日本第一电通DDK电动扳手
DAKE单相耐压 Durapress 10DA 产品说明书

DAKE SINGLE PHASE DURA-PRESSForce 10DAINSTRUCTIONAL MANUALWARNING!Read and understand all instructions and responsibilities before operating. Failure to follow safety instructions and labels could result in serious injury.Dake Corporation Phone: 800.937.3253 TABLE OF CONTENTSDAKE STANDARD LIMITED WARRANTY (2)RETURN & REFUND POLICY (4)SAFEGUARDING THE POINT OF OPERATION (5)SPECIFICATIONS (6)SAFETY (7)SET UP (8)PRESS PLACEMENT (8)FILLING THE PRESS WILL OIL (8)WIRING INSTRUCTIONS (9)OPERATION (9)BEFORE FIRST TIME OPERATION (9)MAINTENANCE (10)LUBRICATION (10)HYDRAULIC LINES AND FITTINGS (10)TROUBLESHOOTING (11)EXPLODED VIEW & PARTS LIST (12)10 DA WORKHEAD DIAGRAM (14)ORDERING INFORMATION (14)DAKE STANDARD LIMITED WARRANTYFinished MachinesDake warrants to the original purchaser the finished machine manufactured or distributed by it to be free from defects in material and workmanship under normal use and service within 1 year (12 months) from the delivery date to the end user.PartsDake warrants to the original purchaser the component part manufactured or distributed by it to be free from defects in material and workmanship under normal use and service within 30 days from the delivery date to the end user.The standard limited warranty includes the replacement of the defective component part at no cost to the end user.Sale of Service (Repairs)Dake warrants to the original purchaser the component part repaired by Dake Corporation at the manufacturing facility to be free from defects in material and workmanship under normal use and service within 90 days from the return date to the end user, as it pertains to the repair work completed. The standard limited warranty includes repair of the defective component part, at no cost to the end user.Warranty ProcessSubject to the conditions hereinafter set forth, the manufacturer will repair or replace any portion of the product that proves defective in materials or workmanship. The manufacturer retains the sole right and option, after inspection, to determine whether to repair or replace defective equipment, parts or components. The manufacturer will assume ownership of any defective parts replaced under this warranty.All requested warranty claims must be communicated to the distributor or representative responsible for the sale. Once communication has been initiated, Dake Customer Service must be contacted for approval:Phone: (800) 937-3253Email: ****************************When contacting Dake, please have the following information readily available:- Model #- Serial #- Sales Order #Purchasers who notify Dake within the warranty period will be issued a Case number and/or a Return Material Authorization (RMA) number. If the item is to be returned per Dake’s request, the RMA number must be clearly written on the exterior packaging. Any item shipped to Dake without an RMA will not be processed.Warranty Exceptions:The following conditions are not applicable to the standard limited warranty:(a) Part installation or machine service was not completed by a certified professional, and is notin accordance with applicable local codes, ordinances and good trade practices.(b) Defects or malfunctions resulting from improper installation or failure to operate or maintainthe unit in accordance with the printed instructions provided.(c) Defects or malfunctions resulting from abuse, accident, neglect or damage outside of prepaidfreight terms.(d) Normal maintenance service or preventative maintenance, and the parts used in connectionwith such service.(e) Units and parts which have been altered or repaired, other than by the manufacturer or asspecifically authorized by the manufacturer.(f) Alterations made to the machine that were not previously approved by the manufacturer, orthat are used for purposes other than the original design of the machine.RETURN & REFUND POLICYThank you for purchasing from Dake! If you are not entirely satisfied with your purchase, we are here to help.ReturnsAll Dake manufactured / distributed machines, parts and couplings include a 30-day return option. These policies are valid from the date of final shipment to the end user.To be eligible for a return, the item must be unused and in the same condition as received.All requested warranty claims must be communicated to the distributor or representative responsible for the sale. Once communication has been initiated, Dake Customer Service must be contacted for approval:Phone: (800) 937-3253Email:****************************Once the return request has been approved by Customer Service, a representative will supply a Return Material Authorization (RMA) number. The returned item must have the provided RMA number clearly marked on the outside packaging. Any item received without an RMA number clearly visible on the packaging will not be processed.An RMA number can only be provided by the Dake Customer Service team and must be obtained prior to the return shipment.RefundsOnce the item has been received and inspected for damages, a representative will notify the requestor referencing the provided RMA number.If the return is approved, a refund will be issued to the original method of payment, less a 20% restocking fee. The restocking fee may be waived if an order is placed at the time of return with like-value merchandise.Transportation costs are the responsibility of the end user and will not be credited upon return approval.Any item that is returned after the initial 30 days or has excessive/obvious use will not be considered for a full refund.SAFEGUARDING THE POINT OF OPERATIONANSI B11.2 - Hydraulic Power Presses -Safety Requirements for Construction, Care, and UseIt is important that Dake press users have a clear understanding of their responsibility involving the care and use of their Dake hydraulic press, including point-of-operation safe guards. Dake strongly recommends that Dake press users obtain a copy of the current American National Standard Institute (ANSI) B11.2 standard, for a more complete understanding of their responsibilities.ANSI B11.2 states the following, relative to point of operation safeguarding:“Normally, only the employer (press user) can determine the requirements of the press productions system components, including the dies and methods for feeding. Therefore, the employer is ultimately responsible to designate and provide the point-of-operation safeguarding system.”The standard also discusses additional responsibilities of the employer. Some of the key responsibilities are:•The employer is responsible for the safety, use, and care of the hydraulic power press production system.•The employer is responsible to consider the sources of hazards for all tasks to be implemented on the hydraulic power press production system.•The employer is required to eliminate, or control identified hazards in the scope of their work activity. •The employer is responsible for the training of personnel, caring for, inspecting, maintaining, and operating hydraulic press production systems to ensure their competence.•The employer is responsible to provide and ensure that point-of-operation safeguarding is used, checked, maintained, and where applicable, adjusted on every production operation performed on a press production system.A complete and current copy of the ANSI B.11.2 standard can be obtained by contacting the following:American National Standards Institute1430 BroadwayNew York, NY 10018AMT – The Association for Manufacturing Technology7901 Westpark DriveMcLean, VA 22102SPECIFICATIONSModel Force 10DA Number 909205 Capacity 10 tons Horse Power 1 HP Voltage 110V Single Phase Ram Travel 10”Pressing Speed20 ipmWidth between uprights 20”Max. ram to table 40”Height 80”Base 29-3/4” x 24”Weight 3,450 lbs.In the space provided record the serial number and model number of the machine. This information is only found on the black and gold Dake tag shown below. If contacting Dake this information must be provided to assist in identifying the specific machine.Serial No.Model No.Install Date:SAFETYThis is the safety alert symbol. When you see this symbol on your press be alert to the potential for personal injury.Employer is responsible to perform a hazard/PPE assessment before work activity.Label Placement ViewFollow recommended precautions and safe operating practices. It is important that the operator understand all safety instruction listed below in order to prevent damage to themselves, others, or the machine:•Carefully read all the safety messages in this manual and on your press safety labels.Keep safety labels in good condition. Replace missing or damaged safety labels.•Do not alter this press from its original design.•Do not make repairs or adjustments to any hydraulic system unless you are competent or working under competent supervision.•Only use Dake original parts.•This machine is intended to be operated by one person. This person should be conscious of the ram movement not only for themselves but also for persons in the immediate area of the machine.•This press is not intended for pulling operations. Personal injury or machine damage can result.SET UPPRESS PLACEMENT•The press needs to be placed so that it has a safety perimeter of 2-1/2 feet on all sides from any other objects or machines.•Press should be placed on level floor with base angles touching the floor at all points.Use shims where necessary.FILLING THE PRESS WILL OILFill the reservoir with DTE 24 Mobil hydraulic oil or equivalent.a. 10DA holds 2 gallons of oil. Make sure the oil is new and be cautious nocontaminants get in while filling the reservoir.b. Oil should be changed about once a year.WIRING INSTRUCTIONSWARNING:A licensed qualified electrician that follows all state and local laws must wire and install electrics on this press.110 VoltWARNING: Machine must have a designated 30 amp drop for 110 volts. This press will not operate correctly without 30 amps.For 110 volts this machine is ready to plug in. The machine can be wired 220-volt single phase. Always follow the wiring diagram provided in the moor cover when converting to 220-volt single phase. A cord and plug that is rated for a specific voltage and amperage must be used. This rating can be found on the motor.220 Volt Single PhaseThe press new is shipped out as a 110-volt machine. If wiring must be changed to suit 220-volt single phase.1. The leads on the motor must be changed to fit 220-volt, 17.2 amps, follow the diagram onthe motor.2. Install plug and wire that fits the rating on the motor, the plug and wire must be rated forthe voltage and amperage listed on the motor.OPERATIONBEFORE FIRST TIME OPERATION1. Make sure the reservoir is filled with 2 gallons of Mobil DTE 24 hydraulic fluid orequivalent.2. Turn the on/off power (toggle) switch to the “on” position (up).3. Move the control lever down, this will advance the ram in the downward position.4. Release the control lever and the ram will stop all movement.5. Move the control lever to the up position and the ram with move up.6. When the press is new be sure to move the ram up and down to work out any air thatmay be in the system.WARNING: When using the control lever in pressing operations or to return the ram stop applying pressure once the handle reaches its positive stop. Applying additional force on the lever does not increase ram speed and will lead to premature damage of the valve.MAINTENANCELUBRICATIONKeep all working parts of press well oiled for easier operation. Also, keep a light film of oil over the entire surface of the ram to prevent rust.HYDRAULIC LINES AND FITTINGSIf there is ever any maintenance done with the hydraulic components below is how to reinstall all components.TROUBLESHOOTINGSYMPTOM CAUSE SOLUTIONRam runs jerky while movingup and down Air is in the system This press has a self-bleeding system, continue to run the ram up and down approximately 15 times.Machine will not build desiredpressure Relief valve needs to be reset Remove octane cap from back of manifold and adjust set screw to correct pressure. WARNING: Do not exceed 2413 PSIPins are shearing or bending Relief valve needs to be reset Remove octane cap from back of manifold and adjust set screw to correct pressure. WARNING: Do not exceed 2413 PSIOil Leaks around the ram Cylinder seals are worn ordamaged Replace cylinder sealsOil leaks around holes otherthan the ram Bolts need to be tightened Tighten bolts around the ram Ram will not extend the full10 inches Oil level is too low Re-fill the reservoir with oil Hydraulic gauge will not readpressure Hydraulic gauge is bad Replace hydraulic gauge Motor will not start No power to press Double check electrical cordMotor overheats and shut down Duty cycle time is exceededCheck the duty cycle time onthe motor. (Has no coolingfan, 15-20 minutes) Extension cord is being usedExtension cord will lower theAPMS and will causeoverheating of the motor.Remove cord.EXPLODED VIEW & PARTS LISTPARTS NOT ILLISTRATEDItem Description Part No. Qty Breather Vent & Elbow Reservoir fill port 300267 1 Gauge Tons/PSI 302937 1Reservoir 2 Gallons 300269 1Valve Kit Fittings, hoses, valve,manifold, bolts, & O-rings 300266KIT 1 Optional Check Valve 302071 1 Optional Relief Valve 290-3625 PSI or 20-250 Bar 301949 1 Optional Relief Valve 43.5-435 PSI or 3-30 Bar 302197 1 Bolts SHC #10-24 x 1-3/4” Mounting bolts for valve only 43403 4Bolts SHC #10-24 x 2-3/4” Mounting bolts for valve,relieve valve, or check valve 76749 4Bolts SHC #10-24 x 4-1/2” Mounting bolts for valve,relieve valve, or check valve 302221 410 DA WORKHEAD DIAGRAMPlease contact factory for current prices.ORDERING INFORMATIONParts are available for direct purchase from Dake or through a distributor. When placing a parts order, you will need to provide the part number, name of part, and model number. All parts shipped F.O.B. Factory in Grand Haven, MI.ItemDescription Part # A Piston86690 B Cylinder Flange86689 C Cylinder86688 D Socket Head Cap Screw43450 E O-Ring 78483 F Seal 78484 G Wear Ring 78485 H Wear Ring 78486 J O-Ring Seal 78487 - Workhead Assembly 716514。
AFC1500拧紧控制器使用方法

扭矩 角度上限 角度下限
扭矩上限
标准扭矩 第二步斜率上限 扭矩下限 第二步斜率下限
交叉扭矩
第一步扭矩 第一步斜率上限 缓冲扭矩 阈值扭矩 第一步斜率下限
角度 第一时间极限 最终时间极限
四、AF1500的参数表
1、拧紧模式:单步、双步。 2、标定扭矩:即工具标定设定。 3、扭矩下限:最终拧紧扭矩的判断下限。 4、扭矩上限:最终拧紧扭矩的判断上限。 5、标准扭矩:目标扭矩。 6、第一步扭矩:第一斜率标定终点。 7、缓冲扭矩:角度测量的扭矩起点。 8、阈值扭矩:第一扭矩斜率标定的起点。 9、交叉扭矩:第二扭矩斜率标定的起点。 10、角度下限:最终拧紧角度判断的角度下限。 11、角度上限:最终拧紧角度判断的角度上限。 12、第一步扭矩斜率上限:第一步扭矩斜率判断上限。 13、第一步扭矩斜率下限:第一步扭矩斜率判断下限。 14、第二步扭矩斜率上限:第二步扭矩斜率判断上限。 15、第二步扭矩斜率下限:第二步扭矩斜率判断下限。 16、第一时间极限:第一步拧紧时间极限。 17、最终时间极限:最后一步拧紧时间极限。
二、外观及接线
21、OUT 22、OUT 23、OUT 24、OUT 25、OUT DATA4(输出数据4):同上。 DATA3(输出数据3):同上。 DATA2(输出数据2):同上。 DATA1(输出数据1):同上。 DATA0(输出数据0):同上。
二、外观及接线
B、轴输出信号 当12、13位不同组合情况下,输出数据含义为:
二、外观及接线
(一)外观 该系统由拧紧控制器和轴驱动器组成。一个系统必须有一个控制器模块, 但可以有多个驱动器模块。一个驱动模块驱动一把拧紧枪。
轴驱动器 拧紧控制器
前桥装配机的 拧紧系统图。 右1为控制器, 右2到4依次为 第一轴到第三 轴。
CKD品牌DD马达--AX系列使用说明

目录
ABSODEX AX 系列[TS 型/TH 型] 使用说明书 No.SMB-55
前言 ······································································································ 1
3. 系统构成与配线 3.1 系统构成 ······················································································· 3- 1 3.1.1 系统构成示例 ········································································ 3- 1 3.1.2 外围设备一览 ········································································ 3- 3 3.2 配线······························································································· 3- 4 3.2.1 驱动装置面板的说明······························································ 3- 4 3.2.2 连接到电源、电机的接线 ······················································ 3- 7 3.2.3 连接到其它端子台的接线 ······················································ 3-10 3.2.4 关于电磁制动器····································································· 3-11 3.2.5 CN3(I/O 信号)的连接························································ 3-16 3.2.6 CN3(I/O 信号)的接口规格················································· 3-19 3.2.7 配线示例················································································ 3-21 3.2.8 安全功能的配线····································································· 3-23
CO-SHARE智能无刷电批特性简介
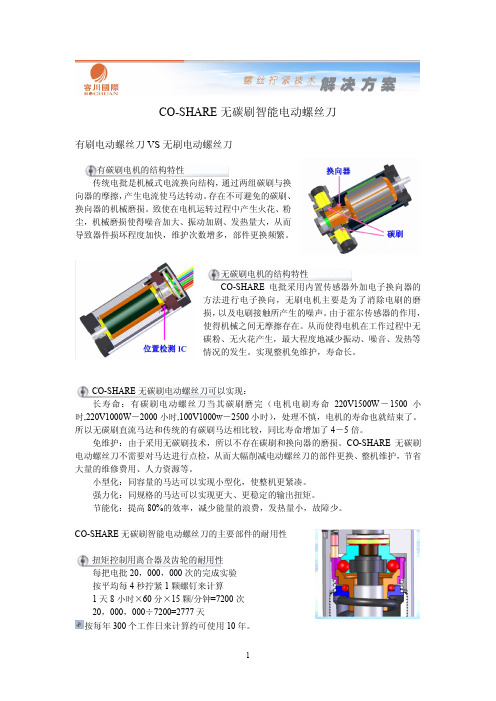
CO-SHARE无碳刷智能电动螺丝刀有刷电动螺丝刀VS无刷电动螺丝刀有碳刷电机的结构特性传统电批是机械式电流换向结构,通过两组碳刷与换向器的摩擦,产生电流使马达转动。
存在不可避免的碳刷、换向器的机械磨损。
致使在电机运转过程中产生火花、粉尘,机械磨损使得噪音加大、振动加剧、发热量大,从而导致器件损坏程度加快,维护次数增多,部件更换频繁。
无碳刷电机的结构特性CO-SHARE电批采用内置传感器外加电子换向器的方法进行电子换向,无刷电机主要是为了消除电刷的磨损,以及电刷接触所产生的噪声。
由于霍尔传感器的作用,使得机械之间无摩擦存在。
从而使得电机在工作过程中无碳粉、无火花产生,最大程度地减少振动、噪音、发热等情况的发生。
实现整机免维护,寿命长。
CO-SHARE无碳刷电动螺丝刀可以实现:长寿命:有碳刷电动螺丝刀当其碳刷磨完(电机电刷寿命220V1500W-1500小时,220V1000W-2000小时,100V1000w-2500小时),处理不慎,电机的寿命也就结束了。
所以无碳刷直流马达和传统的有碳刷马达相比较,同比寿命增加了4-5倍。
免维护:由于采用无碳刷技术,所以不存在碳刷和换向器的磨损。
CO-SHARE无碳刷电动螺丝刀不需要对马达进行点检,从而大幅削减电动螺丝刀的部件更换、整机维护,节省大量的维修费用、人力资源等。
小型化:同容量的马达可以实现小型化,使整机更紧凑。
强力化:同规格的马达可以实现更大、更稳定的输出扭矩。
节能化:提高80%的效率,减少能量的浪费,发热量小,故障少。
CO-SHARE无碳刷智能电动螺丝刀的主要部件的耐用性扭矩控制用离合器及齿轮的耐用性每把电批20,000,000次的完成实验按平均每4秒拧紧1颗螺钉来计算1天8小时×60分×15颗/分钟=7200次20,000,000÷7200=2777天按每年300个工作日来计算约可使用10年。
轴承的耐用性(CO-SHARE无碳刷智能电动螺丝刀采用的是日本NMB-美培亚、日本NSK-精工的轴承)轴承制造厂商的品质保证为40,000小时假设每天需拧紧7200颗螺钉,实际使用时间为4小时(1颗/2秒)40,000小时÷4小时=10,000天10,000天÷300天工作日=33年按国内厂家两班倒制度计算约可使用10年霍尔感应开关(霍尔感应开关功能说明及与传统的微动开关比较说明)传统微动开关微动开关,内部有机械触点影响寿命因素:触点的寿命及机械寿命日本“日开”的寿命保证为100万次大陆国产的寿命为10万次霍尔感应开关CO-SHARE电批采用的霍尔感应开关为非接触型,不存在磨损,因而不存在使用次数的限制,其寿命和其它半导体器件相似,为半永久型,和传统的触点开关比较,其寿命有了等级性的提高,使用寿命约为2000万次。
LINAK制造高级电热线动作器产品说明书,包括功能性、应用领域,以及全球地区生产工厂
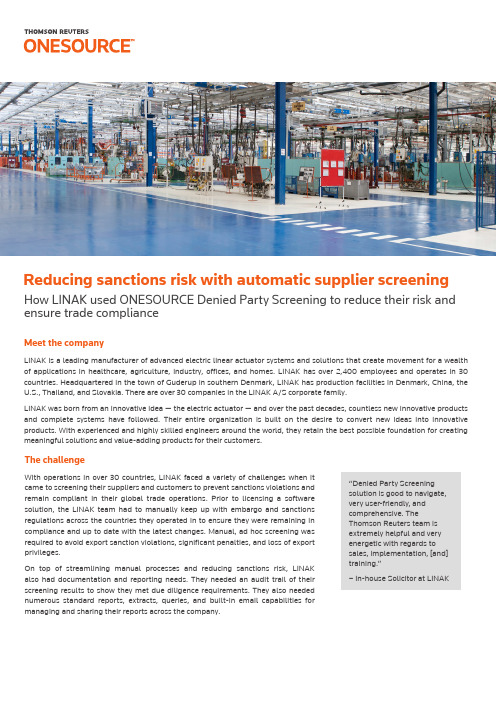
Reducing sanctions risk with automatic supplier screening How LINAK used ONESOURCE Denied Party Screening to reduce their risk and ensure trade complianceMeet the companyLINAK is a leading manufacturer of advanced electric linear actuator systems and solutions that create movement for a wealth of applications in healthcare, agriculture, industry, offices, and homes. LINAK has over 2,400 employees and operates in 30 countries. Headquartered in the town of Guderup in southern Denmark, LINAK has production facilities in Denmark, China, the U.S., Thailand, and Slovakia. There are over 30 companies in the LINAK A/S corporate family.LINAK was born from an innovative idea — the electric actuator — and over the past decades, countless new innovative products and complete systems have followed. Their entire organization is built on the desire to convert new ideas into innovative products. With experienced and highly skilled engineers around the world, they retain the best possible foundation for creating meaningful solutions and value-adding products for their customers.The challengeWith operations in over 30 countries, LINAK faced a variety of challenges when it came to screening their suppliers and customers to prevent sanctions violations and remain compliant in their global trade operations. Prior to licensing a software solution, the LINAK team had to manually keep up with embargo and sanctions regulations across the countries they operated in to ensure they were remaining in compliance and up to date with the latest changes. Manual, ad hoc screening was required to avoid export sanction violations, significant penalties, and loss of export privileges.On top of streamlining manual processes and reducing sanctions risk, LINAK also had documentation and reporting needs. They needed an audit trail of their screening results to show they met due diligence requirements. They also needed numerous standard reports, extracts, queries, and built-in email capabilities for managing and sharing their reports across the company. “Denied Party Screening solution is good to navigate, very user-friendly, and comprehensive. The Thomson Reuters team is extremely helpful and very energetic with regards to sales, implementation, [and] training.”–In-house Solicitor at LINAKLearn more about how ONESOURCE Denied Party Screening and other global trade management solutions can help your company reduce risk and increase efficiency.Contact us today /en/products-services/global-trade-management © 2021 Thomson Reuters TR1459488/03-2021Reducing risk and increasing control with ONESOURCE Denied Party Screening To solve their challenges, LINAK turned to ONESOURCE® Denied Party Screening. Designed to handle the validation of business partners by screening against 350+ global lists for restricted persons, companies, and sanctioned or embargoed countries, ONESOURCE had the coverage that a multinational company like LINAK needed to comply with the various regulations of the countries they do business in. ONESOURCE Denied Party Screening is automatically updated with the latest regulations, so the LINAK team no longer needs to check manually for regulation changes. ONESOURCE also automatically triggers a screening process whenever a new customer or supplier is added to database or there is a change to an existing customer or supplier, and the tool manages appropriate level of risk in minimizing false positives while not missing real hits.LINAK also benefited from the Sanctions Ownership Research data from Dow Jones Risk & Compliance within ONESOURCE, which covers companies owned or controlled by individuals, entities, countries, or regions sanctioned by the U.S. Department of the Treasury’s Office of Foreign Assets Control (OFAC) and/or the European Union. LINAK now has access to more than 200 analysts collectively speaking over 60 languages and records contain over 30 identifiers like name, age, date of birth, locations, citizenships, etc., which aid the classification of searches, thus preventing false positives and also satisfies demands for KYC (Know Your Customer), AML (Anti-Money Laundering), and CFT (Combating the Financing of Terrorism).With ONESOURCE Denied Party Screening, LINAK has been able to transform the compliance risk management of their screening processes by standardizing, automating, and streamlining its work, leading to increased control as well as operational efficiency.“We had a successful implementation process, and…we are very happy with the Denied Party Screening solution.”–In-house Solicitor at LINAK ONESOURCE Indirect Tax 2。
日本古河电工公司开发出全球最高导电率的CNT导体

料 ,但两公司打算短期内改变以水、氢气和C O 为原料 ,
国家橡胶与轮 胎工程技术研 究 中心 、青岛益凯新 材料 有 限公司和意大利 埃尼集 团维萨 雷斯 公司 ,签订 三方 合作 协议 ,青 岛市 由此引进 了绿色轮胎橡胶复合新材料技术 。 意大利埃尼集 团在基础化 学品 、聚乙烯和苯 乙烯 塑料 及合成橡胶 弹性体等领域处 于领 先地位 。此次 引进的新技
Nm。 / h 的合 成气 ( s y n g a s ) ,可用 于制造氢气 、氨 和其 他化
“
德 国 奥 迪 公 司 近 日宣 布 ,与 法 国 全 球 生 物 能 源 公 司共 同成 功 地 开 发 出 不 使 用 化 石 原 料 合 成 的燃 料 e - b e n z i n ”。 “ e — b e n z i n ”采用的是从玉米 中提取 的葡萄 糖为原料 ,先通 过发酵 的 自然蒸 发的方式分离 出异丁烯气
利用太 阳能来合成e — b e n z i n J  ̄料 。 奥迪公 司此前与多 家企业合作 ,进行不使 用化石原料 生产 C O 中和燃料 的开发 。 目前正 以工业 规模 进行量产合 成 甲烷 “ e — g a s ” ,另外还 开发 了合 成乙醇 “ e — e t h a n o l ”和
( 本栏编辑 祖国红 )
损耗化方面的研发 。
着光 原料化 的进展 , 期 待该技术将 能作 为弥补将来 丁二烯 不 足的下一代生产技术 。虽然2 0 1 4 年该技术 已经确立 ,但
日本东日扭力扳手(Tohnichi)(可编辑)

东日扭力扳手操作说明及应用、选型东日扭力扳手,东日扭力扳手数显式,东日扭力扳手棘轮式,东日扭力扳手开口头式,东日扭力扳手可交换头扳手,东日扭力扳手表盘式扭力扳手SP/SP-MH/RSP脱跳式扭力扳手相同螺栓紧固专用扭力扳手。
带开口头(S)/梅花(R)头。
新增加了SP-MH 系列(采用不易打滑的滚花手柄)。
准确度±3%东日扭力扳手,扭力仪器总代理,北京朗科精密仪器欢迎您的来电132****0101张先生************东日扭力扳手,东日表盘式扭力扳手,东日数显扭力扳手,东日开口头扭力扳手,东日棘轮式扭力扳手,东日交换头扭力扳手。
东日扭力扳手,扭力仪器总代理,北京朗科精密仪器欢迎您的来电132****0101张先生************东日扭力扳手,东日表盘式扭力扳手,东日数显扭力扳手,东日开口头扭力扳手,东日棘轮式扭力扳手,东日交换头扭力扳手。
DB/DBE/DBR直读式扭力扳手检查用扭力扳手的基本型。
不受握持位置的影响。
(DBE:带加长手柄、DBR:机械加力型)表盘式清晰直观,适用于测定作业。
(-S:带记忆指针)准确度±3%注1 带记忆指针的型号后为“-S”。
注2 DBR 使用绞盘和手扳葫芦加力。
注3 DBR 为定制产品。
注4 □ 25.4 以上的方形驱动头请使用通孔套筒。
东日扭力扳手,扭力仪器总代理,北京朗科精密仪器欢迎您的来电132****0101张先生************东日扭力扳手,东日表盘式扭力扳手,东日数显扭力扳手,东日开口头扭力扳手,东日棘轮式扭力扳手,东日交换头扭力扳手。
CEM3-G数字式扭力扳手紧固数据用LED 和LCD 组合显示,最大存储数为999 个。
准确度±1%注1 全长指本体的长度。
注2 交换头的详细内容请参见P38 ~41。
注3 可使用DFS 方便地进行简单的统计处理。
(参见P61)注4 使用红外线输出时请参见R-DT999。
扭矩扳手

扭矩扳手扭矩扳手又叫力矩扳手、扭力扳手、扭矩可调扳手,是扳手的一种,一般分为三类:手动力矩扳手、气动扭力扳手和电动力矩扳手。
定扭扳手广泛用于对拧紧工艺有严格要求的装配线,使产品各个紧固件扭矩值一致,生产出来的产品质量有保障。
手动扭矩扳手现阶段分为机械音响报警式,数显式,指针式(表盘式),打滑式(自滑转式). 其中机械音响报警式,采用杠杆原理,当力矩到达设定力矩时会出现"嘭"机械相碰的声音,此后扳手会成为一个死角,及相当于呆扳手,如再用力,会出现过力现象. 数显式和指针式(表盘式)差不多,都是把作用力矩可视化.现阶段的数显和指针都是在机械音响报警式扭矩扳手的基础上工作的. 打滑式(自滑转式)采用过载保护、自动卸力模式,当力矩到达设定力矩时会自动卸力(同时也会出现机械相碰的声音),此后扳手自动复位,如再用力,会再次打滑,不会出现过力现象.此种是最近1,2年才出现的新感念产品. 机械音响报警式是目前市场的主流产品,主要体现在价格便宜,其它3种相对来说,价格昂贵.不过由于各行各业对这方面要求越来越高,以及效率的要求,数显式、指针式(表盘式)及打滑式(自滑转式)的需求会越来越高.电动扭矩扳手一般就是可以设定扭矩值的电动扳手,也叫定扭矩电动扳手。
电动扭矩扳手一般用来紧固大六角高强螺栓,使用时,先把扭矩调到需要规定的扭矩,然后紧固螺栓。
电动定扭扳手分为电流式和动态扭矩传感器式两种,由控制器和拧紧轴组成。
电流式定扭扳手根据电机拧紧过程中电流值的变化来判断扭力值,当达到预定扭力时,电机停止工作。
动态扭矩传感器式是在拧紧轴上安装有传感器,时刻监测扭力值的变化,当达到预定扭力时,电机停止工作。
电动扭矩扳手具有精度高(±2%)、故障率低、寿命长、可编程,可对扭力和角度控制、可多种扭力选择的优点。
因为拧大扭矩螺栓会有反作用力,所以一般在大扭矩拧紧工件上都会设计反作用力臂,防止操作人员出现安全事故。
DDK系列

適 合 電 線
公称断面積(mm2) 最大導体径(mm)
1.25
1.6
3.50
2.5
8.00
4.5
22.00
7.0
50.00
11.0
● 3 ●
A
D/MS
D/MSシリーズ
材質/処理
構成部品 コンタクト インサート(絶縁体) シェル、接続ナット リテナーリング
材 質 銅合金 ジアリルフタレート樹脂 (UL94V-O) アルミニウム合金
Y
(U2)のみで前面取付(U1)ができません。
シェル サイズ
10SL 12S 14S 16S,16 18 20 22 24 28 32 36
二連取付 間隔
Y以上 47 50 53 56 59 62 70 73 80 86 92
取付小ネジ用穴
間隔 R±0.13
18.26
穴径
T
+0.25 -0.12
A
D/MS
結線手順
〈半田付作業〉
コンタクトの半田カップには予備半田を施してから結線作業をして下 さい。
余分なフラックスや半田が半田カップから外に流出しない様に短時間 で行なって下さい。
×○×
〈リテナーリングのはずし方〉
シェルのリテナーリング引き抜き溝に小形のネジ回しの様な先の細いものを差し込んでこじり、リテ ナーリングが飛び出さないよう指で軽くおさえながら、外して下さい。
〈リテナーリングの固定〉
シェルのリテナーリング装着溝にリテナーリングの一方を差し込み、指で軽く押さえながら、もう一 方を小形のネジ回しの様な先の細いもので、押し込んで下さい。
・D/MS、CE02シリーズと嵌合いたします。
Makita WT01 无线电力扳手说明书

011762ENGLISH (Original instructions) SPECIFICATIONSModelWT01 Standard bolt M8 - M12 (5/16" - 1/2")CapacitiesHigh tensile bolt M6 - M10 (1/4" - 3/8")Square drive 9.5 mm (3/8")No load speed (RPM) 0 -2,300/min.Impacts per minute 0 - 3,000Max. fastening torque 110 N.m (1,000 in.lbs)Overall length 163 mm (6-3/8")Net weight 0.95 kg (2.1 lbs)Rated voltage D.C. 10.8V/12VmaxStandard battery cartridges BL1014• Due to our continuing programme of research and development, the specifications herein are subject to change without notice. • Specifications and battery cartridge may differ from country to country.• Weight, with battery cartridge, according to EPTA-Procedure 01/2003GEA006-2 General Power Tool SafetyWARNING Read all safety warnings and all instructions. Failure to follow the warnings and instructions may result in electric shock, fire and/or serious injury.Save all warnings and instructions for future reference. The term "power tool" in the warnings refers to your mains-operated (corded) power tool or battery-operated (cordless) power tool.Work area safety1. Keep work area clean and well lit. Cluttered ordark areas invite accidents.2. Do not operate power tools in explosiveatmospheres, such as in the presence offlammable liquids, gases or dust. Power toolscreate sparks which may ignite the dust or fumes.3. Keep children and bystanders away whileoperating a power tool. Distractions can causeyou to lose control.Electrical safety4. Power tool plugs must match the outlet. Nevermodify the plug in any way. Do not use anyadapter plugs with earthed (grounded) powertools. Unmodified plugs and matching outlets willreduce risk of electric shock.5. Avoid body contact with earthed or groundedsurfaces such as pipes, radiators, ranges andrefrigerators. There is an increased risk ofelectric shock if your body is earthed or grounded.6. Do not expose power tools to rain or wetconditions. Water entering a power tool willincrease the risk of electric shock.7. Do not abuse the cord. Never use the cord forcarrying, pulling or unplugging the power tool.Keep cord away from heat, oil, sharp edges ormoving parts. Damaged or entangled cordsincrease the risk of electric shock.8. When operating a power tool outdoors, use anextension cord suitable for outdoor use. Use ofa cord suitable for outdoor use reduces the risk ofelectric shock.9. If operating a power tool in a damp location isunavoidable, use a ground fault circuitinterrupter (GFCI) protected supply. Use of anGFCI reduces the risk of electric shock.Personal safety10. Stay alert, watch what you are doing and usecommon sense when operating a power tool.Do not use a power tool while you are tired orunder the influence of drugs, alcohol ormedication. A moment of inattention whileoperating power tools may result in seriouspersonal injury.e personal protective equipment. Alwayswear eye protection. Protective equipment suchas dust mask, non-skid safety shoes, hard hat, orhearing protection used for appropriate conditionswill reduce personal injuries.12. Prevent unintentional starting. Ensure theswitch is in the off-position before connectingto power source and/or battery pack, pickingup or carrying the tool. Carrying power tools withyour finger on the switch or energising power toolsthat have the switch on invites accidents.13. Remove any adjusting key or wrench beforeturning the power tool on. A wrench or a key leftattached to a rotating part of the power tool mayresult in personal injury.14. Do not overreach. Keep proper footing andbalance at all times. This enables better controlof the power tool in unexpected situations.15. Dress properly. Do not wear loose clothing orjewellery. Keep your hair, clothing, and glovesaway from moving parts. Loose clothes,jewellery or long hair can be caught in movingparts.16. If devices are provided for the connection ofdust extraction and collection facilities,ensure these are connected and properly used.Use of dust collection can reduce dust-relatedhazards.Power tool use and care17. Do not force the power tool. Use the correctpower tool for your application. The correctpower tool will do the job better and safer at therate for which it was designed.18. Do not use the power tool if the switch doesnot turn it on and off. Any power tool that cannotbe controlled with the switch is dangerous andmust be repaired.19. Disconnect the plug from the power sourceand/or the battery pack from the power toolbefore making any adjustments, changingaccessories, or storing power tools. Suchpreventive safety measures reduce the risk ofstarting the power tool accidentally.20. Store idle power tools out of the reach ofchildren and do not allow persons unfamiliarwith the power tool or these instructions tooperate the power tool. Power tools aredangerous in the hands of untrained users.21. Maintain power tools. Check for misalignmentor binding of moving parts, breakage of partsand any other condition that may affect thepower tool’s operation. If damaged, have thepower tool repaired before use. Many accidentsare caused by poorly maintained power tools. 22. Keep cutting tools sharp and clean. Properlymaintained cutting tools with sharp cutting edgesare less likely to bind and are easier to control. 23. Use the power tool, accessories and tool bitsetc. in accordance with these instructions,taking into account the working conditionsand the work to be performed. Use of the powertool for operations different from those intendedcould result in a hazardous situation.Battery tool use and care24. Recharge only with the charger specified bythe manufacturer. A charger that is suitable forone type of battery pack may create a risk of firewhen used with another battery pack.25. Use power tools only with specificallydesignated battery packs. Use of any otherbattery packs may create a risk of injury and fire.26. When battery pack is not in use, keep it awayfrom other metal objects, like paper clips,coins, keys, nails, screws or other small metalobjects, that can make a connection from oneterminal to another. Shorting the batteryterminals together may cause burns or a fire.27. Under abusive conditions, liquid may beejected from the battery; avoid contact. Ifcontact accidentally occurs, flush with water. Ifliquid contacts eyes, additionally seek medicalhelp. Liquid ejected from the battery may causeirritation or burns.Service28. Have your power tool serviced by a qualifiedrepair person using only identical replacementparts. This will ensure that the safety of the powertool is maintained.29. Follow instruction for lubricating andchanging accessories.30. Keep handles dry, clean and free from oil andgrease.GEB049-2 CORDLESS IMPACT WRENCH SAFETY WARNINGS1. Hold power tool by insulated grippingsurfaces, when performing an operation wherethe fastener may contact hidden wiring.Fasteners contacting a "live" wire may makeexposed metal parts of the power tool "live" andcould give the operator an electric shock.2. Wear ear protectors.3. Check the socket carefully for wear, cracks ordamage before installation.4. Hold the tool firmly.5. Always be sure you have a firm footing.Be sure no one is below when using the tool inhigh locations.6. The proper fastening torque may differdepending upon the kind or size of the bolt.Check the torque with a torque wrench.SAVE THESE INSTRUCTIONS.DO NOT let comfort or familiarity with product (gained from repeated use) replace strict adherence to safety rules for the subject product. MISUSE or failure to follow the safety rules stated in this instruction manual may cause serious personalinjury.USD302-1 SymbolsThe followings show the symbols used for tool.voltsdirect currentno load speedrevolutions or reciprocation per minutenumber of blowENC007-7 IMPORTANT SAFETY INSTRUCTIONSFOR BATTERY CARTRIDGE1. Before using battery cartridge, read allinstructions and cautionary markings on (1)battery charger, (2) battery, and (3) productusing battery.2. Do not disassemble battery cartridge.3. If operating time has become excessivelyshorter, stop operating immediately. It mayresult in a risk of overheating, possible burnsand even an explosion.4. If electrolyte gets into your eyes, rinse themout with clear water and seek medicalattention right away. It may result in loss ofyour eyesight.5. Do not short the battery cartridge:(1) Do not touch the terminals with anyconductive material.(2) Avoid storing battery cartridge in acontainer with other metal objects such asnails, coins, etc.(3) Do not expose battery cartridge to wateror rain.A battery short can cause a large current flow,overheating, possible burns and even a breakdown.6. Do not store the tool and battery cartridge inlocations where the temperature may reach orexceed 50 C (122F).7. Do not incinerate the battery cartridge even ifit is severely damaged or is completely wornout. The battery cartridge can explode in a fire.8. Be careful not to drop or strike battery.9. Do not use a damaged battery.SAVE THESE INSTRUCTIONS. Tips for maintaining maximum battery life1. Charge the battery cartridge before completelydischarged.Always stop tool operation and charge thebattery cartridge when you notice less toolpower.2. Never recharge a fully charged batterycartridge.Overcharging shortens the battery service life.3. Charge the battery cartridge with roomtemperature at 10 C - 40 C (50 F - 104F).Let a hot battery cartridge cool down beforecharging it.4. Charge the battery cartridge once in every sixmonths if you do not use it for a long period oftime.FUNCTIONAL DESCRIPTION• Always be sure that the tool is switched off and the battery cartridge is removed before adjusting or checking function on the tool.Installing or removing battery cartridge• Always switch off the tool before installing or removing of the battery cartridge.• To remove the battery cartridge, withdraw it from the tool while pressing the buttons on both sides ofthe cartridge.• To install the battery cartridge, hold it so that the battery cartridge front shape fits to that of thebattery installment opening and slip it into place.Always insert it all the way until it locks in place witha little click. If not, it may accidentally fall out of thetool, causing injury to you or someone around you. • Do not use force when installing the battery cartridge. If the cartridge does not slide in easily, itis not being inserted correctly.1. Button2. Battery cartridgeSwitch action1• Before inserting the battery cartridge into the tool, always check to see that the switch trigger actuatesproperly and returns to the "OFF" position whenreleased.To start the tool, simply pull the switch trigger. Tool speed is increased by increasing pressure on the switch trigger. Release the switch trigger to stop.Electric brakeThis tool is equipped with an electric brake. If the tool consistently fails to quickly stop after switch trigger release, have tool serviced at a Makita service center. Turning on the front lamp1• Do not look in the light or see the source of light directly.Pull the switch trigger to turn on the light. The lamp keeps on lighting while the switch trigger is being pulled. NOTE:• Use a dry cloth to wipe the dirt off the lens of lamp.Be careful not to scratch the lens of lamp, or it maylower the illumination.Reversing switch actionThis tool has a reversing switch to change the direction of rotation. Depress the reversing switch lever from the A side for clockwise rotation or from the B side for counterclockwise rotation.When the reversing switch lever is in the neutral position,the switch trigger cannot be pulled.• Always check the direction of rotation before operation.• Use the reversing switch only after the tool comes to a complete stop. Changing the direction of rotation before the tool stops may damage the tool. • When not operating the tool, always set the reversing switch lever to the neutral position.ASSEMBLY• Always be sure that the tool is switched off and the battery cartridge is removed before carrying outany work on the tool.Selecting correct socketAlways use the correct size socket for bolts and nuts. An incorrect size socket will result in inaccurate and inconsistent fastening torque and/or damage to the bolt or nut.Installing or removing socketTo install the socket, push it onto the anvil of the tool until it locks into place.To remove the socket, simply pull it off.1. Socket2. Anvil1. Reversingswitch lever1. Lamp1. Switch triggerOPERATIONThe proper fastening torque may differ depending upon the kind or size of the bolt, the material of the workpiece to be fastened, etc. The relation between fastening torque and fastening time is shown in the figures.Hold the tool firmly and place the socket over the bolt or nut. Turn the tool on and fasten for the proper fastening time.NOTE:•When fastening screw M8 (5/16") or smaller, carefully adjust pressure on the switch trigger so that the screw is not damaged.• Hold the tool pointed straight at the bolt or nutwithout applying excessive pressure on the tool. • Excessive fastening torque may damage thebolt/nut or socket. Before starting your job, alwaysperform a test operation to determine the properfastening time for your bolt or nut. Especially for thebolt smaller than M8 (5/16"), perform the above testoperation to prevent the trouble on socket or bolt,etc.• If the tool is operated continuously until the battery cartridge has discharged, allow the tool to rest formore than 15 minutes before proceeding with afresh battery.The fastening torque is affected by a wide variety of factors including the following. After fastening, always check the torque with a torque wrench.1.When the battery cartridge is discharged almostcompletely, voltage will drop and the fasteningtorque will be reduced.2.Socket• Failure to use the correct size socket will causea reduction in the fastening torque.• A worn socket (wear on the hex end or square end) will cause a reduction in the fasteningtorque.3.Bolt• Even though the torque coefficient and the class of bolt are the same, the proper fasteningtorque will differ according to the diameter ofbolt.• Even though the diameters of bolts are the same, the proper fastening torque will differaccording to the torque coefficient, the class ofbolt and the bolt length.4.The use of the universal joint or the extension barsomewhat reduces the fastening force of theimpact wrench. Compensate by fastening for alonger period of time.5.The manner of holding the tool or the material ofdriving position to be fastened will affect thetorque.6.Operating the tool at low speed will cause areduction in the fastening torque.Using holster (optional accessory)• Do not use for tools such as a drill with a bit installed on them.• Turn off a tool and wait until it comes to a complete stop before placing in the holster.Be sure to close the holster securely so that it holdsthe tool firmly.008807Thread a waist belt or similar through holster holder.008808Put the tool in the holster and lock it with the holster button.MAINTENANCE• Always be sure that the tool is switched off and the battery cartridge is removed before attempting toperform inspection or maintenance.• Never use gasoline, benzine, thinner, alcohol or the like. Discoloration, deformation or cracks mayresult.To maintain product SAFETY and RELIABILITY, repairs, any other maintenance or adjustment should be performed by Makita Authorized or Factory Service Centers, always using Makita replacement parts.OPTIONAL ACCESSORIES• These accessories or attachments are recommended for use with your Makita toolspecified in this manual. The use of any otheraccessories or attachments might present a risk ofinjury to persons. Only use accessory or attachment for its stated purpose.If you need any assistance for more details regarding these accessories, ask your local Makita Service Center. • Plastic carrying case• Various type of Makita genuine batteries and chargers• Holster NOTE:• Some items in the list may be included in the tool package as standard accessories. They may differ from country to country.。
DDK电动手持扳手FUSION

方头尺寸
3/8" 3/8" 3/8" 3/8"
转速
1 - 1665 1 - 1665 1 - 900 1 - 694
直 筒 式 工 具 扭 矩 范 围 为 10 ~ 40NM。标 准 工 具 带 有 压杆启动和反转开关。 可 选 配 伸 缩 轴、偏 心 齿 轮、开口头。 推荐的工作扭矩范围为最 大扭矩的80%。
FEB-1312-M5
FEB-1312-M10
41610
名称 主电缆,直头型 主电缆,直头型 主电缆,直头型 主电缆,弯角型 主电缆,弯角型 主电缆,弯角型 加长电缆,直头型 加长电缆,直头型 加长电缆,直头型 加长电缆,直头型 加长电缆,直头型 加长电缆,弯角型 加长电缆,弯角型 加长电缆,弯角型 加长电缆,弯角型 加长电缆,弯角型 空调制解调器电缆(9针串口,电脑-控制器)
长/宽 260mm (10.25”) L x 122mm (4.8”) W 279mm (10.9”) L x 217mm (8.56”) W
特殊拧紧头
● DDK可以提供多种特殊用途的拧紧头,包括:偏心头、棘轮头、夹住并拧紧头、开口头、伸缩轴等。
如您有特殊需求,请即与DDK联系!
DDK — 代理商:北京东方泰阳科技有限公司 — 电话:010-51581018
DDK — 代理商:北京东方泰阳科技有限公司 — 电话:010-51581018
6
AFC用户控制软件
AFC用户控制软件 是基于Windows的编程界面,可以: ֜ 简单快捷的读,写,保存和检查拧紧参数。 ֜ 在电子数据表或图形界面上编辑拧紧参数。 ֜ 显示、保存和打印拧紧结果数据和扭矩/角度曲线。 ֜ 对拧紧结果数据进行统计计算。
上海泽驰携手第一兴商推出新品DAM产品再创佳绩
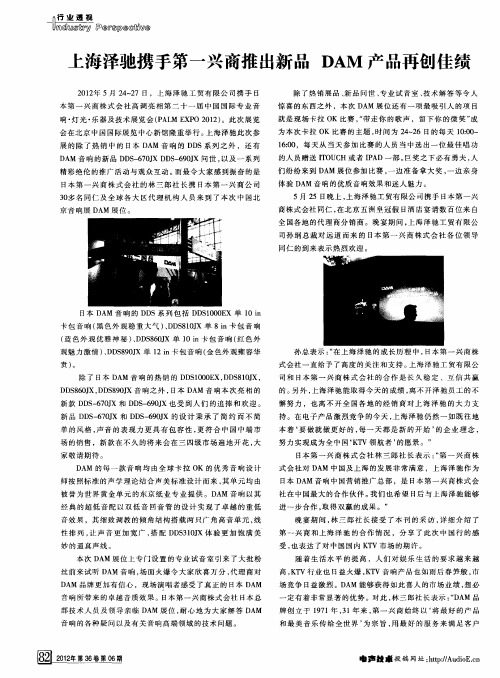
运用 , 大至借助 网络全球覆盖 , 对传统运用提供 了优化
解 决 , 音 频 应 用 瓶 颈 进 行 了突 破 , 现 代 “ 动 ” 活 对 为 移 生 音 频 领 域 增 添 了新 的注 解 。
( 宪 1 续
三 基 音 响 企 业 供 稿
都 安装一个 i t a S 0 r m E 1 ,只需简单 地把它连接到建 Se
京音响展 D M展 位。 A
们 纷 纷 来 到 D M 展 位参 加 比赛 , 边 准 备 拿 大 奖 , 边 亲 身 A 一 一
体 验 D M 音 响 的优 质 音 响 效果 和迷 人 魅 力 。 A 5月 2 5日晚 上 , 海 泽 驰 工 贸 有 限公 司携 手 日本 第 一 兴 上 商 株 式 会 社 同 仁 , 北 京 五洲 皇冠 假 日酒 店 宴请 数 百 位 来 自 在
。 。
/
基于 I P设 备 的 i t a 音 频 应 用 于 公 共 广 播 通 rm se
簟 簟
频 息 输 预 指 的、 有 立 编 P 信 会 入 先 定 具 独 可 址I的
适 合于高品质 I P对讲 和传呼应用 的主机站 , 无需个人
计 算 机 或 服务 器 软件 。 i t a S系 列 I r mE Se P流部 件 可 作 为 酒 店 、商 场 、 娱 乐 公 园 或 零 售 连 锁 店 的 声 音 分 配 系 统 。为 每 一 个 区域
www. g s sc m 3 - y .o
的需 求 。 是 在这 种理 念 的 推 动 和鼓 舞 下 , 过 多 年 发 展 , 正 经 第
一
出 。在 此 之 前 , 们 在 开 拓 海 外 市 场 包 括 欧 美 市 场 的 时候 , 我 也 投 人 了几 百 亿 日元 , 几 年 之 后 也 都 得 到 了 回报 , 在 看 在 现
日东工机 气动手枪钻 ADR-65 ADR-100 说明书

Due to continuous product development/improvement the specifications and configurations in this document are subject to change without prior notice.Manufactured by :NITTO KOHKI Co., Ltd.9-4, Nakaikegami 2-chome, Ohta-ku,Tokyo, 146-8555, Japan Tel :+81-3-3755-1111 Fax :+81-3-3753-8791PNEUMATIC HAND DRILLPlease read this manual carefully before you attempt to use your tool so that you may use it properly and safely.AIR DRILL Model ADR-65 ADR-100PROFESSIONAL TOOLKeep the manual handy – so you can use it whenever necessary.Original InstructionsSpecificationsModelADR-65ADR-100Maximum Operating Pressure 0.6 MPaAir Consumption (No Load)0.55 m 3/min 0.67 m 3/min Stroke Speed (No Load)2900 r/min(min -1)2000 r/min(min -1)Sound Pressure Level 76 dB(A)77 dB(A)Sound Power Level87 dB(A)88 dB(A)Vibration Level [Uncertainty K ] 4.9 m/s 2 [ 2.9 m/s 2 ]2.5 m/s 2 [ 0.75 m/s 2 ]Max. Chuck Size 6.5 mm 10.0 mm Mass (Weight)0.8 kg1.1 kgTQ12825-207/20171The following Safety notations are used throughout the manual to highlight safety precautions for the user and forCaution : Important precautions for tool setup, operation and maintenance.Thank you very much for your purchase of this NITTO KOHKI products.Before using your tool, please read this manual carefully so that you may use it properly to get the most out of it.Please keep the manual handy - so you can use it whenever necessary.・English: P lease ask your dealer ordistributor for instruction manual in local language(s).・German: B itte fragen Sie lhren Händler nach eine Betriebsanleitung in Landessprache.・French: S 'il vous plait, veuillez demandez á votre foumisseur de manuel instruction en langue locale.・Spanish: P or favor, cantacte con su distribuidor para el manual de instrucciones en español.・Portuguese :P or favor pessa ao seo agente ou distribuidor o manual de instrucces ih linguagen local.・Italian: P er Manuale Istruzioni in lingua locale Vi preghiamo di rivolgervi al rivenditore o distributore.・Dutch: V raag uw handelaar om een nederladstalige gebruiksaanwijzing.・Swedish: B e er lokala Åtreförsäljare eller distributör om manualer pá svenska.・Danish: V enligst henvend Dem til den danske distributør for instructions manualer.・Polish: P rosze pytac swojego dealera lub dystrybutora o instrukcje obslugi w jezyku localnym.・中文: 請向當地供應商或経銷商詢問中文使用説明書CONTENTS pageIMPORTANT SAFETY INSTRUCTIONS ........................3GENERAL: TOOLS ...................................................3GENERAL: PNEUMATIC TOOLS ..............................4INSTRUCTIONS FOR THIS TOOL ..............................41. USAGE ............................................................52. CHECK THE CONTENTS OF THE PACKAGE .........53. AIR SUPPLY ......................................................54. HOW TO OPERATE THE TOOL ...........................65. THEREAD SIZE OF HOSE FITTING .....................66. STORAGE .........................................................77. ORDERING SERVICE PARTS ..............................78. OPTIONAL PARTS (7)PICTOGRAMWarning: It might be dangerous to operate the tool if the instructions supplied are not followed.Using this tool improperly could result in serious injury. Read the instruction manual before use.Always wear suitable eye protection.Always wear suitable hearing protection.Always wear respiratory protective equipment (PPE).2California Proposition 65WARNINGSome dust created by power sanding, sawing, grinding, drilling, and other construction activities contains chemicals known [to the State of California] to cause cancer birth defects or other reproductive harm.Some examples of these chemicals are: ●Lead from lead-based paints,●Crystalline silica from bricks and cement and other masonry products, and ●Arsenic and chromium from chemically-treated lumber.Your risk from these exposures varies, depending on how often you do this type of work. To reduce yourexposure to these chemicals: work in a well ventilated area, and work with approved safety equipment, such as those dust masks that are specially desined to filter out microscopic particles.3IMPORTANT SAFETY INSTRUCTIONSWhen using the tool, please observe the safety precautions below to prevent possible accident or injury.GENERAL: TOOLS WARNINGTO OPERATORS●Wear proper clothing for the type of work being done.Take care to avoid entanglement with the moving parts of the tool with clothing, ties, hair etc. If items become entangled it will cause the operator to be pulled towards the tool and lead to possible cause of accident or injury.●Always wear suitable eye protection.Remember, regular glasses are not safety glasses.The lenses are only shock resistant, which will not give you sufficient eye protection you may need in your working environment.●Always wear suitable hearing protection.●Wear respiratory protective equipment (PPE).Wear respiratory protective equipment (PPE) when working in an environment where dust particles are generated in operation.●Avoid working posture that is too stressful.Always ensure a firm footing and well balanced posture.●Do not operate the tool if you are too tired.●Never touch any moving parts of the tool when running.ABOUT WORK AREA●Keep the work area clean.Cluttered work areas (e.g. workbench) invite accidents.●Carefully select the work area.Do not expose tool to rain.Do not use tool in a wet or soaked area.See that the work area is adequately illuminated.●Never work near inflammable liquid or in a potentially explosive atmosphere.●Keep children away from the work area.Keep children and unauthorized people away from the work area to avoid accident or injury.BEFORE OPERATION●Inspect tool before use.Before using, check that screws are securely tightened, that any protective cover or guard is securely in place, other parts are free from damage and that the tool runs as it should.Check that moving parts are properly adjusted for positioning and tightened, that parts are free from damage and properly mounted, and that all other parts are in good condition for normal operation.Should you find any damage to the protective cover or other part, replace it in accordance with the Operation Manual. If there are no instructions in the Manual, please contact the sales agent through which you have purchased your tool or an authorized dealer near you for repair.Likewise, if a switch failure occurs, contact sales agent through which you have purchased your tool or an authorized dealer near you for repair.Do not use the tool if it does not start or stop with the start/stop switch.●Securely mount cutter.An improperly mounted cutter may fly out, causing possible damage to the tool or injury to the operator.●Always remove spanner, wrench, etc., once adjustment has been made with them.●Use a tool appropriate for the application.Avoid heavy-duty application that is beyond the capacity of tool.●Do not use the tool for purposes other than what it is designed for.●Do not abuse tool.Use tool in accordance with the specifications: you’ll get the most out of it while ensuring safety.●Securely fasten workpiece in place.Use a vice or clamp to securely fasten the workpiece in place. It is much safer this way than holding it in your hand, allowing you to operate the tool with both hands.ABOUT HANDLING●How to store tool.When the tool is not used, store it in a dry area and out of reach of children.●How to carry tool.Do not touch the start switch while the tool is being carried.●Do not leave the tool unattended while it is running.Turn off the start switch and disconnect the tool from power source. Do not leave the work area until the tool comes to a complete stop.MAINTENANCE/SERVICE● Do not take apart or modify tool. Disassembly or modification carried out without the supervision of a qualified or authorized service engineer could result in an accident or injury.● Inspect cutting tool and accessories, etc. Always check to see that cutting tool and accessories, etc. are in good operating condition without damage or deterioration before you mount them on the tool. Should you find any damage to an accessory or part, please contact sales agent through which you have purchased your tool or an authorized dealer near you for repair.● Check parts for damage.When you have found damage to accessory or other part, carefully check the damaged part to determine the extent of influence it has upon the functions of the tool – that is, determine whether it can still perform its normal functions.Check to see that the linkage of the moving parts is OK, that all parts are OK without damage, that they are properly mounted, and that the tool functions normally. Should you find any damage to an accessory or part that may hamper proper functioning of the tool, please contact sales agent through which you have purchased your tool or an authorized dealer near you for repair.● Have your tool repaired at an authorized Nitto Service Center.For repair or parts replacement, please contact the sales agent through which you have purchased your tool or an authorized dealer near you.● Use only Nitto genuine parts.Use of improper parts may result in serious occurrence.To obtain a Nitto genuine part, consult this Manual or contact the sales agent from which you have purchased your tool directly.● Do not detach label or nameplate from tool. When a label/nameplate gets damaged, worn or becomes missing, contact the sales agent through which you have purchased your tool or Nitto Kohki Co. Ltd, directly for a replacement.DISPOSAL● When a tool is taken permanently out of service, it is advised that the tool is disassembled, degreased and parts separated by material and recycled locally in the appropriate manner.GENERAL: P NEUMATICTOOLS WARNING● Use appropriate air pressure. Excessively high air pressure will increase the tool number of revolutions or strokes causing not only potential premature failure/breakage but could also lead to an unexpected accident or injury.● Connect tool to air supply line.There are various types of pipes running in a factory in addition to the pneumatic line (such as oxygen, nitrogen, gas and water). For this reason, always ensure that you are connecting to the pneumatic line.● Start tool properly.Turn the start switch OFF before connecting to the air supply line.● Always disconnect the tool from the air supply line before putting on/taking off any accessory and prior to carrying out any maintenance work.● Avoid exposure to exhaust air.Pneumatic tool exhaust air contains oil and contaminated moisture. Make sure the exhaust air is not directed towards your face or anyone else within the work area.● Keep tool off electricity.This pneumatic tool is not electrically insulated. To avoid a potential electric shock do not use where there is a possibility of coming into contact with liveelectricity.CAUTION● Handle tool carefully.Abusive use of tool could invite failure or accident. Do not throw, drop or shock the tool.● Handle air hose carefully.Do not carry the tool by the air hose.Do not pull the air hose to disconnect.4INSTRUCTIONSFOR THIS TOOLAbout Your ToolWARNING● Wear protective glasses and a dustproof mask.Operation generates chips and dust particles, etc.which may cause eye and/or respiratory injury:Always use PPE (Personal Protective Equipment)for eye and respiratory protection.● Always wear suitable hearing protection.The tool generates loud noise. Always use ear plugsfor hearing protection. Take necessary measures tocomply with the local regulatory requirements andlaws with regard to noise level, or do better.● When the drill passes through or locked duringdrilling or tapping, the main body may be Swungaround. If it occurs, release the Trigger quicklyto avoid injury.● Do not tap a blind hole using this air drill.●Never touch moving parts.CAUTION● For tapping, always use tapping paste.● Use sharp taps.● Use a taper tap (No.1) and a plug tap (No.2) fortapping.1. USAGEThis tool is for drilling work with a drill bit. Tapping(right-hand screw) is also possible by using thereversible function.2. CHECK THE CONTENTS OF THE PACKAGECheck the contents and make sure that the tooldoes not have any damage which may haveoccurred during transportation. The contents shouldcorrespond to the list as follows. In case of damage/missing parts, please contact the sales agent fromwhom you purchased the tool.3. AIR SUPPLY3-1. Air PressureAdjust air pressure with the air regulator to the levelappropriate for the pneumatic tool used.Air pressure that is too low will fails the tool tooperate at full capacityAir pressure that is too high may cause damage tothe tool.3-2. Air Line (Fig.1)Use a 9.5mm (3/8”) I.D. connecting hose betweenthe compressor and the tool.Drained water, etc., if flown into the tool, couldcause tool failure. Install an air filter, bsetween thecompressor and the tool.Fig. 13-3. LubricationInstall an oiler between the compressor and the tool.Use the machine oil ISO VG-10. Failure to lubricateas required may result in damage to the tool. Use ofoil that is too thick will reduce the performance of thetool.564. HOW TO OPERATE THE TOOLWARNINGTurn off the air supply and disconnect the air hose before replacing the Drill Bit.4-1. How to Hold the Air Drill (Fig.2)For Stable operation, hold the grip of the Air Drill by one hand with the middle finger put on the Trigger and the index finger extended over the main body, and grip the main body firmly with the other hand asbelow figure.Fig. 24-2. How to Adjust Rotating Speed (Fig.3)Turn the Speed Control Nut to adjust the drill rotating Speed. Adjust the rotating speed for the operation requirement.4-3. How to Change Rotation Direction (Fig.3)Change rotation direction by turning the valve as indicated.Fig. 34-4. Mounting the Drill Bit (Fig.4)Mount the drill bit to the Chuck, and tighten theChuck securely with the accessory Chuck Handle.Fig. 44-5. Start and Stop (Fig.5)(1) C onfirm that the Trigger is OFF and fit the connecting hose onto the Cupla plug on the Air Drill.(2) T o turn on the Air Drill, hold the Air Drill by hands and pull the Trigger.(3) To turn it off, release the Trigger.T riggerONOFF Fig. 54-6. Tapping OperationCAUTION●Make sure the hole as large as possible within the tolerance for strength.(1) Drill a hole before tapping.(2) Apply tapping paste to the tap.(3) C onfirm that the Valve is set for normal rotation direction. (Fig.5)(4) A lign the tap with the hole, and start tapping. If the top end of drill cannot break into the hole when the tap diameter is large, manually rotate the drill in normal rotating direction by several turns with the Trigger set on, and then start tapping.(5) A fter tapping ends, change the rotation direction, and pull out the tap while the drill is rotating reversely.5. THREAD SISE OF HOSE FITTINGThe product comes with a metal-fitting with R thread. Connect the Bushing R thread X NPT thread included as standard accessories. If you would like to have American NPT thread instead.76.STORAGECAUTIONWhen tool is not used, store it out of reach of children.Avoid storing the tool in a location subject to high humidity, if the tool is left as it is used, residual moisture on the inside can cause rusting. Before storing, and after operation, oil the tool at the air inlet with machine oil IS0 VG-10 and run it for a short time.7.ORDERING SERVICE PARTSFor further operational and handling information or for replacement of parts and components, contact the company from whom you purchased the tool or an authorized dealer.In ordering parts and components give each part number, part name and quantity e only NITTO genuine parts.8.OPTIONAL PARTSA hanger to be mounted on the bottom of the grip is available as option. It can be mounted on both ADR-65 and ADR-100.Fig. 6Overseas Affiliates / OfficesNITTO KOHKI U.S.A., INC.46 Chancellor Drive, Roselle, Illinois 60172, U.S.A.For CuplasTel : +1-630-924-5959 Fax : +1-630-924-1174For Machine ToolsTel : +1-630-924-9393 Fax : +1-630-924-0303NITTO KOHKI EUROPE GMBHGottlieb-Daimler-Str. 10, 71144 Steinenbronn, GermanyTel : +49-7157-989555-0 Fax : +49-7157-989555-40 www.nitto-kohki.eu/NITTO KOHKI EUROPE GMBH UK BranchUnit A5, Langham Park Industrial Estate, Maple Road, Castle Donington, Derbyshire DE74 2UT, United KingdomTel : +44-1332-653800 Fax : +44-1332-987273www.nitto-kohki.eu/NITTO KOHKI AUSTRALIA PTY LTD77 Brandl Street, Eight Mile Plains, Queensland 4113, Australia Tel : +61-7-3340-4600 Fax : +61-73340-4640.auNITTO KOHKI (SHANGHAI) CO., LTD.Room1506, Suite C, Orient International Plaza,No.85 Loushanguan Road, Shanghai 200336, ChinaTel : +86-21-6415-3935 Fax : +86-21-6472-6957 NITTO KOHKI (SHANGHAI) CO., LTD. Shenzhen Branch2005C Shenzhen ICC Tower, Fuhuasanlu 168,Futian District, Shenzhen, Guangdong 518048, ChinaTel : +86-755-8375-2185 Fax : +86-755-8375-2187NITTO KOHKI CO., LTD. Singapore Branch10 Ubi Crescent #01-62, Ubi Techpark Lobby D, Singapore 408564 Tel : +65-6227-5360 Fax : +65-6227-0192www.nitto-kohki.co.jp/e/nksb/index.htmlNITTO KOHKI CO., LTD. Bangkok Representative OfficeM&A Business Center, Q-House Convent Bldg.,38 Convent Rd., Silom, Bangrak, Bangkok 10500, ThailandTel : +66-2632-0307 Fax : +66-2632-0308NITTO KOHKI CO., LTD. India Liaison Office3rd Floor, Building No.9-A DLF Cyber City, Phase-III, Gurgaon, Haryana 122002, IndiaTel : +91-124-454-5031 Fax : +65-6227-0192NITTO KOHKI CO., LTD. Mexico Representative OfficeOF1109 Torre Corporativo 1 Piso 11 Central Park Armando Birlain Shaffler #2001 Col Centro Sur, Queretaro, Qro, C.P. 76090, MexicoTel : +52-442-290-1234。
ddk手持工具中文

6
工具
行星齿轮
轻型・小型构造
弯头
追求耐用性的小型弯头
超高速小型马达
分相器方式的高能力马达
第一電通株式会社
判定表示LED
高亮度OK/NG判定、逆转选择表示
前置放大器基板
配备TOOL-ID
扭矩传感器
配备高精度・高可靠性的TD
操作开关
磁性方式 无触点方式 可变速度
连接端口
90°拧扭锁构造 容易取出 牢固的构造
因为扭矩传感器装在前端,所以扭矩的检测精度 和拧紧机是一样的。 一个型号可以对应5NM级到最大40NM的范围。
2个起动按钮可以大幅提高作业效果
10
网络功能(任选功能)
第一電通株式会社
通过与Ethernet对应模块的配备,实现了工件信息的读取(VIN No、发动机No等)、向数据结果的辅助输出。
11
13
HMI 用户控制台
第一電通株式会社
可对应Windows (95,98,NT,ME,2000,Xp)
(日语、英语)
基本功能
设定值编辑・保存 拧紧结果数据收集 / 统计功能 拧紧扭矩曲线表示・文件自动保存 NG・异常文件生成 通用软件 可通过选择菜单进行产品选择
14
HMI 用户控制台
设定画面
控制法的设定可通过选择来方便地完成
下方式的设定选择
第一電通株式会社
15
HMI 用户控制台
设定画面
易懂的图形设定
第一電通株式会社
16
HMI ユーザーコンソール
締付結果画面
第一電通株式会社
拧紧结果收集・统计计算功能・NG异常单独显示
保存的波形数据可以通过Excel等显示