齿轮和轴的计算过程
齿轮的设计计算过程

齿轮的设计计算过程
齿轮的设计计算过程可以分为以下几个步骤:
1. 确定设计参数:确定齿轮的类型、传动功率、转速、齿数、模数等设计参数。
2. 确定齿轮的齿数和模数:根据设计参数中的传动功率和转速,计算出齿轮的齿数和模数。
3. 确定齿轮的几何参数:根据齿数和模数,计算齿轮的几何参数,如分度圆直径、齿高、齿厚等。
4. 确定齿轮的强度参数:根据设计参数中的功率和转速,计算齿轮的强度参数,如接触强度和弯曲强度。
5. 进行强度校核:根据计算出的齿轮强度参数,进行强度校核,确定齿轮的寿命和安全系数。
6. 进行结构设计:根据强度校核的结果,进行齿轮的结构设计,包括齿轮轴的直径、齿轮的材料选择等。
7. 进行CAD绘图和制造:根据设计结果,进行CAD绘图和制造,完成齿轮的设计和制造。
需要注意的是,在设计计算过程中,需要考虑到齿轮的噪音、磨损、振动等问题,以确保齿轮的设计质量和可靠性。
步进电机齿轮计算公式

步进电机齿轮计算公式全文共四篇示例,供读者参考第一篇示例:步进电机是一种常见的电机类型,广泛应用于各种自动控制系统和机械装置中。
而齿轮则是步进电机中常见的传动元件,可以通过齿轮传动实现步进电机的运动。
在设计和制作步进电机齿轮时,需要考虑到齿轮的参数,如模数、齿数、压力角等。
本文将介绍步进电机齿轮的计算公式,帮助读者更好地理解和设计步进电机齿轮。
对于步进电机齿轮的计算,最基本的参数是模数。
模数是齿轮的一个重要参数,用来描述齿轮的尺寸大小。
在步进电机齿轮的设计中,选择适当的模数是非常重要的,可以影响到齿轮的传动性能和寿命。
通常情况下,步进电机齿轮的模数会根据实际需要和设计要求来确定。
在具体计算中,可以使用以下公式来计算步进电机齿轮的模数:\[ m = \frac{d}{z} \]m表示模数,d表示齿轮的分度圆直径,z表示齿轮的齿数。
通过这个公式,我们可以很方便地计算出步进电机齿轮的模数,从而为后续的设计和制作提供参考。
除了模数,步进电机齿轮的齿数也是一个重要参数。
齿数是描述齿轮上齿的数量,可以影响到齿轮的传动效果和传动比。
一般来说,齿数越多,齿轮的传动比就越大,传动效果也会更好。
在计算步进电机齿轮齿数时,可以使用以下公式:这个公式可以根据齿轮的分度圆直径和模数来计算出齿轮的齿数,帮助设计者更好地确定齿轮的结构参数。
\[ \alpha = 20° \]在步进电机齿轮的设计中,通常会选择20°的标准压力角,这样可以更好地保证齿轮的传动效果和寿命。
第二篇示例:步进电机是一种常见的电机类型,其特点是可以通过控制电流来精确控制旋转角度。
而步进电机齿轮计算公式是指在步进电机与齿轮传动系统中计算齿轮参数的公式,用于确定齿轮的种类、参数和传动比等,从而实现步进电机与其他机械部件的传动匹配。
步进电机齿轮计算公式涉及到的主要参数包括齿轮的齿数、模数、分度圆直径、分度圆厚度等。
这些参数是确定齿轮几何形状和传动性能的重要依据,通过合理选择这些参数可以使得步进电机与齿轮传动系统达到最佳匹配,提高传动效率和精度。
定轴齿轮系传动比的计算

构件
太阳轮1 行星轮2 太阳轮3 行星架H
行星齿轮系中的 转化齿轮系中的
转速
转速
1
2
3
H
1H 1 H
H 2
2
H
H 3
3
H
H H
H
H
0
12.2 行星齿轮系传动比的计算
12.2.2 行星齿轮系的传动比计算
12.1.2 空间定轴齿轮系传动比的计算
[例题] 在如图所示的齿轮系中,已知 z1 z2 z3' z4 20 ,齿轮1、3、3’
和5同轴线,各齿轮均为标准齿轮。若已知轮1的转速n1=1440r/min, 求轮5的转速
[解]
该齿轮系为一平面定轴齿轮系,齿轮
2和4为惰轮,齿轮系中有两对外啮合齿
轮,根据公式可得
12.3 齿轮系的应用
12.3.1 获得大的传动比
若想要用一对齿轮获得较大的传动比,则必然有一个齿轮要做得很大, 这样会使机构的体积增大,同时小齿轮也容易损坏。如果采用多对齿轮组 成的齿轮系则可以很容易就获得较大的传动比。只要适当选择齿轮系中各 对啮合齿轮的齿数,即可得到所要求的传动比。在行星齿轮系中,用较少 的齿轮即可获得很大的传动比。
根据齿轮系运转时齿轮的轴线位置相对于机架是否固定,又可将齿 轮系分为两大类:定轴齿轮系和行星齿轮系。
12.1 定轴齿轮系传动比的计算
各种齿轮系
12.1 定轴齿轮系传动比的计算
如果齿轮系运转时所有齿轮的轴线保持固定,称为定轴齿轮系,定轴齿 轮系又分为平面定轴齿轮系和空间定轴齿轮系两种。
设齿轮系中首齿轮的角速度为 A,末齿轮的角速度 K, A 与 K
直齿圆柱齿轮轴向力计算

直齿圆柱齿轮轴向力计算一、前言齿轮是传动机械中常用的元件之一,能够将输入轴的旋转转化为输出轴的旋转。
在齿轮使用的过程中,轴向力是一个重要的参数,需要进行计算和评估。
本文将以直齿圆柱齿轮为例,介绍轴向力的计算方法。
二、直齿圆柱齿轮结构直齿圆柱齿轮的结构简单,主要由圆柱形齿轮和法向于齿轮面的齿(齿廓线为圆弧形)组成。
其尺寸参数包括模数、齿数、压力角等。
三、定义轴向力在直齿圆柱齿轮传动中,齿轮会在轴向方向产生力,这个力被称为轴向力,记为Ft。
轴向力的大小与齿轮的设计参数(齿数、传递力矩等)、工作条件(转速、载荷等)以及齿轮制造精度等因素有关。
四、轴向力计算直齿圆柱齿轮轴向力的计算是根据齿轮端面力平衡原理和渐开线法则进行的。
齿轮端面力平衡原理指出,对于两个啮合的齿轮,它们沿着啮合线方向的力相等,但在法向方向上的力则不相等,具体表现为一个向内的侧向力Fr和一个沿着轴向方向的轴向力Ft。
若忽略摩擦力,则有Ft =F1 - F2,其中F1、F2为相邻两齿轮侧面载荷的水平分量。
而渐开线法则将齿轮啮合时沿任一啮合线处的齿面曲线视为渐开线,其中存在一个渐开线垂线。
将位于渐开线垂线两端的齿轮抽象为两个小齿轮,其啮合时沿任意直线上的受力和力矩为零,即:Fa1 + Fa2 = 0,Ma1 + Ma2 = 0。
其中Fa1、Fa2分别为垂直于直线方向的力,Ma1、Ma2分别为这两个小齿轮的力矩。
综合以上两个原理,可得到直齿圆柱齿轮轴向力的计算公式:Ft = (T1-T2) / (2b sinβ)其中T1、T2为两齿轮传递的传动力矩,b为啮合齿宽,β为压力角。
五、注意事项1. 轴向力的大小对传动系统的正常运转和寿命有重要影响,设计时应充分考虑;2. 齿轮制造精度对轴向力大小影响较大,制造时应尽可能减少误差;3. 不同的统计方法和假设条件可能导致轴向力的计算结果存在差异,需要进行实验验证和修正。
六、结论直齿圆柱齿轮轴向力的计算是根据齿轮端面力平衡原理和渐开线法则进行的,其大小与齿轮的设计参数和工作条件有关。
螺旋齿轮传动设计计算

螺旋齿轮传动设计计算
1.轴速比的计算
轴速比是指两个相邻轴上齿轮的转速比。
根据传动比的定义,轴速比可以通过齿轮的啮合齿数来计算。
假设小齿轮的齿数为N1,大齿轮的齿数为N2,则轴速比为:
轴速比=N2/N1
2.齿轮模数的选择
齿轮模数是指齿轮齿数与齿轮直径的比值。
在选择齿轮模数时,需要根据传动的功率和转速等参数来确定。
根据齿距计算公式,齿轮模数可以选择为:
模数=齿数/齿距
3.齿轮啮合角的计算
齿轮啮合角是指两个啮合齿轮的主动齿与被动齿之间的夹角。
根据传动比和齿轮啮合的齿数,齿轮啮合角可以通过以下公式进行计算:齿轮啮合角 = arccos(N1/N2)
4.齿轮中心距的计算
齿轮中心距是指两个相邻轴上齿轮的中心距离。
在设计计算中,齿轮中心距可以通过以下公式进行计算:
齿轮中心距=(齿数1+齿数2)/2*模数
其中,齿数1和齿数2分别为小齿轮和大齿轮的齿数。
5.齿轮弯曲强度的计算
齿轮的弯曲强度是指齿轮在传动过程中所承受的弯曲应力。
通常,齿轮的弯曲强度可以通过以下公式进行计算:
齿轮弯曲强度=270*Y*(Wt^2*Mt*Kv)/(b*m*Z)
其中,Y为齿轮弯曲系数,Wt为齿轮齿宽压力,Mt为传动扭矩,Kv 为动载荷系数,b为齿轮齿宽,m为齿轮模数,Z为齿轮齿数。
计算过程及计算说明__一、传动方
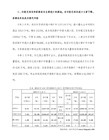
2、 计算各轴的功率(KW)
PI=P工作=2.4KW
PII=PI×η带=2.4×0.96=2.304KW
PIII=PII×η轴承×η齿轮=2.304×0.98×0.96
=2.168KW
3、 计算各轴扭矩(N•mm)
TI=9.55×106PI/nI=9.55×106×2.4/960
由课本图6-35C查得:
σFlim1=290Mpa σFlim2 =210Mpa
由图6-36查得:YNT1=0.88 YNT2=0.9
试验齿轮的应力修正系数YST=2
按一般可靠度选取安全系数SF=1.25
计算两轮的许用弯曲应力
[σF]1=σFlim1 YSTYNT1/SF=290×2×0.88/1.25Mpa
=2×500+1.57(100+200)+(200-100)2/4×500
=1476mm
根据课本P71表(5-2)取Ld=1400mm
根据课本P84式(5-16)得:
a≈a0+Ld-L0/2=500+1400-1476/2
=500-38
=462mm
(4)验算小带轮包角
α1=1800-dd2-dd1/a×57.30
根据课本P107表6-1取标准模数:m=2.5mm
(6)校核齿根弯曲疲劳强度
根据课本P132(6-48)式
σF=(2kT1/bm2Z1)YFaYSa≤[σH]
确定有关参数和系数
分度圆直径:d1=mZ1=2.5×20mm=50mm
d2=mZ2=2.5×120mm=300mm
齿轮系传动比的计算

齿轮系传动比的计算齿轮系统是一种常用的传动装置,通过两个或多个齿轮之间的啮合来实现不同轴的旋转传动。
传动比是指输入轴和输出轴的转速之比,通常用于计算齿轮传动的输出速度以及扭矩的增减。
计算齿轮传动比涉及到齿数和模数的计算,下面将详细介绍齿轮传动比的计算公式和步骤。
1.齿数的计算:齿数是齿轮的一个重要参数,可以用来计算齿轮传动比。
如果已知输入轴齿轮的齿数为N1,输出轴齿轮的齿数为N2,那么传动比K为:K=N2/N12.模数的计算:模数是齿轮的另一个重要参数,用来描述齿轮的齿大小和齿距之间的关系。
模数可以通过以下公式计算:m=D/(Z+2)其中,m为模数,D为齿轮的分度圆直径,Z为齿数。
3.传动比的计算:已知输入轴齿轮的齿数为N1,输出轴齿轮的齿数为N2,齿轮的模数分别为m1和m2,则传动比K为:K=N2/N1=(m2/m1)*(D1/D2)在实际计算中,可以根据已知的参数来计算模数,然后使用模数来计算齿轮的分度圆直径,最后计算出传动比。
齿轮的模数、齿数和分度圆直径的计算公式如下:D=m*(Z+2)m=K*m1N=(π*D)/m其中,D为分度圆直径,m为模数,Z为齿数,N为轮齿数。
除了传动比的计算,齿轮系统在实际应用中还需要考虑一些其他因素,如轴间距的确定、齿轮啮合角等。
这些因素都会对齿轮传动比的计算和实际传动效果产生影响。
总结:齿轮传动比的计算涉及到齿数和模数的计算,传动比可以通过已知的齿数和模数来计算。
同时,在实际应用中还需要考虑一些其他因素的影响,如轴间距和齿轮啮合角。
这些因素的综合作用使得齿轮传动比的计算变得更加复杂,在实际应用中需要综合考虑多个因素来确定传动比。
各种齿轮系传动比的计算
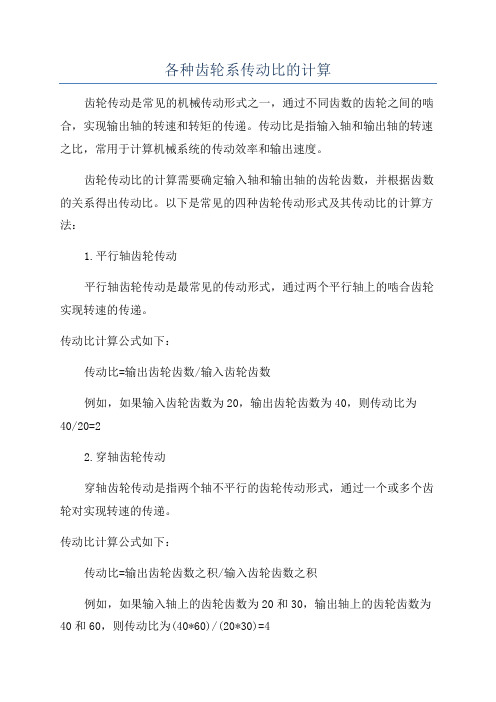
各种齿轮系传动比的计算齿轮传动是常见的机械传动形式之一,通过不同齿数的齿轮之间的啮合,实现输出轴的转速和转矩的传递。
传动比是指输入轴和输出轴的转速之比,常用于计算机械系统的传动效率和输出速度。
齿轮传动比的计算需要确定输入轴和输出轴的齿轮齿数,并根据齿数的关系得出传动比。
以下是常见的四种齿轮传动形式及其传动比的计算方法:1.平行轴齿轮传动平行轴齿轮传动是最常见的传动形式,通过两个平行轴上的啮合齿轮实现转速的传递。
传动比计算公式如下:传动比=输出齿轮齿数/输入齿轮齿数例如,如果输入齿轮齿数为20,输出齿轮齿数为40,则传动比为40/20=22.穿轴齿轮传动穿轴齿轮传动是指两个轴不平行的齿轮传动形式,通过一个或多个齿轮对实现转速的传递。
传动比计算公式如下:传动比=输出齿轮齿数之积/输入齿轮齿数之积例如,如果输入轴上的齿轮齿数为20和30,输出轴上的齿轮齿数为40和60,则传动比为(40*60)/(20*30)=43.内外啮合齿轮传动内外啮合齿轮传动是指一个齿轮位于另一个齿轮的内部并与其啮合的传动形式,通过齿轮的运动将旋转轴方向转换为轴线的转速和转矩。
传动比计算公式如下:传动比=1/(输入齿轮齿数/输出齿轮齿数)例如,如果输入齿轮齿数为40,输出齿轮齿数为20,则传动比为1/(40/20)=0.54.斜齿轮传动斜齿轮传动是通过斜齿轮的啮合实现转速传递的传动形式,常用于垂直传动和传递大转矩的场合。
传动比计算公式如下:传动比=输出齿轮齿数/输入齿轮齿数*齿数系数齿数系数是考虑斜齿轮齿面压力角的修正系数。
以上是常见齿轮传动形式的传动比计算方法,根据实际情况选择适合的传动形式,并根据齿轮齿数和齿数系数计算传动比。
对于复杂的齿轮系统,可以通过级联多个传动,将多个传动比相乘来得到整个系统的传动比。
可以通过合理的设计和计算,实现满足机械系统性能要求的传动比。
齿轮与轴的三种连接方式
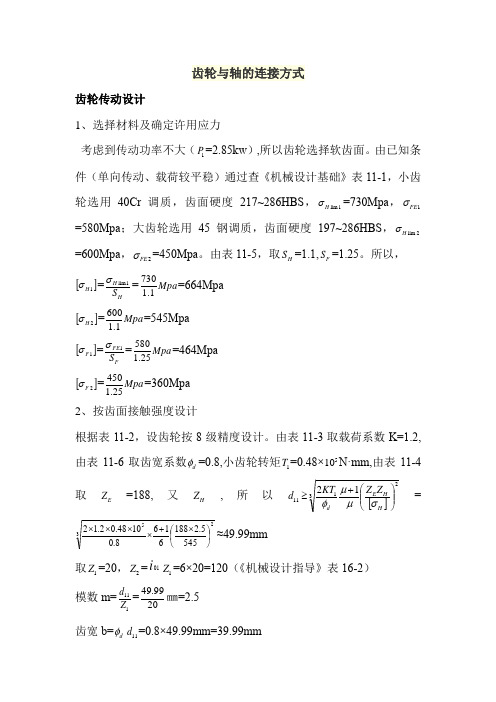
齿轮与轴的连接方式齿轮传动设计1、选择材料及确定许用应力考虑到传动功率不大(1P =2.85kw ),所以齿轮选择软齿面。
由已知条件(单向传动、载荷较平稳)通过查《机械设计基础》表11-1,小齿轮选用40Cr 调质,齿面硬度217~286HBS ,1lim H σ=730Mpa ,1FE σ=580Mpa ;大齿轮选用45钢调质,齿面硬度197~286HBS ,2lim H σ=600Mpa ,2FE σ=450Mpa 。
由表11-5,取H S =1.1,F S =1.25。
所以,[]1H σ=HH S 1lim σ=Mpa 1.1730=664Mpa[]2H σ=Mpa 1.1600=545Mpa[]1F σ=FFE S 1σ=Mpa 25.1580=464Mpa[]2F σ=Mpa 25.1450=360Mpa2、按齿面接触强度设计根据表11-2,设齿轮按8级精度设计。
由表11-3取载荷系数K=1.2,由表11-6取齿宽系数d φ=0.8,小齿轮转矩1T =0.48×510N·mm,由表11-4取EZ =188,又HZ ,所以[]3211112⎪⎪⎭⎫⎝⎛+≥H HE d Z Z KT d σμμφ=3255455.21886168.01048.02.12⎪⎭⎫⎝⎛⨯+⨯⨯⨯⨯≈49.99mm取1Z =20,2Z =01i 1Z =6×20=120(《机械设计指导》表16-2) 模数m=111Z d =2099.49㎜=2.5 齿宽b=d φ11d =0.8×49.99mm=39.99mm大齿轮的齿宽b=40mm 小齿轮的齿宽b=45mm取2b =45mm,1b =50mm,按表4-1取m=2.5mm,实际的11d =1Z m=20×2.5mm=50mm,12d =120×2.5mm=300mm 中心距1a =21211d d +=175mm 验算轮齿弯曲强度齿形系数1Fa Y =2.94(图11-8),1Sa Y =1.56(图11-9)2Fa Y =2.13,2Sa Y =1.811F σ=121112z bm Y Y KT Sa Fa =205.299.3956.194.21048.02.1225⨯⨯⨯⨯⨯⨯⨯=105.7Mpa ≤[]1F σ=464Mpa 2F σ=11221Sa Fa Sa Fa F Y Y Y Y σ=56.194.281.113.27.105⨯⨯⨯Mpa=88.85Mpa ≤[]2F σ=360Mpa,安全。
齿轮的设计计算过程
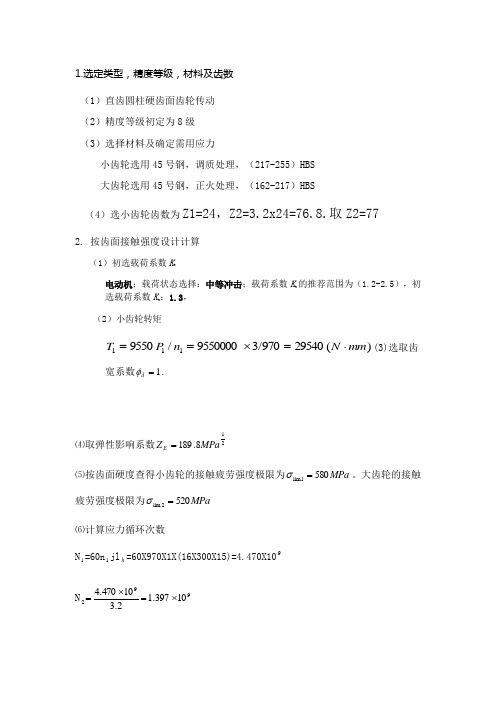
1.选定类型,精度等级,材料及齿数 (1)直齿圆柱硬齿面齿轮传动 (2)精度等级初定为8级 (3)选择材料及确定需用应力小齿轮选用45号钢,调质处理,(217-255)HBS 大齿轮选用45号钢,正火处理,(162-217)HBS (4)选小齿轮齿数为Z1=24,Z2=3.2x24=76.8.取Z2=772. 按齿面接触强度设计计算(1)初选载荷系数K t电动机;载荷状态选择:中等冲击;载荷系数K t 的推荐范围为(1.2-2.5),初选载荷系数K t :1.3, (2)小齿轮转矩)(29540/97039550000/9550111mm N n P T ⋅=⨯==(3)选取齿宽系数1=d φ.⑷取弹性影响系数218.189MPa Z E =⑸按齿面硬度查得小齿轮的接触疲劳强度极限为MPa 5801lim =σ。
大齿轮的接触疲劳强度极限为MPa 5202lim =σ ⑹计算应力循环次数N 1=60n 1jl h =60X970X1X(16X300X15)=4.470X109N 99210397.12.310470.4⨯=⨯=⑺取接触疲劳寿命系数K .89.0,88.021==HN HN K⑻计算接触疲劳许用应力 取失效概率为1%,安全系数S=1[]a HN H MP MPa SK 4.5105709.01lim 11=⨯==σσ[]a HN H MP MPa SK 8.46253095.02lim 22=⨯==σσ⑼按齿面接触强度设计计算 ①试算小齿轮分度圆直径mm Z u u T K d H E d t t 248.56)8.4628.189(2.32.4110954.28.132.2)][(132.23243211=⨯⨯⨯=+〉σφ②计算齿轮圆周转速v 并选择齿轮精度 s m n d V t /48.2100060970248.5610006011=⨯⨯⨯=⨯=ππ③计算齿轮宽度bmm d b t d 248.56248.5611=⨯=⨯=φ④计算齿轮宽度b 与齿高h 之比 模数 mm mm Z d m t 033.22272.44111===齿高 mm mm m h 574.4033.225.225.21=⨯==67.10=hb⑤计算载荷系数根据v=2.27m/s 。
凸轮轴齿轮扭力计算公式

凸轮轴齿轮扭力计算公式在机械传动系统中,凸轮轴齿轮扭力是一个重要的参数,它直接影响着机械传动系统的稳定性和可靠性。
因此,准确计算凸轮轴齿轮扭力是非常重要的。
本文将介绍凸轮轴齿轮扭力的计算公式及其应用。
凸轮轴齿轮扭力的计算公式可以通过以下步骤得到:第一步,计算凸轮轴齿轮的转矩。
凸轮轴齿轮的转矩可以通过以下公式计算得到:T = P 9550 / n。
其中,T为凸轮轴齿轮的转矩,单位为N·m;P为功率,单位为kW;n为转速,单位为r/min。
第二步,计算凸轮轴齿轮的扭矩。
凸轮轴齿轮的扭矩可以通过以下公式计算得到:M = T K。
其中,M为凸轮轴齿轮的扭矩,单位为N·m;T为凸轮轴齿轮的转矩,单位为N·m;K为载荷系数,通常取1.2。
第三步,计算凸轮轴齿轮的扭力。
凸轮轴齿轮的扭力可以通过以下公式计算得到:F = M / r。
其中,F为凸轮轴齿轮的扭力,单位为N;M为凸轮轴齿轮的扭矩,单位为N·m;r为凸轮轴齿轮的半径,单位为m。
通过以上三步计算,我们可以得到凸轮轴齿轮的扭力。
这个扭力值可以帮助工程师们设计和选择合适的凸轮轴齿轮,以确保机械传动系统的稳定性和可靠性。
凸轮轴齿轮扭力的计算公式在机械传动系统的设计和分析中具有重要的应用价值。
通过这个公式,工程师们可以准确地计算凸轮轴齿轮的扭力,从而为机械传动系统的设计和选择提供参考依据。
同时,这个公式也可以帮助工程师们优化机械传动系统的结构,提高其传动效率和可靠性。
在实际工程中,凸轮轴齿轮扭力的计算公式可以通过计算机辅助设计(CAD)软件来实现。
工程师们可以在CAD软件中输入凸轮轴齿轮的参数,然后通过计算公式得到凸轮轴齿轮的扭力。
这样可以大大提高工作效率,同时也可以减少人为误差,保证计算结果的准确性。
总之,凸轮轴齿轮扭力的计算公式是机械传动系统设计和分析中的重要工具。
通过这个公式,工程师们可以准确地计算凸轮轴齿轮的扭力,为机械传动系统的设计和选择提供参考依据,同时也可以实现机械传动系统的优化设计。
齿轮各部分计算公式
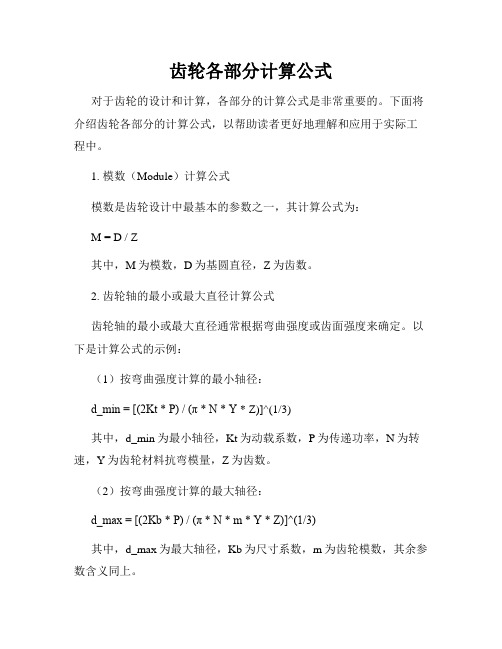
齿轮各部分计算公式对于齿轮的设计和计算,各部分的计算公式是非常重要的。
下面将介绍齿轮各部分的计算公式,以帮助读者更好地理解和应用于实际工程中。
1. 模数(Module)计算公式模数是齿轮设计中最基本的参数之一,其计算公式为:M = D / Z其中,M为模数,D为基圆直径,Z为齿数。
2. 齿轮轴的最小或最大直径计算公式齿轮轴的最小或最大直径通常根据弯曲强度或齿面强度来确定。
以下是计算公式的示例:(1)按弯曲强度计算的最小轴径:d_min = [(2Kt * P) / (π * N * Y * Z)]^(1/3)其中,d_min为最小轴径,Kt为动载系数,P为传递功率,N为转速,Y为齿轮材料抗弯模量,Z为齿数。
(2)按弯曲强度计算的最大轴径:d_max = [(2Kb * P) / (π * N * m * Y * Z)]^(1/3)其中,d_max为最大轴径,Kb为尺寸系数,m为齿轮模数,其余参数含义同上。
3. 齿宽计算公式齿宽是齿轮上两齿间的宽度,其计算公式为:b = m * z其中,b为齿宽,m为模数,z为齿数。
4. 齿顶高计算公式齿顶高是齿轮齿形中顶面的高度,其计算公式为:ha = 0.5m * (α + β)其中,ha为齿顶高,m为模数,α为压力角,β为顶隙角。
5. 齿根高计算公式齿根高是齿轮齿形中根面的高度,其计算公式为:hf = 1.25 * ha其中,hf为齿根高,ha为齿顶高。
6. 齿根圆直径计算公式齿根圆直径是齿轮齿形中根部的圆直径,其计算公式为:df = D - 2hm - 2hf其中,df为齿根圆直径,D为基圆直径,hm为齿顶高。
以上是几个常用的齿轮各部分的计算公式。
通过这些公式,可以更好地进行齿轮设计和计算,确保齿轮的准确性和可靠性。
在实际工程中,根据具体需求和材料特性,还可以进行进一步的调整和优化。
齿轮箱轴设计计算

齿轮箱轴设计计算轴的结构设计及计算一, 轴一的设计1. 轴上的功率P ,转速n 和转矩TP=2.996KWn=576r/min T=49.673N.m2. 求一号齿轮上的力因已知分度圆直径所以:则 Fr1=1505.2424N Ft1=547.863N3. 初步确定最小直径先按公式15-2初步估算轴的最小直径。
选取轴的材料为45号钢,调制处理。
根据表15-3取A0=110,根据实际工作条件A0增大5%于是得:4. mm n P C d mm n P C d mm n P C d A C 85.4640.41763.25.11538.32515.130877.25.11520576996.25.11505.1045315333333322233111=⨯=≥=⨯=≥=⨯=≥⨯=-钢取得:查课本表轴的结构设计 (1) 拟定轴的零件的装配方案:见装配图其其简图如下(2)根据轴向定位的要求确定轴的各段直径1)由于齿轮直径较小故制成齿轮轴齿轮段CD 长度有齿轮宽度决定为66mm,AB,EF段安装轴承考虑到齿轮距箱体内壁的距离以及与其余轴的关系AB=29,EF=29,GH段由于安装带轮,根据所选带轮确定GH=65,直径为最小。
2)初步选择滚动轴承。
因轴承承受大部分为径向力,受轴向力较小,故选择价格低廉的深沟球轴承,根据AB直径,由轴承产品目录中初步选取0游隙组,,标准精度级的单列球轴承6208,其尺寸可查指导手册,右端距齿轮的距离较大故制出轴肩,轴承采用润滑脂润滑,(3)轴的轴向定位见上图,(4)轴上圆角和倒角尺寸的确定参考表15-25求轴上的载荷首先根据上图作出轴的受力简图载荷水平垂直支反力Fn Fnt1=680.258NFnt2=202.459NFnr1=428.158NFnr2=93.5N带轮径向力Fp Fp=1430.58N弯矩133759.25MPa 0总弯矩133759.25 MPa扭矩T 49.673 MPa5.按照弯扭合成应力校核轴的强度进行校核时只校核最大弯矩的截面中的数据,由于轴为单向旋转,为脉动循环变应力,取a=0.6,轴的计算应力:总弯矩M=√Mr 2+Mv2=129409.07N·m<133759.25 N·m由公式σ=√0.6T2+M20.1d=4.8MPa<[σ]=60 MPa前面已经选定轴的材料,查表15-1查得最大极限应力为60MPa。
标准齿轮参数计算
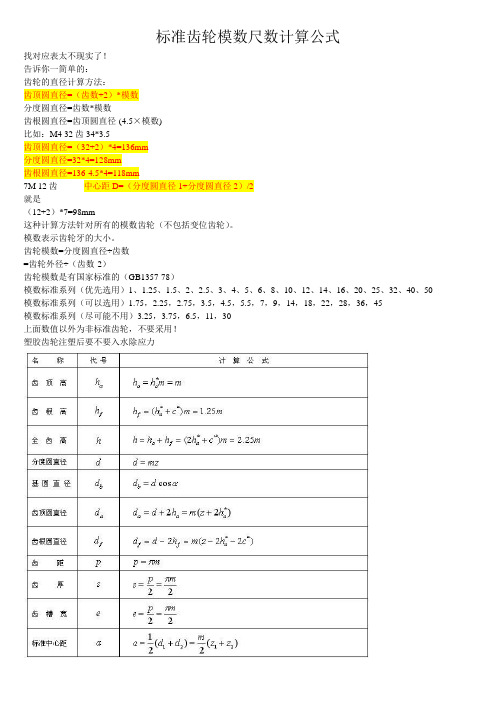
标准齿轮模数尺数计算公式找对应表太不现实了!告诉你一简单的:齿轮的直径计算方法:齿顶圆直径=(齿数+2)*模数分度圆直径=齿数*模数齿根圆直径=齿顶圆直径-(4.5×模数)比如:M4 32齿34*3.5齿顶圆直径=(32+2)*4=136mm分度圆直径=32*4=128mm齿根圆直径=136-4.5*4=118mm7M 12齿中心距D=(分度圆直径1+分度圆直径2)/2就是(12+2)*7=98mm这种计算方法针对所有的模数齿轮(不包括变位齿轮)。
模数表示齿轮牙的大小。
齿轮模数=分度圆直径÷齿数=齿轮外径÷(齿数-2)齿轮模数是有国家标准的(GB1357-78)模数标准系列(优先选用)1、1.25、1.5、2、2.5、3、4、5、6、8、10、12、14、16、20、25、32、40、50 模数标准系列(可以选用)1.75,2.25,2.75,3.5,4.5,5.5,7,9,14,18,22,28,36,45模数标准系列(尽可能不用)3.25,3.75,6.5,11,30上面数值以外为非标准齿轮,不要采用!塑胶齿轮注塑后要不要入水除应力精确测定斜齿轮螺旋角的新方法Circular Pitch (CP)周节齿轮分度圆直径d的大小可以用模数(m)、径节(DP)或周节(CP)与齿数(z)表示径节P(DP)是指按齿轮分度圆直径(以英寸计算)每英寸上所占有的齿数而言径节与模数有这样的关系: m=25.4/DPCP1/8模=25.4/DP8=3.175 3.175/3.1416(π)=1.0106模1) 什么是「模数」?模数表示轮齿的大小。
R模数是分度圆齿距与圆周率(π)之比,单位为毫米(mm)。
除模数外,表示轮齿大小的还有CP(周节:Circular pitch)与DP(径节:Diametral pitch)。
【参考】齿距是相邻两齿上相当点间的分度圆弧长。
2) 什么是「分度圆直径」?分度圆直径是齿轮的基准直径。
齿轮轴计算

4)轴承端盖的总宽度为20mm。根据轴承端盖的装拆以及便于对轴承添加脂润滑的要求,去端盖的外端面与半联轴器右端面间的距离l=30mm,故取L2=50mm。
5)取齿轮距箱体内壁之间距离 ,考虑箱体的铸造误差,在确定滚动轴承位置时,应距箱体内壁一段距离s,取s=8mm,已知滚动轴承宽度T=19.75mm,则
(2)根据轴向定位的要求确定轴的各段直径和长度
1)为了满足半联轴器的轴向定位, - 处应设置一轴肩,故取
2)初步选择滚动轴承。选择7008C轴承。根据dxDxB=40x68x15mm。取
设计计算内容
主要结果
右端轴承采用轴肩进行定位。查手册定位高度h=3.5mm,即
3)取安装齿轮处的直径 ,齿轮的左端与左轴承之间采用套筒定位。已知齿轮轮毂的宽度为84mm,取
设计计算内容
主要结果
1求输出轴上的功率P2,转速n2,和转矩T2
若取齿轮传动的效率为 ,则
又
2求作用在齿轮上的力
各力方向如图所示。
3初步确定轴的最小直径
先按式15-2初步估算轴的最小直径。选取轴的材料为45钢,调质处理。根据表15-3,取A0=112,于是得
输出轴的最小直径显然是安装联轴器处轴的直径。为了使所选的直径与联轴器的孔径相适应,故需同时选择联轴器型号。
(4)确定轴上的圆角和倒角尺寸
如图
5.求轴上的载荷
首先根据轴的结构图做出轴的计算简图。在确定轴承的支点位置,应从手册中查得a的值。对于30208型圆锥滚子轴承,由手册中查得a=16.9mm。因此,作为简支梁的轴的支撑跨距 。根据轴的计算简图做出轴的弯矩图和扭转图。
齿轮轴计算过程

倒档器锥齿轮计算因为转向器没有设置传动比 我选用两个材料和尺寸大小一样的锥齿轮 1)选择齿轮材料,确定许用应力由机械设计书表6.2选两齿轮材料为: 小齿轮40Cr 调质 HBS1=260 HBS大齿轮 45 正火 HBS2=210 HBS 许用接触应力[]H σ 由[]H σ=limminH N H Z S σg接触疲劳极限lim H σ查机械设计 图6-4 lim1H σ=700N/mm2接触强度寿命系数N Z 应力循环次数N lim2H σ=550N/mm N=60njL h =6080001(103004)⨯⨯⨯⨯⨯ N=5.76910⨯ 查图机械设计6-5(如没有特殊说明图表都来源于机械设计书)得N ZN Z =1接触最小安全系数lim H S lim H S =1[]1H σ =700 1/1⨯ []1H σ =700N/mm 2[]25501/1H σ=⨯ []2H σ =550N/ mm 2许用弯曲应力[]F σ 由式[]limminF F N X F Y Y S σσ=弯曲疲劳极限lim F σ 查图6-7 lim1F σ=540N/mm 2, 2lim 2420/F N mm σ= 弯曲强度寿命N Y 查图6-8 12N N Y Y ==1弯曲强度尺寸系数X Y 查图6-9(设模数m 小于5) X Y =1 弯曲强度最小安全系数min F S min F S =1.4 则[]1F σ=54011/1.4⨯⨯ []1F σ=450 N/mm 2 []2F σ= 42011/1.4⨯⨯ []2F σ=300 N/mm 2 2)齿面解除疲劳强度设计计算确定齿轮传动精度等级,估取圆周速度7/t m s υ=,参考表6-7 、6-8选取∏公差等级组7级锥齿轮分度圆直径d(1d ≥+齿宽系数dm ψ 查表6.14 dm ψ=0.3 小齿轮齿数1z =13 1z =13 那么 大齿轮齿数211z z i ==18.2圆整 2z =18 齿数传动比u=1.385 u=1.385 传动比误差为/u u V /(1.4 1.385)/1.40.01070.05u u =-=<V 倒档器输入轴扭矩1T1119550/T P n ==10050 N m g 1T =10050N •mm 载荷系数K= A V K K K βA K ——使用系数 查表6.3 A K =1.1 V K ——动载系数 由推荐值 1.05-1.4 V K =1.2 K β——齿向载荷分布系数 由推荐值1.0-1.2 K β=1.1载荷系数 K1.1 1.2 1.1A V K K K K β==⨯⨯ K=1.452材料弹性系数E Z 查6.4E Z 节点区域系数 H Z 查图6-3 H Z =2.5计算得d1≥44.74 mm d1≥44.74mm 齿轮模数m m=d1/z1=3.44 圆整 m=3.5 小齿轮大端分度圆直径 d1=mz1=3.5⨯13 d1=45.5mm 大齿轮大端分度圆直径 d2=mz2=3.5⨯18 d2=63mm 齿轮平均分度圆直径d m =/(1dd1m =45.5/(1+d 1m =38.7mmd2m ) d 2m =53.59mm圆周速度1m υ=3.141/60000m d n I 1m υ=16.2m/s 2m υ=3.1422/60000m d n2m υ=18.84m/s齿宽b b1=dm ψd 1m =11.61mm 圆整 b1=12mm b2=dm ψd 2m =16.007mm 圆整 b2=16mm 3)齿根弯曲疲劳强度校核计算 由式[]212(1F Fa Sa F KT Y Y bdm σσ=≤当量齿数v z11/cos 3016.04v z z δ===1v z =16.04221z z u υυ==30.75 2z υ=30.75 齿形系数Fa Y 应力修正系数Sa Y 查表 6.5 1Fa Y =3.21,2 2.91Fa Y =1Sa Y =1.46,2Sa Y =1.53计算弯曲疲劳强度1F σ=197.17<[]H σ 所以齿根弯曲强度满足 4)齿轮其他主要尺寸计算 分度锥角1cos δ=0.8107 1δ=35.83o锥距255.1R ==R=55.1mm齿顶高 3a a h h m mm *==齿根高 () 3.6f a h h c m mm **=+=齿顶圆直径2cos 82.24a a d d h mm δ=+=齿根圆直径 2cos 72.9f f d d h mm δ=-=齿顶角 arctan(/) 3.1a a h R θ== 齿根角 arctan(/) 3.7f f h R θ== 4)结构设计及绘制齿轮零件图花键连接强度计算花键轴的内径为20mm,轴与发动机轴用凸缘联轴器连接;选取花键规格N d D B ⨯⨯⨯为620245⨯⨯⨯;因为花键是连接发动机输出轴和转向器轴,因此,他们是动连接。
齿轮计算PPT课件

效率影响因素探讨
01
02
03
齿轮精度
齿轮的加工精度和装配精 度对传动效率有直接影响, 高精度齿轮能够减少摩擦 和振动,提高效率。
润滑条件
良好的润滑条件能够降低 摩擦系数,减少磨损和热 量产生,从而提高传动效 率。
载荷特性
载荷的大小、方向和变化 频率都会对传动效率产生 影响,合理设计和控制载 荷是提高效率的关键。
05
齿轮材料选择与热处理工 艺
常用齿轮材料介绍
碳素钢
具有良好的可加工性和 较低的成本,但强度和
耐磨性相对较低。
合金钢
不锈钢
铸铁
通过添加合金元素提高材料 的强度、硬度和耐磨性,适 用于高负荷和高速齿轮。
具有优异的耐腐蚀性和美 观性,但成本较高,适用 于特殊环境下的齿轮。
具有良好的铸造性能和减震 性能,但强度和耐磨性较差 ,适用于低速和轻载齿轮。
03
齿轮传动比与效率分析
传动比概念及计算公式
传动比定义
传动比是输入转速与输出转速之比,表示了动力传递的速率变化。
计算公式
传动比i = 输入转速n1 / 输出转速n2,其中n1、n2分别为输入轴 和输出轴的转速。
应用场景
传动比的计算在齿轮设计、选型及性能分析中具有重要意义,它直 接影响到齿轮传动的效率和扭矩输出。
剃齿加工
利用剃齿刀从齿轮齿面上剃下一层很 薄的切屑,以提高齿轮精度和表面光
洁度。
插齿加工
利用插齿机上的插齿刀按展成法或成 形法加工齿轮,主要用于加工内齿轮 和多联齿轮。
珩齿加工
利用珩磨轮对淬火后的齿轮进行精整 加工,以改善齿轮表面粗糙度和减小 齿轮噪声。
加工误差来源分析
机床误差
机械设计手册:齿轮传动设计与计算
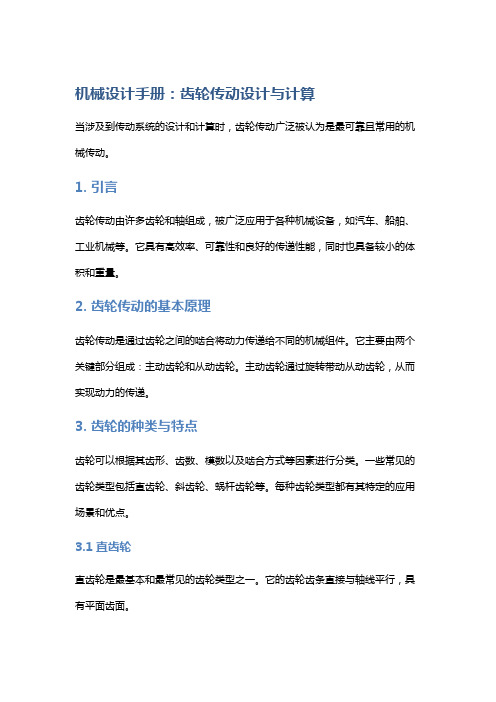
机械设计手册:齿轮传动设计与计算当涉及到传动系统的设计和计算时,齿轮传动广泛被认为是最可靠且常用的机械传动。
1. 引言齿轮传动由许多齿轮和轴组成,被广泛应用于各种机械设备,如汽车、船舶、工业机械等。
它具有高效率、可靠性和良好的传递性能,同时也具备较小的体积和重量。
2. 齿轮传动的基本原理齿轮传动是通过齿轮之间的啮合将动力传递给不同的机械组件。
它主要由两个关键部分组成:主动齿轮和从动齿轮。
主动齿轮通过旋转带动从动齿轮,从而实现动力的传递。
3. 齿轮的种类与特点齿轮可以根据其齿形、齿数、模数以及啮合方式等因素进行分类。
一些常见的齿轮类型包括直齿轮、斜齿轮、蜗杆齿轮等。
每种齿轮类型都有其特定的应用场景和优点。
3.1 直齿轮直齿轮是最基本和最常见的齿轮类型之一。
它的齿轮齿条直接与轴线平行,具有平面齿面。
3.2 斜齿轮斜齿轮具有斜齿面,其齿条与轴线有一定的角度。
斜齿轮能够传动更大的力和扭矩,常用于需要更高传动效率和更大负载能力的应用场景。
3.3 蜗杆齿轮蜗杆齿轮是一种特殊的齿轮装置,由蜗杆和蜗轮组成。
它具有较高的减速比和较大的传动力矩,常用于需要大扭矩输出和减速的设备。
4. 齿轮设计与计算的基本步骤齿轮设计与计算是齿轮传动系统设计的关键步骤。
下面是齿轮设计与计算的基本步骤:4.1 确定传动比传动比是齿轮设计的基本指标之一,它表示主动齿轮和从动齿轮之间的速度比。
传动比的确定需要考虑到所需输出速度和扭矩。
4.2 选择合适的齿轮类型和参数根据传动比和应用需求,选择合适的齿轮类型和参数。
这包括确定齿轮的齿数、模数、齿宽等。
4.3 计算齿轮的尺寸和位置根据选定的齿轮参数,计算齿轮的几何尺寸和位置。
这包括计算齿轮的模数、齿顶间隙、齿底间隙、齿根弯曲半径等。
4.4 验证齿轮设计的可行性和可靠性对齿轮设计进行验证,包括校核齿轮的强度、耐疲劳性能和齿轮啮合的准确性。
这个过程可以使用齿轮设计软件和标准齿轮计算方法。
4.5 进行齿轮传动的弹性变形计算在齿轮传动系统设计中,弹性变形是一个重要的考虑因素。
齿轮和轴的计算过程

倒档器锥齿轮计算因为转向器没有设置传动比 我选用两个材料和尺寸大小一样的锥齿轮 1)选择齿轮材料,确定许用应力由机械设计书表6.2选两齿轮材料为: 小齿轮40Cr 调质 HBS1=260 HBS大齿轮 45 正火 HBS2=210 HBS 许用接触应力[]H σ 由[]H σ=limminH N H Z S σ接触疲劳极限lim H σ查机械设计 图6-4 lim1H σ=700N/mm2接触强度寿命系数N Z 应力循环次数N lim2H σ=550N/mm N=60njL h =6080001(103004)⨯⨯⨯⨯⨯ N=5.76910⨯ 查图机械设计6-5(如没有特殊说明图表都来源于机械设计书)得N ZN Z =1接触最小安全系数lim H S lim H S =1[]1H σ =700 1/1⨯ []1H σ =700N/mm 2[]25501/1H σ=⨯ []2H σ =550N/ mm 2许用弯曲应力[]F σ 由式[]limminF F N X F Y Y S σσ=弯曲疲劳极限lim F σ 查图6-7 lim1F σ=540N/mm 2, 2lim 2420/F N mm σ= 弯曲强度寿命N Y 查图6-8 12N N Y Y ==1弯曲强度尺寸系数X Y 查图6-9(设模数m 小于5) X Y =1 弯曲强度最小安全系数min F S min F S =1.4 则[]1F σ=54011/1.4⨯⨯ []1F σ=450 N/mm 2 []2F σ= 42011/1.4⨯⨯ []2F σ=300 N/mm 2 2)齿面解除疲劳强度设计计算确定齿轮传动精度等级,估取圆周速度7/t m s υ=,参考表6-7 、6-8选取∏公差等级组7级锥齿轮分度圆直径d(1d ≥+齿宽系数dm ψ 查表6.14 dm ψ=0.3 小齿轮齿数1z =13 1z =13 那么 大齿轮齿数211z z i ==18.2圆整 2z =18 齿数传动比u=1.385 u=1.385 传动比误差为/u u /(1.4 1.385)/1.40.01070.05u u =-=< 倒档器输入轴扭矩1T1119550/T P n ==10050 N m 1T =10050N •mm 载荷系数K= A V K K K βA K ——使用系数 查表6.3 A K =1.1 V K ——动载系数 由推荐值 1.05-1.4 V K =1.2 K β——齿向载荷分布系数 由推荐值1.0-1.2 K β=1.1载荷系数 K1.1 1.2 1.1A V K K K K β==⨯⨯ K=1.452材料弹性系数E Z 查6.4E Z 节点区域系数 H Z 查图6-3 H Z =2.5计算得d1≥44.74 mm d1≥44.74mm 齿轮模数m m=d1/z1=3.44 圆整 m=3.5 小齿轮大端分度圆直径 d1=mz1=3.5⨯13 d1=45.5mm 大齿轮大端分度圆直径 d2=mz2=3.5⨯18 d2=63mm 齿轮平均分度圆直径d m =/(1dd1m =45.5/(1+d 1m =38.7mmd2m ) d 2m =53.59mm圆周速度1m υ=3.141/60000m d n I 1m υ=16.2m/s 2m υ=3.1422/60000m d n2m υ=18.84m/s齿宽b b1=dm ψd 1m =11.61mm 圆整 b1=12mm b2=dm ψd 2m =16.007mm 圆整 b2=16mm 3)齿根弯曲疲劳强度校核计算 由式[]212(1F Fa Sa F KT Y Y bdm σσ=≤当量齿数v z2111/cos 3016.04v u z z uδ+===1v z =16.04221z z u υυ==30.75 2z υ=30.75 齿形系数Fa Y 应力修正系数Sa Y 查表 6.5 1Fa Y =3.21,2 2.91Fa Y =1Sa Y =1.46,2Sa Y =1.53计算弯曲疲劳强度1F σ=197.17<[]H σ 所以齿根弯曲强度满足 4)齿轮其他主要尺寸计算分度锥角1cos δ=0.8107 1δ=35.83锥距255.1R ==R=55.1mm齿顶高 3a a h h m mm *==齿根高 () 3.6f a h h c m mm **=+=齿顶圆直径2cos 82.24a a d d h mm δ=+=齿根圆直径 2cos 72.9f f d d h mm δ=-=齿顶角 arctan(/) 3.1a a h R θ== 齿根角 arctan(/) 3.7f f h R θ== 4)结构设计及绘制齿轮零件图花键连接强度计算花键轴的内径为20mm,轴与发动机轴用凸缘联轴器连接;选取花键规格N d D B ⨯⨯⨯为620245⨯⨯⨯;因为花键是连接发动机输出轴和转向器轴,因此,他们是动连接。
- 1、下载文档前请自行甄别文档内容的完整性,平台不提供额外的编辑、内容补充、找答案等附加服务。
- 2、"仅部分预览"的文档,不可在线预览部分如存在完整性等问题,可反馈申请退款(可完整预览的文档不适用该条件!)。
- 3、如文档侵犯您的权益,请联系客服反馈,我们会尽快为您处理(人工客服工作时间:9:00-18:30)。
倒档器锥齿轮计算因为转向器没有设置传动比 我选用两个材料和尺寸大小一样的锥齿轮 1)选择齿轮材料,确定许用应力由机械设计书表6.2选两齿轮材料为: 小齿轮40Cr 调质 HBS1=260 HBS大齿轮 45 正火 HBS2=210 HBS 许用接触应力[]H σ 由[]H σ=limminH N H Z S σ接触疲劳极限lim H σ查机械设计 图6-4 lim1H σ=700N/mm2接触强度寿命系数N Z 应力循环次数N lim2H σ=550N/mm N=60njL h =6080001(103004)⨯⨯⨯⨯⨯ N=5.76910⨯ 查图机械设计6-5(如没有特殊说明图表都来源于机械设计书)得N ZN Z =1接触最小安全系数lim H S lim H S =1[]1H σ =700 1/1⨯ []1H σ =700N/mm 2[]25501/1H σ=⨯ []2H σ =550N/ mm 2许用弯曲应力[]F σ 由式[]limminF F N X F Y Y S σσ=弯曲疲劳极限lim F σ 查图6-7 lim1F σ=540N/mm 2, 2lim 2420/F N mm σ= 弯曲强度寿命N Y 查图6-8 12N N Y Y ==1弯曲强度尺寸系数X Y 查图6-9(设模数m 小于5) X Y =1 弯曲强度最小安全系数min F S min F S =1.4 则[]1F σ=54011/1.4⨯⨯ []1F σ=450 N/mm 2 []2F σ= 42011/1.4⨯⨯ []2F σ=300 N/mm 2 2)齿面解除疲劳强度设计计算确定齿轮传动精度等级,估取圆周速度7/t m s υ=,参考表6-7 、6-8选取∏公差等级组7级锥齿轮分度圆直径d(1d ≥+齿宽系数dm ψ 查表6.14 dm ψ=0.3 小齿轮齿数1z =13 1z =13 那么 大齿轮齿数211z z i ==18.2圆整 2z =18 齿数传动比u=1.385 u=1.385 传动比误差为/u u /(1.4 1.385)/1.40.01070.05u u =-=< 倒档器输入轴扭矩1T1119550/T P n ==10050 N m 1T =10050N •mm 载荷系数K= A V K K K βA K ——使用系数 查表6.3 A K =1.1 V K ——动载系数 由推荐值 1.05-1.4 V K =1.2 K β——齿向载荷分布系数 由推荐值1.0-1.2 K β=1.1载荷系数 K1.1 1.2 1.1A V K K K K β==⨯⨯ K=1.452材料弹性系数E Z 查6.4E Z 节点区域系数 H Z 查图6-3 H Z =2.5计算得d1≥44.74 mm d1≥44.74mm 齿轮模数m m=d1/z1=3.44 圆整 m=3.5 小齿轮大端分度圆直径 d1=mz1=3.5⨯13 d1=45.5mm 大齿轮大端分度圆直径 d2=mz2=3.5⨯18 d2=63mm 齿轮平均分度圆直径d m =/(1dd1m =45.5/(1+d 1m =38.7mmd2m ) d 2m =53.59mm圆周速度1m υ=3.141/60000m d n I 1m υ=16.2m/s 2m υ=3.1422/60000m d n2m υ=18.84m/s齿宽b b1=dm ψd 1m =11.61mm 圆整 b1=12mm b2=dm ψd 2m =16.007mm 圆整 b2=16mm 3)齿根弯曲疲劳强度校核计算 由式[]212(1F Fa Sa F KT Y Y bdm σσ=≤当量齿数v z2111/cos 3016.04v u z z uδ+===1v z =16.04221z z u υυ==30.75 2z υ=30.75 齿形系数Fa Y 应力修正系数Sa Y 查表 6.5 1Fa Y =3.21,2 2.91Fa Y =1Sa Y =1.46,2Sa Y =1.53计算弯曲疲劳强度1F σ=197.17<[]H σ 所以齿根弯曲强度满足 4)齿轮其他主要尺寸计算分度锥角1cos δ=0.8107 1δ=35.83锥距255.1R ==R=55.1mm齿顶高 3a a h h m mm *==齿根高 () 3.6f a h h c m mm **=+=齿顶圆直径2cos 82.24a a d d h mm δ=+=齿根圆直径 2cos 72.9f f d d h mm δ=-=齿顶角 arctan(/) 3.1a a h R θ== 齿根角 arctan(/) 3.7f f h R θ== 4)结构设计及绘制齿轮零件图花键连接强度计算花键轴的内径为20mm,轴与发动机轴用凸缘联轴器连接;选取花键规格N d D B ⨯⨯⨯为620245⨯⨯⨯;因为花键是连接发动机输出轴和转向器轴,因此,他们是动连接。
动连接强度计算条件为: []2mTP P zhld ψ=≤式中,T 为工作转矩,T=6180N.mm ;ψ为各齿间载荷分配不均匀系数,一般取ψ=0.7-0.8,我们取0.8:;z 为花键齿数,取z=6;h m 为花键齿面的工作高度,对矩形花键h=0.5(D-d )-2c,其中d 和D 为花键轴的内径和外径,c 为齿顶的倒圆半径。
计算h=3;d =0.5(D+d) ,计算得22mm ;l 为工作长度40mm ;[]P ——许用挤压应力,N/mm ,查看机械设计书表3.4为10-20:p=261800.8634022⨯⨯⨯⨯⨯=2.93[]P ≤;发动机和转向器连接的联轴器选型(1)转向器输入轴的设计与校核输入功率1 4.851P kw = 转速17500/min n r = 齿宽B=31mm模数 m=3 压力角20α= 1)计算作用在轴上的力转矩 T1=6180N mm 齿轮分度圆直径 d=78mm圆周力112/26180/78206t F T d N ==⨯= 径向力tan 20/cos 45106r t F F N == 轴向力106a r F F N == 2)初步估算轴的直径选用45号钢作为轴的材料,调质处理 轴材料:45号钢由式8-2 d ≥ 计算轴的最小直径并加大3%以考虑键槽的影响 查表8.6 取A =110则 min d ≥ min d =26mm 3)轴的结构设计(1)确定轴的结构方案轴承靠轴肩定位,左端轴承靠套筒与端盖定位。
两轴承之间靠套筒定位,因为是齿轮轴,无须定位齿轮,轴承选用角接触球轴承(2)确定轴各段直径和长度○1段 根据min d 圆整,选择连轴器YL4型,连轴器毂孔长62mm ,该段应比连轴器短1~4mm 取d1=28mm 1l =60mm○2段 为使连轴器定位,轴肩高度 (2~3)h c mm =+,孔倒角C 取3mm,212d d h =+ 且符合标准密封内径,取端盖宽度15mm ,转向器齿轮轴两轴承接在同一个轴肩上,中间用套筒固定,轴承选用角接触球轴承 型号为7001AC 35621418.5d D B a ⨯⨯⨯=⨯⨯⨯ 215277l B =++ 2l =120mm 2d =35mm○3段 为了卡住轴承 d= d2+2h 轴肩h 取5mm 3d =45mm 3l = 10mm○4段 本身这跟齿轮轴就是齿轮与轴连在一起,这段是齿轮 宽4l =42mm4)轴的强度校核齿轮采用的是直齿,因此轴主要承受扭矩,其工作能力按扭转强度条件计算。
扭转强度条件为: []639.55100.2T T T T PW d n ττ==⨯⨯≤ 2/N mmd ≥mm 式中,T τ ―轴的扭转切应力,2/N mm ; T ―轴所受的扭矩,N mm ;T W -轴的抗扭截面模量,3mm ;n -轴的转速,/min r ;P -轴所传递的功率,Kw;[]T τ -轴的许用扭转切应力,2/N mm ,见表8.6;A -取决于轴材料的许用扭转切应力[]T τ的系数,其值可查表 8.6.6633309.55109.55100.20.2287500T T T P W d n τ==⨯⨯=⨯⨯⨯⨯ []228.7/40/T T N mm N mm ττ=≤=5)精确校核轴的疲劳强度 (1)选择危险截面在第一段轴与第二段轴之间有应力集中源,第一段轴上有键,其应力较大,应力集中严重,选其接近第二段轴处截面为危险截面。
(2)计算危险截面上工作应力轴主要承受扭矩,其 扭矩6180T N mm = 其抗弯截面系数:3232()2838 4.3(28 4.3)323228d bt d t W d ππ-⨯⨯⨯-=-=-=1030mm 3抗扭截面系数:3232()2816 4.3(28 4.3)161628T d bt d t W d ππ-⨯⨯⨯-=-=-=2928.08mm 3.截面上的扭剪应力:/6180/2928.08T T W τ===2.112/N mm 扭切应力: /2a m τττ===1.0552/N mm(3)确定轴材料机械性能查表8.2,弯曲疲劳极限 21275mm σ-=,剪切疲劳极限21155/N mm τ-= 碳钢材料特性系数:0.1σϕ=,0.5τσϕϕ= (4)确定综合影响系数K σ,K τ轴肩圆角处有效应力集中系数 k σ,k τ,根据/ 1.6/280.057r d ==,由表8.9插值计算得 1.86k σ=, 1.30k τ=配合处综合影响系数 K σ,K τ,根据d ,b σ ,配合7/6H r ,由表8.11插值计算得 3.4K σ=, 0.40.6 2.44K K τσ=+=键槽处有效应力集中系数k σ,k τ,根据b σ,由表8.10插值计算得 1.80k σ=,1.61k τ=尺寸系数 σε,τε,根据d ,由表8-12查得,0.81σε=,0.75τε=。
表面状况系数σβ,根据 b σ,表面加工方法查图8-2得 0.84στββ==轴肩处的综合影响系数K σ,K τ为:1.802.730.810.84k K σσσσεβ===⨯2.443.870.750.84k K ττττεβ===⨯键槽处综合影响系数K σ,K τ为: 1.802.640.810.84k K σσσσεβ===⨯1.612.560.750.84k K ττττεβ===⨯同一截面上有两个以上应力集中源,取其中较大的综合影响系数来计算安全系数,故按配合处系数K σ,K τ 。
(5)计算安全系数由表8.13取许用安全系数 [] 1.6S = 由式8-6 12753.410.10a m S k σσσσσϕσ-==+⨯+⨯= 80.111552.4416.50.0516.5a m S k τττττϕτ-==+⨯+⨯ 3.77=ca S =5.2=6)轴的弯矩图和扭矩图 (1)求轴承反力H 水平面1103H R N =,2103H R N = V 垂直面160V R N =-, 2166V R N = (2)求第一个轴承处弯矩H 水平面10918H M N mm = V 垂直面16360V M N = mm , 29960V M N = mm 合成弯矩M114080M N mm =, 217680M mm = 扭矩T 6180T N mm = 弯扭合成当量弯矩121456018064.7ca ca M N mm M N mm====弯矩图,扭矩图如下:7)轴上键的设计及校核静联接,按挤压强度条件计算,其计算式为: []4P P Tdhlσσ=≤ 式中,T -转矩,N mm ; d -轴径,mm; h -键的高度,mm;l -键的工作长度,mm, A 型键l L b =-;B 型键l L =;C 型键/2l L b =-,其中L 为键的长度,b 为键的宽度;[]P σ -许用挤压应力,2/N mm ,见表3.2;根据轴径,选用C 型键,b=15mm,h=10mm,L=18-90mm,取L=38mm/23815/2l L b =-=-=30.5446180 2.32281038P T dhl σ⨯===⨯⨯ 按轻微冲击算[]2100~120/P N mm σ=所以此键符合强度要求(2)输出轴的设计与校核输出转速27500/min n r =,转矩25930T N mm =1)计算作用在轴上的力转矩25930T N mm = ,总传动效率取 0.97η=,则输出功率 2300.97P =⨯2)初步估算轴的直径选用 40Cr 作为轴的材料,由式8-2 d ≥ 计算轴的最小直径并加大3%以考虑键槽的影响 查表 8.6 取A =100d ≥= 3)轴的结构设计(1)确定轴的结构方案行星轮上有一与行星轮固联的圆盘,该圆盘与输出轴相连,从而将转矩传递到输出端。