金刚石刀头配方设计依据
金刚石单晶刀具的设计及制备
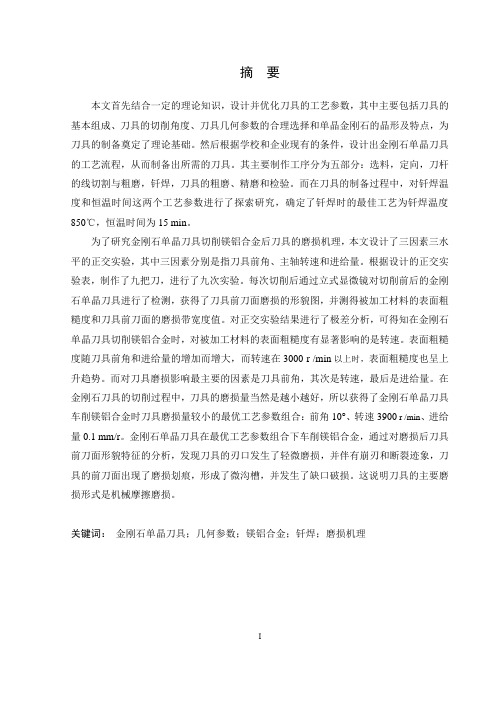
摘要本文首先结合一定的理论知识,设计并优化刀具的工艺参数,其中主要包括刀具的基本组成、刀具的切削角度、刀具几何参数的合理选择和单晶金刚石的晶形及特点,为刀具的制备奠定了理论基础。
然后根据学校和企业现有的条件,设计出金刚石单晶刀具的工艺流程,从而制备出所需的刀具。
其主要制作工序分为五部分:选料,定向,刀杆的线切割与粗磨,钎焊,刀具的粗磨、精磨和检验。
而在刀具的制备过程中,对钎焊温度和恒温时间这两个工艺参数进行了探索研究,确定了钎焊时的最佳工艺为钎焊温度850℃,恒温时间为15 min。
为了研究金刚石单晶刀具切削镁铝合金后刀具的磨损机理,本文设计了三因素三水平的正交实验,其中三因素分别是指刀具前角、主轴转速和进给量。
根据设计的正交实验表,制作了九把刀,进行了九次实验。
每次切削后通过立式显微镜对切削前后的金刚石单晶刀具进行了检测,获得了刀具前刀面磨损的形貌图,并测得被加工材料的表面粗糙度和刀具前刀面的磨损带宽度值。
对正交实验结果进行了极差分析,可得知在金刚石单晶刀具切削镁铝合金时,对被加工材料的表面粗糙度有显著影响的是转速。
表面粗糙度随刀具前角和进给量的增加而增大,而转速在3000 r /min以上时,表面粗糙度也呈上升趋势。
而对刀具磨损影响最主要的因素是刀具前角,其次是转速,最后是进给量。
在金刚石刀具的切削过程中,刀具的磨损量当然是越小越好,所以获得了金刚石单晶刀具车削镁铝合金时刀具磨损量较小的最优工艺参数组合:前角10°、转速3900 r /min、进给量0.1 mm/r。
金刚石单晶刀具在最优工艺参数组合下车削镁铝合金,通过对磨损后刀具前刀面形貌特征的分析,发现刀具的刃口发生了轻微磨损,并伴有崩刃和断裂迹象,刀具的前刀面出现了磨损划痕,形成了微沟槽,并发生了缺口破损。
这说明刀具的主要磨损形式是机械摩擦磨损。
关键词:金刚石单晶刀具;几何参数;镁铝合金;钎焊;磨损机理AbstractFirst, this paper combines with the certain theoretical knowledge, designs and optimizes the process parameters of the cutter, which mainly includes the basic parts of the cutting tool, the selection of proper cutting angle of the cutter, the reasonable choice of geometry parameters of the cutting tool and the crystal shape and characteristics of single crystal diamond. It laid a theoretical basis for the preparation of cutting tool. Then, according to the existing condition of the school and the enterprise, the process of single crystal diamond cutter is designed and the cutting tool is prepared. The main production process is divided into five parts: choosing material, directional, the cutting and coarse grinding of tool rod, brazing, the coarse grinding, fine grinding and inspection of the cutting tool. And in the process of preparing tools, the brazing temperature and constant temperature time were studied, which determines the best technology of the brazing for brazing temperature 850℃, constant temperature time of 15 min.In order to study the wear mechanism of the single crystal diamond cutter after cutting magnesium alloy, this paper designs orthogonal experiment including three factors and three levels. The three factors respectively is refers to the rake angle of cutting tool, spindle speed, and feed. According to orthogonal experiment table, nine experiments were carried out. After each cutting, single crystal diamond cutting tools were detected before and after cutting through vertical microscope. The topography figures of cutter surface wear were gained, and the surface roughness of the processed material and the width values of cutter surface wear were measured. The result of the orthogonal experiment can be made range analysis, which can learn in the single crystal diamond cutter cutting magnesium alloy, the spindle speed has a significant effect on the surface roughness of the processed material. Surface roughness increases significantly with the increase of the cutting tool rake angle and feed, and at the time of the more than 3000 r /min speed, the surface roughness is also on the rise. And the main influencing factors on tool wear is rake angle of cutting tool, the second is spindle speed, the last is feeding. In the cutting process of diamond tool, tool wear volume is as small as possible, so when the single crystal diamond tool cuts magnesium alloy, the optimal process parameters combination of the smallest tool wear is rake angle 10°、spindle speed 3900 r /min、feeding 0.1 mm/r。
一种耐磨金刚石刀头的设计
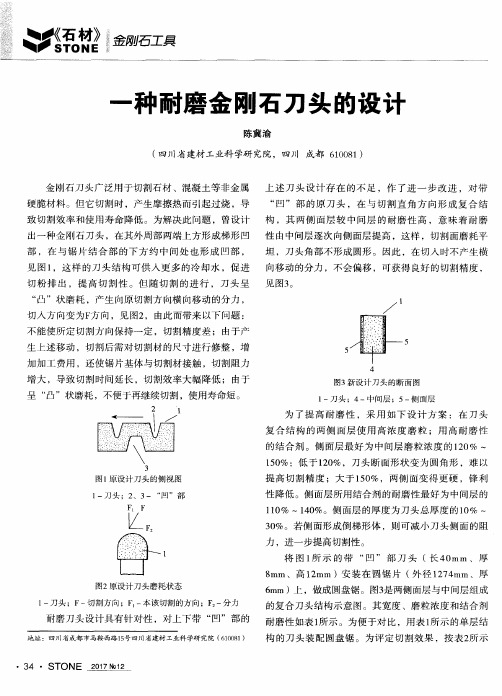
种 耐磨 金 刚石刀 头 的设 计
陈冀 渝
( 四川省 建材 工业科 学研 究院 ,四 川 成都 6 1 0 0 8 1 )
金 刚石 刀 头 广泛 用 于 切割 石 材 、混 凝 土 等 非金 属 上 述 刀 头 设 计 存 在 的 不 足 ,作 了进 一 步 改 进 ,对 带
硬 脆材 料 。但 它切 割 时 ,产 生摩 擦 热 而 引起 过 烧 ,导
・
3 4 ・S TO NE 2 0 1 7 N o ] 2
切割 条 件 ,用两 种 不 同结 构 的金 刚 石 圆盘 锯 ,切割 花 岗 石 ,进 行 对 比试 验 。根据 图4 所 示 的 电耗 指 标 评 定 切 割 性 。图4 中表 明 ,使 用 复 合 结 构 的刀 头 , 电耗 不 仅稳 定 ,而 且较 使 用单 一结 构 的原 刀 头 的低 。 图5 a 和 图5 b 分别 表 明 复合 结 构 刀头 与单 一 结 构 刀头 的磨损 状
。 0 . 0 . ≤
态 ,前种刀头切割作用 面的断面形状仅为平坦磨耗 。 对图5 各部位的说明如表3 所示。表3 列 出两种刀头的磨
损 指 标 。表 3 中 表 明 ,复合 结 构较 单 一 结 构 刀头 的磨 耗 小得 多 。试验 中还依 据 切 割 尺寸 的互差 ,评 定 了两 种 刀 头切 割 精度 。评定 结 果 如表 4 所示 。表4 中表 明 , 不 论 切入 深 度 为 2 7 0 mm,还 是4 5 0 am,复合 结 构 刀头 r 为单 一 刀头 切割精 度 的8—9 倍 。刀 头使 用寿命 如 表5 所 示 。表 5 中表 明 ,在 同 一切 割 条件 下 ,复合 结 构 刀头 较 单一 结构 刀 头 的使 用寿命 约 延长 5 0 %。如 图6 所示 , 由侧 面层 与 中间层 组 成 的复 合 结构 刀 头 ,若 其 前 端形
CVD金刚石刀具材料的制备、性质与应用
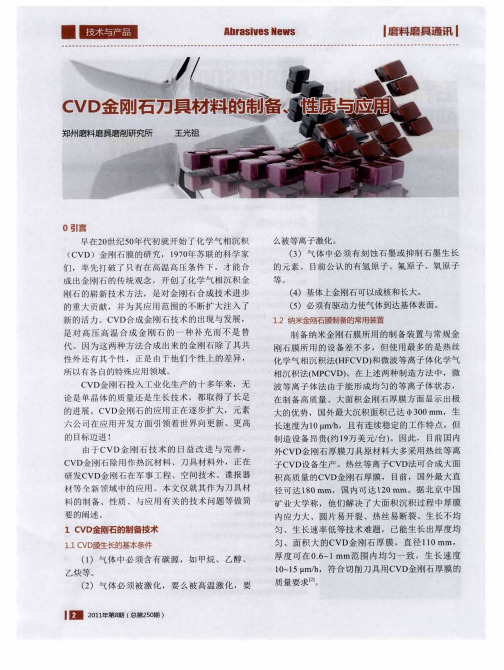
Ar ises b seNw av
■ 叠 曩 ■ 团 嗣
传 统 的CVD法 是 以 大 量 氢 气 为 主 要 反 应 气
体 ,同 时加 入 少 量 的碳 源 气 体 ( 于5 ,沉积 出 少 %)
33要解 决大面 积沉 积 过程 中厚 膜 内应力 大 、圆 片 . 易开 裂 、热 丝 易 断裂 、生 长 不均 匀 、生 长速 率低 等 技术 难题 ,长 期 以来 一直 困扰 着制造 商 。 34C D金 刚石 厚膜 与硬质 合 金基体 之 间 的焊 接 强 . V
Notn 司宣 称 ,其 牌 号 为Dima a 的C r 公 o a P k VD
36干 切 削是 未来 切 削的主 要方 向。随 着切 削速 度 . 的提 高 (20 0m/ n 9 0 mi ),C VD厚膜 切 削刀具 会 成 为干 式高速 切 削某些新 材料 的首 选工 具 。 ]
10 2 0 t %~ 0 % 源自 0美 国NotnFl 司推 出的牌 号 为Dima a r i o m公 a Pk 的C D金 刚石 复 合片 ,也 是03 V - mm或 05mm厚度 . 的C VD金 刚石 层 焊 接 到硬 质 合 金 基底 上 ,刀 片 总 厚度 为 1 .mm,可 根据 用户 需要 提供 各种 形状 。 6
小 晶粒 尺 寸 。在 纳 米 金 刚石 生 长 中 ,C 是 重 要 的 2 参与 者与 决定 性 的成分 。 J
度 ,是 决 定C VD刀具 用 于 断续 切 削 这种 高 要 求机
械 加工 的关键 。
C VD金 刚 石 用 于 切 削有 两 种 形 式 : 聚 晶质 C VD金 刚 石 薄膜 和 单 晶质 C 金 刚石 厚膜 ,可切 VD 割成 不 同形状 。单 晶 质C VD金 刚 石 切割 工 具 主要 用于 加 工 强 度 高而 质 量 轻 的结 构材 料 ,如 金 属基 体 复合 材 料( MMC ) ,存 在 的 问题是 不能制 成 形 S等
石材锯切专用金刚石刀头设计因素分析
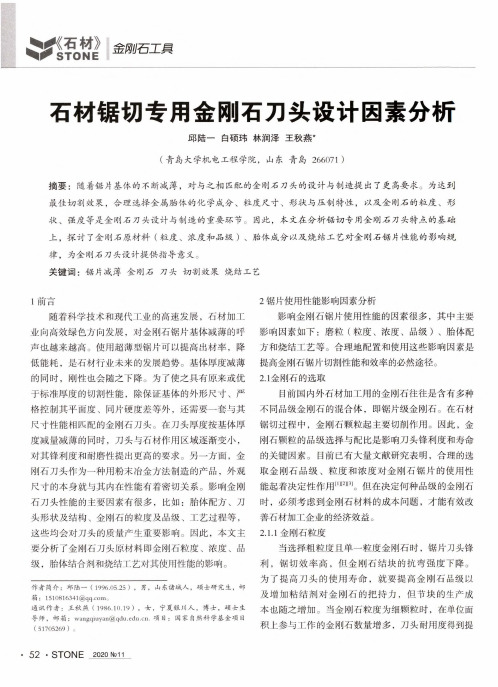
M灘金刚石工具石材锯切专用金刚石刀头设计因素分析邱陆一白硕玮林润泽王秋燕*(青岛大学机电工程学院,山东青岛266071)摘要:随着锯片基体的不断减薄,对与之相匹配的金刚石刀头的设计与制造提出了更高要求。
为达到最佳切割效果,合理选择金属胎体的化学成分、粒度尺寸、形状与压制特性,以及金刚石的粒度、形状、强度等是金刚石刀头设计与制造的重要环节。
因此,本文在分析锯切专用金刚石刀头特点的基础上,探讨了金刚石原材料(粒度、浓度和品级)、胎体成分以及烧结工艺对金刚石锯片性能的影响规律,为金刚石刀头设计提供指导意义。
关键词:锯片减薄金刚石刀头切割效果烧结工艺-、八—X—1刖S随着科学技术和现代工业的高速发展,石材加工业向高效绿色方向发展,对金刚石锯片基体减薄的呼声也越来越高。
使用超薄型锯片可以提高出材率,降低能耗,是石材行业未来的发展趋势。
基体厚度减薄的同时,刚性也会随之下降。
为了使之具有原来或优于标准厚度的切割性能,除保证基体的外形尺寸、严格控制其平面度、同片硬度差等外,还需要一套与其尺寸性能相匹配的金刚石刀头。
在刀头厚度按基体厚度减量减薄的同时,刀头与石材作用区域逐渐变小,对其锋利度和耐磨性提出更高的要求。
另一方面,金刚石刀头作为一种用粉末冶金方法制造的产品,外观尺寸的本身就与其内在性能有着密切关系。
影响金刚石刀头性能的主要因素有很多,比如:胎体配方、刀头形状及结构、金刚石的粒度及品级、工艺过程等,这些均会对刀头的质量产生重要影响。
因此,本文主要分析了金刚石刀头原材料即金刚石粒度、浓度、品级,胎体结合剂和烧结工艺对其使用性能的影响。
作者简介:邱陆一(1996.05.25),男,山东诸城人,硕士研究生,邮箱:1510816341@,通讯作者:王秋燕(1986.10.19),女,宁夏银川人,博士,硕士生导师,邮箱:******************.cn.项目:国家自然科学基金项目(51705269)o 2锯片使用性能影响因素分析影响金刚石锯片使用性能的因素很多,其中主要影响因素如下:磨粒(粒度、浓度、品级)、胎体配方和烧结工艺等。
金刚石刀具制作工艺流程

金刚石刀具制作工艺流程一、原料准备。
咱得先找好金刚石原料呀。
这金刚石可不好找呢,它可是超级硬的家伙。
一般都是从天然金刚石或者人工合成的金刚石里挑。
天然金刚石那可真是大自然的宝藏,不过数量有限而且贵得很。
人工合成的金刚石现在也很厉害啦,品质也很不错。
要选那些晶体结构比较好的金刚石,就像挑水果一样,要挑长得好看、没有啥缺陷的金刚石才行。
在这个过程中,还得考虑金刚石的粒度大小,不同的刀具用途可能需要不同大小的金刚石呢。
二、基体选择。
有了金刚石还不行,还得有个好的基体来搭配它。
基体就像是金刚石的家,得结实又靠谱。
一般会选择金属材料做基体,像硬质合金之类的就很常用。
这就好比给超级英雄(金刚石)找个坚固的基地一样重要。
要根据刀具的使用环境和要求来选择合适的基体材料。
如果是要做那种需要承受很大压力的刀具,那基体的硬度和强度就得足够高。
而且,基体的形状也要根据刀具的设计来确定,有圆形的、方形的等等各种形状呢。
三、金刚石的镶嵌。
接下来就是把金刚石镶嵌到基体上啦。
这可是个技术活呢。
就像给宝石镶嵌到戒指上一样,不过这个难度可大多了。
一种常见的方法是烧结法,把金刚石和基体材料放在一起,通过高温高压让它们融合在一起。
在这个过程中,要控制好温度和压力的参数,要是不小心弄错了,可能金刚石就镶嵌不好,刀具的性能就会大打折扣。
还有一种是电镀法,就像给东西镀上一层漂亮的金属外衣一样,把金刚石镶嵌在基体上。
这个方法可以让金刚石分布得比较均匀,不过也需要很精细的操作。
四、刀具的成型加工。
金刚石镶嵌好之后,刀具还不是最终的样子呢。
还需要进行成型加工。
这时候就需要用到各种加工设备啦,像磨床之类的。
要把刀具的刃口磨得锋利无比,就像给宝剑开刃一样。
这个过程中,要根据刀具的设计要求,精确地控制刃口的角度和形状。
如果刃口角度不对,那刀具在使用的时候就可能不好用,切东西就不顺畅。
而且在加工的时候,还得注意不要损伤到金刚石,毕竟金刚石是刀具的核心部分呀。
金刚石刀头生产工艺
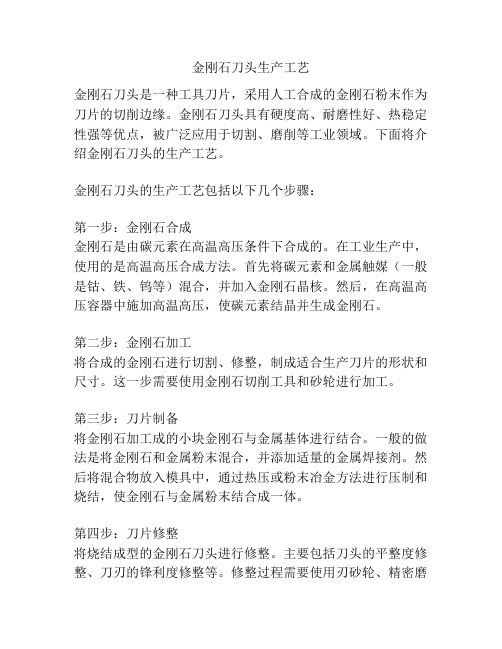
金刚石刀头生产工艺金刚石刀头是一种工具刀片,采用人工合成的金刚石粉末作为刀片的切削边缘。
金刚石刀头具有硬度高、耐磨性好、热稳定性强等优点,被广泛应用于切割、磨削等工业领域。
下面将介绍金刚石刀头的生产工艺。
金刚石刀头的生产工艺包括以下几个步骤:第一步:金刚石合成金刚石是由碳元素在高温高压条件下合成的。
在工业生产中,使用的是高温高压合成方法。
首先将碳元素和金属触媒(一般是钴、铁、钨等)混合,并加入金刚石晶核。
然后,在高温高压容器中施加高温高压,使碳元素结晶并生成金刚石。
第二步:金刚石加工将合成的金刚石进行切割、修整,制成适合生产刀片的形状和尺寸。
这一步需要使用金刚石切削工具和砂轮进行加工。
第三步:刀片制备将金刚石加工成的小块金刚石与金属基体进行结合。
一般的做法是将金刚石和金属粉末混合,并添加适量的金属焊接剂。
然后将混合物放入模具中,通过热压或粉末冶金方法进行压制和烧结,使金刚石与金属粉末结合成一体。
第四步:刀片修整将烧结成型的金刚石刀头进行修整。
主要包括刀头的平整度修整、刀刃的锋利度修整等。
修整过程需要使用刃砂轮、精密磨床等设备进行。
第五步:刀片涂覆为了提高金刚石刀片的工作效率和寿命,一般会对刀片进行涂覆。
涂覆的材料通常是一层个别晶体金刚石膜。
涂覆过程通常采用化学气相沉积法或物理气相沉积法进行。
第六步:刀片检验制成的金刚石刀头需要进行严格的检验,以确保质量符合要求。
常见的检验项目包括刀片的硬度、抗磨性、耐热性等。
第七步:刀片包装经过检验合格的金刚石刀片将进行包装,以便运输和销售。
一般是将刀片放入专用的塑料盒或纸盒中,并附带说明书和标签。
金刚石刀头生产工艺复杂,需要经过多道工序才能完成。
每个步骤都需要严格的操作和控制,以确保金刚石刀头的质量和性能达到要求。
随着科技的发展,金刚石刀头的生产工艺也在不断改进和创新,以提高产能和质量。
金属粉末在刀头中的作用及金刚石的品级及应用
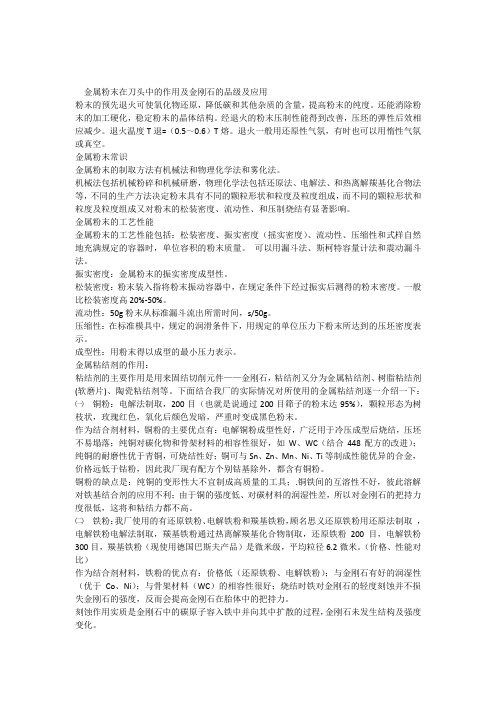
金属粉末在刀头中的作用及金刚石的品级及应用粉末的预先退火可使氧化物还原,降低碳和其他杂质的含量,提高粉末的纯度。
还能消除粉末的加工硬化,稳定粉末的晶体结构。
经退火的粉末压制性能得到改善,压坯的弹性后效相应减少。
退火温度T退=(0.5~0.6)T熔。
退火一般用还原性气氛,有时也可以用惰性气氛或真空。
金属粉末常识金属粉末的制取方法有机械法和物理化学法和雾化法。
机械法包括机械粉碎和机械研磨,物理化学法包括还原法、电解法、和热离解羰基化合物法等,不同的生产方法决定粉末具有不同的颗粒形状和粒度及粒度组成,而不同的颗粒形状和粒度及粒度组成又对粉末的松装密度、流动性、和压制烧结有显著影响。
金属粉末的工艺性能金属粉末的工艺性能包括:松装密度、振实密度(摇实密度)、流动性、压缩性和式样自然地充满规定的容器时,单位容积的粉末质量。
可以用漏斗法、斯柯特容量计法和震动漏斗法。
振实密度:金属粉末的振实密度成型性。
松装密度:粉末装入指将粉末振动容器中,在规定条件下经过振实后测得的粉末密度。
一般比松装密度高20%-50%。
流动性:50g粉末从标准漏斗流出所需时间,s/50g。
压缩性:在标准模具中,规定的润滑条件下,用规定的单位压力下粉末所达到的压坯密度表示。
成型性:用粉末得以成型的最小压力表示。
金属粘结剂的作用:粘结剂的主要作用是用来固结切削元件——金刚石,粘结剂又分为金属粘结剂、树脂粘结剂(软磨片)、陶瓷粘结剂等。
下面结合我厂的实际情况对所使用的金属粘结剂逐一介绍一下:㈠铜粉:电解法制取,200目(也就是说通过200目筛子的粉末达95%),颗粒形态为树枝状,玫瑰红色,氧化后颜色发暗,严重时变成黑色粉末。
作为结合剂材料,铜粉的主要优点有:电解铜粉成型性好,广泛用于冷压成型后烧结,压坯不易塌落;纯铜对碳化物和骨架材料的相容性很好,如W、WC(结合448配方的改进);纯铜的耐磨性优于青铜,可烧结性好;铜可与Sn、Zn、Mn、Ni、Ti等制成性能优异的合金,价格远低于钴粉,因此我厂现有配方个别钴基除外,都含有铜粉。
金刚石刀头配方设计依据
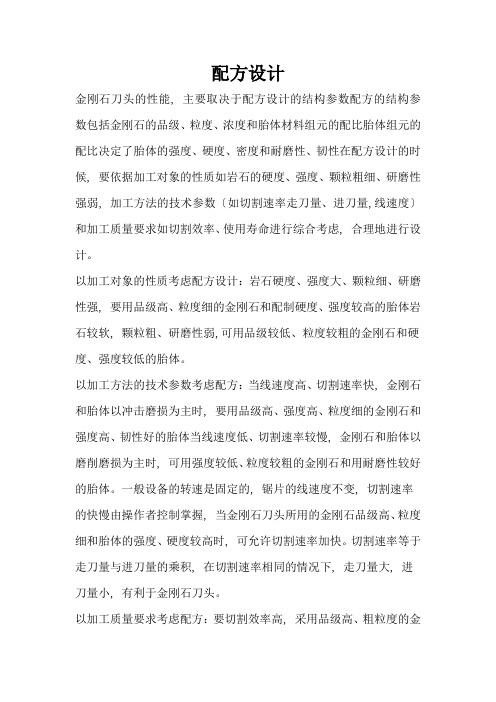
配方设计
金刚石刀头的性能, 主要取决于配方设计的结构参数配方的结构参数包括金刚石的品级、粒度、浓度和胎体材料组元的配比胎体组元的配比决定了胎体的强度、硬度、密度和耐磨性、韧性在配方设计的时候, 要依据加工对象的性质如岩石的硬度、强度、颗粒粗细、研磨性强弱, 加工方法的技术参数〔如切割速率走刀量、进刀量,线速度〕和加工质量要求如切割效率、使用寿命进行综合考虑, 合理地进行设计。
以加工对象的性质考虑配方设计:岩石硬度、强度大、颗粒细、研磨性强, 要用品级高、粒度细的金刚石和配制硬度、强度较高的胎体岩石较软, 颗粒粗、研磨性弱,可用品级较低、粒度较粗的金刚石和硬度、强度较低的胎体。
以加工方法的技术参数考虑配方:当线速度高、切割速率快, 金刚石和胎体以冲击磨损为主时, 要用品级高、强度高、粒度细的金刚石和强度高、韧性好的胎体当线速度低、切割速率较慢, 金刚石和胎体以磨削磨损为主时, 可用强度较低、粒度较粗的金刚石和用耐磨性较好的胎体。
一般设备的转速是固定的, 锯片的线速度不变, 切割速率的快慢由操作者控制掌握, 当金刚石刀头所用的金刚石品级高、粒度细和胎体的强度、硬度较高时, 可允许切割速率加快。
切割速率等于走刀量与进刀量的乘积, 在切割速率相同的情况下, 走刀量大, 进刀量小, 有利于金刚石刀头。
以加工质量要求考虑配方:要切割效率高, 采用品级高、粗粒度的金
刚石有利要使用寿命长, 配制较细粒的金刚石和较高的金刚石浓度以及耐磨性好、强度、韧性较高的胎体。
金刚石锯片刀头胎体材料的研究
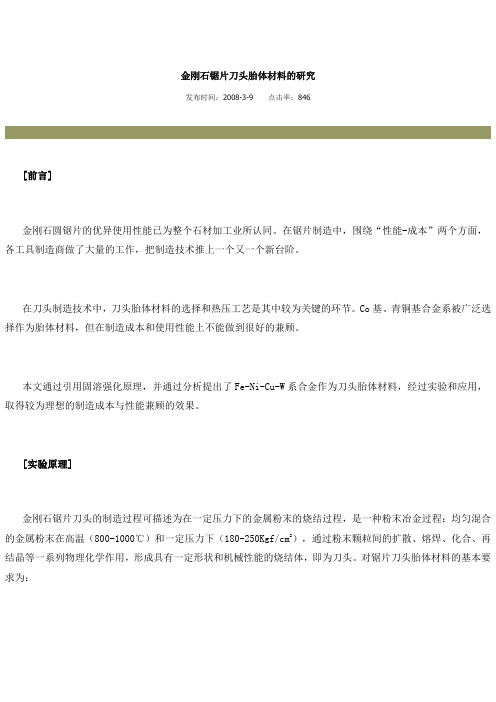
金刚石锯片刀头胎体材料的研究发布时间:2008-3-9点击率:846[前言]金刚石圆锯片的优异使用性能已为整个石材加工业所认同。
在锯片制造中,围绕“性能-成本”两个方面,各工具制造商做了大量的工作,把制造技术推上一个又一个新台阶。
在刀头制造技术中,刀头胎体材料的选择和热压工艺是其中较为关键的环节。
Co基、青铜基合金系被广泛选择作为胎体材料,但在制造成本和使用性能上不能做到很好的兼顾。
本文通过引用固溶强化原理,并通过分析提出了Fe-Ni-Cu-W系合金作为刀头胎体材料,经过实验和应用,取得较为理想的制造成本与性能兼顾的效果。
[实验原理]金刚石锯片刀头的制造过程可描述为在一定压力下的金属粉末的烧结过程,是一种粉末冶金过程:均匀混合的金属粉末在高温(800-1000℃)和一定压力下(180-250Kgf/cm2),通过粉末颗粒间的扩散、熔焊、化合、再结晶等一系列物理化学作用,形成具有一定形状和机械性能的烧结体,即为刀头。
对锯片刀头胎体材料的基本要求为:1、烧结体应具有优良的冲击性能和适当的硬度,以保证对所包裹的金刚石形成良好的机械啮合和对岩石适度的抗磨损能力;2、能够在较低的烧结温度(一般不超过950℃)下和较短的保温时间(一般不超过5分钟)内完成满足上述性能要求的粉末冶金过程,以减缓金刚石单晶的劣化趋势;3、胎体合金中的合金组元可以良好的浸润金刚石单晶,并通过加入的微量元素使合金组元与金刚石间产生化学键合作用,进一步提高对金刚石的把持能力。
研究表明,粉末冶金方式可以使胎体材料获得与一般合金相似的组织,实现合金化。
在合金组织中有若干种相,其中在电化学性质与原子半径相似的组元间,合金倾向于优先生成固溶体相。
由于固溶体相在生成过程中晶格发生畸变,使晶格位错移动时所受到的阻力增大,从而使材料的强度、硬度提高,即产生固溶强化作用,因此,固溶体相成为对综合机械性能要求较高材料的最基本组成相。
可以说,胎体合金能形成固溶体相是实现胎体材料高性能的关键之一。
金刚石刀头制造的详细说明
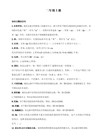
3、 胎体合金中的合金组元可以精采的浸润金刚石单晶,并经由过程插手的微量元素使合金组元与金刚石间孕育产生化学键合浸染,进一步进步对金刚石的哄骗手段。
粉末冶金方法可以使胎体原料得到与一样寻常合金相似的构造,实现合金化。在合金构造中有多少种相,其中在电化学性子与原子半径相似的组元间,合金偏向于优天赋生固溶体相。因为固溶体相在天生历程中晶格产生畸变,使晶格位错移动时所受到的阻力增年夜,从而使原料的强度、硬度进步,即孕育产生固溶强化浸染,是以,固溶体相成为对综合机器机能要求较高原料的最根基组成相。可以说,胎体合金能形成固溶体相是实现胎体原料高机能的关键之一。
金刚石锯片刀头的制造历程可描写为在必然压力下的金属粉末的烧结历程,是一种粉末冶金历程:匀称肴杂的金属粉末在高温(800-1000℃)和必然压力下(180-250Kgf/cm2),经由过程粉末颗粒间的扩散、熔焊、化合、再结晶等一系列物理化学浸染,形成具有必然外形和机器机能的烧结体,即为刀头。
对锯片刀头胎体原料的根基也要有较严的要求:
1、 烧结体应具有精良的抨击袭击机能和恰当的硬度,以保证对所包裹的金刚石形成精采的机器啮合和对岩石适度的抗磨损手段;
2、 能够在较低的烧结温度(一样寻常不赶过950℃)下和较短的保温时刻(一样寻常不赶过5分钟)内完成餍足上述机能要求的粉末冶金历程,以减缓金刚石单晶的劣化趋势;
按照锯片刀头胎体原料的根基要求,应选择易于在胎体合金中形成固溶体相、孕育产生固溶强化浸染的合金系作为胎体的根基因素,Fe-Ni-Cu-W系合金切合这种要求:
Fe-Ni、Cu-Ni可以实现完全互溶;
WC/W-Ni、WC-Cu、Fe-Cu可实现有限互溶并可以孕育产生弥散强化浸染;
Fe、Ni第Ⅷ族元素对金刚石有精采的亲和性。
- 1、下载文档前请自行甄别文档内容的完整性,平台不提供额外的编辑、内容补充、找答案等附加服务。
- 2、"仅部分预览"的文档,不可在线预览部分如存在完整性等问题,可反馈申请退款(可完整预览的文档不适用该条件!)。
- 3、如文档侵犯您的权益,请联系客服反馈,我们会尽快为您处理(人工客服工作时间:9:00-18:30)。
配方设计
金刚石刀头的性能, 主要取决于配方设计的结构参数配方的结构参数包括金刚石的品级、粒度、浓度和胎体材料组元的配比胎体组元的配比决定了胎体的强度、硬度、密度和耐磨性、韧性在配方设计的时候, 要依据加工对象的性质如岩石的硬度、强度、颗粒粗细、研磨性强弱, 加工方法的技术参数〔如切割速率走刀量、进刀量,线速度〕和加工质量要求如切割效率、使用寿命进行综合考虑, 合理地进行设计。
以加工对象的性质考虑配方设计:岩石硬度、强度大、颗粒细、研磨性强, 要用品级高、粒度细的金刚石和配制硬度、强度较高的胎体岩石较软, 颗粒粗、研磨性弱,可用品级较低、粒度较粗的金刚石和硬度、强度较低的胎体。
以加工方法的技术参数考虑配方:当线速度高、切割速率快, 金刚石和胎体以冲击磨损为主时, 要用品级高、强度高、粒度细的金刚石和强度高、韧性好的胎体当线速度低、切割速率较慢, 金刚石和胎体以磨削磨损为主时, 可用强度较低、粒度较粗的金刚石和用耐磨性较好的胎体。
一般设备的转速是固定的, 锯片的线速度不变, 切割速率的快慢由操作者控制掌握, 当金刚石刀头所用的金刚石品级高、粒度细和胎体的强度、硬度较高时, 可允许切割速率加快。
切割速率等于走刀量与进刀量的乘积, 在切割速率相同的情况下, 走刀量大, 进刀量小, 有利于金刚石刀头。
以加工质量要求考虑配方:要切割效率高, 采用品级高、粗粒度的金
刚石有利要使用寿命长, 配制较细粒的金刚石和较高的金刚石浓度以及耐磨性好、强度、韧性较高的胎体。