钻孔动力头的PLC控制
基于PLC控制的数控钻孔机的设计与实现

基于PLC控制的数控钻孔机的设计与实现随着科技的进步和工业自动化水平的提高,数控(Numerical Control)钻孔机在工业生产中得到了广泛的应用。
数控钻孔机的设计与实现基于PLC(Programmable Logic Controller)控制,PLC控制具有可靠性高、灵活性强等优点。
本文将介绍基于PLC控制的数控钻孔机的设计与实现。
首先,在数控钻孔机的设计中,我们需要考虑到几个方面。
首先是机械部分的设计,包括钻头的选择、主轴的设计、夹持装置的设计等。
其次是电气部分的设计,主要包括电机的选择、传感器的选择、电气线路的设计等。
最后是PLC控制程序的编写,需要根据实际需求设计钻孔程序。
在机械部分的设计中,我们需要选择适合的钻头来满足不同的钻孔需求。
常见的钻头有立铣钻头、圆滚钻头等。
主轴的设计需要考虑到主轴的转速和稳定性,可以选择带有变频器的电机来调整主轴的转速。
夹持装置的设计需要满足钻孔材料的夹持需求,可以选择气动夹紧装置或电动夹紧装置。
在电气部分的设计中,我们需要选择适合的电机来驱动主轴。
根据钻孔材料的不同,可以选择不同功率的电机。
传感器的选择需要满足对材料位置和尺寸的检测需求,可以选择接近开关、压力传感器等传感器。
电气线路的设计需要根据实际需求进行布线,保证线路的安全稳定。
在PLC控制程序的编写中,我们需要根据实际需求设计钻孔程序。
首先,我们需要编写一个启动程序,通过点击按钮或接近开关来启动钻孔机的工作。
然后,我们需要编写一个控制程序,通过设定参数来控制钻孔机的运行。
控制程序可以设置钻孔深度、钻孔速度等参数。
最后,我们还需要编写一个停止程序,当钻孔完成或发生异常情况时,通过点击按钮或接近开关来停止钻孔机的工作。
总结起来,基于PLC控制的数控钻孔机的设计与实现需要考虑到机械部分的设计、电气部分的设计以及PLC控制程序的编写。
通过合理的设计和实施,可以实现数控钻孔机的自动化控制,提高生产效率,降低人工成本,提高产品质量。
PLC编程实例之钻孔动力头控制

PLC编程实例之钻孔动⼒头控制某⼀钻床如图35-1 (a)所⽰,⽤于在⼯作台上钻孔,钻床的⼯作过程如下:钻头在原位时,限位开关SQ1受压。
按下启动按钮SB1,动⼒电动机Ml得电,带动钻头转动。
同时⼯进电动机M2得电,钻头快进。
当碰到限位开关SQ2时,⼯进电磁阀YV得电,转为⼯作进给。
当碰到限位开关SQ3时,YV2失电,停⽌⼯进。
5s后,钻头快退,碰到SQ1时,动⼒电动机和电磁阀均失电,停⽌⼯作。
按下停⽌按钮,动机电动机和电磁阀均失电。
控制⽅案设计1.输⼊/输出元件及控制功能如表35-1所⽰,介绍了实例35中⽤到的输⼊/输出元件及控制功能。
2.电路设计钻孔动⼒头控制梯形图如图35-2所⽰。
3.控制原理⽅法1:图35-2 (a)中,钻头在原位时限位开关X1受压,接点闭合。
按下启动按钮XO, MC 主控指令的线圈Y0得电并⾃锁,主轴电动机启动。
此处⽤MC、MCR指令的⽬的是保证只有在主轴电动机Y0得电时钻头才能⼯作,另⼀个⽬的是简化电路(如果⽤OUT Y0指令梯形图较复杂)。
同时Y1得电⾃锁,进给电动机得电快进。
当快进碰到限位开关X2时,Y3 得电⾃锁,⼯进电磁阀得电钻头⼯进。
当⼯进碰到限位开关X3时,M0得电⾃锁,Y1、Y3 失电,钻头停⽌;TO得电延时5s, Y2得电。
进给电动机得电快退。
当快退(中途碰到限位开关X2吋,由于Y2常闭接点断开,不会误使Y3得电)到原位碰到限位开关X1时,X1上升沿接点取反,使主控线圈Y0失电,完成⼀次钻孔过程。
⽅法2:图35-2 (b)中,初始状态,钻头在原位时限位开关X1受压。
按下启动按钮X0,状态器SO置位,由于限位开关X1受压接点闭合,状态器SO⼜复位,S500置位,Y0置位,主轴电动机启动。
Y1线圈得电,进给电动机得电快进。
当快进时碰到限位开关X2时,Y0仍置位,Y1失电,Y3得电,⼯进电磁阀得电钻头前进。
当⼯进碰到限位开关X3时,Y3失电钻头停⽌,TO得电延时5s,Y2得电。
深孔钻机床PLC控制电路的设计

深孔钻机床PLC控制电路的设计深孔钻机床是一种专门用于加工深孔的机床,其加工深孔的工艺复杂,对控制系统的可靠性和精度要求较高。
PLC(Programmable Logic Controller,可编程逻辑控制器)被广泛应用于深孔钻机床的控制系统中,具有可编程性强、可靠性高等特点。
首先,深孔钻机床的PLC控制电路应包括输入模块、输出模块、中央处理器以及电源等组成部分。
输入模块主要负责检测各种传感器的输出信号,例如钻头的位置、进给速度等。
输出模块则负责控制机床的各种执行器,例如钻孔进给和回退等。
中央处理器是PLC的核心部分,负责处理输入信号,并输出相应的控制信号。
其次,深孔钻机床的PLC控制电路的设计要考虑以下几个方面:1.高精度控制:深孔钻机床的加工要求高精度,因此PLC控制电路应具有高精度的脉冲输出端口,以控制机床的进给速度和位置。
可以采用高速计数器模块,实现对脉冲信号的精确计数和控制。
2.多轴控制:深孔钻机床通常包括多个工作轴,如X、Y、Z轴等。
PLC控制电路应支持多轴控制,需要具备多个高速计数器和输出模块,实现对多个轴的独立控制。
3.安全保护:深孔钻机床的加工过程中存在一定的危险,PLC控制电路应包含相应的安全保护措施,如急停开关、过载保护等,确保操作人员和设备的安全。
4.自动化控制:PLC控制电路可以实现深孔钻机床的自动化控制,例如根据加工要求自动调整进给速度和切削参数等。
此外,还可以通过与上位机通信和数据交互,实现远程监控和故障诊断。
在深孔钻机床的PLC控制电路具体设计中,需要根据具体的机床加工要求和实际控制需求进行功能划分和模块选择。
同时,还需要考虑电源和接口电路的设计,确保PLC控制电路的稳定性和可靠性。
总结起来,深孔钻机床的PLC控制电路的设计应当考虑高精度控制、多轴控制、安全保护和自动化控制等方面。
在具体的设计中,需要根据实际需求进行功能划分和模块选择,并确保电路的稳定性和可靠性。
基于PLC控制的数控钻孔机的设计与实现

基于PLC控制的数控钻孔机的设计与实现数控钻孔机是一种通过计算机数控系统实现自动钻孔的设备,可以实现高精度、高效率的钻孔作业。
本文将基于PLC控制的数控钻孔机的设计与实现进行详细介绍。
1.设计概述数控钻孔机主要由机械部分和控制系统两部分组成。
机械部分主要包括电动机、传动装置和钻头等,控制系统则由PLC控制器和人机界面组成。
2.机械部分设计为了实现高精度的钻孔作业,机械部分需要具备较高的稳定性和刚度。
首先,选择质量较好的电动机,通过减速装置将电动机的转速转为稳定的钻头转速。
其次,使用高硬度的刀具材料,以保证钻头在高速转动时不会变形。
最后,选择高精度的导轨和滑块,确保钻孔机在运动过程中无偏差。
3.PLC控制系统设计PLC控制系统是数控钻孔机的核心部分,它通过计算机数控系统来实现自动化的钻孔操作。
首先,选择适合的PLC控制器,通常选择具有高速计算和多IO口的控制器。
其次,编写PLC程序,根据用户输入的坐标参数和钻头尺寸,计算出钻孔的位置和深度。
然后,通过控制器的输出口,控制电动机的转速和钻头的升降运动,实现自动化的钻孔操作。
最后,在控制界面上添加合适的控制按钮和显示界面,方便用户操作和监测钻孔过程。
4.人机界面设计为了方便操作和监测钻孔过程,需要设计一个直观清晰的人机界面。
在界面上添加坐标输入框和尺寸调节按钮,方便用户输入钻孔的坐标和尺寸参数。
同时,添加控制按钮和监测指示灯,方便用户启动和停止钻孔过程,并实时监测钻孔状态。
另外,在界面上添加错误提示功能,当出现异常情况时能及时提示用户,并采取相应的应对措施。
5.钻孔机的实现在完成设计后,将机械部分和控制系统进行组装和调试。
首先,根据设计要求,选择适合的材料和加工工艺,制作机械部分的各个零件。
然后,组装机械部分,确保各个部件的协调配合。
接下来,将PLC控制器和人机界面与机械部分进行连接,并进行电气布线和信号调试。
最后,进行整机调试和测试,检查钻孔机的各项指标是否符合设计要求。
基于PLC的钻孔加工过程自动化控制系统的设计
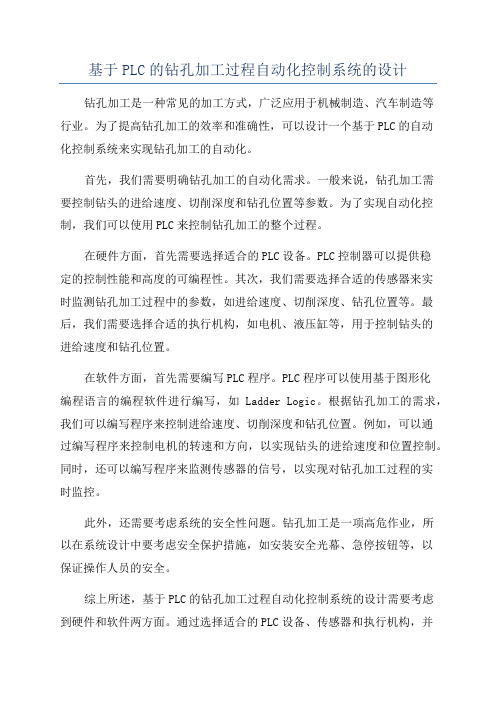
基于PLC的钻孔加工过程自动化控制系统的设计钻孔加工是一种常见的加工方式,广泛应用于机械制造、汽车制造等行业。
为了提高钻孔加工的效率和准确性,可以设计一个基于PLC的自动化控制系统来实现钻孔加工的自动化。
首先,我们需要明确钻孔加工的自动化需求。
一般来说,钻孔加工需要控制钻头的进给速度、切削深度和钻孔位置等参数。
为了实现自动化控制,我们可以使用PLC来控制钻孔加工的整个过程。
在硬件方面,首先需要选择适合的PLC设备。
PLC控制器可以提供稳定的控制性能和高度的可编程性。
其次,我们需要选择合适的传感器来实时监测钻孔加工过程中的参数,如进给速度、切削深度、钻孔位置等。
最后,我们需要选择合适的执行机构,如电机、液压缸等,用于控制钻头的进给速度和钻孔位置。
在软件方面,首先需要编写PLC程序。
PLC程序可以使用基于图形化编程语言的编程软件进行编写,如Ladder Logic。
根据钻孔加工的需求,我们可以编写程序来控制进给速度、切削深度和钻孔位置。
例如,可以通过编写程序来控制电机的转速和方向,以实现钻头的进给速度和位置控制。
同时,还可以编写程序来监测传感器的信号,以实现对钻孔加工过程的实时监控。
此外,还需要考虑系统的安全性问题。
钻孔加工是一项高危作业,所以在系统设计中要考虑安全保护措施,如安装安全光幕、急停按钮等,以保证操作人员的安全。
综上所述,基于PLC的钻孔加工过程自动化控制系统的设计需要考虑到硬件和软件两方面。
通过选择适合的PLC设备、传感器和执行机构,并编写合适的PLC程序,可以实现对钻孔加工过程的自动化控制。
这样可以提高钻孔加工的效率和准确性,降低人工操作的工作强度,提高生产效益。
同时,还需要考虑系统的安全性问题,采取相应的安全保护措施,确保操作人员的安全。
钻孔动力头的plc控制分析

钻孔动力头的PLC控制分析钻孔动力头在各种钻探和钻孔工作中起着关键的作用,其性能直接影响到工作效率和质量。
随着现代工业的快速发展,自动化程度越来越高,PLC控制系统作为一种重要的控制方式得到了广泛应用。
本文将针对钻孔动力头的PLC控制系统进行分析,介绍其控制原理和实现方法。
钻孔动力头的工作原理首先,了解钻孔动力头的工作原理对于我们理解PLC控制系统非常重要。
在石油、水利、地质等领域,钻孔动力头的主要作用是将钻具传递给井下的钻头,同时驱动钻头进行钻孔作业。
具体来说,钻孔动力头主要由钻杆、传动机构、动力机构等部分组成,其工作原理如下:1.钻杆通过传动机构连接到动力机构;2.动力机构通过电机、液压或气动系统提供动力;3.传动机构将动力传递到钻头,驱动钻头旋转钻孔或钻取地质样品。
PLC控制系统的特点PLC即Programmable Logic Controller,可编程逻辑控制器,也是一种数字控制器,广泛应用于各种现代工业控制系统中。
它拥有以下几个特点:1.开放性:PLC控制系统采用国际标准编程语言,具有开放性,易于维护;2.稳定性:PLC控制系统的硬件和软件都比较稳定,能够长时间运行;3.可编程性:PLC控制系统可以方便地进行编程,可根据需要随时修改程序;4.灵活性:PLC控制系统可根据控制参数的变化自动调整输出信号,实现自动化控制。
钻孔动力头的PLC控制系统钻孔动力头的PLC控制系统可分为三个主要部分:硬件平台、软件平台和外部设备。
其中:1.硬件平台:PLC控制系统的硬件平台主要包括PLC主控板、输入输出模块、通信模块、LCD显示屏等,其中,输入输出模块负责收集钻孔动力头的运行数据和操作命令,通信模块负责与上位机进行通讯,LCD显示屏用于显示工作状态和参数。
2.软件平台:PLC控制系统的软件平台主要由控制程序和监控程序组成。
控制程序主要负责控制钻孔动力头的运行,实现自动化控制;监控程序主要负责对钻孔动力头的状态进行监测和报警。
钻孔动力头PLC控制课程设计说明书
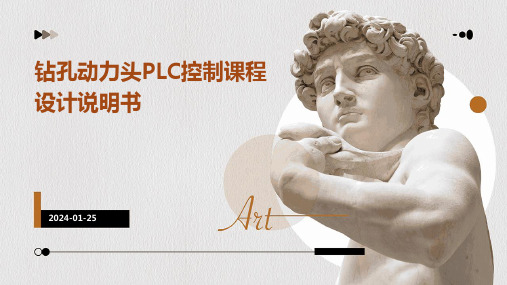
在未来的相关课程中,可以进一步加强对PLC控制理论的学习,包括PLC的工作原理、编程语言、通信协议等方面的知识。
加强PLC控制理论学习
通过增加实践环节,让学生有更多的机会亲自动手进行PLC编程和调试,提高学生的实践能力和动手能力。
增加实践环节
THANKS
感谢您的观看。
04
CHAPTER
软件编程与实现
编程语言选择
模块化
强大的数学运算能力
易于与硬件接口
结构化
特点分析
根据钻孔动力头控制需求,选用结构化文本(ST)作为编程语言。ST语言采用类似于高级编程语言的语法结构,易于理解和维护,同时支持复杂的算法和数学运算,适用于钻孔动力头的精确控制。
ST语言具有以下特点
采用类似于C/C等高级语言的语法结构,代码清晰易懂。
手动/自动模式选择模块
03
根据用户需求选择手动或自动模式,手动模式下用户可以通过操作面板直接控制钻孔动力头的动作,自动模式下则按照预设的程序进行自动控制。
允许用户设置钻孔动力头的运行参数,如转速、进给速度、钻孔深度等。
参数设置模块
当钻孔动力头出现故障时,及时停止设备运行并显示故障信息,方便用户进行维修和调试。
01
实现了钻孔动力头的PLC控制
通过编写PLC程序,成功实现了对钻孔动力头的精准控制,包括启动、停止、转速调节等功能。
02
完成了人机交互界面设计
设计了易于操作的人机交互界面,使得操作人员能够方便地对钻孔动力头进行控制和监控。
通过本次课程设计,我进一步熟悉了PLC编程语言和编程环境,提高了自己的编程能力。
03
在操作面板上显示当前转速、进给速度和位置;
VS
某深孔钻的PLC控制设计
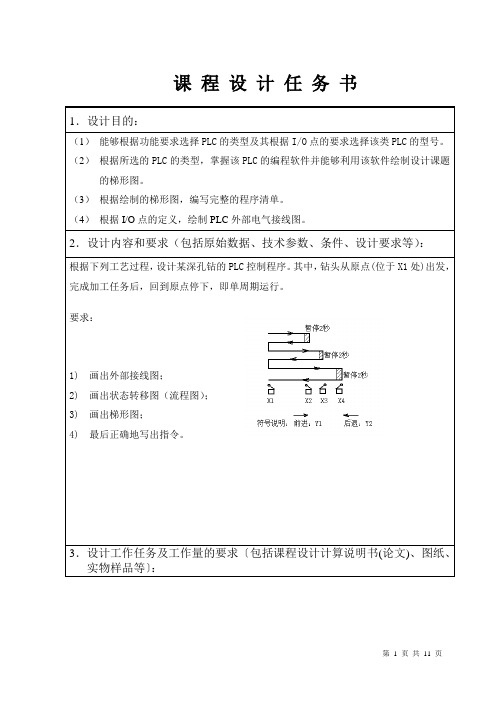
课 程 设 计 任 务 书1.设计目的:(1) 能够根据功能要求选择 PLC 的类型及其根据 I/O 点的要求选择该类 PLC 的型号。
(2) 根据所选的 PLC 的类型,掌握该 PLC 的编程软件并能够利用该软件绘制设计课题 的梯形图。
(3) 根据绘制的梯形图,编写完整的程序清单。
(4) 根据 I/O 点的定义,绘制 PLC 外部电气接线图。
2.设计内容和要求(包括原始数据、技术参数、条件、设计要求等) :根据下列工艺过程, 设计某深孔钻的 PLC 控制程序。
其中, 钻头从原点(位于 X1 处)出发, 完成加工任务后,回到原点停下,即单周期运行。
要求:1) 画出外部接线图; 2) 画出状态转移图(流程图) ; 3) 画出梯形图; 4) 最后正确地写出指令。
3.设计工作任务及工作量的要求〔包括课程设计计算说明书(论文)、图纸、 实物样品等〕 :第 1 页 共 11 页按照任务书要求, 完成课程设计说明书一份; PLC 外部接线图一份; PLC 梯形图一份。
课 程 设 计 任 务 书4.主要参考文献:例如: (根据自己的参考文献写如下内容,与设计说明书中的参考文献一致,以下仅仅是 学生参考的格式) [1] 王阿根. 电气可编程序控制原理与应用.清华大学出版社.2010 [2] 何有华. 可编程序控制器及常用控制电路. 冶金工业出版社.2002 [3] 郭纯生. 可编程序控制器编程实战与提高. 电子工业出版社.2006 [4] 谢克明 夏路易. 可编程控制器. 电子工业出版社.20035.设计成果形式及要求:PLC 外部接线图;梯形图;设计说明书。
6.工作计划及进度:1 月 7 日 ~ 1 月 10 日 根据功能要求及自己的掌握的 PLC 知识选择 PLC 类型及 对该 PLC 进行深入学习。
1 月 11 日 ~ 1 月 17 日 根据设计要求,设计完整的系统程序,并撰写课程设计 说明书。
钻孔动力头的PLC控制
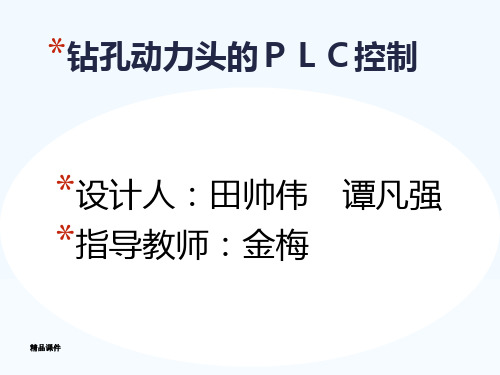
*四、梯形图设计
精品课件
启动后X001置1,F1接通 限位开关K1接通
精品课件
限位开关K2接通
延时10秒后后退 到达K3后停止
*五件
2.组态王设计界面
精品课件
3.运行界面
精品课件
谢谢观赏
精品课件
*二、动力头的工作循环过程
*动力头在原位时,加启动命令后接通电磁阀
F1,动力头快进,碰到限位开关K1时接通电 磁阀F1和F2转为工作进给,碰到限位开关 K2时,停止进给。延时10s后接通电磁阀F3, 动力头快速退回,当原点限位开关K3接通时 动力头快退结束。
精品课件
*三、 I/O地址的分配及接线图
*输入信号 *名称 *启动按钮 *快进限位开关 *工进限位开关 *原点限位开关 *停止按钮
精品课件
代号 启动 K1 K2 K3 停止
输入点编号 X001
X002 X003 X004
X005
*输出信号 *名称
*前进接触器
*转动接触器
*后退接触器
精品课件
代号 KM1 KM2 KM3
输出编号 Y000 Y001 Y002
*钻孔动力头的PLC控制
*设计人:田帅伟 谭凡强 *指导教师:金梅
精品课件
*一、控制任务
1.动力头在原位时,加启动命令后接通电磁阀 F1,动力头快进。 2.动力头碰到限位开关K1后,接通电磁阀F1和 F2,动力头由快进转为工进
3.动力头碰到限位开关K2后,停止进给, 延时10S。 4.延时时间到,接通F3,动力头快速退回。 当原点限位开关K3接通时,动力头快速退 精品课件回结束。
钻孔动力头的plc控制.
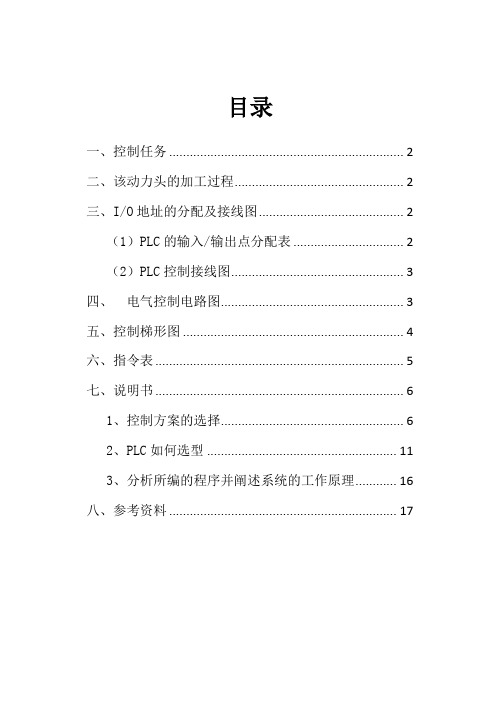
目录一、控制任务 (2)二、该动力头的加工过程 (2)三、I/O地址的分配及接线图 (2)(1)PLC的输入/输出点分配表 (2)(2)PLC控制接线图 (3)四、电气控制电路图 (3)五、控制梯形图 (4)六、指令表 (5)七、说明书 (6)1、控制方案的选择 (6)2、PLC如何选型 (11)3、分析所编的程序并阐述系统的工作原理 (16)八、参考资料 (17)钻孔动力头的PLC控制一、控制任务(1)动力头在原位时开关ST3受压,加启动命令后接通电磁阀F1,动力头快进。
(2)动力头碰到限位开关ST1后,接通电磁阀F1和F2,动力头由快进转为工进。
(3)动力头碰到限位开关ST2后,停止进给,延时10S。
(4)延时时间到,接通F3,动力头快速退回。
(5)当原点限位开关ST3接通时,动力头快速退回结束。
根据上述控制要求,用PLC编制程序实现对钻孔动力头的控制。
二、该动力头的加工过程三、I/O地址的分配及接线图(1) PLC的输入/输出点分配表输入信号名称代号输入点编号启动按钮启动X0停止按钮停止X1 原点限位开关ST3 X2快进限位开关ST1 X3工进限位开关ST2 X4输出信号名称代号输出编号正转接触器KM1 Y0正转接触器KM2 Y1反转接触器KM3 Y2 (2)PLC控制接线图四、电气控制电路图五、PLC控制梯形图六、PLC控制指令语句表七、说明书1、控制方案的选择(1)为何采用PLC控制可编程序控制器PLC是微机技术与传统的继电接触控制技术相结合的产物,它克服了继电接触控制系统中的机械触点的接线复杂、可靠性低、功耗高、通用性和灵活性差的缺点,充分利用了微处理器的优点,又照顾到现场电气操作维修人员的技能与习惯,特别是PLC的程序编制,不需要专门的计算机编程语言知识,而是采用了一套以继电器梯形图为基础的简单指令形式,使用户程序编制形象、直观、方便易学;调试与查错也都很方便。
用户在购到所需的PLC后,只需按说明书的提示,做少量的接线和简易的用户程序编制工作,就可灵活方便地将PLC应用于生产实践。
PLC控制的专用钻孔系统设计

PLC控制的专用钻孔系统设计PLC(可编程逻辑控制器)是一种用于控制工业自动化系统的计算机控制系统,它可以控制和监控各种工艺设备和机器。
钻孔系统是一种常见的工业设备,用于在不同材料上进行钻孔操作。
本文将介绍如何设计一个基于PLC控制的专用钻孔系统。
首先,设计钻孔系统时需要确定系统的功能需求。
主要功能包括控制钻头的进给速度和转速,控制钻孔深度和位置,实现自动钻孔和停止功能。
此外,钻孔系统还可以考虑添加自动刀具更换和质量检测等功能。
接下来,需要选择适用的PLC控制器和其他相关硬件设备。
根据钻孔系统的规模和要求,选择合适的PLC型号和扩展模块。
同时,选择合适的传感器和执行器,用于监测和控制钻孔系统的运行状态。
在进行系统设计时,需要根据功能需求和硬件设备的特性,编写PLC程序。
程序应考虑到钻孔的各种情况和特殊要求,例如不同材料的钻孔参数不同,需要根据材料类型和规格进行调整。
此外,还可以添加故障诊断和报警功能,以便及时发现和修复故障。
图形化编程软件是PLC编程的常用工具,它可以简化编程的过程,并提供友好的用户界面。
使用该软件,可以创建钻孔系统的控制界面,并实现直观的操作和监控功能。
同时,还可以通过通信接口与其他系统进行数据交换,如与上位机进行数据传输和与生产线进行协作。
在钻孔系统设计中,安全性是一个至关重要的因素。
系统应考虑到各种安全措施,包括紧急停止按钮、安全门和传感器等。
此外,还需要进行安全风险评估,并根据评估结果进行相应的控制和优化。
在设计完成后,需要进行系统的调试和测试。
通过模拟真实操作场景,测试PLC程序的功能和性能。
同时,还需要验证系统对各种输入条件的响应和处理能力,并进行必要的调整和改进。
最后,为了确保钻孔系统的可靠性和稳定性,需要进行预防性维护和定期检查。
定期检查系统的各个组件、传感器和执行器的工作状态,并及时更换损坏或老化的部件。
总之,基于PLC控制的专用钻孔系统设计需要综合考虑功能需求、硬件设备、编程软件和安全措施等因素。
plc控制钻机实训

电机与控制模块实训一、PLC控制1.题目:台式电钻机系统程序设计及模拟运行2.所要实现的功能接上电后初始化(回到原点),然后打第一个孔,再打第二个孔,然后回到原位。
电钻机通过三个小电机控制上下、左右、前后的运行,其各端分别有两个行程开关控制其运动的终止,行程开关用常开触点连入PLC的输入端口,公共端与COM端口相连。
其运动由六个继电器分别控制,各继电器控制引线接入PLC的输出端口。
通过PLC控制电钻机实现自动打孔。
具体为电钻机接上15V电压PLC接通电源后等待X0启动按钮接通,接通后电钻机初始化回到原点,然后再从原点行进到第一个点,停顿后开始打孔,再行进到第二个点打孔,然后回到原位。
流程图为3.完整的硬件电路图4.梯形图程序5.实际运行的情况及实训的心得体会我主要负责程序编制部分内容,才开始我们主要研究硬件部分的功能实现所具备的条件,这样便于设计和编写程序,在弄清楚了硬件电路后开始遍了一段简短的程序烧进去实验发现问题很多,才开始直接不会动,检查电路后咨询老师之后改动了连线后简单的程序能运行,但是启动按钮X0却没有效果,在老师的帮助下用万用表检查后发现PLC坏了,重新换了一个后把完整程序烧入,但是却没有按预设运行,很乱,再次咨询老师后发现行程开关长臂触电和常开触点弄反了,导致程序出错了,再重新调整行程开关接线后能实现初始化,对照程序发现刚要开始第一次打点的时候出错了,向左运行和向右运行的行程开关互锁实现了初始化,但是开始打点时离开了行程开关,导致互锁失效,程序出乱,发现问题后加上了定时器互锁便解决了这个问题,之后通过实际操作不断修改完善了程序,最后实现了整个过程。
二、电机控制1、由两个启动按钮控制的长动、点动控制线1)电路图2)工作原理按下SB2后长动,按下SB3后点动。
3)顺利完成该项。
按下SB2后一直在动,按下SB1后动一下。
2、自动往复循环控制线路1)电路图2)工作原理连接好线路后按下SB3后线圈KM2得电,常开触点KM2自锁,电机正传,当碰到行程开关SQ1时常开触点SQ1常闭触点断开,正传停止,同时SQ1常开触点闭合,线圈KM1得电,常开触点KM1闭合,电机反转,当碰到行程开关SQ2时常闭触点SQ2断开,线圈KM1断电,反转停止,常开触点SQ2闭合,KM2得电正传,并循环上述,当按下SB1后停止。
钻孔动力头的plc控制汇总
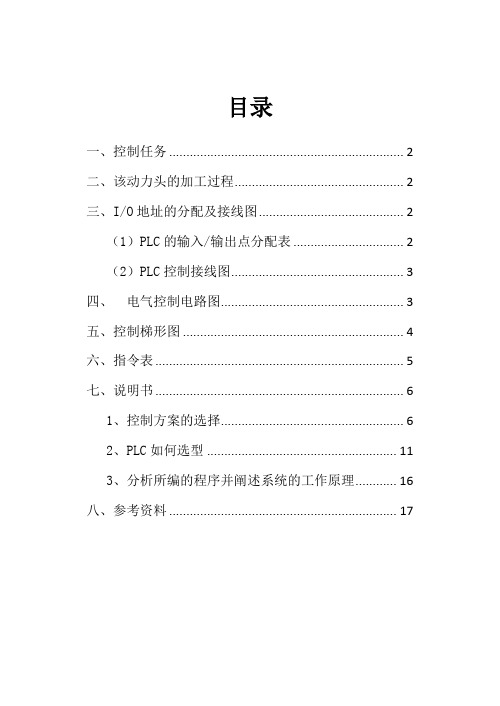
目录一、控制任务 (2)二、该动力头的加工过程 (2)三、I/O地址的分配及接线图 (2)(1)PLC的输入/输出点分配表 (2)(2)PLC控制接线图 (3)四、电气控制电路图 (3)五、控制梯形图 (4)六、指令表 (5)七、说明书 (6)1、控制方案的选择 (6)2、PLC如何选型 (11)3、分析所编的程序并阐述系统的工作原理 (16)八、参考资料 (17)钻孔动力头的PLC控制一、控制任务(1)动力头在原位时开关ST3受压,加启动命令后接通电磁阀F1,动力头快进。
(2)动力头碰到限位开关ST1后,接通电磁阀F1和F2,动力头由快进转为工进。
(3)动力头碰到限位开关ST2后,停止进给,延时10S。
(4)延时时间到,接通F3,动力头快速退回。
(5)当原点限位开关ST3接通时,动力头快速退回结束。
根据上述控制要求,用PLC编制程序实现对钻孔动力头的控制。
二、该动力头的加工过程三、I/O地址的分配及接线图(1) PLC的输入/输出点分配表输入信号名称代号输入点编号启动按钮启动X0停止按钮停止X1 原点限位开关ST3 X2快进限位开关ST1 X3工进限位开关ST2 X4输出信号名称代号输出编号正转接触器KM1 Y0正转接触器KM2 Y1反转接触器KM3 Y2 (2)PLC控制接线图四、电气控制电路图五、PLC控制梯形图六、PLC控制指令语句表七、说明书1、控制方案的选择(1)为何采用PLC控制可编程序控制器PLC是微机技术与传统的继电接触控制技术相结合的产物,它克服了继电接触控制系统中的机械触点的接线复杂、可靠性低、功耗高、通用性和灵活性差的缺点,充分利用了微处理器的优点,又照顾到现场电气操作维修人员的技能与习惯,特别是PLC的程序编制,不需要专门的计算机编程语言知识,而是采用了一套以继电器梯形图为基础的简单指令形式,使用户程序编制形象、直观、方便易学;调试与查错也都很方便。
用户在购到所需的PLC后,只需按说明书的提示,做少量的接线和简易的用户程序编制工作,就可灵活方便地将PLC应用于生产实践。
深孔钻PLC控制系统设计
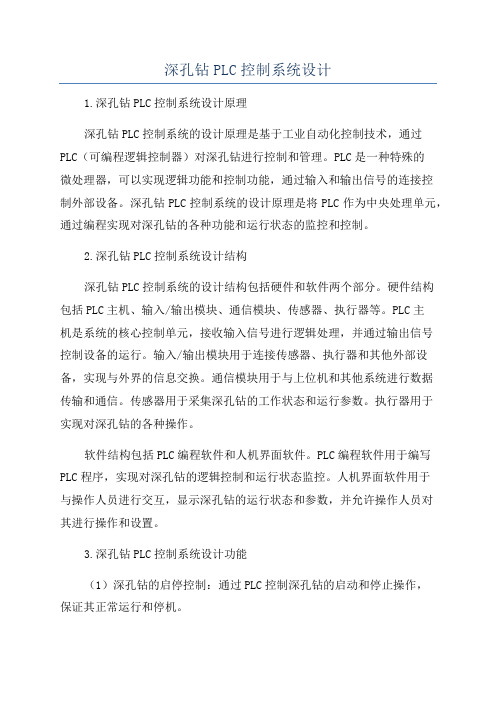
深孔钻PLC控制系统设计1.深孔钻PLC控制系统设计原理深孔钻PLC控制系统的设计原理是基于工业自动化控制技术,通过PLC(可编程逻辑控制器)对深孔钻进行控制和管理。
PLC是一种特殊的微处理器,可以实现逻辑功能和控制功能,通过输入和输出信号的连接控制外部设备。
深孔钻PLC控制系统的设计原理是将PLC作为中央处理单元,通过编程实现对深孔钻的各种功能和运行状态的监控和控制。
2.深孔钻PLC控制系统设计结构深孔钻PLC控制系统的设计结构包括硬件和软件两个部分。
硬件结构包括PLC主机、输入/输出模块、通信模块、传感器、执行器等。
PLC主机是系统的核心控制单元,接收输入信号进行逻辑处理,并通过输出信号控制设备的运行。
输入/输出模块用于连接传感器、执行器和其他外部设备,实现与外界的信息交换。
通信模块用于与上位机和其他系统进行数据传输和通信。
传感器用于采集深孔钻的工作状态和运行参数。
执行器用于实现对深孔钻的各种操作。
软件结构包括PLC编程软件和人机界面软件。
PLC编程软件用于编写PLC程序,实现对深孔钻的逻辑控制和运行状态监控。
人机界面软件用于与操作人员进行交互,显示深孔钻的运行状态和参数,并允许操作人员对其进行操作和设置。
3.深孔钻PLC控制系统设计功能(1)深孔钻的启停控制:通过PLC控制深孔钻的启动和停止操作,保证其正常运行和停机。
(2)深孔钻的运行状态监控:通过PLC采集传感器信号,实时监测深孔钻的工作状态,包括转速、切削力、冷却液流量等,以及机床的运行状态。
(3)深孔钻的切削参数设置:通过人机界面软件,允许操作人员设置深孔钻的切削参数,如进给速度、切削深度、冷却液的流量等。
(4)深孔钻的报警和故障处理:通过PLC程序的逻辑判断,实时检测深孔钻的运行状态和传感器信号,如果发生异常情况或故障,自动报警并采取相应的处理措施。
4.深孔钻PLC控制系统实现方法和工作原理(1)PLC编程:根据深孔钻的工作特点和要求,编写PLC程序,实现对深孔钻的逻辑控制和运行状态监控。
基于PLC及WinCC的冷加工生产线上钻孔动力头的加工过程.
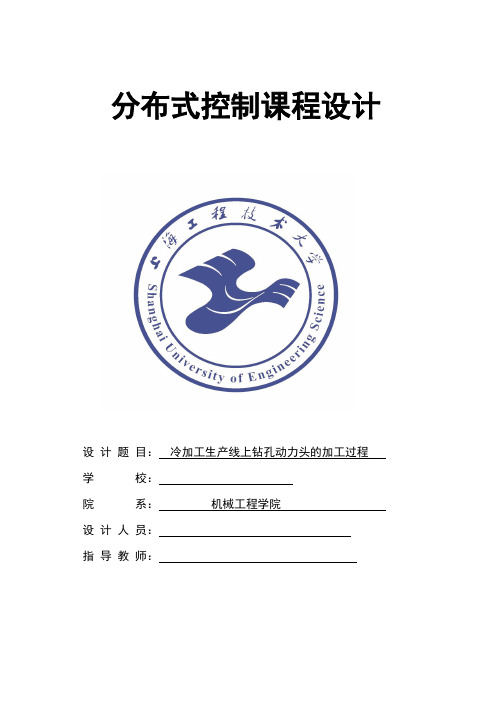
分布式控制课程设计设计题目:冷加工生产线上钻孔动力头的加工过程学校:院系:机械工程学院设计人员:指导教师:目录任务描述 (1)控制任务和要求 (1)方案分析 (2)硬件配置及I/O接线图 (2)(1)PLC外部接线图 (2)(2)系统硬件配置 (2)I/0地址分配 (3)程序设计 (3)(1)创建符号表 (4)(2)创建组织块OB1 (4)STEP 7仿真调试及运行 (5)(1)调试方案确定 (5)(2)软件仿真调试 (6)WINCC 介绍 (7)(1)简介7 (2)突出优点7 SIMATIC WINCC仿真 (8)(1)创建新的驱动程序 (8)(2)建立变量表 (8)(3)创建运行画面 (9)设计总结 (11)参考文献 (12)任务描述在各种形式的工件加工过程中,以快进—工进—快退作为生产流动方式的工艺过程得到了广泛的应用。
设计控制器的原则是:(1)可以根据实际工艺过程,设定具体的控制点。
(2)各具体要求的工艺过程能够很好的保持彼此间的关系。
(3)根据总体规模的大小要求,能够自由调整控制点个数。
为简单起见,将限位开关假设为一开关按钮,系统组成如图1所示。
在每动力头碰到限位开关时,相应的按钮被按下;图1 系统组成控制任务和要求(1)动力头在原为(压下限位开关SL0)时,按启动按钮,接通电磁阀YV1,动力头快进。
(2)动力头碰到限位开关SL1后,接通电磁阀YV1和YV2,动力头由快进转为共进。
(3)动力头碰到限位开关SL2后,延时3s。
(4)延时时间到,接通电磁阀YV3,动力头快退。
(5)动力头退回到原位后(碰到限位开关SL0)停车。
1方案分析动力头加工过程控制装置是由两大部分组成:电动机起停和限位开关。
电动机起停主要有关不同工位电动机的开关与工件所在位置的关系。
能完成任务中的相应要求,避免不工作的工位电机也保持转动。
限位开关主要用于判断工件所处的工位。
两个主要块在编写程序的过程中需注意以下几点:a、各工位要有准确的顺序,不能存在逻辑上的混乱。
钻孔专用机床的PLC控制设计与实现

钻孔专用机床的PLC控制设计与实现摘要钻孔专用机床是典型的机、电、液一体化设备,其先进程度决定了一个国家和地区制造业的生产能力。
可编程序逻辑控制器组成的控制电路相对于继电器控制电路在控制方式、工作方式、控制速度、定时和计数功能的实现,以及可靠性和可维护性方面都有着明显的优势。
本文针对钻孔专用机床的结构和运动部件情况,并根据加工工艺详细分析了其控制要求,通过对比传统的继电器控制和PLC控制性能特点,选用PLC控制系统,并完成了该机床的梯形图设计,实现了其控制功能。
关键词可编程序控制器;钻孔专用机床;逻辑控制随着科学技术的发展,制造业已经成为经济发展的重要支柱,成为衡量一个国家或地区的经济实力、科技水平、生活水准和国防实力的标志。
机床是制造业不可或缺的装备,其决定了制作业的生产能力[3]。
钻孔专用机床是机床中的一种,它是典型的机、电、液一体化设备。
现代钻孔专用机床已对传统的钻床进行了改进,特别是开关量的逻辑控制部分,用PLC 取代了传统的继电器—接触器控制,使生产控制过程更加平稳可靠,提高了效率,减少维修人员的任务量。
本文主要研究了用PLC对其液压系统进行控制,实现对工件的加工。
如图1所示为典型的钻孔专用机床运动过程,主轴电动机为M1,左、右动力头进给运动由液压驱动,液压泵电动机为M2。
a)左、右动力头运动图b)钻孔机床工作示意图1 钻孔专用机床的总体控制要求1)初始状态,主轴电动机及液压泵电动机均停止,电磁阀Y1~Y7均断电。
位置开关SQ1=SQ2=ON,SQ3=SQ4=SQ5=SQ6=SQ7=OFF;2)工作流程:先启动液压泵,按启动按钮后夹紧工件→左、右动力头同时快进,并启动主轴→当行程开关SQ3=SQ4=ON时,转入工进加工→当行程开关SQ5=SQ6=ON时,压下挡铁后,在此处停5秒→左右动力头分别快退→当行程开关SQ1=SQ2=ON时,松开工件,主轴停止转动……如此循环往复,实现半自动循环;3)如需停止,则按下停止按钮后,在完成本次工作循环后方能停止。
自动钻孔攻丝机床的PLC控制

自动钻孔攻丝机床的PLC控制两工位钻孔、攻丝组合机床,能自动完成工件的钻孔和攻丝加工,自动化程度高,生产效率高。
两工位钻孔、攻丝组合机床如图7-32所示。
图7-32 两工位钻孔、攻丝组合机床示意图机床主要由床身、移动工作台、夹具、钻孔滑台、钻孔动力头、攻丝滑台、攻丝动力头、滑台移动控制凸轮和液压系统等组成。
移动工作台和夹具用以完成工件的移动和夹紧,实现自动加工。
钻孔滑台和钻孔动力头,用以实现钻孔加工量的调整和钻孔加工。
攻丝滑台和攻丝动力头,用以实现攻丝加工量的调整和攻丝加工。
工作台的移动(左移、右移),夹具的夹紧、放松,钻孔滑台和攻丝滑台的移动(前移、后移),均由液压系统控制。
其中两个滑台移动的液压系统由滑台移动控制凸轮来控制,工作台的移动和夹具的夹紧与放松由电磁阀控制。
根据设计要求,工作台的移动和滑台的移动应严格按规定的时序同步进行,两种运动密切配合,以提高生产效率。
1. 控制要求系统通电,自动起动液压泵电动机M1。
若机床各部分在原位(工作台在钻孔工位SQ1动作,钻孔滑台在原位SQ2动作,攻丝滑台在原位SQ3动作),并且液压系统压力正常,压力继电器PV动作,原位指示灯HL1亮。
将工件放在工作台上,按下起动按钮SB,夹紧电磁阀YV1得电,液压系统控制夹具将工件夹紧,与此同时控制凸轮电动机M2得电运转。
当夹紧限位SQ4动作后,表明工件已被夹紧。
起动钻孔动力头电动机M3,且由于凸轮电动机M2运转,控制凸轮控制相应的液压阀使钻孔滑台前移,进行钻孔加工。
当钻孔滑台到达终点时,钻孔滑台自动后退,到原位时停,M3同时停止。
等到钻孔滑台回到原位后,工作台右移电磁阀YV2得电,液压系统使工作台右移,当工作台到攻丝工位时,限位开关SQ6动作,工作台停止。
起动攻丝动力头电机M4正转,攻丝滑台开始前移,进行攻丝加工,当攻丝滑台到终点时(终点限位SQ7动作),制动电磁铁DL得电,攻丝动力头制动,0.3s后攻丝动力头电机M4反转,同时攻丝滑台由控制凸轮控制使其自动后退。
PLC任务2钻孔专用机床控制系统

相关知识
二、采用S、R指令设计并行序列控制程序 如图所示是一个并行序列的顺序功能图,采用S、R指令进行并 行序列控制程序设计的梯形图。
SM0.1
M0.0 I0.1
M 0.1 I0.2
M0.2
Q0 .1 Q0.2
M0.3
Q0 .3
I0.3 M 0.4
T37
Q0 . 1
T37 5S
1.并行序列分支的编程 M0.0之后有一个并行序列的分支。当M0.0是活动步,并且转换条 件I0.1为ON时,步M0.1和步M0.3应同时变为活动步,这时用M0.0和 I0.1的常开触点串联电路使M0.1和M0.3同时置位,用R指令使步M0.0 变为不活动步。
相关知识
相关知识
2.并行序列合并的编程 转换条件I0.3之前有一个并行序列的合并。当所有的前级步 M0.2和M0.3都是活动步,并且转换条件I0.3为ON时,实现并行 序列的合并。用M0.2、M0.3和I0.3的常开触点串联电路使后续 步M0.4置位,用R指令使步M0.2和M0.3变为不活动步。
任务准备
(2)某一输出量在多步中都为ON,应将各有关步的常开触点并 联后,驱动该输出量的线圈。例如图2-2-9中Q0.2在M0.1和M0.4这 两步中均应工作,所以用M0.1与M0.4的常开触点并联来驱动Q0.2的 线圈。
扩展知识
扩展知识
一、应知、应会部分
1、S7-200型PLC编译程序时,如显示错误信息为:0 ERR,则表
能力
安全 文明 生产
1.安全意识差,不安安全生产规程操作;扣10
分
2.劳动保护穿戴不整齐;扣10分
10
3.施工后不清理现场;扣5分
定额 15min,每超时5min
- 1、下载文档前请自行甄别文档内容的完整性,平台不提供额外的编辑、内容补充、找答案等附加服务。
- 2、"仅部分预览"的文档,不可在线预览部分如存在完整性等问题,可反馈申请退款(可完整预览的文档不适用该条件!)。
- 3、如文档侵犯您的权益,请联系客服反馈,我们会尽快为您处理(人工客服工作时间:9:00-18:30)。
*输入信号 *名称 *启动按钮 *快进限位开关 *工进限位开关 *原点限位开关 *停止按钮
实用文档
代号 输入点编号
启动
X001
K1
X002
K2
X003
K3
X004
停止
X005
*输出信号 *名称
编号
*前进接触器
*转动接触器
*后退接触器
实用文档
代号
KM1 KM2 KM3
输出
Y000 Y001 Y002
*四、梯形图设计
实用文档
启动后X001置1,F1接通 限位开关K1接通
实用文档
限位开关K2接通
延时10秒后后退 到达K3后停止
*五、组态王设计
1.变量命名
实用文档
2.组态王设计界面
实用文档
3.运行界面
实用文档
谢谢观赏
实用文档
*钻孔动力头的PLC控制
*设计人:田帅伟 谭凡强 *指导教师:金梅
实用文档
*一、控制任务
1.动力头在原位时,加启动命令后接通电磁阀 F1,动力头快进。 2.动力头碰到限位开关K1后,接通电磁阀F1和 F2,动力头由快进转为工进
3.动力头碰到限位开关K2后,停止进给, 延时10S。 4.延时时间到,接通F3,动力头快速退回。 当原点限位开关K3接通时,动力头快速退 实用文档回结束。
*二、动力头的工作循环过程
*动力头在原位时,加启动命令后接通电磁阀
F1,动力头快进,碰到限位开关K1时接通电 磁阀F1和F2转为工作进给,碰到限位开关K2 时,停止进给。延时10s后接通电磁阀F3, 动力头快速退回,当原点限位开关K3接通时 动力头快及接线图