原材料消耗计算
固定资产及原材料消耗核算公式

一、固定资产计算残值:预计卖废品能卖多少钱。
净残值:例:一台机器报废了,为了废品多卖点钱我们先把它拆了,把能卖的摆一志,或者是把这台废机器弄得干净点,预计为这个花的工资等,就叫清理费用,用残值减去清理费就叫净残值。
(1)直线法又称年限平均法,是指将固定资产的应提折旧额均衡地分摊到固定资产预计使用寿命内的各个会计期间的一种方法。
直线法的计算公式如下:年折旧额=(固定资产原值-预计净残值)÷预计使用年限月折旧额=年折旧额÷12例:某公司一台生产用设备原值为30000元,预计清理费为1200元,而预计残值为3000元,使用年限为4年。
那么用直线法怎么计算折旧额呢?年折旧额=【30000-(30000-1200)÷4=7050元月折旧额=7050÷12月科目:借:制造费用 587.5 贷:累计折旧(2)工作量法是指根据固定资产在生产经营过程中实际完成的工作量计算固定资产折旧额一种方法。
计算公式为单位作业量折旧额=(固定资产原值-预计净残值)÷预计总作业量各期折旧额=单位作业量折旧额×各期实际作业量例:某电器厂购置一台专用机床,价值200000元,预计总工作小时数为300000小时,预计净残值2000元,购置的当年便工作了2400小时,则有:每小时折旧额=(200000-2000)300000=0.66(元/小时)当年的折旧额=2400*0.66=1584(元)(3)双倍余额递减法是指在不考虑固定资产预计净残值的情况下,以固定资产年初账面净值作为折旧基数,以直线法的折旧率的双倍作为折旧率来计算折旧额的一种方法。
年折旧率= 2÷预计使用年限*100% 月折旧率=年折旧率/2使用双倍余额递减法要注意两点:1.这种方法使用初期不考虑固定资产的净残值2.在固定资产折旧年限到期以前的两年,也就是使用期的最后两年,把其余还没提的那部分扣除净残值以后,平均分在两年内计入折旧。
净料单位成本的具体计算方法

净料单位成本的具体计算方法净料单位成本是指在生产过程中,每单位产品所需的原材料成本。
计算净料单位成本的具体方法有以下几个步骤:1. 确定原材料成本:首先,需要确定生产过程中所使用的原材料,并计算出其成本。
原材料成本包括购买原材料的费用、运输费用以及其他与原材料相关的费用。
2. 计算净料消耗量:净料消耗量是指在生产过程中,每单位产品所消耗的原材料数量。
它可以通过以下公式计算得出:净料消耗量 = 原材料用量 - 原材料损耗量原材料用量是指生产一单位产品所需的原材料数量,而原材料损耗量是指在生产过程中由于废料、副产品等原因而损失的原材料数量。
3. 计算净料单位成本:净料单位成本是指在生产过程中,每单位产品所需的原材料成本。
它可以通过以下公式计算得出:净料单位成本 = 原材料成本 / 净料消耗量通过将原材料成本除以净料消耗量,可以得出每单位产品所需的原材料成本。
4. 考虑其他因素:除了原材料成本,还有一些其他因素也会对净料单位成本产生影响。
这些因素包括生产效率、设备维护成本、人工成本等。
在计算净料单位成本时,需要综合考虑这些因素,并进行相应的调整。
净料单位成本的计算方法可以帮助企业了解生产过程中的原材料使用情况,并通过优化生产过程来降低成本。
通过减少原材料消耗量、提高生产效率等方法,可以有效地降低净料单位成本,提高企业的竞争力。
净料单位成本是指在生产过程中,每单位产品所需的原材料成本。
通过计算原材料成本、净料消耗量等指标,可以得出净料单位成本,并通过优化生产过程来降低成本。
这对于企业的生产管理和成本控制非常重要,可以帮助企业提高竞争力,提升经济效益。
成本会计主要计算方法公式
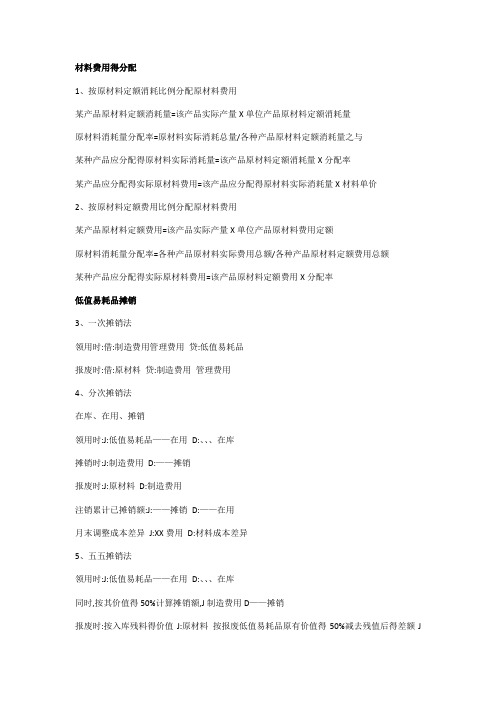
辅助生产车间提供得工具、模具与修理用备件等产品成本,在产品完工时从“辅助生产成本”科目得贷方转入“低值易耗品”、“原材料”科目得借方;
提供供水、供电、供气、修理与运输等劳务所发生得费用,在各受益单位之间进行分配,从“辅助生产成本”科目贷方转入“基本生产成本”、“制造费用”、“管理费用”、“销售费用”等科目得借方
1、直接分配法
单位成本(分配率)=待分配辅助生产费用/(辅助生产劳务总量-其她辅助生产劳务耗用量)
2、顺序分配法
按照受益多少得顺序将辅助生产车间依次排列,受益少得排在前面,先将费用分配出去,受益多得排在后面,后将费用分配出去
3、交互分配法
首先,将各辅助生产车间归集得费用,根据各辅助生产车间相互提供得产品或劳务数量与交互分配前得单位成本(费用分配率),在各辅助生产车间之间进行一次交互分配;然后,将各辅助生产车间交互分配后得实际费用,按提供产品或劳务数量与交互分配后得单位成本(费用分配率),在辅助生产车间以外得各受益单位之间进行分配。
直接用于辅助生产得动力费用,借记“辅助生产成本”总账科目及所属明细账得“直接燃料与动力”成本项目。
如果基本生产与辅助生产未专设“直接燃料与动力”成本项目,发生得动力费用借记“制造费用”科目及其明细账有关项目。
用于基本生产车间、辅助生产车间以及行政管理部门、销售部门得照明用电等,借记“制造费用”、“辅助生产成本”、“管理费用”、“销售费用”等总账科目及其所属明细账有关项目。
报废时:借:原材料贷:制造费用管理费用
4、分次摊销法
在库、在用ቤተ መጻሕፍቲ ባይዱ摊销
领用时:J:低值易耗品——在用D:、、、在库
摊销时:J:制造费用D:——摊销
报废时:J:原材料D:制造费用
木屑颗粒压制损耗计算公式

木屑颗粒压制损耗计算公式引言。
木屑颗粒是一种常见的生物质能源,其生产过程中会产生一定的损耗。
了解和计算木屑颗粒压制损耗对于生产厂家和研究人员来说都是非常重要的。
通过合理的损耗计算,可以帮助生产厂家控制生产成本,提高生产效率,同时也有助于研究人员深入了解木屑颗粒的生产过程和特性。
本文将介绍木屑颗粒压制损耗的计算公式及其相关内容。
木屑颗粒压制损耗计算公式。
木屑颗粒压制损耗的计算公式可以通过以下步骤得出:步骤一,测量原料和成品的重量。
首先需要测量用于生产木屑颗粒的原料(如木屑、秸秆等)的重量,以及生产出的木屑颗粒的重量。
这两个重量将作为计算损耗的基础数据。
步骤二,计算木屑颗粒的压制损耗。
木屑颗粒的压制损耗可以通过以下公式计算得出:损耗 = (原料重量成品重量) / 原料重量× 100%。
步骤三,分析损耗原因。
通过对木屑颗粒压制损耗的计算结果进行分析,可以进一步了解损耗的原因。
可能的原因包括原料的质量、压制工艺、设备性能等。
通过分析损耗的原因,可以采取相应的措施来降低损耗,提高生产效率。
木屑颗粒压制损耗的影响因素。
木屑颗粒压制损耗受到多种因素的影响,主要包括原料的性质、压制工艺和设备性能等。
原料的性质,原料的湿度、粒度、密度等性质都会影响木屑颗粒的压制损耗。
湿度过高会增加原料的粘性,导致压制过程中的损耗增加;而过大或过小的颗粒大小也会影响压制效果,进而影响损耗。
压制工艺,压制工艺包括原料的预处理、压制工艺参数的设定等。
合理的预处理可以提高原料的适应性和可压性,从而降低损耗;而合理的压制工艺参数设定也可以提高生产效率,减少损耗。
设备性能,压制设备的性能对木屑颗粒的压制损耗也有重要影响。
设备的性能包括压制机的结构、压辊的材质和加工工艺等。
优质的设备可以提高压制效率,减少损耗。
降低木屑颗粒压制损耗的措施。
为了降低木屑颗粒的压制损耗,可以采取以下措施:优化原料的选择和预处理,选择合适的原料,并对原料进行合理的预处理,如干燥、粉碎等,以提高原料的适应性和可压性。
材料定额耗用量比例法的计算步骤
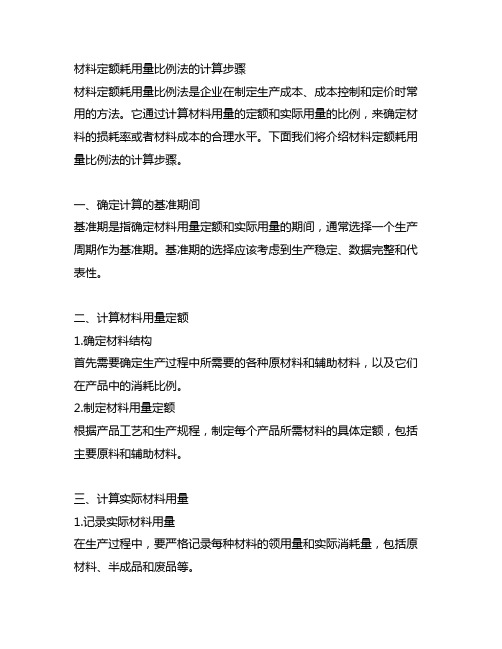
材料定额耗用量比例法的计算步骤材料定额耗用量比例法是企业在制定生产成本、成本控制和定价时常用的方法。
它通过计算材料用量的定额和实际用量的比例,来确定材料的损耗率或者材料成本的合理水平。
下面我们将介绍材料定额耗用量比例法的计算步骤。
一、确定计算的基准期间基准期是指确定材料用量定额和实际用量的期间,通常选择一个生产周期作为基准期。
基准期的选择应该考虑到生产稳定、数据完整和代表性。
二、计算材料用量定额1.确定材料结构首先需要确定生产过程中所需要的各种原材料和辅助材料,以及它们在产品中的消耗比例。
2.制定材料用量定额根据产品工艺和生产规程,制定每个产品所需材料的具体定额,包括主要原料和辅助材料。
三、计算实际材料用量1.记录实际材料用量在生产过程中,要严格记录每种材料的领用量和实际消耗量,包括原材料、半成品和废品等。
2.校核实际材料用量进行材料领用和实际用量的校核,确保数据的准确性和完整性。
四、计算材料定额耗用量比例1.计算材料定额耗用量将材料用量定额和实际用量进行比对,得出每种材料的损耗率或者消耗比例。
2.分析材料定额耗用量比例对比不同材料的定额耗用量比例,分析其变化原因和影响因素,发现问题并加以改进。
五、制定管理措施1.根据材料定额耗用量比例的计算结果,制定相应的管理措施,提高材料利用率,降低损耗率,从而降低成本、提高经济效益。
2.建立监控体系建立材料用量的监控指标和体系,定期进行检查和分析,及时发现问题并采取对策。
六、定期评估定期对材料定额耗用量比例法的执行情况和效果进行评估,根据评估结果对管理措施进行调整和改进,不断提高材料利用率和管理水平。
在企业管理中,材料定额耗用量比例法是一个简单有效的管理工具,可以帮助企业合理控制材料成本、提高生产效率和经济效益。
希望大家在实际工作中,能够根据以上步骤正确应用材料定额耗用量比例法,为企业的发展做出更大的贡献。
材料定额耗用量比例法的执行对企业的经济效益具有重要影响。
材料利用率怎么算

材料利用率怎么算材料利用率是指在生产过程中所使用的原材料与最终产品中所用原材料的比例。
计算材料利用率可以帮助企业评估生产效率、节约成本,提高资源利用效率。
下面将介绍几种常见的计算方法。
首先,最简单的计算材料利用率的方法是通过原材料利用率公式来计算。
原材料利用率=(所用原材料的重量/最终产品的重量)100%。
这个公式可以直观地反映出生产过程中原材料的利用情况,是一个比较直接的计算方法。
其次,还可以通过材料利用效率公式来计算。
材料利用效率=(最终产品的价值/所用原材料的价值)100%。
这个公式可以帮助企业评估生产过程中原材料的利用效率,从价值的角度来考量。
除此之外,还可以通过能源利用率来计算材料利用率。
能源利用率=(生产所需能源/最终产品的能源)100%。
这个公式可以帮助企业评估生产过程中能源的利用情况,从能源的角度来考量材料利用率。
在实际应用中,企业可以根据自身的生产情况和需求选择合适的计算方法来评估材料利用率。
通过计算材料利用率,企业可以及时发现生产过程中存在的问题,采取相应的措施进行改进,提高材料利用率,降低生产成本,提高经济效益。
在进行材料利用率的计算时,需要注意以下几点,首先,要准确地记录生产过程中所使用的原材料的重量、价值和能源消耗情况;其次,要准确地记录最终产品的重量、价值和能源产出情况;最后,要选择合适的计算方法进行材料利用率的评估,根据实际情况进行调整和改进。
总之,材料利用率的计算是企业生产管理中的重要环节,可以帮助企业评估生产效率、节约成本,提高资源利用效率。
通过合理地计算和评估材料利用率,企业可以及时发现问题,采取相应的措施进行改进,提高经济效益,实现可持续发展。
希望本文介绍的方法对您有所帮助。
塑胶产品成本计算公式

塑胶产品成本计算公式
1.原材料成本:
原材料成本是塑胶产品生产的基础成本,通常包括塑胶原料和其他辅
助材料的成本。
原材料成本的计算公式如下:
原材料成本=原材料消耗量×原材料价格
2.加工成本:
加工成本是指将塑料原料转化为塑胶产品的成本,通常包括能耗、设
备折旧、设备维护和设备操作人员的工资等。
加工成本的计算公式如下:加工成本=能耗成本+设备折旧成本+设备维护成本+工资成本
3.设备成本:
设备成本是指用于生产塑胶产品的设备的成本,通常包括设备购置费用、设备安装费用和设备维护费用。
设备成本的计算公式如下:设备成本=设备购置费用+设备安装费用+设备维护费用
4.人工成本:
人工成本是指参与塑胶产品生产的工人的工资和福利费用等。
人工成
本的计算公式如下:
人工成本=工人数量×平均工资+福利费用
5.质量控制成本:
质量控制成本是指用于监督和保证塑胶产品质量的费用,通常包括质
检设备、质检人员工资和质量改进费用等。
质量控制成本的计算公式如下:
质量控制成本=质检设备成本+质检人员工资+质量改进费用
6.其他间接成本:
其他间接成本是指与塑胶产品生产相关的其他费用,如厂房租金、办公费用、物料管理费用等。
其他间接成本的计算公式如下:
其他间接成本=厂房租金+办公费用+物料管理费用
总成本=原材料成本+加工成本+设备成本+人工成本+质量控制成本+其他间接成本
以上是塑胶产品成本计算的基本公式,企业可以根据实际情况对公式进行调整和细化。
在实际生产中,还需要关注成本的优化和控制,以提高企业的竞争力和盈利能力。
材料损耗分析范文
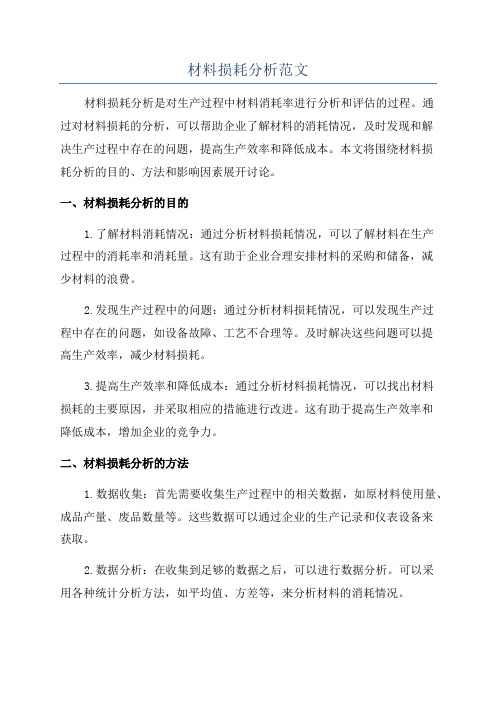
材料损耗分析范文材料损耗分析是对生产过程中材料消耗率进行分析和评估的过程。
通过对材料损耗的分析,可以帮助企业了解材料的消耗情况,及时发现和解决生产过程中存在的问题,提高生产效率和降低成本。
本文将围绕材料损耗分析的目的、方法和影响因素展开讨论。
一、材料损耗分析的目的1.了解材料消耗情况:通过分析材料损耗情况,可以了解材料在生产过程中的消耗率和消耗量。
这有助于企业合理安排材料的采购和储备,减少材料的浪费。
2.发现生产过程中的问题:通过分析材料损耗情况,可以发现生产过程中存在的问题,如设备故障、工艺不合理等。
及时解决这些问题可以提高生产效率,减少材料损耗。
3.提高生产效率和降低成本:通过分析材料损耗情况,可以找出材料损耗的主要原因,并采取相应的措施进行改进。
这有助于提高生产效率和降低成本,增加企业的竞争力。
二、材料损耗分析的方法1.数据收集:首先需要收集生产过程中的相关数据,如原材料使用量、成品产量、废品数量等。
这些数据可以通过企业的生产记录和仪表设备来获取。
2.数据分析:在收集到足够的数据之后,可以进行数据分析。
可以采用各种统计分析方法,如平均值、方差等,来分析材料的消耗情况。
3.材料损耗率计算:通过分析数据,可以计算材料的消耗率。
材料损耗率是指单位产品所用的原材料的消耗量。
可以采用以下公式进行计算:材料损耗率=(原材料消耗量-成品量)/成品量4.原因分析:通过分析数据和计算出的材料损耗率,可以找出材料损耗的主要原因。
可能的原因包括设备故障、工艺不合理、操作不当等。
5.措施改进:根据原因分析的结果,可以采取相应的措施进行改进。
如修理设备、改进工艺、提高员工培训等,以减少材料损耗。
三、影响材料损耗的因素1.设备质量:设备的质量直接影响到生产过程中的材料损耗。
设备质量差、老化、损坏会导致材料的浪费。
2.工艺流程:工艺流程合理与否直接影响到材料的损耗量。
工艺流程不合理可能导致材料的重复使用、过多消耗等问题。
原材料安全库存计算公式
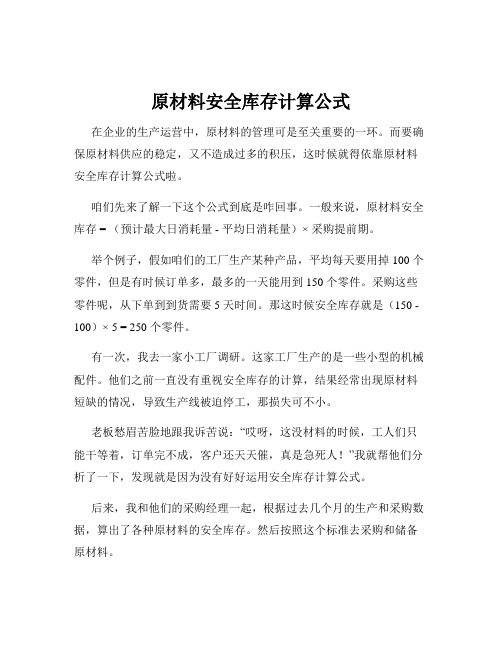
原材料安全库存计算公式在企业的生产运营中,原材料的管理可是至关重要的一环。
而要确保原材料供应的稳定,又不造成过多的积压,这时候就得依靠原材料安全库存计算公式啦。
咱们先来了解一下这个公式到底是咋回事。
一般来说,原材料安全库存 = (预计最大日消耗量 - 平均日消耗量)×采购提前期。
举个例子,假如咱们的工厂生产某种产品,平均每天要用掉 100 个零件,但是有时候订单多,最多的一天能用到 150 个零件。
采购这些零件呢,从下单到到货需要 5 天时间。
那这时候安全库存就是(150 - 100)× 5 = 250 个零件。
有一次,我去一家小工厂调研。
这家工厂生产的是一些小型的机械配件。
他们之前一直没有重视安全库存的计算,结果经常出现原材料短缺的情况,导致生产线被迫停工,那损失可不小。
老板愁眉苦脸地跟我诉苦说:“哎呀,这没材料的时候,工人们只能干等着,订单完不成,客户还天天催,真是急死人!”我就帮他们分析了一下,发现就是因为没有好好运用安全库存计算公式。
后来,我和他们的采购经理一起,根据过去几个月的生产和采购数据,算出了各种原材料的安全库存。
然后按照这个标准去采购和储备原材料。
你还别说,经过一段时间的调整,情况有了很大的改善。
生产线再也没有因为缺料而停工,老板脸上也终于有了笑容。
再深入说说这个公式里的各个因素。
预计最大日消耗量,这可不是随便拍脑袋想出来的,得根据历史数据、市场需求的变化还有生产计划的调整来综合判断。
比如说,要是马上到销售旺季了,那最大日消耗量可能就得往上调一调。
平均日消耗量相对来说好算一些,但也不能马虎。
得把各种影响因素都考虑进去,像设备故障、工人请假这些都可能影响产量,从而影响原材料的消耗。
采购提前期也不是个固定值。
有时候供应商那边出点问题,运输途中遇到点状况,都可能导致提前期延长。
所以在计算的时候,得留有余地,不能卡得太死。
总之,原材料安全库存计算公式虽然看起来简单,但要用好可不容易。
原材料费用分配的方法
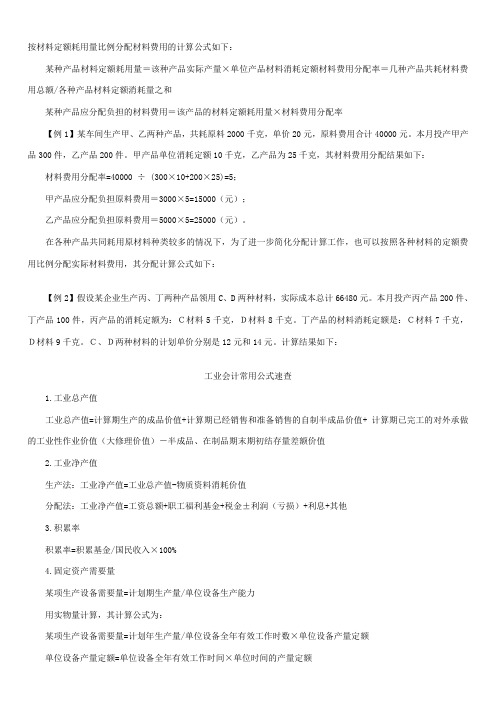
按材料定额耗用量比例分配材料费用的计算公式如下:某种产品材料定额耗用量=该种产品实际产量×单位产品材料消耗定额材料费用分配率=几种产品共耗材料费用总额/各种产品材料定额消耗量之和某种产品应分配负担的材料费用=该产品的材料定额耗用量×材料费用分配率【例1】某车间生产甲、乙两种产品,共耗原料2000千克,单价20元,原料费用合计40000元。
本月投产甲产品300件,乙产品200件。
甲产品单位消耗定额10千克,乙产品为25千克,其材料费用分配结果如下:材料费用分配率=40000 ÷(300×10+200×25)=5;甲产品应分配负担原料费用=3000×5=15000(元);乙产品应分配负担原料费用=5000×5=25000(元)。
在各种产品共同耗用原材料种类较多的情况下,为了进一步简化分配计算工作,也可以按照各种材料的定额费用比例分配实际材料费用,其分配计算公式如下:【例2】假设某企业生产丙、丁两种产品领用C、D两种材料,实际成本总计66480元。
本月投产丙产品200件、丁产品100件,丙产品的消耗定额为:C材料5千克,D材料8千克。
丁产品的材料消耗定额是:C材料7千克,D材料9千克。
C、D两种材料的计划单价分别是12元和14元。
计算结果如下:工业会计常用公式速查1.工业总产值工业总产值=计算期生产的成品价值+计算期已经销售和准备销售的自制半成品价值+ 计算期已完工的对外承做的工业性作业价值(大修理价值)-半成品、在制品期末期初结存量差额价值2.工业净产值生产法:工业净产值=工业总产值-物质资料消耗价值分配法:工业净产值=工资总额+职工福利基金+税金±利润(亏损)+利息+其他3.积累率积累率=积累基金/国民收入×100%4.固定资产需要量某项生产设备需要量=计划期生产量/单位设备生产能力用实物量计算,其计算公式为:某项生产设备需要量=计划年生产量/单位设备全年有效工作时数×单位设备产量定额单位设备产量定额=单位设备全年有效工作时间×单位时间的产量定额单位设备全年有效工作时间=(全年日历数-节假日-设备检修停工天数)×每天工作班次×每班工作小时用台时数计算,其计算公式为:某项生产设备需要量=全年计划生产任务需用设备定额总台时/单位设备全年有效工作台时=∑(计划年产品产量×单位产品台时定额×定额改进系数)/全年单位设备有效工作台时(定额改进系数=计划年度小计新定额/单位允时定额×100%)5.固定资产原值计划年末固定资产原值=上年末固定资产原值+计划年度增加固定资产原值-计划年度减少固定资产原值6.应提折旧固定资产平均总值应提折旧固定资产全年平均总值=1~12月各月应计提折旧的各项固定资产原值的月初余额之和/12增减法,其计算公式为:计划年度应计提折旧固定资产平均总量=期初应计提折旧的固定资产平均总值+计划年内增加应计折旧固定资产平均总值-计划年内减少应计折旧固定资产平均总值式中:年度内增加应计提折旧固定资产平均总值=∑(某月增加应计折旧固定资产总值×该月增加应计提固定资产的当年使用月数)/12年度内减少应计折旧固定资产平均总值=∑(某月减少应计折旧固定资产总值)×(12-该月份减少应计提折旧固定资产的当年使用月数)/127.固定资产折旧率年折旧率=年折旧额/固定资产原始价值×100%年折旧额=(固定资产原值-预计残值+预计清理费用)/固定资产预计使用年限季折旧率=固定资产年折旧率/4=固定资产季折旧额/固定资产原值固定资产季折旧额=固定资产年折旧额/4月折旧率=固定资产年折旧率/12=固定资产月折旧额/固定资产原值月折旧额=固定资产年折旧额/128.固定资产净值固定资产净值=固定资产原值-已提折旧额固定资产净值全年平均余额=1~12月各月月初、月末固定资产净值之和/249.固定资产结构固定资产的比重=某一类固定资产原值/全部固定资产原值×100%10.固定资产增长率固定资产增长率=(本期增加的固定资产原值-本期减少的固定资产原值)/起初固定资产原值×100%11.固定资产更新率固定资产更新率=本期增加固定资产的原值/期末固定资产原值×100%12.固定资产退废率固定资产退废率=本期退废固定资产的原值/期末固定资产原值×100%13.固定资产净值率固定资产净值率=期末固定资产净值/期末固定资产原值×100%固定资产尚可使用年限=固定资产净值率/综合折旧率14.固定资产磨损率固定资产磨损率=期末固定资产折旧余额/期末固定资产原值×100%15.在用固定资产占用率在用固定资产占用率=在用固定资产平均总值/工业总产值×100% =全部固定资产占用率×(在用固定资产平均总值/全部固定资产平均总值=工业生产用固定资产占用率×(在用固定资产平均总值/工业生产用固定资产平均总值)全部固定资产占用率=全部固定资产平均总值/工业总产值16.工业生产用固定资产占用率工业生产用固定资产占用率=工业生产用固定资产平均总值/工业总产值×100% =全部固定资产占用率×工业生产用固定资产平均总值/全部固定资产平均总值=在用固定资产占用率×工业生产用固定资产平均总值/在用固定资产平均总值17.低值易耗品摊销额净值摊销法:低值易耗品摊销额=在用低值易耗品净值×摊销率在用低值易耗品净值=在用低值易耗品计划成本-已经摊销数分期摊销法:低值易耗品月平均消耗额=(低值易耗品价值-预计残值)/预计可使用数产品摊销法:低值易耗品月平均消耗额=(低值易耗品价值-预计残值)/预定使用期内的预计产量×计算期月产量五五摊销法:领用时耗销额=在用低值易摊品计划成本×50%报销时消耗额=在用低值易耗品计划成本×150%-残值18.材料需要量材料需要量=计划产量×单位产品材料消耗定额=(计划产量×计划废品数量)×单位产品材料消耗定额-回收废料数量=[计划产量/(1-废品率)]×材料消耗定额-(1-回收废料率)19.辅助材料需要量辅助材料需要量=计划产量*单位产品消耗定额辅助材料需要量=上期单位产品产值(或工时)辅助材料消耗量×计划期产品产值(工时)×(1-压缩系数)20.工具需要量工具需要量=计划期工具消耗量+计划期末工具周转量-计划期初工具周转量某种工具消耗量=计划期某种产品的计划产量×该单位产品某种工具的消耗定额某种工具的消耗定额=制造一定数量的产品使用某种工具的时间/某种工具的寿命(分)21.材料供应量材料供应量=材料需要量+计划期末储备量-计划期初库存量-企业内部可利用资源22.材料储备量材料经常储备量=供应间隔天数×平均每日耗用量材料保险储备量=保险日数×平均每日耗用量材料最高储备量=(供应间隔日数+检验日数+使用准备日数+保险日数)×平均每日耗用量或=经常储备量+最低储备量材料最低储备量=(检验日数+使用准备日数+保险日数)×平均每日耗用量材料平均储备量=(最高储备量+最低储备量)/2材料季节性储备量=季节性储备日数×平均每日耗用量23.材料采购量材料订购量=(订购时间+订购间隔期)×平均每日需用量+保险储备量-实际库存量-订货余额订货点订购量=订货时间×平均每日需用量+保险储备量24.材料采购次数材料采购次数=材料年需用量/经济采购批量25.材料储备量对生产的保证率材料储备量对生产的保证率(天)=材料储备量/材料计划每日消耗量26.材料储备定额执行情况材料储备定额执行情况=(材料实际储备量/材料计划每日消耗量)×100%27.材料的平均单价移动加权平均法:材料平均单价=[(以前结余+本批收入)×材料实际成本]/(以前结余+本批收入)×材料的数量全月一次加权平均法:材料平均单价=[(月初库存+本月收入)×材料实际成本]/(月初库存+本月收入)×材料数量28.材料价格差异率本月材料累计数计算,其计算公式为:本月材料价格差异率=[材料价格差异额/(月初结存材料的计划价格+本月收入材料的计划价格)]×100% 材料价格差异额=月初结存材料的价格差异+本月收入材料的价格差异=(月初结存材料的实际价格-月初结存材料的计划价格)+(本月收入材料的实际价格-本月收入材料的计划价格)按当月发生数计算,其计算公式为:本月材料价格差异率=(本月收入材料价格差异额/本月发出材料计划价格)×100%本月收入材料的价格差异额=本月收入材料的实际价格-本月收入材料的计划价格按月初结存数计算,其计算公式为:本月材料价格差异率=(月初结存材料价格差异/月初结存材料计划价格)×100%按材料价格差异率和调整率的关系计算,其计算公式如下:本月材料价格差异率=本月材料价格调整率-1本月材料价格调整率=(月末结存材料实际价格/月末结存材料的计划价格)×100%或=[(月初结存材料实际价格+本月收入材料实际价格)/(月初结存材料计划价格+本月收入材料计划价格)]×100%发出材料应分配的价格差异额=发出材料计划价格×材料价格差异率29.材料年平均仓库保管费材料年平均仓库保管费=该种材料单价×材料保管费率材料保管费率=(材料年保管费/材料平均储备价值)×100%材料消耗总量:某种产品材料总消耗量=本期投料量+期初在制品、半成品未入库成品的折料量-期末在制品半成品未入库成品的折料量本期投料量=本期领料量-退料量本期投料量=本期领料量+期初领而未用的余料量-期末领而未用的余料量期末在制品、半成品未入库成品的折料量=∑期末各种在制品、半成品未入库成品的结存量×材料消耗定额30.单位产品材料实际消耗量单位产品材料实际消耗量=材料消耗总量/产品产量31.材料消耗定额执行情况指标一种产品消耗一种材料,其计算公式为:材料消耗定额执行情况指标=(单位产品材料实际消耗量/单位产品材料定额消耗量)×100%一种产品消耗多种材料,其计算公式为:材料消耗定额执行情况指标=[∑(单位产品材料实际消耗量×计划价格)/∑(单位产品材料消耗定额×计划价格)]×100%多种产品消耗一种原材料,其计算公式为:材料消耗定额执行情况指标=[∑(单位产品材料实际消耗量×实际产量)/∑(单位产品材料消耗定额×实际产量)]×100%32.原材料利用率原材料利用率=产品中所包含的原材料数量/生产该产品的原材料总消耗量×100%原材料利用率=产品产量/生产该产品的原材料消耗总量×100%33.原材料损耗率原材料损耗率=原材料的工艺性损耗重量/消耗的原材料重量×100%34.原材料综合利用率原材料综合利用率=不同规格零件净重之和/不同规格零件消耗原材料总重量×100%原材料综合利用率=(主产品重量+副产品重量)/原材料总消耗量×100%35.废料利用率废料利用率=(副产品重量/废料重量)×100%36.原材料利用定额完成情况原材料利用定额完成情况=实际利用率-定额(计划)利用率37.原材料消耗定额完成率原材料消耗定额完成率=(实际消耗/消耗定额)×100%38.原材料节约量原材料节约(或耗损)数量=(实际单耗-消耗定额)×报告期产量39.原材料代用节约额原材料代用而节约的材料数量=原用原材料单位产品消耗量×用代用品生产的产品产量原材料代用而节约材料金额=(原用原材料生产的单位产品原材料价值-代用品生产的单位产品原材料价值)×用代用品生产的产品产量40.材料变动对产量的影响额材料供应量变动对产量的影响额,其计算公式为:材料供应量变动对产量的影响额=(材料实际购入量-材料计划购入量)/单位产品材料计划消耗量材料储备量对产量的影响额,其计算公式为:材料储备量变动对产量的影响额=(材料实际储备量-材料计划储备量)/单位产品材料计划消耗量单位产品材料消耗量变动对产量的影响额,其计算公式为:单位产品材料消耗量变动对产量的影响额=(材料实际消耗量/单位产品材料实际消耗量)-(材料实际消耗量/单位产品材料计划消耗量)41.生产设备需要量生产设备需要量=(计划生产任务/单台设备的生产能力)×100%单台设备的生产能力=单台设备的工作时间×单位时间的产量定额42.设备的生产能力某设备的生产能力:某设备的生产能力=单项设备的生产能力×该类设备的数量×规定的全年开动时间单项设备的生产能力=设备的作业时间数×单位时间的产量定额同类设备的生产能力:同类设备的生产能力=同类设备台数×设备有效工作时间×每一台产量定额=(同类设备允数×设备的有效工作时间)/单位产品的台时定额设备的有效工作时间=(日历天数-节假日)×日制度工作时间-设备修理停歇时间设备组的生产能力:设备组的生产能力=(设备组的设备台数×单位设备有效工作时间)/(单位产品台时定额×改进压缩系数)设备组的生产能力=(设备组的设备台数×设备有效工作时间)/单位代表产品台时定设备有效工作时间=(日历日数-节假日)×班次×每班工作小时数×(1-设备停修率)43.年末的设备生产能力年末的设备生产能力=年初生产能力+本年新增加的生产能力-本年减少的生产能力设备的年平均生产能力=年初生产能力+新增的年平均生产能力-减少的年平均生产能力新增的年平均生产能力=新增设备的年生产能力×(自投入生产到年底的日历日数)/365减少的年平均生产能力=减少设备的年生产能力44.锻锤生产能力锻锤生产能力=锻锤每小时锻件产量(吨/时)×全年有效工作小时化铁炉生产能力(吨/年)=化铁炉每小时产量(吨/小时)×全年有效工作小时×改改进系数=1-(自然损耗率+浇胃口残头等消耗率+废品率)45.电弧炼钢生产能力电弧炼钢生产能力(吨/年)=炼钢炉容量(吨)×(全年有效工作时间/炼钢周期)×改进系数46.生产面积生产能力生产面积生产能力=(现有生产面积×制度工作时间)/(单位产品占用生产面积×单位产品占用时间)47.生产面积负荷系数生产面积负荷系数=完成生产任务所需生产面积的平方米小时数/现有生产面积的平方米小时数设备的全年计划总台时数=日历台时数×(制度台时数/日历台时数)×(计划台时数/制度台时数)=日历台时数×日历台时数利用率×制度台时数利用率48.设备台时平均产量设备台时平均产量=按定额工时计算的产品产量/(设备平均数量×每台设备工作小时数)完成计划任务所需设备台时数完成计划任务所需设备台时数=各种产品计划产量×单位产品台时定额49.设备组的有效台时数设备组的有效台时数=设备组的设备数量×单位设备有效时间50.设备的时间潜力设备的时间潜力(台时)=使用设备台数×平均每台不必要的停台时间51.设备的能力潜力设备的能力潜力=设备设计能力的台时产量-设备的实际台时产量52.设备的时间增长潜力设备的时间增长潜力=设备时间潜力×实际平均台时产量53.设备能力增长潜力设备能力增长潜力=每台设备能力潜力×设备可能利用的台时数设备可能利用的台时数=设备实际运转台时数+设备时间潜力(台时)54.设备全部增长潜力设备全部增长潜力=设备时间增长潜力+设备能力增长潜力55.设备平均数报告期设备平均数=∑报告期每日拥有的设备数量/报告期日历日数=期初设备数量+(报告期增加设备台日数)/报告期日历日数-(报告期减少设备台日数/报告期日历日数)56.实用设备安装率实有设备安装率=已安装设备台数/实有设备台数×100%57.已安装设备完好率已安装设备完好率=完好设备台数/已安装设备台数×100%58.已安装设备利用率已安装设备利用率=实际使用的设备台数/已安装设备台数×100%59.完好设备使用率完好设备使用率=实际使用设备台数×完好设备台数×100%60.设备时间利用率设备时间利用率=实际作业时间/最大可能利用时间×100%61.设备日厉台时利用率设备日历台时利用率=实际工作时间/日历时间×100% =实际使用台时/已安装设备或实际使用设备的日历台时数×100%平炉日历时间利用率=炼钢作业时间/(日历时间-冷炉大修理时间)×100%62.设备制度台时利用率设备制度台时利用率=实际使用台时数/制度工作台时数×100%制度工作台时数=已安装设备台时数(或实际使用设备)×制度工作日数×工作班次×每班次工作小时63.设备计划台时利用率设备计划台时利用率=(实际使用台数/计划使用台数)×100%计划使用台数=计划使用设备×设备计划使用的时间64.设备综合利用指标设备综合利用指标=设备时间利用指标×设备能力利用指标65.高炉综合利用率高炉综合利用率=生铁产量(吨)/[有效容积(立方米)×(日历昼夜数-大中修理昼夜数)]=[生铁产量(吨)/(有效容积×实际作业昼夜数)]×[实际作业昼夜数/(日历昼夜数-大中修理昼夜数)]=高炉生产效率×高炉时间利用率66.平炉综合利用率平炉综合利用率=合格平炉钢产量(吨)/[炉底面积(平方米)×(日历昼夜数-大修理昼夜数)]=平炉生产效率×平炉时间利用率平炉生产效率=合格平炉钢产量(吨)/(有效面积×实际作业昼夜数)平炉时间利用率=实际作业昼夜数/(日历昼夜数-大中修理昼夜数)67.设备现代化的费用节约额设备现代化的费用节约额=采用新设备后的单位产品成本降低额×计划产量+(单位产品出厂价格-采用新设备后的单位产品成本)×实际比计划增加的产量68.设备修理工作量设备修理工作量=设备的修理复杂系数×一个修理复杂系数的工时定额69.设备修理停歇时间设备修理停歇时间=设备修理工作量(工时)/(一个轮班参加修理的工人数×每个轮班工作时间×轮班次数)70.设备维修材料消耗定额设备维修材料消耗定额=用于设备大修理的材料实际消耗量/单台设备修理复杂系数71.设备平均在修日数设备平均在修日数=各台设备在修日数之和/修完设备的台数72.单位产品的设备维修费用单位产品的设备维修费用=设备维修费用/产品生产量73.设备维修费用效率设备维修费用效率=(产品生产量/设备维修费用)×100%74.设备维修计划完成率设备维修计划完成率=(报告期累计完成检修台数/本年计划检修台数)×100%75.设备修理质量平均等级设备修理质量平均等级=[∑(质量等级×修理完毕的各等级设备数)]/∑修理完毕的各等级设备数76.设备修理返修率设备修理返修率=(修理设备返修台数×/修理设备送检台数)×100%77.设备泄漏率设备泄漏率=(泄漏点总数/静密封点总数)×100%78.设备故障率设备故障率=(设备故障停歇时间/设备开动总台时)×100%79.设备事故率以设备事故次数与实际开动的设备台数对比,其计算公式为:设备事故率=报告期设备事故次数/报告期实际开动的设备台数以设备因事故停开台时与设备实际开动台时对比,以百分数表示,其计算公式为:设备事故率=(报告期设备事故停开台时/报告期设备实际开动台时)×100% 80.设备事故损失总金额设备事故损失总金额=设备事故的修理费总额+设备事故造成减产金额设备事故造成减产金额=各种设备事故减产数量×单位产品价格设备事故造成减产数=设备事故停开台时×每台时平均产量81.设备换班系数设备换班系数=设备工作的总台班数/实际使用的设备总台数82.工艺用燃料需要量工艺用燃料需要量=(单位产品标准燃料消耗定额×计划产量)/折算系数折算系数=实际使用的燃料每千克发热量(千焦)/700(千焦)标准燃料=非标准燃料×(每千克非标准燃料发热量(千焦)/700(千焦))83.铸造焦炭需要量铸造焦炭需要量=炉料总重量×熔炼每吨金属的焦炭消耗定额84.焦铁比焦铁比=化焦总量/焦炭消耗量85.标准煤量标准煤量=∑[煤炭数量×每千克煤炭发热量(千焦)]/700(千焦)86.单位产品耗煤量单位产品耗煤量=(全厂用煤总量-全厂非工业生产用煤量)/产品产量单位产品耗煤量=该种产品应分摊的煤消耗量/该种产品产量该种产品应分摊的煤消耗量=工业生产用的煤总消耗量×(该种产品定额消耗量/总的应耗煤量)工业生产用的煤总消耗量=全厂用煤总量-全厂非工业生产用煤量87.锅炉用煤需要量锅炉用煤需要量=锅炉计划开动日数×煤炭日耗定额或=计划产量(产值)×单位产品(产值)耗煤定额88.铸造加热炉熏油需要量铸造加热炉熏油需要量=计划铸件产量(产值)×单位产量(产值)耗油定额每万元产值耗煤量=标准耗煤量/总产值(万元)节约煤消耗的节约额=[上期单位产品耗煤量(千克)-本期单位产品耗煤量(千克)]×本期产品产量×每千克燃料计划价格89.单位产品耗电量单位产品耗电量=(收入电量-转供电量-非生产用电量)/本期产品产量90.每万元产值耗电量每万元产值耗电量=(收入电量-转供电量-非生产用电量)/本期产品产量91.电力消耗定额完成率电力消耗定额完成率=(单位产品耗电量/消耗定额)×100%92.节约电力消耗的节约额节约电力消耗的节约额=(上期单位产品耗电量(度)-本期单位产品耗电量(度))×本期产品产量×每度电费93.技改革新节约电力消耗的节约额技改革新节约电力消耗的节约额=(改进前耗电量(度)-改进后耗电量(度))×使用时间×推广台数×每度电费94.发电机的平均实际能力发电机的平均实际能力=报告期实际发电总量(千瓦时)/报告期实际作业时间总数(小时)发电机的年平均能力=一年发电总量(千瓦时)/8760(小时)95.发电机的平均利用小时数发电机的平均利用小时数=报告期发电总量/报告期被利用设备能力总和(千瓦)96.发电机时间利用率发电机时间利用率(粗放负荷单)=(报告期发电机的实际作业数/报告期日历时数)×100%。
原材料成本怎么算
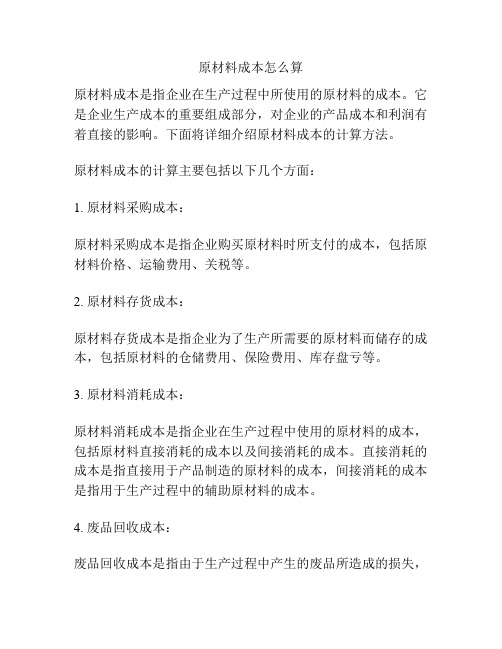
原材料成本怎么算原材料成本是指企业在生产过程中所使用的原材料的成本。
它是企业生产成本的重要组成部分,对企业的产品成本和利润有着直接的影响。
下面将详细介绍原材料成本的计算方法。
原材料成本的计算主要包括以下几个方面:1. 原材料采购成本:原材料采购成本是指企业购买原材料时所支付的成本,包括原材料价格、运输费用、关税等。
2. 原材料存货成本:原材料存货成本是指企业为了生产所需要的原材料而储存的成本,包括原材料的仓储费用、保险费用、库存盘亏等。
3. 原材料消耗成本:原材料消耗成本是指企业在生产过程中使用的原材料的成本,包括原材料直接消耗的成本以及间接消耗的成本。
直接消耗的成本是指直接用于产品制造的原材料的成本,间接消耗的成本是指用于生产过程中的辅助原材料的成本。
4. 废品回收成本:废品回收成本是指由于生产过程中产生的废品所造成的损失,包括废品处理的成本、废品的运输费用等。
通过上述几个方面的成本计算,就能够得出原材料成本的总额。
企业可以根据不同的需求和情况,灵活进行成本计算,并进行相应的管理和控制。
在实际操作过程中,企业可以采用以下方法来计算原材料成本:1. 确定原材料的种类和数量,包括直接使用的原材料和间接使用的辅助原材料。
2. 采集原材料的相关成本信息,包括采购成本、仓储费用、保险费用、运输费用等。
3. 计算直接使用的原材料的成本,即直接消耗成本。
4. 计算间接使用的辅助原材料的成本,即间接消耗成本。
5. 根据废品的产生情况和成本信息,计算废品回收成本。
6. 将上述成本相加,就得到了原材料成本的总额。
原材料成本的计算对于企业的经营和管理有着重要的意义。
合理计算和控制原材料成本,有助于提高产品的竞争力和盈利能力。
企业可以通过精细化管理、优化采购渠道、提高库存周转率等方式,来降低原材料成本,实现更好的经济效益。
合理损耗标准及计算方法
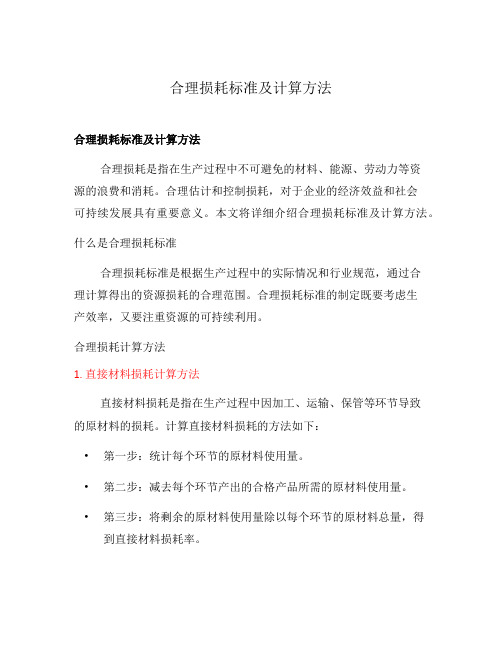
合理损耗标准及计算方法合理损耗标准及计算方法合理损耗是指在生产过程中不可避免的材料、能源、劳动力等资源的浪费和消耗。
合理估计和控制损耗,对于企业的经济效益和社会可持续发展具有重要意义。
本文将详细介绍合理损耗标准及计算方法。
什么是合理损耗标准合理损耗标准是根据生产过程中的实际情况和行业规范,通过合理计算得出的资源损耗的合理范围。
合理损耗标准的制定既要考虑生产效率,又要注重资源的可持续利用。
合理损耗计算方法1. 直接材料损耗计算方法直接材料损耗是指在生产过程中因加工、运输、保管等环节导致的原材料的损耗。
计算直接材料损耗的方法如下:•第一步:统计每个环节的原材料使用量。
•第二步:减去每个环节产出的合格产品所需的原材料使用量。
•第三步:将剩余的原材料使用量除以每个环节的原材料总量,得到直接材料损耗率。
2. 能源损耗计算方法能源损耗是指在生产过程中因能源转换、传输、利用等环节导致的能源的浪费。
计算能源损耗的方法如下:•第一步:统计每个环节的能源消耗量。
•第二步:减去每个环节产出的合格产品所需的能源消耗量。
•第三步:将剩余的能源消耗量除以每个环节的能源总量,得到能源损耗率。
3. 人工损耗计算方法人工损耗是指在生产过程中因误工、操作不当等原因导致的人工资源的浪费。
计算人工损耗的方法如下:•第一步:统计每个环节的工时消耗。
•第二步:减去每个环节产出的合格产品所需的工时消耗。
•第三步:将剩余的工时消耗除以每个环节的总工时,得到人工损耗率。
合理损耗的影响因素合理损耗的多少受到以下因素的影响:1.生产工艺:不同的生产工艺对损耗的要求不同,合理的生产工艺能够降低损耗。
2.设备状态:设备的良好状态能够减少资源的浪费。
3.人员素质:员工的专业素质和操作技能会直接影响损耗的大小。
4.管理水平:科学合理的管理能够有效控制损耗的发生。
合理损耗的重要性合理损耗的控制对企业的经济效益和可持续发展具有重要意义,具体体现在以下几个方面:1.节约成本:合理控制损耗可以降低材料和能源的使用量,减少成本支出。
原材料周转天数公式

原材料周转天数公式原材料周转天数是企业财务管理中的一个重要概念,它能反映出企业在原材料管理方面的效率和运营状况。
咱们先来了解一下原材料周转天数的公式。
简单来说,原材料周转天数 = 计算期天数 ÷原材料周转次数。
而原材料周转次数 = 原材料消耗额 ÷原材料平均库存额。
给您举个例子啊,比如说有一家生产玩具的工厂。
这工厂每个月生产 10 万个玩具,每个玩具需要用到 10 元的原材料。
一个月下来,原材料消耗额就是 100 万元。
同时呢,经过盘点,发现工厂平均原材料库存额是 20 万元。
那这个月的原材料周转次数就是 100÷20 = 5 次。
如果这个月按 30 天算,那原材料周转天数就是 30÷5 = 6 天。
这意味着,这家玩具厂的原材料平均每 6 天就周转一次。
周转天数越短,说明企业原材料的流转速度越快,资金利用效率越高,管理水平相对也就越好。
相反,如果周转天数过长,那就可能存在库存积压、资金占用等问题,这可不利于企业的发展。
在实际的企业运营中,原材料周转天数会受到多种因素的影响。
比如说,采购计划是否合理。
如果采购部门一下子采购了太多的原材料,那库存就会增加,周转天数也就变长了。
还有生产计划的稳定性,如果生产老是停停走走,一会儿需要大量原材料,一会儿又不需要,这也会打乱原材料的周转节奏。
另外,市场需求的变化也很关键。
要是市场突然对某种玩具的需求大增,工厂就得加大生产,原材料消耗加快,周转天数可能就缩短。
但要是市场需求疲软,生产放缓,原材料就可能积压在仓库里,周转天数就变长了。
我之前接触过一家食品加工厂,他们就曾经在原材料周转天数上吃过亏。
一开始,他们没有仔细分析市场需求,盲目采购了大量的某种季节性水果作为原材料。
结果呢,那年这种水果的相关食品市场需求不如预期,生产计划也跟着调整,大量水果堆在仓库里慢慢变质,不仅造成了巨大的浪费,还因为占用了大量资金,影响了企业的正常运转。
原材料费用分配的方法

原材料费用分配的方法按材料定额耗用量比例分配材料费用的计算公式如下:某种产品材料定额耗用量=该种产品实际产量×单位产品材料消耗定额材料费用分配率=几种产品共耗材料费用总额/各种产品材料定额消耗量之和某种产品应分配负担的材料费用=该产品的材料定额耗用量×材料费用分配率【例1】某车间生产甲、乙两种产品,共耗原料2000千克,单价20元,原料费用合计40000元。
本月投产甲产品300件,乙产品200件。
甲产品单位消耗定额10千克,乙产品为25千克,其材料费用分配结果如下:材料费用分配率=40000 ÷ (300×10+200×25)=5;甲产品应分配负担原料费用=3000×5=15000(元);乙产品应分配负担原料费用=5000×5=25000(元)。
在各种产品共同耗用原材料种类较多的情况下,为了进一步简化分配计算工作,也可以按照各种材料的定额费用比例分配实际材料费用,其分配计算公式如下:【例2】假设某企业生产丙、丁两种产品领用C、D两种材料,实际成本总计66480元。
本月投产丙产品200件、丁产品100件,丙产品的消耗定额为:C材料5千克,D材料8千克。
丁产品的材料消耗定额是:C材料7千克,D材料9千克。
C、D两种材料的计划单价分别是12元和14元。
计算结果如下:工业会计常用公式速查1.工业总产值工业总产值=计算期生产的成品价值+计算期已经销售和准备销售的自制半成品价值+ 计算期已完工的对外承做的工业性作业价值(大修理价值)-半成品、在制品期末期初结存量差额价值2.工业净产值生产法:工业净产值=工业总产值-物质资料消耗价值分配法:工业净产值=工资总额+职工福利基金+税金±利润(亏损)+利息+其他3.积累率积累率=积累基金/国民收入×100%4.固定资产需要量某项生产设备需要量=计划期生产量/单位设备生产能力用实物量计算,其计算公式为:某项生产设备需要量=计划年生产量/单位设备全年有效工作时数×单位设备产量定额单位设备产量定额=单位设备全年有效工作时间×单位时间的产量定额单位设备全年有效工作时间=(全年日历数-节假日-设备检修停工天数)×每天工作班次×每班工作小时用台时数计算,其计算公式为:某项生产设备需要量=全年计划生产任务需用设备定额总台时/单位设备全年有效工作台时=∑(计划年产品产量×单位产品台时定额×定额改进系数)/全年单位设备有效工作台时(定额改进系数=计划年度小计新定额/单位允时定额×100%)5.固定资产原值计划年末固定资产原值=上年末固定资产原值+计划年度增加固定资产原值-计划年度减少固定资产原值6.应提折旧固定资产平均总值应提折旧固定资产全年平均总值=1~12月各月应计提折旧的各项固定资产原值的月初余额之和/12增减法,其计算公式为:计划年度应计提折旧固定资产平均总量=期初应计提折旧的固定资产平均总值+计划年内增加应计折旧固定资产平均总值-计划年内减少应计折旧固定资产平均总值式中:年度内增加应计提折旧固定资产平均总值=∑(某月增加应计折旧固定资产总值×该月增加应计提固定资产的当年使用月数)/12年度内减少应计折旧固定资产平均总值=∑(某月减少应计折旧固定资产总值)×(12-该月份减少应计提折旧固定资产的当年使用月数)/127.固定资产折旧率年折旧率=年折旧额/固定资产原始价值×100%年折旧额=(固定资产原值-预计残值+预计清理费用)/固定资产预计使用年限季折旧率=固定资产年折旧率/4=固定资产季折旧额/固定资产原值固定资产季折旧额=固定资产年折旧额/4月折旧率=固定资产年折旧率/12=固定资产月折旧额/固定资产原值月折旧额=固定资产年折旧额/128.固定资产净值固定资产净值=固定资产原值-已提折旧额固定资产净值全年平均余额=1~12月各月月初、月末固定资产净值之和/249.固定资产结构固定资产的比重=某一类固定资产原值/全部固定资产原值×100%10.固定资产增长率固定资产增长率=(本期增加的固定资产原值-本期减少的固定资产原值)/起初固定资产原值×100%11.固定资产更新率固定资产更新率=本期增加固定资产的原值/期末固定资产原值×100%12.固定资产退废率固定资产退废率=本期退废固定资产的原值/期末固定资产原值×100%13.固定资产净值率固定资产净值率=期末固定资产净值/期末固定资产原值×100%固定资产尚可使用年限=固定资产净值率/综合折旧率14.固定资产磨损率固定资产磨损率=期末固定资产折旧余额/期末固定资产原值×100%15.在用固定资产占用率在用固定资产占用率=在用固定资产平均总值/工业总产值×100% =全部固定资产占用率×(在用固定资产平均总值/全部固定资产平均总值=工业生产用固定资产占用率×(在用固定资产平均总值/工业生产用固定资产平均总值)全部固定资产占用率=全部固定资产平均总值/工业总产值16.工业生产用固定资产占用率工业生产用固定资产占用率=工业生产用固定资产平均总值/工业总产值×100% =全部固定资产占用率×工业生产用固定资产平均总值/全部固定资产平均总值=在用固定资产占用率×工业生产用固定资产平均总值/在用固定资产平均总值17.低值易耗品摊销额净值摊销法:低值易耗品摊销额=在用低值易耗品净值×摊销率在用低值易耗品净值=在用低值易耗品计划成本-已经摊销数分期摊销法:低值易耗品月平均消耗额=(低值易耗品价值-预计残值)/预计可使用数产品摊销法:低值易耗品月平均消耗额=(低值易耗品价值-预计残值)/预定使用期内的预计产量×计算期月产量五五摊销法:领用时耗销额=在用低值易摊品计划成本×50%报销时消耗额=在用低值易耗品计划成本×150%-残值18.材料需要量材料需要量=计划产量×单位产品材料消耗定额=(计划产量×计划废品数量)×单位产品材料消耗定额-回收废料数量=[计划产量/(1-废品率)]×材料消耗定额-(1-回收废料率)19.辅助材料需要量辅助材料需要量=计划产量*单位产品消耗定额辅助材料需要量=上期单位产品产值(或工时)辅助材料消耗量×计划期产品产值(工时)×(1-压缩系数)20.工具需要量工具需要量=计划期工具消耗量+计划期末工具周转量-计划期初工具周转量某种工具消耗量=计划期某种产品的计划产量×该单位产品某种工具的消耗定额某种工具的消耗定额=制造一定数量的产品使用某种工具的时间/某种工具的寿命(分)21.材料供应量材料供应量=材料需要量+计划期末储备量-计划期初库存量-企业内部可利用资源22.材料储备量材料经常储备量=供应间隔天数×平均每日耗用量材料保险储备量=保险日数×平均每日耗用量材料最高储备量=(供应间隔日数+检验日数+使用准备日数+保险日数)×平均每日耗用量或=经常储备量+最低储备量材料最低储备量=(检验日数+使用准备日数+保险日数)×平均每日耗用量材料平均储备量=(最高储备量+最低储备量)/2材料季节性储备量=季节性储备日数×平均每日耗用量23.材料采购量材料订购量=(订购时间+订购间隔期)×平均每日需用量+保险储备量-实际库存量-订货余额订货点订购量=订货时间×平均每日需用量+保险储备量24.材料采购次数材料采购次数=材料年需用量/经济采购批量25.材料储备量对生产的保证率材料储备量对生产的保证率(天)=材料储备量/材料计划每日消耗量26.材料储备定额执行情况材料储备定额执行情况=(材料实际储备量/材料计划每日消耗量)×100%27.材料的平均单价移动加权平均法:材料平均单价=[(以前结余+本批收入)×材料实际成本]/(以前结余+本批收入)×材料的数量全月一次加权平均法:材料平均单价=[(月初库存+本月收入)×材料实际成本]/(月初库存+本月收入)×材料数量28.材料价格差异率本月材料累计数计算,其计算公式为:本月材料价格差异率=[材料价格差异额/(月初结存材料的计划价格+本月收入材料的计划价格)]×100% 材料价格差异额=月初结存材料的价格差异+本月收入材料的价格差异=(月初结存材料的实际价格-月初结存材料的计划价格)+(本月收入材料的实际价格-本月收入材料的计划价格)按当月发生数计算,其计算公式为:本月材料价格差异率=(本月收入材料价格差异额/本月发出材料计划价格)×100%本月收入材料的价格差异额=本月收入材料的实际价格-本月收入材料的计划价格按月初结存数计算,其计算公式为:本月材料价格差异率=(月初结存材料价格差异/月初结存材料计划价格)×100%按材料价格差异率和调整率的关系计算,其计算公式如下:本月材料价格差异率=本月材料价格调整率-1本月材料价格调整率=(月末结存材料实际价格/月末结存材料的计划价格)×100%或=[(月初结存材料实际价格+本月收入材料实际价格)/(月初结存材料计划价格+本月收入材料计划价格)]×100%发出材料应分配的价格差异额=发出材料计划价格×材料价格差异率29.材料年平均仓库保管费材料年平均仓库保管费=该种材料单价×材料保管费率材料保管费率=(材料年保管费/材料平均储备价值)×100%材料消耗总量:某种产品材料总消耗量=本期投料量+期初在制品、半成品未入库成品的折料量-期末在制品半成品未入库成品的折料量本期投料量=本期领料量-退料量本期投料量=本期领料量+期初领而未用的余料量-期末领而未用的余料量期末在制品、半成品未入库成品的折料量=∑期末各种在制品、半成品未入库成品的结存量×材料消耗定额30.单位产品材料实际消耗量单位产品材料实际消耗量=材料消耗总量/产品产量31.材料消耗定额执行情况指标一种产品消耗一种材料,其计算公式为:材料消耗定额执行情况指标=(单位产品材料实际消耗量/单位产品材料定额消耗量)×100%一种产品消耗多种材料,其计算公式为:材料消耗定额执行情况指标=[∑(单位产品材料实际消耗量×计划价格)/∑(单位产品材料消耗定额×计划价格)]×100%多种产品消耗一种原材料,其计算公式为:材料消耗定额执行情况指标=[∑(单位产品材料实际消耗量×实际产量)/∑(单位产品材料消耗定额×实际产量)]×100%32.原材料利用率原材料利用率=产品中所包含的原材料数量/生产该产品的原材料总消耗量×100%原材料利用率=产品产量/生产该产品的原材料消耗总量×100%33.原材料损耗率原材料损耗率=原材料的工艺性损耗重量/消耗的原材料重量×100%34.原材料综合利用率原材料综合利用率=不同规格零件净重之和/不同规格零件消耗原材料总重量×100%原材料综合利用率=(主产品重量+副产品重量)/原材料总消耗量×100%35.废料利用率废料利用率=(副产品重量/废料重量)×100%36.原材料利用定额完成情况原材料利用定额完成情况=实际利用率-定额(计划)利用率37.原材料消耗定额完成率原材料消耗定额完成率=(实际消耗/消耗定额)×100%38.原材料节约量原材料节约(或耗损)数量=(实际单耗-消耗定额)×报告期产量39.原材料代用节约额原材料代用而节约的材料数量=原用原材料单位产品消耗量×用代用品生产的产品产量原材料代用而节约材料金额=(原用原材料生产的单位产品原材料价值-代用品生产的单位产品原材料价值)×用代用品生产的产品产量40.材料变动对产量的影响额材料供应量变动对产量的影响额,其计算公式为:材料供应量变动对产量的影响额=(材料实际购入量-材料计划购入量)/单位产品材料计划消耗量材料储备量对产量的影响额,其计算公式为:材料储备量变动对产量的影响额=(材料实际储备量-材料计划储备量)/单位产品材料计划消耗量单位产品材料消耗量变动对产量的影响额,其计算公式为:单位产品材料消耗量变动对产量的影响额=(材料实际消耗量/单位产品材料实际消耗量)-(材料实际消耗量/单位产品材料计划消耗量)41.生产设备需要量生产设备需要量=(计划生产任务/单台设备的生产能力)×100%单台设备的生产能力=单台设备的工作时间×单位时间的产量定额42.设备的生产能力某设备的生产能力:某设备的生产能力=单项设备的生产能力×该类设备的数量×规定的全年开动时间单项设备的生产能力=设备的作业时间数×单位时间的产量定额同类设备的生产能力:同类设备的生产能力=同类设备台数×设备有效工作时间×每一台产量定额=(同类设备允数×设备的有效工作时间)/单位产品的台时定额设备的有效工作时间=(日历天数-节假日)×日制度工作时间-设备修理停歇时间设备组的生产能力:设备组的生产能力=(设备组的设备台数×单位设备有效工作时间)/(单位产品台时定额×改进压缩系数)设备组的生产能力=(设备组的设备台数×设备有效工作时间)/单位代表产品台时定设备有效工作时间=(日历日数-节假日)×班次×每班工作小时数×(1-设备停修率)43.年末的设备生产能力年末的设备生产能力=年初生产能力+本年新增加的生产能力-本年减少的生产能力设备的年平均生产能力=年初生产能力+新增的年平均生产能力-减少的年平均生产能力新增的年平均生产能力=新增设备的年生产能力×(自投入生产到年底的日历日数)/365减少的年平均生产能力=减少设备的年生产能力44.锻锤生产能力锻锤生产能力=锻锤每小时锻件产量(吨/时)×全年有效工作小时化铁炉生产能力(吨/年)=化铁炉每小时产量(吨/小时)×全年有效工作小时×改改进系数=1-(自然损耗率+浇胃口残头等消耗率+废品率)45.电弧炼钢生产能力电弧炼钢生产能力(吨/年)=炼钢炉容量(吨)×(全年有效工作时间/炼钢周期)×改进系数46.生产面积生产能力生产面积生产能力=(现有生产面积×制度工作时间)/(单位产品占用生产面积×单位产品占用时间)47.生产面积负荷系数生产面积负荷系数=完成生产任务所需生产面积的平方米小时数/现有生产面积的平方米小时数设备的全年计划总台时数=日历台时数×(制度台时数/日历台时数)×(计划台时数/制度台时数)=日历台时数×日历台时数利用率×制度台时数利用率48.设备台时平均产量设备台时平均产量=按定额工时计算的产品产量/(设备平均数量×每台设备工作小时数)完成计划任务所需设备台时数完成计划任务所需设备台时数=各种产品计划产量×单位产品台时定额49.设备组的有效台时数设备组的有效台时数=设备组的设备数量×单位设备有效时间50.设备的时间潜力设备的时间潜力(台时)=使用设备台数×平均每台不必要的停台时间51.设备的能力潜力设备的能力潜力=设备设计能力的台时产量-设备的实际台时产量52.设备的时间增长潜力设备的时间增长潜力=设备时间潜力×实际平均台时产量53.设备能力增长潜力设备能力增长潜力=每台设备能力潜力×设备可能利用的台时数设备可能利用的台时数=设备实际运转台时数+设备时间潜力(台时)54.设备全部增长潜力设备全部增长潜力=设备时间增长潜力+设备能力增长潜力55.设备平均数报告期设备平均数=∑报告期每日拥有的设备数量/报告期日历日数=期初设备数量+(报告期增加设备台日数)/报告期日历日数-(报告期减少设备台日数/报告期日历日数)56.实用设备安装率实有设备安装率=已安装设备台数/实有设备台数×100%57.已安装设备完好率已安装设备完好率=完好设备台数/已安装设备台数×100%58.已安装设备利用率已安装设备利用率=实际使用的设备台数/已安装设备台数×100%59.完好设备使用率完好设备使用率=实际使用设备台数×完好设备台数×100%60.设备时间利用率设备时间利用率=实际作业时间/最大可能利用时间×100%61.设备日厉台时利用率设备日历台时利用率=实际工作时间/日历时间×100% =实际使用台时/已安装设备或实际使用设备的日历台时数×100%平炉日历时间利用率=炼钢作业时间/(日历时间-冷炉大修理时间)×100%62.设备制度台时利用率设备制度台时利用率=实际使用台时数/制度工作台时数×100%制度工作台时数=已安装设备台时数(或实际使用设备)×制度工作日数×工作班次×每班次工作小时63.设备计划台时利用率设备计划台时利用率=(实际使用台数/计划使用台数)×100%计划使用台数=计划使用设备×设备计划使用的时间64.设备综合利用指标设备综合利用指标=设备时间利用指标×设备能力利用指标65.高炉综合利用率高炉综合利用率=生铁产量(吨)/[有效容积(立方米)×(日历昼夜数-大中修理昼夜数)]=[生铁产量(吨)/(有效容积×实际作业昼夜数)]×[实际作业昼夜数/(日历昼夜数-大中修理昼夜数)]=高炉生产效率×高炉时间利用率66.平炉综合利用率平炉综合利用率=合格平炉钢产量(吨)/[炉底面积(平方米)×(日历昼夜数-大修理昼夜数)]=平炉生产效率×平炉时间利用率平炉生产效率=合格平炉钢产量(吨)/(有效面积×实际作业昼夜数)平炉时间利用率=实际作业昼夜数/(日历昼夜数-大中修理昼夜数)67.设备现代化的费用节约额设备现代化的费用节约额=采用新设备后的单位产品成本降低额×计划产量+(单位产品出厂价格-采用新设备后的单位产品成本)×实际比计划增加的产量68.设备修理工作量设备修理工作量=设备的修理复杂系数×一个修理复杂系数的工时定额69.设备修理停歇时间设备修理停歇时间=设备修理工作量(工时)/(一个轮班参加修理的工人数×每个轮班工作时间×轮班次数)70.设备维修材料消耗定额设备维修材料消耗定额=用于设备大修理的材料实际消耗量/单台设备修理复杂系数71.设备平均在修日数设备平均在修日数=各台设备在修日数之和/修完设备的台数72.单位产品的设备维修费用单位产品的设备维修费用=设备维修费用/产品生产量73.设备维修费用效率设备维修费用效率=(产品生产量/设备维修费用)×100%74.设备维修计划完成率设备维修计划完成率=(报告期累计完成检修台数/本年计划检修台数)×100%75.设备修理质量平均等级设备修理质量平均等级=[∑(质量等级×修理完毕的各等级设备数)]/∑修理完毕的各等级设备数76.设备修理返修率设备修理返修率=(修理设备返修台数×/修理设备送检台数)×100%77.设备泄漏率设备泄漏率=(泄漏点总数/静密封点总数)×100%78.设备故障率设备故障率=(设备故障停歇时间/设备开动总台时)×100%79.设备事故率以设备事故次数与实际开动的设备台数对比,其计算公式为:设备事故率=报告期设备事故次数/报告期实际开动的设备台数以设备因事故停开台时与设备实际开动台时对比,以百分数表示,其计算公式为:设备事故率=(报告期设备事故停开台时/报告期设备实际开动台时)×100%80.设备事故损失总金额设备事故损失总金额=设备事故的修理费总额+设备事故造成减产金额设备事故造成减产金额=各种设备事故减产数量×单位产品价格设备事故造成减产数=设备事故停开台时×每台时平均产量81.设备换班系数设备换班系数=设备工作的总台班数/实际使用的设备总台数82.工艺用燃料需要量工艺用燃料需要量=(单位产品标准燃料消耗定额×计划产量)/折算系数折算系数=实际使用的燃料每千克发热量(千焦)/700(千焦)标准燃料=非标准燃料×(每千克非标准燃料发热量(千焦)/700(千焦))83.铸造焦炭需要量铸造焦炭需要量=炉料总重量×熔炼每吨金属的焦炭消耗定额84.焦铁比焦铁比=化焦总量/焦炭消耗量85.标准煤量标准煤量=∑[煤炭数量×每千克煤炭发热量(千焦)]/700(千焦)86.单位产品耗煤量单位产品耗煤量=(全厂用煤总量-全厂非工业生产用煤量)/产品产量单位产品耗煤量=该种产品应分摊的煤消耗量/该种产品产量该种产品应分摊的煤消耗量=工业生产用的煤总消耗量×(该种产品定额消耗量/总的应耗煤量)工业生产用的煤总消耗量=全厂用煤总量-全厂非工业生产用煤量87.锅炉用煤需要量锅炉用煤需要量=锅炉计划开动日数×煤炭日耗定额或=计划产量(产值)×单位产品(产值)耗煤定额88.铸造加热炉熏油需要量铸造加热炉熏油需要量=计划铸件产量(产值)×单位产量(产值)耗油定额每万元产值耗煤量=标准耗煤量/总产值(万元)节约煤消耗的节约额=[上期单位产品耗煤量(千克)-本期单位产品耗煤量(千克)]×本期产品产量×每千克燃料计划价格89.单位产品耗电量单位产品耗电量=(收入电量-转供电量-非生产用电量)/本期产品产量90.每万元产值耗电量每万元产值耗电量=(收入电量-转供电量-非生产用电量)/本期产品产量91.电力消耗定额完成率电力消耗定额完成率=(单位产品耗电量/消耗定额)×100%92.节约电力消耗的节约额节约电力消耗的节约额=(上期单位产品耗电量(度)-本期单位产品耗电量(度))×本期产品产量×每度电费93.技改革新节约电力消耗的节约额技改革新节约电力消耗的节约额=(改进前耗电量(度)-改进后耗电量(度))×使用时间×推广台数×每度电费94.发电机的平均实际能力发电机的平均实际能力=报告期实际发电总量(千瓦时)/报告期实际作业时间总数(小时)发电机的年平均能力=一年发电总量(千瓦时)/8760(小时)95.发电机的平均利用小时数发电机的平均利用小时数=报告期发电总量/报告期被利用设备能力总和(千瓦)96.发电机时间利用率发电机时间利用率(粗放负荷单)=(报告期发电机的实际作业数/报告期日历时数)×100%97.发电机能力利用率发电机能力利用率(集约负荷率)=(发电机的平均实际能力/发电机的最大长期有效能力)×100%发电机平均实际能力=报告期实际发电量/报告期实际作业时间发电机的综合利用率(综合负荷率)=[(报告期发电总量(千瓦时))/报告期发电机最大可能发电量(千瓦时)]×100%或=发电机的时间利用率×发电机的能力利用率98.劳动的潜在动力装备系数劳动的潜在动力装备系数=用于工业生产的动力设备总能力(千瓦或马力)/企业最大班工人数用于工业生产的动力设备的总能力=(用于工业生产的全部原动机能力-劳动发电机的原动机能务)+(用于工业生产的全部电动机能力+用于工业生产的电气器械能力)=机械传导设备能力+电力传导设备能力99.劳动的实际动力装备系数劳动的实际动力装备系数=用于工业生产的总动力(千瓦时)/平均工人数或实际工作工日数)用于工业生产的总动力=(全部原动机发生的动力-原动机用以劳动发电机的动力)+(用于工业生产的电动机消耗的动力+用于工业生产的电气器械消耗的动力)=机械传导的动力+电力传导的动力100.劳动的固定资产装备系数劳动的固定资产装备系数=工业生产用固定资产(元)/企业最大班工人数101.劳动机械化程度劳动机械化程度=(报告期从事机械化操作的工人数/报告期全部工人数) ×100%102.生产机械化程度生产机械化程度=(报告期机械化生产的产量/报告期全部产量) ×100%或=劳动机械化程度×(机械化工人劳动生产率/全部工人劳动生产率)103.生产自动化程度生产自动化程度=(报告期自动化设备生产的产量/报告期全部产量)×100%或=设备自动化程度×(自动化设备的生产效率/全部设备的平均生产效率)设备自动化程度=(报告期自动化设备台数/报告期全部设备台数)×100%104.在途日数在途日数=材料运输与验收日数-结算凭证邮递日数-双方开户银行办理结算凭证手续日数-货款承付日数某种材料实际平均在途日数=计算期该种在途材料平均占用额/计算期该种材料每日平均耗用额平均在途日数=[∑(全年供应量×在途日数)]/各供应单位全年供应量之和。
原材料周转天数计算公式

原材料周转天数计算公式
原材料周转天数(Material Turnover Days)是测量企业用于原材料
的库存周转次数的一种指标,它表明原材料从采购,加工,包装至出售的
转换周期,具有重要的参考意义。
原材料周转天数的计算公式为:原材料周转天数=平均原材料库存/(原材料消耗金额/该期(一年)
原材料采购成本)×365天。
其中,原材料平均库存指的是一定时期(一般为一年)的开始的库存
水平和结束的库存水平的平均数。
原材料消耗金额指的是一定时期内(一
般为一年),原材料实际消耗的成本。
原材料采购成本指的是一定时期内(一年)所采购的原材料的总成本。
全面正确地计算原材料周转天数,需要企业正确收集、记录相关信息,包括:原材料库存数量、原材料采购数量、原材料采购成本、原材料实际
消耗金额等数据。
以及原料仓库的库存管理政策、采购管理政策、供货管
理政策的落实情况。
正确掌握原材料周转天数的计算方法,可以为企业更有效地控制原材
料库存,降低存货成本,提高资金的使用效率,有助于企业合理调节物料
供应,提高供应链管理水平,最终使企业实现可持续发展。
电解制备氟气耗能标准
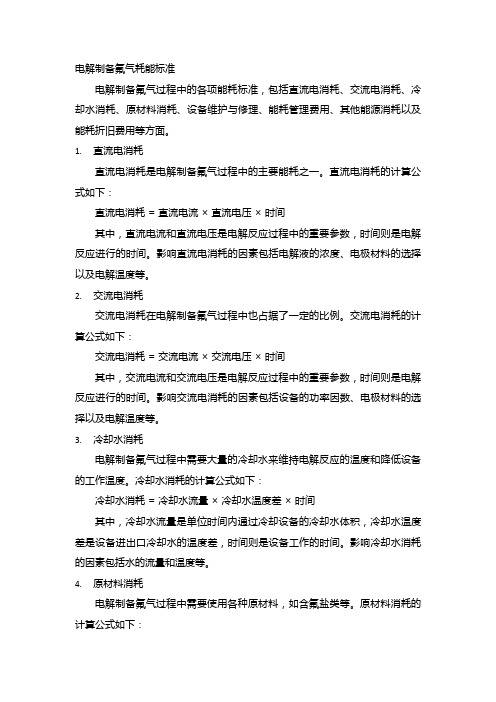
电解制备氟气耗能标准电解制备氟气过程中的各项能耗标准,包括直流电消耗、交流电消耗、冷却水消耗、原材料消耗、设备维护与修理、能耗管理费用、其他能源消耗以及能耗折旧费用等方面。
1.直流电消耗直流电消耗是电解制备氟气过程中的主要能耗之一。
直流电消耗的计算公式如下:直流电消耗 = 直流电流×直流电压×时间其中,直流电流和直流电压是电解反应过程中的重要参数,时间则是电解反应进行的时间。
影响直流电消耗的因素包括电解液的浓度、电极材料的选择以及电解温度等。
2.交流电消耗交流电消耗在电解制备氟气过程中也占据了一定的比例。
交流电消耗的计算公式如下:交流电消耗 = 交流电流×交流电压×时间其中,交流电流和交流电压是电解反应过程中的重要参数,时间则是电解反应进行的时间。
影响交流电消耗的因素包括设备的功率因数、电极材料的选择以及电解温度等。
3.冷却水消耗电解制备氟气过程中需要大量的冷却水来维持电解反应的温度和降低设备的工作温度。
冷却水消耗的计算公式如下:冷却水消耗 = 冷却水流量×冷却水温度差×时间其中,冷却水流量是单位时间内通过冷却设备的冷却水体积,冷却水温度差是设备进出口冷却水的温度差,时间则是设备工作的时间。
影响冷却水消耗的因素包括水的流量和温度等。
4.原材料消耗电解制备氟气过程中需要使用各种原材料,如含氟盐类等。
原材料消耗的计算公式如下:原材料消耗 = 原材料使用量×价格其中,原材料使用量是进行电解反应所需消耗的原材料数量,价格则是原材料的单价。
影响原材料消耗的因素包括反应物的浓度、电解设备的效率以及原材料的质量等。
5.设备维护与修理电解制备氟气过程中,设备的维护与修理是保证生产顺利进行的重要环节。
设备维护与修理费用的计算公式如下:设备维护与修理费用 = 人数×工时×维护与修理单价其中,人数是进行设备维护与修理所需的技术人员数量,工时是进行设备维护与修理所需的时间,维护与修理单价则是进行设备维护与修理的单价。