低压精密铸造轮毂时形成冷热裂纹的原因
压铸件出现裂纹的原因

压铸件出现裂纹的原因可能有多种,以下是一些常见的原因:
1. 温度梯度引起的热裂纹:在冷却过程中,不均匀的温度分布会导致部分区域产生较大的收缩应力,从而引发裂纹。
2. 疲劳裂纹:长时间的循环加载和应力集中会导致材料疲劳,最终导致裂纹的形成。
3. 内部气孔:在铸造过程中,如果存在气体未能完全排除,会在压铸件内部形成气孔。
这些气孔可能会成为裂纹的起点。
4. 不合适的材料选择:选择了强度或韧性不足的材料,无法承受所需的工作条件下的应力和载荷,从而导致裂纹的形成。
5. 设计缺陷:不合理的设计、结构薄弱或应力集中的区域,可能会导致压铸件在使用过程中产生裂纹。
6. 制造工艺问题:制造过程中操作不当、工艺参数设置不正确等因素,如铸造温度、冷却速度、注射压力等,都可能导致压铸件出现裂纹。
为了避免压铸件出现裂纹,可以采取以下措施:
-优化设计,避免应力集中区域的存在。
-选择合适的材料,以满足所需的工作条件和要求。
-严格控制制造工艺,确保温度、压力和冷却速度等参数符合要求。
-检查和修复内部气孔,以减少裂纹的起始点。
-定期进行检测和维护,及时发现并处理潜在的问题。
1。
分析铸造热裂缺陷形成的原因及改进对策

分析铸造热裂缺陷形成的原因及改进对策铸造热裂缺陷是铸造过程中常见的一种缺陷形态,会对铸件的性能和质量造成重大影响。
为了解决这一问题,需要深入分析其成因,并制定改进对策。
本文将从铸造热裂缺陷的原因以及改进措施两个方面展开讨论,旨在为铸造工艺提升提供思路和指导。
一、铸造热裂缺陷的形成原因铸造热裂缺陷通常在铸件冷却过程中产生,以下是其形成的主要原因:1. 温度梯度引起的应力集中铸件冷却过程中,由于各部分温度变化不一致,会导致内部产生温度梯度,从而引起局部局部应力集中。
当材料的强度无法承受这种应力时,就会发生热裂缺陷。
2. 晶粒的收缩行为铸件在凝固过程中,晶粒会出现收缩。
若凝固过程中晶粒收缩不一致,就会引起内部应力的不平衡,从而产生热裂。
3. 液态膨胀引起的应力铸造过程中,液态金属体积较大,当其冷却凝固时,体积会缩小,引起内部应力。
若应力超过材料的承载能力,就会发生热裂缺陷。
二、改进对策为了解决铸造热裂缺陷问题,可以采取以下改进对策:1. 优化铸造工艺参数通过调整铸造温度、冷却速度以及铸件尺寸等参数,使得整个铸造过程中的温度分布更加均匀,减小温度梯度和晶粒收缩不一致性,从而减轻应力集中的程度,降低热裂的风险。
2. 控制液态膨胀行为合理控制铸造合金的成分,通过合金设计等方法来调整材料的液态膨胀行为。
降低材料在冷却凝固过程中产生的应力,减少热裂的概率。
3. 采用合适的铸型材料选择合适的铸型材料也是防止铸造热裂缺陷的关键。
材料的导热性能和热传导能力会影响铸件冷却的速度,因此在选择铸型材料时要充分考虑其导热性和热传导性能。
4. 进行合理的余热处理通过对已铸造完成的铸件进行合理的余热处理,使其内部温度均衡分布,减少应力集中和热裂的风险。
此外,适当的余热处理还能改善铸件的织构和力学性能。
5. 严格控制冷却速度合理控制冷却速度是防止铸造热裂缺陷的重要措施之一。
通过对冷却介质的选择以及冷却方式的优化,可以实现对冷却速度的有效控制,降低热裂的风险。
铸件裂纹产生的原因
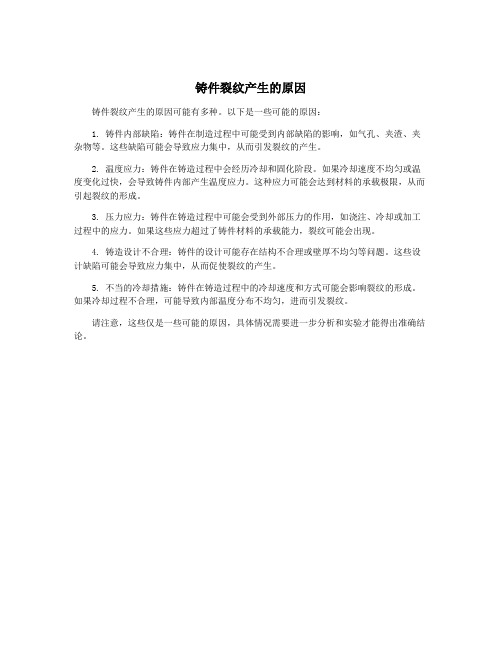
铸件裂纹产生的原因
铸件裂纹产生的原因可能有多种。
以下是一些可能的原因:
1. 铸件内部缺陷:铸件在制造过程中可能受到内部缺陷的影响,如气孔、夹渣、夹杂物等。
这些缺陷可能会导致应力集中,从而引发裂纹的产生。
2. 温度应力:铸件在铸造过程中会经历冷却和固化阶段。
如果冷却速度不均匀或温度变化过快,会导致铸件内部产生温度应力。
这种应力可能会达到材料的承载极限,从而引起裂纹的形成。
3. 压力应力:铸件在铸造过程中可能会受到外部压力的作用,如浇注、冷却或加工过程中的应力。
如果这些应力超过了铸件材料的承载能力,裂纹可能会出现。
4. 铸造设计不合理:铸件的设计可能存在结构不合理或壁厚不均匀等问题。
这些设计缺陷可能会导致应力集中,从而促使裂纹的产生。
5. 不当的冷却措施:铸件在铸造过程中的冷却速度和方式可能会影响裂纹的形成。
如果冷却过程不合理,可能导致内部温度分布不均匀,进而引发裂纹。
请注意,这些仅是一些可能的原因,具体情况需要进一步分析和实验才能得出准确结论。
镁合金铸件低压铸造出现裂纹缩松的原因分析论文

镁合金铸件低压铸造出现裂纹缩松的原因分析论文在镁铸件生产中,常见的铸件缺陷有显微疏松、松孔、气孔、裂纹(热裂、冷裂、冷隔、欠铸、夹砂、夹杂(氧化皮、熔剂等)、偏析等。
通常,产生这些缺陷的原因不单是自身的合金成分问题,有时还有造型制芯、熔炼浇注、型砂质量、落砂处理等许多生产工序的问题,因此必须具体分析,以便采取相应的合理措施加以解决。
生产镁铸件时,与合金自身有直接关系的某些缺陷及其原因分析与防止方法如下:氧化冷隔特征:金属液流被氧化皮隔开而未熔合为一体。
严重时成为欠铸。
常出现在铸件的顶壁上、薄的水平或垂直面上、厚薄转接处或薄肋条上原因分析:1.浇注温度过低,合金流动性差2.型腔排气不良,阻碍合金液的流动3.直浇道、横浇道或内浇道的面积不够,金属液充填的速度缓慢或流动的距离太远4.型芯错位或移动,使某一部位的壁厚明显变薄5.浇注时金属液流中断或不稳定防止办法:1.适当提高浇注温度和金属型温度2.增加铸型、型芯的排气能力3.合理选择浇注系统的位置、数量和面积4.增加铸件某一部位的厚度5.保持金属液流平稳、均匀而无紊流地进入铸型特征:断口呈深灰、黑和浅黄色而不规则的点或小块状存在于铸件内部,外形上呈薄片、皱皮或团絮状,有时还带有少量的熔剂。
薄壁铸件则常露于表面原因分析:1.合金熔炼过程中因生成氧化物而造成的夹杂。
主要原因是炉料不清洁,熔剂不干燥,精炼作用不完全,浇注前的静置时间不够以及熔炼操作不当2.浇注过程中因形成氧化皮而造成。
主要原因是浇注系统设计不合理,浇注时合金剧烈氧化或产生涡流以及浇注操作不当3.铸型本身原因:主要是砂型及型芯烘烤不良,保护剂不足,合箱后停放时间过长,型砂过湿,砂型捣得太实等防止办法:1.保持炉料清沽、熔剂干燥、仔细精炼。
充分静置并往合金中加人少量铍2.正确设计浇注系统,采用过滤器,起动坩埚要平稳,正确浇注,避免氧化和燃烧。
浇注时不断撒以硫黄、硼酸防护剂或喷以保护气氛3.造型操作要正确,控制型砂水分,砂芯要干透,控制好合箱时间1.大块熔剂夹杂在铸件内呈水滴状,常与熔渣同时出现。
分析铸造热裂缺陷形成的机理及改进措施

分析铸造热裂缺陷形成的机理及改进措施铸造热裂缺陷是铸造过程中常见的一种缺陷,它对铸件的质量和性能产生严重的影响。
了解和分析铸造热裂缺陷形成的机理,并采取适当的改进措施,对于提高铸件的质量和性能具有重要意义。
一、铸造热裂缺陷的机理分析铸造热裂缺陷的形成主要与铸造过程中的温度变化和应力积累有关。
具体的机理可以从以下几个方面进行分析:1. 温度梯度引起的热应力在铸造过程中,液态金属流注入型腔中后,由于型腔的温度梯度不均匀,会导致金属在冷却过程中产生温度梯度,从而引起不均匀的热收缩和热应力的积累。
当应力达到材料的承载极限时,就会发生裂纹的形成。
2. 金属的热固性和热收缩不匹配不同金属具有不同的热膨胀系数和热收缩系数,当金属与型腔或其他部件接触时,由于温度变化而引起的热收缩不匹配,也会导致热应力的产生。
3. 相变引起的应力集中在铸造过程中,液态金属在冷却过程中会发生相变,如固态化、固相转变等。
这些相变对金属的体积变化和应力产生有着重要影响。
当相变速率较快时,容易引起应力集中,从而形成裂纹。
二、改进措施为了减少铸造热裂缺陷的发生,可以采取以下改进措施:1. 控制铸造温度和温度梯度合理控制铸造过程中的温度和温度梯度对于减少热应力的产生具有重要作用。
可以通过调整浇注温度、冷却速度等参数来控制温度梯度的变化,减少热应力的积累。
2. 选择合适的金属材料选择具有匹配热膨胀系数和热收缩系数的金属材料,可以减少热收缩不匹配引起的应力积累。
同时,还应选择具有较好耐热性能的材料,以降低温度梯度引起的热应力。
3. 优化铸造工艺合理设计铸造工艺,采用预热、降温等措施,可以有效降低热应力的产生。
此外,还应注意避免温度梯度过大的情况,避免铸件过厚或形状复杂等导致热应力增加的问题。
4. 消除应力集中点铸造热裂缺陷的形成与应力集中有关,因此,要尽量消除或减少应力集中点。
对于已经存在的应力集中点,可以采取修补、改进设计等方式进行处理,以减少裂纹的产生。
铸造裂纹产生的原因和避免的措施

铸造裂纹产生的原因和避免的措施铸造是一种重要的金属成型工艺,广泛应用于汽车、航空、航天、军工等领域。
然而,铸造件在生产中常常会出现裂纹缺陷,导致产品质量下降,甚至造成安全事故。
本文将就铸造裂纹的产生原因和避免措施进行简要介绍。
铸造裂纹产生的原因铸造裂纹主要有以下几个原因。
1. 材料缺陷铸造材料在生产过程中,常常会出现缺陷,如气孔、夹杂、杂质等,这些缺陷会在铸造冷却过程中形成应力集中区域,导致裂纹的产生。
2. 铸造工艺不合理铸造工艺不合理也是造成铸造件裂纹的重要原因。
如浇口不当、冷却不均、浇注速度过快等,都会导致铸造件的应力不均匀,从而形成裂纹。
3. 设计不合理铸造件的设计也会影响裂纹的产生。
当设计不合理时,会使铸造件应力分布不均匀,从而形成裂纹。
4. 环境因素环境因素也可能导致铸造件裂纹的产生。
如温度过高或过低、环境湿度过高、风力过大等,都会影响铸造件的冷却速度,从而形成裂纹。
避免铸造裂纹的措施为了避免铸造裂纹的产生,我们可以采取以下措施。
1. 优化材料在生产过程中,对铸造材料进行优化,去除缺陷,可以有效减少铸造裂纹的产生。
2. 检查工艺在生产过程中,对铸造工艺进行检查,保证浇口、浇注速度等符合要求,可以有效减少铸造件裂纹的产生。
3. 合理设计设计时要考虑到铸造件内部的应力分布,合理设计无疑可以减少铸造裂纹的产生。
4. 控制环境在铸造过程中,要控制环境温度、湿度和风力等因素,使铸造件冷却均匀,从而减少裂纹的产生。
结语本文介绍了铸造裂纹的产生原因和避免措施。
铸造件裂纹的产生很大程度影响了铸造件的质量和使用寿命,因此,为了提高产品质量,我们必须采取措施避免铸造裂纹的产生。
镁合金铸件低压铸造出现裂纹缩松的原因分析论文

镁合金铸件低压铸造出现裂纹缩松的原因分析论文缩松裂纹不同于晶界裂纹,其裂纹较为明显,裂纹表面常常凹凸不平,并且在裂文处出现较多的缩松、缩孔以及杂物存在,由于模具在热胀冷缩过程中可能又气体的掺杂,因此在裂纹的端部会出现大的气孔,气孔膨胀导致表面凸起,因此促使产品表面不平整,导致出现缩松裂纹,与晶界裂纹一样缩松裂纹的出现同样会导致杂质在裂纹处的聚集,大量的聚集以后导致截面处的韧性大大降低,同时介于产品的整体性被严重的破坏,会极大的降低铸件自身的塑性与强度,并且在其裂纹的前沿形成应力的集中区,导致材料自身对自己就有应力的存在,一旦受到外力的作用就很容易在此处产生剪切力,并且发生断裂。
缩松裂纹的产生很大程度上是因为铸件有一定刚度的先凝固部分对收缩部位产生损害,促使局部形成收缩应力,该应力超过了铸件在该温度的塑性极限,因此导致裂纹的产生,在此过程中由于工艺的不成熟还会导致气泡的掺杂从而导致裂纹缩松,表面的不平整,破坏了此处金相组织的连续性,导致产品的塑性和强度降低。
铸件热裂原因
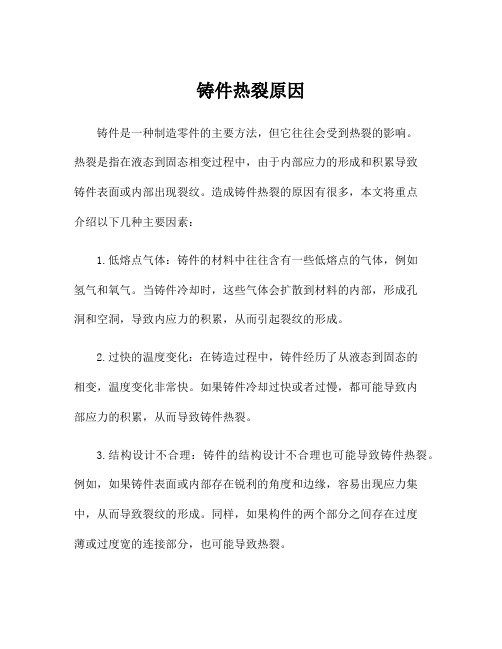
铸件热裂原因
铸件是一种制造零件的主要方法,但它往往会受到热裂的影响。
热裂是指在液态到固态相变过程中,由于内部应力的形成和积累导致
铸件表面或内部出现裂纹。
造成铸件热裂的原因有很多,本文将重点
介绍以下几种主要因素:
1.低熔点气体:铸件的材料中往往含有一些低熔点的气体,例如
氢气和氧气。
当铸件冷却时,这些气体会扩散到材料的内部,形成孔
洞和空洞,导致内应力的积累,从而引起裂纹的形成。
2.过快的温度变化:在铸造过程中,铸件经历了从液态到固态的
相变,温度变化非常快。
如果铸件冷却过快或者过慢,都可能导致内
部应力的积累,从而导致铸件热裂。
3.结构设计不合理:铸件的结构设计不合理也可能导致铸件热裂。
例如,如果铸件表面或内部存在锐利的角度和边缘,容易出现应力集中,从而导致裂纹的形成。
同样,如果构件的两个部分之间存在过度
薄或过度宽的连接部分,也可能导致热裂。
4.金属成分的变化:铸件的金属成分对铸件的热裂性能有很大的影响。
例如,硅、铜、锰等元素的含量过高,会导致内部应力的增加,从而导致铸件热裂。
5.冷却方式不适当:铸造过程中冷却方式不合理也常常是引起热裂的原因之一。
如果冷却过程中所用的冷却剂温度过低或过高,或者冷却的速度过快或过慢,都会导致铸件内部产生应力,从而引起铸件热裂。
综上所述,铸件热裂的原因复杂,需要进行全面的分析和研究。
在铸造中要避免热裂,需要在制作工艺与工作水平的不断提升上进行不断地思考和改进。
冷热裂纹形成机理影响因素防治措施

冷热裂纹形成机理影响因素防治措施引言冷热裂纹是一种常见的材料力学性能问题,其在工业领域中广泛存在,并对材料的性能和寿命产生负面影响。
了解冷热裂纹的形成机理、影响因素以及相应的防治措施对于提高材料的可靠性和使用寿命至关重要。
本文将深入探讨冷热裂纹的相关知识,帮助读者了解该问题,并提供有效的防治措施。
冷热裂纹形成机理冷热裂纹的形成机理是由于材料在冷却或加热过程中产生的内部应力超过了其破坏强度,导致裂纹的生成和扩展。
一般来说,冷热裂纹的形成可以归结为以下几个主要机制:1.温度差异引起的热应力:在材料冷却或加热的过程中,温度变化引起了材料的热膨胀或收缩,从而产生内部应力。
当这些内部应力超过材料的破坏强度时,就会形成裂纹。
2.材料组织的不均匀性:材料内部的组织不均匀性会导致不同部分的热膨胀或收缩程度不同,从而引起内部应力的积累。
这种内部应力的不均匀分布会促使裂纹的形成。
3.金属材料中的相变:某些金属材料在冷却或加热过程中会发生相变,进而引起内部应力的产生。
这种内部应力可以导致裂纹的形成。
4.加工工艺缺陷:不合理的加工工艺,如快速冷却或加热,过高的加工温度等,可能会导致材料内部应力过大,从而引发冷热裂纹。
影响因素冷热裂纹的形成受到多种因素的影响,下面将介绍其中一些主要因素:1.材料特性:材料的热膨胀系数、热导率、弹性模量等性质会影响材料在温度变化时的应变和应力分布,从而对冷热裂纹的形成起到重要作用。
2.加工工艺:加工工艺的合理性直接关系到冷热裂纹的形成。
材料的加工温度、冷却速率、加热速率以及冷却或加热时所采用的手段等都会对冷热裂纹的发展起到影响。
3.材料结构:材料的晶体结构和晶粒尺寸也会影响冷热裂纹的形成。
晶体结构不完善或晶粒尺寸过大都会削弱材料的抗裂性能,增加冷热裂纹的发生风险。
4.环境条件:环境因素如湿度、氧化性、腐蚀性等也会对冷热裂纹的形成产生一定影响。
特别是在存在湿度和腐蚀性较高的环境中,冷热裂纹的形成更容易发生。
铸件开裂的原因

铸件开裂的原因
铸件开裂是在铸造过程中经常发生的问题,可能会造成产品质量下降甚至损坏。
下面将从几个方面分析铸件开裂的原因。
温度控制不当是导致铸件开裂的主要原因之一。
在铸造过程中,如果铸件冷却过快或温度变化过大,容易造成内部应力过大,从而导致铸件开裂。
因此,对于不同材料和结构的铸件,需要合理控制铸造温度和冷却速度,避免温度梯度过大造成应力集中。
金属液体的浇注方式也会影响铸件的质量。
如果浇注速度过快或浇注过程中存在气泡和气体混入,会导致铸件内部存在气孔和夹杂物,降低铸件的强度和韧性,容易发生开裂。
因此,在铸造过程中需要采取适当的浇注方式和控制浇注速度,确保金属液体充分填充模具且不受气体污染。
金属合金的成分和熔炼工艺也会影响铸件的质量。
如果金属合金成分不均匀或存在杂质,会导致铸件内部组织不均匀,容易出现晶粒过大或过小的情况,从而影响铸件的力学性能,导致开裂。
因此,在选择合金材料和熔炼工艺时,需要严格控制合金成分和熔炼温度,确保合金均匀混合且无杂质。
模具设计和制造也会对铸件开裂产生影响。
如果模具设计不合理或制造精度不高,会导致铸件表面粗糙或存在凹凸不平的情况,容易造成应力集中和裂纹产生。
因此,在模具设计和制造过程中,需要
考虑铸件的结构和形状,确保模具表面光洁度和精度要求,减少铸件在脱模过程中的变形和损伤。
铸件开裂是由多种因素综合作用导致的问题,需要在铸造过程中综合考虑温度控制、浇注方式、合金成分、模具设计等多个方面的因素,以避免铸件开裂的发生,提高铸件的质量和性能。
只有在铸造过程中严格控制每个环节,才能确保铸件的质量和稳定性,避免开裂等质量问题的发生。
低压铸铝加工后出现的问题

低压铸铝加工后出现的问题
低压铸铝加工后可能出现以下问题:
1. 气孔:低压铸铝过程中,若铝液中存在气体或其他杂质,则在铸造过程中会形成气孔,影响铝件的质量和强度。
2. 破损:低压铸铝过程中,如果铝液进入模具时速度过快或压力过大,可能导致模具破裂或铝件损坏。
3. 热裂纹:低压铸铝件在冷却过程中可能会产生热应力,导致铝件出现裂纹。
这通常是由于铝液冷却过快或不均匀,导致铝件表面和内部产生不同程度的收缩。
4. 变形:低压铸铝件在冷却过程中,由于内部和外部温度不均匀,可能会出现变形。
这种变形可能导致铝件无法满足设计要求或无法与其他部件组装。
5. 肉眼可见的疵点:低压铸铝过程中,由于模具不良或操作不当,可能会在铝件表面形成肉眼可见的疵点,如斑点、划痕等。
6. 尺寸偏差:低压铸铝时,模具和铝液的热膨胀和收缩导致尺寸偏差。
这可能需要通过后期加工或热处理来纠正。
7. 冷隔:低压铸铝过程中,如果铝液填充模具过程中存在的空隙不能完全填满,就会产生冷隔。
冷隔会导致铝件的局部强度降低。
要解决这些问题,可以通过提高工艺控制、优化模具设计、优化铝合金配方、选择合适的冷却方式等措施来改善低压铸铝加工的质量。
铸件热裂纹的原因及其防治措施
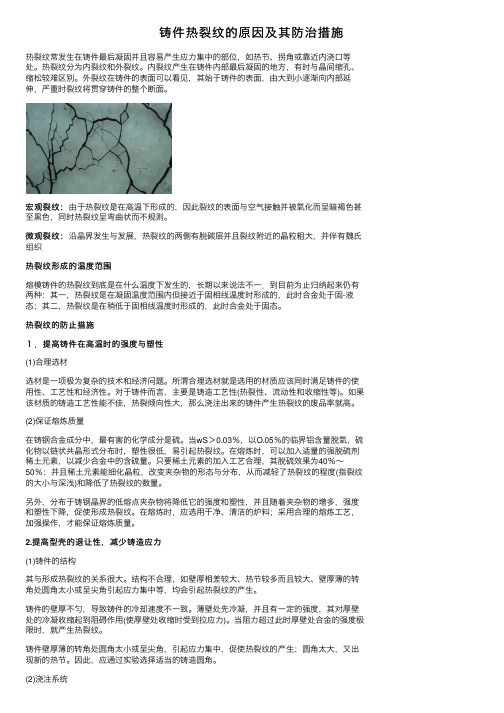
铸件热裂纹的原因及其防治措施热裂纹常发⽣在铸件最后凝固并且容易产⽣应⼒集中的部位,如热节、拐⾓或靠近内浇⼝等处。
热裂纹分为内裂纹和外裂纹。
内裂纹产⽣在铸件内部最后凝固的地⽅,有时与晶间缩孔、缩松较难区别。
外裂纹在铸件的表⾯可以看见,其始于铸件的表⾯,由⼤到⼩逐渐向内部延伸,严重时裂纹将贯穿铸件的整个断⾯。
宏观裂纹:由于热裂纹是在⾼温下形成的,因此裂纹的表⾯与空⽓接触并被氧化⽽呈暗褐⾊甚宏观裂纹:⾄⿊⾊,同时热裂纹呈弯曲状⽽不规则。
微观裂纹:沿晶界发⽣与发展,热裂纹的两侧有脱碳层并且裂纹附近的晶粒粗⼤,并伴有魏⽒微观裂纹:组织热裂纹形成的温度范围熔模铸件的热裂纹到底是在什么温度下发⽣的,长期以来说法不⼀.到⽬前为⽌归纳起来仍有两种:其⼀,热裂纹是在凝固温度范围内但接近于固相线温度时形成的,此时合⾦处于固-液态;其⼆,热裂纹是在稍低于固相线温度时形成的,此时合⾦处于固态。
热裂纹的防⽌措施1.提⾼铸件在⾼温时的强度与塑性(1)合理选材选材是⼀项极为复杂的技术和经济问题。
所渭合理选材就是选⽤的材质应该同时满⾜铸件的使⽤性、⼯艺性和经济性。
对于铸件⽽⾔,主要是铸造⼯艺性(热裂性、流动性和收缩性等)。
如果该材质的铸造⼯艺性能不佳,热裂倾向性⼤,那么浇注出来的铸件产⽣热裂纹的废品率就⾼。
(2)保证熔炼质量在铸钢合⾦成分中,最有害的化学成分是硫。
当wS>0.03%,以O.05%的临界铝含量脱氧,硫化物以链状共晶形式分布时,塑性很低,易引起热裂纹。
在熔炼时,可以加⼊适量的强脱硫剂稀⼟元素,以减少合⾦中的含硫量。
只要稀⼟元素的加⼊⼯艺合理,其脱硫效果为40%~50%:并且稀⼟元素能细化晶粒,改变夹杂物的形态与分布,从⽽减轻了热裂纹的程度(指裂纹的⼤⼩与深浅)和降低了热裂纹的数量。
另外,分布于铸钢晶界的低熔点夹杂物将降低它的强度和塑性,并且随着夹杂物的增多,强度和塑性下降,促使形成热裂纹。
在熔炼时,应选⽤⼲净、清洁的炉料;采⽤合理的熔炼⼯艺,加强操作,才能保证熔炼质量。
铸造裂纹的产生原因及种类

铸造裂纹的产生原因及种类
铸造裂纹的产生原因主要有以下几个方面:
1.材料原因:铸造材料质量不良,有夹杂物或缺陷,导致铸件强度不足,易产生裂纹。
2.工艺原因:铸造工艺控制不当,例如铸造温度不均匀、浇注方式不
正确、冷却速率不协调等都会导致铸件内部应力过大,从而产生裂纹。
3.设计原因:铸件设计不合理、结构形状复杂、壁厚过薄等都是容易
产生裂纹的原因。
铸造裂纹主要有以下几种类型:
1.热裂纹:在铸造过程中,铸件受到热应力的作用,从而产生的裂纹。
2.冷裂纹:指铸件在自然冷却过程中,由于内部应力大、冷却不均等
因素导致的裂纹。
3.拉伸裂纹:在铸件拉伸过程中,由于应力集中导致铸件表面产生的
裂纹。
4.疲劳裂纹:铸件经过长时间的载荷作用,由于应力交替的影响,会
产生裂纹。
5.焊接裂纹:铸造件经焊接后,由于热应力、冷却速率不协调等因素,容易产生的裂纹。
铸造裂纹产生的原因和避免的措施

在所有的铸造缺陷中,对产品质量影响最大的是铸造裂纹,按照其特征可将其分为热裂纹和冷裂纹,它们是不允许存在的缺陷。
(1)热裂纹热裂纹是铸件在凝固末期或凝固结束后不久,铸件尚处于强度和塑性都很低的高温阶段,形成温度在1250~1450℃,因铸件固态收缩受阻而引起的裂纹。
热裂纹的主要特征有:•在晶界萌生并沿晶界扩展,形状粗细不均匀、曲折不规则;•通常呈龟裂的网状;•裂纹的表面呈氧化色,无金属光泽,铸钢件裂纹表面呈近似黑色;•裂纹末端圆钝,两侧有明显的氧化和脱碳,有时有明显的疏松、夹杂、孔洞等缺陷。
按照热裂纹在铸件中的形成位置,又可将其分为外裂纹和内裂纹。
•在铸件表面可以看到的热裂纹为外裂纹,外裂纹常产生在铸件的拐角或局部凝固缓慢、容易产生应力集中的位置,其特征是:表面宽,心部窄,呈撕裂状,有时断口会贯穿整个铸件断面。
•内裂纹一般发生在铸件内部最后凝固的部位,其特征是:形状不规则,裂纹面常伴有树枝晶。
通常情况下,内裂纹不会延伸到铸件表面,内裂纹的一个典型例子是冒口切除后根部所显露的裂纹。
热裂纹的形成原因可归纳为:1.浇铸冷却过程中收缩应力过大;2.铸件在铸型中收缩受阻;3.铸件冷却不均匀;4.铸件结构设计不合理,存在几何尺寸突变;5.有害杂质在晶界富集;6.铸件表面与涂料之间产生了相互作用。
(2)冷裂纹冷裂纹是铸件凝固结束后继续冷却到室温的过程中,因铸件局部受到的拉应力大于铸件本体的破断强度而引起的开裂。
冷裂纹的主要特征有:1.总是发生在承受拉应力的部位,特别是铸件形状、尺寸发生变化的应力集中部位;2.裂纹宽度均匀、细长,呈直线或折线状,穿晶扩展;3.裂纹面比较洁净、平整、细腻,有金属光泽或呈轻度氧化色;4.裂纹末端尖锐,裂纹两侧基本无氧化和脱碳,显微组织与基体的基本相同。
冷裂纹产生的原因,可归纳为:1.铸件结构系统设计不合理,铸件壁厚不均匀会导致铸造应力,有时会产生冷裂纹,刚性结构的铸件,由于其结构的阻碍,温度降低导致的收缩应力容易使铸件产生冷裂纹,薄壁大芯、壁薄均匀的铸件非常容易产生冷裂纹;2.浇冒口系统设计不合理,对于壁厚不均匀的铸件,如果内浇口设置在铸件的厚壁部分时,将使铸件厚壁部分的冷却速度更加缓慢,导致或加剧铸件各部分冷却速度的差别,增大了铸造热应力,容易使铸件产生冷裂纹,浇冒口位置设计不当时,也会直接阻碍铸件收缩,使铸件容易产生冷裂纹;3.型砂或型芯的强度太高,高温退让性差,或舂砂过紧,使铸件收缩受到阻碍,产生很大的拉应力,导致铸件产生冷裂纹;4.钢的化学成分不合格,有害元素磷含量过高,使钢的冷脆性增加,容易产生冷裂纹5.铸件开箱过早,落砂温度过高,或者在清砂时受到碰撞、挤压等都会引起铸件的开裂。
铸造可能遇到的问题和解决方案

铸造可能遇到的问题和解决方案标题,铸造中常见问题及解决方案。
在铸造过程中,常常会遇到一些问题,这些问题可能会影响产品的质量和生产效率。
以下是一些铸造中常见的问题以及可能的解决方案。
1. 气孔和气泡。
气孔和气泡是铸造中常见的质量问题,可能会导致产品强度不足或者外观质量不佳。
这可能是由于熔融金属中的气体未能完全排除所致。
解决方案,采取适当的浇注系统设计,确保熔融金属能够充分充填模具,同时使用合适的除气剂和浇口设计来减少气孔和气泡的产生。
2. 热裂纹。
热裂纹是由于金属在冷却过程中产生的应力超过了其承受能力
而引起的。
这可能会导致产品在使用过程中出现裂纹。
解决方案,通过合理的冷却控制和合适的金属合金选择,可以减少热裂纹的发生。
此外,预热模具和采用合适的退火工艺也可以有效减少热裂纹的产生。
3. 金属收缩。
金属在冷却过程中会收缩,如果不加以控制,可能会导致产品尺寸不准确甚至变形。
解决方案,通过合理的浇注系统设计和冷却控制,可以减少金属收缩对产品质量的影响。
此外,采用合适的模具设计和金属合金选择也可以减少金属收缩带来的问题。
总之,铸造过程中可能会遇到各种质量问题,但通过合理的工艺控制和技术手段,这些问题是可以得到解决的。
只有不断改进工艺和技术,才能确保铸造产品的质量和稳定性。
低压铸造铝合金轮毂裂纹形成及原因分析

对低压铸造铝合金轮毂裂纹形成原因进行分析,就影响裂纹产升的各种因素,如铸件结构、工艺参数、模具温度等进行研究,通过合理控制和调整这些因素,消除裂纹对轮毂铸件的影响,从而进步企业的经济效益。
铝合金轮毂具有许多钢质轮毂无法比拟的特性,因此铝合金轮毂在轿车、摩托车等车辆上已开始广泛应用。
到2002年,我国轿车铝合金轮毂的装车率已接近45%。
由于汽车轮毂质量要求较高,本身结构又适合于低压铸造,且需求量大,因此,极大地推动了低压铸造技术的发展。
目前,低压铸造已成为铝合金轮毂升产的主要工艺方法,国内的铝合金轮毂制造企业多数采用此工艺升产。
低压铸造可实现高度机械化、自动(di ya zhu zao ke shi xian gao du ji xie hua _zi dong)化,既进步升产率(10~15型/h),又可减少众多的不利于升产工艺的人为因素,进步成品率,且可大大减轻工人的劳动强度。
然而低压铸造件的质量受到诸如工艺方案、工艺参数、模具结构及人工操作等因素,以及它们之间的相互影响,任何一个环节设计不合理或操作不当都有可能导致低压铸造件产升缺陷。
其中,铝合金轮毂裂纹的产升是影响企业升产成本、升产效率的重要因素,且轮毂裂纹是汽车安全性的重大隐患。
因此,对低压铸造铝合金轮毂裂纹成因的探讨就显得尤为重要。
一、低压铸造铝合金轮毂裂纹形成的原因低压铸造铝合金轮毂裂纹主要产升在应力集中的部位,或轮毂顶出时因受力不均,或升液管处液体凝固造成的开裂。
裂纹一般分为冷裂和热裂两种。
冷裂纹是指合金在低于其固相线温度时形成的裂纹。
通俗地说,冷裂是铸件冷却到低温时,作用在铸件上的铸造应力超过铸件本身强度或塑性所允许的程度而产升的。
冷裂多在铸件表面上出现,裂口表面有轻微的氧化;而热裂通常认为是在合金凝固过程中产升的,由于型壁的传热作用,铸件总是从表面开始凝固的。
当铸件表面出现大量的枝品并搭接成完整的骨架时,铸件就会出现固态收缩(常以线收缩表示)。
铸件开裂的原因
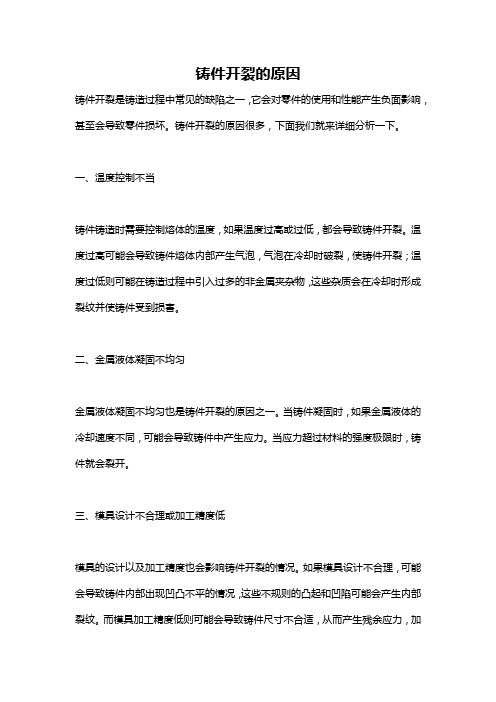
铸件开裂的原因
铸件开裂是铸造过程中常见的缺陷之一,它会对零件的使用和性能产生负面影响,甚至会导致零件损坏。
铸件开裂的原因很多,下面我们就来详细分析一下。
一、温度控制不当
铸件铸造时需要控制熔体的温度,如果温度过高或过低,都会导致铸件开裂。
温度过高可能会导致铸件熔体内部产生气泡,气泡在冷却时破裂,使铸件开裂;温度过低则可能在铸造过程中引入过多的非金属夹杂物,这些杂质会在冷却时形成裂纹并使铸件受到损害。
二、金属液体凝固不均匀
金属液体凝固不均匀也是铸件开裂的原因之一。
当铸件凝固时,如果金属液体的冷却速度不同,可能会导致铸件中产生应力。
当应力超过材料的强度极限时,铸件就会裂开。
三、模具设计不合理或加工精度低
模具的设计以及加工精度也会影响铸件开裂的情况。
如果模具设计不合理,可能会导致铸件内部出现凹凸不平的情况,这些不规则的凸起和凹陷可能会产生内部裂纹。
而模具加工精度低则可能会导致铸件尺寸不合适,从而产生残余应力,加
剧铸件开裂的可能性。
四、材料质量差
材料质量也是铸件开裂的重要原因之一。
比如,含有大量氧、硫等元素的材料,容易在铸造过程中形成气孔,令铸件在高温和不和谐的应力情况下容易产生裂纹;低品质的材料,或者生产工艺不严格,可能含有大量的夹杂物,这些杂质容易在铸造过程中产生应力集中的区域,使得铸件容易裂开。
综上所述,铸件开裂的原因有很多,主要包括温度控制不当、金属液体凝固不均匀、模具设计和加工问题、材料质量等。
为了减少铸件开裂的情况,需要对这些问题进行细致的分析,并针对性地进行改进和优化。
压铸裂纹的成因和预防措施
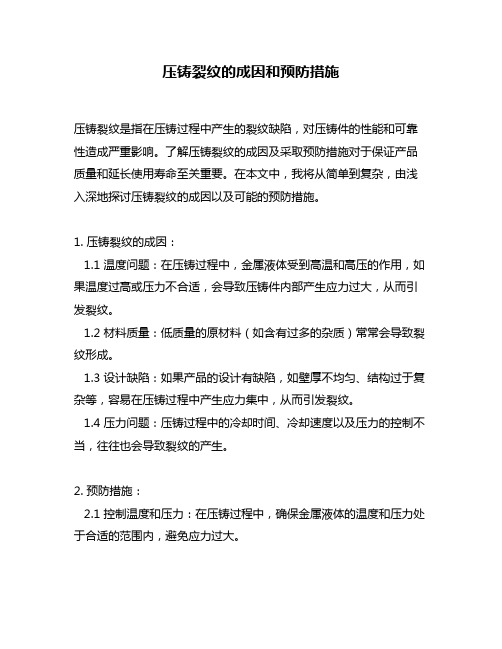
压铸裂纹的成因和预防措施压铸裂纹是指在压铸过程中产生的裂纹缺陷,对压铸件的性能和可靠性造成严重影响。
了解压铸裂纹的成因及采取预防措施对于保证产品质量和延长使用寿命至关重要。
在本文中,我将从简单到复杂,由浅入深地探讨压铸裂纹的成因以及可能的预防措施。
1. 压铸裂纹的成因:1.1 温度问题:在压铸过程中,金属液体受到高温和高压的作用,如果温度过高或压力不合适,会导致压铸件内部产生应力过大,从而引发裂纹。
1.2 材料质量:低质量的原材料(如含有过多的杂质)常常会导致裂纹形成。
1.3 设计缺陷:如果产品的设计有缺陷,如壁厚不均匀、结构过于复杂等,容易在压铸过程中产生应力集中,从而引发裂纹。
1.4 压力问题:压铸过程中的冷却时间、冷却速度以及压力的控制不当,往往也会导致裂纹的产生。
2. 预防措施:2.1 控制温度和压力:在压铸过程中,确保金属液体的温度和压力处于合适的范围内,避免应力过大。
2.2 优化材料选择:选择高质量的原材料,并对原材料进行严格的检测,以确保杂质含量在合理范围内。
2.3 设计合理性:在产品设计阶段,要考虑材料的性能和加工过程中的应力分布情况,尽量避免应力集中的情况发生。
2.4 控制压力和冷却过程:在压铸过程中,合理控制压力和冷却过程,确保产品快速冷却,减少应力积累。
2.5 严格的质量控制:在生产过程中,要加强对每个环节的质量控制,确保每个压铸件的质量符合标准要求。
压铸裂纹作为一种常见的缺陷,对于压铸产品的性能和可靠性有着重要的影响。
通过探究压铸裂纹的成因,我们可以有针对性地采取预防措施,从而减少压铸裂纹的发生。
尽管无法完全消除压铸裂纹的风险,但通过合理的措施和严格的质量控制,可以有效降低其发生的概率,提高压铸产品的质量和可靠性。
以上就是关于压铸裂纹的成因和预防措施的文章,希望对您有所帮助。
如有任何问题或需要进一步了解,欢迎随时与我沟通。
一、选择高质量的原材料,并对原材料进行严格的检测,以确保杂质含量在合理范围内。
探讨铸造热裂缺陷的形成原因及预防措施
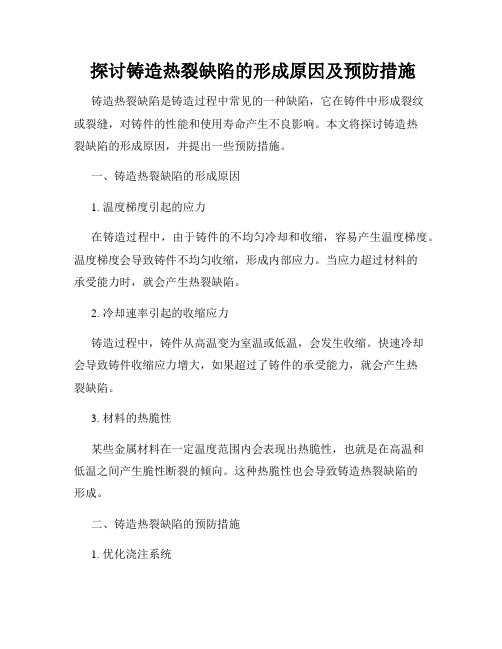
探讨铸造热裂缺陷的形成原因及预防措施铸造热裂缺陷是铸造过程中常见的一种缺陷,它在铸件中形成裂纹或裂缝,对铸件的性能和使用寿命产生不良影响。
本文将探讨铸造热裂缺陷的形成原因,并提出一些预防措施。
一、铸造热裂缺陷的形成原因1. 温度梯度引起的应力在铸造过程中,由于铸件的不均匀冷却和收缩,容易产生温度梯度。
温度梯度会导致铸件不均匀收缩,形成内部应力。
当应力超过材料的承受能力时,就会产生热裂缺陷。
2. 冷却速率引起的收缩应力铸造过程中,铸件从高温变为室温或低温,会发生收缩。
快速冷却会导致铸件收缩应力增大,如果超过了铸件的承受能力,就会产生热裂缺陷。
3. 材料的热脆性某些金属材料在一定温度范围内会表现出热脆性,也就是在高温和低温之间产生脆性断裂的倾向。
这种热脆性也会导致铸造热裂缺陷的形成。
二、铸造热裂缺陷的预防措施1. 优化浇注系统铸造过程中,合理设计浇注系统可以帮助铸件更均匀地冷却,减少温度梯度的产生。
例如,合理设置浇口、冷却器和冷却垫等措施,可以提高铸件的冷却均匀性,降低热裂缺陷的风险。
2. 控制冷却速率合理控制铸件的冷却速率可以减少收缩应力的产生。
通过改变冷却介质或调整冷却周期等方法,可以使铸件的冷却过程更加平缓,降低热裂缺陷的发生概率。
3. 选择适当的材料对于存在热脆性的金属材料,可以选择具有更好耐热性和耐脆性的材料。
例如,添加合适的合金元素,调整材料的成分,改善材料的热稳定性,从而减少热裂缺陷的风险。
4. 加强预热处理在铸造前进行适当的预热处理可以改变铸件的组织结构,提高材料的抗裂性能。
通过加热铸件,可以减轻材料内部的应力,预防热裂缺陷的生成。
5. 控制冷却过程中的应力在铸件冷却过程中,可以采取一些措施来控制应力的产生和释放,避免应力积累导致热裂缺陷。
例如,采用合适的保温措施、调整冷却速率等。
总结:铸造热裂缺陷是铸造过程中常见的一种缺陷,其形成原因主要包括温度梯度引起的应力、冷却速率引起的收缩应力以及材料的热脆性。
铸钢件裂纹产生的原因
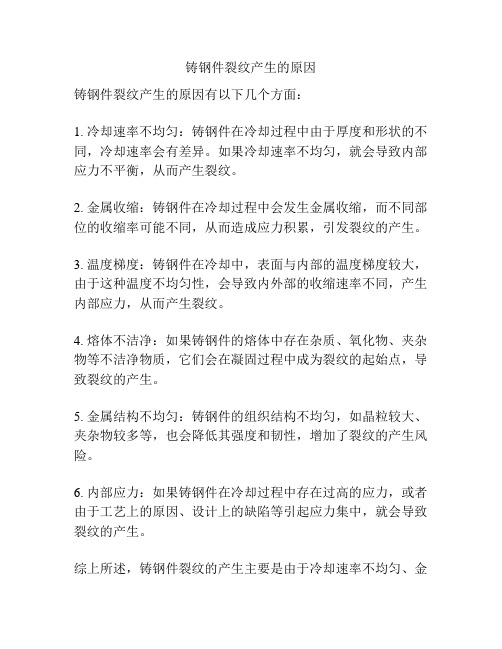
铸钢件裂纹产生的原因
铸钢件裂纹产生的原因有以下几个方面:
1. 冷却速率不均匀:铸钢件在冷却过程中由于厚度和形状的不同,冷却速率会有差异。
如果冷却速率不均匀,就会导致内部应力不平衡,从而产生裂纹。
2. 金属收缩:铸钢件在冷却过程中会发生金属收缩,而不同部位的收缩率可能不同,从而造成应力积累,引发裂纹的产生。
3. 温度梯度:铸钢件在冷却中,表面与内部的温度梯度较大,由于这种温度不均匀性,会导致内外部的收缩速率不同,产生内部应力,从而产生裂纹。
4. 熔体不洁净:如果铸钢件的熔体中存在杂质、氧化物、夹杂物等不洁净物质,它们会在凝固过程中成为裂纹的起始点,导致裂纹的产生。
5. 金属结构不均匀:铸钢件的组织结构不均匀,如晶粒较大、夹杂物较多等,也会降低其强度和韧性,增加了裂纹的产生风险。
6. 内部应力:如果铸钢件在冷却过程中存在过高的应力,或者由于工艺上的原因、设计上的缺陷等引起应力集中,就会导致裂纹的产生。
综上所述,铸钢件裂纹的产生主要是由于冷却速率不均匀、金
属收缩、温度梯度、熔体不洁净、金属结构不均匀和内部应力等因素的综合作用所导致的。
- 1、下载文档前请自行甄别文档内容的完整性,平台不提供额外的编辑、内容补充、找答案等附加服务。
- 2、"仅部分预览"的文档,不可在线预览部分如存在完整性等问题,可反馈申请退款(可完整预览的文档不适用该条件!)。
- 3、如文档侵犯您的权益,请联系客服反馈,我们会尽快为您处理(人工客服工作时间:9:00-18:30)。
低压精密铸造轮毂时形成冷热裂纹的原因
铝合金轮毂具有许多钢质轮毂无法比拟的特性,因此铝合金轮毂在轿车、摩托车等车辆上已开始广泛应用。
到2002年,我国轿车铝合金轮毂的装车率已接近45%。
由于汽车轮毂质量要求较高,本身结构又适合于低压精密,且需求量大,因此,极大地推动了低压铸造技术的发展。
目前,低压铸造已成为铝合金轮毂生产的主要工艺方法,国内的铝合金轮毂制造企业多数采用此工艺生产。
低压精密铸造铝合金轮毂裂纹主要产生在应力集中的部位,或轮毂顶出时因受力不均,或升液管处液体凝固造成的开裂。
裂纹一般分为冷裂和热裂两种。
冷裂纹是指合金在低于其固相线温度时形成的裂纹。
通俗地说,冷裂是精密铸造件冷却到低温时,作用在铸件上的精密铸造应力超过铸件本身强度或塑性所允许的程度而产生的。
冷裂多在铸件表面上出现,裂口表面有轻微的氧化;而热裂通常认为是在合金凝固过程中产生的,由于型壁的传热作用,铸件总是从表面开始凝固的。
当铸件表面出现大量的枝品并搭接成完整的骨架时,铸件就会出现固态收缩(常以线收缩表示)。
但此时枝晶之间还存在一层尚未凝固的液体金属薄膜(液膜),如果铸件的收缩不受任何阻碍,那么枝晶层不受力的作用,可以自由收缩,也就不会出现应力。
当枝晶层的收缩受到阻碍时,不能自由收缩或受到拉力的作用,就会出现拉应力,这时枝晶间的液膜将受到拉伸的作用而变形。
当拉应力超过液膜的强度极限时,枝晶间就会被拉开。
但是被拉裂部分的周围还存在一些液体金属,如果液膜被拉开的速度很慢,且周围有足够的液体并及时流人拉裂处,那么拉裂处将得到填补和“愈合”,精密铸造产品不会出现热裂纹。
如果拉裂处不能重新“愈合”,精密铸造产品就会出现热裂纹。
热裂断口处表面被强烈氧化,呈现无金属光泽的暗色或黑色。
(end) 文章内容仅供参考() (2012-7-16)
本文由风机盘管 斜管填料 联合整理发布。