电动执行器英文说明书
电动阀门执行器出口英文使用说明书
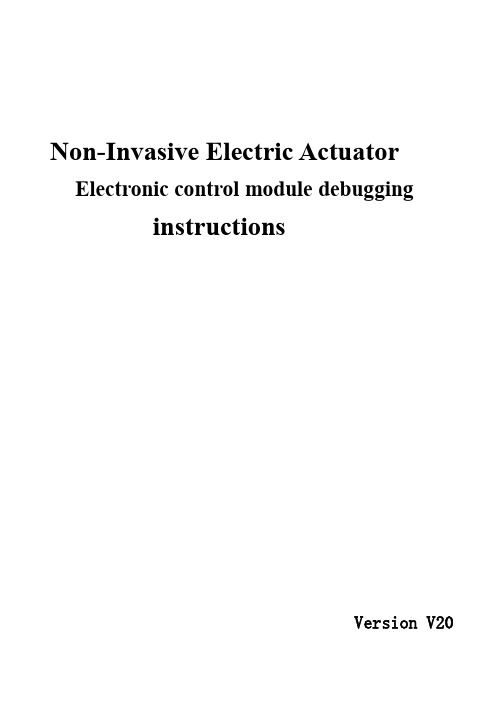
Non-Invasive Electric Actuator Electronic control module debugginginstructionsVersion V201SummaryThis component can receive the DCS system on-off signals (passive dry contact of active, active 24 v, 220 v, keep running can switch) or analog signals (DC4-20 ma, 0 to 10 v, etc.), direct drive electric actuators switch action or adjust the action. Output DC4-20 ma feedback current and contact/remote control state instructions. The component integration the servo control unit, solid-state drive unit, liquid crystal display unit, knobs and other ancillary units and aluminum shell assembly operation.The product operates as a fool camera is simple, like intelligent perfect protection function.2Operating Instructions2.1Knob Operating InstructionsThe red knob is the mode button, can be switched between Local/Stop/Remote. Or in a set state, to save the menu contents (from the stop bit screwed to the site) or to exit the menu(from the stop bit screwed into the remote).Black knob for the operating button can be opened or closed operation at the local.Or to plus or minus in the set state.With button operation, short time effect for the inching mode. When the operation button is effective for more than 3 seconds, in the lower right corner of the LCD, the bc is displayed automatically entered into the hold mode. When actuator movement, click the action button reverse rotation or spin mode button to Stop, the actuator Array stops.2.2 setting tool description (setting tool are optional, needto please when ordering special instructions)"Up" button = Open calibration key, "Down" button = close calibrationkey, "Enter" button = Confirm key or Save key"Stop" button = stop key, "Open" button = open key, "Close" button =close key.When mode button at Local location, press "Open" button to performopen, press "Close" button to perform off. In the action, press the"Stop" button to stop the move, short press "Close" to stop the openingprocess, short press "Open" to stop the closing process.In local mode, even by three "Up" key to enter the open position calibration status, "Open", "Close" and "Stop" keys to control the electric actuator to open, close and stop, "Enter" key to save the trip, "Stop "key is used to return.In local mode, even by three "Down" key to enter the closed position calibration status, like the rest of the operation as above.3Signal query (LCD lower left corner for a signal check area) 3.1 Remote control signal inquiryWhen the mode button is screwed into the Remote, the remote control signal received is displayed in the lower-left corner of the LCD. Switch type: show OP represents a open signal, show CL represents a close signal, show BC represents a keep signal (multi state of coexistence of alternate display). Regulating type: to display the received control current value or voltage value.3.2 Valve position signal queryWhen the mode button is screwed onto the Local, the LCD shows the valve position signal in lower left corner. When using a potentiometer, show the percentage of resistance (d01 ~ d99); When using 12 encoder, shows the percentage of the encoder (b01 ~ b99); When using 18 encoder, display micrometer ratio of the encoder (001 to 999).4 4 Stroke calibrations4.1 Calibration for close limit:The mode button at the Stop position, the rotary operation knob to the Close position for about 3 seconds, until the letter L is flashing of the LCD to release operation button, then the mode button to the Local position, now letter L no longer flashes and the system into the closed position calibration status. The actuator can open or close by the operating button. When the actuator operates to the closed position, then the mode button to spin the Stop position, and back to the Local position, at this time the red LED flashing two times said the closed position calibration is completed. If the mode button is screwed to the Remote position from Stop position, that exit travel calibration.4.2 Calibration for open limitThe mode button at the Stop position, the rotary operation knob to the Open position for about 3 seconds, until the letter H is flashing of the LCD to release operation button, then the mode button to the Local position, now letter H no longer flashes and the system into the open position calibration status. The actuator can open or close by the operatingmode button to spin the Stop position, and back to the Local position, at this time the green LED flashing two times said the open limit position calibration is completed. If the mode button is screwed to the Remote position from Stop position, that exit travel calibration.Note: When you save a stroke, display Fu or Fn characters on the LCD, please re-adjust potentiometer or rotary encoder range, and recalibrate the trip.5Feedback current trimming5.1 Feedback current 4mA trimmingThe mode button at the Stop position, the rotary operation knob to the Open position for about 10 seconds, until the letter LF is flashing of the LCD to release operation button, then the mode button to the Local position and back to the Stop position, and the system into the 4mA current trimming status. At this point,the size of the output current can be adjusted by the operating button. When adjusting the output current reaches 4mA, then mode button to spin the Local position, this time the red LED flashes three times, said 4mA output current trim is complete. If the mode button to Stop position from Remote position, which exit status of the output current trim.5.2 Feedback current 20mA trimmingThe mode button at the Stop position, the rotary operation knob to the Open position for about 10 seconds, until the letter HF is flashing of the LCD to release operation button, then the mode button to the Local position and back to the Stop position, and the system into the 20mA current trimming status. At this point,the size of the output current can be adjusted by the operating button. When adjusting the output current reaches 4mA, then mode button to spin the Local position, this time the green LED flashes three times, said 20mA output current trim is complete. If the mode button to Stop position from Remote position, which exit status of the output current trim.6About dead zoneThe dead zone to adapt automatically, without setting can ensure that in any conditions without oscillation, and the positioning precision is higher.7Alarm description (error code displayed on the LCD in the lower right corner) FaultcodeFault informationFA Actuator running direction errorFu V alve position potentiometer or encoder Angle is too largeFn V alve position potentiometer or encoder Angle is too smallFP Power phaseFF Broken valve position potentiometer, rotary to blind or pick the wrong line, or encoder failure.FC Over closed torqueFO Over open torqueFH Remote control signals to open and close signals exist (only on-off type)FS Control current signal is lost (only positioning)Fb Current control signal calibration error(only positioning)Fd Stall or other causes the valve position does not changeFL Limit contact line or torque contact line reversedFE The motor is too hot or the torque public terminal is openNOTE: The green LED is the open limit position light on the screen, the red LED is closed position light on the screen.8Advanced SettingsNOTE: All the Advanced Settings can be set after the mode button in the "Local" position. Advanced settings must open the electrical box cover and you can operate. The Close Key and Open Key mentioned below are in the electronic control board.8.1 Action when the control current loss:(Only positioning type, default: Remain in Situ)8.1.1 To press the “Close Key” and power up for 3 seconds until the red LED on the board is lit. And you release the key, then the red LED flashes three times; the “FullClose” setup is completed.8.1.2 To press the “Open Key” and power up for 3 seconds until the green LED on the board is lit. And you release the key, then the green LED flashes three times; the “Full Open” setup is completed.8.1.3 Simultaneously press two keys and power up for 3 seconds until the green and red LEDs on the board are lit. And you release the two keys simultaneously, then the two LEDs flashes three times; the “Remain in Situ” setup is completed.8.2 Control current calibration:(Only positioning type)8.2.1 To send 4mA control current to the module from the outside, press the “Close Key” and power up for 10 seconds until the red LED on the board is lighted second times. And you release the key, then the red LED flashes three times; and the4mA calibration is completed.8.2.2 To send 20mA control current to the module from the outside, press the “Open Key” and power up for 10 seconds until the green LED on the board is lighted second times. And you release the key, then the green LED flashes three times; and the20mA calibration is completed.8.3 Polarity for the control current:(Only positioning type)20mA = Full Open /4mA = Full Open (default:20mA = Full Open) Simultaneously press “Open Key” and “Close Key” and then power up for 10 seconds. To release the key after the red LED and green LED second lights up. Short press “Open Key” or “Close Key” to alternately lit red LED or green LED. The red LED light represents “20mA = Full Open”, the green LED light represents “4mA = Full Open”. Simultaneously press “Open Key” and “Close Key” for 3 seconds. To release two keys after the two LEDs lights up. Then corresponding LED flashes three times, the polarity for the control current setup is complete.8.4 Two-Wire Control:(Only on-off type)Disable or Open First or Close First (default: Disable)8.4.1Close FirstYou press “Close Key” and then power up for 10 seconds. The key is released after the red LED second light up. And the red LED flashes three times, this setup is complete. This Close First refers to the actuator close operation when voltages signal on the “Remote Close” terminal of the actuator. But no voltage signal, actuators open operation. When wiring, “Remote Open” terminal connected to 24V +.8.4.2Open FirstYou press the “Open Key” and then power up for 10 seconds. The key is released after the green LED second light up. And the green LED flashes three times, this setup is complete.This Open First refers to the actuator open operation when voltages signal on the “Remote Open” terminal of the actuator. But no voltage signal, actuators close operation. When wiring, “Remote Close” terminal connected to 24V +.8.4.3 DisableYou press the two keys simultaneously and then power up for 10 seconds. The key is released after the two LEDs second lights up. Then the two LEDs flashes three times, this setup is complete.8.5 Close direction:Clockwise /Anti-clockwise (default:Clockwise)You press the “Open Key” and “Close Key” simultaneously and then power up for 20 seconds. The keys are released after the red LED and green LED third lights up. Short press “Open Key” or “Close Key” to alternately lit red LED or green LED. Red LED light represents “Clockwise”, green LED light represents “Anti-clockwise”. You press the two keys simultaneously for 3 seconds. The keys is released after the two LEDs light up. Then corresponding LED flashes three times, the Close direction setup is complete.9Common problems to deal withPower LED is not lit or digital display does not show 1. Power is not actually access. 2. voltage is too low 3. Wiring fault. 4. Module badLEDs and digital display abnormal 1. See fault code.2. Query information.3. Replace the moduleAfter power on ,actuator can be not control in the LOCAL and REMOTE mode 1. Wiring fault or loose wiring. 2. Fault Protection.3. Motor bad or stuck.4. Bad start capacitor.5. module badLOCAL mode work is normal but the REMOTE mode can't control 1. No signal or junction anti- , 2. Bad or no knob plate in Remote3. Positive / reaction set wrong.4. Module badREMOTE mode work is normal but the LOCAL mode can't control 1. Not in LOCAL mode. 2. Knobs board bad or not at the scene mode. 3. Operation button is not properly screwed in placeActuator can open but not close or can close but not open 1. Torque wiring fault or loose wiring. 2. to limit position or over torque3. Motor bad or stall or wiring fault.4. Module badThe action immediately after power on 1. Wiring fault. 2. control signal is present3. Implementation the action when the control current loss4. Set the wrong.5. module badThe middle position can move but to the limit position does not move 1. Reverse limit switch line. 2. Motor bad or loose wiring 3. Module badThe direction of movement is the anti 1. Motor lines reversed. 2. Anti valve calibration.3. Signal Reverse4. Polarity for the control current or closing direction set wrong.No output current or sometimes no 1. The output wiring fault or bad. 2. Module bad 3. potentiometer wiring fault or loose wiringFeedback current is larger or smaller or unchanged 1.Potentiometer failure. 2. Calibration error.3. module bad4. potentiometer meshing with drive gear not wellNote: Please strictly in accordance with the wiring diagram electrical wiring connection.Like has the change, without notice。
电动执行器-RCEL005 RCEL006-250说明书

Top Quality Valve ActuatorsMade in SwedenHigh quality electric actuatorsRCEL005 / RCEL006-250 www.remotecontrol.seROTORK SWEDEN ABRCEL005RCEL006-250RCEL – series meet all International Standards for easy and quick mounting of actuators on valves.The RCEL Actuator has a smooth and easy operation which considerably increases the life expectancy of the valve.The technical advantages of the electrical actuators produced by Remote Control are much appreciated by our customers.“Power Start”The RCEL-series has an unique rising of the rpm prior to start which results in a higher starting torque. This is necessary when valves have been sitting idle for a long time and initially need more force to be manoeuvred.RCEL006-250 is also available with extended rotation angle and in explosion-safe design.Accessories such as local control units or digital regulation cards and positioners can easily be installed.For On-Off regulation.Torque range: 50 Nm - 2,452 Nm.443 Ibf.in - 21,702 Ibf.in.Mounting kits for all 90° valves.RCEL006-250 also for 120°, 135°, 180°, 270° och 300°.Connections and hole constellations in compliance with International standard ISO5211 (DIN 3337) and DIN 79.Permanently lubricated and self locking gear drive.Temp: RCEL005: -20° to + 70 °C RCEL006-250: -30 to + 70 °C Feed Voltage:RCEL005: 24 VDC (Option 24 VAC).110 / 230 VAC, 1-phase.RCEL006-250: 24 VDC (Option 24 VAC).110 / 230 VAC, 1-phase.380/400/440 VAC, 3-phase.Safety Class:RCEL005: IP 67RCEL006-250: IP 67 (Option 68)CE labelled.Approval CSA - UL.ATEX (Option).Manual Override in case of power failure.Smooth pact proportions.Built-in heater preventing condensation.Housing made from centrifugally cast anodized and epoxy painted aluminium.Long life, maximum dependability.Limit Switches2 potential-free Switches2 limit-position SwitchesConnectionVibration-safe plinthsNo special tools neededSpace HeaterPrevents condensationCabel inputM20 x 1,5Highest Surface FinishCentrifugally cast aluminiumExternally and internally anodizedDry Powder Epoxy paintedIndicatorIlluminated indicator for visualindication of end positionMotorFully enclosedQuiet operationThermal motor protectionScrewsExternal screws stainless steelSelf-locking gearsMechanical breaks notneededPermanently lubricatedEmergency OperationManually with 6 mm hex keyRotation axleComplies with Internatioal standardfor square spindles, ISO 5211 ochDIN 79, 14 mmMounting FlangeISO 5211 (DIN 3337)F03 - F05 - F07High casing on RCEL005LTo facilitate mounting ofaccessoriesIndicatorFor visual indication of end positionEEx- design without domeLimit Switches2 potential-free Switches2 limit-position SwitchesManual OverrideHand WheelManuallyemployed andautomaticallydeclutched Torque SwitchesOpen/Closed position(RCEL015-250Space HeaterPrevents condensationSelf-locking gearsMechanical breaksnot neededPermanently lubricatedConnectionVibration-safe plinthsNo special toolsneededMotorFully enclosedQuiet operationThermal motorprotectionHighest Surface FinishCentrifugally cast aluminiumExternally and internally anodizedDry Powder Epoxy paintedPullerEasy dismantling of the drivingbush by use of existing screws.No puller needed.Driving Bush enclosedDelivered unfinished (without holes, for your own adaption) oradapted to International standard for square spindles, DIN 79,standard from 22 to 75.Can be adapted according to customer specification.Mounting FlangeISO 5211 (DIN 3337)F07, F10, F12, F14, F16Individualized MountingAngleFor each 45°8 screwsEnd of travel stopsMechanical and adjustableCable inputM20 x 1,5ScrewsExternal screwsstainless steelType Torque Nm Flange ISO 5211 D Max Ø (mm)Std hole /axle (mm)Total height (mm)Total width (mm)Totalt depth (mm)00550F03-05-07 14148168132005L50F03-05-0714208168132RCEL005RCEL005LRef 007363Ref 007364H e i g h tH e i g h tWidthD e p t hType TorqueNmFlangeISO 5211D MaxØ (mm)Std hole /axle (mm)Total height(mm)Total widht(mm)Totalt depth(mm)RCEL 00658F0722 17273231181 RCEL 00988F0722 17273231181 RCEL 015147F07 - F1022 17273261224 RCEL 019186F07 - F1022 17273261224 RCEL 028274F10 - F1232 22320285258 RCEL 038373F10 - F1232 22320285258 RCEL 050490F10 - F1232 22320285258 RCEL 060588F12 - F1442 27361325307 RCEL 080785F12 - F1442 27361325307 RCEL 100981F12 - F1442 27361325307 RCEL 1501471F14 - F1675 36556388318 RCEL 2001962F14 - F1675 36556388318 RCEL 2502452F14 - F1675 36556388318RCEL006-100RCEL150-250Max DiameterWidth Underside Max DiameterWidth UndersideHeightDepthDepthHeightRef 007883Ref 008737 Ref 007884Ref 008739AdaptationA driving bush is delivered as a standard with all actuators,for customers own adaptation or adapted as below.RCEL 005-005L: 14 mm, ISO 5211 and DIN 79RCEL 006-019: 22 mm, DIN 79RCEL 028-050: 32 mm, DIN 79RCEL 060-100: 42 mm, DIN 79RCEL 150-250: 75 mm, DIN 79Rotork Sweden has blueprints of more than 6,000 different valvesfor manufacturing valve adaption kits.Rotork Sweden also offers adapted driving bushes accordingto customer requirements.Mounting kit, console and driving bushWhen direct mounting is not possible.Standard design according to ISO 5211 and DIN 3337.Measurements F07, F10, F12, F14, F16.Individually adapted to valves according to customer specifications.Mounting actuator on valveRotork Sweden offers mounting of the actuator onto the valve.The complete unit is calibrated and test run prior to delivery.PIU. Potentiometer kitFor modulating actuators.Continually monitors the actuator position throughout the full rotation motion. PIU is built into the actuator at factory. Can also be mounted later. Available to RCEL005L, RCEL006-250 and EEx-actuators.Mounting details are enclosed.Operating panelCustomized control panel.CPT. Continuous Position TransmitterFor externally controlled actuators.4 - 20 mA, 0 - 1 kΩ, R/I converter.Safety Class IP 67.RCEL005L: To be ordered as a complete unit.RCEL006-009: CPT built into the PCU housing.RCEL015-250: CPT built into the actuator.Not for EEx-actuators.PCU PB90. Position Control Unit for RCEL 006-250.4 - 20 mA or 0 - 10 V input signal; split range.Return signal 4 - 20 mA. Max load 300Ω.Safety Class IP 67.For 3-phase 380/400/440V:RCEL006-019: PCU PB90 built into the PCU housing.RCEL028-250: PCU PB90 built into the actuator.For 24VDC:RCEL006-019: PCU PB90 built into the PCU housing.RCEL028: PCU PB90 built into the actuator.Not for EEx-actuators.LCU. Local Control Unit for RCEL005LIntegrated in the actuator cover.Lockable 3-position selector knob for Remote - Stop - Local.3-position control knob for Open - Stop - Close.Safety Class IP67.For On-Off applications.Not for retro fitting on installed actuators.Not for Ex-protected actuators.LCU4 & 5. Local Control Unit for RCEL006-250Compact epoxy painted aluminium housing.Lockable 3-position selector knob for Remote - Stop - Local.3-position control knob for Open - Stop - Close.LED indicators for Remote - Local - Open - Over Torque - Closed.Built in anti-condensation space heater.Safety Class IP67.LCU 4 for On-Off applications.LCU 5 for control applications.For actuator mounting or wall mounting.Not for Ex-protected actuators.LCU6 Ex-proof Local Control Unit for RCEL015 -250Epoxy painted aluminium housing.Lockable 3-position selector knob for Remote - Stop - Local.Push buttons for Open - Stop - Close.LED indicators for Remote - Local - Open - Over Torque - Closed.LCD display.Built in self diagnostic.Built in anti-condensation space heater.Safety Class IP67.ExdIIBT4 -20°C - +55°C.Available for On-Off, On-Off with position feed-back signal or Control applications. Not for retro fitting on installed actuators.PCU DHC-100D. Digital modulating card.Resolution: 450 points per 90° movement.Is mounted in the actuator at delivery if requested, can also easily be mounted later.Input signal: 4 - 20 mA, 0 - 5V and 0 - 10V.Easily calibrated with buttons on the front panel.Simple configuration of all parameters.Optional rotation direction.Adaptable control function continually modulating the load ofthe electric actuator.Safety function for overloading (detection).Faulty signal indicated by flashing LED.Eliminates overload through operation-time protection.Programmable function wrong input signal open, stop or close.Can be combined with transmitter type OTX-100 or OTR-100 for return signal 4 - 20 mA. For 1-phase 230 V, not for EEx-actuators or actuator RCEL005 with low cover.OTX-100. Transmitter for return signal.Return signal: 4 - 20 mA.Simple installation. Plugged directly into PCU DHC-100D.Eliminates extra wiring. Easily calibrated with buttons on thePCU DHC-100D.Voltage or current output can be adjusted to optional range within0 - 10 V DC with steps of 0,0016 V or within 0 - 20 mA with stepsof 0,0031 mA.OTX-100 can be mounted at a later point in time.For 1-phase 230 V, not for EEx-actuators.OTR-100. Transmitter for return signal and faulty information.Return signal: 4 - 20 mA.Simple installation. Plugged directly into PCU DHC-100D.Eliminates extra wiring. Easily calibrated with buttons on thePCU DHC-100D.Voltage or current output can be adjusted to optinal range within0 - 10 V DC with steps of 0,0016 V or within 0 - 20 mA with stepsof 0,0031 mA.Relay outputs, 2 pcs programmable + 1 pc for faulty function alarm.OTR-100 can be mounted at a later point in time.For 1-phase 230 V, not for EEx-actuators.AMM-100. Manual Override Module.Makes it possible to combine Local Control Unit type LCU5with Position Control Unit PCU DHC-100D.Simple installation. 2-thread communication.Can be combined with push buttons or handle.AMM-100 can be mounted at a later point in time.For 1-phase 230 V, not for EEx-actuators.Strength: Safety: Delivery:Warranty: Mounting:Material Quality:“Power Start” delivers higher torque during the start.Consultation worldwide.Technical support from specialists, and direct customer support. Service / spare parts from factory.Training in the factory or at the customer’s location.CE labelled.Approval CSA –UL.ATEX (option). RCEL006-250.Self locking gear.Manual override wheel in case of power loss. (RCEL006-250)Allen key for manual operation. (RCEL005-005L)4 Limit Switches as standard, of which 2 pcs are potential free. Thermal motor protection. (Not for 24VDC).Mechanical end of travel stops.Vibration-safe plinthsFast deliveries from warehouse in Falun, Sweden.Delivery inspection of all Actuators.Unattached Actuators have basic settings at delivery.Actuators mounted on valves are calibrated before delivery.1 year warranty.Compact dimensions on the Actuators.Remote Control has blueprints for the manufacturing of more than 6000 different valve adaption kits.Customer adapted special applications.Mounting Kits: International standard ISO 5211, DIN 79 and DIN 3337. Centrifugally cast aluminium.Exterior and interior anodized.Dry powder painted.Fully enclosed, low noise motor.Built-in heater preventing condensation.Stainless steel.QualityRotork Sweden AB is certified according toISO 9001 and ISO 14001.All Rotork Sweden electric actuators are manu-factured under rigorous quality control.The RCEL-actuators comply with all International standard demands.All products are CE-labeled and manufactured according to EMC and the ATEX-directive.The recognized high quality of RCEL’s Actuators safeguards Actuators of Highest Class to our customers.ReliabilityThe design is simple and robust. We only use material of the highest quality in manufacturing, which results in Actuators with high life expectancy.StrengthRCEL Actuators are strong and unique. The secret lies in the “Power Start” which gives an increased torque during the start-up mode, exactly when thevalve needs the most force. www.remotecontrol.seRotork Sweden AB’s quality system ISO 9001 also encompasspacking and delivery.Ref No 787D / Art No 980787 We reserve the right to make changes without notice www.remotecontrol.seROTORK SWEDEN AB Box 80, Kontrollvägen 15, SE-791 22 Falun, SwedenTel:+46(0)23-58700•Fax:+46(0)23-58745•*********************Enviroment Control ISO 14001:2004Quality Assurance ISO 9001:2015RCEL 005Electric Actuator50 Nmmounted on Valve RCEL 006-250Electric Actuator 58 Nm to 2,450 Nm mounted on Valve RCE-SR Electric Actuator with spring return mounted on Valve。
丹佛斯(Danfoss) 电动执行器 AME 55QM 数据表说明书
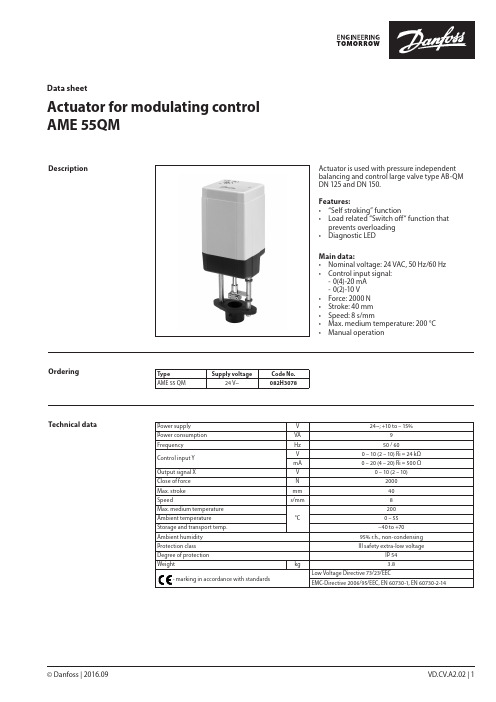
© Danfoss | 2016.09VD.CV.A2.02 | 1Actuator for modulating control AME 55QMData sheetActuator is used with pressure independent balancing and control large valve type AB-QM DN 125 and DN 150.Features:• “Self stroking” function• Load related “Switch off“ function that prevents overloading • Diagnostic LEDMain data:• Nominal voltage: 24 VAC, 50 Hz/60 Hz • Control input signal: - 0(4)-20 mA - 0(2)-10 V • Force: 2000 N • Stroke: 40 mm • Speed: 8 s/mm• Max. medium temperature: 200 °C • Manual operationDescriptionOrderingType Supply voltageCode No.AME 55 QM24 V~082H3078Technical dataPower supply V 24~; +10 to – 15%Power consumption VA 9Frequency Hz 50 / 60Control input Y V 0 – 10 (2 – 10) Ri = 24 kΩmA 0 – 20 (4 – 20) Ri = 500 ΩOutput signal X V 0 – 10 (2 – 10)Close of force N 2000Max. stroke mm 40Speeds/mm 8Max. medium temperature °C200Ambient temperature 0 – 55Storage and transport temp. –40 to +70Ambient humidity 95% r.h., non-condensing Protection class III safety extra-low voltageDegree of protection IP 54Weight kg 3.8- marking in accordance with standardsLow Voltage Directive 73/23/EECEMC-Directive 2006/95/EEC, EN 60730-1, EN 60730-2-14Data sheet Actuator for modulating control AME 55 QM2 | © Danfoss | 2016.09VD.CV.A2.02Installation MechanicalThe actuator should be mounted with the valvestem in either horizontal position or pointingupwards. Use a 4 mm Allen key (not supplied) tofit the actuator to the valve body.Allow for necessary clearance for maintenancepurposes.The valve has position indication ringswhich should be pushed together beforecommissioning; after stroking they indicate theends of the stroke.ElectricalElectrical connections can be accessed byremoving the cover. Two M16 × 1.5 cable entriesare provided. Both entries are provided with arubber grommet for use with flexible cable. Notethat in order to maintain the enclosure IP rating,appropriate cable glands must be used.Wiring The actuator must be dismantled and the elements sorted into various material groups before disposal.Disposal 24 Vac only.Wiring length Recommendedsquare of the wiring0-50 m0.75 mm2> 50 m 1.5 mm2Automatic self stroking featureWhen power is first applied, the actuator willautomatically adjust to the length of the valvestroke. Subsequently, the self stroking featurecan be re-initialised by changing position of SW9.Diagnostic LEDThe red diagnostic LED is located on the pcbunder the cover. It provides indication of threeoperational states:• Actuator Healthy (Permanently ON),• Self Stroking (Flashes once per second),• Error (Flashes 3 times per second - seektechnical assistance).Data sheetActuator for modulating control AME 55 QM© Danfoss | 2016.09 | 3VD.CV.A2.02DIP switch settingThe actuator has a function selection DIP switch under the removable cover. In particular, if SW6 is set to ON, the actuator will perform as 3-point actuator.The switch provides the following functions:• SW1: U/I - Input signal type selector:If set to OFF position, voltage input is selected. If set to ON position, current input is selected.• SW2: 0/2 - Input signal range selector:If set to OFF position, the input signal is in the range from 2 V to 10 V (voltage input)or from 4 mA to 20 mA (current input). If set to ON position, the input signal is in the range from 0 V to 10 V (voltage input) or from 0 mA to 20 mA (current input).• SW3: D/I - Direct or inverse acting selector:If set to OFF position, the actuator is direct acting (stem contracts as voltage increases). If actuator is set to ON position the actuator is inverse acting (stem extracts as voltage increases).• SW4: —/Seq - Normal or sequential modeselector:If set to OFF position, the actuator is working in range 0(2)..10V or 0(4)..20mA. If set to ON position, the actuator is working in sequential range; 0(2)..5 (6)V or (0(4)..10 (12)mA) or (5(6)..10V) or (10(12)..20mA).• SW5: 0..5V/5...10V - Input signal range insequential mode:If set to OFF position, the actuator is working in sequential range 0(2)..5 (6)V or 0(4)..10 (12)mA. If set to ON position, the actuator is working in sequential range; 5(6)..10V or 10(12)..20mA.• SW6: Prop./3-pnt - Modulating or 3-point modeselector:If set to OFF position, the actuator is working normally according to control signal. If set to ON position, the actuator is working as 3-point actuator.For this operation please refer to page 2(wiring 3-point control).When DIP switch SW6 is set to ON than allfunctions from other DIP switch become inactive.• SW7: LOG/LIN - Equal percentage or linear flowthrough valve selector:If set to OFF position, the flow through valve is equal percentage. If set to ON position, the flow through valve is linear according to control signal.• SW8: 100% K VS/Reduced K VS :To be set to OFF position (no sense in combination with AB-QM).• SW9: Reset:Changing this switch position will cause the actuator to go through a self stroking cycle.Complete the mechanical and electricalinstallation and perform the necessary checks and tests:• Isolate control medium. (e.g. self stroking in a steam application without suitable mechanical isolation could cause a hazard).• Apply the power. Note that the actuator will now perform the self stroking function.• Apply the appropriate control signal and check the valve stem direction is correct for the application.• Ensure that the actuator drives the valve over its full stroke, by applying the appropriate control signal. This action will set the valve stroke length.The unit is now fully commissioned.CommissioningCommissioning / testing featureThe actuator can be driven to the fully open or closed positions (depending on valve type) by connecting SN to terminals 1 or 3.VD.CV.A2.024 | © Danfoss | DHS-SRMT/SI | 2016.09Data sheetActuator for modulating control AME 55 QMActuator - valve combinationsThe manual override is applied by rotating the 4 mm Allen key (not supplied) to the required position. Observe the direction of the rotation symbol.• Disconnect power supply• Adjust valve position using an Allen key • Set valve to closed position •Restore power supplyIf manual override has been used then X and Y signal are not correct until the actuator reaches its end position. If this is not accepted reset the actuator, or apply accessory active return signal kit.DimensionsManual override。
电动执行器规格说明书

SPECIFICATIONSPart number . . . . . . . . . . . . . . . . . . .875-1029-000Power supply . . . . . . . . .24 V AC ±20%, 50–60 Hz, . . . . . . . . . . . . . . . . . . . . . . . .24 V DC ±20%Power consumptionIn operation . . . . . . . . . . . . .2 W @ nominal torque At res . . . . . . . . . . . . . . . . . . . . . . . . . . . . . . .0 .4 W For wire sizing . . . . . . . . . . . . . . . . . . . . . . . . . .4 VA Connection cable . . . . . . .1 m (3 .3 ft), 4×0 .75 mm 2(AWG 18)Control signal X . . . . . . . . . . . . . . . . . . .0–10 V DC Input resistance . . . . . . . . . . . . . . . . . .100 k Ohm Operating range . . . . . . . . . . . . . . . . . . .2–10 V DC(for set angle of rotation)Synchronisation tolerance . . . . . . . . . . . . . . . . .±5%Position feedback Y . . . . . .2–10 V DC (max . 1 mA) Direction of rotation . . .Reversible with switch 0 / 1Angle of rotation . . . . . . . . . . . . . . . . . . . .max . 95° (adjustable by mechanical stops)Torque . .min . 20 Nm (180 in-lb) @ nominal voltage Running time . . . . . . . . . . . . . . . . . . . . . . . . .150 s Position indication . . . . . . . . . . . . . . . .mechanical Manual override . . . . . . .Gearing latch disengaged with pushbutton, self-resetting, manual locking Standards conformityEMC, emission . . . . . . . . . . . . . . . .SS EN 50081-1EMC, immunity . . . . . . . . . . . . . . . .SS EN 50082-1Protection class . . . . . . .III Safety extra-low voltage Enclosure rating . . . . . . . . . . . . . . . . . . . . . . .IP 54Ambient humidity . . . . . . . . .95% r .H (EN 60730-1)MD20A - 24Modulating Damper Actuator Action 20 Nm (180 in-lb)MD20A-24 damper actuators for operating air control dampers in ventilation and air-conditioning systems for building services installations• For air control dampers up to approx. 4 m 2(4 .8 yard 2)• Torque 20 Nm (180 in-lb)• Nominal voltage AC/DC 24 V • Control: Modulating 0 – 10 V • Position feedback: 2 – 10 VAmbient temperatureOperation . . . . . . . .–30 to +50 °C (–22 to +122 °F)Storage . . . . . . . . .–40 to +80 °C (–40 to +176 °F)Sound power level . . . . . . . . . . . . . .max . 45 dB (A)Maintenance . . . . . . . . . . . . . . . . .Maintenance-free Weight . . . . . . . . . . . . . . . .Approx 1 .05 kg (2 .3 lb .)6441(1,6)109(4,3)30(1,2)Damper spindle (in.)Length mm (in.)mmClamp on top min . 42 (1 .65)10 . . . 20 (0 .39 . . . 0 .78)Clamp on bottommin . 20 (0 .78)10 . . . 20 (0 .39 . . . 0 .78)WIRINGWIRINGMD10B-230Connection via safety isolatingtransformer.Measuring voltage Y for position indication or as master-slave signal .Parallel connection of several actuators is possible . Power consumption must be observed .ACCESSORIESPlease refer to data sheet G-30-90“Accessories Damper Actuators” (part . no . 0-003-2251) .On October 1st, 2009, TAC became the Buildings Business of its parent company Schneider Electric. This document reflects the visual identity of Schneider Electric, however there remains r eferences to TAC as a corporate brand in the body copy. As each document is updated, the body copy will be changed to reflect appropriate corporate brand changes.Schneider Electric Telephone Europe: Malm ö, Sweden +46 40 38 68 50 Telephone Asia Pacific: Singapore +65 6776 3166 /buildings003-2234-3February 2006 mf© 2009 S c h n e i d e r E l e c t r i c . A l l r i g h t s r e s e r v e d .FUNCTIONMode of operationThe actuator is controlled by means of as tandard control signal DC 2-10 V . It opens to the position dictated by this signal . Them easuring voltage Y allows the damper position (0 . . . 100%)to be electrically indicated and serves as a follow-up control signal for other actuators .Simple direct mountingSimple direct mounting on the damper spindle with a universal spindle clamp, supplied with an anti-rotation strap to prevent the actuator from rotating .Manual overrideManual operation is possible with the self-resetting pushbutton (the gearing latch remains disengaged as long as the pushbutton is pressed or detented) .Adjustable angle of rotationAdjustable angle of rotation with mechanical end stops .High functional reliabilityThe actuator is overload-proof, requires no limit switches and automatically stops when the end stop is reached .SAFETY NOTESThe damper actuator is not allowed to be used outside the specified field ofa pplication, especially in aircraft.The device may only be opened at the manufacturer’s site. It does not c ontain any parts that can be replaced orr epaired by the user.The cable must not be removed from the device.When calculating the required torque, the specifications supplied by thedamper manufacturers (cross section, design, installation site), and the air flowc onditions must be observed.lectronic components and is not allowed All locally valid regulations and require-ments must be observed.。
KEYSTONE EPI-2电动执行器 使用说明书

GENERAL APPLICATIONThe EPI-2 is available in six sizes and is designed for on/off or modulating control of butterfly, ball, rotary plug valves or dampers in a wide range of heavy industrial, chemical and petrochemical plants on and offshore.KEYSTONE EPI-2 ELECTRIC ACTUATORSFEATURES• Low or high voltage single phase DC or AC power supply with 3-phase option• Multiple adjustable stroking times to suit specific applications• Interchangeable base plate and range ofshaft inserts enable simple connection to any valve type• Intelligent control unit prevents overheating • Epicyclical gearing ensures reliable and smooth operation• Top-mounted position indicator• Constantly-engaged, hand wheel-operated manual override in case of power failure • Bluetooth™ wireless connectivity fornon-intrusive configuration, operation and diagnostics• Optional local control panel for manual valve operation with additional open/close indicator • Simple upgrade options for modulating control and network communication via DeviceNet or Profibus DP protocols• Latched-type output contacts for fully open/fully close remote indication. Output contacts for monitor and blinker/local selector indication are also availableBluetooth™ is a trademark of Bluetooth SIG. Inc, USAThe EPI-2 series are compact, intelligent quarter-turn electric actuators for the accurate control of valves with torques from 35 to 2000 Nm / 308 to 17,700 lb.in.APPROVALS Waterproof:IP66/68 or NEMA 4/4X/6(NEMA ICS6/NEMA 250)CAN/CSA C22.2 No 139-10and UL 429-2009Explosionproof: Ex d e IIB T5 Gb (Gas) Ex tb IIIC T100°C Db (Dust) (prefix c for model 2000)TECHNICAL DATA Power supply:Single phase from 24 to 48 V DC or AC at 50/60 HzSingle phase from 100to 240 V DC or AC at 50/60 Hz3-phase from 208-240V AC, 380-480 V AC and 500-575 V ACVoltage fluctuations: +/-10%Frequency: +/- 5%Torque output: From 35 to 2000 Nm /308 to 17,700 lb.in.Ambient temperature Standard range: -25°C to +70°C /-13°F to 158°FLow temp range: -40°C to +70°C /-40°F to 158°FConduit entry: M25/1” NPT4016131731383426203930353633372322282524151812464841492732474219101114434544292150835476912COMPONENT PARTS - MODELS 063/E006-125/E013-250/E025-500/E051-1000/E091Part DescriptionQuantity1 Nut UNI5588 M6 22 Nut UNI5588 M8 23 Eccentric14 Planocentric gear 25 Spacer16 Ball bearing type 16002 17 Ball bearing type 16004 28 Ball bearing type 600119 ESH screw UNI5931- M6x8 110 HSHC screw UNI5931- M6x16 411 HSHC screw UNI5931- M4x14 712 HSHC screw UNI5931- M6x18 213 HSHC screw UNI5931- M6x25 414 HSHC screw UNI5931- M8x20 415 HSSC screw UNI5933- M4x10 116 Cover assembly117 Drive and control unit 118 Handwheel119 Output drive assembly 120 Standard housing 121 Stopper222 Terminal block 123 Worm shaft flange124 Anti-loosening washer UNI 8842-J6 125 Base plate ISO 5211 / F05-F07 126 Cover gasket1*27 Dowel pin UNI EN 22338 128 Earth stud 129 Fixed anulus 130 Gasket 1*31 Indicator132 Indicator shaft133 Manual worm shaft 134 Motor pinion135 O-ring Di=10.77/W=2.62 1*36 O-ring Di=18.77/W=1.78 1*37 O-ring Di=52.07/W=2.62 1*38 O-ring Di=6.07/W=1.78 1*39 Plug140 Position label141 Power clamps protection 142 Ring243 Ring for pins alignement 144 Ring RW 7 UNI7433 245 Seal washer 8.3 246 Sliding ring147 Snap ring for shaft D.6 148 Terminal block cover 149 Terminal board gasket 1*50Wheel1* Indicates recommended spare partsCOMPONENT PARTS - MODEL 2000/E171Part Description Quantity1Nut M20 ISO 4032 EN 24032 22Ball bearing type 6006 13Ball bearing type 16004 14Ball bearing type 61908 15HSHC screw UNI5931- M6x16 36HSHC screw UNI5931- M12x30 47HSHC screw UNI5931- M12x65 48HSHC screw UNI5931- M8x25 A4-7069EPI-2 actuator1 10Base housing1 11Base plate ISO 5211 / F12-F16 1 12Bearing support1 13Bushing2 14Bushing1 15Bushing1 16Bushing1 17Dowel pin UNI EN 22338 D 8x20 type B4 18Gasket 1* 19Hex head screw M20x80 UNI EN 240172 20Idle wheel shaft1 21Needle bearing type NKI 22/162 22O-ring Di=82.22/W=2.62 1* 23Position wheel1 24Seal washer 20.3 2 25Selector gear1 26Sliding ring1 27Upper vover1 28Wheel2* Indicates recommended spare partsDESIGN FEATURESMechanical connection to the valveEPI-2 actuators feature a multi drilled base plate and a range of drive inserts to allow direct mounting to almost all valve types according the EN ISO 5211 and other manufacturers’ standards.Power supplyEPI-2 can simply be connected to the local power supply. It accepts any single phase input voltages (from 24 to 48 V DC or AC and 100 to 240 V DC or AC). Alternatively 3 phase voltages from 208-240 V AC, 380-480 V AC and 500-575 V AC are also availableElectric motor thermostatA thermostat to protect the motor temperature in hot applications is included as standard in the control circuit of the electric actuator. HeaterA heater is standard available within theunit and is powered from the motor power supply. It is automatically activated when the temperature drops below 10°C in order to prevent condensation.Actuator serviceThe standard actuator is suitable for open/close and modulating applications.Compact and light designEPI-2 actuators are very compact and balanced for easy installation to small valves minimizing pipe work stress or loads to the valve shaft. Actuator configurationEach actuator is equipped with 2 rotary switches on the logic board to configureeach function and parameter like position, torque, open/close speed and output contacts. Additionally each optional module has itsown additional switches for its specific configuration.Local manual overrideA constantly engaged manual override (not rotating during motor operation) is fitted to all EPI-2 actuators.Torque and sizingThe EPI-2 range comprises of six models,for operating torques of up to 2000 Nm /17,700 lb.in. with a configurable operation time from 15 to 180 seconds. The nominal output torque value is constant along the entire stroke. Non-intrusive configurationWith Bluetooth® wireless technology enabled on your PDA or PC all configuration requirements can be undertaken without opening the unit. Direct access to the EPI-2 is then availablefor configuration and predictive/preventative maintenance information, including valve position, actuator speed, output torque, alarm and status.Position monitoringThe EPI-2 provides a local mechanical position indication. For remote indication the positionis detected by a non-contact sensor. The open and close position are configured via the electronic control card.Electronic controlsInternal drive to reverse the actuator rotation direction via remote control signals with internal 24 V DC or external 24 V DC/AC up to 120 V DC/AC power supply.Output contacts4 latched-type output contacts for fully open/ fully close remote indication; 1 output contact for monitor (loss of power, torque alarm, high temperature alarm, travel alarm, position sensor, hardware malfunction, local interface malfunction, local selector in LOCAL); 1 output contact for blinker/local selector indication (local selector feature only with OM3 installed).P1✓PA ✓✓✓P6✓✓P7✓✓P3✓5P ✓✓6P ✓✓✓5D ✓✓6D ✓✓✓PG✓OPTIONAL MODULES AND PERFORMANCEOPTIONAL MODULESOPTIONAL MODULES SELECTION TABLEOrder code OM1 I/Oadditional moduleOM3 local interfaceBluetooth componentOM9 PDP V0/V1OM11 DeviceNet OM133-wires moduleNOTES1. Each optional module (OMx) will be provided with its own installation and maintenance instructions.2. All modules except OM13 are available for both single phase and 3-phase voltage versions.3. Bluetooth component is integrated in the OM1, OM9 and OM11 card: not available for integration by localorganizations, as a stand alone unit.4. OM13 is not available with 3-phase supply and for LV version (single phase voltage from 24 to 48 V DC/V AC).OM1 I/0 additional moduleAnalog position INPUT 4-20 mA or 0-10 V DC Analog position OUTPUT 4-20 mA or 0-10 V DC 4 additional SPST output contacts Optional Bluetooth interfaceMonitor relayInformation about loss of input signal andBluetooth failure are available on monitor relay output contact.OM3 local interface Local/remote selector OP/CL pushbuttons2 LEDs for local indication Available in WP versionOM13 3-wire module 110/240 V AC3-wire control module for open/close Bus communication – network interfaces OM9) Profibus DP V0/V1OM11) DeviceNet063/E00663/600152848125/E013125/1300152848250/E025250/2500152848500/E051500/51001528481000/E0911000/91002445802000/E1712000/1770053100180PERFORMANCE AND APPROVALSOPERATING TIMESNominal torque Operating time (secs 90°) at selected step Model (Nm / lb.in.)864Times are guaranteed with a tolerance of ±10% on the 90° strokeApprovalsWaterproof IP66/68 or NEMA 4/4X/6 (NEMA ICS6/NEMA 250)CAN/CSA C22.2 No 139-10 and UL 429-2009ExplosionproofEx d e IIB T5 Gb (Gas)Ex tb IIIC T100°C Db (Dust)(prefix c for model 2000)PaintingESPC for 1000 hrs salt spray resistance (ASTM D 2247-02 and ASTM B117-97)Vibration and noise1 to 500 Hz with2 g peak acceleration (IEC60068-2-6-appendix B)65 dB (grade A) (EN 21680)063/E0069.410.78.3 4.5 3.3 4.6 2.7 3.1 2.5 1.3 1.4 2.6 2.7 4.9 6.9F0717 125/E0139.410.79.1 4.5 3.3 4.6 2.7 3.1 2.5 1.3 2.1 3.4 3.4 4.9 6.9F1021 250/E02511.613.111.3 5.1 4.3 6.1 2.7 3.7 3.0 1.3 2.5 3.7 3.67.19.1F1236 500/E05111.613.111.3 5.1 4.3 6.1 2.7 3.7 3.0 1.3 2.5 3.7 3.67.19.1F1240 1000/E09113.413.714.3 5.5 4.3 6.7 2.7 4.1 3.2 1.3 5.5 6.8 6.59.49.1F1657 063/E006239272210114.0851186980.0633235.567.067.5125175F077.5 125/E013239272230114.0851186980.0633253.586.086.5125175F109.5 250/E025295332287129.010********.0763263.595.092.0180230F1216.5 500/E051295332287129.010********.0763263.595.092.0180230F1218.0 1000/E091340349364138.510917169104.58132140.0172.5164.0240230F1626.0 OVERALL DIMENSIONS - MODELS 063/E006-125/E013-250/E025-500/E051-1000/E091EPI-2 BASE UNIT MODELS 063/E006 TO 1000/E091 - METRIC (mm / kg)Model A B H a1b1b2b3c d e h1h2h3øv x F kgEPI-2 BASE UNIT MODELS 063/E006 TO 1000/E091 - IMPERIAL (in / lb)Model A B H a1b1b2b3c d e h1h2h3øv x F lb NOTESW = Nr. 4 cable entries M25x1.5 acc. to ISO 724/965-1 (others available as special versions)X = Space for cover removalF = ISO 5211 Standard flange (others available)2000/E17113.415.219.918.3 5.57.310.5 6.7 2.7 4.1 3.2 1.39.410.710.49.49.1F10-F14992000/E17113.415.219.918.35.57.310.5 6.7 2.7 4.1 3.2 1.39.410.710.49.49.1F12-F161032000/E171340387506464138.5185.526617169104.58132240272.5264240230F10-F1445.02000/E171340387506464138.5185.526617169104.58132240272.5264240230F12-F1646.5EPI-2 MODEL 2000/E171 - METRIC (mm / kg)Model A A1B H a1a11b1b2b3c d e h1h2h3øv x F kg EPI-2 MODEL 2000/E171 - IMPERIAL (in / lb)Model A A1B H a1a11b1b2b3c d e h1h2h3øv x F lb NOTESW = Nr. 4 cable entries M25x1.5 acc. to ISO 724/965-1 (others available as special versions)X = Space for cover removalF = ISO 5211 Standard flange (others available)063/E0069.411.2 4.5 6.38.310.6 6.910.41718125/E0139.411.2 4.5 6.39.111.4 6.910.42122250/E02511.613.4 5.1 6.911.313.79.113.03435500/E05111.613.4 5.1 6.911.313.79.113.037391000/E09113.415.25.57.314.316.79.113.05158063/E006239285114.0160.02102701752657.58.0125/E013239285114.0160.02302901752659.510.0250/E025*********.0175.028734723033015.516.0500/E0512********.0175.028734723033017.017.51000/E091340387138.5185.536442523033023.026.5EPI-2 WITH OPTIONAL MODULES - METRIC (mm / kg)Model A A1a1a11H H1X X1kg [1]kg [2]EPI-2 WITH OPTIONAL MODULES - IMPERIAL (in / lb)Model A A1a1a11H H1X X1lb [1]lb [2]1. Weight with Beacon option module 2. Weight with local interface moduleNOTES1. Dimensions a1 and A are for the standard unit.2. Dimensions a11 and A1 are for the standard unit plus a local interface option.3. Dimensions H and X are for the standard unit.4. Dimensions H1 and X1 are for the standard unit plus a Beacon type indicator.5. X / X1 indicates the space for cover removal.6. All other dimensions are as the standard unit.E006 1.1251/4 x 1/4 1.34 1.751/4" - 20 UNC3.253/8" - 16 UNC -- 1.37E013 1.37510 x 8 mm 2.05-- 3.253/8" - 16 UNC 1.1251/4 x 1/4 2.12E025 1.8751/2 x 3/8 2.05 3.253/8" - 16 UNC 5.001/2" - 13 UNC 1.1251/4 x 1/4 2.12E051 1.8751/2 x 3/8 2.05 3.253/8" - 16 UNC 5.001/2" - 13 UNC 1.6251/4 x 1/4 2.44E091 2.2501/2 x 3/84.805.001/2" - 13 UNC6.503/4" - 10 UNC 1.8751/2 x 3/8 4.25E171 2.2501/2 x 3/84.805.001/2" - 13 UNC6.503/4" - 10 UNC1.8751/2 x 3/84.25OUTPUT DRIVE DIMENSIONSKEYSTONE DIRECT MOUNT SYSTEM The same direct mounting brought to the market place by Keystone for valves and actuators, with even more flexibility.Keystone Valve pioneered the direct mounting compact valve actuator system.The EPI 2 continues this customer oriented system with additional flexibility aimed at allowing the customer more actuator with every purchase.Actuator BaseShaft InsertsB ADEFCThe EPI 2 has dual mounting bolt circles and dual shaft acceptance with most units.This feature allows coverage of more valve sizes and types with less actuator models.DIMENSIONS (INCHES)Standard BoreBolt CircleStandard Shaft Inserts KeyedDepthA BCF Key Size Model Bore Dia.Key Depth Dia.Holes Dia.HolesL1L2L335363233342021CLC1CLC2OPC1OPC222232425262728293031123432WIRING DIAGRAM - BASE VERSIONNOTES1. Power connection L1-L2 for V DC or V AC single phase motor supply from 24 V to 48 V or from 100 V to 240 V.Power connection L1-L2-L3 for 3 phase motor supply from 208 V to 575 V (check the actuator label for the correct voltage to be applied).2. Remote command options.Note 1Note 6Remote commands(Note 2, 5)MONITORRELAYGROUNDBLINKERLOCALSELECTORRELAYOutput contacts(Note 3, 4)Optional moduleOM33. Contacts shown in intermediate position CLC1-CLC2 end of travel signaling in closing.Contacts shown in intermediate position OPC1-OPC2 end of travel signaling in opening.4. Output contact rating 240 V AC / 5 A ; 30 V DC / 5A ; 120 V DC / 0.5 A.5. Control command rating 24 to 120 V AC or DC.6. Blinker or local selector monitoring function (when OM3 is present) to be configured.External supply 24 / 120 V AC External supply 24 / 120 V DC063/E006815 2.26 1.010.5900.4730.3340.289 2.02 1.010.6050.4760.2220.196628 1.600.840.4050.3340.2530.217 1.530.750.4150.3430.1580.138448 1.380.730.3170.2650.2090.176 1.300.640.3180.2600.1200.106125/E013815 4.20 1.700.9800.8100.4300.420 4.50 1.81 1.0400.8200.3900.340628 2.60 1.280.7800.6300.3700.340 2.65 1.270.8100.6400.3000.260448 2.04 1.000.6800.5600.3400.290 2.100.960.7200.5700.2700.220250/E02581510.30 4.90 2.440 1.9700.9200.8009.70 4.80 2.520 1.9500.9000.7806288.20 3.80 1.650 1.3500.6400.5707.20 3.60 1.650 1.3200.6300.540448 6.40 3.30 1.440 1.1700.5600.500 6.80 3.20 1.460 1.1400.5400.470500/E05181514.50 6.80 3.200 2.520 1.150 1.00014.007.00 3.220 2.530 1.1200.9806289.50 4.60 1.900 1.5500.7600.6709.30 4.50 1.920 1.5400.7200.6204487.00 3.40 1.550 1.2400.6000.5307.10 3.40 1.510 1.2400.5800.5001000/E09182414.50 6.80 3.200 2.520 1.150 1.00014.007.00 3.220 2.530 1.1200.9806459.50 4.60 1.900 1.5500.7600.6709.30 4.50 1.920 1.5400.7200.6204807.00 3.40 1.550 1.2400.6000.5307.10 3.40 1.510 1.2400.5800.5002000/E17185314.50 6.80 3.200 2.520 1.150 1.00014.007.00 3.220 2.530 1.1200.98061009.50 4.60 1.900 1.5500.7600.6709.30 4.50 1.920 1.5400.7200.62041807.003.401.5501.2400.6000.5307.103.401.5101.2400.5800.500CURRENT ABSORPTION - SINGLE PHASE AND DC VOLTAGECURRENT ABSORPTION - SINGLE PHASE AND DC VOLTAGEModel Selected step Operating time (secs/90°)Current absorption (A)24 V AC48 V AC 90 V AC 110 V AC 230 V AC 264 V AC 24 V DC 48 V DC 90 V DC 110 V DC 230 V DC 264 V DC063/E0068150.2260.1760.1076280.1650.1010.0804480.1320.0830.057125/E0138150.3440.2270.1716280.2950.1800.1434480.2450.1550.125250/E0258150.8000.730.520.490.370.3406280.5900.560.410.350.290.2804480.5300.500.370.300.270.250500/E051815 1.0730.970.650.580.460.4306280.7200.640.470.390.320.3104480.5900.550.410.320.290.2801000/E091824 1.0730.970.650.580.460.4306450.7200.640.470.390.320.3104800.5900.550.410.320.290.2802000/E171853 1.0730.970.650.580.460.43061000.7200.640.470.390.320.31041800.5900.550.410.320.290.280CURRENT ABSORPTION - THREE PHASE VOLTAGECURRENT ABSORPTION - THREE PHASE VOLTAGEModel Selected stepOperating time (secs/90°)Current absorption (A)208 V AC 240 V AC380 V AC 400 V AC 480 V AC500 V AC 575 V ACSELECTION GUIDEExample KPD063LV PD P12D4 ProductKPD ISO 5211 with double star insertKPE ISO 5211 with flat or key insertKPU Non-ISO flangeKPB ISO 5211 flange - insert not machinedKPK Key non-ISO flange - insert not machinedKEU(NPT) US version ISO 5211 flangewith ISO insert, 4x 1"NPT entriesModels063Model 063/E00606B Model 063/E006 with Beacon125Model 125/E01312B Model 125/E013 with Beacon250Model 250/E02525B Model 250/E025 with Beacon500Model 500/E05150B Model 500/E051 with Beacon1K0Model 1000/E0911KB Model 1000/E091 with Beacon2K0Model 2000/E1712KB Model 2000/E171 with BeaconVoltageLV1-phase 24-48 V AC/DC3A3-phases 208-240 V ACHV1-phase 100-240 V AC/DC3B3-phases 380-480 V AC3C3-phases 500-575 V ACSpeed/DutyPD Standard speed range and standard duties for model 063/E006 to 500/E051PE Standard speed range and standard duties for model 1000/E091PF Standard speed range and standard duties for model 2000/E171Option modules00No optional modules P7 OM1/Bluetooth5D OM11/BluetoothP1 OM1P3 OM36D OM11/OM3/BluetoothPA OM1/OM3/Bluetooth5P OM9/Bluetooth PG OM13P6 OM1/OM36P OM9/OM3/BluetoothApprovals/Protections0Standard protection NEMA 4/4X/6 (IP66/68M) - CSA certificate T°amb from -40°C to +60°C / -40°F to +140°F2Standard protection NEMA 4/4X/6 (IP66/68M) T°amb from -25°C to +70°C / -13°F to +158°F3Standard protection NEMA 4/4X/6 (IP66/68M) T°amb from -40°C to +70°C / -40°F to +158°F4Explosionproof IP66/68 (NEMA 4/4X/6) + Ex d e IIB T5 Gb - EX tb IIC T100°C Db T°amb from -20°C to +65°C / -4°F to +149°F (prefix c for model 2000)9Explosionproof IP66/68 (NEMA 4/4X/6) + Ex d e IIB T5 Gb - EX tb IIIC T100°C Db T°amb from -40°C to +65°C / -40°F to +149°F (prefix≈c for model 2000)Flange/Insert00No flange insertB4Model 063/E006 flange ISO 5211/F05/F07 - insert not machined (KPB)B5Model 125/E013 flange ISO 5211/F07/F10 - insert not machined (KPB)B5Model 250/E025 flange ISO 5211/F07/F10/F12 - insert not machined (KPB)B6Model 500/E051 flange ISO 5211/F10/F12 - insert not machined (KPB)B7Models 1000/E091-2000/E171 flange ISO 5211/F10/F14 - insert not machined (KPB)BA Models 1000/E091-2000/E171 flange ISO 5211/F12/F16 - insert not machined (KPB)D4Model 063/E006 ISO 5211 (KPD)D5Models 125/E013-250/E025 ISO 5211 (KPD)D6Model 500/E051 ISO 5211 (KPD)D7Models 1000/E091-2000/E171 F10 to F14 ISO 5211 (KPD)DA Models 1000/E091-2000/E171 F12 to F16 ISO 5211 (KPD)E3Model 063/E006 ISO 5211 (KPE)E5Models 125/E013-250/E025 ISO 5211 (KPE)E6Model 500/E051 ISO 5211 (KPE)E9Models 1000/E091-2000/E171 F12 to 16 ISO 5211 (KPE)K4Model 063/E006 flange key 44.45-82.6 - insert not machined (KPK)K8Model 125/E025 flange key 82.6 - insert not machined (KPK)K8Model 250/E025 flange key 82.6-127 - insert not machined (KPK)KA Model 500/E051 flange key 82.6-127 - insert not machined (KPK)KC Models 1000/E091-2000/E171 flange key 127-165 - insert not machined (KPK)U4Model 063/E006 non-ISO (KPU)U8Models 125/E013-250/E025 non-ISO (KPU)UA Model 500/E051 non-ISO (KPU)UC Models 1000/E091-2000/E171 non-ISO (KPU)ORDERING INFORMATION - US MARKETS ONLYExample E006A L W5000 ModelE EPI-2 quarter-turn electricSize006Model E006013Model E013025Model E025051Model E051091Model E091171Model E171Local indicatorA Standard windowVoltage ratingsL1-phase 24-48 V AC/DCH1-phase 100-240 V AC/DCA3-phases 208-240 VACB3-phases 380-480 VACC3-phases 500-575 VACClassification and temperature ratingW1NEMA 4/4X/6 (IP66/68M)Ambient temp: -13°F to 158°F (-25°C to 70°C)W2NEMA 4/4X/6 (IP66/68M)Ambient temp: -40°F to 158°F (-40°C to 70°C)W5CSA 139 (C-US)NEMA 4/4X/6 (IP66/68M)AWWAAmbient temp: -40°F to 140°F (40°C to 60°C)Option modules00NONE, standard On-Off configurationP1Servoamp w/retransmission (OM1)P3Local interface (OM3)P6Servoamp w/retransmission, local interface (OM1/OM3)P7Servoamp w/retransmission, Bluetooth® communication (OM1/Bluetooth)PA Servoamp w/retransmission, local interface, Bluetooth® communication (OM1/OM3/Bluetooth)3D DeviceNet™ bus communication (OM11)5D DeviceNet™ bus communication, Bluetooth® communication (OM11/Bluetooth)6D DeviceNet™ bus communication, local interface, Bluetooth® communication (OM11/OM3/Bluetooth)3P PDP V0/V1 bus communication (OM9)5P PDP V0/V1 bus communication, Bluetooth® communication (OM9/Bluetooth)6P PDP V0/V1 bus communication, local interface, Bluetooth® communication (OM9/OM3/Bluetooth)PG3-wire interface card (OM13)Special option code0Standard。
flowserve limiterque mx系列电动执行器手册说明书

11
11 Absolute encoder
12 Cast aluminum housing
13 Declutch lever
14 Handwheel
10
Flowserve Corporation has established industry leadership in the design and manufacture of its products. When properly selected, this Flowserve product is designed to perform its intended function safely during its useful life. However, the purchaser or user of Flowserve products should be aware that Flowserve products might be used in numerous applications under a wide variety of industrial service conditions. Although Flowserve can (and often does) provide general guidelines, it cannot provide specific data and warnings for all possible applications. The purchaser/user must therefore assume the ultimate responsibility for the proper sizing and selection, installation, operation, and maintenance of Flowserve products. The purchaser/user should read and understand the Installation Operation Maintenance (IOM) instructions included with the product, and train its employees and contractors in the safe use of Flowserve products in connection with the specific application.
EMA电动直线执行器安装和维护说明书
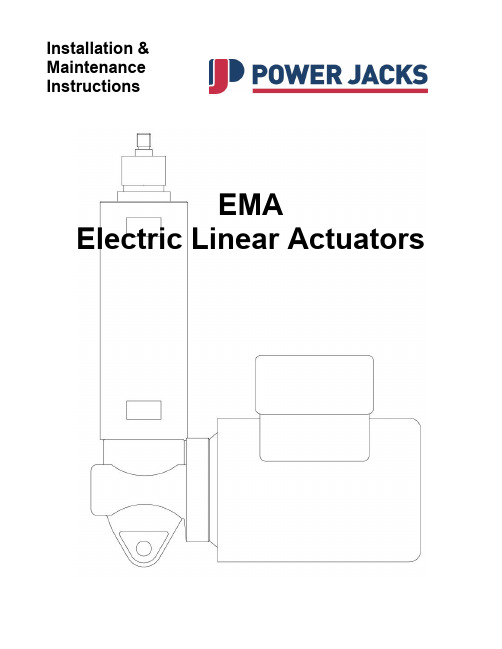
Electric Linear ActuatorsContents1. SAFETY AUTHORISED USE (3)1.1R ESIDUAL RISK AND HAZARDS (3)1.2O PERATING PERSONNEL (3)1.3C OMMISSIONING (4)1.4M ODIFICATIONS AND ALTERATIONS TO THE UNIT (4)2. DESCRIPTION (5)3. TECHNICAL DATA (6)3.1M ODEL I-I NTERMITTENT (LESS THAN 10 STARTS/DAY,10 HOURS/DAY) (6)3.2M ODEL C-C ONTINUOUS (MORE THAN 10 STARTS/DAY) (6)3.3M ODEL H-H IGH S PEED C ONTINUOUS (6)4. MOUNTING A SINGLE ACTUATOR (7)4.1U NPACKING AND I NSTALLATION (7)4.2M OUNTING (7)4.3M OUNTING O PTIONS (8)5. ADJUSTING THE LIMIT SWITCHES (9)6. ADJUSTING THE CLUTCH (10)6.1EMA C LUTCH G ENERAL A SSEMBLY (11)6.2EMA C LUTCH S ETTINGS (11)7. ELECTRICAL INSTALLATION (12)7.1L IMIT S WITCH –E LECTRO-M ECHANICAL T YPE (12)7.2M OUNTING THE DRIVE MOTOR (12)7.3S TANDARD M OTOR T ERMINAL B OX P OSITION (13)7.4O PTIONS (13)7.5M OTOR C ONNECTION (13)7.5.1 Three Phase Motor Connections (13)7.5.2 Single Phase Motor Connections (14)7.5.3 DC Motor (14)8. MAINTENANCE AND LUBRICATION (14)9. PARTS LIST - GENERAL (15)9.1EMA E LECTRIC L INEAR A CTUATOR (G ENERAL A SSEMBLY) (16)1. Safety Authorised useEMA electric linear actuators are exclusively designed for carrying out lifting, lowering and feeding movements with the lifting forces up to 10 kN. Any other application other than specified or one going beyond the above mentioned capacity is unauthorised. The manufacturer is not liable for damages resulting from such applications. The user alone has to bear the risk.Since the actuators can be applied in various areas, the user is responsible for the specific application of use.In compliance with the regulations concerning the electromagnetic compatibility of machines, the EMA linear actuators may only be used in industrial areas according to the definition EN 50 081-2.Safety instructions in the operating manualThis symbol indicates potential dangers to people. Comply withthe instructions in order to avoid injury.This symbol indicates potential dangers to the unit. Comply withthe instructions in order to avoid damage to the unit.This symbol indicates special information on:∙the best possible use of the unit∙how to facilitate operation of the unit1.1 Residual risk and hazardsShould a risk of damage to material or injury to persons remain despite the structural safety of the EMA actuators, the user must employ other safety measures and draw attention to such hazards by means of suitable warning notices and written instructions indicating safety precautions.1.2 Operating personnelThe EMA electric linear actuators are designed according to state-of-the-art technology and are in line with applicable safety regulations.However, the general risks of personal injury or damage to property connected with the use of such machinery cannot be completely eliminated. Therefore the units may only be assembled and operated by competent and qualified personnel and only be used for the authorised application. Therefore a careful study of this operating manual should be made before attempting to use or service the unit and particular attention should be paid to the safety instructions.Work to be performed on electrical parts, such as:∙installation of limit switches∙mounting of the drive∙Checking of the direction of rotation may only be carried out by qualified electricians.The linear actuators and the installation should be inspected by the operating and supervising personnel for externally visible damage and defects at least once every shift. Any changes (including the operational conditions) which may affect the safety are to be reported immediately.1.3 CommissioningThe EMA electric linear actuators must not be put into service before the machinery into which it is to be incorporated fulfils all provisions of the EC directive relating to machinery.1.4 Modifications and alterations to the unitIt is not permitted to make any alterations to the safety features or design of the EMA electric linear actuators without our written consent. Power Jacks declines any responsibility in the event of such alterations. Worn and spare parts may only be replaced after consultation with our service technicians or by them personally. It is not permitted to disassemble or disconnect any safety or protection device. When using special accessories the assembly instructions of the manufacturer must be observed! The following regulations must be complied with:∙the relevant regulations for the prevention of accidents∙generally recognised safety regulations∙EC guidelines and∙National regulationsTo comply with the regulations concerning the electromagnetic compatibility of machines, the units must be connected according to EC rules & regulations. Therefore the norms EN 50 081-2 and EN 50 082-2 should be observed, to avoid electromagnetic interference.2. DescriptionEMA electric linear actuators are mainly used whenever precisely controlled lifting, lowering or feeding movements are required. The actuators consist of either a trapezoidal or ball lead screw, driven by an electric motor through spiroid gearing. The screw converts the rotary motion into linear movement. As the screw rotates, the nut extends and retracts the ram, which is attached to the load.There are 3 standard EMA models, all available in a right-angle drive configuration.∙Intermittent model, incorporating a trapezoidal screw.∙Continuous model, incorporating a ball screw∙High Speed Continuous model, incorporating a ball screw.Where the standard range does not meet the application specification, special actuators can be designed to meet customers’ specific requirements.As standard, the units are available with 240V / 415VAC 3phase or 240VAC 1 phase or 24VDC motors, with or without a brake. The type of motors required is dependent on the customer’s application. The motors are mounted to the actuator on an IEC 63C Face Flange Mounting.3. Technical Data3.1 Model I - Intermittent (less than 10 starts/day, 10 hours/day)3.2 Model C - Continuous (more than 10 starts/day)3.3 Model H - High Speed Continuous4. Mounting a single actuator4.1 Unpacking and InstallationRemove the EMA electric linear actuator from its container. Dispose of the packaging material and the desiccant in an environmentally friendly way. If it is necessary and in order to avoid damages, please use soft straps to transport or mount the actuator.In order to avoid damage; do not attach the straps to the inner tube but to theouter housing of the drive or to the gearbox.4.2 MountingThere are two possible ways of mounting the EMA actuator at the gearbox end:By means of bearing journals for trunnion mounting or clevis mount.Rear Clevis∙Mount the actuator by attaching the desired bracket and pin to the clevis end. Refer to section 4.2.1 for ram mounting options.∙Verify that the ram attachment is aligned throughout the actuator stroke before connecting the ram. The ram attachment will either be pinned or bolted in place depending on chosen model.Trunnion Mount∙Mount the actuator by attaching the desired bearings (or mounting feet) to the trunnion pins. Refer to section 4.2.1 for ram mounting options.∙Verify that the ram attachment is aligned throughout the actuator stroke before connecting the ram. The ram attachment will either be pinned or bolted in place depending on chosen model.Always ensure that clevis holes align correctly and that they allow for thecorrect angle of pivoting for the application before operating the actuator.Side loads on the actuator ram should be avoided by ensuring that theload is guided. The load guide mechanism should resist the torquedeveloped at the ram by the screw mechanism. A guided ram can besupplied on request, which utilises a keyway in the inner ram, eliminatesthe need for torsional restraint and therefore allows flexibility in the choiceof end fitting.The desired mounting orientation will be determined when placing the order; this orientation must be maintained at installation.4.3 Mounting OptionsClevis End Fork EndThreadedEnd Top PlateTrunnionMount Rear Clevis at 90° Standard Rear Clevis5. Adjusting the limit switchesElectrical connections may only be performed by licensed electricians. Standard mechanical limit switches are used to cut off the electrical drive before the final position is reached. The limit switch is triggered by a cam on the lifting nut assembly. The positions of these limit switches are fixed and are not adjustable. The position is determined by the length of stroke specified by order and cannot be changed at a later date. The mounting of a position-measuring system is possible as an option.Suitably rated mechanical safety limit switches must be used if the non-disconnection of the electrical drive constitutes a potential danger topeople.Adjusting the best possible sensing distance:1. Position the cam on the lifting nut assembly to cover the opening of the switch.2. Screw the switch into the housing until the unit switches over.3. Lock the switch in place with the lock nut.4. Check the correct function of the switches by moving the lifting-nut assemblymanually.5. If the switch works correctly then repeat the procedure for the next switch.Otherwise repeat procedure for this switch.6. Once all the limit switches are set ensure that the cam on the lifting nut is restingin a position in between both end of travel limit switches.The drive must not be put into service before all limit switches have beenmounted and correctly adjusted.6. Adjusting the ClutchThe clutch is a device mounted on the actuator inner tube (ram) which will slip when the torque to drive the load exceeds the limit set. (refer 6.1)The clutch spindle, (6) that is attached to the load via an end fitting, is supported on bearings (8) and clamped from rotating by interlocking conical rings (7). The clamping load is applied by a locknut (5) with keyways to engage a tab washer (4). The clutch housing (3) is attached to the inner tube (1) and the clamping effort of the conical rings (7) carries the residual torque of lifting to the clutch spindle (6).If the load is axially locked or if a torque greater than the clutch setting is required to move the load, the conical rings will rotate within each other, disengaging the spindle to inner tube drive and preventing the motor from overloading the actuator components or the load guides etc.Under normal operation and with no overload experienced the clutch requires no regular maintenance or adjustment. If however the clutch slips regularly in operation the setting of the clutch will reduce to a point where the normal operating torque will overcome the clutch and the load will not move. Under these circumstances the clutch can be adjusted as follows:1. Remove the actuator from the installation.2. Extend the inner tube (1) and clamp in soft jaws in a vice.3. Bend out the tab of the washer (4) from the keyway of locknut (5).4. With a suitable fitting screwed on to the clutch spindle (6) tighten the locknut untila torque is indicated in table 1 (refer 6.2) is measured, e.g. Clutch lever forces intable are for a 254mm (10in) lever inserted through clevis.5. When the torque has been set, bend a tab of the washer into an adjacent keywayin the locknut. The actuator is ready to reinstall.6. The clutch is selected from either of the following:a) Ringspan Cone Clamping Element TLK 250:-i) 4202015.001 - 27Nm max.ii) 4202025.001 - 74Nm max.7. When assembling the clutch a small quantity of oil (3 in 1) should bea pplied to the cone (7) surfaces.6.1 EMA Clutch General Assembly6.2 EMA Clutch SettingsT - Trapezoidal B-Ball Screw7. Electrical Installation7.1 Limit Switch – Electro-Mechanical Type7.2 Mounting the drive motorThe electrical installations and the checking of the direction of rotation may only be carried out be a licensed electrician.Connect the motor in compliance with the electro-technical regulationBefore mounting the motor, check the direction of rotation / linear travel of the EMA actuator and the operation of the limit switches (if fitted). In order to do this:1. Place the motor at the mounting position near the gearbox input.2. Switch on the motor and check the direction of rotation.3. Check the direction of rotation / linear travel by manually turning the gearbox inputshaft. Change the direction of the motor rotation if necessary by changing motor connections.4. Where necessary, attach coupling halves to motor shaft.5. Mount motor onto gearbox input flange using screws provided.7.3 Standard Motor Terminal Box Position7.4 Options∙ Delivery with mounted brake motor (DC or AC brake).∙ Delivery with non-standard motor types e.g. servo motor, 48VDC motor. ∙ Special request, motor being supplied by the customer.7.5 Motor ConnectionThe electrical connections for the standard three-phase, single-phase or DC-permanent-magnet motor are within the terminal box. Appropriate rated and insulated cables require to be selected in accordance with the rated power. If motors are supplied with flying leads please consult Power Jacks.All electrical connections are to be carried out by a qualified electrician.7.5.1 Three Phase Motor ConnectionsStar and Delta connections for dual wound motors7.5.2 Single Phase Motor ConnectionsThis diagram is typical for motors with on board capacitors connected to the motor for the correct start and run characteristics. For motors with loose capacitors consult Power Jacks or the motor manufacturer.7.5.3 DC Motor8. Maintenance and LubricationUnless otherwise specified the actuators are shipped with their full requirement ofgrease for normal operation. The actuators should not need a lubrication refill within their standard life provided they have been installed and used correctly. Should the unit require lubrication then use one of the following extreme pressure greases or their equivalent:Shell Alvania WR2 BP Energrease LC2 Castrol Spheerol L-EP2 Mobil Mobilux EP2If ambient temperatures exceed 50°C (122°F) consult Power Jacks.ForwardReverse +ve-ve9. Parts List - General(refer to section 9.1 for EMA Electric Linear Actuator general assembly diagram)9.1 EMA Electric Linear Actuator (General Assembly)Power Jacks Ltd Balmacassie Commercial Park Ellon AB41 8BXScotland Tel: +44 (0) 1358 285100 Email:******************** 。
AUMA A-Series 工业电动执行器说明书

Technical InstructionsDocument No. A6V12035775July 7, 2020A-Series IndustrialElectric Actuators AUMA (21,300 and 40,680 lb-in)Siemens Industry, Inc.DescriptionA-Series Industrial Electric AUMA actuators provide precise, durable control of quarter turn Siemens resilient seat butterfly valves. The compact industrial housing is rated to NEMA 6P (IP 68) standards for outdoor use. All models include integrated controls and a manual override handwheel.The standard AUMA models are 120V single phase. All AUMA actuators include six auxiliary switches, torque switches, a position indicator and a heater. Modulating units provide position feedback as standard. Features• Compact, lightweight design and direct mounting • Manual, declutchable override handwheel • Position and motion indicator lights • Push button controls • CE Certified• On/off or modulating control• Output torque 21,300 lb-in (2,407 Nm) to 40,680 lb-in (4,596 Nm) • ISO 5210 for direct mounting• All actuators include a heater to prevent condensation build-up •All modulating units include a feedback potentiometerOrderingActuators can be ordered separately or together with a valve as an assembly.Product NumbersTable 1. A-Series AUMA Industrial Electric Actuators, 120V.Product Number Operating Mode Voltage 50/60 HzTorque 90° Stroke Time*Current Draw (Amps) (lb-in) (Nm) Full Load LockedRotorA226.21K On/Off120 Vac21,300 2,407 60 sec.6.514A226.41K 40,680 4,596 A266.21K Modulating21,300 2,407 A266.41K40,6804,596* Operating times shown are with 60 Hz power supply. Actuators with 50 Hz power supply will be 20% slowerWarning/Caution Notations WARNING: Personal injury or loss of life may occur if you do not perform a procedure as specified.CAUTION:Equipment damage may occur if you do not perform a procedure as specified.Technical Instructions A-Series Industrial Electric Actuators AUMA Document Number A6V12035775June 15, 2020CAUTION:Do not install or use the A-Series Industrial Electric Actuator in or near environmentswhere corrosive substances or vapors could be present. Exposure of the electricactuator to corrosive environments may damage the internal components of thedevice and will void the warranty.Application These actuators are ideal for use on valves for chillers, cooling towers, boilers, heatexchangers and other outdoor applications. The actuators’ advanced electronicsassure reliable compatibility with virtually any analog control signal used in today’sbuilding automation and temperature control systems. The NEMA 6P rated housingprevents any water ingress in outdoor applications. The built-in heater prevents anycondensation build-up inside the housing.NOTE: Use a “liquid tight” conduit connector to maintain NEMA 6P rating. SpecificationsOperating Conditions Ambient Temperature -22°F to 158°F (-30°C to 70°C)Fail Position Loss of supply power - fail-in-placeDuty Cycle On/Off – 15 min. continuous, max. six starts/minuteModulating – 25% intermittent duty Physical Description Motor 120 Vac, Single-Phase, Reversible, PermanentSplit Capacitor Induction MotorMotor Protection 1 Ph-1 thermal switch 284°F (140°C)Class F insulation, tropicalized windingControl Voltage A226.21K and A226.41K: 120 VacA266.21K and A266.41K:Input 4 to 20 mAModular Power Supply 24 VdcOutput Aux. Voltage A226.21K and A226.41K: 115 Vac – 30 mAA266.21K and A266.41K: 24 Vdc – 100 mAFeedback Signal 4 to 20 mAOutput Contacts 6 Output contacts: 6 NO/NC without common 5AOutput Signals Default setting: Fault, End pos. CLOSEDEnd pos. OPEN, Selector sw. REMOTE, Torquefault CLOSE, Torque fault OPENTerminal StripPower Terminals 8 to 10 AWG (6 to 10 mm2)Controls Contacts 14 AWG (2.5 mm2)Heater 24V Internal Supply (5 Watt)Dimensions See Figure 3 and Figure 4.Weight A2x6.21K – 165 lbs. (75 kg)A2x6.41K – 195 lbs. (88 kg)Enclosure NEMA types 6P (IP68)Corrosion Protection: KSConduit entries Plug/socket 100 mm, 2 × 3/4” NPT; 1 × 1-1/4” NPTManual operation To close the valve, turn handwheel clockwise.Drive shaft (valve) turns clockwise in closedirection. 52:1 drive ratioAngle of Rotation 92° maximumCertifications CE CertifiedCSA - Classes C322102 and C3221812(available upon request)A-Series Industrial Electric Actuators AUMA Technical InstructionsDocument Number A6V12035775July 7, 2020Product NumbersTable 2. Product Numbers.Use the product numbers in the following table to order a valve or a valve and actuator assembly. The valve product number consists of the type, action, valve size, disc type, and valve configuration.To order an assembly, add a (-) after the valve product number and then choose the application, actuator, voltage, control signal, end switches followed by a separator (.) and the actuator torque.Siemens Industry, Inc. Page 3Technical InstructionsA-Series Industrial Electric Actuators AUMADocument Number A6V12035775 July 7, 2020Page 4Siemens Industry, Inc.Mounting and InstallationAll A-Series industrial electric actuators are suitable for direct mounting on Siemens resilient seat butterfly valves.NOTE:The standard mounting position for the actuator is to orient the base of the actuator parallel to the pipeline. •To mount an actuator on a vertical pipe, position the unit with the conduit entries on the bottom to prevent condensation from entering the actuator through its conduits.• Use a “liquid tight” conduit connector to maintain NEMA 6P rating.Service The resilient seat butterfly valve and actuator are maintenance-free.WiringCAUTION: •When wiring an A-Series Industrial Electric Actuator for two-position(on/off) control and the power to the actuator is commanded to be off, you must ensure that there is no extraneous or leakage voltage between hot and common. Leakage voltage greater than 3 Vac can cause actuator failure.• When wiring an A-Series Industrial Electric Actuator for two-positioncontrol, the controller should use at minimum a one-second time delay for command signal reversal. Instantaneous command reversals may cause actuator failure.Figure 1.. On/Off .NOTE:Use this A-Series Industrial Electric Actuator only to control equipment under normal operating conditions. Where failure or malfunction of the electric actuator could lead to personal injury or property damage to the controlled equipment or other property, additional precautions must be designed into the control system. Incorporate and maintain other devices such as supervisory or alarm systems or safety or limit controls intended to warn of, or protect against, failure or malfunction of the electric actuator.Figure 2. Modulating.A-Series Industrial Electric Actuators AUMA Technical InstructionsDocument Number A6V12035775July 7, 2020 Information in this publication is based on current specifications. The company reserves the right to make changes in specifications and models as design improvements are introduced. Products or company names mentioned herein may be the trademarks of their respective owners. © 2020 Siemens Industry, Inc.Siemens Industry, Inc. Smart Infrastructure1000 Deerfield Parkway Buffalo Grove, IL 60089 USA + 1 847-215-1000Your feedback is important to us. If you havecomments about this document, please send themto***************************************Document No. A6V12035775Printed in the USAPage5of 5DimensionsFigure 3. Model A2x6.21K Actuators.Figure 4. Model A2x6.41K Actuators.。
3810L电动执行器使用说明中英文.

3810L电动执行器使用说明书3810L Electric Actuator Instructions目录Table of Contents1. 产品概述Product Overview2. 主要技术参数The main technical parameters3. 产品型号规格Product Specification4、结构与原理The structure and principles5、安装Installation6、调整Adjusting7、外形尺寸Dimension8、配套支架The supporting bracket9、故障和解决办法fault and solutions10 、订货须知Ordering Information 11 、安全使用注意事项Safety Precautions使用本执行器时,请先认真阅读和理解本说明书,通过正确的使用和维护,充分发挥其效能。
When using this actuator, please read and understand the present specification, by the proper use and maintenance, full play to its effectiveness.1 产品概述Product Overview3810L 系列直行程电子式电动执行器有以220V 交流单相电源和380V 三相交流电源两种驱动电源的机型,接受来自调节器控制信号( D C 4 ~ 20m A 或DC 1 ~ 5V ),实现预定直线往复运动的新型执行器。
本系列执行器被用作调节阀的执行机构时,几乎具备了调节阀本身所要求的各种动作变换功能以及阀开度信号功能和手动功能。
因此被广泛应于发电、冶金、石化、轻工及环保等工业部门。
主要特点:main feature:1.1执行器设计有伺服系统(无需另配伺服放大器),只需接入DC4〜20mA (或D C1~5V )信号和对应的电源即可工作。
EIM-HQ Series 电动执行机构使用手册说明书
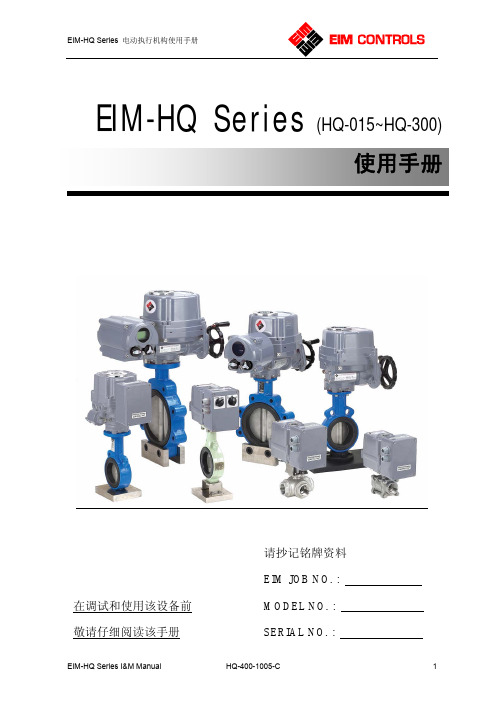
请抄记铭牌资料EIM JOB NO. :MODEL NO. : SERIAL NO. :在调试和使用该设备前 敬请仔细阅读该手册EIM-HQ Series(HQ-015~HQ-300)使用手册目录1.0 概述 (3)2.0 电动执行机构与阀门的装配 (3)3.0 外部结构 (4)4.0 电气接线图 (5)5.0 供电电源 (6)6.0 工作制式 (6)7.0 手动操作 (6)8.0 机械限位的调整 (6)9.0 电气接线 (7)10.0 行程开关的设置 (7)11.0 力矩开关的设置........ (8)12.0 反向运动(逆时针关闭) (8)13.0 润滑 (8)14.0 机械位置指示器(MDPI)的调整 (9)15.0 一般保养 (9)16.0 储藏与存放 (9)17.0 机械接口详细说明 (10)18.0 驱动轴套详细说明 (11)19.0 故障诊断和排除 (12)20.0 HQ系列产品标准功能配置 (13)重要:EIM 公司在对该使用手册的编撰及修订时已经考虑了多方面的使用和应用,然而EIM 公司不保证该手册中的内容无任何错误,也无法对误操作或使用该手册而导致的产品损坏和连带损失负责。
EIM 公司有权利对本手册进行修改,请恕不另行通知。
1.0 概述EIM-HQ系列电动执行机构可以为90º旋转的阀门提供可靠和有效的控制,如球阀,蝶阀及风门挡板等。
警告:在安装、调试、使用和维护HQ系列电动执行机构前,必须仔细阅读本手册,对该产品不熟悉或未阅读本手册前,请勿启动。
警告:当人员在阀门和电动执行机构附近时,必须小心高温、高压、易燃、易爆、有毒、腐蚀性介质和高电压、强大外力等危险状况。
警告:必须严格按照规范、图纸和手册等的要求进行正确的安装、接线、调试、使用、储存和维护,否则有可能导致严重伤害、损坏设备和失去质量保证。
安装之前的检查:仔细核对设备的铭牌信息,必须确认以下参数的正确:型号,力矩,操作速度,电源电压,防护/防爆等级等。
NA Series电动执行器手册说明书

NA SeriesNoah NA Series of Electric Actuators are particularysuited for quarter turn applications in piping, ductingand in various plants such as water treatment, pulp,paper, ship building and air conditioning combinedwith ball, butterfly, plug valves and dampers.Its compact and simple design will ensure reliabilityand quality for customers even in hazardouslocations. Noah NA Series of Electric Actuators givethe best automation solutions to you with its variousmodels (60Nm ~ 2,500Nm) and options.n SEALINGStandard enclosure with o-ring sealing is watertight to IECIP67, NEMA4 and 6.The actuator is available with optional explosion proof enclosure.n WIRINGElectric wiring of control circuit is standardized for single and three phase power supply in a single module. Multiple terminal contacts sufficiently cover additional requirements such as auxiliary contactors for DCS, interlocking and other options.n COMPONENT ARRANGEMENTMechanical and electrical module can be separated easily to improve assembling, maintenance and alteration of electrical requirements. Actuator has enough internal space for optional accessories.n HANDWEELSize of handwheel is designed for safe and efficient emergency manual operation.n MANUAL OVERRIDEWhen operated the manual override lever engages the handwheel. Manual override is automatically disengaged when motor power is applied.n ADAPTIONBase mounting is standard to ISO 5211.Drive bush is removable for machining to valve stem requirement. The actuator position on the valve can be selected for 4 positions by means of 4 bolt holes in the drive bush.n HEATERA space heater inside the actuator prevents condensation due to temperature and weather changes. Standard 200W heater keeps all electrical components in the actuator clean and dry.n LIMIT SWITCHESThe limit switch is activated by means of a simple and yet reliable cam mechanism mounted and driven by the center column. The valve position can be accurately and easily set with a simple adjustable switch mechanism. The set position is permanent and is not affected by over-travel resulting from manual operation.n TORQUE SWITCHESCam activated torque switches are easily adjustable to provide over-load protection.n SELF-LOCKINGRolled steel wormgear on aluminium bronze wormwheel self-locks to prevent valve back drive on control signal or power failure and transfers high torque with high efficiency at low sound levels.11111213171819222325687070Weight(kg f)n ATS (Auxilary Torque Switches)Providing a dry contact signal to send to customer’s panel to indicate over-torque.n ALS (Auxilary Limit Switches)Providing a dry contact signal to verify valve’s positions and interface with customer’s controls.n CPT (Current Position Transmitter)Combined with a PIU to transfer an output signal (DC : 4~20mA) from PIU’s resistance value power : AC 110/240V±10% 50/60Hz DC24V output signal : DC 4~20mAn PCU (Proportional Control Unit)Combined with PIU to control the valve’s position proportionally by an input signal and provide an output signal in relation to valves position.l Input signal : DC 4~20mA/DC 2~10V/DC 1~5V l Output signal : DC 4~20mAl Power : AC 110/240V±10% 50/60Hz DC24V l Size : 120mm×135mml Operating temperature : -10˚C~55˚C l Resolution : Min. 1/500 l Operating Humidity :90% RH Max.(Non condensing)n LCU (Local Control Unit)A small unit that is mounted to the actuator to operate the valve’s position locally, complete with Local/Remote switch and Open/Stop/Close switchesn PIU (Position Indication Unit)Providing resistance value (0~1KΩ) according to valve’s position.n IMS (Integral Motor Starter)Integrated reversing contactors and control transformer provides various control voltages tothe actuator from the main power (380VAC/440VAC).。
JFE W X系列NEMA 4,4X,7电动执行器说明书

Electric Actuator JFE W/X SeriesINTRODUCTION- JFLOW controls designs, produces and provideshigh quality actuators and automated and manual valves- Our years ofexperience in the automation field enables us to launch our JFE series electricactuator which hascompact size, robust construction, reliable performance and ability to integrate fully into sophisticated control systems.- Jflow controls is always ready to provide you withthe JFE series actuator and accessories, with quality service.FEATURES- Compact and robust construction, light weight providing high output torque(Max 80,000 In-lbs / 9000Nm).- Wide range of torque variation (From min 885In-Lbs to max 80,000 In-Lbs).- Hard anodized aluminum housing inside and outside with external powder coated against severe industrial environment.- Enclosure using radial seals & O-rings that provide protection to waterproof IP67 (Nema 4 & 6) and optional watertight IP68- Mounting base according to ISO5211 standard.- Removable drive bushing for easy machining and mounting.- Self-locking provided by double worm gearing (no brake required).- Auto-declutching manual override handwheel with padlockable auto / manualswitchable lever.- Reliable Mechanical Torque sensing system providing safe operation in overload condition.- Large size window and indicator provides better position indication from a distance.- Various Local position control options providing easy commissioning and operation in field.- Digitalized control component.Cable entries- Standard 2-3/4NPTExternal mechanical stopper- Prevents over run of travel angle when limit switch fails.Removable drivebushing and ISO5211 mounting base- (F07~F30) for easy mounting on valve.GearingSelf locking- Provided by double worm gearing to keep position of valve unchanged against reverse torque from valve.CONSTRUCTIONCaptive cover bolts- Designed to prevent losing it during maintenance or installation.* All external bolts are stainless steel for rust prevention.- HousingSealing- By O-ring in all interfacesIP67(standard), and double o-ring for IP68 (option)Handwheel- Different sizes depending on actuator torque, and knob on handwheel for easy operation.Motor- Specially designed induction motor to generate high starting torque and high efficiency equipped with thermal protector to prevent damage from over heating.- Insulation class F- Hard anodized Aluminum casting and external epoxy powder coated against severe industrial environment.- Precisely machined double worm gear c/w minimumback-lash, low noise, high output torque.Tapered interface between cover and lower housing- For easy lifting cover up from lower housing for wiring or maintenance.StandardIndicator- Continuous mechanical position indicator and window with dialLimit switches- Directly engaged with driving shaft to setaccurate position of valve.- 2 ea for each travel end (open/close).- Optional Extra Limit Switches (Max 4 ea for each end) : Except for JFE 0100Torque switches- Protect actuator from damage caused byoverload from the driven valve over the whole travel.- 1 each for open / closeSpace Heater- Anti-condensationTerminal- Spring loaded push type terminal for tight wiring connection under severe vibration.Manual override- Auto / Manual switchable lever and handwheel engagement for emergency manual operation.- Drive force automatically resorted by motor start, unless lever padlocked toprevent this occuring.TECHNICAL INFORMATIONSTANDARD SPECIFICATIONModelJFE 0100JFE 0160JFE 0240JFE 0350JFE 0500JFE 0800JFE 1100JFE 2000JFE 3000JFE 6000JFE 9000MechanicalOPTIONS AVAILABLERemote monitoring and controlLocal controlLp4 for 1 & 3 Phase (JFEW 0100~9000)Lm4 for 3 Phase (JFEW 0100~9000)Including the same functions as LP4Control power : Free Voltage (85~265VAC) 50/60Hz, Option : 24VDC Magnetic selector switches, SMPS (Switching Module Power Supply) : Open/Close & Local/Stop/RemoteLocal lamp indicationReversing electric contactors, Transformer: Power - White(on), Remote : Blue(on), : In case of Close Torque Switch Trip - Yellow(on) + Green (flickering : only at Local Position): In case of Open Torque Switch Trip - Yellow(on) + Red (flickering : only at Local Position): Full Close - Green(on), Closing - Green(flickering : only at Local Position): Full Open - Red(on), Opening - Red(flickering : only at Local Position)* Options Available : PK, CT, RPC(Modulating), IP68, Explosion proofPKCTLP4 / LM4DHC SeriesICM2 for 1 & 3 phase (integral with LCD Display) (JFEW 0160~9000)ICM3 for 1 & 3 phase (integral with LCD Display/IP68 Enclosure) (JFEW 0160~9000)Reversing electric contactors, Transformer,Auto-Phase Discriminator, LCD Display Including the same functions as ICM1Including the same functions as ICM2Reversing electric contactors, Transformer, Auto-Phase Discriminator,LCD Display, IP68, Explosion Proof, RPC(Modulating), Bus Communication, 34pins seperate compartment for terminal blockLocal controlFail safeBP for 1 Phase (JFEW 0160~0500)Rechargeable Battery back up - Fail safe function / Optional: Super Capacitors When Main power is alive, actuator works as normally.Once power fails, actuator will move to pre-set fail safe position. Input power : Free Voltage (85~265 VAC) 50/60Hz Output contacts : open/close/Alarm relayLED signal indication : 4 LEDs (Full Open/Close, Over Torque and Power)Rechargeable battery : 2.0AH 27.5VDC(Ni-Cd)ICM1 for 1 & 3 Phase (Integral Control Module) (ITQ 0160~9000)Control power : 24 VDC (Internal Power) (Option : 110 VAC, 220 VAC (External Power)) Main Power : 3Ph / 220/380/440 VAC1Ph / 110/220 VACMagnetic selector switches: Open/Close & Local/Stop/RemoteReversing electric contactors, Transformer, Phase Detector Auto-Phase DiscriminatorLocal lamp indication: Power - White(on), Remote : Blue(on),: In case of Close Torque Switch Trip - Yellow(on) + Green(flickering): In case of Open Torque Switch Trip - Yellow(on) + Red(flickering): Full Close - Green(on), Closing - Green (flickering): Full Open - Red(on), Opening - Red (flickering):Single & Reverse Phasing : (Yellow + Green + Red) all flickering * Options Available : Explosion Proof, IP68* Options Available : CT, RPC(Modulating), Explosion Proof,IP68, Bus CommunicationICM1ICM2BASIC ACTUATOR DIMENSIONSWith Gear BoxJFE 6000JFE 9000SWITCHCLS 1-2CLS 1-3OLS 1-2OLS 1-3ACLS1-2ACLS1-3AOLS1-2AOLS1-3CTS 1-3OTS 1-3TORQUE AND LIMIT SWITCHES OPERATION CLOSEINTERMEDIATEOPENTYPICAL WIRING (JFE W/X 0100)110/220VAC/50/60Hz, 1Ph(On-Off)110/220VAC/50/60Hz, 1Ph(Modulating : RPC)380/440VAC/50/60Hz, 3Ph(On-Off)**Important Notice**1. The Electric Wiring Diagrams shall be modified withterminal no and wires in Red Color for our customers’ convenience from 1st of June 2009.2. Please only refer to the Wiring Diagram Sticker or separate Wiring Diagram inside of each actuator. If there is any confusion please contact our distributor.Closing Torque Switch interrupts control if Mechanical overload occurs during closing cycle Opening Torque Switch interrupts control if Mechanical overload occurs during opening cycleJFEW 0100-80000-FEARTHBASE CLOSECOMNC H E A T E R2G /FG /FG /FW H ICOM1NO32NC 1NO 3B R OW H IR E DB L UG R EG R EP U RW H IB L AR E DB L UTP LAMPOPEN CLOSE LAMPCC OC C C531364264O C512PROPOSED CUSTOMER'S WIRING ACTUATOR WIRINGOPEN STOP 3223NC RED1COMNO NC 1COMNOP U RG R EB L U10UAC 3PH ( V)WV MAIN POWER MTPMTP MCLSOLSC723451CC6AC 1PH or DC 24VOC O89CONTROL POWER ACLSAOLS 12131114OPTION A U X . A C L SA U X . A O L SA U X . C O MCOM380/440VAC/50/60Hz, 3Ph(On-Off)110/220VAC/50/60Hz, 1Ph(Modulating : RPC)110/220VAC/50/60Hz, 1Ph(On-Off)ALS : Auxiliary Limit SwitchAOLS : Auxiliary Open Limit Switch (Dry contact)ACLS : Auxiliary Close Limit Switch (Dry contact)O : Open Lamp C : Close Lamp OT : Over Torque LampCLS : Close Limit Switch (250VAC 10A)OLS : Open Limit Switch (250VAC 10A)CTS : Close Torque Switch (250VAC 10A)OTS : Open Torque Switch (250VAC 10A)CC : Close Magnetic CoilOC : Open Magnetic CoilM : MotorTP : Thermal Protector (250VAC 15A option)MTP : Thermal Protector built in motor* Each actuator should be powered through its ownindividual switch or relay contacts to prevent crossfeed between two or more actuators.* In case of 3ph actuator, make sure to place actuator on the middle of travel angle before electrical operation to avoid "Jamming"* All internal wiring is done as color coding.TYPICAL WIRING (ITQ 0160 ~ ITQ 9000)ITQ0160-70000-FITQ0160-80000-FLAMP CLOSE B L UNO 32NC 1COM W H I1COMNC NO23B L A3NONC 2TP1COM1W H IG /FB R OCOMNO NC 32Y E LR E DG R EB L UR E DB L UW H IBLA CAPACITOROPTIONR E DMTPH E A T E R 5WACTUATOR WIRINGPROPOSED CUSTOMER'S WIRING L I V EN E U T R A LREDBLUOVER TORQUE LAMP G /FR E DB L UG R EP U RP U RR E DG R EB L U1COMNO32NC EARTHBASE 1COMNC 23NOSTOP OPEN CLOSE COMOPENLAMP AC 1PH ( V)INCOMING POWER OTMOLS OTSCLSCTS ACLSAOLSMAX. 250VAC 10AAUX. CONTACT OC 26543781615141312101191817PROPOSE CUSTOMER'S WIRING ACTUATOR WIRINGBASE EARTHCLOSESTOP OPENLAMPCLOSE OVER TORQUE LAMPOPENLAMPNO COM COM NOG R EB L AR E DR E DB L UW H IHEATER 5WNC 2112NCB R OG /FW H ITPR E DB L UG R EP U RW H IY E LB L UCOM1NO32NC3W H I3NC23NOCOM1B L UG R ER E DP U RNC 23NOCOM1NO32NC COM1MTPMTPCONTROL POWER AC 1PH ( V) or DC 24VOC U AC 3PH ( V)MAIN POWER CC WV C OT OM98745623161718111213151410ACLSAOLSCTSCLSOTS OLS C C531364264O C512CCOC AUX.FULL CLOSE 250VAC, 10A AUX.FULL OPEN250VAC, 10AL WIRING (ICM2 for 3phase) TYPICAL WIRING (ICM2 for 3phase TYPICThe details of this catalog are subject to change without prior notification.4665 Interstate Drive - Cincinnati OH 45246TOLL FREE PHONE: 866.95J.FLOW Phone: 513.731.2900 - Fax: 513.731.6939AdditionalJflow Controls ProductsElectric ActuatorMULTI-TURN 0180 / 0450 / 0750 / 1800 / 3000。
Bray AU系列电动执行器使用说明书

clude two auxiliaryswitches, torque switches, a position indicator and a heater. Modulating units provide position feed-back as standard.AU series actuators mount directly to Bray butterfly valves and ball valves without the need for adapter bracket. Thermal overload protection is provided by means of PTC thermistors connected directly to the motor windings.AU Series - Specifications & Model SelectionModel NumberF e a t u r eT o r q u eO n /O ffM o d u l a t i n gH e a t e rA u x i l i a r y S w i t c h e s••••••••••••••••••AU-213021,300AU-2130SV 21,300AU-406840,680AU-4068SV 40,680AU-708070,800AU-7080SV70,800Technical SpecificationsOn/Off, Floating and Modulating 120 Vac, 60 Hz, +/- 10%, Single-Phase, Reversible, Permanent Split Capacitor Induction Motor Power Supply Full Load Locked Rotor14 APower Terminals 8 to 10 AWG (6 to 10 mm2)Controls Contacts14 AWG (2.5 mm2)24 V internal (12.5 W)Current DrawControl Module Voltage On/Off, Floating ModulatingModulating 24 VDC – 100 mA 115 VAC – 30 mA Output Aux.Voltage On/Off, Floating Modulating On/Off, Floating Declutchable Override Handwheel ModulatingMotor Protection 1 Ph-1 thermal switch 284°F (140°C) Class F insulation, tropicalized windingFeedback SignalControl Input Signal 4 to 20 mA 4 to 20 mAOutput Signals Terminal Strip Fault, End pos. CLOSED End pos. OPEN, Selector sw. REMOTE, Torque fault CLOSE, Torque fault OPEN Output Contacts 6 Output contacts: 6 NO/NC without common 5AEnclosure Heater NEMA types 6P (IP68) Corrosion Protection: KSWarranty3 Years limited from time of shipment.Manual Operation To close the valve, turn handwheel clockwise.Drive shaft (valve) turns clockwise in close direction.Conduit Entries Plug/socket 100 mm, 2 × 3/4” NPT; 1 × 1-1/4” NPT Dimensions See Page 4WeightAU-2130AU-4068AU-7080165 lbs. (75 kg)195 lbs. (88 kg)AU-2130AU-4068 & AU-7080 5.9 A 6.4 A278 lbs. (127 kg)Angle of Rotation 92° maximumOperating Time 60 Seconds Life Cycle 15,000 Full Stroke Cycles; 2,500,000 Repositions at Rated Running Torque Ambient TemperatureFail Position -13°F to 158°F (-25°C to 70°C)Duty Cycle Disclaimer - The performance specifications are nominal and conform to acceptable industry standards. For application at conditions beyond these specifications, consult the local Bray office. Bray, Inc. shall not be liable for damages resulting from misapplication or misuse of its products.AU-xxxx On/Off or Floating Control Type AU-xxxxSVModulating24 VDC 110 – 120 VAC 120 V internal (12.5 W)S4 – 25% Intermittent dutyOn/Off, Floating ModulatingS2 -15 min continuous, max. six starts/minute Default Setting Loss of supply power - Fail-in-placeCertifications CEAU Series - Model SelectionAU Series - WiringFIELD WIRING ACTUATORBCD-WD-A048NOTES:1. POWER INPUT FROM FIELD CONTROL PANEL TO ACTUATOR2. 120VAC COMMAND SIGNAL INPUT FROM FIELD CONTROL PANEL TO ACTUATOR (LIVE AND NEUTRAL BOTH REQUIRED FOR OPERATION)3. OPTIONAL: POWER OUTPUT FROM ACTUATOR TO BE USED BY FIELD CONTROL PANEL CONTACTS FOR ACTUATOR INPUTS4. OPTIONAL: 120VAC COMMAND SIGNAL INPUT FROM FIELD CONTROL PANEL TO ACTUATOR (LIVE AND NEUTRAL BOTH REQUIRED FOR OPERATION). FUNCTIONAL PURPOSE IS DETERMINED BY PROGRAMMING SELECTION5. OPTIONAL: DIGITAL OUTPUT FROM ACTUATOR, VOLTAGE FREE CONTACT. RATING: 250V 5AMP6. OPTIONAL: ANALOG OUTPUT FROM ACTUATOR TO BE USED BY FIELD PLC FROM MONITORING. 4-20mA @ 500 OHM MAXLEGEND:TERMINAL SYMBOLS FIELD WIRING FCTORY WIRING GROUNDCALIBRATION SEQUENCE:ACTUATOR THAT WAS FACTORY MOUNTED TO VALVE WAS CALIBRATED BY THE FACTORY IN ACCORDANCE WITH THE APPLICABLE AUMA OPERATION MANUAL.ON/OFF WIRINGAU Series - WiringFIELD WIRING ACTUATORBCD-WD-A049NOTES:1. POWER INPUT FROM FIELD CONTROL PANEL TO ACTUATOR2. 0/4-20mA COMMAND SIGNAL INPUT FROM FIELD CONTROL PANEL TO ACTUATOR3. OPTIONAL: POWER OUTPUT FROM ACTUATOR TO BE USED BY FIELD CONTROL PANEL CONTACTS FOR ACTUATOR INPUTS4. OPTIONAL: 120VAC COMMAND SIGNAL INPUT FROM FIELD CONTROL PANEL TO ACTUATOR (LIVE AND NEUTRAL BOTH REQUIRED FOR OPERATION)5. OPTIONAL: 120VAC COMMAND SIGNAL INPUT FROM FIELD CONTROL PANEL TO ACTUATOR (LIVE AND NEUTRAL BOTH REQUIRED FOR OPERATION). FUNCTIONAL PURPOSE IS DETERMINED BY PROGRAMMING SELECTION6. OPTIONAL: DIGITAL OUTPUT FROM ACTUATOR, VOLTAGE FREE CONTACT. RATING: 250V 5AMP7. OPTIONAL: ANALOG OUTPUT FROM ACTUATOR TO BE USED BY FIELD PLC FROM MONITORING. 4-20mA @ 500 OHM MAXLEGEND:TERMINAL SYMBOLS FIELD WIRING FCTORY WIRING GROUNDCALIBRATION SEQUENCE:ACTUATOR THAT WAS FACTORY MOUNTED TO VALVE WAS CALIBRATED BY THE FACTORY IN ACCORDANCE WITH THE APPLICABLE AUMA OPERATION MANUAL.MODULATING WIRINGAU Series - Dimensions AU-2130AU-4068AU-7080XXX10.4" [265] 6.8" [173]11.8" [300]5.9" [150]6.8" [173]4.9" [125]5.6" [143]1.6" [40]3.0" [75]5.8" [147]12.3" [313]8.9" [225]13.5" [342]11.8" [300]32.9" [836]ø 6.3" [160]10.6" [270]6.5" [166]XXX7.2" [182] 6.8" [173]8.3" [210]4.1" [105]5.8" [148]3.9" [100]6.0" [153]2.0" [50]3.0" [75]5.6" [143]12.7" [323]8.9" [225]10.6" [270]11.8" [300]29.9" [759]ø 7.9" [200]10.6" [270]5.7" [146]6.3" [160]9.8" [250]13.0" [330]6.3" [160]6.5" [165]8.6" [218]11.8" [300]16.5" [418]39.7" [1008]3.0" [75]6.1" [155]12.3" [312](2) 3/4"Conduit Entries(1) 1 1/4"5.6" [143]21.8" [553]11.7" [298]XXX。
AVC 电动执行器手册说明书

1Technical Data Sheet123451 – Manual operation clutch.2 –LED display – rotating the valve to left.3 – LED display – AUX switch is ON.4 – LED display – rotating the valve to right.5 – Button.AVC actuators are intended for the control of rotary mixing and ball valves.Typical application-For controlling mixing valves in heating or cooling systems. -Switchover between heating and cooling.-Switchover between heating and domestic hot water heating. -Switchover between various heat sources. -In solar systems.-In domestic hot water heating systems. -Controls ventilation system elements.-As a component in central heating devices.Features-Robust construction.-Four possible installation positions.-Actuator protection in case of mixing valve blockage. -Signalisation of operation with LED technology. -It can be installed on rotary mixing or ball valves.-Possibility of a proportional control of mixing valves.-Option of an adjustable auxiliary switch for activating the circulation pump in any actuator position.ActuatorsAVC | AVC S | AVC R | AVC RS | AVC YT echnical Data SheetActuators AVC2Seltrond.o.o.|Tržaškacesta85A|SI-2000Maribor|+386(0)26719600|****************|www.seltron.eu3Signalisation of operationThe signalisation of operation with LEDs on the actuator shows the direction in which the mixing valve is moving. The user always has an overview whether theactuator is stationary or moving.Manual mode clutch When the button is in theposition, the actuator operates automatically.When the button is in the position, the valve position can be set with abutton or the manual turning lever.Four possible installation positionsThe AVC actuator can be installed on the mixing valve in four positions (upper,lower, left, right).Direct installation onto more than 20 different valvesThe actuators are available with suitable accessories, which enable direct installation onto more than 20 mixing valves of different manufacturers.T echnical Data SheetActuators AVC4Seltrond.o.o.|Tržaškacesta85A|SI-2000Maribor|+386(0)26719600|****************|www.seltron.eu5Three-point actuator AVC 1AVC0532M210-030Actuator SELTRON AVC05, 3-point, 5 Nm, 2 min, 230 V~Three-point actuator AVC S – with an end-limit switch 1AVC05C2M210-030Actuator SELTRON AVC05S, 3-point, with a switch, 5 Nm, 2 min, 230 V~1AVC15C2M220-030Actuator SELTRON AVC15S, 3-point, with a switch, 15 Nm, 2 min, 230 V~Two-point actuator AVC R 1AVC0521M210-030Actuator SELTRON AVC05R, 2-point, 5 Nm, 1 min, 230 V~Two-point actuator AVC RS – with an end-limit switch 1AVC05B1M210-030Actuator SELTRON AVC05RS, 2-point, with a switch, 5 Nm, 1 min, 230 V~1AVC15B1M220-030Actuator SELTRON AVC15RS, 2-point, with a switch, 15 Nm, 1 min, 230 V~Proportional actuator AVC 10Y 1AVC10Y1M510-030Actuator SELTRON AVC10Y , proportional, 10 Nm, 1 min, 24 V~Accessories1ASCAVMSA000+NN0Seltron, Acaso, Brv, Esbe, Hora, Imit, Imp, Ivar, Paw, Somatherm, Wip(5Nm) (basic version for AVC05)1ASCAVMSB000+NN0Seltron, Acaso, Brv, Esbe, Hora, Imit, Imp, Ivar, Paw, Somatherm, Wip(10Nm+) (basic version for AVC10 and AVC15)1ASCAVMSC000+NN0Centra – type DR/ZR 1ASCAVMSD000+NN0Centra – type DRU1ASCAVMSE000+NN0Landis & Gyr, Siemens – type VBI, VBF 1ASCAVMSF000+NN0Meibes, Wita1ASCAVMSG000+NN0Esbe VRG 1ASCAVMSH000+NN0Firšt 1ASCAVMSI000-NN0Honeywell – type V5442.., type V5433..1ASCAVMSJ000-NN0Paw K32, K33, K341ASCAVMSK000+NN0Danfoss HRB31ASCAVMSM000-NN0Ball valve ISO5211, F03, L (9 mm)1ASCAVMSN000-NN0Ball valve ISO5211, F03, L (11 mm)1ASCAVMSO000-NN0Ball valve Belimo R2..xx-S.., F04, L (10 mm)6S e p t e m b e r 2019. W e r e s e r v e t h e r i g h t t o m a k e c h a n g e s d u e t o p r i n t i n g e r r o r s o r t e c h n i c a l m o d i f i c a t i o n s . I m a g e s a r e s y m b o l i c .©Copyright 2019 Seltron Inc.T: +386 (0)2 671 96 00F: +386 (0)2 671 96 66****************www.seltron.euSeltron d.o.o.Tržaška cesta 85 A SI-2000 Maribor Slovenia。
执行器使用英文说明书
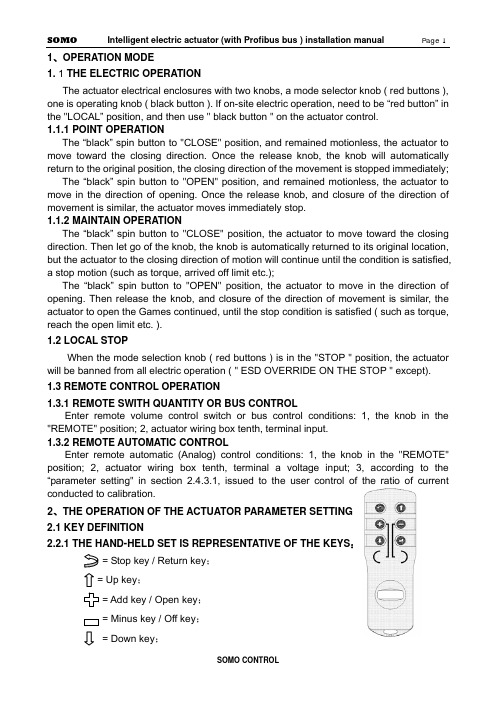
1、OPERATION MODE1. 1 THE ELECTRIC OPERATIONThe actuator electrical enclosures with two knobs, a mode selector knob ( red buttons ), one is operating knob ( black button ). If on-site electric operation, need to be “red button” in the "LOCAL” position, and then use " black button " on the actuator control.1.1.1 POINT OPERATIONThe “black” spin button to "CLOSE" position, and remained motionless, the actuator to move toward the closing direction. Once the release knob, the knob will automatically return to the original position, the closing direction of the movement is stopped immediately;The “black” spin button to "OPEN" position, and remained motionless, the actuator to move in the direction of opening. Once the release knob, and closure of the direction of movement is similar, the actuator moves immediately stop.1.1.2 MAINTAIN OPERATIONThe “black” spin button to "CLOSE" position, the actuator to move toward the closing direction. Then let go of the knob, the knob is automatically returned to its original location, but the actuator to the closing direction of motion will continue until the condition is satisfied, a stop motion (such as torque, arrived off limit etc.);The “black” spin button to "OPEN" position, the actuator to move in the direction of opening. Then release the knob, and closure of the direction of movement is similar, the actuator to open the Games continued, until the stop condition is satisfied ( such as torque, reach the open limit etc. ).1.2 LOCAL STOPWhen the mode selection knob ( red buttons ) is in the "STOP " position, the actuator will be banned from all electric operation ( " ESD OVERRIDE ON THE STOP " except).1.3 REMOTE CONTROL OPERATION1.3.1REMOTE SWITH QUANTITY OR BUS CONTROLEnter remote volume control switch or bus control conditions: 1, the knob in the "REMOTE" position; 2, actuator wiring box tenth, terminal input.1.3.2 REMOTE AUTOMATIC CONTROLEnter remote automatic (Analog) control conditions: 1, the knob in the "REMOTE" position; 2, actuator wiring box tenth, terminal a voltage input; 3, according to the “parameter setting" in section 2.4.3.1, issued to the user control of the ratio of currentconducted to calibration.2、THE OPERATION OF THE ACTUATOR PARAMETER SETTING2.1 KEY DEFINITION2.2.1THE HAND-HELD SET IS REPRESENTATIVE OF THE KEYS:= Stop key / Return key;= Up key;= Add key / Open key;= Minus key / Off key;= Down key;= Confirm key;2.2.2MODE BUTTON REPRESENTS THE KEY:Confirm key: mode button from the "STOP" - > “LOCAL" position, hereinafter referred to as the "Confirm key;Return key: mode button from the "STOP" - > “REMOTE" position, hereinafter referred to as the "return key;2.2.3THE OPERATION BUTTON REPRESENTS THE KEYDown key: the operating button - > " CLOSE" position, hereinafter referred to as the "Down key;Add key: the operating button - > " OPEN" position, hereinafter referred to as the "Add key;2.2 LCDThe actuator is equipped with a bitmap type liquid crystal display. Its layout is the region Ⅰ,Ⅱ,Ⅲ zone.I zone for valve position display area, the valve opening position percentage in the form of real-time display the current valve position value;II zone for the control of display area;III zone for running state and alarm information display area ( see behind the " five, alarm information." );When entering the working parameter setting menu, the LCD screen will use a unified region Ⅰ,Ⅱ,Ⅲ zone.2.3 POWER ON OR RESET2.3.1 POWER ON SELF TEST SYSTEMThe actuator after power on, the actuator control system based on instruction, program area, data region and a A/D conversion function in self. If the test were normal, LCD liquid crystal display valve position display area shows the current valve opening position percentage, alarm area contents are cleared. If the self-test one is not normal, warning zone will always show the abnormal code, the control system not to accept any operation, pending.The actuator power after initialization, the liquid crystal display screen in large font to display the percentage of valve opening. In the valve position limit position, the valve opening display simulation butterfly valve graphical display ( see below ).2.3.2 SYSTEM RESETIn any case, the mode button on the " STOP" position, the operation button is placed on the " CLOSE" position and maintain 5S above the clock, until the liquid crystal screen above the lighted indicator lights, and then release the operation knob away from the "CLOSE" position, the control system reset.2.4 WORKING PARAMETER SETTINGNote 1: in the menu operation, if the user in 1 minutes without key operation, display will automatically return to a setting screen. In addition, in the menu operation, should use the return key to exit the setup screen, before the motor rotates at a setting screen when the valve opening position.Note 2: in the menu operation, first display settings or first display setting value is set after the last stored value, the user can use this feature to view previously set value.2.4.1ENTER MENUThe mode button on the “LOCAL" position, according to the hand-held set on 1, 2, 5, 6 keys of any key can enter the working set menu. Or will the mode button on the " STOP" position, the operation button is placed on the " OPEN" position and maintain 3S above the clock, control system into the working set main menu.Note: In order to behind the narrative and display with convenient, " [ ] " the representationof the selected menu, in the liquid crystal screen menu display, the selected item is to reverse display mode ( i.e. black white ) indicating the cursor position; not the selected itemin a conventional manner ( i.e. black text on a white background ).2.4.2 BASIC SETTINGS MENUIn [ 1 ] on the menu, with a "Up key " or " Down key " to select the desired item, then press " Confirm key ", show will enter the corresponding menu as shown above. Basic settings [ 2 ] on the menu of 4 options, namely, " CHANGE CLOSE DIRECTION ", " LOCAL CONTROL MODE ", " ACCEPT VALVE LIMIT CLOSED VALVE LIMIT OPEN " and " ACCEPT ".2.4.2.1 CHANGE CLOSE DIRECTIONIn [ 2 ] on the menu " CHANGE CLOSE DIRECTION ", the selected item, the line of the right will show a previously set value ( " CLOCKWISE " or " COUNTER CLOCKWISE " ). Click the " Return key" to return to the previous menu, does not alter the previously set value. Users can use these characteristics to query a previously set value ( following similar, no longer has the ). Use the "Add key ", " Minus key " can make the setting value in " CLOCKWISE " and " COUNTER CLOCKWISE " switching between. Use the "Confirm key " save the selected set value.2.4.2.2 LOCAL CONTROLIn [ 2 ] on the menu " LOCAL CONTROL MODE ", the selected item, the line of the right will show a previously set value ( " INCHING " or " MAINTAIN " ). Use the "Add key ", " Minus key " can make the setting value in " INCHING " and " MAINTAIN " switching between. Use the "Confirm key " save the selected set value.2.4.2.3 ACCEPT VALVE LIMIT CLOSEDLimit set order is unlimited, the user can set off again on a set, can also open a set off again.In [ 2 ] on the menu, " ACCEPT VALVE LIMIT CLOSED " selected item, the rows of the right will show the current absolute encoder output current location for thousands of ratio of (0~ 1000). Manual mode will be available to the valve rotation limit; can also be mode button on the " LOCAL " position, according to the hand-held set is Open key/Off key or by operating the button with means of the electric motor valve rotating to limit at. Click the " Confirm key ", LCD screen above the red indicator light flashing 2 exhibit of lanterns before, said actuator has the position calibration for clearance limit. According to the " Confirm key " to " Return key " before, do not set off the limit, and return to the previous menu.2.4.2.4 ACCEPT VALVE LIMIT OPENIn [ 2 ] on the menu, " ACCEPT VALVE LIMIT OPEN " selected item, the rows of the rightwill show the current absolute encoder output current location for thousands of ratio of (0~1000). Available manually valve rotates to the open limit; can also be mode button on the "LOCAL" position, according to the hand setting device on a "Open key/Off key " or by the operating knob with means of the electric motor valve rotating to open limit position. Click the " Confirm key ", when the liquid crystal screen above the green indicator exhibit of lanterns flashing 2 after light, said actuator has the position calibration for open limit. According to the " Confirm key " to " Return key " before, do not set the open limit, and return to the previous menu.Note 1: 1000 ratio 0 and 1000 respectively for absolute encoder minimum code value and the maximum code value, the two is the coincidence. Open, close to set the limit of the whole trip can after this point, but should guarantee the full travel beyond that represent the range of absolute encoder. Note 2: if the set limit is set at one end and another end limit, should not withdraw from the original set, and run to the other end of the limiting office, then enters the other end limit setting item for confirmation, otherwise there will be a " blocking " warning error.2.4.2.5 CHANGE THE LCD DISPLAYIn [ 3 ] on the menu, with a "Up key " or " Down key " selected " CHANGE THE LCD DISPLAY", the bank's right will show a previously set value ( " INVERT " or " POSITIVE " ). Use the "Add key ", " Minus key " to select the desired value, use the "Confirm key " save the selected revision.2.4.3 SECOND SETUPIn [1] on the menu, selected " SECOND SETUP" and press "confirm " [ 3 ] into the menu. As shown in the following illustration.2.4.3.1 4-20mA OF ACC. CALIBRATIONIn [ 3 ] on the menu, with a "Up key " or " Down key " selected " 4-20mA OF ACC. CALIBRATION" and press "Confirm key " [ 4 ] on screen display menu content.When a user sends the actuator 4mA~ 20mA current and actuator previous calibration value is different, use this function is issued to the user 's current recalibrated, causes the actuator and the user's 4mA~ 20mA current transmission device with the same measure, in order to improve the accuracy of the actuator control system.In order to describe convenience, defines 4mA signal low-end (referred to as low signal ), 20mA signals for high-end (referred to as the high letter).CALIBRATE 4mA FOR ACC in [ 4 ]: on the menu, with a "Down key " selected " CALIBRATE 4mA FOR ACC", the bank's right will show the actuator to collect the control current value ( mA ); the user can send the control current to the actuator end of the signal, and when the current is stable after according to the " Confirm key " save the collected current value.CALIBRATE 20mA FOR ACC in [ 4 ]: on the menu, with a "Down key " selected " CALIBRATE 20mA FOR ACC", the bank's right will show the actuator to collect the control current value ( mA ); the user can send the control current to the actuator end signal, and to the current stability according to the " Confirm key " save the current value.At any time the user can control the current calibration menu to query the user sends the current value, but in the control current signal without calibration, inquires into the value is not accurate.2.4.3.2 POSITIONING CONTROL SETUPIn [ 3 ] on the menu, with a "Up key " or " Down key " select " POSITIONING CONTROL SETUP" and click " Confirm key " [ 5 ] on screen display menu content.2.4.3.2.1 DEADBAND ADJUSTMENTDead meaning: the functions of the remote automatic control method. In this mode, the actuator according to the control current to calculate the user wishes to valve position value, then the value and the current valve position values are compared, and if the absolute value of the difference is greater than the zone value, the actuator to action, so that the current valve valve position close to the goal orientation. If the current valve position and the user wants the valve position of the absolute value of the difference in the dead zone range, then the actuator stop motion. Set proper dead-time prevents the actuator in a valve position oscillation.In [ 5 ] on the menu, with a "Down key " selected " DEADBAND ADJUSTMENT " item, the line of the right will show a previously set value ( 0.1%~9.9% ) or " SELF ADAPTING ". The user can use the " Add key ", " Minus key " to change the deadband values. Select the desired deadband value, using " Confirm key " to save your changes.2.4.3.2.2 POLARITY FOR ACCPOLARITY FOR ACC: in current control mode, the lower end of the signal ( 4mA current)Note corresponding to the valve opening position value.In [ 5 ] on the menu, with a "Down key " selected " POLARITY FOR ACC", the bank's right will show a previously set value " 4mA = CLOSED " or " 4mA = OPEN ". The user can use the " Add key ", " Minus key " to change the selection. Select the desired value, using the " Confirm key " to save your changes.Note: the current and low current corresponding to the valve opening position values are mutually exclusive. For example, when setting the low-side current corresponding valve position switch, current automatic corresponding valves full open. Conversely, low signal valve set corresponding valve fully open, the high-end automatic current corresponding to the valve position switch.2.4.3.2.3 ACTION ON LOSS SIGNALLost letter: when the actuator is in the remote automatic control mode, and the control current is less than the low current 1/2, actuators that control signal is lost, referred to as the lost letter.ACTION ON LOSS SIGNAL:ACTION ON LOSS SIGNAL defined in the event of lost letter when the actuator should run into position. The "STAY UP ", " CLOSED ", " OPEN " 3 selectable values. The " STAY UP " refers to remain in situ.In [ 5 ] on the menu, with a "Down key " ACTION ON LOSS SIGNAL " selected " item, the bank's right will show a previously set value ( " STAY UP " or " CLOSED " or " OPEN " ). Use the "Add key ", " Minus key " to select the desired value, use the "Confirm key " save the selected revision.2.4.3.2.4 BRAKE TIME WITH TURN IN REVERSEBRAKE TIME WITH TURN IN REVERSE refers to the movement of the actuator to the target position, and then a short reverse rotation, to compensate for actuator motion inertia, to improve the control precision of the objective.In [ 5 ] on the menu, with a "Down key " " BRAKE TIME WITH TURN IN selected REVERSE " item, the bank's right will show the previous set of actuators rotate in reverse time value ( mS ). Use the "Add key ", " Minus key " in 0~ 50mS time range to select the desired value ( 0mS said without brake ), using " Confirm key " to save your changes.2.4.3.3 ESD SETUPIn [ 3 ] on the menu, with a "Up key " or " Down key " select the "ESD SETUP" and click " Confirm key " [ 6 ] on screen display menu content. : select “ESD SETUP” and " Add key ", according to the " Minus key " will cause the system reset, is a normal phenomenon ( the factory when tested with ).2.4.3.3.1 ESD ACTIONESD: refers to emergency situations (i.e., the actuator control signal terminal to detect ESD ESD appear on the effective signal) actuator which actions to perform. There are 3 kinds of ESD action: " OPEN ", " CLOSED " and " STOP ".In [ 6 ] on the menu, with a "Up key " or " Down key " selected " ESD ACTION " item, the line of the right will show a previously set value ( " CLOSED " or " OPEN " or " STOP " ). Use the "Add key ", " Minus key " to select the desired value, use the "Confirm key " save the selected revision.2.4.3.3.2 ESD ACTION WHEN ESD SIGNAL ISThe actuator ESD control signal terminal input signal can be two levels: no voltage signal is called the low level, a voltage signal is called the high level.In [ 6 ] on the menu, with a "Down key " " ESD ACTION WHEN ESD SIGNAL selectedIS " item, the bank's right will show a previously set value ( " ABSENT " or " PRESENT " ). Use the "Add key ", " Minus key " to select the desired value, use the "Confirm key " save the selected revision.2.4.3.3.3 ESD OVERRIDE ON THERMALESD OVERRIDE ON THERMAL refers to " MOT.OVERTHERMAL " even if the alarm will execute ESD control action, otherwise, to stop the implementation of ESD control action.In [ 6 ] on the menu, with a "Up key " or " Down key " ESD OVERRIDE ON THERMAL " selected " item, the bank's right will show a previously set value ( " YES " or " NO " ). Use the " Add key ", " Minus key " to select the desired value, use the "Confirm key " save the selected revision.2.4.3.3.4 ESD OVERRIDE ON THE STOPESD OVERRIDE ON THE STOP refers to the even mode button in position "STOP" to perform ESD control action, otherwise, to stop the implementation of ESD control action.In [ 6 ] on the menu, with a "Up key " or " Down key " " ESD OVERRIDE ON THE STOP selected " item, the bank's right will show a previously set value ( " YES " or " NO " ). " Add key ", " Minus key " to select the desired value, use the" Confirm key " save the selected revision.2.4.3.4 NETWORK SETUPNot When the actuator through the Profibus field bus control, need to enter the items set in advance. If using a dual channel redundant configuration, need to set of channels and II channel address, or simply set Ⅰchannel address. Channel address refers to the bus control can be the main control system ( Master) and their identification code. e: This machine address reset, the actuator must first off, turn power can guarantee the normal work of the Profibus bus control.In [ 3 ] on the menu, with a "Up key " or " Down key " select the "NETWORK SETUP" and click " Confirm key " [ 7 ] on screen display menu content.2.4.3.5.1 SLAVE ADDRESS1In [ 7 ] on the menu, with a "Up key " or " Down key " select the "SLAVE ADDRESS1 " item, the right will be displayed before the set address value. Use the " Add key ", " Minus key" may be in the 1 to 126 range selection of the desired value, use the "Confirm key " tosave your changes.2.4.3.5.2 SLAVE ADDRESS2In [ 7 ] on the menu, with a "Up key " or " Down key " select the "SLAVE ADDRESS2 " item, the right will be displayed before the set address value. Use the " Add key ", " Minus key" may be in the 1 to 126 range selection of the desired value, use the "Confirm key " to save your changes.2.4.3.6 TWO-SPEED TIMERTWO-SPEED TIMER refers to the operation of the actuator is not continuous, but stop-and-go. This operation is directed to those in need in the valve to be opened or closed in the process of setting the clearance action. TWO-SPEED TIMER allows the actuator topulsating implementation of closing / opening action, so as to effectively increase the travel time, to prevent the hydraulic shock and fluid surge.If the choice is "DISABIE ", the operation of the actuator is normal continuous operation process; if you choose to "ENABLE", show [ 8 ] to enter the menu, according to the requirements of users on TWO-SPEED TIMER [ 8 ] on the menu in the child set.2.4.3.6.1 START POSITION IN OPENINGSTART POSITION IN OPENING refers to the actuator in the opening direction during the operation of opening “TWO-SPEED TIMER “start position. Use the "Add key ", " Minus key " in 0~100% opening range to select a desired value, use the "Confirm key " to save your changes.2.4.3.6.2 STOP POSITION IN OPENINGSTOP POSITION IN OPENING refers to the actuator in the opening direction of operation process termination " TWO-SPEED TIMER " end position. Use the "Add key ", " Minus key " in 0~ 100% opening range to select the desired value ( Note: STOP POSITION IN OPENING must be greater than START POSITION IN OPENING ), "Confirm key " to save your changes.2.4.3.7.3 PULSE ON IN OPENINGPULSE ON IN OPENING refers to the actuator in the opening direction of implementation of "TWO-SPEED TIMER " operation in each TWO-SPEED TIMER required during operation of the travel value. Use the "Add key ", " Minus key " in 2~ 100% opening range to select a desired value, use the "Confirm key " to save your changes.2.4.3.6.4 PULSE OFF IN OPENINGPULSE OFF IN OPENING refers to the actuator in the opening direction of implementation of "TWO-SPEED TIMER” operation in each discontinuous stop required during the time value. Use the "Add key ", “Minus key " in 1 to 255 seconds to select a desired value, use the "Confirm key " to save your changes.2.4.3.6.5 START POSITION IN CLOSINGSTART POSITION IN CLOSING refers to the actuator in the closing direction during the operation of opening “TWO-SPEED TIMER " start position. Use the "Add key ", " Minus key " in 0~100% opening range to select a desired value, use the "Confirm key " to save your changes.2.4.3.6.6 STOP POSITION IN CLOSINGSTOP POSITION IN CLOSING refers to the actuator in the closing direction in the running process of the termination of “TWO-SPEED TIMER " end position. Use the "Addkey ", " Minus key " in 0~100% opening range to select the desired value ( Note: STOP POSITION IN CLOSING must be less than START POSITION IN CLOSING ), "Confirm key " to save your changes.2.4.3.6.7 PULSE ON IN CLOSINGPULSE ON IN CLOSING refers to the actuator in the closing direction of implementation of "TWO-SPEED TIMER” operation in each intermittent operation required during operation of the travel value. Use the "Add key ", " Minus key " in 2~ 100% opening range to select a desired value, use the "Confirm key " to save your changes.2.4.3.6.8 PULSE OFF IN CLOSINGPULSE OFF IN CLOSING refers to the actuator in the closing direction of implementation of "TWO-SPEED TIMER” operation in each discontinuous stop required during the time value. Use the "Add key ", " Minus key " in 1 to 255 seconds to select a desired value, use the "Confirm key " to save your changes.2.4.4 POS.FDBK.CALThe actuator will current location to 4mA~20mA current delivered to the control room. When the user that sent 4mA ~20mA current is not on time, you can use this feature to be calibrated. In [ 1 ] on the menu, select " POS.FDBK.CAL" and press the " Confirm key " [ 9 ] into the menu. As shown in the following illustration.2.4.4.1 ADJUST 4MA FOR CPFIn [ 9 ] on the menu, with a "Up key " or " Down key " selected " ADJUST 4MA FOR CPF", the bank's right will show the previously set value. When the actuator force feedback 0% valve position corresponding to the current value (4mA), in order to offer user detection. If the 4mA current feedback is not accurate, the user can press the " Add key ", " Minus key " to adjust the actuator feedback current value, meet the requirements for " Confirm key " to save your changes.2.4.4.2 ADJUST 20MA FOR CPFIn [ 9 ] on the menu, with a "Up key " or " Down key " selected " ADJUST 20MA FOR CPF", the bank's right will show the previously set value. When the actuator force feedback 100% valve position corresponding to the current value ( 20mA ), in order to offer user detection. If the 20mA current feedback is not accurate, the user can press the " Add key ", " Minus key " to adjust the actuator feedback current value, meet the requirements for " Confirm key " to save your changes.2.4.4.3 POLARITY FOR CPFIn [ 9 ] on the menu, with a "Up key " or " Down key " select " POLARITY FOR CPF", the bank's right will show the previously set value ( 4MA=CLOSED or 4MA=OPEN ). The lower end of said feedback current value ( 4mA ) on behalf of the valve position value ( close / open ). Select the desired value, using the " Confirm key " to save your changes." POLARITY FOR CPF" is selected, the feedback current value ( 20mA ) on behalf of the valve position value is then determined, and the low-side current corresponding to the valve opening position values are mutually exclusive. Such as " POLARITY FOR CPF" selected " off ", is the current representative of the valve position value to "4MA= OPEN ".2.4.5 STATUS MENUIn [1], “SIGNAL VIEW menu, select " and press "Confirm key " [ 10 ] into the menu. As shown in the following illustration.2.4.5.1MODE BUTTON POSITIONIn [ 10 ] on the menu, with a "Up key " or " Down key " " POSITION OF THE SELECTOR KNOB selected " item, the right hand will display " mode button " location. The user can on the knob position query:When the mode knob ( red buttons ) in " STOP " position, [ 10 ] menu " POSITION OF THE SELECTOR KNOB" right "STOP " as normal, otherwise is not normal;When the mode knob ( red buttons ) in " LOCAL " position, [ 10 ] menu " POSITION OF THE SELECTOR KNOB" right "LOCAL " as normal, otherwise is not normal;When the mode knob ( red buttons ) in " REMOTE " position, [ 10 ] menu " POSITION OF THE SELECTOR KNOB" right "REMOTE " as normal, otherwise is not normal.Note: in this way, with the knob “return “operation does not play role.2.4.5.2THE OPERATION BUTTON POSITIONIn [ 10 ] on the menu, with a "Up key " or " Down key " " POSITION OF THE OPERATOR KNOB selected " item, the bank's right will show the mode button position. The user can on the knob position query:When the operation knob ( black button ) in " OPEN " position, [ 10 ] menu " POSITION OF THE OPERATOR KNOB" right "OPEN " as normal, otherwise is not normal;When the operation knob ( black button ) in " CLOSE " position, [ 10 ] menu " POSITION OF THE OPERATOR KNOB" right "CLOSE " as normal, otherwise is not normal;When the operation knob ( black button ) in " NOTHING " position, [ 10 ] menu " POSITION OF THE OPERATOR KNOB" right "NOTHING " as normal, otherwise is not normal.Note: in this entry, with the operation knob " down" operation or the query "CLOSE" position when the screen to display " CLOSE " after a second move to the next item.2.4.5.3 REMOTE OPEN SIGNAL APPEARIn [ 10 ] on the menu, select " REMOTE OPEN SIGNAL APPEAR", the right to display。
努托克NTE系列电动执行器使用说明书

NUTORK CORPORATIONNTE Series Quarter Turn Electric ActuatorActuators & ValvesVisual Indicator +Handwheel (Option)NTE - 02L ABS EnclosureNTE - 02S TypeInternal MagnetContactor For 24VDC(Option)Modulating TypeStandard TypeApproved by:Low Voltage Directive 2006/95/EC Machinery Directive 2006/42/EC Electromagnetic Compatibility Directive 2004/108/EC5. The captive cover bolt prevents bolt from dropping when cover is opened.1. Due to characteristics of valve, the electric actutor must be able to provide high start up torque with full load whenever the valve is at open, closed or any other position. NUTORK NTE series electric actuators are designed for such working requirement.2. Gear driving unit is made of alloy steel with heat treatment featuring high strength, excellent wear resistance and long term fatigue load impact.3. The crank handle is designed as detachable to minimize the dimension of the actuator.4. The integral construction of the wormgear and drive shaft provides long term dependable operation with high output torque.6. The stainless steel stroke bolt and cam provide 0 - 90° adjustability.7. The tempered glass visual position indicator provides anti-aging, temperature resistance and anti-deformation.8. The epoxy encapsulated control servo unit provides heat insulation, moisture and dust proofing, thus suitable for various industrial process requirements.Electric Actuator – Featuresw w w.n u t o r k.c o m112345678Wiring Diagram18/1609/8018/1609/801261260.28 0.151.2/2.65Weight(Kg/Lbs)Enclosure Mounting DirectionAmbient Temp.Valve ConnectionDimension(mm)ModelPowerOutput Torque(Nm/in.lbs)Operation Speed(sec.)Power Consumption(W)Rated Current(A)Insulation ResistanceWithstand Voltage1.10100M Ω@500VDC Ω100M @250VDC Die-casting aluminum alloy72(W) x 75(L) x 120(H)NTE-02S110/220VAC 24VDC 861500VAC@1 Min.550VAC@1 Min.IP68All directions -30°C ~ +60°CISO5211,9/11mm x F03/F04/F05Housing Material standard accessory, built-in,auto-reset typeThermal Protection w w w.n u t o r k.c o m210235.55016.53638.5729x9 11x11Crank HandleG1/4" with cable gland & 30cm lead wire4-M 68-M5503642Depth:17mmBottom ViewBottom ViewModel : NTE-02S Power Supply 200VAC Rated Current : 0.15A Frequency 50/60Hz Amb Temp : 30℃~60℃Output Torque 18NM Operation Time : 12S Enclosure : IP168Manual OperationCD V 42B: e p y T B :e p y T A :e p y T OLSK CCLSPEMLNBlueRed Black BrownCloseOpnenGreyY&GFull-close signalFull-open signal COM OLS K CCLSPEMLN BlueRed Black WhiteBrown Grey CloseOpen Y&G Full-close signal Full-open signal Full-open signal Full-close signal COMOLS CLSPE MRedBlack White Brown Grey Close OpenY&G D1D2Wiring DiagramType: B 10987654321MACPE NO NCNO NCOLSCLSYellow Green Purple Orange Grey Brown WhiteBlackRedBlueOpenStop Close Type: B1Model Power Output Torque Operation Speed(sec.)Power Consumption(W)Rated Current(A)Insulation Resistance Withstand Voltage Thermal Protection Mounting Direction Ambient Temperature Valve Connection Dimension(LxWxH),mm Enclosure Housing Material Weight(Kg)NTE-02L 24VAC25Nm(222in.lbs)100M Ω@500VDC 1500VAC @ 1 minStandard accessory ,built-in ,auto-reset typeAll Direction -30°C ~ +60°C12x12x12mm square drive shaft x F05160(L)x100(W)x133(H)mmIP65ABS 1.4Kg10 sec.20W 1.118W 0.218W 0.1110VAC 220VACFull-open signal EarthFull-closed signal COM1Full-open signal Full-closed signal COM2COMCrank Handle100351235124M516011013303w w w.n u t o r k.c o mw w w.n u t o r k.c o m4NTE-03NTE-05NTE-10NTE-20NTE-40NTE-60NTE-100NTE-160NTE-200NTE-400NTE-6003015/30/5050/60/10080/100/150/200150/250/300/400600300/800/100016002000400060002010/20/30(std.)15/20/30(std.)9/15/20/30(std.)9/15/20/30(std.)3015/30/50(std.)881001001500-360°0-360°0-90°0-90°0-90°0-90°0-90°0-90°0-90°0-90°0-90°◇14/17-F05/F07◇17/22-F07/F10DC motor 202040409090..............................AC motor 10102340909010010010020020024VDC22 2.48.511.511.811.5........................110VAC 0.480.480.640.92 2.06 2.2 2.2 2.2 4.10 4.10220VAC 0.240.240.320.480.920.95 1.20 1.20 1.20 2.10 2.10380VAC0.150.150.190.250.450.460.480.480.480.900.902.22.2477.87.811.211.511.83131ModelOutput Torque(Nm)Operation Speed (Sec.)@0-90°/ 50Hz Operation Angel(Max.)Power (Watts)Valve Conn./ ISO5211◇9/11-F03/F05or ◇14-F05/F07◇17/22/27-F07/F10◇22/27 - F10/F12or ◇36 - F14/F16Rated Current 50HZ(A)Weight-(Kg)Duty Cycle (ON/OFF)Duty Cycle (Modulating)S4 : 30~50%, 300~1200 Start/HourPower Supply 1 Phase:110/220VAC±10%@50/60Hz, 3 Phase:380/440VAC±10%@50/60Hz, 12VDC.24VDC/VAC S2 : 35%,10min. ~ 30min.Stall Protection standard accessory , built-in , auto-reset type Anti-Vibration XYZ 10g , 0.2~34Hz , 10 minutes Ambient Humidity90%RH Max.(non-condensing)Ambient Temperature -30ºC ~ +60ºC Mounting Direction All DirectionsElectrical Conduit M20×1.5 with cable gland for standard type(2 - M20×1.5 with cable gland for modulating type)7. H : Space heater 8. Torque switches(2 units)9. Various mounting bracketsManual Operation Detachable Crank Allen-Key (standard accessory)StopperIn operation : limit switches at full & closed position ; manual operation:mechanical stopper Housing MaterialDie-casting aluminum alloy Bare Shaft Enclosure Rating IP67(standard), IP68(option)Various Option1. Type A standard type2. Type B additional limit switches (2xSPST) or Type B1 additional limit switches(2xSPDT)3. Type C potentiometer unit (1K Ω or 5K Ω)4. Type D potentiometer unit (1K Ω or 5K Ω) with additional limit switches (2xSPST)5. Type E modulating controller (input signal : 4-20mA or 1-5VDC.output signal : 4-20mA )6. Type F current position transmitter(output signal : 4-20mA)Techanical Data(NTE Series Electric Actuator)Type A: Standard TypeOutput Signal:2xSPST(NO) with line power switchInput Signal:4-20mDC or 0-5VDC Output Signal: 4-20mADCOutput Signal: 4-20mADCOutput Signal: 1xSPST(NO)micro-switch each at open & close position.Output Signal: 1xSPST(NO)micro-switch each at open & close position.Output Signal: 1xSPST(NO)micro-switch each at open & close position.Output Signal: 1xSPDT(NC/NO) micro-switch each at open & close positionOutput Signal:0-500Ω or 0-1000ΩType B: 2xSPST(NO)w w w.n u t o r k.c o m5Type E: Modulating ControlType F: R/I ConverterDC Motor with 2xSPST(NO)3 Phase, 380/415/440VAC Motor with 2xSPST(NO)Type C: PotentiometerType B1: 2xSPDT(NO/NC)blue yellow redbrownblack brown greenwhite brown green RHOXSCXSols cls MTPOPEN-SIGNAL SHUT-SIGNAL NC1NC2COM1COM2OPEN STOPSHUTElectric Actuator - Dimension Tablew w w.n u t o r k.c o m6Model NTE-03NTE-05NTE-10NTE-20NTE-40NTE-60NTE-100NTE-160NTE-200NTE-400NTE-600A A1MMNUTORKRso8-M10soO PTU KAA1HH 1ETNUTORKRsoLBDØFDØGXV 4-Z4-S XV 4-Z4-S PBracket + CouplerBare ShaftBare ShaftBare ShaftISO5211NUTORKRE H H1TK L B X V PSZØG ØF D115221**********12686013836509/11/144-M54-M67028F o l l o w e d b y V a l v e115221**********12686013836509/11/144-M54-M67028123222081241915*15827010550709/11/144-M64-M89035148222581482223*2311884178701024-M84-M101254814/17148222581482223*2311884178701024-M84-M101254817/22148222581482223*2311884178701024-M84-M101254817/2215627.52801592530*30148841871021254-M101356522/2715627.52801592530*30148841871021254-M101356522/2715627.52801592530*30148841871401654-M1617565362664391794852*521801802661592544-M18522664391794852*521801802661592544-M1852NTE Series Quarter Turn Electric Actuatorw w w.n u t o r k.c o m7Ordering InformationA. Output Torque / Operation Time1.Code:02S,(18Nm)-12 sec.8.Code:60,(600Nm)- 30 sec.2.Code:02L,(22Nm)-15 sec.9.Code:100,(1000Nm)-50 sec.3.Code:03,(30Nm)-20 sec.10.Code:160,(1600Nm)-88 sec.4.Code:05,(50Nm)-30 sec.11.Code:200,(2000Nm)-100 sec.5.Code:10,(100Nm)-30 sec.12.Code:400,(4000Nm)-100 sec.6.Code:20,(200Nm)-30 sec.13.Code:600,(6000Nm)-150 sec.7.Code:40,(400Nm)-30 sec.14.Code:XX (the other output Torque & Operation Time)Note: 1. The quick operation speed is available upon request.B. Type(Control function)2.Code B: 1xSPST(NO) micro switch for each at open & close3.Code B1: 1xSPDT micro switch for each at open & close4.Code C: 1K Ω potentiometer5.Code D: 1xSPST,NO micro-switch+ 1K Ω potentimeter C. Power Voltage:1.Code A:24VDC 5.Code E:380VAC 2.Code B:24VAC6.Code F:440VAC 3.Code C:110~120VAC7.Code X: others4.Code D:220~240VACNote: 02S only available in 24/120/240VAC, 24VDC 02L only available 240VACD. Accessories:1.Code: H - Heater(02S is not available)E. Enclosure1.Code:IP67, IP67 enclosure(standard)2.Code IP68: IP68 enclosureNote: 1. 02S only available in type A & B control function 2. 02L only available Type B control function 7.Code F: position transmitter (output signal:4-20mADC)NTEOutput TorqueControlType Power AccessoriesEnclosure6.Code E: modulating control (input/output singal:4-20mADC)1.Code A: StandardNUTORK CORP. manufactures a wide range of pneumatic actuators, electric actuators and theaccessories of pneumatic actuator (limit switchbox, solenoid valve, manual override ---etc.) for quarter turn valvesNutork Corp. supply the following product range:NUTORKNK series rack & pinion type (CE-ATEX certified and PED compliant)14 models, the output torque from 9Nm(80in.lbs) to 3,920Nm(34,660in.lbs) at 6 bar air supply.ISO5211/DIN3337 for valve connection, VDI/VDE 3845(Namur) standard connection for solenoid valve and shaft top end(limit switchbox or E/P positioner), +/-5 degree stroke adjustment. 25~30um standard hard anodizedtreatment on actuator body and over 120um epoxy coated on end caps which meet ASTM B117 qualification(salt spread test over 1,000 hours and no corrosion.PTFE, Polyester, Nickel, Ceramic and Epoxy coated are available on request.NSF series scotch yoke type pneumatic and hydraulic actuators (CE-ATEX certified and PED compliant)The output torque from 978Nm(8,656in.lbs) to 226,200Nm (2,001,870in.lbs) at 6 bar air supply.Anti-corrosion painting on outer body and cylinder as standard. VDI/VDE 3845(Namur) standard connection for shaft top end(limit switchbox or E/P positioner), +/-10 degree stroke adjustment. ISO5211 standard for valve connection. PTFE coated on inner cylinder surface. Hydraulic manual override is available for big size actuator.NTE series electric actuator, CE approval13 models and the output torque from 18Nm(159in.lbs) to 6000Nm(53,106in.lbs), compact design, die-casting aluminum alloy housing, alloy steel with heat treatment gear driving unit, integral wormgear & drive shaft, 30% duty rating, detachable crank handle, ISO5211(option), IP67 enclosure.IP68 for option.NTQ electric actuator, CE approval(IP67 & EExdIIBT4 enclosure)13 models, the output torque from 100Nm(885in.lbs) to 6,000Nm(53,106in.lbs), de-clutchable manual override, 2xSPDT each for open & close, torque switch: 1xSPDT each for open & close. space heater, self-lock, IP67 & EExdIIBT4 enclosure.The fully range accessories(Limit Switchbox, Solenoid Valve,Declutchable Manual Override, Air Filter regulator, E/P Positioner ---etc).NTE-02L Quarter Turn Electric ActuatorOutput torque 25Nm(222in.lbs),operation time 10Sec;voltage 24VAC,110VAC & 220VAC for option,ABS housing,30% duty rating,IP65 enclosure.NUTORK Corp.China Office:No.10,Lane 899, Zhuguang Road, Qingpu Area, Shanghai,ChinaTel*************/59888463/59888436Fax*************Email:*****************USA Office:5010 Wright RD. Suite 200B Stafford, TX 77478Tel: +1-281-222-0018 Email:*********************Website: 。
MP 型MP-3xx MP-4xx 电动执行器 使用说明书

137Reversible and Proportional Electric ActuatorsThe MP Series Actuators are used for two-position, floating, and proportional control of dampers, valves, and program switches in heating,ventilation, and air conditioning applications or similar applications.Features:•Proportional actuators with built-in feedback potentiometers.•Spring return and non-spring return models available.•24 Vac, 120 Vac, and 240 Vac models are available.•Die cast housings with four 1/2 in. conduit openings.•Oil-immersed motor and gear train.MP-3xx Series.Model No.ApplicationSolid State Drive CP-8301-xxx CP-9301CP-9302Power RequirementsOutput Shaft Aux.Switch Built-in Transformer aa Units with a “-2” suffix, e.g. MP-xxxx-xxx-2-x, include a built-in transformer (used for Microtherm or with AE-504) with secondary loadswired externally to terminals seven and eight of the actuator. Red (24 Vac) to terminal eight and Blue (12 Vac) to terminal seven. When these actuators are used with controllers other than Microtherm or AE-504, disconnect the Red and Blue leads and tape off. Note: Models prior to “-2” suffix had transformer wired directly to potentiometer. To disconnect the transformer, remove the back plate of the actuator,disconnect, and tape the transformer leads.Volts Hz Amps Torquelb.-in.(N-m)Timing Seconds (No Load)Degrees of Rotation Spring ReturnMP-361ProportionalAvailable 24602.550 (5.6)90180 (Adj.b )bRotation adjustable 45 to 320°. Caution: On actuators with proportional input signals changing the rotation will affect the control, since the internal feedback potentiometer’s travel is fixed.CWSPDT⎯MP-361-600c c Integral solid state drive CP-8301 accepts 6-9 Vdc voltage with 20 Vdc power supply included.CP-8301-024 Included MP-361-691d d Integral solid state drive CP-9301 accepts 6-9 Vdc voltage.CP-9301 Included MP-367Sequencing —SPSTMP-371ProportionalAvailable 180 (non Adj.)CCWSPDTMP-371-600 c CP-8301-024 Included MP-371-691 d CP-9301 IncludedMP-377Sequencing —SPST MP-379Five position None MP-381Proportional Available2.2220 (24.9)130180 (Adj. b )NoSPDTMP-382130 to 1300 (Adj.)MP-387Sequencing Available130SPST MP-389Five position None MP5-381Proportional502.5156SPDT138MP-4xx SeriesModel No.Application Solid StateDriveCP-9301CP-9302Power Requirements Output Shaft Aux.Switch Built-in Transformer aVoltsHzAmpsTorque lb.-in. (N-m)Timing Seconds (No Load)Degrees of RotationSpring ReturnMP-421Proportional Available 120600.6560 (6.8)25180 (Adj.b )NoSPDT⎯MP-42225 to 250 (Adj.)MP-4231390 (Adj. b )MP-42413 to 130 (Adj.)MP-451220 (24.9)80180 (Adj. b )MP-45280 to 800 (Adj.)MP-4534090 (Adj. b )MP-45440 to 400 (Adj.)MP-461-600refer to footnote cCP-8301-120 Included 0.550 (5.6)90180 (Adj. b )CWMR-461-691CP-9301MP-465Proportional Available YesMP-470Five position —180 (non-Adj.)CCWNoneMP-471-600refer to footnote cCP-8301-120 Included SPDT⎯MP-471-691CP-9301 IncludedMP-475Proportional Available YesMP-480Five position—220 (24.9)130180 (Adj. b )NoNone MP-481Proportional Available SPDT⎯MP-481-600refer to footnote cCP-8301-120 Included SPDTMP-481-691 c CP-9301 IncludedMP-483Proportional Available6590 (Adj. b )YesMP-485130180 (Adj. b )MP-486130 to 1300 (Adj.)MP-4950.95450 (50.9)130MP5-483—500.5220 (24.9)7890 (Adj. b )NoSPDTaUnits with a “-2” suffix, e.g. MP-xxxx-xxx-2-x, include a built-in transformer (used for Microtherm or with AE-504) with secondary loads wired externally to terminals seven and eight of the actuator. Red (24 Vac) to terminal eight and Blue (12 Vac) to terminal seven. When these actuators are used with con-trollers other than Microtherm or AE-504, disconnect the Red and Blue leads and tape off. Note: Models prior to “-2” suffix had transformer wired directly to potentiometer. To disconnect the transformer, remove the back plate of the actuator, disconnect, and tape the transformer leads.bRotation adjustable 45 to 320°. Caution: On actuators with proportional input signals changing the rotation will affect the control, since the internal feed-back potentiometer’s travel is fixed.c6 to 9V proportional.139MP-2xxx Series.Model No.ApplicationSolid State Drive CP-9301CP-9302Power RequirementsOutput ShaftAux.Switch Built-in Transformer aaUnits with a “-2” suffix, e.g. MP-xxxx-xxx-2-x, include a built-in transformer (used for Microtherm or with AE-504) with secondary loads wired externally to terminals seven and eight of the actuator. Red (24 Vac) to terminal eight and Blue (12 Vac) to terminal seven. When these actuators are used with controllers other than Microtherm or AE-504, disconnect the Red and Blue leads and tape off. Note: Models prior to “-2” suffix had transformer wired directly to potentiometer. To disconnect the transformer, remove the back plate of the actuator, disconnect, and tape the transformer leads.Volts Hz AmpsTorque lb.-in. (N-m)TimingSeconds(No Load)Degrees ofRotationSpring ReturnMP-2113-500Proportional Available24602.250 (5.6)25180 (non-Adj.)NoSPDT⎯MP-2130-5001200.590 (non-Adj.)YesMP-2150-500180 (non-Adj.)MP-2151-5002400.2230MP-4xxx Series.Model No.ApplicationSolid State DriveCP-9301CP-9302Power Requirements Output ShaftAux.SwitchBuilt-in Transformer aaUnits with a “-2” suffix, e.g. MP-xxxx-xxx-2-x, include a built-in transformer (used for Microtherm or with AE-504) with secondary loads wired externally to terminals seven and eight of the actuator. Red (24 Vac) to terminal eight and Blue (12 Vac) to terminal seven. When these actuators are used with con-trollers other than Microtherm or AE-504, disconnect the Red and Blue leads and tape off. Note: Models prior to “-2” suffix had transformer wired directly to potentiometer. To disconnect the transformer, remove the back plate of the actuator, disconnect, and tape the transformer leads.VoltsHz Amps Torque lb.-in. (N-m)Timing Seconds (No Load)Degrees of Rotation Spring Return MP5-4651Proportional Available240500.2550 (5.6)108180 (Adj.b )bRotation adjustable 45 to 320°. Caution: On actuators with proportional input signals changing the rotation will affect the control, since the internal feedback potentiometer’s travel is fixed.CW SPDT YesMP-4701Five position—6090180 (non-Adj.)CCW NoneMP5-4751ProportionalAvailable50108SPDTMP-485160220 (24.9)130180 (Adj. b )NoMP5-485150156Part Numbers for Hazardous Locations Applications.Hazardous Locations aaClass 1, Groups C and D, and Class 2, Groups E, F, and G Hazardous Locations; Ref. EN-56-2.Hz ListingMP6-4xx60UL Listed and CSA CertifiedMP7-3xx, MP7-4xx50Input Control signals Refer to the Model Charts for input control signal capability versus specific actuator models.Floating Requires one Single Pole Double Throw (SPDT) switch with floating (center off) position rated at 0.9 amps at 24 Vac or two Single Pole Single Throw (SPST) switches rated at 0.9 amps at 24Vac.Two-position SPDT: Requires snap acting switch rated at 0.9 amps at 24 Vac.SPST: Can be used with certain spring return actuators. Switch must be rated to handle actuator power requirements.Microtherm®Proportional electrical system with the following typical controllers: PP-22x Series, TP-1xx Series, TP-2xx Series, TP-3xx Series, TP-4xx Series, TP-1xxx Series, and TP-1xxxx Series.Standard: Control of a single actuator.Sequencing: Control of two actuators in sequence.Five-position: Used typically for adjustable minimum position (five positions) of an economizer actuator.Slidewire and paralleling Requires AE-504 paralleling relay. AE-504 accepts 100 Ω to 1000 Ω slidewires.Voltage Vdc (System 8000)Requires CP-8301-xxx or CP-9301-xxx Series of solid state actuator drives. Refer to the Model Charts.Current mAdc Requires CP-9302-xxx Series of solid state actuator drives. Refer to the Model Charts. ConnectionsMP-3xx, 4xx, 2xxx, 4xxx Coded screw terminals.Models -600 Suffix Coded screw terminals except for input signal which are color coded pigtails.Power Requirements Refer to the Model Charts to determine power requirements.Torque Refer to the Model Charts to determine the actuator torque rating.Nominal damper area Actuator sizing should be done in accordance with damper manufacturer’s specifications. Spring return Refer to the Model Charts for models that are spring return.EnvironmentAmbient temperature limits Shipping and storage: -40 to 160°F (-40 to 71°C). Operating: -40 to 136°F (-40 to 58°C).Humidity 5 to 95% RH, non-condensing.Locations NEMA 1.NEMA 4 for non-spring return actuators with AM-363.DimensionsMP-3xx, 4xx, 2xxx, 4xxx7 H x 5-3/8 W x 6-5/16 D in. (178 x 136 x 160 mm) NSR.Models -600 Suffix7 H x 5-3/8 W x 8-1/8 D in. (178 x 136 x 206 mm) SR plus actuator drive housing. Agency ListingsUL 873File E9429 Temperature Indicating and Regulating Equipment.CUL Canadian Standard #LR 3728.European Community EMC Directive 89/336/EEC and 92/31 EEC. Low voltage Directive 72/23EEC. Units with a "-xxx-x-2" suffix identify models that are in compliance with CE. Example: MP-xxxx-xxx-x-2.General Instructions Refer to F-15479.140141Figure 1 Typical Reversible Floating Wiring.Model No.Description Damper linkage accessories AM-111Crank arm for 5/16in. (7.9 mm) diameter damper shaft.AM-112Crank arm for 3/8in. (9.5 mm) diameter damper shaft.AM-113Crank arm for 1/2in. (12.7 mm) diameter damper shaft.AM-115Crank arm for 7/16in. (11.1 mm) diameter damper shaft.AM-116Splined crank arm for actuator.AM-122Linkage connector, straight type.AM-123Damper clip.AM-1255/16 x 20in. (7.9 mm x 0.5 m) damper rod.AM-125-0485/16 x 48in. (7.9 mm x 1.2 m) damper rod.AM-132Ball joint connector.AM-161Damper linkage kit.AM-161-1Damper linkage kit.AM-30190 degree mounting bracket.Miscellaneous actuator accessories AM-321Two step switch kit.AM-332Potentiometer kit.AM-341Four step switch kit.AM-342Two step switch and potentiometer kit.AM-363NEMA 4 gasket kit for non-spring return actuators only.CP-8301Electronic drive, voltage input 1 to 20 Vdc.CP-9301Electronic drive, voltage input 6 to 9 Vdc.CP-9302Electronic drive, voltage input 4 to 20 mAdc.TOOL-201Calibration kit for System 8000.TOOL-209135 Ω slidewire calibration kit.Valve linkage for 50 lb.-in. minimum, 180° actuator.AV-391Valve linkage for 1/2 to 2 in. VB-7XXX and 1/2 to 1-1/4in. discontinued VB-9XXX.AV-392Valve linkage for 1-1/2 and 2in. discontinued VB-9XXX.AV-395Valve linkage for 2-1/2 to 4in. VB-9213 or VB-9313.Valve linkage for 130 lb.-in. minimum, 180° actuator.AV-352Valve linkage for 2-1/2 to 6in VB-9213 or VB-9313, 4 to 6 in. VB-9323.AV-393Valve linkage for 1/2 to 2 in. VB-7XXX and 1/2 to 1-1/4in. discontinued VB-9XXX.AV-394Valve linkage for 1-1/2 and 2in. discontinued VB-9XXX.AV-396Valve linkage for 2-1/2 to 4in. VB-9213 or VB-9313.1 Terminals 1,5, & 6 are used for built-inauxiliary switch.2 Rotates CW or Lowers Valve Stem.3 Rotates CCW or Raises Valve Stem.4 These terminal are marked L1 & L2 on line voltage actuators.5 Remove green wire to unground actuator.6 SPDT Neutral Off Switch may be used on manual positioning applications.7 Switch control circuit is 0.5 amp at approx. 24 Vac on either low or line voltage actuators.8 Install under cover of actuator.Figure 2 Adjustable Auxiliary Switch SPDT.Figure 3 Typical PP-2xx Wiring. 142143Figure 4 Typical for Proportional Slidewire.Figure 5 Typical Proportional Electronic ⎯ Voltage.Wiring for MP-461-600, MP-471-600, MP-481-600.1 Typical controllers.2 Actuator rotates clockwise on increase in input signal. To rotate actuator counterclockwise on an increase in input signal reverse Blue/Black and Red/Black leads and reverseBrown/Black and Brown/ White leads.3 Terminals 1, 5 & 6 are used for built-in auxilliary switch. 1- 5NC, 1 -ENO 4 Only 24 Vac actuators have this ground.5 6 20 Vdc. 50 mA power supply in CP-8301-xxx.Part Number Vac Color CP-8301-120White Black/Blue CP-8301-024CP-8301-24012024240White/BlackFigure 6 Typical Proportional Electronic -Current/Voltage Wiring for CP-930x to MP-3xx, MP-4xx, and MP-21xxx Series Actuators. 144。
GBB系列执行器说明书(英文)

DC 0...10 V
Max. permissible input voltage
DC 35 V
Input voltage Y (wires 8-2) Non-adjustable characteristic function
DC 0...35 V DC 0...10 V
Adjustable characteristic function
Feedback potentiometer 1 kΩ
135.1E 136.1E 331.1E 335.1E Three-position control
X
X
X
X
X
X
336.1E X
161.1E X
X X
163.1E 164.1E 166.1E Modulating control
X
X
X
X
X
X
X
X
X
This data sheet provides a brief overview of these actuators. Please refer to the Technical Basics in document Z4626E for a detailed description as well as information on safety, engineering notes, mounting and commissioning.
Auxiliary switches (two)
X
X
X
X
X
X
Rotary direction switch
Powerpack (two actuators, tandem-mounted)
Moog电动执行器手册说明书

ACTUATION AND MOTION SYSTEMS PRODUCT GUIDEUTILITY ACTUATORS AND SERVOACTUATORSAEROSPACE AND DEFENSE | UTILITY ACTUATORSCAPABILITYMoog has been developing specialized high technology and utility electromechanical actuators for over 35 years. Our capability includes in-house design, manufacturing expertise, engineering support and qualification for these products.PRODUCT RANGEProducts range from 25 to 2,500 in-lb for rotary and 100 to 2,000 lbf for linear configurations. We can offer our assemblies with integral servo control electronics. Moog offers a variety of communication interfaces including analog, (+/- 10 VDC for example), RS232 / 422 / 485, R/C PWM and CAN Bus. We design for redundancy if required by our customer.Moog is a FAA certified repair station and can offer hardware in support of repairs, upgrades or overhauls.FAA / EASA Approved Repair Station Location, Blacksburg, VA FAA Repair Station: 21MR057C Cage Code: 999321501 North Main StreetBlacksburg VA 24060-3127 USA Tel: +1-540-552-3011Fax: +1-540-557-6719AS9100:2016 Certified ISO9001:2005 CertifiedThese products were previously manufactured at Moog’s Springfield, PA, facility.ABOUT MOOGMoog’s multi-purpose actuators and servoactuators can be used for a variety of high performance applications and are standard building blocks used in ruggedized systems. We utilize our expertise in DC electromagnetics, gearing, rate and position loop servo electronics and mechanical design in these assemblies. Moog rotary and linear electromechancial actuators are used in:• Fixed and Rotary Wing Aircraft• Unmanned Vehicles / Remotely Operated Vehicles • Ground Vehicles • Radar Systems• Remote Weapon Stations • EO / IR Sensor Pods• Valve / Damper Actuators• eVTOL / Advanced Air MobilityROTARY ACTUATORSModel Size in (mm)Load T orque in-lbs Stroke Weight lbs Operating Voltagevdc2200.90 x 2.7 x 4.1(22.9 x 68.6 x 104.1)50 or 100Depending on Output Configuration±45°0.628820 1.5 x 3.2 x 4.3(38.1 x 81.3 x 114.1)80 Rated 150 Peak ±45° 2.828863 1.6 x 4.1 x 4.5(40.6 x 103.9 x 113.0)150 Rated 320 Peak ±45° 2.028935 2.3 x 4.8 x 6.6(58.4 x 121.9 x 167.6)150 Rated 600 Peak ±45° 3.9289653.5 x 7.1 x 9.8(88.9 x 180.3 x 248.9)2,200 Rated 2,500 Peak±90°11.528ROTARY ACTUATORSRotary servoactuators utilize brush and brushless type DC motors using both neodymium and rare earth magnets. These units have been designed with separate or integrated analog or digital amplifiers, spur gearing and potentiometers or rotary magnetic encoders (RME) as feedback devices. Typical applications include Unmanned Aerial Vehicles (UAVs) , Remotely Piloted Vehicles (RPVs), electric Vertical Take-Off and Landing (eVTOL) vehicles, target drones and utility aircraft applications.CUSTOM DESIGNSMoog’s experience makes us familiar with numerous types of rotary and linear electromechanical actuation requirements. Weoffer our customers a solution from dozens of product configurations or a baseline design. We recognize that it is not always possible to utilize an existing design, so we are equally comfortable in offering customization to meet individual customer needs. Customizations often include expanded angular deflection, unique mounting provisions and/or relocation of connectors or other mechanical parts. Moog works closely with each customer to help select the appropriate model with a focus towards meeting program milestones and goals.Moog is committed to work with our customers in providing a solution to customer specific requirements if an existing design is not available. We are experts in design, development, qualification and certification. In addition to the hardware development, our sites include program management professionals who can support SDRL creation, milestone reporting and overall risk mitigation. Moog offers extensive engineering experience in mechanical, electrical and system disciplines to our customers.MODEL 220MODEL 820MODEL 863MODEL 935MODEL 965LINEAR ACTUATORSModel Size in (mm)Force lbs Stroke in Weight lbs Power vdc 981Integrated Electronics2.50 x 4.05 x 14.00 (63.5 x 102.9 x 355.6)10 Rated 30 Stall ±.654.75289092.5 x3.57 x 2.5(63.5 x 90.68 x 63.5)12 Rated 0.750.7528973Dual Motor Construction 3.25 x 3.56 x 11.17 (82.6 x 90.4 x 283.7)350 Rated 1,120 Stall 4.50 6.3028290Integrated Electronics 15 x 4.27 x 1.9(381 x 108.46 x 48.26)1,500 Rated 2,500 Stall 7.75 6.0028974Dual Motor Construction3.88 x4.75 x 14.75 (98.6 x 120.7 x 374.6)1,500 Rated 2,150 Stall7.258.1028LINEAR ACTUATORSLinear actuators translate rotary motion to linear motion. They have the same features and similar applications as rotary units. This actuator configuration is used to control linear motion. It utilizes high performance DC motors coupled to high efficiency gearing. A ball screw or lead screw / nut assembly is typically used to translate the rotary to linear motion. It typically integrates a position transducer and fail-safe brake in a robust structural design. Moog can couple the actuator with position loop servo control electronics. We can also offer several actuators with redundancy through the motor and feedback device.MODEL 973MODEL 290MODEL 909MODEL 974MODEL 981HIGHER LEVEL SOLUTIONSMoog’s unique product offering of motion technology (slip rings, motors, resolvers, drives and actuators) and fiber optic products provides the capital assets and engineering capabilities to design, manufacture and integrate these discrete products into an integrated gimbaled mechanism. In today’s business environment where many corporate strategies are to focus on core competencies, let Moog take the design and integration of these discrete components into fully functional and tested subassemblies that are ready for installation into the end-item assembly. If your strategy is to outsource these assemblies on a build-to-print basis, we are ready to apply our resources so you can achieve those goals too.Our integrated assemblies range from simple combinations of slip rings and resolvers to sophisticated electromechanical assemblies including the motor, drive electronics, fiber optic rotary joints, hydraulic and pneumatic swivels and RF rotary joints. We also offer and provide fully integrated servo and utility actuators complete with precision gearing, clutches, brakes and closed-loop control electronics.Our business strategy is simple, let Moog focus on what we do best so our customer can focus on what they do best. This strategy provides our customers with many measurable benefits.SOLUTIONSChallengeCustomer needed to rapidly develop a higher reliability, digital interface source for servoactuators on a new eVTOL platform. The actuators are a drop-in replacement on all flight control surfaces and improve environmental and EMI performance.SolutionMoog responded with a DSP-based control design that moves flaps, aileron and ruddervator positions despite the varying loads. Because aerodynamic loads are doubled at several positions on the vehicle, Moog developed a second stage bolt-on gearbox that doubles the output torque from 50 to 100 in-lbs, allowing use of the same basic configuration at multiple positions. Moog also designed a highly reliable solid-state solution for position feedback utilizing a magnetic encoder. We have continued to evolve the digital electronics, as well as our unique interface protocol. Moog is aware of and working towards industry standards regarding certification for use in civil airspace.ChallengeCustomer needed to develop a higher reliability, digital interface source for servoactuators on a tactical class UAV operating in a high altitude environment. The actuators offered meet the requirements for multiple flight control surfaces.SolutionMoog provided a standard 150 in-lb rated rotary electromechanical servoactuator and developed a thermal management system that detects cold temperature environments (as low as -85°C). The actuator employs a fully integrated servo controller and film potentiometer position feedback along with a high reliability stainless steel gear train. The thermal system and integrated heater circuit allows operation at 100% performance through all operating extremes.ROTARY JOINTS AND SLIP RINGSThese high performance products are used in systems that require unrestrained, continuous rotation while transmitting power, data and media from a stationary device to a rotating structure. High bandwidth options include Ethernet, high definition video and other industry standard formats. Moog also has solutions including fiber optic rotary joints, fluid rotary unionsand position sensors.DIRECT DRIVE DC TORQUE MOTORS AND ALTERNATORSFrameless torque motors are used in defense applications that require high power density and quick accelerations. The motors are optimized to minimize input power for maximum efficiency. Alternators in the same mechanical configuration can be used for mobile power generation.RESOL VERSMoog offers rugged resolvers that provide accurate positioning and velocity feedback, as well as commutation of brushless motors. These models withstand the shock and vibration levels often encountered in aerospace and military applications. They are used for vertical integration with motors and slip ring assemblies.ACTUATORSMulti-purpose electromechanical actuators are available in both rotary and linear configurations and are standard building blocks in a variety of systems. Some of our actuators integrate servoelectronics. These actuators are used on air, ground and unmanned applications.DEFENSE PRODUCTSHIGH SPEED DATA COMMUNICATIONSM oog provides innovative components and communication sub-systems for both copper and optical fiber based systems used in harsh environments. Moog meets the demanding high speed and secure networking equipment requirements of todays modern defense systems. The product range includes electro-optical transceivers, link extenders, Ethernet media converters and switches, data aggregators and multiplexer/de-multiplexer solutions.INTEGRATED MOTION ASSEMBLIESOur higher level solutions range from simple combinations of individual products to sophisticated electromechanical assemblies including the motor, drive electronics, slip ring, fiber optic rotary joint, fluid / pneumatic swivel and RF rotary joint. Moog’s single-axis gimbal stage supports most payloads, and all the rotary components are integrated into one assembly. This design reduces set-up time andsimplifies the installation process.AMERICAS1501 North Main Street, Blacksburg, Virginia 24060 +1(540)**************************** EUROPE30 Suttons Business Park, Reading Berkshire, RG6 1AW +44(0)*******************************Moog Space and Defense @MoogSDG @MoogSDG @MoogSDG @MoogInc©2022 Moog, Inc. All rights reserved.Products listed herein are subject to U.S. Export Regulations and may require export licensing. Contact Moog to obtain specific export control requirements.。