机械加工精度计算
机械加工精度设计举例

M27
Φ30 K5 E Φ35
Φ40
Φ30K5 E
(2) Φ35(与齿轮基准孔的配合)轴颈的尺寸公差带
齿轮精度等级为7级,则内孔尺寸公差为IT7 ,与其配合的轴 为IT6。此处属于小间隙的滑动配合且对定位精度要求高。
根据优先配合 ,选轴的基本偏差代号为g,则轴的公差带代号为Φ35g6
E
其配合代号为 Φ35H7/g6
6×26h5×32a11×6h8
Page 6
M27
Φ30 Φ35
Φ40
Φ30
(4) 为保证Φ30,Φ35, Φ28和M27轴线与A-B同轴,应规定它们的径向圆跳
动公差 齿轮精度为7级, tr= 0.3FP=0.3×0.038=0.011 按尺大小类比法,Φ35的径向圆跳动公差tr= 0.012, Φ30的径向圆
Page 1
1. 确定尺寸精度 (1) Φ30(与6级滚动轴承6306内圈配合)轴颈尺寸公差
该轴承的当量径向负荷P 1804 额定动负荷C 26700 0.067 0.07
属于轻负荷。
轴承工作时承受定向负荷作用。内圈与轴一起转 动,故内圈承受旋转负荷。查表得两轴颈的公差带代号为Φ30k6
E
Page 2
Φ30 Φ35
Φ40
Φ30
2. 确定几何公差
(1)与轴承内圈、齿轮内孔、花键毂配合轴颈表面采用包容要求 ;
(2) 与轴承内圈配合表面要求圆柱度公差,按6级轴承查 表, 得圆柱度 公差值为0.003。
(3)Φ40轴肩两端面对Φ30k6 两轴线的公共基准 A-B轴向圆跳
动公差,由表6.6查得0.006。
跳动公差tr= 0.011, Φ28的径向圆跳动公差tr= 0.010, M27的径向圆跳 动公差tr= 0.009.
机械制造工艺课件第三章机械加工精度
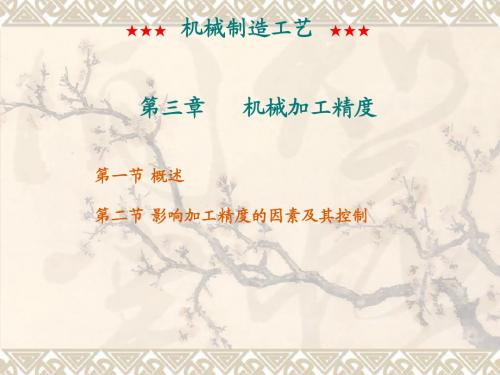
★★★
机械制造工艺
★★★
三、影响加工精度的原始误差
机械加工时,机床、刀具、夹具和工件等组成了一个工艺系统, 工艺系统的各个部分在加工过程中,应该保持严格的相对位臵关系。 由于受到许多因素的影响,系统的各个环节难免会产生一定的偏移, 使工件和刀具间相对位臵的准确性受到影响,从而引起加工误差。 原始误差即导致工艺系统各环节产生偏移的这些因素的总称。原始 误差中,有的取决于工艺系统的初始状态,有的与切削过程有关。 当原始误差的方向发生在加工表面法线方向时,引起的加工误 差最大;当原始误差的方向发生在加工表面的切线方向时,引起的 加工误差最小,一般可以忽略不计。为了便于分析原始误差对加工 精度的影响程度,我们把对加工精度影响最大的那个方向(即通过 切削刃的加工表面的法向)称为误差的敏感方向。而把对加工精度 影响最小的那个方向(即通过切削刃的加工表面的切向)则称为误 差的不敏感方向。
★★★
机械制造工艺
★★★
一、加工原理误差
原理误差即是在加工中由于采用近似的加 工运动、近似的刀具轮廓和近似的加工方法而 产生的原始误差。 完全符合理论要求的加工方法,有时很难实 现,甚至是不可能的。这种情况下,只要能满 足零件的精度要求,就可以采用近似的方法进 行加工。这样能够使加工难度大为降低有利于 提高生产效率降低成本。
★★★
机械制造工艺
ห้องสมุดไป่ตู้
★★★
3)定尺寸刀具法:是直接利用刀具的相应尺寸来 保证加工尺寸的方法。如用钻头钻孔,铰刀铰孔,用拉 刀、铣刀加工键槽等。加工尺寸精度的高低主要与刀具 的制造精度,安装精度和磨损及机床运动精度等因素有 关。这种加工方法加工精度稳定,生产率也高。 4)自动获得尺寸法:是利用测量装臵、调整装臵 和控制系统等组成的自动化加工系统,在加工过程中能 自动测量、补偿调整,当工件达到尺寸要求时,能自动 退回停止加工的方法。
机械加工方法与零件的粗糙度及精度等级之间的对应表

机械加工方法与零件的粗糙度及精度等级之间的对应表本文章由里氏硬度计/官方网站发布。
序号=1Ra值不大于μm=100表面状况=明显可见的刀痕加工方法=粗车、镗、刨、钻应用举例=粗加工的表面,如粗车、粗刨、切断等表面,用粗镗刀和粗砂轮等加工的表面,一般很少采用-------------------------------------------------- ---------序号=2Ra值不大于μm=25、50表面状况=明显可见的刀痕加工方法=粗车、镗、刨、钻应用举例=粗加工后的表面,焊接前的焊缝、粗钻孔壁等-------------------------------------------------- ---------序号=3Ra值不大于μm=12.5表面状况=可见刀痕加工方法=粗车、刨、铣、钻应用举例=一般非结合表面,如轴的端面、倒角、齿轮及皮带轮的侧面、键槽的非工作表面,减重孔眼表面-------------------------------------------------- ---------序号=4Ra值不大于μm=6.3表面状况=可见加工痕迹加工方法=车、镗、刨、钻、铣、锉、磨、粗铰、铣齿应用举例=不重要零件的配合表面,如支柱、支架、外壳、衬套、轴、盖等的端面。
紧固件的自由表面,紧固件通孔的表面,内、外花键的非定心表面,不作为计量基准的齿轮顶圈圆表面等-------------------------------------------------- ---------序号=5Ra值不大于μm=3.2表面状况=微见加工痕迹加工方法=车、镗、刨、铣、刮1~2点/cm^2、拉、磨、锉、滚压、铣齿应用举例=和其他零件连接不形成配合的表面,如箱体、外壳、端盖等零件的端面。
要求有定心及配合特性的固定支承面如定心的轴间,键和键槽的工作表面。
不重要的紧固螺纹的表面。
需要滚花或氧化处理的表面-------------------------------------------------- ---------序号=6Ra值不大于μm=1.6表面状况=看不清加工痕迹加工方法=车、镗、刨、铣、铰、拉、磨、滚压、刮1~2点/cm^2铣齿应用举例=安装直径超过80mm的G级轴承的外壳孔,普通精度齿轮的齿面,定位销孔,V型带轮的表面,外径定心的内花键外径,轴承盖的定中心凸肩表面-------------------------------------------------- ---------序号=7Ra值不大于μm=0.8表面状况=可辨加工痕迹的方向加工方法=车、镗、拉、磨、立铣、刮3~10点/cm^2、滚压应用举例=要求保证定心及配合特性的表面,如锥销与圆柱销的表面,与G级精度转动轴承相配合的轴径和外壳孔,中速转动的轴径,直径超过80mm的E、D级转动轴承配合的轴径及外壳孔,内、外花键的定心内径,外花键键侧及定心外径,过盈配合IT7级的孔(H7),间隙配合IT8~IT9级的孔(H8,H9),磨削的齿轮表面等-------------------------------------------------- ---------序号=8Ra值不大于μm=0.4表面状况=微辨加工痕迹的方向加工方法=铰、磨、镗、拉、刮3~10点/cm^2、滚压应用举例=要求长期保持配合性质稳定的配合表面,IT7级的轴、孔配合表面,精度较高的齿轮表面,受变应力作用的重要零件,与直径小于80mm的E、D级轴承配合的轴径表面、与橡胶密封件接触的轴的表面,尺寸大于120mm的IT13~IT16级孔和轴用量规的丈量表面-------------------------------------------------- ---------序号=9Ra值不大于μm=0.2表面状况=不可辨加工痕迹的方向加工方法=布轮磨、磨、研磨、超级加工应用举例=工作时受变应力作用的重要零件的表面。
机械加工方法与零件的粗糙度及精度等级之间的对应表

机械加工方法与零件的粗糙度及精度等级之间的对应表序号=1Ra值不大于呵=100表面状况=明显可见的刀痕加工方法=粗车、镗、刨、钻应用举例=粗加工的表面,如粗车、粗刨、切断等表面,用粗镗刀和粗砂轮等加工的表面,一般很少采用序号=2Ra值不大于呵=25、50表面状况=明显可见的刀痕加工方法=粗车、镗、刨、钻应用举例=粗加工后的表面,焊接前的焊缝、粗钻孔壁等序号=3Ra值不大于呵=12.5表面状况=可见刀痕加工方法=粗车、刨、铣、钻应用举例=一般非结合表面,如轴的端面、倒角、齿轮及皮带轮的侧面、键槽的非工作表面,减重孔眼表面序号=4Ra值不大于呵=6.3表面状况=可见加工痕迹加工方法=车、镗、刨、钻、铣、锉、磨、粗铰、铣齿应用举例=不重要零件的配合表面,如支柱、支架、外壳、衬套、轴、盖等的端面。
紧固件的自由表面,紧固件通孔的表面,内、外花键的非定心表面,不作为计量基准的齿轮顶圈圆表面等序号=5Ra值不大于呵=3.2表面状况=微见加工痕迹加工方法二车、镗、刨、铣、舌I」1~ 2点/cm A2、拉、磨、锂、滚压、铣齿应用举例=和其他零件连接不形成配合的表面,如箱体、外壳、端盖等零件的端面。
要求有定心及配合特性的固定支承面如定心的轴间,键和键槽的工作表面。
不重要的紧固螺纹的表面。
需要滚花或氧化处理的表面序号=6Ra值不大于呵=1.6表面状况=看不清加工痕迹加工方法二车、镗、刨、铣、铰、拉、磨、滚压、舌J 1 ~ 2点/盯八2铣齿应用举例二安装直径超过80mm的G级轴承的外壳孔,普通精度齿轮的齿面,定位销孔,V型带轮的表面,外径定心的内花键外径,轴承盖的定中心凸肩表面---序号=7Ra值不大于呵=0.8表面状况=可辨加工痕迹的方向加工方法二车、镗、拉、磨、立铣、舌J 3~ 10点/cm A2、滚压应用举例=要求保证定心及配合特性的表面,如锥销与圆柱销的表面,与G 级精度滚动轴承相配合的轴径和外壳孔,中速转动的轴径,直径超过80mm 的E、D 级滚动轴承配合的轴径及外壳孔,内、外花键的定心内径,外花键键侧及定心外径,过盈配合IT7级的孔(H7),间隙配合IT8〜IT9级的孔(H8,H9),磨削的齿轮表面等序号=8Ra值不大于呵=0.4表面状况=微辨加工痕迹的方向加工方法二铰、磨、镗、拉、舌J 3~ 10点/盯八2、滚压应用举例二要求长期保持配合性质稳定的配合表面,IT7级的轴、孔配合表面,精度较高的齿轮表面,受变应力作用的重要零件,与直径小于80mm 的E、D级轴承配合的轴径表面、与橡胶密封件接触的轴的表面,尺寸大于120mm 的IT13〜IT16级孔和轴用量规的测量表面序号=9Ra值不大于呵=0.2表面状况=不可辨加工痕迹的方向加工方法=布轮磨、磨、研磨、超级加工应用举例=工作时受变应力作用的重要零件的表面。
加工精度
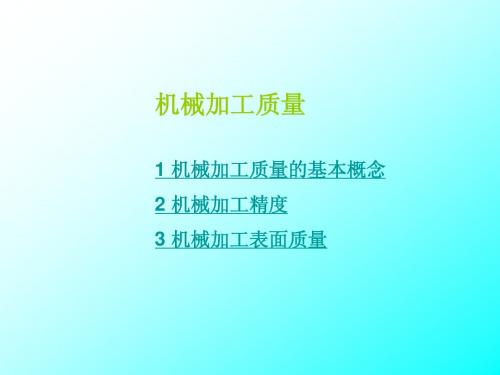
返回本章目录
工件回转(车削)的情况: ①工件回转在1处: R1 = R - A ②工件回转在2处: R2 = R ③工件回转在3处: R3 = R + A ④工件回转在4处: R4 = R D1-3= R1+R2=2R D2-4= 2R = D1-3
返回本章目录
工件孔轴心线
α
主轴回转轴心线
主要影响工件的形状精度
垂直误差
两者比较
R y 400Rz
结论:普通机床导轨水平误差比垂直误差对加 工误差影响大得多。(此例两者相差400倍)
返回本章目录
误差敏感方向— 对加工误差影响大的加工表面的法线方向。 平面磨床误差敏感方向为
导轨垂直误差。
返回本章目录
2)主轴误差
主轴回转误差
—主轴实际回转中心的瞬时位置 与理想位置的最大偏差。 一般把主轴误差分解为三种独立运动形式: ①纯轴向窜动△x ②纯径向移动△r ③纯角度摆动△α
机械加工质量
1 机械加工质量的基本概念 2 机械加工精度 3 机械加工表面质量
机械加工质量
1 机械加工质量的基本概念
机器零件的加工质量决定了机器的: 1.性能 2.质量 3.寿命 机器产品加工质量的内容: 1.加工精度 2.加工表面质量
返回本章目录
机器产品加工质量要求越来越高(近30年) 加工精度 (普通)从0.01mm →0.005mm (精密)从1μm → 0.02μm (超精密)从0.1μm →0.001μm 加工表面质量粗糙度方面已获得小于 0.0005μ m的粗糙度。 加工质量与设备、工艺方法、工艺措施有关。
返回本章目录
(4)工艺系统受力变形 工艺系统在加工过程中受: ①切削力; ②惯性力; ③重力; ④夹紧力 力作用→产生工艺系统变形→加工误差
机械加工中尺寸精度的测量方法

机械加工中尺寸精度的测量方法试切法试切法是通过“试切-测量-调整-再试切”的操作流程,反复开展,直到到达要求的尺寸精度为止。
先从加工表面上试切出一个很小的部分,对这部分的尺寸开展测量。
接下来,根据测量结果和加工要求,对刀具的切削刃与工件相对的位置开展适当地调整。
然后再试切,再测量。
经过如此往复的两三次试切和测量之后,当被加工工件的尺寸到达要求后,再切削整个待加工表面。
例如,箱体孔系的试镜加工就应用了试切法测量尺寸精度。
采用试切法测量尺寸精度不需要复杂的装置,而且可以到达一个很高的精度值。
但这种方法的缺点是工序比较复杂,需要开展多次的调整、试切、测量和计算,这样做效率较低,而且费时费力。
再有,这种方法对于工人的技术水平和计量器具的精度有严重的依赖,质量不够稳定,所以往往只适用于较小批量的生产。
试切法中有一种特殊的类型,称为配作。
配作是以已经加工好的工件尺寸为基准,对另一个或者多个相配的工件组合在一起开展加工。
对被加工工件的尺寸须要到达的要求,是以与已加工工件的配合要求为准的。
调整法调整法是利用样件或标准件,如机床上的定程装置、对刀装置或是预先调整好的刀架,修正机床、夹具、刀具和工件之间的准确相对位置,使之到达需要的尺寸精度,然后再以此标准对一批工件开展加工的方法。
因为尺寸已经在加工之前调整到位,所以加工时不再需要开展试切,并在一批零件的加工过程中保持不变。
例如,采用铳床夹具时,刀具的位置靠对刀块确定。
相比于试切法,调整法拥有更加稳定的加工精度和更高的生产率。
这种方法对机床操作员工的要求不是很高,但是对机床调整员工的要求比较高,因此,调整法常用于零件的成批生产和大量生产。
在机床上按照已经事先确定的刻度盘刻度进刀,然后再开展切削,这也是调整法的一种类型。
这种方法需要在大批量生产之前,先采用试切法,确定刻度盘上的刻度。
定尺寸法定尺寸法是用刀具的相应尺寸来保证工件被加工部位尺寸精度的方法。
它开展加工所使用的刀具,如较刀、扩孔钻、钻头等,都具有非常标准的尺寸精度,利用该刀具的尺寸来决定加工面的尺寸,以保证工件被加工部位可以得到较高的精度。
各种机械加工方法的加工精度

各种机械加工方法的加工精度
机械加工方法是指利用机床和切削工具对金属、合金、塑料等材料进行切削、锻造、焊接、抛光等操作,以达到工件设计尺寸、形状和表面粗糙度要求的一系列工艺过程。
不同的机械加工方法有着不同的加工精度,下面将对常见的几种机械加工方法的加工精度进行详细介绍。
1.车、铣、刨、磨加工:
车、铣、刨、磨加工是最常见的机械加工方法之一,其加工精度通常可达到0.01mm级别。
其中,精度最高的是磨加工,其加工精度可达到0.001mm级别。
而车、铣、刨加工的加工精度相对较低,通常在0.01mm 至0.015mm之间。
2.钻削加工:
钻削加工是通过钻头旋转和轴向进给运动,以及工件的切削超前量来进行的。
其加工精度一般可达到0.02mm级别。
3.线切割加工:
线切割是利用金属丝或者金刚线经过电火花腐蚀加工,从而将工件切割成所需形状的加工方法。
其加工精度可达到0.005mm级别。
4.电火花加工:
电火花加工是利用放电现象进行切削的一种加工方法,其加工精度可达到0.001mm级别。
5.冲压加工:
冲压加工是通过冲床对金属板材进行冲裁、弯曲、深冲等形变加工的方法。
其加工精度一般在0.05mm至0.1mm之间。
6.锻造加工:
锻造加工是通过加热和机械力的作用,改变金属原始形状并获得所需形状的一种加工方法。
其加工精度通常为0.2mm至0.5mm之间。
7.激光加工:
激光加工是利用激光束对工件进行切割、焊接等加工的方法。
其加工精度通常可以达到0.01mm级别。
机械加工产品公差精度等级标准
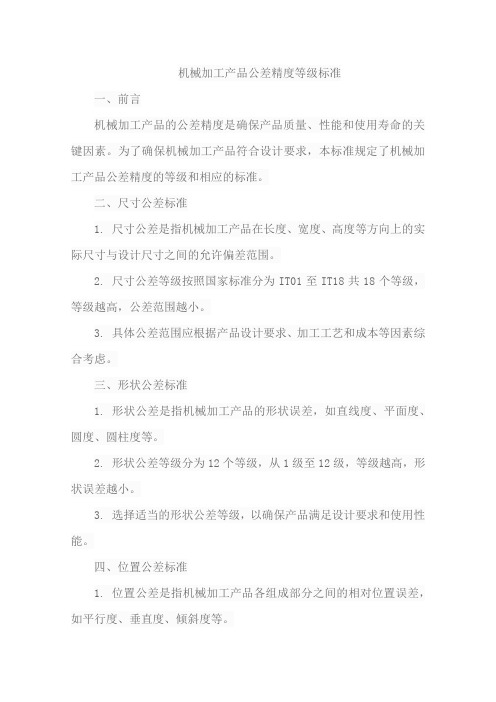
机械加工产品公差精度等级标准一、前言机械加工产品的公差精度是确保产品质量、性能和使用寿命的关键因素。
为了确保机械加工产品符合设计要求,本标准规定了机械加工产品公差精度的等级和相应的标准。
二、尺寸公差标准1. 尺寸公差是指机械加工产品在长度、宽度、高度等方向上的实际尺寸与设计尺寸之间的允许偏差范围。
2. 尺寸公差等级按照国家标准分为IT01至IT18共18个等级,等级越高,公差范围越小。
3. 具体公差范围应根据产品设计要求、加工工艺和成本等因素综合考虑。
三、形状公差标准1. 形状公差是指机械加工产品的形状误差,如直线度、平面度、圆度、圆柱度等。
2. 形状公差等级分为12个等级,从1级至12级,等级越高,形状误差越小。
3. 选择适当的形状公差等级,以确保产品满足设计要求和使用性能。
四、位置公差标准1. 位置公差是指机械加工产品各组成部分之间的相对位置误差,如平行度、垂直度、倾斜度等。
2. 位置公差等级分为11个等级,从1级至11级,等级越高,位置误差越小。
3. 选择适当的位置公差等级,以确保产品装配精度和使用性能。
五、表面粗糙度标准1. 表面粗糙度是指机械加工产品表面微观几何形状的不平度。
2. 表面粗糙度等级分为Ra、Rz、Ry等多种评定参数,每个参数分为不同等级,等级越高,表面越光滑。
3. 选择适当的表面粗糙度等级,以确保产品表面质量和使用性能。
六、材料公差标准1. 材料公差是指机械加工产品所用材料的物理性能、化学成分等与设计要求之间的允许偏差范围。
2. 材料公差标准应根据产品使用环境和性能要求综合考虑,选择符合国家标准和行业标准的材料。
七、热处理公差标准1. 热处理公差是指机械加工产品在热处理过程中产生的尺寸、形状和性能变化与设计要求之间的允许偏差范围。
2. 选择适当的热处理工艺和参数,以确保产品热处理后的稳定性和性能。
八、装配公差标准1. 装配公差是指机械加工产品在装配过程中各零部件之间的相对位置误差和配合间隙。
孔的最大实效尺寸的公式

孔的最大实效尺寸的公式
(实用版)
目录
1.孔的最大实体尺寸的概念
2.孔的最大实体实效尺寸的公式
3.孔的最大实体实效尺寸的应用
正文
孔的最大实体尺寸是指在孔的尺寸中,最大的实际尺寸,它是控制加工精度的重要参数。
在机械加工中,孔的最大实体实效尺寸的公式可以通过以下步骤计算得出:
1.首先,根据设计图纸,确定孔的基本尺寸,即孔的直径。
2.其次,根据加工工艺和设备能力,确定孔的最大实体尺寸,即孔的最大直径。
3.最后,根据孔的最大实体尺寸和基本尺寸,使用以下公式计算孔的最大实体实效尺寸:
最大实体实效尺寸 = 最大实体尺寸 - 直线度公差
其中,直线度公差是指孔的直线度允许偏差的最大值。
孔的最大实体实效尺寸在机械加工中具有重要的应用。
它可以用于控制加工精度,保证产品的质量。
还可以用于确定加工工艺和设备的能力,以满足生产需要。
第1页共1页。
机械加工精度与加工误差
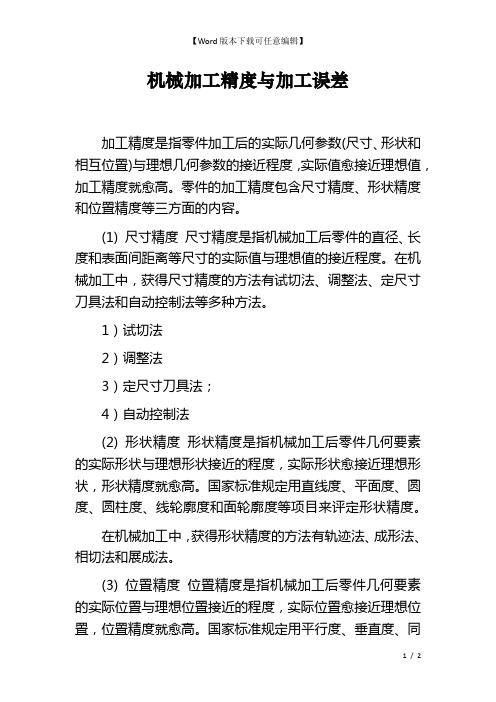
机械加工精度与加工误差加工精度是指零件加工后的实际几何参数(尺寸、形状和相互位置)与理想几何参数的接近程度,实际值愈接近理想值,加工精度就愈高。
零件的加工精度包含尺寸精度、形状精度和位置精度等三方面的内容。
(1) 尺寸精度尺寸精度是指机械加工后零件的直径、长度和表面间距离等尺寸的实际值与理想值的接近程度。
在机械加工中,获得尺寸精度的方法有试切法、调整法、定尺寸刀具法和自动控制法等多种方法。
1)试切法2)调整法3)定尺寸刀具法;4)自动控制法(2) 形状精度形状精度是指机械加工后零件几何要素的实际形状与理想形状接近的程度,实际形状愈接近理想形状,形状精度就愈高。
国家标准规定用直线度、平面度、圆度、圆柱度、线轮廓度和面轮廓度等项目来评定形状精度。
在机械加工中,获得形状精度的方法有轨迹法、成形法、相切法和展成法。
(3) 位置精度位置精度是指机械加工后零件几何要素的实际位置与理想位置接近的程度,实际位置愈接近理想位置,位置精度就愈高。
国家标准规定用平行度、垂直度、同轴度、对称度、位置度、圆跳动和全跳动等项目来评定位置精度。
在机械加工中,获得位置精度的方法有直接找正法、划线找正法和夹具装夹法。
加工过程中有很多因素影响加工精度,实际加工不可能把零件做得与理想零件完全一致;零件加工后的实际几何参数(尺寸、形状和相互位置)对理想几何参数的偏离量称为加工误差。
加工过程中有很多因素影响零件的加工精度,即使是同一种加工方法只要工作条件稍有变化它们所能到达的加工精度也不一样。
例如,采用较高精度的设备,适当选用切削用量,精心完成加工过程中的每一个操作,就能得到较高的加工精度,但这会增加加工成本。
加工经济精度是指在正常生产条件下(采用符合质量标准的设备、工艺装备和标准技术等级的工人,不延长加工时间)所能保证的加工精度。
机床行业机械加工精度标准

机床行业机械加工精度标准近年来,随着科技的不断进步和工业化的快速发展,机床行业在制造领域扮演着至关重要的角色。
机床作为一种关键的生产设备,对于产品的加工精度有着决定性的影响。
在机床行业中制定和遵守机械加工精度标准是非常重要的,它可以确保产品质量和生产效率,并为行业的发展提供基础和指导。
本文将分为四个小节,分别从机床行业中的精度标准、精度等级划分、精度的测量以及机床使用中的注意事项等方面进行详细论述。
1. 精度标准在机床行业中,精度标准是评估和控制产品加工质量的重要依据。
通常来说,机床加工精度标准包括直线度、圆度、平行度、垂直度、位置精度等。
这些标准的要求是由国家相关机构制定的,通常在产品设计和生产过程中都需要遵守。
通过执行这些标准,可以保证产品的尺寸、形状和位置的精度符合要求,从而确保产品质量的稳定和可靠。
2. 精度等级划分为了便于评估和比较不同产品或工件的加工精度,在机床行业中通常会将精度分为不同的等级。
常见的精度等级包括高精度、中精度和普通精度。
高精度要求最严格,适用于一些对精度要求极高的领域,如航空航天和精密仪器制造。
中精度适用于大部分机械加工领域,可以满足一般工件的加工要求。
普通精度则适用于一些对精度要求较低的工件。
在实际生产中,根据具体需求和成本因素,选择合适的精度等级,保证产品的合理加工。
3. 精度的测量机床行业中,精度的测量是确保产品加工质量的关键环节。
为了评估产品的加工精度,可以使用各种测量工具和设备,如游标卡尺、三坐标测量仪、光学测量仪等。
在测量过程中,可以通过与标准进行比对,来判断产品是否符合要求,并进行相应的调整和改进。
精确的测量不仅可以提高产品的加工质量,还可以提高生产效率和降低成本。
4. 机床使用中的注意事项在机床行业中,除了遵守精度标准和进行精度测量外,还需要注意一些使用中的事项,以确保机床的正常运行和延长其使用寿命。
首先,需要定期进行设备维护和保养,包括清洁、润滑和紧固等,以保持机床的良好状态。
机械加工精度定位误差--例题

例4:工件尺寸及工序要求如图a)所示,欲加工键槽 并保证尺寸45mm及对内孔中心的对称度0.05mm,试 计算按图b)方案定位时的定位误差。
解:(1)求45的定位误差 1)工序基准是外圆下母线, 定位基准是外圆的轴线,两 者不重合, ΔB =0.11/2=0.055mm。 2)以外圆在V型块上定位,
解:(1)求45的定位误差 1)工序基准是外圆下母线, 定位基准是孔的轴线,两者 不重合, ΔB =0.11/2=0.055mm。 2)以孔在间隙心轴上水平 放置定位,
ΔY=(0.021+0.042-0.007)/2≈0.028mm
3)工序基准不在定位基面上
ΔD=ΔY+ΔB=0.028+0.105=0.133mm
0.11 Y 2sin 45 0.078mm
ቤተ መጻሕፍቲ ባይዱ
3)工序基准在定位基面上 ΔD=ΔY±ΔB “+”、“-”的判别: 当定位基面直径由大变小,
定位基准朝下变动;若定位基准 位置不动时,工序基准朝上变动; 两者的变动方向相反,取“-”号。 所以45的定位误差为
ΔD=ΔY-ΔB=0.078-0.055 =0.023mm
(2)求对称度0.05的定位 误差 1)工序基准是孔轴线,定 位基准是外圆轴线,两者不 重合, ΔB =0.05=0.05mm。 2)以外圆在V型块上定位, 定位基准在水平方向无位移,
ΔY=0 3)ΔD=ΔB=0.05mm
例1:下图所示为工件铣槽工序简图,求ΔB。 ΔB = 2ΔL
例2:如图所示,以A面定位加工φ20H8孔,求加工尺 寸40±0.1mm的定位误差。
解: 工序基准B与定位基准A
不重合,因此存在基准不重 合误差。
ΔB=0.05+0.1=0.15mm
机械加工精度

误差增大,加工最 低成本不变
加工成本与加工误差之间的关系
一种加工方法介于A、B之间的精度为经济加工精度
6
二、获得加工精度的方法
1.获得尺寸精度的方法 1)试切法 2)调整法 3)定尺寸刀具法 4)自动控制法 2.获得形状精度的方法 1)成形刀具法 2)轨迹法 3)展成法 3.获得位臵精度的方法 1)直接找正法 2)划线找正法 3)夹具定位法
尺寸精度、形状精度和位臵精度三者之间关系
:
通常形状公差限制在位置公差内,而位置误差一般限制 在尺寸公差之内。当尺寸精度要求高时,相应的位置精度、 形状精度也要求高。但形状精度或位置精度要求高时,相应 的尺寸精度不一定要求高,这要根据零件的功能要求来决定。 4
第一节 机械加工精度概述 一、加工精度概念
态下的误差 传动误差 工艺系统受力变形(包括夹紧变形) 工艺系统受热变形 刀具磨损 测量误差 工件残余应力引起的变形
19
原始误差构成
三、影响加工精度的因素(原始误差)
热变形 对刀误差 F 设计基准 夹紧误差
定位误差
菱形销
定位基准 导轨误差
活塞销孔精镗工序中的原始误差
20
三、影响加工精度的因素(原始误差)
误差敏感方向
21
四、研究加工精度的方法
1.通过分析计算或实验、测试等方法
7
1.获得尺寸精度的方法
1)试切法 先试切部分加工表面,测量后,适当调整刀具相 对工件的位臵,再试切,再测量,当被加工尺寸达 到要求后,再切削整个待加工面。
试切
测量
调整车刀
试切法效率低,精度主要取决于工人技术,用于单
件小批生产。
8
1.获得尺寸精度的方法
机械加工中获得工件尺寸精度的常用方法

机械加工中获得工件尺寸精度的常用方法!加工精度是指零件加工后的实际几何参数(尺寸、形状和位置)与图纸规定的理想几何参数符合的程度。
这种相符合的程度越高,加工精度也越高。
在加工中,由于各种因素的影响,实际上不可能将零件的每一个几何参数加工得与理想几何参数完全相符,总会产生一些偏离。
这种偏离,就是加工误差。
从以下三个方面探讨:1.获得零件尺寸精度的方法2.获得形状精度的方法3.获得位置精度方法1.获得零件尺寸精度的方法(1)试切法即先试切出很小部分加工表面,测量试切所得的尺寸,按照加工要求适当调刀具切削刃相对工件的位置,再试切,再测量,如此经过两三次试切和测量,当被加工尺寸达到要求后,再切削整个待加工表面。
试切法通过“试切-测量-调整-再试切”,反复进行直到达到要求的尺寸精度为止。
例如,箱体孔系的试镗加工。
试切法达到的精度可能很高,它不需要复杂的装置,但这种方法费时(需作多次调整、试切、测量、计算),效率低,依赖工人的技术水平和计量器具的精度,质量不稳定,所以只用于单件小批生产。
作为试切法的一种类型——配作,它是以已加工件为基准,加工与其相配的另—工件,或将两个(或两个以上)工件组合在一起进行加工的方法。
配作中最终被加工尺寸达到的要求是以与已加工件的配合要求为准的。
(2)调整法预先用样件或标准件调整好机床、夹具、刀具和工件的准确相对位置,用以保证工件的尺寸精度。
因为尺寸事先调整到位,所以加工时,不用再试切,尺寸自动获得,并在一批零件加工过程中保持不变,这就是调整法。
例如,采用铣床夹具时,刀具的位置靠对刀块确定。
调整法的实质是利用机床上的定程装置或对刀装置或预先整好的刀架,使刀具相对于机床或夹具达到一定的位置精度,然后加工一批工件。
在机床上按照刻度盘进刀然后切削,也是调整法的一种。
这种方法需要先按试切法决定刻度盘上的刻度。
大批量生产中,多用定程挡块、样件、样板等对刀装置进行调整。
调整法比试切法的加工精度稳定性好,有较高的生产率,对机床操作工的要求不高,但对机床调整工的要求高,常用于成批生产和大量生产。
机械设计分度误差计算公式
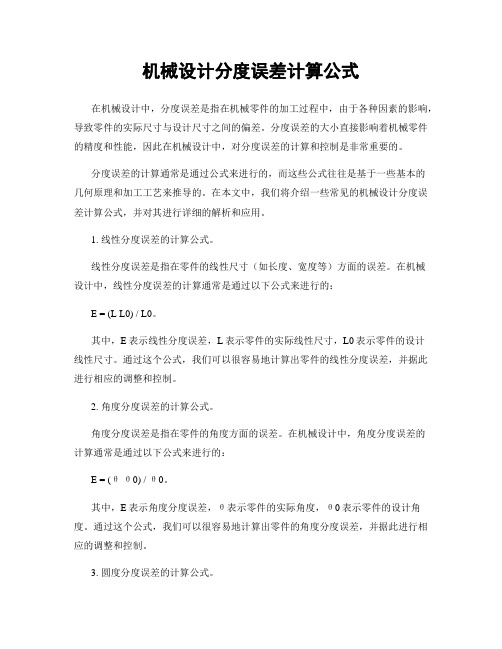
机械设计分度误差计算公式在机械设计中,分度误差是指在机械零件的加工过程中,由于各种因素的影响,导致零件的实际尺寸与设计尺寸之间的偏差。
分度误差的大小直接影响着机械零件的精度和性能,因此在机械设计中,对分度误差的计算和控制是非常重要的。
分度误差的计算通常是通过公式来进行的,而这些公式往往是基于一些基本的几何原理和加工工艺来推导的。
在本文中,我们将介绍一些常见的机械设计分度误差计算公式,并对其进行详细的解析和应用。
1. 线性分度误差的计算公式。
线性分度误差是指在零件的线性尺寸(如长度、宽度等)方面的误差。
在机械设计中,线性分度误差的计算通常是通过以下公式来进行的:E = (L L0) / L0。
其中,E表示线性分度误差,L表示零件的实际线性尺寸,L0表示零件的设计线性尺寸。
通过这个公式,我们可以很容易地计算出零件的线性分度误差,并据此进行相应的调整和控制。
2. 角度分度误差的计算公式。
角度分度误差是指在零件的角度方面的误差。
在机械设计中,角度分度误差的计算通常是通过以下公式来进行的:E = (θθ0) / θ0。
其中,E表示角度分度误差,θ表示零件的实际角度,θ0表示零件的设计角度。
通过这个公式,我们可以很容易地计算出零件的角度分度误差,并据此进行相应的调整和控制。
3. 圆度分度误差的计算公式。
圆度分度误差是指在零件的圆形度方面的误差。
在机械设计中,圆度分度误差的计算通常是通过以下公式来进行的:E = (D D0) / D0。
其中,E表示圆度分度误差,D表示零件的实际直径,D0表示零件的设计直径。
通过这个公式,我们可以很容易地计算出零件的圆度分度误差,并据此进行相应的调整和控制。
4. 平面度分度误差的计算公式。
平面度分度误差是指在零件的平面度方面的误差。
在机械设计中,平面度分度误差的计算通常是通过以下公式来进行的:E = (H H0) / H0。
其中,E表示平面度分度误差,H表示零件的实际平面度,H0表示零件的设计平面度。