化学镀的发展简史
第8章2019化学镀

被还原析出的金属应具有催化活性,这样 镀层才能增厚。
反应生成物不防碍镀覆过程的正常进行, 即溶液有足够的使用寿命。
三、化学镀与电镀的比较 P:253
镀液与镀层的性能 镀层沉积驱动力
镀液的组成 溶液组成的变复化 受 pH 值影响的程度 受温度影响的程度
沉积速度
镀液寿命 镀层结晶 膜层厚度分布 溶液管理
6)、最大优点耐磨,耐蚀。在酸性腐蚀介 质中随镀层中含磷量的增加,耐蚀性增加 (抗酸腐蚀),由酸性镀液化学沉积镍-磷 合金层的抗蚀性比碱性镀液优越,它在盐、 碱、氨和海水中有很好的抗蚀性
7)、 硬度高,一般500~600HV
400℃热处理1000HV
可代替硬铬镀层
韧性比镀镍层差
8)、易钎焊,但是熔焊性能比镍镀层差 9)、 某些化学镀镍层外观与不锈钢相似,
• 1966年,Metzger等开始试验化学复合镀 ,得到了化学镀Ni-P-Al2O3,化学镀Ni-PSiC化学复合镀层,并首先应用于工业生产
• 我国化学复合镀技术研究开始于20世纪70 年代
• 直至今日,化学复合镀的研究与开发一直 是表面工程技术最为活跃的研究领域
化学复合镀的固体颗粒
• 氧化物、碳化物、氮化物、硼化物等 几乎所有类型的陶瓷颗粒
零部件和工模具的表面强化
• 15)成本低 • 16)工艺简单,操作方便,工艺过程温度低
化学镀镍磷层应用
化工设备的抗蚀镀层 复杂机械零件的耐磨镀层 电子元器件的钎焊镀层 电子仪器的电磁屏蔽镀层 非导体的金属化
电镀镍层与化学镀镍层的主要性质差别
结构与性能
电镀镍层
化学镀镍层
镀层晶体结 fcc(面心立方) 随含磷量的增加由晶态经过微晶最终转变成
基体 成本
4.2-现代表面工程学导论--化学镀篇课件

2 化学性能
• 化学镀Ni-P合金镀层耐蚀性很好,几乎不受碱液,中性盐 水,淡水和海水的腐蚀。 • Ni-P镀层作为防蚀基底材料在高温(565℃~625℃), 高压(125kg/mm2)空气或水蒸汽中,其耐蚀性具有重 要的实用价值。含磷6~12 % 的Ni-P镀层在这种条件下 的耐蚀性比无镀层的提高约90倍。 • Ni-P化学镀层在石油、天然气工业环境中有非常好的耐蚀 性。H2S环境------腐蚀使无镀层的设备很快损坏-----Ni-P镀层设备在该环境中能生产致密的钝化膜而增加抗蚀 能力。
表面技术概论
——— 4.6 化学镀
山东科技大学材料科学与工程学院
2014
4.6.1 发展概况:
• 已有100多年历史 • 1845年, Wurtz试验时注意到次磷酸盐的 还原现象 • 1916年,Roux使用次磷酸盐的化学镀镍 获第一个美国专利 。但镀液极不稳定,自 分解严重。 • 1944年,A.布伦纳(A. Brenner)和G.黑 得尔(G.Riddell)找到控制稳定性的配方。 • Electroless(化学沉积、化学镀、无电解 电镀、自催化电镀等 )
(3)在模具工业中的应用
采用化学镀镍强化模具,既能 保证硬度和耐磨性,又能起到 固体润滑的效果 。 例如,45钢( 50 HRC)黄铜零 件拉伸模在使用过程中,粘铜现象严重,极易拉 伤零件,所以在生产过程中需要频繁地修理模 具,有的加工几件或几十件就要进行修理 。 化 学镀 10μ m厚的镍磷合金层后,经热处理钢模 表面硬度达到 1000HV,连续加工 5000次仍 不需要修模,而且加工的零件表面质量明显提 高。
• 电磁屏蔽保护镀层
• 化学镀镍层用于防电磁干扰特别有效。采用组合 镀层可达到屏蔽的效果,在塑料制品盒或其它罩 壳上,先镀一层很薄的铜,铜有良好的导电性能, 屏蔽效果很好,但铜易被氧化,不能耐久,然后 再化学镀一层镍,镍磷化学镀层有良好的耐磨和 耐蚀性能,可以保护底层铜免遭氧化,长期保持 良好的屏蔽性能。 • 电磁屏蔽保护镀层化学镀镍层的合金元素与含量, 影响镀层的屏蔽效果、在 Ni-P合金镀层中,磷含 量越低,镀层的导电性越好,电磁波的初屏蔽效 果就越好。
化学镀的发展

化学镀的发展
1944年,A.Brenner和G.Riddell进行了化学镀镍的实验,开发了可以工作的镀液。
20世纪80年代以后,化学镀镍有了很大的突破,解决了长期存在的一些问题,如镀液寿命、稳定性等,基本实现了镀液的自动控制,使连续化的大型生产有了可能。
近20年来,化学镀发展迅速,同时化学镀的应用领域不断拓宽。
2004年第七届全国化会议(深圳)上,在论及化学镀镍产业所面临的挑战时,曾对End-of-Life Vehicle Di-rectlve(欧盟ELV指令)作过简介,此后的化学镀的研究开始转向环境保护和清【电镀设备厂】洁生产,即开发无铅无镉的化学镀工艺,已有商品化镀液出现。
1947年,Narcus首先报道了化学镀铜。
初始阶段化学镀铜液的稳定性很差,溶易自动分解,且施镀范围不能控制,所有与溶液接触的地方都有沉积物。
而真正意义上的商品化学镀铜出现于20世纪50年代,随着印制线路板(PCB)通孔金属化的发展,化学镀铜得到了最早的应用。
第一个类似现代的化学镀铜溶液由Cahill公开发表于1957,镀液为碱性酒石酸铜镀液,甲醛为还原剂。
现在,经过50多年的开发研究,形成了相对完善的化学镀的溶液化学知识以及工艺技术基础,并建立了初步的基础理论体系。
由于甲醛具有致癌作用,化;学镀铜的研究者开始寻找替代甲醛的还原剂。
目前化学镀铜的发展方向是:①采用非甲醛还原剂;②超声波辐射化学镀;③激光增强化镀;④无钯催化化学镀铜。
化学镀特点及应用

50年代后期出现了商品镀铜液,主要用于制造印刷电路板,其后 开发出一系列用于多层印刷电路板通孔镀的化学镀铜液。
化学镀铜技术目前广泛用于材料表面金属化、电连接、电磁屏蔽 等方面。
化学镀钴、化学镀贵金属
化学镀钴及其合金具有很好的磁性能,随着计算机工 业的发展而迅速开展起来。
化学镀镍
化学镀的发展史主要就是化学镀镍(Electroless nickel plating,简写:EN)的发展史。
化学镀镍是在1944年由美国的A.Brenner 和G.Riddell发 现的。为了纪念他们的伟大贡献,A.布伦纳和G.里德 尔的论文50年重新被发表。
化学镀镍的最早工业应用是二战后美国通用运输公司 (GATC)。
目前化学镀贵金属Ag、Au、Pd、Pt等均有报道,相应 地出现了很多的专利,
特别是化学镀Au在电子工业上得到了工业化的应用。
化学复合镀、化学镀镍基多元合金
值得注意的是化学镀镍技术的新进展。 为了满足更复杂工况的要求,化学复合镀、化学镀镍基多元合金
、Ni-P镀层的着色工艺也逐渐发展起来。 如Ni-P/SiC、Ni-P/PTFE复合镀层比Ni-P镀层有更佳的耐磨性及自
属(Me2)覆盖,过程马上停止。 所以其最大厚度是很小的,而且结合力没有真正的化学镀那么好。 由于镀层质量差,厚度有限,所以应用非常有限。
这种工艺又称为浸镀(Immersion plating) ,目前应用的有化学镀镍/ 浸金工艺在集成电路电路板制造行业。
接触镀(contact process)
20世纪70年代以后,槽容量每年增长15%。 80年代以后,化学镀镍技术取得巨大突破。(如镀液
化学镀技术(图尔荪江·亚森)

化学镀技术摘要化学镀是一种在无电流通过的情况下,金属离子在同一溶液中还原剂的作用下通过可控制的氧化还原反应在具有催化表面(催化剂一般为钯、银等贵金属离子)的镀件上还原成金属,从而在镀件表面上获得金属沉积层的过程,也称自催化镀或无电镀。
化学镀最突出的优点是无论镀件多么复杂,只要溶液能深入的地方即可获得厚度均匀的镀层,且很容易控制镀层厚度。
与电镀相比,化学镀具有镀层厚度均匀、针孔少、不需直流电源设备、能在非导体上沉积和具有某些特殊性能等特点;关键词:化学镀,表面工程,金属;化学镀技术及发展概况近年来, 化学镀技术得到了越来越广泛的应用,在各种非金属纤维、微球、微粉等粉体材料上施镀成为研究的热点之一;用化学镀方法可以在非金属纤维、微球、微粉镀件表面获得完整的非常薄而均匀的金属或合金层,而且镀层厚度可根据需要确定。
这种金属化了的非金属纤维、微球、微粉镀件具有良好的导电性,作为填料混入塑料时能获得较好的防静电性能及电磁屏蔽性能,有可能部分取代金属粉用于电磁波吸收或电磁屏蔽材料。
毛倩瑾等采用化学镀的方法对空心微珠进行表面金属化改性研究,发现改性后的空心微珠具有较好的吸波性能,可用于微波吸收材料、轻质磁性材料等领域。
化学镀所需仪器电热恒温水浴锅;8522型恒温磁力搅拌器控温搅拌;增力电动搅拌机。
化学镀工艺流程机械粗化→化学除油→水洗→化学粗化→水洗→敏化→水洗→活化→水洗→解胶→水洗→化学镀→水洗→干燥→镀层后处理。
1化学镀预处理需进行化学镀的镀件一般不溶于水或者难溶于水。
化学镀工艺的关键在于预处理,预处理的目的是使镀件表面生成具有显著催化活性效果的金属粒子,这样才能最终在基体表面沉积金属镀层。
由于镀件微观表面凸凹不平,必须进行严格的镀前预处理,否则易造成镀层不均匀、密着性差,甚至难于施镀的后果。
1.1 化学除油镀件材料在存放、运输过程中难免沾有油污,为保证预处理效果,必须首先进行除油处理,去除其表面污物,增加基体表面的亲水性,以确保基体表面能均匀的进行金属表面活化。
《化学化学镀》课件

前处理阶段主要是对基材进行表面处 理,包括除油、除锈、活化等步骤, 以获得适合沉积的清洁表面。
后处理阶段主要是对沉积层进行清洗 、干燥等处理,以提高镀层的耐腐蚀 性和外观质量。
03
化学镀的种类与工艺
酸性化学镀镍
总结词
。
缺点分析
01
02
03
成本较高
化学镀所需的设备和试剂 成本较高,导致生产成本 增加。
镀层厚度难以控制
化学镀过程中,镀层厚度 受到多种因素的影响,难 以精确控制。
表面质量不稳定
化学镀过程中,工件表面 容易出现颗粒、气泡等缺 陷,影响表面质量。
改进措施
优化化学镀工艺参数
加强表面处理
通过调整温度、浓度、pH值等工艺参 数,提高镀层质量和均匀性。
在化学镀前对工件表面进行预处理, 去除杂质和油污,提高表面质量。
开发新型化学镀溶液
研究新型的化学镀溶液,降低成本和 提高镀层性能。
05
化学镀的发展趋势与展望
新型化学镀技术的研发
纳米化学镀技术
利用纳米材料和纳米技术 ,在化学镀过程中实现纳 米级镀层,提高镀层的硬 度和耐磨性。
复合化学镀技术
结合多种化学镀技术,如 复合电镀、复合化学转化 等,以提高镀层的综合性 能。
高温化学镀技术
在高温条件下进行化学镀 ,以实现高熔点金属的沉 积,提高镀层的稳定性和 耐腐蚀性。
环保型化学镀技术的探索
无氰化学镀
开发无氰化合物的化学镀工艺, 减少对环境的污染和危害。
低毒化学镀
降低化学镀过程中的有害物质含量 ,减少对操作人员的健康危害。
循环利用化学镀
化学镀资料

化学镀铝和铝合金有易产生晶间腐蚀,表面硬度低,不耐磨损等弱点。
在其表面进行化学镀处理,可以改善一些性能:改善耐腐蚀性,提高耐磨性,良好的耐磨性,高硬度,提高装饰性。
而纳米TiO2的加入,可以显著提高镀层的耐磨性,硬度,自润滑性,耐腐蚀性等性能。
化学镀概述化学镀:也称无电解镀,是在无外加电流的化学沉积过程。
借助合适的还原剂,使镀液中金属离子还原成金属,并沉积到零件表面的一种镀覆方法。
也叫做”自催化镀”,”无电解电镀”。
化学镀可以分为“置换法”,“接触度”,“还原法”。
一.化学镀相对电镀优点①化学镀可以用于各种基体,包括金属,非金属以及半导体。
②化学镀镀层均匀,无论工件如何复杂,只要采用合适的施镀方法,都可以在工件上得到均一镀层。
③对于可以自催化的化学镀而言,理论上可以得到任意厚度的镀层。
④化学镀所得到的镀层有很好的化学,机械,磁性性能。
⑤化学镀相对电镀而言最大的优点是镀层厚度均匀,针孔率低。
二.发展概况1.1844年,A.Wurtz通过亚磷酸盐还原镍得到了金属镍的镀层。
2.1911年,Bretean发表有关沉积过程是镍与次磷酸盐的催化过程的化学镀研究报告。
3.1916年,Roux从柠檬酸盐一次亚磷酸盐体系中得到了镀镍层,注册了第一份化学镀镍专利。
4.1944年,美国国家标准局从事轻武器改进研究的A.Brenner与G.Riddel在枪管实验中证实了次亚磷酸钠催化还原镍,1946年,1947年,两人公布了研究结果。
5.20世纪五十年代,美国通用运输公司对化学镀镍溶液组成与工艺进行系统研究。
为后来化学镀镍工业应用奠定基础。
6.1955年,开发出“Kanigen”技术;1964年,开发出“Durapositli”技术;1968年,开发出“Durnicoat”技术;1978年至1982年,开发成“诺瓦泰克”商品镀液。
7.20世纪六十年代,小规模化学镀镍工艺进入美国市场。
8.20世纪七十年代末至八十年代初,化学镀镍研究重点转向高磷镀层。
其他化学镀

其他化学镀在化学镀领域中,除应用最广的化学镀镍、化学镀铜和化学镀银以外,其他类型的化学镀也逐渐发展。
第一节其他金属化学镀一、化学镀钴1962年R.D.Fisher报告了电镀钴的磁特性作为高密度磁记录器镀层,引起广泛的重视,随之研究化学镀钴作为强磁性薄膜。
钴的标准电极电势为-0.28V,比镍的-0.25V负,在用次磷酸盐做还原剂的酸性溶液中C0的沉积速度很慢,甚至得不到钴的镀层。
只有在碱性溶液中才能有合适的沉积速度。
化学镀钴的机理与化学镀镍相类似。
用次磷酸钠作还原剂的化学镀钻的氧化还原反应如下:式中:x表示配位体。
(一)化学镀钴的工艺规范t表7—4—1是常用化学镀钴的工艺规范。
表7—4—1 常用化学镀钴的工艺规范(g·L-1)化学镀钴通常采用柠檬酸盐、酒石酸盐和铵盐为配位体。
配位体除能防止产生碱性盐沉淀外,会对镀液的沉积速度和镀层性能产生影响。
ph值调整剂采甩氨水,不采用氢氧化钠,因为后者会使镀液的沉积速度变慢。
(二)化学镀钴溶液的配制用纯水溶解计算量的配位体,然后在搅拌下加入溶解好的钴盐,若出现混浊,继续搅拌至全部溶解,然后加入溶解好的次磷酸盐,加纯水接近总体积,然后用氨水调节pH值至规范,加纯水至总体积,过滤后即可使用。
(三)化学镀钴层的特性和用途化学镀钴层是以P在01—C0中的过饱和固溶体为主,x射线衍射图谱在2Θ≈53。
,570及610处分别出现hcp结构的Co(100)、(102)、(101)晶面衍射峰。
镀态硬度HV500~HV600(叫(P)为4%~6%时),经5000C1h热处理可析出大量的C02P相,硬度上升为HV900~HVl000。
钴的居里温度(失去磁性的温度)是1150℃,而铁的是769℃,镍的是358℃。
钴是磁化一次能保持磁性的少数金属之一。
化学镀钴层的矫顽力依磷含量不同而异,即随次磷酸盐增加和pH值下降而增大。
因化学镀钴可获得各种十分不同的磁性能,所以广泛用于记忆存储器元件。
化学镀简介

简介化学镀简介化学镀一、化学镀(chemical plating)化学镀是一种新型的金属表面处理技术,该技术以其工艺简便、节能、环保日益受到人们的关注。
化学镀使用范围很广,镀金层均匀、装饰性好。
在防护性能方面,能提高产品的耐蚀性和使用寿命;在功能性方面,能提高加工件的耐磨导电性、润滑性能等特殊功能,因而成为全世界表面处理技术的一个发展。
化学镀技术是在金属的催化作用下,通过可控制的氧化还原反应产生金属的沉积过程。
与电镀相比,化学镀技术具有镀层均匀、针孔小、不需直流电源设备、能在非导体上沉积和具有某些特殊性能等特点。
另外,由于化学镀技术废液排放少,对环境污染小以及成本较低,在许多领域已逐步取代电镀,成为一种环保型的表面处理工艺。
目前,化学镀技术已在电子、阀门制造、机械、石油化工、汽车、航空航天等工业中得到广泛的应用。
二、化学镀原理化学浸镀(简称化学镀)技术的原理是:化学镀是一种不需要通电,依据氧化还原反应原理,利用强还原剂在含有金属离子的溶液中,将金属离子还原成金属而沉积在各种材料表面形成致密镀层的方法。
化学镀常用溶液:化学镀银、镀镍、镀铜、镀钴、镀镍磷液、镀镍磷硼液等。
目前以次亚磷酸盐为还原剂的化学镀镍的自催化沉积反应,已经提出的理论有“原子氢态理论”、“氢化物理论”和“电化学理论”等。
在这几种理论中,得到广泛承认的是“原子氢态理论”。
三、对非金属的化学镀需要敏化活化处理敏化就是使非金属表面形成一层具有还原作用的还原液体膜。
这种具有还原作用的处理液就是敏化剂。
好的敏化效果要求具有还原作用的离子在一定条件下能较长时间保持其还原能力,并且能控制其还原反应的速度,要点是敏化所要还原出来的不是连续的镀层,而只是活化点。
目前最适合的还原剂只有氯化亚锡。
目前,对于非金属化学镀镍用得最多的是Pd活化工艺。
当吸附有Sn的非金属表面接触到Pd活化液时,Pd会被Sn还原而沉积到非金属表面形成活化中心,从而顺利进行化学镀。
公共基础知识化学镀基础知识概述

《化学镀基础知识综合性概述》一、引言化学镀作为一种重要的表面处理技术,在现代工业生产中发挥着至关重要的作用。
它不仅可以提高材料的耐腐蚀性、耐磨性和硬度等性能,还可以赋予材料特殊的电磁、光学和催化等功能。
本文将对化学镀的基础知识进行全面的阐述与分析,包括基本概念、核心理论、发展历程、重要实践以及未来趋势等方面,旨在为读者提供一个清晰、系统且深入的理解框架。
二、基本概念1. 定义化学镀,又称为无电解镀或自催化镀,是一种在无外加电流的情况下,利用处于同一溶液中的金属盐和还原剂在具有催化活性的基体表面上进行的自催化氧化还原反应,从而在基体表面沉积出金属镀层的方法。
2. 特点(1)无需外接电源,操作简便,适用于各种形状复杂的工件。
(2)镀层均匀,孔隙率低,与基体结合力强。
(3)可以在非导体材料如塑料、陶瓷等表面进行镀覆。
(4)可根据需要选择不同的金属镀层,如镍、铜、金、银等。
3. 应用领域化学镀广泛应用于航空航天、汽车制造、电子电器、机械加工、化工等领域。
例如,在航空航天领域,化学镀镍可以提高零部件的耐腐蚀性和耐磨性,延长其使用寿命;在电子电器领域,化学镀铜可以提高印制电路板的导电性和焊接性能。
三、核心理论1. 自催化反应机理化学镀的自催化反应机理主要包括以下几个步骤:(1)还原剂在催化表面上被氧化,释放出电子。
(2)金属离子在催化表面上获得电子,被还原成金属原子。
(3)金属原子在催化表面上聚集,形成金属镀层。
2. 动力学模型化学镀的动力学模型主要用于描述反应速率与各种因素之间的关系。
其中,影响反应速率的因素主要包括温度、溶液浓度、pH 值、搅拌速度等。
通过建立动力学模型,可以优化化学镀工艺参数,提高镀层质量和生产效率。
3. 镀层结构与性能关系化学镀镀层的结构和性能取决于多种因素,如镀液组成、工艺参数、基体材料等。
一般来说,镀层的结构可以分为晶态和非晶态两种。
晶态镀层具有较高的硬度和耐磨性,非晶态镀层则具有较好的耐腐蚀性和电磁性能。
第3章 2-化学镀
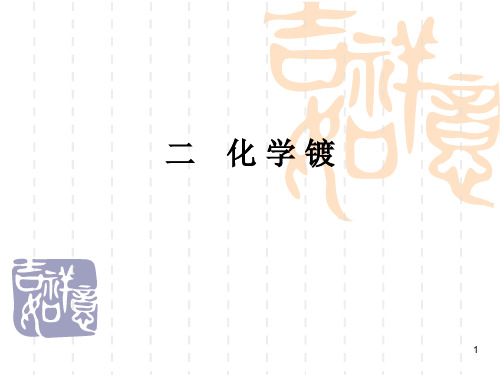
化学镀
1
主要内容
一、学镀概述
化学镀基本概念、基本原理及其特点
二、化学镀镍
概述、 基体材料 、动力学 、镀液基本组成 、 次磷酸盐型镀液镀Ni层、 镀层的组成和特性
2
一、化学镀概述 1. 化学镀基本概念
化学镀(chemical plating)是属镀层的一种化学处理 方法。在还原剂的作用下,使金属盐溶液中的金属离 子还原成原子,在具有催化作用的基板表面上沉积成
39
(6)缓冲剂
化学镀镍过程中由于有H+产生,使溶液pH值随施镀进 程而逐渐降低。为了稳定镀速及保证镀层质量,化学 镀镍体系必须具备缓冲能力,pH值不变化太大。 某些弱酸(或碱)与其盐组成的混合物就能抵消外来 少许酸或碱以及稀释对溶液pH值变化的影响,使之在 一个较小范围内波动,这种物质称为缓冲剂。
15
第二类:
大多数材料属于第二类,即无催化活性的材料。这 些材料表面不具备催化活性,必须通过在它表面沉 积的第一类本身具备催化活性的金属,使这种表面 具有催化活性之后才能引发化学沉积。
第二类无催化活性材料又可分为三种: 比镍活泼的金属材料 比镍稳定的金属 非金属材料
16
比镍活泼的金属材料: 如铁金属材料浸入化学镀液时,由于置换反应开始在 铁表面上沉积镍,成为引发化学镀反应的成核中心, 继而使化学镀镍反应可以在大面积上持续进行。
“三高特性”:高耐蚀性、高耐磨性及高均匀。 (1)化学镀镍层的结晶细致,孔隙率低,硬 度高,镀层均匀,可焊性好,镀液深镀能力 好,化学稳定性高,目前已广泛用于电子、 航空、航天、机械、精密仪器、日用五金、 电器和化学工业中。
10
(2)化学镀镍在原子能工业(如生产核燃料系统中的 零件和容器),以及火箭、导弹、喷气式发动机的零 部件上已采用。(熔点1455℃) (3)化工设备中压缩机等的零部件为防腐蚀、抗磨, 而用化学镀镍层是很有利的。 (4)化学镀镍层还能改善铝、铜、不锈钢材料的焊接 性能,减少转动部分的磨耗,减少不锈钢与钛合金的 应力腐蚀。
化学镀的研究现状
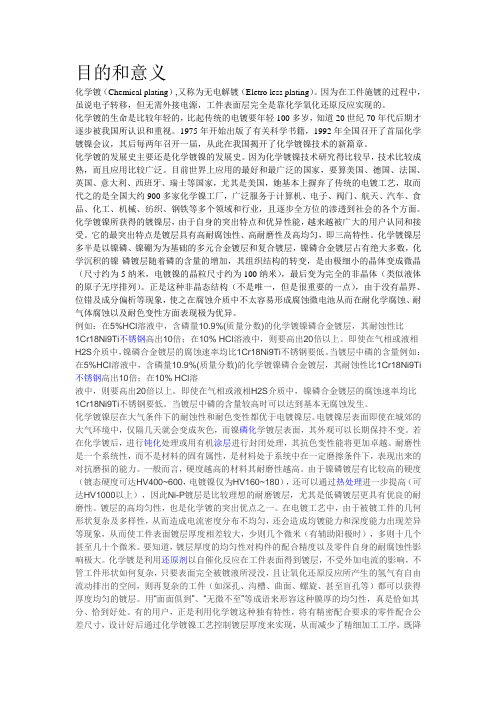
目的和意义化学镀(Chemical plating),又称为无电解镀(Eletro less plating)。
因为在工件施镀的过程中,虽说电子转移,但无需外接电源,工件表面层完全是靠化学氧化还原反应实现的。
化学镀的生命是比较年轻的,比起传统的电镀要年轻100多岁,知道20世纪70年代后期才逐步被我国所认识和重视。
1975年开始出版了有关科学书籍,1992年全国召开了首届化学镀镍会议,其后每两年召开一届,从此在我国揭开了化学镀镍技术的新篇章。
化学镀的发展史主要还是化学镀镍的发展史。
因为化学镀镍技术研究得比较早,技术比较成熟,而且应用比较广泛。
目前世界上应用的最好和最广泛的国家,要算美国、德国、法国、英国、意大利、西班牙、瑞士等国家,尤其是美国,她基本上摒弃了传统的电镀工艺,取而代之的是全国大约900多家化学镍工厂,广泛服务于计算机、电子、阀门、航天、汽车、食品、化工、机械、纺织、钢铁等多个领域和行业,且逐步全方位的渗透到社会的各个方面。
化学镀镍所获得的镀镍层,由于自身的突出特点和优异性能,越来越被广大的用户认同和接受。
它的最突出特点是镀层具有高耐腐蚀性、高耐磨性及高均匀,即三高特性。
化学镀镍层多半是以镍磷、镍硼为为基础的多元合金镀层和复合镀层,镍磷合金镀层占有绝大多数,化学沉积的镍-磷镀层随着磷的含量的增加,其组织结构的转变,是由极细小的晶体变成微晶(尺寸约为5纳米,电镀镍的晶粒尺寸约为100纳米),最后变为完全的非晶体(类似液体的原子无序排列)。
正是这种非晶态结构(不是唯一,但是很重要的一点),由于没有晶界、位错及成分偏析等现象,使之在腐蚀介质中不太容易形成腐蚀微电池从而在耐化学腐蚀、耐气体腐蚀以及耐色变性方面表现极为优异。
例如:在5%HCl溶液中,含磷量10.9%(质量分数)的化学镀镍磷合金镀层,其耐蚀性比1Cr18Ni9Ti不锈钢高出10倍;在10% HCl溶液中,则要高出20倍以上。
即使在气相或液相H2S介质中,镍磷合金镀层的腐蚀速率均比1Cr18Ni9Ti不锈钢要低。
化学镀铜工艺的历史
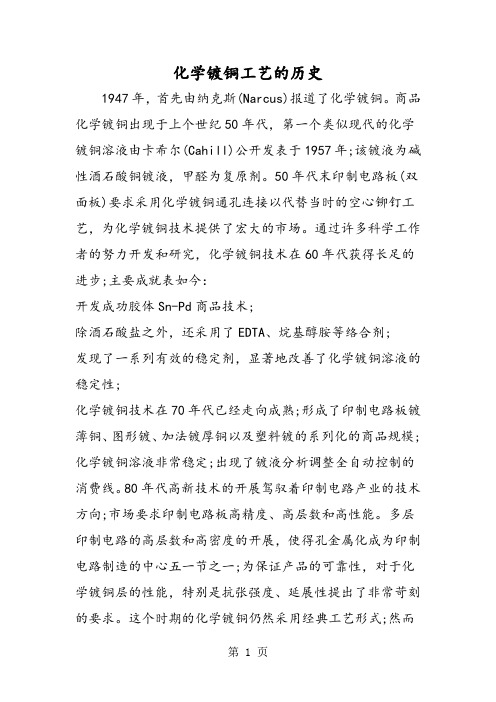
化学镀铜工艺的历史1947年,首先由纳克斯(Narcus)报道了化学镀铜。
商品化学镀铜出现于上个世纪50年代,第一个类似现代的化学镀铜溶液由卡希尔(Cahill)公开发表于1957年;该镀液为碱性酒石酸铜镀液,甲醛为复原剂。
50年代末印制电路板(双面板)要求采用化学镀铜通孔连接以代替当时的空心铆钉工艺,为化学镀铜技术提供了宏大的市场。
通过许多科学工作者的努力开发和研究,化学镀铜技术在60年代获得长足的进步;主要成就表如今:开发成功胶体Sn-Pd商品技术;除酒石酸盐之外,还采用了EDTA、烷基醇胺等络合剂;发现了一系列有效的稳定剂,显著地改善了化学镀铜溶液的稳定性;化学镀铜技术在70年代已经走向成熟;形成了印制电路板镀薄铜、图形镀、加法镀厚铜以及塑料镀的系列化的商品规模;化学镀铜溶液非常稳定;出现了镀液分析调整全自动控制的消费线。
80年代高新技术的开展驾驭着印制电路产业的技术方向;市场要求印制电路板高精度、高层数和高性能。
多层印制电路的高层数和高密度的开展,使得孔金属化成为印制电路制造的中心五一节之一;为保证产品的可靠性,对于化学镀铜层的性能,特别是抗张强度、延展性提出了非常苛刻的要求。
这个时期的化学镀铜仍然采用经典工艺形式;然而有关工艺材料的控制技术,从内容和程度两方面发生了重大革新。
目前,化学镀铜不仅在宽广的操作条件下长时间镀液保持稳定,而且,过程状态可以预测,镀层性能优秀。
有的化学镀淮在孔径0.15mm,板厚与孔径之比为10时,平均镀层为65μm,镀厚比为100%;抗张强度为400MPa时,延展性大于10%;有的镀层延展性高达15%。
由于甲醛的固有缺点,不少人开场浓度采用次磷酸盐、肼或硼化合物作为复原剂替代。
在化学镀铜30多年的历史中经历了开展和巨的进步,已成为相对新的领域;为电子产品的可靠性和丰富人民生活作出了奉献。
由于环境和价格的因素,引发了研究代替化学镀铜的其他金属化方法;而环境、顾客品位的改烃,塑料装饰的电镀量也有明显的减少;但用于射频和磁屏蔽(EMI)的化学镀铜市场却在看好。
化学镀镍-第1篇
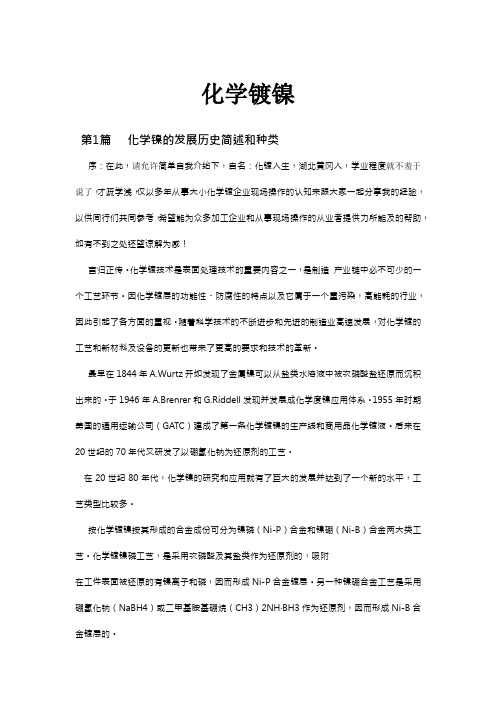
化学镀镍第1篇化学镍的发展历史简述和种类序:在此,请允许简单自我介绐下,自名:化镀人生,湖北黄冈人,学业程度就不羞于说了,才疏学浅,仅以多年从事大小化学镀企业现场操作的认知来跟大家一起分享我的经验,以供同行们共同参考,希望能为众多加工企业和从事现场操作的从业者提供力所能及的帮助,如有不到之处还望谅解为感!言归正传。
化学镀技术是表面处理技术的重要内容之一,是制造产业链中必不可少的一个工艺环节。
因化学镀层的功能性、防腐性的特点以及它属于一个重污染,高能耗的行业,因此引起了各方面的重视。
随着科学技术的不断进步和先进的制造业高速发展,对化学镀的工艺和新材料及设备的更新也带来了更高的要求和技术的革新。
最早在1844年A.Wurtz开如发现了金属镍可以从盐类水溶液中被次磷酸盐还原而沉积出来的。
于1946年A.Brenrer和G.Riddell发现并发展成化学度镍应用体系。
1955年时期美国的通用运输公司(GATC)建成了第一条化学镀镍的生产线和商用品化学镀液。
后来在20世纪的70年代又研发了以硼氢化钠为还原剂的工艺。
在20世纪80年代,化学镍的研究和应用就有了巨大的发展并达到了一个新的水平,工艺类型比较多。
按化学镀镍按其形成的合金成份可分为镍磷(Ni-P)合金和镍硼(Ni-B)合金两大类工艺。
化学镀镍磷工艺,是采用次磷酸及其盐类作为还原剂的,吸附在工件表面被还原的有镍离子和磷,因而形成Ni-P合金镀层。
另一种镍硼合金工艺是采用硼氢化钠(NaBH4)或二甲基胺基硼烷(CH3)2NH·BH3作为还原剂,因而形成Ni-B合金镀层的。
化学镀镍磷中的磷含量是0.5% - 14%(质量),按溶液的PH值又可分为酸性和碱性两大类。
碱性化学镀镍溶液的磷含量较低,稳定性较差。
主要用在作为非金属材料或铝及其合金等材料的镀前预镀层,以提高后续镀层跟基材的镀层结合力,突出的典型例子如汽车轮毂中的应用。
目前在我们现实生产中应用最为广泛的还是酸性化学镀镍溶液的工艺。
化学镀——重现千百年前的美丽
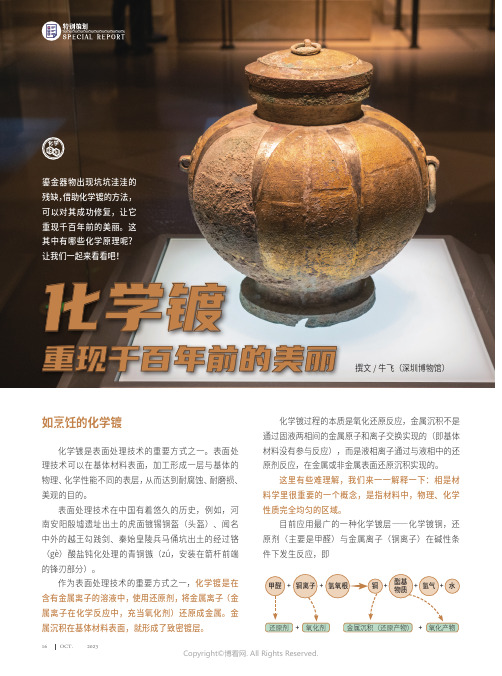
重现千百年前的美丽如烹饪的化学镀化学镀是表面处理技术的重要方式之一。
表面处理技术可以在基体材料表面,加工形成一层与基体的物理、化学性能不同的表层,从而达到耐腐蚀、耐磨损、美观的目的。
表面处理技术在中国有着悠久的历史,例如,河南安阳殷墟遗址出土的虎面镀锡铜盔(头盔)、闻名中外的越王勾践剑、秦始皇陵兵马俑坑出土的经过铬(gè)酸盐钝化处理的青铜镞(zú,安装在箭杆前端的锋刃部分)。
作为表面处理技术的重要方式之一,化学镀是在含有金属离子的溶液中,使用还原剂,将金属离子(金属离子在化学反应中,充当氧化剂)还原成金属。
金属沉积在基体材料表面,就形成了致密镀层。
撰文/牛飞(深圳博物馆)鎏金器物出现坑坑洼洼的残缺,借助化学镀的方法,可以对其成功修复,让它重现千百年前的美丽。
这其中有哪些化学原理呢?让我们一起来看看吧!化学镀化学镀过程的本质是氧化还原反应,金属沉积不是通过固液两相间的金属原子和离子交换实现的(即基体材料没有参与反应),而是液相离子通过与液相中的还原剂反应,在金属或非金属表面还原沉积实现的。
这里有些难理解,我们来一一解释一下:相是材料学里很重要的一个概念,是指材料中,物理、化学性质完全均匀的区域。
目前应用最广的一种化学镀层——化学镀铜,还原剂(主要是甲醛)与金属离子(铜离子)在碱性条件下发生反应,即甲醛铜离子+还原剂 +17因此,化学镀并非直接作用在文物本体,而是作用在补配部位。
所谓补配,是在文物残缺部位,使用各种修复前 修复前、后对比(供图/牛飞)修复后修复前修复后化学镀铜后扫描电镜(介于透射电镜和光学显微镜之间仿生瓷器金饰残缺部位修复效果(供图/牛飞). All Rights Reserved.。
化学镀技术 班级.doc孔倩倩

化学镀技术班级:1385011 学号:138501103 姓名:孔倩倩引言化学镀作为一种优良的表面处理技术能够施镀于导体和非导体材料,镀层均匀,操作简便。
因此一直受到工业上和学术界的关注。
综述了化学镀的研究现状和主要化学镀层的应用领域,包括化学镀镍,化学镀钴,化学镀银,化学镀锡,化学镀金以及化学镀钯等技术,并提出了化学镀技术的发展趋势。
化学镀由于镀层本身具有独特的优良性能,且工艺与其他表面处理技术相比,化学镀不需要外加电源,操作方便,工艺简单,镀层均匀,孔隙率低和外观良好,而且能在塑料,陶瓷等多种非金属基体上沉积,并具有优良的包覆性(因不用外加电源,凡镀液能浸到的部位,任何复杂零件包括微小孔,盲孔都可以获得均匀的镀层),高的附着力,优良的抗腐蚀,耐腐蚀性能以及优异的功能性能等而使其在世界范围内得到了迅速的发展和广泛的应用。
一 . 概述化学镀是在金属的催化作用下,通过可控制的氧化还原反应产生金属沉淀的过程。
它被称为自催化(Auocatalytic Plating)或无电镀(Chemical Composition electroless plating)。
实现化学镀应具备下述条件:1)溶液中还原剂被氧化的电位要显著地与金属离子被还原的电位,以使金属有可能被沉积出来。
2)配好的溶液不产生自发分解,当与催化表面接触时,才发生金属沉积过程。
3)调节溶液的PH,温度时,可以控制温度的还原速度,即可以调节镀覆速度。
4)被还原析出的金属应具有催化作用,这样镀层才能增厚。
5)反应生成物不妨碍镀覆过程的正常进行,即溶液有足够的使用寿命。
化学镀溶液的成分包括金属盐、还原剂、络合剂、缓冲剂、PH调节剂、稳定剂、加速剂、润湿剂和光亮剂等。
二、化学镀的发展过程化学镀作为一种表面处理技术,从开发到应用经历了一个历史发展的过程。
1844年,Wurtz通过次亚磷酸盐得到了金属镍的镀层。
1911年,Bretean发表了有关化学镀镍的研究报告,认为沉积过程是Ni在次亚磷酸盐上的催化反应。
化学镀

• 80年代后,化学镀镍技术有很大的突破,如镀液 寿命、稳定性等得到初步解决,基本实现镀液的 自动控制,是连续化的大型生产有了可能。 • 近年来,各种期刊上发表了很多有关化学镀镍的 论文,综述,书评和会议纪要。主要研究集中在 化学镀镍机理的研究、镀液成分的研究及寿命的 延长以及复合镀的方面。
化学镀的基本原理
⑦湿润剂(表面活性剂):降低镀液与镀件的表面 张力,提高镀件表面的浸润性。如硫化脂肪酸、 硫酸酯。 ⑧光亮剂:增强化学镍层的光亮度,提高装饰效果。 主要有丁炔二醇、炔丙醇 等。 ⑨去应力剂:降低镀层的内应力(张应力),提高 镀层与基体的结合力。如糖精等。 ⑩PH值调整剂:连续调整 PH 值。如HCl、NaOH、 氨水等。
③缓冲剂:长期控制 pH 值,使其稳定。常用的 有柠檬酸、丙酸、乙二酸、硼酸及其钠盐。 ④稳定剂:通过吸附遮蔽催化活性核心,防止镀 液分解。如:铅离子、锡的硫化物、钼酸盐、 碘酸盐、偏硫化物等。 ⑤还原剂:主要有次磷酸钠,硼氢化钠,二甲基 胺硼烷,二乙基胺硼烷等。 ⑥加速剂:活化次亚磷酸盐离子,加速沉积反应 的进行。如氟化物、硼酸盐等
• 化学镀不依赖外加电流,仅靠镀液中的还原剂进 行氧化还原反应,在金属表面的催化作用下使金 属离子不断沉积于金属表面的工艺方法叫化学镀。 由于化学镀必须在具有自催化性材料表面进行, 因而化学镀又称“自催化镀”。由置换反应或其 他化学反应,而不是自催化还原反应而获得金属 镀层的方法,不能称之为化学镀。化学镀过程中, 还原金属离子所需的电子由还原剂Rn+供给,电子 转移情况可表述为: • Rn+→R(n+z)++ze • Mez++ze→Me
盖子
尼龙丝
镀镍试样烧杯恒温水锅化学镀的特点1.化学镀镀层分散能力好,无明显的边缘效应,几 乎不受工件复杂外形的限制,镀层厚度均匀。 镀层厚度易于控制,表面光洁平整,一般不需 要镀后加工。 2. 化学镀可用在非金属材料表面上沉积金属镀层。 3. 对能自动催化的化学镀,理论上可获得任意厚度 的镀层。
- 1、下载文档前请自行甄别文档内容的完整性,平台不提供额外的编辑、内容补充、找答案等附加服务。
- 2、"仅部分预览"的文档,不可在线预览部分如存在完整性等问题,可反馈申请退款(可完整预览的文档不适用该条件!)。
- 3、如文档侵犯您的权益,请联系客服反馈,我们会尽快为您处理(人工客服工作时间:9:00-18:30)。
化学镀的发展史主要就是化学镀镍的发展史。
虽然早在1844年A.Wurtz 就发现次磷酸盐在水溶液中还原出金属镍,但化学镀镍技术的奠基人是美国国家标准局的A.Brenner和G.Ridell。
他们在1947年提出了沉积非粉末状镍的方法,弄清楚了形成涂层的催化特性,使化学镀镍技术工业应用有了可能性。
所以,化学镀镍技术的历史还很短暂,真正大规模工业还是70年代末期的事。
早期只有含磷5%-8%(重量)的中磷镀层,80年代初发展出磷含量为9%-12%的高磷非晶结构镀层,使化学镀镍向前迈进一步。
80年代末到90年代初又发展了磷含量为1%-4%的低磷镀层。
含磷量不同的镀层物理化学镀性能也不同。
化学镀镍的最早工业应用是二战后在美国通用运输公司(GATC)。
他们在系统研究该技术后于1955年建立的第一条生产线,发展出的化学镀镍溶液商品名称为"Kanigen"(是CatalyticNickelGeneRation学缩写)。
70年代又发展出仍以次磷酸钠还原剂的Durnicoat工艺、用硼氢化钠做还原剂Ni-B层的Nibodur工艺,以后又出现了用肼做还原剂的化学镀镍方法。
化学镀镍技术的核心是镀液的组成及性能,所以化学镀镍发展史中最值得注意的是镀液本身的进步。
在60年代之前由于镀液化学知识贫乏,只有中磷镀液配方,镀液不稳定,往往只能稳定数小时,因此为了避免镀液分解只有间接加热,在溶液配制、镀液管理及施镀操作方面必须十分小心,为此制定了许多操作规程给以限制。
此外,还存在沉积速度慢、镀液寿命短等缺点。
为了降低成本,延长镀液使用周期,只好使镀液“再生”,再生的实质就是除去镀液中还原剂的反应产物,次磷酸根氧化产生的亚磷酸根。
当时使用的方法有弃去部分旧镀液添加新镀液、加FeCl3或Fe2(SO4)3以沉淀亚磷酸根(形成Na2
[Fe(OH)(HPO3)2])·20H2O黄色沉淀)、离子交换法等,这些方法既麻烦又不适用。
70年代以后多种络合剂、稳定剂等添加剂的出现,经过大量的试验研究、筛选、复配以后,新发展的镀液均采用“双络合、双稳定”、甚至“双络合、双稳定、双促进”配方,这样不仅使镀液稳定性提高、镀速加快,更主要的是大幅度增加了镀液对亚磷酸根容忍量,最高达600-800g/LNa2HPO3·5H2O,这就使镀液寿命大大延长,一般均能达到4-6个周期,甚至10-12个周期,镀速达17-25μm/h。
这样,无论从产品质量和经济效益角度考虑,镀液已不值得进行“再生”,而直接做废液处理。
近来,为了改革镀层质量、减少环境污染,已改用新型有机稳定剂,
不再使用重金属离子,从而显著提高了镀层的耐蚀性能。
目前,化学镀液均已商品化,根据用户要求有各种性能化学镀的开缸及补加浓缩液出售,施镀过程中只需按消耗的主盐、还原剂、pH调节剂及适量的添加剂进行补充,使用十分方便。
据不完全统计,目前世界上至少有两百种以上的成熟化学镀镍配方,一些有代表性出售镀液的公司有:美国的
M&TChemicalsLtd.,Allied-KeliteDiv.,WitcoChemicalCorp.,EnthoneInc.,Ship leyCompany,HidilityCo.Wear-CoteInternationalInc.;英国的
W.CanningMaterialsLtd.,HarshawChemicalsLimited;德国的
Friedr.BlasbergGmbh.&Co.KG,AutoTech;日本的上村株式会社、奥野株式会社等。
我国化学镀工业目前正逐步走向成熟。
从1959年美国召开第一届化学镀镍学术会议以后,陆续发表了大量的论文及专利,还出版了有关专著,如
G.G.Gawrilov:Chemical(Electroless)Nickel-plating1974;
G.O.Mallory:ElectrolessPlatingFundmentalsandApplication1990。
美国电化学学会秋季年会(暨美国固体电路制造学会年会),于1989年开始建立化学镀学术研究报告专集,由此可见化学镀学术研究的普遍性。
由于电子计算机、通信等高科技产业的迅猛发展,为化学镀技术提供了巨大的市场。
80年代是化学镀技术的研究、开发和应用飞跃发展时期,西方工业化国家化学镀镍的应用,在与其他表面处理技术激烈竞争的形势下,年净增长速率曾在到15%;这是金属沉积史上空前的发展速度。
预期化学镀技术将会持续高速发展,平均年净增速率将降至6%,而进入发展成熟期。
我国的化学镀市场与国际相比起步晚、规模小,但近十几年发展极期迅速,不仅有大量的论文发表,还举行了全国性的专业会议,相信在今后几年内会越来越广泛的应用该项技术,并逐步走向稳定和成熟。
kajbzon 阳极氧化设备/。