昆钢棒材
昆钢棒材厂穿水冷却设施除雾
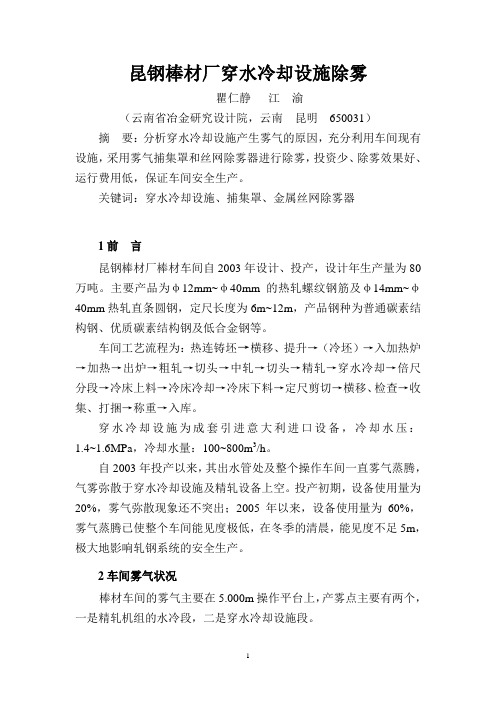
昆钢棒材厂穿水冷却设施除雾瞿仁静江渝(云南省冶金研究设计院,云南昆明650031)摘要:分析穿水冷却设施产生雾气的原因,充分利用车间现有设施,采用雾气捕集罩和丝网除雾器进行除雾,投资少、除雾效果好、运行费用低,保证车间安全生产。
关键词:穿水冷却设施、捕集罩、金属丝网除雾器1前言昆钢棒材厂棒材车间自2003年设计、投产,设计年生产量为80万吨。
主要产品为φ12mm~φ40mm的热轧螺纹钢筋及φ14mm~φ40mm热轧直条圆钢,定尺长度为6m~12m,产品钢种为普通碳素结构钢、优质碳素结构钢及低合金钢等。
车间工艺流程为:热连铸坯→横移、提升→(冷坯)→入加热炉→加热→出炉→粗轧→切头→中轧→切头→精轧→穿水冷却→倍尺分段→冷床上料→冷床冷却→冷床下料→定尺剪切→横移、检查→收集、打捆→称重→入库。
穿水冷却设施为成套引进意大利进口设备,冷却水压:1.4~1.6MPa,冷却水量:100~800m3/h。
自2003年投产以来,其出水管处及整个操作车间一直雾气蒸腾,气雾弥散于穿水冷却设施及精轧设备上空。
投产初期,设备使用量为20%,雾气弥散现象还不突出;2005年以来,设备使用量为60%,雾气蒸腾已使整个车间能见度极低,在冬季的清晨,能见度不足5m,极大地影响轧钢系统的安全生产。
2车间雾气状况棒材车间的雾气主要在5.000m操作平台上,产雾点主要有两个,一是精轧机组的水冷段,二是穿水冷却设施段。
穿水冷却设备一共有五台,使用三台,布置在5.000m平台上,设备下设有钢架,钢架上铺设有钢筋台面,便于冷却水落入集水槽。
平台下设有一个大的循环水池,在生产使用时,产生大量的雾气。
穿水冷却设备产雾点主要在出水管和出水箱。
冷却水一进入集水槽,便有大量的蒸汽腾起。
在春冬季节清晨及晚间,雾气弥漫于车间中段。
棒材厂曾经密封了平台上钢筋台面,并将排水管延长至钢筋平面以下,但不能止住雾汽,大量的雾汽从平台下逸出,主轧跨与轧辊间汽雾弥漫,安全生产仍受到响。
首席技师先进事迹材料

首席技师先进事迹材料3月春暖花开之时,中国十九冶根据《四川省中长期人才发展规划纲要(2020-2020)》关于加快高技能人才队伍建设的相关要求,向四川省人力资源和社会保障厅提出了成立“周树春焊接技能大师工作室”的申请。
“技能大师工作室”,是高技能人才培养的一种创新模式,旨在给技能领军人才创造良好环境、提升高技能人才培养能力和成效。
周树春,这名从20年前走进工厂的毛头小伙儿,历练成了以响当当的操作技术和优秀品质而闻名行业内外的技能大师、蓝领劳模,成为中国工人阶级最骄傲的一份子!这位曾经带领徒弟在世界技能大赛赛场上为中国获得首枚银牌,响亮喊出“中国焊工,焊接世界”口号的全国技术能手,是如何从一名普通工人成长为焊接首席技师,达到自己事业的辉煌顶点的呢?冰炭不言,冷热自明青春在焊花中闪耀刚踏进电焊工这个行当时,周树春并不觉得自己的人生也可以精彩。
皮肤被高温灼伤、常年出差在外、时间在埋头焊接的枯燥与疲惫中流逝,他也曾面临过诸多质疑,也曾打过退堂鼓,但是,与焊花共舞二十载,慢慢的,他发现了自己的价值。
从1992年参加工作以来,周树春先后参加了攀钢热轧板厂工程、昆钢焦炉工程、涟钢烧结机工程、攀企球团工程、韶钢、安钢、唐山国丰、柳钢转炉等上百个工程施工建设。
从最开始业主对这个毛头小子“他能行吗?”的挑剔眼光,到后来“把焊接项目交给周树春我们放心”的高度评价,十几年来,他以从没有无故耽搁一天,没有一条不合格的焊缝的实际行动回击质疑、回报信任。
由于他技术过硬,作风顽强,经常从一个工地,被叫到另一个工地。
不管在哪里,他都是勤勤恳恳、任劳任怨,敢于挑战自我,敢于拼搏。
1997年,还在攀钢冷轧干活的周树春接到紧急通知,连夜赶往昆钢棒材加热炉检修现场。
周树春赶到时,刚停下来的炉子温度有300多度,用了10多个风机降温,可炉内温度还是有70多度,无奈之下,抢修小组只能在炉膛下面垫了一层木板防止脚部烧伤,当时的木板还冒着白烟,周树春穿上打湿的棉衣毅然钻进了加热炉。
70Mn2合金钢的生产实践

70Mn2合金钢的生产实践黄静;陈寿红【摘要】通过分析70Mn2的性能、组织、成分,结合昆钢炼钢厂的具体工况研发试制了70Mn2,并对成品钢质量进行跟踪检测和分析,逐步建立了较为稳定的70Mn2生产工艺,为开发高碳合金钢奠定了基础.%Based on the specific working condition in the Steel Making Plant of Kunming Iron and Steel Co. , Ltd. , 70Mn2 Steel was developed and trial - produced by analyzing its performance, structure and composition. In the meanwhile, the fairly steady productive technology of 70Mn2 has been set up gradually by tracking testing and analyzing the quality of finished steel, which provided the foundation for development of high - carbon alloy steel.【期刊名称】《云南冶金》【年(卷),期】2012(041)003【总页数】5页(P42-46)【关键词】70Mn2;生产工艺;分析;实践【作者】黄静;陈寿红【作者单位】昆明工业职业技术学院,云南昆明650302;昆明钢铁股份有限公司炼钢厂,云南昆明650302【正文语种】中文【中图分类】TF70370Mn2是广泛应用于煤矿、有色金属矿山和铁矿上的开采等行业中球磨机、棒磨机等机械设备上的研磨体材料,具有良好的市场前景。
为此,昆明钢铁股份有限公司 (以下简称昆钢)炼钢厂、技术中心根据市场需求共同试制开发70Mn2。
棒材倍尺飞剪的控制与优化
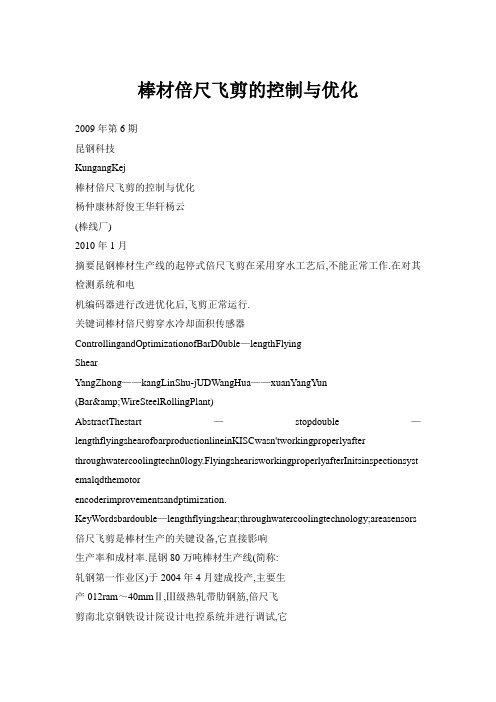
棒材倍尺飞剪的控制与优化2009年第6期昆钢科技KungangKej棒材倍尺飞剪的控制与优化杨仲康林舒俊王华轩杨云(棒线厂)2010年1月摘要昆钢棒材生产线的起停式倍尺飞剪在采用穿水工艺后,不能正常工作.在对其检测系统和电机编码器进行改进优化后,飞剪正常运行.关键词棒材倍尺剪穿水冷却面积传感器ControllingandOptimizationofBarD0uble—lengthFlyingShearYangZhong——kangLinShu-jUDWangHua——xuanYangYun(Bar&WireSteelRollingPlant)AbstractThestart—stopdouble—lengthflyingshearofbarproductionlineinKISCwasn'tworkingproperlyafter throughwatercoolingtechn0logy.FlyingshearisworkingproperlyafterInitsinspectionsyst emalqdthemotorencoderimprovementsandptimization. KeyWordsbardouble—lengthflyingshear;throughwatercoolingtechnology;areasensors 倍尺飞剪是棒材生产的关键设备,它直接影响生产率和成材率.昆钢80万吨棒材生产线(简称:轧钢第一作业区)于2004年4月建成投产,主要生产012ram~40mmⅡ,Ⅲ级热轧带肋钢筋,倍尺飞剪南北京钢铁设计院设计电控系统并进行调试,它操作简单,维护方便,工作稳定,剪切精度高,能够获得最大的产品收得率.该系统在生产线采用穿水冷却新技术后,出现了不剪切的问题,经过改进优化,倍尺飞剪动作的可靠性和倍尺精度得到保证.1设计原理起停式飞剪在不剪切时是静止的,此位置称之为原位,当控制系统发出剪切信号时,剪刀机从静止迅速加速到最高速度对轧件进行分断剪切,剪切完成后迅速停止于原位,其运转不大于一周.整个倍尺飞剪由机械部分和电气部分组成.剪机为组合式结构,分3种形式:回转式,曲柄式,曲柄+飞轮式;传动系统为美国GE公司全数字直流调速装置6KDV31350Q4F40D3型;电机采用上海南洋电机厂生产的ZTFS一315—42型280KW低惯量电机(满足起,停要求),额定电压440V,额定电流704A,基速650r/min,励磁电压220V,励磁电流24A.控制系统由CPU,高速计数器模块(HSC),轴定位模块(APM),数字输人输出模块(DI/D0)等组成.检测系统由HMD一0,HMD一1,HMD一2(热金属检测器),轧线出口脉冲编码器,电机轴脉冲编码器组成,见图1.昆钢科技2009年第6期(誓0谁牦I乏一一.0一:二j0二二圈lIs控利糸统Figure1ControlSystemofFlyingShear1.1轧件长度测量及剪切长度控制原理式中:LPP一一脉冲当量,mm;飞剪系统对轧件长度的测量及剪切长度控制原Dw——工作辊径,ram;理如式(1),轧件通过长度与单位脉冲对应,当PPR一一编码器每转脉冲数;成品轧机工作辊径不变时,LPP基本为常数,L与Ni一一轧机减速箱速比,倍. 成正比,长度测量变成脉冲计数.通过两个HMD测量脉冲当量的方法称为测量L:N×LPP(1)优先,即直接测量法,计算公式为式(3):式中:L一一轧件长度,mm;N——成品轧机编码器输出脉冲数,个;LPP一一脉冲当量,mm.式(1)可理解为:假设HMD一1,HMD一2之间的距离为10米,所需分段的倍尺长度为100米,轧件头部通过此l0米的时间为1秒,计数器所记录的出口机架脉冲数为10240个,那么在轧件速度稳定的情况下lO秒后计数器所记录的出口机架脉冲数为102400个,轧件通过长度为100米,此时达到设定长度,控制系统发出命令启动飞剪,从而得到一个倍尺品.1.2脉冲当量的计算脉冲当量的计算有两种方式:辊径优先和测量优先.从工作辊径计算脉冲当量的方法称为辊径优先(理论计算法),计算公式为式(2):LPP=竹Dw/(PPRxi1(2)LPP=L/N(3)式中:LPP一一脉冲当量,mm;L一一HMD一1~HMD一2之间的距离,mm;N一一轧件头部通过HMD一1~HMD一2时记录的脉冲数,个.两种计算方法各有优,缺点.对于辊径优先而言,其优点是:脉冲当量值稳定不变,即脉冲当量的稳定度非常好;缺点是:1)辊径估计不准.工艺上有两个辊径,即工作辊径和辊环直径.轧线上设置的出口线速度是按照工作辊径计算出来的,而轧件实际行走的线速度是比设置的出口线速度快的,轧件经过轧辊的挤压有一定的前滑量,前滑值一般在3%~5%之间,因此,在飞剪设置工作辊径时可以按工艺工作辊径×5%进行设置.辊环直径是所安装的轧辊的最大辊径,因此在辊径估计不准时,可以先按辊环直径进行设置.2)辊径变化2009年第6期杨仲康,林舒俊,王华轩等:棒材倍尺飞剪的控制与优化不能自适应.在轧钢的过程中,随着时间的推移,因为下列原因可导致工作辊径的变化:轧辊压下量调整,轧辊磨损,轧辊温度变化引起的轧辊变形等等.而辊径优先法永远按照设定辊径进行测长,测速,剪切,对辊径的变化不能自动改变.对于测量优先而言,其优点是:脉冲当量值准确度高,能自动适应辊径变化;缺点是:易产生随机误差.测量优先的脉冲当量值完全依赖于轧件头部瞬间经过HMD一1和HMD一2热金属检测器时,能否被检测到.对于辊径优先和测量优先的使用通常是根据两种测量方法的优势和缺陷,可以在轧钢的初期,即调试完成后第一次轧钢,或更换热检后或调整热检角度及灵敏度后或调整热检位置后的第一次轧钢,或增加水冷以后的第一次轧钢,操作人员对热检检测不信任时,先用辊径优先法,待在轧辊压下量调整完毕,轧件尺寸合格后,经过几根钢的轧制,十个脉冲当量的测量值偏差均在2‰以内,确认热检测量准确后,再使用测量优先.1.3应急剪切模式倍尺飞剪的应急剪切模式,是针对当来自出口机架脉冲信号有故障时或HMD一1或HMD一2有故障时,在轧线速度稳定时,也可获得较好的剪切精度.所选定的关键热金属检测器(通常为HMD一2)必须完好.进入应急剪切状态后,系统根据设定的轧件线速度及分段长度给出分段参考时间来对轧件进行分断剪切.但在实际生产过程中,轧线速度往往不稳定,从而倍尺得不到优化,有时成材率和定尺率不能满足要求.2倍尺飞剪系统的优化2.1倍尺飞剪存在的问题倍尺飞剪检测系统工作时,通过热金属检测器采集可见红外光源,经光电处理输出一个高电平信号,进入PLC系统.比如:轧件HMD一1到HMD一2之间的距离为A,HMD一2到倍尺剪之间的距离为B.各个品种的线速度不同,所以通过A所需的时间也不同,在PLC系统中,倍尺的长度是根据出口机架编码器的脉冲数量来计算的.假设轧件的头部在通过A这段距离时PLC系统共测得N个脉冲数量,倍尺长度为L,则:(L/A)×N就等于当前倍尺长度对应的脉冲数量,当PLC系统的高速记数模块计够当前倍尺长度对应的脉冲数量时,发出剪切信号使剪刀机动作,剪切出符合要求的倍尺产品.同时在剪刀机的剪刃闭合瞬问倍尺剪PLC系统发出一个剪刃闭合信号给冷床PLC系统,延时以后冷床裙板动作.当尾钢倍尺剪不进行剪切时,冷床裙板动作的HMD2信号消失,同时剪刀机的剪刃未闭合,倍尺剪PLC系统同样发出一个信号给冷床PLC系统, 延时以后冷床裙板动作.当应用穿水冷却工艺生产时,在精轧机出口,即穿水冷却系统的人口处,HMD1检测到轧件信号至轧件通过HMD2(穿水冷却系统出口处)的一段距离内,由HMD2发出两路高电平信号分别送到倍尺剪控制系统和高速计数模块,这时高速计数模块开始采集成品出口机架电机编码器的脉冲数量,并与倍尺剪控制系统所设定的倍尺长度对应的脉冲数量进行比较,在达到设定倍尺长度对应的脉冲数量时,控制系统发出剪切信号使倍尺剪动作,进行剪切.由此可以看出,决定倍尺剪能否正常剪切的关键是:HMD1,HMD2能否准确,稳定的检测到轧件通过信号,而通常所选用的低温型热金属检测器检测的被测物的表面辐射温度需~E300~C~1400~C 之间才能正常工作.在穿水轧制过程中,因为轧件的表面温度过低(300cC左右),导致了HMD2不能检测到轧件信号,破坏了剪刀机正常工作的条件,导致剪刀机不能剪切.为了解决这个问题,采用剪刀机"应急剪切"功能,只能选择HMD1为关键检测器.这样一来,第一段倍尺是HMD1检测到轧件信号才开始计时,所以倍尺长度比设定值短了25m(穿水管道的长度),而尾钢则长出25米,从而使得尾钢上不了冷床.因此,导致成品的倍尺长度不能调整,尾钢上不了冷床等一系列问题.此外,倍尺剪电机的编码器控制着倍尺剪的剪切和定位,若编码器出现故障则会出现堆钢事故,因编码器的电源出现问题而导致的跳轧事故是较为常见的原因.编码器的工作电源取自数字调速装昆钢科技2009年第6期置.通过对比发现:不同的数字调速装置所提供的编码器电源的电压并不相同,即使是同一台数字调速装置所提供的电源电压也不稳定,而编码器工作在一个电源不稳定的条件下,它的数据反馈也就变得不稳定甚至是错误的,最终出现速度反馈信号丢失而跳闸.2.2检测系统的优化由于倍尺剪的控制程序受设计单位的知识产权保护,不能通过修改或优化控制程序中的相关部分来解决和改善这一问题.第一作业区以简单可行,稳定运行,投入少,并能保证实现倍尺剪的全部功能为思路,设计了优化方案.1)保持原有的控制程序,仍然采用光电检测元件进行检测,重新改制一个检测元件替代原有的HMD2安装在穿水冷却系统出口处,以使轧件通过信号得到有效检测.2)保证在较宽视场范围内(垂直视场70ram)有效检测跳动较大的小物体,如:直径012mm的轧件,以避免因轧件跳动后脱离视场范围而产生信号误动作;检测距离在0.6~1.8m范围.3)保证改制的光电检测元件能同时输出两个常开性质的高电平接点信号给控制系统和高速计数模块,以满足控制条件.4)现场的安装条件不作任何变更.发射器接收器5)为编码器提供稳定的工作电源.2.3优化措施实施2.3.1检测系统通过对比测试多种光电检测元件,选择以面积传感器作为改进的基本检测元件.面积传感器是一种特殊的光电开关,可以在较宽的视场范围内检测很小的目标,它不受被测物温度高低的影响,只要有物体从面积传感器的发射器和接收器之间通过,传感器问的光束被挡住,就会输出检测信号.在原产品的基础上将普通光敏二极管更换为高灵敏度光敏管,数量由l0只增加到12只;检测视窗范围由55mm增加至70mm.为保证检测距离在0.6~1.8m范围,将光敏管工作电压提高了3V,仍然保持在额定范围内.经过72/bt~通电老化试验,元件温升保持在27~35℃正常范围内;至此,改制的传感器已具备装机条件.由于普通面积传感器输出接点均为一常开一常闭,而控制系统和高速计数模块进入控制状态需要的是两个常开性质的高电平接点,为此需将其进行输出改制,在传感器无空间容纳更多元件的情况下,新增输出接点采取了以面积传感器输出信号推动一个外接的带两常开,两常闭接点的中间继电器给出两个常开信号的方式,满足了控制要求.改进后的电气控制系统见图2.棕色701—24V棕色电源电源蓝色70一0V蓝色电源电源白色白色3S4—24V\70103(3S4.16)同步信号同步信号黑色黑色3S4—24V\701—03SH/HMD-2输出输出701—01(24V)厂—]701-0Vll…一电骡々1日怂器一…,,自弃图2改进后的飞剪控制系统Figure2ImprovedControlSystemofFlyingShear(下转44页)呲斛至至昆钢科技2009年第6期模拟量的遥测;支持2路4~20mA直流模拟量输出.⑤通讯接口:双以太网,双RS485,电力行业标准DL/T667—1999(IEC60870—5—103标准)的通讯规约.⑥对时功能:软件报文对时;硬件脉冲对时功能(支持IRIG—B码对时).⑦保护信息方面的主要功能:装置描述的远方查看;装置参数的远方查看;保护定值,区号的远方查看,修改功能;保护功能软压板状态的远方查看,投退;装置保护开入状态的远方查看;装置运行状态(包括保护动作元件的状态和装置的自检信息)的远方查看;远方对装置实现信号复归;故障录波(包括波形数据上送)功能.⑧具备冶金,钢铁行业系统的防爆认证.7结束语采用综合自动化控制方式和测控继电保护分层布置方案,并实施无人值班管理模式是变电站自动化技术的发展趋势,不仅技术上先进可行,功能完善,而且也极具经济性.鉴于变电站综合自动化系统当前缺乏统一的国家标准,因此,在草铺新区供配电网络的综合自动化系统的功能组合和设计优化过程中,应根据项目的具体情况,遵循科学,严谨的工作原则,集思广益,用发展的眼光来进行变电站综合自动化系统的建设,以保证电网安全,经济,可靠运行.参考文献:[1]丁书文,黄训诚,胡启迪,变电站综合自动化原理及应用[M].北京中国电力出版社,2002 (上接32页)因HMD2的安装位置与控制系统中的运算值是相对应的,因此在现场安装上,把改制的面积传感器安装于原HMD2的位置处.在使用中,又出现穿水管的水和蒸汽干扰了HMD2信号的问题,倍尺剪不能正常工作.为此提出了新的优化方案:将HMD2的安装位置由倍尺剪前移到倍尺剪后,并对PLC程序进行相应的修改,实现倍尺剪的稳定运行.2.3.2电机编码器编码器的工作电源直接由直流24V稳压电源提供,从根本上解决了电源的不稳定性.2.4优化效果2.4.1检测系统HMD2由热金属检测器换为面积传感器,并将其移到倍尺剪之后,保证了检测信号的可靠性又避免了外界对信号的干扰因素,确保了倍尺剪的稳定性和剪切精度.投入使用后,穿水轧制钢种的定尺率及成材率得到大幅提高,避免了"应急剪切"中出现的首段倍尺短,末段倍尺长且不能上冷床的情况.2.4.2电机编码器编码器采用工作电源单独供电后,没有出现过"速度反馈丢失"报警,从而保证了生产顺行.3结束语经过对倍尺剪的优化,达到了预期的目标;"轧机倍尺剪控制检测装置"成为公司实用新型技术专利;优化过程中积累的经验,为今后让设备发挥更好的性能提供了借鉴和参考.。
攀钢110万吨棒线材生产线建设与发展

攀钢110万吨棒线材生产线建设与发展宋建国;陈文灶【摘要】攀钢抓住市场机遇,在攀枝花本部搬迁建设一条110万吨的棒线材生产线,本文对该生产线的工艺布局、主要装备特点、产品定位及后期发展等进行了介绍.【期刊名称】《四川冶金》【年(卷),期】2018(040)005【总页数】3页(P38-40)【关键词】棒材;高线;生产工艺;技术改造【作者】宋建国;陈文灶【作者单位】攀钢集团攀枝花金属制品有限公司,四川攀枝花617023;攀钢集团攀枝花金属制品有限公司,四川攀枝花617023【正文语种】中文【中图分类】TG33根据攀钢产线结构调整需求,攀钢集团利旧搬迁攀成钢闲置设备,在攀枝化本部建设一条年产50万吨高速线材生产线和60万吨的棒材生产线。
棒材于2017年3月1日热负荷试车,高线于2017年5月9 日热负荷试车。
在一年的时间内,完成项目的搬迁建设与达产达效,实现当年投资、当年建成、当年赢利的任务,成为攀钢新的利润增长点。
截止2017年12月底,全年累计生产建筑用钢40.8万吨,棒材实现了Φ14~40mm规格、高线实现了Φ6.5~12 mm规格的螺纹钢、圆钢生产。
现今,高速线材生产线正致力于高端金属制品用线材的开发,逐步打造西南地区最具竞争力的建材生产基地和金属制品材生产基地。
1 平面布置根据地理位置条件,为有效节约占地和工程投资,尽可能利旧闲置设备及设施,高速线材与棒材车间平行相邻布置,依次布置线材主轧跨(231.0 m×24.0 m+135.0 m×21.0 m)、棒材主轧跨(428.5 m×24.5 m)、原料跨(440.5 m×33.0 m)、成品跨(256.5 m×18.5 m,预留184.0 m×18.5 m)。
车间最大长度440.5 m,最大宽度100 m,线材主轧线设备布置在+5.0 m平台上。
工艺平面布置示意图如图1所示。
2 主要装备2.1 棒材生产线主要由1台蓄热推钢式加热炉、18架轧机、3台飞剪、1台冷剪机、1台步进齿式冷床、检查收集设备等组成。
棒材工艺优化提升产能改造

新 建的高炉和转炉 投产后 ,炼钢达 到 2 0 0万 吨 / 年规
模 ,而 目前 轧钢 为 5 0万 吨 / 年 中宽 带 钢 生 产线 和 1 0 0万 吨 / 年 棒材 生产 线 ,富余 了约 5 0万 吨 / 年 钢 坯 ,因此需 要 在棒 材生 产线 年产 量 1 0 0万 吨的基 础 上 ,通过 实施轧 钢工 艺优 化 、设 备 改造 ,提 升棒 材
线提 升产能的的改造方案 :
( 1 )坯料 改 为 :1 6 5 m m ×1 6 5 m m×1 2 0 0 0 m m, 单重 2 5 0 0 k g 。 ( 2)带肋 钢筋 2 2 m m 由单 线 轧制 改 为两切 分 轧制 ; 1 6 m m、 1 8 m m 由两 切 分 改 为 三 切 分 ;
e c o no mi c b e ne it f .
Ke y W or ds b a r p r o d u c t i o n — l i n e ; p r o c e s s o p t i mi z a t i o n ; e q u i p me n t t r ns a f o r ma t i o n ; b o o s t i n g o u t p u t
2 0 1 3年 第 4期
王晓松 : 棒 材 工 艺 优 化 提 升 产 能 改 造
①1 4 m m 由三切分改为 四切分 。
( 3 )调整减速机速 比。
1 6 5方 ( 自产坯) 和 1 5 0 方 ( 外 购坯)两种 ,设计 的
1 6 5方孔型系统必须 能满 足轧制两种坯料 ,并且 与 目
昆 钢 科 技
2 01 3年 第 4期
K u n g a n g K e j i
昆钢简介(科学材料)

炼铁厂昆钢炼铁厂始建于1939年,至今已有70年的发展历史,主要产品为炼钢生铁。
拥有5座高炉,高炉总容积为3760 m3,其中为六高炉2000 m3。
炼铁厂年生产能力340万吨铁、240万吨球团矿、592万吨烧结矿。
共有9个辅助作业区,各作业区生产及技术装备均达到国内先进水平。
“九·五”之初,从钢铁冶炼技术较先进发达的卢森堡引进C高炉,在国内进行了大量的修配改工作,定型为昆钢2000m3高炉,于1997年2月1日正式开工建设,1998年12月26日顺利投产出铁,建设工期仅为23个月,技术装备达到国内同类型高炉先进水平。
开炉后,69天达产,创造了国内同类型高炉达产的最快纪录,现生产水平已跻身国内先进行列,已达170万吨的生产能力。
原料系统三烧配置2台工艺比较完善的130m2烧结机,1998年8月建成并投产,其设备装备、自动化控制水平达到国内二十世纪九十年代先进水平;四烧配置一台300 m2烧结机,于2008年8月投产;球团作业区有链篦机—回转窑球团生产线2条,年设计产球团矿260万吨。
炼钢厂昆钢炼钢厂是武钢集团昆明钢铁股份有限公司主要的生产单位之一,2006年11月20日,昆钢集团进行了资源优化组合和结构调整,原昆钢第二炼钢厂、昆钢第三炼钢厂合并成立昆钢炼钢厂,重组后的钢厂具备年产360万吨钢的生产能力。
炼钢厂第一作业区(原第二炼钢厂)1970年11月建成投产时有15吨顶吹转炉3座,600吨混铁炉一座,设计能力为年产38万吨钢。
1981年从德国Mannesmann-Demag引进小方坯连铸生产线,1982年投产,生产断面为90×90mm 的小方坯,被赞誉为“全国小方坯连铸一枝花”;1996年停止铸模生产,至此昆钢实现了全连铸生产。
2002年钢产量突破100万吨;2003年,进行了转炉扩容改造,转炉由15t扩容为25t,2004年1月,150万吨产能工程改造完成,通过技术改进、连铸机易地改造、风机改型等,达到了优化工艺流程、提高浇铸能力、提升产能的目的,实现了与80万吨棒材线直接热装轧制生产工艺;随着工艺、设备的不断完善,生产水平稳步提高,并使生产能力提高至设计能力的 3.8倍,达到了150万吨钢的实际生产能力。
棒材生产线穿水区域除雾装置的设计

2 1 年9 0 0 月
棒材生产线穿水 区域 除雾装置 的设计
彭 智 业 詹 道 平
( 昆钢 集 团设计 院有 限公 司 )
摘 要 昆钢棒 线)8 TP 棒材生产作业 区生产时产生雾汽,对操作人 员和设备危 害较大 ,并可造成3≠ - 0YE - ≠ 飞剪 信 号 中断 ,造成堆钢 事故 。经设计采用顶部喷淋压 雾、底部收 集 ,混流风机导 出厂外 的方式 ,减 少 了雾气 污染,降低 了设备事故 。
关键词 棒材 生产线 除雾 设计
Dei sgn fD e i t r f e por ton a r a of o m s e or D va a i tA e Coo i t oug W a e fBa oduc i n’lne lng hr h t r o r Pr to _ i _ -
Pe gZh- e Zh nda — i g n iy a o— n p
(ei sttC . doK n ig r d t l ru ) D s nI tue o t u m n o a e op g ni L f I n n S eG
Absr c t r d c dage t e l fv p r u i gtep o uci ni e8 0t o s n — 0 sb r r s p ta t I o u e r a a a o sd rn r d t t 0 u a d tn a swo k ho p d o h o nh h
a o t dfo t etp s r ywae op e st ev p r n ol ci o t eb to te sn h x a s d pe r m h o p a trt r s h a osa d c l t f m h otm h n u igt ee h u t e ng r fn g v f ev p r ot eo tie o ewo k h p I e u e h ol to ft ev p ra d d c e s d a a e o t a st h u sd ft r s o . tr d c dt ep l in o h a o n e r a e h o h u t ea cd n so ee u p n s h c ie t f h q i me t. t
“四切分轧制”的生产技术要点
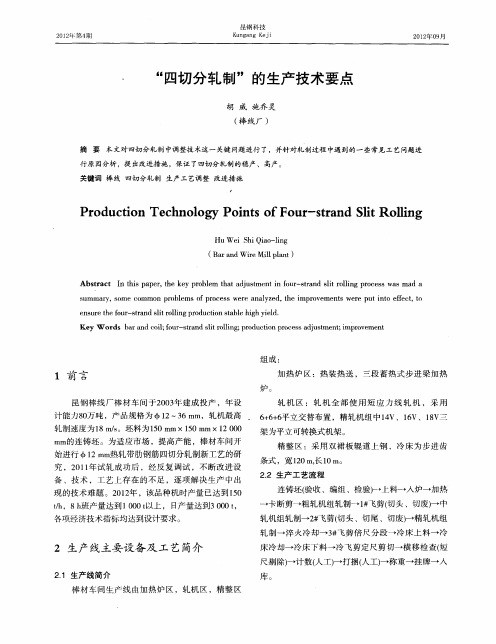
坏 ;2 分刀粘钢 :造成切分刀粘钢主要原因有 :①开 切
轧温度过高 ,切分带形状不规则 ,引起切分刀粘钢 ;
②切分刀被封闭在箱体 内,由于冷却不足 ,刀片两侧
会粘 附氧化铁皮 。③切分箱的安装 必须保证切分 环 、 切分轮 、切分刀三点一线 ,对中 良好 ,若 安装不 正 ,
1 四切 分 生 产 工 艺 相 对 于其 他 钢 种 较 为 复 2 杂 ,对 坯料质 量 、加热温 度及 轧制要 求都 很 高 。特 别 是 轧 制 过 程 中 ,更 是 需 要对 料 形 尺 寸 、轧 制 速 度 、导 卫调整 严格 要求 ,而且 需要 职工过 硬 的操作
水 平 。料形控 制是 四切分 生产 工艺 中最 为重要 的环 节 ,料 型 的控 制 又牵涉 到轧制 温度 、速度 、导 卫 、
H i h Q a—i u We S i i —n olg
( a n r lpa t B r dWi Mi ln ) a e l
Ab ta t nti p p r tek ypo lm a du t n nfu - t n l ol gpo e sw sma sr c I hs a e, h e rbe t t j s h a me t o r sr dsi rln rc s a da i a t i
行 原 因分析 ,提 出改进措施 ,保证 了四切分轧制的稳产 、高产。
关 键 词 棒 线 四切 分 轧制 生产 工 艺调 整 改 进 措 施
Pr u to c no o y Po n so o r。ta d S i Rol od c i n Te h l g i t fF u ‘sr n l l ng - t i
昆钢棒材钢坯使用高温防氧化涂料的试验分析
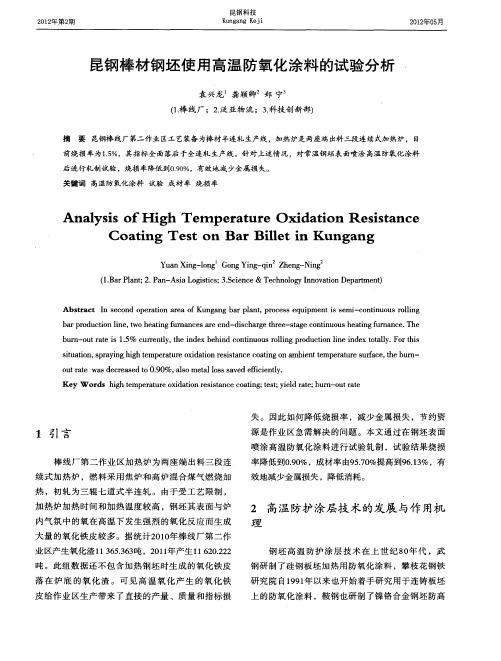
A bsr c I e o d o r t n a e fKu g n a l n , r c s q p e ti e -c ni u usrli g t a t n s c n pea i r ao n a gb rpa t p o e se uim n ss mi o t o oln o n
源 是作 业 区急需解 决 的 问题 。本 文通 过在 钢坯表 面
喷涂 高温 防氧化 涂料进 行试 验轧 制 ,试验 结果烧 损
率 降低到0 0 . %,成材率 由9 . %提高到9 . %,有 9 57 0 61 3 效地减少金属损失 ,降低 消耗 。
2 高温 防 护 涂 层 技 术 的 发展 与 作 用机
st a in s r y n i htmp r tr xd t nr ssa c o tn n a in mp r tr u f c ,h u - i t , p a i gh g e e au eo iai e it n ec ai go mb e t e e au es ia e teb r u o o t n
b r -o tr t s15 c r nl . h n e e i d c n i u u oln r d cin ln n e oal . o i u n u a ei .% ure t t ei d x b h n o tn o sr l gp o u to ie i d xttly F rt s y i h
理
钢 坯 高温 防护 涂 层 技 术 在 上 世 纪 8 年 代 ,武 0 钢研 制 了硅钢 板坯 加热 用 防氧化 涂料 ,攀枝 花钢 铁
内气 氛 中 的氧在 高温 下 发生 强烈 的氧化 反 应而 生成
大量 的 氧化铁 皮较 多 。据 统计 2 1 年棒 线 厂第 二作 00
昆钢质量信息管理系统棒材站子系统的构建
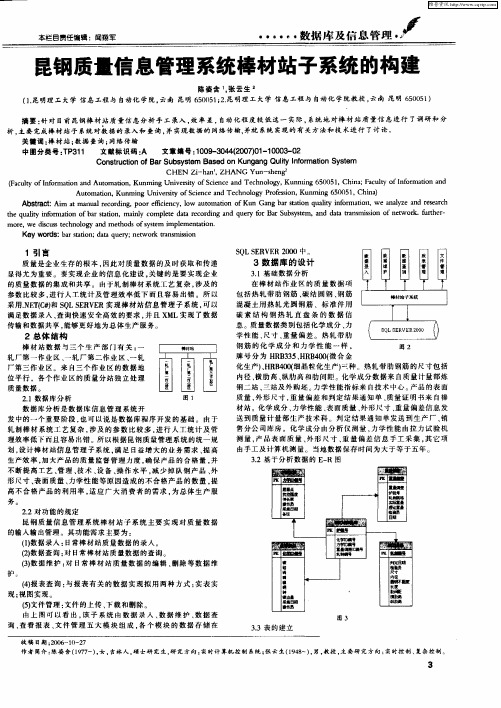
中圈分类号 :P 1 T 3 1
文献标识码 : A
传 输 和 数据 共 享 . 能够 更 好 地 为 总 体 生 产 服 务 。
T j 入 萋
数
棒 材站子 幕坑
2总体 结构
棒材站数 据与三个 生产 部 门有关 : 一
学 性 能 、 寸 、 量 偏 差 。 热 轧 带 肋 尺 重 钢筋 的化 学成 分和 力学性 能一样 . 牌 号 分 为 HR 3 5 H B 0 ( 合 金 B 3 、 R 4 0微
t e q ai f m ̄t n o a  ̄t n h u l y i o a o fb rs i .many c mp ee d t e o d n n u r 0 r S b y tm。a d d t rn mi i n o ewo k u t e — t n i o i l o lt aa r c r ig a d q ey f rBa u s s e n a t s s o f t r .f r r a a s n h m0 l we d c s tc n l g n t o so se i lme tt n t . l u s e h o o y a me h d f y tm e 坞 d s mp e n i a o
A tma o 。 u migUnvrt f c neadTeh o g rfso , u mig6 0 5 , hn) u o t n K n n i s yo i c n cn ly Poe in K n n 50 C ia i ei Se o s 1
2024年特钢棒材制造市场发展现状
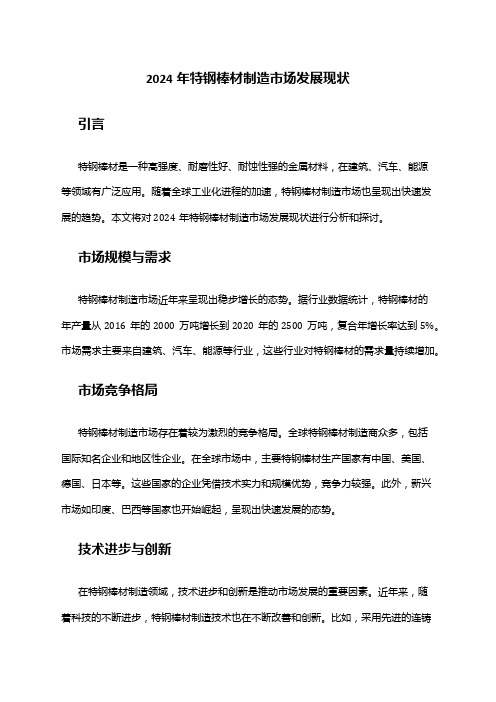
2024年特钢棒材制造市场发展现状引言特钢棒材是一种高强度、耐磨性好、耐蚀性强的金属材料,在建筑、汽车、能源等领域有广泛应用。
随着全球工业化进程的加速,特钢棒材制造市场也呈现出快速发展的趋势。
本文将对2024年特钢棒材制造市场发展现状进行分析和探讨。
市场规模与需求特钢棒材制造市场近年来呈现出稳步增长的态势。
据行业数据统计,特钢棒材的年产量从2016年的2000万吨增长到2020年的2500万吨,复合年增长率达到5%。
市场需求主要来自建筑、汽车、能源等行业,这些行业对特钢棒材的需求量持续增加。
市场竞争格局特钢棒材制造市场存在着较为激烈的竞争格局。
全球特钢棒材制造商众多,包括国际知名企业和地区性企业。
在全球市场中,主要特钢棒材生产国家有中国、美国、德国、日本等。
这些国家的企业凭借技术实力和规模优势,竞争力较强。
此外,新兴市场如印度、巴西等国家也开始崛起,呈现出快速发展的态势。
技术进步与创新在特钢棒材制造领域,技术进步和创新是推动市场发展的重要因素。
近年来,随着科技的不断进步,特钢棒材制造技术也在不断改善和创新。
比如,采用先进的连铸连轧技术可以提高生产效率和产品质量;应用新型合金材料可以满足不同行业对特定性能的要求。
技术进步和创新的推动,为特钢棒材制造市场的发展注入了新的动力。
市场挑战与机遇特钢棒材制造市场面临着一些挑战,但也有着发展的机遇。
首先,环保问题是特钢棒材制造面临的重要挑战之一。
特钢棒材的制造过程涉及大量的能源消耗和环境污染,因此提高生产过程的环保性和可持续性是当前亟待解决的问题。
其次,市场竞争激烈,企业需要通过技术创新和提高产品质量来保持竞争力。
同时,市场的快速发展也为企业带来了机遇,适应市场需求和扩大市场份额是企业的发展方向。
发展趋势与前景展望特钢棒材制造市场将继续保持快速发展的态势。
未来,市场需求将持续增加,特钢棒材的应用领域也将进一步拓展。
与此同时,技术进步和创新将不断推动市场发展,新型材料和新工艺的应用将提高特钢棒材的性能和品质。
昆钢650全连轧工艺系统优化改造实践

安 宁公司于 2 0 1 3年 1 月停 产实施 了全连 轧工 艺系统 优化 节 能升级 改造 。此 次改 造 以调 整用 能 结构 、降
低 能耗 为 目标 ,进 一步 优化 工 艺 和设备 配 置 ,提高 能 源利 用效 率和 生产效 率 ;坚持 工 艺技 术 与经 济相
昆 钢 科 技
现就 改造 的 主要 内容 、改造 后 的全连 轧 生产线 的工
艺特点及改造后 的效果做一个 简要 的分析。
2 实施 改 造
2 . 1 原 有 主要 工艺 装备 条件
原半 连轧主要工艺装备 为 :2座推钢式煤气加 热
炉 ;原 半连 轧生 产线 布 置为 粗轧  ̄6 5 0×1( 7道 轧
时 ,粗轧 机组采用 不 同的孑 L 型系统 ,但 经粗 轧机 组 轧制后 ,轧件 断面一致 ( 8 V机架 出 口料形均为 8 8
7 ) 主厂 房加 固改 造 。原料 跨保 持不 变 ,利用 原 物流坯 料库作 为原料 场地 。主轧 跨加 热炉 至粗 轧 段厂房加 固,经核算主轧跨加固长度 7 8 m。
并 兼顾 城市 煤气供 应 ,原有 两 座传统 的推 钢式 加热 炉拆 除 ,新建 一座 蓄热式推 钢煤 气加 热炉 。煤 气和 空气均预热 1 0 0 0 o C以上 ,加热环节采用 工业 微机和
P L C构 成热 工控 制 系统 ,具 有生 产操 作灵 活 、钢 坯 加 热均匀 、减少 能源 消耗 、氧化烧 损 少和节 能 等优
点。
2)产 能。改造后为 1 2 0万吨 / 年。 3)加 热炉 改造 。改造 前 为两座 推钢 式煤气 加
热 炉 ;改 造 为 一 座 双 蓄 热 煤气 推 钢 式 加 热 炉 ,加
首席技师先进事迹材料
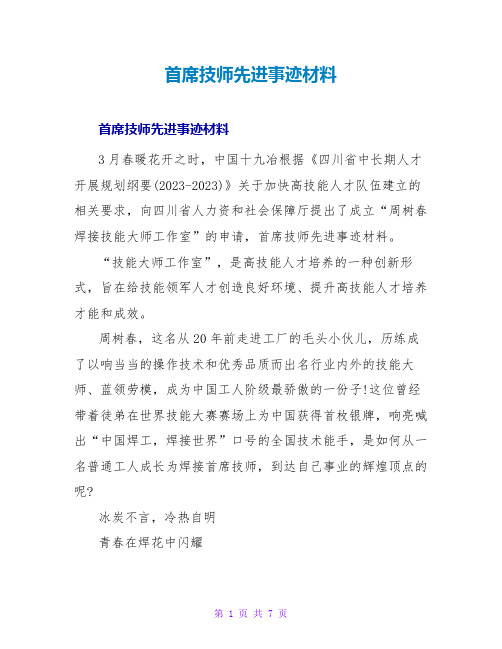
首席技师先进事迹材料首席技师先进事迹材料3月春暖花开之时,中国十九冶根据《四川省中长期人才开展规划纲要(2023-2023)》关于加快高技能人才队伍建立的相关要求,向四川省人力资和社会保障厅提出了成立“周树春焊接技能大师工作室”的申请,首席技师先进事迹材料。
“技能大师工作室”,是高技能人才培养的一种创新形式,旨在给技能领军人才创造良好环境、提升高技能人才培养才能和成效。
周树春,这名从20年前走进工厂的毛头小伙儿,历练成了以响当当的操作技术和优秀品质而出名行业内外的技能大师、蓝领劳模,成为中国工人阶级最骄傲的一份子!这位曾经带着徒弟在世界技能大赛赛场上为中国获得首枚银牌,响亮喊出“中国焊工,焊接世界”口号的全国技术能手,是如何从一名普通工人成长为焊接首席技师,到达自己事业的辉煌顶点的呢?冰炭不言,冷热自明青春在焊花中闪耀刚踏进电焊工这个行当时,周树春并不觉得自己的人生也可以精彩。
皮肤被高温灼伤、常年出差在外、时间在埋头焊接的枯燥与疲惫中流逝,他也曾面临过诸多质疑,也曾打过退堂鼓,但是,与焊花共舞二十载,渐渐的,他发现了自己的价值。
从1992年参加工作以来,周树春先后参加了攀钢热轧板厂工程、昆钢焦炉工程、涟钢烧结机工程、攀企球团工程、韶钢、安钢、唐山国丰、柳钢转炉等上百个工程施工建立。
从最开场业主对这个毛头小子“他能行吗?”的挑剔目光,到后来“把焊接工程交给周树春我们放心”的高度评价,十几年来,他以从没有无故耽误一天,没有一条不合格的焊缝的实际行动回击质疑、回报信任。
由于他技术过硬,作风顽强,经常从一个工地,被叫到另一个工地。
不管在哪里,他都是勤勤恳恳、任劳任怨,敢于挑战自我,敢于拼搏。
1997年,还在攀钢冷轧干活的周树春接到紧急通知,连夜赶往昆钢棒材加热炉检修现场。
周树春赶到时,刚停下来的炉子温度有300多度,用了10多个风机降温,可炉内温度还是有70多度,无奈之下,抢修小组只能在炉膛下面垫了一层木板防止脚部烧伤,当时的木板还冒着白烟,周树春穿上打湿的棉衣决然钻进了加热炉。
红河钢铁有限公司位于蒙自县城以西15公里处的雨过铺镇

红河钢铁有限公司位于蒙自县城以西15公里处的雨过铺镇,隶属于武钢集团昆钢股份有限公司,是云南省精品建筑钢材生产基地。
自2003年建厂以来,红钢一直以“创造价值,创造文明,造福社会”为企业宗旨,走新型工业化道路,加强企业管控,参与市场竞争,并将文化建设与企业发展战略目标相结合,以企业文化服务于企业未来的发展战略使企业逐渐成长壮大。
2003年,州委、州政府与昆钢控股公司合作,充分利用红河州与东南亚国家越南接壤的区位优势,由昆钢控股公司投资建设了涵盖从原料场、烧结、炼铁、炼钢到轧钢完整工艺流程的钢铁联合企业——红河钢铁有限公司。
红钢的诞生结束了我州“有铁无钢”的历史,翻开了红河工业发展的新篇章。
红钢工程项目在初期按年产100万吨钢的规模一次设计、分步实施。
2003年11月18日举行奠基仪式,2005年2月23日,第一座容积为450立方米的高炉(一期工程)顺利开炉出铁,4月1日第一座炼钢转炉炼出第一炉钢水,由此红钢具备了年产50万吨钢铁的生产能力。
2005年11月18日,第2座容积为450立方米的高炉(二期工程)开始建设,于2006年9月17日高炉顺利出铁。
2006年9月30日,第2座炼钢转炉出钢,至此,红钢达到年产100万吨钢铁的生产规模。
根据市场需求,2005年10月1日,年产40万吨高速线材生产线开工建设,并于2006年9月1日投产。
2006年9月29日,年产80万吨棒材生产线项目开工建设,并于2007年8月16日热负荷试车成功。
红钢达到了年产100万吨钢铁、40万吨线材、80万吨棒材的生产规模。
2007年1月31日开工建设建水钢铁厂移地大修改建项目(新建1350立方米高炉),于2008年7月9日竣工投产。
3号50吨转炉及连铸于2009年5月31日热负荷试车成功,3号260平方米烧结机工程也正在建设中,预计2010年3月中旬投产。
届时,3期配套工程全部完工后,红钢将达到年产200万吨钢的综合生产能力。
《棒线材轧制的发展方向》课件

2023/12/18
3
连铸坯热装热送或直接轧制
2023/12/18
直接轧制定义:连铸坯不经过再加热而直接 送至成品轧机轧制成材的一种方法;
直接轧制可省掉钢坯冷却和清理仓库存放及 中间加热工序;
前提保证无缺陷钢坯,在线检查和在线清理; 保证轧制温度。
4
柔性轧制技术
对于小批量、多品种的生产,改变规格和品 种时,轧机停机时间增加。
研究表明,在棒线材的轧 制中,2道次低温轧制的面 缩率应控制在24%~31%, 4道次低温轧制的面缩率应 控制在46%~57%。在更 多道次中采用大变形量的 低温轧制,会导致晶粒尺 寸的不均匀。
2023/12/18
低温精轧工艺的温度范围
14
低温轧制的优缺点
减少加热能耗; 减少氧化烧损; 提高轧钢加热炉的加热产量; 延长加热炉的寿命; 减少轧辊的热应力疲劳裂纹以及氧化皮引起的磨损; 降低脱碳层深度; 提高产品的表面质量; 细化晶粒; 改善产品性能。 缺点: 加大了轧材的变形抗力,从而加大了轧制力和轧制功率; 降低了轧制时轧材的塑性,从而影响轧材的咬入。
利用超快速冷却技术,进行TMCP和冷却路径控制,可明显提高线材强度,提高钢材产品利 用率,有十分广阔的应用前景。
利用了线材轧机连续大变形的特点,通过轧后的快速冷却过程抑制线材的再结晶,最后通 过相变过程的控制实现线材的细晶化。
2023/12/18
27
盐浴控冷工艺
线材的在线熔融盐浴直接韧化处理(简称DLP)是新日铁最先开 发的工艺,应用品种主要是桥梁缆索用线材、高级弹簧钢线材、 特殊用途钢丝绳用线材等高档线材。
在生产中采用的方法是低温轧制 实际效果并不好: 1)轧制不方便, 2)质量不稳定
2023/12/18
- 1、下载文档前请自行甄别文档内容的完整性,平台不提供额外的编辑、内容补充、找答案等附加服务。
- 2、"仅部分预览"的文档,不可在线预览部分如存在完整性等问题,可反馈申请退款(可完整预览的文档不适用该条件!)。
- 3、如文档侵犯您的权益,请联系客服反馈,我们会尽快为您处理(人工客服工作时间:9:00-18:30)。
昆钢棒材冷飞剪剪切控制功能的改进和完善
内容摘要:本文介绍了冷飞剪的控制原理,主要叙述了昆钢棒材冷飞剪剪切控制功能的改进和完善。
通过对冷飞剪控制功能的改进和完善,使冷飞剪剪切倍尺的精度大大的提高,直接提高了产品的成材率,为生产企业带来了巨大
内容摘要:本文介绍了冷飞剪的控制原理,主要叙述了昆钢棒材冷飞剪剪切控制功能的改进和完善。
通过对冷飞剪控制功能的改进和完善,使冷飞剪剪切倍尺的精度大大的提高,直接提高了产品的成材率,为生产企业带来了巨大的经济效益。
关键词:倍尺剪LPP 辊径优先测量优先
前言
昆钢棒材生产线始建于2004年,该条生产线由12套PLC组成,完成各区域控制,其中主轧线控制系统配备两级自动化系统,通过三类通讯网络连接,组成资源共享的分布式计算机控制系统。
该控制系统是以美国GE公司90-70、90-30系列可编程控制器(PLC)为核心,控制信息和系统状态信息通过监控网(ETHERNET)、传动网(PROFIBUS-DP)和分布式I/O网(GENIUS网)交换。
冷飞剪(也称为倍尺剪)电气控制系统为控制及传动一体化的产品,其可编程控制器(PLC)采用美国通用电气公司的GE90-30型,安装在传动控制柜中;传动部分采用了美国GE公司的DV300。
冷飞剪的基本原理就是通过采集相关的现场信号,送至剪子PLC程序,经PLC程序的计算和执行发出剪切信号送至传动装置以驱动倍尺剪执行启动、剪切和复位这一动作周期并做往复执行。
在投产使用近两年时间以后发现,由于检测元件以及现场其他一些非人为因素的影响造成倍尺剪的误动作或者不动作,引起倍尺剪切的长度或长或短甚至于不剪切倍尺现象时有发生。
由于轧线采用的是顺控的模式和思路,倍尺剪动作的异常直接导致了下游设备裙板分钢和冷床的运动过程,同时还会引发堆钢造成对设备的损坏,加大了精整区工人的劳动强度,由此造成的停车将直接影响生产作业率和产品成材率等经济指标,日益成为抑制生产顺利有序进行的瓶颈。
基于上述原因决定对其做出相应的改进和完善,通过改造我们要达到预期的目的,保证正常的剪切并提高剪切的精度,同时也抑制了外界环境因素造成的不利影响,实现、
一.冷飞剪测长原理
冷飞剪的关键设备是剪前两个热金属探测器
冷飞剪测长原理是由PLC计算LPP(每个脉冲所代表的长度),剪切长度设定值由PLC换算成脉冲个数,当钢头到2#热检时计数器2开始计数,达计数值后给传动发送剪切命令切钢。
计算LPP使用两种方法:辊经优先和测量优先
1.辊径优先:利用轧机出口机架的辊径和减速比来直接计算即
LPP=3.1415926*D/(1024*K1) 其中:D为轧机出口机架的轧辊辊径,K1为轧机出口机架齿轮箱的减速比。
2.测量优先:利用剪前的两个热检。
当每根钢头部到1#热检时,PLC计数器1从0开始计数,当钢头部2#热检时捕捉计数器中的值假定为n,每次测得的LPP=L/n ,取10个LPP 的平均值
经过较长时间的观察发现,倍尺剪不剪切或是剪切长度与设定值有较大的出入,主要是与轧制速度和剪前的热检信号有直接的联系。
因此我们改造就从这些方向入手。
服务于生产的目的。
二、剪切动作的完善和改造
首先,更换冷飞剪测长的关键设备:两个热金属探测器。
热金属探测器由继电器输出换成NPN输出的DANIELI ID2000型热金属探测器,提高检测设备的可靠性。
其次,对剪切程序进行修改和完善。
保证在剪前两个信号出现问题的时候保证倍尺剪正常动
作。
我们根据设备来确定末架轧机与两个热检探测器的距离然后根据轧制速度来确定末架轧机有钢到两个热检响应的时间分别是多少。
机架有钢且达到两个热检的响应时间时,控制系统中的高速计数器正常清零、计数;当计数的设定值一到则发出剪切脉冲沿,通过轴定位模块送出一模拟电压量到传动系统,从而实现正常的剪切。
如果热金属探测器中的一个或二个在应当响应的时候没有响应,从而造成高速计数器不能正常取值,就不能实现正常剪切。
于是我们就又添加了一个动作信号,这个信号的动作原理是无论外部采集的信号正常与否,在机架有钢时,倍尺剪到达正常剪切的时间内而没有剪切动作的时候直接将正常剪切复位掉而发出一个单剪切的动作信号,驱动倍尺剪切钢来完成剪切动作。
此外,我们还在程序中做了两个计数器,分别对两个热金属检测器的误动作进行计数,以便于我们在实际工作中来分析确定元件的好坏,和受到外界的影响而造成信号采集有误,为我们的日常检修维护工作提供依据.这样就避免了由于两个热金属探测器采集信号有误或元件本身有问题而造成的不切倍尺的现象。
到目前为止,我们已经能够实现了每一次倍尺的剪切,但是剪切后的倍尺忽长忽短还是个问题,下面我们就来介绍一下通过造是如何提高剪切精度的。
三、剪切精度的完善和改进
首先,更换剪冷飞测长的关键设备:两个热金属探测器。
并对2#热金属探测器进行了移位,重新测量1#热检与2#热检间及2#热检与剪刃闭合点的距离,最大限度的消除人为误差。
热金属探测器由继电器输出换成NPN输出的DANIELI ID2000型热金属探测器。
使热检信号的响应速度更加灵敏。
使LPP更准确,从而提高了倍尺精度。
其次,棒材生产线倍尺剪正常剪切采用的是两种方式:一种是测量LPP值优先,一种是工作辊径优先。
在采用测量优先的计算方式时为了提高倍尺长度准确,原程序是通过采集脉冲当量后求算术平均值作为执行剪切的脉冲当量,最终是取十次的测量值做平均并且进行刷新来完成。
但是由于轧机存在换品种更换轧槽、轧辊和对轧制速度进行调整的现象,会对LPP值的采集产生一些影响,造成倍尺或长或短存在误差从而影响生产经济指标。
针对这种情况我们采用了一种较为稳妥的方式和思路,简单地说就是为采集脉冲当量值设限来提高倍尺优化剪切的精度。
新编写的逻辑程序所要达到的目的就是如此,首先最先测取的五个LPP 值暂不调用,依然按原程序执行剪切。
待到产品质量调整好且轧制速度亦达到稳定后,测取的新的脉冲当量值与以前的LPP平均值做比较,如果新的LPP值在99%―101%之间则参与LPP平均值的计算,如果超出此范围则不采用这个LPP值而采用上一根钢的LPP值剪切,这样就保证了倍尺钢的剪切精度。
不过此次采集的误差超限的LPP仍然会送到PLC,此值依然会参与LPP平均值一的计算;为避免这种情况的发生,我们就把这个新采集的LPP值与原LPP值做比较,将所得的偏差与这个LPP值相加,令其等于被采用的LPP平均值后,在送入PLC程序参与计算。
这样
一来就实现了我们改造的目的。
结束语:通过对冷飞剪控制功能的改进和完善,使冷飞剪剪切倍尺的精度大大的提高,并且再也没有因为倍尺剪不切造成停车而减少轧机的作业时间,使生产作业率受到限制。
进入轧线的钢坯除正常切头切尾的损耗,全部轧制剪切为成品,直接提高了产品的成材率,为生产企业带来了巨大的经济效益。