选矿工艺流程
选矿工艺流程

选矿工艺流程选矿工艺流程是指将矿石中有用矿物从矿石中分离出来的一系列工艺流程。
这个过程是矿石开采后的重要环节,其目的是提高矿石的品位,减少废石的含量,从而提高矿石的经济价值。
选矿工艺流程通常包括破碎、磨矿、浮选、重选等环节,下面将详细介绍这些环节的工艺流程。
1. 破碎破碎是将原始矿石通过机械设备进行粉碎的过程。
首先是粗碎,将原始矿石从大块破碎成较小的颗粒,然后是细碎,将颗粒再次破碎成更小的颗粒。
破碎的目的是为了方便后续的磨矿操作,提高矿石的表面积,促进矿石中有用矿物的释放。
2. 磨矿磨矿是将破碎后的矿石通过磨矿设备进行细磨的过程。
磨矿的目的是将矿石中的有用矿物和废石分离开来,提高有用矿物的品位。
磨矿设备通常包括球磨机、砂磨机等,通过磨矿设备的旋转和摩擦作用,使矿石中的有用矿物得到释放和细磨。
3. 浮选浮选是利用有机物或无机物对矿石中有用矿物和废石进行分离的工艺。
首先是矿石的湿法研磨,将矿石研磨成一定粒度的矿浆。
然后是药剂的添加,根据矿石中有用矿物和废石的特性,添加相应的浮选药剂。
接着是气泡的注入,通过气泡的吸附作用,使有用矿物与气泡形成浮沫,从而分离出来。
4. 重选重选是利用重力或离心力对矿石中有用矿物和废石进行分离的工艺。
首先是矿石的干法选矿,将矿石通过重力分选设备进行干法选矿,将矿石中的有用矿物和废石分离开来。
然后是矿石的湿法选矿,将矿石研磨成一定粒度的矿浆,通过离心设备进行湿法选矿,进一步提高有用矿物的品位。
以上就是选矿工艺流程的基本环节,通过这些工艺流程,可以将矿石中的有用矿物和废石进行有效分离,提高矿石的品位,从而提高矿石的经济价值。
选矿工艺流程是矿石加工过程中的重要环节,对于提高矿石的综合利用率和降低生产成本具有重要意义。
铝土矿选矿工艺流程

铝土矿选矿工艺流程铝土矿的选矿主要涉及矿石的破碎、磨矿、分选、选后处理等过程。
接下来,我们详细了解每一个步骤。
一、破碎选矿的第一步是破碎。
铝土矿的硬度较高,需要使用颚式破碎机、圆锥破碎机等设备进行初步破碎。
破碎的目的在于将大块的矿石破碎成小块,以便于后续的磨矿过程。
二、磨矿经过破碎后,矿石被送入磨矿阶段。
磨矿的目的是使矿石中的矿物颗粒达到适合分选的粒度。
通常使用球磨机、棒磨机等设备进行磨矿,以将矿石磨成粉末状。
磨矿过程中需添加水和化学药剂,以促进磨矿效率并方便后续的分选。
三、分选在经过破碎和磨矿后,矿石进入分选阶段。
这一阶段的目标是利用矿物间的物理化学性质差异,将有价值的矿物与脉石矿物分离。
分选的方法包括重力分选、浮选、磁选等。
重力分选:对于比重差异较大的矿物,可以利用不同比重矿物在水中的沉降速度不同来进行分离。
这种方法主要用于铝土矿中的铁矿物的分离。
浮选:这是铝土矿选矿中常用的方法。
主要利用铝土矿与脉石矿物的表面物理化学性质差异,通过添加特定的浮选药剂,使铝土矿颗粒附着在气泡上并浮到水面,从而达到分离的目的。
磁选:对于具有磁性的矿物,可以利用磁场将其从非磁性矿物中分离出来。
这种方法在铝土矿选矿中不常用,但如果矿石中含有磁铁矿物,就需要采用磁选法进行分离。
四、选后处理经过分选后,有价值的矿物得到富集。
此时需要进行脱水、脱泥、浓缩等处理,以提高矿物的品位并方便后续的加工利用。
这一阶段还涉及尾矿的处理和堆放,需要合理规划以减少对环境的影响。
总结:铝土矿的选矿工艺流程包括破碎、磨矿、分选和选后处理等步骤。
每个步骤都至关重要,需精心操作以确保获得高质量的铝土矿产品。
选矿工艺流程
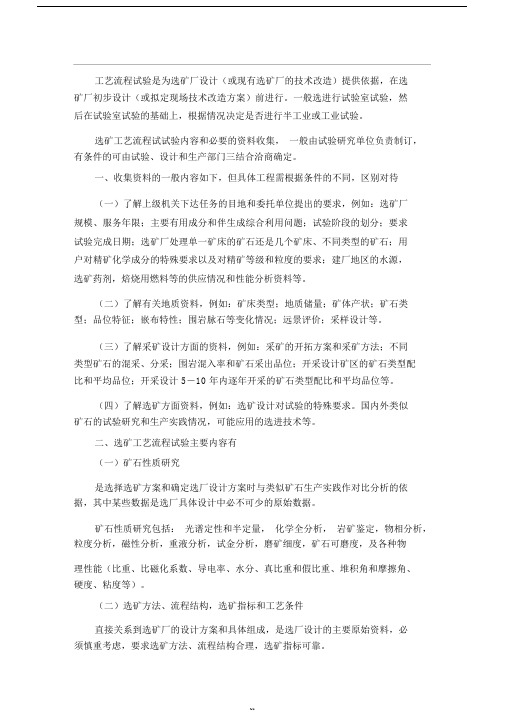
工艺流程试验是为选矿厂设计(或现有选矿厂的技术改造)提供依据,在选矿厂初步设计(或拟定现场技术改造方案)前进行。
一般选进行试验室试验,然后在试验室试验的基础上,根据情况决定是否进行半工业或工业试验。
选矿工艺流程试试验内容和必要的资料收集,一般由试验研究单位负责制订,有条件的可由试验、设计和生产部门三结合洽商确定。
一、收集资料的一般内容如下,但具体工程需根据条件的不同,区别对待(一)了解上级机关下达任务的目地和委托单位提出的要求,例如:选矿厂规模、服务年限;主要有用成分和伴生成综合利用问题;试验阶段的划分;要求试验完成日期;选矿厂处理单一矿床的矿石还是几个矿床、不同类型的矿石;用户对精矿化学成分的特殊要求以及对精矿等级和粒度的要求;建厂地区的水源,选矿药剂,焙烧用燃料等的供应情况和性能分析资料等。
(二)了解有关地质资料,例如:矿床类型;地质储量;矿体产状;矿石类型;品位特征;嵌布特性;围岩脉石等变化情况;远景评价;采样设计等。
(三)了解采矿设计方面的资料,例如:采矿的开拓方案和采矿方法;不同类型矿石的混采、分采;围岩混入率和矿石采出品位;开采设计矿区的矿石类型配比和平均品位;开采设计 5-10 年内逐年开采的矿石类型配比和平均品位等。
(四)了解选矿方面资料,例如:选矿设计对试验的特殊要求。
国内外类似矿石的试验研究和生产实践情况,可能应用的选进技术等。
二、选矿工艺流程试验主要内容有(一)矿石性质研究是选择选矿方案和确定选厂设计方案时与类似矿石生产实践作对比分析的依据,其中某些数据是选厂具体设计中必不可少的原始数据。
矿石性质研究包括:光谱定性和半定量,化学全分析,岩矿鉴定,物相分析,粒度分析,磁性分析,重液分析,试金分析,磨矿细度,矿石可磨度,及各种物理性能(比重、比磁化系数、导电率、水分、真比重和假比重、堆积角和摩擦角、硬度、粘度等)。
(二)选矿方法、流程结构,选矿指标和工艺条件直接关系到选矿厂的设计方案和具体组成,是选厂设计的主要原始资料,必须慎重考虑,要求选矿方法、流程结构合理,选矿指标可靠。
铜矿选矿工艺流程
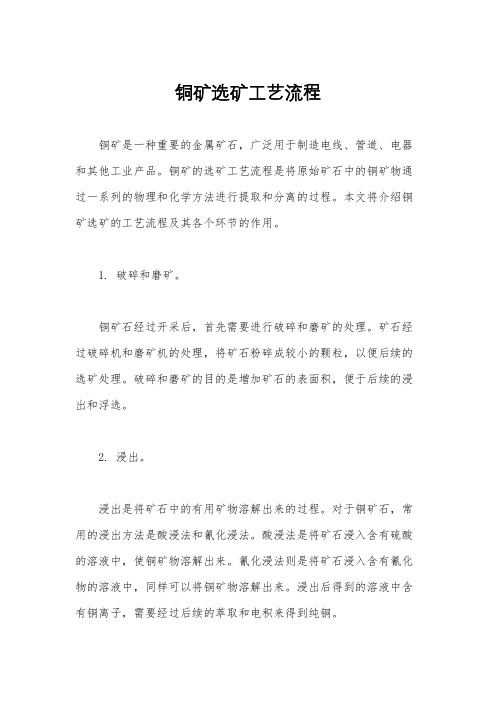
铜矿选矿工艺流程铜矿是一种重要的金属矿石,广泛用于制造电线、管道、电器和其他工业产品。
铜矿的选矿工艺流程是将原始矿石中的铜矿物通过一系列的物理和化学方法进行提取和分离的过程。
本文将介绍铜矿选矿的工艺流程及其各个环节的作用。
1. 破碎和磨矿。
铜矿石经过开采后,首先需要进行破碎和磨矿的处理。
矿石经过破碎机和磨矿机的处理,将矿石粉碎成较小的颗粒,以便后续的选矿处理。
破碎和磨矿的目的是增加矿石的表面积,便于后续的浸出和浮选。
2. 浸出。
浸出是将矿石中的有用矿物溶解出来的过程。
对于铜矿石,常用的浸出方法是酸浸法和氰化浸法。
酸浸法是将矿石浸入含有硫酸的溶液中,使铜矿物溶解出来。
氰化浸法则是将矿石浸入含有氰化物的溶液中,同样可以将铜矿物溶解出来。
浸出后得到的溶液中含有铜离子,需要经过后续的萃取和电积来得到纯铜。
3. 浮选。
浮选是将矿石中的有用矿物通过气泡的吸附和分离来实现的。
对于铜矿石,常用的浮选方法是将矿石浸入含有吸附剂的浮选剂中,通过气泡的作用使铜矿物粘附在气泡上,然后分离出来。
浮选后得到的铜精矿含有较高的铜含量,需要经过后续的冶炼和精炼来得到纯铜。
4. 冶炼和精炼。
铜精矿经过冶炼和精炼的处理,可以得到纯铜。
冶炼是将铜精矿加热至高温,使其中的铜矿物氧化还原,得到粗铜。
精炼是将粗铜经过电解或火法处理,使其中的杂质得到去除,得到纯铜。
冶炼和精炼是铜矿选矿工艺流程中非常重要的环节,直接影响着最终铜的品质。
5. 废水处理。
铜矿选矿过程中会产生大量的废水,其中含有铜离子和其他有害物质。
废水处理是铜矿选矿工艺流程中必不可少的环节,通过沉淀、过滤、离子交换和电解等方法,将废水中的有害物质去除,得到清洁的水体,以保护环境和节约资源。
以上就是铜矿选矿工艺流程的主要环节及其作用。
铜矿选矿是一个复杂的过程,需要各种物理和化学方法的配合,才能最终得到纯铜。
在实际生产中,还需要根据矿石的特性和工艺条件进行调整和改进,以提高选矿效率和降低成本。
选矿工艺流程介绍

选矿工艺流程介绍(附流程图)[导读]:选矿是冶炼前的准备工作,从矿山开采下来矿石以后,首先需要将含铁、铜、铝、锰等金属元素高的矿石甄选出来,为下一步的冶炼活动做准备。
选矿一般分为破碎、磨矿、选别三部分。
其中,破碎又分为:粗破、中破和细破;选别依方式不同也可分为:磁选、重选、浮选等。
本专题将详细向大家讲述选矿的一些具体工艺常识,以及主要选矿设备的大致工作原理,主要控制要点等知识。
由于时间的仓促和编辑水平有限,专题中难免出现遗漏或错误的地方,欢迎大家补充指正。
选矿的目的:提高矿石品位。
选矿方法:◆重力选矿法。
根据矿物密度的不同,在选矿介质中具有不同的沉降速度而进行选矿。
◆磁力选矿法。
磁力选矿法是利用矿物的磁性差别,在不均匀的磁场中,磁性矿物被磁选机的磁极吸引,而非磁性矿物则被磁极排斥,从而达到选别的目的。
◆浮游选矿法。
浮游选矿法是利用矿物表面不同的亲水性,选择性地将疏水性强的矿物用泡沫浮到矿浆表面,而亲水性矿物则留在矿浆中,从而实现不同矿物彼此分离。
选矿后的产品:精矿、中矿和尾矿。
◆精矿是指选矿后得到的含有用矿物含量较高的产品。
◆中矿为选矿过程中间产品,需进一步选矿处理。
◆尾矿是经选矿后留下的废弃物。
选矿的流程:(一)矿石破碎我国选矿厂一般采用粗破、中破和细破三段破碎流程破碎铁矿石。
粗破多用1.2m或1.5m旋回式破碎机,中破使用2.1m或2.2m标准型圆锥式破碎机,细破采用2.1m或2.2m短头型圆锥式破碎机。
通过粗破的矿石,其块度不大于1m,然后经过中、细破碎,筛分成矿石粒度小于12mm的最终产品送磨矿槽。
(二)磨矿工艺我国铁矿磨矿工艺,大多数采用两段磨矿流程,中小型选矿厂多采用一段磨矿流程。
由于采用细筛再磨新工艺,近年来一些选矿厂已由两段磨矿改为三段磨矿。
采用的磨矿设备一般比较小,最大球磨机 3.6m×6m,最大棒磨机 3.2m×4.5m,最大自磨机5.5m×1.8m,砾磨机2.7m×3.6m。
选矿厂工艺流程

选矿厂工艺流程
选矿厂工艺流程是指将矿石中有用的矿物和有用的矿石分离出来的一系列工艺过程。
选矿厂工艺流程的主要目的是提高矿石的品位,降低生产成本,实现资源的有效利用。
下面我们将详细介绍选矿厂工艺流程的主要步骤。
首先,矿石的破碎和磨矿是选矿厂工艺流程的第一步。
矿石经过破碎设备的破碎和磨矿设备的磨矿,将矿石破碎成较小的颗粒,以便后续的选矿操作。
这一步是整个选矿过程的基础,破碎和磨矿的效果直接影响后续工艺的进行。
接下来是矿石的分类和分级。
经过破碎和磨矿后的矿石颗粒并不是均匀的,其中含有有用矿物的颗粒和废石的颗粒。
因此,需要通过分类设备将矿石进行分级,将有用矿物和废石进行分离,以便后续的选矿操作。
然后是矿石的浮选和重选。
浮选是利用有机物或无机物的表面活性剂,使有用矿物和废石在水中产生疏水性和亲水性的差异,从而达到分离的目的。
而重选是利用重力、离心力、阻力等原理,将矿石中的有用矿物和废石进行分离。
最后是矿石的脱水和干燥。
经过前面的工艺步骤,矿石中的有用矿物已经得到了分离,但其中还含有一定的水分。
因此,需要通过脱水和干燥设备将矿石中的水分去除,以便后续的运输和加工。
总的来说,选矿厂工艺流程是一个复杂的过程,需要经过多个步骤的精细操作才能达到预期的效果。
只有严格按照工艺流程进行操作,才能保证选矿厂的生产效率和产品质量。
希望本文对选矿厂工艺流程有所帮助,谢谢阅读!。
选矿厂工艺流程范文

选矿厂工艺流程范文矿厂是一种特殊的工业企业,用于处理含有矿物质的原材料并提取出有用的金属元素。
工艺流程是指在矿石处理过程中所采取的一系列技术步骤,用于将矿石转化为有用产品的过程。
下面是一份关于工艺流程的范文,供参考:一、概述选矿厂是矿产资源综合利用的工厂,主要用于对矿石进行加工,从中提取出有用的金属元素。
矿石的处理流程通常包括破碎、磨矿、选矿和精矿等环节。
通过对矿石进行加工处理,可以实现矿石中金属元素的分离和提取。
二、矿石破碎矿石破碎通常是将原始的矿石进行粉碎,使其达到适合进一步处理的细度。
常见的破碎设备包括颚式破碎机、圆锥破碎机、冲击破碎机等。
矿石破碎的目的是将矿石从大块状分解为较小的颗粒,以便提高后续步骤中的处理效果。
三、磨矿磨矿是将矿石进行进一步细化的过程,通常使用的磨矿设备包括球磨机、砂石磨机等。
磨矿的目的是将矿石中的金属矿物颗粒进一步细化,使其达到适合进行选矿操作的细度。
此外,磨矿还可以促使金属矿物与其他杂质的分离。
四、选矿选矿是将矿石中的有用金属矿物与其他无用杂质进行分离的过程。
选矿通常采用物理或化学方法来实现。
物理选矿通常是利用矿石中有用矿物和无用矿物在物理特性上的差异进行分离,常见的物理选矿方法包括重选、浮选等;化学选矿是通过物质的化学性质来实现分离,例如利用溶液中金属离子与特定化学试剂的反应来使金属矿物与杂质分离。
选矿工艺的选择取决于矿石的成分和性质,以及需要提取的金属元素。
五、精矿精矿是指通过选矿步骤分离出的含有较高金属含量的矿石。
精矿的处理通常包括砂浆搅拌、烘干、熔炼等过程,以提取出金属元素。
砂浆搅拌通常采用搅拌机将精矿与一定量的水混合,形成矿浆;烘干是将矿浆中的水分蒸发掉,使精矿达到熔点;熔炼是将矿石中的金属元素通过高温熔炼的方式分离出来,通常使用的设备有电炉、熔炉等。
六、尾砂处理尾砂是指经过精矿处理后所剩下的杂质和废料,其中包含了一定量的有用金属矿物。
尾砂处理可以将这些金属元素进一步提取出来,以实现矿石资源的综合利用。
选矿的工艺流程

选矿的工艺流程
选矿的工艺流程一般分为以下几步:
1. 破碎:将原矿物料经过破碎机等设备进行物理性分解,使其变成较小的块状物质,为后续工艺处理创造条件。
2. 磨矿:采用球磨机或磨矿机等设备对原矿进行细磨,使其粒度进一步细化。
3. 选别:采用重选机、浮选机等设备,利用矿物的物理和化学性质差异进行选择性分离,将其中的有用矿物分离出来。
4. 混合:将不同矿物分离出来后进行混合,得到符合要求的混合矿。
5. 精矿:将混合矿物料进行再次选别、磨矿等处理,得到更加纯净的矿物产品。
6. 焙烧:这一步主要针对金属矿物,在高温下进行物理或化学反应,得到金属元素。
选矿重选工艺流程
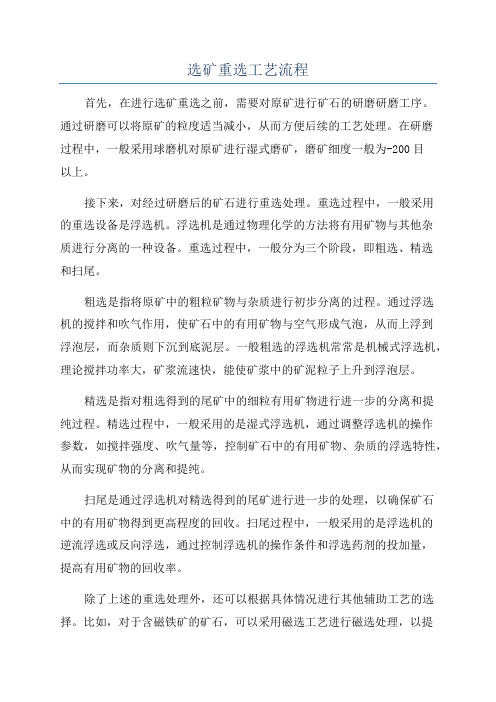
选矿重选工艺流程首先,在进行选矿重选之前,需要对原矿进行矿石的研磨研磨工序。
通过研磨可以将原矿的粒度适当减小,从而方便后续的工艺处理。
在研磨过程中,一般采用球磨机对原矿进行湿式磨矿,磨矿细度一般为-200目以上。
接下来,对经过研磨后的矿石进行重选处理。
重选过程中,一般采用的重选设备是浮选机。
浮选机是通过物理化学的方法将有用矿物与其他杂质进行分离的一种设备。
重选过程中,一般分为三个阶段,即粗选、精选和扫尾。
粗选是指将原矿中的粗粒矿物与杂质进行初步分离的过程。
通过浮选机的搅拌和吹气作用,使矿石中的有用矿物与空气形成气泡,从而上浮到浮泡层,而杂质则下沉到底泥层。
一般粗选的浮选机常常是机械式浮选机,理论搅拌功率大,矿浆流速快,能使矿浆中的矿泥粒子上升到浮泡层。
精选是指对粗选得到的尾矿中的细粒有用矿物进行进一步的分离和提纯过程。
精选过程中,一般采用的是湿式浮选机,通过调整浮选机的操作参数,如搅拌强度、吹气量等,控制矿石中的有用矿物、杂质的浮选特性,从而实现矿物的分离和提纯。
扫尾是通过浮选机对精选得到的尾矿进行进一步的处理,以确保矿石中的有用矿物得到更高程度的回收。
扫尾过程中,一般采用的是浮选机的逆流浮选或反向浮选,通过控制浮选机的操作条件和浮选药剂的投加量,提高有用矿物的回收率。
除了上述的重选处理外,还可以根据具体情况进行其他辅助工艺的选择。
比如,对于含磁铁矿的矿石,可以采用磁选工艺进行磁选处理,以提高品位。
另外,对于含黄铁矿的矿石,可以采用重选-磨矿-重选的工艺流程,以实现黄铁矿的优先回收。
总之,选矿重选工艺流程是对原矿进行进一步处理的过程,通过研磨和重选等工序,可以提高矿石的品位和回收率。
在工艺的选择上,需要结合矿石的性质和选矿目标来确定合适的工艺流程。
同时,还可以根据具体情况进行其他辅助工艺的选择,以进一步提高选矿效果。
萤石选矿工艺流程

萤石选矿工艺流程
萤石选矿的工艺流程主要包括破碎、磨矿和浮选等步骤。
1. 破碎:萤石矿石一般比较坚硬,需要通过破碎设备将其破碎成适当大小的颗粒。
常用的破碎设备有颚式破碎机、圆锥破碎机等,通过不同设备的组合使用,可以得到适合后续磨矿工艺的矿石颗粒。
2. 磨矿:为了提高萤石矿的磨矿效果,一般采用湿式磨矿工艺。
常用的磨矿设备包括球磨机、湿式自由撞击磨机等。
在磨矿过程中,将矿石与磨矿介质(如水、钢球等)一起放入磨矿机中,通过不断的磨矿撞击,将矿石进一步细磨,使得矿石颗粒大小更加均匀。
3. 浮选:浮选是萤石选矿的关键步骤。
通过向磨矿后的矿石浆中加入适量的浮选剂,如油酸或其衍生物,可以有效地将萤石与其它矿物分离。
在浮选过程中,萤石颗粒会附着在气泡上,并随着气泡上升到矿浆表面,形成萤石泡沫层。
通过刮板将萤石泡沫刮入精矿槽中,实现萤石与其他矿物的分离。
通过上述步骤,可以有效地提取出高品质的萤石矿物,同时尽可能地减少对环境的污染。
如需更多信息,建议咨询相关选矿工程师或查阅相关文献资料。
锰铁矿选矿工艺流程

锰铁矿选矿工艺流程锰铁矿是一种重要的金属矿石,广泛应用于冶金、化工、建材等行业。
为了提高锰铁矿的品位和回收率,需要进行选矿处理。
本文将介绍锰铁矿选矿工艺流程。
一、锰铁矿选矿的目标和原则锰铁矿选矿的目标是提高矿石的品位,即提高锰和铁的含量,同时降低杂质的含量,提高回收率。
选矿的原则是根据矿石的物理性质和化学性质,采取合适的工艺方法进行处理,以实现目标。
二、锰铁矿选矿的工艺流程1. 粗选阶段:将原矿经过破碎、磨矿等工序后,进行粗选。
首先采用重介质浮选法,利用锰铁矿和杂质的密度差异,通过重介质浮选机进行分离。
锰铁矿沉降到底部,杂质浮在上层,实现初步分离。
2. 精选阶段:将粗选后的锰铁矿进行进一步处理,以提高品位和回收率。
常用的精选方法有重介质分选、磁选和浮选等。
重介质分选是利用锰铁矿和杂质的密度差异,通过重介质分选机进行分离。
磁选是利用锰铁矿和杂质的磁性差异,通过磁选机进行分离。
浮选是利用锰铁矿和杂质的浮力差异,通过浮选机进行分离。
3. 过滤和干燥:经过精选后的锰铁矿进行过滤和干燥处理。
过滤是将矿浆中的水分和杂质分离,常用的过滤设备有压滤机和离心机等。
干燥是将过滤后的锰铁矿进行干燥,常用的干燥设备有旋转干燥机和烘箱等。
4. 精矿处理:经过过滤和干燥后的锰铁矿为精矿,可以进一步提取锰和铁。
常用的处理方法有磁选、重选和浮选等。
磁选是利用锰铁矿和杂质的磁性差异,通过磁选机进行分离。
重选是利用锰铁矿和杂质的密度差异,通过重选机进行分离。
浮选是利用锰铁矿和杂质的浮力差异,通过浮选机进行分离。
5. 尾矿处理:选矿过程中产生的尾矿需要进行处理,以减少环境污染。
常用的尾矿处理方法有干堆和浸铁法。
干堆是将尾矿进行干燥后,堆积在指定场地进行固体废物处理。
浸铁法是将尾矿进行浸铁处理,将其中的铁和锰进行回收利用。
三、锰铁矿选矿工艺的优化与创新为了提高选矿效果和经济效益,锰铁矿选矿工艺不断进行优化与创新。
一方面,研究人员通过改进设备和工艺参数,提高了选矿的效率和品位。
选矿厂工艺流程

选矿厂工艺流程
采矿:采矿工艺是从矿石中提取有价值的金属元素的过程。
常用的采
矿工艺有间断采矿、深部采矿和潜水采矿等。
破碎:破碎工艺是将矿石打碎,使其尺寸符合提炼要求的工序。
破碎
工艺可以将大块矿石粉碎成小颗粒,以便进行下一个提炼工序。
浮选:浮选基本原理是利用重金属物质和轻金属物质在液体中的不同
沉淀速率的特点,利用沉淀率的不同将重金属物质和轻金属物质分离开来,从而实现重金属的提取。
加热:加热工艺是通过高温将金属元素从其他含量较低的轻金属物质
中提炼出来的过程。
这个步骤是使用高温将含金量较低的金属物质从高温
熔融中提炼出金属元素的过程。
熔解:熔解工艺是一种用来提取不同物质中的金属元素的工艺,它将
提取的金属元素以液态形式收集起来,然后再进行净化等操作。
净化:净化工艺是指将提炼的金属元素进行再加工,以去除其中的杂质,从而使其具有技术使用要求的过程。
例如,可以通过电解、熔炼、精
细加工等方法进行净化操作。
选矿工艺流程

选矿工艺流程选矿工艺流程是指将矿石中有用的矿物从矿石中分离出来的过程。
选矿工艺流程的主要目的是提高矿石的品位,降低矿石的含杂量,从而达到提高矿石的经济价值的目的。
选矿工艺流程通常包括矿石的破碎、磨矿、浮选、脱水等环节。
下面将对选矿工艺流程的主要环节进行介绍。
首先是矿石的破碎。
矿石经过开采后,通常是以较大的块状存在的,需要经过破碎过程将其破碎成较小的颗粒。
破碎的目的是为了方便后续的磨矿和浮选操作,提高矿石的表面积,使有用矿物更容易与药剂接触,从而提高选矿效果。
接下来是磨矿环节。
磨矿是将矿石中的有用矿物从矿石中分离出来的关键环节。
磨矿通常采用球磨机、破碎机等设备进行,将矿石磨成一定粒度的矿浆。
磨矿的目的是将矿石中的有用矿物和杂质分离,使有用矿物暴露在矿浆中,为后续的浮选操作提供条件。
然后是浮选环节。
浮选是通过对矿浆中的有用矿物和杂质进行化学处理,使有用矿物与药剂发生吸附作用,从而使有用矿物浮在矿浆表面,而杂质沉入矿浆底部的物理化学过程。
浮选的目的是将有用矿物从矿石中分离出来,提高有用矿物的品位。
最后是脱水环节。
脱水是将浮选后的矿浆进行脱水处理,使矿浆中的水分含量降低,得到干燥的有用矿物产品的过程。
脱水的目的是降低矿石的含水率,提高有用矿物的成品率,方便后续的运输和加工。
在选矿工艺流程中,每个环节都起着至关重要的作用。
只有每个环节都能够得到严格控制和合理操作,才能够最大限度地提高矿石的经济价值。
因此,在选矿工艺流程中,需要对每个环节进行精心设计和合理安排,以确保整个选矿过程的顺利进行。
总的来说,选矿工艺流程是一个复杂的过程,需要综合运用矿石学、化学、机械等多个学科的知识,通过合理的工艺设计和操作控制,实现矿石中有用矿物的有效分离和提取。
只有在不断的实践中总结经验,不断的改进工艺流程,才能够不断提高选矿工艺的效率和经济效益,实现矿产资源的最大利用。
选矿设备工艺流程

选矿设备工艺流程选矿是矿山生产中的重要环节,其工艺流程对矿石的提取和提纯起着关键作用。
选矿设备工艺流程是指通过一系列设备和工艺步骤,将原始矿石中的有用矿物和杂质分离出来,从而达到提取有用矿物的目的。
下面将介绍典型的选矿设备工艺流程。
1. 破碎和磨矿阶段矿石从矿山中采出后,首先需要进行破碎和磨矿处理。
破碎设备通常包括颚式破碎机、圆锥破碎机和冲击破碎机等,其作用是将原始矿石从较大的块状物破碎成较小的颗粒。
而磨矿设备则包括球磨机、矿石磨等,其作用是将破碎后的矿石进行细磨,以便后续的浮选或者选矿过程。
2. 浮选阶段浮选是选矿中常用的一种分离方法,其原理是利用矿物与浮选剂的亲疏性差异,使有用矿物和杂质分离。
浮选设备通常包括浮选机、搅拌桶和浮选槽等。
在浮选过程中,首先将矿石经过破碎和磨矿处理后,与浮选剂混合,然后通过浮选机的搅拌和气泡作用,使有用矿物浮到矿浆表面形成浮渣,而杂质则沉入矿浆底部形成尾渣,从而实现有用矿物和杂质的分离。
3. 磁选阶段磁选是利用矿石中的铁磁性矿物与非铁磁性矿物的差异,通过磁场作用将二者分离的方法。
磁选设备通常包括磁选机和磁选槽等。
在磁选过程中,矿石经过破碎和磨矿处理后,通过磁选机的磁场作用,使铁磁性矿物被吸附在磁选机表面形成磁渣,而非铁磁性矿物则被带走形成尾渣,从而实现有用矿物和杂质的分离。
4. 重选阶段重选是利用矿石中的密度差异进行分离的方法。
重选设备通常包括重选机和重选槽等。
在重选过程中,矿石经过破碎和磨矿处理后,通过重选机的水流作用,使密度较大的有用矿物沉降到重选机底部形成重选渣,而密度较小的杂质则被带走形成尾渣,从而实现有用矿物和杂质的分离。
5. 脱水和干燥阶段脱水和干燥是选矿过程中的最后一道工艺环节,其目的是将分离出来的有用矿物进行脱水和干燥处理,以便后续的运输和储存。
脱水设备通常包括脱水筛和脱水离心机等,而干燥设备则包括回转干燥机和烘干机等。
综上所述,选矿设备工艺流程是一个复杂的系统工程,其涉及到破碎、磨矿、浮选、磁选、重选、脱水和干燥等多个工艺环节。
铁矿石选矿工艺流程
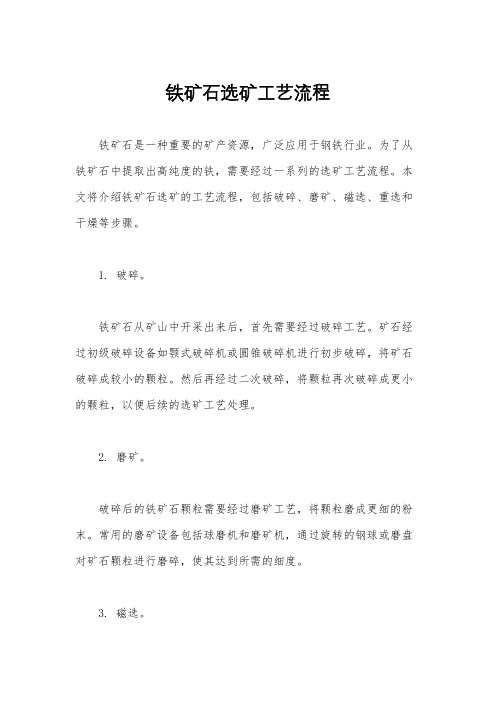
铁矿石选矿工艺流程
铁矿石是一种重要的矿产资源,广泛应用于钢铁行业。
为了从铁矿石中提取出高纯度的铁,需要经过一系列的选矿工艺流程。
本文将介绍铁矿石选矿的工艺流程,包括破碎、磨矿、磁选、重选和干燥等步骤。
1. 破碎。
铁矿石从矿山中开采出来后,首先需要经过破碎工艺。
矿石经过初级破碎设备如颚式破碎机或圆锥破碎机进行初步破碎,将矿石破碎成较小的颗粒。
然后再经过二次破碎,将颗粒再次破碎成更小的颗粒,以便后续的选矿工艺处理。
2. 磨矿。
破碎后的铁矿石颗粒需要经过磨矿工艺,将颗粒磨成更细的粉末。
常用的磨矿设备包括球磨机和磨矿机,通过旋转的钢球或磨盘对矿石颗粒进行磨碎,使其达到所需的细度。
3. 磁选。
磨矿后的铁矿石粉末含有一定的磁性矿物,可以通过磁选工艺进行分离。
磁选设备包括湿式磁选机和干式磁选机,通过磁场作用将磁性矿物和非磁性矿物分离,从而提高铁矿石的品位。
4. 重选。
经过磁选后的铁矿石粉末还会含有一定的杂质,需要通过重选工艺进行进一步的分离。
重选设备包括重介质分离机和震动台,通过密度差异将铁矿石和杂质进行分离,提高铁矿石的品位。
5. 干燥。
最后,经过重选的铁矿石粉末需要进行干燥处理,以便后续的加工和运输。
常用的干燥设备包括回转烘干机和热风炉,通过热风对铁矿石进行干燥,使其达到所需的含水率。
通过以上工艺流程,铁矿石可以得到高品位的铁精矿,可以进一步进行冶炼和加工,用于生产各种钢铁产品。
铁矿石选矿工艺流程的优化和改进,可以提高铁矿石的选矿效率和品位,降低生产成本,对于钢铁行业具有重要的意义。
选矿重选工艺流程

选矿重选工艺流程选矿重选工艺流程是一种用于对矿石进行分级处理的过程。
在矿石开采和粗选过程中,矿石通常具有较低的品位和较高的杂质含量。
因此,矿石需要经过重选工艺流程,以去除杂质并提高品位,从而使之适用于下一步的冶炼或炼化过程。
以下是一个典型的选矿重选工艺流程。
1.研磨和浸染:矿石首先经过破碎和细磨过程,以将其细化为较小颗粒的矿石粉末。
然后将矿石浸入浸出液中,以消除一部分杂质。
2.浮选:经浸染后的矿石进入浮选池中。
在浮选池中,通过添加特定的药剂,使具有相同物理化学性质的矿石矿物团块浮在液面上,而将其他矿物沉入液体底部。
3.磁选:经过浮选处理的矿石通过磁选流程,以去除磁性矿物。
在磁选过程中,矿石通过磁场,使磁性矿物被吸附在磁力线上,而非磁性矿物则不受影响。
4.重选:通过离心或震荡装置将经过浮选和磁选处理的矿石进行分级。
这种过程根据其大小和密度,将矿石分为不同的等级,并将杂质的含量进一步降低,提高矿石的品位。
5.过滤和干燥:在重选过程中,将矿石与水和化学药剂混合。
在过滤和干燥过程中,将矿石与水分离,并将矿石的含水量降至可接受的水平。
过滤和干燥后的矿石具有较高的精度和较低的含水量。
6.储存和包装:最后,经过重选、过滤和干燥的矿石被储存在特定的储存设施中。
矿石可以被包装成袋或罐,以方便运输和使用。
总结来说,选矿重选工艺流程是一个复杂的过程,包括研磨、浸染、浮选、磁选、重选、过滤和干燥等步骤。
通过这些过程,矿石的杂质含量可以降低,品位可以提高,从而使其适用于下一步的冶炼或炼化过程。
这种流程可以根据特定的矿石类型和要求进行调整,以达到最佳的处理效果。
铬矿选矿工艺流程
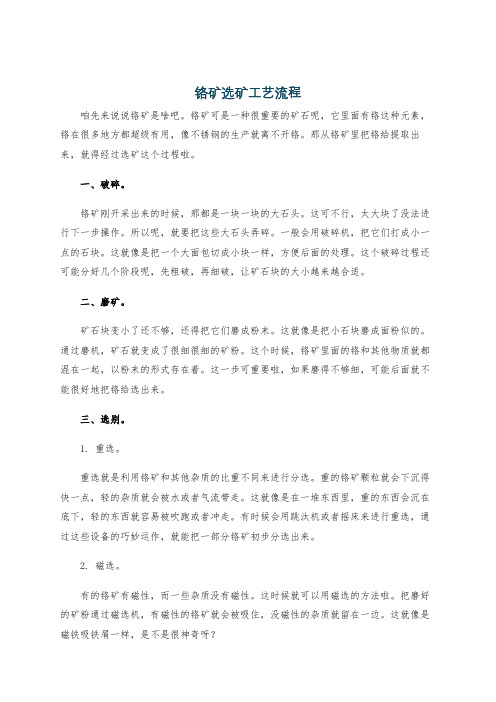
铬矿选矿工艺流程咱先来说说铬矿是啥吧。
铬矿可是一种很重要的矿石呢,它里面有铬这种元素,铬在很多地方都超级有用,像不锈钢的生产就离不开铬。
那从铬矿里把铬给提取出来,就得经过选矿这个过程啦。
一、破碎。
铬矿刚开采出来的时候,那都是一块一块的大石头。
这可不行,太大块了没法进行下一步操作。
所以呢,就要把这些大石头弄碎。
一般会用破碎机,把它们打成小一点的石块。
这就像是把一个大面包切成小块一样,方便后面的处理。
这个破碎过程还可能分好几个阶段呢,先粗破,再细破,让矿石块的大小越来越合适。
二、磨矿。
矿石块变小了还不够,还得把它们磨成粉末。
这就像是把小石块磨成面粉似的。
通过磨机,矿石就变成了很细很细的矿粉。
这个时候,铬矿里面的铬和其他物质就都混在一起,以粉末的形式存在着。
这一步可重要啦,如果磨得不够细,可能后面就不能很好地把铬给选出来。
三、选别。
1. 重选。
重选就是利用铬矿和其他杂质的比重不同来进行分选。
重的铬矿颗粒就会下沉得快一点,轻的杂质就会被水或者气流带走。
这就像是在一堆东西里,重的东西会沉在底下,轻的东西就容易被吹跑或者冲走。
有时候会用跳汰机或者摇床来进行重选,通过这些设备的巧妙运作,就能把一部分铬矿初步分选出来。
2. 磁选。
有的铬矿有磁性,而一些杂质没有磁性。
这时候就可以用磁选的方法啦。
把磨好的矿粉通过磁选机,有磁性的铬矿就会被吸住,没磁性的杂质就留在一边。
这就像是磁铁吸铁屑一样,是不是很神奇呀?3. 浮选。
浮选也是一种很常用的方法。
浮选会在矿浆里加入一些特殊的药剂,这些药剂能让铬矿或者杂质产生不同的反应。
有的会附着在气泡上,然后随着气泡浮到表面,有的就留在下面。
就好像在一个大泳池里,有的人能抓住浮板浮起来,有的人就只能在水底待着。
通过浮选,可以把铬矿和其他物质进一步分离。
四、脱水。
选别完了之后,得到的铬矿精矿里面还有很多水分呢。
这时候就需要脱水。
可以先自然沥干一部分水,然后再用一些专门的设备,像过滤机之类的,把水尽量都去掉。
金属矿主要选矿方法的工艺流程

金属矿主要选矿方法的工艺流程
重选法:重选法是根据矿物相对密度(通常称比重)的差异来分选矿物的。
密度不同的矿物在运动介质(水、空气与重滚)中受到流体动力和各种机械力的作用,造成适宜的松散分层和分离条件,从而使不同密度的矿粒得到分离。
浮选法:浮选法是根据矿物表面物理化学性质的差别,经浮选药剂处理,使用矿物选择性地附着在气泡上,达到分选的目的。
有色金属矿石的选矿,如铜、铅、锌、硫、钼等矿主要用浮选法处理,某些黑色金属、稀有金属和一些非金属矿石,如石墨矿、磷灰石等也用浮选法选别。
磁选法:磁选法是利用各种矿石或物料的磁性差异,在磁力及其他力作用下进行选别的过程。
电选法:电选法是利用矿物在电场中的电荷性质差异进行分选的方法。
化学选矿:化学选矿是利用矿物的化学性质差异,通过化学反应或物理化学效应,使有用矿物与脉石或其他有害矿物分离的方法。
细菌选矿法:细菌选矿法是利用微生物的生物化学作用,使有用矿物与脉石或其他有害矿物分离的方法。
选矿生产流程
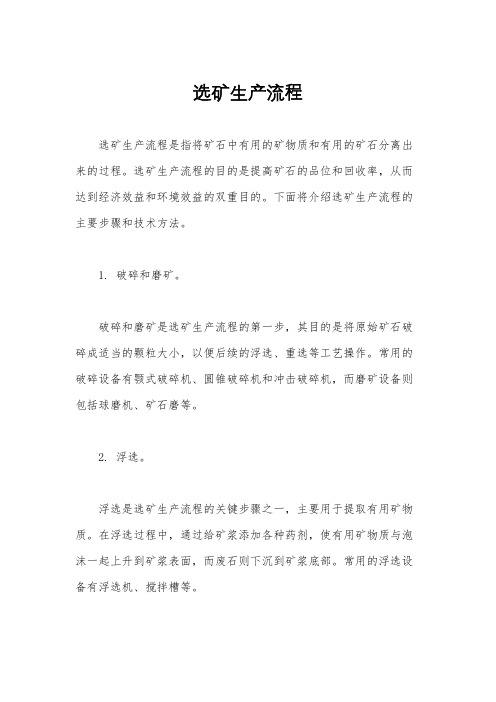
选矿生产流程选矿生产流程是指将矿石中有用的矿物质和有用的矿石分离出来的过程。
选矿生产流程的目的是提高矿石的品位和回收率,从而达到经济效益和环境效益的双重目的。
下面将介绍选矿生产流程的主要步骤和技术方法。
1. 破碎和磨矿。
破碎和磨矿是选矿生产流程的第一步,其目的是将原始矿石破碎成适当的颗粒大小,以便后续的浮选、重选等工艺操作。
常用的破碎设备有颚式破碎机、圆锥破碎机和冲击破碎机,而磨矿设备则包括球磨机、矿石磨等。
2. 浮选。
浮选是选矿生产流程的关键步骤之一,主要用于提取有用矿物质。
在浮选过程中,通过给矿浆添加各种药剂,使有用矿物质与泡沫一起上升到矿浆表面,而废石则下沉到矿浆底部。
常用的浮选设备有浮选机、搅拌槽等。
3. 重选。
重选是对浮选尾矿进行的分选过程,目的是进一步提高有用矿物质的品位和回收率。
重选过程通常采用离心机、重介质分选机等设备,通过不同密度的矿石在离心力或重力作用下的分选,实现矿石的分离。
4. 脱水。
脱水是将选矿过程中产生的浮选浓缩液或重选浓缩液进行固液分离的过程,其目的是获得干燥的矿产品和减少废水排放。
常用的脱水设备有压滤机、离心机等。
5. 尾矿处理。
尾矿是指经过浮选、重选等工艺后剩余的废石和未被提取的有用矿物质。
尾矿处理是选矿生产流程中不可或缺的环节,其主要方法包括尾矿回收、填埋和综合利用等。
总结。
选矿生产流程是一个复杂的系统工程,需要各种工艺设备和技术方法的有机组合。
通过合理的选矿生产流程设计和优化,可以实现矿石的高效利用,提高矿石的经济价值和资源利用率。
在未来的发展中,随着科技的不断进步,选矿生产流程将会更加智能化、自动化,为矿山企业带来更大的经济效益和社会效益。
- 1、下载文档前请自行甄别文档内容的完整性,平台不提供额外的编辑、内容补充、找答案等附加服务。
- 2、"仅部分预览"的文档,不可在线预览部分如存在完整性等问题,可反馈申请退款(可完整预览的文档不适用该条件!)。
- 3、如文档侵犯您的权益,请联系客服反馈,我们会尽快为您处理(人工客服工作时间:9:00-18:30)。
矿产资源开发利用方案编写内容要求及审查大纲
矿产资源开发利用方案编写内容要求及《矿产资源开发利用方案》审查大纲一、概述
㈠矿区位置、隶属关系和企业性质。
如为改扩建矿山, 应说明矿山现状、
特点及存在的主要问题。
㈡编制依据
(1简述项目前期工作进展情况及与有关方面对项目的意向性协议情况。
(2 列出开发利用方案编制所依据的主要基础性资料的名称。
如经储量管理部门认定的矿区地质勘探报告、选矿试验报告、加工利用试验报告、工程地质初评资料、矿区水文资料和供水资料等。
对改、扩建矿山应有生产实际资料, 如矿山总平面现状图、矿床开拓系统图、采场现状图和主要采选设备清单等。
二、矿产品需求现状和预测
㈠该矿产在国内需求情况和市场供应情况
1、矿产品现状及加工利用趋向。
2、国内近、远期的需求量及主要销向预测。
㈡产品价格分析
1、国内矿产品价格现状。
2、矿产品价格稳定性及变化趋势。
三、矿产资源概况
㈠矿区总体概况
1、矿区总体规划情况。
2、矿区矿产资源概况。
3、该设计与矿区总体开发的关系。
㈡该设计项目的资源概况
1、矿床地质及构造特征。
2、矿床开采技术条件及水文地质条件。