铝合金轮毂铸造裂纹缺陷及预防
《低压铸造铝合金车轮主要缺陷分析与控制》

《低压铸造铝合金车轮主要缺陷分析与控制》篇一一、引言随着汽车工业的快速发展,低压铸造铝合金车轮因其轻量化、强度高、耐腐蚀等优点,在汽车制造领域得到了广泛应用。
然而,在生产过程中,铝合金车轮常会出现一些主要缺陷,这些缺陷不仅影响产品的外观质量,还可能对车辆的安全性能造成潜在威胁。
因此,对低压铸造铝合金车轮的主要缺陷进行分析与控制显得尤为重要。
本文旨在探讨低压铸造铝合金车轮的主要缺陷类型、成因及相应的控制措施。
二、铝合金车轮低压铸造工艺概述低压铸造是一种常用的铝合金车轮制造工艺,其基本原理是在较低的压力下将熔融的铝合金注入模具中,通过控制压力和温度,使铝合金在模具中结晶并形成车轮。
这一工艺具有设备简单、操作方便、成本低等优点。
三、主要缺陷类型及分析1. 表面缺陷:主要包括气孔、夹渣、裂纹和表面粗糙等。
气孔和夹渣的产生主要是由于熔融铝合金中气体和杂质未能有效排除;裂纹则多由于铸造过程中热应力过大或合金成分不均所致;表面粗糙则与模具表面处理不当有关。
2. 尺寸及形状缺陷:主要表现为车轮的直径、圆度、厚度等尺寸超差,以及轮辐形状不符合设计要求等。
这些缺陷多由于模具设计不合理、铸造工艺参数控制不当或设备精度不足所致。
3. 内部组织缺陷:包括晶粒粗大、组织不均等。
这些缺陷会影响车轮的力学性能和耐腐蚀性,其产生原因主要与合金成分、铸造温度和时间等工艺参数有关。
四、缺陷控制措施1. 优化熔炼工艺:严格控制合金成分,确保熔融铝合金的纯净度,减少气体和杂质的含量。
2. 改进模具设计:优化模具结构,提高模具表面光洁度,减少表面缺陷的产生。
3. 控制铸造工艺参数:合理设置铸造压力、温度和时间等参数,确保铝合金在模具中均匀结晶。
4. 加强设备维护:定期检查和维护铸造设备,确保设备运行稳定,减少因设备精度问题导致的尺寸及形状缺陷。
5. 实施质量监控:建立严格的质量监控体系,对铝合金车轮进行定期抽检和全检,确保产品质量的稳定性和可靠性。
《低压铸造铝合金车轮主要缺陷分析与控制》范文
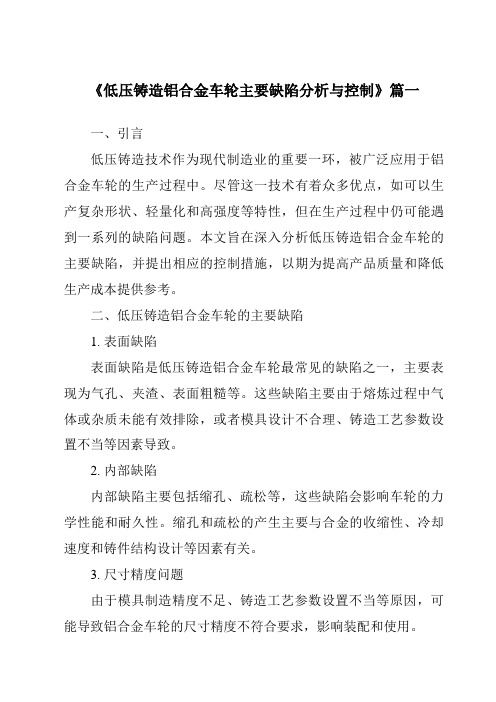
《低压铸造铝合金车轮主要缺陷分析与控制》篇一一、引言低压铸造技术作为现代制造业的重要一环,被广泛应用于铝合金车轮的生产过程中。
尽管这一技术有着众多优点,如可以生产复杂形状、轻量化和高强度等特性,但在生产过程中仍可能遇到一系列的缺陷问题。
本文旨在深入分析低压铸造铝合金车轮的主要缺陷,并提出相应的控制措施,以期为提高产品质量和降低生产成本提供参考。
二、低压铸造铝合金车轮的主要缺陷1. 表面缺陷表面缺陷是低压铸造铝合金车轮最常见的缺陷之一,主要表现为气孔、夹渣、表面粗糙等。
这些缺陷主要由于熔炼过程中气体或杂质未能有效排除,或者模具设计不合理、铸造工艺参数设置不当等因素导致。
2. 内部缺陷内部缺陷主要包括缩孔、疏松等,这些缺陷会影响车轮的力学性能和耐久性。
缩孔和疏松的产生主要与合金的收缩性、冷却速度和铸件结构设计等因素有关。
3. 尺寸精度问题由于模具制造精度不足、铸造工艺参数设置不当等原因,可能导致铝合金车轮的尺寸精度不符合要求,影响装配和使用。
三、缺陷控制措施1. 表面缺陷控制为减少表面缺陷的产生,可以采取以下措施:一是优化熔炼工艺,确保合金液中气体和杂质的有效排除;二是改进模具设计,提高模具的排气性能;三是合理设置铸造工艺参数,如温度、压力和时间等。
2. 内部缺陷控制针对内部缺陷,可以采取以下措施:一是优化合金成分,提高合金的收缩性;二是改进铸件结构设计,合理布置浇注系统和冷铁等;三是控制冷却速度,避免产生过大的热应力。
3. 尺寸精度控制为提高尺寸精度,可以采取以下措施:一是提高模具制造精度,确保模具的尺寸精度和表面质量;二是优化铸造工艺参数,确保铸件在凝固过程中得到合理的补缩和冷却;三是采用先进的检测设备和方法,对铸件进行严格的尺寸检测。
四、结论通过对低压铸造铝合金车轮的主要缺陷进行分析和控制,可以有效提高产品质量和降低生产成本。
在生产过程中,应注重优化熔炼工艺、模具设计和铸造工艺参数等方面,以减少表面和内部缺陷的产生。
《2024年低压铸造铝合金车轮主要缺陷分析与控制》范文

《低压铸造铝合金车轮主要缺陷分析与控制》篇一一、引言随着汽车工业的快速发展,低压铸造铝合金车轮因其轻量化、强度高、耐腐蚀等优点,在汽车制造领域得到了广泛应用。
然而,在生产过程中,由于多种因素的影响,铝合金车轮可能会出现各种缺陷,影响产品的质量和性能。
本文将针对低压铸造铝合金车轮的主要缺陷进行分析,并提出相应的控制措施。
二、低压铸造铝合金车轮主要缺陷1. 表面缺陷表面缺陷是铝合金车轮最常见的缺陷之一,主要表现为气孔、夹渣、麻面等。
这些缺陷的形成主要与铸造过程中的气体排除、材料选择、熔炼工艺等因素有关。
2. 尺寸精度问题尺寸精度问题包括轮毂尺寸超差、轮辐厚度不均等。
这些问题直接影响车轮的装配和使用性能,严重时可能导致安全事故。
3. 内部结构问题内部结构问题主要包括气孔、夹杂物等。
这些问题的产生主要与熔炼温度、铸造压力、保温时间等因素有关,严重影响车轮的强度和耐久性。
三、主要缺陷的原因分析1. 工艺因素低压铸造过程中,工艺参数的设定不合理、铸造压力不足、气体排除不彻底等都会导致各种缺陷的产生。
此外,模具设计不合理、模具表面粗糙度不够等因素也会影响产品质量。
2. 材料因素铝合金材料的成分、杂质含量等都会对车轮的质量产生影响。
此外,熔炼过程中使用的熔剂、炉渣等也会对产品质量造成影响。
3. 操作因素操作人员的技能水平、操作规范程度等都会对产品质量产生影响。
操作不当可能导致熔炼不充分、气体排除不彻底等问题。
四、控制措施1. 优化工艺参数根据产品特点和生产需求,合理设定铸造压力、熔炼温度、保温时间等工艺参数,确保产品质量。
同时,加强气体排除,减少气孔和夹渣等缺陷的产生。
2. 改进模具设计优化模具设计,提高模具表面粗糙度,减少模具对产品的挤压和摩擦,降低表面缺陷的产生。
同时,改进模具排气系统,确保气体顺利排出。
3. 严格控制材料质量加强铝合金材料的检测和筛选,确保材料成分和杂质含量符合要求。
同时,优化熔炼工艺,减少熔剂和炉渣的使用,降低对产品的污染。
《低压铸造铝合金车轮主要缺陷分析与控制》

《低压铸造铝合金车轮主要缺陷分析与控制》篇一一、引言低压铸造铝合金车轮以其轻量化、高强度、良好的耐腐蚀性等特点,在汽车制造领域得到了广泛应用。
然而,在生产过程中,由于多种因素的影响,常常会出现一些主要缺陷,这些缺陷不仅影响产品的性能,还可能对使用安全构成潜在威胁。
因此,对低压铸造铝合金车轮的主要缺陷进行分析和控制显得尤为重要。
本文将就低压铸造铝合金车轮的主要缺陷进行深入分析,并提出相应的控制措施。
二、低压铸造铝合金车轮主要缺陷分析1. 气孔缺陷气孔是低压铸造铝合金车轮中常见的缺陷之一。
其主要原因是铸造过程中熔体中溶解的气体在凝固时未能及时逸出,导致在铸件内部形成气孔。
气孔的存在会严重影响车轮的力学性能和耐腐蚀性。
2. 缩松和缩孔缺陷缩松和缩孔是由于铝合金在凝固过程中收缩而未能得到充分补缩所引起的缺陷。
这种缺陷会导致车轮的力学性能下降,甚至出现裂纹和断裂等现象。
3. 表面质量问题表面质量问题主要包括轮毂表面的砂眼、夹杂物等。
这些问题的出现往往是由于模具清洁度不够、涂料选择不当或操作工艺不当等原因造成的。
三、主要缺陷的控制措施1. 气孔缺陷控制为减少气孔的产生,可以采取以下措施:一是严格控制熔炼温度和时间,保证熔体充分溶解和净化;二是合理设计浇注系统和排气系统,确保气体能够顺利排出;三是优化铸造工艺参数,如铸造压力、保压时间等。
2. 缩松和缩孔缺陷控制为防止缩松和缩孔的产生,可以采取以下措施:一是合理设计铸件结构,保证其具有良好的补缩能力;二是通过提高铸造压力和延长保压时间等方式,增强铝合金的补缩效果;三是采用预热和后热处理等方式,降低铸件内部的应力。
3. 表面质量控制为提高轮毂表面的质量,可以采取以下措施:一是保持模具的清洁度,定期对模具进行清洗和维护;二是选择合适的涂料和涂料工艺,提高模具的表面质量和耐热性;三是优化操作工艺,如调整浇注速度、温度等参数,减少表面问题的产生。
四、结论低压铸造铝合金车轮的缺陷控制是保证产品质量、提高生产效率的关键环节。
低压铸造铝合金车轮缺陷探讨

低压铸造铝合金车轮缺陷探讨随着铝合金车轮技术生产技术水平的提升,低压铸造技术作为重要技术得到了技术人员的重视。
通过技术的应用,可以有效减少实际生产的成本,提升铝合金车轮的耐用性和可靠性。
但是根据实际生产的情况,低压铸造铝合金车轮存在一定的缺陷,不仅影响了车轮的美观,而且增加了车辆行驶安全隐患。
从而影响了汽车的正常行驶。
因此,本文首先分析低压铸造铝合金车轮存在的缺陷,然后提出相应的改进措施。
标签:低压铸造;铝合金;车轮;缺陷;探讨就目前而言,我国汽车数量不断增加,作为关键部件的车轮,生产企业需要重视车辆质量,消除潜在的缺陷,充分利用低压铸造铝合金车轮技术,降低实际投入,提升车轮的耐久性,延长车轮的使用寿命。
随着我国汽车行业的发展,铝合金车轮制水平不断提升,创造更多的经济利益,适应当前市场经济迅速发展的基本要求。
但是从当前的铝合金车轮制造与国外相比,存在一定的差距。
因此,本文主要低压铸造铝合金车轮缺陷展开论述,并且结合实际生产情况,提出一些借鉴和帮助。
一、铝合金车轮的低压铸造技术在当前我国工业经济迅速发展的背景下,对周围环境造成了破坏,人们环保意识不断提升,环保汽车生产数量不断增加,受到了人们的欢迎。
铝合金材料密度比较低,能够有效减轻车辆的重量,降低了油耗。
与此同时,随着低压铸造技术的应用,提升了车轮生产的环保性,满足了节能型社会发展的要求。
铝合金车轮低压铸造技术主要利用压缩空气,把熔融的铝合金压进磨具内,让其固化,通过降低空气的压力,让后未凝固的液态金属重新回流。
通过这種技术的应用,可以提升车轮的耐久性,在世界范围内得到了广泛的应用。
改革开放以来,我国汽车行业得到了快速发展,在不断引进国外先进生产技术的前提下,不断提升铝合金车轮生产水平。
但是由于我国铝合金车轮生产技术发展时间比较短,与国外相比,尤其低压铸造铝合金车轮生产技术工艺和生产设备性能上,还存在比较大的差距。
因此,本文对低压铸造过程中容易出现的铸造缺陷进行了分析,并且结合实际情况,找到了缺陷的形成机理及其危害,然后提出相应的控制策略,为当前车轮车轮生产提供借鉴和帮助。
铝合金的铸造缺陷及其解决方案

铝合金的铸造缺陷及其解决方案关键信息项:1、铝合金铸造缺陷的类型名称:____________________________描述:____________________________2、造成铸造缺陷的原因因素:____________________________详细解释:____________________________3、解决方案的具体措施方法:____________________________实施步骤:____________________________4、预防铸造缺陷的策略策略:____________________________执行要点:____________________________11 铝合金铸造缺陷的类型111 气孔气孔是铝合金铸造中常见的缺陷之一。
气孔通常呈圆形或椭圆形,其尺寸大小不一。
112 缩孔和缩松缩孔是由于铸件在凝固过程中,金属液补缩不足而形成的较大孔洞。
缩松则是分散的细小缩孔。
113 夹渣夹渣指在铸件内部或表面存在的非金属夹杂物。
114 裂纹裂纹分为热裂纹和冷裂纹。
热裂纹在凝固末期高温下形成,冷裂纹则在较低温度下产生。
12 造成铸造缺陷的原因121 熔炼工艺不当熔炼过程中,如果温度控制不合理、熔炼时间过长或过短、搅拌不均匀等,都可能导致合金成分不均匀,气体和夹杂物含量增加。
122 浇注系统设计不合理浇注系统的结构和尺寸如果设计不当,可能导致金属液的流动不畅,产生卷气、冲砂等问题,从而形成气孔、夹渣等缺陷。
123 模具问题模具的温度不均匀、模具的排气不畅、模具的表面粗糙度不合适等,都可能影响铸件的质量,导致缺陷的产生。
124 铸造工艺参数不合理包括浇注温度、浇注速度、冷却速度等参数,如果选择不当,会直接影响铸件的凝固过程,从而引发各种缺陷。
13 解决方案的具体措施131 优化熔炼工艺严格控制熔炼温度和时间,采用合适的搅拌方式,确保合金成分均匀,减少气体和夹杂物的含量。
《2024年低压铸造铝合金车轮主要缺陷分析与控制》范文

《低压铸造铝合金车轮主要缺陷分析与控制》篇一一、引言随着汽车工业的快速发展,低压铸造铝合金车轮因其良好的机械性能和轻量化特点,在汽车制造领域得到了广泛应用。
然而,在生产过程中,铝合金车轮常常会出现一些缺陷,这些缺陷不仅影响产品的外观质量,还可能对车辆的安全性能产生严重影响。
因此,对低压铸造铝合金车轮的主要缺陷进行分析和控制显得尤为重要。
本文将探讨铝合金车轮的常见缺陷,并探讨相应的控制措施。
二、铝合金车轮常见缺陷1. 气孔与夹渣缺陷在低压铸造过程中,铝合金车轮可能因为气体无法顺利排出而形成气孔。
同时,如果炉料中的杂质未能被完全净化,可能产生夹渣。
这些气孔和夹渣都会影响车轮的机械性能和抗腐蚀性能。
2. 缩孔与缩松缺陷缩孔和缩松是由于凝固过程中液体金属收缩不足或收缩补偿不足引起的,通常出现在轮辐或轮盘等壁厚较薄的区域。
这些缺陷会降低车轮的强度和韧性。
3. 表面粗糙与凹坑缺陷由于模具设计不合理或铸造工艺控制不当,铝合金车轮表面可能出现粗糙、凹坑等缺陷,影响产品的外观质量。
三、缺陷成因分析1. 工艺参数控制不当铸造过程中的温度、压力、速度等工艺参数对铝合金车轮的质量有着重要影响。
如果这些参数控制不当,可能导致上述缺陷的产生。
2. 模具设计与制造问题模具的设计和制造质量直接影响产品的形状和尺寸精度。
模具设计不合理或制造精度不足可能导致铸造过程中出现各种缺陷。
3. 原材料质量铝合金原材料的化学成分、杂质含量等也会对车轮的质量产生影响。
如果原材料质量不稳定或不符合要求,可能引发各种铸造缺陷。
四、控制措施1. 优化工艺参数控制通过合理设置铸造温度、压力、速度等工艺参数,以及控制铸造周期,可以有效减少气孔、夹渣、缩孔等缺陷的产生。
同时,加强过程监控和质量控制,确保工艺参数的稳定性和可靠性。
2. 模具设计与制造优化模具设计应充分考虑铝合金的流动性、收缩性等特点,确保产品形状和尺寸的准确性。
同时,提高模具的制造精度和表面质量,减少模具对产品表面质量的影响。
铸轧铝合金裂边缺陷产生原因及改进措施

铸轧铝合金裂边缺陷产生原因及改进措施1. 引言铸轧铝合金是一种广泛应用于航空、汽车、电子等领域的重要材料。
然而,在生产过程中,铸轧铝合金裂边缺陷的产生成为了一个严重的问题。
裂边缺陷不仅会影响产品的外观和质量,还可能导致零部件在使用过程中的性能损失甚至失效。
深入探讨铸轧铝合金裂边缺陷的产生原因及改进措施,对于提高产品质量和生产效率具有重要意义。
2. 裂边缺陷的产生原因2.1 材料原因铸轧铝合金裂边缺陷的产生与材料的性质有密切关系。
原材料的质量和纯度对铝合金的力学性能和成型性能具有重要影响。
杂质和氧化物的存在会导致合金中存在脆性相,从而增加裂边的产生概率。
合金的熔炼过程中,温度和冷却速率的控制不当也会导致合金组织不均匀,从而进一步增加裂边的发生。
2.2 工艺原因铸轧铝合金的生产过程涉及多个环节,如铸造、加热、轧制等。
在每个环节中,不当的工艺参数设置或操作方法可能会导致裂边缺陷的产生。
铸造过程中,浇注温度过高会导致合金存在大量气孔和夹杂物,增加裂边的概率。
加热过程中,温度梯度过大或保持时间不足,也会导致合金的形态不稳定,导致裂边的形成。
3. 改进措施3.1 优化材料选择在铝合金生产中,选择高质量、纯净度高的原材料是降低裂边缺陷的重要措施之一。
对原材料进行严格的质量检测和筛选,以确保合金中的杂质和氧化物含量尽可能低,并优化熔炼过程的温度和冷却速率,以提高合金的均匀性和稳定性。
3.2 优化工艺参数在各个工艺环节中,优化参数设置和改进操作方法是降低裂边缺陷的关键。
在铸造过程中,控制浇注温度、填充速度和冷却速率,提高铸造的质量稳定性;在加热过程中,控制温度梯度和保持时间,降低合金的形态不稳定性。
3.3 引入先进技术随着科学技术的不断进步,先进的制造技术也逐渐应用于铸轧铝合金的生产中。
利用激光熔化等先进的合金制备技术,可以使合金的组织更加均匀,减少裂边缺陷的发生。
利用先进的在线检测技术,可以及时监测裂边缺陷的发生,实现快速响应和纠正。
《低压铸造铝合金车轮主要缺陷分析与控制》范文
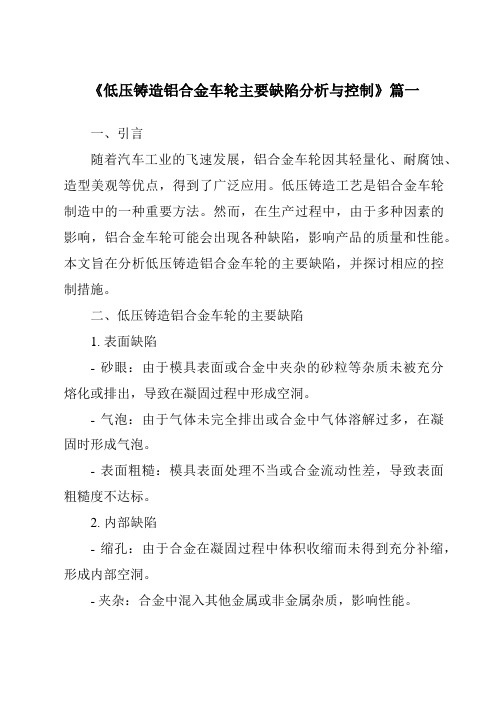
《低压铸造铝合金车轮主要缺陷分析与控制》篇一一、引言随着汽车工业的飞速发展,铝合金车轮因其轻量化、耐腐蚀、造型美观等优点,得到了广泛应用。
低压铸造工艺是铝合金车轮制造中的一种重要方法。
然而,在生产过程中,由于多种因素的影响,铝合金车轮可能会出现各种缺陷,影响产品的质量和性能。
本文旨在分析低压铸造铝合金车轮的主要缺陷,并探讨相应的控制措施。
二、低压铸造铝合金车轮的主要缺陷1. 表面缺陷- 砂眼:由于模具表面或合金中夹杂的砂粒等杂质未被充分熔化或排出,导致在凝固过程中形成空洞。
- 气泡:由于气体未完全排出或合金中气体溶解过多,在凝固时形成气泡。
- 表面粗糙:模具表面处理不当或合金流动性差,导致表面粗糙度不达标。
2. 内部缺陷- 缩孔:由于合金在凝固过程中体积收缩而未得到充分补缩,形成内部空洞。
- 夹杂:合金中混入其他金属或非金属杂质,影响性能。
- 裂痕:铸造过程中因应力集中或合金成分不均等导致车轮出现裂纹。
3. 尺寸及形状偏差- 尺寸超差:由于模具设计、制造精度不足或铸造工艺控制不当,导致车轮的尺寸不符合标准要求。
- 形状不规整:模具变形或铸造过程中温度控制不当,导致车轮形状不规整。
三、缺陷产生的原因及控制措施1. 表面缺陷控制- 原因:模具清洁度不足、合金成分不纯、浇注温度过高等。
- 控制措施:定期清理模具、选用优质合金、控制浇注温度和速度、加强排气设计等。
2. 内部缺陷控制- 原因:合金熔炼不均、冷却速度过快、补缩不足等。
- 控制措施:优化熔炼工艺、合理设计浇注系统和冷却系统、保证补缩效果等。
3. 尺寸及形状偏差控制- 原因:模具设计制造精度不足、工艺参数设置不当等。
- 控制措施:提高模具设计制造精度、优化工艺参数设置、定期校准模具等。
四、结论低压铸造铝合金车轮的缺陷问题涉及多个方面,包括材料、工艺、设备和管理等。
要有效控制和减少这些缺陷,需要从以下几个方面着手:一是优化材料选择,确保合金的纯度和性能;二是改进工艺流程,提高铸造过程的稳定性和可控性;三是加强设备维护和校准,确保模具和铸造设备的精度和可靠性;四是强化管理措施,包括加强生产过程的质量监控和人员培训等。
《2024年低压铸造铝合金车轮主要缺陷分析与控制》范文
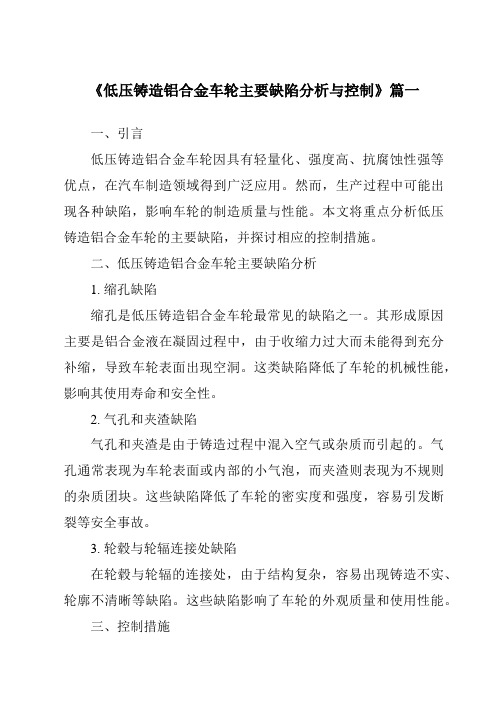
《低压铸造铝合金车轮主要缺陷分析与控制》篇一一、引言低压铸造铝合金车轮因具有轻量化、强度高、抗腐蚀性强等优点,在汽车制造领域得到广泛应用。
然而,生产过程中可能出现各种缺陷,影响车轮的制造质量与性能。
本文将重点分析低压铸造铝合金车轮的主要缺陷,并探讨相应的控制措施。
二、低压铸造铝合金车轮主要缺陷分析1. 缩孔缺陷缩孔是低压铸造铝合金车轮最常见的缺陷之一。
其形成原因主要是铝合金液在凝固过程中,由于收缩力过大而未能得到充分补缩,导致车轮表面出现空洞。
这类缺陷降低了车轮的机械性能,影响其使用寿命和安全性。
2. 气孔和夹渣缺陷气孔和夹渣是由于铸造过程中混入空气或杂质而引起的。
气孔通常表现为车轮表面或内部的小气泡,而夹渣则表现为不规则的杂质团块。
这些缺陷降低了车轮的密实度和强度,容易引发断裂等安全事故。
3. 轮毂与轮辐连接处缺陷在轮毂与轮辐的连接处,由于结构复杂,容易出现铸造不实、轮廓不清晰等缺陷。
这些缺陷影响了车轮的外观质量和使用性能。
三、控制措施1. 优化铸造工艺参数针对缩孔、气孔和夹渣等缺陷,可以通过优化铸造工艺参数来控制。
例如,调整铝合金液的浇注温度、压力和速度,确保铝合金液在凝固过程中得到充分的补缩。
同时,控制铸造过程中的气体和杂质含量,减少气孔和夹渣的产生。
2. 改进模具设计及制造工艺针对轮毂与轮辐连接处的缺陷,可以通过改进模具设计及制造工艺来控制。
例如,优化模具结构,使轮毂与轮辐的过渡更加平滑;提高模具的制造精度,确保轮廓清晰。
此外,对模具进行预热处理,减少模具与铝合金液之间的温度差异,有助于提高铸造质量。
3. 加强质量检测与控制在生产过程中,应加强质量检测与控制。
采用X射线、超声波等无损检测技术对车轮进行全面检测,及时发现并处理各类缺陷。
同时,建立严格的质量管理体系,对生产过程中的每个环节进行严格控制,确保产品质量符合标准。
四、结论低压铸造铝合金车轮的制造质量直接关系到汽车的性能和安全性。
通过分析主要缺陷并采取相应的控制措施,可以有效提高车轮的制造质量。
铝合金压铸常见缺陷解决方案与预防措施

铝压铸十大缺陷解决方案与预防措施一、流痕和花纹外观检查:铸件表面上有与金属液流动方向一致的条纹,有明显可见的与金属基体颜色不一样的无方向性的纹路,无发展趋势。
1.流痕产生的原因有如下几点:1)模温过低2)浇道设计不良,内浇口位置不良3)料温过低4)填充速度低,填充时间短5)浇注系统不合理6)排气不良7)喷雾不合理2.花纹产生的原因是型腔内涂料喷涂过多或涂料质量较差,解决和防止的方法如下:1)调整内浇道截面积或位置2)提高模温3)调整内浇道速度及压力4)适当的选用涂料及调整用量二、网状毛翅(龟裂纹)外观检查:压铸件表面上有网状发丝一样凸起或凹陷的痕迹,随压铸次数增加而不断扩大和延伸。
产生原因如下:1)压铸模腔表面有裂纹2)压铸模预热不均匀解决和防止的方法为:1)压铸模要定期或压铸一定次数后,应作退火处理、消除型腔内应力2)如果型腔表面已出现龟裂纹,应打磨成型表面,去掉裂纹层3)模具预热要均匀三、冷隔外观检查:压铸件表面有明显的、不规则的、下陷线性型纹路(有穿透与不穿透两种)形状细小而狭长,有时交接边缘光滑,在外力作用下有断开的可能。
产生原因如下:1)两股金属流相互对接,但未完全熔合而又无夹杂存在其间,两股金属结合力又很薄弱2)浇注温度或压铸模温度偏低3)浇道位置不对或流路过长4)填充速度低解决和防止的方法为:1)适当提高浇注温度2)提高压射比压缩短填充时间,提高压射速度3)改善排气、填充条件四、缩陷(凹痕)外观检查:在压铸件厚大部分的表面上有平滑的凹痕(状如盘碟)。
产生原因如下:1)由收缩引起压铸件设计不当壁厚差太大浇道位置不当压射比压低,保压时间短压铸模局部温度过高2)冷却系统设计不合理3)开模过早4)浇注温度过高解决和防止的方法为:1)壁厚应均匀2)厚薄过渡要缓和3)正确选择合金液导入位置及增加内浇道截面积4)增加压射压力,延长保压时间5)适当降低浇注温度及压铸模温度6)对局部高温要局部冷却7)改善排溢条件五、印痕外观检查:铸件表面与压铸模型腔表面接触所留下的痕迹或铸件表面上出现阶梯痕迹。
《低压铸造铝合金车轮主要缺陷分析与控制》

《低压铸造铝合金车轮主要缺陷分析与控制》篇一一、引言随着汽车工业的快速发展,低压铸造铝合金车轮因其轻量化、强度高、耐腐蚀等优点,已成为现代汽车制造的重要部分。
然而,在生产过程中,该类产品可能出现多种缺陷,这些缺陷不仅影响产品的性能和外观,还可能对车辆的安全性能造成潜在威胁。
因此,对低压铸造铝合金车轮的主要缺陷进行分析和控制显得尤为重要。
本文将就低压铸造铝合金车轮的主要缺陷进行详细分析,并提出相应的控制措施。
二、低压铸造铝合金车轮主要缺陷分析1. 气孔与夹杂物气孔和夹杂物是低压铸造铝合金车轮中常见的缺陷类型。
由于合金液在充型过程中混入气体或夹杂物,导致在凝固过程中形成气孔或夹杂物。
这些缺陷会降低车轮的强度和耐腐蚀性,严重时甚至可能导致车轮断裂。
2. 缩松与缩孔缩松和缩孔是铝合金车轮在凝固过程中因收缩不均而形成的缺陷。
这些缺陷通常表现为车轮的表面粗糙,尺寸精度低,严重时会降低车轮的承载能力。
3. 轮毂与轮辐错位在铸造过程中,由于模具设计不合理或操作不当,可能导致轮毂与轮辐错位。
这种缺陷不仅影响车轮的外观,还可能影响车轮的装配和使用性能。
三、控制措施1. 原料控制选择优质的原材料和熔剂,保证原材料的纯度和成分稳定。
在熔炼过程中,应严格控制温度和时间,以减少合金液中气体和夹杂物的含量。
2. 模具设计及制造模具的设计和制造对铸造过程及产品质量具有重要影响。
模具应具有良好的排气性能,以减少气孔的形成。
同时,模具的尺寸精度和表面粗糙度应满足生产要求,以保证铸造产品的尺寸精度和外观质量。
3. 铸造工艺控制在铸造过程中,应严格控制充型速度、压力和时间等参数。
充型速度过快或压力不足可能导致气孔和夹杂物的形成。
此外,铸造过程中的保温措施和冷却速度也应合理控制,以减少缩松和缩孔的产生。
4. 质量检测与监控建立严格的质量检测与监控体系,对铝合金车轮进行全面的质量检查。
包括外观检查、尺寸精度检测、金相组织分析等。
对于发现的不合格产品,应立即进行原因分析并采取相应的纠正措施。
《2024年低压铸造铝合金车轮主要缺陷分析与控制》范文
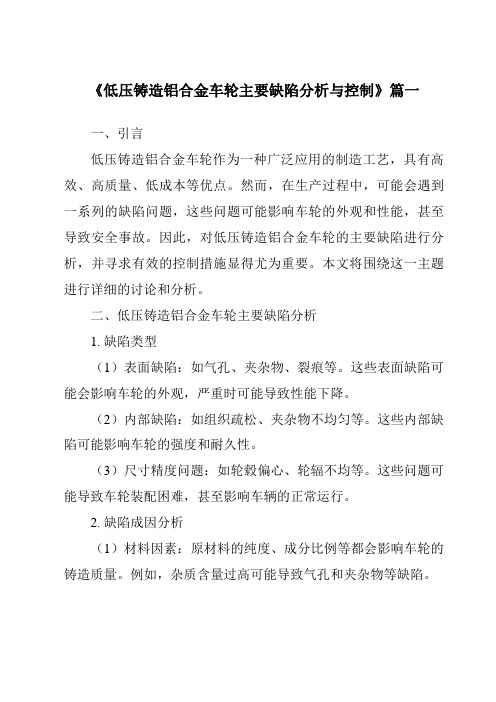
《低压铸造铝合金车轮主要缺陷分析与控制》篇一一、引言低压铸造铝合金车轮作为一种广泛应用的制造工艺,具有高效、高质量、低成本等优点。
然而,在生产过程中,可能会遇到一系列的缺陷问题,这些问题可能影响车轮的外观和性能,甚至导致安全事故。
因此,对低压铸造铝合金车轮的主要缺陷进行分析,并寻求有效的控制措施显得尤为重要。
本文将围绕这一主题进行详细的讨论和分析。
二、低压铸造铝合金车轮主要缺陷分析1. 缺陷类型(1)表面缺陷:如气孔、夹杂物、裂痕等。
这些表面缺陷可能会影响车轮的外观,严重时可能导致性能下降。
(2)内部缺陷:如组织疏松、夹杂物不均匀等。
这些内部缺陷可能影响车轮的强度和耐久性。
(3)尺寸精度问题:如轮毂偏心、轮辐不均等。
这些问题可能导致车轮装配困难,甚至影响车辆的正常运行。
2. 缺陷成因分析(1)材料因素:原材料的纯度、成分比例等都会影响车轮的铸造质量。
例如,杂质含量过高可能导致气孔和夹杂物等缺陷。
(2)工艺因素:铸造过程中的温度、压力、时间等参数控制不当,都可能导致车轮出现缺陷。
例如,温度过高可能导致组织疏松,压力不足可能导致充型不完整等。
(3)设备因素:铸造设备的精度、稳定性等也会影响车轮的铸造质量。
例如,模具的精度不足可能导致尺寸精度问题。
三、缺陷控制措施1. 材料控制:严格控制原材料的纯度和成分比例,确保原材料质量符合要求。
同时,对原材料进行严格的检验和筛选,防止杂质进入生产过程。
2. 工艺控制:优化铸造过程中的温度、压力、时间等参数,确保车轮的铸造过程在最佳状态下进行。
同时,加强对工艺过程的监控和记录,以便及时发现和解决问题。
3. 设备维护:定期对铸造设备进行维护和保养,确保设备的精度和稳定性。
对模具进行定期检查和更换,防止因模具问题导致的尺寸精度问题。
4. 质量检测:加强质量检测力度,对生产出的车轮进行严格的外观和性能检测,确保产品符合要求。
同时,建立完善的质量追溯体系,以便在出现问题时能够迅速找到原因并采取措施。
《2024年低压铸造铝合金车轮主要缺陷分析与控制》范文
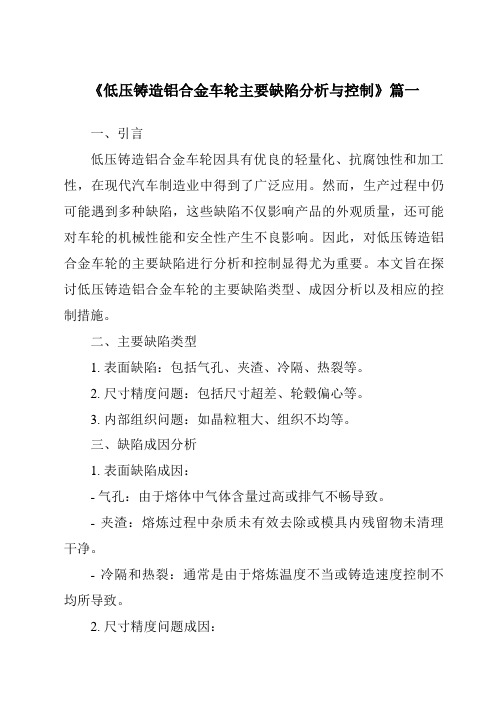
《低压铸造铝合金车轮主要缺陷分析与控制》篇一一、引言低压铸造铝合金车轮因具有优良的轻量化、抗腐蚀性和加工性,在现代汽车制造业中得到了广泛应用。
然而,生产过程中仍可能遇到多种缺陷,这些缺陷不仅影响产品的外观质量,还可能对车轮的机械性能和安全性产生不良影响。
因此,对低压铸造铝合金车轮的主要缺陷进行分析和控制显得尤为重要。
本文旨在探讨低压铸造铝合金车轮的主要缺陷类型、成因分析以及相应的控制措施。
二、主要缺陷类型1. 表面缺陷:包括气孔、夹渣、冷隔、热裂等。
2. 尺寸精度问题:包括尺寸超差、轮毂偏心等。
3. 内部组织问题:如晶粒粗大、组织不均等。
三、缺陷成因分析1. 表面缺陷成因:- 气孔:由于熔体中气体含量过高或排气不畅导致。
- 夹渣:熔炼过程中杂质未有效去除或模具内残留物未清理干净。
- 冷隔和热裂:通常是由于熔炼温度不当或铸造速度控制不均所导致。
2. 尺寸精度问题成因:- 模具设计不合理或加工精度不足。
- 铸造过程中压力控制不稳定。
- 材料收缩率估算不准确。
3. 内部组织问题成因:- 合金成分不均或合金元素含量超标。
- 铸造温度过高或保温时间过长导致晶粒长大。
四、控制措施1. 表面缺陷控制:- 控制熔体中的气体含量,采取真空除气技术。
- 严格清理模具,确保无杂质残留。
- 优化铸造工艺参数,如温度、压力和速度等。
2. 尺寸精度控制:- 提高模具设计及加工精度,确保尺寸稳定性。
- 采用先进的压力控制系统,确保铸造过程中压力稳定。
- 准确估算材料收缩率,合理设计模具补缩系统。
3. 内部组织控制:- 严格控制合金成分及含量,确保合金质量。
- 优化铸造温度和保温时间,避免晶粒长大。
- 采用合金化及热处理技术,改善内部组织结构。
五、结论低压铸造铝合金车轮的缺陷控制是保证产品质量和性能的关键环节。
通过对表面缺陷、尺寸精度问题和内部组织问题的成因分析,我们采取了相应的控制措施,如优化熔炼工艺、提高模具精度和优化合金成分等,从而有效地减少了产品缺陷的发生率,提高了产品的质量和性能。
《低压铸造铝合金车轮主要缺陷分析与控制》范文

《低压铸造铝合金车轮主要缺陷分析与控制》篇一一、引言低压铸造铝合金车轮以其优越的力学性能和外观品质在汽车行业中广泛应用。
然而,在生产过程中,由于多种因素的影响,可能会出现一些主要缺陷,这些缺陷不仅影响产品的性能,还可能对车辆的安全性和使用寿命产生不良影响。
因此,对低压铸造铝合金车轮的主要缺陷进行分析和控制显得尤为重要。
本文旨在探讨低压铸造铝合金车轮的主要缺陷及其控制措施,以提高产品质量和降低生产成本。
二、低压铸造铝合金车轮主要缺陷分析1. 气泡和气孔气泡和气孔是低压铸造铝合金车轮常见的缺陷之一。
这些缺陷主要是由于熔炼过程中气体未充分排出或熔体中含气量过高所导致。
气泡和气孔的存在会降低车轮的强度和耐腐蚀性,严重时可能导致车轮在使用过程中出现断裂等问题。
2. 轮毂与轮辐结合处不紧密轮毂与轮辐结合处不紧密是低压铸造铝合金车轮的另一个常见缺陷。
这主要是由于模具设计不合理、铸造工艺参数设置不当或铸件在凝固过程中受到外部振动等因素导致。
这一缺陷会影响车轮的整体性能,严重时可能导致轮毂与轮辐分离。
3. 表面质量差表面质量差主要表现在车轮表面出现砂眼、夹杂物、划痕等问题。
这主要是由于熔炼过程中杂质未充分去除、模具表面粗糙度不足或铸件在凝固过程中受到外力等因素导致。
表面质量差会严重影响车轮的外观品质,降低其市场竞争力。
三、低压铸造铝合金车轮缺陷控制措施1. 优化熔炼工艺为减少气泡和气孔等缺陷,应优化熔炼工艺。
具体措施包括控制熔体中的含气量、调整熔炼温度和速度、保持炉内气氛的稳定性等。
此外,还可以通过加入适当的合金元素和细化晶粒等方法提高熔体的流动性,从而减少气泡和气孔的产生。
2. 改进模具设计及制造工艺为解决轮毂与轮辐结合处不紧密的问题,需要改进模具设计及制造工艺。
首先,应确保模具设计合理、尺寸精确;其次,在制造过程中,应控制好模具的表面粗糙度、热处理工艺等;最后,应采取防震措施,减少铸件在凝固过程中受到的外部振动。
铸轧铝合金裂边缺陷产生原因及改进措施

《铸轧铝合金裂边缺陷产生原因及改进措施》1. 引言铸轧铝合金在工业生产中具有重要的应用价值,然而在生产过程中,裂边缺陷是较为常见的质量问题之一。
本文将从裂边缺陷产生的原因和可能的改进措施进行探讨,以期加深对这一问题的理解并改进生产工艺。
2. 原因分析2.1 温度控制不当铸轧铝合金在轧制过程中需要严格控制温度,若温度过高或过低都会导致晶界移动不畅,从而形成裂边缺陷。
2.2 润滑不足良好的润滑能够降低金属板材与轧辊之间的摩擦,减少表面缺陷的产生,然而润滑不足会导致裂痕的形成。
2.3 材质问题铸轧铝合金的材质不均匀或含有太多的杂质也会导致裂边缺陷的产生。
2.4 设备故障轧制设备的故障隐患会影响板材的表面质量,从而产生裂边缺陷。
3. 改进措施3.1 加强温度控制通过对轧制温度的严格控制和监测,确保在合适的温度范围内进行轧制,从而减少裂边缺陷的产生。
3.2 改善润滑条件完善润滑系统,保证每一块板材表面都获得均匀的润滑,降低摩擦,减少裂边缺陷的出现。
3.3 优化原材料选择优质的原料,并对原料进行严格的检测和筛选,排除掺杂和不均匀的材料,降低裂边缺陷的风险。
3.4 设备维护对轧制设备进行定期的维护和保养,消除故障隐患,保证设备的正常运行,减少裂边缺陷的产生。
4. 个人观点和理解作为铝合金轧制行业的从业者,我深知裂边缺陷给生产带来的质量和效益损失。
在实际工作中,我也发现了裂边缺陷的产生往往伴随着多种因素的综合作用,解决起来并不容易。
但只要我们采取科学的改进措施,严格把关每个环节,相信裂边缺陷问题是可以得到有效控制和改进的。
5. 总结与展望通过对铸轧铝合金裂边缺陷的原因和改进措施进行全面的分析和讨论,我们不仅更深入地了解了该问题的成因和解决方法,也为今后的生产实践提供了有益的启示。
相信在不久的将来,随着技术的不断升级和管理的不断完善,铸轧铝合金裂边缺陷将会逐步得到有效控制和解决,为行业的发展注入新的动力。
6. 参考文献- 张三, 张四.《铝合金轧制工艺》. 浙江大学出版社, 2005.- 李四, 王五.《钢铁轧制设备维护与故障诊断》. 机械工业出版社, 2010.结语:通过对铸轧铝合金裂边缺陷产生原因及改进措施的探讨,希望能够为相关行业提供一些有益的帮助,指导大家更好地避免和解决这一问题。
探讨铸造铝合金热裂缺陷的成因及对策

探讨铸造铝合金热裂缺陷的成因及对策铸造铝合金热裂缺陷是在铸造过程中常见的一种问题,它会对产品的质量和可靠性产生不良影响。
本文将探讨该缺陷的成因,并提出相应的对策。
1. 问题描述铸造铝合金热裂缺陷,指的是在铝合金铸件冷却过程中产生的裂纹。
这些裂纹可以沿晶界或内部形成,导致铸件的破裂或性能下降。
该缺陷通常在高温下出现,尤其在熔点附近的温度范围内更加明显。
2. 成因分析2.1 温度梯度铸造过程中,由于铸型和铸件的几何形状不同,冷却速度也会有所差异,导致温度梯度的形成。
当铸件冷却速度不均匀时,快速冷却部分与慢速冷却部分之间会产生相对较大的温度梯度,从而引起热应力的积累,进而导致裂纹的形成。
2.2 冷却收缩铝合金在冷却过程中会收缩,而铸件内部的阻塞性大于外界环境,导致内部应力的积累。
当外部的阻塞性释放时,内部应力会发生突然释放,引发裂纹。
2.3 结构设计不合理的结构设计也是造成铝合金热裂缺陷的重要原因之一。
例如,壁厚过大、壁薄部件的变形、角部或尖部的过渡不平滑等,都会导致温度梯度的形成,增加裂纹的风险。
3. 对策措施3.1 控制温度梯度为了减少温度梯度,可以采取一些措施,如增加浇注温度、改变冷却介质等。
通过调整铸造参数,尽量使铸件内外温度差异较小,减少裂纹的发生。
3.2 预热处理在铸造前对合金材料进行预热处理,可以改善其热传导性能,降低内部应力的积累。
预热处理还可以提高合金的形变能力,减少变形产生的应力,从而降低热裂缺陷的风险。
3.3 优化结构设计在产品设计阶段,应该考虑减少壁厚差异、优化过渡部位的设计,避免部件过于尖锐,以减少温度梯度的产生。
采用流线型结构或增加倒角等措施,有助于降低内应力的积累,减少热裂缺陷的出现。
3.4 控制冷却速度调整冷却速度在一定程度上可以减少内外界温度差异,减轻热应力的积累。
可通过优化冷却条件、改变冷却介质以及控制冷却时间等手段来实现。
4. 结论铸造铝合金热裂缺陷是造成产品质量问题的重要原因之一。
《低压铸造铝合金车轮主要缺陷分析与控制》
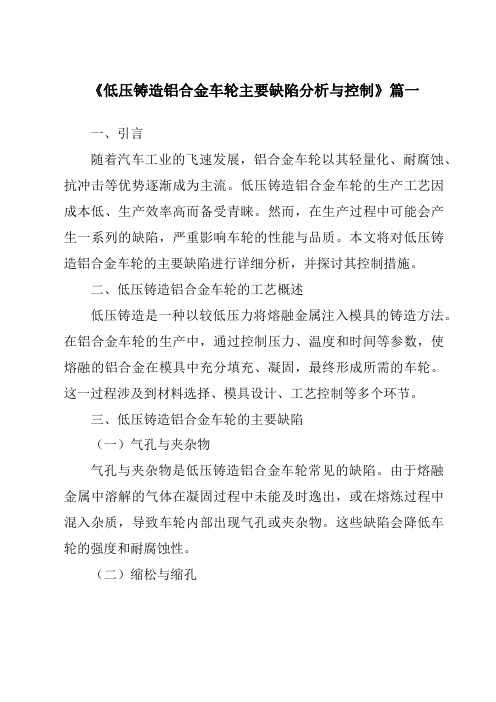
《低压铸造铝合金车轮主要缺陷分析与控制》篇一一、引言随着汽车工业的飞速发展,铝合金车轮以其轻量化、耐腐蚀、抗冲击等优势逐渐成为主流。
低压铸造铝合金车轮的生产工艺因成本低、生产效率高而备受青睐。
然而,在生产过程中可能会产生一系列的缺陷,严重影响车轮的性能与品质。
本文将对低压铸造铝合金车轮的主要缺陷进行详细分析,并探讨其控制措施。
二、低压铸造铝合金车轮的工艺概述低压铸造是一种以较低压力将熔融金属注入模具的铸造方法。
在铝合金车轮的生产中,通过控制压力、温度和时间等参数,使熔融的铝合金在模具中充分填充、凝固,最终形成所需的车轮。
这一过程涉及到材料选择、模具设计、工艺控制等多个环节。
三、低压铸造铝合金车轮的主要缺陷(一)气孔与夹杂物气孔与夹杂物是低压铸造铝合金车轮常见的缺陷。
由于熔融金属中溶解的气体在凝固过程中未能及时逸出,或在熔炼过程中混入杂质,导致车轮内部出现气孔或夹杂物。
这些缺陷会降低车轮的强度和耐腐蚀性。
(二)缩松与缩孔缩松与缩孔是由于熔融金属在凝固过程中体积收缩而未能得到充分补缩所导致的。
这些缺陷通常出现在车轮的厚大部位或热节处,会严重影响车轮的力学性能。
(三)轮辐不均与错位轮辐不均与错位主要源于模具设计不合理或制造精度不足。
这些缺陷会导致车轮的动平衡性能下降,影响车辆的行驶稳定性。
四、缺陷控制措施(一)优化熔炼工艺为减少气孔与夹杂物,应优化熔炼工艺,如采用高真空度熔炼、使用精炼剂等措施,以降低金属中的气体含量和杂质含量。
同时,应严格控制熔炼温度和时间,避免过烧或欠烧现象。
(二)改进模具设计及制造工艺针对缩松与缩孔问题,应改进模具设计及制造工艺,如优化浇注系统设计、提高模具的制造精度等。
此外,还应合理设置工艺参数,如浇注温度、压力等,以确保金属液在模具中充分填充和凝固。
(三)提高制造精度及检测水平为解决轮辐不均与错位问题,应提高制造精度及检测水平。
在生产过程中,应严格控制各道工序的加工精度,确保车轮的尺寸和形状符合要求。
《低压铸造铝合金车轮主要缺陷分析与控制》

《低压铸造铝合金车轮主要缺陷分析与控制》篇一一、引言低压铸造技术因其良好的可操作性和生产效率,已成为铝合金车轮制造中的常用工艺。
然而,在生产过程中可能会出现一系列的缺陷,对车轮的制造质量和最终的使用效果造成不利影响。
因此,本文主要探讨了低压铸造铝合金车轮的主要缺陷及其控制方法。
二、低压铸造铝合金车轮的主要缺陷1. 表面缺陷表面缺陷是低压铸造铝合金车轮中最为常见的缺陷类型。
包括气孔、缩孔、砂眼等。
气孔通常是由于熔炼过程中气体未及时排出或排气系统设计不合理造成的;缩孔则是由于合金在凝固过程中体积收缩造成的;而砂眼则是由于模具表面杂质或砂粒未清理干净导致的。
2. 内部缺陷内部缺陷包括夹杂物、偏析等。
夹杂物主要是由于原材料中含有的杂质未被有效去除或熔炼过程中外部杂质进入;偏析则是由于合金在凝固过程中元素分布不均匀导致的。
3. 结构缺陷结构缺陷包括车轮尺寸偏差、形位误差等。
这些误差主要是由于模具设计制造不当或工艺参数控制不准确造成的。
三、控制措施1. 表面缺陷控制为减少表面缺陷,应优化熔炼工艺,确保气体及时排出;加强模具的清洁和保养,防止杂质进入;同时,合理设计排气系统,确保熔融金属中的气体能够顺利排出。
2. 内部缺陷控制为减少内部缺陷,应严格控制原材料的质量,去除原材料中的杂质;优化熔炼工艺,使合金元素分布均匀;同时,加强生产过程中的质量控制和检测。
3. 结构缺陷控制为减少结构缺陷,应提高模具的设计和制造精度,确保车轮的尺寸和形状符合要求;同时,严格控制工艺参数,如铸造压力、铸造温度等,以减少形位误差的产生。
四、结论低压铸造铝合金车轮的制造过程中,应注重对各种缺陷的预防和控制。
通过优化熔炼工艺、加强模具的清洁和保养、提高模具的设计和制造精度等措施,可以有效减少表面、内部和结构缺陷的产生。
同时,严格控制原材料的质量和生产过程中的质量控制与检测,也是确保产品质量的重要手段。
在未来的生产过程中,我们应继续探索和研究新的技术和方法,以提高铝合金车轮的生产质量和效率,满足市场的需求。
- 1、下载文档前请自行甄别文档内容的完整性,平台不提供额外的编辑、内容补充、找答案等附加服务。
- 2、"仅部分预览"的文档,不可在线预览部分如存在完整性等问题,可反馈申请退款(可完整预览的文档不适用该条件!)。
- 3、如文档侵犯您的权益,请联系客服反馈,我们会尽快为您处理(人工客服工作时间:9:00-18:30)。
铝合金轮毂铸造裂纹缺陷及预防
裂纹,铝合金轮毂铸造常见缺陷之一;它是产品失效的直接原因。
现场对裂纹的认知缺少,难以采取有效解决办法,本文主要介绍毛坯中主要裂纹缺陷。
低压铸造铝合金轮毂常见裂纹缺陷,按缺陷位置分可分为:内轮缘裂纹、外轮缘裂纹、冒口裂纹、胎圈座裂纹、轮辐夹角裂纹、螺栓孔裂纹等。
按裂纹冷热性质分可分为:热裂纹、冷裂纹,其中内外轮缘裂纹一般属于冷裂纹,它主要出现在成品车轮,由疲劳源产生裂纹。
以下将按照部位一一解释、
在解释毛坯裂纹之前,需先解释热裂与冷裂的定义及区别。
热裂的形成温度是在合金形成金属骨架,线收缩开始温度到固相线温度区内,这一温度区间称为“有效结晶温度区间”。
目前,关于热裂的形成机理主要有两种解释:强度理论和液膜理论。
强度理论认为:合金存在热脆区以及热脆区内合金的断裂应变低是产生热裂的重要原因,铸件内变形集中是热裂形成的必要条件;因此,合金凝固过程中,收缩受到外界阻碍时,如果产生的外应力超过合金的强度,则会有裂纹产生。
液膜理论认为:热裂的形成是由于铸件在凝固末期晶间存在液膜和铸件在凝固过程中受到拉应力共同作用的结果;如果铸件收缩受到阻碍,拉应力和变形主要集中在液膜上,使液膜被拉长,当应力足够大时,液膜开裂形成晶间裂纹。
目前比较主流的原因是:液膜的存在是形成热裂的主要原因,铸件收缩受阻是形成热裂的必要条件;主要集中作用于晶间液膜上,使液膜开裂。
冷裂是由于模具温度低,外表面将凝固成一个薄的固态壳层。
内部未凝固的金属液受压力直接作用于刚凝固的外表壳层上,使其受拉应力,而这个外表固态壳层是凝固时间不长、内部又受到高温液体加热的高温层,其边缘温度处在液固两相的临界温度上,根据液膜理论,从而使其形成裂纹源,在冷却过程中,受拉应力作用,不断生长,最终将成为裂纹
内外轮缘裂纹,严格来讲不属于铸造裂纹范畴;在铸造过程中内外轮缘作为产品延伸率最佳区域,极少出现铸造裂纹。
经常出现在汽车行驶几万公里后,主要成形原因为疲劳或外力作用开裂。
冒口裂纹,典型的热裂;一般由于冒口凝固不足,强度较低或冒口造型不佳造成起拔模力大产生拉裂。
典型状况为冒口内裂、冒口表层横向开裂、冒口内纵
向裂纹、机加后裂纹等,形状特征不一,产生原因各异。
可通过观察裂纹方向、裂纹颜色,结合轮型结构来判断产生原因及控制方法。
主要调整方向:增强冷却、修改造型、调整充型等。
胎圈座位置裂纹,属于铸造裂纹,发生于两块边模接缝处,主要形成原因有两点:第一点:边模夹铝。
残留铝片进入下一件毛坯,造成应力集中,产生裂纹源,该类裂纹在热处理后,机加工过程中容易发现;热处理过程释放应力及机加刀具切削力均会裂纹源扩大、产生明显裂纹。
目前防止此类缺陷主要靠加强筋解决,尤其冷却水盘位置所对的胎圈座。
第二点:边模冷却强度不足或毛坯冷却时间较短,强行起模造成应力过大开裂或热处理后开裂。
防范此类问题主要靠工艺调整和毛坯冷却时间控制。
轮辐夹角裂纹,多由于产品设计不合理、充型异常造成,一般为热裂,经常发生在铸造、热处理过程后。
按照裂纹原因可分为应力裂纹、氧化膜裂纹。
典型轮型夹角设计角度过小、筋部造型特殊,造成应力裂纹。
其中有一部分包含氧化膜裂纹,氧化膜裂纹,顾名思义,由氧化膜造成的裂纹,多数由于充型异常、铝液激射造成铝液翻滚产生大量氧化膜。
热处理过后,毛坯释放应力,裂纹现象较明显。
出现轮型较多,以偏距较小或法兰较小产品。
螺栓孔裂纹,位置多在螺栓孔靠近冒口一侧;形成原因较多,冷却强度不足、中心温度过高、氧化膜裂纹、拔模角度不合理、螺栓孔深度大等;铸造本序发生较少,多数发生在机加工过程中,尤其螺栓孔过深产品,切削应力造成应力开裂;另一部分为充型不当造成的氧化膜裂纹,伴随氧化裂纹而生的是中心气孔缺陷,裂纹产生原因复杂、多变,具体解决办法需根据裂纹形状、位置来判定,在此不在一一叙述,但一点比较普遍,毛坯裂纹多为温度高位置产生。
难以解决的裂纹主要是突发性裂纹,由于过程无法再现,难以判断。
另预防裂纹,除有效加强或降低冷却、加强筋、修改造型平衡应力之外,加强自检、过程控制保持最小变差亦为有效措施之一。