铸坯表面缺陷图谱及产生原因
板坯外观缺陷图谱
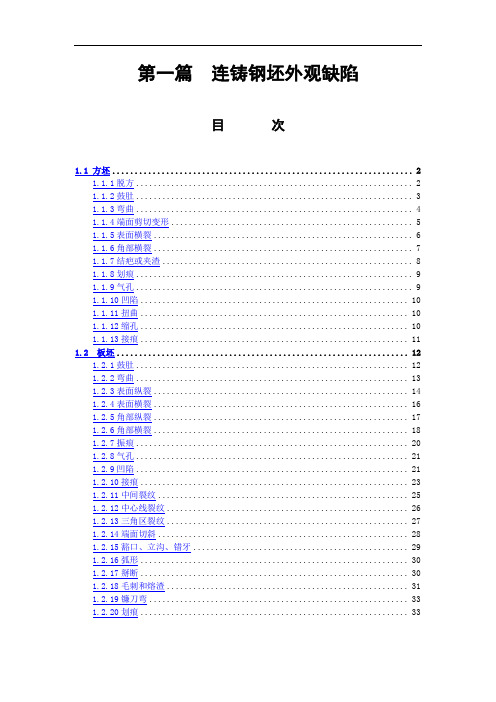
第一篇连铸钢坯外观缺陷目次1.1 方坯 (2)1.1.1脱方 (2)1.1.2鼓肚 (3)1.1.3弯曲 (4)1.1.4端面剪切变形 (5)1.1.5表面横裂 (6)1.1.6角部横裂 (7)1.1.7结疤或夹渣 (8)1.1.8划痕 (9)1.1.9气孔 (9)1.1.10凹陷 (10)1.1.11扭曲 (10)1.1.12缩孔 (10)1.1.13接痕 (11)1.2 板坯 (12)1.2.1鼓肚 (12)1.2.2弯曲 (13)1.2.3表面纵裂 (14)1.2.4表面横裂 (16)1.2.5角部纵裂 (17)1.2.6角部横裂 (18)1.2.7振痕 (20)1.2.8气孔 (21)1.2.9凹陷 (21)1.2.10接痕 (23)1.2.11中间裂纹 (25)1.2.12中心线裂纹 (26)1.2.13三角区裂纹 (27)1.2.14端面切斜 (28)1.2.15豁口、立沟、错牙 (29)1.2.16弧形 (30)1.2.17掰断 (30)1.2.18毛刺和熔渣 (31)1.2.19镰刀弯 (33)1.2.20划痕 (33)1.1 方坯1.1.1脱方英:Off square【定义与特征】脱方是方坯横截面上两个对角线不相等。
【原因分析】方坯结晶器内各边冷却不均匀,造成凝固壳厚度不均。
结晶器铜板水缝不均匀,铜板磨损不均匀,下口锥度过大,水口不对中。
【鉴别与判定】用量具测量铸坯横截面两个对角线的长度,如两对角线之差超出标准要求,做判废或改尺处理。
1.1.2鼓肚英:Protuberance【定义与特征】铸坯表面凝固壳受到钢水静压力的作用导致一个或几个表面鼓胀成凸面。
【原因分析】二冷喷嘴阻塞,水压不足或偏离;钢水过热度过高;拉速过快,冷却强度不足。
【鉴别与判定】用量具测量鼓肚量,如超出标准要求,做判废或改尺处理。
1.1.3弯曲英:Bending【定义与特征】弯曲是长度或宽度方向不平直。
【原因分析】在冷床上冷却不均匀;摆放不当。
铸坯表面缺陷图谱及产生原因
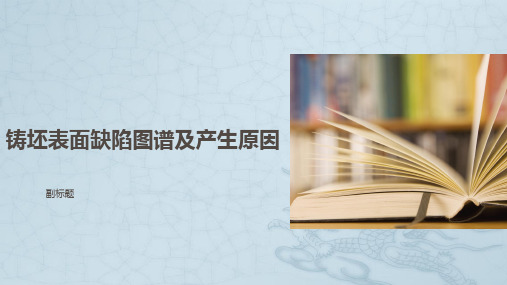
5.结 疤
1. 结晶器弯月面处初生坯壳生长不均匀,薄弱处与结晶器壁粘结后又在振动作用 下脱开形成;
2. 保护渣化渣效果差,润滑不均匀;
6.凹 陷
1. 边部凹陷原因为保护渣润滑效果差,另一原因为宽窄面冷却差异。 2. 中部凹陷原因为保护渣流入过大,减缓传热,使局部凝固坯壳变薄;
7.接 痕
1. 结晶器专家报警后拉速瞬间降至0.1m/min; 2. 浇注过程其他异常人为停机; 3. 开浇过程结晶器液面下跌。
8.夹 (卷渣)
1. 结晶器液面波动大,窄侧液面翻腾严重; 2. 水口插入深度过浅造成钢流股冲击液面; 3. 拉钢速度与水口内径不匹配,水口侧孔钢流速度过大,回流到达液面产生较大
切应力导致渣卷入。
9.角 部 掉 肉
1. 结晶器保护渣粘度大,液渣流入困难,润滑不良。
10.角 裂
1. 结晶器保护渣碱度小,坯壳冷却不均匀; 2. 铸坯角部冷却强度大。
3.纵 裂
1. 水口与结晶器不对中而产生偏流冲刷初生凝固坯壳; 2. 保护渣熔化性能不良、液渣层过厚或过薄; 3. 结晶器液面波动(液面波动≥±5㎜,纵裂发生几率≥30%); 4. 受钢种特性影响:钢中S>0.02%,P>0.017%,发生纵裂趋向增大;
4.横 裂
1. 振痕过深刻导致连铸坯横向裂开; 2. 钢中含A1、Nb,刻促使质点(A1N)、Nb(C,N)在晶界沉淀,诱发横裂纹; 3. 铸坯在第二脆性区间矫直; 4. 二次冷却太强。
谢谢各位的聆听
铸坯表面缺陷图谱及产生原因
副标题
1.保护渣压坑
1. 弯月面处保护渣润滑不良,坯壳较薄处积聚较多固体渣膜铸机内冲刷后产生; 2. 铸机辊面积渣深,浇注过程积渣压入坯壳后产生,此类渣坑有较强的规律性。
方坯铸坯缺陷产生原因及预防措施

方坯铸坯缺陷产生原因及预防措施1.前言由于连铸坯质量问题多发于连铸,因此对连铸质量缺陷进行了分析,总结出发生原因,以减少连铸坯质量问题的发生。
2.铸坯主要有以下几种缺陷:2.1卷渣2.1.1表面卷渣(见图1)2.1.2内部卷渣(见图2)图1 图22.2裂纹2.2.1表面裂纹:头部表面裂纹(图3 )、尾部表面裂纹(见4)。
图3 图42.2.2内部裂纹(见图5)图52.3气泡缺陷(见图6、见图7)图6 图73、缺陷产生原因及预防措施3.1卷渣产生原因及预防措施3.1.1表面卷渣产生原因及预防措施产生原因:(1)结晶器内形成渣条,当结晶器内钢液面波动量大于熔渣层厚度时、或挑渣条未挑净时、或在挑渣条过程中将渣条带入结晶器坯壳上时形成卷渣。
(2)在换包或等包降速过程中,由于操作不当造成中包液位较浅,导致中包内钢液形成涡流将中包渣卷进结晶器内,在上浮过程中被坯壳捕作形成卷渣。
(3)调整渣线高度超过液渣层厚度、或有渣条未挑净、等原因时造成颗粒渣被卷到坯壳上而形成卷渣。
(4)在开浇升速前液渣厚度未达到标准,造成颗粒渣或予熔层的保护渣直接与钢液接触,升速过程中在结晶器内造成钢液面发生波动,导致保护渣被卷入到坯壳上,形成卷渣。
(5)中包掉料或有杂物,开浇过程中被钢水冲到结晶器内,从而形成卷渣。
(6)中包内钢液面剧烈波动时,造成中包内覆盖剂被卷入中包钢液中,此时被卷入的覆盖剂受两个力作用:向上的钢水的浮力和向下的钢流股吸力作用,当向下的钢流股吸力大于向上钢水的上浮力时,卷入的覆盖剂就被卷入到结晶器内,在钢流流股的作用下,如被坯壳捕作而形成皮下卷渣,如被向下流股带入液相穴深处而形成内部卷渣。
(7)挑渣条用8#钢线(或细铁线),在钢线上结钢瘤或渣块,有钢瘤的8#线熔断到结晶器钢液内部,如被坯壳捕作到而形成皮下卷渣,如进入液相穴深处而形成内部卷渣。
(8)拉速波动,特别是在升速或降速过程,由于拉矫机电机转速发生变化,从而造成结晶器液面波动,从而形成渣条,形成的渣条被卷入结晶器坯壳上形成卷渣。
铸造缺陷特征原因及预防措施图文并茂
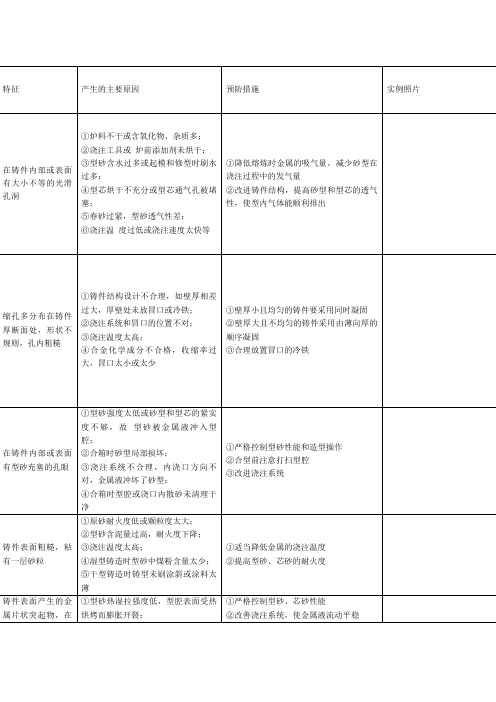
特征产生的主要原因预防措施实例照片在铸件内部或表面有大小不等的光滑孔洞①炉料不干或含氧化物、杂质多;②浇注工具或炉前添加剂未烘干;③型砂含水过多或起模和修型时刷水过多;④型芯烘干不充分或型芯通气孔被堵塞;⑤春砂过紧,型砂透气性差;⑥浇注温度过低或浇注速度太快等①降低熔炼时金属的吸气量,减少砂型在浇注过程中的发气量②改进铸件结构,提高砂型和型芯的透气性,使型内气体能顺利排出缩孔多分布在铸件厚断面处,形状不规则,孔内粗糙①铸件结构设计不合理,如壁厚相差过大,厚壁处未放冒口或冷铁;②浇注系统和冒口的位置不对;③浇注温度太高;④合金化学成分不合格,收缩率过大,冒口太小或太少①壁厚小且均匀的铸件要采用同时凝固②壁厚大且不均匀的铸件采用由薄向厚的顺序凝固③合理放置冒口的冷铁在铸件内部或表面有型砂充塞的孔眼①型砂强度太低或砂型和型芯的紧实度不够,故型砂被金属液冲入型腔;②合箱时砂型局部损坏;③浇注系统不合理,内浇口方向不对,金属液冲坏了砂型;④合箱时型腔或浇口内散砂未清理干净①严格控制型砂性能和造型操作②合型前注意打扫型腔③改进浇注系统铸件表面粗糙,粘有一层砂粒①原砂耐火度低或颗粒度太大;②型砂含泥量过高,耐火度下降;③浇注温度太高;④湿型铸造时型砂中煤粉含量太少;⑤干型铸造时铸型未刷涂斜或涂料太薄①适当降低金属的浇注温度②提高型砂、芯砂的耐火度铸件表面产生的金属片状突起物,在①型砂热湿拉强度低,型腔表面受热烘烤而膨胀开裂;①严格控制型砂、芯砂性能②改善浇注系统,使金属液流动平稳金属片状突起物与铸件之间夹有一层型砂②砂型局部紧实度过高,水分过多,水分烘干后型腔表面开裂;③浇注位置选择不当,型腔表面长时间受高温铁水烘烤而膨胀开裂;④浇注温度过高,浇注速度太慢③大平面铸件要倾斜浇注④适当调整浇注温度和浇注速度铸件沿分型面有相对位置错移①模样的上半模和下半模未对准;②合箱时,上下砂箱错位;③上下砂箱未夹紧或上箱未加足够压铁,浇注时产生错箱④砂箱或模板定位不准确,或定位销松动①定期检查砂箱、模板的定位销及销孔、并合理地安装;②定期对套箱整形,脱箱后的铸型在搬运时要小心。
连铸板坯缺陷图谱及产生的原因分析(新)

第二篇连铸板坯缺陷(AA)第二篇连铸板坯缺陷(AA) (1)2.1表面纵向裂纹(AA01) (4)2.2表面横裂纹(AA02) (6)2.3星状裂纹(AA03) (7)2.4角部横裂纹(AA04) (8)2.5角部纵裂纹(AA05) (10)2.6气孔(AA06) (11)2.7结疤(AA07) (12)2.8表面夹渣(AA08) (13)2.9划伤(AA09) (14)2.10接痕(AA13) (15)2.11鼓肚(AA11) (16)2.12脱方(AA10) (17)2.13弯曲(AA12) (18)2.14凹陷(AA14) (19)2.15镰刀弯(AA15) (20)2.16锥形(AA16) (21)2.17中心线裂纹(AA17) (22)2.18中心疏松(AA18) (23)2.19三角区裂纹(AA19) (25)2.20中心偏析(AA20) (27)2.21中间裂纹(AA21) (28)2.1表面纵向裂纹(AA01)图2-1-11、缺陷特征表面纵向裂纹沿浇注方向分布在连铸板坯上下表面,裂纹深度一般为2mm~15mm,裂纹部位伴有轻微凹陷。
在连铸浇注过程中,当连铸板坯坯壳在结晶器内所受到的应力超过了坯壳所能承受的抗拉强度时,即产生表面纵向裂纹。
表面纵向裂纹缺陷在结晶器内产生,出结晶器后若二次冷却不良,裂纹将进一步加剧。
2、产生原因及危害产生原因:①钢中碳含量处于裂纹敏感区内;②结晶器钢水液面异常波动。
当结晶器钢水液面波动超过10mm时,表面纵向裂纹缺陷易于产生;③结晶器保护渣性能不良。
保护渣液渣层过厚、过薄或渣膜厚薄不均,使连铸板坯凝固壳局部过薄而产生表面纵向裂纹;④中间包浸入式水口与结晶器对中不良,钢水产生偏流冲刷连铸板坯凝固壳,而产生表面纵向裂纹。
危害:轻微的表面纵裂纹经火焰清理后均能消除;表面纵向裂纹严重时可能会造成漏钢;表面纵向裂纹若送热轧进行轧制可能导致热轧产品出现分层、开裂缺陷。
国际铸造缺陷图谱--给学生

铸件缺陷分析与铸件质量保证(国际铸造缺陷图谱)铸造教研室一、铸件缺陷分析铸件缺陷是在铸造生产过程中,由于种种原因,在铸件表面和内部产生的各种缺陷的总称。
铸件缺陷是导致性能低下,使用寿命短、报废和失效的重要原因。
分析铸件的形貌、特点、产生原因和形成过程,目的是防止、减少和消除铸件缺陷。
消除或减少铸件缺陷是铸件质量控制的重要组成部分。
二、铸件缺陷种类铸件缺陷种类繁多,形貌各异,各国分类方法不统一。
我国国家标准GB/T5611-1998《铸造术语》将铸件缺陷分为八类:1.多肉类缺陷:铸件表面各种多肉类缺陷总称。
2.孔洞类缺陷:是铸件表面和内部产生的不同大小、形状的孔洞类缺陷的总称。
3.裂纹、冷隔类缺陷。
4.表面缺陷,是铸件表面产生的各类缺陷的总称。
5.残缺类缺陷:是铸件由于各种原因造成的外形缺损缺陷的总称。
6.形状及重量差错类缺陷:铸件的形状、尺寸、重量和铸件图样或技术条件的规定不符合。
7.夹杂类缺陷:是铸件中各种金属和非金属夹杂物的总称。
8.性能、成分、组织不合格:铸件由于化学成分不符合铸件技术条件的要求,或由于熔炼、金属液处理、铸造、热处理工艺不当,导致显微组织异常,物理性能或力学性能不合格。
三、铸件挽救铸件上的某些缺陷,如气孔、夹渣、夹砂、裂纹、冷隔、渗漏等,如果超过有关标准、验收文件或订货协议中所允许的范围,可以按规定进行修复。
经修复、检验,确认合格的铸件,不应列入废品。
四、铸件的品质(质量)等级JB/JQ82001-1990《铸件分等通则》规定了铸件的品质(质量)原则,品质(质量)等级、品质(质量)检测方法和评定方法。
它是铸件品质(质量)考核、分等定级的依据,亦是评定企业等级的重要依据。
连铸方坯缺陷图谱PDF

伤划 8
9
。理处废判作陷缺方脱重严对 �量测尺卡用�查检眼肉用 理处查检 。匀、勤、少应入加渣护保�6� 。好良中对口水式入浸证保�5� 。却冷匀均面个四坯铸区冷二证保�嘴喷理清时及�4� 。塞堵物异被缝水止防�质水水却冷器晶结高提�3� 。匀均度厚缝水面四证保�形变不�量质砌修器晶结证保�2� 。器晶结换更时及�1� 法方除消及防预 。型孔入咬能不或叠折生产会能可部角时制轧在�钢堆生发会能可时钢推内炉热加钢轧在�时 mm01 �7�b�a 当即�大过方。钢漏成造会重严方脱。纹裂线角对生产位部角钝在会度程定一到方脱 。均不度厚膜渣器晶结�6� 。中对不口水式入浸�5� 。匀均不却冷面个四坯铸区冷二�塞堵嘴喷�4� 。匀均不却冷壳坯�塞堵物异被缝水器晶结�3� 。匀均不却冷壳坯�匀均不度厚缝水面四器晶结�2� 。匀均不却冷壳坯�化老器晶结�1� 害危及因成 。方脱为称时等相不度长线角对个两上面截横坯方当 观外与义定
渣夹面表 6
7
。废判接直格合不理清�理清焰火行进须必 �查检眼肉用 理处查检 。弧对格严段却冷次二与口出器晶结�3� 。 �力用作械机的间之器晶结与坯铸低降�滑润高提�能性化理的渣护保器晶结整调�2� 。数参动振器晶结化优�率脱滑负低降�1� 法方除消及防预 。象现块掉及疤结现出上材轧�合焊能不纹 裂中程过制轧来带这。杂夹铁化氧成形�化氧被下温高在纹裂�纹裂观微的量大着布分部谷下痕振 。良不弧对段却冷次二与口出器晶结�4� 。结粘壁铜与壳坯�良不滑润器晶结�3� 。当不数参动振器晶结�2� 。迹痕 叠折成形面表在固凝刻立水钢的出漏处裂撕在�冷强器晶结于由�裂撕壳固凝使挂悬内器晶结�1� 害危及因成 。纹裂向横有时重严�迹痕叠折的 向横有面表坯铸在�象现结搭现出时重严�在存纹裂小微有下皮�渣粘、皱起面表坯铸、凸外痕振 观外与义定
连铸方坯缺陷图谱PDF

�4� 保证结晶器钢水流动合理性 ◆结晶器液面波动±3�±5mm ◆水口对中 ◆合适的水口插 入深度。
�5� �6�
�7�
保证结晶器初始坯壳均匀生长 ◆合适结晶器锥度◆结晶器弱冷◆热顶结晶器。 合适的结晶器振动 ◆合适的负滑脱值 ◆合适的频率和振幅 ◆振动偏差�纵向、横向� 0.2mm�。 良好的连铸机设备状况�保证出结晶器铸坯运行良好 ◆结晶器与零段、二冷区上部对弧要 准 ◆冷却均匀性良好。
锥度不合适��7�结晶器钢液流动 ◆水口不对中�◆水口插入深度不合适。�8�结晶器振动 ◆振痕深�
◆负滑脱时间增大。
裂纹严重时会造成漏钢和钢坯废品。
预防及消除方法
防止纵裂纹产生的根本措施就是使结晶器弯月面区域坯壳厚度均匀生长。
�1� �2� �3�
尽量降低钢中[S]、[P]含量�提高 Mn/S。 合适的拉坯速度。 合适的保护渣 ◆ η·ν=2�4 ◆液渣层厚度 10�15mm ◆高结晶温度的保护渣 ◆均匀 渣膜厚度�150μm/0.3�0.5kg/m2�。
1.表面纵裂纹
连铸方坯缺陷图谱
定义与外观
沿拉坯方向�铸坯表面中心位置附近产生的裂纹�裂纹长 10�1500mm�宽 0.1�3.5mm�深�5mm。 成因及危害
在结晶器弯月面区�钢液面下 170mm�左右�钢液凝固在固相线以下发生δ→γ转变�导致凝固 厚度生产的不均匀性�由于热收缩使坯壳产生应力梯度�在薄弱处产生应力集中�坯壳在表面形成纵向
4
5.星状裂纹
定义与外观 裂纹位于铸坯表面常被 FeO 覆盖�经酸洗后才能被发现�表面之�结晶器弯月面区凝固壳厚度不均匀性是产生表面纵裂纹的根本原因�
在二冷区铸坯裂纹进一步扩展。导致表面纵裂纹指数增加的因素有��1�钢水成分 ◆[S]�0.020%�[P]
钢坯常见缺陷图谱PPT课件

20
多发生在小方坯,主要由于两架轧机的对中性不好造成的。
21
因为轧制原因造成。
22
主要是由压缩比不够,造成的。
23
部分合金钢由于硬度比较高,在火焰切割后由于受热而产 生应力使得端部切割后产生裂缝。
24
主要在轧制过程中产生的,孔型对中不好。
25
此为带锯锯切的端面不平整,主要发生在钢种比较硬,或钢坯厚度比较厚,
常见缺陷图谱
板、方、管区域精整的坯料中存在的缺 陷种类很多,具有一定的特点,下面对钢坯 存在的缺陷的形状和部分产生原因进行介绍
1
形成原因:多为角裂的扩展
2
钢锭浇注凝固时,发生体积收缩,先凝固部分的体积收缩可由尚未凝固的钢液 补充,当钢液由外向内,由下向上冷却的过程中,在铸锭上部中间最后凝固的 部分,因得不到钢液的补充,集中形成了倒圆锥形的收缩孔洞,称为缩孔。这 3 里主要因为剪切不够,在剪切端面上的缩孔。
某些钢坯需要进行热火焰清理,表面会产生点火坑的深度比较深,影
响外观和用户使用。在精整用火焰枪清理的过程中也会产生点火坑超
13
标。
此缺陷因为均热炉夹钳吊的夹钳印在轧制后形成的缺陷
14
此缺陷主要因轧机的翻钢钩引起 的表面压痕,为与钢坯长度方向 平行的纵向缺陷。
此缺陷主要由推钢机滑块突出造 成。
15
缝缺陷在精整为最常见缺陷之一,小方坯可以用磁粉探伤设备进行探测,在板坯目前
使用肉眼进行人工检查标记。
6
形成原因:可能为钢锭浇铸时钢水飞溅,致使飞溅钢水无法与钢锭本身融合,形成 结疤,也有可能为钢材料加热表面产生厚氧化铁皮,轧制时嵌入钢材表面,形成结 疤。此类缺陷在头部发生的情况比较多。
7
多发生在小方坯,主要因为原料角部尖锐,在轧制的过程中角部
铸坯缺陷图谱及预防
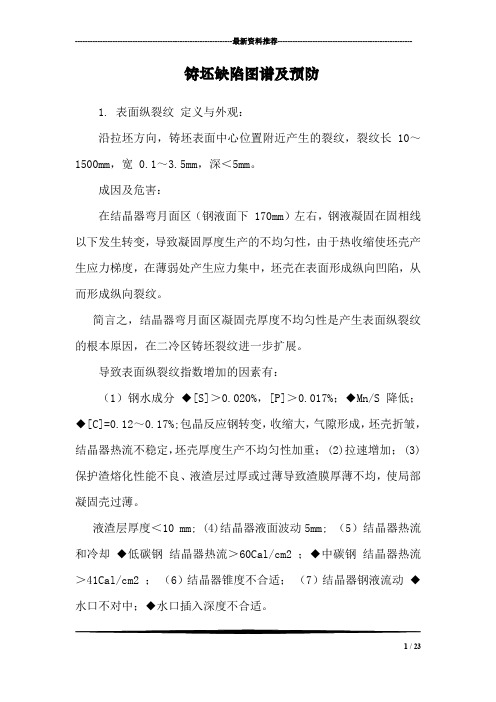
---------------------------------------------------------------最新资料推荐------------------------------------------------------铸坯缺陷图谱及预防1. 表面纵裂纹定义与外观:沿拉坯方向,铸坯表面中心位置附近产生的裂纹,裂纹长 10~1500mm,宽 0.1~3.5mm,深<5mm。
成因及危害:在结晶器弯月面区(钢液面下 170mm)左右,钢液凝固在固相线以下发生转变,导致凝固厚度生产的不均匀性,由于热收缩使坯壳产生应力梯度,在薄弱处产生应力集中,坯壳在表面形成纵向凹陷,从而形成纵向裂纹。
简言之,结晶器弯月面区凝固壳厚度不均匀性是产生表面纵裂纹的根本原因,在二冷区铸坯裂纹进一步扩展。
导致表面纵裂纹指数增加的因素有:(1)钢水成分◆[S]>0.020%,[P]>0.017%;◆Mn/S 降低;◆[C]=0.12~0.17%;包晶反应钢转变,收缩大,气隙形成,坯壳折皱,结晶器热流不稳定,坯壳厚度生产不均匀性加重; (2)拉速增加; (3)保护渣熔化性能不良、液渣层过厚或过薄导致渣膜厚薄不均,使局部凝固壳过薄。
液渣层厚度<10 mm; (4)结晶器液面波动5mm; (5)结晶器热流和冷却◆低碳钢结晶器热流>60Cal/cm2 ;◆中碳钢结晶器热流>41Cal/cm2 ;(6)结晶器锥度不合适;(7)结晶器钢液流动◆水口不对中;◆水口插入深度不合适。
1 / 23(8)结晶器振动◆振痕深;◆负滑脱时间增大。
裂纹严重时会造成漏钢和钢坯废品。
预防及消除方法:防止纵裂纹产生的根本措施就是使结晶器弯月面区域坯壳厚度均匀生长。
(1)尽量降低钢中[S]、[P]含量,提高 Mn/S。
(2)合适的拉坯速度。
(3)合适的保护渣◆ =2~4 ◆液渣层厚度 10~15mm ◆高结晶温度的保护渣◆均匀渣膜厚度(150m/0.3~0.5kg/m2 )。
铸造缺陷特征、原因及预防措施(图文并茂)

缺陷名称特征产生的主要原因预防措施实例照片气孔在铸件内部或表面有大小不等的光滑孔洞①炉料不干或含氧化物、杂质多;②浇注工具或炉前添加剂未烘干;③型砂含水过多或起模和修型时刷水过多;④型芯烘干不充分或型芯通气孔被堵塞;⑤春砂过紧,型砂透气性差;⑥浇注温度过低或浇注速度太快等①降低熔炼时金属的吸气量,减少砂型在浇注过程中的发气量②改进铸件结构,提高砂型和型芯的透气性,使型内气体能顺利排出缩孔与缩松缩孔多分布在铸件厚断面处,形状不规则,孔内粗糙①铸件结构设计不合理,如壁厚相差过大,厚壁处未放冒口或冷铁;②浇注系统和冒口的位置不对;③浇注温度太高;④合金化学成分不合格,收缩率过大,冒口太小或太少①壁厚小且均匀的铸件要采用同时凝固②壁厚大且不均匀的铸件采用由薄向厚的顺序凝固③合理放置冒口的冷铁编辑版word砂眼在铸件内部或表面有型砂充塞的孔眼①型砂强度太低或砂型和型芯的紧实度不够,故型砂被金属液冲入型腔;②合箱时砂型局部损坏;③浇注系统不合理,内浇口方向不对,金属液冲坏了砂型;④合箱时型腔或浇口内散砂未清理干净①严格控制型砂性能和造型操作②合型前注意打扫型腔③改进浇注系统粘砂铸件表面粗糙,粘有一层砂粒①原砂耐火度低或颗粒度太大;②型砂含泥量过高,耐火度下降;③浇注温度太高;④湿型铸造时型砂中煤粉含量太少;⑤干型铸造时铸型未刷涂斜或涂料太薄①适当降低金属的浇注温度②提高型砂、芯砂的耐火度夹砂铸件表面产生的金属片状突起物,在金属片状突起物与铸件之间夹有一层型砂①型砂热湿拉强度低,型腔表面受热烘烤而膨胀开裂;②砂型局部紧实度过高,水分过多,水分烘干后型腔表面开裂;③浇注位置选择不当,型腔表面长时间受高温铁水烘烤而膨胀开裂;④浇注温度过高,浇注速度太慢①严格控制型砂、芯砂性能②改善浇注系统,使金属液流动平稳③大平面铸件要倾斜浇注④适当调整浇注温度和浇注速度编辑版word错型铸件沿分型面有相对位置错移①模样的上半模和下半模未对准;②合箱时,上下砂箱错位;③上下砂箱未夹紧或上箱未加足够压铁,浇注时产生错箱④砂箱或模板定位不准确,或定位销松动①定期检查砂箱、模板的定位销及销孔、并合理地安装;②定期对套箱整形,脱箱后的铸型在搬运时要小心。
板坯外观缺陷图谱
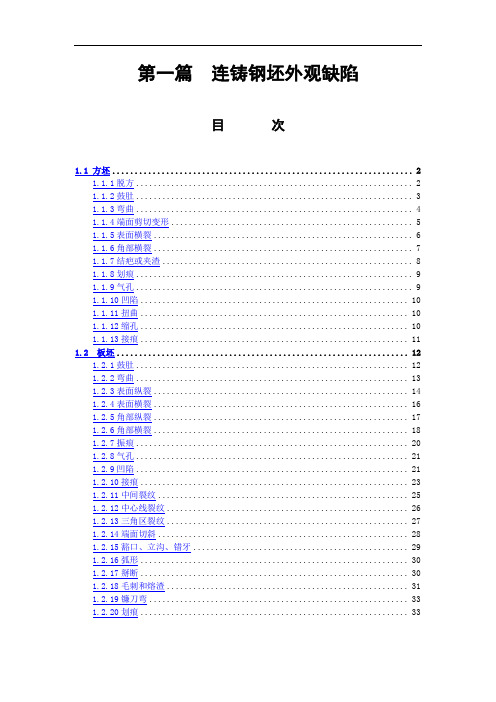
第一篇连铸钢坯外观缺陷目次1.1 方坯 (2)1.1.1脱方 (2)1.1.2鼓肚 (3)1.1.3弯曲 (4)1.1.4端面剪切变形 (5)1.1.5表面横裂 (6)1.1.6角部横裂 (7)1.1.7结疤或夹渣 (8)1.1.8划痕 (9)1.1.9气孔 (9)1.1.10凹陷 (10)1.1.11扭曲 (10)1.1.12缩孔 (10)1.1.13接痕 (11)1.2 板坯 (12)1.2.1鼓肚 (12)1.2.2弯曲 (13)1.2.3表面纵裂 (14)1.2.4表面横裂 (16)1.2.5角部纵裂 (17)1.2.6角部横裂 (18)1.2.7振痕 (20)1.2.8气孔 (21)1.2.9凹陷 (21)1.2.10接痕 (23)1.2.11中间裂纹 (25)1.2.12中心线裂纹 (26)1.2.13三角区裂纹 (27)1.2.14端面切斜 (28)1.2.15豁口、立沟、错牙 (29)1.2.16弧形 (30)1.2.17掰断 (30)1.2.18毛刺和熔渣 (31)1.2.19镰刀弯 (33)1.2.20划痕 (33)1.1 方坯1.1.1脱方英:Off square【定义与特征】脱方是方坯横截面上两个对角线不相等。
【原因分析】方坯结晶器内各边冷却不均匀,造成凝固壳厚度不均。
结晶器铜板水缝不均匀,铜板磨损不均匀,下口锥度过大,水口不对中。
【鉴别与判定】用量具测量铸坯横截面两个对角线的长度,如两对角线之差超出标准要求,做判废或改尺处理。
1.1.2鼓肚英:Protuberance【定义与特征】铸坯表面凝固壳受到钢水静压力的作用导致一个或几个表面鼓胀成凸面。
【原因分析】二冷喷嘴阻塞,水压不足或偏离;钢水过热度过高;拉速过快,冷却强度不足。
【鉴别与判定】用量具测量鼓肚量,如超出标准要求,做判废或改尺处理。
1.1.3弯曲英:Bending【定义与特征】弯曲是长度或宽度方向不平直。
【原因分析】在冷床上冷却不均匀;摆放不当。
- 1、下载文档前请自行甄别文档内容的完整性,平台不提供额外的编辑、内容补充、找答案等附加服务。
- 2、"仅部分预览"的文档,不可在线预览部分如存在完整性等问题,可反馈申请退款(可完整预览的文档不适用该条件!)。
- 3、如文档侵犯您的权益,请联系客服反馈,我们会尽快为您处理(人工客服工作时间:9:00-18:30)。
1.
弯月面处保护渣润滑不良,坯壳较薄处积聚较多固体渣膜铸机内冲刷后产生;
2.
铸机辊面积渣深,浇注过程积渣压入坯壳后产生,此类渣坑有较强的规律性。
2.振痕紊乱、深振痕
1. 振动参数设计不合理,负滑脱时间长,振幅较大可导致振痕深;
2. 结晶器液面波动大,波动≥± 3mm;
3. 初生坯壳冷却不均,保护渣润滑不稳。
切应力导致渣卷入。
9.角 部 掉 肉
1.
结晶器保护渣粘度大,液渣流入困难,润滑不良。
10.角 裂
匀;
2.
铸坯角部冷却强度大。
7.接 痕
1. 2. 3.
结晶器专家报警后拉速瞬间降至0.1m/min; 浇注过程其他异常人为停机; 开浇过程结晶器液面下跌。
8.夹 渣(卷渣)
1. 2.
结晶器液面波动大,窄侧液面翻腾严重; 水口插入深度过浅造成钢流股冲击液面;
3.
拉钢速度与水口内径不匹配,水口侧孔钢流速度过大,回流到达液面产生较大
3.纵 裂
1.
水口与结晶器不对中而产生偏流冲刷初生凝固坯壳;
2.
3. 4.
保护渣熔化性能不良、液渣层过厚或过薄;
结晶器液面波动(液面波动≥± 5㎜,纵裂发生几率≥30%); 受钢种特性影响:钢中S>0.02%,P>0.017%,发生纵裂趋向增大;
4.横 裂
1. 振痕过深刻导致连铸坯横向裂开; 2. 钢中含A1、Nb,刻促使质点(A1N)、Nb(C,N)在晶界沉淀,诱发横裂纹;
3. 铸坯在第二脆性区间矫直;
4. 二次冷却太强。
5.结 疤
1.
结晶器弯月面处初生坯壳生长不均匀,薄弱处与结晶器壁粘结后又在振动作用
下脱开形成;
2. 保护渣化渣效果差,润滑不均匀;
6.凹 陷
1.
边部凹陷原因为保护渣润滑效果差,另一原因为宽窄面冷却差异。
2.
中部凹陷原因为保护渣流入过大,减缓传热,使局部凝固坯壳变薄;