数控雕刻机治具加工实例
20多种雕刻机做橱柜门铣型刀具及加工效果,再也不用到处找了

20多种雕刻机做橱柜门铣型刀具及加工效果,再也不用到处找了首先从橱柜门、衣柜门的生产工艺说起。
现在用来做橱柜门、衣柜门所用的材质主要有密度板、刨花板、三聚氰胺板及实木板等板材。
根据所用材质给工艺分类有以下几个:橱柜门、衣柜门生产工艺一:造型(雕刻)、抛光、覆膜这条生产工艺主要是针对密度板、刨花板这种板材的,那么他所需要的设备主要有:数控雕刻机:数控开料机主要是用来造型,也就是雕刻。
木工橱柜门雕刻可以说是橱柜门凸显档次和产品销量的关键步骤,现在市场上雕刻设备的刀具头数对雕刻步骤的效率影响很大,普通木工雕刻机可以进行简单的线条雕刻,但是复杂的图形需要用到2把以上的刻刀,那么普通木工雕刻机就无能为力,这时可以选择多工序木工雕刻机或者一步到位直接选择上木工加工中心。
多工序雕刻机可以自动换刀比人工换刀雕刻的精度要高,速度也更快,适合5把刀以下的雕刻图形,如果需要5把以上的图形雕刻那么最好是选择木工加工中心,标配刀库是8把,省心省力,适合任何高级图形的雕刻。
全自动砂光机:全自动砂光机主要是用来抛光。
原来橱柜门、衣柜门造型以后表面不是特别光滑,会有毛刺等影响板材表面的光滑度,所以会使用砂光机抛光。
但是现在我们所生产的数控雕刻机加工出来的表面还是非常不错的,只有少量毛刺。
所以一般产量不高的情况下不建议选用砂光机,手动抛光就可以。
橱柜门、衣柜门生产工艺二:造型(雕刻)、烤漆主要是针对烤漆门,他只需要数控雕刻机雕刻就可以,然后烤漆。
所以这条生产线只需要数控雕刻机就可以。
橱柜门、衣柜门生产工艺三:封边像三聚氰胺板表面是经过加工的,所以只需要封边机进行封边就可以。
现在我们给大家带来的是20多种常用橱柜门铣型刀具详细尺寸及加工效果。
数控加工技术学习中的实际应用案例分享

数控加工技术学习中的实际应用案例分享随着科技的不断发展,数控加工技术在各个行业中得到了广泛的应用。
作为一种高效、精确的加工方式,数控加工技术在机械制造、航空航天、汽车制造等领域发挥着重要的作用。
在学习数控加工技术的过程中,实际应用案例的分享对于学习者来说是非常有价值的。
本文将分享几个实际应用案例,帮助读者更好地理解和掌握数控加工技术。
案例一:汽车零部件加工在汽车制造过程中,数控加工技术被广泛应用于零部件的加工。
以发动机缸体为例,传统的加工方式需要多道工序,耗时且精度难以保证。
而采用数控加工技术,可以通过预先编写加工程序,将加工路径和刀具轨迹精确控制,大大提高了加工效率和精度。
同时,数控加工技术还可以实现复杂形状的加工,如内腔、倒角等,满足了汽车零部件对于精度和质量的要求。
案例二:航空航天零部件制造在航空航天领域,数控加工技术是不可或缺的。
航空航天零部件通常具有复杂的形状和高精度的要求,传统的加工方式往往难以满足需求。
而数控加工技术通过高速、高精度的切削,可以实现复杂零部件的加工。
例如,飞机发动机叶片的制造,采用数控加工技术可以精确控制叶片的形状和尺寸,提高了叶片的工作效率和可靠性。
案例三:电子产品外壳加工在电子产品制造中,外壳的加工是一个重要环节。
传统的加工方式往往需要多道工序,效率低下且不易控制。
而数控加工技术可以通过编写加工程序,一次性完成外壳的加工,大大提高了加工效率。
同时,数控加工技术还可以实现复杂形状的加工,如圆弧、凹凸等,使得外壳的外观更加美观。
此外,数控加工技术还可以通过刀具的自动更换,实现不同型号外壳的加工,提高了生产的灵活性。
案例四:模具制造在模具制造中,数控加工技术是必不可少的工具。
模具通常具有复杂的形状和高精度的要求,传统的加工方式往往难以满足需求。
而数控加工技术通过高速、高精度的切削,可以实现复杂模具的加工。
例如,塑料注塑模具的制造,采用数控加工技术可以精确控制模具的形状和尺寸,提高了塑料制品的质量和生产效率。
五轴数控编程加工案例.docx

、尸■、■前言当前模具制造行业中,三轴数控加工技术已经普遍应用并且相对成熟,但随着五轴数控技术的发展与推进,先进的五轴数控加工技术在市场上体现出了明显的优越性,故而引进五轴数控加工技术,建立一个高效率、高质量、短周期、低成本的产品生产框架来适应市场的发展,以求在市场竞争中立于不败之地已经成为我们必须面对的问题。
近段时间,珠海某大型电器模具厂采购我司的五轴数控编程软件PowerMILL,本人接受公司的任务,为该客户进行五轴技术的培训辅导,并结合实际加工进行模具的试切,实例指导客户应用五轴加工技术,让客户看到了客观具体的三轴加工与五轴加工两者的效率和质量对比数据。
本文即以此次培训五轴工件试切为例,禅述在电器注塑模具加工当中,五轴数控加工技术相对于传统的三轴数控加工技术的若干优越性。
一、五轴数控加工技术简述1、五轴刀轴和五轴刀轴控制五轴是由 3 个线性轴(Linear axis) 加上 2 个旋转轴(Rotary axis) 组成。
五轴刀轴控制是CAM系统五轴技术的核心。
五轴CAM系统计算出每个切削点刀具的刀位点(X,Y,Z)和刀轴矢量(l,J,K),五轴后处理器将刀轴矢量(I,J,K) 转化为不同机床的旋转轴所需要转动的角度(A,B,C) 其中的两个角度;然后计算出考虑了刀轴旋转之后线性移动的各轴位移(X,Y,Z)。
2、五轴机床类型按两旋转轴的运动位置结构来划分,可分为Table-Table 、Head-Head、Table-Head 三种类型。
1)Table-Table :此类型机床主轴方向不动,两个旋转轴均分布在工作平台上;工件加工时旋转轴随工作台旋转,加工时必须考虑装夹承重,可加工的工件尺寸比较小。
2)Head-Head此类机床工作台不动,两个旋转轴均在主轴上。
机床可加工的工件尺寸比较大。
3)Table-Head :此类机床的两个旋转轴分别处于主轴和工作台上,工作台可以旋转,可装夹尺寸较大的工件;主轴可摆动,改变刀轴方向灵活。
数控车削加工编程及实例模板
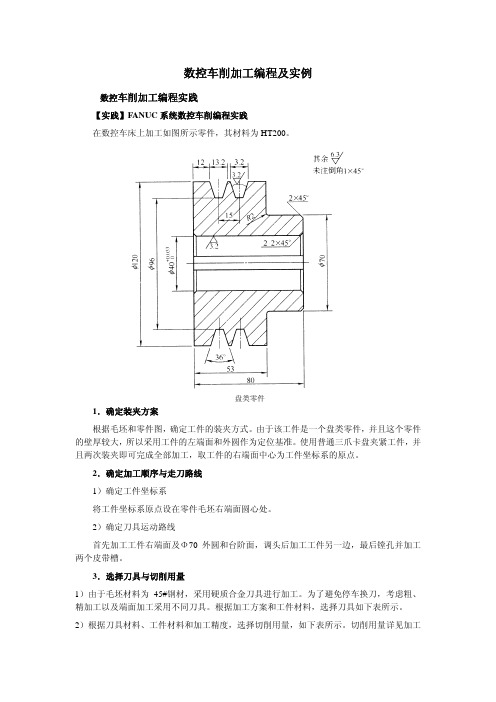
数控车削加工编程及实例数控车削加工编程实践【实践】FANUC系统数控车削编程实践在数控车床上加工如图所示零件,其材料为HT200。
盘类零件1.确定装夹方案根据毛坯和零件图,确定工件的装夹方式。
由于该工件是一个盘类零件,并且这个零件的壁厚较大,所以采用工件的左端面和外圆作为定位基准。
使用普通三爪卡盘夹紧工件,并且两次装夹即可完成全部加工,取工件的右端面中心为工件坐标系的原点。
2.确定加工顺序与走刀路线1)确定工件坐标系将工件坐标系原点设在零件毛坯右端面圆心处。
2)确定刀具运动路线首先加工工件右端面及Φ70外圆和台阶面,调头后加工工件另一边,最后镗孔并加工两个皮带槽。
3.选择刀具与切削用量1)由于毛坯材料为45#钢材,采用硬质合金刀具进行加工。
为了避免停车换刀,考虑粗、精加工以及端面加工采用不同刀具。
根据加工方案和工件材料,选择刀具如下表所示。
2)根据刀具材料、工件材料和加工精度,选择切削用量,如下表所示。
切削用量详见加工程序。
表数控加工工艺卡4.编制程序根据所用机床的数控系统和工艺设计编制加工程序,最后粗精加工程序如下表所示。
表程序编制表设备数控车床系统 FAUNC 零件号程序注释N10 M03 S400 T0101 N20 G00 X121 Z6N30 G01 X-55 F0.15 X122N40 G00 Z1N50 G01 X30 F0.15 加工零件左端的主程序设定工件坐标系,选择外圆车刀 粗车零件外圆,端面Z0N60 M03 S500N70 G01 X120 F0.05 Z-55N80 G00 X150 Z200 N90 T0303 S300 M03 N100 G00 Z4X39.4N110 G01 X-82 F0.1 X39 F0.5N120 G00 Z4X44N130 S400 M03N140 G01 Z0 F0.05X40.01 Z-2Z-82X39N150 G00 Z200X150N160 T0202N170 G00 X121Z-18.752N180 G01 X96 F0.1Z-21.113N190 G01 X121Z-33.752N200 G01 X96Z-36.113N210 G00 X150 精车外圆、端面,主轴转速500r/min退至换刀点换镗孔刀粗镗内孔精镗内孔换皮带槽刀加工两个皮带槽退至换刀点X200 N220 M05 M30主轴停转,主程序结束【实践】FANUC系统数控车削编程实践在数控车床上加工如图所示零件,毛坯为Φ60mm ×95mm 。
数控铣床典型零件加工实例图文稿
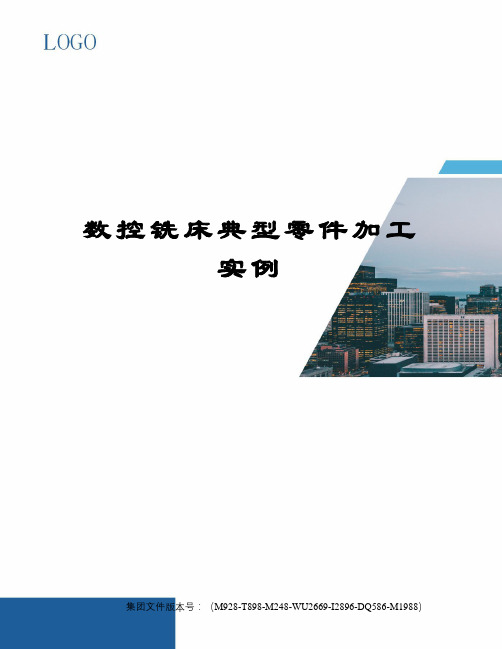
数控铣床典型零件加工实例集团文件版本号:(M928-T898-M248-WU2669-I2896-DQ586-M1988)模块五 数控铣床典型零件加工实例本单元从综合数控技术的实际应用出发,列举了典型数控铣削编程实例,如果希望掌握这门技术,就应该仔细的理解和消化它,相信有着举一反三的效果。
一、数控铣床加工实例1——槽类零件 毛坯为70㎜×70㎜×18㎜板材,六面已粗加工过,要求数控铣出如图2-179所示的槽,工件材料为45钢。
图2-179 凹槽工件1.根据图样要求、毛坯及前道工序加工情况,确定工艺方案及加工路线1)以已加工过的底面为定位基准,用通用机用平口虎钳夹紧工件前后两侧面,虎钳固定于铣床工作台上。
2)工步顺序① 铣刀先走两个圆轨迹,再用左刀具半径补偿加工50㎜×50㎜四角倒圆的正方形。
② 每次切深为2㎜,分二次加工完。
2.选择机床设备根据零件图样要求,选用经济型数控铣床即可达到要求。
3.选择刀具现采用φ10㎜的平底立铣刀,定义为T01,并把该刀具的直径输入刀具参数表中。
4.确定切削用量切削用量的具体数值应根据机床性能、相关的手册并结合实际经验确定,详见加工程序。
5.确定工件坐标系和对刀点在XOY 平面内确定以工件中心为工件原点,Z 方向以工件上表面为工件原点,建立工件坐标系,如图2-118所示。
采用手动对刀方法(操作与前面介绍的数控铣床对刀方法相同)把点O 作为对刀点。
学习目标知识目标: ●学会对工艺知识、编程知识、操作知识的综合运用 能力目标: ●能够对适合铣削的典型零件进行工艺分析、程序编制、实际加工。
6.编写程序考虑到加工图示的槽,深为4㎜,每次切深为2㎜,分二次加工完。
为编程方便,同时减少指令条数,可采用子程序。
该工件的加工程序如下:O0001; 主程序N0010 G90 G00 Z2. S800 T01 M03;N0020 X15.Y0 M08;N0030 G01 Z-2. F80;N0040 M98 P0010; 调一次子程序,槽深为2㎜N0050 G01 Z-4.F80;N0060 M98 P0010; 再调一次子程序,槽深为4mmN0070 G00 Z2.N0080 G00 X0 Y0 Z150. M09;N0090M02 主程序结束O0010 子程序N0010G03 X15. Y0 I-15.J0;N0020 G01 X20.;N0030 G03 X20. YO I-20. J0;N0040 G41 G01 X25. Y15.;左刀补铣四角倒圆的正方形N0050 G03 X15. Y25. I-10. J0;N0060G01 X-15.;N0070 G03 X-25. Y15. I0 J-10.;N0080G01 Y-15.N0090 G03 X-15. Y-25. I10. J0;N0100 G01 X15.;N0110 G03 X25. Y-15. I0 J10.;N0120 G01 Y0;N0130 G40 G01 X15. Y0; 左刀补取消N0140 M99; 子程序结束7.程序的输入(参见模块四具体操作步骤)8.试运行(参见模块四具体操作步骤)9.对刀(参见模块四具体操作步骤)10.加工选择“自动方式”,按“启动”开始加工。
数控车加工案例分析

进行分析该零件先用 :1$ 进行粗加工选用 '% 度外圆车 刀切除多余余料和端面再用 :1( 进行精加工根据零件的 形状选定尖刀加工圆弧先加工大端 然后夹持住大端再 加工小端 大端长度刚开始给了 $%DD为了装夹强度考虑 可以加长大端长度增至 $9DD
5$)% Yg$$%% 5$)$ :1% ;)% `$)% 5$)9 :%% W99&%% 5$(% W$9%&% Y)%%&%% 5$($ b%(%( <3%%% :%% W9%&% Yg$%'% :%$ W% e%&$9% :%% W0%&%% W$9%&% Y$9%&%% 5$(9 @%9% 5$3% @(%% #加工 (&$ 试切 在试切外轮廓加工应注意.)/ 处的夹刀现象"同时要注 意如图所示的 $$( 两个位置# $ 为圆弧"半径较小"在切削时 会出现产生的切屑流出后翻转到半径为 ^$9&9 的圆弧面"划 伤其表面# )$( 的右侧均为锥面"一方面要注意刀具的副后 刀面与工件已车削轮廓表面是否干涉"另外也要注意"在切 削时会出现产生的切屑流出后翻转到锥面上造成划伤# 为 避免干涉也可采用直头刀杆车削"如图 ( 所示# (&) 加工中的问题及解决方法 为了避免上面提到的问题"可采取如下方法予以解决# ($)如在试切时.)/处出项夹刀现象"应改变.)/ 处的外 圆尺寸"进行外圆粗加工"再用 :1( 进行局部精加工# ()) 对整个工件预留不超过 %&$DD的余量"在加工完工 件后"再将预留的 加 工 余 量 切 去" 可 对 划 伤 的 表 面 进 行 修 复 或者 采 取 在 编 程 时" 分 别 对 $$)$( 三 个 位 置 预 留 不 超 过 %E$DD的余量"通过切除余量"修复划伤的表面# 后一种办 法会更为简便一些# 加工效果如图 3 所示#
数控木工砂光机在厨房家具制造中的应用案例分享

数控木工砂光机在厨房家具制造中的应用案例分享随着科技的不断发展,数控技术在各行业中的应用越来越广泛。
在家具制造行业中,数控木工砂光机的应用也得到了越来越多的关注和应用。
本文将就数控木工砂光机在厨房家具制造中的应用进行案例分享,探讨其优势和效果。
一、案例一:高效精确的砂光处理在厨房家具制造中,木材的表面处理是非常重要的一环。
传统的手工砂光处理需要耗费大量的时间和人力,而且难以达到一致的效果。
而采用数控木工砂光机进行砂光处理,不仅可以提高工作效率,还能保证砂光效果的一致性。
以某厨房家具制造企业为例,他们采用数控木工砂光机进行家具的表面砂光处理。
数控技术使得砂光机能够按照预设的程序进行砂光,精确控制砂光的深度、速度和力度。
这样一来,不仅能够减少砂光处理的时间,更重要的是能够保证每个家具的砂光效果一致,提高了产品的质量和品质。
二、案例二:多功能的加工能力数控木工砂光机不仅能够进行砂光处理,还可以具备多种功能的加工能力,进一步提高了生产的效率和灵活性。
例如,数控木工砂光机可以配备多种刀具,如平刀、V形刀、圆弧刀等,可以进行开槽、榫卯加工等工序,实现不同家具的定制化生产。
某家具制造企业采用数控木工砂光机进行厨房家具的定制化生产。
在该企业的生产线上,数控木工砂光机不仅进行砂光处理,还可以进行开槽、榫卯等加工工序。
通过数控编程,能够根据不同的产品要求,精准控制加工的深度和形状,满足不同顾客的定制需求。
这种灵活的生产方式不仅能够提高工作效率,也有利于满足市场的多样化需求。
三、案例三:提高产品质量和一致性在传统的手工加工过程中,操作者的技术水平和疲劳度都会影响到产品的质量和一致性。
而数控木工砂光机的应用可以有效地解决这个问题,提高产品的质量和一致性。
以某家具制造企业为例,他们在生产线上引入了数控木工砂光机。
在原来的手工加工过程中,产品的砂光效果因不同人员的操作技术和疲劳度而存在差异。
而引入数控木工砂光机后,可以通过预设的程序和参数,保证每个产品的砂光效果一致。
第七章数控铣床加工中心零件加工综合实例课件

2.工艺处理
1)工件的装夹。本例工件毛坯的外形为长方 体,为使定位和装夹准确、可靠,选择机用虎 钳来进行装夹。
2)刀具的选择。该工件的材料为硬铝,切削 性能较好,选用高速钢立铣刀即可满足工艺要 求。工件上表面铣削用φ60mm端铣刀(T01) ,凸台轮廓选用φ12mm立铣刀(T02),凹槽 加工用8mm键槽铣刀(T03),孔加工用φ9.7 麻花钻(T04)和φ10H8铰刀(T05)。
精铣凹槽:用φ10mm键槽铣刀,主轴转速为 1000r/min ,进给速度为80mm/min。
钻孔:用φ9.7麻花钻,主轴转速为1000r/min ,进给速 度为100mm/min。
铰孔:用φ10H8铰刀,主轴转速为1200r/min ,进给速 度为80mm/min。
3.数学处理
建立工件坐标系:原点设在工件表面中 心点位置。工件各坐标计算简单,五边 形各坐标如下:A(-23.512,-31.944) 、B(-37.82,12.6)、C(0,40)、D (37.82,12.36)、E(23.512,31.944)。
N100 X34 Y29; N110 Y10; N120 G03 X34 Y-10 R10; N130 G01 X34 Y-29; N140 G02 X29 Y-34 R5; N150 G01 X0 Y-34; N160 G03 X-16 Y-50 R16; N170 G40 G01 X0 Y-50; N180 M99;
第七章 数控铣床加工中心 零件加工综合实例
数控铣床加工中心零件加工综合实例
教学目标
1. 学会数控铣床程序编制的方法 2. 学会在数控仿真软件上校验程序的方
法 3.了解在数控铣床上加工零件的方法与
步骤
教学重点难点
数控铣床典型零件加工实例

数控铣床典型零件加工实例模块五如果希望掌握这门技列举了典型数控铣削编程实例,本单元从综合数控技术的实际应用出发,术,就应该仔细的理解和消化它,相信有着举一反三的效果。
学习目标知识目标:●学会对工艺知识、编程知识、操作知识的综合运用能力目标:●能够对适合铣削的典型零件进行工艺分析、程序编制、实际加工。
——槽类零件一、数控铣床加工实例1所示的槽,工×㎜毛坯为70×70㎜18㎜板材,六面已粗加工过,要求数控铣出如图2-179 钢。
件材料为45图2-179 凹槽工件1.根据图样要求、毛坯及前道工序加工情况,确定工艺方案及加工路线1)以已加工过的底面为定位基准,用通用机用平口虎钳夹紧工件前后两侧面,虎钳固定于铣床工作台上。
2)工步顺序四角倒圆的正方形。
㎜50×㎜50铣刀先走两个圆轨迹,再用左刀具半径补偿加工①.②每次切深为2㎜,分二次加工完。
2.选择机床设备根据零件图样要求,选用经济型数控铣床即可达到要求。
3.选择刀具现采用φ10㎜的平底立铣刀,定义为T01,并把该刀具的直径输入刀具参数表中。
4.确定切削用量切削用量的具体数值应根据机床性能、相关的手册并结合实际经验确定,详见加工程序。
5.确定工件坐标系和对刀点在XOY平面内确定以工件中心为工件原点,Z方向以工件上表面为工件原点,建立工件坐标系,如图2-118所示。
采用手动对刀方法(操作与前面介绍的数控铣床对刀方法相同)把点O作为对刀点。
6.编写程序考虑到加工图示的槽,深为4㎜,每次切深为2㎜,分二次加工完。
为编程方便,同时减少指令条数,可采用子程序。
该工件的加工程序如下:O0001;主程序N0010 G90 G00Z2.S800T01M03;N0020X15.Y0M08;N0030G01 Z-2. F80;N0040M98 P0010;调一次子程序,槽深为2㎜N0050G01Z-4.F80;N0060M98 P0010; 再调一次子程序,槽深为4mmN0070G00 Z2.Z150. M09;Y0X0N0080 G00.N0090M02主程序结束O0010 子程序N0010G03X15.Y0I-15.J0;N0020G01X20.;N0030G03X20.YO I-20.J0;N0040G41G01X25.Y15.;左刀补铣四角倒圆的正方形;I-10.J0 Y25.N0050G03X15.;G01X-15.N0060;I0J-10.N0070 G03X-25.Y15.Y-15.G01N0080 J0; I10.G03X-15.Y-25.N0090 X15.;G01N0100 J10.; I0X25.Y-15.N0110G03 Y0;G01N0120左刀补取消X15.Y0; N0130G40G01 子程序结束N0140 M99;程序的输入(参见模块四具体操作步骤)7. 8.试运行(参见模块四具体操作步骤)对刀(参见模块四具体操作步骤)9. 10.加工选择“自动方式”,按“启动”开始加工。
数控铣床加工实例

数控铣床加工实例——钻孔类零件
工艺分析及处理
(4)刀具和切削用量的选择 影响切削用量的因素很多,工件的材料和硬度、加工
的精度要求、刀具的材料和耐用度、是否使用切削液等都 直接影响到切削用量的大小。在数控程序中,决定用量的 参数是主轴转速S和进给速度F,主轴转速S、进给速度F 值的选择与在普通机床上加工时的值相似,可以通过计算 的方法得到,也可查阅金属切削工艺手册,或根据经验数 据给定。本例S设为1000 r/min 。
数控铣床加工实例——挖槽类零件
工艺分析及处理
(1)零件图的分析
工件毛坯为100 mm× 80 mm×25 mm的长方体零件, 材料为45钢,要加工成型中间的环 形槽。
数控铣床加工实例——挖槽类零件
工艺分析及处理
(2)加工方案及刀具选择 根据零件图分析,要加工的部位是一个环形 槽,中间的凸台作为槽的岛屿,外轮廓转角处的 半径是R4,槽较窄处的宽度是10 mm,所以选用 直径¢6mm的直柄键槽铣刀较合适。
N600 M30 ;
程序结束
数控铣床加工实例——平面轮廓类零件
数控铣床加工实例——平面轮廓类零件
工艺分析及处理
(1)零件图的分析
工件毛坯为¢85mm ×30mm的圆柱 件,材料为硬铝,加工其上部轮廓后形成 如图所示的凸台。加工部分凸台的精度不 高,可以按照图纸的基本尺寸进行编程, 一次铣削完成。
数控铣床加工实例——挖槽类零件
注意:
(1)根据以上特征和要求,对于挖槽的编程和加工要选择合适的刀具 直径,刀具直径太小将影响加工效率,刀具直径太大可能使某些转角处 难以切削,或由于岛屿的存在形成不必要的区域。
(2)由于圆柱形铣刀垂直切削时受力情况不好,因此要选择合适的刀 具类型,一般可选择双刃的键槽铣刀,并注意下刀时的方式,可选择斜 向下刀或螺旋形下刀,以改善下刀切削时的刀具受力情况。
数控车床零件加工综合实例解析21张幻灯片课件

数控机床编程与操作
②数控加工程序的编制 5.2.4 零件的数控加工
1、机遇对于有准备的头脑有特别的亲和力。
2、不求与人相比,但求超越自己,要 哭就哭 出激动 的泪水 ,要笑 就笑出 成长的 性格! 3、在你内心深处,还有无穷的潜力, 有一天 当你回 首看时 ,你就 会知道 这绝对 是真的 。 4、无论你觉得自己多么的了不起,也 永远有 人比你 更强; 无论你 觉得自 己多么 的不幸 ,永远 有人比 你更加 不幸。
32、滴水穿石不是靠力,而是因为不 舍昼夜 。 33、忍别人所不能忍的痛,吃别人所 别人所 不能吃 的苦, 是为了 收获得 不到的 收获。
34、时间是个常数,但也是个变数。 勤奋的 人无穷 多,懒 惰的人 无穷少 。—— 字严 35、不同的信念,决定不同的命运!
36、只有你学会把自己已有的成绩都 归零, 才能腾 出空间 去接纳 更多的 新东西 ,如此 才能使 自己不 断的超 越自己 。 37、突破心理障碍,才能超越自己。
数控机床编程与操作 ④刀具的选择
数控机床编程与操作 ⑤切削用量的确定
数控机床编程与操作
5.1.3基点坐标的计算及加工程序的编制 ①基点坐标的计算
数控机床编程与操作 ①基点坐标的计算
数控机床编程与操作
②数控加工程序的编制 5.1.4 零件的数控加工
数控机床编程与操作
5.2套类零件的编程与加工 5.2.1零件图纸及加工要求
25、我学习了一生,现在我还在学习, 而将来 ,只要 我还有 精力, 我还要 学习下 去。— —别林 斯基
13、你不能左右天气,但可以改变心 情。你 不能改 变容貌 ,但可 以掌握 自己。 你不能 预见明 天,但 可以珍 惜今天 。 14、我们总是对陌生人太客气,而对 亲密的 人太苛 刻。
数控机床加工工艺实例分析

数控机床加工工艺实例分析第9章数控机床加工工艺实例分析9.1 大批量生产零件数控车削加工工艺maxbook118com.零件介绍maxbook118com 工艺分析1.加工技术要求分析2.定位基准的选择3.工艺方案拟定maxbook118com 铜接头综合工艺过程卡和工序卡1.铜接头综合工艺过程卡2.工序卡3数控加工走刀路线图4.刀具调整图5.专用夹具9.2 数控铣削加工工艺实例分析maxbook118com 零件介绍maxbook118com 工艺分析1.工艺分析2.选择装夹和定位3.选择铣刀和切削用量4.确定走刀路线maxbook118com 加工工序卡片和刀具使用卡片9.3 加工中心加工工艺实例分析maxbook118com 零件介绍maxbook118com 工艺分析1.零件图工艺分析2.确定装夹方案3.确定加工顺序及走刀路线4.刀具的选择5.切削用量的选择maxbook118com 填写数控加工工序卡片9.4 数控线切割机床加工工艺实例分析maxbook118com 零件介绍maxbook118com 工艺分析小结与复习思考题图912 锪4-φ16孔进给路线return 图913 钻螺纹底孔攻螺纹进给路线return 铣AB表面时为缩短进给路线提高加工效率减少接刀痕迹同时考虑切削力矩不要太大选择φ100硬质合金可转位面铣刀孔螺纹孔加工刀具尺寸根据加工尺寸选择所选刀具见表912 铣AB表面时留02mm精铣余量精镗φ60H7孔留01mm余量4-φ12H8孔留01mm铰孔余量查表确定切削速度和进给量然后根据式vc πdn1000vf nfvf nZfz计算各工步的主轴转速和进给速度将各工步的加工内容所用刀具和切削用量填入表913 盖板零件数控加工工序卡片表912 盖板零件数控加工刀具卡片产品名称或代号×××零件名称盖板零件图号×××序号刀具号刀具加工表面备注规格名称数量刀长/mm 1 2 3 4 5 6 7 8 9 10 11 T01 T02 T03 T04 T05 T06 T07 T08 T09 T10 Tll φ100可转位面铣刀φ3中心钻φ58镗刀φ599镗刀φ60H7镗刀φ119麻花钻φ16阶梯铣刀φ12H8铰刀φ14麻花钻90°φ16铣刀机用丝锥M16 l 1 l l 1 l 1 1 1 1 1 铣AB表面钻中心孔粗螳φ60H7孔半精镗φ60H7孔精镗φ60H7孔钻4-φ12H8底孔锪4-φ16阶梯孔铰4-φ12H8孔钻4-M16螺纹底孔4-M16螺纹孔倒角攻4-M16螺纹孔编制×××审核×××批准×××年月日共页第页表913 盖板零件数控加工工序卡片单位名称×××产品名称或代号零件名称零件图号×××盖板×××工序号程序编号夹具名称使用设备车间××××××平口虎钳TH5660A 数控中心工步号工步内容刀具号刀具规格mm 主轴转速r·min-1 进给速度mm·min-1 背侧吃刀量mm 备注1 2 3 4 5 6 7 8 9 lo 11 12 13 14 粗铣A面精铣A面粗铣B面精铣B面保证尺寸15 钻各光孔和螺纹孔的中心孔粗镗φ60H7孔至φ58 半精镗φ60H7孔至φ599 精镗φ60H7孔钻4-φ12H8底孔至φ119 锪4-φ16阶梯孔铰4-φ12H8孔钻4-M16螺纹底孔至φ14 4-M16螺纹孔端倒角攻4-M16螺纹孔T0l T01 T0l T01 T02 T03 T04 T05 T06 T07 T08 T09 T10 T11 φ100 φ100 φ100 φ100 φ3 φ58 φ599 φ60H7 φ119 φ16 φ12H8 φ14 φ16 M16 250 320 250 320 1000 400 460 520 500 200 100 350 300 100 80 40 80 40 40 60 50 30 60 30 30 50 40 200 38 02 38 02 自动自动自动自动自动自动自动自动自动自动自动自动自动自动编制×××审核×××批淮×××年月日共页第页按照技术要求完成图914所示内花键扳手零件的加工此零件毛坯料为100mm×32mm×6mm板料图图914 内花键扳手零件1.零件图工艺分析此零件尺寸要求精度不高但内外两个型面都要加工有一定的位置要求2.确定装夹位置及走刀路线因为该零件毛坯料为100mmX 32mmX 6mm板料为防止工件翘起或低头装夹采用两端支承方式走刀路线是先切割内花键然后再切割外形轮廓如图915所示图915 零件装夹位置3.穿丝点的位置根据图纸所给参数编制程序单生成切割轨迹时注意穿丝点的位置见图915所示可以用轨迹跳步9.1 大批量生产零件数控车削加工工艺9.2 数控铣削加工工艺实例分析9.3 加工中心加工工艺实例分析9.4 数控线切割机床加工工艺实例分析图91所示为铜接头零件简图该零件材料为HPb591毛坯为30铜六方冷拔型材是国内某精密仪器厂接洽日本的定单零件为大批量生产类型产品该零件为外圆柱面内外螺纹内圆柱孔内圆锥孔内外环槽等表面组成的零件加工表面较多适合在数控车床上加工图91 铜接头零图该零件有众多的精度要求大端内螺纹RC12大端内螺纹倒角1×45°小端内孔直径φ连接小端内孔与大端内螺纹的内锥孔长165大径φ107小端外径φ11外螺纹G12大端端面2φ29大端外表面刻字68以及其它各轴向尺寸粗糙度要求等此外零件上不得有毛刺伤痕及油污未注公差±01φ68孔P处不得有毛刺但倒角不得大于03零件上φ11外圆φG12螺纹Rc12内螺纹68孔与G12螺纹Rc12内螺纹有同轴度要求φ68与G12一次装夹加工以保证同心上述技术要求决定了需加工的表面及相应加工方案见表91 因该零件为大批量采用普通机床和数控机床共同加工完成见表91综合工艺过程卡按工序分散原则先粗后精原则划分工序其整个工艺流程分两大部分一部分是下料和粗加工部分在普通机床上完成粗加工的定位基准是用三爪卡盘以外六方各端面配合定位另一部分是精加工和螺纹加工部分在数控车床上完成按装夹方式划分为两个工序外螺纹加工等以外六方和大端面定位是一个工序内螺纹加工等使用专用夹具如图94所示以外螺纹面大端左端面定位是另一个工序见表92~表98 1下料车端面切断2外表面各部分粗车精车3钻孔小端钻盲孔φ55大端钻孔φ15 4钻锥孔锥形钻头钻锥孔5切退刀槽外螺纹切槽25×φ18精车螺纹G12 6切内槽内螺纹切内槽25×φ22精车内螺纹Rc12 表91 铜接头综合工艺过程卡零件名称零件材料毛坯种类毛坯硬度毛重kg 净重kg 车型每车件数铜接头HPb591 冷拔型材工序号工序名称设备名称夹具进给量mmr 主轴转速rmin 切削速度mmin 冷却液负荷 1 下料卧式车床三爪平卡盘 2 粗车小端外圆卧式车床三爪平卡盘 3 粗车小端面及钻孔卧式车床三爪平卡盘 4 粗车大端面及钻孔卧式车床三爪平卡盘 5 钻锥孔卧式车床三爪平卡盘 6 精车小端面各部数控机床三爪平卡盘7 精车大端面各部数控机床专用夹具编制审核批准共1页第1页表92 铜接头工序卡机械加工工序卡零件图号零件名称文件编号第页CF-AD316Z0 铜接头工序号工序名称材料 1 下料HPb59-1 加工车间设备型号夹具CW6140A 三爪平卡盘工步号工步内容刀具量具及检具 1 车端面切断刀1 2 切断切断刀1 游标卡尺编制校对审定批准表93 铜接头工序卡机械加工工序卡零件图号零件名称文件编号第页CF-AD316Z0 铜接头工序号工序名称材料2 车小端外圆HPb59-1 加工车间设备型号夹具C6140A1 三爪平卡盘工步号工步内容刀具量具及检具 1 粗车φ11外圆至φ126 外圆车刀1 游标卡尺2 粗maxbook118com 外圆车刀2 游标卡尺编制校对审定批准表94 铜接头工序卡机械加工工序卡零件图号零件名称文件编号第页CF-AD316Z0 铜接头工序号工序名称材料 3 粗车小端面及钻孔HPb59-1 加工车间设备型号夹具CM6125 三爪平卡盘工步号工步内容刀具量具及检具 1 车小端面车刀游标卡尺2 钻φ6孔至φ55孔深18 φ55钻头编制校对审定批准表95 铜接头工序卡机械加工工序卡零件图号零件名称文件编号第页CF-AD316Z0 铜接头工序号工序名称材料 4 粗车大端面及钻孔HPb59-1 加工车间设备型号夹具CM6125 三爪平卡盘工步号工步内容刀具量具及检具 1 车大端面车刀游标卡尺 2 钻Rc12螺纹底孔孔深17 φ15钻头编制校对审定批准表96 铜接头工序卡机械加工工序卡零件图号零件名称文件编号第页CF-AD316Z0 铜接头工序号工序名称材料 5 钻锥孔HPb59-1 加工车间设备型号夹具CM6125 三爪平卡盘工步号工步内容刀具量具及检具 1 成形钻头钻锥形孔锥形钻头编制校对审定批准表97 铜接头工序卡数控加工工序卡零件图号零件名称文件编号第页CF-AD316Z0 铜接头工序号工序名称材料 6 精车小端面各部HPb59-1 加工车间设备型号夹具CNC6132 三爪平卡盘工步号工步内容刀具走刀次数量具及检具1 精车小端面φ11外圆φ208端面G12螺纹底径至φ209和车大端左端面倒角及退刀槽车刀T01 游标卡尺 2 精车φ68到尺寸车刀T02 1 塞规3 精车G12螺纹到尺寸外螺纹车刀T03 6 螺纹环规编制校对审定批准表98 铜接头工序卡数控加工工序卡零件图号零件名称文件编号第页CF-AD316Z0 铜接头工序号工序名称材料7 精车大端面各部HPb59-1 加工车间设备型号夹具CNC6132 专用夹具工步号工步内容刀具走刀次数量具及检具 1 精车大端面至215靠倒角2-φ29 30°精车内螺纹Rc12大径车内槽25×φ22 专用车刀T01 游标卡尺2 精车内螺纹Rc12到尺寸内螺纹车刀T02 7 螺纹塞规3 精车内锥孔到尺寸车刀T03 1 塞规编制校对审定批准表99 数控加工走刀路线图数控加工走刀路线图零件图号CF-AD316Z0 工序号 6 工步号 1 程序号O0099 机床型号CNC6132 程序段号加工内容精车小端外圆柱面端面倒角及退刀槽共1页第页符号含义抬刀下刀编程原点起刀点走刀方向走刀线相切爬斜坡铰孔行切图92 工序6小端外轮廓精加工刀具调整图图93 工序7大端外轮廓精加工刀具调整图图94 工序7专用夹具零件图典型零件如图95所示该零件为铸造件灰口铸铁铣削上表面最大外形轮廓挖深度为25mm的凹槽钻maxbook118com公差按ITl0级自由公差确定加工表面粗糙度Ra≤6.3制订加工工序图95 盖板零件该零件形状较典型并且为轴对称图形也便于装夹和定位该例在数控铣削加工中有一定的代表性1图样分析该零件以φ22mm孔的中心线为基准尺寸标注齐全且无封闭尺寸及其他标注错误尺寸精度要求不高2加工工艺该零件为铸造件灰口铸铁其结构并不复杂但对要求加工部分需要一次定位二次装夹根据数控铣床工序划分原则先安排平面铣削后安排孔和槽的加工对于该工件加工顺序为先铣削上平面铣削轮廓用中心钻点窝钻φ55mm的孔钻φ65mm的孔然后先用压板压紧工件再松开定位销螺母进行挖φ25mm深的中心槽该零件在生产时可采用一面两销的定位方式以工件底面为第一定位基准定位元件采用支撑面限制工件在Xy方向的旋转运动和Z方向的直线运动两个φ22mm的孔作为第二定位基准定位元件采用带螺纹的两个圆柱定位销进行定位和压紧限制工件在Xy 方向的直线运动和Z方向的旋转运动挖φ25mm深的中心槽时先用压板压紧工件再松开定位销螺母在批量生产加工过程中应保证定位销与工作台相对位置的稳定铣削上表面选取φ25mm立铣刀由于采用两个中心孔定位不能使用端面铣刀先进行粗铣留02~05mm余量再进行精铣最大外形轮廓铣削可选用直径较大的刀根据余量决定铣削次数最后余量加工应≤φ05mm挖深度为25mm选用直径≤φ8 mm的立铣刀maxbook118com先用φ3的中心钻点窝再分maxbook118com麻花钻钻削盖板挖槽走刀线路如图96所示采用由内向外平行环切并清角或采用由外向内平行环切并清角的切削方式盖板钻孔走刀线路如图97所示编程与工件坐标系大端φ22mm孔的中心点为坐标系原点对刀点根据实际情况而定定位销与工作台固定以后可以套装一标准块然后再进行定位图96 盖板挖槽走刀路线图97 盖板钻孔走刀路线盖板零件数控铣加工工序卡片和刀具使用卡片见表910和表611 表910 盖板零件数控铣加工工序卡片单位名称数控加工工序卡零件名称零件图号材料02 盖板HT 32-52 工艺序号02 夹具名称夹具编号使用设备XK5025 工步号加工内容程序号刀具名称刀具规格mm 补偿号补偿值主轴转速r·min-1 进给速度mm·min-1 进给倍率切削深度mm 加工余量mm 1 铣平面粗立铣刀φ25 202 200 30 精402 200 20 05 2 铣外轮廓粗立铣刀φ25 H1 202 200 30 精φ25 H1 402 200 10 05 3 挖槽键槽铣刀φ8 402 200 10 4 点窝中心钻φ3 800 100 20 5 钻孔麻花钻φ55 602 200 20 6 钻孔麻花钻φ6602 50 10 注意事项①启动机床回零后检查机床零点②换刀后应松开主轴锁定并对Z轴进行对刀③正确操作机床注意安全文明生产表911 盖板零件数控铣加工刀具使用卡片编号刀具名称刀具规格mm 数量用途刀具材料1 立铣刀φ25 1 铣平面轮廓合金镶条2 键槽铣刀φ8 1 挖孔高速刀HSS 3 麻花钻φ55 1 钻孔高速刀HSS 4 麻花钻φ65 1 钻孔高速刀HSS 在立式加工中心上加工如图98 所示盖板零件零件材料为HT200铸件毛坯尺寸长×宽×高为170mm×170mm×23mm 图98 盖板零件图该零件毛坯为铸件外轮廓4个侧面为不加工面主要加工AB面及孔系包括4个M16螺纹孔4个阶梯孔及1个φ6OH7尺寸精度要求一般最高为IT7级4-φ12H8φ60H7孔的表面粗糙度要求较高达到只Ra08其余加工表面粗糙度要求一般根据上述分析AB面加工可采用粗铣-精铣方案φ6OH7孔为已铸出毛坯孔因而选择粗镗-半精镗-精镗方案4-φ12H8宜采用钻孔-铰孔方案以满足表面粗糙度要求该零件形状比较规则简单加工面与不加工面的位置精度要求不高可采用平口虎钳夹紧但应先加工A面然后以A面主要定位基面和两个侧面定位用虎钳从侧面夹紧按照先面后孔先粗后精的原则确定加工顺序总体顺序为粗精铣AB面-粗镗半精镗精镗φ60H7孔-钻各中心孔-钻锪铰4-φ12H8和4-φ16孔-钻4-M16螺纹底孔-攻螺纹由零件图可知孔的位置精度要求不高因此所有孔加工的进给路线按最短路线确定图99 图910图911图912图913为孔加工各工步的进给路线图99 镗φ60H7孔进给路线return 图910 钻中心孔进给路线return 图911 钻铰4-φ12H8孔进给路线return。
数控铣削加工工艺及编程实例

(2)加工过程 1)粗、精铣B面。平面B采用铣削加工,表面粗糙度Ra 值为6.3μm,依据经济加工精度,选用粗铣→精铣加工 方案。B面的粗、精铣削加工进给路线根据铣刀直径 (φ100mm),确定为沿X方向两次进刀。
2)粗镗、半精镗、精镗φ60H7孔镗孔。φ60H7孔采用镗 削加工,精度等级IT7,表面粗糙度 Ra 值为0.8μm,依 据经济加工精度,选用粗镗→半精镗→精镗三次镗削加 工方案。所有孔加工进给路线按最短路线确定,孔的位 置精度要求不高,所以机床的定位精度完全能保证。
4.评分标准
3.6.2 平面内轮廓零件的编程与操作
平面内轮廓零件如图3-101所 示。已知毛坯尺寸为 70mm×70mm×20mm的长方 料,材料为45钢,按单件生产 安排其数控加工工艺,试编写 出该型腔加工程序并利用数控 铣床加工出该工件。
1.加工工艺方案 (1)加工工艺路线 1)切入、切出方式选择。铣削封闭内轮廓表面时,刀具 无法沿轮廓线的延长线方向切入、切出,只有沿法线方 向切入、切出或圆弧切入、切出。切入、切出点应选在 零件轮廓两几何要素的交点上,而且进给过程中要避免 停顿。 2)铣削方向选择。一般采用顺铣,即在铣削内轮廓时采 用沿内轮廓逆时针的铣削方向比较好。 3)铣削路线。凸台轮廓的粗加工采用分层铣削的方式。 由中心位置处下刀,采用环切的切削方法进行铣削,去 除多余材料。粗加工与精加工的切削路线相同。
图3-103所示为零件,已 知材料为45钢,毛坯尺 寸为 80mm×80mm×20mm, 所有加工面的表面粗糙 度值为Ra1.6μm。试编 写此工件的加工程序并 在数控铣床上加工出来。
1.确定加工工艺 (1)加工工艺分析 按长径比的大小,孔可分为深孔和浅孔两类。 (2)加工过程 确定加工顺序时,按照先粗后精、先面后孔的原则,其 加工顺序为: 1)编程加工前,应首先钻孔前校平工件、用中心钻钻 6×φ8mm的中心孔; 2)同φ10mm铣刀铣削型腔; 3)用φ8mm钻头钻6×φ8mm的通孔,加工路线: L→M→N→I→J→K;
数控车加工实例
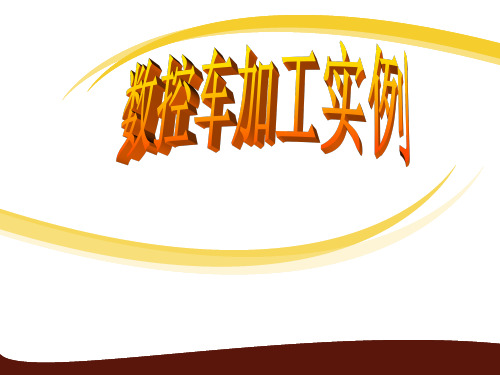
3、精密圆弧加工
3、精密圆弧加工
该圆弧槽如果用劣弧R编 程,程序如下: G02 W-40.0 R20.0; 加工后,φ60.25±0.03不符 合图纸要求。 用圆心坐标编程,程序如下: G02 W-40.0 I0.125 K-20.0; 加工后,φ60.25±0.03就符 合图纸要求。
测量尺寸
4、中心轨迹、刀尖转移编程 实例1:橡胶硫化模模芯
数控车床加工的球面工件常见的是加工部分球面, 其加工圆弧的角度受刀具副偏角的限制。即使采用 R刀或切断刀加工纯圆球。
上述的几种加工方法,在切断部位总是存在瑕疵。
1、圆球加工
下面介绍一种数控车加工纯圆球的方法: (1)按下图b所示加工部分球面,圆弧长度在 垂直轴线两侧夹角各大于45°以上(例V形刀可接 近50° ),在两端各余量加工余量(便于测量)。 (2)切断。 (3)在机床卡盘、尾座顶尖上,加工、安装如 图所示辅助工装,将根据如图安装并顶紧。加工完 成。
9、子程序应用实例 实例1:切槽
9、子程序应用实例 实例1:切槽子程序1 (左刀尖对刀)
O0010 T0202 G97 S750 M03 G00 X55.0 Z10.0
Z-20.0 X52.0 N98 P130011 G00 X150.0 Z10.0 M30
O0011 G01 X38.0 F0.08 G04 X0.1 G01 X52.0 F0.4 G00 W-10.0 M99
9、子程序应用实例
工艺分析:
X58.0 Z-1.0 Z-6.8 G03 U-1.6 W-1.6 R2.0 N98 P50002 G02 W-3.2 R2.0 G03 U1.6 W-1.6 R2.0 G01 Z-52.0 G00 G40 X150.0 Z150.0 M30
MTS数控铣床加工案例 发那科 fanuc 0-M

7
Abdeckplatte5.fnc
刀具列表 1
1 SK40 14.03.2017
钻铣刀
BNF-B 14x16(73) R_SZF-40 ER25x60 2 SK40
精加工铣刀,高速钢制,短型
SLF HSS-k 14x26(83) R_SZF-40 ER25x60 4 SK40
当前刀具 ?
( ( ?T0 1
刀具修 ? 盗 斜
? ( ( ( ( ( ( ( ( ( ( ( ( ( ( ( T01 T02 T04 T05 T05 T05 T06 T06 T06 T07 T08 T12 T13 TC1: TC1: TC1: TC1: TC2: TC3: TC1: TC2: TC3: TC1: TC1: TC1: TC1: TT340 TT340 TT340 TT220 TT220 TT220 TT230 TT230 TT230 TT250 TT340 TT340 TT340 KR007.000 KR007.000 KR003.000 KR008.000 KR008.000 KR008.000 KR002.450 KR002.450 KR002.450 KR003.000 KR015.000 KR003.000 KR012.500 KZ+098.100 KZ+108.100 KZ+077.100 KZ+140.300 KZ+140.100 KZ+132.300 KZ+133.800 KZ+132.365 KZ+133.837 KZ+082.100 KZ+126.100 KZ+093.100 KZ+190.100 NZ2 NZ4 NZ2 NZ2 NZ2 NZ2 NZ2 NZ2 NZ2 NZ4 NZ2 NZ3 NZ5 SL16 DB14 Ds12 Aw90 AE90 SL26 DB14 Ds12 Aw90 AE90 SL8 DB6 Ds6 Aw90 AE90 SL35 DB16 Ds16 Aw90 SL35 DB16 Ds16 Aw90 SL35 DB16 Ds16 Aw90 SL52 DB4.9 Ds4.9 Aw118 SL52 DB4.9 Ds4.9 Aw118 SL52 DB4.9 Ds4.9 Aw118 SL19 DB6 Ds4.5 SL26 DB30 Ds25 Aw90 AE90 SL24 DB6 Ds6 Aw90 AE90 SL90 DB25 Ds25 Aw90 AE90
数控加工中心典型零件编程实例精选全文完整版
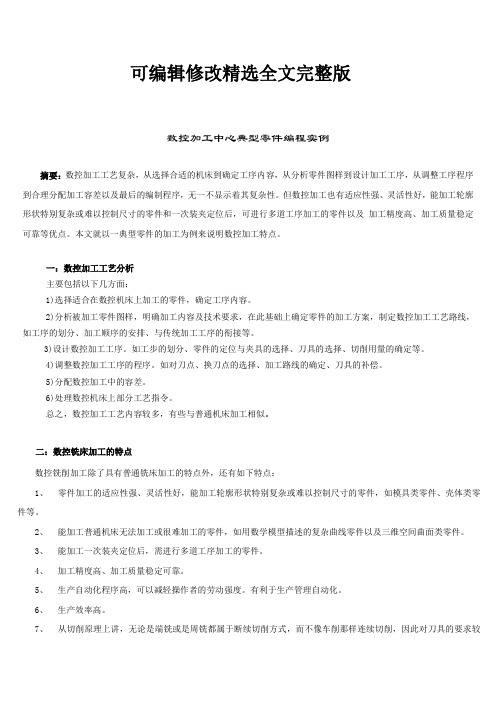
可编辑修改精选全文完整版数控加工中心典型零件编程实例摘要:数控加工工艺复杂,从选择合适的机床到确定工序内容,从分析零件图样到设计加工工序,从调整工序程序到合理分配加工容差以及最后的编制程序,无一不显示着其复杂性。
但数控加工也有适应性强、灵活性好,能加工轮廓形状特别复杂或难以控制尺寸的零件和一次装夹定位后,可进行多道工序加工的零件以及加工精度高、加工质量稳定可靠等优点。
本文就以一典型零件的加工为例来说明数控加工特点。
一:数控加工工艺分析主要包括以下几方面:1)选择适合在数控机床上加工的零件,确定工序内容。
2)分析被加工零件图样,明确加工内容及技术要求,在此基础上确定零件的加工方案,制定数控加工工艺路线,如工序的划分、加工顺序的安排、与传统加工工序的衔接等。
3)设计数控加工工序。
如工步的划分、零件的定位与夹具的选择、刀具的选择、切削用量的确定等。
4)调整数控加工工序的程序。
如对刀点、换刀点的选择、加工路线的确定、刀具的补偿。
5)分配数控加工中的容差。
6)处理数控机床上部分工艺指令。
总之,数控加工工艺内容较多,有些与普通机床加工相似。
二:数控铣床加工的特点数控铣削加工除了具有普通铣床加工的特点外,还有如下特点:1、零件加工的适应性强、灵活性好,能加工轮廓形状特别复杂或难以控制尺寸的零件,如模具类零件、壳体类零件等。
2、能加工普通机床无法加工或很难加工的零件,如用数学模型描述的复杂曲线零件以及三维空间曲面类零件。
3、能加工一次装夹定位后,需进行多道工序加工的零件。
4、加工精度高、加工质量稳定可靠。
5、生产自动化程序高,可以减轻操作者的劳动强度。
有利于生产管理自动化。
6、生产效率高。
7、从切削原理上讲,无论是端铣或是周铣都属于断续切削方式,而不像车削那样连续切削,因此对刀具的要求较高,具有良好的抗冲击性、韧性和耐磨性。
在干式切削状况下,还要求有良好的红硬性。
三:数控加工案例例1:如图9.1所示,为一长方形板类零件,工件材料为45号钢,六面已加工,试分析孔加工工艺及编写该零件的加工程序。
数控车床加工编程典型实例[1]
![数控车床加工编程典型实例[1]](https://img.taocdn.com/s3/m/97435b0654270722192e453610661ed9ad515506.png)
数控车床加工编程典型实例[1]数控机床是一种技术密集度及自动化程度很高的机电一体化加工设备,是综合应用计算机、自动控制、自动检测及精密机械等高新技术的产物。
随着数控机床的发展与普及,现代化企业对于懂得数控加工技术、能进行数控加工编程的技术人才的需求量必将不断增加。
数控车床是目前使用最广泛的数控机床之一。
本文就数控车床零件加工中的程序编制问题进行探讨。
一、编程方法二、编程步骤拿到一张零件图纸后,首先应对零件图纸分析,确定加工工艺过程,也即确定零件的加工方法(如采用的工夹具、装夹定位方法等),加工路线(如进给路线、对刀点、换刀点等)及工艺参数(如进给速度、主轴转速、切削速度和切削深度等)。
其次应进行数值计算。
绝大部分数控系统都带有刀补功能,只需计算轮廓相邻几何元素的交点(或切点)的坐标值,得出各几何元素的起点终点和圆弧的圆心坐标值即可。
最后,根据计算出的刀具运动轨迹坐标值和已确定的加工参数及辅助动作,结合数控系统规定使用的坐标指令代码和程序段格式,逐段编写零件加工程序单,并输入CNC装置的存储器中。
三、典型实例分析数控车床主要是加工回转体零件,典型的加工表面不外乎外圆柱、外圆锥、螺纹、圆弧面、切槽等。
例如,要加工形状如图所示的零件,采用手工编程方法比较合适。
由于不同的数控系统其编程指令代码有所不同,因此应根据设备类型进行编程。
以西门子802S数控系统为例,应进行如下操作。
(1)确定加工路线按先主后次,先精后粗的加工原则确定加工路线,采用固定循环指令对外轮廓进行粗加工,再精加工,然后车退刀槽,最后加工螺纹。
(2)装夹方法和对刀点的选择采用三爪自定心卡盘自定心夹紧,对刀点选在工件的右端面与回转轴线的交点。
(3)选择刀具根据加工要求,选用四把刀,1号为粗加工外圆车刀,2号为精加工外圆车刀,3号为切槽刀,4号为车螺纹刀。
采用试切法对刀,对刀的同时把端面加工出来。
(4)确定切削用量车外圆,粗车主轴转速为500r/min,进给速度为0.3mm/r,精车主轴转速为800r/min,进给速度为0.08mm/r,切槽和车螺纹时,主轴转速为300r/min,进给速度为0.1mm/r。
数控雕刻机治具加工实例

一.数控雕刻机雕刻从加工原理上讲是一种钻铣组合加工,雕刻机多种数据输入模式根据需要游刃有余。
电脑雕刻机有激光雕刻和机械雕刻两类,这两类都有大功率和小功率之分。
因为雕刻机的应用范围非常广泛,因此有必要了解各种雕刻机的最合适的应用范围。
小功率的只适合做双色板、建筑模型、小型标牌、三维工艺品等。
由于功率太小而大大影响了其应用的范围。
大功率雕刻机可以做小功率雕刻机的东西。
最适合做大型切割、浮雕、雕刻。
工作原理:是通过计算机内配置的专用雕刻软件进行设计和排版,并由计算机把设计与排版的信息自动传送至雕刻机控制器中,再由控制器把这些信息转化成能驱动步进电机或伺服电机的带有功率的信号(脉冲串),控制雕刻机主机生成X,Y,Z三轴的雕刻走刀路基径。
同时,雕刻机上的高速旋转雕刻头,通过按加工材质配置的刀具,对固定于主机工作台上的加工材料进行切削,即可雕刻出在计算机中设计的各种平面或立体的浮雕图形及文字,实现雕刻自动化作业。
1.使用数控雕刻机型号及说明:设备名称: SD1212设备说明:刚:整体铸造机身,内嵌式导轨,确保设备结构稳定,钢性最佳精:采用德国滚珠丝杆,双螺母消隙,国际领先的三轴承定位传动方式劲:标配2.2KW水冷变频高速电机(1325以上机型标配3千瓦变频水冷电机)跃:采用最先进的DSP数控系统机型特点高速度加工:曲直线速度一致,空运行速度可达12米/分(选配)大容量储存:标配128M储存空间,可同时保存30个文件,并可支持U盘直接输出,随意加工快速数据传输:采用先进的USB接口,全脱机工作,不占电脑资源,多种软件兼容:兼容Type3/Artcam/Casmate/CAXA/文泰等多种国内外CAD/CAM 软件高效无忧作业:拥有断电恢复、断点续雕,自动对刀等功能,并支持9个坐标系定位,真正的人性化设计适用范围:本系列机型功能强劲,使用方便,坚固耐用,性能可靠,且价格经济,广泛应用于各种广告标牌、铭牌、胸牌、印章、烫金板、压痕板、指示牌、建筑模型、仪表面板、木工制品、工业模具等产品的加工和制作,并可雕刻铁、铜、铝、塑料板、木板等金属或非金属。
- 1、下载文档前请自行甄别文档内容的完整性,平台不提供额外的编辑、内容补充、找答案等附加服务。
- 2、"仅部分预览"的文档,不可在线预览部分如存在完整性等问题,可反馈申请退款(可完整预览的文档不适用该条件!)。
- 3、如文档侵犯您的权益,请联系客服反馈,我们会尽快为您处理(人工客服工作时间:9:00-18:30)。
一.数控雕刻机雕刻从加工原理上讲是一种钻铣组合加工,雕刻机多种数据输入模式根据需要游刃有余。
电脑雕刻机有激光雕刻和机械雕刻两类,这两类都有大功率和小功率之分。
因为雕刻机的应用范围非常广泛,因此有必要了解各种雕刻机的最合适的应用范围。
小功率的只适合做双色板、建筑模型、小型标牌、三维工艺品等。
由于功率太小而大大影响了其应用的范围。
大功率雕刻机可以做小功率雕刻机的东西。
最适合做大型切割、浮雕、雕刻。
工作原理:是通过计算机内配置的专用雕刻软件进行设计和排版,并由计算机把设计与排版的信息自动传送至雕刻机控制器中,再由控制器把这些信息转化成能驱动步进电机或伺服电机的带有功率的信号(脉冲串),控制雕刻机主机生成X,Y,Z三轴的雕刻走刀路基径。
同时,雕刻机上的高速旋转雕刻头,通过按加工材质配置的刀具,对固定于主机工作台上的加工材料进行切削,即可雕刻出在计算机中设计的各种平面或立体的浮雕图形及文字,实现雕刻自动化作业。
1.使用数控雕刻机型号及说明:设备名称: SD1212设备说明:刚:整体铸造机身,内嵌式导轨,确保设备结构稳定,钢性最佳精:采用德国滚珠丝杆,双螺母消隙,国际领先的三轴承定位传动方式劲:标配2.2KW水冷变频高速电机(1325以上机型标配3千瓦变频水冷电机)跃:采用最先进的DSP数控系统机型特点高速度加工:曲直线速度一致,空运行速度可达12米/分(选配)大容量储存:标配128M储存空间,可同时保存30个文件,并可支持U盘直接输出,随意加工快速数据传输:采用先进的USB接口,全脱机工作,不占电脑资源,多种软件兼容:兼容Type3/Artcam/Casmate/CAXA/文泰等多种国内外CAD/CAM 软件高效无忧作业:拥有断电恢复、断点续雕,自动对刀等功能,并支持9个坐标系定位,真正的人性化设计适用范围:本系列机型功能强劲,使用方便,坚固耐用,性能可靠,且价格经济,广泛应用于各种广告标牌、铭牌、胸牌、印章、烫金板、压痕板、指示牌、建筑模型、仪表面板、木工制品、工业模具等产品的加工和制作,并可雕刻铁、铜、铝、塑料板、木板等金属或非金属。
技术参数▇可选购日本松下伺服系统▇可选配吸尘装置▇可选配真空吸附装置▇可选配水冷和气冷装置▇可选配意大利ELTE、HSD、哥伦布等进口主轴▇可根据客户需求,更改机身颜色2.系统特点:①.3.5英寸TFT真彩色液晶显示,240*320高分辨率,显示内容丰富;②.完全脱机操作,内置2GB超大存储空间;③.可以直接读取U盘上的文件,读写速度快;④.可以加工超大的文件;⑤.具有加工文件预检查能力,防止加工文件的书写或设计错误,防止物料摆放位置超出加工范围;⑥.具有良好的自我诊断能力,可以诊断跟中输入输出信号,提高远程维护的能力;⑦.可以全自动升级;⑧.加工过程加减速更加平稳,有效的降低机械震动;⑨.可以兼容精雕转NC代码,过滤和优化太刀动作,提高加工效率和品质;⑩.支持G代码中的F和S指令。
3.注意事项:①.严禁在强干扰、强磁场环境中使用本产品;②.运行过程中严禁插拔U盘;③.注意防水、防尘、防火;④.防止金属等导电物质进入壳内;⑤.严禁非授权的拆卸,内部无用户可修复部件;⑥.插拔U盘和其他连接线时用力要适度;⑦.长时间不使用,请注意断电,并妥善保存。
4.手柄加工操作流程①.在断电情况下先将机床各部分电缆线正确连接;②.打开电源,手柄屏幕出现是否回机械零点提示,点击确认键,这是机床Z轴会先上升至Z轴零点位置并停止,然后X和Y轴同时会向XY轴零点位置运动并停止,机床处于待机状态;③.机床回零动作完成后,机械坐标全部归零,系统处于待机状态,等待用户操作;④.这时用户可在机床台面上固定需加工零件,在主轴上安装相应的刀具;⑤.定义加工原点操作:将刀具移动到工件上,按XY→0定义好加工的XY 原点,Z轴的原点一般是工件的表面,即将刀尖慢速下降到工件表面,再按Z→0定义好Z轴的原点;⑥.按F4键,调出文件列表窗口,用F2和F3键选择“内部文件列表”或“U盘文件列表”,按回原点键进入,选择要加工的文件,按回原点键确认,再按运行键,出现加工的参数设置界面,按修改键进行修改,可按数字键进行修改数值,再按确认键进行参数确认,按Y+和Y-键可以进行上下选择,再按确认键进行加工,且主轴和水冷却自动开启,加工完成后主轴和水冷却自动关闭。
加工完成之后,如需要更换加工文件,请按F4键,执行上面的步骤即可;⑦.加工中可随时按“暂停”键暂停加工,再按“运行”键即可重新出现加工参数设置窗口,再按“确认”键就可以继续加工了;⑧.加工中可随时按“停止”键停止加工。
5.雕刻机安全操作规程目的:保证雕刻机安全运转,杜绝设备、人身事故。
对象:雕刻机操作人员。
1. 准备作业:1.1 设备上电前先检查台面上有无物品,各运动部件是否正常;检查急停按钮是否正常。
1.2 旋转急停按钮,设备上电。
1.3 在加工过程中,应注意有无异常声音情况。
2. 主体作业:3. 结束作业:3.1 加工结束后,做好5S工作。
3.2 关闭电源开关。
4.1 雕刻前及雕刻过程中必须检查并确认主轴的冷却系统和设备润滑状况,确保设备正常运行。
4.2 工作过程中严禁戴手套操作设备。
4.3 使用的刀具应与机床允许的规格相符,有严重破损的刀具要及时更换。
4.4 装夹工件时,必须遵循“装实、装平、装正”的原则,严禁在悬空的材料上雕刻;为了防止材料的变形,材料的厚度要比雕刻的深度大2mm以上。
4.5 刀具露出卡头的长度须根据雕刻深度、工件与夹具是否干涉来共同决定,在满足以上条件下尽量取短。
4.6 在开始加工(下刀)前,须把手放在红色紧急开关按钮处,一有意外情况立即按下。
4.7 某一项工作如需要俩人或多人共同完成时,应注意相互间的协调一致,确保安全。
4.8 禁止用手接触刀尖和切削碎屑,碎屑必须要用毛刷来清理;4.9 禁止用手或其它任何方式接触正在旋转的主轴、工件或其它运动部位。
4.10 设备运转中,操作者不得离开岗位,机床发现异常现象立即停车。
4.11 严格遵守岗位责任制,机床由专人使用,杜绝设备、人身事故。
4.12 机床的横梁及档板上严禁放任何物品。
4.13 操作过程中严禁趴在机床上,更不允许坐或倚靠在机床架上。
4.14 卸刀时严禁用扳手敲打卡头。
4.15 操作人员在作业过程中必须佩戴防护耳罩和防护眼镜。
6.数控雕刻机的日常维护1、雕刻机工作时必须严格接地!!供电稳定且采用三芯电源插头!2、工作时必须保证水路通畅!! 特别是在夏季,注意电机温度、勤换水!3、当天工作结束后,请将台面清理干净。
4、雕刻机直线导轨每2~3个月维护一次:加少许黄油。
5、雕刻机滚珠丝杆每2~3个月维护一次:加少许机油,严禁加黄油。
二.加工零件1.零件名称:光栅2.零件材质:电木(胶木)3.零件形状尺寸如下图:零件厚度3mm4.技术要求:表面光滑,无毛刺。
三.数控雕刻机加工工艺制定1.选定加工零件,确定工序内容。
2.分析零件图样,确定加工内容及技术要求,确定加工工艺路线。
3.确认各加工工序所需完成的内容。
4.将零件图纸转化为数控雕刻机的程序语言(使用TYPE3软件)。
5.按照工艺路线进行加工。
6.最终进行确认加工零件是否符合尺寸要求及技术要求标准。
四.光栅零件加工实例1.零件确定:选定加工零件为光栅。
2.加工毛坯选定:根据上面光栅零件的加工要求,选定加工毛2.坯为3mm厚电木板。
3.刀具选型:∮3.175*3 一个,∮2*3 一个。
4.数控雕刻机(以SD1212雕刻机为例)加工参数:主轴转速:24000r/min加工速度:1000mm/min5.光栅零件加工程序:此零件加工共分为三个程序:①内部孔∮6.35*1和孔∮3.175*3的加工程序:首先将光栅零件CAD图纸转化为DXF格式,然后由雕刻机软件TYPE3读入,如图所示将图纸所有线条转化为封闭曲线,再点击按钮进入CAM模块,如图选中中心的三个∮3.175的孔,选择创建刀具路径中的钻孔命令,设定钻孔参数:刀具3.175,深度3.2mm,选中钻标志点和框中心,点击确定,如下图操作:再选定中心∮3.35孔,在创建刀具路径窗口中选择二维切割指令,选择3.175刀具,深度3.2mm,选中内切割,并在经过参数选项中,将分步次数改为2,点击确定按钮,在层次3中点击右键,选择机器工作,如下图:选择机器工作指令,弹出点击执行,生成文件。
程序内容如下:G90 G17 G71T1 M6M91 1G0 X20.436 Y22.788Z11.G1 Z0. F300Z-3.2Z0. F600G0 Z10.X26. Y32.425G1 Z0. F300Z-3.2Z0. F600G0 Z10.X31.564 Y22.788G1 Z0. F300Z-3.2Z0. F600G0 Z20.X0. Y0.M90 1T1 M6M91 1X27.588 Y26.Z11.G1 Z0. F300Z-1.6X27.548 Y26.353 F600 X27.43 Y26.689X27.241 Y26.99X26.99 Y27.241X26.689 Y27.43X26.353 Y27.548X26. Y27.588X25.647 Y27.548X25.311 Y27.43X25.01 Y27.241X24.759 Y26.99X24.57 Y26.689X24.452 Y26.353X24.413 Y26.X24.452 Y25.647X24.57 Y25.311X24.759 Y25.01X25.01 Y24.759X25.311 Y24.57X25.647 Y24.452X26. Y24.412X26.353 Y24.452X26.689 Y24.57X26.99 Y24.759X27.241 Y25.01X27.43 Y25.311X27.548 Y25.647X27.588 Y26.Z-3.2 F300X27.548 Y26.353 F600 X27.43 Y26.689X27.241 Y26.99X26.99 Y27.241X26.689 Y27.43X26.353 Y27.548X26. Y27.588X25.647 Y27.548X25.311 Y27.43X25.01 Y27.241X24.759 Y26.99X24.57 Y26.689X24.452 Y26.353X24.413 Y26.X24.452 Y25.647X24.57 Y25.311X24.759 Y25.01X25.01 Y24.759X25.311 Y24.57X25.647 Y24.452X26. Y24.412X26.353 Y24.452X26.689 Y24.57X26.99 Y24.759X27.241 Y25.01X27.43 Y25.311X27.548 Y25.647X27.588 Y26.G0 Z20.X0. Y0.M90 1M30②20个方格的加工程序:选中一圈20个方格,点击CAM模块,在创建刀具路径窗口中选择二维切割,选择∮2刀,加工深度3.2mm,选中内切割,经过参数中设置分步次数2,如下图点击确定按钮,选择机器工作同样生成文件。