磨削硬质合金刀具的磨料粒度选择
硬质合金刀片的材料分类性能选用(摘要)剖析

一、概述: 切削过程的主要矛盾是刀具的切除与工
件的反切除。影响刀具切削能力的外在因素 有刀具结构、几何角度、磨损情况以及工件 材料、切削用量选用情况等,而刀具材料的 性能则是决定切削能力的内在因素;因此, 在切削加工实践中,进行编制工艺、选择刀 具和优选切削用量,都必须以刀具材料的性 能为依据。
硬质合金刀具是在较大的切削力和较高 的切削温度下切除金属的,并且和切屑与工 件表面不断地发生摩擦,因此,作为刀具切 削部份的刀片材料,应具备以下几方面的性 能:
P. M. K. H. S. N.
H类(包括 H01~H30): 适用于加工硬度为HRC40~65 的高硬度材料 (如:切削淬火钢、合 金钢、硬铸铁等),以褐色为标志;
S类(包括S01~S30): 适用于切削高温合金、耐热合 金材料 (如:钛合金、镍基高温合金 等),以棕色为标志;
N类(包括N10~N30): 适用于加工有色金属及非金属 材料 (如:铝合金、纤维强化型塑料 等) ,以绿色为标志。
锻铸铁
钢、铸钢、
车削、铣削、刨削、中或低切削速度中
P30 长切屑的可 或大切削截面,在不利条件下加工
锻铸铁
钢、有夹
车削、刨削、插削、低切削速度、大切
P40 砂和孔隙的 削截,可以用于不利条件下加工的大切削角
铸钢件
和在自动机床上使用
钢、有夹
适于要求韧性很高的硬质合金的工序车
P50
砂和孔隙中 削、刨削、插削、低切削速度、大切削截面, 或低抗拉强 可以在不利条件下以大切削角加工和在自动
M30
奥氏体钢、灰口铸 铁、耐高温合金
中或大切削截面
高速切削软钢、 车削、切断、特别适于自动机床的 低抗拉强度钢、有 成形车削
硬质合金刀具的常用切削用量及注意事项?

硬质合金刀具的常用切削用量及注意事项?
在工厂的实际生产过程中,切削用量一般根据经验并通过查表的方式进行选取,常用硬质合金或涂层硬质合金切削不同材料时的切削用量见下表:
这是常用的切削用量推荐表,W18Cr4V为高速钢
这些参数的选择不仅要看推荐值,更要根据实际加工状况来选择,
需要注意一下几点:
1、主轴转速
可以根据零件上被加工处的直径,并结合零件和刀具的材料特性及切削加工性等条件所限定的切削速度来定。
切削速度除了计算(Vc=πDn/1000)和査切削手册选取外,还可根据实践经验确定,需要注意的是交流变频调速数控车床低速输出力矩小,因而切削速度不能太低。
应根据切削速度可以计算出主轴转速(n=1000Vc/πD)。
2、车螺纹时的主轴转速
在车削螺纹时,主轴转速将受到螺纹的螺距P(或导程)大小、驱动电机的升降频特性,以及螺纹插补运算速度等多种因素影响,故对于不同的数控系统,推荐不同的主轴转速选择范围。
根据以上几点,我们不能完全根据切削手册上的推荐值进行加工,还需要综合分析,避免因为切削参数选择不当造成零件报废。
数控机床铣削刀具的刃磨与调试技巧
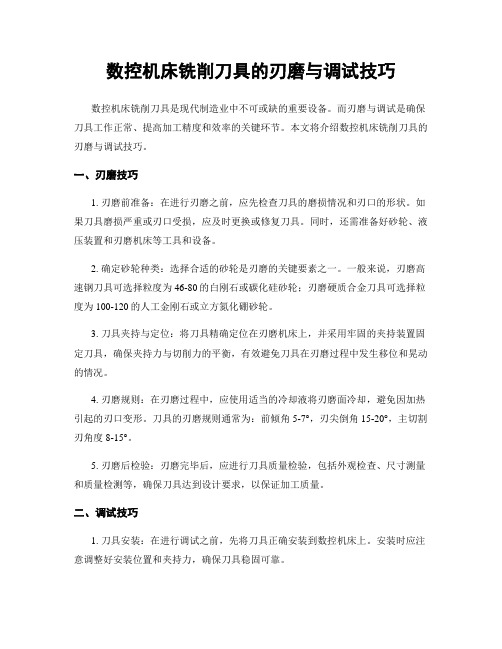
数控机床铣削刀具的刃磨与调试技巧数控机床铣削刀具是现代制造业中不可或缺的重要设备。
而刃磨与调试是确保刀具工作正常、提高加工精度和效率的关键环节。
本文将介绍数控机床铣削刀具的刃磨与调试技巧。
一、刃磨技巧1. 刃磨前准备:在进行刃磨之前,应先检查刀具的磨损情况和刃口的形状。
如果刀具磨损严重或刃口受损,应及时更换或修复刀具。
同时,还需准备好砂轮、液压装置和刃磨机床等工具和设备。
2. 确定砂轮种类:选择合适的砂轮是刃磨的关键要素之一。
一般来说,刃磨高速钢刀具可选择粒度为46-80的白刚石或碳化硅砂轮;刃磨硬质合金刀具可选择粒度为100-120的人工金刚石或立方氮化硼砂轮。
3. 刀具夹持与定位:将刀具精确定位在刃磨机床上,并采用牢固的夹持装置固定刀具,确保夹持力与切削力的平衡,有效避免刀具在刃磨过程中发生移位和晃动的情况。
4. 刃磨规则:在刃磨过程中,应使用适当的冷却液将刃磨面冷却,避免因加热引起的刃口变形。
刀具的刃磨规则通常为:前倾角5-7°,刃尖倒角15-20°,主切割刃角度8-15°。
5. 刃磨后检验:刃磨完毕后,应进行刀具质量检验,包括外观检查、尺寸测量和质量检测等,确保刀具达到设计要求,以保证加工质量。
二、调试技巧1. 刀具安装:在进行调试之前,先将刀具正确安装到数控机床上。
安装时应注意调整好安装位置和夹持力,确保刀具稳固可靠。
2. 刀具配合检查:调试过程中,需要检查刀具与夹头、刀杆的配合是否紧密,避免出现松动和摆动等问题,影响加工精度。
3. 设定刀具参数:根据加工要求和刀具特点,设定合适的切削速度、进给量和切削深度等刀具参数,以提高加工效率和保证加工质量。
4. 初次试切:进行初次试切时,应逐步加工,确保刀具和零件之间的配合与加工精度。
观察切削状况,根据需要适当调整刀具参数。
5. 精细调试:在初次试切的基础上,进行进一步的磨调试双重工作。
通过微小的调整,提高加工精度和效率,并确保刀具运行平稳可靠。
硬质合金切削刀具的材料选择与表面涂层优化
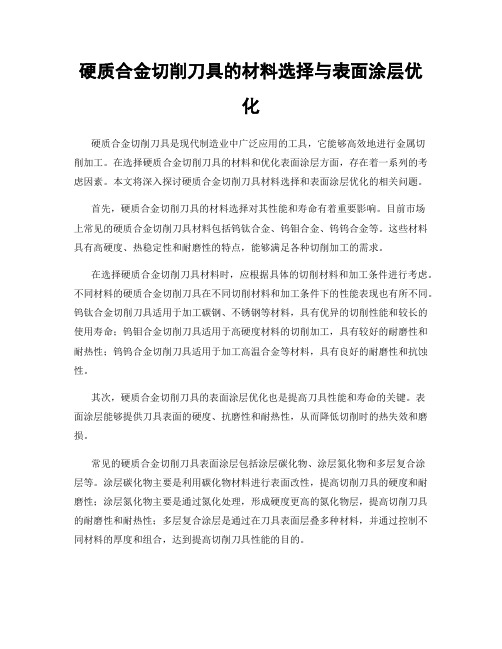
硬质合金切削刀具的材料选择与表面涂层优化硬质合金切削刀具是现代制造业中广泛应用的工具,它能够高效地进行金属切削加工。
在选择硬质合金切削刀具的材料和优化表面涂层方面,存在着一系列的考虑因素。
本文将深入探讨硬质合金切削刀具材料选择和表面涂层优化的相关问题。
首先,硬质合金切削刀具的材料选择对其性能和寿命有着重要影响。
目前市场上常见的硬质合金切削刀具材料包括钨钛合金、钨钼合金、钨钨合金等。
这些材料具有高硬度、热稳定性和耐磨性的特点,能够满足各种切削加工的需求。
在选择硬质合金切削刀具材料时,应根据具体的切削材料和加工条件进行考虑。
不同材料的硬质合金切削刀具在不同切削材料和加工条件下的性能表现也有所不同。
钨钛合金切削刀具适用于加工碳钢、不锈钢等材料,具有优异的切削性能和较长的使用寿命;钨钼合金切削刀具适用于高硬度材料的切削加工,具有较好的耐磨性和耐热性;钨钨合金切削刀具适用于加工高温合金等材料,具有良好的耐磨性和抗蚀性。
其次,硬质合金切削刀具的表面涂层优化也是提高刀具性能和寿命的关键。
表面涂层能够提供刀具表面的硬度、抗磨性和耐热性,从而降低切削时的热失效和磨损。
常见的硬质合金切削刀具表面涂层包括涂层碳化物、涂层氮化物和多层复合涂层等。
涂层碳化物主要是利用碳化物材料进行表面改性,提高切削刀具的硬度和耐磨性;涂层氮化物主要是通过氮化处理,形成硬度更高的氮化物层,提高切削刀具的耐磨性和耐热性;多层复合涂层是通过在刀具表面层叠多种材料,并通过控制不同材料的厚度和组合,达到提高切削刀具性能的目的。
在进行硬质合金切削刀具表面涂层优化时,应根据切削材料、加工条件和切削过程中的磨损机理来选择合适的涂层类型。
以增加刀具的硬度和抗磨性为主要目标,选择碳化物涂层;以提高刀具的耐热性和耐磨性为主要目标,选择氮化物涂层。
同时,在选择涂层材料时,还应考虑成本、制备工艺和刀具几何形状等因素。
此外,刀具表面涂层的结构和性能也需要进行优化。
车刀磨修

车刀磨修一、砂轮的选择:粗磨车刀应选磨粒号数小的砂轮,精磨车刀应选号数大( 即磨粒细) 的砂轮。
刃磨高速钢车刀和硬质合金车刀时应选软或中软的砂轮。
刃磨高速钢车刀时,应选用粒度为46号到60号的软或中软的氧化铝砂轮。
刃磨硬质合金车刀时,应选用粒度为60号到80号的软或中软的碳化硅砂轮,两者不能搞错二、车刀刃磨的步骤1、磨主后刀面,同时磨出主偏角及主后角;2、磨副后刀面,同时磨出副偏角及副后角3、磨前面,同时磨出前角;4、修磨各刀面及刀尖。
三、刃磨车刀的姿势及方法1、人站立在砂轮机的侧面,以防砂轮碎裂时,碎片飞出伤人;2、两手握刀的距离放开,两肘夹紧腰部,以减小磨刀时的抖动;3、磨刀时,车刀要放在砂轮的水平中心,刀尖略向上翘约3°~8°,车刀接触砂轮后应作左右方向水平移动。
当车刀离开砂轮时,车刀需向上抬起,以防磨好的刀刃被砂轮碰伤;4、磨后刀面时,刀杆尾部向左偏过一个主偏角的角度;磨副后刀面时,刀杆尾部向右偏过一个副偏角的角度;5、修磨刀尖圆弧时,通常以左手握车刀前端为支点,用右手转动车刀的尾部。
四、磨刀安全知识1、刃磨刀具前,应首先检查砂轮有无裂纹,砂轮轴螺母是否拧紧,并经试转后使用,以免砂轮碎裂或飞出伤人。
2、刃磨刀具不能用力过大,否则会使手打滑而触及砂轮面,造成工伤事故。
3、磨刀时应戴防护眼镜,以免砂砾和铁屑飞入眼中。
4、磨刀时不要正对砂轮的旋转方向站立,以防意外。
5、磨小刀头时,必须把小刀头装入刀杆上。
6、砂轮支架与砂轮的间隙不得大于3mm,入发现过大,应调整适当。
五、车刀几何参数的综合选择车刀刃磨水平的高低直接关系到产品的生产效率、加工质量、设备能耗和产品成本,甚至关系到操作者的人身安全,也反映出操作者对加工主体的特性和切削用量的灵活应变能力。
合理选择车刀的几何参数是决定刃磨质量的关键,其主要体现于对车刀角度和前面形状的合理选择。
两者既相互依赖又相互制约,一把车刀不能只有一个角度,如果只有一个角度选择合理,它的切削效果也不一定理想,操作者必须根据工件材料、车刀材料、切削用量,以及工件、车刀、夹具和车床的刚性等各方面因素,全面分析,找出切削过程中的主要矛盾,合理选择车刀的角度和前面形状。
刀具磨削加工时如何正确选择砂轮?

刀具磨削加工时如何正确选择砂轮?一、普通砂轮的选择1、磨料的选择磨料选择主要取决于工件材料及热处理方法。
a.磨抗张强度高的材料时,选用韧性大的磨料。
b.磨硬度低,延伸率大的材料时,选用较脆的磨料。
c.磨硬度高的材料时,选用硬度更高的磨料。
d.选用不易被加工材料发生化学反应的磨料。
最常用的磨料是棕刚玉(A)和白刚玉(WA),其次是黑碳化硅(C)和绿碳化硅(GC),其余常用的还有铬刚玉(PA)、单晶刚玉(SA)、微晶刚玉(MA)、锆刚玉(ZA)。
棕刚玉砂轮:棕刚玉的硬度高,韧性大,适宜磨削抗拉强度较高的金属,如碳钢、合金钢、可锻铸铁、硬青铜等,这种磨料的磨削性能好,适应性广,常用于切除较大余量的粗磨,价格便宜,可以广泛使用。
白刚玉砂轮:白刚玉的硬度略高于棕刚玉,韧性则比棕刚玉低,在磨削时,磨粒容易碎裂,因此,磨削热量小,适宜制造精磨淬火钢、高碳钢、高速钢以及磨削薄壁零件用的砂轮,成本比棕刚玉高。
黑碳化硅砂轮:黑碳化硅性脆而锋利,硬度比白刚玉高,适于磨削机械强度较低的材料,如铸铁、黄铜、铝和耐火材料等。
绿碳化硅砂轮:绿碳化硅硬度脆性较黑碳化硅高,磨粒锋利,导热性好,适合于磨削硬质合金、光学玻璃、陶瓷等硬脆材料。
铬刚玉砂轮:适于磨削刀具,量具、仪表,螺纹等表面加工质量要求高的工件。
单晶刚玉砂轮:适于磨削不锈钢、高钒高速钢等韧性大、硬度高的材料及易变形烧伤的工件。
微晶刚玉砂轮:适于磨削不锈钢、轴承钢和特种球墨铸铁等,用于成型磨,切入磨,镜面磨削。
锆刚玉砂轮:适于磨削奥氐体不锈钢、钛合金、耐热合金,特别适于重负荷磨削。
2、粒度的选择主要取决于被磨削工件的表面粗糙度和磨削效率。
粒度是指磨料的颗粒尺寸,其大小则用粒度号表示。
用粗粒度砂轮磨削时,生产效率高,但磨出的工件表面较粗糙;用细粒度砂轮磨削时,磨出的工件表面粗糙度较好,而生产率较低。
在满足粗糙度要求的前提下,应尽量选用粗粒度的砂轮,以保证较高的磨削效率。
一般粗磨时选用粗粒度砂轮,精磨时选用细粒度砂轮。
金刚石砂轮加工整体硬质合金刀具的磨削参数选择

n d i n g a r e c i t e d . T h e c a u s e s o f t h e p r o b l e ms a r e a n a l y z e d a n d t h e me a s u r e s i n t e r ms o f g r i n d i n g p a r a me t e r s h a v e b e e n t a k e n . A me t h o d f o r r a p i d i d e n t i f i c a t i o n o f s u i t a b l e g r i n d i n g p ra a me t e r s i s i n t r o d u c e d f o r t h e g r i n d i n g p ra a me t e s r f r o m e mp i ic r a l d a t a t o e x p a n d t h e n e w s p e c i f i c a t i o n t o o l p r o c e s s i n g . Ke y wo r d s :d i a mo n d g i r n d i n g wh e e l ;c e me n t e d c a r b i d e ;g r i n d i n g p a r a me t e r
6 0
工 具 技 术
金 刚石 砂 轮 加 工整 体 硬 质 合 金 刀具 的磨 削 参 数 选 择
袁剑
哈尔 滨量 具刃具 集 团有 限公 司
摘要 :磨 削参数会影响磨削质量 、 砂轮 的使用寿命 以及加 工效率 , 本文 阐述 了磨削 整体硬质 合金刀具所 用 的 砂轮类型 , 列举 了在磨 削中常见 的问题并分析 了问题产生 的原 因及在磨削参数方 面应采取 的措施 。介绍 了一种快 速确定合适的磨 削参数 的方法 , 该方法用于将磨 削参 数经验数据扩展至新规 格刀具的加工 中。
硬质合金刀片切削参数推荐表
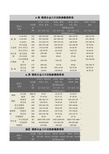
P类硬质合金刀片切削参数推荐表被加工材料布氏硬度HBYC10、YT30YT05、K7HYC20、ZP10YT15、K45YC30、ZP30YT5、K21YC40、YT540K25进给量(mm/转)0.1~0.3~0.50.2~0.4~0.60.2~0.5~1.00.3~0.6~1.2切削速度(m/min)碳钢C=0.15% 125 395 270 225 355 260 195 190 135 95 160 115 85 C=0.35% 150 355 250 205 265 190 155 169 125 95 155 105 80 C=0.6% 200 315 220 175 230 170 115 140 95 80 125 100 70合金钢退火状态180 250 170 140 150 135 95 125 105 90 95 70 50 淬火并回火275 170 115 90 120 90 65 85 65 50 70 50 35 淬火并回火350 135 90 70 85 70 50 70 45 35 55 40 25高合金钢退火状态200 220 140 130 95 105 70 85 65 40 淬火状态325 100 65 80 65 55 40 40 30 20不锈钢马氏体/铁素体100 230 190 150 125 110 80120 100 80 奥氏体175 200 165 115 95 90 60 120 100 75铸钢低合金200 150 105 150 115 85 90 70 50 60 50 35 高合金225 120 85 120 90 65 70 50 30 45 35 25K类硬质合金刀片切削参数推荐表;;;;;;;;;;;;被加工材料布氏硬度HBYD10.2、ZK10UFCG10、K11YD20、ZK20YG8、K6YD10.1、ZK10YG6X、K68进给量(mm/转)0.1~0.3~0.50.2~0.5~1.00.2~0.5~1.0切削速度(m/min)硬钢淬火钢HRC55 36 25 26 15 10 31 20 15 锰钢250 57 43 28 62 37 15 47 28 20锻铁铁素体130 180 146 117 100 70 42 190 155 125 珠光体230 120 96 83 70 58 28 120 92 52低合金铸铁180 230 169 130 130 87 52 205 140 86 高合金铸铁260 165 115 90 92 62 38 155 110 56球墨铸铁铁素体160 185 140 115 110 75 42 175 130 82 珠光体250 165 125 105 95 76 36 155 115 72 冷硬铸铁400 30 16 16 10 23 14铝合金不可热处理60 2400 1950 1550 1650 1200 950 2200 1750 1400 可热处理100 810 600 460 470 320 220 780 550 400 硬塑料670 460 340 200 550 420涂层硬质合金刀片切削参数推荐表被加工材料布氏硬度HBYB415、KC910ZC312N、GC415YB125、KC810ZC302N、GC425YB435、KC935ZC314N、GC435进给量(mm/转)0.10~0.4~0.80.1~0.4~0.80.2~0.5~1.0 ; ; ; ; ; ;; ; ;; ; ; ; ;切削速度(m/min)碳 钢C=0.5% 125 480 340 250 440 300 210 320 230 160 C=0.35% 150 440 310 230 400 270 200 300 210 150 C=0.6% 200 380 270 200 340 230 180 260 180 130 合金钢退火状态 180 380 260 190 290 190 140 200 140 90 淬火并回火 275 260 180 130 200 130 95 130 95 65 淬火并回火 300 240 165 120 185 120 90 125 90 60 淬火并回火 350 205 145 105 160 105 75 110 75 55 高合金钢 退火状态 200 350 230 170 265 175 130 175 115 80 淬火状态 325 170 110 95 65 50 85 55 40不锈钢马氏体/铁素体 100 295 240 170 265 195 155 220 175 145 奥氏体 175 285 240 160 240 190 140 195 160 125 铸 钢非合金 180 260 185 145 190 130 100 135 105 75低合金200255 160 120160 115 85120 90 60 高合金225190 130 95135 90 7095 70 55。
刀具的刃磨技术
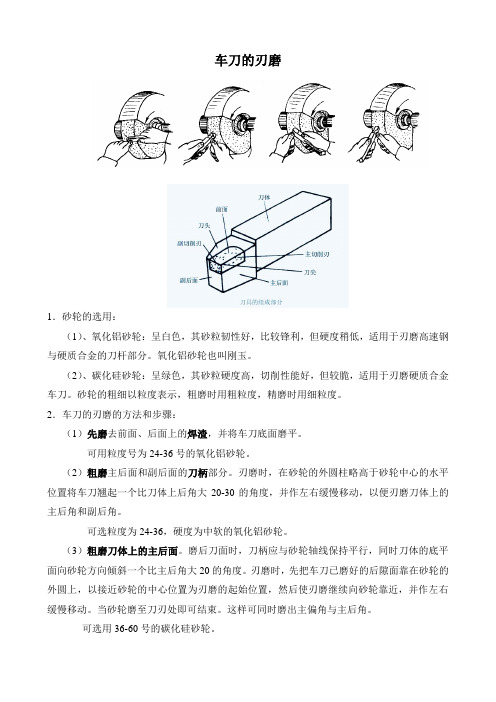
车刀的刃磨1.砂轮的选用:(1)、氧化铝砂轮:呈白色,其砂粒韧性好,比较锋利,但硬度稍低,适用于刃磨高速钢与硬质合金的刀杆部分。
氧化铝砂轮也叫刚玉。
(2)、碳化硅砂轮:呈绿色,其砂粒硬度高,切削性能好,但较脆,适用于刃磨硬质合金车刀。
砂轮的粗细以粒度表示,粗磨时用粗粒度,精磨时用细粒度。
2.车刀的刃磨的方法和步骤:(1)先磨去前面、后面上的焊渣,并将车刀底面磨平。
可用粒度号为24-36号的氧化铝砂轮。
(2)粗磨主后面和副后面的刀柄部分。
刃磨时,在砂轮的外圆柱略高于砂轮中心的水平位置将车刀翘起一个比刀体上后角大20-30的角度,并作左右缓慢移动,以便刃磨刀体上的主后角和副后角。
可选粒度为24-36,硬度为中软的氧化铝砂轮。
(3)粗磨刀体上的主后面。
磨后刀面时,刀柄应与砂轮轴线保持平行,同时刀体的底平面向砂轮方向倾斜一个比主后角大20的角度。
刃磨时,先把车刀已磨好的后隙面靠在砂轮的外圆上,以接近砂轮的中心位置为刃磨的起始位置,然后使刃磨继续向砂轮靠近,并作左右缓慢移动。
当砂轮磨至刀刃处即可结束。
这样可同时磨出主偏角与主后角。
可选用36-60号的碳化硅砂轮。
(4)粗磨刀体上的副后角。
磨副后面时,刀柄尾部应向右转过一个副偏角的角度,同时车刀底平面向砂轮方向倾斜一个比副后角大20的角度,具体刃磨方法与粗磨刀体上主后面大体相同,不同的是粗磨副后面时砂轮应磨到刀尖处为止。
也可同时磨出副偏角和副后角。
(5)粗磨前面。
以砂轮的端面粗磨出车刀的前面,并在磨前面的同时磨出前角。
(6)磨断屑槽。
断屑槽有两种,一种是直线型,适用于切削较硬的材料;一种是圆弧型,适用于较软的材料。
手工刃磨的断屑槽一般为圆弧型,须将砂轮的外圆和端面的交角处用修砂轮的金刚石笔修磨成相应的圆弧。
若刃磨出直线型断屑槽,则砂轮的交角须修磨得很尖锐。
刃磨时可向下磨或向上磨,但选择刃磨断屑槽部位时,应考虑留出刀头倒棱的宽度。
刃磨断屑槽的注意事项:砂轮交角处应经常保持尖锐或具有一定形状的圆弧,当砂轮的棱边有较大的棱角时,应及时修整。
磨具磨料粒度及硬度选用原则

磨料是磨具起磨削作用的重要因素,磨料的选择主要根据工件材料的性质,如硬度、抗张强度、韧性等来确定,选择磨具磨料的基本原则是:磨削硬度高的工件材料时,应选择硬度更高的磨料;磨削抗张强度高的工件材料时,应选用韧性大的磨料;磨削抗张强度低的材料时,应选用较脆或强度高的碳化硅磨料。
具体说,棕刚玉适应磨削碳钢、铸铁合金钢、硬青铜等;白刚玉适应磨削淬火钢、合金钢、高速钢、工具钢等;黑碳化硅适应磨削有色金属、橡胶、皮革、塑料等;绿碳化硅适应磨削硬质合金、光学玻璃、陶瓷材料等;SG、CBN陶瓷磨具广泛用于难磨材料。
此外,为了充分发挥各种磨料在磨削中的优点,目前在磨具制造中己广泛采用混合磨料,以提高磨具磨削效率。
如:磨球墨铸铁时,一般采用A/WA混合磨料;棕、白刚玉两种混合磨料,磨削时既有棕刚玉高韧性的特点,又发挥了白刚玉兼有一定脆性和导热性较好的特点。
(如磨曲轴砂轮多采用棕、白混合,粒度60#~80#,硬度中软2到中1)(粗磨钴基合金齿轮齿形砂轮,可用单晶和微晶两种混合)(磨铝高速钢砂轮,采用棕刚玉、绿碳化硅混合)(磨球面轴承内外套圈砂轮,应采用棕、白混合,代表规格是:GZ/GB80#P600×36×305是粗磨滚道。
GZ/GB80#P600×510×355.6是终磨外径等。
磨具粒度选择原则?选择磨料粒度时,主要应根据加工精度、表面粗糙度和磨削效率的要求来选择。
一般原则如下:要求被磨工件粗糙度高,应选择粗粒度;要求表面粗糙度低,应选择细粒度。
工件要求较高的几何精度和较低的表面粗糙度时,应选择混合粒度。
工件几何精度要求高,当砂轮与工件接触面积小时,应选择细粒度;接触面积大时,选择粗粒度。
工件材质硬而脆,应选择细粒度;工件材料软而韧,应选择粗粒度。
工件的导热性差,易发热变形,易烧伤,应选择较粗粒度。
磨具硬度选择原则?选择磨具硬度时,主要根据工件材料的性质、磨削方式来选择。
砂轮的硬度是指砂轮表面上的磨粒在磨削力作用下脱落的难易程度。
硬质合金刀具选用指导
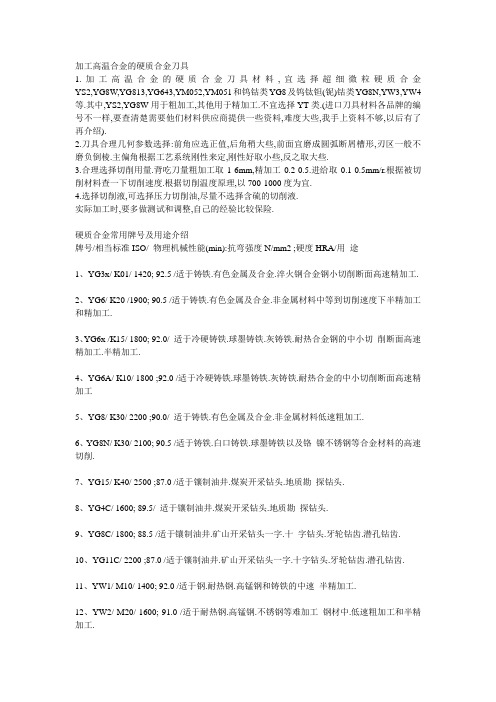
加工高温合金的硬质合金刀具1.加工高温合金的硬质合金刀具材料,宜选择超细微粒硬质合金YS2,YG8W,YG813,YG643,YM052,YM051和钨钴类YG8及钨钛钽(铌)钴类YG8N,YW3,YW4等.其中,YS2,YG8W用于粗加工,其他用于精加工.不宜选择YT类.(进口刀具材料各品牌的编号不一样,要查清楚需要他们材料供应商提供一些资料,难度大些,我手上资料不够,以后有了再介绍).2.刀具合理几何参数选择:前角应选正值,后角稍大些,前面宜磨成圆弧断屑槽形,刃区一般不磨负倒棱.主偏角根据工艺系统刚性来定,刚性好取小些,反之取大些.3.合理选择切削用量.背吃刀量粗加工取1-6mm,精加工0.2-0.5.进给取0.1-0.5mm/r.根据被切削材料查一下切削速度.根据切削温度原理,以700-1000度为宜.4.选择切削液,可选择压力切削油,尽量不选择含硫的切削液.实际加工时,要多做测试和调整,自己的经验比较保险.硬质合金常用牌号及用途介绍牌号/相当标准ISO/ 物理机械性能(min):抗弯强度N/mm2 ;硬度HRA/用途1、YG3x/ K01/ 1420; 92.5 /适于铸铁.有色金属及合金.淬火钢合金钢小切削断面高速精加工.2、YG6/ K20 /1900; 90.5 /适于铸铁.有色金属及合金.非金属材料中等到切削速度下半精加工和精加工.3、YG6x /K15/ 1800; 92.0/ 适于冷硬铸铁.球墨铸铁.灰铸铁.耐热合金钢的中小切削断面高速精加工.半精加工.4、YG6A/ K10/ 1800 ;92.0 /适于冷硬铸铁.球墨铸铁.灰铸铁.耐热合金的中小切削断面高速精加工5、YG8/ K30/ 2200 ;90.0/ 适于铸铁.有色金属及合金.非金属材料低速粗加工.6、YG8N/ K30/ 2100; 90.5 /适于铸铁.白口铸铁.球墨铸铁以及铬镍不锈钢等合金材料的高速切削.7、YG15/ K40/ 2500 ;87.0 /适于镶制油井.煤炭开采钻头.地质勘探钻头.8、YG4C/ 1600; 89.5/ 适于镶制油井.煤炭开采钻头.地质勘探钻头.9、YG8C/ 1800; 88.5 /适于镶制油井.矿山开采钻头一字.十字钻头.牙轮钻齿.潜孔钻齿.10、YG11C/ 2200 ;87.0 /适于镶制油井.矿山开采钻头一字.十字钻头.牙轮钻齿.潜孔钻齿.11、YW1/ M10/ 1400; 92.0 /适于钢.耐热钢.高锰钢和铸铁的中速半精加工.12、YW2/ M20/ 1600; 91.0 /适于耐热钢.高锰钢.不锈钢等难加工钢材中.低速粗加工和半精加工.13、GE1/ M30/ 2000; 91.0 /适于非金属材料的低速粗加工和钟表齿轮耐磨损零件.14、GE2 /2500; 90.0 /硬质合金顶锤专用牌号.15、GE3/ M40/ 2600; 90.0 /适于制造细径微钻.立铣刀.旋转挫刀等.16、GE4/ 2600; 88.0/ 适于打印针.压缸及特殊用途的管. 棒.带等.17、GE5 /2800 ;85.0 /适于轧辊.冷冲模等耐冲击材料.。
磨刀石参数
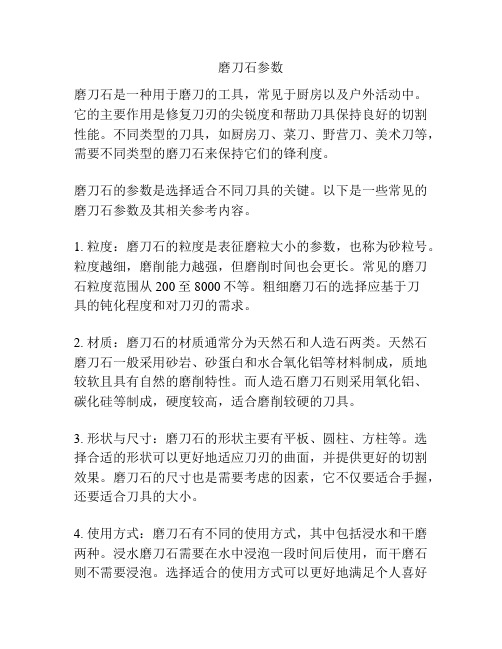
磨刀石参数磨刀石是一种用于磨刀的工具,常见于厨房以及户外活动中。
它的主要作用是修复刀刃的尖锐度和帮助刀具保持良好的切割性能。
不同类型的刀具,如厨房刀、菜刀、野营刀、美术刀等,需要不同类型的磨刀石来保持它们的锋利度。
磨刀石的参数是选择适合不同刀具的关键。
以下是一些常见的磨刀石参数及其相关参考内容。
1. 粒度:磨刀石的粒度是表征磨粒大小的参数,也称为砂粒号。
粒度越细,磨削能力越强,但磨削时间也会更长。
常见的磨刀石粒度范围从200至8000不等。
粗细磨刀石的选择应基于刀具的钝化程度和对刀刃的需求。
2. 材质:磨刀石的材质通常分为天然石和人造石两类。
天然石磨刀石一般采用砂岩、砂蛋白和水合氧化铝等材料制成,质地较软且具有自然的磨削特性。
而人造石磨刀石则采用氧化铝、碳化硅等制成,硬度较高,适合磨削较硬的刀具。
3. 形状与尺寸:磨刀石的形状主要有平板、圆柱、方柱等。
选择合适的形状可以更好地适应刀刃的曲面,并提供更好的切割效果。
磨刀石的尺寸也是需要考虑的因素,它不仅要适合手握,还要适合刀具的大小。
4. 使用方式:磨刀石有不同的使用方式,其中包括浸水和干磨两种。
浸水磨刀石需要在水中浸泡一段时间后使用,而干磨石则不需要浸泡。
选择适合的使用方式可以更好地满足个人喜好和实际需求。
5. 附件:一些磨刀石会配备附件,如磨刀角度固定器、底座等。
磨刀角度固定器可以帮助用户保持合适的刀刃角度,提供更一致的切割效果。
底座则可以提供更稳定的工作平台,减少石板移动的可能性。
总的来说,选择合适的磨刀石参数是保证刀具保持锋利的重要因素。
粒度、材质、形状与尺寸、使用方式以及附件都是需要根据个人的需求和偏好来综合考虑的。
除了以上提到的参数,还有一些其他因素,如磨刀石的品牌、价格、耐久性等也是需要考虑的。
因此,在购买磨刀石时,建议根据自己的真实需求,选择适当的参数来满足刀具的保养和使用。
合金车刀磨刀方法及怎么磨【纯干货】
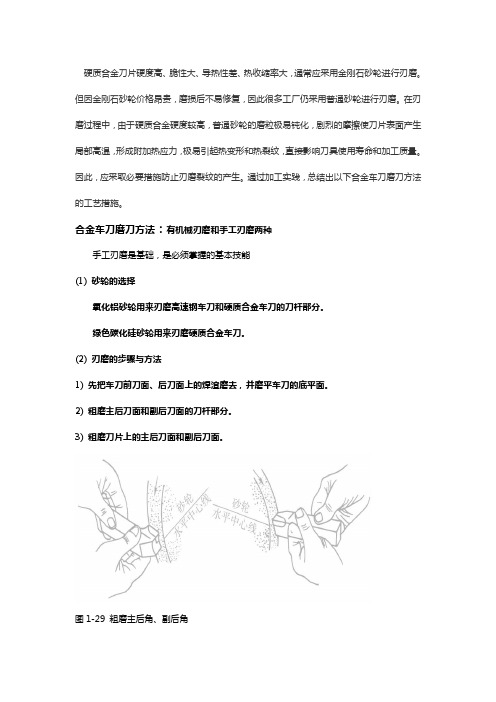
硬质合金刀片硬度高、脆性大、导热性差、热收缩率大,通常应采用金刚石砂轮进行刃磨。
但因金刚石砂轮价格昂贵,磨损后不易修复,因此很多工厂仍采用普通砂轮进行刃磨。
在刃磨过程中,由于硬质合金硬度较高,普通砂轮的磨粒极易钝化,剧烈的摩擦使刀片表面产生局部高温,形成附加热应力,极易引起热变形和热裂纹,直接影响刀具使用寿命和加工质量。
因此,应采取必要措施防止刃磨裂纹的产生。
通过加工实践,总结出以下合金车刀磨刀方法的工艺措施。
合金车刀磨刀方法:有机械刃磨和手工刃磨两种手工刃磨是基础,是必须掌握的基本技能(1) 砂轮的选择氧化铝砂轮用来刃磨高速钢车刀和硬质合金车刀的刀杆部分。
绿色碳化硅砂轮用来刃磨硬质合金车刀。
(2) 刃磨的步骤与方法1) 先把车刀前刀面、后刀面上的焊渣磨去,并磨平车刀的底平面。
2) 粗磨主后刀面和副后刀面的刀杆部分。
3) 粗磨刀片上的主后刀面和副后刀面。
图1-29 粗磨主后角、副后角4) 磨断屑槽图1-30 刃磨断屑槽的方法5) 精磨主后刀面和副后刀面图1-31 精磨主后角和副后角6) 磨负倒棱图1-32 磨负倒棱a)直磨法b)横磨法7) 磨过渡刃图1-33 磨过渡刃a)磨直线形过渡刃b)磨圆弧形过渡刃防止或减少刃磨裂纹的合金车刀磨刀方法1 负刃刃磨法负刃刃磨法是指在刃磨刀具前,先在前刀面或后刀面上磨出一条负刃带。
硬质合金属于硬脆材料,刃磨时因砂轮振动使刀具受到冲击载荷,容易发生振裂;同时,磨削区的瞬间升温与冷却使热应力可能超过硬质合金的强度极限而产生热裂纹。
采用负刃刃磨法可提高刀片强度,增强刀片抗振性和承受冲击载荷的能力,并增大受热面积,防止磨削热大量导向刀片,从而减少或防止裂纹产生。
2 用二硫化钼浸润砂轮在常温状态下,将粉状二硫化钼与无水乙醇制成混合溶液,然后在密闭容器内(防止乙醇挥发)将新的普通砂轮浸泡在混合溶液中,14小时后取出,自然干燥18~20小时,使砂轮完全晾干。
经上述处理的砂轮内部空隙中充满二硫化钼,对磨粒可起到润滑作用,使砂轮排屑良好,不易堵塞。
车刀的标准修磨方法
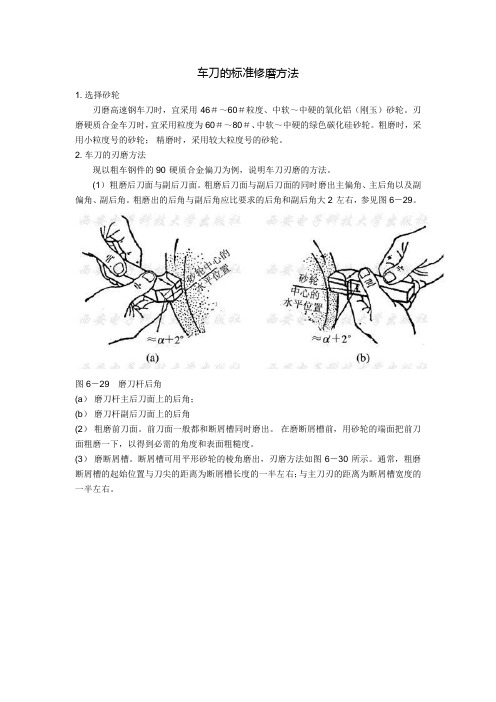
车刀的标准修磨方法1. 选择砂轮刃磨高速钢车刀时,宜采用46#~60#粒度、中软~中硬的氧化铝(刚玉)砂轮。
刃磨硬质合金车刀时,宜采用粒度为60#~80#、中软~中硬的绿色碳化硅砂轮。
粗磨时,采用小粒度号的砂轮;精磨时,采用较大粒度号的砂轮。
2. 车刀的刃磨方法现以粗车钢件的90°硬质合金偏刀为例,说明车刀刃磨的方法。
(1)粗磨后刀面与副后刀面。
粗磨后刀面与副后刀面的同时磨出主偏角、主后角以及副偏角、副后角。
粗磨出的后角与副后角应比要求的后角和副后角大2°左右,参见图6-29。
图6-29磨刀杆后角(a)磨刀杆主后刀面上的后角;(b)磨刀杆副后刀面上的后角(2)粗磨前刀面。
前刀面一般都和断屑槽同时磨出。
在磨断屑槽前,用砂轮的端面把前刀面粗磨一下,以得到必需的角度和表面粗糙度。
(3)磨断屑槽。
断屑槽可用平形砂轮的棱角磨出,刃磨方法如图6-30所示。
通常,粗磨断屑槽的起始位置与刀尖的距离为断屑槽长度的一半左右;与主刀刃的距离为断屑槽宽度的一半左右。
图6-30粗磨断屑槽(a) 向下磨;(b) 向上磨2)精磨车刀(1)精磨断屑槽。
为使断屑槽的形状修整得更正确,表面粗糙度更细些,粗磨后的断屑槽还需精磨,精磨断屑槽的方法与粗磨相同。
(2)磨负倒棱。
负倒棱一般用杯形砂轮的端面磨出,砂轮的粒度为100#~200#,刃磨方法如图6-31所示。
图6-31磨负倒棱(a)沿刀刃方向的磨刀位置;(b)垂直刀刃方向的磨刀位置(3)精磨后刀面与副后刀面,刃磨方法如图6-32所示,采用的砂轮与磨负倒棱时相同。
当主刀刃全部磨出并且负倒棱宽度达到要求时停止刃磨。
(4)磨过渡刃,刃磨方法如图6-33所示,图6-33(a)所示为刃磨直线形过渡刃,图6-33(b)为刃磨圆弧形过渡刃。
图6-32精磨后刀面和副后刀面(a)精磨后刀面;(b)精磨副后刀面图6-33磨过渡刃(a)刃磨直线形过渡刃;(b)刃磨圆弧形过渡刃(5)磨修光刃,刃磨方法如图6-34所示。
硬质合金刀具的性能评估与选用指南

硬质合金刀具的性能评估与选用指南硬质合金刀具是现代切削工具中的重要成员之一,其在工业生产中起到关键的作用。
为了确保合理选用硬质合金刀具,并实现最佳的切削效果和使用寿命,必须对其性能进行评估和选择。
本文将对硬质合金刀具的性能评估和选用指南进行探讨。
首先,评估硬质合金刀具的性能需要考虑以下几个方面:1. 切削性能:切削性能是衡量硬质合金刀具的重要指标之一。
切削性能包括切削力、表面质量和切削速度等。
切削力越小,表面质量越好,切削速度越高,刀具的切削性能越好。
2. 耐磨性:硬质合金刀具耐磨性是指其在切削过程中能够抵御磨损的能力。
一般来说,硬质合金刀具的耐磨性越好,使用寿命越长。
耐磨性的评估可以通过刀具磨损的量来进行,磨损量越小,耐磨性越好。
3. 抗折性:硬质合金刀具在切削负荷下容易发生断裂,抗折性就是刀具在切削过程中抵御断裂的能力。
抗折性的评估可以通过刀具的折断率来进行,折断率越低,刀具的抗折性越好。
4. 刚性:刚性是指硬质合金刀具在切削过程中的抗变形能力。
刀具的刚性越好,切削过程中的变形越小,切削精度越高。
在评估硬质合金刀具的性能之后,下面是硬质合金刀具选用的指南:1. 根据切削材料来选择合适的刀具:不同的材料对刀具的要求也不同。
例如,对于钢铁材料,一般推荐使用钨钛合金刀具;对于铸铁材料,一般推荐使用氮化钨刀具;对于不锈钢材料,一般推荐使用钛铝合金刀具等。
因此,根据切削材料的不同来选择合适的刀具至关重要。
2. 根据加工类型和切削条件来选择刀具:不同的加工类型和切削条件对刀具的要求也不同。
例如,对于粗加工,一般需要使用强度较高的刀具;对于精加工,一般需要使用刀具的刚性和耐磨性较好的刀具。
因此,在选择刀具时,要考虑加工类型和切削条件的因素。
3. 参考推荐表格和经验数据:根据厂家提供的推荐表格和经验数据,可以了解不同硬质合金刀具的适用范围和性能指标。
通过参考推荐表格和经验数据,可以有效地选用合适的刀具。
4. 考虑成本和效益:选择刀具时,不仅要考虑刀具的性能,还要考虑其成本和效益。
磨削加工中的磨料选择

磨削加工中的磨料选择磨削加工是一种重要的金属加工方式,通过磨料在工件表面上切削去除不需要的材料,达到精密加工目的。
而在磨削加工中,磨料的选择对于加工效果至关重要。
不同种类的磨料,具有不同的物理特性和化学成分,使用时需要根据具体情况进行选择。
1. 刚玉磨料刚玉磨料是一种常见的人工磨料,具有硬度高、耐磨性好、化学稳定、导热性能好等优点,适用于对硬度大的金属材料进行磨削加工。
同时,粒度大小也会影响到加工效果,细小的刚玉磨料适用于高精度的磨削,而粗颗粒刚玉磨料则适用于快速粗磨。
2. 碳化硅磨料碳化硅磨料是一种非常硬的天然磨料,适用于对硬度较高的金属材料进行粗磨和中磨,具有高耐磨性、热稳定性和低密度等特点,同时也能够在高温下使用。
但是,碳化硅磨料的弱点是容易受到化学腐蚀,使用时需要避免对其带来损害。
3. 钻石磨料钻石磨料是一种最硬的人造磨料,使用时具有很高的磨削效果和磨削速度,同时也很耐磨。
因此,钻石磨料适用于对硬度非常高的金属材料进行磨削加工,如硬质合金等。
但是,钻石磨料成本较高,使用时需要谨慎考虑。
4. 氧化铝磨料氧化铝磨料是一种较为常见的磨料,具有较好的耐磨性和化学稳定性,适用于对铜、铝等较为软的金属材料进行中磨和精磨。
同时,氧化铝磨料的化学活性较低,使用时对工件不会造成损伤。
5. 涂布磨料涂布磨料一般是指将磨料涂布在轮胎上,磨削时采用旋转方式进行加工。
这种磨料适用于对大型工件的磨削加工,具有速度快、使用寿命长等优缺点,适用于需要大量高效量产的企业。
综上所述,不同种类的磨料具有不同的优缺点,使用时需要针对不同的加工需求进行选择。
同时,磨料的选择也需要考虑硬度、耐磨性和化学稳定性等多方面因素。
在实际加工过程中,需要根据工件的形状、材料等具体情况进行选择,才能够达到最佳的磨削效果。
磨具磨料粒度及硬度选用原则(甲类精制)

磨具磨料粒度及硬度选用原则,总结的还挺全面磨料是磨具起磨削作用的重要因素,磨料的选择主要根据工件材料的性质,如硬度、抗张强度、韧性等来确定,选择磨具磨料的基本原则是:磨削硬度高的工件材料时,应选择硬度更高的磨料;磨削抗张强度高的工件材料时,应选用韧性大的磨料;磨削抗张强度低的材料时,应选用较脆或强度高的碳化硅磨料。
具体说,棕刚玉适应磨削碳钢、铸铁合金钢、硬青铜等;白刚玉适应磨削淬火钢、合金钢、高速钢、工具钢等;黑碳化硅适应磨削有色金属、橡胶、皮革、塑料等;绿碳化硅适应磨削硬质合金、光学玻璃、陶瓷材料等;SG、CBN陶瓷磨具广泛用于难磨材料。
此外,为了充分发挥各种磨料在磨削中的优点,目前在磨具制造中己广泛采用混合磨料,以提高磨具磨削效率。
如:磨球墨铸铁时,一般采用A/WA混合磨料;棕、白刚玉两种混合磨料,磨削时既有棕刚玉高韧性的特点,又发挥了白刚玉兼有一定脆性和导热性较好的特点。
(如磨曲轴砂轮多采用棕、白混合,粒度60#~80#,硬度中软2到中1)(粗磨钴基合金齿轮齿形砂轮,可用单晶和微晶两种混合)(磨铝高速钢砂轮,采用棕刚玉、绿碳化硅混合)(磨球面轴承内外套圈砂轮,应采用棕、白混合,代表规格是:GZ/GB80#P600×36×305是粗磨滚道。
GZ/GB80#P600×510×355.6是终磨外径等。
磨具粒度选择原则?选择磨料粒度时,主要应根据加工精度、表面粗糙度和磨削效率的要求来选择。
一般原则如下:要求被磨工件粗糙度高,应选择粗粒度;要求表面粗糙度低,应选择细粒度。
工件要求较高的几何精度和较低的表面粗糙度时,应选择混合粒度。
工件几何精度要求高,当砂轮与工件接触面积小时,应选择细粒度;接触面积大时,选择粗粒度。
工件材质硬而脆,应选择细粒度;工件材料软而韧,应选择粗粒度。
工件的导热性差,易发热变形,易烧伤,应选择较粗粒度。
磨具硬度选择原则?选择磨具硬度时,主要根据工件材料的性质、磨削方式来选择。
磨削硬质合金刀具的磨料粒度选择
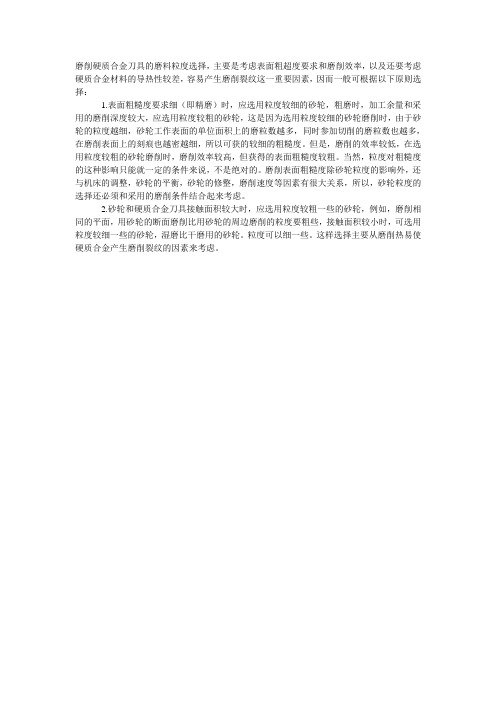
磨削硬质合金刀具的磨料粒度选择,主要是考虑表面粗超度要求和磨削效率,以及还要考虑硬质合金材料的导热性较差,容易产生磨削裂纹这一重要因素,因而一般可根据以下原则选择:
1.表面粗糙度要求细(即精磨)时,应选用粒度较细的砂轮,粗磨时,加工余量和采用的磨削深度较大,应选用粒度较粗的砂轮,这是因为选用粒度较细的砂轮磨削时,由于砂轮的粒度越细,砂轮工作表面的单位面积上的磨粒数越多,同时参加切削的磨粒数也越多,在磨削表面上的刻痕也越密越细,所以可获的较细的粗糙度。
但是,磨削的效率较低,在选用粒度较粗的砂轮磨削时,磨削效率较高,但获得的表面粗糙度较粗。
当然,粒度对粗糙度的这种影响只能就一定的条件来说,不是绝对的。
磨削表面粗糙度除砂轮粒度的影响外,还与机床的调整,砂轮的平衡,砂轮的修整,磨削速度等因素有很大关系,所以,砂轮粒度的选择还必须和采用的磨削条件结合起来考虑。
2.砂轮和硬质合金刀具接触面积较大时,应选用粒度较粗一些的砂轮,例如,磨削相同的平面,用砂轮的断面磨削比用砂轮的周边磨削的粒度要粗些,接触面积较小时,可选用粒度较细一些的砂轮,湿磨比干磨用的砂轮。
粒度可以细一些。
这样选择主要从磨削热易使硬质合金产生磨削裂纹的因素来考虑。
加工硬质合金刀具磨削参数确定方法

科技与创新┃Science and Technology & Innovation ·96·文章编号:2095-6835(2015)18-0096-02加工硬质合金刀具磨削参数确定方法张慈恩(东莞市森鑫刀具有限公司,广东东莞 523852)摘 要:确定合适的加工硬质合金刀具磨削参数有利于提高磨削质量、加工效率和延长金刚石砂轮的使用寿命。
介绍了磨削硬质合金的砂轮种类,分析了在磨削中常遇到的问题,给出了相应的解决措施,提出了一种在生产中确定磨削参数的方法,并将该方法应用在了新规格刀具的加工中。
关键词:金刚石砂轮;硬质合金;磨削参数;磨削裂纹中图分类号:TG580.6 文献标识码:A DOI:10.15913/ki.kjycx.2015.18.096随着我国经济的不断增长,制造业得到了明显的发展,硬质合金刀具的生产数量也越来越多。
如果没有确定好硬质合金刀具的磨削参数,则会影响到刀具的生产质量和生产效率。
因此,如何确定有效的磨削参数以提高刀具的生产质量成为了工作人员需要解决的问题。
1 磨削硬质合金砂轮的种类硬质合金是以碳化钨、碳化钛等金属碳化物作为硬质相,以钴等金属作为黏接剂,通过粉末冶金的方法制成,具有较高的硬度(可达HRA89-93,显微硬度为1 300~1 800 N/mm2)、较低的导热系数(16.75~79.55 W/m·K)、较低的抗弯强度(3.0~4.5 GPa)和较大的弹性磨量(540~650 GPa),常温下为硬脆性材料,表现出与钢件等材料不同的磨削要求。
以往,硬质合金常使用绿色碳化硅砂轮磨削,但因碳化硅磨粒硬度不足(显微硬度32 000~34 000 N/mm2),在磨削硬质合金时磨粒易磨耗钝化,导致磨削力增大、磨削温度过高,进而使刀具表面形成裂纹等缺陷。
同时,碳化硅砂轮脱粒过快,砂轮形状不易保持,易造成刀具尺寸不稳定。
2 磨削中的常见问题及其解决措施2.1 磨削裂纹硬质合金刀具在磨削过程中有时会产生裂纹,这是因刀具表面形成了拉应力,当拉应力超过刀具材料的抗拉极限时会产生裂纹。
- 1、下载文档前请自行甄别文档内容的完整性,平台不提供额外的编辑、内容补充、找答案等附加服务。
- 2、"仅部分预览"的文档,不可在线预览部分如存在完整性等问题,可反馈申请退款(可完整预览的文档不适用该条件!)。
- 3、如文档侵犯您的权益,请联系客服反馈,我们会尽快为您处理(人工客服工作时间:9:00-18:30)。
矿产资源开发利用方案编写内容要求及审查大纲
矿产资源开发利用方案编写内容要求及《矿产资源开发利用方案》审查大纲一、概述
㈠矿区位置、隶属关系和企业性质。
如为改扩建矿山, 应说明矿山现状、
特点及存在的主要问题。
㈡编制依据
(1简述项目前期工作进展情况及与有关方面对项目的意向性协议情况。
(2 列出开发利用方案编制所依据的主要基础性资料的名称。
如经储量管理部门认定的矿区地质勘探报告、选矿试验报告、加工利用试验报告、工程地质初评资料、矿区水文资料和供水资料等。
对改、扩建矿山应有生产实际资料, 如矿山总平面现状图、矿床开拓系统图、采场现状图和主要采选设备清单等。
二、矿产品需求现状和预测
㈠该矿产在国内需求情况和市场供应情况
1、矿产品现状及加工利用趋向。
2、国内近、远期的需求量及主要销向预测。
㈡产品价格分析
1、国内矿产品价格现状。
2、矿产品价格稳定性及变化趋势。
三、矿产资源概况
㈠矿区总体概况
1、矿区总体规划情况。
2、矿区矿产资源概况。
3、该设计与矿区总体开发的关系。
㈡该设计项目的资源概况
1、矿床地质及构造特征。
2、矿床开采技术条件及水文地质条件。