磨料粒度的分类及适用范围讲解学习
磨料的种类简介
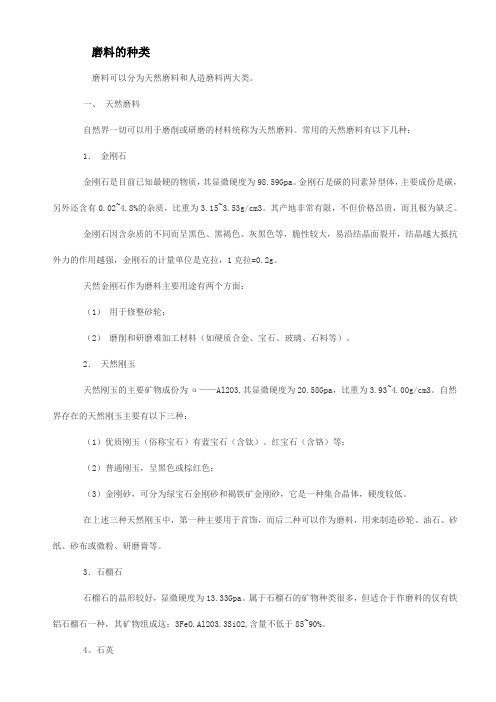
磨料的种类磨料可以分为天然磨料和人造磨料两大类。
一、天然磨料自然界一切可以用于磨削或研磨的材料统称为天然磨料。
常用的天然磨料有以下几种:1.金刚石金刚石是目前已知最硬的物质,其显微硬度为98.59Gpa。
金刚石是碳的同素异型体,主要成份是碳,另外还含有0.02~4.8%的杂质,比重为3.15~3.53g/cm3。
其产地非常有限,不但价格昂贵,而且极为缺乏。
金刚石因含杂质的不同而呈黑色、黑褐色、灰黑色等,脆性较大,易沿结晶面裂开,结晶越大抵抗外力的作用越强,金刚石的计量单位是克拉,1克拉=0.2g。
天然金刚石作为磨料主要用途有两个方面:(1)用于修整砂轮;(2)磨削和研磨难加工材料(如硬质合金、宝石、玻璃、石料等)。
2.天然刚玉天然刚玉的主要矿物成份为α——Al2O3,其显微硬度为20.58Gpa,比重为3.93~4.00g/cm3。
自然界存在的天然刚玉主要有以下三种:(1)优质刚玉(俗称宝石)有蓝宝石(含钛)、红宝石(含铬)等;(2)普通刚玉,呈黑色或棕红色;(3)金刚砂,可分为绿宝石金刚砂和褐铁矿金刚砂,它是一种集合晶体,硬度较低。
在上述三种天然刚玉中,第一种主要用于首饰,而后二种可以作为磨料,用来制造砂轮、油石、砂纸、砂布或微粉、研磨膏等。
3.石榴石石榴石的晶形较好,显微硬度为13.33Gpa。
属于石榴石的矿物种类很多,但适合于作磨料的仅有铁铝石榴石一种,其矿物组成这:3FeO.Al2O3.3SiO2,含量不低于85~90%。
4。
石英石英的化学成份为SiO2,常夹杂有Al2O3、Fe2O3、 CaO MgO Fe2O3等。
显微硬度为8.04 Gpa,可用作磨料的石英矿有脉石英、石英岩及石英砂等。
随着科学技术的发展,人造磨料的品种已达几十种之多,天然磨料由于自身的缺陷,已被越来越多的人造磨料所取代,目前除了天然金刚石、石榴石外,其它种类的天然磨料用量甚微。
二、人造磨料人造磨料分刚玉系列、碳化物系列、超硬系列等几大类。
磨料粒度的分类及适用范围讲解学习

磨料粒度的分类及适用范围第6章宝石加工常用的工艺耗材第1节磨料磨料指可用于是研磨或抛光的材料,它们是一些具有棱角和一定硬度及韧性的粉状物质,可直接研磨工件和制成磨具用。
6.1.1 磨料的基本特性(1)硬度较高,一般不应低于被加工材料的硬度。
(2)韧性较好,不能因有研磨压力而易变形和被磨损。
(3)自锐性较好,即当受研磨压力而碎裂时,破碎后的各部分仍保持尖锐的多棱角状。
自锐性示意图(4)熔点或软化点较高,在研磨发热作用下,磨料尖角不易熔化或变软。
(5)化学稳定性较好,不与被加工的材料起反应。
(6)形状和粒度较均匀,每号磨料粒度在一定范围内。
6.1.2 磨料粒度的分类及适用范围1、磨料的粒度等级磨料粒度表示法:粒度号“#”、“w”粒径尺寸“μm”磨料粒度分类:磨粒 2000~40 μm (17种)微粉 40~0.5 μm (12种)(1)磨粒分级:12#、14#、16#、20#、24#、30#、36#、46#、60#、70#、80#、100#、120#、150#、180#、240 # 、280#磨粒的粒度号用筛号表示,例如:12#表示12#筛以下~14#筛以上的颗粒级(2)微粉分级:W40 W28 W20 W14W10 W7 W5 W3.5 W2.5 W1.5 W1.0 W0.5微粉的粒度号以微米值表示,例如:W40表示粒径40~28 μm级(上限)磨料的粒度号与粒径尺寸的对应关系见下表:2、不同磨料粒度的适用范围在宝石加工中,不同粒度磨料的适用范围如下表:6.1.3 磨料的种类和性能磨料主要是一些具有一定硬度和韧性的粒状或粉状的矿物质材料。
按成因可分为天然磨料和人造磨料两大类。
天然磨料:金刚石、刚玉、石榴石、石英,等等。
人造磨料:金刚石系、碳化物系、刚玉系,等三大系列。
1、金刚石•包括天然和人造金刚石。
•Hm=10,Hv=10000kg/mm2。
•有一定韧性,但脆性相对较大,因易沿八面体完全解理方向破裂,自锐性较高。
磨料粒度的分类及适用范围

第6章宝石加工常用的工艺耗材第1节磨料磨料指可用于是研磨或抛光的材料,它们是一些具有棱角和一定硬度及韧性的粉状物质,可直接研磨工件和制成磨具用。
6.1.1 磨料的基本特性(1)硬度较高,一般不应低于被加工材料的硬度。
(2)韧性较好,不能因有研磨压力而易变形和被磨损。
(3)自锐性较好,即当受研磨压力而碎裂时,破碎后的各部分仍保持尖锐的多棱角状。
自锐性示意图(4)熔点或软化点较高,在研磨发热作用下,磨料尖角不易熔化或变软。
(5)化学稳定性较好,不与被加工的材料起反应。
(6)形状和粒度较均匀,每号磨料粒度在一定范围内。
6.1.2 磨料粒度的分类及适用范围1、磨料的粒度等级磨料粒度表示法:粒度号“#”、“w”粒径尺寸“μm”磨料粒度分类:磨粒 2000~40 μm (17种)微粉 40~0.5 μm (12种)(1)磨粒分级:12#、14#、16#、20#、24#、30#、36#、46#、60#、70#、80#、100#、120#、150#、180#、240 # 、280#磨粒的粒度号用筛号表示,例如:12#表示12#筛以下~14#筛以上的颗粒级(2)微粉分级:W40 W28 W20 W14W10 W7 W5 W3.5 W2.5 W1.5 W1.0 W0.5微粉的粒度号以微米值表示,例如:W40表示粒径40~28 μm级(上限)磨料的粒度号与粒径尺寸的对应关系见下表:粒度号粒径(μm)粒度号粒径(μm)粒度号粒径(μm)12# 2000-1600 80# 200-160 W1414-714# 1600-1250 100# 160-125 W1010-516# 1250-1000 120# 125-100 W77-3.520# 1000-800 150# 100-80 W57-3.524# 800-630 180# 80-63 W3.5 3.5-1.530# 630-500 240# 63-50 W2.5 2.5-1.036# 500-400 280# 50-40 W1.5 1.5-0.546# 400-315 W4040-28 W1.0<1 60# 315-250 W2828-20 W0.5<0.5 70# 250-200 W2020-142、不同磨料粒度的适用范围在宝石加工中,不同粒度磨料的适用范围如下表:粒度号适用范围46#-80# 大料切割,毛坯倒棱100#-120# 小料切割,毛坯倒棱,预形150#-1803 成型粗磨,预形,穿孔,小石切磨及修整240#-W40 成型细磨,穿孔W28-W14 成型精磨,粗抛光W10-W0.5 细抛光,精抛光6.1.3 磨料的种类和性能磨料主要是一些具有一定硬度和韧性的粒状或粉状的矿物质材料。
磨料的粒度

磨料的粒度磨料的粒度是指磨料颗粒的粗细程度,磨料的粒度规格用粒度号来表示。
*粒度号用目或粒度表示,是1英寸*1英寸的面积内有多少个颗粒数(是指磨料颗粒的大小相当于1平方英寸的多少分之一)。
例:1000,表示砂粒大小是25.4微米。
磨料的国家标准把粒度规格分为两类:一类是用于固结磨具、研磨、抛光的磨料粒度规格,其粒度号以"F"打头,称为"F粒度号磨料";另一类是用于涂附磨料的磨粒粒度规格,其粒度号以"P"打头,称为"P粒度号磨料".(1)F粒度号规格普通磨料粒度按颗粒尺寸大小,分为39个粒度号,其筛比为1.1892,即粗磨粒F4、F5、F6、F7、F8、F10、F12、F14、F16、F20、F22、F24、F30、F36、F40、F46、F54、F60、F70、F80、F90、F100、F120、F150、F180、F220、微粉F230、F240、F280、F320、F360、F400、F500、F600、F800、F1000、F1200、F1500、F2000.根据磨料生产工艺,磨料粒度在F4~F220部分的称为"粗磨粒"、其磨粒尺寸在63µm以上,多用筛分法生产;磨料粒度在F230~F2000范围内,磨粒尺寸小于63µm的称为"微粉",多用于水选法生产。
F4~F220粗磨粒磨料粒度组成、F230~F2000微粉磨料粒度组成(光电沉降粒度)及F230~F2000微粉磨料粒度组成参见GB-T 2481-2009标准。
(2)P粒度号规格在涂附磨具中使用P粒度号磨料(P为popular的第一个字母)。
国标规定磨料有28个粒度号,即粗磨料P12、P16、P20、P24、P36、P40、P50、P60、P80、P100、P120、P150、P180、P220、细磨料P240、P280、P320、P360、P400、P500、P600、P800、P1000、P1200、P1500、P2000、P2500.P12~P220磨料较粗,其筛比为1.892.P240~P2500磨料为粒度较系及分为磨料,所用筛分比为1.120→1.589→1.196.P12~P220磨料粒度组成与P240~P250磨料粒度组成参见GB-T 9258-2000标准。
粒度分析原理与应用

<D>对D求微商,可以获得分布函数F<D>即频率分布.
消光沉降法
消光沉降法原理:对于单位体积中含有n个迎光面积都同为a的悬浮液, 若以悬浮液的浊度 表示
ln<I0/I>/l=nKa 其中K是颗粒的消光系数,一般与颗粒尺寸有关.上式表明,相同强度的
平行入射光束经过长度为l的均匀悬浮液光路后,因衰减达到的光 强I与空白光强〔通过同样长度沉降介质连同槽壁后的光强〕I0的 关系.浊度 的数值等于单位体积中这n个颗粒的消光截面之和.
主要缺点:分辨率较低,不适于测量粒度分布范围很窄的样品.
Stokes重力沉降公式
考察一个球体在无界流体受重力、浮力和阻力的运动情况:
mdu/dt=W-f-F 其中阻力
F=3 Du 其中 为流体粘滞系数,D为球体直径.当F=W-f时,du/dt=0,球体达 到一恒定的最终沉降速度ust,又称Stokes速度.可求出Stokes速度 与球直径的关系为:
在光路中的颗粒大小是不同时,设光路中单位体积含有某颗粒直径为Di的颗粒ni个, 该颗粒的迎光截面积ai= iDi2, i是与Di相关的迎光截面积形状系数,其值与颗粒 的形状及其对光的取向有关.又颗粒的消光系数Ki一般随Di而异.在现在情况
ln<I0/I>/l= niKi iDi2
若令消光度
G log<I0/I>
二 粒度的测量方式
对于粒度的测试方法应根据粉末粒度范围、颗粒的形 态材质以及测试的目的等不同要求而确定.目前,粉末 粒度的测试方法主要有以下几种测试方法:
1.筛分法;
2.显微镜法〔SEM或TEM〕;
3.离心沉降法;
磨料及砂轮的适用范围(刚玉系与碳化系)

磨料及砂轮的适用范围(刚玉系与碳化系)在节省成本的前提下,用最低的成本取得较好的磨削效果是磨削时必须考虑的。
而各种磨料不同,砂轮磨具的成本也就不同。
下面介绍几种磨料的大致适用范围,当然,这也视实际情况而定,本人的观点仅供参考吧。
棕刚玉砂轮(A)--磨抗张强度较高的金属,如碳素钢、合金钢、可锻铸铁、硬青铜等白刚玉砂轮(WA)--磨淬火钢、合金钢、高速钢、高碳钢、薄壁零件等单晶刚玉砂轮(SA)-- 磨不锈钢等韧性大、硬度高的材料及易变形烧伤的工件微晶刚玉砂轮(MA)--磨轴承钢和特种球墨铸铁等。
用于成型磨、切入磨、镜面磨等铬刚玉砂轮(PA)--磨刀具、量具、仪表螺纹等工件表面粗糙度值要求低的工件锆刚玉砂轮(ZA)--磨钛合金、耐热合金等镨钕刚玉(NA)--磨合金工具钢、超硬高速钢、高温合金钢等黑刚玉(BA)--适用于电镀底面抛光、铝制品和不锈钢的抛光黑碳化硅(C)--磨铸铁、黄铜、铅、锌、皮革、塑料、木材、矿石等绿碳化硅(GC)--磨硬质合金、光学玻璃、陶瓷等硬脆材料立方碳化硅(SC)--不锈钢及轴承钢的大、小、微型轴承沟道的超精加工碳化硼(BC)--适于对硬质合金和宝石等材料的研磨抛光铈碳化硅(CC)--磨硬质合金、钛合金、超硬高速钢等砂轮的选择及诺顿砂轮介绍砂轮选择及诺顿砂轮介绍砂轮选择及诺顿砂轮介绍砂轮选择在磨削中的重要性磨削加工一般作为工件加工的终工序,其任务就是要保证产品零件能达到图纸上所要求的精度和表面质量。
磨削表面粗糙度与零件精度有密切关系,一定的精度应有相应的表面粗糙度。
一般情况下,对尺寸要进行有效的控制,则粗糙度Ra值应不超过尺寸公差的八分之一,磨削表面粗糙度对零件使用性能的影响是:表面粗糙度值越小,则零件的耐磨性,耐蚀性,耐疲劳性越好。
反之则相反。
因此,在磨削加工中,必须注意降低表面粗糙度。
影响磨削加工表面粗糙度的主要工艺因素中砂轮粒度对其有显著影响,砂轮粒度越细,同时参与磨削的磨粒就越多,则磨削表面粗糙度就越低。
磨料粒度的分类及适用范围

第6章宝石加工常用的工艺耗材第1节磨料 磨料指可用于是研磨或抛光的材料,它们是一些具有棱角和一定硬度及韧性的粉状物质,可直接研磨工件和制成磨具用。
6.1.1 磨料的基本特性(1)硬度较高,一般不应低于被加工材料的硬度。
(2)韧性较好,不能因有研磨压力而易变形和被磨损。
(3)自锐性较好,即当受研磨压力而碎裂时,破碎后的各部分仍保持尖锐的多棱角状。
自锐性示意图(4)熔点或软化点较高,在研磨发热作用下,磨料尖角不易熔化或变软。
(5)化学稳定性较好,不与被加工的材料起反应。
(6)形状和粒度较均匀,每号磨料粒度在一定范围内。
6.1.2 磨料粒度的分类及适用范围 1、磨料的粒度等级磨料粒度表示法:粒度号“#”、“w” 粒径尺寸“μm”磨料粒度分类:磨粒 2000~40 μm (17种) 微粉 40~0.5 μm (12种)(1)磨粒分级:12#、14#、16#、20#、24#、30#、36#、 46#、60#、70#、80#、100#、120#、 150#、180#、240 # 、280#磨粒的粒度号用筛号表示,例如:12# 表示12#筛以下~14#筛以上的颗粒级(2)微粉分级:W40 W28 W20 W14W10 W7 W5 W3.5 W2.5 W1.5 W1.0 W0.5微粉的粒度号以微米值表示,例如: W40 表示粒径40~28 μm级(上限) 磨料的粒度号与粒径尺寸的对应关系见下表:粒度号粒径(μm)粒度号粒径(μm)粒度号粒径(μm)12#2000-160080#200-160W1414-714#1600-1250100#160-125W1010-516#1250-1000120#125-100W77-3.520#1000-800150#100-80W57-3.524#800-630180#80-63W3.5 3.5-1.530#630-500240#63-50W2.5 2.5-1.036#500-400280#50-40W1.5 1.5-0.546#400-315W4040-28W1.0<160#315-250W2828-20W0.5<0.570#250-200W2020-14 2、不同磨料粒度的适用范围 在宝石加工中,不同粒度磨料的适用范围如下表:粒度号适用范围46#-80#大料切割,毛坯倒棱100#-120#小料切割,毛坯倒棱,预形150#-1803成型粗磨,预形,穿孔,小石切磨及修整240#-W40成型细磨,穿孔W28-W14成型精磨,粗抛光W10-W0.5细抛光,精抛光 6.1.3 磨料的种类和性能 磨料主要是一些具有一定硬度和韧性的粒状或粉状的矿物质材料。
磨料的分类及属性

磨料的分类及属性磨料(Abrasive)是在磨削、研磨和抛光中起作用的材料;磨粒(Abrasive Grains)是用人工方法制成特定粒度,用以制造切除材料余量的磨削、抛光和研磨工具的颗粒材料。
在爱锐网中,共有18个产品分类,其中4个分类涉及到磨料,分别是Abrasive Grains(磨粒)、Superhard Materials(超硬材料)、Sand Blasters & Media(喷砂、抛丸)、Mass Finishing & Media(抛磨机、抛磨块)、Buffing & Polishing(抛光材料及制品)。
爱锐网结合了大量了国内外网站、产品手册和大部分行业人士的使用习惯,认为用于制造普通磨具,比如陶瓷砂轮、树脂磨具、砂布、砂带等的磨料应该放入Abrasive Grains (磨粒)分类;用于制造超硬磨具、金刚石工具,比如金刚石砂轮、cBN砂轮、金刚石锯片等的磨料应该放入Superhard Materials(超硬材料);用于喷砂、喷丸的游离磨料,应该放入Sand Blasters & Media(喷砂&抛丸);用于大面积抛磨、抛光的研磨石,则放到Mass Finishing & Media(光饰机&研磨石) ,至于研磨石是磨具还是磨料,我们这里不过多的讨论,在爱锐网中先放入这个分类中。
抛光蜡、抛光粉等光整材料,爱锐网认为应该放入专门的Buffing & Polishing(抛光材料和制品)分类,与布轮、麻轮同时存在比较好!本篇为磨粒的分类及属性说明。
如图1所示,在爱锐网“磨粒”被分为7个二级分类。
事实上,刚玉和碳化硅是本分类中供需最多的产品,所以刚玉又被分了7个三级分类,碳化硅又被分成2个三级分类。
每个最终分类都有相对应的属性字段和值。
比如说,刚玉虽然是磨粒的分类,但不是最终分类,棕刚玉才是,所以棕刚玉就有相应的属性及值;锆刚玉是磨粒的二级分类也是最终分类,也有相应的属性及值。
磨料种类
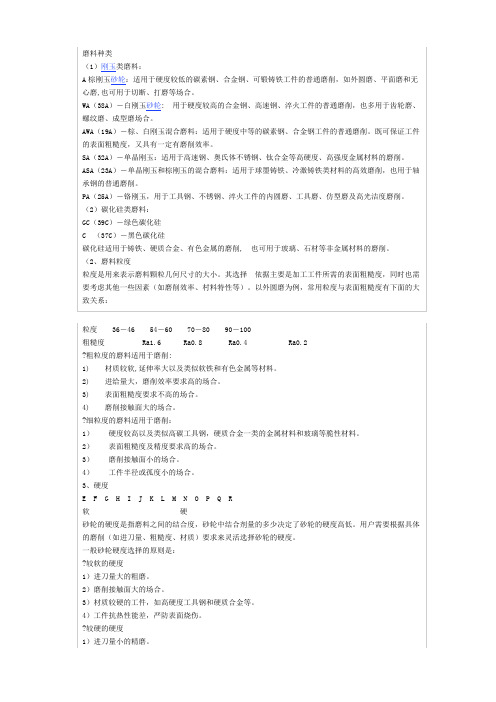
粒度36-46 54-60 70-80 90-100
粗糙度Ra1.6 Ra0.8 Ra0.4 Ra0.2
?粗粒度的磨料适用于磨削:
1) 材质较软,延伸率大以及类似软铁和有色金属等材料。
2) 进给量大,磨削效率要求高的场合。
3) 表面粗糙度要求不高的场合。
4) 磨削接触面大的场合。
?细粒度的磨料适用于磨削:
1)硬度较高以及类似高碳工具钢,硬质合金一类的金属材料和玻璃等脆性材料。
2)表面粗糙度及精度要求高的场合。
3)磨削接触面小的场合。
4)工件半径或孤度小的场合。
3、硬度
E F G H I J K L M N O P Q R
软硬
砂轮的硬度是指磨料之间的结合度,砂轮中结合剂量的多少决定了砂轮的硬度高低。
用户需要根据具体的磨削(如进刀量、粗糙度、材质)要求来灵活选择砂轮的硬度。
一般砂轮硬度选择的原则是:
?较软的硬度
1)进刀量大的粗磨。
2)磨削接触面大的场合。
3)材质较硬的工件,如高硬度工具钢和硬质合金等。
4)工件抗热性能差,严防表面烧伤。
?较硬的硬度
1)进刀量小的精磨。
粒度是磨料微粉最重要的技术指标之一

然而由于它的抽象性和实际测试存在的困难,许多用户甚至部分制造商对“粒度”的理解都比较模糊,这实际上成了我国磨料技术水平提高的一大障碍。
为此对“粒度”的基本概念作一通俗{TodayHot}介绍。
“粒度”是指一个粉体样品颗粒大小的总体描述。
详细的要用粒度分布来表示,在实用中一般只取几个关键参数,例如磨料JIS标准中的D50、D94、D3。
由于实际的微粉颗粒是不规则的,而且同一样品中各颗粒之间也不一致,所谓颗粒的大小,用不同方法就会得出不同的结果。
因此任何一个粉体产品的粒度标准,都必须注明所用测量仪器的原理。
有的标准允许用几种原理的仪器,这时标准数据也是不同的。
下面对几种国内常用的中国国家(W)标准和日本JIS 标准作具体说明。
国家标准:俗称W标准,因在粒度号前冠以字母W而得名,W是汉语“微粉”中“微”字的拼音(WEI)的字头。
实际上该标准已于1998年废止,但现在还在技术设备比较落后的磨料制造商和广大用户中流行。
W标准是建立在用显微镜刻度尺测量颗粒大小的方法上的。
这种方法规定用颗粒的最大宽度代表颗粒的大小。
该标准以大致为公比对颗粒大小(又称“粒径”)分档,例如40、28、20、14、10等等(单位为“μm”),又把一个粉体样品中的颗粒按上述分档法为基本粒、混合粒、细粒、粗粒和最大粒。
以粒度W14{HotTag}为例。
基本粒:10-14μm混合粒: 7-14μm细粒:<7μm粗粒: 14-28μm最粗粒: 28-40μm基本粒是磨料中最有用的部分,希望比例越高越好,国标要求在50%以上。
混合粒则占磨料的主要部分,比例当然也是越高越好,国标要求在80%以上。
W 标准粒径的定义日本标准推荐的仪器有两种原理:一是电气抵抗法(即电阻法或称库尔特法),二是沉降管法。
两种方法由于原理不同,标准值也不同,例如,JIS#1500,电阻法D50值为8.0±0.6μm,而沉降管法的D50为10.51μm。
砂轮片按所用磨料的种类

精心整理砂轮磨料品种、代号及其应用范围
砂轮片的分类
砂轮片按所用磨料可分为普通磨料(刚玉和碳化硅等)砂轮和天然磨料超硬磨料和(金刚石和立方砂轮氮化硼等)砂轮;
金刚石砂轮
以金刚石磨料为原料,分别用金属粉、树脂粉、陶瓷和电镀金属作结合剂,制成的中央有通孔的圆
想
首先A
Q
用,
使
1.磨料及其选择原则
磨料是砂轮的基本材料,在磨削时主要起切削的作用。
磨料硬度是指磨料这种物质本身所具有的硬度。
磨料分为天然磨料和人造磨料两大类。
天然磨料包括:石英、石榴石、天然刚玉及天然金刚石等。
人造磨料包括:刚玉系和碳化物系等普通磨料;人造金刚石、立方碳化硼等超硬磨料;以及硬度较低的的磨料氧化铬、氧化铁、玻璃粉等。
磨具,系指用结合剂或粘结剂将磨料按一定要求粘结而成的砂轮、油石、砂纸、砂带等以及用油料、水剂调合而成的研磨膏等用于磨削的工具。
现代磨具制造业主要选用人造磨料来制造磨具。
普通磨料的固结磨具(本书表述的是砂轮),由磨粒、结合剂和空隙三部分组成。
磨粒以其裸露在表面部分的棱角作为切削刃;结合剂将磨粒粘结在一起,经加压与熔烧使之具有一定的形状和强度;空隙则在磨削中起容纳切屑、磨削液和散逸磨削热的作用。
磨料、粘结剂和空隙构成砂轮结构的三要素。
磨料选择注意事项
●须考虑被加工材料的性质。
抗张强度较高的材料,应选用韧性大的磨料;硬度低、延伸率
●
●。
磨料粒度文档

磨料粒度简介磨料粒度是磨料材料中颗粒大小的度量标准。
磨料是一种用于磨削、抛光、切割和其他加工工艺中的材料,常用于制造砂纸、砂轮等工具。
磨料粒度的大小直接影响了磨料的磨削效果和加工质量。
在本文中,我们将探讨磨料粒度的概念、分类及其在不同应用场景中的选择原则。
磨料粒度的概念磨料粒度是指磨料颗粒的大小和分布情况。
常见的磨料粒度表示方法是通过筛网的孔径来定义的。
即,在一定的筛网上,通过该筛网的磨料颗粒被视为合格的磨料。
筛网的编号越大,孔径越小,通过该筛网的磨料颗粒越细。
磨料粒度的分类磨料粒度按照颗粒大小的不同可以分为粗磨料、中磨料和细磨料。
1.粗磨料:粗磨料的颗粒直径较大,一般在几十至几百微米之间。
粗磨料适用于对工件进行粗磨和修整的加工工艺,能够快速去除工件上的大颗粒杂质和粗糙面。
常见的粗磨料有碳化硅、氧化铝等。
2.中磨料:中磨料的颗粒直径介于粗磨料和细磨料之间,一般在几十至几百纳米之间。
中磨料适用于对工件进行加工和磨削的中等精度要求。
常见的中磨料有二氧化硅、金刚石等。
3.细磨料:细磨料的颗粒直径较小,一般在几个纳米至几十纳米之间。
细磨料适用于对工件进行高精度加工和磨削的工艺,能够获得更高的加工精度和表面质量。
常见的细磨料有氮化硼、莫来石等。
磨料粒度在不同应用场景中的选择磨料粒度的选择需要根据具体的加工工艺和要求来决定。
不同的工件和加工要求对磨料粒度有不同的要求。
1.粗磨料适用于对材料进行切削、打磨和修整的加工工艺。
通常,对于需要去除材料表面大颗粒杂质或者需要迅速将工件修整为一定形状的情况,可以选择粗磨料。
2.中磨料适用于对工件进行中等精度加工和磨削的情况。
对于要求较高的表面光洁度和加工精度的工件,中磨料能够更好地满足要求。
3.细磨料适用于对工件进行高精度加工和磨削的情况。
当需要获得非常高的加工精度和表面质量时,细磨料是不可或缺的选择。
除了磨料粒度,磨料的硬度、结构和磨削机械等因素也需要考虑。
不同的磨料特性会对加工效果产生直接影响,因此在选择磨料粒度时,需要综合考虑多个因素。
磨料粒度的分类及适用范围

磨料粒度的分类及适用范围第6章宝石加工常用的工艺耗材第1节磨料磨料指可用于是研磨或抛光的材料,它们是一些具有棱角和一定硬度及韧性的粉状物质,可直接研磨工件和制成磨具用。
6.1.1 磨料的基本特性(1)硬度较高,一般不应低于被加工材料的硬度。
(2)韧性较好,不能因有研磨压力而易变形和被磨损。
(3)自锐性较好,即当受研磨压力而碎裂时,破碎后的各部分仍保持尖锐的多棱角状。
自锐性示意图(4)熔点或软化点较高,在研磨发热作用下,磨料尖角不易熔化或变软。
(5)化学稳定性较好,不与被加工的材料起反应。
(6)形状和粒度较均匀,每号磨料粒度在一定范围内。
6.1.2 磨料粒度的分类及适用范围36# 500-400 280# 50-40 W1.5 1.5-0.5 46# 400-315 W4040-28 W1.0<160# 315-250 W2828-20 W0.5<0.5 70# 250-200 W2020-142、不同磨料粒度的适用范围在宝石加工中,不同粒度磨料的适用范围如下表:粒度号适用范围46#-80# 大料切割,毛坯倒棱100#-120# 小料切割,毛坯倒棱,预形150#-1803 成型粗磨,预形,穿孔,小石切磨及修整240#-W40 成型细磨,穿孔W28-W14 成型精磨,粗抛光W10-W0.5 细抛光,精抛光6.1.3 磨料的种类和性能磨料主要是一些具有一定硬度和韧性的粒状或粉状的矿物质材料。
按成因可分为天然磨料和人造磨料两大类。
天然磨料:金刚石、刚玉、石榴石、石英,等等。
人造磨料:金刚石系、碳化物系、刚玉系,等三大系列。
1、金刚石•包括天然和人造金刚石。
•Hm=10,Hv=10000kg/mm2。
•有一定韧性,但脆性相对较大,因易沿八面体完全解理方向破裂,自锐性较高。
因而,耐磨性强,磨削性能好。
•耐热性良好,在无氧化条件下加热1000℃无变化。
•化学性质稳定,与酸碱物质不起反应。
2、碳化硅(SiC)•以石英、石油焦碳为主要原料在1800℃以上高温下炼成的结晶化合物,是一种常用人造成磨料。
磨料粒度的分类及适用范围

第6章宝石加工常用的工艺耗材第1节磨料磨料指可用于是研磨或抛光的材料,它们是一些具有棱角和一定硬度及韧性的粉状物质,可直接研磨工件和制成磨具用。
6.1.1 磨料的基本特性(1)硬度较高,一般不应低于被加工材料的硬度。
(2)韧性较好,不能因有研磨压力而易变形和被磨损。
(3)自锐性较好,即当受研磨压力而碎裂时,破碎后的各部分仍保持尖锐的多棱角状。
自锐性示意图(4)熔点或软化点较高,在研磨发热作用下,磨料尖角不易熔化或变软。
(5)化学稳定性较好,不与被加工的材料起反应。
(6)形状和粒度较均匀,每号磨料粒度在一定范围内。
6.1.2 磨料粒度的分类及适用范围1、磨料的粒度等级磨料粒度表示法:粒度号“#”、“w”粒径尺寸“μm”磨料粒度分类:磨粒 2000~40 μm (17种)微粉 40~0.5 μm (12种)(1)磨粒分级:12#、14#、16#、20#、24#、30#、36#、46#、60#、70#、80#、100#、120#、150#、180#、240 # 、280#磨粒的粒度号用筛号表示,例如:12#表示12#筛以下~14#筛以上的颗粒级(2)微粉分级:W40 W28 W20 W14W10 W7 W5 W3.5 W2.5 W1.5 W1.0 W0.5微粉的粒度号以微米值表示,例如:W40表示粒径40~28 μm级(上限)磨料的粒度号与粒径尺寸的对应关系见下表:2、不同磨料粒度的适用范围在宝石加工中,不同粒度磨料的适用范围如下表:6.1.3 磨料的种类和性能磨料主要是一些具有一定硬度和韧性的粒状或粉状的矿物质材料。
按成因可分为天然磨料和人造磨料两大类。
天然磨料:金刚石、刚玉、石榴石、石英,等等。
人造磨料:金刚石系、碳化物系、刚玉系,等三大系列。
1、金刚石•包括天然和人造金刚石。
•Hm=10,Hv=10000kg/mm2。
•有一定韧性,但脆性相对较大,因易沿八面体完全解理方向破裂,自锐性较高。
因而,耐磨性强,磨削性能好。
粒度的相关知识和筛分粒度法
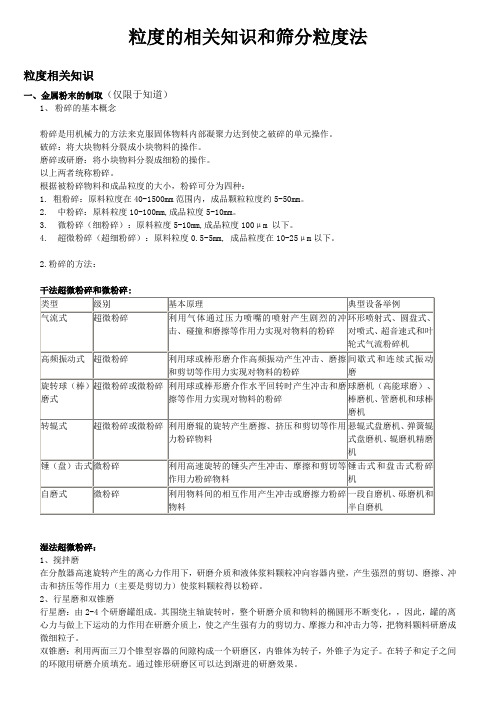
粒度的相关知识和筛分粒度法粒度相关知识一、金属粉末的制取(仅限于知道)1、粉碎的基本概念粉碎是用机械力的方法来克服固体物料内部凝聚力达到使之破碎的单元操作。
破碎:将大块物料分裂成小块物料的操作。
磨碎或研磨:将小块物料分裂成细粉的操作。
以上两者统称粉碎。
根据被粉碎物料和成品粒度的大小,粉碎可分为四种:1. 粗粉碎:原料粒度在40-1500mm范围内,成品颗粒粒度约5-50mm。
2. 中粉碎:原料粒度10-100mm,成品粒度5-10mm。
3. 微粉碎(细粉碎):原料粒度5-10mm,成品粒度100μm 以下。
4. 超微粉碎(超细粉碎):原料粒度0.5-5mm, 成品粒度在10-25μm以下。
2.粉碎的方法:湿法超微粉碎:1、搅拌磨在分散器高速旋转产生的离心力作用下,研磨介质和液体浆料颗粒冲向容器内壁,产生强烈的剪切、磨擦、冲击和挤压等作用力(主要是剪切力)使浆料颗粒得以粉碎。
2、行星磨和双锥磨行星磨:由2-4个研磨罐组成。
其围绕主轴旋转时,整个研磨介质和物料的椭圆形不断变化,,因此,罐的离心力与做上下运动的力作用在研磨介质上,使之产生强有力的剪切力、摩擦力和冲击力等,把物料颗料研磨成微细粒子。
双锥磨:利用两面三刀个锥型容器的间隙构成一个研磨区,内锥体为转子,外锥子为定子。
在转子和定子之间的环隙用研磨介质填充。
通过锥形研磨区可以达到渐进的研磨效果。
3、胶体磨和均质机原理:胶体磨:又称分散磨,工作构件由一个固定的磨体(定子)和一个高速旋转磨体(转子)组成。
两磨体之间有一个可以调节的微小间隙。
当物料通过这个间隙时,由于转子的高速旋转,使附着于转子面上的物料速度最大,而附着于定子面的物料速度为零。
这样产生了急剧的速度梯度,从而使物料受到强烈的剪切、磨擦和湍动骚扰,产生了超微粉碎作用。
均质机:当高压物料在阀盘与阀座间流过时产生了急剧的速度梯度,速度以缝隙的中心为最大,而附于阀盘与阀座上的物料流速为零。
由于急剧的速度梯度产生强烈的剪力,使液滴或颗粒发生变形和破裂以达到微粒化的目的。
磨具磨料粒度及硬度选用原则(甲类精制)

磨具磨料粒度及硬度选用原则,总结的还挺全面磨料是磨具起磨削作用的重要因素,磨料的选择主要根据工件材料的性质,如硬度、抗张强度、韧性等来确定,选择磨具磨料的基本原则是:磨削硬度高的工件材料时,应选择硬度更高的磨料;磨削抗张强度高的工件材料时,应选用韧性大的磨料;磨削抗张强度低的材料时,应选用较脆或强度高的碳化硅磨料。
具体说,棕刚玉适应磨削碳钢、铸铁合金钢、硬青铜等;白刚玉适应磨削淬火钢、合金钢、高速钢、工具钢等;黑碳化硅适应磨削有色金属、橡胶、皮革、塑料等;绿碳化硅适应磨削硬质合金、光学玻璃、陶瓷材料等;SG、CBN陶瓷磨具广泛用于难磨材料。
此外,为了充分发挥各种磨料在磨削中的优点,目前在磨具制造中己广泛采用混合磨料,以提高磨具磨削效率。
如:磨球墨铸铁时,一般采用A/WA混合磨料;棕、白刚玉两种混合磨料,磨削时既有棕刚玉高韧性的特点,又发挥了白刚玉兼有一定脆性和导热性较好的特点。
(如磨曲轴砂轮多采用棕、白混合,粒度60#~80#,硬度中软2到中1)(粗磨钴基合金齿轮齿形砂轮,可用单晶和微晶两种混合)(磨铝高速钢砂轮,采用棕刚玉、绿碳化硅混合)(磨球面轴承内外套圈砂轮,应采用棕、白混合,代表规格是:GZ/GB80#P600×36×305是粗磨滚道。
GZ/GB80#P600×510×355.6是终磨外径等。
磨具粒度选择原则?选择磨料粒度时,主要应根据加工精度、表面粗糙度和磨削效率的要求来选择。
一般原则如下:要求被磨工件粗糙度高,应选择粗粒度;要求表面粗糙度低,应选择细粒度。
工件要求较高的几何精度和较低的表面粗糙度时,应选择混合粒度。
工件几何精度要求高,当砂轮与工件接触面积小时,应选择细粒度;接触面积大时,选择粗粒度。
工件材质硬而脆,应选择细粒度;工件材料软而韧,应选择粗粒度。
工件的导热性差,易发热变形,易烧伤,应选择较粗粒度。
磨具硬度选择原则?选择磨具硬度时,主要根据工件材料的性质、磨削方式来选择。
“砂轮磨料颗粒粒径分析方法”汇总大全

“砂轮磨料颗粒粒径分析方法”汇总大全一、相关概念:1、粒度与粒径:颗粒的大小称为粒度,一般颗粒的大小又以直径表示,故也称为粒径。
2、粒度分布:用一定方法反映出一系列不同粒径区间颗粒分别占试样总量的百分比称为粒度分布。
3、等效粒径:由于实际颗粒的形状通常为非球形的,难以直接用直径表示其大小,因此在颗粒粒度测试领域,对非球形颗粒,通常以等效粒径(一般简称粒径)来表征颗粒的粒径。
等效粒径是指当一个颗粒的某一物理特性与同质球形颗粒相同或相近时,就用该球形颗粒的直径代表这个实际颗粒的直径。
其中,根据不同的原理,等效粒径又分为以下几类:等效体积径、等效筛分径、等效沉速径、等效投影面积径。
需注意的是基于不同物理原理的各种测试方法,对等效粒径的定义不同,因此各种测试方法得到的测量结果之间无直接的对比性。
4、颗粒大小分级习惯术语:纳米颗粒(1-100 nm),亚微米颗粒(0.1-1 μm),微粒、微粉(1-100 μm),细粒、细粉(100-1000 μm),粗粒(大于1 mm)。
5、平均径:表示颗粒平均大小的数据。
根据不同的仪器所测量的粒度分布,平均粒径分、体积平均径、面积平均径、长度平均径、数量平均径等。
6、D50:也叫中位径或中值粒径,这是一个表示粒度大小的典型值,该值准确地将总体划分为二等份,也就是说有50%的颗粒超过此值,有50%的颗粒低于此值。
如果一个样品的D50=5 μm,说明在组成该样品的所有粒径的颗粒中,大于5 μm的颗粒占50%,小于5 μm 的颗粒也占50%。
7、最频粒径:是频率分布曲线的最高点对应的粒径值。
8、D97:D97指一个样品的累计粒度分布数达到97%时所对应的粒径。
它的物理意义是粒径小于它的的颗粒占97%。
这是一个被广泛应用的表示粉体粗端粒度指标的数据。
二、粒度测试的基本方法及其分析激光法激光法是通过一台激光散射的方法来测量悬浮液,乳液和粉末样品颗粒分布的多用途仪器。
纳米型和微米型激光料度仪还可以通过安装的软件来分析颗粒的形状。
砂轮的粒度名词解释

砂轮的粒度名词解释砂轮是工业生产中常用的一种磨料工具,在金属加工、玻璃加工、木材加工等领域广泛应用。
而砂轮的粒度是指砂轮中磨料颗粒的大小。
不同粒度的砂轮适用于不同的加工需要,粒度的选择对加工效果有着重要影响。
本文将解释砂轮的粒度名词,并对其影响进行简要探讨。
在砂轮的粒度名词中,常见的有数字和字母表示。
比如,常见的粒度名词有36、60、80、120等数字表示,还有相对粗糙度和细糙度的字母标记,如C、D、F 等。
这些标记代表了磨料颗粒的大小及其分布情况。
具体来说,数字越小表示磨料颗粒越粗糙,数字越大表示磨料颗粒越细腻;字母标记中,粗糙度由“A”到“Z”递增,细糙度由“A”到“Z”递减。
当选择砂轮时,粒度的选择至关重要。
粗糙的砂轮适用于初次加工,可以快速将材料表面的粗糙度去除,但却不能获得很高的光洁度。
换言之,粗糙的砂轮通常用于粗加工或快速磨削。
而细糙的砂轮则适用于精细加工,可以获得较高的光洁度。
细糙的砂轮常用于完成产品的抛光、光亮处理等工序。
根据实际需求,选择合适的砂轮粒度可以提高加工效果,同时也能延长砂轮的使用寿命,减少加工成本。
不仅如此,砂轮的粒度还会影响加工过程中的散热情况。
在加工过程中,由于砂轮与工件的摩擦,会产生大量的热。
粒度较大的砂轮表面覆盖的是较宽的磨料颗粒,因此,单位面积的磨料颗粒相对较少,磨削过程中摩擦产生的热量较少,散热较快。
而粒度较小的砂轮则相反,它的磨料颗粒更密集,摩擦所产生的热量更多,因此散热速度较慢。
这就需要在实际加工过程中根据工件材料的热敏感性和加工要求,选择合适的砂轮粒度,以确保加工过程中的热不会对工件造成不可逆的影响。
不同砂轮粒度的选择也与加工效率和工件使用寿命息息相关。
通常情况下,粗糙度较高的砂轮可以提高加工效率,但也容易导致材料的损耗和变形;细糙度较高的砂轮则能够提供更高的加工精度和光洁度,同时也会降低砂轮的磨损速度。
因此,在实际工程中,选取合适的砂轮粒度是平衡加工效率和产品质量之间的重要考量。
磨具磨料粒度及硬度选用原则

磨料是磨具起磨削作用的重要因素,磨料的选择主要根据工件材料的性质,如硬度、抗张强度、韧性等来确定,选择磨具磨料的基本原则是:磨削硬度高的工件材料时,应选择硬度更高的磨料;磨削抗张强度高的工件材料时,应选用韧性大的磨料;磨削抗张强度低的材料时,应选用较脆或强度高的碳化硅磨料。
具体说,棕刚玉适应磨削碳钢、铸铁合金钢、硬青铜等;白刚玉适应磨削淬火钢、合金钢、高速钢、工具钢等;黑碳化硅适应磨削有色金属、橡胶、皮革、塑料等;绿碳化硅适应磨削硬质合金、光学玻璃、陶瓷材料等;SG、CBN陶瓷磨具广泛用于难磨材料。
此外,为了充分发挥各种磨料在磨削中的优点,目前在磨具制造中己广泛采用混合磨料,以提高磨具磨削效率。
如:磨球墨铸铁时,一般采用A/WA混合磨料;棕、白刚玉两种混合磨料,磨削时既有棕刚玉高韧性的特点,又发挥了白刚玉兼有一定脆性和导热性较好的特点。
(如磨曲轴砂轮多采用棕、白混合,粒度60#~80#,硬度中软2到中1)(粗磨钴基合金齿轮齿形砂轮,可用单晶和微晶两种混合)(磨铝高速钢砂轮,采用棕刚玉、绿碳化硅混合)(磨球面轴承内外套圈砂轮,应采用棕、白混合,代表规格是:GZ/GB80#P600×36×305是粗磨滚道。
GZ/GB80#P600×510×355.6是终磨外径等。
磨具粒度选择原则?选择磨料粒度时,主要应根据加工精度、表面粗糙度和磨削效率的要求来选择。
一般原则如下:要求被磨工件粗糙度高,应选择粗粒度;要求表面粗糙度低,应选择细粒度。
工件要求较高的几何精度和较低的表面粗糙度时,应选择混合粒度。
工件几何精度要求高,当砂轮与工件接触面积小时,应选择细粒度;接触面积大时,选择粗粒度。
工件材质硬而脆,应选择细粒度;工件材料软而韧,应选择粗粒度。
工件的导热性差,易发热变形,易烧伤,应选择较粗粒度。
磨具硬度选择原则?选择磨具硬度时,主要根据工件材料的性质、磨削方式来选择。
砂轮的硬度是指砂轮表面上的磨粒在磨削力作用下脱落的难易程度。
粗磨砂轮粒度

粗磨砂轮粒度磨料是机械加工中必不可少的工具,而粗磨砂轮作为一种常用砂轮,具有较大粒度的特点,被广泛应用于各类研磨加工过程中。
本文将对粗磨砂轮粒度进行探讨,并介绍其特点以及适用范围。
一、粗磨砂轮粒度的定义及分类粗磨砂轮粒度是指砂轮的磨料颗粒大小,常用万分之一毫米(μm)或米(m)作为单位进行表示。
根据国际标准ISO9001,粗磨砂轮粒度一般可分为以下几个等级:40、46、54、60、70、80、90、100、120、150等。
其中,数字越大表示砂轮的粒度越细。
二、粗磨砂轮粒度的特点1. 高效研磨:粗磨砂轮具有较大的砂粒,可实现对工件表面的快速研磨,提高加工效率。
2. 适应性广泛:粗磨砂轮适用于各类金属、非金属以及硬质材料的研磨加工,具有广泛的适应性。
3. 耐磨性强:粗磨砂轮的砂粒较大,经久耐用,在长时间的研磨过程中,砂轮的砂粒消耗较少,寿命较长。
三、粗磨砂轮的应用范围1. 金属加工:粗磨砂轮广泛应用于金属加工行业,可进行钢材、铸铁、铜、铝等金属材料的表面研磨,去除毛刺、氧化层等。
2. 木工加工:在木工行业中,粗磨砂轮可用于对木材表面进行打磨,使其光滑细腻,进一步提高木制品的质量。
3. 玻璃加工:粗磨砂轮亦可用于玻璃加工领域,对玻璃的边角进行研磨,修整和抛光,提高玻璃制品的精度和美观度。
4. 磨具制造:粗磨砂轮还可以作为一种磨具基体,与其他磨料颗粒结合制成各类研磨工具,如砂轮、内外圆磨盘等。
四、粗磨砂轮粒度的选择注意事项1. 工件材料:根据不同的工件材料选择合适的粗磨砂轮粒度,以确保研磨效果和加工质量。
2. 研磨要求:根据加工要求,选择适当的粗磨砂轮粒度,以获得合理的加工效果。
3. 砂轮硬度:粗磨砂轮除了粒度以外,硬度也是一个重要指标,根据需要选择适当的硬度,以确保砂轮的寿命和加工效果。
4. 砂轮粒度的匹配:在多道研磨过程中,应根据磨削工艺要求,合理匹配粗、中、精三种粒度的砂轮,以获得更好的加工效果。
- 1、下载文档前请自行甄别文档内容的完整性,平台不提供额外的编辑、内容补充、找答案等附加服务。
- 2、"仅部分预览"的文档,不可在线预览部分如存在完整性等问题,可反馈申请退款(可完整预览的文档不适用该条件!)。
- 3、如文档侵犯您的权益,请联系客服反馈,我们会尽快为您处理(人工客服工作时间:9:00-18:30)。
磨料粒度的分类及适
用范围
第6章宝石加工常用的工艺耗材
第1节磨料
磨料指可用于是研磨或抛光的材料,它们是一些具有棱角和一定硬度及韧性的粉状物质,可直接研磨工件和制成磨具用。
6.1.1 磨料的基本特性
(1)硬度较高,一般不应低于被加工材料的硬度。
(2)韧性较好,不能因有研磨压力而易变形和被磨损。
(3)自锐性较好,即当受研磨压力而碎裂时,破碎后的各部分仍保持尖锐的多棱角状。
自锐性示意图
(4)熔点或软化点较高,在研磨发热作用下,磨料尖角不易熔化或变软。
(5)化学稳定性较好,不与被加工的材料起反应。
(6)形状和粒度较均匀,每号磨料粒度在一定范围内。
6.1.2 磨料粒度的分类及适用范围
1、磨料的粒度等级
磨料粒度表示法:粒度号“#”、“w”
粒径尺寸“μm”
磨料粒度分类:磨粒 2000~40 μm (17种)
微粉 40~0.5 μm (12种)
(1)磨粒分级:12#、14#、16#、20#、24#、30#、36#、
46#、60#、70#、80#、100#、120#、
150#、180#、240 # 、280#
磨粒的粒度号用筛号表示,例如:
12#表示12#筛以下~14#筛以上的颗粒级
(2)微粉分级:W40 W28 W20 W14W10 W7 W5 W3.5 W2.5 W1.5 W1.0 W0.5微粉的粒度号以微米值表示,例如:
W40表示粒径40~28 μm级(上限)
磨料的粒度号与粒径尺寸的对应关系见下表:
2、不同磨料粒度的适用范围
在宝石加工中,不同粒度磨料的适用范围如下表:
6.1.3 磨料的种类和性能
磨料主要是一些具有一定硬度和韧性的粒状或粉状的矿物质材料。
按成因可分为天然磨料和人造磨料两大类。
天然磨料:金刚石、刚玉、石榴石、石英,等等。
人造磨料:金刚石系、碳化物系、刚玉系,等三大系列。
1、金刚石
•包括天然和人造金刚石。
•Hm=10,Hv=10000kg/mm2。
•有一定韧性,但脆性相对较大,因易沿八面体完全解理方向破裂,自锐性较高。
因而,耐磨性强,磨削性能好。
•耐热性良好,在无氧化条件下加热1000℃无变化。
•化学性质稳定,与酸碱物质不起反应。
2、碳化硅(SiC)
•以石英、石油焦碳为主要原料在1800℃以上高温下炼成的结晶化合物,是一种常用人造成磨料。
•黑碳化硅Hv=3100~3280kg/mm2,性脆,自锐性好;
•绿碳化硅Hv=3200~3400kg/mm2,性脆,自锐性好。
•但绿碳化硅含杂质少,硬度和脆性比黑碳化硅高,自锐性更好,磨削能力更强。
•具良好导热性、耐高温和不受腐蚀等特性。
•常用来制造砂轮、砂带、砂布等磨具,或供自由研磨用。
3、碳化硼(B4C)
•人造成磨料的一种,由硼酸与碳在电炉中2000 ℃以上的高温下合成。
•暗灰至黑色,硬度很高,耐磨性好,Hv=4000~5000kg/mm2
•属高级磨料,常代替金刚石用作研磨和抛光中、高档宝石。
4、刚玉(Al2O3)
•包括天然和多种人造成刚玉(棕刚玉、微晶刚玉、单晶刚玉、白刚玉、锆刚玉等)。
•硬度高,Hm=9,Hv=1800~2400kg/mm2,韧性较大,切削力强,但自锐性相对较低。
•适于磨削韧性较大的翡翠、软玉、虎睛石等材料,而对其它宝石材料的磨削能力不如金刚石、碳化硅和碳化硼。
6.1.4 抛光剂的种类和性能
抛光剂是磨料中的一些可用于抛光的微粉状特殊材料。
宝石加工常用的抛光剂有:
1、钻石粉(C)
•将天然或人造的工业级金刚石压碎成粉未,经分级,即可制成不同型号的钻石粉,呈灰白色,极精细(W10以下)的可用作抛光
剂。
•用法:干钻石粉与缝纫机油调成糊状;钻粉研磨膏可加适量缝纫机油稀释。
•可用于抛光任何宝石,效果好,但成本高,一般仅用于抛光硬度>7的宝石。
2、氧化铝(Al2O3)
•铝氧化粉:纯度低,抛光性能差,但价格低廉,适合大量用于珠型和随型宝石的抛光。
•铝钒土:纯度较低,抛光性能较差,价格低廉,用途同铝氧化粉。
•红宝粉:人造刚玉粉,红色,抛光性能好,主要用于刻面型和部分弧面型宝石的抛光。
•蓝宝粉:人造刚玉粉,多呈白色,性能和用途与红宝粉一样。
3、氧化铈(Ce2O3)
•呈微黄粉红色,粉状。
•易溶于浓硫酸或浓硝酸,不溶于稀酸和水。
•适用于抛光脆性的中硬度宝石,如水晶、橄榄石、锆石、绿柱石、电气石等,效果可达极佳。
4、氧化锡(SnO2)
•呈白色粉未状。
•可用于各种中硬宝石的抛光,但效果一般。
5、氧化锆(ZrO2)
•呈浓艳的红棕色粉未状,外观似红宝粉。
•可用于中硬以下宝石的抛光,但效果不及红宝粉。
6、氧化铬(Cr2O3)
•呈深绿色粉状,俗称绿粉。
•硬度中等(Hm=5~7)。
性质稳定,不溶于水。
•适于中硬~中软(Hm=6~3)宝石的抛光,如翡翠、绿松石、孔雀石等,效果好。
•缺点:
o常因颗粒粗细均匀,若掌握不好,易在抛光面上留下擦
痕;
o易污染工件、工具、手指、衣物等,故对裂隙或孔隙的宝石不适合。
7、氧化铁(Fe2O3)
•呈深棕红色,俗称红粉、铁丹。
•性质稳定,不溶于水,但溶液于盐酸。
•粉状粒度一般在0.25~0.75μm,细腻均匀。
•可用于多种中硬以下宝石的抛光,效果一般。
•缺点:易污染宝石材料,难清除。
8、硅藻土(SiO2)
•用含硅藻壳骸的生物岩经粉碎、分选、提纯而成。
•呈灰白~微黄色粉状,质地细腻。
•硬度中等,Hm=5.5~5.6。
•化学性质稳定,不溶于水,仅易溶于氢氟酸。
•可用于玛瑙、翡翠等韧性较大或其它中硬宝石的抛光,对部分高硬度宝石如蓝宝石、海蓝宝石的抛光也可这到很好效果。