梭式窑设计

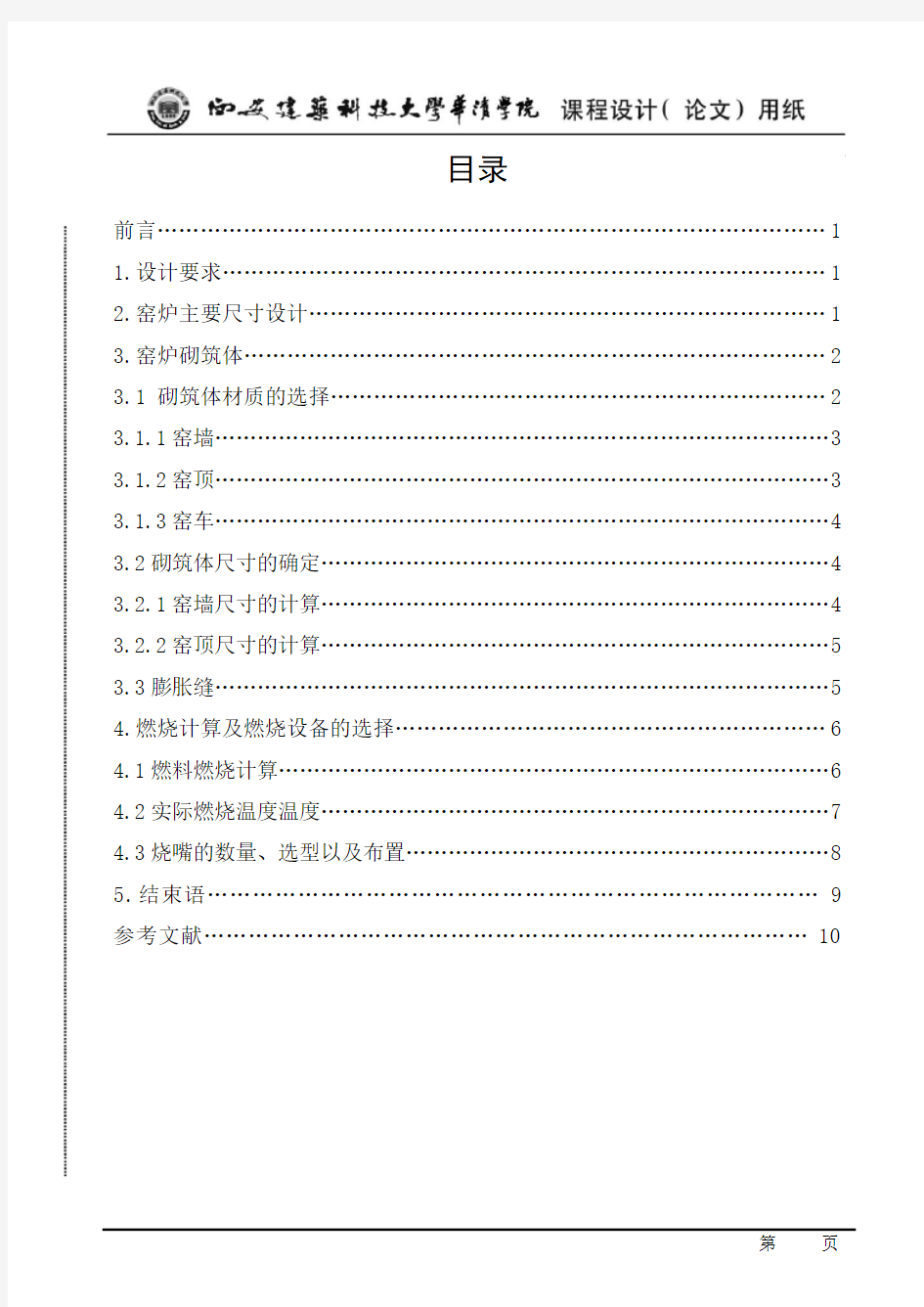
35m3烧成电瓷制品梭式窑设计
摘要:梭式窑是一种间歇式的工业烧成设备,跟火柴盒的结构类似,窑车推进窑内烧成,烧完了再往相反的方向拉出来,卸下烧好的陶瓷,窑车的往复运动如同织布时的“梭子”,故而称为梭式窑。在陶瓷材料、耐火材料以及建筑材料等烧成方面,尽管目前大规模生产所使用的是隧道窑或更为先进的辊道窑,但是由于梭式窑对所生产制品的适应性较强,可以适应不同尺寸、不同形状、不同材质制品的烧成,所以梭式窑特别适应于小批量、多品种产品的生产,使其满足市场多样化的需求,梭式窑能够非常方便的改变其烧成曲线,因而它还被许多科研单位所采用,用来进行一些新产品的实验,随着保温效果极佳且耐高温的轻质保温耐火砖和耐火纤维的出现,使得梭式窑的烧成热耗大大降低,于是出现的高效节能梭式窑的耗能指标甚至可以与隧道窑相媲美,所以梭式窑至今仍具有强大的生命力。本文主要介绍了梭式窑窑体尺寸的设计计算、窑炉砌筑体的设计计算、燃烧系统的设计计算。
关键词:梭式窑,设计,计算
目录
前言 (1)
1.设计要求 (1)
2.窑炉主要尺寸设计 (1)
3.窑炉砌筑体 (2)
3.1砌筑体材质的选择 (2)
3.1.1窑墙 (3)
3.1.2窑顶 (3)
3.1.3窑车 (4)
3.2砌筑体尺寸的确定 (4)
3.2.1窑墙尺寸的计算 (4)
3.2.2窑顶尺寸的计算 (5)
3.3膨胀缝 (5)
4.燃烧计算及燃烧设备的选择 (6)
4.1燃料燃烧计算 (6)
4.2实际燃烧温度温度 (7)
4.3烧嘴的数量、选型以及布置 (8)
5.结束语 (9)
参考文献 (10)
前言
梭式窑(Spindle type kiln ,也称:往复窑,或称:台式车窑)是从传统的倒焰窑演变而来,故梭式窑属于“间歇式”或“半连续式”窑炉。自80年代来,我国引进了不少的梭式窑,在借鉴的基础上,自行研制开发了许多梭式窑,因其具有操作灵活方便、升降温度速度较快、受热较均匀、便于维修等特点,近年来梭式窑得到了飞速发展,在冶金、化工、陶瓷、无机材料等领域得到了广泛应用。为了让我们掌握梭式窑的特点及结构、增强工程设计能力、提高计算能力和理论分析能力,我们设计了一个35m3最高烧成温度为1280℃的烧成电瓷制品的梭式窑。
1.设计要求
① 窑内有效容积:35m3 ② 最高烧成温度:1280℃ ③ 燃料的种类及组成:净化煤气 煤气组成:
④ 空气过系数:α=1.1 ⑤ 燃料消耗量:160kg/h ⑥ 成品率:95%
⑦ 装窑密度:1.2吨/立方米 ⑧ 窑容积系数:0.9
⑨ 当地气候条件:夏季平均温度为27℃,年平均大气压力96000Pa 。
2.窑炉主要尺寸设计
成分 CO 2 CO
H 2
CH 4
C 2H 4
H 2S
N 2
含量(%)
4.5
29
14
1.8
0.2
0.3
50.2
窑体的尺寸主要依据被煅烧制品的产量要求、产品性能、烧嘴喷射能力、温度分布均匀性等各方面因素综合确定。
①梭式窑内高为窑车台面至窑顶的空间高度。根据材料所能允许的对多高度
来确定窑的内高。如镁砖由于其荷重软化温度和它的烧成温度接近,故砖跺高度不宜太高,通常其窑内高在1米左右;而硅砖由于其荷重软化温度高,其窑内高通常在1.9-2.1米;现有粘土砖和高铝砖窑内高分别为1.5-1.9米和1.1-1.5米。砖跺上下所允许的温差也是考虑窑内高时应注意的影响因素之一。窑高增加,上下温度加大,容易造成烧成质量不均匀。本设计中窑内高H取1.6米,即H=1.6m。
②梭式窑的内宽为窑内两侧窑墙之间的距离。窑的内宽与窑的产量和允许的
温差有关。产量随窑的宽度增加而增大,太宽则中心温度偏低。现代梭式窑多采用扁宽型断面设计,窑的宽高比一般为B/H≈2,其中B为窑内宽,H为窑的内高。梭式窑内宽一般在1—3米之间,国外最宽梭式窑已达6.4米。则本设计中B=3.2m,查设计指导书附录2取B=3.248m。
③烧成温度较低断面较宽的陶瓷梭式窑则常采用平吊顶的窑顶结构。平吊顶
结构是由异型轻质耐火砖或耐火纤维叠块所构成,用吊杆将其单独的或成组的吊挂在窑体的钢梁上。综合考虑以上各因素,该窑采用平顶结构。
④当梭式窑的内高、内宽确定后,可以计算出梭式窑的横截面积,从而确定
出梭式窑的总长度L:L=V
F(式中:V-窑容积,可由装窑密度、产量要
求及窑容积系数求出,在本设计中V=35m3;F-窑横截面积,可由B与H 之积求得)。
由于B=3.248m,H=1.6m可得:
F=B×H=3.248×1.6=5.12m2
则
V
L=
F
=
5.12
35
=6.84 m
3.窑炉砌筑体的设计
3.1砌筑体材质的选择
选择砌筑体材质窑充分考虑砌筑体所处的工作条件,其中包括:
①工作温度:窑炉因用途不同,工作温度相差很大,应区别选用不同品种或不同等级的制品砌筑。
②温度应力:承受温度应力较大的窑炉或部位,应选择稳定性好的材料,特别是间歇操作的窑炉更应该充分注意。
③承重荷载:承受荷重大的部位应选择强度大的砖。轻质砖和硅藻土砖不能用于砌筑承重拱顶或拱角砖,也不能用于砌筑同钢结构立柱相接触的窑墙。在温度下承重还要考虑材料的荷重软化点。
④机械损伤:如煅烧原料的竖窑和回转窑都要考虑受料的冲击和磨损。
⑤化学侵蚀:不同种类的耐火制品砌筑接触时,要考虑它们之间的反应。
对于整个窑体来说,还要防止由于局部砌体过早损坏而导致停产。
查课本《无机非金属材料热工设备》选用粘土砖、轻质粘土砖、红砖以及高炉矿渣作为砌筑体材料,其最高使用温度、体积密度及导热系数如下表所示:
硅砖轻质粘土砖红砖高炉矿渣
最高使用
温度(℃)
1300~1400 1300 600 600
体积密度
(Kg/m3)
1000 1900~2300 500~550
导热系数[W/(m·℃)] 0.698+0.64-3
10
?t 0.291+0.256-3
10
?t
0.7~1.2
0.093+0.291-3
10
?t
3.1.1窑墙
窑墙窑要有一定的强度才能承受荷重、支持窑顶,同时还要耐高温、能保温,以维持窑内煅烧温度,减少热量损失,降低环境温度。一般窑墙都由能够承受高温的耐火材料、保温隔热材料及外表面维护结构组成。本设计中窑墙由内至外分别采用了粘土砖、轻质粘土砖、红砖砌筑。
3.1.2窑顶
窑顶除了要有一定的强度、耐热、保温性能,还要不漏气、重量轻、推力小等要求。本设计中窑顶由内至外分别采用粘土砖、轻质粘土砖,并用高炉矿渣填充,窑顶表面铺上一层红砖以便于行走。
3.1.3窑车
窑车衬砖是梭式窑的活动窑底,它是用来保护金属窑车和装载制品烧成的。它每经过窑内一次,就会被加热冷却一次,经受周期性的温度变化。同时还要在窑车衬砖面上进行经常性的装卸工作,因此窑车衬砖较容易松动和损坏,严重时阻碍窑车在窑内正常运行。所以窑车表面和周围要选用能承受高温、温度变化,并能承受荷重的耐火材料。窑车内部衬砖砌筑,为了减少窑车重量,并减少窑车本身蓄热及散热,宜采用容重小,热容小,热容量小及热导率小的轻质保温材料。由于本设计窑长L=6.84m ,故选择2个长度为3.42m 的窑车。
3.2砌筑体尺寸的确定
砌筑体的各种材料的厚度可用公式 q =
δ
λ
(t 内–t 外)来确定。对于高温窑炉,窑墙外表面温度一般取100℃-120℃,空气温度一般取20℃。在本设计中窑墙外表面温度取100℃,空气温度取20℃。
同时砌筑体的长、宽、高的尺寸都应该考虑到砖行,计算时还要考虑灰缝在内。耐火砖灰缝一般为2mm-3mm 。标准耐火砖尺寸为230×113×65mm 。耐火砖墙高度砌筑尺寸取68的倍数,耐火砖墙水平砌筑尺寸取116的倍数,其值可由指导书的附录表格中查出。
窑顶厚度也用同样的方法计算。通常吊平顶厚200-250mm 。
本设计中窑墙外表面温度取100℃,空气温度取20℃。窑墙由内至外分别采用粘土砖、轻质粘土砖、红砖砌筑,温降分别为1280℃、1100℃、450℃、100℃。窑顶由内至外分别采用粘土砖、轻质粘土砖,并用高炉矿渣填充,温降分别为1280℃、1100℃、600℃、100℃,窑顶表面铺上一层红砖以便于行走。
3.2.1窑墙尺寸的计算
查指导书附录3可得:窑墙外表面温度为100℃,空气温度为20℃时,窑墙的散热量为q=1000千卡/(米2·时),
即q =1000×4.184÷3600×1000=1162 J/(m 2·s)
粘土砖:λ=0.698+0.64×10-3t×(1280+1100) ÷2=1.46 [W/(m·℃)]δ1=λ/q1 (t内–t外)=1.46÷1162×(1280-1100)=0.226m
查指导书附录5后取δ1=232mm。
轻质粘土砖:λ=(0.291+0.256×10﹣3)×(1100+450)÷2=0.489 [W/(m·℃)]δ2=λ/q1(t内–t外)=0.489÷1162×(1100-450)=0.274m
查指导书附录5后取δ2=348mm。
红砖:λ=0.7 [W/(m·℃)]
δ3=λ/q1(t内–t外)=0.7÷1162×(450-100)=0.211m
查指导书附录5后取δ3=232mm。
3.2.2窑顶尺寸的计算
查指导书附录4可得:空气温度为20℃时,窑顶的散热量为
q=1200千卡/(米2·时)即q=1200×4.184÷3600×1000=1395 J/(m 2·s)
粘土砖:δ4=λ/q2(t内–t外)=1.46÷1395×(1280-1100)=0.188m
查指导书附录5后取δ4=204mm
轻质粘土砖:δ5=λ/q2(t内–t外)=0.509÷1395×(1100-600)=0.182m
查指导书附录5后取δ5=204mm
高炉矿渣:λ=(0.093 +0.291×10﹣3)×(600+100)÷2=0.195 [W/(m·℃)] δ6=λ/q2(t内–t外)=0.195÷1395×(600-100)=0.070m=70mm 3.3膨胀缝
几种常用的耐火材料每米砌体的膨胀缝按下列尺寸留设。
耐火粘土砖和轻质粘土砖砌体5~6mm/m
硅砖砌体12mm/m
镁砖砌体10~12mm/m
高铝砖砌体6~8mm/m
由于上述所用的材料的工作温度都大于80℃,都应设膨胀缝,且膨胀缝的位置应避开受力部位和骨架,关应按间距2米左右均布。
窑墙膨胀缝的内层与外层之间留成锯齿形,上下层之间留成锁口形式以保证密封。
窑顶膨胀缝,单层拱顶留直缝,为保证密封应在拱顶压一层砖;多层拱顶膨胀缝应错开,最上一层应拱顶也应压一层砖保证密封。如下图:
4.燃烧计算及燃烧设备的选择
4.1燃料燃烧计算
设窑炉使用的煤气组成干基如下表:
其中含水率为4%,α=1.1时。
基准:1Nm3湿煤气x u×1=x d(1-H2O)
换算成湿煤气组成:x u=x d
100O
H
1002
-
=0.96x d
换算后的煤气组成如下表:
成分CO2CO H2CH4C2H4H2S N2H2O 含量
(%) 4.32 27.84 13.44 1.73 0.19 0. 29 48.19 4.0 (1) 1Nm3煤气燃烧所需要的空气量
理论空气量为:
V 0
a=(1/2 CO+1/2 H2+2CH4+3 C2H4+3/2 H2S)×100/21
=(
2
0.2784
+
2
0.1344
+0.0173×2+0.0019×3+0.0029×
2
3
)×
21
100
成
分
CO2CO H2CH4C2H4H2S N2含
量(%) 4.5 29 14 1.8 0.2 0.3 50.2
=1.195 Nm 3 / Nm 3煤气 实际空气量为: Va=αVa 0 =1.1×1.195=1.315 Nm 3 / Nm 3煤气 (2) 1Nm 3煤气燃烧理论生成烟气量为:
V 0=(CO+ H 2+3CH 4+4 C 2H 4+2 H 2S+ CO 2+ N 2+ H 2O )+Va 0×79/100 =(0.2784 +0.1344+3×0.0173+4×0.0019+2×0.0029+0.0432+0.4819+0.04)+1.195
×79/100
=1.99 Nm 3 / Nm 3煤气
1Nm 3煤气燃烧实际生成烟气量为:
V= V 0
+(α-1)V 0a
=1.99+(1.1-1)×1.195=2.11 Nm 3 / Nm 3煤气 烟气组分:
2CO V =( CO 2+ CO+CH 4+2 C 2H 4)/V ×100%
=11
.20.001920.01730.27840.0432?+++×100%
=16.24%
O H V 2 =( H 2O+ H 2+2CH 4+2 C 2H 4+ H 2S )/V ×100%
=11
.20.017320.00290.001920.13440.04?++?++×100%
=10.22% 2SO V = H 2S /V ×100%
=11
.20029.0×100% =0.14%
2N V = (N 2+αV 0
a
×79%)/V ×100%
=(0.4819+1.195×1.1×79%)÷2.11×100% =72.05%
2O V =(α-1) V
0a
×0.21/V
=(1.1-1) × 1.195 ×0.21/2.11×100%
=1.19%
4.2实际燃烧温度温度
查《材料工程基础》公式6.14知:气体燃料的低位发热量:
Q net =12600 CO +10800H 2+35800CH 4+59000C 2H 4+63700C 2H 6+80600C 3H 6
+91200C 3H 8+118700C 4H 10+146000C 5H 12+23200H 2S(KJ/Nm 3) Q net =126×27.84+108×13.44+358×1.73+590×0.19+232×0.29
=5758 KJ/(Nm 3·℃)
燃烧所需空气量: V a =1.315 Nm 3/ Nm 3煤气 实际烟气量: V=2.11 Nm 3/ Nm 3煤气
发生燃烧时煤气温度t g 与空气温度t a 均为20℃,其中空气在0~20℃的平均比热容为1.296 KJ/Nm 3 理论燃烧温度: t th =
c
a
a a g g net V t C V t C Q ++
=c
11.220296.1315.12032.15758??+?+
=c
11.25.5818 即2.11ct th =5818.5 设t th ′=1700℃,查《材料工程基础》表6.16知发生煤气燃烧产物的平均比容C′=1.67。
则Q′=2.11×1.67×1700=5990.29>5818.5
设t th ′′=1600℃,C′′=1.65则Q′′=2.11×1.65×1600=5570.4<5818.5 此时,t th 的值必在t th ′与t th ′′之间,可用内插法以求t th 值,即:
''t 't t 't th th th th --='
Q'Q'Q
Q'--
16001700t 1700th --=4
.557029.59905
.581829.5990--
t th =1659℃ 实际燃烧温度t p =ηt th
设取高温系数η=0.78(陶瓷倒焰窑)
∴t p=0.78×1659.1=1294℃
4.3烧嘴的数量、选型以及布置
现代的梭式窑基本上采用先进的高速调温烧嘴,或者更新型、节能的脉冲(高速调温)烧嘴。这次设计的梭式窑采用性能优良的高速调温烧嘴。
高速调温烧嘴属无焰烧嘴,它是指燃气和空气在烧嘴内“完全”进行燃烧,再与二次空气(调温空气)混合来调节所喷出的气体温度。使用高速调温烧嘴,燃烧效率高,燃烧室的体积小,燃烧室的容积能力强度非常高,最高可达2.1×108W/ m3,且窑内温度均匀,这样有利于消除窑内的过热部位,减小窑体的蓄热损失和散热损失。同时在窑内,温度均匀气流的强烈循环与搅拌作用又强化了烟气对制品的传热,这样既可以实现安全快速的加热,又可以降低烟气排除的温度,使窑炉的燃料消耗量下降。调温方便,而且高温烟气高速喷出,喷出的速度通常在70m/s以上,高达200~300m/s。
本次设计选择2对高速调温烧嘴,且布置在半窑车位处,在窑的高度方向上,高速烧嘴往往是设置在梭式窑的偏上部,这样的布置有利于窑内气体形成强烈的循环。
5.结束语
本次热工课程设计时间为三周,经过设计计算、绘制梭式窑剖面图、撰写设计计算说明书这三个阶段。三周的时间虽然很短,但我觉得受益匪浅,不仅仅是学习到了相关的知识、方法,而且深深感受到了老师敬业的工作态度,很值得我们学习。此外,通过这一次的锻炼,现在已经可以熟练运用CAD画图,相信无论是以后的工作还是学习,我都能从这次设计中受益。这次的设计计算说明书经过细心地编写,由于自己能力有限,学习中不乏有浅尝辄止的时候,其中还有很多不足之处,希望老师批评指正。
最后,非常感谢马林老师、杨晓凤老师以及其他几位老师三周来的耐心指导,在这里道一声您们辛苦了。当然也要感谢同学给予的帮助和支持!
参考文献
[1]热工课程设计任务书(自编)
[2]徐德龙,谢峻林.《材料科学与工程》.武汉:武汉理工大学出版社,2008
[3]姜洪舟.《无机非金属材料热工设备》.武汉:武汉理工大学出版社,2005
50 梭式窑设计
前言 这次设计的是50立方米的燃煤气梭式窑炉,在设计前期阶段收集和查阅了相关资料和文献。中间进行了大量的计算,也学到了不少的东西。在设计过程中综合运用了自己大学四年来所学的的知识,在运用知识的同时,才深深感到所学知识面的狭窄和不够深。第一部分主要是参照江西萍乡远洋出口电瓷厂的窑炉确定了我此次设计的窑体尺寸,第二部分再根据实习过程中收集到的相关数据和资料确定了烧成制度和烧成周期,根据指导老师的意见和建议,再加上自己的设计思路,确定了工作系统,燃烧系统和排烟系统等。 窑体结构采用了三层材料,多晶莫来石纤维,轻质莫来石砖和普通硅酸铝纤维,窑车结构主要是多晶莫来石纤维,轻质莫来石砖和轻质耐火粘土砖。采用窑车中部开烟道,窑车两侧墙各设两个烟道,窑顶集中排烟,设有风机抽风。燃烧器采用高速喷射式烧嘴。还用到了打入急冷风快速冷却制品的设计思路。 在设计过程中,得到了各位老师和同学的大力支持和帮助,特别是指导教师童剑辉老师提出了许多很有建设性的意见和建议,在此谨致以诚挚的谢意。同时也感谢江西萍乡远洋出口瓷厂提供了我前后共三次的窑炉实体观摩机会。 限于设计者水平,书中难免有不妥之处,诚请各位专家、老师批评指正!
第1章设计任务及原始资料 1.1设计任务书 景德镇陶瓷学院毕业设计(论文)任务书 院(系)热能工程系08年1月5日
1.2原始资料 1.2.1设计技术指标及参数 有效容积:50立方米 燃料:城市煤气 低发热值:16515KJ,湿煤气含水量4%。 最高烧成温度:1270℃ 烧成周期:72h 1.2.2产品名称及规格 名称:电瓷 规格高:150mm 直径:110mm 产品单位重量:1.0㎏ 坯体总线收缩率:1.9% 入窑水分:2% 产品合格率:95%
之水泥回转窑电气控制系统设计说明
(括号里填学校名称)本科毕业论文 ¢3.5/3×60m水泥回转窑电气控制系统 设计 学生姓名: *** 学生学号: 0000000 院(系): ******学院 年级专业: ****级**** 指导教师: **** 助理指导教师: 二〇一一年六月
摘要 在建材、冶金、化工、矿物加工和环保等许多行业中,广泛地使用回转圆筒型设备对散装或浆状物料进行物理或化学处理,这种回转圆筒设备被称为回转窑。 水泥生产是由原料预处理(均化、破碎、烘干等)、生料制备(配料、粉磨、均化)、熟料锻烧(分解预热、锻烧、煤磨)、水泥制成(水泥配料、粉磨、包装)四大部分组成,其中水泥熟料的煅烧是水泥生产中最重要的过程,所用的设备水泥回转窑,常被称为水泥厂的心脏。水泥回转窑由机械、电气、液压等部分组成。通过研究设计主要用PLC为核心控制水泥回转窑系统,主要包括有: ①回转窑辅助电机的正常运转控制。②主电机的变频调速控制。③燃烧器移动小车的正反转运行控制。④主减速机润滑站的控制应按TE525润滑站的压力、温度、液位等控制。⑤挡轮液压站TE326的控制。 结论控制方案包括: ①主电机为变频调速电机,故采用变频器控制其调速运行。②辅助电机、燃烧小车的控制比较简单,直接用继电接触器控制其运行。③挡轮液压站、主减速机润滑站因控制容多,工艺复杂,两者均采用由PLC控制的方式,利用PLC的硬件电路与软件结合,实现挡轮液压站、主减速机润滑站的正常运转与故障报警等控制功能。 关键词水泥,回转窑,PLC,控制系统
ABSTRACT In building materials,metallurgy,chemical,mineral processing,envir onmental pr-otection,and many other industries,people widespread use o f rotating cylindrical device on the bulk or slurry material to do phy sical or chemical treatment,which-h is known as rotary kiln that with rotating cylinder device. Cement production is composed by the raw material pretreatment (ho mog-e-nizing,crushing,drying,etc.),raw material preparationing redient s,grinding,homogeniz-ation),clinker calcination(decomposition and preh eating,calcination,coal mill),ceme-nt products (Cement batching,grindi ng,packaging).And calcining cement clinker which is the most important cement production process,so its equipment–cement rotary kiln,often referred to as the heart of cement.Cement kiln consist of mec-hanical, electrical,hydraulic and other components.By studying and the design o f cement rotary kiln system we will use PLC as the main core of the co ntrol.Tha-t including: Firstly, rotary control of the normal operation of auxiliary motors.S-condly, the main motor of the variable frequenc y control.Thirdly, move the car reversing the burner operation control. The fourth is the main reducer lubrication station control stations s hall TE525 lubrication pressure,temperature,liquid level control. The fifth is gear wheel hydraulic TE326 control. Conclusions control program include: First of all, main motor for frequency conversion motor,which inverter control its speed operation. Secondly,auxiliary m-otors,combustion car’s control is relatively simp le,which direct contacts with the relay control its operation. Last bu t not least,because of gear wheel hydraulic s-tation,the main gearbox lubrication station’s control contents and more complex process,both a dopted by the PLC control method,the use of PLC combination of hardwar e and software to achieve gear wheel hydraulic station,the main gearbo x lubrication Stop the normal operation and fault alarm control functi ons.
毕业设计设计说明书范文
第一章塑件分析 1.1塑件结构分析 图1-1 塑件结构图 此制品是消声器上盖,现实生活中经常看到用到,是一个非常实际的产品。且生产纲领为:中批量生产,所以我们采用注射模具注射成型。 1.2 成型工艺性分析[1] 塑件材料为尼龙,因塑件用在空压机内,表面无光洁度要求。具有良好的力学性能,其抗冲击强度比一般的塑料有显著的提高,具有良好的消音效果和自润滑性能。密度1.15 g/cm3, 成型收缩率:0.4~0.7%,平均收缩率为0.55%。 第二章确定模具结构
2.1模具结构的确定 塑料模具的种类很多,大体上分为:二板模,三板模,热流道模。 二板模缺点是浇口痕迹明显,产生相应的流道废料,不适合高效生产。本模具选择二板模其优点是二板模结构简单,制作容易,成本低,成型周期短。 支撑板 分型面 定模侧 动模侧 图2.1 典型的二板模结构 模架为非标准件 定模座板: 400*200*25mm 定模板: 315*200*40mm 动模板: 315*200*32mm 支承板: 315*200*25mm 推秆固定板:205*200*15mm 推板: 205*200*20mm 模脚: 50*200*60mm 动模座板 400*200*25mm 2.2确定型腔数目 2.2.1塑件体积的计算 a. 塑件体积的计算 体积为:
V a = S a ×L a =(37×35-8×25)×10-(33×36-10.5×25) ×8 =12.60cm 3 b.计算塑件的重量 根据《塑料模具设计手册》查得密度ρ取1.12g/cm 3 所以,塑件单件的重量为:m=ρV =12.60?1.12 =14.11g 浇注系统的体积为:主流道+分流道+浇口=(6280+376.8*2+12*2)/1000 ≈7.05 cm 3 粗略计算浇注系统的重量:7.05*1.12=7.90g ≈8.0g(含有冷料穴料重) 总重量:14.11*2+8.0=36.22g 2.2.2 模具型腔数目的确定 模具型腔的数目决定了塑件的生产效率和模具的成本,确定模具型腔的方法也有许多种,大多数公司采用“按经济性确定型腔的数目”。根据总成型加工费用最小的原则,并忽略准备时间和试生产原料的费用,仅考虑模具费用和成型加工费,则模具费用为 21C nC Xm += 式中Xm ——模具费用,元; 1C ——每一个型腔的模具费用,元 2C ——与型腔数无关的费用,元。 成型加工费用为 n Y N X t j 60= 式中j X ——成型加工费用,元 N ——需要生产塑件的总数; t Y ——每小时注射成型的加工费,元/h ;n ——成型周期,min 。 总的成型加工费用为n Y N C nC X X X t j m 6021++=+= 为了使成型加工费用最小,令 0=dn dX ,则 n=2 上式为按经济性确定型腔数目为2。考虑到模具成型零件和抽芯结构的设计,模具
PLC控制梭式窑燃烧系统设计
PLC控制梭式窑燃烧系统设计 摘要 近年来来随着电力电子技术的发展,梭式窑的控制上也越来越多的应用自动化的控制技术。梭式窑燃烧系统是由燃气燃烧器(烧嘴)、燃气阀组、助燃风机、流量计、压力变送器、点火装置、燃气/空气压力检测装置、火焰监控装置等组成,确保系统在安全、合理的情况下稳定运行。由温度控制系统、燃烧控制系统、压力控制系统、故障报警系统等组成。 本文以梭式窑燃烧控制系统为主要研究目标,在深入研究了梭式窑燃烧的工作过程,详细分析了控制系统的需求后,结合PLC的应用对梭式窑燃烧的控制系统进行了设计研究,针对梭式窑炉运行过程中温度分布不均匀、压力调节繁琐、气氛不可控及抗扰能力差等问题,通过对炉内燃气热值数据分析得出数值模型,结合专家系统在各类温度控制系统中的优点,提出了模糊PID控制算法控制相结合的控制方法。对窑内温度的控制利用了PID的控制方式,引入了先进的控制算法,利用模糊控制算法对控制系统做了优化设计,系统的动态响应快对系统的控制效果好。系统能够根据各个传感器检测到的信息数据传送到控制中心进行决策,PLC根据这些变化的电信号,输出变频器控制信号控制相关的电机的工作状态,完成系统的自动化工作,设计的控制系统自动化水平高,应用前景较大,具有很高的现实意义。 关键词:梭式窑,PLC,模糊PID,温度控制,
Abstract In recent years, with the development of power electronics technology, more and more automated control technologies have been applied to the control of shuttle kiln. The shuttle kiln combustion system is composed of a gas burner (burner), a gas valve group, a combustion air blower, a flow meter, a pressure transmitter, an ignition device, a gas/air pressure detecting device, a flame monitoring device, etc., to ensure that the system is safe. Stable operation under reasonable conditions. It consists of a temperature control system, a combustion control system, a pressure control system, and a fault alarm system. In this paper, the shuttle kiln combustion control system is the main research goal. After studying the working process of shuttle kiln combustion in detail, after analyzing the requirements of the control system in detail, combined with the application of PLC, the control system of the shuttle kiln combustion control system is designed. For the problem of uneven temperature distribution, cumbersome pressure regulation, uncontrollable atmosphere and poor anti-interference ability during the operation of the shuttle kiln, the numerical model is obtained by analyzing the calorific value data of the furnace gas, combined with the expert system at various temperatures. The advantages of the control system are proposed, and the control method combined with fuzzy PID control algorithm control is proposed. The control of the temperature in the kiln utilizes the PID control method, introduces an advanced control algorithm, and uses the fuzzy control algorithm to optimize the control system. The dynamic response of the system is fast and the control effect of the system is good. The system can transmit the information data detected by each sensor to the control center for decision. According to these changed electrical signals, the PLC outputs the inverter control signal to control the working state of the relevant motor, completes the automation of the system, and designs the automation level of the control system. High, the application prospect is large, and has a high practical significance.
北京机电院回转窑设计部分文献总结
北京机电院高技术股份有限公司回转窑焚烧危废文献总结
目录 第一部分回转窑处理危险废物的工程设计 (1) 一、回转窑运转形式的确定 (1) 二、回转窑处理危险废物的设计 (1) 三、回转窑处理危险废物工程中的问题 (4) 第二部分回转窑焚烧系统的控制参数及调节方法 (6) 一、回转窑焚烧系统流程图 (6) 二、焚烧过程的主要控制参数 (7) 三、焚烧系统的实际控制参数 (7) 四、回转窑焚烧系统的调节方法 (8) 第三部分二噁英的控制 (10) 一、危险废物处置中二恶英产生机理 (10) 二、危险废物处置中二恶英的控制 (11) 第四部分回转窑耐火砖的砌筑 (13) 一、回转窑砌筑 (13) 二、烘炉 (15)
第一部分回转窑处理危险废物的工程设计 一、回转窑运转形式的确定 1.1回转窑操作方式的选择 按气、固体在回转窑内流动方向的不同,回转窑可分为顺流式回转窑(co-currentflowkiln)和逆流式回转窑(counter-currentflowkiln)两种。 1.2回转窑燃烧模式的选择 依据回转窑内燃烧时灰渣状态和炉内温度的不同,回转窑可分为熔渣式回转窑和非熔渣式回转窑。其中,非熔渣式又称“灰渣式”。 二、回转窑处理危险废物的设计 2.1回转窑尺寸和运转方式的设计 用于危险废物处理的回转窑,其典型的长径比值为3.4~4.2,而回转窑的尺寸须根据容积热负荷参数来确定。回转窑容积热负荷参数关系到炉内燃烧状况的好坏,文献中给出回转窑容积热负荷的范围为(4.2~104.5)×104kJ/(m3·h)。 回转窑尺寸采用的方法是:首先,根据危险废物的成分计算出废物的热值,再根据废物的处理量确定出每小时废物在回转窑内燃烧所产生的热量,然后根据选定的容积热负荷确定出回转窑的容积,最后结合回转窑的长径比,确定回转窑的尺寸。 对于回转窑的运转方式,在工程实践中,回转窑的倾斜角度一般在1°~3°,转速为0.2~5r/min,回转窑的转动方向结合进料方式和助燃方式确定。处理难焚烧的危险废物可采用大长径比与低转速的回转窑;而热值较高、容易燃烧的危险废物,燃烧需要的时间稍短一些,可采用较大倾斜角与较高转速的回转窑来处理。 2.2回转窑耐火材料设计 根据《危险废物集中焚烧处置工程建设技术规范》(HJ/T176-2005)的要求,危险废物
回转窑设计方案手册
回转窑的设计 一、窑型和长径比 1.窑型 所谓窑型是指筒体各段直径的变化。按筒体形状有以下几种窑型: (1)直筒型:制造安装方便,物料在窑内移动速度较均匀一致,操作控制较易掌握,同时窑 体砌造及维护较方便; (2)热端扩大型:加大单位时间内燃烧的燃料量及传热量,在原窑直径偏小的情况下,扩大 热端将相应提高产量,适用于烧成温度高的物料; (3)冷端扩大型:便于安装热交换器,增大干燥受热面,加速料浆水分蒸发,降低热耗及细 尘飞损,适用于处理蒸发量大、烘干困难的物料; (4)两端扩大型(哑铃型):中间的填充系数提高,使物料流动的机会减少,还可以节约部分 钢材;还有单独扩大烧成带或分解带的“大肚窑”,这种窑型易挂窑皮,在干燥带及烧成带 能力足够时,可以显著提高产量。但这种窑型操作不便。 总之,不论扩大哪一带,必须保持预烧能力和烧结能力趋于平衡。只有在生产窑上,经过生产实践和充分调查研究(包括必要的热工测定和计算),发现某一带确为热工上的薄弱环节,在这种特定条件下将该带扩大,才会得出较明显的效果。 目前国内外发展趋势仍以直筒型窑为主,而且尺寸向大型方面发展。其他有色金属工业用回转窑(还原、挥发、硫化精矿焙烧、氯化焙烧、离析、烧结转化等)多采用较短的直筒窑。 2.长径比 要得长径比有两种表示方法:一是筒体长度L与筒体公称直径D之比;另一是筒体长 度L与窑的平均有效直径D均之比。L/D便于计算,L/D均反映要的热工特点更加确切, 为了区别起见,称L/D均为有效长径比。窑的长径比是根据窑的用途、喂料方式及加热方 法来确定的。根据我国生产实践的不完全统计,各类窑的长径比示于表1中。长径比太大,窑尾废气温度低,蒸发预热能力降低,对干燥不利;长径比太小,则窑尾温度高,热效率低。同类窑的长径比与窑的规格有关,小窑取下限,大窑取上限。 表1各类窑的长径比 窑的名称公称长径比有效长径比 氧化铝熟料窑(喷入法)20~2522~27 氧化铝焙烧窑20~2321.5~24 碳素煅烧窑13.5~1917~24 干法和半干法水泥窑11~15—— 湿法水泥窑30~42—— 单筒冷却机8~12—— 铅锌挥发窑14~1716.7~18.3 铜离析窑——15~16 氯化焙烧窑——12~17.7 二、回转窑的生产率 回转窑生产是一个综合热工过程,其生产率受多方面因素影响。分析其内在规律性, 可以建立以下几个方面的数量 关系。
8立方梭式窑讲解
8立方米日用瓷梭式窑方案及报价 1、8m3日用瓷梭式窑 1.1、结构概述 本梭式窑广泛吸收国内外先进的热工设备制造技术,广泛应用于结构陶 瓷、功能陶瓷、电子陶瓷、磁性材料及高档耐火材料等方面,结合我公司多 年设计、制造、调试的经验标准化设计,具有以下特点: 1、采用明焰裸烧,燃烧完全。热气流与烧成制品接触面大,热交换率 高,制品受热均匀。 2、耐火/保温材料全部采用高热阻、低蓄热、热稳定性好的轻质隔热材料,升降温度快速,保温性能好,窑外侧温度低、能耗低,操作环境安全可 靠。 3、窑炉工作灵活,调节范围广,易实现一窑烧制多规格产品,烧成合 格率高。 设备组成:本窑由窑体单元,燃烧冷却工作系统,控制显示系统三大部 分组成。 1.2、窑体单元 窑体既是窑炉主体,又是各种管路和热工控制一次仪表及执行机构等的 支撑体。该窑由砌体、窑车及烟道组成。 窑墙选材:厚度650mm(其中50mm多晶莫来石纤维+230mmJM28轻质莫来石砖+230mm轻质粘土砖+40mm高铝纤维毯+40mm标准纤维毯+60mm普通纤维毡)。 窑顶选材:厚度450mm(其中50mm多晶莫来石纤维+260mmJM28轻质莫来石砖+40mm高铝纤维毯+40mm标准纤维毯+60mm普通纤维毯)。 窑门采用侧开门,内部结构从内到外依次为50mm多晶棉块+JM28轻质莫来石砖+40mm高铝纤维毯+50mm标准纤维毯+30mm普通纤维毡。 窑体采用砖棉结构降低了窑体承重,减少了窑体蓄热,具有较好的保温
性能,减少窑体散热,达到节能降耗的目的。 1.3、燃烧及通/排风系统 该系统按功能类别分为燃料供应系统、助燃/冷却系统、排烟系统。 A、燃料供应系统 燃气管道均为优质不锈管制作而成。阀门为密封良好的优质球阀,燃气 经过总管、过滤、稳压、支管等到烧嘴。为保证供气系统安全,在供气主管 上配置有手动阀、过滤器、压力表、调压阀、上下限压力开关、电磁阀、溢 流放散阀等,旁路前后各有一块压力表现场显示进出口管路压力。压力开关 分别控制燃气压力最高限和最低限。主管经总成进入窑体范围后分成6组支路,每支烧咀设有火焰监测和自动点火,每个喷嘴前带一个电磁阀。 B、助燃系统控制 助燃系统包括高压离心送风机、调节闸阀、送风管路及变频调节器等装 置。送风压力通过安装在主风管路上的压力检测装置检测并传送给仪表间压 力自控仪显示并控制。 C、燃烧部分控制 为使烧成温度控制调节灵活,截面温差小,该窑设计选用高速节能烧咀 交错对称分上下两排布置,烧咀内芯为耐热不锈钢,燃烧充分不结焦。 D、通/排风控制 梭式窑的燃烧、冷却、排烟系统一般都结合在一起。每支烧咀配有自动 点火,火焰监测器、安全切断阀,通过电动阀和变频自控助燃风实现燃烧、 冷却工序的完成,排烟采用窑底车面两头排烟方式,冷却主要靠烧咀喷射的 冷风进行冷却制品,在窑炉开始进入急冷阶段时,冷却风根据冷却曲线,自 动降温。 该窑配备有排烟、助燃风机共2台。排烟、助燃风机均采用变频控制, 其中排烟根据窑压(取零压点附近的位置)来控制,助燃通过主管检测压力 来控制。变频器采用进口日本三菱公司产品。这些控制不仅能维护窑炉压力 制度,而且节省电耗。
回转窑系统热平衡计算资料
回转窑系统热平衡计算 1 热平衡计算基准、范围及原始数据 1.1 热平衡计算基准 物料基准:一般以1kg 熟料为基准; 温度基准:一般以0℃为基准; 1.2 热平衡范围 热平衡范围必须根据回转窑系统的设计或热工测定的目的、要求来确定。在回转窑系统设计时,其平衡范围,可以回转窑、回转窑加窑尾预热分解系统、或再加冷却机和煤磨作平衡范围。范围选得大,则进出口物料、气体温度较低,数据易测定或取得,但往往需要的数据较多,计算也烦琐。因此一般选回转窑加窑尾预热分解系统作为平衡范围。 1.3 原始数据 根据确定的计算基准和平衡范围,取得必要的原始数据,这是一项非常重要的工作。计算结果是否符合实际情况,主要取决于所选用的数据是否合理。对新设计窑或改造窑来说,主要是根据同类型窑的生产资料,结合工厂具体条件和我国实际情况、合理地确定各种参数;对于生产窑来说,主要通过热工测定取得实际生产中各种参数。若以窑加窑尾预热系统为平衡范围,一般要取得如下原始数据:生料用量、化学组成、水分、入窑温度;燃料成分、工业分析和入窑温度;一、二次空气的比例和温度;空气过剩系数、漏风系数;废气温度;飞灰量、灰温度及烧失量;收尘器收尘效率;窑体散热损失;熟料形成热等等。熟料形成热可根据熟料形成过程中的各项物理化学热效应求得,也可用经验公式计算或直接选定。 2 物料平衡与热量平衡 计算方法与步骤说明于下: 窑型:预分解窑 基准:1kg 熟料;0℃ 平衡范围:窑+预热器系统 根据确定的平衡范围,绘制物料平衡图和热量平衡图,如图1和图2所示。 图1 物料平衡图 图2 热量平衡图
2.1 物料平衡计算 2.1.1 收入项目 (1)燃料消耗量 m r (kg/kg 熟料) 设计新窑或技术改造时,m r 是未知量,通过热平衡方程求得,已生产的窑,通过热工测定得到。 (2)入预热器物料量 ① 干生料理论消耗量 s ar r gsL 100100L a A m m --= 式中,m gsL —干生料理论消耗量,kg/kg 熟料;A ar —燃料收到基灰分含量,%;a —燃料灰分掺入熟料中的量,%;L s —生料的烧失量,%。 ② 入窑回灰量和飞损量 ηfh yh m m = )1(fh Fh η-=m m 式中,m yh —入窑回灰量,kg/kg 熟料;m fh —出预热器飞灰量,kg/kg 熟料;m Fh —出收尘器飞灰损失量,kg/kg 熟料;η—收尘器、增湿塔综合收尘效率,%。 ③ 考虑飞损后干生料实际消耗量 s fh Fh gsL gs 100100L L m m m --?+= 式中,m gs —考虑飞损后干生料实际消耗量,kg/kg 熟料;L fh —飞灰烧失量,%。 ④ 考虑飞损后生料实际消耗量 s gs s 100100W m m -?= 式中,m s —考虑飞损后生料实际消耗量,kg/kg 熟料;W s —生料中水分含量,%。 ⑤ 入预热器物料量 yh s m m +=入预热器物料量(kg/kg 熟料) (3)入窑系统空气量 ① 燃料燃烧理论空气量 )O 0.033(S 0.267H 0.089C ar ar ar ar LK -++='V LK LK 293.1V m '='
加工站毕业设计说明书
开封大学 毕业设计说明书 设计题目亚龙YL-335B型自动生产线---加工站院系电子电气工程学院 专业电气自动化技术 学生姓名王鹏 指导教师高明远(副教授)
摘要 随着社会的进步科技的发展,人们不愿再花很大力气去手工操作机器,而PLC技术在正好应用于这一点,通过PLC内部的处理能把许多之前手动操作的加工机器改为自动运行,这样不仅解放了人力,生产效率也有很大的提升。PLC以其高抗干扰能力、高可靠性、高性能价格比且编程简单而广泛地应用在现代化的自动生产设备中,担负着生产线的大脑——微处理单元的角色。 对本设计而言,加工站机构采用气动驱动技术,系统控制方式采用一台PLC承担其控制任务,加工单元的功能是完成把待加工工件从物料台移送到加工区域冲压气缸的正下方;完成对工件的冲压加工,然后把加工好的工件重新送回物料台的过程。 在TPC7062KS人机界面上组态画面,触摸屏上电并进行权限检查后运行,将直接切换到“运行界面”。人机界面上增加了操作加工站的操作方式,易于观察,提供了远程控制使加工与控制分离,易于操作。 关键词:加工站 PLC 人机界面组态
目录 前言 (2) 一、加工单元的结构 (3) (一)加工单元结构认知 (3) 1.物料台及滑块机构 (3) 2.磁性开关 (4) 3.漫射式光电接近开关 (5) (二)加工(冲压)机构 (6) (三)加工单元的气动元件 (7) 1.薄型气缸 (7) 2.气动手指(气爪) (7) 3.电磁阀组 (8) 4.磁感应接近开关 (9) 二、加工单元的气路设计与连接 (10) 三、加工单元的PLC及编程 (11) (一)加工单元PLC的选择及其介绍 (12) (二)加工单元的PLC的接线分配表及I/O分配表 (12) (三)加工单元的PLC的I/O接线图 (14) (四)加工单元的PLC的编程 (14) 1.工作任务 (15) 2.子程序流程图 (15) 3.PLC程序的编写 (15) 四、加工单元的本地控制 (16) 五、加工单元的人机界面控制 (17) 1.根据工作任务,对工程分析并规划 (17) 2.“运行画面”组态 (17) 3.制作指示灯 (18) 4.数据显示 (19) 5.工程通信 (20) 6.工程下载 (21) 7.工程运行 (22) 六、总结 (23) 七、参考文献 (24) 八、附录 (25)
3自吸梭式窑
3 m3燃气自吸式梭式窑 一、主要技术参数: 1. 烧成产品:日用陶瓷 2. 窑炉全容积:3 m3 3. 窑炉设计温度:1350℃ 4. 正常烧成温度:1350℃ 5. 窑炉内尺寸:L×W×H=3200×1460×1100mm 6. 窑车台面尺寸:L×W×H=3000×1030×1000mm 7. 窑炉装载量:有效装载3立方 8. 棚板材质:碳化硅 10. 燃料:天然气,热值8600kcal/bm3, 总管压力要求稳定在0.02—0.08兆帕 11. 烧成方式:自吸式烧嘴,两侧布置,车台面烟道 12. 制品烧成方式:棚板装载,明焰祼烧; 13. 控制方式:窑内压力手动控制,温度通过燃气压力控制,。 14. 主要配置:窑车2辆,托车1辆,窑门1个,停车道2条; 二、设备概况: 该窑炉由可窑体、窑车、托车、侧开窑门、停车道、燃烧系统、排烟系统、热电偶、数显仪表、补偿导线等几部分组成。 1. 窑体
窑体内衬选材满足最高烧成温度要求。内层为50mm多晶棉,中间为230mm厚莫来石砖,外层200mm厚优质硅酸铝纤维,最外层为A3钢板。 2. 燃烧系统 选用文丘里自吸式烧嘴,助燃风自行吸入,烧嘴结构简单,无须动力。该窑设28支烧嘴,于两侧墙底部布置,火焰由两侧墙上升至窑顶后向下流经料垛,进入车台面烟道。窑炉采用车底排烟,火焰呈倒焰形式,窑内温度均匀。窑体钢结构底部设有环行供气管路,每支烧嘴前设有阀门调节。 3. 排烟系统 烟气由车台面棚板吸火孔进入窑车中部的3个排烟口,经汇总烟道由排烟风机引入厂方的钢制烟囱排空。在排烟机入口前装有温度表,检测烟道温度,并设有冷风配入口,根据烟气温度调节配风量,使排烟机在安全工作温度下运行。 4. 温度测量控制及窑压控制系统 窑顶安装1支热电偶显示窑内温度。更换烧成工艺时通过人工调节燃气管路各阀门、吸风口风盘间隙等,达到要求后投入温度及窑压的自动控制,以满足生产工艺要求。 为提高温度调节的精度,本方案的温度测量信号由带温度偏差报警功能的数显程序仪处理,当实际烧成温度与预先设定的烧成温度产生偏差,且超过了预先设定的偏差数值时,该数显程序仪输出报警信号给声光报警器,提示现场操作人员
水泥回转窑结构图及水泥回转窑流程宏科
水泥回转窑结构图及水泥回转窑原理讲解 水泥回转窑结构图水泥回转窑模型图解 1 水泥回转窑生产工艺简介 整个工艺流程主要有生料粉末预均化,五级旋风预热,预分解,窑内煅烧,蓖冷机冷却及熟料粉碎等工序组成。 2 水泥回转窑原理讲解:水泥回转窑生产自动化对DCS系统的要求 对于年产30万吨水泥生产线,按工艺及实现生产过程控制对DCS系统有如下要求: (1)根据厂方的具体技术要求,目前DCS主要监控生产线的四大部分:窑头、窑中、窑尾和煤粉制备。共设置560个I/O点,其中模拟量输入72点,模拟量输出25点,数字量输入267点,数字量输出139点,热电偶及热电阻分别为22点和35点。 窑头、窑中(点) 窑尾(点) 煤粉制备(点) AI 21 11 40 AO 7 6 12 DI 112 48 107 DO 64 20 55 RTD 5 16 14 T/C 3 4 15 (2)根据该水泥厂实际情况和生产工艺,整个回转窑系统共设置12个控制回路,其它各设备则采用直接控制和顺序控制方式。12个控制回路中,压力控制回路6个,流量控制回路3个,料位控制回路1个,温度控制回路2个。 (3)为减轻人工操作强度,提高自动化程度和系统可靠性,由DCS系统实现联锁保护功能。同时为了操作方便和直观,在工作站界面中,将工艺流程及各种运行设备工况按比例设计操作界面,并随时对各部位进行动态显示。测量值如温度、压力、流量、料位等数据实现动态
显示,阀位开度以百分比表示,料位用彩色棒图动态模拟。不同物料管道用不同颜色来区别,其物料流向用箭头表示。 (4)为了对生产进行有效监控,以便优化工艺条件如故障查找,对32个重要参数用历史趋势曲线进行汇总。如回转窑各段的窑温,五级旋风及窑尾分解炉等处的温度、压力等,以及各控制回路的测量值等,以上就是关于水泥回转窑原理讲解和水泥回转窑结构图的讲解。
机械毕业设计说明书
机械毕业设计说明书 【篇一:机械类毕业设计说明书】 河北工业大学 毕业设计说明书 作者:杲宁学号: 090365 学院:机械工程学院 系(专业):机械设计制造及其自动化 题目:药板装盒机结构设计 指导者:张建辉副教授 (姓名)(专业技术职务) 评阅者: (姓名)(专业技术职务) 2013年 6 月 4 日 毕业设计(论文)中文摘要 毕业设计(论文)外文摘要 ? 目录 1 引言(或绪论)???????????????????????? 1 1.1课题研究的目的与意义?????????????????????? 1 1.2 本课题国内外研究现状和发展趋势????????????????? 1 1.3 本课题主要研究内容??????????????????????? 3 1.4 药板装盒机工艺流程分析????????????????????? 3 2 总体方案确定??????????????????????????4 3 药板装盒机详细结构设计 ????????????????????6 3.1 总体结构组成及其工作原理???????????????????? 7 3.2 主要技术参数的确定??????????????????????? 10 结 论 ???????????????????????????????20 参考文献??????????????????????????????21 致谢??????????????????????????????22 【篇二:机械制造毕业设计说明书模板】 (中文题目) (二号、黑体、居中,段后空一行)
摘要(小四号、黑体):离心式压缩机在国民生产中占有重要地位。可用于化肥、制药、制氧及长距离气体增压输送等装置。本次设计 的主要工作包括:确定合成氨工段循环离心压缩机的结构形式、主 体结构尺寸,并确定主要零、部件的结构尺寸及其选型。首先进行 强度和稳定性计算,主要进行了筒体、端盖的壁厚计算、水压试验 应力校核以及叶轮、轴的强度校核。其次,对这些零部件进行结构 设计。整个设计过程都是依据设计规范和标准进行的,设计结果满 足工程设计要求。关键词(小四号、黑体):离心压缩机;叶轮; 结构设计;应力校核;转子轴(英文题目) .engineering design results meet the design requirements. key words: centrifugal compressor; impeller; structural design;stress check;rotor shaft 目录 1 前言 (1) 1.1本次毕业设计课题的目的、意义 (1) 1.2 合成氨工艺简介 (1) 2 离心式压缩机概况 (3) 2.1离心压缩机的优缺点 (3) 2.2离心压缩机的结构组成 (3) 2.3离心压缩机的发展趋势 (4) 3 离心式压缩机选型及计算依据 (5) 3.1离心式压缩机的气动热力学 (5) 3.1.1连续方程 (5) 4 离心压缩机设计和选型计算 (7) 4.1工艺条件 (7) 4.2容积多变指数和压缩性系数的计算 (7) 4.2.1确定混合气体的分子量和气体常数 (7) 4.2.2容积多变指数和压缩系数的确定 (8) 4.3离心压缩机的热力计算 (8) 4.3.1压缩机级数确定 (8) 5 结论 (10) 符号说明 (11) 参考文献 (12) 致谢 (13)
刚玉制品高温梭式窑设计全解
19M31650℃刚玉制品高温梭式窑设计 班级:材料科学1101 姓名: 指导教师:徐长海 设计总说明 梭式窑,或称抽屉窑,也叫车底式窑或活底式窑,是从传统的倒焰窑演变而来,故而属于“间歇式”或“半连续式”窑型。随着国内陶瓷工业燃料结构由煤、油向煤气、液化石油气的过渡,梭式窑已被广泛地用于陶瓷、耐火材料以及建筑材料等行业。本文是对19m3 1650℃氧化铝制品高温梭式窑的设计,主要包括窑墙与窑顶尺寸的设计和燃烧计算与燃烧设备的选择,等等。本文中梭式窑选用重油燃料。 关键词:梭式窑,重油,高温,刚玉制品 19m3,1650 ℃ Corundum Products High Temperature Shuttle Kiln Design Design Description The shuttle kiln is also called drawer kiln, or by the name of the kiln underneath the car or the kiln live upstairs, which is evolved from the traditional down draft kiln. so this kind of kiln belongs to "intermittent" or "semi-continuous"
kiln type. The domestic ceramic industry fuel structure has experienced the change from coal and oil to coal gas, oil, liquefied petroleum gas, the shuttle kiln has been widely used in ceramics, refractory materials and building materials industries under this transformation circumstance. This thesis describes the design of 19m3 1650℃high-temperature shuttle kiln which can fabricate corundun products. It mainly includes the dimension design of kiln wall and kiln crown, the calculation of combustion and the choice of combustion equipment, etc. The shuttle kiln using heavy oil as fuel in this article. Key words: shuttle kiln, heavy oil, high temperature,corundun products
4000吨每天水泥回转窑烟气除尘工程设计
本科毕业设计(论文)4000t/d水泥回转窑烟气除尘工程设计 学院环境科学与工程学院 专业环境工程 年级班别 20XX级(X)班 学号 310X008XXX 学生姓名 XXX 指导教师 XX 20XX年 X 月
设计总说明 设计任务由来: 为了控制水泥工业的大气污染物排放,促进水泥工业产业结构调整,国家环境保护总局组织中国环境科学研究院、合肥水泥研究设计院、中国材料工业科工集团公司起草了新的《水泥工业大气污染物排放标准》(GB4915-2004)。水泥回转窑窑尾是水泥生产环节中粉尘排放量最大的排放点,窑外分解窑尾烟尘浓度为60g/m3~80g/m3,这一环节的污染物成分复杂,除粉尘、烟尘外,还有二氧化硫、氮氧化物、氟化物等有害气体,而粉尘对大气污染最为严重。 设计依据标准: 现有生产线工艺、操作方式及其有关技术资料、文件资料; 广东省《大气污染物排放限值》(DB44/27-2001) 《工业企业设计卫生标准》(TJ36-79) 《水泥工业污染物排放标准》(GB4915-85) 回转窑有关技术参数如下: 水泥产量:4000吨/天; 烟气温度:45~200℃; 烟气含尘浓度:5000~30000mg/Nm3; 烟气湿度:5%~15%。 设计原则: 1)设计中要认真贯彻国家的经济建设方针、政策。 2)应充分考虑资源的充分利用。 3)选用的技术要先进适用。 4)工程设计要坚持安全可靠、质量第一的原则。 5)坚持经济合理原则 6)必须遵循国家有关环境保护法律、法规,合理开发和充分利用各种自然 资源,严格控制环境污染,保护和改善生态环境 7)建设项目需要配套建设的环境保护设施,必须与主体工程同时设计、同 时施工、同时投产使用。 8)必须遵守污染物排放的国家标准和地方标准。 9)应当在建设项目中采用能耗物耗小、污染物产生量少的清洁生产工艺。关键词:水泥回转窑,烟气,除尘