内螺纹铜管基本参数对换热的影响
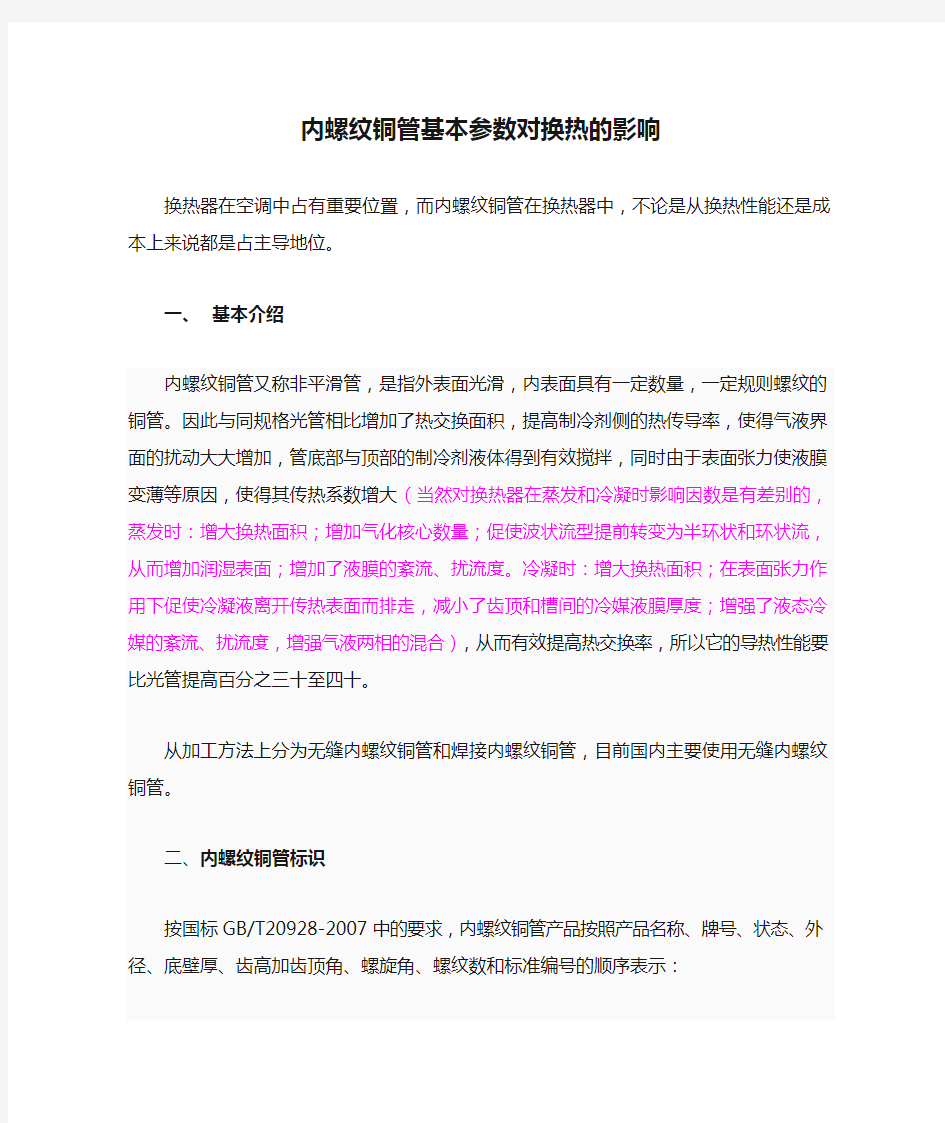

内螺纹铜管基本参数对换热的影响
换热器在空调中占有重要位置,而内螺纹铜管在换热器中,不论是从换热性能还是成本上来说都是占主导地位。
一、基本介绍
内螺纹铜管又称非平滑管,是指外表面光滑,内表面具有一定数量,一定规则螺纹的铜管。因此与同规格光管相比增加了热交换面积,提高制冷剂侧的热传导率,使得气液界面的扰动大大增加,管底部与顶部的制冷剂液体得到有效搅拌,同时由于表面张力使液膜变薄等原因,使得其传热系数增大(当然对换热器在蒸发和冷凝时影响因数是有差别的,蒸发时:增大换热面积;增加气化核心数量;促使波状流型提前转变为半环状和环状流,从而增加润湿表面;增加了液膜的紊流、扰流度。冷凝时:增大换热面积;在表面张力作用下促使冷凝液离开传热表面而排走,减小了齿顶和槽间的冷媒液膜厚度;增强了液态冷媒的紊流、扰流度,增强气液两相的混合),从而有效提高热交换率,所以它的导热性能要比光管提高百分之三十至四十。
从加工方法上分为无缝内螺纹铜管和焊接内螺纹铜管,目前国内主要使用无缝内螺纹铜管。
二、内螺纹铜管标识
按国标GB/T20928-2007中的要求,内螺纹铜管产品按照产品名称、牌号、状态、外径、底壁厚、齿高加齿顶角、螺旋角、螺纹数和标准编号的顺序表示:
示例1:用TP2制造的,供应状态为M2,外径为9.52mm,底壁厚为0.30mm,齿高为0.20mm,齿顶角为53度,螺旋角为18度,螺纹数为60的无缝内螺纹盘管,标记为:
无缝内螺纹盘管TP2 M2 φ9.52×0.30+0.20-53-18/60
TP2:牌号,是磷脱氧铜,磷脱氧铜是熔解高纯度的原材料,把熔化铜中产生的氧气用亲氧性的磷(P)脱氧,使其氧含量降低到100PPm以下,从而
提高其延展性、耐蚀性、热传导性、焊接性、抽拉加工性,在高温中也不发生氢脆现象。
三、内螺纹铜管齿形基本参数及对其传热性能的影响
齿形图
1、外径D
我们蒸发器目前用φ7管径(C型蒸发器用6.35),冷凝器用φ9.52与φ7管径;由于成本压力,铜管都趋近于细经化,铜管细径化的优点:由于管与管之间距离缩小,使得肋片效率提高、传热有效面积增加、空气流过时的流动阻力减小,强化传热(仅指管外换热,但管内换热面减少的影响远远大于这点,如果实际使用过程中,相同结构能保证管内换热面积相同则细径化优点就能体现出来),但管径太小会造成冷媒阻力变大;对R410A来说,其本身压力较高,能克服这种阻力对它的影响,因此铜管细径化对R22不利。
2、底壁厚Tw
目前内螺纹管底壁厚一般在0.20~0.30mm范围内,底壁厚越薄传热效果越好,但底壁厚过薄会削弱管材的强度以及齿的稳定性,不仅不利于后道工序的U形弯管质量与焊接质量,而且同样也会因齿的稳定性差,影响传热效果。φ7*0.22,φ9.52*0.27
3、齿高H f
齿高是影响传热的重要因素,增加齿高会使内表面换热面积和刺破液膜能力增加,内螺纹管传热效果增强,但齿高的增大受加工技术的限制。目前内螺纹管齿高一般在0.10~0.25mm范围内。φ7*0.10,φ9.52*0.16
4、螺旋角β
螺旋角的存在是为了使流体旋转,使管道中流体产生与径向不同的二次流,增加湍流的强度,从而使对流换热得到加强,换热系数随之增加,所以螺旋角增大能增强换热系数,但随着螺旋角的增大,压力损失也随之增加,故螺旋角也不是越大越好,而是有一个合理的范围。通常在10°~25°范围内(经验值:在此范围内,蒸发管螺旋角小些较好,冷凝管螺旋角大些较好;管径较小时,冷媒流动阻力大,螺旋角应取小值,反之取大值)
5、齿顶角α
齿顶角小,有利于增加内表面换热面积,减薄冷凝传热的液膜厚度,增加蒸发传热的汽化核心,但齿顶角过小,则内螺纹管齿的抗胀管强度过小,齿高在胀管后被压低的程度及齿型的变形量增加会引起传热效率减低,因此在保证齿的抗胀管强度的前提下,内螺纹管的齿顶角尽可能小些。目前一般在40°~60°之间,现国内一些厂家做出的内螺纹瘦高齿齿顶角能达到20°左右。
6、齿数(螺纹数)n
增加齿数即螺纹条数能够增加汽化核心的数目,有利于沸腾换热举措,增加内表面换热面积。但是齿数增加过多,会使齿间距过小,反而减弱了管内流体的被搅拌强度,且加大了齿间液膜厚度,增大了热阻,而降低了换热能力,使得螺纹管的换热效率趋近于光管,故齿数应控制在一定的范围内为宜。
7、槽底宽 W
槽底宽尺寸大有利于传热,但槽底宽尺寸过大,胀管后齿高被压低的程度及齿型的变形量增加,传热效率将降低,因此在保证抗胀管强度的前提下,槽底宽大些好。
8、润周长
增加润周长可以增加汽化核心数,使蒸发传热效率显著提高。因此,对于蒸发器用管,管内横截面润周长越大越好。润周长的增加,可以通过增加齿高和减少齿顶角来实现。
四、齿形分类
为提高空调能效比,最直接的技术途径就是提高换热器传热性能,而控制空调产品成本,最有效的技术措施就是研究并运用传热强化技术,提高换热器单位面积的传热量。因此通过改变齿形参数来提高传热系数,就产生了不同种类的高效内螺纹管,按旋向和齿形分类如下:
单旋向:等高齿(通用C型齿)、高低齿、瘦高翅、M型齿
双旋向:断续齿、交叉齿
图形如下:
现在大量使用的还是普通等高齿,因为复杂齿形的加工难度大,成本较高,还未广泛使用。
瘦高齿:齿顶角减小,槽底宽增大,来提高换热系数
M型齿:在齿上开小槽,增加槽底宽,增加换热面积
断续齿:增加换热面积,促使气液两相转换平稳
交叉齿:形成多个蒸发核心,增加换热面积,强化了紊流,蒸发用管改善较明显
交叉齿与瘦齿铜管能明显改善蒸发性能,M形齿、瘦齿、断续齿也能明显改善冷凝性能,提高能效比
五、加工工艺对螺纹管的影响
1、U形弯管工序
首先,要选择直径大小合适的弯管芯头,芯头的直径一般比内螺纹管内径小0.2~0.4mm,如果芯头选取过大,U形管尾部外侧易开裂,如果选取过小则U形管尾部内侧易起皱;
其次,弯管速度和芯头离U形管尾部位置也很重要,太近尾部外侧易开裂,太远尾部内侧易起皱;
最后,弯管时所用润滑油的黏度和数量也很重要,如果黏度过低或喷油量少,则易造成开裂,并且在之后的胀管过程中,倒齿程度会加大,影响传热效果;反之则易起皱且油脂不易去除,影响传热还会影响焊接。当然做到绝对不起皱很难,大U管折皱质量判定标准:折皱高度0.05mm以下轻微,
0.05-0.2mm严重,0.2m以上折管。
2、胀管工序
胀管目的是为了消除传热管与翅片间缝隙,实现相互之间的连接和传热。一般采用机械胀管,操作简单、成本低,但机械胀管时胀头对螺纹管齿形和
参数有破坏作用。其破坏程度与胀接量大小有关,即胀头大小有关,过胀时管子会有过大的塑性变形,加工硬化现象严重,易产生裂纹,特别会造成倒齿严重,同时冷凝器折弯时容易折管;欠账时铜管未产生足够塑性变形,会使传热管和翅片间产生较大接触热阻,从而降低传热效率。一般铜管胀后齿高降低量应在0.01~0.02之间为妥。
因此,每次内螺纹管规格改变,如壁厚减薄后,都需更换弯管芯头和涨头尺寸,否者就会影响两器换热效果
六、内螺纹管的成型工艺
1、无缝内螺纹铜管成型
从示意图可看出无缝内螺纹管是拉制而成的,管坯ΦD×S经过减径模ΦD6减径后,在高速旋转的钢球ΦD3滚压下,铜管内表面的金属被压进螺纹芯头ΦD5的齿槽,在铜管内表面形成齿高为H0的齿形(底壁厚为S0);在拉拔力F的作用下,铜管不断向前运动,在铜管内壁就形成连续的螺纹;最后通过定径模ΦD1定径后,成为符合要求的螺纹管ΦD0×S0×H0。
2、焊接内螺纹铜管成型
焊接内螺纹铜管成型工艺过程大致如下
高精度铜带→对焊连接→两次滚压成齿→多辊卷制成管→高频焊接
+气体保护→定径切割等工序最后成为螺纹管。
由此可看出,焊接内螺纹管与无缝管最大不同就是,先成型螺纹齿,再成管形(而无缝管则相反),此种方式可加工复杂高难度齿形,且成型过程免润滑可保持管内清洁度;但是成型过程会产生焊接晶粒同时焊缝会切断螺纹齿,使得成品管的抗拉强度和延伸率降低;因此这对成型过程中的工艺要求非常高,由此加工成本也随之提高。如果这种工艺成熟后,可容易地加工出高效率齿形的内螺纹管,以提升两器换热效率。
内螺纹铜管齿形参数对传热性能的影响_图文(精)
第 9卷第 6期制冷与空调 2009年 12月 REFRIGERA TION AND A IR CONDITIONIN G 35238 收稿日期 :2009208225 通信作者 :郭宏林 ,Email :guohonglin2@126. com 内螺纹铜管齿形参数对传热性能的影响 董志强郭宏林蔡运亮安鹏涛 (金龙精密铜管集团股份有限公司 摘要利用 R 22单管传热试验台 , 对相同工况下不同结构参数的内螺纹强化管进行蒸发冷凝换热试验。通过对比分析试验数据 , 发现改变齿形参数对内螺纹管换热系数影响较大 , 且 Tube 2N EW 换热性能优于其他管型。 关键词内螺纹强化管 ; 蒸发 ; 冷凝 ; 换热系数 ; 齿形 ; 制冷 ; 空调 Influence of tooth prof ile parameters of inner 2grooved copper tube on heat transfer performance Dong Zhiqiang Guo Honglin Cai Yunliang An Pengtao (G olden Dragon Precise Copper Tube Group Inc. ABSTRACT By using of t he single t ube laboratory for R 22, test s and compares t he evap 2oration and co ndensation heat t ransfer performance wit h different toot h p rofile parameters of inner 2grooved t ube. The result s show t hat toot h p rofile
5mm管径内螺纹铜管换热器分析
Ф5与Ф7换热器比较分析 背景: 近年来,由于国际铜价节节攀升且居高不下,如果降低空调器铜用量各大厂家也是八仙过海,比如铝制换热器,ACC管,小管径铜管替代原有较大管径的铜管等。随着环保节能的考虑,家用空调用冷媒逐渐由R22过渡到R410A,整机中R410A运行压力要比R22高出60%,因此系统性能受冷媒压力损失的影响较小,更适合于采用小管径铜管换热器。 空调换热器采用小管径铜管后,管内换热和压降特性会随之改变,根据换热器试验研究表明:在冷媒质量流量相同情况下,Ф5铜管管内制冷剂的摩擦压降比Ф7的大20-40%。因此在实际应用Ф5铜管时,需要针对Ф5铜管的换热和压降特性,对换热器型式进行优化调整,如翅片或流路,同时制冷剂充注量可以减少了10-20%,需要对系统的其他部件,如膨胀阀的开度进行调整,以求系统的性能接近甚至优于原有系统性能。 一、行业Ф5翅片方面的应用情况: 1)日本应用情况 小结: ◆换热器越来越细管径化,Φ5换热器在室内机上有4家公司使用。2家是跟其他管径的组 合构成的圆弧换热器。大金使用的更细的φ4。 ◆φ5以下的細管各公司几乎都是用在能力2.2~7.1kW的室内机上。这是因为室内机箱体 从小到大共都是通用的,φ5可以使用在家用空调上限7.1kW。 ◆作为日本冷暖变频室外机,各企业的设计中没有使用φ5换热器,一般是Φ7或φ7.94。
因为用φ5的话分流回路数多分流太复杂。φ7换热器在4.0kW机上都要分4路,φ5的就太复杂了。 ◆室内机的φ5换热器几种管径(φ5和φ6.35等)组合,可以简化分流并提高性能。2)韩国应用情况 3)国内应用情况 Ф5管技术在2005年以后引入国内,在2007年国内相应的产品设计和生产工艺已经成熟。经向冲床及模具厂家调研,近3年以来美的、格力在Ф5换热器设备方面投入较大,Ф5换热器的产能各达到100万件/月的大批量生产规模。 ◆美的2009年以前陆续购入5条Ф5换热器生产线,2009~2010年进口了10条日本日高 公司Ф5换热器生产线,已经在今年旺季实现规模效益。2011年还将预计投入5条。 ◆格力2010年前陆续购入10条Ф5换热器生产线以后,2011年已经向日本日高公司一次 性订购了12条Ф5换热器生产线(今年12月开始陆续交货),预计在2012年旺季可实现规模效益。格力Ф5换热器生产线有3台为国产设备,其余19台均为进口设备。 ◆行业内其他竞争对手格兰仕、志高等均有3条以上Ф5换热器生产线,以面向国际市场 的生产订单为主,产能预计各将达到12万件以上/月的生产规模。 4)海信科龙的情况 海信科龙到目前为止,Ф7和Ф5换热器有以下几种:
内螺纹铜管
简介 2发展简史 3传热性能 4生产过程 ?生产工艺 ?生产标准 ?应用领域 1简介 内螺纹铜管又称非平滑管,英文名称INNER GROOVED COPPER TUBE(IGT),是指外表面光滑,内表面具有一定数量,一定规则螺纹的内螺纹TP2紫铜管。 由于内螺纹铜管内表面积的增加,所以它的导热性能要比光管提高百分之二十到三十。 随着世界能源紧张和国内能效比空调准入制度的实行,内螺纹铜管将 会被广泛应用到空调制冷行业中。 2发展简史 内螺纹铜管的发展大致经历了如下几个发展阶段: (1)山型齿内螺纹管; (2)梯型槽内螺纹管; (3)顶角型内螺纹管; (4)细高齿型内螺纹管。(又称瘦高齿内螺纹铜管) 目前,国外又陆续推出了高低齿齿型、齿顶开槽、双旋向等内螺纹管。 3传热性能 按照国标GB/T20928-2007中的要求,内螺纹铜管产品按照产品名称、牌号、状态、外径、底壁厚、齿高加齿顶角、螺旋角、螺纹数和标准编号的顺序表示:
示例1:TP2 M2 φ9.52×0.30+0.20-53-18/60 GB/T20928-20072、(用TP2制造的,供应状态为M2,外径为9.52mm,底壁厚为0.30mm,齿高为0.20mm,齿顶角为53度,螺旋角为18度,螺纹数为60的无缝内螺纹盘管,)标记为: 无缝内螺纹盘管TP2 M2 φ9.52×0.30+0.20-53-18/60 GB/T20928-20072、内螺纹铜管尺寸参数及对其传热性能的影响(1)外径 早期空调换热器中使用得较普遍的铜管直径为9.52mm左右,进入1990年以后一些空调器生产企业已经将换热器的传热管管径细化成7.0mm,其中蒸发器管径细化的现象最为普遍。这种细管径的换热器,由于管与管之间距离缩小,使得肋片效率提高、传热有效面积增加、空气流过时的流动阻力减小,强化传热。1995年以后,一些家用空调器生产企业又将传热管的管径进一步细化为6mm,甚至5mm,传热效率又进一步提高,尤其是在应用于替代制冷剂R410A的室内机时,由于R410A制冷剂系统的压力比R22的高1.6倍左右,使用细径管有利于提高安全可靠性。 目前国内的内螺纹管管径主要有12.7mm,9.52mm,7.94mm,7mm,6.35mm和5mm 等几种规格,其中9.52mm与7mm应用最为普遍。并且随着铜价等原材料上涨及国家对空调能效的要求,铜管正朝着细径薄壁的方向发展,但管径太小会造成冷媒阻力变大,薄壁会使工作中管子出现泄漏或者爆裂的可能性增加。 (2)底壁厚 目前内螺纹管底壁厚一般在0.20~0.30mm范围内,底壁厚越薄传热效果越好,但底壁厚过薄会削弱管材的强度以及齿的稳定性,不仅不利于后道工序的U形弯管质量与焊接质量,而且同样也会因齿的稳定性差,影响传热效果。 (3)齿高 齿高是影响传热的重要因素,增加齿高会使内表面换热面积和刺破液膜能力增加,内螺纹管传热效果增强,但齿高的增大受加工技术的限制。目前内螺纹管齿高一般在0.10~0.25mm范围内。 (4)螺旋角 螺旋角的存在是为了使流体旋转,使管道中流体产生与径向不同的二次流,增加湍流的强度,从而使对流换热得到加强,换热系数随之增加,所以螺旋角增大能增强换热系数,但随着螺旋角的增大,压力损失也随之增加,故螺旋角也不是越大越好,而是有一个合理的范围。 (5)齿顶角 齿顶角小,有利于增加内表面换热面积,减薄冷凝传热的液膜厚度,增加蒸发传热的汽化核心,但齿顶角过小,则内螺纹管齿的抗胀管强度过小,齿高在胀管后被压低的程度及齿型的变形量增加会引起传热效率减低,因此在保证齿的抗胀管强度的前提下,内螺纹管的齿顶角尽可能小些。目前国内一些厂家做出的内螺纹瘦高齿齿顶角能达到20°左右。 (6)齿数(螺纹数) 增加齿数即螺纹条数能够增加汽化核心的数目,有利于沸腾换热举措,增加内表面换热面积。但是齿数增加过多,会使齿间距过小,反而减弱了管内流体的被搅拌强度,且加大
内螺纹铜管基本参数对换热的影响
内螺纹铜管基本参数对换热的影响换热器在空调中占有重要位置,而内螺纹铜管在换热器中,不论是从换热性能还是成本上来说都是占主导地位。 一、基本介绍 内螺纹铜管又称非平滑管,是指外表面光滑,内表面具有一定数量,一定规则螺纹的铜管。因此与同规格光管相比增加了热交换面积,提高制冷剂侧的热传导率,使得气液界面的扰动大大增加,管底部与顶部的制冷剂液体得到有效搅拌,同时由于表面张力使液膜变薄等原因,使得其传热系数增大(当然对换热器在蒸发和冷凝时影响因数是有差别的,蒸发时:增大换热面积;增加气化核心数量;促使波状流型提前转变为半环状和环状流,从而增加润湿表面;增加了液膜的紊流、扰流度。冷凝时,增大换热面积;在表面张力作用下促使冷凝液离开传热表面而排走,减小了齿顶和槽间的冷媒液膜厚度;增强了液态冷媒的紊流、扰流度,增强气液两相的混合,,从而有效提高热交换率,所以它的导热性能要比光管提高百分之三十至四十。 从加工方法上分为无缝内螺纹铜管和焊接内螺纹铜管,目前国内主要使用无缝内螺纹铜管。 二、内螺纹铜管标识 按国标GB/T20928-2007中的要求,内螺纹铜管产品按照产品名称、牌号、状态、外径、底壁厚、齿高加齿顶角、螺旋角、螺纹数和标准编号的顺序表示: 示例1:用TP2制造的,供应状态为M2,外径为9.52mm,底壁厚为0.30mm,齿高为0.20mm,齿顶角为53度,螺旋角为18度,螺纹数为60的无缝内螺纹盘管,标记为: 无缝内螺纹盘管TP2 M2 φ9.52×0.30+0.20-53-18/60
TP2:牌号,是磷脱氧铜,磷脱氧铜是熔解高纯度的原材料,把熔化铜中产生的氧气用亲氧性的磷(P)脱氧,使其氧含量降低到100PPm以下,从而提高其延展性、耐蚀性、热传导性、焊接性、抽拉加工性,在高温中也不发生氢脆现象。 三、内螺纹铜管齿形基本参数及对其传热性能的影响 齿形图 1、外径D 我们蒸发器目前用φ7管径(C型蒸发器用6.35),冷凝器用φ9.52与φ7管径;由于成本压力,铜管都趋近于细经化,铜管细径化的优点:由于管与管之间距离缩小,使得肋片效率提高、传热有效面积增加、空气流过时的流动阻力减小,强化传热(仅指管外换热,但管内换热面减少的影响远远大于这点,如果实际使用过程中,相同结构能保证管内换热面积相同则细径化优点就能体现出来),但管径太小会造成冷媒阻力变大;对R410A来说,其本身压力较高,能克服这种阻力对它的影响,因此铜管细径化对R22不利。 2、底壁厚Tw 目前内螺纹管底壁厚一般在0.20,0.30mm范围内,底壁厚越薄传热效果越好,但底壁厚过薄会削弱管材的强度以及齿的稳定性,不仅不利于后道工序的U形弯管质量与焊接质量,而且同样也会因齿的稳定性差,影响传热效果。φ7*0.22, φ9.52*0.27
内螺纹管资料
内螺纹铜管又称非平滑管,英文名称INNER GROOVED COPPER TUBE(IGT),是指外表面光滑,内表面具有一定数量,一定规则螺纹的内螺纹TP2紫铜管。 由于内螺纹铜管内表面积的增加,所以它的导热性能要比光管提高百分之二十到三十。 内螺纹铜管的发展大致经历了如下几个发展阶段: (1)山型齿内螺纹管; (2)梯型槽内螺纹管; (3)顶角型内螺纹管; (4)细高齿型内螺纹管。(又称瘦高齿内螺纹铜管) 目前,国外又陆续推出了高低齿齿型、齿顶开槽、双旋向等内螺纹管 传热性能: 按照国标GB/T20928-2007中的要求,内螺纹铜管产品按照产品名称、牌号、状态、外径、底壁厚、齿高加齿顶角、螺旋角、螺纹数和标准编号的顺序表示: 示例1:TP2 M2 φ9.52×0.30+0.20-53-18/60 GB/T20928-20072、(用TP2制造的,供应状态为M2,外径为9.52mm,底壁厚为0.30mm,齿高为0.20mm,齿顶角为53度,螺旋角为18度,螺纹数为60的无缝内螺纹盘管,)标记为: 无缝内螺纹盘管TP2 M2 φ9.52×0.30+0.20-53-18/60 GB/T20928-20072、内螺纹铜管尺寸参数及对其传热性能的影响(1)外径 早期空调换热器中使用得较普遍的铜管直径为9.52mm左右,进入1990年以后一些空调器生产企业已经将换热器的传热管管径细化成7.0mm,其中蒸发器管径细化的现象最为普遍。这种细管径的换热器,由于管与管之间距离缩小,使得肋片效率提高、传热有效面积
增加、空气流过时的流动阻力减小,强化传热。1995年以后,一些家用空调器生产企业又将传热管的管径进一步细化为6mm,甚至5mm,传热效率又进一步提高,尤其是在应用于替代制冷剂R410A的室内机时,由于R410A制冷剂系统的压力比R22的高1.6倍左右,使用细径管有利于提高安全可靠性。 目前国内的内螺纹管管径主要有12.7mm,9.52mm,7.94mm,7mm,6.35mm和5mm 等几种规格,其中9.52mm与7mm应用最为普遍。并且随着铜价等原材料上涨及国家对空调能效的要求,铜管正朝着细径薄壁的方向发展,但管径太小会造成冷媒阻力变大,薄壁会使工作中管子出现泄漏或者爆裂的可能性增加。 (2)底壁厚 目前内螺纹管底壁厚一般在0.20~0.30mm范围内,底壁厚越薄传热效果越好,但底壁厚过薄会削弱管材的强度以及齿的稳定性,不仅不利于后道工序的U形弯管质量与焊接质量,而且同样也会因齿的稳定性差,影响传热效果。 (3)齿高 齿高是影响传热的重要因素,增加齿高会使内表面换热面积和刺破液膜能力增加,内螺纹管传热效果增强,但齿高的增大受加工技术的限制。目前内螺纹管齿高一般在0.10~0.25mm范围内。 (4)螺旋角 螺旋角的存在是为了使流体旋转,使管道中流体产生与径向不同的二次流,增加湍流的强度,从而使对流换热得到加强,换热系数随之增加,所以螺旋角增大能增强换热系数,但随着螺旋角的增大,压力损失也随之增加,故螺旋角也不是越大越好,而是有一个合理的范围。 (5)齿顶角 齿顶角小,有利于增加内表面换热面积,减薄冷凝传热的液膜厚度,增加蒸发传热的汽化核心,但齿顶角过小,则内螺纹管齿的抗胀管强度过小,齿高在胀管后被压低的程度及齿型的变形量增加会引起传热效率减低,因此在保证齿的抗胀管强度的前提下,内螺纹管的齿顶角尽可能小些。目前国内一些厂家做出的内螺纹瘦高齿齿顶角能达到20°左右。 (6)齿数(螺纹数) 增加齿数即螺纹条数能够增加汽化核心的数目,有利于沸腾换热举措,增加内表面换热面积。但是齿数增加过多,会使齿间距过小,反而减弱了管内流体的被搅拌强度,且加大了齿间液膜厚度,增大了热阻,而降低了换热能力,使得螺纹管的换热效率趋近于光管,故齿数应控制在一定的范围内为宜。 (7)槽底宽 槽底宽尺寸大有利于传热,但槽底宽尺寸过大,胀管后齿高被压低的程度及齿型的变形量增加,传热效率将降低,因此在保证抗胀管强度的前提下,槽底宽大些好。 (8)润周长 增加润周长可以增加汽化核心数,使蒸发传热效率显著提高。因此,对于蒸发器用管,管内横截面润周长越大越好。润周长的增加,可以通过增加齿高和减少齿顶角来实现。
内螺纹铜管
铜管,配管类标准 内螺纹铜管 定义 本标准采用下列定义。 1:内螺纹铜管 管材内表面具有一定数量、一定螺旋角度的金属肋。 2:圆度 管材任一端面上测量的最大与最小直径之差。 3:平均壁厚 指内螺纹铜管按称重法算出相应公称外径的无缝光管的壁厚值。 4:分类与命名 产品分类:热交换器用铜管的种类及牌号见表 5:型号命名:产品型号命名如下: 示例1:内螺纹铜管,外经Φ、底壁厚、齿高、齿数60、螺旋角18度、供应形式(LWC),牌号TP2,铜管供应状态M,执行标准GB20928。 标记为:内螺纹铜管Φ××LWC ×60×18 TP2M GB20928。 示例2:内螺纹铜管,外经Φ、底壁厚、齿高、齿数60、螺旋角18度、供应形式(LWC),牌号C1100T,铜管供应状态OL,执行标准JISH 3300。 标记为:内螺纹铜管Φ××LWC ×60×18 C1100T OL JISH 3300。 技术要求 1:外观质量:内外表面质量 管材的内外表面无针孔、裂缝、起皮、气泡、粗拉道、夹杂、海绵、铜粉、积碳层、绿锈、脏污和严重的氧化膜(内螺纹铜管内表面齿型均匀、正常)。 内外表面颜色要求不得呈(灰)黑色、蓝色,呈轻微灰黑色时不能被擦除,不能有油污流出。用气吹内外表面不得有粉沫,且吹后表面不得变成白色。不允许存在明显的划伤、凹坑和斑点等缺陷。 2:管材质量
管材不应有分层和明显呈暗裂状粗燥感。 3:结构尺寸:内螺纹铜管尺寸、规格 热交换器用内螺纹铜管的尺寸、规格应符合表的规定: 注:外径允许误差计算公式:+│(Dmax+Dmin )÷2 -Dnom │ Dmax :同一截面上最大直径; Dmin :同一截面上最小直径; Dnom :名义直径。 4:圆度 圆度允许误差见表: 注: 计算公式:不圆度=(最大外径-最小外径)/标称外径*100% 5:性能要求 压扁试验 观察压扁后的试样,试样不应有肉眼可见的微小裂纹。 管内清洁度 铜管两端应采用胶塞或其他方式封堵,以防止水汽和灰尘进入,管内应充满保护性气体氮气。清洁度参照表 力学性能与晶粒度:铜管力学性能与晶粒度应符合表 扩口试验:铜管进行扩口试验时,从铜管的端
内螺纹铜管
内螺纹铜管 This manuscript was revised on November 28, 2020
铜管,配管类标准 内螺纹铜管 定义 本标准采用下列定义。 1:内螺纹铜管 管材内表面具有一定数量、一定螺旋角度的金属肋。 2:圆度 管材任一端面上测量的最大与最小直径之差。 3:平均壁厚 指内螺纹铜管按称重法算出相应公称外径的无缝光管的壁厚值。 4:分类与命名 产品分类:热交换器用铜管的种类及牌号见表 5:型号命名:产品型号命名如下: 示例1:内螺纹铜管,外经Φ、底壁厚、齿高、齿数60、螺旋角18度、供应形式(LWC),牌号TP2,铜管供应状态M,执行标准GB20928。 标记为:内螺纹铜管Φ××LWC ×60×18 TP2M GB20928。 示例2:内螺纹铜管,外经Φ、底壁厚、齿高、齿数60、螺旋角18度、供应形式(LWC),牌号C1100T,铜管供应状态OL,执行标准JISH 3300。 标记为:内螺纹铜管Φ××LWC ×60×18 C1100T OL JISH 3300。 技术要求 1:外观质量:内外表面质量 管材的内外表面无针孔、裂缝、起皮、气泡、粗拉道、夹杂、海绵、铜粉、积碳层、绿锈、脏污和严重的氧化膜(内螺纹铜管内表面齿型均匀、正常)。 内外表面颜色要求不得呈(灰)黑色、蓝色,呈轻微灰黑色时不能被擦除,不能有油污流出。用气吹内外表面不得有粉沫,且吹后表面不得变成白色。不允许存在明显的划伤、凹坑和斑点等缺陷。 2:管材质量
管材不应有分层和明显呈暗裂状粗燥感。 3:结构尺寸:内螺纹铜管尺寸、规格 热交换器用内螺纹铜管的尺寸、规格应符合表的规定: 注:外径允许误差计算公式:+│(Dmax+Dmin)÷2 -Dnom│ Dmax:同一截面上最大直径; Dmin:同一截面上最小直径; Dnom:名义直径。 4:圆度 圆度允许误差见表: 注:计算公式:不圆度=(最大外径-最小外径)/标称外径*100% 5:性能要求 压扁试验 观察压扁后的试样,试样不应有肉眼可见的微小裂纹。 管内清洁度 铜管两端应采用胶塞或其他方式封堵,以防止水汽和灰尘进入,管内应充满保护性气体氮气。清洁度参照表 力学性能与晶粒度:铜管力学性能与晶粒度应符合表 扩口试验:铜管进行扩口试验时,从铜管的端部切取适当的长度作试验,试验结果应符合表
内螺纹铜管
内螺纹铜管 Document number:WTWYT-WYWY-BTGTT-YTTYU-2018GT
铜管,配管类标准 内螺纹铜管 定义 本标准采用下列定义。 1:内螺纹铜管 管材内表面具有一定数量、一定螺旋角度的金属肋。 2:圆度 管材任一端面上测量的最大与最小直径之差。 3:平均壁厚 指内螺纹铜管按称重法算出相应公称外径的无缝光管的壁厚值。 4:分类与命名 产品分类:热交换器用铜管的种类及牌号见表 5:型号命名:产品型号命名如下: 示例1:内螺纹铜管,外经Φ、底壁厚、齿高、齿数60、螺旋角18度、供应形式(LWC),牌号TP2,铜管供应状态M,执行标准GB20928。 标记为:内螺纹铜管Φ×××60×18TP2MGB20928。 示例2:内螺纹铜管,外经Φ、底壁厚、齿高、齿数60、螺旋角18度、供应形式(LWC),牌号C1100T,铜管供应状态OL,执行标准JISH3300。 标记为:内螺纹铜管Φ×××60×18C1100TOLJISH3300。 技术要求 1:外观质量:内外表面质量 管材的内外表面无针孔、裂缝、起皮、气泡、粗拉道、夹杂、海绵、铜粉、积碳层、绿锈、脏污和严重的氧化膜(内螺纹铜管内表面齿型均匀、正常)。 内外表面颜色要求不得呈(灰)黑色、蓝色,呈轻微灰黑色时不能被擦除,不能有油污流出。用气吹内外表面不得有粉沫,且吹后表面不得变成白色。不允许存在明显的划伤、凹坑和斑点等缺陷。 2:管材质量 管材不应有分层和明显呈暗裂状粗燥感。
3:结构尺寸:内螺纹铜管尺寸、规格 热交换器用内螺纹铜管的尺寸、规格应符合表的规定: 注:外径允许误差计算公式:+│(Dmax+Dmin)÷2-Dnom│ Dmax:同一截面上最大直径; Dmin:同一截面上最小直径; Dnom:名义直径。 4:圆度 圆度允许误差见表: 注:计算公式:不圆度=(最大外径-最小外径)/标称外径*100% 5:性能要求 压扁试验 观察压扁后的试样,试样不应有肉眼可见的微小裂纹。 管内清洁度 铜管两端应采用胶塞或其他方式封堵,以防止水汽和灰尘进入,管内应充满保护性气体氮气。清洁度参照表 力学性能与晶粒度:铜管力学性能与晶粒度应符合表 扩口试验:铜管进行扩口试验时,从铜管的端部切取适当的长度作试验,试验结果应符合表
内螺纹铜管标识及标准
内螺纹铜管标识及标准 内螺纹铜管的发展大致经历了如下几个发展阶段:(1)山型齿内螺纹管;(2)梯型槽内螺纹管;(3)顶角型内螺纹管;(4)细高齿型内螺纹管。目前,国外又陆续推出了高低齿齿型、齿顶开槽、双旋向等内螺纹管。 内螺纹铜管参数及对其传热性能的影响 1、内螺纹铜管标识 按照国标GB/T20928-2007中的要求,内螺纹铜管产品按照产品名称、牌号、状态、外径、底壁厚、齿高加齿顶角、螺旋角、螺纹数和标准编号的顺序表示:示例1:用TP2制造的,供应状态为M2,外径为9.52mm,底壁厚为0.30mm,齿高为0.20mm,齿顶角为53度,螺旋角为18度,螺纹数为60的无缝内螺纹盘管,标记为:无缝内螺纹盘管TP2 M2 φ9.52×0.30+0.20-53-18/60 GB/T20928-20072、内螺纹铜管尺寸参数及对其传热性能的影响 (1)外径早期空调换热器中使用得较普遍的铜管直径为9.52mm左右,进入1990年以后一些空调器生产企业已经将换热器的传热管管径细化成7.0mm,其中蒸发器管径细化的现象最为普遍。这种细管径的换热器,由于管与管之间距离缩小,使得肋片效率提高、传热有效面积增加、空气流过时的流动阻力减小,强化传热。1995年以后,一些家用空调器生产企业又将传热管的管径进一步细化为6mm,甚至5mm,传热效率又进一步提高,尤其是在应用于替代制冷剂R410A的室内机时,由于R410A制冷剂系统的压力比R22的高1.6倍左右,使用细径管有利于提高安全可靠性。目前国内的内螺纹管管径主要有12.7mm,9.52mm,7.94mm,7mm,6.35mm和5mm等几种规格,其中9.52mm与7mm应用最为普遍。并且随着铜价等原材料上涨及国家对空调能效的要求,铜管正朝着细径薄壁的方向发展,但管径太小会造成冷媒阻力变大,薄壁会使工作中管子出现泄漏或者爆裂的可能性增加。(2)底壁厚目前内螺纹管底壁厚一般在0.20~0.30mm范围内,底壁厚越薄传热效果越好,但底壁厚过薄会削弱管材的强度以及齿的稳定性,不仅不利于后道工序的U形弯管质量与焊接质量,而且同样也会因齿的稳定性差,影响传热效果。 (3)齿高齿高是影响传热的重要因素,增加齿高会使内表面换热面积和刺破液膜能力增加,内螺纹管传热效果增强,但齿高的增大受加工技术的限制。目前内螺纹管齿高一般在0.10~0.25mm范围内。 (4)螺旋角螺旋角的存在是为了使流体旋转,使管道中流体产生与径向不同的二次流,增加湍流的强度,从而使对流换热得到加强,换热系数随之增加,所以螺旋角增大能增强换热系数,但随着螺旋角的增大,压力损失也随之增加,故螺旋角也不是越大越好,而是有一个合理的范围。 (5)齿顶角齿顶角小,有利于增加内表面换热面积,减薄冷凝传热的液膜厚度,
冷凝器换热面积计算方法
冷凝器换热面积计算方法 制冷量+压缩机电机功率/200~250=冷凝器换热面 例如:(3SS1-1500压缩机)CT=40℃:CE=-25℃压缩机制冷量=12527W+压缩机电机功率11250W=23777/230=风冷凝器换热面积103m2 水冷凝器换热面积与风冷凝器比例=概算1比18(103/18)=6m2 蒸发器的面积根据压缩机制冷量(蒸发温度℃×Δt相对湿度的休正系数查表)。 制冷量的计算方法 制冷量=温差×重量/时间×比热×设备维护机构 例如:有一个速冻库 1库温-35℃ 2速冻量1T/H 3时间2/H内 4速冻物质(鲜鱼) 5环境温度27℃ 6设备维护机构保温板 计算:62℃×1000/2/H×0.82×1.23=31266kcal/n 可以查压缩机蒸发温度CT=40CE-40℃制冷量=31266kcal/n 关于R410A和R22翅片管换热器回路数比的探讨晨怡热管(特灵亚洲研发中心上海200001)申广玉2008-6-15 20:10:07 摘要:通过理论计算得出了相同换热量和相同工况下,采用5/16″管径R410A蒸发器(或冷凝器)与采用3/8″管径R22蒸发器(或冷凝器)时回路数的比值,并指出比值是两工质物性差异和盘管的内径及当量摩擦阻力系数差异共同作用的结果。 关键词:R410A;回路数;蒸发器;冷凝器 中图分类号:TQ051 文献标识码: B
1前言 随着人类环保意识的提高,新冷媒技术的发展和应用已成为空调器发展的方向和关注的焦点。目前,国际上一致看好的R22替代物是混合工质R407C和R410A。其中R410A是HFC 32和HFC 125按照50%:50%的质量百分比组成的二元近共沸混合制冷剂,它的温度滑移不超过0.2℃(R407C温度滑移约7℃左右),这给制冷剂的充灌、设备的更换提供了很多方便。另外,由于R410A系统运行的蒸发压力和冷凝压力比R22高60%,所以系统性能对压力损失不敏感,每个回路工质循环流速可以加大,有利于换热器的强化换热,这为提高R410A系统的整体能效创造了有力条件。 正是由于R410A具有上述优点,在R22用量最大的单元式空调和热泵产品中,R410A是其首要的替代品。美国有望在2007年底将R410A产品在单元式空调的应用比例提高到80%,并在2009年底接近100%[1]。 但是R410A和R22物性存在着上述明显差异而不能在原R22系统中直接充注替代使用,应该对新的R410A 系统中的压缩机、蒸发器、冷凝器、节流机构和系统管路等部件重新设计才能达到系统的最佳匹配。本文仅以R410A和R22翅片管蒸发器和冷凝器的回路数相对比进行说明。 2R410A和R22翅片管蒸发器回路数比计算 目前常用的R22换热器一般采用的是3/8″内螺纹管,R410A换热器一般采用的是5/16″内螺纹。无特殊说明,所述的R410A和R22换热器即分别指这两种结构的换热器。 无论采用何种工质,在设计蒸发器时,一般均要保证工质在蒸发器中的饱和温度降ΔT相同,即:
铜管重量和长度换算表
紫铜管理论重量计算公式方法:每米重量=0.02796×壁厚×(外径-壁厚) ,以下为常用的铜管重量计算公式 黄铜管:每米重量(公斤)=0.02670*壁厚*(外径-壁厚)外径(毫米)内径(毫米)壁厚(毫米)理论重量公斤/米 3 2 0.50 0.035 3 1.5 0.75 0.047 4 3 0.50 0.066 4 2. 5 0.75 0.084 5 4 0.50 0.063 5 3.5 0.75 0.089 6 5 0.50 0.077 6 4.5 0.75 0.110 7 6 0.50 0.091 7 5.5 0.75 0.131 8 7 0.50 0.105 8 6.5 0.75 0.152 8 6 1.00 0.196 10 9 0.50 0.133 10 8.5 0.75 0.194 10 8 1.00 0.252 12 10.5 0.75 0.236 12 10 1.00 0.307 12 9 1.50 0.440 14 12 1.00 0.363 14 11 1.50 0.524 16 14 1.00 0.419 16 13 1.50 0.608 16 12 2.00 0.782 19 17 1.00 0.503 19 16 1.50 0.734 19 15 2.00 0.950 22 20 1.00 0.587 22 19 1.50 0.859 22 18 2.00 1.118 25 23 1.00 0.671 25 22 1.50 0.983 25 21 2.00 1.286 25 20 2.50 1.572 28 26 1.00 0.755 28 25 1.50 1.111 28 24 2.00 1.453 34 32 1.00 0.922 34 31 1.50 1.362 34 30 2.00 1.788
内螺纹铜管基本参数对换热的影响
内螺纹铜管基本参数对换热的影响 换热器在空调中占有重要位置,而内螺纹铜管在换热器中,不论是从换热性能还是成本上来说都是占主导地位。 一、基本介绍 内螺纹铜管又称非平滑管,是指外表面光滑,内表面具有一定数量,一定规则螺纹的铜管。因此与同规格光管相比增加了热交换面积,提高制冷剂侧的热传导率,使得气液界面的扰动大大增加,管底部与顶部的制冷剂液体得 到有效搅拌,同时由于表面张力使液膜变薄等原因,使得其传热系数增大(当然对换热器在蒸发和冷凝时影响因数是有差别的,蒸发时:增大换热面积; 增加气化核心数量;促使波状流型提前转变为半环状和环状流,从而增加润湿表面;增加了液膜的紊流、扰流度。冷凝时:增大换热面积;在表面张力作用下促使冷凝液离开传热表面而排走,减小了齿顶和槽间的冷媒液膜厚度;增强了液态冷媒的紊流、扰流度,增强气液两相的混合),从而有效提高热交换率,所以它的导热性能要比光管提高百分之三十至四十。 从加工方法上分为无缝内螺纹铜管和焊接内螺纹铜管,目前国内主要使用无缝内螺纹铜管。 二、内螺纹铜管标识 按国标GB/T20928-2007中的要求,内螺纹铜管产品按照产品名称、牌号、状态、外径、底壁厚、齿高加齿顶角、螺旋角、螺纹数和标准编号的顺序表示: 示例1:用TP2制造的,供应状态为M2,外径为9.52mm,底壁厚为0.30mm,齿高为0.20mm,齿顶角为53度,螺旋角为18度,螺纹数为60的无缝内螺纹盘管,标记为: 无缝内螺纹盘管TP2 M2 φ9.52×0.30+0.20-53-18/60 TP2:牌号,是磷脱氧铜,磷脱氧铜是熔解高纯度的原材料,把熔化铜中产生的氧气用亲氧性的磷(P)脱氧,使其氧含量降低到100PPm以下,从而提
换热器的传热计算
换热器的传热计算 换热器的传热计算包括两类:一类是设计型计算,即根据工艺提出的条件,确定换热面积;另一类是校核型计算,即对已知换热面积的换热器,核算其传热量、流体的流量或温度。这两种计算均以热量衡算和总传热速率方程为基础。 换热器热负荷Q 值一般由工艺包提供,也可以由所需工艺要求求得。Q=W c p Δt ,若流体有相变,Q=c p r 。 热负荷确定后,可由总传热速率方程(Q=K S Δt )求得换热面积,最后根据《化工设备标准系列》确定换热器的选型。 其中总传热系数K= 0011 h Rs kd bd d d Rs d h d o m i i i i ++++ (1) 在实际计算中,总传热系数通常采用推荐值,这些推荐值是从实践中积累或通过实验测定获得的,可以从有关手册中查得。在选用这些推荐值时,应注意以下几点: 1. 设计中管程和壳程的流体应与所选的管程和壳程的流体相一致。 2. 设计中流体的性质(粘度等)和状态(流速等)应与所选的流体性质和 状态相一致。 3. 设计中换热器的类型应与所选的换热器的类型相一致。 4. 总传热系数的推荐值一般范围很大,设计时可根据实际情况选取中间的 某一数值。若需降低设备费可选取较大的K 值;若需降低操作费用可取较小的K 值。 5. 为保证较好的换热效果,设计中一般流体采用逆流换热,若采用错流或 折流换热时,可通过安德伍德(Underwood )和鲍曼(Bowman )图算法对Δt 进行修正。 虽然这些推荐值给设计带来了很大便利,但是某些情况下,所选K 值与实际值出入很大,为避免盲目烦琐的试差计算,可根据式(1)对K 值估算。 式(1)可分为三部分,对流传热热阻、污垢热阻和管壁导热热阻,其中污垢热阻和管壁导热热阻可查相关手册求得。由此,K 值估算最关键的部分就是对流传热系数h 的估算。
内螺纹铜管成型技术与工艺(综述)
内螺纹铜管成型技术与工艺 1 内螺纹铜管生产技术发展过程 1.1国外内螺纹铜管的发展过程 随着空调器制造技术的不断进步, 对高效、节能、环保的要求愈来愈高, 国外从70 年代开始先后开发了用内螺纹铜盘管和亲水铝箔做两器(蒸发器和冷凝器)的新型空调。内螺纹管与光管相比可增加热交换面积 2~ 3 倍, 加之形成的湍流作用,提高热交换效率20% ~ 30%,节能15%。80年代已得到普遍认可的主要铜盘管生产企业的内螺纹盘管的产品比例一般大于 50%。国外内螺纹盘管从开发到大批量生产大约用了近20 a的时间。 1.2 国产内螺纹的发展过程 80 年代末期,国内相继上马空调器生产线,并使用铜光盘管作为热交换的主要材料, 随着环保要求的提高,新的致冷剂使用以及降低成本的需要, 开始研究具有高的换热效率的铜管进行替代, 90 年代初期和中期, 国内有几家设备制造厂家和铜管生产厂家已经研究和试制内螺纹铜管, 并取得了一些成绩,可以在10~ 20 m/ min低速的情况下, 直线拉制内螺纹实现批量生产, 但没有达到大批量高速生产盘管的技术。而国外,如日本、韩国已经开发出较成熟的设备和工艺,但设备和技术价格较高昂,所以这段时期,进口内螺纹铜管成了空调厂家的首选。此时,国内部分厂家也花大价钱进口了一些设备, 但由于光管本身的质量问题和模具等因素的影响, 国产内螺纹管没有太大的批量。 90 年代中期以后,国内设备厂家如江苏兴荣、北京京圣等,加紧对加工设备的开发和研究,铜管生产厂家如河南金龙、湖南光远、江苏名佳利等, 注重研究铜管的品质, 使得内螺纹铜管的生产得到了飞速的发展, 无论采用原挤压法生产的管坯还是采用铸扎生产的管坯,无论是用直线拉伸还是用盘拉, 都能生产出合格的内螺纹管。 90 年代末期,由于设备和工艺的成熟,国内开始批量复制内螺纹铜管生产线, 如张家港的恒荣、华芳、广东太平洋、浙江海亮等, 国内的生产能力不断扩大,国内产品亦开始出现竞争的态势,各个厂家注重降低产品的生产成本,在 3 a 的时间内, 内螺纹铜管的销售价格连下 1x104万元, 目前该产品的价格几乎接近于成本价, 将国外产品基本上排挤在国门之外,国外厂家因为生产成本过高, 出口不利, 开始大批量减产。 内螺纹铜管的发展大致经历了如下几个发展阶段: ( 1)山型齿内螺纹管; ( 2)梯型槽内螺纹管; ( 3)小顶角型内螺纹管; ( 4) 细高齿型内螺纹管。目前,国 外又陆续推出了高低齿齿型、齿顶开槽、双旋向等内螺纹管。 1.3 国产管的优势和劣势 与国外产品相比较, 国产内螺纹管生产成本较低,无论是设备还是人工成本都相对低廉, 这对加工制造业来说是有利的, 特别是来料加工是再好不过的,这对国际国内市场都不错。在国内,各铜管生产厂家亦提供了良好的售后服务, 得到了空调制造厂家的一致好评。但弱势显而易见, 加工设备自动化程度低,过分依赖操作人员的素质和加工技术, 导致成品率低下,产品品质稳定性差, 这对降低生产成本是不利的,也削弱了产品的竞争能力,特别是产品的稳定性问题使出
板式换热器换热面积的计算
板式换热器换热面积的 计算 Company Document number:WTUT-WT88Y-W8BBGB-BWYTT-19998
(1) 求热负荷Q : Q=G .ρ.CP .Δt Q —换热量(取冷热流体换热量的平均值),w; Δt —流体进出口温差,K 。 (2) 求冷热流体进出口温度:t 2=t 1+ Q /G .ρ .CP (3) 冷热流体流量:G=Q / ρ .CP .(t2-t1 ) (4) 求平均温度差Δtm Δtm=(T1-t2)-(T2-t1)/In(T1-t2)/(T2-t1)或Δtm=(T 1-t2)+(T2-t1)/2 (5) 选择板型 若所有的板型选择完,则进行结果分析。 (6) 由K值范围,计算板片数范围Nmin ,Nmax Nmin = Q / Kmax .Δtm .F P .β Nmax = Q / Kmin .Δtm .F P .β (7) 取板片数N (Nmin ≤N≤Nmax ) 若N 已达Nmax ,做(5)。 (8) 取N 的流程组合形式,若组合形式取完则做(7)。 (9) 求Re ,Nu Re = W .de/ ν Nu =a 1.Re a 2.Pr a 3 (10)求a ,K 传热面积F a = Nu .λ/ de K= 1 / 1/a h+1/ a c +γc +γc +δ/λ0
(11)由传热面积F求所需板片数NN NN= F/ Fp+ 2 (12)若N<NN,做(8)。 (13)求压降Δp Eu = a4.Re a5 Δp = Eu .ρ.W2.ф (14) 若Δp>Δ 允,做(8);
翅片式换热器的设计及计算
制冷剂系统翅片式换热器设计及计算 制冷剂系统的换热器的传热系数可以通过一系列实验关联式计算而得,这是因为在这类换热器中存在气液两相共存的换热过程,所以比较复杂,现在多用实验关联式进行计算。之前的传热研究多对于之前常用的制冷剂,如R12,R22,R717,R134a等,而对于R404A和R410A的,现在还比较少。按照传热过程,换热器传热量的计算公式为: Q=KoFΔtm (W) Q—单位传热量,W Ko—传热系数,W/(m2.C) F—传热面积,m2 Δtm—对数平均温差,C Δtmax—冷热流体间温差最大值,对于蒸发器,是入口空气温度—蒸发温度,对于冷凝器,是冷凝温度—入口空气温度。 Δtmin—冷热流体间温差最小值,对于蒸发器,是出口空气温度—蒸发温度,对于冷凝器,是冷凝温度—出口空气温度。 传热系数K值的计算公式为: K=1/(1/α1+δ/λ+1/α2) 但换热器中用的都是圆管,而且现在都会带有肋片(无论是翅片式还是壳管式),换热器表面会有污垢,引入污垢系数,对于蒸发器还有析湿系数,在设计计算时,一般以换热器外表面为基准计算传热,所以对于翅片式蒸发器表述为: Kof--以外表面为计算基准的传热系数,W/(m2.C) αi—管内侧换热系数,W/(m2.C) γi—管内侧污垢系数,m2.C/kW δ,δu—管壁厚度,霜层或水膜厚度,m λ,λu—铜管,霜或水导热率,W/m.C ξ,ξτ—析湿系数,考虑霜或水膜使空气阻力增加系数,0.8-0.9(空调用亲水铝泊时可取1)αof—管外侧换热系数,W/(m2.C) Fof—外表面积,m2 Fi—内表面积,m2 Fr—铜管外表面积,m2 Ff—肋片表面积,m2 ηf—肋片效率, 公式分析: 从收集的数据(见后表)及计算的结果来看,空调工况的光滑铜管内侧换热系数在2000-4000 W/(m2.C)(R22取前段,R134a取后段,实验结果表明,R134a的换热性能比R22高)之间。因为现在蒸发器多使用内螺纹管,因此还需乘以一个增强因子1.6-1.9。 下面这个计算公式来自《制冷原理及设备》(第二版,1996,吴业正主编):
圆钢理论重量表大全
圆钢理论重量表大全
圆钢和螺纹钢理论重量表 建筑工程中,圆钢和螺纹钢是对不同种类钢筋的通俗叫法,它们之间的不同主要有以下五点: 1.外形不同。圆钢的外表面是光滑的;螺纹钢的外表面带有螺旋形的肋。 2.生产标准不同。在现行标准中,圆钢指HPB235级钢筋,它的生产标准是《钢筋混凝土用热轧光面钢筋》(GB13013);螺纹钢一般指HRB335及HRB400级钢筋,它的生产标准是《钢筋混凝土用热轧带肋钢筋》(GB1499)。 3.强度不同。圆钢(HPB235)的设计强度为210MPa;螺纹钢的强度较圆钢要高,HRB335的设计强度为300MPa; HRB400的设计强度为360MPa。 4.钢种不同,(化学成份不同)。圆钢(HPB235)属碳素钢,钢种是Q235;螺纹钢属低合金钢,HRB335级钢筋是20MnSi(20锰硅);HRB400级钢筋是20MnSiV 或20MnSiNb或20MnTi等; 5.物理力学性能不同。由于钢筋的化学成份和强度的不同,因此在物理力学性能方面有所不同。圆钢的冷弯性能较好,可以作180度的弯钩,螺纹钢只能作90度的直钩;圆钢的可焊性较好,用普通碳素焊条即可,螺纹钢须用低合金焊条;螺纹钢在韧性、抗疲劳性能方面较圆钢好。 理论重量(当然,如果你的智能手机或手提方便的话,用预算小软件比这个好使多了,不过基本的东西还是记住一些的好) 用钢筋直径(mm)的平方乘以乘以长度L 是圆10钢筋每米重量。钢筋重量与直径(半径)的平方成正比。 G/m=*D*D/100 每米的重量(Kg)=钢筋的直径(mm)×钢筋的直径(mm)× 其实记住建设工程常用的钢筋重量也很简单φ6=Kg φ=φ8=φ10=φ12=Φ14=Φ16=Φ18=Φ24=Φ22=Φ25=Φ28=............ Φ12(含12)以下和Φ28(含28)的钢筋一般小数点后取三位数,Φ14至Φ25钢筋一般小数点后取二位数 Φ6= Φ8= Φ10= Φ12= Φ14= Φ16= Φ18=2Kg Φ20= Φ22=3Kg Φ25=
内螺纹铜管
铜管,配管类标准
内螺纹铜管 定义 本标准采用下列定义。 1:内螺纹铜管 管材内表面具有一定数量、一定螺旋角度的金属肋。 2:圆度 管材任一端面上测量的最大与最小直径之差。 3:平均壁厚 指内螺纹铜管按称重法算出相应公称外径的无缝光管的壁厚值。 4:分类与命名 产品分类:热交换器用铜管的种类及牌号见表 5:型号命名:产品型号命名如下: ×× 铜管的生产执行标准 铜管的供应状态 铜管牌号 内螺纹铜管参数(齿高×齿数×螺旋角) 铜管的供应形式 铜管的底壁厚 铜管的外径 铜管的种类 示例1:内螺纹铜管,外经Φ9.52mm、底壁厚0.27mm、齿高0.16mm、齿数60、螺旋角18度、供应形式(LWC),牌号TP2,铜管供应状态M,执行标准GB20928。 标记为:内螺纹铜管Φ9.52×0.27×LWC 0.16×60×18 TP2M GB20928。 示例2:内螺纹铜管,外经Φ9.52mm、底壁厚0.27mm、齿高0.16mm、齿数60、螺旋角18度、供应形式(LWC),牌号C1100T,铜管供应状态OL,执行标准JISH 3300。 标记为:内螺纹铜管Φ9.52×0.27×LWC 0.16×60×18 C1100T OL JISH 3300。
技术要求 1:外观质量:内外表面质量 管材的内外表面无针孔、裂缝、起皮、气泡、粗拉道、夹杂、海绵、铜粉、积碳层、绿锈、脏污和严重的氧化膜(内螺纹铜管内表面齿型均匀、正常)。 内外表面颜色要求不得呈(灰)黑色、蓝色,呈轻微灰黑色时不能被擦除,不能有油污流出。用气吹内外表面不得有粉沫,且吹后表面不得变成白色。不允许存在明显的划伤、凹坑和斑点等缺陷。 2:管材质量 管材不应有分层和明显呈暗裂状粗燥感。 3:结构尺寸:内螺纹铜管尺寸、规格 热交换器用内螺纹铜管的尺寸、规格应符合表的规定: 注:外径允许误差计算公式:+│(Dmax+Dmin)÷2 -Dnom│ Dmax:同一截面上最大直径; Dmin:同一截面上最小直径; Dnom:名义直径。 4:圆度 圆度允许误差见表: 注:计算公式:不圆度=(最大外径-最小外径)/标称外径*100% 5:性能要求