Integrated hardware interfaces for modular sensor networks
德尔·艾美 S5148F-ON 25GbE 顶层架(ToR)开放网络交换机说明书

The Dell EMC S5148 switch is an innovative, future-ready T op-of-Rack (T oR) open networking switch providing excellent capabilities and cost-effectiveness for the enterprise, mid-market, Tier2 cloud and NFV service providers with demanding compute and storage traffic environments.The S5148F-ON 25GbE switch is Dell EMC’s latest disaggregated hardware and software data center networking solution that provides state-of-the-art data plane programmability, backward compatible 25GbE server port connections, 100GbE uplinks, storage optimized architecture, and a broad range of functionality to meet the growing demands of today’s data center environment now and in the future.The compact S5148F-ON model design provides industry-leading density with up to 72 ports of 25GbE or up to 48 ports of 25GbE and 6 ports of 100GbE in a 1RU form factor.Using industry-leading hardware and a choice of Dell EMC’s OS10 or select 3rd party network operating systems and tools, the S5148F-ON Series offers flexibility by provision of configuration profiles and delivers non-blocking performance for workloads sensitive to packet loss. The compact S5148F-ON model provides multi rate speedenabling denser footprints and simplifying migration to 25GbE server connections and 100GbE fabrics.Data plane programmability allows the S5148F-ON to meet thedemands of the converged software defined data center by offering support for any future or emerging protocols, including hardware-based VXLAN (Layer 2 and Layer 3 gateway) support. Priority-based flow control (PFC), data center bridge exchange (DCBX) and enhanced transmission selection (ETS) make the S5148F-ON an excellent choice for DCB environments.The Dell EMC S5148F-ON model supports the open source Open Network Install Environment (ONIE) for zero touch installation of alternate network operating systems.Maximum performance and functionalityThe Dell EMC Networking S-Series S5148F-ON is a high-performance, multi-function, 10/25/40/50/100 GbE T oR switch purpose-built for applications in high-performance data center, cloud and computing environments.In addition, the S5148F-ON incorporates multiple architectural features that optimize data center network flexibility, efficiency, and availability, including IO panel to PSU airflow or PSU to IO panel airflow for hot/Key applications •Organizations looking to enter the software-defined data center era with a choice of networking technologies designed to deliver the flexibility they need• Use cases that require customization to any packet processing steps or supporting new protocols• Native high-density 25 GbE T oR server access in high- performance data center environments• 25 GbE backward compatible to 10G and 1G for future proofing and data center server migration to faster uplink speeds. • Capability to support mixed 25G and 10G servers on front panel ports without any limitations• iSCSI storage deployment including DCB converged lossless transactions• Suitable as a T oR or Leaf switch in 100G Active Fabric implementations• As a high speed VXLAN L2/L3 gateway that connects the hypervisor-based overlay networks with non-virtualized • infrastructure•Emerging applications requiring hardware support for new protocolsKey features •1RU high-density 25/10/1 GbE T oR switch with up to forty eight ports of native 25 GbE (SFP28) ports supporting 25 GbE without breakout cables• Multi-rate 100GbE ports support 10/25/40/50 GbE• 3.6 Tbps (full-duplex) non-blocking, cut-through switching fabric delivers line-rate performance under full load**• Programmable packet modification and forwarding • Programmable packet mirroring and multi-pathing • Converged network support for DCB and ECN capability • IO panel to PSU airflow or PSU to IO panel airflow • Redundant, hot-swappable power supplies and fans • IEEE 1588v2 PTP hardware supportDELL EMC NETWORKING S5148F-ON SERIES SWITCHProgrammable high-performance open networking top-of-rack switch with native 25Gserver ports and 100G network fabric connectivity• FCoE transit (FIP Snooping)• Full data center bridging (DCB) support for lossless iSCSI SANs, RoCE and converged network.• Redundant, hot-swappable power supplies and fans• I/O panel to PSU airflow or PSU to I/O panel airflow(reversable airflow)• VRF-lite enables sharing of networking infrastructure and provides L3 traffic isolation across tenants• 16, 28, 40, 52, 64 10GbE ports availableKey features with Dell EMC Networking OS10• Consistent DevOps framework across compute, storage and networking elements• Standard networking features, interfaces and scripting functions for legacy network operations integration• Standards-based switching hardware abstraction via Switch Abstraction Interface (SAI)• Pervasive, unrestricted developer environment via Control Plane Services (CPS)• Open and programmatic management interface via Common Management Services (CMS)• OS10 Premium Edition software enables Dell EMC layer 2 and 3 switching and routing protocols with integrated IP Services,Quality of Service, Manageability and Automation features• Platform agnostic via standard hardware abstraction layer (OCP-SAI)• Unmodified Linux kernel and unmodified Linux distribution• OS10 Open Edition software decoupled from L2/L3 protocol stack and services• Leverage common open source tools and best-practices (data models, commit rollbacks)• Increase VM Mobility region by stretching L2 VLAN within or across two DCs with unique VLT capabilities• Scalable L2 and L3 Ethernet Switching with QoS, ACL and a full complement of standards based IPv4 and IPv6 features including OSPF, BGP and PBR• Enhanced mirroring capabilities including local mirroring, Remote Port Mirroring (RPM), and Encapsulated Remote Port Mirroring(ERPM).• Converged network support for DCB, with priority flow control (802.1Qbb), ETS (802.1Qaz), DCBx and iSCSI TLV• Rogue NIC control provides hardware-based protection from NICS sending out excessive pause frames48 line-rate 25 Gigabit Ethernet SFP28 ports6 line-rate 100 Gigabit Ethernet QSFP28 ports1 RJ45 console/management port with RS232signaling1 Micro-USB type B optional console port1 10/100/1000 Base-T Ethernet port used asmanagement port1 USB type A port for the external mass storage Size: 1 RU, 1.72 h x 17.1 w x 18.1” d (4.4 h x 43.4 w x46 cm d)Weight: 22lbs (9.97kg)ISO 7779 A-weighted sound pressure level: 59.6 dBA at 73.4°F (23°C)Power supply: 100–240 VAC 50/60 HzMax. thermal output: 1956 BTU/hMax. current draw per system:5.73A/4.8A at 100/120V AC2.87A/2.4A at 200/240V ACMax. power consumption: 516 Watts (AC)T yp. power consumption: 421 Watts (AC) with all optics loadedMax. operating specifications:Operating temperature: 32° to 113°F (0° to 45°C) Operating humidity: 5 to 90% (RH), non-condensingFresh Air Compliant to 45CMax. non-operating specifications:Storage temperature: –40° to 158°F (–40° to70°C)Storage humidity: 5 to 95% (RH), non-condensingRedundancyHot swappable redundant power suppliesHot swappable redundant fansPerformanceSwitch fabric capacity: 3.6TbpsPacket buffer memory: 16MBCPU memory: 16GBMAC addresses: Up to 512KARP table: Up to 256KIPv4 routes: Up to 128KIPv6 routes: Up to 64KMulticast hosts: Up to 64KLink aggregation: Unlimited links per group, up to 36 groupsLayer 2 VLANs: 4KMSTP: 64 instancesLAG Load Balancing: User Configurable (MAC, IP, TCP/UDPport)IEEE Compliance802.1AB LLDPTIA-1057 LLDP-MED802.1s MSTP802.1w RSTP 802.3ad Link Aggregation with LACP802.3ae 10 Gigabit Ethernet (10GBase-X)802.3ba 40 Gigabit Ethernet (40GBase-X)802.3i Ethernet (10Base-T)802.3u Fast Ethernet (100Base-TX)802.3z Gigabit Ethernet (1000BaseX)802.1D Bridging, STP802.1p L2 Prioritization802.1Q VLAN T agging, Double VLAN T agging,GVRP802.1Qbb PFC802.1Qaz ETS802.1s MSTP802.1w RSTPPVST+802.1X Network Access Control802.3ab Gigabit Ethernet (1000BASE-T) orbreakout802.3ac Frame Extensions for VLAN T agging802.3ad Link Aggregation with LACP802.3ae 10 Gigabit Ethernet (10GBase-X)802.3ba 40 Gigabit Ethernet (40GBase-SR4,40GBase-CR4, 40GBase-LR4, 100GBase-SR10,100GBase-LR4, 100GBase-ER4) on optical ports802.3bj 100 Gigabit Ethernet802.3u Fast Ethernet (100Base-TX) on mgmtports802.3x Flow Control802.3z Gigabit Ethernet (1000Base-X) with QSAANSI/TIA-1057 LLDP-MEDJumbo MTU support 9,416 bytesLayer2 Protocols4301 Security Architecture for IPSec*4302 I PSec Authentication Header*4303 E SP Protocol*802.1D Compatible802.1p L2 Prioritization802.1Q VLAN T agging802.1s MSTP802.1w RSTP802.1t RPVST+802.3ad Link Aggregation with LACPVLT Virtual Link TrunkingRFC Compliance768 UDP793 TCP854 T elnet959 FTP1321 MD51350 TFTP2474 Differentiated Services2698 T wo Rate Three Color Marker3164 Syslog4254 SSHv2791 I Pv4792 ICMP826 ARP1027 Proxy ARP1035 DNS (client)1042 Ethernet Transmission1191 Path MTU Discovery1305 NTPv41519 CIDR1812 Routers1858 IP Fragment Filtering2131 DHCP (server and relay)5798 VRRP3021 31-bit Prefixes3046 DHCP Option 82 (Relay)1812 Requirements for IPv4 Routers1918 Address Allocation for Private Internets2474 Diffserv Field in IPv4 and Ipv6 Headers2596 Assured Forwarding PHB Group3195 Reliable Delivery for Syslog3246 Expedited Assured Forwarding4364 VRF-lite (IPv4 VRF with OSPF andBGP)*General IPv6 Protocols1981 Path MTU Discovery*2460 I Pv62461 Neighbor Discovery*2462 Stateless Address AutoConfig2463 I CMPv62464 Ethernet Transmission2675 Jumbo grams3587 Global Unicast Address Format4291 IPv6 Addressing2464 Transmission of IPv6 Packets overEthernet Networks2711 IPv6 Router Alert Option4007 IPv6 Scoped Address Architecture4213 Basic Transition Mechanisms for IPv6Hosts and Routers4291 IPv6 Addressing Architecture5095 Deprecation of T ype 0 Routing Headers inI Pv6IPv6 Management support (telnet, FTP, TACACS,RADIUS, SSH, NTP)OSPF (v2/v3)1587 NSSA1745 OSPF/BGP interaction1765 OSPF Database overflow2154 MD52328 OSPFv22370 Opaque LSA3101 OSPF NSSA3623 OSPF Graceful Restart (Helper mode)*BGP 1997 Communities 2385 MD52439 Route Flap Damping 2796 Route Reflection 2842 Capabilities 2918 Route Refresh 3065 Confederations 4271 BGP-44360 Extended Communities 4893 4-byte ASN5396 4-byte ASN Representation 5492Capabilities AdvertisementLinux Distribution Debian Linux version 8.4Linux Kernel 3.16MIBSIP MIB– Net SNMPIP Forward MIB– Net SNMPHost Resources MIB– Net SNMP IF MIB – Net SNMP LLDP MIB Entity MIB LAG MIBDell-Vendor MIBTCP MIB – Net SNMP UDP MIB – Net SNMP SNMPv2 MIB – Net SNMP Network Management SNMPv1/2SSHv2FTP, TFTP, SCP SyslogPort Mirroring RADIUS 802.1XSupport Assist (Phone Home)Netconf APIs XML SchemaCLI Commit (Scratchpad)AutomationControl Plane Services APIs Linux Utilities and Scripting Tools Quality of Service Access Control Lists Prefix List Route-MapRate Shaping (Egress)Rate Policing (Ingress)Scheduling Algorithms Round RobinWeighted Round Robin Deficit Round Robin Strict PriorityWeighted Random Early Detect Security 2865 RADIUS 3162 Radius and IPv64250, 4251, 4252, 4253, 4254 SSHv2Data center bridging802.1QbbPriority-Based Flow Control802.1Qaz Enhanced Transmission Selection (ETS)*Data Center Bridging eXchange(DCBx) DCBx Application TLV (iSCSI, FCoE*)Regulatory compliance SafetyUL/CSA 60950-1, Second Edition EN 60950-1, Second EditionIEC 60950-1, Second Edition Including All National Deviations and Group DifferencesEN 60825-1 Safety of Laser Products Part 1: EquipmentClassification Requirements and User’s GuideEN 60825-2 Safety of Laser Products Part 2: Safety of Optical Fibre Communication Systems FDA Regulation 21 CFR 1040.10 and 1040.11Emissions & Immunity EMC complianceFCC Part 15 (CFR 47) (USA) Class A ICES-003 (Canada) Class AEN55032: 2015 (Europe) Class A CISPR32 (International) Class AAS/NZS CISPR32 (Australia and New Zealand) Class AVCCI (Japan) Class A KN32 (Korea) Class ACNS13438 (T aiwan) Class A CISPR22EN55022EN61000-3-2EN61000-3-3EN61000-6-1EN300 386EN 61000-4-2 ESDEN 61000-4-3 Radiated Immunity EN 61000-4-4 EFT EN 61000-4-5 SurgeEN 61000-4-6 Low Frequency Conducted Immunity NEBSGR-63-Core GR-1089-Core ATT -TP-76200VZ.TPR.9305RoHSRoHS 6 and China RoHS compliantCertificationsJapan: VCCI V3/2009 Class AUSA: FCC CFR 47 Part 15, Subpart B:2009, Class A Warranty1 Year Return to DepotLearn more at /Networking*Future release**Packet sizes over 147 BytesIT Lifecycle Services for NetworkingExperts, insights and easeOur highly trained experts, withinnovative tools and proven processes, help you transform your IT investments into strategic advantages.Plan & Design Let us analyze yourmultivendor environment and deliver a comprehensive report and action plan to build upon the existing network and improve performance.Deploy & IntegrateGet new wired or wireless network technology installed and configured with ProDeploy. Reduce costs, save time, and get up and running cateEnsure your staff builds the right skills for long-termsuccess. Get certified on Dell EMC Networking technology and learn how to increase performance and optimize infrastructure.Manage & SupportGain access to technical experts and quickly resolve multivendor networking challenges with ProSupport. Spend less time resolving network issues and more time innovating.OptimizeMaximize performance for dynamic IT environments with Dell EMC Optimize. Benefit from in-depth predictive analysis, remote monitoring and a dedicated systems analyst for your network.RetireWe can help you resell or retire excess hardware while meeting local regulatory guidelines and acting in an environmentally responsible way.Learn more at/Services。
Endress+Hauser DeviceCare设备配置工具说明书

Configuration tool for devices via fieldbus protocols and Endress+Hauser service protocolsApplicationDeviceCare is the tool developed by Endress+Hauser for the configuration of Endress+Hauser devices. All smart devices in a plant can be configured via a point-to-point or point-to-bus connection. The status information given provides users with a simple yet effective tool for monitoring devices. Automatic functions and wizards guide the user easily through the program. The user-friendly menus enable transparent and intuitive access to the field devices.Your benefits•Fast and easy installation, online application updates, one-click connection to devices •Automatic hardware identification and driver catalog update •Device configuration with DTMs, Heartbeat verification support •Multi-language support, touch-ready for tablet use •Integrated help, wizards and event reporting •The following communication protocols are supported: HART, PROFIBUS DP/PA,FOUNDATION Fieldbus, Modbus, CDI and Endress+Hauser service interfaces •Hardware interfaces for modems (USB/RS232), Bluetooth, TCP/IP and USBProducts Solutions ServicesTechnical Information DeviceCare SFE100Configuration of Endress+Hauser devicesTI01134S/04/EN/06.1771379781DeviceCare SFE1002Endress+HauserTable of contentsDocument information .......................3Symbols for certain types of information .. (3)Function and system design (3)Function ...................................3System design ................................3Operation .................................5System integration . (5)Ordering Information (6)Additional documentation ....................6DeviceCare SFE100............................6FieldCare SFE500.............................6Plant Asset Management (6)Registered trademarks (6)DeviceCare SFE100Endress+Hauser 3Document informationFunction and system designFunction DeviceCare is a free configuration tool for Endress+Hauser devices. It supports devices with the following protocols, provided a suitable device driver (DTM) is installed: HART, PROFIBUS,FOUNDATION Fieldbus, Ethernet/IP, Modbus, CDI, ISS, IPC and PCP. The tool is aimed at customers without a digital network in plants and workshops and Endress+Hauser service technicians. The devices can be connected directly via a modem (point-to-point) or a bus system (point-to-bus).DeviceCare is fast, easy and intuitive to use. It can run on a PC, laptop or tablet with a Windows operating system.System designHART point-to-point connectionFig. 1 shows a HART point-to-point connection with an FXA195 USB/HART modem. If an FXA195 is connected to the computer, DeviceCare can connect to the device automatically.1Point-to-point connection with a HART field device 1DeviceCare 2HART FXA1953Field deviceTo establish communication with the HART device, a resistor of at least 250 Ω must be provided in the circuit. The way in which this is done depends upon the system architecture and power source used. Please read the FXA195 manual carefully.DeviceCare SFE1004Endress+HauserPROFIBUS point-to-bus connectionFig. 2 shows how the connection from PROFIBUS DP to PROFIBUS PA can be established using a Siemens DP/PA Link or a Pepperl+Fuchs SK3.2PROFIBUS point-to-bus connection 1DeviceCare 2FieldgateSFG5003PROFIBUS DP 4Segment coupler 5PROFIBUS PACDI point-to-point connectionFig. 3 shows a CDI point-to-point connection with an FXA291 modem. If an FXA291 is connected tothe computer, DeviceCare can connect to the device automatically.3CDI point-to-point connection to a device 1DeviceCare 2CDI FXA2913Field deviceDeviceCare SFE100Endress+Hauser 5Operation•Standard configurable Windows graphical user interface with icons, short cuts etc.•Hardware: Windows PC, laptop, tablet •Supported operating systems: Windows 7, 8, 8.1, 10 (32/64-bit)•Connection to Endress+Hauser devices automatic or via wizard •Choice of languages in DeviceCare: AR, CS, DE, ES, FI, FR, ID, IT, JA, KO, NL, PL, PT, RU, SA, SV, TH,TR, VI, ZH •DTM graphical user interface and language depend on the device and supplierSystem integrationSystem requirementsOperating systemThe date indicates when standard supports ends. It is possible to extend Microsoft support by another five years.HardwareSoftware required•Microsoft .Net 3.5•Microsoft .Net 4.x •PDF readerInstalled software•DeviceCare •USB driver •CommDTMs •Microsoft .Net 3.5•The DeviceDTMs for your devices must be selected and installed by the user •Endress+Hauser DTMs for SFG500 and SWA70 must be additionally installed •A PDF printer must be installed to save the device reports in PDF format •The DTM for Siemens DP/PA Link must be additionally installed •The DTM for Modbus must be additionally installedDeviceCare SFE1006Endress+HauserOrdering InformationDetailed information about the product structure is available:•In the Product Configurator on the Endress+Hauser web site: /SFE100•From the Endress+Hauser Sales Center: Additional documentationDeviceCare SFE100Innovations IN01047S/04/EN FieldCare SFE500•Getting Started KA01303S/04/EN •Operating Instructions BA00065S/04/EN •Technical Information TI00028S/04/EN •Tutorial for FieldCare projects SD01928S/04/EN •Competence Brochure CP00001S/04/ENPlant Asset Management Fields of Activity FA00024S/04/ENRegistered trademarksPROFIBUS® is a registered trademark of the PROFIBUS User Organization, Karlsruhe/Germany.FOUNDATION Fieldbus TM is the trademark of the FieldComm Group, Austin, TX 78759, USA.HART®, WirelessHART® is the registered trademark of the FieldComm Group, Austin, TX 78759,USA.Ethernet/IP is the registered trademark of ODVA, Michigan USA.Modbus is the registered trademark of Modicon, Incorporated.Microsoft®, Windows 8.1®, Windows XP®, Windows 2008 Server®, Windows 7®, Windows 10®,Internet Explorer® and the Microsoft logo are registered trademarks of the Microsoft Corporation.All other brand and product names are trademarks or registered trademarks of the companies and organizations in question.。
铁路信号专用名词缩写对照表

1.1.1 铁路信号专用名词缩写对照表自动站间闭塞:Automatic inter-sation block铁路信号:Railway singal无绝缘轨道电路:Jointless track circuit综合防雷:Synthesized lightning protection铁路车站电码化技术条件:railway station coding of continuous truck circuits specificationZPW-2000A无绝缘移频轨道电路:ZPW-2000A jointless audio frequency-shift modulate truck circuit电码化:Coding正线电码化:main line coding防雷:lightning protection屏蔽:shielding转辙机:Switching machine机车信号:Cab signal补偿电容:Compensative Capacitor轨道电路:truck circuit电磁兼容:Electromagnetic compatibility (EMC)闭环电码化轨道电路:Closed loop coded track circuit站内电码化系统:Coded System Within Station双机热备:Dual machine hot standby微机监测:Computerized monitoring侧线:side line正线:main line计轴:Axle counter铁路运行:railway transport计算机联锁系统:Computer Interlocking system (CIS)管理信息系统:Manage Information system (MIS)单线:single line信号机:Signal自动控制:Automatic control高速铁路:High-speed line铁路行车调度信号系统:Railway Traffic Control Information system客运专线:passenger special line传输协议:Transport Protocols列车自动保护:Automatic train protection (AIP)应答器:balise固态继电器:Solid State Relay(SSR)发送器:transmitter接收器:receiver低道床电阻:Low ballast bed resistance安全防护:Safety Protection道口信号:Level crossing signal。
HEIDENHANN Connected Machining 产品说明说明书
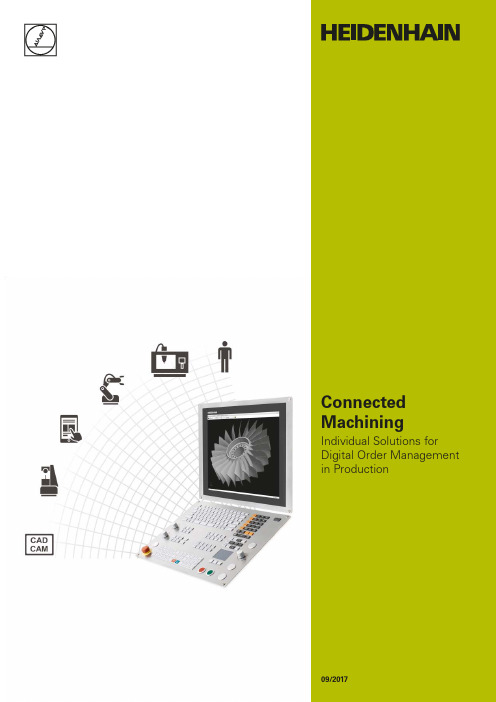
Connected Machining Individual Solutions for Digital Order Management in Production09/20172The center of every metalworking manu-facturing company is the workshop. Highly qualifi ed specialists work here on modern milling machines and lathes. This is where the workpieces are produced. This is where experience and expertise determine the quality of the products and the effi ciency of the manufacturing process.The discussion about digitization raises big expectations in many manufacturing companies, but it also presents new challenges. The main question is how digital networking and software solutions can be used to analyze one’s own manu-facturing processes, improve internal processes, and tailor the use of external services, such as cloud solutions.C onnected Machining With its Connected Machining package of functions, HEIDENHAN offers solutions for individual networking of production pro-cesses. These solutions place the user at the center of digital order management through the control of his milling or turning machine. The HEIDENHAIN control is net-worked with all production-related areas within the company on a very individual ba-sis tailored to the existing structures and open for future developments.Y ou are supported in your work through simple data usage, time-saving workfl ows and transparent processes in all company areas. This applies of course in the work-shop, but also during design and produc-tion planning, as well as in management, logistics, servicing, etc. The production-related strengths of modern machines and plants are thus supplemented through a uniform digital job management with Connected Machining.Contents34Networked manufacturing –Making know-how useable and protecting it at the same timeCreativity and innovative power drive the important and unique features that make a production company successful. This is driven by innovative and motivatedemployees who place their expertise at the service of the company. T o use this private, highly sensitive know-how in a targeted manner and protect it at the same time places manufacturing companies before crucial challenges.Connected Machining deliberately makes control of the machine in the workshop the focal point of digital order management. HEIDENHAIN is therefore consistently pursuing what it already began with the TNC control and the Klartext programming format as a dialog-oriented programming language in the mid-1970s: providing the specialist in the workshop with powerful, intuitive solutions for the production of high-quality workpieces.The realization of uniform digital order management with Connected Machining through HEIDENHAIN control leaves the necessary leeway for individual design and connection of the network. Connected Machining offers the necessary openness with its comprehensive capabilities and digital interfaces.Even a simple TNC control systemintegrated into the company network via Ethernet offers with its standard functions a wide range of options for receiving and using digital job data directly on the control:•PDF viewer, e.g. for displaying of fi xture diagrams and design drawings •DXF viewer, e.g. for displaying 3-D models•Image display, e.g. for displaying fi xture situations and manufacturing notes •Web browser for accessing web-based applications, such as ERP and MESclients, e-mail clients, and HTML5 clientsBeyond this, the following solutions and options are offered:•The StateMonitor software creates transparent processes through data acquisition and data analysis.•The Remote Desktop Manager(option 133) allows access to PCs and the installed software right at the control •The HEIDENHAIN DNC interface (option 18) connects the control to enterprise-resource planning and production-activity control systems •The Extended Workspace display provides clear representation and processing of the job data on the machineThe employees in the company keep the digital threads in their hands to be able to use the internal know-how individually—whether on the machine tool in the workshop, in the design stage or in production planning.In production, on the machine, all the information is quickly and immediately available that is necessary for continuous high-quality production planning and enables a fl exible order management from a batch size of one.5Order data and due datesImportant information such as order number, desired delivery date, order volume and required materials can be viewed directly with the integrated web browser of the HEIDENHAIN controls and corresponding web applications or with the help of the Remote Desktop Manager directly on the order server. Preparations on the machine can be quick, paperless and free of routing slips.Preparation of productionThe necessary production data such as NC programs, fi xture and test plans, or 2-D and 3-D data can be transmitted digitally to the control via the DNC interface. HEIDENHAIN controls offer even as standard features an image display as well as PDF and DXF viewers to view these data.Communication interfaces allow toolmanagement systems to directly compare data with the controller. It is also possible to send confi rmation of fi nished orders via the control automatically, either via DNC interface or the StateMonitor software. With appropriate MES and ERP systems, the user can also enter them manually through a web browser.–Powerful solutions on the controlData access during production Fast and fl exible reaction to changes requires clearly laid out, always available data. If, for example, machining strategies are wrong, or if the part program has to be examined in more detail and even edited, the NC data generation of the CAM system quickly comes into play.The Remote Desktop Manager allows access to the data of the CAM system from the PLC during NC machining. With its help, the user is able to call up the fi rst information on the machine and conduct examinations.Overview and documentation during productionWith the expanded display of Extended Workspace, the user has additionalworkspace available on which he displays the CAM system as needed. He has the NC program running in parallel on the control screen.In addition, Extended Workspace also makes it possible to display other applica-tions such as process monitoring, monitor-ing and status information. Whether a workspace camera or display of multi-ma-chine status at the push of a button—a clear status overview helps the user to quickly locate and correct problems on a machine such as a tool failure.StateMonitor can also send targeted status messages on events via e-mail. The events and recipients of the status e-mails are freely confi gurable.6Networked manufacturing –Support in the offi ceSimple production planningConnected Machining also supports production planning. If all production-relevant data are known and prepared for an order, the order data can be transmitted to the machine tool via a DNC interface or can be provided on a server for retrieval. The user receives information digitally via e-mail or through a web application. He can either use an e-mail client on an IPC or the web browser of the HEIDENHAIN control via the Remote Desktop Manager. This reduces paperwork and eliminates superfl uous communications.The constantly available information about current production orders is also a valuable tool for production planning. This informa-tion can be displayed and tracked quickly and easily via StateMonitor's machine data acquisition. But StateMonitor does not simply display machine data. The software also allows its evaluation and comments on events. This provides important data for optimizing the organizational sequence of production.Data exchange for continuous horizontal integrationIn an automated production setup,Connected Machining can implement a targeted data exchange over the DNC interface. Handover units or tool andworkpiece handling systems for example, then always provide the right information at the right time in order to make the fl ow of automation trouble-free. The communica-tion is over Ethernet interface, supported by commonly available fi eldbus systems.Coordinated order and production planningA good overview of the current production process facilitates further planning, e.g. for the procurement of tools, the preparation of follow-up orders or the logistics around the fi nished parts. In particular the manag-ers of manufacturing and production re-quire simple and easily accessible informa-tion as provided by StateMonitor. These data ensure plannable production that is successful in the long term and offers the necessary security for investments.Systematically reduce unplanned shutdownsStateMonitor provides confi gurable fault messages and, if desired, documents machine messages in the log that are then available as machine history. Their evaluation can show creeping wear and tear or possible disturbances, so that early preventive measures can be planned and production losses can be avoided.For maintenance and service, the DNC in-terface also supports planning in advance. Third party providers, for example, can pick up the necessary machine data via HEIDEN-HAIN DNC from the control for evaluation and use it to assess the maintenance situa-tion or to correct problems.Sound investment planning Machine utilization and the effi ciency of the machines are a key aspect in investment planning. They provide valuable information on whether old machines should be mod-ernized, machinery should be expanded or further automation should be considered. The StateMonitor helps you with these decisions and ensures transparency.7StateMonitor – Acquiring and evaluating machine dataStateMonitor records the states of the machines in production and visualizesthem. By evaluating important data such as current machine status, machine messag-es, override positions and utilization history, StateMonitor provides in-depth information on the machine's degree of utilization. StateMonitor also uses the collected data to show existing optimization possibilities. The operator can enter comments on machine downtimes and set-up times in order to uncover machine-specifi c as well as organizational potential for optimization. Using the messenger function, StateMonitor notifi es the responsible person by e-mail of specifi c events such as program end, machine standstill, or service warnings based on individually combinable machine signals and statuses.State Monitor is installed on a server in the company network and collects machine states of HEIDENHAIN controls via the HEIDENHAIN DNC interface. The software runs in the local network as a client-server application and has a web-based user interface. This allows StateMonitor to be displayed and operated via any device (TNC controls, PCs, mobile devices) that has a web browser and has access to the respective server. No further software or app has to be installed on the respective display and control units. It is suffi cient to enter or store the respective web address. The user interface of StateMonitor adapts to the respective screen resolution and can be operated by mouse as well as by a touchscreen.StateMonitor captures and visualizes the following information of the networked machines:• Operating modes• Override positions (spindle, rapid traverse, feed rate)• Program status and program name, if appropriate also subprograms • Program run time• SIK number and software number • Machine messages StateMonitor is installed on a server or PC with Windows operating system, the so-called host. The hardware prerequisites depend on the number of machines to be connected. The HEIDENHAIN controls to be connected must be accessible from the server through the IP address or DHCP name. Also, HEIDENHAIN control must have HEIDENHAIN DNC (option 18).8k+CAMERPPPSCADTNC 640IPC R emote Desktop Manager– Display and remote control of external computer unitsIn daily operations it can often be neces-sary to make entries in planning and con-trol systems or perform diagnostics usingWindows-based software. The RemoteDesktop Manager option provides theuser with the opportunity to operate one ormore Windows PCs directly from the TNC.It offers complete integration of WindowsPC operation in the user interface of theTNC control’s screen.With a simple keystroke on the machineoperating panel you can switch betweenthe control screen and the screen of a sep-arate Windows PC in your local network.And it makes no difference whether theWindows computer operates as an indus-trial PC (e.g. IPC 6641) in the machine’scontrol cabinet, or as a server in the localnetwork.Possible applications include the centralmanagement of job orders or tools and NCprograms, all the way to remote operationof CAD/CAM systems from the machine.In this way, the machine tool operatingpanel becomes a fl exible and effi cientworkplace for the steps in the CAD/CAM/CNC process chain, including decentralizedorder processing.The Remote Desktop Manager can be setup through the control’s operating system.Remote Desktop Manager Option 133ID 894423-01TNC 640 HSCITNC 620 HSCITNC 320iTNC 530 HSCIiTNC 530As of NC SW 34059x-01As of NC SW 81760x-01–As of NC SW 60642x-02–Installation by IT specialistsFor more information see the T echnical ManualsConnected Machining permits uniformlydigital order management in networkedmanufacturing Y ou also profi t from:• Easy data usage• Time-saving procedures• T ransparent processesDocumentsE-mail9Paperless order management requires the seamless exchange of data about all process steps in the production process. The HEIDENHAIN DNC option enables a Windows application to access data of the TNC, and to edit the data if required. Possible fi elds of application include, for example:• Software solutions controlling the manufacturing process – M achine and operating-data acquisition systems (MDA/PDA) – C onnection to higher -level ERP/MES systems – P lanning of preventive maintenance based on the actual condition of the machine• Standard or customer -specifi c PC software – I ncrease in process reliability and system availability – E rror reporting systems that, for example, send the customer amessage to his smartphone reporting problems with the currently running machining process – O verview plans that provideinformation about the current condition of all machines used in production – C reation of a database for comprehensive data mining RemoT ools SDK development package T o enable you to use the HEIDENHAIN DNC software interface, HEIDENHAIN offers the RemoT ools SDK software devel-opment package. RemoT ools SDK provides a Microsoft COM component for the devel-opment environments on Windows operat-ing systems in order to make communi-cation with the HEIDENHAIN control possible. During the installation of Remo-T ools SDK the COM component is regis-tered in the Windows operating system.HEIDENHAIN DNC– Communication via COM components10Extended Workspace – Expanded displayExtended Workspace makes it possible to work in parallel on the machine and job management directly at the machine and control. A second screen with an integrat-ed computer is simply connected to the controller via Ethernet and confi gured as an additional screen in the TNC operating system. This enables the user to work ef-fectively and knowledgeably with additional applications on the second screen without losing his grasp on the center of his work on the control screen.The applications for the additional screen workspace are multiple:• Parallel work during NC program run on: –Order management–CAD/CAM programming (e.g. via Remote Desktop Manager) –Documentation –Machine-specifi c applications(e.g. the use of maintenance software)• Monitoring the working space• Operating two or more machines by one machine operator, display of StateMonitor's machine overview on the second screenExtended Workspace can be confi gured individually for the desired applications. The computer integrated in the second screen has a powerful processor and thus relieves the main computer of the controller. The applications run natively on the computer of Extended Workspace which, however, receives all necessary data from the TNC controller and can also be used for display processes (e.g. PDF and DXF viewer, web browser and image display) during concurrent processes.11Connected Machining– OverviewY ou can fi nd more information in the brochure titled Options and Accessories.HEIDENHAIN worldwide Mastering nano meter accuracy1225632-20 · 3 · 09/2017 · H · Printed in Germany DR. JOHANNES HEIDENHAIN GmbH Dr.-Johannes-Heidenhain-Straße 583301 Traunreut, Germany +49 8669 31-0 +49 8669 32-5061******************。
XMC4500自动化输入输出芯片模块说明书

XMC4500 Satellite-kit: Automation I/O Kit Part Number: KIT_XMC4X_AUT_ISO_001Features∙Connection to CPU board via ACT Satellite Connector∙ISOFACE OUT, up to 8 channels∙ISOFACE IN, up to 8 channels∙I2C based IO expander up to 8 channels∙Single side assembly of all parts∙ 2 LEDs indicating power (3.3 Volt, 5 Volt)∙Power supply:-Power jack for external 24V supply-From CPU Board via ACT Satellite ConnectorPLEASE SEE THE FOLLOWING PAGES FOR USERS MANUALHexagon Application Kit For XMC4000 FamilyAUT_ISO-V1Automation I/O CardBoard User's Manual Revision 1.0, 2012-02-28Edition 2012-02-28Published byInfineon Technologies AG81726 Munich, Germany© 2012 Infineon Technologies AGAll Rights Reserved.Legal DisclaimerThe information given in this document shall in no event be regarded as a guarantee of conditions or characteristics. With respect to any examples or hints given herein, any typical values stated herein and/or any information regarding the application of the device, Infineon Technologies hereby disclaims any and all warranties and liabilities of any kind, including without limitation, warranties of non-infringement of intellectual property rights of any third party.InformationFor further information on technology, delivery terms and conditions and prices, please contact the nearest Infineon Technologies Office ().WarningsDue to technical requirements, components may contain dangerous substances. For information on the types in question, please contact the nearest Infineon Technologies Office.Infineon Technologies components may be used in life-support devices or systems only with the express written approval of Infineon Technologies, if a failure of such components can reasonably be expected to cause the failure of that life-support device or system or to affect the safety or effectiveness of that device or system. Life support devices or systems are intended to be implanted in the human body or to support and/or maintain and sustain and/or protect human life. If they fail, it is reasonable to assume that the health of the user or otherTrademarks of Infineon Technologies AGAURIX™, C166™, CanPAK™, CIPOS™, CIPURSE™, EconoPACK™, CoolMOS™, CoolSET™, CORECONTROL™, CROSSAVE™, DAVE™, EasyPIM™, EconoBRIDGE™, EconoDUAL™, EconoPIM™, EiceDRIVER™, eupec™, FCOS™, HITFET™, HybridPACK™, I²RF™, ISOFACE™, IsoPACK™, MIPAQ™, ModSTACK™,my-d™, NovalithIC™, OptiMOS™, ORIGA™, PRIMARION™, PrimePACK™, PrimeSTACK™, PRO-SIL™, PROFET™, RASIC™, ReverSave™, SatRIC™, SIEGET™, SINDRION™, SIPMOS™, SmartLEWIS™, SOLID FLASH™, TEMPFET™, thinQ!™, TRENCHSTOP™, TriCore™.Other TrademarksAdvance Design System™ (ADS) of Agilent Technologies, AMBA™, ARM™, MULTI-ICE™, KEIL™, PRIMECELL™, REALVIEW™, THUMB™, µVision™ of ARM Limited, UK. AUTOSAR™ is licensed by AUTOSAR development partnership. Bluetooth™ of Bluetooth SIG Inc. CAT-iq™ of DECT Foru m. COLOSSUS™, FirstGPS™ of Trimble Navigation Ltd. EMV™ of EMVCo, LLC (Visa Holdings Inc.). EPCOS™ of Epcos AG. FLEXGO™ of Microsoft Corporation. FlexRay™ is licensed by FlexRay Consortium. HYPERTERMINAL™ of Hilgraeve Incorporated. IEC™ of Commission Electrotechnique Internationale. IrDA™ of Infrared Data Association Corporation. ISO™ of INTERNATIONAL ORGANIZATION FOR STANDARDIZATION. MATLAB™ of MathWorks, Inc. MAXIM™ of Maxim Integrated Products, Inc. MICROTEC™, NUCLEUS™ of Mentor Graphics Corporation. Mifare™ of NXP. MIPI™ of MIPI Alliance, Inc. MIPS™ of MIPS Technologies, Inc., USA. muRata™ of MURATA MANUFACTURING CO., MICROWAVE OFFICE™ (MWO) of Applied Wave Research Inc., OmniVision™ of OmniVision Technologies, Inc. Openwave™ Openwave Systems Inc. RED HAT™ Red Hat, Inc. RFMD™ RF Micro Devices, Inc. SIRIUS™ of Sirius Satellite Radio Inc. SOLARIS™ of Sun Microsystems, Inc. SPANSION™ of Spansion LLC Ltd. Symbian™ of Symbian Software Limited. TAIYO YUDEN™ of Taiyo Yuden Co. TEAKLITE™ of CEVA, Inc. TEKTRONIX™ of Tektronix Inc. TOKO™ of TOKO KABUSHIKI KAISHA TA. UNIX™ of X/Open Company Limited. VERILOG™, PALLADIUM™ of Cadence Design Systems, Inc. VLYNQ™ of Texas Instruments Incorporated. VXWORKS™, WIND RIVER™ of WIND RIVER SYSTEMS, INC. ZETEX™ of Diodes Zetex Limited.Last Trademarks Update 2011-02-24Table of ContentsTable of Contents1Overview (7)1.1Key Features (7)1.2Block Diagram (8)2Hardware Description (8)2.1ISOFACE OUT (9)2.2ISOFACE IN (9)2.3IO Expander (10)2.4Power (11)2.5Satellite Connector (12)3Production Data (13)3.1Schematics (13)3.2Layout and Geometry (16)3.3Bill of Material (17)List of FiguresFigure 1Automation I/O Card (AUT_ISO-V1) (8)Figure 2Automation I/O Card Interfaces (8)Figure 3Power Circuit (11)Figure 4ACT Satellite Connector (12)Figure 5Satellite Connector Type ACT (12)Figure 6Satellite Connector, IO Expander, Power (14)Figure 7ISOFACE (15)Figure 8Automation I/O Card Layout (16)List of TablesTable 1ISOFACE OUT Connector Pinout (9)Table 2ISOFACE OUT signal connection to the Satellite Connector (9)Table 3ISOFACE IN Connector Pinout (9)Table 4ISOFACE IN signal connection to the Satellite Connector (10)Table 5GPIO channel LED/SMD pad mapping (10)Table 6IO Expander I2C signal connection to the Satellite Connector (10)Table 7Power LED’s (11)Table 8PowerScale Jumper (11)Table 9Automation I/O Card BOM (17)OverviewIntroductionThis document describes the features and hardware details of the Automation I/O Card (AUT_ISO-V1) designed to work with Infineon’s XMC4500 CPU board. This board is part of Infineon’s Hexagon Application Kits.1 OverviewThe AUT_ISO-V1 board is an application expansion satellite card of the Hexagon Application Kits. The satellite card along with a CPU board (e.g. CPU_45A-V2 board) demonstrates ISOFACE capabilities together with XMC4500. The focus is safe operation under evaluation conditions. The satellite card is not cost optimized and cannot be seen as reference design.1.1 Key FeaturesThe AUT_ISO-V1 satellite card is equipped with following featuresConnection to CPU board (e.g. CPU_45A-V2) via satellite connector ACTISOFACE OUT, up to 8 channelsISOFACE IN, up to 8 channelsI2C based IO expander up to 8 channelsPower supplyo Powerjack for external 24 V supplyo From CPU board via ACT satellite connector1.2Block DiagramFigure 1 shows the block diagram of the AUT_ISO-V1 satellite card. There are following building blocks:Figure 1Automation I/O Card (AUT_ISO-V1)2 Hardware DescriptionThe following sections give a detailed description of the hardware and how it can be used.Figure 2 Automation I/O Card InterfacesISOFACE OUT (ISO1H812G)ISOFACE IN (ISO1I811T)Power 3.3 V (IFX1763SJV33)ISOFACE IN ConnectorACT Satellite ConnectorPower Jack24 V2.1 ISOFACE OUTISOFACE output device used in AUT_ISO-V1 satellite card is ISO1H812G. It is supplied by VDD3.3 on the CPU side and VDD24 for the ISOFACE OUT side. VDD24 and GNDISO can to be connected either by X300 or by X240(24 V external power jack). This is the same net that supplies the DC/DC converter. VDD24 is +24 Vdc (referred to GNDISO)Table 1 below gives the signal details of ISOFACE OUT connector.Table 12 below gives the details of SPI signal connection to the satellite connector.2.2 ISOFACE INISOFACE input device used in AUT_ISO-V1 satellite card is ISO1I811T. It is supplied by 3.3 V on the CPU side and VBB (24V) for the ISOFACE IN side. VBB and GNDBB need a separate connection to 24 V external power source through connector X320.Resistor R337 is used on board for setting input type to IEC61131-2 Type 1.Resistors R326 and R327 sets the frequency of ISOFACE IN to 100 kHz (default).Table 3 gives the details of ISOFACE IN connector pin mapping.Table 3 ISOFACE IN Connector PinoutISOFACE IN shares the same SPI lines with ISOFACE OUT except the chip select as shown in Table 4.2.3 IO ExpanderThe AUT_ISO-V1 satellite card supports GPIO expansion though I2C IO-Expander on board (U230). The I2C Address for IO expander device is 0x1001000X. The satellite card supports 8 such GPIO’s. All t he GPIO’s are connected to LEDs (V230-V237) and SMD-Pads (TP230 – TP237). The Table 5 gives the GPIO channel and corresponding LED/PAD mapping.Table 6 shows the connection of the IO Expander device to the ACT satellite connector.2.4 PowerThe AUT_ISO-V1 satellite card can be supplied by an external power supply (24 V / 1 A) to be connected to the power jack X240 or by a 5 V supply via the 80-pin ACT satellite connector. An external power supply is necessary only in case the current coming via the ACT satellite connector is not sufficient.A DC-DC converter on board (U240) steps down the input voltage from the power jack X240 to 5 V (VDD5). The input voltage can be in the range from 12 V to 24 V. An on board linear voltage regulator is generating a 3.3 V (VDD3.3) power supply out of the VDD5.Figure 3 Power CircuitA Diode V242 protects the reverse flow of current to an external source. Therefore a simultaneous power supply of the satellite boards via both the power jack and the satellite connector with not harm.LED V210 indicates the presence of 5 V power and LED V211 indicates the presence of 3.3 V power.Table 7 Power LED’sThe AUT_ISO-V1 satellite card supports a PowerScale probe for power measurement purpose.Table 8 PowerScale Jumper2.5 Satellite ConnectorThe satellite connector of the AUT_ISO-V1 satellite card interfaces it’s the signals to a CPU board e.g. CPU_45A-V2. Take care to connect the ACT satellite card always to the corresponding ACT satellite connector of the CPU board only.Figure 4 ACT Satellite ConnectorThe signal mapping of the ACT satellite connector and correponding CPU function are provided in figure 6Figure 5 Satellite Connector Type ACT3 Production Data3.1 SchematicsThis chapter contains the schematics for the Automation I/O Card:Satellite Connector, IO Expander, PowerISOFACEFigure 6 Satellite Connector, IO Expander, PowerFigure 7 ISOFACE3.2 Layout and GeometryFigure 8 Automation I/O Card Layout3.3 Bill of MaterialTable 9 Automation I/O Card BOMTable 9 Automation I/O Card BOMw w w.i n f i n e o n.c o m。
SPARC V8处理器基于PC 104嵌入式计算机模块设计说明书
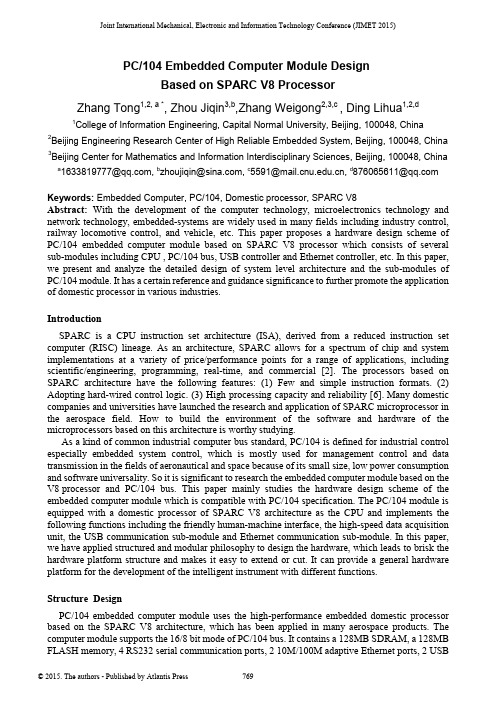
Joint International Mechanical, Electronic and Information Technology Conference (JIMET 2015)PC/104 Embedded Computer Module DesignBased on SPARC V8 ProcessorZhang Tong1,2, a *, Zhou Jiqin3,b,Zhang Weigong2,3,c , Ding Lihua1,2,d1College of Information Engineering, Capital Normal University, Beijing, 100048, China2Beijing Engineering Research Center of High Reliable Embedded System, Beijing, 100048, China 3Beijing Center for Mathematics and Information Interdisciplinary Sciences, Beijing, 100048, China a*****************,b******************,c*************,d****************Keywords: Embedded Computer, PC/104, Domestic processor, SPARC V8Abstract: With the development of the computer technology, microelectronics technology and network technology, embedded-systems are widely used in many fields including industry control, railway locomotive control, and vehicle, etc. This paper proposes a hardware design scheme of PC/104 embedded computer module based on SPARC V8 processor which consists of several sub-modules including CPU , PC/104 bus, USB controller and Ethernet controller, etc. In this paper, we present and analyze the detailed design of system level architecture and the sub-modules of PC/104 module. It has a certain reference and guidance significance to further promote the application of domestic processor in various industries.IntroductionSPARC is a CPU instruction set architecture (ISA), derived from a reduced instruction set computer (RISC) lineage. As an architecture, SPARC allows for a spectrum of chip and system implementations at a variety of price/performance points for a range of applications, including scientific/engineering, programming, real-time, and commercial [2]. The processors based on SPARC architecture have the following features: (1) Few and simple instruction formats. (2) Adopting hard-wired control logic. (3) High processing capacity and reliability [6]. Many domestic companies and universities have launched the research and application of SPARC microprocessor in the aerospace field. How to build the environment of the software and hardware of the microprocessors based on this architecture is worthy studying.As a kind of common industrial computer bus standard, PC/104 is defined for industrial control especially embedded system control, which is mostly used for management control and data transmission in the fields of aeronautical and space because of its small size, low power consumption and software universality. So it is significant to research the embedded computer module based on the V8 processor and PC/104 bus. This paper mainly studies the hardware design scheme of the embedded computer module which is compatible with PC/104 specification. The PC/104 module is equipped with a domestic processor of SPARC V8 architecture as the CPU and implements the following functions including the friendly human-machine interface, the high-speed data acquisition unit, the USB communication sub-module and Ethernet communication sub-module. In this paper, we have applied structured and modular philosophy to design the hardware, which leads to brisk the hardware platform structure and makes it easy to extend or cut. It can provide a general hardware platform for the development of the intelligent instrument with different functions.Structure DesignPC/104 embedded computer module uses the high-performance embedded domestic processor based on the SPARC V8 architecture, which has been applied in many aerospace products. The computer module supports the 16/8 bit mode of PC/104 bus. It contains a 128MB SDRAM, a 128MB FLASH memory, 4 RS232 serial communication ports, 2 10M/100M adaptive Ethernet ports, 2 USBports and a VGA display port with 1600*1200 display resolution. In this PC/104 module, we have configured VxWorks operating system including BSP, USB keyboard mouse driver, Ethernet driver, UART driver, TFFS file system and other software driver [1]. Drivers are designed for the corresponding hardware devices, such as USB, Ethernet, UART and display control circuit to manage the underlying hardware, which can provide a standardized and hardware-independent interface to the high-level application software. Fig. 1 shows the main block diagram of PC/104 embedded computer module.Fig. 1 The main block diagram of PC/104 embedded computer moduleHardware Module Design Based on Domestic ProcessorCPU Sub-module A 32-bit microprocessor based on SPARC V8 architecture with the high degree of integration and high performance is adopted in this design. Fig. 2 shows the internal structure of the processor. From Fig. 2, we can see the processor chip contains an on-chip integer processing unit IU, a floating-point unit (FPU), independent data caches and instruction caches, 5 stage pipeline, hardware multiplier and divider and so on. Moreover, interrupt controller, hardware debug unit with tracking buffer storage (DSU), two common timer (timer0, timer1), serial interface, PCI interface, watchdog timer and memory controller supporting PROM, SRAM, SDRAM and I/O space accessing and so on are integrated in this processor chip[4].Fig. 2 The structure diagram of SPARC V8 CPUPC/104 Bus Sub-module The electrical logic of PC/104 specification uses ISA bus specification. It defines two types ofaddress space including I/O space and memory space, supporting 8-bit and 16-bit data accessing. The hardware of PC/104 can configure 11 interrupt sources and provide 7 DMA Channels. Due to the characteristics of V8 processor chip, in the designing of PC/104 module, we use dual space mapping mode to support the 8/16 read-write functions of PC/104 bus. The I/O space of V8 processor has the following two regions:(1) One region is used to deal with the 16-bit read-write functions of PC/104 bus, which can be divided into two subspaces, namely I/O space and memory space. The PC/104 bus accessing operations to this space are all considered to be 16-bit read-write mode. In this region, the MEMCS16# and IOCS16# signals are all ignored (assuming the device accessed is 16 bits).(2) Another region is specifically designed for 8-bit read-write functions of PC/104 bus, which can also be divided into two subspaces, namely IO space and storage space. The PC/104 bus accessing operations to this space are considered to be 8-bit read-write mode. The accessed device is served as an 8-bit device or a 16-bit device by the MEMCS16# and IOCS16# signal and the PC/104 data bus is mapped into the corresponding space of the processor.In order to improve the efficiency of bus accessing and the controlling flexibility, we implement the bus sequential control logic circuits on a FPGA chip. Through this designing method, the PC/104 bus sequence can be set flexibly by configuring the software, for example, the length (T1) of the address latch signal (BALE) or the default length (T2) of the bus access cycle can be changed by modifying the control register. The PC/104 bus sequence waveforms are shown in Fig. 3. In this figure, the term T4 is the time gap between the BALE falling edge and read-write signal falling edge, which has a minimum value of zero.As shown in Fig. 3, the length of T1 can be set by the BALEW domain of PC/104 bus sequence control register (ISATIMING). The length of T4 is 0~10ns. The length of T3 is T2-T1-T3. The default value of T2 is set by the ISAW domain of ISATIMING register.Fig. 3 PC/104 bus waveform DiagramUSB Sub-module In this paper, we use CH374U (produced by Nanjing QinHeng Electronics Co.,Ltd.) as the USB controller of PC/104 embedded computer module and implement two USB1.0 ports (usb0, usb1), which can connect keyboard, mouse, or the other USB external devices. The interface of USB adopts PulseGuard ESD protection circuit to implement the over-voltage protection. CH374U supports both USB-HOST and USB-DEVICE mode with root hub of 3 ports. It has multiple transmission method, including low speed and full speed control transmission, bulk transmission, interrupt transmission, and synchronous transmission. CH374U uses four I/O registers to interact with the CPU and can generate an interrupt request to CPU. The four registers are all adopted 16-bit accessing mode, but only low 8 bits are effective. High 8 bits are read with constant zero and writing in is arbitrary. The hardware block diagram of USB is shown in Fig. 4.Fig. 4 USB signal connection diagramEthernet Sub-module The two-way 10M/100M adaptive Ethernet interface (LAN1, LAN2) is implemented with the module using DM9000CIEP owned by Davicom Semiconductor, Inc. In order to improve the reliability of the internal work of the PC/104 embedded computer module, the double isolation interface scheme is adopted in the Ethernet interface, namely the input and output signals separated by the transformer. Two way Ethernet interfaces can work independently and also can be redundant backup for each other used under the driver management [5]. The hardware block diagram is shown in Fig. 5.ADRESSBALER/WIOCHRDYRead DataWrite DataFig. 5 Ethernet signal connection DiagramTest resultsThe cast plate is made according to the above design and the module real figure is shown in Fig. 6. The PCB boards are put to the test and the tests are mainly about the validity of the various functions modules of the PC/104 embedded computer module. The tests are mainly as follows:Fig. 6 Module physical Diagram(1) CPU functional testing, the main function is to test the cache, perform the same cycle, it is 19us to open the cache code, 195us to close the cache code time.(2) In order to test the PC/104 module more fully, we design a motherboard with a CPLD chip which implements several registers including ISA bus interrupt request control register, accessing latency control register, clock-timing registers.The V8 PC/104 computer module can access these functional registers by internal ISA bus in order to control the CPLD to generate the bus interrupts or modify the bus latency. Using these control method, we can implement the test of PC/104 module.The generation and clear of the PC/104 bus interrupt signal is controlled by the interrupt request register and the interrupt enable register, which is how the bus interrupt signal is tested.The bus access cycle controller is mainly to test the validity of the bus access after inserting the different length of wait states the maximum of which is 256us. These waiting for the cycle controllers is only effective for testing the functional registers (IO address 0000 ~ 00FFH). The signal IOCHRDY is in the state of high resistance and the default cycle is adopted while the registers are accessed by other ISA address.The timer is set with a kind of bus clock when the clock timing is tested. And firstly the 33MHz (CPLD operating clock), 14.318MHz (bus BCLK clock), 14.318MHz (bus OSC clock) are respectively divided into 1MHz by an internal frequency divider, and then the signal is stipulated-timing-controlled by a set of registers. When it comes to overflowing in the timer, the interrupt request is applied to the ISA bus by the interrupt request signal (IRQ12, 14 or 15). And the timer can be tested by software reading the timer count.(3) Ethernet communication test: Two way Ethernet are connected to the test monitoring computer with the router. Ethernet transferring the data is normal and the average transfer rate is about 1Mbps, and the error rate is zero, and the packet loss rate is zero.(4) In the operating system, SDRAM memory which is not occupied by the operating system is accessing tested. In order to accurately test the validity of the data bus, writing-in data must have wide adaptability, including 0x55555555、0xaaaaaaaa、0x1、0x2、0x4、0x8、0x10、……、0x80000000. The data in two formats is mainly tested for reading the preliminarily stored data in the FLASH memory. One is the binary data stored in the space that is not changed into the file system, the other is a file stored in the file system, and the test results are correct. Display images and memory access test: After receiving the test command, the specific graphics display functions are called so that the specific graphics can be displayed on the display and the read and write accessing to the display buffer memory is normal. In the RS232 communication test, four RS232 interfaces of the V8 PC/104 computer module are two-two interconnected to send and receive data, and serial data transmission is normal, and the average Baud rate is about 90kbps, and the error rate is zero.ConclusionsThe embedded system has been widely used in the field of industrial control, such as industrial process control, intelligent instrument, and numerical control system. Especially with the network technology and communication technology rapidly booming, the networked site of the industrial control has become a trend. In this paper, after studying the development situation of the embedded system at home and abroad, the relatively complete solution to the embedded application system is designed with a high-performance domestic embedded processor based on SPARC V8 architecture. And the 128MB bytes of FLASH that is used to store all the program codes and parameters is extended in this system and the 128MB bytes of SDRAM that is used to store running programs and data is extended in this system and PC/104 bus is extended in this system to improve the efficiency of bus access and control flexibility. Moreover, USB, Ethernet communication interface and etc. are designed in this system. The testing results indicate that the function indexes and performance indexes meet the requirements. This module is featured in a small size, powerful functions, low power consumption, high reliability, good compatibility and low cost [3], which means it can be applied in different fields of the industrial occasions.AcknowledgmentsThis work was supported in part by the National Natural Science Foundation of China (No.61170009, No.61472260, No.61402302); Beijing Natural Science Foundation of China (No.4132016, No.4143060); the Project of Construction of Innovative Teams and Teacher Career Development for Universities and Colleges Under Beijing Municipality(No.IDHT20150507); the Scientific Research Base Development Program of the Beijing Municipal Commission of Education. References[1] Zhang Lihong, Ren Yu, Chen Jianzheng, Data Acquisition System Based On PC/104, Engineering and Test,2009,3[2] The SPARV Architecture Manual, Version 8[3] Cao Zhijin, Hou Xia, Wu Qiuping, Master-slave data acquisition systems and applications based on PC/104,Electrical Measurement and Instrumentation, 2003,4[4] Yu Dan, Zhang Zhuancheng, Feng Lijie, Lai Yuqiang, LEON2 processor-based SoC designs based on LEON2 processor, Modern electronic technology, 2005[5] Chen Yi, Wang Lei, Zhou guojia, Li Zhe, Radiation Monitoring Network and Ethernet Interface Based On CAN bus, Nuclear Electronics and Detection Technology,2011[6] Zhu Xiaoyan, Zhang Weigong, Wang Jianfeng, Duan Qingya, and Liu Shurong, “The design of high reliable serial system BUS”. Proceedings of Computer Design and Applications, Qinhuangdao,Hebei, China, 25-27 June 2010; pp.V4-14-V4-17.。
莫萨公司MGate MB3180 MB3280 MB3480系列1、2和4端口标准串行到以太网Mod

MGate MB3180/MB3280/MB3480Series1,2,and4-port standard serial-to-Ethernet Modbus gatewaysFeatures and Benefits•Supports Auto Device Routing for easy configuration•Supports route by TCP port or IP address for flexible deployment•Converts between Modbus TCP and Modbus RTU/ASCII protocols•1Ethernet port and1,2,or4RS-232/422/485ports•16simultaneous TCP masters with up to32simultaneous requests permaster•Easy hardware setup and configurationCertificationsIntroductionThe MB3180,MB3280,and MB3480are standard Modbus gateways that convert between Modbus TCP and Modbus RTU/ASCII protocols.Up to 16simultaneous Modbus TCP masters are supported,with up to31RTU/ASCII slaves per serial port.For RTU/ASCII masters,up to32TCP slaves are supported.Routing through the serial ports can be controlled by IP address,TCP port number,or ID mapping.Serial-port routing by TCP port and IP address allows access for up to4TCP clients/masters(MB3280/MB3480models),while routing by ID mapping allows access for up to16 TCP clients/masters(MB3180/MB3280/MB3480).Standard Modbus Network IntegrationThe three standard MGate™models(MB3180,MB3280,and MB3480)are designed for easy integration of Modbus TCP and RTU/ASCII networks. With these models,Modbus serial slave devices can be seamlessly incorporated into an existing Modbus TCP network,and Modbus TCP slaves can be made accessible to serial masters.The MB3180,MB3280,and MB3480offer features that make network integration easy,customizable, and compatible with almost any Modbus network.High Density,Cost-Effective GatewaysThe MGate™MB3000gateways can effectively connect a high density of Modbus nodes to the same network.The MB3280can manage up to62 serial slave nodes,and the MB3480can manage up to124serial slave nodes.Each RS-232/422/485serial port can be configured individually for Modbus RTU or Modbus ASCII operation and for different baudrates,allowing both types of networks to be integrated with Modbus TCP through one Modbus gateway.Auto-Device Routing for Easy Configuration(patented)Moxa’s Auto-Device Routing function helps eliminate many of the problems and inconveniences encountered by engineers who need to configure large numbers of Modbus devices.A single mouse click is all that’s required to set up a slave ID routing table and configure Modbus gateways to automatically detect Modbus requests from a supervisory control and data acquisition(SCADA)system.By removing the need to manually create the slave ID routing table,the Auto-Device Routing function saves engineers significant time and cost.SpecificationsEthernet Interface10/100BaseT(X)Ports(RJ45connector)Auto MDI/MDI-X connectionMagnetic Isolation Protection 1.5kV(built-in)Ethernet Software FeaturesIndustrial Protocols Modbus TCP Client(Master)Modbus TCP Server(Slave)Configuration Options All models:Web Console(HTTP),Device Search Utility(DSU),MGate Manager,MCCTool,Telnet ConsoleMGate MB3280/MB3480only:Web Console(HTTPS)Management All models:ARP,DHCP Client,DNS,HTTP,SNMPv1/v2c/v3,TCP/IP,Telnet,UDPMGate MB3280/MB3240only:HTTPS,SMTP,SNMP Trap,NTP ClientMIB RFC1213,RFC1317Time Management NTP Client(MGate MB3180Excluded)Security FunctionsAuthentication Local databaseEncryption HTTPSAES-128AES-256SHA-256Security Protocols SNMPv3HTTPS(TLS1.2)(except MGate MB3180)Serial InterfaceNo.of Ports MGate MB3180:1MGate MB3280:2MGate MB3480:4Connector DB9maleSerial Standards RS-232/422/485(software selectable)Baudrate50bps to921.6kbpsData Bits7,8Parity NoneEvenOddSpaceMarkStop Bits1,2Flow Control DTR/DSRRTS Toggle(RS-232only)RTS/CTSRS-485Data Direction Control ADDC(automatic data direction control)Pull High/Low Resistor for RS-4851kilo-ohm,150kilo-ohmsTerminator for RS-485MGate MB3180:NoneMGate MB3280/MB3480:120ohmsSerial SignalsRS-232TxD,RxD,RTS,CTS,DTR,DSR,DCD,GNDRS-422Tx+,Tx-,Rx+,Rx-,GNDRS-485-2w Data+,Data-,GNDRS-485-4w Tx+,Tx-,Rx+,Rx-,GNDSerial Software FeaturesIndustrial Protocols Modbus RTU/ASCII MasterModbus RTU/ASCII SlaveModbus(Transparent)Max.No.of Client Connections16Max.No.of Server Connections32Power ParametersInput Voltage12to48VDCInput Current MGate MB3180:200mA@12VDCMGate MB3280:250mA@12VDCMGate MB3480:365mA@12VDCPower Connector MGate MB3180:Power jackMGate MB3280/MB3480:Power jack and terminal blockPhysical CharacteristicsHousing MetalIP Rating IP301Dimensions(with ears)MGate MB3180:22x75x80mm(0.87x2.95x3.15in)MGate MB3280:22x100x111mm(0.87x3.94x4.37in)MGate MB3480:35.5x102.7x181.3mm(1.40x4.04x7.14in)Dimensions(without ears)MGate MB3180:22x52x80mm(0.87x2.05x3.15in)MGate MB3280:22x77x111mm(0.87x3.03x4.37in)MGate MB3480:35.5x102.7x157.2mm(1.40x4.04x6.19in)Weight MGate MB3180:340g(0.75lb)MGate MB3280:360g(0.79lb)MGate MB3480:740g(1.63lb)Environmental LimitsOperating Temperature MGate MB3180:0to55°C(32to131°F)MGate MB3280:0to60°C(32to140°F)MGate MB3480:0to55°C(32to131°F)Storage Temperature(package included)-40to85°C(-40to185°F)Ambient Relative Humidity5to95%(non-condensing)Standards and CertificationsEMC EN55032/35EMI CISPR32,FCC Part15B Class AEMS IEC61000-4-2ESD:Contact:4kV;Air:8kVIEC61000-4-3RS:80MHz to1GHz:3V/mIEC61000-4-4EFT:Power:1kV;Signal:0.5kVIEC61000-4-5Surge:Power:1kV(MB3180/MB3280)IEC61000-4-5Surge:Power:1kV;Signal:2kV(MB3480)IEC61000-4-6CS:3VIEC61000-4-8PFMFIEC61000-4-11Safety MB3180Models:EN62368-1and UL60950-1MB3280/3480Models:IEC/UL62368-11.For the MGate MB3480,the two screws provided with the wall-mounting kit must be used to fasten the kit to the bottom of the MGate,and the MGate must beproperly attached to the terminal block for power input.MTBFTime MGate MB3180:2,762,384hrsMGate MB3280:749,455hrsMGate MB3480:1,213,993hrsStandards Telcordia SR332WarrantyWarranty Period5yearsDetails See /warrantyPackage ContentsDevice1x MGate MB3180/MB3280/MB3480Series gatewayPower Supply1x power adapter,suitable for your regionDocumentation1x quick installation guide1x warranty cardDimensionsOrdering InformationModel Name No.of Serial Ports MGate MB31801MGate MB32802MGate MB34804 Accessories(sold separately)CablesCBL-F9M9-150DB9female to DB9male serial cable,1.5mCBL-F9M9-20DB9female to DB9male serial cable,20cmConnectorsMini DB9F-to-TB DB9female to terminal block connectorDIN-Rail Mounting KitsDK35A DIN-rail mounting kit,35mmWall-Mounting KitsWK-35-01Wall-mounting kit with2plates(35x44x2.5mm)and6screws©Moxa Inc.All rights reserved.Updated Aug07,2023.This document and any portion thereof may not be reproduced or used in any manner whatsoever without the express written permission of Moxa Inc.Product specifications subject to change without notice.Visit our website for the most up-to-date product information.。
MX行业领先云管理系统说明书

INDUSTRY-LEADING CLOUD MANAGEMENT• Unified firewall, switching, wireless LAN, and mobile device man-agement through an intuitive web-based dashboard• Template based settings scale easily from small deployments to tens of thousands of devices• Role-based administration, configurable email alerts for a variety of BRANCH GATEWAY SERVICES• Built-in DHCP, NAT, QoS, and VLAN management services • Web caching: accelerates frequently accessed content• Load balancing: combines multiple WAN links into a single high-speed interface, with policies for QoS, traffic shaping, and failover FEATURE-RICH UNIFIED THREAT MANAGEMENT (UTM) CAPABILITIES• Application-aware traffic control: bandwidth policies for Layer 7 application types (e.g., block Y ouTube, prioritize Skype, throttle BitTorrent)• Content filtering: CIPA-compliant content filter, safe-seach enforcement (Google/Bing), and Y ouTube for Schools• Intrusion prevention: PCI-compliant IPS sensor using industry-leading SNORT® signature database from Cisco• Advanced Malware Protection: file reputation-based protection engine powered by Cisco AMP• Identity-based security policies and application managementINTELLIGENT SITE-TO-SITE VPN WITH MERAKI SD-WAN• Auto VPN: automatic VPN route generation using IKE/IPsec setup. Runs on physical MX appliances and as a virtual instance within the Amazon AWS or Microsoft Azure cloud services• SD-WAN with active / active VPN, policy-based-routing, dynamic VPN path selection and support for application-layer performance profiles to ensure prioritization of the applications types that matter • Interoperates with all IPsec VPN devices and services• Automated MPLS to VPN failover within seconds of a connection failure• Client VPN: L2TP IPsec support for native Windows, Mac OS X, iPad and Android clients with no per-user licensing feesOverviewCisco Meraki MX Security & SD-WAN Appliances are ideal for organizations considering a Unified Threat Managment (UTM) solution fordistributed sites, campuses or datacenter VPN concentration. Since the MX is 100% cloud managed, installation and remote management are simple. The MX has a comprehensive suite of network services, eliminating the need for multiple appliances. These services includeSD-WAN capabilities, application-based firewalling, content filtering, web search filtering, SNORT® based intrusion detection and prevention, Cisco Advanced Malware Protection (AMP), web caching, 4G cellular failover and more. Auto VPN and SD-WAN features are available on our hardware and virtual appliances, configurable in Amazon Web Services or Microsoft Azure.Meraki MXCLOUD MANAGED SECURITY & SD-WANRedundant PowerReliable, energy efficient design with field replaceable power suppliesWeb Caching 128G SSD diskDual 10G WAN Interfaces Load balancing and SD-WAN3G/4G Modem Support Automatic cellular failover1G/10G Ethernet/SFP+ Interfaces 10G SFP+ interfaces for high-speed LAN connectivityEnhanced CPU Layer 3-7 firewall and traffic shapingAdditional MemoryFor high-performance content filteringINSIDE THE CISCO MERAKI MXMX450 shown, features vary by modelModular FansHigh-performance front-to-back cooling with field replaceable fansManagement Interface Local device accessMulticolor Status LED Monitor device statusFRONT OF THE CISCO MERAKI MXMX450 shown, features vary by modelCryptographic AccelerationReduced load with hardware crypto assistCisco Threat Grid Cloud for Malicious File SandboxingIdentity Based Policy ManagementIronclad SecurityThe MX platform has an extensive suite of security features including IDS/IPS, content filtering, web search filtering, anti-malware, geo-IP based firewalling, IPsec VPN connectivity and Cisco Advanced Malware Protection, while providing the performance required for modern, bandwidth-intensive yer 7 fingerprinting technology lets administrators identifyunwanted content and applications and prevent recreational apps like BitT orrent from wasting precious bandwidth.The integrated Cisco SNORT® engine delivers superior intrusion prevention coverage, a key requirement for PCI 3.2 compliance. The MX also uses the Webroot BrightCloud® URL categorization database for CIPA / IWF compliant content-filtering, Cisco Advanced Malware Protection (AMP) engine for anti-malware, AMP Threat Grid Cloud, and MaxMind for geo-IP based security rules.Best of all, these industry-leading Layer 7 security engines and signatures are always kept up-to-date via the cloud, simplifying network security management and providing peace of mind to IT administrators.Organization Level Threat Assessment with Meraki Security CenterSD-WAN Made SimpleTransport independenceApply bandwidth, routing, and security policies across a vari-ety of mediums (MPLS, Internet, or 3G/4G LTE) with a single consistent, intuitive workflowSoftware-defined WAN is a new approach to network connectivity that lowers operational costs and improves resource us-age for multisite deployments to use bandwidth more efficiently. This allows service providers to offer their customers the highest possible level of performance for critical applications without sacrificing security or data privacy.Application optimizationLayer 7 traffic shaping and appli-cation prioritization optimize the traffic for mission-critical applica-tions and user experienceIntelligent path controlDynamic policy and perfor-mance based path selection with automatic load balancing for maximum network reliability and performanceSecure connectivityIntegrated Cisco Security threat defense technologies for direct Internet access combined with IPsec VPN to ensure secure communication with cloud applications, remote offices, or datacentersCloud Managed ArchitectureBuilt on Cisco Meraki’s award-winning cloud architecture, the MX is the industry’s only 100% cloud-managed solution for Unified Threat Management (UTM) and SD-WAN in a single appliance. MX appliances self-provision, automatically pulling policies and configuration settings from the cloud. Powerful remote management tools provide network-wide visibility and control, and enable administration without the need for on-site networking expertise.Cloud services deliver seamless firmware and security signature updates, automatically establish site-to-site VPN tunnels, and provide 24x7 network monitoring. Moreover, the MX’s intuitive browser-based management interface removes the need for expensive and time-consuming training.For customers moving IT services to a public cloud service, Meraki offers a virtual MX for use in Amazon Web Services and Microsoft Azure, enabling Auto VPN peering and SD-WAN for dynamic path selection.The MX67W, MX68W, and MX68CW integrate Cisco Meraki’s award-winning wireless technology with the powerful MX network security features in a compact form factor ideal for branch offices or small enterprises.• Dual-band 802.11n/ac Wave 2, 2x2 MU-MIMO with 2 spatial streams • Unified management of network security and wireless • Integrated enterprise security and guest accessIntegrated 802.11ac Wave 2 WirelessPower over EthernetThe MX65, MX65W, MX68, MX68W, and MX68CW include two ports with 802.3at (PoE+). This built-in power capability removes the need for additional hardware to power critical branch devices.• 2 x 802.3at (PoE+) ports capable of providing a total of 60W • APs, phones, cameras, and other PoE enabled devices can be powered without the need for AC adapters, PoE converters, or unmanaged PoE switches.MX68 Port ConfigurationVirtual MX is a virtual instance of a Meraki security appliance, dedicated specifically to providing the simple configuration benefits of site-to-site Auto VPN for customers running or migrating IT services to the public cloud. A virtual MX is added via the Amazon Web Services or Azure marketplace and then configured in the Meraki dashboard, just like any other MX. It functions like a VPN concentrator, and features SD-WAN functionality like other MX devices.• An Auto VPN to a virtual MX is like having a direct Ethernetconnection to a private datacenter. The virtual MX can support up to 500 Mbps of VPN throughput, providing ample bandwidth for mission critical IT services hosted in the public cloud, like Active Directory, logging, or file and print services.• Support for Amazon Web Services (AWS) and AzureMeraki vMX100MX68CW Security ApplianceLTE AdvancedWhile all MX models feature a USB port for 3G/4G failover, the MX67C and MX68CW include a SIM slot and internal LTE modem. This integrated functionality removes the need for external hardware and allows for cellular visibility and configuration within the Meraki dashboard.• 1 x CAT 6, 300 Mbps LTE modem • 1 x Nano SIM slot (4ff form factor)• Global coverage with individual orderable SKUs for North America and WorldwideMX67C SIM slotSmall branch Small branch Small branch Small branch50250 Mbps250 Mbps250 Mbps200 Mbps1Requires separate cellular modemMX67MX67C MX68MX68CW 1Requires separate cellular modemMedium branch Large branch Campus orVPN concentrator Campus orVPN concentratorRack Mount Models 1Requires separate cellular modemVirtual AppliancesExtend Auto-VPN and SD-WAN to public cloud servicesAmazon Web Services (AWS) and Microsoft Azure1 + VirtualIncluded in the BoxPackage Contents Platform(s)Mounting kit AllCat 5 Ethernet cable (2)AllAC Power Adapter MX64, MX64W, MX65, MX65W, MX67, MX67W, MX67C, MX68, MX68W, MX68CWWireless external omni antenna (2)MX64W, MX65W, MX67W, MX68W250W Power Supply (2)MX250, MX450System Fan (2)MX250, MX450SIM card ejector tool MX67C, MX68CWFixed external wireless and LTE paddle antennas MX68CWRemovable external LTE paddle antennas MX67CLifetime Warranty with Next-day Advanced ReplacementCisco Meraki MX appliances include a limited lifetime hardware warranty that provides next-day advance hardware replacement. Cisco Meraki’s simplified software and support licensing model also combines all software upgrades, centralized systems management, and phone support under a single, easy-to-understand model. For complete details, please visit /support.ACCESSORIES / SFP TRANSCEIVERSSupported Cisco Meraki accessory modulesNote: Please refer to for additional single-mode and multi-mode fiber transceiver modulesPOWER CABLES1x power cable required for each MX, 2x power cables required for MX250 and MX450. For US customers, all required power cables will beautomatically included. Customers outside the US are required to order power cords separately.SKUMA-PWR-CORD-AUThe Cisco Meraki MX84, MX100, MX250, MX450 models support pluggable optics for high-speed backbone connections between wir-ing closets or to aggregation switches. Cisco Meraki offers several standards-based Gigabit and 10 Gigabit pluggable modules. Each appliance has also been tested for compatibility with several third-party modules.Pluggable (SFP) Optics for MX84, MX100, MX250, MX450AccessoriesManagementManaged via the web using the Cisco Meraki dashboardSingle pane-of-glass into managing wired and wireless networksZero-touch remote deployment (no staging needed)Automatic firmware upgrades and security patchesTemplates based multi-network managementOrg-level two-factor authentication and single sign-onRole based administration with change logging and alertsMonitoring and ReportingThroughput, connectivity monitoring and email alertsDetailed historical per-port and per-client usage statisticsApplication usage statisticsOrg-level change logs for compliance and change managementVPN tunnel and latency monitoringNetwork asset discovery and user identificationPeriodic emails with key utilization metricsDevice performance and utilization reportingNetflow supportSyslog integrationRemote DiagnosticsLive remote packet captureReal-time diagnostic and troubleshooting toolsAggregated event logs with instant searchNetwork and Firewall ServicesStateful firewall, 1:1 NAT, DMZIdentity-based policiesAuto VPN: Automated site-to-site (IPsec) VPN, for hub-and-spoke or mesh topologies Client (IPsec L2TP) VPNMultiple WAN IP, PPPoE, NATVLAN support and DHCP servicesStatic routingUser and device quarantineWAN Performance ManagementWeb caching (available on the MX84, MX100, MX250, MX450)WAN link aggregationAutomatic Layer 3 failover (including VPN connections)3G / 4G USB modem failover or single-uplinkApplication level (Layer 7) traffic analysis and shapingAbility to choose WAN uplink based on traffic typeSD-WAN: Dual active VPN with policy based routing and dynamic path selection CAT 6 LTE modem for failover or single-uplink1MX67C and MX68CW only Advanced Security Services1Content filtering (Webroot BrightCloud CIPA compliant URL database)Web search filtering (including Google / Bing SafeSearch)Y ouTube for SchoolsIntrusion-prevention sensor (Cisco SNORT® based)Advanced Malware Protection (AMP)AMP Threat Grid2Geography based firewall rules (MaxMind Geo-IP database)1 Advanced security services require Advanced Security license2 Threat Grid services require additional sample pack licensingIntegrated Wireless (MX64W, MX65W, MX67W, MX68W, MX68CW)1 x 802.11a/n/ac (5 GHz) radio1 x 802.11b/g/n (2.4 GHz) radioMax data rate 1.2 Gbps aggregate (MX64W, MX65W), 1.3Gbps aggregate (MX67W,MX68W, MX68CW)2 x 2 MU-MIMO with two spatial streams (MX67W, MX68W, MX68CW)2 external dual-band dipole antennas (connector type: RP-SMA)Antennagain:*************,3.5dBi@5GHzWEP, WPA, WPA2-PSK, WPA2-Enterprise with 802.1X authenticationFCC (US): 2.412-2.462 GHz, 5.150-5.250 GHz (UNII-1), 5.250-5.350 GHZ (UNII-2), 5.470-5.725 GHz (UNII-2e), 5.725 -5.825 GHz (UNII-3)CE (Europe): 2.412-2.484 GHz, 5.150-5.250 GHz (UNII-1), 5.250-5.350 GHZ (UNII-2)5.470-5.600 GHz, 5.660-5.725 GHz (UNII-2e)Additional regulatory information: IC (Canada), C-Tick (Australia/New Zealand), RoHSIntegrated Cellular (MX67C and MX68CW only)LTE bands: 2, 4, 5, 12, 13, 17, and 19 (North America). 1, 3, 5, 7, 8, 20, 26, 28A, 28B, 34, 38, 39, 40, and 41 (Worldwide)300 Mbps CAT 6 LTEAdditional regulatory information: PTCRB (North America), RCM (ANZ, APAC), GCF (EU)Power over Ethernet (MX65, MX65W, MX68, MX68W, MX68CW)2 x PoE+ (802.3at) LAN ports30W maximum per portRegulatoryFCC (US)CB (IEC)CISPR (Australia/New Zealand)PTCRB (North America)RCM (Australia/New Zealand, Asia Pacific)GCF (EU)WarrantyFull lifetime hardware warranty with next-day advanced replacement included.Specificationsand support). For example, to order an MX64 with 3 years of Advanced Security license, order an MX64-HW with LIC-MX64-SEC-3YR. Lifetime warranty with advanced replacement is included on all hardware at no additional cost.*Note: For each MX product, additional 7 or 10 year Enterprise or Advanced Security licensing options are also available (ex: LIC-MX100-SEC-7YR).and support). For example, to order an MX64 with 3 years of Advanced Security license, order an MX64-HW with LIC-MX64-SEC-3YR. Lifetime warranty with advanced replacement is included on all hardware at no additional cost.*Note: For each MX product, additional 7 or 10 year Enterprise or Advanced Security licensing options are also available (ex: LIC-MX100-SEC-7YR).and support). For example, to order an MX64 with 3 years of Advanced Security license, order an MX64-HW with LIC-MX64-SEC-3YR. Lifetime warranty with advanced replacement is included on all hardware at no additional cost.*Note: For each MX product, additional 7 or 10 year Enterprise or Advanced Security licensing options are also available (ex: LIC-MX100-SEC-7YR).。
Labview图形化编程语言中英文对照外文翻译文献
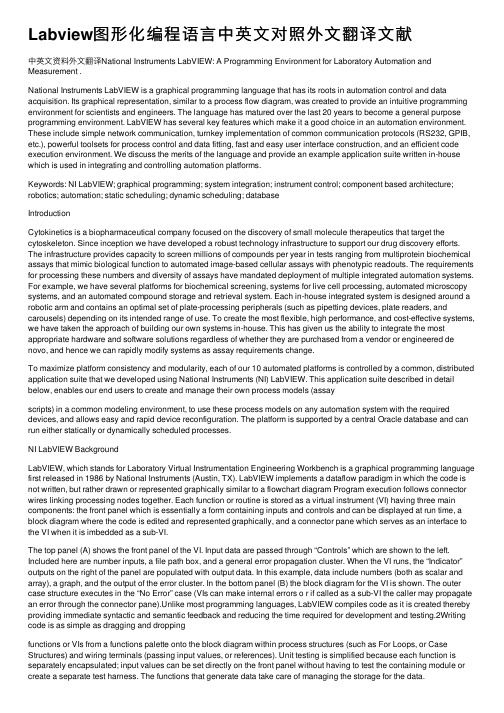
Labview图形化编程语⾔中英⽂对照外⽂翻译⽂献中英⽂资料外⽂翻译National Instruments LabVIEW: A Programming Environment for Laboratory Automation and Measurement .National Instruments LabVIEW is a graphical programming language that has its roots in automation control and data acquisition. Its graphical representation, similar to a process flow diagram, was created to provide an intuitive programming environment for scientists and engineers. The language has matured over the last 20 years to become a general purpose programming environment. LabVIEW has several key features which make it a good choice in an automation environment. These include simple network communication, turnkey implementation of common communication protocols (RS232, GPIB, etc.), powerful toolsets for process control and data fitting, fast and easy user interface construction, and an efficient code execution environment. We discuss the merits of the language and provide an example application suite written in-house which is used in integrating and controlling automation platforms.Keywords: NI LabVIEW; graphical programming; system integration; instrument control; component based architecture; robotics; automation; static scheduling; dynamic scheduling; databaseIntroductionCytokinetics is a biopharmaceutical company focused on the discovery of small molecule therapeutics that target the cytoskeleton. Since inception we have developed a robust technology infrastructure to support our drug discovery efforts. The infrastructure provides capacity to screen millions of compounds per year in tests ranging from multiprotein biochemical assays that mimic biological function to automated image-based cellular assays with phenotypic readouts. The requirements for processing these numbers and diversity of assays have mandated deployment of multiple integrated automation systems. For example, we have several platforms for biochemical screening, systems for live cell processing, automated microscopy systems, and an automated compound storage and retrieval system. Each in-house integrated system is designed around a robotic arm and contains an optimal set of plate-processing peripherals (such as pipetting devices, plate readers, and carousels) depending on its intended range of use. To create the most flexible, high performance, and cost-effective systems, we have taken the approach of building our own systems in-house. This has given us the ability to integrate the most appropriate hardware and software solutions regardless of whether they are purchased from a vendor or engineered de novo, and hence we can rapidly modify systems as assay requirements change.To maximize platform consistency and modularity, each of our 10 automated platforms is controlled by a common, distributed application suite that we developed using National Instruments (NI) LabVIEW. This application suite described in detail below, enables our end users to create and manage their own process models (assayscripts) in a common modeling environment, to use these process models on any automation system with the required devices, and allows easy and rapid device reconfiguration. The platform is supported by a central Oracle database and can run either statically or dynamically scheduled processes.NI LabVIEW BackgroundLabVIEW, which stands for Laboratory Virtual Instrumentation Engineering Workbench is a graphical programming language first released in 1986 by National Instruments (Austin, TX). LabVIEW implements a dataflow paradigm in which the code is not written, but rather drawn or represented graphically similar to a flowchart diagram Program execution follows connector wires linking processing nodes together. Each function or routine is stored as a virtual instrument (VI) having three main components: the front panel which is essentially a form containing inputs and controls and can be displayed at run time, a block diagram where the code is edited and represented graphically, and a connector pane which serves as an interface to the VI when it is imbedded as a sub-VI.The top panel (A) shows the front panel of the VI. Input data are passed through “Controls” which are shown to the left. Included here are number inputs, a file path box, and a general error propagation cluster. When the VI runs, the “Indicator”outputs on the right of the panel are populated with output data. In this example, data include numbers (both as scalar and array), a graph, and the output of the error cluster. In the bottom panel (B) the block diagram for the VI is shown. The outer case structure executes in the “No Error” case (VIs can make internal errors o r if called as a sub-VI the caller may propagate an error through the connector pane).Unlike most programming languages, LabVIEW compiles code as it is created thereby providing immediate syntactic and semantic feedback and reducing the time required for development and testing.2Writing code is as simple as dragging and droppingfunctions or VIs from a functions palette onto the block diagram within process structures (such as For Loops, or Case Structures) and wiring terminals (passing input values, or references). Unit testing is simplified because each function is separately encapsulated; input values can be set directly on the front panel without having to test the containing module or create a separate test harness. The functions that generate data take care of managing the storage for the data.NI LabVIEW supports multithreaded application design and executes code in an inherently parallel rather than sequential manner; as soon as a function or sub-VI receives all of its required inputs, it can begin execution. In Figure 1b, all the sub-VIs receive the array input simultaneously as soon as the For Loop is complete, and thus they execute in parallel. This is unique from a typical text-based environment where the control flows line by line within a function. When sequential execution is required, control flow can be enforced by use of structures such as Sequences, Events, or by chaining sub-VIs where output data from one VI is passed to the input of the next VI.Similar to most programming languages, LabVIEW supports all common data types such as integers, floats, strings, and clusters (structures) and can readily interface with external libraries, ActiveX components, and .NET framework. As shown in Figure 1b, each data type is graphically represented by wires of different colors and thickness. LabVIEW also supports common configuration management applications such as Visual SourceSafe making multideveloper projects reasonable to manage.Applications may be compiled as executables or as Dynamic Link Libraries (DLLs) that execute using a run-time engine similar to the Java Runtime Environment. The development environment provides a variety of debugging tools such as break-points, trace (trace), and single-step. Applications can be developed using a variety of design patterns such as Client-Server, Consumer-Producer, andState-Machine. There are also UML (Unified Modeling Language) modeling tools that allow automated generation of code from UML diagrams and state diagrams.Over the years, LabVIEW has matured into a general purpose programming language with a wider user base.NI LabVIEW as a Platform for Automation and InstrumentationOur experience creating benchtop instrumentation and integrated automation systems has validated our choice of LabVIEW as an appropriate tool. LabVIEW enables rapid development of functionally rich applications appropriate for both benchtop applications and larger integrated systems. On many occasions we have found that project requirements are initially ill defined or change as new measurements or new assays are developed.. There are several key features of the language that make it particularly useful in an automation environment for creating applications to control and integrate instrumentation, manage process flow, and enable data acquisition.Turnkey Measurement and Control FunctionLabVIEW was originally developed for scientists and engineers .The language includes a rich set of process control and data analysis functions as well as COM, .NET, and shared DLL support. Out of the box, it provides turnkey solutions to a variety of communication protocols including RS232, GPIB, and TCP/IP. Control structures such as timed While Loops allow synchronized and timed data acquisition from a variety of hardware interfaces such as PCI, USB, and PXI. DataSocket and VI ServerDeployment of an integrated system with multiple control computers requires the automation control application to communicate remotely with instrument drivers existing on remote computers. LabVIEW supports a distributed architecture by virtue of enabling seamless network communication through technologies such as VI Server and DSTP (data sockets transfer protocol). DSTP is an application layer protocol similar to http based on Transmission Control Protocol/Internet Protocol (TCP/IP). Data sockets allow easy transfer of data between remote computers with basic read and write functions. Through VI server technology, function calls can be made to VIs residing on remote computers as though they are residing on the local computer. Both Datasockets and VI server can be configured to control accesses privileges.Simple User Interface (UI) ImplementationIn addition to common interface controls such as text boxes, menu rings, and check-boxes, LabVIEW provides a rich set of UI controls (switches, LEDs, gauges, array controls, etc.) that are pertinent to laboratory equipment. These have their origins in LabVIEWs laboratory roots and help in development of interfaces which give scientists a clear understanding of a system's state. LabVIEW supports UI concepts including subpanels (similar to the Multiple Document Interface), splitter bars, and XControls (analogous to OCX controls).Multithreaded Programming EnvironmentThe inherent parallel environment of LabVIEW is extremely useful in the control of laboratory equipment. Functions can have multiple continuous While Loops where one loop is acquiring data rapidly and the other loop processes the data at a much slower rate. Implementing such a paradigm in other languages requires triggering an independent function thread for each process and developing logic to manage synchronization. Through timed While Loops, multiple independent While Loops can be easily synchronized to process at a desired period and phase relative to one another. LabVIEW allows invoking multiple instances of the same function witheach maintaining its own data space. For instance, we could drag many instances of the Mean sub-VI onto the block diagramin Figure 1b and they would all run in parallel, independent of one another. To synchronize or enforce control flow within the dataflow environment, LabVIEW also provides functions such as queues, semaphores, and notification functions.NI LabVIEW Application Example: The Open System Control Architecture (OSCAR)OSCAR is a LabVIEW-based (v7.1) automation integration framework and task execution engine designed and implemented at Cytokinetics to support application development for systems requiring robotic task management. OSCAR is organized around a centralized Oracle database which stores all instrumentation configuration information used to logically group devices together to create integrated systems (Fig. 2). The database also maintains Process Model information from which tasks and parameters required to run a particular process on a system can be generated and stored to the database. When a job is started, task order and parameter data are polled by the Execution Engine which marshals tasks to each device and updates task status in the database in real time. Maintaining and persisting task information for each system has two clear benefits. It allows easy job recovery in the event of a system error, and it also provides a process audit trail that can be useful for quality management and for troubleshooting process errors or problems.Each OSCAR component is distributed across the company intranet and communicates with a central database. Collections of physical devices controlled through OSCAR Instrument packages (OIP) make up systems. Users interact with systems through one of the several applications built on OSCAR. Each application calls the RTM which marshals tasks from the database to each OIP. OSCAR has sets of tools for managing system configurations, creating Process Models, monitoring running processes, recovering error-state systems, and managing plate inventory in storage devices.OSCAR uses a loosely coupled distributed component architecture, enabled in large part by LabVIEWs DSTP and remote VI technologies that allow system control to be extended beyond the confines of the traditional central control CPU model. Any networked computer or device can be integrated and controlled in an OSCAR system regardless of its physical location. This removes the proximity constraints of traditional integrated systems and allows for the utilization of remote data crunchers, devices, or even systems. The messaging paradigm used shares many similarities with current Service Oriented Architectures or Enterprise Service Bus implementations without a lot of required programming overhead or middleware; a centralized server is not required to direct the XML packets across the network. An additional benefit to this loosely coupled architecture is the flexibility in front-end application design. OSCAR encapsulates and manages all functionality related to task execution and device control, which frees the developer to focus on the unique requirements of a given application. For example, an application being created for the purpose of compound storage and retrieval can be limited in scope to requirements such as inventory management and LIMS integration rather than device control, resource allocation, and task synchronization.The OSCAR integration framework consists of multiple components that enable device and system configuration, process modeling, process execution, and process monitoring. Below are descriptions of key components of the framework. Integration PlatformThe Oscar Instrument Package (OIP) is the low level control component responsible for communicating with individual devices. It can support any number of devices on a system (including multiple independent instances of the same type of device) and communicates to the Runtime Manager (RTM) via serialized XMLstrings over DSTP. This allows the device controller and RTM components to exist on separate networked computers if necessary. Additionally, the OIP controller communicates with a device instance via LabVIEW remote VI calls which provide a lower level of distribution and allow the device drivers to exist on a separate networked computer from the controller. At Cytokinetics, we currently support approximately 100 device instances of 30 device types which are distributed across 10 integrated systems.System ManagementAn OSCAR system is a named collection of device instances which is logically represented in the database. The interface for each device (commands and parameters) is stored in the database along with the configuration settings for each device instance (i.e., COM port, capacity). The System Manager component provides the functionality to easily manipulate this information (given appropriate permissions). When a physical device is moved from one system to another, or a processing bottleneck alleviated by addition of another similar device, system configuration information is changed without affecting the processes that may be run on the system.Process ModelingA process model is the logical progression of a sequence of tasks. For example, a biochemical assay might include the following steps (1) remove plate from incubator, (2) move plate to pipettor, (3) add reagent, (4) move plate to fluorescent reader, (5) read plate, and (6) move plate to waste. The Process Modeler component allows the end user to choose functions associated with devices and organize them into a sequence of logical tasks. The resulting process model is then scheduled via a static schedule optimization algorithm or saved for dynamic execution (Fig. 3). Aprocess model is not associated with a physical system, but rather a required collection of devices. This has two importantbenefits: (1) the scientist is free to experiment with virtual system configurations to optimize the design of a future system or the reconfiguration of an existing system, and (2) any existing process model can be executed on any system equipped with the appropriate resources.The top panel (A) shows the Process Schedule Modeler, an application that graphically displays statically scheduled processes. Each horizontal band represents a task group which is the collection of required tasks used by a process; tasks are color coded by device. The bottom panel (B) shows the UI from the Automated Imaging System application. The tree structure depicts the job hierarchy for an imaging run. Jobs (here AIS_Retrieval and AIS_Imaging) are composed of task groups. As the systems runs, the tasks in the task group are executed and their status is updated in the database.Process ExecutionProcess execution occurs by invoking the OSCAR RTM. The RTM is capable of running multiple differing processes on a system at the same time allowing multiple job types to be run in parallel. The RTM has an application programming interface (API) which allows external applications to invoke its functionality and consists of two main components, the Task Generator Module (TGM) and the Execution Engine. External applications invoke an instance of a Process Model through the TGM at which point a set of tasks and task parameters are populated in the OSCAR database. The Execution Engine continually monitors the database for valid tasks and if a valid task is found it is sent to the appropriate device via the OIP. The OSCAR system supports running these jobs in either a static or dynamic mode. For processes which must meet strict time constraints (often due to assay requirements), or require the availability of a given resource, a static schedule is calculated and stored for reuse.The system is capable of optimizing the schedule based on actual task operation times (stored in the database).Other types of unconstrained processes benefit more from a dynamic mode of operation where events trigger the progress of task execution as resources become available in real-time. When operating dynamically, intelligent queuing of tasks among multiple jobs allows optimal use of resources minimizing execution time while allowing for robust error handling.Process MonitoringAll systems and jobs can be monitored remotely by a distributed application known as the Process Monitor. This application allows multiple users to monitor active jobs across all systems for status and faults and provides email notification for fault situations.ConclusionCytokinetics has built and maintains an automation software infrastructure using NI LabVIEW. The language has proven to be a powerful tool to create both rapid prototype applications as well as an entire framework for system integration and process execution. LabVIEW's roots in measurement instrumentation and seamless network communication protocols have allowed systems to be deployed containing multiple control computers linked only via the network. The language continues to evolve and improve as a general purpose programming language and develop a broad user base.。
特斯拉 Model S 高性能版用户指南说明书

Altium - 12-400-NB2DSK01 - NANOBOARD NB2 WITH XILINXSPARTAN-3Product Overview:Altium's NanoBoard architecture is unique in thattarget programmable devices are housed onseparate satellite boards, referred to as daughterboards. These boards plug-in to the NanoBoard. Bykeeping each programmable device on its owndaughter board, engineers can easily change thetarget project architecture, while retaining a trulyFPGA vendor-independent development board.Altium's Xilinx Spartan 3 daughter board DB30provides an XC3S1500-4FG676C device, as wellas a range of on-board memories available for use by a design running within that device.The NanoBoard NB2 provides application-specific plug-in peripheral boards to give complete flexibility in system architecture and provide a simple andcost-effective method for rapid prototyping ofhardware concepts.The NanoBoard NB2 caters for the use of up to threeperipheral boards, and is delivered with the followingstandard peripheral boards:▪Audio/Video Peripheral Board (PB01)o Composite and S-Video output andcapture, 24-bit VGA output,high-performance I2S stereo audiocodec▪Mass Storage Peripheral Board (PB02)o Compact Flash, SD card slot, ATA hard-drive interfaces▪USB-IrDA-Ethernet Peripheral Board (PB03)o10/100 Ethernet interface, USB 2.0 interface, 4Mbits/sec IrDAKit Contents:Following are included with NanoBoard NB2DSK01:The NanoBoard NB2 includes a 12-month subscription to an Altium Designer Soft Design license which is linked to the NanoBoard in the box. This license option provides functionality to quickly start designing FPGA-based embedded systems, including:▪FPGA design entry in C, Open Bus, Schematic, VHDL and Verilog▪VHDL simulation engine, integrated debugger and waveform viewer▪Support for a range of 32-bit soft processors for use in FPGA design▪ A rich set of royalty-free IP core libraries including peripherals and user-configurable custom logic ▪Full software development tool chain with libraries and source code▪Programmable FPGA-based instruments for hardware debug and deployment▪Support for importing third-party FPGA IP cores, developing and reusing IP librariesKey Features of Motherboard Altium NanoBoard NB2:Following are the below Main Features for Altium NanoBoard NB2:▪Integrated colour TFT LCD panel (320x240) with touch screen that facilitates dynamic application interaction.▪Stereo analog audio system with high-quality on-board amplifiers, mixer, line in/out and stereo speakers.▪Standard communication interfaces – RS-232 serial, CAN,PS/2 mini-DIN.▪SD card reader – for additional I/O flexibility including the ability to download a variety of files ▪Four channel, 8-bit ADC and 10-bit DAC, I2C-compatible.▪User definable PDA-style push button switches that function as generic design inputs▪General purpose switches and LEDs.▪Programmable clock, 6 to 200 MHz.▪Power sensing system allows real-time monitoring of system and device power consumption.▪SPI Real-Time Clock with 3V battery back-up▪Onboard memory accessible by NanoTalk Controller – 256K x 32-bit common-bus SRAM (1MB), 16M x 32-bit common-bus SDRAM (64MB), 16M x 16-bit common-bus 3.0V Page Mode Flashmemory (32MB), 256K x 32-bit independent SRAM (1MB)▪Dual User Board JTAG headers for direct interaction.▪Home/Reset button – Home button enables firmware to take control of TFT panel; Reset provides NanoBoard reset functionality.▪NanoTalk Controller – manages real time proprietary communication with Altium Designer, the board, and the NanoBoard firmware using a Xilinx® Spartan-3TM (XC3S1500-4FG676C)controller with JTAG accessible Flash configuration PROM▪Master-Slave connectors for chaining multiple development boards – allowing multiple-FPGA system development.▪Board ID memory – 1-Wire® ID system uniquely identifies each daughter board and peripheral board.▪Power – Dual 5V DC power daisy-chain connectors with power switch, 5V DC power output connector, power supply test points for all supply levels available on the board, four GND points.▪High-speed PC interconnection through USB 2.0The following is a list of generic features, common to NB30 board:∙Protective casing – all daughter boards have a protective casing that helps protect the topside of the board.∙100-way connectors – these 100-way Male docking connectors are used to connect the daughter board to the NB2DSK01 motherboard, which has corresponding 100-way Female dockingconnectors ('NANOCONNECT' interfaces). Daughter boards available with the DesktopNanoBoard NB2DSK01 and beyond each have three connectors (top, bottom and left). Thoseavailable previously for the NanoBoard-NB1 have two such connectors (top and bottom).∙Power LED – this will light (RED) when the daughter board is correctly plugged into the NB2DSK01 motherboard and the NB2DSK01's power is switched on.∙Program LED – this will light (GREEN) when the target device on the daughter board has been successfully programmed with an FPGA design.3-connector daughter boards also have three holes that align with threaded standoffs on the NB2DSK01. These can be used to affix the board securely to the motherboard.Key Features of Spartan 3 daughter board DB30:Altium's Xilinx Spartan 3 daughter board DB30 provides an XC3S1500-4FG676C device, as well as a range of on-board memories available for use by a design running within that device.The Daughter Board DB30 has the following features:▪Xilinx Spartan-3 FPGA (XC3S1500-4FG676C)▪On-board memories available for use by FPGA design:o256K x 32-bit common-bus SRAM (1MByte)o16M x 32-bit common-bus SDRAM (64MByte)o16M x 16-bit common-bus Flash memory (32MByte)o Dual 256K x 16-bit independent SRAM (512KByte each)▪Wire® memory device used to store board ID and related information▪Three 100-way connectors for attachment to NB2DSK01 motherboard. These connectors provide:o Interface to resources on the NB2DSK01 motherboard and plugged-in peripheral boardso SPI bus interfaceo I2C bus interfaceo1-Wire bus interfaceo JTAG, power and additional control lines from the motherboard.Ordering InformationProducts:Part Number Manufacturer Farnell P/N Newark P/N12-400-NB2DSK0 1-DB30 Altium 171440925R5626Associated Products:Part Number Manufacturer Description FarnellP/NNewarkP/NDaughter Board Altium Spartan-3 174414 10R0249ADAPTER AltiumJTAGUSB171442610R0257Flash Memory ST Micro Serial SPI FlashMemory1099669 26M1754Transceiver MaximRS-232137976968K4632CAN Bus Maxim Transceiver NA 24R9638ADC MaximADC-ICNA68K9410 DAC MaximDACICNA78C3271 Amplifier MaximCurrentSenseNA67K5237 FPGA XilinxSpartan3176247622M4732 Flash Memory Spansion Flash 1567823 42K8611Switch Maxim Switch Addressable 96B0597 *******Power Supply Maxim Power Supply IC NA 67K4263SDRAMMicron Memory 1216280 97K6120 ALTERA CYCLONE III DB40 DAUGHTER BOARD Altium Cyclone III 1714419 10R0253 XILINX SPARTAN-3AN DB41 DAUGHTER BOARD Altium Spartan 3AN 1714420 10R0254 XILINX SPARTAN-3A DSP DB42 DAUGHTER BOARD Altium Spartan 3A 1714421 10R0255 BOARD, DAUGHTER, DB46, VIRTEX-4 SX Altium Virtex-4 1714422 10R0256 BOARD, DAUGHTER, DB30,Spartan 3 Altium Spartan-3 174414 10R0249 BOARD, PERIPHERAL, PB01Altium AUDIO/VIDEO171442310R0258BOARD, PERIPHERAL, PB02Altium MASS STORAGE171442410R0259 BOARD, PERIPHERAL, PB03AltiumUSB / IRDA /ETHERNET1714425 10R0260Similar Products:Part NumberManufa cturerDescription Support DeviceFarnell P/NNewark P/N12-400-NB2DSK01 (ALTERA)AltiumDESKTOPNANOBOARD WITH ALTERACYCLONE II Cyclone IINA10R024512-400-NB2DSK01 (LATTICE)AltiumDESKTOPNANOBOARD WITH LATTICEECP Lattice ECPNA10R024612-400-NB2DSK01 (XILINX)AltiumDESKTOPNANOBOARD WITH XILINXSPARTAN-3 Spartan 3NA10R024712-401-NB2DS-K01-DB30 Altium NANOBOARDKIT NB2 SPARTAN-3Spartan 325R562612-400-NB2DSK01-DB31 Altium NANOBOARD KITNB2, CYCLONE IICyclone II171440725R562712-400-NB2DSK01-DB32 Altium NANOBOARD KITNB2, LATTICE ECPLattice ECP171441025R5628Document List: Datasheets:Part Number DescriptionSize Xilinx’s Spartan Series Spartan 3 User guide Spartan 3 Datasheet 8.94MB 5.1MB DS2406Dual Addressable Switch Plus 1Kb Memory 240KBMT48LC16M16A2TG Common-Bus SDRAM2.9MBS29GL256N11FFIV10 Common-Bus Flash memory 4.8MB MAX8860 Linear Regulator 168KBMAX1831Voltage Regulator106KBApplication Notes:File NameSize XAPP058 - Xilinx In-System Programming Using an Embedded Microcontroller641KBXAPP195 - Implementing Barrel Shifters Using Multipliers 52KBXAPP452 - Spartan-3 FPGA Family Advanced Configuration Architecture 574KBXAPP453 - The 3.3V Configuration of Spartan-3 FPGAs 215KBXAPP454 - DDR2 SDRAM Interface for Spartan-3 Generation FPGAs 328KBHardware & Software Resources:File NameSizeDownload the latest release of Altium Designer Viewer 129MBDownload the Altium Instrument Dashboard 31.7MBAutotrax Freeware Version Download 821KBEasytrax Freeware Download 485 KB。
诺基亚7950可扩展路由系统说明书
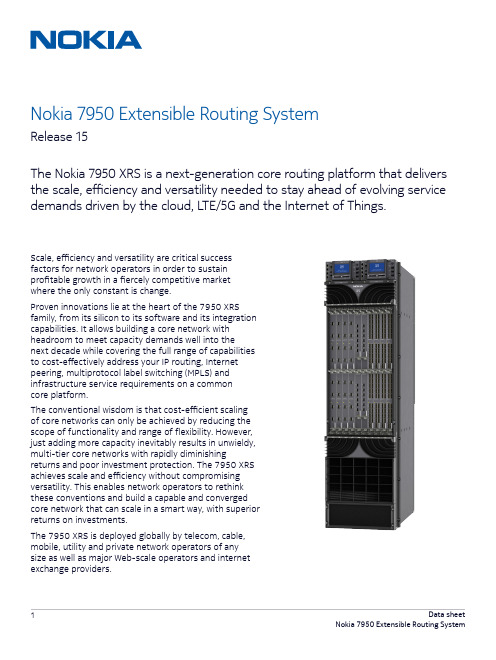
Nokia 7950 Extensible Routing SystemRelease 15The Nokia 7950 XRS is a next-generation core routing platform that delivers the scale, efficiency and versatility needed to stay ahead of evolving service demands driven by the cloud, L TE/5G and the Internet of Things.Scale, efficiency and versatility are critical successfactors for network operators in order to sustainprofitable growth in a fiercely competitive marketwhere the only constant is change.Proven innovations lie at the heart of the 7950 XRSfamily, from its silicon to its software and its integrationcapabilities. It allows building a core network withheadroom to meet capacity demands well into thenext decade while covering the full range of capabilitiesto cost-effectively address your IP routing, Internetpeering, multiprotocol label switching (MPLS) andinfrastructure service requirements on a commoncore platform.The conventional wisdom is that cost-efficient scalingof core networks can only be achieved by reducing thescope of functionality and range of flexibility. However,just adding more capacity inevitably results in unwieldy,multi-tier core networks with rapidly diminishingreturns and poor investment protection. The 7950 XRSachieves scale and efficiency without compromisingversatility. This enables network operators to rethinkthese conventions and build a capable and convergedcore network that can scale in a smart way, with superiorreturns on investments.The 7950 XRS is deployed globally by telecom, cable,mobile, utility and private network operators of anysize as well as major Web-scale operators and internetexchange providers.7950 XRS family overview The 7950 XRS family consists of three systems that are designed to meet the needs of global, national, regional and private network operatorsof all sizes: the 7950 XRS-20, -20e and -40.It offers a common platform that addresses the full spectrum of networking needs for public and private internet backbones and peering points, metropolitan and regional aggregation hubsas well as cloud, data center and mobile core infrastructure. This will enable network operators to deliver the immersive ultra-broadband service experiences that consumers aspire to todayand will expect tomorrow.One platform for all servicesThe 7950 XRS addresses the full range of core routing requirements using common hardware that is powered by programmable FP3 routing silicon and runs the proven, resilient and feature-rich Service Router Operating System (SR OS).A flexible, pay-as-you-go software licensing model allows you to build a versatile, reliable and converged core network that evolves with your needs while protecting your hardware investments. Scale with superior economicsA modular and extensible hardware design ensures granular and economical scaling of switching capacity and port density. A 7950 XRS chassis equipped with FP3 hardware delivers up to 16 Tb/s (up to 80 100GE or 800 10GE ports) in a single 19-in rack, and consumes only a single Watt per gigabit of traffic switched. System capacity can be expanded to 32 Tb/s in a back-to-back chassis configuration and each chassis is designed to scale much higher with next generation FP hardware. IP/optical integrationTunable 10G and integrated 100G coherentPM-QPSK tunable DWDM optics enable the7950 XRS to directly interface with the photonic transport layer without requiring optical transponders.A standards-based GMPLS user-network interface (UNI) enables IP/optical control plane integration, allowing the 7950 XRS to efficiently coordinateIP routing and transport requirements across administrative boundaries and to dynamically set up optical segments and end-to-end transport connections.Cross-domain managementThe 7950 XRS is managed by the Nokia Network Services Platform (NSP), supporting integrated element and network management with end-to-end orchestration of network resource provisioning and assurance operations. Operational tools, including the Nokia 5650 Control Plane Assurance Manager (CPAM), provide additional visibility and flexibilityin monitoring and trouble-shooting IP control plane issues.Carrier SDN integrationThe 7950 XRS and SR OS enable multivendor SDN control integration through OpenFlow, PCEP and NETCONF/YANG. Network operators can leverage the 7950 XRS in combination with the NSP to introduce scalable and integrated carrier SDN control across IP, MPLS, Ethernet and optical transport layers.The NSP supports unified service automation and network optimization with comprehensive path computation capabilities to enable source-based routing and traffic steering with segment routing support, online traffic engineering and resource optimization, and elastic bandwidth services for dynamic cloud applications.7950 XRS-40The Nokia 7950 XRS-40 provides32 Tb/s of routing capacity in a single system when fully equipped with FP3 hardware. The system comprises 40 slots in a dual-chassis configuration of two 7950 XRS-20or two 7950 XRS-20e systems, with each slot supporting 400 Gb/s of full duplex aggregate interface capacity. The two systems are interconnected through optical backplane cabling and can be placed up to 30 meters apart. One chassis will act as the master and assume system control overthe extension chassis as well. Designed to meet the needs of today’s largest Internet backbones and aggregation points, a single 7950 XRS-40 core router can handle up to 160 100GE or 1600 10GE interfaces without oversubscription and achieve full port density without requiring cabling breakout panels.7950 XRS-20The Nokia 7950 XRS-20 provides16 Tb/s of routing capacity in a single19-in rack when fully equipped withFP3-based hardware, and its chassisand common hardware is designedto scale much higher in the future.With 20 slots, each initially capableof 400 Gb/s of full duplex aggregateinterface capacity, the systemsupports up to 80 100GE or 80010GE ports in a single rack usingstandards-based pluggable opticsand without requiring additionalbreakout panels for cabling.The 7950 XRS-20 system is availablein an extensible and a stand-aloneconfiguration. The extensibleconfiguration is equipped with opticalbackplane connectors and can beupgraded in-service to a 7950 XRS-40back-to-back configuration to doublesystem capacity. The standaloneconfiguration can be made extensibleby exchanging the Switch FabricModules.7950 XRS-20eThe Nokia 7950 XRS-20e runsSR OS release 13.0 or higher andis functionally compatible withthe XRS-20. All XRS-20 hardwarecomponents except the fan traysand XRS Control Modules areinterchangeable.The “Universal” chassis variantsupports all AC and DC poweroptions and is equipped with aPower Connection Panel at the rear.The “AC/HVDC” variant is cabled atthe front and has a blank rear panel.The 7950 XRS-20e introduces anew XRS Control Module (XCM)with additional air-intake capacity.Air movement and noise levelsare further improved through anupgraded cooling fan assemblywith slanted centrifugal impellertrays and 2+1 redundancy.Common elements and attributesThe 7950 XRS core router family shares fundamental attributes that ensure consistency, operational ease of use, and investment protection for network operators.Routing siliconThe 7950 XRS leverages internally developedNPU routing silicon to ensure optimal performance and scaling of a rich and complete Layer 2 and Layer 3 feature set that addresses all core deployment scenarios. The 400G FP3 chipset is the third-generation NPU and provides the perfect geometry for high-density 10, 40, 100 and 400G interface modules. It offers deterministic forwarding performance with advanced traffic management features and energy-efficient power gating techniques.These silicon innovations drive the high levelof flexibility and performance needed for converged backbone and metro core deployments, including IP routing and peering, MPLS switching, VPN infrastructure services and data center interconnection applications.Interface modulesThe Nokia 7950 XRS uses a pair of complementary modules to support current and future interfaces. XMA Control Modules (XCMs) contain a slot-level control plane subsystem and switch fabric interface. XRS Media Adapters (XMAs) contain the forwarding complex and provide a wide range of GE, 10GE,40GE and 100GE interface options.A flexible software licensing scheme allowsfor customizing XMAs for diverse core router applications, with configurable quality of service (QoS) granularity. This enables operators to consolidate core routing systems on a single platform, and to rapidly respond to evolving requirements with minimal impact and maximum investment protection.Operating systemThe 7950 XRS family is based on the proven SR OS, carrying forward over a decade of experience in the IP networks of more than 750 network operators worldwide. With a single common OS across the Nokia routing portfolio, network operators benefit froman extensive track record of reliability in the field and a full suite of features to enable resiliency, high availability and in-service software upgrade (ISSUs). Optical integrationMany operators are looking to optimize the overall efficiency of the core through closer integrationof the IP and optical domains. Tunable, pluggable DWDM optics for 10GE and 100GE interfaces are available for all platforms. Multi-vendor IP/optical control plane integration is supported by meansof the GMPLS UNI.Power and cooling efficiencyThe 7950 XRS system design incorporates intelligent power management capabilitiesto monitor power consumption of individual components, assure power safety thresholds,and manage power-up and power-down priorities in the event of degraded power availability. Other key enhancements include clock gating techniques that dynamically reduce power to system components not in use.Redundant, modular fan trays that are linearly modulated provide appropriate and efficient cooling with reduced noise levels. The 7950 XRS-20 uses two linear, 1+1 redundant fan trays in a stacked configuration for primary system cooling whilethe XRS-20e uses three impeller fan trays in aside-by-side configuration.A “pull” airflow design, in combination with impedance panels and air guides, ensures an even distribution of air to every section of the system. Hot air exhaust through the back of the chassis ensures a clean separation between the hot and cold aisles. An optional top plenum accessory is available for the 7950 XRS-20 to enable hot air exhaust at the top of the chassis for additional cooling efficiency.Hardware overviewAll common equipment components are redundant and field replaceable to maximize system uptime. Chassis Control Modules (CCMs)Redundant CCMs support operator access tothe Nokia 7950 XRS control and management interfaces. The CCMs are located at the top, and each CCM has an LCD touch-screen display and supports interfaces for timing, management, alarms and memory expansions.Advanced Power Equalization Modules (APEQs) APEQs provide power for the 7950 XRS and include built-in intelligence to monitor and communicate available power budget versus actually consumed power. The low voltage DC APEQs deliver up to 2800W each. The high voltage DC APEQs take260-400 V and provide 3000W each. AC APEQs take 200-240 V single phase and deliver 3000W each. APEQs support cost-effective modular expansion as required.Fan traysFan trays provide system cooling for the 7950 XRS. Redundant fans can be controlled independently and fan speed is linearly modulated to allow for the optimal balancing of cooling, power and noise. The 7950 XRS-20 supports two stacked horizontal fan trays with 1+1 redundancy. The XRS-20e chassis variants support three side-by-side impeller fan trays with 2+1 redundancy.Switch Fabric Modules (SFMs)SFMs enable the line-rate connectivity betweenall slots of a 7950 XRS chassis. The fabric cardsare N+1 redundant with active redundancy and graceful capacity degradation in case multiple SFMs fail. There are two types of SFMs. The first is dedicated to standalone system operation of the 7950 XRS-20 and XRS-20e. The second is equipped with optical connectors to support back-to-back configuration in a 7950 XRS-40 system.Control Processor Modules (CPMs)CPMs provide the management, security and control plane processing for the Nokia 7950 XRS. Redundant CPMs operate in a hitless, stateful, failover mode. Central processing and memoryare intentionally separated from the forwarding function on the interface modules to ensure utmost system resiliency. Each CPM contains a full FP3 complex to protect against Denial of Service attacks. XRS Media Adapters (XMAs)XMAs provide the interface options for the7950 XRS, including high-density GE, 10GE, 40GE and 100GE interfaces. They contain an FP3-based forwarding complex that performs typical functions such as packet lookups, traffic classification, processing and forwarding, service enablement and QoS. Each XMA also provides specific interface ports, physical media and optical functions. The range of interface modules and slot capacitywill expand over time, along with overall system capacity, in order to accommodate the evolving needs of network operators while protectingtheir 7950 XRS hardware investments.XRS Control Modules (XCMs)XMAs are equipped in an appropriate XCM. The XCMs contain a slot-level control plane subsystem and fabric interface to interconnect to the switch fabric modules (SFMs) via the chassis mid-plane. XMCs connect via a mid-plane to deliver 800 Gb/s full duplex slot capacity to a pair of 400G XMAs or 200G C-XMAs. The XCM variants for the 7950 XRS-20 and XRS-20e each deliver 800 Gb/s full duplex slot capacity and support the full range of FP3 XMAs and C-XMAs. The flexibility and modularity of XCMs and XMAs allow network operators to granularly configure each Nokia 7950 XRS with its desired range of Ethernet interfaces to meet the demands of growing core networks.Technical specificationsTable 1. Technical specifications for the Nokia 7950 XRS familySystem expansion—32 Tb/s (back-to-back)32 Tb/s (back-to-back) System design Mid-plane Mid-plane Mid-planeInterface slots402020Number of XMAs (400G line card)40 per system20 per system20 per system Number of C-XMAs (200G linecard)40 per system20 per system20 per systemCommon equipment redundancy CPM (1+1), CCM (1+1), DC APEQ(N+1), AC APEC (N+N), SFM (14+2),fan trays (1+1), power termination(1+1)CPM (1+1), CCM (1+1), DC APEQ(N+1), AC APEC (N+N), SFM (7+1),fan trays (1+1), power termination(1+1)CPM (1+1), CCM (1+1), DC APEQ(N+1), AC APEC (N+N), SFM (7+1),fan trays (2+1), power termination(1+1)Hot-swappable modules CPM, CCM, XCM, XMA, C-XMA,APEQ, SFM, fans CPM, CCM, XCM, XMA, C-XMA,APEQ, SFM, fansCPM, CCM, XCM, XMA, C-XMA,APEQ, SFM, fansDimensions 2 x standard 19-in racks39 RU• Height: 173 cm (68.25 in)• Width: 44.5 cm (17.5 in)• Depth: 91 cm (36 in)1 standard 19-in rack39 RU (44 RU with top plenum)• Height: 173 cm (68.25 in)• Width: 44.5 cm (17.5 in)• Depth: 91 cm (36 in)1 standard 19-in rack44 RU (no top plenum)• Height: 195.6 cm (77 in)• Width: 44.5 cm (17.5 in)• Depth: 106.3 cm (41.9 in)Weight* (max)1,070.5 kg (2360 lb)535.2 kg (1180 lb)612.35 (1350 lb)Power• -48 V DC (2 x 12 60A/80A inputs)• 260-400 V DC (2 x 12 inputs)• 200-240 V AC (2 x 12 inputs)• -48 V DC (12 60A/80A inputs)• 260-400 V DC (12 inputs)• 200-240 V AC (12 inputs)• -48 V DC (12 60A/80A inputs)• 260-400 V DC (12 inputs)• 200-240 V AC (12 inputs)Cooling Front/bottom to top/back Front/bottom to top/back Front/bottom to back * Weights and dimensions are approximate and subject to change. Refer to the appropriate installation guide for the current weights and dimensions.Table 2. Nokia 7950 XRS XMA/C-XMA support per chassis type10GBASE (200G C-XMA)20SFP+800400400 10GBASE (400G XMA)40SFP+1600800800 40GBASE (200G C-XMA)6QSFP+240120120 100GBASE (200G C-XMA)2CFP804040 100GBASE (400G XMA)4CXP, CFP21608080 100G DWDM (200G XMA)2LC (OTU4)804040 400G DWDM (400G XMA)1LC (dual carrier)402020Feature and protocol support highlights Protocol support within the 7950 XRS family includes (but is not limited to):• Intermediate System-to-Intermediate System (IS-IS), Open Shortest Path First (OSPF), and Multiprotocol Border Gateway Protocol (MBGP) IPv4 and IPv6 unicast routing• Internet Group Management Protocol (IGMP), Multicast Listener Discovery (MLD), Protocol Independent Multicast (PIM), and Multicast Source Discovery Protocol (MSDP) IPv4 andIPv6 multicast routing• MPLS Label Edge Router (LER) and Label Switching Router (LSR) functions, with support for seamless MPLS designs• Label Distribution Protocol (LDP) and Resource Reservation Protocol (RSVP) for MPLS Signaling and Traffic Engineering with Segment Routing support, Point-to-Point (P2P) and Point-to-Multipoint (P2MP) Label Switched Paths (LSPs) with Multicast LDP (MLDP) and P2MP RSVP, weighted Equal-Cost Multi-path (ECMP),Inter-AS Multicast VPN (MVPN) and Next Generation Multicast VPN (NG-MVPN)• P2P Ethernet virtual leased lines (VLLs), Ethernet VPNs (EVPNs), EVPN-MLDP, EVPN-VPWS, Virtual Extensible LAN (VXLAN), EVPN-VXLAN to VPLS/ EVPN-VPLS gateway functions• Multipoint Ethernet VPLS and IP VPNs for usein delivering core infrastructure services• Ethernet port expansion through remote Nokia 7210 Service Access Switch (SAS) Ethernet satellites, each offering 24/48GE ports over a4 x 10GE Link Aggregation Group (LAG) under 7950 XRS control• Unicast Reverse Path Forwarding (uRPF), RADIUS/TACACS+, and comprehensive control plane protection features for security • Extensive OAM features, including Cflowd, Ethernet Connectivity Fault Management (CFM) (IEEE 802.1ag, ITU-T Y.1731), Ethernet in the First Mile (EFM) (IEEE 802.3ah), Two-Way Active Measurement Protocol (TWAMP), Bi-Directional Fault Detection (BFD), and a full suite of MPLS OAM tools including GMPLS UNI• Intelligent packet classification, queue servicing, policing and buffer management• Industry-leading high availability, including nonstop routing, nonstop services, ISSU,fast reroute, pseudowire redundancy, ITU-T G.8031 and G.8032, weighted mixed-speed link aggregation• Management via CLI, SNMP MIBs, NETCONF/ YANG and service assurance agent (SAA) with comprehensive support through the Nokia 5620 SAM• Multivendor SDN control integration through OpenFlow, PCEP, BGP-LS interface support Environmental specifications• Operating temperature: 5°C to 40°C(41°F to 104°F)• Operating relative humidity: 5% to 85%• Operating altitude: Up to 4000 m (13,123 ft)at 30°C (86°F)Safety standards and compliance agency certifications • IEC/EN/UL/CSA60950-1 Ed2 Am2• FDA CDRH 21-CFR 1040• IEC/EN 60825-1• IEC/EN 60825-2Nokia is a registered trademark of Nokia Corporation. Other product and company names mentioned herein may be trademarks or trade names of their respective owners. Nokia Oyj Karaportti 3 FI-02610 Espoo FinlandTel. +358 (0) 10 44 88 000Product code: SR1702007527EN (March)EMC emission• ICES-003 Class A• FCC Part 15 Class A(with EMI/Protection panel)• EN 55032 Class A • CISPR 32 Class A • AS/NZS CISPR 32 Class A • VCCI Class A • KN 32 Class A • EN 61000-3-2• EN 61000-3-3EMC immunity• ETSI EN 300 386• EN 55024• KN 35Environmental• ETSI EN 300 019-2-1 Storage Tests, Class 1.2• ETSI EN 300 019-2-2 Transportation Tests, Class 2.3• ETSI EN 300 019-2-3 Operational Tests, Class 3.2• ETSI EN 300 019-2-4, pr A 1 Seismic• ETSI EN 300 132-2 DC Power Supply Interface • ETSI EN 300 132-3-1 HVDC Power Supply Interface • WEEE • RoHS • China CRoHSNetwork Equipment Building System (NEBS)• NEBS Level 3• RBOC requirements –ATIS-0600020 –ATIS-0600010.3 –ATIS-0600015 –ATIS-0600015.03 –ATT-TP-76200 –VZ.TPR.9205 TEEER –VZ.TPR.9305MEF certifications• CE 2.0–Certified (on E-LAN, E-Line, E-Tree and E-Access MEF service types) –100G Certified (on E-Line and E-Access MEF service types)• CE 1.0 (MEF 9 and MEF 14) –Certified。
FPGA的英文文献及翻译
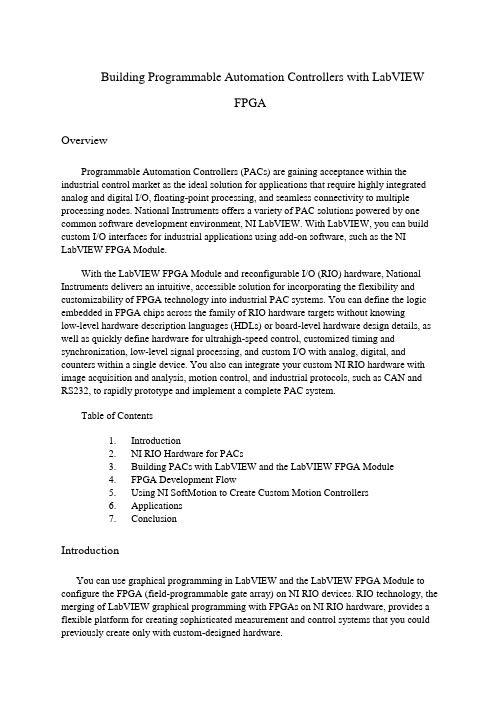
Building Programmable Automation Controllers with LabVIEWFPGAOverviewProgrammable Automation Controllers (PACs) are gaining acceptance within the industrial control market as the ideal solution for applications that require highly integrated analog and digital I/O, floating-point processing, and seamless connectivity to multiple processing nodes. National Instruments offers a variety of PAC solutions powered by one common software development environment, NI LabVIEW. With LabVIEW, you can build custom I/O interfaces for industrial applications using add-on software, such as the NI LabVIEW FPGA Module.With the LabVIEW FPGA Module and reconfigurable I/O (RIO) hardware, National Instruments delivers an intuitive, accessible solution for incorporating the flexibility and customizability of FPGA technology into industrial PAC systems. You can define the logic embedded in FPGA chips across the family of RIO hardware targets without knowinglow-level hardware description languages (HDLs) or board-level hardware design details, as well as quickly define hardware for ultrahigh-speed control, customized timing and synchronization, low-level signal processing, and custom I/O with analog, digital, and counters within a single device. You also can integrate your custom NI RIO hardware with image acquisition and analysis, motion control, and industrial protocols, such as CAN and RS232, to rapidly prototype and implement a complete PAC system.Table of Contents1.Introduction2.NI RIO Hardware for PACs3.Building PACs with LabVIEW and the LabVIEW FPGA Module4.FPGA Development Flowing NI SoftMotion to Create Custom Motion Controllers6.Applications7.ConclusionIntroductionYou can use graphical programming in LabVIEW and the LabVIEW FPGA Module to configure the FPGA (field-programmable gate array) on NI RIO devices. RIO technology, the merging of LabVIEW graphical programming with FPGAs on NI RIO hardware, provides a flexible platform for creating sophisticated measurement and control systems that you could previously create only with custom-designed hardware.An FPGA is a chip that consists of many unconfigured logic gates. Unlike the fixed, vendor-defined functionality of an ASIC (application-specific integrated circuit) chip, you can configure and reconfigure the logic on FPGAs for your specific application. FPGAs are used in applications where either the cost of developing and fabricating an ASIC is prohibitive, or the hardware must be reconfigured after being placed into service. The flexible,software-programmable architecture of FPGAs offer benefits such as high-performance execution of custom algorithms, precise timing and synchronization, rapid decision making, and simultaneous execution of parallel tasks. Today, FPGAs appear in such devices as instruments, consumer electronics, automobiles, aircraft, copy machines, andapplication-specific computer hardware. While FPGAs are often used in industrial control products, FPGA functionality has not previously been made accessible to industrial control engineers. Defining FPGAs has historically required expertise using HDL programming or complex design tools used more by hardware design engineers than by control engineers.With the LabVIEW FPGA Module and NI RIO hardware, you now can use LabVIEW, a high-level graphical development environment designed specifically for measurement and control applications, to create PACs that have the customization, flexibility, andhigh-performance of FPGAs. Because the LabVIEW FPGA Module configures custom circuitry in hardware, your system can process and generate synchronized analog and digital signals rapidly and deterministically. Figure 1 illustrates many of the NI RIO devices that you can configure using the LabVIEW FPGA Module.Figure 1. LabVIEW FPGA VI Block Diagram and RIO Hardware PlatformsNI RIO Hardware for PACsHistorically, programming FPGAs has been limited to engineers who have in-depth knowledge of VHDL or other low-level design tools, which require overcoming a very steep learning curve. With the LabVIEW FPGA Module, NI has opened FPGA technology to a broader set of engineers who can now define FPGA logic using LabVIEW graphical development. Measurement and control engineers can focus primarily on their test and control application, where their expertise lies, rather than the low-level semantics of transferring logic into the cells of the chip. The LabVIEW FPGA Module model works because of the tightintegration between the LabVIEW FPGA Module and the commercial off-the-shelf (COTS) hardware architecture of the FPGA and surrounding I/O components.National Instruments PACs provide modular, off-the-shelf platforms for your industrial control applications. With the implementation of RIO technology on PCI, PXI, and Compact Vision System platforms and the introduction of RIO-based CompactRIO, engineers now have the benefits of a COTS platform with the high-performance, flexibility, and customization benefits of FPGAs at their disposal to build PACs. National Instruments PCI and PXI R Series plug-in devices provide analog and digital data acquisition and control for high-performance, user-configurable timing and synchronization, as well as onboard decision making on a single device. Using these off-the-shelf devices, you can extend your NI PXI or PCI industrial control system to include high-speed discrete and analog control, custom sensor interfaces, and precise timing and control.NI CompactRIO, a platform centered on RIO technology, provides a small, industrially rugged, modular PAC platform that gives you high-performance I/O and unprecedented flexibility in system timing. You can use NI CompactRIO to build an embedded system for applications such as in-vehicle data acquisition, mobile NVH testing, and embedded machine control systems. The rugged NI CompactRIO system is industrially rated and certified, and it is designed for greater than 50 g of shock at a temperature range of -40 to 70 °C.NI Compact Vision System is a rugged machine vision package that withstands the harsh environments common in robotics, automated test, and industrial inspection systems. NICVS-145x devices offer unprecedented I/O capabilities and network connectivity for distributed machine vision applications.NI CVS-145x systems use IEEE 1394 (FireWire) technology, compatible with more than 40 cameras with a wide range of functionality, performance, and price. NI CVS-1455 and NI CVS-1456 devices contain configurable FPGAs so you can implement custom counters, timing, or motor control in your machine vision application.Building PACs with LabVIEW and the LabVIEW FPGA Module With LabVIEW and the LabVIEW FPGA Module, you add significant flexibility and customization to your industrial control hardware. Because many PACs are already programmed using LabVIEW, programming FPGAs with LabVIEW is easy because it uses the same LabVIEW development environment. When you target the FPGA on an NI RIO device, LabVIEW displays only the functions that can be implemented in the FPGA, further easing the use of LabVIEW to program FPGAs. The LabVIEW FPGA Module Functions palette includes typical LabVIEW structures and functions, such as While Loops, For Loops, Case Structures, and Sequence Structures as well as a dedicated set of LabVIEWFPGA-specific functions for math, signal generation and analysis, linear and nonlinear control, comparison logic, array and cluster manipulation, occurrences, analog and digital I/O, and timing. You can use a combination of these functions to define logic and embed intelligence onto your NI RIO device.Figure 2 shows an FPGA application that implements a PID control algorithm on the NI RIO hardware and a host application on a Windows machine or an RT target that communicates with the NI RIO hardware. This application reads from analog input 0 (AI0), performs the PID calculation, and outputs the resulting data on analog output 0 (AO0). While the FPGA clock runs at 40 MHz the loop in this example runs much slower because each component takes longer than one-clock cycle to execute. Analog control loops can run on an FPGA at a rate of about 200 kHz. You can specify the clock rate at compile time. This example shows only one PID loop; however, creating additional functionality on the NI RIO device is merely a matter of adding another While Loop. Unlike traditional PC processors, FPGAs are parallel processors. Adding additional loops to your application does not affect the performance of your PID loop.Figure 2. PID Control Using an Embedded LabVIEW FPGA VI with Corresponding LabVIEW HostVI.FPGA Development FlowAfter you create the LabVIEW FPGA VI, you compile the code to run on the NI RIO hardware. Depending on the complexity of your code and the specifications of your development system, compile time for an FPGA VI can range from minutes to several hours.To maximize development productivity, with the R Series RIO devices you can use abit-accurate emulation mode so you can verify the logic of your design before initiating the compile process. When you target the FPGA Device Emulator, LabVIEW accesses I/O from the device and executes the VI logic on the Windows development computer. In this mode, you can use the same debugging tools available in LabVIEW for Windows, such as execution highlighting, probes, and breakpoints.Once the LabVIEW FPGA code is compiled, you create a LabVIEW host VI to integrate your NI RIO hardware into the rest of your PAC system. Figure 3 illustrates the development process for creating an FPGA application. The host VI uses controls and indicators on the FPGA VI front panel to transfer data between the FPGA on the RIO device and the host processing engine. These front panel objects are represented as data registers within the FPGA. The host computer can be either a PC or PXI controller running Windows or a PC, PXI controller, Compact Vision System, or CompactRIO controller running a real-time operating system (RTOS). In the above example, we exchange the set point, PID gains, loop rate, AI0, and AO0 data with the LabVIEW host VI.Figure 3. LabVIEW FPGA Development FlowThe NI RIO device driver includes a set of functions to develop a communication interface to the FPGA. The first step in building a host VI is to open a reference to the FPGA VI and RIO device. The Open FPGA VI Reference function, as seen in Figure 2, also downloads and runs the compiled FPGA code during execution. After opening the reference, you read and write to the control and indicator registers on the FPGA using the Read/Write Control function. Once you wire the FPGA reference into this function, you can simply select which controls and indicators you want to read and write to. You can enclose the FPGA Read/Write function within a While Loop to continuously read and write to the FPGA. Finally, the last function within the LabVIEW host VI in Figure 2 is the Close FPGA VI Reference function. The Close FPGA VI Reference function stops the FPGA VI and closes the reference to the device. Now you can download other compiled FPGA VIs to the device to change or modify its functionality.The LabVIEW host VI can also be used to perform floating-point calculations, data logging, networking, and any calculations that do not fit within the FPGA fabric. For added determinism and reliability, you can run your host application on an RTOS with the LabVIEW Real-Time Module. LabVIEW Real-Time systems provide deterministicprocessing engines for functions performed synchronously or asynchronously to the FPGA. For example, floating-point arithmetic, including FFTs, PID calculations, and custom control algorithms, are often performed in the LabVIEW Real-Time environment. Relevant data can be stored on a LabVIEW Real-Time system or transferred to a Windows host computer for off-line analysis, data logging, or user interface displays. The architecture for this configuration is shown in Figure 4. Each NI PAC platform that offers RIO hardware can run LabVIEW Real-Time VIs.Figure 4. Complete PAC Architecture Using LabVIEW FPGA, LabVIEW Real-Time and Host PC Within each R Series and CompactRIO device, there is flash memory available to store a compiled LabVIEW FPGA VI and run the application immediately upon power up of the device. In this configuration, as long as the FPGA has power, it runs the FPGA VI, even if the host computer crashes or is powered down. This is ideal for programming safety power down and power up sequences when unexpected events occur.Using NI SoftMotion to Create Custom Motion ControllersThe NI SoftMotion Development Module for LabVIEW provides VIs and functions to help you build custom motion controllers as part of NI PAC hardware platforms that can include NI RIO devices, DAQ devices, and Compact FieldPoint. NI SoftMotion provides all of the functions that typically reside on a motion controller DSP. With it, you can handle path planning, trajectory generation, and position and velocity loop control in the NI LabVIEW environment and then deploy the code on LabVIEW Real-Time or LabVIEW FPGA-based target hardware.NI SoftMotion includes functions for trajectory generator and spline engine and examples with complete source code for supervisory control, position, and velocity control loop using the PID algorithm. Supervisory control and the trajectory generator run on a LabVIEW Real-Time target and run at millisecond loop rates. The spline engine and the control loop can run either on a LabVIEW Real-Time target at millisecond loop rates or on a LabVIEW FPGA target at microsecond loop rates.ApplicationsBecause the LabVIEW FPGA Module can configure low-level hardware design of FPGAs and use the FPGAs within in a modular system, it is ideal for industrial controlapplications requiring custom hardware. These custom applications can include a custom mix of analog, digital, and counter/timer I/O, analog control up to 125 kHz, digital control up to 20 MHz, and interfacing to custom digital protocols for the following:•Batch control•Discrete control•Motion control•In-vehicle data acquisition•Machine condition monitoring•Rapid control prototyping (RCP)•Industrial control and acquisition•Distributed data acquisition and control•Mobile/portable noise, vibration, and harshness (NVH) analysis ConclusionThe LabVIEW FPGA Module brings the flexibility, performance, and customization of FPGAs to PAC platforms. Using NI RIO devices and LabVIEW graphical programming, you can build flexible and custom hardware using the COTS hardware often required in industrial control applications. Because you are using LabVIEW, a programming language already used in many industrial control applications, to define your NI RIO hardware, there is no need to learn VHDL or other low-level hardware design tools to create custom hardware. Using the LabVIEW FPGA Module and NI RIO hardware as part of your NI PAC adds significant flexibility and functionality for applications requiring ultrahigh-speed control, interfaces to custom digital protocols, or a custom I/O mix of analog, digital, and counters.使用LabVIEW FPGA〔现场可编程门阵列〕模块开发可编程自动化控制器综述工业控制上的应用要求高度集成的模拟和数字输入输出、浮点运算和多重处理节点的无缝连接。
sv modport用法 -回复
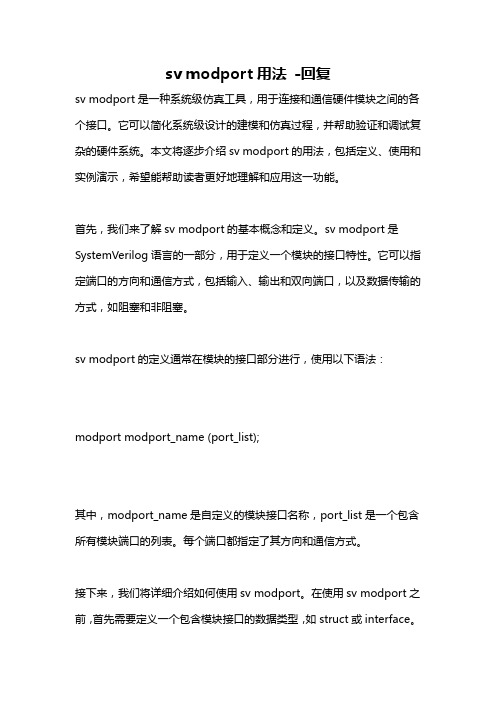
sv modport用法-回复sv modport是一种系统级仿真工具,用于连接和通信硬件模块之间的各个接口。
它可以简化系统级设计的建模和仿真过程,并帮助验证和调试复杂的硬件系统。
本文将逐步介绍sv modport的用法,包括定义、使用和实例演示,希望能帮助读者更好地理解和应用这一功能。
首先,我们来了解sv modport的基本概念和定义。
sv modport是SystemVerilog语言的一部分,用于定义一个模块的接口特性。
它可以指定端口的方向和通信方式,包括输入、输出和双向端口,以及数据传输的方式,如阻塞和非阻塞。
sv modport的定义通常在模块的接口部分进行,使用以下语法:modport modport_name (port_list);其中,modport_name是自定义的模块接口名称,port_list是一个包含所有模块端口的列表。
每个端口都指定了其方向和通信方式。
接下来,我们将详细介绍如何使用sv modport。
在使用sv modport之前,首先需要定义一个包含模块接口的数据类型,如struct或interface。
然后,在模块的接口声明中使用modport来定义具体的接口特性。
例如,假设我们有一个顶层模块top_module,它包含两个子模块child_module1和child_module2。
我们可以定义一个包含所有端口的接口数据类型interface_type,并在每个子模块的接口声明中使用sv modport来指定模块端口的特性。
typedef struct {logic [7:0] data;logic enable;} interface_type;module child_module1 (input sv_interface_type::modport_name1 port);...endmodulemodule child_module2 (input sv_interface_type::modport_name2 port);...endmodulemodule top_module;sv_interface_type port1, port2;child_module1 u1 (port1.modport_name1);child_module2 u2 (port2.modport_name2);...endmodule在上面的例子中,我们首先定义了一个接口数据类型interface_type,其中包含了两个信号data和enable。
PR Electrical 电子产品 - 基本原理 - 通用旋转操作器 238说明书
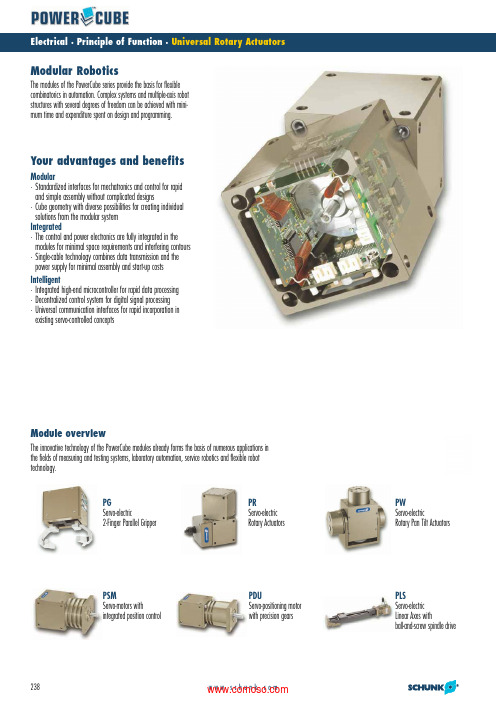
PRElectrical · Principle of Function ·Universal Rotary ActuatorsModular RoboticsModular·Standardized interfaces for mechatronics and control for rapid and simple assembly without complicated designs·Cube geometry with diverse possibilities for creating individual solutions from the modular system Integrated·The control and power electronics are fully integrated in the modules for minimal space requirements and interfering contours ·Single-cable technology combines data transmission and the power supply for minimal assembly and start-up costs Intelligent·Integrated high-end microcontroller for rapid data processing ·Decentralized control system for digital signal processing ·Universal communication interfaces for rapid incorporation in e xisting servo-controlled conceptsYour advantages and benefitsThe modules of the PowerCube series provide the basis for flexible c ombinatorics in automation. Complex systems and multiple-axis robot structures with several degrees of freedom can be achieved with mini-mum time and expenditure spent on design and programming.Module overviewThe innovative technology of the PowerCube modules already forms the basis of numerous applications in the fields of measuring and testing systems, laboratory automation, service robotics and flexible robot t echnology.PGServo-electric2-Finger Parallel Gripper PRServo-electric Rotary Actuators PWServo-electricRotary Pan Tilt ActuatorsPSMServo-motors with integrated position control PDUServo-positioning motor with precision gearsPLSServo-electric Linear Axes withball-and-screw spindle drivePRUniversal Rotary ActuatorsMethod of actuationThe PowerCube modules work completely independently. The master control system is only required for generating the sequential program and sending it step by step to the connected modules. Therefore, only the current sequential command is ever stored in the modules, and the subsequent command is stored in the buffer. The current, rotational speed and positioning are controlled in the module itself. Likewise, functions such as t emperature and limit monitoring are performed in the module itself. Real-time capability is not absolutely essential for the master control or bus system.Control version AB C Hardware Control with SPC (S7)Control with PC Control with PC Interface Profibus DPCAN bus / RS-232CANopenSoftwareWindows operating system LINUX operating system Development platformsPowerCube (LabView, Diadem)standard software PowerCube on request on request on request (gsd file, programming examples)standard software (e.g. Eckelmann CNC 55)Included with the “PowerCube Standard Software“ CD-ROM (ID 0307700): Assembly and operating manual with manufacturer’s declaration, quick-step software, demo and d iagnosticprogram plus various driver files.1234567889ᕃ24 VDC / 48 VDC power supply provided by the customerᕄControl system provided by the customer (see control versions A, B and C)ᕅPAE 130 TB terminal block for connecting the voltage supply, the communication and the hybrid cable ᕆPDU servo-motorᕇLinear axis with PLS ball-and-screw spindle drive and PSM servo-motorᕈHybrid cable (single-cable technology) for connecting the PowerCube modules (voltage supply and communication)ᕉPW Servo-electric Rotary Pan Tilt Actuator ᕊPG Servo-electric 2-Finger Parallel Gripper ᕋPR Servo-electric Rotary ActuatorPRL· Universal Rotary ActuatorsSizes 60 .. 120Weight1.0 kg .. 3.6 kg Torque4.5 Nm .. 216 Nm Axial force 120 N .. 800 N Bending moment 20 Nm .. 320 NmApplication exampleMobile platform with autonomous loading and unloading possibility for workpiece transportation3-Finger Electric Gripping HandLWA 3 Light-weight Arm consists of 7 PRL modulesPRLElectrical · Rotary Actuators ·Universal Rotary ActuatorsHollow shaft for media feed-throughfor minimizing interfering contours and break of cable High torques at smallest space requirements for short cyclesAbsolute position encoder without additional set-up Magnetic brakefor save hold in case of power outageFully integrated control and power electronics for creating a decentralized control systemVersatile actuation optionsfor simple integration in existing servo-controlled concepts via P rofibus DP, CAN bus or RS-232Standard connecting elements and uniform control conceptfor extensive combinatorics with other PowerCube modules (see explanation of the PowerCube system)Single-cable technology for data transmission and power supply (plug & play)for low assembly and start-up costsServo-electric rotary actuator with > 360° rotating angleUniversal Rotary ActuatorArea of applicationFor universal use in clean to slightly dirty environments as handling or positioning system components; for workpiece or sensor p ositioning in measuring and testing applications; as extension axes and axes for industrial and service robots and in machining centers.Your advantages and benefitsGeneral information on the seriesWorking principlewith Harmonic Drive ®gear driven by a brushless DC servo-motor Housing materialAluminum alloy, hard-anodizedActuationservo-electric, with brushless servo-motor and incremental encoder for position and speed control Warranty 24 monthsScope of delivery“PowerCube Standard Software“ CD-ROM, containing assembly and operating m anual with manufacturer’s declaration, quick-step software, demo and diagnostic program and various driver files (see explanation of PowerCube system).Other information · 2 digital EIA 24 VDCPRL· Universal Rotary ActuatorsComplete performance and control electronicsIntegrated brake Brushless servo-motor Harmonic Drive ®gearThe rotary actuator is equipped with a Harmonic Drive ®precision gear, which is d riven directly by a brushless DC servo-motor.Function descriptionThe PRL rotary actuator is electrically actuated by the fully integrated control andpower electronics. In this way, the module does not require any additional external control units.A varied range of interfaces, such as Profibus DP, CAN-Bus or RS-232 are available as methods of communication. This enables you to create industrial bus networks, and ensures easy integration in control systems. You can make use of our hybrid cables for conveying the supply voltage and for communication.If you wish to create combined systems (e.g. a rotary gripping module), various other modules from our PowerCube series are at your disposal.Electrical actuationSectional diagramPRLUniversal Rotary ActuatorsRepeat accuracyRepeat accuracy is defined as the spread of the limit position after 100 consecutive swiveling cycles.Position of driveThe position of the motor shaft is always shown in the drawing in the zero position (0°). From here, it can be rotated clockwise and anti-clockwise.The turning range may exceed 360° several times, depending on the type of application. After switch on the module reports its position as an absolute value (last position before switch off).Swiveling timeSwiveling times are purely the times of the output cube to rotate from rest position to rest position. Relay switching times or SPC reaction times are not included in the above times and must be taken into consideration when determining cycle times.Load-dependent rest periods may have to be included in the cycle time.General information on the seriesElectrical accessories PAE terminal blockPAM standardc onnecting elementsAccessoriesHybrid cableFor the exact size of the required accessories, availability of this size and the designation and ID, please refer to the additional views at the end of the size in question. You will find more detailed information on our accessory range in the …Accessories“ catalog section.PRL 80· Universal Rotary ActuatorsThe peak torques act as a temporary drive reserve on acceleration and braking. *Higher accuracy on requestTechnical data Moment loadMoments and forces may occur simultaneously.Description PRL 80-552ID0306915 Mechanical operating dataNominal torque[Nm]20.7 Peak torque[Nm]41.4 Rotating angle (>)[°]360.0 IP class65 Weight[kg] 1.2 Swiveling time (90°) with mean attached load[s] 4.25 Min. ambient temperature[°C] 5.0 Max. ambient temperature[°C]55.0 Repeat accuracy*[°]0.02 Max. angular velocity[°/s]25.0 Max. acceleration[°/s2]100.0 Gear ratio552:1 Electrical operating dataNominal voltage[VDC]24.0 Nominal power current[A] 3.0 Max. current[A] 6.0 Resolution[arcsec] 1.0 Control electronicsIntegrated electronics Yes Voltage supply[VDC]24.0 Nominal power current[A]0.5 Sensor systemInterfaces RS-232; Profibus-DP; CAN-Bus-PRL 80Universal Rotary Actuatorsᕃ24 VDC voltage supply provided by customer ᕄControl (SPC, etc.) provided by customerᕅPAE 130 TB terminal block for connecting the voltage supply, the communication and thehybrid cableᕆHybrid cable for connecting the PowerCube modulesMain viewsThe drawing shows the rotary actuator with damp-proof cap in the basic version with closed jaws, the dimensions do not include the options described below.1234ᕎᕞThrough-boreᕑᕠElectronics connectionActuationDescriptionID Terminal block PAE 130 TB 0307725PowerCube Communication cable0307759PowerCube Hybrid cable, straight (per meter)9941120You can find further cables in the “Accessories“ catalog section.Interconnecting cable。
15. Interfaces_Module_V1.0

In both cases, the project runs the risk of future interface incompatibility, since the subsystems mature their concepts (and their interfaces) independently. The solution is to explicitly identify the owner of every interface.
So, optimal system decomposition considers both the implications for subsystem requirements and the implications for subsystem interfaces.
Space Systems Engineering: Interfaces Module
Space Systems Engineering: Interfaces Module 6
GLAST — Gamma-ray Large Area Space Telescope Launched 6/11/08
Interface Design Heuristics
In system decomposition, choose subsystems so that they are as independent as possible; that is, they have simple interfaces. As a result these subsystems will be easier to develop and test independently and when they are integrated there will be fewer problems with compatibility. Group like functions within a subsystem. This reduces the exchange of common data and focuses development expertise. Consider the use of standard interfaces, e.g., mechanical, electrical and data (e.g., data exchange standards from the Consultative Committee for Space Data Systems).
IND570工业称量终端说明书
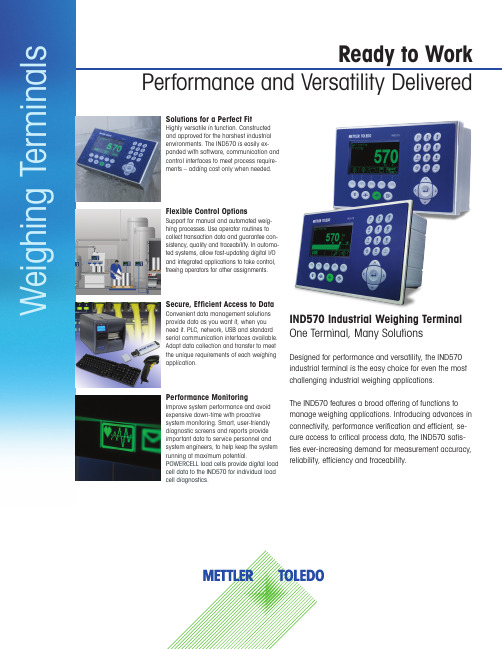
W e i g h i n g T e r m i n a l sW e i g h i n g T e r m i n a l s Technical Specifications Physical and ElectricalEnclosures Harsh environment model : 304 Stainless steel, IP69K certified. Includes fixed-angle brackets forwall mounting. Panel mount model : Stainless steel front panel, aluminum chassis and integratedmounting hardware. Certified IP65 protectionWeight 3.2 kg (7 lbs)Operating environment -10°C to +40°C (14°F to 104°F), 10% to 95% relative humidity, non-condensingInput power AC: 100-240 VAC, 50-60 Hz, 500 mA (harsh and panel enclosure types)DC: 24 VDC, 1.25A (panel-mounted enclosure only; not available for POWERCELL version)Scale Interface Supported scale types Analog : Up to 12 350 Ω load cells, 2 or 3 mV/V cells. 10 VDC excitation. A/D update rate >366 Hz SICSpro : High-Precision digital platforms and junction boxes that support Advanced Setup Mode (ASM ), including Bluetooth-based ACW520 Cable-Free Floor Scale. 90 Hz update rate.IDNet : High-Precision K-Line, +12V versions only, including T-Brick cell, M-Cell and Point-ADCPOWERCELL : Supports one PowerDeck floor scale or a network of up to 14 POWERCELL PDX loadcells, or PowerMount platformsUnits kg, lb, tons, metric tons, g, dwt, lb-oz, oz, ozt, custom unitCapacity & increments Analog and POWERCELL: 2,000,000 maximum capacity; maximum 100,000 display incrementsIDNet and SICSpro: Determined by platform Human-Machine InterfaceDisplayHigh contrast, high resolution display with clear weight indication and low power consumption Status indicatorsGross, Net, active Range/Interval, Units, Motion, Center of Zero, MinWeigh, Service Icon Metrology lineDisplays capacity, increments and approval class System lineDisplays weighing system messages and application information Auxiliary displaySelect from SmartTrac™ (graphic display of weighing status), rate (weight/time) or discrete I/O status Keypad Tactile keypad for enhanced operator experience. Clear, Tare, Print, Zero keys. Navigation keyset.Alphanumeric keypad. 5 softkeys, programmable with up to 15 unique functions to customizeoperator interaction with a weighing application ConnectivityUSB Host USB Host (standard): Type A connection, +5V at 500mA for connected devices. Supports externalkeyboards, barcode scanners and USB memory devicesSerial Standard: COM1 (isolated in POWERCELL versions) suports RS-232/422/485.COM4, isolated (standard in POWERCELL versions only)Optional: COM2 (RS232) and COM3 (RS-232/522/485)Network Optional Ethernet interface supports speeds of 10 Mb/s and 100 Mb/s using 10 Base-T, 100Base-TX, 100 Base-FX, and 100 Base-T4. Fully compliant with IEEE standard 802.3 and 802.3x.Full duplex flow control supported. Supports 3 simultaneous socket connections.Protocols MT Continuous Output, MT Continuous Extended, CTPZ input, Demand Print, Continuous Templateoutput, ARM100 Remote I/O, Shared Data Server access, SICS, ASCII inputFieldbus Supports any one of the following options: EtherNet/IP, Analog Output (4-20 mA or 0-10 VDC),PROFIBUS ® DP, PROFINET ®, ControlNet™, DeviceNet™, Modbus TCPDiscrete I/O Either 2 inputs and 5 outputs or 5 inputs and 8 outputs available internallyARM100 Remote I/O modules expand total I/O support to 13 inputs and 20 outputsInterface update rates PLC cyclic data: 25 Hz. Int. Discrete I/O: 50 Hz. Ext. Discrete I/O (ARM100): 25 Hz2METTLER TOLEDO IND570Performance Diagnostics Error and Maintenance Logs record system events. Service icon () displays to indicate an event requiring user/serviceattention. Terminal Status Report provides real-time system performance data, including POWERCELL load cell dataEmail Integrated email function can deliver system notifications to designated recipients. Proxy server login supportedTest Manager GWP ®Supports routine testing of weighing system for performance verification and compliance. Test procedures are stored in theterminal and users prompted when testing is required. GWP Log and reports support compliance efforts.Web ServerBuilt-in web server provides tools for examining terminal and POWERCELL operation over a network using just a webbrowser Optional Application PACsCOM-570Retains advanced features and functions of the IND570 while communicating with existing systems via legacy METTLERTOLEDO product protocols, including 8142 Host, 8530 Host, PT6S3 and SMA. Input Command Template allows the IND570to recognize and respond to customer-specific commandsDrive-570Supports Inbound/Outbound vehicle weighing. Refer to Drive-570 data brief for detailsDyn-570Specialized solutions for in-motion package weighing and multi-zone checkweighing. Refer to DYN-570 data brief for detailsFill-570Advanced control of automatic filling, dosing and blending of up to six materials. Refer to Fill-570 data brief for detailsTaskExpert™TaskExpert gives qualified programmers the ability to adapt the standard capabilities of the IND570 to more closely alignwith a user’s specific application requirements Integrated ApplicationsGeneralSimple, manual weighing, vehicle, silo and hopper weighing, transaction counter, accumulation/totalization, automatic tare/print/clear, auto-zero maintenance, x10 weight display Material TransferStandard software supports single material filling or dosing with integrated I/O control CheckweighingStatic checkweighing with intuitive graphical display and integrated I/O support Remote DisplayFunctions as a remote display (via a serial or ethernet connection) for another METTLER TOLEDO terminal. Simple function control (clear, tare, zero, print) provided through the HMI Data tablesTarget Table stores values for up to 200 material IDs. Tare Table stores up to 99 tare weights Alibi MemoryStores individual transaction data. Export as .csv file for further use Printing10 customizable templates. Manual and automatic print triggers. Standard data and service reports available. Print via serial and Ethernet ports. Direct print to connected USB memory device. Direct print to USB printer is not supported ID PromptingStore up to four 30-step custom routines to guide users through an operating sequence. Use to assure consistency and col-lection of transaction data. Add external keyboard or barcode scanner to facilitate data entryUSB File Transfer 3IND570 METTLER TOLEDOApprovals/IND570 For more information Mettler-Toledo, LLC1900 Polaris ParkwayColumbus, OH 43240Subject to technical changes© 04/2021 Mettler-Toledo, LLC30237957 EN.LTRTerminal DimensionsEnclosure for Harsh Environments Panel-Mounted EnclosureBrackets and Accessories Wall Mounting Brackets[Included with harsh terminal]Positionable Bracket[22020286]USB Extension Kit [30139559]Ethernet Extension Kit[30139561]WiFi Kit,Terminal mounted[30499148]WiFi Kit, Remotely mounted [30499149]。
fortigate-fortiwifi-40f-series-快速入门指南说明书

F ortiGate FortiWiFi 40F SeriesFG-40F, FG-40F-3G4G, FWF-40F, FWF-40F-3G4GConverged Next-Generation Firewall (NGFW) and SD-WAN The FortiGate Next-Generation Firewall 40F series is ideal for building security-driven networks at distributed enterprise sites and transforming WAN architecture at any scale.With a rich set of AI/ML-based FortiGuard security services and our integrated Security Fabric platform, the FortiGate FortiWiFi 40F series delivers coordinated, automated, end-to-end threat protection across all use cases.FortiGate has the industry’s first integrated SD-WAN and zero-trust network access (ZTNA) enforcement within an NGFW solution and is powered by one OS. FortiGate 40F automatically controls, verifies, and facilitates user access to applications, delivering consistency with a seamless and optimized user experience.HighlightsGartner Magic QuadrantLeader for both Network Firewalls and SD-WAN.Security-DrivenNetworking with FortiOS delivers convergednetworking and security.Unparalleled Performance with Fortinet’s patented SoC processors.Enterprise Security with consolidated AI / ML-powered FortiGuard Services.Simplified Operations with centralized management fornetworking and security, automation, deep analytics, and self-healing.IPS NGFW Threat Protection Interfaces1 Gbps800 Mbps600 MbpsMultiple GE RJ45 | WiFi variantsData SheetFortiOS EverywhereFortiOS, Fortinet’s Advanced Operating SystemFortiOS enables the convergence of high performing networking and security across the Fortinet Security Fabric. Because it can be deployed anywhere, it delivers consistent and context-aware security posture across network, endpoint, and multi-cloud environments.FortiOS powers all FortiGate deployments whether a physical or virtual device, as acontainer, or as a cloud service. This universal deployment model enables the consolidation of many technologies and use cases into organically built best-of-breed capabilities, unified operating system, and ultra-scalability. The solution allows organizations to protect all edges, simplify operations, and run their business without compromising performance or protection.FortiOS dramatically expands the Fortinet Security Fabric’s ability to deliver advanced AI/ML-powered services, inline advanced sandbox detection, integrated ZTNA enforcement, and more. It provides protection across hybrid deployment models for hardware, software, and Software-as-a-Service with SASE.FortiOS expands visibility and control, ensures the consistent deployment and enforcement of a simplified, single policy and management framework. Its security policies enable centralized management across large-scale networks with the following key attributes: •Interactive drill-down and topology viewers that display real-time status•On-click remediation that provides accurate and quick protection against threats and abuses •Unique threat score system correlates weighted threats with users to prioritize investigationsFortiConverter ServiceFortiConverter Service provides hassle-free migration to help organizations transition from a wide range of legacy firewalls to FortiGate Next-Generation Firewalls quickly and easily. The service eliminates errors and redundancy by employing best practices with advanced methodologies and automated processes. Organizations can accelerate their network protection with the latest FortiOS technology.Intuitive easy to use view into the network andendpoint vulnerabilitiesVisibility with FOS Application SignaturesAvailable inCloudHostedVirtualApplianceContainerFortiGuard ServicesFortiGuard AI-Powered SecurityFortiGuard’s rich suite of security services counter threats in real time using AI-powered, coordinated protection designed by FortiGuard Labs security threat researchers, engineers, and forensic specialists.Web SecurityAdvanced cloud-delivered URL, DNS (Domain Name System), and Video Filtering providing complete protection for phishing and other web born attacks while meeting compliance. Additionally, its dynamic inline CASB (Cloud Access Security Broker) service is focused on securing business SaaS data, while inline ZTNA traffic inspection and ZTNA posture check provide per-sessions access control to applications. It also integrates with the FortiClient Fabric Agent to extend protection to remote and mobile users.Content SecurityAdvanced content security technologies enable the detection and prevention of knownand unknown threats and file-based attack tactics in real-time. With capabilities like CPRL (Compact Pattern Recognition Language), AV, inline Sandbox, and lateral movement protection make it a complete solution to address ransomware, malware, and credential-based attacks.Device SecurityAdvanced security technologies are optimized to monitor and protect IT, IIoT, and OT (Operational Technology) devices against vulnerability and device-based attack tactics. Its validated near-real-time IPS intelligence detects, and blocks known and zero-day threats, provides deep visibility and control into ICS/OT/SCADA protocols, and provides automated discovery, segmentation, and pattern identification-based policies.Advanced Tools for SOC/NOCAdvanced NOC and SOC management tools attached to your NGFW provide simplified and faster time-to-activation.SOC-as-a-ServiceIncludes tier-one hunting and automation, log location, 24x7 SOC analyst experts, managed firewall and endpoint functions, and alert triage.Fabric Rating Security Best PracticesIncludes supply chain virtual patching, up-to-date risk and vulnerability data to deliver quicker business decisions, and remediation for data breach situations.Secure Any Edge at Any ScalePowered by Security Processing Unit (SPU)Traditional firewalls cannot protect against today’s content- and connection-based threats because they rely on off-the-shelf hardware and general-purpose CPUs, causing a dangerous performance gap. Fortinet’s custom SPU processors deliver the power you need—up to520Gbps—to detect emerging threats and block malicious content while ensuring your network security solution does not become a performance bottleneck.ASIC AdvantageSecure SD-WAN ASIC SOC4•Combines a RISC-based CPU with Fortinet’s proprietary Security Processing Unit (SPU) content and network processors for unmatched performance•Delivers industry’s fastest application identification and steering for efficient business operations•Accelerates IPsec VPN performance for best user experience on direct internet access •Enables best of breed NGFW Security and Deep SSL Inspection with high performance •Extends security to access layer to enable SD-Branch transformation with accelerated and integrated switch and access point connectivityFortiCare ServicesFortinet is dedicated to helping our customers succeed, and every year FortiCare Services help thousands of organizations get the most from our Fortinet Security Fabric solution. Our lifecycle portfolio offers Design, Deploy, Operate, Optimize, and Evolve services. Operate services offer device-level FortiCare Elite service with enhanced SLAs to meet our customer’s operational and availability needs. In addition, our customized account-level services provide rapid incident resolution and offer proactive care to maximize the security and performance of Fortinet deployments.Use CasesNext Generation Firewall (NGFW)•FortiGuard Labs’ suite of AI-powered Security Services—natively integrated with your NGFW—secures web, content, and devices and protects networks from ransomware and sophisticated cyberattacks•Real-time SSL inspection (including TLS 1.3) provides full visibility into users, devices, and applications across the attack surface•Fortinet’s patented SPU (Security Processing Unit) technology provides industry-leading high-performance protectionSecure SD-WAN•FortiGate WAN Edge powered by one OS and unified security and management framework and systems transforms and secures WANs•Delivers superior quality of experience and effective security posture for work-from-any where models, SD-Branch, and cloud-first WAN use cases•Achieve operational efficiencies at any scale through automation, deep analytics, and self-healingUniversal ZTNA•Control access to applications no matter where the user is and no matter where the application is hosted for universal application of access policies•Provide extensive authentications, checks, and enforce policy prior to granting application access - every time•Agent-based access with FortiClient or agentless access via proxy portal for guest or BYODHardwareFortiGate FortiWifi 40F SeriesHardware FeaturesInterfaces1. 1 x USB Port2. 1 x Console Port3. 1 x GE RJ45 WAN Port4. 1 x GE RJ45 FortiLink Port5.3 x GE RJ45 Ethernet PortsHardware FeaturesFortiGate FortiWifi 40F-3G4GInterfaces1. 1 x USB Port2. 1 x Console Port3. 1 x GE RJ45 WAN Port4. 1 x GE RJ45 FortiLink Port5. 3 x GE RJ45 Ethernet PortsCompact and Reliable Form FactorDesigned for small environments, you can place it on a desktop or wall-mount it. It is small, lightweight, yet highly reliable with a superior MTBF (Mean Time Between Failure), minimizing the chance of a network disruption.Access Layer SecurityFortiLink protocol enables you to converge security and the network access by integrating the FortiSwitch into the FortiGate as a logical extension of the NGFW. These FortiLink enabledports can be reconfigured as regular ports as needed.SpecificationsNote: All performance values are “up to” and vary depending on system configuration.1IPsec VPN performance test uses AES256-SHA256.2 IPS (Enterprise Mix), Application Control, NGFW and Threat Protection are measured with Logging enabled.3 SSL Inspection performance values use an average of HTTPS sessions of different cipher suites.4 NGFW performance is measured with Firewall, IPS and Application Control enabled. 5Threat Protection performance is measured with Firewall, IPS, Application Control andMalware Protection enabled.Interfaces and ModulesHardware Accelerated GE RJ45 WAN / DMZ Ports1111 Hardware Accelerated GE RJ45 Internal Ports3333 Hardware Accelerated GE RJ45 FortiLink Ports(Default)1111 Hardware Accelerated GE RJ45 PoE/+ Ports0000 Cellular Modem--3G4G LTE3G4G LTEWireless Interface0Single Radio(2.4GHz/5GHz) 802.11/a/b/g/n/ac-W20Single Radio(2.4GHz/5GHz), 802.11a/b/g/n/ac-W2Antenna Ports (SMA)0336 USB Ports1111 Console Port (RJ45)1111 SIM Slots (Nano SIM)0022 Onboard Storage0000 Included Transceivers0000 System Performance — Enterprise Traffic MixIPS Throughput 2 1 GbpsNGFW Throughput 2, 4800 MbpsThreat Protection Throughput 2, 5600 MbpsSystem Performance and CapacityIPv4 Firewall Throughput (1518 / 512 / 64 byte, UDP) 5 / 5 / 5 GbpsFirewall Latency (64 byte, UDP) 2.97 μsFirewall Throughput (Packet per Second)7.5 MppsConcurrent Sessions (TCP)700 000New Sessions/Second (TCP)35 000Firewall Policies5000IPsec VPN Throughput (512 byte) 1 4.4 GbpsGateway-to-Gateway IPsec VPN Tunnels 200Client-to-Gateway IPsec VPN Tunnels250SSL-VPN Throughput490 MbpsConcurrent SSL-VPN Users(Recommended Maximum, Tunnel Mode)200SSL Inspection Throughput (IPS, avg. HTTPS) 3310 MbpsSSL Inspection CPS (IPS, avg. HTTPS) 3320SSL Inspection Concurrent Session(IPS, avg. HTTPS) 355 000Application Control Throughput (HTTP 64K) 2990 MbpsCAPWAP Throughput (HTTP 64K) 3.5 GbpsVirtual Domains (Default / Maximum)10 / 10Maximum Number of FortiSwitches Supported8Maximum Number of FortiAPs (Total / Tunnel)16 / 8Maximum Number of FortiTokens500High Availability Configurations Active-Active, Active-Passive, ClusteringSpecificationsModem Model N/A Sierra Wireless EM7565(2 SIM Slots, Active/Passive)LTE Category N/A CAT-12LTE Bands N/A B1, B2, B3, B4, B5, B7, B8, B9, B12, B13, B18, B19, B20, B26, B28, B29,B30, B32, B41, B42, B43, B46, B48, B66UMTS/HSPA+N/A B1, B2, B4, B5, B6, B8, B9, B19WCDMA N/A-CDMA 1xRTT/EV-DO Rev A N/A-GSM/GPRS/EDGE N/A-Module Certifications N/A FCC, ICES, CE, RCM, VCCI, BSMI, UL/cUL, CB Diversity N/A YesMIMO N/A YesGNSS Bias N/A YesFortiGuard BundlesFortiGuard Labs delivers a number of security intelligence services to augment the FortiGate firewall platform.You can easily optimize the protection capabilities of your FortiGate with one of these FortiGuard Bundles.FortiCare EliteFortiCare Elite services offers enhanced service-level agreements (SLAs) and accelerated issue resolution. This advanced support offering provides access to a dedicated support team. Single-touch ticket handling by the expert technical team streamlines resolution. This option also provides Extended End-of-Engineering-Support (EoE’s) of 18 months for added flexibility and access to the new FortiCare Elite Portal. This intuitive portal provides a single unified view of device and security health.Fortinet CSR PolicyFortinet is committed to driving progress and sustainability for all through cybersecurity, with respect for human rights and ethical business practices, making possible a digital world you can always trust. You represent and warrant to Fortinet that you will not use Fortinet’s products and services to engage in, or support in any way, violations or abuses of human rights, including those involving illegal censorship, surveillance, detention, orexcessive use of force. Users of Fortinet products are required to comply with the Fortinet EULA and report any suspected violations of the EULA via the procedures outlined in the Fortinet Whistleblower Policy .SUBSCRIPTIONSService Category Service Offering A-la-carteBundlesEnterprise ProtectionUnified Threat ProtectionAdvanced ThreatProtectionSecurity ServicesFortiGuard IPS Service••••FortiGuard Anti-Malware Protection (AMP) — Antivirus, Mobile Malware, Botnet, CDR, Virus Outbreak Protection and FortiSandbox Cloud Service••••FortiGuard Web Security — URL and web content, Video and Secure DNS Filtering •••FortiGuard Anti-Spam••FortiGuard IoT Detection Service ••FortiGuard Industrial Security Service ••FortiCloud AI-based Inline Sandbox Service1•NOC ServicesFortiGate Cloud (SMB Logging + Cloud Management)•FortiGuard Security Fabric Rating and Compliance Monitoring Service ••FortiConverter Service••FortiGuard SD-WAN Underlay Bandwidth and Quality Monitoring Service•SOC ServicesFortiAnalyzer Cloud•FortiAnalyzer Cloud with SOCaaS •Hardware and Software SupportFortiCare Essentials •FortiCare Premium ••••FortiCare Elite•Base ServicesFortiGuard Application Control included with FortiCare SubscriptionFortiCloud ZTNA Inline CASB Service 1Internet Service (SaaS) DB Updates GeoIP DB UpdatesDevice/OS Detection Signatures Trusted Certificate DB Updates DDNS (v4/v6) Service1.Available when running FortiOS 7.2Ordering Informationcompatible FortiGate products, visit our Documentation website, AC Power Adaptor SP-FG-40F-PA-10(-XX)Pack of 10 AC power adaptors for FG/FWF-40F, come with interchangeable power plugs. (XX=various countries code). Wall Mount Kits SP-FG60F-MOUNT-20Pack of 20 wall mount kits for FG/FWF-40F series, FG/FWF-60F series, FG-80F, FG-81F and FG-80F-Bypass.[RC] = regional code: A, B, D, E, F, I, J, N, P, S, V, and Y Copyright © 2023 Fortinet, Inc. All rights reserved. Fortinet, FortiGate, FortiCare and FortiGuard, and certain other marks are registered trademarks of Fortinet, Inc., and other Fortinet names herein may also be registered and/or common law trademarks of Fortinet. All other product or company names may be trademarks of their respective owners. Performance and other metrics contained herein were attained in internal lab tests under ideal conditions, and actual performance and other results may vary. Network variables, different network environments and other conditions may affect performance results. Nothing herein represents any binding commitment by Fortinet, and Fortinet disclaims all warranties, whether express or implied, except to the extent Fortinet enters a binding written contract, signed by Fortinet’s General Counsel, with a purchaser that expressly warrants that the identified product will perform according to certain expressly-identified performance metrics and, in such event, only the specific performance metrics expressly identified in such binding written contract shall be binding on Fortinet. For absolute clarity, any such warranty will be limited to performance in the same ideal conditions as in Fortinet’s internal lab tests. Fortinet disclaims in full any covenants, representations, and guarantees pursuant hereto, whether express or implied. Fortinet reserves the right to change, modify, transfer, or otherwise revise this publication without notice, and the most current version of the publication shall be applicable.March 29, 2023FGFWF-40F-DAT-R29-20230329。
毕业设计的英文翻译----开放式控制器体系结构 - 过去,现在和未来
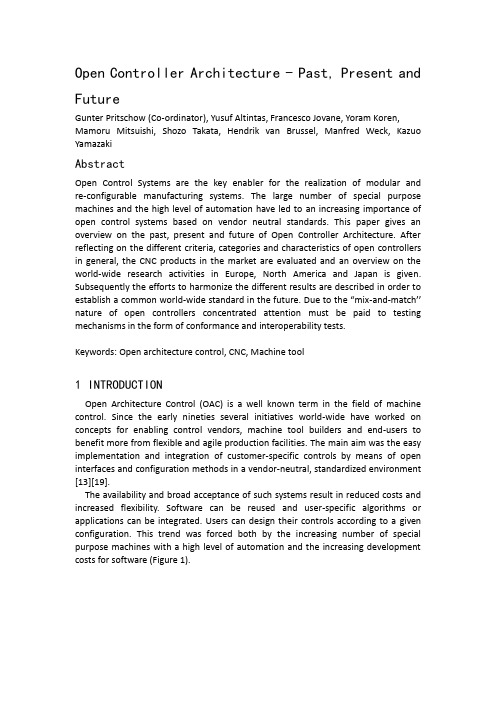
Open Controller Architecture - Past, Present and FutureGunter Pritschow (Co-ordinator), Yusuf Altintas, Francesco Jovane, Yoram Koren, Mamoru Mitsuishi, Shozo Takata, Hendrik van Brussel, Manfred Weck, Kazuo YamazakiAbstractOpen Control Systems are the key enabler for the realization of modular and re-configurable manufacturing systems. The large number of special purpose machines and the high level of automation have led to an increasing importance of open control systems based on vendor neutral standards. This paper gives an overview on the past, present and future of Open Controller Architecture. After reflecting on the different criteria, categories and characteristics of open controllers in general, the CNC products in the market are evaluated and an overview on the world-wide research activities in Europe, North America and Japan is given. Subsequently the efforts to harmonize the different results are described in order to establish a common world-wide standard in the future. Due to the “mix-and-match’’ nature of open controllers concentrated attention must be paid to testing mechanisms in the form of conformance and interoperability tests.Keywords: Open architecture control, CNC, Machine tool1 INTRODUCTIONOpen Architecture Control (OAC) is a well known term in the field of machine control. Since the early nineties several initiatives world-wide have worked on concepts for enabling control vendors, machine tool builders and end-users to benefit more from flexible and agile production facilities. The main aim was the easy implementation and integration of customer-specific controls by means of open interfaces and configuration methods in a vendor-neutral, standardized environment [13][19].The availability and broad acceptance of such systems result in reduced costs and increased flexibility. Software can be reused and user-specific algorithms or applications can be integrated. Users can design their controls according to a given configuration. This trend was forced both by the increasing number of special purpose machines with a high level of automation and the increasing development costs for software (Figure 1).Figure 1: CNC Hardware and software -Actual trend existingIn the past the CNC market was dominated by heterogeneous, device-oriented systems with proprietary hardware and software components. The tight coupling of application software, system software and hardware led to very complex and inflexible systems. Great efforts were made to maintain and further develop the products according to new market requirements. Modern CNC approaches, which comprise extensive functionality to achieve a high quality and flexibility of machining results combined with a reduced processing time, favor PC- based solutions with a homogenous, standardized environment (Figure 2). The structure is software- oriented and configurable due to defined interfaces and software platforms. Open control interfaces are necessary for continuously integrating new advanced functionality into control systems and are important for creating re-configurable manufacturing units [17]. Unbundling hardware and software allows profiting from the short innovation cycles of the semiconductor industry and information technology. With the possibility for reusing software components, the performance of the overall system increases simply by upgrading the hardware platform.Figure 2: PC-based, software-oriented Control SystemsThere are a lot of benefits for suppliers and users of open control systems (Figure 3) [7]. CNC designers and academics benefit from a high degree of openness coveringalso the internal interfaces of the CNC. For CNC users the external openness is much more important. It provides the methods and utilities for integrating user-specific applications into existing controls and for adapting to user-specific requirements, e.g. adaptable user interfaces or collection of machine and production data. The external openness is mainly based on the internal openness but has functional or performance Iimitations .2 STATE OF THE ART2.1 Control Systems and their interfacesControls are highly sophisticated systems due to very strict requirements regarding real-time and reliability. For controlling the complexity of these systems hardware and software interfaces are an essential means. The interfaces of control systems can be divided into two groups-external and internal interfaces (Figure4).External InterfacesThese interfaces connect the control system to superior units, to subordinate units and to the user. They can be divided into programming interfaces and communication interfaces. NC and PLC programming interfaces are harmonized by national or international standards, such as RS-274, DIN 66025 or IEC 61131-3. Communication interfaces are also strongly influenced by standards. Fieldbus systems like SERCOS, Profibus or DeviceNet are used as the interface to drives and 110s. LAN (Local Area Network) networks mainly based on Ethernet and TCP/lP do reflect the interfaces to superior systems.Internal InterfacesInternal interfaces are used for interaction and data- exchange between components that build up the control- system core. An important criterion in this area is the support of real-time mechanisms. To achieve a re-configurable and adaptable control the internal architecture of the control system is based on a platform concept. The main aims are to hide the hardware-specific details from the software components and to establish a defined but flexible way of communication between the software components. An application programming interface(API) ensures these requirements. The whole functionality of a control system is subdivided into several encapsulated, modular software components interacting via the defined API.2.2 Hardware and software structure of control systemsFigure 5 shows different variants for the hardware structures of control systems. Variant a) shows an analog drives interface with position controller in the control system core. Each module of this structure uses its own processor which leads to a large variety of vendor-specific hardware. Combining modules leads to a significant reduction of the number of processors. Variant b) shows intelligent digital drives with integrated control functionality, which result from higher capacity, miniaturization and higher performance of the processors. Variant c) shows a PC-based single processor solution with a real-time extension of the operating system. All control-functions run as software tasks in the PC-based real-time environment.2.3 Market overviewThe controls available in the market provide different levels of openness according to the criteria shown in Figure 6. An important criterion is the use of a standardized computing platform (i.e. hardware, operating system and middleware) as an environment to execute the HMI and CNC software. Besides this, the connectivity of the CNC to upper and lower factory levels must be guaranteed. Application Programming Interfaces (API) are used to integrate third party software in the CNC products. Al though most of today’s controls offer openness concerning the operator-related control functions (Human-Machine Interface, HMI) only few controls allow users to modify their low-level control algorithms to influence the machine-related control functions.Figure 7 gives an overview of the characteristics of today’s control s ystems regarding the degree of openness.Although many control systems provide open interfaces for software integration (e.g. OPC) there is still no common definition of data which is passed back and forth via the programming interface. Therefore, the control systems available on the market today do not implicitly support “plug-and-play” features. To improve this situation, the fieldbus systems can serve as a role model (see Figure 8). The variety of different fieldbus systems has led to the broad consensus that harmonizing the application-oriented interfaces is desirable in order to hide the plurality and the complexity of the systems from the user. Most fieldbus organizations are already using so-called device profiles in order to support the interchangeability of the devices of different vendors.For example, the SERCOS interface standard (IEC61491) for the cyclic and deterministic communication between CNC and drives has defined the semantics forapprox. 400 parameters describing drive and control functions which are used by the devices of different vendors.3 DEFINITIONS AND CATEGORIES OF OPENNESS3.1 DefinitionsThe “Technical Committee of Open Systems” of IEEE defines an open system as follows: “An open system provides capabilities that enable properly implemented applications to run on a variety of platforms from multiple vendors, interoperate with other system applications and present a consistent style of interaction with the user” (IEEE 1003.0).To estimate the openness of a controller the following criteria can be applied (Figure 9):Portability. Application modules (AM) can be used on different platforms without any changes, while maintaining their capabilities.Extendibility. A varying number of AM can run on a platform without any conflicts.Inferoperability. AM work together in a consistent manner and can interchange data in a defined way.Scalability. Depending on the requirements of the user, functionality of the AM and performance and size of the hardware can be adapted.To fulfill the requirements of the IEEE-definition and these criteria of openness, an open control system must be:vendor neutral. This guarantees independence of single proprietary interests.consensus-driven. It is controlled by a group of vendors and users (usually in the form of a user group or an interested group).standards-based. This ensures a wide distribution in the form of standards (national/international standards or de-facto standards).freely available. It is free of charge to any interested party.3.2 Categories of Open Control SystemsIf we speak of openness in control systems, the following categories can be identified (Figure 10):Open HMl: The openness is restricted to the non-real-time part of the control system. Adaptations can be made in user oriented applications.Kernel with restricted openness: The control kernel has a fixed topology, but offers interfaces to insert user-specific filters even for real-time functions.Open Control System: The topology of the control kernel depends on the process. It offers interchangeability, scalability, portability and interoperability.Open control systems that are available today mostly offer the possibility for modifications in the non-real-time part in a fixed software topology. They lack the necessary flexibility and are not based on vendor-neutral standards.3.3 RequirementsA vendor-neutral open control system can only be realized if the control functionality is subdivided in functional units and if well-defined interfaces between these units are specified (Figure 11). Therefore modularity can be identified as the key for an open system architecture. In determining the module complexity there is an obvious trade-off between the degree of openness and the cost of integration [6]. Smaller modules provide a higher level of openness and more options, but increase the complexity and integration costs. Furthermore such a low level of granularity can lead to much higher demands for resources and it may even deteriorate the real-time performance of the overall system.Combining modules in the manner of “mix-and-match’’ requires a comprehensive set of standard Application Programming Interfaces (APIs). For vendor-neutral open control systems the interfaces need to be standardized and broadly accepted. Due to the complexity of such modular systems the definition of a system architecture is recommendable and helpful. This leads to the introduction of so-called system platforms (Figure 12). These platforms encapsulate the specifics of a computing system by absorbing the characteristics of hardware, operating system and communication. The availability of such middleware systems facilitates the easy porting of application software and also the interoperability of application modules even in distributed heterogeneous environments.Due to the possibility to “mix-and-match’’ modules via standardized interfaces the quality of the overall system is determined by the degree of the interoperability between the single modules (see Section 5).4 SYSTEMS ON THE WAY TO THE MARKET4.1 Major international activitiesOSEC (Japan)The OSE (Open System Environment for Manufacturing) consortium was established in December 1994. Three project phases were carried out until March 1999 [1][2][3]. The OSEC Architecture was intended to provide end users, machine makers, control vendors, software vendors, system integrators, etc. a standard platform for industrial machine controllers, with which they can add their own unique values to the industrial machines, and hence promote the technical and commercial development of the industrial machines. The OSEC API is defined in the form of an interface protocol, which is used to exchange messages among controller software components representing the functionality and the real- time cycle. Each functional block can be encapsulated as an object so it is not necessary to deal with how a functional block processes messages to it at architecture level (Figure 13). Although the structure of functional blocks can be defined uniquely by the OSEC architecture from a logical point of view, the system is neither determined nor limited at its implementation phase because there are so many options for implementations. These options may include system contrivances such as device driver, interprocess communication, installation mechanisms such as static library and DLL, hardware factors like selection of controller card, and implementations of software modules added for execution control and/or monitoring of various software. In other words, the implementation model to realize the architecture model is not limited to a particular model. In this way, it is assured to incorporate various ideas in the implementation model depending on the system size or its hardware implementation and/or utilization.JOP (Japan)In parallel to the OSE consortium activities, MSTC formed the Open-Controller Technical Committee (OC- TC) from 1996 to 2000, under the umbrella of JOP (Japanese Open Promotion Group). The objectives of OC-TC were to provide the opportunities for various companies to discuss and work together on the standardization of open controller technologies. The OC- TC was also expected to act as liaison between domestic and international activities in this field. OC-TC was participated by approximately 50 members, which included major Japanese controller vendors, machine tool builders, integrators, users, and academics. Some of the members represented the other groups concerning open controllers such as the OSE consortium and the FA Intranet Promotion Group .One of the working groups was engaged in developing a standard API for interfacing between NC and PC-based HMI. It should be also effective for the communication between NC and an upper level management controller. The work was carried out based on the proposals from the major controller vendors and that from the OSE consortium. The developed specifications were named PAPI and released July, 1999 [4] [5]. PAPI was approved as a JIS (Japan Industrial Standard) technical report and published in October, 2000. To demonstrate the effectiveness of the specifications developed by OC-TC, in Nagoya in October 1999, two CNCs manufactured by different vendors were connected to a Windows NT machine in which the same HMI systems developed by the University of Tokyo were implemented (Figure 14). Since any specific controller architecture is not assumed, PAPI can be implemented in various types of existing CNC systems, such as PC + proprietary NC, PC + NC board, and Software NC on PC+110 board. The HMI system communicates with the CNCs via PAPI which is a function-oriented software library in the programming language C. The PAPI interface is neutralizing the vendor-specific interface by mapping the PAPI calls to the vendor-specific API and protocol.OMAC (USA)The Open Modular Architecture Controllers (OMAC) Users Group is an industry forum to advance the state of controller technology [l0]. An effort was undertaken within OMAC to define API specification for eventual submittal to an established standards body. The OMAC API adopted a component-based approach to achieve plug-and-play modularization, using interface classes to specify the API [11]. For distributed communication, component-based technology uses proxy agents to handle method invocations that cross process boundaries. OMAC API contains diffe rent “sizes” and “types” of reusab le plug-and-play components - component, module, and task - each with a unique Finite State Machine (FSM) model so that component collaboration is performed in a known manner. The term component applies to reusable pieces of software that serves as a building block within an application while the term module refers to a container of components. Tasks are components used to encapsulate programmable functional behavior consisting of a series of steps that run to completion, including support for starting, stopping, restarting, halting, and resuming, and may be run multiple times while a controller is running. Tasks can be used to build controller programs consisting of a series of Transient Tasks, with ability to restart and navigate, or as standalone Resident Tasks to handle specialized controller requirements, (e.g., axis homing or ESTOP).To integrate components, a framework is necessary to formalize the collaborations and other life cycle aspects in which components operate. The OMAC API uses Microsoft Component Object Model (COM) as the initial framework in which to develop components, with the expected benefit that control vendors could then concentrate on application-specific improvements that define their strategic market-share - as opposed to spending valuable programming resources reinventing and maintaining software “plumbing.”The primary problem with COM framework, specifically under the Windows 2000 operating system, is the lack of hard, real-time preemptive scheduling, but third party extensions to Windows 2000 can be used to overcome this requirement.Figure 15 illustrates a sketch of OMAC API controller functionality. The HMI module is responsible for human interaction with a controller including presenting data, handing commands, and monitoring events and in the OMAC API “mirrors” the actual controller with references to all the major modules and components via proxy agents. The Task Coordinator module is responsible for sequencing operations and coordinating the various modules in the system based on programmable Tasks. The Task Coordinator can be considered the highest level Finite State Machine in the controller. A Task Generator module translates an application-specific control program (e.g., RS 274 part program) into a series of application-neutral Transient Tasks. The Axis Group module is responsible for coordinating the motions of individual axes, transforming an incoming motion segment specification into a sequence of equi-time- spaced setpoints for the coordinated axes. The Axis module is responsible for servo control of axis motion, transforming incoming motion setpoints into setpoints for the corresponding actuators 10 points. The Control Law component is responsible for servo control loop calculations to reach specified setpoints. OSACA (Europe)In Europe the ESPRIT project OSACA (Open System Architecture for Controls within Automation Systems) was initiated in 1992 with the aim to unite European interests and to create a vendor-neutral standard for open control systems[9][16].It was supported by major European control vendor and machine tool builders. OSACA reached a mature state already in April 1996 having at its disposal a stable set of specifications and a tested pool for system software. Based on these results, several application-oriented projects were carried out. In 1988 two pilot demonstrators in the automotive industry proved the interoperability of OSACA-compliant controllers and applications. The OSACA association eth currently 35 members from all over the word is the lasting organization to keep and maintain the OSACA-related specifications.The basic technical approach of the OSACA architecture is the hierarchical decomposition of control functionality into so-called functional units (Figure 16).For each of these functional units (e.g. motion control, motion control manager, axescontrol, logic control, etc.) the interfaces are specified by applying object-oriented information models. This technique is similar to the approach of MAP/MMS but with a limited and manageable number of object classes.The data interface consists of several variable objects that support the read and/or write access to data structure(data flow).The data can be of a simple type or of a complex type(array, structure, union).By using formal templates(Figure17) all the characteristics of a single interface object are specified. These elements cover the name (e.g, “mc-active-feed-override”), the type (e.g. UNS32: 32-bit unsigned value), the scaling (e.g. 0.l%),the range and the access rights (read only, to all the major modules and components via proxy write only, read/write) of the data. An additional description is to avoid misinterpretations of the use of the data. The process interface consists of several process objects that are used to describe the dynamic behavior (control flow) of the application modules by means of finite state machine (FSM). The state machines are described by static states, dynamic states and transitions to change the states of a given state-machine. The transitions can handle input and output parameters to pass data between application modules via the communication platform. The formal template for such process interfaces consists of an unambiguous description and the following attributes: list of static states (identifier, list of possible transitions), list of dynamic states (identifier) and a list of transitions (input parameters, output parameters, return codes). The process interface can also be used to activate application-specific functions in form of procedure calls. The interoperability of distributed application modules is supported by an infrastructure (so-called OSACA platform) which comprises client-server principles, synchronous and asynchronous calls and event handling via any underlying communication protocol and media (e.g. by using the TCP/lP protocol). A dedicated configuration runtime system is handling the system’s startup and shutdown. Besides, it also allows an easy reconfiguration of the system.开放式控制器体系结构- 过去,现在和未来摘要开放式控制系统是用于模块化和可重新配置制造系统实现的关键推动者。
Mettler Toledo IND890 PC Weighing Terminal说明书
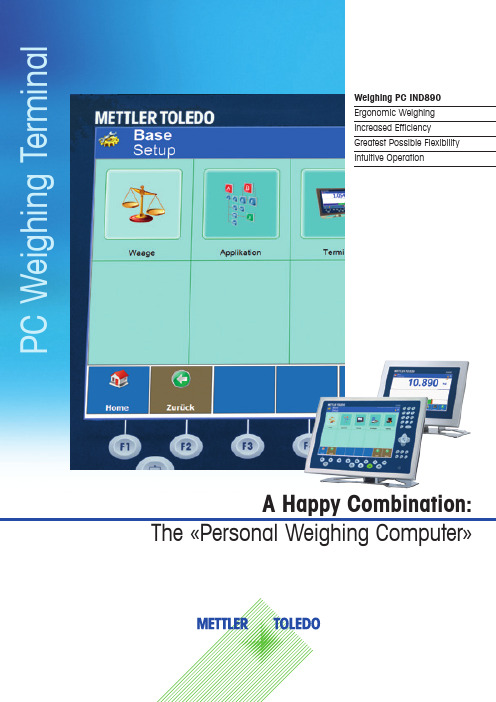
P C W e i g h i n g T e r m i n a lA Happy Combination:The «Personal Weighing Computer»Weighing PC IND890Ergonomic Weighing Increased EfficiencyGreatest Possible FlexibilityIntuitive Operation2M ETTLER T OLEDO IND890 PC Weighing TerminalThe IND890 is designed to be ergonomic and extremely user-friendly. It offers the following advantages:• Uncomplicated, fast operation: – Touchscreen– Self-explanatory and visually appealing icons – Optimized, simple operator guidance – Only relevant information is displayed • Flexible use:– User-dependent, intuitive software structure– Customer-specific adaptations through free programmability – Freely configurable softkeys– Country and language-specific screen layouts • Perfect readability:– Especially large display option for weight values– Simultaneous display of 4 balances plus sum scale possible – Different status messages can be viewed concurrentlyThe answer’s easy: “touch it!” With the standard touchscreen, the operation of the IND890 is simple and reliable even in the harshest environments. The application terminal also sets new standards in highly complex weigh-ing processes. It provides the perfect connection between PC and scale with powerful and reliable industrial quality – the elegant industrial weigh-ing solution for all sectors.Weighing PC with «Mouse-free» Zone:Clear – Efficient – UniversalI n n o v a t i v e T e c h n o l o g yOne for All!The IND890 can be used everywhere. In modern in-dustrial systems, instruments are designed in such a way that they optimally fulfill their intended purpose. If processes change, weighing equipment must also be adapted. The IND890 offers the necessary flexibility in weighing station arrangement in just one version. Combined with a range of stands and fastening ele -ments, the IND890 can be mounted on a table or on the wall, can stand freely on the floor or can be in -stalled in a switch cabinet./IND890/PC-based-Terminals3M ETTLER T OLEDO IND890 PC Weighing TerminalSharper, More Attractive, Better!The large displays using widescreen technology with 10" or 15" screen diagonals and a resolution of 1024 x 600 up to 1280 x 800 pixels ensure better and easier readability from virtually any viewing angle.100 % Hygiene in Harsh ConditionsThe IND890 stainless steel terminal with its design which is free of dirty edges was developed for use in even the harshest of industrial environments. With the all-round IP66 and IP69k protection, it can be cleaned conveniently and in a time-saving manneru sing a high-pressure cleaner. The cleanability is also supported by:• E asy to disconnect cable connections: quick and easy separation of connections • A voidance of dirty edges: the surfaces and screw connections permit virtually no contamination • T he stainless steel surface has a roughness of Ra < 0.8 µm • P ower supply unit integrated in housing • R esistant to most cleaning agents and disinfectantsA New World of Weighing:• Different user profiles• Up to 4 balances can be calibrated – plus sum scale • V ariable adaptability through settings for display, region (time zone), user, language, softkeys • W ide range of configuration options (e.g. interfaces)• N umerous weighing and standard functions: – DeltaTrac ® – Tare deduction – Setpoints – Identcodes– dynamic weighing (animal weighing) • V ersatile options for evaluating the saved data (alibi, tare, messages, target values, interfaces)• M aintenance functions with diagnosis routines • S imple software updates4M ETTLER T OLEDO IND890 PC Weighing TerminalThe IND890-15 (the large version of the IND890) consists of a slimline flat screen and a separate ELO box 1. Both components are connected with as ingle cable. This ensures extremely flexible and ergonomic workplace layout. Furthermore, the convenient IND890-10 compact version offers an a ll-in- o ne solution: small, compact and supplies real-time data thanks to Windows CE.A Completely New Weighing PC The ELO box 1 contains the entire weighing and PC technology: the PC and the weighing t echnology thus form a single unit, which, with its rapid internal communica -tion, performs impressively even in challenging applications.The IND890-HMI (Human Machine Interface) can generally be smoothly adapted to a wide variety of condi -tions. This ensures individual work -place arrangement as well as c onvenient operation and reliable reading: quick and easy!The Right Version for Every ApplicationWhether as a real-time-capable compact terminal with Windows CE, or as a high-performance application with a large display – the IND890 product family has different versions with different configuration levels:• I ND890-10: Compact versionwith 10" touchscreen display and Windows CE • I ND890-15-HMI: Human MachineInterface with 15" touchscreendisplay and additional function keys • I ND890 ELO box: Electronics unitfor connection with the 15" HMIFlexible and Ergonomic – Quick and Easy!I n n o v a t i v e T e c h n o l o g yIND890-15-HMI IND890-ELO-Box IND890-10 Compact version1ELO box: The electronics box, or ELO box for short, contains the entire PC hardware including interfaces.5M ETTLER T OLEDO IND890 PC Weighing TerminalDetermining the Minimum Weight – MinWeigh ®The advantageous MinWeigh ® tech-nology ensures reliability. Because the accuracy of a measuring device is quantified by the measurement uncertainty. Every weighing system has a minimum weight at which the measurement uncertainty does not exceed the stipulated weighing tolerance. With the MinWeigh ® technology, the minimum weight is determined and certified, in order to ensure that the necessary weighing tolerances are complied with. If the weight falls below the minimum weight, this can be indicated via an icon or a weight value which changes color./minweighKey information at a glanceDepending on the configuration, all weighing data and weight values from up to 4 balances plus the sum scale are displayed simultaneously in the large, clear, certified weight value window. Here, the weightd ata can be displayed in parallel with other application data. This mean all information about all data is available at a glance. The bal -ances can be quickly activated and switched via the softkeys and smartkeys. Values are input via the country-specific touchscreen key-board.Operator Guidance • I ntuitive work with the IND890: working with the IND890 is very easy thanks to the self-explanatory icons, which are also supported by text instructions • S ettings can be made quickly and effectively: no matter whether you have to adapt data from the connected balances or the inter-faces used. Everything can be found in the respective submenu with a few touches of the screen • E very user is shown only the e lements required for the task in hand • D eltaTrac ® uses the bar color to indicate quickly and easily whether or not the target weight has yet been reached, or exceeded. This simplifies and accelerates processes./IND8906M ETTLER T OLEDO IND890 PC Weighing TerminalTouch it …… direct input:Touchscreens in every IND890 as standardNaturally intuitive …… credible, simple and new:• U nique software design – self-explanatory icons combined with an attractive, logical software structureC o n v i n c i n g A r g u m e n t sImpressively … …clear:• O ptimized navigation and input for operation via touchscreen • M enu path display for improved navigationHealthy outlook …… clear and unmistakable:• A dvantageous display options • P rogressive designwith ELO boxPin-sharp ……outstanding display even at an unfavorable viewing angleDisplays with 1A resolution 1024 x600 with IND890-101280 x 800 with IND890-157M ETTLER T OLEDO IND890 PC Weighing TerminalHygienic … … easy to clean:• P rotection rating IP69k: Cleaning with high-pressure cleaner • S urface roughness of RA < 0.8 µm • A voidance of dirty edges thanks to easy-to-clean designWhatever you want …… Individually adaptable thanks to the free programmability of the IND890.How much can it do?Numerous applications possible:• U p to 4 balances at the same time • C ertifiable • S um scale • A nalog or digitalBest connections …… easy connection and disconnectionof cables thanks to simple plug connec-tions – IP protection remains.Top condition … … top performance:Ideal performance combination of processor, RAM and mass storage.Any location … … is suitable for use:VESA 2 Mount 100 x 100 for using standard mounting systems.Universal …… with VGA interface as standard:• Connection of a standard PC to the HMI box• Connection of a standard monitor to the ELO box 11ELO box: Electronics box2VESA: Video Electronics Standards Association8M ETTLER T OLEDO IND890 PC Weighing TerminalInSite™ – the Global, PC-based Configuration ToolConfiguring the IND890 could not be simpler: e ither connected ino nline mode or for preparation as off-line configuration. This hasproven to be particularly time-saving if the configuration also has to be transfered to further IND890 ter-minals. The functions for the com-position and archiving as well as the saving and retrieval of docu-ments are also particularly useful. /insiteThe IND890 weighing software has been specially developed for use on a touchscreen. With its icons, it offers a completely new type of weight data recording, not previously available in weighing terminals.Innovative – Simple – Intuitive:Modern Weight Data RecordingS o f t w a r e a n d T o o l sReal-time Weight Values for Time-critical Control Processes The IND890 can autonomously control weight-dependent processes. A connected dosing system also shuts down correctly if the operating system is executing a different task at this precise moment. This is particularly advantageous in fast or automated processes, where re -liability is the top priority. In some cases, this function may mean that it is not necessary to have thec onnection to a PLC 2 . IND890-Base – Standard Application IncludedThe multilingual IND890-Base soft-ware is a universally applicable weighing and service program for basic weighing tasks. It is a com-prehensive weighing solution for customers, but also providess upport for calibration officers and METTLER TOLEDO service techni -cians.Today’s Sophisticated Solutions – Simple ImplementationIf a standard application solution is no longer appropriate, speciala pplications can also be implement-ed. The integrated Microsoft ® technology offers software developers an ideal tool for fast and efficient implementation of customized solutions.Irrespective of the development en-vironment, there is simple drag-and-drop access to a wide range of system and weighing functions.Globally ConnectedThe use of the Windows operating systems allows remote configu-ration and maintenance of your ap-plication on the IND890. Software updates and e-mail services take place via the internet, VNC 1 or InSite ®.1VNC: Virtual Network Computing 2PLC: Programmable logic controller9M ETTLER T OLEDO IND890 PC Weighing Terminalmanually by operator guidance or by a regulation intervention from a dynamic checkweigher.Unnecessary material losses are thus avoided and statutory fill quantities and net weight specifica -tions are complied with. The soft -ware conforms to internal as wellas external, international standardssuch as ISO and GMP . In combina -tion with the IND890 for immediatedata recording, analysis and pro -cess control, supplies the necessary statistical data forassessing, documenting and control -ling the cost-effectiveness of a fill-ing process./freeweighnet The ® dosing and formulation system simplifies formu-lation processes. The intuitiveo perator guidance throughout the whole formulation process ensures uniform batch quality. At the same time, material use and process speed are optimized and the amount of manual work is reduced.Whether you are in the food, pharma -ceutical, chemical, cosmetic or manufacturing industry – ® has many advan-tages and can bring great benefit to your company:• Increased productivity• Complete batch documentation • G uaranteed consistently high product quality • R eliability and stability of pro -cesses • M ore efficient batch production/formweighnetThe quality of industrial filling pro -cesses ranges from stable and easy to control through to highly dispersive and difficult to control.Irrespective of the requirements forthe filling process, the use of enables systematicmonitoring and control of fillingprocesses, ensures conformity andhelps control losses arising fromoverfilling.As the fill quantities of liquid, pasty,powdery or solid products arechecked by taking random samplesimmediately after filling, precise system settings are ensured – eitherThe use of * for statistical quality control and * for professional formulation processing has proven to be a particularlys uccessful combination. These profitable tools can be used with the IND890 directly in production.A New Standard: IND890 and * or * ® ®* In preparation – more information at your local METTLER TOLEDO representative10M ETTLER T OLEDO IND890 PC Weighing TerminalTests and DiagnosisDimensionsT e c h n i c a l D a t aThe status of the IND890 terminal is analyzed using the integrated test and diagnosis functions. If neces -sary, direct measures for optimizing the system are taken.Communication with connected devic -es and balances can thus be tested very easily at any time, in order to avoid possible downtime, before amalfunction occurs.IND890-10 DeskIND890-10 PanelIND890-15-HMI Desk11M ETTLER T OLEDO IND890 PC Weighing TerminalHousing dimensions (maximum: H x W x D)IND890-10:253 x 320 x 241 mm IND890-15-HMI:350 x 490 x 349 mm IND890 ELO box:50 x 122 x 400 mmOperating environment–10°C to 40°C (14°F to 104°F), at 10 % to 85% relative humidity, non-condensingDisplayIND890-1010.2" Widescreen TFT Touchscreen display, resolution 1024 x 600IND890-1515,4" Widescreen TFT Touchscreen display, resolution 1280 x 800Processor typesIND890-10AMD Geode LX800 Processor IND890 ELO boxIntel Atom Processor 1.6 GHz RAM memoryFrom 256 MB to 2 GB Power supply unitWide-range power supply unit 100 – 240 V AC, 50/60 Hz, 250 mA with country-specific power lineData interfacesEthernet (standard), RS232, RS422, RS485, USBWeighing interfacesIDNet, analog, SICSGross dispatch weight (including packaging)IND890-10Desk: 5.5 kg Panel: 4.5 kg IND890-15-HMIDesk: 11.4 kg Panel: 8.5IND890 ELO box6.3 kg ApprovalsEC Conformity CE marking with declaration of conformity – admission for certification or pattern approval EC Directive 2009/23/EEC; EN 45 501; OIML R76; NTEP compliant – Electrical Safety EC Directive 2006/95/EEC; EN 61010-1, UL, CSA approved Electromagnetic compatibility EC Directive 2004/108/EEC; EN 61000-6-2, EN 61000-6-3Order numbersIND890-10 110/230 VDesk: 22019982Panel: 22019983IND890-15-HMI 110/230 VDesk: 22019984Panel: 22019985IND890 ELO box 110/230 VDesk: 22019986Data interfacesEthernet standardRS232: 22020258RS422/485: 22020259Balance interfacesAnalog: 22020254IDNet: 22020253SICS-RS232: 22020255 SICS-RS422: 22020256Technical DataIND890-15-HMI Panel IND890-ELO-BoxFor more information /ind890Mettler-Toledo AGIndustrialCH-8606 GreifenseeTel. +41-44-944 22 11Fax +41-44-944 31 70Subject to technical changes© 04/2011 Mettler-Toledo AGPrinted in Switzerland MTSI 44098080ServiceAdvantages Installation &Set-up • Precise, reproducible results through correct installation• Tried and tested data exchange with peripheral devices and systems• Predetermined operating sequences improve user productivity• Integration in work and maintenance processes• Fast and efficient process start-upInstrument qual-ification • Documented performance in line with process requirements• Regular inspections when used in production processes• Risk of infringing regulations is minimizedCalibration • Accuracy check over entire weighing range• Accuracy check at different points on weighing platform• Brief and compliant calibration certificate• Use of industry-specific and statutory tolerance standards• Reduction in product loss and/or overfilling• Reduction in liability risk due to products which do not comply with specifications Preventive maintenance• Inspection of critical components to identify potential faults• Inspection of audit and error logs to prevent unexpected downtime• Test operation for determining weighing and application performance• Reliable operation, avoidance of unexpected costs• Increased service life and yield return of balances The first step is selecting the right scale. Whether the desired results can be achieved is then dependent on factors such as precise installation, set-up,c alibration, maintenance, product and service, which ensure the performance,r eliability and durability of the scale.Through efficient maintenance and the adaptation of our service to your process and operating requirements, we can help you achieve accurate, reliable and comprehensible weighing results as well as the desired increase in productivity.Lifelong Constant Performancethrough Precision ServiceOur global service organization offers the following significant advantages:• Properly maintained devices which ensure productivity and optimize process performance.• Problem-free compliance with industry-specific standards and regulations • Clear and precise documentation to minimize the risk of infringements17025。
HNC Electric 2020 HC系列卡型PLC与远程模块说明说明书

HNC Electric Limited 2020HC series Card-Type PLC&Remote modulesContentsHardware featuresProgramming software featuresProgramming instructions featuresSpecification1+15Single PLC MPU can expand 15 modules, up to 256 pointsCloud EngineRemote program & monitor PLC through HNC CloudMotion ControlUp to 200KHz high speed pulse which support linear&circularinterpolation, homimg, etc.Mix-type MPUPLC MPU integrated with digital and analog IOEthernet +Support Ethernet + RS485 work simultaneouslyEasy WiringDirect pressure terminal block, easy connectingPLC HC series 1/2Easy selectionProduct model naming is easy to understand and convenient for model selectionOptimized structure design, compact size, beautiful appearance, saving installation spaceEasy wiringDirect insert terminal, humanized design, more convenient wiringThe PLC main unit integrates DI/DO and AI/AO with flexible configuration and higher cost performanceEthernet +Ethernet and RS485 interfaces are standard on the PLC main unit, supporting simultaneous operation of twocommunication ports. Each communication port can be programmed and networked as a master or slave station1+15+256A single main unit can expand up to 15 modules, with a maximum expansion capacity of 256 pointsUnlimited networkingPLC main unit can be networking, theoretically can form unlimited points control network, aperfect substitute for medium or even large PLC system.PLC main unit supports up to 4 channels A/B phase (8 points) 200KHz high-speed pulse input/output.Perfect temperature controlThermal resistance, thermocouple and unique temperature& humidity sensor modules, etc., perfectlymeet the application requirements of process controlCommunication extension module with isolation to meet stable communication extension requirements.Card-Type PLC & Remote modulesProgramming software featuresThree programming languagesHPMaster is a PLC programming software conforming to IEC 61131-3, which supports LD (ladderdiagram), FBD (function block diagram) and IL (instruction table).Good compatibilityStable operation in Win98, Win200X, WinXP, Win7, Win8, Win10 and otheroperating systemsPrompt message and help functionAll instructions and detailed information of hardware modules can be opened in thesoftware through F1 key to find the answer. Even if HPMaster programming software is usedfor the first time, the program can be easily written.Three-level password protectionPassword for project files, password for PLC, password for individual program blocks,and protection functions such as preventing program upload.Modular program project structureUp to 63 program blocks can be established (including main program, subroutine, interruptprogram), programming language can be chosen arbitrarily, execution order of program blockscan be adjusted arbitrarily, each block can be imported and exported separately and has thesame password protection as program project.Cloud programmingThe built-in cloud engine enables PLC remote programming, download, firmware upgrade,diagnosis, monitoring and debugging through HNC cloud, enabling easy remoteconnection and detecting on-site conditions at any time.Locally, the PLC can beprogrammed with a cloud engine built into the HT3000 series HMI.Program simulatorCan be simulated running PLC program in the case of complete separation from PLC,greatlyreducing field debugging time and improving debugging efficiency.Communication simulatorEquipped with a communication simulation tool specially designed for debuggingcommunication instructions, it can simulate the process of PLC executingcommunication instructions and processing the data returned from the slave computer.Interpolation simulatorTrack and draw the motion trajectory generated by motion control instructions such as linearinterpolation and circular interpolation, display the current position, mechanical origin position,output mode, etc., of the channel, or set the axis length and unit pulse number.Online monitoring and debugging functionProvide up to 10 pages of component monitoring table, can choose to display data in different dataformats, support mixed monitoring of bit components and register components and displaycomponent notes at the same time.Unique real-time curve functionReal-time curve monitoring can be carried out on any register components to facilitate processcontrol and debugging.PLC execution fileThe PLC source program can be generated into a PLC execution file that can be independentlyreleased and executed, convenient and safe to give the PLC execution file to the end user todownload, there is no need to worry about the user knowing the source program content.Firmware upgrade functionNo matter MPU or extension module, firmware can be upgraded for free. Even the previouslypurchased products can have various latest functions continuously introduced.Powerful online PLC functionIt can search out all PLC connected with the PC, show the information and status of all onlinePLC, and can choose any PLC for online monitoring, program download, firmware upgrade,control PLC running stop, etc.Card-Type PLC & Remote modulesProgramming instructions featuresPowerful innovation convenience instructionsOn the basis of analyzing and absorbing various EXISTING PLC instructions, many powerfulinnovation convenience instructions are launched.Such as communication instruction (MODR, MODW HWRD HWWR), PID control (PID), valve control (VC), upper and lower alarm (HAL, LAL), send (SC), the temperature curve radius (TTC), only one instruction can implement other brand PLC need multiple instructions to realize the function, greatly improve the efficiency ofprogramming and program run faster.Instruction routinesIn the help document, all instructions are explained in detail and corresponding routines are supported to be opened and downloaded into PLC.Rich communication protocolsBuilt-in Modbus TCP, Modbus RTU/ASCII protocol, free communication protocol and PLCbus high-speed communication protocol instructions independently developed by HNC.Powerful communication instructionNo matter use what kind of communication protocol is simply a communication instruction can complete complex communication function, no conflict, to send and receive control for communication port,communication interrupt handling problems such as trouble, and the same communication port can use different protocols, complete the required all sorts of data exchange easily.Powerful analog input processingAI register can be used to directly access analog input, analog input support engineeringconversion, sampling times setting and zero correction.Powerful analog output processingThe analog output can be directly controlled by AQ register. The analog output can support engineering conversion and can be configured with blackout output holding function.PID control functionSupport 32 incremental PID, 32 self-tuning PID, 32 fuzzy temperature control, with TTC temperature curve control, VC valve control and other instructions to easily achieve a variety of complex control requirements of industrial site.High-speed pulse instructionSupports acceleration and deceleration pulse output.The unique synchronous pulse output instruction can easily realize accurate synchronizationcontrol. The single machine supports 8-channel pulse width modulation output (PWM) and candrive 8 servo or stepper motors at the same time.Motion control functionThe single machine supports 8-axis 200KHz motion control, linear interpolation and circular interpolation of any 2-axis, absolute position, relative position, reverse clearance compensation, origin regression, electric origin definition and other functions.Simulator Powerful analogprocessing PLC executable file generationOnline help with demo Local refinement Rich instruction Curve monitoringPLC HC series 5/6Card-Type PLC & Remote modulesHCS Series - Economic PLC MPU40×95×65 HCG Series - Standard PLC MPUHCM Series - High Performance PLC MPU40×95×6525×95×65Digital I/O Modules25×95×65PLC HC series7/8*HCM series supports linear interpolation and circular interpolation of any 2 axes, and supports absolute position, relative position, backlash compensation, origin point return, electrical origin point definition and other functionsCard-Type PLC & Remote modulesAnalog I/O Modules25×95×65Temperature I/O ModulesDimension25×95×65 Communication I/O Modules25×95×6593×95×82131×95×82177×95×82Digital I/O ModulesPLC Remote Module9/10Remote IO Module&FunctionsSupport serial bus, running independently.Can be installed independently without PLC system points limitation.Long distance. Flexible configuration. Low cost.HNC PLC Remote IO ModuleHMI and PC can read&control the devices through RS485 of remote HNC PLC moduleTemperature module DI/DO module AI/AO module DT moduleThermalresistancesensorPhotoelectric switchSolenoid valve Temperature transmitter32pcs ofDS18B20AThermocouple sensor RelayPressure transmitter MeterHMI OR PCWidely used in data acquisition, equipment monitoring,environmental monitoring and industrial process control, etc.Card-Type PLC & Remote modulesAnalog I/O Modules70×95×8293×95×82 Temperature & Humidity Modules30×95×8270×95×8293×95×82 Load Cell Modules30×95×82 Note: All remote modules do not support direct connection with HC series card PLC; Can communicate via RS485 or Ethernet portHNC ELECTRIC LIMITED is a company dedicated to the development and production of intelligent industrial automation solutions based on national strategic needs.Supported by its outstanding electrical and electronic technology and strong control technology, it provides control, display, drive and system solutions and other related products and services to customers worldwide.With 25 years of hard work, we have developed and produced professional CNC systems, industrial robots, servo drives, servo motors, reducers, inverters, PLCs, HMIs, etc.In more than 50 countries and regions around the world, we have established a comprehensive agent system and after-sales service system. In the future, we will, as always,provide more professional services for global industrial automation.Thanks for choosing HNC productAny technique support,please feel to contact our support teamURL:Email:********************。
- 1、下载文档前请自行甄别文档内容的完整性,平台不提供额外的编辑、内容补充、找答案等附加服务。
- 2、"仅部分预览"的文档,不可在线预览部分如存在完整性等问题,可反馈申请退款(可完整预览的文档不适用该条件!)。
- 3、如文档侵犯您的权益,请联系客服反馈,我们会尽快为您处理(人工客服工作时间:9:00-18:30)。
Integrated hardware interfaces for modular sensor networksJ. Portilla1, A. de Castro2, A. Abril1, T. Riesgo 11Universidad Politécnica de Madrid. Centro de Electrónica Industrial.c/ José Gutiérrez Abascal, 2. 28006 Madrid (Spain)2Universidad Autónoma de Madrid. Escuela Politécnica Superior.Avda. Tomás y Valiente, 11. 28049 Madrid (Spain)ABSTRACTSensor networks have reached a great relevance during the last years. The idea is to use a large number of nodes measuring different physical parameters in several environments, which implies different research challenges (low power consumption, communication protocols, platform hardware design, etc). There is a tendency to use modular hardware nodes in order to make easier rapid prototyping as well as to be able to redesign faster and reuse part of the hardware modules. One of the main obstacles for rapid prototyping is that sensors present heterogeneous interfaces. In this paper, a VHDL library for sensors/actuators interfaces is proposed. The purpose is to have a set of different sensor interfaces that include the most common in the sensors/actuators world, enabling the rapid connection to a new sensor/actuator. Moreover, the concept presented here may be used for new interfaces that can be easily developed. The VHDL implementation is independent of the final platform (any FPGA or ASIC) in order to minimize redesign effort and make easier rapid prototyping. The interfaces are installed in a UPM platform for sensor networks.Keywords: sensor networks, hardware interfaces, modular design, reuse1.INTRODUCTIONWireless sensor networks (WSNs) are a new and promising technology that is rapidly being introduced in the market and in everyone’s life. The ubiquitous behavior, the transparency to the final user and the variety of applications foreseen are some of the most important features of this technology. Several fields are involved in WSN, like sensor technology, communication protocols, low power consumption techniques, hardware design of the nodes, algorithms, etc [1]. The tendency is promising, and it is expected that the sensor networks market will grow up to $43 billion in 2008 [2].The hardware node design becomes critical in WSN, in order to achieve the targets already commented. In this way, several approaches exist in the state of the art, but there is a tendency to make the node hardware platform modular [3], [4], [5]. With a modular approach, it is easy to redesign the platform to adapt the system to different scenarios and applications. Moreover, modularity allows rapid prototyping. This concept was developed in previous works of this research group, and a modular platform is actually available as a niche for researching and developing [6]. Fig. 1 shows the four-layered platform developed by UPM-CEI, whose main features are: modularity, low cost, medium size and easy adaptation to different applications.This modular platform is divided in four functional layers: communication, processing, power supply and sensing/actuating layer. The processing layer includes a microcontroller and an FPGA (Field Programmable Gate Array), which gives much processing power to the platform, as well as flexibility. Modularity in the hardware node must be combined with flexibility in the processing devices in order to obtain the maximum adaptability. In this context, sensors present heterogeneous interfaces, which make difficult developing applications in a fast way. When adopting a new sensor, most of the work must be started from scratch.teresa.riesgo@upm.es. Phone: +34 91 3363191, fax: +34 91 5645966. www.upmdie.upm.es6 cm2 cm4 cm Fig. 1 Four layer architecture for sensor nodes in WSNDifferent works have been done in order to minimize this fact, the most of them with a software point of view [7]. It would be desirable to standardize in some manner sensor interfaces to accelerate development time. Some efforts have been done as the IEEE 1451 standards family, for smart sensors [8].In this paper, a VHDL library for transducers (sensors or actuators) interfaces is presented, which allows implementation in any custom hardware device (FPGA or ASIC). Different common interfaces for commercial sensors have been chosen, like PWM or I2C among others. The purpose is to minimize redesign time when new sensors are integrated in the system, because the interface is standardized. The designer deals with each transducer as a “channel”, but all the channels are used in the same way independently of the interface that transducer has.2. LIBRARY OF INTERFACES FOR SENSORS/ACTUATORSAt the present time, there are a lot of different transducers (sensors/actuators) interfaces. Although there are some interfaces that have reached much diffusion, like I2C, probably there will never be a common unique interface for all the transducers due to commercial interests and special features of every transducer or application.In order to simplify the connection and use of transducers, it would be desirable to have a library with the most common interfaces for sensors, and to improve and to extend this library with more interfaces for new transducers in the market. This situation would make easier rapid prototyping and redesign.Fig. 2 shows a diagram of the implementation strategy used for the interfaces presented along the paper, using the UPM platform as the base for the WSN.ADuC831Fig. 2. Interfaces for transducer control adapted to WSN platformA VHDL library has been developed in order to achieve this purpose. Different interfaces have been described in VHDL, which makes the solution independent of the final implementation as long as it is based on custom hardware (FPGA or ASIC). The library is composed of different modules which deal directly with every transducer (analog or digital) and present a common interface with the rest of the circuit independently of the specific transducer. The transducer is connected to the corresponding module of the library, which is different for every interface, and finally this module is connected through the common interface to the rest of the circuit (see Fig.3).Commoninterfacefor all thesensorsFig. 3 General structure chosen for the control of a transducerThe signals that compose this interface are the following ones:Inputso NTrigCh (1 bit): Used to request the module to take a measure from a sensor or to write a value in an actuator.o DataToDAC (8 bits): The data to be written in the actuator is received by this bus (not included in sensor channels).Outputso NAckCh (1 bit): Acknowledge that shows that a sensor has been read or a value has been written in an actuator.o ReadN (1 bit): Used to request data to be written in the actuator (not included in sensor channels).o WriteN (1 bit): Used to alert that a value read from a sensor is put in the bus DataFromADC (not included in actuator channels).o ByteNumber (8 bits): Used to assign a number to each byte sent by DataFromADC or received from DataToDAC. Each data can include up to 256 bytes.o DataFromADC (8 bits): The data to be read from the sensors is received by this bus (not included in actuator channels).Every module has been designed following a philosophy inspired in the IEEE 1451 family of standards, but can be used without being compatible with them. Each transducer is “seen” as a channel (or set of channels) by the transducer controller. Two kinds of channels are recognized: sensor channel and actuator channel. Some sensors, like the SHT11 from Sensirion, supply different measures (in this case, humidity and temperature). So, for the same sensor two different channels are needed. This will be explained in more detail in the following section.The heart of every module is a set of nested FSMs (Finite States Machines). At the top, there is a main state machine, TrigStates, common to every module, which responds to the trigger signal. It controls the lower level FSMs and theacknowledge signal. This FSM follows the 1451 philosophy. At a second level there is another FSM, DataStates, that controls the data acquisition process and the communication through the common interface with the rest of the system (see Fig. 4). This second FSM exists in all the modules of the library, but changes from module to module depending on the specific needs of each interface. Finally, some modules use a third or even fourth FSM if the communication with the transducer is complex. This will be detailed in section 3.DataStatesTrigStatesFig. 4 Top FSM, TrigStates and secondary FSM DataStates.The different modules developed in the proposed library are used for the following transducer interfaces: PWMFrequency/Period modulationI2CSensirion interface (similar to I2C)Interface for analog transducers (module to interact with ADCs and DACs)1-Wire ®3.TRANSDUCER INTERFACESIn this section, more detailed information of every transducer interface is given.3.1 PWMSome sensors in the market give their measurements using PWM (Pulse Width Modulation). Basically, the sensor generates a signal with fixed period and variable duty cycle depending on the value of the measurement.Reading this signal demands a lot of resources if done via software. The microprocessor should be reading it continuously during at least one cycle, which is usually in the order of tenths or thousands of µs, or even ms, stopping the rest of tasks during this time. In the other side, an FPGA can process this signal in parallel with the rest of system, without stopping it, and with higher precision thanks to its high processing speed. Therefore, this is a good example of the benefits of implementing transducer interfaces in hardware.A module for the family of accelerometers ADXL from Analog Devices has been developed. This module may be adapted to any other sensor with PWM interface with a minimal effort.The acceleration would be normally calculated using the value T 1/T 2 (where T 1 is the time during which the output signal is ‘1’ and T 2 is the period) which implies including a divider in the design, that consumes many resources in hardware terms. In order to avoid the divider, it has been supposed that T 2 is constant. This assumption is valid once R SET (resistance value that fixes the period of the signal) is fixed. A parameter that represents T 2 is included in the module as a constant, so adjusting the module to different periods only needs correcting this constant, but there is no divider circuit.3.2 Period/FrequencyThere are a lot of sensors whose output is codified in period or frequency. The library includes modules designed for these coding strategies, which have been applied to two specific temperature sensors. These sensors are MAX6576 and MAX6577 from Maxim. The former gives the temperature codified in period and the latter in frequency. The modules in the library are easily adaptable to other sensors with similar output signals.If a period interface is used, the measurement consists on counting the number of clock cycles in each output cycle. In the case of the frequency coding strategy, the same interface could be used, calculating the inverse of the period. However, in order to avoid the divider, which demands a lot of hardware resources, a different measurement method has been used. It is based on counting the number of output cycles in a certain constant time, as this number is proportional to the frequency.3.3 I2CI2C (Inter-Integrated Circuit) is a serial bidirectional bus developed by Philips which uses two lines (SCL or clock and SDA or data). It was thought to make easier the communication between peripherals in a motherboard or an embedded system.This kind of interface is very usual in sensors today, probably the most popular, so it has been included in the library. As an example, a module for the DS1629 temperature sensor from Maxim has been designed. This temperature sensor also includes a real time clock.The sensor is treated as two sensor channels (temperature and real time clock) and an actuator channel (for programming the clock), using the IEEE 1451 philosophy: including a different channel for each functionality (Fig. 5). TemperatureRealDS1629Sensor TimeClock Sensor Channel →TemperatureSensor Channel →Read clock Actuator Channel →Clock ConfigurationFig. 5 Module structure for I2C interfaceDue to the complexity of this interface compared to the previous ones, the structure of this module uses four levels of nested FSMs. Each level has the following functionality:Attending triggers from each channel. There is a separate TrigStates FSM for each channel but, as the I2Cinterface is shared, if all the channels are triggered simultaneously they receive access to the interface depending on their priority level, which is set in the module.Managing the requests to the sensor. This second level (DataStates) is common in all the modules of the library.The difference is that, in this case, it is not in charge of controlling directly the interface signals due to the complexity of the process. Its task is managing the FSMs at lower levels.Sending and receiving I2C frames. The third level is in charge of managing the frames sent or received from the sensor. Two different FSMs control each kind of frame: ReadStates for receiving data and WriteStates for sending data.Sending and receiving bytes. As all the information in I2C is sent in separate bytes, the task of sending or receiving each individual byte is done in this fourth level. Again, there are two FSMs: SendStates, for sending a byte to the sensor, and ReceiveStates, for receiving a byte from the sensor.3.4 Sensirion interface (similar to I2C)There is a series of sensors (SHT1x/SHT7X) from Sensirion that use an interface similar to I2C. These sensors are very common in sensor networks applications due to their low size and digital output. The Sensirion interface presents mainly the following differences from I2C. Signals are named SCK and DATA, instead of SCL and SDA. SCK is not open-drain, and its default value is ‘0’ instead of ‘1’. The “start” sequence is also different and there is no “stop” sequence in the Sensirion interface. The communication finishes when there is no acknowledge to a byte.The chosen sensor, SHT11, is seen as two different channels, because it includes two different measurements: temperature and humidity. In this case, a three level FSMs strategy was used, instead of the four level strategy in the I2C module. However, the main idea is similar to the previous one.3.5 Analog transducersMany sensors in the market have analog outputs. Because of this, the interfaces library must include a way of dealing with these sensors.All the previous modules deal with digital signals, so a VHDL implementation can be in charge of them directly. However, for analog transducers an ADC or a DAC will be necessary, depending on whether it is a sensor or an actuator respectively. Therefore, the control of an analog transducer is equivalent to the control of an ADC or a DAC.In the library, modules for controlling two different ADCs and a DAC have been included. The ADCs have been chosen because they represent the two most usual interfaces in ADCs, in particular:o AD0808: this ADC has 8 analog multiplexed inputs. This is a problem if every analog input has to be defined asa sensor channel. The reason is that the number of signals in the interface with the rest of the system would bemultiplied by 8. The solution was to include an actuator channel in order to tell the interface module which input must be used at each time. In this way, the controller can set the active input from the ADC. Regarding the conversion interface, it is controlled through two signals: “start of conversion” and “end of conversion”.o HI5805: this ADC converts its input continuously. It only needs an external clock input (0.5-5 MHz) as interface. The analog to digital conversion is done using a pipelined flash structure, which introduces a latency of 3 clock cycles. This is taken into account in the module to synchronize the measurement with high accuracy.o DAC8562: this DAC has a 12-bit parallel input. It has a 12-bit latch controlled by the CE signal, and an additional clear signal.All these three modules include two FSMs, TrigStates and DataStates, as explained in the previous section. This interface is difficult to be generalized as there are many different types of ADCs or DACs and each has its own interface.3.6 The 1-Wire® interfaceThe 1-Wire interface is a proprietary communication protocol from Dallas Semiconductor. The 1-Wire bus is a simple signaling scheme that performs half-duplex bidirectional communications between a host/master controller and one or more slaves sharing a common data line [9]. The slaves can take the energy from the data line, charging an internal capacitor when this data line is high state (actually, the 1-Wire protocol is a “two wire” because of the ground signal). There are a lot of different products available with this standard, like temperature sensors, memories (EEPROM, EPROM and SRAM) and analog to digital converters from Dallas, among others. In this context, and foreseeing future new devices from this and other manufacturers, a hardware interface for the 1-Wire protocol has been developed. Dealing with the 1-Wire signals using a microprocessor demands performing the timing functions (bit-banging). TheCPU is idled for up to 60 microseconds for every bit sent and at least 480 microseconds when generating a 1-Wire Reset [10].Dallas distributes a 1-Wire master (Fig. 6) available in VHDL, in order to make easier 1-Wire integration without overload the microprocessor.The host only has to load commands into the 1-Wire master and read and write data. Depending on the application, it will be better to implement the 1-Wire master into the microcontroller or outside. This is a clear example of the use of generic hardware interfaces to deal with sensors and actuators. In this case, the interface is based in a public core from Dallas, and can be easily adapted to the general structure for the library of interfaces. It is necessary only to include a module to adapt the core from Dallas to the generic architecture for the interfaces presented in this paper. In this way, the microcontroller will send a trigger every time a measure has to be taken, and the interface will make all the rest of tasks. The development effort is short and the generality of the interface allows adapting it to different 1-Wire devices in an easy way.Fig. 6. 1-Wire bus master schematic.4.VERIFICATION AND EXPERIMENTAL RESULTSAll the modules in the library have been tested using a Xilinx Spartan 3 XC3S200 FPGA. But before starting with the experimental verification, exhaustive simulations have been carried out for each module. In order to do so, a functional model of each sensor has been written in VHDL. This model is connected with its respective module, and the test bench generates the different values that are measured by the model of the sensor. Furthermore, the test bench is also in charge of the signals for every channel, such as the trigger.Then, two kinds of simulations have been accomplished for every module. The first simulation is a simple one, just to know if the module works correctly with its sensor. This simulation was verified watching the waveforms. The second simulation guarantees that the module works appropriately even in bizarre conditions. For instance, conditions such as simultaneous triggers of different channels, rapid changes in the sensor values for synchronization verification, errors in the sensor communication, etc, were tested. Very long simulations were necessary for these exhaustive verifications, so visual inspection of waveforms was inappropriate. Therefore, automatic verification mechanisms were included in the test bench, making use of VHDL procedures and functions. All these conditions were reported through text messages. The simulation tool was ModelSim.After simulations were correct, experimental tests were made in hardware using real sensors. In this way, the interface modules were synthesized in the FPGA and the different sensors were attached to the system. In order to complete the hardware verification, additional VHDL blocks were developed for managing the channels of each module and showing the results through LEDs and displays. The last step is to include these interfaces in the modular platform for wireless sensor networks (Fig. 7).Fig. 7 Modular platform for wireless sensor networks and sensor layer with ADXL213 accelerometer, MAX 6576,DS18S20 and DS1629 temperature sensors5.CONCLUSIONSA VHDL library for sensor/actuator interfaces has been presented. The library is used on a modular platform for wireless sensor networks. The library makes the sensor almost transparent for the user, who always sees the same signals independently of the sensor being used.Exhaustive simulations have been carried out in order to make sure that the modules are correct. Furthermore, experimental tests have also been accomplished for every module in the library. Finally, the transducer interface modules have been integrated in the modular platform for wireless sensor networks.These interfaces integrated in the UPM platform are currently being used for different applications that are being developed: structural control of walls, mining industry application, fruit transportation control and an amusement application made to produce effects on music.REFERENCES1.Chee-Yee Chong, Srikanta P. Kumar, “Sensor Networks: Evolution, Opportunities and Challenges,” Proc. of theIEEE, vol. 91, Nº 8, Aug. 2003, pp. 1247–1256.2.Y. Zhang, Y. Gu, V. Vlatkovic, X. Wang, “Progress of Smart Sensors and Smart Sensor Networks,” Proc. of the5th IEEE World Congress on Inteligent Control and Automation, Jun. 2004, pp. 3600–3606.3. A.Y. Benbasat, J.A. Paradiso, “A Compact Modular Wireless Sensor Platform,” Proc. of the 4th IEEEInternational Symposium on Information Processing in Sensor Networks, Apr. 2005, pp. 410–415.4.L. Nachman, R. Kling, R. Adler, J. Huang, V. Hummel, “The Intel Mote Platform: a Bluetooth-Based SensorNetwork for Industrial Monitoring,” Proc. of the 4th IEEE International Symposium on Information Processing in Sensor Networks, Apr. 2005, pp. 437-442.5.S. Yamshita, T. Shimura, K. Aiki, K. Ara, Y. Ogata, I. Shimokawa, T. Tanaka, H. Kuriyama, K. Shimada, K.Yano, “A 15x15, 1 µA, Reliable Sensor-Net Module: Enabling Application-Specific Nodes,” Proc. of the 5th IEEE/ACM International Conference on Information Processing in Sensor Networks, April. 2006, pp. 383–390. 6.J. Portilla, A. de Castro, E. de la Torre, T. Riesgo, “A Modular Architecture for Nodes in Wireless SensorNetworks”, Journal of Universal Computer Science, vol. 12, nº 3, March 2006, pp. 328-339.7. D. Chu, K. Lin, A. Linares, G. Nguyen, J. M. Hellerstein, "Sdlib: a Sensor Network Data and CommunicationsLibrary for Rapid and Robust Application Development," Proc. of the 5th IEEE/ACM International Conference on Information Processing in Sensor Networks, April 2006, pp. 432–440.8.K. B. Lee, R. D. Schneeman, “Distributed measurement and control based on the IEEE 1451 smart transducerinterface standards,” IEEE Transactions on Instrumentation and Measurement, vol. 49, issue 3, pp. 621–627, Jun.2000.9.Dallas Semiconductor 1-Wire web page: /appnotes.cfm/appnote_number/398910.Specification for the Synthesizable 1-Wire Bus Master: /en/ds/DS1WM.pdf。