DEMO9RS08KB12_QSG_0
NuMicro N9H30系列开发板用户手册说明书

NuMicro®FamilyArm® ARM926EJ-S BasedNuMaker-HMI-N9H30User ManualEvaluation Board for NuMicro® N9H30 SeriesNUMAKER-HMI-N9H30 USER MANUALThe information described in this document is the exclusive intellectual property ofNuvoton Technology Corporation and shall not be reproduced without permission from Nuvoton.Nuvoton is providing this document only for reference purposes of NuMicro microcontroller andmicroprocessor based system design. Nuvoton assumes no responsibility for errors or omissions.All data and specifications are subject to change without notice.For additional information or questions, please contact: Nuvoton Technology Corporation.Table of Contents1OVERVIEW (5)1.1Features (7)1.1.1NuMaker-N9H30 Main Board Features (7)1.1.2NuDesign-TFT-LCD7 Extension Board Features (7)1.2Supporting Resources (8)2NUMAKER-HMI-N9H30 HARDWARE CONFIGURATION (9)2.1NuMaker-N9H30 Board - Front View (9)2.2NuMaker-N9H30 Board - Rear View (14)2.3NuDesign-TFT-LCD7 - Front View (20)2.4NuDesign-TFT-LCD7 - Rear View (21)2.5NuMaker-N9H30 and NuDesign-TFT-LCD7 PCB Placement (22)3NUMAKER-N9H30 AND NUDESIGN-TFT-LCD7 SCHEMATICS (24)3.1NuMaker-N9H30 - GPIO List Circuit (24)3.2NuMaker-N9H30 - System Block Circuit (25)3.3NuMaker-N9H30 - Power Circuit (26)3.4NuMaker-N9H30 - N9H30F61IEC Circuit (27)3.5NuMaker-N9H30 - Setting, ICE, RS-232_0, Key Circuit (28)NUMAKER-HMI-N9H30 USER MANUAL3.6NuMaker-N9H30 - Memory Circuit (29)3.7NuMaker-N9H30 - I2S, I2C_0, RS-485_6 Circuit (30)3.8NuMaker-N9H30 - RS-232_2 Circuit (31)3.9NuMaker-N9H30 - LCD Circuit (32)3.10NuMaker-N9H30 - CMOS Sensor, I2C_1, CAN_0 Circuit (33)3.11NuMaker-N9H30 - RMII_0_PF Circuit (34)3.12NuMaker-N9H30 - RMII_1_PE Circuit (35)3.13NuMaker-N9H30 - USB Circuit (36)3.14NuDesign-TFT-LCD7 - TFT-LCD7 Circuit (37)4REVISION HISTORY (38)List of FiguresFigure 1-1 Front View of NuMaker-HMI-N9H30 Evaluation Board (5)Figure 1-2 Rear View of NuMaker-HMI-N9H30 Evaluation Board (6)Figure 2-1 Front View of NuMaker-N9H30 Board (9)Figure 2-2 Rear View of NuMaker-N9H30 Board (14)Figure 2-3 Front View of NuDesign-TFT-LCD7 Board (20)Figure 2-4 Rear View of NuDesign-TFT-LCD7 Board (21)Figure 2-5 Front View of NuMaker-N9H30 PCB Placement (22)Figure 2-6 Rear View of NuMaker-N9H30 PCB Placement (22)Figure 2-7 Front View of NuDesign-TFT-LCD7 PCB Placement (23)Figure 2-8 Rear View of NuDesign-TFT-LCD7 PCB Placement (23)Figure 3-1 GPIO List Circuit (24)Figure 3-2 System Block Circuit (25)Figure 3-3 Power Circuit (26)Figure 3-4 N9H30F61IEC Circuit (27)Figure 3-5 Setting, ICE, RS-232_0, Key Circuit (28)Figure 3-6 Memory Circuit (29)Figure 3-7 I2S, I2C_0, RS-486_6 Circuit (30)Figure 3-8 RS-232_2 Circuit (31)Figure 3-9 LCD Circuit (32)NUMAKER-HMI-N9H30 USER MANUAL Figure 3-10 CMOS Sensor, I2C_1, CAN_0 Circuit (33)Figure 3-11 RMII_0_PF Circuit (34)Figure 3-12 RMII_1_PE Circuit (35)Figure 3-13 USB Circuit (36)Figure 3-14 TFT-LCD7 Circuit (37)List of TablesTable 2-1 LCD Panel Combination Connector (CON8) Pin Function (11)Table 2-2 Three Sets of Indication LED Functions (12)Table 2-3 Six Sets of User SW, Key Matrix Functions (12)Table 2-4 CMOS Sensor Connector (CON10) Function (13)Table 2-5 JTAG ICE Interface (J2) Function (14)Table 2-6 Expand Port (CON7) Function (16)Table 2-7 UART0 (J3) Function (16)Table 2-8 UART2 (J6) Function (16)Table 2-9 RS-485_6 (SW6~8) Function (17)Table 2-10 Power on Setting (SW4) Function (17)Table 2-11 Power on Setting (S2) Function (17)Table 2-12 Power on Setting (S3) Function (17)Table 2-13 Power on Setting (S4) Function (17)Table 2-14 Power on Setting (S5) Function (17)Table 2-15 Power on Setting (S7/S6) Function (18)Table 2-16 Power on Setting (S9/S8) Function (18)Table 2-17 CMOS Sensor Connector (CON9) Function (19)Table 2-18 CAN_0 (SW9~10) Function (19)NUMAKER-HMI-N9H30 USER MANUAL1 OVERVIEWThe NuMaker-HMI-N9H30 is an evaluation board for GUI application development. The NuMaker-HMI-N9H30 consists of two parts: a NuMaker-N9H30 main board and a NuDesign-TFT-LCD7 extensionboard. The NuMaker-HMI-N9H30 is designed for project evaluation, prototype development andvalidation with HMI (Human Machine Interface) function.The NuMaker-HMI-N9H30 integrates touchscreen display, voice input/output, rich serial port serviceand I/O interface, providing multiple external storage methods.The NuDesign-TFT-LCD7 can be plugged into the main board via the DIN_32x2 extension connector.The NuDesign-TFT-LCD7 includes one 7” LCD which the resolution is 800x480 with RGB-24bits andembedded the 4-wires resistive type touch panel.Figure 1-1 Front View of NuMaker-HMI-N9H30 Evaluation BoardNUMAKER-HMI-N9H30 USER MANUAL Figure 1-2 Rear View of NuMaker-HMI-N9H30 Evaluation Board1.1 Features1.1.1 NuMaker-N9H30 Main Board Features●N9H30F61IEC chip: LQFP216 pin MCP package with DDR (64 MB)●SPI Flash using W25Q256JVEQ (32 MB) booting with quad mode or storage memory●NAND Flash using W29N01HVSINA (128 MB) booting or storage memory●One Micro-SD/TF card slot served either as a SD memory card for data storage or SDIO(Wi-Fi) device●Two sets of COM ports:–One DB9 RS-232 port with UART_0 used 75C3232E transceiver chip can be servedfor function debug and system development.–One DB9 RS-232 port with UART_2 used 75C3232E transceiver chip for userapplication●22 GPIO expansion ports, including seven sets of UART functions●JTAG interface provided for software development●Microphone input and Earphone/Speaker output with 24-bit stereo audio codec(NAU88C22) for I2S interfaces●Six sets of user-configurable push button keys●Three sets of LEDs for status indication●Provides SN65HVD230 transceiver chip for CAN bus communication●Provides MAX3485 transceiver chip for RS-485 device connection●One buzzer device for program applicationNUMAKER-HMI-N9H30 USER MANUAL●Two sets of RJ45 ports with Ethernet 10/100 Mbps MAC used IP101GR PHY chip●USB_0 that can be used as Device/HOST and USB_1 that can be used as HOSTsupports pen drives, keyboards, mouse and printers●Provides over-voltage and over current protection used APL3211A chip●Retain RTC battery socket for CR2032 type and ADC0 detect battery voltage●System power could be supplied by DC-5V adaptor or USB VBUS1.1.2 NuDesign-TFT-LCD7 Extension Board Features●7” resolution 800x480 4-wire resistive touch panel for 24-bits RGB888 interface●DIN_32x2 extension connector1.2 Supporting ResourcesFor sample codes and introduction about NuMaker-N9H30, please refer to N9H30 BSP:https:///products/gui-solution/gui-platform/numaker-hmi-n9h30/?group=Software&tab=2Visit NuForum for further discussion about the NuMaker-HMI-N9H30:/viewforum.php?f=31 NUMAKER-HMI-N9H30 USER MANUALNUMAKER-HMI-N9H30 USER MANUAL2 NUMAKER-HMI-N9H30 HARDWARE CONFIGURATION2.1 NuMaker-N9H30 Board - Front View Combination Connector (CON8)6 set User SWs (K1~6)3set Indication LEDs (LED1~3)Power Supply Switch (SW_POWER1)Audio Codec(U10)Microphone(M1)NAND Flash(U9)RS-232 Transceiver(U6, U12)RS-485 Transceiver(U11)CAN Transceiver (U13)Figure 2-1 Front View of NuMaker-N9H30 BoardFigure 2-1 shows the main components and connectors from the front side of NuMaker-N9H30 board. The following lists components and connectors from the front view:NuMaker-N9H30 board and NuDesign-TFT-LCD7 board combination connector (CON8). This panel connector supports 4-/5-wire resistive touch or capacitance touch panel for 24-bits RGB888 interface.Connector GPIO pin of N9H30 FunctionCON8.1 - Power 3.3VCON8.2 - Power 3.3VCON8.3 GPD7 LCD_CSCON8.4 GPH3 LCD_BLENCON8.5 GPG9 LCD_DENCON8.7 GPG7 LCD_HSYNCCON8.8 GPG6 LCD_CLKCON8.9 GPD15 LCD_D23(R7)CON8.10 GPD14 LCD_D22(R6)CON8.11 GPD13 LCD_D21(R5)CON8.12 GPD12 LCD_D20(R4)CON8.13 GPD11 LCD_D19(R3)CON8.14 GPD10 LCD_D18(R2)CON8.15 GPD9 LCD_D17(R1)CON8.16 GPD8 LCD_D16(R0)CON8.17 GPA15 LCD_D15(G7)CON8.18 GPA14 LCD_D14(G6)CON8.19 GPA13 LCD_D13(G5)CON8.20 GPA12 LCD_D12(G4)CON8.21 GPA11 LCD_D11(G3)CON8.22 GPA10 LCD_D10(G2)CON8.23 GPA9 LCD_D9(G1) NUMAKER-HMI-N9H30 USER MANUALCON8.24 GPA8 LCD_D8(G0)CON8.25 GPA7 LCD_D7(B7)CON8.26 GPA6 LCD_D6(B6)CON8.27 GPA5 LCD_D5(B5)CON8.28 GPA4 LCD_D4(B4)CON8.29 GPA3 LCD_D3(B3)CON8.30 GPA2 LCD_D2(B2)CON8.31 GPA1 LCD_D1(B1)CON8.32 GPA0 LCD_D0(B0)CON8.33 - -CON8.34 - -CON8.35 - -CON8.36 - -CON8.37 GPB2 LCD_PWMCON8.39 - VSSCON8.40 - VSSCON8.41 ADC7 XPCON8.42 ADC3 VsenCON8.43 ADC6 XMCON8.44 ADC4 YMCON8.45 - -CON8.46 ADC5 YPCON8.47 - VSSCON8.48 - VSSCON8.49 GPG0 I2C0_CCON8.50 GPG1 I2C0_DCON8.51 GPG5 TOUCH_INTCON8.52 - -CON8.53 - -CON8.54 - -CON8.55 - -NUMAKER-HMI-N9H30 USER MANUAL CON8.56 - -CON8.57 - -CON8.58 - -CON8.59 - VSSCON8.60 - VSSCON8.61 - -CON8.62 - -CON8.63 - Power 5VCON8.64 - Power 5VTable 2-1 LCD Panel Combination Connector (CON8) Pin Function●Power supply switch (SW_POWER1): System will be powered on if the SW_POWER1button is pressed●Three sets of indication LEDs:LED Color DescriptionsLED1 Red The system power will beterminated and LED1 lightingwhen the input voltage exceeds5.7V or the current exceeds 2A.LED2 Green Power normal state.LED3 Green Controlled by GPH2 pin Table 2-2 Three Sets of Indication LED Functions●Six sets of user SW, Key Matrix for user definitionKey GPIO pin of N9H30 FunctionK1 GPF10 Row0 GPB4 Col0K2 GPF10 Row0 GPB5 Col1K3 GPE15 Row1 GPB4 Col0K4 GPE15 Row1 GPB5 Col1K5 GPE14 Row2 GPB4 Col0K6GPE14 Row2GPB5 Col1 Table 2-3 Six Sets of User SW, Key Matrix Functions●NAND Flash (128 MB) with Winbond W29N01HVS1NA (U9)●Microphone (M1): Through Nuvoton NAU88C22 chip sound input●Audio CODEC chip (U10): Nuvoton NAU88C22 chip connected to N9H30 using I2Sinterface–SW6/SW7/SW8: 1-2 short for RS-485_6 function and connected to 2P terminal (CON5and J5)–SW6/SW7/SW8: 2-3 short for I2S function and connected to NAU88C22 (U10).●CMOS Sensor connector (CON10, SW9~10)–SW9~10: 1-2 short for CAN_0 function and connected to 2P terminal (CON11)–SW9~10: 2-3 short for CMOS sensor function and connected to CMOS sensorconnector (CON10)Connector GPIO pin of N9H30 FunctionCON10.1 - VSSCON10.2 - VSSNUMAKER-HMI-N9H30 USER MANUALCON10.3 - Power 3.3VCON10.4 - Power 3.3VCON10.5 - -CON10.6 - -CON10.7 GPI4 S_PCLKCON10.8 GPI3 S_CLKCON10.9 GPI8 S_D0CON10.10 GPI9 S_D1CON10.11 GPI10 S_D2CON10.12 GPI11 S_D3CON10.13 GPI12 S_D4CON10.14 GPI13 S_D5CON10.15 GPI14 S_D6CON10.16 GPI15 S_D7CON10.17 GPI6 S_VSYNCCON10.18 GPI5 S_HSYNCCON10.19 GPI0 S_PWDNNUMAKER-HMI-N9H30 USER MANUAL CON10.20 GPI7 S_nRSTCON10.21 GPG2 I2C1_CCON10.22 GPG3 I2C1_DCON10.23 - VSSCON10.24 - VSSTable 2-4 CMOS Sensor Connector (CON10) FunctionNUMAKER-HMI-N9H30 USER MANUAL2.2NuMaker-N9H30 Board - Rear View5V In (CON1)RS-232 DB9 (CON2,CON6)Expand Port (CON7)Speaker Output (J4)Earphone Output (CON4)Buzzer (BZ1)System ResetSW (SW5)SPI Flash (U7,U8)JTAG ICE (J2)Power ProtectionIC (U1)N9H30F61IEC (U5)Micro SD Slot (CON3)RJ45 (CON12, CON13)USB1 HOST (CON15)USB0 Device/Host (CON14)CAN_0 Terminal (CON11)CMOS Sensor Connector (CON9)Power On Setting(SW4, S2~S9)RS-485_6 Terminal (CON5)RTC Battery(BT1)RMII PHY (U14,U16)Figure 2-2 Rear View of NuMaker-N9H30 BoardFigure 2-2 shows the main components and connectors from the rear side of NuMaker-N9H30 board. The following lists components and connectors from the rear view:● +5V In (CON1): Power adaptor 5V input ●JTAG ICE interface (J2) ConnectorGPIO pin of N9H30Function J2.1 - Power 3.3V J2.2 GPJ4 nTRST J2.3 GPJ2 TDI J2.4 GPJ1 TMS J2.5 GPJ0 TCK J2.6 - VSS J2.7 GPJ3 TD0 J2.8-RESETTable 2-5 JTAG ICE Interface (J2) Function●SPI Flash (32 MB) with Winbond W25Q256JVEQ (U7); only one (U7 or U8) SPI Flashcan be used●System Reset (SW5): System will be reset if the SW5 button is pressed●Buzzer (BZ1): Control by GPB3 pin of N9H30●Speaker output (J4): Through the NAU88C22 chip sound output●Earphone output (CON4): Through the NAU88C22 chip sound output●Expand port for user use (CON7):Connector GPIO pin of N9H30 FunctionCON7.1 - Power 3.3VCON7.2 - Power 3.3VCON7.3 GPE12 UART3_TXDCON7.4 GPH4 UART1_TXDCON7.5 GPE13 UART3_RXDCON7.6 GPH5 UART1_RXDCON7.7 GPB0 UART5_TXDCON7.8 GPH6 UART1_RTSCON7.9 GPB1 UART5_RXDCON7.10 GPH7 UART1_CTSCON7.11 GPI1 UART7_TXDNUMAKER-HMI-N9H30 USER MANUAL CON7.12 GPH8 UART4_TXDCON7.13 GPI2 UART7_RXDCON7.14 GPH9 UART4_RXDCON7.15 - -CON7.16 GPH10 UART4_RTSCON7.17 - -CON7.18 GPH11 UART4_CTSCON7.19 - VSSCON7.20 - VSSCON7.21 GPB12 UART10_TXDCON7.22 GPH12 UART8_TXDCON7.23 GPB13 UART10_RXDCON7.24 GPH13 UART8_RXDCON7.25 GPB14 UART10_RTSCON7.26 GPH14 UART8_RTSCON7.27 GPB15 UART10_CTSCON7.28 GPH15 UART8_CTSCON7.29 - Power 5VCON7.30 - Power 5VTable 2-6 Expand Port (CON7) Function●UART0 selection (CON2, J3):–RS-232_0 function and connected to DB9 female (CON2) for debug message output.–GPE0/GPE1 connected to 2P terminal (J3).Connector GPIO pin of N9H30 Function J3.1 GPE1 UART0_RXDJ3.2 GPE0 UART0_TXDTable 2-7 UART0 (J3) Function●UART2 selection (CON6, J6):–RS-232_2 function and connected to DB9 female (CON6) for debug message output –GPF11~14 connected to 4P terminal (J6)Connector GPIO pin of N9H30 Function J6.1 GPF11 UART2_TXDJ6.2 GPF12 UART2_RXDJ6.3 GPF13 UART2_RTSJ6.4 GPF14 UART2_CTSTable 2-8 UART2 (J6) Function●RS-485_6 selection (CON5, J5, SW6~8):–SW6~8: 1-2 short for RS-485_6 function and connected to 2P terminal (CON5 and J5) –SW6~8: 2-3 short for I2S function and connected to NAU88C22 (U10)Connector GPIO pin of N9H30 FunctionSW6:1-2 shortGPG11 RS-485_6_DISW6:2-3 short I2S_DOSW7:1-2 shortGPG12 RS-485_6_ROSW7:2-3 short I2S_DISW8:1-2 shortGPG13 RS-485_6_ENBSW8:2-3 short I2S_BCLKNUMAKER-HMI-N9H30 USER MANUALTable 2-9 RS-485_6 (SW6~8) FunctionPower on setting (SW4, S2~9).SW State FunctionSW4.2/SW4.1 ON/ON Boot from USB SW4.2/SW4.1 ON/OFF Boot from eMMC SW4.2/SW4.1 OFF/ON Boot from NAND Flash SW4.2/SW4.1 OFF/OFF Boot from SPI Flash Table 2-10 Power on Setting (SW4) FunctionSW State FunctionS2 Short System clock from 12MHzcrystalS2 Open System clock from UPLL output Table 2-11 Power on Setting (S2) FunctionSW State FunctionS3 Short Watchdog Timer OFFS3 Open Watchdog Timer ON Table 2-12 Power on Setting (S3) FunctionSW State FunctionS4 Short GPJ[4:0] used as GPIO pinS4Open GPJ[4:0] used as JTAG ICEinterfaceTable 2-13 Power on Setting (S4) FunctionSW State FunctionS5 Short UART0 debug message ONS5 Open UART0 debug message OFFTable 2-14 Power on Setting (S5) FunctionSW State FunctionS7/S6 Short/Short NAND Flash page size 2KBS7/S6 Short/Open NAND Flash page size 4KBS7/S6 Open/Short NAND Flash page size 8KBNUMAKER-HMI-N9H30 USER MANUALS7/S6 Open/Open IgnoreTable 2-15 Power on Setting (S7/S6) FunctionSW State FunctionS9/S8 Short/Short NAND Flash ECC type BCH T12S9/S8 Short/Open NAND Flash ECC type BCH T15S9/S8 Open/Short NAND Flash ECC type BCH T24S9/S8 Open/Open IgnoreTable 2-16 Power on Setting (S9/S8) FunctionCMOS Sensor connector (CON9, SW9~10)–SW9~10: 1-2 short for CAN_0 function and connected to 2P terminal (CON11).–SW9~10: 2-3 short for CMOS sensor function and connected to CMOS sensorconnector (CON9).Connector GPIO pin of N9H30 FunctionCON9.1 - VSSCON9.2 - VSSCON9.3 - Power 3.3VCON9.4 - Power 3.3V NUMAKER-HMI-N9H30 USER MANUALCON9.5 - -CON9.6 - -CON9.7 GPI4 S_PCLKCON9.8 GPI3 S_CLKCON9.9 GPI8 S_D0CON9.10 GPI9 S_D1CON9.11 GPI10 S_D2CON9.12 GPI11 S_D3CON9.13 GPI12 S_D4CON9.14 GPI13 S_D5CON9.15 GPI14 S_D6CON9.16 GPI15 S_D7CON9.17 GPI6 S_VSYNCCON9.18 GPI5 S_HSYNCCON9.19 GPI0 S_PWDNCON9.20 GPI7 S_nRSTCON9.21 GPG2 I2C1_CCON9.22 GPG3 I2C1_DCON9.23 - VSSCON9.24 - VSSTable 2-17 CMOS Sensor Connector (CON9) Function●CAN_0 Selection (CON11, SW9~10):–SW9~10: 1-2 short for CAN_0 function and connected to 2P terminal (CON11) –SW9~10: 2-3 short for CMOS sensor function and connected to CMOS sensor connector (CON9, CON10)SW GPIO pin of N9H30 FunctionSW9:1-2 shortGPI3 CAN_0_RXDSW9:2-3 short S_CLKSW10:1-2 shortGPI4 CAN_0_TXDSW10:2-3 short S_PCLKTable 2-18 CAN_0 (SW9~10) Function●USB0 Device/HOST Micro-AB connector (CON14), where CON14 pin4 ID=1 is Device,ID=0 is HOST●USB1 for USB HOST with Type-A connector (CON15)●RJ45_0 connector with LED indicator (CON12), RMII PHY with IP101GR (U14)●RJ45_1 connector with LED indicator (CON13), RMII PHY with IP101GR (U16)●Micro-SD/TF card slot (CON3)●SOC CPU: Nuvoton N9H30F61IEC (U5)●Battery power for RTC 3.3V powered (BT1, J1), can detect voltage by ADC0●RTC power has 3 sources:–Share with 3.3V I/O power–Battery socket for CR2032 (BT1)–External connector (J1)●Board version 2.1NUMAKER-HMI-N9H30 USER MANUAL2.3 NuDesign-TFT-LCD7 -Front ViewFigure 2-3 Front View of NuDesign-TFT-LCD7 BoardFigure 2-3 shows the main components and connectors from the Front side of NuDesign-TFT-LCD7board.7” resolution 800x480 4-W resistive touch panel for 24-bits RGB888 interface2.4 NuDesign-TFT-LCD7 -Rear ViewFigure 2-4 Rear View of NuDesign-TFT-LCD7 BoardFigure 2-4 shows the main components and connectors from the rear side of NuDesign-TFT-LCD7board.NuMaker-N9H30 and NuDesign-TFT-LCD7 combination connector (CON1).NUMAKER-HMI-N9H30 USER MANUAL 2.5 NuMaker-N9H30 and NuDesign-TFT-LCD7 PCB PlacementFigure 2-5 Front View of NuMaker-N9H30 PCB PlacementFigure 2-6 Rear View of NuMaker-N9H30 PCB PlacementNUMAKER-HMI-N9H30 USER MANUALFigure 2-7 Front View of NuDesign-TFT-LCD7 PCB PlacementFigure 2-8 Rear View of NuDesign-TFT-LCD7 PCB Placement3 NUMAKER-N9H30 AND NUDESIGN-TFT-LCD7 SCHEMATICS3.1 NuMaker-N9H30 - GPIO List CircuitFigure 3-1 shows the N9H30F61IEC GPIO list circuit.Figure 3-1 GPIO List Circuit NUMAKER-HMI-N9H30 USER MANUAL3.2 NuMaker-N9H30 - System Block CircuitFigure 3-2 shows the System Block Circuit.NUMAKER-HMI-N9H30 USER MANUALFigure 3-2 System Block Circuit3.3 NuMaker-N9H30 - Power CircuitFigure 3-3 shows the Power Circuit.NUMAKER-HMI-N9H30 USER MANUALFigure 3-3 Power Circuit3.4 NuMaker-N9H30 - N9H30F61IEC CircuitFigure 3-4 shows the N9H30F61IEC Circuit.Figure 3-4 N9H30F61IEC CircuitNUMAKER-HMI-N9H30 USER MANUAL3.5 NuMaker-N9H30 - Setting, ICE, RS-232_0, Key CircuitFigure 3-5 shows the Setting, ICE, RS-232_0, Key Circuit.NUMAKER-HMI-N9H30 USER MANUALFigure 3-5 Setting, ICE, RS-232_0, Key Circuit3.6 NuMaker-N9H30 - Memory CircuitFigure 3-6 shows the Memory Circuit.NUMAKER-HMI-N9H30 USER MANUALFigure 3-6 Memory Circuit3.7 NuMaker-N9H30 - I2S, I2C_0, RS-485_6 CircuitFigure 3-7 shows the I2S, I2C_0, RS-486_6 Circuit.NUMAKER-HMI-N9H30 USER MANUALFigure 3-7 I2S, I2C_0, RS-486_6 Circuit3.8 NuMaker-N9H30 - RS-232_2 CircuitFigure 3-8 shows the RS-232_2 Circuit.NUMAKER-HMI-N9H30 USER MANUALFigure 3-8 RS-232_2 Circuit3.9 NuMaker-N9H30 - LCD CircuitFigure 3-9 shows the LCD Circuit.NUMAKER-HMI-N9H30 USER MANUALFigure 3-9 LCD Circuit3.10 NuMaker-N9H30 - CMOS Sensor, I2C_1, CAN_0 CircuitFigure 3-10 shows the CMOS Sensor,I2C_1, CAN_0 Circuit.NUMAKER-HMI-N9H30 USER MANUALFigure 3-10 CMOS Sensor, I2C_1, CAN_0 Circuit3.11 NuMaker-N9H30 - RMII_0_PF CircuitFigure 3-11 shows the RMII_0_RF Circuit.NUMAKER-HMI-N9H30 USER MANUALFigure 3-11 RMII_0_PF Circuit3.12 NuMaker-N9H30 - RMII_1_PE CircuitFigure 3-12 shows the RMII_1_PE Circuit.NUMAKER-HMI-N9H30 USER MANUALFigure 3-12 RMII_1_PE Circuit3.13 NuMaker-N9H30 - USB CircuitFigure 3-13 shows the USB Circuit.NUMAKER-HMI-N9H30 USER MANUALFigure 3-13 USB Circuit3.14 NuDesign-TFT-LCD7 - TFT-LCD7 CircuitFigure 3-14 shows the TFT-LCD7 Circuit.Figure 3-14 TFT-LCD7 CircuitNUMAKER-HMI-N9H30 USER MANUAL4 REVISION HISTORYDate Revision Description2022.03.24 1.00 Initial version NUMAKER-HMI-N9H30 USER MANUALNUMAKER-HMI-N9H30 USER MANUALImportant NoticeNuvoton Products are neither intended nor warranted for usage in systems or equipment, anymalfunction or failure of which may cause loss of human life, bodily injury or severe propertydamage. Such applications are deemed, “Insecure Usage”.Insecure usage includes, but is not limited to: equipment for surgical implementation, atomicenergy control instruments, airplane or spaceship instruments, the control or operation ofdynamic, brake or safety systems designed for vehicular use, traffic signal instruments, all typesof safety devices, and other applications intended to support or sustain life.All Insecure Usage shall be made at customer’s risk, and in the event that third parties lay claimsto Nuvoton as a result of customer’s Insecure Usage, custome r shall indemnify the damagesand liabilities thus incurred by Nuvoton.。
KSZ8851-16MLL DEMO BOARD 48-PIN ETHERNET CONTROLLE

SD13
SD7 40
CPU_D14 3
6
SD14
SD8 39
CPU_D15 4
5
SD15
SD9 36
SD10 35
33
SD11 34
CPU_CMD
33
SD12 33
R10
SD13 32
CPU_CSN
33
SD14 31
R12
SD15 30
CPU_WRN
33
CMD
11
R14
CPU_RDN
33
CSN
12
R16
5 6 7 8
TANT
C27
R28 10uF
470pF 2.49K
Power 3.3V 0.1uF (red LED)
CSN CMD
4.7K R27 4.7K R29
GBLC03C_0 D3
GND 2 GND
VR 5 3.3VA
INTRN 4.7K R30
VOUT = 1.24 X [ 1 + ( 2.49k/ 1.5K ) ]
5
4
3
KSZ8851-16MLL (48-pin) Demo Board Black Diagram
D
Headers 20x2
RJ45
LAN1 T
KSZ8851-16MLL
Reset
Power
+1.8V
+2.5V
+3.3V
STATUS LEDs
OSC
EEPROM
C
MIC5209YM
25 MHz
AT93C46
x2
2
1
DATE:
MC9RS08KA8微控制器单元说明书

Target Applications • High-brightness LED • Lighting systems control • Toys• Small handheld devices• Space-constrained applications • Small appliances• AC line voltage monitoring • Battery charger • ASIC replacement OverviewThe MC9RS08KA8 microcontroller unit (MCU) is an extremely cost-effective and highly integrated, device intended for home appliances, health care equipment and as a general-purpose microcontroller. This device is composed of standard on-chip modules including a very small and highly efficient RS08 CPU core, 254 bytes RAM, 8K bytes flash, two 8-bit modulo timers,12-channel 10-bit ADC, 2-channel 16-bit timer/PWM, inter-integrated circuit bus module, keyboard interrupt and analog comparator. The device is available in 16- and 20-pin packages.Cost-Effective Development toolsFor more information on development tools, please refer to the Freescale Development Tool Selector Guide (SG1011).CodeWarrior ® Development Studio for Microcontrollers 6.1Complimentary*CodeWarrior Development Studio for Microcontrollers is an integrated tool suite that supports software development for Freescale’s 8-bit or 32-bit microcontrollers. Designers can further accelerate application development with the help of the Processor Expert™ tool, which is an award-winning rapid application development tool in the CodeWarrior tool suite.DEMO9RS08KA8$50 MSRPCost-effective demonstration board with potentiometer, LEDs and a built-in USB-BDM cable for debugging and programming.8-bit MicrocontrollersMC9RS08KA8/4Package OptionsPart NumberPackageTemp. Range* Subject to license agreement and registrationFreescale and the Freescale logo are trademarks or registered trademarks of Freescale Semiconductor, Inc. in the U.S. and other countries. All other product or service names are the property of their respective owners. © Freescale Semiconductor, Inc. 2008.Document Number: MC9RS08KA8/4FSREV 1。
NSG 435 ESD Simulator User Manual

1NSG 435 ESD SIMULATORUSER MANUAL5.4 Air/Contact-discharge 28 5.5 Voltage 29 5.6 Polarity 30 5.7 Repetition frequency 31 5.8 Counter 31 5.9 Preselect counter 32 5.10 Automatic polarity switching 34 5.11 Continuous operation 375.12 Storing voltage settings 396 Test procedures 41 6.1 Standard-conforms procedures 416.2 Other conditions 417 Verification of the pulse data 438 Maintenance 44 8.1 Servicing 44 8.2 Calibration 44 8.3 Exchanging the R/C network 47 8.3.1 Derating of pulse repetition at increased capacitance 49 8.4 Repairs 508.5 Disposal 509 Declaration of Conformity CE 5110 Technical specifications 5211 ESD standards 5412 Warranty 5513 Odering information 5614 Addresses 57discharge network (exchangeable)measuring electronicshigh voltage relaypolarity changeovertrigger connection Test finger (exchangeable)Earth cableconnectionPulse triggerExchangeablebattery packTripod bushUNC1/4-20HandgripF1 Toggle between air and contact-discharge (and vice versa) Increment voltage and counterF2 Activation of voltage settingDecrement voltage and counterF3 Polarity switching:Selection of pre-programmed test levelsPreselect counter on/offF4 Selection of discharge mode:Single discharge Repetitive discharge at 0.5, 1, 5, 10, 20, 25 Hzfor air-dischargeRepetitive discharge at 0.5, 1, 5, 10 Hz for contact-dischargeAutomatic polarity switchingStorage of programmed test levelsF5 Resets the counterReturn from second functionNSG 435 ESD simulatorposes.The handgrip adapter is an integral part of this power supply unit. It contains electrical components that are necessary for this mode of operation. It is not per-missible to operate the NSG 435 with a power supply unit from another system.The power supply unit can be used on all common AC mains supplies without having to make any adjustments, thus:80 to 240 V (50/60 Hz) with 3-pin IEC connectorMatching 3-core mains cable20NSG 435 ESD simulator The power supply unit must be connected to a mains outlet having a protectiveearth.The protective earth connection does not replace the earth cable for the opera-tion of the NSG 435. To ensure safe and valid test operation the earth cable must be correctly connected as the pulse return path in every case.The mains power supply unit is constructed in conformity with the relevant safety standards and carries the appropriate test symbol.3.3.5 Discharge networksThe basic set contains a discharge network and test fingers that conforms to IEC/EN 61000-4-2, Ed. 1.2:2001.Alternative networks can be installed for testing in accordance with other standards.The discharge network and test fingers form a mutually matched combination. They are labeled with a corresponding INA number. The specified pulse data are only achieved while this combination is maintained.Several combinations are given in the order list. The C and R values of the discharge network can also be specified for other applications.Networks conforming to other standards can be built upon request. The speci-fications of the standard must be fully defined.Exchanging the discharge network is described in section «Exchanging the R/C network».The normal remote trigger unit consists of a «triggerbox» and 5 m (197 “) of optical cable. The remote trigger works in parallel with the «trigger-button» on the NSG 435. Pulse triggering, or the on/off switching in the case of repetitive discharges, can be effected by a push-button or an electrical signal applied to the triggerbox.The electrical signal at the BNC connector must fulfill the following condi tions:On: V = 2.4...10 V, I >2 mA, t >10 msOff: V <0.8 VRepetition rate: <5 HzThe remote trigger is powered by a conventional 9 volt battery. The current consumption is so low that a battery switch has been dispensed with. If NSG 435 provided with two optical connectors connect the optical cable to the blue terminal.It is recommended to remove the battery if the unit is not going to be used forMounting flangeContact surfaceThe measurement adapter type MD 101 as per informative annex B of IEC/EN 61000-4-2 serves to verify pulse amplitudes and pulse shapes. It is designed for mounting in the side wall of a Faraday cage in which an oscilloscope has been installed. This measurement adapter, also known as a «Pellegrini-Target» has the flat impedance curve to well over 1 GHz that is necessary for the purpose. Use of this adapter is only worthwhile in conjunction with a test rig that is laid out in strict conformity with the relevant standard (see section 7).24NSG 435 ESD simulatorSwitch the simulator on with the main switch.A display appears in the window showing values representing the status of the instrument before it was last switched off.A typical set of values might look like this:The instrument performs audible switching functions for a while that result from various self-tests and calibration procedures.High voltage generation is activated by pressing and holding the trigger button. By bringing the test finger close to the earthing point an discharge occurs which is acknowledged acoustically and the display shows the effective discharge voltage in a frame. (This applies under the following conditions: air-discharge, single-pulse, preselect counter off).The instrument is now ready to use.26NSG 435 ESD simulatorThe instrument is ready for use immediately after the execution of a self-testand calibration procedure.Press and hold the trigger button to activate the high voltage generation. The active high voltage state is shown on the display by the “kV” indication blink-ing.The measured value of the breakdown voltage in air-discharge mode will be displayed. Differentiation from the display of the set value is made by the frame around the kV readings.The effective discharge voltage depends on various factors such as the distance to the discharge point, speed of approach, nature of the EUT, etc.In the case of a contact-discharge this measurement is not carried out since only a discharge current can occur.The instrument switches itself off automatically after a period of 30 minutes of non-use although the parameters that have been set will remain stored in memory.The change to contact-discharge is prevented if:The voltage set for this operating mode is too high, i.e. over 9 kVThe repetition frequency set for this operating mode is too high, i.e.over 10 pulses/sThe instrument notifies the error with a beep and the erroneous setting blinks for 5 s.When working with fixed voltage levels, the relevant value is automatically loaded upon toggling between the air/contact-discharge mode.12Free setting Call stored values level 1-4(4 values each for air-dischargeand contact discharge) Pressing F1 or F2 raises or lowers Press F3 to select the four stored the voltage respectively in steps of voltage values in each case. 100 V. Pressing the buttons (To change a stored value, see continuously changes the voltage section 5.12).level with increasing rapidity.30NSG 435 ESD simulatorPress F5 to return to the starting menu level. (This return will also be madeautomatically after about 10 s).5.6 PolarityF3 toggles between positive and negative polarity. The sign shown in the displayalters correspondingly.In the SINGLE mode a discharge is released each time the trigger button is pressed. The discharge is confirmed by a beep. In the REPETITIVE mode dis charges are released at the chosen rate for as long as the trigger button remains pressed (no acoustic confirmation).32NSG 435 ESD simulatorF5 sets the counter either back to 0000 or to the preset value if the preselect counter mode has been chosen.Pressing F5 a second time causes a branch to the preselect counter menu.5.9 Preselect counterA specified number of discharges (0...9999) can be pre-programmed with this function. These can then be triggered single by hand or automatically.F5 first resets the counter then, when pressed a second time, branches into the preselect counter menu.F3 switches the preselect counter operation on and off (PRESELECT ON/OFF). Use F1 and F2 to raise or lower the preset value. Keeping either button pressed causes the change to occur with increasing rapidity.34NSG 435 ESD simulatorPress F5 to return to the original menu level. (This return also occurs automati-cally after about 10 s)The preselect counter mode can be used with either single or with repetitive discharges.Each time there is a discharge the counter content is decremented by 1.In the repetitive mode the discharge sequence is started when the trigger button is first pressed and is halted when the button is pressed a second time. The sequence can be continued by pressing it again.Pulse triggering is terminated when the counter content reaches 0000.F5 reloads the preselect counter with the original value.Once the counter reaches 0000 and the procedure has been stopped, the counter can also be reloaded with the original value again and the test sequence started anew simply by pressing the trigger button.5.10 Automatic polarity switchingThe IEC standards call for equal quantities of positive and then negative dis-charges to be applied to a test point. The NSG 435 can execute this function automatically.The automatic polarity switch operates in conjunction with the preselect counter.F5 branches into the preselect counter menu.F4 switches the function «Automatic polarity change» on and off (Precondition: PRESELECT ON). The active state is shown by the polarity sign in front of the voltage alternating on the display.36NSG 435 ESD simulatorUse F5 to return to the original menu level. (This return also occurs automatically after about 10 s). The «Automatic polarity change» function is identified by «ALT.POL.» over F4 and +/- over F3.The instrument switches over from positive to negative polarity once half of the preset number of pulses has been released (the sign on the display changes).This automatic function works in both the single pulse mode as well as with repetitive discharges.Reinitialize the operation in single pulse mode after each cycle. Reset the counter and select the counter menu again (press F5 three times).Select the repetition frequency in the basic menu with F4. By F5 branch into the preselect counter menu.38NSG 435 ESD simulatorHold F2 down until the counter content is 0000. Press F2 again to activate continuous operation. The display shows - - - -.Use F5 to return to the original menu level.Switching off continuous operation:By F5 branch into the preselect counter menu. Press F1 or F2. The counter shows 0000 or 9999 respectively. Continuous operation is switched off.Use F5 to return to the original menu level.5.12 Storing voltage settingsPre-programmed discharge voltage values can be stored in four memory loca-tions for both air and contact-discharges. As delivered, the instrument has the test levels set according to IEC/EN 61000-4-2, Ed. 1.2:2001.The values stored in memory can be altered arbitrarily.Level Test voltage contact-discharge 1234 2 kV 4 kV 6 kV 8 kV40NSG 435 ESD simulator Press F4 and a memory location (1 ... 4) appears over F3.Use F3 to specify the required memory location. Press F4 again and the value is stored.Use F5 to return to the original menu level.Set the required voltage with F1 or F2.Range for air: 0.2 ... 16.5 kVRange for contact: 0.2 ...9 kVThe «LEVEL» indication shown over F3 disappears. «STORE» appears over F4.simulator46 537A yellowB black8C yellow/green48NSG 435 ESD simulator Procedure:1 Switch the instrument off2 Remove the earth cable3 Take out the battery4 Unscrew the test finger5 Pull out the trigger button6 Remove the rear cover(the cover locks into 3 notches in the housing on both sides. The cover can be removed by carefully lifting it at the points where the notches are and gradually sliding it back).7 Lay the instrument on its side and remove the screws8 Remove the screw in the printed circuit board9 Remove the upper part of the housing with a rocking movement 10 Note the arrangement of the wiring11 Release the network connecting screws in the given order12 Remove the network13 Insert the replacement network14 Firmly screw the color-coded network connections into place as shown in the illustration15 Take care with the placement of the wires so that none becoming trapped while re-assembling the generator16 Carefully screw the upper part of the housing back into place17 Continue re-assembly in the reverse order of points 8 .. 1 above (attach the test finger belonging to the set!)18 Check the operation of the generator by observing the spark-gap (the high voltage generator adjusts itself automatically to the newnetwork)19 If in doubt, a voltage check can be carried out as given in section 8.220 A calibration measurement is not normally necessary50NSG 435 ESD simulator 8.4 RepairsRepair work is to be executed exclusively by authorized Teseq repair depart-ments. Only original replacement parts and accessories are to be used.Do not continue to use the instrument in the event of mechanical damage occurring. The molded housing also performs insulating and protective func-tions which are only assured as long as it is in its original condition. A damaged instrument should be returned without delay to a Teseq service centre.8.5 DisposalThe following list shows the principal materials that are used in the construction of the NSG 435. The relevant national regulations are to be observed when disposing of the instrument.Item Material RemarkHousing Control unit LCD-display LCD-window Chassis plate HV unit/network HV relay Test finger Battery Charger Carrying case ABS with glass-fiberEpoxy circuit board with SMD componentsGlassAcrylicGalvanized steelPolyurethane block with electr.components and copper wireVarious metals, ceramicvarious insulating MagerialsBrass, plastics, electrical componentsNickel-metal hybrid (>2002) ABS hosuing Epoxy circuit board ABS housing with transformer, PCB with electr, componentsPolyethyleneObserve any specialregulations regardingdisposal of Ni-MHs。
FANUC 0系列参数说明
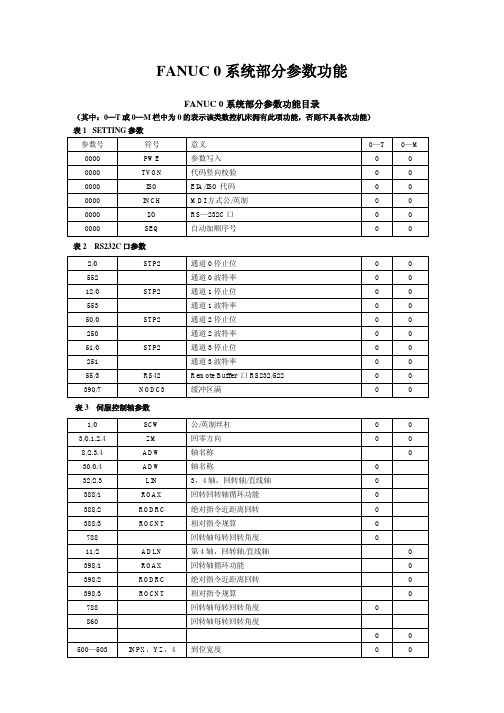
0 0 0 0
0
0
0
0
0
0
0
0
0
0
0
0
0
0
0
0
0
0
0
0
0
0
0
0
0
0
0
0
0
0
0
0
0Hale Waihona Puke 0000
0
0
0
0
0
0
0
0
0
0
0
0
0
0
0
0
0
0
0
0
0
0
0
表 9 编程参数
10/4 15/7 28/4 29/5 389/2 394/6
PRG9 CPRD EXTS MABS PRG8 WKZRST
O9000—O9999 号程序保护 小数点的含义 外部程序号检索 MDI—B 中,指令取决于 G90/G91 设定 O8000—O8999 号程序保护 自动设工件坐标系时设为 G54
PPD 1:坐标系设定时,相对坐标值亦被预置。 0:坐标系设定时,相对坐标值不被预置。
STP2 1:阅读/穿孔接口的停止位由此 2 位设定。 0:阅读/穿孔接口的停止位由此 1 位设定。 (设定参数 I/O “0”时有效) 注:波特率由参数 NO.0522 设定。
0004 0006 0005 0007
0:坐标值显示的是加上偏置值的实际位置。
SCW 1:最小指令值为英制(机床为英制) 0:最小指令值为米制(机床为米制)
0002
7
6
5
4
3
2
1
0
NFED TFHD HSLE
电脑主板纠错灯指示信息及含义

现在(xiànzài)很多人买的主板都带有DEBUG侦错灯,借此把搜集回来的DEBUG侦错灯指示信息及其含义;拿来共享下........CF 测试(cèshì) CMOS R/W 功能性。
C0 早期的主板设定初始值: - 禁用(jìn yònɡ) shadow RAM - 禁用 L2cache(SURPER 7 构架及后期兼容构架) - 检测基本 chipset 寄存器。
C1 检测内存: -Auto- 检测DRAM(动态随机存取储存器)大小,类型(lèixíng) 和 ECC。
-Auto- 检测L2 cache (SURPER 7 构架及后期兼容构架)C3 映射(yìngshè)BIOS编码到DRAM。
C5 允许chipset将BIOS复制到地址为E000 F000的shadow RAM。
01 将Xgroup编码定位在内存地址中的1000到003 初始化Superio(超级输入输出)_Early(响应)_Init(启动)开关。
053.将空白输出到荧屏。
4.清除CMOS错误。
071.清除 8042 接口。
2.初始化 8042接口自检。
081.检测特殊的键盘控制器型号为Winbond 977 系列超级I/O(输入/输出)芯片。
2.允许使用键盘接口。
0A1.禁用PS/2 老鼠接口.(可选)2.在端口和交换接口检测完成后自动检测键盘和鼠标端口。
(可选)3.重置键盘在发现型号为Winbond 977 系列超级I/O输入/输出芯片后。
0E 检测内存地址为F000h段图像以证明是否它支持 R/ W.如果检测失败,机箱扬声器将发出警报。
10 自动检测FlashROM类型以读取合适的FlashROM R/W 编码。
在ESCD和DMI支持的情况下进入运行时间和区域的地址位F000。
12 使用步骤1’s 运算方式以确定CMOS电路的接口。
MC9RS08KA4_8中文数据手册
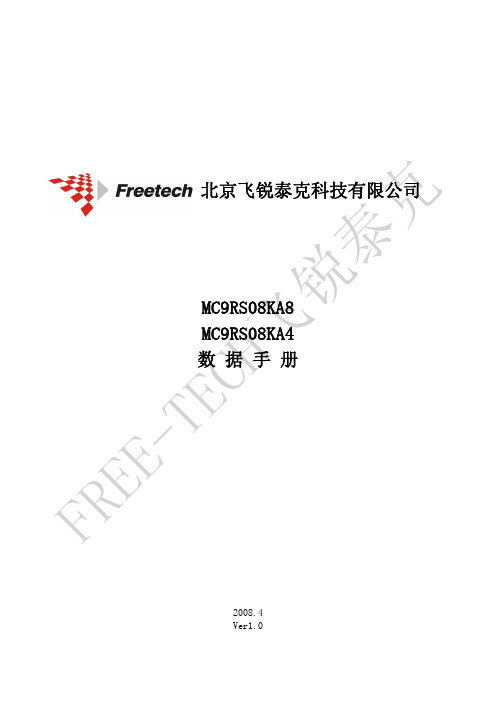
3FFE
3FFF
BC(JMP 机器码)
跳转地址高字节
跳转地址低字节
飞 3.4 激活背景调试模式 背景调试功能是由 RS08 核内的 BDC 管理的。在软件开发过程中,BDC 提供了
H 一种分析 MCU 操作方法。 C 有 4 种激活背景调试的方法:
*在 POR 期间或发出背景调试强制复位命令之后,拉 BKGD/MS 引脚为低
3
北京飞锐泰克科技有限公司 tel:010-59831537 fax:010-59831536
手机解锁密码大全

手机解锁密码大全三、GSM手机密笈&e r.b]'a D:V(一)摩托罗拉摩托罗拉所有机锁:按MENU+5+1/2 2f} o U%AT190解锁密码: 20010903T191解锁密码:199807223X8/2X88/998/8088/L2000/7689/T189/C289等初始密码为1234 ;话机密码为000000 ;解锁方法:如无测试卡,则先输入1234,如密码已更改,先按Menu键会出现“修改开锁密码”,按OK键,然后输入000000就会显示四位数的话机密码,如保密码已更改,则只能用测试卡或软件工具解。
2C&r/_F3@X!JT2688/2988万能解锁码:19980722C300解话机锁:20020801摩托罗拉手机出现“话机坏,请送修”:可利用测试卡,输入0205#、0205068#即可修复,无须重写码片。
T2688/2988/988d设置中文:*#0000# ok(插卡)V60/V66/V70解锁:插入测试卡,开机后输入menu+048263*进入测试状态后按18*1总清除,输入18*0是主复位。
V998外文改中文:MENU—左方向键按3下—OK—左方向键按5下—OK—Simplified—CHINESE摩托罗拉2688时间不走修复密诀:将电源1脚和8脚用漆包线短接,必杀!(二)诺基亚初始保密码:12345 W"w2K z k#i)A n5110锁码机解码:在保密码锁死,输入正确保密码无效的情况下,可1、按C键不放,2、按*键不放,3、按*键不放,4、输入04*PIN*PIN*PIN# 解除锁码。
;z8N M4s y!q3210解 SP 锁: 1、按C键 2、按向下键 3、按C键直到屏幕清除 4、按住*键直到其闪烁 5、再按住*键直到其闪烁,输入04*PIN码*PIN 码*PIN 6~,O Y)^/W"K vTN7650恢复出厂设置:*#7370#诺基亚手机省30%电密码:*#746025625# |(H3K诺基亚手机查出厂日期:*#0000#诺基亚能打过进不能呼出:如果显示屏左上角有“2”字,按住#键两秒,再按确认即可;如果没有显示“2”,则按“功能键”+6+1+4+2再按确认即可。
AORUS MODEL S 电竞台式电脑 (GB-AMSR9N8I-20A1) 使用手册说明书

版权© 2021年,技嘉科技股份有限公司,版权所有。
本使用手册所提及的商标与名称,均属其合法注册的公司所有。
责任声明本使用手册受著作权保护,所撰写的内容均为技嘉所拥有。
本使用手册所提及的产品规格或相关信息,技嘉保留修改的权利。
本使用手册所提及的产品规格或相关信息有任何修改或变更时,恕不另行通知。
未事先经由技嘉书面允许,不得以任何形式复制、修改、转载、传送或出版本使用手册内容。
产品使用手册类别简介为了协助您使用技嘉主板,我们设计了以下类别的使用手册:如果您要快速安装,可以参考包装内所附的【快速入门手册】。
如果您要了解产品详细规格数据,请仔细阅读【使用手册】。
产品相关信息,请至网站查询:https:///目清点配件 (4)第一章硬件安装 (5)1-1 安全性注意事项 (5)1-2 硬件信息 (6)系统总览 (6)系统正面 (6)系统背面-A (7)系统背面-B (9)1-3 准备就绪 (10)连接集成外设 (10)连接电源线 (11)开启电脑 (11)第二章BIOS 程序设置 (12)2-1 进入BIOS设置程序 (12)2-2 设置BIOS设置程序使用语言 (13)2-3 设置管理员/用户密码 (14)2-4 载入最佳化预设值 (15)2-5 存储BIOS设置值及退出BIOS选单 (16)第三章附录 (17)如何执行Q-Flash Plus (17)Regulatory Notices (18)技嘉科技全球服务网 (22)- 3 -清点配件5AORUS MODEL S电竞台式电脑5快速入门手册5天线5电源线上述附带配件仅供参考,实际配件请以实物为准,技嘉科技保留修改的权利。
- 4 -第一章硬件安装1-1 安全性注意事项•连接电源插座之前,请确保电源线的额定电压与您所在国家/地区的电源规格兼容。
•电源线插头必须连接至正确接线且接地的电源插座。
•请将电源线插入容易取得的电源插座中,位置应尽可能靠近系统用户。
FANUC系统数控机床参数
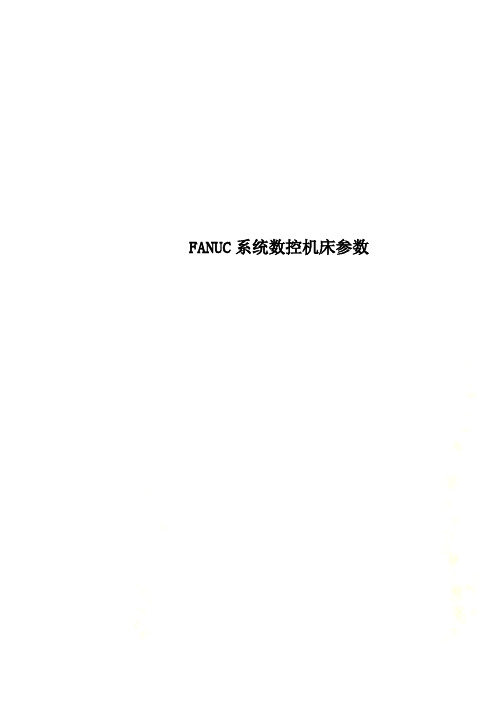
FANUC系统数控机床参数FANUC系统数控机床参数一、掌握数控机床参数的重要性:无论哪个公司的数控系统都有大量的参数,如日本的FANUC公司6T-B系统就有294项参数。
有的一项参数又有八位,粗略计算起来一套CNC系统配置的数控机床就有近千个参数要设定。
这些参数设置正确与否直接影响数控机床的使用和其性能的发挥。
特别是用户能充分掌握和熟悉这些参数,将会使一台数控机床的使用和性能发挥上升到一个新的水平。
实践证明充分的了解参数的含义会给数控机床的故障诊断和维修带来很大的方便,会大大减少故障诊断的时间,提高机床的利用率。
同时,一台数控机床的参数设置还是了解CNC系统软件设计指导思想的窗口,也是衡量机床品质的参考数据。
在条件允许的情况下,参数的修改还可以开发CNC系统某些在数控机床订购时没有表现出来的功能,对二次开发会有一定的帮助。
因此,无论是那一型号的CNC系统,了解和掌握参数的含义都是非常重要的。
另外,还有一点要说明的是,数控机床的制造厂在机床出厂时就会把相关的参数设置正确、完全,同时还给用户一份与机床设置完全符合的参数表。
然而,目前这一点却做的不尽如人意,参数表与参数设置不符的现象时有发生,给日后数控机床的故障诊断带来很大的麻烦。
对原始数据和原始设置没有把握,在鼓掌中就很难下决心来确定故障产生的原因,无论是对用户和维修者本人都带来不良的影响。
因此,在购置数控机床验收时,应把随机所带的参数与机床上的实际设置进行校对,在制造厂的服务人员没有离开之前落实此项工作,资料首先要齐全、正确,有不懂的尽管发问,搞清参数的含义,为将来故障诊断扫除障碍。
数控机床在出厂前,已将所采用的CNC系统设置了许多初始参数来配合、适应相配套的每台数控机床的具体情况,部分参数还需要调试来确定。
这些具体参数的参数表或参数纸带应该交付给用户。
在数控维修中,有时要利用机床某些参数调整机床,有些参数要根据机床的运行状态进行必要的修正,所以维修人员要熟悉机床参数。
内存条说明书

Qualified Vendors List (QVL) Standard table for user manual & MKTA*B*C*256MB Kingston KVR533D2N4/256N/A Elpida SS E5116AB-5C-E Pass Pass N/A 256MB Kingston KVR533D2N4/256N/A Elpida SS E5116AF-5C-E Pass Pass N/A 512MB Kingston KVR533D2N4/512N/A Hynix DS HY5PS56821Pass Pass N/A 512MB Kingston KVR533D2N4/512N/A Infineon SS HYB18T512800AF3733336550Pass Pass N/A 1G Kingston KVR533D2N4/1G N/A Kingston DS D6408TE7BL-37Pass Pass N/A 1G Kingston KVR533D2N4/1G N/A Micron DS 5YD11D9GCT Pass Pass N/A 256MB Kingston KVR667D2N5/256N/A Elpida SS E2508AB-6E-E Pass Pass N/A 512MB Kingston KVR667D2N5/512N/A Kingston SS D6408TE8WL-27Pass Pass N/A 512MB Kingston KVR667D2E5/512N/A Elpida SS E5108AE-6E-E Pass Pass N/A 1G Kingston KVR667D2N5/1G N/A Kingston DS D6408TE8WL-3Pass Pass N/A 256MB Samsung M378T3253FG0-CD5N/A Samsung SS K4T56083QF-GCD5Pass Pass N/A 512MB SamsungM378T6553BG0-CD54Samsung SS K4T51083QB-GCD5Pass Pass N/A 512MB Samsung KR M378T6553CZ0-CE6N/A Samsung SS K4T51083QC Pass Pass N/A 512MB Samsung KR M378T6453FZ0-CE6N/A Samsung DS K4T56083QF-ZCE6Pass Pass N/A 1G Samsung KR M378T2953CZ0-CE6N/A Samsung SS K4T51083QC-ZCE6Pass Pass N/A 256MB Infineon HYS64T32000HU-3.7-A 4Infineon SS HYB18T512160AF-3.7AFSS31270Pass Pass N/A 512MB Infineon HYS64T64000GU-3.7-A 4Infineon SS HYB18T512800AC37SSS11511Pass Pass N/A 512MB Infineon HYS64T64000HU-3.7-A N/A Infineon SS HYB18T512800AF37SSS12079Pass Pass N/A 512MB Infineon HYS64T64000HU-3.7-A N/A Infineon SS HYB18T512800AF37FSS29334Pass Pass N/A 256MB Infineon HYS64T32000HU-3S-A N/A Infineon SS HYB18T512160AF-3SSSS17310Pass Pass N/A 512MB Infineon HYS64T32000HU-3S-A N/A Infineon SS HYB18T5128000AF-3SSSS27416Pass Pass N/A 512MB Infineon HYS64T64000HU-3S-A N/A Infineon SS HYB18T512800AF3SFSS05346Pass Pass N/A 1G Infineon HYS64T128020HU-3S-AN/A Infineon DS HYB18T512800AF3SSSS28104Pass Pass N/A 512MB Micron MT 16HTF6464AG-53EB2 4Micron DS D9BOM Pass Pass N/A 512MB Micron MT 16HTF6464AG-53EB24Micron DS Z9BQT Pass Pass N/A 1G Micron MT 16HTF12864AY-53EA14Micron DS D9CRZ Pass Pass N/A 512MB Corsair VS512MB533D2N/A Corsair DS MIII0052532M8CEC Pass Pass N/A 512MB Corsair VS512MB667D2N/A Corsair DS MIII0052532M8CEC Pass Pass N/A 512MB HY HYMP564U64AP8-Y4 AA N/A Hynix SS HY5PS12821AFP-Y4Pass Pass N/A 512MB HY HYMP564U64AP8-Y5 AA N/A Hynix SS HY5PS12821AFP-Y5Pass Pass N/A 1G HY HYMP512U64AP8-Y5 AB N/A Hynix DS HY5PS12821AFP-Y5Pass Pass N/A 512MB Elpida EBE51UD8ABFA-5C-E N/A Elpida SS E5108AB-5C-E Pass Pass N/A 512MB Kingmax KLBC28F-A8KB4N/A Kingmax SS KKEA88B4IAK-37Pass Pass N/A 256MB Kingmax KLBB68F-36EP4N/A Elpida SS E5116AB-5C-E Pass Pass N/A 512MB Kingmax KLBC28F-A8EB4N/A Elpida SS E5108AE-5C-E Pass Pass N/A 512MB Kingmax KLCC28F-A8EB5N/A Elpida SS E5108AE-6E-E Pass Pass N/A 512MB Kingmax KLCC28F-A8KB5N/A Kingmax SS KKEA88B4LAUG-29DX Pass Pass N/A 1G Kingmax KLCD48F-A8KB5N/A Kingmax DS KKEA88B4LAUG-29DXPass Pass N/A 512MB Apacer 78.91092.420N/A Elpida SS E5108AE-6E-E Pass Pass N/A 512MB Apacer AU512E667C5KBGC5Apacer SS AM4B5708MIJS7E0627BPass Pass N/A 1G Apacer 78.01092.4205Elpida DS E5108AE-6E-E Pass Pass N/A 1G Apacer AU01GE667C5KBGC 5Apacer DS AM4B5708MIJS7E0627BPass Pass N/A 512MB ADATA M20EL5G3H3160B1C0Z N/A Elpida SS E5108AE-6E-E Pass Pass N/A 512MB VDATA M2GVD5G3H31A4I1C52N/A VDATA SS VD29608A8A-3EC20615Pass Pass N/A 512MB VDATA M2YVD5G3H31P4I1C52N/A VDATA SS VD29608A8A-3EG20627Pass Pass N/A 1G VDATA M2GVD5G3I41P6I1C52N/A VDATA DS VD29608A8A-3EG20627Pass Pass N/A 1G VDATA M2GVD5G3I41C4I1C52N/A VDATA DS VD29608A8A-3EC20620Pass Pass N/A 256MB Nanya NT256T64UH4A1FY-3C N/A Nanya SS NT5TU32M16AG-3C Pass Pass N/A 512MB Nanya NT512T64U88A1BY-3CN/A Nanya SS NT5TU64M8AE-3C Pass Pass N/A 512MB PQI MEAB-323LA N/A PQI SS D2-E04180W025Pass Pass N/A 1G PQI MEAB-423LA N/A PQI DS D2-E04230W107Pass Pass N/A 512MB AENEON AET660UD00-370A98Z 4AENEON SS AET93F370A G 0513Pass Pass N/A 256MB AENEON AET560UD00-370A98Z 4AENEON SS AET94F370AWVV34635G0520Pass Pass N/A 512MBAENEONAET660UD00-370A98Z4AENEONSSAET93F370A 3VV36328G 0522PassPassN/ASize Vendor Model CL Brand SS/DS Component DIMM socket support (Optional)512MB AENEON AET660UD00-370A98X N/A AENEON SS AET93F370A 0518Pass Pass N/A 512MB AENEON AET660UD00-370A88S N/A AENEON DS AET82F370A 0550Pass Pass N/A 1G AENEON AET760UD00-370A98Z N/A AENEON DS AET93F370A 0551Pass Pass N/A 1G AENEON AET760UD00-370A98S N/A AENEON DS AET92F370A 0606Pass Pass N/A 2G AENEON AET860UD00-370A08X N/A AENEON DS AET03F370AFVV26176G 0542Pass Pass N/A 512MB AENEON AET660UD00-30DA98Z N/A AENEON SS AET93F30DA 0552Pass Pass N/A 1G AENEON AET760UD00-30DA98Z N/A AENEON DS AET93F30DA8EE47414G 0540Pass Pass N/A 512MB AENEON AET660UD00-30DA98Z N/A AENEON SS AET93F300A 0606Pass Pass N/A 1G AENEON AET760UD00-30DA98Z N/A AENEON DS AET93F30DA 0604Pass Pass N/A512MB VERITECHGTP512HLTM46DG N/AVERITECHSS VTD264M8PC6G01A164129621Pass Pass N/A1G VERITECHGTP01GHLTM56DG N/AVERITECHDS VTD264M8PC6G01A164129621Pass Pass N/A512MB VERITECHGTP512HLTM45EG N/AVERITECHSS VTD264M8PC6G01A164129621Pass Pass N/A1G VERITECHGTP01GHLTM55EG N/AVERITECHDS VTD264M8PC6G01A164129621Pass Pass N/A512MB GEIL GX21GB5300DC4GEIT SS Heat-Sink Package Pass Pass N/A 512MB Century CENTURY 512MB N/A Nanya SS NT5TU64M8AE-3C Pass Pass N/A 512MB Century CENTURY 512MB N/A Hynix SS HY5PS12821AFP-Y5Pass Pass N/A 1G Century CENTURY 1G N/A Hynix DS HY5PS12821AFP-Y5Pass Pass N/A 1G Century CENTURY 1G N/A Nanya DS NT5TU64M8AE-3C Pass Pass N/A 512MB KINGBOX512MB 667MHz N/A KINGBOX SS EPD264082200-4Pass Pass N/ANote:A* : Supports one module inserted in any slot as Single-channel memory configurationB* : Supports one pair of modules inserted into eithor the blue slots or the black slots as one pair of Dual-channel memory configurationC* : Supports 4 modules inserted into both the blue and black slots as two pairs of Dual-channel memory configuration。
Freescale Kinetis E 系列 KE06 微控制器开发板用户指南说明书
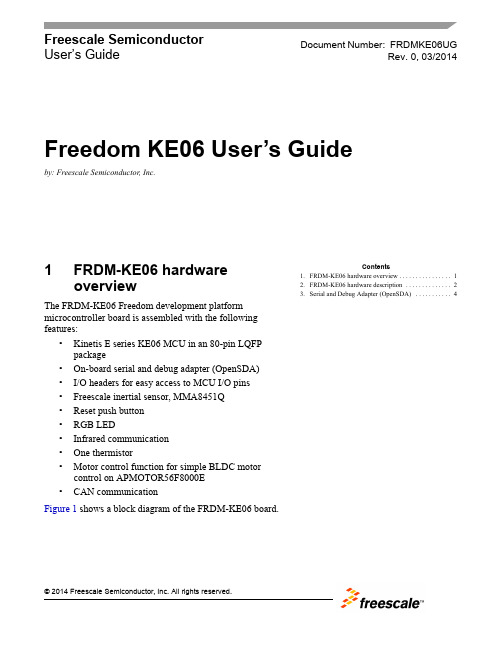
Freescale Semiconductor User’s Guide1FRDM-KE06 hardware overviewThe FRDM-KE06 Freedom development platform microcontroller board is assembled with the following features:•Kinetis E series KE06 MCU in an 80-pin LQFP package•On-board serial and debug adapter (OpenSDA)•I/O headers for easy access to MCU I/O pins •Freescale inertial sensor, MMA8451Q •Reset push button •RGB LED•Infrared communication •One thermistor•Motor control function for simple BLDC motor control on APMOTOR56F8000E •CAN communication Figure 1 shows a block diagram of the FRDM-KE06 board.Document Number:FRDMKE06UGRev. 0, 03/2014Contents1.FRDM-KE06 hardware overview . . . . . . . . . . . . . . . . 12.FRDM-KE06 hardware description . . . . . . . . . . . . . . 23.Serial and Debug Adapter (OpenSDA) . . . . . . . . . . . 4Freedom KE06 User’s Guideby: Freescale Semiconductor, Inc.FRDM-KE06 hardware descriptionFigure1. FRDM-KE06 block diagramThe FRDM-KE06 features two microcontrollers, the target MCU and a serial and debug adapter (OpenSDA) MCU. The target MCU is a Kinetis E series KE06 family device. The OpenSDA MCU is a Kinetis K series K20 family device, the K20DX128VFM5.2FRDM-KE06 hardware description2.1Power supplyThe FRDM-KE06 offers a design with multiple power supply options. It can be powered from the USB connector, the V IN pin on the I/O header, an off-board 1.71-3.6V supply from the 3.3V pin on the I/O header or 3.3V from motor control board. The USB and V IN supplies are regulated on-board using a 3.3V linear regulator to produce the main power supply. The other two sources are not regulated on-board. Note that KE06 on FRDM board can be powered by 5V or 3.3V.The following figure shows the schematic drawing for the power supply inputs and the on-board voltage regulator.FRDM-KE06 hardware descriptionFigure 2. FRDM-KE06 power supplyTable 1 provides the operational details and requirements for the power supplies.Note that the OpenSDA circuit is only operational when a USB cable is connected and supplying power to J6. However, the protection circuitry is in place to allow multiple sources to be powered at once.Table 1. Power supply requirementsSupply Source Valid RangeOpenSDA Operational?Regulated on-board?OpenSDA USB (J6)5VYes Yes V IN Pin on I/O header 4.3-9V Yes Yes 3.3V Pin on I/O header 1.71-3.6V Yes No 3.3V Pin on motor control header3.3VYesNoTable 2. Power suppliesPower Supply Name DescriptionVDD_PERIPHPeripheral power supply, including RGB LED, Key buttons, infrared, thermistor, reset circuit.J14 Pin1&2 connected, 3.3V power supply;J14 Pin2&3 connected, 5V power supply.Serial and Debug Adapter (OpenSDA)Notes:1.J9 and J10 are not populated by default on the production version. The two pins of these headers are shorted together by 0 ohm resistor R12 and R26 on the PCB. To measure the energyconsumption of either the KE06 or the OpenSDA MCU, the 0 ohm resistor between these pins must first be cut. A current probe or a shunt resistor and voltage meter can then be applied to measure the energy consumption on these rails. When the MCU current measurement is done, this 0 ohm resistor can be soldered on again.2.To better get ADC accuracy on KE06, it is recommended that a 0 ohm resistor R13 be soldered on. Ensure there is no power supply from P3V3_MOTOR and P3V3 sourced from I/O headers.3Serial and Debug Adapter (OpenSDA)OpenSDA is an open-standard serial and debug adapter. It bridges serial and debug communications between a USB host and an embedded target processor as shown in Figure 3.VDD_KE06KE06 MCU power supply.Header J9 provides a convenient means for KE06 energy consumption measurements.Header J14 for KE06 power supply selection: 3.3V or 5V.J14 Pin1&2 connected, 3.3V power supply,J14 Pin2&3 connected, 5V power supply.P3V3_SDAOpenSDA circuit power supply. Can be 3.3V only.Header J10 provides a convenient means for K20 energy consumption measurements.P5V_SDA INPUT [J6 Pin1] Input 5V Power supplied from the OpenSDA USB connector. P5-9V_VIN INPUT [J4 Pin16] Power supplied from the V IN pin of the I/O headers.P3V3_MOTOR INPUT [J2 Pin13] Input 3.3V power supplied from motor control header.P5V_USB OUTPUT[J4 Pin10] Output 5V to the I/O headers.Sourced from J6 USB (P5V_SDA) supply through a back drive protection Schottky diode.Table 2. Power suppliesSerial and Debug Adapter (OpenSDA)Figure3. OpenSDA block diagramOpenSDA is managed by a Kinetis K20 MCU built on the ARM® Cortex™-M4 core. The OpenSDA circuit includes a status LED (D4) and a reset pushbutton (SW1). The pushbutton asserts the reset signal to the KE06 target MCU. It can also be used to place the OpenSDA circuit into Bootloader mode by holding down the reset pushbutton while plugging the USB cable to USB connector J6. Once the OpenSDA enters bootloader mode, other OpenSDA applications such as debug app can be programmed. SPI and GPIO signals provide an interface to the SWD debug port of the KE06. Additionally, signal connections are available to implement a UART serial channel. The OpenSDA circuit receives power when the USB connector J6 is plugged into a USB host.3.1Debugging InterfaceSignals with SPI and GPIO capability are used to connect directly to the SWD of the KE06. These signals are also brought out to a standard 10-pin (0.05”) Cortex Debug connector (J7) as shown in Figure 4. It is possible to isolate the KE06 MCU from the OpenSDA circuit and use J7 to connect to an off-board MCU. To accomplish this, cut the 0 ohm resistor R58. This will disconnect the SWD_CLK pin to the KE06 so that it will not interfere with the communications to an off-board MCU connected to J7.When KE06 on FRDM board is 5V powered, and the OpenSDA is power off, there need to connect an external debugger to debug KE06 on board.Serial and Debug Adapter (OpenSDA)Figure4. SWD debug connector to KE063.2Virtual Serial PortA serial port connection is available between the OpenSDA MCU and UART1 pin PTC7 (TXD1) and PTC6 (RXD1) of KE06. Several of the default OpenSDA applications provided by Freescale, including the MSD Flash Programmer and the P&E Debug Application, provide a USB Communications Device Class (CDC) interface that bridges serial communications between the USB host and this serial interface on the KE06.3.3KE06 Microcontroller3.3.1Clock SourceThe Kinetis KE06 microcontrollers feature an on-chip oscillator compatible with two ranges of input crystal or resonator frequencies: 32 kHz (low frequency mode), 4-20 MHz (high frequency mode).The KE06 on the FRDM-KE06 is clocked from an 8 MHz crystal.3.3.2Serial PortThe serial port interface signals used with OpenSDA are UART1 pin PTC7 (TXD1) and PTC6 (RXD1). These signals are also connected to I/O header J1.3.3.3ResetThe PTA5/RESET signal on the KE06 is connected externally to a pushbutton SW1. The reset button can be used to force an external reset event in the target MCU. The reset button can also be used to force the OpenSDA circuit into bootloader mode when plugging the USB cable to J6. See Section3, “Serial and Debug Adapter (OpenSDA)” section for more details.Serial and Debug Adapter (OpenSDA)3.3.4DebugThe sole debug interface on all Kinetis E Series devices is a Serial Wire Debug (SWD) port. The primary controller of this interface on the FRDM-KE06 is the onboard OpenSDA circuit. However, a 2x5-pin (0.05”) Cortex Debug connector, J7, provides access to the SWD signals for the KE06 MCU. The following table shows SWD connector signals description for KE06:3.4ThermistorOne thermistor (RT1) is connected to two ADC inputs (PTF4/ADP12, PTF5/ADP13) of KE06 for evaluating the ADC module.Figure 5. Thermistor connectionTable 3. ARM JTAG/SWD mini Connector DescriptionPin FunctionConnection to KE061VTref 3.3V or 5V KE06 power supply (VDD_KE06)2SWDIO/TMS PTA4/SWD_DIO 3GNDGND4SWDCLK/TCK PTC4/SWD_CLK 5GND GND 6SWO/TDO NC 7NC NC 8TDI NC 9NC NC10RESETPTA5/RESETSerial and Debug Adapter (OpenSDA)3.5Infrared PortOne infrared Rx port and one Tx port (as shown in the following figure) are connected to ACMP0 input pin (ACMP0_IN1) and UART0 TXD0 pin of KE06 to demonstrate the capability of SCI0 modulated by a flextimer to generate infrared signals and use ACMP0 as a filter to receive the SCI data via infrared signal.Figure6. Infrared connection3.6Key buttonsTwo key buttons are connected to PTH3/4 to demonstrate KBI function of KE06, which can capture both falling edge and rising edge of key button input, as shown in the following figure.Serial and Debug Adapter (OpenSDA)Figure7. Key buttons connection3.7Three-axis accelerometerA Freescale MMA8451Q low power, three-axis accelerometer is interfaced through an I2C bus and two GPIO signals as shown in the following table. By default, the I2C address is 0x1D (SA0 pulled high).Table4. Accelerometer signal connectionsMMA8451Q KE06SCL PTA3SDA PTA2INT1 PTD4INT2 PTD3Serial and Debug Adapter (OpenSDA)Figure8. Accelerometer connection3.8RGB LEDThree PWM-capable pins are connected to a red, green, blue LED. The signal connections are shown in the table below.Table5. RGB LED Signal ConnectionsRGB LED KE06Red Cathode PTG5/FTM2CH3Green Cathode PTG6/FTM2CH4Blue Cathode PTG7/FTM2CH5Serial and Debug Adapter (OpenSDA)Figure9. GB LED connection3.9CANThe CAN phy on KE06 FRDM board is 3.3V powered.Table6. CAN signal connectionCAN Phy KE06D CAN_TXR CAN_RXSerial and Debug Adapter (OpenSDA)Figure10. CAN3.10Input/Output HeadersThe KE06 microcontroller is packaged in an 80-pin LQFP. Some pins are utilized in on-board circuitry, but many are directly connected to one of four I/O headers (J1, J2, J3, J4 and J5). J1 and J2 also function as motor control headers to provide access to a motor control board such as simple BLDC motor driving board APMOTOR56F8000E.Serial and Debug Adapter (OpenSDA)Figure11. I/O headers3.11Arduino CompatibilityThe I/O headers on the FRDM-KE06 are arranged to allow compatibility with peripheral boards (known as shields) that connect to Arduino and Arduino-compatible microcontroller boards. The pins on the headers share the same mechanical spacing and placement as the I/O headers on the Arduino Uno Revision 3 board design. See Figure11 for compatible signals.Document Number:FRDMKE06UG Rev. 003/2014Information in this document is provided solely to enable system and software implementers to use Freescale products. There are no express or implied copyright licenses granted hereunder to design or fabricate any integrated circuits based on the information in this document.Freescale reserves the right to make changes without further notice to any products herein. Freescale makes no warranty, representation, or guarantee regarding the suitability of its products for any particular purpose, nor does Freescale assume any liability arising out of the application or use of any product or circuit, and specifically disclaims any and all liability, including without limitation consequential or incidental damages. “Typical” parameters that may be provided in Freescale data sheets and/or specifications can and do vary in different applications, and actual performance may vary over time. All operating parameters, including “typicals,” must be validated for each customer application by customer’s technical experts. Freescale does not convey any license under its patent rights nor the rights of others. Freescale sells products pursuant to standard terms and conditions of sale, which can be found at the following address: /SalesTermsandConditions.How to Reach Us:Home Page:Web Support:/supportFreescale, the Freescale logo, and Kinetis, are trademarks of FreescaleSemiconductor, Inc., Reg. U.S. Pat. & Tm. Off. All other product or service names arethe property of their respective owners. ARM and Cortex are the registered trademarksof ARM Limited. ARMCortex-M4 is the trademark of ARM Limited.© 2014 Freescale Semiconductor, Inc.。
Lenovo RackSwitch G8272 Networking OS 8.2 Release

Lenovo RackSwitch G8272Release Notes For Networking OS 8.2Note: Before using this information and the product it supports, read the general information in the Safety information and Environmental Notices and User Guide documents on the Lenovo Documentation CD and the Warranty Information document that comes with the product.First Edition (April 2015)© Copyright Lenovo 2015Portions © Copyright IBM Corporation 2014.LIMITED AND RESTRICTED RIGHTS NOTICE: If data or software is delivered pursuant a General Services Administration “GSA” contract, use, reproduction, or disclosure is subject to restrictions set forth in Contract No. GS-35F-05925.Lenovo and the Lenovo logo are trademarks of Lenovo in the United States, other countries, or both.Release NotesThis release supplement provides the latest information regarding LenovoNetworking OS 8.2 for the Lenovo RackSwitch G8272 (referred to as G8272throughout this document).This supplement modifies and extends the following Lenovo N/OS documentationfor use with N/OS 8.2:●Lenovo Networking OS 8.2 Application Guide●Lenovo Networking OS 8.2 ISCLI Reference●Lenovo RackSwitch G8272 Installation GuideThe publications listed above are available from the following website:/infocenter/systemx/documentation/index.jspPlease keep these release notes with your product manuals.© Copyright Lenovo 2015 Release Notes 3Hardware SupportN/OS 8.2 software is supported on the G8272, a high performance Layer 2-3network switch.The G8272 is a 1U rack-mountable aggregation switch with unmatched line-rateLayer 2 performance. The G8272 uses a wire-speed, non-blocking switching fabricthat provides simultaneous wire-speed transport of multiple packets at lowlatency on all ports.The switch unit contains the following switching ports:●Forty-eight 10 Gigabit Ethernet (GbE) Small Form Pluggable Plus (SFP+) portswhich also support legacy 1 GbE connections●Six 40 GbE Quad Small Form Pluggable Plus (QSFP+) ports, each of which canoptionally be used as four 10 GbE SFP+ portsFigure1.RackSwitch G8272 front panel4 Lenovo G8272: Release NotesUpdating the Switch Software ImageThe switch software image is the executable code running on the G8272. A versionof the image comes pre-installed on the device. As new versions of the image arereleased, you can upgrade the software running on your switch. To get the latestversion of software supported for your G8272, go to the following website:/supportTo determine the software version currently used on the switch, use the followingswitch command:The typical upgrade process for the software image consists of the following steps:●Load a new software image and boot image onto an SFTP, FTP, or TFTP serveron your network.●Transfer the new images to your switch.●Specify the new software image as the one which will be loaded into switchmemory the next time a switch reset occurs.●Reset the switch.For instructions on the typical upgrade process, see “Loading New Software toYour Switch” on page5.Loading New Software to Your SwitchThe G8272 can store up to two different switch software images (called image1and image2) as well as special boot software (called boot). When you load newsoftware, you must specify where it should be placed: either into image1, image2,or boot.For example, if your active image is currently loaded into image1, you wouldprobably load the new image software into image2. This lets you test the newsoftware and reload the original active image (stored in image1), if needed.Attention: When you upgrade the switch software image, always load the newboot image and the new software image before you reset the switch. If you do notload a new boot image, your switch might not boot properly (To recover, see“Recovering from a Failed Software Upgrade” on page7).To load a new software image to your switch, you will need the following:●The image and boot software loaded on an SFTPFTP or TFTP server on yournetwork.Note:Be sure to download both the new boot file and the new image file.●The hostname or IP address of the SFTP, FTP, or TFTP serverNote:The DNS parameters must be configured if specifying hostnames.●The name of the new software image or boot fileWhen the software requirements are met, use the following procedures todownload the new software to your switch.© Copyright Lenovo 2015 Release Notes 51.In Privileged EXEC mode, enter the following command:RS 8272(config)#copy {sftp|tftp|ftp} {image1|image2|bootimage}2.Enter the hostname or IP address of the SFTP, FTP, or TFTP server.Address or name of remote host: <name or IP address>3.Enter the name of the new software file on the server.Source file name: <filename>The exact form of the name will vary by server. However, the file location isnormally relative to the SFTP, FTP, or TFTP directory (for example, tftpboot).4.If required by the SFTP, FTP, or TFTP server, enter the appropriate username andpassword.5.The switch will prompt you to confirm your request.Once confirmed, the software will begin loading into the switch.6.When loading is complete, use the following commands to enter GlobalConfiguration mode to select which software image (image1 or image2) you wantto run in switch memory for the next reboot:RS 8272#configure terminalRS 8272(config)#boot image {image1|image2}The system will then verify which image is set to be loaded at the next reset:Next boot will use switch software image1 instead of image2.7.Reboot the switch to run the new software:RS 8272(config)# reloadThe system prompts you to confirm your request. Once confirmed, the switch willreboot to use the new software.Note:If you select “No” when asked to confirm the reload, any changes made tothe configuration since the last reboot will be lost.6 Lenovo G8272: Release Notes© Copyright Lenovo 2015 Release Notes 7Supplemental InformationThis section provides additional information about configuring and operating the G8272 and N/OS.The Boot Management MenuThe Boot Management menu allows you to switch the software image, reset the switch to factory defaults, or to recover from a failed software download.You can interrupt the boot process and enter the Boot Management menu from the serial console port. When the system displays Memory Test, press <Shift B>. The Boot Management menu appears.The Boot Management menu allows you to perform the following actions: ●To change the booting image, press I and follow the screen prompts. ●To change the configuration block, press C , and follow the screen prompts. ●To perform a TFTP/Xmodem download, press R and follow the screen prompts.●To reboot the switch, press Q . The booting process restarts ●To exit the Boot Management menu, press E . The booting process continues.Recovering from a Failed Software UpgradeUse the following procedure to recover from a failed software upgrade.1.Connect a PC to the serial port of the switch.2.Open a terminal emulator program that supports XModem Download (forexample, HyperTerminal, SecureCRT, PuTTY) and select the following serial port characteristics:●Speed: 9600 bps ●Data Bits: 8●Stop Bits: 1●Parity: None ●Flow Control: None Resetting at 10:55:49 Sun Apr 19, 2015…Memory Test ................................Boot Management MenuI Change booting imageC Change configuration blockR Boot in recovery mode (tftp and xmodem download of images to recover switch)Q RebootE ExitPlease choose your menu option: ICurrent boot image is 1. Enter image to boot: 1 or 2: 2Booting from image 23.To access the Boot Management menu, you must interrupt the boot process fromthe Console port. Boot the G8272, and when the system begins displaying MemoryTest progress (a series of dots), press <Shift B>. The Boot Management menu willdisplay:Resetting at 10:55:49 Sun Apr 19, 2015…Memory Test ................................Boot Management MenuI Change booting imageC Change configuration blockR Boot in recovery mode (tftp and xmodem download of images to recoverswitch)Q RebootE ExitPlease choose your menu option:4.Select R for Boot in recovery mode. You will see the following display:Entering Rescue Mode.Please select one of the following options:T) Configure networking and tftp download an imageX) Use xmodem 1K to serial download an imageP) Physical presence (low security mode)F) Filesystem checkR) RebootE) ExitOption?:●If you choose option X (Xmodem serial download), go to step 5.●If you choose option T (TFTP download), go to step 6.8 Lenovo G8272: Release Notes5.Xmodem download: When you see the following message, change the Serial Portcharacteristics to 115200 bps:Change the baud rate to 115200 bps and hit the <ENTER> key beforeinitiating the download.a.Press <Enter> to set the system into download accept mode. When the readinessmeter displays (a series of “C” characters), start XModem on your terminalemulator.b.When you see the following message, change the Serial Port characteristics to9600 bps:Change the baud rate back to 9600 bps, hit the <ESC> key.c.When you see the following prompt, enter the image number where you want toinstall the new software and press <Enter>.Install image as image 1 or 2 (hit return to just boot image): 1d.The following message is displayed when the image download is complete.Continue to step 7.Entering Rescue Mode.Please select one of the following options:T) Configure networking and tftp download an imageX) Use xmodem 1K to serial download an imageP) Physical presence (low security mode)F) Filesystem checkR) RebootE) ExitOption?:© Copyright Lenovo 2015 Release Notes 96.TFTP download: The switch prompts you to enter the following information:Performing TFTP rescue. Please answer the following questions (enter 'q'to quit):IP addr :Server addr:Netmask :Gateway :Image Filename:a.Enter the required information and press <Enter>.b.You will see a display similar to the following:Host IP : 10.10.98.110Server IP : 10.10.98.100Netmask : 255.255.255.0Broadcast : 10.10.98.255Gateway : 10.10.98.254Installing image G82728.2.1.0_OS.img from TFTP server 10.10.98.100c.When you see the following prompt, enter the image number where you want toinstall the new software and press <Enter>.Install image as image 1 or 2 (hit return to just boot image): 1d.The following message is displayed when the image download is complete.Continue to step 7.Entering Rescue Mode.Please select one of the following options:T) Configure networking and tftp download an imageX) Use xmodem 1K to serial download an imageP) Physical presence (low security mode)F) Filesystem checkR) RebootE) ExitOption?:7.Image recovery is complete. Perform one of the following steps:●Press r to reboot the switch.●Press e to exit the Boot Management menu●Press the Escape key (<Esc>) to re-display the Boot Management menu.10 Lenovo G8272: Release NotesRecovering from a Failed Boot Image UpgradeUse the following procedure to recover from a failed boot image upgrade.1.Connect a PC to the serial port of the switch.2.Open a terminal emulator program that supports Xmodem download (such asHyperTerminal, CRT, or PuTTY) and select the following serial port characteristics:Speed: 9600 bpsData Bits: 8Stop Bits: 1Parity: None Flow Control: None3.Boot the switch and access the Boot Management menu by pressing <Shift B >while the Memory Test is in progress and the dots are being displayed.4.Select R to boot in recovery mode. Then choose option X (Xmodem serialdownload). You will see the following display:5.When you see the following message, change the Serial Port characteristics to115200 bps:a.Press <Enter > to set the system into download accept mode. When the readinessmeter displays (a series of “C” characters), start Xmodem on your terminalemulator.You will see a display similar to the following:b.When you see the following message, change the Serial Port characteristics to9600 bps: Perform xmodem downloadTo download an image use 1K Xmodem at 115200 bps.Change the baud rate to 115200 bps and hit the <ENTER> key beforeinitiating the download. Extracting images ... Do *NOT* power cycle the switch.**** RAMDISK ****Un Protected 38 sectorsErasing Flash......................................... doneErased 38 sectorsWriting to Flash...9....8....7....6....5....4....3....2....1....doneProtected 38 sectors**** KERNEL ****Un Protected 24 sectorsErasing Flash........................... doneErased 24 sectorsWriting to Flash...9....8....7....6....5....4....3....2....1....Change the baud rate back to 9600 bps, hit the <ESC> key.Boot image recovery is complete.Known IssuesThis section describes known issues for N/OS 8.2 on the RackSwitch G8272.Note:Please review the Change History documentation posted with the SwitchFirmware to check if any of these issues have been fixed in the latest release. FCoE: Configuration Download FCF ErrorWhen you download a configuration file with more than 12 Fibre ChannelForwarder VLANs that differ from those in the running configuration, a“configdownload:fcf error” occurs. (ID: LV304109)FCoE: Only 2048 Maximum Logins Allowed When Area Size is Set to 4096When the area size is set to 4096, maximum number of logins allowed per switchacross all VLANs remains at 2048, and the maximum number of logins allowed ina VLAN remains at 2048. (ID: LV300846)Python Throws Error When Checking Help ModulesA python exception is thrown when checking help (“modules”) in the switchpython shell. The supported modules are those from the python 2.6.8 distributionexcept for bsddb, curses, idlelib, lib-tk, and xml. (ID: LV299048, LV299106). QBG: Changed STG for a Dynamically-Created VLAN Appears “shutdown”If a VLAN is created statically and set to disabled using the VLAN configurationcommand:RS 8272(config-vlan)# shutdownthis will not influence QBG behavior on that VLAN. The user configuration is keptin the running configuration. (ID:XB295275)VLAG: Disconnecting ISL Ports Causes Loss in TrafficTraffic is lost when you disconnect and reconnect the ISL ports in a VLAG setupwith Routing Information Protocol (RIP). Upon reconnection, the ContentAddressable Memory (CAM) table does not synchronize. (ID: LV302019)。
联想电脑驱动光盘安装指引
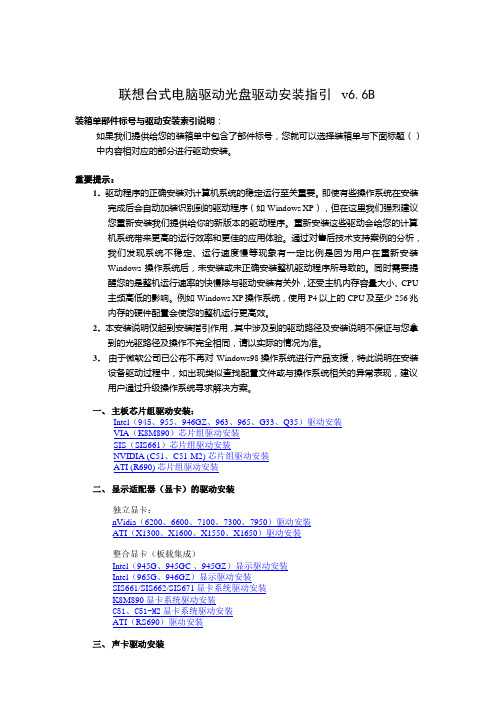
联想台式电脑驱动光盘驱动安装指引v6.6B装箱单部件标号与驱动安装索引说明:如果我们提供给您的装箱单中包含了部件标号,您就可以选择装箱单与下面标题()中内容相对应的部分进行驱动安装。
重要提示:1.驱动程序的正确安装对计算机系统的稳定运行至关重要。
即使有些操作系统在安装完成后会自动加装识别到的驱动程序(如Windows XP),但在这里我们强烈建议您重新安装我们提供给你的新版本的驱动程序。
重新安装这些驱动会给您的计算机系统带来更高的运行效率和更佳的应用体验。
通过对售后技术支持案例的分析,我们发现系统不稳定、运行速度慢等现象有一定比例是因为用户在重新安装Windows操作系统后,未安装或未正确安装整机驱动程序所导致的。
同时需要提醒您的是整机运行速率的快慢除与驱动安装有关外,还受主机内存容量大小、CPU主频高低的影响。
例如Windows XP操作系统,使用P4以上的CPU及至少256兆内存的硬件配臵会使您的整机运行更高效。
2.本安装说明仅起到安装指引作用,其中涉及到的驱动路径及安装说明不保证与您拿到的光驱路径及操作不完全相同,请以实际的情况为准。
3.由于微软公司已公布不再对Windows98操作系统进行产品支援,特此说明在安装设备驱动过程中,如出现类似查找配臵文件或与操作系统相关的异常表现,建议用户通过升级操作系统寻求解决方案。
一、主板芯片组驱动安装:Intel(945、955、946GZ、963、965、G33、Q35)驱动安装VIA(K8M890)芯片组驱动安装SIS(SIS661)芯片组驱动安装NVIDIA (C51、C51-M2) 芯片组驱动安装ATI (R690) 芯片组驱动安装二、显示适配器(显卡)的驱动安装独立显卡:nVidia(6200、6600、7100、7300、7950)驱动安装ATI(X1300、X1600、X1550、X1650)驱动安装整合显卡(板载集成)Intel(945G、945GC 、945GZ)显示驱动安装Intel(965G、946GZ)显示驱动安装SIS661/SIS662/SIS671显卡系统驱动安装K8M890显卡系统驱动安装C51、C51-M2显卡系统驱动安装ATI(RS690)驱动安装三、声卡驱动安装AD1986A\1988A\1882声音系统安装AD1983A声音系统安装ALC655声音系统安装ALC882声音系统安装ALC888声音系统安装四、网卡驱动安装Intel82562(ET/EM/EZ/GZ)、Intel82540(EM)、Intel82547(EI)、Intel(82559/82550)、Intel82541(PI)、Intel82573E、Intel82566DM 驱动安装Realtek8139/8139C/8139D/8100/8100B/8100C/8100D/8110驱动安装Realtek8101E/8111B驱动安装Realtek8169S千兆网卡驱动安装BroadCOM4401网卡驱动安装BroadCOM57XX网卡驱动安装Marvell8039/8071网卡驱动安装五、调制解调器(MODEM)驱动安装Conexant (CX11252-41Z)调制解调器驱动安装Conexant (CX11256)调制解调器驱动安装六、联想电脑双网托盘程序双网托盘程序的安装七、其它驱动程序TPM驱动程序的安装AMT2.1驱动程序的安装INTEL QST驱动程序的安装重要提示:1.下面指引中对光盘盘符统一以“X”为代表。
DEMO9S12PFAME 快速入门指南 Rev. 1.0说明书
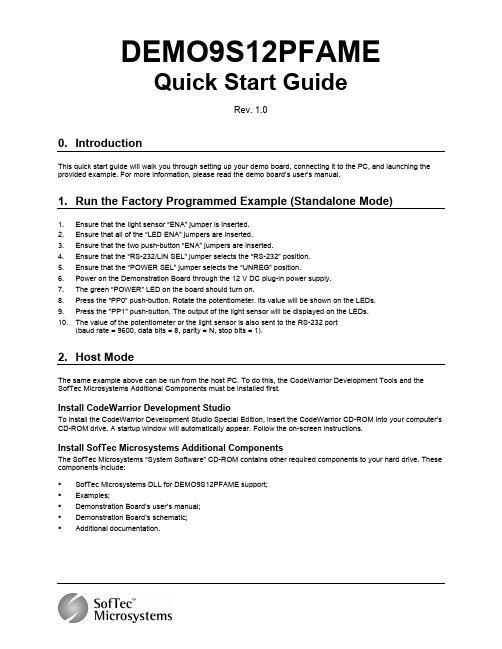
DEMO9S12PFAMEQuick Start GuideRev. 1.00. IntroductionThis quick start guide will walk you through setting up your demo board, connecting it to the PC, and launching the provided example. For more information, please read the demo board’s user’s manual.1. Run the Factory Programmed Example (Standalone Mode)1. Ensure that the light sensor “ENA” jumper is inserted.2. Ensure that all of the “LED ENA” jumpers are inserted.3. Ensure that the two push-button “ENA” jumpers are inserted.4. Ensure that the “RS-232/LIN SEL” jumper selects the “RS-232” position.5. Ensure that the “POWER SEL” jumper selects the “UNREG” position.6. Power on the Demonstration Board through the 12 V DC plug-in power supply.7. The green “POWER” LED on the board should turn on.8. Press the “PP0” push-button. Rotate the potentiometer. Its value will be shown on the LEDs.9. Press the "PP1" push-button. The output of the light sensor will be displayed on the LEDs.10. The value of the potentiometer or the light sensor is also sent to the RS-232 port(baud rate = 9600, data bits = 8, parity = N, stop bits = 1).2. Host ModeThe same example above can be run from the host PC. To do this, the CodeWarrior Development Tools and the SofTec Microsystems Additional Components must be installed first.Install CodeWarrior Development StudioTo install the CodeWarrior Development Studio Special Edition, insert the CodeWarrior CD-ROM into your computer’s CD-ROM drive. A startup window will automatically appear. Follow the on-screen instructions.Install SofTec Microsystems Additional ComponentsThe SofTec Microsystems “System Software” CD-ROM contains other required components to your hard drive. These components include:SofTec Microsystems DLL for DEMO9S12PFAME support;Examples;Demonstration Board’s user’s manual;Demonstration Board’s schematic;Additional documentation.To install the required components, do the following:1. Insert the SofTec Microsystems “System Software” CD-ROM into your computer’s CD-ROM drive. A startupwindow will automatically appear.2. Choose “Install Instrument Software” from the main menu.3. Click on the “Copy SofTec Microsystems DLL to \CodeWarrior for HCS12 V4.7\Prog\gdi” option. An Explorerwindow will open. Copy the “SofTec_BDM12.dll” file to your PC in the “\CodeWarrior for HCS12V4.7\Prog\gdi” folder, relative to the CodeWarrior installation path.4. Click on the “Copy examples for CodeWarrior for HCS12 V.4.7” option. An Explorer window will open. Copythe “DEMO9S12PFAME” folder to your PC, in a location of your choice. These are the examples specific for the demonstration board, and will be used later in the step-by-step tutorial.Note: to install the Additional Components on Windows 2000 or Windows XP, you must log in asAdministrator.First Connection with the PCNote: before to connect the board to the PC, it is important that you install the required system software asdescribed in the previous section.The Evaluation Board connects to a host PC through a USB port. Connection steps are listed below in therecommended flow order:1.Install all the required system software as described in the previous section. 2.Make sure the “POWER SEL” jumper is in the “USB” position. 3.Insert one end of the USB cable into a free USB port. 4.Insert the other end of the USB cable into the USB connector on the Demonstration Board. 5. The first time the Demonstration Board is connected to the PC, Windows recognizes the instrument and starts the“Found New Hardware Wizard” procedure, asking you to specify the driver to use for the instrument. Follow the wizard steps, choosing to install the software automatically when requested.The Evaluation Board’s USB driver is now installed on your system.Step-By-Step Tutorial1. Make sure that the “POWER SEL” jumper selects the “USB” position.2. Ensure that the Demonstration Board is connected to the PC (via the USB cable) and that the board is powered.3. Start CodeWarrior by selecting it in the Windows Start menu.4.From the CodeWarrior main menu, choose “File > Open” and choose the“DEMO9S12PFAME\C\Demo\Demo.mcp” file. This is the board example you copied from the SofTecMicrosystems “System Software” CD-ROM.5. Click “Open”. The Project window will open.6. The C code of this example is contained in the “main.c” file. Double click on it to open it.7. From the main menu, choose “Project > Debug”. This will compile the source code, generate an executable fileand download it to the demo board.8. A new debugger environment will open. From the main menu, choose “Run > Start/Continue”. The programwill be executed in real-time.9. From the main menu, choose “Run > Halt”. The program execution will stop. The next instruction to beexecuted is highlighted in the Source window.10. From the main menu, choose “Run > Single Step”. The instruction highlighted in the Source window will beexecuted, and the program execution will be stopped immediately after.11. From the main menu, choose “Run > Start/Continue”. The application will restart from where it was previouslystopped.TrademarksSMH Technologies is the licensee of the SofTec Microsystems trademark.Freescale™ and the Freescale logo are trademarks of Freescale Semiconductor, Inc.Copyright © 2008 SMH Technologies DC10008Microsoft and Windows are trademarks or registered trademarks of Microsoft Corporation.PC is a registered trademark of International Business Machines Corporation.Other products and company names listed are trademarks or trade names of their respective companies.。
PL2303HXD Datasheet
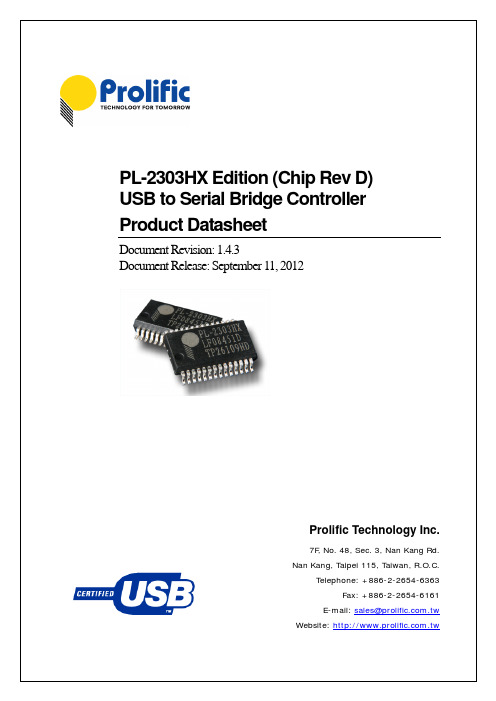
September 11, 2012ds_pl2303HXD_v1.4.3DisclaimerAll the information in this document is subject to change without prior notice. Prolific Technology Inc. does not make any representations or any warranties (implied or otherwise) regarding the accuracy and completeness of this document and shall in no event be liable for any loss of profit or any other commercial damage, including but not limited to special, incidental, consequential, or other damages.TrademarksThe Prolific logo is a registered trademark of Prolific Technology Inc. All brand names and product names used in this document are trademarks or registered trademarks of their respective holders.CopyrightsCopyright © 2005-2012 Prolific Technology Inc., All rights reserved.No part of this document may be reproduced or transmitted in any form by any means without the express written permission of Prolific Technology Inc.ds_pl2303HXD_v1.4.3Revision HistoryRevision Description DateSeptember 11, 20121.4.3 Modify Features and OS Driver Support ListAdded QFN32 Reel Tape Information1.4.2 Modify Section 12.0 Ordering Information Part Number June 25, 20121.4.1 Modify Reel Tape Packing (MOQ) Information May 25, 2012March 16, 20121.4 Added Windows 8 Driver SupportAdded OTPROM Configuration SectionModified BaudRate Support TableAdded Reference Schematic DiagramAdded Chip Marking InformationAdded Tube Packing InformationAdded Worldwide Distributors InformationSeptember 9, 20101.3 Added Windows 7 Logo Driver InformationModified Operating Temperature CharacteristicsModified Baud Rate Settings Table1.2 Sec. 9.0: Modified DC & Temperature Characteristics June 27, 20081.1 Added Windows Vista and XP Logo Driver informationApril 16, 2007 Added USB-IF Logo TID informationJune 30, 20061.0B Sec. 4.2: Modified QFN diagram to add IC bottom PADinformation1.0A PL-2303HX (Chip Rev D) Datasheet – Formal Release November 23, 2005September 11, 2012ds_pl2303HXD_v1.4.3Table of Contents1.0FEATURES (7)1.1Royalty-Free Driver Support (8)1.2Product Applications (8)2.0FUNCTIONAL BLOCK DIAGRAM (9)3.0INTRODUCTION (10)4.0PIN ASSIGNMENT OUTLINE (11)4.1SSOP28 Package (11)4.2QFN32 Package (12)5.0PIN ASSIGNMENT & DESCRIPTION (13)5.1SSOP28 Package (13)5.2QFN32 Package (14)6.0OTPROM CONFIGURATION (15)7.0 DATA FORMATS & PROGRAMMABLE BAUD RATE GENERATOR (17)8.0PL2303HXD REFERENCE SCHEMATIC DIAGRAM (18)9.0DC & TEMPERATURE CHARACTERISTICS (19)9.1Absolute Maximum Ratings (19)9.2DC Characteristics (19)9.3Clock Characteristics (20)9.4Temperature Characteristics (21)9.5Leakage Current and Capacitance (21)9.6 Power-On Reset (21)10.0 O UTLINE DIAGRAM (22)10.1SSOP28 Package (22)10.2 QFN32 Package (23)11.0 PACKING INFORMATION (24)11.1Carrier Tape (SSOP-28) (24)11.2Carrier Tape (QFN32) (25)11.3Reel Dimension (26)11.4 Tube Packing (27)ds_pl2303HXD_v1.4.3 12.0ORDERING AND CHIP MARKING INFORMATION (28)13.0CONTACT INFORMATION (29)September 11, 2012ds_pl2303HXD_v1.4.3List of FiguresFigure 2-1 Block Diagram of PL-2303HX (Rev D) (9)Figure 4-1 Pin Assignment Outline of PL-2303HX (Rev D) SSOP28 (11)Figure 4-2 Pin Assignment Outline of PL-2303HX (Rev D) QFN32 (12)Figure 6-1 PL2303 EEPROM Writer Program (15)Figure 8-1 PL2303HX (Chip Rev D) Reference Schematic Diagram (18)Figure 9-1 Power-On Reset Diagram (21)Figure 10-1 Outline Diagram of PL-2303HX (Rev D) SSOP28 (22)Figure 10-2 Outline Diagram of PL-2303HX (Rev D) QFN32 (23)Figure 11-1 SSOP28 Carrier Tape (24)Figure 11-2 IC Reel Placements (24)Figure 11-3 QFN32 Carrier Tape (25)Figure 11-4 Reel Dimension (26)Figure 11-5 Tube Packing Dimension (27)Figure 12-1 Chip Part Number Information (SSOP) (28)List of TablesTable 5-1 Pin Assignment & Description (SSOP28) (13)Table 5-2 Pin Assignment & Description (QFN32) (14)Table 6-1 EEPROM Writer Configuration (15)Table 7-1 Supported Data Formats (17)Table 7-2 Baud Rate Settings (Supported by Driver) (17)Table 9-1 Absolute Maximum Ratings (19)Table 9-2a Operating Voltage and Suspend Current (19)Table 9-2b 3.3V I/O Pins (19)Table 9-2c VDD_325@3.3V Serial I/O Pins (20)Table 9-2d VDD_325@2.5V Serial I/O Pins (20)Table 9-2e VDD_325@1.8V Serial I/O Pins (20)Table 9-3 Clock Characteristics (20)Table 9-4 Temperature Characteristics (21)Table 9-5 Leakage Current and Capacitance (21)Table 9-6 Power-On Reset (21)Table 10-1 Package Dimension (22)Table 11-1 Reel Part Number Information (26)Table 12-1 Ordering Information (28)Table 12-2 Chip Marking Information (28)September 11, 2012ds_pl2303HXD_v1.4.31.0 FeaturesSingle-chip USB to Serial (RS232/RS422/RS485) asynchronous serial data transfer interface Fully Compliant with USB Specification v2.0 (Full-Speed)USB-IF Logo Compliant with TID 40000100UHCI/OHCI (USB1.1), EHCI (USB 2.0), xHCI (USB 3.0) Host Controller CompatibleIntegrated USB 1.1 Transceiver and 5V to 3.3V RegulatorIntegrated 96MHz clock generator (No external crystal required)Integrated OTPROM (One-Time Programming ROM) – no external EEPROM required.o For writing and storing customer USB VID/PID, Serial Number, Product String, and other device startup configurations. (uses default settings if OTPROM is empty) Supports USB to RS232 Serial UART Interfaceo Full-duplex transmitter and receiver (TXD and RXD)o Six MODEM control pins (RTS, CTS, DTR, DSR, DCD, and RI)o5, 6, 7 or 8 data bitso Odd, Even, Mark, Space, or None parity modeo One, one and a half, or two stop bitso Parity error, frame error, and serial break detectiono Programmable baud rate from 75 bps to 12M bpso External RS232 driver power down controlo Independent power source for serial interfaceSupports RS-422/RS-485 like serial interface (TXD, DTR_N, and RTS_N pins should be externally pulled-up to 5V)Extensive Flow Control Mechanismo Adjustable high/low watermark levelo Automatic hardware flow control with CTS/RTS or DSR/DTRo Automatic software flow control with XON/XOFFo Inbound data buffer overflow detectionConfigurable 512-byte bi-directional data buffero256-byte outbound buffer and 256-byte inbound buffer; oro128-byte outbound buffer and 384-byte inbound bufferSupports Remote Wake-up from RS232 input pin signals (RI, RXD, DSR, DCD, CTS)Four (4) General Purpose I/O (GP0, GP1, GP2, & GP3) pins and Four (4) Auxiliary General Purpose I/O (RI_N, DSR_N, DCD_N, & CTS_N) pins.Supports Windows Selective Suspend by OTPROM configuration (Enable Remote Wakeup) o Suspends power of chip when idle (COM port is closed)Provides royalty-free USB to Virtual COM Port (VCP) drivers for Windows, Mac, Linux-40o C to 85o C Operating TemperatureSmall footprint 28-pin SSOP or 32-pin QFN IC packages (RoHS compliant and Pb-free Green CompoundSeptember 11, 2012ds_pl2303HXD_v1.4.31.1 Royalty-Free Driver SupportWindows 8, 7, Vista, XP, 2000 (Microsoft Certified WHQL Drivers)o Windows Update Driver installation available in Windows Vista, 7, and 8 (32/64-bit) Windows Server 2003, 2008, 2008 R2, 2012Windows CE 4.2, 5.0, 6.0, and Windows Embedded Compact 7o Requires customer SDK image file for customizing WinCE 6.0 and 7.0 drivers.Windows XP Embedded (XPe), Point-of-Service (WEPOS), and POSReadyMac OS 8/9, OS X (supports latest Mac OS X 10.8 Mountain Lion)Linux/Android kernel 2.4.31 and above includes built-in driversProvides Driver Customization for Customer USB VID/PID and special baud rates1.2 Product ApplicationsSingle-chip upgrade solution for Legacy RS232 devices to USB interfaceUSB to RS232/RS422/RS485 converters/cables/dongles/adaptersHealthcare/Medical USB Interface Data Transfer CablePersonal Infotainment/Media Player Docking USB InterfaceCellular/PDA USB Interface Data Transfer CableSerial-over-IP Wireless SolutionUSB Barcode/Smart Card ReadersGPS/Navigation USB InterfacePoint-of-Sale (POS) Terminals/PrintersPC Docking Station/Port ReplicatorsIndustrial/Instrumentation/Automation Control USB InterfaceUSB Modem/Wireless/Zigbee USB InterfaceSet-Top Box (STB) / Home Gateway USB InterfaceMCU-based devices to USB interfaceds_pl2303HXD_v1.4.32.0 Functional Block DiagramUSB HostRS-232/RS-422/RS-485 Like InterfaceFigure 2-1 Block Diagram of PL-2303HX (Rev D)September 11, 2012ds_pl2303HXD_v1.4.33.0 IntroductionPL-2303HX (Chip Rev D) or PL-2303HXD provides a convenient solution for connecting an RS232-like full-duplex asynchronous serial device to any Universal Serial Bus (USB) capable host. PL-2303HXD highly compatible drivers could simulate the traditional COM port on most operating systems allowing the existing applications based on COM port to easily migrate and be made USB ready.By taking advantage of USB bulk transfer mode, large data buffers, and automatic flow control,PL-2303HXD is capable of achieving higher throughput compared to traditional UART (Universal Asynchronous Receiver Transmitter) ports. When real RS232 signaling is not required, baud rate higher than 115200 bps could be used for even higher performance. The flexible baud rate generator of PL-2303HXD could be programmed to generate any rate between 75 bps to 12M bps.PL-2303HXD is exclusively designed for mobile and embedded solutions in mind, providing a small footprint that could easily fit in to any connectors and handheld devices. With very small power consumption in either operating or suspend mode, PL-2303HXD is perfect for bus powered operation with plenty of power left for the attached devices. Flexible signal level requirement on the RS232-like serial port side also allows PL-2303HXD to connect directly to any 3.3V~1.8V range devices.4.0 Pin Assignment Outline4.1 SSOP28 PackageFigure 4-1 Pin Assignment Outline of PL-2303HX (Rev D) SSOP284.2 QFN32 PackageR T S _NN C GN D G N DT E S TR E S E R V E DN CN CT X DD T R _NV D D _325R XD R I_N GN D V D D _33D SR _N D C D _N C T S_NS H T D _NG P 3G P 2N CN CD PD MN CG P 1G P 0N C V D D _5R ESET _NV O _33Figure 4-2 Pin Assignment Outline of PL-2303HX (Rev D) QFN32Warning: The exposed center die pad of the PL-2303HX QFN package is connected (bonded) to thepin VO_33 so it is very important to design the PCB layout wherein this exposed die pad won’t get grounded on the PCB when mounted.5.0 Pin Assignment & DescriptionPin Type Abbreviation:I: Input O: Output B: Bidirectional I/O P: Power/Ground 5.1 SSOP28 PackageTable 5-1 Pin Assignment & Description (SSOP28)Pin # Name Type Description1 TXD O (1)Serial Port (Transmitted Data)2 DTR_N O (1)Serial Port (Data Terminal Ready)3 RTS_N O (1)Serial Port (Request To Send)4 VDD_325 P RS232 VDD. The power pin for the serial port signals. When the serial port is 3.3V, this should be 3.3V. When the serial port is 2.5V, this should be 2.5V. The range can be from 1.8V~3.3V.5 RXD I (2)Serial Port (Received Data)6 RI_N B (2)Serial Port (Ring Indicator); or Auxiliary General Purpose I/O Port when enabled(7).7 GND P Ground8 NC - No Connection9 DSR_N B (2)Serial Port (Data Set Ready); or Auxiliary General Purpose I/O Port when enabled(7).10 DCD_N B (2)Serial Port (Data Carrier Detect); or Auxiliary General Purpose I/O Port when enabled(7).11 CTS_N B (2)Serial Port (Clear to Send); or Auxiliary General Purpose I/O Port when enabled(7).12 SHTD_N O (3)RS232 Transceiver Shut Down Control13 GP3 I/O Auxiliary GPIO Pin 3 (Default output high mode) (6)14 GP2 I/O Auxiliary GPIO Pin 2 (Default output high mode) (6)15 DP B USB Port D+ signal16 DM B USB Port D- signal17 VO_33 P Regulator Power Output, 3.3V18 GND P Ground19 RESET_N I (4)External System Reset (Active Low)20 VDD_5 P USB Port V BUS, 5V Power. (6.5V for OTPROM writing voltage).21 NC - No Connection22 GP0 B (5)General Purpose I/O Pin 023 GP1 B (5)General Purpose I/O Pin 124 NC - No Connection25 GND - Ground26 TEST I Test mode control27 NC - No Connection28 Reserved - Reserved pin (Must be floating)Notes:(1) – Tri-State, Output Pad. Level and Driving Capability decided by VDD_325.(2) – Tri-State, CMOS Input/Output Pad with level shifter. Level and Driving Capability decided by VDD_325.(3) – CMOS Output Pad.(4) – CMOS Input Pad, 5V tolerant.(5) – Tri-State, CMOS Input/Output Pad. (Default mode: Input)(6) – Default output high mode; do not connect to ground.(7) – Enabling Auxiliary GPIO requires special customized driver.5.2 QFN32 PackageTable 5-2 Pin Assignment & Description (QFN32)Notes:(1) – Tri-State, Output Pad. Level and Driving Capability decided by VDD_325.(2)– Tri-State, CMOS Input/Output Pad with level shifter. Level and Driving Capability decided by VDD_325.(3)– CMOS Output Pad.(4)– Tri-State, CMOS Input/Output Pad. (Default mode: Input)(5)– Default output high mode; do not connect to ground.(6)– Enabling Auxiliary GPIO requires special customized driver.6.0 OTPROM ConfigurationThe default configuration descriptors are stored in the chip internally which will be loaded during power-on reset or USB bus reset whenever OTPROM (One-Time Programmable ROM) is empty. Several of the USB descriptors could be modified and stored to the PL2303HXD OTPROM during device startup like Vendor ID (VID), Product ID (PID), Serial Number, Product String, and otherconfiguration descriptors. The OTPROM can be programmed twice using the Prolific PL2303 EEPROM Writer utility software which can be requested from Prolific or authorized distributors.Figure 6-1 PL2303 EEPROM Writer ProgramTable 6-1 EEPROM Writer Configuration7.0 Data Formats & Programmable Baud Rate GeneratorThe PL-2303HXD controller supports versatile data formats and has a programmable baud rate generator. The supported data formats are shown on Table 7-1. The programmable baud rate generator supports baud rates up to 12M bps and standard driver already supports several baud rate settings as shown in Table 7-2.Table 7-1 Supported Data FormatsTable 7-2 Baud Rate Settings (Supported by Driver)Note: For special baud rate requirements, please contact Prolific FAE for driver customization support.8.0 PL2303HXD Reference Schematic DiagramBelow is an example of using the PL-2303HX (Chip Rev D) as a USB to RS232 converter (with RS485 option) where a RS232 transceiver (Sipex SP213EHCA) is used to convert the TTL levels serial interface of the PL2303TA to RS232 levels as well as converting the +5V nominal VCC to the ±9V required by RS232. The SP213EHCA transceiver provides up to 500Kbps data rate transmission which is ideal for many designs requiring high speed performance. Contact Prolific FAE for more PCB design support.Figure 8-1 PL2303HX (Chip Rev D) Reference Schematic Diagram9.0 DC & Temperature Characteristics9.1 Absolute Maximum RatingsTable 9-1 Absolute Maximum Ratings9.2 DC Characteristics9.2.1 Operating Voltage and Suspend CurrentTable 9-2a Operating Voltage and Suspend CurrentNote: (1) – No device connected.9.2.2 3.3V I/O PinsTable 9-2b 3.3V I/O Pins9.2.3 Serial I/O PinsTable 9-2c VDD_325@3.3V Serial I/O PinsTable 9-2d VDD_325@2.5V Serial I/O PinsTable 9-2e VDD_325@1.8V Serial I/O Pins9.3 Clock CharacteristicsTable 9-3 Clock Characteristics9.4 Temperature CharacteristicsTable 9-4 Temperature Characteristics9.5 Leakage Current and CapacitanceTable 9-5 Leakage Current and Capacitance*1. No pull-up or pull-down resistor.9.6 Power-On ResetFigure 9-1 Power-On Reset DiagramTable 9-6 Power-On ResetNote: The delay time is simulated with VIN ramp of 1V/µsec.10.0 Outline Diagram10.1 S SOP28 PackageTable 10-1 Package DimensionFigure 10-1 Outline Diagram of PL-2303HX (Rev D) SSOP2810.2 Q FN32 PackageFigure 10-2 Outline Diagram of PL-2303HX (Rev D) QFN3211.0 Packing Information11.1 Carrier Tape (SSOP-28)Figure 11-1 SSOP28 Carrier TapeFigure 11-2 IC Reel Placements11.2 Carrier Tape (QFN32)Figure 11-3 QFN32 Carrier Tape11.3 Reel DimensionFigure 11-4 Reel DimensionTable 11-1 Reel Part Number Information11.4 Tube PackingFigure 11-5 Tube Packing Dimension12.0 Ordering and Chip Marking InformationTable 12-1 Ordering InformationFigure 12-1 Chip Part Number Information (SSOP)Table 12-2 Chip Marking Information13.0 Contact InformationTaiwan Headquarter7F, No.48, Sec. 3, Nan Kang Rd.,Nan Kang, Taipei, Taiwan 115, R.O.C.Tel: +886-2-2654-6363 Fax: +886-2-2654-6161Website: E-mail: sales@Shenzhen OfficeRoom 1908, Building, No.A. jiahehuaqiang Building,Shennanzhong Rd. Futian District, Shenzhen, ChinaTel: +86-1350-285-4191E-mail: alexyang@Distributors Contact:/eng/contact-distributors.asp Taiwan DistributorsMaxtek Technology Co., Ltd.5F, No. 13-20, Sec. 6, Ming-Chuang E.RD., Nei-Hu, Taipei, Taiwan, R.O.C.Tel: +886-2-2794-6060 Ext.662Fax: +886-2-8792-8921Website: E-mail: sales@Morrihan International Corp.4F, No. 3-2, YuanCyu Street, NanKang District , Taipei 115, Taiwan, R.O.C.Tel: +886-2-2788-5511Fax: +886-2-2788-9366Website: U-CHEER Company Co., Ltd.4F, No. 48, Chow-Tze ST., Nei-Hu, Taipei, Taiwan, R.O.C.Tel: +886-2-8797-6789Fax: +886-2-8797-3388E-mail: arthur.lu36@USA and Canada / Tectona Electronics Inc.250 Wyecroft Road, Unit 6, Oakville, Ontario, Canada L6K 3T7Tel: +905-827-2206Fax: +905-847-9412Corporate Website: Product Website: JapanHitachi High-Tech Trading Corporation1-24-14, Nishi-Shimbashi, Minato-ku, Tokyo, 105-8418 JapanDept.: Electronic Devices 4th Dept., Electonic Devices Sales DivTel: +81-3-3504-3859Fax: +81-3-3504-7903Website: ChinaLacewood International Corp.Hong Kong OfficeUnit B1-B3, 21/F, Block B, Kong Nam Industrial Building, 603-609 Castle peak Road, Tsuen Wan N.T, Hong KongTel: +852-2690-9898Fax: +852-2690-9300Shenzhen OfficeRoom401-3,East, CEC Information Building, No.1 Xin Wen Road, Shenzhen, P.R.C., 518034Tel:+86-755-8296-7018Fax: +86-775-8330-7119Shanghai OfficeRm 208,District B, Building 3,NO.7,Guiqin Rd, Xuhui Area, ShanghaiTel : +86-21-5426-2182 ~6Fax: +86-21-5426-2180China Freelink Asia LimitedRoom 307, 3F Block6, AnHua Industrial Zone, Tairan 8th Road,CheGongMiao, Futian District, Shenzhen, ChinaTel: +86-755-8302-0469China Shenzhen Shiqixinji Science and Technology Co., Ltd.Room 1908, Building NO.A, Jiahehuaqiang Building,Shennanzhong Rd., Futian District, Shenzhen, ChinaTel: +86-755-8329-5310KoreaNevora TechnologyRm 502, Citylife, 441, Amsa-Dong, Kangdong-Gu, Seoul, 134-855, KoreaTel: +82-2-3426-0050Fax: +82-2-3426-0070Website: http://www.nevora.co.krT&C Semitech Co.,LTD#703 J-dong, Gongku-sangga, 636-62, Kuro-dong, Kuro-ku, Seoul. KoreaTel: +82-2-2672-9531Fax: +82-2-2672-9532Website: http://www.tncsemi.co.kr。
帕特莱特灯具 3 线式警示灯 (Lever) 用户手册说明书

- 5 -- 7 -- 8 -- 6 -Thank you very much for purchasing our Patlite products.● Request the installation and wiring be performed by a professional contractor if construction work is involved.● Prior to installation, read this manual thoroughly before using this product to ensure correct use.● In addition, please store this manual for future reference when performing maintenance, repairs or inspections.●For options and repair parts, please visit our website (https://).● If there are any questions concerning this product, refer to the contact information at the end of this document and contact your nearest PATLITE Sales Representative.● Ensure that the product is installed in an environment that meets the following conditions:- Where excessive vibration is not present. - On a sturdy surface. - On a level surface.● When it is necessary to waterproof the backside of the installation surface;- Provide a sealant coating around the nuts of the backside of the installation surface.- Waterproof the cable mounting area.● Ensure that the product is mounted upright when installed outdoors.● Ensure that the speaker is facing forward when installing the buzzer models.● Depending on your operating environment, additional waterproo fing may be required on the Terminal Block openings for SKH-M □T models.● With buzzer ● Red color● Ø100 ● 12 - 24 V DC ● Cabtyre Cable ● With buzze ● Red c olor(1)(1)(2)<Conformity Standards>● EMC Directive (EN61000-6-4, EN61000-6-2)● RoHS Directive (EN50581)● UL508, CSA-C22.2 No.14 (File No. E215660)● FCC Part 15 Subpart B Class A<Conformity requirements for the CE Marking>This product conforms to EN standards and shows the CE Marking.This product has been tested and found to comply with the limits for a Class A device, pursuant to EMC DIRECTIVE. These limits are designed to providereasonable protection against harmful interference when the equipment is operated in a commercial environment. This product must not be used in residential areas.<Conformity to FCC Compliance>This equipment has been tested and found to comply with the limits for a Class A digital device, pursuant to Part 15 of the FCC Rules. These limits are designed to provide reasonable protection against harmful interference when the equipment is operated in a commercial environment. The equipment generates, uses, and can radiate radio frequency energy and, if not installed and used in accordance with the instruction manual, may cause harmful interference to radio communications. Operation of this equipment in aresidential area is likely to cause harmfulinterference in which case the user will be required to correct the interference at his own expense.(Note ) ● Dimensions and specifications may change without notice due tocontinual product improvement.● PATLITE and the PATLITE logo is a trademark, or registered trademark ofthe PATLITE Corporation of Japan and each country.(Importer for EU)PATLITE Europe GmbH Am Soeldnermoos 8, D-85399 Hallbergmoos, GermanyNoticeModel Number Configuration 2■3Model Number ExampleSKH-M1JB-RInstallation Example■ 3-Screw Mounting Type ■ 2-point Hole Type Mounting (SF • SL Models)3-point Hole Type Mounting (SL15 Model Only)TYPETYPE TYPE(1) Use the screws or bolts, nuts. to secure the mounting bracket (accessory) to the mounting surface.(Installation screws and nuts are not included with this product. (2) Check that the O-ring is not twisted.(3) Align the main unit of product with the positioning Indicator and turn it clockwise to lock it.Wire Type : UL2464。
- 1、下载文档前请自行甄别文档内容的完整性,平台不提供额外的编辑、内容补充、找答案等附加服务。
- 2、"仅部分预览"的文档,不可在线预览部分如存在完整性等问题,可反馈申请退款(可完整预览的文档不适用该条件!)。
- 3、如文档侵犯您的权益,请联系客服反馈,我们会尽快为您处理(人工客服工作时间:9:00-18:30)。
Email:
Support: support@
DEMO9RS08KB12 QUICK START GUIDE
Introduction and Default Settings
Install CodeWarrior for Microcontrollers:
Insert the CodeWarrior Development Studio for Microcontrollers CD into a CD / DVD drive. The installation pro-gram will start automatically. If the installation fails to start, start the installation program manually. Open Win-dows Explorer and navigate to the CD / DVD drive where the CodeWarrior disk is inserted. Double click on Launch.exe to launch the installer. Follow the on-screen instructions to install the CodeWarrior IDE and inte-grated programmer.
To Launch the Demo Program:
The DEMO9RS08KB12 ships with a demonstration program preloaded into on-chip FLASH memory. The dem-onstration program converts an analog reading from the POT and the Light Sensor to control the LEDs. The in-ternal TPM is used to flash and LED. ASCII text is echoed to the terminal.
1. Verify the option jumpers are set in default positions. Refer to Figure 1 above.
2. Connect the included A/B USB cable between an open USB port on the host PC and the USB connector on
the target board. Follow the on-screen instructions to install the necessary USB drivers.
3. Rotate the POT fully in both directions. LED1 and LED2 combine to display the POT position.
4. Press SW1. Cover and uncover the light sensor at RZ1. LED1 and LED2 combine to display ambient light
incident on the sensor.
5. Connect a serial cable to the DB9 at J4. Open a terminal program such as AxIDE, and configure for 19200,
8, N, 1. Text typed in the terminal window will echo to the screen
The Quick Start CodeWarrior Project may be downloaded from the Axiom Manufacturing web site at
/support.
Troubleshooting
If the demonstration application fails to function as indicated above, please follow the steps below before contact-ing Freescale Semiconductors. Please refer to the TIC card included in the DEMO9RS08KB12 kit for contact in-formation.
∙Ensure the option jumpers are set to default positions. Refer to Figure 1 above.
∙Ensure the correct version of CodeWarrior is installed and that the KB12 Service Pack is installed
∙Ensure D300 and VDD LED’s are both ON
If the above Troubleshooting Tips fail to correct the problem, please contact Freescale Semiconductors for further assistance. Refer to the Technical Information Card (TIC) included in the kit for contact information. The user may also contact Axiom Manufacturing directly at support@.
2。