机械原理课程设计--粉料压片成形机
机械原理课程设计-压片成型机

先由直齿轮传动实现变速,再经槽轮传动实现间歇运动,然后由 锥齿轮传动实现换向,最后经直齿轮传动达到要求。
②下冲头运动的实现:直齿轮传动。
缺点:传动没有斜齿轮传动平稳。
③上冲头运动的实现:直齿轮传动
返回
①组成:控制装置和被控对象。 ②控制装置:电气控制。 ③控制对象:位移、速度、加速度、 压力等参数的数值大小。
¤圆形转盘机构:
①组成:转盘、主轴、直齿轮、锥齿轮、槽形 机构。
②主要参数:转盘直径500毫米,转盘上 两工作孔直径100毫米,孔底台阶部分高 20毫米,垫片厚10毫米,主轴的转盘传 动部分直径75毫米,连接部分直径120毫 米。齿轮系与下推杆部分共用(下推杆 轮系实现传动比70:1,本机构要求实现 传动比70:1,由齿数为70,35,35的各 齿轮完成,电机原始转速设为1400转/ 分),通过锥齿轮和槽轮实现换向和间 歇运动。
设计成弧状可以成功地将成形片坯扫入成 形槽,传动未皮带传动,转速与圆盘保持一致, 因与物料接触,故材料选定为为奥氏体不锈钢、 聚四氟乙烯材料或采用镀铬等措施。
¤上冲头:因为上冲头压制完后必须退回,我们 考虑过两种方案:
方案A:推杆安装在弹簧内的凸轮机构。 方案B:开槽的凸轮机构。 最终选定方案B 原因:弹簧的弹性模量会随着使用的次数而降 低,机器时间过长后必须更换弹簧才能保证正常工 作,而方案B则不存在这一问题。
主要技术参数 :
最大压片压 Max. Pressure 最大压片直径 Max. Dia. of Table 最大充填深度 Max. Depth of Fill 最大片剂厚度 Max.ThickNess of Table 转盘转速 Turret Speed 电动机 Motor 1.5 kN千牛 100mm毫米 90mm毫米 60mm毫米 5r/min转/分 3千瓦 1400转/ 分 380/50伏/赫 kW-r/min-v/Hz 1200×1000×12 00mm毫米 1800 kg公斤
[机械制造行业]机械原理课程设计粉料压片成形机
![[机械制造行业]机械原理课程设计粉料压片成形机](https://img.taocdn.com/s3/m/d32eb130856a561252d36fe7.png)
(机械制造行业)机械原理课程设计粉料压片成形机一、设计题目3(一)设计题目3(二)设计要求3(三)设计任务4二、方案分析与设计4(一)执行机构的选择与分析41、循环图的分析确定42、运动方案的拟定与选择63、机构的运动分析与设计10(1)上冲头设计10(2)下冲头设计16(3)料筛设计19(二)电动机的选择21(三)传动机构的选择与减速器的设计22(四)飞轮的设计23(五)心得体会25(六)参考文献26机械原理课程设计——粉料压片成形机一、设计题目(一)设计题目1、设计题目及原始数据设计自动压片成形机,将具有一定湿度的粉状原料(如陶瓷干粉、药粉)定量送入压形位置,经压制成形后脱离该位置。
机器的整个工作过程(送料、压形、脱离)均自动完成。
该机器可以压制陶瓷圆形片坯、药剂(片)等。
数据见表1。
表1压片成形机设计数据2、压片成形机的工艺动作(1)干粉料均匀筛入圆筒形型腔(图1a)。
(2)下冲头下沉3mm,预防上冲头进入型腔时粉料扑出(图1b)。
(3)上、下冲头同时加压(图1c),并保持一段时间。
(4)上冲头退出,下冲头随后顶出压好的片坯(图1d)。
(5)料筛推出片坯(图1e)图1(二)设计要求1、上冲头完成往复直移运动(铅垂上下),下移至终点后有短时间的停歇,起保压作用,保压时间为0.4秒左右。
因冲头上升后要留有料筛进入的空间,故冲头行程为90~100mm。
因冲头压力较大,因而加压机构应有增力功能。
2、下冲头先下沉3mm,然后上升8mm,加压后停歇保压,继而上升16mm,将成型片坯顶到与台面平齐后停歇,待料筛将片坯推离冲头后,再下移21mm,到待料位置。
3、料筛在模具型腔上方往复筛料,然后退回。
待批料成型并被推出型腔后,料筛在台面上右移约45~50mm,推卸片坯。
(三)设计任务1、各执行机构应包括:实现上冲头运动的主加压机构、实现下冲头运动的辅助加压机构、实现料筛运动的上下料机构。
满足上述运动可采用连杆机构、凸轮机构等。
机械原理课程设计粉料压片成形机

机械原理课程设计粉料压片成形机引言:在制药和化工等行业中,粉末压片成形机的应用日益增多。
该机的工作原理是将一定数量的粉末材料填入模具中,在应用足够的压力下将粉末材料压缩成特定形状。
在机械原理课程设计中,粉末压片成形机是一种非常重要的机器。
本文将介绍一个可选的设备,即粉末压片成形机,包括其原理、构件和设计。
这个设备非常灵活,可以用来制造各种形状和尺寸的产品,包括塑性、金属等领域的产品。
一、原理粉末压片成形机的工作原理基于物理现象,如惯性、摩擦和力。
在开始工作前,填充粉状物料的模具被装入机器中。
一旦设备运作,将施加巨大的压力来压缩模具中的粉状物料。
这个过程通过一组凸轮和编码器来控制,并在必要时进行更正。
物料的压缩力决定了最终产品的密度和硬度。
二、构件粉末压片成形机的构件包括凸轮、压盘、模具、电动机、液压和机壳。
凸轮是这个机器的控制中心。
它以一定的速率旋转,并通过机械传动作用于其他机器部件。
凸轮的形状和位置是设定压片的形状和尺寸的基础。
压盘是与凸轮直接连接的部件。
它的运动取决于凸轮的形状和位置,它将施加压力到粉末物料上,将其压缩成所需的形状。
模具由基座和顶盖组成,底部可放置粉末材料,在顶盖下面配有压力感应器和形状指示器。
当最低点旋转凸轮时,压盘会施加压力到模具上,并在必要时进行不同位置的、不同速度和方向的转动。
电动机提供凸轮旋转所需的能量。
液压功能分别与压盘、模具和压力传感器连接,为产生足够的压力和控制压力的位置提供重要支持。
机壳是粉末压制机器的保护盖,保护内部机件免受污染或损坏。
三、设计粉末压片成形机的设计涉及到各种考虑因素。
设计过程应考虑以下几个方面:1. 给定的粉末物料,要求输出所需的密度和硬度水平。
2. 所需的产品形状和尺寸。
3. 生产的产品数量和速度。
设计目标是生产高质量、可靠和精度高的输出产品。
在满足这些目标的同时,还应尽可能地减少制造和维护成本。
结论:粉末压片成形机是一种灵活的、高效的制造机器。
机械设计学课程设计-粉料压片机

机械设计学课程设计-粉料压片机(共17页)--本页仅作为文档封面,使用时请直接删除即可----内页可以根据需求调整合适字体及大小--西北工业大学机械设计学课程设计院(系):机电学院班级: 05021103学号:姓名:同组学生:陈波等指导教师:辛洪兵成绩:实践地点:实践时间: 2010 年 6 月 21 日至 2010 年 7 月 2 日2010 年 7 月 2 日目录第一章设计任务目的 (3)设计要求 (4)第二章功能原理设计总功能 (5)功能分析 (5)方案及评价 (6)第三章原理方案设计及分析选定方案的详细说明 (11)各装置选用方案 (11)原理方案总图 (13)第四章机械系统方案设计总体功能机械系统设计方案 (15)第五章结束语 (16)参考文献 (17)第一章设计任务目的1. 设计该装置有利于易拉罐的回收利用,增强大家的环保意识,增加易拉罐的回收利用率。
2. 粉料压片机的工作原理及工艺动作过程(1)粉末压片机是由上冲头、下冲头、料筛传送机构组成,料筛由传送机构把粉料送至上、下冲头之间,通过上、下冲头加压把粉料压成有一定密度的药片。
(2)它的主要动作有:送料、筛料、压料、推出片坯、送成品其工艺动作的分解如下图所示:1-料斗 2-粉料 3-片坯(药片) 4-下冲头 5-模具 6-上冲头1)移动料斗至模具的型腔上方准备将粉料装入型腔,同时将已经成型的药片推出;2)料斗振动,将料斗内的粉料筛入型腔;3)下冲头下沉至一定程度,以防止上冲头向下压制时将型腔内粉料扑出;4)上冲头向下,下冲头下上,将粉料加压并保压一定时间,使药片成型好;5)上冲头快速退出,下冲头将成型的工件(药片)退出型腔,完成压片工艺过程。
设计要求1.原始数据(仅供参考)最大压片压力:50kn最大压片直径:φ16mm最大充填深度:14mm最大片剂厚度:6mm生产能力:3500-4000片/h2设计任务及要求设计一种可以回收易拉罐空瓶的装置,每当将一易拉罐空瓶塞入该装置后自动吐出一角硬币,同时将易拉罐被压缩存放。
机械原理课程设计粉末成形压机答辩
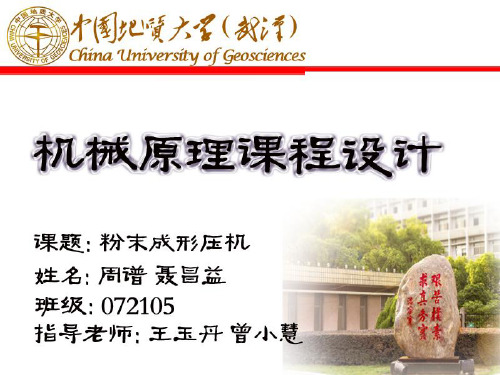
粉末成形压机
送粉器
上模冲下模冲
工作原理
上模冲(上下往复直线运动)
满足运动的机构:
凸轮机构
凸轮连杆机构
偏置曲柄滑块机构
送粉器(左右往复直线运动)满足运动的机构:
偏置曲柄滑块机构
直动推杆圆柱凸轮机构
下模冲(上下往复直线运动)
满足运动的机构:
凸轮机构
凸轮连杆机构
气压传动
优点:能够完成所需功能,而且在加压阶段比凸轮机构优越,结构简单,便于计算。
缺点:保压阶段不够完美。
优点:能够很好地完成停歇保压阶段。
缺点:计算较为复杂,易磨损。
比较之下,我们优先选择了方案二。
方案一:曲柄滑块机构方案二:凸轮机构
√
方案一:偏置曲柄滑块机构
优点:该机构结构简单,基本能实现所需功能,并且在送完料后,可利用该机构的急回特性,节省了空回行程的时间,可以提高劳动生产率。
另外便于计算。
方案二:直动推杆圆柱凸轮机构优点:可以利用凸轮远休过程很好地实现停歇卸料阶段,并且可以很好地控制其周期运动规律。
缺点:结构复杂,计算复杂。
比较之下,我们优先选择了方案二。
√
方案一:气动机构
优点:能够较为完美地实现加压、保压过程。
缺点:往复运动不够稳定,而且设计计算较为复杂。
方案二:凸轮机构
优点:运动过程清晰明朗,能够
很好地完成各个阶段。
缺点:易磨损。
比较之下,我们优先选择了方案二。
√
方案一
方√
案
二。
机械原理课程设计-压片成形机

机械原理课程设计-压片成形机一、设计背景压片成形机是一种常见的机械设备,广泛应用于制药、化工、食品等领域中,用于将各种粉状、颗粒状的原料通过机械压缩成为各种板状、球状或其他形状的制品。
压片成形机主要由进料系统、压制系统、出料系统和控制系统组成。
其中压制系统是压片成形机的核心部分,其设计与性能直接影响着成品质量和生产效率。
本计划设计的压片成形机是一种卧式压片机,其进料方式为自动进料,压制方式为双辊压制。
压制过程中,通过调整辊速、辊距等参数,实现对原料的最佳成形压缩,从而制成各类产品。
为使该设备能够满足不同用户的需求,设备还具有良好的操作性、可靠性、保养性和安全性。
二、设计目标本设计的压片成形机,要求在保证强度和刚度的前提下,具有以下主要技术指标:1.最大压制力:100kN2.最大压制厚度:15mm3.最大压制直径:25mm4.压制速度:0.2-10mm/s5.控制精度:±0.2mm6.电机功率:3kW7.设备外形尺寸:1800×800×1500mm8.设备净重:500kg三、设计方案1. 压制系统设计压制系统是该成形机的核心部分,它由压制辊、强制进料装置、可调式辊距机构、压力调节机构等部件组成。
压制辊为该系统的主要工作部分,其主要由钢材制成,并表面经过热处理,具有很强的耐磨性和抗压弯强度。
强制进料装置为该系统的进料部分,它采用自动进料方式,通过调整强制进料机构的进出角度,使原料经过强制进料后压入两辊压制辊之间进行压制。
可调式辊距机构则为该系统的压制调整部分,通过调整辊距大小,实现对各种原料的最佳压制效果。
压力调节机构为该系统的压力调节部分,通过调整调压阀,实现对压制力大小的精确调节。
2. 设备控制系统设备控制系统采用单片机控制方式,通过脉冲信号和电气信号实现对压制过程的控制。
系统包括压制力传感器、速度检测器、温度传感器等器件,并通过统一的控制接口与压制系统等部件连接。
机械原理课程设计粉末成型压机
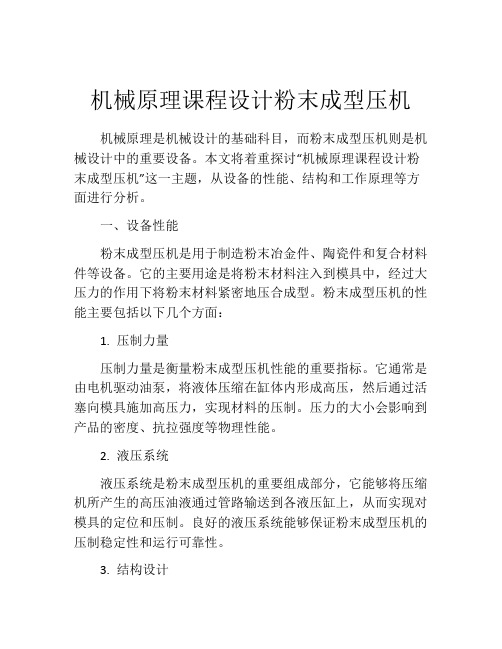
机械原理课程设计粉末成型压机机械原理是机械设计的基础科目,而粉末成型压机则是机械设计中的重要设备。
本文将着重探讨“机械原理课程设计粉末成型压机”这一主题,从设备的性能、结构和工作原理等方面进行分析。
一、设备性能粉末成型压机是用于制造粉末冶金件、陶瓷件和复合材料件等设备。
它的主要用途是将粉末材料注入到模具中,经过大压力的作用下将粉末材料紧密地压合成型。
粉末成型压机的性能主要包括以下几个方面:1. 压制力量压制力量是衡量粉末成型压机性能的重要指标。
它通常是由电机驱动油泵,将液体压缩在缸体内形成高压,然后通过活塞向模具施加高压力,实现材料的压制。
压力的大小会影响到产品的密度、抗拉强度等物理性能。
2. 液压系统液压系统是粉末成型压机的重要组成部分,它能够将压缩机所产生的高压油液通过管路输送到各液压缸上,从而实现对模具的定位和压制。
良好的液压系统能够保证粉末成型压机的压制稳定性和运行可靠性。
3. 结构设计粉末成型压机的结构设计要考虑到平衡性、稳定性和精度,这些因素会影响到设备的定位精度和生产效率。
此外,结构也应具有一定的强度和刚度,这样才能够承受高强度的压制力量和保证设备的安全性。
二、设备结构粉末成型压机的结构是由液压系统、压制平台、油罐、双柱、机身、压盘等组成部分组成,所有部件之间紧密配合,共同作用实现粉末成型压制。
1. 液压系统液压系统是粉末成型压机的核心部分,可以将压缩机所产生的高压油液通过管路输送到各液压缸上,从而实现对模具的定位和压制。
良好的液压系统能够保证粉末成型压机的压制稳定性和运行可靠性。
2. 压制平台压制平台是设置成型模具的平台,由于模具的大小、形状等不同,故而需要根据具体情况制定压制平台的大小和形状。
3. 油罐油罐是储存液压系统所需要的高压油液的容器,其大小也要根据设备的实际需求进行合理的设计,以保证生产的连续性和稳定性。
4. 双柱双柱主要是用来承载压盘、压力导柱、模具等重量部件的力量载荷,以此保证粉末成型压机在运行过程中的平衡性和稳定性。
机械原理课程设计--压片成形机

机械原理课程设计–压片成形机1. 引言压片成形机是一种用于制造工程材料和零部件的机械设备。
其原理基于压力和温度对材料进行塑性变形,使其在特定形状和尺寸范围内得以成型。
在机械原理课程设计中,我们将研究和设计一种压片成形机,旨在学习和应用机械原理的相关知识,并加深对机械成形工艺的理解。
2. 设计目标本次课程设计的目标是设计一台压片成形机,具有以下特点和功能:•高精度成型:机器能够保证成形后零部件的尺寸和形状精度,满足工程需求。
•可调节压力:机器应具备调节压力的功能,以适应不同材料和成形工艺的要求。
•高效率生产:机器应具备较高的生产效率,以提高生产效益。
•安全可靠:机器应具备安全防护措施,确保操作人员的安全。
3. 设计原理3.1 压片成形工艺压片成形是一种通过将材料置于模具中,并施加压力和温度来使其变形的工艺。
压片成形可以用于制造各种复杂形状的零部件,如齿轮、轴承等。
3.2 压片成形机构本设计的压片成形机主要包含以下几个主要机构:•液压系统:用于提供压力给压片机构,控制工作台的运动速度和压力大小。
•压片机构:由机械结构和压片头组成,通过压力和温度对材料进行塑性变形。
•加热系统:用于加热材料,以改变其塑性和流动性。
•控制系统:用于控制整个机器的运行和各个机构的动作。
4. 设计步骤4.1 确定工作台尺寸和形状根据所需成品的尺寸和形状,确定压片机的工作台尺寸和形状。
可以使用CAD软件进行设计和模拟,以确保工作台满足要求。
4.2 设计液压系统设计液压系统,包括选型液压泵和液压缸,并确定所需压力和流量。
根据设计原则,选择合适的液压元件,并进行液压回路的设计和布置。
4.3 设计压片机构根据成形工艺要求和工作台尺寸,设计压片机构,包括压片头的结构、材料和加热方式。
使用CAD软件进行模拟和优化,确保结构合理和稳定。
4.4 设计加热系统根据压片材料的特性和成形温度要求,设计加热系统。
可以选择电加热、燃气加热或其他适合的加热方式,并进行加热功率的计算和布置。
机械原理课程设计压片机
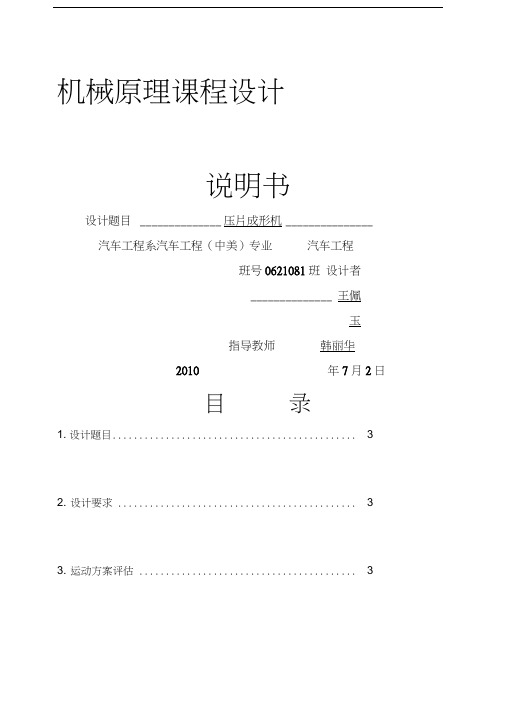
机械原理课程设计说明书设计题目______________ 压片成形机_______________ 汽车工程系汽车工程(中美)专业汽车工程班号0621081班设计者______________ 王佩玉指导教师韩丽华2010 年7月2日目录1. 设计题目 (3)2. 设计要求 (3)3. 运动方案评估 (3)4. 设计内容 (6)5. 设计步骤6. 附录机械原理课程设计――压片成形机一、.设计题目1. 压片成形机介绍设计自动压片成形机,将具有一定湿度的粉状原料(如陶瓷干粉、药粉)定量送入压形位置,经圧制成形后脱离位置。
机器的整个工作过程(送料、压形、脱离)均自动完成。
该机器可以压制陶瓷圆形片坯、药剂(片)等。
2. 压片成形机的工艺动作(1)干粉料均匀筛入圆筒形型腔。
(2)下冲头下沉3mm预防上冲头进入型腔是粉料扑出。
片坯3. 压片成形机设计数据电动机转速/ (r/min ):1450; 生产率1(片/min):10;冲头压力/N : 150 000 ; 机器运转不均匀系数/ 0.10 ;二、设计要求1. 上冲头完成往复直移运动(铅垂上下),下移至终点后有短时间的停歇,起保压作用,保压时间为0.4s左右。
因冲头上升后要留有料筛进入的空间,故冲头行程为100mm 因冲头压力较大,因而加压机构应有增力能力。
2. 下冲头先下沉3mm然后上升8mm加压后停歇保压,继而上升16mm将成形片坯顶到与台面平齐后停歇,待料筛将片坯推离冲头后,再下移21mm到待料位置。
3. 料筛在模具型腔上方往复振动筛料,然后向左退回。
待坯料成型并被推出型腔后,料筛在台面上右移约45~50mm推卸片坯。
三.运动方案评估上冲头设计方案方案1说明:杆1带动杆2运动,杆2使滑块往复运动,同时带动杆3运动,从而达到所要求的上冲头的运动。
此方案可以满足保压要求,但是上冲头机构制作工艺复杂,磨损较大,且需要加润滑油,工作过程中污损比较严重。
方案2说明:凸轮旋转带动滚子运动,使杆1与杆2运动,使上冲头上下往复运动,完全能达到保压要求。
机械原理课程设计-粉末成型压机设计

机械原理课程设计—粉末成型压机小组成员:指导老师:2011年7月中国地质大学(武汉)一.题目与设计要求 (1)题目 (1)设计要求 (1)1.3 尺寸选择 (2)二.方案设计与分析 (2)1. 上模冲压机构 (2)1.1 方案一:凸轮机构 (2)1.2 方案二:曲柄滑块机构 (3)2.送料机构 (3)3.下模冲压机构 (6)三.总体方案 (6)1.上模冲方案............................ 错误!未定义书签。
2.送料机构方案 (10)3.下冲模机构方案 (14)4.传动机构设计方案 (20)四.课程设计小结 (21)五.课题设计环境........................... 错误!未定义书签。
六.参考文献. (22)七.附录 (23)一.题目与设计要求粉末冶金是将金属粉末的混合料通过压制成型和烧结而制成零件或成品材料的一种工艺方法。
在压制长径比h/d=1~1.5的圆柱体压坯时,可采用单向压制,即压制时仅一个方向施力。
压制过程中,阴模固定不动,其他执行构建如图所示。
图.11.上冲模压制机构应具有以下的运动特性:快速接近粉料,慢速压制,压制到位后停歇片刻(约0.4秒左右)保压或接近压制行程终点时再放慢速度而起到保压作用。
2.脱模机构应使下模冲顶出距离准确,复位时要求速度快而冲击小。
3.送粉机构要求严格遵守压制周期的运动规律。
4.进一步要求:上冲模和下冲模的行程可调。
1.3 尺寸选择每分钟压制次数:20次压坯直径:45mm上模冲行程:110mm二.方案设计与分析1. 上模冲压机构对于上模冲机构,要求是需要有几个状态,包括快速接近粉料、慢速压制、保压、离开这几个状态。
其中保压需要0.4秒左右,而且上模冲受到的冲击力为58KN,受到的冲击力较大。
因此我们想到了以下三个方案,其中有凸轮机构、曲柄滑块机构。
1.1 方案一:凸轮机构图.1开始时我们选用的上冲模机构用到了了凸轮机构,它能偶满足我们的运动要求,实现短暂停歇的要求,然而冲题目得知上冲模再冲压时,所受到的力会达到58KN,然而凸轮与上冲模之间形成的是高副,在承受到如此大的力的时候会发生形变,从而影响到凸轮以后的工作以及整个机构的稳定工作,于是我们放弃了这个方案。
机械原理课程设计-粉末成型压机
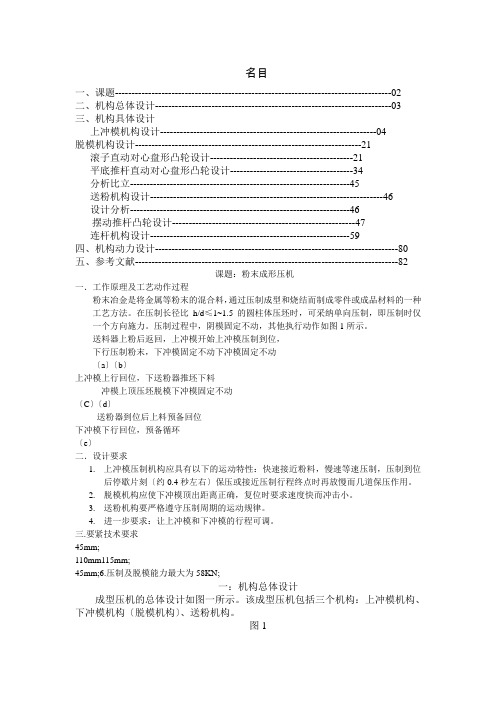
名目一、课题-----------------------------------------------------------------------------------02二、机构总体设计-----------------------------------------------------------------------03三、机构具体设计上冲模机构设计-----------------------------------------------------------------04脱模机构设计--------------------------------------------------------------------21 滚子直动对心盘形凸轮设计-------------------------------------------21平底推杆直动对心盘形凸轮设计-------------------------------------34分析比立------------------------------------------------------------------45送粉机构设计----------------------------------------------------------------------46设计分析------------------------------------------------------------------46摆动推杆凸轮设计-------------------------------------------------------47连杆机构设计------------------------------------------------------------59四、机构动力设计-------------------------------------------------------------------------80五、参考文献-------------------------------------------------------------------------------82课题:粉末成形压机一.工作原理及工艺动作过程粉末冶金是将金属等粉末的混合料,通过压制成型和烧结而制成零件或成品材料的一种工艺方法。
机械原理课程设计-----粉末成型机
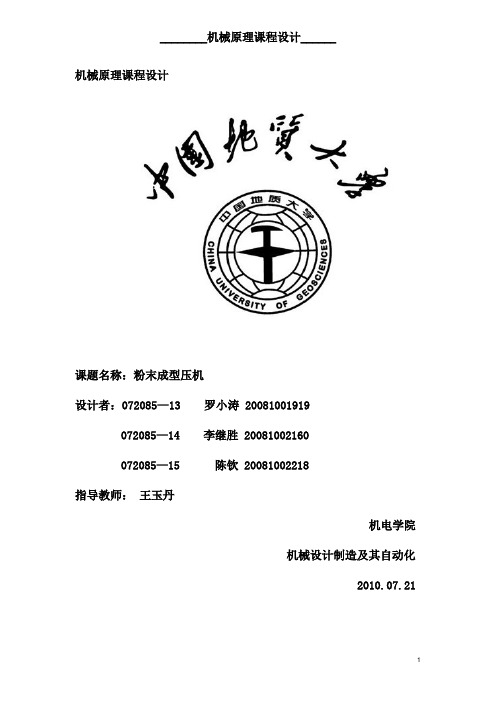
7
________机械原理课程设计______
(2).下冲模为固定移动凸轮和推杆组成。其功能为:推出压坯。在上冲模冲 压的时候下冲模是停歇的,此时推杆可以靠在机架上,而上冲模的作用力就不 会作用到凸轮上。可以实现间歇要求,可靠性高。 (3).送粉器是偏置曲柄滑块机构。其功能为:送料和推离压坯同时实现,并 且具有间歇特性。 其总体机构设计简图如下:
图 18:位移曲线
16
________机械原理课程设计______
图 19:速度曲线 图 20:加速度曲线
17
________机械原理课程设计______
Solidworks 建模结果如下图所示:
图 21:压力角曲线
图 22:下冲模建模
18
________机械原理课程设计______
运动过程分析: 1. 近休止运动阶段(0s~1.2s): 0°~144°:根据周期图可知在这一阶段既要将金属粉末加入到工作 台中去,又要避免与上冲模的推程冲突。 2. 推程阶段(1.2s~1.8s): 144°~216°:这个阶段成型的压坯被推出。加速度曲线为正弦曲线,冲 击力小。 3. 远休止阶段(1.8s~2.1s): 216°~252°:远休止阶段,凸轮位移不变,速度和加速度均为 0。此 时,送粉器将成型的压坯推出。时间设计合理,满足要求 4. 回程阶段:(2.1s~3.0s): 252°~360°,下模进入回程阶段,其运动方式与推程运动方式相同。运 动过程平缓,冲击小。
6
________机械原理课程设计______
艺动作运动循环图如下所示:
图 6:上冲模、下冲模、送粉器位移、速度随时间变化的配合曲线 上述四个动作很简单,关键是时间的配合要非常的恰当,这样一来就对机构提 出了较高的要求。
机械原理课程设计压片成型机

机械原理课程设计压片成型机一、引言压片成型机是一种常见的机械设备,用于将粉末状原料通过压力和模具的作用进行成型。
本文将介绍机械原理课程设计的压片成型机的设计要求、工作原理、结构设计以及相关参数的计算等内容。
二、设计要求1. 成型压力:根据成型材料的特性和要求,确定合适的成型压力范围。
2. 成型速度:根据成型材料的流动性和成型过程的要求,确定合适的成型速度。
3. 成型精度:根据产品的要求,确定合适的成型精度,包括尺寸精度和形状精度。
4. 自动化程度:考虑到生产效率和操作便捷性,设计具有一定自动化程度的压片成型机。
5. 安全性:设计符合相关安全标准,保证操作人员的安全。
三、工作原理压片成型机通过电机驱动传动装置,将动力传递给压力机构,使其产生一定的压力。
同时,通过控制系统控制压力机构的运动,使压力机构按照一定的速度和路径进行运动。
在成型过程中,粉末状原料被放置在模具中,当压力机构施加压力时,原料受到压力的作用,逐渐变形,最终成型为所需的产品。
四、结构设计1. 机架:选择坚固的机架材料,确保机架具有足够的强度和刚度。
2. 传动装置:选择合适的电机和传动装置,确保成型过程中的动力传递稳定可靠。
3. 压力机构:设计合适的压力机构,包括压力传感器、活塞和压力调节装置等,以实现精确的压力控制。
4. 模具:设计适用于不同产品的模具,确保成型过程中的尺寸和形状精度。
5. 控制系统:设计合理的控制系统,包括压力控制、速度控制和路径控制等,以实现自动化生产。
五、参数计算1. 成型压力计算:根据成型材料的特性和要求,结合模具设计,计算所需的成型压力。
2. 传动装置计算:根据所选电机的功率和转速,结合传动装置的传动比,计算所需的传动装置参数。
3. 压力机构计算:根据成型压力和工作面积,计算所需的活塞面积和压力传感器的量程。
4. 控制系统计算:根据成型速度和路径要求,选择合适的控制器和传感器,计算所需的控制系统参数。
六、结论本文详细介绍了机械原理课程设计的压片成型机的设计要求、工作原理、结构设计以及相关参数的计算。
课程设计--粉末成型机
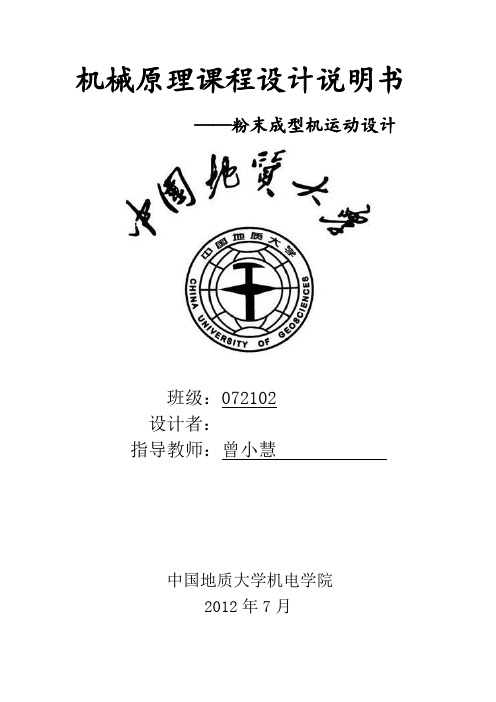
机械原理课程设计说明书——粉末成型机运动设计班级:072102设计者:指导教师:曾小慧中国地质大学机电学院2012年7月目录1.题目 (2)2.设计题目及任务 (2)ξ 2.1工作原理及工艺动作过程 (2)ξ 2.2功能要求及技术参数 (3)3机构方案选择 (4)ξ 3.1上冲模 (4)ξ 3.2送料机构 (6)ξ 3.3下冲模 (7)4.总体方案设计 (8)ξ 4.1机构传动方案 (8)ξ 4.2上下冲头与送粉器动作关系表 (8)ξ 4.3运动循环图 (9)ξ 4.4齿轮传动设计 (9)5.机构设计及分析 (10)ξ 5.1压制机构 (10)ξ 5.2送粉机构 (14)ξ 5.3脱模机构 (20)ξ 5.4传动系统齿轮参数及尺寸确定 (28)6.课程设计小结 (28)7.参考文献 (30)8.附录 (31)1.题目:粉末成形压机设计2.设计题目及任务2.1 工作原理及工艺动作过程设计粉末成形压机,将具有一定湿度的粉状原料(如陶瓷干粉、药粉)定量送入压形位置,经压制成形后脱离该位置。
机器的整个工作过程(送料、压形、脱离)均自动完成。
该机器可以压制陶瓷圆形片坯、药剂(片)等。
粉末成形压机的工作原理及工艺动作过程是:2.2功能要求及技术参数2.2.1上冲头、下冲头、送料筛的设计要求是:1.上模冲压制机构应具有以下的运动特性:快速接近粉料,慢速等速压制,压制到位后停歇片刻保压或接近压制行程终点时在放慢速度而起到保压作用。
2.脱模机构应使下模冲顶出距离准确,复位时要求速度快而冲击小。
3.送粉机构要求严格遵守压制周期的运动规律。
4.进一步要求:让上模冲和下模冲的运动规律可调。
2.2.2主要技术参数要求:1.每分钟压制次数为10-40次;2.压坯最大直径为45mm;3.上模冲最大行程为110mm;4.送粉器行程为115mm;5.脱模最大行程为45mm;6.压制及脱模能力最大为58kN;2.2.3 设计任务1.按个执行件的工艺动作要求拟定运动循环图;2.进行执行机构即压制机构、脱模机构、送粉机构的选型;3.机械运动方案的评价和确定,并进行执行机构运动学尺寸计算和必要的运动分析;4.按选定的电机和执行机构的运动参数拟定机械传动方案,并进行传动机构的运动学尺寸计算;5.画出机械运动简图;6.编制设计说明书(内容包括上述任务的设计、分析计算及结果、图)。
机械原理课程设计-压片成型机
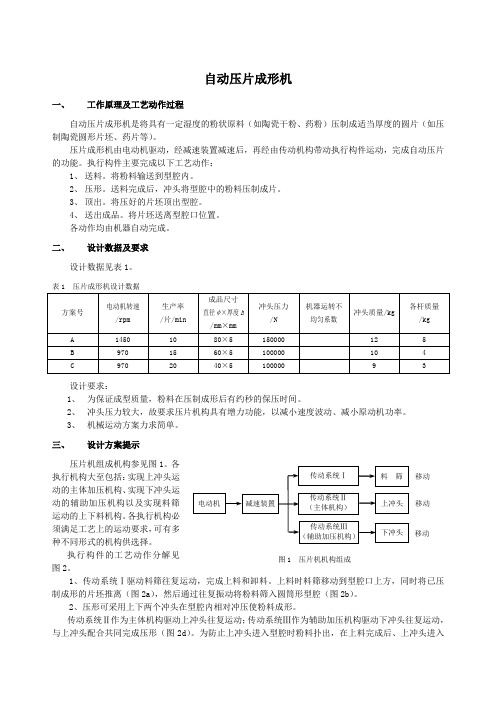
自动压片成形机一、工作原理及工艺动作过程自动压片成形机是将具有一定湿度的粉状原料(如陶瓷干粉、药粉)压制成适当厚度的圆片(如压制陶瓷圆形片坯、药片等)。
压片成形机由电动机驱动,经减速装置减速后,再经由传动机构带动执行构件运动,完成自动压片的功能。
执行构件主要完成以下工艺动作:1、 送料。
将粉料输送到型腔内。
2、 压形。
送料完成后,冲头将型腔中的粉料压制成片。
3、 顶出。
将压好的片坯顶出型腔。
4、 送出成品。
将片坯送离型腔口位置。
各动作均由机器自动完成。
二、设计数据及要求设计数据见表1。
表1 压片成形机设计数据设计要求:1、 为保证成型质量,粉料在压制成形后有约秒的保压时间。
2、 冲头压力较大,故要求压片机构具有增力功能,以减小速度波动、减小原动机功率。
3、 机械运动方案力求简单。
三、设计方案提示压片机组成机构参见图1。
各执行机构大至包括:实现上冲头运动的主体加压机构、实现下冲头运动的辅助加压机构以及实现料筛运动的上下料机构。
各执行机构必须满足工艺上的运动要求,可有多种不同形式的机构供选择。
执行构件的工艺动作分解见图2。
1、传动系统Ⅰ驱动料筛往复运动,完成上料和卸料。
上料时料筛移动到型腔口上方,同时将已压制成形的片坯推离(图2a ),然后通过往复振动将粉料筛入圆筒形型腔(图2b )。
2、压形可采用上下两个冲头在型腔内相对冲压使粉料成形。
传动系统Ⅱ作为主体机构驱动上冲头往复运动;传动系统Ⅲ作为辅助加压机构驱动下冲头往复运动,与上冲头配合共同完成压形(图2d )。
为防止上冲头进入型腔时粉料扑出,在上料完成后、上冲头进入图1 压片机机构组成移动 移动 移动型腔前,下冲头先下沉3mm (图2c )。
可通过对主体机构进行运动分析以及冲头相对于曲柄转角的运动线图,检查保压时间是否满足要求。
3、成形后由下冲头继续上移顶出片坯(图2e )。
4、型腔深度约取28mm 。
5、因上冲头上升后要留出料筛进退的空间,故上冲头行程要求有90~100mm 。
粉末成型压机_机械原理课程设计

机械原理课程设计题目:粉末成型压机设计者: XXX专业:机械设计制造及其自动化指导教师:王玉丹曾小慧2010年7月19日第一部份设计原理及设计要求一、工作原理及工艺动作进程粉末冶金是将金属等粉末的混合料,通过压制成型和烧结而制成零件或成品材料的一种工艺方式。
在压制长径比h/d<1~的圆柱体压坯时,可采纳单向压制,即压制时仅一个方向施压。
压制进程中,阴模固定不动,其它执行件动作如图1所示。
二、设计要求一、上模冲压制机构应具有以下特性:快速接近粉料,慢速等速压制,压制到位后停歇片刻(约秒)保压或接近压制行程终点时再放慢速度而起到保压作用。
二、脱模机构应使下模冲顶出距离准确,复位时要求速度快而冲击小。
3、送分机构要严格遵守压制周期的运动规律。
4、进一步要求:让上冲模和下冲模的行程可调。
三、要紧技术参数要求一、每分钟压制次数为10~40次;二、压坯最大直径为45mm;3、上模冲最大行程为110mm;4、送粉器行程为115mm;五、脱模最大行程为45mm;六、压制及脱模能力最大为58KN;四、课程设计任务要求一、按各个执行件的工艺动作要求拟定运动循环图;二、进行执行机构即压制机构、脱模机构、送粉机构的选型;3、机械运动方案的评判和确信,并进行执行机构运动学尺寸计算和必要的运动分析;4、按选定的电机和执行机构的运动参数拟定机构传动方案,并进行传动机构运动学尺寸计算;五、画出机械运动方案简图;六、编制设计说明书(内容包括上述任务的设计、分析计算及结果、图);7、进一步工作:执行机构的动画演示、凸轮的数控加工等。
第二部份机构运动循环图的确信和各个执行构件的选型一、各执行构件的工艺动作和运动循环图1 功能分析依照任务书要求,有以下图分析得知该系统的主功能为将粉料压制成型,为完成主功能又可分解为四个功能,即上冲头的压下,下冲头的压上,筛料推片和成新模具,如下图。
图图2 上模冲压制机构的工艺动作:上模冲压制机构的曲柄在0º(在那个地址特殊规定0º是使上模冲位于最高位置的极位角度)到150°(那个数值由设计的极位夹角决定)要完成上模冲的下降和冲压进程;在150º到360º内要完成上模冲和粉料离开并使上模冲继续向上升的工艺动作。
- 1、下载文档前请自行甄别文档内容的完整性,平台不提供额外的编辑、内容补充、找答案等附加服务。
- 2、"仅部分预览"的文档,不可在线预览部分如存在完整性等问题,可反馈申请退款(可完整预览的文档不适用该条件!)。
- 3、如文档侵犯您的权益,请联系客服反馈,我们会尽快为您处理(人工客服工作时间:9:00-18:30)。
课程设计(课程实习)机械设计与制造主体实践(一)院(系、部):机械工程学院姓名:同组成员:班级:指导教师签名:目录一、设计题目3(一)设计题目 3(二)设计要求 3(三)设计任务 4二、方案分析与设计4(一)执行机构的选择与分析 41、循环图的分析确定 42、运动方案的拟定与选择 63、机构的运动分析与设计 10(1)上冲头设计 10(2)下冲头设计 16(3)料筛设计19(二)电动机的选择 21(三)传动机构的选择与减速器的设计 22(四)飞轮的设计 23(五)心得体会 25(六)参考文献 26机械原理课程设计——粉料压片成形机一、设计题目(一)设计题目1、设计题目及原始数据设计自动压片成形机,将具有一定湿度的粉状原料(如陶瓷干粉、药粉)定量送入压形位置,经压制成形后脱离该位置。
机器的整个工作过程(送料、压形、脱离)均自动完成。
该机器可以压制陶瓷圆形片坯、药剂(片)等。
数据见表1。
表1 压片成形机设计数据2、压片成形机的工艺动作(1)干粉料均匀筛入圆筒形型腔(图1a)。
(2)下冲头下沉3mm,预防上冲头进入型腔时粉料扑出(图1b)。
(3)上、下冲头同时加压(图1c),并保持一段时间。
(4)上冲头退出,下冲头随后顶出压好的片坯(图1d)。
(5)料筛推出片坯(图1e)图1冲头行程为90~100mm。
因冲头压力较大,因而加压机构应有增力功能。
2、下冲头先下沉3mm,然后上升8mm,加压后停歇保压,继而上升16mm,将成型片坯顶到与台面平齐后停歇,待料筛将片坯推离冲头后,再下移21mm,到待料位置。
3、料筛在模具型腔上方往复筛料,然后退回。
待批料成型并被推出型腔后,料筛在台面上右移约45~50mm,推卸片坯。
(三)设计任务1、各执行机构应包括:实现上冲头运动的主加压机构、实现下冲头运动的辅助加压机构、实现料筛运动的上下料机构。
满足上述运动可采用连杆机构、凸轮机构等。
辅助加压机构可采用凸轮机构2、设计传动系统并确定其传动比分配,并在图纸上画出传动系统图;3、画出机器的运动方案简图与运动循环图。
拟定运动循环图时,可执行构件的动作起止位置可根据具体情况重叠安排,但必须满足工艺上各个动作的配合,在时间和空间上不能出现“干涉”;4、设计机构;5、对机构进行运动设计,绘出运动线图。
进行机构的动态静力分析,计算飞轮转动惯量;6、将机构做成三维模型,实现模拟运动;7、编写设计计算说明书。
二、方案分析与设计(一)执行机构的选择与分析1、循环图的分析确定根据压片机的工艺动作可得各个机构的动作如下:上冲头:往复运动。
下降压紧药片,保压0.4s,上升。
下冲头:复杂的往复运动。
首先下降3mm,接着上升8mm,保压0.4s,上升16mm,间歇一段时间后,下降21mm。
再间歇一段时间。
料筛:将料送出,筛料,返回,间歇一段时间后重复动作。
由各个机构的动作可画出其运动循环图如图2所示:图2下冲头510152025301534567591512135151651819521225242552728533153334536φs则其运动关系如表2所示:表2上冲头进休退下冲头休退进休进休退料筛退休进筛可将其运动表示为树状功能图:图32、运动方案的拟定与选择根据循环图及树状图,可得三个机构都做往复运动,且都有间歇运动。
上冲头是主加压机构,故可选曲柄滑块机构,或六杆机构来实现增力。
下冲头运动和筛料机构可用凸轮机构来实现其运动。
筛料机构做往复运动,故可以使用曲柄滑块机构,也可用凸轮机构实现其运动。
设计各个部分的机构如表3所示表3方案上冲头下冲头料筛1 曲柄滑块机构平底凸轮机构曲柄滑块机构2 六杆机构滚子凸轮机构滚子凸轮机构上冲头方案:方案一:曲柄滑块机构方案二:六杆机构选择:选择方案二。
理由:六杆机构将曲柄滑块的急回特性进一步扩大,同时使行程得到扩大,效率高。
六杆机构接近死点位置所具有的传力特征来实现增力,比曲柄滑块的增力效果好,能够更好的实现加压。
故选择六杆机构作为上冲头的加压机构。
下冲头方案:方案一:平底凸轮机构方案二:滚子凸轮机构选择:选择方案二。
理由:选择凸轮机构易实现下冲头复杂的运动。
首先我们想到的是方案一,因为方案一的压力角为零,传力效果好,但当画出凸轮轮廓线时,有曲率半径小于零的地方,故方案一不可行,选择滚子凸轮机构。
料筛方案:方案一:方案二:选择:选择方案二。
理由:曲柄滑块机构能够实现料筛的往复运动,但不易实现料筛的间歇运动及筛料的过程。
凸轮机构能够很好的实现料筛的间歇运动,且能够实现筛料的过程。
故选用凸轮来控制料筛。
总方案:根据以上分析可得最终方案如图4所示(六杆机构的曲柄与齿轮结合,由不完全齿轮实现机构的间歇)图43、机构的运动分析与设计1.上冲头设计六杆机构的计算设计数据:六杆机构已知的数据如表4,六杆机构的中心距x,构件3的上下极限位置角ψ,ψ1,滑块5的行程H,曲柄的转速n,则要求的为各杆的长度,以及y的长度。
X (mm) K ψ( )ψ1( )H(mm)DE/CD n(r/min)80 1.4 30 90 91 1.6 60数值计算第一步分析:曲柄滑块机构六杆机构示意图(1) 尺寸计算图5将杆3,杆4,滑块5拆下来分析,将图顺时针旋转90°,如图5,以便于分析。
并以C 点为原点,滑块5的道路方向为x 轴方向,垂直方向为y 轴方向。
对CD 1E 1分析:60cos x 31l D = 60sin 31l y D =2121124)-(D D E y x x l += 346.1l l = 由以上各式可求得:3184.1x l E = ①对CD 2E 2分析:432l l x E += 346.1l l =由以上两式可求得:326.2l x E = ②且H x x E =1E2- ③由①②③联立求得:2313=l 1964=l(2)运动分析对于图中所示的曲柄滑块机构已知曲柄的转速n 1=60 r/min ,各从动构件的运动可由表5中所列公式求出。
计算结果见附件一,结果画出的滑块的速度、加速度曲线如图6所示。
此曲柄滑块机构为对心曲柄滑块机构,故无急回特性。
当曲柄不是匀速转动的时候便有了急回特性。
此时最大压力角为38°,小于40°,符合要求。
图6第二步分析:曲柄摇杆机构曲柄滑块机构的曲柄在六杆机构中只做摆动,即曲柄摇杆机构的摇杆。
有上一步分析可得曲柄滑块中曲柄的长度,即曲柄摇杆中摇杆的长度。
由已知数据中的其急回系数为K=1.4,计算可得其极位夹角为 3018014.114.118011=⨯+-=⨯+-=K K θ,则对曲柄摇杆的设计及为已知摇杆的长度、两个极限位置,以及四杆机构的极位夹角,求各杆的长度,则可用图解法进行分析并求解。
如图7图7将图旋转180°,即为六杆机构时的机构,如图8图8对此四杆机构进行运动分析,分析数据见附件二,分析的速度、加速度曲线如图9图9求得1l =23, 2l =62, 3l =123,Y=92。
将此四杆机构在软件中计算得最大压力角为37°,符合压力角的要求,故此机构成立。
故可得1l =23, 2l =62, 3l =123, 4l =196,即六杆机构的各个尺寸已求出,可画出六杆机构的精确结构如图10。
此六杆机构无间歇运动,可让曲柄由不完全齿轮带动,就实现其间歇运动(此齿轮的系数确定见附件三)。
图10四杆机构的摇杆及曲柄滑块的曲柄,将曲柄滑块的曲柄位置改为四杆机构中摇杆的位置,将曲柄滑块的曲柄的速度改为四杆机构中摇杆的速度,可得出一组滑块的速度,加速度曲线,此速度与加速度曲线则为六杆机构中滑块的速度,加速度曲线,如图11。
由图可得,滑块向下运动的速度小于回来时的速度,即实现了急回特性。
图112.下冲头设计下冲头采用滚子凸轮机构完成其动作。
根据循环图构造凸轮。
若直接使用循环图中的位移曲线,则有较大的刚性冲击,使得运动时有较大的惯性力,从而有震动。
为使凸轮工作时无突变的加速度,故计算时采用3—4—5多项式来计算位移。
计算时所用公式如表6,用excel表格计算,计算数据中有确定其位移、速度、加速度曲线,凸轮的理论廓线、实际廓线,确定基圆半径,计算压力角。
计算数据见附件二。
其位移、速度、加速度曲线,及凸轮理论廓线、实际廓线,如图12所示表6 凸轮计算公式图123.料筛的设计料筛机构为滚子凸轮机构。
为使其运动时没有冲击,也是用3-4-5多项式计算位移,筛料的过程中也为3-4-5多项式,计算公式与下冲头相同,见表,计算出的数据表格见附件三,其位移、速度、加速度及凸轮理论廓线、实际廓线如图13图13(二)电动机的选择 1、正确选用电动机的基本原则:1)电动机的机械特性、启动、制动、调速及其它控制性能应满足机械特性和生产工艺过程的要求,电动机工作过程中对电源供电质量的影响(如电压波动、谢波干扰等),应在容许的范围内;2)按预定的工作制、冷却方法基辅在情况所确定的电动机功率,电动机的温升应在限定的范围内;3)根据环境条件、运行条件、安装方式、传动方式,选定电动机的结构、安装、防护形式,保证电动机可靠工作;4)综合考虑一次投资几运行费用,整个驱动系统经济、节能、合理、可靠和安全。
2、常用电动机的结构特征 1)Y 系列三相异步电动机该系列电机能防止水滴、灰尘、铁屑或其他杂物浸入电机内部,它是我国近年来研制成功的新型电动机。
2)电磁调速三相异步电动机YCD 电磁调速三相异步电动机,有组合式和整体式两种机构,这两种调速电动机为防护式,空气自冷,卧式安装,且无碳刷,集电环等滑动接触部件。
3、确定原动机的功率Pnηwn P P =其中,Pw 为工作机要求的功率;η为由电动机到工作机执行机构的总效率。
工作机要求的功率Pw 主要为执行构件在单位时间里克服工作阻力所作的功。
在压片机中,主要为在单位时间里冲头冲压时克服工作阻力所作的功。
则c r w v F P =其中,Fr 为冲头冲压时的工作阻力,主要发生在冲头下压的后半个行程中,且假定为线性变化,我们选择方案一,故行程结束时达到最大值60000N 。
vC为冲头的运动速度,可以通过得曲柄滑块机构的运动分析得到(见附件一)。
由上式可以算得冲头在不同位置时,消耗的功率,列于表7。
可见最大值为15.5千瓦左右。
平均值为10千瓦左右,考虑机构中运动副的摩擦,参照电动机的技术数据选择Y160M-4电机。
输出功率N=11KW,转速n=1350 r/min。
表7Fr vc Pw00.250020106666.6670.28362181890.81213333.330.30876384116.851200000.32556346511.26826666.670.33415898910.90433333.330.334699311156.643400000.327350813094.03246666.670.312306914574.32253333.330.289810615456.565600000.252988415179.304(三)传动机构的选择与减速器的设计1、传动机构的选择如何合理分配各级传动比,将直接影响传动装置的结构尺寸,重量,运行维护,造价及性能,这是设计过程中一个重要的问题,必须认真对待。