CAXA提供的机械制图的一些加工技术要求
机械制图常用的技术要求

机械制图常用的技术要求技术要求是表述视图与标注无法表达的其他要求,技术要求是图纸不可或缺的组成部分一、一般技术要求制件去除表面氧化皮;制件不得有划痕、擦伤等损伤零件表面的缺陷;去除毛刺飞边;锐角倒钝;未注倒角均为0.5×45%%d;未注越程槽均为1.2×0.3;表面平整无毛刺;二、未注公差技术要求(金属件)未注公差尺寸的极限偏差按GB/T 1804-m;未注形位公差按GB/T 1184-K;未注长度尺寸允许偏差±0.5;三、表面处理技术要求表面镀白(黑)锌处理;表面喷漆(喷塑)处理;表面发黑处理;表面电泳处理;表面镀铬处理;表面抛光处理;表面滚花,直纹(网纹)m=0.4 GB/T 6403.3;四、热处理技术要求制件氮化450-480HV;制件毛坯须调质处理220-260HB;制件调质处理30-35HRC;制件高频淬火45~50HRC;制件渗碳处理,深度>0.1;制件进行高温回火处理;制件整体淬火40-45HRC;五、塑料件技术要求未注公差尺寸的极限偏差按GB/T 14486-MT6级;制件应饱满光整、色泽均匀;无缩痕、裂纹、银丝等缺陷;浇口、溢边修剪后飞边≤0.3,且不得伤及本体;未注壁厚3;未注筋板1.5~2;表面打光(喷砂)处理;未注过渡圆角取R0.3~R1,脱模斜度≤0.3%%d;各脱模顶料推杆压痕均应低于该制件表面0.2;与对应装配结合面外形配合错位≤0.5;制件应进行时效处理;制件机械强度须符合GB 3883.1标准规定;制件内腔表面打上材料标记和回收标志;未注尺寸参照三维造型;制件表面处理及其它要求由客户定;六、焊接件技术要求未注形位公差按GB/T 19804-F级;焊缝应均匀平整,焊渣清理干净;焊缝应焊透,不得烧穿及产生裂纹等影响机械性能的缺陷;未注公差线性及角度尺寸的极限偏差均按GB/T 19804-B级;七、齿轮(齿轴)技术要求未注公差尺寸的极限偏差按GB/T 1804-m;未注形位公差按GB/T 1184-K;制件毛坯须调质220~260HB;制件材料的化学成分和力学性能应符合GB/T 3077的规定;齿面接触斑点:按齿高不小于40%,按齿长不小于50%;齿面高频淬火回火至49-52HRC;制件表面不应有锈迹、裂纹、灼伤等影响使用寿命的伤痕及缺陷;最终工序热处理表面不得有氧化皮;八、一般轴芯(无铣齿)技术要求未注公差尺寸的极限偏差按GB/T 1804-m;未注形位公差按GB/T 1184-K;未注倒角均为0.5×45°;未注越程槽均为1.2×0.3;制件毛坯须调质220~260HB;档车正反两条螺旋槽,螺距10,深0.4;螺纹表面不允许有磕碰、乱扣、毛刺等缺陷;热处理:表面处理:九、自锁销轴技术要求未注公差尺寸的极限偏差按GB/T 1804-m;未注形位公差按GB/T 1184-K;未注倒角均为0.5×45%%d;热处理:30-35HRC;表面发黑处理;十、输出轴技术要求未注公差尺寸的极限偏差按GB/T 1804-m;未注形位公差按GB/T 1184-K;未注倒角均为0.5×45%%d;未注越程槽均为1.2×0.3;制件毛坯须调质220~260HB;制件表面不允许有锐边、锈迹、污垢等缺陷;热处理:磨加工前表面发黑处理;十一、弹簧技术要求总圈数=有效圈数=展开长度=旋向:热处理:表面处理:制件定型处理;未标自由尺寸公差GB/T1804-MGB/T1804未注公差的线性和角度尺寸的公差M中等级精度尺寸分段/线性尺寸的极限偏差数值0.5-3/±0.1>3-6/±0.1>6-30/±0.2>30-120/±0.3>120-400/±0.5>400-1000/±0.8>1000-2000/±1.2>2000-4000/±2。
CAXA加工
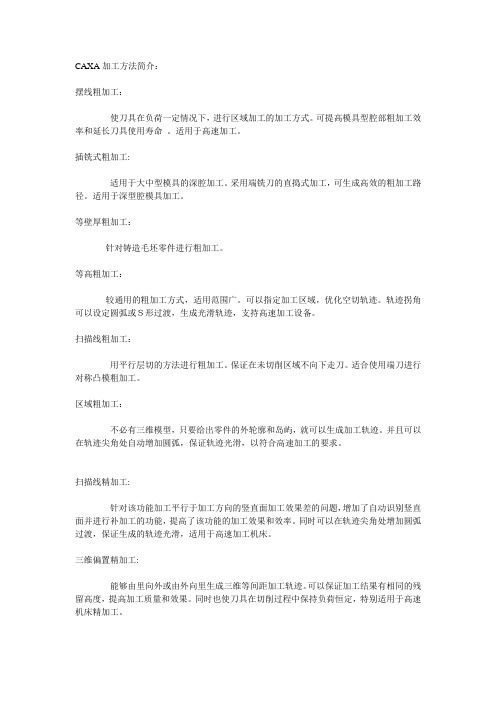
CAXA加工方法简介:摆线粗加工:使刀具在负荷一定情况下,进行区域加工的加工方式。
可提高模具型腔部粗加工效率和延长刀具使用寿命。
适用于高速加工。
插铣式粗加工:适用于大中型模具的深腔加工。
采用端铣刀的直捣式加工,可生成高效的粗加工路径。
适用于深型腔模具加工。
等壁厚粗加工:针对铸造毛坯零件进行粗加工。
等高粗加工:较通用的粗加工方式,适用范围广。
可以指定加工区域,优化空切轨迹。
轨迹拐角可以设定圆弧或S形过渡,生成光滑轨迹,支持高速加工设备。
扫描线粗加工:用平行层切的方法进行粗加工。
保证在未切削区域不向下走刀。
适合使用端刀进行对称凸模粗加工。
区域粗加工:不必有三维模型,只要给出零件的外轮廓和岛屿,就可以生成加工轨迹。
并且可以在轨迹尖角处自动增加圆弧,保证轨迹光滑,以符合高速加工的要求。
扫描线精加工:针对该功能加工平行于加工方向的竖直面加工效果差的问题,增加了自动识别竖直面并进行补加工的功能,提高了该功能的加工效果和效率。
同时可以在轨迹尖角处增加圆弧过渡,保证生成的轨迹光滑,适用于高速加工机床。
三维偏置精加工:能够由里向外或由外向里生成三维等间距加工轨迹。
可以保证加工结果有相同的残留高度,提高加工质量和效果。
同时也使刀具在切削过程中保持负荷恒定,特别适用于高速机床精加工。
等高线精加工:可以用加工范围和高度限定进行局部等高加工;可以自动在轨迹尖角拐角处增加圆弧过渡,保证轨迹的光滑,使生成的加工轨迹适用于高速加工;可以通过输入角度控制对平坦区域的识别,并可以控制平坦区域的加工先后次序。
浅平面精加工:自动识别零件模型中平坦的区域,针对这些区域生成精加工刀具轨迹。
大大提高了零件平坦部分的精加工效率。
等高补加工:自动识别零件粗加工后的残余部分,生成针对残余部分的中间加工轨迹。
可以避免已加工部分的空走刀。
区域补加工:针对前一道工序加工后的残余量区域进行补加工的功能。
多笔清根:生成角落部分的补加工刀具轨迹。
机械设计图纸常用技术要求

机械设计图纸常用技术要求一、机械零件常用技术要求:1、锐边倒钝、去除毛刺飞边。
2、零件去除氧化皮。
3、未注圆角半径R5。
4、未注倒角均为C2°。
5、未注形状公差应符合GB/T 1184-H级要求。
6、未注长度尺寸允许偏差±0.5mm。
7、零件加工表面,不应有划痕、擦伤等损伤零件表面的缺陷。
二、表面处理:1.铝件表面本色阳极氧化处理。
2.铝件表面喷砂处理。
3.零件表面喷塑处理,颜色为银灰色。
4.零件加工后,表面进行拉丝处理。
5.零件表面喷涂黑色面漆,且不得有流挂、气泡、缩孔的表面缺陷。
6. 零件表面镀铬处理。
7. 零件表面镀锌处理,颜色为银白色。
三、铸件技术要求:1、铸件不得有裂纹、气孔、缩孔等铸造缺陷。
2、铸件非加工表面上的铸字和标志应清晰可辨,位置和字体应符合图样要求。
3、铸件非加工表面的粗糙度不大于50μm。
四、热处理要求:1、调质处理HB235~277(45#)。
2、淬火HRC40~45(45# 40Cr)。
3、渗碳淬火,要求渗碳深度不小于0.3mm,HRC56~62。
(20# )4、进行时效处理(自然时效,人工时效)。
5、发黑。
五、焊接技术要求:1、焊缝均匀平滑,不得有裂纹、夹渣、气孔等焊接缺陷。
2、焊缝高度不小于焊接钢板厚度的0.6,采用断续焊时,焊缝长度及间隔应均匀一致。
六、锻件技术要求:1、锻件组织应致密,不得有折叠、裂纹等缺陷。
2、去锐边毛刺,直角处倒钝。
七、装配要求:1、一般装配技术要求:(1)、零件在装配前必须清理和清洗干净,不得有毛刺、飞边、氧化皮、锈蚀、切屑油污、着色剂和灰尘等。
(2)、装配前应对零、部件的主要配合尺寸,特别是过盈配合尺寸及相关精度进行复查。
(3)、装配过程中零件不允许磕、碰、划伤。
(4)、粘接后应清除流出的多余粘接剂。
2、紧固装配技术要求:(1)、螺钉、螺栓和螺母紧固时,严禁打击或使用不合适的旋具和扳手。
紧固后螺钉槽、螺母和螺钉、螺栓头部不得损坏。
CAXA画法标准规定

CAXA机械制图操作规范一、图纸幅面和格式1、图纸幅面利用CAXA进行工程图绘制过程中,在“图幅设置”对话框中标准A3、A4图幅调用Mechanical H A3或Mechanical V A4图框(包含在《CAXA制图标准模板库》内),标准A0、A1、A2图幅调用图框A0,A1,A2图框(包含在《CAXA 制图标准模板库》内,分区图框)。
2、标题栏所有图纸一律采用标准的“汽轮机专用标题栏”。
图纸标题栏中各项内容利用“填写标题栏”工具进行逐项填写,对于零件或小部套其“图框名称”中填写的内容要与装配图明细表中名称保持一致。
“重量”栏填写的零、部件总重对于装配件及中、大型零件保留一位小数或取整数填写;对于重量较轻的小型零件及标准件可以保留四位有效数字填写。
如两个以上零件利用一张图纸绘出时,其对应重量无法在标题栏中填写,可以利用表格的形式在图中列出,以示区分。
填写重量的默认单位是“kg”,如采用其他单位请加注说明。
“材料”栏对于装配图标题栏不填写材料名称及相关技术要求。
零件图中标题栏中材料若有相关技术要求,需两行填写时,在“材料”栏中利用“插入分数”进行填写。
3、明细表装配图利用CAXA“生成序号”功能自动生成明细表。
在实际工作中,为了提高团队设计的效率和一致性,结合CAXA软件明细表的实际操作功能,绘图过程中先填写明细表,必要时输出装配图的明细表为EXCEL格式文件,并把装配图中的明细表与EXCEL文件进行“关联数据库”操作,这样在后序工作中仅需修改对应EXCEL文件或CAXA中的明细表,另一个关联文件即可同步改动。
装配图明细表各零、部件的代号编制方法按照《CAXA机械制图标准》第四章中关于装配图中零、部件序号及其编排方法的相关要求执行。
各零、部件的代号、名称、数量、材料、单重等参数要严格与对应零件图一致。
标准件的代号要查找相关标准,按最新的国家标准代号填写,材料栏中不填写任何材料符号或名称;外购件的代号栏中要准确填写其型号,并在备注栏中注明“外购”。
CAXA机械制图标准

CAXA机械制图标准第一章、图线:参照标准(GB/T457.4-2002)1 线型及其应用:下表列出了在工程图纸中各种线型的主要应用范围,利用CAXA进行工程图绘制过程中,根据图中图素的实际2、图线线宽和图线组别选择。
第二章、剖面符号:参照标准(GB/T457.5-84)1、剖面符号在剖视图和剖面图中,按照CAXA提供的剖面图案的风格,遵守国家制图标准GB/G4457.5-84关于剖面符号的有关规定执行。
2、剖面符号的画法(1)在同一金属零件的零件图中,剖视图、剖面图和剖面线,应画成间隔相等、方向相同而且与水平成45°的平等线。
但当图形中的主要轮廓线与水平成45°时,该图形的剖面线应画成与水平成30°或60°的平行线,其倾斜的方向仍与其他图形的剖面线一致。
(2)相邻辅助零件(或部件),一般不画剖面符号。
当需要画出时,仍按1中的规定绘制。
(3)在装配图中,相互邻接的金属零件的剖面线,其倾斜方向应相反,或方向一致而间隔不等,以示区别。
同一装配图中的同一零件的剖面线应方向相同,间隔相等。
(4)在装配图中,宽度小于或等于2mm的狭小面积的剖面,可用涂黑代替剖面符号。
如果是玻璃或其他材料,而不宜涂黑时,可不画剖面符号。
第三章、视图:参照标准(GB/T458.1-2002)1、局部视图(1)在机械制图中,局部视图的配置可选用以下方式:—按基本视图的配置形式配置—按向视图的配置形式配置—按第三角画法配置在视图上所需表示物体的局部结构的附近,并用细点画线将两者相连。
(2)画局部视图时,其断裂边界用波浪线(No.01.1线型)或双折线(No.01.1线型绘制。
当所表示的局部视图的外轮廓成封闭时,则不必画出其断裂边界线。
(3)标注局部视图时,通常在其上方用大写的拉丁字母标出视图的名称,在相应视图附近用箭头指明投射方向,并注上相同的字母。
当局部视图按基本视图配置,中间又没有其他图形隔开时,则不必标注。
机械制图常用的技术要求

机械制图常用的技术要求技术要求是表述视图与标注无法表达的其他要求,技术要求是图纸不可或缺的组成部分一、一般技术要求制件去除表面氧化皮;制件不得有划痕、擦伤等损伤零件表面的缺陷;去除毛刺飞边;锐角倒钝;未注倒角均为0.5×45%%d;未注越程槽均为1.2×0.3;表面平整无毛刺;二、未注公差技术要求(金属件)未注公差尺寸的极限偏差按GB/T 1804-m;未注形位公差按GB/T 1184-K;未注长度尺寸允许偏差±0.5;三、表面处理技术要求表面镀白(黑)锌处理;表面喷漆(喷塑)处理;表面发黑处理;表面电泳处理;表面镀铬处理;表面抛光处理;表面滚花,直纹(网纹)m=0.4 GB/T 6403.3;四、热处理技术要求制件氮化450-480HV;制件毛坯须调质处理220-260HB;制件调质处理30-35HRC;制件高频淬火45~50HRC;制件渗碳处理,深度>0.1;制件进行高温回火处理;制件整体淬火40-45HRC;五、塑料件技术要求未注公差尺寸的极限偏差按GB/T 14486-MT6级;制件应饱满光整、色泽均匀;无缩痕、裂纹、银丝等缺陷;浇口、溢边修剪后飞边≤0.3,且不得伤及本体;未注壁厚3;未注筋板1.5~2;表面打光(喷砂)处理;未注过渡圆角取R0.3~R1,脱模斜度≤0.3%%d;各脱模顶料推杆压痕均应低于该制件表面0.2;与对应装配结合面外形配合错位≤0.5;制件应进行时效处理;制件机械强度须符合GB 3883.1标准规定;制件内腔表面打上材料标记和回收标志;未注尺寸参照三维造型;制件表面处理及其它要求由客户定;六、焊接件技术要求未注形位公差按GB/T 19804-F级;焊缝应均匀平整,焊渣清理干净;焊缝应焊透,不得烧穿及产生裂纹等影响机械性能的缺陷;未注公差线性及角度尺寸的极限偏差均按GB/T 19804-B级;七、齿轮(齿轴)技术要求未注公差尺寸的极限偏差按GB/T 1804-m;未注形位公差按GB/T 1184-K;制件毛坯须调质220~260HB;制件材料的化学成分和力学性能应符合GB/T 3077的规定;齿面接触斑点:按齿高不小于40%,按齿长不小于50%;齿面高频淬火回火至49-52HRC;制件表面不应有锈迹、裂纹、灼伤等影响使用寿命的伤痕及缺陷;最终工序热处理表面不得有氧化皮;八、一般轴芯(无铣齿)技术要求未注公差尺寸的极限偏差按GB/T 1804-m;未注形位公差按GB/T 1184-K;未注倒角均为0.5×45°;未注越程槽均为1.2×0.3;制件毛坯须调质220~260HB;档车正反两条螺旋槽,螺距10,深0.4;螺纹表面不允许有磕碰、乱扣、毛刺等缺陷;热处理:表面处理:九、自锁销轴技术要求未注公差尺寸的极限偏差按GB/T 1804-m;未注形位公差按GB/T 1184-K;未注倒角均为0.5×45%%d;热处理:30-35HRC;表面发黑处理;十、输出轴技术要求未注公差尺寸的极限偏差按GB/T 1804-m;未注形位公差按GB/T 1184-K;未注倒角均为0.5×45%%d;未注越程槽均为1.2×0.3;制件毛坯须调质220~260HB;制件表面不允许有锐边、锈迹、污垢等缺陷;热处理:磨加工前表面发黑处理;十一、弹簧技术要求总圈数=有效圈数=展开长度=旋向:热处理:表面处理:制件定型处理;未标自由尺寸公差GB/T1804-MGB/T1804未注公差的线性和角度尺寸的公差M中等级精度尺寸分段/线性尺寸的极限偏差数值0.5-3/±0.1>3-6/±0.1>6-30/±0.2>30-120/±0.3>120-400/±0.5 >400-1000/±0.8 >1000-2000/±1.2 >2000-4000/±2。
CAXA制造工程师加工方法介绍
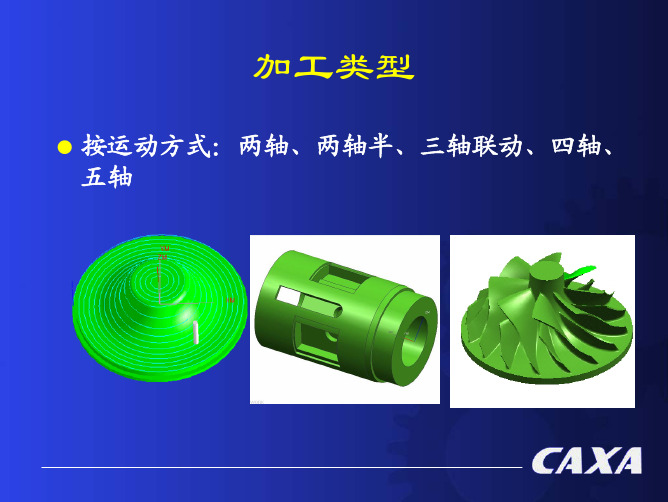
SIEMENS FANUC FIDIA MITSUBISHI FAGOR CINCINNATI OKUMA NUM 华中数控 ………
后置处理机床定义
自动换刀设定 程序头尾格式设定 定义各种G指令,M指令
圆弧插补格式设定 行号格式设定
知识加工
可将某类零件的加工步骤、使用刀具、 工艺参数等加工条件保存为规范化的模 板,形成企业的标准工艺知识库.
槽加工
பைடு நூலகம்
点加工
加工仿真
加工仿真验证模块。
对加工过程进行模拟仿真。仿真过程中可以随意放大、缩小、旋转, 便于观察细节。 能显示多道加工轨迹的加工结果。 仿真过程中可以调节仿真速度。 仿真过程中可以检查刀柄干涉、快速移动过程(G00)中的干涉、刀具 无切削刃部分的干涉情况。 可以把切削仿真结果与零件理论形状进行比较,切削残余量用不同的 颜色区分表示。
插铣式粗加工:
适用于大 中型模具的深 腔加工。采用 端铣刀的直捣 式加工,可生 成高效的粗加 工路径。适用 于深型腔模具 加工。
导动线粗加工
不需要造 型,按照轮廓 线和导动线加 工
半精/精加工
9种常用精加工方式:
参数线精加工 等高线精加工 扫描线精加工 浅平面精加工 限制线精加工 导动线精加工 三维偏置精加工 轮廓线精加工 深腔侧壁加工
笔式清根:
生成角落部分的补加工刀具轨迹。
铣槽加工(扫描式、曲线式):
生成分层和单层的沿导线运动的加工轨迹。
按照等高 粗加工的 方式,对 所选区域 内前一刀 具遗留的 陡峭拐角 部位进行 补加工。
等高补加工
清理所选 区域内平 坦部位两 边间的交 角。
清根补加工
区域补加工
对所选 定的区 域内的 所有拐 角处进 行理。
(精选文档)CAXA机械制图操作规范

CAXA机械制图操作规范一、图纸幅面和格式1、图纸幅面利用CAXA进行工程图绘制过程中,在“图幅设置”对话框中标准A3、A4图幅调用Mechanical H A3或Mechanical V A4图框(包含在《CAXA制图标准模板库》内),标准A0、A1、A2图幅调用图框A0,A1,A2图框(包含在《CAXA制图标准模板库》内,分区图框)。
2、标题栏所有图纸一律采用标准的“汽轮机专用标题栏”。
图纸标题栏中各项内容利用“填写标题栏”工具进行逐项填写,对于零件或小部套其“图框名称”中填写的内容要与装配图明细表中名称保持一致。
“重量”栏填写的零、部件总重对于装配件及中、大型零件保留一位小数或取整数填写;对于重量较轻的小型零件及标准件可以保留四位有效数字填写。
如两个以上零件利用一张图纸绘出时,其对应重量无法在标题栏中填写,可以利用表格的形式在图中列出,以示区分。
填写重量的默认单位是“kg”,如采用其他单位请加注说明。
“材料”栏对于装配图标题栏不填写材料名称及相关技术要求。
零件图中标题栏中材料若有相关技术要求,需两行填写时,在“材料”栏中利用“插入分数”进行填写。
3、明细表装配图利用CAXA“生成序号”功能自动生成明细表。
在实际工作中,为了提高团队设计的效率和一致性,结合CAXA软件明细表的实际操作功能,绘图过程中先填写明细表,必要时输出装配图的明细表为EXCEL格式文件,并把装配图中的明细表与EXCEL文件进行“关联数据库”操作,这样在后序工作中仅需修改对应EXCEL文件或CAXA中的明细表,另一个关联文件即可同步改动。
装配图明细表各零、部件的代号编制方法按照《CAXA机械制图标准》第四章中关于装配图中零、部件序号及其编排方法的相关要求执行。
各零、部件的代号、名称、数量、材料、单重等参数要严格与对应零件图一致。
标准件的代号要查找相关标准,按最新的国家标准代号填写,材料栏中不填写任何材料符号或名称;外购件的代号栏中要准确填写其型号,并在备注栏中注明“外购”。
机械制图常用技术要求

机械制图常用技术要求➢技术要求(冲压件)1、锐边去毛刺,冲压切口粗糙度6、3、2、冲件表面氧化处理:H、Y、或(表面镀锌钝彩、Zn8、DC、)、3、未注公差尺寸的极限偏差按GB/T 1804-92 m级、技术要求(铸件)1、铸件不得有气孔、夹渣、裂纹等缺陷、2、未注明铸造斜度为1~2、5%%d、3、铸造公差按GB6414-86 CT6、4、未注明铸造圆角为R1~R2、5、5、未注公差尺寸的极限偏差按GB/T 1804-92 m级、6、未注形位公差按GB/T1184-96 H级、7、去毛刺,未注倒角0、5x45%%D、➢技术要求(锻件)1、未注锻造圆角半径为R1~R2、2、未注锻造斜度为1~1、5%%D,锻造公差为IT15级、3、锻件组织应致密,不得有折叠、裂纹等缺陷,并去飞边、4、去锐边毛刺,直角处倒钝、5、未注公差尺寸的极限偏差按GB/T 1804-92 m级、6、未注形位公差按GB/T1184-96 H级、技术要求(活塞件)1、未注公差尺寸的极限偏差按GB/T 1804-92 m级、2、未注形位公差按GB/T1184-96 H级、3、去毛刺,未注倒角0、5x45%%D、4、表面磷化处理、➢技术要求(橡胶件)1、零件表面应光洁、(模具表面粗糙度应在Ra0、4以上)且不允许有气泡、杂技级凸凹等缺陷、2、合模缝不允许错位,合模飞边的凸起级厚度不得大于0、02mm、3、邵氏A型硬度65%%P5、4、去净飞边、➢技术要求(塑料件)1、成形前材料应预热干燥、2、成形后制件应光整不得有扭曲变形现象、3、未注圆角为R0、5、4、外表面应光滑,其粗糙度不大于Ra0、4、且不得有划伤,刻痕等缺陷、5、未注尺寸公差按GB/T 1804-92 m级、⏹技术要求(弹簧件)1、旋向:左旋、2、总圈数:no=123、工作圈数:no=104、钢丝硬度:HRC42~48、5、表面氧化处理:H、Y、(俗称发黑)6、单端并紧磨平、再如:⏹如果就是整机安装后的技术要求还应该增加:整机的的性能指标,最后的喷漆要求。
CAXA提供的机械制图的一些加工技术要求
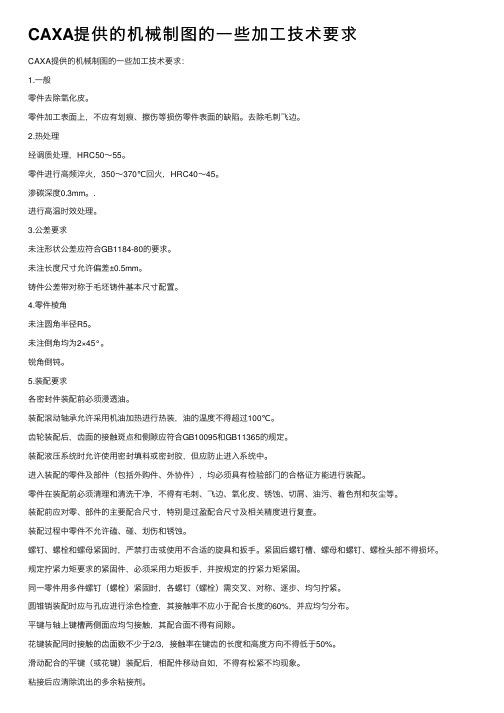
CAXA提供的机械制图的⼀些加⼯技术要求CAXA提供的机械制图的⼀些加⼯技术要求:1.⼀般零件去除氧化⽪。
零件加⼯表⾯上,不应有划痕、擦伤等损伤零件表⾯的缺陷。
去除⽑刺飞边。
2.热处理经调质处理,HRC50~55。
零件进⾏⾼频淬⽕,350~370℃回⽕,HRC40~45。
渗碳深度0.3mm。
.进⾏⾼温时效处理。
3.公差要求未注形状公差应符合GB1184-80的要求。
未注长度尺⼨允许偏差±0.5mm。
铸件公差带对称于⽑坯铸件基本尺⼨配置。
4.零件棱⾓未注圆⾓半径R5。
未注倒⾓均为2×45°。
锐⾓倒钝。
5.装配要求各密封件装配前必须浸透油。
装配滚动轴承允许采⽤机油加热进⾏热装,油的温度不得超过100℃。
齿轮装配后,齿⾯的接触斑点和侧隙应符合GB10095和GB11365的规定。
装配液压系统时允许使⽤密封填料或密封胶,但应防⽌进⼊系统中。
进⼊装配的零件及部件(包括外购件、外协件),均必须具有检验部门的合格证⽅能进⾏装配。
零件在装配前必须清理和清洗⼲净,不得有⽑刺、飞边、氧化⽪、锈蚀、切屑、油污、着⾊剂和灰尘等。
装配前应对零、部件的主要配合尺⼨,特别是过盈配合尺⼨及相关精度进⾏复查。
装配过程中零件不允许磕、碰、划伤和锈蚀。
螺钉、螺栓和螺母紧固时,严禁打击或使⽤不合适的旋具和扳⼿。
紧固后螺钉槽、螺母和螺钉、螺栓头部不得损坏。
规定拧紧⼒矩要求的紧固件,必须采⽤⼒矩扳⼿,并按规定的拧紧⼒矩紧固。
同⼀零件⽤多件螺钉(螺栓)紧固时,各螺钉(螺栓)需交叉、对称、逐步、均匀拧紧。
圆锥销装配时应与孔应进⾏涂⾊检查,其接触率不应⼩于配合长度的60%,并应均匀分布。
平键与轴上键槽两侧⾯应均匀接触,其配合⾯不得有间隙。
花键装配同时接触的齿⾯数不少于2/3,接触率在键齿的长度和⾼度⽅向不得低于50%。
滑动配合的平键(或花键)装配后,相配件移动⾃如,不得有松紧不均现象。
粘接后应清除流出的多余粘接剂。
机械制图技术要求库 常用要求

1.去除毛刺飞边。
2.未注倒角均为1.5×45°。
3.形状公差应符合GB/T 1804-2000 k级的要求。
4.未注长度尺寸允许偏差±0.5mm。
1.各密封件装配前必须浸透油。
2.零件在装配前必须清理和清洗干净,不得有毛刺、飞边、氧化皮、锈蚀、切屑、油污、着色剂和灰尘等。
3.装配过程中零件不允许磕、碰、划伤和锈蚀。
1.未注形状公差应符合GB/T 1804-2000 k级的要求。
2.未注尺寸公差应符合GB/T 1184-1996 m的要求。
1.未注形状公差应符合GB1184-80的要求。
2.未注长度尺寸允许偏差%p0.5mm1.焊缝应连续均匀,坡口面应修的平整圆滑。
2.焊缝质量符合SY5305-87中BK级要求。
1.焊缝应连续均匀,不得有气孔、夹渣等缺陷。
要求耐压25MPa,稳压5分钟,压降不得大于1MPa。
2.安装轴用T型双向旋转组合密封时需对密封基体、密封件及安装工具进行清洗并涂油。
3.件(轴承〕背靠背安装。
1.锐角倒钝。
2.经调质处理。
3.未注倒角均为1.5×45°。
4.未注形状公差应符合GB1184-80的要求。
5.未注长度尺寸允许偏差±0.5mm。
1.进浆段(件4)与扩散段(件5)的同轴度小于0.5mm2.装配后应保证各法兰联接面无渗漏;3.蝶阀开启与关闭应灵活无卡阻,关闭可靠无泄漏;4.装配前将所有液流通道凸凹不平、毛刺之处修整;5.所有内表面涂黑色防锈漆,外露表面先涂一层铁红;6.在外筒体外壁上固定铭牌。
1.与气水分离器、真空泵配焊,焊缝连续,无夹渣、无渗漏。
2.焊后打磨平整。
尖角倒钝1.按图示尺寸焊接,焊缝连续,无夹渣、无渗漏。
2.焊后打磨平整。
钢板的厚度表示方法是钢板t10组合件,焊接件。
1.件1与件2采用断续焊接,焊缝高度5mm,长度50mm,间隔150mm.2.件2下表面与件1接触的部位均需焊接,焊接要求同1。
槽钢的组焊件代号栏可空。
CAXA制造工程师之--平面区域粗加工
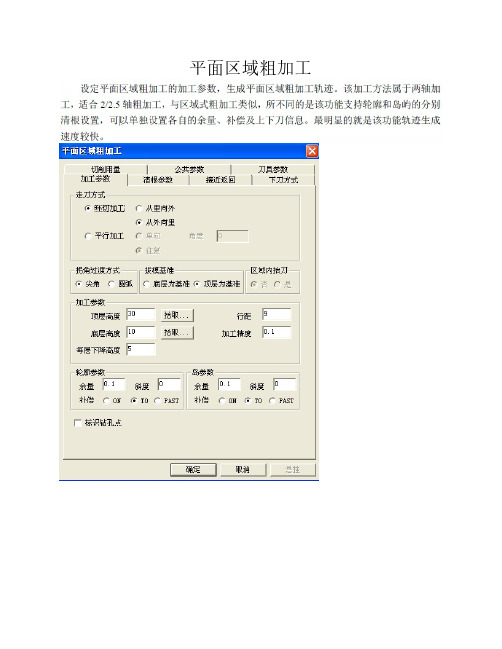
平面区域粗加工走刀方式平行加工 刀具以平行走刀方式切削工件。
可改变生成的刀位行与X轴的夹角。
可选择单向还是往复方式。
单向 刀具以单一的顺铣或逆铣方式加工工件。
往复 刀具以顺逆混合方式加工工件。
环切加工 刀具以环状走刀方式切削工件。
可选择从里向外还是从外向里的方式。
拐角过渡方式 拐角过渡就是在切削过程遇到拐角时的处理方式,以下两种情况。
尖角 刀具从轮廓的一边到另一边的过程中,以二条边延长后相交的方式连接。
圆弧 刀具从轮廓的一边到另一边的过程中,以圆弧的方式过渡。
过渡半径=刀具半径+余量。
拔模基准 当加工的工件带有拔模斜度时,工件顶层轮廓与底层轮廓的大小不一样。
底层为基准 加工中所选的轮廓是工件底层的轮廓。
顶层为基准 加工中所选的轮廓是工件顶层的轮廓。
区域内抬刀 在加工有岛屿的区域时,轨迹过岛屿时是否抬刀,选“是”就抬刀,选“否”就不抬刀。
此项只对平行加工的单向有用。
否 在岛屿处不抬刀。
是 在岛屿处直接抬刀连接。
加工参数顶层高度 零件加工时起始高度的高度值,一般来说,也就是零件的最高点,即Z最大值。
底层高度 零件加工时,所要加工到的深度的Z坐标值,也就是Z最小值。
每层下降高度 刀具轨迹层与层之间的高度差,即层高。
每层的高度从输入的顶层高度开始计算。
行距 是指加工轨迹相邻两行刀具轨迹之间的距离。
加工精度轮廓参数余量 给轮廓加工预留的切削量。
斜度 以多大的拔模斜度来加工。
补偿 有三种方式。
ON:刀心线与轮廓重合。
TO:刀心线未到轮廓一个刀具半径。
PAST:刀心线超过轮廓一个刀具半径。
岛屿参数余量 给轮廓加工预留的切削量。
斜度 以多大的拔模斜度来加工。
补偿有三种方式。
ON:刀心线与岛屿线重合。
TO:刀心线超过岛屿线一个刀具半径。
PAST:刀心线未到岛屿线一个刀具半径。
标识钻孔点 选择该项自动显示出下刀打孔的点。
O1200(NC0006,2010-11-12 ,19:52:54.515 )($stockbase=-50.,-40.,0. )($stockbox=50.,40.,30. )(=========LoadTool=====1===========)($tool_nameD12$tool_rad=6 $tool_corner_rad=0 ) ($tool_num=2 $tool_cutcom_reg=2 $tool_cut_length=40 ) (pathCoordinate:)($pathcoord0=0.,0.,0. )($pathcoordx=10.,0.,0. )($pathcoordy=0.,10.,0. ) 刀具直径12,行距9N8 T2 M6N10 G90 G54 G0 X-30. Y-23.8 S3000 M03N12 G43 H0 Z100. M07N14 Z35.N16 G1 Z25. F100N18 G17 G2 X-33.8 Y-20. I0. J3.8 F1000N20 G1 Y20.N22 G2 X-30. Y23.8 I3.8 J0.N24 G1 X30.N26 G2 X33.8 Y20. I0. J-3.8N28 G1 Y-20.N30 G2 X30. Y-23.8 I-3.8 J0.N32 G1 X-30.N34 X-15. Y-21.2N36 X15.N38 G3 X26.2 Y-10. I0. J11.2N40 G1 Y10.N42 G3 X15. Y21.2 I-11.2 J0.N44 G1 X-15.N46 G3 X-26.2 Y10. I0. J-11.2N48 G1 Y-10.N50 G3 X-15. Y-21.2 I11.2 J0.N52 G1 X-30. Y-23.9N54 G2 X-33.9 Y-20. I0. J3.9N56 G1 Y20.N58 G2 X-30. Y23.9 I3.9 J0.N60 G1 X30.N62 G2 X33.9 Y20. I0. J-3.9N64 G1 Y-20.N66 G2 X30. Y-23.9 I-3.9 J0.N68 G1 X-30.N70 X-15. Y-21.1N72 X15.N74 G3 X26.1 Y-10. I0. J11.1N76 G1 Y10.N78 G3 X15. Y21.1 I-11.1 J0.N80 G1 X-15.N82 G3 X-26.1 Y10. I0. J-11.1N84 G1 Y-10.N86 G3 X-15. Y-21.1 I11.1 J0.N88 G1 Z35. F100N90 G0 Z100.N92 X-30. Y-23.8N94 Z30.N96 G1 Z20.N98 G2 X-33.8 Y-20. I0. J3.8 F1000 N100 G1 Y20.N102 G2 X-30. Y23.8 I3.8 J0.N104 G1 X30.N106 G2 X33.8 Y20. I0. J-3.8N108 G1 Y-20.N110 G2 X30. Y-23.8 I-3.8 J0.N112 G1 X-30.N114 X-15. Y-21.2N116 X15.N118 G3 X26.2 Y-10. I0. J11.2N120 G1 Y10.N122 G3 X15. Y21.2 I-11.2 J0.N124 G1 X-15.N126 G3 X-26.2 Y10. I0. J-11.2N128 G1 Y-10.N130 G3 X-15. Y-21.2 I11.2 J0.N132 G1 X-30. Y-23.9N134 G2 X-33.9 Y-20. I0. J3.9N136 G1 Y20.N138 G2 X-30. Y23.9 I3.9 J0.N140 G1 X30.N142 G2 X33.9 Y20. I0. J-3.9N144 G1 Y-20.N146 G2 X30. Y-23.9 I-3.9 J0.N148 G1 X-30.N150 X-15. Y-21.1N152 X15.N154 G3 X26.1 Y-10. I0. J11.1N156 G1 Y10.N158 G3 X15. Y21.1 I-11.1 J0.N160 G1 X-15.N162 G3 X-26.1 Y10. I0. J-11.1N164 G1 Y-10.N166 G3 X-15. Y-21.1 I11.1 J0.N168 G1 Z30. F100N170 G0 Z100.N172 X-30. Y-23.8N174 Z25.N176 G1 Z15.N178 G2 X-33.8 Y-20. I0. J3.8 F1000 N180 G1 Y20.N182 G2 X-30. Y23.8 I3.8 J0.N184 G1 X30.N186 G2 X33.8 Y20. I0. J-3.8N188 G1 Y-20.N190 G2 X30. Y-23.8 I-3.8 J0.N192 G1 X-30.N194 X-15. Y-21.2N196 X15.N198 G3 X26.2 Y-10. I0. J11.2N200 G1 Y10.N202 G3 X15. Y21.2 I-11.2 J0.N204 G1 X-15.N206 G3 X-26.2 Y10. I0. J-11.2N208 G1 Y-10.N210 G3 X-15. Y-21.2 I11.2 J0.N212 G1 X-30. Y-23.9N214 G2 X-33.9 Y-20. I0. J3.9N216 G1 Y20.N218 G2 X-30. Y23.9 I3.9 J0.N220 G1 X30.N222 G2 X33.9 Y20. I0. J-3.9N224 G1 Y-20.N226 G2 X30. Y-23.9 I-3.9 J0.N228 G1 X-30.N230 X-15. Y-21.1N232 X15.N234 G3 X26.1 Y-10. I0. J11.1N236 G1 Y10.N238 G3 X15. Y21.1 I-11.1 J0.N240 G1 X-15.N242 G3 X-26.1 Y10. I0. J-11.1N244 G1 Y-10.N246 G3 X-15. Y-21.1 I11.1 J0.N248 G1 Z25. F100N250 G0 Z100.N252 X-30. Y-23.8N254 Z20.N256 G1 Z10.N258 G2 X-33.8 Y-20. I0. J3.8 F1000 N260 G1 Y20.N262 G2 X-30. Y23.8 I3.8 J0.N264 G1 X30.N266 G2 X33.8 Y20. I0. J-3.8N268 G1 Y-20.N270 G2 X30. Y-23.8 I-3.8 J0.N272 G1 X-30.N274 X-15. Y-21.2N276 X15.N278 G3 X26.2 Y-10. I0. J11.2N280 G1 Y10.N282 G3 X15. Y21.2 I-11.2 J0. N284 G1 X-15.N286 G3 X-26.2 Y10. I0. J-11.2 N288 G1 Y-10.N290 G3 X-15. Y-21.2 I11.2 J0. N292 G1 X-30. Y-23.9N294 G2 X-33.9 Y-20. I0. J3.9 N296 G1 Y20.N298 G2 X-30. Y23.9 I3.9 J0. N300 G1 X30.N302 G2 X33.9 Y20. I0. J-3.9 N304 G1 Y-20.N306 G2 X30. Y-23.9 I-3.9 J0. N308 G1 X-30.N310 X-15. Y-21.1N312 X15.N314 G3 X26.1 Y-10. I0. J11.1 N316 G1 Y10.N318 G3 X15. Y21.1 I-11.1 J0. N320 G1 X-15.N322 G3 X-26.1 Y10. I0. J-11.1 N324 G1 Y-10.N326 G3 X-15. Y-21.1 I11.1 J0. N328 G1 Z20. F100N330 G0 Z100.N332 M09N334 M05N336 M30。
CAXA机械制图操作规范
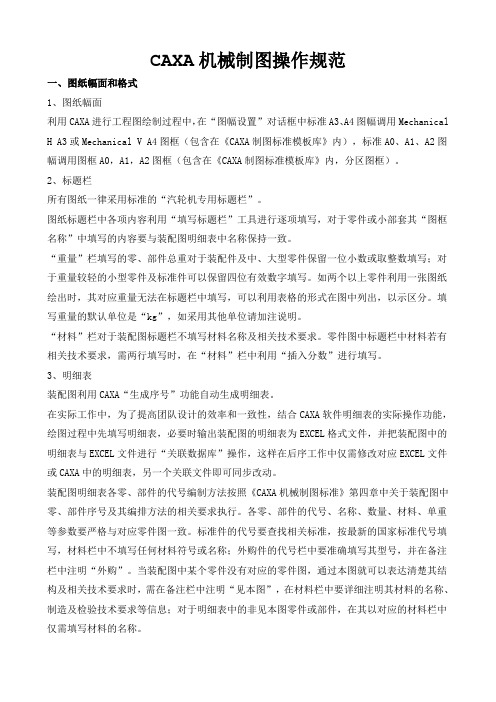
CAXA机械制图操作规范一、图纸幅面和格式1、图纸幅面利用CAXA进行工程图绘制过程中,在“图幅设置”对话框中标准A3、A4图幅调用Mechanical H A3或Mechanical V A4图框(包含在《CAXA制图标准模板库》内),标准A0、A1、A2图幅调用图框A0,A1,A2图框(包含在《CAXA制图标准模板库》内,分区图框)。
2、标题栏所有图纸一律采用标准的“汽轮机专用标题栏”。
图纸标题栏中各项内容利用“填写标题栏”工具进行逐项填写,对于零件或小部套其“图框名称”中填写的内容要与装配图明细表中名称保持一致。
“重量”栏填写的零、部件总重对于装配件及中、大型零件保留一位小数或取整数填写;对于重量较轻的小型零件及标准件可以保留四位有效数字填写。
如两个以上零件利用一张图纸绘出时,其对应重量无法在标题栏中填写,可以利用表格的形式在图中列出,以示区分。
填写重量的默认单位是“kg”,如采用其他单位请加注说明。
“材料”栏对于装配图标题栏不填写材料名称及相关技术要求。
零件图中标题栏中材料若有相关技术要求,需两行填写时,在“材料”栏中利用“插入分数”进行填写。
3、明细表装配图利用CAXA“生成序号”功能自动生成明细表。
在实际工作中,为了提高团队设计的效率和一致性,结合CAXA软件明细表的实际操作功能,绘图过程中先填写明细表,必要时输出装配图的明细表为EXCEL格式文件,并把装配图中的明细表与EXCEL文件进行“关联数据库”操作,这样在后序工作中仅需修改对应EXCEL文件或CAXA中的明细表,另一个关联文件即可同步改动。
装配图明细表各零、部件的代号编制方法按照《CAXA机械制图标准》第四章中关于装配图中零、部件序号及其编排方法的相关要求执行。
各零、部件的代号、名称、数量、材料、单重等参数要严格与对应零件图一致。
标准件的代号要查找相关标准,按最新的国家标准代号填写,材料栏中不填写任何材料符号或名称;外购件的代号栏中要准确填写其型号,并在备注栏中注明“外购”。
机械制图常用技术要求大全

1.零件加工表面上,不应有划痕、擦伤等损伤零件表面的缺陷;2.去除毛刺飞边;3.未注圆角半径R2;4.未注倒角均为0.5×45°;5.未注长度尺寸允许偏差±0.5mm;6.未注形位公差应符合GB/T 1184-H的要求;7.未注尺寸公差符合GB/T 1804-f的要求;8.加工件数:1件。
5.零件去除氧化皮。
6.零件加工表面上,不应有划痕、擦伤等损伤零件表面的缺陷。
7.经调质处理,28~32HRC。
8.零件进行高频淬火,350~370℃回火,40~45HRC。
9.渗碳深度0.3mm。
10.进行高温时效处理。
11.未注形状公差应符合GB1184-80的要求。
12.铸件公差带对称于毛坯铸件基本尺寸配置。
13.锐角倒钝。
14.各密封件装配前必须浸透油。
15.装配滚动轴承允许采用机油加热进行热装,油的温度不得超过100℃。
16.齿轮装配后,齿面的接触斑点和侧隙应符合GB10095和GB11365的规定。
17.装配液压系统时允许使用密封填料或密封胶,但应防止进入系统中。
18.进入装配的零件及部件(包括外购件、外协件),均必须具有检验部门的合格证方能进行装配。
19.零件在装配前必须清理和清洗干净,不得有毛刺、飞边、氧化皮、锈蚀、切屑、油污、着色剂和灰尘等。
20.装配前应对零、部件的主要配合尺寸,特别是过盈配合尺寸及相关精度进行复查。
21.装配过程中零件不允许磕、碰、划伤和锈蚀。
22.螺钉、螺栓和螺母紧固时,严禁打击或使用不合适的旋具和扳手。
紧固后螺钉槽、螺母和螺钉、螺栓头部不得损坏。
23.规定拧紧力矩要求的紧固件,必须采用力矩扳手,并按规定的拧紧力矩紧固。
24.同一零件用多件螺钉(螺栓)紧固时,各螺钉(螺栓)需交叉、对称、逐步、均匀拧紧。
25.圆锥销装配时应与孔应进行涂色检查,其接触率不应小于配合长度的60%,并应均匀分布。
26.平键与轴上键槽两侧面应均匀接触,其配合面不得有间隙。
汽车发动机连杆caxa零件图-及加工规程分析

•夹具使用 •应具备适应“一面一孔一凸台”的统一精基准。而 大小头定位销是一次装夹中镗出,故须考虑“自为 基准”情况,这时小头定位销应做成活动的,当连 杆定位装夹后,再抽出定位销进行加工。
端面间有配合要求,而连杆小头两端面与
活塞销孔座内档之间没有配合要求。连杆
大头端面间距离尺寸的公差带正好落在连
杆小头端面间距离尺寸的公差带中,这给 连杆的加工带来许多方便。
•螺栓孔的技术要求 •在前面已经说过,连杆在工作过 程中受到急剧的动载荷的作用。这 一动载荷又传递到连杆体和连杆盖 的两个螺栓及螺母上。因此除了对
•大、小头孔轴心线在两个互相垂直方向 的平行度
•两孔轴心线在连杆轴线方向的平行度误 差会使活塞在汽缸中倾斜,从而造成汽缸
壁磨损不均匀,同时使曲轴的连杆轴颈产
生边缘磨损,所以两孔轴心线在连杆轴线
方向的平行度公差较小;而两孔轴心线在
垂直于连杆轴线方向的平行度误差对不均
匀磨损影响较小,因而其公差值较大。两
螺栓及螺母要提出高的技术要求外 ,对于安装这两个动力螺栓孔及端 面也提出了一定的要求。规定:螺 栓孔按IT8级公差等级和表面粗糙度 Ra应不大于6.3μm加工;两螺栓孔 在大头孔剖分面的对称度公差为 0.25 mm。
•有关结合面的技术要求 •在连杆受动载荷时,接合面的歪 斜使连杆盖及连杆体沿着剖分面产 生相对错位,影响到曲轴的连杆轴 颈和轴瓦结合不良,从而产生不均 匀磨损。结合面的平行度将影响到 连杆体、连杆盖和垫片贴合的紧密 程度,因而也影响到螺栓的受力情 况和曲轴、轴瓦的磨损。对于本连 杆,要求结合面的平面度的公差为 小头孔处0.004 mm,大头孔处 0.012mm。
机械制图一般专业技术要求

13.铸件表面应平整,浇口、毛刺、粘砂等应清除干净。
14.铸件不允许存在有损于使用的冷隔、裂纹、孔洞等铸造缺陷。
ﻫ
涂装要求
1.所有需要进行涂装的钢铁制件表面在涂漆前,必须将铁锈、氧化皮、油脂、灰尘、泥土、盐和污物等除去。
2.除锈前,先用有机溶剂、碱液、乳化剂、蒸汽等除去钢铁制件表面的油脂、污垢。
1.焊接前必须将缺陷彻底清除,坡口面应修的平整圆滑,不得有尖角存在。
2.根据铸钢件缺陷情况,对焊接区缺陷可采用铲挖、磨削,炭弧气刨、气割或机械加工等方法清除。
3.焊接区及坡口周围20mm以内的粘砂、油、水、锈等脏物必须彻底清理。
4.在焊接的全过程中,铸钢件预热区的温度不得低于350°C。
5.在条件允许的情况下,尽可能在水平位置施焊。
9.螺钉、螺栓和螺母紧固时,严禁打击或使用不合适的旋具和扳手。紧固后螺钉槽、螺母和螺钉、螺栓头部不得损坏。
10.规定拧紧力矩要求的紧固件,必须采用力矩扳手,并按规定的拧紧力矩紧固。
11.同一零件用多件螺钉(螺栓)紧固时,各螺钉(螺栓)需交叉、对称、逐步、均匀拧紧。
12.圆锥销装配时应与孔应进行涂色检查,其接触率不应小于配合长度的60%,并应均匀分布。
7.铸件有倾斜的部位、其尺寸公差带应沿倾斜面对称配置。
8.铸件上的型砂、芯砂、芯骨、多肉、粘沙等应铲磨平整,清理干净。
9.对错型、凸台铸偏等应予以修正,达到圆滑过渡,一保证外观质量。
10.铸件非加工表面的皱褶,深度小于2mm,间距应大于100mm。
11.机器产品铸件的非加工表面均需喷丸处理或滚筒处理,达到清洁度Sa2 1/2级的要求。
2.装配前,所有钢管(包括预制成型管路)都要进行脱脂、酸洗、中和、水洗及防锈处理。
CAXA制造工程师2015几种加工方法介绍
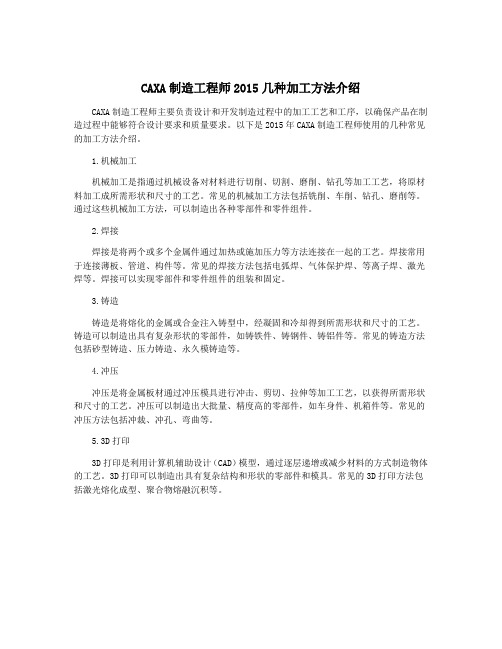
CAXA制造工程师2015几种加工方法介绍
CAXA制造工程师主要负责设计和开发制造过程中的加工工艺和工序,以确保产品在制造过程中能够符合设计要求和质量要求。
以下是2015年CAXA制造工程师使用的几种常见的加工方法介绍。
1.机械加工
机械加工是指通过机械设备对材料进行切削、切割、磨削、钻孔等加工工艺,将原材料加工成所需形状和尺寸的工艺。
常见的机械加工方法包括铣削、车削、钻孔、磨削等。
通过这些机械加工方法,可以制造出各种零部件和零件组件。
2.焊接
焊接是将两个或多个金属件通过加热或施加压力等方法连接在一起的工艺。
焊接常用于连接薄板、管道、构件等。
常见的焊接方法包括电弧焊、气体保护焊、等离子焊、激光焊等。
焊接可以实现零部件和零件组件的组装和固定。
3.铸造
铸造是将熔化的金属或合金注入铸型中,经凝固和冷却得到所需形状和尺寸的工艺。
铸造可以制造出具有复杂形状的零部件,如铸铁件、铸钢件、铸铝件等。
常见的铸造方法包括砂型铸造、压力铸造、永久模铸造等。
4.冲压
冲压是将金属板材通过冲压模具进行冲击、剪切、拉伸等加工工艺,以获得所需形状和尺寸的工艺。
冲压可以制造出大批量、精度高的零部件,如车身件、机箱件等。
常见的冲压方法包括冲裁、冲孔、弯曲等。
5.3D打印
3D打印是利用计算机辅助设计(CAD)模型,通过逐层递增或减少材料的方式制造物体的工艺。
3D打印可以制造出具有复杂结构和形状的零部件和模具。
常见的3D打印方法包括激光熔化成型、聚合物熔融沉积等。
CAXA软件在机械数控加工技术中的应用
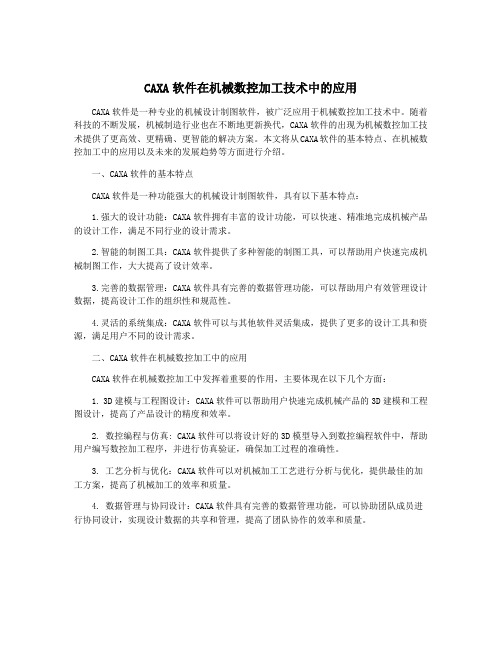
CAXA软件在机械数控加工技术中的应用CAXA软件是一种专业的机械设计制图软件,被广泛应用于机械数控加工技术中。
随着科技的不断发展,机械制造行业也在不断地更新换代,CAXA软件的出现为机械数控加工技术提供了更高效、更精确、更智能的解决方案。
本文将从CAXA软件的基本特点、在机械数控加工中的应用以及未来的发展趋势等方面进行介绍。
一、CAXA软件的基本特点CAXA软件是一种功能强大的机械设计制图软件,具有以下基本特点:1.强大的设计功能:CAXA软件拥有丰富的设计功能,可以快速、精准地完成机械产品的设计工作,满足不同行业的设计需求。
2.智能的制图工具:CAXA软件提供了多种智能的制图工具,可以帮助用户快速完成机械制图工作,大大提高了设计效率。
3.完善的数据管理:CAXA软件具有完善的数据管理功能,可以帮助用户有效管理设计数据,提高设计工作的组织性和规范性。
4.灵活的系统集成:CAXA软件可以与其他软件灵活集成,提供了更多的设计工具和资源,满足用户不同的设计需求。
二、CAXA软件在机械数控加工中的应用CAXA软件在机械数控加工中发挥着重要的作用,主要体现在以下几个方面:1. 3D建模与工程图设计:CAXA软件可以帮助用户快速完成机械产品的3D建模和工程图设计,提高了产品设计的精度和效率。
2. 数控编程与仿真: CAXA软件可以将设计好的3D模型导入到数控编程软件中,帮助用户编写数控加工程序,并进行仿真验证,确保加工过程的准确性。
3. 工艺分析与优化:CAXA软件可以对机械加工工艺进行分析与优化,提供最佳的加工方案,提高了机械加工的效率和质量。
4. 数据管理与协同设计:CAXA软件具有完善的数据管理功能,可以协助团队成员进行协同设计,实现设计数据的共享和管理,提高了团队协作的效率和质量。
CAXA机械制图标准
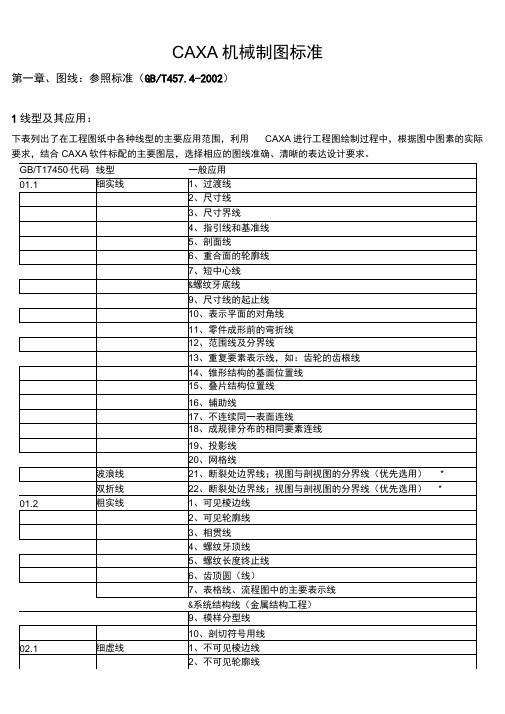
CAXA机械制图标准第一章、图线:参照标准(GB/T457.4-2002)1线型及其应用:下表列出了在工程图纸中各种线型的主要应用范围,利用CAXA进行工程图绘制过程中,根据图中图素的实际要求,结合CAXA软件标配的主要图层,选择相应的图线准确、清晰的表达设计要求。
2、图线线宽和图线组别对于图线线宽的要求见下表,在机械图样中采用粗细两种线宽,其之间的比例为2: 1在实际工作过程中,图线宽度和图线组别的选择应根据图样的类型、尺寸、比例和缩放复制的实际要求进行选择。
第二章、剖面符号:参照标准(GB/T457.5-84)1、剖面符号在剖视图和剖面图中,按照CAX/提供的剖面图案的风格,遵守国家制图标准GB/G4457.5-84关于剖面符号的有关规定执行。
2、剖面符号的画法(1)在同一金属零件的零件图中,剖视图、剖面图和剖面线,应画成间隔相等、方向相同而且与水平成45° 的平等线。
但当图形中的主要轮廓线与水平成45°时,该图形的剖面线应画成与水平成30°或60°的平行线, 其倾斜的方向仍与其他图形的剖面线一致。
(2)相邻辅助零件(或部件),一般不画剖面符号。
当需要画出时,仍按1中的规定绘制。
(3)在装配图中,相互邻接的金属零件的剖面线,其倾斜方向应相反,或方向一致而间隔不等,以示区别。
同一装配图中的同一零件的剖面线应方向相同,间隔相等。
(4)在装配图中,宽度小于或等于2mm勺狭小面积的剖面,可用涂黑代替剖面符号。
如果是玻璃或其他材料,而不宜涂黑时,可不画剖面符号。
第三章、视图:参照标准(GB/T458.1-2002)1、局部视图(1)在机械制图中,局部视图的配置可选用以下方式:—按基本视图的配置形式配置—按向视图的配置形式配置—按第三角画法配置在视图上所需表示物体的局部结构的附近,并用细点画线将两者相连。
(2)画局部视图时,其断裂边界用波浪线(No.01.1线型)或双折线(No.01.1线型绘制。
- 1、下载文档前请自行甄别文档内容的完整性,平台不提供额外的编辑、内容补充、找答案等附加服务。
- 2、"仅部分预览"的文档,不可在线预览部分如存在完整性等问题,可反馈申请退款(可完整预览的文档不适用该条件!)。
- 3、如文档侵犯您的权益,请联系客服反馈,我们会尽快为您处理(人工客服工作时间:9:00-18:30)。
CAXA提供的机械制图的一些加工技术要求:
1.一般
零件去除氧化皮。
零件加工表面上,不应有划痕、擦伤等损伤零件表面的缺陷。
去除毛刺飞边。
2.热处理
经调质处理,HRC50~55。
零件进行高频淬火,350~370℃回火,HRC40~45。
渗碳深度0.3mm。
.
进行高温时效处理。
3.公差要求
未注形状公差应符合GB1184-80的要求。
未注长度尺寸允许偏差±0.5mm。
铸件公差带对称于毛坯铸件基本尺寸配置。
4.零件棱角
未注圆角半径R5。
未注倒角均为2×45°。
锐角倒钝。
5.装配要求
各密封件装配前必须浸透油。
装配滚动轴承允许采用机油加热进行热装,油的温度不得超过100℃。
齿轮装配后,齿面的接触斑点和侧隙应符合GB10095和GB11365的规定。
装配液压系统时允许使用密封填料或密封胶,但应防止进入系统中。
进入装配的零件及部件(包括外购件、外协件),均必须具有检验部门的合格证方能进行装配。
零件在装配前必须清理和清洗干净,不得有毛刺、飞边、氧化皮、锈蚀、切屑、油污、着色剂和灰尘等。
装配前应对零、部件的主要配合尺寸,特别是过盈配合尺寸及相关精度进行复查。
装配过程中零件不允许磕、碰、划伤和锈蚀。
螺钉、螺栓和螺母紧固时,严禁打击或使用不合适的旋具和扳手。
紧固后螺钉槽、螺母和螺钉、螺栓头部不得损坏。
规定拧紧力矩要求的紧固件,必须采用力矩扳手,并按规定的拧紧力矩紧固。
同一零件用多件螺钉(螺栓)紧固时,各螺钉(螺栓)需交叉、对称、逐步、均匀拧紧。
圆锥销装配时应与孔应进行涂色检查,其接触率不应小于配合长度的60%,并应均匀分布。
平键与轴上键槽两侧面应均匀接触,其配合面不得有间隙。
花键装配同时接触的齿面数不少于2/3,接触率在键齿的长度和高度方向不得低于50%。
滑动配合的平键(或花键)装配后,相配件移动自如,不得有松紧不均现象。
粘接后应清除流出的多余粘接剂。
轴承外圈与开式轴承座及轴承盖的半圆孔不准有卡住现象。
轴承外圈与开式轴承座及轴承盖的半圆孔应接触良好,用涂色检查时,与轴承座在对称于中心线120°、与轴承盖在对称于中心线90°的范围内应均匀接触。
在上述范围内用塞尺检查时,0.03mm的塞尺不得塞入外圈宽度的1/3。
轴承外圈装配后与定位端轴承盖端面应接触均匀。
滚动轴承装好后用手转动应灵活、平稳。
上下轴瓦的结合面要紧密贴和,用0.05mm塞尺检查不入。
用定位销固定轴瓦时,应在保证瓦口面和端面与相关轴承孔的开合面和端面包持平齐状态下钻铰、配销。
销打入后不得松动。
球面轴承的轴承体与轴承座应均匀接触,用涂色法检查,其接触不应小于70%。
合金轴承衬表面成黄色时不准使用,在规定的接触角内不准有离核现象,在接触角外的离核面积不得大于非接触区总面积的10%。
齿轮(蜗轮)基准端面与轴肩(或定位套端面)应贴合,用0.05mm
塞尺检查不入。
并应保证齿轮基准端面与轴线的垂直度要求。
齿轮箱与盖的结合面应接触良好。
组装前严格检查并清除零件加工时残留的锐角、毛刺和异物。
保证密封件装入时不被擦伤。
6.铸件要求
铸件表面上不允许有冷隔、裂纹、缩孔和穿透性缺陷及严重的残缺类缺陷(如欠铸、机械损伤等)。
铸件应清理干净,不得有毛刺、飞边,非加工表明上的浇冒口应清理与铸件表面齐平。
铸件非加工表面上的铸字和标志应清晰可辨,位置和字体应符合图样要求。
铸件非加工表面的粗糙度,砂型铸造R,不大于50μm。
铸件应清除浇冒口、飞刺等。
非加工表面上的浇冒口残留量要铲平、磨光,达到表面质量要求。
铸件上的型砂、芯砂和芯骨应清除干净。
铸件有倾斜的部位、其尺寸公差带应沿倾斜面对称配置。
铸件上的型砂、芯砂、芯骨、多肉、粘沙等应铲磨平整,清理干净。
对错型、凸台铸偏等应予以修正,达到圆滑过渡,一保证外观质量。
铸件非加工表面的皱褶,深度小于2mm,间距应大于100mm。
机器产品铸件的非加工表面均需喷丸处理或滚筒处理,达到清洁
度Sa2 1/2级的要求。
铸件必须进行水韧处理。
铸件表面应平整,浇口、毛刺、粘砂等应清除干净。
铸件不允许存在有损于使用的冷隔、裂纹、孔洞等铸造缺陷。
7.涂装要求
所有需要进行涂装的钢铁制件表面在涂漆前,必须将铁锈、氧化皮、油脂、灰尘、泥土、盐和污物等除去。
除锈前,先用有机溶剂、碱液、乳化剂、蒸汽等除去钢铁制件表面的油脂、污垢。
经喷丸或手工除锈的待涂表面与涂底漆的时间间隔不得多于6h。
铆接件相互接触的表面,在连接前必须涂厚度为30~40μm防锈漆。
搭接边缘应用油漆、腻子或粘接剂封闭。
由于加工或焊接损坏的底漆,要重新涂装。
8.配管要求
装配前所有的管子应去除管端飞边、毛刺并倒角。
用压缩空气或其他方法清楚管子内壁附着的杂物和浮锈。
装配前,所有钢管(包括预制成型管路)都要进行脱脂、酸洗、中和、水洗及防锈处理。
装配时,对管夹、支座、法兰及接头等用螺纹连接固定的部位要拧紧,防止松动。
预制完成的管子焊接部位都要进行耐压试验。
配管接替或转运时,必须将管路分离口用胶布或塑料管堵封口,防止任何杂物进入,并拴标签。
9.补焊要求
补焊前必须将缺陷彻底清除,坡口面应修的平整圆滑,不得有尖角存在。
根据铸钢件缺陷情况,对补焊区缺陷可采用铲挖、磨削,炭弧气刨、气割或机械加工等方法清除。
补焊区及坡口周围20mm以内的粘砂、油、水、锈等脏物必须彻底清理。
在补焊的全过程中,铸钢件预热区的温度不得低于350°C。
在条件允许的情况下,尽可能在水平位置施焊。
补焊时,焊条不应做过大的横向摆动。
铸钢件表面堆焊接时,焊道间的重叠量不得小于焊道宽度的1/3。
10.锻件要求
每个钢锭的水口、冒口应有足够的切除量,一以保证锻件无缩孔和严重的偏折。
锻件应在有足够能力的锻压机上锻造成形,以保证锻件内部充分锻透。
锻件不允许有肉眼可见的裂纹、折叠和其他影响使用的外观缺陷。
局部缺陷可以清除,但清理深度不得超过加工余量的75%,锻件非加工表面上的缺陷应清理干净并圆滑过渡。
锻件不允许存在白点、内部裂纹和残余缩孔。
11.切削加工件的要求
零件应按工序检查、验收,在前道工序检查合格后,方可转入下道工序。
加工后的零件不允许有毛刺。
精加工后的零件摆放时不得直接放在地面上,应采取必要的支撑、保护措施。
加工面不允许有锈蛀和影响性能、寿命或外观的磕碰、划伤等缺陷。
滚压精加工的表面,滚压后不得有脱皮现象。
最终工序热处理后的零件,表面不应有氧化皮。
经过精加工的配合面、齿面不应有退火、发蓝、变色的现象。
加工的螺纹表面不允许有黑皮、磕碰、乱扣和毛刺等缺陷。