净水器安装说明 英文
雨人水制器安装说明(附录2)说明书

Rainman WatermakerInstallation Instructions (Appendix 2 of General Instruction Manual)Rainman Technology Pty Ltd#17 / 10-18 Orchard RoadBrookvale, NSW 2100Australia************************+61 433 826 626Version 3.4Table of ContentsInstallation Overview1Physically Mounting Your Watermaker1Mounting Naked Pressure Supply Unit (PSU)1 Mounting Cased Pressure Supply Unit (PSU)5 Mounting Naked Reverse Osmosis (RO) Unit6 Mounting Cased Reverse Osmosis (RO) Unit9Plumbing Watermaker Into Your Vessel10Stage 1 - Seawater Intake10 Stage 2 - Brine outlet (waste overboard)12 Stage 3 - Product (fresh) water connection to fresh water tank13 Extra items you may need13Installation OverviewThe Rainman installation system consists of parts that will allow you to install your AC electric or 12VDC watermaker. This is a guide only. Installation will vary from vessel to vessel.All electric Rainman systems can be installed. The systems in the traditional blue case can be either installed or run as portable. The Rainman Naked systems are specifically designed for a minimum footprint installation. The plumbing hardware described in this manual is included with a Rainman Naked system, or available as an optional item for the classic Rainman system in a blue case.A system installation can be divided into the physical installation process and then plumbing the system into your vessel.Physically Mounting Your WatermakerThe mounting system is moulded from rugged fiberglass filled nylon and has been designed to make the physical installation of your system as quick and easy as possible. The white blemishes that may exist on some parts are normal residual from the moulding process.Mounting Naked Pressure Supply Unit (PSU)The mounting system for the Naked PSU has three parts. The mounting seat on the base and two mounting frames on each side.The PSU needs to be correctly oriented when placed in themounting assembly. The embossed diagram on the seatshows the correct orientation. The two side frames arelabelled A or B, and must be used on the correct sides of thebase seat. There are notches to prevent you from installingthem on the incorrect side.When selecting a suitable mounting position, consider the following points:•The mounting kit should be secured to a level surface and positioned in such a way that there is a minimum 100mm (4”) of clearance on one side to allow for working space to complete the assembly. •Each hose run between the PSU and the pre-filter should be no more than 2 meters (six feet). •Ensure that both the high pressure output fitting and the on/off switch are accessible.•The motor on PSU is air cooled and has a fan to push air over the motor. The motor is rated to stay under its max operating temperature in a max surrounding air temperature of 40C (104F). If the unit is mounted in an enclosed space without adequate ventilation, the air in the space will heat to over 40C (104F) very easily. If you are mounting the PSU in an enclosure with other machinery (e.g. in an engine room), it is very important to ensure that the ambient temperature remains below 40C (104F) whilst your watermaker is running concurrently with other machinery.Instructions1.Before you fasten the mounting seat to thesurface, attach the frame to the seat on theside that will have the least clearance whenthe unit is installed. Use two of thecountersunk M6X20mm machine screwssupplied for this.2.Fasten the mounting seat to a level surfaceusing all four holes. Use the self-tappingscrews provided, or your choice of alternatefastener.3.Slide the PSU into the mounting seat asshown. Ensure the PSU orientationmatches the embossed diagram on themounting seat.4.As you place the unit in the mounting seat,taking care to align the black rubbervibration isolators on the PSU with thecorresponding holes in the side frame.5.Slide the other mounting frame onto themounting seat, taking care to align theholes in the frame with the black rubbervibration isolators on the PSU. This mayrequire lifting the PSU slightly.6.Fasten the side rail to the mounting seat using the remaining two countersunk machine screws.7.Mount the prefilter bracket as close to thePSU as possible, not exceeding two meters(six feet). Before installing the prefilter,consider how you will run the tubing tothe ‘IN’ and ‘OUT’ sides of the prefilter. Itis very important that the tube from thebrass lift pump runs to the “IN” side andthe tube from the “OUT” side runs to thehigh pressure pump. Note that the screwsmounting the bracket to the wall arelarger than the ones mounting thehousing to the bracket.ing the white ½” tube supplied, connect the ‘IN’ side of the prefilter to the corresponding fitting onbrass lift pump on the PSU. Now connect the ‘OUT’ side to the push fitting on the side of the high pressure pump.Mounting Cased Pressure Supply Unit (PSU)The cased PSU can be mounted using the mounting seat and strap provided.When selecting a suitable mounting position, consider the following points:●The mounting seat should be secured to a level surface.●Ensure that both the high pressure output fitting and the on/off switch are accessible.●The motor on PSU is air cooled and has a fan to push air over the motor. The motor is rated to stayunder its max operating temperature in a max surrounding air temperature of 40C (104F). If the unit is mounted in an enclosed space without adequate ventilation, the air in the space will heat to over 40C (104F) very easily. If you are mounting the PSU in an enclosure with other machinery (e.g. in an engine room), it is very important to ensure that the ambient temperature remains below 40C (104F) whilst your watermaker is running at the same time as other machinery.●The PSU should be placed in the mounting assembly in the correct orientation. The embossed diagramon the mounting seat shows the correct position.Instructions1.Fasten the mounting seat using all four holes with the self-tapping screws provided or your choice ofalternate fastener.2.Slide the strap through the slot on the underside of the mounting seat.3.Place the PSU in the seat.4.If the pickup hose is coiled in the side pocket, pass the strap outside the pocket. If the pickup hose isnot in the side pocket, pass the strap through the pocket. The external pocket of the case can beremoved if desired to slightly reduce size.5.Tighten the strap.Mounting Naked Reverse Osmosis (RO) UnitThe mounting system for Rainman RO High Output (twin 40” membranes) or Economy (single 40”membrane) are the same and consist of three parts. One back bracket and two mounting saddles. The Compact unit (twin 21” membranes) consists of four parts, including two abbreviated back brackets and two mounting saddles.The RO units can be mounted either horizontally or vertically.For most mounting surfaces, a total of four fasteners will be adequate. More mounting holes have been provided for placing up to 12 fasteners. 4 x 14 Gauge countersunk self-tappers are provided in the kit. Instructions1.Fasten the back bracket using the appropriate fasteners. It isusual to mount against a wall, but the back bracket also hasangled holes for mounting on a floor if desired. If you have aCompact RO unit (2 x 21” membranes), the abbreviated backbrackets should be mounted 250mm (10”) apart as in the photoabove. The lower part of the back bracket extends further so youcan rest the RO unit while attaching the mounting saddles.2.Ensure all four rubber pads are in place.3.Place RO assembly in the back bracket.Note that the Economy RO unit (single40” membrane) will only occupy one slotin the mounting bracket.4.Secure the RO unit by attaching the two saddles firmly usingthe four M6 x 40 cap screws provided.e slots on the back bracket with zip ties to tie off hoses, keeping the set up tidy.6.Mount the product water flow meter at a convenient locationin line with the white product water hose. Two screws holdthe bracket in place and the flow meter itself slots in. Thehose from the RO unit inserts into the bottom of the flowmeter push-fit connector. The hose from the top of the flowmeter connects to the product water three way valve.7.Mounting pressure control valve / gauge assembly can be up to 5 meters (15 ft) away from the ROunit. This configuration allows for a minimalist installation or integration with a broader control function. It provides significant flexibility on how to physically install the assembly, as per sample images.Mounting Cased Reverse Osmosis (RO) UnitThe cased RO units include plates and screws to assist with mounting the systems while in the case.Instructions1.Place each mounting plate inside the case, over the two holes inthe rear. Use double sided tape or other adhesive to hold theplates in position during installation.2.Fasten the unit to the surface using the screws provided, or yourchoice of appropriate fastener.Plumbing Watermaker Into Your VesselRegardless of whether you have a Rainman Naked system or the traditional Rainman in the blue case, the process of plumbing it into your vessel is the same. The plumbing installation is broken into 3 stages.1.Seawater intake2.Brine outlet (waste over board)3.Product (fresh) water connection to fresh water tankStage 1 - Seawater Intake5 x 3/4” hose barbs1 x 3/4” BSP tee female1 x 3/4” BSP 3 way valve 316 S/S with reversable handle sleeve12 x Hose clamps1 x 1/2” hose barb1 x 1/4”-1/2” hex nippleThe installation kit provides enough hose clamps to double clamp each hose barb. You will need to use sealant (example SikaFlex or similar) on each hose barb before connecting hoses.Option 1 - Dedicated Through HullIf you already have a spare through hull or plan to install a new 3/4” through hull fitting with valve for your Rainman seawater intake, follow these steps to complete the intake install.1.Make sure the through hull fitting and valve are 3/4” inner diameter.2.Connect the intake hose non-return valve from the PSU to the middle port (Port A) of the 3 way valve.Use thread sealant to ensure no leaks.3.You will need a sea strainer fitted directly to or off the 3/4” valve. (not supplied by Rainman)4.Plumb the 3/4” 3 way valve supplied from the sea strainer to the seawater intake port of the 3 wayvalve (Port B).5.Connect a loose hose to the fresh water / pickle intake. (Port C)Option 2 - Shared Through HullIf you do not plan to install a new through hull or have a spare 3/4” through hull fitting and valve, you can also explore teeing into a seawater supply hose that already exists. For example, teeing into the 3/4” supply hose for a deck water pump or similar.Ensure your Rainman system is not competing for water while running with a shared through hull.1.Cut the existing 3/4” supply hose (example: deck wash pump) and add the tee piece supplied.2.Connect the intake hose non-return valve from the PSU to the middle port of the 3 way valve (Port A).Use thread sealant to ensure no leaks.3.Plumb the tee piece to the seawater inlet of the 3 way valve. (Port B)4.Connect a loose hose to the fresh water / pickle Inlet. (Port C)Stage 2 - Brine outlet (waste overboard)2 x 3/4” hose barbs1 x 3/4” BSP tee female1 x 3/4”-1/4” bush1 x 1/4” - 10mm push-fit4 x Hose clampsThe brine waste water hose will come from the RO unit in the traditional blue cased version of the system. If you have a Rainman Naked system, the green brine hose will come from the remote pressure control valve / gauge assembly.Run the green brine hose from the RO unit to an above water through hull fitting, cable tying along the way to secure. Parts are supplied so you can easily connect to an existing 3/4” hose connected to an above water through hull fitting. Tee into the existing 3/4” hose with the tee supplied and plug the green brine hose into the brine push-fit (Port D).If you have a spare above water through hull fitting, you may need to source parts to connect to the 1/4” - 10mm push-fit.Stage 3 - Product (fresh) water connection to fresh water tank1 x Plastic 3 way valve (diverter valve fresh water tank and for testing)1 x 8mm push-fit1.Run the white product water hose from the RO unit to your fresh water tank, cable tying along theway to secure.2.Tap the 8mm push-fit into the tank and push the end of the white product water hose into the push-fit(Port H).3.In a convenient place, cut the white product water hose and install the 3 way valve by pushing oneside of the hose into the “in”(Port E) and the other side into the “out”(Port F) port. In the other out port (Port G) connect a loose hose (this loose end will become your testing hose).Use a sharp knife to cut the white product water hose. Make sure the hose is cut straight to ensure correct fitting into the push-fit fitting.The white product water hose can be plumbed different ways, such as:1.Direct to your fresh water tank by tapping the supplied fitting as described above.2.Connecting it to the filler hose to your fresh water tank.3.Leave the white product water hose loose and manually putting it into your deck filler each time youuse your Rainman watermaker.Extra items you may needThere are some items you may require for your installation that are not part of the plumbing installation kit.1.Sea strainer2.Extra 3/4” hose3.3/4” through hull fitting and valves。
厨下纯水机英文说明书

INSTALLATION & SERVICE MANUAL Under-the-sink Reverse Osmosis Water SystemsModel:RO 585 5-Stage RO system, 85 gal/day at 80 psi.RO 585A 5-Stage RO system with digital Water Quality TDS meter RO6100DINT 6-Stage RO+DI system, 100GPD, single outputRO6100+DI 6-Stage RO+DI system, 100GPD, dual output+tank+faucetPRODUCT SPECIFICATION5- Stage Reverse Osmosis Water Purification SystemsModel no: RO585Capacity: Generates 45 to 85 gallons per day depends on water temperature, pressure, chemistry variations)System includes•RO unit: 5-stage unit, all filters included.•Storage Tank: Pressurized tank with pre-charge pressure of 7~10 psi., powder coated steel construction with Food Grade butyl water bladder. NSF listed•Water Dispensing Faucet: lead-free, long reach goose neck type, chrome steel, locking lever for continuous dispensing.•Hardware: feed water adapter, feed water valve, drain saddle valve, tank valve, and screws.•Installation & Service manualSystem Requirements•Working pressure: 40 to 80 psi feed water pressure required, if below 40 psi, a booster pump is needed. We have a RO system with booster pump assembly. If the input pressure is above 80 psi, you MUST put a pressure regulator to reduce the pressure below 80 psi.•Working temperature: 100 ~ 40 deg. F ( 37 ~ 4 deg. C )•pH range: 2-11•If feed water has hardness level above 300 ppm, we recommend putting a water softener prior to the RO system.•If feed water has iron, rust problem, we recommend putting a iron filter prior to the RO system.•If feed water has bacteria problem, we recommend putting an ultra violet sterilizing system prior to RO system.Filter Service Life•1st Stage Sediment filter: Recommend changing every 6 ~12 months. Replacement filter Part no. 201 •2nd Stage Carbon block filter: Recommend changing every 6 ~12 months. Replacement filter Part no. 205 • 3rd Stage Carbon block filter: Recommend changing every 6 ~12 months. Replacement filter Part no. 205 •4th Stage TFC/TFM membrane: Recommend changing every 2~3 years. Replacement filter Part no. 385 •5th Stage Inline carbon filter: Recommend changing every 6 ~12 months. Replacement filter Part no. 213The filters & membrane used are all standard sizes.Dimension•RO unit: Length 15 inch, Width 5 ½ inch, Height 16 inch•Storage tank: Diameter 10 ¾ inch, Height 15 ¼ inch•Faucet: 9 ½ inch above counter topWarranty• 1 years Limited Warranty on parts, components. Filters are not under warranty.Performance•Average Rejection rate: 92 to 98% of dissolved solids after ROPurification Processes/ Filter specificationsRemoves microbiological contaminants like Cysts (protozoan), inorganic/Radiological contaminants like Barium,Cadmium, Copper, Chromium (hexvavalent), Chromim (trivalent), Fluoride, Lead, Radium 226/228, Selenium, etc.Ammonia, Arsenic, chloramines, chlorine, copper, lead, nitrate, phosphate, silica, hardness, calcium, magnesium, other dissolved solids.•1st stage: 5 micron sediment filter, 2 3/4”. x 9 7/8” height, made by 100% pure polypropylene fibers•2nd & 3rd stage: carbon filter, 2 3/4” x 9 ¾” height, composed of high-performance coconut shell carbon.•4th stage: TFC/TFM type membrane, 75 GPD, 1 ¾” x 11 ¾” long•5th stage: Inline carbon filter (polishing filter, improves taste): 2” x 10”T hank you for choosing Watergeneral Reverse Osmosis Water Systems. You now own a superb Reverse Osmosis (RO) system that effectively reducing most contaminants, organic and inorganic compound, unwanted taste and odor from tap water. It is designed to transform your tap water into distill water.Read carefully and follow the instruction in this manual before proceeding with actual installation. Failure to do so could result in personal injury or damage to the equipment or other properties. Be sure to follow any special plumbing codes in your area.CHECK LIST:1.Reverse Osmosis Unit2.Water storage tank3.Installation kit consists tank ball valve, drain saddle valve, feed water adapter, feed water needle valve, faucetassembly, tubing, tube inserts4.Installation manualINSTALLATION KIT:1.Chrome dispensing faucet2.Tank ball valve or On/Off valve3.Drain saddle clamp4.¼” tubing5.Bottom filter housing wrench6.tube insert *7.½” feed water adapter8.chrome ball valve for water supply* NOTE: Item #6 tube inserts are not required in the installation, but you can put them in three places; (1) tubing connection at 1st stage filter, (2) tubing connection at tank ball valve, (3) tubing connection at dispensing faucet.RECOMMENDED TOOLS LISTVariable speed drill1/8” ¼”, 7/16”, ½”, and 5/8” drill bit5/8, 9/16 open-end wrench, or adjustable wrench, pliers Phillips screwdriverUtility knife, or scissor Teflon tapeOPERATING PARAMETER•Working pressure: 40 to 80 psi feed water pressure required. If input pressure is below 40 psi, a booster pump or a permeate pump is needed. We have a RO system with built-in permeate pumps, and we also carry booster pumps.If the input water pressure is above 80 psi (you must use a pressure regulator to step down the pressure). We also carry small pressure regulators just for the RO system.•Working temperature: 100 ~ 40 deg. F ( 37 ~ 4 deg. C )•If feed water has hardness level above 300 ppm, we recommend putting a water softener prior to the RO system.•If feed water has iron, rust problem, we recommend putting an iron filter prior to the RO system.•If feed water has bacteria problem, we recommend putting an ultra violet sterilizing system prior to RO system. WARNING: Do not use this RO+DI system alone to treat water with bacteria problem or water source with unknown quality.WARNING: Do not connect HOT water source to this unit.WARNING: Incorrect installation will VOID the warranty.WARNING: Input pressure must not exceed 80 psi. Pressure regulator must be installed to reduce pressure. WARNING: Using other brand of replacement filters and parts will void the warranty.About the systemReverse Osmosis process is a separation process. Tap water enters the system, and it is separated at the 4th stagemembrane filter. One side would go to the storage tank (purified water); the other side carrying all the minerals is purged to the drain. The ratio of purified water to drain water is 1:3. That means for every gallon of water you use, it will drain 3 to 4 gallons. The drain is required for the RO process to work. If the drain is intentionally shut off, all the minerals will be accumulated inside the membrane, and it would permanently damaged the membrane filter. All Reverse Osmosis units require purging of water when it’s producing water.Production rate: The system uses a 75 GPD (gallons per day) RO membrane. The actual production rate will depend on water input pressure, temperature, and water chemistry. At optimal condition the membrane will make 85 GPD, but on average, it would make about 45 to 60 gallons per day, or about 2 to 3 gallons per hour.Drain rate: The drain rate of the system is set at 600 mL/min. using a flow restrictor. This drain rate is constant,independent of input pressure. If the input water supply is very hard (> 17 grains) or the TDS reading is above 700 ppm, it would be advantageous to change the membrane to 50GPD, in order to get better rejection and prolong the life of the membrane filter.ASSEMBLY QUICK V IEWCarbon Carbon Sediment1. Remove plastic wrap on the filters2. Insert the filters as shown above.1. Put upper portion of the unit on top of the filter housing2. Screw on filter housing vertically to the filter housing cap by hand3. Then use filter housing wrench to tighten the each housingINSTALLATION QUICK VIEW4 connectionsColor of tubing A Feed water valveRed or orange B Dispensing FaucetBlue C Drain saddle valveBlack DTank ball valveYellowINSTALLATION (for under-the-sink installation) STEP 1: TAPPING INTO COLD WATER SUPPLY:• The water supply to your RO unit MUST come from COLD water line . Hot water will damage your RO system.1. Locate cold water shut off valve under the sink and turn it off. Open cold-water faucet to release the pressure, and make surethere is no water.2. Put 3 turns of Teflon tape on threaded ends of the angle needle valve, or the ball valve.3. Determine the best location for putting the feed water adapter. Do you have a flexible line or a solid copper tube? Is theflexible line with smooth surface or spiral line? Is there enough space for installing feed water adapter? More radius or more space is required if you first joint the feed water adapter with the needle valve. Is the size of fitting thread the same as the feed water adapter?4. You can either joint the angle needle valve to the feed water adapter first, or install adapter to cold water supply line first. Itdepends on how much space is available under the sink.5. For FLEX line: Loosen nut and separate cold water riser tube from faucet shank. Gently bend riser tube so that feed wateradapter fits onto faucet shank. Use the Existing cone washer (if the existing cone water is badly damaged, use the new cone water provided in the kit). NOTE: If you have a spiral type flex tube riser, you NEED to use the existing cone water, since the cone washer we provided is straight, not spiral). Use Teflon tape on threaded parts to prevent leaks. Then tighten the connection.6. For Solid Copper riser: Same procedure as flex tubing except you must cut a piece of the riser tube about 3/ 4” to 1” so theadapter can fit between faucet and riser tube. Use Teflon tape to prevent leaks. 7. Install the angle needle valve to adapter if you have not done so in procedure #4.8. For connecting red tubing to angle needle valve, refer to the photo below. Then push tubing through the brass nut, then thesleeve, then put plastic insert inside the tubing, then push sleeve against the insert, then screw on the brass nut. Don’t over tighten it. But it has to be tight.1. feed water adapter ½” connect tobase of kitchen faucet1. buy a ½ pipe to ½” pipe hose2. ½ to ½” nipple fitting.3. adapter.4. your existing faucet pipe• Many times, it is easier to use the existingcone washer than using the new one.• If there is not enough space under the sinkbase, or it’s difficult to get to, you candisconnect the riser from the cold-water valve side. If the fitting size does not match, buy size-changing fittings, or buy a new flex riser with matching sizes.• Many times, it is easier to buy an additionalstainless steel braded flex riser and a ½” nipple to put in between the bottom of the faucet male thread and the feed water adapter (Don’t buy the spiral type) so you can easily put the feed water adapter between two risers. This is the EASIEST way. Spend additional$5 on the riser may save you a lot of time.Feed water adapter with Ball valve1. put Teflon tape on the thread, put only 3 turns2. push tubing through the nut,3. push tubing all the way into the connection,4. screw on the nut tight using a wrenchNOTE: The system uses compression fitting connections: When connecting tubing tothe system, first, you must unscrew the compression nut off the fitting, then pass the tubing through the compression nut about 1”, then screw on to the fitting, then use a 5/8” wrench to tighten th e nut until the thread is not visible. Don’t over-tighten it.STEP 2: INSTALLING THE DISPENSING FAUCET1. faucet base2. small washer+ chrome plate3. large washer4. kitchen sink5. bottom plate6. lock washer7. lock nut8. tube insert9. sleeve 10. faucet nutdrill 5/8” hole on the sinkThe faucet should be positioned with aesthetics, function and convenience in mind. An ample flat surface isrequired for the faucet base so that it can be drawn down tight. Also check the under sink area of the desired location to see if there is ample space to complete the faucet installation.If the space is not available on the upper sink area, the faucet could be positioned on the counter top at the edge of the sink. Be sure to watch for obstructions below, i.e., drawers, cabinet walls, support braces, etc. If the counter top is ceramic tile, the method for drilling the hole should be the same as for porcelain sink.NOTE : The sink drilling process, although notcomplicated, requires a certain amount of caution and forethought. Porcelain sink can chip if care is not exercised.PORCELAIN ENAMEL SINK/ STAINLESS STEEL SINK/ ALUMIUM SINKA 5/8” hole is required for the faucet. It is recommended that you get special drill bi t for porcelain and tile counter.1. Place a piece of masking tape or duct tape on the determined location where the hole is to be drilled.2. Use a variable speed drill at slow speed with 1/8” drill bit, and drill a centering hole in the center of the desiredfaucet location.3. Enlarge the hole using a 1/ 4” drill bit.4. Enlarge the hole using 7/16”, 1/ 2”, and 5/8” drill bit. Pause occasionally to cool drill bits.5. File or clean the surrounding area and remove the masking or duct tape. (NOTE: the metal chips on porcelain willstain very fast)6. DON’T put Teflon tape at the tip of the threaded mounting base of the faucet since it’s a compression fitting.7. Put the small rubber washer, the chrome base plate, large rubber washer according to the diagram through thethreaded mounting tube at the base of the faucet.8. From under the sink, install the bottom plate, lock washer, and nut. Then screw on tightly.9. According to the diagram, put the brass nut through the BLUE tubing first, then plastic sleeve (preferred), or brasssleeve, then the plastic insert. Push the white plastic sleeve against the insert.10. Screw on the Blue tubing with brass nut to the faucet base. Uses wrench to tighten the nut but don’t over tightenit. Too tight would cause leak.11. The spout can swivel 360-degrees. The faucet lever can be pushed down for dispensing or pulled up forcontinuing dispensing.STEP 3: MOUNTING THE TANK BALL VALVEDo not release air from the air valve on the lower side of the storage tank. It is pre-charged at 7 psi at the factory.put Teflon tape, 6-8 turnsscrew on ball valve hand tight,push tubing through the nut, put tube insert, screw on the nutthe tank can be positionedlaying down or standing uprightSTEP 4: MOUNTING THE DRAIN SADDLE VALVE (don’t put in blue area)The drain saddle valve should fit most standard drain pipe. It should be installed above the trap and on the horizontal pipe(1) or vertical pipe (2).DON’T put on position (3), (4), or blue sectionPosition the drain saddle in desired location, mark spot. You need to consider available space for drain tubingDrill 1/ 4” hole into the drainpipe above the water line of the pipe.Clean the surface of the pipe.Pear off the sticky foam pad, then align the center hole around thedrilled pipe hole. Then tape it. Align the drilled hole in the drain pipe with the drain saddleusing a drill bit or narrow screwdriverput the complementary piece and clamp them together with the two bolts. (1) Tighten the two bolts evenly. (2) Connect tubingSTEP 5: SYSTEM START-UP2.Turn Tank Valve to OFF position.3.Turn RO faucet lever to continuous flow position. Lever points up.4.Turn cold water supply main valve on slowly. Also turn input ball valve ON. When the system is pressurized,check for leaks. If a leak is found, tighten the connection.5.Wait 5 minutes, the water should start dripping out of the RO faucet, and then wait 10 more minutes to allowwater to flow through the system, and air inside the system can be purged.6.Turn Tank Valve to ON position, lever is parallel to the tubing.7.Turn the RO faucet lever to OFF. Now the purified water will start filling the storage tank.8.Wait 2 hours for the storage tank to be filled up.9.DO NOT DRINK THE FIRST BATCH OF WATER PRODUCED BY THE SYSTEM.10.After storage tank is full, turn the RO faucet lever to continuous flow position, (Lever points up) to discharge thefirst batch of water. It takes about 5 minutes to completely discharge the tank. When the tank is discharged, you will notice just a steady trickle of water coming out.11.After discharging the tank or about 5 minutes, turn the RO faucet to OFF position. Now the RO system isrefilling the tank.12.After the tank is filled up again, you can start enjoy the purified water. Job Well Done!NOTE: Check for leaks daily for the first week after installation.Flow Diagram for 5-Stage Reverse Osmosis Water SystemsSERVICE RECORD:DATE OF PURCHASE:DATE OF INSTALLATION/SERVICE:Service Date Date Date Date Date1st stage sediment2nd stage carbon3rd stage carbon4th stage membrane5th stage inline carbonChanging Filters Procedures•Shut off the system by turning off the water supply, and turn off the tank valve, openthe spigot to depressurize•Prepare a towel under the unit for water spills•Use a filter wrench (part no. 566) or use hands to open the filter housing, unscrew itfrom right to left. To open is clockwise looking from the top.•Throw away the used filter, and clean the inside of the housing by rinsing orscrubbing it with dish soap.•Check condition of the O-ring. It should be replaced every 3 years to prevent leak•Place the new filter inside the filter housing. For carbon filters, the rubber gasketsshould be on both ends.•Put some Vaseline or silicon-based O-ring lubricant on the side of the housing threadand the O-rings (optional procedure)•Use a filter wrench or both hands to screw the housing back by turning it from left toright (Don’t lay down the unit when turning it, the unit should be standing upright toprevent the o-ring or filters from misalignment)•Repeat the above steps for other filters•The 5th stage inline carbon filter has penny-sized protective caps on both ends.Please use a screw driver or knife to pry open the caps.Replace inline carbon filter: (white inline filter)* if you have compression fitting *unscrew fitting off to replacefilterFor part no. 213 inline carbon filter, remove fittings from bothends of the filter then replace new filter.After all housings are tight, turn on the water supply and tankvalve.Check for leaks, if there is a leak; tighten the housing or re-aligning the o-ring.Open the spigot to drain all the water out of the storage tank.If you are changing a carbon filter or membrane, you mustdrain the first tank of water after restart the system.Refer to the next page for recharging tank procedure (ifnecessary)Changing Membrane Procedure•Lift the membrane housing from the U-clips, and remove the tubing from the membrane fitting (the inlet side of the membrane housing, or the side with the membrane housing cap). Unscrew the membrane housing cap off (counter-clockwise)•Use pliers to pull the membrane out of the membrane housing, and discard the used membrane.•Put some Vaseline or lubricant on the small black O-rings. Insert the new membrane into the membrane housing (THE SIDE WITH DOUBLE BLACK O-RINGS SHOULD GO IN FIRST) Push the membrane all the way in (some force is required to make sure the membrane is all the way in). Put some Vaseline or silicon based lubricant to the side of the housing threads.•Screw the me mbrane-housing cap back (clockwise). Make sure O-ring is in place. Connect the tubing to its elbow fittings.•Turn on the water supply and tank valve to restart the system. Check for leaks, if there is a leak, tighten the cap•Wait 2 to 3 hours for the tank to be filled then you must drain the first tank of water by opening up the spigot to flush the system.TROUBLE SHOOTING* For more detailed tech support notes & troubleshooting go to NOTE: Turn off the system before servicing.Installation TroubleshootingPROBLEM POSSIBLE CAUSE SOLUTIONNo or low water production 1. Feed water valve in not turn on2. Tank valve is not turn on3. Tubing is kinked 1. Turn on feed water valve2. Turn on tank valve3. Straighten the tubingLeak at filter housing 1. Housing is not tighten2. Damaged or misaligned O-ring3. Housing has cracks1. Tighten housing2. Re-aligned O-ring or replace3. Replace housingLeak at fitting thread 1. Not properly tighten2. Fitting has cracks 1. Use Teflon tape, re-tighten2. Replaced itBad-tasting water 1. Not yet flush the system2. Tubing connection incorrect 1. Discharge water from tank2. Check flow diagramMilky/Cloudy water 1. Air in system/filters 1. This is normal, continue use it for 2 weeksNoise from drain 1. Saddle valve mounted too high 1. Lower the saddle valveWhen system is making water, waste water todrain is normal, when storage tank is full, drainshould stopTroubleshootingPROBLEM POSSIBLE CAUSE SOLUTIONWhen turn on the RO faucet, only small amount of water come out. 1. Lifting the tank to see if there isstill water inside. Heavy or light ?1. If it’s heavy, you need to recharge tank,following recharge procedure1b. If its light, the water either is not goingin or the system is not making water.Vibrating noise or very loud high pitch noise 1. From the auto shut-off valve 1. If the noise is too unbearable, shut-offvalve should be replaced.Drain water never shut off 1. Auto shut-off valve is worn outor becoming ineffective2. Storage tank not enough pressure3. Water supply pressure is near 40psi or below4. Cold water temperature5. Filters are clogged up1. Replace auto shut-off valve2. Follow recharging tank procedure3. Increase feed water pressure4. Can’t do anything about it.5. Replace filtersLow water production 1. Storage tank problem2. Clogged filters3. Kinked tubing4. Clog flow restrictor1. Follow recharging tank procedure2. Replace filters3. Straighten the tubing4. Replace flow restrictorNote: Clogged filters: How do you know if the filters are clogged up? For the pre-filters, sediment filters and carbon filters; check the pressure difference before and after the filters. If there is significant difference in pressure that means the filter is clogged. Turn OFF tank valve and cold water main valve then open the RO faucet to depressurize the system, then disconnect the tubing after the bottom three pre-filters, then turn ON the cold water main valve. If you get very strong water pressure, (as strong as water going into the system) then the bottom 3 pre-filters are not clogged. If the water pressure is much smaller, unlike a burst of water pressure, then the bottom 3 pre-filters need to be replaced. Note: Checking a clogged membrane uses different method. Use a water quality meter TDS meter to check the condition and performance of the RO membrane (4th stage filter)Note: Clogged flow restrictor: When you disconnect the black tubing going into the saddle valve, and the RO system is in the processing of making water (by turning on the RO faucet), there should be a small steady flow of drain water. If you do not get any drain water, the flow restrictor may be clogged, then you need to replace a new flow restrictor ASAP, and discontinue using the system.Instruction for Water Quality TDS Meter (included with Model: RO 585A only) Part No. 578 Specifications:Range 0 to 9990 ppm (mg/L) EMC Deviation + 1% Temperature Compensation 5 to 50C or 41-122F Resolution 1 ppm Environment 32F to 122 F BatteriesAccuracy + 2% full scale Weight 2 oz or 85 g Dimension•Hold function: Freezes measurements for convenient reading & recording.•Auto-Off function: Turns off meter after 10 minutes of idle to conserve batteries.•High operating limit: Measures from 1 to 9990 ppm, when reading is over 999, it converts to x10’Operation•Remove the protective cap , then turn TDS meter on, press ON button•Immerse into water sample up to the about 1 ½ “ from tipwithout touching the bottom of the water sample container•Stir gently and wait until the display stabilizes, and theTDS meter compensates for the temperature variance automatically.•To hold the reading, press HOLD, Turn off meter, press OFF buttonBattery ReplacementWhen the TDS mater cannot be switched on or the display fades, pull out the battery compartment and replace two 1.5V batteries, paying attention to their polarity.Interpreting the ResultsExample:Reading #1 Reading from Reverse Osmosis water : 30 ppm:: Reading #2 Reading from tap water: 350 ppmDivide Reading #1 by Reading #2 Reading #1/ Reading #2 = 0.086one minus the value obtain above the multiply by 100 to get the Rejection of the R.O. membrane or RO system1-0.086 = 0.914 0.914 x 100 = 91.4 or 91% rejection rateYour Reading:Reading #1 Reading from Reverse Osmosis water : ppmReading #2 Reading from tap water: ppmDivide Reading #1 by Reading #2 Reading #1/ Reading #2 =one minus the value obtain above the multiply by 100 to get the Rejection of the R.O. membrane or RO system1- ( ) = x 100 = % (rejection rate)• A new RO system or a new membrane should have rejection rate of 90 to 95%•Over years of usage the membrane performance will degrade, and membrane should be replaced when rejection rate reaches 80% or below.RECHARGING TANK PROCEDUREPROBLEMS:•When you turn on the spigot you get small water pressure and water flow.•When you turn on the spigot, only a quick burst of water comes out of the system, then it dies down to trickles.•When you turn on the spigot in the morning, you only can get less than a gallon of water.If you have above problems, you should recharge the tank. The tank should have about 7 psi of air pressure when it is completely empty. The storage tank has a water bladder inside, and it is surrounded by compressed air, so when you turn on the spigot, the compressed air would squeeze or compress the water bladder to force the water out of the tank. When the tank is full the tank pressure can reach about 35 to 50 psi depending on your feed water pressure, but to accurately recharge the storage tank, you should empty the tank then set the air pressure to 7 psi.TOOLS NEEDED: An air compressor or air pump (like a bicycle tire air pump. An air pressure gauge that is able to read less than 10 psi. Adjustable wrench or 9/11” wrenchSTEPS:1. Shut off the water supply to the RO system. Turn on the spigot to allow water to run until it stops (you can collect the water if youwant)2. Check to see if there is still water in the storage tank by lifting the tank. If the tank feels heavy, that means you need to rechargeto tank, then continue the following steps. If the tank feels light, that means you don’t need to recharge your storage tank at this time.3. Locate the air valve on the side or on the bottom of the tank. It looks like the air valve on tires.4. Use an air compressor or air pump to pump air into the tank. Keep the spigot on while pumping air, so that all water inside thetank can be purged out. Don’t over charged it, just keep around 20 psi.5. After all water is been discharged, use an air pressure gauge to check the tank pressure.6. The tank should have 7 psi of pressure when it’s empty. Add or purge air if necessary.7. Turn the feed water valve back on, and turn off the spigot to allow refilling of the tank. It may take couple hours to refill thestorage tank.8. FinishedNOTE: If after few days of running the system, the problem comes back, then you may need to replace a new tank.。
科勒厨房超滤净饮机利奥系列 K-24634T-KT700-01R 安装使用说明书
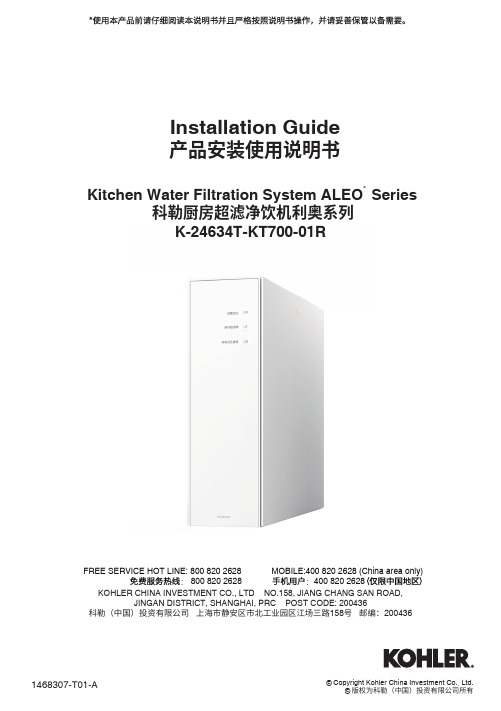
Installation Guide产品安装使用说明书KOHLER CHINA INVESTMENT CO., LTD NO.158, JIANG CHANG SAN ROAD,JINGAN DISTRICT, SHANGHAI, PRC POST CODE: 200436科勒(中国)投资有限公司 上海市静安区市北工业园区江场三路158号 邮编:200436Kitchen Water Filtration System ALEO Series科勒厨房超滤净饮机利奥系列K-24634T-KT700-01R®FREE SERVICE HOT LINE: 800 820 2628 MOBILE:400 820 2628 (China area only): 800 820 2628 :400 820 26281. PRODUCT FUNCTION (1)2. INTENDED USE (2)3. PRODUCT SPECIFICATION (3)4. INSTALLATION (7)5. OPERATION INSTRUCTIONS (11)6. FILTER CARTRIDGE REPLACEMENT (12)7. TROUBLESHOOTING GUIDE......................................13一、产品功能 (1)二、安装之前 (2)三、产品规格 (3)四、安装步骤 (7)五、产品使用 (11)六、滤芯更换 (12)七、常见问题及解决方法 (13)• Thank you for choosing the Kitchen WaterFiltration System ALEO Series.• Please read this Installation Guide carefully prior to installation and operation of this system.• You can also visit for an electronic copy of the Installation Guide or obtain the latest product information by following the official Kohler WaterFiltration wechat account: kohlerwater.• 感谢您选择科勒厨房超滤净饮机利奥系列。
英文设备安装说明说明书

Installation InstructionEnglishUNPACKING INSTRUCTIONS! Carefully open the carton, remove contents and lay out on cardboard or other protective surface to avoid damage.! Check package contents against the Supplied Parts List in the next page to assure that all components were received undamaged. Do not use damaged or defective parts.! Carefully read all instructions before attempting installation.IMPORTANT SAFETY INFORMATIONInstall and operate this device with care. Please read this instruction before beginning the installation, and carefully follow all instructions contained herein. Use proper safety equipment during installation.Please call a qualified installation contractor for help if you:! If you don't understand these directions or have any doubts about the safety of the installation.! If you are uncertain about the nature of your wall, consult a qualified installation contractor.Do not use this product for any purpose or in any configuration not explicitly specified in this instruction. We hereby disclaims any and all liability for injury or damage arising from incorrect assembly, incorrect mounting, or incorrect use of this product.CAUTION!WARNING !This TV mount must be securely attached to the vertical wall. If the mount is not properly installed it may fall, resulting in possible injury and/or damage.Note: The mounting components and hardware supplied in this package are not designed for installations to walls with steel studs or to cinder block walls. If the hardware you need for your installation is not included, please consult your local hardware store for proper mounting hardware for the application.Tools Required 3/16" Drill BitPhillips Screwdriver 1/2" Masonry Bit Stud Finder Wrench or Socket Set Carpenter's Level(4)M4x12 Bolt-e (4)M5x12 Bolt-f (4)M6x12 Bolt-g (4)M8x16 Bolt-h(4)M4x30 Bolt-i (4)M5x30 Bolt-j (4)M6x35 Bolt-k (4)M8x40 Bolt-l(1)Wall Plate-a (1)Right Monitor Bracket-c (1)Allen Key-d(1)Left Monitor Bracket-b Supplied Parts List(2)Safety Bolt-u (6)Lag Bolt-v (6)Lag Bolt Washer-w (6)Concrete Anchor-x(4)M4/M5 Space-q (4)M6/M8 Space-r (8)M4/M5 Washer-s (4)M6/M8 Washer-t(4)M4 Lock Washer-m (4)M5 Lock Washer-n (4)M6 Lock Washer-o (4)M8 Lock Washer-pFirst of all, Once you have determined the correct diameter, please see the relative diagram as below. You will thread the Bolt into the TV using the correct Lock Washer(m,n,o,p), Washer(s,t) and spacer(q,r). For the M4 or M5 diameter bolt, you will need another M4/M5 Washer between the Monitor Bracket and the Spacer. Please make sure the Monitor Brackets are vertically centered and level with each other.make sure the diameter of the Bolt(i,j,k,l) your TV requires. First of all, make sure the diameter of the Bolt(e,f,g,h) your TV requires. Once you have determined the correct diameter, please see the relative diagram as below. You will thread the Bolt into the TV using the correct Lock Washer(m,n,o,p) and Washer(s,t). Please make sure the Monitor Brackets(b,c) are vertically centered and level with each other.Mounting the Monitor Brackets to a TV with Flat BackStep 1A Step 1B Mounting the Monitor Brackets to a TV with Curved Backem s b f n sb got chp t c M4 Diameter Bolt M5 Diameter Bolt M6 Diameter BoltM8 Diameter BoltDiagram 1A M4 Diameter Bolt M5 Diameter Bolt M6 Diameter BoltM8 Diameter BoltDiagram 1B i m sb s q b j n ss q cr t o kc lp t rBrick, Solid Concrete and Concrete Block mounting:Use the Wall Plate(a) as a template to mark 6 hole locations on the wall. Three in the top row of slots and three more in the bottom row. Make sure these holes are level and there is at least 6" distance between any two holes. Pre-Drill these holes with a 1/2" masonry bit to at least 2.5" in depth. Insert a Concrete Anchor(x) into each of these holes. Make sure the anchor is seated completely flush with the concrete surface even if there is a layer of drywall or other material in front. Attach the Wall Plate to the wall using 6pcs Lag Bolts(v) and 6pcs Lag Bolt Washers(w), shown in Diagram 2A.Wood Stud mounting:The Wall Plate(a) must be mounted to two wood studs at least 16" apart. Use a stud finder to locate two adjacent studs. It is a good idea to verify where the studs are located with an awl or thin nail shown in Diagram 2B. Pre-drill a 2.5" deep hole at the desired height in each stud using a 3/16" drill bit. Make sure these holes are in the center area of the studs and level with each other. Use the Wall Plate as a template to mark the location of the second hole in each stud. Drill 2.5" deep holes using the 3/16" drill bit in the marked locations. Attach the Wall Plate to the wall using the 4pcs Lag Bolts(v) and 4pcs Lag Bolt Washers(w).Warning : Some TVs may require two people to lift ! We are not responsible for personal injury or product damage .First hook the Monitor Brackets(b,c) over the top of the wall Plate(a), then let the bottom of the Monitor Brackets rotated to the bottom of the Wall Plate as shown in the Diagram 3A. Insert the Safety Bolts(u) into the threaded holes in the bottom of the Monitor Brackets. Use the Allen Key(d) to tighten the bolts. Then the Monitor Bracket will sit behind the bottom tab on the Wall Plate as shown in the Diagram 3B.Mounting the Wall Plate to the WallStep 2Attaching Monitor to Wall Plate and Adding the Safety Bolts Step 3Diagram 3A Diagram 3B16 inch 16 inch16 inchDiagram 2BDiagram 2Av w a a b,c b,cauThanks for choosing our products, enjoy the using.Stud Finderwall wall。
带式浓缩压滤机安装、调试、维护保养说明书英文版

Installation debugging and maintenance of condensed beltpress-filterA. Scope of application:ZDNY Belt-style condensing press-filter is a solid-liquid separating machine combining condensation, pressing and filtering and can work continuously and high-efficiently. It is applicable to any kind of solid-liquid sedimentation and separation of suspend material widely in chemical industry, metallurgy, mining, food, paper making, urban water supply, draining and many other fields. This equipment features easy craft flow, good applicability, small area occupation, short sludge stay and high ifficiency, saving investment in sludge removing condensation machine and pondB. Features:1. This equipment combines condensation, press and filering, reducting investment in pond.2. This equipment features high automation, designed with pneumatic filtering belt deviation correcting device.3. This equipment adopts condensation filtering water as flushing water, decreasing operation fee.4. This equipment features easy craft flow, good applicability, reasonable structure, small area occupation, short sludge stay and high efficiency.C. Equipment structure:The ZDNY machine consists of machine frame, conveying device, gravity dewatering, prepressing dewatering, upper/lower filtering belts, cloth device, filtering device, press roller, guide roller, discharge device, auto protection device, pneumatic control cabinet and electrical control.Working theories: the sludge mixed with flocculated suspend material goes into gravity centrifugal dewatering system, and under gravity, squeezing and overturning, the sludge will lose most of the free water. The sludge that goes through predewatering, goes through cloth chute and spreads evenly between the two sealed belts and into the rift between the two belts to be pre-dewatered. It then passesthrough rollers in the form of “s” from the least diameter one to the biggest, squeezing and cutting the filtered cake correspondingly to dewater. The material after being dewatered will be discharged from the outlet at the end of the machine.1.Machine frame: welded with chute steel used for fixing other parts and tails.2.Conveying parts: including motor, speed reducer, conveying shaft and gearwheel.3.Gravity dewatering: consists of rolling siege used for further stirring andcondensing the sludge and flocculant.4.Pre-pressing dewatering: After passing through gravity dewatering, the sludgehas fully mixed with the flocculant and will go into double belts to prepare for afterwards filtering.5.Upper/lower filtering belts: called so because they include upper and lowerfiltering belts in between. They force the sludge to go into filtering stage and divided the sludge into two passages and then make the sludge circulate.6.Cloth device: evenly spreads the sludge on the filtering belts afterdewatering.7.Filtering belts cleaning device: the meshes are filled with sludge aftergravity dewatering and press filtering and have lost dewatering function. To clean away the sludge, high water pressure is required.8.Series of rollers: they are the center parts of the press filtering system,made up of rollers of different sizes. The rollers lies in descending order of the radium but the cutting force and pressure go up on the contrary with the order. This structure is called “S-shaped” series of rollers.9.Guide roller system: consists of guide rollers and deviation correcting devicewhich will correct filtering deviation making the belts work only within required range.10.Filtered cake discharge device: after the press filtering is completed, thedischarge device with filtered cake will scrape the cake into the conveyor.11.Auto protection device: mainly controls the machine when some errors occurto the press filtering machine to prevent malfunction.12.Pneumatic control system: corrects deviations and tighten air cylinders. Itis equipped with vacuum press, pressure adjustor and barometer.13.Electrical control system: includes feed line, control cabinet, distancecontrol, electromagnetic valve, approach switch and control chamber.D. Installation and debugging:The base of site should be injected with concrete and equipped with bicycles and electric hoists.Test base plane level with allowable deviation of ±5mm.Size deviation of ±10mm is allowable.Debugging:1.Every drive, conveying parts including speed reducer, bearings and gear wheelsshould be lubricated before operation.2.After connecting PC, check to see if drive parts turn in the same direction andif switches installation positions and movements meet requirements. Should there be any deviation, adjust and correct it in time.(Note:First remove the two scraping boards before connecting PC to avoid damage to scraping boards due to reverse operation of speed reducer.)3.Check to see if there is any leaking problem with the ports of pneumatic system.Should there be any, replace in time.(The pressure of pressure reducing valve should be less than the minimal pressure of vacuum press, or else it will bring about malfunction of parts.)4.Let the machine work for several hours before test run to make sure all partsare working normally.5.Parts tests: Observe the barometer during empty run to see if the value on themeter accords with requirements. Touch the deviation correcting device to see if it works normally. Check protection device and scraping board to make sure they are normal.6.Cleaning machine inside: there shouldn’t be any matter that could damagefiltering belts inside the box or else the belts might get damaged.Preliminary run:Start up, inject running water and open in order the vacuum press, conveyor, speed reducer and water pump(at first there is no filtering water so that waterpump will be constant). When the sludge comes into the main machine, drain the waste water until the water comes out comparatively clean.(open and close for several times). When the cleaning nozzle is silted, turn the cleaning brush and draining the waste water.Observe the distribution amount of sludge which can be adjusted by sludge pump, normally thickness of 15-20mm, width same as valid width. When the sludge is too much and affects the feed-in amount of sludge pump, speed up the turning rate of filtering, less than ≤5m.The speed reducer should be adjusted to 2.4r/min at condensing phase.Adjusting turning rate of reducer can change the sludge outlet amount in a short time and change distribution situations.The tightening air cylinder should be adjusted to 0.4Mp. Observe the sludge outlet. When the water containing rate is comparatively high, then add air pressure, normally ≤0.7Mp. The pressure can’t be too big or else it will bring about problems with cleaning and is recommended on 0.4±0.1Mp.When big range of sludge won’t fall off, adjust the spring at the end to put on pressure. Too big pressure will cause speedy ware to belts.Let the machine run for several turns before shutdown, and the pump can starts and shuts according to water compensation until the belts are cleaned.Not frequently used cleaning pipes such as bearing plate cleaning, water reserving plate cleaning should be flushed twice a day to avoid silting inside pipes.Empty the water tank after all the cleaning.Flush the machine body, filtering belts after shutdown to keep clean.Repeat these activities at startup afterwards.The tank inside should be cleaned for long time standby.The above is the reference value of desilted sludge containing water of 99%~99.5%. The value varies according to different parameters of sludge component and water containing rate.E. Commonly-met errors:1. Deviation of belt can be caused by: a. nearby switch broken; b. electromagneticvalve broken; c. pressure reducing valve broken; d. leak from air pipe; e. pressure in pressure reducer bigger than minimal pressure of vacuum press; f. metal touching nearby switch is out of range of detection (8mm).2.Bad effect of cleaning may be caused by: a. nozzle holes small, easily silted;b. pump too small, insufficient water or pressure;c. flocculant not stirred evenly,filtering water too dirty and causes silting.3.Not clean scraping may be caused by: a. scraping board not quite match filtering cloth; b. spring too loose; c. too much stretch of filtering belts.F. Maintenance notes:1. After the speed reducer, motor and all roller bearing have turned for 100 hours, they should be all be cleaned and lubricated with new grease and the same thing should be done every 6-12 months.2. Check the touch point of all switches once or twice a month. Should there be any singe, it should be made up. When it’s severe, replace the contact.3. The press-filter should be shut down periodically to give a full check on all the connections of all parts to make sure there is no loose ones or falling off or leakage or damage. Should there be any, they must be replaced in time; if there is paint falling off, the rest of it should be shoveled before repainting.。
沛亿超纯水机Professional 系列说明书

沛亿超纯水机Puring water purification systems Professional系列使用说明书V2.1成都沛亿科技有限公司警告用户尊敬的用户:感谢您选购沛亿超纯水机!在使用沛亿超纯水机前,请务必仔细阅读本使用说明书!您能成为我们的用户,是我们莫大的荣幸。
为了使您尽快掌握沛亿超纯水机的使用方法,我们特别为您编写了此说明书资料(包括随机光盘,相关技术文件等,内容视机型而异。
)。
我们对产品说明书的编排力求全面而又简捷。
从中您可以获得有关沛亿超纯水机的设备配置、安装步骤及设备操作维护的方法等方面的一些知识。
我们强烈建议您在使用本产品之前,务必先仔细阅读,这会有助于您更好地使用沛亿超纯水机。
如果您未按本手册的要求操作沛亿超纯水机而由此引起的任何损失,成都沛亿科技有限公司将不承担责任。
我们已经尽我们最大的努力尽量避免人为的失误,以确保本说明书中所提供的信息是正确可靠的,但我们不能完全保证:不会有在印刷之前未曾发现或检查出的差错,以及那些我们无法控制的印刷、装订、分发等环节的疏漏,请您多加包涵!有时,我们为了提高部件及整机的性能和可靠性,可能会对产品的配置作了一些小的调整,这样有可能会导致机器的实际情况与说明书有某些不一致的地方,但这应该不会实质性地影响您对机器的使用,请您能够谅解。
如果您在使用本手册过程中发现手册中有任何错误或者您有什么问题,请与沛亿客户服务中心联系。
谢您的合作!成都沛亿科技有限公司郑重声明本说明书使用的商标、商号及图标均属于成都沛亿科技有限公司或其授权人,并受中华人民共和国法律及国际条约保护。
本手册提及的其他产品的注册商标归其相应公司所有。
本说明书仅适用于书中所介绍的沛亿超纯水机同型号产品的使用和使用条件及环境要求的说明,本说明书并不一定能够适用于其他型号和配置的沛亿超纯水机产品,沛亿也不保证本说明书能够适用于其他品牌的产品。
本说明书中资料的正确性已经认真审核,但成都沛亿有限公司对其内容不作保证。
纯净水设备英文版说明书(FINAL)
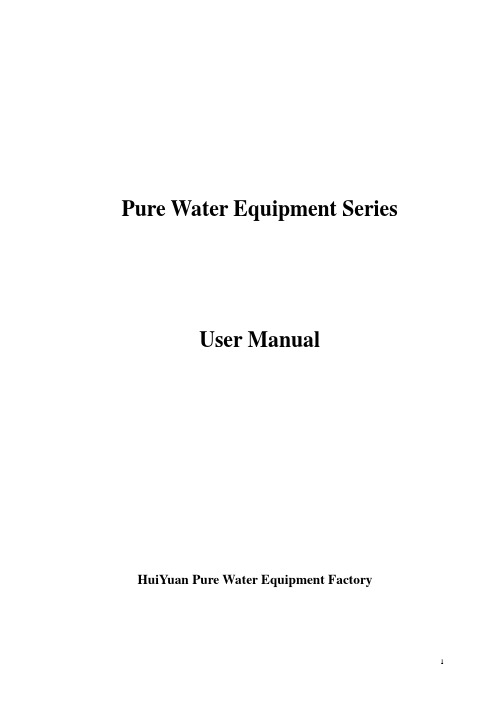
Pure Water Equipment SeriesUser ManualHuiYuan Pure Water Equipment Factory1. Company BriefHuaiBei HuiYuan Pure Water Device Factory is a high-tech company incorporated with design, development, manufacture and management. We are specialized in pure water equipment, mineral water equipment, and undertaking water treatment project with a strong technical force, perfect supporting facilities, timely after-sales services and regulated management system. With the pure water equipment series passed the examination charged by national quality supervision institute, we made the recording effective enterprise standard and successfully passed ISO19001 quality management system certification.2. Preliminary Introduction before Operation2.1 With the equipment placed into the workshop building, make a stable installation. Connect waterinlet of booster pump to source water. Attach pure water outlet and wastewater outlet to water outlet pipeline. Connect main line of distributor box to the power supply. For safety, joint the antapical horn screws of high-pressure pump and booster pump to the ground wire.2.2 With the equipment power on, check whether high-pressure pump, booster pump, ozonegenerator or ultraviolet sterilizer, and water break protector are in normal operating condition.2.3 Start up booster pump to clean multiple media filter repeatedly until its inner water flow turnsclear. Then clean active carbon filter until its inner water flow turns clear. Close the control valve of active carbon filter, and clean the ion-exchanger until its inner water flow turns clear. And working of pretreatment system cleaning is completed.2.4Start up booster pump to make the water flow pass through the pretreatment system intoprecision filter. Open the air vent valve of precision filter, and close it until the air is discharged completely. Start up high-pressure pump to make the water flow into reverse osmosis system, open the pressure regulating valve fully and clean RO membrane repeatedly. The working of antiosmosis system cleaning is completed 60 minutes later.3. Equipment Operation Instructions3.1 Open the source water, start up booster pump until the water shortage indicator lights off andlaunch high-pressure pump immediately. Regulate the control valve to make the pure water flowrate at rated condition. Please refer to the flowmeter for p ure water and wastewater’s flowrate.3.2 Ozone generator or ultraviolet sterilizer works synchronously when the equipment is in normalworking condition. The equi pment’s circuit will turn into automatic guard mode if source water is in shortage, then the equipment will shut down. High-pressure pump and booster pump should not be started up forcibly under the water break condition.3.3 When the operation is completed, close high-pressure pump firstly, then booster pump, ozonegenerator, or ultraviolet sterilizer in right turn. Shut down the power and the primary power ultimately.4. Equipment Maintenance Instructions4.1 Frequently check whether high-pressure pump, booster pump, ozone generator or ultravioletsterilizer, water break protector and power supply system are in good condition.4.2 The positive ion in saturation adsorption condition should be reactivated when it adsorbs calciumion and magnesian ion in the water for a long time. Its regenerate cycle is related to the pure water yield and quality of source water. Regeneration method: put the saturated brine into the regenerated water tank, close the normal operating water outlet valve of the ion-exchanger, open the regenerated valve, start up booster pump (acid & alkali resisting pump) to pump the saturated brine into the ion-exchanger, and flow into the regenerated water tank, keep the saturated brine water recycling for 30 minutes repeatedly through the on-exchanger, and close booster pump (acid & alkali resisting pump), regulate water conduit into normal working condition. After theion-exchanger is soaked by saturated brine for 12 hours, clean out positive ion according to the flushing procedure of the ion-exchanger. Now, the equipment could work normally. Wick filter element should be cleaned frequently and replaced regularly.4.3 Quality condition of source water and pure water yield determine service lifetime of ROmembrane directly. In order to keep RO membrane in operating condition, it will be maintained regularly. This job should be charged or instructed by the professional personnel. The untrained personnel should not clean, remove RO membrane, or adopt other measures on it without authorization. With out the permission from this manufacturer’s professional personnel, the manufacturer will not be liable for any damages resulting from removing high-pressure pump, booster pump, water break protector, reverse osmosis system, host machine or other main parts.4.4 With the equipment standing idle, source water and power supply must be shut down, dischargeall the water in the equipment, and the equipment should not be placed in high temperature and subzero temperature.5. Standard Water Yield EquationP PI-πIP1- PQ N=Q0× 2 ×TCF1P1-PP P0-πO TCF O2WhereQ N = Standard Water YieldN O = Actual Water YieldP1 = Operating Pressure in Preliminary TestP O = Actual Operating Pressure= Pressure Difference in Preliminary TestP= Actual Pressure DifferencePP PI = Water Yield in Preliminary TestP PO = Actual Water YieldπI = Osmotic Pressure in Preliminary TestπO= Actual Osmotic PressureTCF= Temperature Correction Factor in Preliminary Test1TCF= Actual Temperature Correction FactorO6. Equipment Process Flow and Cleaning Method水泵:Water Pump 石英砂过滤器:Quartz Sand Filter活性炭过滤器:Active Carbon Filter 软水器:Water Softener压力表:Manometer 精密过滤器:Precision Filter压力保护器:Pressure Protector 高压泵:High-pressure Pump加药箱:Dosing Tank地漏:Floor Drain6.1 In running condition, start up booster pump, open K1, K4, K5, K8, K9, K12, K13, regulate K17,close K3, K2, K7, K6, K11, K10, K14, K16, K18, start up high-pressure pump when the booster pressure is above 0.2MPa.6.2 In cleaning condition, start up source water pump to clean quartz sand filter, open K3, K2, K7, K8,K11, K12, K14, close K1, K2, K5, K8, K10, K13, K18, the work will be completed within 10~20 minutes.6.3 While cleaning active carbon filter, start up source water pump and open K3, K4, K7, K6, K11, K12,K14, close K12, K5, K8, K9, K10, K13, K18, the time same as above.6.4 To clean water softener, start up source water pump and open K3, K4, K7, K8, K11, K10, K14, closeK1, K2, K5, K6, K9, K12, K13, K8, the time same as above.6.5 RO membrane cleaning prescriptions and method:The above table describes the working prescription of cleaning solution, however professional cleaning agent would be more appreciated in most condition. Most of the professional agents is compatible with RO membrane. The actual effectiveness depends on the results from chemical cleaning for more time. Cleaning method:Put the prepared cleaning solution into the acid and alkaline resistant container as backup, open precision filter and take out the filter element. Put the cleaning solution into precision filter (Put cleaning water into membrane-washing tank if the equipment is provided with membrane-washing tank), contra rotate the regulating valve to fully open, connect the wastewater outlet to precision filter (membrane-washing tank), start up high-pressure pump, and allow the cleaning solution flow into precision filter (membrane-washing tank) from water conduit through RO membrane ultimately. This work will last for 40 minutes. Discharge cleaning solution thoroughly when the above work is completed and make use of pure water to wash the cleaning container, high-pressure pump, RO membrane, pipeline and others with the same method. Restore the equipment to the normal working condition.Notice:1) PH value should be regulated between 11 and 12 while preparing alkaline cleaning solution. PH valueshould be regulated between 2 to 3 while preparing acid cleaning solution. It will be processing caustic washing firstly and acid cleaning secondly when the two cleaning patterns are needed at the same time.Determine the prescription and temperature of cleaning solution with the lifetime services of RO membrane and contamination condition. In the actual operating process, you can make certain what kind of cleaning solution will be used for long time through checking the running quality of the RO membrane after being cleaned.2) Personnel charging cleaning should not leave their posts. Observe changes from solution all the time.Prevent cleaning solution overflow from wastewater conduit, replenish cleaning water or pure water timely to avoid high-pressure pump from idle running.3) In the cleaning condition, a small quantity of water flowing out of pure water outlet should bedischarged. It could not be drunk or mixed with pure water.4) While the cleaning is completed and the equipment goes into normal operating condition, the purewater produced initially should be discharged. When data displayed by the conductivity meter is normal, it could be stepped into normal producing stage.7. General TroubleshootingBooster pump and high-pressure pump could not pump water.When the input voltage is 380v, check whether booster pump and high-pressure pump are reverse or not. If they are reverse, exchange two connector lugs of three at random. If not, open the air vent valve to discharge the contained air or fill the pump body with water fully. When the input voltage is 220v, booster pump and high-pressure pump will not be reverse, just open the air vent valve to discharge the contained air or fill the pump body with water fully.Booster pump could not start up.Firstly, check whether the master machine is connected with the power supply, the wire lead come adrift or off, and the relay is operating.High-pressure pump could not start up.Check whether the relay abutting with high-pressure pump is operating, the wire lead come adrift or off or the water break indicator lights on. If the indicator lights on, it reveals that the source water is insufficient to the usage of booster pump. In order to avoid damage of high-pressure pump resulting from its running idle, apply water break protector to cut off power supply for sake of protecting high-pressure pump. With sufficient water provided, water break protector's pressure will meet the requirement of high-pressure pump’s working pressure, water break protector’s indicator lights off, and then start up high-pressure pump. High-pressure pump sends abnormal noise.Check whether high-pressure pump is running idle. Sometimes, high-pressure pump will send abnormal noise when the water is not pumped in thoroughly. Generally the noise will automatically disappear in 1 to 3 minutes. If it does not disappear 3 minutes later, open the air vent valve to discharge the contained air or fill it with water fully.Pipelines outbreak.Since water from some regions has poor quality and more impurities, or wick filter and RO membrane have not been replaced for a long time, these problems will lead to blockage of RO membrane, increasing of the pipeline’s inner pressure, and make the pipeline outbreak ultimately. Wi th this abnormal turn of events comes, check whether it is necessary to clean or replace wick filter element, and clean RO membrane. Antisludging agent should be added into the source water with poor quality that will lead to blockage of RO membrane frequently to remove the impurities from water, improve water quality and prolong RO membrane’s service life.Water yield runs down.Some operators will find that water yield runs down (Generally, this abnormal turn of events will not come with the tap water as source water.), resulting from partly blockage of RO membrane since water from some regions has poor quality and more impurities. At this time, back flush the pretreatment system, replace wick filter element, clean RO membrane regularly, or replace the underground water having very poor quality with tap water (It will be better to install a set of antisludging system where there is no tap water provided. This measure will avoid the problems basically.)White or black tiny particles are suspended in pure water.This problem is resulted from the infected bacteria caused by the contamination of pipeline. Put resolved sodium hydroxide into precision filter, adjust the regulating valve to shut off the wastewater, and lift the pure water at highest point. Start up high-pressure pump, import water from pure water outlet into precision filter and keep the water recycling for 30 minutes repeatedly through precision filter (Please refer to 6.5, RO membrane cleaning prescriptions and method). If the pipeline sterilization machine is provided with the equipment, timely start up sterilization machine to disinfect the pure water pipelines.24 hours after-sales service hotline: 0561-*******HuaiBei HuiYuan Pure Water Equipment FactoryImportance: Any changes for the above circuit without notice.交流接触器AC Contactor 控制继电器Control Relay漏电保护断器Earth Leakage Circuit Breaker 主控引出Master Controller Output主控输入Master Controller Output 主控信号输入Master Signal Input主控信号输出Master Signal Output KA自锁开关KA Self-locking SwitchKA指控按钮KA Finger-controlled Button KB自锁开关KB Self-locking SwitchKB指控按钮KB Finger-controlled Button 电压表输出Voltmeter Output电源信号输出Power Signal Output KA工作信号指示KA Working Signal Indicator KB工作信号指示KB working signal indicator 参照点Reference PointD1输入接口D1 Input Interface D2输入接口D2 Input Interface电源输入接口Power Input Interface。
Coway P-5600N净水器用户手册说明书

12345特点大流量NANO-TRAP 纳米滤芯直饮水系统大容量过滤滤芯持续供应纯净水。
三级大容量过滤系统采用可选择性去除漂浮颗粒、金属颗粒(汞、铅、铁、铝) 和细菌(大肠杆菌) 和病毒(诺如病毒) 等微生物的NANO-TRAP 纳米滤芯,以及去除水中异味物质的INNO-SENSE 后置活性炭棒滤芯滤芯,使得水的口感更佳。
专为商用和家庭用而设计用户可通过旋钮式水龙头轻松放出大量净水,最多可装满 1.75 升的瓶子。
外形小巧,适用于狭小的空间小巧的外观设计,放在小厨房使用也很方便。
无电环保系统本产品是环保产品,而不需要电,不用担心电费。
21感谢您使用 Coway 净水器。
请阅读本《用户手册》,以便正确使用和维护本产品。
如果您在使用本产品的过程中遇到任何问题,可以参考《用户手册》来解决问题。
本手册附有产品保修卡,请妥善保管。
尊敬的顾客:- 请将《用户手册》放在便于取阅或寻找的地方 -目录特点/目录C O W A Y用户须知维护使用方法其他| 03 | 安全信息| 05 | 部件名称| 06 | 净水程序| 07 | 注意事项| 08 | 如何卫生地使用| 09 | 接水方法| 11 | 安装方法| 13 | 清洁方法| 14 | 更换滤芯| 15 | 滤芯更换方法| 16 | 如何阻止漏水| 17 | 故障排除| 18 | 规格| 19 | 水路图| 22 | 保修卡安全信息请妥善保管此安全信息。
请阅读此信息以避免财产损失并确保您的安全。
电器安全: 如果不按规定操作,可能会导致重伤或死亡。
• 切勿将本产品安装在电热器附近。
• 如果有水进入本产品内部,或者本产品周围出现一滩水, 请关闭供水阀并拔下产品电源插头,然后致电服务中心。
• 切勿将蜡烛或打火机等放在本产品上。
• 切勿在设备上方放置任何盛有水、化学品、食物、小金属物品或任何易燃物的容器。
安装安全: 如果不按规定操作,可能会导致重伤或财产损坏。
• 切勿在本产品附近使用或存放易燃气体或易燃材料。
家用净水器的安装流程

家用净水器的安装流程1.首先确定净水器安装位置和水源位置。
First, determine the installation location and water source for the home water purifier.2.开始安装前先准备好所需的工具和材料。
Prepare the necessary tools and materials before starting the installation.3.关闭水源,拧下水龙头的水管。
Turn off the water source and unscrew the water pipe from the tap.4.清洁水管连接处以确保紧密连接。
Clean the water pipe connection to ensure a tight fit.5.安装净水器的进水管道并将其连接到水源。
Install the inlet pipe of the water purifier and connect it to the water source.6.安装净水器的出水管道并将其连接到家中的水龙头。
Install the outlet pipe of the water purifier and connect it to the tap in the house.7.确保所有管道连接处都安装牢固并且没有漏水。
Ensure that all pipe connections are securely installed and free from leaks.8.打开水源,检查净水器的进出水是否正常。
Turn on the water source and check if the inlet andoutlet of the water purifier are working properly.9.打开净水器,进行排气和冲洗处理。
Kinetico 水净化器 安装说明书

INSTALLATION & USE MANUALReview these instructions before beginning installation. Be sure that installationconforms to all plumbing, electrical and other applicable codes.When installation is complete, ensure these instructions are left with building owner for future reference.Service to be performed by authorized service personnel only.NOTE: It is common practice to ground electrical hardware such as telephones, computers and other devices to available water lines. This can, however, cause electrical feedback in the plumbing circuit, which results in an “electrolysis” effect occurring in the fountain. This may result in water which has a metallic taste to it or has a noticeable increase in the metallic content of the water.When inspecting plumbing circuit, remember the line may be grounded some distance from theinstallation, and may occur outside the building or area in which the unit is being installed.This condition can be avoided (in most cases) by using recommended materials during installation.Any drain fittings provided by the installer should be made of plasticfountain from the remainder of the building’s plumbing circuits.Special ToolsItem Description QuantityNONEAdditional MaterialsI tem Description Quantity1 Unplated copper inlet pipe2 Service StopREQUIRED TOOLS AND MATERIALSThese tables show special tools and/or additional materials(not provided) which are necessary to complete installation ofthese units:Figure 2 - Chiller InstallationCHILLERINLETCHILLEROUTLET23222422Figure 3 - ENO Tube Routing221. Install chiller: Remove front panel of chiller. Slide chilleronto the shelf and position it to the left as per dimensionsin Figure 1.Note: Building construction must allow foradequate air flow on both sides, top andback of chiller. A minimum of 4” (102mm) onboth sides and top is required. See chillerinstallation for additional instructions.2. Attach solenoid valve assembly to the underside ofcross member of mounting frame on electronicsensor unit. (See Fig. 7).3. Make water supply connections. Inlet port is marked on thechiller (1/4” O.D. copper tube). Bend the copper tube (provided)at an appropriate length from the chiller to opening in frame.Install the in-line strainer (provided with chiller) by pushing it inuntil it reaches a positive stop, approximately 3/4” (19mm) onthe marked chiller inlet port (See Figs. 3) (Refer to Fig. 12 onpage 7 for details on assembling quick connect fittings). Attachan unplated and deburred copper water inlet line and a servicestop (not provided) to the chiller. Turn on the water supply andflush the line thoroughly.Caution:DO NOT SOLDER tubes insertedinto the strainer as damage too-rings may result.4. Make connection between remote chiller outlet tube andsolenoid valve assembly. Outlet port is marked on the chiller(1/4” O.D. copper tube). Install a 1/4” union (provided) on themarked chiller outlet port. Insert one end of 1/4” poly tubinginto the union and the other end into the straight fitting on thesolenoid valve assy (See Fig. 3)5. Hang the upper panel on the mounting frame hanger. Besure that the panel is engaged with hanger at the top offrame before releasing it. Align holes in the panel with holesin the mounting frame. Install two (2) #10-24 x 5/8” (16mm)screws (Item 27 - Figure 4) in holes and tighten securely.Figure 4 - Upper Panel Installation27256. Install the fountain. Remove the screw (Item 28) from coverplate (Item 12) and slide cover plate toward basin. Mount thefountain to the upper panel and frame with (4) 5/16” x 1”(25mm) long bolts (Item 30), bracket (Item 34) and nuts(Item 33) provided. Tighten securely. Brackets (Item 34)must be installed as shown to properly supportfountain. (See Figure 5)7. Attach waste tube (1-1/4” O.D.) to 1-1/4” O.D. slip trap(provided by others).8. Connect the fountain drain waste tube to the buildingsanitary sewer system. Connection should be made incompliance with local plumbing code requirements.(Note: Plumbing trap is not included with the fountain).9. Make connection between solenoid valve assembly andfountain(s). Insert the 1/4” poly tubing coming from the fountainwith sensor into the solenoid valve. (See Fig. 3)Figure 4 - Upper Panel InstallationFigure 5 - Fountain InstallationFigure 6 - Lower Panel Installation302827272526View From Rear34331210. Connect power cord of sensor to solenoid valve assembly byrunning it through the back panel and connecting it to termianl shown in Fig. 8. 11. Turn on water supply and check for leaks. Release air from tankby interrupting infrared beam; a steady stream of water assures all air is removed. The sensor has a 30 second maximum ON time. It may be necessary to step away from beam a few times to allow chiller tank to fill.DO NOT SOLDER tubes while inserted into the strainer as damage to o-rings may result.12. These products are designed to operate on 20-105 PSI supplyline pressure. If inlet pressure is above 105 PSI, a pressure regulator must be installed in the supply line.Any damage caused by connecting these products to a supply line with pressure lower than 20 PSI or higher than 105 PSIIS NOT covered under warranty.13. Make electrical connections to the chiller. See chiller instructions.14. Check stream height from bubbler. Stream height isfactory set at 35-40 PSI. If supply pressure varies greatly from this, please do the following. For Electronic sensor unitsonly , remove lower panel (Item 26 - Fig. 6) and turn adjustment screw on the regulator (Item 17 - Fig. 8). Clockwise adjustment will raise stream height and counterclockwise movement will lower stream height. For best adjustment stream should hit basin approximately 6-1/2” from the bubbler.15. Mount lower panel. Loosen the two (2) #10-24 x 5/8”(16mm) screws (Item 27 - Figure 5) at frame bottom lip. Slide upper tongue of lower panel (Item 26 - Figure 6) under lower edge of already installed upper panel. Tighten previously loosened screws securely. (See Figure 6)17311636342, 3, 42918357Figure 7 - Solenoid Assembly WIRING CONNECTORSee Fig. 102132091912101113153237275146Figure 9 - Exploded View2738Figure 11 – Water Supply ConnectionsActuation of Quick Connect Water Fittings: Cooler is provided with lead-free connectors which utilize an o-ring water seal. To remove tubing from the fitting, relieve water pressure, push in on the gray collar while pulling on thetubing. (See Figure 12) To insert tubing, push tube straight into fitting until it reaches a positive stop approximately 3/4”).OPERATION OF QUICK CONNECT FITTINGSOPERATION OF QUICK CONNECT FITTINGS NOTE: WATER FLOW DIRECTIONSERVICE STOP (NOT FURNISHED)。
Rainman水制器安装指南说明书

Although the Rainman watermaker is designed as a portable system not requiring installation, many of our customers choose to partially or fully install the system in their boat. The variations can range widely, including installation of both the pressure supply unit and reverse osmosis case to installing one or the other of the units. An install process should be undertaken by a skilled and experienced technician. As such, this is not a comprehensive guide but a document of tips and issues for consideration.Pressure Supply Unit:•If taking water in from through hull, ensure a sea strainer is in place to catch coarse matter prior to getting in to pre-filter assembly.•Ensure through hull location will not let air into the system. Account for healing of sailing vessel and avoid through hull too near the bow.•Mount pressure supply unit in a cool dry location.•Ensure you leave access to easily view and change the pre-filter.•Intake hose should be minimum of 1/2” diameter.•Pressure supply unit has in built lift pump. Do not exceed 2 metres (6 ft) above the water line. •We recommend not installing any petrol powered device in an enclosed area.• A 10 litre (2.5 gallon) bucket should be used and accessible through a T valve for fresh water rinsing and membrane pickling purposes. Vessel tank water should not be used for fresh water rinsing or membrane pickling as there may be residual chlorine in the tank from previous filling with city water. This chlorine will damage your reverse osmosis membrane.•If you wish to draw water from the vessel tank for fresh water rinsing, an inline active carbon filter can remove the residual chlorine.• A dedicated through hull is best. If shared with other appliances, it is critical to ensure your Rainman watermaker is not being starved of feed water by competing with other appliances. Reverse Osmosis Case:•The brine output should be above the water line to avoid back pressure. Use the easiest method to dump brine overboard, including internal sinks, etc.•The product water hose should have T valve for water tasting/testing, fresh water flushing, and membrane pickling.•The product water hose should feed into top of vessel tank to avoid back pressure.•There is practically no limit on length of high pressure hose, product water hose, or brine outputhose.•The reverse osmosis pressure vessel housings may be mounted within the Rainman case orremoved and mounted on their own.。
淘汰者水过滤器安装指南说明书

THE ELIMINATOR WATER FILTERINSTALLATIONDiscount Water Softeners recommends using a licensed plumber to install your water filter. The following installation instructions are for use with the water filter system you now own. Discount Water Softeners assumes no responsibility for improper installation or injury.Additional instructions are also in your water filter manual. Please print these instructions and use them in conjunction with your manual for installing and programming your system.Step 1:Location of your filter is important. It should be in a protected dry, level and non-freezing area (34-120 degrees F). The 2 tanks should be set close to each other. The small round tank is your solution tank (chlorine solution) and it is the tank that you will have to refill with chlorine and water from time to time, so make it the more accessible of the 2 tanks. Do not put anything in this tank until you have put the filter into service and have tested the cycles. If you have a water softener, be sure to install the eliminator first inline in your home.Step 2:You will need a standard outlet that is not controlled by a switch. You should also have a floor drain located nearby.Step 3: The single riser tube should be placed in the filter tank with the distributor basket end down. The filter tank (fiberglass construction) is the taller of the two tanks and shown in the following picture. Turn the tube a couple times to make sure that the bottom basket seats properly in the bottom of the tank. Make sure the riser tube is in the tank BEFORE YOU ADD THE CARBON! If your system came with a small bag of gravel, add the gravel before the carbon.Step 4:Make sure you place the filter tank shown above where you want to connect it to your water line because it will be heavy and difficult to move after the carbon is added. Make sure you install your filter in line before your water softener.Step 5:Be sure to cover the open upper end of the riser tube with tape or a cap as shown below to keep any gravel or carbon from falling into the riser tube while pouring the gravel or carbon into the filter tank. Try to pour the carbon in slowly as it can causea black dust that is unhealthy to inhale. Remove the tape after filling the tank.Step 6: Place the funnel into the filter tank as shown below, and slowly pour the gravel and carbon into the filter tank. Caution: If you purchased a filter that came with a bag containing gravel, you must add the gravel first before the carbon.Step 7: Be careful to keep the riser tube centered as best you can, while filling. Once the filling of the filter tank is completed,carefully remove the tape from the riser tube. Do not pull upwards on the riser tube.If you purchased a Fleck 5600 Eliminator system, continue to step 9. If you purchased a Fleck 7000 Eliminator skip to step 13Step 9: The control valve head can now be screwed onto the filter tank. Be sure the large O-ring is in place, and lubricated. As you start to screw the control valve onto the tank, make sure the hole in the center of the control valve fits over the riser tube. The control valve should be hand tightened, snug and tight to eliminate a possible leak, clockwise.Step 10:You are now ready to install the bypass valve and yoke to the control valve. Turn off main water valve. Water connections to and from filter should now be connected. For Fleck 5600SE filter systems you will need to install your bypass along with either your plastic male threaded connections or stainless steel threaded connections. The plastic or stainless steel fittings will need to be screwed on to yourexisting piping. CAUTION: YOU MUST PAY ATTENTION TO THE IN AND OUT ARROWS ON THE VALVE TO BE SURE THE FILTER IS PIPED PROPERLY.Step 11:You will need a drain for the backwashing cycles. This should be no longer than 20 feet from the water softener. You will need to purchase this flexible 1/2 i.d. plastic pipe (can be vinyl, polyethylene etc.) and a small clamp to hold the tubing over the fitting. This backwashing drain line will be under high pressure when the backwash cycle is working. Make sure the drain line is secured. The drain line will need to drain into a drain, which should be a minimum of 1 1/2” size, and ideally be below the top of the head of your softener. Local codes should be adhered to. (be sure to use teflon tape on this step).Step 12: You will now need to connect the solution tank line to the water filter valve. Attach the clear tubing provided from the solution tank to the connection fitting on the valve as shown below. You may need to connect the pick up screen inside the tank and run the tubing through the top hole in the solution tank and connect to the compression fitting elbow.If you purchased a Fleck 5600 Eliminator system, skip to step 16. If you purchased a Fleck 7000 Eliminator continue to step 13Step 13:You are now ready to install the bypass valve to the control valve Use the red clips provided to hold the connection fittings to the bypass and the bypass to the valve. Be careful not to force the red clips on or off the valve as they can break. Turn off main water valve. Water connections to and from softener should now be connected. For Fleck 7000 systems you will need to install your bypass along with either your plastic threaded connections or brass “sweat” fittings. The plastic fittings can just be screwed onto your connections. Brass connections will need to be “sweated” in. CAUTION: YOU MUST PAY ATTENTION TO THE IN AND OUT ARROWS ON THE VALVE TO BE SURE THE SOFTENER IS PIPED PROPERLY.NEVER REMOVE ANY RED CLIPS FROM THE FLECK 7000 SYSTEM WHILE UNDER PRESSURE.NEVER REMOVE ANY RED CLIPS FROM THE FLECK 7000 SYSTEM WHILE UNDER PRESSURE.Step 14:You will need a drain for the backwashing cycles. This should be no longer than 20 feet from the water softener. You will need to purchase this flexible 1/2 i.d. plastic pipe (can be vinyl, polyethylene etc.) and a small clamp to hold the tubing over the hose barb fitting supplied. This backwashing drain line will be under high pressure when the backwash cycle is working. Make sure the drain line is secured. The drain line will need to drain into a drain, which should be a minimum of 1 1/2” size, and ideally be below the top of the head of your softener. Local codes should be adhered to. On the Fleck 7000 there is a side connection where you will connect this drainline.Note: Never connect the drain line directly into a drain. Allow an air-gap between the drain line and waste line to prevent possibility of back- siphoning.Step 15: You will now need to connect the solution tank line to the control valve. Attach the clear tubing provided from the solution tank to the connection fitting on the valve First attach the connection fitting to the valve then attach the tubing to the valve.On the other end, attach the tubing to the solution tank compression fitting elbow.Step 16: INITIAL POWER UP1. Add 1 gallon of regular household bleach (approx. 5.25% strength) to the solution tank after moving it to the desired spot that is accessible for refill. Next add 14 more gallons of water to the solution tank. Make a mark on your solution tank for future reference when refilling. For larger Eliminators with the 35 gallon solution tank,add 2 gallons of bleach and 28 gallons of water.2. Set your bypass in bypass mode and slowly turn on the main water valve to your home until all pipes are pressurized. Now open the bypass valve SLOWLY. You do not want to be surprised by leaks. Let the filter tank fill completely, then open the bypass valves the rest of the way.CAUTION If opened too rapidly or too far, carbon may be lost out of the tank into the valve or the plumbing. In the 1/4 open position, you should hear air slowly escaping from the valve drain line.3. Plug the power supply transformer into a socket that is not controlled by a switch or timer.4. Program your water filter. Be sure you set the control valve as a time clock delayed system. Set the time of day, days to backwash, and backwash times. Here is where you will need to refer your owner's manual and special eliminator programming instructions that should have been emailed to you for your particular water filter settings and programming.5. Once your filter is programmed advance your controller to manual backwash. The backwash process can take a while. Upon initial installation, some carbon “fines” could pass into your water supply to your home. Be sure to clear all lines after installation to minimize the carbon “fines” in your water.6. Check for any leaks during this initial backwash.8. Your filter should now be providing you with odor free water.。
水果汁机滤芯安装指南说明书
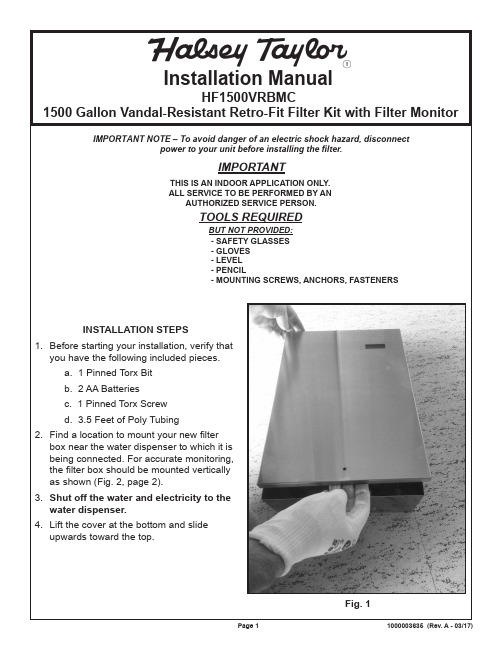
IMPORTANT NOTE – To avoid danger of an electric shock hazard, disconnect power to your unit before installing the filter.INSTALLATION STEPS 1. Before starting your installation, verify thatyou have the following included pieces.a. 1 Pinned Torx Bitb. 2 AA Batteriesc. 1 Pinned Torx Screwd. 3.5 Feet of Poly Tubing2. Find a location to mount your new filterbox near the water dispenser to which it isbeing connected. For accurate monitoring,the filter box should be mounted verticallyas shown (Fig. 2, page 2).3. Shut off the water and electricity to thewater dispenser.4. Lift the cover at the bottom and slideupwards toward the top.Fig. 1IMPORTANTTHIS IS AN INDOOR APPLICATION ONLY. ALL SERVICE TO BE PERFORMED BY AN AUTHORIZED SERVICE PERSON.TOOLS REQUIREDBUT NOT PROVIDED:- SAFETY GLASSES - GLOVES - LEVEL - PENCIL - MOUNTING SCREWS, ANCHORS, FASTENERS1500 Gallon Vandal-Resistant Retro-Fit Filter Kit with Filter MonitorInstallation ManualHF1500VRBMCNOTE: All installations must becompliant with ADA regulationsFig. 2Fig. 3Fig. 46. Cut a hole in the wall anywhere inside themarked location to allow room for the waterlines to come into the back of the box.7. Remove any protective covering from theoutside of the filter box.8. Using the appropriate fasteners (Not Supplied),mount the box to the wall.Fig. 5Fig. 6Inlet Fitting not included 10. Connect the poly tubing from inlet of the waterdispenser to the outlet fitting on the flow meterFig. 8Fig. 7Inlet fitting not includedinstall on the filter head turning clockwise.Fig. 913. Turn on the water and check for leaks. Repair as needed14. Run approximately 1 gallon of water thru the fixture. This flushing procedure purges air and fine carbon particles from the filter. After 1 gallon of water has been purged carefully inspect all water connections for leaksFig. 1012. Remove the filter monitor from the back of the box and insert the supplied batteries. Once installed, the monitor will light up. The monitor can now be put back on the back of the box. Make sure it is positioned so that it can be viewed thru the window in the front cover once it is installed.15. After peeling the protective covering from the front cover, hook the tabs on the top into the slots on the top of the box. Slide the cover down and install the supplied screw. Once done keep the bit as it will be needed for replacing the filter.OPERATING INSTRUCTIONS FOR THE FILTER MONITOR 1. The filter monitor backlight automatically turns on when there is water flowing through it. The blue backlight will turn off after approximately 10 seconds but will display the remaining capacity the entire time water is flowing. To conserve battery life, the display will automatically turn off in 10 seconds when there is no water flowing. The power of the two batteries could last for approximately one year.2. The flow meter will generates an audible alert and the digits on the LCD will blink red when the remaining capacity reaches zero.3. To reset, press the reset button for four seconds. The “RESET” on the LCD blinks twice and the remaining capacity is reset to the original programming value.4. When the battery power is low the monitor generates an audible alert and the empty battery symbol on the upper right corner blinks. The alert status will be released when the batteries are replaced with new one. NOTE: the data of the last status will be memorized when powered off.PRINTED IN U.S.A.2222 CAMDEN COURTOAK BROOK, IL 60523630.574.3500FOR PARTS CONTACT YOUR LOCAL DISTRIBUTOR OR VISIT OUR WEBSITE - Fig. 11Fig. 12To receive maximum benefit from your Halsey Taylor ®WaterSentry ® VII filters, note the installation dates below,and change according to the following guidelines.Halsey Taylor ® Part No. 55897C WaterSentry ® VII -- Lead Reduction Filter Change every 1,500 gallons, or once a year -- whichever occurs first.- - KEEP THIS SHEET IN A HANDY LOCATION - -NOTICEFOR PARTS, CONTACT YOUR LOCAL DISTRIBUTOR OR VISIT OUR WEBSITE 2222 CAMDEN COURTOAK BROOK, IL 60523630.574.3500PRINTED IN U.S.A.DATE INSTALLED MODEL (TYPE OF FILTER)SERVICE PERSON DATE INSTALLED MODEL (TYPE OF FILTER)SERVICE PERSON。
美国迪士尼(Duracraft)冷水饮水机说明书

Installation / Care / Use ManualOriginal InstructionsModels: FD70010LF2YJO, FD70010SF2YJO, FD70010TF2YJODescriptionRefrigerated Drinking Fountain (Cooler) delivers chilled, clean potable drinking water. Water Cooler houses the refrigeration and delivers a steady stream of water for direct drinking at the press of the pushbutton.Ratings• Electrical: 230Vac, 50Hz, (See nameplate for Amperage), 1 phase. • Ambient Air Temperature: 50-100.4 °F (10-38 °C).• Water Pressure: 20-100 psig (0.14-0.69 MPa).• Maximum Water Temperature: 90 °F (32 °C).• Refrigerant: HFC-R134a • Ingress Protection: IP21• For Indoor Commercial Use only.• Water Inlet: 3/8”O.D. unplated copper tube. • Waste Water Outlet: 1-1/4” O.D. tubeDANGER– Indicates death or serious injury will result if proper precautions are not taken.WARNING – Indicates death, serious injury or property damage can result if proper precautions are not taken.CAUTION – Indicates some injury or property damage may result if proper precautions are not taken.DefinitionsAuthorized Service Personnel – Factory trained personnel or personnel having working knowledge of electrical, plumbing andmachine (appliance) maintenance procedures.SafetyDANGER• Please read these instructions completely before starting the installation or performing any service. Failure to follow the instructions andsafety precautions in this manual can result in serious injury or death.• After installation, keep these instructions in a safe location for future reference.• Electric supply must be identical in voltage, cycle, and phase to that specified on nameplate.• Electrical supply must have Ground Fault Circuit Interrupter (GFCI) protection.• A means for disconnecting electrical supply to the unit must be incorporated in the fixed wiring in accordance with wiring rules. This is toallow electrical disconnection of the unit from electrical supply after installation.WARNING• For use with clean, clear potable drinking water only. Do not use with water that is microbiologically unsafe or of unknown quality without adequate disinfection before the system.• Installation and connection to water and electrical mains must be in compliance with local and national laws.• All Installation and Service work must be performed by an authorized service personnel.CAUTION• This appliance can be used by children aged from 8 years and above and persons with reduced physical, sensory, or mental capabilities or lack of experience and knowledge if they have been given supervision or instructions concerning use of the appliance in a safe way andunderstand the hazards involved. Children shall not play with the appliance. Cleaning and user maintenance shall not be made by children without supervision.• To prevent a metallic taste or increased metal content in the water due to an electrolysis process caused by electrical feedback from thegrounding of electrical equipment to water supply and water waste mains, connect to these mains using non-conductive materials. Theprovided non-metallic In-line Strainer meets this requirement.InstallationFor correct and safe installation, please read these instructions completely.• All Installation work must be performed by an authorized service personnel.• Disconnect electrical supply serving the Installation area to reduce risk of electrocution. • Unit not suitable for installations where water jets could be used.DANGERWARNING• Shut off water supply serving the Installation area to reduce risk of water damage.• Ensure proper ventilation by maintaining clearance from cabinet louvers to wall on each side of Cooler as specified in Rough-In. • Never wire compressor directly to electrical supply.• Do not solder tubes inserted into the In-line Strainer as damage to the o-rings may result. • Thoroughly flush all water lines and fittings of all foreign matter before connecting to Cooler.• Warranty is void if the plumbing kit or glass filler is not specified for use by the Manufacturer for this particular model. • Warranty is void if Installation is not made in accordance with current Manufacturing instructions.CAUTION• Hose-sets are not to be used for connecting to water mains.• If inlet pressure is above 100 psig (0.69 MPa), a pressure regulator must be installed in water supply line. Any damage caused by reason of connecting this product to water supply line pressure outside its rated pressure, is not covered by warranty.• This cooler is manufactured in such a manner that it does not in any way cause taste, odor, color, or sediment problems. If a taste, odor or sediment problem is prevalent, try installing our water filter on the supply line. • Tools/Items required but not provided.o Water Shut-off Valve with 3/8” (9.5mm) compression outlet. o 1-1/4" (31.8mm) Waste Trap (non-metallic) o Safety Glasses o Protective Gloveso 5/16" (7.9mm) Hex Driver or Flathead Screwdriver o C-13 Modular International Power Cord SetInstallation: Cooler Mounting1. Select installation location. Installation location must be a flat surface. Installation location should ensure proper ventilation by maintaining 4"(102mm) minimum clearance from cabinet louvers to wall.2. Remove front panel (Item 26) by unscrewing (2) 5/16" (7.9mm) Hex Head screws. Set panel aside.3. Installation area must also include water supply, electrical supply and suitable drain. Water, drain and electrical supply systems must complywith local code requirements.Installation: Water Line connection1. Ensure Mains Water Supply has Water Shut-off Valve with 3/8” (9.5mm) compression outlet.2. Connect loose end of supplied 3/8” (9.5mm) unplated copper tube to Water Shut-off Valve. See Figure 1.• NOTE: If 3/8” (9.5mm) copper tube must be cut for proper fit, remove all burrs from the outside of tube and re-flush before use.3. Install waste trap. Remove the slip nut and gasket from the waste trap and install them on the Cooler waste line making sure that the end of thewaste line fits into the waste trap. Assemble the slip nut and gasket to the trap and tighten securely.4. Turn on building water supply and open Water Shut-off Valve. Check all connections for leaks and correct any found.Installation: Electrical connection1. Rotate fan to insure proper clearance and free fan action.2. Connect modular (C-13) end of International Power Cord Set (sold separately) into Power Inlet on unit and ensure plug-end reaches electricaloutlet. Do not plug into electrical outlet!NOTE: WATER FLOWDIRECTIONBUILDING WATER SUPPLYWATER SHUT-OFF VALVE(NOT PROVIDED)1/4" O.D. TUBE WATER INLET3/8" (9.5mm) O.D.UNPLATED COPPER TUBEIN-LINE STRAINER (PROVIDED)Figure 1Figure 2A = White (Neutral)B = Black (230Vac)C = Ground (Earth)D = FanE = Freeze Control (when provided)F = Cold Control (Water)G = Hot Tank Switch (When Provided)H = Hot Tank (when provided)I = Capacitor (when provided)POWER INLETRough-In: SCWT14AOperation: Start-Up1. Turn on the building water supply and check all connections for leaks.2. Purge air from all water lines by activating pushbutton with your hand.3. Recheck all water and drain connections with water flowing through system.4. Rotate fan to ensure proper clearance and free fan action.5. Connect plug-end of International Power Cord Set (sold separately) into electrical outlet.6.After verifying that the water cooler is properly connected and operational, replace and reattach cooler front panel (Item 26) by tightening (2) screws.A = Water Mains Supply, 3/8” (9.5mm) O.D. compression outlet of Shut-off Valve (not provided) to be 1-1/2” (38mm) from WallB = Waste Outlet, 1-1/4” (31.8mm) O.D. Drain TubeC = 1-1/4” (31.8mm) Trap (not provided)D = Power Inlet. Electrical Mains Supply Duplex Outled, 3-wire in Recessed Box. Must have Ground Fault Circuit Interrupter (GFCI) protectionE = Ensure proper ventilation by maintaining 4” (102mm) minimum clearance from cabinet louvers to wallF = To level unit, loosen screws to adjust base for contact with floor. Tighten screws after unit has been leveled.Figure 3ServiceFor proper and safe servicing, please read these instructions completely.• All Service and Maintenance must be performed by an authorized service personnel.• Disconnect electrical supply to the unit before any service work to reduce risk of electrocution. • Shut off water supply serving the unit before any service work to reduce risk of water damage.DANGERCAUTION• Tools/Items required but not provided, for Servicing: o Safety Glasses o Protective gloveso 5/16" (7.9mm) Hex Driver or Flathead ScrewdriverService: Adjustments1. Temperature Control: Factory set for 50ºF ± 5º (10ºC ±2.8º) water under normal conditions. To adjust water temperature, remove front panel(Item 26) by unscrewing (2) 5/16" (7.9mm) Hex Head screws. Set panel aside. Turn screw on cold control (Item 15) clockwise for colder, counter clockwise for warmer. See Figure 10.2. Water Stream Height: Stream height is factory set at 35 psig (0.24MPa). If supply varies greatly from this, remove items 1 and 2 and adjustscrew on item 4. Clockwise adjustmentwill raise stream height and counter-clockwise adjustment will lower stream. For best adjustment, stream should hit basin approximately 6-1/2" (165mm) from bubbler. See Figure 5 and 10.3. Water coming out of Bubbler continuously: When this occurs at the end of the compressor cycle, turn the cold control warmer (Item 15) counter-clockwise 1/4 of a turn. See Figure 10.DService: Inspection/Cleaning• Inspect Cooler twice each year for proper operation and performance.• Inspection of the unit will require disconnecting electrical supply, removal of panels, etc. and reassembly and return to service practices.1. Cleaning: Warm, soapy water or mild household cleaning products can be used to clean the exterior panels. Extra caution should be used to clean the mirror finished stainless steel panels. They can be easily scratched and should only be cleaned with mild soap and water or Windex glass cleaner and a clean, soft cloth. Use of harsh chemicals or petroleum based or abrasive cleaners will void the warranty.2. Bubbler : Mineral deposits on the orifice can cause water flow to spurt or not regulate. Mineral deposits may be removed from the orifice with a small round file not over 1/8” (3 mm) diameter or small diameter wire.• CAUTION : DO NOT file or cut orifice material. Care must be taken not to damage the orifice(s)3. Condenser Fan Motor : Confirm condenser fan turns freely. If the condenser fan does not spin freely, have an authorized service personnel replace.4. Ventilation : Cabinet louvers and condenser fins should be periodically cleaned with a brush, air hose or vacuum cleaner. Cleaning should be done twice each year or more frequently if needed due to environment. Excess dirt or poor ventilation can cause no cold water and compressor cycling on the compressor overload protector.5. Water Flow : Confirm proper water flow. If water flow is slow, inspect filter or inline strainer for restriction. Replace filter cartridge if required. Disassemble inline strainer and clean if required See Figure6.6. Lubrication: Motors are lifetime lubricated.7.Actuation of Quick Connect Water Fittings: Cooler is provided with lead-free connectors which utilize o-ring water seal. To remove tubing from the fitting, relieve water pressure, push in on the gray collar before pulling on the tubing. To insert tubing, push tube straight into fitting until it reaches a positive stop, approximately 3/4” (19mm). See Figure 7.Service: Inspection/Replacement• Inspect Cooler twice each year for proper operation and performance.• Inspection of the unit will require disconnecting electrical supply, removal of panels, etc. and reassembly and return to service practices.1. Bubbler : To remove the bubbler, first disconnect the electrical supply. Remove the Front Panel by removing (2) screws. To remove the bubbler,loosen locknut from the underside of the basin and remove the tubing from the quick connect fitting (see Figure 7 for actuation of Quick Connect Fittings). When installing replacement bubbler, tighten nut only to hold parts snug in position. Do Not Overtighten. After servicing, replace the front panel and two (2) screws.2. Cleaning Strainer : Restricted water flow may be caused by clogged screen. Remove plug and screen. Clean screen and replace. LubricateO-Ring with food grade pharmaceutical mineral oil. Do not overtighten plug or fittings. See Figure 6.A = Plug with 7/8" (22.2mm) HexB = O-ringC = ScreenD = Strainer Body with 1" (25.4mm) HexFigure 6Figure 7Figure 4Figure 5Figure 8Filter Assy - 1500 GallonKit - Filter Head Fitting includes John Guest Fitting & 3/8" Elbow FittingAssy - Filter & Bracket includes Fltr Head/Mtg Bkt/John Guest Ftgs/Screws51299C 98926C 51469C123Item No.Part No.DescriptionReplacement Parts: Filter Parts ListItem No.Part No.DescriptionReplacement Parts: 230V-50Hz Parts List*Includes Relay & Overload. If under Warranty, replace with same Compressor used in original assembly.NOTE: All correspondence pertaining to any of the above water cooler or orders for repair parts MUST include Model number and Serial number of cooler, name and part number of replacement part.For Replacement Parts, contact your local distributor or call 1.800.834.4816Elkay Manufacturing Co. 2222 Camden Court – Oak Brook, IL 60523 U.S.A – 630.574.8484SEE FIG.57131523252829, 30,31, 372624271417, 18,19 & 20SEE FIG.421, 22, 353236Figure 10Glass Filler shown for Reference OnlyFigure 9393840089C 40048C 15005C 61313C 40169C 50986C 22543C 56073C 40322C 56011C 55997C 75580C 55996C 66810C 35839C 31430C 30664C 70018C 20282C 50144C 1903700066202C 66508C 66305C 21958C 21482C 20460C 21959C 21487C 21486C 21239C 28196C 100000214735768C 36222C 36221C 56092C 10032274056015009C 75706C 50189C 98751C 35826C 35827C 31455C 31457C 31458C 31459C 70682C 75583C 27115C 27117C 27116C 27361C1234567891011121314151718192021222324252627*2829303132333435363738NS NS NS NS NSCover ButtonRetainer Nut Regulator Hex NutHolder Regulator Basin & Drain Assy Bubbler Assy Orifice Assy Housing Assy Pedestal Locknut StrainerEvaporator Assy Cold Control Motor-Fan Blade-FanNut (Motor Mtg.) Bracket-Fan MotorGrommet - Compressor Mtg.Clip - Compressor Mtg.DrierHeat Exchanger Assy CondenserFront-Pnl (Almond)Front-Pnl (Sandalwood)Front-Pnl ( Stainless Steel)Front-Pnl (Light Grey)Cabinet (Almond)Cabinet (Sandalwood)Cabinet (Stainless Steel)Cabinet (Light Grey)Compressor Serv. Pak Cover - Relay Overload RelayTubing - Poly (Cut to Length)Gasket (GF)Bubbler Nipple Assy. (GF)Stud - Compressor Mtg.Shroud - FanKit - Relay/OverLoad/Cover Power InletCord-Power (230V/50Hz)Power Cord "JB"Power Cord "JD"Power Cord "JJ"Power Cord "JS"Tee 1/4"Elbow - 5/16" x 1/4"Cover-Rear (Almond)Cover-Rear (Sandalwood)Cover-Rear (Stainless Steel)Cover-Rear (Light Grey)38。
VERTEX水产品纯水暖饮水器安装说明书

VERTEX Water ProductsPureWaterCoolerWater Dispenser OWNERS INSTALLATIONMANUAL™VERTEXWATER PRODUCTS Countertop ModelsPWC-400 FPWC-400 RMontclair, CA - USA–2–Figure 2.Flow Schematic–3–Figure 3.Back View of Cooler–4––5–4.0 Installation4.1Positioning the CoolerThere are some precautions to take when positioning and using the PureWaterCooler™. See the items in Figure 4a and 4b. In addition, the cooler must be located near the supply water, and for the “R” version with the reverse osmosis fil-ter, there must be access to a drain trap to which the reject water from the RO is deliv-ered. Normally, this can be found in a bathroom, or kitchen sink. Flexible 1/4-inch plastic tubing may be used for the feed and discharge connections. Normally, these connections should be within 25-feet of the cooler.Important Note:Do not cover air intake vent as this will prevent proper chill-ing from occurring.Figure 4a.Installation Precautions6 i n 4 in Keep at least 6 in. distance between the cooler and the wall.AirIntakevent4.2 Cooler Water ConnectionsWhen received, the water connections on the back have color coded tube sections with red shipping caps on them. These tube sections must be removed before making water connections. To remove the tube sections see Figure 8. The 1/4” plastic tubing should be used for making the Feed Water and Drain connections. If hard copper tubing is used for the Feed Water and Drain connections, the bulkhead fittings on the cooler must be changed to metal fittings.4.3 Feed Water ConnectionsTo connect the feed water, used the supplied self-piercing saddle valve to connect to the cold water supply line under the sink. Attach the 1/4” tubing to the compression fit-ting on the side of the valve. Clamp the saddle valve over the copper or plastic feed line (cold water only). Turn the handle on the valve until the needle stem pierces the tube.Then retract the needle 1-2 turns to start water flow. See Figure 5.–6–Figure 4b.Installation PrecautionsDo not place cooler next tooven or dishwasher. Keepout of direct sunlight Be sure to use correct power voltage. Plug power cord directly into electrical socketFigure 5.Saddle Valve4.4Drain Connection (Applies to models wit Reverse Osmosis “R-version”)The black drain line in the back must be hooked to the drain line ahead of the normal sink water trap.See Figure 6 below. Place the 2 part drain saddle on the drain pipe before the drain trap. Allow proper space for the drilling operation. Tighten the sad-dle bolts evenly on both sides. Using the opening in the drain outlet saddle as a guide, drill a 1/4” hole in the pipe. Clean any debris out of the drain saddle connection.Connect the drain line to the cooler using the 1/4” black tubing supplied.Figure 6.Drain Connection for RO Filter–7–4.5 Quick Connect FittingsThe standard tubing connections on the PureWaterCooler™are of Quick Connect 0-ring seal design and manufacture. Use the tubing and follow the instruc-tions below to make the connections. If you cut the tubing make sure it is a square cut, fits squarely in the fitting and seals properly.Figure 7.Quick Connect Fittings–8–5.0 Operation5.1Start UpThe PWC 400 Cooler is shipped to you complete and ready to operate. Connect all tubing according to instructions.b. Make sure Cold and Hot power switches at back of cooler are OFF beforeplugging the cooler into 110-volt wall socket. (See Figure 8a)c. Filter pre-flush. The carbon filter must be flushed of carbon fines before use. Release the tubing from the carbon filter at the top of the tank. Run this to a container to collect water. Let water run until it is clear. Unplug the power cord. Reconnect tub-ing. For complete instructions see Section 7.1.d. Plug in the power cord. The feed water solenoid valve will open automatically (a “click” can be heard from inside the cooler when this occurs).e. Water will now start to flow through the filtration system and enter the water tanks inside the cooler. DO NOT TURN ON THE HOT & COLD POWER YET!f. When the ‘tank full’light on the front panel (Figure 8b) comes on, the tanks are full and water production has stopped.1) For the “R” version with reverse osmosis, it will take 2 hours.2) For the “F” standard filter version, it will take about 15 minutes.–9–Figure 8a.Hot/Cold Power SwitchesFigure 8b.Control Panelg. Completely drain all of the water from the cooler using the hot water dispens-ing button. After the first tank is drained, let the tanks refill and drain a second time in the same manner. You must drain (2) complete tanks of water before use to ensure car-bon fines and membrane preservative have been removed.h. Once the cooler has refilled for the 3rd time, turn on hot power switch on the back. Heating will start and the “Heating” light will come on the front panel.i. Dispense hot water (Figure 8c). Hot water dispensing utilizes a child safety device to help prevent accidental dispensing of hot water by young children. To operate the hot water tap, first push the “key” button. Then within 30 seconds, push the hot water tap button and hot water will be dispensed.Figure 8c.Control Panel j. Turn on the cold power switch in the back. The compressor will start and cooling will begin. The “cooling” light, located on the front panel, will come on.k. To dispense cold water, push the Cold Water Tap button.l. The temperature of cold water is set at midpoint at the factory. Using a flat screw-driver, the temperature can be adjusted by turning the temperature control slot Clockwise for colder and Counterclockwise for warmer (See Figure 3).CAUTION:If you turn the COLD POWER button off, WAIT AT LEAST3 MINUTES before turning on again to protect the compressor from damage.–10–5.2Tank DrainOccasionally, it may be desirable to drain both tanks. There is a drain plug on the bottom of the cooler frame. See Figure 9. First, make sure all power is off. The cooler must be moved so that the water can be drained from the bottom into a container to collect the water (about 11/4 gal).Figure 9.Tank Drain–11–6.0 Leak Detection SystemThere is a water leak detection system installed in the cooler. If a water leak should occur inside the cooler, power will automatically be shut off.When power is cut off due to water leak:a. Un-plug the cooler and remove the left side panel (See Figure 10).b. Remove any excess water in the bottom lift and wipe the detection probes dry. Replace.c. Plug in the unit and check for leaks.7.0 Filter Replacement ProcedureThe filter elements must be replaced at regular intervals to maintain the quality of the water.The “F” Model 400 has 2-stages of mechanical filtration. A1st stage 5-micron sediment filter and a 2nd stage activated carbon filter. Both stages must be replaced every 6-12 months.The “R” Model 400 has the 2-stages of mechanical filtration plus an additional 50 GPD Reverse Osmosis membrane element. The 2 pre-filters must be replaced every 6-12 months. The Reverse Osmosis membrane must be replaced every 3 years. The RO unit produces filtered water at a rate of 2 gal/hour.Figure 11.Filter Access7.1 Sediment and Carbon Filter Replacement Procedurea. Unplug the cooler from the wall socket.b. To access the filter compartment, remove the two screws that secure theright side panel. (See Figure 11).c. Remove the right side panel by sliding it backwards and then lifting the panel out.d. To remove the sediment and carbon filters, rotate the filter 90 degrees and pull down.e. Install a new carbon and sediment filter in the indicated positions.Use these replacement filters for PWC 400 shipped before 03/01/2008:1st stage sediment filter, P/N TF-40562nd stage Carbon filter, P/N TF-4057Use these replacement filters for PWC 400 shipped after 04/01/08:1st stage in-line sediment filter, P/N IFA-40352nd stage in-line carbon filters, P/N IFA-4034f. On the Model 400F The carbon filter must be flushed of carbon fines before use. Release the tubing from the carbon filter at the top of the tank. To access the tank, remove the top cover by removing the two hold down screws and sliding back the top (See Figure 1). Run this tubing to a container to collect water.g. Plug in the power cord. The inlet water valve opens and water will run through the filters. Let water run until it is clear. Unplug the cooler and re-connect tubing. Plug in the power cord.-14-7.2 Stage 3 Reverse Osmosis Membrane ReplacementUse the same procedure as in paragraph 7.1 above section a-f. With the cooler unplugged and the filter compartment open, disconnect the 3 tubes of the RO filter housing. Remove the RO housing from the filter clips. Remove the cap from the housing by unscrewing it.Using a pair of pliers, remove the RO element from the housing by grasping the tube end and pulling it out. Use RO filter replacement P/N ma-4203(50 gpd TFC membrane). Insert the element into the housing with the double “o”-ring end going in first, toward the bottom of the housing. Make sure the “o”-rings are seated. Replace the cap. Reconnect the tubing and replace housing in filter clips.Replace cover and plug in cooler. Flush 3 tanks of water before drinking to remove preservative in the RO membrane.Membrane Installation8.0 Options8.1 UV StageAn additional stage is available for both models. The UV stage provides a UV light which is continuously on when the cooler is plugged in. This option is installed at the factory as an additional stage of the filter system. The UV light bulb must be replaced once per year. The replacement part number is UV-4061.-15-9.0 Trouble Shooting Guide-16-11.0 Specifications Model No.Voltage/Frequency DimensionsWeight (empty)Hot Water Tank CapacityCold Water tank CapacityPower ConsumptionElectric Power Cord Length PWC-400AC110V (L) 16 x (W) 13 x (H) 16 1/242 lb..25 gal.1.0 gal.Hot Water: 500W Cold Water: 100W 6Ft.Conforms to UL STD.399- 17 -LIMITED WARRANTYVertex Water Products (“Manufacturer”) sell its products through independent retailer dealers (“Dealer”) who re-sell to the end-user customer. In this limited warranty, “Vertex” refers to Vertex Water Products and not to the Dealer.WHO IS COVERED BY THIS WARRANTYThis limited warranty covers only the first purchaser of the V ertex PureWaterCooler™ from a Dealer for use by that purchaser, and is not transferrable. “Consumer Use” means personal residential household use by a consumer or consumers. “Commercial Use” means all other uses, including (but not limited to) use for commercial, income producing purposes and/or when purchased by a business and/or when purchased for use in an office, business, or industrial setting. “Purchaser” means the end-user customer, and not a V ertex re-seller Dealer.PERIOD OF COVERAGE OF THIS WARRANTYManufacturer warrants the complete water cooler (“the unit”) against defects in material and workmanship, subject to the exclusions described below, for a period of ONE YEAR, beginning on the later of either (a) the date of purchase or (b) the date of manufacture as identified by the Vertex unit’s serial number. Manufacturer additionally warrants the compressor for a period of THREE YEARS from the above date. The purchaser must provide the original sales receipt as proof of the date of purchase. If the purchaser is unable to produce the original sales receipt, the Warranty Period commencement date will be determined by Manufacturer, in its sole and absolute discretion, based upon the unit’s serial number. This warranty does not apply if the original serial number affixed by Manufacturer is removed, defaced, altered, obscured, tampered with, or obliterated. If Manufacturer provides a replacement part or parts, or repairs a part or parts, under this limited warranty, then the replacement part(s) or repaired part(s) will be covered under this limited warranty for the time remaining under the original Warranty Period applicable to the part(s) repaired or replaced.The duration of ALL OTHER WARRANTIES, INCLUDING ANY AND ALL IMPLIED WARRANTIES, INCLUDING BUT NOT LIMITED TO MERCHANTABILITY AND FITNESS FOR A PARTICULAR PURPOSE, ARE RESTRICTED TO THE TWO-YEAR LIMITED WARRANTY PERIOD. Some states do not allow limitations on how long an implied warranty lasts, so the above limitation may not apply to purchaser.WHAT IS COVERED BY THIS WARRANTYThis limited warranty covers defects in materials or workmanship, subject to the exclusions below and for the time period stated above. Manufacturer promises to repair or to replace, at Manufacturer’s sole and absolute discretion, any part of this water cooler that proves to be inoperative due to a defect in material or workmanship under normal use.WHAT IS NOT COVERED BY THIS WARRANTYThis limited warranty does not extend to and expressly excludes:• conditions, losses, malfunctions, or damages not resulting from defects in material or workmanship; • conditions, malfunctions, losses, or damages or the inability to operate the Vertex unit resulting from conditions beyond Manufacturer’s control, including but not limited to failure of the unit or any of its parts due to damage caused by: improper installation; accident; fire; flood; windstorm; acts of God; rodent and/or insect infestation; vandalism; modification; alteration; combination with any other device or machine; abuse and/or misuse of the unit; negligence by purchaser or third parties; any part of the water system that has become fouled due to liming, dirt, unsatisfactory/unsanitary water conditions, corrosion, or faulty plumbing; failure to install, maintain, assemble, mount or place the Vertex unit in accordance with Manufacturer’s instructions and/or local, state, or national plumbing and electrical codes; wear and tear expected to occur in the normal course of use, including but not limited to cosmetic rust, scratches, dents or comparable and reasonably expected losses or damages; exposure to extreme variations in ambient environmental conditions (including but not limited to changes in heat, humidity, moisture, or exposure to sunlight).• labor for installation or deinstallation of the unit or any of its parts; shipping of the unit or any of its parts to Manufacturer for repair/replacement.In addition to the above exclusions, this limited warranty does not apply if any of the following conditions of operation are not met: System Pressure 35 - 100 psi, Temperature 40 - 100 degrees F, PH range 4 - 10, Max TDS 1500 PPM Max., Turbidity <1.0NTU, Hardness <20gpg, R version: <3.5 gpg, F version, Iron <0.1 mg/l, Manganese <0.1 mg/l, Hydrogen Sulfid e <0.00 mg/l.- 18 -NO OTHER EXPRESS OR IMPLIED WARRANTY APPLIESThis limited warranty is the sole and exclusive warranty provided to the purchaser identified above. No other express warranty, written or verbal, applies. No agent, employee, deal or other person or entityis authorized to alter this limited warranty or make any other warranty on behalf of Manufacturer. The terms of this limited warranty shall not be modified by the Manufacturer, the purchaser/end user, or their respective successors or assigns.WHAT WE WILL DO TO CORRECT PROBLEMS/ HOW TO GET WARRANTY PARTSIf the Vertex unit does not operate in accordance with the documentation provided to purchaser, or purchaser have questions concerning purchaserr Vertex unit, please contact the Dealer from whom the unit was purchased. If the original Dealer is not available or the purchaser does not know who the Dealer is, please call or email the Manufacturer, Vertex, using the contact information provided below. We will try to find a Dealer in purchaserr geographical area to assist purchaser. If a Dealer cannot be conveniently located, the Manufacturer, in its sole and absolute discretion, may offer two (2) options. First, we will attempt to troubleshoot the issue with purchaser over the phone. If the purchaser is comfortable making a repair/ replacing a part, once we understand the problem and its solution, we will send the replacement part(s) for the cooler. This warranty is for the replacement of part(s) ONLY; it does not cover the cost of labor for either the Dealer or the end user/purchaser. The second option is that the end user/purchaser may, after notifying Manufacturer and receiving written authorization/approval from Manufacturer to do so, send the unit back to Manufacturer and we will repair it. The end user purchaser must pay the freight/ shipping costs to return the unit to Manufacturer. Manufacturer will pay the freight/shipping to return the unit to the end user/purchaser following repair.If the end user/purchaser contacts the Dealer and the Dealer repairs the unit pursuant to this limited warranty, Manufacturer will provide parts to the Dealer at no charge; labor is not included in this limited warranty.The Dealer may, in his or her sole and absolute discretion, decide to repair the unit on-site or take the unit to a shop to repair.This limited warranty covers replacement or repair of parts only. Manufacturer will not replace the entire unit if a part can be replaced or repaired to restore the unit to full operational function. On the rare occasion that a unit cannot be restored to full operation by a part or parts, Manufacturer will replace the unit after the end user/purchaser has shipped the unit to Manufacturer and Manufacturer has determined, in its sole and absolute discretion, that the unit cannot be repaired and must be replaced. T he end user/purchaser must pay the freight/shipping costs to return the unit to Manufacturer. Manufacturer will pay the freight/ shipping to return the unit to the end user/purchaser following repair or will ship a new unit if repair is not possible. If Manufacturer does provide a replacement unit, then the Warranty Period (as specified above) for the replacement unit would begin at the time of its delivery to the end user/purchaser.LIMITATION OF LIABILITY AND DISCLAIMER OF WARRANTIESTO THE EXTENT PERMITTED BY LAW, IN NO EVENT SHALL MANUFACTURER BE LIABLE TO PURCHASER OR ANY THRID PARTIES FOR ANY INCIDENTAL, SPECIAL, INDIRECT,OR CONSEQUENTIAL DAMAGES, INCLUDING ANY ECONOMIC LOSS, WHETHER RESULTING FROM NON-PERFORMANCE, USE, MISUSE, OR INABILITY TO USE THE VERTEX UNIT. MANUFACTURER SHALL NOT BE LIABLE FOR DAMAGES CAUSED BY DELAY IN PERFORMANCE AND IN NO EVENT, REGARDLESS OF THE FORM OF THE CLAIM OR CAUSE OF ACTION (WHETHER BASED IN CONTRACT, WARRANTY, TORT, INFRINGEMENT, NEGLIGENCE, STRICT LIABILTY, OTHER TORT OR ANY OTHER LEGAL THEORY) SHALL MANUFACTURER’S ENTIRE LIABILTY EXCEED THE PRICE PAID BY THE ORIGINAL PURCHASER FOR THE VERTEX UNIT. THE TERM “CONSEQUENTIAL DAMAGES” SHALL INCLUDE, BUT NOT BE LIMITED TO, LOSS OF ANTICIPATED PROFITS, BUSINESS INTERRUPTION, LOSS OF USE OR REVENUE, COST OF CAPITAL, OR LOSS OR DAMAGE TO PROPERTY OR EQUIPMENT.Contact information:Vertex Water Products 5138 Brooks Street Montclair, California 91763email:*************************- 19 -。
K3 内联净水器安装指南说明书

Installation of K3 Inlinewater filtersK3 RangeMarch 10, 2021INSTRUCTIONSThere are several types of K3 inline water filters that we produce, they are all the same dimensions so are quite easily interchangeable.Model Description Water Use Capacity Dimensions-mm K3 1 Micron carbon block Cold 9600L 295-92-102 K3P 1 Micron carbon block with scale inhibitor Hot/Cold 9600L 295-92-102 K3G Granulated Activated Carbon Low Pressure 9600L 295-92-102 K3B K3 Filter BracketWe added the K3G filters to our inline range in 2020 to provide filtered water for low pressure water fed machines that are needed occasionally.Installation.1.Turn off the cold-water supply.2.Locate an easily accessible location or section of tubing where you want to install the filter.3.Cut the tubing using a tube cutter – ensure that the edges of the cut tube are clean and freefrom sharp edges or burrs (use steel wool or a file if required on copper tubing). Do not cut tubing on an angle as this may cause the unit to leak during service. See figure 3. Remove protective film from filter & Remove red clip from both ends of filter.4.NOTE: There is a directional flow arrow on the filter. The incoming water should be routedto the inlet and the filtered water should be coming from the outlet or arrowhead end of the flow arrow. Figure 1. There is also a mount bracket available – see K3 Filter Bracket below.K3 Filter Bracket5.Insert the water supply tubing (1/4” plastic) into the end of the filter. Push firmly until thetubing bottoms out. Attach the red safety collet ring (Figure 2).6.Hold the filter over a bucket or other suitable container and Turn on the water supply, flushfilter thoroughly until the water runs clear.7.Turn water off8.Insert outlet tubing (1/4” plastic) into the other end of the filter. Push firmly until the tubingbottoms out, making sure to install the outlet tubing firmly and until it bottoms out in the fitting. Attach the red safety collet ring (Figure 2).9.Turn the water supply back on and check immediately for leaks.Important: The operational, maintenance and replacement requirements must be followed for this unit to perform as sold.Replacement:1.Turn off the cold-water supply.2.Remove the red safety Collet clips from either end of filter.3.Remove the tubing from the ends of the filterSee figure 2 above for using the built in quick connect fittings -14.Trim off a short section(5-10mm) of tubing on both ends using a tube cutterSee figure 3.5.Insert supply tubing (1/4” plastic) into the end of the filter. Push firmly until the tubingbottoms out.6.Turn on the water supply. Hold the filter over a bucket or other suitable container andflush until the water runs clear.7.Turn water off8.Repeat step 5 for the outlet side of the filter, making sure to install the tubing firmly anduntil it bottoms out in the fitting.9.Turn the water supply back on and check immediately for leaks.Install this filter on cold water only. Do not use on water lines exceeding 100°F (38°). Water pressure minimum is 20psi and the Maximum is 125psi. Please note that all pipework should always be fitted with a Pressure Limiting Valve.•Intended for indoor use only.•For extended periods of non-use, turn water off and dispose of filter. Replace with new filter prior to turning back on water supply.•Tubing and hose dimensions are ¼”•Before using the water, flush the new filter for until clear.•Change the cartridge at manufacturers suggested interval or sooner if you notice a change in taste, odor or color of the water or low water pressure.•It is advised that this operation is carried out by an experienced engineer or qualified plumber.•All filters in water coolers should be fitted as in accordance with the recommendations of Watercoolers Europe or The Water Hydration Association (UK) Guidelines. This includesfitting a pressure reducer (PRV) and Water Block, prior to any installation.•Information in this leaflet is for guidance only and H2O Direct take no responsibility for installation. Please consult with professional engineers.Tools & Fittings that may be needed on installation or replacements:•Container for flushing the filters•Filter•¼” Tubing•¼” Isolator•Water Block and Reset Adaptor / Install Rail•PRV (if not using Install Rail)•Tube Cutter•Gloves•K3 BracketApprovals and Certifications.BS 6920-1:2014 CertifiedNSF42 CertifiedMeets and exceeds certification for:EuropeUK Germany Belgium/Holland SpainFrance“EU guidelines for Good Hygienic Practice for Distributors and operators of Plumbed-in POU (Point of Use) Water Coolers issued by Watercoolers Europe, pursuant to Article 9 of Regulation (EC) NO 852/2004 of the European Parliament” section 6.7 The type of water filters installed must be adapted to the local circumstances (e.g. the water quality) and be certified with the minimum NSF Standard 42 Class 1 or any equivalent European Standard.For more information please feel free to contact us:Jim RedfordEmail: ************************.ukMobile : +44(0) 7968894355Office: +44 (0) 1892669628。
墨道克喝水机安装说明书

1. Remove drinking fountain access panel and shut off water supply, thenactuate valve to relieve pressure.ROUGH-IN FOR THE FOLLOWING:2. Drill ½” dia. hole thru drinking fountain deck (where shown). Deburr hole and install grommet provided.Drilling Notes:— Wear approved safety glasses when drilling.— Use a short, sharp high-speed drill bit and drill speed of 400-600 RPM;applying heavy pressure. Drill must cut at all times. DO NOT allow drill bit to ride, this will cause work hardening and will make it very difficult to drill or tap. Bibb washers, placed on drill shank will help to prevent marring the surface after the drill has broke through.— Prior to drilling stainless steel, adhere masking tape over drilling areato protect finish and provide marking surface.8. Align mounting frame and horizontal mounting channels to the anchors (as shown) and attach to wall with mounting fasteners (by others).INSTALLATION INSTRUCTIONS:4. Carefully disassemble bottle filler. Remove the top, frame, horizontal mounting channels, and disconnect the PE tubing from the filler tube. 3. Mark vertical (plumb) center line on the wall, at the center of the drinking cooler deck.5. Use the frame as template, align notches in the frame with the vertical center line, and with the frame sitting on the deck NOTE: FOUNTAIN SHOULD BE LEVEL.6. Mark four mounting holes.7. Install the four wall anchors (by others).To Filler Tube MODELS BF1SC & BF2SCI N S TA L L AT I O N /M A I N T E N A N C E I N S T R U CT I O N S I N S TA L L AT I O N I N S T R U C T I O N S212I N S TA L L AT I O N /M A I N T E N A N C E I N S T R U CT I O N S I N S TA L L AT I O N I N S T R U C T I O N S 7014-441-00111. Reassemble and install top with #8-32 truss head screws provided.10. To reassemble housing to mounting frame assembly, engage the left side of the housing behind the horizontal mountingchannels, then stretch the housing over the right end of the horizontal mounting channels, make sure that the rubber trim on the housing is touching the fountain deck. Secure the housing to the top channel, with #10-32 truss head screws provided.INSTALLATION INSTRUCTIONS Cont’d:9. See below for piping detail.12. Turn on the water supply stop, test unit and check for leaks, then reinstall access panel.1414" TeeNON-REFRIGERATED REFRIGERATED2 of 2RVA 07/07/21。
- 1、下载文档前请自行甄别文档内容的完整性,平台不提供额外的编辑、内容补充、找答案等附加服务。
- 2、"仅部分预览"的文档,不可在线预览部分如存在完整性等问题,可反馈申请退款(可完整预览的文档不适用该条件!)。
- 3、如文档侵犯您的权益,请联系客服反馈,我们会尽快为您处理(人工客服工作时间:9:00-18:30)。
Retract pin before
CAUTION:
fitting to pipe
The water supply to your system must be the cold mains, as hot water will severly
damage your system.
Turn the water on at the mains and open the swan neck tap.
Filter Replacement Filters should be replaced every 6000 litres or 6 months. To replace filter, turn off water at mains and self-piercing valve. Open Swan Neck Tap to release water pressure. Carefully release housings with ring spanner supplied. Replace filter and ensure large “O” ring in top of housing is seated evenly before re assembling the housing to the unit. Finally tighten with to the self-cutting valve using the internal ferrule, olive & nut supplied.
Ensure the piercing pin is fully retracted in the Quick Fit Self Piercing Valve.
All of the air is expelled and the water will begin to flow.
You should allow the water to flow for approximately 10 minutes to remove any debris in the system.
Select a suitable place to mount your swan neck tap either through the top
of the sink or mounted onto a work surface, ensuring that the tap can
discharge fully into your sink without flooding any work surfaces.
Fixing bracket
1/2
Cold water supply
Filter housing head
Filter housing body
Self piercing value unit
Internal ferrule
Olive Nut
Cabinet side wall
40mm min clearance
WARNING: When assembling these units if any leaks occur turn water off. Tighten any seeping joints and then turn water back on. Mains water pressure can vary, therefore it is essential to check for leaks daily during first week and periodically there after.
Clamp the valve to the 15mm cold mains and run the 1/4” plastic pipe to the port
on the filter housing marked “IN”. Pierce the pipe by turning the ‘T’ bar fully in, and then fully out.
NW2915
Then drill a 1/2” hole and mount the tap using the fittings supplied, make sure the tap is secure &
rigid.
Connect the 1/4” pipe using the internal ferrule, olive & nut supplied to the tap and tighten. Connect the other end of the loose pipe to the port on the filter housing marked “OUT”.
Installation Instructions
Product Code: NW 4310
One Stage, Point of Use, Dual Acting Water Filtration System
This water filtration system will remove chlorine, odours, bad tastes, sediment and provides great tasting water. The system can be easily installed beneath the kitchen sink. Replace filter every 6000 litres or 6 months.
Clamping screw
Parts List 1 x Swan Neck with ceramic ¼ turn valve 1 x 10” Filter Housing 1 x Dual Action Sediment/Chlorine Filter. Product Code NW 2915 (single sealing ring on blue top) 1 x Quick fit self cutting valve 1 x Wall mounting bracket with screws 1 x key / wrench 2 metres ¼” plastic connecting tube Installation Instructions
Issue 2005/9
2/2
Important
Remove the outer wrapping from the filter taking care not to lose the fitted sealing ring.
Check that the large “o” ring is seated evenly in the top of the filter housing.
Installation Instructions
single stage, point of use, dual acting water filtration system
Select a suitable place to mount your system. Ensure that there is at least 40mm clear space between filter housing body and any fixture below to allow filter changing. Using screws supplied fix the housing head to bracket. Then mount the bracket into position.
Place filter into housing and screw onto filter housing head. (See Filter Replacement
for filter orientation)
Turn the water off.
Replace filter
this way up
Tap Unit Fitting
Instalation Schematic
TAP
WORKTOP
SINK
Nut
Top plate
Small rubber washer Large rubber seal
Black plastic washer Star washer Locking nut Internal Ferrule Olive
If for any reason you experience a problem with this system. Please call NOGA WATERCARE TECHNICAL HELP LINE. On 0208 400 2020 Mon-Fri 9-5pm
© Copyright LinearTools Ltd 2005