14机械加工工艺规程设计2ccx
机械加工工艺规程
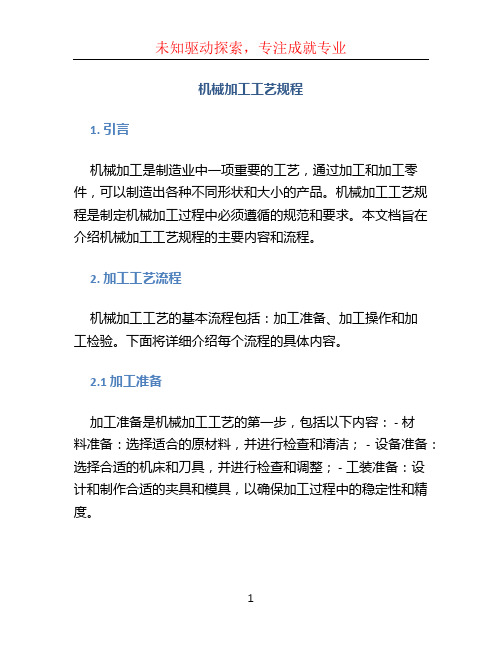
机械加工工艺规程1. 引言机械加工是制造业中一项重要的工艺,通过加工和加工零件,可以制造出各种不同形状和大小的产品。
机械加工工艺规程是制定机械加工过程中必须遵循的规范和要求。
本文档旨在介绍机械加工工艺规程的主要内容和流程。
2. 加工工艺流程机械加工工艺的基本流程包括:加工准备、加工操作和加工检验。
下面将详细介绍每个流程的具体内容。
2.1 加工准备加工准备是机械加工工艺的第一步,包括以下内容: - 材料准备:选择适合的原材料,并进行检查和清洁; - 设备准备:选择合适的机床和刀具,并进行检查和调整; - 工装准备:设计和制作合适的夹具和模具,以确保加工过程中的稳定性和精度。
2.2 加工操作加工操作是机械加工工艺的核心步骤,包括以下内容: -加工方案确定:根据零件的要求和材料的特性,确定合适的加工方案,包括切削速度、进给速度和切削深度等; - 加工工序选择:根据零件的形状和要求,选择合适的加工工序,包括车削、铣削、钻削等; - 加工操作执行:根据加工方案和加工工序,进行具体的加工操作,包括上下刀具、进给和主轴转速的控制等。
2.3 加工检验加工检验是机械加工工艺的最后一步,用于检查加工结果的质量和精度,包括以下内容: - 尺寸检测:使用合适的测量工具和设备,检测加工后零件的尺寸和几何形状; - 表面质量检查:使用合适的表面检测设备,检查加工后零件的表面平整度和光洁度; - 功能检测:根据零件的要求,进行功能性测试,确保零件能够正常工作。
3. 常用加工工艺机械加工工艺的选择取决于零件的形状、材料和要求。
以下是常用的机械加工工艺之一:3.1 车削车削是通过旋转工件和固定刀具相对运动,将工件的一部分材料切削掉,从而得到所需的形状和尺寸。
车削常用于制造圆柱形零件,如轴、套筒等。
3.2 铣削铣削是通过旋转刀具和固定工件相对运动,将工件的一部分材料切削掉,从而得到所需的形状和表面质量。
铣削常用于制造平面和曲面零件,如平面、凸台等。
机械加工工艺规程设计课件

机械加工工艺规程设计课件1. 引言机械加工工艺规程是指在机械加工过程中的一系列操作步骤和要求的规范性文件。
它包含了加工工序的选择、设备的使用、工艺参数的确定、工装夹具的设计等内容,是保证产品质量和生产效率的重要因素。
本课件将介绍机械加工工艺规程设计的基本概念、步骤和设计要点,帮助学习者掌握机械加工工艺规程设计的方法和技巧。
2. 机械加工工艺规程设计的基本概念2.1 机械加工工艺规程的定义机械加工工艺规程是指在机械加工过程中,根据产品的设计要求和加工设备的特点,制定出一系列的操作步骤和要求的规范性文件。
它规定了加工工序、设备使用、工艺参数、工装夹具等内容,用于保证产品的质量和生产效率。
2.2 机械加工工艺规程设计的意义机械加工工艺规程设计是机械加工的关键环节之一,它直接影响到产品的质量和生产效率。
正确设计的机械加工工艺规程能够确保产品的尺寸精度、表面质量和装配性能满足设计要求,同时减少加工时间和成本。
2.3 机械加工工艺规程设计的步骤机械加工工艺规程设计包括以下几个步骤: 1. 分析产品设计要求和加工工艺特点,确定加工工序和加工顺序。
2. 确定加工设备和工具的选择,包括机床、刀具、夹具等。
3. 确定工艺参数,包括切削速度、切削深度、进给速度等。
4. 设计工装夹具,确保工件在加工过程中的固定和定位。
5. 确定检验工具和检验方法,用于检测产品的质量和尺寸精度。
6. 编制加工工艺文件和工艺卡,用于指导实际生产操作。
3. 机械加工工艺规程设计的要点3.1 加工顺序的确定在机械加工工艺规程设计中,确定加工顺序是非常重要的。
加工顺序应该从易到难,从粗加工到精加工,以确保加工过程的顺利进行。
同时,还需要考虑到夹持刀具的方便性和工装夹具的设计。
3.2 加工设备和工具的选择加工设备和工具的选择直接影响加工效果和成本。
在机械加工工艺规程设计中,需要根据产品的尺寸、形状和材料特性来选择合适的机床、刀具和夹具。
同时,还需要考虑加工设备的可用性和性能,以及工具的耐用性和切削性能。
机械加工工艺规程设计大纲
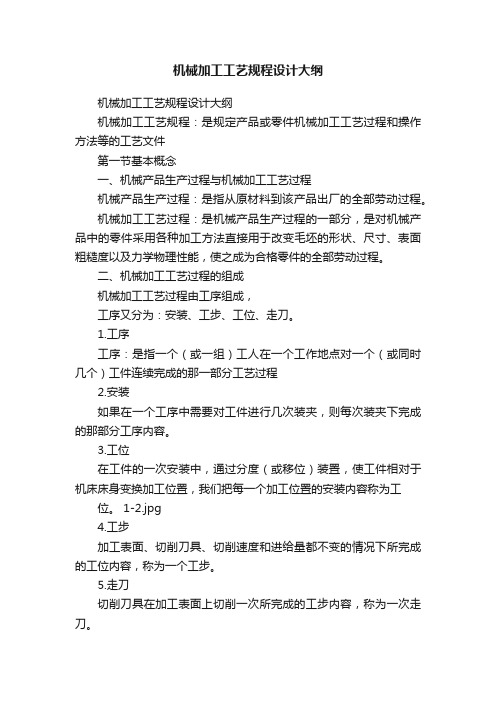
机械加工工艺规程设计大纲机械加工工艺规程设计大纲机械加工工艺规程:是规定产品或零件机械加工工艺过程和操作方法等的工艺文件第一节基本概念一、机械产品生产过程与机械加工工艺过程机械产品生产过程:是指从原材料到该产品出厂的全部劳动过程。
机械加工工艺过程:是机械产品生产过程的一部分,是对机械产品中的零件采用各种加工方法直接用于改变毛坯的形状、尺寸、表面粗糙度以及力学物理性能,使之成为合格零件的全部劳动过程。
二、机械加工工艺过程的组成机械加工工艺过程由工序组成,工序又分为:安装、工步、工位、走刀。
1.工序工序:是指一个(或一组)工人在一个工作地点对一个(或同时几个)工件连续完成的那一部分工艺过程2.安装如果在一个工序中需要对工件进行几次装夹,则每次装夹下完成的那部分工序内容。
3.工位在工件的一次安装中,通过分度(或移位)装置,使工件相对于机床床身变换加工位置,我们把每一个加工位置的安装内容称为工位。
1-2.jpg4.工步加工表面、切削刀具、切削速度和进给量都不变的情况下所完成的工位内容,称为一个工步。
5.走刀切削刀具在加工表面上切削一次所完成的工步内容,称为一次走刀。
三、生产类型与机械加工工艺规程用工艺文件规定的机械加工工艺过程,称为机械加工工艺规程。
(一)年生产纲领和生产批量企业根据市场需求和自身的生产能力决定生产计划。
生产纲领:在计划期内,应当生产的产品产量和进度计划。
年生产纲领:计划期为一年的生产纲领。
N=Qn(1+ %+ %) 件/年生产批量:是指一次投入或产出的同一产品(或零件)的数量。
(二)生产类型根据工厂(或车间、工段、班组、工作地)生产专业化程度的不同,可将生产类型分为:大量生产,成批生产和单件生产。
(三)机械加工工艺规程的作用(四)机械加工工艺规程的格式通常,机械加工工艺规程被填写成表格(卡片)的形式。
在我国各厂使用的表格的形式不尽一致,但是其基本内容是相同的。
四、机械加工工艺规程的设计原则、步骤和内容(一)机械加工工艺规程的设计原则设计机械加工工艺规程应遵循如下原则:1)必须可靠地保证零件图纸上所有的技术要求的实现。
14 机械加工工艺规程
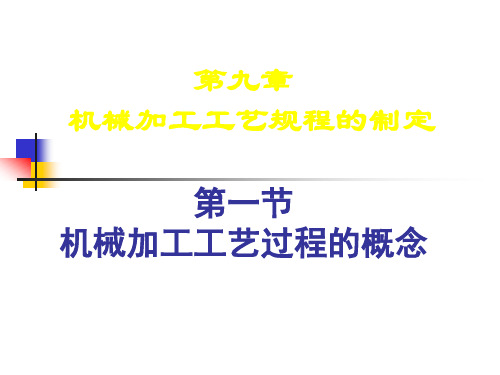
2.粗基准的选择
1) 若工件必须首先保证某重要表面的加工 余量均匀,则应选择该表面为粗基准。
图7-11 床身加工粗基准的两种方案比较
2.粗基准的选择
2) 在没有要求保证重要表面加工余量均 匀的情况下,若零件的所有表面都要加工, 则应以加工余量最小的表面作为粗基准。
图7-12 阶梯轴粗基准的选择
2.粗基准的选择
文件,称工艺规程。其中规定零件机械加工工艺过 程和操作方法等的工艺文件称为机械加工工艺规程。
四、机械加工工艺规程
1. 机械加工工艺规程的作用
(1) 机械加工工艺规程是机械加工工艺过 程的主要技术文件,是指挥现场生产的依据。
(2)机械加工工艺规程是新产品投产前, 进行有关的技术准备和生产准备的依据。
4.所选加工方法要与企业的生产类 型相适应 ;
5.加工方法要与工厂现有生产条件 相适应
三、加工阶段的划分
1.粗加工阶段 2.半精加工阶段 3.精加工阶段 4.光整加工阶段
3.确定毛坯
确定的毛坯是否合适,对零件的质量、材料消 耗、加工工时都有很大的影响。显然,毛坯的尺寸 和形状越接近成品零件,机械加工的工作量就越少, 但是毛坯的制造成本就越高。所以,应根据生产纲 领,综合考虑毛坯制造和机械加工的费用,合理地 确定毛坯,以求得最好的经济效益
1)毛坯的制造类型;
2)毛坯的制造精度;
P153 表5-3 (内孔加工) P77 表3-1 (外圆加工)
P116 图4-4 (平面加工)
二、加工方法的选择
2.所选加工方法要能保证加工表面
的几何形状精度和表面相互位置精度要 求。见P311 表9-8 表9-9 表9-1
3.所选加工方法要与零件的结构、 加工表面的特点和材料等因素相适应
机械加工工艺规程设计

机械加工工艺规程设计1. 引言机械加工工艺规程是指在特定的工艺条件下,完成机械零部件加工任务的一系列工艺过程和要求的技术文件。
机械加工工艺规程设计是指根据零部件的材料、结构和加工要求,确定合理的加工工艺,编制相应的操作工艺文件,以保证零部件的加工质量和效率。
本文将介绍机械加工工艺规程设计的主要内容和步骤。
2. 设计流程机械加工工艺规程设计的流程一般包括以下几个步骤:(1)零部件分析在设计工艺规程之前,首先需要对要加工的零部件进行全面的分析。
这包括对零部件的材料、尺寸、形状和加工要求等进行仔细研究和了解。
通过对零部件的分析,可以确定出合理的加工方法和工艺路线。
(2)加工工艺选择在零部件的分析基础上,选择合适的加工工艺是至关重要的。
根据零部件的特点和加工要求,考虑到加工质量、效率和成本等因素,确定出最佳的加工工艺。
常用的机械加工工艺包括车削、铣削、钻孔、切割、抛光等。
(3)工艺参数确定在确定了加工工艺之后,需要进一步确定具体的工艺参数,以保证零部件的加工质量和工艺效果。
这包括加工切削速度、进给速度、切削深度、切削用液和刀具的选择等。
根据不同的材料和加工情况,需要进行试验和实际加工来确定最佳的工艺参数。
(4)工艺文件编制根据上述的分析和确定,编制相应的工艺文件是必不可少的。
工艺文件包括工艺路线、加工工序、工艺参数、工装夹具和工艺设备等。
工艺文件的编制需要准确详细,以便操作人员按照文件要求进行操作和监控。
(5)工艺评定和改进在实际加工过程中,需要对工艺进行评定和改进。
通过对加工质量、效率和成本等方面的评估,发现问题并及时进行调整和改进。
这包括对工艺文件的修订和优化,以提高加工质量和效率。
3. 工艺规程设计的要求机械加工工艺规程设计需要满足以下几个要求:(1)合理性加工工艺规程需要在保证加工质量的前提下,尽量减少加工成本和时间。
设计工艺时,需要考虑到工艺的可行性、经济性和适用性等因素,以保证加工的效果和效率。
机械加工工艺规程设计

机械加工工艺规程设计机械加工工艺规程是保证加工质量、提高生产效率的重要文件。
下面就机械加工工艺规程的设计进行详细介绍。
一、规程的编制制定机械加工工艺规程时,应根据产品性质、要求和加工设备现状等因素考虑,并严格按照国家相关标准和规范进行编制。
规程的编制应当包括以下内容:1.加工设备的选型和安装要求;2.工序的排列和加工方法;3.加工刀具的选择和使用要求;4.加工质量的标准和检验方法;5.加工过程中的安全措施;6.加工过程中模板和资料的保管;7.加工过程中的质量控制等方面。
二、规程的执行规程的执行是保证加工质量和生产效率的重要保障。
为了使规程得到有效执行,应当注意以下几点:1.严格执行规程,严格按照规程要求选用设备、工具和材料;2.严格执行工艺流程和加工标准,确保加工质量达到要求;3.严格执行安全防护措施,确保操作人员的人身安全;4.加强管理,保证各个环节的质量得到有效控制。
三、规程的更新在生产过程中,根据设备改进和新技术的应用,加工工艺规程也需要不断更新。
规程的更新应当按照以下步骤进行:1.搜集信息,了解新设备和新技术的应用情况;2.评估新设备和新技术的应用效果,是否能够提高生产效率和加工质量;3.更新规程,根据新设备和新技术的应用情况,重新编制规程,确保规程能够适应新的生产需求。
四、规程的评估为了保证规程的有效性和实用性,应当对规程进行定期评估。
评估的内容包括:1.规程执行情况的检查,了解规程的有效性;2.加工效率和质量的检测,根据规程要求进行比较;3.对规程进行修改和完善,确保规程的科学性和可操作性。
总之,机械加工工艺规程的设计和执行是机械加工过程中至关重要的环节。
只有科学合理地编制工艺规程,并严格按照规程要求进行操作,才能保证加工质量和生产效率。
机械加工工艺规程设计

机械加工工艺规程设计本规程适用于机械加工工艺的设计和操作。
其目的是为了保证加工过程的质量,提高生产效率,降低生产成本。
2. 适用范围本规程适用于金属、塑料等材料的机械加工过程。
3. 设计要求3.1 确定加工材料的种类、规格和数量。
3.2 按照零件图纸和工艺要求,确定加工工艺路线和工序。
3.3 确定加工设备、刀具、量具和夹具的选用及加工工艺参数。
3.4 设计并编制加工工艺图纸和工艺文件。
4. 工艺操作4.1 准备工作:清洁加工设备、检查刀具、量具和夹具的状况。
4.2 装夹工件:根据加工图纸和工艺文件要求,正确安装工件到加工设备上。
4.3 调试设备:进行设备的调试,确保设备运转正常。
4.4 加工操作:按照工艺文件要求进行加工操作,保证加工质量。
4.5 定期检查:对加工设备和加工质量进行定期检查,及时调整和改进加工工艺。
5. 质量控制5.1 加工过程中,严格执行工艺文件要求。
5.2 定期对加工零件进行抽样检验,确保产品质量符合标准要求。
5.3 对加工设备进行定期维护和保养,确保设备正常运转,避免出现质量问题。
5.4 对加工工艺进行评估和改进,提高生产效率和产品质量。
6. 安全生产6.1 加工人员必须严格遵守操作规程,做好个人防护工作。
6.2 对加工设备进行定期检查,确保设备安全可靠。
6.3 对加工环境进行安全检查,保证生产过程安全无隐患。
7. 文档管理工艺文件必须完整、准确、清晰,确保加工操作得以正确进行。
实施过程中发现不合适或需要改进的地方,应及时修改工艺文件,并通知相关人员。
8. 培训针对新员工和新设备,必须进行相关的培训工作,使其能够熟悉并掌握加工工艺的操作规程。
9. 结论本规程的实施将有助于规范机械加工工艺的操作流程,提高产品质量,降低生产成本,增强企业竞争力。
10. 审核和改进为确保机械加工工艺规程的有效性和实用性,需要定期进行审核和改进。
可以安排专门的质量管理团队负责对工艺规程进行审查,包括对操作流程、质量控制要求、安全生产要求等方面进行评估。
机械加工工艺规程设计的内容及步骤
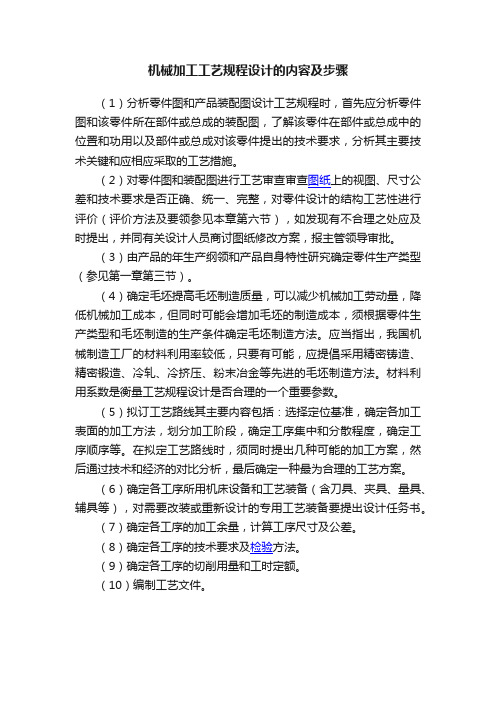
机械加工工艺规程设计的内容及步骤(1)分析零件图和产品装配图设计工艺规程时,首先应分析零件图和该零件所在部件或总成的装配图,了解该零件在部件或总成中的位置和功用以及部件或总成对该零件提出的技术要求,分析其主要技术关键和应相应采取的工艺措施。
(2)对零件图和装配图进行工艺审查审查图纸上的视图、尺寸公差和技术要求是否正确、统一、完整,对零件设计的结构工艺性进行评价(评价方法及要领参见本章第六节),如发现有不合理之处应及时提出,并同有关设计人员商讨图纸修改方案,报主管领导审批。
(3)由产品的年生产纲领和产品自身特性研究确定零件生产类型(参见第一章第三节)。
(4)确定毛坯提高毛坯制造质量,可以减少机械加工劳动量,降低机械加工成本,但同时可能会增加毛坯的制造成本,须根据零件生产类型和毛坯制造的生产条件确定毛坯制造方法。
应当指出,我国机械制造工厂的材料利用率较低,只要有可能,应提倡采用精密铸造、精密锻造、冷轧、冷挤压、粉末冶金等先进的毛坯制造方法。
材料利用系数是衡量工艺规程设计是否合理的一个重要参数。
(5)拟订工艺路线其主要内容包括:选择定位基准,确定各加工表面的加工方法,划分加工阶段,确定工序集中和分散程度,确定工序顺序等。
在拟定工艺路线时,须同时提出几种可能的加工方案,然后通过技术和经济的对比分析,最后确定一种最为合理的工艺方案。
(6)确定各工序所用机床设备和工艺装备(含刀具、夹具、量具、辅具等),对需要改装或重新设计的专用工艺装备要提出设计任务书。
(7)确定各工序的加工余量,计算工序尺寸及公差。
(8)确定各工序的技术要求及检验方法。
(9)确定各工序的切削用量和工时定额。
(10)编制工艺文件。
二、工艺路线的拟订拟订工艺路线是设计工艺规程最为关键的一步,需顺序完成以下几个方面的工作。
(一)选择定位基准在工艺规程设计中,正确选择定位基准,对保证零件技术要求、确定加工先后顺序有着至关重要的影响。
定位基准有精基准与粗基准之分。
机械加工工艺规程设计
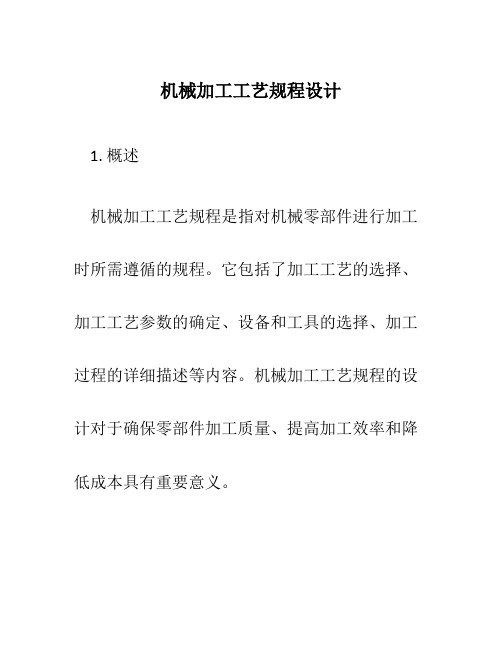
机械加工工艺规程设计1. 概述机械加工工艺规程是指对机械零部件进行加工时所需遵循的规程。
它包括了加工工艺的选择、加工工艺参数的确定、设备和工具的选择、加工过程的详细描述等内容。
机械加工工艺规程的设计对于确保零部件加工质量、提高加工效率和降低成本具有重要意义。
2. 加工工艺选择在进行机械加工工艺规程设计之前,首先需要进行加工工艺选择。
加工工艺选择是根据零部件的材料、形状、尺寸和要求等因素确定的,其目的是选择出能满足零部件要求的最佳加工工艺。
在进行加工工艺选择时,需要综合考虑以下因素:•零部件的材料属性,包括硬度、强度、耐磨性等。
•零部件的形状和尺寸要求,包括平面度、圆度、直线度等。
•零部件的表面质量要求,包括光洁度、粗糙度等。
•加工工艺的可靠性和稳定性。
•加工工艺的经济性和效率。
3. 加工工艺参数确定在确定了加工工艺之后,接下来需要确定具体的加工工艺参数。
加工工艺参数是指在进行机械加工时,控制加工过程中各种参数的数值。
合理的加工工艺参数能够保证零部件的加工质量,提高加工效率。
常见的加工工艺参数包括:•速度:主要指切削速度和进给速度。
切削速度是切削刀具与工件接触时的相对速度,进给速度是工件在切削过程中移动的速度。
•切深:指刀具每次进给时在工件上所切下的厚度。
•切削液的使用:切削液可以降低切削温度,减少摩擦,延长刀具寿命。
•切削刃数:切削刃数多少可以影响加工效率和加工质量。
•夹紧力:指夹持零部件的夹紧力大小,需要根据零部件的材料和形状进行合理调整。
4. 设备和工具选择进行机械加工时,需要选择合适的设备和工具。
设备和工具的选择直接影响到加工工艺的实施效果和加工质量。
在选择设备和工具时,需要考虑以下因素:•设备的精度和稳定性,以确保能够满足零部件的加工要求。
•设备的加工能力和加工范围,以确保能够满足零部件的材料和尺寸要求。
•工具的材料和硬度,以确保能够满足零部件的切削要求。
•工具的耐磨性和寿命,以提高加工效率和降低成本。
机械加工工艺规程
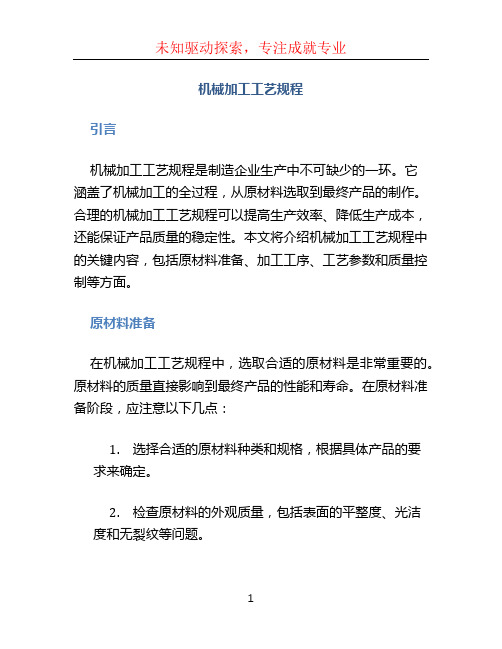
机械加工工艺规程引言机械加工工艺规程是制造企业生产中不可缺少的一环。
它涵盖了机械加工的全过程,从原材料选取到最终产品的制作。
合理的机械加工工艺规程可以提高生产效率、降低生产成本,还能保证产品质量的稳定性。
本文将介绍机械加工工艺规程中的关键内容,包括原材料准备、加工工序、工艺参数和质量控制等方面。
原材料准备在机械加工工艺规程中,选取合适的原材料是非常重要的。
原材料的质量直接影响到最终产品的性能和寿命。
在原材料准备阶段,应注意以下几点:1.选择合适的原材料种类和规格,根据具体产品的要求来确定。
2.检查原材料的外观质量,包括表面的平整度、光洁度和无裂纹等问题。
3.检查原材料的化学成分和机械性能,确保符合相关标准要求。
4.对于特殊材料,如不锈钢和铝合金等,还需进行材料的腐蚀性测试以及硬度测试等。
加工工序机械加工的过程一般包括以下几个工序:车削、铣削、钻削、刨削、磨削、螺纹加工等。
每个工序都有不同的工艺要求和特点,需要根据具体产品的要求来选择适合的加工工序。
以下是常见的加工工序的要点:车削车削是利用车床进行加工,将工件固定在主轴上,然后由刀具旋转切削工件。
车削过程中应注意以下几点:1.工件夹紧要稳定可靠,以防止加工过程中发生错位。
2.刀具选择合适的刀具材料和刀具形状,以达到预期的加工效果。
3.控制刀具的进给速度和切削深度,以适应不同材料的加工需求。
4.注意冷却液的选择和使用,以避免加工过程中产生过多的热量。
铣削铣削是利用铣床进行加工,通过刀具旋转和工件在进给运动下相对运动来实现切削加工。
铣削过程中应注意以下几点:1.工件夹紧要牢固可靠,以避免加工过程中的晃动和错位。
2.刀具选择合适的铣刀和刀具材料,以满足不同材料和加工需要。
3.确定铣削的进给速度和切削深度,以达到预期的加工效果。
4.控制冷却液的使用,以避免过热和损坏刀具。
钻削钻削是利用钻床进行加工,通过刀具对工件进行旋转切削加工。
钻削过程中应注意以下几点:1.工件夹紧要稳定可靠,以防止加工过程中发生错位。
机械加工工艺规程 (2)

机械加工工艺规程
机械加工工艺规程是指在机械加工过程中,根据产品工艺
要求和加工技术条件,制定的一系列技术规范和工艺流程。
它包括了加工工艺的选定、排料方案、加工顺序、工序参数、工装夹具设计、质量控制要求等。
机械加工工艺规程的编制过程包括以下几个步骤:
1. 产品分析与工艺评审:对产品进行全面分析,了解产品
的结构特点、工艺要求和加工难点,并进行工艺评审,确
定加工工艺的可行性。
2. 工艺方案设计:根据产品的结构特点和工艺要求,确定
加工工艺的方案,包括加工方法、工序顺序、加工工艺参
数等。
3. 工艺路线制定:按照工序的先后顺序,确定整个加工过
程的工序路线,并绘制工艺路线图。
4. 工装夹具设计:根据加工工序和产品结构要求,设计相应的工装夹具,确保产品加工的精度和质量。
5. 工序参数设定:根据工艺方案和产品要求,确定各个工序的加工参数,包括进给速度、切削速度、切削深度等。
6. 质量控制要求确定:制定相应的质量控制计划,包括加工过程中的自检、互检、专检要求,以及对最终产品的质量检验标准。
7. 编写工艺文件:将上述内容整理成工艺文件,包括工艺路线图、加工工艺参数表、工装夹具设计图纸等。
机械加工工艺规程的编制是保证产品加工质量和工艺可靠性的关键环节,它对于提高生产效率和产品质量具有重要意义。
机械加工工艺规程设计
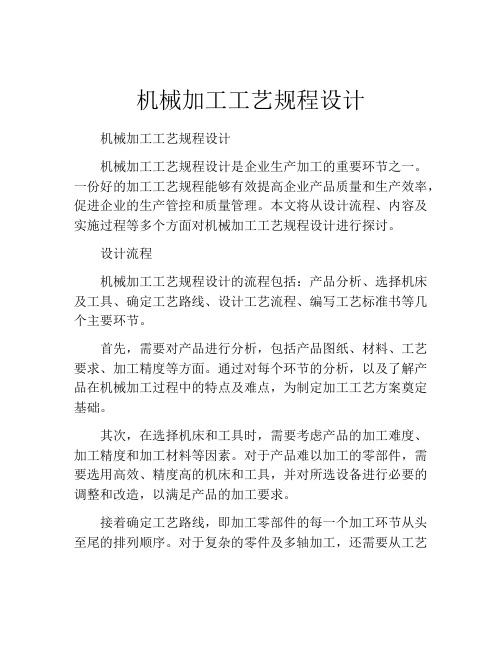
机械加工工艺规程设计机械加工工艺规程设计机械加工工艺规程设计是企业生产加工的重要环节之一。
一份好的加工工艺规程能够有效提高企业产品质量和生产效率,促进企业的生产管控和质量管理。
本文将从设计流程、内容及实施过程等多个方面对机械加工工艺规程设计进行探讨。
设计流程机械加工工艺规程设计的流程包括:产品分析、选择机床及工具、确定工艺路线、设计工艺流程、编写工艺标准书等几个主要环节。
首先,需要对产品进行分析,包括产品图纸、材料、工艺要求、加工精度等方面。
通过对每个环节的分析,以及了解产品在机械加工过程中的特点及难点,为制定加工工艺方案奠定基础。
其次,在选择机床和工具时,需要考虑产品的加工难度、加工精度和加工材料等因素。
对于产品难以加工的零部件,需要选用高效、精度高的机床和工具,并对所选设备进行必要的调整和改造,以满足产品的加工要求。
接着确定工艺路线,即加工零部件的每一个加工环节从头至尾的排列顺序。
对于复杂的零件及多轴加工,还需要从工艺上进行分析和确定合理的加工方案,并根据实际操作中的难点和风险,确定样本加工的步骤并验证。
在设计工艺流程时,需要将加工零件的每个工序步骤详细列出,并规定好工艺参数、机床设备、刀具种类、加工精度要求等,确保生产过程中的标准化和规范化。
最后,编写工艺标准书,包括步骤和参数、工具夹持方式、机床的操作指南、工序检验标准等内容。
通过编写工艺标准书,确保加工过程的标准化和工序符合要求。
内容要点机械加工工艺规程设计需包含以下几个方面的内容:1、产品零部件的加工工艺方案,包括加工路线、机床选择、刀具、夹具、工艺控制等。
工艺方案应考虑到生产的实际情况,确定好各加工工序的先后顺序,确保加工的高效性和质量。
2、各个加工工序的工艺参数详细规定,包括每个工序中所需的工具、加工精度、表面质量要求等。
这些参数是确保生产加工的精度和品质的重要基础。
3、机床和设备的选择,考虑到产品的加工难度、加工精度和加工材料等因素,选用合适的机床进行加工。
机械加工工艺规程设计

机械加工工艺规程设计一、引言机械加工是制造业中的重要生产环节,工艺规程设计对于确保产品质量、提高生产效率具有至关重要的作用。
本文将探讨机械加工工艺规程设计的基本原则、步骤和方法。
二、工艺规程设计的基本原则1.精确性:工艺规程应确保产品能够按照设计要求制造。
2.经济性:工艺规程应尽可能减少生产成本,提高资源利用率。
3.安全性:工艺规程应保证生产过程的安全,减少事故发生的可能性。
4.可靠性:工艺规程设计应考虑设备和材料的可靠性,避免因工艺问题导致产品质量不稳定。
三、工艺规程设计步骤1.产品分析:了解产品的设计要求和特性,确定加工所需的工艺过程。
2.工艺路线设计:根据产品要求和生产设备,确定加工工序和顺序。
3.工艺参数确定:确定加工过程中的各项参数,如切削速度、进给速度等。
4.工艺检验:通过样件或小批量试验验证工艺参数的正确性和合理性。
5.工艺文件编制:撰写完整的工艺文件,包括加工程序、工艺卡等。
四、工艺规程设计方法1.模块化设计:将工艺过程分解成多个模块,便于管理和修改。
2.先进技术应用:引入先进的加工技术和设备,提高生产效率和产品质量。
3.优化设计:通过工艺参数优化和生产流程优化,提高生产效率和降低生产成本。
4.定期评估:定期对工艺规程进行评估,发现问题及时调整和改进。
五、总结机械加工工艺规程设计是确保产品质量和生产效率的关键环节。
设计规程时应遵循精确、经济、安全和可靠的原则,通过产品分析、工艺路线设计、工艺参数确定、工艺检验和工艺文件编制等步骤,制定出科学合理的工艺规程。
在设计过程中,应采用模块化设计、先进技术应用、优化设计和定期评估等方法,不断提高生产水平和产品质量。
本文对机械加工工艺规程设计进行了简要介绍,希望能为相关人员提供参考和指导,促进工艺规程设计水平的提升和工业生产的发展。
- 1、下载文档前请自行甄别文档内容的完整性,平台不提供额外的编辑、内容补充、找答案等附加服务。
- 2、"仅部分预览"的文档,不可在线预览部分如存在完整性等问题,可反馈申请退款(可完整预览的文档不适用该条件!)。
- 3、如文档侵犯您的权益,请联系客服反馈,我们会尽快为您处理(人工客服工作时间:9:00-18:30)。
1、尺寸链的定义 、
尺寸链:尺寸链就是在零件加工或机器装配过程中, 尺寸链:尺寸链就是在零件加工或机器装配过程中,由相互
联系且按一定顺序首尾相接的封闭尺寸组合。 联系且按一定顺序首尾相接的封闭尺寸组合。 它是揭示零件加工和装配过程中尺寸内在联系的重要手段。 它是揭示零件加工和装配过程中尺寸内在联系的重要手段。 根据用途不同分为工艺尺寸链和 根据用途不同分为工艺尺寸链和装配尺寸链 工艺尺寸链 工艺尺寸链: 工艺尺寸链:是由单个零件在工艺过程中的有关尺寸形成的尺 寸链; 寸链; 装配尺寸链: 装配尺寸链:指机器在装配过程中由相关零件的尺寸或相互位 置关系所组成的尺寸链
Ф100 +0.035 0 Ф99.9 +0.045 0 Ф99.4 +0.14 0 Ф97 +0.35 0 Ф92 -+1 2
2)工艺基准与设计基准不重合 )
必须通过工艺尺寸的计算才能得到, 必须通过工艺尺寸的计算才能得到, 设计基准
+ δA2
A2
A1
+ δA1
A3 −δ
定位基准
第六节 工艺尺寸链
同一表面经多次加工达到图纸尺寸要求, 同一表面经多次加工达到图纸尺寸要求 , 其 中间工序尺寸根据零件图尺寸加上或减去工序余 量即可得到,即从最后一道工序向前推算, 量即可得到,即从最后一道工序向前推算,得出 相应的工序尺寸,一直推算到毛坯尺寸。 相应的工序尺寸,一直推算到毛坯尺寸。
计算工序间尺寸、确定其上下偏差的步骤: 计算工序间尺寸、确定其上下偏差的步骤:
在尺寸链图中用首尾相接的单向 箭头顺序表示各尺寸环,其中与 封闭环箭头方向相反者为增环, 与封闭环箭头方向相同者为减环。
增环
A1 A0 A2 A3
举例: 举例:
封闭环
减环
尺寸链的建立
1、加工顺序或装配顺序 确定后才能确定封闭环。 2、封闭环的基本属性为“ 派生”,表现为尺寸间接 获得。 1、设计尺寸往往是封闭 环。 2、加工余量往往是封闭 环(靠火花磨除外)。 1、封闭环确定后才能确定 2、直接获得。 3、对封闭环有影响
孔:Zi = Di – Di–1
由于各工序尺寸都有公差, 由于各工序尺寸都有公差,故实际切除的余量也有一定的 公差范围, 公差范围,其公差大小等于本道工序尺寸公差与上道工序尺寸 公差之和。 公差之和。
Tz = Zmax–Zmin = Tb + Ta
一般情况下,工序尺寸公差按“入体原则”标注。 一般情况下,工序尺寸公差按“入体原则”标注。即对于 被包容尺寸(轴的外径,实体长、 ),其最大的工序尺 被包容尺寸(轴的外径,实体长、宽、高),其最大的工序尺 寸就是基本尺寸(上偏差为零);对于包容尺寸(孔的直径、 );对于包容尺寸 寸就是基本尺寸(上偏差为零);对于包容尺寸(孔的直径、 槽的宽度),其最小工序尺寸就是基本尺寸(下偏差为零)。 ),其最小工序尺寸就是基本尺寸 槽的宽度),其最小工序尺寸就是基本尺寸(下偏差为零)。 毛坯尺寸公差按双向对称偏差形式标注。 毛坯尺寸公差按双向对称偏差形式标注。
(1)、确定各加工工序的加工余量。(一般查 、确定各加工工序的加工余量。 一般查 表法) 表法 (2)、从最终加工工序开始,即从设计尺寸 、从最终加工工序开始, 开始,到第一道加工工序, 开始 , 到第一道加工工序 , 逐次考虑每道 工序的加工余量, 工序的加工余量 , 以得到各工序的基本尺 包括毛坯尺寸): 寸(包括毛坯尺寸 : 包括毛坯尺寸 前道工序基本尺寸=本道工序基本尺寸± 前道工序基本尺寸 本道工序基本尺寸±本 本道工序基本尺寸 道工序余量 被包容特征( “+”——被包容特征(轴) 被包容特征 包容特征( “-” ——包容特征面 粗、半精、精加工的工序余量; - 半精、精加工的工序余量; b-包容面 粗、半精、精加工的工序余量 半精、 -
2 、影响加工余量的因素
1)上工序留下的表面粗糙度值Rz和表面缺陷 )上工序留下的表面粗糙度值 层深度H 层深度 a
本工序必须把上工序留下的表面粗糙度和表面缺陷层 全部切去,因此本工序余量必须包括这两项因素。 全部切去,因此本工序余量必须包括这两项因素。
A1
A0 A2
A1和A2是在加工过程中直接获得,尺寸 0是间接保证的, 是在加工过程中直接获得 尺寸A 间接保证的 直接获得, A1、A2 和A0构成一个封闭的尺寸组,都叫尺寸链的环。 构成一个封闭的尺寸组,都叫尺寸链的环。
3、尺寸链计算的关键: 、尺寸链计算的关键: 正确画出尺寸链图,找出封闭环, 正确画出尺寸链图,找出封闭环,确定增环和减环
计算工序间尺寸、确定其上下偏差的步骤: 计算工序间尺寸、确定其上下偏差的步骤:
(3)、除最终加工工序外,其他各加工工序 、除最终加工工序外, 按各自所采用的加工方法所对应的经济精 度确定工序尺寸公差。 度确定工序尺寸公差。
现以查表法确定工序余量并计算工序尺寸及其上 下偏差。 下偏差。 例题1 例题1: )、表面粗糙度为 某心轴直径为φ - (IT5)、 某心轴直径为φ6000.013 IT5)、表面粗糙度为 0.04μ 心轴毛坯为锻件,并要求高频淬火。 Ra0.04μm,心轴毛坯为锻件,并要求高频淬火。已 知心轴工艺路线为: 知心轴工艺路线为: 粗车–––半精车 高频淬火–––粗磨 半精车–––高频淬火 粗磨–––精磨–––研磨 。 粗车 半精车 精磨 现计算各工序尺寸及其上下偏差。 现计算各工序尺寸及其上下偏差。
从封闭环开始,给每一个环画出箭头, 从封闭环开始,给每一个环画出箭头, 最后再回到封 闭环,像电流一样形成回路。凡箭头方向与封闭环方 闭环,像电流一样形成回路。 箭头方向与封闭环方向相 向相反者为增环(如A2),箭头方向与封闭环方向相 相反者为增环( 同者为减环( 同者为减环(如A1)。
增、减环判别方法
2、尺寸链的基本术语 、
尺寸链的环: 尺寸链的环:是指尺寸链中的每一个 尺寸。 尺寸。 组成环: 组成环:加工过程中直接获得的尺寸 是组成环; 。如A1、A2是组成环; 封闭环: 封闭环:在加工或装配过程中最后被 间接获得的尺寸或间接保证精度的尺 称为封闭环。 是封闭环。 寸,称为封闭环。如A0是封闭环。 增环: 增环:它增大将使封闭环随之增大 的组成环。 叫增环; 的组成环。如A2叫增环; 减环: 减环:它增大反使封闭环随之减小 的组成环。 叫减环。 的组成环。如A1叫减环。
工序尺寸及其偏差 工序名称 工序余量 工序经济精度 工序基本尺寸 工序尺寸及偏差 浮动镗孔 精镗孔 半精镗孔 粗镗孔 毛坯孔 0.1 0.5 2.4 5 IT7(H7) ( ) IT8(H8) ( ) IT10(H10) ( ) IT12(H12) ( )
+1 -2
100 100-0.1=99.9 99.9-0.5=99.4 99.4-2.4=97 97-5=92
2)上道工序的尺寸公差Ta )上道工序的尺寸公差
上道工序的加工误差包括尺寸误差和位置误差, 上道工序的加工误差包括尺寸误差和位置误差,如平面 圆柱度等,其总和不超过T 度、圆柱度等,其总和不超过 a ,为使本工序能切去这些 误差,工序余量应包括T 误差,工序余量应包括 a项。
加工表面的粗糙度与缺陷层
n
Z0 = ∑Z
i =1
i
单边余量 对于非对称表面, 对于非对称表面,其加工余量用单边余量 Zi 表示 Zi =li - 1 -li 双边余量 对于外圆内圆等对称表面加工余量用双边余量表示
加工B面 加工 面:Z1 = A0 – A1 加工C面 加工 面: Z2 = A1 – A2
B C
轴:Zi = di–1 – di
(二) 加工余量的确定 1)计算法 )
掌握影响加工余量的各种因素具体数据的条件下, 掌握影响加工余量的各种因素具体数据的条件下, 计算法比较科学,但目前统计资料较少。 计算法比较科学,但目前统计资料较少。
2)经验估计法 )
为避免出现废品,估计余量一般偏大,用于单件小 为避免出现废品,估计余量一般偏大, 批生产。 批生产。
关键
1、确定封闭环 、
要领
2、组成环确定 、
关键
尺寸链的分类 1、按应用范围分类 、
①作尺寸链图 按照加工顺序依次画出各工序尺寸及零件 图中要求的尺寸,形成一个封闭的图形。 图中要求的尺寸,形成一个封闭的图形。 ②找封闭环 根据工艺过程,找出间接保证的尺寸 根据工艺过程,找出间接保证的尺寸A0 为 封闭环。 封闭环。 ③ 确定增环和减环 可用以下简便的方法得到: 可用以下简便的方法得到:
二、加工余量的确定
(一)加工余量的定义
1、加工总余量与工序余量 加工总余量:毛坯尺寸与零件设计尺寸之差称为总余量。 加工总余量:毛坯尺寸与零件设计尺寸之差称为总余量。 工序余量:每一道工序切除的金属层厚度称为工序余量。 工序余量:每一道工序切除的金属层厚度称为工序余量。 总余量Z0与工序余量Zi 的关系: 的关系:
3)查表法 )
以生产实践和实验研究为基础制成数据表格, 以生产实践和实验研究为基础制成数据表格,查表 并结合实际情况加以修正。查表法确定加工余量, 并结合实际情况加以修正。查表法确定加工余量, 方法简便,较接近实际,应用广泛。 方法简便,较接近实际,应用广泛。
三、 工序尺寸及其公差的确定
1)工艺基准与设计基准重合 )
0 Ф60 -0.013
Ф60.01 Ф60.11 Ф60.41 Ф60.51
0 - 0.019 0 - 0.046 0 - 0.12 0 - 0.3
66± Ф66±2
例题2 例题2: 确定某箱体零件上孔加工的各工序尺寸和公差。 确定某箱体零件上孔加工的各工序尺寸和公差。 设毛坯为带孔铸件, 设毛坯为带孔铸件,零件孔要求达到Φ100H7(+0.035),Ra ( 0 为0.8μm,材料为 μ ,材料为HT200。 。 其工艺路线为粗镗→半精镗→精镗→浮动镗 其工艺路线为粗镗→半精镗→精镗→