UM_H4Silver_CS_REVC_WEB-4银使用手册
微 bit服务扩展板用户手册说明书

Servo Driver for Micro:bitUser ManualOVERVIREThis Servo Driver board is an PWM/servo expansion board for micro:bit. UsePCA9685 chip, expands up to 16 channels and support 12-bits resolution for each channel. Using I2C interface. This board also integrates 5V regulator, up to 3A output current, can be powered from battery through VIN terminal. It could be used to for Robot applications.FEATURES➢Power supply: 6V~12V (VIN terminal)➢Servo voltage: 5V➢Logic voltage: 3.3V➢Driver: PCA9685➢Control interface: I2C➢Dimension: 65mm x 36mm➢Mounting hole size: 3.0mmHARDWAREYou can connect battery to the green socket VIN on the left for power supply, for VIM, voltage range 6V~12V. 5V regulator on board could output 3A (MAX) current. You can also connect 5V power supply to the POWER interface on the right, and it could power micro:bit via 3.3V regulator.GPIOs on top are interfaces of servo. Black pins are connected to GND (mostly connect to brown wire of servo). Red pins are VCC pin connected to 5V. Yellow GPIOs are signal wires of PWM, channel 0~15 supports 16 servos connected at the same time.【Note】1.If you only connect 5V power supply to USB interface, servo cannot be driven.2.You should connect higher power supply for higher-power servo.3.Make sure servo are connected properly, otherwise they will not move.The website of typescript: https:///# ,Open browser and type the address as below:Click Projects -> New Project to create a new project.Then click Advanced->Add Package In the pop-up dialog box, click the search field box to copy the URL: https:///waveshare/pxt-ServoClick Servo searched to add the package.After adding, you can see that Servo block class appears to block area. In the class, two blocks are included.: This block is used to control the angle of servo in range 0°~180°. Channel can be change from 0 to 15.: Use this block, you can set the PWM pulse in range: 500~2500.The relationship between start pulse and degree is as below:500 ------- 0°1000 ------- 45°1500 ------- 90°2000 ------- 135°2500 ------- 180°You can control servo just by setting channel, degree and pulse, it is simple.DEMO CODESWe provide three demo codes (HEX file) for this module. You can copy them to micro:bit for testing. Drag HEX file to the web page directly could get details information of demo code: https:///MICROBIT-SERVOThis demo code is used to rotate 16 servos in range 0~180 all the timeitem: current angleFlag: step length for every change. Positive value stands for co-rotating, and negative for reverse, interval is 20s.After running the code, y ou can see that 16 servos turn from 0° to 180°, then turn 0° again all the time, you can adjust its speed by change the pause on code. MICROBIT-SERVO-KEYThis demo uses A and B keys to control rotation of servo 0. It moves forward when A button is pressed and moves backward when B button is pressed.MICROBIT-SERVO-BLUETOOTHmicrobit-Servo-Bluetooth, the function of this code is to rotate four servos 0~4 via Bluetooth. If you assemble servo to robot arm, it could control robot ram via Bluetooth.This is the Bluetooth remote control code. pos0~pos3 are current degrees of channel 0~3. step0~step3 are step length.When command are received by micro:bit from app, micro:bit will change the step as received to control servo. If step is not equal to 0, change the pos and let servo move. (Note that the value of pos should in: 0~180)To use this demo code, you should first install APP for Bluetooth communication. (Only support Android)⚫Bluetooth App (for Android)Open APP, click Settings on the right top, uncheck Filter unpaired micro:bit from scan results?.Scanning BBCC micro:bit device and connect it. After connecting, you can enter the control page by click the Joystick icon.There are 8 buttons, could be used t control servos from channel0 to channel3.Note: If you want to create new Bluetooth project, don’t forget to setting project that, choose No Pairing Required:Anyone can connect via Bluetooth.MICROBIT-SERVO-RADIOThis code we use 2.4Ghz RF function of micro:bit. To test this code, you need two micro:bit, one is connected to Joystick for mciro:bit as sender, and another connected to Servo Driver for micro:bit as receiver which will control robot.Code if sender:Code of receiver:Similar to Bluetooth code, pos0~pos3 are current degree of servos from channel 0 to channe 3, step0~step3 are step length.You should flash sender code to micro:bit which connect Joystick module and flash receiver one to servo module. Then you can control servo by module Joystick for micro:bit.For more details about Bluetooth and 2.4G, you can refer to the user guide of KitiBot for micro:bit:https:///wiki/Chapter_8_of_KitiBot-Microbithttps:///wiki/Chapter_9_of_KitiBot-Microbit。
NANO-PLC EM4系列产品说明书

› U p to 46 I/Os - Base 16 DI (4 HighSpeed/ 12 AI ), 8 DO + 2 Solid State Relays › A nalog Inputs 4-20 mA, 0-10 V c and 0-Vdc 12 bits › E thernet Modbus TCP/IP (Client/Server) and Modbus RTU RS485 via interface(Master/Slave)› E vent management & datalog via mail or FTP server › P LC performance with the shape and ease of use of a logic controllerEM4B26-ETBase 26 I/O EthernetEM4B26Base 26 I/O LocalFinishGlossy black On front panel color Black RAL 9011On terminal block color Blue RAL 5017Protection rating(in accordance with IEC/EN 60529)IP 40 on front panel IP 20 on terminal block Weight Without packing: 345 g With packing: 395 gWithout packing: 310 g With packing: 355 gDimensionsWithout packing: 124.6 x 90 x 60.6 mm / 4.91 x 3.54 x 2.38 inchWith packing: 148 x 103 x 65 mm / 5.83 x 4.06 x 2.56 inchWithout packing: 124.6 x 90 x 60.4 mm / 4.91 x 3.54 x 2.38 inchWith packing: 148 x 103 x 65 mm / 5.83 x 4.06 x2.56 inchLCD display Display with 4 lines of 18 characters, white characters on a black background, reverse displayfunctionProgramming method FBD (Function Block Diagram), including SFC (Sequential Function Chart) (Grafcet) Program size Function blocks: typically 1000 blocksMacro blocks: 127 max. (255 blocks per macro)Program memory FlashRemovable memory N.AData memory 2 k octetsBack-up time(in the event of power failure)Program and settings in the controller: 10 years Data memory: 10 yearsData back-up Data backup in the flash memory is guaranteed if the product is powered on more than 10 seconds Cycle time From 2 ms* to 90 ms, default value: 10 ms*: Depending on configurationFrom 2 ms to 90 ms, default value: 10 ms Clock data retention10 years (lithium battery) at 25 °C (77 °F)Clock drift Drift < 12 min/year (at 25 °C (77 °F))6 s / month (at 25 °C (77 °F) with user-definable correction of drift).Synchronizable by networkTimer block accuracy0.5 % ± 2 cycle timeStart up time on power up< 10 s base alone, < 5 s base + 2 expansions +1 accessory (RS485)< 3 s base alone, < 1.5 s base +2 expansions + 1 accessory (USB, RS485…)Self test Test firmware integrity (checksum memory)Stability of the internal power supplyCheck the conformity of the em4 device configuration with the configuration in the applicationInput voltage24 V c (-15% / +20%)Input current***********2.1 mA @ 24 V***********Input impedance11.6 kΩLogic 1 voltage threshold≥ 15 V cMaking current at logic state 1≥ 1.3 mALogic 0 voltage threshold≤ 10 V cRelease current at logic state 0≤ 0.8 mAResponse time 1 to 2 cycle timesSensor type Contact or 3-wire PNPConforming to IEC/EN 61131-2Type 1Input type ResistiveIsolation between power supply and inputs NoneIsolation between inputs NoneProtection against polarity inversions YesStatus indicator On LCD screenMaximum counting frequency 3 channels encoder (I1, I2, I3): 20 kHz*2 independent counters (I1, I2) (I3, I4) (Cumul, IND, DIR): 2 channels: 40 kHz*, 4 channels:20 kHz*,2 independent counters (I1, I2) (I3, I4) (PH, PH2): 2/4 channels: 20 kHz*4 independent counters (I1, I2, I3, I4) (Up/Down): 1 channel: 60 kHz*, 2 channels: 40 kHz*, >2 channels: 20 kHz** with a time cycle ≤ 10 ms and a ton / toff = 50% ± 5%, level 0 < 2V and level 1 > 20.4V Other functions 4 chronometers (I1, I2, I3, I4 )4 tachometers (I1, I2, I3, I4 )Input voltage24 V c (-15% / +20%)Input current***********1.7 mA @ 24 V*********** Input impedance13.9 kΩLogic 1 voltage threshold≥ 11 V cMaking current at logic state 1≥ 0.8 mALogic 0 voltage threshold≤ 8 V cRelease current at logic state 0≤ 0.5 mAResponse time 1 to 2 cycle timesSensor type Contact or 3-wire PNPConforming to IEC/EN 61131-2Type 1Input type ResistiveIsolation between power supply and inputs NoneIsolation between inputs NoneProtection against polarity inversions NoStatus indicator On LCD screenBreaking voltage10 → 28.8 V cNominal voltage12 / 24 V cNominal current0.5 A on resistive load @ 25 °C (77 °F) Max. breaking current0.625 ANon repetitive overload current 1 AMaximum breaking current in the common 1 AVoltage drop< 1 V for I = 0.5 AResponse time Make = 1 cycle time + 30 µs typicalRelease = 1 cycle time + 40 µs typicalBuilt-in protections Against overloads and short-circuits: YesAgainst over voltages (*): YesAgainst inversions of power supply: Yes(*) In the absence of a volt-free contact between the output of the logic controller and the load Min. load 1 mAGalvanic isolation NoCable length≤ 10 mTruth table of the default Command Output FaultNormal condition 0 0 No1 1 NoOverheating 0 0 No1 0 YesUnderpowered 0 0 X1 0 XShort circuit (current limit) 0 0 No1 0 YesPWM frequency14.11 Hz; 56.45 Hz; 112.90 Hz; 225.80 Hz; 451.59 Hz; 1758.24 HzPWM cyclic ratio0 → 100 % 100 stepsPWM Max. error≤ 2 % (from 10 % → 90 %)Status indicator On LCD screenCable length≤ 10 m with shielded twisted cableDistance between the power source and the ≤ 30 mBreaking voltage250 V a maxBreaking current 6 ADerating: UL: ≥ 45 °C (113 °F): 4A max6AMaximum breaking current in the common IEC @ 25 °C (77 °F): 12 AIEC @ 60 °C (140 °F) or UL: 10 AMechanical life 5 000 000 operations (cycles)Electrical durability for 50 000 operating cycles 24 V c tau = 0 ms: 6 A, tau = 7 ms: 3 A, tau = 15 ms: 1.8 A Usage category DC-12: 24 V, 6 AUsage category DC-14: 24 V, 1.8 A250 V a cos phi = 1: 6 A, cos phi = 0.7: 5 A, cos phi = 0.4: 2.5 A Usage category AC-12: 250 V, 6 AUsage category AC-13: 250 V, 5 AUsage category AC-15: 250 V, 2 AMinimum switching capacity100 mA (at minimum voltage of 12V)Maximum operating rate Off load: 10 HzAt operating current: 0.1 HzVoltage for withstanding shocks In accordance with IEC/EN 60947-1 and IEC/EN 60664-1: 4 kV Response time Make = 1 cycle time + 8 ms typicalRelease = 1 cycle time + 4 ms typicalBuilt-in protections Against short-circuits: NoneAgainst over voltages and overload: NoneStatus indicator On LCD screenBreaking voltage250 V a maxBreaking current8 ADerating: CEI ≥ 55 °C (131 °F) or UL: ≥ 45 °C(113 °F): 6A max8 A, ≥ 55 °C: 6 AMaximum breaking current in the common IEC @ 25 °C (77 °F): C3, C6: 8A; C4, C5: 16 AIEC @ 60 °C (140 °F) or UL: C3, C6: 8 A; C4, C5: 10 A Mechanical life20 000 000 operations (cycles)Electrical durability for 50 000 operating cycles 24 V c tau = 0 ms: 8 A, tau = 7 ms: 3 A, tau = 15 ms: 1.5 A Usage category DC-12: 24 V, 8 AUsage category DC-14: 24 V, 1.5 A250 V a cos phi = 1: 8 A, cos phi = 0.7: 4.75 A, cos phi = 0.4: 3 A Usage category AC-12: 250 V, 8 AUsage category AC-13: 250 V, 4.3 AUsage category AC-15: 250 V, 1.5 AMinimum switching capacity100 mA (at minimum voltage of 12V)Maximum operating rate Off load: 10 HzAt operating current: 0.1 HzVoltage for withstanding shocks In accordance with IEC/EN 60947-1 and IEC/EN 60664-1: 4 kV Response time Make = 1 cycle time + 10 ms typicalRelease = 1 cycle time + 5 ms typicalBuilt-in protections Against short-circuits: NoneAgainst over voltages and overload: NoneStatus indicator On LCD screenEthernetLocalI1 ... IG 0/124V(2)I5 ... IC UID ... IG U / I24V(2)I1 ... I4 2604I1 ... I4 2604I1 ... I4 260424V(2)O3 ... OA12…240 V 50 / 60 Hz or 12…24 VN / –N / – 6 A, 8 A(3)Inductive load+–I1I2I3I4I5I6I7I8I9IA IB IC ID IE IF IG O2C1O1C2O3O4C3O5C4O6O7C5O8O9C6OAOA/。
Web网络版说明书
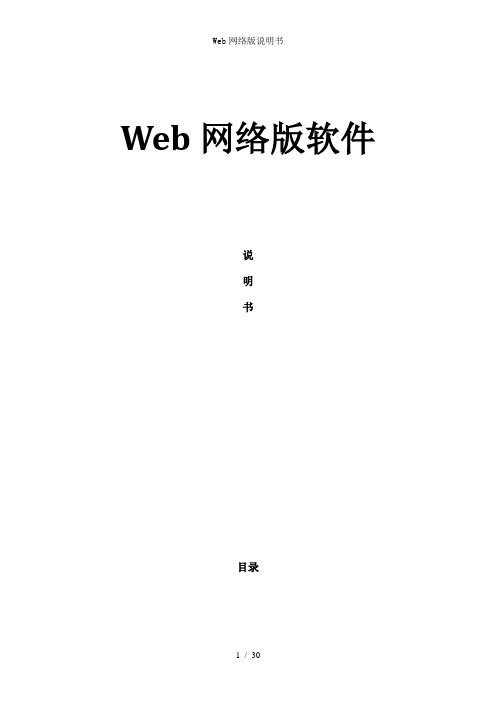
Web网络版软件说明书目录USB驱动安装 (3)一、驱动安装 (3)二、查看设备 (5)使用说明 (6)一、软件操作流程 (6)1. 软件使用操作流程 (6)2. 客户端远程通讯初始化 (7)3. GPRS类设备设置工具 (8)二、软件功能详细介绍 (10)1. 权限设置 (10)2. 棒号管理 (12)3. 人员管理 (16)4. 地点管理 (18)5. 线路管理 (21)6. 计划设置 (22)7. 地图设置 (23)8. 采集数据 (24)9. 通过远程通讯工具上传数据 (25)10. 历史记录 (27)11. 计划考核 (28)12. 数据统计 (28)13. 地图演示 (29)USB驱动安装一、驱动安装第一次安装完软件后,请将巡检器用USB传输线及电脑连接好,系统自动出现如下画面:选择第一个选项(是,仅此一次),单击下一步,出现:选择第二个选项(从列表或指定位置安装),单击下一步,出现:选择在搜索中包括这个位置,点击浏览,选择USB驱动所在的文件夹,单击下一步,出现:单击完成,则USB驱动安装成功。
二、查看设备安装完USB驱动后,您可以在设备管理器中查看所用的串口号,选择我的电脑按右键选择属性,在属性中选择硬件,点击设备管理器,在管理器中选择端口(COM和LPT),出现CP2101 USB to UART Bridge Controller (COM3),则您在软件中应用的串口号则为COM3。
具体过程如下图所示:使用说明一、软件操作流程1.软件使用操作流程(1)GPRS类型设备登录系统→→权限设置(添加部门和相应登录人员以及设置其权限等操作)→→通过刷棒号工具设置服务器公网IP地址和棒号→→上传棒号(设置该棒的工作状态)→→上传人员(若未购买人员卡则该步操作可以省略)→→上传地点(将巡逻钮数据上传服务器并)→→线路设置→→计划设置→→正式巡逻→→采集数据(将巡检器内的数据上传服务器保存并考核巡逻情况)→→查看相关巡逻数据和考核情况。
维智WSDA系列伺服驱动器用户手册(EtherCAT总线通信型)-R4
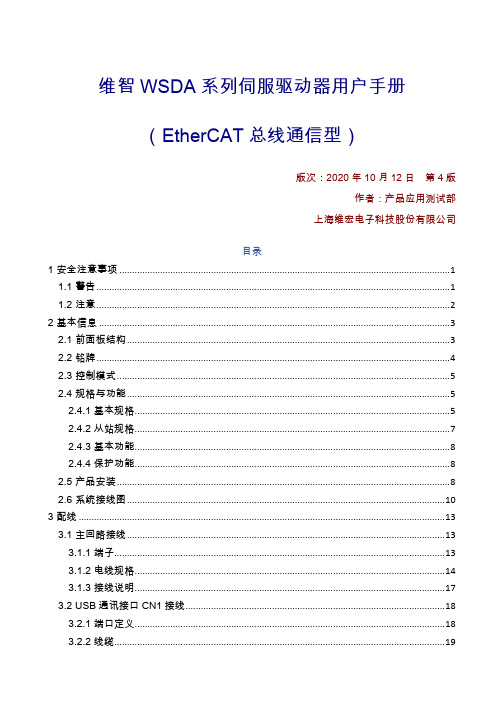
维智WSDA系列伺服驱动器用户手册(EtherCAT总线通信型)版次:2020年10月12日第4版作者:产品应用测试部上海维宏电子科技股份有限公司目录1 安全注意事项 (1)1.1 警告 (1)1.2 注意 (2)2 基本信息 (3)2.1 前面板结构 (3)2.2 铭牌 (4)2.3 控制模式 (5)2.4 规格与功能 (5)2.4.1 基本规格 (5)2.4.2 从站规格 (7)2.4.3 基本功能 (8)2.4.4 保护功能 (8)2.5 产品安装 (8)2.6 系统接线图 (10)3 配线 (13)3.1 主回路接线 (13)3.1.1 端子 (13)3.1.2 电线规格 (14)3.1.3 接线说明 (17)3.2 USB通讯接口CN1接线 (18)3.2.1 端口定义 (18)3.2.2 线缆 (19)3.3 总线接口 CN2A/B 接线 (20)3.3.1 接线图 (20)3.3.2 线缆 (20)3.4 电机编码器线接口CN4接线 (21)3.4.1 端口定义 (21)3.4.2 说明 (22)3.4.3 线缆 (23)3.5 外置再生制动电阻器连接 (24)4 驱动器面板 (29)4.1 概述 (29)4.2 监视器模式 (31)4.3 参数设定模式 (41)4.4 EEPROM 写入模式 (41)4.5 辅助功能模式 (42)4.5.1 概述 (42)4.5.2 设置站别名 (44)4.5.3 解除报警 (44)4.5.4 试运行电机 (45)4.5.5 清零绝对值编码器 (45)4.5.6 初始化参数 (46)4.5.7 解除前面板锁定 (46)4.5.8 注册驱动器 (46)4.5.9 初始化对象字典 (47)4.6 驱动器面板锁定 (48)5 电机试运行 (48)5.1 准备工作 (48)5.2 进行基本设定 (48)5.2.1 打开伺服 (49)5.2.2 选择电机旋转方向 (49)5.2.3 启用超程防止功能 (49)5.2.4 设定电机过载率 (50)5.2.5 启用制动器 (50)5.2.6 伺服断开及报警时停止电机 (50)5.3.1 使用 iMotion 软件 (51)5.3.2 使用驱动器面板 (51)5.4 故障排查 (51)6 控制系统连接 (54)6.1 选择系统类型 (54)6.2 设置关联参数 (54)6.2.1 设置控制系统参数 (54)6.2.2 设置维智伺服驱动器参数 (55)6.3 设置站别名 (55)6.4 设定基准或回机械原点 (55)6.4.1 设定基准 (55)6.4.2 回机械原点 (56)6.5 运行电机 (56)7 绝对式系统 (56)7.1 安装与更换电池 (56)7.2 自制绝对式编码器电缆 (58)7.3 启用绝对值功能 (58)7.4 启用无限旋转绝对式功能 (58)8 增益调整 (58)8.1 准备工作 (58)8.1.1 设定驱动禁止输入 (59)8.1.2 设定转矩限制 (59)8.1.3 设定过速度保护 (59)8.1.4 设定位置偏差过大保护 (59)8.1.5 设定电机可动范围 (60)8.2 推定惯量比 (60)8.3 设置自适应滤波器 (61)8.3.1 操作步骤 (62)8.3.2 故障排查 (62)8.3.3 相关信息 (63)8.4 自动调整增益 (63)8.4.1 操作步骤 (64)8.4.3 相关信息 (65)8.5 手动调整增益 (67)8.5.1 执行基本调整 (68)8.5.2 切换增益 (69)8.5.3 抑制机械共振 (75)8.5.4 设置 2 段转矩滤波器 (76)8.6 总线控制系统调整增益 (77)9 驱动器注册 (77)9.1 获取序列号 (77)9.1.1 通过 iMotion 软件 (78)9.1.2 通过驱动器面板 (79)9.2 获取注册码 (80)9.3 注册驱动器 (81)10 异常与对策 (82)10.1 异常时应对思路 (82)10.2 警告 (83)10.2.1 查找警告 (83)10.2.2 警告码 (83)10.3 SDO传输中止码 (84)10.4 错误码一览表 (85)10.5 错误码详情 (90)10.5.1 Err10系列 (90)10.5.2 Err20系列 (97)10.5.3 Err30系列 (101)10.5.4 Err40系列 (105)10.5.5 Err50系列 (108)10.5.6 Err70系列 (112)10.5.7 Err80系列 (115)10.5.8 Err90系列 (124)10.5.9 其他错误码 (125)10.5.10 解除错误 (125)11 参数 (126)11.2 [分类 0]基本设定 (126)11.2.1 Pr001 (126)11.2.2 Pr002 (127)11.2.3 Pr003 (127)11.2.4 Pr004 (128)11.2.5 Pr011 (128)11.2.6 Pr012 (129)11.2.7 Pr013 (130)11.2.8 Pr014 (131)11.2.9 Pr015 (131)11.2.10 Pr016 (132)11.2.11 Pr017 (132)11.2.12 Pr018~Pr019 (133)11.2.13 Pr024 (134)11.3 [分类 1]增益调整 (134)11.3.1 Pr100~Pr104 (134)11.3.2 Pr105~Pr109 (136)11.3.3 Pr110 (137)11.3.4 Pr111 (138)11.3.5 Pr112 (138)11.3.6 Pr113 (138)11.3.7 Pr114 (139)11.3.8 Pr115 (140)11.3.9 Pr116 (142)11.3.10 Pr117 (142)11.3.11 Pr118 (142)11.3.12 Pr119 (143)11.3.13 Pr120 (143)11.3.14 Pr121 (144)11.3.15 Pr122 (144)11.3.16 Pr123 (144)11.3.17 Pr124 (145)11.3.19 Pr126 (145)11.3.20 Pr127 (146)11.4 [分类 2]控制抑制功能 (146)11.4.1 Pr200 (146)11.4.2 Pr201~Pr203 (146)11.4.3 Pr204~Pr206 (147)11.4.4 Pr207~Pr209 (149)11.4.5 Pr210~Pr212 (150)11.4.6 Pr214~Pr215 (151)11.4.7 Pr216~Pr217 (151)11.4.8 Pr218~Pr219 (152)11.4.9 Pr220~Pr221 (152)11.4.10 Pr222 (153)11.4.11 Pr223 (154)11.5 [分类 3]速度/转矩控制 (155)11.5.1 Pr300 (155)11.5.2 Pr302 (156)11.5.3 Pr304 (156)11.5.4 Pr312~Pr313 (157)11.5.5 Pr314 (158)11.5.6 Pr317、Pr318、Pr321、Pr322 (158)11.5.7 Pr323 (160)11.5.8 Pr326 (160)11.5.9 Pr327 (161)11.5.10 Pr343 (161)11.5.11 Pr344 (161)11.5.12 Pr345 (162)11.5.13 Pr346 (162)11.6 [分类 4] I / F 监视器设定 (162)11.6.1 Pr400~Pr406 (162)11.6.2 Pr408~Pr411 (165)11.6.3 Pr430 (167)11.6.5 Pr432 (168)11.6.6 Pr433 (168)11.6.7 Pr434 (169)11.6.8 Pr435 (169)11.6.9 Pr436 (170)11.6.10 Pr437 (171)11.6.11 Pr438 (171)11.6.12 Pr439~Pr440 (172)11.6.13 Pr441 (173)11.6.14 Pr449 (173)11.6.15 Pr450 (174)11.7 [分类 5]扩展设定 (174)11.7.1 Pr503 (174)11.7.2 Pr504 (174)11.7.3 Pr505 (175)11.7.4 Pr506 (176)11.7.5 Pr507 (177)11.7.6 Pr508 (177)11.7.7 Pr509 (177)11.7.8 Pr510 (178)11.7.9 Pr511 (179)11.7.10 Pr512 (179)11.7.11 Pr513 (179)11.7.12 Pr514 (180)11.7.13 Pr516 (180)11.7.14 Pr520 (180)11.7.15 Pr521 (181)11.7.16 Pr522 (181)11.7.17 Pr523 (181)11.7.18 Pr524 (181)11.7.19 Pr525 (182)11.7.20 Pr526 (182)11.7.22 Pr533 (184)11.7.23 Pr535 (184)11.7.24 Pr540 (184)11.7.25 Pr541 (185)11.8 [分类 6]特殊设定 (185)11.8.1 Pr601 (185)11.8.2 Pr602 (185)11.8.3 Pr604 (185)11.8.4 Pr607 (186)11.8.5 Pr608 (186)11.8.6 Pr609 (186)11.8.7 Pr611 (187)11.8.8 Pr612 (187)11.8.9 Pr615 (187)11.8.10 Pr617 (188)11.8.11 Pr623 (188)11.8.12 Pr624 (189)11.8.13 Pr627 (189)11.8.14 Pr628 (189)11.8.15 Pr629 (189)11.8.16 Pr630 (190)11.8.17 Pr632 (190)11.8.18 Pr633 (192)11.8.19 Pr638 (192)11.8.20 Pr640 (193)11.8.21 Pr642 (193)11.8.22 Pr643 (194)11.8.23 Pr647 (194)11.8.24 Pr650 (194)11.8.25 Pr651 (195)11.8.26 Pr660 (195)12 EtherCat通信规格 (195)12.2 帧结构 (196)12.3 ESC地址空间 (197)12.4 通信状态 (197)12.5 SDO (198)12.6 PDO (198)12.6.1 PDO映射 (199)12.6.2 分配对象 (200)12.6.3 映射配置 (200)12.7 DC通信同步模式 (201)12.8 SII EEPROM (201)12.9 寻址模式 (201)13 对象字典 (202)13.1 概述 (202)13.1.1 分类 (202)13.1.2 数据类型 (203)13.1.3 相关用语 (203)13.2 通信对象 (204)13.2.1 设备信息 (204)13.2.2 同步管理器通讯类型 (208)13.2.3 PDO通讯 (210)13.2.4 同步管理器 2 和 3 同步对象 (240)13.2.5 对象写入 EEPROM (250)13.2.6 对象恢复出厂 (251)13.2.7 故障履历 (252)13.3 驱动器参数对象 (259)13.3.1 2100h (259)13.3.2 2101h (260)13.3.3 2102h (262)13.3.4 2103h (263)13.3.5 2200h (264)13.4 厂商定义对象 (265)13.5 辅助功能对象 (266)13.5.1 信息监视器对象 (266)13.5.2 多圈绝对式编码器清零 (277)13.6 驱动协议对象 (277)13.6.1 功率驱动系统状态机 (277)13.6.2 控制模式设置 (283)13.6.3 位置控制模式 (287)13.6.4 速度控制模式 (325)13.6.5 转矩控制模式 (335)13.6.6 模式共通功能 (343)14 对象字典一览表 (370)14.1 1000h~1FFFh (370)14.2 2000h~2FFFh (378)14.3 3000h~30FFh (379)14.4 3100h~37FFh (392)14.5 6000h~6FFFh (394)1安全注意事项注意事项根据不遵守可能会造成危害的程度,分为警告和注意类型:警告:特别需要提示的内容,如果不遵守此类信息,可能会造成人身伤害甚至是死亡、机器损坏、或者其他财产损失。
UMC-4全局电动机控制器用户指南说明书
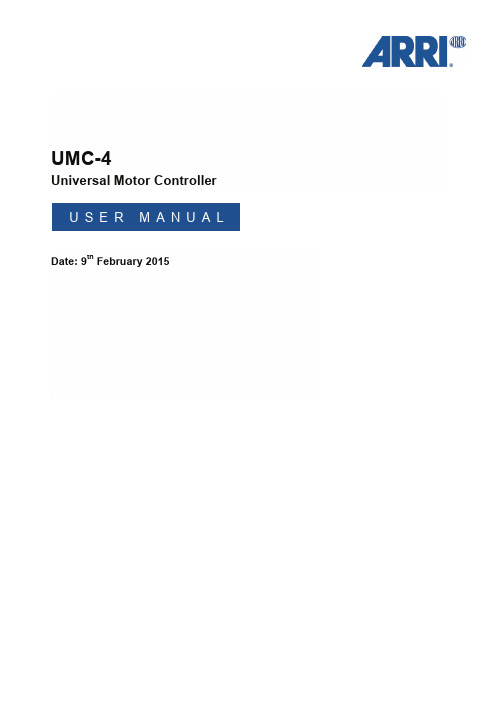
UMC-4Universal Motor Controller U S E R M A N U A L Date: 9th February 2015•Wireless Zoom Unit WZU-3•Controlled Lens Motor CLM-2•Controlled Lens Motor CLM-3•Controlled Lens Motor CLM-4•Lens Data Encoder LDE-1•Ultrasonic Distance Measure UDM-1Note: Use only one lens motor per lens axis.Note: Up to three hand units can be connected to one UMC-4 in parallel to form a radio network.Connector PinoutsSerial1 GND Ground2 +12V 12V output, max 200mA3 TxD/Tx– RS232/RS485 – RS4224 RxD/Rx+ RS232/RS485 – RS4225 Tx+ RS422 line6 Rx– RS422 lineLCS1GND Ground 2n.c. 3CAN-L CAN bus 4CAN-H CAN bus 5 +V-BAT Battery supply outputCAM1GND Ground 2+V-BAT 9.5 V to 34 V DC IN 3CAM-TYPE Camera type sense, analog input 4Rx- RS422 line 5RUN-SW1 Opto switch1 connects to pin 13 @REC (max. 100 mA/50 V) 6Tx+ RS422 line 7CAN-L CAN bus 8n.c.9 TALLY Tally, analog input, active high (default value:1.25 V transition level)10 D-CAMTally, digital input, active low,TALLY11 DAC-CAM REC analog output, active high (default value@REC: 3.3 V)12 R/S ARRI R/S13 RUN-SW2 Opto switch 2 connects to pin 5 @REC (max.100 mA/50 V)14 RxD/Rx+ RS232/RS485 – RS422 together with pins 4, 6,1515 TxD/Tx- RS232/RS485 – RS422 with pins 4, 6, 1416 CAN-H CAN busFOCUS/IRIS/ZOOM1 GND Ground2 MTYPE-A Motor type sense3 MTYPE-B Motor type sense4 MTYPE-C Motor type sense5 +5V Encoder supply6 Encoder-A Encoder input A7 Encoder-B Encoder input B8 n.c.9 n.c.10 n.c.11 Motor + Motor drive output12 Motor – Motor drive outputRS IN1GND Ground 2+V-BAT 9.5 V to 34 V DC IN 3R/S ARRI R/STC1GND Ground 2LTC-IN Timecode input 3n.c. 4n.c. 5LTC-OUT Timecode outputDimensions and WeightWeight (including antenna): 428 gElectrical DataSupply Voltage: 9.5 V to 34 V DC (full motor speed) Current Consumption: 135 mA@12 V (radio on/ready)70 mA@24 V (radio on/ready) Operating Temperature: -20 to +50 °C (-4 to +122 °F)Radio SystemThe UMC-4 contains a radio unit that enables wireless lens control and lens data communication with a white coded radio module. A white ring at the base of the antenna mount point identifies it. It offers 8 channels to choose from:Channel Frequency0 2.410 GHZ1 2.415 GHZ2 2.430 GHZ3 2.435 GHZ4 2.450 GHZ5 2.455 GHZ6 2.470 GHZ7 2.475 GHZWhite radio and legacy yellow radio cannot be mixed in the same radio network of camera and hand units. It is possible to use both systems in parallel within different radio networks.。
SIWAREX JB 钢铁锈防爆规格权重系统操作说明说明书

Weighing systemsSIWAREX JB stainless steel with ATEX certificateCompact Operating InstructionsLegal information Warning notice systemThis manual contains notices you have to observe in order to ensure your personal safety, as well as to prevent damage to property. The notices referring to your personal safety are highlighted in the manual by a safety alert symbol, notices referring only to property damage have no safety alert symbol. These notices shown below aregraded according to the degree of danger.DANGERindicates that death or severe personal injury will result if proper precautions are not taken.WARNINGindicates that death or severe personal injury may result if proper precautions are not taken.CAUTIONwith a safety alert symbol, indicates that minor personal injury can result if proper precautions are not taken.CAUTIONwithout a safety alert symbol, indicates that property damage can result if proper precautions are not taken.NOTICEindicates that an unintended result or situation can occur if the corresponding information is not taken into account.If more than one degree of danger is present, the warning notice representing the highest degree of danger willbe used. A notice warning of injury to persons with a safety alert symbol may also include a warning relating to property damage.Qualified PersonnelThe product/system described in this documentation may be operated only by personnel qualified for the specific task in accordance with the relevant documentation for the specific task, in particular its warning notices and safety instructions. Qualified personnel are those who, based on their training and experience, are capable of identifying risks and avoiding potential hazards when working with these products/systems.Proper use of Siemens productsNote the following:WARNINGSiemens products may only be used for the applications described in the catalog and in the relevant technical documentation. If products and components from other manufacturers are used, these must be recommended or approved by Siemens. Proper transport, storage, installation, assembly, commissioning, operation andmaintenance are required to ensure that the products operate safely and without any problems. The permissible ambient conditions must be adhered to. The information in the relevant documentation must be observed.TrademarksAll names identified by ® are registered trademarks of the Siemens AG. The remaining trademarks in thispublication may be trademarks whose use by third parties for their own purposes could violate the rights of the owner.Disclaimer of LiabilityWe have reviewed the contents of this publication to ensure consistency with the hardware and software described. Since variance cannot be precluded entirely, we cannot guarantee full consistency. However, the information in this publication is reviewed regularly and any necessary corrections are included in subsequent editions.Siemens AG Industry Sector Postfach 48 4890026 NÜRNBERG A5E01257284C-01 Ⓟ 07/2010 Copyright © Siemens AG 2010. Technical data subject to changeTable of contents1 Introduction (4)1.1 Purpose of this documentation (4)1.2 History (4)1.3 Trademarks (4)1.4 Environmental protection (4)2 Notes on handling the product (5)3 Description (7)3.1 Applications (7)3.2 Properties (8)3.3 Design (8)4 Application planning (10)4.1 Alternative EMC cable glands (10)4.2 Selection of suitable cables (10)5 Installing and connecting (12)5.1 Qualified personnel (12)5.2 Mounting (12)5.3 Connecting principle (13)5.4 Connection (15)5.4.1 Installing the EMC cable glands and the screw plugs (15)5.4.2 Connecting the shielding (16)5.4.3 Installing the spring-loaded terminal block in the enclosure (16)5.4.4 Connecting spring-loaded terminals (17)5.4.5 Screwing on the cover (18)6 Technical data (19)6.1 Ambient conditions (19)6.2 Mechanical and electrical data (19)6.3 Explosion protection (20)6.4 Electromagnetic compatibility (20)6.5 Dimension drawing (21)7 Ordering data (22)7.1 Order no (22)7.2 Accessories (22)A Appendix (23)A.1 Technical support (23)SIWAREX JB stainless steel with ATEX certificateIntroduction 1 1.1Purpose of this documentationThese instructions contain all the information you need for commissioning and using thedevice.They are directed at persons who mechanically assemble, connect, start up, and use thedevice.1.2HistoryThe following versions of this documentation have been released to date. The changes applyto the previous version:Edition Comment / change06/2010 Initial release1.3TrademarksSIWAREX ® is a registered trademark of Siemens AG.All other names appearing in these instructions may be trademarks whose use by thirdparties for their own purposes may infringe upon owners rights.1.4Environmental protectionDevices described in this programming manual can be recycled owing to the low content ofnoxious substances in their version. Please contact a certified waste disposal company foreco-friendly recycling and to dispose of your old devices.SIWAREX JB stainless steel with ATEX certificateNotes on handling the product 2Proper usageProper usage means that this product must only be used within the scope of the technicalspecifications and intended purposes of these operating instructions.If this device is used properly in compliance with the safety notices, this device will notpresent any danger.This device can only function correctly and safely if it is transported, stored, set up andmounted correctly.Correct operation of the device must be ensured by complying with the technicalspecifications.Improper handling can result in death, personal injury or property damage.Notes on liability for defectsWe expressly point out that the product quality is exclusively and conclusively described inthe sales contract. The content of this product documentation is neither part of a previous orexisting agreement, promise or legal relationship, nor is it intended to modify these. Allobligations on the part of Siemens AG are contained in the respective sales contract, whichalso contains the complete and solely applicable liability provisions. The provisions definedin the sales contract for the responsibility for defects are neither extended nor limited by theremarks in this document.Delivery informationThe current scope of delivery is listed on the shipping documents enclosed with the deliveryin accordance with the valid sales contract.When opening the packaging, please observe the relevant information. Check the deliveryfor completeness and undamaged condition. In particular, the order number on the ratingplate must be compared to the ordering data.Before you start work, please read these operating instructions. They contain importantinformation and data whose observation ensures the general safety and functionality of thisdevice. The manual will help you to handle this product more easily and efficiently, allowingyou to achieve reliable measuring results.SIWAREX JB stainless steel with ATEX certificateNotes on handling the productSIWAREX JB stainless steel with ATEX certificateQualified personnelIn the context of this documentation, qualified personnel are people who are familiar with the installation, mounting, commissioning, and operation of the product. These people must have the following qualifications:● They must be trained, instructed and authorized to operate and maintain devices and systems in accordance with their place of work and in compliance with the safety engineering standards for – Electrical circuits – High pressures– Corrosive and hazardous media● They must be trained, instructed and authorized to maintain and use appropriate safety equipment according to the standards for safety engineering. ● In the case of devices with explosion protection, qualified persons must be trained, instructed and authorized to perform work on electrical circuits in plants subject to explosion hazards.Important notes on connectingWARNINGElectric shockThe SIWAREX JB junction box must only be used with extra-low voltages ≤ 30 V.Important notes on cleaningCAUTIONMalfunctionDo not subject the junction box directly to the jet from a high-pressure cleaner.Explosion protectionWARNINGDanger of explosionObserve the test certificates, provisions and laws applicable in your country during connection, assembly and operation. For hazardous areas, these are for example: • IEC 60079-14 (international)• EN 60079-14 (previously VDE0165, T1) (EU, Germany) • The operational safety directive (Germany)All work undertaken on electrical circuits in hazardous areas must only be performed by skilled personnel.Description 3 3.1ApplicationsField of applicationThe stainless steel SIWAREX JB junction box is used in weighing systems with extra-lowvoltages ≤ 30 V.The junction box can connect up to four load cells to the weighing module at the same time.Operating principleLoad cells with 4-wire and 6-wire strain gauges can be connected.The cable connection from the junction box to the weighing module is implemented with a 6-wire cable.LC Load cellJB SIWAREX JB junction boxW Weighing moduleFigure 3-1 Principle of applicationSIWAREX JB stainless steel with ATEX certificate3.2 Properties3.2PropertiesThe SIWAREX JB junction box has the following properties:●It consists of stainless, acid-resistant steel 1.4301.●It is protected against dust and jet water according to protection class IP66.●The junction box is maintenance-free.●The cables are fed into the junction box via EMC cable glands.–The cable glands are made of nickel-plated brass.–Unneeded openings for cable glands are sealed with a cap screw.●Electromagnetic compatibility:Installing the shield in the cable glands provides a high degree of protection againstinterference.3.3DesignSIWAREX JB stainless steel with ATEX certificate①Cover②Screw for cover (4x)③Rear side with nameplate and ATEX plate④Lower part⑤Support for mounting⑥EMC cable glandFigure 3-2 DesignSIWAREX JB stainless steel with ATEX certificate3.3 DesignSIWAREX JB stainless steel with ATEX certificateNameplateThe nameplate shows the order number and other important product information.The following example explains the information on the nameplate.① Product name ② Degree of protection③ Consult operating instructions ④ Development stage ⑤ Manufacturer ⑥ Country of origin ⑦ Serial number ⑧Order no.Figure 3-3NameplateATEX plate①Certification data in accordance with ATEXFigure 3-4ATEX plateSIWAREX JB stainless steel with ATEX certificateApplication planning44.1 Alternative EMC cable glandsIf you need stainless steel EMC cable glands, you can purchase them from corresponding suppliers. Please note that the cable glands must be approved for the respective applications. See Service and support(/automation/service&support )Note4.2Selection of suitable cablesSignal cableThe junction box is connected to the weighing module by means of a signal cable. Use a shielded cable with six cores as the signal cable. We recommend the SIWAREX cable Li2Y2x0.75St+2x(2x0.34St)-CY:● For standard applications: 7MH4702-8AG, orange sheath color.● For intrinsically safe Ex applications: 7MH4702-8AF, light blue sheath color.The cables and lines must correspond to the installation regulations according to EN 60079-14. In hazardous areas, the diameter of individual conductors must not be smaller than 0.1 mm.WARNINGShort circuit/explosion hazardAt an ambient temperature T ≥ 60 °C, use heat-resistant cables which are approved for an ambient temperature at least 20 K higher.NoteThe maximum cable length between the load cell and the weighing module is stated in the weighing module documentation.Application planning4.2 Selection of suitable cablesSuitable cables for spring-loaded terminalsThe following cables are suitable for connecting to the spring-loaded terminalsCross section Design0.08 ... 1.5 mm² AWG 28 ... 16 •Solid•Stranded•Finely-stranded - with galvanized individual wires •Finely-stranded - compacted strands•Finely-stranded with gas-tight crimped-on pin cable lug0.08 ... 1 mm²AWG 28 (18)•Finely-stranded with gas-tight crimped-on end sleevesCAUTIONShort-circuitUse end sleeves for small conductor cross-sections.Otherwise the stripped litz wire may buckle when it is inserted into the terminal. In this case,the line is clamped onto the insulation, which will cause contact problems.Load cell cablesDMS load cells are supplied with connecting cables.Connecting a PAL cableFor non-intrinsically safe use of the junction box, a PAL cable must be connected. An M6x12bolt is provided for this on the mounting flange. The PAL cable must be protected againstbecoming loose on its own, which is achieved by a cable eye crimped to the cable.WARNINGDanger of explosionPlease observe that in the case of shielded cables of intrinsically safe circuits in hazardousareas, only one grounding is permissible.If grounding is to be on both sides, an equipotential bonding conductor with at least 4 mm²must be connected.Installing and connecting 5WARNINGDanger of explosionObserve the test certificates, provisions and laws applicable in the country of operationduring connection, assembly, and operation.For hazardous areas in Europe, for example, this is EN 60079-14.5.1Qualified personnelThe SIWAREX JB junction box must only be mounted and connected by qualified personnel.5.2MountingYou can mount the SIWAREX JB junction box in any position. Preferrably, the cable glandsshould point downward.1.Prepare the location for mounting. Position the corresponding drill holes, see Dimensiondrawing (Page 21).2.Screw the junction box tight with four screws.5.3 Connecting principle 5.3Connecting principleLoad cells with four-wire system1.Connect the load cells to the weighing module according to the circuit diagram.2.Install the following jumpers:Jumper From terminal To terminal1 EXC SENSE2 EXC+ SENSE+NOTICEIf the jumpers are missing, the weighing module will report a wire break.5.3 Connecting principleLoad cells with six-wire systemConnect the load cells to the weighing module according to the circuit diagram.1.6 VKLHOG FRQQHFWLRQ HOHPHQWFigure 5-2 Connecting principle for load cells with six-wire system5.4 Connection 5.4Connection5.4.1Installing the EMC cable glands and the screw plugsLC Input for the connecting cable of a load cellW Output to the weighing module or to the "Ex barrier"PAL Equipotential bonding conductorFigure 5-3 Assignment of the cable glands1.Install an EMC cable gland for each load cell that is to be connected. The position of thecable glands is shown in the figure above.2.Open the cover of the junction box.3.Close any unused openings in the SIWAREX JB enclosure using a cap screw.WARNINGMeasurement inaccuracies/risk of explosionThe cables must be matched to the cable glands.If you use the provided M16x1.5 cable glands, only cables with a diameter of 7 to 12mm may be laid into the device.After installation, make sure that the cables are positioned securely and that the sealsare in the correct position.5.4 Connection5.4.2Connecting the shielding1.Connect the cable shielding in the EMC cable glands so that it covers a broad area.Figure 5-4 Connecting the shielding in the EMC cable gland5.4.3Installing the spring-loaded terminal block in the enclosureFigure 5-5 Mounting the spring-loaded terminal block on the mounting rail1.Tighten the two screws on the mounting rail by one turn each.2.Slide the spring-loaded terminal block on one side under the applied screw ①.3.Insert the spring-loaded terminal block ②.4.Screw the spring-loaded terminal block firmly into place.5.4 Connection5.4.4 Connecting spring-loaded terminals(;&6,* 6(16( 6(16(6,*(;&Figure 5-6Pin assignment of the spring-loaded terminalsIn order to connect the spring-loaded terminals, you require a screwdriver with a maximum blade width of 2.5 mm.1. Strip the insulation from the cables as shown.Figure 5-7 Strip cable2. Push the screwdriver into the rectangular opening ①. This opens the spring clip of the spring-loaded terminal.Figure 5-8 Connection of spring-loaded terminals3. Insert the stripped wire into the round opening as far as the stop ②.4. Remove the screwdriver from the rectangular opening ③.The spring clip firmly holds the stripped wire and establishes the contact.The use of spring-loaded terminals ensures that the contact pressure being exerted is permanently maintained.NoteThe use of spring-loaded terminals ensures that the contact pressure being exerted is permanently maintained.5.4 Connection5.4.5Screwing on the coverRequirementsCAUTIONLoss of degree of protectionPrior to closing the cover, check to ensure that:•No dirt or cable residues are in the enclosure.Such residues could lead to faults or short-circuits.•The sealing surfaces are clean.•The necessary cable glands are installed and screwed tightly in place.•Unused openings are closed using the supplied screw plugs.WARNINGLoss of degree of protectionDegree of protection IP66 is only guaranteed if the device was installed perfectly.Please note that if the device is open or not completely closed, this degree of protection isno longer guaranteed.Procedure1.Place the cover and screw it on properly.Technical data 6 6.1Ambient conditionsAmbient condition ValueAmbient temperature - 50 °C ... + 80 °CStorage temperature - 50 °C ... + 100 °CType of protection: IP66, DIN 605296.2Mechanical and electrical dataEnclosure material Stainless steel 1.4301Weight Approx. 1.5 kgColor Polished stainless steelElectrical connection Spring-loaded terminals 1.5/1 mm2Cable glands •Load cells •Signal cable Screw connectionM16 x 1.5 mmM20 x 1.5 mmTerminal area5 ... 7 mm7 ... 12 mmVibration test of the terminals Acc. to DIN EN 60068-2-6: 1996-0510 ... 150 ... 10 Hz, amplitude 0.35 mmVariable ValueRated voltage max. AC 250 VRated current max. 10 A per terminalConductor cross-section max. 1.5 mm²Technical data6.3 Explosion protection6.3Explosion protectionIn hazardous areas, it is only permitted to use components with the appropriate Ex approval.The junction box can be used in hazardous areas even for connecting an intrinsically safecircuit according to EN 60079-14 or EN 61241-14.In zone 20, certified circuits in category ia, ib or iaD, ibD are permitted.The terminals meet the requirements for disconnecting intrinsically safe circuits: Thecreepage distance and clearance are greater than 8 mm.Only connect the device to circuits that comply with the technical data specified on thenameplate or on the certificates and approvals (e.g., the EC-type examination certificates). Ifthe circuits do not comply with the information in the certificates and approvals, then thesafety required for the approval is longer guaranteed.When using the junction box for type of protection nA, the junction box must be included inthe local potential equalization. The external and internal connection in the cover must beused for this purpose. Use a cable eye that is crimped to the cable to do this. The minimumcross-section of the PAL connecting cable must be the same or greater than the cross-section of the phase conductor. The washer that is also to be used must ensure that thecontact pressure is permanently maintained. The four cover screws must be screwed tight.Before loosening the cover screws, all of the circuits must be de-energized.The circuits that are connected must be either only intrinsically safe or only non-intrinsicallysafe. Mixing is not allowed.If the SIWAREX JB junction box is operated with the markingII 1 D Ex tb + ib IIIC T85°C Da IP66 in hazardous zone 20, then the feeding circuit mustmeet the requirements of protection type "intrinisically safe" Cat. ia or Cat. ib in connectionwith another recognized protection type.6.4Electromagnetic compatibilityThe SIWAREX JB junction box meets the following EMC requirements:●EN 61326: 1999●EN 45501: 1992●NAMUR NE21: 2004To maintain the electromagnetic compatibility, for example,●ensure that the cables are routed with electromagnetic compatibility (even withincabinets!).●lay the signal cable segregated from cables with voltages > 60 V or high currents.●avoid sites neighboring large electrical systemsTechnical data6.5 Dimension drawing6.5Dimension drawingFigure 6-1Dimension drawingOrdering data 7 7.1Order no.Junction boxDesignation Order no.7MH4710-1EA01SIWAREX JB stainless steel with ATEXcertificate7.2AccessoriesEMC cable glands, stainless steelRecommended suppliers:RST Rabe-System-Technik und Vertriebs-GmbHOtto-Lilienthal-Str. 1949134 WallenhorstGermanyPhone: +45 (0) 54 07 / 87 66 – 0Fax: +45 (0) 54 07 / 87 66 – 98Internet: RST in the Internet ()Signal cableRecommended cable:SIWAREX cable Li2Y2x0.75St+2x(2x0.34St)-CYApplication Sheath color Order no.Standard applications Orange 7MH4702-8AGIntrinsically safe Ex application Light blue 7MH4702-8AFAppendix A A.1Technical supportTechnical SupportYou can contact Technical Support for all IA and DT products:●Via the Internet using the Support Request:Support request (/automation/support-request)●E-mail (mailto:******************************)●Phone: +49 (0) 180 5050 222(0.14 €/min on German landlines, prices may vary for mobile systems)●Fax: +49 (0) 180 5050 223(0.14 €/min on German landlines, prices may vary for mobile systems)Further information about our technical support is available in the Internet atTechnical Support (/automation/csi/service)Service & Support on the InternetIn addition to our documentation, we offer a comprehensive knowledge base online on theInternet at:Services & Support (/automation/service&support)There you will find:●The latest product information, FAQs, downloads, tips and tricks.●Our newsletter, providing you with the latest information about your products.● A Knowledge Manager to find the right documents for you.●Our bulletin board, where users and specialists share their knowledge worldwide.●You can find your local contact partner for Industry Automation and Drives Technologiesin our partner database.●Information about field service, repairs, spare parts and lots more under "Services."Additional SupportPlease contact your local Siemens representative and offices if you have any questionsabout the products described in this manual and do not find the right answers.Find your contact partner at:Partner (/partner)A signpost to the documentation of the various products and systems is available at:Documentation (/weighing/documentation)AppendixA.1 Technical support。
夏米尔操作指南4
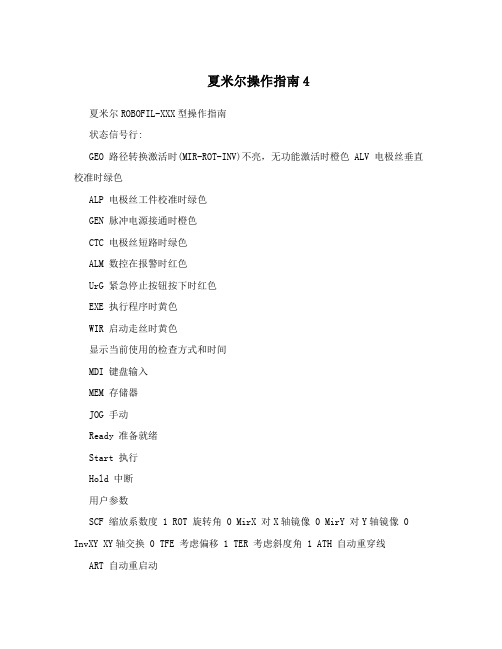
夏米尔操作指南4夏米尔ROBOFIL-XXX型操作指南状态信号行:GEO 路径转换激活时(MIR-ROT-INV)不亮,无功能激活时橙色 ALV 电极丝垂直校准时绿色ALP 电极丝工件校准时绿色GEN 脉冲电源接通时橙色CTC 电极丝短路时绿色ALM 数控在报警时红色UrG 紧急停止按钮按下时红色EXE 执行程序时黄色WIR 启动走丝时黄色显示当前使用的检查方式和时间MDI 键盘输入MEM 存储器JOG 手动Ready 准备就绪Start 执行Hold 中断用户参数SCF 缩放系数度 1 ROT 旋转角 0 MirX 对X轴镜像 0 MirY 对Y轴镜像 0 InvXY XY轴交换 0 TFE 考虑偏移 1 TER 考虑斜度角 1 ATH 自动重穿线ART 自动重启动SIM 空运行MLK 无移动模拟(程序校验)BLK 单段执行BLD 跳段有效,表示程序前有/的就不执行(如/M00) OSP 考虑可选停止制作:尹承效夏米尔ROBOFIL-XXX型操作指南BLK 打勾后,ISO程序单段执行OSP M01无效打勾后,M01有效(M01为暂停)BLD /开头的语句执行打勾后,/开头的语句跳过0、自动穿丝无效即断丝后不会自动穿丝ATH 1、断丝后回起割点自动穿丝再空走到断丝点切2、如果穿丝穿不进就直接加工下一个孔VSIM 空运行速度(6-900)1、机床坐标操做指令:SMA,X10 设制X轴机床坐标值为本10.00 SMA 设定机床坐标值X Y U V 同时为零MOV,X10 机床坐标系中的绝对移动将机床坐标X移到10处(注意无插补,各轴速度一样,路徑不是线性的) MOV XYUV都回零MOV,Z10 Z轴机床坐标移到10处绝对 Z轴不能同其他轴联动移动MVR 机床坐标的相对移动MVR,Z10 Z轴在现在的位置上向上移动10mm(不考虑转换、镜像、缩放,如果数控系统先前为绝对方式,移动后重新回到这一方式)制作:尹承效夏米尔ROBOFIL-XXX型操作指南CTR,X20 在此位置X轴向正方向加工20mm EDG,X-,X0.1252、工件坐标操作指令:SPA,X1 更新坐标SPA 同时更新XY的坐标为零MPA 绝对移动(不带值XY同时移动到零处) MPR 相对移动CPA 绝对加工CPR 相对加工3、预定义的移动GOH,Hh 按照工件高度H移动Z轴以定位喷嘴位 SEP,CPp 存储绝对坐标系中当前点的坐标p=点号,从0-5 GOP,p 移动到所定义的点位上,p=点号,从0-54、工艺和加工规准TEC<,表名> 激活含有准备使用的规准的工艺 WIR<,表名>激活准备使用的电极丝特性表HPA,h 修改当前高度h=新高度单位mm REX,Ee,(Hh)在所用工艺表中选择工艺规准Ee可选修改当高度(Hh) CLE(,c) 引入附加间隙(c=附加间隙,mm) CLE 设定附加间隙为零制作:尹承效夏米尔ROBOFIL-XXX型操作指南5、辅助功能AUX,m 辅助M功能(m=功能号)WTC 电极丝准备和切(拉)断WPR 断丝后的穿丝准备THR 自动穿丝(在WCT或WPR或人工丝准备之后) MDI模式常用指令:CT 相应的G\M代码SMA,XO,YO G74X0Y0 设定机床坐标的0,0点 SPA,XO,Y0 G92X0Y0 设定工件坐标的0,0点 MOV,X0,Y0 G75X0Y0 移动到机床坐标的0,0点 MVR,X2.0 X 方向相对移动2mm THD M60 穿丝WCT M50 剪丝SEP,CP1 G910 A1 设定当前点为1号点 GOP,1 G911 A1 从当前点移动到1号点EDG,Y,Y-0.125 Y方向对边,并把所对面设0CEN,R45 45度找孔中心 MID,R90 90度方向找中 CTR,X10 X方向相对切割10mm简单加工举例:TEC,LT25AREX,E2,H25制作:尹承效夏米尔ROBOFIL-XXX型操作指南CTR,X10程序执行:ZCL 加工计数器设回到零 SIM,I 激活(i=1) 不激活(i=0) EDG,s轴(,轴v) 找边CEN(,Xx)(,Yy)(,Rr) 找孔中心MID(,Xx)(,Yy)(,Rr) 在两个平行面之间找中GG00 快速移动G01 直线插补G02 顺时针圆弧插补G03 逆时针圆弧插补G04 暂停G09 准备停止一次移动到位 G10 指定偏移量/可选责程序跳步值 G11 自动加工顺序G17 编辑面选择G20 英制输入(英寸)G21 公制输入(mm)G22 存储行程极限功能ON(有效) G23 存储行程极限功能OFF G28 返回到第一参考点G29 从参考点返回到用户点 G30 返回到第二、第三、第四用户点 G32 存储当前点为用户第二、第三、第四参考点G33 设定用户点2,3,4G40 取消丝径补偿G41 电极丝左补偿G42 电极丝右补偿G46 最佳反向控制ONG47 最佳反向控制OFFG48 自动角部倒圆ONG49 自动角部倒圆OFFG50 取消斜度G51 左锥度G52 右锥度G53 在绝对坐标系中移动G61 恒定拐角半径制作:尹承效夏米尔ROBOFIL-XXX型操作指南G62 锥形拐角半径(最小) G63 锥形拐角半径(平均) G64 (最大) G65 宏调用(局部)G66 宏调用(全程)G67 取消宏调用(全程) G68 切割进给方式G69 准确停止方式G70 找边G71 找孔中心G72 找槽中心G73 电极丝校准和导向器设定循环 G74 设定测量点/机床坐标系设定 G75 在机床坐标系中定位 G76 定位-找边点类型1或2 G77 定位-测量点类型1、2或3 G78 定位-拐角点G79 计算工件倾斜角G86 取消支撑功能G87 “用支撑保留废芯”方式G88 “切除支撑”方式G90 绝对方式指令G91 相对G93 局部坐标系设定G94 恒速进给G95 伺服进给MM00 停止M01 可选停止(可用来建立支撑以保留废芯)M02 程序结束M06 穿丝水射流ON M07 上导电块退回ON M14 重穿丝块初始化 M15 锥度方式编成 M16 穿丝射水OFF M17 上导电块回退OFF M23 几何精度策略OFF M24 几何精度策略ON M27 保护策略OFF制作:尹承效夏米尔ROBOFIL-XXX型操作指南M28 一级粗加工策略ON M29 二级粗加工策略ON M30 程序结束和重绕 M31 预置计时器M32 检查水的离子度(电导率) M33 检查水的温度M34 工作液槽上水M35 放水M36 工作液槽位记忆+加载液位ON M37 加载液位OFF M40 空运行状态M42 走丝OFFM43 上、下冲液OFF M44 丝张力OFF M50 CUT 切丝M59 穿丝准备M60 穿丝M68 关闭循环泵M69 接通循环泵M70 轨迹返回功能M70 《执行有效》信号的管理 M71M73M74M80 加工状态M82 走丝开M83 下冲液开M87 存储功能1 ON M88 存储功能1 OFF M89 存储功能2 ON M90 存储功能2 OFF M91 遥控器报警有效 M92 遥控器报警无效 M93 遥控器报警接通ON M94 遥控器报警断开OFF M95 脉冲输出功能M96 完成加工M97 镜向反向加工M98 子程序调用M99 子程序结束制作:尹承效夏米尔ROBOFIL-XXX型操作指南穿丝射流水调整:EXE-service-calibration cyeles-wire calibration 激活卸下丝移动上加工头到相对于待加工工件所需的穿丝位置上接通穿丝射流水手动移动U/V轴以便使穿丝射流水对准下导向器的中心并在其周围分布均匀按memorize threading (记忆穿丝)ZUV 键,保存达到的位置存储UV位置;其值在穿丝操作中会自动用到。
WIZORD 4 安装手册说明书
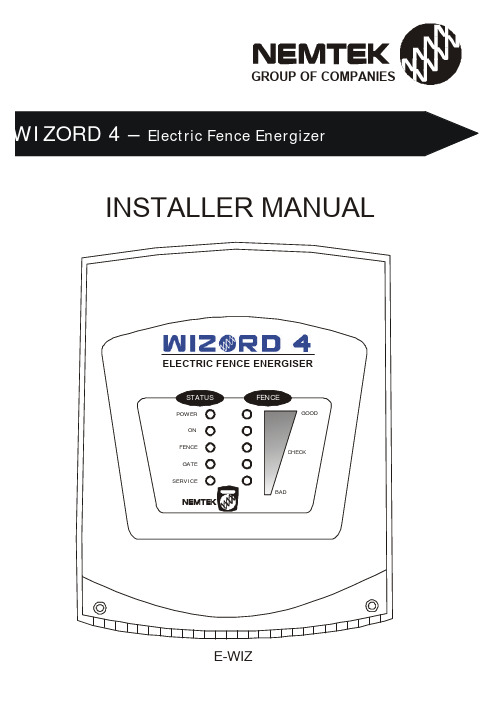
GROUP OF COMPANIESINSTALLER MANUALELECTRIC FENCE ENERGISERINTRODUCTION (3)DISCLAIMER (3)MOUNTING / BATTERY REPLACEMENT PROCEDURES (4)CONNECTION TO THE FENCE (5)CONNECTION / CONFIGURATION DIAGRAM (6)PC BOARD REPLACEMENT PROCEDURES (7)SERVICE CONDITIONS (8)APPENDIX A…………………………………………………………………………………. 9-11I N T R O D U C T I O NThe WIZORD 4 is a battery (12V 7AH nominal) operated energizer suitable for connection to mains (230V 50Hz nominal).The batteries to be used are rechargeable lead-acid batteries. Non-rechargeable batteries must NOT be used. The lead-acid batteries require venting and it is imperative that the energizer be situated in a well-ventilated area.D I S C L A I ME RNEMTEK Holdings (Pty) Ltd or any of its subsidiary companies does not guarantee that the operation of the product will be uninterrupted or totally error free.Energizer specifications may be altered without prior notification.The installer is referred to the definitions and general requirements in Appendix A.The installer must take into consideration the applicable municipal laws concerning the installation of electric fences. General guidelines are available, or refer to the website: . International standards can be viewed at http://www.iec.ch and South African standards on http://www.sabs.co.za.*Energizer to be mounted vertically against a flat surface, in well ventilated area.OPTION 1: NO EARTH LOOP MONITORINGBridge the earth OUT to earth RETURN. The unit will now function as per theold version WIZORD.OPTION 2: EARTH LOOP MONITORING; GOOD SOIL EARTHINGOPTION 3: EARTH LOOP MONITORING; POOR SOIL EARTHING EARTHFEARTHFJUMPER OPERATION:Jumper Description: Inserted: Removed:JP1 Switch input enabled See next tableJP2 Switch input delay (4 minutes) Switch input instantaneous Jumper Description: Inserted: Removed:JP1 See previous table Remote on/off enabled JP2 Plastic tab switch enabled Plastic tab switch disabled * JP3 – Reserved for future use* JP4 – Bypass safety switch. Not to be installed during normal use.terminals if connected PC Board back) into place the PC Board into place.Also ensure that the opto-coupler PC Board REMOVAL: REPLACEMENT:S E R V I C E C O N D I T I O N SOn removing the energizer lid and disconnecting JP3, one or more of the following service conditions may be displayed (Lit LED):FUSE DESCRIPTION & FAULT SYMPTOMSHOW TO CHECK: (ALL FUSES ARE 2 AMPERE FAST BLOW)F1: Energizer does not operate when mains is switched offF2: Siren or strobe light does not operate (ensure that the unit wasswitched off with no fault conditions)F3:Power light is not lit, even when mains is presentGOODSystem TimeoutFence Interference Over-temperature Energizer Faulty or Tampered withBattery Flat SERVICEBASIC DEFINITIONS:Electric Fence: a barrier which includes one or more electric conductors, insulated from earth, to which electric pulses are applied by an energiserConnecting Lead: an electric conductor, used to connect the energiser to the electric fence or the earth electrodeElectric Security Fence: a fence used for security purposes which comprises an electric fence and a physical barrier electrically isolated from the electric fencePublic Access Area: any area where persons are protected from inadvertent contact with pulsed conductors by a physical barrier.Pulsed Conductors: conductors which are subjected to high voltage pulses by the energiser.Secure Area: an area where a person is not separated from pulse conductors below 1,5m by a physical barrier.GENERAL REQUIREMENTS FOR ELECTRIC SECURITY FENCES:Electric fences shall be installed and operated so that they cause no electrical hazard to persons, animals or their surroundings.Electric fence constructions which are likely to lead to the entanglement of animals or persons shall be avoided.An electric fence shall not be supplied from two different energizers or from independent fence circuits of the same energiser.For any two different electric fences, each supplied from a different energiser independently timed, the distance between the wires of the two electric fences shall be at least 2m. If this gap is to be closed, this shall be effected by means of electrically non-conductive material or an isolated metal barrier.Barbed wire or razor wire shall not be electrified by an energiser.Any part of an electric fence which is installed along a public road or pathway shall be identified at frequent intervals by prominently placed warning signs securely fastened to the fence posts or firmly clamped to the fence wires. The size of the warning signs shall be at least 100mm x 200mm. The background colour of both sides of the warning plate shall be yellow. The inscription on the plate shall be black . The warning sign shall typically appear as depicted in Figure x. The inscription shall be indelible, inscribed on both sides of the warning plate and have a height of at least 25 mm.Warning signs shall be placed at- each gate- each access point- intervals not exceeding 10m- adjacent to each sign relating to chemical hazards for the information of emergency services.Gates in electric security fences shall be capable of being opened without the person receiving an electric shock.The energiser earth electrode shall penetrate the ground to a depth of at least 1m. The distance between any electric security fence earth electrode and other earth systems shall not be less than 2m.Connecting leads that are run inside buildings shall be effectively insulated from the earthed structural parts of the building. This may be achieved by using insulated high voltage cable.Connecting leads that are run underground shall be run in a conduit of insulating material or else insulated high voltage cable shall be used. Care shall be taken to avoid damage to the connecting leads due to external factors.Connecting leads shall not be installed in the same conduit as the mains supply wiring, communication cables or data cables.Connecting leads and electric fence wires shall not cross above overhead power or communication lines.Mains supply wiring shall not be installed in the same conduit as signalling leads associated with the electric security fence installation.Crossings with overhead power lines shall be avoided wherever possible. If such a crossing cannot be avoided, it shall be made underneath the power line and as nearly as possible at right angles to it.If connecting leads and electric fence wires are installed near an overhead power line, the clearances shall not be less than those shown in Table 1. Power Line Voltage (V) Clearance(m)Equal or less than 1 000 3>1 000 and equal or less than 33 000 4>33 000 8Table 1If connecting leads and electric fence wires are installed near an overhead power line, their height above the ground shall not exceed 3m.11 Where an electric security fence passes below bare power line conductors, the highest metallic element shall be effectively earthed for a distance of not less than 5m on either side of the crossing point.This height applies either side of the orthogonal projection of the outermost conductors of the power line on the ground surface, for a distance of- 2m for power lines operating at a nominal voltage not exceeding 1 000 V- 15m for power lines operating at a nominal voltage exceeding 1 000V Electric security fences and their ancillary equipment shall be installed, operated and maintained in a manner that minimizes danger to persons, and reduces the risk of persons receiving an electric shock unless they attempt to penetrate the physical barrier, or are in a secure area without authority. Exposed conductive parts of the physical barrier shall be effectively earthed. A spacing of 2.5 m shall be maintained between uninsulated electric fence conductors or uninsulated connecting leads supplied from different energizers. This spacing may be less where conductors or connecting leads are covered by insulating sleeving, or consist of insulated cables, rated to at least 10kV.This requirement need not apply where the separately energized conductors are separated by a physical barrier, which does not have any openings greater than 50mm.A vertical separation of not less than 2m shall be maintained between pulsed conductors fed from different energizers.Ensure that all ancillary equipment connected to the electric security fence circuit provides a degree of isolation between the fence circuit and the supply mains equivalent to that provided by the energiser. Protection from the weather shall be provided from the ancillary equipment unless this equipment is certified by the manufacturer as being suitable for use outdoors, and is of a type with a minimum degree of protection IPX4.。
SHARP电子现金机 Model ER-A410 A420 使用手册说明书

• If the register malfunctions, call your local dealer for service - do not try to repair the register yourself. • For a complete electrical disconnection, pull out the mains plug.
EXTERNAL VIEW OF THE ER-A420 ·························································································8 Front view ···············································································································································8 Rear view················································································································································8
HP X24c模型维护与服务指南说明书

Maintenance and Service GuideX24c modelSUMMARYThis guide provides information about spare parts, removal and replacement of parts, diagnostic tests, problem troubleshooting, and more.© Copyright 2020 HP Development Company, L.P.AMD is a trademark of Advanced Micro Devices, Inc. Bluetooth is a trademark owned by its proprietor and used by HP Inc. under license. NVIDIA is a trademark and/or registered trademark of NVIDIA Corporation in the U.S. and other countries. USB Type-C and USB-C are registered trademarks of USB Implementers Forum. DisplayPort and the DisplayPort logo are trademarks owned by the Video Electronics Standards Association (VESA) in the United States and other countries.The information contained herein is subject to change without notice. The only warranties for HP products and services are set forth in the express warranty statements accompanying such products and services. Nothing herein should be construed as constituting an additional warranty. HP shall not be liable for technical or editorial errors or omissions contained herein.First Edition: April 2021Document Part Number: L89666-X24C-MSG-V1Assembly part number: L89666-001Table of Contents1 Getting started (1)Important safety information (1)Important service information and precautions (1)RoHS (2002/95/EC) requirements (2)General descriptions (2)Firmware updates (2)Before returning the repaired product to the customer (2)2 Monitor features (3)Features (3)Front components (4)Rear components (5)Locating the serial number and product number (6)3 Illustrated parts catalog (7)How to order parts (8)4 Removal and replacement procedures (9)Preparation for disassembly (9)Power board ........................................................................................................................................ ..12Connector repair .................................................................................................................................. ..13 Audio connector M1 .................................................................................................................. ..14HDMI connector J2 ................................................................................................................... ..14DP connector J3 ....................................................................................................................... ..15 Function test (17)Function test (17)Support and troubleshooting ............................................................................................................... ..17Index .................................................................................................................................................... ..19iii11 Getting startedRead this chapter to learn about safety information and where to find additional HP resources.Important safety informationCarefully read the cautions and notes within this document to minimize the risk of personal injury to service personnel. The cautions and notes are not exhaustive. Proper service methods are important to the safe, reliable operation of equipment. Improper service methods can damage equipment.The service procedures recommended and described in this service manual provide effective methods of performing service operations. Service engineers should have prior repair knowledge and experience as well as appropriate training for the product before performing service procedures.●Be sure your working environment is dry and clean and meets all government safety requirements. ●Be sure that other persons are safe while you are servicing the product. ●Do not perform any action that can cause a hazard to the customer or make the product unsafe. ●Use proper safety devices to ensure your personal safety. ●Always use approved tools and test equipment for servicing. ●Never assume the product’s power is disconnected from the main power supply. Check that it is disconnected before opening the product’s cabinet. ●Modules containing electrical components are sensitive to electrostatic discharge (ESD). Follow ESD safety procedures while handling these parts. ●Some products contain more than one battery. Do not disassemble or expose a battery to high temperatures, such as throwing into fire, or the battery may explode. ● Refer to government requirements for battery recycling or disposal.This information provides general service information for the monitor. Adherence to theprocedures and precautions is essential for proper service.IMPORTANT: Only trained service personnel who are familiar with this HP product should perform service or maintenance for it. Before performing any service or maintenance, personnel must read the important safety information.IMPORTANT: You must disconnect the power cord from the power source before opening the monitor to prevent component damage.Important service information and precautions●Repair must be performed by professional service technicians in a repair center. End users should not perform these procedures. ●Please note during servicing that the primary side is the high voltage area. ●This monitor meets ROHS requirements. Be sure to use lead-free solder wire when soldering. ●If you must change a capacitor, be sure to match the polarity as printed on the PCB. ●If you must replace a capacitor, make sure the specification and part number match the BOM and location.●If you must replace a capacitor, insert new parts carefully to avoid a short circuit caused by thenear pin.●Do not get the board wet. Water and moisture can cause a short circuit that causesmalfunctions.●To avoid damage, be sure to use lead-free solder.●When soldering, work quickly to avoid overheating the circuit board.●Keep the soldering iron tip clean and well tinned when replacing parts.●After repair, perform a close inspection of the circuit board to confirm it is in good condition.●After repair, perform a function test to confirm the power supply is working properly.ERP Lot5 requirement1. A professional repairer must have the technical competence to repair electronic displays andcomply with the applicable regulations for repairers of electrical equipment in the Member Stateswhere the repairer operates. Reference to an official registration system as professional repairer,where such a system exists in the Member States, shall be accepted as proof of compliance.2. A professional repairer must have insurance that covers liabilities resulting from repairs,regardless of whether required by the Member State.RoHS (2002/95/EC) requirementsApplied to all countries that require RoHS.The RoHS (Restriction of Hazardous Substance in Electrical and Electronic Equipment Directive) is alegal requirement by the EU (European Union) for the global electronics industry sold in the EU andother countries. Any electrical and electronics products launched in the market after June 2006 shouldmeet this RoHS requirement. Products launched in the market before June 2006 are not required to becompliant with RoHS parts. If the original parts are not RoHS complaint, the replacement parts can benon-ROHS complaint. If the original parts are RoHS compliant, the replacement parts MUST be RoHScomplaint.If product service or maintenance requires replacing parts, confirm the RoHS requirement beforereplacement.General descriptionsThis manual contains general information. There are two levels of service:Level 1: Cosmetic/appearance/alignment serviceLevel 2: Circuit board or standard parts replacementFirmware updatesFirmware updates for the monitor are available at . If no firmware is posted, the monitordoes not need a firmware update.Before returning the repaired product to the customer Perform an AC leakage current check on exposed metallic parts to be sure the product is safe tooperate without the potential of electrical shock. Do not use a line isolation transformer during thischeck.Measurements that are not within specified limits present a possible shock hazard. You must check andrepair the product before returning it to the customer.232 Monitor featuresThis chapter provides an overview of the monitor’s features.FeaturesDepending on the model, your monitor might include the following features:● 59.94 cm (23.6-inch) diagonal viewable screen area with 1920 x 1080 resolution, plus full-screen support for lower resolutions; includes custom scaling for maximum image size while preserving original aspect ratio● Anti-Glare panel with an LED backlight● Wide viewing angle to allow viewing from a sitting or standing position, or when moving from side to side● Tilt capability● Swivel and height adjustment capabilities● Removable stand for flexible monitor head mounting solutions● Display Port video input● High-Definition Multimedia Interface● Audio headphone● Plug-and-play capability if supported by your operating system● Security cable slot provision on rear of monitor for optional security cable● On-Screen Display (OSD) adjustments in several languages for easy setup and screenoptimization● High-Bandwidth Digital Content Protection (HDCP) copy protection on all digital inputs●Energy saver feature to meet requirements for reduced power consumptionNOTE: For safety and regulatory information, refer to the Product Notices provided in yourdocumentation kit. To access the latest user guides or manuals for your product, go to/support and follow the instructions to find your product. Then select Manuals .4Front componentsTo identify the components on the front of the monitor, use this illustration and table. 123456ControlDescription 1Menu button Press to open the OSD menu, select a menu item from the OSD, or close the OSD menu.2-4Function buttonsWhen the OSD menu is open, press the buttons to navigate through the menu. The function light icons indicate the default button functions. For a description of these functions, see Using the function buttons on page 14.You can reassign the function buttons to quickly select the most commonly used operations. See Reassigning the function buttons on page 14.5Power Turns the monitor on or off.6Power light White: The monitor is on.Amber: The monitor is in standby mode.5Rear componentsTo identify the components on the rear of the monitor, use this illustration and table. 1234ComponentDescription 1Power connector Connects the power cable to the monitor 2HDMI connector Connects the HDMI cable to the monitor 3DisplayPort connectorConnects the DisplayPort cable to the monitor 4Audio-out (headphone)jack Connects headphones to the monitor.CAUTION: To reduce the risk of personal injury, adjust the volume before using headphones or earbuds. For additional safety information, see the Product Notices provided in your documentation kit.Locating the serial number and product numberThe SPEC label (1) and Barcode label (2) are located on the rear of the monitor. The serial number and product number are located on a Safety label. You may need these numbers when contacting HP about the monitor model.For worldwide models (except India): LabelFor India:label673 Illustrated parts catalogTo identify the monitor major components, use this illustration and table.How to order partsThe HP authorized repair center can purchase the power board from HP.Power boardDescription HP spare part number Manufacturer part numberPSU X24c 21204-00925-S01M84714-00121204-00925 Capacitors and connectors are available for purchase from the following EU distributors:Digi-Key: Capacitors by distributorComponent description Location ComponentdistributorDistributor part numberEC_470uF_25V_10*13C811、C817 Digi-Key399-6656-1-NDEC_470uF_25V_10*13 RS- Component 862-3175 Connectors by manufacturerComponent description LocationidentifierComponentdistributorDistributer part numberDisplayPort P105Digi-Key670-2430-NDHDMI P111Digi-Key1175-2000-1-2-30-00-BK-TR-ND Audio P602Digi-KeyCP1-3525NG-NDNOTE: The connector may need to be modified to meet functionality, regulatory and safetyrequirements if it is not an exact match.You can purchase cables from the HP part store at https:///Search.aspx.NOTE: HP continually improves and changes product parts. For complete and current informationabout supported parts for your computer, go to , select your country or region,and then follow the on-screen instructions.894 Removal and replacement proceduresAdherence to these procedures and precautions is essential for proper service.Preparation for disassemblyUse this information to properly prepare to disassemble and reassemble the monitor.1) Read the “Important safety information” and “Important service information and precautions”sections in the “Getting started” chapter of this guide. 2) Clean the room for disassembly. 3) Identify the disassembly area.4) Check the position that the monitors are to be placed along with the number of monitors. Prepare thearea for material flow according to the disassembly layout. 5) Be sure to have the following equipment and materials:∙ Press fixture ∙ Working table ∙ Screwdriver ∙ Knife ∙ Gloves ∙ Cleaning cloth ∙ ESD protection ∙Scraper bar in the following dimensions:▲ Prepare the monitor for disassembly.1) Rotate the screw from counterclockwise to remove base102) Disassembly VESA cover by hexagon keys, turn the four screws clockwise to remove the arm fromthe display head.3) Use knife to sparated the rear cover from the MNT head through the tear down slots which on thebottom side.4) a.Remove the acetate tape (red frame)/unplug the backlight (green frame), remove the aluminumfoil (yellow frame) to release wire and the shielding case.b. Remove screws(red circles) and remove shielding(need to pull-out the wires first).115) a.Release screw from shielding case bottom side.b. Remove Main board from shielding case6) Remove the screws*11 which around bezel, then remove bezel from panel rear side.7) a.Remove screw from red portion.b. Release screws from mylars.c. Remove screws fromM/B(yellow)&P/B(red).12Power boardThe power board part number is 21204-01047. Before removing the power board, follow these steps: ▲ Prepare the monitor for disassembly. Remove the power board:1) The HP X24c power board connector position is as follows:132) Locate the part number location on the board.Connector repairThis procedure includes HDMI, DisplayPort and audio connectors. The connectors are on the main board (board part number 60104-09513). The connectors identifiers are as follows:Connector LocationHDMI P111 DisplayPort P105 AudioP60214Before repairing connectors, follow these steps:▲ Prepare the monitor for disassembly. See Preparation for disassembly on page 9.Audio connector P602Repair the audio connector:1) Use a hot air gun to melt the solder on the pins. Pin solder with soldering iron and absorber. Youcan gently push down with the soldering iron once everything is molten to move the P602 out of the through holes.2) Lift the P602 connector from the circuit board.3) Place the new component on the circuit board. Be sure that it matches the footprint. 4) Solder the new component.HDMI connector P111Repair the HDMI connector:1)Use a soldering iron and a de-soldering pump to remove as much solder as possible from the pin.152) Use a hot air gun to melt the solder on the pins.3) Lift the P111 connector from the circuit board.4) Place the new component on the circuit board. Be sure that it matches the footprint. 5) Solder the new component.DP connector P105Repair the DP connector:1) Use a soldering iron and a de-soldering pump to remove as much solder as possible from the pin.2)Use a hot air gun to melt the solder on the pins.3) Lift the P105 connector from the circuit board.4) Place the new component on the circuit board. Be sure that it matches the footprint.5) Solder the new component.1617Function testAfter repair, be sure to confirm that all functions are working.Support and troubleshootingThe following table lists possible problems, the possible cause or each problem, and the recommended solutions.Table 4-1: Function test Test item Operating descriptionTool usedHDMI test Confirm whether image displays and sound plays correctly on the monitor.Computer or DVD player DP test Confirm whether image displays and sound plays correctly on the monitor.Computer or DVD playerAudio testChange volume and balance to confirm whether volume is smooth and loud enough.Speaker Table 4-2: Solving common problems Problem Possible cause Solution Screen is blank or video is flashing. Power cord is disconnected.Connect the power cord.Monitor is off.Power the power button. NOTE: If pressing the Power button has noeffect, press and hold the power button for 10 seconds to disable the Power button lockout feature.Video cable is improperly connected. Connect the video cable properly.System is in Sleep mode.Press any key on the keyboard or move the mouse to exit Sleep mode. Video card is incompatible.Open the OSD menu and select the Input Control menu. Set Auto-Switch Input to Off and manually select the inputImage appears blurred,indistinct, or tooBrightness is too low. Open the OSD menu and select Brightness toadjust the brightness scaledark. asneeded.Check Video Cable is displayed on screen. Monitor video cable is disconnected. Connect the appropriatevideo signal cablebetween the computer andmonitor. Be sure that thecomputer power is offwhile you connect thevideo cable.Input Signal Out of Range is displayed on screen. Video resolution and/or refresh rate are sethigher than what the monitor supports.Change the settings to asupported setting.The monitor is off, but it did not seem to enter into Sleep mode. The monitor’s power saving control is disabled.Open the OSD menu andselect Power Control >Auto-Sleep Mode and setauto-sleep to On.On-Screen Menus are Locked is displayed. The monitor’s OSD lock function is enabled. Press and hold the Menubutton on the front bezel to10 seconds to disable theOSD lockout function.Power Button is Locked is Displayed The monitor’s power button is locked. Press and hold the powerbutton for 10 seconds todisable the power buttonlock function.1819Indexcomponents front, 4 rear, 5connector repair, 13 features, 3firmware updates, 2 front components, 4 function test, 17HDMI connector location, 14 how to order parts, 8 illustrated parts catalog, 7 parts, 8power board, 12precautions, 1preparation for disassembly, 9 rear components, 5 removalpower board, 12removal and replacement procedures, 9 RoHS (2002/95/EC) requirements, 2 safety information, 1 service information, 1 spare parts, 9support and troubleshooting, 17 troubleshooting, 17DP connector location, 15。
eView MD204L V4 说明书

目录第一章产品概述 (1)1.1功能 (1)1.2一般规格 (1)1.3各部分名称 (2)1.4外型尺寸及安装方法 (4)第二章编辑软件TP200 (5)2.1 TP200基本概述 (5)2.2编辑用户画面 (5)2.3保存工程 (29)2.4下载画面 (30)2.5 导入旧工程 (30)第三章操作方法 (32)3.1联机通讯 (32)3.2切换画面 (32)3.3系统口令 (32)3.4修改数据 (33)3.5开关量控制 (34)第四章与PLC的连接方法 (35)4.1三菱FX系列 (35)4.2西门子S7-200系列 (36)4.3欧姆龙C系列 (36)4.4施耐德NEZA/TWIDO系列 (37)4.5 台达DVP系列 (38)4.6松下FP系列 (38)4.7 LG Master-K CNet系列 (39)4.8 LG系列 Modbus 协议 (40)4.9 LG Master-K 120S 编程口通讯 (41)4.10 FACON永宏系列 (41)4. 11 光洋S系列 (42)4.12 ECOSTEP 系列 (43)4.13 AB Micrologix系列 (44)4.14 MODBUS RTU/ASCII/EMERSON/RTU EXTEND (45)4.15 MODBUS SERVER (46)4.16 eView自由协议 (47)4.17 SAIA PCD S-BUS协议 (48)4.18 VIGOR PLC (49)4.19 EMERSON EC20系列PLC (49)4.20 KEYENCE KV系列PLC (50)eView TP200 V4.0.0 组态软件Release Note (51)附录1:自由协议文档 (56)附录2:其它注意事项 (58)第一章产品概述1.1功能MD204L是一个小型的人机界面,主要与各类PLC(或带通信口的智能控制器)配合使用,以文字或指示灯等形式监视、修改PLC内部寄存器或继电器的数值及状态,从而使操作人员能够自如地控制机器设备。
REVO C REVEX 服务器面板工程手册说明书

Engineering manualREVO C / REVEX service terminal PLEASE READ THIS MANUAL BEFORE ATTEMPTING TO CONNECT AND/OR SWITCHING POWER ON THE MODULES. THIS DOCUMENT CONTAINS VERY IMPORTANT INFORMATION THAT WILL PREVENT WRONG CONNECTIONS THAT CAN CAUSE DAMAGE TO THE UNITS.Thank you for choosing the “REVO C/REVEX service terminal”This manual should enable you to use your machine to full satisfaction.Every effort has been made to provide you with maximum performance, ergonomics and benefits from this premium quality product. Version History:07-02-2020 Initial version V1.0 for software version V100.001.This document describes the installation, service and configuration of the REVOC/REVEX service terminal application in Pro-Face GP4116 touchscreen. It is a technical manual for the equipment manufacturer. For the normal operation of this equipment we refer to the user manual. You can use parts of this manual for the manual that you supply with the equipment.REMARK: CasCade strongly advises you read this manualthoroughly before starting up the system. This canprevent damage and a dangerous situation for yourselfand the end user of the equipment.WARNING: The configuration/setup must be performed bytechnically educated personnel. This can preventdamage and a dangerous situation for yourself and theend user of the equipment.This system consists of:1x Pro-face GP4116 touchpanel with COM1 3 wire RS-485 interface1x REVO C/REVEX power module (1, 2 or 3 phase versions)Care has been taken for the correctness of this manual. When there should be errors in this manual, CasCade, nor her employees, can be held responsible for any consequential damage that could be caused by this.TABLE OF CONTENTSTABLE OF CONTENTS4 READ THIS FIRST5 Explanation of symbols5 Touchscreen introduction6 Touchscreen maintenance6 Touchscreen cleaning7 1. CONNECT REVO C/REVEX MODULE AND GP-4116 screen8 1.1 Connect communication cable between REVO C/REVEX and GP4116.81.5 Connect power to GP-4116112. CONFIGURING THE REVO C/REVEX COMMUNICATION PORT SETTINGS123. SETUP of GP4116 touchpanel17READ THIS FIRSTExplanation of symbolsThe following signs have been used throughout this manual to draw your attention.Hint: Useful hints for ease of operation.Printed in Blue.Info: Information you should know to fully understand your system andbenefit from its properties. Printed in green.Warning: Read these important messages before executing the desiredoperation. Printed in red.Warning: Read these important messages before executing the desiredoperation. Printed in red.Touchscreen introductionYour machine has been equipped with a “Human Machine Interface” or HMI or -more popular called-: A touch screen.If you are familiar with touch screen operation, found nowadays on modern cell phones, navigation systems, informational displays etc. you may want to skip this section. If however, this is the first time you are using a touch screen, please keep in mind that in contradiction with older fashioned operating panels utilizing mechanical buttons, lamps and displays, both the displays and images on a touch screen can be interactive too, meaning they will react on a touch by your finger. The interface on the touch screen is optimized for ergonomic operation. In practice this means that all objects are positioned and sized such, that they can be touched easily with your finger without the need for a stylus or precise positioning. A soft tipped stylus can be used if preferred, but is normally not required for proper operation.Touching objects on a touch screen can be compared with a mouse-click on a computer screen. Based on the shown graphical user interface and your finger’s position on the screen, the system can determine what action it should take when an object is touched.To prevent accidental, unwanted actions some objects may require a prolongedtouch, meaning you should keep your fingers pressed longer on a certain object (like a button or display) to invoke the required action. Touchscreen maintenanceIMPORTANT - READ THIS FIRSTNever operate a machine until you have fully understood it’s safe workingconditions and operating principles.Never operate the machine unless you are authorized to do soNORMAL EVERY DAY USAGEYour touch screen utilizes a sensitive touch mechanism. The technique used provides reliable operation, even when the screen is modestly covered with moist and dirt. It also allows the wear of rubber gloves. And even under these conditions it should normally react already on a gentle touch .Some buttons may require a prolonged touch to prevent unwanted actions.If the touch screen fails to respond, ask yourself first whether you have applied a validcommand. If in doubt, you could check the responsiveness of the touch screen by using other commands.Each valid command will invoke a short beep, confirming the reception of the touch. However, whether or not the actual action is performed depends also on other conditionsAvoid applying excessive force on the touch screen and never use sharp or hardobjects (e.g. nails, tools, kitchenware or a pencil) to operate it ! In either case you might damage the screen and void your warranty.Touchscreen cleaningYour touch screen is provided with a durable front sheet which is water, oil and fat resistant. The best way to clean the front sheet is with a soft, lukewarm and mildly moist cloth.Special, disposable front cover protection sheets that will reinforce and protect your touch screen, are available through your dealer.Never use solvents (e.g. thinner, tri, turpentine) hot water, soda, abrasives orother aggressive matter for cleaning.1. CONNECT REVO C/REVEX MODULE AND GP-4116 screenThis part describes how to connect the power supply and communication cable to the REVOC/REVEX. Also consult the CD Automation manual that was supplied with the REVO C/REVEX module.1.1 Connect communication cable between REVO C/REVEX and GP4116.You can connect the RS485 modbus communication cable between the REVO C M5 port and the GP4116 COM1 connector.REVO C:M5 point 9=B and M1 point A+ (white wire to GP4116) and M1 point B- (brown wire to GP4116)REVEX: different connections depending on the size of the thyristorFor 30-40A and 60-90A: use M3For the larger thyristors, use M1 point 11-12Here is the REVEX communication port for higher currents than above.For good EMC/EMI immunity, use a Lapp RS-485 modbus communication cable that is 120ohm impedance corrected. Use Lapp Unitronic bus LD 2x2x0.22 article number 2170204. You can order per meter at Conrad electronic.Please also note the red and blue wires that are bridging signals on the GP-4116 connector.For completeness here an extra informative picture from the Pro-face manual. You see here a description of all signals that are present on the GP4116 COM1 connector.1.5 Connect power to GP-4116The touchscreen must be supplied with 24VDC. This must be connected to the power supply connector of the touchscreen.Please regard the polarity of the +24VDC signals This is also marked on the touch screen. The incorrect connection of the power supply can result inirrepairable damage that is outside the normal warranty.The FG (functional ground) must also be connected to the central PE (protective earth) connection of the unit. This can prevent damage to the touchscreen in caseof an electrostatic discharge.2. CONFIGURING THE REVO C/REVEX COMMUNICATION PORT SETTINGSTo configure the REVO C/REVEX communication port (i.e. set to correct Modbus address 1, 2, 3 or 4 and 19200bps N81) you must make use of the thyristor configurator tool that you can download from the CD automation website.https:///product/software/#grefHere you can also download the drivers for the USB interfaceFor the service touchscreen, you need to adjust the Modbus slave port on each REVO C/REVEX to a Modbus address 1, 2, 3 or 4 and 19200bps N81.First connect the 24VDC power supply to the Revo C or REVEX unit (see manual) and make sure you have connection with it via a micro-usb cable (maybe your mobile phone has it).First check in windows on which comport the interface to the Revo C/REVEX has been mapped. Keep on using always the same USB port because windows mappes other COMport number to each differen t USB port (don’t know why?).Start the thyristor configuration tool and adjust the comport settings to what you found in the device settings. Do this with setting-communicationSelect Revo C or REVEX and push “upload from unitSet address 1 and push read”. All parameters will now be read from the Revo C/REVEX (takes a short while, just wait).Push test, click on the blue actual level 0 and login with 1111 when you want to make changesNow move the window a bit to the left and push ONLINE, to go online with the Revo C/REVEX. Push communicationsSet the COM1 comport speed to 19200bps and the desired Modbus address of the module (either 1, 2, 3 or 4).3. SETUP of GP4116 touchpanelWhen the Revo C/REVEX thyristor modules are configured properly we can start the GP4116 screen for the first time.First we need to configure the touchpanel in the initial setup. This will only be necessary when the screen starts for the first time. After that the settings are stored and the screen will start automatically.First select the language and push nextThen select which modules are present in the system.There can be a mix of both the REVEX and REVO C modules of different sizes, since the communication protocol of the REVEX and the REVO C is the same.This is an overview what has been selected in the setup. Push next and the settings will be stored in the screen and the system is ready for use.。
SilverSchmidt 和 Hammerlink 操作说明说明书

目录1. 安全和责任2. 如何着手2.1 SilverSchmidt 基础知识 4 2.2 SilverSchmidt 的部件 5 2.3 SilverSchmidt 显示屏 6 2.4 用户界面基本原理 72.5 正确使用回弹仪 73. 可选设置3.1 单位8 3.2 统计信息 8 3.3 转换曲线 9 3.4 形状因数 9 3.5 碳化修正系数 103.6 检查当前设置104. 应用11 4.1 均匀性评估11 4.2 估算现场抗压强度12 4.2.1 碳化12 4.2.2 配合使用形状因数和 SilverSchmidt 134.2.3 测试低强度混凝土145. 操作仪器5.1 单击模式 16 5.2 测量序列 17 5.3 删除上次冲击(异常值) 185.4 使用数据列表 186. 订购信息 197. 技术规格 208. 保养和支持 219. 启动 Hammerlink 22 9.1 查看数据23 9.2 调整设置24 9.3 调整日期和时间 24 9.4 导出数据 25 9.5 删除和恢复数据 26 9.6 其它功能 26 9.7 自定义统计信息 27 9.8 自定义曲线 281. 安全和责任安全和使用预防措施本手册包含了 Silverschmidt回弹仪的安全、使用和保养等方面的重要信息。
请在首次使用仪器前仔细阅读本手册。
请安全保管本手册以备将来参考。
责任和保修Proceq 的“销售和交付一般条款和条件”适用于所有情形。
由于下列某种或多种原因造成的人身伤害或财产损失,我们不予担保,也不承担任何责任:• 未按照本手册所述的使用方法使用该仪器。
• 错误进行操作性能检查和对仪器及其组件进行不当维护。
• 未按照本手册的说明对仪器及其组件进行性能检查、操作和保养。
• 未经授权对仪器及其组件进行结构更改。
• 因异物、事故、故意破坏和不可抗力而造成的严重损坏。
Proceq SA出于善意提供本文档的所有信息,并相信这些信息正确无误。
HP 外部设备用户指南.pdf_1701934686.821407说明书

External Devices User Guide© Copyright 2008 Hewlett-Packard Development Company, L.P.The information contained herein is subject to change without notice. The only warranties for HP products and services are set forth in the express warranty statements accompanying such products and services. Nothing herein should be construed as constituting an additional warranty. HP shall not be liable for technical or editorial errors or omissions contained herein.First Edition: July 2008Document Part Number: 482360-001Product noticeThis user guide describes features that are common to most models. Some features may not beavailable on your computer.iiiiv Product noticeTable of contentsUsing a USB deviceConnecting a USB device (2)Stopping and removing a USB device (3)Using USB legacy support (3)Index (4)vviUsing a USB deviceUniversal Serial Bus (USB) is a hardware interface that can be used to connect an optional externaldevice, such as a USB keyboard, mouse, drive, printer, scanner, or hub.Some USB devices may require additional support software, which is usually included with the device.For more information about device-specific software, refer to the manufacturer's instructions.The computer has 4 USB ports, which support USB 1.0, USB 1.1, and USB 2.0 devices. A USB hubprovides additional USB ports that can be used with the computer.1Connecting a USB deviceCAUTION:To prevent damage to a USB connector, use minimal force to connect a USB device.▲To connect a USB device to the computer, connect the USB cable for the device to the USB port.You will hear a sound when the device has been detected.NOTE:The first time you connect a USB device, the “Installing device driver software” message isdisplayed in the notification area, at the far right of the taskbar.2Using a USB deviceStopping and removing a USB deviceCAUTION:To prevent loss of information or an unresponsive system, stop a USB device beforeremoving it.CAUTION:To prevent damage to a USB connector, do not pull on the cable to remove the USB device.To stop and remove a USB device:1.Double-click the Safely Remove Hardware icon in the notification area, at the far right of thetaskbar.NOTE:To display the Safely Remove Hardware icon, click the Show Hidden Icons icon (< or<<) in the notification area.2.Click the name of the device in the list.NOTE:If the USB device is not listed, you do not have to stop the device before you remove it.3.Click Stop, and then click OK.4.Remove the device.Using USB legacy supportUSB legacy support (enabled by default) permits the following actions:●Using a USB keyboard, mouse, or hub connected to a USB port on the computer during startup orin an MS-DOS-based program or utility●Starting or restarting from an optional external MultiBay or an optional USB bootable deviceUSB legacy support is enabled at the factory. To disable or reenable USB legacy support in Computer Setup, follow these steps:1.Turn on or restart the computer, and then press esc while the “Press ESC key for Startup Menu”message is displayed at the bottom of the screen.2.Press f10 to enter the BIOS Setup.e a pointing device or the arrow keys to select System Configuration>DeviceConfiguration s.4.To disable USB legacy support, click Disabled next to USB legacy support. To reenable USBlegacy support, click Enabled next to USB legacy support.5.To save your changes and exit Computer Setup, click Save in the lower-left corner of the screen,and then follow the on-screen instructions.– or –Use the arrow keys to select File>Save changes and exit, and then follow the on-screeninstructions.Your changes go into effect when the computer restarts.Stopping and removing a USB device3IndexCcablesUSB2Hhubs1PportsUSB1UUSB cable, connecting2 USB devicesconnecting2description1removing3stopping3USB hubs1USB legacy support3 USB ports, identifying1 4Index。
smart reverb 说明书

m a n u a ls m a r t :r e v e r b s mart:re ve rbm a n u a ls m a r t :r e v e r b Welcome to smart:reverb3Install 4Authorization 5User Interface6Global Reverb Controls 7Global Reverb Controls 8Custom-tailored Reverb 9The Reverb Matrix 10The Particle Display 11The Temporal Shaper 12The Spectral Shaper Grid 13Pre-Filter EQ14Settings 15contentso v e r v i e wc o n t e n tsm a n u a ls m a r t :r e v e r b w e l c o m e t o s m a r t :r e v e r bWelcome to smart:reverbBecause no two audio tracks are the same, smart:reverb’s processing focuses on the individuality of each signal. With a single click, the plug-in quickly analyzes the source material to create each reverb from scratch. By custom-fitting the reverb to the spectral and temporal characteristics of the input signal, typical problems such as disturbing resonances or muddy reverb tails are avoided from the very beginning.Simultaneously, smart:reverb computes a matrix that provides a range of styles for the reverb at hand—each of them tailored to the input signal. Guided by descriptive properties, users can quickly find the style that best suits their creative visions without having to search through hundreds of presets.For maximum control, the plug-in provides an interactive view of the reverb’s anatomy. A detailed interface makes it easy to manipulate the deep-structure of the reverb by modifying its frequency and time-dependent decay rate as well as the reverb’s spread or density evolvement over time.smart:reverb is a source-adaptive reverb plug-in. It delivers custom-tailored reverb by adjusting its processing to the individual characteristics of the input material. In addition, smart:reverb creates an intuitively navigable reverb matrix for quickly finding the right sound.m a n u a ls m a r t :r e v e r b m i n i m u m r e q u i r e m e n t s | W i n d o w s | O S Xi n s t a l l Mac OSXTo start the installation process, please open the disk image sonible_smartreverb.dmg . This will mount the image and open a finder window showingthe content of the installation package.To install smart:reverb on your system, run theinstallation file smartreverb_installer.pkg .The installer will now guide you through the necessary steps to install smart:reverb on your computer. smart:reverb will automatically be installed in the default locations for audio plug-ins.Default folders:Audio Unit/Library/Audio/Plug-Ins/Components/VST/Library/Audio/Plug-Ins/VST/System requirementsInstallWindows To start the installation process, extract the downloaded zip-file sonible_smartreverb.zip onto your hard disk and run the installer.The installer will now guide you through thenecessary steps to install smart:reverb on your computer.During installation, you can select which version(s)of smart:reverb you want installed. You can also select custom installation folders for the VST version or simply use the default folder suggested by the installer.The VST3 and AAX versions of the plug-in will be automatically installed in their respective default folders.Default folders:VST3 (on a 64 bit operating system):..\Program Files\Common Files\VST3\..\Program Files(x86)\Common Files\VST3\AAX (on a 64 bit operating system)..\Program Files\Common Files\Avid\Audio\Plug-Ins ..\Program Files(x86)\Common Files\Avid\Audio\CPU RAMOperating systemsIntel Core Duo, i52GBWindows 10 (64 bit)Mac OSX 10.7+m a n u a ls m a r t :r e v e r b l i c e n s i n g s y s t e m | u n l o c k i n g | t r i a l v e r s i o na u t h o r i z a t i o n AuthorizationUnlockingIf you purchased a license for smart:reverb online, you will receive your license key via email.Machine-based unlockingWhen opening smart:reverb for the first time, a notification window will be displayed asking you to unlock smart:reverb with a valid license key.Please make sure that your computer is connected to the internet before starting the registration process.Enter your license key and click "register." The plug-in will now communicate with our server to check if the license is valid. If it is – enjoy!iLokIf you transferred your license to an iLok, simply attach the iLok to your computer. The plug-in will then be automatically registered – enjoy!If you don’t receive the email within minutes please check your junk folder first before contacting our support (*******************).Trial versionTo run smart:reverb in demo-mode, simply click "try" and you will then be able to use smart:reverb for a couple of days without any limitations. (Please refer to our website to find out more about the current demo period of smart:reverb)When the demo period expires, you will need to purchase a full license in order to continue using the plug-in.Licensing systemYou can select between two licensing systems: machine-based or iLok (USB dongle).By creating a user account on and registering your products – if they are not already visible in your Dashboard – you can manage your plug-in activations.Machine-basedEach license key allows you to install smart:reverb on two computers with unique system IDs. These system IDs are registered during license activation.The same license can be used by multiple users, but each user has to individually unlock the full version of smart:reverb under their account.In the case of a system-ID being changed (e.g. replacement of the hard drive), you can revoke/activate the plug-in next to the respective system-ID in the Dashboard of your sonible user account.iLokIf you want to transfer one activation to your iLok, first make sure the plug-in is registered in your sonible user account. Click on the button "transfer to iLok" next to the plug-in in your Dashboard and follow the instructions.Note: 1st gen iLok dongles and the iLok Cloud arecurrently not supported.m a n u a ls m a r t :r e v e r bu s e r i n t e r f a c e User InterfaceLearning section Learn and recall a tailored reverb for your track.Reverb ControlSet the reverb time and pre-delay.EffectsFreeze the current reverb tail or enable an infinite reverb time to create sound layers.Filter SectionApply a pre-filter EQ to quickly adapt the spectral shape of your signal.o v e r v i e wSettingsAccess the settings page.Particle Display Monitor the reverb’s anatomy and its current activity in different frequency bands. Once the learning process is finished, you can also freely adjust the decay rates in different bands using the inter-active spectral shaper grid.Temporal ShaperMonitor the reverb’s decay, spread and density evolvement over time. Once the learning process is finished, you can freely adjust the temporal behavior using the interactive shaper lines.Reverb Character Manually fine-tune the width, clarity and color of your reverb.Reverb MatrixTo intuitively browse through different reverb styles use the reverb matrix as an XY pad.State handlingSave different states of parameter settings for easy A/B comparison or to store personal presets.m a n u a ls m a r t :r e v e r bWidthLimit or expand the perceived width of the reverb effect within the stereo field.ColorDetermine if the reverb should have a darker or brighter sound.ClarityUnmask direct signal components to increase the transparency of the reverb effect.o v e r v i e wg l o b a l r e v e r b c o n t r o l s The left-hand section of the user interface provides you with all the necessary controls to start the learning process for a new reverb and to modify all global reverb parameters.Profile & Learning Although smart:reverb can be used without applying its source-adaptive features, it’s highly recommended to always start off with the learning process. This adapts the processing of smart:reverb to your audio material and enables all detailed reverb controls. Please refer to page 9 for more details on the learning process.Reverb MatrixThe Reverb Matrix is a parameter space covering different reverb styles. Guided by the semantic descriptors, you can easily navigate via the XY pad. By moving across the XY pad, you can see how the reverb’s anatomy inside the Particle Display (see page 11) and the Temporal Shaper (see page 12) changes in real-time. Please refer to page 10 for more details on the Reverb Matrix.Global Reverb Controls13542m a n u a ls m a r t :r e v e r b Reverb TimeSet the reverberation time. This is the length of time over which the reverb tail has decayed by 60dB. Please note, changing the reverberation time will scale (extend or shorten) your current reverb effect and its internal temporal and spectral structure accordingly.Pre-DelaySet a pre-delay. The pre-delay refers to the length of time between the original dry sound and the audible onset of early reflections.Dry / WetMix the dry (direct) and wet (reverberated) signal. When using smart:reverb as an insert effect, you typically want to use a mix of both signals. When using smart:reverb as a send effect, you may stick to 100% wet signal since the output will later be mixed with the dry signal inside the mixer of your DAW.If you want to change the two parameters proportionately (so that they always sum up to 100%), enable the chain symbol.FreezeClick on Freeze to capture the current reverb tail. This will create a layered sound of the reverb effect.InfiniteClick on Infinite for an infinite reverb time. This setting will overrule the current settings of the reverberation time. Disable to return to your previously set reverberation time.Global Reverb Controls5678956789m a n u a ls m a r t :r e v e r b c u s t o m -t a i l o r e d r e v e r b1. Select a ProfileA profile calibrates the processing of smart:re-verb to a specific sound source. You can always start the learning process with the "Universal" profile and switch to a more specific profile later. 2. Start the audio playback & begin learning smart:reverb needs incoming audio material for the learning process. Once the playback started, click the green record button. A pulsating pause icon and a progress bar inside the profile dropdown indicate that smart:reverb is actively analyzing.3. Done!When the learning process is finished, smart:re-verb will automatically set all learned parameters, the Reverb Matrix is adjusted to your signal (see page 10) and the Spectral Shaper Grid (see page 13) as well as the Temporal Shaper (see page 12) are enabled.With the learning process complete, the thumb ofthe Reverb Matrix and the smart state button will turn green. This indicates that the current reverb settings lie within the custom parameter space computed for your signal.LearningClick the record button to start or pause learning. While learning, a pause symbol will be displayed instead of the record button.Profile dropdownExpand the dropdown menu to select a profile that best matches your audio material.Smart State buttonThis button indicates whether you are currently in a smart state (the button is GREEN ) or if one or multiple parameters have been manually modified (the button turns BLACK).Although it’s simply impossible to automatically generate something as subjective as a perfectly sounding reverb effect, the intelligent processing of smart:reverb ensures that every reverb computed by the plug-in fits to the spectral and temporal characteristics of your input signal. This way, problems such as disturbing resonances, muddy reverb tails or reverbs that just don’t fit are avoided right from the start.Custom-tailored Reverbm a n u a ls m a r t :r e v e r b t h e r e v e r b m a t r i xFinding the right reverb for a track can be a time-consuming and challenging task and often involves searching through dozens of presets. To keep you in the creative flow, smart:reverb comes with a new way of finding the right style of reverb: the Reverb Matrix.The Reverb Matrix is a parameter space covering different reverb styles. Using XY pad functionality and semantic descriptors, it can be easily and efficiently explored to find the reverb style that matches your creative vision.IntimateAn intimate reverb gives your sound a warm and personal touch. It’s great if you work with soft vocals or solo instruments, since it makes your signal sound like it’s been recorded at a relatively small, slightly homey location.RichA rich reverb creates a full and multi-layeredsound. Go for rich if you want to fully immerse your signal in a dense and vibrant reverb, for example when working with synth pads or orchestral sounds.NaturalA natural reverb sounds as if the reverberated signal was recorded in a real environment as the reverb effect is very cohesive and unobtrusive. This reverb will give your signal finishing touches without changing its character too much. It works very well when working with acoustic instruments or clean vocals.ArtificialAn artificial reverb does not try to simulate an actual room but rather plays with different reverb characteristics. Use an artificial sounding reverb if you want to intentionally change the character of a signal and make the reverb audible as a distinct creative effect.The Reverb Matrixm a n u a ls m a r t :r e v e r b t h e p a r t i c l e d i s p l a yThe Particle DisplayThe Particle Display shows your reverb’s anatomy and the current reverb activity in different frequency bands. The reverb particles indicate the energy, density and structure of the reverb. The horizontal axis represents the reverb time (the right end of this axis shows the current reverb time) while the vertical axis represents different frequency bands:When there is no audio playback, the Particle Display shows the static structure of the reverb. Large, opaque particles indicate a lot of potential reverb energy while small, more transparent particles indicate low reverb levels.When a signal is running through, the reverb particles are triggered by the incoming signal. The level and size of the particles show the dynamicspectral behavior of the reverb components.m a n u a ls m a r t :r e v e r b t h e t e m p o r a l s h a p e rThe Temporal ShaperDecayThe Decay curve shows how the reverb’s energy decreases or increases over time.SpreadThe Spread curve shows the reverb’s stereo spread over time. This parameter is similar to the global Width parameter, but allows control of the spread’s temporal progression.You can restrict the affected frequency range by dragging the line inside the spectral display.DensityThe Density curve shows the density evolvement of the reverb.The Temporal Shaper allows you to monitor the temporal evolvement of your reverb’s Decay (green), Spread (yellow) and Density (pink). Once smart:reverb hascreated a custom Reverb Matrix for the current signal, you can freely shape the three temporal curves using interactive thumbs and lines.m a n u a ls m a r t :r e v e r b Once smart:reverb has generated a custom Reverb Matrix for the current signal (see page 9), the Spectral Shaper Grid is enabled. This grid lets you control the decay shape of the reverb over frequency ranges and time using interactive thumbs and lines.Moving a thumb to the left decreases the decay time of the reverb within the respective time frame and frequency band. You can also select the decay line between two points to move both frequency bands.While changing the Decay lines, you will also see how the reverb’s anatomy (Particle Plot) is changing.If you manually change the reverb’s anatomy by using the Spectral Shaper Grid or the Temporal Shaper, you leave the computed parameter space: the thumb inside the Reverb Matrix then changes into a white circle and the smart state button turns black.To return to the automatically generated reverb settings you can simply click on the smart state button or move the thumb inside the Reverb Matrix.The Spectral Shaper Gridt h e s p e c t r a l s h a p e rm a n u a ls m a r t :r e v e r b p o s t -fi l t e r e qPre-Filter EQThe Pre-Filter EQ, allows you to shape the wet signal using two thumbs. Choose from five filter types (bell, high and low pass, high and low shelf). Set the frequency and gain by dragging the thumbs or entering a precise value in the text box. You can change the Q value by scrolling or holding ALT while dragging verti-cally. Deactivate a filter by clicking on the pink and yellow icon.You can also change frequency and gain values as well as turn filters on or off when the filter is collapsed.m a n u a ls m a r t :r e v e r b SettingsAll of these parameters are global settings. This means that they will be applied to ALL instances of smart:reverb (in all your projects).To visit the settings page, click the little cogwheel in the upper right corner of the plug-in.Use 100% wet signal per defaultEnable if you want to change the default balance of dry/wet to 0/100.Show tooltipsDisable to hide show tooltips when hovering over selected control elements.Use OpenGL:Enable for GPU powered graphics processing. It is recommended to only disable this switch in case of graphics problems, since the system load may significantly increase without OpenGL.Share anonymous user data:Enable to share fully anonymous user data with sonible and help us improve smart:reverb.Plug-in informationH ere you can find the name and version of your plug-in. You can start the welcome tour by clicking on "show tutorial".Update notice When a new release of the plug-in is available, you‘llreceive a notification on the smart:reverb settings page. Click on the blue label to download the latest version of the plug-in.License informationThis will display your license state and number (when not licensed via iLok).s e t t i n g s11223344556677m a n u a ls m a r t :r e v e r b sonible GmbH Haydngasse 10/18010 Graz Austriaphone: +43 316 912288*******************All specifications are subject to change without notice.©2020, sonible GmbH. All rights reserved.Engineered & designed by sonible in Austria./smartreverb。
Ivium电化学工作站中文操作手册

电化学工作站软件简要操作手册(版本:1.633)目录一软件的安装 (6)1.仪器安装 (6)2.软件安装 (6)3.驱动程序安装 (8)二佼器介绍 (11)1.IVIUMSOFT软件 (11)2.IVIUMSTAT仪器 (11)3.COMPACTSTAT型 (12)4.仪器的安装和设置 (12)5.增压器的安装 (12)6.多样品切换器的安装 (13)7.PLUS部件的安装 (13)三开机操作 (14)1.启动仪器 (14)2.电极的连接方法 (15)3.界面简介 (17)4.内置模拟电解池 (18)5.外置标准测量池 (18)6.标准测量1:使用内置模拟电解池1 (18)7.标准测量2:使用外置标准测量池 (19)8.标准测量3:使用外置标准测量池和双恒电位模块 (20)四直接控制模式 (21)1.直接控制 (21)2.示波器窗口 (22)五标准方法控制模式 (23)1. 标准方法控制模式 (23)2. 测量的顺序 (23)3. 方法列表 (23)4. 测量结果 (24)5. 图形选项 (25)6. 图例说明窗 (25)7. 数据显示工具菜单 (26)8. 图形工具单 (27)9. 图形弹出式菜单 (29)10. 测量结果数据列表 (29)11. 文件菜单 (30)12. 选项菜单 (30)13. 工具菜单 (31)14. 帮助菜单 (32)六电化学测量技术 (33)1.标准线性扫描法 (33)2.线性扫描——电流平均法 (34)3.线性扫描——真正线性法 (34)4.线性扫描——动电流扫描法 (34)5.标准循环伏安法 (35)6.循环伏安——电流平均法 (35)7.循环伏安——真正线性法 (35)8.循环伏安——动电流扫描法 (36)9.暂态计时电流法 (36)10.暂态计时电位法 (37)11.暂态法——混合模式 (38)12.暂态法——电化学噪声法 (41)13.电分析——安培测定法 (41)14.电分析——差分脉冲法 (41)15.电分析——方波伏安 (42)16.电分析——交流伏安法 (42)17.电分析——恒电位溶出分析 (42)18.电分析——交流测量 (42)19.电分析——常规脉冲 (43)20.交流阻抗——控制电位 (43)21.交流阻抗——控制电流 (44)22.交流阻抗——电位扫描 (44)23.交流阻抗——电流扫描 (45)24.交流阻抗——外部设备控制的电化学交流阻抗EIS (45)七批处理 (47)1.批处理程序 (47)八数据分析及处理 (51)1.电流密度曲线 (51)2.坐标调整及放大 (51)3.粘贴板功能 (51)4.数据平滑处理 (51)5.腐蚀曲线分析 (52)6.电化学噪声分析方法 (53)7.阻抗等效电路分析 (54)8.找峰和基线校正功能 (56)9.寻找突变点 (60)九仪器特别功能 (62)1.仪器的校正 (62)2.仪器内部软件(固件)的升级方法 (62)3.仪器的恢复功能 (62)4.软件开发程序DLL (63)十软件参数说明 (64)第一章仪器及其软件的安装一、仪器安装1. 从包装箱中取出仪器,清除杂物。
GOPRO HERO4 Silver中文说明书

/ 摄像机显示屏
Swipe up/down Swipe left/right
向右滑动 显示最新拍摄的视频和相片。
Double tap
Tap
Press + hold Swi
Swipe right Double tap
向左/向右滑动 显Sw示ip图e u库p/d图ow像n(回放模式)。
Tap
Press + hold
/ 摄像机菜单
Camera Reset
21
/ 摄像机模式
HERO4 Silver 具备若干摄像机模式。要浏览这些模式,请在触摸显 示屏上向左滑动,或反复按 Power/Mode 按钮 [ ]。
这些模式有:
Video(视频) 录制视频
Photo(照片) 拍摄单张照片
Multi-Shot (连拍)
拍摄一组照片(延时、连拍等)
Swipe down
使用这些手势来操作触摸显示屏:
om
Swipe left
Press for 3 sec Slide down and hold
ge
Swipe down
Swipe right
ttom p
Swipe up from bottom edge
向左滑动
显示摄像机的模式。
Swipe left
Press for 3 sec
关
专业提示:在触摸屏上向上滑动或按 Settings/Tag 按钮 [ ],可 以打开当前模式的 Settings(设置)菜单。
10
/ 入门
开机和关机 要开机: 按一下 Power/Mode 按钮 [ ]。摄像机状态指示灯(红色)会闪烁 三次,而声音指示器则会发出三声嘟嘟声。当摄像机状态屏幕显示出 信息时,摄像机即开启。 要关机: 按住 Power/Mode 按钮 [ ] 两秒钟。摄像机状态指示灯(红色)会 闪烁若干次,而声音指示器则会发出七声嘟嘟声。 专业提示:当相机关闭且 QuikCapture 功能启用时,只要按下 Shutter/Select 按钮 [ ] 启动相机,就能立刻开始拍摄视频或延 时拍照。单击可拍摄视频,持续按住则可开始延时拍照。再单击即 可停止录制并关闭相机电源。如需详细信息,请参阅设置模式中的 QuikCapture。
HP Secure Web Console (J3591A) 用户手册说明书

If your HP Secure Web Console requires warranty service, contact your HP-authorized reseller or local HP representative for assistance.
For defects that occur during the warranty period, HP will, at its option, either repair or replace the defective product, or refund the purchase price. For information on how to contact HP, consult the WEB site http:// /go/webconsole.
This warranty does not apply to defects resulting from improper or inadequate maintenance by the customer; customer-supplied software, interfacing, supplies, unauthorized modification or improper use, operation outside the published environmental specifications for the product, or improper site preparation or maintenance by the customer.
HP Manufacturing Part Number J3591-90101
Edition 2 E08/98 Printed in U.S.A.
TWN4 MultiTech HF Mini 用户手册说明书

TWN4 MULTITECH HF MINI TWN4 Mini Reader MIFARE NFCUSER MANUALTABLE OF CONTENTS1INTRODUCTION (3)1.1ABOUT THIS MANUAL (3)1.2ELATEC SUPPORT (3)1.3REVISION HISTORY (3)2INTENDED USE (3)3SAFETY INFORMATION (4)4TECHNICAL DATA (5)5MODE OF OPERATION (6)5.1OPERATING MODE (6)5.2POWER UP (6)5.3ENUMERATION (6)5.4INITIALIZATION (6)5.5NORMAL OPERATION (6)5.6DETECTION OF A TRANSPONDER (6)5.7SUSPEND MODE (6)6COMPLIANCE STATEMENTS (7)6.1EU (7)6.2FCC (7)6.3IC (7)6.4RF EXPOSURE COMPLIANCE (7)APPENDIX (8)A – TERMS AND ABBREVIATIONS (8)B – RELEVANT DOCUMENTATION (8)1INTRODUCTION1.1ABOUT THIS MANUALThis user manual is intended for the user and enables a safe and appropriate handling of the product. It gives a general overview, as well as important technical data and safety information about the product. Before using the product, the user should read and understand the content of this user manual.For the sake of better understanding and readability, this user manual might contain exemplary pictures, drawings and other illustrations. Depending on your product configuration, these pictures might differ from the actual design of your product.1.2ELATEC SUPPORTIn case of any technical questions, refer to the ELATEC website () or contact ELATEC technical support at:***********************In case of questions regarding your product order or if you wish additional copies of this user manual, contact your Sales representative or ELATEC customer service at:********************1.3REVISION HISTORYVERSION CHANGE DESCRIPTION EDITION08/202101 First edition(replaces Transponder Reader TWN4 Mini Reader MIFARE NFC Quick Start Guide)2INTENDED USEELATEC TWN4 MultiTech HF Mini reader is designed for integration into machines, handheld computers or any other human interface devices such as displays, panels, etc. The focus has especially been set on size, flexibility and price. Thanks to its compact dimensions, integration directly on a PC board is possible.The product is intended to be integrated into a host device.Any use other than the intended use described in this section, as well as any failure to observe the safety information listed in this document, will be considered misuse and will void the warranty. ELATEC is not responsible for any damage or injuries resulting from any misuse of the product.3SAFETY INFORMATIONInstallation•The installation of the product should be done by a trained and qualified personnel only.Do not install the product by yourself.•Metallic materials on or in direct vicinity to the product might reduce the reading performance of the product. In some circumstances, plastic screws should be preferred to metallic screws when installing the product. Refer to the installation instructions or integration manual of the product for more information.Handling•Depending on your product configuration, the product might be equipped with one or more light-emitting diodes (LED).Avoid direct eye contact with the blinking or steady light of the light-emitting diodes.•The product has been designed for a use under following conditions:o Temperature range: -25 °C – 80 °C (operating conditions)o Relative humidity: 5% – 95% (non-condensing)o Integration into a host device.Any use of the product under different conditions might damage the product or alter its reading performance.•The use of other RFID readers or reader modules in direct vicinity to the product, or in combination with the product might damage the product or alter its reading performance. In case of doubts, contact ELATEC for more information.•The user is liable for the use of spare parts or accessories other than the ones sold or recommended by ELATEC.ELATEC is not responsible for any damage or injuries resulting from the use of spare parts or accessories other than the ones sold or recommended by ELATEC.•Like most electronic devices, RFID systems generate electromagnetic waves that can vary in amplitude and frequency. It is generally known and accepted that some RFID devices might potentially interfere with personal medical devices, like pacemakers or hearing aids.Users with a pacemaker or any other medical device should use TWN4 MultiTech HF Mini carefully and refer to the information given by the manufacturer of their medical devices before using TWN4 MultiTech HF Mini or any host device containing TWN4 MultiTech HF Mini.Maintenance and cleaning•Any repair or maintenance work should be done by a trained and qualified personnel only.Do not try to repair or carry out any maintenance work on the product by yourself.Do not allow any repair or maintenance work on the product by an unqualified or unauthorized third party.•The product does not need any special cleaning.Do not use any detergents or other cleaning agents on the product.Disposal•The product must be disposed of in accordance with the EU directive on waste electrical and electronic equipment (WEEE) or other applicable local regulations.Product modifications•The product has been designed, manufactured and certified as defined by ELATEC.Any product modifications not expressly approved by ELATEC, including – but not limited to – modifications of antennas or other radio-related components, is not allowed and will void the warranty and all approvals granted to the product.If you are unsure about any part of the safety information above, contact ELATEC support.Any failure to observe the safety information above will be considered misuse and will void the warranty. ELATEC is not responsible for any damage or injuries resulting from any misuse of the product.4TECHNICAL DATAThe reader module is equipped with the following antenna:TWN4 MultiTech HF MiniHF antenna (13.56 MHz)Dimensions: 27.5 x 25 mmNumber of turns: 4For more information, refer to the related product data sheet or other technical documents.5MODE OF OPERATION5.1OPERATING MODEIn order to start operating TWN4 MultiTech HF Mini, it simply has to be connected directly to a host device.5.2POWER UPIn case of an external power supply unit is used, the following requirements must be satisfied:•Limited power source according to the safety norms listed in the respective declaration(s) of conformity•Short-circuit current < 8 A5.3ENUMERATIONThis is only applicable for the USB version: Once the device has been powered up, it is waiting for completion of the enumeration by the USB host. As long as the device is not enumerated, it is entering a minimum power consumption mode5.4INITIALIZATIONAfter powering up and enumeration (in USB mode), the device is turning on the built-in transponder reader logic. Some RFID reader modules need some kind of initialization, which is performed in this step.5.5NORMAL OPERATIONAs soon as the reader module has completed the initialization, it is entering normal operation. During normal operation, the reader module is searching for a transponder continuously.5.6DETECTION OF A TRANSPONDERIf a transponder is detected by the reader module, following actions are performed:•Send the ID to the host. By default, the USB device sends by emulating keystrokes of a keyboard.Within the two seconds timeout, the transponder, which just has been recognized will not be accepted again. This prevents the reader module from sending identical IDs more than one time to the host.If during the two seconds timeout a different transponder is detected, the complete sequence restarts immediately.5.7SUSPEND MODEThe USB version of the reader module supports the USB suspend mode. If the USB host is signaling suspend via the USB bus, the reader module is turning off most of its power consuming peripherals. During this operation mode, no detection of transponders is possible. Once the host is resuming to normal operation mode, this is also signaled via the USB bus. Therefore, the reader module will resume to normal operation too.6COMPLIANCE STATEMENTS6.1EUTWN4 MultiTech HF Mini is in compliance with the EU directives and regulations as listed in the respective declaration of conformity (cf. TWN4 Mini Reader MIFARE NFC EC Declaration of Conformity).6.2FCCThis device complies with Part 15 of the FCC Rules. Operation is subject to the following two conditions:(1) this device may not cause harmful interference, and(2) this device must accept any interference received, including interference that may cause undesired operation.CautionThe Federal Communications Commission (FCC) warns the users that changes or modifications to the unit not expressly approved by the party responsible for compliance could void the user's authority to operate the equipment.FCC §15.105 (b)Note: This equipment has been tested and found to comply with the limits for a Class B digital device, pursuant to part 15 of the FCC Rules. These limits are designed to provide reasonable protection against harmful interference in a residential installation. This equipment generates, uses and can radiate radio frequency energy and, if not installed and used in accordance with the instructions, may cause harmful interference to radio communications. However, there is no guarantee that interference will not occur in a particular installation. If this equipment does cause harmful interference to radio or television reception, which can be determined by turning the equipment off and on, the user is encouraged to try to correct the interference by one or more of the following measures: •Reorient or relocate the receiving antenna.•Increase the separation between the equipment and receiver.•Connect the equipment into an outlet on a circuit different from that to which the receiver is connected.•Consult the dealer or an experienced radio/TV technician for help.FCC ID: WP5TWN4F156.3ICThis device complies with Industry Canada’s license-exempt RSSs. Operation is subject to the following two conditions:(1) This device may not cause interference; and(2) This device must accept any interference, including interference that may cause undesired operation of the device.Le présent appareil est conforme aux CNR d’Industrie Canada applicables aux appareils radio exempts de licence. L’exploitation est autorisée aux deux conditions suivantes:(1) l’appareil ne doit pas produire de brouillage;(2) l’utilisateur de l’appareil doit accepter tout brouillage radioélectrique subi, même si le brouillage est susceptible d’en compromettre le fonctionnement.IC: 7948A-TWN4F156.4RF EXPOSURE COMPLIANCERF exposure statement (mobile and fixed devices)This device complies with the RF exposure requirements for mobile and fixed devices. However, the device shall be used in such a manner that the potential for human contact during normal operation is minimized.APPENDIXA – TERMS AND ABBREVIATIONSTERM EXPLANATION FCC Federal Communications CommissionHF high frequencyIC Industry CanadaNFC near field communicationRFID radio frequency identificationWEEE Waste of electrical and electronic equipment.Refers to Directive 2011/65/EU of the European Parliament and of the Council of the European UnionB – RELEVANT DOCUMENTATION ELATEC documentation•ELATEC quick start guide•TWN4 MultiTech HF Mini data sheet •TWN4 MultiTech HF Mini integration manual •TWN4 MultiTech Mini technical handbookElatec reserves the right to change any information or data in this document without prior notice. Elatec declines all responsibility for the use of this product with any other specification but the one mentioned above. Any additional requirement for a specific customer application has to be validated by the customer himself at his own responsibility. Where application information is given, it is only advisory and does not form part of the specification. Disclaimer: All names used in this document are registered trademarks of their respective owners.ELATEC GMBHZeppelinstr. 1 • 82178 Puchheim • Germany P +49 89 552 9961 0 • F +49 89 552 9961 129 • E-mail:********************。
FatWire Web Support System 教程说明书

Go Live Checklist1Ensure that publishing is working correctly (3)1.1Analyze Firewall (3)1.2Ensure that all information published is correct (3)1.3Review Page Cache (3)1.4Review batch host configuration (4)2Load Testing (4)2.1Load Test Delivery (4)2.2Verify cluster configuration (4)2.3Simulate Editorial Load (5)3Performance Testing (5)3.1Performance Test Publishing (5)3.2Performance Test Content Server (5)3.3Performance Test additional components egfile system,Engage (6)4Perform a security audit of all external-facing environments (6)4.1Review Passwords (6)4.2Harden servlets (7)4.3Harden non-delivery pages (7)4.4Protect against remote calls (8)5Additional standard tests (8)5.1Reviewfilesystem configuration (8)5.2Review Database configuration and response times (9)5.3Review and assess total number offile-descriptors (9)5.4Perform sizing on the java heap size (10)5.5Review Page caching strategy (10)6Backup Testing (10)6.1Test database backups (10)6.2Test application backups (10)6.3Test application server backups (11)6.4Test disaster recovery (11)7Information transfer (11)7.1Provide go-live implementation plan to support (11)7.2Document all customizations to product behavior,eg UI elements,modified jars (11)7.3Document all known outstanding issues and any action plan for their resolution (11)7.4Supply names/contact details of persons responsible for managing the customer go-live (11)7.5Provide all design documentation describing site design,asset models etc (11)7.6Provide architectural map and details such as CS versions,database,webservers,load-balancers,etc (11)7.7Provide an export of database,FatWire directory,Shared Filesystem and web applicationto support (11)7.8Confirm completion(or otherwise)and results of all items above (11)Appendix A:Checklist (12)1Ensure that publishing is working correctlyAt least one publishing test must be completed from your management environment to your delivery environment.1.1Analyze FirewallCheck Firewall ports and timeouts for the connection between source and destination.Content Server requires communications on different ports between different instances.For the development server(s)they will need to have thefirewall opened for the ports specified in your publishing destinations.If you’re running a cluster,the ports for the batchhost and eventhost need to be setup on thefirewall.If you’re using a HA setup that requires for traffic to pass through a Firewall for localhost traffic,you will need to open these locally as well.For the management servers,you will need to configure exactly as listed above for the development servers but for management.For the delivery servers,you will need to make sure that your webservers communication ports have been allowed on thefirewall.For each of your different environments you should check the actualfirewall and router setup rules to make sure that sockets are not forcibly disconnected after a period of time.1.2Ensure that all information published is correctPerform a complete publish and compare the environments to make sure that all content was published correctly.1.3Review Page CacheEnsure page cache is operating as intended;content isflushing when assets are published.Check your system page cache and system item cache before a publish and record its contents. After a publish check the assets that were published to ensure that they have been updated in the system page cache and system item cache.You can also turn on debugging for publishing on the host to ensure that the correct IDswereflushed.1.4Review batch host configurationEnsure batch host is set correctly on source and destination.The batch host should be set to one server on each of the instances,for example if you’re running publishes on your management instance you should set the batch host on each member of the cluster to be one member.The properties for batchhost can be located in the futuretense_xcel.ini,the properties are; xcelerate.batchhostxcelerate.batchuserxcelerate.batchpass2Load TestingA load test should be performed on all parts of your environment to ensure that the current architecture setup meets the metrics defined for FatWire.2.1Load Test DeliveryComprehensive load test of delivery system,all pages with simulated load no less than the predicted amount of page views.Calculate based on current trends the amount of pageviews that your site current is undergoing. From thosefigures setup a Jrun,LoadRunner etc script to simulate the usage patterns of your users against your site.Ensure that the load test is a comprehensive test that covers the actual patternof usage and not just one page.During the load test record statistics on each of your different components,the components that you should monitor are;Database(CPU,Memory,Shared Memory,Cursors),Application Server(CPU,Memory,JVM Heap Space,File Handles),Webservers (CPU,Memory,Sockets,File Handlers).2.2Verify cluster configurationEnsure that ft.sync and edisksync is enabled even if no cluster is present,so that any issues with shared disk are discovered early and do not present a surprise when embarking on a cluster later. Check your futuretense.inifiles to make sure that you have settings for the ft.sync and theedisksync properties.If you need information about each of these properties refer to the property guide available on e-docs.2.3Simulate Editorial LoadSimulate load on staging system,eg expected number of editorial users all performing normal tasks. Perform load testing on your staging system by using either people or an automated testing tool (JRun,LoadRunner,etc)to simulate your editorial load on the system.During this load testing you should monitor the statistics of your components,eg Database(CPU,Memory,Shared Memory, Cursors),Application Server(CPU,Memory,JVM Heap Space,File Handles),Webservers(CPU,Memory, Sockets,File Handlers)3Performance TestingYou should complete performance testing on your environment so that it meets your metrics.3.1Performance Test PublishingPerformance testing should be similar to load testing but with a different outcome in mind.When you performance test your publishing procedures you should monitor the same components as listed in the load testing however you should address the areas of each of these components that are performing slowly.When performance testing publishing you should turn on several different debug logging options, they are;publishing debug,time debug,cs debug and db debug.These four debugs will allow you to see the different activities undertaken during the publishing process and will allow you to tune the different areas of your Content Server installation with publishing in mind.3.2Performance Test Content ServerTo performance test Content Server you should turn on three different debugs,cs debug,db debug and time debug.These will allow you to see how Content Server is performing under normal operating scenarios.Ensure that no publishing activity is occurring during normal Content Server testing. Based on the logfiles you can address different areas of your setup that are performing slowly.3.3Performance Test additional components egfile system,EngageAny additional component that your server requires outside of the normal Content Server installation should be performance tested.Some common areas that need to be analyzed and corrected are; File Systems on shared cluster instances.Engage tables if engage is being used.Database performance.Network traffic performance.4Perform a security audit of all external-facing environments4.1Review PasswordsEnsure all passwords have been changed from the default users.Many passwords are defaulted to different common passwords,for example fwadmin is usually defaulted to xceladmin.Review all default passwords to ensure that people with priorContent Server experience can not login or perform unwanted actions on your installation.You should review all entries in your systemusers table to ensure that any user that has the sitegod privilege changes their password on a regular basis.The list of usernames that you should change is;fwadminSatelliteServer4.2Harden servletsOnly the necessary servlets are exposed to the world,if all access goes through Satellite Server then only Satellite and CookieServer servlets need to be exposed.Ensure that your webservers are setup correctly to only allow access to the parts of the servlet that you need to provide pages.For example,if you’re going to be serving all your content from Satellite Server,then make sure that you block the Content Server servlet.The complete list of servlets to block against is;HelloCSCatalogManagerTreeManagerDebugServerCacheServerInventoryPageDispatcherServerDispatchManagerSyncSeedDispatchServerSeedDispatchServerFlushServer4.3Harden non-delivery pagesDisable outside access to all non-delivery pages such as support tools,UI pages,WebServices.If any of the non delivery pages are installed on your delivery system make sure that you have the correct settings in your webserver to deny outside access to these pages.You should set rules on your webserver to deny access to these specific pages externally and only allow internal traffic to these webpages.From support tools you can perform a variety of operations that can damage your system if used improperly therefore it should be restricted to internal users only.4.4Protect against remote callsEither with webserver rules,or by setting csstatus=pending on SiteCatalog entries(the latter is more extreme).The publishing endpointOpenMarket/Xcelerate/PrologActions/Publish/<your_delivery_type>/RemoteCall needs to remain accessible from the staging system to delivery,but can be blocked to the outside world.Like4.3you should create rules in your webserver to prevent people from executing commands using CatalogManager,ftcmd ing the csstatus=pending is an extreme method of restricting access to remote calls and should only be used if you can not configure your webserver torestrict access.5Additional standard testsThis task is to head offany possible problems that could arise from factors within your control.5.1Reviewfilesystem configurationThefilesystem configuration needs to be reviewed to ensure that configuration is appropriate to your needs.You should check with your Operating System Administrator(s)to getfiner detailconfiguration information.Some areas of yourfile system that you should review are;Unix/LinuxFile HandlesMax InodesPermissionsFree Space ConsiderationsWindowsPermissionsFree Space Considerations5.2Review Database configuration and response timesYour database configuration should be reviewed on a regular basis as this is a frequently changing component of your system.When going live you should review the database configuration and address some specific areas such as;OracleTablespace growth optionsMax cursorsRecalculate statisticsAnalyze all indexesMS SQL ServerDB2Sybase5.3Review and assess total number offile-descriptorsYou should analyze your operating systems needs to determine if you need to change yourfile descriptors.This is very important because if youfile descriptors are set too low then your system may not be able to open newfiles or sockets to connect with other Content Servers or write information to disk.Consult your Operating System Administrator for more information on the correct setting of yourfile descriptors.SolarisFor solaris,to see and set thefiledescriptors type;ulimit–aRedhat LinuxFor redhat linux to see and set thefiledescriptors type;ulimit–aWindowsThere is no easy way to view and set thefiledescriptors for windows,you will need to write a small program to retrieve thefile descriptors.More information can be found on Microsoft support site.5.4Perform sizing on the java heap sizeDuring your load testing and performance testing you should monitor the JVM heap size to increase or decrease it depending on load and garbage collection.Too much garbage collection could indicate that you’re running out of heap and that you should increase it.Many JVMs allow you to write out garbage collection logs that you can use to analyze the heap GC activities.An example of the switches that you need to add for garbage collects is as follows;-verbose:gc-XX:+PrintGCTimeStamps-XX:+PrintGCDetailsTo adjust your max and min heap size an example of the JVM;-Xms512m-Xmx1024mTo adjust your perm gen size an example of the parameter is;-XX:MaxPermSize=128m5.5Review Page caching strategyYou should check to see which pages that you have cached and which that you do not.Make sure that you cache pages that very rarely change and do not cache pages that frequently change.Cache pages that are requested a lot.For more information on caching strategies please consult your Pro-fessional Services Account Executive.6Backup TestingEvery system should be tested for backup and restoration.6.1Test database backupsPerform a hot and cold backup of your database aswell as a test export of the schema that Content Server is using.Please follow the procedure that you are planning on following for every day backups.6.2Test application backupsPerform a backup of Content Server and the relevantfiles to Content Server so that you’re familiar with all the dependants of Content Server.Remember are the following components to backup; Content Server install directoryShared File systemAny other directory referenced within Content ServerAlso remember that you should perform this backup when Content Server is not running.6.3Test application server backupsPerform a backup of your application server and webcomponents so that you’re familiar with the process and location of thefiles.6.4Test disaster recoveryPerform a cold backup of all the above pieces and then restore them on a completely separate server so that you’re comfortable with disaster recovery of Content Server.7Information transferEnsuring that all information is communicated with the rest of the team dealing with FatWire is essential to a successfully rollout.7.1Provide go-live implementation plan to supportGo-live plan actions and dates,at minimum a week’s notice.7.2Document all customizations to product behavior,eg UI elements,modified jars 7.3Document all known outstanding issues and any action plan for their resolution 7.4Supply names/contact details of persons responsible for managing the go-live event 7.5Provide all design documentation describing site design,asset models etc7.6Provide architectural map and details such as CS versions,database,webservers,load-balancers,etc.7.7Provide an export of database,FatWire directory,Shared Filesystem andweb application to supportIn order to support your golive process with maximum efficiency you should provide a cold backup of your database schema,FatWire directory,Sharedfilesystem and web application to FatWire Support so that we can replicate your system inhouse to troubleshoot any golive problems.7.8Confirm completion(or otherwise)and results of all items aboveConfirm completion(or otherwise)and results of all items above.。
- 1、下载文档前请自行甄别文档内容的完整性,平台不提供额外的编辑、内容补充、找答案等附加服务。
- 2、"仅部分预览"的文档,不可在线预览部分如存在完整性等问题,可反馈申请退款(可完整预览的文档不适用该条件!)。
- 3、如文档侵犯您的权益,请联系客服反馈,我们会尽快为您处理(人工客服工作时间:9:00-18:30)。
用户手册To download this user manual in a different language, visit /support.Pour télécharger ce manuel de l’utilisateur dans une autre langue, rendez-vous sur /support.Wenn Sie dieses Benutzerhandbuch in einer anderen Sprache herunterladen möchten, besuchen Sie /support.Per scaricare questo manuale utente in un’altra lingua, visita /support.Para descargar este manual de usuario en otro idioma, visite /support.Para baixar este manual do usuário em outro idioma, acesse /support./support/support如需下载本用户手册的其他语言版本,请访问/support。
45/ 目录使用底座83常见问题解答86客户支持88商标88监管信息88基本结构6入门8摄像机显示屏14相机图标18摄像机菜单20摄像机模式22掌握设置菜单23视频模式25照片模式36连拍模式43回放模式52设置模式56连接到 GoPro App 63将文件传输至电脑中64Protune ™65电池71重要信息76摄像机保护盒78/ 目录10. 麦克风11. HERO 端口12. 触摸显示屏13. Touch Display Sleep/Wake按钮 [ ]14. Settings/Tag 按钮15. 电池盖/ 基本结构1.摄像机状态指示灯2. Shutter/Select 按钮3.4.摄像机状态屏幕5. Power/Mode 按钮6. Micro HDMI 端口(不含数据线)7. microSD™卡槽(不含 microSD 卡)8. Mini-USB 端口(支持 A/C 复合数据线/不含 3.5mm 立体声麦克风适配器)9.语音报警/基本结构6789Slim housing remove camera 1. 将相机从保护盒中取出。
2. 卸下相机侧边护盖,并插入 microSD 存储卡(另售)。
存储卡必的容量。
。
3. 开启底盖,装入电池,然后关上底盖。
4. 要为电池充电时,请使用随附的 USB 传输线连接相机与计算机或其他 USB 充电适配器。
充电时,相机状态指示灯会亮起,充电以外的壁式充电器可能会导致 5V 1A 的充电器。
请使用随附的 USB 传输线,电池充电。
如需详细信息,请访问 。
如需更多电池相关信息,请参阅电池部分。
警告:在动感活跃的生活中使用 GoPro 时请务必提高警觉。
请随时留意周遭状况,避免自身或他人受到伤害。
使用 GoPro 与相关的固定座及配件时,请遵守当地各项法律规范。
1011开机和关机要开机:按一下 Power/Mode 按钮。
摄像机状态指示灯(红色)会闪烁三次,当摄像机状态屏幕显示出信息时,摄像机即开启。
要关机:按住 Power/Mode 按钮两秒钟。
摄像机状态指示灯(红色)会闪烁若干次,专业提示:功能启用时,只要按下Shutter/Select 按钮启动相机,就能立刻开始拍摄视频或延时拍照。
持续按住则可开始延时拍照。
再单击即可停止录制并关闭相机电源。
如需详细信息,请参阅设置模式中的 QuikCapture 。
摄像机软件更新若希望您的 HERO4 相机获得最新功能并发挥最佳效能,请确 保您所使用的相机软件为最新版本。
您可以通过 GoPro App 或 GoPro 软件更新您的相机软件。
如需更多信息,请访问 /getstarted 。
摄像机默认设置HERO4 Silver摄像机在开机时将默认以下设置:关1213要取出 microSD 卡: 用指甲抵住存储卡边缘,将其向摄像机内侧轻按。
存储卡随即弹出且可轻松取出。
注意事项:装卸存储卡时请务必小心。
避免接触液体、灰尘和碎屑。
为谨慎起见,插入或取出存储卡前请关闭摄像机。
查看相应的厂家指导以了解其支持的操作温度范围。
插入和取出 MICROSD 卡HERO4 Silver 相机可兼容 4GB 、8GB 、16GB 、32GBmicroSD、microSDHC 及 microSDXC 存储卡microSD 存储卡必须具备 Class 10 或 UHS-1 卡推荐清单,请访问 /support 。
)GoPro 品牌的存储卡产品,您的 HERO4 Silver 摄像机正面有一个状态屏幕,背面有一个更大的触摸显示屏。
摄像机状态屏幕摄像机正面的状态屏幕显示以下模式和设置信息:1. 摄像机模式/FOV(视野)2. 摄像机设置3. 分辨率/fps(帧/秒)4. Protune™5. 拍摄的文件数量6. 时间/存储量/文件7. Wireless(无线网络)8. 电池使用时间注意:摄像机状态屏幕上显示的图标,将随所的模式不同而有所差异。
触摸显示屏借助摄像机背面的集成触摸显示屏,您可以操控摄像机,调整设置,还能预览和回放视频与照片。
您也可以将它用作取景器,这样您就可以看见摄像机镜头中的内容,轻松调整取景范围。
打开/关闭触摸显示屏您打开/关闭摄像机时,触摸显示屏会自动打开/关闭。
专业提示:为在摄像机开机时节省电池电量,在不使用屏幕时,请按 Touch Display Sleep/Wake(触摸屏睡眠/唤醒)按钮 [ ] 调低屏幕亮度。
14151617手势使用这些手势来操作触摸显示屏:Press for 3 secttomTapPress + holdSwipe from top/bottomSwipe from left edgeSwipe left/rightDouble tapTapPress + holdSwi/ 相机图标/ 相机图标自动低光拍照自动关闭视野每秒帧数间隔ISO限制屏幕显示锐度点测光白平衡无线网络1819/ 摄像机菜单/ 摄像机菜单20212223HERO4 Silver 具备若干摄像机模式。
请在触摸显示屏上向左滑动,或反复按 Power/Mode 按钮。
这些模式有:(连拍)拍摄一组照片(延时、连拍等)Playback 回放视频和照片/ 摄像机模式每一种摄像机模式都有自己的设置菜单。
在您的 HERO4 Silver 上,您可以使用触摸显示屏或摄像机上的按钮来操作设置菜单。
使用触摸显示屏操作:1. 确认摄像机处于所需的摄像机模式。
如果在触摸显示屏左上角没有显示该模式的图标,向左滑动,然后点按该模式。
2. 从屏幕底部向上滑动,打开该模式的设置菜单3. 向上或向下滑动,以滚动浏览该模式的设置。
4. 根据需要点按和滑动,以选择新的设置选项。
5.点按Exit (退出),或按下 Settings/Tag按钮,即可退出设置菜单。
/ 掌握设置菜单2425使用摄像机按钮操作:1. 确认摄像机处于所需的摄像机模式。
显示该模式的图标,请不断重复按 Power/Mode 按钮, 直到该图标出现。
2. 按 Settings/Tag 按钮,打开该模式的设置菜单。
3. 按 Power/Mode 按钮,浏览各个设置。
4. 按 Shutter/Select 按钮,浏览设置内的各个选项。
要选择一个选项,然后转移至另一屏幕。
5.或要退出设置菜单,请按 Settings/Tag 按钮。
/ 掌握设置菜单/ 视频模式Video (视频)模式包括三种拍摄模式:Video (视频)、Video + Photo (视频 + 照片)和 Video Looping (视频循环)。
拍摄模式说明Video (默认) (默认)拍摄视频。
Video + Photo (视频 + 照片)同时拍摄视频和照片。
您可以将摄像机设置为在录制视频时,以选定的时间间隔拍摄照片。
有关更多详细信息,请参阅本节的“视频和照片时间间隔”部分。
Looping (循环)用户可以连续录制,并仅保存最精彩的瞬间,有助于节省 microSD 卡的空间。
Looping (循环)仅在 Protune ™ 关 闭时可用。
专业提示:使用免费的 GoPro 软件,可以轻松制作 GoPro 风格的经典视频。
请访问 /getstarted 获取更多信息,并下载该软件。
2627重点标记录制视频的过程中,您可以随时使用 HiLight Tag 功能标记特定时刻的画面。
HiLight Tag 可让您轻松找到想要分享的重点片段。
您可以利用相机、GoPro App 或 Smart Remote (另售)来添加标记。
使用 GoPro App 或 GoPro 软件播放视频时,可以清楚看见标记。
专业提示:进入应用程序后,只要在播放时点按屏幕,即可在进度列上显示 HiLight Tag 。
新增 HiLight Tag : 录制视频时,按下 Settings/Tag 按钮。
拍摄视频:1. 向左滑动以显示摄像机模式,然后点按左上方的图标(Video (视频)模式)。
2. 如有需要,可选择其他视频拍摄模式(Video (视频)、Video + Photo (视频 + 照片)或 Video Looping (视频循环)):a. 向上滑动以打开设置菜单。
b. 点按 Mode (模式),然后点按所需的拍摄模式。
c. 向下滑动以关闭设置菜单。
选定的拍摄模式图标将显示在摄像机屏幕的左上角。
3. 请按 Shutter/Select 按钮。
摄像机会发出一声嘟嘟声,而在录制时,4. 要停止拍摄,请按 Shutter/Select 按钮。
摄像机状态指示灯将会闪烁三次,并发出三声嘟嘟声。
当存储卡已满或电池没电时,摄像机将自动停止录制。
您的视频会在摄像机关闭前予以保存。
专业提示:QuikCapture 时,只需按下Shutter/Select 按钮,即可开机,并立即开始拍摄视频。
再按一次即停止拍摄,有关更多详细信息,请参阅“设置模式”部分。
视频设置Video(视频)模式有三种可用的拍摄模式:Video(视频)、Video + Photo(视频 + 照片)和 Video Looping(视频循环)。
您选择的拍摄模式决定了出现在菜单其余部分的 Video(视频)设置。
有关如何更改以下设置的说明,请参阅“掌握设置菜单”部分。
专业提示:在触摸屏上向上滑动或按 Settings/Tag按钮,可以快速打开当前模式的 Settings(设置)菜单。
时间间隔Interval(时间间隔)设置应用于 Video + Photo(视频和照片)及 Looping(循环)两个模式。