刀具课件第13章
刀具知识ppt课件
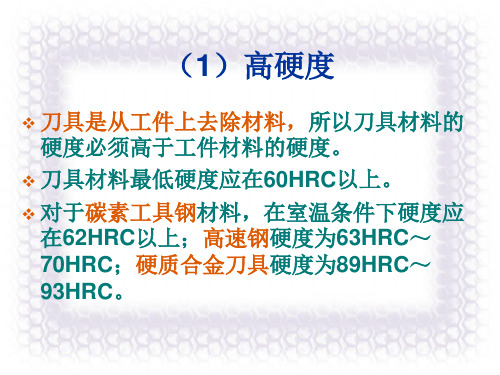
2.刀具几何参数
❖ 由图2-7可以看到,当刀具
前角γO增大时,沿刀面流出
的金属切削层将比较平缓的 流出,金属切屑的变形也会 变小。
❖ 刀尖圆弧半径对切削变形也
有影响,刀尖圆弧半径越大,
表明刀尖越钝,对加工表面 挤压也越大,表面的切削变 形也越大。
❖ 1、切削速度υc 、进给量f 、背吃刀量 ap哪一个对温度的影响最显著?说明 原因?
❖ 刀具材料导热性好,其抗耐热冲击和抗热裂 纹性能也强。
(5)良好的工艺性与经济性
❖ 刀具不但要有良好的切削性能,本身还应该 易于制造,这要求刀具材料有较好的工艺性, 如锻造、热处理、焊接、磨削、高温塑性变 形等功能。
❖ 经济性也是刀具材料的重要指标之一,选择 刀具时,要考虑经济效果,以降低生产成本。
❖ (5)适用范围:主要用于车削、铣削等加工,由于 成本较高,还不能完全取代未涂层刀具的使用。不适 合受力大和冲击大的粗加工,高硬材料的加工以及进 给量很小的精密切削。
课堂问题
避免积屑瘤的发生的措施?
避免积屑瘤的发生的措施P45
❖ ①、首先从加工前的热处理工艺阶段解决。通过热处理,
提高零件材料的硬度,降低材料的加工硬化。 ❖ ②、调整刀具角度,增大前角,从而减小切屑对刀具前
❖ 2.当刀具前角γO增大时,金属切屑的
变形趋势?
❖ 刀尖圆弧半径越大,表面的切削变形是
增大还是减小?
变形系数 ζ
1.工件材料
❖ 通过试验,可以发 现工件材料强度和 切屑变形有密切的 关系。
❖ 从图可以看出,随 着工件材料强度的 增大,切屑的变形 越来越小。
材料强度 σ
图2-10 材料强度对变形系数的影响
❖ 如车削45钢,在背吃刀量ap=4㎜,进给量f =0.5㎜/r的条件下,刀片所承受的切削力达 到4000N,可见,刀具材料必须具有较高的 强度和较强的韧性。
第十三章零件毛坯成形方法和选择原则

塑性好,变形抗力小 中碳钢, 低碳钢和 合金结构 非铁合金 钢 薄板 自由锻件 简单,模 可较复杂 锻件可较 复杂
强度好,塑性好 切削加 液态下化学稳定性 工性好 碳钢, 低碳钢和低合金 合金钢 结构钢 非铁合金 简单, 一般为 圆形或 平面
6
适宜的 形状
形状不受限
2015/11/17
4.1、不同毛坯的应用特征
11
2015/11/17
4.2.2、满足材料的工艺性能要求
工艺性能要求: (1)可行性:毛坯的加工方法能把毛坯 制造出来; (2)简便性:毛坯的加工方法能容易把 毛坯制造出来(成形难易程度); (3)可靠性:生产的毛坯能保证质量 (尺寸精度、表面质量)。
2015/11/17 12
4.2.2、满足材料的工艺性能要求
2015/11/17 21
4.3.1、轴杆件分析与毛坯选择
2、按受力分类 (1)转轴:受 弯矩、扭矩; (2)心轴:受 弯矩; (3)传动轴: 受扭矩。
2015/11/17
22
4.3.1、轴杆件分析与毛坯选择
(二)工作条件 1、分别承受弯、扭、拉、压等多种 应力,并多为循环应力,有时有冲击 应力。 2、局部颈部、滑动表面承受摩擦, 会产生各种断裂、磨损及塑性变形失 效。
2015/11/17 15
4.2.3、毛坯成形要适应经济性
2015/11/17
16
4.2.4、符合生产条件
量体裁衣 选用毛坯生产方法时,必须分析本单 位的设备条件和技术水平、工人的技术 能力等。 充分考虑外协的可能性(专业化生产 企业协同生产),降低成本、减少投入、 保证质量。
2015/11/17 17
2015/11/17
数控机床编程与操作 第4版 第13章 极坐标编程及习题课
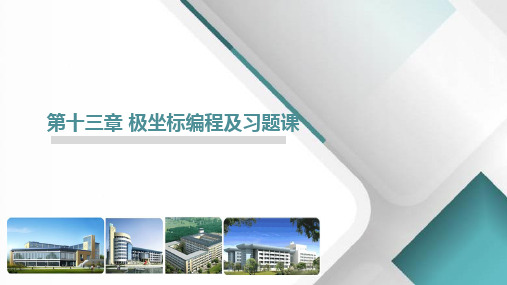
一、极坐标编程
4、举例
【例3-12】 试用极坐标编写图示铣削正六边形的刀具轨迹。
若采用G91方式极坐标编程,则编程如下:
O0012;
此程序为不加半径补偿刀具轨迹程序
……
G01 X25.0 Y-43.3; 刀具移至A点
G91 G17 G16;
设定刀具当前位置A点为极坐标系原点
G01 X50.0 Y120.0; 极半径AB长为50.0mm,极角是OA方向与AB方向的夹角为120º
3、极坐标的应用
一、极坐标编程
➢采用极坐标编程,可以大大减少编程时的计算工作量,因此在编程中得到广泛应用。
➢通常情况下,圆周分布的孔类零件(如法兰类零件)以及图样尺寸以半径与角度形 式标示的零件(如铣正多边形的外形),采用极坐标编程较为合适。
一、极坐标编程
4、举例
【例3-11】用极坐标指令编写如图3-45所示图形起点到终点的轨迹。
G1Z-2 F100
G41 X-50 D01 F200; E点为切削起点
G90 G17 G16; 设定工件坐标系原点为极坐标系原点
G1 X50 Y120;
极坐标半径为50.0,极坐标角度为120º
Y60;
顺时针切削
Y0
Y-60
Y-120
Y180
G15;
取消极坐标
G0 Z50
G40 X-60 Y0
M30
......
G90 G16 G1 X40 Y0 F200; →A
X40 Y45;
→B
Y90;
→C
G3 Y210 R40;
→D
G15;
......
一、极坐标编程
4、举例 【例3-12】 试用极坐标编写图示铣削正六边形的刀具轨迹。
数控机床第13章 其他辅助装置

14
2.执行机构部分
• (1)液压缸。液压缸是液压系统中的执行元件,它是一种 把液体的压力能转变为直线往复运动机械能的装置。它可 以很方便地获得直线往复运动和很大的输出力,结构简单、 工作可靠,制造容易,因此应用广泛,是液压系统中最常 用的执行元件。液压缸按结构特点的不同可分为活塞缸、 柱塞缸和摆动缸三类,活塞缸和柱塞缸用以实现直线运动, 输出推力和速度;摆动缸(或称摆动马达)用以实现小于 360°的转动,输出转矩和角速度。
2021/1/20
16
4.辅件部分
• 液压辅助元件包括过滤器、油箱、管道及管接头、密封件 等。这些元件,从在液压系统中的作用看,仅起辅助作用, 但从保证完成液压系统的任务看,它们是非常重要的。它 们对系统的性能、效率、温升、噪声和寿命影响极大,必 须给予足够的重视。除油箱常需自行设计外,其余的辅助 元件已标准化和系列化,皆为标准件,但应注意合理选用。 是系统中除上述三部分以外的所有其他元件,如油箱,压 力表、滤油器、管路、管接头、加热器和冷却器等。
用液压系统传动功率大、效率高、运行安全可靠的优点。 该加工中心主要实现链式刀库的刀链驱动、上下移动的主 轴箱的配重、刀具的安装和主轴高低速的转换等辅助动作 的完成。图13-6所示为VP1050加工中心的液压系统工作 原理图。整个液压系统采用变量叶片泵为系统提供压力油, 并在泵后设置止回阀2用于减小系统断电或其他故障造成 的液压泵压力突降而对系统的影响,避免机械部件的冲击 损坏。压力开关 YK1 用以检测液压系统的状态,如压力 达到预定值,则发出液压系统压力正常的信号,该信号作 为CNC系统开启后PLC高级报警程序自检的首要检测对象, 如YK1无信号,PLC自检发出报警信号,整个数控系统的 动作将全部停止。
• 数控机床的超程限位保护一般有硬限位和软限位 两种双重保护。硬限位靠行程开关碰撞机械撞块 后,自动切断进给驱动电源,为可靠起见,通常 在硬限位前又设定了软限位。其尺寸距离可通过 修改系统参数来设定,软限位需要在机床回参考 点后才起作用。
机械制图电子课件第十三章尺寸的标注方法 第十四章表面粗糙和公差配合

3、当零件所有表面具有相同的表面粗糙度要求 时,其代(符)号可在图样的右上角统一标注。 4、当零件的大部分表面具有相同的表面粗糙度 要求时,对其中使用最多的一种代(符)号可 以统一注在图样的右上角,并加“其余”两字。 5、为了简化标注方法,或者标注位置受到限制 时,可以标注简化代号,也可以采用省略的注 法,但必须在标题栏附近说明简化代号的意义。 6、对不连续的同一表面,可用细实线连接,只 注一次表面粗糙度符号。对连续表面及重复要 素(孔、槽、齿、……等)的表面,其表面粗 糙度代(符)号只标注一次。
2、当组合体具有交线时,要注意:不要直 接标注交线的尺寸,而应该标注产生交 线的形体或截面的定形及定位尺寸。
§13-2 尺寸的清晰布置
为了看图方便,在标注尺寸时,应当考虑使尺寸 的布置整齐清晰。一般有以下几种处理方法: 1、为了使图面清晰,应当将多数尺寸注在视图 外面,与两视图有关的尺寸注在两视图之间。
三、退刀槽及越程槽 切削过程中,为了不致使刀具损坏,并易退出刀具,同 时与相关零件装配时易于靠紧,所以被加工零件预先要 加工出退刀槽或越程槽,这样被加工的表面的根部就不 会有残留部分,一般叫“清根”。 退刀槽一般可按“槽宽*直径”或“槽宽*槽深”的形式 标注。 四、各种形式的孔 螺孔、沉孔及圆锥销孔等可采用旁注的方法标注。
二.简单物体的尺寸标注 方法: 先将简单物体分解为基本体 再注出各基本体所需要的尺寸 然后再分别注出变化部分的尺寸
简单物体的尺寸可分为两类: 1、定形尺寸——决定组成简单物体的各基本体 的形状及大小的尺寸。 2、定位尺寸——决定各基本体在简单物体上的 相互位置的尺寸。
三、组合体的尺寸标注
1、形体分析法是标注组合体尺寸的基本方法
第十三章 尺寸的标注方法
刀具培训资料PPT课件
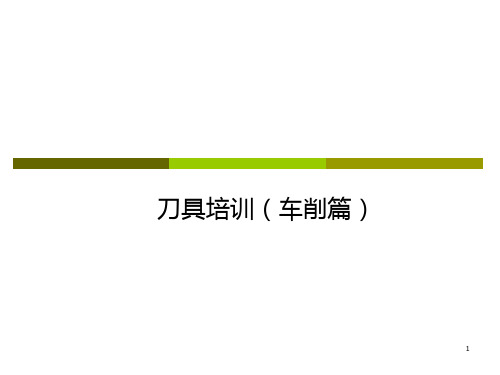
•副切削刃
•切削刃上除主切削刃以外的刃,亦起始于切削刃上主偏角为零的点,但它向背离
主切削刃的方向延伸。
。化 学 蒸 汽 堆 积
特点:
1)1000(C) 涂层温度提高了
生产率
2)5-15 微米厚度
3)多涂层
优点:
1)涂层强度和附着力好(涂层强度比母材稍低
)
2)50%-100% 提高了切削速度
3)多至400%地提高了刀具寿命
4)提高了抗热冲击性
5)对母材的形状无限制
18
PVD方法
Physical Vapor Deposition 物理蒸汽堆 积
8
刀具材料陶瓷
9
陶瓷粗车球铁差速器壳
10
刀具材料CBN
CBN方氮化硼是由六方氮化硼和触媒在高温高压下合成的,是继人造金刚石问世后出 现的又一种新型高新技术产品。它具有很高的硬度、热稳定性和化学惰性,以及良好 的透红外形和较宽的禁带宽度等优异性能,它的硬度仅次于金钢石,但热稳定性远高 于金钢石,对铁系金属元素有较大的化学稳定性。
陶瓷
涂层
劣 劣
金属陶瓷
硬质合金 高速钢
韧性
优
4
切削刀具分类及标志
P类 用于加工长切屑的钢件
M类
用于加工
不锈钢件
K类
用于加工短切屑的
铸铁件
N类
用于加工短切屑的
非铁材料
S类
用于加工
难加工材料
H类
用于加工
硬料
5
刀具材质高速钢
定义;又名风钢或锋钢,又称白钢。它是一种成分复杂的合金钢,含有
钨、钼、铬、钒、钴等碳化物形成元素。合金元素总量达10~25%左右。它 在高速切削产生高热情况下(约500℃)仍能保持高的硬度,HRC能在60以上。 高速钢的工艺性能好,强度和韧性配合好,在刀具制造过程中应用广泛
第13章 机械加工误差分析(2)

L
Δβ
18
一面两孔定位时定位误差计算公式:(教材图13.10) 任意位臵水平尺寸B1、B2、B3 Δ Y=X1max(孔与销的最大间隙) 与定位销对齐的垂直尺寸A2 Δ Y=X1max A4 Δ Y=X2max 在定位销之间的垂直尺寸A3 Δ Y=X1max+2B2tanΔ α 在定位销之外的垂直尺寸A1 Δ Y=X1max+2B1tanΔ β A5 Δ Y=X2max+2B3tanΔ β tanΔ α =(X2max- X1max)/2L tanΔ β =(X2max+ X1max)/2L Δα
8
2、基准位移误差的计算 (2)工件以圆孔在圆柱销上定位 当定位基准在任意方向偏移时,其最大偏移量即为 定位副直径方向的最大间隙,即 ΔY=Xmax=Dmax—d0min=δD+δd0+Xmin 当基准偏移为单方向时,在其移动方向最大偏移量 为半径方向的最大间隙,最小偏移量为半径方向的最 小间隙,加工前预先将刀具向下调低Xmin/2,这时Xmin 不影响定位精度。 ΔY=(Xmax – Xmin)/2 =(Dmax-d0min- Xmin)=(δD+δd0)/2 如果基准偏移的方向与工件加工尺寸的方向不一 致时,应将基准的偏移量向加工尺寸方向上投影,投 影后的值才是此加工尺寸的基准位移误差。 采用弹性可涨心轴为定位元件时,则定位元件与 定位基准之间无相对位移,因此基准位移误差为零。 9
D B Y (0.053 0.007 )mm 0.06 mm
15
(4) 一面两孔组合定位时的定位误差计算
在加工箱体、支架类零件时,常用工件的一 面两孔定位,以使基准统一。这种组合定位方式 所采用的定位元件为支承板、圆柱销和菱形销。 工件以平面作为主要定位基准,限制三个自由度, 圆柱销限制二个自由度,菱形销限制一个自由度。 菱形销作为防转支承,其长轴方向应与两销中心 连线相垂直。 工件以一面两孔定位时,主要在确定两销的 中心距及公差、圆柱销的直径及公差、菱形销的 直径及公差,最后进行定位误差计算。
第13章 ProE NC后置处理

第13章 Pro/E NC后置处理
13.2 Pro/E NC配置文件的制作
13.2.2 打开后处理器 2.File Formats
第13章 Pro/E NC后置处理
13.2 Pro/E NC配置文件的制作
13.2.2 打开后处理器 3.Start/End of Program
第13章 Pro/E NC后置处理
13.1 Pro/E NC后置处理简介
在数控加工过程中,系统会生成模型加工的刀 具运动轨迹文件,即刀具数控文件(CL文件), 这些数据文件不能再被机床控制器直接识别,因 此有必要将这些数据文件转换成机床能够识别的 文件,然后再输入到数控机床中进行加工,这些 过程称为后处理。
13.2.2 打开后处理器 6.Operator Messages
第13章 Pro/E NC后置处理
13.2 Pro/E NC配置文件的制作
13.2.2 打开后处理器 7.Advanced
第13章 Pro/E NC后置处理
13.3 创建后处理器
Define Option File Location对话框
第13章 Pro/E NC后置处理
13.2 Pro/E NC配置文件的制作
13.2.1 后处理器模式 4.Help菜单
第13章 Pro/E NC后置处理
13.2 Pro/E NC配置文件的制作
13.2.2 打开后处理器 “应用程序”→“NC后处理器”
第13章 Pro/E NC后置处理
13.2 Pro/E NC配置E NC配置文件的制作
机床的后置处理程序由于数控机床的输入格式不同而有 所不同,因此不同的机床也要求有不同的后处理器。 Pro/ENGINEER Wildfire 4.0为设计人员提供了一些经常使用 的后置处理器,以方便用户根据实际需要选择,用户也可以根 据具体需要自行创建所需的后处理器。
第13章(96)教材配套课件

第 13 章 轴
图13-14 轴肩的圆角和倒角
第 13 章 轴
3.
在满足使用要求的情况下,轴的形状和结构应力求简
单,精度要求应合理以便于降低制造成本。为此,应注意:
各轴段的直径不宜相差太大(一般取5~10 mm),以便能选
用合适的圆钢和减少切削加工量;一根轴上的圆角应尽可
能取相同的半径,以便减少换刀或刃磨刀具的次数;一根
图13-4 转动心轴
第 13 章 轴
按轴线的形状轴可分为直轴(见图13-1~图13-4)、 曲轴 (见图13-5)和挠性轴(见图13-6)。
曲轴主要用于内燃机等作往复运动的机械中。挠性钢 丝轴通常是由几层紧贴在一起的钢丝层构成的,可以把转 矩和运动灵活地传到任何位置。它适用于受连续振动的场 合,具有缓和冲击的作用,常用于振捣器等设备中。轴按 其截面又可分为圆形截面轴和非圆形截面轴。另外,为减 轻轴的重量,还可以将轴制成空心的形式,如图13-7所示。
第 13 章 轴
13.3.2
轴的结构设计就是使轴的各部分具有合理的形状和尺 寸。其主要要求是: ① 要便于轴上零件的装拆;② 轴和 轴上零件要有准确的工作位置,各零件要可靠地相对固定; ③ 轴的结构要便于加工和节省材料;④ 满足强度要求, 尽量减少应力集中等。下面结合图13-9所示的单级齿轮减
第 13 章 轴
第 13 章 轴
1. 碳素钢 35、 45、 50等优质碳素结构钢因具有较好的综合机 械性能,故应用较多,特别是45钢应用最为广泛。为了改 善其机械性能,应进行正火或调质处理。不重要或受力较 小的轴,可采用Q235、 Q275
第 13 章 轴
2. 合金钢 合金钢具有较高的机械性能,可淬性也较好,但价格 较贵,多用于有特殊要求的轴。例如采用滑动轴承的高速 轴,常用20Cr、20CrMnTi等低碳合金钢,经渗碳淬火后 提高轴颈耐磨性;汽轮发电机转子轴在高温、 高速和重 载条件下工作,必须具有良好的高温机械性能,常采用 40CrNi、 38CrMoAlA等合金结构钢。
13机械制造基础2_齿加工和磨削

动画7 剃齿
第 16 页
视频5 剃齿
第 17 页
12.4.2 刀具、夹具、工件的安装
1.剃齿刀的安装 剃齿的安装角ψ按下式计算: ψ=β工+β刀 式中:β刀——刀具分度圆螺旋角; β工——被剃齿轮分度圆螺旋角。 剃齿面的安装精度、刀杆的径向圆跳动量一般小于0.003mm; 刀具安装好后,刀具端面圆跳动量一般小于0.006mm。
7
8~7
1.6~0.4
3.2~1.6
高
一般较滚齿低 较高 高 很高 成形高于展成
拉床
插齿机 滚齿机 剃齿机 珩齿机 磨齿机
大批大量生产7级精度的内齿 轮
单件成批生产中等质量的内外 圆柱齿轮、多联齿轮 单件成批生产中等质量的外圆 柱齿轮、蜗轮 精加工未淬火的圆柱齿轮 成批大量光整加工已淬火的圆 柱齿轮 精加工已淬火的圆柱齿轮
插齿过程如同一对齿轮作无侧隙的啮合运动,其中一个是被加 工齿轮,另一个是插齿刀(在每一个齿上磨出前角和后角以形成刀刃, 切削时插齿刀作上下往复运动,从工件上切除切屑。插齿刀的
模数和压力角必须与被加工齿轮的模
数和压力角相同。如动画6所示,当 插削圆柱直齿轮时,插齿机必须有以 下几个运动: ①切削运动; ②周向进给运动; ③分齿运动; ④径向进给运动; ⑤退 刀运动。
动画10 常用剃齿法
0.03mm)。
动画11 鼓形齿剃削
第 21 页
12.5 珩齿(见视频6)
12.5.1 珩齿加工原理
珩齿加工是应用珩轮与被珩齿轮作自由啮合传动,利用其齿面间 的相对滑动速度和压力来进行珩削的一种齿面精加工方法。珩齿运 动和剃齿基本相同,一般用于淬硬齿轮的最终加工,与剃齿不同的 是珩齿加工余量很少,只需一次进行到底,故开始时齿面压力较大, 随后逐渐减小,直至压力消失时,珩齿便告结束。
刀具基础知识课件
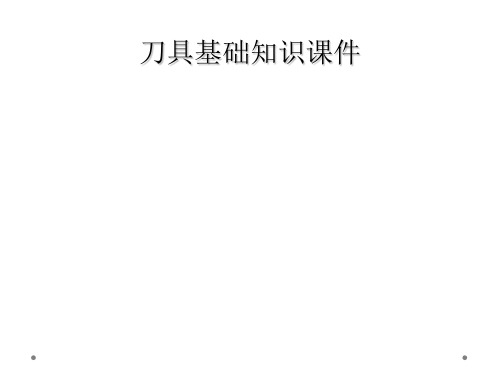
(2)增加磨刀次数。
(三)边界磨损(前、后刀面同时磨损)
边界磨损--切钢料时,主刃、副刃与工件待加工表面或已加
工表面接触处磨出沟纹。边界处的加工硬化层、硬质点、较大的应
力梯度和温度梯度所造成。
刀具基础知识----失效及耐用度
二、刀具磨损过程及磨钝标准
4.切削液对刀具耐用度T的影响 切削液的种类 冷却润滑方式
刀具基础知识----失效及耐用度
工件:HT250 刀具:PCBN
切削速度、切削路程与刀尖磨损量的关系
刀具基础知识----失效及耐用度
工件:HT250 刀具:PCBN
进给量与表面粗糙度的关系
刀具基础知识----失效及耐用度
切削速度与表面粗糙度的关系
一、刀具的磨损形式
前刀面磨损 最少 后刀面磨损 边界磨损 最多
(一)前刀面磨损
原因:(1)切塑性材料; (2)切削速度v较高; (3)切削厚度ac较大时。
特点:切削时间↑→月牙洼深度↑ →崩刃 措施:(1)冷却、润滑
(2)刀具材料刀具基础知识---失效及耐用度(二)后刀面磨损
原因:(1)切削铸铁等脆性材料; (2)v 和ac较小切塑性材料时。
工件:HT250 刀具:PCBN
刀具基础知识----失效及耐用度
工件:HT250 刀具:PCBN
切深与刀具磨损量的关系
刀具基础知识----刀具材料
刀具材料及其选用:刀具材料主要指刀 具切削部分的材料。刀具切削性能的优劣, 直接影响着生产效率、加工质量和生产成 本。而刀具的切削性能,首先取决于切削 部分的材料;其次是几何形状及刀具结构 的选择和设计是否合理。
刀具基础知识----几何角度
第13章 成形车刀

限制,精确度较低。而计算法虽较复杂,但精确 度较高。生产中常用计算法进行设计,再用图形 法校验。
1. 设计前的准备工作 (1) 确定成形表面廓形的组成点。对图13.20 所示成形表面进行分析表明:任何一个复杂表面 均可看成是由很多个平面、圆柱面和圆锥面组成 的。取各组成表面轮廓线的起始点和终(拐)点 作为成形表面廓形的组成点(如图中的1、2、3、 4、a、b、c、d、5各点),求出与之对应的刀具 廓形上的点,这样可以简化设计过程。
为简化结构,可在成形车刀端面上直接做出端
面齿(图13.11(a))。对切削刃总长度不长、切 削力较小的圆体成形车刀,只在其端面上滚花,靠 增大断面的摩擦力来实现车刀在刀夹中的夹紧(图 13.11(b)),也可以通过销子与可换端面齿环连 接(图13.11(c))。
13.3 成形车刀的前角与后角
成形车刀必须具有合理的切削角度。由于成形 车刀切削刃形状复杂(图13.12),各段切削刃的 正交平面方向各不相同,难于做到切削刃各点的切 削角度合理。一般只给假定工作(进给) 平面的前角γf与后角αf 。
13.4 径向成形车刀的廓形设计
成形车刀的廓形设计就是根据工件的已知 径向和轴向尺寸求出刀具法剖面N—N内的形状 尺寸,即刀具的廓形。有图13.17知,刀具法剖 面N—N内的廓形深度Px与刀具前刀面上对应切 削刃的廓形深度Cx有关, Cx则是根据工件轴向 剖面内的廓形深度Pwx及刀具的前角γf与后角
显然,与径向成形车刀相比,它的切削力小且工作过 程较平稳;但工作行程长,生产效率低。故仅用于 加工廓形深度不大、细长、刚度较差的工件。 3. 按工作时与工件轴线的相互位置分 按工作时与工件轴线的相互位置可分为正装(图 13.3~13.5)和斜装(图13.7)两种。 成形车刀一般都用高速钢整体制造。近年来, 为提高刀具使用寿命,也采用镶焊硬质合金的成形 车刀(图13.8),但目前国内还用得不多。
机修钳工工艺学第四版教学课件第十三章机床夹具

(3)定位件。定位件主要用于工件的定位和确定元 件与元件之间的相对位置,如各种定位销、定位盘、定 位支承、V 形支承、 定位键等。
(4)导向件。导向件是用来确定刀具与工件之间相 对位置的元件,包括各种尺寸规格的钻套、钻模板、导 向支承等。
3. 扩大机床加工范围
使用夹具可以扩大机床的加工范围,实现一机多用,解 决缺乏某种设备的困难。
三、机床夹具的分类
常用金属切削机床夹具的分类
§13-2 工件的定位
一、工件定位原理
1. 六点定位规则
确定工件在机床或夹具中占有正确位置的过程称为定位。 一个尚未定位的工件,在空间直 角坐标系中,可沿3个坐标轴自由移 动和绕这3个坐标轴自由转动。通常 把这种运动的可能性称为自由度。
二、机床夹具的作用
1. 保证加工精度
使用机床夹具能保证加工精度的稳定性。零件的加工精 度主要取决于夹具的制造精度。
2. 提高劳动生产率,降低加工成本
采用机床夹具省去了划线、找正等工序,且装夹方便、 迅速、安全、可靠,缩短了辅助时间。在导向元件的作用 下可加大切削用量。能有效提高生产率,降低加工成本。
自由度,该面称为止推定位基准面。
(2)长轴类工件定位
长轴类工件加工实例
长轴类工件定位支承点分布
(3)盘类工件定位 端面定位支承点1、3、4限制了工件的
三个自由度;短心轴的定位支
承点5、6限制了工件的
两个自由度
;防转支承点2限制了工件的 自由度。
通过以上分析可知:件加工时应限制的自由度取决于 加工要求,定位支承点的分布取决于工件形状。
刀具介绍及运用课件
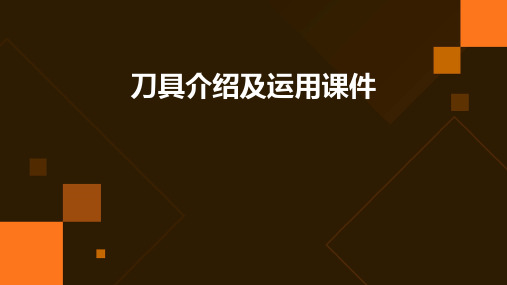
绿色制造与环保刀具的推广使用
环保材料
采用可再生、可降解的环保材料制造刀具,减少对环境的污染。
节能减排
优化刀具结构和切削参数,降低切削能耗和切削液的使用,实现绿色制造。
刀具行业的未来展望和挑战
新材料与新技术
随着新材料和新技术的不 断涌现,刀具行业将迎来 更多的发展机遇和挑战。
市场需求变化
随着制造业的转型升级, 刀具市场将更加注重个性 化、定制化和高端化需求 。
• 几何参数:刀具的几何参数包括前角、后角、主偏角、副偏角等,这些参数对 切削力、切削热、切削刃磨损和加工表面质量有很大影响。
• 涂层技术:涂层技术可以提高刀具的硬度、耐磨性、耐热性和抗氧化性。常见 的涂层材料有氮化钛、氧化铝、金刚石等。
• 选用原则:在选择刀具时,需要考虑加工材料、加工精度、加工效率、刀具寿 命等因素。应根据具体加工需求,选用合适的刀具类型、材料和几何参数。同 时,定期检查和更换磨损严重的刀具,以保证加工质量和效率。
02
种类
包括砂轮、砂带、磨头等。
03
特性
磨削刀具通过磨料颗粒与工件表面的摩擦和切削作用实现材料去除,其
加工精度高,表面质量好。选择合适的磨料、粒度、结合剂和硬度是磨
削刀具的关键。
刀具的特性与选用原则
• 刀具材料:刀具材料应具备高硬度、高强度、良好的耐磨性和耐热性。常用的 刀具材料有高速钢、硬质合金、陶瓷、立方氮化硼(CBN)和金刚石等。
刀具介绍及运用课件
目录
• 刀具概述 • 刀具的种类与特性 • 刀具的运用技术 • 现代刀具技术发展趋势
01
刀具概述
刀具定义和分类
定义
刀具是机械制造中用于切削、车 削、铣削、钻孔等加工工件的专 用工具。
刀具课件第13章共46页

第13章成形刀具、拉刀及组合刀具刀具切削刃形状决定于工件轮廓形状的刀具,称为成形刀具。
但成形刀具的廓形尺寸与工件并不完全一致,需要进行设计计算。
成形刀具的主要优点是生产率高。
其产品质量主要取决于刀具精度,而与操作者水平关系不大,因此,成形刀具的使用寿命长,用其加工出的工件一致性好(可保证工件的互换性)。
成形刀具的缺点是制造比较麻烦,成本较高,因此,其主要适用于成批和大量生产。
成形刀具多用高速钢制造。
拉刀是一种多齿刀具,它的刀体上有许多排刀齿,并且刀齿尺寸是逐渐增加的。
它除了具有切削部分外,还能保证拉削后的工件获得较高光洁度与准确度的加工表面。
组合刀具是机械加工中多快好省地完成和超额完成生产任务的重要方法之一。
13.1 成形车刀13.1.1 成形车刀的分类成形车刀是一种专用刀具,它多用于车床、六角车床、自动和半自动车床加工内、外回转体成形表面。
成形车刀制成后,其后面为成形表面,每次重磨时只磨前面。
1.按结构和形状分类成形车刀按其结构和形状可分为平体成形车刀、棱体成形车刀和圆体成形车刀。
1)平体成形车刀平体成形车刀的外形与普通车刀相似,只是切削刃有一定形状。
如图13-1所示的螺纹车刀和铲齿车刀就属于平体成形车刀。
它一般可用来加工宽度不大,且较简单的成形表面,但刀具重磨次数不宜过多。
(a)螺纹车刀(b)铲齿车刀图13-1 平体成形车刀2)棱体成形车刀如图13-2所示为棱体成形车刀。
其外形为多棱柱体,由于结构尺寸限制,只能用来加工外成形表面。
棱体成形车刀的刀体可根据结构设计得长些,故其重磨次数较平体成形车刀多,且刚性较高。
3)圆体成形车刀如图13-3所示为圆体成形车刀。
其外形为回转体,重磨次数比棱体成形车刀多。
圆体成形车刀不但可加工外成形表面,还可加工内成形表面。
因其刀体本身为回转体,制造容易,故生产中应用较多。
图13-2 棱体成形车刀图13-3 圆体成形车刀2.按进给方向分类成形车刀按其进给方向可分为径向成形车刀和切向成形车刀。
通用刀具培训教材(共 34张PPT)

相关概念的介绍 车削刀具 铣削刀具
攻丝工艺
主运动及从运动的概念 切削三要素
线性切削速度Vc,切深ap和每转走刀量f是切 削三要素。 Vc: m/min 米/分钟 ap: mm 毫米 fr(fn): mm/r 毫米/转
车削刀具---焊接车刀和机夹车刀
焊接车刀的优点在于单刀价格便宜,多次重 磨,容易获得锋利刃口,缺点在于速度低 (70米以下),寿命短,刃口安全性差。
影响车刀片寿命的原因有切削热,摩擦和切削抗力,这三者随着切 削速度的增加而加剧最为强烈。
刀片材料和切削线速度
高速钢车刀:20-30米/分钟 硬质合金:70-90米/分钟 涂层硬质合金:100-300米/分钟
氧化铝涂层:200-400米/分钟
金属陶瓷: 200-350米/分钟 陶瓷刀片:500米/分钟以下 CBN刀片:400-1000米/分钟 金刚石刀片:1000-3000米/分钟
切削力和切削方向的突变
刀具中心点频繁切削
特别对于高速加工
切削转角处
过切
碎屑接触中心点
ae
ae
如果铣宽 ae 等于和小于 1/2 刀盘直径,切屑厚度有何不同 ?
ae ≥ 50% fz = 最大切屑厚度 ae < 50% 时, fz > 最大切屑厚度
fz =.006
.004
ae.75
最大切屑厚度 hex
经济核算
效率的压力
振动的影响
表面质量要求
工件直径120mm, 主轴转速350转/ 分钟,则切削速度为
Vc=120x3.14x350/1000
=132m/min
车削三要素与刀具寿命
T
ap fr Vc
切削速度增加20%刀片磨损增加50%; 走刀量增加20%刀片磨损增加20%; 切深增加50%刀片磨损增加20%。
- 1、下载文档前请自行甄别文档内容的完整性,平台不提供额外的编辑、内容补充、找答案等附加服务。
- 2、"仅部分预览"的文档,不可在线预览部分如存在完整性等问题,可反馈申请退款(可完整预览的文档不适用该条件!)。
- 3、如文档侵犯您的权益,请联系客服反馈,我们会尽快为您处理(人工客服工作时间:9:00-18:30)。
第13章成形刀具、拉刀及组合刀具刀具切削刃形状决定于工件轮廓形状的刀具,称为成形刀具。
但成形刀具的廓形尺寸与工件并不完全一致,需要进行设计计算。
成形刀具的主要优点是生产率高。
其产品质量主要取决于刀具精度,而与操作者水平关系不大,因此,成形刀具的使用寿命长,用其加工出的工件一致性好(可保证工件的互换性)。
成形刀具的缺点是制造比较麻烦,成本较高,因此,其主要适用于成批和大量生产。
成形刀具多用高速钢制造。
拉刀是一种多齿刀具,它的刀体上有许多排刀齿,并且刀齿尺寸是逐渐增加的。
它除了具有切削部分外,还能保证拉削后的工件获得较高光洁度与准确度的加工表面。
组合刀具是机械加工中多快好省地完成和超额完成生产任务的重要方法之一。
13.1 成形车刀13.1.1 成形车刀的分类成形车刀是一种专用刀具,它多用于车床、六角车床、自动和半自动车床加工内、外回转体成形表面。
成形车刀制成后,其后面为成形表面,每次重磨时只磨前面。
1.按结构和形状分类成形车刀按其结构和形状可分为平体成形车刀、棱体成形车刀和圆体成形车刀。
1)平体成形车刀平体成形车刀的外形与普通车刀相似,只是切削刃有一定形状。
如图13-1所示的螺纹车刀和铲齿车刀就属于平体成形车刀。
它一般可用来加工宽度不大,且较简单的成形表面,但刀具重磨次数不宜过多。
(a)螺纹车刀(b)铲齿车刀图13-1 平体成形车刀2)棱体成形车刀如图13-2所示为棱体成形车刀。
其外形为多棱柱体,由于结构尺寸限制,只能用来加工外成形表面。
棱体成形车刀的刀体可根据结构设计得长些,故其重磨次数较平体成形车刀多,且刚性较高。
3)圆体成形车刀如图13-3所示为圆体成形车刀。
其外形为回转体,重磨次数比棱体成形车刀多。
圆体成形车刀不但可加工外成形表面,还可加工内成形表面。
因其刀体本身为回转体,制造容易,故生产中应用较多。
图13-2 棱体成形车刀 图13-3 圆体成形车刀2.按进给方向分类成形车刀按其进给方向可分为径向成形车刀和切向成形车刀。
1)径向成形车刀图13-1~图13-3均为径向成形车刀。
此类成形车刀工作时,是沿工件半径方向进给的,整个切削刃同时切入,工作行程短、生产效率高。
但其同时参加切削的切削刃的长度长,径向力较大,容易引起振动,影响加工质量。
2)切向成形车刀如图13-4所示为切向成形车刀。
此类成形车刀是沿工件切线方向进给的,由于切削刃与工件端面(进给方向)偏斜角度r κ,故切削刃逐渐切入工件,只有当切削刃上最后一点通过工件外轮廓的铅垂面后,工件上的成形表面才被加工完成。
显然,与径向成形车刀相比,其切削力小且工作过程较平稳。
但由于其工作行程长,因而生产效率较低。
切向成形车刀仅用于加工廓形深度不大、细长、刚性较差的工件。
成形车刀一般都用高速钢制成整体结构。
近年来,为提高刀具耐用度,也采用镶焊硬质合金的成形车刀,但目前国内还用得不多。
图13-4 切向成形车刀13.1.2 成形车刀的前角和后角成形车刀切削刃形状较复杂,为了便于设计、制造和重磨,一般规定成形车刀的前角和后角均在假定工作平面内表示,并以加工工件上半径最小处的切削刃上点(称为基准点)的基面与前面的夹角f γ,切削平面与后面的夹角f α。
f γ和f α分别被定义为成形车刀的前角和后角。
对于如图13-5所示的棱体成形车刀,它的外形为棱体,其重磨次数比平体成形车刀多。
使用时靠燕尾体与刀杆的燕尾槽连接,并用螺钉夹紧,刀体下端的螺钉可用来调整刀尖的高度,并可承受部分切削力。
制造棱体成形车刀以及重磨时只控制前、后角之和,装夹时装在倾斜f α角度的刀杆上,从而形成前角f γ和后角f α。
图13-5 棱体成形车刀的几何角度及安装对于如图13-6所示的圆体成形车刀,其安装时刀具中心高于工件中心,刀具前面与工件径向线(水平线)之间的夹角即为前角f γ。
由于刀具中心高于工件中心,自然形成了后角f α。
图13-6 圆体成形车刀的几何角度及安装成形车刀的前角可根据工件材料选择,后角可按下列数据选取:平体成形车刀为 25°~30°,棱体成形车刀为12°~17°,圆体成形车刀为10°~15°。
13.1.3 成形车刀的廓形设计成形车刀的廓形设计有作图法和计算法两种。
作图法简单、直观,但受图形放大倍数限制,精确度较低。
计算法虽较复杂,但精确度较高。
生产中常采用计算法进行设计,再用作图法进行校验。
1.廓形设计前的准备工作设计前的准备工作如下:(1)确定成形车刀廓形的组成点。
对如图13-7所示的成形车刀廓形进行分析表明,一个复杂表面可以看成是由很多个平面、圆柱面和圆锥面组成的。
取各组成表面轮廓线的起始点和终(拐)点作为成形车刀廓形的组成点,图13-7中的1、2、3、4、a 、b 、c 、d 、5各点,求出与之对应的成形车刀廓形上的点,这样可以简化设计过程。
图13-7 对成形车刀廓形的分析(2)画出工件的主视图和俯视图,确定工件上最小半径圆与水平轴线的交点为基准点(当不考虑附加切削刃时),并依次标出其余组成点及相应的径向、轴向尺寸。
(3)确定成形车刀的合理前角f γ和后角f α,对圆体成形车刀还须确定外径1R 。
2.廓形设计的作图法1)棱体成形车刀的作图法棱体成形车刀的廓形设计如图13-8所示。
其作图步骤如下:图13-8 棱体成形车刀的廓形设计(1)以适当的放大比例画出工件的端视图和俯视图。
(2)在端视图上,从基准点1分别作与水平线成f γ和与铅垂线成f α的直线,并作为前面和后面的投影线。
前面投影线与工件各组成点所在圆相交于2’、3’(4’)点,这些点就是刀具前面上与工件各组成点相对应的点。
(3)从前面投影线上的2’、3’(4’)各点分别作平行于后面投影线的直线。
这些直线即为棱体成形车刀廓形上各点所在后面的投影线,它们与基准点1所在后面投影线间的距离P 2、P 3(P 4)即为棱体成形车刀N -N 剖面对应点间的廓形深度。
(4)延长各后面投影线,在基准点1后面投影线延长线上取1’’点并作该线的垂线,以该垂线作为起始线,分别在过2’、3’(4’)点的后面投影线的延长线上截取32l l =和4l 得交点2’’、3’’、4’’,用直线(或平滑曲线)连接这些点,即得棱体成形车刀N -N 剖面内廓形。
2)圆体成形车刀的作图法圆体成形车刀的廓形设计如图13-9所示。
其作图步骤如下:(1)以适当的放大比例画出工件的端视图和俯视图;(2)在端视图上,从基准点1作与水平线夹角为f γ的直线作为前面的投影线,分别与工件各组成点所在圆相交于2’、3’(4’)点,这些点即为前面廓形的组成点。
(3)再从基准点1作与水平线夹角为f α的斜向右上方的直线,在其上截取圆体成形车刀外圆半径的长度得点c O ,c O 即为圆体成形车刀的轴心。
(4)以c O 为圆心,分别以c O 1’、c O 2’、c O 3’(c O 4’)为半径作同心圆,与过c O 的水平线分别相交于1’’、 2’’、 3’’(4’’)点。
1R 、2R 、3R (4R )即为圆体成形车刀廓形各组成点的半径。
1R 、2R 、3R (4R )各半径之差,即为刀具廓形各组成点在轴向剖面的廓形深度。
(5)根据已知的工件轴向尺寸及1R 、2R 、3R (4R ),利用投影原理,即可求出圆体成形车刀轴向剖面内的廓形。
图13-9 圆体成形车刀的廓形设计1、2、3、4—工件廓形; 1’、2’、3’、4’—切削刃投影; 1’’、2’’、3’’、4’’—刀具廓形3.廓形设计的计算法1)棱体成形车刀廓形设计的计算图13-8中,作棱体成形车刀前面投影线的延长线,再从工件中心1O 作该延长线的垂线得交点b ,工作中心1O 到交点b 的距离为h ,再标出2C 、3C 、4C 及1A 、2A 、3A 、4A 。
设r 1、r 2、r 3、r 4为工件轮廓上各点的半径,P 2、P 3、P 4为棱体成形车刀廓形深度。
由直角三角形1O b 1可得f 1sin γr h = (13-1)f 11cos γr A =由直角三角形1O b 2’可得22f 2cos A r γ= (13-2)又因为221C A A =-所以22f f cos()P C γα=+同理,前面上任意点n 的各参数为f cos n n n A r γ= (13-3)1C n n A A =- (13-4)f f cos()n n P C γα=+ (13-5)2)圆体成形车刀廓形设计的计算图13-9中,过基准点1作前面投影线的延长线,工件中心1O 至该延长线的距离为h ,c O 至该延长线的距离为c h ,分别标出工件和圆体成形车刀廓形上的尺寸1A 、2A 、3A (4A )、2C 、3C 、(4C )、1B 、2B 、3B (4B )。
设r 1、r 2、r 3、r 4为工件轮廓上各点的半径,R 1、R 2、R 3、R 4为圆体成形车刀廓形上各点的半径。
由图13-9可知)sin(f f 1c αγ+=R h (13-6))(c o s f f 11αγ+=R B c 1arctan h B ε= 212C B B -=c 22sin h R ε=同理,前面上任意点n 的各参数为 n 1n C B B -=c n narctan h B ε= c n nsin h R ε= (13-7) 13.2 铲齿成形铣刀成形铣刀是具有成形切削刃的铣刀,它与成形车刀相同之处是刀具切削刃的廓形都要根据工件廓形设计。
用成形铣刀可在通用铣床上加工复杂形状的表面,能获得较高的精度和表面质量,并有较高的生产率。
成形铣刀在生产中应用比较广泛,如发动机蜗轮叶片成形面、齿轮齿廓表面、花键槽、成形螺旋槽(麻花钻螺旋糟)等的加工。
按照齿背的加工方法及重磨方法的不同,成形铣刀可分为尖齿成形铣刀和铲齿成形铣刀,如图13-10所示。
(a )尖齿成形铣刀 (b )铲齿成形铣刀图13-10 成形铣刀在大批量生产中,用来在铣床上铣削成形表面或成形沟槽的以铲齿成形铣刀居多,其切削刃廓形是根据工件的廓形设计、计算的。
13.2.1 铲齿成形铣刀刀齿的要求铲齿成形铣刀刀齿的前面,多取为轴向平面,即前角f γ为零。
这种成形铣刀的设计、制造、检验都比较简单,刃磨比较方便。
铲齿成形铣刀刀齿的后面的齿背表面,应能保证铣刀重磨后的切削刃形状不变,并具有一定的后角f α。
为达到这个要求,铣刀的后面应该是由切削刃绕轴线回转,又同时沿轴向平面向铣刀轴心移动所形成的表面。
只要能得到这样的齿背表面,就能保证铣刀在重磨后切削刃形状不变,如图13-11所示A -A 、B -B 各剖面形状相同。
实现这种齿背(后面)加工的方法叫做铲齿,就是用铲齿成形车刀(刃形与被铲的成形铣刀切削刃形相同,但凹凸相反的平体成形车刀)在铲齿车床上加工出来的。