不锈钢钻削加工有限元仿真及试验研究
316l不锈钢的铣削仿真试验与试验研究

1.1 建 立 仿 真 模 型 本 研 究 在 模 型 建 立 时 袁采 用 标 准 建 模 方 式 与 自 定 义
功 能 建 立 工 件 模 型 袁 同 时 将 SolidWorks 中 建 立 的 刀 具 模 型 导 入 Deform3D 软 件 中 袁 其 中 刀 具 选 用 直 径 为 5mm 的 硬 质 合 金 立 铣 刀 曰 工 件 为 棱 长 是 3mm 的 立 方 体 遥 为 了 仿 真 更 加 接 近 于 实 际 加 工 中 稳 定 铣 削 的 阶 段 袁建 立 几 何 模 型 时 进 行 预 切 遥 工 件 与 刀 具 的 仿 真 装 配 模 型 如 图 1所 示 袁同 时 铣 刀 走 刀 方 向 为 X 正 方 向 遥
Science & Technology Vision
科技视界
316L 不锈钢的铣削仿真试验与试验研究
李本泉 李 阳 马曰红 渊 山 东 理 工 大 学 机 械 工 程 学 院 袁 山 东 淄 博 255000 冤
揖 摘 要 铱 本 文 以 316L 不 锈 钢 材 料 的 铣 削 加 工 为 研 究 对 象 袁 进 行 铣 削 仿 真 和 实 际 铣 削 试 验 遥 先 利 用 软 件 Deform3D 的 铣 削 仿 真 功 能 进 行 单 因 素 的 铣 削 仿 真 袁 并 根 据 实 验 结 果 选 择 合 理 铣 削 用 量 来 设 计 尧 进 行 正 交 仿 真 试 验 遥 再 利 用 软 件 MATLAB 将 正 交 仿 真 试 验 所 得 到 的 数 据 拟 合 袁 构 建 铣 削 力 的 预 测 方 程 遥 最 后 袁 设 计 正 交 试 验 并进行实际铣削袁对比测得的实际铣削力和仿真试验的铣削力袁验证预测方程以及仿真试验结果的准确性遥 对 比显示袁该预测公式以及铣削仿真可以准确地预测铣削力遥
金属切削过程模拟的有限元仿真

金属切削过程模拟的有限元仿真摘要: 本文在建立车削三维有限元模拟基础上,运用有限元对车削过程中车削的变形系数,工件与刀具的温度分布,切削力进行了模拟,并对结果进行了分析讨论。
该模拟的结果对实际工作有重要的现实作用。
关键词:切削 有限元 模拟1 绪 论1.1本课题的研究背景1.1.1微电子等领域突出的散热问题在现代工业领域,有很多专门用途的设备,它们的工作性能和工作效率取决于关键零件的结构和性能,如空气冷却器,热交换器的散热管,激光器热辐射表面,环保设备的过滤表面,螺纹表面等等。
我们把这类起特定作用的表面统称为“功能表面”。
这些表面大多数采用组装式结构(套装、镶嵌、钎焊、高频焊)、切削、滚压等方法加工。
早在19世纪中期,Jone 就提出在管内插入螺旋线以强化蒸汽的冷凝过程,从此人们就开始了在传热管等传热材料上进行翅加工技术的研究。
70年代出现能源危机,研究翅化管的加工技术及其强化传热机理有了进一步的发展,随着加工制造技术的不断进步,近20年来对强化换热元件的研究在化工、能源、制冷、航空、电子等工业部门有了很大的进展,各式各样的强化换热元件层出不穷,为提高传热效率作出了重要的贡献。
但是随着微电子及化工等领域,尤其是微电子领域对产品性能的无限追求,芯片集成度不断提高,带来致命的高热流密度,电子器件的冷却问题越来越突出。
英特尔公司负责芯片设计的首席执行官帕特-盖尔欣格指出,如果芯片耗能和散热的问题得不到解决,到2005年芯片上集成了2亿个晶体管时,就会热得象“核反应堆”,2010年时会达到火箭发射时高温气体喷射的水平,而到2015年就会与太阳的表面一样热。
目前芯片发热区域(cm cm 5.15.1 )上的功耗已超过105W ,且未来有快速增加的趋势。
芯片产生的这些热量如果不能及时散出,将使芯片温度升高而影响到电子器件的寿命及工作的可靠性,因而电子器件的有效散热方式已成为获得新一代电子产品的关键科学问题之一。
两种典型金属高速切削过程有限元模拟与分析的开题报告
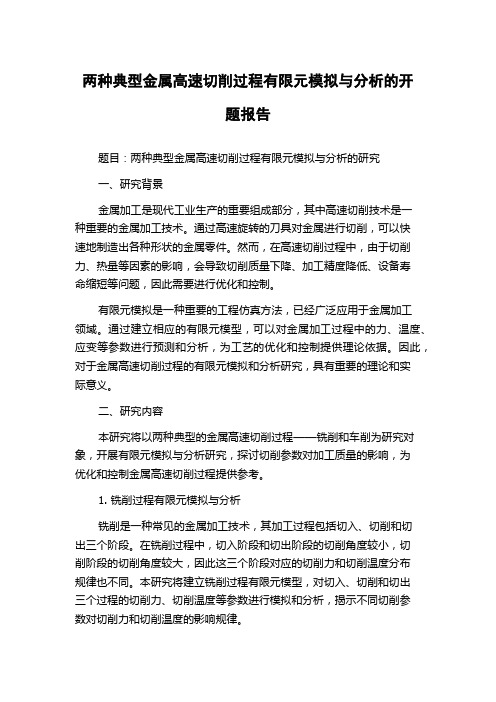
两种典型金属高速切削过程有限元模拟与分析的开题报告题目:两种典型金属高速切削过程有限元模拟与分析的研究一、研究背景金属加工是现代工业生产的重要组成部分,其中高速切削技术是一种重要的金属加工技术。
通过高速旋转的刀具对金属进行切削,可以快速地制造出各种形状的金属零件。
然而,在高速切削过程中,由于切削力、热量等因素的影响,会导致切削质量下降、加工精度降低、设备寿命缩短等问题,因此需要进行优化和控制。
有限元模拟是一种重要的工程仿真方法,已经广泛应用于金属加工领域。
通过建立相应的有限元模型,可以对金属加工过程中的力、温度、应变等参数进行预测和分析,为工艺的优化和控制提供理论依据。
因此,对于金属高速切削过程的有限元模拟和分析研究,具有重要的理论和实际意义。
二、研究内容本研究将以两种典型的金属高速切削过程——铣削和车削为研究对象,开展有限元模拟与分析研究,探讨切削参数对加工质量的影响,为优化和控制金属高速切削过程提供参考。
1. 铣削过程有限元模拟与分析铣削是一种常见的金属加工技术,其加工过程包括切入、切削和切出三个阶段。
在铣削过程中,切入阶段和切出阶段的切削角度较小,切削阶段的切削角度较大,因此这三个阶段对应的切削力和切削温度分布规律也不同。
本研究将建立铣削过程有限元模型,对切入、切削和切出三个过程的切削力、切削温度等参数进行模拟和分析,揭示不同切削参数对切削力和切削温度的影响规律。
2. 车削过程有限元模拟与分析车削是一种高效的金属加工技术,可以用于加工圆形、柱形等各种形状的零件。
在车削过程中,刀具切入工件后,与之接触的区域产生高温,导致金属发生塑性变形。
本研究将建立车削过程有限元模型,对切削力、切削温度等参数进行模拟和分析,揭示不同切削参数对加工质量的影响规律。
三、研究意义通过本研究,可以深入了解金属高速切削过程中的力学、热学和材料学等基本规律,为优化和控制切削过程提供理论依据。
此外,通过对不同切削参数对切削力、切削温度等参数的影响规律的分析,可以为金属加工工艺的优化和改进提供实用的建议和方法。
金属切削原理中切削力效果的仿真模拟研究

金属切削原理中切削力效果的仿真模拟研究随着工业技术的快速发展,金属切削加工在各个领域中都扮演着重要的角色。
而在金属切削加工过程中,切削力效果的研究对于提高切削加工的效率和质量具有重要的影响。
本文将以金属切削原理中切削力效果的仿真模拟研究为题,探讨金属切削过程中切削力的影响因素以及仿真模拟的方法。
首先,我们需要了解金属切削加工中切削力的概念和作用。
切削力是指在金属切削过程中刀具对工件产生的力。
它是通过与工件表面接触形成的摩擦力和切削力的合力,用于克服金属材料的强度和硬度,从而将金属材料切削成预定形状和尺寸的零件。
切削力直接影响着切削加工的效率、切削工具的寿命以及加工表面质量等方面。
在金属切削过程中,切削力的大小和方向受到多种因素的影响。
首先是刀具的几何形状和刀具材料的选择。
刀具的刃角、刃宽以及刀具材料的硬度和耐磨性等因素都会直接影响切削力的大小。
其次是被切削材料的性质。
材料的硬度、塑性和热导率等特性都会对切削力产生影响。
此外,切削速度、进给量和切削深度等工艺参数也会对切削力产生影响。
因此,研究这些影响因素对切削力的影响是非常必要的。
为了研究金属切削过程中切削力效果,研究人员常常采用仿真模拟的方法。
仿真模拟可以通过建立切削力的数学模型和计算机模拟技术,准确预测切削过程中的切削力大小和方向,并分析各种影响因素对切削力的影响。
其中,有限元法是一种常用的仿真模拟方法。
有限元法是一种数值计算方法,广泛应用于工程领域中的结构力学和材料力学问题。
在金属切削过程中,有限元法可以通过将切削区域划分成许多小块,建立小块上的切削力模型,并通过求解数学方程组来计算切削力的大小和方向。
通过调整模型中的参数,如刀具几何形状、工件材料特性、切削速度等,可以得到不同情况下的切削力效果。
此外,还可以使用商业仿真软件来进行金属切削过程中切削力效果的仿真模拟研究。
这些软件通过提供各种切削过程的模型和计算工具,能够更加方便地进行切削力的预测和分析。
切削加工有限元仿真教学设计与研究
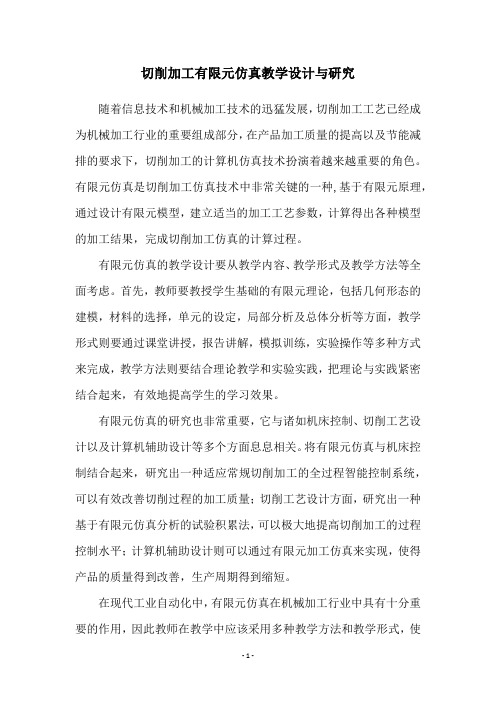
切削加工有限元仿真教学设计与研究随着信息技术和机械加工技术的迅猛发展,切削加工工艺已经成为机械加工行业的重要组成部分,在产品加工质量的提高以及节能减排的要求下,切削加工的计算机仿真技术扮演着越来越重要的角色。
有限元仿真是切削加工仿真技术中非常关键的一种,基于有限元原理,通过设计有限元模型,建立适当的加工工艺参数,计算得出各种模型的加工结果,完成切削加工仿真的计算过程。
有限元仿真的教学设计要从教学内容、教学形式及教学方法等全面考虑。
首先,教师要教授学生基础的有限元理论,包括几何形态的建模,材料的选择,单元的设定,局部分析及总体分析等方面,教学形式则要通过课堂讲授,报告讲解,模拟训练,实验操作等多种方式来完成,教学方法则要结合理论教学和实验实践,把理论与实践紧密结合起来,有效地提高学生的学习效果。
有限元仿真的研究也非常重要,它与诸如机床控制、切削工艺设计以及计算机辅助设计等多个方面息息相关。
将有限元仿真与机床控制结合起来,研究出一种适应常规切削加工的全过程智能控制系统,可以有效改善切削过程的加工质量;切削工艺设计方面,研究出一种基于有限元仿真分析的试验积累法,可以极大地提高切削加工的过程控制水平;计算机辅助设计则可以通过有限元加工仿真来实现,使得产品的质量得到改善,生产周期得到缩短。
在现代工业自动化中,有限元仿真在机械加工行业中具有十分重要的作用,因此教师在教学中应该采用多种教学方法和教学形式,使学生充分了解到有限元仿真的重要性;研究方面也要联系实际,研究出一系列先进的方法,以提高切削加工的加工质量和效率。
本文从教学和研究的角度,讨论了有限元仿真的重要性及其在切削加工中的应用,给出了一些实用的建议,以帮助技术人员和学生在切削加工领域更好地应用有限元仿真仿真技术,促进了机械加工行业的发展和切削加工仿真技术的普及应用。
基于DEFORM-3D的不锈钢切削力有限元仿真

涉及到材料学、 学、 力 热学 及摩擦学等相关 知识 。以
前, 学者 通 常通过 试 验和解 析 的手段 来研 究切 削过 程 ,
往往耗时 、 耗力 、 成本高 , 难以精确测量切削力 、 应力应 变、 温度场分布等关键数据 , 而计算机技术的飞速发展 使 得利 用有 限元 方法 来研 究 切削加 工成 为 了可能 ¨ 引。
内牌 号 为 0 r8 i ClN9不锈 钢 ) 。
金属切削过程中, 刀具切人工件 , 使被加工材料发 生变形成为切屑所需要 的力称为切削力 , 它包含主切 削力 、 进给力 和背 向力 3 部分 。因为主切 削 力 是计算车刀强度 、 设计机床零件和确定机床功率 的主要依据 , 因此 , 择主切削 力 作为研究 对象。 选 相关 的仿真参数见表 1 。 表 1 仿真切削参数表
体常应变单元划分网格 。通常在一些场变量变化梯度 较大的区域 , 划分较为致密的网格 , 反之则应划分较为
稀疏 的 网格 。
4 2 相关结果分析 . 图2 表示主切削力 仿真曲线。从图中可看 出, 主切削力 先由零线性增大至最大值 , 然后减少并逐 步接近稳定 , 这与实际的切削过程一致。当刀具 开始
削过程进行 了建模与仿真 , 分析 O r8 i C lN9不锈钢的切 削力 变化 规律 以及切 削速 度和进 给量对其 切削 力的影响 . 同理 并 论计算 结果进行对比验证。研究表明 , E O M-D软件 所得仿 真数据与理论计 算结果吻合度 较高 , 明仿真 结果具 有 DFR 3 说 较 高的可信 度 , 系统 地研 究金 属的切削过程提供 了一种新 的途 径。图 4表 1参 1 为 0 关 键 词 : 削加 工; E O M一D软件 ; 切 DFR 3 有限元仿 真; 削力 切
基于Deform 3D的不锈钢车削加工仿真研究
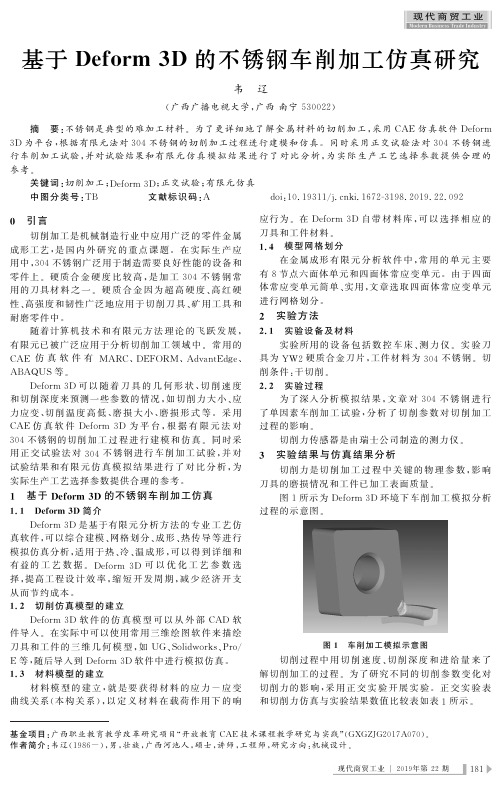
现代商贸工业2019年第22期181㊀基金项目:广西职业教育教学改革研究项目 开放教育C A E 技术课程教学研究与实践 (G X G Z J G 2017A 070).作者简介:韦辽(1986-),男,壮族,广西河池人,硕士,讲师,工程师,研究方向:机械设计.基于D e f o r m3D 的不锈钢车削加工仿真研究韦㊀辽(广西广播电视大学,广西南宁530022)摘㊀要:不锈钢是典型的难加工材料.为了更详细地了解金属材料的切削加工,采用C A E 仿真软件D e f o r m3D 为平台,根据有限元法对304不锈钢的切削加工过程进行建模和仿真.同时采用正交试验法对304不锈钢进行车削加工试验,并对试验结果和有限元仿真模拟结果进行了对比分析,为实际生产工艺选择参数提供合理的参考.关键词:切削加工;D e f o r m3D ;正交试验;有限元仿真中图分类号:T B ㊀㊀㊀㊀㊀文献标识码:A㊀㊀㊀㊀㊀㊀d o i :10.19311/j.c n k i .1672G3198.2019.22.0920㊀引言切削加工是机械制造行业中应用广泛的零件金属成形工艺,是国内外研究的重点课题.在实际生产应用中,304不锈钢广泛用于制造需要良好性能的设备和零件上.硬质合金硬度比较高,是加工304不锈钢常用的刀具材料之一.硬质合金因为超高硬度㊁高红硬性㊁高强度和韧性广泛地应用于切削刀具㊁矿用工具和耐磨零件中.随着计算机技术和有限元方法理论的飞跃发展,有限元已被广泛应用于分析切削加工领域中.常用的C A E 仿真软件有MA R C ㊁DEF O R M ㊁A d v a n t E d ge ㊁A B A Q U S 等.D e f o r m3D 可以随着刀具的几何形状㊁切削速度和切削深度来预测一些参数的情况,如切削力大小㊁应力应变㊁切削温度高低㊁磨损大小㊁磨损形式等.采用C A E 仿真软件D e f o r m 3D 为平台,根据有限元法对304不锈钢的切削加工过程进行建模和仿真.同时采用正交试验法对304不锈钢进行车削加工试验,并对试验结果和有限元仿真模拟结果进行了对比分析,为实际生产工艺选择参数提供合理的参考.1㊀基于D e f o r m3D 的不锈钢车削加工仿真1.1㊀D e f o r m3D 简介D e f o r m3D 是基于有限元分析方法的专业工艺仿真软件,可以综合建模㊁网格划分㊁成形㊁热传导等进行模拟仿真分析,适用于热㊁冷㊁温成形,可以得到详细和有益的工艺数据.D e f o r m 3D 可以优化工艺参数选择,提高工程设计效率,缩短开发周期,减少经济开支从而节约成本.1.2㊀切削仿真模型的建立D e f o r m3D 软件的仿真模型可以从外部C A D 软件导入.在实际中可以使用常用三维绘图软件来描绘刀具和工件的三维几何模型,如U G ㊁S o l i d w o r k s ㊁P r o/E 等,随后导入到D e f o r m3D 软件中进行模拟仿真.1.3㊀材料模型的建立材料模型的建立,就是要获得材料的应力-应变曲线关系(本构关系),以定义材料在载荷作用下的响应行为.在D e f o r m3D 自带材料库,可以选择相应的刀具和工件材料.1.4㊀模型网格划分在金属成形有限元分析软件中,常用的单元主要有8节点六面体单元和四面体常应变单元.由于四面体常应变单元简单㊁实用,文章选取四面体常应变单元进行网格划分.2㊀实验方法2.1㊀实验设备及材料实验所用的设备包括数控车床㊁测力仪.实验刀具为YW 2硬质合金刀片,工件材料为304不锈钢.切削条件:干切削.2.2㊀实验过程为了深入分析模拟结果,文章对304不锈钢进行了单因素车削加工试验,分析了切削参数对切削加工过程的影响.切削力传感器是由瑞士公司制造的测力仪.3㊀实验结果与仿真结果分析切削力是切削加工过程中关键的物理参数,影响刀具的磨损情况和工件已加工表面质量.图1所示为D e f o r m3D 环境下车削加工模拟分析过程的示意图.图1㊀车削加工模拟示意图切削过程中用切削速度㊁切削深度和进给量来了解切削加工的过程.为了研究不同的切削参数变化对切削力的影响,采用正交实验开展实验.正交实验表和切削力仿真与实验结果数值比较表如表1所示.工程管理与技术现代商贸工业2019年第22期182㊀㊀图2㊀切削力仿真曲线表1㊀正交实验表和切削力仿真与实验结果数值比较表序号切削深度(a p )进给量(f)切削速度(V c )仿真值(N )实验值(N )误差(%)10.40.2060706763.48.120.40.2365745789.35.930.40.2670772802.84.040.60.2065796824.53.650.60.2370823806.2-2.060.60.2660836847.71.470.80.2070872897.32.980.80.2360841875.14.190.80.2665862873.61.3㊀㊀在实际加工过程中,由于环境温度变化㊁刀具磨损状况㊁加工参数对排屑情况等因素的影响,可能会导致实际数值与模拟数值产生一定的误差.同时,因为金属切削过程是一个非线性问题,具有连续性和动态性特征,在D e f o r m3D 中对于刀具和工件的网格划分不同也将会导致误差产生,在仿真切削过程中一些单元可能被挤压或变形,严重影响切削精度,导致计算过程不收敛,也会产生误差.从表1可以看出,考虑到实际切割中材料的失效和摩擦条件非常复杂,误差在8%以内,所以模拟结果是可以接受的.D e f o r m3D 模拟在理想条件下,实际加工过程中存在各种影响因素,可以看出实验值和切削力模拟值存在一定的误差.但总体误差很小,在可接受的范围内.㊀㊀从图2可以看出,当刀具开始切削工件后,切削力开始比较小,随着时间的增加不断增加,到了一定时间后才会达到稳定值,数值在一定范围内也存在不断波动情况,这与在实际试验中利用测力仪所获取的图表变化趋势是一致的.4㊀结语文章以C A E 仿真软件D e f o r m3D 为研究平台,根据有限元法对304不锈钢的切削加工过程进行建模和仿真.同时采用正交试验法对304不锈钢进行车削加工试验,并对试验结果和有限元仿真模拟结果进行了对比分析,为实际生产工艺选择参数提供合理的参考和理论指导.参考文献[1]VB o u n h o u r e a ,SL a ya ,SC o i n d e a u ab ,e t a l .E f f ec t o f C r ad d i t i o n o n s o l i d s t a te s i n t e r i n g o fW C -C o a l l o y s [J ].I n t e r n a t i o n a l J o u r Gn a l o fR ef r a c t o r y Me t a l s a n dH a r d M a t e r i a l s ,2015,52:21G28.[2]S u W e i ,S u nY e x i ,J i a oF e n g ,e t a l .I nf l u e n c e so f t h e p r e pa r a Gt i o nm e t h o d so f W C-C o p o w d e r so nt h es i n t e r i n g an d m i c r o Gs t r u c t u r e o fc o a r s e g r a i n e d W C-8C oh a r d m e t a l s [J ].I n t e r n a Gt i o n a l J o u r n a lo fR e f r a c t o r y Me t a l sa n d H a r d M a t e r i a l s ,2015,48:369G375.[3]R u m m a n M R ,X i eZ ,H o n g SJ ,e t a l .Ef f e c t o f s pa r k p l a s m a s i n t e r i n gp r e s s u r eo n m e c h a n i c a l p r o pe r t i e sof W C-7.5w t %N a n oC o [J ].M a t e r i a l s&D e s i gn ,2015,68:221G227.[4]温效朔,王克琦.切削加工有限元仿真与应力分析[J ].工具技术,2006,40(7):30G32.[5]方刚.切削加工过程数值模拟的研究进展[J ].力学进展,2001,31(3):394G404.[6]张磊光.三维金属切削过程的有限元模拟[D ].北京:华北电力大学,2008.[7]于贻鹂.金属切削过程有限元法仿真研究[D ].大连:大连理工大学,2005.[8]章振翔,张金明,王来钱等.基于D e f o r m-3D 的不锈钢切削力有限元仿真[J ].轻工机械,2011,29(4):40G42.[9]聂闻,李成让,张伟等.基于D e f o r m 的304不锈钢的车削仿真与实验研究的影响[J ].装备制造技术,2014,(5):55G57.建筑工程项目管理的重要性与创新方法探析张海波(吉林省辽源市人防办工程管理处,吉林辽源136200)摘㊀要:随着我国经济建设的高速发展,我国的建筑工程建设也取得了令人瞩目的成绩.建筑工程的发展,满足了人民群众对生活水平的日益增长的要求,也满足了我国国际竞争力的不断增强的目标.为了保证我国在建筑工程领域能够不断的取得进步和发展,就必须认识到建筑工程管理的重要性.只有采取了行之有效的管理方法,建筑工程水平才能够不断提高,我国的建筑工程事业才能得到健康有序的发展与进步.关键词:建筑工程;项目管理;重要性;创新方法中图分类号:T B ㊀㊀㊀㊀㊀文献标识码:A㊀㊀㊀㊀㊀㊀d o i :10.19311/j .c n k i .1672G3198.2019.22.093㊀㊀在当今社会的新的发展阶段,建筑工程的质量和效率,影响着我们社会的进步和人民的满意程度.在当代经济高速发展的大环境下,如何促进建筑工程项目管理水平的进步,也是我们现阶段要重点要研究的问题.只有改变现有的建筑工程管理方法,才能使建筑工程管理水平的提高得以实现.通过建筑工程项目管理方法的研究,可以对我国建筑工程管理方法创新的目标提供有效的途径.1㊀建筑工程项目管理的现状在我国改革开放以后,为了满足社会进步的需求。
金属微切削过程的有限元仿真及实验研究(一)
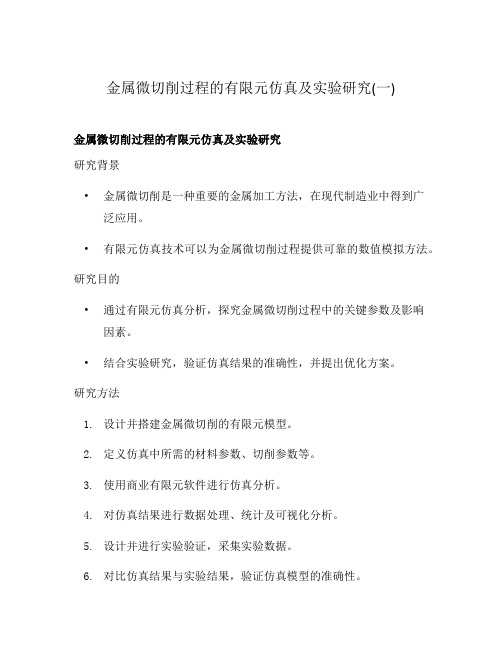
金属微切削过程的有限元仿真及实验研究(一)金属微切削过程的有限元仿真及实验研究研究背景•金属微切削是一种重要的金属加工方法,在现代制造业中得到广泛应用。
•有限元仿真技术可以为金属微切削过程提供可靠的数值模拟方法。
研究目的•通过有限元仿真分析,探究金属微切削过程中的关键参数及影响因素。
•结合实验研究,验证仿真结果的准确性,并提出优化方案。
研究方法1.设计并搭建金属微切削的有限元模型。
2.定义仿真中所需的材料参数、切削参数等。
3.使用商业有限元软件进行仿真分析。
4.对仿真结果进行数据处理、统计及可视化分析。
5.设计并进行实验验证,采集实验数据。
6.对比仿真结果与实验结果,验证仿真模型的准确性。
研究结果与讨论1.通过有限元仿真,得到了金属微切削过程中切削力、切削温度、表面质量等关键参数的变化规律。
2.实验结果与仿真结果一致,验证了有限元仿真模型的准确性和可靠性。
3.对比不同切削参数下的仿真结果与实验结果,发现切削速率、进给量等参数对金属微切削过程有显著影响。
4.提出了优化金属微切削过程的建议,例如调整切削参数,优化刀具设计等。
研究结论•通过有限元仿真及实验研究,我们深入了解了金属微切削过程的相关参数及影响因素。
•我们验证了有限元仿真模型的准确性,并提出了优化金属微切削过程的建议。
•本研究为金属微切削过程的优化与改进提供了重要的理论依据和实验支持。
研究展望•本研究在金属微切削过程的有限元仿真及实验研究方面取得了一定成果,但仍存在一些局限性。
•今后,可以进一步扩大研究样本和范围,优化有限元模型,提高仿真精度。
•进一步研究金属微切削过程中的机理,探索更有效的优化方法。
以上是关于”金属微切削过程的有限元仿真及实验研究”的相关研究报告。
金属切削过程有限元仿真关键技术及应考虑的若干问题_李涛
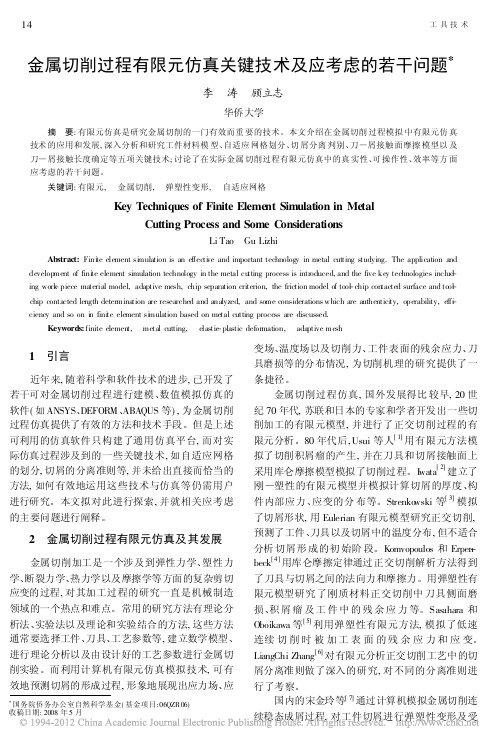
*国务院侨务办公室自然科学基金(基金项目:06QZR06)收稿日期:2008年5月金属切削过程有限元仿真关键技术及应考虑的若干问题*李 涛 顾立志华侨大学摘 要:有限元仿真是研究金属切削的一门有效而重要的技术。
本文介绍在金属切削过程模拟中有限元仿真技术的应用和发展,深入分析和研究工件材料模型、自适应网格划分、切屑分离判别、刀)屑接触面摩擦模型以及刀)屑接触长度确定等五项关键技术;讨论了在实际金属切削过程有限元仿真中的真实性、可操作性、效率等方面应考虑的若干问题。
关键词:有限元, 金属切削, 弹塑性变形, 自适应网格Key Techniques of Finite Element Simulation in MetalCutting Process and Some C onsiderationsLi Tao Gu LizhiAbstract:Fini te element si mulation is an effecti ve and important technology in metal cutting studying.The application and develop ment of fini te element simulation technology in the metal cu tting process is introduced,and the five key technologies includ -ing work -piece material model,adaptive mesh,chip separation criterion,the friction model of too-l chip con tacted surface and too-l chip contacted length determination are researched and analyzed,and some considerations which are authentici ty,operability,eff-i ciency and so on i n fini te element si mulation based on metal cutting process are discussed.Keywords:finite elemen t, metal cutting, elastic -plastic deformation, adaptive mesh1 引言近年来,随着科学和软件技术的进步,已开发了若干可对金属切削过程进行建模、数值模拟仿真的软件(如ANSYS 、DEFORM 、ABAQUS 等),为金属切削过程仿真提供了有效的方法和技术手段。
钻削过程的数值模拟仿真分析论文
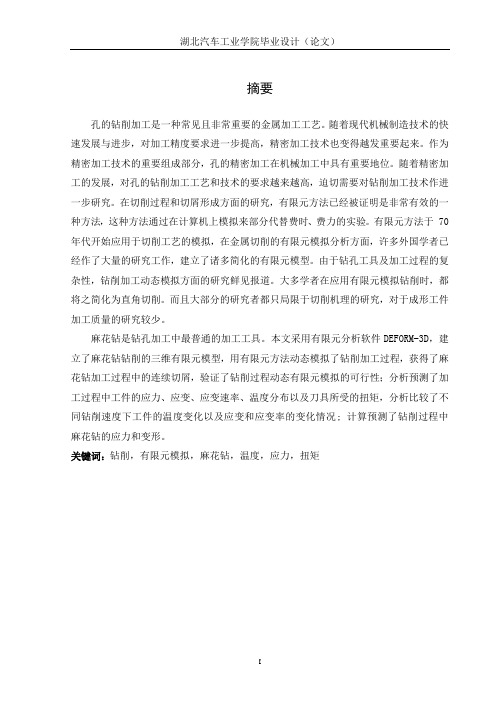
摘要孔的钻削加工是一种常见且非常重要的金属加工工艺。
随着现代机械制造技术的快速发展与进步,对加工精度要求进一步提高,精密加工技术也变得越发重要起来。
作为精密加工技术的重要组成部分,孔的精密加工在机械加工中具有重要地位。
随着精密加工的发展,对孔的钻削加工工艺和技术的要求越来越高,迫切需要对钻削加工技术作进一步研究。
在切削过程和切屑形成方面的研究,有限元方法已经被证明是非常有效的一种方法,这种方法通过在计算机上模拟来部分代替费时、费力的实验。
有限元方法于70 年代开始应用于切削工艺的模拟,在金属切削的有限元模拟分析方面,许多外国学者已经作了大量的研究工作,建立了诸多简化的有限元模型。
由于钻孔工具及加工过程的复杂性,钻削加工动态模拟方面的研究鲜见报道。
大多学者在应用有限元模拟钻削时,都将之简化为直角切削。
而且大部分的研究者都只局限于切削机理的研究,对于成形工件加工质量的研究较少。
麻花钻是钻孔加工中最普通的加工工具。
本文采用有限元分析软件DEFORM-3D,建立了麻花钻钻削的三维有限元模型,用有限元方法动态模拟了钻削加工过程,获得了麻花钻加工过程中的连续切屑,验证了钻削过程动态有限元模拟的可行性;分析预测了加工过程中工件的应力、应变、应变速率、温度分布以及刀具所受的扭矩,分析比较了不同钻削速度下工件的温度变化以及应变和应变率的变化情况; 计算预测了钻削过程中麻花钻的应力和变形。
关键词:钻削,有限元模拟,麻花钻,温度,应力,扭矩ABSTRACTDrilling is one of the most commonly used and important machining operations. As modern machinery manufacturing technology continues to envolve and progress , the requirement of precision machining is more exigent than before and the precision machining technology is much more important. Nowadays, a lot of work is urgent to do on drilling in order to meet the needs of precision machining. In recent years, the application of finite element method (FEM) to cutting operations has proved to be effective to study the cutting process and chip formation. It can reduce the experimental cost replace some experimental testing which may be difficult or impossible to obtain by numerical simulation on the computer. The first time FEM was applied in machining simulation was in 1970s. Many papers are available now on simulation of orthogonal and oblique cutting process but little of drilling because of the complexity of drilling processes. Though some is on drilling, they are simplified to orthogonal cutting. The cutting mechanism of drilling is similar to 3D orthogonal cutting but not the same. Little research has been done on the FEM simulation of the drilling processes. Further more, most researchers just studied the cutting mechanism. V ery little has been investigated on machining quality of the workpiece.Twist drills are the most widely used tools for drilling holes.The present work aims to simulate three-dimensional drilling operations and 3D FE model of twist drilling is developed for the drilling simulation process. 3D FEM simulation of twist drilling is presented in the paper and get the continuous chip formation and indicate the feasibility of FEM simulation of drilling processes. FEM simulation of twist drilling is carried out to identify the characteristics and to analyze the drilling quality of these two classes of drilling, including stress, strain, strain rate and temperature distribution, material flow and chip formation in the workpiece, drilling torque, stress and elastic deformation of drilling tools.KEY WORDS:drilling, FEM simulation, twist drill,temperature,stress,torque目录摘要 (I)ABSTRACT (II)1 绪论 (1)1.1 本课题的来源、目的及意义 (1)1.1.1课题来源 (1)1.1.2 本课题研究的目的 (1)1.1.3 本课题研究的意义 (1)1.2 国内外研究现状及发展方向 (2)1.2.1有限元方法(FEM)在切削方面的研究应用 (2)1.2.2切削加工过程有限元模拟的研究现状 (3)1.2.3切削加工有限元模拟的发展方向 (4)1.3 本课题研究的主要内容 (4)2 有限元模拟原理 (6)2.1 有限元法理论基础 (6)2.1.1 有限元理论简介 (6)2.1.2 弹塑性有限元分析 (7)2.1.3 刚塑性有限元法 (8)2.2 切削理论 (8)2.2.1 金属的晶体结构 (9)2.2.2 塑性变形机理 (9)2.3 切屑断裂准则 (10)2.4 DEFORM V6.1 软件简介 (13)2.5 小结 (15)3 钻削模型的建立及参数设置 (16)3.1 引言 (16)3.2 三维建模 (16)3.3 麻花钻的三维模型 (16)3.4 模型初始网格划分及边界条件设定 (18)3.5 参数设置 (19)3.5.1 切削用量的设定 (19)3.5.2 材料设置 (19)3.5.3 运动参数的设定 (19)3.5.4 模拟参数的设定 (21)3.6 本章小结 (22)4 钻削过程的仿真结果及分析 (23)4.1 钻削过程仿真分析 (23)4.1.1 温度分布 (23)4.1.3 等效应力 (25)4.1.4 等效应变及等效应变率 (27)4.1.5 刀具所受扭矩 (31)4.2 本章小结 (32)5 总结与展望 (33)5.1 总结 (33)5.1.1 研究结果 (33)5.1.2 现存问题 (33)5.2 展望 (34)致谢 (35)参考文献 (36)1 绪论1.1 本课题的来源、目的及意义1.1.1课题来源本课题源于教学科研,对麻花钻钻削加工过程进行科学整理、归纳和完善,以期最终形成最佳的加工工艺。
金属切削过程有限元仿真技术

阅读感受
书中,作者还借助Abaqus软件对典型仿真案例进行了详细介绍,包括刀具的 磨损、切削过程的控制以及金属车削和铣削过程的仿真分析等。这些案例让我了 解到有限元仿真技术在解决实际问题中的强大作用,也让我对金属切削过程有了 更直观的理解。
阅读感受
值得一提的是,本书最后对不同仿真软件的研究结果进行了特性对比,帮助 我认识到各种仿真软件的优缺点,为我在未来的学习和实践中选择合适的工具提 供了宝贵的参考。
目录分析
接下来,本书的第2章到第7章,详细介绍了切削过程有限元仿真的关键技术。 这些技术包括有限元模型的建立、材料本构模型的选取、边界条件的处理、切削 过程的动态仿真等。这些章节不仅提供了详尽的理论知识,也给出了具体的实例, 使读者能够更好地理解和掌握这些关键技术。
目录分析
在第8章和第9章,本书分别对金属车削和铣削过程进行了仿真分析。这两章 的内容是本书的核心,它们详细阐述了如何使用有限元方法对金属切削过程进行 模拟,并给出了具体的仿真结果和分析。这些章节的内容对于理解金属切削过程 的有限元仿真具有非常重要的意义。
谢谢观看
阅读感受
阅读感受
《金属切削过程有限元仿真技术》——深化对机械制造工艺的理解 在我阅读《金属切削过程有限元仿真技术》这本书的过程中,我深深地被书 中深入浅出的理论知识和丰富的实际应用案例所吸引。这本书不仅为我揭示了金 属切削过程的奥秘,也让我对有限元仿真技术在机械制造领域的应用有了更深入 的认识。
内容摘要
这个模型可以用来预测切削过程中的各种现象,如切屑的形成,切削力的变化,以及工件的变形 等。 本书通过大量的实例展示了如何利用有限元模型对切削过程进行优化。这些实例包括如何优化刀 具设计,如何调整切削参数以改善加工质量,以及如何预测和避免加工过程中可能出现的问题等。 《金属切削过程有限元仿真技术》这本书是一本关于如何利用有限元方法模拟和优化金属切削过 程的实用指南。这本书对于从事机械制造、材料科学、力学等领域的研究者和工程师来说,是一 本非常有价值的参考书籍。
基于ABAQUS的不锈钢材料切削过程的模拟与数值分析

ing commercial finite element software ABAQUS to simulate the cutting process, researched the influence of cutting speed, feed rate and other processing parameters on stress, strain and temperature during the cutting processes. Compare and analysis the causes of chip formation, and finally compared the different geometry of the simulation results of cutting force under the same conditions.
3.Simplified the geometric model of end mill, established a three-dimensional cutting model. By compare the results of simulation and experimental, the paper discussed the impact of the cutting speed, feed per tooth and other processing parameters on the force.
不锈钢微钻削的切屑形成与仿真分析

p r o c e s s o f mi c r o—d r i l l i n g o f s t a i n l e s s s t e e l ma t e ia r l , t h e c h i p s a r e p r o n e t o t a n g l e o n t h e mi c r o—d r i l l ,i t
i s d i ic f u l t t o b r e a k a n d e va c ua t e t h e c h i ps . I n t h i s pa pe r ,t he c h i p mo r p ho l o g i e s i n t he mi c r o—d il r l i ng o f 0Cr l 8 Ni 9 s t a i n l e s s s t e e l we r e o bs e r v e d,a n d t h e i n lu f e nc e o f c u t t i n g s pe e d a n d f e e d s p e e d o n t h e c h i p mo ph r o l o g y we r e s t ud i e d. Ba s e d o n t he FEM a na l y s i s s o f t wa r e,t h e c h i p f o r ma t i o n p r o c e s s wa s a n a l y z e d t h r o u g h s i mu l a t i o n a n d t h e o r e t i c a l a n a l y s i s .
ZHAN GHa o q i a n g,HOU S u o x i a,CHANG Ch u n r u i ,AN Li b a o,W ANG Li n a
《316L微孔钻削特性仿真与试验研究》范文
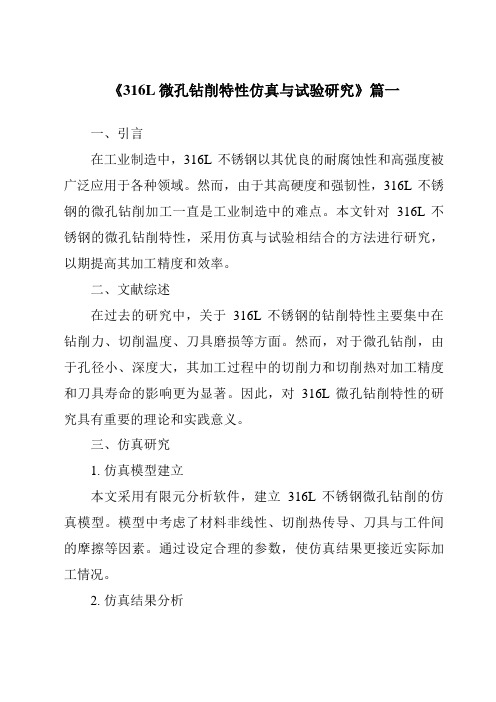
《316L微孔钻削特性仿真与试验研究》篇一一、引言在工业制造中,316L不锈钢以其优良的耐腐蚀性和高强度被广泛应用于各种领域。
然而,由于其高硬度和强韧性,316L不锈钢的微孔钻削加工一直是工业制造中的难点。
本文针对316L不锈钢的微孔钻削特性,采用仿真与试验相结合的方法进行研究,以期提高其加工精度和效率。
二、文献综述在过去的研究中,关于316L不锈钢的钻削特性主要集中在钻削力、切削温度、刀具磨损等方面。
然而,对于微孔钻削,由于孔径小、深度大,其加工过程中的切削力和切削热对加工精度和刀具寿命的影响更为显著。
因此,对316L微孔钻削特性的研究具有重要的理论和实践意义。
三、仿真研究1. 仿真模型建立本文采用有限元分析软件,建立316L不锈钢微孔钻削的仿真模型。
模型中考虑了材料非线性、切削热传导、刀具与工件间的摩擦等因素。
通过设定合理的参数,使仿真结果更接近实际加工情况。
2. 仿真结果分析仿真结果表明,在微孔钻削过程中,切削力和切削热对加工精度和刀具寿命的影响显著。
随着切削深度的增加,切削力逐渐增大,切削热逐渐累积,导致工件材料发生热软化,进而影响加工精度。
此外,刀具的磨损也随着钻削过程的进行而加剧。
四、试验研究1. 试验材料与方法试验选用316L不锈钢为工件材料,采用不同参数的钻头进行微孔钻削试验。
试验中记录了切削力、切削温度、刀具磨损等数据。
2. 试验结果分析(1)切削力:随着切削深度的增加,切削力逐渐增大。
适当减小进给量和转速可降低切削力。
(2)切削温度:切削温度随着钻削过程的进行而逐渐升高。
通过合理选择冷却液和优化切削参数,可降低切削温度。
(3)刀具磨损:刀具磨损是影响加工精度和效率的重要因素。
在微孔钻削过程中,刀具的磨损主要表现为刃口磨损和扩散磨损。
通过优化切削参数和选用合适的刀具材料,可延长刀具的使用寿命。
五、结论与展望本文通过仿真与试验相结合的方法,对316L微孔钻削特性进行了深入研究。
结果表明,在微孔钻削过程中,切削力和切削热对加工精度和刀具寿命的影响显著。
《316L微孔钻削特性仿真与试验研究》范文

《316L微孔钻削特性仿真与试验研究》篇一一、引言随着现代工业的快速发展,微孔加工技术在许多领域中得到了广泛的应用,如电子、航空、医疗等。
316L不锈钢因其优异的耐腐蚀性和良好的机械性能,在微孔加工领域具有重要地位。
然而,由于微孔加工的特殊性,其加工过程中的切削力、切削热以及孔的精度和表面质量等问题一直是研究的热点。
本文旨在通过仿真与试验相结合的方法,对316L不锈钢的微孔钻削特性进行研究,为实际生产提供理论依据。
二、仿真研究1. 仿真模型建立本文采用有限元分析软件,建立了316L不锈钢微孔钻削的仿真模型。
模型中考虑了切削力、切削热、材料去除等多方面因素,以及刀具的几何形状、切削速度、进给量等工艺参数。
2. 仿真结果分析通过仿真研究,我们发现:在一定的工艺参数下,316L不锈钢的微孔钻削过程中,切削力随着切削深度的增加而增大;切削热主要集中于切削区域,对工件表面质量有一定影响;合理的工艺参数可以有效地减小切削力和切削热,提高孔的加工精度和表面质量。
三、试验研究1. 试验材料与设备试验材料选用316L不锈钢,试验设备包括钻床、测力仪、显微镜等。
2. 试验方案试验中,我们设定了不同的切削速度、进给量和钻头类型,以研究这些工艺参数对微孔钻削特性的影响。
同时,我们还对加工后的孔的尺寸精度、表面质量等进行了检测和分析。
3. 试验结果分析通过试验研究,我们发现:切削速度和进给量对微孔钻削过程有显著影响,合理的工艺参数可以有效地提高孔的加工精度和表面质量;不同类型的钻头在微孔钻削过程中表现出不同的性能,应根据具体需求选择合适的钻头。
四、结论与展望通过仿真与试验相结合的方法,本文对316L不锈钢的微孔钻削特性进行了深入研究。
我们发现,合理的工艺参数和钻头类型对提高微孔的加工精度和表面质量具有重要作用。
此外,仿真与试验结果还可以为实际生产过程中的工艺优化提供理论依据。
展望未来,我们将进一步研究其他材料和工艺条件下的微孔钻削特性,以及如何通过优化工艺参数和钻头设计来进一步提高微孔的加工质量和效率。
钻削过程切屑受力建模及有限元仿真研究

钻削过程切屑受力建模及有限元仿真研究【文章】钻削过程切屑受力建模及有限元仿真研究一、引言钻削作为金属加工中的一种重要工艺,其切屑受力情况一直备受关注。
本文旨在通过建模及有限元仿真研究,探讨钻削过程中切屑受力的特点及影响因素,从而提供深度的理论指导和实践应用价值。
二、切屑受力特点1. 切屑形成与受力关系在钻削过程中,切屑形成与受力密切相关。
切屑的形成主要受到切削力、切削温度和材料力学性能等因素的影响。
其中,切削力是切屑形成的主要驱动因素,在切削过程中产生的切削力将直接影响切屑的形态和受力情况。
2. 切屑受力影响因素切屑的受力情况受到多种因素的影响,包括钻具结构、切削参数、工件材料等。
钻具结构的合理设计和切削参数的选择对于降低切屑受力具有重要意义。
工件材料的硬度、塑性等力学性能也会对切屑受力产生影响。
3. 切屑受力模型建立针对切屑受力情况的复杂性,需要建立合理的数学模型来描述其受力特点。
基于切屑形成机理和材料力学性能,可以建立切屑受力模型,从而深入分析切屑在钻削过程中的受力情况。
三、有限元仿真研究1. 有限元建模通过有限元方法,可以对钻削过程中切屑受力进行深入研究。
在建立切屑受力模型的基础上,采用有限元方法进行建模和仿真,可以模拟实际的钻削过程,并获取切屑受力的详细信息。
2. 仿真结果分析通过有限元仿真,可以获取切屑受力的分布情况、受力大小和变化规律。
还可以对不同工艺参数和材料性能对切屑受力的影响进行系统分析,为钻削过程的优化提供理论依据。
四、个人观点与总结在钻削过程中,切屑受力的研究对于提高钻削效率和延长工具寿命具有重要意义。
通过深入分析切屑受力的特点和影响因素,可以为钻削工艺的优化提供理论依据。
有限元仿真作为一种重要的研究手段,为切屑受力的深入研究提供了新的途径和方法。
钻削过程切屑受力建模及有限元仿真研究具有重要的理论和应用价值,值得深入探讨和研究。
以上是本次文章的初稿,具体的细节和论证可以进一步完善。
钻削过程切屑受力建模及有限元仿真研究

钻削过程切屑受力建模及有限元仿真研究一、概述钻削过程是金属加工中常见的加工工艺之一,其切削过程中切屑的形成和受力情况对加工质量和工件表面粗糙度有着重要影响。
本文将针对钻削过程中切屑受力建模及有限元仿真研究展开深入探讨,从宏观和微观两个角度分析切屑的形成机理和受力情况,旨在为钻削工艺提供更深入的理论基础和实用指导。
二、切屑形成机理分析1. 切屑形成的基本过程在钻削过程中,切屑的形成是由刀具对工件进行切削,其中金属材料在刀具作用下形成的薄层即为切屑。
切屑形成的基本过程可以简要概括为切屑的起始、发展和脱离三个阶段。
切屑的形成机理主要包括切削热、切削变形、切削厚度和切屑形状等因素的综合作用。
2. 切屑形成的影响因素切屑形成受到诸多因素的影响,包括工件材料性能、刀具的材料和几何形状、切削参数、冷却液的使用等。
不同的工件材料、刀具材料和切削参数组合会导致切屑的形态、厚度和温度等特性的差异,从而影响切屑的排屑能力、切屑的排屑性能和对切屑的进一步加工。
三、切屑受力情况分析1. 切屑的受力特点切屑在形成过程中会承受来自刀具的切削力、切削热和切屑自身的重力等多种力的作用。
其中,切削力是切屑受力的主要载荷,其大小和方向直接影响切屑的形状和质量。
切屑受力还与刀具的几何形状、切削参数和切削状态等因素相关。
2. 切屑的受力模型有限元分析是研究切屑受力的有效方法之一,通过建立钻削加工的切屑受力模型,可以分析切屑在加工过程中的受力情况。
通过有限元仿真可以得到切屑的应变、应力分布以及切屑的变形情况,从而为钻削工艺的优化提供理论支持。
四、有限元仿真研究1. 切屑受力的有限元模型建立在进行有限元仿真时,首先需要建立钻削过程中切屑受力的有限元模型。
该模型需要考虑刀具、工件、切屑和切削液等多个物理对象及其之间的相互作用,同时要考虑切屑受力的非线性、瞬态和热传导等特性。
通过对切屑受力的有限元模型建立,可以准确地模拟切屑在切削过程中的受力情况。
金属切削变形过程的有限元仿真初探
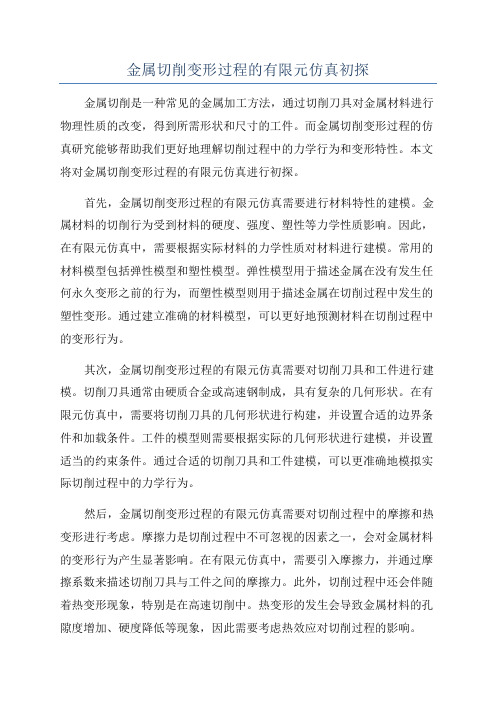
金属切削变形过程的有限元仿真初探金属切削是一种常见的金属加工方法,通过切削刀具对金属材料进行物理性质的改变,得到所需形状和尺寸的工件。
而金属切削变形过程的仿真研究能够帮助我们更好地理解切削过程中的力学行为和变形特性。
本文将对金属切削变形过程的有限元仿真进行初探。
首先,金属切削变形过程的有限元仿真需要进行材料特性的建模。
金属材料的切削行为受到材料的硬度、强度、塑性等力学性质影响。
因此,在有限元仿真中,需要根据实际材料的力学性质对材料进行建模。
常用的材料模型包括弹性模型和塑性模型。
弹性模型用于描述金属在没有发生任何永久变形之前的行为,而塑性模型则用于描述金属在切削过程中发生的塑性变形。
通过建立准确的材料模型,可以更好地预测材料在切削过程中的变形行为。
其次,金属切削变形过程的有限元仿真需要对切削刀具和工件进行建模。
切削刀具通常由硬质合金或高速钢制成,具有复杂的几何形状。
在有限元仿真中,需要将切削刀具的几何形状进行构建,并设置合适的边界条件和加载条件。
工件的模型则需要根据实际的几何形状进行建模,并设置适当的约束条件。
通过合适的切削刀具和工件建模,可以更准确地模拟实际切削过程中的力学行为。
然后,金属切削变形过程的有限元仿真需要对切削过程中的摩擦和热变形进行考虑。
摩擦力是切削过程中不可忽视的因素之一,会对金属材料的变形行为产生显著影响。
在有限元仿真中,需要引入摩擦力,并通过摩擦系数来描述切削刀具与工件之间的摩擦力。
此外,切削过程中还会伴随着热变形现象,特别是在高速切削中。
热变形的发生会导致金属材料的孔隙度增加、硬度降低等现象,因此需要考虑热效应对切削过程的影响。
最后,金属切削变形过程的有限元仿真需要进行切削参数的优化。
切削参数包括切削速度、进给量和切削深度等,它们会直接影响到金属切削过程中的力学行为和变形特性。
通过对切削参数进行优化,可以获得更理想的切削效果和更大的加工效率。
在有限元仿真中,可以通过改变切削参数的数值来模拟不同的切削条件,并通过参数优化来确定最佳的切削参数组合。
高强度钢钻削过程的加工仿真与实验研究

高强度钢钻削过程的加工仿真与实验研究高强度钢在切削加工过程中存在断屑困难,切削温度高,单位面积上的切削力大等问题,利用传统的切削试验方法耗时耗财,效率不高且对切削的预见性不强。
针对上述问题,本文研究了高强度钢钻削过程的加工仿真技术,并对钻削过程进行了实验研究。
论文的主要内容包括以下几个方面:首先,本文利用三维建模软件(SolidWorks)建立了麻花钻的模型,采用双因素无重复试验设计方法设计了仿真试验表,在DEFORM-3D软件中对高强度钢钻削仿真实验表中的数据进行仿真。
分析了仿真过程中会遇到的一些问题,并针对这些问题提出了相应的解决方法。
得到不同切削参数下钻削高强度钢时的轴向力、转矩,以及钻削温度等所对应的形象直观的仿真结果。
并将仿真的具体数据导出,对导出的数据进行滤波来消除大误差点,得到相应的仿真实验数据,采用图表的形式对数据的变化情况进行呈现。
其次,利用方差分析法即就是变异数分析对受切削参数影响的轴向力,扭矩及温度等进行显著性分析。
仿真的数据表导入Design expert软件中,研究仿真试验指标和试验因素之间的回归关系(响应面分析),并就有交互关系的试验因素生成的响应曲面进行分析。
对钻削参数、钻削轴向力与扭矩之间的响应关系进行二次非线性拟合及分析,获得钻削轴向力、扭矩与切削参数间的函数关系,为进一步优化加工参数提供参考。
最后,结合MATLAB中的遗传算法工具箱,采用多目标优化的方法,来对加工参数进行优化,获得了钻削加工的Pareto最优解集。
从Pareto最优解集中获得了部分优化的切削参数,并对优化出的部分切削参数进行钻削实验。
对实验中切屑的形态,钻削时的振动情况,孔的质量等进行观察、测量和分析。
将实验中获得的数据进行整理分析,以此验证了仿真优化后的结果与实验结果的一致性以及优化的有效性和仿真的可行性。
本文采用有限元方法分析钻削加工过程,获得了硬质合金麻花钻在钻削AISI4340时的切削参数。
- 1、下载文档前请自行甄别文档内容的完整性,平台不提供额外的编辑、内容补充、找答案等附加服务。
- 2、"仅部分预览"的文档,不可在线预览部分如存在完整性等问题,可反馈申请退款(可完整预览的文档不适用该条件!)。
- 3、如文档侵犯您的权益,请联系客服反馈,我们会尽快为您处理(人工客服工作时间:9:00-18:30)。
分类号密级UDC学位论文不锈钢钻削加工有限元仿真及试验研究作者姓名:闫鹏飞指导教师:邹平教授东北大学机械工程与自动化学院申请学位级别:硕士学科类别:工学学科专业名称:机械制造及其自动化论文提交日期:2010年6月论文答辩日期:2010年6月学位授予日期:2010年7月答辩委员会主席:评阅人:东北大学2010年6月A Thesis in Mechanical Manufacturing and AutomationFinite Element Simulation and Experimental Study of Stainless SteelDrilling ProcessBy Yan PengfeiSupervisor: Professor Zou PingNortheastern UniversityJune 2010独创性声明本人声明,所呈交的学位论文是在导师的指导下完成的。
论文中取得的研究成果除加以标注和致谢的地方外,不包含其他人己经发表或撰写过的研究成果,也不包括本人为获得其他学位而使用过的材料。
与我一同工作的同志对本研究所做的任何贡献均己在论文中作了明确的说明并表示谢意。
学位论文作者签名:日期:学位论文版权使用授权书本学位论文作者和指导教师完全了解东北大学有关保留、使用学位论文的规定:即学校有权保留并向国家有关部门或机构送交论文的复印件和磁盘,允许论文被查阅和借阅。
本人同意东北大学可以将学位论文的全部或部分内容编入有关数据库进行检索、交流。
作者和导师同意网上交流的时间为作者获得学位后:半年 □ 一年□ 一年半□ 两年□学位论文作者签名:导师签名:签字日期:签字日期:不锈钢钻削加工有限元仿真及试验研究摘 要随着航空、航天、石油、化工、冶金、食品、环保、汽车等工业的蓬勃发展,不锈钢材料已得到广泛地应用,生产实践中,钻削是十分常见的不锈钢加工方法。
不锈钢属于难加工材料,其特殊的材料性能使其加工效率比较低下,加工成本较大。
因此研究不锈钢的钻削性能,提高不锈钢钻削加工效率具有重要的意义,同时也为其它难加工材料的研究提供借鉴。
建立麻花钻的数学模型是对麻花钻进行几何设计、制造、切削性能分析和对钻削过程进行建模的基础。
根据麻花钻后刀面刃磨原理,利用Pro/E软件完成锥面麻花钻、螺旋面钻尖三维造型。
在金属切削加工中,对切削过程的研究有着重要的意义。
切削力、切削温度和刀具磨损是反映切削过程的主要指标,特别是切削力,其使用范围更广。
切削过程的建模和仿真在改进切削刀具的设计和优化切削参数方面有很大的发展潜力。
有限元法逐渐成为切削过程的研究和仿真的一种有效手段。
本文应用DEFORM-3D有限元软件,将工件、刀具材料的一些特性参数结合起来,分析和定义了载荷边界条件、刀具前刀面与切屑之间摩擦状况,确定了切屑分离准则和网格重划标准,完成了有限元分析仿真的预处理工作。
利用有限元仿真分析,分析了切削用量对不锈钢钻削性能的影响,建立普通麻花钻钻削加工仿真模型,分析切削用量对不锈钢钻削轴向力和扭矩的影响规律,并得到了钻削温度场和钻头磨损的情况;研究麻花钻主要几何参数对不锈钢钻削性能的影响,将麻花钻的横刃缩短,将横刃形状修磨成“S”形(螺旋面钻尖)、建立不同顶角的钻尖,并且在相同的切削参数下,对这些不同几何参数麻花钻进行有限元分析,研究麻花钻几何参数对轴向力、扭矩和刀具磨损的影响。
本课题用普通麻花钻做了钻削试验,对正交试验所得结果进行多元线性回归分析,建立在试验范围内的钻削力经验公式,并将试验数据与仿真数据对比,发现切削力的试验值与预测值对指标的影响具有相同的发展趋势。
也用螺旋面钻头做了钻削不锈钢试验,该钻头是由沈阳东北大学研制的SD-2型手动复杂刃磨机床上刃磨而成的,通过试验,得知:在相同的切削参数下,螺旋面麻花钻的轴向力和扭矩比普通麻花钻要小很多,证实了螺旋面钻头的优越性。
关键词:不锈钢;刃磨;有限元仿真;钻削试验;多元线性回归Finite Element Simulation and Experimental Study of Stainless Steel Drilling ProcessAbstractWith the aviation,aerospace, petroleum, chemical metallurgy, food, environmental, automotive and other industries flourish, stainless steel has been widely used. Production practice, drilling is a very common method of stainless steel processing. Stainless steel is difficult to process materials, because of its unique material properties; we can not get better processing efficiency and lower processing costs. Therefore, it’s of great significance to study Drilling Performance of Stainless steel for improving the processing efficiency, but also for other difficult to machine materials for reference.Mathematical model to establish drill bit is the geometric design, manufacture, cutting analysis and modeling on the basis of the drilling process. According to Twist Drill Grinding principle, using Pro/E to complete three-dimensional modeling of Twist drill.In Metal Cutting, cutting process of great significance. Cutting force, cutting temperature and tool wear are the major indicators reflecting the cutting process, especially the cutting force, the use of a broader range. Modeling and simulation of cutting process the cutting tool in improving the design and optimization of cutting parameters have great potential for development. Finite element method has become the research and simulation of cutting process is an effective means.Application of finite element software DEFORM, the work piece, cutting tool material combination of a number of parameters, analysis and definition of the load boundary conditions, defines a tool rake face and chip friction between the state, chip separation criteria and remeshing criteria, completed finite element analysis simulation of pretreatments.Finite element simulation analysis of the cutting performance of stainless steel drilling, establish ordinary twist drills drilling a simulation model of cutting stainless steel axial force and torque on the impact of the law, and has been drilling temperature and the drill wear condition; of the main geometric parameters on the stainless steel twist drill drilling performance, will reduce the twist drill chisel edge, the chisel edge ground into the shape ofrepair "S" shape (Helical Drill Point), to establish different vertex The drill tip, and the same cutting parameters, geometric parameters of these different twist on the finite element analysis to study the twist drill geometry parameters on the axial force, torque and tool wear.This topic made with ordinary twist drill drilling test results on the orthogonal multiple linear regression analysis, the test drilling force within the empirical formula and comparison of test data and simulation data and found that the cutting force of experimental and predicted values of the indices of the same trends. Also done a bit with a helical stainless steel test drilling, the drill was developed by the Northeastern University, Shenyang, SD-2 hand-grinding machine tool grinding complex formed through the test, the cutting parameters in the same helical twist drilling thrust and torque much smaller than ordinary twist drill, drill confirmed the superiority of the spiral surface.Key words: Stainless steel; grinding; finite element simulation; drilling test; multiple linear regressions目 录独创性声明 (I)摘要 (II)Abstract (III)第1章绪论 (1)1.1难加工材料概述 (1)1.1.1 材料切削加工性指标及其衡量标准 (1)1.1.2 难加工材料定义及其切削加工特点 (2)1.1.3 国内外难加工材料切削加工现状及其发展 (3)1.2不锈钢概述 (3)1.2.1 不锈钢定义及其分类 (3)1.2.2 不锈钢切削加工特点 (4)1.3钻削加工及其有限元仿真概述 (5)1.3.1 麻花钻基本结构及其几何参数 (5)1.3.2 钻削力建模的发展及其组成 (6)1.3.3 国内外钻削加工仿真研究现状 (7)1.4本文研究的主要内容 (8)1.5本章小结 (8)第2章麻花钻后刀面刃磨方法 (9)2.1平面刃磨法 (9)2.2锥面刃磨法 (10)2.2.1 锥面刃磨法原理 (10)2.2.2 锥面刃磨法后刀面数学模型 (10)2.2.3 锥面麻花钻3D模型 (12)2.3螺旋面刃磨法 (15)2.3.2 螺旋面刃磨法后刀面数学模型 (15)2.3.3 螺旋面麻花钻3D模型 (18)2.4本章小结 (18)第3章钻削加工有限元仿真模型的建立 (19)3.1有限元分析法基本理论 (19)3.1.1 有限元分析法概述 (19)3.1.2 刚塑性有限元法基本原理 (19)3.1.3 金属切削加工有限元仿真关键技术 (21)3.1.4 金属切削有限元软件的选择 (25)3.2DEFORM-3D软件介绍 (25)3.3钻削有限元模型的建立 (26)3.4本章小结 (30)第4章仿真分析 (31)4.1切削用量对不锈钢钻削性能的影响 (31)4.1.1 普通麻花钻钻削过程中轴向力分析 (33)4.1.2 普通麻花钻钻削过程中扭矩分析 (36)4.2钻削温度场以及刀具磨损分析 (39)4.3麻花钻几何参数对不锈钢钻削性能的影响 (41)4.3.1 横刃对钻削性能的影响 (41)4.3.2 顶角对不锈钢钻削性能的影响 (44)4.4本章小结 (46)第5章钻削试验及钻削力经验公式的建立 (47)5.1钻削试验 (47)5.1.1 试验目的 (47)5.1.2 试验条件 (47)5.1.3 测力仪标定 (49)5.2结果对比 (54)5.3钻削力经验公式的建立 (57)5.4多元线性回归方程的方差分析 (60)5.5本章小结 (64)第6章结论与建议 (65)6.1结论 (65)6.2建议 (66)参考文献 (67)致谢 (70)第1章绪论1.1 难加工材料概述随着航天航空工业、核工业、兵器工业、化学工业、电子工业及其现代机械工业的发展,对产品零部件材料的性能提出了各种各样的新的和特殊的要求。