注塑模的排位设计
塑胶模具排位的过程
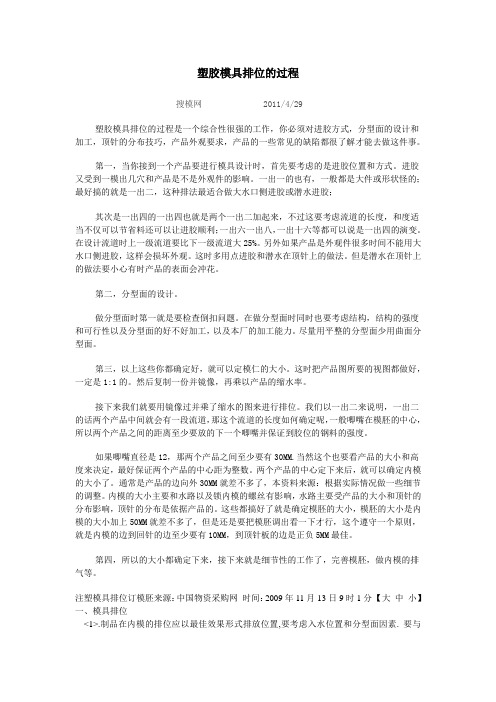
塑胶模具排位的过程搜模网 2011/4/29塑胶模具排位的过程是一个综合性很强的工作,你必须对进胶方式,分型面的设计和加工,顶针的分布技巧,产品外观要求,产品的一些常见的缺陷都很了解才能去做这件事。
第一,当你接到一个产品要进行模具设计时,首先要考虑的是进胶位置和方式。
进胶又受到一模出几穴和产品是不是外观件的影响。
一出一的也有,一般都是大件或形状怪的;最好搞的就是一出二,这种排法最适合做大水口侧进胶或潜水进胶;其次是一出四的一出四也就是两个一出二加起来,不过这要考虑流道的长度,和度适当不仅可以节省料还可以让进胶顺利;一出六一出八,一出十六等都可以说是一出四的演变。
在设计流道时上一级流道要比下一级流道大25%。
另外如果产品是外观件很多时间不能用大水口侧进胶,这样会损坏外观。
这时多用点进胶和潜水在顶针上的做法。
但是潜水在顶针上的做法要小心有时产品的表面会冲花。
第二,分型面的设计。
做分型面时第一就是要检查倒扣问题。
在做分型面时同时也要考虑结构,结构的强度和可行性以及分型面的好不好加工,以及本厂的加工能力。
尽量用平整的分型面少用曲面分型面。
第三,以上这些你都确定好,就可以定模仁的大小。
这时把产品图所要的视图都做好,一定是1:1的。
然后复制一份并镜像,再乘以产品的缩水率。
接下来我们就要用镜像过并乘了缩水的图来进行排位。
我们以一出二来说明,一出二的话两个产品中间就会有一段流道,那这个流道的长度如何确定呢,一般唧嘴在模胚的中心,所以两个产品之间的距离至少要放的下一个唧嘴并保证到胶位的钢料的强度。
如果唧嘴直径是12,那两个产品之间至少要有30MM.当然这个也要看产品的大小和高度来决定,最好保证两个产品的中心距为整数。
两个产品的中心定下来后,就可以确定内模的大小了。
通常是产品的边向外30MM就差不多了,本资料来源:根据实际情况做一些细节的调整。
内模的大小主要和水路以及锁内模的螺丝有影响,水路主要受产品的大小和顶针的分布影响,顶针的分布是依据产品的。
基于AutoCAD的注塑模具排位设计

的
模
具 排
设
( 江西现代职业技术学院, 江西 南昌 3 09) 3 05
( a g i d m oyeh i C l g ,i g i n h n 3 0 5 J n x Mo e P lt nc ol e J n x ca g3 0 9 ) i c e a Na
位
计
f
和产品基准为整数 。 一般情况下, 型腔之间没有流道 时, 一般取 1 ̄2 1T 如图一 中 B值)设置流道时 2 0T I I( I , 正常可取 2  ̄3 0 0 mm, 由于产品中心相对模具中心
具设计 中, 使用 U X、r E等软件做全 3 已经 GN Po / D
不能胜任复杂的模具和公司要求,D排位能快速直 2 观地体现模具结构, 便于讨论和修改, 通过对排位的
检查 可以消除隐患, 减少返工次数, 目前常用的一 是 种手段 。 很多工厂使用 A tC D进行模具 2 u A o D排位 设计, 而使用 U X、r/ 做 分模。 GN Po E
p un d. o de
K y rsA tC D; jcinModD s ; ry e wod : uo A I et l ei Ar n o n g a
0 引言 随着我 国模具行业的 日 益发展,在现代注塑模
细检查产品尺寸、 公差 、 脱模斜度 、 厚度等 , 确保产品 能够顺利出模。同时注意检查产 品是否已经放过缩
在设计过程 中,有不少零件都是模具常用的标 准件, 以直接调 用, 可 此时需要使用 A t A 的外 u CD o
挂程 序 ,其 中燕 秀 工具箱 是 目前使 用较 多 的一款 外
缩率 ,实 际设计 中即在 A t A 中放 大 比例 为 uC D o ( S 。 设计中要注意对 2 图形的镜像( I ) + D 产品是完
【模具设计】注胶模具的排位设计PPT

·无冷却水孔或制品较小时,h1取15~20mm。
·冷却水孔边到型腔的距离取1.5d,或取10~15 mm。
制品平面投影面积(cm2)
h1(mm)
d(mm)
<40(6.32)
20~25(20)
6
40~77(8.72)
25~32(30)
8
77~116(10.72)
32~38(35)
10
116~154(12.42)
B(cm) 15、20
25
30、35
40
45、50
h7(mm)
30
35最低
45
50
60
③B板厚度h8=后模芯厚度h6+ B板开框背后厚度h7
完整版ppt
12
此课件下载可自行编辑修改,供参考! 感谢您的支持,我们努力做得更好!
55
140
45
300
65
170
350
65
220
50 L0 = L - 2 LK
55
400
75
250
55
450
85
280
60
500
95
310
完整版p6p0t
10
三、高度尺寸的确定
注塑模具的排位设计
1、前模部分(前模厚度=产品的高度+10水孔深度+15~20,再取接近的整数)
①型腔背后模芯厚度h1,h1与冷却水孔的布置及制品的平面投影面积有关。
完整版ppt
3
注塑模具的排位设计
3、对高精度制品,型腔数目尽可能少。因为每增加一个型腔,制品精度下降4%。 精密模具型腔数目一般不超过4个。
4、相同颜色、相同原料。
注塑模的排位设计

注塑模的排位设计一、设计原则1、力求平衡、对称。
①各型腔在相同温度下同时充模。
·采用平衡布局·非平衡布局可通过调节浇口尺寸达到平衡②浇口平衡③大小制品对称布置④模具力平衡,即注射压力中心与主流道中心重合,防止飞边。
2、流道尽可能短,以降低废料率、成型周期和热损失。
H型排位优于环形和对称型。
3、对高精度制品,型腔数目尽可能少。
因为每增加一个型腔,制品精度下降4%。
精密模具型腔数目一般不超过4个。
4、相同颜色、相同原料。
5、结构紧凑,节约钢材。
6、大近小远。
7、高度相近。
8、先大后小,见缝插针。
9、同一制品,大近小远。
10、工艺性好。
二、平面尺寸的确定1、型腔到型芯边的距离aa = 0.2×l + 17 经推算得知20≤a≤40·对模芯边走冷却水的深腔模具或带侧抽芯的模具,a可适当增加。
2、型腔之间的距离bb≧a/2 ,一般取12~20mm。
·对于特别小的制品,b可取3mm。
·型腔之间布置有流道时,b′可取25~30mm,一般取30mm。
3、模芯尺寸B0×L0模芯尺寸= 制品尺寸+型腔到型芯边的距离+型腔之间的距离·模芯尺寸超过200×200时,必须做成拼块结构。
4、推算模架①模具尺寸系列(CM)②模架之成型范围(MM)三、高度尺寸的确定1、前模部分(前模厚度=产品的高度+10水孔深度+15~20,再取接近的整数)①型腔背后模芯厚度h1,h1与冷却水孔的布置及制品的平面投影面积有关。
·无冷却水孔或制品较小时,h1取15~20mm。
·冷却水孔边到型腔的距离取1.5d,或取10~15 mm。
A、B板的宽度:由模芯单边+50~55②A板开框背后厚度h3 = 最低25~35 mm③前模芯厚度h2 = 制品厚度h+型腔背后模芯厚度h1④A板厚度h4 =前模芯厚度h2+ A板开框背后厚度h32、后模部分(主要承受来自型腔的注射压力,取最低值35,总尺寸在80,90,100间)①后模芯厚度h6,主要起藏core作用,一般取20~35 mm。
塑料端盖注塑模的型腔数排列
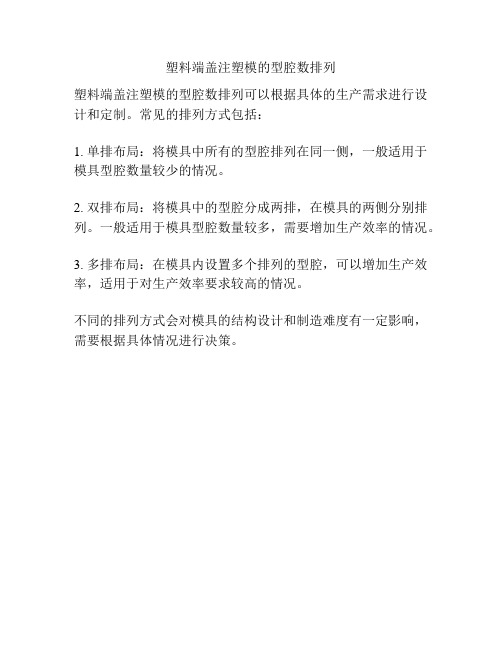
塑料端盖注塑模的型腔数排列
塑料端盖注塑模的型腔数排列可以根据具体的生产需求进行设计和定制。
常见的排列方式包括:
1. 单排布局:将模具中所有的型腔排列在同一侧,一般适用于模具型腔数量较少的情况。
2. 双排布局:将模具中的型腔分成两排,在模具的两侧分别排列。
一般适用于模具型腔数量较多,需要增加生产效率的情况。
3. 多排布局:在模具内设置多个排列的型腔,可以增加生产效率,适用于对生产效率要求较高的情况。
不同的排列方式会对模具的结构设计和制造难度有一定影响,需要根据具体情况进行决策。
塑胶模CAD设计、排位技巧归纳

塑胶模CAD设计、排位技巧归纳1.把產品的3D图档转到2D图档上,需将倒勾或有组织处做剖面,要留意比例问题。
(1:1)2.转到2D图档上的產品图要加缩水和镜像。
留意:完结以上两步骤后有必要查看,能够丈量產品在加缩水前后的同一当地,来查看缩水加的是否正确。
3.排组立前要定制品基准线。
即把產品上boss或大平面等易找到的特征定X,Y,Z三轴,特征的寻觅需尽量接近于制品中心,若是两上下盖相配合,基原则尽量為同一点。
制品基准线相对模具中心要為整数。
4 按照制品基准线把模仁排出来。
步骤舆表示重点:1. 删去制品上的虚线。
2. 如侧视图為剖面要将侧视图的实线改為虚线,仅留剖面处為实线。
3.要把制品的分型面表明出来,要点表明主分型面,斜销,滑块处置型面。
分型面上的插破,靠破也需表明。
4. 还需把模仁拆入子处表明清楚,正视图入子遍界用黄色线表明,且入子沉头也需表明。
入子舆入子间要防止有薄铁现象,一般不行小于1mm。
(模仁需拆入子部位一般為整体欠好加工处或肋较深处及一些boss处)。
5.排顶针,水路,最后排模仁螺丝。
要注意三者不能干与,三者距离不小于3mm,拆入子时也要一起考虑.画模架时的注意事项:A. KO孔一般放在模具的正中,当有多个时,它们之间的间隔一般為100mm。
B.支撑柱应尽量往模具中心排即靠著KO孔,且尺度尽量做大。
要注意不能和顶针,斜销等组织干与。
相比较下,六合侧比左右侧更需求支撑柱。
C. 当顶针小于2mm时,模具需加EGP。
但也有特殊要求的。
方位放在模具的六合侧。
D. 吊模孔在舆其它组织不干与的情况下要放在模板中心,如有干与则要移位,并要标示尺度。
E.当模具六合侧长度超越350mm时,需添加顶出板螺丝和ST,且鄙人固定板舆模脚之间要加锁左右各两个M10螺丝。
F.如一副模架的模板都很厚超越规范模架所列出的模板厚度的中心数字,那么GP需加大一绩。
如是不规范模架,六合侧或左右侧有拉长,那么GP需加大一绩。
注塑模具设计第3讲 实例3-2D-03 产品排位确定型腔、型芯尺寸

注塑模具设计实例教程
图3-1-10型芯的长宽尺寸(型芯视图)
型腔、型芯厚度的尺寸一般是由产品的结构和高度尺寸来确定,本例有 定模滑块,型腔厚度应比常规结构的模具适当加大。 设计型腔、型芯的厚度时先确定产品的主分型线,本例的分型面为曲面 ,因此需顺着曲面延伸10mm左右,再拉平创建主分型线。创建出主分型 线后,利用【偏移】命令,将主分型线向上偏移55mm,向下偏移35mm, 所得到的型腔、型芯厚度如图3-1-11所示,此图为正剖视图。
完成练习三以下部分内容: 产品排位确定型腔、型芯尺寸
4
2
四、产品排位确定型腔、型芯尺寸
2. 型腔、型芯厚度尺寸的确定
一般25~30左右
型腔
注塑模具设计实例教程
主分型线
一般延伸10mm左右
型芯
图3-1-11 型腔、型芯的厚度尺寸(正剖视图)
型芯视图和正剖视图绘制出来后,根据 投影关系可绘出型腔视图和侧剖视图, 其中型腔视图取图3-1-9中的“型腔排 位用图”来绘制;侧剖视图取图3-1-9 中的“侧剖排位用图”来绘制。所绘制 的排位图如图3-1-12所示。
主分型线一般2530左右一般延伸10mm左右型腔型芯图3111型腔型芯的厚度尺寸正剖视图图3112产品排位图注塑模具设计实例教程4四产品排位确定型腔型芯尺寸?注意
实例三 玩具面壳注塑模具2D设计
复习:产品工程图的创建与处理方法
注塑模具设计实例教程
检查上次布置作业的完成情况
新课:
四、产品排位确定型腔、型芯尺寸 产品排位是模具设计的重要步骤,通过产品排位可确定型腔、型芯尺寸,进 而确定模架的规格。 1. 型腔、型芯长宽尺寸的确定 型腔、型芯尺寸一般是由产品的尺寸来确定,可查实例一提供的经验值。 本例产品最大外形尺寸为116.67 mm×90.30 mm,总高度为25.90mm。一般 产品边到型腔、型芯边的距离取30mm左右,以保证型腔、型芯的强度,同 时也为螺钉、冷却水道的布置留下足够的距离。 另外,产品的中心线到型腔、型芯中心的距离要取整数;型腔、型芯的长 宽尺寸一定要取整数,并尽可能取为10的倍数,以便更好取数加工。 1
塑料模具型腔的排列方式及分流道布置

塑料模具型腔的排列⽅式及分流道布置
塑料模具多腔注塑模具的排位和分流道布置,往往有很多选择,在实际⼯作中应遵循以下设计原则。
(1)⼒求平衡对称。
⼀模多腔的模具,应尽量采⽤平衡布局,使各型腔在相同温度下同时充模。
流道平衡。
塑料模具⼤⼩型腔对⾓布置,使模具保持压⼒平衡,即注射压⼒中⼼与锁模压⼒中⼼(主流道中⼼)重合,防⽌塑件产⽣飞边。
(2)流道尽可能短以降低废料率、成型周期和热损失。
在这⼀点上H形排位优于环形和对称形状。
(3)对⾼精度塑料制品,型腔数⽬应尽可能少因为每增加⼀个型腔,塑料制品精度下降5%。
精密模具型腔数⽬⼀般不宜超过4个。
(4)浙江塑料模具加⼯⼚设计塑料模具结构紧凑,节约钢材。
(5)⼤近⼩远。
(6)⾼度相近⾼度相差悬殊的塑料制品不宜排在⼀起。
(7)先⼤后⼩,见缝插针⼀模多腔时,相同的塑料制品采⽤对称进浇⽅式;对于不同塑料制品,在同⼀模具中成型时,优先将最⼤塑料制品放在靠近主流道的位置。
(8)同⼀塑料制品,⼤近⼩远塑料制品⼤头应靠近模具中⼼。
(9)⼯艺性好排位时必须考虑模具注射的⼯艺性要好,并保证模具型腔的压⼒和温度平衡。
塑胶模具排位的过程

塑胶模具排位的过程塑胶模具排位的过程引导语:下面是店铺为大家精心整理出来的一些关于塑胶模具排位的过程的资料,希望可以帮助到大家哦!塑胶模具排位的过程是一个综合性很强的工作,你必须对进胶方式,分型面的设计和加工,顶针的分布技巧,产品外观要求,产品的一些常见的缺陷都很了解才能去做这件事。
第一,当你接到一个产品要进行模具设计时,首先要考虑的是进胶位置和方式。
进胶又受到一模出几穴和产品是不是外观件的影响。
一出一的也有,一般都是大件或形状怪的;最好搞的就是一出二,这种排法最适合做大水口侧进胶或潜水进胶;其次是一出四的一出四也就是两个一出二加起来,不过这要考虑流道的长度,和度适当不仅可以节省料还可以让进胶顺利;一出六一出八,一出十六等都可以说是一出四的演变。
在设计流道时上一级流道要比下一级流道大25%。
另外如果产品是外观件很多时间不能用大水口侧进胶,这样会损坏外观。
这时多用点进胶和潜水在顶针上的做法。
但是潜水在顶针上的做法要小心有时产品的表面会冲花。
第二,分型面的设计。
做分型面时第一就是要检查倒扣问题。
在做分型面时同时也要考虑结构,结构的强度和可行性以及分型面的好不好加工,以及本厂的加工能力。
尽量用平整的分型面少用曲面分型面。
第三,以上这些你都确定好,就可以定模仁的大小。
这时把产品图所要的视图都做好,一定是1:1的。
然后复制一份并镜像,再乘以产品的缩水率。
接下来我们就要用镜像过并乘了缩水的图来进行排位。
我们以一出二来说明,一出二的话两个产品中间就会有一段流道,那这个流道的长度如何确定呢,一般唧嘴在模胚的中心,所以两个产品之间的距离至少要放的下一个唧嘴并保证到胶位的钢料的`强度。
如果唧嘴直径是12,那两个产品之间至少要有30MM.当然这个也要看产品的大小和高度来决定,最好保证两个产品的中心距为整数。
两个产品的中心定下来后,就可以确定内模的大小了。
通常是产品的边向外30MM就差不多了,根据实际情况做一些细节的调整。
模具排位(新)
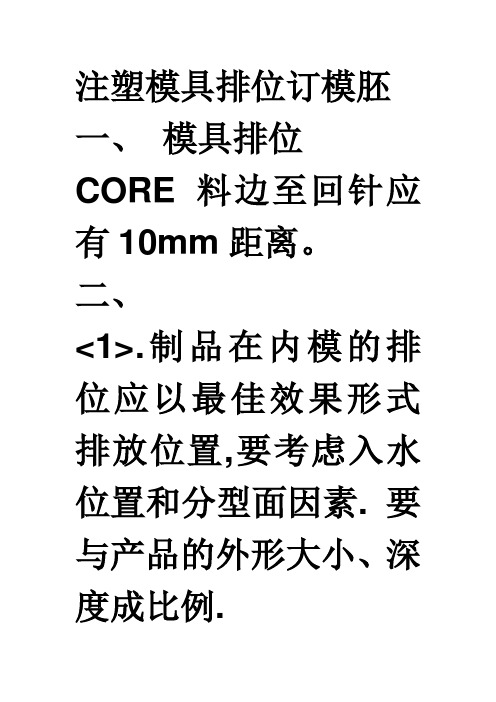
注塑模具排位订模胚一、模具排位CORE料边至回针应有10mm距离。
二、<1>.制品在内模的排位应以最佳效果形式排放位置,要考虑入水位置和分型面因素. 要与产品的外形大小、深度成比例.<2>.制品到精框边的距离:A).小件的制品:距离为25mm~30mm之间,成品之间为15mm~20mm,如有镶件则为25mm左右,成品间有流道的最少要15mm.B).大件的制品:距边为35~50mm,如果有突出块,按小件产品边。
有镶件最小为35mm,如1件钢件出多件小产品,则其之间的距离应12~15mm左右.成品长度在200mm以上,宽度在150mm以上其产品距边应不少于35mm.<3>.制品排位时选择基准的原则:A).优先选取具明显特征(如柱位、碰穿孔、骨位中)的部分分中.B).若选取PRO/E 3D 基准时,要注明CSO 或CSI或DTM的名字.C).形状特别,难以确定基准的制品,要与CAM 讨论再确定其基准. D).制品基准与模胚中心一定要为整数,并在标注尺寸时于数字上加方框以示区别.<4>.排位时确定内模精框X,Y坐标方向的原则:若内模精框长宽尺寸差明显,必须取较长一方之方向为X轴方向放置模胚排位,以配合工场机床加工方向,减少出错几率.二、订模胚<1>.尽量采用标准模胚(LKM标准或鸿丰标准).A).由工字模改直身模时,不要移动方铁,要直接在方铁上锣码模坑.B).不标准模胚要经过主管同意并要在排位图上注明.<2>.用CH型和CT型模胚要做码模坑,高度和宽度为25~35mm左右,长度按模胚的高度确定.< 3>.顶棍孔应按模胚的大细长宽加工1个或2个或4个孔(加工1个以上顶棍孔时,要做长顶棍,模胚中心的顶棍孔不做).孔径为。
注塑模行位(滑块)设计

倒勾处理(滑块)一‧斜撑销块的动作原理及设计要点是利用成型的开模动作用,使斜撑梢与滑块产生相对运动趋势,使滑块沿开模方向及水平方向的两种运动形式,使之脱离倒勾。
如下图所示:上图中:β=α+2°~3°(防止合模产生干涉以及开模减少磨擦)α≦25°(α为斜撑销倾斜角度)L=1.5D (L为配合长度)S=T+2~3mm(S为滑块需要水平运动距离;T为成品倒勾)S=(L1xsina-δ)/cosα(δ为斜撑梢与滑块间的间隙,一般为0.5MM;L1为斜撑梢在滑块内的垂直距离)二‧斜撑梢锁紧方式及使用场合简图说明适宜用在模板较薄且上固定板与母模板不分开的情况下配合面较长,稳定较好适宜用在模板厚、模具空间大的情况下且两板模、三板板均可使用配合面L≧1.5D(D为斜撑销直径)稳定性较好适宜用在模板较厚的情况下且两板模、三板板均可使用,配合面L≧1.5D(D为斜撑销直径)稳定性不好,加工困难.适宜用在模板较薄且上固定板与母模板可分开的情况下配合面较长,稳定较好三‧拔块动作原理及设计要点是利用成型机的开模动作,使拔块与滑块产生相对运动趋势,拨动面B拨动滑块使滑块沿开模方向及水平方向的两种运动形式,使之脱离倒勾。
如下图所示:上图中:β=α≦25°(α为拔块倾斜角度)H1≧1.5W (H1为配合长度)S=T+2~3mm(S为滑块需要水平运动距离;T为成品倒勾)S=H*sinα-δ/cosα(δ为斜撑梢与滑块间的间隙,一般为0.5MM;H为拔块在滑块内的垂直距离)C为止动面,所以拨块形式一般不须装止动块。
(不能有间隙)四‧滑块的锁紧及定位方式由于制品在成型机注射时产生很大的压力,为防止滑块与活动芯在受到压力而位移,从而会影响成品的尺寸及外观(如跑毛边),因此滑块应采用锁紧定位,通常称此机构为止动块或后跟块。
常见的锁紧方式如下图:简图说明简图说明滑块采用镶拼式锁紧方式,通常可用标准件.可查标准零件表,结构强度好.适用于锁紧力较大的场合.采用嵌入式锁紧方式,适用于较宽的滑块滑块采用整体式锁紧方式,结构刚性好但加工困难脱模距小适用于小型模具.采用嵌入式锁紧方式适用于较宽的滑块.采用拔动兼止动稳定性较差,一般用在滑块空间较小的情况下采用镶式锁紧方式,刚性较好一般适用于空间较大的场合.五.滑块的定位方式滑块在开模过程中要运动一定距离,因此,要使滑块能够安全回位,必须给滑块安装定位装置,且定位装置必须灵活可靠,保证滑块在原位不动,但特殊情况下可不采用定位装置,如左右侧跑滑块,但为了安全起见,仍然要装定位装置.常见的定位装置如下:简图说明利用弹簧螺钉定位,弹簧强度为滑块重量的1.5~2倍,常用于向上和侧向抽芯.利用弹簧钢球定位,一般滑块较小的场合下,用于侧向抽芯.利用弹簧螺钉和挡板定位,弹簧强度为滑块重量的1.5~2倍,适用于向上和侧向抽芯利用弹簧挡板定位,弹簧的强度为滑块重量的1.5~2倍,适用于滑块较大,向上和侧向抽芯.六‧滑块入子的连接方式滑块头部入子的连接方式由成品决定,不同的成品对滑块入子的连接方式可能不同,具体入子的连接方式大致如下:简图说明简图说明滑块采用整体式结构,一般适用于型芯较大,强度较好的场合. 采用螺钉固定,一般型芯或圆形,且型芯较小场合.采用螺钉的固定形式,一般型芯成方形结构且型芯不大的场合下. 采用压板固定适用固定多型芯.七‧滑块的导滑形式块在导滑中,活动必须顺利、平稳,才能保证滑块在模具生产中不发生卡滞或跳动现象,否则会影响成品质品,模具寿命等。
塑胶模具的排位.ppt
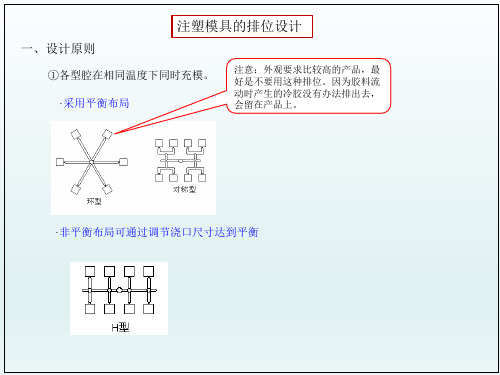
45
√√√
50
√√√
注塑模具的排位设计
②模架之成型范围(MM)
B
BK
B0
LK
L0
150
35
80
35
200
45
110
40
250
55
140
45
300
65
170
350
65
220
50 L0 = L - 2 LK
55
400
75
250
55
450
85
28060500来自9531060
三、高度尺寸的确定
注塑模具的排位设计
注塑模具的排位设计
一、设计原则
①各型腔在相同温度下同时充模。 ·采用平衡布局
注意:外观要求比较高的产品,最 好是不要用这种排位。因为胶料流 动时产生的冷胶没有办法排出去, 会留在产品上。
·非平衡布局可通过调节浇口尺寸达到平衡
②浇口平衡
注塑模具的排位设计
③大小制品对称布置
④模具力平衡,即注射压力中心与主流道中心重合,防止飞边。
77~116(10.72) 116~154(12.42) 154~193(13.92)
>193
h1(mm) 20~25(20) 25~32(30) 32~38(35) 38~50(45) 44~64(50) 50~76(60)
d(mm) 6 8 10 12 16 20
注塑模具的排位设计
A、B板的宽度:由模芯单边+50~55 ②A板开框背后厚度h3 = 最低25~35 mm ③前模芯厚度h2 = 制品厚度h+型腔背后模芯厚度h1 ④A板厚度h4 =前模芯厚度h2+ A板开框背后厚度h3 2、后模部分(主要承受来自型腔的注射压力,取最低值35,总尺寸在80,90,100间) ①后模芯厚度h6,主要起藏core作用,一般取20~35 mm。 ②B板开框背后厚度h7,主要承受来自型腔的注射压力,可以查选标准托板厚度。
塑胶模具设计规范
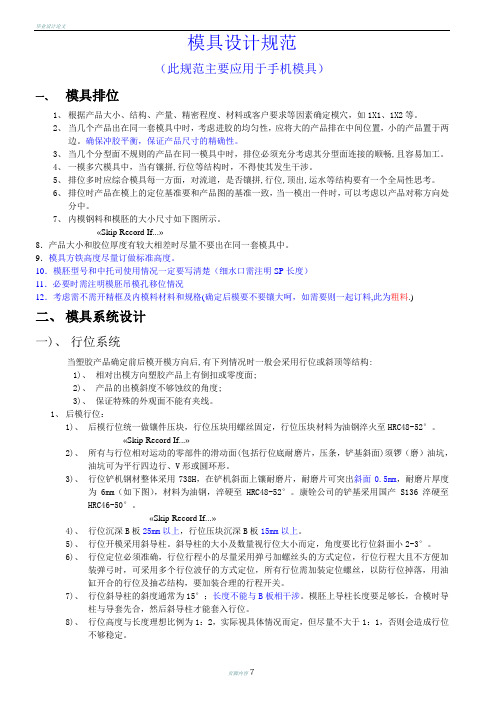
模具设计规范(此规范主要应用于手机模具)一、模具排位1、根据产品大小、结构、产量、精密程度、材料或客户要求等因素确定模穴,如1X1、1X2等。
2、当几个产品出在同一套模具中时,考虑进胶的均匀性,应将大的产品排在中间位置,小的产品置于两边。
确保冲胶平衡,保证产品尺寸的精确性。
3、当几个分型面不规则的产品在同一模具中时,排位必须充分考虑其分型面连接的顺畅,且容易加工。
4、一模多穴模具中,当有镶拼,行位等结构时,不得使其发生干涉。
5、排位多时应综合模具每一方面,对流道,是否镶拼,行位,顶出,运水等结构要有一个全局性思考。
6、排位时产品在模上的定位基准要和产品图的基准一致,当一模出一件时,可以考虑以产品对称方向处分中。
7、内模钢料和模胚的大小尺寸如下图所示。
«Skip Record If...»8.产品大小和胶位厚度有较大相差时尽量不要出在同一套模具中。
9.模具方铁高度尽量订做标准高度。
10.模胚型号和中托司使用情况一定要写清楚(细水口需注明SP长度)11.必要时需注明模胚吊模孔移位情况12.考虑需不需开精框及内模料材料和规格(确定后模要不要镶大呵,如需要则一起订料,此为粗料.)二、模具系统设计一)、行位系统当塑胶产品确定前后模开模方向后,有下列情况时一般会采用行位或斜顶等结构:1)、相对出模方向塑胶产品上有倒扣或零度面;2)、产品的出模斜度不够蚀纹的角度;3)、保证特殊的外观面不能有夹线。
1、后模行位:1)、后模行位统一做镶件压块,行位压块用螺丝固定,行位压块材料为油钢淬火至HRC48-52°。
«Skip Record If...»2)、所有与行位相对运动的零部件的滑动面(包括行位底耐磨片,压条,铲基斜面)须锣(磨)油坑,油坑可为平行四边行、V形或圆环形。
3)、行位铲机钢材整体采用738H,在铲机斜面上镶耐磨片,耐磨片可突出斜面0.5mm,耐磨片厚度为6mm(如下图),材料为油钢,淬硬至HRC48-52°。
ts16949注塑件形位标准_解释说明以及概述

ts16949注塑件形位标准解释说明以及概述1. 引言1.1 概述TS16949注塑件形位标准是指在汽车零部件制造过程中,针对注塑件的形位测量和要求而制定的一系列标准规范。
这些标准规定了注塑件在尺寸和位置上的公差范围,以确保注塑件能够正确安装和与其他零部件精确配合。
1.2 文章结构本文主要围绕TS16949注塑件形位标准展开详细说明和解释,并探讨其在质量管理中的应用。
文章分为五个部分:引言、TS16949注塑件形位标准解释说明、形位标准的具体要点解析与示例说明、注塑件形位标准在质量管理中的应用、结论与展望。
1.3 目的本文旨在向读者介绍和解释TS16949注塑件形位标准,包括其定义和背景,作用和重要性,以及分类和要求方面的内容。
同时,我们将对形位标准的具体要点进行深入解析,并提供示例说明。
此外,文章还将探讨注塑件形位标准在质量管理中的应用,并分析其对生产过程、质量检验和评估的影响与控制措施。
最后,我们将总结文章主要观点和研究成果,并展望注塑件形位标准研究的不足之处和未来发展方向。
2. TS16949注塑件形位标准解释说明:2.1 定义和背景:TS16949是汽车行业质量管理体系标准,也是ISO/TS 16949:2009技术规范的简称。
注塑件形位标准是该标准中的一个重要部分,用于规范和约束汽车注塑件在尺寸、位置以及相关要求方面的质量控制。
2.2 形位标准的作用和重要性:注塑件形位标准在汽车零部件制造过程中起着至关重要的作用。
通过明确注塑件尺寸公差、位置公差等要求,可以保证零部件在装配过程中的一致性和互换性。
形位标准可以有效地指导产品设计与制造,并为供应商提供参考,从而提高整个供应链上各环节的生产效率和产品质量。
2.3 注塑件形位标准的分类和要求:注塑件形位标准可以分为两大类:尺寸公差和位置公差。
尺寸公差是指允许零部件实际尺寸与理论尺寸之间的偏差范围;而位置公差则主要描述了零部件之间或其它基准面之间的相对位置关系要求。
QW-RD-004 注塑模具技术标准

1.4浇口
常见浇口类型有直接浇口﹑侧浇口﹑潜伏式浇口﹑点浇口等多种。设计时应根据产品的不同要求选择适合的类型.尤其当制品外观有要求时,要慎重选择。
1.4.1直接浇口
对大型单一型腔制品成型效果好,需注意唧嘴底部与产品之间隔10MM。例如底壳类制品.其尺寸要求如图:
1.2.4梯形流道: W一般为5~8 H一般为4~6 H/W=2/3如图1-1:
1.3冷料井
为防止冷却的树脂流入型腔,在不通向型腔的流道末端要设置冷料井,包括主流道的大端和分流道拐角处.
1.3.1大水口模主流道大端的冷料井与顶针配合有抓料的作用。 常见形式如图1-2
1.3.2分流道拐角处冷料井设置如图:
5.1.5行位斜销角度一般为15o~25o,最大不能超过25o,斜销角度比行位小2o,一般尽量不采用细小的斜销,以保证行位运动的顺利
5.1.6行位弹弓长度的确定,应保证弹弓空间足够,防止弹弓失效。
设定行位行程为M,弹弓总长为L,设弹簧压缩40%,行位完全退出后,弹弓仍预压10则有
(40%﹣10%)L=M
6.1.2顶出位置
正确的顶出位置,应设在制品脱模困难的地方,制品的骨位﹑柱位以及对内模有包紧力的地方均应考虑设置顶出机构.同时还应考虑顶出机构应设置在不影响制品外观的部位,并且不能与其它零件(如撑头﹑螺丝等)发生干涉。
6.1.3设计中尽量选用大的顶针,大模不用小顶针,当在产品有相互配合的地方设置顶针时,顶针应高出后模面0.5MM。
7.产品胶位边与模仁边需有25-30mm,模仁边与模胚边需保证50mm(模胚大模边亦要加大),产品胶位底部与模仁底部需有25-30mm,模仁底与模胚底:前模需有25mm,后模需有35mm,(模胚大模底亦相应加厚)见图:
塑胶产品排位设计,模仁尺寸及模架大小的确认

产品排位设计,模仁尺寸及模架大小的确定
1.产品排位设计:
1.1产品与产品之间的间距:
其它确定内模尺寸要点
排位应保证流道、唧咀距前模型腔边缘有一定的距离,以满足封胶要求。
一般要求:
D1≥6.0mm,D2≥10.0mm (如下图)
2.1 模仁尺寸的确定:
产品边到模仁边的距离(X,Y方向的确认):
模仁厚度(高度)尺寸的确认(Z方向尺寸的确认):
2.模架大小的确认:
模架的宽与长由模仁的宽与长和模仁边到A板边或B板边的距离确定。
模仁边到A板边或B板边的距离一般取50-70mm,于是:
模架宽=模仁宽+2×(50~70)mm
模架长=模仁长+2×(50~70)mm
A.B板的厚度:
大水口模
小水口模具。
注塑模行位(滑块)设计

倒勾处理(滑块)一‧斜撑销块的动作原理及设计要点是利用成型的开模动作用,使斜撑梢与滑块产生相对运动趋势,使滑块沿开模方向及水平方向的两种运动形式,使之脱离倒勾。
如下图所示:上图中:β=α+2°~3°(防止合模产生干涉以及开模减少磨擦)α≦25°(α为斜撑销倾斜角度)L=1.5D (L为配合长度)S=T+2~3mm(S为滑块需要水平运动距离;T为成品倒勾)S=(L1xsina-δ)/cosα(δ为斜撑梢与滑块间的间隙,一般为0.5MM;L1为斜撑梢在滑块内的垂直距离)二‧斜撑梢锁紧方式及使用场合简图说明适宜用在模板较薄且上固定板与母模板不分开的情况下配合面较长,稳定较好适宜用在模板厚、模具空间大的情况下且两板模、三板板均可使用配合面L≧1.5D(D为斜撑销直径)稳定性较好适宜用在模板较厚的情况下且两板模、三板板均可使用,配合面L≧1.5D(D为斜撑销直径)稳定性不好,加工困难.适宜用在模板较薄且上固定板与母模板可分开的情况下配合面较长,稳定较好三‧拔块动作原理及设计要点是利用成型机的开模动作,使拔块与滑块产生相对运动趋势,拨动面B拨动滑块使滑块沿开模方向及水平方向的两种运动形式,使之脱离倒勾。
如下图所示:上图中:β=α≦25°(α为拔块倾斜角度)H1≧1.5W (H1为配合长度)S=T+2~3mm(S为滑块需要水平运动距离;T为成品倒勾)S=H*sinα-δ/cosα(δ为斜撑梢与滑块间的间隙,一般为0.5MM;H为拔块在滑块内的垂直距离)C为止动面,所以拨块形式一般不须装止动块。
(不能有间隙)四‧滑块的锁紧及定位方式由于制品在成型机注射时产生很大的压力,为防止滑块与活动芯在受到压力而位移,从而会影响成品的尺寸及外观(如跑毛边),因此滑块应采用锁紧定位,通常称此机构为止动块或后跟块。
常见的锁紧方式如下图:简图说明简图说明滑块采用镶拼式锁紧方式,通常可用标准件.可查标准零件表,结构强度好.适用于锁紧力较大的场合.采用嵌入式锁紧方式,适用于较宽的滑块滑块采用整体式锁紧方式,结构刚性好但加工困难脱模距小适用于小型模具.采用嵌入式锁紧方式适用于较宽的滑块.采用拔动兼止动稳定性较差,一般用在滑块空间较小的情况下采用镶式锁紧方式,刚性较好一般适用于空间较大的场合.五.滑块的定位方式滑块在开模过程中要运动一定距离,因此,要使滑块能够安全回位,必须给滑块安装定位装置,且定位装置必须灵活可靠,保证滑块在原位不动,但特殊情况下可不采用定位装置,如左右侧跑滑块,但为了安全起见,仍然要装定位装置.常见的定位装置如下:简图说明利用弹簧螺钉定位,弹簧强度为滑块重量的1.5~2倍,常用于向上和侧向抽芯.利用弹簧钢球定位,一般滑块较小的场合下,用于侧向抽芯.利用弹簧螺钉和挡板定位,弹簧强度为滑块重量的1.5~2倍,适用于向上和侧向抽芯利用弹簧挡板定位,弹簧的强度为滑块重量的1.5~2倍,适用于滑块较大,向上和侧向抽芯.六‧滑块入子的连接方式滑块头部入子的连接方式由成品决定,不同的成品对滑块入子的连接方式可能不同,具体入子的连接方式大致如下:简图说明简图说明滑块采用整体式结构,一般适用于型芯较大,强度较好的场合. 采用螺钉固定,一般型芯或圆形,且型芯较小场合.采用螺钉的固定形式,一般型芯成方形结构且型芯不大的场合下. 采用压板固定适用固定多型芯.七‧滑块的导滑形式块在导滑中,活动必须顺利、平稳,才能保证滑块在模具生产中不发生卡滞或跳动现象,否则会影响成品质品,模具寿命等。
模具2D排位设计经验技巧

模具2D排位设计经验技巧一、当把成品图调进模图时,成品图必须乘缩水。
(模具尺寸=产品尺寸×缩水)必须把成品图MIRROR(镜射)一次,即模圈里的成品图是反像的(成品是完全对称的除外)在前模,应把不属于前模的线条删除。
在后模,应把不属于后模的线修删除。
二、成品在模具里应遵循分中的原则,特别是对称的,成品如果不分中,到工场加工时很可能出错。
三、所有枕位之模具,枕位必须避开入水,无法避开时要加水口铁。
四、成品之间12—20mm(特殊情况下,可以作3mm)当入水为潜水时,应有足够的潜水位置,成品至CORE边15-50mm,成品至CORE的边距与制品的存度有关,一般制品可参考下表经验数值选定。
制品的厚度(mm)成品至CORE边数值(mm)2015—2020—3020—3030—4030—40﹥4050五、藏CORE(内模料)深度28mm以上,前后模内模料厚度与制品的平面投影面积有关,一般制品可参考下表,经验数值选定。
CORE 料边至回针应有10mm距离。
制品平面投影面积前模内模料厚度A+型腔深度后模内模料厚度B+型腔深度SP、CMmmMm﹤77253277—1163238116—1543850154—1934464≧1935076 CORE(内模料)料宽度一般比顶针极宽或窄5—10mm,最低限度成品胶位应在顶针板内不影响落顶针,CORE(内模料)边至模胚边一般应有45—80mm六、当在一块内模料上出多个CAVITY时,内模料大小不超过200×200mm。
七、模内镶入模框中圆角一般取10mm,如要开精框时则取16mm 或更大,铍铜模模内不倒圆角。
八、任何一种塑胶入水位置应避免从唧咀直行入型腔。
九、镜面透明之啤塑(K料、亚加力、PC等)应注意,冷料井入水流量及入水位置不能直衡(冲),一般作成“S”型缓冲入水,扇形浇品,使成品表面避免产生气级流雲。
十、选模胚的一般原则:当模胚阔度在250mm(包括250mm)以下时,用工字型模胚口型,模胚阔度在250—350mm时,用直力有面板模胚(T型)。
塑胶模具排模原则

塑胶模具排模原则塑胶模具排模原则是指在进行塑胶模具排模时应遵循的一些基本原则。
本文将从人类视角出发,详细描述塑胶模具排模的原则和注意事项。
塑胶模具排模时需要考虑产品的形状和尺寸。
合理的模具设计能够提高生产效率和产品质量。
为了避免浪费材料和时间,我们应该选择适当的模具尺寸,并确保模具与产品的形状相匹配。
模具排列的密度也是一个重要的考虑因素。
密度过高会导致模具之间的干涉,影响生产效率;密度过低则会造成模具的浪费。
因此,我们应该根据产品的尺寸和形状来确定模具的排列密度,使其既能提高生产效率,又能减少模具的使用。
模具的排列方向也需要注意。
一般来说,模具的排列方向应与产品的主要外形保持一致。
这样可以减少模具的变形和损坏,提高产品的质量。
同时,合理的排列方向还能够提高生产效率,减少模具的更换次数。
模具排列时还需要考虑产品的结构和表面质量。
一些复杂的产品可能需要多个模具来进行生产,而一些表面要求较高的产品可能需要特殊的模具处理。
因此,在进行模具排列时,我们应该根据产品的特点来选择合适的模具,并确保产品的结构和表面质量得到保证。
模具排列还需要考虑生产流程的合理性。
我们应该合理安排模具的顺序,使其能够顺利地进行生产。
同时,我们还应该考虑模具之间的配合关系,确保生产过程中的协调性和连贯性。
塑胶模具排模原则是一个综合考虑多个因素的过程。
我们应该根据产品的特点和要求,选择合适的模具尺寸、排列密度和方向,并考虑产品的结构、表面质量和生产流程的合理性。
只有这样,我们才能够提高生产效率,保证产品质量,实现模具排模的最佳效果。
- 1、下载文档前请自行甄别文档内容的完整性,平台不提供额外的编辑、内容补充、找答案等附加服务。
- 2、"仅部分预览"的文档,不可在线预览部分如存在完整性等问题,可反馈申请退款(可完整预览的文档不适用该条件!)。
- 3、如文档侵犯您的权益,请联系客服反馈,我们会尽快为您处理(人工客服工作时间:9:00-18:30)。
注塑模的排位设计
一、设计原则
1、力求平衡、对称。
①各型腔在相同温度下同时充模。
·采用平衡布局
·非平衡布局可通过调节浇口尺寸达到平衡
②浇口平衡
③大小制品对称布置
④模具力平衡,即注射压力中心与主流道中心重合,防止飞边。
2、流道尽可能短,以降低废料率、成型周期和热损失。
H型排位优于环形和对称型。
3、对高精度制品,型腔数目尽可能少。
因为每增加一个型腔,制品精度下降4%。
精密模具型腔数目一般不超过4个。
4、相同颜色、相同原料。
5、结构紧凑,节约钢材。
6、大近小远。
7、高度相近。
8、先大后小,见缝插针。
9、同一制品,大近小远。
10、工艺性好。
二、平面尺寸的确定
1、型腔到型芯边的距离a(20~25mm)
a = 0.2×l + 17
·对模芯边走冷却水的深腔模具或带侧抽芯的模具,a可适当增加。
2、型腔之间的距离b
b≧a/2 ,一般取12~20mm。
·对于特别小的制品,b可取3mm。
·型腔之间布置有流道时,b′可取25~30mm,一般取30mm。
3、模芯尺寸B0×L0
模芯尺寸= 制品尺寸+型腔到型芯边的距离+型腔之间的距离·模芯尺寸超过200×200时,必须做成拼块结构。
4、推算模架
①模具尺寸系列
②模架之成型范围
三、高度尺寸的确定
1、前模部分
①型腔背后模芯厚度h1,h1与冷却水孔的布置及制品的平面投影面积有关。
·无冷却水孔或制品较小时,h1取15~20mm。
·冷却水孔边到型腔的距离取1.5d,或取10~15 mm。
②A板开框背后厚度h3 = 25~35 mm
③前模芯厚度h2 = 制品厚度h+型腔背后模芯厚度h1
④A板厚度h4 =前模芯厚度h2+ A板开框背后厚度h3
2、后模部分
①后模芯厚度h6,主要起藏core作用,一般取20~35 mm。
②B板开框背后厚度h7,主要承受来自型腔的注射压力,可以查选标准托板厚度。
③B板厚度h8=后模芯厚度h6+ B板开框背后厚度h7。