高光亮挤出方案
影响高光黑色ABS树脂光泽度因素分析

影响高光黑色ABS树脂光泽度因素分析作者:***来源:《神州·下旬刊》2020年第01期摘要:ABS树脂(丙烯腈一丁二烯一苯乙烯共聚物)在目前市场上的产量较高,也是应用最为广泛的聚合物,具有着韧、硬等优良的力学性能,本文主要研究了橡胶的含量、色母种类、光泽度改善剂、成型条件等对ABS树脂光泽度的影响。
得出影响ABS树脂光泽度测试准确性的主要因素,通过实验结果的准确性和实验过程当中的变量因素进行对比分析,结果表明,橡胶含量、色母种类是决定ABS树脂光泽度的关键因素。
在同一个样件上不是同一处的光泽度也会存在着一定的差异,经过不断的尝试还会给测试的样品造成一定程度的磨损,最后降低了测量值。
关键词:丙烯腈一丁二烯一苯乙烯树脂;橡胶含量;色母;成型条件;光泽度ABS树脂是由丙烯腈、丁二烯以及苯乙烯这三个单体共同汇聚而成的,是五大合成树脂之一,具有抗冲击性、耐低温性以及耐化学药品性等优点,同时还具有易加工、表面光泽性良好的特点,更容易涂装和着色,同时它还是目前产量最大,应用最为广泛的聚合物。
而高光黑色丙烯腈一丁二烯一苯乙烯(ABS)树脂是一种黑色、表面光亮度高的ABS专用料产品,它也是没有毒的,本身的性质是稳定的,有一些塑料的添加剂当中是有毒的,在一定条件下会产生有毒物质,但是ABS树脂大部分都是环保的产品,对人体是没有影响,大多数应用于家用电器等产品当中,例如LED电视机外壳,边框、底座等表面光泽度高的电器设备,具有较高的抗冲击性能和机械强度,光泽度也是极高的。
光泽是材料反射光线的一种表现,一般光泽度较高的产品,它的致密性就越高,也更加的容易清洁,一个材料的光泽度不仅取决于材料的表面形状,还与材料的组成有关,对于高滚滚黑色ABS树脂来说,一般反射角和入射角的角度是20°,本文主要研究探讨了ABS橡胶含量、色母类型、润滑剂、光泽改善助剂、成型条件等对高光黑色ABS产品光泽度的影响。
1.实验部分1.1原材料实验主要采用表面光泽度较高的ABS专用料产品,有着光泽度高和易于加工的特点,同时还有ABS高胶粉、SAN树脂、黑字母以及相关的助剂。
双向拉伸聚酯薄膜BOPET综述

BOPET双向拉伸聚对苯二甲酸乙二酯(BOPET)薄膜最初是在20世纪50年代由英国ICI公司开发的。
经过几十年的发展,产品已由原来的单一绝缘膜发展到现在的电容器用膜、包装用膜、感光绝缘膜等;按厚度有从0. 5μm到250μm数十个规格;其生产工艺也从最简单的釜式间歇式生产发展到多次拉伸与同步双向拉伸,其产品形式也由平膜发展到多层共挤膜、强化膜及涂覆膜等。
1.生产工艺及改善聚酯薄膜已成为世界上发展最快的薄膜品种之一,目前国内主要采用两步法双向拉伸工艺生产[1]。
1.1 BOPET的生产工艺BOPET薄膜的生产工艺流程一般为: PET树脂干燥→挤出铸片→厚片的纵向拉伸→横向拉伸→收卷→分切包装→深加工。
1.1.1PET树脂的干燥PET树脂由于分子中含有极性基团,因此吸湿性较强,其饱和含湿量为0. 8%,而水分的存在使PET在加工时极易发生氧化降解,影响产品质量。
因此加工前必须将其含水量控制在0. 005%以下,这就要求对PET进行充分的干燥。
一般干燥方法有两种,即真空转鼓干燥和气流干燥。
其中前一种干燥方法较好,因为真空干燥时PET不与氧气接触,这有利于控制PET的高温热氧老化,提高产品质量。
PET的真空转鼓干燥条件如下:蒸气压力0. 3~0. 5MPa,真空度98. 66~101. 325 kPa,干燥时间8~12h。
1.1.2PET熔体挤出铸片将干燥好的PET树脂熔融挤出塑化后,再通过粗、细过滤器和静态混合器混合后,由计量泵输送至机头,然后经过急冷辊冷却成厚片待用。
挤出铸片的工艺条件为:挤出机输送段温度240~260℃,熔融塑化段温度265 ~285℃,均化段温度270 ~280℃,过滤器(网)温度280~285℃,熔体线温度270~275℃,铸片急冷辊温度18~25℃。
1.1.3PET厚片的双向拉伸薄膜的挤出双轴(向)拉伸是将从挤出机挤出的薄膜或片材在一定温度下,经纵、横方向拉伸,使分子链或待定的结晶面进行取向,然后在拉伸的情况下进行热定型处理。
高光亮面产品作业要求 项目明细
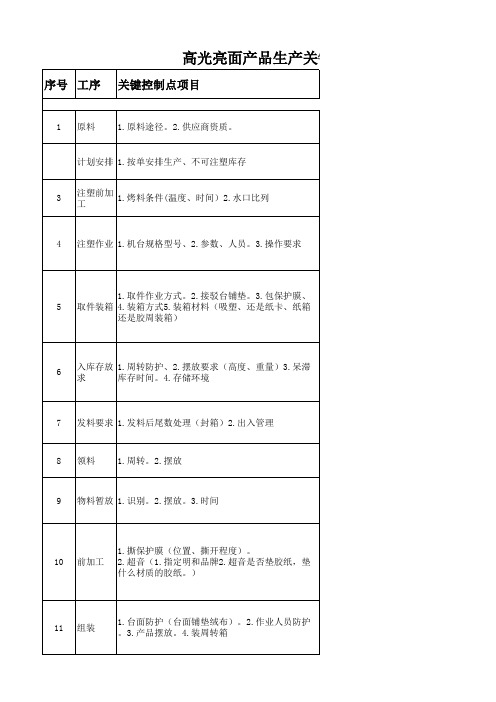
13
包装
14
装箱
1.高光亮外观产品设计装箱要求 2.装机格子间隔(距离产品多少毫米,不松也不 紧) 3.外箱标示设计 (注明:内装高光亮面产品注意 搬运防护)
生产关键控制点
确认执行标准 负责人
一:黑色指定沙伯原料(白色待确认) 二:供应商必须有代理、经销证明,证明其货源 林艳红 正规 一:按PO单,每单按规定备品下单生产。 一:PC料:120度4个小时。 二:不可添加水口 高洪志
6
入库存放 1.周转防护、2.摆放要求(高度、重量)3.呆滞 求 库存时间。4.存储环境
7
发料要求 1.发料后尾数处理(封箱)2.出入管理
8
领料
1.周转。2.摆放
9
物料暂放 1.识别。2.摆放。3.时间
10
前加工
1.撕保护膜(位置、撕开程度)。 2.超音(1.指定明和品牌2.超音是否垫胶纸,垫 什么材质的胶纸。)
高德兴
一:采购找供应商确认定制保护膜单价如可行打 样进行试产。 二:定制保护膜失败后改撕保护膜为撤掉(生产 高德兴 部进行试做) 王成 三:超音设备品牌指定:明和、是否铺垫胶纸及 品牌由工程确认11月30日回复) 一:定线增铺绒布对台面进行防护(先试行一条 线) 二:凡接触高光亮面 高德兴 外壳的均需要戴手指套,并不可佩戴首饰。 三:指定塑胶周转箱并在内璧增加PE袋进行防护
一:上下架防护:一个手拿一个产品循环进行作 业。二:装箱防护参考11点要求
高德兴
一:作业台面铺装绒布(先试行一条线), 二:测试一次一个手拿一个产品循环进行作业。 高德兴 三:凡接触产品带手指套。 一:设计装箱要求:一个格子装一个产品、必须 有单独保护膜、 二:设计刀卡格子能固定产品,不可出现左右严 陈焱 重晃动 。 三:暂不对高光亮面产品包装外箱进行标示
ABS 高光原理
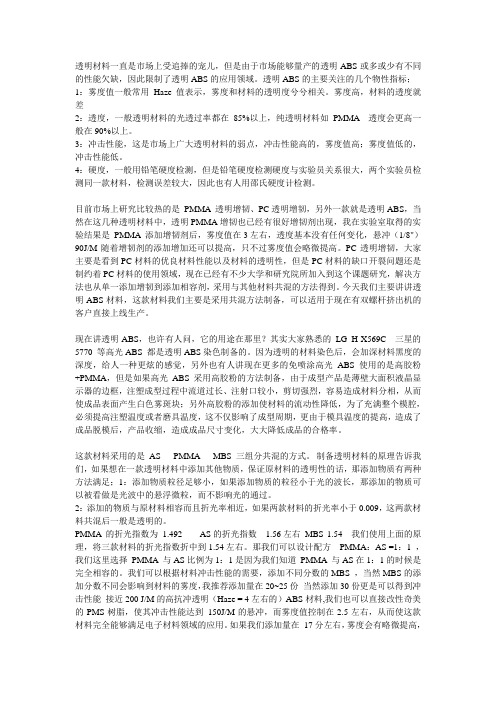
透明材料一直是市场上受追捧的宠儿,但是由于市场能够量产的透明ABS或多或少有不同的性能欠缺,因此限制了透明ABS的应用领域。
透明ABS的主要关注的几个物性指标;1:雾度值一般常用Haze 值表示,雾度和材料的透明度兮兮相关。
雾度高,材料的透度就差2:透度,一般透明材料的光透过率都在85%以上,纯透明材料如PMMA 透度会更高一般在90%以上。
3:冲击性能,这是市场上广大透明材料的弱点,冲击性能高的,雾度值高;雾度值低的,冲击性能低。
4:硬度,一般用铅笔硬度检测,但是铅笔硬度检测硬度与实验员关系很大,两个实验员检测同一款材料,检测误差较大,因此也有人用邵氏硬度计检测。
目前市场上研究比较热的是PMMA 透明增韧、PC透明增韧,另外一款就是透明ABS,当然在这几种透明材料中,透明PMMA增韧也已经有很好增韧剂出现,我在实验室取得的实验结果是PMMA 添加增韧剂后,雾度值在3左右,透度基本没有任何变化,悬冲(1/8")90J/M随着增韧剂的添加增加还可以提高,只不过雾度值会略微提高。
PC透明增韧,大家主要是看到PC材料的优良材料性能以及材料的透明性,但是PC材料的缺口开裂问题还是制约着PC材料的使用领域,现在已经有不少大学和研究院所加入到这个课题研究,解决方法也从单一添加增韧到添加相容剂,采用与其他材料共混的方法得到。
今天我们主要讲讲透明ABS材料,这款材料我们主要是采用共混方法制备,可以适用于现在有双螺杆挤出机的客户直接上线生产。
现在讲透明ABS,也许有人问,它的用途在那里?其实大家熟悉的LG H-X569C 三星的5770 等高光ABS 都是透明ABS染色制备的。
因为透明的材料染色后,会加深材料黑度的深度,给人一种更炫的感觉,另外也有人讲现在更多的免喷涂高光ABS使用的是高胶粉+PMMA,但是如果高光ABS采用高胶粉的方法制备,由于成型产品是薄壁大面积液晶显示器的边框,注塑成型过程中流道过长、注射口较小,剪切强烈,容易造成材料分相,从而使成品表面产生白色雾斑块;另外高胶粉的添加使材料的流动性降低,为了充满整个模腔,必须提高注塑温度或者磨具温度,这不仅影响了成型周期,更由于模具温度的提高,造成了成品脱模后,产品收缩,造成成品尺寸变化,大大降低成品的合格率。
PET膜

PET膜PET膜又名膜耐高温聚酯薄膜。
它具有优异的物理性能、化学性能及尺寸稳定性、透明性、可回收性,可广泛的应用于磁记录、感光材料、电子、电气绝缘、工业用膜、包装装饰等领域。
耐高温聚酯薄膜介绍耐高温聚酯薄膜型号:FBDW(单面哑黑)FBSW(双面哑黑)耐高温聚酯薄膜规格厚度宽度卷径卷芯内径38um~250um 500~1080mm 300mm~650mm 76mm(3〞)、152mm(6〞) 注:宽度规格可依据实际需求生产。
膜卷常规长度相当于25um的3000m或6000目录编辑本段随着特种功能薄膜的开发,聚酯薄膜新的用途也不断出现。
可以生产成手机液晶保护膜、液晶电视保护膜、手机按键、等。
PET薄膜是一种性能比较全面的包装薄膜。
其透明性好,有光泽;具有良好的气密性和保香性;防潮性中等,在低温下透湿率下降。
PET薄膜的机械性能优良,其强韧性是所有热塑性塑料中最好的,抗张强度和抗冲击强度比一般薄膜高得多;且挺力好,尺寸稳定,适于印刷、纸袋等二次加工。
PET薄膜还具有优良的耐热、耐寒性和良好的耐化学药品性和耐油性。
但其不耐强碱;易带静电,尚没有适当的防静电的方法,因此在包装粉状物品时应引起注意。
编辑本段种类(1)PET高光亮膜该薄膜除具有普通聚酯薄膜优良的物理机械性能外,还具有极好的光学性能,如透明度好、雾度低,光泽度高。
它主要用于高档真空镀铝产品,该薄膜镀铝后呈镜面,具有很好的包装装饰效果;它也可用于镭射激光防伪基膜等。
高光亮BOPET薄膜市场容量大,附加值高,经济效益明显。
(2)PET转移膜转移膜又称热转印膜,这种转移膜的特点是拉伸强度高,热稳定性好、热收缩率低,表面平整光洁、剥离性好,可多次反复使用。
它主要用做真空镀铝的载体,就是将PET膜置于真空镀铝机镀铝后,涂胶与纸复合,然后将PET膜剥离,铝分子层通过胶粘作用便转移到纸板表面上,形成所谓的镀铝卡纸。
镀铝卡纸的生产流程是:PET基膜→离型层→色层→镀铝层→涂胶层→转移到卡纸。
PVC管材挤出工艺流程

PVC 管材挤出工艺流程PVC 塑料是一种多组分塑料,根据不同的用途可加入不同添加剂,因组分不同,PVC 制品呈现不同的物理力学性能,针对不同场合应用。
而PVC 塑料管在塑料管中所占的比例较大。
PVC 管材分硬软两种,RPVC 管是将PVC 树脂与稳定剂、润滑剂等助剂混合,经造粒后挤出机成型制得,也可采用粉料一次挤出成型。
RPVC 管耐化学腐蚀性与绝缘性好,主要输送各种流体,以及用作电线套管等.RPVC 管易切割、焊接、粘接、加热可弯曲,因此安装使用非常方便。
SPVC 管是由PVC 树脂加入较大量增塑剂和一定量稳定剂,以及其他助剂,经造粒后挤出成型制造。
SPVC 管材具有优良的化学稳定性,卓越的电绝缘性和良好的柔软性和着色性,此种管常用来代替橡胶管,用以输送液体及腐蚀性介质,也用作电缆套管及电线绝缘管等.PVC 硬管1、原料选择及配方硬管生产中树脂应选用聚合度较低的SG—5 型树脂,聚合度愈高,其物理力学性能及耐热性愈好,但树脂流动性差,给加工带来一定困难,所以一般选用黏度为(1 。
7~1 。
8)×10-3Pa •s 的SG-5 型树脂为宜.硬管一般采用铅系稳定剂,其热稳定性好,常用三盐基性铅,但它本身润滑性较差,通常和润滑性好的铅、钡皂类并用.加工硬管,润滑剂的选择和使用很重要, 既要考虑内润滑降低分子间作用力,使熔体黏度下降有利成型,又要考虑外润滑,防止熔体与炽热的金属粘连,使制品表面光亮. 内润滑一般用金属皂类,外润滑用低熔点蜡.填充剂主要用碳酸钙和钡(重晶石粉),碳酸钙使管材表面性能好,钡可改善成型性,使管材易定型,两者可降低成本,但用量过多会影响管材性能,压力管和耐腐蚀管最好不加或少加填充剂。
2、工艺流程RPVC 管的成型使用SG-5 型PVC 树脂,并加入稳定剂、润滑剂、填充剂、颜料等,这些原料经适当的处理后按配方进行捏合,若挤管采用单螺杆挤出机,还应将捏合后的粉料造成粒,再挤出成型:若采用双螺杆挤出机,可直接用粉料成型,RPVC 管材工艺流程如下:生产流程原料+助剂配制→混合→输送上料→强制喂料→锥型双螺杆挤出机→挤出模具→定径套→喷淋真空定型箱→浸泡冷却水箱→油墨印字机→履带牵引机→抬刀切割机→管材堆放架→成品检测包装3 、PVC 管材生产线设备功能(1)原料混合:是将PVC 稳定剂、增塑剂、抗氧化剂等其它辅料,按比例、工艺先后加入高速混合机内,经物料与机械自摩擦使物料升温至设定工艺温度,然后经冷混机将物料降至40-50 度;这样就可以加入到挤出机的料斗。
说明书高光亮相纸140212
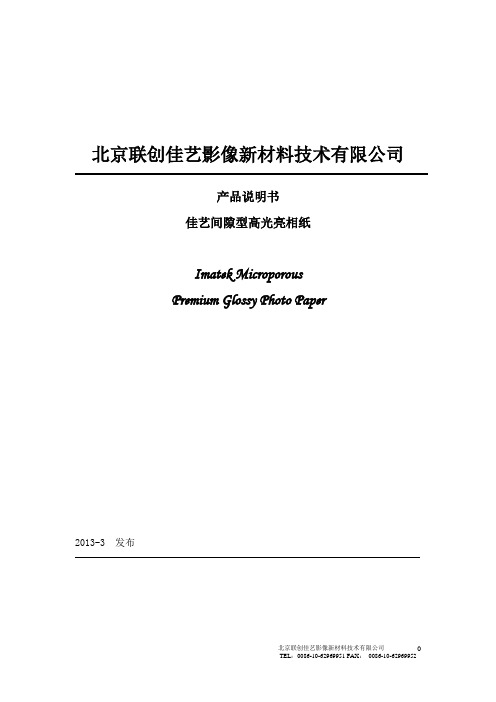
北京联创佳艺影像新材料技术有限公司产品说明书佳艺间隙型高光亮相纸Imatek MicroporousPremium Glossy Photo Paper2013-3 发布佳艺间隙型高光亮相纸Premium Glossy Photo Paper喷墨打印高光相纸从技术角度讲可分为三类结构:膨润型、铸涂型、间隙型结构,从开发的时间来看可分别称之为第一代、第二代、第三代相纸。
膨润型高光相纸(swelling photo paper)使用的双面淋膜相纸纸基(PE lamination),与传统银盐相纸的纸基相同。
其影像吸墨层主要由水溶性聚合物组成,当喷墨打印墨滴落在介质表面时,聚合物吸收水分产生膨胀,从而带来吸墨与防水的基本冲突。
因为具备吸水快速膨胀性能的聚合物必然防水性差,湿强度低。
而且,由于聚合物的膨胀速度有限,吸墨速度在六色压电式打印机上明显不足,图像存在严重的堆积弊病,清晰度很低。
膨润型相纸虽然生产成本低,但由于吸墨性能差,干燥慢,打印完需要覆膜处理,后期工序多,打印质量与传统相片相去甚远,只能作为普通广告类产品使用。
铸涂型高光相纸(cast coating photo paper)产品结构为原纸上以铸涂的加工方式加涂一层光泽固墨层,固墨层采用微米级的二氧化硅颗粒。
打印时依赖原纸纤维吸收印墨中的水分和助溶剂,染料则停留在固墨层内。
产品白度和光泽度高,画面具有较高色彩重现性和精细性。
由于采用微米级颗粒,打印画面与传统相片比,色密度和光泽仍有差距,影像质量有限。
由于纤维原纸吸墨,通常在打印高饱和度画面时由于墨量大存在一定程度变形褶皱,遇水时,相纸直接变形。
间隙型高光亮相纸(microporous photo paper)在双面淋膜相纸纸基涂布一层纳米级涂料,提供象卤化银相纸一样的厚度、挺度、平整度。
吸墨层中含大量纳米级的无机颗粒,颗粒是如此之小,乃至于它们小于可见光波波长的二分之一而变得透明,当入射光到达涂层表面时,大部分光线穿透涂层在RC面上发生镜面反射,因此间隙型高光亮相纸可以得到传统银盐相纸的光泽和平滑度。
TPE原料(颗粒)知识荟萃篇
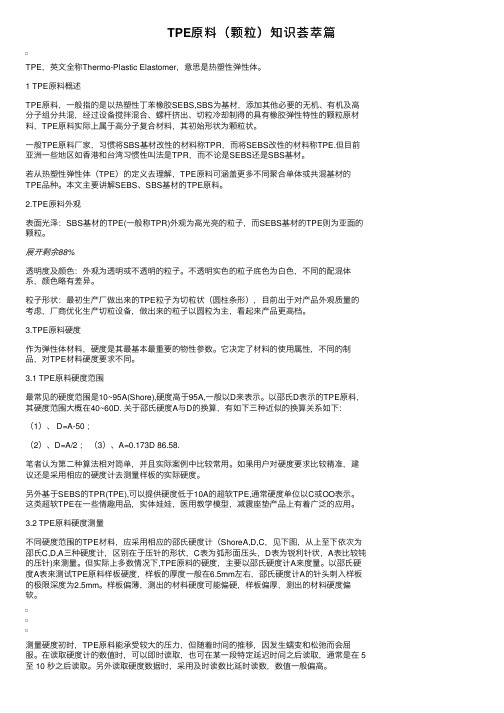
TPE原料(颗粒)知识荟萃篇TPE,英⽂全称Thermo-Plastic Elastomer,意思是热塑性弹性体。
1 TPE原料概述TPE原料,⼀般指的是以热塑性丁苯橡胶SEBS,SBS为基材,添加其他必要的⽆机、有机及⾼分⼦组分共混,经过设备搅拌混合、螺杆挤出、切粒冷却制得的具有橡胶弹性特性的颗粒原材料,TPE原料实际上属于⾼分⼦复合材料,其初始形状为颗粒状。
⼀般TPE原料⼚家,习惯将SBS基材改性的材料称TPR,⽽将SEBS改性的材料称TPE.但⽬前亚洲⼀些地区如⾹港和台湾习惯性叫法是TPR,⽽不论是SEBS还是SBS基材。
若从热塑性弹性体(TPE)的定义去理解,TPE原料可涵盖更多不同聚合单体或共混基材的TPE品种。
本⽂主要讲解SEBS、SBS基材的TPE原料。
2.TPE原料外观表⾯光泽:SBS基材的TPE(⼀般称TPR)外观为⾼光亮的粒⼦,⽽SEBS基材的TPE则为亚⾯的颗粒。
展开剩余88%透明度及颜⾊:外观为透明或不透明的粒⼦。
不透明实⾊的粒⼦底⾊为⽩⾊,不同的配混体系,颜⾊略有差异。
粒⼦形状:最初⽣产⼚做出来的TPE粒⼦为切粒状(圆柱条形),⽬前出于对产品外观质量的考虑,⼚商优化⽣产切粒设备,做出来的粒⼦以圆粒为主,看起来产品更⾼档。
3.TPE原料硬度作为弹性体材料,硬度是其最基本最重要的物性参数。
它决定了材料的使⽤属性,不同的制品,对TPE材料硬度要求不同。
3.1 TPE原料硬度范围最常见的硬度范围是10~95A(Shore),硬度⾼于95A,⼀般以D来表⽰。
以邵⽒D表⽰的TPE原料,其硬度范围⼤概在40~60D. 关于邵⽒硬度A与D的换算,有如下三种近似的换算关系如下:(1)、 D=A-50 ;(2)、D=A/2 ;(3)、A=0.173D 86.58.笔者认为第⼆种算法相对简单,并且实际案例中⽐较常⽤。
如果⽤户对硬度要求⽐较精准,建议还是采⽤相应的硬度计去测量样板的实际硬度。
另外基于SEBS的TPR(TPE),可以提供硬度低于10A的超软TPE,通常硬度单位以C或OO表⽰。
一种家用阻燃耐候高光ABS材料及其制备方法[发明专利]
![一种家用阻燃耐候高光ABS材料及其制备方法[发明专利]](https://img.taocdn.com/s3/m/4b267ce902020740be1e9be9.png)
专利名称:一种家用阻燃耐候高光ABS材料及其制备方法专利类型:发明专利
发明人:李益祖,范保林,黄浩,吴摞,邢纪普
申请号:CN201911288722.0
申请日:20191212
公开号:CN111500011A
公开日:
20200807
专利内容由知识产权出版社提供
摘要:本发明公开了一种家用阻燃耐候高光ABS材料及其制备方法,属于高分子材料技术领域。
所述材料由以下组分按质量份组成:ABS树脂40‑80份,溴系阻燃剂10‑30份,三氧化二锑10‑25份,黑色母0.3‑3份,抗氧剂0.1‑1份,润滑剂1‑5份,稳定剂1‑5份,光亮剂1‑5份,本发明通过选用合适的ABS原材料,从分子结构入手,优选高流动性原材料,采用溴系阻燃剂复配三氧化二锑,结合螺杆组合和挤出工艺进行优化配置,得到的材料阻燃性能优异、耐降解和黄变、光泽性好,机械强度佳和易于成型加工和着色,主要应用在家电中与电接触的外观材料领域,具有优异的性能。
申请人:重庆会通科技有限公司
地址:402560 重庆市铜梁区东城街道办事处金川大道116号
国籍:CN
代理机构:合肥天明专利事务所(普通合伙)
代理人:汪贵艳
更多信息请下载全文后查看。
挤出导光条生产工艺流程

挤出导光条生产工艺流程The production process of extrusion optical light guide strip involves several important steps. 挤出导光条生产过程涉及几个重要步骤。
It begins with the selection of high-quality raw materials such as PMMA or PC, which are then heated and melted before being extruded through a die to form the desired shape. 它始于选择优质的原材料,如聚甲基丙烯酸甲酯或聚碳酸酯,在加热熔化后通过模具挤出,形成所需的形状。
This process requires precise control of temperature and pressure to ensure the consistency and quality of the extruded light guide strips. 这一过程需要精确控制温度和压力,以确保挤出的导光条的一致性和质量。
Once the strips are formed, they undergo further processing such as cutting, polishing, and coating to achieve the final product. 一旦条形成,它们会经过进一步的加工,如切割、抛光和涂层,以达到最终产品。
In terms of the raw materials used in the production process, the selection of high-quality PMMA or PC is crucial to the performance and durability of the extruded light guide strips. 在生产过程中使用的原材料方面,选择优质的聚甲基丙烯酸甲酯或聚碳酸酯对挤出导光条的性能和耐用性至关重要。
注塑产品亮印解决方案

注塑产品亮印解决方案在当今的注塑产品市场上,产品的外观质量和标识对于产品的竞争力和市场占有率起着至关重要的作用。
而亮印技术作为一种常用的表面处理方法,可以有效提升注塑产品的外观质量和标识清晰度,从而满足市场需求。
本文将就注塑产品亮印解决方案进行探讨。
首先,亮印技术可以有效提升注塑产品的外观质量。
通过亮印技术,可以在产品表面形成一层均匀、光滑的印刷层,使产品外观更加美观、整洁。
同时,亮印技术还可以增加产品的光泽度,使产品看起来更加具有质感和高端感,提升产品的附加值和竞争力。
其次,亮印技术可以提升产品标识的清晰度和耐久性。
在注塑产品生产中,产品标识往往是非常重要的,它可以包含产品的型号、品牌、生产日期等信息,而这些信息对于产品的使用和售后维护都具有重要意义。
通过亮印技术,可以实现对产品标识的高清晰度印刷,使标识文字、图案清晰可辨,不易褪色和磨损,从而延长产品标识的使用寿命。
此外,亮印技术还可以实现对产品表面的定制处理。
不同的产品对于表面处理的要求可能有所不同,有些产品需要在表面进行特殊的处理,以增加产品的防水性、耐磨性或者防腐蚀性等。
而亮印技术可以根据产品的特性和需求,实现对产品表面的个性化定制处理,满足不同客户的需求。
总的来说,注塑产品亮印技术作为一种常用的表面处理方法,可以有效提升产品的外观质量和标识清晰度,满足市场需求,提升产品竞争力。
在实际生产中,企业可以根据产品的特性和需求,选择合适的亮印技术及材料,进行定制化的表面处理,从而实现产品的差异化定位和市场竞争优势。
在选择亮印技术时,企业需要考虑产品的材料、形状、尺寸等因素,以及产品的使用环境和需求,综合考虑选择合适的亮印技术和材料。
同时,企业还需要注意亮印工艺的操作规范和质量控制,确保产品表面处理的质量和稳定性。
通过科学合理的亮印技术选择和质量控制,可以为产品的外观质量和标识清晰度提升提供有力保障。
综上所述,注塑产品亮印技术具有重要的意义和应用前景,可以为产品的外观质量和标识清晰度提升提供有效解决方案,满足市场需求,提升产品竞争力。
【熔接痕】注塑工艺中如何更有效的优化熔接痕呢?

【熔接痕】注塑工艺中如何更有效的优化熔接痕呢?塑料熔料从浇口填充型腔时,由于浇口数量和产品结构的原因,熔料在型腔内部相遇时前沿部分已经冷却,使他们不能完全融合,便在汇合处产生线性凹槽,形成熔接痕。
一,通过模流分析优化熔接线。
下面产品为喷漆件改高光的应用,通过模流分析在原始模具上进行优化的方案。
二,通过注塑工艺条件进一步优化1.材料温度太低。
低温熔料的分流汇合性能较差,容易形成熔接痕。
如果塑件的内外表面在同一部位产生熔接细纹时,往往是由于料温太低引起的熔接不良。
对此,可适当提高料筒及喷嘴的温度。
一般情况下,塑件熔接痕处的强度较差,如果对模具中产生熔接痕的相应部位进行局部加热,提高成型件熔接部位的的局部温度,往往可以提高塑件熔接处的强度,减轻熔接痕的程度。
如果由于特殊需要,必须采用低温成型工艺时,可适当提高注射速度及注射压力,从而改善熔料的汇合性能。
也可在原料配方中适当增用少量润滑剂,提高熔料的流动性能。
也可以增大射嘴孔径或进胶口扩大,改善熔体的填充效率,消除或减小熔接痕。
2.模具缺陷。
应尽量采用分流少的浇口形式并合理选择浇口位置,尽量避免充模速率不一致及充模料流中断。
在可能的条件下,应选用一点进胶。
为了防止低温熔料注入模腔产生熔接痕,可在提高模具温度的同时,在模具内设制冷料穴。
也可以通过优化浇口位置,让熔接线的位置处于产品边缘,有利于解决熔接线。
3. 模具排气不良。
首先应检查模具排气孔是否被熔料的固化物或其它物体阻塞,浇口处有无异物。
如果阻塞物清除后仍出现炭化点,应在模具汇料点处增加排气孔,或适当降低合模力,增大排气间隙来加速汇料合流。
在工艺操作方面,也可采取降低料温及模具温度,缩短高压注射时间,降低注射压力等辅助措施。
可以同步增加镶件排气,如遇到排气比较困难,增加排气槽或排气镶块仍然解决不了,可以通过增加溢料包来解决排气,达到优化及消除熔接线的效果。
4. 脱模剂使用不当。
在注塑成型中,一般只在螺纹等不易脱模的部位才均匀地涂用少量脱模剂,原则上应尽量减少脱模剂的用量。
注塑产品亮印解决方案

注塑产品亮印解决方案
《注塑产品亮印解决方案》
注塑产品亮印是一种将文字、图案或标志印在塑料制品表面的工艺技术,常用于电子产品、家居用品、玩具等领域。
亮印产品的外观更加美观,能够提升产品的档次,增加产品的附加值。
然而,由于塑料制品表面不平整、易磨损等特点,亮印工艺面临着一些困难和挑战。
针对这些问题,我们提出了以下几种解决方案。
首先,选择合适的塑料材料非常重要。
在进行亮印工艺之前,需要对所用的塑料材料进行严格的筛选和测试。
选择表面平整度高、抗磨损性强的塑料材料,可以有效提高亮印效果的稳定性和持久性。
其次,合理设置亮印工艺参数。
在亮印产品时,应根据塑料材料的特性以及所需印刷效果,合理设置温度、压力、速度等工艺参数。
通过优化工艺参数,可以有效降低废品率,提高亮印产品的良品率。
另外,选用优质的印刷油墨和印刷设备也是确保亮印品质的关键。
优质的印刷油墨能够提供更好的附着力和耐磨性,而先进的印刷设备则能够提高印刷精度和稳定性。
此外,对于一些特殊形状的塑料制品,可以采用定制的印模或模具,以适应不规则表面的印刷需求。
同时,结合数码亮印、激光雕刻等现代化工艺技术,也可以进一步提高亮印产品的精
度和美观度。
总的来说,注塑产品亮印是一项技术含量高、管理难度大的工艺,但通过合理选择材料、优化工艺参数、选用高品质原材料和设备等措施,可以有效提高亮印产品的质量和稳定性。
随着科技的不断发展,相信注塑产品亮印技术将会不断完善和创新,为塑料制品的外观提升和附加值增加提供更多可能性。
注塑产品亮印解决方案
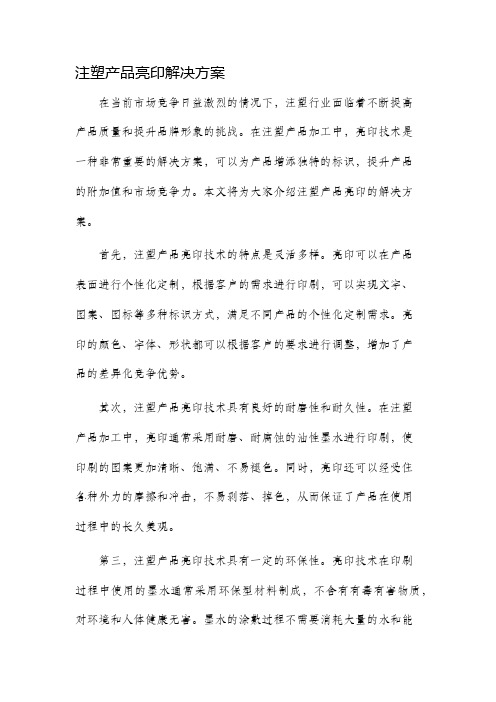
注塑产品亮印解决方案在当前市场竞争日益激烈的情况下,注塑行业面临着不断提高产品质量和提升品牌形象的挑战。
在注塑产品加工中,亮印技术是一种非常重要的解决方案,可以为产品增添独特的标识,提升产品的附加值和市场竞争力。
本文将为大家介绍注塑产品亮印的解决方案。
首先,注塑产品亮印技术的特点是灵活多样。
亮印可以在产品表面进行个性化定制,根据客户的需求进行印刷,可以实现文字、图案、图标等多种标识方式,满足不同产品的个性化定制需求。
亮印的颜色、字体、形状都可以根据客户的要求进行调整,增加了产品的差异化竞争优势。
其次,注塑产品亮印技术具有良好的耐磨性和耐久性。
在注塑产品加工中,亮印通常采用耐磨、耐腐蚀的油性墨水进行印刷,使印刷的图案更加清晰、饱满、不易褪色。
同时,亮印还可以经受住各种外力的摩擦和冲击,不易剥落、掉色,从而保证了产品在使用过程中的长久美观。
第三,注塑产品亮印技术具有一定的环保性。
亮印技术在印刷过程中使用的墨水通常采用环保型材料制成,不含有有毒有害物质,对环境和人体健康无害。
墨水的涂敷过程不需要消耗大量的水和能源,减少了对环境的污染。
同时,亮印的耐磨性和耐久性也大大减少了产品更换带来的资源浪费。
最后,注塑产品亮印技术的实施也需要一套完整的解决方案。
首先是选择合适的印刷设备和工艺。
在选择印刷设备时,应考虑生产规模、产品尺寸和印刷要求等因素,并确定合适的印刷工艺。
其次是选择合适的墨水和印刷材料。
墨水的选择应符合产品的特性和印刷要求,而印刷材料的选择则应考虑与产品的粘附性及外观效果等因素。
最后是制定适当的印刷工艺流程和质量控制标准,确保产品的印刷效果和质量稳定。
综上所述,注塑产品亮印解决方案是一种能够提升产品附加值和竞争力的重要技术。
亮印的灵活性、耐磨性和环保性使其成为注塑行业中不可或缺的一环。
然而,实施亮印技术也需要一套完整的解决方案和专业的团队来保证印刷效果和质量稳定。
在未来的发展中,随着技术的不断创新和完善,注塑产品亮印技术将为企业带来更多的机遇和挑战。
基于模流分析技术的高光双色塑件成型工艺研究

基于模流分析技术的高光双色塑件成型工艺研究潘建新;潘祎【摘要】借助MoldFlow Synergy分析软件,对某双色底壳塑件进行CAE模拟仿真,结合浇注系统的设计原则,确定了该塑件模具浇注系统参数:模具型腔采用l模2腔布置;第一次成型外层PMMA材料,采用点浇口选胶,浇口尺寸为1.3mm;第二次成型内层ABS材料,采用潜伏式点浇口进胶,浇口尺寸为1.81mm.同时,还通过成型窗口分析,得到了PMMA材料和ABS材料的最佳工艺参数范围:PMMA材料的最佳模具温度为100℃、熔体温度控制在300C~340℃、注射时间控制在0.2~1.1s;ABS材料的最佳模具温度为60℃、熔体温度控制在220~260℃、注射时间控制在0.1~1.2s.【期刊名称】《模具制造》【年(卷),期】2017(017)008【总页数】4页(P42-45)【关键词】模流分析;高光;双色;塑件;成型工艺【作者】潘建新;潘祎【作者单位】长沙职业技术学院机械与汽车工程分院湖南长沙410217;中南大学基础医学院湖南长沙410000【正文语种】中文【中图分类】TQ320.66Key words:moldflow analysis;high surface finish;double color;injection parts;molding processAutodesk MoldFlow Synergy是一款专业的模流分析软件,可以对塑件和模具进行深入分析,还可以对注射全过程进行模拟,包括填充、保压、冷却、翘曲、纤维取向、结构应力和收缩,以及气体辅助成型分析等,使模具设计师在设计阶段就能找出未来塑件可能出现的缺陷,提高一次试模的成功率,可在更高程度上进行模拟仿真,提高塑件和模具设计的质量,优化注射工艺。
本文借助此软件,对某公司电子塑件底壳双色塑件的关键成型工艺进行研究,使塑件具有更好的工艺性,并优化模具设计,提高塑件的质量,缩短开发周期,降低生产成本。
- 1、下载文档前请自行甄别文档内容的完整性,平台不提供额外的编辑、内容补充、找答案等附加服务。
- 2、"仅部分预览"的文档,不可在线预览部分如存在完整性等问题,可反馈申请退款(可完整预览的文档不适用该条件!)。
- 3、如文档侵犯您的权益,请联系客服反馈,我们会尽快为您处理(人工客服工作时间:9:00-18:30)。
6月15日高光亮方案分析
1,利用公司设计模具,模具代号为MJ06513~06523,模具结构为前方后圆。
2,方案:按照常规工艺参数设置温度,温度稳定后,记录对应加热温度系列的机头压力,保留切片。
分析:
1,瓷砖亮是因为表面有一层釉,该层的反光度很高。注塑件表面亮度高,应该是配方中的外润滑剂析出在制品表面固化的结果。在微观上讲,瓷砖表面的釉层其实也应该是一种外润滑剂,与挤出制品相比较,为什么相似的配方体系在表面光亮度方面有如此大的差别呢?关键问题应该在成型工艺的区别,不管是瓷砖还是注塑件都是静态成型,静态成型有利于析出的外润滑挤固化在制品表面,提高表面质量。
根据左表,如果将两个面积比相乘的话,乘积分别为0.64\0.69\0.75\0.64\0.8两个问题:
1:从最终的结果看,基本都差不多,但为什么会出现门扇压力比较低的现象呢,关键就在联结头出入口有个很明显的发散过程(比较的前提是尾锥的长度差不多)。
2:从最终制品的表面亮度来看也差不多,个人认为595~597主要的原因是机头压力的原因、而门扇的主要原因是定型模的真空吸附,因为大面宽度尺寸比较大,贴合比较紧密。
问题
1,只要对表面进行结皮,就会出现表面取向增强的问题,意味着尺寸变化率肯定会提高,怎么办?难道冷却温度不能低于玻璃化温度,不让它结皮,只让表面增加阻力,增加致密度
2,重新分析了上面所有的分析,得出这种结论:表面亮只是表面致密度增加,与分子取向无关。怎样增加亮度的过程就是怎样提高表面致密度的过程。如果这种想法正确的话,降低出口温度但同时不让结皮,应该可以提高表面亮度同时也不会提高尺寸变化率。另外一方面,如果压缩过程中不加以固定的话,压缩后是否会重新松弛,亮度没有改变呢?松弛的速率?是否忽略了外润滑在急冷中的作用。
40/80/120/160/200
检验项目
表面亮度
尺寸变化率
高光亮挤出方案
一:在型材表面用热风枪吹
时间
过程记录
现象
分析
设想
人员
备注
2006.3.10
在一根型材外观面上,用热风枪吹热,后用自来水冷却
1,表面的划痕很快消失,光滑度增加。
2,经检验,表面光亮度降低16,加热前为63,加热后为47
型材表面的光亮现象应该取决于两方面,第一,成型后的分子颗粒大小与分子之间的间隙。第二,分子间隙之间的填充物的饱满程度,这两种物质如果填充的很好的话,将会很好的将漫反射转化为镜面反射,大大提高型材的表面光亮度。
根据上面的分析,结合MJ05595~05597三套模具的调试状况(亮度很高,达到60以上)。认为应该从三方面考虑:
1,增加机头压力,让机头压力保证在300左右,这一点要通过更改口模设计来实现。
2,让型材表面快速冷却,在牵引以及真空吸附作用下,尽量让型材内部结构趋向一致。
3,让型材表面充分贴合定型模,要充分考虑真空设计与制品壁厚的关系,同时要考虑定型模之间真空损失对表面质量的影响。
II/I
分流板过流面积、含内筋III
III/II
595
3848
3833
1
2440
0.64
596
3848
4026
1.05
2688
0.66
597
3848
4240
1.1
2877
0.68
562
5026
47730.953195Fra bibliotek0.67
564
5026
6665
1.33
4000
0.6
另外一个现象:
MJ01201(60框),使用的是与MJ05595一样的料,但小面几乎没有光泽,机头压力280,因此怀疑是小面的真空贴附有问题(如果设计尺寸没有问题的话)。
分析:
1,上面三种情况说明冷却水的大小对表面成型质量的影响比较明显,第一种情况容易出现破裂,是因为表面结皮层太薄,强度不够;第二种情况有强度,但外层结皮后,内部出料变快,特别是中间部位,容易出现内鼓。前两种情况在冷却的同时还能保证胚料与冷却板的充分接触,所以表面质量很高。第三种情况因为完全在冷却板中成型,贴附能力变差,所以表面亮度最差。
2,压缩板不加热,调整模头压力,分析对表面质量的影响。通过调整温度,实现机头压力的调整(在结构上怎么实现)
3,是否可以先冷却,在成型后进行表面处理,消除表面应力
1,如果提高机头压力可以明显提高表面质量,可以考虑更改流道设计
2,分析机头压力的提高是否可以提高内筋的成型状态(甚至可能影响出料状态)
温度梯度
结论
1,这种方案可以提高表面亮度
2,因为今天采用的冷却介质是普通的冷却水,无法进行温度控制,因此尺寸变化率偏差比较大,还是应该采用油温冷却比较好,而且冷却温度应该接近玻璃化温度。
3,这种方案应该可以与木塑挤出、发泡挤出的冷却装置统一到一种标准结构。这种结构甚至可以考虑对气体的加热与冷却,方便内腔冷却以及弯曲校正。(有可能的话可以申请专利并加工成标准件)
4月15日讨论记要
参与人员:刘新、翟步荣、王强、高立林、陈猛
备注
议题:高光亮方案设计
内容:
4月14日调研发现以下几个现象:
1,所有瓷砖、注塑件表面亮度都很高。
2,冷挤出(在口模出口设计冷却水)的制品表面亮度都很高。
3,发泡制品与型材制品在配方上的区别就在于是否添加发泡剂,但成型方式不同,结果在表面反光度方面有很大区别。
开始认为,在型材表面用热风吹,应该会让析出物增加,将分子之间的间隙填充的更饱满,但事实证明这种想法是错误的,原因应该有几个方面:第一,析出物不够多,配方中析出物的出现应该从两方面考虑,高温与高压。在成型后的加热,只能提供其中一个条件。第二,没有及时冷却,造成型材表面出现氧化反应,造成表面光滑但发乌的现象,这种想象与切片相似,开始发出油光,但冷却下来后光亮度不高。第三,因为型材表面还残留成型过程中的应力,当重新加热后,表面应力释放,分子重新排布,原来受拉伸的分子链重新收缩,增加漫反射。
3:大面的划伤问题:主要原因:抛光、真空槽的宽度,倒角、特别是第一节定型模前面几道真空槽的影响。还有加工后的清理工作不够到位,经常有残渣出现。
4:模唇加热以及急冷块搭配使用可以将亮度提高,原因是,瞬间加热可以将物料表层形成熔融态,在入定型模中瞬间成型,保证了局部的分子状态。
5:定型模之间漏气现象比较严重,该部位型材与模具的帖附性不好,对表面亮度有影响。
3,实验需要记录的数据:冷却介质的压力与通过量、不同挤出状态对冷却介质的敏感程度。
2006.6.7日增加
根据木塑模具调试现状分析:
1,当冷却水很小时,表面结皮层很薄,表面亮但容易出现破裂。
2,当冷却水比较大时,表面结皮层比较厚,表面亮但中间部位容易鼓,亮度最亮。
3,当冷却水最大时,全部在冷却块中成型,成型可以但表面亮度不高。
刘新
从整个模头部分考虑,机头的压力降可以分成几个区域:联结头区域、分流板区域、压缩板区域、成型段区域,成型段长度通过制品要求壁厚控制(应该不能长于100)。压缩板往前部分部分,如果超出机器调节范围,应该通过调节压缩比进行控制。同时还应该考虑压缩比的调整对内筋供料腔的影响。
代号
连接头入口面积I
联结头出口面积11
2,与发泡制品或冷挤出比较,我们发现同样存在表面反光度差别很大的情况,原因是什么呢?在这些制品的成型过程中,在口模出口均设计有冷却介质存在,冷却板与熔融状态的挤出胚料接触,在保证高压的状态下有利于提高表面光亮度。
结论:
1,在口模出口设计冷却装置应该能明显提高制品的表面光亮度
2,该装置有可能带来的负面作用是:挤出压力增大,口模出料变化,甚至可能影响到制品的物理性能。
6月8日试验记录
项目
高光亮方案调试
备注
参与人员
刘新、陈猛
实验设备
CINCINNATI93
使用模具
MJ06465(门扇)
方案
在正常调试成型后,利用专门装置向模唇加热槽内加冷却介质进行急冷,观察机头压力,出料状态、出料表面亮度、成型后表面亮度、实验表面尺寸变化率的变化。
装置介绍
标准管接头一个,螺纹端用密封件堵平,中间插一根直径2mm的电极铜管
将口模出口面在不同的温度系列下面,检测切片表面亮度的改变情况。调整口模加热圈与加热板的温度参数,
2006.6.19高光亮项目方案讨论
项目
讨论高光亮方案
备注
参与人员
刘新、王强、高立林
方案
1,利用实验模具,用模具温度控制器对口模模唇加热槽用油进行温度控制,油温由低到高设定温度,对胚料表面进行温度调整,分析对表面质量的影响(模具温度控制器外借)。
3月28日会议记要
参与人员:刘新、王强、高立林、陈猛、李洪泗、于洪祥
备注
议题:高光亮方案设计
内容:
1:牵引时口模与定型模尽量靠近,让物料在定型模中膨胀;
2:高速状态下,第一节定型模的冷却能力要提高,大面可以采用缓冷结构;
3:整体上感觉我们现在的表面质量已经不错了,关键问题是表面亮度的均匀性不好。主要要解决口模的内筋供料问题,定型模的尺寸设计问题。
刘新
王强、韩敬华
1,问题有三个方面,怎么保证压力,怎样急冷,怎样保证贴附
2,了解析出物的析出原理
3,感觉我们的工作只是改良性质的,怎样才能有质的提高。
2006.3.11
MJ05595~597以及562、564几套模具进行对比,这几套模具成型后的表面光亮度都在50以上,但原因可能有所区别
MJ05595~597三套模具分别是60框、扇、梃,机头压力在310左右,定型模采用缓冷结构,MJ05562、564分别为70梃、门扇(5腔室),机头压力分别是310、260。