车间对标管理方案
车间开展全面对标管理实施细则

生产车间对标管理实施细则二014年十二月十五日全面对标管理实施细则为了贯彻落实发电公司[2008]110号关于开展全面对标管理的文件精神,转变车间职工和车间管理人员的思想观念,强化成本意识,提高经济运行水平,努力提高经营、管理水平,合理控制各种支出,车间根据车间实际,制定如下全面对标管理实施细则。
一、车间对标管理主要工作思路建立严密的组织制度、严格的量化目标为基础的激励制度,形成严格、经常而详细的成本控制报告,在输煤、除灰各环节各成本要素上,采取增效降耗、先进的技术和有效管理等措施,改善资本管理,运用最合理的运行方式,获取最大的运营效益。
具体工作思路如下:1、基础性对标,即建章建制对标。
讲解对标管理的定义及重要意义,要求车间职工都能够学习和领会对标管理的工作的重要性,努力按照车间对标管理的工作的目标进行实施,并且结合其它电力部门输煤及除灰系统,核查我车间已建立起来的各项制度和标准。
按照分工逐级落实责任。
2、各项指标对标车间拟定指标体系,要求各班组根据自身管辖或业务范围对车间拟定的指标逐一落实和考核,对有异议的指标可以提出,经过车间执行小组商榷后,进行修改。
㈠安全管理类指标表1㈣、燃运车间执行力指标1、严格贯彻、执行、传达上级文件精神。
2、定期召开车间各种工作会议,包括班前会、周安会、班长会、干部碰头会以及其它临时工作会议等。
并做好相关会议记录。
3、严格执行厂级、车间级各种规章制度。
4、严格执行厂级、车间级的其它规定。
二、全面对标管理燃运车间执行小组体系组长:副组长:成员:三、全面对标管理燃运车间执行小组职责㈠组长职责1、监督、管理、指导车间对标工作的日常运营,负责对标管理执行小组进行控制;2、确保车间对标管理活动规范化及其整个流程顺利推行;3、协调公司各部门之间的对标管理活动,减少或避免部门之间协调工作带来的资源浪费及无效劳动;4、排除对标活动中出现的各种阻力,保证对标管理活动及项目的正常运行;5、为对标管理活动及项目调配人力及各种资源。
车间对标管理方案

对标治理方案为确保标杆治理工作取得实效,进一步推动我车间对标治理工作的开展,建立涵盖生产全过程的对标指标体系,提高生产治理水平, 降低生产本钱,依据《“质量效益年”暨标杆治理〔2023-2023 年〕实施方案》要求,我车间打算开展对标治理工作,现提出实施方案如下:一、活动目标:以建设“令人敬重的创型国际能源化工企业”为目标,由少到多,由主及次,渐渐递进。
认真学习对标治理根本学问,以行业对标为主,辅以内部对标和竞争性对标。
在条件成熟时承受一般性对标。
首先,选择内部对标指标以设计值和历史最好水平作为对标基准;其次,将区域内炼油厂的平均和先进水平作为竞争对标基准;再次,以全国炼油厂先进水平为基准。
二、总体要求:比照先进、查错纠弊、持续改善、不断超越。
1、对标治理工作是标准化、精细化治理工作的深入推动,是推动标准提升的有效手段,要充分运用标准化载体来推动对标工作。
2、通过寻标、建标、对标、达标,找准存在的差距,分析缘由, 借鉴同行业同类型企业的成功阅历与做法,制定措施, 全面提醒与先进水平的差距和目标, 促进流程的标准和效率,找到流程的关键掌握节点,增加自我改善的压力和不断超越的动力,不断优化各项指标。
3、通过召开专题会议、沟通研讨等形式,进一步完善内部治理制度和考核方法,将责任落实到各个班组和岗位,实现层层有指标,人人有目标的对标链条,看到业务流程上、治理上的差距和薄弱环节,挖掘隐蔽在指标背后的本质原因,对存在问题进展分析争论,准时制定措施,解决存在的问题,使我车间指标不断得到提升。
定期检验工作成果,不断纠偏与总结,营造“我要对标”的良好气氛。
4、建立对标治理工作长效机制,认真总结对标治理的阅历,不断完善对标治理制度,特别是要完善鼓励约束机制,将对标治理融入预算、业绩、薪酬三位一体的考核机制。
三、对标指标现状及存在问题分析依据炼化公司及我厂统一安排,以同行业先进企业为标杆,制定目标,我车间选取的对标指标主要包括轻质油收率、炼油损失、检修周期及装置能耗四个方面内容。
车间对标实施方案
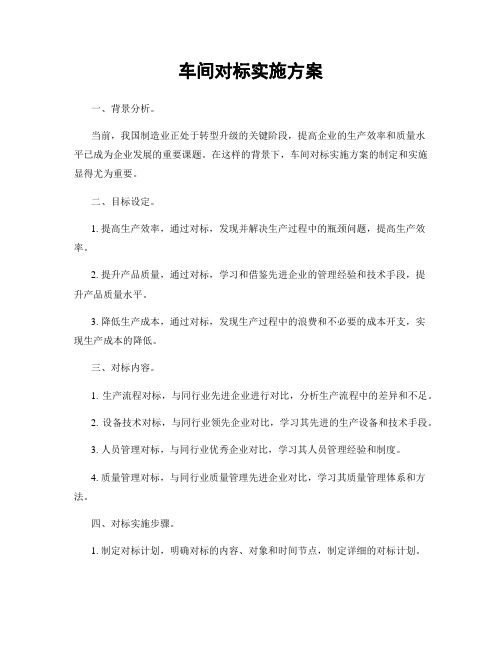
车间对标实施方案一、背景分析。
当前,我国制造业正处于转型升级的关键阶段,提高企业的生产效率和质量水平已成为企业发展的重要课题。
在这样的背景下,车间对标实施方案的制定和实施显得尤为重要。
二、目标设定。
1. 提高生产效率,通过对标,发现并解决生产过程中的瓶颈问题,提高生产效率。
2. 提升产品质量,通过对标,学习和借鉴先进企业的管理经验和技术手段,提升产品质量水平。
3. 降低生产成本,通过对标,发现生产过程中的浪费和不必要的成本开支,实现生产成本的降低。
三、对标内容。
1. 生产流程对标,与同行业先进企业进行对比,分析生产流程中的差异和不足。
2. 设备技术对标,与同行业领先企业对比,学习其先进的生产设备和技术手段。
3. 人员管理对标,与同行业优秀企业对比,学习其人员管理经验和制度。
4. 质量管理对标,与同行业质量管理先进企业对比,学习其质量管理体系和方法。
四、对标实施步骤。
1. 制定对标计划,明确对标的内容、对象和时间节点,制定详细的对标计划。
2. 数据收集与分析,收集相关数据,进行对比分析,找出存在的问题和改进空间。
3. 制定改进方案,根据对比分析的结果,制定具体的改进方案和措施。
4. 实施改进措施,组织实施改进措施,确保各项措施得以落实。
5. 持续跟踪和评估,建立持续改进的机制,对改进效果进行跟踪和评估。
五、对标实施方案的意义。
1. 促进企业发展,通过对标,引进先进的管理经验和技术手段,促进企业发展。
2. 提高企业竞争力,通过对标,提高生产效率和产品质量,提升企业在市场上的竞争力。
3. 降低生产成本,通过对标,降低生产成本,提高企业的盈利能力。
六、对标实施方案的保障措施。
1. 加强组织领导,建立对标工作领导小组,明确工作责任,加强对标工作的组织和领导。
2. 加强宣传和培训,通过宣传和培训,提高员工对对标工作的认识和参与度。
3. 建立激励机制,建立激励机制,鼓励员工积极参与对标工作,推动对标工作的顺利实施。
生产部对标管理工作计划

一、指导思想以提升公司生产管理水平、提高生产效率、降低生产成本、增强企业核心竞争力为目标,以“对标先进、追求卓越”为工作方针,全面开展生产部对标管理工作。
二、工作目标1. 通过对标管理,使生产部各项工作达到行业先进水平。
2. 提高生产效率,降低生产成本,实现经济效益最大化。
3. 提升生产部员工素质,培养一支高素质、高效率的员工队伍。
三、工作内容1. 对标选型(1)选取国内外同行业先进企业作为对标对象,包括生产工艺、设备、管理等方面。
(2)建立对标指标体系,涵盖生产效率、成本、质量、安全等方面。
2. 数据收集与分析(1)收集对标企业相关数据,包括生产效率、成本、质量、安全等。
(2)分析对标企业数据,找出差距和不足。
3. 对标改进(1)针对对标分析中发现的差距和不足,制定改进措施。
(2)优化生产流程,提高生产效率。
(3)加强设备管理,降低设备故障率。
(4)提高员工素质,培养一支高素质、高效率的员工队伍。
4. 持续改进(1)建立对标管理长效机制,定期开展对标活动。
(2)持续关注对标企业动态,及时调整对标策略。
(3)总结对标经验,推广先进做法。
四、工作步骤1. 第一阶段:准备阶段(1个月)(1)成立对标管理工作小组,明确工作职责。
(2)制定对标管理计划,明确工作目标、内容、步骤等。
(3)开展对标企业调研,确定对标对象。
2. 第二阶段:实施阶段(3个月)(1)收集对标企业数据,分析差距和不足。
(2)制定改进措施,优化生产流程。
(3)加强设备管理,降低设备故障率。
(4)提高员工素质,培养高素质员工队伍。
3. 第三阶段:总结阶段(1个月)(1)总结对标管理工作成果,评估改进效果。
(2)形成对标管理报告,提出改进建议。
(3)推广先进做法,提升公司整体管理水平。
五、保障措施1. 加强组织领导,明确工作职责,确保对标管理工作顺利开展。
2. 加大资金投入,为对标管理工作提供必要的物质保障。
3. 强化培训,提高员工对标管理的意识和能力。
车间对标管理工作计划

一、前言为了提升车间管理水平,提高产品质量,降低生产成本,增强企业竞争力,特制定本车间对标管理工作计划。
通过学习先进企业的管理经验,查找自身不足,持续改进,实现车间管理的全面提升。
二、工作目标1. 学习先进企业的管理经验,提高车间管理水平;2. 提升产品质量,降低生产成本,提高生产效率;3. 增强团队凝聚力,提高员工素质;4. 实现车间管理标准化、规范化、精细化。
三、工作内容1. 对标学习(1)选取行业领先企业作为对标对象,了解其先进的管理理念、管理模式、管理制度等;(2)组织车间管理人员、技术人员、生产骨干赴对标企业进行实地考察,学习其先进经验;(3)收集整理对标企业的相关资料,组织内部培训,提升员工对先进管理理念的认识。
2. 查找不足(1)针对车间管理、生产流程、产品质量等方面,进行全面梳理,查找自身不足;(2)组织员工开展自查自纠活动,对发现的问题进行汇总、分析;(3)邀请外部专家对车间进行诊断,查找潜在问题。
3. 持续改进(1)针对查找到的问题,制定整改措施,明确责任人和整改时限;(2)落实整改措施,确保问题得到有效解决;(3)建立长效机制,防止问题再次发生。
4. 优化生产流程(1)优化车间布局,提高生产效率;(2)优化生产设备,提高设备利用率;(3)优化生产计划,确保生产有序进行。
5. 提升产品质量(1)加强原材料采购管理,确保原材料质量;(2)加强生产过程控制,降低不良品率;(3)加强成品检验,确保产品质量。
6. 培训与激励(1)开展各类培训,提升员工技能和素质;(2)建立激励机制,激发员工积极性;(3)开展团队建设活动,增强团队凝聚力。
四、实施步骤1. 制定对标管理工作计划,明确工作目标、内容、步骤等;2. 组织对标学习,了解先进企业管理经验;3. 查找不足,制定整改措施;4. 落实整改措施,持续改进;5. 优化生产流程,提升产品质量;6. 培训与激励,提高员工素质。
五、预期效果通过实施本车间对标管理工作计划,预计在一年内实现以下效果:1. 车间管理水平显著提高;2. 产品质量得到有效提升,不良品率降低;3. 生产成本降低,生产效率提高;4. 员工素质和团队凝聚力得到增强。
车间岗位对标细则

车间岗位对标细则根据集团公司对标管理工作要求,结合车间对标管理实施方案,为进一步弥补班组成员之间技能存在的不足,缩小班组之间的管理水平,不断打牢班组安全生产基础,提高车间班组生产规范化管理水平,经研究决定以各班组表现突出的成员为标杆,开展班组岗位对标工作,使各岗位工作有标可照、以杆找差,实行一流班组管理模式,促进车间管理工作“上台阶、严制度、形规范”,将人员责任内化于心、外化于行,特制定本方案。
一、班组岗位管理“对标”小组为将工作落到实处,有效开展对标工作,实现各项工作闭环管理,成立车间班组岗位管理“对标”小组。
(一)小组成员组长:副组长:成员:(二)职责1、组长职责(1)负责本方案的审核、批准执行。
(2)负责对本方案的内容进行指导、督促。
(3)负责组织对本方案取得的效果进行评价,提炼过程取得的精髓进行固化。
2、副组长职责(1)负责对本方案的内容进行检查指导。
(2)具体负责对本方案取得的效果进行评价,实施过程取得的成果进行固化,形成制度、规范,并进行推广。
(3)负责检查监督成果推广的进度,对其不适应的规范制度进行修编、调整,保证制度规范执行具有针对性、唯一性、实际性。
(4)负责岗位对标工作的评审总结3、成员职责(1)负责组织本班组人员贯彻执行本方案内容,对本方案内容做到熟知,结合本班组实际形成工作规范。
(2)负责组织本班组人员积极参加本方案活动内容,融入班组管理、提炼班组文化。
(3)负责梳理本班组职责、基础管理、安全管理、生产技术管理、文明生产等方面存在的差距,对其进行调整、更新、宣讲、执行;对本班组较优秀的内容负责在全车间推广共享。
(4)负责对照标杆成员管理机制查找本班组存在的差距,制定整改措施,按PDCA流程形成闭环,创建一流班组。
(5)负责将本方案固化的内容在本班组执行,形成长效机制。
二、班组管理对标的基本原则和方法(一)创造条件、固化成绩。
车间创造条件增强班组成员间的学习和交流,通过班组互查、人员轮休到标杆班组跟班学习等活动形式,营造“比、学、赶、帮、超”的良好氛围;总结班组管理的典型经验,提炼最佳实践,有针对性地持续改进班组管理工作。
对标管理实施方案范本(四篇)

对标管理实施方案范本为进一步增强企业核心竞争力,提高企业综合发展水平,让企业向着更高的目标迈进。
经研究决定在____煤矿深入开展“精细管理对标年”活动,特制定本实施方案。
一、指导思想以____为指导,以公司“____”发展规划为目标,以做大做精做强企业为基础,以提升企业核心竞争力,获取最佳劳动效率和经济效益为主要任务,通过在不同企业之间,全面开展对标活动,寻找自身差距,制定和落实追赶先进的战略方案和措施,促使矿井各项指标进一步调整和优化,增强可持续发展能力,实现矿井各项指标的快速增长,跻身于国内同行业先进矿井之列。
二、奋斗目标通过收集近三年来国内外同行业先进煤炭企业的关键参数,建立较为完整的标杆指标体系。
比照标杆指标,分规模、分步骤地在全面开展对标活动,查找存在的差距,分析存在问题的原因,制定改进方案和措施,排出追赶、跨越的路线图和时间表。
通过一段时间的努力,使我矿各项指标逐步缩小与同行业先进企业的差距,各项指标能够逐步达到或接近同行业先进水平,以实现我矿整体经济规模和效益水平跨越式提升。
对标指标体系结合本单位实际情况,按照确定原则选定标杆单位,确定并建立对标指标体系,从而形成全矿从上到下多层面的对标指标体系网络,实现对事关企业发展的各类指标实施全面对标和提升,以实现企业全面快速发展。
2三、组织机构:对标管理领导小组:组长:李井坤、葛春谟副组长:张奇、郭绍坤、于刚、宋文官、刘金龙、马金良、赵明勇、张金华、张国新、丘其祥、李本学、王宪光成员。
巩军伟、冯广东、孙艳娟、南国军、、张国志、张雪光、范思祥、屈武等部门行政正职。
领导小组下设办公室,办公室设在企管办,办公室主任屈武(兼)。
对标活动领导小组主要负责对全矿开展对标活动把关定向,组织、指导各单位开展对标活动;负责组织审定矿井开展对标活动的实施方案、考评奖惩机制及评价结果;组织调度对标活动开展情况,平衡解决在对标活动中出现的重大问题等。
____矿对标活动领导小组办公室在对标活动领导小组领导下,主要负责对我矿开展对标活动情况的调度、督导、反馈、考评等日常业务,同时负责协助对标单位搜集对标指标、对标标准。
对标管理实施方案
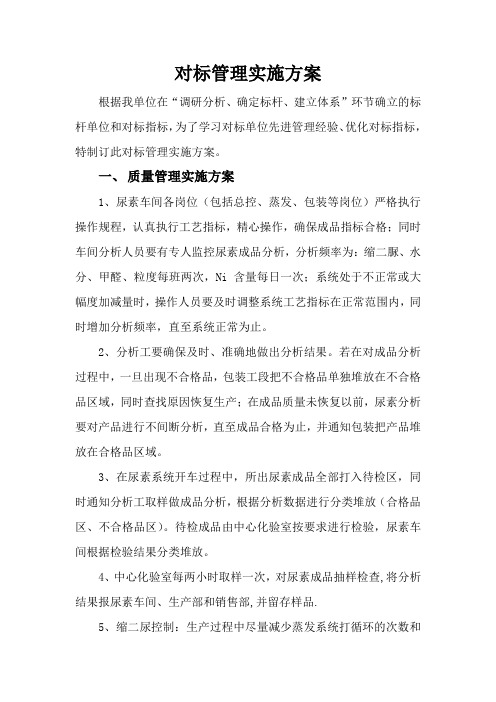
对标管理实施方案根据我单位在“调研分析、确定标杆、建立体系”环节确立的标杆单位和对标指标,为了学习对标单位先进管理经验、优化对标指标,特制订此对标管理实施方案。
一、质量管理实施方案1、尿素车间各岗位(包括总控、蒸发、包装等岗位)严格执行操作规程,认真执行工艺指标,精心操作,确保成品指标合格;同时车间分析人员要有专人监控尿素成品分析,分析频率为:缩二脲、水分、甲醛、粒度每班两次,Ni含量每日一次;系统处于不正常或大幅度加减量时,操作人员要及时调整系统工艺指标在正常范围内,同时增加分析频率,直至系统正常为止。
2、分析工要确保及时、准确地做出分析结果。
若在对成品分析过程中,一旦出现不合格品,包装工段把不合格品单独堆放在不合格品区域,同时查找原因恢复生产;在成品质量未恢复以前,尿素分析要对产品进行不间断分析,直至成品合格为止,并通知包装把产品堆放在合格品区域。
3、在尿素系统开车过程中,所出尿素成品全部打入待检区,同时通知分析工取样做成品分析,根据分析数据进行分类堆放(合格品区、不合格品区)。
待检成品由中心化验室按要求进行检验,尿素车间根据检验结果分类堆放。
4、中心化验室每两小时取样一次,对尿素成品抽样检查,将分析结果报尿素车间、生产部和销售部,并留存样品.5、缩二尿控制:生产过程中尽量减少蒸发系统打循环的次数和时间,避免尿液经两次蒸发浓缩后是缩二尿严重超标;保证系统在高符合下运行、尽量降低尿素系统各设备的液位,减少尿液在隔断停留时间。
6、水份控制:控制好一、二段蒸发压力,同时加强对蒸发系统的冲洗,减少系统真空度的波动;合理控制低压系统压力,减少低压系统对蒸发系统的影响。
7、结块控制:在一定负荷下对应一定的喷头转速,在符合变化是喷头转速应做小幅度的调整;定期对尿素造粒塔壁进行清理和冲洗;防止外部蒸汽和冷凝液进入尿液管线。
二、原料煤耗管理实施方案1、对进厂原料煤的不同层度、不同方位进行混合取样,取样不得少于5个方位点,根据采出的煤样,称出取样总重量,再将取样矸石捡出称出重量,用取样矸石重量除去取样总量,得出数据的百分比就是矸石所占的比例。
车间对标管理工作计划范文

一、背景与意义车间对标管理是一种有效的管理方法,通过与同行对比、学习和竞争,推动车间的管理水平不断提高,增强竞争力,提高产品质量和生产效率。
在当前激烈的市场竞争中,车间对标管理已成为企业提高核心竞争力的必要手段之一。
二、对标管理的基本概念对标管理是指企业通过对外部优秀企业的学习和借鉴,以及内部企业各部门之间的比较,逐步形成自己的管理标准,不断提高企业的管理水平。
车间对标管理是指在车间生产管理中,通过对比外部优秀企业或者内部其他车间的管理水平和经验,进行学习借鉴,不断提升车间的管理水平和效率。
三、车间对标管理的实施步骤(一)确定对标对象确定对标对象是对标管理的第一步。
可以选择外部同行企业或者内部其他车间作为对标对象。
对标外部同行企业可以通过市场调研和行业比较确定,对标内部其他车间可以由企业内部的管理部门或者生产部门协商确定。
(二)收集信息和数据收集对标对象的信息和数据是对标管理的关键步骤。
可以采集对标对象的管理模式、生产流程、质量管控、设备配置、人员组织等相关信息和数据,形成一份对标分析的基础资料。
(三)制定对标方案在收集到对标对象的信息和数据后,需要根据实际情况制定对标方案。
对标方案包括对标的重点、对标的内容、对标的时间安排、对标的目标等。
对标方案需要由企业内部的管理部门或者相关部门共同制定,并经过相关部门的审核同意。
(四)落实对标计划对标计划的落实是对标管理的核心环节。
在制定对标计划后,需要明确责任人和实施方案,对各项对标活动进行跟踪和监督,确保对标计划的有效执行。
(五)总结经验和改进措施对标活动结束后,需要对对标过程进行总结,总结经验和提出改进措施。
总结经验和提出改进措施可以根据实际情况,分析对标活动的成果和不足,提出改进意见和建议,为下一轮对标活动的开展提供参考。
(一)对标对象的确定首先确定对标的对象是外部同行企业,以一家同行业的知名企业A公司为对标对象。
(二)收集信息和数据可以通过市场调研和行业比较,了解A公司的管理模式、生产流程、质量管控、设备配置、人员组织等相关信息和数据。
车间对标学习计划
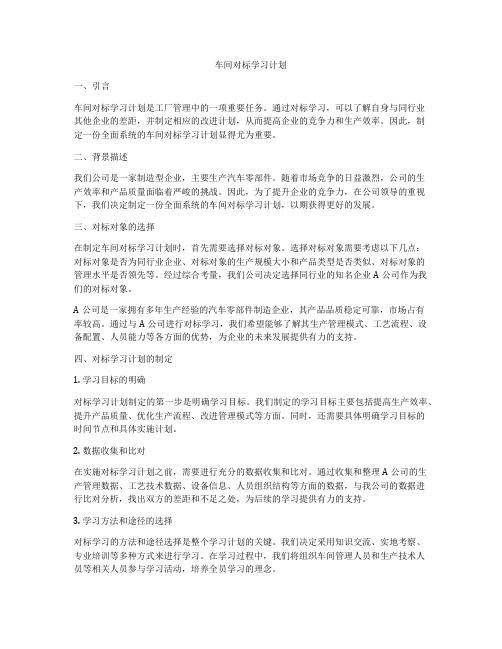
车间对标学习计划一、引言车间对标学习计划是工厂管理中的一项重要任务。
通过对标学习,可以了解自身与同行业其他企业的差距,并制定相应的改进计划,从而提高企业的竞争力和生产效率。
因此,制定一份全面系统的车间对标学习计划显得尤为重要。
二、背景描述我们公司是一家制造型企业,主要生产汽车零部件。
随着市场竞争的日益激烈,公司的生产效率和产品质量面临着严峻的挑战。
因此,为了提升企业的竞争力,在公司领导的重视下,我们决定制定一份全面系统的车间对标学习计划,以期获得更好的发展。
三、对标对象的选择在制定车间对标学习计划时,首先需要选择对标对象。
选择对标对象需要考虑以下几点:对标对象是否为同行业企业、对标对象的生产规模大小和产品类型是否类似、对标对象的管理水平是否领先等。
经过综合考量,我们公司决定选择同行业的知名企业A公司作为我们的对标对象。
A公司是一家拥有多年生产经验的汽车零部件制造企业,其产品品质稳定可靠,市场占有率较高。
通过与A公司进行对标学习,我们希望能够了解其生产管理模式、工艺流程、设备配置、人员能力等各方面的优势,为企业的未来发展提供有力的支持。
四、对标学习计划的制定1. 学习目标的明确对标学习计划制定的第一步是明确学习目标。
我们制定的学习目标主要包括提高生产效率、提升产品质量、优化生产流程、改进管理模式等方面。
同时,还需要具体明确学习目标的时间节点和具体实施计划。
2. 数据收集和比对在实施对标学习计划之前,需要进行充分的数据收集和比对。
通过收集和整理A公司的生产管理数据、工艺技术数据、设备信息、人员组织结构等方面的数据,与我公司的数据进行比对分析,找出双方的差距和不足之处,为后续的学习提供有力的支持。
3. 学习方法和途径的选择对标学习的方法和途径选择是整个学习计划的关键。
我们决定采用知识交流、实地考察、专业培训等多种方式来进行学习。
在学习过程中,我们将组织车间管理人员和生产技术人员等相关人员参与学习活动,培养全员学习的理念。
机物料对标管理实施方案

对标管理实行方案
按照企业管理提高活动旳统一布署及规定,我部对照企业有关制度,通过内部对标学习,在物资申领、仓储管理等方面对照兄弟单位旳原则,全面分析、找差距,现结合部门工作实际,制定出如下实行方案。
一、对标管理旳目旳
(一)物资申领方面,重点对采购物资质量、时效、成本管理等方面工作深挖各项指标,规范工作原则及流程,为现场生产提供物资保障。
(二)仓储管理方面,重点对物资仓库管理、收发料管理方面工作深挖各项指标,规范工作原则及流程,提高整体物资库存管理水平,为项目建设提供有力保障。
二、对标考核方案
三、对标管理旳实行时间与环节
(一)实行时间
2023年x月x日~2023年x月x日
(二)实行环节
1、实行操作。
(实行时间:x月x日~x月x日)按照确定旳对标指标开始实行对标管理。
2、评价反馈。
(实行时间:x月x日~x月x日)对实行操作旳状况进行检查,并对照指标值进行评估,反馈评估意见,深入查找差距,不停向新原则靠近,不停完善对标体系。
3、完善。
(实行时间:x月x日~x月x日)根据对标成果和对标评价状况深入完善制度,规范表单流程,初步形成标杆管理旳体系架构。
4、达标。
(实行时间:x月x日~x月x日)根据标杆管理体系,结合各项对标评价状况,持续改善,最终实现达标。
xxxx部
2023.xxxx。
车间对标管理工作计划范文
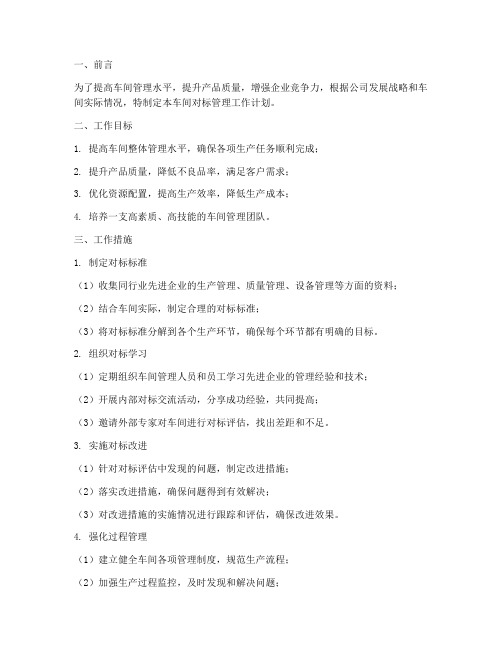
一、前言为了提高车间管理水平,提升产品质量,增强企业竞争力,根据公司发展战略和车间实际情况,特制定本车间对标管理工作计划。
二、工作目标1. 提高车间整体管理水平,确保各项生产任务顺利完成;2. 提升产品质量,降低不良品率,满足客户需求;3. 优化资源配置,提高生产效率,降低生产成本;4. 培养一支高素质、高技能的车间管理团队。
三、工作措施1. 制定对标标准(1)收集同行业先进企业的生产管理、质量管理、设备管理等方面的资料;(2)结合车间实际,制定合理的对标标准;(3)将对标标准分解到各个生产环节,确保每个环节都有明确的目标。
2. 组织对标学习(1)定期组织车间管理人员和员工学习先进企业的管理经验和技术;(2)开展内部对标交流活动,分享成功经验,共同提高;(3)邀请外部专家对车间进行对标评估,找出差距和不足。
3. 实施对标改进(1)针对对标评估中发现的问题,制定改进措施;(2)落实改进措施,确保问题得到有效解决;(3)对改进措施的实施情况进行跟踪和评估,确保改进效果。
4. 强化过程管理(1)建立健全车间各项管理制度,规范生产流程;(2)加强生产过程监控,及时发现和解决问题;(3)强化员工培训,提高员工操作技能和质量管理意识。
5. 落实绩效考核(1)建立车间绩效考核体系,将对标工作纳入考核范围;(2)定期对车间管理人员和员工进行绩效考核,奖优罚劣;(3)根据绩效考核结果,调整工作计划和资源配置。
四、工作步骤1. 第一阶段(1-3个月):制定对标标准,组织对标学习,开展内部对标评估;2. 第二阶段(4-6个月):实施对标改进,强化过程管理,落实绩效考核;3. 第三阶段(7-9个月):总结对标工作经验,完善对标管理体系;4. 第四阶段(10-12个月):巩固对标成果,持续推进车间对标管理工作。
五、保障措施1. 加强组织领导,明确责任分工,确保对标工作顺利推进;2. 加大资金投入,为对标工作提供必要的硬件和软件支持;3. 强化宣传引导,提高员工对对标工作的认识和支持;4. 定期召开对标工作总结会议,及时总结经验,发现问题,调整工作计划。
检修班对标管理实施方案

检修班对标管理实施方案一、背景随着现代化工业生产的不断发展,设备的维修和检修工作变得越来越重要。
而检修班对标管理作为一种有效的管理手段,能够提高设备的可靠性和稳定性,降低维修成本,提高生产效率,受到了越来越多企业的重视和应用。
二、目的本方案的目的在于建立一套科学、规范的检修班对标管理体系,以提高设备的可靠性和稳定性,降低维修成本,提高生产效率。
三、实施步骤1. 制定检修班对标管理制度首先,需要制定一套完善的检修班对标管理制度,明确各项工作的责任人员、工作流程、工作标准、工作要求等内容,确保制度的科学性和可操作性。
2. 设立检修班对标管理团队在各生产车间设立专门的检修班对标管理团队,负责具体的对标管理工作,包括设备的定期检修、维护、故障排除等工作。
3. 建立设备档案和对标管理台账建立完善的设备档案和对标管理台账,记录设备的基本信息、使用情况、维修记录等内容,为对标管理提供数据支持。
4. 开展对标管理培训对检修班的相关人员进行对标管理培训,提高他们的对标管理意识和操作能力,确保对标管理工作的顺利开展。
5. 定期进行对标管理检查和评估定期对设备的对标管理工作进行检查和评估,发现问题及时整改,确保对标管理工作的有效性和持续性。
四、实施效果通过对标管理实施方案的落实,将会取得以下效果:1. 设备的可靠性和稳定性得到提高,减少了设备的故障率和停机时间,提高了生产效率。
2. 维修成本得到降低,节约了企业的维修成本支出。
3. 对标管理团队的建立和培训,提高了检修班的管理水平和技术水平。
4. 设备档案和对标管理台账的建立,为对标管理提供了数据支持,提高了管理的科学性和规范性。
五、总结检修班对标管理实施方案的落实,对于提高设备的可靠性和稳定性,降低维修成本,提高生产效率具有重要的意义。
希望各相关部门和人员能够认真贯彻落实本方案,确保对标管理工作的有效开展,为企业的可持续发展做出贡献。
XX车间对标排序管理考核分配办法

XX车间对标排序管理考核分配办法为深入贯彻落实公司对标排序管理工作,进一步调动车间员工工作积极性、主动性和创造性,构建你争我赶、不甘落后的竞争氛围,全面提升车间各项管理水平,特制定本办法。
1.管理考核分配小组为保证对标排序管理的考核准确、分配公平,车间成立对标排序管理考核分配小组:小组组长:车间主任小组副组长:车间副主任小组成员:核算员、安全员、企业文化管理员、设备管理员、材料员、创新管理员、班组建设管理员、班长对标排序管理考核分配小组主要负责车间内各项对标排序项目、指标的监督检查指导,对标排序奖罚分配,保证车间对标排序项目的名次、指标的达标。
小组组长:全面负责车间对标排序工作的管理,监督检查指导车间对标排序项目实施、各项指标的完成,对车间对标排序工作负总责。
小组副组长:协助组长管理车间对标排序工作,监督检查指导车间对标排序项目实施、各项指标的完成,对车间对标排序工作负有管理责任。
小组成员:各成员具体负责自己所管理项目的对标检查、接收上级考核、奖罚分配工作。
对所负责项目的对标排序结果负主要责任。
班长:负责协助小组成员对标项目的具体实施工作,对对标项目的实施负有配合、执行责任。
2.奖罚分配2.1 内部市场化工作内部市场化工作对标排序考核中受到公司奖励(处罚),按下表分配系数进行奖励(处罚):2.2 四型班组建设四型班组建设对标排序考核中受到公司奖励(处罚),按四型班组建设奖励班组的班组建设管理员奖罚系数进行奖励(处罚)。
2.3 企业文化工作企业文化工作对标排序考核中受到公司奖励(处罚),按下表分配系数进行奖励(处罚):2.4 物资出库管理物资出库管理对标排序考核中受到公司奖励(处罚),按下表分配系数进行奖励(处罚):2.5 物资需求计划管理物资需求计划管理对标排序考核中受到公司奖励(处罚),按下表分配系数进行奖励(处罚):2.6 机电设备管理机电设备管理对标排序考核中受到公司奖励(处罚),按下表分配系数进行奖励(处罚):2.6 双创工作双创工作对标排序考核中受到公司奖励(处罚),按下表分配系数进行奖励(处罚):3.其他要求3.1 各项目管理人员要充分认识公司开展对标排序管理的积极意义,进一步增强自身责任意识,努力规范、完善所负责项目的各项指标、执行材料,确保所负责对标排序项目多奖少罚。
成品车间对标管理方案
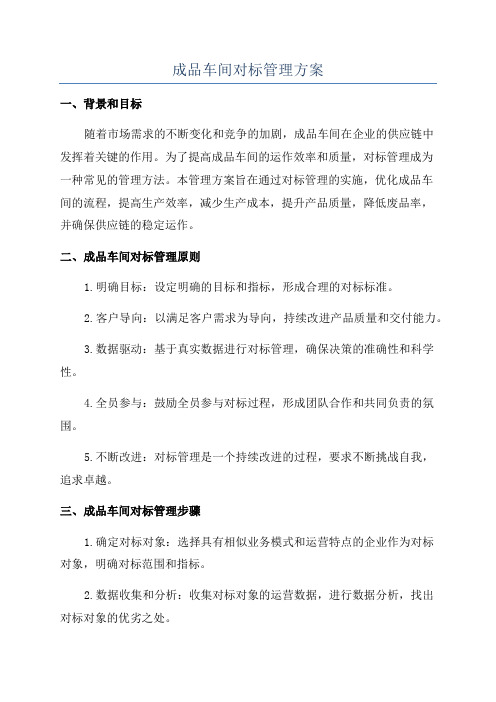
成品车间对标管理方案一、背景和目标随着市场需求的不断变化和竞争的加剧,成品车间在企业的供应链中发挥着关键的作用。
为了提高成品车间的运作效率和质量,对标管理成为一种常见的管理方法。
本管理方案旨在通过对标管理的实施,优化成品车间的流程,提高生产效率,减少生产成本,提升产品质量,降低废品率,并确保供应链的稳定运作。
二、成品车间对标管理原则1.明确目标:设定明确的目标和指标,形成合理的对标标准。
2.客户导向:以满足客户需求为导向,持续改进产品质量和交付能力。
3.数据驱动:基于真实数据进行对标管理,确保决策的准确性和科学性。
4.全员参与:鼓励全员参与对标过程,形成团队合作和共同负责的氛围。
5.不断改进:对标管理是一个持续改进的过程,要求不断挑战自我,追求卓越。
三、成品车间对标管理步骤1.确定对标对象:选择具有相似业务模式和运营特点的企业作为对标对象,明确对标范围和指标。
2.数据收集和分析:收集对标对象的运营数据,进行数据分析,找出对标对象的优劣之处。
3.制定对标计划:根据数据分析结果,制定对标计划,明确改进目标、时间表和责任人。
4.改进实施:执行对标计划,采取适当的改进措施,如优化流程、提高设备利用率、培训提升员工技能等。
5.监控和评估:定期监控改进效果,根据对标指标对成品车间进行评估,及时调整改进措施。
6.知识分享和学习:通过与对标对象的交流和学习,将优秀经验和做法借鉴到成品车间的管理和运作中。
四、关键指标1.生产效率:包括产量、生产周期、设备利用率等指标,着重优化生产流程和设备利用效率,提高生产效率。
2.产品质量:包括合格品率、不良品率、客户投诉率等指标,通过优化质量控制过程和培训提升员工质量意识,提高产品质量。
3.交付能力:包括按时交付率、交货准确率等指标,通过优化生产计划和物流管理,提高交付能力。
4.成本控制:包括人力成本、物料成本、能源成本等指标,通过优化生产过程、降低废品率和能源消耗,实现成本控制和降低。
维修二车间“安全对标管理年”实施方案【精选文档】
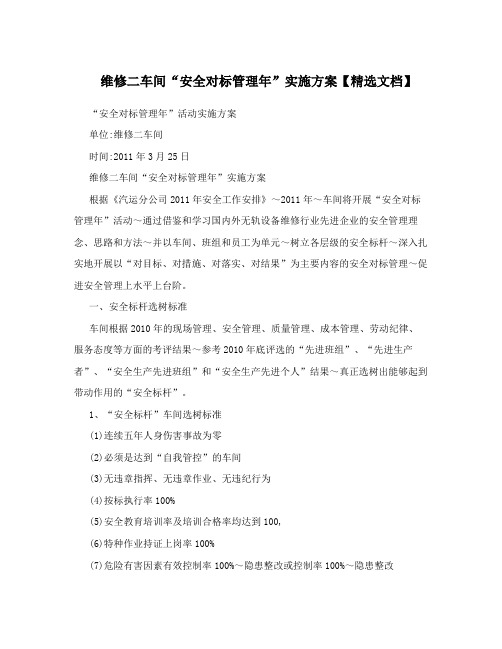
维修二车间“安全对标管理年”实施方案【精选文档】“安全对标管理年”活动实施方案单位:维修二车间时间:2011年3月25日维修二车间“安全对标管理年”实施方案根据《汽运分公司2011年安全工作安排》~2011年~车间将开展“安全对标管理年”活动~通过借鉴和学习国内外无轨设备维修行业先进企业的安全管理理念、思路和方法~并以车间、班组和员工为单元~树立各层级的安全标杆~深入扎实地开展以“对目标、对措施、对落实、对结果”为主要内容的安全对标管理~促进安全管理上水平上台阶。
一、安全标杆选树标准车间根据2010年的现场管理、安全管理、质量管理、成本管理、劳动纪律、服务态度等方面的考评结果~参考2010年底评选的“先进班组”、“先进生产者”、“安全生产先进班组”和“安全生产先进个人”结果~真正选树出能够起到带动作用的“安全标杆”。
1、“安全标杆”车间选树标准(1)连续五年人身伤害事故为零(2)必须是达到“自我管控”的车间(3)无违章指挥、无违章作业、无违纪行为(4)按标执行率100%(5)安全教育培训率及培训合格率均达到100,(6)特种作业持证上岗率100%(7)危险有害因素有效控制率100%~隐患整改或控制率100%~隐患整改核销率100%2、“安全标杆”班组选树标准(1)连续五年人身伤害事故为零(2)必须是“安全标准化班组”(3)无违章指挥、无违章作业、无违纪行为(4)按标执行率100%2(5)安全会组织率100%(6)安全教育培训率及培训合格率均达到100,(7)特种作业持证上岗率100%(8)危险有害因素有效控制率100%~隐患整改或控制率100%~隐患整改核销率100%3、“安全标杆”个人评选标准:(1)安全操作规程掌握100%(2)按规定正确穿戴劳保用品~持证上岗率100%(3)检修安全措施落实率100%(4)作业前安全确认制执行率100%(5)隐患排查执行率、隐患整改100%(6)安全教育培训率及培训合格率均达到100,(7)无违章、违纪行为(8)无安全事故二、活动步骤:,一,现状分析,3月1日—3月31日,车间组织职能人员对车间的安全管理现状、关键作业流程和主要危险有害因素进行深入分析~找出安全管理方面的关键流程节点和关键活动~分析安全管理中存在的主要问题和改进需求。
- 1、下载文档前请自行甄别文档内容的完整性,平台不提供额外的编辑、内容补充、找答案等附加服务。
- 2、"仅部分预览"的文档,不可在线预览部分如存在完整性等问题,可反馈申请退款(可完整预览的文档不适用该条件!)。
- 3、如文档侵犯您的权益,请联系客服反馈,我们会尽快为您处理(人工客服工作时间:9:00-18:30)。
对标管理方案
为确保标杆管理工作取得实效,进一步推进我车间对标管理工作的开展,建立涵盖生产全过程的对标指标体系,提高生产管理水平, 降低生产成本,根据《“质量效益年”暨标杆管理(2012-2015年)实施方案》要求,我车间决定开展对标管理工作,现提出实施方案如下:
一、活动目标:以建设“令人尊敬的创新型国际能源化工企业”为目标,由少到多,由主及次,逐渐递进。
认真学习对标管理基本知识,以行业对标为主,辅以内部对标和竞争性对标。
在条件成熟时采用一般性对标。
首先,选择内部对标指标以设计值和历史最好水平作为对标基准;其次,将区域内炼油厂的平均和先进水平作为竞争对标基准;再次,以全国炼油厂先进水平为基准。
二、总体要求:对照先进、查错纠弊、持续改善、不断超越。
1、对标管理工作是标准化、精细化管理工作的深入推进,是推动标准提升的有效手段,要充分运用标准化载体来推动对标工作。
2、通过寻标、建标、对标、达标,找准存在的差距,分析原因, 借鉴同行业同类型企业的成功经验与做法,制定措施, 全面揭示与先进水平的差距和目标, 促进流程的规范
和效率,找到流程的关键控制节点,增强自我改善的压力和不断超越的动力,不断优化各项指标。
3、通过召开专题会议、交流研讨等形式,进一步完善内部管理制度和考核办法,将责任落实到各个班组和岗位,实现层层有指标,人人有目标的对标链条,看到业务流程上、管理上的差距和薄弱环节,挖掘隐藏在指标背后的本质原因,对存在问题进行分析研究,及时制定措施,解决存在的问题,使我车间指标不断得到提升。
定期检验工作成果,不断纠偏与总结,营造“我要对标”的良好氛围。
4、建立对标管理工作长效机制,认真总结对标管理的经验,不断完善对标管理制度,特别是要完善激励约束机制,将对标管理融入预算、业绩、薪酬三位一体的考核机制。
三、对标指标现状及存在问题分析
根据炼化公司及我厂统一安排,以同行业先进企业为标杆,制定目标,我车间选取的对标指标主要包括轻质油收率、炼油损失、检修周期及装置能耗四个方面内容。
1 、轻质油收率
(1)现状分析
2009年、2010年及2011年轻质油年平均收率分别为46.86%、46.03%、46.71%虽然收率保持平稳趋势,2012年由于生产方案发生变化,最高生产0#柴油,故轻质油收率定为46%,距离46.20%还有一定差距。
(2)存在问题分析
①原油性质的变化影响轻质油收率的提高。
现阶段随着原油日益短缺,性质日益恶化,轻质油收率也逐渐下降,主要表现在原油密度增大(由原先0.810kg/m3左右增大到现阶段0.850 kg/m3左右)及含水率(现阶段原油含水率基本在1%以上)的增大。
②生产方案制约轻质油收率的提高。
由于柴油中硫含量高,一直降不下来,最高生产0#柴油,与生产+5#柴油相比,收率能下降1~2个百分点。
③车间努力实现“两年一修”或“三年一修”,这样检修周期长,塔内浮渣沉积多、结垢严重,不利于轻质油收率的提高。
④计量仪表影响轻质油收率。
统计做报表计算轻质油收率时,与车间质量流量计相比,每月石脑油大约减300来吨,柴油减几十到100来吨,而原油却增加几千吨,这样就使得轻质油收率有所下降,大约下降0.3个百分点。
2、炼油损失
(1)现状分析
2009年、2010年及2011年损失年平均率分别为0.70%、0.86%、0.98%,成逐渐上升趋势,距离0.70%还有一定困难
(2)存在问题分析
①原油性质的变化影响损失率的降低。
现阶段由于原油
性质日益恶化,含水率逐渐增大,故炼油损失也有所提高。
②计量仪表影响损失率的降低。
统计做报表时,与车间质量流量计相比,每月石脑油大约减300来吨,柴油减几十到100来吨,而原油却增加几千吨,这样就使得炼油损失率有所提高。
3、检修周期
(1)现状分析
2003年至2011年,我车间装置一直保持一年一修的状态,历史运行天数最长为384天(2009年-2010年),2011年5月23日开工至今已运行507天,按照现状可以完成目标值690天。
(2)存在问题分析
①部分管线腐蚀减薄严重。
其中拔头油四路进口管线最薄处4.6mm(原厚7.1mm),E-101、E-102至空冷油气管线最薄处为8.7mm(原厚19mm),二级电脱盐罐原油进口管线最薄4.8mm(原厚7.1mm)。
②部分塔盘腐蚀减薄严重。
自2003年开车至今,只对分馏塔塔内1至7层塔盘进行过更换,其他塔盘均未更换过(原计划于2012年大修对塔盘进行更换,但是由于装置长周期运行,未能实施),最薄处为1.6mm(原厚4.0mm)。
③部分机泵不能满足生产需要。
电脱盐注水泵P-114/AB 电机长期发热,超负荷运行,需更换大功率电机;常顶脱水
泵P-112/AB扬程偏低,无法满足生产需要,需更换大扬程泵。
④部分设备本体与管线连接处焊缝发生泄漏。
巡回检查时不易发现,发现后在线堵漏难度大。
⑤操作工对装置存在的薄弱环节重视程度不够,巡回检查不到位,缓解薄弱环节操作有待进一步提高。
4、装置能耗
(1)现状分析
2009年、2010年及2011年能耗平均分别为9.09 kg标油/吨、9.94 kg标油/吨和8.74 kg标油/吨,虽然能耗呈下降趋势,但是由于原油加工量等不稳定因素存在,距离目标值9.5 kg标油/吨还需继续努力。
(2)存在问题分析
①原油加工量(5200t/d)一直处于低负荷状况,但是各类能源消耗却变化不大,导致能耗增大。
②车间努力实现“两年一修”或“三年一修”,这样检修周期长,容易出现一些突发情况影响装置平稳运行,导致能耗上升。
③燃料油消耗计量一直不准确(能耗计算时常估算或者不算),虽然对燃料油计量仪表进行过一次更换,但是计量还存在误差。
④目前车间低压瓦斯完全进入加热炉燃烧(低压瓦斯不
作为能源消耗)。
2013年投用压缩机后低压瓦斯将不再进入加热炉,务必会大大增加燃料油、气的消耗,进一步加大能源消耗。
四、分解落实情况
我车间按照“质量效益年”暨标杆管理(2012-2015年)实施方案的要求,根据车间自身实际情况,制定出现阶段车间轻质油收率的对标指标为46.17%,下一阶段的对标指标为46.20%;炼油损失现阶段的对标指标为0.80%,下一阶段的对标指标为0.70%;现阶段检修周期的对标指标为690天,下一阶段的对标指标为1050天;现阶段装置能耗对标指标为9.20kg标油/吨,下一阶段装置能耗指标为9.0 kg标油/吨。
五、具体措施
1、制定出切实可行的实施办法,同时要将对标指标分解落实到相关班组和个人,充分调动各级管理人员和职工的积极性,全程全面参与对标活动。
2、建议调度协调好上下游关系,搞好原油脱水工作。
3、通过优化工艺操作条件,改变生产方案来提高轻质油收率。
如:柴油加氢装置建成以后,柴油硫含量高的问题可以得到解决,这样就可以提高柴油生产标号,提高轻质油收率。
4、在大修中进行一些及改技措项目,针对管线、塔盘腐蚀减薄及机泵超负荷运行情况,2013年度大修将进行更
换,延长装置运行周期的同时消除影响轻质油收率提高的因素,比如在一线柴油空冷与三线柴油空冷之间增加副线,更换塔内腐蚀、卡死的浮阀等措施来提高轻质油收率。
5、在原有加工量不可控的情况下,积极组织职工进行形式多样的技术培训,找出操作中的不足,提高工人的操作水平,确保装置平稳高效运行。
6、加强与兄弟单位与国内外先进单位交流学习,学习先进的工艺操作方法、节能理念方法,组织相关的人员参加技术、节能培训,进一步提高操作人员调整操作理念,有待进一步提高对比指标。
7、加强巡回检查,发现问题及时处理。
六、对标活动考核内容及考核办法
为了把对标工作落到实处,更好的调动职工工作的积极性,使各项对标指标顺利完成,因此,我车间成立对标活动考核小组:
组长:
副组长:
成员:
1、对标活动考核内容
考核内容包括“四项对标”,即收率对标、炼油损失对标、检修周期对标和装置能耗对标。
2、考核办法
把“四项对标”指标分解落实到五个运行班组,按照完
成情况进行评分。
(1)评分在90分以上按奖金的100%发放。
(2)评分在80分以上按奖金的90%发放。
(3)评分在70分以上按奖金的80%发放。
(4)评分在60分以上按奖金的70%发放。
(5)评分在60分以下全部扣除全部奖金。
(6)连续两次在60以下且每次考核分数没有进步的班组,班组成员必须进行脱产学习培训,直至考试合格后方可上岗。
总之,开展对标管理工作意义重大、任务艰巨。
我车间要从长远发展出发,着力构建长效机制。
要把对标管理的体系、内容等以制度的形式确定下来,把对标活动融入车间各项管理工作中,促进对标管理日常化、规范化和常态化。
要通过对标管理,健全各项管理制度和工作标准,进一步优化体制机制和管理流程,深入推进精细化管理,为延长石油成为名副其实的世界500强企业、打造创新型国际化现代能源化工企业做出新的更大的贡献!。