板坯表面纵裂纹的原因及控制措施
板坯边部纵裂纹产生的原因及解决措施
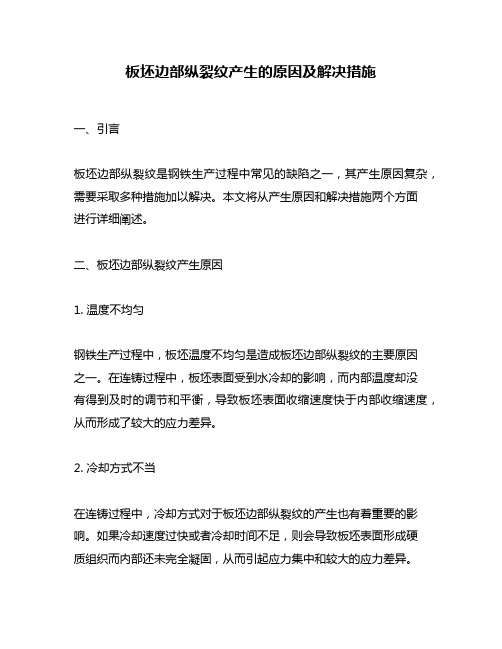
板坯边部纵裂纹产生的原因及解决措施一、引言板坯边部纵裂纹是钢铁生产过程中常见的缺陷之一,其产生原因复杂,需要采取多种措施加以解决。
本文将从产生原因和解决措施两个方面进行详细阐述。
二、板坯边部纵裂纹产生原因1. 温度不均匀钢铁生产过程中,板坯温度不均匀是造成板坯边部纵裂纹的主要原因之一。
在连铸过程中,板坯表面受到水冷却的影响,而内部温度却没有得到及时的调节和平衡,导致板坯表面收缩速度快于内部收缩速度,从而形成了较大的应力差异。
2. 冷却方式不当在连铸过程中,冷却方式对于板坯边部纵裂纹的产生也有着重要的影响。
如果冷却速度过快或者冷却时间不足,则会导致板坯表面形成硬质组织而内部还未完全凝固,从而引起应力集中和较大的应力差异。
3. 连铸机结构问题连铸机的结构问题也会对板坯边部纵裂纹的产生造成影响。
例如,如果连铸机的结构不合理或者设备老旧,就可能导致板坯内部温度不均匀或者冷却方式不当,从而引起板坯边部纵裂纹。
三、解决措施1. 调节温度钢铁生产过程中,调节温度是减少板坯边部纵裂纹的有效措施之一。
可以通过加强温度监测和调节系统来实现。
例如,在连铸过程中可以采用先进的热流体模拟技术来预测板坯内部温度分布情况,并及时调整冷却水量和喷淋位置等参数,以保证板坯内外温度平衡。
2. 改进冷却方式改进冷却方式也是减少板坯边部纵裂纹的有效措施之一。
可以通过增加喷淋头数量、改变喷淋角度、增加喷淋水量等方式来改善连铸过程中的冷却效果,并保证板坯表面和内部同时达到凝固要求。
3. 优化连铸机结构优化连铸机结构也是减少板坯边部纵裂纹的有效措施之一。
可以通过升级设备、改进结构、增加监测仪器等方式来提高连铸机的生产效率和准确性,从而保证板坯内部温度分布均匀和冷却方式合理。
四、总结综上所述,板坯边部纵裂纹是钢铁生产过程中常见的缺陷之一,其产生原因复杂,需要采取多种措施加以解决。
调节温度、改进冷却方式和优化连铸机结构是减少板坯边部纵裂纹的有效措施。
连铸板坯表面纵裂原因探究

连铸板坯表面纵裂原因探究
连铸板坯作为容易变形的金属坯料,在冷却变形过程中容易出现多种裂纹,其中纵裂最为常见。
针对连铸板坯表面纵裂现象,本文就其产生原因进行探究。
首先,表面纵裂常常是由于板坯的表面微细的成形不均匀导致的。
在铸造过程中,由于复杂的铸件形状,往往在表面上凸起或凹陷的微细尺寸会有些出入,并且会加快凝固层的冷却变形,从而使表面裂纹形成。
其次,表面纵裂也可能是由于浇口不合理而出现的。
正常的浇口应该是圆形的,但如果浇口不够均匀,表面纵裂就会产生。
此外,如果浇口太大,会导致板坯储存在浇口中的金属过多,使其凝固太快,从而导致表面纵裂的形成。
再者,当铸件温度过高的时候,表面纵裂也是可能出现的。
当板坯的温度过高时,凝固层会变得很薄,而且会加快凝固变形的过程,从而会出现表面纵裂现象。
最后,表面纵裂也可能是由于模具材料质量不佳导致的。
连铸板坯在流动过程中,会受到模具的影响,因此,模具质量的不佳会直接导致表面纵裂的发生。
总之,连铸板坯表面纵裂的原因多种多样,主要包括表面微细成形不均匀、浇口不合理、板坯温度过高、模具质量不佳等。
因此,为了防止表面纵裂的发生,可以采取一系列技术措施,以确保生产高质量的产品。
板坯纵裂产生原因及控制
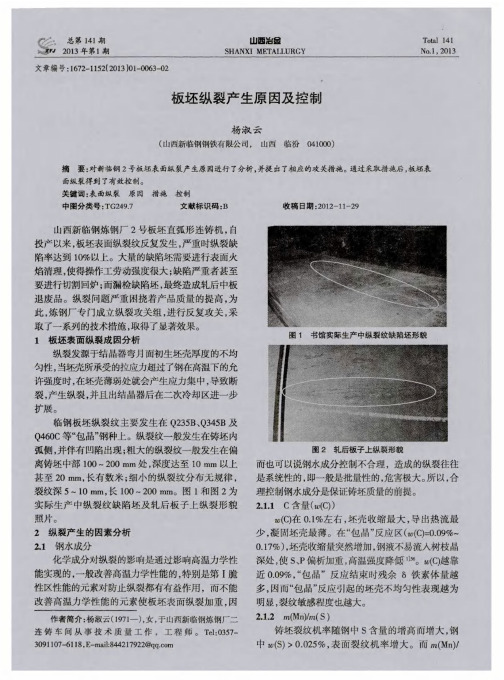
碳钢 m n ( S ) > 2 0 ; 控 制钢 中 ( C ) 尽 可能避 开
0 . 1 0 %~ 0 . 1 3 %的范 围 。
3 . 2 严格控制结 晶器标准 结晶器与二冷段上 口对弧要准 ,倒锥度控制在 5 ~ 8之问 , 出现铜板磨损较严重的情况 时 , 应及时 更换或修复铜板。 3 . 3 控制冷却强度
结 晶器与二冷段上 口对弧不准 ,结晶器倒锥பைடு நூலகம்
不合适( 偏小) , 使用过程铜板磨损严重 , 会造成纵裂
纹机率升高。
2 . 3 冷 却强 度
结晶器内一次冷却 、 一出结晶器足辊冷却 、 二冷
段冷却控制不宜过强。 3 . 4 保证下水 口垂直 、 对 中和水 口插入深度合适 严格检查测量 中包车 、 中包及各相关点 , 保证下 水 口垂 直 、对 中;将 中包下水 口插入深度控制在
YANG S h u y u n
( S t e e l m a k i n g P l a n t o f S h a n x i N e w L i n g a n g I r o n&S t e e l C o . , L t d . , L i n f e n 0 4 1 0 0 0 , C h i n a )
厚度均匀 、 稳定 , 就会使局部凝固坯壳过薄 , 产生纵
裂纹。
( 编辑: 胡玉香 )
3 采取的主要攻关措施
3 . 1 合理控制钢水成分
钢中控制 ( s ) ≯0 . 0 3 0 %, ( P ) ≯0 . 0 3 0 %, 控制普
( 下转 第 8 1页 )
2 0 1 3 年第 1 期
山 西冶金
板坯边部纵裂纹产生的原因及解决措施

板坯边部纵裂纹产生的原因及解决措施板坯边部纵裂纹是钢铁生产过程中常见的问题之一,它会影响钢材的质量和使用寿命,因此必须采取措施加以解决。
本文将从产生原因和解决措施两个方面进行探讨。
一、产生原因
1.板坯温度不均匀:板坯温度不均匀是板坯边部纵裂纹产生的主要原因之一。
当板坯表面温度高于内部温度时,板坯边部会出现温度梯度,导致板坯边部产生应力,从而引起纵裂纹。
2.板坯结晶器结构不合理:板坯结晶器结构不合理也是板坯边部纵裂纹产生的原因之一。
结晶器结构不合理会导致板坯边部温度不均匀,从而引起纵裂纹。
3.轧制工艺不合理:轧制工艺不合理也是板坯边部纵裂纹产生的原因之一。
轧制工艺不合理会导致板坯边部应力过大,从而引起纵裂纹。
二、解决措施
1.优化板坯结晶器结构:优化板坯结晶器结构是解决板坯边部纵裂纹的有效措施之一。
合理的结晶器结构可以使板坯温度均匀,从而减少板坯边部应力,降低纵裂纹的发生率。
2.调整轧制工艺:调整轧制工艺也是解决板坯边部纵裂纹的有效措
施之一。
合理的轧制工艺可以使板坯边部应力适当,从而减少纵裂纹的发生率。
3.控制板坯温度:控制板坯温度也是解决板坯边部纵裂纹的有效措施之一。
合理的板坯温度可以使板坯温度均匀,从而减少板坯边部应力,降低纵裂纹的发生率。
板坯边部纵裂纹是钢铁生产过程中常见的问题之一,产生原因主要有板坯温度不均匀、板坯结晶器结构不合理和轧制工艺不合理等。
解决措施主要包括优化板坯结晶器结构、调整轧制工艺和控制板坯温度等。
只有采取有效的措施,才能有效地解决板坯边部纵裂纹问题,提高钢材的质量和使用寿命。
表面纵裂纹产生原因分析及控制措施
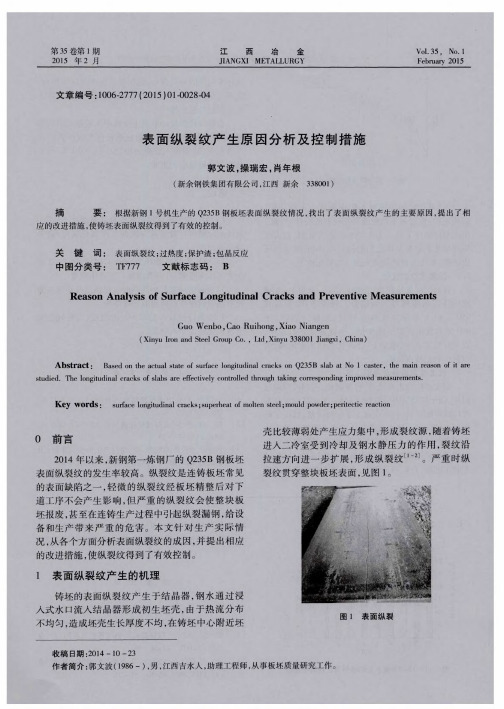
30
40
Mn/S
50
图 3 Mn/S对 纵 裂 纹 的影 响
表 1 Q235B的化学成分
%
裂纹 有 显著 的效果 。但 夹 杂 物 的 Mn/S与铁 的压缩
比不 同 ,在 铸坯 轧 制过程 中 ,对 铸坯 质 量 有一 定 程度
僻
的影 响 ,因此 ,应 从 源 头 上 解 决 硫 高 的 问题 ,如 要 进
行
铁水
预脱
硫及
转
炉放钢1
应执 行渣 洗制 、瓣划 l l 1 1 0
第 35卷第 1期
郭文 波 ,操瑞宏 ,肖年根 :表 面纵 裂纹产生原因分析及控制措施
根 据 对 新 钢 第 一 炼 钢 厂 Q235B板 坯 纵 裂 纹 的 跟 踪 统计 情况 ,对 影 响表 面 纵 裂 纹 产 生 的原 因进 行 了分 析 。 1.1 钢水 的影 响
新 钢第 一 炼 钢 厂 生 产 的 Q235B的 化 学 成 分 见 表 l。 由钢 种 成 分 设 计 可 知 该 钢 种 位 于 包 晶反 应 区 ,且对 W(s)的要求较低 ,这也是该钢种表面纵裂 纹发 生率 较 高 的重要 原 因 。 1.1.1 碳 的影 响
突出,这是高温钢铸坯形成纵裂纹 的主要原 因。
根据钢种液相线温度 的计算公式 ,该钢种的
液相 线为 1 520 ~1 524 oC。过热 度 偏低 ,结 晶器 内
板坯表面纵裂的原因分析及采取的措施
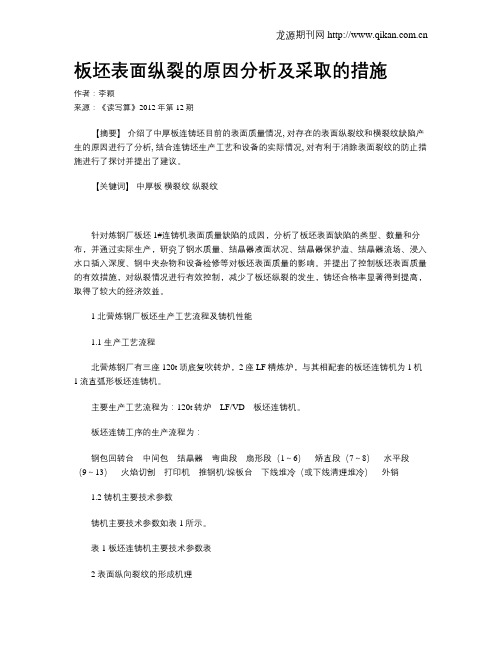
板坯表面纵裂的原因分析及采取的措施作者:李颖来源:《读写算》2012年第12期【摘要】介绍了中厚板连铸坯目前的表面质量情况, 对存在的表面纵裂纹和横裂纹缺陷产生的原因进行了分析, 结合连铸坯生产工艺和设备的实际情况, 对有利于消除表面裂纹的防止措施进行了探讨并提出了建议。
【关键词】中厚板横裂纹纵裂纹针对炼钢厂板坯1#连铸机表面质量缺陷的成因,分析了板坯表面缺陷的类型、数量和分布,并通过实际生产,研究了钢水质量、结晶器液面状况、结晶器保护渣、结晶器流场、浸入水口插入深度、钢中夹杂物和设备检修等对板坯表面质量的影响。
并提出了控制板坯表面质量的有效措施,对纵裂情况进行有效控制,减少了板坯纵裂的发生,铸坯合格率显著得到提高,取得了较大的经济效益。
1 北营炼钢厂板坯生产工艺流程及铸机性能1.1 生产工艺流程北营炼钢厂有三座120t顶底复吹转炉,2座LF精炼炉,与其相配套的板坯连铸机为1机1流直弧形板坯连铸机。
主要生产工艺流程为:120t转炉LF/VD板坯连铸机。
板坯连铸工序的生产流程为:钢包回转台中间包结晶器弯曲段扇形段(1~6)矫直段(7~8)水平段(9~13)火焰切割打印机推钢机/垛板台下线堆冷(或下线清理堆冷)外销1.2 铸机主要技术参数铸机主要技术参数如表1所示。
表1 板坯连铸机主要技术参数表2 表面纵向裂纹的形成机理表面纵裂起因于结晶器弯月面初生坯壳厚度的不均匀性,作用于坯壳上的拉应力和热应力超过高温坯壳的允许强度,在坯壳薄弱处产生应力集中沿树枝晶间或奥氏体晶界产生断裂。
一般来说,裂纹在结晶器弯月面刚形成时是很微小的,只有进入二冷区才不断加深、加宽和加长,即使二冷区冷却均匀,这种裂纹进入二冷区也要扩展,若二冷区冷却不均匀,裂纹扩展更加严重。
2.1 表面纵向裂纹的形成原因北营第二炼钢厂板坯连铸机所浇钢种绝大多数是含碳在0.10%~0.18%范围的亚包晶钢。
亚包晶钢与δ单相凝固钢或过包晶钢相比,该类型钢浇注板坯容易出现表面纵裂,这是由于亚包晶钢初生凝固坯壳收缩大、生长不均匀造成。
连铸板坯表面纵裂原因探究

连铸板坯表面纵裂原因探究
连铸板坯表面纵裂是目前钢铁行业中比较常见的一种缺陷,它主要指的是在铸钢板坯的表面有一条类似裂缝的状况,这种缺陷会降低板坯的使用质量,降低生产效率,影响铸钢行业的运营状况。
因此,研究连铸板坯表面纵裂的原因,对于钢铁行业来说具有重要意义。
首先,连铸板坯表面纵裂形成的原因可以归结为四大类,即工艺因素、材料因素、结构因素、设备因素。
在四大因素中,工艺因素是造成连铸板坯表面纵裂的主要因素,从料头到成品,从工艺流程到参数设置,连铸工艺铸造中几乎每一个环节都可能导致连铸板坯表面纵裂的形成。
其次,在冶炼中缺陷的材料可能会造成连铸板坯表面纵裂,而板坯结构变形也可能导致板坯表面纵裂的出现。
此外,设备故障,如冷却不均匀或设备老化,也会导致连铸板坯表面纵裂的形成。
要有效控制连铸板坯表面纵裂的形成,应从四个方面着手:第一,严格把控连铸工艺参数,做到技术标准控制,定期检验确保各环节工艺符合要求;第二,提升冶炼质量,提高冶炼材料的质量,做到成分精确;第三,优化板坯结构,采用合理的结构和冷作参数,以避免因冷作过度造成表面纵裂;第四,定期检测设备,及时更换老化的设备,保证工艺设备的正常运行。
此外,针对已产生的连铸板坯表面纵裂,也可以采取一些措施来缓解。
一是加大轧制参数,通过轧制平整板坯表面,消除表面缺陷;二是通过焊接和补焊,消除已经存在的表面纵裂;三是采用再结晶技术来填补表面纵裂,提高板坯的力学性能。
综上所述,连铸板坯表面纵裂的原因复杂,要想有效地控制纵裂的发生,就需要从工艺、材料、结构、设备等方面着手,合理采取措施,降低缺陷比例,保证生产质量。
连铸板坯表面从裂纹的原因及防止措施

维普资讯
20 0 2年 l 2月
・
炼
钢
De . 0 2 c2 0
2 ・ 第 1 6 8卷 第 6期
S el kn tema ig
V0 . 8 No 6 11 .
连 铸 板 坯 表 面 纵 裂 纹 的 成 因 及 防 止 措 施
汤 曙 光 焦 兴 利 刘 启 龙
大包 容量 / t
中包 / t
2 铸 机 状况
铸 机 状 况 见 表 1 。
结 晶器
长 9 0 i一 a rn 振幅/ mm
四偏 心 正弦 振动
3 0~ 3 o o
±5
3 铸 坯 表面 裂 纹 的影 响 因素
对 轧 出 的 中厚 板 仔 细 观 察 ,发 现 板 子 表 面有 很 细 的 、 规 则 的 、时 断 时 续 的纵 裂 纹 ,并 且 发 不 生 过 几 次 铸 坯 宽 面 中心 大 宗 纵 裂 纹 ,下 面 主 要 从
纵裂纹 的发生率有显著影 响 ,中包 过热 度每增加
l ℃ ,在 一 定 拉 速 的 条 件 下 ,出 结 晶 器 的坯 壳 厚 0 度 约 减 少 3 ;且 坯 壳 平 均 温 度 升 高 ,在 应 力 不 % 变 的情 况 下 ,由 于坯 壳 温 度 向钢 的 第 1脆 性 区移
联 系人 :汤曙 光 ,高级工 程师 ,安徽 省马鞍 山市 ( 4 0 1马 鞍 山钢 铁股份 公 司第一炼 钢厂 23 1 )
以下 几 方 面进 行 分 析 。
矫直 工作 拉速 / ri m・ n a
冶金 长度 / m
多点矫 直
0. ~ 2. 3 0
2 . 8 8 71
3 1 铸 温铸速 的影 响 .
表面纵裂纹

20
低、中、高碳钢结晶器内坯壳示意图
21
体积收缩大, 气隙就大。
不同碳含量钢坯壳与模壁之间的空隙
22
气隙大,热阻较 大,热流降低。
不同碳含量钢铸坯传热速率的变化
23
裂纹的形成与铸坯的 不均匀凝固有关。
•
•
48
不同类钢适用的保护渣凝固温度示意图
49
保护渣重要的物性参数:结晶温度
•
结晶析出会降低保护渣的润滑效果,拉漏可能 性增加; 结晶温度高可以减弱液体保护渣的发达程度, 减缓传热; 固体保护渣层中结晶相析出,渣膜中易产生微 裂纹和晶界均会增大传热热阻; 降低玻璃相辐射传热的效果。
•
•
•
50
保护渣重要的物性参数:熔化温度和熔化速度 保护渣熔化温度和熔化速度对保护渣液渣层高度及 坯壳与结晶器壁之间的流入有重要影响。 影响保护渣熔化速率的因素: 自由碳含量; 碳颗粒的粒度; 保护渣熔化温度; 保护渣原料粒度; 拉速。
q=hT(TS-TW) =1/RT(TS-TW)
34
热流包括:
■ 钢水向坯壳的对流传热; ■ 凝固坯壳的传导传热; ■ 保护渣膜传导传热; ■ 气隙间的传导和辐射传热; ■ 结晶器铜板传导传热; ■ 冷却水与铜板间对流传热。
总热阻RT可表示为: RT=R1+R2+R3+R4+R5+R6
R1:钢水-坯壳间的热阻, cm2 ℃/W 。 R2:通过坯壳的热阻, cm2 ℃/W ; R3:通过保护渣膜的热阻, cm2 ℃/W ; R4:通过气隙的热阻, cm2 ℃/W ; R5:通过结晶器铜板的热阻, cm2 ℃/W ; R6:结晶器壁-冷却水间的热阻,cm2 ℃/W;
板坯表面纵裂的原因及控制措施
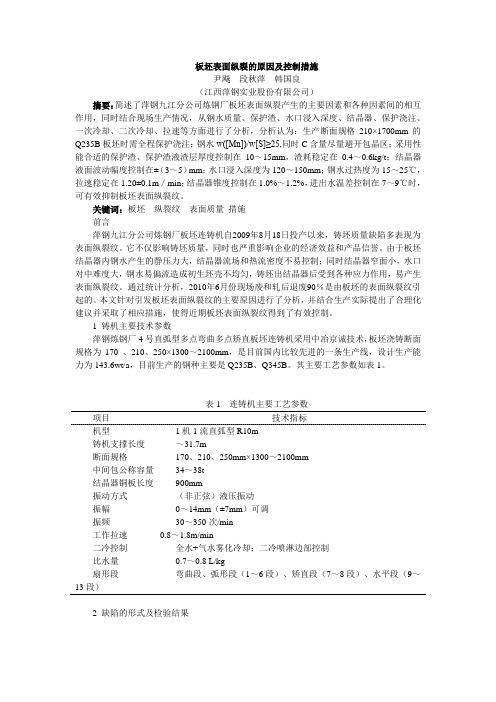
板坯表面纵裂的原因及控制措施尹飚段秋萍韩国良(江西萍钢实业股份有限公司)摘要:简述了萍钢九江分公司炼钢厂板坯表面纵裂产生的主要因素和各种因素间的相互作用,同时结合现场生产情况,从钢水质量、保护渣、水口浸入深度、结晶器、保护浇注、一次冷却、二次冷却、拉速等方面进行了分析,分析认为:生产断面规格210×1700mm的Q235B板坯时需全程保护浇注;钢水w([Mn])/w[S]≥25,同时C含量尽量避开包晶区;采用性能合适的保护渣、保护渣液渣层厚度控制在10~15mm,渣耗稳定在0.4~0.6kg/t;结晶器液面波动幅度控制在±(3~5)mm;水口浸入深度为120~150mm;钢水过热度为15~25℃,拉速稳定在1.20±0.1m/min;结晶器锥度控制在1.0%~1.2%,进出水温差控制在7~9℃时,可有效抑制板坯表面纵裂纹。
关键词:板坯纵裂纹表面质量措施前言萍钢九江分公司炼钢厂板坯连铸机自2009年8月18日投产以来,铸坯质量缺陷多表现为表面纵裂纹。
它不仅影响铸坯质量,同时也严重影响企业的经济效益和产品信誉。
由于板坯结晶器内钢水产生的静压力大,结晶器流场和热流密度不易控制;同时结晶器窄面小,水口对中难度大,钢水易偏流造成初生坯壳不均匀,铸坯出结晶器后受到各种应力作用,易产生表面纵裂纹。
通过统计分析,2010年6月份现场废和轧后退废90%是由板坯的表面纵裂纹引起的。
本文针对引发板坯表面纵裂纹的主要原因进行了分析,并结合生产实际提出了合理化建议并采取了相应措施,使得近期板坯表面纵裂纹得到了有效控制。
1 铸机主要技术参数萍钢炼钢厂4号直弧型多点弯曲多点矫直板坯连铸机采用中冶京诚技术,板坯浇铸断面规格为170 、210、250×1300~2100mm,是目前国内比较先进的一条生产线,设计生产能力为143.6wt/a,目前生产的钢种主要是Q235B、Q345B。
其主要工艺参数如表1。
连铸板坯表面纵裂纹控制

连铸板坯表面纵裂纹控制
一、连铸板坯表面纵裂纹的产生因素
1、造坯温度:过低的造坯温度会导致板坯表面纵裂纹的出现,应在钢
水熔化温度的基础上提高造坯温度;
2、造坯件间距:连铸板坯的冷却过程会产生很强的内应力,如果水冷
却造坯件间距过大,冷却之后会出现拉伸变形,从而产生纵裂纹;
3、连铸熔口处处理不当:当积熔渣正常时,若造坯件分离不平衡,也
会使连铸熔口处出现倾斜度,且不平衡的张力会造成热锻段产生纵裂纹;
4、水冷却喷口结构:水冷却温度不均匀,会在板坯表面形成表面纵裂纹,应采取合理的水冷却喷口结构布置,保证冷却水均匀性;
二、连铸板坯表面纵裂纹的控制措施
1、温度控制:在连铸造坯过程中,采用温度控制措施,确保钢水熔化
温度跨度不要在半钩温度以内,另外,为了减轻连铸板坯表面拉伸应
力也有助于减少纵裂纹;
2、造坯件间距控制:对于比较薄的连铸板坯,如低碳钢、低合金钢等,尤其需要多加注意造坯件间距的控制,相应地采用一定的补偿措施;
3、熔口处理控制:在熔口结构上有要求,要保证熔口垂直度,以保证
熔口平整,以及减少裂纹的出现;
4、水冷却喷口结构控制:采取合理的水冷却喷口结构,尽量取均衡的
喷口布置,以保证冷却的均匀性;。
连铸板坯裂纹的可能原因

连铸板坯裂纹的可能原因连铸板坯裂纹是指在连铸过程中板坯表面或内部出现的裂纹现象。
连铸板坯是制造板材的重要中间产品,其质量直接关系到最终产品的质量。
因此,了解连铸板坯裂纹的可能原因对于提高板材质量具有重要意义。
连铸板坯裂纹的可能原因主要包括以下几个方面:1. 温度控制不当:温度是连铸过程中最重要的控制参数之一。
如果连铸板坯的冷却速度过快或过慢,都会导致板坯表面或内部的温度梯度过大,从而引起裂纹的产生。
此外,连铸机的冷却水温度和流量的不稳定也会对板坯的温度分布产生影响,进而导致裂纹的形成。
2. 铸造过程中的应力:连铸板坯在冷却过程中由于温度变化而产生应力,如果应力超过了材料的承受能力,就会引起裂纹。
铸造过程中的应力主要包括热应力、冷却应力和收缩应力。
热应力是由于连铸板坯的非均匀冷却引起的,冷却应力是由于冷却水的不均匀冷却引起的,而收缩应力是由于连铸板坯的收缩引起的。
3. 材料质量问题:连铸板坯的质量直接关系到裂纹的产生。
如果原料中存在夹杂物、气孔或其他缺陷,都会在连铸过程中发展为裂纹。
此外,连铸板坯的化学成分和物理性能也会对裂纹的形成起到重要影响。
4. 连铸工艺参数调整不当:连铸过程中的各项工艺参数对于连铸板坯的质量具有重要影响。
如果连铸机的浇注速度、结晶器的冷却强度、结晶器的振动频率等参数调整不当,都会导致连铸板坯出现裂纹。
为了避免连铸板坯裂纹的产生,可以采取以下措施:1. 合理控制连铸过程中的温度,保证板坯的均匀冷却。
2. 优化连铸工艺参数,确保连铸板坯的质量稳定。
3. 加强原料检验,确保原料的质量达标。
4. 定期检查和维护连铸机设备,确保设备的正常运行。
5. 引入先进的控制技术,如自动化控制系统和智能监测设备,提高连铸过程的稳定性和可控性。
连铸板坯裂纹的产生是由多种因素共同作用的结果。
通过合理控制连铸过程中的温度、调整工艺参数、优化原料质量以及加强设备维护,可以有效地避免连铸板坯裂纹的产生,提高板材的质量。
薄板坯表面纵裂的形成原因及预防措施
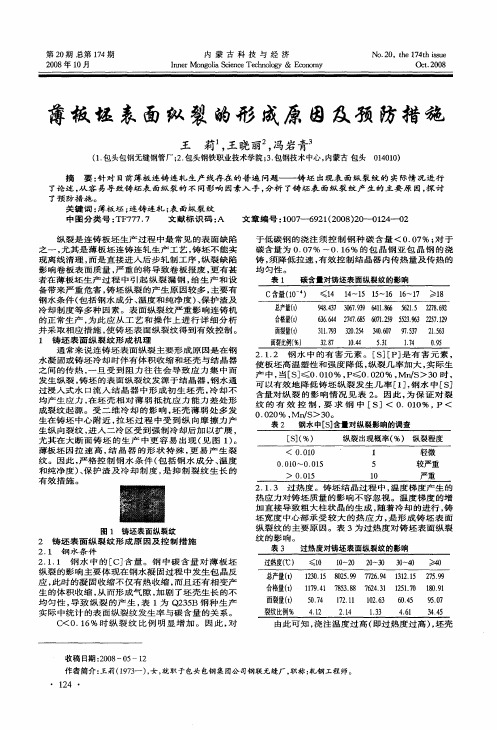
一
图 1 铸坯表面纵裂纹 2 铸 坯 表 面 纵 . 2 1 1 钢 水 中 的 [ 含 量 。 钢 中 碳 含 量 对 薄 板 坯 .. C]
2. . 过 热 度 。铸 坯 结 晶 过 程 中 , 度 梯 度 产 生 的 13 温 热 应 力 对 铸 坯 质 量 的 影 响不 容 忽 视 。 温 度 梯 度 的 增
1 铸坯表 面纵 裂纹形 成机理 通常来 说连铸 坯表 面纵裂 主要形 成原 因是在钢
水 凝 固或 铸 坯 冷 却 时 伴 有 体 积 收 缩 和 坯 壳 与 结 晶 器 之 间 的 传 热 , 旦 受 到 阻 力 往 往 会 导 致 应 力 集 中 而 一 发 生 纵 裂 , 坯 的 表 面 纵 裂 纹 发 源 于结 晶器 , 水 通 铸 钢 过 浸 入 式 水 口流 入 结 晶 器 中 形 成 初 生 坯 壳 , 却 不 冷 均产 生应力 , 坯 壳 相 对薄 弱抵 抗 应 力 能力 差 处形 在 成裂 纹起源 。受 二维 冷 却 的影 响 , 壳薄 弱 处 多发 坯 生在铸 坯 中心 附近 , 坯过 程 中受 到 纵 向摩 擦 力产 拉 生 纵 向裂 纹 , 入 二 冷 区 受 到 强 制 冷 却 后 加 以 扩 展 , 进 尤其 在大 断面 铸 坯 的生 产 中更容 易 出现 ( 图 1 。 见 ) 薄板坯 因拉 速 高 , 晶器 的形 状 特 殊 , 易 产 生 裂 结 更 纹 。因此 , 格控 制 钢水 条 件 ( 括 钢水 成分 、 度 严 包 温 和 纯 净 度 ) 保 护 渣 及 冷 却 制 度 , 抑 制 裂 纹 生 长 的 、 是 有效 措施 。
薄板坯 表面纵裂 的形 成原 因及预 防措施
王 莉 王 晓丽 , , 冯岩青。
(. 1包头包钢无缝钢管 厂 ;. 头钢铁职业技术学院 ;. 2包 3包钢技 术中心 , 内蒙古 包头 04 1) 100 摘 要 : 对 目前 薄 板 连 铸 连 轧 生 产 线 存 在 的 普 遍 问 题 — — 铸 坯 出 现 表 面 纵 裂 纹 的 实 际 情 况 进 行 针 了论 述 , 容 易 导 致 铸 坯 表 面 纵 裂 的 不 同 影 响 因素 入 手 , 析 了铸 坯 表 面 纵 裂 纹 产 生 的 主 要 原 因 , 讨 从 分 探
板坯角部裂纹的原因

板坯⻆部裂纹的原因⼀、引⾔板坯⻆部裂纹是⼀种常⻅的冶⾦缺陷,它发⽣在热轧板卷的⻆部位置,呈现出⼀定深度的裂纹。
这种裂纹的产⽣对产品的质量和使⽤性能产⽣了极⼤的影响,不仅影响产品的美观,⽽且降低了产品的使⽤寿命和安全性。
本⽂旨在深⼊探讨板坯⻆部裂纹产⽣的原因,并提出相应的预防措施。
⼆、板坯⻆部裂纹产⽣的原因1.原料质量:原料的化学成分、微观组织结构和冶⾦性能是影响板坯质量的关键因素。
例如,⾼碳钢、合⾦钢等材料的C、Si、Mn等元素的⽐例不当,或者夹杂物含量较⾼,都可能导致板坯⻆部裂纹的产⽣。
2.加热⼯艺:加热温度、加热速度和加热均匀性等加热⼯艺参数对板坯的⻆部裂纹也有重要影响。
如果加热温度过⾼或加热速度过快,可能导致板坯局部过热,造成内部应⼒集中,引发裂纹的产⽣。
此外,加热不均匀也会导致板坯内部应⼒分布不均,进⽽引发裂纹。
3.轧制⼯艺:轧制过程中的各种⼯艺参数,如轧制温度、轧制速度、轧制道次等,都会影响板坯的⻆部裂纹。
如果轧制温度过⾼或轧制速度过快,可能导致板坯在轧制过程中受到的应⼒过⼤,引发裂纹。
此外,轧制道次不合理也会导致板坯内部应⼒的积累,进⽽引发裂纹。
4.冷却⼯艺:冷却⼯艺也是影响板坯⻆部裂纹的重要因素。
如果冷却速度过快或冷却不均匀,可能导致板坯内部应⼒集中,引发裂纹。
5.设备状况:轧机设备的⼯作状态和精度也是影响板坯⻆部裂纹的因素之⼀。
如果轧机设备磨损严重或维护不当,可能导致轧制的板坯质量受到影响,引发裂纹。
三、预防措施针对以上产⽣原因,可以从以下⼏个⽅⾯进⾏预防:1.严格控制原料质量:对原料进⾏全⾯的质量检测,确保其化学成分、微观组织结构和冶⾦性能符合要求。
同时,加强原料的保管和运输,防⽌其受到有害元素的污染。
2.优化加热⼯艺:通过实验和模拟的⽅法,确定合理的加热温度、加热速度和加热均匀性等参数。
在⽣产过程中,加强加热设备的维护和保养,确保其正常⼯作。
3.轧制⼯艺的优化:通过实验和模拟的⽅法,确定合理的轧制温度、轧制速度和轧制道次等参数。
板坯表面纵裂的原因分析及采取的措施
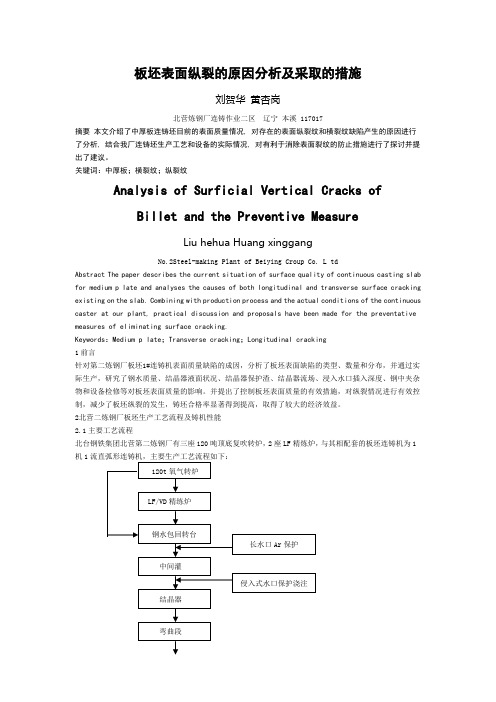
板坯表面纵裂的原因分析及采取的措施刘贺华黄杏岗北营炼钢厂连铸作业二区辽宁本溪 117017摘要本文介绍了中厚板连铸坯目前的表面质量情况, 对存在的表面纵裂纹和横裂纹缺陷产生的原因进行了分析, 结合我厂连铸坯生产工艺和设备的实际情况, 对有利于消除表面裂纹的防止措施进行了探讨并提出了建议。
关键词:中厚板;横裂纹;纵裂纹Analysis of Surficial Vertical Cracks ofBillet and the Preventive MeasureLiu hehua Huang xinggangNo.2Steel-making Plant of Beiying Croup Co. L tdAbstract The paper describes the current situation of surface quality of continuous casting slab for medium p late and analyses the causes of both longitudinal and transverse surface cracking existing on the slab. Combining with production process and the actual conditions of the continuous caster at our plant, practical discussion and proposals have been made for the preventative measures of eliminating surface cracking.Keywords:Medium p late;Transverse cracking;Longitudinal cracking1前言针对第二炼钢厂板坯1#连铸机表面质量缺陷的成因,分析了板坯表面缺陷的类型、数量和分布,并通过实际生产,研究了钢水质量、结晶器液面状况、结晶器保护渣、结晶器流场、浸入水口插入深度、钢中夹杂物和设备检修等对板坯表面质量的影响。
连铸坯表面纵裂产生原因及控制

连铸坯表面纵裂产生的原因及控制一、表面纵裂的危害1、铸坯表面纵裂纹影响轧制产品质量,长300mm、深2.5mm的表面纵裂纹在轧制板材上留下1125mm分层缺陷,纵裂纹严重时会造成拉漏和废品。
2、表面纵裂经修磨后,由于修磨处铸坯厚度小于其他部位,造成轧制时压缩比偏小,板的表面质量和钢质性能不连续,降低板材的等级和钢材的收得率。
二、铸坯表面纵裂纹形成的机理:铸坯的表面纵裂纹产生于结晶器,由于热流分布不均匀,造成坯壳厚度不均匀,在坯壳薄的地方产生应力集中;结晶器壁与坯表面间的摩擦力使坯壳承受较大的负荷,在牵引坯壳向下运动时产生纵向应力,这种应力与从结晶器窄面,到宽面中心线的距离呈直线增加,最大处在板坯的中间,而钢水静压力随着坯壳往下移动呈直线增加,静压力使得坯壳往外鼓,表面裂纹得到进一步扩大。
三、钢坯表面纵裂纹形成的原因及分析:1、保护渣性能的影响,保护渣的黏度过大或过小,都会使渣膜在坯壳与结晶器壁之间,厚薄不均匀,从而影响结晶器的热流分布,导致坯壳凝固不均匀,从而影响结晶器的热流分布,导致坯凝固不均匀,保护渣的融化速率应与其消耗量平衡,熔化速度和熔点均对保护渣渣层的性能有直接关系,熔化过快或过慢均会影响渣膜的厚度及其均匀性,从而影响结晶器的热流分布。
2、结晶器内钢水行为的影响,钢水在结晶器内的流动状态,对结晶器内钢水卷渣、保护渣对夹杂物的捕捉,铸坯裂纹的形成均有一定关系。
当浸入式水口侧孔直径和角度或是水口的浸入深度和对中程度改变时,钢水流场随之改变,钢水对坯壳的冲刷程度也改变,流场不合理也会造成保护渣的铺展性不良,结晶器液面液渣层厚薄不均匀,使流入气隙的渣厚薄不均,造成热流分布不均匀,坯壳凝固不均,而出现表面纵裂纹。
当下水口外径过大时,结晶器内钢水在口区的内外弧处会出现钢水流动“死区”,造成结晶器液面“搭桥”现象,影响保护渣的熔化性,增加了铸坯中部的摩擦应力。
3、钢水过热度的影响,增加钢水过热度,保护渣熔化速度快,液渣层过厚在空隙内流失过快造成结晶器内热流分布不均匀,坯壳凝固不均匀,表面纵裂纹趋势增大。
板坯表面纵裂纹的原因及控制措施

板坯表面纵裂纹的原因及控制措施摘要:通过对安钢第一炼轧厂板坯连铸工艺分析,认为引起板坯纵裂纹的主要原因是钢水成分和质量、结晶器冷却强度、保护渣性能及其吸收夹杂物后成分和性能变化等。
通过采取措施使板坯的表面纵裂纹得到有效的控制,纵裂纹发生率由1.9%控制到0.55%左右。
关键词:连铸板坯纵裂纹保护渣连铸板坯的表面纵裂纹是影响铸机产量和铸坯质量的主要缺陷。
它的出现,轻者须进行精整;严重的导致漏钢或铸坯报废,影响铸机作业率和金属收得率,增加了生产成本也打乱了生产计划。
安钢第一炼轧厂自投产以来,铸坯的表面缺陷主要是表面纵裂纹,而表面横裂纹几乎没有出现过。
纵裂纹增加最严重的月份,纵裂纹率高达3.13%,攻关前,纵裂纹的平均发生率为1.9%,经过两个月的攻关,纵裂纹率控制在0.55%的水平。
1 表面纵裂纹的特征从表面纵裂纹的分布状况看,在板坯的宽面中央区域,即水口区域的表面纵裂纹占整个铸坯表面裂纹的90%,其余的分布在铸坯宽面的1/4和3/4区域,内、外弧都有,内弧的表面纵裂纹比例明显高于外弧的比例。
从裂纹的长短看,大于1m的占表面纵裂纹的多数;从裂纹的深度看,大于10mm的占多数。
2 表面纵裂纹的产生原因与控制措施2.1 钢水质量的影响2.1.1 钢中碳含量的影响C含量在0.10%~0.12%范围内,裂纹敏感性最大;C含量≥0.18%时,板坯表面裂纹的发生率是随碳含量的增加而增加的[1]。
由铁碳相图可知,当碳含量在0.10%~0.14%时,凝固过程发生包晶反应并伴随δ→γ相变,产生较大的体积收缩,铸坯与结晶器壁之间产生空隙,导出热量较小,坯壳最薄,在表面形成凹陷,凹陷部位冷却和凝固速度比其它部位慢,组织粗化,在热应力、摩擦力和钢水静压力等作用下,在凝固坯壳薄弱处产生裂纹,并且在二冷作用下裂纹加深和扩大[2]。
根据数据统计结果来看,C含量在0.12%~0.14%对板坯纵裂有一定的影响。
2.1.2 成品钢中硫含量的影响硫在钢中的溶解度极小,与铁生成FeS,FeS与FeO能形成低熔点的热脆性共晶体,并在晶界析出。
薄板坯表面纵裂的成因及防止措施 精品
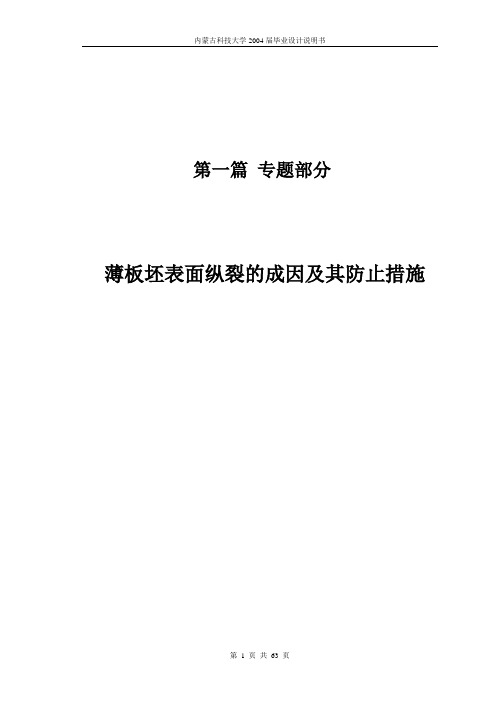
第一篇专题部分薄板坯表面纵裂的成因及其防止措施薄板坯表面纵裂的成因及防止措施摘要对珠钢、包钢薄板坯表面纵裂进行分析后发现,产生薄板坯表面纵裂的主要原因有钢中含碳量、硫含量、结晶器热流密度、拉速。
避免钢中含碳量在敏感区,控制热流密度在临界热流密度以下,选择合理拉速等对提高薄板坯质量,防止表面纵裂有重要作用。
关键词连铸表面纵裂薄板坯Abstract Surface longitudinal cracks on thin slabs which are produced by Zhujiang Iron&Steel Company and Baotou Iron&Steel Company are studied ,and find that there are several factors maybe lead to surface longitudinal cracks on thin slabs. Influences include carbon content ,sulfur content ,thermal energy density,pull speed ,etc .In order to improve the quantity of steel ,it should control the carbon content ,sulfur content ,and thermal energy density,also it should choose appropriate pull speed . It takes great effect to avoid surface longitudinal cracks on thin slabs .Key words continuous casting surface longitudinal crack thin slab薄板连铸连轧是当今世界钢铁工业具有革命性的前沿技术,它集科学,技术和工程为一体,将热轧板卷的生产在一条短流程生产线上完成,充分显示其先进性和科学性。
连铸板坯表面纵裂原因探究

连铸板坯表面纵裂原因探究连铸板坯表面纵裂是一种很常见的问题,这种现象会导致质量问题,影响后续工序,并增加板材的损耗。
因此,对于连铸板坯表面的纵裂机理及其原因的深入探究显得尤为重要。
第一,表面纵裂的形成机理。
在连铸过程中,由于液态铸锭造粒时所作用的拉拔力和铸锭不均的温度场,使各种尺寸的铸锭受力不均,把铸锭表面不平整,针织纹以及其他皱革状物出现,比较大的破坏原有大片薄膜结构,使表面出现纵裂。
第二,表面纵裂的成因。
连铸板坯表面纵裂的主要原因有:铸锭温度不均,液态铸锭造粒时所作用的拉拔力过大,液态铸锭温度不合适,液态铸锭含氧量太高,铸锭结构缺乏稳定性,表面物质含量过高,以及操作不当等。
第三,消除表面纵裂的技术措施。
针对连铸板坯表面纵裂的原因,可以采取以下技术措施来消除表面纵裂:(1)调节液态铸锭温度,把液态铸锭温度控制在一定范围内,使铸锭结构更加稳定;(2)减少熔炼后的液态铸锭氧化,减少表面物质的含量;(3)采用新型的拉拔装置,减少拉拔力的大小;(4)做好连铸操作规程,保证生产工艺的稳定性。
第四,未来的发展方向。
在以上的技术措施的基础上,为了进一步改善连铸板坯表面纵裂现象,未来发展的重点在于以下方面:(1)采用新型材料,使整体板坯结构更加稳定,从而改善表面纵裂现象;(2)实施连铸装备智能化,使连铸工艺运行得更加顺畅、稳定;(3)采用现代化的动力控制系统,改善铸锭的动力分布;(4)开展更多的科学研究,探索更有效的表面纵裂预防技术。
综上所述,连铸板坯表面纵裂是一种很常见的问题,其发生是由于铸锭温度不均、拉拔力过大、液态铸锭含氧量太高和铸锭结构缺乏稳定性等原因所导致,为了消除这一现象,应当调节液态铸锭温度、减少液态铸锭含氧量、采用新型拉拔装置、做好连铸操作规程等,未来还要探索新型材料、连铸装备智能化、现代化的动力控制系统以及更有效的表面纵裂预防技术,以期改善连铸板坯表面纵裂现象。
连铸板坯表面纵裂事故分析及预防措施.doc

YJ0712-连铸板坯表面纵裂事故分析及预防措施案例简要说明:依据国家职业标准和冶金技术专业教学要求,归纳提炼出所包含的知识和技能点,弱化与教学目标无关的内容,使之与课程学习目标、学习内容一致,成为一个承载了教学目标所要求知识和技能的教学案例。
本案例是连续铸钢产品质量缺陷案例,体现了铸坯质量特征、表面纵裂产生的原因、预防措施等知识点和岗位技能,与本专业连续铸钢课程连铸坯质量缺陷单元的教学目标相对应。
连铸板坯表面纵裂事故分析及预防措施1 背景介绍某炼钢厂连铸车间,采用超薄热带生产线,FTSC连铸板坯连铸机,机型直弧形,二冷气水雾化喷嘴,铸机基本半径5m,工作拉速2.8-5.2m/min,生产铸坯厚度87mm,结晶器液面控制方式Cs137射源控制。
主要生产薄板坯。
2 主要内容2.1事故经过2012年5月,FTSC工艺连铸薄板坯出现了大量的表面纵裂。
特别是浇注的ss400钢的裂纹率明显超高,占有缺陷铸坯的60~70%。
其主要发生在距中心四分之一宽度附近,距离中心300~400mm的区域。
当时,取样反馈的情况滞后于铸机生产,发现裂纹缺陷时已经造成至少两炉钢的裂纹质量缺陷。
因缺少铸坯离线检测的中间环节,这种铸坯纵裂纹对轧钢工序影响较大,最终导致质量异议事件2.2事故原因分析连铸板坯的裂纹表面纵裂由于在结晶器内凝固壳的生长不均匀,导致在特定部位拉伸应力的集中而产生。
对于薄板坯连铸来说,由于工艺的特殊性,其原因更为复杂多样。
(见图1)图1:铸坯表面纵裂(1)四孔水口通钢量大,对坯壳冲刷严重,使得在水口射流下方距中心260~430的区域坯壳减薄,导致结晶器出口处坯壳厚度比平均坯壳厚度减薄20%。
(2)钢水射流冲刷作用反映到坯壳表面温度上使得在距中心260~400的区域形成高温区,并随着拉速的增加而被加强,在结晶器出口处铸坯表面横向温度差达到1000C,高温、坯壳薄所造成的应力集中是产生铸坯纵裂纹的一个根源。
(3)结晶器漏斗区宽度为800mm,自由锥度设计较小,漏斗区内坯壳的收缩需要靠挤压窄面进行补充,但过大的局部锥度构成了形成纵裂纹的潜在因素。
- 1、下载文档前请自行甄别文档内容的完整性,平台不提供额外的编辑、内容补充、找答案等附加服务。
- 2、"仅部分预览"的文档,不可在线预览部分如存在完整性等问题,可反馈申请退款(可完整预览的文档不适用该条件!)。
- 3、如文档侵犯您的权益,请联系客服反馈,我们会尽快为您处理(人工客服工作时间:9:00-18:30)。
板坯表面纵裂纹的原因及控制措施
摘要:通过对安钢第一炼轧厂板坯连铸工艺分析,认为引起板坯纵裂纹的主要原因是钢水成分和质量、结晶器冷却强度、保护渣性能及其吸收夹杂物后成分和性能变化等。
通过采取措施使板坯的表面纵裂纹得到有效的控制,纵裂纹发生率由1.9%控制到0.55%左右。
关键词:连铸板坯纵裂纹保护渣
连铸板坯的表面纵裂纹是影响铸机产量和铸坯质量的主要缺陷。
它的出现,轻者须进行精整;严重的导致漏钢或铸坯报废,影响铸机作业率和金属收得率,增加了生产成本也打乱了生产计划。
安钢第一炼轧厂自投产以来,铸坯的表面缺陷主要是表面纵裂纹,而表面横裂纹几乎没有出现过。
纵裂纹增加最严重的月份,纵裂纹率高达3.13%,攻关前,纵裂纹的平均发生率为1.9%,经过两个月的攻关,纵裂纹率控制在0.55%的水平。
1 表面纵裂纹的特征
从表面纵裂纹的分布状况看,在板坯的宽面中央区域,即水口区域的表面纵裂纹占整个铸坯表面裂纹的90%,其余的分布在铸坯宽面的1/4和3/4区域,内、外弧都有,内弧的表面纵裂纹比例明显高于外弧的比例。
从裂纹的长短看,大于1m的占表面纵裂纹的多数;从裂纹的深度看,大于10mm的占多数。
2 表面纵裂纹的产生原因与控制措施
2.1 钢水质量的影响
2.1.1 钢中碳含量的影响
C含量在0.10%~0.12%范围内,裂纹敏感性最大;C含量≥0.18%时,板坯表面裂纹的发生率是随碳含量的增加而增加的[1]。
由铁碳相图可知,当碳含量在0.10%~0.14%时,凝固过程发生包晶反应并伴随δ→γ相变,产生较大的体积收缩,铸坯与结晶器壁之间产生空隙,导出热量较小,坯壳最薄,在表面形成凹陷,凹陷部位冷却和凝固速度比其它部位慢,组织粗化,在热应力、摩擦力和钢水静压力等作用下,在凝固坯壳薄弱处产生裂纹,并且在二冷作用下裂纹加深和扩大[2]。
根据数据统计结果来看,C含量在0.12%~0.14%对板坯纵裂有一定的影响。
2.1.2 成品钢中硫含量的影响
硫在钢中的溶解度极小,与铁生成FeS,FeS与FeO能形成低熔点的热脆性共晶体,并在晶界析出。
极易在晶界处产生裂纹,所以要尽可能降低钢中的硫含量。
成品钢中硫含量与板坯表面纵裂的关系见表1。
从表1可以看出,成品钢中的w(S)>0.030%的炉次,裂纹比是浇铸比的10倍;成品w(S)在0.030%~0.015%之间的,裂纹比与浇铸比的比值迅速下降,但仍然高于平均值;而w(S)0.14%;Q345类钢成品w(C)>0.16%;普通钢种要求终点w(C)>0.08%。
通过技术比武、考核等管理措施使这3项指标的受控率均达到了85%以上。
(2)对硫的控制。
在条件许可的情况下,每炉进行铁水预脱硫,保证铁水w(S)<0.010%,成品w(S)<0.020%的控制率达到95%以上。
2.2 影响液面稳定的因素
由于采用液面自动控制技术,正常拉钢的情况下,液面波动都在±4mm以下,表3为特殊情况影响液面稳定的因素与裂纹的关系的统计。
表3 液面波动因素对裂纹的影响
从表3看,开浇第一炉(或换水口第一炉)易出裂纹,这与开浇、换水口时液面不稳和拉速变化多有关。
换渣和变渣线第一炉出现裂纹的比例也高,说明影响弯月面稳定性的操作与纵裂纹的产生有一定的对应关系。
2.3 保护渣性能的影响
结晶器的润滑对纵向裂纹形成有重要影响,尤其是在大的板坯宽厚比和高的浇铸速度下,这种影响更大。
因为结晶器与坯壳表面之间的摩擦力使坯壳承受较大的负荷,在牵引坯壳向下运动时会产生纵向应力,良好的润滑对降低应力非常有效,若摩擦力不能减小,则坯壳在结晶器内被撕裂。
在浇铸过程中,摩擦阻力稳定在7.5~13kN/m2范围内,一般不会有纵裂纹的产生,若摩擦力过大或波动较大,则易出现纵裂纹。
保护渣粘度过高和过低都容易引起纵裂。
保护渣粘度太低,则渣耗量过高,易引起液渣流入不均匀。
在渣膜最厚的地方,坯壳凝固慢,该处坯壳薄,成为应力集中点,易产生纵裂;粘度过高,则渣耗量太少,渣膜太薄,厚度不均匀,容易形成间断的渣膜,也易产生纵裂。
保护渣必须保证合适的液渣层厚度,过厚或过薄都会使铸坯产生表面纵裂纹。
实践表明,当液渣层厚度在8~15mm时,铸坯的表面纵裂纹很少出现,在此范围之外,纵裂纹显著增加,过厚或过薄,纵裂纹比都上升。
直结晶器加上直立段,共有3.7m的夹杂物上浮空间,使钢水中的夹杂物上浮良好,保护渣吸收夹杂量较大,熔渣成分波动范围较大,对此铸机需要保护渣具有良好的吸收夹杂物能力。
保护渣使用前后成分变化如表4所示。