中低低变换工艺中几个技术问题的探讨
19-变换各工艺简介

Fe3O4 与 FeS 的晶体结构差异大,产生的相变应力大,催化剂颗粒容易 破碎和粉化。 (3)降压速度太快。停车时如降压速度太快,由于这时催化剂颗粒中心的压 力远远高于外表面的压力。以至产生“爆裂”现象,使颗粒破碎粉化。 (4)液态水进入催化剂床层与催化剂接触,会使催化剂粉化。
• 9.延长高变催化剂的寿命应注意哪些问题? • (1)严格控制高变催化剂的还原和操作温度。还原温度越高,活性 最佳期越短,还原温度必须控制在催化剂允许的还原温度范围之内。 • 操作温度要尽量控制在催化剂活性温度低限。随着使用时间的增加, 催化剂活性逐步降低,操作温度可逐步提高,每次提高温度不超过 10℃。 • (2)控制合适的入炉汽气比,合理分配各段变换率。 • (3)进变化工段的半水煤气需脱硫、除尘、防焦油,防止毒物、杂 质和冷凝水进入催化剂床层。 • (4)稳定生产工艺操作条件如温度、压力、半水煤气成分、气量、 汽气比等,半水煤气中氧含量应小于0.5%。热点温度波动每小时不超 过±10℃。 • (5)蒸汽锅炉、合成废锅、饱和热水塔、高变炉段间喷水等都应采 用除盐水,以防止钠、氯的化合物进入高变炉对催化剂造成危害。 • (6)停车时卸压不宜太快,并要防止漏入空气或液态水进入催化剂 床层。
• 空间速度的大小对变换反应有什么影响? • 空间速度简称“空速”,是指单位时间内通过单位面积的催化剂的气 体标准积数。单位为m3(标)/[m3(催化剂).h]或简写成h-1。 • 空间速度的大小,既决定催化剂的生产能力,又关系到变化率的高低。 空速过小,反应热小,催化剂床层温度降低,变换率下降;空速过大, 气体与催化剂接触时间短,来不及反应就离开了催化剂床层,变换率 也下降。空速与催化剂型号有关,不同型号的催化剂确定不同的空速。 高变催化剂空速一般控制在500~1000 h-1,低变催化剂空速一般控 制在1000~2000 h-1,B303Q低变催化剂用于全低变流程,其空速 可控制在2500 h-1左右。催化剂空速的大小还与催化剂的活性有关。 催化剂活性好,反应速度快,可以采用较大的空速;催化剂活性差, 反应速度慢,必须降低空速。
一氧化碳低温变换工艺及应用
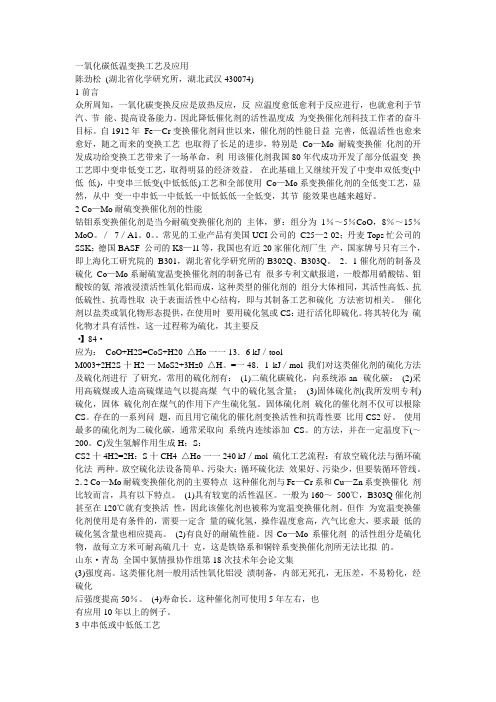
一氧化碳低温变换工艺及应用陈劲松(湖北省化学研究所,湖北武汉430074)1前言众所周知,一氧化碳变换反应是放热反应,反应温度愈低愈利于反应进行,也就愈利于节汽、节能、提高设备能力。
因此降低催化剂的活性温度成为变换催化剂科技工作者的奋斗目标。
自1912年Fe—Cr变换催化剂问世以来,催化剂的性能日益完善,低温活性也愈来愈好,随之而来的变换工艺也取得了长足的进步,特别是Co—Mo耐硫变换催化剂的开发成功给变换工艺带来了一场革命,利用该催化剂我国80年代成功开发了部分低温变换工艺即中变串低变工艺,取得明显的经济效益。
在此基础上又继续开发了中变串双低变(中低低),中变串三低变(中低低低)工艺和全部使用Co—Mo系变换催化剂的全低变工艺,显然,从中变一中串低一中低低一中低低低一全低变,其节能效果也越来越好。
2 Co—Mo耐硫变换催化剂的性能钴钼系变换催化剂是当今耐硫变换催化剂的主体,萝:组分为1%~5%CoO,8%~15%MoO。
/7/A1。
0。
常见的工业产品有美国UCI公司的C25—2-02;丹麦Tops忙公司的SSK;德国BASF 公司的K8—1l等,我国也有近20家催化剂厂生产,国家牌号只有三个,即上海化工研究院的B301,湖北省化学研究所的B302Q、B303Q。
2.1催化剂的制备及硫化Co—Mo系耐硫宽温变换催化剂的制备已有很多专利文献报道,一般都用硝酸钴、钼酸铵的氨溶液浸渍活性氧化铝而成,这种类型的催化剂的组分大体相同,其活性高低、抗低硫性、抗毒性取决于表面活性中心结构,即与其制备工艺和硫化方法密切相关。
催化剂以盐类或氧化物形态提供,在使用时要用硫化氢或CS:进行活化即硫化。
将其转化为硫化物才具有活性,这一过程称为硫化,其主要反·】84·应为:CoO+H2S=CoS+H20 △Ho一一13.6 kJ/toolM003+2H2S十H2一MoS2+3Hz0 △H。
=一48.1 kJ/mol 我们对这类催化剂的硫化方法及硫化剂进行了研究,常用的硫化剂有:(1)二硫化碳硫化,向系统添an--硫化碳;(2)采用高硫煤或人造高硫煤造气以提高煤气中的硫化氢含量;(3)固体硫化剂(我所发明专利)硫化,固体硫化剂在煤气的作用下产生硫化氢。
一氧化碳变换工艺分析

万方数据
第 27卷 化 肥
中低低工艺是在吸收了中串低和全低变工艺 优点的基础上发展起来的,通常设2段Fe-Cr中 变催化剂后串2段Co-Mo耐硫低变催化剂,典 型的工艺流程如图4所示。中变两段之间通常采 用水冷激或原料气冷激降温,低变进口温度通常 仍采用调温水加热器调节。由于保留了一、二段 Fe-Cr中变催化剂,使得后串的Co-Mo耐硫低 变催化剂基本上不需要保护;由于第一、二段远离 平衡,反应推动力较大,在较高的温度下使用Fe -Cr中变催化剂效果也较理想;Co-Mo耐硫低 变催化剂的使用条件与中串低时相近,第一段热 点温度略高,因此对变换系统H2S浓度的要求亦 相对较低(100mg/m3已可满足工艺要求)。
26
段间、二三段间采用水冷激方法降温、增湿;变换 炉出口变换气经热交换器加热入口半水煤气、水 加热器加热热水而降温,再入热水塔回收热量后 离开变换工序。中温变换工艺是合成氨工业中历 史最悠久的,在长期的实践过程中,进行了不断的 改革和创新,主要有:采用活性温度低、催化活性 高 的 Fe-Cr中 变 催 化 剂 , 降 低 了 入 炉 温 度 和 水 汽 比;采用段间水冷激降温措施,减少了系统的热负 荷,降低了系统的阻力降,有利于节省蒸汽;强化 了热量回收系统,提高了系统的热利用率等。
变换工艺催化剂的使用及常见问题的处理
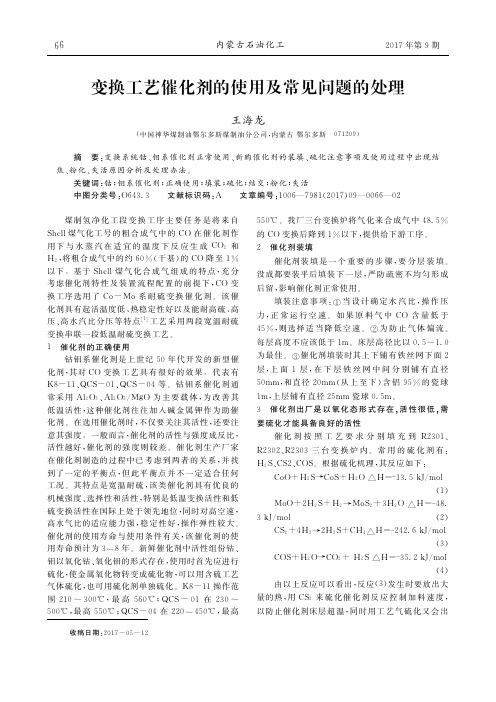
变换工艺催化剂的使用及常见问题的处理王海龙(中国神华煤制油鄂尔多斯煤制油分公司,内蒙古鄂尔多斯 071209) 摘 要:变换系统钴、钼系催化剂正常使用、新购催化剂的装填、硫化注意事项及使用过程中出现结焦、粉化、失活原因分析及处理办法。
关键词:钴;钼系催化剂;正确使用;填装;硫化;结交;粉化;失活 中图分类号:O643.3 文献标识码:A 文章编号:1006—7981(2017)09—0066—02 煤制氢净化工段变换工序主要任务是将来自Shell煤气化工号的粗合成气中的CO在催化剂作用下与水蒸汽在适宜的温度下反应生成CO2和H2,将粗合成气中的约60%(干基)的CO降至1%以下。
基于Shell煤气化合成气组成的特点,充分考虑催化剂特性及装置流程配置的前提下,CO变换工序选用了Co-Mo系耐硫变换催化剂。
该催化剂具有起活温度低、热稳定性好以及能耐高硫、高压、高水汽比分压等特点[1]工艺采用两段宽温耐硫变换串联一段低温耐硫变换工艺。
1 催化剂的正确使用钴钼系催化剂是上世纪50年代开发的新型催化剂,其对CO变换工艺具有很好的效果。
代表有K8-11、QCS-01、QCS-04等。
钴钼系催化剂通常采用Al2O3、Al2O3/MgO为主要载体,为改善其低温活性,这种催化剂往往加入碱金属钾作为助催化剂。
在选用催化剂时,不仅要关注其活性,还要注意其强度。
一般而言,催化剂的活性与强度成反比,活性越好,催化剂的强度则较差。
催化剂生产厂家在催化剂制造的过程中已考虑到两者的关系,并找到了一定的平衡点,但此平衡点并不一定适合任何工况。
其特点是宽温耐硫,该类催化剂具有优良的机械强度、选择性和活性,特别是低温变换活性和低硫变换活性在国际上处于领先地位,同时对高空速,高水气比的适应能力强,稳定性好,操作弹性较大。
催化剂的使用寿命与使用条件有关,该催化剂的使用寿命预计为3~8年。
新鲜催化剂中活性组份钴、钼以氧化钴、氧化钼的形式存在,使用时首先应进行硫化,使金属氧化物转变成硫化物,可以用含硫工艺气体硫化,也可用硫化剂单独硫化。
一氧化碳低温变换工艺及应用综述

国内外高职院校招生制度对比研究2014年9月国务院发布《关于深化考试招生制度改革的实施意见》,其中指出,到2020年,基本建立中国特色的现代教育考试招生制度,形成分类考试、综合评价、多元录取的考试招生模式。
这一意见的提出,将招生考试改革又一次推到了大众面前,引发了广泛的讨论。
与此同时,美国、德国、加拿大等发达国家的招生制度也在不断地发展和完善,我们在思考自身的同时,也可以比较各国的招生制度,通过分析研究促进我国教育招生制度的改革。
标签:高职院校;招生制度改革;国内外对比高校招生制度改革一直是一个热门话题,高校招生制度的优劣直接影响了整个教育体系,高职院校作为高校的一部分,在招生制度的改革中也起着举足轻重的作用。
近年来,高职院校的招生制度随着我国高考制度的改革也一直在调整着,无论从招生方式、考试内容还是管理办法方面,都进行了很大的改革。
一、我国高职院校招生制度的改革及现行招生制度1.我国招生制度的历史沿革我国古代选拔人才的方式可以追溯到秦朝以前的“世卿世禄”制度,直到隋唐年间,随着改革的深入,形成了比较完善的科举制,科举制又经过历次改革,一直沿用到清朝灭亡,但是这些制度主要都是古代为统治者选拔人才服务的,古代的学校数量稀少,学生大都是家境宽裕以及有一定文化程度的,这也体现了当时考试制度的缺失。
直到新中国成立后,我国才逐步建立起了全国统一的招生制度,虽然有一定的弊端,但是当时国家亟须人才,统一的招生考试的确在一定时间内为国家解决了一部分困难。
后来由于“文化大革命”影响,高考制度暂停了一段时间,直到1976年才正式恢复,恢复后的高校仍然主要是通过高考的形式选拔学生,但是高考的内容一直有小的变动,比如英语课程的加入等。
到了21世纪,随着学校数量的增多,考生生源的扩大,不同省份学校、生源的差异越来越明显,部分省份对高考试卷采用自主命题的方式,其他省份还是沿用全国高考卷。
2003年,教育部开始推行自主招生,结束了此前高校只能在每年同一时间通过高考选拔学生的历史,这次改革可以说是比较大的改变,也有很深远的影响。
中低低变换工艺调整的几个问题

催 化剂 型 号 装填 量 / m
经验 , 当半 水 煤 气 中 H S质 量 浓 度 ≥ 10m / 0 gm’ ( 态) , 标 后 该催 化剂 即有 明显硫 中毒 现象 , 即会导 致 中 变 炉 压 差 上 升 、 应 活性 下 降 、 汽 用 量 增 反 蒸
中变催化剂
加。依据机理 ,eO 与 H s发生可逆反应 , F : 半水 煤气 中 H S含 量 大 幅上 升 时 , 应 有 利 于 F S的 反 e 转化 、 生成 , F 减 少 , 化 剂 活性 下 降 。此 使 eO 催 时适 度 加 大 蒸 汽 用 量 , 扫 H s 可 使 FS 向 吹 :, e F, 转化 , 复其 活 性 , 半 水 煤气 中 H S含 量 eO 恢 但 : 过高 的工况 不能持 续时 间过长 。
0 前 言
福 建永安 智胜 化工 股 份有 限 公 司 ( 以下简 称
智胜 公 司 )Ⅱ变 换 系 统 采 用 0 8M a中低 低 工 . P 艺, 设计 与 8 ta合 成 氨 配套 , 际 合 成 氨产 能 0k / 实
超过 9 ta 5k/ 。该 变 换 系统 有 其 特 殊 的生 产 工 艺
操 作 温 度/c q
3 0~ 0 5 50
10 4 0 8 8
3 半水煤气 H: S含量变化 的影响
3 1 H S含量 高 的危害 . 3 1 1 对 中变催 化 剂的影 响 ..
0 2 05 ) 介质工 作 温度 处 于露 点 温度 以下且 .0~ .0 , 在 (0+2 ℃ 以 内 ( 为 工 作 或运 行 压 力 , 6 P) P 即表 压 ) p <9 其 H2 量 浓 度 在 4 ,H , s质 0~10mgm 0 /
净化-7-如何选择耐硫低温变换工艺及技改注意事项
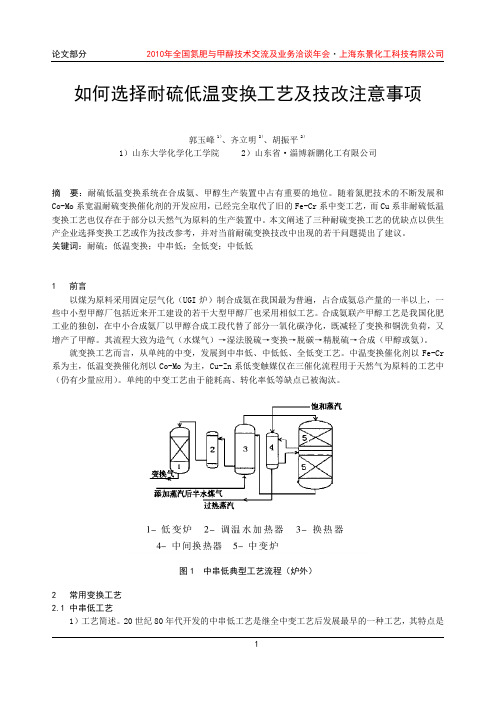
如何选择耐硫低温变换工艺及技改注意事项郭玉峰1)、齐立明2)、胡振平2)1)山东大学化学化工学院 2)山东省·淄博新鹏化工有限公司摘 要:耐硫低温变换系统在合成氨、甲醇生产装置中占有重要的地位。
随着氮肥技术的不断发展和Co-Mo系宽温耐硫变换催化剂的开发应用,已经完全取代了旧的Fe-Cr系中变工艺,而Cu系非耐硫低温变换工艺也仅存在于部分以天然气为原料的生产装置中。
本文阐述了三种耐硫变换工艺的优缺点以供生产企业选择变换工艺或作为技改参考,并对当前耐硫变换技改中出现的若干问题提出了建议。
关键词:耐硫;低温变换;中串低;全低变;中低低1 前言以煤为原料采用固定层气化(UGI炉)制合成氨在我国最为普遍,占合成氨总产量的一半以上,一些中小型甲醇厂包括近来开工建设的若干大型甲醇厂也采用相似工艺。
合成氨联产甲醇工艺是我国化肥工业的独创,在中小合成氨厂以甲醇合成工段代替了部分一氧化碳净化,既减轻了变换和铜洗负荷,又增产了甲醇。
其流程大致为造气(水煤气)→湿法脱硫→变换→脱碳→精脱硫→合成(甲醇或氨)。
就变换工艺而言,从单纯的中变,发展到中串低、中低低、全低变工艺。
中温变换催化剂以Fe-Cr 系为主,低温变换催化剂以Co-Mo为主,Cu-Zn系低变触媒仅在三催化流程用于天然气为原料的工艺中(仍有少量应用)。
单纯的中变工艺由于能耗高、转化率低等缺点已被淘汰。
图1 中串低典型工艺流程(炉外)2 常用变换工艺2.1 中串低工艺1)工艺简述。
20世纪80年代开发的中串低工艺是继全中变工艺后发展最早的一种工艺,其特点是在全中变后加了一段低变催化剂。
具体做法有所不同,有的将Co-Mo低变触媒放在中变炉的第三段,而大部分是在三段中变后,单独再设一个低变炉,两者都是在变换气出中变段后经主热交再进低变段。
为了控制入低变段(炉)的温度,大多数厂在主热交换器和低变炉之间,加一个与循环热水换热的调温水加热器或直接喷水的调温器。
中低低变换工艺及其“准零汽耗”的实现
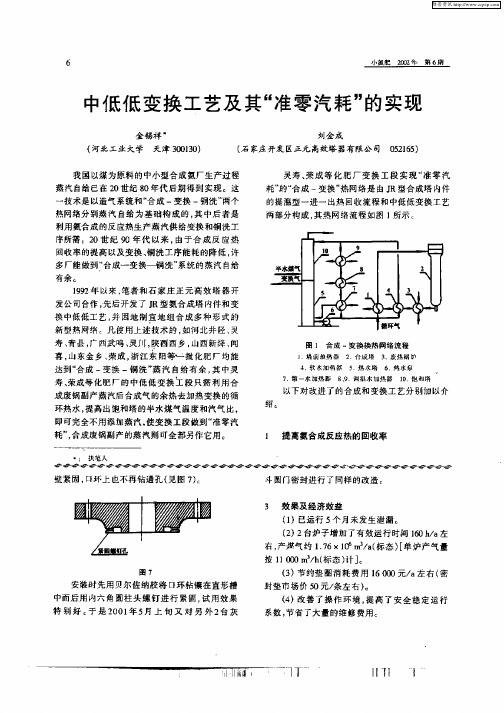
寿 、 县 , 西武鸣 、 川 , 青 广 灵 陕西 西乡 , 山西新 绛 、 闻
喜 , 东金乡 、 山 荣成 , 江 东 阳等一 批 化肥 厂 均能 浙 达到“ 合成 一变换 一铜 洗 ” 汽 自给 有 余 , 中灵 蒸 其 寿、 荣成等 化 肥厂 的 中低 低 变换 工 段 只 需 利用 合
绍
以下对 改进 了的合成 和 变换工 艺分 别加 以介
耗 ”合成废 锅 副产的蒸 汽则 可全 部另作 它用 ,
:
1 提高氨合成反应热的回收率
执 笔人
壁 紧固 , 口环 上 也不再钻通 孔 ( 图 7 见 )
斗 圆r 密封进 行 了同样 的改造 J 3 效果及经 济效 益 ( )已运行 5个月未 发生 泄 漏。 1 () 2 2台炉子增 加 了有 效运 行 时间 10h a左 6 /
维普资讯
6
小氮肥
2O 0 2年
第6 期
中低 低 变 换 工 艺 及 “ 零 汽 耗 实 其 准 ’ ’ 的 现
全锡 祥
刘金成
( 河北工业 大学
天 津 303 ) 0 10
( 家庄 开发 区正元 高效塔 器有 限公 司 石
026 ) 515
操作 控制 、 净 值 高 、 氨 生产 能 力大 、 化 剂使 用 寿 催
4 ~4 0 5℃ , 明没 有回收 的 合 成 反应 热 已经 很 少 表 了, 其合成 反 应热 的回收率在 国内处 于前列 。
与传 统二 进二 出提 温 型氨台 成热 回收 的工 艺
相比 ,R型 氨合成 提温型 一进 一 出热 回收 流 程有 J 所简化 , 氨合成 塔底部 五通 变为 三通 , 在 不增加 且 设 备的 隋况下 , 增加 了蒸汽 回收量 , 以每 吨氨 可 若 多 回收约 30 蒸 汽计 , 个 年 产合成 氨 6万 t 0 】 的
变换工艺技术的发展_陈劲松

变换工艺技术的发展陈劲松 李小定 吴大天(湖北省化学研究院 武汉 430074)摘要 对中温变换、中串低、中低低、全低变的变换技术进行了回顾,并对目前的新技术进行了介绍。
关键词 变换 回顾 发展Development of Shift Conversion TechnologyChen Jinsong,Li Xiaoding and Wu DatianA bstract A review is given on the technology of medium-temperature shift,medium-and low-temper-ature shift in series,medium-,lo w-and low-te mperature shift in series and all lo w-temperature shift,and an introduction is given to new technologies at present.Keywords shift c onversion review development 一氧化碳变换反应是放热反应,催化剂的终态温度又是反应的关键因素和设计的重要技术指标。
当变换气中CO含量为3%时,终态温度与蒸汽用量的关系见表1。
表1 变换气中CO含量3%时不同温度下蒸汽用量项目变换气出口温度(℃) 220250300350400入炉汽气比(R)0.3070.3380.4240.5690.794吨氨入炉蒸汽用量(kg)838.8923.51158.41554.62169.3 显然,变换反应出口温度愈低,对平衡愈有利,蒸汽用量也愈低。
因此降低催化剂的活性温度成为变换催化剂科技工作者的奋斗目标。
自1912年Fe-Cr变换催化剂问世以来,催化剂的性能日益完善,低温活性也愈来愈好,随之而来的变换工艺也取得了长足的进步。
特别是利用Co-Mo耐硫变换催化剂低温活性好的性能开发了部分低温变换工艺,即在原中变降温后串Co-Mo 催化剂的中串低工艺,根据催化剂的低温性能,低变炉(段)入口气体温度一般可控制在180~230℃左右,出口在210~260℃。
中低低和全低变变换工艺的设计与选择
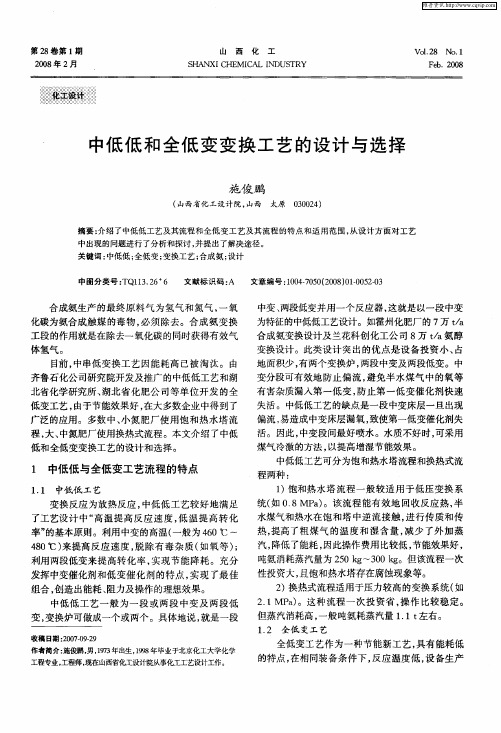
维普资讯
2 0 年 2月 08
施俊鹏 。 中低低 和全低变变换工艺的设计与选择
・5 ・ 3
能力大 。但在 目前 的工 艺 条件 下 , 段催 化剂 因氧 上 化、 反硫 化及硫 酸根 、 化 等污 染 问题 , 氯 会导 致 催 化 剂活性 下降快 , 用寿命 缩短 。基 于此 , 使 一般 应在 一 段入 口前装填保护 剂和抗毒催 化剂 , 防止 出现触媒 老 化、 使用 寿命缩短 、 系统阻力升高较 陕等现象 。 目前 , 全低 变 工艺 大致 可 分 为喷 水增 湿 型 和调 温水 加热器 。全低 变工 艺 一 般为 三 段 , 置一 个 或 设 两个变 换炉 。如 采用 一 低 变 出 口喷 水增 湿 降 温 , 一
1 2 全 低 变 工 艺 .
作者简介: 施俊鹏, 17 男,93年出生,98年毕业于北京化工大学化学 19
全低 变工艺 作 为一 种节 能新 工艺 , 有能 耗低 具
工程专业 , 工程师, 现在山西省化工设计院从事化工工艺设计工作。
的特点 , 在相同装备条件下 , 反应温度低 , 设备生产
中低 低 工 艺 一 般 为一 段 或 两 段 中变及 两 段 低 变 , 换炉可做 成一个 或两个 。具体地 说 , 变 就是 一段
收 稿 日期 :o 7O .9 2 o .92
性投资大, 且饱和热水塔存在腐蚀现象等。 2 )换热式 流程适 用于压力 较高 的变换 系统 ( 如
2 1 a。这种 流 程 一 次投 资 省 , 作 比较 稳 定 。 . MP ) 操 但蒸 汽消耗高 , 一般吨氨 耗蒸汽量 11t . 左右 。
化碳 为氨合 成触 媒 的毒 物 , 必须 除 去 。合 成 氨 变换 工段 的作 用就是在 除去一 氧化碳 的 同时获 得有效 气 体氢气 。 目前 , 中串低 变 换工 艺 因 能耗 高 已被 淘 汰 。 由 齐鲁石 化公 司研究 院开发 及推广 的 中低低 工艺 和湖 北省化学 研究所 、 北省 化 肥公 司等单 位 开发 的全 湖 低 变工艺 , 由于节 能效果好 , 在大 多数企业 中得 到了 广 泛的应用 。 多数 中、 氮肥 厂 使 用饱 和 热水 塔 流 小
3.0MPa中低低加压变换工艺运行总结

a mmo i t2 g,a s vng o 0 W ・ n po r,a d a s v n f1 5 m o o ln tr n a a 03 k a i f3 0i g wae .
Ab t c B s d o h p r h n e ut o h du lw。 w tmp rtr s i rc s t sa t a e n te o ea o rs l fte me im— s o l e eau e hf p o es o t a
3. Pa i h y t e i 0M n t e S n h ssAmm o i a to iua e ia n usr o p Co ,L d. e e t t n na PI n fTa y n Ch m c lI d ty Gr u . t ,apr s n a i o
lw y t m e it n e,a d l r e g ste t n ft e e ui me t o s se r ssa c n a g a r a me to h q p n ,wi t e se m o s m p in pe o f t h ta c n u h t rtn o o
Sh f o e s a . Pa it Pr c s t 3 0 M X aWe e ,S i o g o ,L Y mig ,Y n ei, i a gi,L Y nh n i i i h S nt i u n agD y Q n l w a Y i ica g
i i e ft e p o e s fo ,t c n l gc lc r c e itc nd r s lso d ls lc in o qupme t sg v n o h r c s w l e h o o i a ha a trsis a e u t fmo e e e to fe i n.
中高压电力电子变换中的功率单元及功率器件的级联关键技术研究

中高压电力电子变换中的功率单元及功率器件的级联关键技术研究一、本文概述随着能源结构的转型和电力电子技术的飞速发展,中高压电力电子变换技术在电力系统、新能源发电、工业电机驱动等领域的应用日益广泛。
在这一背景下,功率单元和功率器件的级联关键技术成为了研究热点。
本文旨在探讨中高压电力电子变换中的功率单元及功率器件的级联关键技术,分析其研究现状、发展趋势以及面临的挑战,以期为相关领域的技术研发和应用提供参考。
本文将对中高压电力电子变换的基本概念、技术原理以及应用场景进行简要介绍,为后续研究奠定基础。
接着,重点分析功率单元和功率器件的级联关键技术,包括级联拓扑结构、均流控制策略、热管理和电磁兼容等方面的研究现状。
在此基础上,探讨级联技术在提高变换器容量、效率以及可靠性等方面的优势与局限性。
本文还将关注级联技术在应用中面临的挑战,如高电压大电流下的电磁兼容问题、热管理难题以及成本效益等。
针对这些问题,提出一些可能的解决方案和研究方向,以期推动级联技术的进一步发展。
本文将对中高压电力电子变换中功率单元及功率器件的级联关键技术进行总结,并展望未来的发展趋势和应用前景。
通过本文的研究,希望能为相关领域的技术人员和研究人员提供有益的参考和启示。
二、功率单元级联技术在中高压电力电子变换中,功率单元的级联是实现高电压、大功率输出的关键手段。
级联技术通过将多个低电压、小功率的功率单元在电气上串联或并联,从而构建出高电压、大功率的变换器系统。
这种技术不仅提高了系统的电压和功率等级,还有助于提高系统的可靠性和灵活性。
在功率单元级联过程中,需要解决的关键技术包括单元之间的均压与均流控制、热设计与管理、电磁兼容与干扰抑制等。
均压与均流控制是确保级联系统稳定运行的基础,通过合理的控制策略,使各功率单元在工作过程中保持电压和电流的均衡,避免出现过电压或过电流导致的损坏。
热设计与管理则关注于系统在工作过程中产生的热量,通过有效的散热结构和温度监控,确保功率单元在允许的温度范围内工作,防止热失效。
一氧化碳变换反应工艺流程

一氧化碳变换反应工艺流程一氧化碳变换流程有许多种,包括常压、加压变换工艺,两段中温变换(亦称高变)、三段中温变换(高变)、高-低变串联变换工艺等等。
一氧化碳变换工艺流程的设计和选择,首先应依据原料气中的一氧化碳含量高低来加以确定。
一氧化碳含量很高,宜采用中温变换工艺,这是由于中变催化剂操作温度范围较宽,使用寿命长而且价廉易得。
当一氧化碳含量大于15%时,应考虑将变换炉分为二段或多段,以使操作温度接近最佳温度。
其次是依据进入变换系统的原料气温度和湿度,考虑气体的预热和增湿,合理利用余热。
最后还要将一氧化碳变换和残余一氧化碳的脱除方法结合考虑,若后工序要求残余一氧化碳含量低,则需采用中变串低变的工艺。
一、高变串低变工艺当以天然气或石脑油为原料制造合成气时,水煤气中CO含量仅为10%~13%(体积分数),只需采用一段高变和一段低变的串联流程,就能将CO含量降低至0.3%,图2-1是该流程示意图。
图2-1一氧化碳高变-低变工艺流程图1-废热锅炉2-高变炉3-高变废热锅炉4-预热器5-低变炉6-饱和器7-贫液再沸器来自天然气蒸气转化工序含有一氧化碳约为13%~15%的原料气经废热锅炉1降温至370℃左右进入高变炉2,经高变炉变换后的气体中一氧化碳含量可降至3%左右,温度为420~440℃,高变气进入高变废热锅炉3及甲烷化进气预热器4回收热量后进入低变炉5。
低变炉绝热温升为15~20℃,此时出低变炉的低变气中一氧化碳含量在0.3%~0.5%。
为了提高传热效果,在饱和器6中喷入少量软水,使低变气达到饱和状态,提高在贫液再沸器7中的传热系数。
二、多段中变工艺以煤为原料的中小型合成氨厂制得的半水煤气中含有较多的一氧化碳气体,需采用多段中变流程。
而且由于来自脱硫系统的半水煤气温度较低,水蒸气含量较少。
气体在进入中变炉之前设有原料气预热及增湿装置。
另外,由于中温变换的反应放热多,应充分考虑反应热的转移和余热回收利用等问题。
合成氨变换工段工艺中变串低变换热设计

合成氨变换工段工艺中变串低变换热设计在合成氨的变换工段中,合成气进入变换器,催化剂催化反应生成氨气。
这个过程中,会产生大量的热量,同时还会有一些不完全反应产生的副反应气体。
因此,在变换工艺中需要进行换热以及气体分离。
变换器是合成氨工段中最重要的设备之一,它不仅要能够承受高温高压的工艺条件,还要能够提供足够的接触面积和适宜的操作温度。
在设计变换器时,需要考虑以下几个方面来降低变换热:1.催化剂的选择和设计:催化剂对合成氨的转化率和选择性有很大的影响。
优选高效的催化剂可以提高变换的效率,减少产热量。
同时,还需要根据催化剂的特性设计变换器的结构,以提高反应的效果。
2.换热器的设计:在合成氨变换工艺中,需要进行大量的换热操作以降低温度。
换热器的设计要考虑到换热面积、热传导效果、传热介质的选择等因素。
适当选择换热器的结构和材料,可以提高换热效率,减少能耗。
3.废气的处理:合成氨变换工艺中会产生一些副反应气体,这些气体需要进行分离和处理。
一方面,处理废气可以回收一部分有价值的气体,减少资源浪费;另一方面,处理废气能够降低产生的热量,减少能耗。
4.控制反应温度:合适的反应温度可以提高反应速率和选择性。
通过控制反应温度,可以减少副反应的产生,并且提高变换的效率。
因此,在设计变换工艺时,需要考虑合适的反应温度范围。
总之,合成氨变换工段工艺中的变串低变换热设计是一个综合性的工程问题,需要综合考虑催化剂的选择和设计、换热器的设计、废气的处理以及控制反应温度等因素。
通过合理的设计和优化,可以提高工艺效率,降低能耗,实现工业生产的效益最大化。
单塔和双塔汽提变换低温工艺冷凝液技术探讨

单塔和双塔汽提变换低温工艺冷凝液技术探讨说起单塔和双塔汽提变换低温工艺冷凝液,听起来是不是有点头大?别急,我来给大家捋一捋。
你可千万别小看这东西,它在工业生产中可是个大有作为的角色。
这玩意儿听上去很专业,但如果我给你讲个通俗点的例子,估计你就能马上懂了。
咱得说清楚什么是“汽提变换”。
这其实就是一个用气体处理液体的过程,简单说,就是通过加热或者气体交换把液体中的某些成分分离出来。
是不是有点像你喝的茶,一泡泡出来的就是浓郁的味道,剩下的就是清汤水。
而“低温工艺冷凝液”呢,就是把气体冷却到一定程度,让其中的成分重新变成液体。
这些液体就是我们要处理的宝贵“资源”,它们可能是液化气,也可能是一些化学溶剂,关键是能从这些冷凝液里分离出所需要的成分,做到“物尽其用”。
那单塔和双塔的区别在哪儿呢?别急,我这就给你细细道来。
单塔呢,其实就是一个塔,塔里有液体、气体和一些填料,气体和液体在塔里进行一系列的交换和反应,经过塔顶或者塔底就能得到你需要的液体。
而双塔呢,它的名字就有点“套娃”的意思,两座塔一起工作。
一个塔负责先处理,另一个塔再接着处理,效果当然是更加高效了。
就好比是你请了两个人来干活,一个人在前面分担,你还得接着做,这样才能更快完成任务。
双塔工艺呢,优势就在于分工明确,效率高,产出的冷凝液更加纯净。
哎呀,我得跟你讲个“黄粱一梦”的道理。
很多人看到这两种工艺时,脑袋里总想着:“哎,这个工艺肯定很复杂,搞不好就全是高科技,咱就算了吧。
”但其实没那么夸张。
这些高科技的背后,其实就是一些小心机和聪明的设计,目的就是让我们在生产中能更加节省时间、减少资源浪费。
我突然想起以前在工厂实习的时候,大家都以为“塔”就是那些巨大的金属结构,走在旁边都要小心翼翼。
结果一了解才知道,这些塔的设计其实就像是做菜的配方,塔里加啥,温度是多少,塔底和塔顶之间的区别,每一步都要精准到位。
简直就像是做精致的餐点,丝毫不容忍瑕疵。
说到“冷凝液”,它的作用可是非常重要的,大家千万别小看它。
耐硫变换催化剂使用、硫化中出现的问题及建议

耐硫变换催化剂使用、硫化中出现的问题及建议王立群【摘要】介绍4.0 MPa和6.5 MPa气化系统变换工段的情况.结合生产实际,建议中温变换采用耐硫变换催化剂,还推荐了补硫方法.【期刊名称】《化工设计通讯》【年(卷),期】2011(037)005【总页数】4页(P12-15)【关键词】变换催化剂;使用;硫化;问题;补硫【作者】王立群【作者单位】黑龙江龙煤东化有限公司,黑龙江伊春 154111【正文语种】中文【中图分类】TQ113.26+4.2耐硫变换催化剂近几年在化工行业得到广泛应用,无论是合成氨变换还是甲醇变换都逐渐放弃铁系催化剂,尤其是设计压力较高的系统,耐硫变换催化剂更具优势。
因其制作强度高、不易粉碎、变换效率高、使用时间长等特点深受使用者的青睐。
但是耐硫变换催化剂也有不足之处,在原料气硫含量低、水汽比大的情况下,耐硫变换催化剂极易出现反硫化现象,催化剂使用寿命缩短,尤其是硫含量不稳定,使催化剂在硫化与反硫化之间波动时,更易造成催化剂快速失活。
为此,笔者总结多年的生产实践经验,对耐硫变换催化剂的硫化过程及使用情况阐述一下自己的看法。
1 催化剂的选择近几年国内外催化剂生产厂家生产出一系列耐硫变换催化剂,使用业绩较好的有K811、QCS-01、QCS-04、QDB-04几种型号的催化剂。
国内产品尤其以青岛联信和齐鲁科力两家产品使用较多,使用效果也是说法不一,尤其是在原料气低硫环境下使用的情况差别较大。
由于我公司是以煤为原料生产合成氨的厂家,所采用的工艺是水煤浆气化工艺(设计压力有4.0MPa和6.5MPa两个压力等级)。
6.5 MPa等级采用西北化工研究院多元料浆气化技术,气化装置出口原料气水汽比1.45,温度237℃。
变换入口原料气硫含量500×10-6。
变换采用中低温变换,催化剂采用耐硫变换催化剂,入口硫含量低、水汽比大,对耐硫变换催化剂有着极高的要求,否则就要发生反硫化现象。
青岛联信的催化剂,使用时要求硫含量不低于1 200×10-6;齐鲁科力要求硫含量不能低于400×10-6。
工艺流程指标控制与工艺

工艺流程指标控制与工艺工艺流程指标控制与工艺波动查询处理一、压缩机工艺流程指标的规定1、在合成氨生产过程中,由于需要很多工序(变换、脱碳、碳化(含变脱)),甲醇(含低压甲醇、精炼醇皖化合成),这些工序必须在必要的压力条件下才能顺利的进行,所以需要压缩岗位输送不同的压力级次来对这些岗位进行辅助。
于是就需要压缩机控制工艺,主要是太坏力,其次是温度。
要想操作好压缩机工艺就必须对相关工段有必要的了解。
2、最主要的工艺指标就是各段进出口压力的控制及对系统压力的控制调节,工艺稳定能耗较低,系统压力规定:(1)变换:我厂采用的中低变换一般压力控制在0.8-0.9kg/cm2之间,原因是低变对煤质要求比较宽松,工艺易控制,与高变相皆可节约触煤,并可减少二出、三进压差,这就等于变相降低了压缩机功耗,提高三进压力,缩少三段压缩比,提高三段扩气量,在三段扩气量提高的同时,又可降低变换压力。
(2)脱碳:我厂脱碳分二个压力等级,即18kg/cm2脱碳和27kg/cm2脱碳,此压力等级有利于二氧化碳的吸收,提高气体的净化度。
为什么分二年公斤级脱碳?二氧化碳在碳丙中的溶解度随压力升高而增加,提高吸收压力,有利于提高净化度且27kg/cm2在同样操作工艺下比17kg/cm2气体净化度高,碳丙循环量小,不易带液。
合成氨联醇生产原料损耗低,故现在我们压缩多选七级压缩,就是此原因。
(3)甲醇:提高压力可加快气体与触煤反应,增加甲醇的生成,提高甲醇的质量,抑制副反应,但压力也不能太高,一般中压甲醇100kg/cm2-130kg/cm2之间,若再增高压力,不仅增加动力消耗,而且对设备材料的要求也相应增加。
随着技术革新、进步,低压甲醇越来越普及,较中太坏甲醇相比,低压甲醇投资省、能耗低、工艺稳定、操作方便,而且可以在压缩机中间段降低压力,这样就可以节约电耗,这样就可以节约电耗,一般低压甲醇的压力控制在50kg/cm2-80kg/cm2之间,其作是通过甲醇作用,使压缩机级间压力降低,有利用前段的压力下降,减少气体与铜液的对流量,以及少开铜泵,降低电耗并稳定微量。
- 1、下载文档前请自行甄别文档内容的完整性,平台不提供额外的编辑、内容补充、找答案等附加服务。
- 2、"仅部分预览"的文档,不可在线预览部分如存在完整性等问题,可反馈申请退款(可完整预览的文档不适用该条件!)。
- 3、如文档侵犯您的权益,请联系客服反馈,我们会尽快为您处理(人工客服工作时间:9:00-18:30)。
小氮肥设计技术
东寿光等化肥厂在单醇生产中均采用了上述精脱硫工艺。
目前国内正在设计的单醇厂也基本上都采用此工艺,使其得到较快推广,为以煤为原料的低压合成单醇生产的技术进步作出贡献。
4.2.4在单醇生产中部分脱碳后的常温精脱硫,同联醇生产或合成氨生产完全一样,全国已有
600多个厂次的应用经验。
只是根据不同的工况
选用JTL-1或JTL-4新工艺,没有特别需注意的
地方,在此不再论述。
5小结
5.1实验室与工厂侧流试验数据表明,与常温T504水解催化剂相比,EH-2中温耐硫水解催化
剂有突出的抗硫酸盐化的优异性能。
5.2以煤为原料的低压合成单醇生产中,由于采
用了部分变换工艺,使变换气中有机硫COS含量比全变换中提高约10倍,为保护脱碳溶液不受
污染与降低脱碳后的精脱硫负荷,在部分变换后应加设EH-2中温耐硫水解催化剂,它可放在变换炉外,也可放在变换炉内。
5.3针对以煤为原料的单醇生产的特点,作者提
出的由EH-2催化剂与常温精脱硫工艺组成的精脱硫技术已在安阳、鲁南等单醇生产装置中应用,达到预期效果,并取得甲醇催化剂寿命达3年1个月,生产强度达14000t甲醇/m3催化剂的国内最好水平。
参考文献
1中国专利ZL01106660.1
2孔渝华,王先厚.化肥设计,2004,42(5):463
景汝励等.化肥与催化,1989,(1):13
4孙志强,张震,栗肖红.中氮肥,2002,(2):325
丰中田,李江年,陈发凤.化肥设计,2003,41(6):39
(收稿日期:2005-10-25)
摘
要
对中、低、低变操作中常遇到的几个技术性问题进行了探讨。
关键词
中、低、低变换
工艺
问题
探讨
!!!!!!!!!!!!!!!!!!!!!!!!!!!!!!!!!!!!!!!!!!!!!"
!!!!!!!!!"
!!!!!!!!!!!!!!!!!!!!!!!!!!!!!!!!!!!!!!!!!!!!!"
!!!!!!!!!"
中低低变换工艺中几个技术问题的探讨
胡中光
(湖北双雄催化剂有限公司
432721)
目前在氮肥生产中,中低低变换工艺的推广力度是最大的,也是最成功的。
在工艺设计上针对CO变换的放热反应,较好地满足了高温提高反应速度,低温提高转化率的基本原则。
充分利用低价格的中变催化剂高温反应来提高反应速度,脱除有毒物质,加速有机硫的转化,利用二段低变来提高CO转化率,分层次、有梯度的不同温区,充分发挥了中变催化剂和低变催化剂的特点,实现了最佳组合。
尤其在操作稳定性与操作弹性上比全低变更加优越,并且在改造资金和技改时间方面也有明显的优势。
但针对不同的厂家,各自的生产条件不同,设备状况不同、投资改造力度也各不相同,管理理念上也存在一定的差异,因而所达到的效果也各有不同,但肯定比改造前要好得多。
综合各氮肥生产厂家中低低改造的经验,现就改造中需考虑的几个问题和大家一起探讨。
1搞好半水煤气的冷却和油分离
在原来的理念里认为:进变换饱和塔的半水
煤气温度越高,出饱和塔的半水煤气温度也会提高,从而认为变换所需蒸汽消耗就会越低,甚至将进变换的半水煤气管道进行保温,并取消压缩机二段出口冷却。
而事实上:如果进饱和塔半水煤气温度越高,出饱和塔的水温肯定会升高,从而出热水塔的变换气温度也会越高,且肯定高于进饱和塔的半水煤气温度。
这两种气体相比,半水煤气为干气,而变换气为湿气,其1℃的温升中所含热量的差别很大,后者为前者的十倍以上。
因半水煤气温度升高而引起变换气出热水塔温度升高所造成的热损更大,蒸汽消耗也增加。
另一方面,由于半水煤气温度较高,其中的焦油和压缩机油分离效果不好,从而带入饱和塔、热交############################################
2005年第26卷第6期
28
换器和中变催化剂层,降低了传热传质效率,增加热水排放。
更有甚者,对中变催化剂形成物理性包裹,降低催化剂活性。
因此,加强进变换半水煤气的冷却和油分离是降低变换蒸汽消耗,保障催化剂使用寿命的有效措施之一。
目前所采取的方法是增加压缩二段出口半水煤气的冷却。
将半水煤气温度降至45℃以下,再利用较大的焦炭过滤器或丝网过滤器充分除去煤气中所夹带的焦油和压缩机油污。
2搞好汽水分离,采取有效措施,保障热交长效使用
采取中、低、低工艺以后,变换总汽气比比中串低工艺要低很多,可从0.6~0.7降至0.4~0.5,蒸汽消耗大量减少,每吨氨可降低500~600kg。
由于蒸汽消耗的降低,变换气余热量也减少,饱和塔出口半水煤气加蒸汽后,温度也比中串低工艺要低很多,从而对热交的露点腐蚀加剧。
为保障热交的长效使用,需采取有效措施。
有的厂在热交前增加一个有不锈钢列管的预热交换器,其下部为汽水分离段,将水尽量分离彻底,上部为换热器,将半水煤气温度提至露点以上,从而对主热交起到了很好的保护作用。
3选择适合自己条件的中变催化剂
原有的中温变换工艺和中变串低变工艺,因其汽气比高,对中变催化剂的选择,一般正规生产厂家的中变催化剂都可以使用。
但随着中低低工艺汽气比的大幅降低,传统型中变催化剂要求使用条件是汽气比必须>0.5,显然已不适应于中低低工艺。
因此,在中变催化剂的选型上一定要选择适合低汽气比和相应H2S含量的中变催化剂。
否则,由于汽气比的降低,半水煤气中的H2S、油污和其它杂质对中变催化剂的影响加剧,催化剂的使用寿命和效果将会大打折扣,甚至出现无法正常运行的状况。
4控制适宜的汽气比保障催化剂长效运行汽气比的控制是中低低工艺操作的重要指标。
在一定的负荷下,汽气比的控制应是相对稳定的。
对于没有联醇的厂家,变换出口CO控制1.5%左右是最经济合理的,此时的汽气比应为0.45左右。
过低的CO则需要较高的汽气比,蒸汽消耗明显增加。
而对于有联醇的厂家,变换出口CO达3%~4%,有的甚至达到8%~10%,其汽气比可以很低。
但对于中变催化剂的适应性来说,汽气比是不能太低的。
如果汽气比太低,在生产过程就有可能出现中变催化剂中的Fe3O4
的过度还原:Fe3O4+4CO=3Fe+4CO2
反应生成的铁既可能作为费-托反应的催化剂,又可以与半水煤气中的H2S形成FeS,从而使中变催化剂逐步失去活性。
如果发生此种现象,可以通过一定的办法,即用蒸汽进行热洗的方法使催化剂活性得到部分恢复,我们在山西巴公化肥厂和山东滕州化肥厂都有这样成功处理的经验。
理论上出现过度还原的条件是YCO>YH2O,YH2O/YH2<0.15,而在实测中,当半水煤气中CO为29%~30%,汽气比低于0.38时,都有可能发生过度还原。
因此,我们在实际生产中,最低的汽气比控制应是0.4。
5控制适宜的催化剂使用温度
催化剂温度的控制原则是在保证变换率的前提下达到变换系统自热平衡。
原则上是越低越好。
当生产负荷一定、催化剂装填数量一定的情况下,中变催化剂的热点温度取决于半水煤气中氧含量和催化剂层半水煤气进口温度。
单纯地考核催化剂层热点温度是没有多少实际意义的。
因此对于中变催化剂和低变催化剂而言,在催化剂低温活性很好的情况下,尽可能保障进口温度在相对低温下的操作,从而增加操作弹性、有效延长催化剂使用寿命。
6控制适宜的热水循环量
中低低工艺节能的控制手段是最大限度地提高饱和塔出口半水煤气温度,因此,在饱和塔热水塔传质传热系数一定的条件下,热水循环量的大小和热水温度的高低是提高半水煤气温度的重要手段。
当生产负荷一定时,热水循环量越大,热水温度就会越低,反之越高。
但并不是最高的热水温度就会有最高的煤气饱和度,只有能达到最高煤气饱和度的热水循环量,才是最佳热水循环量,这只有经过实际生产调试才可以得到。
总之,中低低变换工艺已在各氮肥生产厂家得到了广泛的推广和应用,给生产企业带来了很大的经济效益,各生产厂家也积累了很多各自成功的经验,我们希望能为氮肥生产厂家的技术更新和观念更新起到桥梁的作用,为氮肥企业的进一步发展壮大,尽到我们的最大努力。
(收高日期:2005-10-25)
胡中光:中低低变换工艺中几个技术问题的探讨
第6期29。