散热设计热传测试报告
热分析实验报告

热分析实验报告实验目的热分析实验是用于研究物质在升温或降温过程中的物理和化学性质变化的实验方法。
本实验的目的是通过热分析技术,研究样品在升温过程中的热行为,并分析其热性质。
实验原理热分析涉及到一系列技术方法,主要包括差热分析(Differential Thermal Analysis,DTA)、热重分析(Thermogravimetric Analysis,TGA)和热差式量热计(Differential Scanning Calorimetry,DSC)。
在本实验中,我们将主要使用差热分析和热重分析来研究样品的热性质。
差热分析是利用样品与参比样品之间在温度升高或降低过程中吸放热量的差别,来研究样品的物理和化学性质变化。
当样品发生物理或化学变化时,其吸放热量的差别会引起差热曲线的偏移。
通过分析差热曲线的形态和峰的位置,我们可以了解样品的热反应性质。
热重分析则是通过记录样品在升温过程中质量的变化来研究样品的热分解和失水性质。
当样品发生热分解或失水时,其质量会发生变化。
通过分析热重曲线,我们可以确定样品的热分解温度和相应的质量损失。
实验步骤1.准备样品和参比样品。
样品应为已知组成和纯度的物质,参比样品应为不发生物理或化学变化的物质。
2.使用差热分析仪器,将样品和参比样品装入样品盒和参比盒中,并将其放置在差热分析仪中。
3.设置差热分析仪的升温程序和扫描速率。
升温程序应根据样品的性质来选择,扫描速率则应根据实验要求来确定。
4.开始差热分析实验,记录差热曲线。
实验过程中,温度将逐渐升高或降低,样品和参比样品的吸放热量差别将被记录下来。
5.使用热工分析仪器,将样品和参比样品装入热重分析仪器中,并将其放置在恒温器中。
6.设置热重分析仪器的升温程序和扫描速率。
升温程序应根据样品的性质来选择,扫描速率则应根据实验要求来确定。
7.开始热重分析实验,记录热重曲线。
实验过程中,样品和参比样品的质量变化将被记录下来。
实验结果与分析通过对差热曲线和热重曲线的分析,我们可以得到样品的热性质信息。
稳态热工设计实验报告

稳态热工设计实验报告实验目的:本实验旨在通过稳态热工设计,研究热传导的基本规律,并探究不同材料的热导率及热传导特性。
实验原理:稳态热工设计是通过实验测量来确定物体内部温度分布与物体表面热通量之间的关系,进而研究热传导的规律。
对于导热材料,根据傅里叶热传导定律可知,热传导的速率与温度梯度成正比,与材料的热导率成反比。
热传导定律:根据傅里叶热传导定律,单位时间内通过横截面的热流量(Q)与该横截面上的温度梯度(ΔT/Δx)成正比,即:Q = -k * (ΔT/Δx) * A其中,Q为热流量(W),k为热导率(W/m·K),ΔT/Δx为温度梯度(K/m),A为横截面积(m^2)。
实验材料与设备:1. 热传导材料:铜、铝、不锈钢等2. 温度计3. 试样切割工具4. 电炉5. 可变电源6. 恒温水槽7. 数据采集系统1. 准备三种不同热传导材料(铜、铝、不锈钢),并按要求进行切割,得到相同截面积的试样。
2. 在试样两端分别固定热电偶,使其与试样接触紧密。
3. 将试样置于电炉中,设置适当的加热功率和时间,使试样达到稳态。
4. 同时,在试样两端的温度计上测量温度,并记录下相应的温度差ΔT。
5. 根据上述测得的数据,计算得到每个试样的温度梯度(ΔT/Δx)。
6. 根据热传导定律中的公式,计算出热传导材料的热导率(k)。
7. 重复多次实验,取平均值并进行数据处理,得出最终结果。
实验结果与讨论:经过多次实验,我们得到了不同热传导材料的温度差ΔT以及对应的温度梯度(ΔT/Δx)。
通过计算得到的热导率(k)可以比较不同材料的热导性能。
根据实验结果,我们可以发现铜的热导率较高,不锈钢的热导率较低,而铝的热导率介于两者之间。
这与我们对这些材料性质的了解相符。
在实验过程中,我们还发现温度梯度随着加热功率的增加而增大。
这是因为加热功率的增加会导致更大的温度差,从而加大温度梯度。
通过稳态热工设计实验,我们研究了不同材料的热传导特性,并计算得到了它们的热导率。
最新实验报告_实验四

最新实验报告_实验四实验目的:本实验旨在探究特定条件下物质的热传导性能,并验证傅里叶定律在实际应用中的有效性。
通过实验测定不同温度梯度下的物质热传导率,加深对热传导现象的理解。
实验原理:热传导是热能通过物质内部分子振动和自由电子的碰撞传递的过程。
根据傅里叶定律,单位时间内通过单位面积的热量与温度梯度成正比,数学表达式为:q = -kAΔT/Δx,其中q是热流量,k是热传导率,A是传热面积,ΔT是温度差,Δx是传热距离。
实验设备:1. 恒温水浴2. 热传导率测量仪3. 标准样品(如铜、铝块)4. 温度传感器5. 保温材料6. 数据采集系统实验步骤:1. 准备实验设备,确保所有设备均处于良好工作状态。
2. 将标准样品放置在测量仪中央,确保样品与测量仪接触良好。
3. 使用恒温水浴设定两个不同的温度,分别作为实验的高温端和低温端。
4. 将温度传感器固定在样品的两端,以便准确测量温度差。
5. 开始实验,记录不同时间间隔的温度数据。
6. 根据温度数据和傅里叶定律计算热传导率。
7. 改变温度梯度,重复步骤5和6,获得不同温度梯度下的热传导率。
8. 使用数据采集系统整理和分析实验数据,绘制温度梯度与热传导率的关系图。
实验结果:实验数据显示,在一定范围内,随着温度梯度的增加,热传导率呈现上升趋势。
通过对比不同材料的实验结果,可以得出材料的热传导性能与其内部结构和分子振动特性有关。
结论:本次实验成功验证了傅里叶定律在描述热传导现象时的有效性,并通过对不同材料的热传导率进行测定,进一步理解了影响热传导性能的因素。
实验结果对于材料科学和热能工程领域具有一定的参考价值。
散热器(肋片)研究报告

研究总结报告——散热器(肋片)仿真总结一、研究内容散热器设计是决定散热器效能的最重要因素,从散热的过程来看,分为吸热、导热、散热三个步骤。
热量从芯片中产生,散热器与芯片接触端要及时吸取热量,之后传递到散热片上或其它介质当中,最后再将热量发散至环境当中。
因此,散热器设计应从这三个步骤入手,分别将吸热、导热、散热的性能提升,才能获得较好的整体散热效果。
常见的肋片形式有以下几种:平行矩形直肋、平行矩形针肋、交错矩形针肋、平行圆柱针肋、交错圆形针肋。
他们的适用场合、生产工艺、散热性能各不相同,本文就常见强迫风冷散热形式建模,仿真分析以上几种肋片形式散热器的散热性能。
肋片尺寸直接约束着肋片的散热性能,其影响可以在肋片传热的近似解中看到。
图1是常见的矩形等截面直肋的形状尺寸示意图。
图 1 矩形直肋形状尺寸示意图设温度在与x轴垂直的截面上均匀分布,即只是x的函数,肋片导热系数为k,肋表面对周围流体的换热系数为h,周围流体温度为tf,肋根温度为t0,截面不变(等截面面积Ac和周长U为常数),肋厚为U,肋厚为δ。
把肋片的某一微元体dx视为稳态系统,设单位时间导入、导出微元段的热量为Qx和Qx+dx,微元段向周围介质的对流换热热量为Qc,根据能量守恒原理,其热平衡关系为(1-1)根据文献[26]中的推导,可得到肋片的肋效率为(1-2)设肋片表面积为A1,两肋之间的平壁面积为A2,则肋片总换热面积Ah为(1-3)两肋之间平壁温度为t0,肋片表面温度为tl(仍假设沿肋横截面的温度均匀分布,但沿肋x方向tl不是常数),则肋片表面的对流换热热流量为(1-4)式中,为肋表面的平均温度。
根据肋效率的定义,可用肋效率表示成(1-5)于是式(5-4)可变为(1-6)肋片的数量主要是影响肋片与地面的接触面积和类间距两方面,从而改变散热器的散热性能,增加肋片数量,会增大肋片与底面的接触面积,但同时会减小肋间距,所以这一矛盾的存在预示着肋片数目存在着一个最佳数目值,这个值使散热器的散热效率达到最高。
散热片heat sink介绍
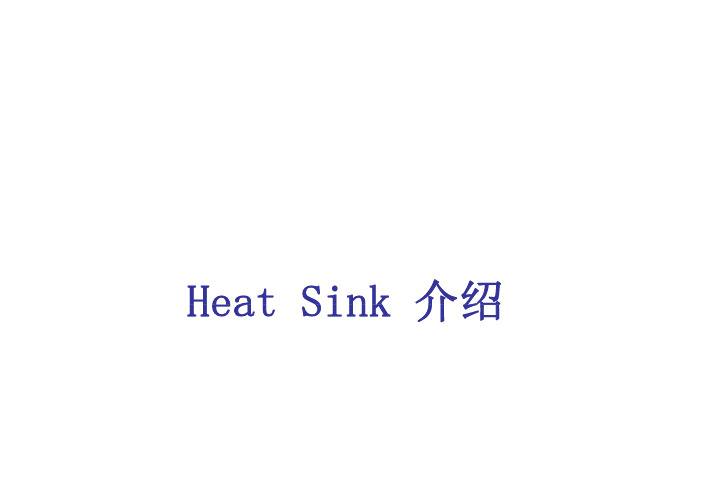
Heat Sink 介绍Heat Sink介绍大纲介绍1.Heat Sink基本热传与设计概念2.Heat Sink各种制程优劣比较3.Malico能提供给客户的服务Heat Sink基本热传与设计概念为什么要散热1.据统计,电子组件的故障,有55%来自温度的影响,而电子组件的温度每1据统计电子组件的故障有55%来自温度的影响而电子组件的温度每提升2℃ ,其信赖性就下降10%2.为了维持产品的稳定性与可靠性,所以要散热。
热的产生:当输入的电能要转换成其它能量,例如灯泡,由于传输阻抗的关系,所以一部份转换成光能,剩下的变为热能发散掉热的三大传播方式传导(Conduction):静止物体之热传递,其利用分子间的碰撞来传递能量对流(Convection):分为(自然对流)与(强制对流)1.自然对流:流体因为密度的不同而引发流体本身的流动而带动能量2强制对流:藉由外加的动力来强制流体流动而传递能量2.强制对流:藉由外加的动力来强制流体流动而传递能量幅射(Radiation):无需介质的热传,另一说为藉由光子(Photon)来传递能量IC与Heat Sink的装置与传导方式•Tj:芯片接口温度•Tc:封装表面温度封装表面温度•Ts:接口材料温度‧Ta:外界温度‧R:热阻•Rjc:Tj到Tc的热阻值热阻公式解说重要公式: R= △T/P(必背)R(℃/W):代表热能通过的难易程度,称为热阻抗(Thermal Resistance) R(℃/W):代表热能通过的难易程度称为热阻抗(Th rm l R i t n)△T( ℃ ):温度差,一般定义为Tc至Ta的温度差P( W ):发热量,一般泛指IC的发热瓦数若将热传递与电学对照,有一相似的物理性质,都是由高处传递至低处,因此可以套用欧姆定义I= V/R I Q ; V △T ; 所以R= △T/Q可以套用欧姆定义I=V/R I~Q;V~△T;所以R=△T/QQ:热传量(单位时间内所能传递的热量,Watt)但一般Q值需经量测才可得知,所以在概略估算时,经常以已知的P来替代Q,所以般将公式解释成R △T/P所以一般将公式解释成R=△T/P上述的公式为初步估算Heat Sink所需的热阻系数,做为判定是否合用的运算标准散热片设计(1)标准散热片设计()Q=h*A*△Tmh:热传系数(对流时套用,需实验得知) A:总热传面积△Tm:有h热传系数(对流时套用需实验得知)A总热传面积△T有效平均温差由上述公式知道提升Q的方式有三:增加h;A或△Tm空气的h要增加或温差△Tm要增加是很困难的事所均所以一般均增加A也就是散热鳍片的高度及散热表面积尽量达到最大在强制对流的状态下,鳍片的几何形状需配合流场的条件,在自然对流下,形状影响不大,但几何尺寸及散热表面积却占了很重要的因素影响散热片的因素主要有两种1.本身的几何设计2.周遭环境的条件周遭环境的条件标准散热片设计(2) 1.本身的几何设计1本身的几何设计影响条件:鳍片-间距,高度,长度,厚度,排列形状,摆置方式间距:过大->散热表面积不足过小->流阻增加,热传性能下降过小流阻增加热传性能下降高度:过高->末端无散热效果不足->无法有效蓄热,热能传递不及,效率不佳长(厚)度:过长(厚)->造成蓄热过度现象,升高环境温度,效能降低长(厚)度过长(厚)造成蓄热过度现象,升高环境温度,效能降低过短(薄)->无法有效蓄热,热能传递不及,效率不佳经验:当间距与Fin的厚度比约为3:1时,效果最好经验:当间距与Fin的厚度比约为3:1时效果最好排列形状:平行状排列比交错状排列效果较好(约20%)摆放方式:垂直摆放比水平摆放佳(PIN FIN刚好相反)摆放方式:垂直摆放比水平摆放佳(PIN FIN刚好相反)标准散热片设计(3)标准散热片设计()2.周遭环境的条件影响因素:环境温度,密闭或开放空间,有无开孔,开孔位置,大小,形状环境温度低->温差越大,散热效果越佳环境温度低>温差越大,散热效果越佳开放空间比密闭空间散热容易->可产生对流开孔可以将密闭空间变成开放空间,可有效散热开孔的考量>位于对流有效区域开孔的考量->位于对流有效区域->风流所造成的噪音->整体机构的机械强度考量>对整体造型的视觉影响->对整体造型的视觉影响如何选择Heat Sink 需要有下列的条件,才能选择合适的Heat Sink需要有下列的条件才能选择合适的Heat Sink1.组件的最大散热量(发热瓦数,P)22.最高的环境温度(Ta)3.容许最大界面温度(Tj or Tc)4.系统限高(最好由芯片算起,不要从PCB)4系统限高(最好由芯片算起不要从PCB)5.底面积大小的限制(MAX)6.系统风流量(否则请告知“自然”或“强制”对流)7.要求热组值范围Heat Sink各种制程优劣比较一般Heat Sink所采用的大约有9种一般H t Sink所采用的大约有9种1. Machining (机械加工)2. Extrusion (挤制成型)g(压铸成)3. Die Casting (压铸成型)4. Stamping (冲压成型)5Skiving(切削成型)5. Skiving (切削成型)6. Inserting or Clamping (插入/夹持成型)7. Folding (折叠成型)7Folding(折叠成型)8. Metal Injection (金属射出成型)9. Forging (锻造成型)9F i(锻造成型)Machining(机械加工)优点:1.不需开模即可成型,省模具费2.几何形状不受限制缺点:1.厚高比仅1:6,加工时Fin的顶部易分岔2.前置与加工时间长,无法应付大量生产的需求2前置与加工时间长无法应付大量生产的需求3.机械加工的费用极高Extrusion(挤制成型)优点:1.模具费用低廉2.成品为一体成型,无热传递损失缺点:1.无法制作铜散热片2.厚高比目前极限1:23,往上有困难高极限,往有困难3.机械加工的费用极高4.Fin因制程呈现下宽上窄,风道变化易造成风压损失Die Casting(压铸成型)优点:1.成型不受几何形状限制1成型不受几何形状限制2.大量生产成本低廉缺点:缺点1.厚高比仅1:15散热总面积受限2.Fin因制程呈现下宽上窄,风道变化易造成风压损失3.低密度材质造成热传递损失4.内部砂孔造成机械加工麻烦5.仅能制作铝散热片6.高昂的模具成本Stamping(冲压成型)缺点:因是用焊接与底座接合,所以接处面的品质与热阻是最大的问题因是用焊接与底座接合所以接处面的品质与热阻是最大的问题Skiving(切削成型)优点:1.能做厚高比高的Fin1能做厚高比高的Fin2.铝与铜的散热片都能生产缺点:1.粗糙的加工面造成风压下降几何形状受极大限制2.几何形状受极大限制3.长时间冷热冲击,隐藏Fin与底部连接处断裂的危险Inserting or Clamping(插入/夹持成型)优点:1.大型散热片才会有模具成本1大型散热片才会有模具成本2.Fin的部份无材料损失3.高厚高比1:1003高厚高比1:100缺点:在夹持区域会有潜在的物理变化,会削弱热传递的效果Folding(折叠成型)缺点:接触面的品质是一个很大的问题g(折成)Metal Injection(金属射出成型)优点:无几何形状限制缺点:1.厚高比仅1:152.只能成型铜散热片尺寸公差控制是困难的3.尺寸公差控制是困难的4.软铜材质对后续机械加工很困难Forging(锻造成型)优点:1.体成型无接口热阻1一体成型无接口热阻2.厚高比可达1:1003.可成型纯铝/铜及合金或是崁铜设计4.Fin上下无变化,不会影响风的流动5.高密度组织增加热传效益6.与压铸相比散热面积更大与压铸相比散热面积更大7.Fin或pin一次成型不需二次加工400倍显微观察,各成型方式组织比较Spec.heat热传导率样品测试件外观V.(MJ /M3K)热扩散率(mm2/S)(W/m·K)±3%Al 356压铸2.37552.63125Al6063Al 6063挤制2.11983.95177.9Al 6063锻造2.37187.77203.3锻Spec.heat 热传导率(/)样品测试件外观V.(MJ /M3K)热扩散率(mm2/S)(W/m·K)±3% CU 1100锻造前3.17497.16308.4CU 110028331395锻造后2.833139.5395CU 1100MIM3.097108.3335.5。
散热器质量检测报告

散热器质量检测报告背景散热器是一种常见的用于散热的设备,广泛应用于电子设备、汽车发动机等领域。
散热器的质量直接影响着散热效果和设备的稳定运行。
因此,进行散热器质量检测非常重要。
检测目标本次散热器质量检测的目标是评估散热器的散热性能和耐久性。
通过检测,我们可以了解散热器在长时间使用和各种环境条件下的表现,并据此为生产厂家提供改进意见。
检测步骤步骤一:材料检测首先,我们需要对散热器的材料进行检测。
散热器通常由铝合金制成,因此我们需要确认散热器使用的材料是否符合要求。
通过目测和化学测试,我们可以确定散热器所用材料的质量和纯度。
步骤二:外观检测外观检测是评估散热器外观质量的重要步骤。
我们需要检查散热器的表面是否平整、无明显瑕疵和划痕。
同时,我们还需要检查散热器的连接件是否完好,无松动或缺失。
步骤三:散热性能测试散热性能是评估散热器质量的关键指标。
我们采用实验测试的方法来评估散热器的散热性能。
具体步骤如下:1.将散热器置于一定温度的环境中,同时将散热器与热源连接。
2.通过测量热源输入和散热器输出的温度,计算散热器的散热效率。
3.重复实验多次,取平均值作为最终的散热效率。
步骤四:耐久性测试耐久性是评估散热器质量的另一个重要指标。
我们需要测试散热器在长时间使用和各种环境条件下的表现。
具体步骤如下:1.将散热器置于高温高湿或低温低湿环境中,模拟极端工作条件。
2.在一定时间内,观察散热器的外观变化和散热性能的衰减情况。
3.通过对比测试前后的散热性能数据,评估散热器的耐久性。
步骤五:数据分析和报告撰写最后,根据步骤三和步骤四的测试数据,进行数据分析和报告撰写。
分析结果应包括散热器的散热性能、耐久性以及任何潜在问题和改进建议。
报告需要详细记录每个步骤的测试方法、实验数据和分析结果。
结论通过以上的散热器质量检测步骤,我们可以得出散热器的质量评估和改进建议。
这些信息对生产厂家来说非常重要,可以帮助他们改进产品设计和生产工艺,提高散热器的质量和性能。
最新实验十四实验报告
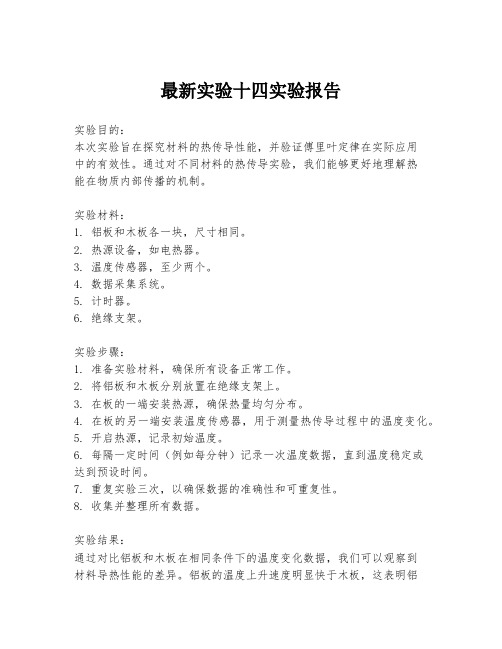
最新实验十四实验报告实验目的:本次实验旨在探究材料的热传导性能,并验证傅里叶定律在实际应用中的有效性。
通过对不同材料的热传导实验,我们能够更好地理解热能在物质内部传播的机制。
实验材料:1. 铝板和木板各一块,尺寸相同。
2. 热源设备,如电热器。
3. 温度传感器,至少两个。
4. 数据采集系统。
5. 计时器。
6. 绝缘支架。
实验步骤:1. 准备实验材料,确保所有设备正常工作。
2. 将铝板和木板分别放置在绝缘支架上。
3. 在板的一端安装热源,确保热量均匀分布。
4. 在板的另一端安装温度传感器,用于测量热传导过程中的温度变化。
5. 开启热源,记录初始温度。
6. 每隔一定时间(例如每分钟)记录一次温度数据,直到温度稳定或达到预设时间。
7. 重复实验三次,以确保数据的准确性和可重复性。
8. 收集并整理所有数据。
实验结果:通过对比铝板和木板在相同条件下的温度变化数据,我们可以观察到材料导热性能的差异。
铝板的温度上升速度明显快于木板,这表明铝的热传导率高于木头。
实验分析:根据傅里叶定律,热流密度与温度梯度成正比。
实验数据显示,铝板的温度梯度变化较大,热流密度也相应较高,这与傅里叶定律的预测一致。
而木板由于热传导率较低,温度梯度变化较小,热流密度也较低。
结论:本次实验验证了傅里叶定律在描述热传导现象中的适用性。
实验结果表明,金属材料(如铝)的热传导性能优于有机材料(如木头)。
这一发现对于材料科学、建筑设计以及能源管理等领域具有重要的实际意义。
未来的研究可以进一步探讨不同温度范围、不同形状和尺寸的材料对热传导性能的影响。
散热风扇检验标准
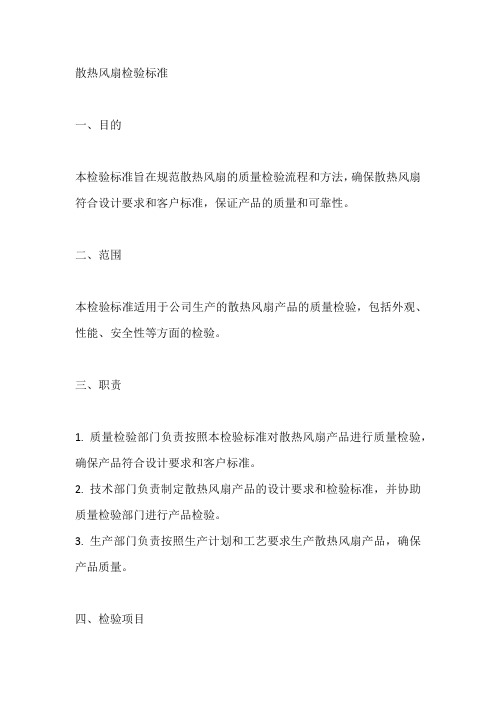
散热风扇检验标准一、目的本检验标准旨在规范散热风扇的质量检验流程和方法,确保散热风扇符合设计要求和客户标准,保证产品的质量和可靠性。
二、范围本检验标准适用于公司生产的散热风扇产品的质量检验,包括外观、性能、安全性等方面的检验。
三、职责1. 质量检验部门负责按照本检验标准对散热风扇产品进行质量检验,确保产品符合设计要求和客户标准。
2. 技术部门负责制定散热风扇产品的设计要求和检验标准,并协助质量检验部门进行产品检验。
3. 生产部门负责按照生产计划和工艺要求生产散热风扇产品,确保产品质量。
四、检验项目1. 外观检验:检查散热风扇的外观是否平滑、整洁,无明显划痕、毛刺、变形等质量问题。
2. 尺寸检验:检查散热风扇的尺寸是否符合设计要求,包括风扇叶片的长度、宽度、厚度等尺寸。
3. 性能检验:测试散热风扇的性能指标,包括风量、噪音、电流等指标,确保符合设计要求和客户标准。
4. 安全性检验:检查散热风扇的安全性能,包括电气安全、机械强度等方面,确保产品安全可靠。
五、检验方法1. 外观检验:采用目视、触摸等方法对散热风扇的外观进行检验,确保外观无明显质量问题。
2. 尺寸检验:采用测量工具对散热风扇的尺寸进行测量,并与设计要求进行比较,确保尺寸符合要求。
3. 性能检验:在规定条件下,采用专业测试设备对散热风扇进行风量、噪音、电流等指标的测试,并将测试结果与设计要求和客户标准进行比较,确保性能符合要求。
4. 安全性检验:采用专业检测设备对散热风扇进行电气安全、机械强度等方面的测试,确保产品安全可靠。
六、检验程序1. 散热风扇生产完成后,由生产部门填写《产品检验申请表》,向质量检验部门申请检验。
2. 质量检验部门收到申请后,按照本检验标准对散热风扇进行逐项检验。
3. 质量检验部门将检验结果记录在《产品检验报告》中,并针对每个项目给出判定结果。
4. 根据检验结果,质量检验部门出具《产品质量检验报告》,对合格产品给予放行,不合格产品进行返修或报废处理。
热管散热器散热性能的实验研究与数值模拟的开题报告

热管散热器散热性能的实验研究与数值模拟的开题报告一、选题背景随着计算机、电子设备的不断发展,散热问题一直是工程设计中需要克服的难题。
高性能的CPU、GPU等集成电路器件在工作时发热量大,需要通过有效的散热方式来维持其正常工作温度。
传统的散热方式主要有风扇散热器、散热片、水冷散热器等,但这些散热器存在着噪音大、寿命短、效率低等问题。
热管散热器作为新型散热器,具有结构简单、散热效率高、寿命长等优点,已经被广泛应用于电子设备、航空航天、医疗器械等领域。
目前的研究主要集中在理论分析和仿真计算上,对热管的热传输特性和结构参数的影响等方面有一定的探究,但对于实验研究的报道很少。
二、研究目的本文的研究目的是通过实验和数值模拟相结合的方式,对热管散热器的散热性能进行研究。
具体包括以下内容:1、设计制作热管散热器样机,测试其散热性能,并与传统散热器进行比较分析;2、通过数值模拟,分析热管散热器的内部流场变化、温度分布情况,探究热管结构参数对散热性能的影响;3、结合实验和数值模拟结果,提出优化建议,改进热管散热器性能。
三、研究内容1、热管散热器的原理和设计制作方法2、实验部分:(1)热管散热器样机的制作和测试(2)传统散热器和热管散热器散热性能的对比分析3、数值模拟部分:(1)建立热管散热器的三维数值模型(2)分析热管散热器内部流动及温度分布情况(3)探究不同结构参数对热管散热器散热性能的影响4、结合实验和数值模拟结果提出优化建议四、研究意义通过研究热管散热器的散热性能,可以从实验和数值模拟两个角度深入探究其内部流场变化和温度分布情况,为后续热管散热器的优化设计和应用提供理论依据和实验数据支持。
散热性能实验报告

散热性能实验报告1. 引言散热是电子设备工作过程中必须解决的重要问题之一。
如今,随着电子设备的不断发展和智能化的普及,设备的功耗越来越大,因此散热问题也变得日益突出。
为了保证设备的正常运行和提高设备的工作效率,对其散热性能进行评估和分析是必要的。
本实验旨在探究不同散热方法对电子设备散热性能的影响,为电子设备的散热设计提供参考依据。
2. 实验装置和方法2.1 实验装置本实验使用以下装置进行散热性能测试:- 电子设备模拟样品- 温度计- 散热系统A:风扇散热系统- 散热系统B:散热片散热系统- 散热系统C:水冷散热系统2.2 实验方法1. 将电子设备模拟样品安装在实验平台上。
2. 接通电源,使电子设备模拟样品开始工作。
3. 使用温度计测量电子设备模拟样品的表面温度,记录初始温度。
4. 启动散热系统A,保持一段时间,记录温度。
5. 关闭散热系统A,让电子设备模拟样品自然冷却,记录温度。
6. 重复步骤4和步骤5,得到散热系统A 的散热效果数据。
7. 重复步骤4至步骤6,分别得到散热系统B 和散热系统C 的散热效果数据。
3. 实验结果与分析根据实验数据,我们得到了以下散热效果数据:散热系统初始温度()散热后温度()A(风扇)50 40B(散热片)50 35C(水冷)50 30通过对比实验数据,我们可以得出以下结论:1. 散热系统C(水冷)具有最好的散热效果,能够将电子设备模拟样品的温度降低到最低的数值。
这是因为水冷能够迅速带走设备的热量,并通过水冷系统的循环往复,保持较低的温度。
2. 散热系统B(散热片)的散热效果次于散热系统C,但优于散热系统A(风扇)。
散热片通过增大表面积以增加散热面,在一定程度上提升了散热效果。
3. 散热系统A(风扇)的散热效果最差,因为其仅通过空气对电子设备模拟样品表面进行散热,限制了散热效果的提升。
4. 结论通过本实验的比较与分析,我们得出以下结论:- 水冷散热系统在电子设备散热中具有良好的效果,能够将设备的温度降低到较低的水平。
寿命试验测试报告
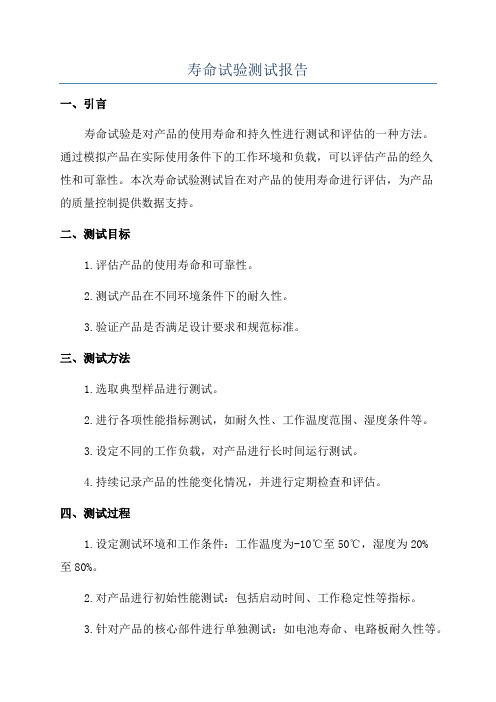
寿命试验测试报告一、引言寿命试验是对产品的使用寿命和持久性进行测试和评估的一种方法。
通过模拟产品在实际使用条件下的工作环境和负载,可以评估产品的经久性和可靠性。
本次寿命试验测试旨在对产品的使用寿命进行评估,为产品的质量控制提供数据支持。
二、测试目标1.评估产品的使用寿命和可靠性。
2.测试产品在不同环境条件下的耐久性。
3.验证产品是否满足设计要求和规范标准。
三、测试方法1.选取典型样品进行测试。
2.进行各项性能指标测试,如耐久性、工作温度范围、湿度条件等。
3.设定不同的工作负载,对产品进行长时间运行测试。
4.持续记录产品的性能变化情况,并进行定期检查和评估。
四、测试过程1.设定测试环境和工作条件:工作温度为-10℃至50℃,湿度为20%至80%。
2.对产品进行初始性能测试:包括启动时间、工作稳定性等指标。
3.针对产品的核心部件进行单独测试:如电池寿命、电路板耐久性等。
4.对产品进行长时间运行测试:设定不同的工作负载,监测产品的工作情况。
5.定期记录产品的性能变化情况,并进行评估和分析。
五、测试结果1.在设定的工作环境和负载条件下,产品正常运行且稳定性良好。
2.经过长时间运行测试,产品的性能并未出现明显衰退。
3.产品的启动时间在规定范围内,满足设计要求。
4.产品的主要部件经受住了长时间运行的考验,没有出现明显缺陷。
六、问题与建议1.在测试过程中,发现产品在高温环境下的发热情况较为严重,建议对散热设计进行优化。
2.部分产品的电池寿命表现不如预期,建议对电池的选用和管理进行改进。
3.长时间运行测试中,产品的外壳出现了一些表面划痕,建议在外壳材料的选择上考虑更耐磨损的材料。
七、结论本次寿命试验测试结果表明,产品的使用寿命和可靠性较好,满足了设计要求和规范标准。
在测试过程中,发现了一些问题和改进的空间,需要在产品设计和制造方面加以改进。
总体而言,本次测试为产品的质量控制提供了有力的数据支持。
八、致谢感谢相关部门的支持和配合,在测试过程中给予的指导和帮助。
传热系数报告模板

传热系数报告模板1. 引言传热系数是研究热传递的一个重要参数。
对于许多实际问题,比如工业生产、环境保护以及生命科学等领域,都需要对传热系数进行研究。
传热系数报告是评估热传递机制和验证数值模拟方法的重要手段。
本文将介绍传热系数的测量方法和报告撰写流程。
2. 传热系数的测量方法传热系数是指在单位时间内,一个体系内的热能通过热量传递的速率与物质温度差之比。
传热系数的测量常采用实验方法,主要包括以下几种:2.1 热阻法热阻法是通过测量导热材料或被测物质的热阻来求得传热系数的一种方法。
具体操作是将被测体系与热流计接在一起,通过施加恒定功率的电热源产生恒定热流,然后测量被测体系两侧的温度差,根据导热材料的热导率求出热阻,进而计算出传热系数。
2.2 微热源法微热源法是通过在被测物质内部嵌入微小加热元件,思路类似于热丝传感器,利用被测物质内部的温度分布将传热系数与测量值联系在一起。
2.3 双温度场法双温度场法是通过在被测物体的两侧形成不同的温度场,通过测量温度场分布,结合传热学的理论模型计算传热系数。
3. 传热系数报告的撰写流程传热系数报告是专门用于说明传热系数实验过程和结果的一份文档。
本章将介绍撰写传热系数报告的流程。
3.1 前置资料准备在开始实验之前,需要做好前期的准备工作。
主要包括实验设备和仪器的选择、检验和校准,实验物质的准备和标准样品的制备,实验流程和步骤的设计、实验数据的处理和计算方法等。
3.2 实验过程记录在实验过程中,需要详细记录实验环境、条件和步骤,实验材料的品种、性质和产地,仪器检定证书和使用情况等相关信息。
对于实验中可能遇到的问题、调整和处理方法,也要进行记录。
3.3 实验结果展示实验结果应该具有可读性和易理解性。
应该通过表格、图形、文字等形式展示实验结果。
在展示实验结果时,应该避免遗漏数据,确保实验过程的完整性。
对于实验结果中可能存在的异常数据和误差原因,应该进行合理分析和解释。
3.4 结果分析和讨论在实验结果展示之后,应该对实验结果进行分析和讨论。
LED灯具散热器检测要求

检测标准和依据
国家标准和行业标准
如GB/T 24824-2009《建筑用LED照明灯具性能试验方法》 等。
客户和企业的要求和规范
针对不同的应用场景和客户需求,可以制定相应的检测标准 和规范。
检测流程和步骤
样品准备
准备需要检测的LED灯具散热器样品, 确保样品的质量和代表性。
环境温度和湿度的控制
根据相关标准和要求,控制实验室的 温度和湿度,以确保检测结果的准确 性和可靠性。
LED灯具散热器检测要求
• LED灯具散热器检测概述 • 散热器材料检测 • 散热器结构检测 • 散热器热性能检测 • 散热器环境适应性检测 • LED灯具散热器检测报告和总结
01
LED灯具散热器检测概述
检测目的和重要性
01
确保LED灯具散热器的性能和质量
通过对LED灯具散热器进行检测,可以评估其性能和质量是否符合相关
06
LED灯具散热器检测报告和总结
检测报告内容
检测目的
评估LED灯具散热器的 性能,确保其满足设计
要求和使用安全。
检测设备
检测环境
检测项目
温度测试仪、风速计、 热成像仪等。
恒温、恒湿的室内环境, 确保测试结果的准确性。
散热器的热传导系数、 风阻、表面温度等。
检测结果分析和评价
01
分析散热器的性能参数,对比设计要求,评估其是否满足使用 需求。
详细描述
耐候性能检测包括对散热器在高温、 低温、潮湿、干燥等环境下的性能表 现进行测试,以确保其在各种气候条 件下都能正常工作,保证LED灯具的 稳定性和使用寿命。
防尘防水性能检测
总结词
防尘防水性能检测是检验LED灯具散热器是否能抵御外部环境中的灰尘和水分侵袭的重 要手段。
热设计规范 散热设计 Thermal
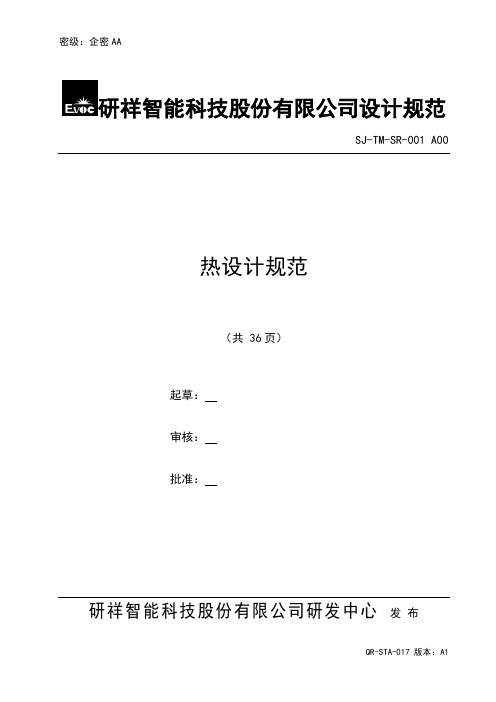
密级:企密AA研祥智能科技股份有限公司设计规范SJ-TM-SR-001 A00热设计规范(共 36页)起草:审核:批准:研祥智能科技股份有限公司研发中心发布目次前言 (I)修订履历 (II)1 范围 (1)2 规范性引用文件 (1)3 定义和基本术语 (1)4 产品热设计的基本原则 (2)5 产品的热设计流程 (3)5.1 项目启动阶段 (4)5.2 方案设计阶段 (5)5.3 样机设计阶段 (5)5.4 样机制作、调试和测试阶段 (5)5.5 试产阶段 (5)6 单板产品的热设计 (5)6.1 PCB热特性 (5)6.2 PCB散热 (5)6.3 器件布局原则 (6)7 整机产品的热设计 (8)7.1 冷却方式的选择 (8)7.2 自然冷却计算 (9)7.3 强迫风冷计算 (11)8 导热填充介质的使用 (16)8.1 导热间隙填充材料 (17)8.2 导热双面胶带 (17)8.3 导热相变化材料 (17)8.4 导热膏 (17)8.5 导热凝胶 (17)9 热仿真 (18)9.1热仿真分析过程 (18)9.2建模 (18)9.3 设定边界条件和求解域 (23)9.4 参数的输入 (24)9.5 网格的划分 (24)9.6监控点或监控区域设置 (26)9.7 收敛与后处理 (26)10 机箱壁上通风孔的标准化 (27)10.1 钣金类材料(冲压加工)箱壁上的通风孔形状 (27)10.2 铝合金类材料(铣削加工)箱壁上的通风孔形状 (29)10.3 机箱前面板上的通风孔形状 (31)前言为了有效控制整机系统内电子元器件的工作温度,使整机系统在指定的工况条件下运行时其系统内电子元器件的温度不超过相应的界定规格或规范所规定的最高温度,保证整机系统持续而稳定地工作;为了使EVOC 产品的热设计进一步规范化、标准化,有效控制散热模组的成本,特制订此规范。
本规范由研祥智能科技股份有限公司研发中心整机专业委员会提出并归口管理。
高温测试报告范文模板

高温测试报告范文模板高温测试报告范文模板一、测试目的本次高温测试的目的是评估产品在高温环境下的性能稳定性和安全可靠性,以确定产品是否符合相关的质量标准和客户的需求。
二、测试背景针对我们公司生产的产品,在使用过程中可能会遭遇高温环境,对产品进行高温测试可有效评估产品在高温条件下的适应能力和稳定性。
三、测试环境1. 温度范围:40℃至60℃2. 湿度:相对湿度控制在30%至50%3. 其他条件:保持环境空气流通,无露点出现四、测试设备1. 温度控制箱:用于设定和控制所需的高温环境2. 温湿度传感器:用于监测测试环境的温度和湿度3. 数据采集器:用于记录和分析温度、湿度等数据五、测试流程1. 将产品置于预热室中,并保持待测温度2. 开始测试前对测试设备进行校准,确保测试数据的准确性3. 将待测产品放入温度控制箱内,测试箱的温度逐渐升高至设定温度,并保持一定时间4. 在每个设定温度下,记录下产品的运行状态、温度、湿度等参数5. 当温度达到最高设定值后,继续保持一段时间,观察产品的反应和性能表现6. 结束测试后,将产品从高温环境中取出,观察是否出现异常现象六、测试数据与结果分析根据测试流程所得到的相关数据,对测试结果进行分析,以评估产品在高温环境下的性能稳定性和安全可靠性。
通过比对测试前后各项参数的变化情况及异常现象的出现与否,得出测试结论。
七、测试结论根据本次测试结果,结合产品设计和使用条件,得出以下结论:1. 产品在高温环境下表现稳定,性能符合设计要求;2. 产品在高温环境中无异常现象出现;3. 产品的材料和结构能够适应高温环境下的使用需求。
八、建议与改进根据本次测试结果,提出以下建议与改进意见:1. 进一步优化产品的散热设计,以提高产品在高温环境下的稳定性;2. 对关键部件进行高温环境下的可靠性测试,以保证整体产品的安全性;3. 结合测试结果,对产品的使用说明书进行相应的更新。
九、测试总结通过本次高温测试,我们对产品在高温环境下的性能和可靠性进行了全面评估。
散热片heat sink介绍
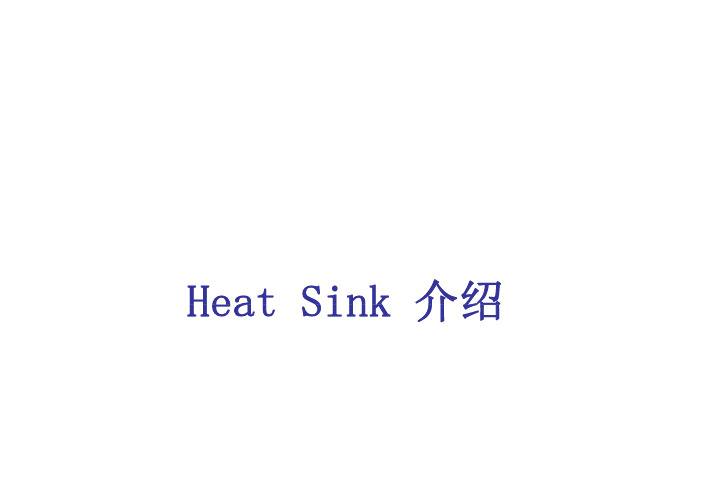
Heat Sink 介绍Heat Sink介绍大纲介绍1.Heat Sink基本热传与设计概念2.Heat Sink各种制程优劣比较3.Malico能提供给客户的服务Heat Sink基本热传与设计概念为什么要散热1.据统计,电子组件的故障,有55%来自温度的影响,而电子组件的温度每1据统计电子组件的故障有55%来自温度的影响而电子组件的温度每提升2℃ ,其信赖性就下降10%2.为了维持产品的稳定性与可靠性,所以要散热。
热的产生:当输入的电能要转换成其它能量,例如灯泡,由于传输阻抗的关系,所以一部份转换成光能,剩下的变为热能发散掉热的三大传播方式传导(Conduction):静止物体之热传递,其利用分子间的碰撞来传递能量对流(Convection):分为(自然对流)与(强制对流)1.自然对流:流体因为密度的不同而引发流体本身的流动而带动能量2强制对流:藉由外加的动力来强制流体流动而传递能量2.强制对流:藉由外加的动力来强制流体流动而传递能量幅射(Radiation):无需介质的热传,另一说为藉由光子(Photon)来传递能量IC与Heat Sink的装置与传导方式•Tj:芯片接口温度•Tc:封装表面温度封装表面温度•Ts:接口材料温度‧Ta:外界温度‧R:热阻•Rjc:Tj到Tc的热阻值热阻公式解说重要公式: R= △T/P(必背)R(℃/W):代表热能通过的难易程度,称为热阻抗(Thermal Resistance) R(℃/W):代表热能通过的难易程度称为热阻抗(Th rm l R i t n)△T( ℃ ):温度差,一般定义为Tc至Ta的温度差P( W ):发热量,一般泛指IC的发热瓦数若将热传递与电学对照,有一相似的物理性质,都是由高处传递至低处,因此可以套用欧姆定义I= V/R I Q ; V △T ; 所以R= △T/Q可以套用欧姆定义I=V/R I~Q;V~△T;所以R=△T/QQ:热传量(单位时间内所能传递的热量,Watt)但一般Q值需经量测才可得知,所以在概略估算时,经常以已知的P来替代Q,所以般将公式解释成R △T/P所以一般将公式解释成R=△T/P上述的公式为初步估算Heat Sink所需的热阻系数,做为判定是否合用的运算标准散热片设计(1)标准散热片设计()Q=h*A*△Tmh:热传系数(对流时套用,需实验得知) A:总热传面积△Tm:有h热传系数(对流时套用需实验得知)A总热传面积△T有效平均温差由上述公式知道提升Q的方式有三:增加h;A或△Tm空气的h要增加或温差△Tm要增加是很困难的事所均所以一般均增加A也就是散热鳍片的高度及散热表面积尽量达到最大在强制对流的状态下,鳍片的几何形状需配合流场的条件,在自然对流下,形状影响不大,但几何尺寸及散热表面积却占了很重要的因素影响散热片的因素主要有两种1.本身的几何设计2.周遭环境的条件周遭环境的条件标准散热片设计(2) 1.本身的几何设计1本身的几何设计影响条件:鳍片-间距,高度,长度,厚度,排列形状,摆置方式间距:过大->散热表面积不足过小->流阻增加,热传性能下降过小流阻增加热传性能下降高度:过高->末端无散热效果不足->无法有效蓄热,热能传递不及,效率不佳长(厚)度:过长(厚)->造成蓄热过度现象,升高环境温度,效能降低长(厚)度过长(厚)造成蓄热过度现象,升高环境温度,效能降低过短(薄)->无法有效蓄热,热能传递不及,效率不佳经验:当间距与Fin的厚度比约为3:1时,效果最好经验:当间距与Fin的厚度比约为3:1时效果最好排列形状:平行状排列比交错状排列效果较好(约20%)摆放方式:垂直摆放比水平摆放佳(PIN FIN刚好相反)摆放方式:垂直摆放比水平摆放佳(PIN FIN刚好相反)标准散热片设计(3)标准散热片设计()2.周遭环境的条件影响因素:环境温度,密闭或开放空间,有无开孔,开孔位置,大小,形状环境温度低->温差越大,散热效果越佳环境温度低>温差越大,散热效果越佳开放空间比密闭空间散热容易->可产生对流开孔可以将密闭空间变成开放空间,可有效散热开孔的考量>位于对流有效区域开孔的考量->位于对流有效区域->风流所造成的噪音->整体机构的机械强度考量>对整体造型的视觉影响->对整体造型的视觉影响如何选择Heat Sink 需要有下列的条件,才能选择合适的Heat Sink需要有下列的条件才能选择合适的Heat Sink1.组件的最大散热量(发热瓦数,P)22.最高的环境温度(Ta)3.容许最大界面温度(Tj or Tc)4.系统限高(最好由芯片算起,不要从PCB)4系统限高(最好由芯片算起不要从PCB)5.底面积大小的限制(MAX)6.系统风流量(否则请告知“自然”或“强制”对流)7.要求热组值范围Heat Sink各种制程优劣比较一般Heat Sink所采用的大约有9种一般H t Sink所采用的大约有9种1. Machining (机械加工)2. Extrusion (挤制成型)g(压铸成)3. Die Casting (压铸成型)4. Stamping (冲压成型)5Skiving(切削成型)5. Skiving (切削成型)6. Inserting or Clamping (插入/夹持成型)7. Folding (折叠成型)7Folding(折叠成型)8. Metal Injection (金属射出成型)9. Forging (锻造成型)9F i(锻造成型)Machining(机械加工)优点:1.不需开模即可成型,省模具费2.几何形状不受限制缺点:1.厚高比仅1:6,加工时Fin的顶部易分岔2.前置与加工时间长,无法应付大量生产的需求2前置与加工时间长无法应付大量生产的需求3.机械加工的费用极高Extrusion(挤制成型)优点:1.模具费用低廉2.成品为一体成型,无热传递损失缺点:1.无法制作铜散热片2.厚高比目前极限1:23,往上有困难高极限,往有困难3.机械加工的费用极高4.Fin因制程呈现下宽上窄,风道变化易造成风压损失Die Casting(压铸成型)优点:1.成型不受几何形状限制1成型不受几何形状限制2.大量生产成本低廉缺点:缺点1.厚高比仅1:15散热总面积受限2.Fin因制程呈现下宽上窄,风道变化易造成风压损失3.低密度材质造成热传递损失4.内部砂孔造成机械加工麻烦5.仅能制作铝散热片6.高昂的模具成本Stamping(冲压成型)缺点:因是用焊接与底座接合,所以接处面的品质与热阻是最大的问题因是用焊接与底座接合所以接处面的品质与热阻是最大的问题Skiving(切削成型)优点:1.能做厚高比高的Fin1能做厚高比高的Fin2.铝与铜的散热片都能生产缺点:1.粗糙的加工面造成风压下降几何形状受极大限制2.几何形状受极大限制3.长时间冷热冲击,隐藏Fin与底部连接处断裂的危险Inserting or Clamping(插入/夹持成型)优点:1.大型散热片才会有模具成本1大型散热片才会有模具成本2.Fin的部份无材料损失3.高厚高比1:1003高厚高比1:100缺点:在夹持区域会有潜在的物理变化,会削弱热传递的效果Folding(折叠成型)缺点:接触面的品质是一个很大的问题g(折成)Metal Injection(金属射出成型)优点:无几何形状限制缺点:1.厚高比仅1:152.只能成型铜散热片尺寸公差控制是困难的3.尺寸公差控制是困难的4.软铜材质对后续机械加工很困难Forging(锻造成型)优点:1.体成型无接口热阻1一体成型无接口热阻2.厚高比可达1:1003.可成型纯铝/铜及合金或是崁铜设计4.Fin上下无变化,不会影响风的流动5.高密度组织增加热传效益6.与压铸相比散热面积更大与压铸相比散热面积更大7.Fin或pin一次成型不需二次加工400倍显微观察,各成型方式组织比较Spec.heat热传导率样品测试件外观V.(MJ /M3K)热扩散率(mm2/S)(W/m·K)±3%Al 356压铸2.37552.63125Al6063Al 6063挤制2.11983.95177.9Al 6063锻造2.37187.77203.3锻Spec.heat 热传导率(/)样品测试件外观V.(MJ /M3K)热扩散率(mm2/S)(W/m·K)±3% CU 1100锻造前3.17497.16308.4CU 110028331395锻造后2.833139.5395CU 1100MIM3.097108.3335.5。
高温测试报告范文
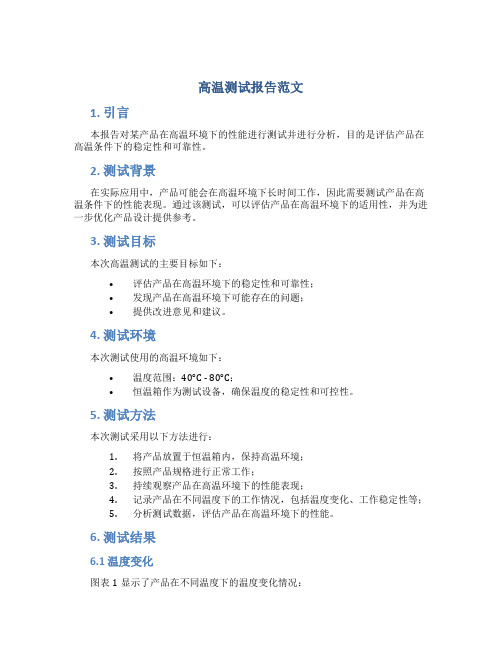
高温测试报告范文1. 引言本报告对某产品在高温环境下的性能进行测试并进行分析,目的是评估产品在高温条件下的稳定性和可靠性。
2. 测试背景在实际应用中,产品可能会在高温环境下长时间工作,因此需要测试产品在高温条件下的性能表现。
通过该测试,可以评估产品在高温环境下的适用性,并为进一步优化产品设计提供参考。
3. 测试目标本次高温测试的主要目标如下:•评估产品在高温环境下的稳定性和可靠性;•发现产品在高温环境下可能存在的问题;•提供改进意见和建议。
4. 测试环境本次测试使用的高温环境如下:•温度范围:40°C - 80°C;•恒温箱作为测试设备,确保温度的稳定性和可控性。
5. 测试方法本次测试采用以下方法进行:1.将产品放置于恒温箱内,保持高温环境;2.按照产品规格进行正常工作;3.持续观察产品在高温环境下的性能表现;4.记录产品在不同温度下的工作情况,包括温度变化、工作稳定性等;5.分析测试数据,评估产品在高温环境下的性能。
6. 测试结果6.1 温度变化图表1显示了产品在不同温度下的温度变化情况:温度(°C)时间(分钟)温度变化(°C)40 0 050 10 +1060 20 +1070 30 +1080 40 +10图表1:产品温度变化从图表1可以看出,在不同温度下,产品的温度有明显的变化。
6.2 工作稳定性图表2显示了产品在不同温度下的工作稳定性情况:温度(°C)时间(分钟)工作情况40 0 正常50 10 正常60 20 异常70 30 异常80 40 异常图表2:产品工作稳定性从图表2可以看出,随着温度的升高,产品的工作情况出现了异常。
7. 分析和讨论根据测试结果,可以得出以下结论:1.在高温环境下,产品的温度会明显上升,可能会影响产品的性能;2.在温度达到一定程度时,产品的工作情况出现了异常,可能影响产品的稳定性和可靠性。
8. 结论本次高温测试结果显示,在高温环境下,产品的温度变化明显,且在一定温度范围内出现了工作异常情况。
高温测试报告范例
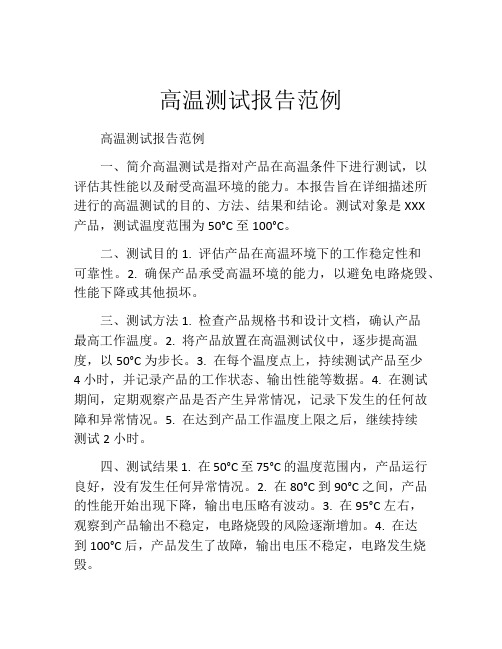
高温测试报告范例高温测试报告范例一、简介高温测试是指对产品在高温条件下进行测试,以评估其性能以及耐受高温环境的能力。
本报告旨在详细描述所进行的高温测试的目的、方法、结果和结论。
测试对象是XXX产品,测试温度范围为50°C至100°C。
二、测试目的1. 评估产品在高温环境下的工作稳定性和可靠性。
2. 确保产品承受高温环境的能力,以避免电路烧毁、性能下降或其他损坏。
三、测试方法1. 检查产品规格书和设计文档,确认产品最高工作温度。
2. 将产品放置在高温测试仪中,逐步提高温度,以50°C为步长。
3. 在每个温度点上,持续测试产品至少4小时,并记录产品的工作状态、输出性能等数据。
4. 在测试期间,定期观察产品是否产生异常情况,记录下发生的任何故障和异常情况。
5. 在达到产品工作温度上限之后,继续持续测试2小时。
四、测试结果1. 在50°C至75°C的温度范围内,产品运行良好,没有发生任何异常情况。
2. 在80°C到90°C之间,产品的性能开始出现下降,输出电压略有波动。
3. 在95°C左右,观察到产品输出不稳定,电路烧毁的风险逐渐增加。
4. 在达到100°C后,产品发生了故障,输出电压不稳定,电路发生烧毁。
五、结论根据测试结果,可以得出以下结论:1. 本产品的最高工作温度应控制在90°C以内,才能保持较好的性能和稳定性。
2. 在高温环境下,产品的承受能力明显有限,存在烧毁的风险。
3. 对于承受高温工作要求的场景,建议使用外部散热装置降低产品温度。
六、改进建议1. 对产品设计进行优化,提高产品的散热能力,以扩大产品的高温工作范围。
2. 添加过温保护电路,以便在温度超出安全工作范围时,自动切断产品电源,以避免烧毁风险。
3. 进一步测试和验证改进后的产品,在更高温度范围内的工作情况。
七、测试注意事项1. 高温测试需要有专门的测试设备和环境,要确保测试设备的稳定性和准确性。
高温测试报告范例大全最新版本
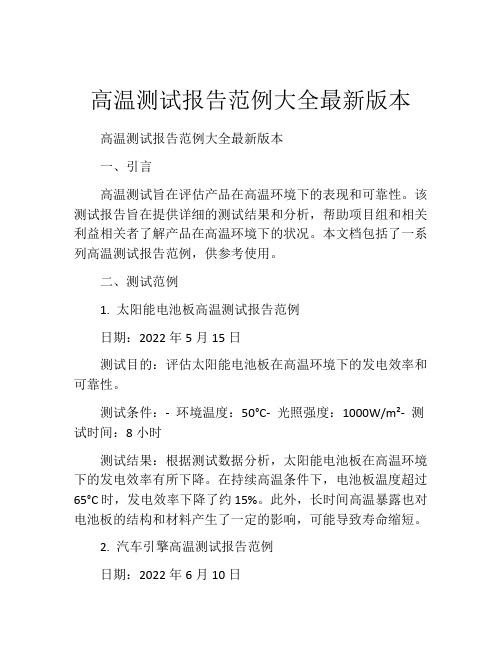
高温测试报告范例大全最新版本高温测试报告范例大全最新版本一、引言高温测试旨在评估产品在高温环境下的表现和可靠性。
该测试报告旨在提供详细的测试结果和分析,帮助项目组和相关利益相关者了解产品在高温环境下的状况。
本文档包括了一系列高温测试报告范例,供参考使用。
二、测试范例1. 太阳能电池板高温测试报告范例日期:2022年5月15日测试目的:评估太阳能电池板在高温环境下的发电效率和可靠性。
测试条件:- 环境温度:50°C- 光照强度:1000W/m²- 测试时间:8小时测试结果:根据测试数据分析,太阳能电池板在高温环境下的发电效率有所下降。
在持续高温条件下,电池板温度超过65°C时,发电效率下降了约15%。
此外,长时间高温暴露也对电池板的结构和材料产生了一定的影响,可能导致寿命缩短。
2. 汽车引擎高温测试报告范例日期:2022年6月10日测试目的:评估汽车引擎在高温环境下的工作能力和可靠性。
测试条件:- 环境温度:60°C- 连续运行时间:2小时- 负载:正常驾驶负载测试结果:在高温环境下,汽车引擎的冷却系统表现出良好的效果,能够稳定保持引擎温度在正常工作范围内。
引擎性能方面,高温环境对功率输出和燃油效率有一定的影响,但在可接受范围内。
测试还表明,在连续高温运行2小时后,引擎各部件的温度升高速度逐渐趋缓,未出现过热现象。
3. 电子设备高温测试报告范例日期:2022年7月5日测试目的:评估电子设备在高温环境下的运行稳定性和可靠性。
测试条件:- 环境温度:55°C- 运行时间:24小时- 电源供应:正常商业电源测试结果:在高温环境下,电子设备的运行稳定性良好,未发现系统崩溃或数据损坏的情况。
然而,长时间高温暴露导致设备散热效果下降,可能会影响设备的长期运行稳定性和寿命。
因此,建议在设计中考虑有效的散热解决方案,并进行适当的温度管理。
三、结论高温测试报告范例大全最新版本中的测试结果表明,在高温环境下,各种产品的性能和可靠性均会受到一定影响。
- 1、下载文档前请自行甄别文档内容的完整性,平台不提供额外的编辑、内容补充、找答案等附加服务。
- 2、"仅部分预览"的文档,不可在线预览部分如存在完整性等问题,可反馈申请退款(可完整预览的文档不适用该条件!)。
- 3、如文档侵犯您的权益,请联系客服反馈,我们会尽快为您处理(人工客服工作时间:9:00-18:30)。
热测试报告
产品名称:LED-engine
报告人:
测试日期:
报告日期:
目录
热测试报告 (1)
产品名称 (1)
一、系统配置 (3)
二、热传测试 (3)
1测试目的 (3)
2测试说明 (3)
3测试设备 (3)
4测试条件 (4)
5测试步骤 (4)
6测试点分布描述 (5)
三、测试结果与分析 (5)
一、系统配置
系统组件图:
图1-1 系统测试照片
二、热传测试
1 测试目的
评估LED-engine内部关键器件工作温度是否满足规格要求。
2 测试说明
2.1 测试对象选择
LED-engine。
2.2 测试方案选择
1、光机打白光功率最大情况测试。
3 测试设备
3.1 FLUKE手持温度巡检仪(见图3-1);
3.2 OMEGA 36#K型热电偶(见图3-2);
3.3 OMEGA快速接头(见图3-3);
3.4 Kapton高温胶布(见图3-4);
图3-1 FLUKE手持温度巡检仪图3-2 OMEGA 36#K型热电偶
图3-3 OMEGA快速接头图3-4 Kapton高温胶布
4 测试条件
测试环境温度:常温
5 测试步骤
5.1 在常温下运行系统以检查系统是否正常工作;
5.2 按测试点的位置安装好热电偶;
5.3 启动系统,运行测试模式;
5.4 记录温度读数结果,运行至各测试点温度基本保持稳定;
5.5 重复动作5.1~5.6,直到完成所有方案的测试;
5.6 测试过程中进行相关拍照;
5.7 测试完成后,关闭系统电源。
6 测试点分布描述
图6-1 LED-engine测试报告主要器件
三、测试结果与分析
序号位号名称常温推算高温45℃Rjc Tj 规格降额结论
1 环境/ 24 45 / / / / /
2 MOS1 斩波 MOS靠近风扇54 75 2.5 77.5 150 120 PASS
3 MOS2 斩波 MOS中间55 76 2.5 78.5 150 120 PASS
4 MOS3 斩波 MOS远离风扇62 83 2.
5 85.5 150 120 PASS
5 L1 DC/DC电感靠近风扇50 71 / 71 125 100 PASS
6 L2 DC/DC电感远离风扇53 74 / 74 125 100 PASS
7 U1 8104靠近风扇58 79 8.5 87.5 150 120 PASS
8 U2 8104中间51 72 8.5 80.5 150 120 PASS
9 U3 8104远离风扇56 77 8.5 85.5 150 120 PASS
结论与分析:
1.LED-engine在光机系统处于最大功率运行状态下关键器件温度符合温升要求,并且有比较大裕量。