810m3高炉开炉料计算
高炉开炉配料计算
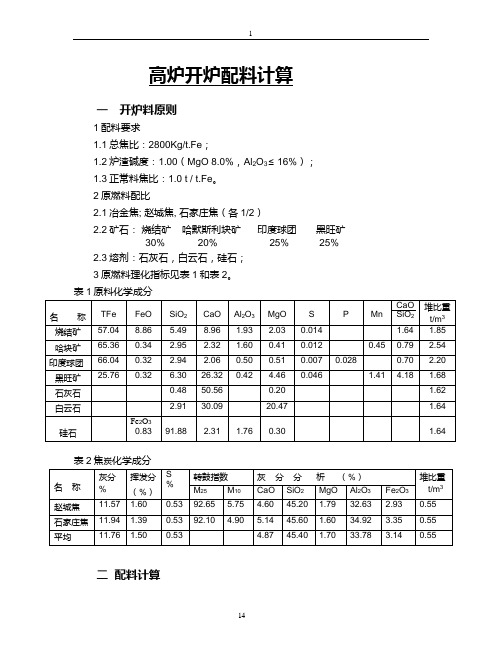
高炉开炉配料计算一开炉料原则1配料要求1.1总焦比:2800Kg/t.Fe;1.2炉渣碱度:1.00(MgO 8.0%,Al2O3≤16%);1.3正常料焦比:1.0 t / t.Fe。
2原燃料配比2.1冶金焦; 赵城焦, 石家庄焦(各1/2)2.2矿石:烧结矿哈默斯利块矿印度球团黑旺矿30% 20% 25% 25%2.3熔剂:石灰石,白云石,硅石;3原燃料理化指标见表1和表2。
二配料计算1、预计生铁成分元素Fe C Si Mn S含量(%) 92.47 4.0 3.0 0.5 0.032 、Fe、Mn回收率Fe回收率: 99.0%;Mn回收率 60.0%; S 分配率:85%进入炉渣,5%进入生铁。
3、以100 Kg混合矿计算:3.1 100 Kg混合矿平均含Fe:30×57.04%+20×65.36%+25×66.04+25×25.76% = 53.134,100 Kg混合矿出铁:100×53.13%×0.99 / 0.9247 = 56.886 Kg。
3.2炉渣成分核算:(1)生铁中Si消耗SiO256.886×3.0%×60 / 28 = 3.657(2)炉渣中FeO量53.134×1.0%×72 / 56 = 0.683(3)入炉料的S负荷30×0.014%+20×0.012%+25×0.007%+25×0.046%+56.886×0.53%=0.321(4)炉渣中的CaS0.321×85%×72 / 32=0.614(5)脱硫消耗CaO0.614×56/72=0.478(6)原燃料成分中进入炉渣的数量(7)炉渣成分调整为使炉渣成分达到要求标准,加白云石和硅石进行调整。
硅石加入量为:x白云石加入量为:y3.927+91.88% x +2.91% y =10.096+2.31% x+30.09% y2.045+0.30% x +20.47% y= 8.0%20.652+96.25% x+53.47% y解方程:x = 7.422 Kg。
高炉开炉配料计算

灰分 0.1313
Fe 57.7 63.9 59.25
10.83
4.13
1.353
0.75 0.25
挥发分 0.0131
SiO2 4.87 6.3 5.23 2.29 11.84 97.67 48.83
5000
Kg
2、则应装净焦的批数为:
二、虚拟矿批及虚拟总批数的计算 矿批=焦批*铁的回收率/(全炉焦比*品位) 1、一批正常料压缩后的体积为: 2、开炉料总批数为:
混合矿的R2=
烧结矿所占的比例:X= 球团矿所占的比例为:1-X=
一、净焦装入的批数(炉缸及炉腹) 1、净焦批重为:
Ⅵ
D3=
Ⅶ
h7=
h"=
料线
正常料焦比 0.86
Mn的回收率 0.5
石灰石 1.6
空料(X) 0.12
料线 1.67
Si 3
渣焦比 0.4
烧结 1.85
正常料(H) 0.12
布料角度 25°×13
h'' D3
Dx5
h7 V7
h6 V6 Dx4
h' Dx3
h5
V5
Dx2 h4 V4
D2 h3 V3
h2
h2-h2' h2'
h-h1 V2
h Dx1
h1
V1
D1 h0
蓝色为人为输入 红色为高炉本身参数 黑色为自动生成
Ⅰ
Ⅱ Ⅲ Ⅳ
D1= h0= h1= Dx1= h=
h-h1= h2= h2’= D2= h3= Dx2=
质量 329.75 142.19 472.16 320.57 448.86
CaO %
810m3高炉开炉料计算

810m3高炉开炉料计算810m高炉开炉料计算开炉工作有两个方面的要求:一是安全顺利地完成开炉工作,即做到炉温适中,铁口易开,下料顺畅,并且无人身、设备事故:二是在开炉后能较快平稳地过渡到正常生产,以获得较好的经济效益。
为此开炉时应该使炉内各区域适时地达到所需要的温度,故开炉料的选择,开炉焦比的确定,以及炉段的安排至关重要。
36.1 开炉焦比的选择所谓开炉焦比(总焦比是指开炉料的总焦量与理论出铁量之比。
开炉时由于高炉炉衬温度、料柱的温度都很低,炉料未经充分的预热和还原直接到炉缸,直接还原增多,渣量打,需要消耗的热量也多,所以开炉焦比要比正常焦比高几倍。
具体数值应该根据高炉容积大小,原燃料条件、风温高低、设备状况及技术操作水平等因素进行选择。
一般情况见表6-1:表6-1 开炉焦比的选择炉容/m 焦比/t?t铁?13100以下 >4100-500 3-4500-1000 2.5-31000以上 <2.6选择合适的开炉焦比对开炉进程有决定性的影响。
焦比选择过高,既不经济,又可能导致炉况不顺,即导致高温区上移,在炉身中上部容易产生炉墙结厚现象,更严重的是延长了开炉时间;焦比选择过低,会导致炉缸温度不足,出渣出铁困难,渣铁流动不畅,严重时会造成炉缸冻结。
一般要求开炉前几次含硅量为3%-3.5%。
6.2 开炉造渣制度的选择为了改善渣铁流动性能,冶炼合格生铁,加热炉缸,稀释渣中的Al2O3(Al2O3含量大于18%时,开炉配料中需增加低Al2O3的造渣剂),开炉时渣量要大一些,渣铁比一般为0.4-0.5.如渣量小,可加干渣调节。
开炉时炉渣碱度SiO2?0.90-1.05。
控制生铁含?Mn?0.8%,为了改善炉渣流动性,可提高渣中的MgO含量,使之维持在8%-10%左右,也可适当加些萤石来稀释炉渣。
小高炉在用全天然矿冷风开炉时,焦比特高,可在空料(即焦炭+石灰石)段加些硅石来调整炉渣成分。
不用干渣,既可以节约焦炭,而且铁口见渣较晚,可以延长喷吹铁口时间,有利于加热炉缸。
1高炉配料计算

高炉炼铁主要经济技术指标 选定 (1) 高炉有效容积利用系数(v η)高炉有效容积利用系数即每昼夜生铁的产量与高炉有效容积之比,即每昼夜1m³有效容积的生铁产量。
可用下式表示:有V Pη=v 式中: v η——高炉有效容积利用系数,t /(m 3·d) P ——高炉每昼夜的生铁产量,t /d有V ——高炉有效容积,m 3V η是高炉冶炼的一个重要指标,有效容积利用系数愈大,高炉生产率愈高。
目前,一般大型高炉超过2.3,一些先进高炉可达到2.9。
小型高炉的更高。
本设计中取2.7。
(2) 焦比(K )焦比即 每昼夜焦炭消耗量与每昼夜生铁产量之比,即冶炼每吨生铁消耗焦炭量。
可用下式表示:式中 K ——高炉焦比,kg/tP ——高炉每昼夜的生铁产量,t /dK Q ——高炉每昼夜消耗焦炭量,kg/d焦比可根据设计采用的原燃料、风温、设备、操作等条件与实际生产情况进行全面分析比较和计算确定。
当高炉采用喷吹燃料时,计算焦比必须考虑喷吹物的焦炭置换量。
本设计中取K = 330 kg/t (3) 煤比(Y )冶炼每吨生铁消耗的煤粉为煤比。
本设计中取煤比为180 kg/t . (4) 冶炼强度(I )和燃烧强度(i )高炉冶炼强度是每昼夜31m 有效容积燃烧的焦炭量,即高炉每昼夜焦炭消耗量与有V 的比值, 本设计I =1.1 t/m 3∙d 。
燃烧强度i 既每小时每平方米炉缸截面积所燃烧的焦炭量。
本设计i = 30 t/m 2∙d 。
(5) 生铁合格率化学成分符合国家标准的生铁称为合格生铁,合格生铁占总产生铁量的百分数为生铁合格率。
它是衡量产品质量的指标。
(6) 生铁成本生产一吨合格生铁所消耗的所有原料、燃料、材料、水电、人工等一切费用的总和,单位为 元/t 。
(7) 休风率休风率是指高炉休风时间占高炉规定作业时间的百分数。
先进高炉休风率小于1%。
(8) 高炉一代寿命高炉一代寿命是从点火开炉到停炉大修之间的冶炼时间,或是指高炉相邻两次大修之间的冶炼时间。
高炉一般计算

高炉一般计算第一篇:高炉一般计算工作总结在繁忙的工作中不知不觉又迎来了新的季度,回顾前几个月的工作历程,在部门领导和同事们的关心与帮助下圆满的完成了生产任务,并在前辈师傅的授受中努力提高高炉冶炼理论知识,学习他们在工作中积累的丰富经验,为了更好地做好以后的工作,现将上季度学到的专业知识做如下总结:冶炼周期可以估计改变装料制度(如变料等)后渣铁成分、温度、流动性等发生变化的时间,从而及时注意观察、分析判断、掌握炉况变化动向;当高炉计划休风或停炉时,根据冶炼周期可以推测休风料到达时间,以便掌握休风或停炉的时机。
(1)用时间表示:t=24V有PV'(1-C)P=V有hη有t=24hη有V'(1-C)式中t——冶炼周期,h;V有——高炉有效容积,m3;P——高炉日产量,t/d;V’——1t铁的炉料体积,m3/t;C——炉料在炉内的压缩系数,大中型高炉C≈12%,小高炉C≈10%。
(2)用料批表示:生产中常采用由料线平面到达风口平面时的下料批数,作为冶炼周期的表达方法。
如果知道这一料批数,又知每小时下料的批数,同样可求出下料所需的时间。
VN=批(V矿+V焦)(1-C)式中N批——由料线平面到风口平面曲的炉料批数;V——风口以上的工作容积,m3;V矿——每批料中矿石料的体积(包括熔剂的),m3; V焦——每批料中焦炭的体积,m3。
通常矿石的堆积密度取2.0~2.2t/m3,烧结矿为1.6t/m3,焦炭为0.55t/m3,冶炼周期是评价冶炼强化程度的指标之一。
冶炼周期越短,利用系数越高,意味着生产越强化。
风口以上高炉工作容积的计算公式:V=V效—n/4(D²*H+d²*h)式中 V效——高炉有效容积,m³;D——炉缸直径,m H——铁口中心线至风口中心线的距离,m d——炉喉直径mh——高炉料线,m 理论出铁量的计算通过计算出铁量,可以检查放铁的好坏和铁损的情况,如发现差距较大时,应及时找出产生原因,尽快解决P理论出铁量=G矿石消耗量×Fe矿石品位×0.997/0.945 理论出渣量的计算渣量批=QcaO批//CaO渣安全容铁量计算安全容铁量=0.6×ρ铁×1/4πd2h h取低渣口中心线到铁口中线间距离,m ρ铁——铁水密度,7t/m3; d——炉缸直径,m 全焦冶炼实际入炉风量计算VB =0.933C焦×CΦ×K×P/﹙0.21+0.29f﹚×1440 式中VB——入炉实际风量,m³/min0.933——1kgC燃烧需要的氧量,m³/kg(0.21+0.29f﹚——湿空气含氧量,其中f为鼓风量湿分,%C焦——综合燃料含碳量,%CΦ——风口前燃烧的碳量占入炉量的比率,一般去65-75%,中小高炉取较小值K——综合燃料比,kg/tP——昼夜产铁量,t 根据碳平衡计算入炉风量(V风,m3)(1)风口前燃烧的碳量(C风,kg):由碳平衡得:C风=C焦+C煤+C料+C碎-C铁-C尘-C甲烷-Cd1224126012Fe还⋅rd+Si铁+Mn铁+P铁+bCO2⋅CO2熔5628556244bCO2——熔剂中CO2被还原的系数,本例为0.4。
高炉简易配料计算
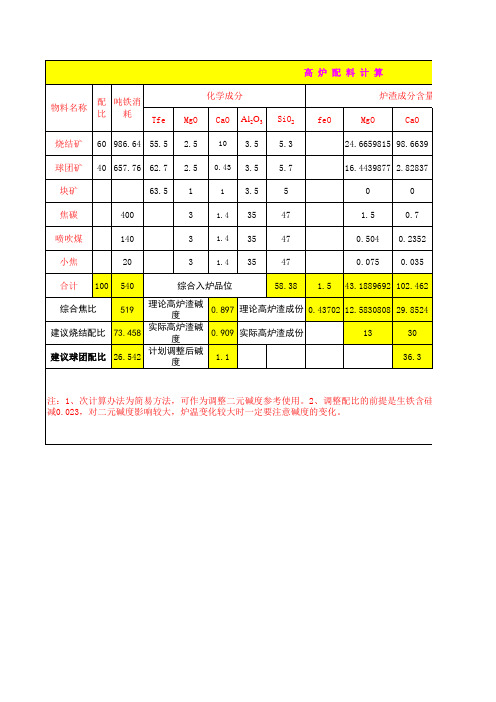
Al2O0 986.64 55.5 40 657.76 62.7 63.5
24.6659815 98.6639 16.4439877 2.82837 0 1.5 0.504 0.075 0 0.7 0.2352 0.035
综合入炉品位
43.1889692 102.462
高 炉 配 料 计 算 吨铁消 物料名称 配比 耗 烧结矿 球团矿 块矿 焦碳 喷吹煤 小焦 合计 100 400 140 20 540 519 化学成分 Tfe MgO 2.5 2.5 1 3 3 3 CaO
10 0.43 1 1.4 1.4 1.4
炉渣成分含量 SiO2 5.3 5.7 5 47 47 47 58.38 1.5 feO MgO CaO
炉渣成分含量 Al2O3 SiO2
吨铁渣 量
灰分
原料带 吨铁耗 入铁量 矿 547.585 412.415 0
34.5324 52.2919 23.0216 37.4923 0 17.5 5.88 0.875 81.809 0 23.5 7.896 1.175 114.27 343.23 生铁含硅量 12.5 12 12.5
综合焦比
理论高炉渣碱度 0.897 理论高炉渣成份 0.43702 12.5830808 29.8524 13 30 36.3
建议烧结配比 73.458 实际高炉渣碱度 0.909 实际高炉渣成份 建议球团配比 26.542 计划调整后碱度 1.1
注:1、次计算办法为简易方法,可作为调整二元碱度参考使用。2、调整配比的前提是生铁含硅不变 减0.023,对二元碱度影响较大,炉温变化较大时一定要注意碱度的变化。
1.6444
960 0.38
23.835 33.2925 20 33
高炉开炉配料自动计算表(专利)

7.30 20
0.00 0.00 0.87 7.30
45 45 45 45
总铁量 总渣量 渣铁比 正常料负荷 硫负荷 全炉焦比 226.8957 168.1047097 740.8899 2.164383562 3.658487 2.863431
渣碱度 及成分
212.18736 211.1264232 1.0609368 R2 0.886529628
MgO 批含量 0.000% 0 0.000% 0 3.000% 0.02616 1.470% 0.013532 0.039692
S 0.000% 0.000% 0.150% 0.820%
批含量
0 0 0.001308 0.007548346 0.008856346 (CaO+MgO)/(SiO2+Al2O3) 0.741313276 MgO 3.150% 1.630% 0.000% 0.000% 0.000% 批含量 0.3528 0 0.07009 0 0 0 0
45
586.112
22
447.503
汇 总 配 料 表
名称 烧结 矿烧 球团 澳矿 锰矿 海南矿 硅石 萤石 石灰石 焦炭 合计 入铁 入渣 参数计算
批重
批重
空焦 批数
24 24 24 24 24 24
Tfe 54.200% 0.000% 63.180% 0.000% 18.000% 0.000%
总重 145.6896 0 65.20176 0 1.296 0
8.84114 8.796934 0.044206 批铁量 渣量 渣铁比 参数计算 9.453986 4.02181317 425.4092
炉料分类 净焦
空焦 料 批 计 算 正常料
高炉开炉配料计算
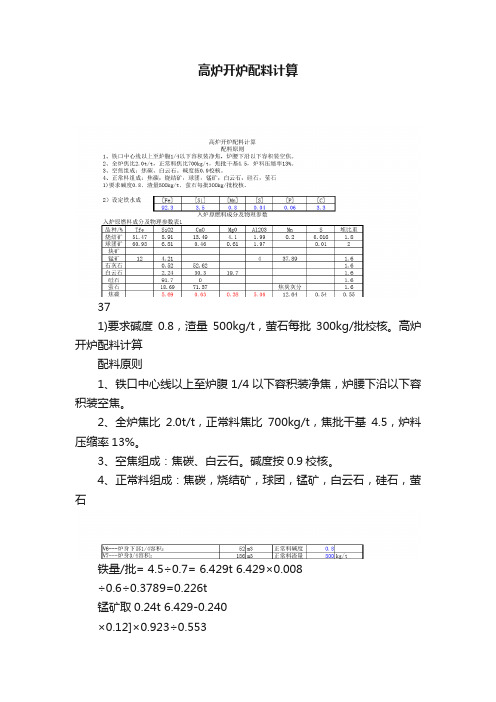
高炉开炉配料计算371)要求碱度0.8,渣量500kg/t,萤石每批300kg/批校核。
高炉开炉配料计算配料原则1、铁口中心线以上至炉腹1/4以下容积装净焦,炉腰下沿以下容积装空焦。
2、全炉焦比2.0t/t,正常料焦比700kg/t,焦批干基4.5,炉料压缩率13%。
3、空焦组成:焦碳、白云石。
碱度按0.9校核。
4、正常料组成:焦碳,烧结矿,球团,锰矿,白云石,硅石,萤石铁量/批= 4.5÷0.7= 6.429t 6.429×0.008÷0.6÷0.3789=0.226t锰矿取0.24t 6.429-0.240×0.12]×0.923÷0.553=10.691t混合矿取11t 焦炭: 4.5t 烧结矿: 6.6t 球团: 4.4t 锰矿:0.2t6.429×500= 3.214t锰矿量/批=混合矿量/批=[根据计算正常料批组成:上述计算的正常料炉渣成分校对见表2一批正常料需配渣量=配渣前炉渣成分表2配渣调整炉渣成分变化见表3硅石量=[ 2.239×(0.2369×0.8-0.4194)]÷0.917÷0.8=-0.702t0.702t 3.214- 2.883=0.332t 0.332×0.4073÷0.917=0.147t 0.147×0.917×0.8÷(0.5262-0.0052×0.8)=0.207t0.207×1×52.62÷30.300=0.359t 0.207×0.000=0.000t0.702+0.147=0.849t硅石取0.849t 石灰石取0t 白云石取0.359t焦炭:4.5t烧结矿: 6.6t配平碱度硅石量取需要配渣量=需配硅石量=需配石灰石量=正常料配硅石=配渣后的正常料组成:石灰石100%换成白云石=石灰石00%量=球团: 4.4t 锰矿:0.240t硅石:0.849t 石灰石:0t 萤石:0.3t 白云石:0.359t 6.6÷ 1.8+(0.240+0.849+0+0.3+0.359)÷1.6+ 4.4÷2+ 4.5÷0.55]×0.87=13.17m3/批R31.090.632)÷(30.3- 2.24×0.9)=0.714t0.714×0.5×30.3÷52.62=0.206t正常料体积=[正常料炉渣成分校对见表4空焦白云石0%换成石灰石=0.714×0.5=0.357t 白云石取0.714t 石灰石取0t 焦炭: 4.5t白云石:0.714t 石灰石:0t 4.5÷0.55+(0.714+0)÷1.6)×0.87=7.506m3=7.12m3/批空焦=7.506m3/批正常料=13.17m3/批69+41=110m3110÷7.118182=15.45批净焦取16.00批7.506X+13.17Y =3114.5×16+ 4.5×(X+Y)÷( 6.429×Y)=213.173Y+7.51X=311(3)开炉料组成空焦白云石100%量=空焦组成:空焦体积计算=((1)净焦批数:净焦容积为炉腹1/4以下容积;净焦容积=V3+1/4V4=净焦批数=(2)空焦与正常料设X——空焦 Y——正常料列方程为:整理方程得:8.357143Y - 4.5X =72110.0858Y +62.73222X =2599.071110.0858Y-59.27696X =948.4313X=13.53批正常料取16批Y=15.90批空焦取13批61.5m3加空焦=61.5÷7.506=8.19批取8.00批3OC+Cn 3OC+Cn 3OC+Cn 7OC+2cn死铁层+16C +8Cn ++++7OC+2cn202.5÷( 6.429×16)= 1.97t/t7.118182×16+7.506×13+13.17×16=422.237m3422.2369÷421=100.29%全炉开炉料按排:3OC+Cn解方程:空焦与正常料按排:炉腹3/4容积3/4V4=其余炉身和炉喉的容积炉料按排:3OC+Cn 3OC+Cn 其中:C——为净焦;Cn——为空焦;OC——正常料。
高炉主要工艺参数计算公式

高炉主要工艺参数计算公式1、风口标准风速:V标=Q/(F×60)式中V标--风口标准风速,m/sQ――风量,m3/minF――风口送风总面积,m22.风口实际风速:V实= V标×(T+273)×0.1013/ (0.1013+P)X×(273+20)式中V实--风口实际风速m/sV标--风口标准风速m/sT--风温℃P--鼓风压力MPa3、鼓风动能:E=0.412 ×1/n × O3/F2 × (T+273)2/(P+P0)2式中E--鼓风动能,j/sQ--风量m3/minn--风口数目个F--风口总截面积m3T--热风温度℃P--热风压力MPaP0--标准大气压,等于101325PaV――炉缸煤气量m3V――炉缸煤气量m3 公式中未使用;(不用)4、焦炭负荷:P=Q矿/Q焦式中P--焦炭负荷Q矿--矿石批重kgQ焦--焦炭(干基)批重kg5、综合负荷:P=Q矿/Q焦式中P--综合负荷Q矿--矿石批重kgQ综焦--综合干焦量批重(干焦量十其它各种燃料量×折合干焦系数批重)kg6、休风率:u=t/T×100%式中u――休风率%t ——高炉休风停产时间minT——规定日历作业时间(日历时间减去计划达中休时间)min.7、生铁合格率生铁合格率是指检验合格生铁占全部检验生铁的百分比。
其计算公式为:生铁合格率(%)= 生铁检验合格量(t)×100%生铁检验总量(t)生铁检验合格量不进行折算,而焦比中合格生铁产量要进行折算计算说明:(1)高炉开工后,不论任何原因造成的出格生铁,均应参加生铁合格率指标的计算。
出格生铁指炼钢生铁S>0.070%,铸造铁生铁S>0.060% (2)用于炼钢的不合格铁水,不允许混罐,应按罐判定。
(3)入库前的混号铁,按出格铁计算。
8、生铁一级品率生铁一级品率是指一级品生铁量占合格生铁总量的百分比。
计算
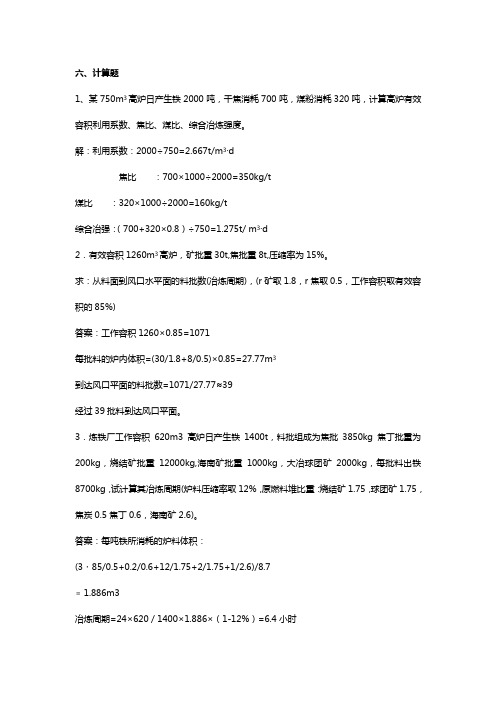
六、计算题1、某750m3高炉日产生铁2000吨,干焦消耗700吨,煤粉消耗320吨,计算高炉有效容积利用系数、焦比、煤比、综合冶炼强度。
解:利用系数:2000〔750=2.667t/m3〃d焦比:700〓1000〔2000=350kg/t煤比:320〓1000〔2000=160kg/t综合冶强:(700+320〓0.8)〔750=1.275t/ m3〃d2.有效容积1260m3高炉,矿批重30t,焦批重8t,压缩率为15%。
求:从料面到风口水平面的料批数(冶炼周期),(r矿取1.8,r焦取0.5,工作容积取有效容积的85%)答案:工作容积1260〓0.85=1071每批料的炉内体积=(30/1.8+8/0.5)〓0.85=27.77m3到达风口平面的料批数=1071/27.77≈39经过39批料到达风口平面。
3.炼铁厂工作容积620m3高炉日产生铁1400t,料批组成为焦批3850kg焦丁批重为200kg,烧结矿批重12000kg,海南矿批重1000kg,大冶球团矿2000kg,每批料出铁8700kg,试计算其冶炼周期(炉料压缩率取12%,原燃料堆比重:烧结矿1.75,球团矿1.75,焦炭0.5焦丁0.6,海南矿2.6)。
答案:每吨铁所消耗的炉料体积:(3﹒85/0.5+0.2/0.6+12/1.75+2/1.75+1/2.6)/8.7﹦1.886m3冶炼周期=24〓620/1400〓1.886〓(1-12%)=6.4小时4、某800m3高炉富氧率为2%,利用系数3.0,全焦冶炼正常焦炭负荷2.5t/t,高炉吨铁耗矿量为1.65t/t,求全焦冶炼条件下,高炉鼓风量应为多少?(跑风率忽略不计,鼓风湿度1%,焦炭C固85%,燃烧率为70%)。
解:日焦炭消耗量:800〓3.0〓1000〓1.65〔2.5=1584000kg每千克焦炭耗风量∨风=0.933〔[(21%+2%)(1-1%)+0.5f]=4.0m3每分钟鼓风量应为1584000〓0.85〓0.7〓4.0〔1440=2618m35.请按下列要求变料已知:矿批20t(全烧结矿),焦批6350kg(干),不加熔剂,生铁含硅0.6%,炉渣碱度1.15,生铁含铁94%,石灰石有效熔剂性50%,当矿批不变,焦比不变时,换用球团矿2000kg, 计算熔剂的变动量烧结矿含SiO2:18000〓8.7%=1566kg球团矿含SiO2:2000〓9%=180kg焦炭含SiO2:6482〓7%=453.74kg还原si消耗SiO2:(18000〓53%/94%+2000〓64%/94%)〓2..14〓0.6%=147.8kg总SiO2=1566+180+453.74-147.8=2051.94kg烧结矿含CaO量:18000〓11.75%=2115kg球团矿含CaO:2000〓0.6%=12kg设所需石灰石量为y,则:Y*50%+2115+12∕2051.94=1.15Y=465kg(取470kg)6.假定100m3鼓风为基准,其鼓风湿度为f=2.0%,计算炉缸煤气成份的百分含量?(以100m3鼓风计算)答案:由反应式2C焦+O2+(79/21)N2=2CO+(79/21)N2得一个O2将生成两个COCO=100[(1-f)〓0.21+0.5〓f]〓2=100[(1―0.02)〓0.21+0.5〓2]〓2=43.16m3N2=100(1―f)〓0.79=98〓0.79=77.42m3H2=100〓2%=2.00m3∴CO+H2+N2=122.58m3∵CO=43.16/122.58〓100%=35.21%N2=77.42/122.58〓100%=63.16%H2=2/122.58〓100%=1.63%炉缸煤气成份CO为35.21%,N2为63.16%,H2为1.63%。
高炉的开炉方法

高炉的开炉和停炉方法新建的高炉和高炉大中修后,顺利开炉是生产稳定顺行的前提。
1、高炉开炉前的准备试车:鼓风机、水泵及电器设备安装检修完毕后,进行不少于8小时的试车,满足正常生产的条件。
试水:高炉冷却系统,包括冷却设备、风口、渣口、管道;热风炉的热风阀、烟道阀等要按正常生产时的用水量、水压进行连续8小时的通水试验。
保证设备部漏水、阀门开关灵活、管道畅通,给排水系统无问题时,再进行验收。
高炉试水时,要进入炉内,检查是否有漏水现象。
出现跑冒滴漏,要及时处理。
如是冬季,处理时要将水放净,防止管路冻坏。
试风:鼓风压力达最高水平,先试冷风管道,再看每座热风炉的各阀门和炉皮;再看冷风调节阀、热风管道、鼓风支管和直吹管,最后送入高炉。
要打压8小时以上,按操作规程,开启各阀门。
要记录下各漏风点,判断出漏风的程度,决定停风后的补救措施。
堵漏和补焊后,还要进行试风。
试气:炉顶设备、煤气系统、泥炮等用蒸汽的部位,要用大于0.4MPa 的压力进行试压。
不漏气、阀门开关灵活、压力达标准、管路有保温。
用氮气也要试压。
上料系统(炉顶设备、卷扬机、、探尺、布料器、料车或皮带、称量设备等均要进行8小时以上的连续运行。
运行的节奏、容量、各种炉料的搭配等均要满足设计要求。
炉前设备(开口机、泥炮、堵渣机、天车、炉前的工具等)也要进行试车,场地布置是否满足设计要求值班室内各仪表配备齐全、进行调试后,要随各设备试车时能反映出相关数据,要稳定、及时、连续、可靠、准确,达到设计水平。
2、烘炉热风炉:要把炉底固定螺丝松开、按规定的烘炉曲线操作(开始炉顶温度低于150℃,以后每个班升温30℃,达到300℃,要恒温16小时,以下每个班升温50℃,顶温达到600℃,要保温16~30小时,,再以每个班升温100℃,升到规定的顶温即可)、要连续烘炉、不允许废气稳定大于300℃、定期检验废气成分和水分。
炉顶温度达到700~800℃时,可以用于烘高炉;温度达到1000℃时,可以用于高炉开炉送风。
高炉炉型计算

第三章高炉炉型及各系统设计3.1高炉炉型设计计算(1)已知:高炉有效容积V U=2000m3,高炉利用系数ηV=2.2t/ m3d,则高炉日产铁量P=V u×ηV=2000×2.2=44000t/d (式3-1);(2)炉缸尺寸:1)炉缸直径:d=0.4078V U0.4205=0.4078×20000.4205=9.97 m 取10m (式3-2);2)炉缸高度:h1=1.4206V U0.159-34.8707V U-0.841=4.815 m 取5m (式3-3);(3)死铁层厚度h0≥0.0937V U d-2=0.0937×2000×10-2=1.87m 取2m (式3-4);(4)炉腰直径(D)、炉腹角(α)、炉腹高度(h2)1)D=0.5684V U0.3942=11.37m取11.7m (式3-5);2)取炉腹角α=78o;3)炉腹高度:h2=(1.6818V U+63.5879)×(V U0.7848+0.719V U0.8129+0.517V U0.841)-1=(1.6818×2000+63.5879)×(20000.7848+0.7190.8129+0.517×20000.841)-1=3.28 m 取3.3 m (式3-6);校核α:tgα=2 h2/(D-d)=4.71 α=78.01o(5)炉喉直径(d1)、炉喉高度(h5)、炉身角(β)、炉身高度(h4)、炉腰高度(h3)1) d1=0.4317V U0.3777=7.62 m 取7.6 m (式3-7);2)h5=0.3527V U0.2446+28.3805V U-0.7554=0.3527×20000.2446+28.3805×2000-0.7554 =2.35 m取2.4 m (式3-8);3)取炉身角(β)=80o;4)h4=(6.3008V U-47.7323)×(V U0.7848+0.7833V U0.8129+0.5769V U0.7554)-1 =(6.3008×2000-47.7323)×(20000.7848+0.7833×20000.8129+0.5769×20000.7554)-1=13.26 m 取13.3 m (式3-9);5)h 3=0.3568V U 0.2152-6.3278V U -0.7848=0.358620000.2152-6.3278×2000-0.7848=1.824 m 取1.8m (式3-10)(6)炉容校核:V 1=π4 ×h 1d 2=3.144 ×5×102=392.5 m 3V 2=π12 ×h 2(D 2+d 2+Dd )=3.1412 ×3.3×(11.72×102×11.7×10)=305.58 m 3 V 3=π4 h 3D 2=3.144 ×1.8×11.72=193.43 m 3V 4=π12 h 4(D 2+d 12+Dd 1)=3.1412 ×13.3×(11.72×7.62×11.7×7.6)=986.87 m 3 V 5=π4 h 5d 12=3.144 ×2.4×7.62=108.82 m 3V u ,= V 1 +V 2+V 3 +V 4 +V 5=392.5+305.58+193.43+986.87+108.82=1987.2 m 3 误差:△V=(V U -Vu ,)/V U ×100%=(2000-1987.2)/2000×100%=0.64%<1%(7)风口数和铁口数1)风口数 n=2×(d+2)=2×(10+2)=242)铁口数 按照每个铁口每日出铁量2300t ,取出铁口3个3.2 高炉各系统设计3.2.1 高炉冷却设备选择在炉底炉缸部位,本设计采用灰口铸铁冷却壁;炉腹部位和炉身上部采用镶砖冷却壁,炉腰和炉身中、下部分采用铜冷却壁。
1080高炉开炉方案最新解析

开炉料计算及装入方法一、参数的选择1、全炉焦比3.0t/t,正常料焦比800kg/t。
2、全炉压缩率13.5%,全炉碱度0.93,正常料碱度1.0,净焦不参与碱度计算,焦炭中的铁不参与配料计算。
3、各种料的堆比重:焦炭0.55,烧结矿1.8,球团矿2.1,锰矿1.7,萤石1.5。
4、矿批20吨,铁中含铁92%,铁水收得率99.4%。
5、死铁层及炉缸填充枕木,炉缸剩余部分及炉腹炉腰加净焦,炉身1/5加空焦,炉身上部至料线加空焦与正常料组合,料线1.5米。
二、正常料与空焦的组成1、正常料的组成2、空焦的组成9.27t焦炭+1t锰矿+0.5t萤石三、装料安排1、炉料装入安排2、高炉总装入容积1102m3,高炉装入料总体积1106m3,基本吻合。
3、设定全炉碱度0.93,实际碱度0.87,主要是因为空焦没有配加碱性料。
如果铁中Si达到4.0%,全炉碱度可达0.93,视情况后续料可适当提高炉渣碱度。
4、设定全炉焦比3.0t/t,实际全炉焦比为2.981t/t,基本吻合。
5、全炉渣铁比487kg/tFe,偏低。
6、设定料线1.5米,开炉料装完后,计算料线为1.37米。
7、由于高炉容积较大,一些物料的堆比重和压缩率采用经验值,可能会有一些偏差,一般情况下,开炉料装入有一两批的偏差属正常。
8、净焦加入角度17°,空焦焦炭加入角度17°,熔剂按15°加入,如果熔剂量小,不容易称量,可两到三批集中加入。
第四段开始焦炭可布5档,圈数32222,矿布2档,圈数44,第七段焦的档位圈数不变,矿布3档,圈数244,后续正常料视炉况进程调整。
开炉枕木与木柴填充方案一、目的和意义:1.易点火,有利于开炉后的煤气安全。
2.送风后有利于炉料下降,不易悬料,有利于开炉炉况顺行。
3.便于均匀加热炉缸,铁口中心线上部不易结成硬壳,铁口好开。
二、作业前提条件:1.高炉烘炉结束,凉炉完毕,炉内温度≯50℃。
2.拆除烘炉导管,安装好煤气导出管。
九江1080立方米高炉开炉配料计算

九江1080立方米高炉开炉配料计算
一、配料参数的选择
全炉焦比3.2t/t,正常料焦比0.9t/t.
全炉碱度R2=0.86,正常料碱度R2=1.06,全炉Al2O3≤14%全炉压缩率13%
生铁成分及元素回收率
二、炉型参数,装料料线为1.6米
三、原燃料成分及全炉用料计算结果
装料情况
炉渣成分
四、正常料计算
1、焦批设定为6吨/批,焦比0.9吨/吨,碱度=1.06
2、矿批数确定:批铁量为:6/0.9=6.67吨/批,正常料批数=20批
3、锰矿量为:0.41吨/批,共计20批
五、炉料安排
1、全炉料批数为71批,其中正常料为20批,净焦20批,空焦
1段19批,空焦2段12批
2、依据经验净焦从风口中心线开始一直加至炉腹上沿,则净焦批
数为(22.68+174.584)/10.38=19.652批,取20批
3、空焦2段组成:石灰石:0.73吨/批,白云石:0.63吨/批,硅
石:0.18吨/批,萤石:0.2吨/批
4、空焦1段组成:依据经验空焦1段炉身高度的18%处,体积
为130.19立方米,则空焦1段批数为(97.31+130.19/11.78)
=19.31,取19批。
空焦2段和正常料占容积为429.71立方米。
5、空焦1段组成:石灰石:1.2吨/批,白云石1吨/批,萤石0.2
吨/批
六、计算结果
1、风口中心线一下装木柴
2、表中焦炭量为干焦量,上料时按实际焦炭水份计算成湿
焦碳量。
【2017年整理】高炉主要工艺参数计算公式_第三次讨论(10.13)

高炉主要工艺参数计算公式1、风口标准风速:V标=Q/(F*60)式中V标--风口标准风速,m/sQ――风量,m3/minF――风口送风总面积,m22、风口实际风速:V实= V标*(T+273)*0.1013/ (0.1013+P)*(273+20)式中V实--风口实际风速,m/sV标--风口标准风速,m/sT--风温,℃P--鼓风压力,MPa3、鼓风动能:E=0.412 * 1/n * O3/F2 * (T+273)2/(P+P0)2式中E--鼓风动能,j/sQ--风量,m3/minn--风口数目,个F--风口总截面积,m3T--热风温度,℃P--热风压力,MPaP0--标准大气压,等于101325PaV――炉缸煤气量,m3宝信疑问:O3是否就是Q3?Q:风量,m3/min;(是的)(动能公式按确认文件中宝信理解计算)V――炉缸煤气量,m3,公式中未使用;(不用)6、焦炭负荷:P=Q矿/Q焦式中P--焦炭负荷Q矿--矿石批重,kgQ焦--焦炭(干基)批重,kg7、综合负荷:P=Q矿/Q焦式中P--综合负荷Q矿--矿石批重,,kgQ综焦--综合干焦量批重(干焦量十其它各种燃料量×折合干焦系数批重,)kg宝信疑问:报表上的负荷采取焦炭负荷还是综合负荷;其中干基是否就是干焦(是的);(参照新发给你的报表)8、休风率: u=t/T×100%式中 u――休风率,%t ——高炉休风停产时间,minT——规定日历作业时间(日历时间减去计划达中休时间),min9、生铁合格率生铁合格率是指检验合格生铁占全部检验生铁的百分比。
其计算公式为:生铁合格率(%)= 生铁检验合格量(吨)×100%生铁检验总量(吨)生铁检验合格量是否同下面焦比中合格生铁产量一个概念(不是,生铁检验合格量不进行折算,而焦比中合格生铁产量要进行折算)或者说它们的关系如何计算说明:(1)高炉开工后,不论任何原因造成的出格生铁,均应参加生铁合格率指标的计算。
高炉工长常用公式

工长公式1.透气性指数透气性指数=风量/(风压-顶压)2.压差压差=风压-顶压3.综负综负=矿石批重/(焦批干基+焦丁干基+煤粉×1000/小时料批)+0.005+0.000014.理燃理燃(迁钢)=1500+0.74×风温-1.6×煤粉×1000/(小时料批×批铁量)-7.6×鼓风湿度+40×(0.995×氧量+0.21×(风量-0.995×氧量)/(风量-0.21))理燃(1,3炉)=1530+0.763×风温+[4970×氧量/(1.088×60×风量)-3770×煤量/(1.088×60×风量)]5.炉腹煤气炉腹煤气=1.21×风量+氧量/30+鼓风湿度/1000×44.8/18×(风量+氧量/60)+煤粉×1000/60×3.6/100×22.4/26.标准风速标准风速=风量/(风口面积×60)7.实际风速实际风速=((标准风速×(风温+273)×1.033)/((1.033+风压)×(273+20))8.鼓风动能鼓风动能=1.471×风量3/风口面积2×(风温+273)2/(风压×101325+101325)2×10-5×103/9.806659.二元碱度二元碱度=CaO / (SiO2-矿批×含铁量×Si系数×2.14)10.三元碱度三元碱度=(CaO+MgO)/ (SiO2-矿批×含铁量×Si系数×2.14) 11.渣铁比渣铁比=CaO×96000/Fe×CaO系数12.硫负荷硫负荷=S/Fe×96013.批铁量批铁量=Fe×0.995/0.9514.炉渣碱度R2=CaO/SiO2R3=(CaO+MgO)/SiO2R4=(CaO+MgO)/(SiO2+Al2O3)15.冶炼周期冶炼周期=风口中心线至料线炉容/(每批料体积×(1-0.12)16. 出铁流速出铁流速=估重/出铁时间。
- 1、下载文档前请自行甄别文档内容的完整性,平台不提供额外的编辑、内容补充、找答案等附加服务。
- 2、"仅部分预览"的文档,不可在线预览部分如存在完整性等问题,可反馈申请退款(可完整预览的文档不适用该条件!)。
- 3、如文档侵犯您的权益,请联系客服反馈,我们会尽快为您处理(人工客服工作时间:9:00-18:30)。
810m3高炉开炉料计算810m高炉开炉料计算开炉工作有两个方面的要求:一是安全顺利地完成开炉工作,即做到炉温适中,铁口易开,下料顺畅,并且无人身、设备事故:二是在开炉后能较快平稳地过渡到正常生产,以获得较好的经济效益。
为此开炉时应该使炉内各区域适时地达到所需要的温度,故开炉料的选择,开炉焦比的确定,以及炉段的安排至关重要。
36.1 开炉焦比的选择所谓开炉焦比(总焦比是指开炉料的总焦量与理论出铁量之比。
开炉时由于高炉炉衬温度、料柱的温度都很低,炉料未经充分的预热和还原直接到炉缸,直接还原增多,渣量打,需要消耗的热量也多,所以开炉焦比要比正常焦比高几倍。
具体数值应该根据高炉容积大小,原燃料条件、风温高低、设备状况及技术操作水平等因素进行选择。
一般情况见表6-1:表6-1 开炉焦比的选择炉容/m 焦比/t?t铁?13100以下 >4100-500 3-4500-1000 2.5-31000以上 <2.6选择合适的开炉焦比对开炉进程有决定性的影响。
焦比选择过高,既不经济,又可能导致炉况不顺,即导致高温区上移,在炉身中上部容易产生炉墙结厚现象,更严重的是延长了开炉时间;焦比选择过低,会导致炉缸温度不足,出渣出铁困难,渣铁流动不畅,严重时会造成炉缸冻结。
一般要求开炉前几次含硅量为3%-3.5%。
6.2 开炉造渣制度的选择为了改善渣铁流动性能,冶炼合格生铁,加热炉缸,稀释渣中的Al2O3(Al2O3含量大于18%时,开炉配料中需增加低Al2O3的造渣剂),开炉时渣量要大一些,渣铁比一般为0.4-0.5.如渣量小,可加干渣调节。
开炉时炉渣碱度SiO2?0.90-1.05。
控制生铁含?Mn?0.8%,为了改善炉渣流动性,可提高渣中的MgO含量,使之维持在8%-10%左右,也可适当加些萤石来稀释炉渣。
小高炉在用全天然矿冷风开炉时,焦比特高,可在空料(即焦炭+石灰石)段加些硅石来调整炉渣成分。
不用干渣,既可以节约焦炭,而且铁口见渣较晚,可以延长喷吹铁口时间,有利于加热炉缸。
开炉焦比高,硫负荷就会随之增大,此时炉渣碱度(CaOSiO2)不宜低于正常时的下限,同时还可以选用含硫较低的开炉料。
6.3 开炉配料计算6.3.1计算条件(1)高炉各部位的容积(2)开炉使用的原料、燃料、熔剂等的化学成分、体积密度。
(3)选定开炉焦比与正常料焦比。
(4)确定炉缸的填充方法。
(5)选定铁、锰、硫等元素在渣铁、煤气中的分配率。
(6)选定生铁成分与炉渣碱度,一般要求渣中Al2O3含量不大于18%。
(7)确定开炉料使用料种之间的比例。
(8)选定焦炭或矿石的批重。
6.3.2选定数据全焦填充,炉缸装净焦(C),炉腹以上装空料(x),炉腰上部1/3容积开始过渡至装正常聊(N)。
料线1.75m。
炉料压缩率15%(炉缸净焦19%,炉腹空料16%,其余13%)。
填充容积(已扣除料线以上空间及铁口泥包):表5-1 填充容积部位炉喉 36炉身 447炉腰 75炉腹 135炉缸 112死铁 48.6合计 853.6开炉料成分及其它数据:表5-2 开炉料成分(%)FeSiO2CaOMgOMnAl2O3SP堆密度t/m3烧结矿锰矿石灰石焦炭52.55 16.9 0.6111.04 19.21 1.02 6.3211.09 0.55 51.08 0.681.09 0.322.82 0.190.16 25.240.95 2.01 0.03 4.730.03 0.17 0.630.01 0.42 0.01 0.0051.6 1.9 1.52 0.45焦炭工业分析:灰分14.18%,挥发分0.94%,硫0.63%,水分4.4% 焦炭强度:M4078%, M108% 预订生铁成分,表5-3预定生铁成分,%Fe Si Mn P S 92.67 2.5 0.5 0.04 0.05铁的回收率 99.6%,锰的回收率60%焦炭批重9000Kg/批,总焦比2.5,正常焦比0.9 (每批出铁10000Kg)炉渣碱度CaO/SiO2=1.0C 4.01)以铁和猛的平衡列方程解出正常料的烧结矿和锰矿的批重:设:x—―烧结矿批重,Kg;y—―锰矿批重,Kg;Fe烧、Fe锰、Fe焦—―分别为烧结矿、锰矿、焦炭的含铁量,%; Mn烧、Mn锰—―分别为烧结矿、锰矿的含锰量,%。
列方程(x·Fe + y·Fe锰 + 焦炭批重×Fe焦)×铁的回收率=每批出铁量生铁含Fe(x·Mn烧 + y·Mn锰)×锰的回收率=每批出铁量×生铁含Mn (145)99.6??(0.5255x?0.169y?9000?0.0061)??10000即 ? 92.67??0.6?10000?0.005?(0.0016x?0.2524y)解方程得 x=17543 y=218.8取烧结矿批重为17500kg,锰矿批重为220kg。
2)每批正常料的石灰石用量:已知原燃料带入 SiO2,,kg CaO,kg烧结矿带入 17500×0.1104=1932 17500×0.1109=1940.8 (146)锰矿带入 220×0.1921=42.3 220×0.0055=1.2 焦炭带入 9000×0.0632=568.8 9000×0.0068=61.2 合计 2543.1kg 2003.2kg生铁含Si消耗SiO2 10000×0.025×60=535.7kg (147) 进入渣中28的SiO2 2543.1-535.7=2007.4kg (148)渣碱度 1.0,尚需CaO 2007.4-2003.2=4.2kg (149) 石灰石有效CaO 51.08-1.02=50.06% (150) 每批正常料需要的石灰石量 4.2÷0.5006=8.4kg (151)为取料方便,每6批正常料取石灰石1次,每次量50kg。
3)每批石灰石用量:取值1000kg/批568.8?61.2=1014kg (152)0.50064)每批净焦、空料、正常料的体积:9000×0.81=16.2m3/批 (153) 45090001000?)?0.84=17.353m3/批 (154) 空料Ⅰ(炉腹) (450152090001000?)?0.87=17.972m3/批 (155) 空料Ⅱ(炉腰上部以上) (45015209000175002208.4???)?0.87=27.021m3/批 (156) 正常料 (450160019001520净焦(炉缸)5)炉缸(包括死铁层空间)填充用净焦批数:48.6?112?=9.9取10批 (157)16.26)炉腹及炉腰下部2/3容积装空料批数;(135?75?)?17.353=10.7 取11批 (158)237)按照总焦比和炉腰上部以上至料线的容积来计算空料和正常料的批数:设:x1—正常料批数;13y1—空料批数。
列方程 x1×正常料体积+y1×空料体积=炉吼+炉身+1 32焦炭批重?(炉缸?炉腹?炉腰等空间已填充批数)?焦炭批重?(x1?y1)3 x1?每批正常料出铁量=总焦比1?27.021x?17.972y?36?447??7511??3即 ? (159)(910?11)?(9x1?y1)?2.5??10x1?解方程得 x1=15.01 y1=5.6取值:正常料为15批空料为6批其分配为:①炉腰上部1及炉身下部装空料4批及正常料4批,本段计算焦比为2.087 t焦/t铁;3加上其下的空料11批空料,计算焦比为4.21t焦/t铁。
②炉身中部装空料2批及正常料11批,本段计算焦比为1.348 t焦/t铁。
③炉身上部及炉喉装正常料装料制度COOC↓至料线1.75m为止。
为使炉缸热量充沛,且经高炉解剖研究证实,正常生产时炉腰以下几乎全被焦炭填充,不应有未还原矿石,所以开炉装料时含有矿石的正常料应装在炉腰以上。
9)校核:根据以上计算列出校核表如表8-7. 序号装料部位内容体积m1死铁层及炉缸10C 11X3(2x+n)+6(x+n)=12X+9N8(x+2n)=8X+16N10N 11C+31X+35N=97 41x+35N=76 160.6 1853炉料构成,t焦炭石灰石烧结矿锰矿 189 234 26出铁量 t焦比 t焦/t铁1.244 1.5402 炉腹及2/3炉腰1/3炉腰及炉身下部炉身中部3 174 162 9.076 157.5 1.98 90.377 2.0874 149 185 853.6198 90 873 6846.314 0.084 41.474 41.474280.0 175.0 612.5 612.53.52 2.20 7.70 7.70160.081 99.829 353.06 351.881.348 0.9022.473 1.9695 炉身上部及炉喉6 7合计不计净焦表8-7 开炉料计算校核(续表)序号 1进入生铁,t Si,折成SiO2S 0.045 0.080 0.050 0.175P 0.012 0.035 0.062 0.031 0.140SiO2 12.669 24.985 36.740 20.083 94.477 CaO进入炉渣,t MgOAl2O3 9.372MnOS 1.247 1.221 1.371 0.573 4.412渣碱度Cao/SiO2 0.993 0.998 0.999 0.999 0.998渣量 t 38.869 64.247 92.149 49.213 242.6582 0.0693 4.5814 8.5825 5.348 67 18.8512.584 0.99724.931 2.423 10.479 0.388 36.695 3.703 12.950 0.690 20.074 2.0885.9640.43194.284 9.211 38.765 1.509注:1.不计净焦的渣铁比:242.658/351.88=0.690;2.硫负荷:(0.175+4.412)/351.88=13.03kg/t铁;炉渣含硫:(4.412/242.658)×100=1.82% 3.生铁含磷:(0.14/351.88)×100=0.04% 4.炉渣含Al2O3:(38.765/242.658)×100=15.98% 5.总开炉焦比2.473,正常料焦比0.902高炉内型参数序号 1 2 3 4 5 6 7 8 9 10 11 12 13 14 15 16项目有效容积Vu/m 炉缸直径d/mm 炉腰直径D/mm 炉喉直径d1/mm 死铁层深度h0/mm 炉缸高度h1/mm 炉腹高度h2/mm 炉腰高度h3/mm 炉身高度h4/mm 炉喉高度h5/mm 有效高度Hu/mm 炉腹角α炉身角β Hu/D铁口数/个风口数/个3数值 800 6900 8000 5600 13003500 3100 1500 12200 1500 27000 80° 84.4° 2.725 1(夹角90°) 16。