外文资料翻译(变频调速)
变频调速的工作原理

变频调速的工作原理
变频调速(Variable Frequency Drive,VFD)是一种用于调节电
动机转速的技术。
其工作原理基于改变电机输入电压频率来控制其转速。
变频调速主要由变频器(Inverter)和电动机两部分组成。
变
频器通过将输入电源的交流电转换为直流电,然后再将直流电通过逆变电路转换为可调频率的交流电输出给电动机。
电动机则根据所提供的频率进行运转。
当变频器的输出频率增加时,电动机的转速也相应增加。
因此,通过控制变频器输出的频率,我们就能实现对电动机转速的调节。
变频器中的控制电路可以通过监测电动机运行状态,收集反馈信号,并根据预设的转速要求进行调整。
通过比较预设转速与实际转速之间的差异,控制电路可以自动调整变频器的输出频率,从而实现对电动机转速的精确控制。
在变频调速过程中,我们可以通过调整变频器的输出频率来实现不同转速的控制。
例如,当我们需要电动机运行在低速状态时,可以降低变频器的输出频率;当需要电动机运行在高速状态时,可以增加变频器的输出频率。
变频调速技术的应用广泛,可以用于工业生产线、空调系统、泵站、机械设备等领域。
通过实现电动机的精确调速,可以提高设备的效率和运行稳定性,同时节约能源和减少设备的损耗。
变频调速的原理及应用教案

变频调速的原理及应用教案变频调速(Variable Frequency Drive,简称VFD)是一种电气设备,用于控制电机的转速和运行。
它通过改变电机的供电频率和电压来调节电机的转速。
以下是一个关于变频调速原理及应用的教案。
一、教学目标:1. 了解变频调速的原理;2. 掌握变频调速的应用范围和优势;3. 能够解释变频调速与传统调速方式的区别;4. 能够应用变频调速解决实际工程问题。
二、教学内容:1. 变频调速的原理1.1 变频调速的基本原理变频调速的基本原理是通过改变电源的频率和电压来改变电机的转速。
变频器将电网的交流电转换为直流电,然后再将直流电转换为可调频率和可调电压的交流电,供给电机。
通过改变输出电压的频率和幅值,可以调整电机的转速。
1.2 变频调速的控制方法变频调速的控制方法主要有开环控制和闭环控制两种。
开环控制是根据负载要求预先设定电机的转速,而闭环控制则通过传感器对电机的运行状态进行监测,并根据监测结果调整电机的输出转速。
2. 变频调速的应用2.1 工业领域在工业领域中,变频调速被广泛应用于各种需要控制转速的设备,如风机、泵、压缩机等。
通过调节设备的转速,可以实现能量的节约和运行效率的提高。
2.2 电梯电梯是另一个应用变频调速的领域。
通过变频调速可以实现电梯的平稳运行和快速响应,提升乘客的舒适度和安全性。
2.3 交通运输在交通运输领域,变频调速被广泛应用于地铁、电车和高速列车等。
通过调节电机的转速,可以实现车辆的平稳起动和制动控制。
三、教学方法:1. 学生讨论法:教师提出问题,学生进行小组讨论,然后在班内进行展示和讨论。
2. 实例分析法:通过实际工程案例,引导学生分析和解决问题,提高理论知识与实践能力的结合。
四、教学过程:1. 引入(10分钟)引入话题,向学生介绍变频调速的应用领域和优势。
2. 知识讲解(30分钟)2.1 讲解变频调速的基本原理和控制方法。
2.2 结合实例,展示变频调速在工程中的应用和效果。
变频器外文翻译文献
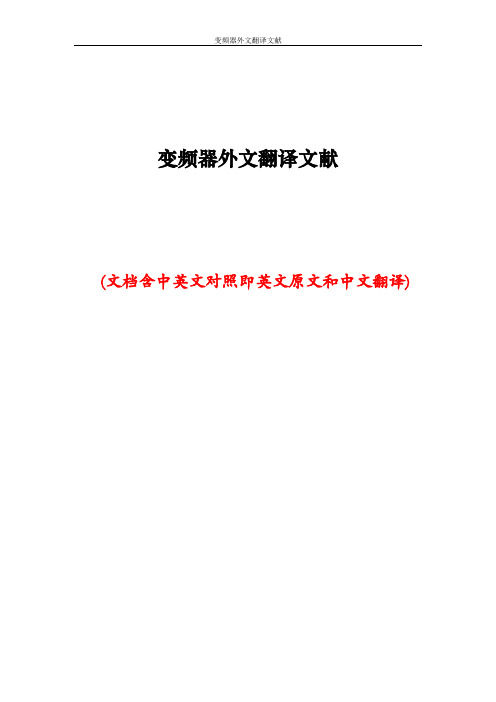
变频器外文翻译文献(文档含中英文对照即英文原文和中文翻译)外文:Converter reference design(1)Converter Selection:Selection to determine the frequency converter when the following points:1) The purpose of a variable frequency; constant pressure to control or constant current control.2) the load converter types such as leaves or pump volume pumps, with special attention to load the performance curve, the performance curve of the decision of the ways and means.3) the frequency converter and load matchingVoltage match: a rated voltage converter with a rated voltage line with the load. Current matches: ordinary pump, the rated current inverter and motor rated current match. For special load such as deep-water pumps, and so on need to refer to the electrical performance parameters to determine the most current inverter current and Guozainengli.Torque match: in this case constant torque load or slow down when the device may have occurred.4) the use of high-speed motor drive inverter, because of the high-speed motor, anti-small, high harmonics lead to increased output current value increases. So for high-speed motor inverter Selection, its capacity to be slightly larger than the ordinary motor selection.5) If the frequency converter to a long cable run, this time to take measures to curb the long cable to the impact of capacitive coupling, inadequate efforts to avoid converter, so in this case, the drive to enlarge the capacity of a file or the converter Output installed output reactor.6) For the application of some special occasions, such as high temperatures, high altitude, at this time would cause the down converter capacity, the drive to enlarge the capacity of a block.(2) inverter control schematic design:1) First confirmation of the installation environment ConverterOperating temperature: high-power converter is the internal electronic components, vulnerable to the effects of temperature, product general requirementsfor 0 ~ 55 ℃, but in order to ensure the safe, reliable, the use of room to be taken into account, the best control in 40 ℃below. In the control box, the converter box should generally be installed in the upper and strictly comply with the Manual of installation requirements, absolutely not be allowed to heating elements or components easily fever close to the converter installed at the bottom.Ambient temperature: the temperature is too high and large temperature changes, within easy converter there is dew, the insulation properties will be greatly reduced,or even short-circuit caused the accident. When necessary, to be added to the desiccant in the box and heater. In water treatment, generally heavier than water vapor, if the temperature changes, then this problem would be more prominent.Corrosive gases: the use of the environment if the corrosive gas concentrations, will not only lead corrosion of components, printed circuit boards, but it will also accelerate the aging of plastic devices, reducing insulation properties.Vibration and shock: the control cabinet with converter by vibration and mechanical shocks will cause electrical connection is bad. Huaian thermoelectric there such a problem. Apart from raising the control cabinet at this time of the mechanical strength, vibration and shock away from the source, we must also use seismic rubber pad fixed within and outside the control cabinet, such as electromagnetic switches have a vibration components. Equipment operation after a period of time and should conduct inspections and maintenance.Electromagnetic interference: Inverter at work due to rectification and frequency, produce around a lot of electromagnetic interference, these high-frequency electromagnetic waves in the vicinity of the instrument, apparatus, a certain interference. Therefore, the cabinet instrumentation and electronic systems, it should be optional metal, shielding the inverter instrument interference. All the components should be reliable grounding, in addition, the electrical components, equipment andinstrumentation should use the connectivity between the shielding control cables, and the shield should be grounded. If handled properly electromagnetic interference, often cause the entire system does not work, leading to the control unit failure or damage.2) Drives and determine the distance between the electrical cables and wiring methodsDrives and motor the short distance should be as much as possible. This reduces the capacitance of the cable, reducing the emission source of interference.Control cables optional shielded cable, power cable or optional shielding from the cable converter to use all the threads of the electrical shield.Electric cables should be independent of the other cable alignment, the minimum distance of 500 mm. At the same time should avoid the electrical cables and other long-running cable lines, in order to reduce the output voltage inverter rapid changes in the electromagnetic interference. If the control cables and power cables cross, as far as possible so that they cross the 90-degree angle. Converter and analog signals on the line and back to the main line of separation of alignment, even in the case also in the control cabinet.And the analog signal converter line the best choice of unshielded twisted pair, shielded power cables selection of the three-core cable (its specifications than ordinary electrical cables in the files) or to comply with the user manual converter.3) inverter control schematicsMain circuit: the role of reactor is to prevent the high-frequency converter harmonic power through the input circuit to return to the grid by the impact of other electronic devices, in accordance with the capacity size converter to decide whether to increase reactor; filter Converter is installed in the output, the output of high-frequency converter to reduce harmonics, when the electrical inverter to the longer distance, we should install filters. Although the frequency converter itself has all kinds of protection, but the lack of protection is not perfect, the main circuit breaker played overload, lack the same protection, selection, in accordance with the capacity to choose the frequency converter. Converter itself can be used to replace thermal overload protection relay.Control loop: the frequency with the frequency manually switch to the failure frequency can be manually cut-operation, not because of output voltage, frequency and frequency-be interlocked.4) Inverter groundingInverter correct grounding is to improve the system stability, the ability to inhibit an important means of noise. Inverter grounding resistance grounding terminal of the smaller the better, the grounding wire cross-section of not less than 4 mm, the length of not more than 5 m. Inverter should be grounded and power equipment to the sites separately, not in total. The shield signal converter from one end of the grounding end, the other floating air. Inverter and control of electrical between the same counter.(3) Inverter Control DesignConverter should be installed in the control cabinet internal control counters in the design should pay attention to the following issues1) heat: Inverter fever is the internal loss. In the frequency converter in the main part of the loss mainly to the main circuit, or about 98 percent, accounting for 2% of control circuits. In order to ensure reliable operation of the normal inverter, Thermal must inverter are usually used for cooling fan; converter fan of the contents of the converter box can be removed internal heat, if the fan does not work, should immediately stop inverter Operation; the high-power inverter also need to increase control Guishang fan, Control of the wind, to design a reasonable, all outlet into the net to set up dust, exhaust open, to avoid over the counter in a swirl, in a fixed location dust Accumulation, according to the statement converter ventilation fans to select the match, fans installed to the attention of earthquake problems.2) the problem of electromagnetic interferenceConverter in its work due to rectification and frequency, produce around a lot of electromagnetic interference, these high-frequency electromagnetic waves in the vicinity of the instrument, apparatus, a certain interference, and will produce high harmonics, the high harmonics will be available for adoption Xinhua loop into the whole power supply network, thus affecting other instruments. If the power inverter system as a whole lot of more than 25 percent, to be considered the anti-jammingmeasures to control supply.When the system in the high-frequency welding machine such as the impact load, electroplating power, the converter itself will appear as interference protection, to consider the whole system of power quality problems.3) protection issues need to pay attention to the following pointsWaterproof anti-condensation: If the converter on the scene, the need to pay attention to the frequency converter Guishang not have the flange or other pipeline leak, the inverter can not be near the water splash, sum up the scene OEM Switchgear Kits & level of security to IP43 above.BOOT: All outlet into the net to set up dust debris into the barrier floc, dust network should be designed to be removable, to facilitate the clean-up, maintenance. Dust of the grid network in accordance with the specific circumstances at the scene determined that dust around the net and Control Department to handle the combination of tight.Anti-corrosive gases: the chemical industry in this relatively Most of this can be on the frequency counters in the control room.(4) converter cable normsSignal lines and power lines must be separately alignment: the use of analog signal converter for remote control, in order to reduce the analog converter and other equipment from the interference, please control signal converter line with the strong electric circuit (H Circuit-and-loop) separate alignment. Distance should be 30 cm above. Even in the control cabinet, the same connection to maintain such a standard. The signal converter and the control should not be longer than the road back to 50 m. Signal lines and power lines must be placed in different metal pipe or metal hose internal: connect PLC and the signal converter if not placed in metal tubes, Drives and vulnerable to external interference equipment; because the converter No built-in the reactor, so the converter input and output level of external power line will have a very strong interference, placing the signal lines of metal or metal hose has to be extended to the inverter control terminal, to ensure that the signal Line and the complete separation of power lines.1) analog control signal line should use two-strands shielding line, cable specifications for 0.75 mm2. When the wiring must pay attention to, to the extent possible, the cable Baoxian short (5-7 mm or so), while Bao Xian after the shield should wrap insulating tape to prevent shielding lines and other equipment contact with the introduction of interference.2) To improve the simple wiring and reliability, signal recommend the use of online video pressure bar.(5) converter and the operation of the relevant parameters setInverter setting parameters, the parameters of each have a certain range of options, often encountered in the use of individual set of parameters for misconduct, leading converter does not work phenomenon.Control: that is, speed control, transferred from the control, PID control or other means. To take control, according to the general control precision, the need for static or dynamic identification.Running a minimum of: that is, the minimum speed motor running, the motor running at low speed, its poor performance cooling, electrical long run on low speed, it can cause burning motor. And at low speed, the cable will increase in the current, cable will lead to fever.The maximum operating frequency: the general maximum frequency converter to 60 Hz, and some even to 400 Hz, high-frequency will enable high-speed motor operation, which the ordinary motor, its bearings can not be over-speed long run, whether the motor rotor To be capable of such a centrifugal force.Carrier frequency: the higher the carrier frequency setting its high harmonics greater weight, and the length of cable, the electrical heating, cable converter fever fever and other factors are closely related.Electrical parameters: the frequency converter to set parameters of the motor power, current, voltage, speed, maximum frequency, these parameters can be directly in the motor nameplate.FH: In a frequency point, there may be a resonance phenomenon, particularly in the relatively high when the entire device in control of the compressor, thecompressor to avoid the surge point.(6) common fault analysis1) flow failure: over-current fault can be divided into acceleration, deceleration, constant speed over-current. May be due to the increase in frequency converter too little time to slow down, load mutations, the unequal distribution of load, output short-circuit, and other causes. At this time can be extended by the general acceleration and deceleration time, reduce the load of mutations, plus braking energy components, load distribution design, the lines to be checked. If off-load converter ora failure that has been Central converter inverter circuits, to be replaced converter.2) overload fault: overload fault, including frequency and overload the electrical overload. May be accelerated their time is too short, too low voltage power grids, Fuzaiguochong and other causes. General can be accelerated through the extension of time to extend the braking time, such as check-voltage power grid. Fuzaiguochong, selected motor and inverter can not drag the load, but also may be due to poor machinery lubrication caused. If the former is the need to replace high-power motors and inverter, if the latter will have to carry out maintenance on production machinery.3) under-voltage: the importation of some of the power inverter that there are problems, need to check before you can run.变频器设计使用参考(1)变频器选型:变频器选型时要确定以下几点:1) 采用变频的目的;恒压控制或恒流控制等。
中英文对照变频调速
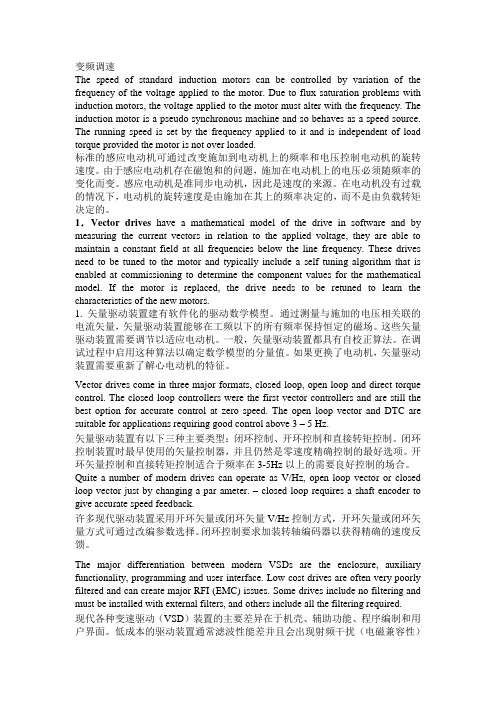
变频调速The speed of standard induction motors can be controlled by variation of the frequency of the voltage applied to the motor. Due to flux saturation problems with induction motors, the voltage applied to the motor must alter with the frequency. The induction motor is a pseudo synchronous machine and so behaves as a speed source. The running speed is set by the frequency applied to it and is independent of load torque provided the motor is not over loaded.标准的感应电动机可通过改变施加到电动机上的频率和电压控制电动机的旋转速度。
由于感应电动机存在磁饱和的问题,施加在电动机上的电压必须随频率的变化而变。
感应电动机是准同步电动机,因此是速度的来源。
在电动机没有过载的情况下,电动机的旋转速度是由施加在其上的频率决定的,而不是由负载转矩决定的。
1.Vector drives have a mathematical model of the drive in software and by measuring the current vectors in relation to the applied voltage, they are able to maintain a constant field at all frequencies below the line frequency. These drives need to be tuned to the motor and typically include a self tuning algorithm that is enabled at commissioning to determine the component values for the mathematical model. If the motor is replaced, the drive needs to be retuned to learn the characteristics of the new motors.1. 矢量驱动装置建有软件化的驱动数学模型。
Application of Frequency Control System PLC(PLC变频调速系统应用研究) 外文翻译

Application of Frequency Control System PLC Abstract: This paper introduces the principle of frequency control heating system, focuses on the structural features of PLC control system, and system hardware and software design.Key words:programmable controller, frequency control, VVVF, heating system.One, IntroductionWith the rapid development of the information age, environmental protection, water and energy saving is no longer a regional topic. According to national statistics from related departments, AC motors, pumps and load for 40% of the country's total power consumption, so large a wide range of pumps and machinery is one of the key areas of energy efficiency. As environmental issues become increasingly accepted by the people in major cities is gradually heating the dispersion of the original into a central heating system. By the microcontroller and relays and other control system composed of short life, system failure rate, is bound by a simple function to the computer, and flexible, the advantages of universal set of one of the devices replaced. The current PLC electrical control system has become the most widely used heart devices. It not only can implement complex logic control, but also to complete the order or timing of various closed-loop control and high reliability, good stability, strong anti-interference, in the harsh environment a long time,uninterrupted operation, and programming Simple, easy maintenance, and is equipped with various communication interfaces and module processing, can be easily connected at all levels.Two, and SelectionIndoor heating, in order to make heating pipe without air, we must maintain a pipeline pressure of the water, or heating system does not work. We use PLC, accompanied by different functions of sensor, according to the pressure of the pipeline, through the inverter to control the pump speed, so that the pipeline pressure is always maintained at the appropriate range, and coupled with over-current, over voltage, overload, without water overpressure protection device set. System has two sets of the same device, to achieve a preparation for one. In addition, PLC by expanding the I / O interface for monitoring, control and communications functions. Control Principle 3The system is PLC real-time device monitoring system. 20 Circulating water pumps, 16 sets of constant pressure up water pumps to PLC's time from the stop control, including the standby pump (pump, constant pressure up water pumps) in the time switch, pump the front of the flow signal detection and alarm, pump overload short-circuit fault alarm.The 36 pump electrical control and protection devices were installed in 7 surface counters, the following detailed description of the first cabinet of the control surface and the initial component selection. Principles of theremaining cabinet features side with the first cabinet.The first control object surface power distribution equipment, including two 2.2 kW pumps and constant pressure up 3 sets of circulating water pump. Pump up work as a set pressure value with a comparison to PID regulator output, and drive up constant pressure water pump work. PLC time to under two pump switch, the specific process for the first frequency converter soft stop, stop receiving the transducer signal the end of the pump disconnect contactor current work, while spare pump contactor to connect operations then start the inverter, the switch to complete the work of the main standby pump. The switching time can be set as needed (using programming device or laptop to the PLC within the original set of switching time parameter changes). Two pump contactor for electrical interlocking. PLC detect the switching state of all contacts.Because the inverter has a short circuit, overload protection, so when the current inverter driven pump failure occurs when the converter will automatically cut off a power supply circuit, into the protection of the state and the output alarm signal. PLC on the alarm signal detection, and then to spare pump input. Specific process for the PLC after the first alarm signal is detected off the current pump contactor, after the inverter reset, and then connected back-pump contactor, start to run back-pump inverter. While the output of the pump failure alarm signal.The cabinet also includes 3 sets of 30 kW pump, a dual-use equipment forthe work, carried out by the PLC according to the time the rotation of 3 water pumps working switch. As the circulating pump is not controlled by inverter, the PLC only need 3 sets of pumps were on time and the disconnect contactor can be connected to operate. Electrical protection components used GV3, GV2 motor protection switch. Motor protection switch with release of the indicator, when the water pump short circuit, overload, etc. for release when the motor protector to protect and output alarm signal, PLC to detect the signal to cut off the pump and standby pump contactor contactor connected, run the standby pump. Pump failure alarm also issued instructions. PLC simultaneous detection of all the pump contactor switch state.All circulating pumps are installed in the outlet water flow sensors, PLC to detect the flow sensor output signal, to determine whether the water pump starts output, and normal work instructions or abnormal alarm indicator. Two constant pressure water pump up a public water sensor works ibid. The system has a number of electric control valve, its distribution by the supply control cabinet, operation control of its installation in control cabinet from the surface of the instrument weather compensator control. PLC to control its power circuit. When the electric control valve corresponding to one or a few circulating pump shut down or failure, the electric control valve will not be able to open.System Settings manual automatic conversion selector switch. PLC willswitch the state of the real-time detection, when you select manual functions, PLC only for signal detection, fault alarm and power supply circuit with the electric valve interlock. All pumps switches and switch start-stop converter installed in the control cabinet by the manual button control panel. When you select automatic state of all control and alarm by the PLC to complete.Overall system diagram in Figure 3-1.Fore, hardware4.1 System block diagramPLC not only to control the circulating pump starts and stops, but also indirectly control up constant pressure from the pump stop working and the alarm output. Following a heat transfer station on the structure of explanation, several other similar basic structure, heat transfer station. Assumption P1, P2, P3 for the 3 sets of circulating pump, P4, P5 up to 2 sets of constant pressure pumps, P6 alarm output for the PLC, then the heat stops the hardware shown in Figure 4-1 to connect.4.2 The job description of all hardwareIn addition to the sensors, other hardware are all installed in a distribution cabinet.(1) converterCounters on each side by the constant pressure pump direct control inverter, inverter installed in the control cabinet, two public a constant pressure water pump converter, two pump electrical interlock. Start-stop control of the inverter is divided into manual and PLC control. There is one pressure sensor transducer input signal (feedback amount), all the way potentiometer signal (reference volume), three-way switch volume (two-way road from the stop signal and reset signal). There are two output signal (along fault protection alarm signal, lower than 5Hz run signal). Inverter parking parking are soft, manual control to stop when the counter has two buttons, one for the sub-contactor off button, a soft-stop button for the inverter. Note that because of the frequency converter soft parking parking are located, so when the manual stop button should press the soft-stop, soft stop and then disconnect the contactor end (this time fromthe actual case may be). Inverter fault reset signal is also equipped with manual and automatic two-way input.(2) Each side cabinet has a weather compensator to require distribution N = 250 W 230 VAC, the input from the external sensor input, output control electric control valve. Weather compensator to counter installation, including the sensor input and control output needs, including a total of 27 secondary terminals. Climate compensator with alarm, alarm lamp power distribution cabinet left.(3) flow switchPump starts the flow switch to detect whether there is any water after the pipe through, if the pump is running for the dual purpose of a front-end equipment is installed on each pump a flow sensor, a total of three. Or one of two pumps with a total installed equipment is a flow sensor. Specific process is: PLC after the start of a pump, after some delay (this delay can be set based on experience), PLC will detect the pump flow sensor output signal, if the signal indicative of the water flow is determined PLC pump failure, resulting in failure alarm signal, while the pump power and the standby pump pump put into operation.When the pipeline pressure tends to set the value of converter operating frequency is low, then the pump speed is very low, the flow switch may also issue non-flow signals. This is not failure, PLC will detect low-frequency transducer output signal to different (less than 5 Hz the waywhen the inverter output signal).(4) 24 hours under normal conditions and automatically switch the water pump, standby pump to run.(5) manual and automatic selection switchEach side cabinets are equipped with a manual / automatic transfer switch, the switch to a three selector switch, installed in the secondary control loop.1 to select Auto,2 to select Manual, 0 for the power left vacant.Select a button to manually power off, manual / automatic instructions breaker pull, PLC test the relay state, the implementation of control procedures, from the PLC to control all the water pump starts and stops and switching, including the frequency converter from the stop and alarm. Select 2 for the manual, then manually / automatically disconnect relay instructions, PLC detect the state of the relay, the implementation of manual procedures. PLC was detected only alarm. At this point all the counter control buttons by hand through the counter on the buttons and switches and switch starts and stops pumps, including the frequency converter from the stop. Note that the PLC in manual mode is still in working condition.Select 0 for the vacant state, now part of the counter button manual control circuit is cut off, can not control the device. Manual / Auto disconnect relay instructions. The PLC signal is detected at this time and when you select Manual as the PLC to perform manual procedures. Fault alarm.(6) supply water solenoid valve cabinets on each side there is a replenishment valve require distribution N = 100 W 220 VAC (7 号cabinet for the two), solenoid valves supply water from the corresponding box of the float switch to control. Replenishment box has two float switches, one at a high, a bit at the bottom. By two different water levels in the different relay contact output, through the intermediate relay to control the electromagnetic valve for starting, stopping and ultra-underground water level alarm. The device also has a set of solenoid valve manually switch the button, installing and counter. Choice through a two-phase control switch and float switch. Select Manual when the water level alarm is also low. Five,System SoftwarePLC software is modular programming system by manual operation module, the module automatically and fault diagnosis and alarm output module and other components.(1) Manual operation modulesAccording to system requirements, the system is run manually, PLC circuit protection only to receive the signal and the sensor signals, and thus judge the work of running the pump in case of failure, the output alarm signal. Chart 5-1 is a flowchart of this module.(2) the module automaticallyAccording to system requirements, the system is running automatically, PLC to complete the work are: to receive the signal circuit protection; to receive the sensor signal; time work in order to switch pumps and backup pumps; in case of failure, the output alarm signal. Figure 5-2 is a flowchart of this module.(3) fault diagnosis and alarm output moduleIn the fault diagnosis and alarm output module, the procedure receives the signal and sensor signal circuit protection, under certain conditions, diagnostic results obtained. If there is no fault, then the process to continue; if there is fault, the output alarm signal, notify the staff for processing. Specific fault are:a. The work of the pump over-current protection signal is valid;b. Working pump starts, the detector can not detect water flow (constant pressure water pump up the work in the frequency converter does not applywhen the ultra-low frequency);c. Pump water up to the constant pressure of reservoir water level is low;d. Other failure.Six, ConclusionThe system is simple, reliable, easy to maintain, is convenient for people living in the PLC in a successful application. PLC frequency current heating system used in the South of use in Urumqi, more than a year without trouble, and compact, precise movement, is an ideal heating system.PLC变频调速系统应用研究论文摘要:本文介绍了变频调速供暖系统的原理,重点介绍了PLC控制系统的结构特点,以及系统硬件和软件设计方法。
外文翻译---PLC变频调速的网络反馈系统的实现
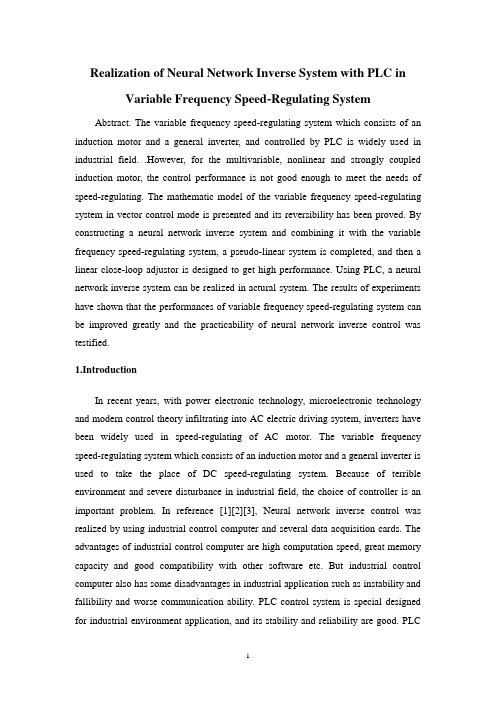
Realization of Neural Network Inverse System with PLC in Variable Frequency Speed-Regulating System Abstract. The variable frequency speed-regulating system which consists of an induction motor and a general inverter, and controlled by PLC is widely used in industrial field. .However, for the multivariable, nonlinear and strongly coupled induction motor, the control performance is not good enough to meet the needs of speed-regulating. The mathematic model of the variable frequency speed-regulating system in vector control mode is presented and its reversibility has been proved. By constructing a neural network inverse system and combining it with the variable frequency speed-regulating system, a pseudo-linear system is completed, and then a linear close-loop adjustor is designed to get high performance. Using PLC, a neural network inverse system can be realized in actural system. The results of experiments have shown that the performances of variable frequency speed-regulating system can be improved greatly and the practicability of neural network inverse control was testified.1.IntroductionIn recent years, with power electronic technology, microelectronic technology and modern control theory infiltrating into AC electric driving system, inverters have been widely used in speed-regulating of AC motor. The variable frequency speed-regulating system which consists of an induction motor and a general inverter is used to take the place of DC speed-regulating system. Because of terrible environment and severe disturbance in industrial field, the choice of controller is an important problem. In reference [1][2][3], Neural network inverse control was realized by using industrial control computer and several data acquisition cards. The advantages of industrial control computer are high computation speed, great memory capacity and good compatibility with other software etc. But industrial control computer also has some disadvantages in industrial application such as instability and fallibility and worse communication ability. PLC control system is special designed for industrial environment application, and its stability and reliability are good. PLCcontrol system can be easily integrated into field bus control system with the high ability of communication configuration, so it is wildly used in recent years, and deeply welcomed. Since the system composed of normal inverter and induction motor is a complicated nonlinear system, traditional PID control strategy could not meet the requirement for further control. Therefore, how to enhance control performance of this system is very urgent.The neural network inverse system [4][5] is a novel control method in recent years. The basic idea is that: for a given system, an inverse system of the original system is created by a dynamic neural network, and the combination system of inverse and object is transformed into a kind of decoupling standardized system with linear relationship. Subsequently, a linear close-loop regulator can be designed to achieve high control performance. The advantage of this method is easily to be realized in engineering. The linearization and decoupling control of normal nonlinear system can realize using this method.Combining the neural network inverse into PLC can easily make up the insufficiency of solving the problems of nonlinear and coupling in PLC control system. This combination can promote the application of neural network into p r a c t i c e t o a c h i e v e i t f u l l e c o n o m i c a n d s o c i a l b e n e f i t s In this paper, firstly the neural network inverse system method is introduced, and mathematic model of the variable frequency speed-regulating system in vector control mode is presented. Then a reversible analysis of the system is performed, and the methods and steps are given in constructing NN-inverse system with PLC control system. Finally, the method is verified in experiments, and compared with traditional PI control and NN-inverse control.2.Neural Network Inverse System Control MethodThe basic idea of inverse control method [6] is that: for a given system, anα-th integral inverse system of the original system is created by feedback method, and combining the inverse system with original system, a kind of decoupling standardized system with linear relationship is obtained, which is named as a pseudo linear system as shown in Fig.1. Subsequently, a linear close-loop regulator will be designed toachieve high control mathematic model of the variable performance.Inverse system control method with the features of direct, simple and easy to understand does not like differential geometry method [7], which is discusses the problems in "geometry domain". The main problem is the acquisition of the inverse model in the applications. Since non-linear system is a complex system, and desired s t r i c t a n a l y t i c a l i n v e r s e i s v e r y obtain, even impossible. The engineering application of inverse system control doesn’t meet the expectations. As neural network has non-linear approximate ability, especially for nonlinear complexity system, it becomes with the powerful e x p e c t a t i o n s t o o l t o s o l v e t h e p r o b l e m.a − th NN inverse system integrated inverse system with non-linear ability of the neural network can avoid the troubles of inverse system method. Then it is possible to apply inverse control method to a complicated non-linear system. a − th NN inverse system method needs less system information such as the relative order of system, and it is easy to obtain the inverse model by neural network training. Cascading the NN inverse system with the original system, a pseudo-linear system is completed. Subsequently, a linear close-loop regulator will be designed.3. Mathematic Model of Induction Motor Variable FrequencySpeed-Regulating System and Its ReversibilityInduction motor variable frequency speed-regulating system supplied by the inverter of tracking current SPWM can be expressed by 5-th order nonlinear model in d-q two-phase rotating coordinate. The model was simplified as a 3-order nonlinear model. If the delay of inverter is neglected system original system, the model is e x p r e s s e d a s f o l l o w s:(1)where denotes synchronous angle frequency, and is rotate speed.a r e s t a t o r’s c u r r e n t,a n d a r e r o t o r’s f l u x l i n k a g e i n(d,q)axis.is number of poles. is mutual inductance, and is rotor’sinductance. J is moment of inertia.is rotor’s time constant, and is l o a d y n c h r o n o u s a n g l e f r e q u e n c y t o r q u e.I n v e c t o r m o d e,t h e nSubstituted it into formula (1), then(2) Taking reversibility analyses of forum (2), thenThe state variables are chosen as followsInput variables areTaking the derivative on output in formula(4), then(5)(6) Then the Jacobi matrix is Realization of Neural Network Inverse System with PLC(7)(8)As so and system is reversible.Relative-order of system isWhen the inverter is running in vector mode, the variability of flux linkage can be neglected (considering the flux linkage to be invariableness and equal to the rating). The original system was simplified as an input and an output system concluded by forum (2).According to implicit function ontology theorem, inverse system of formula (3) can be expressed as(9)When the inverse system is connected to the original system in series, the pseudolinear compound system can be built as the type of4. Realization Steps of Neural Network Inverse System4.1 Acquisition of the Input and Output Training SamplesTraining samples are extremely important in the reconstruction of neural network inverse system. It is not only need to obtain the dynamic data of the original system, but also need to obtain the static date. Reference signal should include all the work region of original system, which can be ensure the approximate ability. Firstly the step of actuating signal is given corresponding every 10 HZ form 0HZ to 50HZ, and the responses of open loop are obtain. Secondly a random tangle signal is input, which is a random signal cascading on the step of actuating signal every 10 seconds, and theclose loop responses is obtained. Based on these inputs, 1600 groups should includea l l t r a i n i n g s a m p l e s a r e g o t t e n.4.2 The Construction of Neural NetworkA static neural network and a dynamic neural network composed of integral is used to construct the inverse system. The structure of static neural network is 2 neurons in input layer, 3 neurons in output layer, and 12 neurons in hidden layer. The excitation function of hidden neuron is monotonic smooth hyperbolic tangent function. The output layer is composed of neuron with linear threshold excitation function. The training datum are the corresponding speed of open-loop, close-loop, first order derivative of these speed, and setting reference speed. After 50 times training, the training error of neural network achieves to 0.001. The weight and threshold of the neural network are saved. The inverse model and a dynamic neural network c o m p o s e d o f o r i g i n a l s y s t e m i s o b t a i n e d.5 .Experiments and Results5.1 Hardware of the SystemThe hardware of the experiment system is shown in Fig 5. The hardware system includes upper computer installed with Supervisory & Control configuration software WinCC6.0 [8], and S7-300 PLC of SIEMENS, inverter, induction installed with m o t o r a n d C o n t r o l p h o t o e l e c t r i c c o d e r.PLC controller chooses S7-315-2DP, which has a PROFIBUS-DP interface and a MPI interface. Speed acquisition module is FM350-1. WinCC is connected with the e x p e r i m e n t s y s t e m S7-300b y C P5611u s i n g M P I p r o t o c o l.The type of inverter is MMV of SIEMENS. It can communicate with SIEMENS PLC by USS protocol. ACB15 module is added on the inverter in this system.5.2 Software Program5.2.1 Communication IntroductionMPI (MultiPoint Interface) is a simple and inexpensive communication strategy using in slowly and non-large data transforming field. The data transforming between W i n C C a n d P L C i s n o t l a r g e,s o t h e M P I c h o s e n.The MMV inverter is connected to the PROFIBUS network as a slave station, which is mounted with CB15 PROFIBUS module. PPO1 or PPO3 data type can be chosen. It permits to send the control data directly to the inverter addresses, or to use t h e s y s t e m f u n c t i o n b l o c k s o f S T E P7V5.2 SFC14/15.OPC can efficiently provide data integral and intercommunication. Different type servers and clients can access data sources of each other. Comparing with the traditional mode of software and hardware development, equipment manufacturers only need to develop one driver. This can short the development cycle, save manpower resources, and simplify the structure the experiment system of the entire c o n t r o l s y s t e m.Variety data of the system is needed in the neural network training of Matlab, which can not obtain by reading from PLC or WinCC directly. So OPC technology can be used l to obtain the needed data between WinCC and Exce. Setting WinCC as OPC DA server, an OPC client is constructed in Excel by VBA. System real time data is readed and writen to Excel by WinCC, and then the data in Excel is transform to M a t l a b f o r o f f l i n e training to get the inverse system of original system.5.2.2 Control ProgramUsed STL to program the communication and data acquisition and control algorithm subroutine in STEP7 V5.2, velocity sample subroutine and storage subroutine are programmed in regularly interrupt A, and the interrupt cycle chooses 100ms. In order to minimum the cycle time of A to prevent the run time of A exceeding 100ms and system error, the control procedure and neural network a l g o r i t h m a r e p r o g r a m m e d i n m a i n procedure B.In neural network algorithm normalized the training samples is need to speed up the rate of convergence by multipl ying a magnification factor in input and output data before the final training.5.3 Experiment ResultsWhen speed reference is square wave signal with 100 seconds cycle, where thei n v e r t e r i s r u n n i n g i n v e c t o r m o d e.T h e r e s u l t s s h o w t h a t t h e tracking performance of neural network control is better than traditional PI control.When speed reference keeps in constant, and the load is reduced to no load at 80 seconds, and increased to full load at 120 seconds, the response curves of speed with traditional PI control and neural network inverse control are shown in Fig. 11 and 12 respectively. It is clearly that the performance of resisting the load disturbing with neural network inverse control is better than the traditional PI control.(Speed response in PI control)(Speed response in neural network inverse control)6. ConclusionIn order to improve the control performance of PLC Variable Frequency Speed-regulating System, neural network inverse system is used. A mathematic model of variable frequency speed-regulating system was given, and its reversibility was testified. The inverse system and original system is compound to construct the pseudo linear system and linear control method is design to control. With experiment, neural network inverse system with PLC has its effectiveness and its feasibility in industryPLC变频调速的网络反馈系统的实现变频调速系统,包括一个异步电动机和通用逆变器、且PLC控制被广泛地应用于工业领域。
变频技术中英文翻译资料
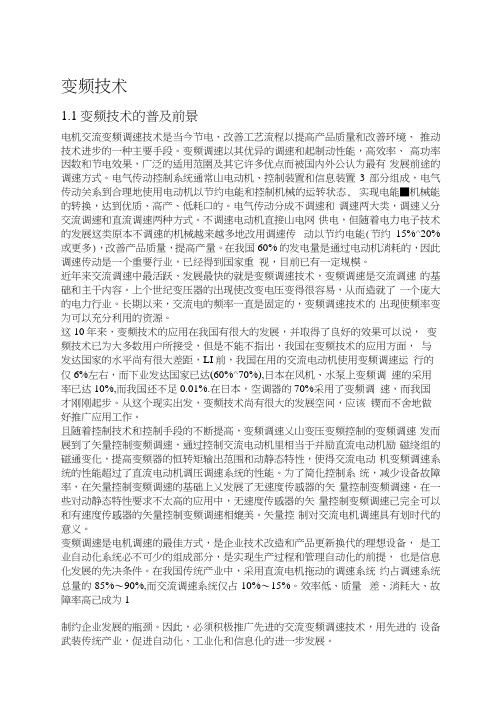
变频技术1.1变频技术的普及前景电机交流变频调速技术是当今节电、改善工艺流程以提高产品质量和改善环境、推动技术进步的一种主要手段。
变频调速以其优异的调速和起制动性能,高效率、高功率因数和节电效果,广泛的适用范圉及其它许多优点而被国内外公认为最有发展前途的调速方式。
电气传动控制系统通常山电动机、控制装置和信息装置3 部分组成,电气传动关系到合理地使用电动机以节约电能和控制机械的运转状态, 实现电能■机械能的转换,达到优质、高产、低耗口的。
电气传动分成不调速和调速两大类,调速乂分交流调速和直流调速两种方式。
不调速电动机直接山电网供电,但随着电力电子技术的发展这类原本不调速的机械越来越多地改用调速传动以节约电能(节约15%^20%或更多),改善产品质量,提高产量。
在我国60% 的发电量是通过电动机消耗的,因此调速传动是一个重要行业,已经得到国家重视,目前已有一定规模。
近年来交流调速中最活跃、发展最快的就是变频调速技术,变频调速是交流调速的基础和主干内容。
上个世纪变压器的出现使改变电压变得很容易,从而造就了一个庞大的电力行业。
长期以来,交流电的频率一直是固定的,变频调速技术的出现使频率变为可以充分利用的资源。
这10年来,变频技术的应用在我国有很大的发展,并取得了良好的效果可以说,变频技术已为大多数用户所接受,但是不能不指出,我国在变频技术的应用方面,与发达国家的水平尚有很大差距,LI前,我国在用的交流电动机使用变频调速运行的仅6%左右,而下业发达国家已达(60%^70%),日本在风机、水泵上变频调速的采用率已达10%,而我国还不足0.01%.在日本,空调器的70%采用了变频调速,而我国才刚刚起步。
从这个现实出发,变频技术尚有很大的发展空间,应该锲而不舍地做好推广应用工作。
且随着控制技术和控制手段的不断提高,变频调速乂山变压变频控制的变频调速发而展到了矢量控制变频调速,通过控制交流电动机里相当于并励直流电动机励磁绕组的磁通变化,提高变频器的恒转矩输出范围和动静态特性,使得交流电动机变频调速系统的性能超过了直流电动机调压调速系统的性能。
变频调速的原理及应用教案

变频调速的原理及应用教案变频调速(Variable Frequency Drive,缩写为VFD)是一种用于调节电机转速的技术,它通过调整电机供电的频率和电压来控制电机的转动速度。
变频调速技术广泛应用于工业领域,如制造业、水泵、风机、压缩机、输送带等。
1.基本构成:变频调速系统由三个部分组成,即电源、变频器和电动机。
电源将交流电转换为直流电,然后经过变频器将直流电转换为可调的交流电,最后通过电动机将电能转换为机械能。
2.频率调节:变频器可以通过改变输出电压的频率来改变电机的转速。
当输出频率增大时,电机的转速也会相应增加;当输出频率减小时,电机的转速也会相应减小。
3.电压调节:变频器还可以通过改变输出电压的幅值来调节电机的转矩。
当输出电压增加时,电机的转矩也会相应增加;当输出电压减小时,电机的转矩也会相应减小。
1.节能:变频调速可以根据实际工作负荷来调节电机的转速,避免了电机运行时的过度能耗,从而实现节能的目的。
2.系统平稳:传统的启停方式容易产生冲击和振动,而变频调速可以使电机平稳启动和停止,减小震动和冲击,延长机械设备的使用寿命。
3.精度控制:变频调速系统可以精确地控制电机的转速,实现对生产过程的精细控制,提高生产效率和产品质量。
4.降噪:由于变频调速使得电机运行平稳,减少了机械设备的震动和噪音,从而改善了工作环境。
5.起重和运输:变频调速广泛应用于起重机和运输设备中,可以实现对货物的平稳提升和运输,提高生产效率和安全性。
6.水泵和风机控制:变频调速可以根据实际需要调节水泵和风机的运行速度,使其在不同负载下工作,提高工作效率和节能效果。
教案设计如下:一、教学目标1.了解变频调速的基本原理和应用。
2.掌握变频调速系统的组成和工作原理。
3.了解变频调速在工业领域的应用。
二、教学内容1.变频调速的原理和基本构成。
2.变频调速系统的工作原理和调节方法。
3.变频调速在工业领域的应用案例。
三、教学过程1.提出问题:请同学们简单介绍一下变频调速的基本原理和应用。
外文翻译-变频器基本参数调试
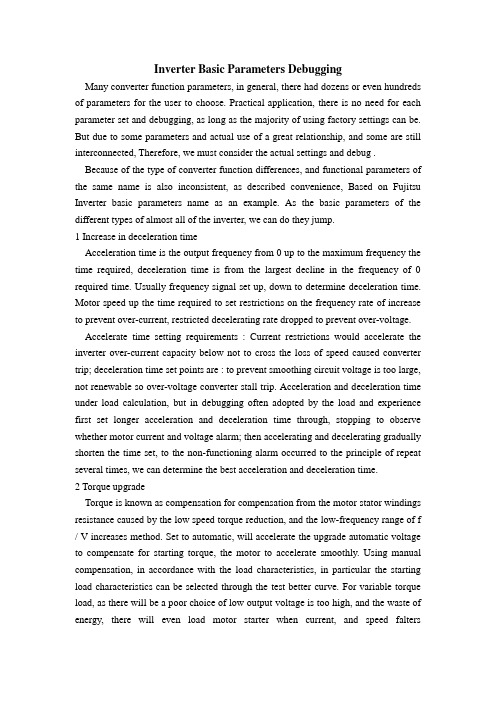
Inverter Basic Parameters DebuggingMany converter function parameters, in general, there had dozens or even hundreds of parameters for the user to choose. Practical application, there is no need for each parameter set and debugging, as long as the majority of using factory settings can be. But due to some parameters and actual use of a great relationship, and some are still interconnected, Therefore, we must consider the actual settings and debug . Because of the type of converter function differences, and functional parameters of the same name is also inconsistent, as described convenience, Based on Fujitsu Inverter basic parameters name as an example. As the basic parameters of the different types of almost all of the inverter, we can do they jump.1 Increase in deceleration timeAcceleration time is the output frequency from 0 up to the maximum frequency the time required, deceleration time is from the largest decline in the frequency of 0 required time. Usually frequency signal set up, down to determine deceleration time. Motor speed up the time required to set restrictions on the frequency rate of increase to prevent over-current, restricted decelerating rate dropped to prevent over-voltage. Accelerate time setting requirements : Current restrictions would accelerate the inverter over-current capacity below not to cross the loss of speed caused converter trip; deceleration time set points are : to prevent smoothing circuit voltage is too large, not renewable so over-voltage converter stall trip. Acceleration and deceleration time under load calculation, but in debugging often adopted by the load and experience first set longer acceleration and deceleration time through, stopping to observe whether motor current and voltage alarm; then accelerating and decelerating gradually shorten the time set, to the non-functioning alarm occurred to the principle of repeat several times, we can determine the best acceleration and deceleration time.2 Torque upgradeTorque is known as compensation for compensation from the motor stator windings resistance caused by the low speed torque reduction, and the low-frequency range of f / V increases method. Set to automatic, will accelerate the upgrade automatic voltage to compensate for starting torque, the motor to accelerate smoothly. Using manual compensation, in accordance with the load characteristics, in particular the starting load characteristics can be selected through the test better curve. For variable torque load, as there will be a poor choice of low output voltage is too high, and the waste of energy, there will even load motor starter when current, and speed faltersphenomenon.3 Electronic Thermal Overload ProtectionThe function of the motor overheating protection setup, It is within the CPU frequency converter operating under the current value and frequency of the motor calculated temperature rise, for the protection of overheating. This function only applies to "drag a" occasion, and "a number of tractors," should be in the retrofitting Motors thermal relay.Electronic thermal protection settings (%)=[ motor rated current (A) / Rated output current converter (A)] × 10 0%.4 Frequency restrictionsThat the inverter output frequency, amplitude threshold. Frequency limitation is to prevent the misoperation or external frequency setting signal failure, which leads to the output frequency is too high or too low. prevent damage to the equipment of a protective function. The application on the actual situation can be set. This function may also be used for the speed limit, if the conveyor belt, due to transportation of materials is not much, To reduce the mechanical and wear belts, use inverter-driven, and will limit frequency inverter settings for a particular frequency, This would enable the conveyor belt running on a fixed, low speed work.5 Frequency OffsetSome deviation is known as the frequency or frequency deviation settings. When their use is by the external frequency analog signal (voltage or current) settings, This function can be adjusted frequency signal set at the lowest level of the output frequency, as illustrated in figure 1. When some frequency transducer signal set for 0%, the error values role of the range 0 ~ HBT, Some converter (such as electricity for homes, Sanken) may also bias polarity settings. Debugging in frequency when the signal is set at 0%, the inverter output frequency is 0 Hz, for xHz. At this time it will be set to the frequency offset the negative xHz will enable inverter output frequency is 0 Hz.6 Set the frequency signal gainThis function only with external analog signal frequency setting was effective. It is used to cover external set voltage and signal transducer voltage (+10 v) the inconsistencies; facilitating simulation setting signal voltage options set, when the analog input signal for a maximum (10 v, 5v or 20mA), the output can be obtained f / V graphics frequency and percentage of this parameter can be set; If external signalsset to 0-5v, if the inverter output frequency of 50Hz ~ 0. Gain signal will be set to 200% can be.7 Torque limitCan be divided into driving torque and braking torque limit restricted. It is based on inverter output voltage and current values, the CPU torque, can increase its deceleration constant speed operation and the impact of load recovery characteristics are significantly improved. Torque limit function for automatic acceleration and deceleration control. Assuming acceleration and deceleration time is less than inertia load time, the motor can be guaranteed in accordance with the torque settings automatically accelerate and decelerate.Driving torque functions provide a powerful starting torque, in steady state operation, the torque control motor functions will turn bad, Motor torque and will limit the maximum value set, when suddenly increased load torque, or even in accelerated time setting off a short time, Inverter is unlikely to cause tripping. Accelerating time setting off a short time, motor torque will not exceed the maximum values. Drivers of large start-up torque advantageous to set to 80 ~ 100% more properly.Braking torque setting numerical smaller, the greater the braking force, acceleration and deceleration for emergency occasions, If braking torque setting numerical Assembly set off alarm occurred pressure phenomena. If braking torque set at 0%, added to the main capacitor will enable the renewable total closer to 0, so that the slowdown in the motor, the non-use of braking deceleration resistance can not turn to stop tripping. But in some loads, such as brake torque set at 0%, the slowdown will be temporary idling, Starting inverters, repeatedly, the current significant fluctuations serious converter Trip will be to attract attention.8 Acceleration and deceleration mode selectionKnown as the acceleration and deceleration curves choice. General converter is linear, nonlinear, and three S curve, usually will choose linear curve; Nonlinear curve applies to variable torque load, such as fan; S curve in constant torque load, slowdown in the rate of change is slow. Settings can load torque characteristic curve corresponding options, but there are exceptions. Debugging a writer in Taiwan Boiler fan of inverters, the first acceleration and deceleration curves choice nonlinear curve, get going on the trip inverter operation, adjusting to change many parameters without results, later renamed the S-curve after the normal. It is the reason : Starting op fan asflue gas flow on its own rotation and inversion as a negative load, This selection of the S-curve, starting just when the frequency increased slowly, in order to avoid a trip to the converter, Of course, this is not starting against DC converter brake function of the method used.9 Torque Vector ControlVector Control is based on the theory that : asynchronous motors and DC motors have the same mechanism of torque. Vector control of the stator current is divided into the current and magnetic torque current, respectively control, while both the synthesis of the stator current output to the motor. Therefore, based on the principle of DC motors available with the same performance. Using torque vector control function, motor in various operating conditions can output maximum torque, especially in the low-speed motor running regional.Now almost all of the inverter by using feedback vector control, As the transducer based on the size and the load current phase of deterioration in compensation, and the motor is the mechanical characteristics are strong, For most occasions have been able to meet the requirements without the external converter installed speed feedback circuit. This function settings, according to the actual situation in the effective and ineffective one can choose.With the transfer function is poor compensation control, whose role is to compensate by load fluctuations caused by the speed deviation can be added corresponding to the load current to the frequency difference. The main function for positioning control.10 Energy-saving controlFans, pumps are reduced torque load, with the speed of that decline, load torque and speed proportional to the square of decreases, and control functions with energy-saving design of the inverter exclusive V / f mode, This model can be improved motor and the inverter efficiency, may reduce the load current automatic converter output voltage, so as to achieve energy-saving purposes, in accordance with the specific circumstances set to be valid or invalid.I need Explained 9、10 these two parameters are very advanced, but some users to upgrade equipment, not simply the opening of these two parameters, that is, after the opening of inverter frequent tripping, suspended after all normal. It is because : (1) original parameters of the inverter and the motor request for the electrical parameters that much difference. (2) for the creation of inadequate understanding of thefunctional parameters, such as energy-saving control function can only be used for V / f controlled manner, not for vector control approaches. (3) the opening of the vector control methods, but no electrical parameters of the manual and automatic settings to read, read or improper methods.From IEEE Trans Automat Control by Engin Yaz变频器基本参数调试变频器功能参数很多,一般都有数十甚至上百个参数供用户选择。
外文文献、译文

外文文献Automatic Frequency tower without constant pressure water system1 .IntroductionWith industrial control levels. Inverter constant pressure water supply device technology has been relatively mature. In the market to be good reflect. from the economical operation of the system is stable and reliable has been recognized by society. Along with the system controller and inverter technology development is continuously updated and developed. Controllers on the run. From the relay logic, microprocessor, PLC, dedicated controller steps. From Frequency Control, its development has undergone a number of speed control, Simulation given exclusive control of the controller. Every step of development mean that newer and better devices replace traditional methods. The system uses more advanced programmable logic control PLC as a controller to complete the frequency constant pressure water system based on the use of water in different Remote control through online pressure transmitter signal input to the PLC, PID automatic adjustment, pump control operations, to maintain pressure on the water supply pipe network. The system uses a more extensive and can be used for living, Fire and water supply industries in many respects. Below constant pressure to district water supply system as an example. Converter Technology in industrial control system applications.2. Introduction ProcessMost of the water supply system prior to using the traditional towers, water tanks, or high-pressure-boosting equipment, But they must pump water higher than the actual height of the pressure referred to "upgrade" of water, The result of the increase in the pump shaft power and energy loss disc, and the user is not a constant pressure. pressure over the need for regular inflation. equipment increased the danger. Frequency is usedwithout constant pressure water tower technology, can make up for these shortcomings. Frequency - control system through measurement of the pressure on the pipe network, by the PLC was built PID regulator after the operation. the converter output frequency to achieve the constant pressure of the water supplynetwork, and from the water company for supply to the purification of water inflow of water east district, followed by a transducer control of the two motors and two-frequency pump the water to the district each user's home. According to users within the water pipe network to control the pressure of four pumps work mode. When the user less water consumption, only one pump operating frequency Taiwan to guarantee the constantmotor and the motor from a B inverters to control, Frequency Motor collectively. in the smaller water consumption, According to two inverter pump controller mutual switching time. to extend motor life.To prevent water users in a very, storage tanks water level is too high and aids out pools, Therefore, the increase in a Level interlock alarm control, to improve system security. 50,000 increase in the bottom of a venting valve, to be able to regularly clean water tanks to ensurethat users of water cleanliness.3 System control theory and compositionThis system uses single-loop feedback control loop, The continuous acquisition system pressure pipe network signal and given SP (pressure settings), After Operators will deviation gave PID controller PID controller then signals gave implementing agencies, namely the electrical group, implementing agencies receiving the regulator orders to change their ways of operating, so that the pressure of change. So the cycle implementation. until the pressurepipe network in a constant state of the pressure. from this system from the environment (such as temperature) interference factors more pressure control belongs to lag control, Therefore, using PID control operation, to reduce the environmental interference. improve system stability and speed.System testing tube pressure, and then judge of the pressure and the low-pressure limit set the difference between, if less than lower limit set pressure. Inverter system will be activated pump. Frequency pump power and the size depends on the size of the pressure signal. If the maximum frequency pump Gong the rate had not been run under control so that the pressure to achieve lower limit set value, then a system will be activated # motor, If this time limit has been set to achieve a low value, the system will return to the state at the beginning, Detection of continued pressure. Similarly, when the pump and an inverter frequency # pump running, Tube pressure limit has not yet been reached, low pressure setting, the system will activate the motor # 2. If this time limit has been set to achieve a low value, The system will be returned to the state at the beginning, Detection of continued pressure. If the pipe pressure has been limited to low-pressure setting. System will judge the pressure of a huge in the high-limit values. If there is no limit set to achieve the high pressure values, the system will return to the state at the beginning, Detectionof continued pressure, has been set to achieve the high pressure limit value. The system will be parked motor # 2, If the limit is greater than the high-pressure setting value, the system will stop a # motor, If the limit is greater than the high-pressure setting value. Inverter system will regulate the pump power until ceases. With a transducer frequency to control two motors, when only one operating frequency pump at work state, and running for some time, the system will automatically switch to another frequency pump Taiwan,In exceptional circumstances or failure of the state, they can manually start each motor. And four motors are equipped with overload protection, short circuit protection, over-voltage protection and phase protection, overheating protection, over-current protection and overvoltage transient power outages automatic restart function restored.3.2The system has a programmable logic controller, a converter, a converter, various conventional remote instrument, Motor Group, warning devices and other pipeline equipment, and the completion of major PLC the overall control system, receive the signals, the corresponding calculation the completion of various chain. Flowmeter selection is the instantaneous flow rate and total flow functions of the flowmeter, it ispossible to calculate the total amount of water district.4 Interlock SystemBecause all the pumps stop operating conditions the same, it only sets out a stop pump interlock, If a motor in the 5 for any one to meet the conditions. then stopped a motor. If 2 in 5 of the Motor any pieces meet a condition, then stopped 2 motor. Frequency of two pumps stopped pumping conditions and a motor, 2pump motor stopped the same conditions.5 SummaryBased on principles of fluid mechanics, water pumps and the flow Tong motor speed proportional to the pressure and motor speed is proportional to the square. So pump technology using frequency effects than conventional methods of water saving 40% ~ 50% and the saving of 7%. The system can be based on the different requirements, they can beconstant pressure control, constant current control. temperature contro. also under differenload increase in the numberof pumps, and system stability. ease of maintenance.译文自动变频恒压供水系统设计引言变频调速恒压供水设备是采用变频调速器、可编程控制器(PLC)和PID调节器等构成的新型供水设备,本设备具有给水压力设定方便、显示直观、成本低,调试容易的特点。
电气及自动化专业 外文翻译 (10)
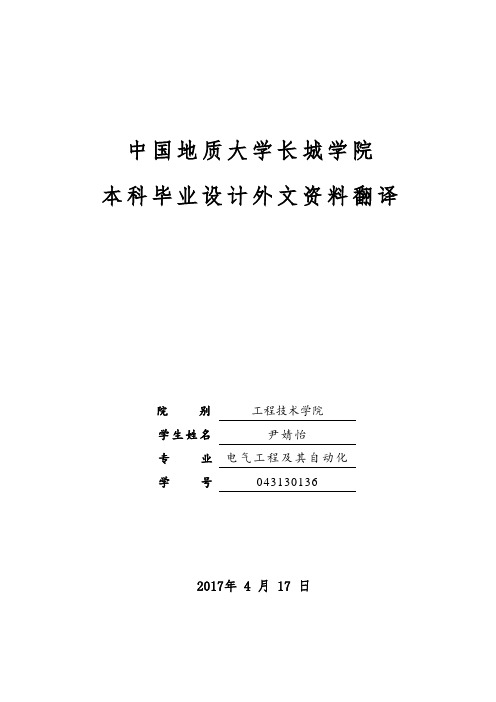
中国地质大学长城学院本科毕业设计外文资料翻译院别工程技术学院学生姓名尹婧怡专业电气工程及其自动化学号0431301362017年 4 月 17 日外文翻译译文三相感应电动机速度控制方法三相异步电动机转速公式为:n=60f/p(1-s) 从上式可见,改变供电频率f、电动机的极对数p及转差率s均可大到改变转速的目的。
从调速的本质来看,不同的调速方式无非是改变交流电动机的同步转速或不改变同步转两种。
在生产机械中广泛使用不改变同步转速的调速方法有绕线式电动机的转子串电阻调速、斩波调速、串级调速以及应用电磁转差离合器、液力偶合器、油膜离合器等调速。
改变同步转速的有改变定子极对数的多速电动机,改变定子电压、频率的变频调速有能无换向电动机调速等。
从调速时的能耗观点来看,有高效调速方法与低效调速方法两种:高效调速指时转差率不变,因此无转差损耗,如多速电动机、变频调速以及能将转差损耗回收的调速方法(如串级调速等)。
有转差损耗的调速方法属低效调速,如转子串电阻调速方法,能量就损耗在转子回路中;电磁离合器的调速方法,能量损耗在离合器线圈中;液力偶合器调速,能量损耗在液力偶合器的油中。
一般来说转差损耗随调速范围扩大而增加,如果调速范围不大,能量损耗是很小的。
一、变极对数调速方法这种调速方法是用改变定子绕组的接红方式来改变笼型电动机定子极对数达到调速目的,特点如下:1、具有较硬的机械特性,稳定性良好;2、无转差损耗,效率高;3、接线简单、控制方便、价格低;4、有级调速,级差较大,不能获得平滑调速;5、可以与调压调速、电磁转差离合器配合使用,获得较高效率的平滑调速特性。
本方法适用于不需要无级调速的生产机械,如金属切削机床、升降机、起重设备、风机、水泵等。
二、变频调速方法变频调速是改变电动机定子电源的频率,从而改变其同步转速的调速方法。
变频调速系统主要设备是提供变频电源的变频器,变频器可分成交流-直流-交流变频器和交流-交流变频器两大类,目前国内大都使用交-直-交变频器。
机械 外文翻译 外文文献 英文文献 直流电动机调速控制

Speed Control of DC MotorAbstract Conditioning system is characterized in that output power to maintain stability. Different speed control system can use a different brake system, high starting and braking torque, quick response and quick adjustment range of degree requirements of DC drive system, the use of the electric braking mode. Depends on the speed control of DC motor armature voltage and flux. To zero speed, or U = 0 or Φ = ∞. The latter is impossible, it only changes through the armature voltage to reduce speed. To speed to a higher value can increase or decrease the U Φ.Keyword DC Speed Feedback BrakeRegulator SystemsA regulator system is one which normally provides output power in its steady-state operation.For example, a motor speed regulator maintains the motor speed at a constant value despite variations in load torque. Even if the load torque is removed, the motor must provide sufficient torque to overcome the viscous friction effect of the bearings. Other forms of regulator also provide output power; A temperature regulator must maintain the temperature of, say, an oven constant despite the heat loss in the oven. A voltage regulator must also maintain the output voltage constant despite variation in the load current. For any system to provide an output, e.g., speed, temperature, voltage, etc., an error signal must exist under steady-state conditions.Electrical BrakingIn many speed control systems, e.g., rolling mills, mine winders, etc., the load has to be frequently brought to a standstill and reversed. The rate at which the speed reduces following a reduced speed demand is dependent on the stored energy and the braking system used. A small speed control system (sometimes known as a velodyne) can employ mechanical braking, but this is not feasible with large speed controllers since it is difficult and costly to remove the heat generated.The various methods of electrical braking available are:(1)Regenerative braking.(2)Eddy current braking.(3) Dynamic braking.(4) Reverse current braking(plugging)Regenerative braking is the best method, though not necessarily the most economic. The stored energy in the load is converted into electrical energy by the work motor (acting temporarily as a generator) and is returned to the power supply system. The su pply system thus acts as a”sink”into which the unwanted energy is delivered. Providing the supply system has adequate capacity, the consequent rise in terminal voltage will be small during the short periods of regeneration. In the Ward-Leonard method of speed control of DC motors, regenerative braking is inherent, but thyristor drives have to be arranged to invert to regenerate. Induction motor drives can regenerate if the rotor shaft is driven faster than speed of the rotating field. The advent of low-cost variable-frequency supplies from thyristor inverters have brought about considerable changes in the use of induction motors in variable speed drives.Eddy current braking can be applied to any machine, simply by mounting a copper or aluminum disc on the shaft and rotating it in a magnetic field. The problem of removing the heat generated is severe in large system as the temperature of the shaft, bearings, and motor will be raised if prolonged braking is applied.In dynamic braking, the stored energy is dissipated in a resistor in the circuit. When applied to small DC machines, the armature supply is disconnected and a resistor is connected across the armature (usually by a relay, contactor, or thyristor).The field voltage is maintained, and braking is applied down to the lowest speed. Induction motors require a somewhat more complex arrangement, the stator windings being disconnected from the AC supply and reconnected to a DC supply. The electrical energy generated is then dissipated in the rotor circuit. Dynamic braking is applied to many large AC hoist systems where the braking duty is both severe and prolonged.DC Motor Speed ControlThe basis of all methods of DC motor speed control is derived from the equations:ωΦ∝Ea a R I E U +=the terms having their usual meanings. If the IaRa drop is small, the equations approximate to ωΦ∝U or Φ=U ω。
中英文对照变频调速
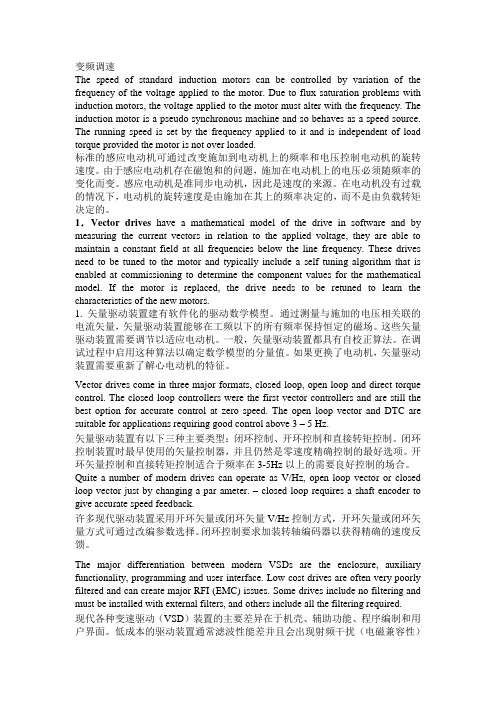
变频调速The speed of standard induction motors can be controlled by variation of the frequency of the voltage applied to the motor. Due to flux saturation problems with induction motors, the voltage applied to the motor must alter with the frequency. The induction motor is a pseudo synchronous machine and so behaves as a speed source. The running speed is set by the frequency applied to it and is independent of load torque provided the motor is not over loaded.标准的感应电动机可通过改变施加到电动机上的频率和电压控制电动机的旋转速度。
由于感应电动机存在磁饱和的问题,施加在电动机上的电压必须随频率的变化而变。
感应电动机是准同步电动机,因此是速度的来源。
在电动机没有过载的情况下,电动机的旋转速度是由施加在其上的频率决定的,而不是由负载转矩决定的。
1.Vector drives have a mathematical model of the drive in software and by measuring the current vectors in relation to the applied voltage, they are able to maintain a constant field at all frequencies below the line frequency. These drives need to be tuned to the motor and typically include a self tuning algorithm that is enabled at commissioning to determine the component values for the mathematical model. If the motor is replaced, the drive needs to be retuned to learn the characteristics of the new motors.1. 矢量驱动装置建有软件化的驱动数学模型。
外文翻译--抽水系统PLC和变频调速
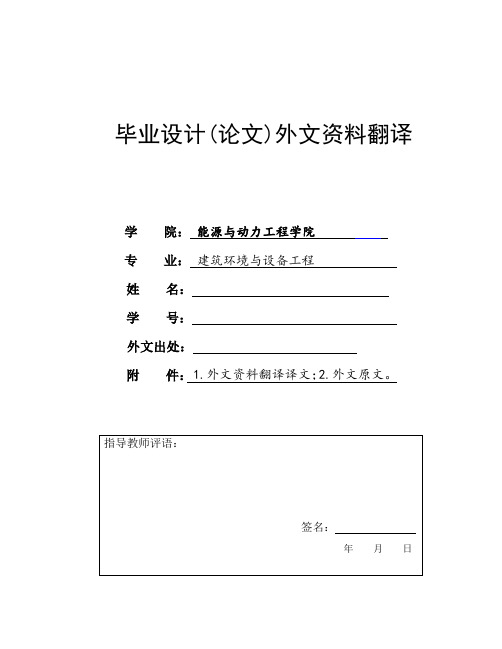
毕业设计(论文)外文资料翻译学院:能源与动力工程学院专业:建筑环境与设备工程姓名:学号:外文出处:附件: 1.外文资料翻译译文;2.外文原文。
附件1:外文资料翻译译文抽水系统PLC和变频调速萨拉赫Addallah改造中应注意的一些技术问题(1)高压变频调速凝结水泵运行时上水调整门打开,利用改变凝结水泵的转速调节除氧器水位造成凝结水压力较低,最大不超过2.8MPa。
运行中凝结水压力随负荷降低而下降,为了保证其它设备所需凝结水的压力,所以凝结水母管压力低联锁值应重新整定,但不能太低。
例如设定变频调速系统的最低转速为30Hz(变频器最低转速设为750r/min)。
(2)变频凝结水泵变频运行时,凝结水至除氧器副调节阀全开,主调节阀全关,所以凝结水母管压力最低低至0.85MPa。
为了保证定速凝结水泵低水压不动作(工频运行时定值为1.8 MPa),将定值修改为低于0.6MPa,联动备用泵,母管压力0.7 MPa 时热控光字牌报警。
变频器跳闸,系统发出12s脉冲信号,将除氧器水位总手操指令由50%减至20%,对应副调节阀开度约在43%左右,其它热控保护不变。
(3)运行变频凝结水泵跳闸备用定速凝结水泵联锁启动后凝结水压力突然升高;对凝结水供其它辅助设备影响很大,特别是给水泵机械密封冷却水系统,由于给水泵机械密封冷却水差压一般维持在0.1MPa。
针对此问题在给水泵机械密封冷却水调整门上预置一个与汽轮机调速级压力具有函数关系的指令,当备用工频凝结水泵联锁启动后将该指令输出至给水泵机械密封冷却水调整门,延时一段时间后系统切换至给水泵机械密封水差压自动调整回路。
(4)运行变频凝结水泵跳闸备用定速凝结水泵联锁启动后凝结水压力突然升高对凝结水供其它辅助设备影响很大,因此在由变频切到工频运行时应适当关小除氧器水位调节的两个调节门的开度,以免除氧器水位过高。
(5)改造前,正常情况下凝结水母管压力为2.5MPa左右。
当母管水压低于1.8MPa或运行的水泵发生故障时,备用水泵必须在5s内启动到全速运转,提升到1.0MPa,否则系统联锁保护动作。
外文翻译-变频调速技术在风机、泵类中的应用分析
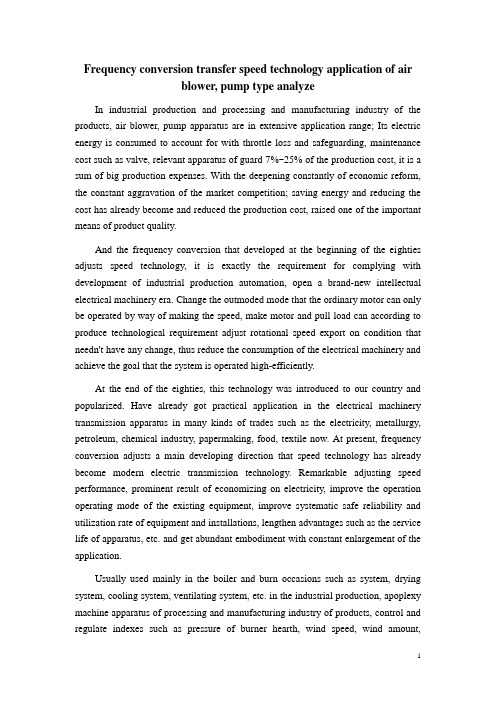
Frequency conversion transfer speed technology application of airblower, pump type analyzeIn industrial production and processing and manufacturing industry of the products, air blower, pump apparatus are in extensive application range; Its electric energy is consumed to account for with throttle loss and safeguarding, maintenance cost such as valve, relevant apparatus of guard 7%~25% of the production cost, it is a sum of big production expenses. With the deepening constantly of economic reform, the constant aggravation of the market competition; saving energy and reducing the cost has already become and reduced the production cost, raised one of the important means of product quality.And the frequency conversion that developed at the beginning of the eighties adjusts speed technology, it is exactly the requirement for complying with development of industrial production automation, open a brand-new intellectual electrical machinery era. Change the outmoded mode that the ordinary motor can only be operated by way of making the speed, make motor and pull load can according to produce technological requirement adjust rotational speed export on condition that needn't have any change, thus reduce the consumption of the electrical machinery and achieve the goal that the system is operated high-efficiently.At the end of the eighties, this technology was introduced to our country and popularized. Have already got practical application in the electrical machinery transmission apparatus in many kinds of trades such as the electricity, metallurgy, petroleum, chemical industry, papermaking, food, textile now. At present, frequency conversion adjusts a main developing direction that speed technology has already become modern electric transmission technology. Remarkable adjusting speed performance, prominent result of economizing on electricity, improve the operation operating mode of the existing equipment, improve systematic safe reliability and utilization rate of equipment and installations, lengthen advantages such as the service life of apparatus, etc. and get abundant embodiment with constant enlargement of the application.Usually used mainly in the boiler and burn occasions such as system, drying system, cooling system, ventilating system, etc. in the industrial production, apoplexy machine apparatus of processing and manufacturing industry of products, control and regulate indexes such as pressure of burner hearth, wind speed, wind amount,temperature, etc. so as to meeting the needs of craft and operation operating mode according to the need of producing. The most frequently used control means is to regulate the air door, size of making degree of guard to adjust the controlled target. In this way, no matter the demand size of production, the air blowers should all operate at full speed, but the change of the operation operating mode makes energy consume with the throttle losses of air door, guard. In process of production, not only control the precision and is limited but also cause a large amount of energy to waste losing with the apparatus. Thus lead to the fact the production cost increases, the service life of apparatus is shortened, the plant maintenance, maintenance cost can not be ranked.The pump apparatus has broad application space on the production field too, propose water pump station, pond store pot give system of arranging, industry water circulatory system, hot exchange system use centrifugal pump, axial-flow pump, gear wheel pump, column fill in apparatus such as the pump Moreover adopt, adjust according to different production demand valve, reflux valve, stop valve, etc. reduce expenditure apparatus carry on flow, pressure, water level control of signal often. In this way, not merely cause a large number of energy to waste, the destruction of sealing properties such as the pipeline, valve, etc.; also accelerate wearing and tearing and vapors of the pump, body of valve and lose, damage the apparatus, influence production, jeopardize product quality when being serious.Most of air blower, pump apparatus adopt the way in which the asynchronous motor drive directly and run, store in and start the electric current greatly, machinery is assaulted, protect the bad shortcoming of the characteristic electrically. Not only influence by apparatus service life, but also not at load can twinkling of an eye movement protect by apparatus, often present the pump and damage the phenomenon that the electrical machinery is burnt too at the same time.In recent years, for the energy-conserving urgent need and requirement for improving constantly in product quality, in addition the adoption frequency conversion governor (abbreviated as the frequency converter) is easy to use, non-maintaining and controlling the precision high, and can realize the high functional characteristic; Therefore the scheme of adopting the frequency converter and driving begins to replace the control scheme of air door, guard, valve progressively.The basic principle of adjusting speed technology of frequency conversion is toimport the relation that frequency is directly proportional to according to rotational speed and working power of electrical machinery: n =60f (1-s) / p, (n, f, s, p show the rotational speed, input frequency, electrical machinery and transfer to difference rate, electrical machinery magnetic pole logarithm respectively in type); Achieve the goal of changing the rotational speed of the electrical machinery through changing the motor working power frequency. The frequency converter is on the basis of principle described above adopts handing in - straight - hand in the power and vary technology, electric electron, microcomputer are controlled, etc. the comprehensive electric products that technology is all over.Can know through the hydro mechanical philosophy: Air blower, pump apparatus belong to the torque load of square, its rotational speed n and flow Q, pressure H and power P of axle have the following relations: Q ∝ n, H∝ n2, P∝ n3;I.e., the flow is proportional to rotational speed, the pressure is proportional to the square of rotational speed, the axle power is proportional to the cube of rotational speed.Take a water pump as an example, its export presses the head for H0 (export presses the quiet pressure difference that the head i.e. entry to the pump and pipeline exports), the specified rotational speed is n0, it is r0 that the tube when the valve is made completely hinders the characteristic, under the specified operating mode and its corresponding pressure is H1, it is Q1 to export the flow.In controlling at the scene, usually adopt the water pump to operate and export the valve to control the flow rapidly definitely. When the flow reduces 50% to Q2 from Q1, valve turn on degree reduce, make pipe network drag characteristic turn r0 into r1, systematic operating point order, move, order along direction me from original A to B; The pressure H1 of function reduced expenditure by it turns into H2. Water pump axle power actual value can by the formula: P =Q* H/ (η c* η b) *10-3 is obtained. Among them, P, Q, H, η c, η b express the power, flow, pressure, water pump efficiency, transmission device efficiency respectively, transmit as 1 directly. Suppose the total efficiency (η c* η b) 1, water pump order, move, order work, from A to B then, consumption that electrical machinery save for AQ1OH1 and area of BQ2OH2 bad. If adopt and adjust rotational speed n that the speed means changes the water pump, when the flow is reduced from Q1 by 50% to Q2, pipe network drag characteristic the same curve r0 then, systematic operating point order, move, orderalong direction II from original A to C, the operation of the water pump is also more rational. All open in the valves, there are only pipe networks.Under the situation of resistance, the system meets the flow requirement of the scene, energy consumption certainly will be reduced. At this moment, the consumption that the electrical machinery saves is bad for the area of AQ1OH1 and CQ2OH3. Degree is regulated and the rotational speed of water pump is controlled to relatively adopt the valve to be driven, obviously use the rotational speed of the water pump to control more valid and more reasonable, have prominent energy-conserving results.In addition, valve make systematic pressure H rise regulate, this transform to pipeline and sealing property of valve into, threaten and destroy; And when the rotational speed is regulated, the systematic pressure H will be reduced with reducing of the rotational speed n of the pump, so will not exert a bad influence on the system.It is easy to obtain from the comparison above: When demand for the flow of the water pump is dropped from 100% to 50% at the scene, adopt the rotational speed to regulate and regulate the power size corresponding to save BCH3H2 than the original valve, the energy-conserving rate is above 75%.Similar to this, adopt frequency conversion transfer speed technology change pump type, air blower apparatus rotational speed come, control on-the-spot pressure, temperature, water level, etc. other course control the parameter, can control the characteristic and draw out the curve of relation and obtain the comparative result described above according to the system too. Namely adopt frequency conversion transfer speed technology change electrical machinery method of rotational speed, than adopt valve, guard regulate economic for energy-conservation, the apparatus operation operating mode will be obviously improved too.变频调速技术在风机、泵类中的应用分析在工业生产和产品加工制造业中,风机、泵类设备应用范围广泛;其电能消耗和诸如阀门、挡板相关设备的节流损失以及维护、维修费用占到生产成本的7%~25%,是一笔不小的生产费用开支。
变速器外文文献翻译、中英文翻译、外文翻译
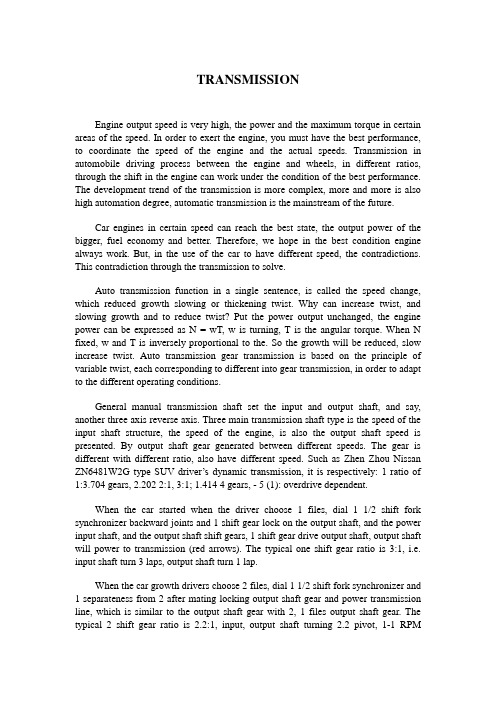
TRANSMISSIONEngine output speed is very high, the power and the maximum torque in certain areas of the speed. In order to exert the engine, you must have the best performance, to coordinate the speed of the engine and the actual speeds. Transmission in automobile driving process between the engine and wheels, in different ratios, through the shift in the engine can work under the condition of the best performance. The development trend of the transmission is more complex, more and more is also high automation degree, automatic transmission is the mainstream of the future.Car engines in certain speed can reach the best state, the output power of the bigger, fuel economy and better. Therefore, we hope in the best condition engine always work. But, in the use of the car to have different speed, the contradictions. This contradiction through the transmission to solve.Auto transmission function in a single sentence, is called the speed change, which reduced growth slowing or thickening twist. Why can increase twist, and slowing growth and to reduce twist? Put the power output unchanged, the engine power can be expressed as N = wT, w is turning, T is the angular torque. When N fixed, w and T is inversely proportional to the. So the growth will be reduced, slow increase twist. Auto transmission gear transmission is based on the principle of variable twist, each corresponding to different into gear transmission, in order to adapt to the different operating conditions.General manual transmission shaft set the input and output shaft, and say, another three axis reverse axis. Three main transmission shaft type is the speed of the input shaft structure, the speed of the engine, is also the output shaft speed is presented. By output shaft gear generated between different speeds. The gear is different with different ratio, also have different speed. Such as Zhen Zhou Nissan ZN6481W2G type SUV driver’s dynamic transmission, it is respectively: 1 ratio of 1:3.704 gears, 2.202 2:1, 3:1; 1.414 4 gears, - 5 (1): overdrive dependent.When the car started when the driver choose 1 files, dial 1 1/2 shift fork synchronizer backward joints and 1 shift gear lock on the output shaft, and the power input shaft, and the output shaft shift gears, 1 shift gear drive output shaft, output shaft will power to transmission (red arrows). The typical one shift gear ratio is 3:1, i.e. input shaft turn 3 laps, output shaft turn 1 lap.When the car growth drivers choose 2 files, dial 1 1/2 shift fork synchronizer and 1 separateness from 2 after mating locking output shaft gear and power transmission line, which is similar to the output shaft gear with 2, 1 files output shaft gear. The typical 2 shift gear ratio is 2.2:1, input, output shaft turning 2.2 pivot, 1-1 RPMincreases, torque shift.When gas growth drivers choose 3, dial 1 1/2 shift fork to synchronizer, and back to space three/four file synchronizer will move until 3 gear lock in the output shaft, make the power from the first shaft -- -- on the output shaft transmission gears, 3 through the output shaft gear shifting speed. The typical 3 ratio was 1.7:1, the input shaft turning circle, the output shaft 1.7 turn 1 ring, is further growth.When gas growth drivers choose 4 gears, fork will 3/4 file synchronizer from 3 gear directly with the input shaft driving gear engagement, power transmission directly from the input shaft to the output shaft, and the output shaft is 1:1 ratio and the input shaft speed. Due to the force, and the direct oart shift, the gear transmission efficiency ratio. Cars run most time in order to achieve the best directly file fuel economy.Shift to go into space, transmission in the transmission gears have locked in the output shaft, they cannot drive the output shaft rotation, no power output.General car manual transmission ratio main points above 1-4, usually designers to first identify the lowest (1) and (4) transmission, the ratio between after general distribution according to form. In addition, there is a reverse and overdrive, overdrive called 5 files.When the car to accelerate whether isolated car drivers choose more than 5, 5 gear transmission is typical 0.87:1, namely with big gear drive pinion gear turns, when active 0.87 lap, passive gear has turned over one lap.When the reverse in the opposite direction to the output shaft rotation. If a gear when reverse rotation, plus a gear will become a positive spin. Using this principle, will add a reverse gear do "medium", the direction of rotation axis, so has reversed a reverse axis. Reverse transmission shaft independent in housing, and parallel axis, when oart in gear and gear and oart output shaft gear, output shaft to will instead.Usually the reverse synchronizer is controlled by the jointing, so May 5 files and reverse position is in the same side. Due to the middle, reverse gear transmission is generally greater than 1 gear transmission ratio, twist, some cars met with forward instead of steep open up in reverse.From driving gear transmission is smooth; more is better, more adjacent gear shift between the transmission ratio, shift easy and smooth. But the gear transmission fault is more complex structure, big volume and light auto transmission is now commonly 4-5. At the same time, the transmission ratio is not an integer, but with the decimal point, this is not the whole number of meshing gears, two gear ratio is the euploid number will lead to two gear surface non-uniform wear, tooth surface quality of differences.Manual transmission and synchronizerManual transmission is one of the most common transmissions, referred to as MT. Its basic structure in a single sentence is a central axis, two input shaft, namely, the axial and axial oart, they constituted the transmission of the subject, and, of course, a reverse axis. Manual transmission gear transmission and manual, contain can in axial sliding gears, through different meshing gears to change gear of torsional purpose. The typical structure and principle of the manual transmission.Input shaft also says, it's in front of the spline shaft directly with clutch platen, thus the spline set by the engine relay of torque. The first shaft gear meshing gears, often with oart as input shaft, and the gear on oart will turn. Also called shaft, because even more solid shaft of gear. The output shaft, and the second shaft position have the drive shaft gear, may at any time and under the influence of the control devices and the corresponding oart gear, thus changing the speed and torque itself. The output shaft is associated with tail spline shaft torque transmission shaft, through to drive to gear reducer.Predictably, transmission gear drive forward path is: input shaft gear - oart gnaws gear - because the second shaft gear - corresponding gear. Pour on the axle gear can also control device, by moving axis in the strike, and the output shaft gear and oart gear, in the opposite direction.Most cars have five forward and reverse gear, each one has certain ratio, the majority of gear transmission more than 1, 4 gears transmission is 1, called directly, and ratio is less than 1 of article 5 gear shift accelerated called. The output axis gear in the mesh position, can accept power transmission.Due to the gearbox output shaft to input shaft and the speed of their gear rotating, transform a "synchronization problem". Two rotating speed different meshing gears forcibly inevitable impact and collision damage gear. Therefore, the old transmission shift to use "two feet on-off" method, accelerate in neutral position shift to stay for a while, in the space location on the door, in order to reduce gear speed. But this operation is more complex, difficult to grasp accurately. Therefore designers to create "synchronizer", through the synchronizer will make the meshing gears reach speed and smooth.Currently the synchronous transmission adopts is inertial synchronizer, it mainly consists of joints, synchronizer lock ring etc, it is characteristic of the friction effect on achieving synchronization. Mating, synchronizer and mating locking ring gear tooth circle have chamfering (locking horns), the synchronizer lock ring inside surface of gear engagement ring and the friction surface contact. The lock horns with cone when designing the proper choice, has been made to the surface friction of meshinggears with gear synchronous, also can rapid produces a locking function, prevent the synchronous before meshing gears. When synchronous lock ring of gear engagement with surface contact surface, the outer circle in friction torque under the action of gear speed rapid decrease (increase) or to synchronous speed equal, both locking ring spun concurrent, relative to lock ring gear synchronous speed is zero, thus inertia moment also disappear, then in force, driven by the junction of unimpeded with synchronous lock ring gear engagement, and further to engagement with the engagement ring gear tooth and complete shift process变速器发动机的输出转速非常高,最大功率及最大扭矩在一定的转速区出现。
外文翻译--变频器使用浅谈-精品
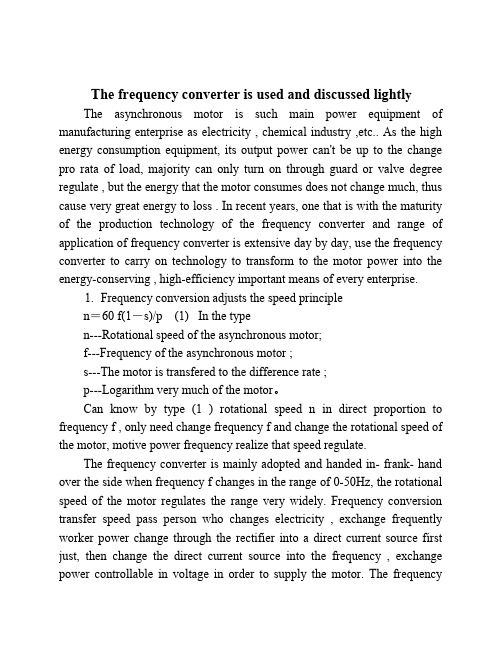
The frequency converter is used and discussed lightl yThe asynchronous motor is such main power equipment of manufacturing enterprise as electricity , chemical industry ,etc.. As the high energy consumption equipment, its output power can't be up to the change pro rata of load, majority can only turn on through guard or valve degree regulate , but the energy that the motor consumes does not change much, thus cause very great energy to loss . In recent years, one that is with the maturity of the production technology of the frequency converter and range of application of frequency converter is extensive day by day, use the frequency converter to carry on technology to transform to the motor power into the energy-conserving , high-efficiency important means of every enterprise.1. Frequency conversion adjusts the speed principlen=60 f(1-s)/p (1) In the typen---Rotational speed of the asynchronous motor;f---Frequency of the asynchronous motor ;s---The motor is transfered to the difference rate ;p---Logarithm very much of the motor。
交流变频调速技术第四版

交流变频调速技术第四版English Answer:Introduction.Adjustable speed drives (ASDs) are a type of motor controller that allows the speed of an electric motor to be varied. This is achieved by varying the frequency of the alternating current (AC) power supply to the motor. ASDs are used in a wide range of applications, including industrial machinery, fans, pumps, and compressors.Types of ASDs.There are two main types of ASDs:Voltage-source inverters (VSIs) convert DC power to AC power. VSIs are typically used in high-power applications.Current-source inverters (CSIs) convert AC power to DCpower. CSIs are typically used in low-power applications.Benefits of ASDs.ASDs offer a number of benefits, including:Energy savings: ASDs can save energy by reducing the speed of motors when they are not needed to run at full speed.Improved process control: ASDs can improve process control by allowing the speed of motors to be precisely controlled.Reduced wear and tear: ASDs can reduce wear and tear on motors by reducing the amount of time that they operate at full speed.Applications of ASDs.ASDs are used in a wide range of applications, including:Industrial machinery: ASDs are used to control the speed of motors in industrial machinery, such as conveyors, robots, and machine tools.Fans: ASDs are used to control the speed of fans in buildings, ventilation systems, and air conditioning units.Pumps: ASDs are used to control the speed of pumps in water distribution systems, sewage treatment plants, andoil pipelines.Compressors: ASDs are used to control the speed of compressors in refrigeration systems, compressed air systems, and gas turbines.Conclusion.ASDs are a versatile and efficient way to control the speed of electric motors. They offer a number of benefits, including energy savings, improved process control, and reduced wear and tear. ASDs are used in a wide range ofapplications, from industrial machinery to fans, pumps, and compressors.中文回答:变频调速技术。
变频器工作原理外文文献翻译、中英文翻译

外文资料Converter working principleMain circuit is for induction motors provide voltage variable frequency power source power conversion part, the inverter main circuit in general can be divided into two categories [1]: voltage is voltage source DC converter for AC inverter, the DC loop filter is capacitance. Current model is the current source of the direct streamization AC inverter, the DC circuit filter inductance. It consists of three parts, the power supply conversion for DC power rectifier, absorption produced in converter and inverter voltage ripple "flat wave circuit, and DC power converter for AC power" inverter ".(1) rectifier: Recently a lot of use is diode converter, it is the power supply conversion for the DC power supply. Also available two groups of transistor converters constitute a reversible converter, due to its power direction reversible can regeneration operation.(2) the flat wave circuit: in the rectifier DC voltage, containing 6 times the frequency of power supply ripple voltage, furthermore the inverter produces a pulsating current the DC voltage changes. In order to suppress the voltage fluctuation, the inductance and capacitance absorption pulsating voltage (current). Device volume hours, if power supply and a main circuit component in margin can save inductance of the simple flat wave circuit.(3) inverter: Contrary to rectifier, inverter is the DC power conversion is the desired frequency AC power and to determine the time the six switch device turn-on and off you can get 3 phase AC output. By voltage type PWM converter as exemplifying the switching time and voltage waveform.Control circuit is to provide a loop control signal to the asynchronous motor power supply (voltage, frequency) of the main circuit, the frequency, the voltage "operation circuit", the main circuit of the "voltage and current detection circuit, the motor" speed detection circuit, operation circuit of control signal amplification drive circuit ", and the inverter and the motor" protection circuit.(1) arithmetic circuit: the external speed, torque and other instructions with the detection circuit of the current, voltage signal comparison operation, determine the output voltage of the inverter, frequency.(2) voltage, current detection circuit: with the main circuit potential isolation detection voltage, current and so on.(3) driving circuit, driving circuit of main circuit devices. It and control isolation circuit enable device in the main circuit turn-on, turn off.(4) speed detection circuit installed in asynchronous motor shaft machine speed detector (TG, PLG) signal for speed signal into the computing circuit, according to the instruction and operation can make the motor run in the speed command.(5) protection circuit: detection of the main circuit of the voltage, current and so on, when the occurrence of overload or over voltage, etc., in order to prevent the inverter and asynchronous motor damage, so that the inverter to stop working or inhibit voltage, current value.中文翻译变频器工作原理主电路是给异步电动机提供调压调频电源的电力变换部分,变频器的主电路大体上可分为两类[1]:电压型是将电压源的直流变换为交流的变频器,直流回路的滤波是电容。
- 1、下载文档前请自行甄别文档内容的完整性,平台不提供额外的编辑、内容补充、找答案等附加服务。
- 2、"仅部分预览"的文档,不可在线预览部分如存在完整性等问题,可反馈申请退款(可完整预览的文档不适用该条件!)。
- 3、如文档侵犯您的权益,请联系客服反馈,我们会尽快为您处理(人工客服工作时间:9:00-18:30)。
淮阴工学院毕业设计(论文)外文资料翻译学院:机械工程学院专业:机械设计制造及其自动化姓名:许斌学号:1071101215外文出处:Design of PWM Controller in a MCS-51 Compatible MCU(用外文写)附件: 1.外文资料翻译译文;2.外文原文。
注:请将该封面与附件装订成册。
附件1:外文资料翻译译文基于C51兼容微处理器单片机的PWM控制器设计导言PWM技术,是一种电压调节方法,通过控制具有固定电压的直流电源的开关频率来调整两端负荷电压。
这种技术能用于各种应用包括电机、温度、和压力的控制,等等。
在电机系统中的应用,如图1所示,通过调整电源开关的占空比,来控制电机的速度,如图2所示,平均电压通过改变占空比来控制电机的速度(在图中D=t1/T),这样当电机的电源打开时,它的速度加快,相反,当电源关闭时,速度下降。
图1 PWM控制框图图2 电压的电枢和占空比之间的关系所以,通过定期地调整时间的开通和关断来控制电机的转速:这儿有三种方法可以完成占空比的调整(1)通过脉宽来调整频率;(2)通过同时调整频率和脉宽;(3)通过频率来调整脉宽。
一般情况下,有四中方法可以产生PWM信号,正如以下:(1)由独立逻辑元件组成的装置产生,这种是原始的方法,现在已被淘汰;(2)通过软件产生,这种方法需要CPU持续操作代码来控制I/O口,以致于CPU不能做其他任何事。
所以,这种方法也渐渐被淘汰;(3)通过ASIC产生,ASIC减少了CPU的负担,并获得了稳定的工作,一般有几个功能,如电流保护、死区时间调整等等;然而这种方法现在已被广泛用于许多场合;(4)通过单片机的PWM功能模块产生,只有当需要改变占空比的时候CPU失控,这样就不能产生PWM信号,否则通过在单片机里嵌入PWM功能模块,并使这功能初始化,单片机的PWM口也能自动产生PWM 信号。
这种方法将在文章中讲述。
在本文中,我们建议在8051单片机里嵌入一个PWM模块。
该PWM模块,通过初始化控制寄存器和寄存器的占空比,可以支持PWM脉冲信号,用刚才提到的上述三种方法调整占空比和几个操作模式,以增加用户弹性。
以下这部分解释PWM模块和基本功能模块的结构。
第三部分描述两种操作模式。
这部分还讲述了实验和仿真的结果验证了合适的系统操作。
通过操作模式,PWM模块产生一个或更多的脉宽模块信号,它们的比率可以自主调整。
在单片机上执行PWM模块PWM模块的概述PWM模块如图3所示,从图中,可以很清楚得看到整个模块有两部分组成:PWM 信号产生器和带有频道选择逻辑的死区时间产生器。
用户可以通过执行一些代码使PWM模块初始化,从而启动其功能。
在特殊情况下,支持以下电源和运动控制应用:1.直流电机2.持续电源供应PWM模块也有以下特征:1.两个PWM输出信号以互补或独立的方式运行2.带有互补模式的硬件死区电动机3.占空比更新设置应立刻或与PWM同步图3 PWM模块的结构结构的详细组成PWM电动机二输出PWM电动机的结构如图2.1所示,该结构是基于能产生脉宽调制信号上的16位计数器。
该系统由四分频或十二分频的系统时钟信号合成,时钟信号的频率可通过对在特殊寄存器PWMCON中的PWM0电机的T3M或PWM1电机的T4M的值进行设置而调整,如图4所示:对于PWM0电机,当T3M设置为零时,16位计数器时钟将被默认预分为四分频,当T3M设置为1时,始终将被十二分频;PWM同样有这种功能。
在PWMCON中的其它位的定义,详见表1图4 PWMCON的位的位置表1:PWMCON的位的定义通道选择逻辑通道选择逻辑在互补模式中很有用,如图5所示。
从表中可以清楚得看出,信号的CP和CPWM控制PWM1和PWML的来源,这两个控制信号的详细情况将在第三部分讲述,死区时间电机的结构也将在一下部分的连续性互补模式中讲述。
图5 通道选择逻辑表运行模式和仿真结果这种设计有两种运行模式:独立模式和互补模式。
通过在PWMCON寄存器中设置相应的位CPWM,如图四所示,用户可以选择其中一个运行模式。
当CPWM设置为0时,PWM模式将工作在独立模式,COWM设置为1时,将工作在互补模式。
在这部分两种模式将分别被详细讲述,从VCS EDA平台的PWM模块的仿真结果证明这种设计。
独立PWM输出模块独立PWM输出模块对于驱动负荷很有用,如图6所示。
当在PWMCON寄存器中相应的CP位设置为0,特殊的PWM输出模块是在独立的输出模式里。
在这种情况下,PWM的两种通道输出是相互独立的。
在PWM0/PWML口的信号是从PWM0电机产生的。
通道选择逻辑完成单独情况,如图6所示。
PWM I/O口通过默认意见复位设置为独立模式,但死区时间电机不能在独立模式下工作。
仿真结果如图6所示。
Tr4和Tr3分别与PWM0和PWM1相连,实际上,从图看,单片机的P1[5]/P[4]口被用做PWMH/PWML 或是一般的I/O口。
图6 独立模式下的PWM波形互补PWM输出模式互补输出模式可以用于驱动逆变器负载,如图7所示。
这种逆变器拓扑学是典型的直流装置。
在互补输出模式,PWM的两个输出不能同时用。
PWM通道和输出口都是通过通道选择逻辑内部配置的,如图7所示。
死区时间是在两端输出的开关装置没有工作的短时期时可以选择插入的。
图7 PWM互补输出的典型电路PWM I/O口通过在PWMCON中设置适当的CPWM位选择互补模式,在这种情况下,PSWL是有效果的。
当PSEL设置为0时,PWMH和PWML将来自PWM0电机,这时来自PWM1电机的信号是没用的,而当PSEL设置为1时,PWMH和PWML将来自PWM1电机,这时来自PWM0电机的信号是没用的。
在互补模式时产生PWM输出信号的过程中,死区时间将被插入在以下这部分讲述。
死区时间控制当PWM I/O口在互补输出模式运行时,死区时间是自动启用生成的,因为电源输出装置不能瞬间开关,在互补对模式下,一个PWM输出的关闭与其它晶体管打开之间要一定的时间,2输出的PWM模块有一个带有8位寄存器的可编程死区时间。
PWM模块的互补输出对已有一个用于产生死区时间插入的8位计数器。
死区时间单元有一个上升沿和下降沿探测器,而这个探测器与PWM电机产生的PWM信号连接。
当到达PWM边沿时,死区时间被载入计时器,根据是否是上升沿或下降沿,在互补输出端口上的其中一个过度被延迟,直到计数器降为0。
PWM输出对的死区时间表,如图8a所示:图8a 死区时间单元模块图图8b 互补模式的PWM输出波形总结:本文,我们设计了基于8位兼容8051单片机的PWM模块,这种设计能产生2通道带有两种运行模式的可编程周期PWM信号,即可插入死区时间的独立模式和互补模式。
这种在EDA平台的仿真结果已证明了它的和谐性和有用性。
附件2:外文原文(复印件)Design of PWM Controller in a MCS-51 Compatible MCUIntroductionPWM technology is a kind of voltage regulation method by controlling the switch frequency of DC power with fixed voltage to modify the two-end voltage of load. This technology can be used for a variety of applications including motor control, temperature control and pressure control and so on. In the motor control system shown as Fig. 1, through adjusting the duty cycle of power switch, the speed of motor can be controlled. As shown in Fig. 2, under the control of PWM signal, the average of voltage that controls the speed of motor changes with Duty-cycle ( D = t1/T in this Figure ), thus the motor speed can be increased when motor power turn on, decreased when power turn off.Fig.1: The Relationship between Voltage of Armature and Fig.2Architecture of PWM ModuleTherefore, the motor speed can be controlled with regularly adjusting the time of turn-on and turn-off. There are three methods could achieve the adjustment of duty cycle: (1) Adjust frequency with fixed pulse-width. (2) Adjust both frequency and pulse-width. (3) Adjust pulse-width with fixed frequency.Generally, there are four methods to generate the PWM signals as thefollowing: (1) Generated by the device composed of separate logic components. This method is the original method which now has been discarded. (2) Generated by software. This method need CPU to continuously operate instructions to control I/O pins for generating PWM output signals, so that CPU can not do anything other. Therefore, the method also has been discarded gradually. (3) Generated by ASIC. The ASIC makes a decrease of CPU burden and steady work generally has several functions such as over-current protection, dead-time adjustment and so on. Then the method has been widely used in many kinds of occasion now. (4) Generated by PWM function module of MCU. Through embedding PWM function module in MCU and initializing the function, PWM pins of MCU can also automatically generate PWM out signals without CPU controlling only when need to change duty-cycle. It is the method that will be implemented in this paper.In this paper, we propose a PWM module embedded in a 8051 microcontroller. The PWM module can support PWM pulse signals by initializing the control register and duty-cycle register with three methods just mentioned above to adjust the duty cycle and several operation modes to add flexibility for user.The following section explains the architecture of the PWM module and the architectures of basic functional blocks. Section3 describes two operation modes. Experimental and simulation results verifying proper system operation are also shown in that section. Depending on mode of operation, the PWM module creates one or more pulse-width modulated signals, whose duty ratios can be independently adjusted.Implementation of PWM module in MCUOverview of the PWM moduleA block diagram of PWM module is shown in Fig.3. It is clearly from the diagram that the whole module is composed of two sections: PWM signal generator and dead-time generator with channel select logic. The PWM function can be started by the user through implementing some instructionsfor initializing the PWM module. In particular, the following power and motion control applications are supported:• DC Motor• Uninterruptablel Power Supply (UPS)·The PWM module also has the following features:• Two PWM signal outputs with complementary or independent operation• Hardware dead-time generators for complementary mode• Duty cycle updates are configurable to be immediated or synchronized to the PWMFig.3 Architecture of PWM ModuleDetails of the architecturePMW generatorThe architecture of the 2-output PWM generator shown in Fig.4 is based on a 16-bit resolution counter which creates a pulse-width modulated signal. The system is synthesized by a system clock signal whose frequency can be divided by 4 times or 12 times through setting the value of T3M for PWM0 or T4M for PWM1 in the special register PWMCON as shown in Fig.4. To PWM0 generator, the clock to 16-bit counter will be pre-divided by 4 times by default when T3M is set to zero. And the clock will be divided by 12 times when T3M is set to 1. This is also true for PWM1. The other bits in PWMCON are explained in detail in Table 1.Fig .4 Bit Mapping of PWMCONTable 1: The Bit Definition in PWMCONChannel-select logicThe follow Fig. 5 shows the channel-select logic which is useful in Complementary Mode. From this diagram, it is clear to know that signal CP and CPWM control the source of PWMH and PWML. And the details about the two control signals will be discussed in the section 3, and the architecture of dead-time generator will also be discussed in section 5 for the continuity of Complementary Mode.Fig. 5 Diagram of Channel-select LogicOperation Mode and Simulation ResultsThe design has two operation modes: Independent Mode and Complimentary Mode. By setting the corresponding bit CPWM in register PWMCON shown in Fig.6 user can select one of the two operation modes. When CPWM is set to zero, PWM module will work in Independent Mode, whereas, PWM module will work in Complimentary Mode. In the following of this section, the two operation mode will be explained respectively in detail and the simulation results of the PWM module from the Synoposys VCS EDA platform which verify the design will also be shown.Independent PWM Output ModeAn Independent PWM Output mode is useful for driving loads such as the one shown in Figure 6. A particular PWM output is in the Independent Output mode when the corresponding CP bit in the PWMCON register is set to zero.In this case, two-channel PWM outputs are independent of each other. The signal on pin PWM0/PWMH is from PWM0 generator, and the signal on pin PWM1/PWML is from PWM0 generator. The separate case is achieved by the channel-select logic shown in Fig. 6. The PWM I/O pins are set to independent mode by default upon advice reset. The dead-time generator is disabled in the Independent mode. The simulation result is shown in Figure 6 as the following Fig.6 Tr4 and tr3 are run bits to PWM0 and PWM1, respectively. Actually, from this diagram, Pin P1[5]/ P1[4] of MCU is used for PWMH/ PWML or normal I/O ,alternatively.Fig6 the Waveform of PWM Outputs in Independent ModeComplementary PWM Output ModeThe Complementary Output mode is used to drive inverter loads similarto the one shown in Figure 7. This inverter topology is typical for DC applications. In Complementary Output Mode, the pair of PWM outputs cannot be active simultaneously. The PWM channel and output pin pair are internally configured through channel-select logic as shown in Figure7. A dead-time may be optionally inserted during device switching where both outputs are inactive for a short period.Fig 7 : Typical Load for Complementary PWM Outputs The Complementary mode is selected for PWM I/O pin pair by setting the appropriate CPWM bit in PWMCON. In this case, PSEL is in effect. PWMH and PWML will come from PWM0 generator when PSEL is set to zero, when the signals from PWM1 generator is useless, whereas PWMH and PWML will come from PWM1 generator when PSEL is set to 1, when the signals from PWM0 generator is useless. In the process of producing the PWM outputs in Complementary Mode, the dead-time will be inserted to be discussed in the following section.Dead-time ControlDead-time generation is automatically enabled when PWM I/O pin pair is operating in the Complementary Output mode. Because the power output devices cannot switch instantaneously, some amount of time must be provided betweenthe turn-off event of one PWM output in a complementary pair and the turn-on event of the other transistor. The 2-output PWM module has one programmable dead-time with 8-bit register.The complementary output pair for the PWM module has an 8-bit down counter that is used to produce the dead-time insertion. As shown in Figure 8, the dead time unit has a rising and falling edge detector connected to PWM signal from one of PWM generator. The dead times is loaded into the timer on the detected PWM edge event. Depending on whether the edge is rising or falling, one of the transitions on the complementary outputs is delayed until the timer counts down to zero. A timing diagram indicating the dead time insertion for the pair of PWM outputs is shown in Figure 8a.Fig 8a Dead-time Unit Block DiagramFig. 8b the Waveforms of PWM Outputs in Complementary ModeConclusionsIn this paper, we have designed PWM module based on an 8-bit MCU compatible with 8051 family. The design can generate 2-channel programmable periodic PWM signals with two operation mode, Independent Mode and Complementary Mode in which dead-time will be inserted. The simulation results on the EDA platform have proven its correctness and usefulness.。