制造一种将材料成型转换成产品的过程(精)
材料成型原理及工艺

材料成型原理及工艺材料成型是指将原料通过一定的工艺过程,使其获得所需形状的过程。
在材料成型中,最常见的方式包括热成型、冷成型和粉末冶金成型等。
这些成型工艺的原理和应用在各个领域都有广泛的应用。
热成型是指通过加热材料使其软化并塑性变形以达到所需形状的一种成型方法。
主要包括热压成型、热拉伸成型、热挤压成型等。
其原理是通过加热使材料达到一定的软化点或熔点,然后通过外力施加,使材料塑性变形并成型。
热成型适用于塑料、玻璃、金属等材料的成型,并且可以制造复杂形状的产品。
冷成型是通过机械力作用在室温下进行的成型方法。
冷成型主要包括挤压成型、压铸成型、冷轧成型等。
其中,冷挤压是常见的一种冷成型方式,主要应用于金属材料的成型。
其原理是通过施加机械力,使材料在室温下产生塑性变形,并达到所需形状。
具有高精度、高效率的特点。
粉末冶金成型是一种将粉末材料在一定温度下进行成型的方法。
其主要过程包括压制和烧结两个过程。
首先将粉末材料经过一定的工艺处理得到一定的物理性质,然后该粉末被用来制造一种新型的成型工艺。
原理是通过压制使粉末粒子结合,并在一定的温度下进行烧结,最终得到所需形状的产品。
其优点是可以制造复杂形状的产品,同时可以利用废料进行再利用。
在材料成型过程中,还有一些辅助工艺和辅助设备的应用,以实现更好的成型效果。
例如模具是实现材料成型的重要工具,通过对模具进行设计和制造,可以获得不同形状和尺寸的产品。
在热成型过程中,需要控制加热温度、保持时间、冷却速率等参数,以确保产品的质量。
在冷成型过程中,需要选择合适的冷却介质和冷却方式,以使产品达到所需的硬度和强度。
在粉末冶金成型过程中,需要控制压制力、压制时间和烧结温度等参数,以实现产品的致密度和力学性能。
总结起来,材料成型的原理和工艺非常丰富多样,根据不同材料和产品的要求选择合适的成型方式可以实现高效率、高质量的制造。
随着科技的进步和工艺的改进,材料成型在各个行业的应用也越来越广泛。
材料成型原理

材料成型原理材料成型是制造业中一项非常重要的工艺过程,它涉及到原材料的加工和成型,对于产品的质量和性能起着至关重要的作用。
在材料成型过程中,需要考虑材料的性质、成型工艺、设备和模具等多个因素,以确保最终产品能够满足设计要求。
首先,材料成型的原理是基于材料的塑性变形特性。
大多数材料在一定条件下都具有塑性,即可以在外力作用下发生形变而不破坏。
利用这一特性,可以通过加工成型将材料变成所需形状。
塑性变形的原理是在外力作用下,材料分子间发生相对位移,从而形成新的结构,使材料发生形变。
这种形变可以通过压力、拉伸、弯曲等方式来实现,从而得到所需的产品形状。
其次,材料成型的原理还涉及到材料的流变性能。
流变性能是材料在加工过程中的变形行为和变形特性,包括材料的屈服点、流变应力、流变指数等参数。
了解材料的流变性能可以帮助选择合适的成型工艺和设备,并且可以预测材料在成型过程中可能出现的问题,从而采取相应的措施进行调整和优化。
另外,材料成型的原理还与成型工艺和设备密切相关。
不同的成型工艺和设备对于材料的成型过程有着不同的影响。
例如,压铸、注塑、挤压等成型工艺都有其独特的特点和适用范围,需要根据产品的要求和材料的性质选择合适的成型工艺。
同时,成型设备的性能和精度也会直接影响到产品的质量和成型效率。
最后,材料成型的原理还包括模具设计和制造。
模具是实现材料成型的重要工具,它的设计和制造质量直接关系到产品的成型质量和精度。
模具的设计需要考虑材料的流动性、收缩率、成型温度等因素,以确保产品能够满足设计要求。
同时,模具的制造精度和表面处理也对产品的外观和尺寸精度有着重要影响。
综上所述,材料成型的原理涉及到材料的塑性变形特性、流变性能、成型工艺和设备以及模具设计和制造等多个方面。
只有充分理解和把握这些原理,才能够有效地进行材料成型工艺的设计和优化,确保最终产品的质量和性能达到预期要求。
材料成型工艺技术

材料成型工艺技术材料成型工艺技术是指将材料通过一定的工艺方法,经过加工、成形、塑造等过程,使其达到特定的形状和性能要求的一种技术。
这种技术可以广泛应用于各个行业,如汽车、航空、电子、家电等领域。
材料成型工艺技术的发展,为各个行业提供了更多的可能性和选择。
材料成型工艺技术主要包括压力成型、热成型、造型、粉末冶金等多种方法。
其中,压力成型是一种将材料放入模具中,在给定的条件下施加一定的压力,使材料在模具内成型的方法。
这种方法适用于加工金属、塑料、陶瓷等材料。
压力成型工艺技术具有成形精度高、表面光洁度好等特点,被广泛应用于制造各种零部件。
热成型是一种通过加热材料使其变软,然后通过外界力的作用使其变形的方法。
这种方法适用于加工塑料、橡胶等材料。
热成型工艺技术能够使材料保持一定的形状稳定性,并且在加工过程中能够消除材料内部的应力,提高产品的性能。
造型是一种通过模板、模具等工具对材料进行塑造的方法。
这种方法适用于加工陶瓷、玻璃等材料。
造型工艺技术能够使材料呈现出各种复杂的形状,满足设计师的要求,并且能够提高生产效率。
粉末冶金是一种通过将金属粉末进行成型、烧结等处理,制造出具有特定形状和性能的材料的方法。
这种方法适用于生产精密零部件、高温合金等材料。
粉末冶金工艺技术能够扩大材料的应用范围,提高产品的性能。
在材料成型工艺技术中,工艺参数的控制是非常重要的。
工艺参数包括温度、压力、速度等多个方面。
通过合理控制这些参数,可以使成型产品具有更好的性能。
材料成型工艺技术的发展,对于提高产品质量、降低产品成本、增加产品种类等方面具有重要作用。
随着科技的不断进步,材料成型工艺技术也在不断创新和发展,为各行各业的发展提供更多的机会和挑战。
lom成型原理

lom成型原理
LOM(Laminated Object Manufacturing)是一种快速成型技术,它使用一种特殊的成型材料和一台激光切割机来创建三维实物模型。
以下是LOM成型的基本原理:
1. 准备模型数据:首先,需要使用计算机辅助设计(CAD)
软件或其他三维建模工具,将所需物体的几何数据转换成电脑可读的格式。
2. 切割材料:LOM的关键是使用激光切割机将薄片材料切割
成所需形状。
切割材料通常是纸张或塑料片,厚度约为0.1-
0.5毫米。
3. 涂敷胶水:切割好的薄片会被粘贴在一张基板上。
这时,切割机会在每个薄片上涂敷一层胶水,以将其固定在基板上。
4. 堆叠薄片:切割好并涂敷胶水的薄片会被依次叠放在一起,直到构成整个模型。
每个薄片的位置和叠放顺序会根据模型设计进行确定。
5. 粘合薄片:切割机通过涂敷胶水的方式,将每个薄片与上一层薄片粘合在一起。
这样,逐层堆叠构建模型的树脂间会被胶水粘接。
6. 移除废材:当模型的所有层次被叠加完成后,需要去除多余的废材。
这些废材通常是模型的轮廓和内部空洞部分。
7. 表面处理:一旦剩余的废材被移除,就可以进行表面处理,例如去除残留的胶水或修整边缘,使模型更加光滑和精确。
LOM成型原理的关键点在于使用激光切割机将薄片材料进行切割,并通过涂敷胶水和粘合薄片的方式逐层堆叠,最终形成完整的三维模型。
这种成型技术具有较高的精度和成品质量,适用于快速制造原型和小批量生产。
简述增材制造工作流程

简述增材制造工作流程下载温馨提示:该文档是我店铺精心编制而成,希望大家下载以后,能够帮助大家解决实际的问题。
文档下载后可定制随意修改,请根据实际需要进行相应的调整和使用,谢谢!并且,本店铺为大家提供各种各样类型的实用资料,如教育随笔、日记赏析、句子摘抄、古诗大全、经典美文、话题作文、工作总结、词语解析、文案摘录、其他资料等等,如想了解不同资料格式和写法,敬请关注!Download tips: This document is carefully compiled by theeditor. I hope that after you download them,they can help yousolve practical problems. The document can be customized andmodified after downloading,please adjust and use it according toactual needs, thank you!In addition, our shop provides you with various types ofpractical materials,such as educational essays, diaryappreciation,sentence excerpts,ancient poems,classic articles,topic composition,work summary,word parsing,copy excerpts,other materials and so on,want to know different data formats andwriting methods,please pay attention!增材制造(Additive Manufacturing,AM)又称 3D 打印,融合了计算机辅助设计、材料加工与成型技术、以数字模型文件为基础,通过软件与数控系统将专用的金属材料、非金属材料以及医用生物材料,按照挤压、烧结、熔融、光固化、喷射等方式逐层堆积,制造出实体物品的制造技术。
挤出成型的产品叫什么
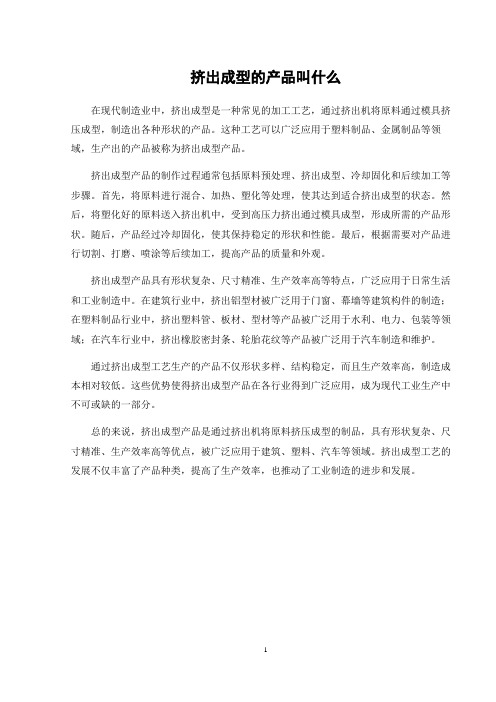
挤出成型的产品叫什么
在现代制造业中,挤出成型是一种常见的加工工艺,通过挤出机将原料通过模具挤压成型,制造出各种形状的产品。
这种工艺可以广泛应用于塑料制品、金属制品等领域,生产出的产品被称为挤出成型产品。
挤出成型产品的制作过程通常包括原料预处理、挤出成型、冷却固化和后续加工等步骤。
首先,将原料进行混合、加热、塑化等处理,使其达到适合挤出成型的状态。
然后,将塑化好的原料送入挤出机中,受到高压力挤出通过模具成型,形成所需的产品形状。
随后,产品经过冷却固化,使其保持稳定的形状和性能。
最后,根据需要对产品进行切割、打磨、喷涂等后续加工,提高产品的质量和外观。
挤出成型产品具有形状复杂、尺寸精准、生产效率高等特点,广泛应用于日常生活和工业制造中。
在建筑行业中,挤出铝型材被广泛用于门窗、幕墙等建筑构件的制造;在塑料制品行业中,挤出塑料管、板材、型材等产品被广泛用于水利、电力、包装等领域;在汽车行业中,挤出橡胶密封条、轮胎花纹等产品被广泛用于汽车制造和维护。
通过挤出成型工艺生产的产品不仅形状多样、结构稳定,而且生产效率高,制造成本相对较低。
这些优势使得挤出成型产品在各行业得到广泛应用,成为现代工业生产中不可或缺的一部分。
总的来说,挤出成型产品是通过挤出机将原料挤压成型的制品,具有形状复杂、尺寸精准、生产效率高等优点,被广泛应用于建筑、塑料、汽车等领域。
挤出成型工艺的发展不仅丰富了产品种类,提高了生产效率,也推动了工业制造的进步和发展。
1。
材料成型案例

材料成型案例材料成型是指将原料经过一定的加工工艺,通过成型设备得到所需形状和尺寸的零件或制品的过程。
本文将以塑料材料成型为例,介绍其在实际生产中的应用案例。
首先,我们来看一个注塑成型的案例。
注塑成型是将塑料颗粒加热熔融后,通过高压注射到模具腔内,冷却后形成所需的零件或制品。
某汽车零部件厂家在生产汽车车灯壳时采用了注塑成型工艺。
他们选用了耐高温、耐冲击的工程塑料作为原料,通过注塑成型工艺,生产出了具有优良光学性能和高强度的车灯壳产品。
这些车灯壳不仅外观精美,而且具有良好的耐候性和耐腐蚀性,满足了汽车在复杂环境下的使用要求。
其次,我们来看一个挤出成型的案例。
挤出成型是将塑料加热熔融后,通过挤出机的螺杆挤压成型,常用于生产管材、板材等产品。
某家建材公司在生产PVC塑料门窗型材时采用了挤出成型工艺。
他们选用了优质的PVC树脂作为原料,通过挤出成型工艺,生产出了表面光滑、色彩丰富的门窗型材产品。
这些产品具有优良的隔热、隔音性能,且耐腐蚀、耐老化,受到了市场的广泛好评。
最后,我们来看一个压缩成型的案例。
压缩成型是将塑料粉末或颗粒置于模具中,通过热压成型机的高温和高压使其成型。
某电子产品制造厂家在生产塑料外壳时采用了压缩成型工艺。
他们选用了具有良好机械性能和耐高温性能的塑料粉末,通过压缩成型工艺,生产出了外观精美、尺寸精准的电子产品外壳。
这些外壳不仅具有良好的阻燃性能,还具有良好的绝缘性能,保护了内部电子元器件的安全运行。
通过以上案例的介绍,我们可以看到,在实际生产中,不同的材料成型工艺可以满足不同产品的生产需求。
注塑成型适用于生产复杂形状的零部件或制品;挤出成型适用于生产管材、板材等产品;压缩成型适用于生产外壳、壳体等产品。
材料成型工艺的选择对产品的质量、性能和生产效率都有着重要影响,因此在实际生产中,需要根据产品的具体要求选择合适的材料成型工艺,以确保产品能够达到设计要求并满足市场需求。
总之,材料成型在现代工业生产中具有重要地位,通过不同的成型工艺,可以满足不同产品的生产需求。
材料成型技术
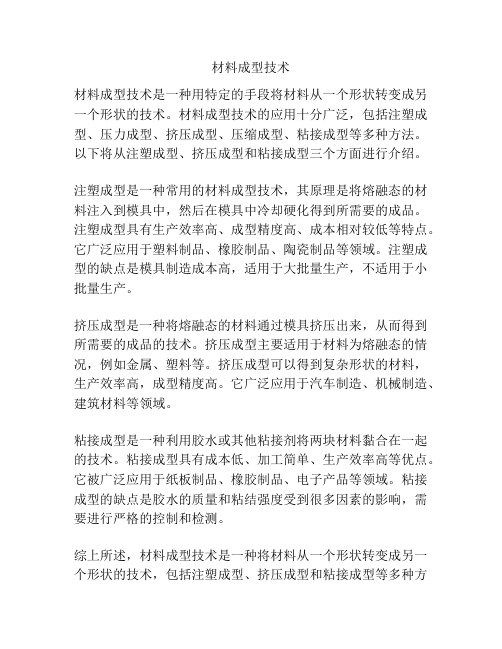
材料成型技术
材料成型技术是一种用特定的手段将材料从一个形状转变成另一个形状的技术。
材料成型技术的应用十分广泛,包括注塑成型、压力成型、挤压成型、压缩成型、粘接成型等多种方法。
以下将从注塑成型、挤压成型和粘接成型三个方面进行介绍。
注塑成型是一种常用的材料成型技术,其原理是将熔融态的材料注入到模具中,然后在模具中冷却硬化得到所需要的成品。
注塑成型具有生产效率高、成型精度高、成本相对较低等特点。
它广泛应用于塑料制品、橡胶制品、陶瓷制品等领域。
注塑成型的缺点是模具制造成本高,适用于大批量生产,不适用于小批量生产。
挤压成型是一种将熔融态的材料通过模具挤压出来,从而得到所需要的成品的技术。
挤压成型主要适用于材料为熔融态的情况,例如金属、塑料等。
挤压成型可以得到复杂形状的材料,生产效率高,成型精度高。
它广泛应用于汽车制造、机械制造、建筑材料等领域。
粘接成型是一种利用胶水或其他粘接剂将两块材料黏合在一起的技术。
粘接成型具有成本低、加工简单、生产效率高等优点。
它被广泛应用于纸板制品、橡胶制品、电子产品等领域。
粘接成型的缺点是胶水的质量和粘结强度受到很多因素的影响,需要进行严格的控制和检测。
综上所述,材料成型技术是一种将材料从一个形状转变成另一个形状的技术,包括注塑成型、挤压成型和粘接成型等多种方
法。
这些方法具有各自的优缺点,应根据实际需求选择合适的成型技术。
材料成型技术的应用广泛,对于现代工业的发展至关重要。
材料成型工作总结

材料成型工作总结
材料成型工作是制造业中不可或缺的一环,它涉及到对原材料进行加工、成型
和制造成最终产品的过程。
在这个过程中,工作人员需要具备丰富的经验和技能,以确保产品的质量和生产效率。
在过去的一段时间里,我们团队在材料成型工作中取得了一些成绩和经验,现在我将对这些工作进行总结和分享。
首先,我们在材料成型工作中注重了生产设备的维护和管理。
我们意识到生产
设备的稳定性和运行效率对产品质量和生产效率有着至关重要的影响。
因此,我们加强了对设备的定期检查和维护,及时发现和解决设备问题,确保生产过程的顺利进行。
其次,我们在材料成型工作中注重了工艺流程的优化和改进。
我们深入分析了
生产过程中的瓶颈和问题,通过技术改进和工艺优化,提高了生产效率和产品质量。
我们还注重了工艺参数的监控和调整,以确保产品的一致性和稳定性。
此外,我们在材料成型工作中注重了团队合作和员工培训。
我们意识到材料成
型工作需要团队协作和员工技能的提升。
因此,我们加强了团队的沟通和协作,建立了相互信任和支持的工作氛围。
同时,我们还加强了员工的培训和技能提升,确保他们具备了应对各种生产工艺和设备操作的能力。
总的来说,材料成型工作是一个复杂而重要的工作环节,我们团队在这方面取
得了一定的成绩和经验。
我们将继续加强生产设备的管理和维护,优化工艺流程,加强团队合作和员工培训,以进一步提高材料成型工作的质量和效率。
希望我们的经验和总结能够对其他从事材料成型工作的团队有所帮助。
快速成型工艺的基本流程

快速成型工艺的基本流程快速成型工艺简介什么是快速成型工艺快速成型工艺(Rapid Prototyping,简称RP)是一种利用计算机辅助设计和制造技术,通过相继固化材料,逐层堆积形成所需产品的一种快速制造工艺。
它通过直接处理数据文件,并通过逐层叠加材料的方式,不用模具,实现了从CAD模型到实体产品的快速转化。
快速成型工艺的意义快速成型工艺是工业制造领域中的一项重要技术,它的出现大大缩短了产品开发周期,提高了产品设计的灵活性和精确度,降低了制造成本,促进了现代制造业的发展。
快速成型工艺的基本流程快速成型工艺的一般流程快速成型工艺的一般流程包括:1.CAD设计:首先,通过计算机辅助设计软件(CAD)进行产品的三维建模。
2.STL文件生成:将设计好的产品模型文件导出为标准三维打印格式的文件,通常是STL文件格式。
3.制造参数设置:根据所选的快速成型工艺方法和材料的特性,设置好相应的制造参数,如层厚、填充密度等。
4.打印准备工作:根据所选快速成型工艺的要求,准备相应的打印设备和材料。
5.快速成型工艺的处理:将STL文件导入快速成型机器中,通过计算机控制,逐层叠加材料,并按照预设的层厚进行固化或粘接。
6.后处理:完成打印后,对产品进行去除支撑结构、研磨平整、喷涂、热处理等后续处理工作,以获得符合要求的成品。
快速成型工艺常用方法光固化造型(Stereolithography,缩写SLA)SLA是一种常见的快速成型工艺方法,它利用紫外线激光束逐层照射光敏感树脂,使其固化成固体。
具体流程如下:1.准备工作:准备好SLA设备和液体光敏感树脂。
2.数据预处理:将CAD设计好的模型转换为STL文件,并设置切片参数。
3.光固化:在液体树脂中,利用激光束逐层照射,使树脂固化。
4.后处理:将固化后的产品从液体中取出,去除支撑结构,使用紫外线曝光设备进行后固化。
熔融沉积成型(Fused Deposition Modeling,缩写FDM)FDM是另一种常见的快速成型工艺方法,它利用熔融的热塑性材料通过喷头逐层堆积成型。
综述SLS工艺
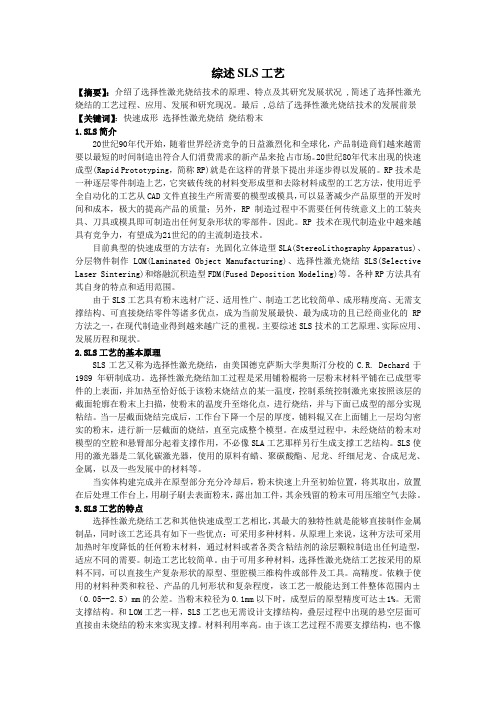
综述SLS工艺【摘要】:介绍了选择性激光烧结技术的原理、特点及其研究发展状况 ,简述了选择性激光烧结的工艺过程、应用、发展和研究现况。
最后 ,总结了选择性激光烧结技术的发展前景【关键词】:快速成形选择性激光烧结烧结粉末1.SLS简介20世纪90年代开始,随着世界经济竞争的日益激烈化和全球化,产品制造商们越来越需要以最短的时间制造出符合人们消费需求的新产品来抢占市场。
20世纪80年代末出现的快速成型(Rapid Prototyping,简称RP)就是在这样的背景下提出并逐步得以发展的。
RP技术是一种逐层零件制造上艺,它突破传统的材料变形成型和去除材料成型的工艺方法,使用近乎全自动化的工艺从CAD文件直接生产所需要的模型或模具,可以显著减少产品原型的开发时间和成本,极大的提高产品的质量;另外,RP制造过程中不需要任何传统意义上的工装夹具、刀具或模具即可制造出任何复杂形状的零部件。
因此。
RP技术在现代制造业中越来越具有竞争力,有望成为21世纪的的主流制造技术。
目前典型的快速成型的方法有:光固化立体造型SLA(StereoLithography Apparatus)、分层物件制作LOM(Laminated Object Manufacturing)、选择性激光烧结SLS(Selective Laser Sintering)和熔融沉积造型FDM(Fused Deposition Modeling)等。
各种RP方法具有其自身的特点和适用范围。
由于SLS工艺具有粉末选材广泛、适用性广、制造工艺比较简单、成形精度高、无需支撑结构、可直接烧结零件等诸多优点,成为当前发展最快、最为成功的且已经商业化的RP 方法之一,在现代制造业得到越来越广泛的重视。
主要综述SLS技术的工艺原理、实际应用、发展历程和现状。
2.SLS工艺的基本原理SLS工艺又称为选择性激光烧结,由美国德克萨斯大学奥斯汀分校的C.R. Dechard于1989年研制成功。
成形工艺过程
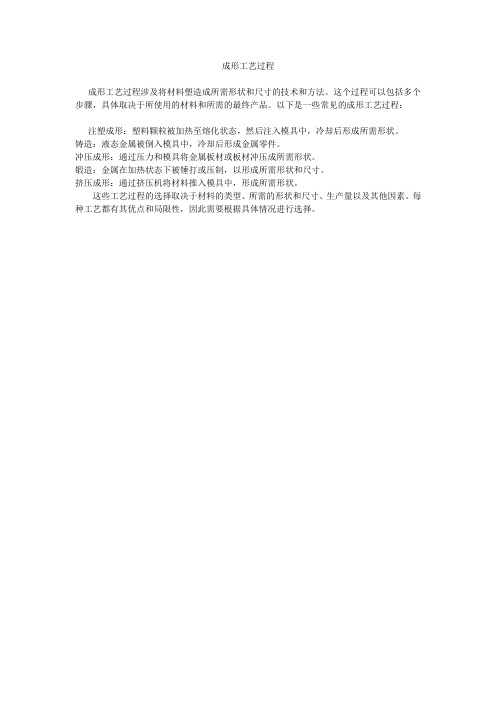
成形工艺过程
成形工艺过程涉及将材料塑造成所需形状和尺寸的技术和方法。
这个过程可以包括多个步骤,具体取决于所使用的材料和所需的最终产品。
以下是一些常见的成形工艺过程:
注塑成形:塑料颗粒被加热至熔化状态,然后注入模具中,冷却后形成所需形状。
铸造:液态金属被倒入模具中,冷却后形成金属零件。
冲压成形:通过压力和模具将金属板材或板材冲压成所需形状。
锻造:金属在加热状态下被锤打或压制,以形成所需形状和尺寸。
挤压成形:通过挤压机将材料推入模具中,形成所需形状。
这些工艺过程的选择取决于材料的类型、所需的形状和尺寸、生产量以及其他因素。
每种工艺都有其优点和局限性,因此需要根据具体情况进行选择。
介绍工艺流程举例

介绍工艺流程举例
《手工陶瓷制作工艺流程》
手工陶瓷制作是一门古老而精湛的工艺,其制作工艺流程需要经过多道复杂的工序。
下面就介绍一下手工陶瓷制作的工艺流程。
第一步:挑选原料
首先,需要挑选合适的陶土作为制作陶瓷的原料。
合适的陶土要求细腻、易于成型、可塑性好以及烧结后颜色均匀。
第二步:搅拌和制泥
将选好的陶土放入搅拌机中,加入适量的水,然后开始搅拌。
搅拌的目的是让陶土和水充分混合,形成柔软的陶泥。
第三步:成型
制作陶瓷的形状可以通过手工成型或者采用模具成型。
手工成型需要陶工经过长时间的练习和技巧,而采用模具成型则可以提高生产效率和产品质量。
第四步:干燥
成型完成后的陶瓷制品需要在通风干燥的环境下进行处理,目的是使陶瓷制品中的水分慢慢被蒸发掉,从而增加陶瓷制品的硬度和稳定性。
第五步:修整和涂釉
干燥后的陶瓷制品需要进行修整,包括去除表面的瑕疵和毛刺。
然后涂上适量的釉料,使其增加光泽和色彩,以及提高瓷器的耐磨性。
第六步:装瓷制品
经过修整和涂釉的陶瓷制品需要经过高温烧制,使其变得坚硬并具有一定的透明度。
第七步:包装和销售
经过烧制的陶瓷制品需要进行包装,然后投入市场销售。
以上就是手工陶瓷制作的工艺流程。
手工陶瓷制作需要耐心和技巧,每一个环节都需要经过精心的操作才能制作出精美的陶瓷制品。
橡胶成型工艺

橡胶成型工艺橡胶成型工艺是指以橡胶和其它组件作为原料,经过加工,最终形成各种橡胶制品的一系列工艺。
橡胶是一种多功能材料,具有抗磨性能强、弹性好、抗腐蚀性能强等优点,被广泛应用于汽车、机械、电子、航空航天、船舶等行业。
目前,它以其特殊的功能和结构,已得到越来越多的应用和重视。
主要橡胶成型工艺有注射成型、压延成型、挤出成型、模压成型和滚压成型等。
注射成型是将橡胶原料放入注射机内,经压缩空气把原料压入模具内,在模具内不同位置进行冷却,当橡胶冷却并固化,最后将成型好的橡胶产品从模具中推出。
由于注射机有很强的动力和大范围作用,塑料注射成型工艺用于生产一般型、复杂型制品效果明显。
压延成型是在压延机给定的温度和压力下,将橡胶原料压入模具内,然后通过冷却区保持模具温度并获得固定形状,从而获得特定的成型产品。
由于平坦的表面,这种工艺适合制作无缝水管、软管等制品。
挤出成型是以橡胶原料为原料,经过挤出机的均匀加压,螺杆挤压将橡胶固体原料转换成可流动状态,进入到模具室,经过模具内的冷凝,最终形成各种橡胶制品。
挤出工艺制作出的产品表面光滑,精度较高。
模压成型是在模压机上安装并配备相应模具,将橡胶原料填充到模具内,经过加热和压力处理,通过模具室的冷凝,可以获得不同形状的成型产品。
该工艺具有制造精度高、细节精细、生产效率高的特点,是生产复杂形状的橡胶制品的理想工艺。
滚压成型是将原料经过热压滚轮将热塑性橡胶压制成球形原料,再经过摆动杆拉伸滚压,最后压入模具内进行冷凝,形成成型产品。
该工艺具有制造精度高、制品均匀、无破裂等特点,常用于生产各种大型橡胶制品。
橡胶成型工艺具有相对简单,机械设备结构简单,成本低等优点,广泛应用于不同行业的制品制作,大大提高了生产效率,为社会发展做出重要的贡献。
熔融沉积成型制造工艺特点

熔融沉积成型制造工艺特点熔融沉积成型(Fused Deposition Modeling,简称FDM)是一种广泛应用于快速成型领域的制造工艺。
它以熔融的塑料材料为原料,通过控制挤出机将材料逐层堆积,最终构建出三维实体模型。
这种制造工艺具有以下特点。
熔融沉积成型工艺具有较高的制造效率。
它采用了一种连续的层叠方式,可以快速地构建出复杂的三维结构。
对于较小的零件,制造时间可能只需要几个小时,而对于较大的零件,也只需要几天的时间。
相比于传统的加工方法,熔融沉积成型可以大大缩短制造周期,提高生产效率。
熔融沉积成型工艺具有较低的制造成本。
传统的制造方法通常需要制造模具,而模具的制造成本较高。
而熔融沉积成型不需要制造模具,只需要使用计算机辅助设计软件将产品的三维模型转换为切片信息,并通过控制挤出机实现材料的逐层堆积。
这种无模具的制造方式不仅可以节约制造成本,还可以避免模具加工过程中可能出现的误差和问题。
熔融沉积成型工艺具有较高的制造精度。
在熔融沉积成型过程中,挤出机会根据切片信息将材料逐层堆积,因此可以实现较高的制造精度。
同时,通过调整挤出机的工作参数以及优化切片信息,还可以进一步提高制造精度。
这种精度可以满足大多数产品的制造要求,尤其适用于制造具有复杂形状或细节的产品。
熔融沉积成型工艺具有较好的材料适应性。
在熔融沉积成型过程中,可以使用多种类型的塑料材料作为原料,如ABS、聚碳酸酯、尼龙等。
不同种类的塑料材料具有不同的特性,可以满足不同产品的要求。
熔融沉积成型工艺具有较好的环境友好性。
相比于传统的加工方法,熔融沉积成型不需要使用大量的切削液和冷却液,减少了对环境的污染。
此外,熔融沉积成型工艺还可以回收利用材料废料,减少了材料的浪费。
这种环境友好性符合现代制造工艺的发展趋势,也符合社会对可持续发展的要求。
总结起来,熔融沉积成型工艺具有高效、低成本、高精度、材料适应性强和环境友好等特点。
它的出现和应用使得快速成型技术更加普及和便捷,为产品设计和制造带来了许多便利。
材料成型技术
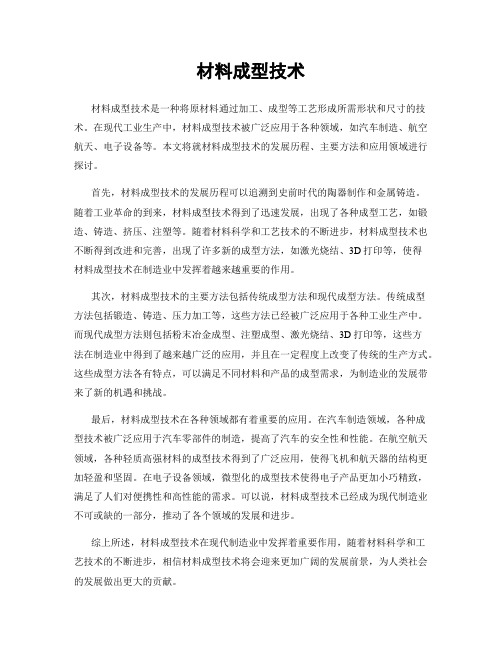
材料成型技术材料成型技术是一种将原材料通过加工、成型等工艺形成所需形状和尺寸的技术。
在现代工业生产中,材料成型技术被广泛应用于各种领域,如汽车制造、航空航天、电子设备等。
本文将就材料成型技术的发展历程、主要方法和应用领域进行探讨。
首先,材料成型技术的发展历程可以追溯到史前时代的陶器制作和金属铸造。
随着工业革命的到来,材料成型技术得到了迅速发展,出现了各种成型工艺,如锻造、铸造、挤压、注塑等。
随着材料科学和工艺技术的不断进步,材料成型技术也不断得到改进和完善,出现了许多新的成型方法,如激光烧结、3D打印等,使得材料成型技术在制造业中发挥着越来越重要的作用。
其次,材料成型技术的主要方法包括传统成型方法和现代成型方法。
传统成型方法包括锻造、铸造、压力加工等,这些方法已经被广泛应用于各种工业生产中。
而现代成型方法则包括粉末冶金成型、注塑成型、激光烧结、3D打印等,这些方法在制造业中得到了越来越广泛的应用,并且在一定程度上改变了传统的生产方式。
这些成型方法各有特点,可以满足不同材料和产品的成型需求,为制造业的发展带来了新的机遇和挑战。
最后,材料成型技术在各种领域都有着重要的应用。
在汽车制造领域,各种成型技术被广泛应用于汽车零部件的制造,提高了汽车的安全性和性能。
在航空航天领域,各种轻质高强材料的成型技术得到了广泛应用,使得飞机和航天器的结构更加轻盈和坚固。
在电子设备领域,微型化的成型技术使得电子产品更加小巧精致,满足了人们对便携性和高性能的需求。
可以说,材料成型技术已经成为现代制造业不可或缺的一部分,推动了各个领域的发展和进步。
综上所述,材料成型技术在现代制造业中发挥着重要作用,随着材料科学和工艺技术的不断进步,相信材料成型技术将会迎来更加广阔的发展前景,为人类社会的发展做出更大的贡献。
高分子材料成型加工

高分子材料成型加工
高分子材料成型加工是指通过热压、冷压、注塑、挤出等
成型技术,将高分子材料转变成所需形状和尺寸的产品的
过程。
高分子材料成型加工可以分为热固性塑料成型和热
塑性塑料成型两种形式。
热固性塑料成型是指在加热过程中,高分子材料经化学交
联形成三维网络结构的过程。
常见的热固性塑料成型加工
方式有热压、注塑和挤出。
热压是通过将高分子材料置于
加热板之间,加热和加压使其熔融并填充模具中,然后冷
却硬化成形。
注塑是将高分子材料加热熔融后注入模具中,冷却硬化成形。
挤出是通过高分子材料在加热和压力的作
用下,从模具口中挤出成型,然后冷却硬化形成。
热塑性塑料成型是指高分子材料在一定温度范围内,经过
塑化加工后,能够通过冷却形成所需产品的过程。
常见的
热塑性塑料成型加工方式有注塑、挤出和吹塑。
注塑的原
理与热固性塑料成型相似,但材料在加热过程中并不发生
交联反应。
挤出是通过高分子材料在加热和压力的作用下,从模具口中挤出成型,然后冷却硬化形成。
吹塑是将高分
子材料加热熔融后,通过压缩空气使其膨胀成薄壁容器形状,然后冷却硬化成型。
总之,高分子材料成型加工是将高分子材料通过加热、压力、塑化等工艺,转变成所需形状和尺寸的产品的过程,广泛应用于各个领域的塑料制品生产中。
材料成型技术

材料成型技术
材料成型技术是一种将原材料加工成所需形状和尺寸的工艺方法。
它是制造业
中非常重要的一环,涉及到各种材料的加工和成型,包括金属、塑料、陶瓷等。
在现代工业生产中,材料成型技术的应用非常广泛,可以说是制造业的基础。
首先,材料成型技术可以分为传统成型技术和现代成型技术两大类。
传统成型
技术包括铸造、锻造、冲压等,这些技术已经有着悠久的历史,经过长期的发展和改进,已经非常成熟。
而现代成型技术则包括注塑成型、3D打印、激光切割等,
这些技术在近年来得到了快速的发展,为制造业带来了革命性的变化。
其次,材料成型技术的发展对制造业起到了至关重要的作用。
它不仅可以大大
提高生产效率,降低生产成本,还可以实现复杂产品的加工和成型。
比如,注塑成型技术可以生产出各种形状复杂的塑料制品,而3D打印技术更是可以实现个性化
定制,为制造业带来了更多的可能性。
此外,材料成型技术的发展也带动了材料科学的进步。
随着材料科学的不断发展,新型材料的涌现为材料成型技术的应用提供了更多的可能性。
比如,高强度、高韧性的新型金属材料可以大大提高传统成型技术的加工性能,而具有特殊功能的复合材料也为现代成型技术的发展带来了新的动力。
总的来说,材料成型技术是制造业发展的重要支撑,它的发展不仅可以提高生
产效率,降低生产成本,还可以推动材料科学的进步。
随着科技的不断进步和创新,相信材料成型技术在未来会有更加广阔的发展空间,为制造业带来更多的惊喜和可能性。
简述熔融沉积成型的成型原理

简述熔融沉积成型的成型原理熔融沉积成型(FDM)是一种三维打印技术,它通过熔化固体材料并将其逐层堆积以构建物体。
本文将简述熔融沉积成型的成型原理。
熔融沉积成型的成型原理主要包括三个步骤:建模、切片和成型。
首先,使用计算机辅助设计(CAD)软件创建三维模型。
然后,将模型导入切片软件中进行处理。
在切片软件中,将三维模型分解成一系列水平的切片层,并将每个切片层转换为机器可以理解的指令。
最后,将切片数据传输到熔融沉积成型机器中,机器按照指令逐层构建物体。
在成型过程中,熔融沉积成型机器使用热塑性材料,如ABS(丙烯腈-丁二烯-苯乙烯共聚物)或PLA(聚乳酸)等,作为原材料。
这些材料以线状形式从机器的喷嘴中喷出,并在喷嘴附近加热到熔化状态。
然后,喷嘴按照切片数据中的指令在工作台上移动,将熔化的材料沉积在正确的位置上,逐层堆积以构建物体。
在沉积过程中,熔融沉积成型机器的喷嘴会在需要的时候停止喷射材料,以便给材料足够的时间冷却和固化。
这有助于确保每层之间有良好的粘接,并增强构建物体的结构强度。
此外,在每层沉积完成后,工作台会下降一个固定的高度,以便开始下一层的沉积。
这个过程将一直重复,直到整个物体构建完成。
熔融沉积成型的成型原理基于热塑性材料的特性,即可以在加热后变软和可塑,并在冷却后变硬和保持形状。
通过控制材料的温度和喷嘴的运动,熔融沉积成型可以实现复杂物体的构建。
此外,由于熔融沉积成型使用的材料具有良好的可塑性和可加工性,因此可以实现更高精度和更复杂的结构。
总结来说,熔融沉积成型的成型原理是通过将热塑性材料逐层堆积以构建物体。
这种成型方法具有灵活性高、构建速度快、成本低等优点,因此在制造、设计和教育领域得到了广泛应用。
随着技术的不断发展,熔融沉积成型将进一步推动创新和生产的进程。
快速成型工艺的基本流程

快速成型工艺的基本流程快速成型工艺的基本流程快速成型(Rapid Prototyping,RP)是指通过计算机辅助设计、制造和快速成型技术,将CAD模型直接转换为实体模型的一种技术。
它是一种快速、准确、灵活的制造方法,能够大大缩短产品从设计到生产的周期。
下面将详细介绍快速成型工艺的基本流程。
一、CAD建模CAD(Computer Aided Design)是计算机辅助设计技术的简称,是利用计算机进行产品设计和制图的过程。
在进行快速成型之前,需要先进行CAD建模,即利用CAD软件进行产品三维建模。
通过CAD建模可以精确地描述产品的形状、尺寸和结构等信息,并可以对其进行修改和优化。
二、STL文件生成STL(Standard Triangulation Language)文件是三角形数据格式文件,由三角形组成一个个小面片来表示物体表面。
在CAD建模完成后,需要将其转换为STL格式的文件。
这个过程通常由专门的软件完成,如3D MAX等软件。
三、SLA光固化SLA(Stereolithography Apparatus)光固化是一种利用紫外线激光束逐层扫描液态光敏树脂,使其固化成固态模型的快速成型技术。
在进行SLA光固化之前,需要先将STL文件导入到SLA机器中,并设置好加工参数。
SLA机器会根据STL文件逐层扫描光敏树脂,使其逐渐固化成实体模型。
四、SLS激光烧结SLS(Selective Laser Sintering)激光烧结是一种利用激光束逐层扫描粉末材料,使其熔融并凝固成实体模型的快速成型技术。
在进行SLS激光烧结之前,需要先将STL文件导入到SLS机器中,并设置好加工参数。
SLS机器会根据STL文件逐层扫描粉末材料,使其逐渐熔融并凝固成实体模型。
五、FDM熔丝沉积FDM(Fused Deposition Modeling)熔丝沉积是一种利用塑料丝材料经过加热后从喷头中挤出,并在平台上依次堆叠形成实体模型的快速成型技术。
- 1、下载文档前请自行甄别文档内容的完整性,平台不提供额外的编辑、内容补充、找答案等附加服务。
- 2、"仅部分预览"的文档,不可在线预览部分如存在完整性等问题,可反馈申请退款(可完整预览的文档不适用该条件!)。
- 3、如文档侵犯您的权益,请联系客服反馈,我们会尽快为您处理(人工客服工作时间:9:00-18:30)。
Cast steel
Al Brass
1╱4 in╱ft 14mm╱m
5╱32 3╱16
2.5 模型:可由木材、塑膠,或金屬製成,材料的選用乃依據
鑄造工件大小、形狀、尺寸精度,鑄件量多寡及鑄 造方法而定。
由鑄件形狀來決定模型的製作一般可分為單件模型(onepiece pattern)及分離式模型(split patterns)。 Split patterns are used for the casting having the complicated shape.
2.3 Major components of sand molds
◎Gating system(澆口系統):使熔化金屬進入模穴的通 道,通常由豎澆池,豎澆口或垂直通路和一澆口所組成。 ◎Pouring basin or pouring cup:熔化金屬入口 ◎Sprue(豎澆口道):熔化金屬流入之通道(downward) ◎Riser(冒口):有二種open riser and blind riser. 供應額外熔化金屬得以進入鑄件模穴中, 以補償鑄件之收縮,其剖面應大,以便熔 化時間儘可能加長,且位置應靠近厚剖面 的地方,以補償較大的收縮,若位於頂部 ,重力會幫助金屬進入鑄件的適當地方。 Blind riser:鐘頂形冒口,位於上砂箱 ,通常是直接 置於澆口上方,即金屬進 入模穴處,如此在澆鑄時,該處金屬進入 時間較模穴內晚,溫度較高。 ◎Cores(砂心):由模砂製,置入模穴中,以產生中空區。 ◎Vents(通汽口):藉以帶走當熔融金屬進入和砂模接觸時 所產生的氣體,及原在模內的氣體。
2.4製造砂模過程:
1.置模型於造模板上(molding board),且將下砂箱置於此 板上。 2.放面砂(乾分模砂,parting sand,細晶粒的乾細砂,沒有 強度,防止相黏) 3.堆砂:(模砂經篩選後覆於模型上,並壓實,須完全填滿 下砂箱) (如搥擊不實,在搬運或以澆入熔鐵產生衝擊時, 模型會分裂,若過緊,則水汽和汽體無法逸出) 4.加底板,並翻轉下砂箱,除去造模板,並加上一上砂箱。 5.置模型,並於二模型間加一些分離砂。 6.將一錐形豎澆口銷(sprue pin),直立置於離模型約1吋 (25m)處,以便能留一直立豎澆口。 7.如製造下砂箱之方法填砂,搥擊,並於模型四周刺穿若干 透氣孔。 8.抽出豎澆銷,並於頂部漏斗形開口,以便澆注金屬。 9.分離上、下砂箱,取出模型。 10.切出模穴和豎澆口間的通道,Gate(runner)(由深入淺,由 寬而窄,與模穴相接處截面最小,以便金屬澆入後,可在 澆口處,敲斷通道的金屬。 11.復合上、下砂箱。 12.開冒口。 13.澆注後敲掉多餘的部份,打掉即成型。
•產品設計及製造流程
• • • • Conceptual design and evaluation ; feasibility study. • Detrition of product need marketing information maybe new product or பைடு நூலகம்evised products.
產品定義及 市場調查
產品概念設計 及可行性評估
Design analysis;codes/seanded review physical and analytical 分析模型及實體
設計分析(產品 模型)
models.
Including: forces ,stresser deflection ,and optimalpart shape.
一、Introduction
製造:一種將材料成型轉換成產品的過程,其包含產品設計 及生產方式,和技術的研發
製造過程整合須符合下列要求: 1.產品須完全符合設計要求與規格。 2.產品須由最經濟的加工方法完成。 3.品質控制須包含在每一加工程序中。 4.保持高度競爭能力,製造方法須具有高度彈性(彈性製造系 統),以利於及時反映市場需求,變化產品,製造比例、數量及 交貨期限。 5.整體製造程序為一大系統,每一單元加工程序彼此關連。可以模 型分析來研究關於市場變化,產品設計,材料費用,和製造方法 等對產品質的成本之影響。 6.高度產能的追求-材料、機器、能源、資金、即技術的最佳化使 用。
Furnace
Solidification
shake out Removal of risers and gates.
製造優良鑄件的重要因素
造模程序、模型、模砂、砂心、機械設備、金屬,和澆注以及 鑄件的清洗。
2.2 Type Of Sand Molds
1.Green─Sand Molds:the most common mold material ,which is mixed of sand、(least expensive) clay,and water.由溼模 砂 所製成,其為砂、黏土及水(溼砂模)的組成,顏色為 深棕色或黑色。(未曬乾之砂) 2.Skin─Dried Molds:一般常用有二種。(表面乾砂模) A.在模型外圍四周堆上一層厚約1╱2吋(約12.7 mm)的一 種混合黏結劑之模砂,當乾燥後,會在模型上留一層硬的 表面,而模型內部的砂仍填以溼砂。 B.整個模型皆用溼砂製成,而以噴霧劑或噴液劑來塗敷表面 ,然後加熱以硬化之。所用之噴料:亞麻子油、糖蜜水、 膠化澱粉…等。 優點:a. Generally used for large casting by their higher strength. b. Stronger then green─sand molds and impart better dimensional accuracy and surface finish to the casting. 缺點:a. Distortion of mold is greater. b. Production rate is slower. 3.Dry─Sand Molds:完全由粗模砂及黏結劑相混合而得,此砂 模在鑄造前(乾砂模)須先在爐中烘乾,所以砂箱須是金屬 製成。 優點:澆鑄時不易變形,且不會發生有害汽泡。
澆口系統設計應考慮之因素
a.金屬流入砂模內時,擾流應愈少愈好。澆鑄小鑄件 時,澆口應在模穴的底部或靠近底部的地方。 b.藉控制金屬流動或使用乾砂心的方式來避免沖蝕通道 或模穴表面。 c.金屬進入模內,使之具方向性的凝固,由模子表面向 最熱的金屬處進行,以保持都有熔化金屬來補償鑄件 的收縮。 d.防止熔渣或其他外物進入模內,通往模子的澆口須稍 加限,以使有時間讓顆粒浮起,進入撇渣器,澆池也 可作成以烘乾的砂或陶瓷材料做成的過濾器,以過濾 金屬液及控制金屬流動。
Prototype production ; easting and evaluation
Prototype 原型 製作與測試評估
(
Computer- aided Design(CAD)
•
Cuality control either at this slage or periodically during production. These is an important aspect of Product drawings; Instruction manuals Product drawings; product manut. Instruction manuals (better way control through out the manufacturing process) (修正產品的設計,材料選 用or製造方法) Material specification;process and equipment selection;safety review
鑄造程序圖 Molding――Pattern making、Core making、Gate making ↓ Sand → Mold ↓ Melting of →Pouring into →Casting →Heat treatment →Cleaning →Inspection metal mold & finishing Defects Additional heat pressure treatment. tightness dimensions
二、Casting
鑄造:傳統鑄造法,現代鑄造。 鑄造程序:製模→熔融金屬→澆注(入模)→[冷卻]→鑄件清洗→回 收鑄模。
2.1砂模鑄造Sand Casting:
砂模種類(依pattern來分) 1.可取出模:用模砂包覆於模型的四周,然後自砂中取出模 型,以融化的金屬來填補所產生的鑄穴。 2.可消失模:用聚苯乙烯所製埋入砂中不取出,當熔化金屬注 入鑄模時,聚苯乙烯被汽化而從砂之孔隙逸出模 化。
Computer-aided manufacturing and process planning. (CAM and CAPP)
Pilot production Production Computer-inter manufacturing. (CIM)
Inspection and quality Assurance
Packaging market and Sales literature
Product
製造程序的分類
1.改變材料形狀的加工:casting,cold forming,hot forming, rolling,forging,extrusion,drawing, power metallurgy,injection molding. 2.按尺寸切削加工:a. turning,boring(搪),drilling, milling, grinding,hobbing,routing(切槽) b.非傳統: ultrasonic(超音波),electrical discharge(放電加工),optical lasers(雷射 切割),eolectro arc rasive-jet maching(磨 料 噴射切削), 3.Joint(聯結):a. welding(熔接),b. soldering(軟焊), c. brazing(硬焊),d. sintering(燒結) , e.pressing(壓接),f. riveting(鉚接), g.screw fastening(螺絲接), h. adhesive joining(黏接). 4.Finishing operation(表面加工):polishing(磨光),honing (搪磨),lapping(研磨), surface treating coating.