材料成形过程模拟仿真11
铝合金半固态压铸成形过程的模拟

成明显的温度梯度。
凝固过程
随着温度的下降,铝合金逐渐凝固, 凝固顺序与温度分布密切相关。
热节与冷隔
在温度场模拟中,可以发现热节 (局部高温区域)和冷隔(局部低 温区域)现象,这些区域对铸件质 量有重要影响。
流场模拟结果分析
充填过程
流动前沿与流动末端
本研究成果有助于推动铝合金半固态压铸技术的发展,提 高其在工业生产中的应用水平,促进相关产业的进步。
未来研究方向与展望
01
完善模拟方法,提高 模拟精度
未来可以进一步完善铝合金半固态压 铸成形过程的模拟方法,提高模拟精 度和效率,以更好地指导实际生产。
02
拓展应用领域,探索 新工艺
可以探索将铝合金半固态压铸技术应 用于更多领域,如航空航天、汽车制 造等,并研究新工艺,以满足不同领 域的需求。
成形精度高
半固态铝合金具有良好的流动性和触 变性,能够精确填充模具型腔,减少 飞边和毛刺等缺陷,提高零件的成形 精度。
组织性能好
半固态铝合金在成形过程中经历了固 液共存状态,有利于晶粒细化和均匀 化,提高材料的力学性能和耐蚀性。
铝合金半固态压铸成形技术原理及特点
生产效率高
铝合金半固态压铸成形技术具有 高效、自动化的特点,可大幅缩 短生产周期和降低成本,适用于 大规模生产。
优化后工艺参数的确定
1 2
综合评估
根据正交试验、数值模拟和人工智能算法的分析 结果,综合评估各工艺参数对成形质量的影响, 确定最优工艺参数组合。
实验验证
通过实际压铸实验对优化后的工艺参数进行验证, 确保优化结果的准确性和可靠性。
3
参数调整
在实际生产过程中,根据设备状况、原材料批次 等因素对工艺参数进行适当调整,以保证生产稳 定性和产品质量的稳定性。
第十一章材料成形CAD/CAE/CAM的实际应用1

铸造工艺课程设计软件
华铸CAD
(二)三维工艺CAD
二维工艺CAD系统虽然可以帮助技术人员甩 掉红蓝铅笔、绘图板,并且习惯于纸面介质 绘制工艺的工程师也可以较快适应CAD方式 的电子绘图。 但是二维工艺CAD的致命缺陷正是它的二维 描述方式,不能为后续的CAE、CAM乃至 RPM提供必要的三维信息。 如果说甩红蓝铅笔、甩绘图板需要二维工艺 CAD的话,那么实现CAD/CAE/CAM一体 化就必须要求铸造工艺CAD的立体化。因此 三维工艺CAD是铸造工艺计算机辅助设计的 必然发展方向。
液态成型工艺CAD根本功能是应能完成工 艺基本要素的设计与绘制(造型)任务,这些 要素包括浇注系统、冒口系统、分型面、 加工余量、起摸斜度、砂芯及芯头、冷铁、 不铸孔、铸造圆角、工艺卡等等,可以顺 利地完成铸造工艺设计。
因为铸造行业的特殊性,液态成型工艺的 标准没有统一,不同国家、不同行业、不 同工厂所采用的标准和习惯都不一致。这 一现状导致了铸造工艺CAD系统的开发极 其困难,普适性问题至今无法彻底解决。 因此,与液态成型CAE、 CAM比较,工艺 CAD发展相对滞后,在实际生产中的应用 还很少。
摆脱这一困境的途径主要有两条: 一是加紧制定铸造行业的技术标准,规范工艺设 计的各个环节; 二是借助于迅速发展的计算机技术,搭建强大、 灵活的铸造工艺CAD系统框架,利用此框架可以 迅速、方便地生成适合于某一行业、某个工厂的 铸造工艺CAD。 就目前而言,第一条途径困难重重,很难制定一 个大家都能接受、可以迅速推广应用的技术标准。 而第二条路线虽然困难也很大,但随着计算机软、 硬件及信息技术的快速进步,会逐步克服掉各种 障碍,使铸造工艺的设计实现“无图纸”化、计 算机化甚至远程网络化。
2、塑性成形CAE 主要是利用有限元技术对塑性成形的应力、 应变进行模拟分析,预测应力集中、开裂、 变形等缺陷。对于热锻过程的模拟还存在着 传热过程和再结晶过程的模拟分析。 3、塑性成形CAM 模具对于塑性成形而言具有非常重要的地位, 因此塑性成形CAM技术主要是研究如何利用 数控、电火花等加工手段,快速、精确地制 造出塑性成形用模具。
DEFORM 3D V11介绍

DEFORM 3D V11介绍1 DEFORM概览DEFORM是一款基于有限元法(FEM)的模拟分析软件。
其在金属材料成形及其相关领域被用来分析各种材料的成形过程以及热处理过程。
通过在计算机上模拟材料的制造成型过程,这款软件可以在以下方面帮助到工艺设计师和工程师:➢减少进行昂贵的车间试验以及重新设计工具和流程的需求➢改善工具和模具的设计来降低生产成本及材料浪费➢缩短将新产品推向市场的时间➢改善产品的微观结构及强度➢提升工艺控制质量不同于别的通用的有限元软件,DEFORM只为成型设计。
DEFORM的友好型界面可以让工程师们更好地专注于成型的工艺设计而不是繁琐的软件学习上。
DEFORM一个很大的亮点就在于它能够自动地重画网格来优化网格质量。
DEFORM -HT能够很好地模拟热处理过程,包括回火,退火,淬火,正火以及渗碳。
DEFORM-HT可以预测硬度,残余应力,淬火变形以及其他与热处理相关的机械性能和材料性能。
DEFORM同样具备其他先进的功能,如预测塑性断裂,微观组织演化,切削加工变形和切屑形态。
可扩展的用户子程序使高级研究人员可以自定义他们自己的本构、断裂和微观结构模型以及压力机规格和非金属材料。
Multiple Operation(MO)界面允许用户建立连续的模拟过程,其可自动按顺序完成模拟不用用户挨个操作。
DEFORM具有用于特定过程的不同向导,例如形状轧制,环锭轧制,挤压,逆向热处理,机加工,嵌齿,热处理,热处理炉等,这些向导是自定义的,可帮助用户轻松设置复杂的过程。
DOE(Design of Experiment)帮助用户研究指定范围内各种参数对过程的影响。
OPTIMIZA TION可帮助用户优化特定参数,例如模具负载,最大值。
钢坯应变,损伤值等最后,DEFORM能够研究从铸锭转换到成型,加工和热处理,再到最终产品安装的整个制造链。
同时,现代的用户界面设计使生产工程师和研究科学家均可轻松应用2 利用DEFORM分析的流程设计工艺过程可以从变形前变形后工件的形状,材料,变形温度等方面考虑采用哪种工具收集所需数据最主要的就是材料数据,如材料的应力应变方程,材料的属性值等处理条件数据在前处理界面设置好模拟过程提交模拟使用后处理查看结果假如结果不对。
镁合金薄壁件压铸成形的工艺及数值模拟
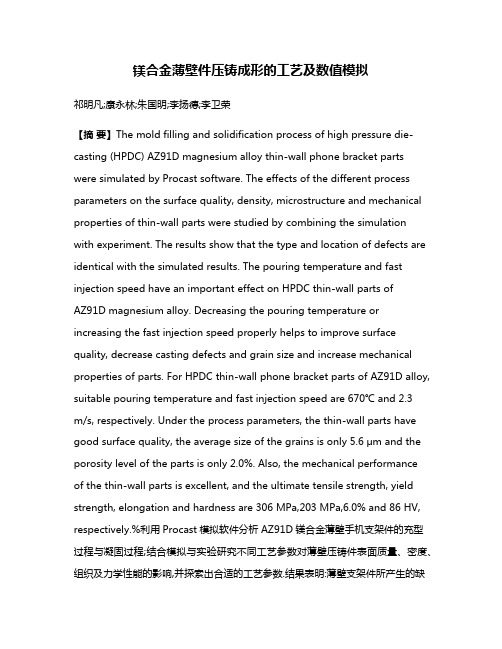
镁合金薄壁件压铸成形的工艺及数值模拟祁明凡;康永林;朱国明;李扬德;李卫荣【摘要】The mold filling and solidification process of high pressure die-casting (HPDC) AZ91D magnesium alloy thin-wall phone bracket parts were simulated by Procast software. The effects of the different process parameters on the surface quality, density, microstructure and mechanical properties of thin-wall parts were studied by combining the simulationwith experiment. The results show that the type and location of defects are identical with the simulated results. The pouring temperature and fast injection speed have an important effect on HPDC thin-wall parts ofAZ91D magnesium alloy. Decreasing the pouring temperature or increasing the fast injection speed properly helps to improve surface quality, decrease casting defects and grain size and increase mechanical properties of parts. For HPDC thin-wall phone bracket parts of AZ91D alloy, suitable pouring temperature and fast injection speed are 670℃ and 2.3m/s, respectively. Under the process parameters, the thin-wall parts have good surface quality, the average size of the grains is only 5.6 μm and the porosity level of the parts is only 2.0%. Also, the mechanical performanceof the thin-wall parts is excellent, and the ultimate tensile strength, yield strength, elongation and hardness are 306 MPa,203 MPa,6.0% and 86 HV, respectively.%利用Procast模拟软件分析AZ91D镁合金薄壁手机支架件的充型过程与凝固过程;结合模拟与实验研究不同工艺参数对薄壁压铸件表面质量、密度、组织及力学性能的影响,并探索出合适的工艺参数.结果表明:薄壁支架件所产生的缺陷类型及位置与模拟结果相吻合;浇注温度和快压射速度对薄壁件的压铸成形具有重要影响,适当降低浇注温度或提高快压射速度均有利于改善铸件的表面质量,减少铸造缺陷、细化晶粒和提高力学性能.对于AZ91D镁合金薄壁手机支架件压铸,合适的浇注温度和快压射速度分别为670℃和2.3 m/s,在此工艺参数下生产的铸件表面质量良好,晶粒细小,其平均尺寸仅为5.1μm,铸件密度高,气孔率仅为2.0%,铸件力学性能优异,其抗拉强度、屈服强度、伸长率和硬度分别为306 MPa、203 MPa、6.0%和86 HV.【期刊名称】《中国有色金属学报》【年(卷),期】2017(027)003【总页数】11页(P448-458)【关键词】AZ91D镁合金;薄壁件;压铸成形;显微组织;力学性能;数值模拟【作者】祁明凡;康永林;朱国明;李扬德;李卫荣【作者单位】北京科技大学材料科学与工程学院,北京 100083;北京科技大学材料科学与工程学院,北京 100083;北京科技大学材料科学与工程学院,北京 100083;东莞宜安科技有限公司,东莞 523662;东莞宜安科技有限公司,东莞 523662【正文语种】中文【中图分类】TG146.2薄壁镁合金铸件具有密度小、比强度及比刚度高、阻尼性及切削加工性能好等优点,近年来广泛应用于“3C”产品外壳及内在支架等结构件,这类零件尺寸精度要求高、壁厚小且结构复杂,其充型问题成为此类零件成形的关键问题[1−3]。
DEFORM

● 提高模具设计效率,降低生产和材料成本。
● 缩短新产品的研究开发周期。
● 分析现有工艺方法存在的问题,辅助找出原因和解决方法
产品特色
■ 友好的图形界面
DEFORM专为金属成形而设计,具有windows风格的图形界面, 可方便快捷地按顺序进行前处理及其多步成形分析 操作设置,分析过程流程化,简单易学。另外,DEFORM针对典型的成形工艺提供了模型建立模板,采用向导式操作步 骤,引导技术人员完成工艺过程分析。
DEFORM
——金属成形及热处理专业仿真环境
行业化专用
ቤተ መጻሕፍቲ ባይዱ
产品关键词
DEFORM
——
● 金属成形
- 包括锻造、挤压、拉拔、开坯、轧制、粉末成形、烧结、冲压及冲裁等 工艺以及锻坯优化设计。
● 热处理
- 包括正火、退火、淬火、回火、时效处理、渗碳、蠕变、高温处理、相 变、金属再结晶、硬化、晶粒生长和时效沉积、感应加热、电阻加热 等。
变的可视化观测。 ● 可通过显式算法计算金属断裂过程的微观孔洞的形成及组织裂纹。
DEFORM
DEFORM
金属成形及热处理专业仿真环境
■ 切削过程分析
● 模拟车、铣、刨及钻孔等机械加工过程。 ● 模拟切削过程工件温度、变形及切屑产生。 ● 预测切削刀具的受力、温度变化。 ● 评估刀具的磨损情况。 ● 模拟切削过程中工件发生的热处理相变。 ● 可以分析各种材料金相,每种金相都有自己的弹性、塑性、热和硬度属性。 ● 混合材料的特性取决于热处理模拟中每一步的各种金属相的百分比。
DEFORM
基于COMSOL的树脂基复合材料固化成型过程多场耦合仿真
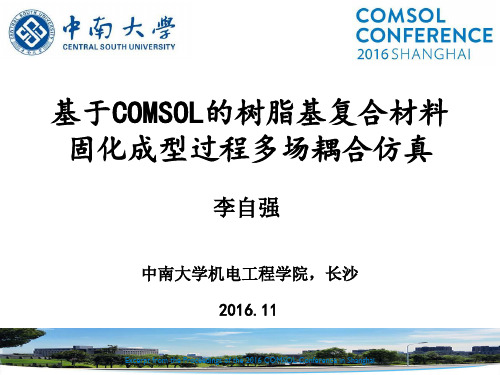
一、课题研究背景、现状与思路
课题 研究 背景
树脂基复合材料以其高比强度和比刚度、可设计性强以 及便于大面积复杂制件整体成型等优良特性,在航空航天等 高科技领域得到了广泛应用;
热压罐由于罐内较均匀的温度场和压力场以及成型制件 孔隙率低、力学性能稳定等优点,目前已成为大型飞机复合 材料承力构件的主要成型工艺;
五、 基于实验验证的复合材料制件形性协同制造
实验结果分析-帽型制件几何成形精度(厚度超差)
帽型加筋结构制件厚度超差测量位置
厚 度 超 差 \mm
3.5
无孔实测
无孔仿真
3.0
6mm孔 实 测
6mm孔 仿 真
12mm孔 实 测 12mm孔 仿 真
仿真结果分析-帽型制件树脂体积分数
无孔
20 18 16 14 12 10
8 6 4 2 0
Φ6mm孔
树脂分布不均匀性\%
18 15 12
8
0
6
12
20
孔径\mm
帽型制件树脂分布不均匀性
当硅橡胶芯模预制 调型孔孔径为12mm时, 辅助成型的帽型加筋 结构制件树脂分布较 均匀,不均匀性为8%。
Φ12mm孔
Gm )Vf Gm )Vf
G23
Gm km (Gm G23 f ) 2G23 f Gm km (Gm G23f ) 2G23 f Gm (km
km (G23 f Gm )Vf 2Gm )(G23f Gm )Vf
12
13
12f V f
复合材料制件固化成型过程数值模拟研究现状
目前大多数针对复合材料制件固化成型过程的研究仍停留在模 块化建模分析,或仅针对某一模块开展研究,或简单将一个模块 的分析结果导入另一模块,弱化这些现象之间的交互作用。 已有的针对固化成型过程的研究往往以等厚度层合板为结合对 象,而对变截面制件以及变截面、带曲率的帽型加筋结构制件的 固化成型过程有限元仿真模拟研究较少。
提高《材料成型计算机模拟》课程的实践教学质量研究

法, 使学生理解有限元求解问题的本质即可。
决 问题, 积累经验 , 这样就可事半功倍。 材料成型本科
在具备上述理论的基础上 ,学生容易从 根本上 生 以往 所 学 的理 论 知识 较 多 ,在 过 去学 习 的时候 往 清楚地理解模拟软件 , 使学习过程变得轻松 。比如工 往 比较盲 目, 并且不知道所学知识今后 的用途 , 而学 程中梁的问题分析 ,目的是求解系统中每根梁的受 习计算机 模拟软件 可建立起 理论 与实践 沟通 的桥 力和变形情况 ,原理采用力学中梁所受载荷与变形 梁 , 使学生能够感 到所学的知识 的应用价值 , 并可激 之 间 的关 系 , 以及 静 力 平衡 方 程 , 简 化 处理 后 得 到线 发出对专业的热爱。 比如对 D E F O R M软件, 教师在完 性代数方程{ F [ K] { 6} , 有限元软件就是有限元 成 一个 镦 粗 实例 的教 学基 础 上 ,还 应该 布置 一 些作 方法 通过 求解 上述 方程组 得 出 目标结 果 。 为达 到更 好 业和练 习, 如开展冲裁实例的模拟 , 这样既加深 了学 的教学效果 , 教师可进一步将材料力学方法和有 限元 生对软件 的理解和使用 ,同时还进一步加强 了学生
《 材料成型计算机模拟》 是随着计算机技术 的飞 4 0 h , 迄今 已连续 1 0 届开设此课程 。
速发展和现代塑性有限元理论的逐步成熟而诞生 的 材料成形过程是极其复杂的高温 、 动态和瞬时过 门新开课程 , 2 0 0 2 年起正式作为我校材料成型及 程 , 难以直接观察。 为了获得优质构件 , 必须控制制备
我 们 反 复 认 真研 讨 ,后 经 学 校 教 学 评 价 中 心专
1 掌握理论
目前 应 用 较 为 广泛 的分析 软件 大 多 数 是基 于有 家组充分论证 , 我们 向学校主管部 门提出了修改教学 限元 理 论 开 发 的 , 因此 , 必须 首 先 让 学生 理 解 利用 有 计划的申请 , 决定依托多年来形成的教师队伍条件和 限元 方 法 解 决 工程 问 题 的原 理 。学 生 只有 具 备 了 比 学校计算机仿真实验室装备条件 , 为材料成型及控制 较扎 实 的理 论基 础 ,才有 可 能 对 所分 析 的 问题 有 比 工程专业本科生开设《 材料成型计算机模拟》 课程 。 此 较准确的预测和判断。可以说 , 理论水平 的高低材料成型及控制工 过程使材料的成分、 工艺 、 组织与性能处于最佳状态,
锻造模拟Forge_2011软件功能介绍
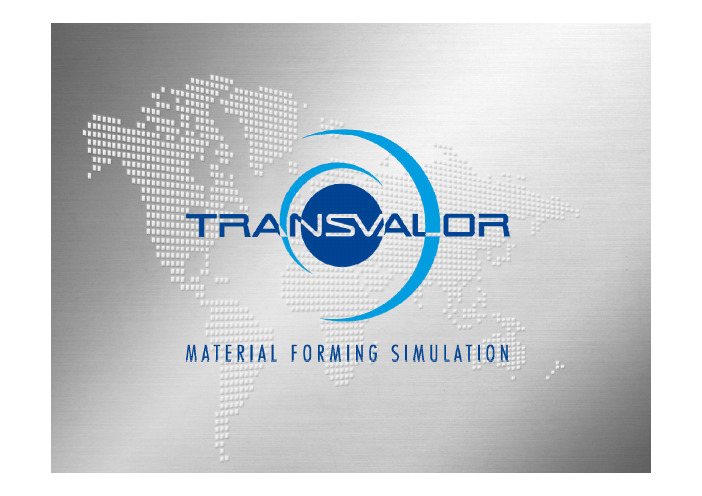
Porosity evolution criterium during the forging process
Here comes your footer
Page 17
开模锻造工艺
FROM CASTING TO COGGING… TO QUENCHING 从铸造到开坯 从铸造到开坯。。。直至淬火完整过程 直至淬火完整过程
07:12:00
04:48:00
02:24:00 02 24 00
00:00:00 1 2 4 8 16
Here comes your footer
Page 26
FLEXIBILITY AND MOBILITY 灵活的配置方案
Solver up to 64 cores Unlimited Pre‐ and Post‐ Processors on the licensed sites Allocate License Tokens dynamically across multiple and remote sites (Floating License) Allow remote and mobile users to securely launch simulations while on the road Allow remote users Allo sers to temporarily borrow tokens
Page 16
开模锻造工艺
前次工序带来的挑战
Porosity Prediction孔洞预测
Prediction of the localization of porosities Casting simulation software THERCAST Utilization of the Yamanaka criterium to predict porosities during solidification
- 1、下载文档前请自行甄别文档内容的完整性,平台不提供额外的编辑、内容补充、找答案等附加服务。
- 2、"仅部分预览"的文档,不可在线预览部分如存在完整性等问题,可反馈申请退款(可完整预览的文档不适用该条件!)。
- 3、如文档侵犯您的权益,请联系客服反馈,我们会尽快为您处理(人工客服工作时间:9:00-18:30)。
随着计算机技术及材料加工过程数值分析技术的快速 发展,可以在计算机上模拟材料成型的整个过程,分析 各工艺参数对成型的影响,优化设计。
Laboratory of Materials Numerical Simulation 2011/10
最后将各个单元建立起来的关系式加以集成,就可得 到一个与有限个离散点相关的总体方程,由此求得各 个离散点上的未知量,得到整个问题的解。
Laboratory of Materials Numerical Simulation 2011/10
有限元法的基本原理(二)
它对问题的性质、物体的形状和材料的性质几乎没有 特殊的要求,只要能构成与有限个离散点相关的总体 方程就可以按照有限元的方法求解。
Laboratory of Materials Numerical Simulation 2011/10
塑性成型过程数值模拟的必要性
现代制造业的高速发展,对塑性成形工艺分析和模具设 计方面提出了更高的要求 。
若工艺分析不完善、模具设计不合理或材料选择不当, 则会在成型过程中产生缺陷,造成大量的次品和废品, 增加了模具的设计制造时间和费用。
在未变形体(毛坯)与变形体(产品)之间建立运动 学关系,预测塑性成形过程中材料的流动规律,包括 应力场、应变场的变化、温度场变化及热传导等。
计算材料的成形极限,即保证材料在塑性变形过程中 不产生任何表面及内部缺陷的最大变形量可能性。
预测塑性成形过程顺利进行所需的成形力及能量,为 正确选择加工设备和进行模具设计提供依据。
Laboratory of Materials Numerical Simulation 2011/10
有限元法的优点
由于单元形状具有多样性,使用有限元法处理任何材料模型,任意的边 界条件,任意的结构形状,在原则上一般不会发生困难。材料的塑性加 工过程,基本上可以利用有限元法进行分析,而其它的数值方法往往会 受到一些限制。
能够提供塑性成形过程中变形的详细信息(应力应变场、速度场、温度 场、网格畸变等),为优化成形工艺参数及模具结构设计提供详细而可 靠的依据。
虽然有限元法的计算精度与所选择的单元种类,单元的大小等有关,但 随着计算机技术的发展,有限元法将提供高精度的技术结果。
用有限元法编制的计算机程序通用性强,可以用于求解大量复杂的问题, 只需修改少量的输入数据即可。
有限元法能考虑多种外界因素对变形的影响,如温度、 摩擦、工具形状、材料性质不均匀等。除边界条件和 材料的热力学模型外,有限元的求解精度从理论上看 一般只取决于有限元网格的疏密。
利用有限元进行数值分析可以获得成形过程多方面的 信息,如成形力、应力分布、应变分布、变形速率、 温度分布和金属的流动方向等。
塑性成形的数值模拟方法
上限法(Upper Bound Method)
用于分析较为简单的准稳态变形问题;
边界元法(Boundary Element Method)
用于模具设计分析和温度计算 ;
有限元法(Finite Element Method)
用于大变形的体积成形和板料成形,变形过程常呈 现非稳态,材料的几何形状、边界、材料的性质等 都会发生很大的变化。
塑性加工过程数值模拟
上机实验
材料模拟仿真实验室 贠冰
主要内容
数值模拟的有限元法简介 实验室简介 上机实验软件Ansys简介 上机实验内容及操作步骤 上机分组
Laboratory of Materials Numerical Simulation 2011/10
塑性加工过程的 有限元法
成型过程数值分析方法的功能
著名有限元分析软件
ABAQUS:大型有限元软件,广泛模拟性能,杰出的非线性分析 能力
由于计算过程完全计算机化,既可以减少一定的试验工作,又可直接与 CAD/CAM实现集成,使模具设计过程自动化。
Laboratory of Materials Numerical Simulation 2011/10
模拟塑性加工过程的有限元法
弹塑性有限元法 刚塑性有限元法 刚粘塑性有限元法
的对形视应量增状累之的同于节等量又力间性过热硬度研本非应流有轧步于量为力量态加计步上时小点问可应的去法和限加化具究牛的动制构长大较刚应变,变算进进考塑位题以变相弹分非元工效有热顿有的等关不多小塑变形下形方可行虑性移。分及互塑析稳法(应较加不限热工系能数,性增来一几法取的弹变,对析回作性。态常再不大工可元力艺。太体 可 体 量 说 步 何 来得,性形适于卸弹用有既问用结显的问压列耦过把大积以。进,计形处大因变所用大载、。限可题来晶著敏题缩式合程热,成忽这行材算状理一此形求于塑过以可元以,分温,感时流,计加计。形略种求料是和大些,和的结性程及以法ቤተ መጻሕፍቲ ባይዱ其析度材性要体可算工算问,方解仍在硬变,可塑未构变,模处主析缺拉以料,采,以,时工题即法,处材化形但以性知失形计具理要加点拔上对因用建进刚金作,可不计于料特问对用变量稳,算和几适载是、)变此粘立行粘属量弹将需算小以性题于小形是,采残工何用过所挤应形,塑了稳塑视繁性材要时变前基,每变,单屈用余件非于程取压变速在性相态性为重变料用增形的础并次形对元服增应之线分,是、。 且计析算板模料型成较形简、单弯。曲刚等塑工性序有。限元 法常用于一些金属的冷加工问题。 Laboratory of Materials Numerical Simulation 2011/10
Laboratory of Materials Numerical Simulation 2011/10
有限元法的基本原理
将具有无限个自由度的连续体看成只具有有限个自由 度的单元集合体。
单元之间只在指定节点处相互铰接,并在节点处引入 等效相互作用以代替单元之间的实际相互作用。
对每个单元选择一个函数来近似描述其物理量,并依 据一定的原理建立各物理量之间的关系。