PCB孔金属化几种制作工艺的分析
多层板孔金属化工艺探讨

多层板孔金属化工艺探讨本文主要论述了多层板的去钻污和沉铜工艺,剖析了各工步的原理及作用。
一、前言众所周知,孔金属化是多层板生产过程中最关键的环节,她关系到多层板内在质量的好坏。
孔金属化过程又分为去钻污和化学沉铜两个过程。
化学沉铜是对内外层电路互连的过程;去钻污的作用是去除高速钻孔过程中因高温而产生的环氧树脂钻污(特别在铜环上的钻污),保证化学沉铜后电路连接的高度可靠性。
二、孔金属化多层板工艺分凹蚀工艺和非凹蚀工艺。
凹蚀工艺同时要去除环氧树脂和玻璃纤维,形成可靠的三维结合;非凹蚀工艺仅仅去除钻孔过程中脱落和汽化的环氧钻污,得到干净的孔壁,形成二维结合,单从理论上讲,三维结合要比二维结合可靠性高,但通过提高化学沉铜层的致密性和延展性,完全可以达到相应的技术要求。
非凹蚀工艺简单、可靠,并已十分成熟,因此在大多数厂家得到广泛应用。
高锰酸钾去钻污是典型的非凹蚀工艺。
工艺流程环氧溶胀→二级逆流漂洗→高锰酸钾去钻污→二级逆流漂洗→中和还原→二级逆流漂洗→调整→二级逆流漂洗→粗化→二级逆流漂洗→预浸→离子钯活化→二级逆流漂洗→还原→水洗→化学沉铜→二级逆流漂洗→预浸酸→预镀铜工艺原理及控制溶胀目的:溶胀环氧树脂,使其软化,为高锰酸钾去钻污作准备。
配方环氧树脂是高聚形化合物,具有优良的耐蚀性。
其腐蚀形式主要有溶解、溶胀和化学裂解(如:浓硫酸对环氧树脂主要是溶解作用,其凹蚀作用是十分明显的)。
根据“相似相溶”的经验规律,醚类有机物一般极性较弱,且有与环氧树脂有相似的分子结构(R-O-R'),所以对环氧树脂有一定的溶解性。
因为醚能与水发生氢键缔合,所以在水中有一定的溶解性。
因此,常用水溶性的醚类有机物作为去钻污的溶胀剂。
溶胀液中的氢氧化钠含量不能太高,否则,会破坏氢键缔合,使有机链相分离。
在生产中,常用此中方法来分析溶胀剂的含量。
去钻污目的:利用高锰酸钾的强氧化性,使溶胀软化的环氧树脂钻污氧化裂解。
配方高锰酸钾是一种强氧化剂,在强酸性溶液中,与还原剂作用,被还原为Mn2+;在中性和弱碱性环境中,被还原为MnO2;在NaOH浓度大于2moL/L,被还原为MnO42-。
第八讲 孔金属化技术

作用:
1、去除铜面上的氧 化物及其他杂质。 2 、粗化铜表面,增 强 铜 面 与电 解铜 的 咬合力。
B、硫酸 -H2O2系列:
Cu+H2SO4+H2O2CuSO4 +2H2O
20
第八讲 孔金属化技术
二 化学镀铜 3、预浸
作用: 1、防止板子带杂质污染物进入昂贵的 Pd槽。
化学镀也叫做自催化镀、无电解镀。 常用还原剂:次磷酸钠、硼氢化钠、二甲基胺硼烷、甲醛等。
14
第八讲 孔金属化技术
二 化学镀铜
印制板生产工艺中的化学镀 :
化学镀 铜 化学镀 钯
• 孔金属化
化学镀 镍金
化学镀 铑
印制板生 产工艺中 的化学镀
激光化 学镀金
化学镀 银
化学镀 锡 • 焊接+图形保护层
15
第八讲 孔金属化技术
由于 H2SO4具有强的氧化性和吸水性, 能将环氧树脂炭化并形成溶于水的烷基磺 化物而去除。反应式如下:
Cm(H2O)nn 浓H2SO4 mC+nH2O
除钻污的效果与浓 H2SO4的浓度、处 理时间和溶液的温度有关。用于除钻污的 浓 H2SO4 的 浓 度 不 得 低 于 86 % , 室 温 下 20~40 秒钟,如果要凹蚀,应适当提高溶 液温度和延长处理时间。
物理反应:
利用正离子撞击分子表 面的方式,使需要处理 的物质,脱离 PCB而达 成 处 理 的 目 的 。 ( Ar 可以更换为其他惰性气 体,如 N2等)
9
第八讲 孔金属化技术
一 去钻污 等离子体处理法(Plasma)
等离子体处理工艺过程
10
双面板孔金属化的制作方法详解
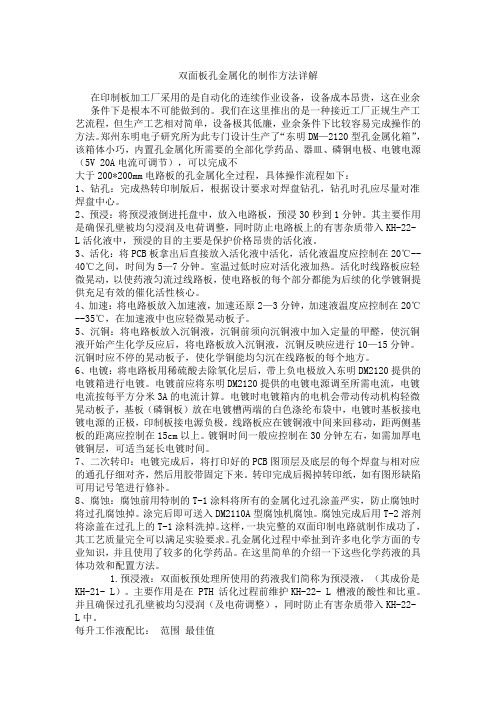
双面板孔金属化的制作方法详解在印制板加工厂采用的是自动化的连续作业设备,设备成本昂贵,这在业余条件下是根本不可能做到的。
我们在这里推出的是一种接近工厂正规生产工艺流程,但生产工艺相对简单,设备极其低廉,业余条件下比较容易完成操作的方法。
郑州东明电子研究所为此专门设计生产了“东明DM—2120型孔金属化箱”,该箱体小巧,内置孔金属化所需要的全部化学药品、器皿、磷铜电极、电镀电源(5V 20A电流可调节),可以完成不大于200*200mm电路板的孔金属化全过程,具体操作流程如下:1、钻孔:完成热转印制版后,根据设计要求对焊盘钻孔,钻孔时孔应尽量对准焊盘中心。
2、预浸:将预浸液倒进托盘中,放入电路板,预浸30秒到1分钟。
其主要作用是确保孔壁被均匀浸润及电荷调整,同时防止电路板上的有害杂质带入KH-22- L活化液中,预浸的目的主要是保护价格昂贵的活化液。
3、活化:将PCB板拿出后直接放入活化液中活化,活化液温度应控制在20℃--40℃之间,时间为5—7分钟。
室温过低时应对活化液加热。
活化时线路板应轻微晃动,以使药液匀流过线路板,使电路板的每个部分都能为后续的化学镀铜提供充足有效的催化活性核心。
4、加速:将电路板放入加速液,加速还原2—3分钟,加速液温度应控制在20℃--35℃,在加速液中也应轻微晃动板子。
5、沉铜:将电路板放入沉铜液,沉铜前须向沉铜液中加入定量的甲醛,使沉铜液开始产生化学反应后,将电路板放入沉铜液,沉铜反映应进行10—15分钟。
沉铜时应不停的晃动板子,使化学铜能均匀沉在线路板的每个地方。
6、电镀:将电路板用稀硫酸去除氧化层后,带上负电极放入东明DM2120提供的电镀箱进行电镀。
电镀前应将东明DM2120提供的电镀电源调至所需电流,电镀电流按每平方分米3A的电流计算。
电镀时电镀箱内的电机会带动传动机构轻微晃动板子,基板(磷铜板)放在电镀槽两端的白色涤纶布袋中,电镀时基板接电镀电源的正极,印制板接电源负极。
PCB孔金属化与电镀
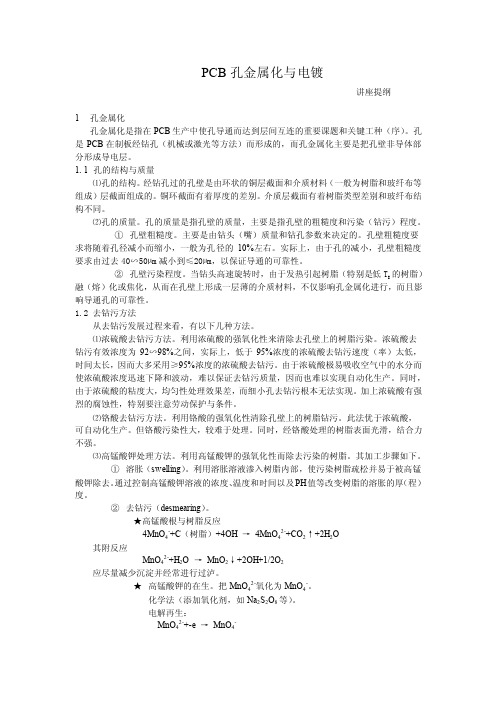
PCB孔金属化与电镀讲座提纲1孔金属化孔金属化是指在PCB生产中使孔导通而达到层间互连的重要课题和关键工种(序)。
孔是PCB在制板经钻孔(机械或激光等方法)而形成的,而孔金属化主要是把孔壁非导体部分形成导电层。
1.1 孔的结构与质量⑴孔的结构。
经钻孔过的孔壁是由环状的铜层截面和介质材料(一般为树脂和玻纤布等组成)层截面组成的。
铜环截面有着厚度的差别。
介质层截面有着树脂类型差别和玻纤布结构不同。
⑵孔的质量。
孔的质量是指孔壁的质量,主要是指孔壁的粗糙度和污染(钻污)程度。
①孔壁粗糙度。
主要是由钻头(嘴)质量和钻孔参数来决定的。
孔壁粗糙度要求将随着孔径减小而缩小,一般为孔径的10%左右。
实际上,由于孔的减小,孔壁粗糙度要求由过去40∽50µm减小到≤20µm,以保证导通的可靠性。
的树脂)②孔壁污染程度。
当钻头高速旋转时,由于发热引起树脂(特别是低Tg融(熔)化或焦化,从而在孔壁上形成一层薄的介质材料,不仅影响孔金属化进行,而且影响导通孔的可靠性。
1.2 去钻污方法从去钻污发展过程来看,有以下几种方法。
⑴浓硫酸去钻污方法。
利用浓硫酸的强氧化性来清除去孔壁上的树脂污染。
浓硫酸去钻污有效浓度为92∽98%之间,实际上,低于95%浓度的浓硫酸去钻污速度(率)太低,时间太长,因而大多采用≥95%浓度的浓硫酸去钻污。
由于浓硫酸极易吸收空气中的水分而使浓硫酸浓度迅速下降和波动,难以保证去钻污质量,因而也难以实现自动化生产。
同时,由于浓硫酸的粘度大,均匀性处理效果差,而细小孔去钻污根本无法实现。
加上浓硫酸有强烈的腐蚀性,特别要注意劳动保护与条件。
⑵铬酸去钻污方法。
利用铬酸的强氧化性清除孔壁上的树脂钻污。
此法优于浓硫酸,可自动化生产。
但铬酸污染性大,较难于处理。
同时,经铬酸处理的树脂表面光滑,结合力不强。
⑶高锰酸钾处理方法。
利用高锰酸钾的强氧化性而除去污染的树脂。
其加工步骤如下。
①溶胀(swelling)。
PCB的CAM制作之金属化包边制作

PCB的CAM制作之金属化包边制作CAM制作方法(仅限交流与学习使用,请勿用于其它作用)A、金属化包边的定义•金属化包边实际上就是板边要金属化。
•英文描述:Edge plating、Border plated、plated contour、sideplating 、side metal等。
B、金属化包边流程•金属化包边流程为:•-----钻孔-----铣金属化槽孔----去钻污----沉铜----C、金属化包边的实际效果•金属化包边做出来的实际效果如下图:•从上图我们得知,板边金属化一共有两种效果:一是板边镀铜,二是镀铜上面做有表面处理(如上图则为无铅喷锡)。
D、金属化包边工程文件的制作1.需要判断客户需要金属化包边的区域!!!!1.1 大多数顾客在设计线路时,铜是伸在板的外形边。
当出现这种情况时,就需要考虑板边是否需要包边?肯定它是金属化包边必须要客户的正式说明信息。
1.2 包边信息的来源:一是Gerber文件;二是Gerber之外的PDF、TXT、DWG等里面。
2. 金属化包边板的线路制作及注意事项2.1 将需包边的外形拷贝到pthrou层,做成封闭的长槽。
注意,由于包边处需要镀铜,铜厚是有一定厚度的。
所以在制作包边外形时,应考虑补偿问题。
2.2 做好包边槽之后,接下来要判断包边的电气连接性。
判断包边应该连接哪一层,应遵循下面顺序:1)查找顾客要求连接哪些层、区域;2)如果没有,则要通过判断了。
3)清楚了各层连接要求,在制作时就要注意,不连接则需隔离,连接处则需导通。
2.3金属化包边线路制作注意事项1)包边的板,为防止碎膜,必须保证焊盘单边10MIL无论是板内还是附边上或板外的部分都要求有10MIL的焊盘,对于客户原来交货单元上没有满足10MIL环,需要增加或更改的,必须反馈确认;包边附近有焊盘的,焊盘距包边盘至少8MIL间距,无法满足的,需要反馈确认。
2)包边后必须检查内外层连接情况,确定层间连接方式,避免包边后引起电地短路。
PCB制造工艺详解

PCB制造工艺详解一PCB制造行业术语1. Test Coupon: 试样test coupon是用来以TDR (Time Domain Reflectometer) 测量所生产的PCB板的特性阻抗是否满足设计需求一般要控制的阻抗有单根线和差分对两种情况,所以 test coupon 上的走线线宽和线距(有差分对时)要与所要控制的线一样,最重要的是测量时接地点的位置为了减少接地引线(ground lead)的电感值 TDR探棒(probe)接地的地方通常非常接近量信号的地方(probe tip) ,所以 test coupon上量测信号的点跟接地点的距离和方式要符合所用的探棒2. 金手指在线路板板边节点镀金Edge-Conncetion也就是我们经常说的金手指(Gold Finger),是用来与连接器(Connector)弹片之间的连接进行压迫接触而导电互连,这是由于黄金永远不会生锈且电镀加工有非常的容易外观也好看,故电子工业的接点表面几乎都要选择黄金线路板金手指上的金的硬度在140 Knoop以上,以便卡插拔时确保耐磨得效果,故一向采用镀硬金的工艺其镀金的厚度平均为在30u in 但在封装载板上(Substrate)上,设有若干镀金的承垫用来COBchip on board晶片间以"打金线"wire bond是一种热压式熔接的办法互连故另需使用较软的金层与金线融合,一般金的硬度在100 Knoop以下称为软金其品质要求较硬金更为严格此外镀金层具有焊锡性与导热性故也常用于焊点与散热表面的用途3. 硬金,软金硬金:Hard Gold;软金soft Gold电镀软金是以电镀的方式析出镍金在电路板上它的厚度控制较具弹性一般适合用于IC封装板打线用金手指或其它适配卡内存所用的电镀金多数为硬金因为必须耐磨在化学金方面基本上有所谓的浸金和化学金两种浸金指的是以置换的方式将金析出于镍表面因为是置换方式其厚度相当薄且无法继续成长但是化学金是采用氧化还原剂的方式将金还原在镍面上并非置换因此它的厚度可以成长较厚一般这类的做法是用于无法拉出导线的电路板因为化学金在整体的稳定度上控制较难因此较容易产生品质问题一般此类应用多集中在焊接方面打线方面的应用很少4. SMT基本名词术语解释Additive Process(加成工艺)一种制造PCB导电布线的方法通过选择性的在板层上沉淀导电材料(铜锡等) Angle of attack(迎角)丝印刮板面与丝印平面之间的夹角Anisotropic adhesive(各异向性胶)一种导电性物质其粒子只在Z轴方向通过电流Application specific integrated circuit (ASIC特殊应用集成电路)客户定做的用于专门用途的电路Artwork(布线图)PCB的导电布线图用来产生照片原版可以任何比例制作但一般为3:1或4:1 Automated test equipment (ATE自动测试设备)为了评估性能等级设计用于自动分析功能或静态参数的设备也用于故障离析Blind via(盲通路孔)PCB的外层与内层之间的导电连接不继续通到板的另一面 Buried via(埋入的通路孔)PCB的两个或多个内层之间的导电连接(即从外层看不见的) Bonding agent(粘合剂)将单层粘合形成多层板的胶剂3 Bridge(锡桥)把两个应该导电连接的导体连接起来的焊锡引起短路Circuit tester(电路测试机)一种在批量生产时测试PCB的方法包括针床元件引脚脚印导向探针内部迹线装载板空板和元件测试Cladding(覆盖层)一个金属箔的薄层粘合在板层上形成PCB导电布线CTE---Coefficient of the thermal expansion(温度膨胀系数)当材料的表面温度增加时测量到的每度温度材料膨胀百万分率(ppm)Cold cleaning(冷清洗)一种有机溶解过程液体接触完成焊接后的残渣清除Component density(元件密度)PCB上的元件数量除以板的面积Conductive epoxy(导电性环氧树脂)一种聚合材料通过加入金属粒子通常是银使其通过电流Copper foil(铜箔)一种阴质性电解材料沉淀于电路板基底层上的一层薄的连续的金属箔它作为PCB的导电体它容易粘合于绝缘层接受印刷保护层腐蚀后形成电路图样Copper mirror test(铜镜测试)一种助焊剂腐蚀性测试在玻璃板上使用一种真空沉淀薄膜Defect(缺陷)元件或电路单元偏离了正常接受的特征Delamination(分层)板层的分离和板层与导电覆盖层之间的分离Desoldering(卸焊)把焊接元件拆卸来修理或更换方法包括用吸锡带吸锡真空(焊锡吸管)和热拔DFM(为制造着想的设计)以最有效的方式生产产品的方法将时间成本和可用资源考虑在内Environmental test(环境测试)一个或一系列的测试用于决定外部对于给定的元件包装或装配的结构机械和功能完整性的总影响Functional test(功能测试)模拟其预期的操作环境对整个装配的电器测试Fiducial(基准点)和电路布线图合成一体的专用标记用于机器视觉以找出布线图的方向和位置Fine-pitch technology (FPT密脚距技术)表面贴片元件包装的引脚中心间隔距离为 "或更少Fixture (夹具)连接PCB到处理机器中心的装置Lead configuration(引脚外形)从元件延伸出的导体起机械与电气两种连接点的作用Machine vision(机器视觉)一个或多个相机用来帮助找元件中心或提高系统的元件贴装精度Mean time between failure (MTBF平均故障间隔时间)预料可能的运转单元失效的平均统计时间间隔通常以每小时计算结果应该表明实际的预计的或计算的Photo-plotter(相片绘图仪)基本的布线图处理设备用于在照相底片上生产原版PCB布线图(通常为实际尺寸)Pick-and-place(拾取-贴装设备)一种可编程机器有一个机械手臂从自动供料器拾取元件移动到PCB上的一个定点以正确的方向贴放于正确的位置Placement equipment(贴装设备)结合高速和准确定位地将元件贴放于PCB的机器分为三种类型SMD的大量转移X/Y定位和在线转移系统可以组合以使元件适应电路板设计Reflow soldering(回流焊接)通过各个阶段包括预热稳定/干燥回流峰值和冷却把表面贴装元件放入锡膏中以达到永久连接的工艺过程Schematic(原理图)使用符号代表电路布置的图包括电气连接元件和功能Solder bump(焊锡球)球状的焊锡材料粘合在无源或有源元件的接触区起到与电路焊盘连接的作用Soldermask(阻焊)印刷电路板的处理技术除了要焊接的连接点之外的所有表面由塑料涂层覆盖住4 Type I, II, III assembly(第一二三类装配)板的一面或两面有表面贴装元件的PCB(I)有引脚元件安装在主面有SMD元件贴装在一面或两面的混合技术(II)以无源SMD元件安装在第二面引脚(通孔)元件安装在主面为特征的混合技术(III)Ultra-fine-pitch(超密脚距)引脚的中心对中心距离和导体间距为或更小Void(空隙)锡点内部的空穴在回流时气体释放或固化前夹住的助焊剂残留所形成Yield(产出率)制造过程结束时使用的元件和提交生产的元件数量比率5 Keying Slot 在线路板金手指区为了防止插错而开的槽6. Mounting Hole 安装孔此词有两种意思一是指分布在板脚的较大的孔是将组装后的线路板固定在终端设备上使用的螺丝孔其二是指插孔焊接零件的脚孔后者也称Insertion Hole ,Lead Hole7. Laminate :基材指用来制造线路板用的基材板也叫覆铜板CCLCopper per Claded Laminates8. Prepreg 树脂片也称为半固化片9. Silk Screen 网板印刷用聚酯网布或不锈钢网布当载体将正负片的图案以直接乳胶或间接版膜方式转移到网框的网布上形成的网版作为对线路板印刷的工具10. Screen Printing 网版印刷是指在已有图案的网布上用刮刀刮挤压出油墨将要转移地图案转移到板面上也叫丝网印刷11. Screen ability 网印能力指网版印刷加工时其油墨在刮压之作用下具有透过网布之露空部分而顺利漏到板上的能力12. Solder Bump 焊锡凸块为了与线路板的连接在晶片的连接点处须做上各种形状的微焊锡凸块13. Substractive Process 减成法是指将基材上部分无用的铜箔减除掉而达成线路板的做法称为减成法14. Surface-Mount Device(SMD) 表面装配零件不管是具有引脚或封装是否完整的各式零件凡能够利用锡膏做为焊料而能在板面焊垫上完成焊接组装者皆称为SMD15. Surface Mount Technology 表面装配技术是利用板面焊垫进行焊接或结合的组装技术有别于采用通孔插焊的传统的组装方式称为SMT16. Thin Core 薄基材多层板的内层是由薄基材制作17. Through Hole Mounting 通孔插装是指早期线路板上各零件之组装皆采用引脚插孔及填锡方式进行以完成线路板上的互连18. Twist板翘指板面从对角线两侧的角落发生变形翘起称为板翘其测量的方法是将板的三个叫落紧台面再测量翘起的角的高度二PCB制造工艺综述1. 印制板制造技术发展50年的历程PCB制造技术发展的50年历程可划分为6个时期1PWB诞生期1936年~制造方法加成法5绝缘板表面添加导电性材料形成导体图形称为加成法工艺使用这类生产专利的印制板曾在1936年底时应用于无线电接收机中2PWB试产期1950年~制造方法减成法制造方法是使用覆铜箔纸基酚醛树脂层压板PP基材用化学药品溶解除去不需要的铜箔留下的铜箔成为电路称为减成法工艺在一些标牌制造工厂内用此工艺试做PWB以手工操作为主腐蚀液是三氯化铁溅上衣服就会变黄当时应用PWB的代表性产品是索尼制造的手提式晶体管收音机应和PP基材的单面PWB3PWB实用期1960年~新材料GE基材登场PWB应用覆铜箔玻璃布环氧树脂层压板GE基材由于PWB的国产GE基板在初期有加热翘曲变形铜箔剥离等问题材料制造商逐渐改进而提高1965年起日本有好几家材料制造商开始批量生产GE基板工业用电子设备用GE基板民用电子设备用PP基板已成为常识 4PWB跌进期1970~MLB登场新安装方式登场这个时期的PWB从4层向50层更多层发展同时实行高密度化细线小孔薄板化线路宽度与间距从向发展PWB单位面积上布线密度大幅提高PWB上元件安装方式开始了革命性变化原来的插入式安装技术TMT改变为表面安装技术SMT 引线插入式安装方法在PWB上应用有20年以上了并都依靠手工操作的这时也开发出自动元件插入机实现自动装配线SMT更是采用自动装配线并实现PWB两面贴装元件 5MLB跃进期1980年~超高密度安装的设备登场在1982年~1991年的10年间日本PWB产值约增长3倍1982年产值3615亿日元1991年10940亿日元MLB的产值1986年时1468亿日元追上单面板产值到1989年时2784亿日元接近双面板产值以后就MLB占主要地位了 1980年后PCB高密度化明显提高有生产62层玻璃陶瓷基MLBMLB高密度化推动移动电话和计算机开发竞争6迈向21世纪的助跑期1990年~积层法MLB登场1991年后日本泡沫经济破灭电子设备和PWB受影响下降到1994年后才开始恢复MLB和挠性板有大增长而单面板与双面板产量却开始一直下跌 1998年起积层法MLB进入实用期产量急速增加IC元件封装形式进入面阵列端接型的BGA和CSP走向小型化超高密度化安装今后的展望50多年来PWB发展变化巨大自1947的发明半导体晶体管以来电子设备的形态发生大变样半导体由ICISIVLSI向高集成度发展开发出了 MCMBGACSP等更高集成化的IC21世纪初期的技术趋向就是为设备的高密度化小型化和轻量化努力主导21世纪的创新技术将是纳米技术会带动电子元件的研究开发 2初步认识PCB PCB是英文(Printed Circuit Board)印制线路板的简称通常把在绝缘材上按预定设计制成印制线路印制元件或两者组合而成的导电图形称为印制电路而在绝缘基材上提供元器件之间电气连接的导电图形称为印制线路这样就把印制电路或印制线路的成品板称为印制线路板亦称为印制板或印制电路板PCB几乎我们能见到的电子设备都离不开它小到电子手表计算器通用电脑大到计算机通迅电子设备军用武器系统只要有集成电路等电子无器件它们之间电气互连都要用到PCB 它提供集成电路等各种电子元器件固定装配的机械支撑实现集成电路等各种电子元器件之间的布线和电气连接或电绝缘提供所要求的电气特性如特性阻抗等同时为自动锡焊提供阻焊图形为元器件插装检查维修提供识别字符和图形PCB是如何制造出来的呢我们打开通用电脑的健盘就能看到一张软性薄膜挠性的绝缘基材印上有银白色银浆的导电图形与健位图形因为通用丝网漏印方法得到这种图形所以我们称这种印制线路板为挠性银浆印制线路板而我们去电脑城看到的各种电脑主机板显卡网卡调制解调器声卡及家用电器上的印制电路板就不同了它所用的基材是由纸基常用于单面或玻璃布基常用于双面及多层预浸酚醛或环氧树脂表层一面或两面粘上覆铜簿再层压固化而成这种线路板覆铜簿板材我们就称它为刚性板再制成印制线路板我们就称它为刚性印制线路板单面有印制线路图形我们称单面印制线路板双面有印制线路图形再通过孔的金属化进行双面互连形成的印制线路板我们就称其为双面板如果用一块双面作内层二块单面作外层或二块双面作内层二块单面作外层的印制线路板通过定位系统及绝缘粘结材料交替在一起且导电图形按设计要求进行互连的印制线路板就成为四层六层印制电路板了也称为多层印制线路板现在已有超过100层的实用印制线路板了为进一认识PCB我们有必要了解一下单面双面印制线路板及普通多层板的制作工艺加深对它的了解单面刚性印制板单面覆铜板下料刷洗干燥网印线路抗蚀刻图形固化检查修板蚀刻铜去抗蚀印料干燥钻网印及冲压定位孔刷洗干燥网印阻焊图形常用绿油UV固化网印字符标记图形UV 固化预热冲孔及外形电气开短路测试刷洗干燥预涂助焊防氧化剂干燥检验包装成品出厂双面刚性印制板双面覆铜板下料钻基准孔数控钻导通孔检验去毛刺刷洗化学镀导通孔金属化全板电镀薄铜检验刷洗网印负性电路图形固化干膜或湿膜曝光显影检验修板线路图形电镀电镀锡抗蚀镍/金去印料感光膜蚀刻铜退锡清洁刷洗网印阻焊图形常用热固化绿油贴感光干膜或湿膜曝光显影热固化常用感光热固化绿油清洗干燥网印标记字符图形固化外形加工清洗干燥电气通断检测喷锡或有机保焊膜检验包装成品出厂贯通孔金属化法制造多层板工艺流程:内层覆铜板双面开料刷洗钻定位孔贴光致抗蚀干膜或涂覆光致抗蚀剂曝光显影蚀刻与去膜内层粗化去氧化内层检查外层单面覆铜板线路制作B阶粘结片板材粘结片检查钻定位孔层压数控制钻孔孔检查孔前处理与化学镀铜全板镀薄铜镀层检查贴光致耐电镀干膜或涂覆光致耐电镀剂面层底板曝光显影修板线路图形电镀电镀锡铅合金或镍/金镀去膜与蚀刻检查网印阻焊图形或光致阻焊图形印制字符图形热风整平或有机保焊膜数控洗外形成品检查包装出厂从工艺流程图可以看出多层板工艺是从双面孔金属化工艺基础上发展起来的它除了继了双面工艺外还有几个独特内容金属化孔内层互连钻孔与去环氧钻污定位系统层压专用材料我们常见的电脑板卡基本上是环氧树脂玻璃布基双面印制线路板其中有一面是插装元件另一面为元件脚焊接面能看出焊点很有规则这些焊点的元件脚分立焊接面我们就叫它为焊盘为什么其它铜导线图形不上锡呢因为除了需要锡焊的焊盘等部分外其余部分的表面有一层耐波峰焊的阻焊膜其表面阻焊膜多数为绿色有少数采用黄色黑色蓝色等所以在PCB行业常把阻焊油叫成绿油其作用是防止波焊时产生桥接现象提高焊接质量和节约焊料等作用它也是印制板的永久性保护层能起到防潮防腐蚀防霉和机械擦伤等作用从外观看表面光滑明亮的绿色阻焊膜为菲林对板感光热固化绿油不但外观比较好看便重要的是其焊盘精确度较高从而提高了焊点的可靠性相反网印阻焊油就比较差我们从电脑板卡可以看出元件的安装有三种方式一种为传动的插入式安装工艺将电子元件插入印制线路板的导通孔里这样就容易看出双面印制线路板的导通孔有如下几种一是单纯的元件插装孔二是元件插装与双面互连导通孔三是单纯的双面导通孔四是基板安装与定位孔另二种安装方式就是表面安装与芯片直接安装其实芯片直接安装技术可以认为是表面安装技术的分支它是将芯片直接粘在印制板上再用线焊法或载带法倒装法梁式引线法等封装技术互联到印制板上其焊接面就在元件面上表面安装技术有如下优点:1 由于印制板大量消除了大导通孔或埋孔互联技术提高了印制板上的布线密度减少了印制板面积一般为插入式安装的三分阶之一同时还可降低印制板的设计层数与成本2 减轻了重量提高了抗震性能采用了胶状焊料及新的焊接技术提高了产品质量和可靠性3 由于布线密度提高和引线长度缩短减少了寄生电容和寄生电感更有利于提高印制板的电参数4 比插装式安装更容易实现自动化提高安装速度与劳动生产率相应降低了组装成本从以上的表面安技术就可以看出线路板技术的提高是隋芯片的封装技术与表面安装技术的提高而提高现在我们看的电脑板卡其表面粘装率都不断地在上升实际上这种的线路板再用传动的网印线路图形是无法满足技术要求的了所以普通高精确度线路板其线路图形及阻焊图形基本上采用感光线路与感光绿油制作工艺也许过不多久人们该把印制线路板叫作感光线路板了现在我们再来看成组芯片直接安装技术多芯片模块MCM技术它是将多块未封装的集成电路芯片高密度安装在同一基板上构成一个完整的部件的新思路即现在人们普遍称之的多芯片模块简称MCM是(Multi Chip Module的缩写)随着MCM的兴起使封装的概念发生了本质的变化在年代以前所有的封装都是面向器件的而MCM可以说是面向部件的或者说是面向系统或整机的MCM技术集先进印刷线路板技术先进混合集成电路技术先进表面安装技术半导体集成电路技术于一体是典型的垂直集成技术对半导体器件来说它是典型的柔性封装技术是一种电路的集成MCM的出现使电子系统实现小型化模块化低功耗高可靠性提供了更有效的技术保障其中MCM-D型Mulit Chip ModuleDeposited Thin Film是采用薄膜技术将金属材料淀积到陶瓷或硅铝基板上光刻出信号线电源线地线并依次做成多层基板多达几十层主要用在500Mhz以上的高性能产品中线宽和间距可做到10-25 孔径在1050因而具有组装密度高信号通道短寄生效应小噪声低等优点可明显地改善系统的高频性能现在我们可以看到如今的高新技术PCB已经不是我们所认为的印制线路板了也许又该提升一步叫光刻线路板了3表面贴装技术(SMT)的介绍1) SMT的特点组装密度高电子产品体积小重量轻贴片元件的体积和重量只有传统插装元件的1/10左右一般采用SMT之后电子产品体积缩小40%~60%重量减轻60%~80%可靠性高抗振能力强焊点缺陷率低高频特性好减少了电磁和射频干扰易于实现自动化提高生产效率降低成本达30%~50% 节省材料能源设备人力时间等2) 为什么要用表面贴装技术(SMT)电子产品追求小型化以前使用的穿孔插件元件已无法缩小电子产品功能更完整所采用的集成电路(IC)已无穿孔元件特别是大规模高集成IC不得不采用表面贴片元件产品批量化生产自动化厂方要以低成本高产量出产优质产品以迎合顾客需求及加强市场竞争力电子元件的发展集成电路(IC)的开发半导体材料的多元应用电子科技革命势在必行追逐国际潮流3) SMT技术的发展趋势随着电子产品向便携式/小型化网络化和多媒体方向迅速发展表面贴装技术Surface Mount Technology简称SMT在电子工业中正得到越来越广泛的应用并且在许多领域部分或全部取代了传统电子装联技术SMT的出现使电子装联技术发生了根本的革命性的变革在应用过程中SMT正在不断地发展与完善主要表现在以下几方面SMT生产线的发展SMT生产线是生产的基础目前其有如下几个发展趋势计算机集成制造系统CIMS的应用SMT 生产线正向高效率方向发展SMT生产线向绿色环保方向发展SMT设备的发展包括丝印设备贴装设备的发展FMS多功能等方向发展表面贴装元器件的发展SMT工艺材料的发展4PCB电镀金工艺介绍作用与特性印制板上的金镀层有几种作用金作为金属抗蚀层它能耐受所有一般的蚀刻液它的导电率很高其电阻率为微欧厘米由于它的负的氧化电位使得它是一种抗锈蚀的理想金属和接触电阻低的理想的接触表面金属金作为可焊性的基底是多年来争论的问题之一只要说明金在控制条件的情况下已经成功地用来作为一种焊接的辅助手段就够了近年来已经发展了一些新的镀金工艺它们大多数是专利性的这表明为避开以典的碱性氰化物镀金及其对电镀抗蚀剂的破坏作用所作的努力金价格成本高促使发展金的合金槽浴作为降低成本的手段5PCB电镀铜工艺介绍铜作为印制电路制造中的基本的导线金属已经得到了广泛的承认它具有极为优越的导电性仅次于银容易电镀成本低并给出高度可靠的结果铜是很容易活化的因此在铜和其它电镀的金属之间可以获得良好的金属金属键合电子设备用的印制电路MILSTD275指出金属化应该镀铜孔中铜镀层的厚度应不小于英寸有三种最常用的镀铜溶液焦磷酸盐硫酸盐以及氟硼酸盐溶液6多层板孔金属化工艺众所周知孔金属化是多层板生产过程中最关键的环节她关系到多层板内在质量的好坏孔金属化过程又分为去钻污和化学沉铜两个过程化学沉铜是对内外层电路互连的过程去钻污的作用是去除高速钻孔过程中因高温而产生的环氧树脂钻污特别在铜环上的钻污保证化学沉铜后电路连接的高度可靠性多层板工艺分凹蚀工艺和非凹蚀工艺凹蚀工艺同时要去除环氧树脂和玻璃纤维形成可靠的三维结合非凹蚀工艺仅仅去除钻孔过程中脱落和汽化的环氧钻污得到干净的孔壁形成二维结合单从理论上讲三维结合要比二维结合可靠性高但通过提高化学沉铜层的致密性和延展性完全可以达到相应的技术要求非凹蚀工艺简单可靠并已十分成熟因此在大多数厂家得到广泛应用高锰酸钾去钻污是典型的非凹蚀工艺7. PCB表面处理技术虽然以产品生命周期短和迅猛的技术改变闻名电子工业还不得不采用一种工业应用广泛的热空气焊锡均涂(HASL, hot air solder leveling)的替代技术长期影响环境的关注通常集中在潜在的铅泄漏到环境中去仅管在北美的立法禁止铅的使用还是几年后的事情但是原设备制造商(OEM, original equipment manufacturer)必须满足欧洲和日本的环境法令以使其产品作全球销售这个考虑已经孕育出许多课题评估在每一个主要的OEM 那里消除铅的可选方法HASL的替代方法允许无铅印刷电路板(PWB, printed wiring board)也提供平坦的共面性表面满足增加的技术要求更密的间距和区域阵列元件已允许增加电子功能性通常越高的技术对立着降低成本可是大多数替代方法改进高技术装配和长期的可靠性而还会降低成本成本节约是整个过程成本的函数包括过程化学劳力和企业一般管理费用(图一)象OSP浸银和浸锡等替代技术可提供最终表面处理成本的20 ~ 30%的减少虽然每块板。
浅析印制电路板孔金属化及其工艺改进途径

浅析印制电路板孔金属化及其工艺改进途径摘要:PBC孔金属化技术被认为是印制电路板生产过程中的关键环节,本文将深入探讨这一技术的概念,并结合实际应用,提出有效的改善方案。
此外,本文还将探讨如何通过整平、氧化、催化和电镀等技术来提高PBC的性能,以及如何通过这些技术来实现PBC的长期可持续发展。
关键词:印制电路板。
孔金属化;工艺现状;优化方法引言:随着电子IT的飞速发展,印刷电路板(PBC)行业迎来了前所未有的机遇,而孔金属化则成为PBC生产过程中不可或缺的一部分。
随着PBC孔金属化技术的不断发展,其工艺已经变得越来越成熟,制造质量也越来越稳定,但仍然存在着复杂的工艺流程、昂贵的成本以及严重的环境污染问题。
因而,提升PBC孔金属化技术的效率与质量显得尤为重要,本文将从多方面探讨这一问题,以期达到更好的效果。
1 PBC孔金属化概念覆铜板(CCP)为PCB制造。
CCP是一种具有重要应用价值的基础材料,它可以通过精心设计的加工工艺,如电镀铜、刻蚀等,制作出具有良好导电性能的电路,从而实现高性能的PCB电路。
在PCB盘面上的每个孔都被完全封装之前,才能够将其与PCB电路连接起来,并安装相应的电子元器件。
从宏观视角来看,孔金属化技术指的是采用电化学镀、电镀或其他技术,将一层导电金属覆盖在PCB板孔壁上,以增强电路与电子元件之间的联系,以达到改善电路效率和电子元件耐久性的目的。
金属化是PCB制造过程中至关重要的一步,它需要确保金属化孔的机械强度和导电性能达到最佳水平。
此外,铜镀层的结构必须完善,分布均匀,厚度也应该适中(一般为25~30μm)。
同时,孔洞内部也应避免出现分层和气泡等缺陷,并且孔的电阻值应小于<1000MΩ。
近年来,随着高密度封装技术的普及,PCB结构的创新和发展得到了显著推动,成为工业界的一大亮点。
通过安装金属孔,可以有效地将不同电路连接起来,从而提高电子元件的性能和可靠性。
通过表面安装技术的应用,可以有效地缩小金属化孔空洞的尺寸,从而推动PCB制造技术的发展,实现微纳通孔和薄型化的生产。
PCB化金流程介绍
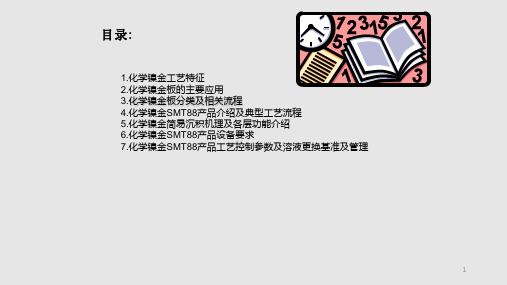
钯
高度活性触媒引发镍沉积(单分子层)
镍
此层为含磷9-11%的镍-磷合金,可焊接。
真正的焊接基地。
金
金本身的高贵特性(惰性金属)
及极好的导电性,作为镍层的
保护层,也可作为最终电气触
点。
9
化学镍金设备条件
缸体材料
打气搅拌
机械震荡
除油
PP
热自来水洗 PP
自来水洗
PP
自来水洗
PP
微蚀
PP
× √(轻微) √(轻微) √(轻微) √
铜,脱镍不良
浓度
同上
高出标准上限 攻击 S/M 同上
药水调整:H2SO4(98%)补充量(L)=(50-分析值)X 槽体积(L)/1000
H2SO4(50%)补充量(L)= H2SO4(98%)补充量(L)X2.6
备注:若药水补充量>配槽量的1/3,请理化室重新取样确认分析
18
钯槽反应机理及主要控制参数:
温度(℃)
35-45℃
40-60
室温 室温 25-35℃ 室温 室温 20-30℃ 室温 室温 室温 80-88℃ 室温 78-90℃
室温 室温 40-50℃
时间(min)
4-6
1-2
1-2 1-2 1-1.5 1-2 1-1.5 0.5-3.0 0-1 1-1.5 1-1.5 18-25 0.5-1.5 8-15
1L原液Catalyst CF可生产1000SF
20
后浸槽反应机理及主要控制参数:
作用:去除阻焊膜及基板上多余之钯离子
主要控制参数:1.浓度:硫酸10-20-30ml/l, 2.温度:20-25-30°C 3.寿命:生产面积达10KSF
印刷线路板孔的金属化工艺及配方
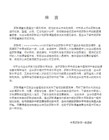
配方2 焦磷酸铜(以铜计)21-31克/升,焦磷酸钾(以P2O7计)150-1210克/升,氢氧化铵(25%)8毫升/升,硝酸钾5-10克/升,柠檬酸铵20克/升,PH值8-9,温度18-58度,阴极电流密度1-3安/分实2,阴极移动需要,
加厚镀铜:在电镀其他金属之前,必须进行加厚镀铜,其溶液的配方和工艺规范与孔内镀铜溶液相同,电镀时间约为1—1.5小时,厚度约为25-30微米。
孔内硫酸型镀铜水液配方:
配方1 硫酸铜80-100克/升,硫酸200克/升,2—四氢基噻唑硫铜0.001克/升,聚二硫二丙烷磺酸钠0.01克/升,聚醚化物0.15克/升,亚甲基磺酸钠(D—1)0.2克/升,氯离子20毫升/升,阳极含磷0.01—0.03%的铜板,电流密度1—3安/分米2,溶液温度10-25度,沉积速度1.5微米/时。
有关工艺及配方如下:
脱膜剂配方:海鸥洗涤剂1份,水10份。
涂保护漆:用过氯乙烯防腐清漆浸2-3次,再晾干或烘干。
新水处理:在5-10%的氢氧化钠水溶液中,于室温下浸10分钟左右,去除Байду номын сангаас内残留的油污。
孔壁粗化:在浓硫酸溶液中,于室温下浸1-2分钟,使孔壁非常清洁,但表面粗糙(微观),粗化时间不能太长,粗化后孔内环氧玻璃钢的表面应呈现均匀的暗红色。
配方3(浓度)硫酸铜10克/升,酒石酸钾钠40克/升,氢氧化钠20克/升,十二烷基硫酸钠0.2-0.3克/升,2—巯基苯并噻唑0.01—0.02克/升,甲醛(37%)20-25毫升,温度20-25度,时间15-25分钟。
配方4(浓度)硫酸铜28克/升,乙二胺四乙酸二钠50克/升,氢氧化钠20克/升,甲醇250毫升/升,甲醛(37%)12毫升/升,温度32—34度,PH值13,时间15-25分;沉铜配方中的甲醛用量,由温度高低而定,当温度高时取下限,反之取上限,只有当溶液有较强的碱性时,甲醛对铜才有足够的还原能力,所以PH值太低,反应便慢,甚至不反应,太高,则反应太快,难于控制。
浅析印制电路板孔金属化及其工艺改进途径

浅析印制电路板孔金属化及其工艺改进途径作者:苗奇来源:《科学与信息化》2019年第13期摘要孔金属化是印制电路板(PBC)生产制造工艺的核心,文章首先阐述了PBC孔金属化概念做出解析,其次从整平、氧化、催化与电镀等方面阐述了PBC孔金属化工艺显著,最后站在促进PBC孔金属化持续发展的角度,对优化工艺的方式方法做出研究。
关键词印制电路板;孔金属化;工艺现状;优化方法在电子信息技术的促动下,印制电路板(PBC)行业获得巨大发展空间,孔金属化是PBC 生产制造的关键一环。
当下国内PBC孔金属化技术工艺日趋成熟、制造质量相对稳定,但还存在工艺流程繁杂、造价成本高及环境污染严重等特征。
故而加强PBC孔金属化工艺改造完善具有很大现实意义,本文基于此做出相关研究与分析。
1 PBC孔金属化概念覆铜板(CCP)为PCB制造。
的基础材料之一,以CCP为载体,在其上部有目的性的进行加工,电镀铜,刻蚀等操作,进而获得导电图形电路并构建PCB。
只有确保PCB盘面上通孔进入化后,方可和PCB电路衔接与安设电子零部件。
从宏观的角度上分析,孔金属化实质上就是采用电化学镀与电镀等方法,在PCB板孔绝缘孔壁上镶镀一层导体金属,其目的在于促使制印导线之间的连通性。
在PCB生产制造期间,孔金属化是核心工艺流程,在具体生产中要求金属化孔具备优良的机械韧性与导电性能、铜镀层结构完整、分布均匀、厚度适中(通常为25~30μm),孔洞内部可有分层、气泡等不良现象,孔电阻指标最近几年中,高密度封装技术在工业领域中有广泛应用,带动了PCB结构的创新发展进程。
在安装插孔过程中,金属孔设置目的是有效连接不同电路,并促进各个电子元件功能正常发挥。
在表面安装技术的协助下,金属化孔空洞内径应适量减少,同时助力于PCB制造技术朝着为微纳通孔、薄型化生产进程。
2 PBC孔金属化工艺研究在孔金属化生产工艺期间,直接采用导电性有机聚合物的方法称之为dms2工艺,其可以划分为前处理,形成导电性聚合物膜以及硫酸铜电镀三阶段,在板面、板面图形及整体图形电镀领域中均有广泛应用,且取得的效果较为优良,本文如下的主要工艺流程做出阐述:(1)整平。
新的环保型PCB金属化孔技术——石墨烯金属化孔工艺和失效模式分析

新的环保型PCB金属化孔技术——石墨烯金属化孔工艺和失效模式分析陈伟元 (深圳市赛姆烯金科技有限公司有限公司,广东 深圳 518125 )摘 要 文章综述PCB传统化学沉铜工艺存在的问题,石墨烯金属化工艺的优良特性和技术亮点,石墨烯金属化原理,及与黑孔工艺的区别,石墨烯的核心性能,石墨烯金属化工艺流程,本工艺的检测方法,石墨烯金属化工艺失效模式分析。
预测了石墨烯金属化取代传统的化学沉铜和黑孔工艺发展方向。
关键词 石墨烯性能;石墨烯金属化孔;失效模式中图分类号:TN41 文献标识码:A 文章编号:1009-0096(2020)03-0043-07New technology of PCB metallization holes withenvironmental protection—— Graphene metallization hole process and failure modeleffectiveness analysisChen WeiyuanAbstract This paper summarizes the problems of traditional PTH process for PCB, the excellent characteristics and technical highlights of graphene metallization process, the principle of graphene metallization, the difference with black hole process, the core performance of graphene, the process flow of graphene metallization, the detection method of this process, and the failure mode analysis of graphene metallization process. It is predicted that graphene metallization will replace the traditional PTH process and black hole process.Key words Performance of Graphene; Graphene Metallization Hole; Failure Model Analysis1 引言随着科技的快速发展,电子产品不仅向“轻薄短小”方向发展,也进一步向5G高频高速方向发展。
孔金属化工艺流程
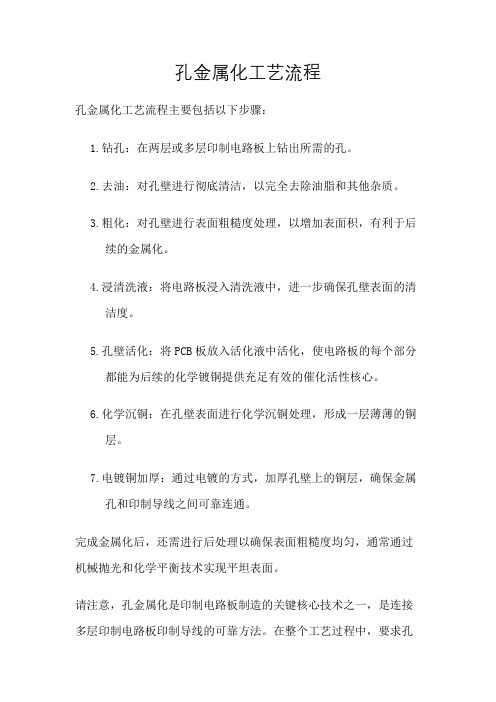
孔金属化工艺流程
孔金属化工艺流程主要包括以下步骤:
1.钻孔:在两层或多层印制电路板上钻出所需的孔。
2.去油:对孔壁进行彻底清洁,以完全去除油脂和其他杂质。
3.粗化:对孔壁进行表面粗糙度处理,以增加表面积,有利于后
续的金属化。
4.浸清洗液:将电路板浸入清洗液中,进一步确保孔壁表面的清
洁度。
5.孔壁活化:将PCB板放入活化液中活化,使电路板的每个部分
都能为后续的化学镀铜提供充足有效的催化活性核心。
6.化学沉铜:在孔壁表面进行化学沉铜处理,形成一层薄薄的铜
层。
7.电镀铜加厚:通过电镀的方式,加厚孔壁上的铜层,确保金属
孔和印制导线之间可靠连通。
完成金属化后,还需进行后处理以确保表面粗糙度均匀,通常通过机械抛光和化学平衡技术实现平坦表面。
请注意,孔金属化是印制电路板制造的关键核心技术之一,是连接多层印制电路板印制导线的可靠方法。
在整个工艺过程中,要求孔
壁内的金属均匀、完整,与铜箔连接可靠,电性能和力学性能符合标准。
孔金属化技术
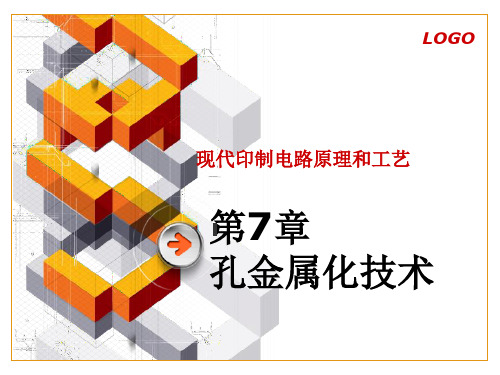
LOGO
孔金属化技术
7.3.1等离子体处理法 1.等离子体去钻污凹蚀原理 等离子体是电离的气体,整体上显电中性,是一种带电粒 子组成的电离状态,称为物质第四态。 2.等离子体去钻污凹蚀系统 印制板专用的等离子体化学处理系统-等离子体去腻污凹 蚀系统
3.还原 去除高锰酸钾去钻污残留的高锰酸钾、锰酸钾和二氧化锰
LOGO
孔金属化技术
7.3.4 PI调整法去钻污
1.浸去离子水 用去离子水浸泡,去掉一些钻污和自来水 2.去钻污 添加剂把聚酰亚胺和丙烯酸胶膜腻污溶涨,使其容易被分 解和去除。接着聚酰亚胺钻污与联胺(胫)反应分解,从 而去除掉相应的钻污。
LOGO
孔金属化技术
(2). Nd:YAG激光钻孔工艺方法
Nd:YAG激光技术在很多种材料上进行徽盲孔与 通孔的加工。其中在聚酰亚胺覆铜箔层压板上钻 导通孔,最小孔径是25μ m。
LOGO
孔金属化技术
1).根据两类激光钻孔的速度采取两种并用的工
LOGO
导电膜上电镀铜工艺
整平
把钻孔后的印制板浸在65℃的整平剂溶 液中3min,然后取出,在25℃,于去离子 水中漂洗2min。氧化DMSⅡ过程综合处 理的目的是在孔壁内(含表面)生成一层连 续的、无空洞的、结合牢固的致密沉积铜 催化剂是有机物的单体溶液.当覆盖有二 氧化锰氧化层的印制板孔壁接触酸性单体 溶液,便在非导体孔壁表面上生成不溶性 导电聚合物层,作为以后直接电镀的基底 导电层 将涂覆有导电性有机聚合物膜的印制板置 于普通电镀铜溶液中电镀.电镀时间取决 于印制板的板厚/孔径比,一般30min内 完成孔金属化.
CmH2 nOn 浓H2SO4 mC+nH2O
PCB化学镀铜工艺流程解读(一)
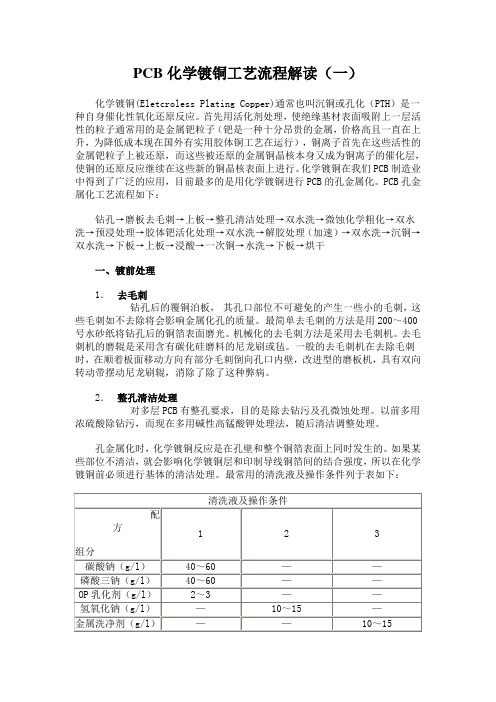
PCB化学镀铜工艺流程解读(一)化学镀铜(Eletcroless Plating Copper)通常也叫沉铜或孔化(PTH)是一种自身催化性氧化还原反应。
首先用活化剂处理,使绝缘基材表面吸附上一层活性的粒子通常用的是金属钯粒子(钯是一种十分昂贵的金属,价格高且一直在上升,为降低成本现在国外有实用胶体铜工艺在运行),铜离子首先在这些活性的金属钯粒子上被还原,而这些被还原的金属铜晶核本身又成为铜离子的催化层,使铜的还原反应继续在这些新的铜晶核表面上进行。
化学镀铜在我们PCB制造业中得到了广泛的应用,目前最多的是用化学镀铜进行PCB的孔金属化。
PCB孔金属化工艺流程如下:钻孔→磨板去毛刺→上板→整孔清洁处理→双水洗→微蚀化学粗化→双水洗→预浸处理→胶体钯活化处理→双水洗→解胶处理(加速)→双水洗→沉铜→双水洗→下板→上板→浸酸→一次铜→水洗→下板→烘干一、镀前处理1.去毛刺钻孔后的覆铜泊板,其孔口部位不可避免的产生一些小的毛刺,这些毛刺如不去除将会影响金属化孔的质量。
最简单去毛刺的方法是用200~400号水砂纸将钻孔后的铜箔表面磨光。
机械化的去毛刺方法是采用去毛刺机。
去毛刺机的磨辊是采用含有碳化硅磨料的尼龙刷或毡。
一般的去毛刺机在去除毛刺时,在顺着板面移动方向有部分毛刺倒向孔口内壁,改进型的磨板机,具有双向转动带摆动尼龙刷辊,消除了除了这种弊病。
2.整孔清洁处理对多层PCB有整孔要求,目的是除去钻污及孔微蚀处理。
以前多用浓硫酸除钻污,而现在多用碱性高锰酸钾处理法,随后清洁调整处理。
孔金属化时,化学镀铜反应是在孔壁和整个铜箔表面上同时发生的。
如果某些部位不清洁,就会影响化学镀铜层和印制导线铜箔间的结合强度,所以在化学镀铜前必须进行基体的清洁处理。
最常用的清洗液及操作条件列于表如下:3.覆铜箔粗化处理利用化学微蚀刻法对铜表面进行浸蚀处理(蚀刻深度为2-3微米),使铜表面产生凹凸不平的微观粗糙带活性的表面,从而保证化学镀铜层和铜箔基体之间有牢固的结合强度。
常见pcb表面处理工艺的特点、用途和发展趋势.doc
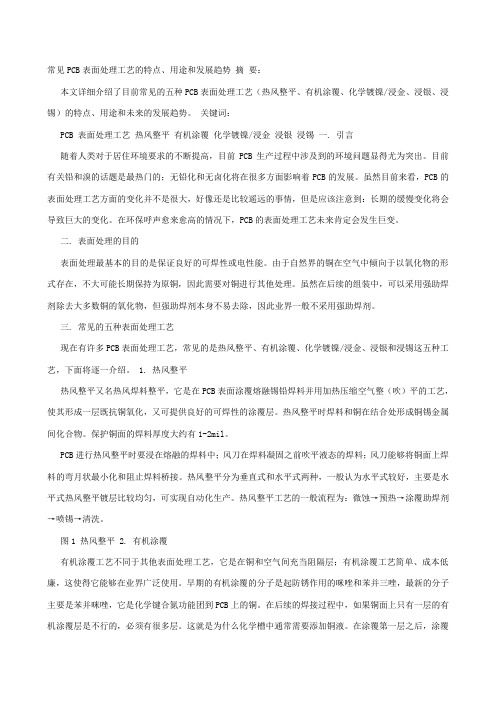
常见PCB表面处理工艺的特点、用途和发展趋势摘要:本文详细介绍了目前常见的五种PCB表面处理工艺(热风整平、有机涂覆、化学镀镍/浸金、浸银、浸锡)的特点、用途和未来的发展趋势。
关键词:PCB 表面处理工艺热风整平有机涂覆化学镀镍/浸金浸银浸锡一. 引言随着人类对于居住环境要求的不断提高,目前PCB生产过程中涉及到的环境问题显得尤为突出。
目前有关铅和溴的话题是最热门的;无铅化和无卤化将在很多方面影响着PCB的发展。
虽然目前来看,PCB的表面处理工艺方面的变化并不是很大,好像还是比较遥远的事情,但是应该注意到:长期的缓慢变化将会导致巨大的变化。
在环保呼声愈来愈高的情况下,PCB的表面处理工艺未来肯定会发生巨变。
二. 表面处理的目的表面处理最基本的目的是保证良好的可焊性或电性能。
由于自然界的铜在空气中倾向于以氧化物的形式存在,不大可能长期保持为原铜,因此需要对铜进行其他处理。
虽然在后续的组装中,可以采用强助焊剂除去大多数铜的氧化物,但强助焊剂本身不易去除,因此业界一般不采用强助焊剂。
三. 常见的五种表面处理工艺现在有许多PCB表面处理工艺,常见的是热风整平、有机涂覆、化学镀镍/浸金、浸银和浸锡这五种工艺,下面将逐一介绍。
1. 热风整平热风整平又名热风焊料整平,它是在PCB表面涂覆熔融锡铅焊料并用加热压缩空气整(吹)平的工艺,使其形成一层既抗铜氧化,又可提供良好的可焊性的涂覆层。
热风整平时焊料和铜在结合处形成铜锡金属间化合物。
保护铜面的焊料厚度大约有1-2mil。
PCB进行热风整平时要浸在熔融的焊料中;风刀在焊料凝固之前吹平液态的焊料;风刀能够将铜面上焊料的弯月状最小化和阻止焊料桥接。
热风整平分为垂直式和水平式两种,一般认为水平式较好,主要是水平式热风整平镀层比较均匀,可实现自动化生产。
热风整平工艺的一般流程为:微蚀→预热→涂覆助焊剂→喷锡→清洗。
图1 热风整平 2. 有机涂覆有机涂覆工艺不同于其他表面处理工艺,它是在铜和空气间充当阻隔层;有机涂覆工艺简单、成本低廉,这使得它能够在业界广泛使用。