连铸坯热送热装工艺技术应用研究
连铸坯热送热装的生产与实践

第3 O卷第 4期
20 0 8
Vo. O No 4 13 .
Au . 2 0 g ,0 8
GANS U METAL LURGY
文 章 编 号 :6 24 6 (0 8 0 -0 90 17 - 1 20 )40 1 -3 4
Ke od :ocsn ie; oo o cag gpoest hoo ngmetepr ne yW rs cnat gbltm tr t hr n r s; c lg maae n;xe ec i l h i c en y i
1 引 言
能 源是 国 民经 济发 展 的物 质基 础 , 节约 能 源 对 保 证我 国经 济 的 快 速 发 展 起 着 重 要 的作 用 。 近 年 来, 随着 连铸 技术 的不 断进 步及 全连铸 工艺 的实 施 , 推 动 了连铸 坯热 送 热装 工 艺 的发 展 , 铸坯 热 送 热 连 装 工艺 是冶 金行 业 内重 点推 广 的 l 节 能增 效 的 8个
的生 产 向连续化 、 成木 、 质 量 、 效 益 的 方 向发 低 高 高
展 ¨。
cag gpoes pou ecni rbeeoo i b nf doe x r nefr eeazt nadapi t n hr n rcs, r c os eal cn mc eet f r pi c nr i i pl ai . i d d ia n ee e og lao n c o
中 图分 类 号 :下 7 . 17 7 2 文献标识码 : A
Th o uc i n a d Ex e i n e o t Ch r i g Pr c s f Co c si g Bi e e Pr d to n p re c f Ho a g n o e s o n a tn l t l
连铸坯热装热送过程中的传质特性研究与模拟

连铸坯热装热送过程中的传质特性研究与模拟连铸坯是一种常见的金属产品,在生产过程中,通过连铸技术将熔融的金属注入到连续结晶器中,形成连续的坯料。
在连铸坯热装热送过程中,传质特性的研究对于优化生产工艺、提高产品品质具有重要意义。
本文将通过模拟和研究连铸坯热装热送过程中的传质特性,探索其影响因素及优化方法。
一、传质特性的定义与重要性传质特性是指在连铸坯热装热送过程中,金属中各组分之间质量或能量的传递过程。
在连铸过程中,金属中的成分不断发生变化,通过传质特性的研究可以了解金属成分变化的规律,从而控制坯料的化学成分,提高产品质量。
二、连铸坯热装热送传质特性的主要因素1. 温度梯度:传质过程受温差驱动,温度梯度的存在将加剧金属中成分的传递速度。
因此,在连铸坯热装热送过程中,合理控制温度梯度有利于提高传质效率。
2. 流动条件:金属在热装热送过程中形成的流动状态对传质特性有着重要影响。
尤其是在液态金属中,流动条件的改变将导致金属中成分的重新分布。
3. 传质界面:传质界面是传质特性研究的重点之一。
在连铸过程中,液态金属与结晶器壁的接触界面处,传质速率较快,属于传质界面。
合理设计传质界面可以提高传质速率,达到优化生产工艺的目的。
三、连铸坯热装热送传质特性模拟方法1. 数值模拟:利用计算机数值模拟方法,可以对连铸坯热装热送传质特性进行模拟与分析。
通过求解相应的传质方程和动量方程,得到金属流动和成分的分布情况。
2. 物理模拟:采用物理实验方法,通过建立实验平台模拟连铸坯热装热送过程。
利用高温熔融金属和结晶器模拟实际工况,通过观察和测试,研究传质特性的变化规律。
四、连铸坯热装热送传质特性研究的意义和应用1. 优化生产工艺:通过深入研究连铸坯热装热送过程中的传质特性,提出相应的优化措施,可以改善金属组织结构,减少气孔、夹杂等缺陷的产生,提高产品品质。
2. 节约能源:传质特性研究有助于优化连铸过程中的能源消耗。
通过控制传质速率和界面条件,实现能源的高效利用,提高连铸过程中的能源利用率。
连铸坯热送热装中MES技术应用的要点分析
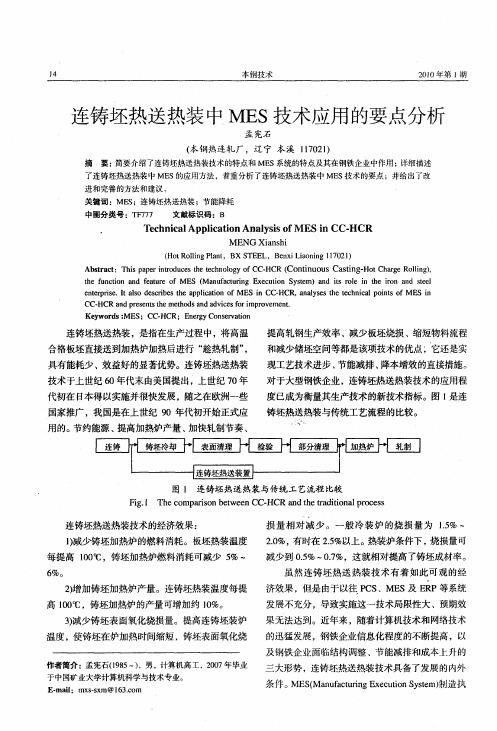
技术于上世纪 6 年代末由美国提出, 0 上世纪 7 年 0 代初在 日本得以实施并很快发展 ,随之在欧洲一些 国家推广 ,我国是在上世纪 9 o年代初开始正式应 用的。 节约能源 、 提高加热炉产量 、 加快轧制节奏 、
对于大型钢铁企业 ,连铸坯热送热装技术的应用程
度 已成为衡量其生产技术的新技术指标。图 l 是连 铸坯热送热装与传统工艺流程的比较。
J ) 减少铸坯加热炉的燃料消耗。板坯热装温度
每提高 I0C O  ̄ ,铸坯加热炉燃料消耗可减少 5 %一
6 。 %
2增加铸坯加热炉产量。连铸坯热装温度每提 )
高1  ̄ 0 E,铸坯加热炉的产量可增加约 1%。 0 0 3减少铸坯表面氧化烧损量。提高连铸坯装炉 ) 温度,使铸坯在炉加热时间缩短 , 铸坯表面氧化烧
CC. HCR n r s n s h t o s n d ie o r v me t a d p e e t emeh t d d a vc s r mp o e n . a f i Ke wo d M E y r s: S;CC・ HCR; E e g o s r ai n n ryC n ev t o
作者简介 :盂宪石(9 5~ ,男,计算机高工 ,20 年 毕业 18 ) 07 于中国矿业大学计算机科学与技术专业。
E- i: mx ・x ma l s s m@ 1 3c r 6 .o n
连铸大方坯热装热送技术研究
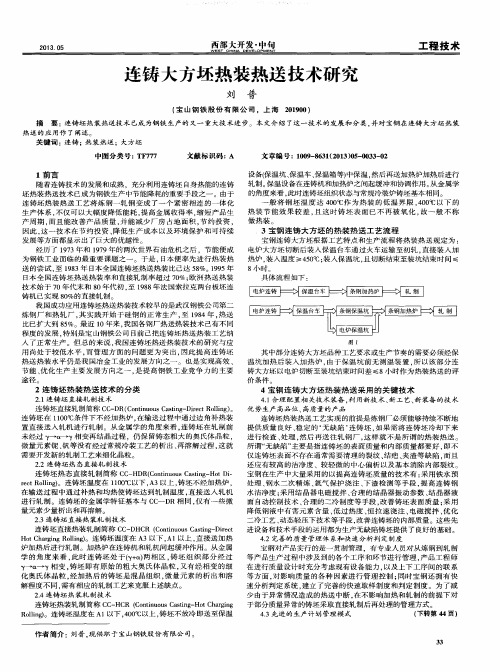
设备 温 坑 、 保 温车 、 保 温箱 等) 中保 温 , 然 后再 送加 热炉 加热 后进 行 轧制 。 保温设 备在 连铸 机和加 热炉 之 间起 缓 冲和协调 作用 。 从金 属学 的角 度来 看 , 此 时连铸 坯组织 状态 与常规 冷装 炉铸坯 基本 相 同。 般将钢坯温度达 4 0 0 ℃作 为 热 装 的 低 温 界 限 . 4 0 0 ℃以 下 的 热装节能效果较差 , 且 这 时铸 坯 表 面 已 不 再 被 氧 化 , 故 一 般 不 称 做 热装 。
1前 言 随着 连铸 技术 的发展 和成 熟 .充分利 用 连铸 坯 自身热 能 的连 铸 坯 热装 热送 技术 已成 为钢 铁生 产 中节能 降 耗的 重要 手段 之一 。由于 连 铸坯 热装 热送 工 艺 将 炼 钢 一轧 钢 变成 了一 个 紧 密相 连 的一 体 化 生产 体 系 , 不仅 可 以大 幅度 降低 能 耗 , 提 高金 属收 得 率 , 缩 短 产 品 生 产周 期 , 而且 能 改善 产 品 质 量 , 并 能减 少 厂 房 占地 面 积 , 节约投资 , 因此。 这 一技 术 在节 约投 资 、 降低 生 产成 本 以及 环境 保 护 和 可 持续 发展 等方 面都 显示 出了 巨大 的优越 性 。 经历 了 1 9 7 3 年和 1 9 7 9 年 的两 次世 界石 油危 机 之后 .节 能便 成 为钢 铁 工业 面 临 的最重 要 课题 之一 。于是 , 日本便 率 先进 行 热 装热 送 的尝试 , 至 1 9 8 3年 日 本 全 国连铸 坯 热送 热装 比己达 5 8 %。 1 9 9 5 年 日本 全 国连 铸坯 热 送热 装率 和 直接 轧制 率 超过 7 0 %; 欧洲 热 送热 装 技 术始 于 7 0 年 代末 和 8 0 年代 初 . 至 1 9 8 8 年法 国索拉 克两 台板 坯连 铸 机 已实 现 8 0 %的直 接轧 制 。 我 国成 功应 用 连铸 坯热 送热 装技 术较 早 的是武 汉 钢铁 公 司第 二 炼钢厂和热轧厂, 其 实践 开 始 于硅 钢 的正 常 生产 , 至 1 9 8 4年 , 热 送 比 已扩 大 到 8 5 %。最 近 1 0年来 , 我 国各钢 厂热 送热 装技 术 己有不 同 程 度 的发 展 . 特 别是 宝 山钢 铁公 司 目前 己把 连铸 坯 热送 热 装 工艺 纳 入 了正 常 生产 。但 总 的来 说 , 我 国连 铸坯 热 送热 装技 术 的研 究 与 应 用 尚处 于较 低 水平 , 而 管 理方 面 的 问题 更 为 突 出 , 因此 提高 连 铸 坯 热 送 热装 水 平仍 是 我 国冶金 工 业 的发展 方 向之 一 。也 是实 现 高效 、 节能 、 优 化 生产 主 要 发展 方 向之 一 . 是 提 高 钢铁 工 业 竞 争力 的主 要
钢坯热送热装高温快轧新工艺的研究与应用

1 蓄 热 式 加 热 炉 热 送 热 装 加 热 工 艺
分 析
采 用连 铸 坯 热 装 轧 制 工 艺 时 , 于 连 铸 坯 本 由 身 温度 较高 , 因此 可 以 不 考 虑 热 应 力 对 加 热 速 度 的限制 , 可采 用快 速 加热工 艺 。
16 元 。 2万
长2 7米 , 有 预热 段 。冷 装 时 , 坯 与 炉 内温 差 没 钢 大 , 热 温度 不能 过快 , 且 加 热段 供 热 量 受 到 限 加 并
维普资讯
4
20 0 8年第 2期
钢 坯 热送 热装 高 温快 轧 新 工 艺 的研 究 与应 用
黄 俊 萍
( 阿城钢 铁股 份有 限公 司 , 阿城
摘
10 0 ) 5 30
要: 本文研究 了连铸坯热送热装技术 与蓄热式加热炉相结合 , 成高温快轧新 工艺 。
由于加 热 炉 改 用 高 效 蓄热 式 热 交 换 技 术 , 加 热 炉没 有 预热段 , 坯一 进 炉 即进行 高 温 加 热 , 钢 因 此 钢坯 入 炉温 度 尽 量 高 , 不 仅 可 保 证 加 热 炉 的 这 加 热能 力 和 高效 率 , 可 以减 轻 钢 坯 因进 炉 温 差 也 产 生 的温 差应力 对加 热质 量 的影 响 。 22 热装连 铸坯 的 轧制 。 由于 采 用 热 装 工 艺 的 连 铸 坯 热 装 温 度 低 于 A 度 , r温 钢坯 加热 时也有 相变 过 程 使 组织 得 到 细
8 , 均 单 位 能 耗 为 25 Jt % 平 .G /。蓄 热 式 加 热 炉 冷
装 时 由于采 用 蓄 热 式余 热 回收 , 位 能 耗 可 大 幅 单 降低 , 均 单 位 能 耗 为 18 Jt而 热 装 时 的节 能 平 .G/, 效果更 明显 , 热装 时可 节 能 2 % ~2 % ,0 全 0 5 5 %热
湘钢连铸坯热送热装技术的现状与展望
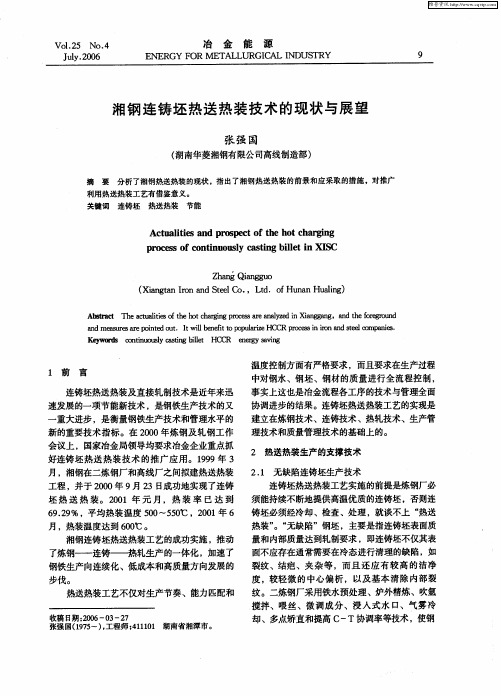
了炼钢——连铸——热轧生产的一体化 ,加速了 钢铁生产向连续化 、低成本和高质量方向发展的
步伐。 热送热装工艺不仅对生产节奏、能力匹配和
收稿 日期 :0 6 3 7 20 —0 —2 张强 国(9 5 ) 工程师 ;1 1 1 湖南省湘潭市 ,到建立炼钢一轧钢一体化生产管理 系统 ,采取 了根 据与客户的合 同,制定生 产计
2 2 适应不同铸坯热履历的轧制技术 . 不同类型的热送热装工艺改变了连铸坯在装 炉、轧制前的热履历 ,而连铸坯热履历 的变化 , 又会影响到轧制产品的质量。我们从金属学的角 度研究了连铸坯不 同热履历对奥氏体晶粒度的影 响 ,连铸坯不同热履历对微合金元素析出行为的
A  ̄re T eata t s fh o a n rcs e nJz i i ga g n h oerud l at h uli o teht h  ̄ gpoes r ay ̄ nXa gn ,adtef go n c ie c a a n r
a dn % Ie aep itd o t I Hb n f t o ua i n K s rs r on e u . twi e ei op p lrz 】 t eHC CR poesi i na dse l o rcs n r n te mm ne . o o is Kq啊0 d cn iu u l a t g bl t HC- r s o t o s csi ie n y n l L  ̄ e哪 n svn aig
理技术和质量管理技术的基础上的。
2 热 送热 装生产 的支 撑技术
重大进步 ,是衡量钢铁生产技术和管理水平的
新的重要技术指标。在 2 0 00年炼钢及轧钢工作
连铸坯热装热送攻关方案的技术难点及应对措施

连铸坯热装热送攻关方案的技术难点及应对措施连铸坯热装热送技术作为钢铁行业的关键环节,具有重要的意义。
然而,在实践中,我们面临着一些技术难题,需要采取相应的应对措施。
本文将重点探讨连铸坯热装热送技术的技术难点以及解决方案。
一、技术难点1. 温度控制难题连铸坯热装热送过程中,要求保持合适的温度范围,既不能过高导致坯料变形,也不能过低导致结冻。
然而,由于连铸坯的体积大、温度变化快,温度控制成为技术上的难点之一。
2. 坯料质量保证难题连铸坯热装热送需要确保坯料质量,这涉及到坯料的化学成分、结构组织以及表面质量等多方面因素。
然而,在实际操作中,由于操作环境复杂、设备条件有限等原因,坯料质量的保证成为一项技术挑战。
3. 设备性能要求难题连铸坯热装热送需要使用具备高温耐受性能、高密封性能以及稳定运行能力的设备,然而,目前市场上存在的设备往往无法满足这些要求。
因此,如何提高设备性能成为技术难点之一。
二、应对措施1. 温度控制方案为了解决温度控制难题,我们可以采取以下措施:(1)优化热装热送工艺流程,合理调整热压时间和温度,确保坯料温度在适宜范围内;(2)引入先进的温度控制设备,如红外线测温系统,实时监测和调控坯料温度,提高温度控制的准确性。
2. 坯料质量保证方案为了保证坯料质量,我们可以采取以下措施:(1)建立完善的质量管理体系,从原料配制、工艺操作到产品质量,全面把关;(2)优化热装热送工艺参数,调整合适的热处理时间和温度,确保坯料化学成分和组织结构的稳定。
3. 设备性能提升方案为了提升设备性能,我们可以采取以下措施:(1)引入具备高温耐受性能的设备,如优质耐火材料,以增强设备的耐高温能力;(2)改进设备结构,提高设备的密封性能,减少热装热送过程中的热量损失;(3)加强设备维护和保养,及时发现设备故障并进行修复,确保设备的稳定运行。
三、总结连铸坯热装热送攻关方案的技术难点主要包括温度控制难题、坯料质量保证难题以及设备性能要求难题。
连铸坯热送热装工艺热技术概述

连铸坯热送热装工艺热技术概述蒋扬虎肖坤伟王德仓肖世华丁翠娇(技术中心)摘要简要回顾了连铸坯热送热装工艺的历史,介绍了该项技术的应用现状及可取得的技术经济效果,并重点从“通用高温坯生产技术”和“温度均匀性保证技术”两个方面介绍了连铸坯热送热装工艺的各项“热技术”。
关键词连铸坯热送热装直接轧制加热炉1前言连铸坯热送热装工艺,是一项具有降低热轧加热炉燃耗、减少钢坯氧化烧损和提高热轧产量等多方面经济效益的技术。
该项工艺是连铸技术的一项重大突破,它不仅对节能有重要意义,而且对改革传统的钢铁工业结构有深远的意义,它涉及从炼钢到热轧之间各个生产环节,是一项系统工程。
目前世界许多钢铁企业根据自身的特点不同程度上采用了该项技术。
本文将对该项技术作一个初步的概括。
2连铸坯热送热装技术的历史及现状1968年美国麦克劳斯钢公司将连铸板坯装入感应加热炉,从而迈出了热装技术的第一步。
70年代初期,由于石油危机的冲击,日本钢铁工业面临严重的能源问题,日本钢铁界以此为契机,开始研究和应用连铸坯热送热装工艺,1973年日本钢管公司鹤见厂首先实现连铸坯热装轧制工艺(CC—HCR);1981年6月新日铁土界厂研究成功并在生产中实现了近程(连铸机终点和轧机始点之间距离为130m)连铸—直接轧制工艺(CC—DR);1987年6月新日铁八幡厂在生产中实现了远程CC—DR工艺(连铸机终点和轧机始点之间距离为620m)。
日本在该项技术上的成功,促进了世界各国对该项技术的研究和应用。
经过80年代世界各国钢铁界的努力,连铸坯热装和直接轧制工艺正日趋完善。
按照温度的高低,连铸坯热送工艺可分为三种情况。
(1)热装轧制HCR(Hot Charge Rolling)。
将经过(或不经过)表面处理的热板坯在大约400~700℃装入加热炉。
(2)直接热装轧制DHCR(Direct Hot Charge Rolling)。
按照和连铸同一序号,将经过(或不经过)表面处理的热板坯在大约700~1000℃装入加热炉。
连铸坯热装热送中的温度分布监测与控制技术改进与优化
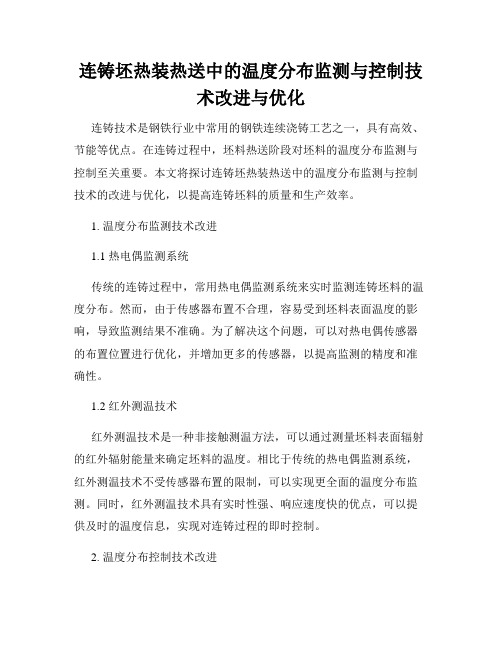
连铸坯热装热送中的温度分布监测与控制技术改进与优化连铸技术是钢铁行业中常用的钢铁连续浇铸工艺之一,具有高效、节能等优点。
在连铸过程中,坯料热送阶段对坯料的温度分布监测与控制至关重要。
本文将探讨连铸坯热装热送中的温度分布监测与控制技术的改进与优化,以提高连铸坯料的质量和生产效率。
1. 温度分布监测技术改进1.1 热电偶监测系统传统的连铸过程中,常用热电偶监测系统来实时监测连铸坯料的温度分布。
然而,由于传感器布置不合理,容易受到坯料表面温度的影响,导致监测结果不准确。
为了解决这个问题,可以对热电偶传感器的布置位置进行优化,并增加更多的传感器,以提高监测的精度和准确性。
1.2 红外测温技术红外测温技术是一种非接触测温方法,可以通过测量坯料表面辐射的红外辐射能量来确定坯料的温度。
相比于传统的热电偶监测系统,红外测温技术不受传感器布置的限制,可以实现更全面的温度分布监测。
同时,红外测温技术具有实时性强、响应速度快的优点,可以提供及时的温度信息,实现对连铸过程的即时控制。
2. 温度分布控制技术改进2.1 水箱布置优化连铸过程中,水箱对冷却坯料起到重要作用。
优化水箱的布置可以提高冷却效率,进而改善坯料的温度分布。
通过建立数值模拟模型,分析坯料在水箱中的流动和冷却情况,确定最优的水箱布置方案。
此外,可考虑引入新型的冷却装置,如水雾喷淋系统或喷水帘,以提高水箱的冷却效果。
2.2 温度自动调控系统为了实现连铸坯料的精确温度控制,可以采用温度自动调控系统。
该系统通过对连铸坯料的温度实时监测,并通过控制流量调节阀、喷水量等参数,自动调整冷却水的供应,以实现坯料温度的精确控制。
同时,为了提高系统的控制精度和稳定性,可以引入先进的控制算法,并结合联合控制策略,如模糊控制或神经网络控制,以进一步优化控制效果。
3. 技术改进与优化带来的效益3.1 提高坯料质量通过优化温度分布监测与控制技术,可以实现对连铸坯料温度的精确控制,避免温度偏差过大而导致坯料质量不稳定。
新钢公司连铸坯热送热装的实践

4 主 要措 施
2 0 年轧材单位全年分别完成产量: 03 中板厂
1 4 4万 t一 线 厂 4 . 9 t 二线 厂 5 0. 、 23 万 、 2万 t 棒 、
材 厂 9 t棒材厂设计能力年产 4 万 t 。 万 ( o )综合 以 上情况分析, 从炼钢、 轧钢工序配置上来说 , 具备
维普资讯
第l 2卷第 6 期
’1 ’ 2 0 4 0 6年 1 2月
克■板
WI DE AND HEAVY ATE PL
VO _ 2 No 6 l1. .
Dee b r 2 0 cm e 0 6
ቤተ መጻሕፍቲ ባይዱ
新钢公司连铸坯热送热装 的实践
李文华 李春华 付遥宜 王少锋
究。
连铸坯热送热装技术能充分利用连铸坯 自 身
热能, 提高轧钢加热炉能力, 降低煤气消耗, 缓解
煤气整体不足和平衡困难的矛盾。新钢公司根据
主体轧材单位均采用 自产连铸坯 , 且三钢厂和新 投产的炼钢厂装备及地理位置与主体轧钢单位中 板厂、 线材厂 ( 一线、 二线)棒材厂临近的实际情 、 况。 将连铸坯热送热装项 目列入攻关计划, 并成功 完成了攻关 目标 。
台 R 的全 弧形 方坯 连铸机 , =8m 其连铸坯 生产
规格 为 : 1 2 0mmX14 0mm, 3 n 3 0 1 0mrX1 0mm,
设备要适合热送热装要求 ; 22 炼钢、 . 连铸及轧钢工序的综合生产状况正常
稳定 , 序能力 大致 匹配 。 工 23 为保 证 冶 炼 、 . 连铸 和 轧机 的 连续 性 生 产 , 必
一
连铸坯的热送热装工艺研究

连铸坯的热送热装是钢铁生产过程中常用的一种热处理方法,它可以使连铸坯达到所需的温度,以满足下一工序的要求。
热送热装的主要装置有热板装置和火焰喷射装置。
热板装置是通过将坯料放置在预热好的热板上进行加热的方法,可以使坯料快速达到所需温度。
火焰喷射装置则是通过喷射燃气使坯料表面产生燃烧反应,将燃烧产生的热量传递给坯料内部,使其达到所需温度。
两种方法各有优缺点,应根据具体情况选择。
在热送热装的过程中,需要注意以下几点:
1.控制加热速率和温度均匀性。
加热速率过快或温度分布不均匀都会导致坯料内部应力过大
或不均匀,从而影响坯料性能。
2.确保热板或火焰喷射装置的稳定性和可靠性。
热板或火焰喷射装置的故障会影响整个生产
线的正常运转,应及时进行检修和维护。
3.合理控制加热时间和温度。
过长的加热时间或过高的温度都会使坯料受到过度加热,影响
其性能。
4.加强坯料表面保护。
在热送热装的过程中,坯料表面易受氧化、腐蚀等影响,应采取措施
进行保护。
热送热装是钢铁生产中重要的热处理方法,其研究对于提高连铸坯质量和生产效率具有重要意义。
石钢连铸方坯热送热装系统翻钢装置的设计研究开发与应用
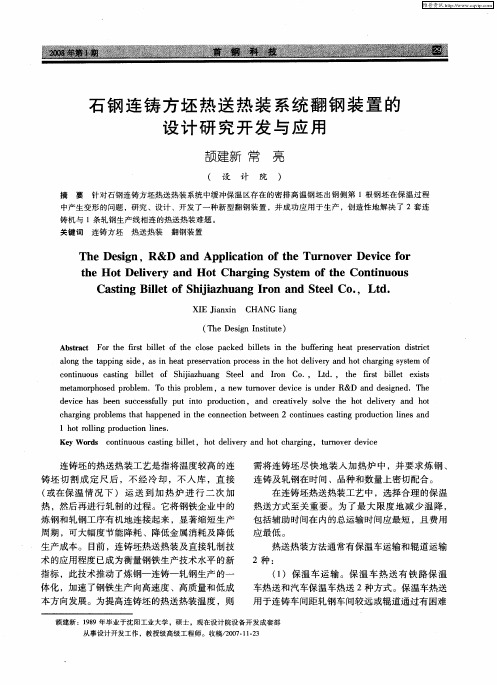
石 钢 连 铸 方 坯 热 送 热 装 系统 翻 钢 装 置 的 设 计 研 究 开 发 与 应 用
颉建 新 常
( 设
摘 要
亮
计 院 )
针对石钢连铸方坯 热送 热装系统 中缓 冲保温 区存 在 的密 排高温钢 坯 出钢侧 第 1根钢坯 在保温 过程
Байду номын сангаас
周 期 ,可大 幅度 节能 降耗 、降低金 属 消耗及 降低
生产成本 。目前 ,连铸坯热送热装及直接轧制技
术 的应用 程度 已成 为衡 量钢 铁 生产 技术 水平 的新 指标 ,此 技术 推动 了炼 钢一 连 铸一 轧钢 生产 的一 体化 ,加 速 了钢铁 生产 向高速 度 、高质 量和 低 成 本 方 向发展 。为提 高 连铸坯 的热送 热装 温 度 ,则
cniuu at g ie f h i h ag t l n I n o , Ld , te i t ie x t o t os cs n bl t S ia u n Se a d r C . n i l o jz e o t. h fs l t is r b l e s
mea r ho e o lm. T h sprblm ,a n w u n v rd vc s u d rR&D n e i n d.T e t mo p s d pr b e o t i o e e t r o e e i e i n e a d d sg e h d v c a b e s c e su l p t n o r d to e ie h s e n u c sf ly u i t p o uci n, a d r ai ey o v h h t ei e a d o n c e tv l s le t e o d l r vy n h t c a g n r b e ha a e e n te c n e t n bewe n 2 c ni ue a tn r d to i e n h r i g p o l ms t th pp n d i h o n c i t e o t o n s c si g p o ucin ln sa d 1 h tr li g p o u to ie . o oln r d ci n l s n Ke r s c ni uo a tn l t h td l e n o h r i g, t r o e e ie y Wo d o t n usc si g bi e , o e i r a d h tc a gn l vy u n y rd vc
热送热装工艺的研究
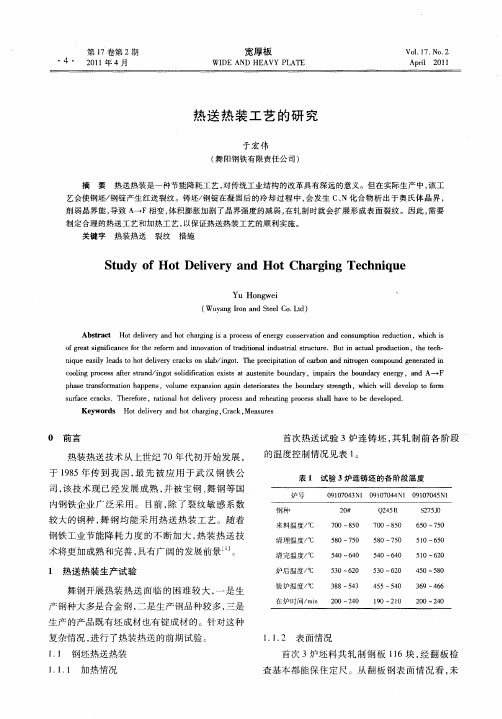
钢 板性能 检验 7批 ,全部合 格 。
1.2 钢锭 热送 热装 1.2.1 加 热及 轧制情 况
热送 试验 2炉 钢锭 ,各 阶段 温 度见表 2。
2 热送 热装存 在 的问题 通过 前期 试验 ,发 现 热 送 热装 过 程 中存 在 以
下 问题 。
表 2 试 验 2炉 钢 锭 的 各 阶段 温度
第 17卷第 2期 · 4 ‘ 2011年 4月
宽厚板
W IDE AND HEAVY PLATE
V01.17.No.2 April 2011
热 送 热 装 工 艺 的 研 究 ቤተ መጻሕፍቲ ባይዱ
于 宏 伟 (舞 阳钢 铁 有 限 责 任 公 司 )
摘 要 热送热装是 一种节能降耗工艺 ,对传统工业结构 的改革具有深远的意义。但在实际生产中 ,该工 艺会使钢坯/钢锭产生红送裂纹。铸坯/钢锭在凝 固后的冷却过 程中 ,会发生 C、N化合物析 出于奥 氏体晶界 , 削弱晶界能 ,导致 A—F相变,体积膨胀加剧 了晶界强度的减弱,在轧制时就会扩展形成表面裂纹 。因此 ,需要 制定合理的热送 工艺 和加热工艺 ,以保证热送热装工艺的顺利 实施 。
of great significance for the reform and innovation of traditional industr ial structure. But in actual production,the tech— nique easily leads to hot delivery cracks on slab/ingot. The pr ecipitation of carbon a n d nitrogen com pound generated in cooling process after strand/ingot solidification exists at austenite boundary,impaim the boundary energ y ,a n d A F phase transformation happens,volume expan sion again deteriorates the boundary str ength,which will develop to f orm sur face cracks.Therefore,rational hot delivery process a n d reheming pro c ess shall have to be developed.
连铸坯热装热送攻关方案的技术规范与标准制定

连铸坯热装热送攻关方案的技术规范与标准制定连铸坯热装热送技术在钢铁行业中被广泛应用,它能够提高连铸生产线的效率和质量,为钢铁企业带来巨大经济效益。
为确保连铸坯热装热送技术的顺利实施和运行,制定相应的技术规范与标准是至关重要的。
本文就连铸坯热装热送攻关方案的技术规范与标准制定进行探讨。
一、背景介绍连铸坯热装热送技术是一种通过炉后立即对坯料进行热装盘融炉的工艺,然后再以热坯的形式送往连铸机进行连铸的技术。
与传统的冷装冷送相比,连铸坯热装热送技术能够有效提高连铸生产线的能源利用率和产能,并降低产品表面缺陷的发生概率。
然而,应用连铸坯热装热送技术还面临一些技术难题,需要科研人员通过攻关方案进行解决。
二、技术规范制定连铸坯热装热送技术规范的制定对于确保技术的可行性和稳定性至关重要。
制定连铸坯热装热送技术规范时,可以参考以下几个方面的内容。
1. 设备要求:包括热装盘融炉、热装盘运输系统、连铸机等设备的选型和性能要求。
例如,热装盘融炉应具备快速加热、坯料预热温度控制等功能。
2. 工艺参数:包括热装盘融炉的加热温度、保温时间、坯料预热温度等工艺参数的设定。
这些参数对于确保连铸坯的质量和坯料热装热送工艺的稳定性至关重要。
3. 操作规程:包括设备的使用、维护和操作等方面的规程。
例如,规定热装盘融炉的操作人员需要接受专业培训,并定期进行设备检修和保养。
4. 质量控制:规定连铸坯热装热送过程中应进行的质量控制措施。
例如,严格监测和记录热装盘融炉的温度、坯料的预热温度等参数,并进行质量检验和分析。
三、标准制定连铸坯热装热送技术的标准是指对连铸坯热装热送技术进行统一规范和评价的标准。
制定连铸坯热装热送技术标准时,可以考虑以下几个方面。
1. 坯料质量标准:规定连铸坯的化学成分、物理性能以及表面质量等方面的要求。
这些要求能够保证连铸坯在热装热送过程中的质量稳定。
2. 过程控制标准:规定热装盘融炉的加热温度控制范围、预热时间等过程参数的要求。
连铸坯热送热装技术简介

按照温度 的高低, 连铸坯热送 工艺可分为三 种 情况 。 () 1热装 轧制HC ( t hre ol g。 RHo ag l ) C R i n 将 经 过( 不 经 过 ) 面 处 理 的热 板 坯 或 表 在 大 约4 0 0 ℃ 装入加 热 炉 。 0  ̄7 0 () 接 热 装 轧 制 DHC Di c Ho 2直 R( r t t e
连铸坯热送热装技术简介
陈朴璞
摘 要 :提 出 了十二 五期 间钢铁 行业 节能 减排 的迫切 需 求 ,简要 回顾 了连 铸 坯 热送 热装 工
艺的历史, 介绍 了连铸坯热装热送]艺实现的条件,概括了连铸坯热送热装 _ 艺在钢铁生 . ] = 产 中的优 点,并指 出热 送热 装工 艺发 展还 需要优 化和 完 善 。
处 理 后再 加 热 进行 轧 制 ,就 谈 不 上热 送 热 装 。 无缺 陷” “ 钢坯 主要 是指 连 铸坯表 面质 量
C ag ol g 。 h e ln ) r R i 按 照 和 连 铸 同 一 序 号 , 经 过 ( 不 经 将 或
过 面 处 理 的 热板 坯 在 大 约 7 0 10 ℃ 表 0 00
装入 加 热炉 。
() 接 轧制D Dic ol g。 3直 r t ln ) e R i
l8 年 热 装 比在 7% 以上 , 装 温 度 高 于 97 5 热 6 0 。 新 日铁 土 界厂 于 l8 年 6 8℃ 9 1 月实 现 了
CC DRS 艺,9 4 3 C D - I 1 8 年 月C — R占连 铸 坯 L
( )由于连铸 坯缺 陷难 以在线进 行热 2 坯清 理 , 钢 、 铸工序 必 须 具备无 缺 陷连 炼 连 铸坯 的 生产技术 , 无须清 理 的 无缺 陷连铸坯 应达 到 9 %以上 。无缺 陷连 铸 坯生 产技术 , 0 是炼 钢厂 必须 能持续 不 断地 提供 高温 、 质 优 的连 铸坯 ,否 则连铸 坯必 须 经冷 却 、检 查 、
连铸坯热装热送攻关方案的技术创新与突破

连铸坯热装热送攻关方案的技术创新与突破近年来,钢铁冶炼领域一直在寻求提高生产效率和品质的方法。
连铸坯热装热送技术作为一项新的工艺创新,得到了广泛的应用。
本文将探讨连铸坯热装热送攻关方案的技术创新与突破,分析其在钢铁冶炼中的应用前景。
1. 连铸坯热装热送技术概述连铸坯热装热送技术是一种将炼钢厂的热钢坯直接运输到轧钢厂进行连续轧制的技术。
传统的钢坯运输方式需要将炼钢厂生产的热钢坯冷却到固态,然后再进行运输,这就浪费了大量的时间和能源。
而连铸坯热装热送技术通过改进传统运输方式,将炼钢厂的热钢坯保持高温状态进行运输,从而使得钢坯可以直接进行轧制,大大提高了生产效率。
2. 技术创新与突破为了实现连铸坯热装热送技术,需要解决以下几个关键问题:2.1 坯料温度保持问题传统的运输方式需要将钢坯降温至合适的温度进行运输,而连铸坯热装热送技术要求保持钢坯在高温状态。
为了解决这个问题,研发人员通过引入保温设施和隔热材料,有效地减少了热量的损失,从而保持了钢坯的高温状态。
2.2 坯料运输安全问题由于热钢坯处于高温状态,对运输设备和人员的安全提出了更高的要求。
为了解决这个问题,研发人员对运输设备进行了改进,采用了耐高温材料和先进的隔热措施,同时也进行了相关的培训,提高了工人的操作安全意识。
2.3 坯料质量保障问题热钢坯的高温状态可能对坯料的质量产生一定的影响。
为了解决这个问题,研发人员通过对运输设备进行优化设计,减少了可能对钢坯造成损害的因素,从而确保了坯料质量的稳定。
3. 连铸坯热装热送技术的应用前景连铸坯热装热送技术的应用前景广阔。
首先,该技术能够大幅度提高钢铁冶炼的生产效率,降低生产成本,提高企业竞争力。
其次,由于连铸坯热装热送技术能够保持钢坯的高温状态,使得钢坯的品质更加稳定,满足了对高质量钢材的需求。
此外,连铸坯热装热送技术还能够节约大量的能源和减少对环境的污染,符合可持续发展的要求。
4. 结论连铸坯热装热送技术作为一项具有创新性和突破性的冶金技术,正在逐渐得到广泛的应用。
钢轧一体化生产暨热送热装调研报告
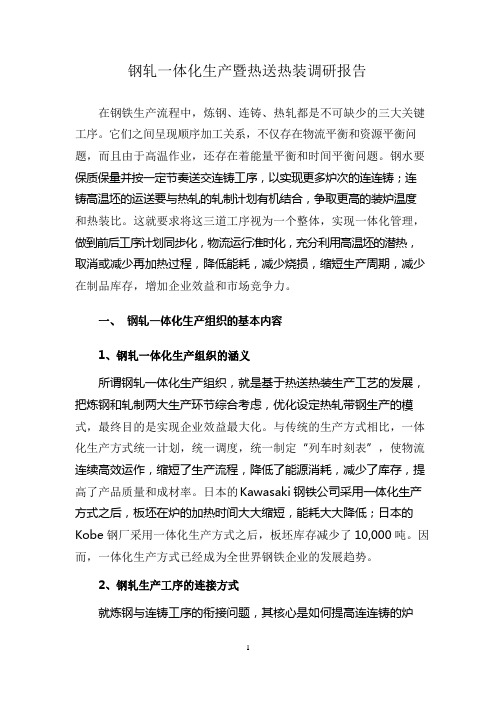
钢轧一体化生产暨热送热装调研报告在钢铁生产流程中,炼钢、连铸、热轧都是不可缺少的三大关键工序。
它们之间呈现顺序加工关系,不仅存在物流平衡和资源平衡问题,而且由于高温作业,还存在着能量平衡和时间平衡问题。
钢水要保质保量并按一定节奏送交连铸工序,以实现更多炉次的连连铸;连铸高温坯的运送要与热轧的轧制计划有机结合,争取更高的装炉温度和热装比。
这就要求将这三道工序视为一个整体,实现一体化管理,做到前后工序计划同步化,物流运行准时化,充分利用高温坯的潜热,取消或减少再加热过程,降低能耗,减少烧损,缩短生产周期,减少在制品库存,增加企业效益和市场竞争力。
一、钢轧一体化生产组织的基本内容1、钢轧一体化生产组织的涵义所谓钢轧一体化生产组织,就是基于热送热装生产工艺的发展,把炼钢和轧制两大生产环节综合考虑,优化设定热轧带钢生产的模式,最终目的是实现企业效益最大化。
与传统的生产方式相比,一体化生产方式统一计划,统一调度,统一制定“列车时刻表”,使物流连续高效运作,缩短了生产流程,降低了能源消耗,减少了库存,提高了产品质量和成材率。
日本的Kawasaki钢铁公司采用一体化生产方式之后,板坯在炉的加热时间大大缩短,能耗大大降低;日本的Kobe钢厂采用一体化生产方式之后,板坯库存减少了10,000吨。
因而,一体化生产方式已经成为全世界钢铁企业的发展趋势。
2、钢轧生产工序的连接方式就炼钢与连铸工序的衔接问题,其核心是如何提高连连铸的炉数。
由于连铸对钢水的成分、温度和到达时间有着严格的要求,因此局部的一体化管理早就引起人们的重视,各钢铁公司将炼钢车间与连铸车间放在同一厂内,就从生产指挥和过程控制上为一体化管理创造了良好的条件。
而连铸与热轧工序之间的连接问题,除包括物流的衔接外,还包括温度的衔接问题,一般有如下四种形式(见图1):图1:连铸与热轧工序间的四种连接方式(1)CC-CCR,连铸-冷坯装炉轧制,简称冷装。
连铸坯因种种原因无法在高温情况下送入热轧加热炉,只好送到板坯库堆放,根据轧制计划的需要,一定时间后再由库中吊至炉前辊道,装炉加热。
唐钢连铸坯热送热装工艺设计分析

70~ 00C)加热 ,再进行 轧制 ,去除 了炼钢 0 10 o 连铸与轧钢之间的保温坑缓冲仓库 ,只保留了 加 热炉 作 为进行 生 产节 奏 的缓 冲或调 节手 段 。与
一
原有 的热 送装 炉 轧制 相 比 ,直 接装 炉轧制 提 高了 炼 钢 一连 铸 与 轧 钢 生 产 的 连 续 化 程 度 和节 能 效 果 。真正 实现 了连铸坯 的热送 热装 。
分半钟 , 即节省设备投资又可保证铸坯温度 。 ( ) 链式 提升 机 采 用链 条 上 安 装 两 个 托 爪 2 的形式 ( 如图2 , ) 将钢坯提升 5 m,向过渡辊道
运 送铸 坯 ,提高 了铸 坯运送 的速 度 ,提升速 度 为
02 . 5m/s 。
唐钢棒材厂与唐钢二炼钢厂三期连铸工艺匹
配 ,非 常适 合连 铸坯 的热送 热装 ,从 图 l 工艺 布 置 图中可 以看 出 ,二 炼 钢 6 连 铸 机 和 棒 材 厂 加 #
唐钢 棒材 厂原 来采 用 的连铸 坯热送 形式 是热 送 装 炉轧 制 ,将高 温热 清理 后 的铸 坯 ,离线装 入
连铸 坯热送 热装 工艺 具 有节省 能 源 ,提 高加 热炉生产能 力,减少连铸坯烧 损 ,降低 轧制故
障,提高成材率 ,加快物流运动 ,减少储坯库房 和流动资金 占用 等优 点 ,因 而被众 多钢铁 企 业所
c n i o s c s ng sa a ng a g o tnu u a t l b t Ta g n i
Da J n Z a gYa fn i u h n nag
( a g hnS i c n eh o g cu ai o ee T n S a c n ea dT c nl yO cp t nC H g ) e o o
连铸坯热装热送

蔡 开 科 北京科技大学冶金与生态工程学院 2004年11月
目录
1 2 3 4 前言 生产高温连铸坯技术 生产无缺陷铸坯技术 结语
前言
连铸坯热送热装工艺 主要有连铸坯直接热装轧制和连铸坯热送热装两种工艺 连铸坯直接热装轧制:典型工艺是薄板坯连铸连轧流程 (如CSP、FTSR),其优点: 液芯长度短,减轻了铸机重量,简化了铸机结构 完全凝固时间短(1min) 拉速高(4~6m/min) 冷却快,枝晶细化,铸坯质量好 板坯温度高,节能,不会产生第二相质点沉淀(AlN, Nb(CN)),减少裂纹
无缺陷铸坯生产-铸坯表面纵裂纹
(9) 结晶器变形 对于小方坯常出现角部纵裂纹(靠近角部棱边或离开角部1015mm),它是与凝固前沿热撕裂有关的。它的产生决定于: 方坯菱变; 结晶器圆角半径R(R大,纵裂沿棱角;R小,纵裂离开角部); 结晶器变形与磨损。 保持结晶器合适锥度,较大的圆角半径(R=6-8mm),准确对弧 和支承,防止结晶器磨损,均匀的冷却等可消除小方坯角部纵裂。 (10)出结晶器下口的冷却 足辊和零段二冷水过强,板坯宽面纵裂加剧,如水流密度由 110l/m2· min 降到60 l/m2 ·min,纵裂指数由纵裂指数的影响
无缺陷铸坯生产-铸坯表面纵裂纹
250×1400mm板坯,结晶的宽面平均热流与板坯纵裂指数如图2-11。 结晶的侧面热流与纵裂纹指数如图2-12。由图可知:结晶器的宽面 铜板平均热流为1.4- 1.6MW/m2 ,侧面平均热流为1.1-.3MW/ m2, 板坯表面纵裂纹发生率最小。
前言
连铸坯热送热装工艺 是传统的板坯和方坯普遍采用的。它的主要优点是: 节能。500℃热装,减少燃耗30%;800℃热装,可 降燃耗50%。 提高金属收得率2~3% 缩短生产周期(板坯→热轧卷节约1小时左右) 降低生产成本(节约生产费用8~10%)
- 1、下载文档前请自行甄别文档内容的完整性,平台不提供额外的编辑、内容补充、找答案等附加服务。
- 2、"仅部分预览"的文档,不可在线预览部分如存在完整性等问题,可反馈申请退款(可完整预览的文档不适用该条件!)。
- 3、如文档侵犯您的权益,请联系客服反馈,我们会尽快为您处理(人工客服工作时间:9:00-18:30)。
连铸坯热送热装工艺技术应用研究赵海峰1龙正民2(1. 河北钢铁集团邯郸钢铁集团有限责任公司技术中心;2. 河北钢铁集团邯郸钢铁集团有限责任公司生产制造部,邯郸 056015)摘 要 对连铸坯热送热装工艺技术的发展、现有工艺流程、品种、质量、温度等进行了应用研究,要达到好的热送热装效果,必须要保证热装率≥60%以上。
好的工艺线热装率应达到80%以上。
温度必须在400℃以上。
好的工艺线应该达到650℃以上。
从运输方式看,倾向于辊道运输,另有火车、汽车及天车运输。
辊道近距离运输是将来设计的趋势。
从热送热装的品种、质量看,能热送的品种较多,质量能够满足工艺要求。
采用该工艺可以增加产量,提高加热能力及质量,降低了加热炉燃气消耗和加热炉吨钢消耗,减少氧化烧损,提高成材率等,并取得了一定的经济效益。
关键词 连铸坯热送热装发展工艺流程品种质量温度Research of Hot Delivery and Hot Charging Technology ofContinuous Casting BilletZhao Haifeng1 Long Zhengmin2(1.Technical Center;2.Production Manufacturing Department,Hebei Iron & Steel Group Handan Iron & SteelGroup Co., Ltd. , Handan, 056015)Abstract This paper used and studied the development of hot delivery and hot charging technology,existent technology process,variety,quality,temperature and so on, in order to reach good effect of hot delivery and hot charging technology,hot charging rate above 60% must be assured. Hot charging rate of good technology process is to reach above 80%. The℃℃temperature must be above 400, good technology process is to reach above 650.From transportation way, tend to roll transportation, other having train, automobile and overhead transportation. Roll short cut transportation is the tread of in the future plan.From the variety、the quality of hot delivery and hot charging, the variety of hot delivery is more than, the quality can meet technology requirement. Using the technology can add output, raise heat up ability and quality ,lower heat up stove fuel consumption and ton steel consumption, reduce oxidize burn loss, raise lumber rate and so on, some economics benefit is obtained.Key words continuous casting billet, hot delivery and hot charging, development, technology process, variety, quality, temperature1 引言连铸坯热送热装技术是钢铁生产中节能减排降耗的重要工艺技术之一,是钢铁工业进步的具体体现,是衡量钢铁生产技术和管理水平的新的重要技术指标。
该工艺具有增产,节能,降耗,提高加热质量,提高经赵海峰(1960—),男,工程硕士,高级工程师,从事钢铁工艺技术研究。
第八届(2011)中国钢铁年会论文集济效益的作用。
国内外一些钢铁公司广泛地采用了这一技术,并在不断的完善、提高和发展。
2 连铸坯热送热装技术的发展1968年,美国麦克劳斯钢公司将热连铸板坯装入感应加热炉,从而迈出了连铸坯热送热装技术的第一步。
20世纪70年代,由于两次石油危机的冲击使日本钢铁工业面临严重的能源问题,促使日本钢铁企业开始研究和应用连铸坯热送热装技术。
根据资料显示,日本在研究应用连铸坯热送热装工艺方面起步较早,1973年首先试验了连铸坯热装轧制工艺。
日本对该工艺进行了深入的研究和应用,实施的各个工艺环节很细,发展很快,效益显著。
并推动和促进了全世界对该技术的研究和应用。
随后,德国、法国、比利时、奥地利、意大利、美国、加拿大、韩国等国相继进行了这项技术的研究和应用。
我国连铸坯热送热装工艺的应用始于20世纪80年代,武钢率先进行了工艺试验,随后,国家大力推广连铸坯热送热装工艺技术。
90年代,宝钢、韶钢、邯钢、鞍钢、三明钢厂、攀钢、邢钢、洛钢、石钢、承钢、莱钢等相继采用了这项技术。
2000年,国家冶金局又要求冶金企业重点抓好连铸坯热送热装技术的推广应用,又有一批钢铁公司采用了这一技术[1,3,4]。
本文从理论和各个钢铁公司应用这一技术进行研究和分析,总结该工艺的运行情况。
3 连铸坯热送热装典型工艺运行特点自从1968年开始试验连铸坯热送热装至2010年,该工艺发生了很大的变化,并随着钢铁工艺技术设备的改造,为该工艺创造了良好的条件。
从2000年以后的新线建设和老线改造,一些钢铁公司从钢铁厂设计就考虑了热送热装工艺,直接把炼钢厂和轧钢厂建在一条工艺线,出坯即进加热炉,工艺流畅,设计合理。
老线改造也是围绕这个方面进行。
连铸连轧工艺的采用又是对该工艺的延伸,这是最有特点的、典型的连铸坯热送热装工艺流程。
进入21世纪,连铸坯热送热装工艺又是如何运行的,现结合一些资料的典型范例说明如下。
3.1武钢新线工艺特点[7]武钢是最早应用该工艺的钢铁公司,技术成熟,工艺较为合理。
2003年5月份和8月份武钢第二热轧厂和第三炼钢厂3号连铸机相继投产,与原有的第一热轧厂构成了两条连铸坯热送热装工艺线。
其流程为:(1)第三炼钢厂1号和2号连铸机铸坯→火车加盖保温→第一热轧厂→热装轧制(HCR)(2)第三炼钢厂2号和3号连铸机铸坯→辊道输送(出坯辊道和热轧辊道直接相连)→第二热轧厂→直接热装轧制(DHCR)这是两条比较有代表性的工艺路线。
第三炼钢厂从2000年采用了火车加盖保温运输,保证了入炉温度550℃以上,加盖与不加盖的效果如表1所示。
表1火车加盖与不加盖保温运输效果表项目运输时间/min 平均温降/℃·min-1小时温降/℃·h-1185 -0.2316 -13.88加盖608 0.337 0.474120 0.466 28.00无罩566 0.474 28.44 从表1看出加盖运输,时间短,温度还有回升,时间长,温降较低。
无罩降温大,10个小时降温约284℃。
加盖运输保温效果好。
3号连铸机铸坯出机温度大约在950℃左右,直接热装时入炉温度平均在680℃。
2003年热装率达到75%。
表2 2003年第三炼钢厂→第一热轧厂热送热装效果表年度热装率(>400℃)/% 节能/万元减少烧损/万元增产/万元合计/万元2003年68.2 1830.35 1911.26 6802.95 10544.56连铸坯热送热装工艺技术应用研究3.2 鞍钢新轧钢工艺特点[2]鞍钢热轧带钢厂是鞍钢自行设计、制造,国内首条具有自主知识产权的短流程中薄板坯(板坯料厚度135mm )连铸连轧生产线,于2000年11月30日投产。
该生产线有两台中薄板坯连铸机,两座步进式加热炉,一架二辊轧机,一架四辊轧机,热卷箱,飞剪,层流冷却系统和两台卷取机,从4号连铸机火切机到2号加热炉只有55m ,连铸机输出辊道与上料辊道直接相连,5号连铸机生产的板坯通过横移小车输送到4号连铸机输出辊道上,比薄板坯连铸连轧生产线连铸机切割到加热炉距离远50多米。
2005年热装率达到90~95.5%,平均煤气单耗1.014GJ/t ,板坯装炉温度达到900℃,坯料在加热炉内时间50~60min ,连铸机拉速2.4m/min ,最高2.8m/min 。
从几项指标看,效果很好。
3.3 马钢工艺特点[8]马钢第三炼钢厂50t 顶底复吹转炉3座,冶炼周期34min ,LF 精炼,异型坯连铸机为三机三流,采用的热送热装工艺路线是:异型连铸坯→火焰切割机→横向移钢机/冷床→火车加盖保温→热轧H 型钢厂→热装轧制(HCR ) 异型坯在装车时的温度平均在532~674℃,平均温降速率大规格异型坯0.89~1.49℃/min ,小规格异型坯1.26~1.63℃/min ,装车至入加热炉总耗时:大规格异型坯84~138min ,小规格异型坯75~133min ,运输时间最长2个多小时,温降67~225℃。
生产周期由30h →11h ,冷装轧制成材率95.03%,热装轧制成材率94.91%,变化不大,轧钢工序能耗热装65.20kg/t ,冷装69.82kg/t ,降低了4.62 kg/t 。
3.4 唐钢工艺特点唐钢棒材厂采用的工艺路线:连铸方坯→火焰切割→输送辊道→旋转辊道→输送辊道→加热炉→热装轧制(HCR )连铸坯到达热送辊道时温度约850℃,为了保证热装温度达到700℃,运送要在10min 内完成,从三期连铸到棒材厂的距离为140m ,平均运送速度14m/min 。
实际运送时间一般为4~5min 。
吨钢可以节约重油8kg 。
3.5 华菱湘钢工艺特点[3]华菱湘钢介绍的工艺路线:(1)二炼钢厂连铸方坯→火焰切割→输送辊道→高线厂加热炉→热装轧制(HCR )→热装效果较好(2)二炼钢厂连铸方坯→火焰切割→汽车运输(距离较近)→二高线厂加热炉→热装轧制(HCR )→热装效果较好(3)二炼钢厂连铸方坯→火焰切割→汽车运输(距离较远)→棒材厂加热炉→热装轧制(HCR )→不很理想(4)二炼钢厂连铸方坯→火焰切割→汽车运输(距离较近)→二棒材厂加热炉→热装轧制(HCR )→热装效果较好二炼钢厂→高线厂热送热装效果如表3所示。