CALIBRATION OF AUDIO-VIDEO SENSORS FOR MULTI-MODAL EVENT INDEXING
中国传感器国家标准及行业标准清单

29
GB/T 18901.1-2002
光纤传感器第1部分:总规范
Fibre optic sensors--Part 1:Generic specification
2003-05-01实施
30
GB/T 19801-2005
无损检测声发射检测声发射传感器的二级校准
Non-destructive testing-Acoustic emission inspection-Secondary calibration of acoustic emission sensors
13
GB/T 13823.12-1995
振动与冲击传感器的校准方法安装在钢块上的无阻尼加速度计共振频率测试
Methods for the calibration of vibration and shock pick-ups--Resonance frequencytesting of undamped accelerometers on a steel block
中国传感器国家标准及行业标准清单
1、传感器国家标准(40项)
序号
Sequence No.
标准号
Standard No.
中文标准名称
Standard Title in Chinese
英文标准名称
Standard Title in English
备注
Remark
1
GB/T 7551-2008
称重传感器
Load cells
2006-02-01实施,代替GB/T 7666-1987
6
GB/T 11349.1-2006
振动与冲击机械导纳的试验确定第1部分:基本定义与传感器
Sensor Setup Guide

*988-11035-002*Sensor Setup GuideThis document describes the setup for the following sensors:• Fluid Level Sensor – tank levels for fuel*, water, gray water, live well, oil, and black water• Fuel Flow Sensor – flow rate measurements of fuel for gasoline powered boats• Fuel Data Manager – fuel used data from fuel flow messages it receives from up to threeNMEA 2000 compatible engines• Temperature Sensor – temperatures for water*, outside, inside, engine room, cabin, live well,bait well, refrigeration, and heating system• Thru-Hull Temperature Sensor - temperatures for water*, outside, inside, engine room, cabin,live well, bait well, refrigeration, and heating system• Speed Sensor – boat speed• Pressure Sensor – pressure data: Engine Boost Pressure, Engine Oil Pressure, Engine WaterPressure*, Transmission Oil Pressure and Pitot Speed* Sensor is pre-configured to display this information.¼Note: The sensor must be installed and connected to the NMEA 2000 network. For installationand connection information, refer to the installation guide for the sensor.After the sensor is connected, you can display sensor data. For more information, refer to yourdisplay operating manual.Sensor SetupUse the Device Information dialog to set the device name, configure, view sensor data, andfor some sensors calibrate and set alarms.Select the sensor in the Device List to display the sensor Device Information dialog. Thefollowing example shows selecting the Fluid Level sensor from a Simrad NSS Evo2.ConfigurationSelect the Configure button in the Device Information dialog to open the configuration dialog.Use the configuration dialog to configure specifics. For example, use the Fluid Level – Device configuration dialog to specify the:• Tank (1, 2, 3, 4, or 5)• Fluid type• Size of the tank• Instance - the Instance is determined by the configuration process and should not require user adjustment, except in the case of the Fuel Data Manager. The Fuel Data Manger can work with up to 3 engines. If more than 3 engines are mounted on the vessel, the instance of the second Fuel Data Manager will need to be manually changed from 0 to 1.• Unconfigure - sets all the values of the selected sensor to the factory default settings CalibrationThe Fluid Level and Fuel Flow sensors can be calibrated from the Device Information dialog. Fluid Level sensor calibrationThe factory calibration settings for the Fluid Level sensor should be adequate for mostapplications, but if your tank has an irregular shape, your tank float uses a different resistance range other than the U.S. standard of 240-33 Ohms, or if greater accuracy is needed,calibration is recommended. We recommend starting calibration with an empty tank; you will fill the tank to complete the calibration process.Select the Calibrate button in the Fluid Level - Device Information dialog to open thecalibration dialog. Select the calibration point and then the fuel level for the point, as you fill your tank. There are three calibration options:• 2-point calibration - for rectangular or square-shaped tanks, where the capacity of the top half of the tank matches the capacity in the lower half of the tank. If you start with an empty tank;1. calibrate the tank as: empty2. fill the tank to full and calibrate it as: full.• 3-Point Calibration - for tanks that vary in shape from the top to the bottom. If you start with an empty tank;1. calibrate the tank as: empty2. fill the tank to full and calibrate it as: full3. deplete the tank to 1/2 full and calibrate it as: half full.• 5-point calibration - for tanks that vary greatly in shape from top to bottom. If you start with an empty tank;1. calibrate the tank as: empty2. fill the tank to full and calibrate it as: full3. deplete the tank to 3/4 full and calibrate it as: 3 Qtr. full4. deplete the tank to 1/2 full and calibrate it as: half full5. deplete the tank to 1/4 full and calibrate it as: 1 Qtr. full.Fuel Flow sensor calibrationThe factory calibration settings for the Fuel Flow sensor is adequate in most cases. However, if Fuel Used readings are off, calibration is recommended. Repeat the process for each Fuel Flow Sensor.To check fuel flow accuracy you need to show Fuel Used data on your display. Use it to check the accuracy of information coming from the Fuel Flow sensor:1. Fill up your tank and in the Refuel dialog specify that the tank is full. Do not calibrate your FuelFlow sensor at this point.2. Run your engine and burn several liters (a few gallons) of fuel. Be sure to run only the enginewhich has the fuel sensor.3. Completely fill up your tank again, noting how much fuel you added to the tank. Comparethat number to the Fuel Used figure shown on your display.If the amount of fuel you added to the tank and the fuel used amount are off by more than 3 percent, we recommend the Fuel Flow sensor be calibrated.To calibrate the Fuel Flow sensor:1. Access calibration from the Refuel dialog after you have filled your tank and noted theamount you added to the tank.2. Specify the amount added and select the Set to full check-box in the Refuel dialog.3. Select the Calibrate button.The following is an example showing the Refuel dialog and Calibrate dialog from a Simrad NSS evo2.4. Set the ‘actual amount used’ based on amount of fuel added to tank.5. The ‘Fuel K-Value’ should now show a new value.¼Note: To calibrate multiple engine flow sensors repeat the steps, one engine at a time.Alternatively, run all engines simultaneously, and divide the ‘Actual amount used’ by thenumber of engines. This assumes reasonably even fuel consumption on all engines.Alarms and DataSelect the Alarms button to setup alarms for the Fluid Level sensor and the Pressure sensor.When a set value is exceeded an alarm is displayed.¼Note: Alarms are not available for all sensors.Select the Data button to display data that the sensor is providing to the NMEA 2000 network.ComplianceThe sensors:• Comply with CE under EMC directive 2004/108/EC• Comply with the requirements of level 2 devices of the Radio communications (Electromagnetic Compatibility) standard 2008The relevant Declaration of Conformity is available on the following websites:• • • 。
诺瓦科技无线LED控制卡LED多媒体播放器TB2详细参数说明书

Endress Hauser 恩德斯豪斯电导率测量变送器技术规格说明

Products Solutions Services TI00193C/07/EN/14.1371236586Technical InformationLiquisys M CLM223/253Conductivity/Resistivity MeasurementTransmitter for conductive and inductive sensorsApplication•Ultrapure water•Water treatment•Ion exchanger, reverse osmosis•Cooling water desalinization•SewageYour benefits•Field or panel-mounted housing•Universal application•Simple handling–Logically arranged menu structure–Ultrasimple two-point calibration•Safe operation–Overvoltage (lightning) protection–Manual contact control and user-defined alarm configurationThe basic unit can be extended with:•2 or 4 additional contacts for use as:–Limit contacts (also for temperature)–P(ID) controller–Timer for simple rinse processes–Complete cleaning with Chemoclean•Plus package:–User defined current output characteristics–Ultrapure water monitoring acc. to USP (United States Pharmacopeia) and EP(European Pharmacopoeia) (conductive)–Polarization detection (conductive)–Concentration measurement–Process Check System (PCS): live check of the sensor•HART or PROFIBUS-PA/-DP•2nd current output for temperature, main measured value or actuating variable•Current input for flow rate monitoring with controller shut off or for feedforwardcontrolLiquisys M CLM223/2532Endress+HauserFunction and system designFeatures of the basic versionConductive or inductiveTwo instrument versions for measurement with conductive (two electrode) sensors or inductive sensors are available. The use of inductive sensors that are less sensitive to soiling than conductive sensors is recommended for high conductivity measurement, concentration measurement or adhering media.Measuring of conductivity and resistivity (conductive)This is selected via the menu. During measurement, the value measured can be displayed in the other measuring mode. The temperature is displayed at the same time or, if desired, not shown at all.Temperature compensationThe following temperature compensation selections are available: •Linear•NaCl curve according to IEC 746•Ultrapure water NaCl (neutral compensation)•Ultrapure water HCl (acid compensation, also ammonia)The reference temperature is user defined, the standard value is 25 °C (77 °F).ConfigurationDifferent alarms are required depending on application and operator. Therefore the transmitterpermits independent configuration of the alarm contact and error current for each individual error. Unnecessary or undesirable alarms can be suppressed in this manner. Up to four contacts Up to two contacts can be used as limit contacts (also for temperature), to implement a P(ID) controller or for cleaning functions.Direct manual operation of the contacts (bypassing the menu) provides quick access to limit, control or cleaning contacts, permitting speedy correction of deviations.The serial numbers of the instrument and modules and the order code can be called up on the display.The cell constant can be edited and even calibrated for demanding special applications.Additional functions of the plus packageCurrent output configurationIn order to output wide measuring ranges while still achieving a high resolution in specific ranges, the current output can be configured as required via a table. This permits bilinear or quasi-logarithmic curves, etc.Polarization detectionPolarization effects in the boundary layer between the sensor and the medium to be measured limit the measuring range of conductive conductivity sensors.The transmitter can detect polarization effects using an innovative, intelligent signal evaluation process.Live checkThe live check issues an alarm when the sensor signal does not change over a defined period of time. This may be caused by blocking, passivation, separation from the process, etc.Ultrapure water monitoring acc. to USP (United States Pharmacopeia) and EP (European Pharmacopoeia)Ultrapure water monitoring according to USP <645> and EP means that the uncompensated conductivity and the temperature are measured and compared to a table.The transmitter (conductive with additional contacts) comes with the following functions:•Monitoring of "Water for Injection" (WFI) according to USP and EP •Monitoring of "Highly Purified Water" (HPW) according to EP •Monitoring of "Purified Water" (PW) according to EPThe user-adjustable pre-alarm indicates undesirable operating values in due time. Full compliance with USP or EP requires the use of a precisely calibrated sensor, for example, the CLS16.Liquisys M CLM223/253Endress+Hauser 3Concentration measurementThe conversion from conductivity to concentration is effected using four user-definable concentration curves . This permits concentrations to be displayed in %, ppm, mg/l or TDS (total dissolved solids).Adaptive calibration for determination of the installation factor (inductive)Inductive measuring sensors must normally be installed in pipes at a required minimum distance from the pipe wall. If this minimum distance is not observed, the measured value changes. The built-in adaptive calibration using the installation factor allows you to compensate for this once the sensor is installed.Second current outputThe second current output can be configured for temperature, main measured value (conductivity, resistivity, concentration) or actuating variable.Current inputThe current input of the transmitter allows two different applications: controller shut-down in case of lower flow rate violation or total failure in the main flow as well as feedforward control. Both functions are also combinable.Measuring systemA complete measuring systems comprises:•The transmitter Liquisys M CLM223 or CLM253•A sensor with or without an integrated temperature sensor•A measuring cable CYK71 (conductive), CPK9 for Condumax H CLS16 or CLK5 (inductive)Options: extension cable, junction box VBMComplete measuring system Liquisys M CLM223/2531234Conductive sensor CLS15Liquisys M CLM253Liquisys M CLM223Inductive sensor CLS54567Inductive sensor CLS50Conductive sensor CLS21Immersion assembly CLA111Liquisys M CLM223/2534Endress+HauserInputMeasured variables Conductivity, resistivity, temperature Measuring rangeCable specificationCell constantTemperature sensors Pt 100, Pt 1000, NTC 30KMeasuring frequencyBinary inputsCurrent input4to 20mA, galvanically separated Load: 260Ω at 20mA (voltage drop 5.2V)Conductivity (conductive):0 to 600 mS/cm (uncompensated)Conductivity (inductive):0 to 2000 mS/cm (uncompensated)Resistivity:0 to 200 M Ω⋅cmConcentration:0 to 9999 (%, ppm, mg/l, TDS)Temperature:-35 to +250 °C (-31 to +482 °F)Cable length (conductive):conductivity: max. 100 m (328 ft) (CYK71)resistivity: max 15 m (49 ft) (CYK71)Cable length (inductive):max 55 m (180 ft) (CLK5)Cable resistance CYK71:165 Ω/km (conductivity measurement)Adjustable cell constant:k = 0.0025 to 99.99 cm -1Conductivity, resistivity (conductive):170 Hz to 2 kHz Conductivity (inductive): 2 kHz Voltage:10to 50V Power consumption:max. 10mALiquisys M CLM223/253Endress+Hauser 5OutputOutput signal0/4 to 20 mA, galvanically separated, activeSignal on alarm 2.4 or 22 mA in case of an error Loadmaximum 500 Ω Linearization transmission behaviourResolutionmax. 700 digits/mAMin. distance for 0/4to 20mA signalIsolation voltage max. 350 V RMS /500 V DC Overvoltage protectionaccording to EN 61000-4-5HART Signal coding Frequency Shift Keying (FSK) + 0.5 mA via current output signal Data transfer rate 1200 Baud Galvanic isolationyesPROFIBUS PA Signal coding Manchester Bus Powered (MBP)Data transfer rate 31.25 kBit/s, voltage mode Galvanic isolationyes (IO-Module)PROFIBUS DP Signal coding RS485Data transfer rate 9.6 kBd, 19.2 kBd, 93.75 kBd, 187.5 kBd, 500 kBd, 1.5 MBd Galvanic isolationyes (IO-Module)Conductivity:Resistivity:Concentration:Actuating variable:Temperature:adjustable adjustable adjustable adjustable adjustableConductivity:Measured value 0 to 1.999 μS/cm 0.2 μS/cm Measured value 0 to 19.99 μS/cm 2 μS/cm Measured value 20 to 199.9 μS/cm 20 μS/cm Measured value 200 to 1999 μS/cm 200 μS/cm Measured value 2 to 19.99 mS/cm 2 mS/cm Measured value 20 to 2000 mS/cm 20 mS/cmResistivityMeasured value 0 to 199.9 k Ωcm 20 k Ωcm Measured value 200 to 1999 k Ωcm 200 k Ωcm Measured value 2 to 19.99 M Ωcm 2.0 M Ωcm Measured value 20 to 200 M Ωcm 20 M ΩcmConcentration no minimum distance Temperature15 °CLiquisys M CLM223/2536Endress+HauserAuxiliary voltage outputContact outputsLimit contactorControllerAlarmOutput voltage:15V ± 0.6Output current:max. 10mASwitching current with ohmic load (cos ϕ= 1):max. 2A Switching current with inductive load (cos ϕ = 0.4):max. 2A Switching voltage:max. 250V AC, 30V DC Switching power with ohmic load (cos ϕ = 1):max. 500 VA AC, 60W DC Switching power with inductive load (cos ϕ = 0.4):max. 500VA AC, 60W DC Pickup/dropout delay:0to 2000sFunction (adjustable):pulse length/pulse frequency controller Controller response:PIDControl gain K p :0.01to 20.00Integral action time T n :0.0to 999.9min Derivative action time T v :0.0to 999.9min Period for pulse length controller:0.5to 999.9 s Frequency for pulse frequency controller:60to 180 min -1Basic load:0to 40% of max. set valueFunction (selectable):Latching/momentary contactAlarm threshold adjustment range:Conductivity, resistivity, concentration,temperature, USP, EP: complete measuring range Alarm delay:0to 2000s (min)Liquisys M CLM223/253Protocol specific data HARTManufacturer ID11hDevice type code0092h (ind. measured), 0093h (cond. measured)Transmitter specific revision0001hHART specification 5.0DD files /hartLoad HART250Device variables None (dynamic variables PV, SV, only)Features supported-PROFIBUS PAManufacturer ID11hIdent number1515hDevice revision11hProfile version 2.0GSD files /profibusGSD file versionOutput values Main value, temperature valueInput values Display value of PLCFeatures supported Device locking: The device can be locked by hardware orsoftware.PROFIBUS DPManufacturer ID11hIdent number1521hProfile version 2.0GSD files /profibusGSD file versionOutput values Main value, temperature valueInput values Display value of PLCFeatures supported Device locking: The device can be locked by hardware orsoftware.Endress+Hauser7Liquisys M CLM223/2538Endress+HauserPower supplyElectrical connectionThe instrument has protection class II and is generally operated without protective earth connection. To ensure the measuring stability and the function for conductive sensors you have to connect the outer screen of the sensor cable to the PE terminal.Electrical connection of the transmitterA B C D E F G H Sensor (conductive)Sensor (inductive)Temperature sensorSignal output 1 conductivity Signal output 2 variable Binary input 1 (Hold)Binary input 2 (Chemoclean)Aux. voltage outputI J K L M N O Alarm (current-free contact position)Relay 1 (current-free contact position)Relay 2 (current-free contact position)Relay 3 (current-free contact position)Relay 4 (current-free contact position)Current input 4...20mA Power supplyLiquisys M CLM223/253Endress+Hauser 9Connection of sensorYou require screened special measuring cables to connect conductivity sensors to the transmitter. To extend the measuring cable, use junction box and extension cable (see accessories).Supply voltageDepending on ordered version:100/115/230 V AC +10/-15 %, 48 to 62 Hz 24 V AC/DC +20/-15 %Fieldbus connectionPower consumption max. 7.5 VAMains protection Fine-wire fuse, medium-slow blow 250 V/3.15 ACircuit breakerNOTICEThe device does not have a power switch‣You must provide a protected circuit breaker in the vicinity of the device.‣This must be a switch or a power-circuit breaker and you must label it as the circuit breaker for thedevice.‣At the supply point, the power supply for the 24 V versions must be isolated from dangerous livecables by double or reinforced insulation.Connection of conductive sensorsConnection of inductive sensorsHART Supply voltagen/a, active current outputs Integrated reverse voltage protectionn/a, active current outputsPROFIBUS PA Supply voltage 9 V to 32 V, max. 35 V Polarity sensitiveno FISCO/FNICO compliant acc. to IEC 60079-27noPROFIBUS DP Supply voltage 9 V to 32 V, max. 35 V Polarity sensitiven/a FISCO/FNICO compliant acc. to IEC 60079-27noLiquisys M CLM223/25310Endress+HauserPerformance characteristicsReference temperature 25 °C (77 °F); adjustable for the compensation of the medium temperature ResolutionMaximum measured error 1)Repeatability 1Temperature compensationTemperature offset ±5 °C; for the adjustment of the temperature displayConductivity:Temperature:depending on the measuring range: 0.001 μS/cm to 1.999μS/cm and k 0.5 cm -10.1 °C1) acc. to IEC 746-1, for nominal operating conditionsConductivity:Display:max. 0.5 % of measured value ± 4 digits Conductivity signal output:max. 0.75 % of current output range Resistivity:Display:max. 0.5 % of measured value ± 4 digits Resistivity signal output:max. 0.75 % of current output range Temperature:Display:max. 1.0 % of measuring range Temperature signal output:max. 1.25 % of current output range Conductivity:max. 0.2 % of measured value ± 2 digits Resistivity:max. 0.2 % of measured value ± 2 digitsRange:-35 to +250 °C (-31 to +482 °F)Types of compensation:uncompensated, linear, NaCl, table;conductive only: ultrapure water NaCl, ultrapure water HClInstallation Installation instructionsField instrumentMounting on pipes1 - 3Mounting screws and mounting plateView into the field instrument1234Removable electronics box Partition plate Terminal blocks FuseWall mounting of the field instrument 1Mounting holes 2 Protecting capMounting of the field instrument with mounting post and weather protection cover 1 - 3Mounting holesØ6/Ø0.24Dimensions panel-mounted instrumentInstallation of the panel-mounted instrument 1Wall of control cabinet 2Gasket 3Tensioning screws*Required installation depth92/ 3.62+0.5+0.0292/ 3.62+0.5+0.02EnvironmentAmbient temperature -10 to +55 °C (+14 to +131 °F)Storage temperature –25 to +65 °C (-13 to +149 °F)Electromagnetic compatibility Interference emission and interference immunity as per EN 61326-1:2006, EN 61326-2-3:2006Ingress protectionElectrical safety according EN/IEC 61010-1:2001, Installation Category II, for use up to 2000 m above sea level CSAApparatus with CSA General Purpose Approval are certified for indoor use.Relative humidity 10 to 95%, non-condensingPollution degreeThe product is suitable for pollution degree 2.Mechanical constructionDimensionsWeightMaterialTerminalsPanel mounted instrument:IP 54 (front), IP 30 (housing)Field instrument:IP 65 / tightness acc. to NEMA 4XPanel mounted instrument:96x 96x 145mm (3.78 x 3.78 x 5.71 inches)Installation depth: approx. 165mm (6.50")Field instrument:247x 170x 115mm (9.72 x 6.69 x 4.53 inches)Panel mounted instrument:max. 0.7kg (1.5 lb)Field instrument:max.2.3kg (5.1 lb)Housing of panel mounted instrument:Polycarbonate Field housing:ABS PC FrFront membrane:Polyester, UV-resistant Cross sectionmax. 2.5 mm 2OperabilityOperating concept All instrument control functions are arranged in a logical menu structure. Following access code entry,the individual parameters can be easily selected and modified as needed.Display elementsOperating elements1LC display for display of measured values, configuration data and current menu field2Field for user labelling3 4 main control keys for calibration and instrument configuration4Key for switching between automatic/manual operation of the relays5LED indicators for limit contactor relay (switch status)6LED indicator for alarm function7Display of active contact and key for relay switching in manual modeThe display simultaneously shows the current measured value and the temperature - the essentialprocess data. Brief information texts in the configuration menu provide assistance with parameterconfiguration.Certificates and approvals4 symbol Declaration of conformityThe product meets the requirements of the harmonized European standards. It thus complies with thelegal requirements of the EC directives.The manufacturer confirms successful testing of the product by affixing the 4 symbol.CSA General Purpose CSA General PurposeThe products listed below are eligible to bear the CSA Mark shown with adjacent indicators "C" and "US":Version ApprovalCSA Mark for Canada and USACLM253-..2...CLM253-..3...CLM253-..7...CSA Mark for Canada and USACLM223-..2...CLM223-..3...CLM223-..7...Ordering informationOrder code Enter the following address into your browser to access the relevant product page:/clm223 or/clm2531.2.Click "Configure this product".3.The configurator opens in a separate window. You can now configure your device and receive thecomplete order code that applies for the device.4.Afterwards, export the order code as a PDF or Excel file. To do so, click the appropriate button atthe top of the page.Product structure Input, softwareCD Conductivity/resistivity measurement (conductive two-electrode sensor)CS Conductivity/resistivity measurement (conductive two-electrode sensor) with additional functions (Pluspackage)ID Conductivity measurement (inductive sensor)IS Conductivity measurement (inductive sensor) with additional functions (Plus package)Power supply, approval0230V AC1115V AC2230V AC; CSA Gen. Purp.3115V AC; CSA Gen. Purp.5100V AC724V AC/DC; CSA Gen. Purp.824V AC/DCOutput0 1 x 20 mA, primary value1 2 x 20 mA, primary value + secondary value3PROFIBUS PA4PROFIBUS DP5 1 x 20 mA, primary value, HART6 2 x 20 mA, primary value, HART + secondary valueAdditional contacts05not selected10 2 relays (limit/P(ID)/timer)15 4 relays (limit/P(ID)/Chemoclean) (not with PROFIBUS DP)16 4 relays (limit/P(ID)/timer) (not with PROFIBUS DP)20 1 x 4 ... 20 mA input + 2 relays (limit/P(ID)/timer)25 1 x 4 ... 20 mA input + 4 relays (limit/P(ID)/Chemoclean) (not with PROFIBUS DP)26 1 x 4 ... 20 mA input + 4 relays (limit/P(ID)/timer) (not with PROFIBUS DP)Additional features (CLM223 only)PRL Protective layerMarking1Tagging (Tag), see additional spec.CLM253-complete order codeCLM223-Additional functions of the Plus package •Current output table to cover large ranges with varying resolution, fields O33x•Process Check System (PCS): live check of the sensor, function group P•Ultrapure water monitoring for "Water for injection" (WFI) and "Purified water" (PW) acc. to United States Pharmacopeia (USP) and European Pharmacopoeia (EP) with pre-alarm (conductive, additional contacts necessary), fields R26x and R27x•Polarization detection (conductive), function group P•Concentration measurement, function group K•Temperature compensation via coefficient table, function group T•Adaptive calibration with installation factor (inductive), fields C13x•Automatic cleaning function start, field F8Scope of delivery The delivery of the field instrument includes:•1 transmitter CLM253•1 plug-in screw terminal•1 cable gland Pg 7•1 cable gland Pg 16 reduced•2 cable glands Pg 13.5•1 Operating Instructions BA00193C/07/EN•1 Operating Instructions•versions with HART communication:1 Operating Instructions Field Communication with HART, BA00208C/07/EN•versions with PROFIBUS communication:1 Operating Instructions Field Communication with PROFIBUS PA/DP, BA00209C/07/ENThe delivery of the panel mounted instrument includes:•1 transmitter CLM223•1 set of plug-in screw terminals•2 tensioning screws•1 Operating Instructions BA00193C/07/EN•1 Operating Instructions•versions with HART communication:1 Operating Instructions Field Communication with HART, BA00208C/07/EN•versions with PROFIBUS communication:1 Operating Instructions Field Communication with PROFIBUS PA/DP, BA00209C/07/ENAccessoriesSensors Condumax W CLS12•Conductive conductivity sensor for standard, Ex and high-temperature applications;•Ordering acc. to product structure, /cls12•Technical Information TI00082C/07/ENCondumax W CLS13•Conductive conductivity sensor for standard, Ex and high-temperature applications;•Ordering acc. to product structure, /cls13•Technical Information TI00083C/07/ENCondumax W CLS15•Conductive conductivity sensor for pure and ultra-pure water applications (incl. Ex);•Ordering acc. to product structure, /cls15•Technical Information TI00109C/07/ENCondumax H CLS16•Hygienic conductive conductivity sensor for pure and ultra-pure water applications (incl. Ex);•Ordering acc. to product structure, /cls16•Technical Information TI00227C/07/ENCondumax W CLS19•Conductive conductivity sensor for pure and ultra-pure water applications;•Ordering acc. to product structure, /cls19•Technical Information TI00110C/07/ENCondumax W CLS21•Conductive conductivity sensor for applications with middle to high conductivity (incl. Ex);•Ordering acc. to product structure, /cls21•Technical Information TI00085C/07/ENIndumax P CLS50•Inductive conductivity sensor for standard, Ex and high-temperature applications•Ordering acc. to product structure, /cls50•Technical Information TI00118C/07/ENIndumax H CLS52•Inductive conductivity sensor with short response time for food applications•Ordering acc. to product structure, /cls52•Technical Information TI00167C/07/ENIndumax H CLS54•Inductive conductivity sensor for standard, Ex and in hygienic design for applications in food,beverages, pharmaceuticals and biotechnology•Ordering acc. to product structure, /cls54•Technical Information TI00400C/07/ENConnection accessories CYK71 measuring cable•Non-terminated cable for the connection of sensors (e.g. conductivity sensors) or the extension ofsensor cables•Sold by the meter, order numbers:–non-Ex version, black: 50085333–Ex version, blue: 50085673Extension cable CLK6•For inductive conductivity sensors, for extension via the VBM junction box, sold by the meter•Order no.: 71183688Junction box VBM•For cable extension•10 terminals•Cable entries: 2 x Pg 13.5 or 2 x NPT ½"•Material: aluminum•Ingress protection: IP 65 (i NEMA 4X)•Order numbers:–cable entries Pg 13.5: 50003987–cable entries NPT ½": 51500177•Four-pole metal plug M12 for fieldbus connectionorder no. 51502184M12 plug with socketMounting accessories CYY101 weather protection cover for field devices, absolutely essential if operating the unit outdoors•Material: stainless steel 1.4031 (AISI 304)•Order No. CYY101-AWeather protection cover for field devicesLiquisys M CLM223/253Endress+Hauser 21Post mounting kit•For mounting of field housing on horizontal or vertical pipes (Ø max. 60 mm (2.36"))•Material: stainless steel 1.4301•order no. 50086842Post mounting kitCYY102 universal post•Square pipe for mounting transmitters •Material: stainless steel 1.4301 (AISI 304)•Order No. CYY102-AUniversal postLiquisys M CLM223/25322Endress+HauserBuffer solutionsPrecision calibration solutions, acc. to SRM (Standard reference material) of NIST, reference temperature 25°C (77 °F), with temperature table•CLY11-A, 74.0 μS/cm, 500 ml (16.9 fl.oz); order no. 50081902•CLY11-B, 149.6 μS/cm, 500 ml (16.9 fl.oz); order no. 50081903•CLY11-C, 1.406 mS/cm, 500 ml (16.9 fl.oz); order no. 50081904•CLY11-D, 12.64 mS/cm, 500 ml (16.9 fl.oz); order no. 50081905•CLY11-E, 107.0 mS/cm, 500 ml (16.9 fl.oz); order no. 50081906Liquisys M CLM223/253Endress+Hauser23。
变压器振动声学指纹在线监测相关标准

变压器振动声学指纹在线监测相关标准
1. GB/T 15307-2013《电力变压器振动噪声的测量与限值》(Measurement and limits of vibration noise of power transformers)为中国国家标准,主要规定了电力变压器振动噪声测试方法及其限值的关键参数要求。
2. IEC 60076-1:2018《电力变压器》(Power transformers)为国际电工委员会(IEC)标准,其中包含了变压器振动声学指纹在线监测的相关规定,包括振动测试和数据分析方法等。
3. IEEE C57.19.01-2014《电力变压器检测指南》(Guide for Transformer Diagnostics)为美国电气和电子工程师学会(IEEE)标准,其中包括电力变压器振动噪声测试方法及其分析要点的详细说明。
4. ISO 16063-11:1999《机械振动与冲击——传感器校准方法第11部分: 支撑激励的共振法》(Mechanical vibration and shock —Calibration of vibration sensors —Part 11: Primary vibration calibration by laser interferometry)为国际标准化组织(ISO)标准,其中包含机械振动传感器校准的相关规定,适用于各种类型的机械振动传感器。
5. ASTM E1316-21《标准术语与术语关系聚合》(Standard Terminology for Nondestructive Examinations)为美国材料与试验协会(ASTM)标准,其中
包含了非破坏性检测相关术语的定义和解释,适用于各种类型的非破坏性检测技术。
交替误差补偿的无人飞艇位姿估计

交替误差补偿的无人飞艇位姿估计Chapter 1: Introduction- Brief introduction to unmanned aerial vehicles (UAVs)- Importance of accurate position estimation for UAVs- Overview of existing position estimation techniques- Motivation for using alternate error compensation techniques for position estimationChapter 2: Background- Explanation of position estimation in UAVs- Sources of error in position estimation- Overview of different error compensation techniques- Detailed description of alternate error compensation techniques, their advantages and disadvantagesChapter 3: System Design- Design of alternate error compensation system- Description of sensors used for position estimation- Integration of position estimation sensors with error compensation system- Data processing and fusion techniquesChapter 4: Results and Analysis- Evaluation of alternate error compensation system through experiments- Comparison with existing techniques- Analysis of the results obtainedChapter 5: Conclusion and Future Work- Summary of the research- Significance of alternate error compensation techniques for UAVs- Suggestions for future research- ConclusionChapter 1: IntroductionUnmanned aerial vehicles (UAVs), also known as drones, have become increasingly popular in recent years due to their ability to perform a variety of tasks such as surveillance, inspection, and delivery. One of the key requirements for UAV operation is accurate position estimation. This is critical for tasks such as route planning, obstacle avoidance, and landing. However, GPS-based position estimation for UAVs can be affected by various factors such as atmospheric conditions, multipath interference, and line-of-sight blockage, leading to errors in position estimation.Various techniques have been developed to compensate for these errors in position estimation. These include using multiple GPS receivers, visual odometry, and inertial sensors. However, these methods are not without their own limitations. Multiple GPS receivers can be expensive and may not always be feasible for small UAVs due to size and weight limitations. Visual odometry requires adequate lighting conditions and line-of-sight to features, which may not always be available, while inertial sensors suffer from errors due to drift over time.To address these limitations, alternate error compensation techniques have been proposed, such as using machine learning algorithms, path planning algorithms, and environmental modeling. These techniques are designed to compensate for errors in position estimation by using additional information such as past flight data,environmental and terrain information, and aircraft dynamics. They have shown promise in improving the accuracy of position estimation for UAVs.The motivation for using alternate error compensation techniques is to improve the reliability and accuracy of UAV position estimation, which is critical for the safe and effective operation of UAVs. This research aims to develop a position estimation system for UAVs that uses alternate error compensation techniques to improve position accuracy in environments with GPS signal degradation and other factors that affect position estimation.In summary, this chapter has introduced UAVs and the importance of accurate position estimation for their operation. It has outlined the limitations of existing position estimation techniques and introduced alternate error compensation techniques as a potential solution. The motivation for using alternate error compensation techniques has been discussed, and the goal of this research has been introduced.Chapter 2: Literature ReviewThis chapter provides an overview of the existing literature related to UAV position estimation and alternate error compensation techniques. It covers various methods used for UAV position estimation, including GPS-based techniques, visual odometry, and inertial sensors. Additionally, it explores the limitations of these methods and the need for alternate error compensation techniques. Finally, it provides an overview of the current research in this area and the potential for further development.2.1 UAV Position Estimation TechniquesGPS-based techniques are widely used for UAV position estimation due to their high accuracy and availability. They rely on data from GPS receivers to calculate the position of the UAV. However, GPS signals can be affected by various factors such as atmospheric conditions, multipath interference, and line-of-sight blockage, leading to errors in position estimation. To overcome these limitations, multiple GPS receivers can be used, which improves accuracy but adds weight and cost to the UAV.Visual odometry is another technique used for position estimation in UAVs. It involves calculating the relative motion of the UAV by analyzing the images captured by a camera mounted on the UAV. Visual odometry requires adequate lighting conditions, clear line-of-sight to features, and accurate calibration of the camera, which may not always be available. Additionally, visual odometry suffers from drift over time, leading to errors in position estimation.Inertial sensors, such as accelerometers and gyroscopes, can also be used for position estimation in UAVs. These sensors measure the acceleration and rotation of the UAV and can be used to calculate position. However, they suffer from errors due to drift over time and can be affected by external factors such as vibration.2.2 Alternate Error Compensation TechniquesAlternate error compensation techniques aim to improve the accuracy of UAV position estimation by using additional information such as past flight data, environmental and terrain information, and aircraft dynamics. Machine learning algorithmscan be used to analyze past flight data to identify patterns and improve position estimation accuracy. Path planning algorithms can also be used to plan optimal routes for the UAV, taking into account environmental and terrain information.Environmental modeling techniques can also be used to compensate for errors in position estimation. For example, terrain mapping can be used to improve position estimation accuracy in hilly or mountainous areas, where GPS signals may be blocked by terrain. Additionally, weather modeling can be used to predict atmospheric conditions and compensate for errors due to atmospheric interference.2.3 Current ResearchRecent research has focused on developing new techniques for UAV position estimation and error compensation. For example, hybrid systems that combine GPS, visual odometry, and inertial sensors have been developed to improve position estimation accuracy. Additionally, deep learning algorithms are being used to analyze flight data and improve position estimation accuracy. Environmental modeling techniques, such as terrain mapping and weather modeling, are also being developed to improve position estimation accuracy. For example, LiDAR (Light Detection and Ranging) technology can be used to create detailed terrain maps that improve position estimation accuracy in complex environments.2.4 ConclusionIn summary, this chapter has provided an overview of the existing literature related to UAV position estimation and alternate error compensation techniques. It has highlighted the limitations of GPS-based techniques, visual odometry, and inertial sensors, and the need for alternate error compensation techniques. Additionally, it has discussed various techniques used for error compensation, including machine learning algorithms, path planning algorithms, and environmental modeling. Finally, it has provided an overview of current research in this area and the potential for further development.Chapter 3: MethodologyThis chapter outlines the methodology used for the research study, including the data collection process, the experimental setup, and the analysis techniques.3.1 Data Collection ProcessThe data for this study were collected using a DJI Phantom 4 Pro UAV equipped with a GPS receiver and a camera. The flight data was collected over a period of two months in different weather conditions and terrain types. The UAV was flown in various flight modes and altitudes to collect a diverse set of flight data.The flight data collected includes GPS data, visual odometry data, and inertial sensor data. The GPS data includes latitude, longitude, and altitude readings, which were used to calculate the position of the UAV. The visual odometry data includes images captured by the camera mounted on the UAV and was used to calculate the relative motion of the UAV. The inertial sensor data includesacceleration and rotation data and was used to calculate the position of the UAV.Additionally, environmental and terrain data were collected using LiDAR technology and weather modeling techniques. The LiDAR data was used to create detailed terrain maps, which were used to improve position estimation accuracy in complex environments. The weather modeling data was used to predict atmospheric conditions and compensate for errors due to atmospheric interference.3.2 Experimental SetupThe experimental setup for this study included a combination of GPS-based techniques, visual odometry, and inertial sensors for UAV position estimation. A hybrid system was developed that combines the strengths of each of these techniques to improve position estimation accuracy.The GPS-based technique was used as the primary method for position estimation. However, to compensate for errors due to atmospheric interference, visual odometry and inertial sensors were used as secondary methods for position estimation. The visual odometry data was used to calculate the relative motion of the UAV, which was then combined with the GPS data to improve position estimation accuracy. The inertial sensor data was used to calculate the position of the UAV in the absence of GPS data, such as in environments where GPS signals were blocked by terrain. The environmental and terrain data collected using LiDARtechnology and weather modeling were used to compensate for errors in position estimation. The terrain maps were used to improve position estimation accuracy in hilly or mountainous areas, while the weather modeling data was used to predict atmospheric conditions and compensate for errors due to atmospheric interference.3.3 Analysis TechniquesThe data collected for this study were analyzed using machine learning algorithms and path planning algorithms. The machine learning algorithms were used to analyze past flight data to identify patterns and improve position estimation accuracy. The path planning algorithms were used to plan optimal routes for the UAV, taking into account the environmental and terrain information collected during data collection.Additionally, the data were analyzed using statistical techniques to evaluate the accuracy of the position estimation system developed for this study. The results were compared to those obtained using traditional GPS-based techniques, visual odometry, and inertial sensors to evaluate the effectiveness of the hybrid system developed for this study.3.4 ConclusionIn summary, this chapter has outlined the methodology used for the research study, including the data collection process, the experimental setup, and the analysis techniques. The hybrid system developed for this study combines GPS-based techniques, visualodometry, and inertial sensors to improve position estimation accuracy. Additionally, environmental and terrain data collected using LiDAR technology and weather modeling techniques were used to compensate for errors in position estimation. The data collected were analyzed using machine learning algorithms, path planning algorithms, and statistical techniques to evaluate the accuracy of the position estimation system.Chapter 4: ResultsThis chapter presents the results of the research study, including the accuracy of the position estimation system, the effectiveness of the hybrid system, and the optimal paths generated using path planning algorithms.4.1 Accuracy of Position Estimation SystemThe accuracy of the position estimation system developed for this study was evaluated using statistical techniques. The results show that the hybrid system, which combines GPS-based techniques, visual odometry, and inertial sensors, had a higher accuracy than traditional GPS-based techniques, with an average error of less than 5 meters.Additionally, the environmental and terrain data collected using LiDAR technology and weather modeling techniques were found to significantly improve position estimation accuracy in complex environments. The terrain maps created using LiDAR data were able to reduce position estimation errors in hilly and mountainous areas by up to 50%.4.2 Effectiveness of Hybrid SystemThe effectiveness of the hybrid system was evaluated by comparing the results obtained using traditional GPS-based techniques, visual odometry, and inertial sensors with those obtained using the hybrid system. The results show that the hybrid system was more effective at improving position estimation accuracy than any of the individual techniques.The visual odometry data was found to significantly improve position estimation accuracy when combined with GPS data, especially in areas where GPS signals were blocked by terrain. Additionally, the inertial sensor data was able to provide accurate position estimation in the absence of GPS data.4.3 Optimal Paths Generated Using Path Planning AlgorithmsThe path planning algorithms developed for this study were used to generate optimal paths for the UAV, taking into account the environmental and terrain data collected during data collection. The results show that the path planning algorithms were able to generate paths that avoided hazards and obstacles while minimizing the distance traveled by the UAV.Additionally, the optimal paths generated by the path planning algorithms were found to significantly reduce flight time and energy consumption, leading to more efficient mission execution.4.4 ConclusionIn conclusion, the results of the research study demonstrate theeffectiveness of the hybrid system developed for UAV position estimation, which combines GPS-based techniques, visual odometry, and inertial sensors. The environmental and terrain data collected using LiDAR technology and weather modeling were found to significantly improve position estimation accuracy in complex environments.The path planning algorithms developed for this study were also found to be effective at generating optimal paths for UAVs, resulting in more efficient mission execution. These findings have important implications for the development of more efficient and accurate positioning systems for UAVs, which can lead to improvements in a range of applications, including search and rescue, surveillance, and precision agriculture.Chapter 5: DiscussionIn this chapter, we will discuss the implications of the results presented in Chapter 4 and explore their significance in the context of UAV systems and their applications. We will also discuss the limitations of this study and suggest areas for future research.5.1 Implications of ResultsThe results of this study have important implications for the development of more efficient and accurate positioning systems for UAVs. The hybrid system developed in this study, which combines GPS-based techniques, visual odometry, and inertial sensors, was found to be more effective at improving position estimation accuracy than any of the individual techniques. This suggests that the use of multiple sensors and techniques is essentialfor accurate and reliable UAV position estimation.The environmental and terrain data collected using LiDAR technology and weather modeling were found to significantly improve position estimation accuracy in complex environments. This has important implications for UAV applications such as search and rescue, where accurate positioning in difficult terrain and weather conditions can be critical.The path planning algorithms developed in this study were also found to be effective at generating optimal paths for UAVs, resulting in more efficient mission execution. This has important implications for UAV applications such as precision agriculture, where efficient use of resources and reduced environmental impact are key factors.5.2 LimitationsThis study was conducted in a specific geographical location and may not be representative of other regions or environments. The results obtained may therefore not be directly applicable to other locations or applications.Additionally, the accuracy of the position estimation system may have been affected by external factors such as GPS accuracy and weather conditions, which were not controlled during the data collection phase.Furthermore, the path planning algorithms developed in this study did not take into account dynamic obstacles such as movingvehicles or pedestrians, which may affect the efficiency and safety of UAV missions.5.3 Future ResearchFuture research could focus on expanding the scope of this study by testing the hybrid system in different environments and regions, and evaluating its effectiveness for different applications.Additionally, future research could explore the integration of dynamic obstacle avoidance techniques into the path planning algorithms developed in this study, to further improve the efficiency and safety of UAV missions.Furthermore, advances in sensor technology and machine learning techniques could be incorporated into the hybrid system and path planning algorithms to further improve the accuracy and efficiency of UAV systems.Overall, the findings of this study have significant implications for the development of more efficient and accurate positioning systems for UAVs, as well as for the development of optimal path planning algorithms for UAV applications.。
Additel 761A自动高压测量仪说明书

Series Automated Pressure CalibratorsAdditel 761AAutomated and self-contained pressure generation and control to 1,000 psi ( 70 bar)Standard accuracy to 0.02%FSOptional precision accuracy models to 0.01%FSTwo removable internal pressure modules for multi-range selection Control stability to 0.003%FSPortable, designed for use in the field and in the lab Ability to measure two external pressure modules Wi-Fi, Bluetooth, USB and Ethernet communication HART and profibus communication Data logging and task managementPatented electric pump technology and improved speed OVERVIEWAt Additel, innovation and continuous improvement are part of our company's culture and the products we introduce. When we set out to deliver the Additel 761A series calibrators, we knew we needed to provide breakthrough improvements and additional value to the existing line of calibrators (Additel 761 series). The ADT761A has many improvements: increased pressure range to 1,000 psi (70 bar), removable internal pressure modules, optional precision models to 0.01%FS, increased speed to pressure, ability to read two external pressure modules, touch screen display, Wi-Fi, Bluetooth, and Ethernet communications, double the original battery life, and more!Just like the first generation, this second generation product is completely self-contained and automated with a built-in pump for pressure generation and precision control technology. Simply set the desired pressure and watch the calibrator do thework.ADT761A-LLPThe Additel 761A-LLP is designed for low pressure calibration and comes with a ±30 inH2O (±75 mbar) high range module and a low range module of your choice ranging from ±20 inH2O to as low as ±0.25 inH2O (±50 to ±0.62 mbar). This unit has an accuracy of 0.05%FS with control stability better than 0.005%FS. All measurements can be made in differential or gaugepressures.ADT761A-DThe Additel 761A-D also provides differential and gauge measurement which covers the range of -13.5 to 35 psi (-0.95 to 2.5 bar). This unit comes with a CP35 module (-13.5 to 35 psi) and one low range module of your choice rangeing as low as ±10 inH2O (25 mbar). Each ADT761A-D can be preconfigured with the modules that fit your need to give you the best precision at the pressures you perform calibrations.ADT761A-500The Additel 761A-500 will generate and control from vacuum pressures upto 500 psig (35 bar.g). Both gauge and absolute pressures can be realizeddue to a built-in barometer. Each unit comes with a CP500 module (-13 to500 psig) for the high range and the low range can be preconfigured basedon the variety of modules available down to 10 psig (0.7 bar.g).ADT761A-1KThe Additel 761A-1K will generate and control from vacuum pressures up to 1,000 psig (70 bar.g). This unit can typically achieve 1,000 psi in less than 45 seconds. Like the ADT761A-500, both gauge and absolute pressures can be realized due to a built-in barometer. Each unit comes with a CP1K module (-13 to 1,000 psig) for the high range and the low range can be preconfigured based on the variety of modules available down to 30 psig (2 bar.g).ADT761A-APXR Precision Accuracy OptionsThe Additel 761A series includes a precision accuracy option whichprovides an accuracy of 0.01%FS. This calibrator option includes a singlenon-removable sensor and can measure absolute and gauge pressures.Model configurations are available from 15 to 1,000 psig (1 to 7 bar.g).ADT761A-BPThe Additel 761A-BP is designed for calibration of barometer sensors. Witha range of 100 to 1200 hPa and an accuracy of 0.01%FS, this unit is idealfor calibration on the bench or in the field.Pressure SpecificationsElectrical Specifications[1] One year accuracy (including 1 year stability). FS specification applies to the span of the module range.[2] Specification based on gauge measurement. An additional 60 pa uncertainty will need to be included when measuring in absolute mode. Applicable only for use with the ADT761A-500 and ADT761A-1K* Additel 761A calibrators support 160A series intelligent digital pressure modules that are available for gauge, vacuum and absolute pressure from -15 psi to 60,000 psi (-1 bar to 4200 bar). For detailed specifications refer to the 160A series pressure modules data sheet.Internal Module Specification and Compatibility[1] FS specification applies to the span of the module range. Accuracy includes one-year stability, except for DP025 to DP10 modules.[2] Accuracy is a 6 months spec, 1-year long-term drift is 0.2%FS.[3] Accuracy is a 6 months spec, 1-year long-term drift is 0.1%FS.[4] Accuracy is a 6 months spec, 1-year long-term drift is 0.05%FS.[5] Specification based on gauge measurement. An additional 60 pa uncertainty will need to be included when measuring in absolute mode.Applicable only for use with the ADT761A-500 and ADT761A-1KPressure gauge / transmitter / switch calibrationGeneral SpecificationsPressure RangeHigh-Range Pressure ModuleLow-Range Pressure Module Accuracy RangeAccuracyDP30: -75 to 75 mbar 0.05%FSUser selectable fromDP20 to DP025See Internal ModuleTable CP35: -0.95 to 2.5 bar 0.02%FSUser selectable from DP10 to CP30See Internal ModuleTable Task ManualHigh Pressure Automated CalibrationORDERING INFORMATIONModel NumberNPressure Range。
诺瓦科技WIFI-LED控制卡TB4规格书

5 Product Specifications ................................................................................................................ 10 6 Audio and Video Decoder Specifications .............................................................................. 11
Taurus Series
Multimedia Players
Document Version: Document Number:
V1.3.2 NS120100359
TB4 Specifications
Copyright © 2018 Xi'an NovaStar Tech Co., Ltd. All Rights Reserved.
4 Software Structure ........................................................................................................................ 9
与术语imu相关的经典文献

与术语imu相关的经典文献与术语IMU(Inertial Measurement Unit)相关的经典文献有很多,以下是一些具有代表性的文献:1. 《Modeling Inertial sensors errors using allan variance》:这篇硕士论文介绍了如何使用 Allan 方差分析对惯性传感器误差进行建模。
该方法可以帮助理解惯性传感器的工作原理,提高其测量精度和可靠性。
2. 《A New Calibration Method for Strapdown Inertial Navigation Systems》:这篇文章介绍了一种新的校准算法,用于对捆绑式惯性导航系统进行校准。
该算法可以提高系统的定位精度和稳定性。
3. 《CALIBRATION OF A MEMS INERTIAL MEASUREMENT UNIT》:这篇文章介绍了一种基于微电子机械系统(MEMS)的惯性测量单元的校准方法。
该方法可以提高 MEMS 惯性传感器的测量精度和稳定性。
4. 《Calibration of a Novel MEMS Inertial Reference Unit》:这篇文章介绍了一种新型的基于 MEMS 的惯性参考单元的校准方法。
该方法可以提高 MEMS 惯性参考单元的测量精度和稳定性。
5. 《Visual-Inertial Odometry for Robust and Precise Estimation of Camera and Robot Motion》:这篇文章介绍了一种基于视觉和惯性的里程计方法,可以用于机器人和无人机的精确姿态估计和运动轨迹规划。
6. 《Visual-Inertial SLAM for Monocular and Stereo Cameras》:这篇文章介绍了一种基于视觉和惯性的同步定位与地图构建(SLAM)方法,可以用于单目和立体相机的姿态估计和环境地图构建。
遥感传感器定标的流程

遥感传感器定标的流程英文回答:Radiometric Calibration of Remote Sensing Sensors.Radiometric calibration is a process that corrects the raw data from a remote sensing sensor to ensure the accuracy and consistency of the measurements. It involves removing systematic errors and converting the raw data into physical units that are meaningful for scientific analysis. The calibration process typically involves the following steps:1. Pre-flight calibration: This is typically done in the laboratory before the sensor is deployed. It involves characterizing the sensor's response to known radiance levels using a calibration target or a reference source. The results of the pre-flight calibration are used to generate calibration coefficients that are applied to the raw data.2. In-flight calibration: This is done during the sensor's operation to monitor and correct for any changes in the sensor's calibration over time. It typically involves using on-board calibration targets or observing natural targets with known radiance values. The results of the in-flight calibration are used to update thecalibration coefficients if necessary.3. Post-flight calibration: This is done after the sensor has been deployed to assess the overall performance of the calibration and to make any final adjustments to the calibration coefficients. It typically involves comparing the sensor's measurements to data from other sensors or ground-based measurements.Methods of Radiometric Calibration.There are various methods for performing radiometric calibration, including:Absolute calibration: This involves using a referencesource with known radiance values to determine the sensor's response function. It is considered the most accurate method but can be complex and expensive to implement.Relative calibration: This involves comparing the sensor's measurements to those of another sensor that has been calibrated. It is less accurate than absolute calibration but is simpler and more cost-effective.Vicarious calibration: This involves using natural targets with known radiance values, such as sun or moon, to calibrate the sensor. It is a low-cost method but can be less accurate than the other methods.Importance of Radiometric Calibration.Radiometric calibration is crucial for ensuring the accuracy and reliability of remote sensing data. It allows scientists to compare data from different sensors and platforms, and to track changes in the Earth's surface over time. Without proper calibration, the data collected by remote sensing sensors would be unreliable and unusable forscientific analysis.中文回答:遥感传感器定标流程。
envi的radiometric calibration工具原理 -回复

envi的radiometric calibration工具原理-回复Radiometric calibration is a crucial step in the field of remote sensing, as it ensures the accuracy and comparability of the data collected by different sensors and platforms. The radiometric calibration tool used by the ENVI software package employs a set of algorithms and mathematical transformations to convert raw image data into radiometrically calibrated imagery. In this article, we will explore the principles behind the radiometric calibration process and understand how it works in the context of ENVI.Step 1: Understanding Radiometric CalibrationRadiometric calibration involves converting the raw digital numbers (DN) recorded by the sensor into physical units of radiance or reflectance. The calibration process compensates for sensor variations, atmospheric effects, and other factors that affect the radiometric values of the captured data. It essentially establishes a quantitative relationship between the recorded DN values and the corresponding physical measurements.Step 2: Sensor Calibration ParametersTo perform radiometric calibration in ENVI, accurate knowledge of the sensor calibration parameters is essential. These parametersinclude gain, offset, saturation values, and wavelength-dependent response functions. The calibration process utilizes these parameters to transform DN values into radiometric values.The gain factor represents the conversion factor from DN to radiance units, while the offset compensates for any potential bias in the sensor's measurements. Saturation values indicate the maximum DN value that can be recorded by the sensor without saturating. Lastly, the wavelength-dependent response functions describe the sensor's sensitivity to different wavelengths.Step 3: Dark Current and Read Noise CorrectionsDark current and read noise are two common sources of noise in remote sensing data that can affect the accuracy of radiometric calibration. Dark current refers to the electrical signal generated by the sensor even in the absence of incident light. Read noise arises during the process of converting analog signals to digital values.ENVI's radiometric calibration tool applies dark current and read noise corrections to remove these sources of noise. By subtracting the dark current signal from the raw data and reducing the read noise, the tool enhances the accuracy of the radiometric calibrationprocess.Step 4: Atmospheric CorrectionsThe radiometric values collected by satellite sensors are often affected by atmospheric interference. Atmospheric gases and particles scatter and absorb solar radiation, leading to errors in the measured radiance or reflectance values. ENVI's radiometric calibration tool employs atmospheric correction techniques to account for these atmospheric effects.Atmospheric corrections utilize radiative transfer models and atmospheric parameters to estimate and remove the atmospheric interference. By estimating the atmospheric path radiance and transmittance, the tool can accurately reconstruct the true radiance or reflectance values at the sensor level.Step 5: Spectral Response Function CorrectionsDifferent sensors have varying spectral response functions, which define their sensitivity to different wavelengths. ENVI's radiometric calibration tool accounts for these spectral response function variations by applying corrections to ensure consistency among different sensors.The tool utilizes the known spectral response function of the sensor to correct the radiometric values accordingly. This correction aligns the measurements from different sensors to a common radiometric scale, facilitating comparison and analysis of imagery collected by multiple platforms.Step 6: Validation and VerificationThe radiometric calibration process is not complete without validation and verification steps. ENVI's radiometric calibration tool provides the capability to compare the calibrated data against ground-truth measurements or reference data. This step allows users to evaluate the accuracy and reliability of the radiometric calibration results.By comparing the calibrated imagery with field measurements or reference datasets, users can quantify the uncertainties associated with the radiometric calibration and assess the suitability of the calibrated data for various applications.ConclusionENVI's radiometric calibration tool plays a vital role in ensuring theaccuracy and comparability of remote sensing data. By applying a series of corrections for sensor variations, atmospheric effects, and spectral response function variations, the tool transforms raw digital numbers into radiometrically calibrated imagery. This calibrated imagery provides researchers and analysts with reliable and accurate data for a wide range of applications, including land cover mapping, agriculture monitoring, and environmental modeling.。
TBS系列插入扬声器说明书

Installation fittings are standard 1-1/2" (TBS-XSX Models) or directly on the flow sensor or mounted remotely. The Series
2” (TBS-XLX Models) male NPT. Fittings such as saddles and RTI (loop powered) provides digital rate and total display, as
4 to 20 mA analog output. The BAT is a blind analog (4 to 20
mA) transmitter. Programmable pulse for pump pacing is
Ruby bearings and a non-drag pickoff give these adjustable available with the PWD.
GENERAL INFORMATION
The Series TBS is an adjustable depth insertion turbine that
comes in brass or 316 stainless models to fit 3” to 40” pipe. If desired, a modular system of electronics can be installed
F-TBS
SERIES TBS
INSERTION TURBINE instructions
-0XX
TBS-1XX
Table of Contents
General Information Features, Specifications........................................................................................................................................ Page 1 Installation Piping, Immersion, Positioning the Meter............................................................................................................ Page 2 Straight Pipe Recommendations..........................................................................................................................Page 3 Full Pipe Recommendations.................................................................................................................................. Page 4 Fitting Installation, Meter Installation................................................................................................................... Page 5 Proper Depth Setting, Dimension C, Pipe Wall Thickness................................................................................... Page 6 Set-Up Connection, Calibration, K-Factors....................................................................................................................... Page 7 Operation Flow Range, Flow Rates......................................................................................................................................... Page 8 Parts List Parts Exploded View.............................................................................................................................................. Page 9 Troubleshooting & Repair Troubleshooting, Repair, Rotor Replacement.......................................................................................................... Back
维美德t191说明书

A128 Error in function of the clutch -or the accelerator pedal electrical circuits,which may change the tractor functions:the clutch pedal function,the Powershift-functions or the shuttle functions.The tractor can normally be driving direction.When disengaging the transmission use the HiShift-switches or the shuttle lever.错误在离合器的功能或油门踏板的电路,它可以改变拖拉机功能,动力换挡功能,或穿梭功能。
拖拉机通常可以行驶方向。
当分离传输使用快速换挡按钮开关或操纵杆。
A192A293 Fuel sensor information is incorrect.Driving can be continued normally.Incorrect display of the fuel gauge.燃油传感器信息错误,燃料表显示不正确。
可以继续正常驾驶。
A215 Error in function of the engine fuel system.The engine output will be limited and the maximum running speed is1500 rpm.发动机燃油系统功能错误。
发动机的输出是有限的,最大运行速度是1500转。
A236 Error in the engine controlling system.The engine works but malfunctions may occur (ck of output,smoking).Driving can be continued temporarily,but the malfunction must be repaired as soon as possible.发动机控制系统误差。
TRCIII冰点参考室说明书

K-12K The TRCIII ice point TM Calibration Reference Chamber relies on the equilibrium of ice and distilled, deionized water at atmospheric pressure to maintain 6 reference wells at precisely 0°C (32°F). The wells extend into a sealed cylindrical chamber containing the distilled, deionized water. The outer walls of the chambers are cooled by thermo-electric cooling elements. The increase in volume produced by the creation of ice crystals within thecell is sensed by the expansion of a bellows, which operates a microswitch and controls the cooling elements. The alternate freezing and thawing of the ice accurately maintains a 0°C (32°F) environment around the reference wells.The automatic operational features of this instrument eliminate the need for frequent attention, required of common ice baths. On/off cycling of a pilot light indicates proper operation of the unit at ice point temperature.Any combination of thermocouples may be used with this instrument by simply inserting the reference probes in the reference wells. Calibration of other types of temperature sensors at 0°C (32°F) may also be performed.When accurate temperature measurements are required, the TRCIII ice point TM Chamber delivers the precision you need. The reference wells are maintained at 0°C (32°F) to within ±0.1°C and a stability of ±0.04°C for constant ambient. Continuous cycling operation maintains constant equilibrium conditions within the cell, eliminating the slow drift often experienced in common ice baths as meltingice point ™ Calibration Reference Chamber High Precision—Uses FreezingWater to Maintain 0°C (32°F)U A 0°C (32°F) Thermoelectric “Refrigerator”U E liminates Old Fashioned “Ice Bath”U F or Versatile Use in the Factory, Laboratory, Instrument Shop U C alibration of All Temperature Instruments and Sensors U R ugged Outer Case for Safe Portability U Accepts Up to 6 Probes U A vailable in 120 or 220 Vac Models U N IST Traceable Calibration Available U C ompanion Dry Block Probe Calibrator Available (Model CL900/950)TRCIII ice point™ shown with companion CL950 dry block probe calibrator. See for details.TRCIII occurs. TRP reference probes, used with the TRCIII, provide a junction from thermocouple alloys to copper wire, at the probe tip. When inserted into the TRCIII, TRP probes enable the change from thermocouple alloy to copper at 0°C (32°F), for accurate cold junction compensation.U s e U p t o 6 P r o b e s a t O n e T i m e w i t h T R C I II K-13SpecificationsReference Wells: 6 wells, 5⁄32" ID, 33⁄4" deep; wells are thermally and electrically grounded to each other; accepts 1⁄8" OD probes Reference Temperature: 0°C Accuracy: ±0.1°C or betterStability: ±0.04°C for constant ambient Environmental Ambient: 2 to 32°C (35 to 90°F)Power Required: 115/220 V, 60 Hz, 100 Watts Stabilization Time: 2 or 3 hours depending on ambient temperature and thermal loadDimensions:305 H x 159 W x 322 mm D (12.0 x 6.25 x 12.7")Weight: 9.5 kg (21 lb)suffix “-24” or “-36” to model number, for an additional cost.For thermocouple Types R, S, B, C, G, D, standard length is 6". Add appropriate suffix for each additional 6", for an additional cost.VoltmeterCuCu TRC Copper Wire Sturdy handle for easy portability.U M ade with Special Limits of Error Material U A ll StandardCalibrations Available U C omes Complete with Mating Connectors U C an Be Ordered with 12, 24 or 36" Leads Thermocouple TRP FeaturesOrdering Example: TRCIII, ice point™ reference cell, TRP-K, TRP-J, TRP-T, TRP-E,Type J, K, T and E temperature reference probes. OCW-3, OMEGACARE SM extends standard 1-year warranty to a total of 4 years.OMEGACARE SM extended warranty program is available for models shown on this page. Ask your sales representative for full details when placing an order. OMEGACARE SM covers parts, labor and equivalent loaners.。
Fluke Calibration温度传感器校准指南说明书
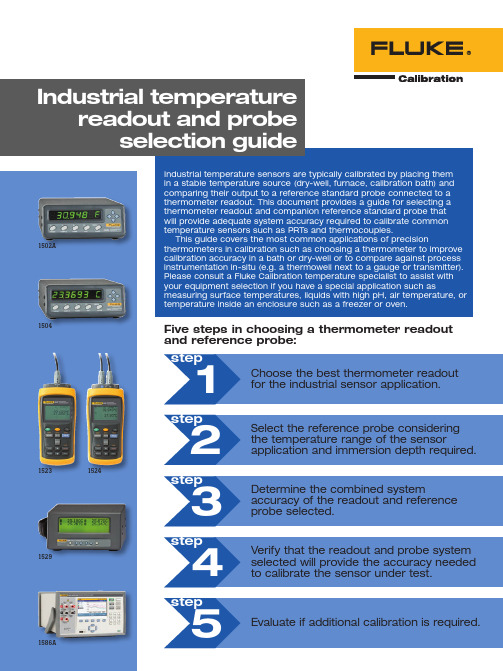
Five steps in choosing a thermometer readoutand reference probe:12345stepstepstepstepstepChoose the best thermometer readoutfor the industrial sensor application.Evaluate if additional calibration is required.Select the reference probe consideringthe temperature range of the sensorapplication and immersion depth required.Determine the combined systemaccuracy of the readout and referenceprobe selected.Verify that the readout and probe systemselected will provide the accuracy neededto calibrate the sensor under test.1502A1504152315291524Several questions should be considered in selecting the right thermometer readout:•Which temperature sensors need to be calibrated—PRTs/RTDs, thermistors, thermocouples?•Will the readout be used in the field or in a calibration lab?•How many channels are needed on the readout?•What level of data logging, graphing and recording features are required?•Is temperature source control of dry-wells, baths, or furnaces desired to help automate sensor calibration? The following table provides a guide for selecting a readout with these technical needs in mind.2No calibration included. Check with your distributor for calibration options.3NIST traceable calibration included. NVLAP accredited calibration optional.4“Basic Accuracy” includes calibration uncertainty and short-term repeatability. It does not include long-term drift.It is important to select a reference probe that covers the full temperature range of the sensor application. Table 2 summarizes temperature ranges for selected reference probes.Table 2: Temperature ranges for select Fluke Calibration probes.Consider the lengthMake sure the reference probe is long enough to reach the bottom of the dry-well or the sensing element of the unit under test in a bath. The sensing element of a PRT is usually in the bottom one inch of the probe. A thermistor sensing element is only a few millimeters at the bottom of the probe. The measurement junction of a thermocouple is where the two dissimilar wires connect.To ensure the reference and the unit under test are at the same temperature during comparison calibration, the sensing element of the unit under test needs to be vertically aligned with the center of the sensing element of the reference probe. Also, inaccurate measurements can occur if either the reference probe or the unit under test is not sufficiently immersed in the dry-well or bath.Consider the diameterMinimum immersion is the minimum depth the probe needs to be inserted into the bath or dry-well for accurate measurement. It is determined by the diameter of the selected probe and the length of its internal sensing element.A general rule is the minimum probe immersion needs to be 15 times the probe diameter plus the sensor length. Fluke Calibration 6-inch and 9-inch PRTs have a 3/16 inch diameter rather than a 1/4 inch diameter and can be a better choice for calibrating shorter probes. See Table 2 for minimum immersion depths for select probes.Safety and other considerationsSome applications may require exposing more of the probe to extreme temperatures than is desirable. Exposing the probe handle to extreme temperatures poses safety concerns for the user, since it may be too hot or cold to touch without safety gear. Also, the transition junction is located inside the probe handle base where the probe connects to the cable and can be damaged by extreme temperatures. Finally, if high temperatures in the transition junction cause the insulation resistance to decrease below 100 MΩ, the performance of the probe might also decrease.For example, a 5615-12 Secondary Reference PRT can operate over a range from –200 °C to 420 °C. However, the 5615-12 transition junction range is –50 °C to 200 °C. This means the probe is designed to measure tempera-tures from –200 °C to 420 °C, but the probe will be damaged if the handle is exposed to temperatures outside the range of –50 °C to 200 °C. Even if the probe is not damaged, touching a probe handle that is extremely hot or cold with bare hands could result in burns.In this example, the 5615-12 can be used to calibrate sensors as low as -200 °C, but would be damaged if placed in a freezer at -80 °C since the transition junction lower limit is -50 °C. For a freezer application, the 5606 Full Immersion PRT would be the right choice since the probe and transition junction can operate at a lower limit of -200 °C.Table 3 shows the system accuracy for Fluke Calibration 1523/1524, 1502A/1504, 1529, and 1586A Super-DAQ thermometer readouts and selected reference probes (5615, 5627A, 5628, 5605, 5610) or Type T and K thermo-couples. For example, the 1586A Super-DAQ with DAQ-STAQ Multiplexer and a 5628 Secondary Standard PRT has a system accuracy of ± 0.011 °C at 0 °C.Reference probes are connected to the thermometer readout, but readouts don’t all share the same connection scheme. When a readout and probe are paired, be sure to choose a model terminated with the right connector. For your convenience, probe models with the correct termination for the readout are shown in Table 3. Note that the readout accuracy with a 5606 probe assumes that the probe has received an optional calibration.A Lemo-to-Unversal Thermocouple adapter 2373-LTC is available for connection to thermocouples.The 1524 can measure two channels at a time, but only one channel can be a thermocouple.5615-6 range is -200 °C to 300 °C. 5615-9, -12 range is -200 °C to 420 °C. 5627A-6, -9 range is -200 °C to 300 °. 5627A-12 range is -200 °C to 420 °. Connector type: DThis is a standard DIN connector and does not contain a microchip with the probe coefficients.5615-6 range is -200 °C to 300 °C. 5615-9, -12 range is -200 °C to 420 °C. 5627A-6, -9 range is -200 °C to 300 °C. 5627A-12 range is -200 °C to 420 °C.The 1529 works with probes that are terminated with the type L connector. These are gold plated mini spade lugs. The 1529 is also compatible with gold pins, mini banana plugs, and bare wire probe terminations. This version of the 1529 is also compatible with mini thermocouple connectors.5616-6 range is -200 °C to 300 °C. 5615-9, -12 range is -200 °C to 420 °C. 5627A-6, -9 range is -200 °C to 300 °C. 5627A-12 range is -200 °C to 420 °C. Connector type: LThe 1529 works with probes that are terminated with the type L connector. These are gold plated mini spade lugs.The 1529 is also compatible with gold pins, mini banana plugs, and bare wire probe terminations.5615-6 range is -200 °C to 300 °C. 5615-9, -12 range is -200 °C to 420 °C. 5627A-6, -9 range is -200 °C to 300 °C.5627A-12 range is -200 °C to 420 °C.Connector type: LThe 1586A works with probes that are terminated with the type L connector. These are gold plated mini spade lugs.The 1586A is also compatible with gold pins, mini banana plugs, bare wire, and mini thermocouple probe terminations.5615-6 range is -200 °C to 300 °C. 5615-9, -12 range is -200 °C to 420 °C. 5627A-6, -9 range is -200 °C to 300 °C. 5627A-12 range is -200 °C to 420 °C. Table 3: Readout accuracy with selected probes.The calibration system comprised of a readout and reference probe needs to have a higher level of accuracy than the temperature sensor being calibrated. A “test accuracy ratio” (TAR) of 4:1 or 3:1 is commonly used as a guide-line. A 4:1 TAR means the calibration system is four times more accurate than the sensor being calibrated. In this example, the system with a 4:1 TAR would be more accurate than a system with 3:1 TAR.Table 4 shows the minimum system accuracy required to calibrate common temperature sensors (Grade A and B PRTs, Type T and K thermocouples). For example, a readout and reference probe system with a combined accuracy of ± 0.06 °C would be needed to calibrate a Grade B PRT at 0 °C with a 4:1 TAR.Assume the 1586A Super-DAQ with DAQ-STAQ Multiplexer and a 5628 Secondary Standard PRT were selected as the readout-and-probe system. The 1586A/5626 system would be a good choice to calibrate a Grade B PRT. The 1586A/5626 system accuracy of ± 0.011 °C at 0 °C is much better than the ± 0.06 °C system accuracy at 0 °C required to calibrate a Grade B PRT with a 4:1 TAR.*ASTM Specification E1137 “Standards Specification for Industrial Platinum Resistance Thermometers”Table 4: Minimum system accuracy required for PRT and thermocouple calibration (± °C).Factory calibrationIt is standard practice for all Fluke instruments to include a factory calibration that is traceable to national stan-dards. Traceability means that there is an unbroken chain of comparisons between the instrument and a national standard providing assurance that measurements obtained with the instrument correlate to a national standard at a particular level of uncertainty.In a few cases, probes such as the 5606 do not include a factory calibration, but a calibration is an avail-able option. If you purchase an uncalibrated probe, then the chain of traceability is broken until a calibration is performed.With many Fluke instruments, the factory calibration is also accredited to ISO 17025. Table 5 summarizes the factory calibrations for the instruments discussed in this guide. Typically, type T and type K thermocouples are provided uncalibrated by the manufacturer. Check with your distributor about temperature instrument calibrationoptions available.Table 5: Factory calibration included with selected Fluke readouts and probes.System calibrationIn addition to a factory calibration for both the probe and read-out, you may desire to verify the performance of the probe andreadout together with a “system calibration.” This system cali-bration provides a higher level of assurance that the instruments are performing as expected when combined together and all probe coefficients are entered correctly into the readout. Check with your distributor about system calibration options available. SummaryThis guide has covered the steps to follow when choosing a readout and probe appropriate for your application. Tempera-ture range of the application and accuracy required are key considerations, but other factors discussed in this guide should be evaluated. If you have a special application such as measur-ing surface temperatures, liquids with high pH, air temperature, or temperature inside an enclosure such as a freezer or oven, please consult a Fluke Calibration temperature specialist to assist with your equipment selection.Fluke CalibrationPO Box 9090, Everett, WA 98206 U.S.A.Fluke Europe B.V.PO Box 1186, 5602 BDEindhoven, The NetherlandsWeb access: http://www.flukecal.euFor more information call:In the U.S.A. (877) 355-3225 orFax (425) 446-5716In Europe/M-East/Africa +31 (0) 40 2675 200 or Fax +31 (0) 40 2675 222In Canada (800)-36-FLUKE orFax (905) 890-6866From other countries +1 (425) 446-6110 or Fax +1 (425) 446-5716Web access: ©2014 Fluke Calibration.Specifications subject to change without notice. Printed in U.S.A. 2/2015 6004176a-enPub-ID 13281-engModification of this document is not permitted Fluke Calibration. Precision, performance, confidence.™。
Audioengine B2 蓝牙声音器快速引导说明书

Quickstart GuideAudioengine B2 Premium Bluetooth ® SpeakerQuick SetupSetup and pairing is really easy. The following instructions will help you connect B2 with your tablet, computer, or smartphone.Step 1: Connect the Bluetooth antenna to the B2 rear panel.The B2 will not function without the antenna connected.Step 2: Connect the power cable to the B2 rear panel and plug the power cable into an AC outlet.Step 3: Turn on the B2 power switch, which is located on the rear panel. B2 will automatically go into pair mode and the Pair button on the B2 rear panel should be ashing.Step 4: On your device, turn on Bluetooth and go to Bluetooth preferences.Step 5: Select “Audioengine B2” to pair and connect. The Pair indicator on the B2 rear panel should be solid.Step 6: Play your music and adjust volume levels on B2 and your device.Repeat Steps 3 thru 6 to add additional devices. B2 can connect to only one device at a time, however it will remember up to six devices.To disconnent B2 from a paired device and put B2 back into pair mode, press and hold the Pair button on the B2 rear panel until the indicator begins ashing.12CleaningWe don’t recommend using any solvents or cleaners on Audioengine cabinets or speakers. Just wipe down with a soft, dry cloth.Break-In PeriodB2 sounds great right out of the box and will sound even better over time. However, give it 40 to 50 hours break-in time before doing any critical listening.Troubleshooting TipsB2 is connected but the Pair button does not light up.Verify that the B2 is plugged into a functioning AC outlet.My device will not pair with B2.Verify that Bluetooth on the device is turned on.Con rm that the B2 Pair button is blinking (in Pair/Discovery mode).Make sure your device is within range of the B2.The B2 Pair light is solid, but I cannot connect my device.Make sure no other devices are connected. If so, either disconnect or turn o Bluetooth on the other devices or press and hold the B2 Pair button until it ashes, then try connecting.Try unpairing and re-pairing your device to the B2.Cycle power by turning the B2 power switch o and back on again.B2 pair light is solid and my device is connected but no audio output.Check the volume levels on your computer OS and player app.Try unpairing and re-pairing your device to the B2.Cycle B2 power by disconnecting and reconnecting the power cable.The volume output level from B2 seems low.Check the volume levels on your computer OS and player app.Also check the volume level on the rear panel of your B2.Only one side of the B2 plays music.Check your music player app and/or OS audio controls to ensure that the audio balance is centered.345Troubleshooting Tips (cont’d)The sound quality is poor and/or audio is cutting out.Move B2 or your device away from cordless phones, routers, micro-wave ovens, or other Bluetooth devices.Try moving your device closer to B2.Try another location.Turn o your device’s Wi-Fi.Try unpairing and re-pairing your device to the B2.Unplug power from B2 and power back on.Check that your device’s OS is updated to the latest version.More InfoMore product information and setup tips can be found on our website: Contact SupportIf you have any questions or feel you may need service, contact us via email: **************************or call toll-free in the United States: (877) 853-4447B2 Rear ViewSafety Instructions1. Please read these instructions before using this product.2. Keep these instructions for future reference.3. Heed all warnings on the product and in this guide.4. Follow all instructions.5. Do not use this apparatus near water or moisture.6. Clean only with a dry cloth and as directed by the manufacturer.7. Do not block any ventilation openings. Install in accordance with the manufacturer's instructions.8. Do not install near any heat sources, such as radiators, heat registers, stoves or other apparatus that produce heat.9. Do not defeat the safety purpose of the polarized or grounding-type plug. A polarized plug has two blades with one wider than the other. A grounding-type plug has two blades and a third grounding prong. The wider blade or third prong are provided for your safety.10. Protect the power cord from being walked on or pinched, particularly at plugs, convenience receptacles, and the point where they exit from the apparatus.11. Use only attachments or accessories speci ed by the manufacturer.12. Use only with the cart, stand, tripod, bracket or table speci ed by the manufacturer or sold with the apparatus. When a cart is used, use caution when moving the cart/apparatus combination to avoid injury from tip-over.13. Unplug this apparatus during lightning storms or when unused for long periods of time to prevent damage to this product.14. Refer all servicing to quali ed service personnel. Servicing is required when the apparatus has been damaged in any way such as power supply cord or plug is damaged, liquid has been spilled or objects have fallen into the apparatus, the apparatus has been exposed to rain or moisture, does not operate normally, or has been dropped.IntroductionWelcome to the Audioengine family and congratulations on your purchase of the Audioengine® B2 Premium Bluetooth® Speaker! The Audioengine team is dedicated to bringing you the highest-qualitylistening experience possible and the Audioengine B2 was designed with the same attention to detail and operational simplicity as all otherAudioengine products. Our goal is to get you to your music as simply as possible without all the “gadget tinkering” many other products require. As with our other past e orts we thank our customers, distributors and resellers for the inspiration to create another great product.What’s in the box B2 Bluetooth Speaker Power cableMicro ber speaker bag Quickstart guideFeaturesStreams audio from any Bluetooth-enabled device Easy setup, connects in secondsCustom Kevlar woofers and silk tweeters Hand-built wood cabinet Detachable magnetic grill Aux audio inputOverviewYour computer, iDevice, or Android phone already has Bluetooth, so get more out of your music with the B2 wireless speaker. Experience award-winning Audioengine® sound, including hand-built wood cabinets, Bluetooth® aptX® coding and extended wireless range.561 Volume control2 Pair button/power indicator3 Bluetooth antenna4 Aux audio input (mini-jack)5 AC power inlet6 Power on/o switchWarranty InformationAll Audioengine products have a 3-year Limited Warranty on parts and labor from date of purchase. The Limited Warranty applies only toAudioengine products purchased in the United States. Your warranty is automatic, so there is no need to register. For Limited Warranty coverage elsewhere, please contact your Audioengine dealer, reseller, or distribu-tor.What is coveredAll defective parts or faulty workmanship.What is not coveredThe Audioengine Limited Warranty does not cover damage caused by accident, misuse, abuse, neglect, excessive moisture, lightning, power surges, other acts of nature, unauthorized product modi cation or repairs, or failure to follow the instructions outlined in this guide.What we will doWe will repair or replace any defective parts, at our option, within a reasonable amount of time and free of charge any time during the warranty period. After service, we will be responsible for shipping the product back to you at our expense.What we ask from youYou will be responsible for shipping charges to Audioengine or to an authorized dealer. We recommend you keep the original shippingmaterials to prevent shipping damage if service is needed. Audioengine cannot be responsible for any damages incurred during shipping due to poor packing, so please pack well and make sure to insure your shipment.Tech StuHigh- delity Bluetooth® with aptX® transmission and extended range Supports all Bluetooth-enabled devicesHand-built wood cabinet with magnetic speaker grill Auxiliary analog mini-jack input Built-in power supplySpeci cations Type 2.0 powered Bluetooth speaker Ampli er type Dual class AB monolithic Power output 60W peak total (15W RMS/30W peak per channel), AES Drivers 2.75” Kevlar woofers 3/4“ Silk dome tweeters Inputs Bluetooth, 3.5mm stereo mini-jack Input voltages 100-240V 50/60Hz auto-switching SNR >90db (typical A-weighted)THD+N <0.05% at all power settings Crosstalk -50dB Frequency response 65Hz-22kHz (±2.0dB)Supported Bluetooth pro les aptX, A2DP and AVRCP D/A converter TI PCM5102A Wireless operation range up to 100ft (30m) typical Product dimensions 4”(H) x 12”(W) x 5.25”(D)Shipping weight 4.6kg/10lbsFor additional speci cations go to: How to obtain Audioengine Warranty serviceIf you have any questions about your warranty coverage or you feel you may need service, email the Audioengine US Service Center:************************** or call toll-free in the US: (877) 853-4447 We will do everything we can to answer your questions and resolve any issues as quickly as possible.Exclusive RemedyThis Limited Warranty is fully transferable provided the current owner furnishes the proof of purchase and that the serial number on theproduct is intact. THE MAXIMUM LIABILITY OF AUDIOENGINE SHALL NOT EXCEED THE ACTUAL PURCHASE PRICE PAID BY YOU FOR THE PRODUCT. IN NO EVENT SHALL AUDIOENGINE BE LIABLE FOR SPECIAL, INCIDENTAL, CONSEQUENTIAL OR INDIRECT DAMAGES.Product Returns and RefundsWe sincerely hope you get as much enjoyment from our products as we've had creating them. However, should you have an issue or are not satis ed with any Audioengine product for any reason contact the reseller where you purchased your product or email us directly: **************************or call toll-free if in the US: (877) 853-4447About AudioengineAudioengine designs and builds innovative audio products with all your music in mind. Great sound, simple but elegant designs, high quality materials, and truly useful features are what Audioengine is about. We sincerely hope you get as much enjoyment from our products as we’ve had creating them!Information for Users on Disposal of Old Equipment [European Union]This symbol indicates that the electrical and electronic equipment should not be disposed as g eneral household waste at its end-of-life. Instead, the product should be handed over to the applicable collection point for the recycling in accordance with your national legislation.By disposing of this product correctly, you will help to conserve the environment and human health that could otherwise be caused by inappropriate waste handling of this product. For more information about collection point and recycling of this product, please contact your household waste disposal service or the shop where you purchased the product. Penalties may be applicable for incorrect disposal of this waste, in accordance with national legislation.[Other Countries outside the European Union]If you wish to dispose of this product, please do so in accordance with applicable national legislation or other rules in your country for the treatment of old electrical and electronic equipment.FCC Part 15 NoticeThis device complies with Part 15 of the FCC Rules. Operation is subject to the following two conditions:1) This device may not cause harmful interference.2) This device must accept any interference received, including interference that may cause undesired operation.Changes or modi cations not expressly approved by the partyresponsible for compliance could void the user's authority to operate the equipment.FCC Part 15 Notice (cont’d)This equipment has been tested and found to comply with the limits for a Class B digital device, pursuant to Part 15 of the FCC Rules. These limits are designed to provide reasonable protection against harmful interference in a residential installation.This equipment generates, uses, and can radiate radio frequency energy and, if not installed and used in accordance with theinstructions, may cause harmful interference to radio communica-tions. However, there is no guarantee that interference will not occur in a particular installation. If this equipment does causeharmful interference to radio or television reception, which can be determined by turning the equipment o and on, the user isencouraged to try to correct the interference by one or more of the following measures:Reorient or relocate the receiving antenna.Increase the separation between the equipment and receiver.Connect the equipment into an outlet on a circuit di erent from that to which the receiver is connected.Consult the dealer or an experienced radio/TV technician for help.FCC Radiation Exposure StatementThis equipment complies with FCC radiation exposure limits set forth for an uncontrolled environment. This equipment should be installed and operated with minimum distance 20cm between the radiator & your body.© 2014 Audioengine. All Rights Reserved.Audioengine and Audioengine B2 are trademarks of Audioengine.The Bluetooth name and the Bluetooth trademarks are owned by Bluetooth SIG, Inc. and are used by Audioengine under license.The aptX® mark and logos are registered trademarks of CSR plc.The Bluetooth® word mark and logos are registered trademarksowned by Bluetooth SIG, Inc.0700。
Jofra RTC-700高温参考温度校准器商品说明书

RTC SeriesReference Temperature CalibratorRTC-700Product DescriptionA METEK continues to develop new techniques to improve the performance, accuracy, convenience,and functionality of the popular Jofra calibration products. By doing so, we maintain our position as the leading worldwide manufacturers of temperature dry-block calibrators.We are proud to introduce our new high temperature model RTC (Reference Temperature Calibrator), which is no exception to the above and even more sophisticated than any existing calibrators. Features & ModelsThe RTC offers many new fantastic features such as:⏹ Patented DLC (Dynamic Load Compensation) system for perfect temperature uniformity in the insert.⏹ Unique, intelligent sensors for plug n’ play connection.⏹ USB connector for communication.⏹ Easy-to-read color VGA display with a perfect overview of the actual status.⏹ Intuitive, fast, and user-friendly navigation.⏹ Lightweight and easy to carry around.⏹ New functional carrying case design.⏹ New multi-hole insert kits covering all of the most used sensor sizes.⏹ High profile design and well-known, long lasting Jofra quality.The new RTC calibrator comes in three different models—A, B, and C.⏹ RTC-A reference temperature calibrator.⏹ RTC-B reference temperature calibrator with input for reference sensor, DLC sensor, and sensors-under-test.⏹ RTC-C reference temperature calibrator with input for reference sensor and DLC sensor.Key Features◆High AccuracyDown to ± 0.11°C using the external reference sensor. 4-wire True-Ohm Measurement technology is used.◆Excellent Stability, 0.008°C◆Wide Temperature RangeFrom 33 to 700°C (91 to 1292°F).◆Improved Temperature HomogeneityUnique, active triple-zone block ensures good temperature homogeneity in thecalibration zone.◆DLC (Dynamic Load Compensation)Perfect temperature uniformity in the insert, even when calibrating large sensors or many sensors at a time. (B and C models only.)◆Display Indicator for Temperature UniformityShows the degree of temperature uniformity in the insert when using the new DLCtechnology. (B and C models only.)◆Intelligent Reference SensorsJofra reference sensors are supplied with intelligent plugs, holding the calibration data (coefficients) of the reference sensor. This is a truly plug n’play calibration system.◆USB CommunicationAll RTC calibrators communicate via an easy-to-use USB port.◆Time SavingSuper high-speed cooling.◆EURAMETBest performing dry-block with regard to the EURAMET/cg-13v.01 guideline for thetesting of dry-blocks.DLC –Dynamic Load CompensationTo bring our well documented active dual-zone technology to an even higher level, we have developed the patented DLC system, making it possible to perform top calibration specifications without being affected by the actual load, e.g. many sensors or very big sensors.The RTC-700 adds active triple-zone temperature control.The DLC sensor improves the homogeneity even more, by controlling it not only the well, but inside the insert where the sensors-under-test are placed during calibration. The DLC sensor measures the temperature homogeneity in the insert and provides feedback to the active triple-zone sys-tem, which compensates the temperature difference to a minimum inside the insert. In this way, the DLC function makes the homogeneity indepen-dent of the different loads of the insert, making the RTC the best performing dry-block calibrator on the market when calibrated and tested according to the globally accepted EURAMET/cg-13v.01 guideline for calibration and testing of dryblocks.The DLC system is comprised of a special differential temperature sensor designed especially for the RTC. The sensor is placed in the insert and con-nected to the calibrator. When the DLC function is enabled, the calibrator will automatically equalize the temperature homogeneity inside the insert, along with the normal temperature control and stabilization.SlaveDLCMaster1000.050.100.15Axial Temperature Homogeneity in °CD i s t a n c e t o B o t t o m o f I n s e r t i n m m0.200.25DLC Function On DLC Function O Thermo Sensitive LengthDLC SensorDLC –User AdvantagesCalibrating with the DLC sensor offers the following advantages:1 Calibration of several sensors simultaneously.2 Calibration of thick sensors.3 Gives TSL (Thermo Sensitive Length) independency. It is no longer necessary to know the TLS of the sensor.4 Compensates for sensor production tolerances like the PT100 element being mounted in vari-ous positions in the sensor.5 Trouble free calibration of sensors with PT100 elements up to 60 mm length.6 The DLC indicator proves that the dual-zone is active and functioning well.7 Proves that the calibrator is working perfectly. The DLC value should be very close to 0.00 when the calibrator is loaded with DLC sensor and an external reference sensor.8 Together with the stability indication, the DLC indicates when the calibration values can be read.Axial temperature curves for an RTC calibrator with and without the DLC functionality activated.Unique Triple Zone Temperature PerformanceThe RTC series of calibrators provide precision temperature calibration of sensors, what-ever the type or format. This is accomplished through an innovative active triple-zone heat-ing technology.With the RTC-700’s active triple-zone heating technology, each heating zone is indepen-dently controlled for precision temperature calibration. The homogeneity in the lower part is close to that of a laboratory liquid bath. The lower zone ensures optimum heat dissipa-tion throughout the entire calibration zone. The upper zone compensates for heat loss from the sensor-under-test, and from the open top. This design also eliminates the need for extra insulation of sensors-under-test and makes it possible to calibrate liquid-filled and other mechanical sensors.USB and LAN/Ethernet ConnectionA USB connection facilitates easy communication with JofraCal. The USB connection also sup-ports easy download of future firmware upgrades. The USB connection provides fast and easy access to all laptops without the need of RS-232 to USB converters.Future-proof through e.g. a flash capability for easy firmware upgrades as well as already integrat-ed LAN communication, SD-card slot, and USB host connectors for future use.Intelligent Reference SensorsThe JOFRA STS-200 intelligent reference sen-sors and the DLC sensor contain individual cali-bration data regarding the sensor. Firstly, this means that the time-consuming coefficientdownloading sequence with risk of errors is no longer necessary. Secondly, the user can change the reference sensor and be up and running immediately.With the intelligent sensors, AMETEK has eliminated a source of error, and the system is now giv-ing a fail-safe plug’n’play calibration system.Unique Reference SensorsThe STS-200 reference sensors and the DLC sensors have been specially designed. They are both angled 90˚ and have been customized to fit the calibrator so that they are only slightly higher than the top of the RTC calibrator.The unique design makes it possible to calibrate threaded sensors and sensors with connection heads without any problems.Easy to Carry Only 24.9 lbs/11.3 kgA calibrator is carried from one job to another. Therefore, it is essential that the weight of the calibrator is as low as possible.We have thoroughly included the weight issue in our design and have developed design tech-niques that have made the RTC calibrator lightweight and easy to carry around without compro-mising its quality, durability, and functionality. The purpose of minimizing the weight of the RTC calibrator is to protect, especially frequent users from overload.Long Inserts for Accurate CalibrationThe new extended insert length increases the maximum possible diameter of the sensor under test to 16 mm. Switch tests of long bulb sensors can be carried out with very high accuracy.SetTemperatureInternal ReferenceTemperature Di erenceSensor-Under-TestU p p e r Z o n eM a i n Z o n eWide Temperature Range 700°CThe RTC-700 can perform calibration over a very wide temperature range starting from 33°C and up to 700°C (91 to 1292°F). This makes it possible to perform calibration jobs over a range of 667° C (1232° F) with only one calibrator.Easy to Read Color Display and User-Friendly NavigationThe 5.7" full color VGA display is very easy to read. The main temperatures, like SET, READ, TRUE and SUT (Sensor under test), are always displayed at all stages of the programming or calibration procedure.The navigation is menu-driven and very logical to use, and the display shows any important information needed for the current function in use. The communication windows pop up andare followed by discrete sound messages. The display is very bright, and the main information can easily be read from a distance. The advanced simplicity RTC user interface is available in English, German, Chinese, and Japanese.The large display contains more detailed information at a glance, such as:Up to five temperature readings simultaneously. Stability status.Load compensation status. Real time clock.Serial number of reference sensor. Sensor-under-test status.Fast Temperature CalibrationTime is money! This is why all the RTC calibrators have an increased heating and cooling speed compared to all other calibrators. With its newly developed heating block, the RTC-700 is able to perform a unique combination of high speed and high accuracy, resulting in savings in both production downtime and general calibration costs.Multi-Hole Insert KitsTwo special multi-hole insert kits have been developed to comply with the calibration of almost any sensor diameter without having to buy numerous inserts.The first kit is a metric insert kit consisting of only four inserts covering all diameters from 3 to 13mm. The other is an imperial insert kit consisting of only three inserts covering six different sizes from 1/8" to ½".All inserts have holes for both STS reference sensors and DLC sensors.With this insert kit in the carrying case, the user is now able to calibrate all commonly known sensor sizes. These insert kits are part of the JOFRA lightweight strategy.Special Designed Carrying CaseAMETEK has designed an all-in-one-handle carrying case that makes it possible to store both the STS reference sensors and DLC sensors in the carrying case with optimum physical protection. There is room for inserts and insulation plugs to cover all dimensions and compartments for the integrated support rod set, wires, manuals, certificates, plugs, insert tools etc.All compartments are specially designed to hold one of the above mentioned items. This makes it very easy to keep track of any accessories.For optimum protection of the calibrator and the accessories, the compartments are designed to hold the accessories fixed during transportation.Integrated Support RodThe integrated support rod is part of the reduced weightphilosophy. It is lightweight and very easy to mount onthe RTC. Two fixing holes are integrated in the calibratorwhere the support rods can be mounted. And even thoughits weight has been reduced by 50%, the support rod willremain very firmly positioned.MVI–Secure Temperature StabilityMVI stands for ’’Mains power Variance Im-munity’’. Unstable mains power is a majorcontributor to on-site calibration inaccura-cies. Traditional temperature calibrators oftenbecome unstable in production environ-ments where large electrical motors, heatingelements, and other devices are periodicallycycled on or off. The cycling of supply powercan cause the temperature regulator to per-form inconsistently, leading to both inaccurate readings and unstable temperatures.The JOFRA RTC calibrators all employ the MVI functionality, thus avoiding such stability problems. The MVI functionality is obtained by running the calibrator on stabilized DC voltage.Highest Accuracy (models B & C only)The RTC series calibrators may be supplied with a built-in reference thermometer to be used with an external reference sensor. This feature allows the instrument to perform calibrations on-site, while maintaining high accuracy.A special 90° angled external reference sensor has been designed to accommodate the calibration of sensors with a transmitter head, top connector, or similar arrangement. The user can decide whether to read the built-in reference sensor or the more accurate angled reference sensor from the large, easy-to-read LCD display of the calibrator. The external sensor and the internal sensor readings are independent of one another.SET-Follows-TRUE (models B & C only)Available on B and C models only, the “SET-Follows-TRUE” makes the instrument tune in until the temperature reading of the external reference “TRUE” meets the desired “SET” temperature. This feature is important when it is critical that the temperature of the calibration zone matches the desired temperature when measured with accurate external reference sensors.Reading of Sensor-Under-Test (model B only)Model B of the RTC is equipped with a built-inaccurate measuring circuit for sensor-under-test(input), which enables measurement of virtu-ally any type of temperature sensors including:Resistance thermometers (RTD), thermocouples(TC), transmitters, milliamps (mA), voltage (V) andthermostats.The RTC calibrators can be user-programmed fromthe keyboard for fully automatic sensor calibra-tions. Once the unit is programmed, the instrument is self-operating and performs the configured calibration routine. All calibration data is stored and can be read on the display.Switch Test (model B only)Users may perform a thermoswitch test and find “Open”, “Closed” and the hysteresis (deadband) automatically. The instrument retains the last twenty test results.MVI NORMAL MAINSAuto-SteppingUp to 20 different temperature steps may be pro-grammed including the hold time for each step.Upon completion of an auto-step routine, the usercan easily read the results for the sensor-under-test on the RTC display. Results from twenty auto-step calibrations are stored.The “Set temperature” feature allows the user toset the exact desired temperature with a resolu-tion of 0.001°.Enhanced StabilityA stability indicator shows when the RTC calibrator has reached the desired temperature and is stable. The user may change the stability criteria for the external reference and the sensor-under-test quickly and simply. The stability criterion is the user’s security of a correct calibration. A count-down timer is displayed next to the temperature read-out.Instrument SetupsThe RTC series allows the user to store up to ten (10) complete instrument setups. You may store all sorts of information including temperature units, stability criteria, use of external reference sensors, resolutions, sensors-under-test (SUT), conversions to temperature, display contrasts, etc. The setup may be recalled at any time.Maximum and Minimum TemperatureFrom the setup menu, the user can select the maximum and minimum temperature limit for the calibrator. This function prevents damage to the sensor-under-test caused by excessive tempera-tures, and it helps reducing sensor drift from exposures of too high temperatures. This feature can be locked with an access code.Silent OperationThe RTC calibrator can be programmed to run in silent operation. This function is an advantage if calibrating in a laboratory or in an office. If used in silent operation, the calibrator is not using its full speed potential.As Found/As Left (model B only)When running a calibration initiated from a work order, the user can select the calibration as an As Found or an As Left calibration.Sync OutputA synchronization output signals when the instrument is stable and may be used with ancillary devices such as video recorders, digital cameras or as an input to a data logging device. The SYNC output may be useful for automating and documenting your calibrations when calibrating exter-nal reading devices.Calibration of Indication DevicesWhen calibrating an indicating device in the work order mode, users may key in the results during or after the test. Using the “Calibration info” function, the user may view the complete calibration task, including the “Scenario” before the calibration takes place.JofraCal Hardware RequirementsINTEL™ PENTIUM™ 1.4 GHz processor. 128 MB RAM (256 MB recommended).80 MB free disk space on hard disk (120 MB recommended) prior to installation. USB input device for installation of program. 1 free USB and 1 free RS-232 serial port.Microsoft Windows® XP or Microsoft Windows® Vista. MS San Serif and Arial system fonts.Calibration of Up To 24 Sensors with the Jofra ASM ScannerUsing the JOFRA RTC series together with the ASM, Advanced Signal Multi-scanner, offers a great time-saving automatic solution to calibrate multiple temperature sen-sors at the same time. The ASM series is an eight channel scanner controlled by the JOFRACAL software on a PC. Up to 3 ASM units can be stacked to calibrate up to 24 sen-sors at a time. It can handle signals from 2-, 3- and 4 wire RTD’s, thermocouples, transmitters, temperature switches, and voltage.JofraCal Calibration SoftwareJofraCal is a highly versatile calibration soft-ware that is supplied together with the RTC calibrators. The software ensures easy calibra-tion of all kinds of temperature sensors, such as RTD´s, thermocouples, transmitters, and thermoswithes. Furthermore, it can be used for pressure calibration i.e. pressure gauges and pressure switches. JofraCal integrates with Jofra calibration instruments. As for temperature calibrators, it is the whole rangeof temperature calibrators. Regarding pressure calibrators, it integrates with the Crystal XP2i and nVision. JofraCal also has full integration with the series of signal calibrators.JofraCal may also be used for manual calibrations, as it can be set up to accept manual entry of calibration data together with other liquid baths, ice points, or dry-block heat sources.The calibration data collected can be stored on a PC for later recall or analysis. The RTC calibra-tor stores the calibration procedure and may be taken out to the process site without bringing a personal computer.This allows the RTC calibrator to:Operate as a stand-alone instrument, using advanced calibration routines without the assis-tance of a personal computer on site. The work order functionalityPrevent unauthorized changes to a calibration routine. Personnel who are not authorized toalter a calibration routine cannot do soOnce all calibrations are completed, the data may be uploaded to JOFRACAL for the printing of certificates. The data collected may be stored on the personal computer for later recall or analysis.JOFRACAL offers extended output formats of the captured calibration data such as PDF file format and ASCII/ semicolon separated text format for further processing and calculation of data in spreadsheets and word processors.Multi-Hole Inserts—Metric (mm)All inserts are supplied with an insulation plug drilled with the necessary holes.InstrumentInsert Type Insert Code*RTC-700 (A/B/C)Multi-hole Type 1M01127200Multi-hole Type 2M02127201Multi-hole Type 3M03127202Multi-hole Type 4M04127203Multi-hole Type 7M07127244Multi-hole Type 8M08127245Multi-hole Type 9M09127246Set of 4 Metric Multi Inserts, 3 to 13 mm. (Includes 127203, 127244, 127245, and 127246)SM127252* Use the insert code, when ordering a JOFRA standard multi-hole insert together with the RTC calibrator.1/4"4 mm4 mm 7 mm13 mm1/4" 4 mm4 mm5 mm6 mm3 mm4 mm9 mmInsert Code SMFunctional ComparisonNo part of this document may be reproduced or modified in any form or by any means, electronic or mechanical, without express written permission from Crystal Engineering Corporation.©2021 AMETEK IncorporatedUSA , FloridaTel +1 (800) 527 9999*******************USA , California *Tel +1 (800) 444 1850******************IndiaTel +91 22 2836 4750****************SingaporeTel +65 6484 2388****************China , Shanghai Tel +86 21 5868 5111**********************.cn China , BeijingTel +86 10 8526 2111**********************.cn United KingdomTel +44 (0) 1243 833 302**********************FranceTel +33 (0) 30 68 89 40***********************************GermanyTel +49 (0) 2159 9136 510*********************Denmark *Tel +45 4816 8000*****************ISO 17025 accredited calibration lab.。
2024科技前沿《自动驾驶车辆的雷达传感器校准》实施报告英文版

2024科技前沿《自动驾驶车辆的雷达传感器校准》实施报告英文版2024 Technology Frontier: Implementation Report on Radar Sensor Calibration for Autonomous Vehicles In the fast-evolving landscape of technology, the field of autonomous vehicles has seen significant advancements. One crucial aspect of ensuring the safety and efficiency of autonomous vehicles is the calibration of radar sensors. This report delves into the implementation of radar sensor calibration for autonomous vehicles in 2024.IntroductionAutonomous vehicles rely on various sensors, including radar sensors, to navigate and make decisions on the road. The accurate calibration of these sensors is paramount to ensure the proper functioning of the autonomous driving system. In this report, we willdiscuss the importance of radar sensor calibration and the steps involved in its implementation.Importance of Radar Sensor CalibrationRadar sensors play a crucial role in detecting objects, pedestrians, and other vehicles on the road. Proper calibration of these sensors ensures accurate and reliable data collection, which is essential for safe autonomous driving. Without accurate calibration, the autonomous vehicle may misinterpret its surroundings, leading to potential accidents or malfunctions.Implementation ProcessThe implementation of radar sensor calibration for autonomous vehicles involves several key steps. These steps include:1. Sensor Positioning: Ensuring that the radar sensors are properly positioned on the vehicle to have a clear line of sight and maximum coverage.2. Data Collection: Collecting data from the radar sensors to understand their performance and accuracy.3. Calibration Algorithm: Utilizing advanced calibration algorithms to optimize the sensor readings and minimize errors.4. Validation Testing: Conducting validation tests to verify the accuracy of the calibrated radar sensors in real-world scenarios.Results and BenefitsBy implementing radar sensor calibration for autonomous vehicles, we can achieve several benefits, including:- Improved Safety: Accurate sensor calibration enhances the safety of autonomous vehicles by reducing the risk of collisions and accidents.- Enhanced Performance: Calibrated radar sensors can improve the performance of autonomous driving systems, leading to smoother and more efficient operations.- Regulatory Compliance: Proper calibration of radar sensors ensures compliance with industry standards and regulations, enhancing the legal and ethical aspects of autonomous vehicle deployment.ConclusionIn conclusion, the implementation of radar sensor calibration for autonomous vehicles is essential for ensuring their safety, performance,and regulatory compliance. By following the steps outlined in this report, we can effectively calibrate radar sensors and contribute to the advancement of autonomous driving technology in 2024.。
- 1、下载文档前请自行甄别文档内容的完整性,平台不提供额外的编辑、内容补充、找答案等附加服务。
- 2、"仅部分预览"的文档,不可在线预览部分如存在完整性等问题,可反馈申请退款(可完整预览的文档不适用该条件!)。
- 3、如文档侵犯您的权益,请联系客服反馈,我们会尽快为您处理(人工客服工作时间:9:00-18:30)。
CALIBRATION OF AUDIO-VIDEO SENSORS FOR MULTI-MODAL EVENT INDEXING Thorsten K¨u hnapfel1,Tele Tan1,Svetha Venkatesh1and Eric Lehmann2 1Department of Computing,Curtin University of Technology,Western Australia2Western Australian Telecommunications Research Institute,Western AustraliaABSTRACTThis paper addresses the coordinated use of video and au-dio cues to capture and index surveillance events with multi-modal labels.The focus of this paper is the development of a joint-sensor calibration technique that uses audio-visual ob-servations to improve the calibration process.One significant feature of this approach is the ability to continuously check and update the calibration status of the sensor suite,mak-ing it resilient to independent drift in the individual sensors. We present scenarios in which this system is used to enhance surveillance.Index Terms—Calibration,Multimedia system1.INTRODUCTIONIn recent years,surveillance systems have become increas-ingly sophisticated by combining different types of sensors to enhance mon choices of sensors are cameras and microphones,which are used predominantly for tracking and identifying the speaker[1,2,3,4].This paper explores the introduction of an audio array in a video surveil-lance domain,to explore the use of extracting and indexing ”coordinated”audio and video events.For example,consider a video and audio stream in an area where there are2groups of people-one speaking German and the other English.Our system detects the video event,say”gathering of more than one person”,and than extracts”beam-steered”audio from the direction of the video event.Thus,in the above example, the two video events”gathering1”and”gathering2”will be indexed by their corresponding beam-steered audio,thereby allowing”gathering1”to be indexed by the enhanced Ger-man audio content,and”gathering2”to be indexed by the enhanced English audio.Note that the video event detection is not the focus of this paper.We focus on the calibration of the coordinated video-audio array,and demonstrate its use for video surveillance.Such calibration can be done in a static setting,but drift often perturbs such systems over time.In-stead,we propose a dynamic calibration system triggered by a single,talking person walking across the visualfield of view.Thanks to Anders Johansson2for his support on sound processing and audio hardware advices.In previous work,audio-video information is fused for tracking purposes,mainly in video conferencing systems. These systems use video segmentation techniques,such as background subtraction,motion detection,shape detection or skin colour detection to locate a speaker.As tracking is sensi-tive to light changes,people in the background or occlusion, there is a need for these systems to incorporate sound source localisation algorithms to enhance tracking.For this purpose, the proposed approaches in[1,2,3,4]all assume known geo-metrical alignment of the sensors.In[5]the number of audio and video sources are assumed to be known at all times.Like-wise,in[4,2]a linear mapping between the audio and video data is assumed.We focus on the issue of dynamic audio-visual sensor cal-ibration based on audio-video observations.This involves es-timating a calibration function that maps the two dimensional video coordinates of a stationary camera to the one dimen-sional audio angle of arrival in a linear microphone array.Im-portantly,the calibration function is automatically computed from a sequence of audio-visual observations and does not assume linear mapping or known relative audio-video sensor orientation.To enhance the accuracy of the calibration func-tion,the estimated sound source location is smoothed by a novel approach.After the calibration function is estimated, the system is able to steer an audio beam towards a”target”based on the image location.Targets can be a wide range of video events such as single people,multiple people and so on.We demonstrate our system in a surveillance situation by enhancing speech for detected visual events.The novelty of such a system is the self calibration of audio-video sensor pairs that combine audio and video information,and its appli-cation for surveillance in which video events are indexed by enhanced audio.The paper is organised as follows:Section2provides an overview of related work.Section3presents the methodology and the results of our experiments are shown in section4. Section5concludes our work.2.RELATED WORKThe authors in[4]propose a sensor fusion model based on Bayesian networks,where a probabilistic graphical model is chosen to approximate a linear mapping between the videoand audio with known sensor geometry.Another way to fuse the data is via the Sequential Monte Carlo method(SMC)[1,5].Here the location of the fore-ground objects in the video stream and the location of sound sources are converted into a probability density function(pdf). In[1]the pdf is computed based on the assumption that the optical center of a static camera is aligned with the middle of the audio array.In[5]a prerecorded sequence with a known number of objects is used to estimate the correlation of the video and audio signals.The speaker tracking system proposed in[3]uses a sim-ple summing voter to combine all sound sources,skin colour and motion locations.In order to map the video based infor-mation with the audio information,the authors discretise the audio information into30◦sectors and the video in sectors according to their alignment setup.The audio information is also normalised to a reference power profile,generated in an anechoic chamber.In comparison to all these methods,the system proposed in this paper does not require any prior cross sensor measure-ments,known relative audio-video sensor geometry or any linearity assumptions in mapping audio-video pairs.3.METHODOLOGYThis section details the tasks in the proposed surveillance sys-tem.First,the sound source localisation algorithm and the smoothing is discussed.Then,the video segmentation and face detection algorithms are presented,followed by the cali-bration approach.Finally,the surveillance system is described to demonstrate the indexing of video events with enhanced audio.3.1.Angle of Arrival AlgorithmFor a sound source in the far-field region,the time delay of ar-rival(TDOA),τ,between two microphones can be computed by the general cross-correlation with PHAT weighting(GCC-PHAT)[6].The generalization of the GCC-PHAT is the SRP-PHAT[7]algorithm and it is used to compute a distributionβ, for a one dimensional,uniform alignment,microphone array as:β(τ)=ν2πNl=1Nk=1+∞−∞Γlk(ω)|Γlk(ω)|e jωτ(l−k)dω(1)whereτis the time delay,l and k are microphones indices ranging from1to N,andΓlk denotes the cross power den-sity spectrum.In this discretised distribution,τranges from −τmax to+τmax,which corresponds to a scan for soundsources from−π2toπ2,relative to the center of the array.Thedistributionβis normalised usingν.An estimate of a sound source’s TDOA,ˆτs,is obtained as the lagτthat maximises β(τ),and can then be converted to an angle of arrival(AOA),α,as follows[7]:α(τ)=arccoscdF sτ(2) where F s is the sampling frequency,d the distance between the microphones and c the speed of sound.Thus,β(τ)can be translated toβ(α).The max ofβ(α), α,is called AOA.Since the distributionβ(α)can be estimated at every sampling in-stance t,we refer to this distribution asβt(α).3.1.1.Smoothing of AOA resultThe estimated AOA has quite a large variance around the true direction of the source.To reduce this variance in estimation, we propose a smoothing approach based on the entropy,H, of the discrete AOA distributionβt(α).For smoothing,we use exponential forgetting to combineβt andβt−1asβt(α)=1−uβt−1(α)+uβt(α)(3) where is a appropriate normalising factor,and u as update factor computed as:u=11+e1σ[H−µ](4) whereµis the mean andσthe variance.To understand u, assume without loss of generality thatµ=0,σ=1.Then, when the distributionβis not uniform(i.e.very peaked),H= 0,and u=1.This corresponds to the update factor being1 when there is little uncertainty inβ.Conversely,when the distributionβis uniform,H=1,and u=0.µandσcontrol the rate of”fall”as shown infigure1(a).Figure1(b)presents the sound source location,in relation to the center of the array, based on the unsmoothed and smoothedβt.−5050.10.20.30.40.50.60.70.80.91Hu(a)024681012−1−0.8−0.6−0.4−0.20.20.40.60.81time in secondsangleinrad(b)Fig.1.Smoothing:(a)shows two functions of u,withµ=0 andσ=1(dark)and with forµ=1andσ=0.3(light).(b)shows the result of the sound source localisation with a frequency range from800Hz to3000Hz,for the smoothed (dark)and unsmoothed(light)AOA.3.2.Video segmentationObjects in the video stream are detected by background sub-traction[8].For calibration purposes,we use the AdaBoost face detection algorithm[9]to locate the face regions.3.3.CalibrationThe calibration function for the proposed system maps the video coordinates to the one dimensional audio information of a linear microphone array.To accurately estimate such a calibration function,3restrictions apply:Only one fore-ground object must be detected in the image,the object has to emit sound and the sound has to be directed towards the mi-crophones.This proposed system uses a single person as the calibration object and speech as the sound source.Therefore, the system must have the ability to detect speech and faces. We use the support vector machine(SVM)[10],trained with Mel Frequency Cepstral Coefficients(MFCC)[11]of speech and background noise samples.The face detection algorithm computes the probability of a frontal face.For the mapping, the image is divided into I vertical bins.This discretisation allows the system to categorise the estimated AOA’s to a bin i,based on the mean position of the person.Given n obser-vations[AOA k,p(face k)],where AOA k and p(face k)are the angle of arrival and the probability that the person is fac-ing the microphones in the k th observation,for each of the bins,a mean AOA is computed asAOA i= nk=1AOA ikp(face k)nk=1p(face k)(5)where i∈1:I.Afitted polynomial function with degree3 is shown infigure2.The calibration function is quite linear, which is expected from the sensor geometry.The Levenberg-Marquardt algorithm is used forfitting the calibration func-tion,which interpolates a correlated AOA for all vertical im-age locations.3.4.Video surveillanceThe aim of the dynamic calibration is to enhance the recorded sounds of a corresponding image events.When the spatial distance between individuals is within a certain threshold,the visual event”crowd”is detected,suggesting a possible con-versation.Due to noisy backgrounds or other groups of peo-ple,the recorded conversation from a single microphone is inadequate.Therefore,the system can steer an audio beam towards the groups,based on the calibration,to enhance the audio signal in the given direction.To steer an audio beam,a delay and sum beamformer is implemented in the frequency domain[12]as follows:B(k,α)=Nn=1W n(k)X n(k)e−j2πf k d c(n−1)sinα(6)f k=kF sM(7)where k is the frequency index andαis the steering angle. The side lobe level is controlled with W n(k),X n(k)is the complex value of the FFT transformed audio signal,where n is the index of the microphone and M the size of the FFT.4.EXPERIMENTSThe performance of the proposed system was evaluated by a set of3experiments.For all experiments,the sound was emitted in a2to3meters range from the microphones and the camera was mounted behind the microphones,so that it faces in approximately the same direction as the microphones.The array consists of7omnidirectional,condenser microphones with a spacing of4cm.The AOA analysis was performed in a frequency range from800Hz to3000Hz.Audio en-hancement was done over the full frequency range from0Hz to4000Hz.The calibration function was estimated from a single,talking person walking in front of the sensor system. Audio was captured at8000Hz,16bits per sample.The im-age resolution was320x240pixels,captured at15frames per second.050100150200250300−0.8−0.6−0.4−0.20.20.40.60.8Vertical video locationAngleinradFig.2.Calibration:The×are the AOA for each video bin and the line is the calibration function.4.1.CalibrationThe accuracy of the calibration was tested by using two pure sine waves,with different frequencies.Two audio speakers were placed on the far right and left sides of the camerafield of view,at a distance of3meters.Then the audio beam was first steered towards the speaker with the3500Hz sine wave, and then towards the one emitting2500Hz,based on the im-age location.The difference in the enhanced to original signal strange at2500Hz was16.3dB and29.5dB at3500Hz.4.2.Indexing audio-video eventsTwo stationary groups of people converse in English and Ger-man,each group consists of two people,located on the right and left sides of the camera view,at about3meters.Two beamformed audio streams were produced,each from a beam steered towards the center of each group.To evaluate the quality of the beamformed audio streams,they werefirst nor-malised to the same signal strength as that of a single micro-phone.Then a test group listened to the resulting beamformed audio and gave a mean opinion score(MOS),expressed as asingle number in the range 1(Bad)to 5(Excellent).This score was based on the understanding of the conversation.The beamformed audio streams achieved an average score of 3.62and the original signal an average score of 1.6,as shown in figure3.(a)Video MOS Event Steered Orig Group 04 1.7Group 1 3.75 1.5(b)Fig.3.Indexing audio-video events:(a)shows a screenshot of the video event detection.The table (b)shows the mean opinion score between the beam steered audio and the original audio stream.4.3.Audio events for moving targetsThe last experiment consists of two people walking in front of the camera and having a conversation.To increase the back-ground noise,a radio is playing in the far right end of the room.This experiment proves the ability to steer an audio beam towards a moving target.The results were evaluated again by using the MOSfor the original and the normalised beamformed audio stream.As shown in figure 4the average MOS for the beam steered audio stream was 3.9compared with the original scored of 2.(a)Video MOS Event Steered Orig Group 0 3.92(b)Fig.4.Audio events for moving targets:(a)shows a screenshot of the video event detection.Table (b)shows the mean opinion score between the beam steered audio and the original audio stream.A video file that demonstrates the calibration and the last two experiments can be downloaded from:.au/∼thorsten/AudioVideoIndexing.avi.5.CONCLUSIONS AND FUTURE WORK We have demonstrated that the system can steer an audio beam towards a detected video event based on the video and audio observation.Experiments have demonstrated the ability of the system for surveillance.In future,we will extend the system with a pan tilt and zoom camera to give the system the potential to detect a per-son based on an audio event,even so he might not be in the view of the camera.Also the system will be able to re-adjust itself should drifts amongst the video-audio sensors occur.6.REFERENCES[1]Y .Chen and Y .Rui,“Real-time speaker tracking using particlefilter sensor fusion,”Proc.of the IEEE ,vol.92,no.03,pp.485–494,2004.[2]J.Vermaak,M.Gangnet,A.Blake,and P.Perez,“Sequentialmonte carlo fusion of sound and vision for speaker tracking,”ICCV ,vol.01,pp.741,2001.[3] D.Lo,R.A.Goubran,R.M.Dansereau,G.Thompson,andD.Schulz,“Robust joint audio-video localization in video conferencing using reliability information,”IEEE Trans.on Instrumentation and Measurement ,vol.53,no.4,pp.1132–1139,2004.[4]M.J.Beal,H.Attias,and N.Jojic,“Audio-video sensor fusionwith probabilistic graphical models,”ECCV (1),pp.736–752,2002.[5]H.Asano et al.,“An application of a particle filter to bayesianmultiple sound source tracking with audio and video informa-tion fusion,”Proc.Int.Conf.on Information Fusion ,pp.805–812,2004.[6] C.Knapp and G.Carter,“The generalized correlation methodfor estimation of time delay,”IEEE Trans.Acoust.Speech Sig-nal Process ,vol.24,no.4,pp.320–327,1976.[7] A.Johansson,N.Grbic,and S.Nordholm,“Speaker localisa-tion using the far-field SRP-PHAT in conference telephony,”in International Symposium on Intelligent Signal Processing and Communication Systems ,2002.[8] C.Stauffer,W.Eric,and L.Grimson,“Learning patterns of ac-tivity using real-time tracking,”IEEE Trans.on Pattern Anal-ysis and Machine Intelligence ,vol.22,pp.747–757,2000.[9]P.Viola and M.Jones,“Robust real-time object detection,”Proc.IEEE Conf.on Computer Vision and Pattern Recogni-tion ,2001.[10]S.Gunn,“Support vector machines for classification and re-gression,”Tech.Rep.,Department of Electronics and Com-puter Science,University of Southampton,1998.[11]S.Davis and P.Mermelstein,“Comparison of parametric rep-resentation for monosyllable word recognition in continuously spoken sentences,”IEEE Trans.Acoust.,Speech,Signal Pro-cessing ,vol.ASSP-28,pp.357–366,1980.[12] B.Maranda,“Efficient digital beamforming in the frequencydomain,”Journal of Acoustic Society of America ,vol.86,pp.1813–1819,1989.。