顶吹转炉炼钢法冶炼历程分析
顶吹转炉吹炼工艺

顶吹转炉吹炼工艺1. 引言顶吹转炉吹炼工艺是一种常用于钢铁冶炼的工艺方法。
它通过将氧气从炉顶喷吹到炉内,以加速燃烧和化学反应的进行。
本文将介绍顶吹转炉吹炼工艺的原理、特点以及工艺参数的控制。
2. 工艺原理顶吹转炉吹炼工艺的基本原理是在转炉顶部设计一个氧气喷嘴,通过喷吹氧气使炉内燃烧温度升高,并加快燃烧反应速率。
同时,顶吹转炉还可以通过调节氧气喷吹速度和位置,控制炉内气流和熔池运动,以提高炉内物料的混合程度,促进冶炼反应的进行。
3. 特点顶吹转炉吹炼工艺相比传统的底吹转炉有着以下特点:3.1 高温燃烧顶吹转炉通过喷吹氧气,可以使炉内燃烧温度达到更高水平,加速燃烧和还原反应的进行。
这样可以提高冶炼速度和效率,减少焦炭、助熔剂等辅助物料的消耗。
3.2 均质混合通过控制氧气喷吹速度和位置,顶吹转炉可以在转炉内形成旋转的气流,从而实现物料的均质混合。
这样可以提高冶炼反应的均匀性,减小冶炼过程中的不均匀性带来的负面影响。
3.3 炉渣处理顶吹转炉可以通过调整氧气喷吹位置和速度,将炉渣浮于熔池表面,有效地减少炉渣与熔池的接触面积,从而降低炉渣对冶炼过程的干扰。
这样可以提高冶炼过程的稳定性和控制精度。
4. 工艺参数控制顶吹转炉吹炼工艺中,需要控制的主要工艺参数包括氧气喷吹速度、氧气喷吹位置以及燃烧温度等。
4.1 氧气喷吹速度氧气喷吹速度决定了氧气进入炉内的速度和能量。
过高的喷吹速度会导致氧气无法有效混合,影响冶炼反应的进行。
而过低的喷吹速度则会导致燃烧不充分,影响冶炼速度和效率。
因此,控制合适的氧气喷吹速度对工艺的稳定性和冶炼效果具有重要影响。
4.2 氧气喷吹位置氧气喷吹位置决定了氧气进入炉内的位置和气流的运动情况。
不同的冶炼反应需要不同的氧气喷吹位置。
例如,在氧气位于熔池表面的情况下,可以加速还原反应的进行;而位于熔池中部时,可以提高燃烧温度。
因此,合理控制氧气喷吹位置可以调节冶炼反应的速率和效果。
4.3 燃烧温度燃烧温度对冶炼反应速率和效果有着直接影响。
世界氧气顶吹转炉炼钢技术发展史

世界氧气顶吹转炉炼钢技术发展史氧气顶吹转炉炼钢(oxygen top blown converter steelmaking)由转炉顶部垂直插入的氧枪将工业纯氧吹入熔池,以氧化铁水中的碳、硅、锰、磷等元素,并发热提高熔池温度而冶炼成为钢水的转炉炼钢方法。
它所用的原料是铁水加部分废钢,为了脱除磷和硫,要加入石灰和萤石等造渣材料。
炉衬用镁砂或白云石等碱性耐火材料制作。
所用氧气纯度在99%以上,压力为0.81~1.22MPa(即8~12atm)。
简史空气底吹转炉和平炉是氧气转炉出现以前的主要炼钢设备。
炼钢是氧化熔炼过程,空气是自然界氧的主要来源。
然而空气中4/5的气体是氮气,空气吹炼时,这样多的氮气在炉内穿行而过,白白带走大量的热且有部分氮溶解在铁液中,成为恶化低碳钢品质的重要原因。
平炉中,氧在用于燃烧燃料之后,过剩的氧要通过渣层传入钢水,所以反应速率极慢,这也就增加了热损失。
因此,直接把氧气吹入熔池炼钢,成为许多冶金学家向往的目标。
早在19世纪,现代炼钢法的创始人贝塞麦(H.Bessemer)就有了纯氧炼钢的设想,但因没有大量氧气而未进行试验。
20世纪20年代后期,以空气液化和分馏为基础的林德一弗兰克(Linde—Frankel)制氧技术开发成功,能够生产可供工业使用的廉价氧气,氧气炼钢又为冶金界所注意。
从1929年开始,柏林工业大学的丢勒尔教授(R.Durrer)在实验室中研究吹氧炼钢,第二次世界大战开始后转到瑞士的冯•罗尔(V.Roll)公司继续进行研究。
1936~1939年勒莱普(O.Lellep)在奥伯豪森(Oberhausen)进行了底吹氧炼钢的试验,由于喷嘴常损坏未能成功。
1938年亚琛(Aachen)工业大学的施瓦茨(C.V.Schwarz)提出用超音速射流向下吹氧炼钢,并在实验室进行了试验,将托马斯生铁吹炼成低氮钢,但因熔池浅而损坏了炉底。
1948年丢勒尔(R.Durrer)等在冯•罗尔(VonRoll)公司建成2.5t的焦油白云石衬的试验转炉,以450的斜度将水冷喷嘴插入铁水吹氧炼钢,无论贝塞麦生铁或托马斯生铁都能成功炼成优质钢水,而且认识到喷嘴垂直向下时,最有利于喷嘴和炉衬的寿命。
炼钢工艺简介(1)
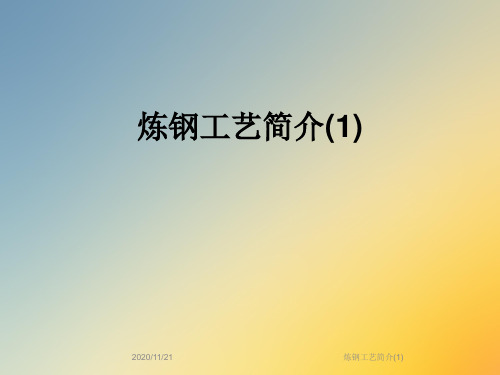
氧气顶吹转炉炼钢法的特点
• 利于自动化生产和开展综合利用 • 氧气顶吹转炉炼钢冶炼时间短,生产率高
,其机械化程度较高,有利于实现生产过程 的自动化,也有利于开展综合利用,如回收 煤气、炉尘(做烧结矿原料)等。
炼钢工艺简介(1)
四、炼钢基本原理
炼钢基本原理
一、什么叫钢
一般把碳小于2.11%的铁碳合金称为钢。 二、什么叫炼钢
炼钢工艺简介(1)
氧气顶吹转炉炼钢法的特点
• 原料消耗少,热效率高、成本低 • 氧气顶吹转炉炼钢的金属消耗一般为1100~1140
公斤/吨钢,稍高于平炉(但在良好燥作情况下 ,金属消耗与平炉接近)。但由于顶吹转炉的热 源是利用铁水本身的物理热和化学热,热效率高 ,不需外加热源,因此在燃料和动力消耗方面均 较平炉、电炉低。由于氧气顶吹转炉炼钢法具有 高的生产率和低的消耗,所以钢的成本也较低。
四、一炼钢技术经济指标
一炼钢在今年前几个月与国内部分同类生产厂指标相比, 在钢铁料消耗、日历作业率上差别较大.而与全国平均水平相 比各项指标均好于同时期的全国平均水平。 ➢ 钢铁料消耗比莱钢高21kg/t,比全国平均低了7.4 kg/t ➢ 日历作业率上比南京低15.56%,比全国平均高2.64% ➢ 氧气消耗比莱钢高3.78m3/t,比全国平均低3.85m3/t。 ➢ 转炉冶炼周期比安阳多1.56min,比全国平均低6.9min。 ➢ 炉衬寿命比莱钢略低。 ➢ 具体对比数据见附表。
➢音频化渣技术:2000年转炉与上海工业大学合作开发的音 频化渣技术,该项技术能根据炉内反应的声音,分析炉渣 的性质,及时指导氧枪枪位控制,促进化渣
炼钢工艺简介(1)
➢ 转炉数据静态模拟控制:2001年,转炉与上海阿塞克自动 化公司合作,开发出转炉数据静态模拟控制系统,使小转炉 炼钢局部实现自动化,降低了劳动强度,改善了生产环境, 提高了转炉作业率及生产效率。
转炉炼钢工艺流程

转炉炼钢工艺流程这种炼钢法使用的氧化剂是氧气。
把空气鼓入熔融的生铁里,使杂质硅、锰等氧化。
在氧化的过程中放出大量的热量(含1%的硅可使生铁的温度升高200摄氏度),可使炉内达到足够高的温度。
因此转炉炼钢不需要另外使用燃料。
转炉炼钢是在转炉里进行。
转炉的外形就像个梨,内壁有耐火砖,炉侧有许多小孔(风口),压缩空气从这些小孔里吹炉内,又叫做侧吹转炉。
开始时,转炉处于水平,向内注入1300摄氏度的液态生铁,并加入一定量的生石灰,然后鼓入空气并转动转炉使它直立起来。
这时液态生铁表面剧烈的反应,使铁、硅、锰氧化(FeO,SiO2 , MnO,) 生成炉渣,利用熔化的钢铁和炉渣的对流作用,使反应遍及整个炉内。
几分钟后,当钢液中只剩下少量的硅与锰时,碳开始氧化,生成一氧化碳(放热)使钢液剧烈沸腾。
炉口由于溢出的一氧化炭的燃烧而出现巨大的火焰。
最后,磷也发生氧化并进一步生成磷酸亚铁。
磷酸亚铁再跟生石灰反应生成稳定的磷酸钙和硫化钙,一起成为炉渣。
当磷与硫逐渐减少,火焰退落,炉口出现四氧化三铁的褐色蒸汽时,表明钢已炼成。
这时应立即停止鼓风,并把转炉转到水平位置,把钢水倾至钢水包里,再加脱氧剂进行脱氧。
整个过程只需15分钟左右。
如果空气是从炉低吹入,那就是低吹转炉。
随着制氧技术的发展,现在已普遍使用氧气顶吹转炉(也有侧吹转炉)。
这种转炉吹如的是高压工业纯氧,反应更为剧烈,能进一步提高生产效率和钢的质量。
转炉一炉钢的基本冶炼过程。
顶吹转炉冶炼一炉钢的操作过程主要由以下六步组成:(1)上炉出钢、倒渣,检查炉衬和倾动设备等并进行必要的修补和修理;(2)倾炉,加废钢、兑铁水,摇正炉体(至垂直位置);(3)降枪开吹,同时加入第一批渣料(起初炉内噪声较大,从炉口冒出赤色烟雾,随后喷出暗红的火焰;3~5min后硅锰氧接近结束,碳氧反应逐渐激烈,炉口的火焰变大,亮度随之提高;同时渣料熔化,噪声减弱);(4)3~5min后加入第二批渣料继续吹炼(随吹炼进行钢中碳逐渐降低,约12min后火焰微弱,停吹);(5)倒炉,测温、取样,并确定补吹时间或出钢;(6)出钢,同时(将计算好的合金加入钢包中)进行脱氧合金化。
炼钢的发展历史

拉碳测温取样: 拉碳测温取样 根据判断确定钢水含碳量和温度同时到达终点时, 立即提枪停止吹氧,当氧枪提出炉口后倒炉测温,取样,进行炉 前化学成分快速分析。铁水温度用装有铂—铑快速热电偶的测温 枪插入钢液内测量。化验室主要分析钢水中的化学成分,含碳量 也可通过钢花的分叉多少凭经验判断确定。当钢水温度和成分合 格后便组织出钢。
炼钢的发展历史
炼钢方法的发展过程
钢铁是工业的粮食,对工业的发展、国家经济力量的水平及其 增长都有很大的作用。 钢是碳、硅、锰及其他元素在铁中的固熔体。钢中存在的元素 可大致分为两大类:碳、硅、锰等是用以改善钢的性能,以满足工 程材料要求的有益元素;另一类如磷、硫、氧、氢及氮等,是从炉 ; 料或大气中进入钢中的,它们的存在会使大部分钢的性能变坏。炼 钢的任务在于通过化学反应,除去主原料(铁水和废钢等)中的杂 质,并调整钢水成分和温度,达到规定要求。最后铸成合格的铸坯 或钢锭。
3)冶炼的钢质量好、品种多 氧气顶吹转炉能冶炼平炉熔炼的全部钢种和电炉熔炼的部分钢 种。从钢中含碳量来看,氧气顶吹转炉可以冶炼微碳(C<0.015%) 、低碳、中碳、直到含碳达1.30一1. 50% 的高碳钢种;以钢中含 合金元素来看,从含微量元素的工业纯铁,低合金钢、中合金钢、 直到镍铬含量高达30%的超低碳不锈钢等,都能冶炼。 氧气顶吹转炉钢的质量与平炉钢基本相同或略优,如氧气顶吹 转炉钢的气体和夹杂含量一般均低于平炉钢。氧气顶吹转炉钢的深 冲性能和延展性好,适宜轧制板、管丝、带等钢材,而这类钢材往 往占钢材总量的50%一60%或更高。
脱氧合金化: 脱氧合金化 出钢过程中向钢包内加入铁合金进行脱氧和合金化 操作,然后镇静或送去炉外精炼,之后浇铸成钢锭(坯)。
70年代以前建成的一批小型氧气顶吹转炉有天津钢厂20t、济南 钢厂13t、安阳钢厂15t、邯郸钢厂15t;中型的有太原钢铁公司50t 、包头钢铁公司50t、武汉钢铁公司50t、马鞍山钢铁公司50t;大型 的有鞍山钢铁公司150t、本溪钢铁公司120t、攀枝花钢铁公司120t 。80年代又建成具有70年代末期世界先进水平的宝钢300t转炉。到 1993年我国转炉钢产量已达到5474.6万t,占总钢产量8868万的 61.7%.。
转炉炼钢工艺流程

这种炼钢法使用的氧化剂是氧气。
把空气鼓入熔融的生铁里,使杂质硅、锰等氧化。
在氧化的过程中放出大量的热量(含1%的硅可使生铁的温度升高200摄氏度),可使炉内达到足够高的温度。
因此转炉炼钢不需要另外使用燃料。
转炉炼钢是在转炉里进行。
转炉的外形就像个梨,内壁有耐火砖,炉侧有许多小孔(风口),压缩空气从这些小孔里吹炉内,又叫做侧吹转炉。
开始时,转炉处于水平,向内注入1300摄氏度的液态生铁,并加入一定量的生石灰,然后鼓入空气并转动转炉使它直立起来。
这时液态生铁表面剧烈的反应,使铁、硅、锰氧化 (FeO,SiO2 , MnO,) 生成炉渣,利用熔化的钢铁和炉渣的对流作用,使反应遍及整个炉内。
几分钟后,当钢液中只剩下少量的硅与锰时,碳开始氧化,生成一氧化碳(放热)使钢液剧烈沸腾。
炉口由于溢出的一氧化炭的燃烧而出现巨大的火焰。
最后,磷也发生氧化并进一步生成磷酸亚铁。
磷酸亚铁再跟生石灰反应生成稳定的磷酸钙和硫化钙,一起成为炉渣。
当磷与硫逐渐减少,火焰退落,炉口出现四氧化三铁的褐色蒸汽时,表明钢已炼成。
这时应立即停止鼓风,并把转炉转到水平位置,把钢水倾至钢水包里,再加脱氧剂进行脱氧。
整个过程只需15分钟左右。
如果空气是从炉低吹入,那就是低吹转炉。
随着制氧技术的发展,现在已普遍使用氧气顶吹转炉(也有侧吹转炉)。
这种转炉吹如的是高压工业纯氧,反应更为剧烈,能进一步提高生产效率和钢的质量。
转炉一炉钢的基本冶炼过程。
顶吹转炉冶炼一炉钢的操作过程主要由以下六步组成:(1)上炉出钢、倒渣,检查炉衬和倾动设备等并进行必要的修补和修理;(2)倾炉,加废钢、兑铁水,摇正炉体(至垂直位置);(3)降枪开吹,同时加入第一批渣料(起初炉内噪声较大,从炉口冒出赤色烟雾,随后喷出暗红的火焰;3~5min后硅锰氧接近结束,碳氧反应逐渐激烈,炉口的火焰变大,亮度随之提高;同时渣料熔化,噪声减弱);(4)3~5min后加入第二批渣料继续吹炼(随吹炼进行钢中碳逐渐降低,约12min 后火焰微弱,停吹);(5)倒炉,测温、取样,并确定补吹时间或出钢;(6)出钢,同时(将计算好的合金加入钢包中)进行脱氧合金化。
转炉炼钢主要过程及特点

脱氧及合金化
脱氧
吹炼终点钢水 [O]=0.02~0.08%, 向 钢 中 加 入一种(或几种)与氧亲和力 比 Fe 大 的 元 素 , 常 用 脱 氧 剂 Fe-Si 、 Fe-Mn 、 Al 、 Si-AlCa、Si-Al-Ba等;
合金化
向钢水中加入合金元素使其 达到成品钢成分要求
❖ 供料系统 ❖ 转炉系统 ❖ 供气系统 ❖ 净化系统 ❖ 辅助设备
炼钢原料
转炉炼钢的原材料分为金属料、非金属料和气 体。金属料包括铁水、废钢、铁合金,非金属料包 括造渣料、熔剂、冷却剂,气体包括氧气、氮气、 氩气、二氧化碳等。非金属料是在转炉炼钢过程 中 为了去除磷、硫等杂质,控制好过程温度而加入的 材料。主要有造渣料(石灰、白云石),熔剂(萤 石、氧化铁皮),冷却剂(铁矿石、石灰石、废 钢),增碳剂和燃料(焦炭、石墨籽、煤块、重 油)。
(3)基建投资和生产费用低 纯氧顶吹转炉的基 建投资相当于同样生产量的平炉车间的60~70%, 生产费用也低于平炉。
温度制度
随铁水中元素氧 化,金属液相线温度升 高,浇注也要求过热度, 升温是炼钢重要任务 之一.
出钢温度T的确定:
T= 浇 注 钢 种 液 相 线 温 度 + 浇 注过热度+钢水镇静及炉 外精炼温度降+出钢温度 降
出钢
出钢过程
先测定[C]、[P]、 [S]及T,判断是否满足 出钢要求,否则补吹;采 用挡渣技术与红包出 钢.
转炉设备
转炉冶炼的基本原理 ----物料平衡及热平衡
纯氧顶吹转炉炼钢优点
(1)生产速度快 因为用纯氧吹炼,会高速降碳, 快速提温,大大缩短冶炼时间。。
(2)品种多、质量好 纯氧顶吹转炉既能炼普通 钢,也能炼普通低碳钢。如首钢采用这种方法成功 地试炼了一百多种钢材。用纯氧吹炼,钢中氮、氢 等有害气体含量较低。
顶吹转炉炼钢法冶炼历程分析

顶吹转炉炼钢法冶炼历程分析摘要:通过对转炉冶炼历程各种元素的氧化规律进行分析,探索出一条能够充分降低钢液中磷、硫两大有害元素含量的工艺制度,为实际生产提供理论依据。
关键词:转炉冶炼历程氧化规律Analysis on Steel-making Process In Top Blowing ConverterZhuo Wei-wei Xu Yu-song Zhang Rongliang Ji Kai(Metallurgy and Material College,JiangSu University of Science and Technolog,ZhangJiaGang SuZhou ,215600,China)Abstract: Through the analysis on oxidation rule of various elements in the process of smelting in converter, to find out a technological condition which can reduce the phosphorus and sulphur that are harmful to molten steel and offer a theoretical foundation to actual production.Key words:conert process of smelt oxidation rule.一、冶炼过程概述从装料到出钢,倒渣,转炉冶炼一炉钢的冶炼过程包括装料、吹炼、脱氧出钢、溅渣护炉和倒渣几个阶段。
一炉钢的吹氧时间通常为12~18min,冶炼周期为30min左右。
转炉出钢完后,倒净炉渣,堵住出钢口,兑铁水和加废钢,降枪供氧,开始吹炼。
在送氧开吹的同时,加入第一批渣料,加入量相当于全炉总渣量的三分之二,开吹4~6分钟后,第一批渣料化好,再加入第二批渣料。
炼钢的过程
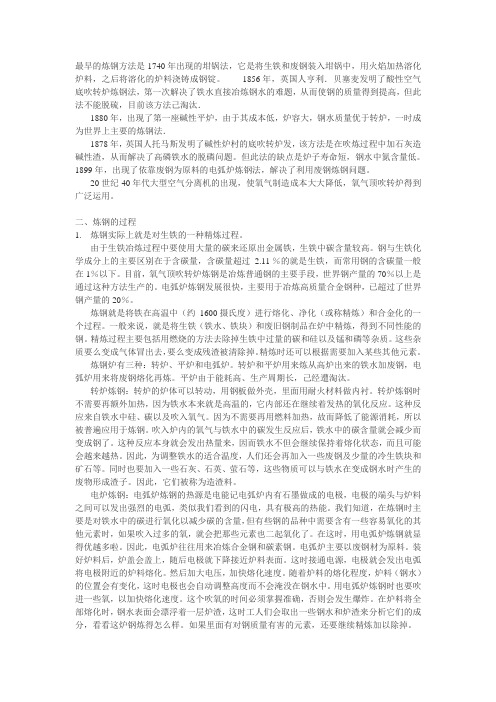
最早的炼钢方法是1740 年出现的坩锅法,它是将生铁和废钢装入坩锅中,用火焰加热溶化炉料,之后将溶化的炉料浇铸成钢锭。
1856 年,英国人亨利.贝塞麦发明了酸性空气底吹转炉炼钢法,第一次解决了铁水直接冶炼钢水的难题,从而使钢的质量得到提高,但此法不能脱硫,目前该方法己淘汰.1880 年,出现了第一座碱性平炉,由于其成本低,炉容大,钢水质量优于转炉,一时成为世界上主要的炼钢法.1878 年,英国人托马斯发明了碱性炉村的底吹转炉发,该方法是在吹炼过程中加石灰造碱性渣,从而解决了高磷铁水的脱磷问题。
但此法的缺点是炉子寿命短,钢水中氮含量低。
1899 年,出现了依靠废钢为原料的电弧炉炼钢法,解决了利用废钢炼钢问题。
20 世纪40 年代大型空气分离机的出现,使氧气制造成本大大降低,氧气顶吹转炉得到广泛运用。
二、炼钢的过程1.炼钢实际上就是对生铁的一种精炼过程。
由于生铁冶炼过程中要使用大量的碳来还原出金属铁,生铁中碳含量较高。
钢与生铁化学成分上的主要区别在于含碳量,含碳量超过 2.11 %的就是生铁,而常用钢的含碳量一般在1%以下。
目前,氧气顶吹转炉炼钢是冶炼普通钢的主要手段,世界钢产量的70%以上是通过这种方法生产的。
电弧炉炼钢发展很快,主要用于冶炼高质量合金钢种,已超过了世界钢产量的20%。
炼钢就是将铁在高温中(约1600 摄氏度)进行熔化、净化(或称精炼)和合金化的一个过程。
一般来说,就是将生铁(铁水、铁块)和废旧钢制品在炉中精炼,得到不同性能的钢。
精炼过程主要包括用燃烧的方法去除掉生铁中过量的碳和硅以及锰和磷等杂质。
这些杂质要么变成气体冒出去,要么变成残渣被清除掉。
精炼时还可以根据需要加入某些其他元素。
炼钢炉有三种:转炉、平炉和电弧炉。
转炉和平炉用来炼从高炉出来的铁水加废钢,电弧炉用来将废钢熔化再炼。
平炉由于能耗高、生产周期长,己经遭淘汰。
转炉炼钢:转炉的炉体可以转动,用钢板做外壳,里面用耐火材料做内衬。
炼钢的生产流程及原理

级论文题目:炼钢的生产流程及原理专业班级姓名学号指导教师日期炼钢的生产流程及原理摘要本文概述了炼钢生产的现状及发展趋势,介绍了炼钢生产的流程、原理及现代炼钢方法。
炼钢生产之初的造渣对钢的冶炼起到决定性作用,而碳、磷、硫、氧等成分的含量对钢的冶炼起着关键性作用,除此之外,钢中所含的气体和夹杂物对钢的质量也有影响。
本文就造渣过程及脱碳、脱磷、脱硫、脱氧过程进行了详细的阐述。
总之,炼钢的生产过程可归纳为:“四脱”(脱碳、脱磷、脱硫、脱氧),“二去”(去气和去夹杂)“二调整”(调整成分和温度)。
关键词:目录摘要第一章引言 (1)第二章现代炼钢方法简介 (3)2.1 氧气转炉炼钢 (3)2.1.1 氧气顶吹转炉炼钢法特点 (3)2.1.2 氧气底吹转炉炼钢法特点 (3)2.1.3 复合炼钢法特点 (4)2.2电弧炉炼钢 (4)第三章炼钢的生产流程及原理 (6)3.1炼钢的基本任务 (6)3.2 炼钢原材料的来源 (7)3.3 装料 (7)3.4 炼钢炉渣 (7)3.4.1 造渣 (8)3.4.2 炼钢炉渣的作用 (10)3.4.3 炼钢炉渣的来源 (11)3.4.4 炼钢炉渣的分类与组成 (11)3.4.5 炼钢炉渣的主要性质 (11)3.5 炼钢过程的基本反应 (13)3.5.1 碳的氧化 (13)3.5.2 硅的氧化和还原 (14)3.5.3 锰的氧化和还原 (15)3.5.4 脱磷反应 (15)3.5.5 脱硫反应 (17)3.5.6 脱氧 (18)3.6 去除钢中的气体 (21)3.7降低钢中的非金属夹杂物 (22)3.8 出钢 (24)结论 (25)参考文献 (26)致谢 (27)第一章引言(三号黑体)我国有丰富的铁矿石、有色金属、煤炭和水力资源等,是发展钢铁工业的基本条件。
我国是世界上钢铁冶金起源最早的国家之一,早在春秋战国时代(公元前8世纪~5世纪)就出现了生铁冶炼,制造出了很锋利的宝剑和其他用具,在历史上有着极其辉煌的成就。
炼钢方法
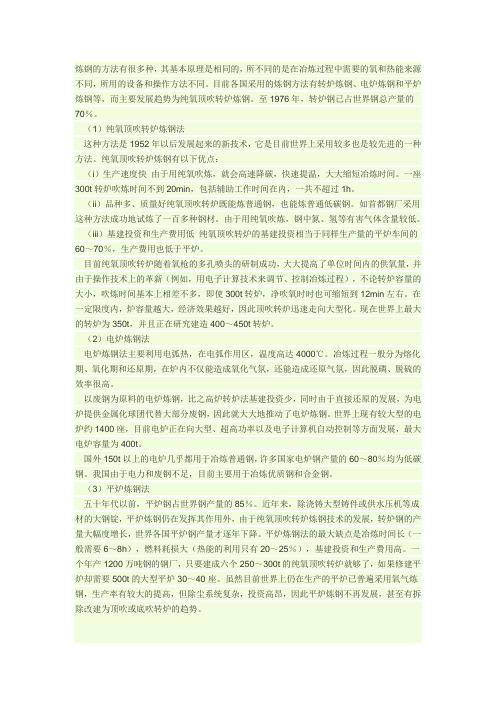
炼钢的方法有很多种,其基本原理是相同的,所不同的是在冶炼过程中需要的氧和热能来源不同,所用的设备和操作方法不同。
目前各国采用的炼钢方法有转炉炼钢、电炉炼钢和平炉炼钢等,而主要发展趋势为纯氧顶吹转炉炼钢。
至1976年,转炉钢已占世界钢总产量的70%。
(1)纯氧顶吹转炉炼钢法这种方法是1952年以后发展起来的新技术,它是目前世界上采用较多也是较先进的一种方法。
纯氧顶吹转炉炼钢有以下优点:(i)生产速度快由于用纯氧吹炼,就会高速降碳,快速提温,大大缩短冶炼时间。
一座300t转炉吹炼时间不到20min,包括辅助工作时间在内,一共不超过1h。
(ii)品种多、质量好纯氧顶吹转炉既能炼普通钢,也能炼普通低碳钢。
如首都钢厂采用这种方法成功地试炼了一百多种钢材。
由于用纯氧吹炼,钢中氮、氢等有害气体含量较低。
(iii)基建投资和生产费用低纯氧顶吹转炉的基建投资相当于同样生产量的平炉车间的60~70%,生产费用也低于平炉。
目前纯氧顶吹转炉随着氧枪的多孔喷头的研制成功,大大提高了单位时间内的供氧量,并由于操作技术上的革新(例如,用电子计算技术来调节、控制冶炼过程),不论转炉容量的大小,吹炼时间基本上相差不多,即使300t转炉,净吹氧时时也可缩短到12min左右。
在一定限度内,炉容量越大,经济效果越好,因此顶吹转炉迅速走向大型化。
现在世界上最大的转炉为350t,并且正在研究建造400~450t转炉。
(2)电炉炼钢法电炉炼钢法主要利用电弧热,在电弧作用区,温度高达4000℃。
冶炼过程一般分为熔化期、氧化期和还原期,在炉内不仅能造成氧化气氛,还能造成还原气氛,因此脱磷、脱硫的效率很高。
以废钢为原料的电炉炼钢,比之高炉转炉法基建投资少,同时由于直接还原的发展,为电炉提供金属化球团代替大部分废钢,因此就大大地推动了电炉炼钢。
世界上现有较大型的电炉约1400座,目前电炉正在向大型、超高功率以及电子计算机自动控制等方面发展,最大电炉容量为400t。
转炉炼钢原理及工艺介绍

2[P] + 5(FeO) = (P2O5) + 5[Fe]
3(FeO) +(P2O5) = (3FeO·P2O5) 在炼钢过程中,由于上述化学反应是一个放热反应,炼钢初期,炉温不高时对 脱磷反应是有利的。由于生成的磷酸铁( 3FeO·P2O5)在高温下是不稳定的化合物, 当炉温升高时,它可以重新分解,使磷又进入金属。为了使磷酸铁不发生分解反应, 需向炉内加入石灰,使磷酸铁转比为稳定的磷酸钙,其反应为: (3FeO·P2O5) + 4(CaO) = (4CaO·P2O5 + 3(FeO) 综上所述,碱性炼钢炉内脱磷的总反应为: 2[P] + 5(FeO) + 4(CaO) =(4CaO·P2O5) + 5[Fe]
(4)碳的氧化与还原
碳的氧化反应又称脱碳反应或碳氧反应,它是炼钢过程中最基本的一 个反应,贯穿炼钢过程的始终。 在炼钢过程中碳可以被氧直接氧化成CO气体,反应式为; 2(C)+{O2}=2{CO}
熔渣中的(FeO)与氧化性气体接触被氧化成高价氧化铁
(FeO) + 1/2{O2}= (Fe2O3) (Fe2O3)从炉渣表面扩散到渣与金属液交界面,与金属接触被还原 成低价氧化铁 (Fe2O3) + [Fe] = 3(FeO) 在渣与金属界面上,氧溶解到金属液中 ( FeO) = [O] + [Fe] 碳与溶于金属的氧发生反应,生成CO气体并排出到炉气中 [C] +[O] ={CO}
(4)碳的氧化与还原
碳的这种氧化反应在炼钢过程中有着极为重要的作用: 1)使铁水中的含碳量降低到所炼钢种的规格范围内o 2)脱碳反应的产物——CO气体从熔池中排出时产生佛腾现象,使熔 池受到激烈地搅动,从而增大了反应接触界面,加速了传质和传热过程, 有刮于冶金物化反应的进行。同时均匀了熔池的成分和温度; (3)上浮的CO气体有利千清除钢中气体和夹杂物,从而提高钢的质量。 为了加速碳的氧化,保持熔池内良好的沸腾状态,就必须提高炉温, 并改善炉渣的流动性以及向炉内加入氧化剂(铁矿石、氧气等)。
转炉炼钢发展历史

转炉炼钢工艺流程

转炉炼钢工艺流程转炉炼钢工艺流程这种炼钢法使用的氧化剂是氧气。
把空气鼓入熔融的生铁里,使杂质硅、锰等氧化。
在氧化的过程中放出大量的热量(含1%的硅可使生铁的温度升高200摄氏度),可使炉内达到足够高的温度。
因此转炉炼钢不需要另外使用燃料。
转炉炼钢是在转炉里进行。
转炉的外形就像个梨,内壁有耐火砖,炉侧有许多小孔(风口),压缩空气从这些小孔里吹炉内,又叫做侧吹转炉。
开始时,转炉处于水平,向内注入1300摄氏度的液态生铁,并加入一定量的生石灰,然后鼓入空气并转动转炉使它直立起来。
这时液态生铁表面剧烈的反应,使铁、硅、锰氧化(FeO,SiO2 , MnO,) 生成炉渣,利用熔化的钢铁和炉渣的对流作用,使反应遍及整个炉内。
几分钟后,当钢液中只剩下少量的硅与锰时,碳开始氧化,生成一氧化碳(放热)使钢液剧烈沸腾。
炉口由于溢出的一氧化炭的燃烧而出现巨大的火焰。
最后,磷也发生氧化并进一步生成磷酸亚铁。
磷酸亚铁再跟生石灰反应生成稳定的磷酸钙和硫化钙,一起成为炉渣。
当磷与硫逐渐减少,火焰退落,炉口出现四氧化三铁的褐色蒸汽时,表明钢已炼成。
这时应立即停止鼓风,并把转炉转到水平位置,把钢水倾至钢水包里,再加脱氧剂进行脱氧。
整个过程只需15分钟左右。
如果空气是从炉低吹入,那就是低吹转炉。
随着制氧技术的发展,现在已普遍使用氧气顶吹转炉(也有侧吹转炉)。
这种转炉吹如的是高压工业纯氧,反应更为剧烈,能进一步提高生产效率和钢的质量。
转炉一炉钢的基本冶炼过程。
顶吹转炉冶炼一炉钢的操作过程主要由以下六步组成:(1)上炉出钢、倒渣,检查炉衬和倾动设备等并进行必要的修补和修理;(2)倾炉,加废钢、兑铁水,摇正炉体(至垂直位置);(3)降枪开吹,同时加入第一批渣料(起初炉内噪声较大,从炉口冒出赤色烟雾,随后喷出暗红的火焰;3~5min后硅锰氧接近结束,碳氧反应逐渐激烈,炉口的火焰变大,亮度随之提高;同时渣料熔化,噪声减弱);(4)3~5min后加入第二批渣料继续吹炼(随吹炼进行钢中碳逐渐降低,约12min后火焰微弱,停吹);(5)倒炉,测温、取样,并确定补吹时间或出钢;(6)出钢,同时(将计算好的合金加入钢包中)进行脱氧合金化。
转炉炼钢工艺(主要是热平衡计算)

3 氧气顶吹转炉炼钢工艺3.1 一炉钢的操作过程要想找出在吹炼过程中金属成分和炉渣成分的变化规律,首先就必须熟悉一炉钢的操作、工艺过程。
在下面的图3-1中示出了氧气顶吹转炉吹炼一炉钢的操作过程与相应的工艺制度。
由图可以清楚地看出,氧气顶吹转炉炼钢的工艺操作过程可分以下几步进行:1)上炉钢出完并倒完炉渣后,迅速检查炉体,必要时进行补炉,然后堵好出钢口,及时加料。
2)在装入废钢和兑入铁水后,把炉体摇正。
在下降氧枪的同时,由炉口上方的辅助材料溜槽,向炉中加入第一批渣料(石灰、萤石、氧化铁皮、铁矿石),其量约为总量的2/3~1/2。
当氧枪降至规定的枪位时,吹炼过程正式开始。
当氧气流与溶池面接触时,碳、硅、锰开始氧化,称为点火。
点火后约几分钟,炉渣形成覆盖于熔池面上,随着Si、Mn、C、P的氧化,熔池温度升高,火焰亮度增加,炉渣起泡,并有小铁粒从炉口喷溅出来,此时应当适当降低氧枪高度。
3)吹炼中期脱碳反应剧烈,渣中氧化铁降低,致使炉渣的熔点增高和粘度增大,并可能出现稠渣(即―返干‖)现象。
此时,应适当提高氧枪枪位,并可分批加入铁矿石和第二批造渣材料(其余的1/3),以提高炉渣中的氧化铁含量及调整炉渣。
第三批造渣料为萤石,用以调整炉渣的流动性,但是否加第三批造渣材料,其加入量如何,要视各厂生产的情况而定。
4)吹炼末期,由于熔池金属中含碳量大大降低,则使脱碳反应减弱,炉内火焰变得短而透明,最后根据火焰状况,供氧数量和吹炼时间等因素,按所炼钢种的成分和温度要求,确定吹炼终点,并且提高氧枪停止供氧(称之为拉碳)、倒炉、测温、取样。
根据分析结果,决定出钢或补吹时间。
5)当钢水成分和温度均已合格,打开出钢口,即可倒炉出钢。
在出钢过程中,向钢包内加入铁合金,进行脱氧和合金化(有时可在打出钢口前向炉内投入部分铁合金)。
出钢完毕,将炉渣倒入渣罐。
通常将相邻两炉之间的间隔时间(即从装钢铁材料到倒渣完毕),称为冶炼周期或冶炼一炉钢的时间。
氧气顶吹转炉炼钢工艺介绍

氧气顶吹转炉炼钢工艺介绍
冶炼过程概述
从装料到出钢、倒完渣止,转炉一炉钢的冶炼过程包括装料、吹炼、脱氧出钢和倒渣几个阶段。
工艺流程图见图4-11。
工艺制度
1、装入制度
装入量指炼一炉钢时铁水和废钢的装入数量,它是决定转炉产量、炉龄及其他技术经济指标的重要因素之一。
在转炉炉役期的不同时期,有不同的合理装入量。
转炉公称容量有三种表示方法:平均炉金属料(铁水和废钢)装入量、平均炉产钢水量、平均炉产良坯量。
这三种表示方法因出发点不同而各有特点,均被采用,其中以炉产钢水量使用较多。
用铁水和废钢的平均装入量表示公称容量,便于物料平衡和热平衡计算。
2、供氧制度
氧射流及其熔池的相互作用
供氧参数a供氧压力b氧气流量和供氧强度
供氧操作供氧操作是指调节氧压或者枪位,达到调节氧气流量、喷头出口气流压力及射流与熔池的相互作用程度,以控制化学反应进程的操作。
供氧操作分为恒压变枪、恒枪变压、和分阶段恒压变枪几种方法。
我厂采用恒压变枪操作方式。
3、造渣制度
造渣是转炉炼钢的一项重要操作。
由于转炉冶炼时间短,必须快速成渣,才能满足冶炼过程和强化冶炼的要求。
此外,造渣对避免喷溅、减少金属损失和提高炉衬寿命都有直接关系。
4、温度制度
出钢温度的确定
冷却剂及其加入量确定终点控制和出钢
脱氧和合金化。
- 1、下载文档前请自行甄别文档内容的完整性,平台不提供额外的编辑、内容补充、找答案等附加服务。
- 2、"仅部分预览"的文档,不可在线预览部分如存在完整性等问题,可反馈申请退款(可完整预览的文档不适用该条件!)。
- 3、如文档侵犯您的权益,请联系客服反馈,我们会尽快为您处理(人工客服工作时间:9:00-18:30)。
顶吹转炉炼钢法冶炼历程分析
摘要:通过对转炉冶炼历程各种元素的氧化规律进行分析,探索出一条能够充分降低钢液中磷、硫两大有害元素含量的工艺制度,为实际生产提供理论依据。
关键词:转炉冶炼历程氧化规律
一、冶炼过程概述
从装料到出钢,倒渣,转炉冶炼一炉钢的冶炼过程包括装料、吹炼、脱氧出钢、溅渣护炉和倒渣几个阶段。
一炉钢的吹氧时间通常为12~18min,冶炼周期为30min左右。
转炉出钢完后,倒净炉渣,堵住出钢口,兑铁水和加废钢,降枪供氧,开始吹炼。
在送氧开吹的同时,加入第一批渣料,加入量相当于全炉总渣量的三分之二,开吹4~6分钟后,第一批渣料化好,再加入第二批渣料。
如果炉内化渣不好,则加入第三批萤石渣料。
当吹炼到所炼钢种要求的终点碳范围时,即停吹,倒炉取样,测定钢水温度,取样快速分析[C]、[S]、[P]的含量,当温度和成分符合要求时就出钢。
当钢水流出总量的四分之一时,向钢包中加脱氧剂,进行脱氧和合金化,由此一炉钢冶炼完毕。
二、熔池内各元素氧化规律分析
1.Si的氧化规律
在吹炼初期,铁水中的[Si]和氧的亲和力大,而且[Si]氧化反应为放热反应,低温下有利于此反应的进行,因此[Si]在吹炼初期就大量被氧化为(SiO2),(SiO2)先是与(FeO)反应生成(2FeO・SiO2),随着吹炼的进行,石灰逐渐溶解,由于钙镁橄榄石中的FeO和MnO 与SiO2的亲合力比CaO低、,故被CaO置换,生成(2CaO・SiO2)稳定化合物[1]。
在吹炼中期,碳氧化反应剧烈的情况下,该化合物也不会被还原。
图2.1 转炉冶炼各试验炉次钢水硅含量[Si]随冶炼时间的统计平均变化
图2.1表明,随着吹炼的进行,钢水硅含量逐渐降低;在钢水硅含量逐渐接近目标硅时,这种逐渐降低的速度越来越缓慢。
这一规律可由随着吹炼的进行,钢水硅含量逐渐降低,炉温逐渐升高,碳-氧反应逐渐为主,硅-氧反应速率逐渐降低而得到解释。
2.Mn的氧化规律
吹炼初期,[Mn]也迅速氧化,但不如[Si]氧化得快。
[Mn]被氧化为(MnO)同(SiO2)反应生成(MnO・SiO2)。
随着吹炼进行,温度升高加速石灰溶解,渣中(CaO)增加将(MnO)置换出来,(MnO)被C还原成[Mn]重新进入钢液中,吹炼后期炉温持续升高,部分[Mn]重新被氧化成(MnO)回到炉渣中,吹炼终了时,钢中的锰含量也称余锰或残锰。
图2.2 转炉冶炼各试验炉次钢水锰含量[Mn]随冶炼时间的统计平均变化
图2.2表明,吹炼中期(5min~10min)随着吹炼的进行,钢水锰含量逐渐升高,而吹炼后期(10min~15min)则逐渐降低。
这是因为吹炼前期炉温较低,锰同氧的亲和力比碳同氧的亲和力大,锰大量被氧化生成氧化锰;中期由于温度的升高,脱碳反应剧烈,并有氧化锰被碳还原成锰重新进入钢液,所以中期锰含量有明显升高;后期随着吹炼的进行,碳的氧化反应逐渐趋于平缓,锰重新被大量氧化,所以钢水中锰含量逐渐降低。
3.C的氧化规律
影响碳氧化速度变化规律的主要因素有:熔池温度、熔池金属成分、熔渣中(FeO)含量和炉内搅拌强度。
在吹炼的前、中、后期,这些因素在不断发生变化,从而体现出吹炼各期不同的碳氧化速度。
图2.3转炉冶炼试验炉次钢水碳含量[C]随冶炼时间的统计平均变化
图2.3表明,随着吹炼的进行,钢水碳含量逐渐降低;在钢水碳含量逐渐接近目标碳时,这种逐渐降低的速度越来越缓慢。
这一规律可由随着吹炼的进行,钢水碳含量逐渐降低,碳
-氧反应速率逐渐降低而得到解释。
吹炼前期(0min-5min):熔池平均温度低于1400~1500℃,[Si]、[Mn]含量高且与[O]的亲和力均大于[C]同[O]的亲和力,虽然(FeO)较高,但化渣、脱碳消耗的(FeO)较少,而且熔池搅拌不强烈,碳的氧化速度不如中期高。
吹炼中期(5min-10min):熔池温度高于1500℃,[Si]、[Mn]含量降低,[P]-[O]亲和力小于[C]-[O]亲和力,熔池搅拌强烈,反应区乳化效果好,结果此期碳氧化速度高。
吹炼后期(10min-15min):熔池温度很高,超过1600℃,[C]含量较低,搅拌也不如中期,碳氧化速度比中期低。
4.P的氧化规律
转炉脱磷的有利条件为:低温、高碱、高氧化性及较好的炉渣流动性。
图2.4转炉冶炼各试验炉次炉渣去磷能力随冶炼时间的统计平均变化
图2.4表明,随着吹炼的进行,磷在炉渣和钢水中的分配比还是逐步降低,即炉渣的脱磷能力逐步减小。
前期不利于脱磷的因素是炉渣碱度偏低,因此,及早形成碱度较高的炉渣,是前期脱磷的关键。
转炉冶炼前期采用高氧枪操作,可以加强熔池表面的搅拌作用,促进石灰的溶解,有助于提高炉渣碱度,高氧枪操作氧枪射流主要作用在熔池表面,同时也提高了熔渣中(FeO)含量,而且前期温度比较低,这些条件都有利于脱磷的进行。
到了冶炼中期,碳氧反应激烈,熔池温度升高加速了石灰的溶解,炉渣碱度持续上升,炉渣流动性也得到了较好的提高,炉渣高碱度及较好的流动性有助于脱磷反应。
到了后期,过高的熔池温度限制了脱磷反应的进行,因此后期不利于脱磷反应。
综上所述,脱磷主要集中在前期-中期。
5.S的氧化规律
转炉脱硫的有利条件为:高温、高碱、低氧化性及较好的炉渣流动性。
图2.5 转炉冶炼各试验炉次炉渣去硫能力随冶炼时间的统计平均变化
图2.5表明,随着吹炼的进行,硫在炉渣和钢水中的分配比还是逐步升高,即炉渣的脱硫能力逐步升高。
在吹炼前期,由于温度和碱度较低,(FeO)较高,渣的流动性差,各个条件均不利脱硫反应的进行,因此脱硫能力较低,脱硫速度较慢;吹炼中期,脱碳反应强烈,释放出大量的热量,熔池温度逐渐升高,同时由于碳氧化反应消耗了炉渣中大量(FeO),(FeO)比前期有所降低,且随着温度升高,大量石灰熔化碱度增大,熔池的乳化比较好,高温、高碱、低氧化性炉渣有利于脱硫反应进行,因此中期是脱硫的较好时期;到了吹炼后期,熔池温度已经升至出钢温度,碱度持续升高,脱硫速度持续上升。
综上所述,脱硫主要集中在中期-后期。
三、建议及小结
炼钢过程中,除了保证正常脱碳外,如何降低钢液中的P、S两大危害元素的含量是我们考虑的重点。
综上所述,脱P主要集中在前期-中期,为了提高脱P的效果,建议前期采用高氧枪操作,除了可以加强熔池表面搅拌,促进石灰熔解,在最短的时间内提高熔渣碱度外,高氧枪操作还可以提高熔渣的富氧量,前期高碱、高氧化性、低温的熔渣生成将大大提高脱P的效果;中期主要问题是在保证较好的脱P条件下,如何防止返干,为了避免返干,可以适当降低氧枪,避免碳氧反应过于激烈消耗过多(FeO),同时可以向熔池表面加入适量氧化铁皮或铁矿石,并加强熔池表面搅拌促进其熔解,保证熔渣中一定的(FeO)从而避免返干。
脱S主要集中在中期-后期,由于脱S需要在低氧化性气氛下进行,通常氧气转炉单渣操作的脱S效率只有30%~40%[2]。
我国炼钢技术规程要求入炉铁水的硫含量不超过0.05%,因此如果入炉铁水硫含量较高情况下,建议入炉前进行铁水预处理。
除此之外,为了达到较
好的控制钢液中的硫含量,可以在以下的几个方面有所改进:
1.尽可能选用低含硫量的金属原料;
2.配制适合成分及流动性好的炉渣,以创造能得到高硫分配比的条件;
3.从有利于脱硫考虑采用较大的渣量;
4.冶炼过程中正确认识及运用去硫“三高一低”原则。
参考文献:
[1]祝真祥.本钢180t转炉造渣工艺研.本钢技术.2008年3期.
[2]朱苗勇.现代冶金学[M].北京:冶金工业出版社,2008.。