丁辛醇的生产工艺与技术路线的选择
丁辛醇

丁辛醇丁辛醇是重要的基本有机化工原料,主要的产品品种:丁醇、辛醇。
1、用途正丁醇直接用作溶剂以及油脂、药物、香料等的萃取剂。
辛醇可直接用作照相造纸涂料和纺织等行业的溶剂,柴油和润滑油的添加剂,陶瓷行业釉浆分散剂、矿石浮选剂、消泡剂、清净剂、表面活性剂等。
作为化工原料可以用来生产以下产品:2、推荐项目在化学工业领域,丁辛醇主要用于生产丙烯酸酯和增塑剂两大酯类,因此根据丁辛醇上述用途以及当前市场情况选择5万吨邻苯二甲酸二丁酯(DBP )和7万吨邻苯二甲酸二辛酯(DOP )、16/20万吨万吨丙烯酸及丙烯酸酯作为重点策划项目。
3、市场分析 (1)国际市场增塑剂是目前塑料橡胶用量最大的助剂,以邻苯二甲酸酯类增塑剂的生产与消费量最大,在增塑剂总消费量中,约90%用于PVC 树脂,其余10%用于各种纤维素树脂、不饱和聚酯、环氧树脂、醋酸乙烯树脂和部分合成橡胶制品中。
邻苯二甲酸酯类仍是全球生产与消费的主导增塑剂,主要消费地区在亚洲,其中我国是世界最大的增塑剂消费国之一。
丁酸醋酸丁酯 丙烯酸丁酯 邻苯二甲酸二丁酯 癸二酸二丁酯丁醛 辛醇 邻苯二甲酸二辛酯内烯酸辛酯 己二酸二辛酯对苯二甲酸二辛酯溶剂、表活剂等各种溶剂、添加剂国外主要增塑剂生产厂家及产能。
(2)国内主要增塑剂生产厂家及产能。
目前,我国制品仍以软制品为主的情况下,增塑剂消费量呈增长趋势。
因国内增塑剂产量不足,每年需有大量进口,且呈逐年上升之势。
进口品种主要是邻苯二甲酸醋类,DOP进口量最大,其次为为DBP/DINP/DIDP,每年进口均超过万吨。
4、工艺技术路线1)DBP由苯酐和丁醇进行酯化反应制得,DOP由苯酐和辛醇进行酯化反应制得,酯化反应的核心是催化剂。
工艺技术路线主要有两条:一是酸性路线,常用的酸类催化剂有硫酸、对甲苯磺酸、磷酸、苯磺酸、2-萘磺酸。
二是非酸催化工艺。
它是国外研究开发的热点,典型代表有西德鲁尔公司采用的铝酸钠催化剂以及英国B.F.公司采用的钛酸酯类(如钛酸四丁酯、钛酸四异丙酯、钛酸四苯酯)催化剂。
丁辛醇工艺技术进展及选择
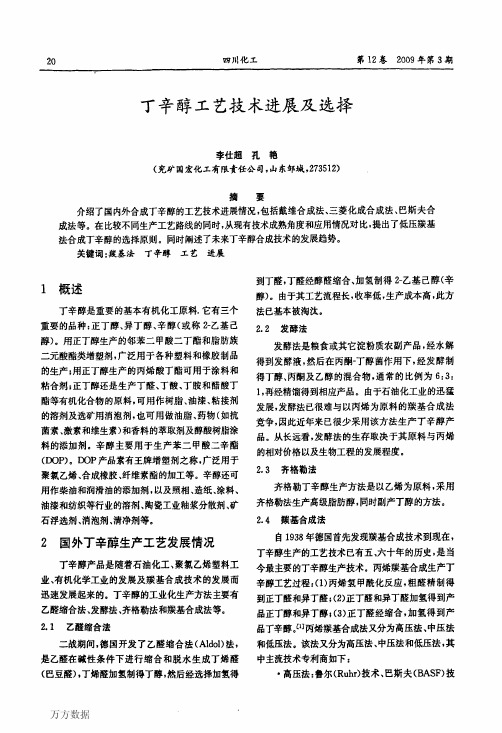
1。[2t引
(2)吉林石化公司研究院于2001年成功开发了 国内首创的辛烯醛高压液相加氢制辛醇催化剂,经 在吉化化肥厂丁辛醇装置上两年的应用证明,可以
丙爆一
问1j】换
谨记翘再 生与琅缩 I
I糯辛尊(:.乙基己尊)
蛩吨囹一异丁啐
对材质的要求最低,大部为碳钢,少量的为304不锈 钢;从流程的长度和装置的复杂性来说,戴维的最 短、最简单;从使用的情况看,戴维合成工艺使用最 多;但是伊斯曼乙烯一丙烯共迸料工艺技术可同时生 产丁醛和丙醛,产品灵活多样,对市场变化有较好的
法合成丁辛醇的选择原则。同时阐述了未来丁辛醇合成技术的发展趋势。
关键词:羰基法丁辛醇工艺进展
1概述
丁辛醇是重要的基本有机化工原料.它有三个
重要的品种:正丁醇、异丁醇、辛醇(或称2一乙基己
到丁醛,丁醛经醇醛缩合、加氢制得2一乙基己醇(辛 醇)。由于其工艺流程长,收率低,生产成本高,此方
法已基本被淘汰。
125 2.5 3~10/l ~9l 332
50
无铁丁醛 三苯基膦羰基铑 催化剂 蒸发分离、 液相循环 ∞~95
1.8~1.9 4~25/I 91~93
278.8
5
催化剂 催化剂 蒸发分离,
6
催化剂分离方式 液相循环 温度℃ 1∞
2 8~9/1
%
7
主要技术参 数
压力-眈
正/异比 转化率 循环水 电
~%
巴斯夫羰基合成工艺采用铑化合物为催化剂,
万方数据
四川化工 近年来,联碳与戴维公司又开发了第四代低压
丁辛醇生产工艺
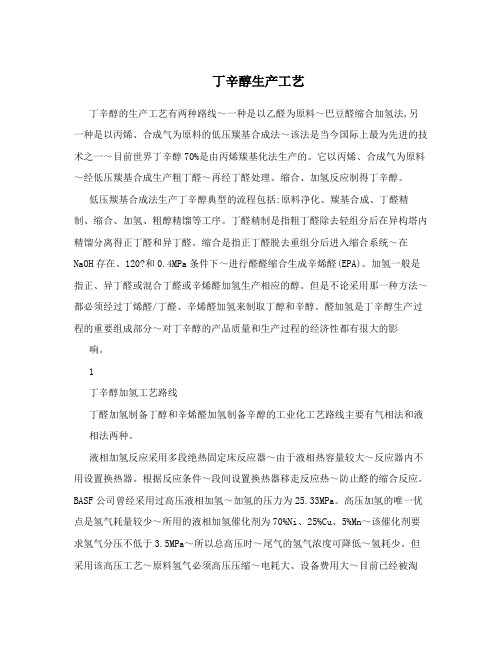
丁辛醇生产工艺丁辛醇的生产工艺有两种路线~一种是以乙醛为原料~巴豆醛缩合加氢法,另一种是以丙烯、合成气为原料的低压羰基合成法~该法是当今国际上最为先进的技术之一~目前世界丁辛醇70%是由丙烯羰基化法生产的。
它以丙烯、合成气为原料~经低压羰基合成生产粗丁醛~再经丁醛处理、缩合、加氢反应制得丁辛醇。
低压羰基合成法生产丁辛醇典型的流程包括:原料净化、羰基合成、丁醛精制、缩合、加氢、粗醇精馏等工序。
丁醛精制是指粗丁醛除去轻组分后在异构塔内精馏分离得正丁醛和异丁醛。
缩合是指正丁醛脱去重组分后进入缩合系统~在NaOH存在、120?和0.4MPa条件下~进行醛醛缩合生成辛烯醛(EPA)。
加氢一般是指正、异丁醛或混合丁醛或辛烯醛加氢生产相应的醇。
但是不论采用那一种方法~都必须经过丁烯醛/丁醛、辛烯醛加氢来制取丁醇和辛醇。
醛加氢是丁辛醇生产过程的重要组成部分~对丁辛醇的产品质量和生产过程的经济性都有很大的影响。
1丁辛醇加氢工艺路线丁醛加氢制备丁醇和辛烯醛加氢制备辛醇的工业化工艺路线主要有气相法和液相法两种。
液相加氢反应采用多段绝热固定床反应器~由于液相热容量较大~反应器内不用设置换热器。
根据反应条件~段间设置换热器移走反应热~防止醛的缩合反应。
BASF公司曾经采用过高压液相加氢~加氢的压力为25.33MPa。
高压加氢的唯一优点是氢气耗量较少~所用的液相加氢催化剂为70%Ni、25%Cu、5%Mn~该催化剂要求氢气分压不低于3.5MPa~所以总高压时~尾气的氢气浓度可降低~氢耗少。
但采用该高压工艺~原料氢气必须高压压缩~电耗大、设备费用大~目前已经被淘汰。
BASF公司和三菱化成工艺中醛的加氢采用中压液相加氢工艺~加氢压力为4.0-5.0MPa~加氢反应器形式采用填充床~反应温度为60-190?。
气相加氢法由于操作压力相对较低~工艺设备简单而被广泛应用。
目前~工业上丁辛醇装置上大多采用铜系催化剂气相加氢工艺。
如U.D.J联合工艺中采用低压气相加氢~压力为0.59-0.69MPa。
丁辛醇生产工艺流程图
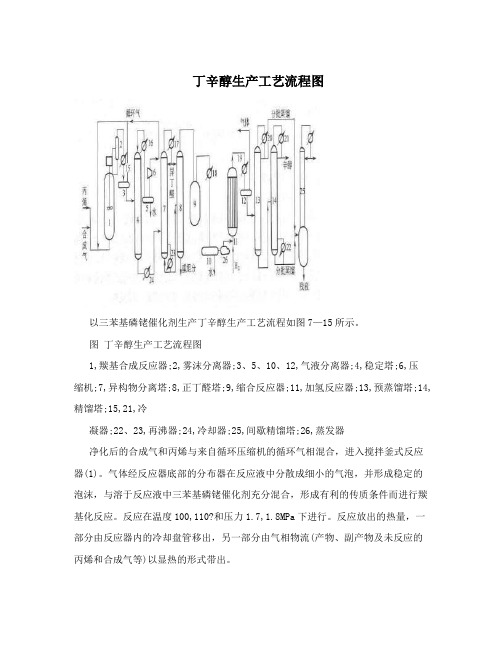
丁辛醇生产工艺流程图以三苯基磷铑催化剂生产丁辛醇生产工艺流程如图7—15所示。
图丁辛醇生产工艺流程图1,羰基合成反应器;2,雾沫分离器;3、5、10、12,气液分离器;4,稳定塔;6,压缩机;7,异构物分离塔;8,正丁醛塔;9,缩合反应器;11,加氢反应器;13,预蒸馏塔;14,精馏塔;15,21,冷凝器;22、23,再沸器;24,冷却器;25,间歇精馏塔;26,蒸发器净化后的合成气和丙烯与来自循环压缩机的循环气相混合,进入搅拌釜式反应器(1)。
气体经反应器底部的分布器在反应液中分散成细小的气泡,并形成稳定的泡沫,与溶于反应液中三苯基磷铑催化剂充分混合,形成有利的传质条件而进行羰基化反应。
反应在温度100,110?和压力1.7,1.8MPa下进行。
反应放出的热量,一部分由反应器内的冷却盘管移出,另一部分由气相物流(产物、副产物及未反应的丙烯和合成气等)以显热的形式带出。
在反应器内,液面高度的控制是很重要的,液面高度过高,会加大液体的夹带量而造成催化剂的损耗,液面太低又会减少反应物的实际停留时间,反应效果差。
由反应器出来的气流首先进入雾沫分离器(2),将夹带出来的极小液滴捕集下来返回反应器,气体进入冷凝器(15)。
气相产物被冷凝,未冷凝的气体循环回反应器。
经冷凝后的液相产物中溶解有大量的丙烷和丙烯,可在稳定塔(4)中蒸馏脱除。
稳定塔为板式塔,塔顶压力为0.62MPa,温度为93?,塔釜温度为140?左右。
塔顶蒸出的气体经冷却分出其中的液滴,并增压后循环回反应器。
稳定塔釜的粗产品冷却后送异构物分离工序。
异构物分离工序由异构物分离塔(7)及正丁醛塔(8)组成,其任务是在进行缩合加氢前,分离出异丁醛,并除去粗产品中的重组分。
异构物塔顶得到质量分数为99,的异丁醛,塔釜得到99.64,的正丁醛,其中异丁醛含量应小于0.2,。
由于正,异丁酯的沸点差较小(正、异丁醛沸点分别是75.9?和63,64?),故异构物分离塔的塔板数较多,且回流比较大。
丁辛醇生产工艺
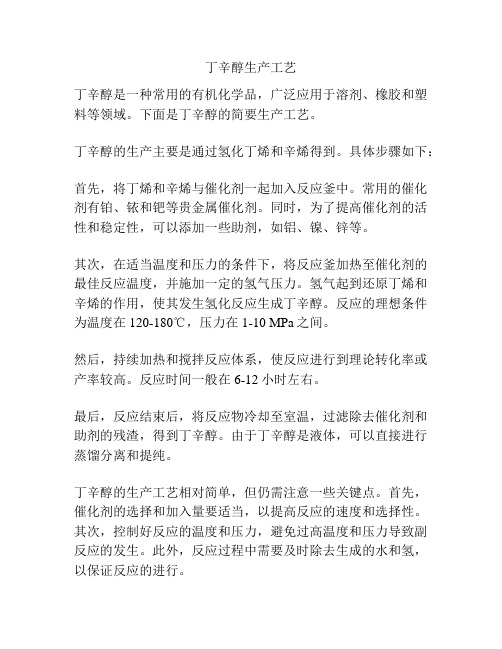
丁辛醇生产工艺
丁辛醇是一种常用的有机化学品,广泛应用于溶剂、橡胶和塑料等领域。
下面是丁辛醇的简要生产工艺。
丁辛醇的生产主要是通过氢化丁烯和辛烯得到。
具体步骤如下:
首先,将丁烯和辛烯与催化剂一起加入反应釜中。
常用的催化剂有铂、铱和钯等贵金属催化剂。
同时,为了提高催化剂的活性和稳定性,可以添加一些助剂,如铝、镍、锌等。
其次,在适当温度和压力的条件下,将反应釜加热至催化剂的最佳反应温度,并施加一定的氢气压力。
氢气起到还原丁烯和辛烯的作用,使其发生氢化反应生成丁辛醇。
反应的理想条件为温度在120-180℃,压力在1-10 MPa之间。
然后,持续加热和搅拌反应体系,使反应进行到理论转化率或产率较高。
反应时间一般在6-12小时左右。
最后,反应结束后,将反应物冷却至室温,过滤除去催化剂和助剂的残渣,得到丁辛醇。
由于丁辛醇是液体,可以直接进行蒸馏分离和提纯。
丁辛醇的生产工艺相对简单,但仍需注意一些关键点。
首先,催化剂的选择和加入量要适当,以提高反应的速度和选择性。
其次,控制好反应的温度和压力,避免过高温度和压力导致副反应的发生。
此外,反应过程中需要及时除去生成的水和氢,以保证反应的进行。
总结起来,丁辛醇的生产主要是通过氢化丁烯和辛烯得到,条件是适当温度和压力下,在催化剂的作用下进行反应。
这种生产工艺简单可行,但仍需要注意控制好关键条件,以提高产率和纯度。
丁辛醇生产技术及其发展趋势
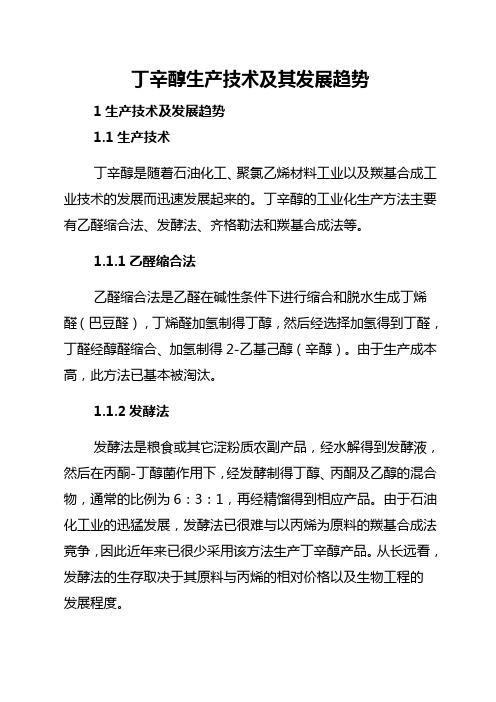
丁辛醇生产技术及其发展趋势1生产技术及发展趋势1.1生产技术丁辛醇是随着石油化工、聚氯乙烯材料工业以及羰基合成工业技术的发展而迅速发展起来的。
丁辛醇的工业化生产方法主要有乙醛缩合法、发酵法、齐格勒法和羰基合成法等。
1.1.1乙醛缩合法乙醛缩合法是乙醛在碱性条件下进行缩合和脱水生成丁烯醛(巴豆醛),丁烯醛加氢制得丁醇,然后经选择加氢得到丁醛,丁醛经醇醛缩合、加氢制得2-乙基己醇(辛醇)。
由于生产成本高,此方法已基本被淘汰。
1.1.2发酵法发酵法是粮食或其它淀粉质农副产品,经水解得到发酵液,然后在丙酮-丁醇菌作用下,经发酵制得丁醇、丙酮及乙醇的混合物,通常的比例为6:3:1,再经精馏得到相应产品。
由于石油化工业的迅猛发展,发酵法已很难与以丙烯为原料的羰基合成法竞争,因此近年来已很少采用该方法生产丁辛醇产品。
从长远看,发酵法的生存取决于其原料与丙烯的相对价格以及生物工程的发展程度。
1.1.3齐格勒法齐格勒丁辛醇生产方法是以乙烯为原料,采用齐格勒法生产高级脂肪醇,同时副产丁醇的方法。
1.1.4羰基合成法羰基合成法是当今最主要的丁辛醇生产技术。
丙烯羰基合成生产丁辛醇工艺过程:丙烯氢甲酰化反应,粗醛精制得到正丁醛和异丁醛,正丁醛和异丁醛加氢得到产品正丁醇和异丁醇;正丁醛经缩合、加氢得到产品辛醇。
丙烯羰基合成法又分为高压法、中压法和低压法。
丙烯羰基合成法的主流技术专利商如下:高压法:鲁尔 (Ruhr)技术、巴斯夫(BASF)技术、三菱(MCC)技术、壳牌(Shell)技术。
中压法:壳牌(Shell)技术、鲁尔-化学(Ruhr-chemic)技术、三菱(MCC)铑法技术。
低压法:雷普法(Reppe)技术、伊士曼(Eastman)技术、戴维(Davy UCC Johnson Matthey)技术、三菱化成(MCC)技术。
高压的羰基合成技术由于选择性较差、副产品(丙烷和高沸物)多,已被以铑为催化剂的低压羰基合成技术所取代。
丁醇和辛醇的生产工艺

② 催化剂和反应器
铜基催化剂 (气相加氢反应) (主要成分 CuO 和ZnO) 压力 0.6MPa; 温度 155℃ 反应器 管式固定床反应器(带有加热蒸发器,防止液体带入)
催化剂优点:加氢选择性好,副反应少,生产能力大;但催化剂力学性能差, 遇液体易破碎等。(即反应器外带有加热蒸发器)
4.20 丁醇和辛醇的生产工艺
① 乙醛为原料的路线 (如,乙醛发酵法和乙醛缩合法)现已淘汰 ② 丙烯为原料的路线(丙烯羰基合成法) (也称氢甲酰化合成法)
全球生产丁、辛醇的主要方法。
4.20 丁醇和辛醇的生产工艺
(3)丙烯羰基合成法制丁醇和辛醇的主要反应
① CH3CH=CH2 + CO+H2 催化→剂 CH3CH2CH2CHO ② CH3CH2CH2CHO +H2 O→H-1 CH3CH2CH2CH2OH
平行副反应
CH3CH=CH2+CO+H2 → (CH3)2CHCHO CH3CH =CH2+H2 →C3H8
连串副反应
CH3CH2CH2CHO+H2 →CH3CH2CH2CH2OH CH3CH2CH2CHO+CO+H2 →C4H9COOH 必须控制反应条件,拟制副反应
ΔHϴ298K= -123.8kJ/mol
3. 生产丁、辛醇的主要工艺条件
(1)丙烯羰基合成制丁醛的工艺条件
液相催化反应,反应条件比较温和。
➢ 原料
丙烯、合成气
➢ 催化剂
铑、三苯基膦
➢ 溶剂
正异构丁醛
➢ 操作压力 1.6~1.8MPa
➢ 反应温度 100~110℃
➢ 转化率
91~93%
➢ 反应选择性好,正/异丁醛超过(7~10) : 1。
丁辛醇生产工艺
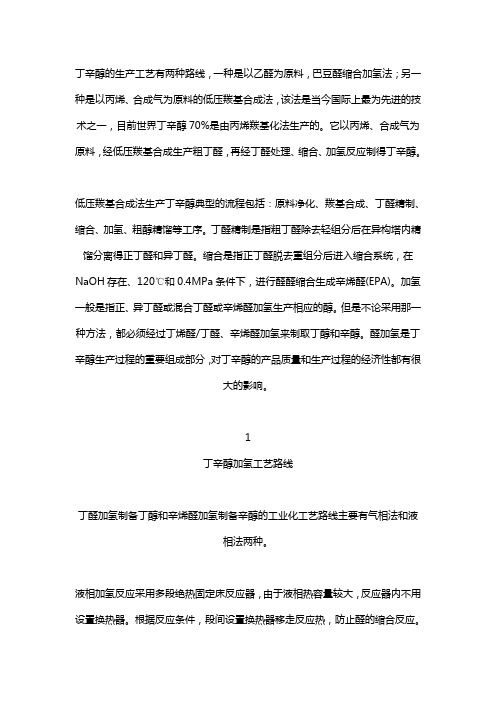
丁辛醇的生产工艺有两种路线,一种是以乙醛为原料,巴豆醛缩合加氢法;另一种是以丙烯、合成气为原料的低压羰基合成法,该法是当今国际上最为先进的技术之一,目前世界丁辛醇70%是由丙烯羰基化法生产的。
它以丙烯、合成气为原料,经低压羰基合成生产粗丁醛,再经丁醛处理、缩合、加氢反应制得丁辛醇。
低压羰基合成法生产丁辛醇典型的流程包括:原料净化、羰基合成、丁醛精制、缩合、加氢、粗醇精馏等工序。
丁醛精制是指粗丁醛除去轻组分后在异构塔内精馏分离得正丁醛和异丁醛。
缩合是指正丁醛脱去重组分后进入缩合系统,在NaOH存在、120℃和0.4MPa条件下,进行醛醛缩合生成辛烯醛(EPA)。
加氢一般是指正、异丁醛或混合丁醛或辛烯醛加氢生产相应的醇。
但是不论采用那一种方法,都必须经过丁烯醛/丁醛、辛烯醛加氢来制取丁醇和辛醇。
醛加氢是丁辛醇生产过程的重要组成部分,对丁辛醇的产品质量和生产过程的经济性都有很大的影响。
1丁辛醇加氢工艺路线丁醛加氢制备丁醇和辛烯醛加氢制备辛醇的工业化工艺路线主要有气相法和液相法两种。
液相加氢反应采用多段绝热固定床反应器,由于液相热容量较大,反应器内不用设置换热器。
根据反应条件,段间设置换热器移走反应热,防止醛的缩合反应。
BASF公司曾经采用过高压液相加氢,加氢的压力为25.33MPa。
高压加氢的唯一优点是氢气耗量较少,所用的液相加氢催化剂为70%Ni、25%Cu、5%Mn,该催化剂要求氢气分压不低于3.5MPa,所以总高压时,尾气的氢气浓度可降低,氢耗少。
但采用该高压工艺,原料氢气必须高压压缩,电耗大、设备费用大,目前已经被淘汰。
BASF公司和三菱化成工艺中醛的加氢采用中压液相加氢工艺,加氢压力为4.0-5.0MPa,加氢反应器形式采用填充床,反应温度为60-190℃。
气相加氢法由于操作压力相对较低,工艺设备简单而被广泛应用。
目前,工业上丁辛醇装置上大多采用铜系催化剂气相加氢工艺。
如U.D.J联合工艺中采用低压气相加氢,压力为0.59-0.69MPa。
丁辛醇生产工艺

丁辛醇的生产工艺有两种路线,一种是以乙醛为原料,巴豆醛缩合加氢法;另一种是以丙烯、合成气为原料的低压羰基合成法,该法是当今国际上最为先进的技术之一,目前世界丁辛醇70%是由丙烯羰基化法生产的。
它以丙烯、合成气为原料,经低压羰基合成生产粗丁醛,再经丁醛处理、缩合、加氢反应制得丁辛醇。
低压羰基合成法生产丁辛醇典型的流程包括:原料净化、羰基合成、丁醛精制、缩合、加氢、粗醇精馏等工序。
丁醛精制是指粗丁醛除去轻组分后在异构塔内精馏分离得正丁醛和异丁醛。
缩合是指正丁醛脱去重组分后进入缩合系统,在NaOH 存在、120℃和0.4MPa条件下,进行醛醛缩合生成辛烯醛(EPA)。
加氢一般是指正、异丁醛或混合丁醛或辛烯醛加氢生产相应的醇。
但是不论采用那一种方法,都必须经过丁烯醛/丁醛、辛烯醛加氢来制取丁醇和辛醇。
醛加氢是丁辛醇生产过程的重要组成部分,对丁辛醇的产品质量和生产过程的经济性都有很大的影响。
1丁辛醇加氢工艺路线丁醛加氢制备丁醇和辛烯醛加氢制备辛醇的工业化工艺路线主要有气相法和液相法两种。
液相加氢反应采用多段绝热固定床反应器,由于液相热容量较大,反应器内不用设置换热器。
根据反应条件,段间设置换热器移走反应热,防止醛的缩合反应。
BASF公司曾经采用过高压液相加氢,加氢的压力为25.33MPa。
高压加氢的唯一优点是氢气耗量较少,所用的液相加氢催化剂为70%Ni、25%Cu、5%Mn,该催化剂要求氢气分压不低于3.5MPa,所以总高压时,尾气的氢气浓度可降低,氢耗少。
但采用该高压工艺,原料氢气必须高压压缩,电耗大、设备费用大,目前已经被淘汰。
BASF公司和三菱化成工艺中醛的加氢采用中压液相加氢工艺,加氢压力为4.0-5.0MPa,加氢反应器形式采用填充床,反应温度为60-190℃。
气相加氢法由于操作压力相对较低,工艺设备简单而被广泛应用。
目前,工业上丁辛醇装置上大多采用铜系催化剂气相加氢工艺。
如U.D.J联合工艺中采用低压气相加氢,压力为0.59-0.69MPa。
丁辛醇生产工艺技术

丁辛醇生产工艺技术丁辛醇是一种重要的有机化工原料,广泛应用于化学、医药、农药、塑料等行业。
下面我们来介绍一下丁辛醇的生产工艺技术。
丁辛醇的主要生产工艺有两步法和一步法。
首先介绍两步法。
两步法生产丁辛醇主要包括醇酸法和醇醚法。
醇酸法是利用丁烯为原料,通过醇酸浓度温和酸催化剂进行酸醇缩合反应,生成丁辛醇。
这个过程需要在合适的温度和压力下进行。
反应结束后,通过蒸馏分离纯化,即可得到丁辛醇。
醇醚法是将丁醇和辛醇分别与硫酸或磷酸等酸催化剂进行酯交换反应,生成对应的丁酯和辛酯。
然后,将丁酯和辛酯在高温下进行酯加成反应,生成丁辛醇。
这个过程同样需要进行蒸馏纯化,从而得到纯净丁辛醇。
两步法生产工艺相对比较复杂,需要多个步骤和反应器,并且对催化剂和温度等条件有较高的要求。
因此,虽然两步法可以得到高纯度的丁辛醇,但生产成本较高,工艺相对繁琐。
另外一步法是将1,3丁二醇和辛醇通过一步法直接脱羟酯化反应得到丁辛醇。
这个过程相对简单,只需要进行一次反应即可得到丁辛醇。
首先将1,3丁二醇和辛醇与脱水剂进行酯化反应,生成丁辛酸酯。
然后通过加热脱羟反应,将丁辛酸酯脱羟生成丁辛醇。
最后进行蒸馏纯化即可得到丁辛醇。
这个工艺相对比较简单,生产成本较低。
无论采用哪种生产工艺,丁辛醇的生产工艺都需要严格控制反应的条件和过程,以保证产品的质量。
同时,在生产过程中需要注意安全生产,避免发生事故。
总的来说,丁辛醇的生产工艺技术涉及到酯交换、酯加成、酸醇缩合等反应,采用两步法或一步法进行。
无论采用哪种工艺,都需要严格控制反应条件和过程,以获得高纯度的丁辛醇。
同时,生产过程中需要注重安全生产,避免事故发生。
丁辛醇的生产工艺随着科技的发展和技术的进步,也在不断的改进和完善。
丁辛醇生产工艺
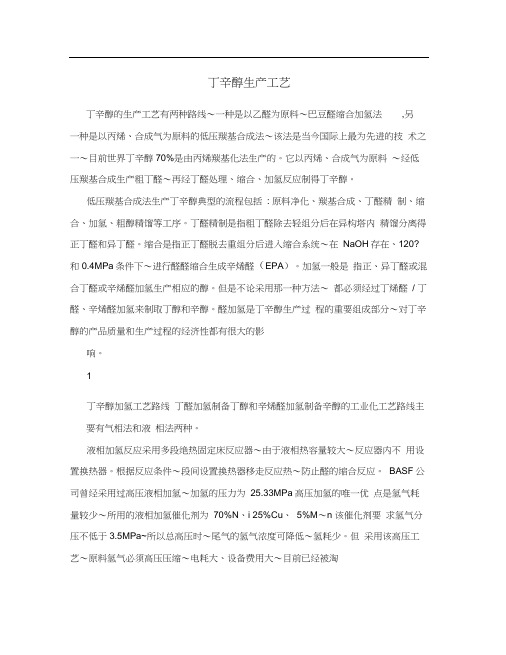
丁辛醇生产工艺丁辛醇的生产工艺有两种路线〜一种是以乙醛为原料〜巴豆醛缩合加氢法,另一种是以丙烯、合成气为原料的低压羰基合成法〜该法是当今国际上最为先进的技术之一〜目前世界丁辛醇70%是由丙烯羰基化法生产的。
它以丙烯、合成气为原料〜经低压羰基合成生产粗丁醛〜再经丁醛处理、缩合、加氢反应制得丁辛醇。
低压羰基合成法生产丁辛醇典型的流程包括: 原料净化、羰基合成、丁醛精制、缩合、加氢、粗醇精馏等工序。
丁醛精制是指粗丁醛除去轻组分后在异构塔内精馏分离得正丁醛和异丁醛。
缩合是指正丁醛脱去重组分后进入缩合系统〜在NaOH存在、120?和0.4MPa条件下〜进行醛醛缩合生成辛烯醛(EPA)。
加氢一般是指正、异丁醛或混合丁醛或辛烯醛加氢生产相应的醇。
但是不论采用那一种方法〜都必须经过丁烯醛/ 丁醛、辛烯醛加氢来制取丁醇和辛醇。
醛加氢是丁辛醇生产过程的重要组成部分〜对丁辛醇的产品质量和生产过程的经济性都有很大的影响。
1丁辛醇加氢工艺路线丁醛加氢制备丁醇和辛烯醛加氢制备辛醇的工业化工艺路线主要有气相法和液相法两种。
液相加氢反应采用多段绝热固定床反应器〜由于液相热容量较大〜反应器内不用设置换热器。
根据反应条件〜段间设置换热器移走反应热〜防止醛的缩合反应。
BASF公司曾经采用过高压液相加氢〜加氢的压力为25.33MPa高压加氢的唯一优点是氢气耗量较少〜所用的液相加氢催化剂为70%N、i 25%Cu、5%M〜n 该催化剂要求氢气分压不低于3.5MPa~所以总高压时〜尾气的氢气浓度可降低〜氢耗少。
但采用该高压工艺〜原料氢气必须高压压缩〜电耗大、设备费用大〜目前已经被淘汰。
BASF公司和三菱化成工艺中醛的加氢采用中压液相加氢工艺〜加氢压力为 4.0-5.0MPa〜加氢反应器形式采用填充床〜反应温度为60-190?。
气相加氢法由于操作压力相对较低〜工艺设备简单而被广泛应用。
目前〜工业上丁辛醇装置上大多采用铜系催化剂气相加氢工艺。
丁辛醇生产工艺技术规程

丁辛醇生产工艺技术规程丁辛醇是一种无色透明的液体,具有良好的溶解性和稳定性。
它广泛应用于合成树脂、塑料、溶剂和涂料等行业。
下面是丁辛醇的生产工艺技术规程。
一、原料准备1. 丁辛醇的主要原料为丁烯和辛醇。
2. 丁烯和辛醇的纯度需达到99%以上。
3. 其它辅助原料包括催化剂、溶剂和助剂等。
二、工艺流程1. 玉米糖浆获得丁烯:将玉米糖浆经过酸液处理和蒸馏,获得纯度达到90%以上的丁烯。
2. 丁辛醇制备:将丁烯与辛醇在反应釜中进行氢化反应,反应温度控制在100-120℃,压力控制在1-3 MPa范围内,反应时间为4-6小时。
3. 分离提纯:经过氢化反应后,将产物进行脱氢反应,去除未反应的氢气。
再通过蒸馏、结晶等工艺过程,分离得到纯度达到99%以上的丁辛醇。
三、关键工艺参数1. 反应温度:控制在100-120℃,过高温度会导致副反应的发生,过低温度则反应速率较慢。
2. 压力:控制在1-3 MPa范围内,高压有利于反应的进行,但过高压力会增加设备的投资和能耗。
3. 反应时间:反应时间为4-6小时,过长时间会导致副反应的发生,过短时间则反应不完全。
四、设备要求1. 反应釜:选择耐高温、耐腐蚀的材质制成,容积应根据生产规模进行选择。
2. 蒸馏塔:采用分馏和萃取等工艺,需要具备高效脱水和分离的能力。
3. 精馏塔:用于去除未反应的氢气,要求具备高效脱气的能力。
五、安全措施1. 工艺过程中要保持设备的密封性,防止气体泄漏和溶剂挥发造成爆炸和污染环境。
2. 操作人员应佩戴防护装备,避免直接接触有毒物质。
3. 严格控制反应温度和压力,防止设备过热或过压造成事故。
六、产品质量检验1. 丁辛醇的外观应无色透明,无杂质。
2. 需经过色度检验,颜色不能超过标准。
3. 根据工业标准进行纯度检验,纯度需达到99%以上。
4. 根据用户要求进行包装和出厂检验。
以上是丁辛醇的生产工艺技术规程,通过合理的生产工艺和严格的质量检验,可保证生产出高质量的丁辛醇产品。
丁辛醇生产工艺技术标准

丁辛醇生产工艺技术标准丁辛醇是一种重要的有机合成原料,被广泛应用于化工、医药、农药等领域。
为了确保丁辛醇的质量稳定和生产效率,制定和实施相应的工艺技术标准是非常重要的。
一、原料选用1. 丁烯:99%以上的纯度,含水量不超过0.1%。
2. 硫酸:纯度大于98%,含水量不超过0.1%。
3. 氢气:氧气含量低于10ppm,水含量不超过0.1%。
二、生产工艺流程1. 丁烯和硫酸的反应:将丁烯和硫酸按照一定的摩尔比加入反应釜中,反应温度控制在100℃-130℃,反应时间需要根据具体情况进行调整,通常为2-3小时。
反应后,将反应物进行分离处理。
2. 含硫酸分离:将反应后得到的含硫酸混合液进行净化处理,通过蒸馏、过滤等方法去除杂质。
3. 脱硫反应:将净化后的含硫酸混合液与氢气进行反应,反应温度在120℃-150℃之间,反应时间约为1-2小时,将反应后得到的产物经过分离处理。
4. 脱水反应:将脱硫后的产物与氢气进行反应,反应温度控制在150℃-200℃,反应时间约为1-2小时,将反应后得到的产物进行分离处理。
5. 丁辛醇的提纯:通过蒸馏、结晶等方法,对产物进行多次提纯,确保丁辛醇的纯度达到99%以上。
三、工艺控制1. 温度控制:根据不同的反应步骤,控制反应温度在适宜的范围内,以确保反应的进行和产物质量的稳定。
2. 气体流量控制:控制氢气的流量,以保证反应物料中的氧气含量在合理的范围内,避免氧气对反应的干扰。
3. 反应时间控制:根据反应的速度和产物的品质要求,控制反应时间,以确保充分反应。
4. 生产过程监控:通过对反应釜内压力、温度、气体流量等参数的实时监控,掌握生产过程中的动态变化,及时调整工艺参数,确保生产的连续性和稳定性。
四、安全和环保要求1. 生产过程中严格遵守相关安全操作规程,确保操作人员的人身安全和设备的正常运行。
2. 定期对生产设备进行检修和保养,保证设备的正常运行和安全性。
3. 对反应废水、废气以及废酸等进行合理处理,遵守环保法规,减少对环境的污染。
丁辛醇残液的提纯工艺流程和注意事项

丁辛醇残液的提纯工艺流程和注意事项
嘿呀!今天咱们来聊聊丁辛醇残液的提纯工艺流程和注意事项!
首先呢,咱来说说这提纯工艺流程。
第一步呀,得对丁辛醇残液进行预处理,把里面的杂质啥的先过滤掉一部分哇!这一步可重要啦,要是没做好,后面的工作可就难搞了呢!
然后呢,会用到一些化学方法来进行分离,比如说萃取呀!哎呀呀,这萃取剂的选择可得小心谨慎哟,选不好就白搭啦!
接下来就是蒸馏环节啦!通过控制温度和压力,把不同的成分给分开哟!这可需要精准的操作呢,稍微有点差错,结果就不理想啦!
再说说注意事项哈!
第一,安全绝对是第一位的呀!处理这些化学物质的时候,一定要做好防护措施,不然受伤了可咋办呢?
第二,设备的维护不能马虎哇!定期检查和保养,不然关键时刻掉链子可就糟糕啦!
第三,操作流程要严格遵守呢,不能随心所欲呀,不然出了问题谁负责呀?
第四,原材料的质量要把关好哟,不好的原材料会影响整个提纯效果的呀!
第五,注意环境的保护哇,不能让这些化学物质随意排放,污染环境可不行呢!
第六,操作人员得有足够的专业知识和经验呀,不然怎么能应对各种突发情况呢?
第七,监控系统要时刻保持正常运行哟,及时发现问题及时解决呀!
第八,实验室的卫生也要搞好哇,干净整洁的环境有助于提高工作效率呢!
哎呀呀,总之,丁辛醇残液的提纯可不容易呀,工艺流程和注意事项都得牢记在心,才能做好这项工作哟!。
丁辛醇的生产工艺与技术路线的选择

丁/辛醇的生产工艺与技术路线的选择2.1 丁辛醇生产方法丁辛醇是随着石油化工、聚氯乙烯材料工业以及羰基合成工业技术的发展而迅速发展起来的。
丁辛醇的工业化生产方法主要有乙醛缩合法、发酵法、齐格勒法和羰基合成法等。
2.1.1乙醛缩合法二战期间,德国开发了乙醛缩合法(Aldo1)法。
……2.1.2发酵法发酵法是粮食或其它淀粉质农副产品,经水解得到发酵液,然后在丙酮-丁醇菌作用下,经发酵制得丁醇、丙酮及乙醇的混合物,通常的比例为……2.1.3齐格勒法齐格勒丁辛醇生产方法是以乙烯为原料,采用齐格勒法生产高级脂肪醇,同时副产丁醇的方法。
2.1.4羰基合成法……2.2 丁辛醇生产工艺技术比较及选择2.2.1 国外丁辛醇生产工艺对比……丁辛醇主要生产工艺的比较见表2.1。
表2.1 丁辛醇主要生产工艺的比较关于丁辛醇生产的几种主要工艺技术方法列表如下。
表2.2 丁辛醇工艺技术方案对比表2.2.2 国外丁辛醇生产工艺选择……2.3 丁辛醇合成工艺技术进展及发展趋势2.3.1 国外丁辛醇合成工艺技术进展丁醇和辛醇是用途广泛的重要精细化工原料,随着生产规模的不断扩大,丁辛醇技术发展重点集中在合成工艺和催化剂的研究和开发上,国外生产商改进丁辛醇合成工艺形成了各具特色的专有技术,引起了业内人士的极大关注。
……2.3.2 国内丁辛醇合成工艺技术进展……2.3.3 国内丁辛醇合成工艺技术发展趋势随着世界经济全球化及规模生产经济最大化,丁辛醇工业发展的重点将集中在催化剂的研究和开发上。
其技术发展趋势是:……2.4 丁辛醇质量指标2.4.1 丁醇质量指标工业正丁醇:执行标准:GB/T 6027/1998,该标准适用于合成法与发酵法生产的工业正丁醇。
要求:外观:透明液体,无可见杂质。
表2.3 正丁醇质量指标项目指标分析方法优等品一等品合格品色度,Hazen单位(铂-钴色号)≤10 15 GB/T3143密度(20℃)g/cm30.809~0.811 0.808~0.812 GB/T4472 沸程(0℃,101.325Kpa)包括(117.7℃),℃≤ 1.0 2.0 3.0 GB/T7534 正丁醇含量,% ≥99.5 99.0 98.0 色谱法硫酸显色试验(铂-钴色号)≤20 40 比色法酸度(以乙酸计),% ≤0.003 0.005 0.01 容量法水分,% ≤0.1 0.2 GB/T6283 蒸发残渣,% ≤0.003 0.005 0.01 重量法2.4.2 辛醇质量指标辛醇:执行标准:GB/T 6818/1993,本标准适用于由丙烯羰基合成法及乙醛缩合法制得的工业辛醇。
丁辛醇合成工艺评价及选择

丁辛醇合成工艺评价及选择摘要:本文介绍了合成丁辛醇技术,对丁辛醇装置主要专利技术的特点做了评价,并举例炼油化工一体化企业中建设丁辛醇装置技术选择及总体平衡。
关键词:羰基法丁辛醇工艺技术炼化一体化一、概述丁辛醇是重要的基本有机原料,包括正丁醇、异丁醇和辛醇(或称2-乙基己醇)三个重要品种。
正丁醇可作溶剂、生产邻苯二甲酸二丁脂、醋酸丁脂、磷酸脂类增塑剂、丁醛、丁酸、丁胺和和乳酸丁酯等化工产品。
异丁醇可以用于生产石油添加剂、抗氧剂、醋酸异丁酯等有机产品;辛醇主要用于制造邻苯二甲酸二辛酯(DOP)和对苯二甲酸二辛酯,还用于柴油添加剂、合成润滑剂、抗氧剂、溶剂、消泡剂等。
二、丁辛醇生产工艺情况丁辛醇的工业化生产方法主要有乙醛缩合法、发酵法、齐格勒法和羰基合成法等。
1.乙醛缩合法二战期间,德国开发了乙醛缩合法(Aldol)法。
利用乙醛在碱性条件下进行缩合和脱水,生产丁烯醛(巴豆醛),丁烯醛加氢制得丁醇,丁醇经选择性加氢得到丁醛,丁醛经醇醛缩合、加氢制得辛醇。
由于此方法工艺流程长、收率低、生产成本高,现已基本被淘汰。
2.发酵法利用粮食或其它淀粉农副产品,经水解得到发酵醇,然后在丙酮-丁醇菌作用下,经发酵制得丁醇、丙酮及乙醇的混合物,再经精馏得到相应的产品。
由于近几十年石油化工的高速发展,发酵法已经难于以丙烯为原料的羰基合成法竞争,因此近年来很少采用该方法生产丁辛醇产品。
3.齐格勒法该方法以乙烯为原料,利用齐格勒法(Ziegler)生产高级脂肪醇,同时副产丁醇的方法。
4.羰基合成法羰基合成法主要以丙烯与合成气(一氧化碳和氢气)为原料生产丁辛醇,其主要工艺过程为①丙烯氢甲酰化反应,粗醛精制得到正丁醛和异丁醛;②正丁醛和异丁醛加氢得到产品正丁醇和异丁醇;③正丁醛经缩合,加氢得到产品辛醇。
④进行反应生成丁醛,加氢得到丁醇。
丙烯羰基合成法又分为高压法、中压法和低压法。
4.1高压法高压法羰基合成技术是四十年代开发成功的,六十年代建了大量装置,主要技术专利商有鲁尔(Ruhr)技术、巴斯夫(BASF)技术、三菱(MCC)技术、壳牌(Shell)技术。
丁辛醇装置生产原理及工艺解读
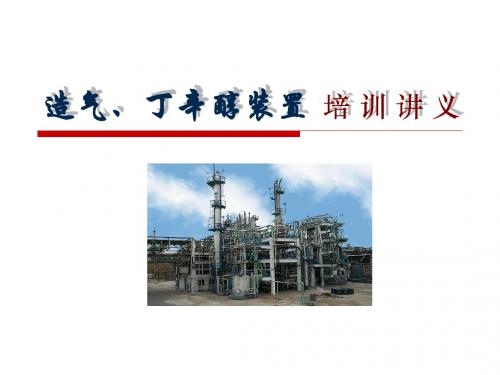
大庆石化公司
一、产品用途 二、工艺技术路线及流程 三、装置存在问题 四、装置发展趋势 五、生产受控开展情况
大庆石化公司
一、产品用途
1.辛醇 辛醇,化学名为2-乙基己醇,主要用于生产 邻苯二甲酸二辛酯(DOP)和对苯二甲酸二辛酯, DOP产品素有王牌增塑剂之称,广泛用于聚氯乙烯、 合成橡胶、纤维素树脂的加工等。 2. 正丁醇 正丁醇属脂肪族饱和四碳醇,主要用于生产邻 苯二甲酸二丁酯和脂肪族二元酸脂类增塑剂,广泛 用于各种塑料和橡胶制品生产。
大庆石化公司
大庆石化公司
大庆石化公司
大庆石化公司
大庆石化公司
丁辛醇装置
丁辛醇装置采用以丙烯、合成气为原料,以 羰基铑/三苯基膦络合物为催化剂的低压羰基合成 方法生产混合丁醛(正丁醛和异丁醛),若丁醇生
产,混合丁醛进入加氢系统,生成混合丁醇,再经
过精馏脱出轻重组份、异构物分离生成正丁醇和异 丁醇。若辛醇生产,混合丁醛先经过异构物分离, 分离出的正丁醛醛醛缩和,生成辛烯醛,再加氢、 精馏脱出轻重组份,最后生成辛醇。
大庆石化公司
为了更好地完成2007大检修任务,车间从4月初开 始,严格按照生产受控要求准备大检修材料,编制节点 式大检修统筹图、节点式开工统筹图和节点式停工统筹 图各一套,对大检修开停工操作卡进行细化,最终将《 丁辛醇装置大检修停工操作卡》细化为446步;《丁辛 醇装置大检修开工操作卡》细化为774步;《造气装置 大检修停工操作卡》细化为296步,《造气装置大检修 开工操作卡》细化为304步。将操作卡及确认单编制成 表格形式,每一步都记录具体的动作时间,执行人每完 成一个动作都要在相应位置签字,避免因漏项导致的操 作事故。大检修全过程严格执行“四有工作法”和“四 有一卡”,真正实现了“安全、绿色、优质”的检修理 念。实现一次开车成功。
丙烯羰基合成生产丁辛醇
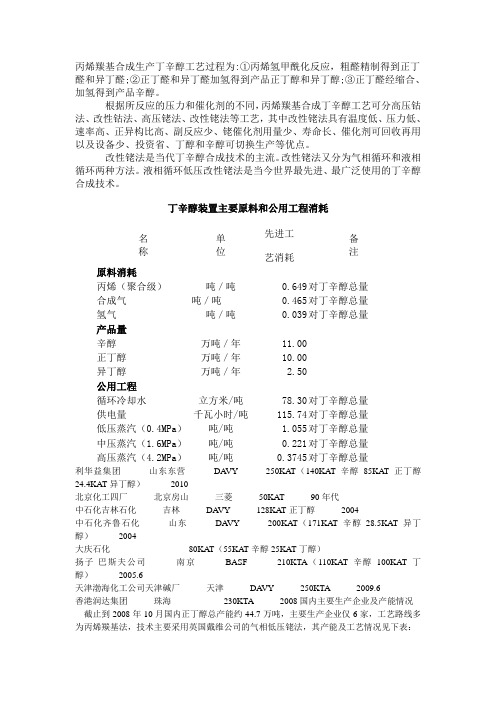
丙烯羰基合成生产丁辛醇工艺过程为:①丙烯氢甲酰化反应,粗醛精制得到正丁醛和异丁醛;②正丁醛和异丁醛加氢得到产品正丁醇和异丁醇;③正丁醛经缩合、加氢得到产品辛醇。
根据所反应的压力和催化剂的不同,丙烯羰基合成丁辛醇工艺可分高压钴法、改性钴法、高压铑法、改性铑法等工艺,其中改性铑法具有温度低、压力低、速率高、正异构比高、副反应少、铑催化剂用量少、寿命长、催化剂可回收再用以及设备少、投资省、丁醇和辛醇可切换生产等优点。
改性铑法是当代丁辛醇合成技术的主流。
改性铑法又分为气相循环和液相循环两种方法。
液相循环低压改性铑法是当今世界最先进、最广泛使用的丁辛醇合成技术。
丁辛醇装置主要原料和公用工程消耗名称单位先进工艺消耗备注原料消耗丙烯(聚合级)吨/吨0.649 对丁辛醇总量合成气吨/吨0.465 对丁辛醇总量氢气吨/吨0.039 对丁辛醇总量产品量辛醇万吨/年11.00正丁醇万吨/年10.00异丁醇万吨/年 2.50公用工程循环冷却水立方米/吨78.30 对丁辛醇总量供电量千瓦小时/吨115.74 对丁辛醇总量低压蒸汽(0.4MPa)吨/吨 1.055 对丁辛醇总量中压蒸汽(1.6MPa)吨/吨0.221 对丁辛醇总量高压蒸汽(4.2MPa)吨/吨0.3745 对丁辛醇总量利华益集团山东东营DA VY 250KAT(140KAT辛醇85KAT正丁醇24.4KAT异丁醇)2010北京化工四厂北京房山三菱50KAT 90年代中石化吉林石化吉林DA VY 128KAT正丁醇2004中石化齐鲁石化山东DAVY 200KAT(171KAT辛醇28.5KAT异丁醇)2004大庆石化80KAT(55KAT辛醇25KAT丁醇)扬子-巴斯夫公司南京BASF 210KTA(110KAT辛醇100KAT丁醇)2005.6天津渤海化工公司天津碱厂天津DA VY 250KTA 2009.6香港润达集团珠海230KTA 2008国内主要生产企业及产能情况截止到2008年10月国内正丁醇总产能约44.7万吨,主要生产企业仅6家,工艺路线多为丙烯羰基法,技术主要采用英国戴维公司的气相低压铑法,其产能及工艺情况见下表:表2 国内主要生产企业及产能情况单位:万吨企业名称产能工艺中石化齐鲁石化 5.0 英国戴维气相低压铑法北京东方石油化工 4.0 日本三菱液相低压循环工艺中石油吉林石化17 英国戴维气相低压铑法大庆石化 2.5 英国戴维气相低压铑法中石化与BASF合资扬子一巴斯夫公司10 巴斯夫技术吉安生化 6.0 粮食发酵法其它0.2合计44.7正丁醇生产供需状况近年来国内正丁醇生产供需情况见下表:表3 近年来国内正丁醇生产供需情况单位:万吨年份2001 2002 2003 2004 2005 2006 2007 2 008(1-10)产能21.2 21.2 21.2 28.0 38.0 38.0 44.5 44.5 产量16.0 17.5 20.4 20.5 29.4 38.0 40.0进口量22.28 24.3 29.6 29.35 23.99 23.58 29.4 19.05出口量0.07 0.06 0.1 0.19 0.20 0.09 0.026 0.11 表观消费量39.91 41.8 50.0 49.66 53.19 61.49 69.37自给率,% 40.1 41.9 40.8 41.3 55.3 61.8 57.7从以上分析可知:国内正丁醇自给率不足60%,长期依赖进口。
丁辛醇装置生产原理及工艺解读
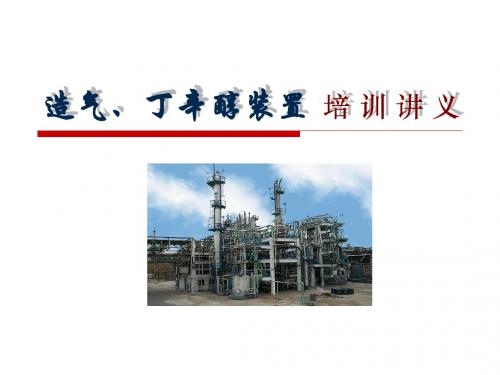
辛烯醛
加 氢 系 统
粗辛醇
醇 精 馏 系 统
辛醇
大庆石化公司
造气装置 造气装置是以重油、氧气、蒸汽为原料 通过工艺烧嘴进入气化炉,在气化炉内 1350度左右的高温条件下发生部分氧化 反应,生成合成气(CO和H2),生成的 合成气通过碳洗涤塔脱出气体中的游离碳 后进入合成气净化系统,脱出CO2、H2S、 COS,然后进入丁辛醇装置。
大庆石化公司
造气、丁辛醇装置工艺流程简图
丙 烯
氧气
蒸汽
油 气 化 系 统
粗合成气
重油
合 成 气 洗 涤 系 统
碳 黑 水
粗合成气
合 成 气 净 化 系 统
合成气
OXO 合 成 系 统
丁醛
加 氢 系 统
粗丁醇
醇 精 馏 系 统
正/异丁醇
丁 醛
氢气
碳
黑
碳 回 收 系 统
2%NaOH
丁 醛 缩 合 系 统
大庆石化公司
国内外工艺发展情况 1、造气装置工艺发展情况 德士古部分氧化法生产合成气工艺是德士古 于1946~1953年间在蒙太伯罗研究实验室开发 的,该工艺最初开发时是使用天然气作为原料, 而后该工艺进一步发展,事实上可用任何烃类作 为原料(气态、液态、固态)。该工艺在全世界 75%工厂采用德士古技术用于工业化生产。 德士古燃料油部分氧化法生产合成气工艺可 根据羰基合成用合成气要求采用不同的流程,从 热量的合理利用方面考虑,对于制氢、合成氨生 产一般采用急冷流程。对于不需制氢的羰基合成 反应采用废热锅炉流程较为合理。
大庆石化公司
为了更好地完成2007大检修任务,车间从4月初开 始,严格按照生产受控要求准备大检修材料,编制节点 式大检修统筹图、节点式开工统筹图和节点式停工统筹 图各一套,对大检修开停工操作卡进行细化,最终将《 丁辛醇装置大检修停工操作卡》细化为446步;《丁辛 醇装置大检修开工操作卡》细化为774步;《造气装置 大检修停工操作卡》细化为296步,《造气装置大检修 开工操作卡》细化为304步。将操作卡及确认单编制成 表格形式,每一步都记录具体的动作时间,执行人每完 成一个动作都要在相应位置签字,避免因漏项导致的操 作事故。大检修全过程严格执行“四有工作法”和“四 有一卡”,真正实现了“安全、绿色、优质”的检修理 念。实现一次开车成功。
- 1、下载文档前请自行甄别文档内容的完整性,平台不提供额外的编辑、内容补充、找答案等附加服务。
- 2、"仅部分预览"的文档,不可在线预览部分如存在完整性等问题,可反馈申请退款(可完整预览的文档不适用该条件!)。
- 3、如文档侵犯您的权益,请联系客服反馈,我们会尽快为您处理(人工客服工作时间:9:00-18:30)。
丁/辛醇的生产工艺与技术路线的选择
2.1 丁辛醇生产方法
丁辛醇是随着石油化工、聚氯乙烯材料工业以及羰基合成工业技术的发展而迅速发展起来的。
丁辛醇的工业化生产方法主要有乙醛缩合法、发酵法、齐格勒法和羰基合成法等。
2.1.1乙醛缩合法
二战期间,德国开发了乙醛缩合法(Aldo1)法。
……
2.1.2发酵法
发酵法是粮食或其它淀粉质农副产品,经水解得到发酵液,然后在丙酮-丁醇菌作用下,经发酵制得丁醇、丙酮及乙醇的混合物,通常的比例为……
2.1.3齐格勒法
齐格勒丁辛醇生产方法是以乙烯为原料,采用齐格勒法生产高级脂肪醇,同时副产丁醇的方法。
2.1.4羰基合成法……
2.2 丁辛醇生产工艺技术比较及选择
2.2.1 国外丁辛醇生产工艺对比
……
丁辛醇主要生产工艺的比较见表2.1。
表2.1 丁辛醇主要生产工艺的比较
关于丁辛醇生产的几种主要工艺技术方法列表如下。
表2.2 丁辛醇工艺技术方案对比表
2.2.2 国外丁辛醇生产工艺选择……
2.3 丁辛醇合成工艺技术进展及发展趋势
2.3.1 国外丁辛醇合成工艺技术进展
丁醇和辛醇是用途广泛的重要精细化工原料,随着生产规模的不断扩大,丁辛醇技术发展重点集中在合成工艺和催化剂的研究和开发上,国外生产商改进丁
辛醇合成工艺形成了各具特色的专有技术,引起了业内人士的极大关注。
……
2.3.2 国内丁辛醇合成工艺技术进展……
2.3.3 国内丁辛醇合成工艺技术发展趋势
随着世界经济全球化及规模生产经济最大化,丁辛醇工业发展的重点将集中在催化剂的研究和开发上。
其技术发展趋势是:……
2.4 丁辛醇质量指标
2.4.1 丁醇质量指标
工业正丁醇:执行标准:GB/T 6027/1998,该标准适用于合成法与发酵法生产的工业正丁醇。
要求:外观:透明液体,无可见杂质。
表2.3 正丁醇质量指标
项目指标分析方法
优等品一等品合格品
色度,Hazen单位(铂-钴色号)≤10 15 GB/T3143
密度(20℃)g/cm30.809~0.811 0.808~0.812 GB/T4472 沸程(0℃,101.325Kpa)包括(117.7℃),℃≤ 1.0 2.0 3.0 GB/T7534 正丁醇含量,% ≥99.5 99.0 98.0 色谱法硫酸显色试验(铂-钴色号)≤20 40 比色法酸度(以乙酸计),% ≤0.003 0.005 0.01 容量法水分,% ≤0.1 0.2 GB/T6283 蒸发残渣,% ≤0.003 0.005 0.01 重量法
2.4.2 辛醇质量指标
辛醇:执行标准:GB/T 6818/1993,本标准适用于由丙烯羰基合成法及乙醛缩合法制得的工业辛醇。
要求:外观:透明液体,无悬浮物。
表2.4 辛醇质量指标
项目指标分析方法
优等品一等品合格品
色度(铂-钴色号)≤10 10 15 GB/T3143 密度(20℃)g/cm30.831~0.833 0.831~0.834 GB/T4472 2-乙基己醇含量,% ≥99.5 99.0 98.0 色谱法
酸度(以乙酸计),% ≤0.01 0.02 容量法
羰基化合物含量(以2-乙基己醛计),≤0.05 0.10 0.20 容量法
硫酸显色试验(铂-钴色号)≤25 35 50 比色法
水分,% ≤0.10 0.20 GB/T6283 详细内容参见六鉴网()发布《丁/辛醇技术与市场调研报告》。