第二章 数控系统及工作原理
数控系统的结构和工作原理

伺服放大器,则再从COP10A 到 COP10B。 FANUC 0iC I/O:I/O Link NC上的口为JD1A, 接I/O单元上JD1B,如再有一个I/O单元,从上一
单元JD1A接至下一个单元JD1B。CB104— CB107为4根扁平电缆,每根50芯,通向机床面板和
机床
FSSB和I/O Link体现 FANUC 公司硬件结构思想, 主运动信息和辅助运动信息分离
四、SIEMENS(西门子)802D系统结构
一、数控系统主要部件
数控控制器 伺服(主轴)放大器、电机(反馈) I/O装置 机床
二、数控机床装配过程
1、机床厂选型购置 2、电器、机械连接 3、PLC编程(辅助功能) 4、参数确定(主运动) 5、联调
三、FANUC 0iC 系统的结构
ቤተ መጻሕፍቲ ባይዱ
FSSB 主运动信息
I/O Link 辅助运动信息
数控机床的工作原理及工作过程

数控机床的工作原理及工作过程数控机床是利用数字控制系统来控制机床进行加工的一种先进的机械设备。
它通过预先编写好的数控程序来控制机床的运动,实现对工件的加工。
本文将详细介绍数控机床的工作原理及工作过程。
一、工作原理数控机床的工作原理主要包括数控系统、伺服系统、传感器和执行机构等几个关键部分。
1. 数控系统:数控系统是数控机床的核心部件,它由硬件和软件组成。
硬件部分包括中央处理器、存储器、输入设备和输出设备等,软件部分则包括数控程序和操作界面等。
数控系统负责接收操作者输入的指令,并将其转化为机床能够理解的控制信号,从而控制机床的运动。
2. 伺服系统:伺服系统是数控机床中的关键部分,它负责控制机床的运动轴。
伺服系统由伺服电机、编码器和驱动器等组成。
伺服电机接收数控系统发出的控制信号,通过编码器反馈机床的实际位置,驱动器则根据反馈信号调整电机的转速和转向,从而实现机床的精确运动。
3. 传感器:传感器用于检测机床的状态和工件的位置等信息,并将其转化为电信号传输给数控系统。
常见的传感器包括光电传感器、接近开关和压力传感器等。
传感器的准确性和可靠性对于数控机床的工作精度和稳定性至关重要。
4. 执行机构:执行机构是数控机床的动力部分,它负责将数控系统发出的控制信号转化为机床的实际运动。
常见的执行机构包括伺服电机、液压缸和气动缸等。
执行机构的性能和可靠性直接影响到机床的工作效率和加工质量。
二、工作过程数控机床的工作过程主要包括数控程序的编写、数控系统的设置和机床的加工操作等几个步骤。
1. 数控程序的编写:数控程序是数控机床工作的指令集,它由一系列的代码和参数组成。
编写数控程序需要根据工件的加工要求和机床的特性来确定加工路径、刀具的选择和切削参数等。
编写好的数控程序可以通过输入设备导入到数控系统中。
2. 数控系统的设置:在进行加工操作之前,需要对数控系统进行设置。
设置包括选择合适的数控程序、设定工件的初始位置和坐标系、调整刀具的补偿和设定加工速度等。
数控技术-第2讲-CNC

数控技术-第2讲-CNCCNC系统第2章CNC系统了解数控系统的组成、原理、分类和功能及开放式数控体系结构。
掌握CNC系统的数据转换及处理过程和进给速度控制过程。
C系统组成与工作原理1 ) CNC 系统概念:计算机数控系统( CNC ,Computerized Numerical Control ),是在硬件数控(NC)系统的基础上发展起来的,用一台计算机完成数控装置的所有功能。
CNC 系统由硬件和软件组成。
CNC系统组成框图3C系统组成与工作原理2)CNC系统功能结构:数控机床的结构组成C系统组成与工作原理输入:输入CNC 装置的有零件程序、控制参数和补偿数据。
输入形式有光电阅读机纸带输入、键盘输入、磁盘输入、通信接口输入及连接上级计算机的DNC(直接数控)接口输入。
从CNC装置工作方式看,有存储工作方式和NC 工作方式输入。
通常在输入过程中CNC装置还要完成无效码删除,代码校验和代码转换等工作。
5C系统组成与工作原理存储方式:是将加工的零件程序一次且全部输入到CNC 装置内部存储器中,加工时再从存储器把一个个程序段调出;所谓NC工作方式是指CNC装置一边输入一边加工,即在前一个程序段正在加工时,输入后一个程序段内容。
C系统组成与工作原理译码:译码处理,是将零件程序以一个程序段为单位进行处理,把其中的各种零件轮廓信息,加工速度信息(F代码)和其他辅助信息按照一定的语法规则解释成计算机能够识别的数据形式,并以一定的数据格式放在指定的内存专用区间。
在译码过程中,还要完成对程序段的语法检查,若发现语法错误便立即报警。
7C系统组成与工作原理刀具补偿:刀具补偿包括刀具长度补偿和刀具半径补偿。
CNC装置的零件程序是以零件轮廓轨迹来编程,刀具补偿的作用是把零件轮廓轨迹的数据转换成刀具中心轨迹的数据。
目前在比较好的CNC装置中,刀具补偿的工作还包括程序段间的转接(即尖角过渡)和过切削判别,这就是所谓C刀具补偿。
第二章数控系统及工作原理_图文
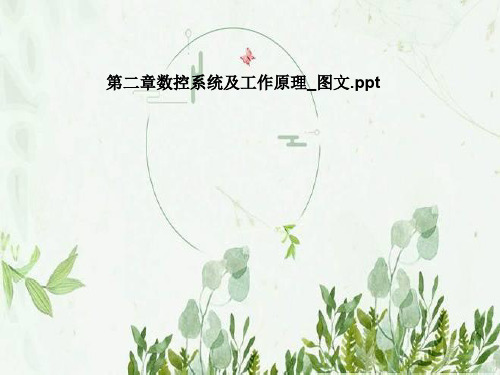
char G0;
//以标志形式存放G指令。
char G1;
char M0;
//以标志形式存放M指令。
char M1;
char T;
//存放本段换刀的刀具号。
char D;
//存放刀具补偿的刀具半径值。
};
以标志形式存放G指令示例
在系统软件中各程序间的数据交换方式一般都 是通过缓冲区进行的。该缓冲区由若干个数据结构 组成,当前程序段被解释完后便将该段的数据信息 送入缓冲区组中空闲的一个。后续程序(如刀补程 序)从该缓冲区组中获取程序信息进行工作。
• 6.位移与速度检测装置
• 位移检测装置:测量装置按各坐标轴方向安装在 机床的工作台或丝杠上,将机床工作台各坐标轴 的实际位移转变成电信号反馈给数控装置,供数 控装置与指令值相比较产生误差信号,以控制机 床向消除该误差的方向移动。
• 速度检测装置:将进给速度反馈给进给伺服驱动 单元;将主轴转速反馈给主轴调速驱动单元。
• (7)I/O处理
• I/O处理是指CNC与机床之间电气信号的输入、输出处理 和控制(如换刀、主轴速度换挡、冷却等)。
• (8)显示
• 显示:零件程序、参数、刀具位置、机床状态、报警信息 等。
• 有些CNC还有刀具加工轨迹的静态和动态图形显示。
• (9)诊断
• 联机诊断:是指CNC中的自诊断程序融合在各部分,随 时检查不正常的事件。
刀补处理的主要工作:
Y
• 根据G90/G91计算零件轮
廓的终点坐标值。
• 根据R和G41/42,计算本 段刀具中心轨迹的终点 (P’e/P〃e)坐标值。
• 根据本段与前段连接关 系,进行段间连接处理 。
Pe’ G41
数控系统的组成及工作原理
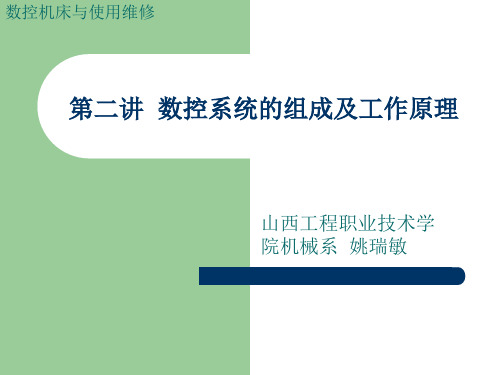
3.刀具半径补偿原理(2): .刀具半径补偿原理( ):
X ′ = X + ∆X Y ′ = Y + ∆Y Y ∆X = R ⋅ sin α = R X 2 +Y 2 X ∆Y = − R ⋅ cos α = − R X 2 +Y2 Y X′= X +R X 2 +Y 2 X Y ′ = Y − R X 2 +Y 2
上面讨论的是单段轮廓的刀补情况,通常工件轮 廓由多段曲线组成,如直线与直线、直线与圆弧、 圆弧与圆弧、圆弧与直线等,这就存在一个轮廓 交接处如何过渡的问题。C刀具补偿能自动地处 理两段程序之间的刀具中心轨迹的转接,编程人 员完全按工件轮廓编程。
刀具补偿原理( ) 4.C刀具补偿原理(2) 刀具补偿原理
图例给出了左刀补和右刀补时轮廓过渡处的处理 情形。从图可以看出:轮廓过渡时,为了避免过 切或间断,需要采用缩短、延长或插入的方式。
C刀具补偿原理图(1) 刀具补偿原理图( ) 刀具补偿原理图
C刀具补偿原理图(2) 刀具补偿原理图( ) 刀具补偿原理图
刀具补偿原理( ) 4.C刀具补偿原理(3) 刀具补偿原理
速度控制程序:根据给定的速度值控制插补运算的 频率,保证预定的进给速度。并能根据反馈值的正 与负自动地调节速度的大小。 管理程序:负责对数据输入、数据处理、插补运算 等各种程序进行调度管理;对诸如面板命令、时钟 信号、故障信号等引起的中断进行处理;子程序的 调用;共享资源的分时享用等。 诊断程序:通过识别程序中的一些标志符来判断故 障的类型和所在地。
数控机床与使用维修
第二讲 数控系统的组成及工作原理
山西工程职业技术学 院机械系 姚瑞敏
本讲主要内容
数控系统工作原理简介PPT课件( 66页)

按所用进给伺服系统
开环数控系统 半闭环数控系统 控制系统 闭环数控系统
步进电机
数控装置
伺服马达
数控装置
机床工作台
伺服马达
机床工作台
机床工作台
位置检 测器 位置检测器
按数控系统加工功能
点位控制系统(Positioning Control System)
特点:只要求保证点与点之间的准确定位,即只控制行程的终点 坐标值,而对点与点之间刀具所移动的轨迹不加控制.在移动过 程中,刀具不进行切削,采用机床设定的最高进给速度进行定位 运动,接近终点需要低速趋近。如:钻床、冲床
+Y
F 4F 3Xe154 E=E-1=5-1=4≠0
F4 40 F5 10
+X F5F4Ye431 E=E-1=4-1=3≠0
+X
F 6F 5Ye132 E=E-1=3-1=2≠0
F6 20
+Y
F 7F 6Xe253 E=E-1=2-1=1≠0
•数字积分原理 •数字积分(DDA)直线插补
① 原理
Y
y f (t)
例:右图下,若要使从O点到E点的插补过程进
给脉冲均匀,就必须使分配给x,y方向的单位增
量成正比。设需要在t=10秒内使加工到达终点E,
则每单位时间间隔△t内,x和y的增量分别为
△t
△x’=xe/10=0.7
y
△y’=ye/10=0.4
F i 1 ,i X e Y i X i 1 Y e X e Y i ( X i 1 ) Y e X e Y i X i Y e Y e
即
i 1 F i-Y e F
当偏差值F <0时,刀具从现加工点 (Xi,Yi ) 向Y正向前进一步,到达 新加工点 (Xi,Yi1)则新加工点的偏差值为
数控系统原理介绍

第二章数控系统原理2.1 插补理论简介在CNC数控机床上,各种轮廓加工都是通过插补计算实现的,插补计算的任务就是对轮廓线的起点到终点之间再密集的计算出有限个坐标点,刀具沿着这些坐标点移动,来逼近理论轮廓。
插补方法可分两大类:脉冲增量插补和数据采样插补。
脉冲增量插补是控制单个脉冲输出规律的插补方法。
每输入一个脉冲,移动部件都要相应的移动一定距离,这个距离成为脉冲当量。
因此,脉冲增量插补也叫做行程标量插补。
如逐点比较法、数字积分法。
根据加工精度的不同,脉冲当量可取0.01~0.001mm。
移动部件的移动速度与脉冲当量和脉冲输出频率有关,由于脉冲输出频率最高为几万Hz,因此,当脉冲当量为0.001mm时,最高移动速度也只有2m/min。
脉冲增量插补通常用于步进电机控制系统。
数字增量插补法(也称数据采样插补法)是在规定的时间(称作插补时间)内,计算出各坐标方向的增量值(X,Y,Z),刀具所在的坐标位置及其它一些需要的值。
这些数据严格的限制在一个插补时间内(如8ms)计算完毕,送给伺服系统,再由伺服系统控制移动部件运动。
移动部件也必须在下一个插补时间内走完插补计算给出的行程,因此数据采样插补也称作时间标量插补。
由于数据采样插补是用数值量控制机床运动,因此,机床各坐标方向的运动速度与插补运算给出的数值量和插补时间有关。
根据计算机运行速度和加工精度不同,有些系统的插补时间选用,12ms 、10.24ms 、8ms ,对于运行速度较快的计算机有的已选2ms 。
现代数控机床的进给速度已超过15m/min ,达到30m/min ,有些已到60m/min.数据采样法适用于直流伺服电机和交流伺服电机的闭环和半闭环控制系统。
2.2 插补原理——逐点比较法逐点比较法是我国数控机床和线切割机应用很广的一种插补运算方法。
它的特点是加工每走一步,就进行一次偏差计算和偏差判别,即比较到达的新位置和理想线段上对应点的理想位置坐标之间的偏差程度,然后根据偏差大小确定下一步的走向。
第二章--数控系统组成原理
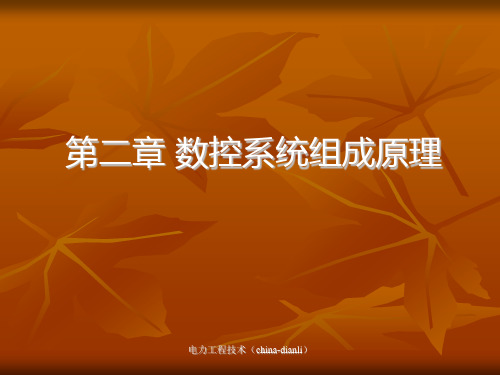
➢ 数控装置
数控装置是数控机床的核心,它包括CPU、存储器、各 种I/O接口、通用输入输出(I/O)接口以及相应的软件。
数控装置接受输入装置送来的程序,进行编译、运算和逻辑 处理后,输出各种信号控制机床的各个部分进行相应的动作。这 些控制信号包括:各坐标轴的进给量、进给方向和速度的指令, 经伺服驱动系统驱动各执行部件运动;主运动部件的变速、换向 和启停信号;选择和交换刀具的刀具指令信号;控制冷却、润滑 的启停、工件和机床部件松开、夹紧、分度工作台转位等辅助指 令信号等。
电力工程技术(china-dianli)
计算机数控系统软件
计算机数控系统为典型的实时多任务系统,体系层次如图 2.6所示。
➢ 数控系统电软力工件程特技点术(china-
dianli)
➢ 数控系统软件典型结构
电力工程技术(china-dianli)
数控功能程序 (加工程序译码,刀补处理和插补计算,编辑器,加工模拟
电力工程技术(china-dianli)
➢ 可编程程序控制器(PLC)
主要作用是接收数控装置输出的主运动变速、刀具选择 交换、辅助装置动作等指令信号,经必要的编译、逻辑判断、 功率放大后直接驱动相应的电器、液压、气动和机械部件, 以完成指令所规定的动作,此外还有行程开关和监控检测等 开关信号也要经过PLC送到数控装置进行处理。
系统中有两个或两个以上的带CPU的功能部件,它们对系 统资源都有控制或使用权。功能部件之间采用紧耦合,有集中的 操作系统,通过总线仲裁器(软件和硬件)来解决争用总线问题, 通过公共存储器来交换系统信息。
特点:
能实现真正意义上的并行处理,处理速度快,可以实现较 复杂的系统功能。
第二章 计算机数控系统CNC与控制原理总结

速度处理要做的工作是根据合成速度来计算各运动坐标 的 分速度。 开环系统:通过控制向步进电机输出脉冲的频率来实现。
速度计算的方法是根据程编的F值来确定该频率值。 半闭环和闭环系统:采用数据采样方法进行插补加工,速度
计算是根据程编的F值,将轮廓曲线分割为采样周期的轮 廓步长。
可以实现较复杂的系统功能。容错能力强,在某模块出 故障后,通过系统重组仍可断继续工作。
12
2.2 CNC装置的硬件结构
结构形式:可分:分布式、主从式、总线式。
分布式:各CPU独立、完整,通过外部通信链路连接起来,
数据交换和资源共享通过网络技术实现。
主从式:主控CPU、从控CPU,主控CPU才能控制和访问总
第二章 计算机数控系统CNC与控制原理
本章主要内容
第一节 概述 第二节 CNC装置的硬件结构 第三节 CNC装置的软件结构
第四节 可编程控制器(PLC)
第五节 典型的CNC系统简介
2
2.1概述
1. CNC系统?
从自动控制的角度来看,CNC系统是一种位置、速 度
(还包括电流)控制系统,其本质上是以多执行部件(各运 动轴)的位移量、速度为控制对象并使其协调运动的自动控 制系统,是一种配有专用操作系统的计算机控制系统。 从外部特征来看,CNC系统是由硬件(通用硬件和专 用硬件)和软件(专用)两大部分组成的。
两个以上任务处理。
♦ 并行处理的实现方式: ☆ 资源分时共享(单CPU)
☆ 资源重叠流水处理(多CPU)
34
Have a Rest!
2.3 CNC系统的软件
资源分时共享并行处理(对单一资源的系统)
♦ 在单CPU结构的CNC系统中,可采用 “资源分时共
数控机床的基本组成与工作原理

数控机床的基本组成与工作原理数控机床是一种通过计算机控制的自动化机械设备,它在现代制造业中起着至关重要的作用。
本文将介绍数控机床的基本组成和工作原理。
一、数控机床的基本组成1. 主机部分:数控机床的主机部分由机床本体、主轴和伺服系统组成。
机床本体是数控机床的主体结构,包括床身、工作台、滑枕等。
主轴是机床用来转动刀具或工件的主要部件。
伺服系统则负责控制主轴和工作台的运动。
2. 数控系统:数控机床的核心部分是数控系统,它由硬件和软件两部分组成。
硬件包括数控装置、输入输出设备和传感器等,而软件则是指数控程序和数控编程软件。
数控系统负责接收和处理指令,控制机床的运动。
3. 刀具系统:数控机床的刀具系统包括刀具、刀柄和刀库等。
刀具是用来加工工件的工具,刀柄则负责固定刀具。
刀库是用来存放刀具的地方,可以根据需要自动更换刀具。
4. 辅助设备:数控机床还需要一些辅助设备来完成加工任务。
常见的辅助设备有冷却液系统、夹具和自动送料装置等。
冷却液系统用来冷却刀具和工件,夹具用来固定工件,而自动送料装置则负责将工件送入机床。
二、数控机床的工作原理数控机床的工作原理可以简单概括为以下几个步骤:1. 编写数控程序:操作人员首先需要编写数控程序,该程序包含了加工工件所需的各种指令和参数。
数控程序可以通过专门的数控编程软件编写,然后通过输入设备输入到数控系统中。
2. 加工准备:在开始加工之前,操作人员需要进行加工准备工作。
这包括选择合适的刀具和夹具,调整机床的工作台和主轴位置,以及设置好冷却液系统和自动送料装置等。
3. 启动数控系统:当加工准备完成后,操作人员可以启动数控系统。
数控系统将根据编写的数控程序,控制机床的运动。
它会发送指令给伺服系统,控制主轴和工作台的运动,同时监测加工过程中的各种参数。
4. 加工工件:一旦数控系统启动,机床就会开始自动加工工件。
数控系统会根据编写的数控程序,控制刀具的进给速度、切削深度和切削速度等。
数控机床的工作原理及工作过程

数控机床的工作原理及工作过程数控机床是一种通过计算机数控系统控制工作过程的机床。
它能够自动执行各种加工操作,具有高精度、高效率和灵活性等优点。
下面将详细介绍数控机床的工作原理及工作过程。
一、工作原理数控机床的工作原理主要包括数控系统、伺服系统、传动系统和执行系统。
1. 数控系统:数控系统是数控机床的核心部件,它由硬件和软件两部分组成。
硬件包括主机、数控装置和输入输出设备等,软件包括数控程序和参数等。
数控系统通过计算机控制,将加工图纸转化为数控程序,并通过数控装置将程序传输给机床进行加工操作。
2. 伺服系统:伺服系统是数控机床的动力系统,它由伺服电机、传感器和伺服控制器等组成。
伺服电机通过传感器检测位置和速度等信息,并将信号传输给伺服控制器,控制电机的转动。
伺服系统能够实现高精度的位置控制,确保机床的精确加工。
3. 传动系统:传动系统是数控机床的动力传输系统,它由主轴、伺服电机和传动装置等组成。
主轴通过伺服电机驱动,将切削刀具转动起来,完成加工操作。
传动装置包括齿轮、皮带和螺杆等,能够将电机的转动传递给切削刀具。
4. 执行系统:执行系统是数控机床的执行部件,它包括工作台、刀库和切削刀具等。
工作台能够实现工件的定位和夹紧,确保加工的准确性。
刀库可以存放多种切削刀具,根据加工要求自动选择合适的刀具进行加工。
二、工作过程数控机床的工作过程主要包括工件加工准备、数控程序编制、机床调试和加工操作等步骤。
1. 工件加工准备:在进行数控机床加工之前,需要进行工件的准备工作。
包括选择合适的工件材料、制定工件加工方案、制定数控程序和准备切削刀具等。
2. 数控程序编制:根据工件的加工要求,使用专门的数控编程软件编写数控程序。
数控程序包括加工路径、加工速度和切削参数等信息。
编写好的数控程序通过输入输出设备传输给数控机床。
3. 机床调试:在进行正式加工之前,需要对数控机床进行调试。
主要包括安装切削刀具、调整工作台位置和设置切削参数等。
第二章计算机数控系统
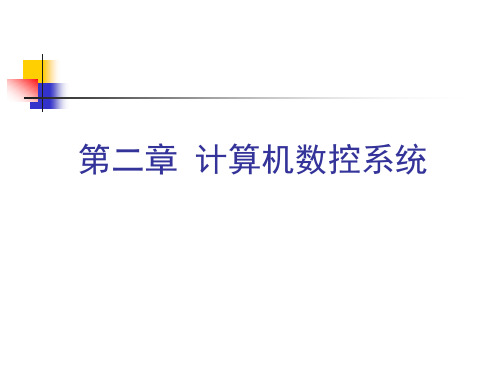
单机或主从结构模块的功能
模块化设计方法:将控制系统按功能划分成若干具有独立功 能的单元模块,并配上相应的驱动软件。系统设计时按功能的 要求选择不同的功能模块,并将其插入控制单元母板上,即 可组成一个完整的控制系统的方法。其中单元母板一般为总 线结构的无源母板,它提供模块间互联的信号通路图2-4。 实现CNC系统模块化设计的条件是总线(BUS)标准化。 1、计算机主板和系统总线(母板) 2、显示模块(显示卡) 3、 输入/输出模块(多功能卡) 4、电子盘(存储模块) 5、设备辅助控制接口模块 6、位置控制模块 7、功能接口模块
首先要将被加工零件图的几何信息和工艺信息 数字化,即将刀具与工件的相对运动轨迹,用 代码按规定的规则和格式编成加工程序,数控 系统则按照程序的要求,进行相应的运算、处 理,然后发出控制命令,使各坐标轴、主轴以 及辅助动作相互协调运动,实现刀具与工件的 相对运动,自动完成零件的加工。 1.逼近处理 2.插补运算 3.指令输出
2.点位运动与移动功能(G功能 )
准备功能(G功能)
—— 指令机床动作方式的功能。
如:基本移动、程序暂停、平面选择、坐
标设定、刀具补偿、基准点返回和固定 循环等。
3.插补功能
插补功能
—— 插补功能是数控系统实现零件轮廓 (平面或空间)加工轨迹运算的功能。 精插补和粗插补;硬件插补和软件插补
DNC接口,可实现直接数控,
MAP(制造自动化协议)模块,
网卡:适应FMS、CIMS、IMS等制造系统集成的
要求。
13.程序编制功能
手工编程 背景(后台)编程 自动编程
数控系统原理介绍

数控系统原理介绍数控系统原理介绍数控系统是一种在机床加工或其他工业领域中使用的先进加工工具,可以大大提高生产效率和制造质量。
数控系统是由软件和硬件两部分组成,它的核心部分是控制器。
控制器通过图形化界面、编程语言和运算器等方式,将计算机程序转化为机器指令,控制机床进行加工操作。
下面我们来介绍数控系统的原理。
一、数控系统的基本组成数控系统由五大基本部分组成:电源系统、机床及工作台部分、传感器及执行器部分、数控装置及软件系统部分、执行机构。
电源系统提供所需的电源电压和电流,以保证数控系统运行所需的稳定电力供应。
机床及工作台部分是数控系统的重要组成部分,包括各类机床、传动装置、定位装置、夹紧装置、转载装置和其他辅助装置等,用于在不同的加工条件下完成加工操作。
传感器及执行器部分包括各种传感器和执行器,能够对各种物理量进行测量和控制。
数控装置及软件系统部分是数控系统的核心部分,由计算机、处理器、输入输出设备组成,主要负责进行控制指令的运作和数据传输。
执行机构包括各种驱动装置和执行机构,如步进电机、伺服电机等,主要用于控制零件的移动位移和加工力度。
二、数控系统的基本工作原理数控系统的基本工作原理是通过输入控制指令,驱动执行机构完成零件的加工操作。
首先,根据工件的设计图纸,制定数控程序。
数控程序一般采用高级编程语言,比如G代码和M代码。
G代码用于描述加工轨迹,M代码用于控制机床运行状态。
接下来,将数控程序输入电脑,通过计算机进行处理和解析。
计算机将程序转换为机器指令,并将其发送到数控装置。
数控装置根据指令的类型和内容,对执行机构进行控制,并将指令转换成相应的控制信号送给执行机构。
执行机构接收信号后,根据指令进行动作,控制零件的受力和轨迹,实现零件的加工操作。
加工过程中,传感器可以实时的监测加工状态,并将监测结果反馈给数控装置,以便下一步的程序控制。
最后,加工完成后,数控系统自动停机,操作人员可以通过电脑或连接到数控机床的监视系统对加工质量进行检查,以确保零件符合要求。
数控系统工作原理

数控系统工作原理
数控系统是一种通过计算机控制数控设备进行加工的自动化系统。
其工作原理如下:
1. 设计制作程序:数控系统首先需要根据加工要求进行程序的设计。
程序可以使用专门的数控编程软件,根据加工零件的几何形状和加工工艺,编写出一系列代码,用于定义刀具的路径、速度、进给等参数。
2. 程序传输与存储:编写完成的数控程序可以通过计算机与数控设备之间的传输设备进行传输。
一般情况下,数控系统会根据需要将程序存储在内部存储器中,方便以后的重复使用。
3. 数控系统解释程序:数控系统会将程序进行解释,并将其转化为数控设备可以理解的指令。
解释程序会根据编写的代码,将刀具路径、速度、进给等信息转化为用来驱动数控设备的指令。
4. 发送指令:解释程序将指令发送给数控设备的控制部分。
控制部分会根据指令控制伺服电机、螺杆传动系统等驱动部件,实现刀具的运动。
5. 加工控制:数控系统会监控刀具的运动状态,并根据需要控制刀具的速度、进给以及切削时刻等参数。
通过对实时的反馈信号进行分析,数控系统可以实现加工过程中的自动控制和调整。
总的来说,数控系统通过计算机对程序进行设计和存储,并将其转化为数控设备可以执行的指令。
通过控制刀具的运动和加工参数,数控系统实现对工件的自动化加工。
数控系统的构成、工作原理和功能

数控系统的构成、工作原理和功能一、数控装置数控(NC)装置是数控装备的控制核心,通常由一台专用计算机和输入输出设备构成,如下图所示。
▲数控(NC)装置的组成1、信息信息、程序可以通过键盘人工编程输入,也可以在专门的编程系统中完成程序编制,将信息、程序存储在移动硬盘、光盘、U盘上输入数控系统,在通信控制的数控机床上,程序还可以由计算机接口传送。
2、专用计算机它由信息输入装置、运算器、控制器和输出装置组成。
专用计算机对信息进行处理,如计算各执行元件的移动量,另外通过固定、内置的逻辑单元操作程序控制动作信息(如:电动机开停、电动机正反转、刀具更换、检测等)。
3、伺服系统伺服系统控制驱动装备的执行元件,实现伺服电动机的起动、回转、编码检测、反馈、控制回转位置、减速、停止等。
通过上述组成部分可以看出,数控装置的工作过程是:将信息、程序通过专用计算机的输入装置,由控制器中的译码器对输入的信息进行识别,将识别结果向专用计算机的输出装置发出控制信号,执行规定的操作;最后由输出装置实现对伺服系统的数据输出,以实现对伺服系统的控制。
数控装置根据输入的指令进行译码、处理、计算和控制实现数控功能。
该类装置是20世纪50~70年代随着计算机技术发展而产生的一种控制技术。
从本质上讲,数控装置所具有的功能都是采用专用的硬件电路来实现的,因此也称为硬件数控装置。
从现代计算机技术和装备技术要求的角度来讲,这种专用数控装置结构复杂,功能扩展困难并受到一定限制,适应性及灵活性差,设计、制造周期长,制造成本高,稳定可靠性较差。
现代数控装置已发展成为计算机数控装置,也称为软件数控装置。
二、计算机数控系统以小型通用计算机或微型计算机的系统控制程序来实现部分或全部数控功能,简称为计算机数控(CNC)。
CNC系统是现代的主流数字控制系统。
用CNC系统控制的数控机床,简称CNC机床。
1、CNC装置的组成CNC装置由硬件和软件两大部分组成。
(1)硬件由CPU、存储器、总线、输入/输出接口、MDI/CRT接口、位置控制、通信接口等组成。
数控系统工作原理

数控系统工作原理
数控系统是一种通过计算机程序来控制机床运动的自动化设备。
它能够精确地控制机床的运动,实现复杂的加工操作。
数控系统的工作原理是将加工工艺的要求通过计算机编程转换成数学模型和控制命令,然后将这些命令传输给数控系统的主机。
主机根据接收到的控制命令,将其转化为相应的电信号,通过伺服驱动系统将电信号转换为适合机床执行的运动信号。
数控系统主机通过数学运算和逻辑控制,根据加工工艺要求来判断机床的运动轨迹,然后控制伺服驱动系统将机床的坐标轴移动到相应的位置。
在机床运动的过程中,数控系统主机会不断接收反馈信号,通过与目标位置进行比较,实时调整控制命令,使机床保持在预定的运动轨迹上。
在数控系统中,还需要进行坐标转换、速度控制、插补计算等操作,以使机床能够按照工艺要求进行精确的加工。
数控系统还可以实现自动工件换刀、自动测量、自动修正等功能,提高了加工的自动化程度和加工精度。
总之,数控系统通过计算机编程和控制命令,实现对机床运动的精确控制,使得机床能够按照预定的轨迹进行加工操作,提高了加工效率和精度。
数控技术原理与系统

数控技术原理与系统数控技术是一种通过计算机软硬件控制机床和工具进行自动加工的先进制造技术。
它在传统机床的基础上,引入了计算机数字控制系统,以提高加工精度、效率和自动化程度。
本文将对数控技术的原理和系统进行分析和探讨。
一、数控技术原理数控技术的核心原理是通过编程指令将加工工艺要求转化为机床的加工轨迹和切削参数,并通过计算机控制系统实现对机床的自动控制。
数控技术的原理主要包括以下几个方面:1. 数字化表示和储存:数控系统将机床的加工轨迹和切削参数等信息以数字的形式进行表示和储存。
通过数字化的数据表示,方便了工艺参数的调整和加工过程的优化。
2. 程序控制:数控系统通过编程指令实现对机床运动轨迹和切削参数的控制。
通过编程,可以指定机床的加工路径、进给速度、刀具的切削深度等参数,从而实现工件的精确加工。
3. 传感器反馈:数控系统通过传感器实时感知机床和工件的状态,并将感知到的信息反馈给控制系统进行处理。
传感器可以监测机床的位置、速度、加速度等参数,以及工件的尺寸和表面质量等指标,从而实现对加工过程的实时监控和调整。
4. 闭环控制:数控系统采用闭环控制的方式对机床进行控制。
即通过传感器反馈的信息进行实时比较,将实际加工结果与期望结果进行对比,从而对控制指令进行修正和调整,以达到更高的加工精度和稳定性。
二、数控系统数控系统是数控技术实现的关键,它由硬件和软件两部分组成。
数控系统的硬件包括计算机、控制器、伺服电机等主要设备,而软件则包括编程软件、操作系统以及相应的应用软件。
1. 计算机:计算机是数控系统的核心设备,它负责将加工工艺的要求转化为机床的控制指令,并实时监控和调整加工过程。
计算机采用高性能的处理器和大容量存储器,以满足复杂加工任务的需求。
2. 控制器:控制器是数控系统的指挥中心,它接收计算机发送的控制指令,并对机床的运动和切削参数进行实时控制。
控制器通常采用专用的硬件电路,以实现高速稳定的信号处理和输出。
数控原理与系统数控原理概述总结

第一章 数控系统概述
1.2数控系统与计算机数控系统(CNC系统)
(2)数控装置—是数控系统的核心
o 由输入/输出接口线路、控制器、运算器和存储器等部分组成 o 作用是将输入装置输入的数据,通过内部的逻辑电路或控制软件进行编译、运算
第一章 数控系统概述
1.1数字控制技术
1.1.2NC机床、加工中心、FMC、FMS与CIMS
o 凡是采用了数控技术进行控制的机床统称NC机床 o 带有自动刀具交换装置(Automatic Tool Changer—ATC)的数控机床(带有回转刀架的 数
控车床除外)称为加工中心(Machine Center—MC) o 在加工中心的基础上,通过增加多工作台(托盘)自动交换装置(Auto Pallet Changer—APC)
第一章 数控系统概述
1.2数控系统与计算机数控系统(CNC系统)
•1.2.3 CNC系统的特点与功能 •C的特点 •1)灵活性 •2)通用性 •3)可靠性 •4)数控功能多样性 •5)使用维修方便 •6)易于实现机电一体化
第一章 数控系统概述
1.2数控系统与计算机数控系统(CNC系统)
o 2.CNC系统的功能
G92 X400. Z250.
位置等),其控制信息主要来源于数控加工或运动控制程序 o 数控系统的最基本组成应包括:程序的输入/输出装置、数控装置、
伺服驱动这三部分
第一章 数控系统概述
1.2数控系统与计算机数控系统(CNC系统)
(1)输入/输出装置—作用是进行数控加工或运动控 制程序、加工与控制数据、机床参数以及坐标轴 位置、检测开关的状态等数据的输入、输出
数控设备的工作原理

数控设备的工作原理
数控设备的工作原理主要由以下几个部分组成:
1. 控制系统:数控设备的控制系统是整个设备的核心部分。
它由计算机和相应的软件组成,用于产生控制指令,并通过接口将指令传递给执行系统。
2. 执行系统:执行系统负责将控制指令转化为实际的运动控制。
它由伺服系统和执行机构组成。
伺服系统通过对电机的电流进行控制,使其达到所需的运动速度和位置,从而实现精确的运动控制。
执行机构包括各种传动装置和工具刀具,用于实际加工工件。
3. 传感器系统:传感器系统用于实时监测数控设备的运动状态和加工过程。
常见的传感器包括编码器、光电开关、压力传感器等,它们将所测量到的信号反馈给控制系统进行处理。
4. 人机界面:数控设备通常会配备人机界面设备,如操作台、显示器、键盘等,用于人机交互和参数设置。
操作人员可以通过人机界面设备输入加工程序和参数,监控设备的运行状态,并进行相关的操作控制。
在工作过程中,数控设备通过接收控制系统发出的控制指令,通过执行系统实现工件的精确运动控制。
控制系统根据工件的几何特征和加工要求生成相应的数控程序,经过编译和加工调整后发送给执行系统。
执行系统根据数控程序中的指令,通过伺服系统调节电机的运动参数,控制执行机构执行相应的加工
操作。
同时,传感器系统实时监测设备的运动状态和加工过程,并将反馈信号传递给控制系统,从而实现加工过程的闭环控制。
最终,通过合理的操作人员在人机界面上进行操作和监控,完成工件的精确加工。
- 1、下载文档前请自行甄别文档内容的完整性,平台不提供额外的编辑、内容补充、找答案等附加服务。
- 2、"仅部分预览"的文档,不可在线预览部分如存在完整性等问题,可反馈申请退款(可完整预览的文档不适用该条件!)。
- 3、如文档侵犯您的权益,请联系客服反馈,我们会尽快为您处理(人工客服工作时间:9:00-18:30)。
• (7)I/O处理
• I/O处理是指CNC与机床之间电气信号的输入、输出处理 和控制(如换刀、主轴速度换挡、冷却等)。
• (8)显示
• 显示:零件程序、参数、刀具位置、机床状态、报警信息 等。 • 有些CNC还有刀具加工轨迹的静态和动态图形显示。
• (9)诊断
• 联机诊断:是指CNC中的自诊断程序融合在各部分,随 时检查不正常的事件。 • 脱机诊断:是在CNC不工作情况下的诊断,这种诊断通 过配备的各种脱机诊断程序对存储器、外围设备(CRT、 阅读机、穿孔机等)接口和I/O接口等进行检查。脱机诊 断也可采用远程诊断。
• (4)进给速度处理
• 按合成速度来计算各坐标方向的分速度,为插补计算做准 备。
• 处理机床的最低和最高速度的限制以及软件的自动加减速 处理。
• (5)插补
• 插补:按一定的方法确定加工轨迹的过程就叫插补。是在 曲线的起点和终点之间自动进行“数据点密化”。
• 插补是在规定的周期(称插补周期)内执行一次,按指令 进给速度计算出一个微小的直线数据段。通常经过若干个 插补周期后,插补完一个程序段加工。常有直线、圆弧及 螺旋线等插补。
• 3.强电控制部分和辅助装置电动执行器
• 控制除进给运动之外的其它辅助操作的装置。 • 强电控制装置接受数控装置的指令信号,通过可 编程控制器(PLC)控制主轴变速、换向、启动 或停止,刀具的选择和更换,分度工作台的转位 和锁紧,工件的夹紧或松夹,切削液的开或关等 辅助操作。
• 4. 进给伺服驱动单元及进给电动机 •定义—以移动部件的位臵和速度作为控制量的 自动控制系统。 •伺服驱动系统:包括伺服单元与驱动装置。
第二章 数控系统及工作原理
第一节 概述
第二节 数控插补原理
第三节 数控补偿原理 第四节 位移与速度检测
第五节 伺服系统与控制
第六节 CNC装置 第七节 CNC系统中的可编程控制器
第一节 概 述
一、 CNC系统的组成和功用
CNC系统主要由硬件和软件两大部分组成。
其核心是计算机数控装置(CNC装置)。
01:G41; 10;G42
在系统软件中各程序间的数据交换方式一般都 是通过缓冲区进行的。该缓冲区由若干个数据结构 组成,当前程序段被解释完后便将该段的数据信息
送入缓冲区组中空闲的一个。后续程序(如刀补程
序)从该缓冲区组中获取程序信息进行工作。
N06 G90 G41 D11 G01 X200 Y300 F200 ; 1 2 3 4 5 6 7 8 9 ----------------------------------------Struct PROG_BUFFER { char buf_state; 0:(开始);1(;)⑨ int block_num; 06(N06)① double COOR[20]; COOR[1]=200000;(X200)⑥ COOR[2]=300000;(Y300)⑦ int F,S; F=200;(F200)⑧ char G0; D5=0;(G90)② D6,D7=0,1(G41)③ D1=1;(G01)⑤ …… char D; D=11(D11)④ };
⒌ 位置控制处理
插补输出 △X1 △Y1 指令位置 X1新Y1新 跟随误差 △X3 △Y3 f() 速度指令 VX、VY
+
+
X1旧Y1旧
+
+
+
实际位置 X2新Y2新
X2旧Y2旧
反馈位置增量 △X2、△Y2
位置控制转换流程
第二节 数控插补原理
一、插补的基本概念
• 在数控机床中,刀具不能严格地按照要求加工的曲 线运动,只能用折线轨迹逼近所要加工的曲线。
⒋ 插补计算
主要功能:
根据操作面板上“进给修调”开关的设定值,计算本 次插补周期的实际合成位移量:
△L1=△L*修调值
将△ L1 按插补的线形(直线,园弧等)和本插补点所 在的位置分解到各个进给轴,作为各轴的位置控制指 令(△X1、△Y1)。 经插补计算后的数据存放在运行缓冲区中,以供位置控 制程序之用。本程序以系统规定的插补周期△t定时运行。
• PLC主要处理开关量的逻辑控制。控制:主轴变速、换向、 启动或停止,刀具的选择和更换,分度工作台的转位和锁 紧,工件的夹紧或松夹,切削液的开或关等辅助操作。
• PLC分为两类: • 一类是将数控系统和PLC综合起来设计,称为内装型(或 集成型) PLC; • 另一类是以独立专业化的PLC生产厂家的产品来实现顺序 控制功能,称为独立型(或外装型) PLC。
CNC装置 • (1) 输入接口。负责接收输入介质或操作面板上的信息,并 将信息代码加以识别,经译码后送入相应的存储器,作为控 制和运算的原始依据。
• (2) 控制器。根据输入的指令控制运算器和输出接口,使机 床按规定的要求协调地进行工作。 • (3) 运算器。接收控制器的指令,对输入数据进行运算,并 将控制信号以脉冲形式送至输出接口。 • (4) 输出接口。根据控制器的指令,接收运算器的控制信号, 经过功率放大驱动伺服系统,使机床按规定要求运动。 • (5) 存储器。CNC装置的存储器分为只读存储器 (ROM)和读 写存储器 (RAM)。 ROM用于存放系统控制程序;RAM用 于存放零件的加工程序和系统运行时的中间结果。 • 数控机床的功能强弱主要由数控装置来决定,所以它是数控 机床的核心部分。
• (2)译码
• 译码处理:以程序段为单位,把零件的轮廓(起点、终 点、直线或圆弧)、进给速度(F)和其他辅助信息(M 、S、T)按照一定的语法规则解释成计算机能够识别的 数据形式并保存,同时还要完成程序段的语法检查。
• (3)刀具补偿
• 刀具补偿是指刀具长度和刀具半径的补偿。 • 目前,在较高档的CNC中,刀具补偿还包括程序段之间的 自动转接和过切削判别,这就是所谓C刀具补偿功能。
• 6.位移与速度检测装置 • 位移检测装置:测量装置按各坐标轴方向安装在 机床的工作台或丝杠上,将机床工作台各坐标轴 的实际位移转变成电信号反馈给数控装置,供数 控装置与指令值相比较产生误差信号,以控制机 床向消除该误差的方向移动。 • 速度检测装置:将进给速度反馈给进给伺服驱动 单元;将主轴转速反馈给主轴调速驱动单元。
CNC控制器由数控系统硬件、软件构成的专用计算机与可编程控制器 PLC组成。前者主要处理机床轨迹运动的数字控制,后者主要处理开关量 的逻辑控制。
• 1. 输入/输出设备
• 键盘和磁盘机是数控机床的典型输入设备,还可 以用串行通信的方式进行信息的输入。 • 数控系统一般配有CRT显示器或点阵式液晶显示 器,显示的信息较丰富,并能显示图形信息。
CNC系统通过软件与硬件的配合,合理地组织、管理数 控系统的输入、数据处理、插补和输出信息、控制执行部件运 动,使数控机床按照操作者的要求进行自动加工。 CNC系统采用了计算机作为控制部件,通常由常驻在其 内部的数控系统软件实现部分或全部数控功能,从而对机床运 动进行实时控制。只要改变计算机数控系统的控制软件就能实 现一种全新的控制方式。
二.CNC装置的主要工作及过程
CNC的工作流程
• 二.CNC装置的主要工作及过程
• CNC的工作过程包括:①输入、②译码、③刀具补偿、④ 进给速度处理、⑤插补、⑥位置控制、⑦I/O处理、⑧显示 和⑨诊断等9个方面。
• (1)输入
• 输入内容:向CNC控制器输入零件程序、机床参数和补偿 数据。 • 输入型式:有光电阅读机、键盘、磁盘和联机等输入。 • CNC输入工作方式:有存储方式和NC方式。前者将整个程 序存入存储器中,加工时一个个程序段调出;后者是指一 边输入一边加工,在前一程序段加工时,输入后一个程序 段内容。
• 插补(interpolation)定义:机床数控系统依照一定
方法确定刀具运动轨迹的过程。也可以说,已知曲线上的某 些数据,按照某种算法计算已知点之间的中间点的方法,也 称为“数据点的密化”。
⒊ 速度预处理
主要功能是根据加工程序给定的进给速度,计算在每 个插补周期内的合成移动量,供插补程序使用。
速度处理程序主要完成以下几步计算: 计算本段总位移量:
直线:合成位移量L;
园弧:总角位移量α 。
L
α
该数供插补程序判断减速起点和终点之用。 计算每个插补周期内的合成进给量: Δ L= F*Δ t/60 (μ m) 式中:F--进给速度值(mm/min);△t--数控系统的插 补周期(ms)
2. 刀补处理(计算刀具中心轨迹)
刀补处理的主要工作: • 根据G90/G91计算零件轮
R
Y
G41
Pe’Leabharlann Pe(200,300) Pe”
廓的终点坐标值。
• 根据R和G41/42,计算本
G42
段刀具中心轨迹的终点 (P’e/P〃e)坐标值。 • 根据本段与前段连接关
P0(72,48)
X
系,进行段间连接处理。
•驱动装置:有步进电动机、直流伺服电动机和 交流伺服电动机等。
功能:接受数控装臵发来的指令信号,信号经变 换和放大由执行元件(伺服电机)将其转变为角 位移或直线位移,从而实现驱动数控机床各运动 部件的进给运动。
• 5.主轴调速驱动单元及主轴电动机 • 主轴调速系统:包括主轴调速驱动单元、主轴电 动机、转速检测装置等。以主运动速度为控制目 标。 • 主轴调速驱动单元:是联系CNC装置和机床本体 的中间环节,它将来自CNC装置的微弱指令信号 放大成控制驱动装置的大功率信号。 • 主轴电动机:可分为直流主轴电动机和交流主轴 电动机。
CNC装置的数据转换流程
⒈
译码(解释)
将用文本格式(通常用ASCII码)表达的零件加工程
序,以程序段为单位转换成后续程序(本例是指刀补 处理程序)所要求的数据结构(格式)。
数据结构示例:
Struct PROG_BUFFER { char buf_state; //缓冲区状态,0 空;1 准备好。 int block_num; //以BCD码的形式存放本程序段号。 double COOR[20];//存放尺寸指令的数值(μ m)。 int F,S; //F(mm/min)S(r/min)。 char G0; //以标志形式存放G指令。 char G1; char M0; //以标志形式存放M指令。 char M1; char T; //存放本段换刀的刀具号。 char D; //存放刀具补偿的刀具半径值。 };