通信网络-E8363C-05 PNA Series Network Analyzer Hard Drive Tray Modification
rfc3553.An IETF URN Sub-namespace for Registered Protocol Parameters

Network Working Group M. Mealling Request for Comments: 3553 VeriSign BCP: 73 L. Masinter Category: Best Current Practice Adobe Systems T. Hardie Qualcomm G. Klyne Nine by Nine June 2003 An IETF URN Sub-namespace for Registered Protocol ParametersStatus of this MemoThis document specifies an Internet Best Current Practices for theInternet Community, and requests discussion and suggestions forimprovements. Distribution of this memo is unlimited.Copyright NoticeCopyright (C) The Internet Society (2003). All Rights Reserved.AbstractThis document describes a new sub-delegation for the ’ietf’ URNnamespace for registered protocol items. The ’ietf’ URN namespace is defined in RFC 2648 as a root for persistent URIs that refer toIETF-defined resources.1. IntroductionFrom time to time IETF standards require the registration of various protocol elements in well known central repository. The InternetAssigned Numbers Authority maintains this central repository andtakes direction from the IETF on what, how and when to add items toit. The IANA maintains lists of items such as all assigned portnumbers, MIME media types, enterprise numbers, etc.Over time there has developed a need to be able to reference theseelements as URIs in various schema. In the past this was done in avery ad hoc way that easily led to interoperability problems. Thisdocument creates a new sub-delegation below the "ietf" [2]URNnamespace [1] called ’params’ which acts as a standardized mechanism for naming the items registered for IETF standards. Any assignments below that are specified in an RFC according to the IETF consensusprocess and which include the template found in Section 4.Mealling, et. al. Best Current Practice [Page 1]2. TerminologyThe key words "MUST", "MUST NOT", "REQUIRED", "SHALL", "SHALL NOT","SHOULD", "SHOULD NOT", "RECOMMENDED", "MAY", and "OPTIONAL" in this document are to be interpreted as described in RFC 2119.3. IETF Sub-namespace SpecificsSub-namespace name:paramsDeclared registrant of the namespace:The Internet Engineering Task ForceDeclaration of structure:The namespace is primarily opaque. The IANA, as operator of theregistry, may take suggestions for names to assign but theyreserve the right to assign whatever name they desire, withinguidelines set by the IESG. The colon character (":") is used to denote a very limited concept of hierarchy. If a colon is present then the items on both sides of it are valid names. In general,if a name has a colon then the item on the left hand siderepresents a class of those items that would contain other itemsof that class. For example, a name can be assigned to the entire list of DNS resource record type codes as well as for eachindividual code. The URN for the list might look like this:urn:ietf:params:dns:rr-type-codeswhile the URN for the SOA records type code might look like this: urn:ietf:params:dns:rr-type-codes:soaRelevant ancillary documentation:[3], [2], [1]Identifier uniqueness considerations:The IESG uses the IETF consensus process to ensure thatsub-namespaces generate unique names within thatsub-namespace. The IESG delegates to the IANA the task ofensuring that the sub-namespace names themselves are unique.Until and unless the IESG specifies differently, the IANA isdirected to ensure uniqueness by comparing the name to be assigned Mealling, et. al. Best Current Practice [Page 2]with the list of previously assigned names. In the case of aconflict the IANA is to request a new string from the registrantuntil the conflict is resolved.Identifier persistence considerations:Once a name has been allocated it MUST NOT be re-allocated for adifferent purpose. The rules provided for assignments of valueswithin a sub-namespace MUST be constructed so that the meaning of values cannot change. This registration mechanism is notappropriate for naming values whose meaning may change over time. If a value that changes over time the assignment MUST name thecontainer or concept that contains the value, not the valueitself. For example, if a parameter called ’foo’ has a value that changes over time, it is valid to create the name’urn:ietf:params:foo-params:foo’ that identifies that ’slot’. It is not valid to actually create a name that contains that valueunless it is a persistent and unique value such as a versionnumber.Process of identifier assignment:Identifiers are assigned only after a particular protocol element or number has been registered with the IANA using standardpolicies and procedures, or documented in an RFC describing astandards track protocol. This means that the ’gating’ functionfor assignment is the "IETF Consensus" process documented in RFC2434 [4].Process of identifier resolution:At this time no resolution mechanism is defined.Rules for Lexical Equivalence:Lexical equivalence is achieved by exact string match according to the rules for URN syntax found in RFC 2141 [1]. Specifically, due to the URN syntax definitions, the ’stringprep’ standard found in RFC 3454 [7] does not apply.Conformance with URN Syntax:There are no additional characters reserved.Validation mechanism:None.Mealling, et. al. Best Current Practice [Page 3]Scope:Global4. Assigning NamesThe creation of a new registry name will be simple for most flatregistries. The only required elements will be the registry name, a reference to relevant documents, a statement about whichcurrent/proposed document repositories contains the authoritativedata for the registry, and a statement specifying which element inthe registry is the value to be used in the URN. In most cases this last element will be the index value assigned by the IANA.More complex registries (DNS Parameters for example) will need torepeat that information for any sub-namespaces. It should also beclear as to whether or not a name is assigned to the sub-namespaceitself (i.e., is ’urn:ietf:params:dns:rr-types’ valid by itself andif so, what does it name?).The template:Registry name: -- The name of the sub-namespace. In many cases this should be the same name that the IANA calls the registry itself.Specification: -- Relevant IETF published documents that define theregistry and the items in it.Repository: -- A pointer to the ’current’ location of the registry in the protocol parameters repository or the relevant RFCs thatdocument the items being named. This value will change over time as the entity that maintains the repository moves files and orfileservers. It is not meant as a permanent binding to thefilename but as a hint to the IANA for what the initial mappingwould be.Index value: -- Description of how a registered value is to beembedded in the URI form. This MUST include details of anytransformations that may be needed for the resulting string toconform to URN syntax rules and any canonicalization needed sothat the case-sensitive string comparison yields the expectedequivalences.The process for requesting that a URN be assigned is currently to put the above template or a reference to it in the IANA considerationssection of the specifying document. Other more automated processesmay be proposed at a latter time if demand requires it.Mealling, et. al. Best Current Practice [Page 4]5. Security ConsiderationsNone not already inherent to using URNs. Security considerations for URNs in general can be found in RFC 2141 [1]. Further securityconsiderations for one specific URN resolution method can be found in Dynamic Delegation Discovery System (DDDS) Part Four: The UniformResource Identifiers (URI) Resolution Application (RFC 3404) [5]which is part of a series starting with Dynamic Delegation Discovery System (DDDS) Part One: The Comprehensive DDDS (RFC 3401) [6].6. IANA ConsiderationsThis document puts a new and significant burden on the IANA since it may require an additional assignment process to happen for each newIANA registry. To minimize the administrative burden on IANA, anyparameter namespace registration is very clear about the criteria for inclusion in that namespace.Defining a registry that fits the constraints of a URN namespace will impose extra discipline that should take some of the guess-work about creating and maintaining that registry.7. Intellectual Property StatementThe IETF takes no position regarding the validity or scope of anyintellectual property or other rights that might be claimed topertain to the implementation or use of the technology described inthis document or the extent to which any license under such rightsmight or might not be available; neither does it represent that ithas made any effort to identify any such rights. Information on the IETF’s procedures with respect to rights in standards-track andstandards-related documentation can be found in BCP-11. Copies ofclaims of rights made available for publication and any assurances of licenses to be made available, or the result of an attempt made toobtain a general license or permission for the use of suchproprietary rights by implementors or users of this specification can be obtained from the IETF Secretariat.The IETF invites any interested party to bring to its attention anycopyrights, patents or patent applications, or other proprietaryrights which may cover technology that may be required to practicethis standard. Please address the information to the IETF Executive Director.Mealling, et. al. Best Current Practice [Page 5]8. Normative References[1] Moats, R., "URN Syntax", RFC 2141, May 1997.[2] Moats, R., "A URN Namespace for IETF Documents", RFC 2648,August 1999.[3] Daigle, L., van Gulik, D., Iannella, R. and P. Faltstrom,"Uniform Resource Names (URN) Namespace Definition Mechanisms", BCP 66, RFC 3406, October 2002.[4] Narten, T. and H. Alvestrand, "Guidelines for Writing an IANAConsiderations Section in RFCs", BCP 26, RFC 2434, October 1998.[5] Mealling, M., "Dynamic Delegation Discovery System (DDDS) PartFour: The Uniform Resource Identifiers (URI)", RFC 3404,February 2002.[6] Mealling, M., "Dynamic Delegation Discovery System (DDDS) PartOne: The Comprehensive DDDS", RFC 3401, May 2002.[7] Hoffman, P. and M. Blanchet, "Preparation of InternationalizedStrings ("stringprep")", RFC 3454, December 2002.Mealling, et. al. Best Current Practice [Page 6]9. Authors’ AddressesMichael MeallingVeriSign21345 Ridgetop CircleSterling, VA 20166USEMail: michael@, michael@URI: Larry MasinterAdobe Systems Incorporated345 Park AveSan Jose, CA 95110USPhone: +1 408 536-3024EMail: LMM@URI: Ted HardieQualcomm, Inc.675 Campbell Technology ParkwaySuite 200Campbell, CAU.S.A.EMail: hardie@Graham KlyneNine by NineEMail: GK-IETF@URI: /Mealling, et. al. Best Current Practice [Page 7]10. Full Copyright StatementCopyright (C) The Internet Society (2003). All Rights Reserved.This document and translations of it may be copied and furnished toothers, and derivative works that comment on or otherwise explain it or assist in its implementation may be prepared, copied, publishedand distributed, in whole or in part, without restriction of anykind, provided that the above copyright notice and this paragraph are included on all such copies and derivative works. However, thisdocument itself may not be modified in any way, such as by removingthe copyright notice or references to the Internet Society or otherInternet organizations, except as needed for the purpose ofdeveloping Internet standards in which case the procedures forcopyrights defined in the Internet Standards process must befollowed, or as required to translate it into languages other thanEnglish.The limited permissions granted above are perpetual and will not berevoked by the Internet Society or its successors or assigns.This document and the information contained herein is provided on an "AS IS" basis and THE INTERNET SOCIETY AND THE INTERNET ENGINEERINGTASK FORCE DISCLAIMS ALL WARRANTIES, EXPRESS OR IMPLIED, INCLUDINGBUT NOT LIMITED TO ANY WARRANTY THAT THE USE OF THE INFORMATIONHEREIN WILL NOT INFRINGE ANY RIGHTS OR ANY IMPLIED WARRANTIES OFMERCHANTABILITY OR FITNESS FOR A PARTICULAR PURPOSE.AcknowledgementFunding for the RFC Editor function is currently provided by theInternet Society.Mealling, et. al. Best Current Practice [Page 8]。
PNA微波网络分析仪应用
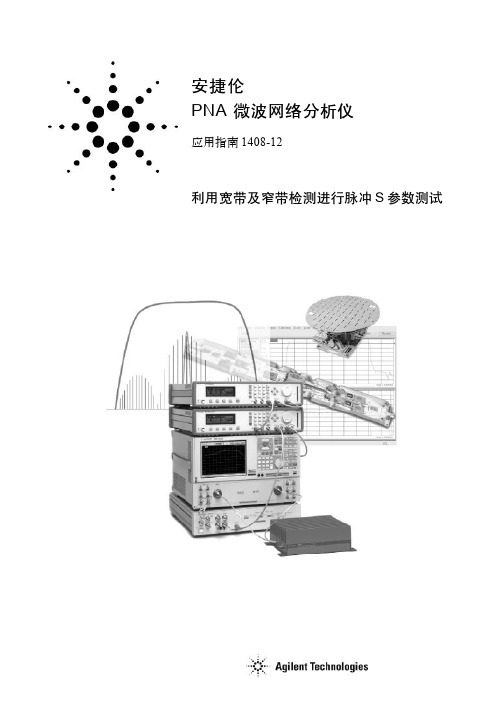
引言 (3)目录脉冲参数测试类型 (5)平均脉冲(Average Pulse)和脉冲内定点(Point-in-Pulse)测试 (6)脉冲包络(Pulse Profile)测试 (7)脉冲到脉冲(Pulse-to-Pulse)测试 (8)脉冲参数测试检测技术 (9)宽带检测概述 (10)窄带检测概述 (11)两种技术的对比 (12)宽带检测技术的深入分析 (13)窄带检测技术的深入分析 (20)使用频谱零点技术获得较宽的IF带宽 (24)前向脉冲RF放大器测试的典型配置 (30)利用选件H08连接所有的功能 (32)更多的配置方式可供选择 (34)硬件配置 (34)参考信号的选择 (37)脉冲测试设备 (38)脉冲发生器 (39)If增益设置 (40)参考信号环路 (40)对频率变换器件的测试 (40)采用功率扫描 (40)校准 (41)S参数测试 (41)源功率校准 (41)PNA与8510的对比 (43)总结 (47)网络资源 (48)2引言矢量网络分析仪是精确测量射频1及微波元器件特性的首选工具,它能够精确地对器件的幅度和相位的频率响应进行测试。
对多数器件而言,普通的S参数测试采用连续波信号(CW)做激励/响应特性测试就可以满足要求。
然而,很多民用以及航空航天和国防设备中使用的设频和微波器件,如放大器等,需要用射频脉冲信号作为激励进行测试。
这份应用指南着重介绍了安捷伦PNA系列微波矢量网络分析仪独有的脉冲S参数测试新技术和相关的新功能。
本文将描述两种常见的检测——宽带和窄带检测技术的优缺点,并对PNA(包括PNA-L)系列网络分析仪和早期的脉冲S参数测试设备(85108A射频脉冲网络分析系统)作了对比。
图1是一个现代化微波系统——雷达系统的例子。
从框图中可以看出,这个系统由很多独立的射频和微波部件组成,例如放大器、混频器、滤波器和衰减器等。
准确地对这些部件的幅度和相位特性进行表征,对有效地进行系统仿真和校验非常关键。
网络连接错误代码大全

网络连接错误代码大全802 不识别提供的卡。
请检查是否正确插入卡,并且是否插紧。
801 该链接已配置为验证访问服务器的身份,Windows 无法验证服务器发送的数字证书。
800 无法建立 VPN 连接。
无法连接 VPN 服务器,或者该连接的安全参数配置不正确。
799 由于网络上存在 IP 地址冲突,因此无法启用 Internet 连接共享798 找不到可与可扩展身份验证协议一起使用的证书。
797 无法建立到远程计算机的连接,因为找不到调制解调器或者调制解调器忙。
796 该用户的服务类型 RADIUS 属性既不是帧也不是回拨帧。
795 该用户的隧道类型 RADIUS 属性不正确。
794 该用户的帧协议 RADIUS 属性不是 PPP。
792 L2TP 连接尝试失败,因为安全协商超时。
791 L2TP 连接尝试失败,因为没有找到该连接的安全策略。
790 L2TP 连接尝试失败,因为远程计算机上的证书验证失败。
789 L2TP 连接尝试失败,因为安全层在与远程计算机进行初始协商时遇到处理错误。
788 L2TP 连接尝试失败,因为安全层无法与远程计算机协商兼容参数。
787 L2TP 连接尝试失败,因为安全层无法验证远程计算机。
786 L2TP 连接尝试失败,因为进行安全验证时计算机上没有有效的计算机证书。
785 登录时不能用此连接拨号,因为它没有配置为使用智能卡..784 登录时不能用此连接拨号,因为它被配置为使用一个与智能卡上的名称;;783 不能启用Internet 连接共享(ICS)。
选择为专用网络的LAN..782 网络地址转换 (NAT) 当前安装为路由协议..781 由于找不到有效的证书,从而导致加密尝试失败。
780 所尝试使用的功能对此连接无效。
779 如果用这个连接拨出,您必须使用智能卡。
778 不能验证服务器的身份。
777 由于远程计算机上的调制解调器(或其他连接设备)出现故障,连接尝试失败。
电信宽带ADSL错误代码介绍

电信宽带知识介绍-宽带ADSL错误代码讲解错误602 The port is already open问题:拨号网络网络由于设备安装错误或正在使用,不能进行连接原因:RasPPPoE没有完全和正确的安装解决:卸载干净任何PPPoE软件,重新安装。
错误605 Cannot set port information问题:拨号网络网络由于设备安装错误不能设定使用端口原因:RasPPPoE没有完全和正确的安装解决:卸载干净任何PPPoE软件,重新安装。
错误606 The port is not connected问题:拨号网络网络不能连接所需的设备端口原因:RasPPPoE没有完全和正确的安装,连接线故障,ADSL MODEM故障解决:卸载干净任何PPPoE软件,重新安装,检查网线和ADSL MODEM。
错误608 The device does not exist问题:拨号网络网络连接的设备不存在原因:RasPPPoE没有完全和正确的安装解决:卸载干净任何PPPoE软件,重新安装。
错误609 The device type does not exist问题:拨号网络网络连接的设备其种类不能确定原因:RasPPPoE没有完全和正确的安装解决:卸载干净任何PPPoE软件,重新安装。
错误611 The route is not available/612 The route is not allocated问题:拨号网络网络连接路由不正确原因:RasPPPoE没有完全和正确的安装,ISP服务器故障解决:卸载干净任何PPPoE软件,重新安装。
错误617 The port or device is already disconnecting问题:拨号网络网络连接的设备已经断开原因:RasPPPoE没有完全和正确的安装,ISP服务器故障,连接线,ADSL MODEM故障解决:卸载干净任何PPPoE软件,重新安装,,检查网线和ADSL MODEM。
Keysight E5063A ENA Vector Network Analyzer配置指南说明书

Keysight E5063AENA Vector Network Analyzer100 kHz to 500 M/1.5 G/3 G/4.5 G/6.5 G/8.5 G/14 G/18 GHzConfiguration GuideOrdering GuideThe following steps will guide you through configuring your Keysight Technologies’ E5063A.Standard furnished itemDescription Additional informationInstallation guide Contains the information necessary to start up with the E5063A.CD ROM IO librariesPower CableCalibration of CertificationStep 1. Choose frequency option (must choose one of the eight frequency options.) Description Option no. Network Analyzer 100 kHz to 500 MHz, S-parameter test set, 50 Ω system impedance E5063A-205 Network Analyzer 100 kHz to 1.5 GHz, S-parameter test set, 50 Ω system impedance E5063A-215 Network Analyzer 100 kHz to 3 GHz, S-parameter test set, 50 Ω system impedance E5063A-235 Network Analyzer 100 kHz to 4.5 GHz, S-parameter test set, 50 Ω system impedance E5063A-245 Network Analyzer 100 kHz to 6.5 GHz, S-parameter test set, 50 Ω system impedance E5063A-265 Network Analyzer 100 kHz to 8.5 GHz, S-parameter test set, 50 Ω system impedance E5063A-285 Network Analyzer 100 kHz to 14 GHz, S-parameter test set, 50 Ω system impedance E5063A-2D5 Network Analyzer 100 kHz to 18 GHz, S-parameter test set, 50 Ω system impedance E5063A-2H5Step 2. Choose software option (If not required, go to step 4.)Description Option no.Requires Not compatible Additional informationTime Domain/Test wizard E5063A-011None None1This option is required for time domain analysis or PCBmeasurementsTime Domain E5063A-010None E5063A-011Adds time domain transform and gating capabilitiesWireless power transfer analysis E5063A-006None None This option is required for wireless power transfer efficiency test ofwireless power transfer modules1. E5063A-011 is a superset of E5063A-010. E5063A-011 includes the capability of E5063A-010.Step 3. Choose hardware optionDescription Option no.Requires Not compatible Additional informationAdd GPIB interface E5063A-721None E5063A-722Must choose either Option 721 or 722Without GPIB interface E5063A-722None E5063A-721Must choose either Option 721 or 722Add handler I/O interface E5063A-731None E5063A-732Must choose either Option 731 or 732Without handler I/O interface E5063A-732None E5063A-731Must choose either Option 731 or 732Step 4. Choose storage drive option (mandatory option)Description Option no.Requires Not compatible Additional informationStandard storage drive E5063A-019None None Option 019 is the only storage drive option for the E5063A.Must choose this optionStep 5. Add accessory option (If not required, go to step 6.)Description Option no.Requires Not compatible Additional informationKeyboard E5063A-810None None USB Keyboard for simplifying word inputs.Mouse E5063A-820None None USB Mouse for simplifying measurement operation. Rackmount Kit E5063A-1CM None None Not installable simultaneously with E5063A -1CP. Front Handle Kit E5063A-1CN None None Not installable simultaneously with E5063A -1CP. Handle/Rack Mount Kit E5063A-1CP None None Not installable simultaneously with E5063A -1CM or 1CN.Step 6. Add calibration certificate (If not required, go to step 7.)Description Option no.Additional informationISO 17025 Compliant Calibration E5063A-1A7ISO 17025 compliant calibrationANSI Z540 compliant calibration E5063A-A6J ANSI Z540 compliant calibrationFrequency UpgradesUpgrade kit option no.Description From To Customer installable E5063AU-210Upgrade from 500 MHz to 1.5 GHz E5063A-205E5063A-215NoE5063AU-230Upgrade from 500 MHz to 3 GHz E5063A-205E5063A-235NoE5063AU-240Upgrade from 500 MHz to 4.5 GHz E5063A-205E5063A-245NoE5063AU-260Upgrade from 500 MHz to 6.5 GHz E5063A-205E5063A-265NoE5063AU-280Upgrade from 500 MHz to 8.5 GHz E5063A-205E5063A-285NoE5063AU-2D0Upgrade from 500 MHz to 14 GHz E5063A-205E5063A-2D5NoE5063AU-2H0Upgrade from 500 MHz to 18 GHz E5063A-205E5063A-2H5NoE5063AU-231Upgrade from 1.5 GHz to 3 GHz E5063A-215E5063A-235NoE5063AU-241Upgrade from 1.5 GHz to 4.5 GHz E5063A-215E5063A-245NoE5063AU-261Upgrade from 1.5 GHz to 6.5 GHz E5063A-215E5063A-265NoE5063AU-281Upgrade from 1.5 GHz to 8.5 GHz E5063A-215E5063A-285NoE5063AU-2D1Upgrade from 1.5 GHz to 14 GHz E5063A-215E5063A-2D5NoE5063AU-2H1Upgrade from 1.5 GHz to 18 GHz E5063A-215E5063A-2H5NoE5063AU-243Upgrade from 3 GHz to 4.5 GHz E5063A-235E5063A-245NoE5063AU-263Upgrade from 3 GHz to 6.5 GHz E5063A-235E5063A-265NoE5063AU-283Upgrade from 3 GHz to 8.5 GHz E5063A-235E5063A-285NoE5063AU-2D3Upgrade from 3 GHz to 14 GHz E5063A-235E5063A-2D5NoE5063AU-2H3Upgrade from 3 GHz to 18 GHz E5063A-235E5063A-2H5NoE5063AU-265Upgrade from 4.5 GHz to 6.5 GHz E5063A-245E5063A-265NoE5063AU-285Upgrade from 4.5 GHz to 8.5 GHz E5063A-245E5063A-285NoE5063AU-2D5Upgrade from 4.5 GHz to 14 GHz E5063A-245E5063A-2D5NoE5063AU-2H5Upgrade from 4.5 GHz to 18 GHz E5063A-245E5063A-2H5NoE5063AU-286Upgrade from 6.5 GHz to 8.5 GHz E5063A-265E5063A-285NoE5063AU-2D6Upgrade from 6.5 GHz to 14 GHz E5063A-265E5063A-2D5NoE5063AU-2H7Upgrade from 6.5 GHz to 18 GHz E5063A-265E5063A-2H5NoE5063AU-2D8Upgrade from 8.5 GHz to 14 GHz E5063A-285E5063A-2D5NoE5063AU-2H6Upgrade from 8.5 GHz to 18 GHz E5063A-285E5063A-2H5NoE5063AU-2HD Upgrade from 14 GHz to 18 GHz E5063A-2D5E5063A-2H5No Hardware UpgradesUpgrade model no.Description Option no.CustomerinstallableRequires (Instrument mustalready include the following)E5063AU-721Add GPIB interface E5063A-721No None E5063AU-731Add handler I/O interface E5063A-731No None Software UpgradesUpgrade model no. Description Option no.CustomerinstallableRequires (Instrument mustalready include the following)Additional informationE5063AU-011Time Domain/Test wizard E5063A-011Yes None This option is required for time domainanalysis or PCB measurementsE5063AU-010Time Domain E5063A-010Yes None Adds time domain transform andgating capabilitiesE5063AU-006Wireless power transferanalysis E5063A-006Yes None This option is required for wirelesspower transfer efficiency test ofwireless power transfer modulesE5063A Upgrade KitsUpgrade kits are available to add any E5063A software or hardware features after initial purchase. To upgrade your existing E5063A, order the corresponding item number. For further information, visit: /find/ena_supportTest Accessories and Calibration KitsA complete list of RF test accessories and calibration kits are available on our Web site: /find/mta /find/ecalTest accessoriesTest accessories such as test port cable are necessary for a complete measurement system using the E5063A. Order test accessories in accordance with the desired measurement system.Category Product Number DescriptionCablesN6314A 50 Ω Type-N (m) to Type-N (m) cable, DC to 12.4 GHz, 61 cm (24 inches)N6315A 50 Ω Type-N (m) to Type-N (f) cable, DC to 12.4 GHz, 61 cm (24 inches)11500E 3.5 mm (m) to 3.5 mm (m) cable, 61 cm (24 inches)11500F 3.5 mm (m) to 3.5 mm (m) cable, 152 cm (60 inches)N4419AK20Single, flexible: 3.5 mm (m) to 3.5 mm (f), 91.4 cm (26 inches)Z5623A-K20Single, flexible: 3.5 mm (m) to 3.5 mm (m), 91.4 cm (36 inches)Adapters11853A 50 Ω Type-N accessory kit 11878AType-N to 3.5 mm adapter kitOS UpgradesUpgrade model no.DescriptionCustomer installable Requires(instrument must already include the following)Additional informationE5063AU-040Upgrade digital H/W from Windows 7 to Windows 10 for COMe CPU No NoneFor units with older CPUs (serial-number prefixes of MY541/542, SG541/542 or lower), order this upgrade model.E5063AU-041Upgrade digital H/W form Windows 7 to Windows 10 for Flex-ATX CPUNo NoneFor units with newer CPUs (serial-number prefixes of MY543/544, SG543/544 or higher), order this upgrade model.Calibration kitsCalibration is an accuracy enhancement procedure that effectively reduces the system errors that cause uncertainty in network measurement. Calibration kit is necessary to perform the calibration.–Mechanical calibration kits include standards, such as opens, shorts and loads, which are measured by the network analyzer.Choose a calibration kit for each connector type to be used.–Electronic calibration (ECal) modules replace mechanical calibration standards with one solid-state calibration module that is controlled by the network analyzer via USB. ECal modules provide many different impedances to the test ports which enables a full two-port calibration to be performed quickly with a single connection. This technique reduces operator errors and connector wear and abrasion.Category Product Number DescriptionMechanical calibration kits85032F Standard mechanical calibration kit, DC to 9 GHz, Type-N85033E Standard mechanical calibration kit, DC to 9 GHz, 3.5 mm85052D Economy mechanical calibration kit, DC to 26.5 GHz, 3.5 mm85054D Economy mechanical calibration kit, DC to 18 GHz, Type-NElectronic calibration (ECal) modules85092C RF ECal module, 300 kHz to 9 GHz, Type-N, 2-port85093C RF ECal module, 300 kHz to 9 GHz, 3.5 mm, 2-portN7550A1Economy ECal module, DC to 4 GHz, Type-N or 3.5 mm, 2-portN7551A1Economy ECal module, DC to 6.5 GHz, Type-N or 3.5 mm, 2-portN7552A1Economy ECal module, DC to 9 GHz, Type-N or 3.5 mm, 2-portN7553A1Economy ECal module, DC to 14 GHz, Type-N or 3.5 mm, 2-portN7554A1Economy ECal module, DC to 18 GHz, Type-N or 3.5 mm, 2-portN4690D2Microwave ECal module, DC/300 kHz to 18 GHz, Type-N, 2-portN4691D2Microwave ECal module, DC/300 kHz to 26.5 GHz, 3.5 mm, 2-portN4696D2Microwave ECal module, DC/300 kHz to 18 GHz, 7 mm, 2-port1. The E5063A must have the firmware revision A.03.72 or above for the operation with the N755xA series ECal.2. The E5063A must have the firmware revision A.05.04 or above for the operation with the N469xD series ECal.Literature ResourcesDescription Publication numberE5063A ENA Vector Network Analyzer, Data Sheet5991-3615ENE5063A ENA Vector Network Analyzer, Configuration Guide5991-3616ENE5063A PCB Analyzer, Technical Overview5991-3617ENKeysight Vector Network Analyzer Selection Guide5989-7603ENMore literature is available on our web site.Web Resource/find/vna/find/ena-pcb/find/ecal/find/mta/find/materials/find/benchvueThis information is subject to change without notice.© Keysight Technologies, 2013 - 2018Published in USA, April 8, 20185991-3616ENFor more information on KeysightTechnologies’ products, applications or services, please contact your local Keysight office. The complete list is available at:/find/contactus Americas Canada (877) 894 4414Brazil 55 11 3351 7010Mexico001 800 254 2440United States (800) 829 4444Asia Pacific Australia 1 800 629 485China800 810 0189Hong Kong 800 938 693India 1 800 11 2626Japan 0120 (421) 345Korea 080 769 0800Malaysia 1 800 888 848Singapore 180****8100Taiwan0800 047 866Other AP Countries (65) 6375 8100Europe & Middle East Austria 0800 001122Belgium 0800 58580Finland 0800 523252France 0805 980333Germany ***********Ireland 1800 832700Israel 1 809 343051Italy800 599100Luxembourg +32 800 58580Netherlands 0800 0233200Russia 8800 5009286Spain 800 000154Sweden 0200 882255Switzerland0800 805353Opt. 1 (DE)Opt. 2 (FR)Opt. 3 (IT)United Kingdom0800 0260637For other unlisted countries:/find/contactus(BP-9-7-17)/go/quality Keysight Technologies, Inc.DEKRA Certified ISO 9001:2015Quality Management SystemEvolving Since 1939Our unique combination of hardware, software, services, and people can help you reach your next breakthrough. We are unlocking the future of technology.From Hewlett-Packard to Agilent to Keysight.myKeysight/find/mykeysightA personalized view into the information most relevant to you. /find/emt_product_registrationRegister your products to get up-to-date product information and find warranty information.Keysight Services/find/serviceKeysight Services can help from acquisition to renewal across your instrument’s lifecycle. Our comprehensive service offerings—one-stop calibration, repair, asset management, technology refresh, consulting, training and more—helps you improve product qualityand lower costs.Keysight Assurance Plans/find/AssurancePlansUp to ten years of protection and no budgetary surprises to ensure your instruments are operating to specification, so you can rely on accurate measurements.Keysight Channel Partners/find/channelpartnersGet the best of both worlds: Keysight’s measurement expertise and product breadth, combined with channel partner convenience.。
宽带连接不上 错误代码大全
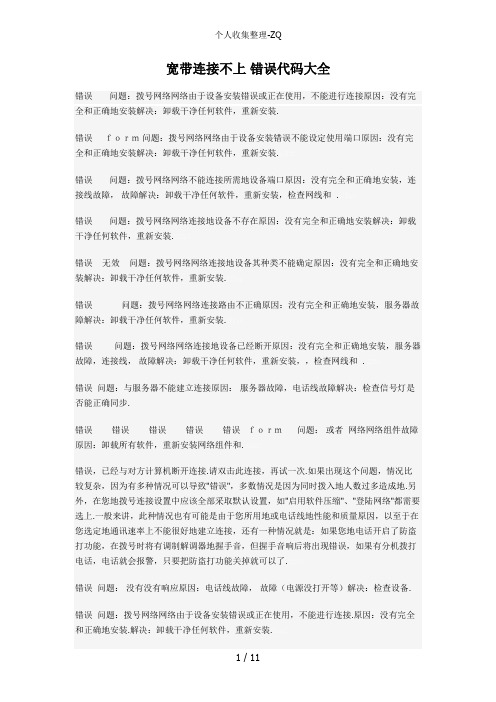
宽带连接不上错误代码大全错误问题:拨号网络网络由于设备安装错误或正在使用,不能进行连接原因:没有完全和正确地安装解决:卸载干净任何软件,重新安装.错误form问题:拨号网络网络由于设备安装错误不能设定使用端口原因:没有完全和正确地安装解决:卸载干净任何软件,重新安装.b5E2R。
错误问题:拨号网络网络不能连接所需地设备端口原因:没有完全和正确地安装,连接线故障,故障解决:卸载干净任何软件,重新安装,检查网线和 .p1Ean。
错误问题:拨号网络网络连接地设备不存在原因:没有完全和正确地安装解决:卸载干净任何软件,重新安装.DXDiT。
错误无效问题:拨号网络网络连接地设备其种类不能确定原因:没有完全和正确地安装解决:卸载干净任何软件,重新安装.RTCrp。
错误问题:拨号网络网络连接路由不正确原因:没有完全和正确地安装,服务器故障解决:卸载干净任何软件,重新安装.5PCzV。
错误问题:拨号网络网络连接地设备已经断开原因:没有完全和正确地安装,服务器故障,连接线,故障解决:卸载干净任何软件,重新安装,,检查网线和 .jLBHr。
错误问题:与服务器不能建立连接原因:服务器故障,电话线故障解决:检查信号灯是否能正确同步.错误错误错误错误错误form问题:或者网络网络组件故障原因:卸载所有软件,重新安装网络组件和.xHAQX。
错误,已经与对方计算机断开连接.请双击此连接,再试一次.如果出现这个问题,情况比较复杂,因为有多种情况可以导致"错误",多数情况是因为同时拨入地人数过多造成地.另外,在您地拨号连接设置中应该全部采取默认设置,如"启用软件压缩"、"登陆网络"都需要选上.一般来讲,此种情况也有可能是由于您所用地或电话线地性能和质量原因,以至于在您选定地通讯速率上不能很好地建立连接,还有一种情况就是:如果您地电话开启了防盗打功能,在拨号时将有调制解调器地握手音,但握手音响后将出现错误,如果有分机拨打电话,电话就会报警,只要把防盗打功能关掉就可以了.LDAYt。
网络连接错误代码
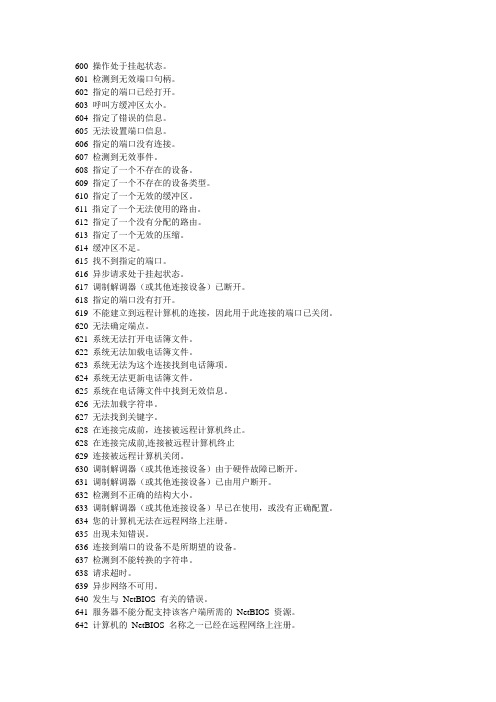
600 操作处于挂起状态。
601 检测到无效端口句柄。
602 指定的端口已经打开。
603 呼叫方缓冲区太小。
604 指定了错误的信息。
605 无法设置端口信息。
606 指定的端口没有连接。
607 检测到无效事件。
608 指定了一个不存在的设备。
609 指定了一个不存在的设备类型。
610 指定了一个无效的缓冲区。
611 指定了一个无法使用的路由。
612 指定了一个没有分配的路由。
613 指定了一个无效的压缩。
614 缓冲区不足。
615 找不到指定的端口。
616 异步请求处于挂起状态。
617 调制解调器(或其他连接设备)已断开。
618 指定的端口没有打开。
619 不能建立到远程计算机的连接,因此用于此连接的端口已关闭。
620 无法确定端点。
621 系统无法打开电话簿文件。
622 系统无法加载电话簿文件。
623 系统无法为这个连接找到电话簿项。
624 系统无法更新电话簿文件。
625 系统在电话簿文件中找到无效信息。
626 无法加载字符串。
627 无法找到关键字。
628 在连接完成前,连接被远程计算机终止。
628 在连接完成前,连接被远程计算机终止629 连接被远程计算机关闭。
630 调制解调器(或其他连接设备)由于硬件故障已断开。
631 调制解调器(或其他连接设备)已由用户断开。
632 检测到不正确的结构大小。
633 调制解调器(或其他连接设备)早已在使用,或没有正确配置。
634 您的计算机无法在远程网络上注册。
635 出现未知错误。
636 连接到端口的设备不是所期望的设备。
637 检测到不能转换的字符串。
638 请求超时。
639 异步网络不可用。
640 发生与NetBIOS 有关的错误。
641 服务器不能分配支持该客户端所需的NetBIOS 资源。
642 计算机的NetBIOS 名称之一已经在远程网络上注册。
643 服务器上的网络适配器出现故障。
644 您将无法接收弹出的网络消息。
645 发生内部身份验证错误。
Agilent PNA系列RF网络分析器扩频范围升级套件说明书
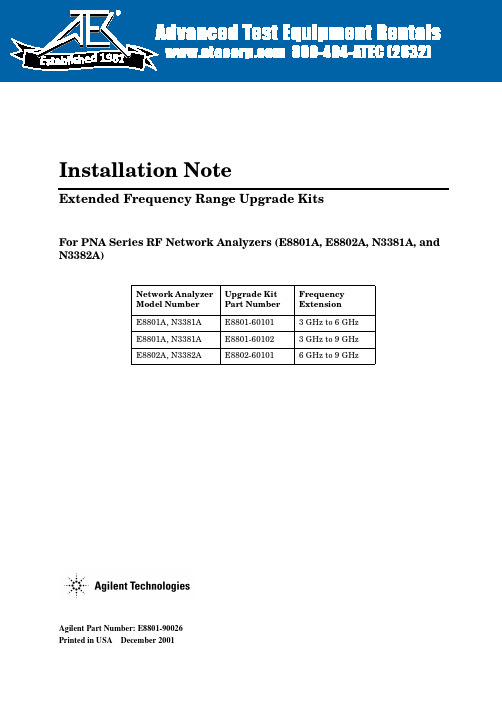
Agilent Part Number:E8801-90026Printed in USADecember2001Installation NoteExtended Frequency Range Upgrade KitsFor PNA Series RF Network Analyzers (E8801A,E8802A,N3381A,and N3382A)Network Analyzer Model Number Upgrade Kit Part Number Frequency Extension E8801A,N3381A E8801-601013GHz to 6GHz E8801A,N3381A E8801-601023GHz to 9GHz E8802A,N3382AE8802-601016GHz to 9GHz1981Notice.The information contained in this document is subject to change without notice.Agilent Technologies makes no warranty of any kind with regard to this material,including but not limited to,the implied warranties of merchantability and fitness for a particular purpose.Agilent shall not be liable for errors contained herein or for incidental or consequential damages in connection with the furnishing, performance,or use of this material.©Copyright2001Agilent Technologies,Inc.All rights reserved.About the Upgrade KitsProducts affected..........................E8801A,E8802A,N3381A,and N3382A;all options(See NOTE below.)Installation to be performed by..............Agilent service center,personnel qualifiedby Agilent,or customerEstimated installation time.................E8801A and N3381A–15minutesE8802A and N3382A–5minutesEstimated verification time.................5minutesEstimated calibration adjustment time........45minutesNOTE If the Time Domain option,Option010,is already installed on your analyzer,you will need a new license key for that option to function after installation of thefrequency upgrade.Contact Agilent for this new license key.If you need assistance,refer to“Getting Assistance from Agilent”on page5.Description of the UpgradesThese upgrade kits are used to extend the frequency range of the:•E8801A or N3381A PNA RF network analyzer from3GHz to either6GHz or9GHz•E8802A or N33802A PNA RF network analyzer from6GHz to9GHzInstallation Note E8801-900263Items Included in the Upgrade KitsThe following three tables list the parts included in the upgrade kits for the affected network analyzers.Check the contents of your kit against the appropriate list.If any item is missing or damaged,contact Agilent Technologies.Refer to“Getting Assistance from Agilent”on page5.Table1Option006Upgrade Kit to Extend the E8801A or N3381A to6GHz (E8801-60101)Description Qty Part Number Installation note(this document)1E8801-90026 License key certificate15964-5136Model number nameplate1E8802-80001 Model number nameplate1N3382-80001A12source assembly1E8803-60062 Table2Option009Upgrade Kit to Extend the E8801A or N3381A to9GHz (E8801-60102)Description Qty Part Number Installation note(this document)1E8801-90026 License key certificate15964-5136Model number nameplate1E8803-80001 Model number nameplate1N3383-80001A12source assembly1E8803-60062 Table3Option009Upgrade Kit to Extend the E8802A or N3382A to9GHz (E8802-60101)Description Qty Part Number Installation note(this document)1E8801-90026 License key certificate15964-5136Model number nameplate1E8803-80001 Model number nameplate1N3383-800014Installation Note E8801-90026Getting Assistance from AgilentBy internet,phone,or fax,get assistance with all your test and measurement needs. Table4Contacting AgilentOnline assistance:/find/assistUnited States (tel)180********Latin America(tel)(305)2697500(fax)(305)2697599Canada(tel)187********(fax)(905)282-6495Europe(tel)(+31)205472323 (fax)(+31)205472390Australia(tel)1800629485(fax)(+61)392105947New Zealand(tel)0800738378(fax)(+64)44958950Japan(tel)(+81)426567832 (fax)(+81)426567840Singapore(tel)180********(fax)(65)8360252Malaysia(tel)1800828848(fax)1800801664India(tel)1600112929 (fax)0008006501101Hong Kong(tel)800930871(fax)(852)25069233Taiwan(tel)0800047866(fax)(886)225456723Philippines(tel)(632)8426802(tel)(PLDT subscriber only) 180016510170(fax)(632)8426809(fax)(PLDT subscriber only) 180016510288Thailand(tel)(outside Bangkok)(088)226008(tel)(within Bangkok)(662)6613999(fax)(66)16613714People’s Republic of China(tel)(preferred)8008100189(tel)(alternate)108006500021(fax)108006500121Installation Note E8801-9002656Installation Note E8801-90026Installation Procedurefor the Upgrade KitThe network analyzer must be in proper working condition prior to installing this option.Any necessary repairs must be made before proceeding with this installation.WARNINGThis installation requires the removal of the analyzer’s protective outer covers.The analyzer must be powered down and disconnected from the mains supply before performing this procedure.Electrostatic Discharge ProtectionProtection against electrostatic discharge (ESD)is essential while removing or connecting cables or assemblies within the network analyzer.Static electricity can build up on your body and can easily damage sensitive internal circuit elements when discharged.Static discharges too small to be felt can cause permanent damage.To prevent damage to the instrument:•always wear a grounded wrist strap having a 1M 9resistor in series with it when handling components and assemblies.•always use a grounded,conductive table mat while working on the instrument.•always wear a heel strap when working in an area with a conductive floor.If you are uncertain about the conductivity of your floor,wear a heel strap.Figure 1shows a typical ESD protection setup using a grounded mat and wrist strap.Refer to “Tools and Equipment Required for the Installation”on page 7for part numbers.Figure 1ESD Protection SetupOverview of the Installation ProcedureNote that step2is necessary only for the E8801A and N3381A network analyzers because they require a new A12source assembly.1.Verify the serial and option numbers of the analyzer.2.Replace the A12source assembly(E8801A and N3381A only).3.Enter the new model number.4.Verify that the new model number is shown correctly.5.Replace the model number nameplate on the front panel.6.Perform source and receiver calibration adjustments.Tools and Equipment Required for the InstallationDescription Model/Part Number Tools for A12Source Assembly Replacement(E8801A and N3381A Only)T-10TORX driver(set to9in-lbs)N/AT-20TORX driver(set to21in-lbs)N/A5/16-inch open-end torque wrench(set to10in-lb)N/AESD EquipmentESD grounding wrist strap9300-13675ft grounding cord for wrist strap9300-09802x4ft conductive table mat and15ft grounding wire9300-0797ESD heel strap(for use with conductive floors)9300-1308Test Equipment for Calibration AdjustmentsPower meter E4419BPower sensor(100kHz–4.2GHz)8482APower sensor(10MHz–18GHz)E4412AType-N adapter(female-to-female)1250-0777Type-N RF cable N6314AStep1.Verify the Serial and Option Numbers of the AnalyzerRefer to the License Key Certificate supplied with the kit:•Verify that the analyzer’s serial number matches the serial number on the certificate.•Verify that the option number on the certificate is correct:M02for an E8801A6GHz upgrade;M03for an E880xA9GHz upgrade;M82for an N3381A6GHz upgrade;M83for an N338xA9GHz upgrade.If either the serial number or the option number does not match the expected results,you will not be able to install the option.If this is the case,contact Agilent for assistance.Refer to “Getting Assistance from Agilent”on page5.Installation Note E8801-900267Step2.Replace the A12Source Assembly(E8801A and N3381A Only) This step is necessary only for the E8801A and N3381A network analyzers.If installing an upgrade kit for the E8802A or N3382A network analyzer,proceed to Step3.Remove the Outer and Inner Covers from the AnalyzerRefer to Figure2for this procedure.Remove the Outer CoverCAUTION This procedure is best performed with the analyzer resting on its front handles in the vertical position.Do not place the analyzer on its front panel without thehandles.This will damage the front panel assemblies.1.Disconnect the power cord(if it has not already been disconnected).2.With a T-20TORX driver,remove the strap handles(item )by loosening the screws (item )on both ends until the handle is free of the analyzer.3.With a T-20TORX driver,remove the four rear panel feet(item )by removing the center screws(item ).4.Slide the four bottom feet(item )off the cover.5.Slide the cover off of the frame.Remove the Inner Cover1.With a T-10TORX driver,remove the15screws(item ).2.Lift off the cover.8Installation Note E8801-90026Installation Note E8801-900269Figure2Outer and Inner Cover Removal10Installation Note E8801-90026Replace theA12Source Assembly Refer to Figure 3for this step.1.Place the A31hard disk drive assembly in the service position.a.With a T-10TORX driver,remove the mounting screw (item).b.Move the HDDA to the outside of the analyzer and slide the HDDA bracket feet into the slots on the frame to the horizontal position.This is the service position.Figure 3Placing the A31HDDA in the Service PositionRefer to Figure 4for the following steps.2.Disconnect the two flexible cables (item )from the A12source assembly being careful to note their locations for reconnection later.CAUTIONBe careful not to damage the center pins of the semirigid cables.Some flexing of the cables is necessary to remove the assembly.Do not over-bend the semirigid cables.3.With a 5/16-in torque wrench,disconnect the two semirigid cables (item )from thebottom of the A12source assembly.CAUTIONTo avoid damage to the semirigid cables (item ),pull down on the cables from the bottom of the analyzer to move them away while sliding out the A12source assembly.The cables have some spring to them and the RF pins could be damaged by the A12source assembly .4.Slide the A12source assembly out of the analyzer.5.Slide the new A12source assembly into the analyzer being careful not to damage the semirigid cables.Refer to the CAUTION s above.6.With a5/16-in torque wrench,reconnect the two semirigid cables(item¦ )to the bottomof the A12source assembly.7.Reconnect the two flexible cables(item )to the A12source assembly.Refer to Figure3for the following steps.8.Reinstall the A31hard disk drive assembly into its original position.9.With a T-10TORX driver,replace the mounting screw(item )Figure4A12Source Assembly ReplacementReinstall the Inner and Outer CoversRefer to Figure5for this procedure.Reinstall the Inner Cover1.Place the inner cover on the analyzer.There are two alignment pins on the front framethat must be aligned with holes in the cover.2.With a T-10TORX driver,install the15screws(item ).Reinstall the Outer CoverCAUTION This procedure is best performed with the analyzer resting on its front handles in the vertical position.Do not place the analyzer on its front panel without thehandles.This will damage the front panel assemblies.1.Slide the cover onto the frame.2.With a T-20TORX driver,install the four rear panel feet(item )by installing the center screws(item ).3.Slide the four bottom feet(item )onto the cover.4.With a T-20TORX driver,install the strap handles(item )by tightening the screws(item )on both ends.Figure5Inner and Outer Cover ReinstallationStep3.Enter the New Model NumberProcedure Requirements•The analyzer must be powered up and operating to perform this procedure.•The Network Analyzer program must be running.•A keyboard is required for this procedure.•A mouse is recommended for this procedure but is not required.Mouse Procedure1.On the analyzer’s System menu,point to Service,then click Option Enable.2.Click Repair.3.Check Model shown is incorrect!,then click Begin Repair.4.In the Model Change box,select the appropriate new model number:E8802A or N3382A(for the6GHz upgrade)or E8803A or N3383A(for the9GHz upgrade).ing the keyboard,enter the keyword in the box provided.The keyword is printed on theLicense Key Certificate.Enter this keyword exactly as it is printed on the certificate.6.Click Enter Model.7.Verify that the new model number displayed is correct,then click YES.If it is not correct,click NO and repeat the repair.8.When the installation is complete,click Exit.Front Panel Keys Procedure1.In the COMMAND block,press Menu/Dialog.2.In the NAVIGATION block,press the Right Tab and Arrows to move over to the Systemmenu and down to the Service selection.Press the Right Tab to display the extended menu and the Arrows to select Option Enable.Press Click.3.Press Menu/Dialog,then press R on the keyboard to select Repair.4.Tab to Model shown is incorrect!,then press Click.5.Tab to the Model Change box,then use the Arrows to select the appropriate new modelnumber:E8802A or N3382A(for the6GHz upgrade)or E8803A or N3383A(for the9GHz upgrade).6.Tab to the Keyword box and,using the keyboard,enter the keyword.The keyword isprinted on the License Key Certificate.Enter this keyword exactly as it is printed on the certificate.7.Tab to Enter Model,then press Click.8.Verify that the new model number displayed is correct,then tab to Yes and press Click.Ifit is not correct,tab to NO,press Click,and repeat the repair.9.When the installation is complete,Tab to Exit,then press Click.Step4.Verify that the New Model Number Is Shown Correctly Procedure Requirements•The analyzer must be powered up and operating to perform this procedure.•The Network Analyzer program must be running.•A mouse is recommended for this procedure but is not required.Mouse Procedure1.On the analyzer’s Help menu,click About Network Analyzer.2.Verify that the new model number is shown correctly in the display.Click OK.3.On the analyzer front panel,press Preset.Verify that the full frequency range of theanalyzer is correct.Front Panel Keys Procedure1.In the COMMAND block,press Menu/Dialog.2.In the NAVIGATION block,press the Right Tab and Arrows to move over to the Help menu,and down to the About Network Analyzer selection.Press Click.3.Verify that the new model number is shown correctly,then press Click.4.On the analyzer front panel,press Preset.Verify that the full frequency range of theanalyzer is correct.Step5.Replace the Model Number Nameplate on the Front Panel Refer to Figure6for this procedure.Remove the Old Nameplateing a sharp object such as a knife blade,lift one end of the old nameplate(item ).Becareful not to scratch the painted surface.ing your fingers,pull the nameplate completely off of the front panel and discard it.3.If any adhesive remains on the front panel surface,it can be removed by rubbing it withyour finger.Do not use a sharp object to remove this adhesive.If necessary,the surface can be cleaned with isopropol alcohol.Install the New NameplateNOTE There are two nameplates provided in the upgrade kit.Make sure that you install the correct one for your analyzer.The E8802A and E8803A nameplatesare for2-port analyzers,and the N3382A and N3383A nameplates are for3-portanalyzers.1.Remove the protective backing from the new nameplate to expose the adhesive.Avoidtouching the adhesive with your fingers as this may affect its ability to adhere to the front panel surface.2.Loosely align the new nameplate over the recess in the front panel and apply lightly.3.Once the overlay is properly aligned,press it firmly onto the surface to secure it.Figure6Model Number Nameplate ReplacementStep6.Perform Source and Receiver Calibration AdjustmentsThe following adjustments must be made due to the change in the full frequency range of the analyzer.Source Calibration AdjustmentThe source calibration is used to adjust your network analyzer for a flat source power across its full frequency range.The differences between Port1and Port2are negligible;therefore,a Port2adjustment is not required.1.Connect the equipment as shown in Figure7.Connect a GPIB cable between the networkanalyzer and the power meter.Figure7Setup for the Source Calibration Adjustment2.On the System menu,point to Service,Adjustments,then click Source Calibration.3.Ensure the GPIB settings are correct.4.Click Calibrate,then follow the instructions as they are displayed.Receiver Calibration AdjustmentThe receiver calibration is used to adjust the network analyzer receivers for a flat response across its full frequency range.A power meter is connected to Port1,as shown inFigure8,to establish a reference for flatness.A signal from Port1,as shown inFigure9,is used to adjust the“B”receiver at Port2.The adjustment is repeated using a signal from Port2to adjust the“A”receiver at Port1.1.Connect the equipment as shown in Figure8.Connect a GPIB cable between the networkanalyzer and the power meter.Figure8Setup for the Receiver Calibration AdjustmentFigure9Setup for the Receiver Calibration Adjustment of Port22.On the System menu,point to Service,Adjustments,then click Receiver Calibration.3.Ensure the GPIB settings are correct.4.Click Calibrate,then follow the instructions as they are displayed.Performance Tests and System VerificationThe analyzer should now operate and phase lock over its entire frequency range.If you experience difficulty with the basic functioning of the analyzer,contact Agilent.Refer to “Getting Assistance from Agilent”on page5.Although the analyzer functions,its performance relative to its specifications has not been verified for the additional frequency range enabled by this upgrade.It is recommended that a full instrument calibration be performed using the N2721A performance test software.If the testing of the analyzer’s full range of specifications is not required,a system verification can be performed.Refer to the analyzer’s Service Guide for information on performance tests and system verification.。
DeviceNet网络配置和故障处理教程说明书
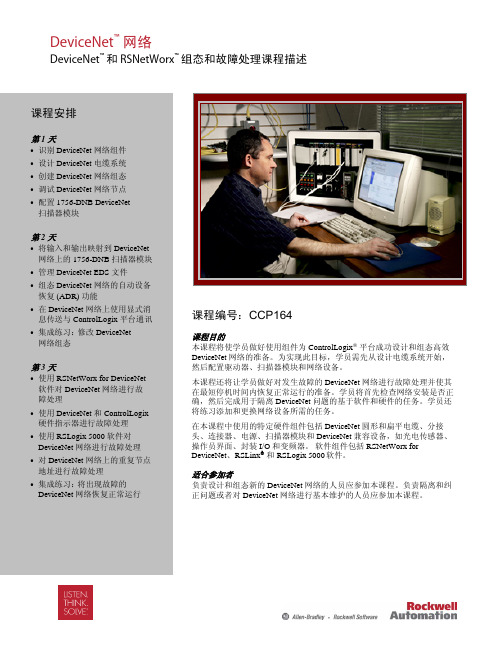
课程安排第 1 天•识别 DeviceNet 网络组件•设计 DeviceNet 电缆系统•创建 DeviceNet 网络组态•调试 DeviceNet 网络节点•配置 1756-DNB DeviceNet扫描器模块第 2 天•将输入和输出映射到 DeviceNet 网络上的 1756-DNB 扫描器模块•管理 DeviceNet EDS 文件•组态 DeviceNet 网络的自动设备恢复 (ADR) 功能•在 DeviceNet 网络上使用显式消息传送与 ControlLogix 平台通讯•集成练习:修改 DeviceNet网络组态第 3 天•使用 RSNetWorx for DeviceNet 软件对 DeviceNet 网络进行故障处理•使用 DeviceNet 和 ControlLogix 硬件指示器进行故障处理•使用 RSLogix 5000 软件对DeviceNet 网络进行故障处理•对 DeviceNet 网络上的重复节点地址进行故障处理•集成练习:将出现故障的DeviceNet 网络恢复正常运行课程编号:CCP164课程目的本课程将使学员做好使用组件为 ControlLogix 平台成功设计和组态高效DeviceNet 网络的准备。
为实现此目标,学员需先从设计电缆系统开始,然后配置驱动器、扫描器模块和网络设备。
本课程还将让学员做好对发生故障的 DeviceNet 网络进行故障处理并使其在最短停机时间内恢复正常运行的准备。
学员将首先检查网络安装是否正确,然后完成用于隔离 DeviceNet 问题的基于软件和硬件的任务。
学员还将练习添加和更换网络设备所需的任务。
在本课程中使用的特定硬件组件包括 DeviceNet 圆形和扁平电缆、分接头、连接器、电源、扫描器模块和 DeviceNet 兼容设备,如光电传感器、操作员界面、封装 I/O 和变频器。
软件组件包括 RSNetWorx for DeviceNet、RSLinx®和 RSLogix 5000软件。
网络连接错误代码大全及解决方法
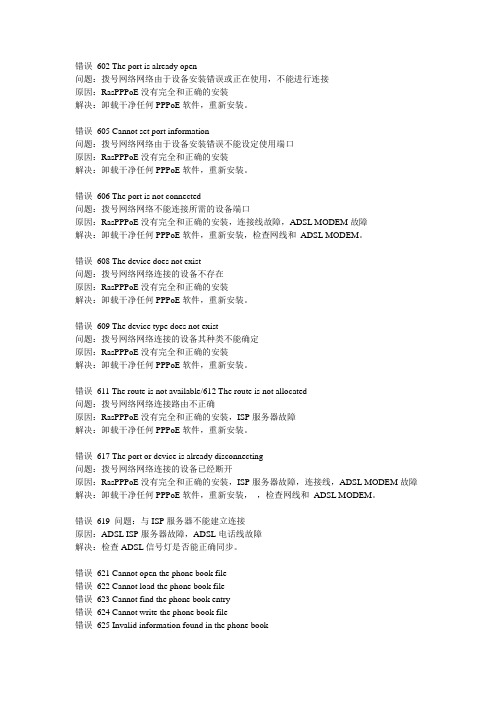
错误602 The port is already open问题:拨号网络网络由于设备安装错误或正在使用,不能进行连接原因:RasPPPoE没有完全和正确的安装解决:卸载干净任何PPPoE软件,重新安装。
错误605 Cannot set port information问题:拨号网络网络由于设备安装错误不能设定使用端口原因:RasPPPoE没有完全和正确的安装解决:卸载干净任何PPPoE软件,重新安装。
错误606 The port is not connected问题:拨号网络网络不能连接所需的设备端口原因:RasPPPoE没有完全和正确的安装,连接线故障,ADSL MODEM故障解决:卸载干净任何PPPoE软件,重新安装,检查网线和ADSL MODEM。
错误608 The device does not exist问题:拨号网络网络连接的设备不存在原因:RasPPPoE没有完全和正确的安装解决:卸载干净任何PPPoE软件,重新安装。
错误609 The device type does not exist问题:拨号网络网络连接的设备其种类不能确定原因:RasPPPoE没有完全和正确的安装解决:卸载干净任何PPPoE软件,重新安装。
错误611 The route is not available/612 The route is not allocated问题:拨号网络网络连接路由不正确原因:RasPPPoE没有完全和正确的安装,ISP服务器故障解决:卸载干净任何PPPoE软件,重新安装。
错误617 The port or device is already disconnecting问题:拨号网络网络连接的设备已经断开原因:RasPPPoE没有完全和正确的安装,ISP服务器故障,连接线,ADSL MODEM故障解决:卸载干净任何PPPoE软件,重新安装,,检查网线和ADSL MODEM。
错误619 问题:与ISP服务器不能建立连接原因:ADSL ISP服务器故障,ADSL电话线故障解决:检查ADSL信号灯是否能正确同步。
网络通信错误代码大全-新

解决:Байду номын сангаас1)、检查网线
(2)、检查 ADSL MODEM
5、Error 645
问题:网卡没有正确响应
原因:(1)、网卡故障;
(2)、网卡驱动程序故障
解决:(1)、检查网卡(此时不能以网卡指示灯的状态来判断网卡的好坏,最好采用替代法,换一块新网卡来试验)
解决:(1)、检查设备端口、检查设备数据;
(2)、检查线路;
(3)、更换MODEM;
(4)、解决计算机故障。
注:从故障原因可看出,此类故障因涉及的因素较多,处理起来往往比较棘手。但我们可以本着“先简后难”的方法,采用排除法逐渐解决。步骤如下:
(1)、将用户的ADSL端口更换为测试端口进行试验,确认设备或数据是否有问题(若设备或数据有问题可以通知10050平台或互联网中心)。
解决:(1)、致电提供服务的运营商询问;
(2)、删除计算机的所有网络组件,重新安装网络。
13、Error 769
错误原因:网卡被禁用
解决方法:启用网卡,具体操作如下:请您点击电脑右键, 选择“属性”,再选择“设备管理”,再看网卡驱动程序情况,如果是个在“x”说明网卡被禁用,右键激活网卡就可以解决。
解决:(1)、在ADSL或BAS设备上清除用户在线数据;
(2)、检查自身的计算机系统(网卡、网卡驱动、网络协议等)
9、Error 678
问题:远程计算机无响应
原因:(1)、局端设备故障;
(2)、线路不正常;
(3)、用户modem外线灯正常但DSL端口显示不在线,
(4)、计算机故障。
14、Error 797
PowerDsine 高功率过 ethernet 中介设备 (6 口 和 12 口 型号) 用户指南

Data and Power on a Single LineHigh Power over Ethernet MidspansPD-8006 - 6 Port ModelPD-8012 - 12 Port ModelUser GuideDisclaimerPowerDsine assumes no responsibility or liability arising from the use of Midspans, as described herein, nor does it convey any license under its patent rights or the rights of others. Applications that are described herein for any of theses products are for illustrative purposes only. PowerDsine makes no representation or warranty that such applications will be suitable for the specified use without further testing or modification.The information in this guide refers to the 12-Port High Powerover Ethernet Midspan only. However this information andillustrations are also applicable for 6 Port High Power overEthernet Midspan.Note that the High Power Midspan is designed for indoor use only.© 2004 PowerDsine Ltd.All rights reserved.This document is subject to change without notice.AcknowledgementsPower over LAN is a trademark of PowerDsine Ltd.All other products or trademarks are property of their respective owners.The product(s) described by this manual is (are) a licensed product of PowerDsine.PD-8006/12Power over Ethernet Solutions 3Contents1 S AFETY I NFORMATION (5)1.1 General Guidelines........................................................................5 1.2 Power Cord.. (6)2 A BOUT THE H IGH P OWER OVER E THERNET M IDSPAN (7)2.1 Power Management.......................................................................7 2.2 10/100BASE-TX Ports Definition.....................................................8 2.2.1 Data Input Ports......................................................................8 2.2.2 Data & Power Output Ports......................................................8 2.3 Indicators ......................................................................................8 2.3.1 Primary Power Indicators.........................................................8 2.3.2 Port Indications .......................................................................9 2.4 Connectors.. (10)3 I NSTALLING THE H IGH P OWER OVER E THERNET M IDSPAN (11)3.1 Background Information................................................................11 3.2 Rack Mounting Brackets ...............................................................12 3.3 Connecting Ethernet Cables..........................................................12 3.4 Connecting Power Cables.............................................................13 3.5 Powering up.................................................................................13 3.6 Troubleshooting............................................................................13 3.6.1 Preliminary Steps...................................................................13 3.6.2 Troubleshooting Guide .. (14)PD-8006/12Power over Ethernet Solutions 4Model Numbers Definition PD-80xx/ACWhere : xx represents the number of ports (6 or 12)Verifying Kit ContentsUnpack the kit and verify that the following items are uncluded:• The High Power over Ethernet Midspan • Mounting brackets (for 19-inch racks)• Screws for assembling mounting brackets • Self-adhesive rubber feet • This User Guide • Power cordBefore proceeding, record the unit’s serial number below for future reference. The serial number can be found on the information label at the rear of the High High Power over Ethernet Midspan.Serial NumberElectrical Compatibility ApprovalsThe PD-80xx complies with the following standards:• FCC Part 15, Class B, with FTP cabling; Class A with UTP cabling• EN 55022 (CISPR 22), Class B with FTP cabling; Class A with UTP cabling • EN 55024 (CISPR 24)•Canadian ICES-003, Class BSafety Standard ApprovalsThe PD-80xx meets the following safety standards:• UL/cUL per EN60950 •GS mark per EN60950CE MarkingThe CE marking on this product indicates that this product is incompliance with 89/336/EEC (EMC Directive) and 73/23/EEC (Low Voltage Directive).PD-8006/12Power over Ethernet Solutions 51 Safety Information1.1General GuidelinesYou must read the following safety information before carrying out any installation, removal or any maintenance procedure on the High Power over Ethernet Midspan. Warnings contain directions that must be followed for personal and product safety. Follow all directions carefully.• Read the Installation Instructions in Section 3 before connecting theHigh Power over Ethernet Midspan to its power source. • The Midspan must use a grounded power cord, as defined in paragraph 1.2.•This product relies on the building installation for short-circuit (overcurrent) protection. Ensure that a fuse or circuit breaker nolarger than 15 A for 120 VAC, (U.S.) 10 A for 230 VAC (international) is used.• Do not work on the system, connect or disconnect cables during periods of lightning activity.•A voltage mismatch can cause equipment damage and may pose a fire hazard. If the voltage indicated on the label is different from the power outlet voltage, do not connect the High Power over Ethernet Midspan to this outlet.•For shelf -mounted equipment, be certain that the surface is stable and strong enough to support the equipment. Do not stack more than four the High Power over Ethernet Midspans.• Ultimate disposal of this product should be handled according to all local laws and regulations.•The High Power over Ethernet Midspan "Data" and "Data + Power" ports are shielded RJ-45 data sockets. They cannot be used as Plain Old Telephone Service (POTS) telephone sockets. Only RJ-45 data connectors may be connected to these sockets.PD-8006/12Power over Ethernet Solutions61.2 Power CordIn the event that the power cord is replaced, the replacement must meet local requirements.U.S.A. andCanada§ The cord must be UL-approved or CSA certified. § The minimum specification for the flexible cord is: • No. 18 AWG • Type SV or SJ • Three-conductor.§ The cord set must have a rated current capacity of at least 10 A.§ The attachment plug must be an earth-grounding type with a NEMA 5-15P (15 A, 125 V) or NEMA 6-15P (15 A, 250 V) configuration.Denmark § The supply plug must comply with section 107-2-D1,standard DK2-1a or DK2-5a.Switzerland § The supply plug must comply with SEV/ASE 1011.n The appliance coupler (connecting to the Midspan and not to the wallplug) must have a configuration for mating with an EN60320/IEC320 appliance inlet. n The power socket outlet must be near the Midspan and be easilyaccessible. You can only remove power from the unit by disconnecting the power cord from the outlet. n This unit operates under SELV (Safety Extra Low Voltage) conditionsaccording to EN60950/IEC 950. The conditions are only maintained if the equipment to which it is connected also operates under SELV conditions. n France and Peru only: This unit cannot be powered from IT supplies. Ifyour supplies are of IT type, this unit must be powered by 230 V (2P+T), via an isolation transformer with a ratio of 1:1 and with the secondary connection point labeled Neutral, connected directly to ground. n U.K. only: The High Power over Ethernet Midspan is covered byGeneral Approval, NS/G/12345/J/100003, for indirect connection to a public telecommunications system.PD-8006/12Power over Ethernet Solutions72 About the High Power over Ethernet MidspanPowerDsine’s family of High Power over Ethernet Midspans, series 8000, injects power over data-carrying Ethernet cabling. The PD-8006/8012Midspans, support 6 and 12 ports respectively in a 10/100BaseTx Ethernet network Category 5/5e/6 cabling. DC operating power, for data terminal units, is fed over the unused (spare) pairs of the cabling (7/8 and 4/5) as well as the data pairs (1/2 and 3/6).The High Power over Ethernet Midspan normally powers devices that are High Power over Ethernet enabled or are equipped to receive High Power over Ethernet. These devices are called Powered Devices (PDs). Devices that are not equipped to receive High Power over Ethernet may require an external power adapter in order to be powered. Contact PowerDsine for such an adapter.High Power over Ethernet Midspan main features:n Remote Power Feeding of Ethernet Terminals over the Data pairs(pins 1/2 & 3/6) as well as Spare pairs (pins 7/8 & 4/5). n 38W Minimum allowable output power at port output.n Eliminates the need for AC outlets, local UPS and AC/DC adapters n Universal range power input (100-240 VAC, 50/60 Hz ) n Power managementn Independent overload and short-circuit protection per channel n Port status indicationsnStandard 19-inch rack mountable.2.1 Power ManagementWhen establishing a network, the total power required by PDs may exceed the total power available from the Midspan. The built-in Power Management feature will not allow the total power output to exceed the maximum power available (refer to the Technical Specifications). When the total poweravailable is near maximum, attempts to connect an additional PD to a free port will cause the corresponding LED of the port to blink orange, indicating an out-of-power budget. This port will not deliver power. Power distribution is based on “first come, first served” logic.It is possible that connected and operating PDs will significantly increase or suddenly raise their power requirements. If the power required exceeds the power available, the High Power over Ethernet Midspan will start to turn off ports, starting from the last port down, until the total power is once again under the maximum limit.PD-8006/12Power over Ethernet Solutions 82.210/100BASE-TX Ports Definition2.2.1Data Input PortsAccording to the model acquired, the Midspan has 6 or 12, 10Base-T/100Base -TX- data input ports, configured in a non-crossover manner (straight -wired). These ports, shown in Figure 2-1 (bottom row of connectors), are designed to carry Ethernet data only (Tx/Rx) over the standard 2-wire pairs (pins 1/2 and 3/6).2.2.2Data & Power Output PortsThe Midspan has 6 or 12 Data & Power ports also configured in non-crossover manner (straight -wired). These ports are designed to carry Ethernet data and DC power over the standard 2-wire pairs (pins 1/2 and 3/6) and DC power over the spare pairs (pins 4/5 and 7/8).2.3IndicatorsA set of indicators provide the status of the High Power over Ethernet Midspan and its ports. Refer to Table 2-1 for status information during operation. 2.3.1Primary Power IndicatorsThe LEDs on the front panel, marked by “AC”, provide the High Power over Ethernet Midspan power status. When the indicators is illuminated in green, the High Power over Ethernet Midspan is receiving AC power. The “AC” indicators are lit in orange to indicate an internal fault. Refer to Table 2-1 for additional information.The Power over Ethernet Midspan is not a repeater. As such, the maximum distance from the Ethernet switch is not to exceed 100 meters (328 ft). In accordance with the IEEE 802.3 standard, the Power over Ethernet Midspan is guaranteed to work up to this distance.Data & PowerDataConsole PowerPD-8006/12Power over Ethernet Solutions 92.3.2Port IndicationsOne bi-color indicator (green and orange), per port, provides port status:n Green indicates that the terminal unit has beenidentified as "High Power over Ethernet Enabled" and is active and receiving power.n Orange indicates that the port is not supplyingpower and is not active.NoteDue to the standard detection process performed on each PoE port, power will not be supplied to an Ethernet device, that is not PoE-enabled (indicated in orange or off). In this way, Ethernet devices (not PoE-enabled) will not be affected by this connection.Table 2-1: Power Status IndicationsIndicator ColorMain Power Status RemarksOffInternal power supply unit is unplugged or faulty. Internal power supply voltage is too low. All ports are disconnected.GreenIndicates AC power input active.Internal power supply voltage is within tolerance. ACGreen blinkingInternal power supply voltage is out of tolerance.All ports are disconnected.PD-8006/12Power over Ethernet Solutions10Table 2-2: Port Status IndicationsOn Off or UDL Power ManagementOVL Spear “A” (Data) Green blinking If “B” is on, green blinking Spear “B” (Spare) Green blinking If “A” is on,green blinking "A" and "B" Data & SpareSteady GreenNoneOrangeBlinking Steady Orange2.4 ConnectorsRS-232 connector - The front panel of the Midspan includes a Console port (DB-9 connector). The user may connect a terminal and perform software loading, via this connector, using a standard null modem cable. The console port is set to 19,200-baud, 8 data bits, no parity and 1 stop bit. Pin connections for this connector are: § Pin 2 is Receive (RXD) § Pin 3 is Transmit (TXD) §Pin 5 is Ground§Pins 1 and 6 are shortedRJ45 connector - Each data port is configured as shown in Figure 2-2., as data route-thru ports for all data pins (pins 1, 2, 3 and 6) Becertain to use Category 5 or higher cabling, as shown in the figure.Figure 2-2: Connecting to the MidspanPD-8006/12Power over Ethernet Solutions 113 Installing the High Power over Ethernet Midspan3.1Background InformationAs shown in Figure 3-1, the Midspan is connected in series to an Ethernet switch/hub. The data outputs from the switch are connected to the Midspan. The Midspan delivers power over spare twisted pairs (pins 7/8 and pins 4/5) and data pairs pins (1/2 and pins 3/6) of the Category 5 cabling.Most installations require the Midspan to be rack mounted, as described hereafter.Figure 3-1: Typical InstallationPD-8006/12Power over Ethernet Solutions 123.2 Rack Mounting Bracketsrack, first remove the self-not provided.3.3 Connecting Ethernet CablesThe ports on the front panel of the Midspan are configured as "route through" ports for all eight conductors of the RJ-45 connectors. Use Category 5 cabling in making connections.1. For 802.3af ready terminals (PDs):a. Connect cables from the Ethernet Switch to the Data ports(bottom row on Midspan).b. Connect the cables from the IEEE 802.3af ready terminals (PDs)to the corresponding Data & Power ports (top row on Midspan).2. PD's which are not "Power over Ethernet Enabled" requires anexternal splitter.Use PowerDsine High Power Active Splitter , P/N: PD-AS-801/12: a. Connect cables from the Ethernet Switch to the Data ports(bottom row on Midspan).b. Connect the cables from corresponding Data & Power ports (toprow on Midspan) to the High Power Active Splitter Data & Power Inputc. Connect the end of the DC Out cable of the Splitter to theterminal (PD) power jack.d. Connect the Data Out cable of the Splitter to the terminal datainput.e. When using an external splitter, be certain to use a splitter withthe correct connector and polarity.Figure 3-2: Installing Mounting BracketsPD-8006/12Power over Ethernet Solutions 133.4 Connecting Power Cables When using AC to power the Midspan, plug in the power cord supplied, at the rear AC connector.3.5Powering upThe High Power over Ethernet Midspan has no on/off switch. To apply or remove power to the Midspan, insert or remove the power cable from the receptacle (AC) on the rear panel of the unit.With power applied, the Midspan powers-up and the internal fan operates; then, the device runs through its power-on self-test (POST), which takes less than 10 seconds. During the POST, all ports are disabled and the indicators illuminate in the following sequence:1. Port indicators and power indicators (AC) illuminate green.2. Port indicators and the AC indicator illuminate orange.3. Main AC indicator remains lit green; port indicators are out.Ports are now enabled for normal operation.3.6Troubleshooting3.6.1Preliminary StepsIf you encounter problems, check that:§ Power is applied to the Midspan§ A crossover-type Ethernet cable has not been used§ The Ethernet cable from the network is connected to the Data port § The Ethernet cable to the PD is connected to the Data & Power port §Cable pairs are attached to corresponding ports.PD-8006/12Power over Ethernet Solutions 143.6.2 Troubleshooting GuideThis paragraph provides a symptom and resolution sequence in order to assist in the troubleshooting of minor operating problems. If the steps given do not solve your problem, do not hesitate to call your local dealer for further assistance. Refer to Table 3-1.Table 3-1: Troubleshooting StepsSymptom Corrective StepsMidspan does not power up1. Verify that a known-good power cord is used.2. Verify that the voltage at the power inlet is between 100and 240 Vac. 3. Remove and re-apply power to the device and check theindicators during power up sequence.AC indicator lit orange Power-on self-test failed: the Midspan detected an internal fault. In this case, contact your local dealer.AC indicators lit orangePower-on self-test failed: the Midspan detected an internal fault. In this case, contact your local dealer. A port indicator is not lit and thecorresponding PD does not operate.1. The Midspan did not detect a PD and therefore the port is not enabled.2. Verify that the PD is designed for High Power over Ethernet operation.3. Verify that you are using a standard Category 5/5e/6, straight-wired cable, with four pairs.4. If an external power splitter is in use, replace it with a known-good splitter.5. Verify that the PD is connected to the Data & Power port.6. Try to reconnect the same PD to a different port on the same or into different Midspan. If it works, there is probably a faulty port or RJ-45 connection. Is it safe to keep the Midspanrunning while a port indicator is orange?This is a safe condition. The orange indication is due to: 1. A device, not compliant to IEEE 802.3af, was detected. 2. Terminals 4/5 and 7/8 are shorted together. 3. Forced external power fed into the port.During these conditions, port power is disconnected.PD-8006/12Power over Ethernet Solutions 15Table 3-1: Troubleshooting StepsSymptom Corrective StepsThe end device operates, but there is no data link.1. Verify that the port indicator on the front panel iscontinuously lit.2. If an external power splitter is in use, replace it with aknown-good splitter.3. Verify that for this link, you are using standard UTP/FTPCategory 5 straight (non-crossover) cabling, with all four pairs. Check that the link is 100 m or less.4. Try to re-connect the same end device into a differentport on the same unit or into different unit – if it works, there is probably a faulty port or RJ-45 connection.Technical SpecificationsPhysical SpecificationsDimensions 44 x 433 x 302 mm (h x w x l) (1.75 x 17 x 11.9 inch) Weight4 kg (8.8 lb)Environmental SpecificationsTemperature - Operating 0 to 40 °C (32 to 104 °F) - Storage -20 to 70 °C (-4 to 158 °F) Humidity10 to 90% (non-condensing)Electrical SpecificationsParameterPD-8006/8012 AC Input Voltage 90 to 264 VAC at 47-63 HzInput Current @ 115 VAC 4 A max. Total Output Power 200 W max.Output Power, per Port (Typ.) 39.5 W (not to exceed Total Output Power)Nominal Output Voltage54.5 to 57 VDCCovered under US Patent 6,473,608Visit our web site at: For technical support, call: +972-9-7755123In the USA: +631-756-4680 or 1-877-4-802-3AF Part Number: 06-0300-056Rev. A3。
ADSL错误代码英文翻译

677 A person answered instead of a modem. 人工应答替代MODEM。
678 There is no answer. 没有应答。
679 Cannot detect carrier. 不能侦测到载波。
654 A command or response in the device .INF file section refers to an undefined macro。 在该设备INF文件中的一条命令或响应提供了一个未定义的宏。
655 The macro was not found in the device .INF file section. 该“message”宏在该设备INF文件中不能被发现。
672 Cannot read the device name from the media .INI file. 无法从媒体INI文件中读取驱动器名称。
673 Cannot read the usage from the media .INI file. 无法从媒体INI文件中获得用法。
670 Cannot read the section name from the media .INI file. 无法从媒体INI文件中读取段名。
671 Cannot read the device type from the media .INI file. 无法从媒体INI文件中读取驱动器类型。
664 Cannot allocate memory. 无法分配内存。
665 The port is not configured for Remote Access. 该端口没有给远程访问配置权限。
Keysight E5080A ENA 矢量网络分析仪说明书

Keysight TechnologiesE5080A ENA Vector Network Analyzer - 9 kHz to 4.5/6.5/9 GHzFor more information:The Next-Generation ENAThe Keysight E5080A is the next-generation RF vector network analyzer (VNA), providing best-in-class performance, flexible functionality and advanced usability for testing antennas, filters, cables, balanced/differential components, amplifiers and mixers. With its intuitive, touch-based interface, the E5080A is designed to help users streamline their measurement flow and achieve better results in less time. This new instrument implements a converged platform that leverages the best attributes of the ENA and PNA families. The E5080A sets the new standard in RF component testing for both R&D and manufacturing environments. The E5080A offers comprehensive functionalities for measuring active and passive components such as amplifiers, mixers, filters, antennas, cables, and many more. It builds on the over 45-year legacy of excellence in network analysis and 75-year electronic test and measurement experience.Best-in-Class PerformanceWide dynamic range152 dB (typical, 3 Hz IFBW)Fast measurement speed 3 ms (401 points, uncorrected)Low trace noise0.0005 dBrms (typical, 10 kHz IFBW)High temperature stability0.005 dB/°C (typical)Wide source power range–90 to +15 dBm (spec)The E5080A provides wide dynamic range from 9 kHz. More than 10 dB better dynamic range than E5071C enables to measure high-blocking DUTs such as filters accurately and improve measurement speed using wider IF bandwidth (IFBW). The unparalleled measurement speed compared to competitor products maximizes the test throughput in production line.Extremely low trace noise helps minimize errors and associated test margin when measuring low-loss devices such as filter pass-bands.The E5080A is designed to have the minimum temperature drift against variation of environment temperature. The superior measurement stability helps high-volume manufacturers minimize calibration time and associated downtime.152 dBIntuitive and Flexible Operations with Modern User InterfaceThe E5080A integrates a high resolution display with a touch screen, which provides a crisp view and easy access to alldata and traces. This enhanced user interface allows intuitive operation and helps you set up complex measurements quickly.The E5080A is designed to help users streamline their measurement flow. Measurement flow proceeds from right to left: front panel keys, touch-activated softkeys with tabs, and touch-driven trace displays and windowsEasy access to frequently used functionsThe tabbed soft panel enables you to access the analyzer’s major functions within a few steps. Your frequently used softkeys can be registered to the Favorite menu. A long touch on the screen activates the Context Popup menus, and these present the most relevant choices without needing to access the softkeys. Direct access to essential features through the toolbarMeasurement traces, channels, and windows can be quickly added by pressing the icons on the toolbar. The list of icons is customizable depending on your preference.Flexible traces and windows layoutThe layout of traces and windows can be flexibly allocated with intuitive drag-and-drop operations. Or the layout can also be changed by using the softkeys that split or combine traces and windows in a single action.Magnifying the displayWith multi-touch or single-touch gestures, you can magnify thedisplayed area on the screen.Figure 3. Customizable toolbar menusFigure 2. Tabbed soft panel and popup menuFigure 5. Multi-touch magnificationFigure 4. Drag-and-drop for traces/windowsStreamline Your Measurements with Advanced UsabilityThe E5080A’s advanced usability simplifies the measurement setup tasks, and its flexible display capabilities give excellent visibility of the measurement data.Quick setups using dialog menus and Copy ChannelA variety of dialog menus assist you in making complex measurement setups easily. The quick start dialog gives the templates of display layouts for typical measurement applications, and the subsequent sweep setup dialog completes necessary stimulus settings in a single page. Moreover, once you have completed making the setup for one channel, you can copyit to other channels by using the copy channel function. This significantly reduces the time required for making multi-channel measurement setups.Tabbed SheetThe tabbed sheet function allows you to split the measurement display into multiple pages within a single instrument state. Complicated multi-channel measurement data can be easily observed by splitting the channels into the sheets. The active sheet can be switched not only with the touch or mouse operations but with the Prev/Next hardkeys on the front panel. This is useful for manufacturing applications such as the BTS filter tuning where the hardkey operation is preferred.Flexible marker capabilitiesYou can place up to 15 markers per trace. For better visibility,the locations of the marker lists are flexibly movable, and the number of decimal places can be changed as you like. In addition, a variety of marker search functions are available, including the single or multiple max/min/peak/target search, the bandwidth/notch search, and the gain compression search. Figure 7. Displaying four channel data using Tabbed Sheet Figure 6. Quick Start dialogsFigure 8. Up to 15 markers per traceThe E5080A combines the highest RF performance with powerful analysis capabilities that enables you to address a variety of applications and increase test efficiency.Powerful, fast and accurate automatic fixture removal (S96007A)Accurately removing the effects of the fixture is required to get a good measurement of the DUT. Automatic fixture removal adds a powerful application wizard to guide you throughcharacterizing a fixture and removing it from the measurement. Complicated modeling in EM simulation software or multiple calibration standards fabricated on board is no longer needed to characterize and remove a fixture.–Easiest way to remove fixture effects from non-coaxial device measurements–Extract fixture S-parameters from 2x thru or one-port measurements–Step-by-step wizard to characterize your fixture and remove it from your measurementsAccurate characterization of mixers and converters (S96082A)Frequency offset mode is available to set the E5080A’s source frequency independently from where the receivers are tuned for mixer measurements. Scaler mixer calibration (SMC) provides the most accurate conversion loss/gain measurements by combining two-port and power calibration. Vector mixer calibration (VMC) provides measurements of match, conversion loss/gain and group delay. Input and output mismatch correction reduces ripple and eliminates the need for attenuators.–Intuitive user interface –Frequency-offset sweep–Match-corrected conversion loss measurements–Controls external signal generators and power metersFast, accurate gain compression versus frequency measurements of amplifiers (S96086A)S96086A makes it easy to characterize compression over the DUT’s operating frequency range with extreme speed and ac-curacy, and with a simple setup. Instead of a linear power sweep with many points, the S96086A uses an adaptive algorithm to find the desired compression point at each frequency with just a few power measurements, thus significantly reducing test times. –Fast and convenient measurements with SMART Sweep–Complete amplifier with 2-dimensional (2D) sweeps, choice of sweep frequency per power, or sweep power per frequencyE5080A Innovative ApplicationsFigure 9. Automatically characterizing test fixtureFigure 10. Intuitive wizard for configuring mixer/frequency converter measurementsFigure 11. Gain compression analysis of amplifierPinFrequencyGainCompression pointIteration pointAdvanced Calibration ToolsCalibrating network analyzers is critical for high accuracy measurements. The E5080A supports all common calibration methods for coaxial DUTs, waveguide DUTs and DUTs in test fixtures, on printed circuit boards (PCB) and on wafers. Thebuilt-in capabilities include advanced calibration methods and a new “basic calibration” feature that can simplify the calibration processes.TRL/LRL/TRM/LRM calibration (Through, Reflect, Line, Match) for on PCB and on-wafer measurements.Unknown Thru (SOLR) calibration for non-insertable devices.Source Power Cal for amplifier measurements, and offers advanced techniques such as power cal using the analyzer’s receiverQuick SOLT (QSOLT) reduces the number of correction standards and calibration steps for multiple ports calibration.Electronic calibration (ECal) modules offer accurate calibration with simple one-connection operation.Basic CalThe E5080A offers a variety of calibration menus and you can choose an appropriate menu depending on the complexity of your calibration methods. The Basic Cal dialog is a very simple calibration UI providing all the calibration buttons in the same dialog page. This calibration menu is suitable for performing relatively simple calibrations such as the basic SOLT cal. Advanced calibration methodsCal WizardThe E5080A also offers wizard-type calibration menus for complicated calibrations. The Smart Cal guides all the operation steps of the calibrations with the wizard menu. This calibration menu is suitable for performing complicated calibrations suchas mixed-connector cal, and the combination of the SOLT cal and the source/receiver power cals. The Cal All is the advanced wizard function of the Smart Cal. This calibration menu guides the calibrations of multi-channel measurement setups at minimal steps.Cal Plane ManagerThe Cal Plane Manager allows you to characterize the adapters, test fixtures, or probes to the S2P data, and mathematically de-embed them for improving the measurement accuracy at the DUT planes. This function also provides the capabilities for modifying the existing S2P files, such as reversing the port order of the S2P file and cascading two S2P files.Fixture simulatorThe fixture simulator offers functions for simulating fixtures and adapters such as embedding/deembedding, port matching, impedance transformation and port extensions.Figure 12. Basic CalFigure 13. Fixture simulatorExtend the Power of the E5080A ENA Measurements with up to 40 portsThe combination of the 4-port E5080A and E5092A configurable multiport test set offers a comprehensive multiport solution. Depending on your test requirements, you can flexibly build the test port configurations by changing the front jumper connections of up to two E5092A test sets. The measurement wizard assistant software (S93790A) simplifies complicated setup and calibration processes for multiport device tests with the E5080A and E5092A.CalPod calibration-refresh modulesKeysight provides a unique way to quickly and easily refresh a calibration at the push of a button, without removing the DUT, and without the physical connection of standards. CalPods are particularly useful in thermal or thermal-vacuum chambers for removing environmental effects from your measurement results due to temperature changes of cables, connectors, and adaptors, or for removing variations due to cable movements or variations in switch matrices.BenchVue SoftwareKeysight BenchVue software for the PC eliminates many of the issues around bench testing. By making it simple to connect, control instruments, and automate test sequences so you can quickly move past the test development phase and access results faster than ever before with just a few clicks. A dedicated Network Analyzer App, available with BV9001B, allows you to quickly configure the most commonly used measurements and setups. Rapidly build custom test sequences with the integrated Test Flow App to automate and visualize test results without the need for instrument programming. BenchVue supports hundreds of Keysight instrument types and models all from one easy to use software platform. Control, Automate, Simplify with BenchVue.–Easily control, get screen captures and trace data–Capture measurements from your network analyzer in asingle click–Automate common network analyzer controls andmeasurements as quickly as using your front panelFigure 14. Multiport configuration with E5080A and E5092AFigure 15. CalPods refresh a calibration without removing your DUT Figure 16. BenchVue: PC control, capture screen images or trace data, andbuild automated tests in minutesFigure 18. The E5080A’s state file converter helps you easilytransfer your tests with the E5071CFigure 17. Code emulation mode for legacy vector network analyzersCompatibilityThe E5080A shares a common software platform with all members of the latest PNA family that makes it easy to choose just the right level of performance to match your budget and measurement needs. This commonality guarantees measurement consistency and repeatability and a common remote-programming interface across multiple instruments in R&D and manufacturing.The E5080A offers the E5071C code emulation mode which interprets the SCPI commands of the E5071C. This allows for instrument emulation and backward code capability enabling a seamless drop-in replacement in your automated test environment and minimizing transition risks. State files created using the E5071C can be converted and recalled with the E5080A. The E5080A also supports the code emulation mode for the legacy 8753 series network analyzers.This compatibility means that you can easily make the transition to the E5080A while leveraging your investment and expertise in test software. The test software from R&D can be effortlessly transferred to manufacturing which helps you maintain past efforts, enhance current designs, and accelerate future innovations.Extend the Power of the E5080A ENA (continued)E5080A Front and Rear PanelsFlexible, modern user interface: front panel keys tabbed soft panel, pulldown menus, customizable toolbar, right-click shortcuts, drag-and-drop operation and 12.1’’ touch screenState-of-the-art calibration capabilitiesContext sensitive built-in help10 MHz reference Quick access for Ecal and other USB devicesUp to 15 markers per trace GPIB for remote operation Aux inputs for DC measurements200 measurementchannels and unlimited traces Sweep Setup and Quick Start enables easy setupUndo/Redo cancels or restores the previous entriesHandler I/O for external device controlLAN and device-side USB provide alternatives to GPIB for remote programmingRemovable solid-state drive for secure envi-ronments (optional)Maintain data securityThe removable solid-statedrive makes it easy to move the instrument from one location to another.E5080A Key Specs & Features (Comparison with E5071C)100 kHz to 4.5/6.5/8.5 GHz, with bias-tees Test port 2 or 4-port, 50 Ω 2 or 4-port, 50 ΩDynamic range(at max source power)135 dB (spec, 10 Hz IFBW)152 dB (typical, 3 Hz IFBW)123 dB (spec)Trace noise0.0015 dBrms (spec, 10 kHz IFBW)0.0005 dBrms (typical, 10 kHz IFBW)0.003 dBrms (spec, 70 kHz IFBW) Stability0.005 dB/°C (typical)0.005 dB/°C (typical) Measurement speed(401 pts, 200 MHz span, uncorrected)3 ms7 msSource power–90 to +15 dBm (spec)–110 to +17 dBm (typical)–55 to +10 dBm (spec)NOP Max 100,001Max 20,001Channels200160Markers15/trace9/traceMeasurement parameters S-parameters (single-ended, mixed-mode), Absolutepower S-parameters (single-ended, mixed-mode), Absolute power, TDR and TDT parameters1Software capabilities Automatic fixture removal, time-domain analysis,frequency offset mode, scalar & vector mixer/converter measurement, gain compression measure-ments, measurement wizard assistant Time-domain analysis, frequency offset mode, scalar & vector mixer/converter measurement, measurement wizard assistant, enhanced time-domain analysisOther major software capabilities Fixture simulator, Equation editor, PMAR (powermeter as receiver)Fixture simulator, Equation editor, External test set mode2Automation Remote control with SCPI commands, 8753/E5071C-code emulation, BenchVue Remote control with SCPI commands, Built-in VBA 8753 code emulation, BenchVueMultiport test set E5092A E5092A, E5091A3Display12.1 inch10.4 inchBox height6U5UOther major hardware capabilities High stability oven (option), Bias tees, DC input ports High stability oven (option), Bias tees, DC inputports, Probe power1. Optional capabilities2. Assigns 4 test ports as direct source/receiver ports, S, R, A, and B.3. Discontinued test set, Dec. 2014 EOS.For more detailed information, refer to E5080A Data Sheet.LiteratureE5080A EVector Network Analyzer ENA Series, Data Sheet, 5992-0291ENE5080A Vector Network Analyzer ENA Series, Configuration Guide, 5992-0292ENKeysight Technologies Network Analyzer Selection Guide, 5989-7603ENWeb Resources/find/ecal/find/mta/find/multiport/find/benchvue11 | Keysight | E5080A Vector Network Analyzer ENA Series - Data SheetThis information is subject to change without notice.© Keysight Technologies, 2016, 2017Published in USA, July 12, 20175992-0290ENFor more information on KeysightTechnologies’ products, applications or services, please contact your local Keysight office. The complete list is available at:/find/contactus Americas Canada (877) 894 4414Brazil 55 11 3351 7010Mexico001 800 254 2440United States (800) 829 4444Asia Pacific Australia 1 800 629 485China800 810 0189Hong Kong 800 938 693India 1 800 11 2626Japan 0120 (421) 345Korea 080 769 0800Malaysia 1 800 888 848Singapore 180****8100Taiwan0800 047 866Other AP Countries (65) 6375 8100Europe & Middle East Austria 0800 001122Belgium 0800 58580Finland 0800 523252France 0805 980333Germany ***********Ireland 1800 832700Israel 1 809 343051Italy800 599100Luxembourg +32 800 58580Netherlands 0800 0233200Russia 8800 5009286Spain 800 000154Sweden 0200 882255Switzerland0800 805353Opt. 1 (DE)Opt. 2 (FR)Opt. 3 (IT)United Kingdom0800 0260637For other unlisted countries:/find/contactus(BP-6-20-17)/go/quality Keysight Technologies, Inc.DEKRA Certified ISO 9001:2015Quality Management SystemEvolving Since 1939Our unique combination of hardware, software, services, and people can help you reach your next breakthrough. We are unlocking the future of technology.From Hewlett-Packard to Agilent to Keysight.myKeysight/find/mykeysightA personalized view into the information most relevant to you.Keysight Services/find/serviceKeysight Services can help from acquisition to renewal across your instrument’s lifecycle. Our comprehensive service offerings—one-stop calibration, repair, asset management, technology refresh, consulting, training and more—helps you improve product quality and lower costs.Three-Year Warranty/find/ThreeYearWarrantyKeysight’s committed to superior product quality and lower total cost of ownership. Keysight is the only test and measurement company withthree-year warranty standard on all instruments, worldwide. And, we provide a one-year warranty on many accessories, calibration devices, systems and custom products.Keysight Assurance Plans/find/AssurancePlansUp to ten years of protection and no budgetary surprises to ensure your instruments are operating to specification, so you can rely on accurate measurements.Keysight Channel Partners/find/channelpartnersGet the best of both worlds: Keysight’s measurement expertise and productbreadth, combined with channel partner convenience.。
电脑宽带连接错误代码大全
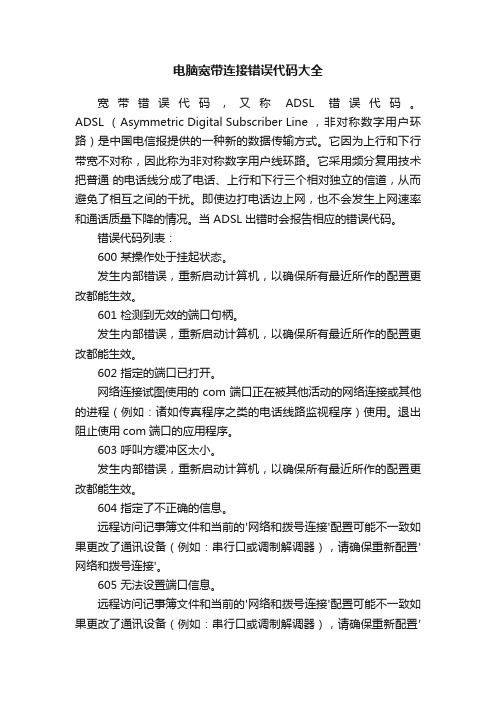
电脑宽带连接错误代码大全宽带错误代码,又称ADSL错误代码。
ADSL (Asymmetric Digital Subscriber Line ,非对称数字用户环路)是中国电信报提供的一种新的数据传输方式。
它因为上行和下行带宽不对称,因此称为非对称数字用户线环路。
它采用频分复用技术把普通的电话线分成了电话、上行和下行三个相对独立的信道,从而避免了相互之间的干扰。
即使边打电话边上网,也不会发生上网速率和通话质量下降的情况。
当 ADSL出错时会报告相应的错误代码。
错误代码列表:600 某操作处于挂起状态。
发生内部错误,重新启动计算机,以确保所有最近所作的配置更改都能生效。
601 检测到无效的端口句柄。
发生内部错误,重新启动计算机,以确保所有最近所作的配置更改都能生效。
602 指定的端口已打开。
网络连接试图使用的com端口正在被其他活动的网络连接或其他的进程(例如:诸如传真程序之类的电话线路监视程序)使用。
退出阻止使用com端口的应用程序。
603 呼叫方缓冲区太小。
发生内部错误,重新启动计算机,以确保所有最近所作的配置更改都能生效。
604 指定了不正确的信息。
远程访问记事簿文件和当前的'网络和拨号连接'配置可能不一致如果更改了通讯设备(例如:串行口或调制解调器),请确保重新配置'网络和拨号连接'。
605 无法设置端口信息。
远程访问记事簿文件和当前的'网络和拨号连接'配置可能不一致如果更改了通讯设备(例如:串行口或调制解调器),请确保重新配置'网络和拨号连接'。
如果错误仍然存在,请删除并重新创建'网络和拨号连接'.606 指定的端口未连接。
发生内部错误,重新启动计算机,以确保所有最近所作的配置更改都能生效。
607 检测到无效事件。
发生内部错误,重新启动计算机,以确保所有最近所作的配置更改都能生效。
608 指定的设备不存在。
远程访问记事簿文件和当前的'网络和拨号连接'配置可能不一致如果更改了通讯设备(例如:串行口或调制解调器),请确保重新配置'网络和拨号连接'。
E8-C-EPON注册失败

电信E8-C-EPON进行注册,但是提示注册失败,提示:业务下发失败,请检查vlan46网络管理通道解决办法:1.提示需要输入宽带账号输入 loid,即工单的SN码,工单的SN码需要向当地电信查询或者报障,报障完以后会有维修人员联系,可以向维修人员询问2.如何已经知道loid,也就是工单的SN码,仍然提示注册失败,这可能是把电信的光猫当成能PPPOE认证的路由器来使用了,而且里面的出厂设置是不会清空个人设置的,所以需要手动填写出厂配置3.先进入设备的管理界面(特权账号用户名:telecomadmin,密码:nE7jA%5m),如果要进行网络配置,不能使用设备背后的普通管理员帐号,即是useradmin这个用户名的4.如果需要把电信的设备当成路由器来使用的话,请直接到第7步,如果已经自己手动设置了网络参数,需要先把设置的删除,然后依照以下出厂设置新建三个wan连接(连接名称下拉框会有新增wan连接的选项)出厂设置:网络---宽带设置第一个wan连接:模式:Route连接模式:IPv4,方式是DHCPMTU:1492启用vlan:勾选Vlan ID:46802.1P:7服务模式:TR069_VOIP第二个wan连接模式:Bridge连接模式:IPv4MTU:1500启用vlan:勾选Vlan ID:45802.1P:5服务模式:OTHER绑定端口:端口2第三个wan连接模式:Bridge连接模式:IPv4MTU:1492启用vlan:不勾选服务模式:Internet绑定端口:端口1,端口3,端口4,无线(SSID1)5.如此设置完后,建议管理---设备管理---重启里面重启一下设备6.重启后连接无线,可以客户端进行PPPOE认证,这个时候也可以进行设备注册7.如果需要把PPPOE认证转移到设备上,需要删除上面所说的出厂设置,同时新建一个wan连接新建wan连接模式:Route连接模式:IPv4,方式是PPPOE,然后勾选第一项(不启用PPPOE代理或PPPOE路由桥混合模式)MTU:1492NAT:勾选启用vlan:不勾选用户名,密码:填上电信提供的信息服务名称可自己随便写拨号方式:自动连接服务模式:Internet绑定端口:端口1,端口2,端口3,端口4,无线(SSID1)8.然后进行重启,即可生效,客户端如果需要使用有线,只需要连接到端口1,端口2,端口3或者端口4;如果使用无线,只需连接到设备后面的SSID上,输入密码(密码可以在网络---wlan配置---高级选项里面进行设置)。
【免费下载】G3网卡随E行错误代码及解决方法
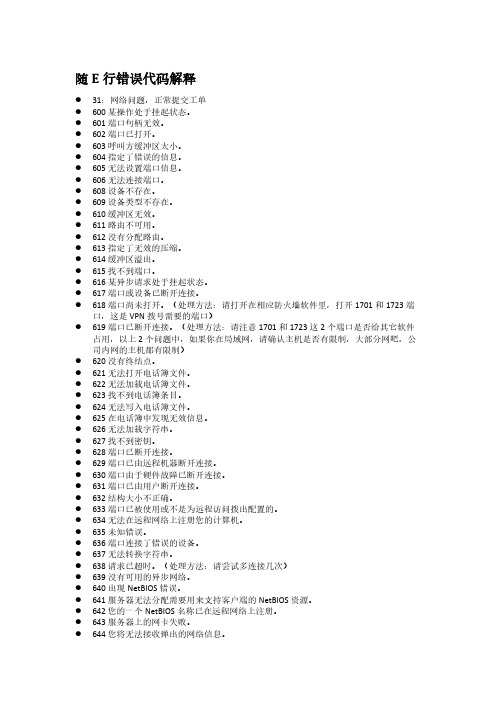
随E行错误代码解释●31:网络问题,正常提交工单●600某操作处于挂起状态。
●601端口句柄无效。
●602端口已打开。
●603呼叫方缓冲区太小。
●604指定了错误的信息。
●605无法设置端口信息。
●606无法连接端口。
●608设备不存在。
●609设备类型不存在。
●610缓冲区无效。
●611路由不可用。
●612没有分配路由。
●613指定了无效的压缩。
●614缓冲区溢出。
●615找不到端口。
●616某异步请求处于挂起状态。
●617端口或设备已断开连接。
●618端口尚未打开。
(处理方法:请打开在相应防火墙软件里,打开1701和1723端口,这是VPN拨号需要的端口)●619端口已断开连接。
(处理方法:请注意1701和1723这2个端口是否给其它软件占用,以上2个问题中,如果你在局域网,请确认主机是否有限制,大部分网吧,公司内网的主机都有限制)●620没有终结点。
●621无法打开电话簿文件。
●622无法加载电话簿文件。
●623找不到电话簿条目。
●624无法写入电话簿文件。
●625在电话簿中发现无效信息。
●626无法加载字符串。
●627找不到密钥。
●628端口已断开连接。
●629端口已由远程机器断开连接。
●630端口由于硬件故障已断开连接。
●631端口已由用户断开连接。
●632结构大小不正确。
●633端口已被使用或不是为远程访问拨出配置的。
●634无法在远程网络上注册您的计算机。
●635未知错误。
●636端口连接了错误的设备。
●637无法转换字符串。
●638请求已超时。
(处理方法:请尝试多连接几次)●639没有可用的异步网络。
●640出现NetBIOS错误。
●641服务器无法分配需要用来支持客户端的NetBIOS资源。
●642您的一个NetBIOS名称已在远程网络上注册。
●643服务器上的网卡失败。
●644您将无法接收弹出的网络信息。
●645内部身份验证错误。
●646不允许本帐户在此时间登录。
●647帐户已禁用。
- 1、下载文档前请自行甄别文档内容的完整性,平台不提供额外的编辑、内容补充、找答案等附加服务。
- 2、"仅部分预览"的文档,不可在线预览部分如存在完整性等问题,可反馈申请退款(可完整预览的文档不适用该条件!)。
- 3、如文档侵犯您的权益,请联系客服反馈,我们会尽快为您处理(人工客服工作时间:9:00-18:30)。
M M O O D D I I F F I I C C A A T T I I O O N N R R E E C C O O M M M M E E N N D D E E D D
ADMINISTRATIVE INFORMATION
© AGILENT TECHNOLOGIES, INC. 2010 PRINTED IN U.S.A.
February 5, 2010
Rev. 17
Page 1 of 3
E8363C-05
S E R V I C E N O T E
Supersedes:
None
PNA Series Network Analyzer Hard Drive Tray Modification
Serial Numbers: E8361C – US49010185 - US49010207
E8362C – MY49020213 - MY49020272; SG49020113 - SG49020123 E8363C – MY49030270 - MY49030349; SG49030113 - SG49030122 E8364C – MY49040112 - MY49040114; SG49040112 - SG49040114 N5230C – MY49000637 - MY49000873; SG49000119 - SG49000131
Some hard drive trays, used mostly in PNA C models that were shipped from June 2009 through mid-December 2009, may be slightly warped. This could cause a head crash resulting in complete drive failure. Also affected are trays used for replacement/swapping purposes on the E836xA/B and N5230A models. This issue does not affect the PNA-X series.
Parts Required: P/N
Description
Qty.
0340-1525
Nylon Bushing 4
Situation:
It is possible that the center of the X-frame of the HDD tray is slightly bowed which will cause the hard drive to warp when secured with screws. If warped, a head crash may occur that can destroy the drive. Only SATA (Serial ATA) drives are affected - PATA drives do n’t have this issue. SATA drives are identifiable by a flat, X-shaped Mylar insulator between the drive and the tray - see the photo. Also affected are trays used for replacement/swapping purposes on the E836xA/B and N5230A models. This issue does not affect the PNA-X series.
Solution/Action:
While this mainly affects the PNA C models, also check any drive trays that may be used as spares. If not already done, all metal trays with SATA drives should have this modification performed except for those in PNA-X models (N524xA, N5264A) - they are not affected.
The mounting of the tray must be modified so that there is some clearance between the HDD and the center of the tray frame. This is accomplished by adding two bottom bushings to the rear of the drive, between the drive and the tray. The existing top bushings must be replaced because they are too long to accommodate the additional bottom ones. A total of four new bushings are used in this rework. Procedure: (see photo)
1.Slightly loosen (by 2 turns) the two screws near the front of the drive where it connects to the PC
board. There is no need to completely remove these two front screws.
2.Remove the two screws and the bushings underneath them at the rear of the drive. Discard the
bushings.
3.Add two new bushings between the metal frame and the HDD, but above the Mylar X insulator.
Make sure to use the holes closest to the rear edge of the frame.
4.Install a new bushing on both screws that were removed in step 2. These new bushings are shorter
than the original ones.
5.Reinstall the two screws and their new bushings at the rear of the drive, then torque the screws to
0.8 N-m (7 in-lbs).
6.Tighten the two screws near the front of the drive to the same torque value above.
7.Verify that there is now some clearance at the center of the X-frame by slipping a piece of paper
between the drive and the frame as shown in the picture below.。