齿轮的设计计算过程
齿轮传动设计与计算

齿轮传动设计与计算
引言
齿轮传动是一种常见且重要的机械传动方式,广泛用于各种机
械设备中。
本文旨在介绍齿轮传动的基本原理、设计方法和计算过程。
齿轮传动基本原理
齿轮传动是通过齿轮之间的啮合来传递力和运动的机制。
主要
包括两个关键参数:模数和齿数。
模数是指齿轮齿廓的比例系数,
齿数是指齿轮上的齿的数量。
通过合理选择模数和齿数,可以满足
传动的要求。
齿轮传动设计步骤
齿轮传动的设计过程一般包括以下步骤:
1. 确定传动比:根据传动要求和输入输出的转速,确定传动比。
2. 选择齿轮类型:根据传动要求和空间限制,选择合适的齿轮
类型,如直齿轮、斜齿轮或蜗杆齿轮。
3. 计算齿轮参数:根据传动比、输入输出转速和齿轮类型,计
算齿轮的模数、齿数和齿轮直径等参数。
4. 验证设计:通过计算齿轮间的啮合角度、啮合强度和齿轮的
受载能力等指标,验证设计的合理性。
齿轮传动计算
齿轮传动的计算过程主要涉及以下几个方面:
1. 齿轮啮合角度计算:根据齿轮的齿数和模数,计算齿轮之间
的啮合角度。
2. 齿轮模数计算:根据传动比和齿轮的模数,计算齿轮的模数。
3. 齿轮齿数计算:根据传动比和齿轮的模数,计算齿轮的齿数。
4. 齿轮直径计算:根据齿轮的模数和齿数,计算齿轮的直径。
以上是齿轮传动设计与计算的基本内容。
齿轮传动的设计和计算过程需要充分考虑传动要求、材料强度和工艺要求等因素,以实现可靠的传动效果。
齿轮上的齿数计算公式

齿轮上的齿数计算公式齿轮是机械传动中常用的一种装置,它通过齿与齿的咬合来传递动力和转速。
在设计和制造齿轮时,齿数是一个非常重要的参数,它直接影响着齿轮的传动比、速比和传动效率。
因此,对于工程师和设计师来说,了解齿轮上的齿数计算公式是非常重要的。
一、齿轮上的齿数计算公式。
齿轮上的齿数计算公式可以根据齿轮的模数、齿轮的压力角和齿轮的分度圆直径来确定。
通常情况下,齿轮的齿数计算公式可以表示为:Z = π D / m。
其中,Z表示齿数,D表示齿轮的分度圆直径,m表示齿轮的模数,π表示圆周率。
在这个公式中,齿数和模数是齿轮设计中最为关键的两个参数。
模数是用来表示齿轮齿的大小的参数,它等于齿轮的分度圆直径与齿数的比值。
而齿数则是用来表示齿轮上的齿的数量。
通过这个公式,我们可以根据齿轮的分度圆直径和模数来计算齿轮上的齿数,从而确定齿轮的尺寸和传动性能。
二、齿数计算公式的应用。
齿数计算公式在齿轮设计和制造中有着广泛的应用。
首先,它可以帮助工程师和设计师确定齿轮的尺寸和形状。
通过计算齿数,可以确定齿轮的分度圆直径,从而确定齿轮的大小和形状。
其次,齿数计算公式还可以帮助工程师和设计师确定齿轮的传动比和速比。
通过计算齿数,可以确定齿轮的传动比,从而确定齿轮传动系统的性能和特性。
除此之外,齿数计算公式还可以帮助工程师和设计师进行齿轮的优化设计。
通过计算齿数,可以确定齿轮的齿形和齿距,从而优化齿轮的传动效率和传动性能。
同时,齿数计算公式还可以帮助工程师和设计师进行齿轮的强度计算。
通过计算齿数,可以确定齿轮的受力情况,从而确定齿轮的强度和耐久性。
三、齿数计算公式的注意事项。
在使用齿数计算公式时,需要注意一些事项。
首先,需要根据实际情况选择合适的齿轮模数。
不同的传动系统和工作环境需要不同的齿轮模数,因此需要根据实际情况选择合适的齿轮模数。
其次,需要根据齿轮的使用要求选择合适的齿数。
不同的传动系统和工作环境需要不同的齿数,因此需要根据实际情况选择合适的齿数。
齿轮的设计计算过程

1.选定类型,精度等级,材料及齿数 (1)直齿圆柱硬齿面齿轮传动 (2)精度等级初定为8级 (3)选择材料及确定需用应力小齿轮选用45号钢,调质处理,(217-255)HBS 大齿轮选用45号钢,正火处理,(162-217)HBS (4)选小齿轮齿数为Z1=24,Z2=3.2x24=76.8.取Z2=772. 按齿面接触强度设计计算(1)初选载荷系数K t电动机;载荷状态选择:中等冲击;载荷系数K t 的推荐范围为(1.2-2.5),初选载荷系数K t :1.3, (2)小齿轮转矩)(29540/97039550000/9550111mm N n P T ⋅=⨯==(3)选取齿宽系数1=d φ.⑷取弹性影响系数218.189MPa Z E =⑸按齿面硬度查得小齿轮的接触疲劳强度极限为MPa 5801lim =σ。
大齿轮的接触疲劳强度极限为MPa 5202lim =σ⑹计算应力循环次数N 1=60n 1jl h =60X970X1X(16X300X15)=4.470X109N 99210397.12.310470.4⨯=⨯=⑺取接触疲劳寿命系数K .89.0,88.021==HN HN K ⑻计算接触疲劳许用应力 取失效概率为1%,安全系数S=1[]a HN H MP MPa SK 4.5105709.01lim 11=⨯==σσ[]a HN H MP MPa SK 8.46253095.02lim 22=⨯==σσ⑼按齿面接触强度设计计算 ①试算小齿轮分度圆直径mm Z u u T K d H E d t t 248.56)8.4628.189(2.32.4110954.28.132.2)][(132.23243211=⨯⨯⨯=+〉σφ②计算齿轮圆周转速v 并选择齿轮精度 s m n d V t /48.2100060970248.5610006011=⨯⨯⨯=⨯=ππ③计算齿轮宽度bmm d b t d 248.56248.5611=⨯=⨯=φ④计算齿轮宽度b 与齿高h 之比模数 mm mm Z d m t 033.22272.44111===齿高 mm mm m h 574.4033.225.225.21=⨯==67.10=hb⑤计算载荷系数根据v=2.27m/s 。
第一对齿轮的设计计算

第一对齿轮的设计计算取机器的工作寿命为10年,每年工作75天,每天工作8小时 1.选定齿轮的类型,精度,材料和齿数 直齿圆柱齿轮;8度精度;小齿轮材料为40Cr 调质,硬度为280HBS ,接触疲劳极限δH1,m /Mpa:650;弯曲疲劳极限δFE 为680Mpa大齿轮材料为45钢(调质),硬度为:240HBS ,接触疲劳极限δH2,m /Mpa:550; 弯曲疲劳极限δFE 为440Mpa2.选取小齿轮齿数Z 1=30,根据u=Z 2/Z 1=2.07,Z 2=2.07×30=62.1,取62。
查表6-28,取齿面接触疲劳安全系数S H =1.0,齿轮弯曲疲劳安全系数S F =1.25 [δH1]=δH1,m SH =650,同理[δH2]=550,取最小值,故[δH ]=550Mpa 。
[δFE1]=δFE1SF=544,同理[δFE1]=352Mpa 。
3.齿轮基本尺寸计算 最小齿轮分度圆直径:d 1≥K-截面系数,取1.3;d Φ-齿宽系数,0.4;Z E -弹性影响系数,189.8Mpa ;Z H -区域系数,2.5 T-转矩,通过计算得8509.9N·mm;计算得:d1≥,取60mm模数:1160230d m z ===mm ;考虑磨损模数加大12%,则m=2×1.2=2.4,取m=3 则齿宽b=φd ·d 1=φd ·Z·m=0.4⨯3⨯30=36mm ; 因为b 2≈b,b 取35mm ;b1=b2+(5~10)mm=40mm ;中心距:()121382ma Z Z mm =⨯+=; 分度圆直径:d 1=mZ 1=3⨯30=90mm ;d 2=mZ 2=3⨯62=186mm ; 齿顶高:h a =m=3mm ;齿根高:h f =1.25⨯h a =3.75mm ;齿顶圆直径:da 1=d 1+2ha=90+2⨯2=94mm ;da 2=d 2+2ha=186+2⨯2=190mm 齿根圆直径:d f1=d 1-2h f =90-2⨯2.5=85mm ,d f2=d2-2⨯h f =186-2.5=183.5mm4.验算齿根弯曲强度根据机械设计手册查表知:取齿形系数;Y fa1=2.9,Y fa2=2.4;取齿根应力集中系数:Y sa1=1.56,Y sa2=1.67. 所以齿根弯曲强度为:111122122 1.38509.9 2.9 1.5678.2[]54416220Fa Fa F F KTY Y Mpa Mpa bm Z ⨯⨯⨯⨯σ===≤σ=⨯⨯2221211 2.4 1.6778.269.2[]3522.9 1.56Fa Sa F F F Fa Sa Y Y Mpa Mpa Y Y ⨯σ=σ⨯=⨯=≤σ=⨯所以两齿轮弯曲强度均满足要求。
齿轮深度的计算公式
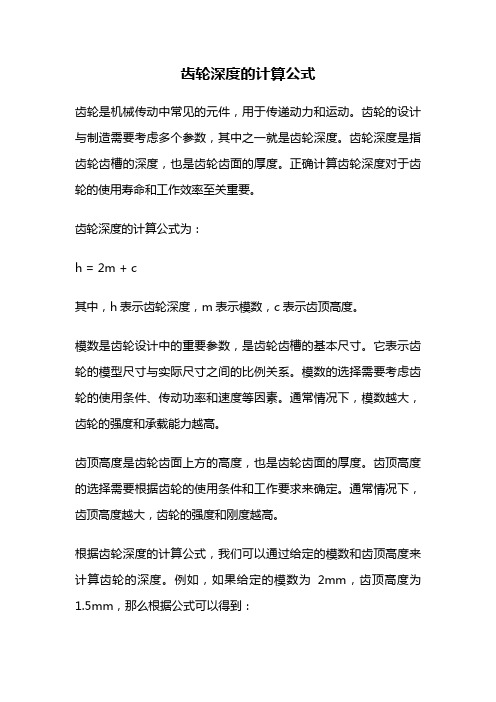
齿轮深度的计算公式齿轮是机械传动中常见的元件,用于传递动力和运动。
齿轮的设计与制造需要考虑多个参数,其中之一就是齿轮深度。
齿轮深度是指齿轮齿槽的深度,也是齿轮齿面的厚度。
正确计算齿轮深度对于齿轮的使用寿命和工作效率至关重要。
齿轮深度的计算公式为:h = 2m + c其中,h表示齿轮深度,m表示模数,c表示齿顶高度。
模数是齿轮设计中的重要参数,是齿轮齿槽的基本尺寸。
它表示齿轮的模型尺寸与实际尺寸之间的比例关系。
模数的选择需要考虑齿轮的使用条件、传动功率和速度等因素。
通常情况下,模数越大,齿轮的强度和承载能力越高。
齿顶高度是齿轮齿面上方的高度,也是齿轮齿面的厚度。
齿顶高度的选择需要根据齿轮的使用条件和工作要求来确定。
通常情况下,齿顶高度越大,齿轮的强度和刚度越高。
根据齿轮深度的计算公式,我们可以通过给定的模数和齿顶高度来计算齿轮的深度。
例如,如果给定的模数为2mm,齿顶高度为1.5mm,那么根据公式可以得到:h = 2m + c = 2 × 2 + 1.5 = 5.5mm这表示该齿轮的深度为5.5mm。
正确计算齿轮深度对于齿轮的设计和制造非常重要。
如果齿轮深度过小,会导致齿轮齿面的强度不足,容易损坏。
如果齿轮深度过大,会增加齿轮的重量和惯性,降低传动效率。
因此,在齿轮设计中,需要根据具体的使用条件和要求来合理选择模数和齿顶高度,确保齿轮深度的合理性。
齿轮深度是齿轮设计中的重要参数之一。
通过正确计算齿轮深度,可以确保齿轮的强度和工作效率。
齿轮深度的计算公式为h = 2m + c,其中m表示模数,c表示齿顶高度。
合理选择模数和齿顶高度,确保齿轮深度的合理性,对于齿轮的设计和制造非常重要。
齿轮齿条设计计算公式

齿轮齿条设计计算公式齿轮和齿条是机械传动中常见的元件,用于传递动力和转速。
齿轮齿条的设计计算是设计师在进行齿轮齿条设计时所必须掌握的知识。
本文将介绍齿轮齿条设计计算的一些基本公式和原理。
一、齿轮设计计算公式1. 齿数计算公式齿数是齿轮设计中最基本的参数之一,可以通过以下公式计算:N = (π * D) / m其中,N为齿数,D为齿轮直径,m为模数。
2. 齿轮间距计算公式齿轮间距是指两个相邻齿轮之间的中心距离,可以通过以下公式计算:P = (N1 + N2) / 2 * m其中,P为齿轮间距,N1和N2分别为两个相邻齿轮的齿数,m为模数。
3. 齿轮传动比计算公式齿轮传动比是指两个相邻齿轮的转速之比,可以通过以下公式计算:i = N2 / N1其中,i为传动比,N1和N2分别为两个相邻齿轮的齿数。
4. 齿轮模数计算公式齿轮模数是指齿轮齿数和齿轮直径之间的比值,可以通过以下公式计算:m = D / N其中,m为模数,D为齿轮直径,N为齿数。
二、齿条设计计算公式1. 齿条模数计算公式齿条模数是指齿条齿数和齿条长度之间的比值,可以通过以下公式计算:m = L / N其中,m为模数,L为齿条长度,N为齿数。
2. 齿条传动比计算公式齿条传动比是指齿条的移动距离与齿轮转动角度之间的比值,可以通过以下公式计算:i = L / (π * D)其中,i为传动比,L为齿条的移动距离,D为齿轮的直径。
3. 齿条齿数计算公式齿条齿数是指齿条上的齿数,可以通过以下公式计算:N = L / m其中,N为齿数,L为齿条长度,m为模数。
三、齿轮齿条设计计算实例假设有一对齿轮,其中一个齿轮的齿数为20,直径为40mm,另一个齿轮的齿数为40,直径为80mm,模数为2mm。
我们可以通过上述公式进行计算。
根据齿数计算公式,可得第一个齿轮的齿数为20,第二个齿轮的齿数为40。
根据齿轮间距计算公式,可得齿轮间距为(20+40)/2*2=60mm。
齿轮齿条设计计算公式
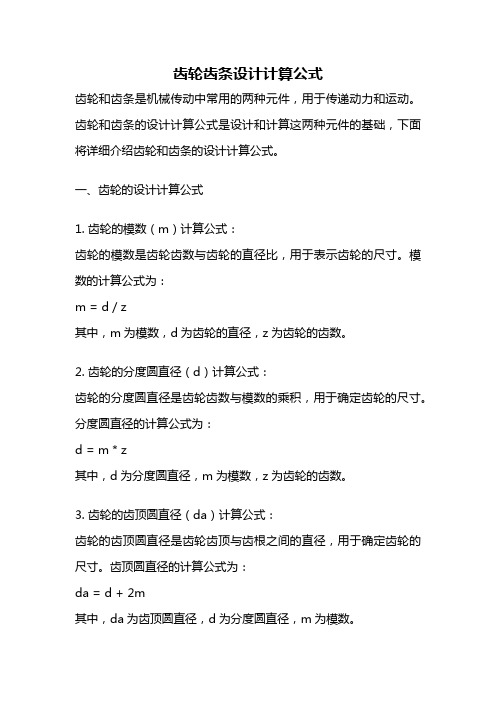
齿轮齿条设计计算公式齿轮和齿条是机械传动中常用的两种元件,用于传递动力和运动。
齿轮和齿条的设计计算公式是设计和计算这两种元件的基础,下面将详细介绍齿轮和齿条的设计计算公式。
一、齿轮的设计计算公式1. 齿轮的模数(m)计算公式:齿轮的模数是齿轮齿数与齿轮的直径比,用于表示齿轮的尺寸。
模数的计算公式为:m = d / z其中,m为模数,d为齿轮的直径,z为齿轮的齿数。
2. 齿轮的分度圆直径(d)计算公式:齿轮的分度圆直径是齿轮齿数与模数的乘积,用于确定齿轮的尺寸。
分度圆直径的计算公式为:d = m * z其中,d为分度圆直径,m为模数,z为齿轮的齿数。
3. 齿轮的齿顶圆直径(da)计算公式:齿轮的齿顶圆直径是齿轮齿顶与齿根之间的直径,用于确定齿轮的尺寸。
齿顶圆直径的计算公式为:da = d + 2m其中,da为齿顶圆直径,d为分度圆直径,m为模数。
4. 齿轮的齿根圆直径(df)计算公式:齿轮的齿根圆直径是齿轮齿根与齿顶之间的直径,用于确定齿轮的尺寸。
齿根圆直径的计算公式为:df = d - 2.2m其中,df为齿根圆直径,d为分度圆直径,m为模数。
5. 齿轮的齿宽(b)计算公式:齿轮的齿宽是齿轮齿根与齿顶之间的宽度,用于确定齿轮的尺寸。
齿宽的计算公式为:b = m * zc其中,b为齿宽,m为模数,zc为齿轮齿数系数。
二、齿条的设计计算公式1. 齿条的模数(m)计算公式:齿条的模数是齿条齿数与齿条的厚度比,用于表示齿条的尺寸。
模数的计算公式为:m = t / z其中,m为模数,t为齿条的厚度,z为齿条的齿数。
2. 齿条的分度圆直径(d)计算公式:齿条的分度圆直径是齿条齿数与模数的乘积,用于确定齿条的尺寸。
分度圆直径的计算公式为:d = m * z其中,d为分度圆直径,m为模数,z为齿条的齿数。
3. 齿条的基圆直径(db)计算公式:齿条的基圆直径是齿条齿槽底部的直径,用于确定齿条的尺寸。
基圆直径的计算公式为:db = d - 2m其中,db为基圆直径,d为分度圆直径,m为模数。
齿轮传动的设计步骤
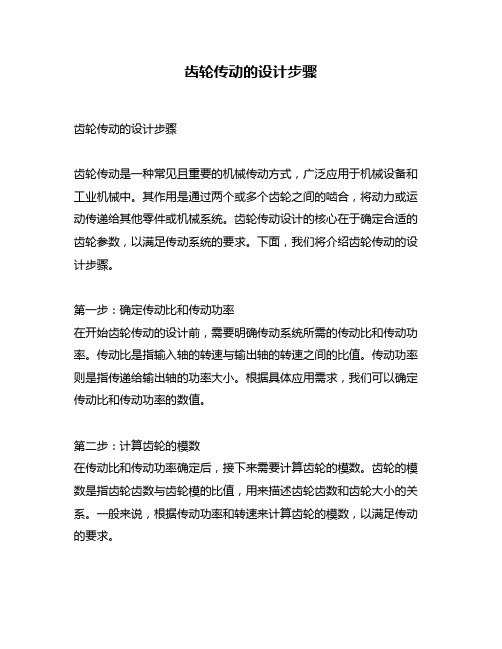
齿轮传动的设计步骤齿轮传动的设计步骤齿轮传动是一种常见且重要的机械传动方式,广泛应用于机械设备和工业机械中。
其作用是通过两个或多个齿轮之间的啮合,将动力或运动传递给其他零件或机械系统。
齿轮传动设计的核心在于确定合适的齿轮参数,以满足传动系统的要求。
下面,我们将介绍齿轮传动的设计步骤。
第一步:确定传动比和传动功率在开始齿轮传动的设计前,需要明确传动系统所需的传动比和传动功率。
传动比是指输入轴的转速与输出轴的转速之间的比值。
传动功率则是指传递给输出轴的功率大小。
根据具体应用需求,我们可以确定传动比和传动功率的数值。
第二步:计算齿轮的模数在传动比和传动功率确定后,接下来需要计算齿轮的模数。
齿轮的模数是指齿轮齿数与齿轮模的比值,用来描述齿轮齿数和齿轮大小的关系。
一般来说,根据传动功率和转速来计算齿轮的模数,以满足传动的要求。
第三步:选择合适的齿轮材料齿轮传动的设计过程中,选择合适的齿轮材料十分重要。
齿轮材料应具有良好的耐磨性、耐蚀性、强度和刚度,以确保传动系统的可靠性和寿命。
常用的齿轮材料包括钢、铸铁、铜合金等。
根据具体的应用需求和工作环境选择合适的齿轮材料。
第四步:确定齿轮的齿数和齿形根据传动比和齿轮模数,确定齿轮的齿数。
齿数的确定需要考虑到齿轮啮合条件的要求,如齿面接触、齿轮强度等。
齿形的设计也是十分重要的一步,合理的齿形设计可以提高齿轮传动的效率和传动能力。
常见的齿形有直齿、斜齿、渐开线齿等。
第五步:计算齿轮的几何参数在确定齿数和齿形后,需要计算齿轮的几何参数。
包括齿轮的分度圆直径、齿顶圆直径、齿根圆直径、齿隙等。
这些参数直接影响着齿轮的传动特性,如传动比、啮合条件等。
通过计算这些几何参数,可以确保齿轮传动的可靠性和稳定性。
第六步:计算齿轮的强度在齿轮传动设计的过程中,还需要计算齿轮的强度。
齿轮的强度是指齿轮在工作过程中能够承受的最大载荷。
通过计算齿轮的强度,可以判断齿轮是否能够满足工作条件下的要求。
齿轮的设计计算过程
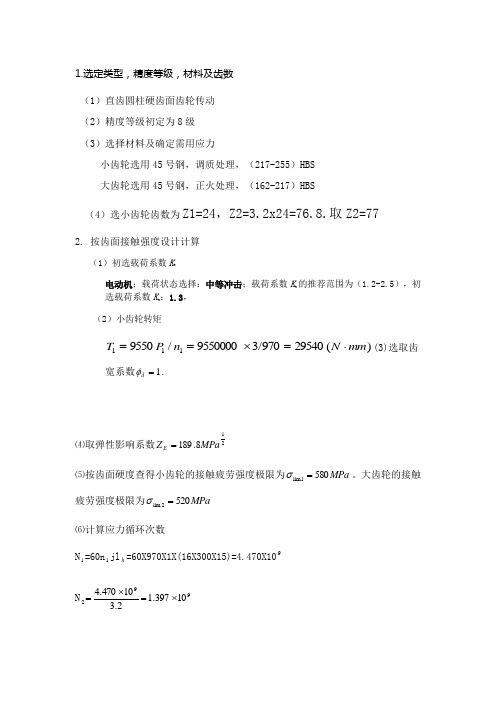
1.选定类型,精度等级,材料及齿数 (1)直齿圆柱硬齿面齿轮传动 (2)精度等级初定为8级 (3)选择材料及确定需用应力小齿轮选用45号钢,调质处理,(217-255)HBS 大齿轮选用45号钢,正火处理,(162-217)HBS (4)选小齿轮齿数为Z1=24,Z2=3.2x24=76.8.取Z2=772. 按齿面接触强度设计计算(1)初选载荷系数K t电动机;载荷状态选择:中等冲击;载荷系数K t 的推荐范围为(1.2-2.5),初选载荷系数K t :1.3, (2)小齿轮转矩)(29540/97039550000/9550111mm N n P T ⋅=⨯==(3)选取齿宽系数1=d φ.⑷取弹性影响系数218.189MPa Z E =⑸按齿面硬度查得小齿轮的接触疲劳强度极限为MPa 5801lim =σ。
大齿轮的接触疲劳强度极限为MPa 5202lim =σ ⑹计算应力循环次数N 1=60n 1jl h =60X970X1X(16X300X15)=4.470X109N 99210397.12.310470.4⨯=⨯=⑺取接触疲劳寿命系数K .89.0,88.021==HN HN K⑻计算接触疲劳许用应力 取失效概率为1%,安全系数S=1[]a HN H MP MPa SK 4.5105709.01lim 11=⨯==σσ[]a HN H MP MPa SK 8.46253095.02lim 22=⨯==σσ⑼按齿面接触强度设计计算 ①试算小齿轮分度圆直径mm Z u u T K d H E d t t 248.56)8.4628.189(2.32.4110954.28.132.2)][(132.23243211=⨯⨯⨯=+〉σφ②计算齿轮圆周转速v 并选择齿轮精度 s m n d V t /48.2100060970248.5610006011=⨯⨯⨯=⨯=ππ③计算齿轮宽度bmm d b t d 248.56248.5611=⨯=⨯=φ④计算齿轮宽度b 与齿高h 之比 模数 mm mm Z d m t 033.22272.44111===齿高 mm mm m h 574.4033.225.225.21=⨯==67.10=hb⑤计算载荷系数根据v=2.27m/s 。
齿轮齿数计算

齿轮齿数计算摘要:一、齿轮齿数计算的背景和意义1.齿轮在机械传动中的应用2.齿轮齿数对传动性能的影响3.计算齿轮齿数的方法在实际工程中的重要性二、齿轮齿数计算的基本原理1.齿轮齿数的定义2.齿轮齿数计算的一般步骤3.影响齿轮齿数计算的因素三、齿轮齿数计算的具体方法1.法向齿距计算法2.切向齿距计算法3.齿轮齿数计算的实践应用案例四、齿轮齿数计算在实际工程中的应用1.在齿轮传动设计中的应用2.在齿轮制造和加工中的应用3.在齿轮检测和故障分析中的应用五、齿轮齿数计算的发展趋势和展望1.齿轮齿数计算方法的优化和改进2.齿轮齿数计算在新型齿轮传动技术中的应用3.齿轮齿数计算未来研究的方向和挑战正文:齿轮齿数计算在机械传动领域具有重要的意义。
齿轮作为机械传动的主要部件,承担着动力传递的重要任务。
齿轮齿数的选择对传动性能有着直接的影响,如传动比、齿面接触疲劳强度、齿根弯曲疲劳强度等。
因此,掌握齿轮齿数计算的方法对于设计和分析齿轮传动系统至关重要。
齿轮齿数计算的基本原理是计算法向齿距和切向齿距。
齿轮齿数的定义是齿轮上的一对相邻齿廓之间的齿数。
齿轮齿数计算的一般步骤包括确定法向齿距、计算切向齿距和得出齿轮齿数。
影响齿轮齿数计算的因素主要有齿轮的类型、传动比要求、齿轮材料、齿轮加工工艺等。
齿轮齿数计算的具体方法主要有法向齿距计算法、切向齿距计算法等。
法向齿距计算法是根据齿轮的齿廓曲线和齿轮的模数、齿数等参数计算法向齿距;切向齿距计算法则是根据齿轮的齿廓曲线和齿轮的齿数计算切向齿距。
通过这两种方法相互配合,可以得出准确的齿轮齿数。
齿轮齿数计算在实际工程中有着广泛的应用。
在齿轮传动设计中,通过齿轮齿数计算可以优化传动比、提高齿轮的疲劳强度;在齿轮制造和加工中,齿轮齿数计算可以为齿轮的加工工艺提供依据,保证齿轮的加工质量;在齿轮检测和故障分析中,齿轮齿数计算可以为齿轮的检测和故障分析提供参考。
随着科技的进步,齿轮齿数计算方法也在不断优化和改进。
齿轮齿条传动设计计算完整版
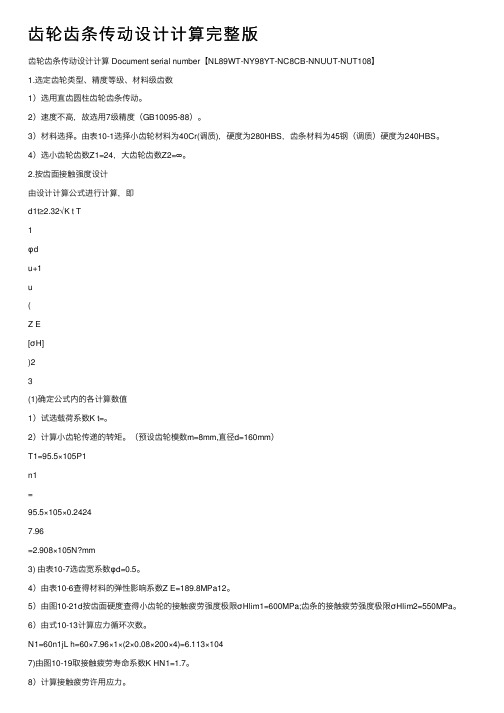
齿轮齿条传动设计计算完整版齿轮齿条传动设计计算 Document serial number【NL89WT-NY98YT-NC8CB-NNUUT-NUT108】1.选定齿轮类型、精度等级、材料级齿数1)选⽤直齿圆柱齿轮齿条传动。
2)速度不⾼,故选⽤7级精度(GB10095-88)。
3)材料选择。
由表10-1选择⼩齿轮材料为40Cr(调质),硬度为280HBS,齿条材料为45钢(调质)硬度为240HBS。
4)选⼩齿轮齿数Z1=24,⼤齿轮齿数Z2=∞。
2.按齿⾯接触强度设计由设计计算公式进⾏计算,即d1t≥2.32√K t T1φdu+1u(Z E[σH])23(1)确定公式内的各计算数值1)试选载荷系数K t=。
2)计算⼩齿轮传递的转矩。
(预设齿轮模数m=8mm,直径d=160mm)T1=95.5×105P1n1=95.5×105×0.24247.96=2.908×105N?mm3) 由表10-7选齿宽系数φd=0.5。
4)由表10-6查得材料的弹性影响系数Z E=189.8MPa12。
5)由图10-21d按齿⾯硬度查得⼩齿轮的接触疲劳强度极限σHlim1=600MPa;齿条的接触疲劳强度极限σHlim2=550MPa。
6)由式10-13计算应⼒循环次数。
N1=60n1jL h=60×7.96×1×(2×0.08×200×4)=6.113×1047)由图10-19取接触疲劳寿命系数K HN1=1.7。
8)计算接触疲劳许⽤应⼒。
取失效概率为1%,安全系数S=1,由式(10-12)得[σH]1=K HN1σHlim1S=1.7×600MPa=1020MPa(2)计算1)试算⼩齿轮分度圆直径d t1,代⼊[σH]1。
d 1t ≥2.32√K t T 1φd u +1u (Z E [σH ])23=2.32√1.3×2.908×1050.5∞+1∞ (189.81020)23=68.89mm2)计算圆周速度v 。
齿轮各部分计算公式

齿轮各部分计算公式
齿轮是一种常见的机械传动装置,由于其结构复杂,设计计算也相对繁琐。
下面将介绍齿轮各部分的计算公式,包括齿数计算、模数计算、齿廓曲线计算等。
一、齿数计算公式:
齿数是齿轮设计中最基本的参数之一、一般情况下,要求输入齿轮中心距、模数和齿数,通过计算可以得到另一个齿轮的齿数。
1.齿数计算公式:
n=(πd)/m
其中,n为齿数,d为齿轮的规定直径,m为模数。
2.齿轮中心距计算公式:
a=m(z1+z2)/2
其中,a为齿轮中心距,m为模数,z1、z2为两个齿轮的齿数。
二、模数计算公式:
模数是齿轮设计中重要的参数之一,是决定齿轮尺寸的关键。
1.模数计算公式:
m=d/z
其中,m为模数,d为齿轮的规定直径,z为齿数。
三、齿廓曲线计算公式:
齿廓曲线是描述齿轮齿形的曲线,常用的齿廓曲线有圆弧、渐开线等。
1.圆弧齿廓曲线计算公式:
y = r - (r' + r' tanα)
其中,y为齿廓偏差,r为齿轮基圆半径,r'为齿轮分度圆半径,α
为压力角。
2.渐开线齿廓曲线计算公式:
x = (r + r α) cosθ + m tanθ - m tanα
其中,x为齿廓偏差,r为齿轮基圆半径,α为压力角,θ为齿廓角。
以上仅是齿轮计算中的一部分公式,实际的齿轮设计计算还需要考虑
到材料强度、结构刚度等因素。
此外,齿轮的传动特性、工作精度也需要
在设计时进行综合考虑。
简述齿轮的设计原理及流程
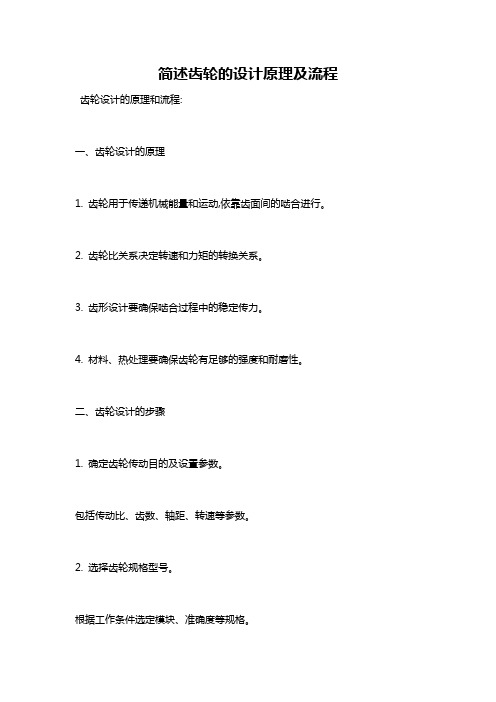
简述齿轮的设计原理及流程齿轮设计的原理和流程:
一、齿轮设计的原理
1. 齿轮用于传递机械能量和运动,依靠齿面间的啮合进行。
2. 齿轮比关系决定转速和力矩的转换关系。
3. 齿形设计要确保啮合过程中的稳定传力。
4. 材料、热处理要确保齿轮有足够的强度和耐磨性。
二、齿轮设计的步骤
1. 确定齿轮传动目的及设置参数。
包括传动比、齿数、轴距、转速等参数。
2. 选择齿轮规格型号。
根据工作条件选定模块、准确度等规格。
3. 设计齿形。
选择直齿轮或斜齿轮,设计齿形修整参数。
4. 设计齿轮强度。
根据负荷设计齿根强度,计算应力。
5. 选择材料及热处理。
根据强度设计要求选择材料,如多种钢型。
6. 设计齿轮制造工艺流程。
详细设计各工序制造、加工、检验过程。
7. 优化设计,提高使用寿命。
改进齿形,增强疲劳强度,延长使用寿命。
三、辅助设计手段
1. 运用计算机辅助设计软件,进行三维建模、运动仿真。
2. 利用有限元分析软件计算齿轮的力学性能。
3. 采用先进制造技术,提高齿轮精度。
综合运用理论计算和现代设计手段,可以设计出工作性能优异的齿轮产品。
齿轮设计的一般步骤
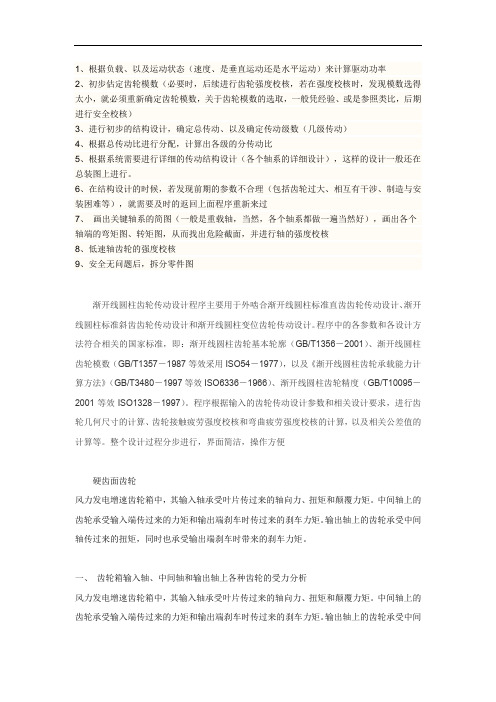
1、根据负载、以及运动状态(速度、是垂直运动还是水平运动)来计算驱动功率2、初步估定齿轮模数(必要时,后续进行齿轮强度校核,若在强度校核时,发现模数选得太小,就必须重新确定齿轮模数,关于齿轮模数的选取,一般凭经验、或是参照类比,后期进行安全校核)3、进行初步的结构设计,确定总传动、以及确定传动级数(几级传动)4、根据总传动比进行分配,计算出各级的分传动比5、根据系统需要进行详细的传动结构设计(各个轴系的详细设计),这样的设计一般还在总装图上进行。
6、在结构设计的时候,若发现前期的参数不合理(包括齿轮过大、相互有干涉、制造与安装困难等),就需要及时的返回上面程序重新来过7、画出关键轴系的简图(一般是重载轴,当然,各个轴系都做一遍当然好),画出各个轴端的弯矩图、转矩图,从而找出危险截面,并进行轴的强度校核8、低速轴齿轮的强度校核9、安全无问题后,拆分零件图渐开线圆柱齿轮传动设计程序主要用于外啮合渐开线圆柱标准直齿齿轮传动设计、渐开线圆柱标准斜齿齿轮传动设计和渐开线圆柱变位齿轮传动设计。
程序中的各参数和各设计方法符合相关的国家标准,即:渐开线圆柱齿轮基本轮廓(GB/T1356-2001)、渐开线圆柱齿轮模数(GB/T1357-1987等效采用ISO54-1977),以及《渐开线圆柱齿轮承载能力计算方法》(GB/T3480-1997等效ISO6336-1966)、渐开线圆柱齿轮精度(GB/T10095-2001等效ISO1328-1997)。
程序根据输入的齿轮传动设计参数和相关设计要求,进行齿轮几何尺寸的计算、齿轮接触疲劳强度校核和弯曲疲劳强度校核的计算,以及相关公差值的计算等。
整个设计过程分步进行,界面简洁,操作方便硬齿面齿轮风力发电增速齿轮箱中,其输入轴承受叶片传过来的轴向力、扭矩和颠覆力矩。
中间轴上的齿轮承受输入端传过来的力矩和输出端刹车时传过来的刹车力矩。
输出轴上的齿轮承受中间轴传过来的扭矩,同时也承受输出端刹车时带来的刹车力矩。
齿轮的设计计算过程

齿轮的设计计算过程
齿轮的设计计算过程可以分为以下几个步骤:
1. 确定设计参数:确定齿轮的类型、传动功率、转速、齿数、模数等设计参数。
2. 确定齿轮的齿数和模数:根据设计参数中的传动功率和转速,计算出齿轮的齿数和模数。
3. 确定齿轮的几何参数:根据齿数和模数,计算齿轮的几何参数,如分度圆直径、齿高、齿厚等。
4. 确定齿轮的强度参数:根据设计参数中的功率和转速,计算齿轮的强度参数,如接触强度和弯曲强度。
5. 进行强度校核:根据计算出的齿轮强度参数,进行强度校核,确定齿轮的寿命和安全系数。
6. 进行结构设计:根据强度校核的结果,进行齿轮的结构设计,包括齿轮轴的直径、齿轮的材料选择等。
7. 进行CAD绘图和制造:根据设计结果,进行CAD绘图和制造,完成齿轮的设计和制造。
需要注意的是,在设计计算过程中,需要考虑到齿轮的噪音、磨损、振动等问题,以确保齿轮的设计质量和可靠性。
齿轮周长计算公式
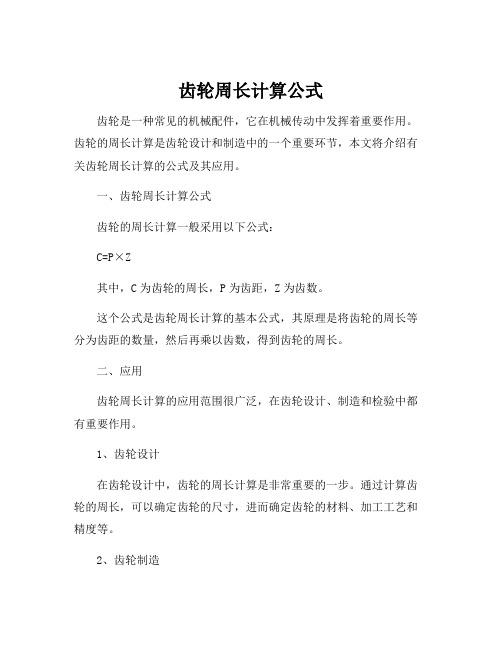
齿轮周长计算公式齿轮是一种常见的机械配件,它在机械传动中发挥着重要作用。
齿轮的周长计算是齿轮设计和制造中的一个重要环节,本文将介绍有关齿轮周长计算的公式及其应用。
一、齿轮周长计算公式齿轮的周长计算一般采用以下公式:C=P×Z其中,C为齿轮的周长,P为齿距,Z为齿数。
这个公式是齿轮周长计算的基本公式,其原理是将齿轮的周长等分为齿距的数量,然后再乘以齿数,得到齿轮的周长。
二、应用齿轮周长计算的应用范围很广泛,在齿轮设计、制造和检验中都有重要作用。
1、齿轮设计在齿轮设计中,齿轮的周长计算是非常重要的一步。
通过计算齿轮的周长,可以确定齿轮的尺寸,进而确定齿轮的材料、加工工艺和精度等。
2、齿轮制造在齿轮制造过程中,齿轮周长计算是制定加工方案的基础。
通过计算齿轮的周长,可以确定齿轮的针齿量、插齿量等工艺参数,从而制定加工方案。
3、齿轮检验在齿轮检验中,齿轮的周长计算可以用于确定齿轮的精度和误差。
通过实测齿轮的周长,可以对齿轮的齿距、齿数等参数进行核对,进而确定齿轮是否符合设计要求。
三、注意事项在进行齿轮周长计算时,需要注意以下几点:1、齿距应该根据齿轮的使用情况和设计要求进行合理选择。
2、齿数应该根据齿轮传动的需求进行选择,不宜太小或太大。
3、齿轮的周长计算应该结合实际情况进行,不同类型的齿轮有不同的计算方法和公式。
四、结语齿轮的周长计算是齿轮设计、制造和检验中的重要环节,也是机械传动中不可或缺的一部分。
通过本文介绍的公式和应用,相信大家对齿轮周长计算有了更深入的了解,从而能够更好地进行齿轮的设计、制造和检验。
单个齿轮和两个齿轮啮合参数计算

单个齿轮和两个齿轮啮合参数计算齿轮是一种常见的传动机构,广泛应用于各种机械设备中。
齿轮主要通过啮合齿轮上的齿来实现动力的传递和转换。
在设计和使用齿轮时,需要进行一些参数计算,以确保齿轮的正常运行和性能满足需求。
单个齿轮的参数计算主要包括模数、齿轮轮齿数、齿轮直径和啮合齿轮的齿轮间隙。
在设计单个齿轮时,需要根据齿轮基本参数计算齿轮的尺寸和齿数。
以下是单个齿轮的参数计算步骤:1.确定齿轮传动比齿轮传动比是齿轮传动的核心参数,决定了输入轴和输出轴的转速比。
根据实际需求和设备的工作条件,确定齿轮传动比。
2.确定模数模数是齿轮齿尺寸的基本参数,通常由制造工艺和实际需求确定。
根据需要的传动比和齿数,确定合适的模数。
3.确定齿轮轮齿数根据传动比和模数,确定输入轴和输出轴上的齿轮齿数。
一般要求两个啮合齿轮的齿数之和为偶数,以确保齿轮传动的平稳性。
4.确定齿轮直径根据齿数和模数,计算齿轮的外径。
外径是齿轮传动中重要的尺寸参数,直接影响传动比和齿轮的承载能力。
5.确定啮合齿轮的齿轮间隙齿轮间隙是啮合齿轮中两相邻齿的间隔大小。
在设计齿轮传动时,需要保证啮合齿轮之间存在一定的间隙,以便齿轮的正常运转。
通过以上步骤计算得到的单个齿轮参数可以用于制造齿轮,并进行齿轮传动的设计和组装。
两个齿轮的啮合参数计算包括传动比、齿宽、齿隙、传动效率等。
在设计和计算两个齿轮的啮合参数时,需要注意以下几点:1.确定传动比:传动比是齿轮传动中非常重要的参数,决定了输入轴和输出轴的转速比。
传动比的计算公式为输出轴齿数除以输入轴齿数。
例如,若输出轴齿数为40,输入轴齿数为20,则传动比为22.确定齿宽:齿宽是齿轮上啮合齿的宽度。
齿宽的计算需要考虑到传递的力矩和承载能力,一般采用公式:齿宽=2*模数。
3.确定齿隙:齿隙是齿轮间的间隔,有助于齿轮的啮合。
齿隙的计算需要考虑到齿轮的精度,一般采用公式:齿隙=齿高-齿厚。
4.确定传动效率:传动效率是指传动过程中输入和输出功率之间的比值。
齿轮齿条计算
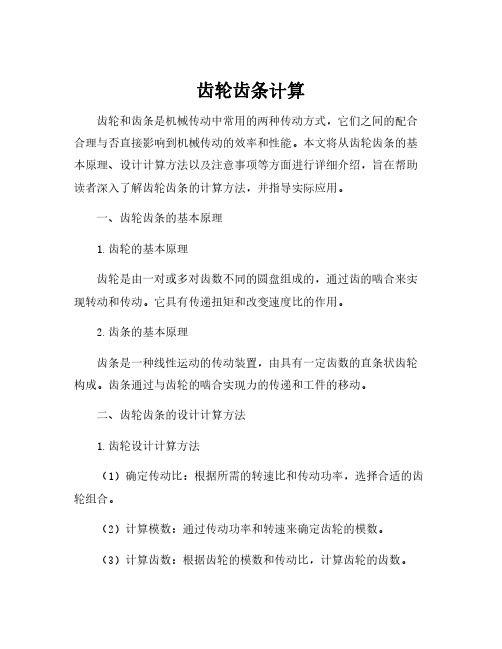
齿轮齿条计算齿轮和齿条是机械传动中常用的两种传动方式,它们之间的配合合理与否直接影响到机械传动的效率和性能。
本文将从齿轮齿条的基本原理、设计计算方法以及注意事项等方面进行详细介绍,旨在帮助读者深入了解齿轮齿条的计算方法,并指导实际应用。
一、齿轮齿条的基本原理1.齿轮的基本原理齿轮是由一对或多对齿数不同的圆盘组成的,通过齿的啮合来实现转动和传动。
它具有传递扭矩和改变速度比的作用。
2.齿条的基本原理齿条是一种线性运动的传动装置,由具有一定齿数的直条状齿轮构成。
齿条通过与齿轮的啮合实现力的传递和工件的移动。
二、齿轮齿条的设计计算方法1.齿轮设计计算方法(1)确定传动比:根据所需的转速比和传动功率,选择合适的齿轮组合。
(2)计算模数:通过传动功率和转速来确定齿轮的模数。
(3)计算齿数:根据齿轮的模数和传动比,计算齿轮的齿数。
(4)计算齿轮尺寸:根据齿数和模数,计算齿轮的直径、齿宽等尺寸。
2.齿条设计计算方法(1)确定齿条的模数:根据工作载荷和所需的尺寸精度,选择合适的齿条模数。
(2)计算齿条的齿数:根据齿条的模数和长度,计算齿条的齿数。
(3)计算齿条的尺寸:根据齿数和模数,计算齿条的宽度、高度等尺寸。
三、齿轮齿条计算的注意事项1.合理设计齿轮齿条的啮合角和啮合线速度,避免啮合不良和过高的载荷。
2.设计时要考虑齿轮齿条的工作环境和要求,选择合适的材料和表面处理方式,以提高其使用寿命和性能。
3.在实际应用中,要注意齿轮齿条的润滑和保养,定期检查和更换磨损严重的齿轮齿条部件。
齿轮齿条作为机械传动中常用的方式之一,其设计计算方法的合理与否对传动效率和性能有着直接的影响。
通过本文的介绍,读者不仅可以全面了解齿轮齿条的基本原理和设计计算方法,还能掌握齿轮齿条计算的注意事项,有助于在实际应用中对齿轮齿条进行准确的计算和选用,以提高机械传动的效率和使用寿命。
齿轮齿面方程
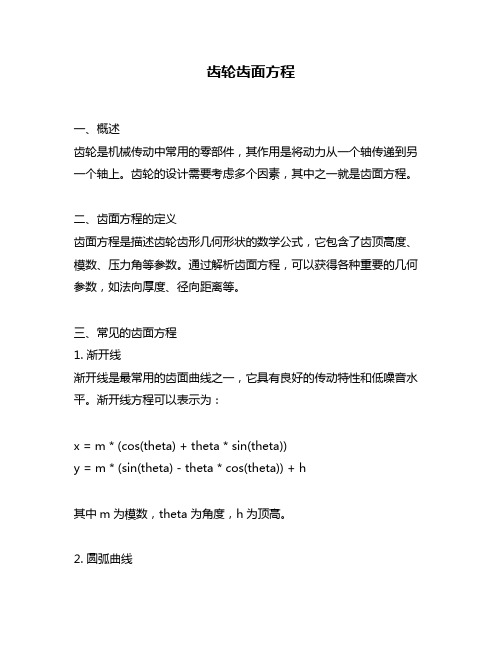
齿轮齿面方程一、概述齿轮是机械传动中常用的零部件,其作用是将动力从一个轴传递到另一个轴上。
齿轮的设计需要考虑多个因素,其中之一就是齿面方程。
二、齿面方程的定义齿面方程是描述齿轮齿形几何形状的数学公式,它包含了齿顶高度、模数、压力角等参数。
通过解析齿面方程,可以获得各种重要的几何参数,如法向厚度、径向距离等。
三、常见的齿面方程1. 渐开线渐开线是最常用的齿面曲线之一,它具有良好的传动特性和低噪音水平。
渐开线方程可以表示为:x = m * (cos(theta) + theta * sin(theta))y = m * (sin(theta) - theta * cos(theta)) + h其中m为模数,theta为角度,h为顶高。
2. 圆弧曲线圆弧曲线也是一种常见的齿面曲线,在低速大扭矩应用中表现良好。
圆弧曲线方程可以表示为:x = r * sin(theta)y = r - r * cos(theta)其中r为半径,theta为角度。
3. 阿基米德螺线阿基米德螺线是一种特殊的曲线,其斜率为常数,因此在制造时易于加工。
阿基米德螺线方程可以表示为:x = r * cos(theta)y = r * sin(theta) + h * theta / (2 * pi)其中r为半径,theta为角度,h为顶高。
四、齿面方程的应用齿面方程是齿轮设计中非常重要的一部分。
通过解析齿面方程,可以计算出各种重要参数,如法向厚度、径向距离等。
这些参数对于齿轮的性能和寿命都有着至关重要的影响。
此外,在制造过程中,齿面方程也起着至关重要的作用。
通过使用数控加工设备和CAD软件,可以精确地制造出符合设计要求的齿轮。
五、总结齿面方程是描述齿轮几何形状的数学公式。
常见的齿面曲线包括渐开线、圆弧曲线和阿基米德螺线等。
通过解析齿面方程,可以计算出各种重要参数,并精确地制造符合设计要求的齿轮。
齿面方程在齿轮设计和制造中起着至关重要的作用。
- 1、下载文档前请自行甄别文档内容的完整性,平台不提供额外的编辑、内容补充、找答案等附加服务。
- 2、"仅部分预览"的文档,不可在线预览部分如存在完整性等问题,可反馈申请退款(可完整预览的文档不适用该条件!)。
- 3、如文档侵犯您的权益,请联系客服反馈,我们会尽快为您处理(人工客服工作时间:9:00-18:30)。
1.选定类型,精度等级,材料及齿数 (1)直齿圆柱硬齿面齿轮传动 (2)精度等级初定为8级 (3)选择材料及确定需用应力
小齿轮选用45号钢,调质处理,(217-255)HBS 大齿轮选用45号钢,正火处理,(162-217)HBS (4)选小齿轮齿数为Z1=24,Z2=3.2x24=76.8.取Z2=77
2. 按齿面接触强度设计计算
(1)初选载荷系数K t
电动机;载荷状态选择:中等冲击;载荷系数K t 的推荐范围为(1.2-2.5),初选载荷系数K t :1.3, (2)小齿轮转矩
)(29540/97039550000/9550111mm N n P T ⋅=⨯==(3)选取齿
宽系数1=d φ.
⑷取弹性影响系数2
1
8.189MPa Z E =
⑸按齿面硬度查得小齿轮的接触疲劳强度极限为MPa 5801lim =σ。
大齿轮的接触疲劳强度极限为MPa 5202lim =σ
⑹计算应力循环次数
N 1=60n 1jl h =60X970X1X(16X300X15)=4.470X109
N 99
210397.12
.310470.4⨯=⨯=
⑺取接触疲劳寿命系数K .89.0,88.021==HN HN K ⑻计算接触疲劳许用应力 取失效概率为1%,安全系数S=1
[]a HN H MP MPa S
K 4.5105709.01lim 11=⨯==σσ
[]a HN H MP MPa S
K 8.46253095.02
lim 22=⨯==σσ
⑼按齿面接触强度设计计算 ①试算小齿轮分度圆直径
mm Z u u T K d H E d t t 248.56)8
.4628.189(2.32.4110954.28.132.2)][(132.232
4
3211=⨯⨯⨯=+〉σφ②计算齿
轮圆周转速v 并选择齿轮精度 s m n d V t /48.21000
60970
248.561000
601
1=⨯⨯⨯=
⨯=
ππ
③计算齿轮宽度b
mm d b t d 248.56248.5611=⨯=⨯=φ
④计算齿轮宽度b 与齿高h 之比
模数 mm mm Z d m t 033.222
72.44111===
齿高 mm mm m h 574.4033.225.225.21=⨯==
67.10=h
b
⑤计算载荷系数
根据v=2.27m/s 。
8级精度得,动载系数08.1=v K
75
.1;1===A F H K K K αα
26.1,342.1==ββF H K K
故载荷系数 403.326.1342.115.175.1=⨯⨯⨯=⨯⨯⨯=βαH H v A K K K K K ⑥按实际的载荷系数校正所算的分度圆直径
mm K K d d t t 616.792
.1403.372.4433
11=⨯== ⑦计算模数m
mm mm Z d m 513.224
616.7911===
3、按齿根弯曲强度设计 ⑴确定各计算值
①MPa MPa FE FE 380,52021==σσ
②弯曲疲劳寿命系数88.0,85.021==FN FN K K ③计算弯曲疲劳许用应力
取弯曲疲劳安全系数S=1.4,由式(10-12)得 小齿轮的弯曲疲劳安全系数为334.29Mpa 大齿轮的弯曲疲劳系数为257.86Mpa 4)计算在载荷系数
K=KaKvK Fa K FB =1.75X1.15X1X1.26=2.536 5)查取齿形系数 Y Fa1=2.65 Y Fa2=2.28 6)查取应力校正系数 由表(10-5)查得 Ysa 1=1.58 Ysa 2=1.83 (2)设计计算
带入公式求得,m ≥1.61mm
对比计算结果,由齿面的接触的接触疲劳强度计算的模数m ≥齿根强度计算的模数,由于齿轮模数m 的大小主要取决于弯曲强度所决定的承载能力,而齿面接触疲劳强度所决定的承载能力,仅于齿轮直径有关,可去弯曲疲劳强度模数2.513,就近圆整为标准值m =3mm ,接触疲劳强度算得分度圆直径为79.616mm ,算出小齿轮齿数
Z1=d1B/m=79.616/3=26.54≈27
Z2=3.2X27=84.9≈85,取Z2=85 4.几何尺寸计算
(1)分度圆直径
d1=z1m=27X3=81mm
d2=z2m=85X3=255mm (2)齿轮宽度b=1X81=81mm 取B2=81mm B1=86mm
齿轮的加工制造
.齿轮的制造主要内容包括确定齿轮毛皮制造方法、选择齿轮的定位基准。
选择吃配和吃面的加工方案、确定齿轮加工工艺过程。
1、确定齿轮毛坯制造方法
齿轮的毛坯形式有棒料。
锻件、铸件三种选择。
锻件用于强度高、耐磨性好、耐冲击的齿轮。
锻件锻后腰进行正火处理,消除锻造应力、改善晶粒组织和切削性能。
2、选择齿轮加工的定位基准。
(1)定位要求、
①齿轮加工时的定位基准应可能的与装配基准、测量基准相一致,以避免基准不重合产生的误差,符合基准重合原则
②在齿轮加工的整个过程中应尽可能的采用相同的定位基准
详细的加工过程的各个基准
(2)滚齿机方案的选择
普通中小型滚齿机的性能特点:
使用广泛,产品型号多。
只具备一般性能,如一次方框工作循环,可顺切、逆切滚齿,滚刀自动窜刀,有车削速度和进给量的变换机构,能做快速机动调整。
多数为工作台径向移动的立式布局,少数有卧式布局。
主要供各类机械加工和修理厂单件小批量生产使用。
加工精度一般为6-7级。
本工件可以采用滚齿加工方法加工齿轮齿面。
滚齿机的型号:Y3150E(机械加工工艺师手册表14-3 P324)
最大加工直径X最大模数 500x8
滚刀工作台最小中心距 30
加工范围齿宽250 螺旋角55 最少加工齿数6 工作台尺寸 510 mm
级数 9
范围 40-250
表面粗糙度 3.2
等级 5-6-7
重量 4.5t
外形尺寸 2439x1272x1770
渐开线齿轮滚刀的选择:
机械加工工艺装备设计手册341页表2-170GB6083-85
选择滚刀型号m3AGB6083-85
D e =80mm ,L =80mm ,Z =14
滚齿机的主运动传动链:
换置计算:两端件:
电动机——滚刀主轴 计算位移
n 电(r/min )——n 刀(r/min )
运动平衡式
u2-3——轴II-III 间的可变传动比;共三种:
刀
n B
A u =⨯⨯⨯⨯
⨯⨯⨯⨯-80
202828282828284221165115143032
u=27/43;31/39;35/35;
A/B ——变速挂轮;三种 A/B=22/44;33/33;44/22 根据滚刀的转速,计算uv ,并决定u2-3的啮合位置和A/B
查表37-15机械加工工艺师手册:fa =1.0mm/r
查表37-18精切齿轮的切削速度 单边余量 0.2,进给量1.0.,则查得切削速度为21m/min.
n 刀=1000X21/πde =83.60r/min
当u 2-3=27/43时,应取A B 为33/33. 取挂轮的A B 为33/33. 滚齿机的展成运动传动链
传动路线:换置计算
两端件 z
k d c b a f e u =⨯⨯⨯⨯⨯⨯⨯⨯721156422828282828282080
1合。