典型天然气液化流程的功耗比较
天然气液化技术介绍
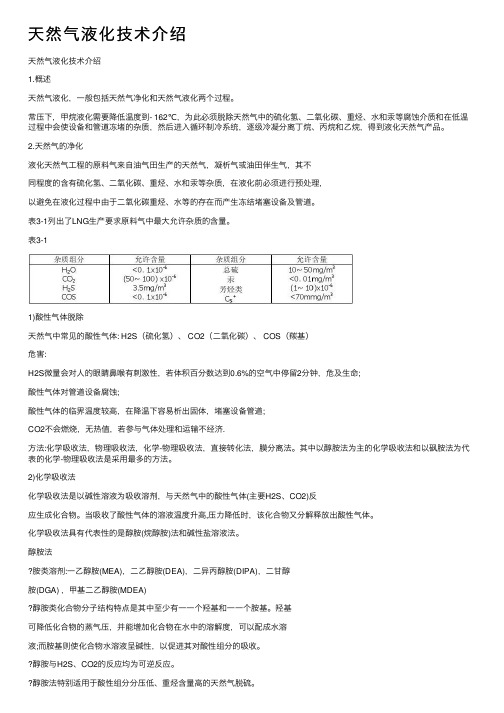
天然⽓液化技术介绍天然⽓液化技术介绍1.概述天然⽓液化,⼀般包括天然⽓净化和天然⽓液化两个过程。
常压下,甲烷液化需要降低温度到- 162℃,为此必须脱除天然⽓中的硫化氢、⼆氧化碳、重烃、⽔和汞等腐蚀介质和在低温过程中会使设备和管道冻堵的杂质,然后进⼊循环制冷系统,逐级冷凝分离丁烷、丙烷和⼄烷,得到液化天然⽓产品。
2.天然⽓的净化液化天然⽓⼯程的原料⽓来⾃油⽓⽥⽣产的天然⽓,凝析⽓或油⽥伴⽣⽓,其不同程度的含有硫化氢、⼆氧化碳、重烃、⽔和汞等杂质,在液化前必须进⾏预处理,以避免在液化过程中由于⼆氧化碳重烃、⽔等的存在⽽产⽣冻结堵塞设备及管道。
表3-1列出了LNG⽣产要求原料⽓中最⼤允许杂质的含量。
表3-11)酸性⽓体脱除天然⽓中常见的酸性⽓体: H2S(硫化氢)、 CO2(⼆氧化碳)、 COS(羰基)危害:H2S微量会对⼈的眼睛⿐喉有刺激性,若体积百分数达到0.6%的空⽓中停留2分钟,危及⽣命;酸性⽓体对管道设备腐蚀;酸性⽓体的临界温度较⾼,在降温下容易析出固体,堵塞设备管道;CO2不会燃烧,⽆热值,若参与⽓体处理和运输不经济.⽅法:化学吸收法,物理吸收法,化学-物理吸收法,直接转化法,膜分离法。
其中以醇胺法为主的化学吸收法和以砜胺法为代表的化学-物理吸收法是采⽤最多的⽅法。
2)化学吸收法化学吸收法是以碱性溶液为吸收溶剂,与天然⽓中的酸性⽓体(主要H2S、CO2)反应⽣成化合物。
当吸收了酸性⽓体的溶液温度升⾼,压⼒降低时,该化合物⼜分解释放出酸性⽓体。
化学吸收法具有代表性的是醇胺(烷醇胺)法和碱性盐溶液法。
醇胺法胺类溶剂:⼀⼄醇胺(MEA),⼆⼄醇胺(DEA),⼆异丙醇胺(DIPA),⼆⽢醇胺(DGA) ,甲基⼆⼄醇胺(MDEA)醇胺类化合物分⼦结构特点是其中⾄少有⼀⼀个羟基和⼀⼀个胺基。
羟基可降低化合物的蒸⽓压,并能增加化合物在⽔中的溶解度,可以配成⽔溶液;⽽胺基则使化合物⽔溶液呈碱性,以促进其对酸性组分的吸收。
典型天然气液化流程的功耗比较

近年来 , 在工 程实践 中 , 用 了许 多天然气 和煤 应 层气 的液化 流程 u“J 。本文对 国内外 常用 的 5种 典 型天 然气液 化流程— — N 膨 胀制 冷 、 H N +C 膨胀
率 为 0 8 .;
除 N 膨胀 制冷 流程外 , : 其他 工艺 均 以优化后 的 制 冷剂 配 比计算 。
第3 0卷
第1 0期
进 行一次 分离 , 可采用 2组 混合制 冷剂 换热器 。 ④ 丙烷 预冷混 合制冷 剂二 次分 离流程 丙烷 预冷部 分 与一次分 离 流程相 同 。混 合制 冷
制冷 、 丙烷预 冷混合 制冷 剂一 次分离制 冷 、 烷预冷 丙 混合 制冷剂 二次 分离 制 冷 、 混合 制 冷 剂 制冷 等 5种 流程 进行 功耗 比较 。
2 流 程要 点
① N 膨胀流程 :
双 机膨胀 , 二级 膨胀 机 出 口不带液 , 增压机 功率
全部有 效利用 。
有效利 用 。
离罐 ; 功耗 计算 中均不 含天然 气压缩 、 净化及 公用耗
③Leabharlann 丙烷预冷混合制冷剂一次分离流程
电; 天然气液相节流后气化分率为 0 制冷剂液相节 ;
流后 压力 为 04M a压 缩 机 水 冷后 温度 为 3 8K; . P ; 0
膨胀 机 的等熵效 率为 0 8 ; 冷剂 压 缩机 的 等熵 效 .5 制
天然气液化工艺流程分析及其优选

天然气液化工艺流程分析及其优选天然气是重要的民生物资,在实际对接市场的过程中往往以液化气的形式而存在。
不同的液化装置在效率、能耗等方面存在一定的差异,故而做好其流程分析与优选对后续具体的工作体系构建与相关的工程建设具有积极意义。
文章以此为切入点在系统探究流程的基础上对不同工艺的特征进行总结,旨在为具体的优选提供必要基础。
标签:天然气;液化工艺;流程分析;工艺优选天然气是重要的清洁能源物质,对人民的生活与生产具有决定性作用。
在实际的运行过程中,往往通过液化技术来做到对天然气的提纯与压缩,进而帮助其更好的参与运输、销售及应用。
在实际的工艺流程中,其大致可以分为如下三个环节,即提纯、液化、分装。
其中提纯与液化为主要的质量控制过程。
而从实践经验来看,不同的工艺选择往往决定于相关液化流程的实际产能、成本规划等,也各自具有不同的特征。
根据企业的实际情况进行合规的优选能够有效的形成对生产成本的控制、对生产质量的控制以及对设备效能的提升。
本文以此为研究目的,对相关流程工艺进行分析,并探究不同模式下的优劣,旨在为后续的优选提供决策参考。
1 天然气液化工艺优化原则分析天然气液化工艺是天然气生产与输送的关键,该环节也是运输与销售过程中的主要耗能环节,并对安全生产有着较高的要求。
在此基础上,现阶段针对其工艺流程的设计与优化成为了研究的重点。
按照现行不同的工艺流程其安全系数、操作难度、设备场地、设备成本、工艺运维均存在较大的不同。
探究各类工艺与设备的原理与工况不同是形成有效选择与工艺优化的基础。
在实际的设计与应用过程中工艺优化应该本着如下原则来进行:一是需要保障工艺的合规性:所谓的合规性主要是指工艺的设计需要符合相关的科学事实以及现阶段的技术特征。
尤其是在天然气液化的过程中由于对生产安全具有较高的要求,更是对其技术的成熟程度有着较高的要求,通过实验工艺以及试运行工艺的方式来确定新型技术的稳定性与参数是一种可行模式,而不能贸然的大范围引入并不成熟的相关技术,以免形成安全生产事故;二是需要保障工艺的适应性:所谓的适应性主要是指不同的天然气液化工艺流程需要根据天然气的原料气特性来进行规划。
2020年常用的天然气液化流程

常用的天然气液化流程常用的天然气液化流程不同液化工艺流程,其制冷方式各不相同。
在天然气液化过程中,常用天然气液化流程主要包括级联式:液化流程、混合制冷剂液化流程与带膨胀机的液化流程,它们的制冷方式如下。
一、级联式液化流程由若干个在不同温度下操作的制冷循环重叠组成,其中的高、中、低温部分分别使用高、中、低温制冷剂。
高温部分中制冷剂的蒸发用来使低温部分中的制冷剂冷凝,低温部分制冷剂再蒸发输出冷量,用几个蒸发冷凝器将这几部分联系起来。
蒸发冷凝器既是高温部分的蒸发器又是低温部分的冷凝器。
对于天然气液化,多采用由丙烷、乙烯和甲烷为制冷剂的三级复叠式制冷循环。
级联式液化流程的优点主要包括:1、逐级制冷循环所需的能耗最小,也是目前天然气液化循环中效率最高的流程。
2、与混合制冷剂循环相比,换热面积较小;3、制冷剂为纯物质,无配比问题;4、各制冷循环系统与天然气液化系统彼此独立,相互影响少、操作稳定、适应性强、技术成熟。
级联式液化流程的缺点:1、流程复杂、所需压缩机组或设备多,至少要有3台压缩机,初期投资大;2、附属设备多,必须有生产和储存各种制冷剂的设备,各制冷循环系统不允许相互渗漏,管线及控制系统复杂,管理维修不方便;3、对制冷剂的纯度要求严格。
根据级联式液化流程的以上特点,该流程无法满足小型撬装式LNG 装置对设备布局要求简单紧凑的要求,因此只适用于大型装置,常用于2X104~5X104m3/d的装置。
通过优化设备的配置,级联式液化流程可以与在基本负荷混合制冷剂厂中占主导地位的带预冷的混合制冷剂循环相媲美。
二、混合制冷剂液化流程该工艺是20世纪60年代末期,由级联式制冷工艺演变而来的,多采用烃类混合物(N2、C1、C2、C3、C4、C5)作为制冷剂,代替级联式制冷工艺中的多个纯组分,其组成根据原抖气的组成和压力确是,利用多组分混合物中重组分先冷凝、轻组分后冷凝的特性,将其依次冷凝、分离、节流、蒸发得到不同温度级的冷量,又据混合制冷剂是否与原料天然气相混合,分为闭式和开式两种混合制冷工艺。
天然气液化工艺技术比较

天然气液化工艺技术比较基本负荷型LNG 大多采用丙烷/ 混合制冷(C3/MR)工艺(C3 是工艺代号),该工艺是由空气产品及化学公司APCI (Air Product s and Chemicals Inc. )于20 世纪70 年代发明的,全世界大约95%的LN G工艺是在该工艺的基础上演变而来的,该工艺通常采用蒸汽轮机或燃气轮机驱动压缩机,冷却方式可采用水冷和空冷等。
近年来,随着低温热交换器制造技术的发展,丙烷/ 混合制冷工艺得到更加广泛的运用,装置的生产规模达到了每年400X104 t 。
近期LNG工业快速增长再次刺激了LN G工艺的技术发展,也使一些传统的LNG 生产工艺得到了关注,尤其是混凝土结构的、驳船型、浮式LNG 装置等小规模LNG 项目的应用。
例如:Phillips 在大西洋LNG 项目(the At lant ic LNGproject )中,采用复迭式工艺,使该工艺再次受到关注。
Pritchard 在PRICO 工艺的基础上对单混合制冷工艺的功耗效率进行了很大改进,使该工艺能用于陆上或海上LN G 生产装置。
一、比较基础由于技术内容无法公开获得,所以在实践中对不同工艺的逐项比较是很困难的。
因此,笔者仅使用相同的条件(冷却介质、原料气、标准、费用)对优化的丙烷/ 混合制冷工艺与其他较好的4 类工艺进行了比较,它们是:丙烷/ 混合制冷工艺(C3/ MR)、复迭式制冷工艺(CCS )、改进的双混合式制冷工艺(DMR)、改进的单混合式制冷工艺(SMR)和带预冷的氮膨胀制冷工艺(工艺代号为N2)。
为方便比较,假定LNG 装置采用相同的预处理单元。
研究的限定条件为:原料气温度为25 C、压力为60 MPa;原料气组分体积含量为甲烷85. 1% 、乙烷6. 5%、丙烷3%、丁烷1. 2% 、戊烷及重组分0. 5%氮气1. 5%、二氧化碳2. 2% ;环境平均温度27 C;回收的LPG 组分重新注入LNG;所有的工艺都采用空气冷却系统;LNG 的贮存及装载设施,通用设施不在研究的范围内。
影响天然气液化流程性能的参数分析研究

维普资讯
1 2
油 气 田地 面 工 程 第 2 5卷 第 6期 ( 0 6 6 20 . )
何 立华 ( 中国石油大学经济管理学院)
摘要 分 析 了钻 井工程 项 目实施过 程 中
部门。
( )项 目组织远 外层 利益 相关 者 。除 了 以上这 3 些 主要 和直接 利益 相关 者 以外 ,还有 一些 机构 和部
门与项 目组织 间接地 发 生联 系 ,包括 政府 部 门 、金 融 机构 、司 法 部 门 、服 务 部 门 、新 闻单 位 和 社 区 单位。 2 .钻 井工 程项 目利 益相 关者 之 间的主 要纷 争 项 目不 同 的参 与 者对 项 目有 不 同 的期 望 和需
量的变 化 对 流 程 性 能 的 影 响情 况 ,改 变 甲 烷 含 量
由图 1可 以得 出 以下结 论 : ( )相 同储 存 压 力 下 ,随着 储 存 温 度 的降 低 , 1 天 然气 的液 化 率逐渐 上 升 。而 且温 度越 接近 泡点温
度 ,天 然气 液化 率上 升 的越快 。
之 间 的关 系 ( 见图 1 。 )
Z UU 2 U0 2 0 Z U 3U ) UU 3 0 2 4 60 U UU 2 4 0 )6 ) uu UU
高压制冷剂压 力(P ) k a
图 2 混 合 制 冷 剂 流量 与 高 压 制 冷 剂 压 力 关 系
( ) 混合 制冷剂 组成 对流 程性 能 的影响 。混 合 2 制 冷剂是 由氮 、甲烷 、乙烷 和丙烷 等组 分组 成 的混 合 物 。各组 分 的 比例一般 是根 据要 液化 的天 然气 的
天然气液化流程工艺选择优化

天然气液化工艺流程方案选择优化液化厂的工艺系统主要包括净化工艺系统、液化工艺系统和存储系统。
工艺优化主要体现在:液化中制冷方式的优化和储存方式的优化。
一、液化制冷方式的选择:天然气液化为低温过程。
天然气液化所需冷量是靠外加制冷循环来提供,配备的制冷系统就是要使得换热器达到最小的冷、热流之温差,并因此获得极高的制冷效率。
天然气液化的制冷系统已非常成熟,常用的工艺有:阶式制冷循环、混合冷剂制冷循环、膨胀机制冷循环。
1、阶式制冷循环阶式制冷循环1939年首先应用于液化天然气产品,装于美国的Cleveland,采用NH、C2H4为第一、第二级制冷剂。
经典阶式制冷循环由三个独立的制冷系统组成。
第一级采用丙烷做制冷剂,经过净化的天然气在丙烷冷却器中冷却到-35〜-40 C,分离出戊烷以上的重烃后进入第二级冷却。
由丙烷冷却器中蒸发出来的丙烷气体经压缩机增压,水冷却器冷却后重新液化,并循环到丙烷冷却器。
第二级采用乙烯做制冷剂,天然气在第二级中被冷却到-80〜-100 C,并被液化后进入第三级冷却。
第三级采用甲烷做制冷剂,液化天然气在甲烷冷却器中被过冷到-150〜-160 C,然后通过节流阀降压,温度降到-162 C后,用泵输送到LNG 贮槽。
甲烷冷却器中蒸发出来的气体经增压、水冷后,在丙烷冷却器中冷却、在乙烯冷却器中液化后,循环到甲烷冷却器。
经典阶式制冷循环,包含几个相对独立、相互串联的冷却阶段,由于制冷剂一般使用多级压缩机压缩,因而在每个冷却阶段中,制冷剂可在几个压力下蒸发,分成几个温度等级冷却天然气,各个压力下蒸发的制冷剂进入相应的压缩机级压缩。
各冷却阶段仅制冷剂不同,操作过程基本相似。
从发展来看,最初兴建LNG装置时就用阶式制冷循环的着眼点是:能耗最低,技术成熟,无需改变即可移植用于LNG 生产。
随着发展要求而陆续兴建新的LNG装置,这时经典的阶式制冷循环就暴露出它固有的缺点:1)经典的阶式制冷循环由三个独立的丙烷、乙烯、甲烷制冷循环复迭而成。
液化工艺及其控制方案的分析

到达下游用户的天然气其热值应达到 3 . JN 。 37M / m 及 以上 。而表 1 出的净化气体 的热值为 3 .9 给 27 , 低于我 国现行 的规定 , 主要原 因就是 富含了约 2% 0 的氮气 。因此 , 化单 元必 须将 不凝气 氮气脱 除 , 液 以 提高 天 然 气 热 值 。 根 据 文 献 [ ] 描 述 , 用 了 1 中 采
起 回换热 器复 热后 , 分 作 为制 冷 气 的补充 气 进 部 入制冷剂循环系统 , 部分在高空放空。
一
冷量 , 精馏塔塔顶出料为氮气和甲烷气的混合物 , 甲 烷 含量 约 为 4 5 , 度 约 为 一15 5C, 产 品气 .% 温 7 . ̄ 与
液分离 器 的 B G( 常 由于 L G过冷 不 产生 B G) O 通 N O 商ຫໍສະໝຸດ *圃 CII2 C
◇ 一
I
.
* 1 * i CI C 0 l l ! , 5 T 册 C 一 T 0
‘
。
一 E l5 、 x0 0、 J 、
), ( / cK << I
!
.
一
J l
【
;
 ̄ 02 f圆 I 10l< < 1 l 1一 03 1 1 0/ 4 一E5
Ke r s: r o—d n ti e t n;n t a a y wo d c y e irf a i i o aur lg s;lq ea to c n r ls se i u f cin; o to y tm
二 十一 世 纪 是 天 然 气 成 为 主 流 清 洁 能 源 的 时
在 图 1中, 化天 然 气 先 经 过 预 冷换 热 器 净 E 0 0 预冷, 152 再进入重烃分离器 S00 , 15 1 气相进入 脱氮塔塔底作为再沸器热源 , 重烃经液化换热器 复 热后出冷箱去储存。天然气在脱氮塔底被冷却后进 入液化换热器 E 00 , 153 温度被进一步降低并全部液 化变成饱和 L G, N 经过节流后温度降为 一 3  ̄ 压 18 C, 力降为 0 4 P G 进入精馏塔脱 氮 , 馏塔压力约 .M a , 精 04 P ( 高 于 L G储 存 压 力 ) 脱 氮后 的饱 和 .M a 略 N , L G从塔底流 出, N 经过 L G过冷器 E 0 0 N 156深冷后 再节流进入 产 品气液 分离器 ¥00 , 152 生成 的少 量 B G与脱氮塔 富氮排放气 汇合经过换热器 复热后 O 部 分作为制 冷循环 系统 的补充 气 ( 10 m / 约 5 N 3
天然气液化流程技术方案的选择与比较
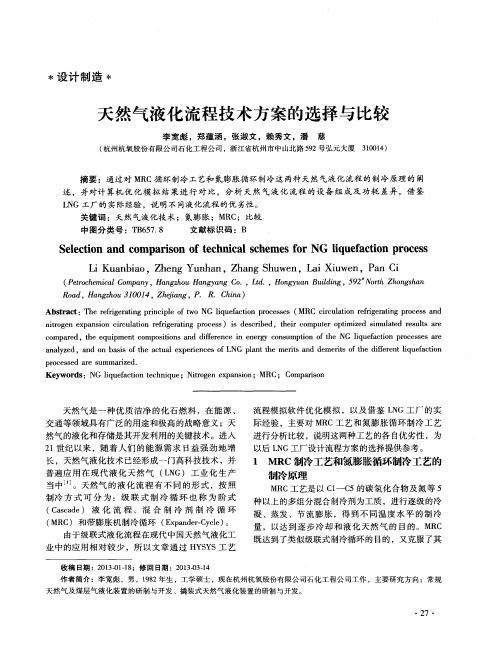
流程模拟软件优 化模拟 ,以及借鉴 L N G工厂的实 际经验 ,主要 对 MR C工 艺 和氮 膨胀 循 环 制 冷 工 艺
进行 分 析 比较 ,说 明这 两种 工艺 的各 自优劣 性 ,为 以后 L N G工 厂设 计 流程方 案 的选择 提供 参考 。
然气 的液化 和存 储是 其 开发 利用 的关 键技 术 。进入 2 1世纪 以来 ,随着 人 们 的 能 源 需 求 日益 强 劲 地 增 长 ,天 然气 液 化技 术 已经形 成 一 门高科 技技 术 ,并 普遍 应 用 在 现 代 液 化 天 然 气 ( L N G) 工 业 化 生 产
a na l y z e d,a n d o n b a s i s o f t he a c t u a l e x pe ie r n c e s o f LNG p l a n t t he me it r s a n d d e me it r s o f t he d i f f e r e n t l i q u e f a c t i o n p r o c e s s e d a r e s u mma r i z e d .
当,按 照
1 MR C制冷 工艺和氮 膨胀循环 制冷工艺 的 制冷原理
MR C工 艺是 以 C 1 一C 5的碳 氢 化 合 物及 氮 等 5 种 以上 的多 组分 混合制 冷剂 为工 质 ,进行 逐级 的冷
凝 、蒸 发 、节 流 膨 胀 ,得 到 不 同 温 度 水 平 的 制 冷
米设 计 制 造 术
天然 气液 化流程技术 方案 的选择与 比较
李 宽彪 ,郑 蕴 涵 ,张淑 文 ,赖 秀 文 ,潘 慈
3 1 0 0 1 4 ) ( 杭 州杭 氧股份有限公 司石化工程公 司 ,浙江省杭州市 中山北路 5 9 2号 弘元大 厦
三、LNG原理

10
1.3混合冷剂液化工艺
11
1.3 混合冷剂液化工艺
12
1.3 混合冷剂液化工艺
工艺特点: 原理:由阶式简化而来,用一种混合制冷剂(C1-C5,N2),利用 其重组分先冷凝,轻组分后冷凝特征,依次节流、气化来 冷凝天然气中对应组分。 优点:工艺简,化设备少,占地小,投资少,维护方便;开启 便捷适合调峰; 缺点:能耗(0.34-0.4 kwh/m^3)比阶式高15%;混合冷剂配比 和液化模拟技术含量高,常涉及专利技术; 适应情况:80年代后基荷性液化装置的工艺,浦东LNG事故调 峰站(20万方/天);新疆广汇( 150万方/天),是目前 最流行的工艺技术。
• 完整的生产线包括冷却、液化及输 送等过程。 • 其生产能力取决于液化工艺流程、 制冷剂、压缩机/驱动设备的最大 功率及所采用的换热器。
23
单级压缩制冷理论循环
降压、降温 节流阀 膨胀机
高 压 液 态
蒸发器
压缩机
吸 热 汽 化
24
天然气液化发展的三个顺序:
•林德过程,依据焦尔-汤姆逊效应, 通过节流阀膨胀,使气体冷却并液 化 •膨胀机过程,使天然气通过膨胀机, 在做外功下降压、冷却和液化 •阶式冷却过程,使天然气在多个冷 却阶中与致冷剂换热、冷却并液化。
13
液化工艺比较
14
液化流程能耗比较
液化流程 阶式液化流程 单级混合制冷剂液化流程 丙烷预冷的单级混合制冷剂液化流程 多级混合制冷剂液化流程 单级膨胀液化流程 能耗比例 1 1.25 1.15 1.05 2
丙烷预冷的单级膨胀液化流程
两级膨胀液化流程
1.7
1.7
15
主要内容
一、天然气液化工艺 二、液化流程优化分析 三、主要设备
2020年常用的天然气液化流程

常用的天然气液化流程常用的天然气液化流程不同液化工艺流程,其制冷方式各不相同。
在天然气液化过程中,常用天然气液化流程主要包括级联式:液化流程、混合制冷剂液化流程与带膨胀机的液化流程,它们的制冷方式如下。
一、级联式液化流程由若干个在不同温度下操作的制冷循环重叠组成,其中的高、中、低温部分分别使用高、中、低温制冷剂。
高温部分中制冷剂的蒸发用来使低温部分中的制冷剂冷凝,低温部分制冷剂再蒸发输出冷量,用几个蒸发冷凝器将这几部分联系起来。
蒸发冷凝器既是高温部分的蒸发器又是低温部分的冷凝器。
对于天然气液化,多采用由丙烷、乙烯和甲烷为制冷剂的三级复叠式制冷循环。
级联式液化流程的优点主要包括:1、逐级制冷循环所需的能耗最小,也是目前天然气液化循环中效率最高的流程。
2、与混合制冷剂循环相比,换热面积较小;3、制冷剂为纯物质,无配比问题;4、各制冷循环系统与天然气液化系统彼此独立,相互影响少、操作稳定、适应性强、技术成熟。
级联式液化流程的缺点:1、流程复杂、所需压缩机组或设备多,至少要有3台压缩机,初期投资大;2、附属设备多,必须有生产和储存各种制冷剂的设备,各制冷循环系统不允许相互渗漏,管线及控制系统复杂,管理维修不方便;3、对制冷剂的纯度要求严格。
根据级联式液化流程的以上特点,该流程无法满足小型撬装式LNG 装置对设备布局要求简单紧凑的要求,因此只适用于大型装置,常用于2X104~5X104m3/d的装置。
通过优化设备的配置,级联式液化流程可以与在基本负荷混合制冷剂厂中占主导地位的带预冷的混合制冷剂循环相媲美。
二、混合制冷剂液化流程该工艺是20世纪60年代末期,由级联式制冷工艺演变而来的,多采用烃类混合物(N2、C1、C2、C3、C4、C5)作为制冷剂,代替级联式制冷工艺中的多个纯组分,其组成根据原抖气的组成和压力确是,利用多组分混合物中重组分先冷凝、轻组分后冷凝的特性,将其依次冷凝、分离、节流、蒸发得到不同温度级的冷量,又据混合制冷剂是否与原料天然气相混合,分为闭式和开式两种混合制冷工艺。
天然气液化装置
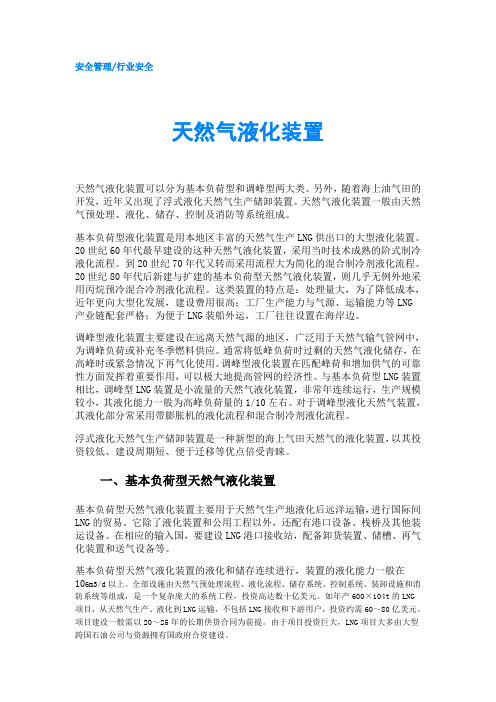
安全管理/行业安全天然气液化装置天然气液化装置可以分为基本负荷型和调峰型两大类。
另外,随着海上油气田的开发,近年又出现了浮式液化天然气生产储卸装置。
天然气液化装置一般由天然气预处理、液化、储存、控制及消防等系统组成。
基本负荷型液化装置是用本地区丰富的天然气生产LNG供出口的大型液化装置。
20世纪60年代最早建设的这种天然气液化装置,采用当时技术成熟的阶式制冷液化流程。
到20世纪70年代又转而采用流程大为简化的混合制冷剂液化流程。
20世纪80年代后新建与扩建的基本负荷型天然气液化装置,则几乎无例外地采用丙烷预冷混合冷剂液化流程。
这类装置的特点是:处理量大,为了降低成本,近年更向大型化发展,建设费用很高;工厂生产能力与气源、运输能力等LNG产业链配套严格;为便于LNG装船外运,工厂往往设置在海岸边。
调峰型液化装置主要建设在远离天然气源的地区,广泛用于天然气输气管网中,为调峰负荷或补充冬季燃料供应。
通常将低峰负荷时过剩的天然气液化储存,在高峰时或紧急情况下再气化使用。
调峰型液化装置在匹配峰荷和增加供气的可靠性方面发挥着重要作用,可以极大地提高管网的经济性。
与基本负荷型LNG装置相比,调峰型LNG装置是小流量的天然气液化装置,非常年连续运行,生产规模较小,其液化能力一般为高峰负荷量的1/10左右。
对于调峰型液化天然气装置,其液化部分常采用带膨胀机的液化流程和混合制冷剂液化流程。
浮式液化天然气生产储卸装置是一种新型的海上气田天然气的液化装置,以其投资较低、建设周期短、便于迁移等优点倍受青睐。
一、基本负荷型天然气液化装置基本负荷型天然气液化装置主要用于天然气生产地液化后远洋运输,进行国际间LNG的贸易。
它除了液化装置和公用工程以外,还配有港口设备、栈桥及其他装运设备。
在相应的输入国,要建设LNG港口接收站,配备卸货装置、储槽、再气化装置和送气设备等。
基本负荷型天然气液化装置的液化和储存连续进行,装置的液化能力一般在106m3/d以上。
天然气液化工艺的对比及应用

天然气液化工艺的对比及应用摘要:随着社会经济的快速发展,天然气已经成为人们日常生活中的重要能源,而液化天然气是天然气利用的一种重要形式,天然气液化是一种要求较高的技术。
天然气液化的工艺一般有两个环节,也就是净化处理与制冷循环。
本文结合工作实践,对天然气液化的工艺方法及选定进行了探讨。
关键词:天然气;净化;液化循环随着我国经济的发展和人口数量增多,人们对能源的需求量也随之日益增长。
天然气是一种清洁、高效、优质的能源与化工原料,逐渐吸引了人们的目光。
目前,天然气主要使用在电力、工业和天然气化工等各个产业,液化天然气(LNG)是一种具有明显优越性的天然气应用形式。
1、天然气的净化1.1 脱酸性气体酸性气体在原料气当中的含量比较多,因此在净化过程中首选就是脱酸性气体,在实践当中技术方法比较多,常见的有醇胺法、Bnefield法、低温甲醇法等。
醇胺法脱除酸性气体是靠醇胺溶液吸收作用来达到净化目的的,常用的醇胺溶剂主要有:一乙醇胺、二乙醇胺、二异丙醇胺等。
在这其中一乙醇胺的碱性最强,脱酸性气体的效果也最好,而且对H2S、C02没有选择项,能够快速、大量的脱除H2S、C02的脱除率,能够达到90%以上。
因此这种方法的适用范围比较广,对脱除装置也没有特殊的要求,但是腐蚀性太强,溶剂损失比较大,成本相对较高。
二乙醇胺的碱性相对一乙弱一些,净化效果也没有前者好,但是在使用缓蚀剂的基础上,可以有效的保证酸性气体的脱除效果,并能大量减少溶液的循环使用量,且腐蚀性较少,成本相对要低一些。
Bnefield法,这种技术方法使用的实际上是碳酸钾与催化剂、防腐剂的多组分水成混合物溶剂,这种方法的适合压力高、酸气含量大的环境,一般来说供气压力需要达到7.0MPa。
酸性气体的含量要达到50%以上最经济、最适合。
1.2 原料气脱水为使天然气中的含水率达到液化的基本要求,需要对原料气进行脱水,这样一方面是为了防止水分析出,在液化的时候结冰堵塞管道或仪表阀门,预防各种天然气液化事故。
LNG原理

− 由两个可逆的绝热过程和两个可逆的等 温过程组成,a-d-c-b-a逆时针循环
38
单级压缩制冷理论循环
•单级压缩制冷性能指标
• ⑴单位制冷量(q0)
−每千克制冷工质在一次循环中所制取 的冷量(亦即在蒸发器内吸收的热量) 称为单位制冷量。
−T-S图上a-d-c-b-a面积。 −也可用式表达:q0=r0(1-x0)
单级压缩制冷理论循环
•工质经过一系列的状态变化后,又 回复到原来状态的过程,热力学上 称为循环过程。 •循环随效果的不同,可分为
−正向循环 −逆向循环
25
单级压缩制冷理论循环
•利用工质的状态变化,将热能转化 为机械能的循环叫作正向循环;
• 所有的热力发动机都是按照这类循 环工作的。 • 正向循环在热力图上依顺时针方向 进行。
39
单级压缩制冷理论循环 • 制冷工质的汽化潜热越大或节流后产生 的蒸汽越少,则循环的单位制冷量越大 • 制冷工质的蒸发潜热因制冷工质的种类 而不同,而节流后干度的大小不仅于制 冷工质的种类有关,而且与节流膨胀前 后的压力范围有关,膨胀的范围越大则 膨胀后的干度(x0)也越大。
40
单级压缩制冷理论循环
− 普通制冷,制冷温度≥-153℃ − 深度制冷,制冷温度≤ -153℃
22
单级压缩制冷理论循环
•制冷方法
−液体蒸发热的利用 −固体融化热的利用 −固体升华热的利用
−气体膨胀热的利用
−利用温差效应
23
单级压缩制冷理论循环
•
•
−
−
基本循环:
一台制冷机的四个基本部件:
压缩机
冷凝器
ห้องสมุดไป่ตู้
−
−
三种混合制冷剂循环液化天然气的比功耗和(佣)对比
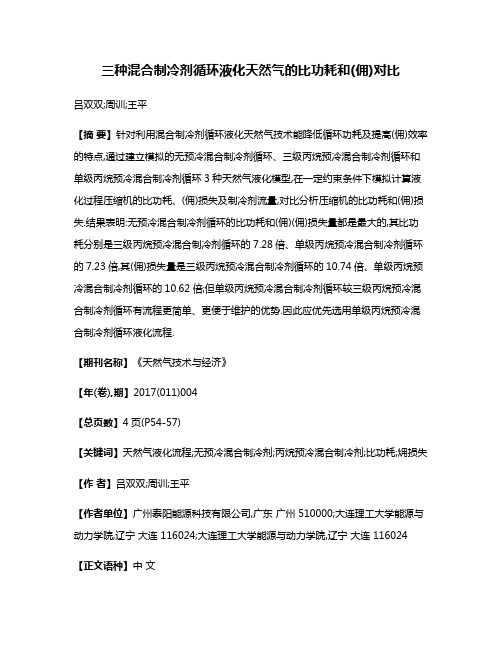
三种混合制冷剂循环液化天然气的比功耗和(佣)对比吕双双;周训;王平【摘要】针对利用混合制冷剂循环液化天然气技术能降低循环功耗及提高(佣)效率的特点,通过建立模拟的无预冷混合制冷剂循环、三级丙烷预冷混合制冷剂循环和单级丙烷预冷混合制冷剂循环3种天然气液化模型,在一定约束条件下模拟计算液化过程压缩机的比功耗、(佣)损失及制冷剂流量,对比分析压缩机的比功耗和(佣)损失.结果表明:无预冷混合制冷剂循环的比功耗和(佣)(佣)损失量都是最大的,其比功耗分别是三级丙烷预冷混合制冷剂循环的7.28倍、单级丙烷预冷混合制冷剂循环的7.23倍,其(佣)损失量是三级丙烷预冷混合制冷剂循环的10.74倍、单级丙烷预冷混合制冷剂循环的10.62倍;但单级丙烷预冷混合制冷剂循环较三级丙烷预冷混合制冷剂循环有流程更简单、更便于维护的优势.因此应优先选用单级丙烷预冷混合制冷剂循环液化流程.【期刊名称】《天然气技术与经济》【年(卷),期】2017(011)004【总页数】4页(P54-57)【关键词】天然气液化流程;无预冷混合制冷剂;丙烷预冷混合制冷剂;比功耗;㶲损失【作者】吕双双;周训;王平【作者单位】广州泰阳能源科技有限公司,广东广州 510000;大连理工大学能源与动力学院,辽宁大连 116024;大连理工大学能源与动力学院,辽宁大连 116024【正文语种】中文关于混合制冷剂循环液化天然气技术,已经有很多学者做过大量研究,都旨在降低循环功耗[1-3],提高㶲效率[4]。
石玉美等对三级丙烷预冷混合制冷循环液化天然气进行了㶲分析,得出压缩机和换热器的㶲损失量分别占流程总㶲损失量的50%和26%,并提出了降低㶲损失量的方法。
尹全森等对单级混合制冷剂循环液化流程进行模拟,从压缩机的运行压力、工质流量与组成方面调整流程,使调整后的流程有了更高的效率。
Alabdulkarem A等采用遗传算法(genetic algorithm,简称GA)在MATLAB优化工具箱中优化丙烷预冷混合制冷剂流程,得到功耗最小的制冷剂配比,并与文献里的两种不同配比的混合制冷剂液化流程的功耗进行对比,分别减少了6.98%和13.6%。
天然气液化计算技术

(4)6点 6压力为天然气冷箱入口压力减去各换热器阻力。然后根据 h6=h24及P、H闪蒸计算T6。 (5) 11点 计算11点前先假定10点状态,根据10点温度、压力迭代计算, 寻找满足T6-T11≥3最大的T11。10点压力工程设计取1.49Mpa, 温度在140K-160K之间,经过膨胀机等熵膨胀迭代试算T11, P11取0.4Mpa。 (6)15点 T15=T11-3,P15=P11-ΔP,ΔP=0.1MPa为冷制冷剂通过三个换 热器的总阻力。
1.2 工艺计算前需已知的参数 在工艺计算前,需确定如下已知参数 (1) 冷箱入口天然气温度、压力、流量及各组分的摩尔分数; (2)LNG储罐的存储温度、压力; (3)换热器端面冷、热流体温差,取3℃; (4) 各种机械设备的效率,如压缩机、膨胀机、增压机; (5) 计算中换热器阻力,本计算冷箱总阻力取0.1Mpa,每个 换热器平均分配,由此引起的误差对计算结果的影响在误差允 许范围内。 在丙烷预冷混合制冷剂流程中,还需确定如下参数: (6) 丙烷压缩机出口压力,设计取1.3Mpa; (7) 混合制冷剂的组成及各摩尔分数; C3/MRC混合制冷剂选4种:分别是甲烷、乙烯(或乙烷)、 丙烷、氮气; MRC混合制冷剂选5种或6种,详见操作手册;
KW Kg/h KJ/kg. ℃ KJ/kg. ℃ K
式中 △Ex——多股流换热器火用损失 Gi——换热器中第i股流的流量 Si1——换热器中第i股流入口熵 Si2——换热器中第i股流出口熵 T0——环境温度
1.3.5 水冷器火用 损失
Q t2 n / 3600 T0 S 2 S1 G T0 t t1
液化天然气(LNG)与液化石油气(LPG)及柴油的经济性比较

名称
容重
低热值
8775 kcal/Nm3 液化天然气(LNG) 0.7505kg/Nm(3 气态)
(11692 kcal/kg)
2.5 kg/Nm3(气态) 液化石油气(LPG)
560kg/m3 (液态)
25000 kcal/Nm3 (10000 kcal/kg)
1 米 3 天然气热值相当于 0.845 公斤或 1.17 升汽油热量 1 米 3 天然气热值相当于 0.792 公斤柴油热量 1 升汽油=0.722-0.725 公斤=7464 大卡 备注:根据适用中实际情况证明,1.1 米 3 天然气约等于 1 公斤石油液化气;1 米 3 天然气相当于 1.17 升汽油。
按热值比较其经济性
备注
1
1.17
假定各种燃
料的燃烧热
1.78
效率相同
1.94
1Nm3 天然气热值相当于 1.17 升汽油(93 号), 0.95 升柴油。 1 升柴油=0.835 公斤=9181 大卡 1 公斤汽油热值为 10296 大卡 1 公斤柴油热值为 10996 大卡 1 公斤液化石油气热值相当于 1.15~1.22 公斤的汽油热量 1 公斤液化石油气热值相当于 1.12~1.2 公斤的柴油热量
柴油
820 kg/m3(液态) 10000 kcal/kg
汽油
732 kg/m3(液态) 10984 kcal/kg
目前市场价
4.5 元/Nm3 (5.13 元/万 kcal)
6.0 元/kg (6.0 元/万 kcal)
7.5 元/升 (9.15 元/万 kcal)
8.0 元/升 (9.95 元/万 kcal)
- 1、下载文档前请自行甄别文档内容的完整性,平台不提供额外的编辑、内容补充、找答案等附加服务。
- 2、"仅部分预览"的文档,不可在线预览部分如存在完整性等问题,可反馈申请退款(可完整预览的文档不适用该条件!)。
- 3、如文档侵犯您的权益,请联系客服反馈,我们会尽快为您处理(人工客服工作时间:9:00-18:30)。
液化天然气典型天然气液化流程的功耗比较杜建梅, 姜东琪, 王文军, 杨 颖, 常玉春(中国市政工程华北设计研究总院,天津300074)摘 要: 比较了典型天然气液化流程(氮气膨胀制冷、氮气甲烷膨胀制冷、丙烷预冷混合制冷剂一次分离制冷、丙烷预冷混合制冷剂二次分离制冷、混合制冷剂制冷)的功耗、冷箱冷负荷、压缩机轴功率、火用损失等技术参数。
关键词: 天然气液化; 功耗; 流程中图分类号:TU996 文献标识码:B 文章编号:1000-4416(2010)10-0B08-03Co m parison of Power Consu mpti on a m ong Typ i cal N aturalGas L i quefacti on ProcessesDU Jian me,i JI ANG Dong q,i WANG W en jun, YANG Y ing, CHANG Yu chun Abst ract: The po w er consum ption,co l d load of co l d box,ax i s po w er of co m pressor,exergy l o ss and o t h er technical para m eters of fi v e typ ical li q uefaction pr ocesses are co m pared.These pr ocesses in clude n itrogen expand i n g refri g eration,nitrogen and m ethane expanding refrigeration,once separate re frigerati o n w ith propane precoo led m ixed refri g eran,t t w ice separate refri g erati o n w ith propane precoo led m ixed refrigerant and m i x ed refri g eran t refri g erati o n.K ey w ords: natural gas li q uefaction; po w er consum ption; process近年来,在工程实践中,应用了许多天然气和煤层气的液化流程[1~4]。
本文对国内外常用的5种典型天然气液化流程 N2膨胀制冷、N2+CH4膨胀制冷、丙烷预冷混合制冷剂一次分离制冷、丙烷预冷混合制冷剂二次分离制冷、混合制冷剂制冷等5种流程进行功耗比较。
1 基本条件比较时采用相同的基本条件,具体为:相同的天然气组成、温度、压力、流量;LNG储罐为常压罐,设计压力为20kPa;按设定天然气组成可不设重烃分离罐;功耗计算中均不含天然气压缩、净化及公用耗电;天然气液相节流后气化分率为0;制冷剂液相节流后压力为0.4MPa;压缩机水冷后温度为308K;膨胀机的等熵效率为0.85;制冷剂压缩机的等熵效率为0.8;除N2膨胀制冷流程外,其他工艺均以优化后的制冷剂配比计算。
2 流程要点N2膨胀流程双机膨胀,二级膨胀机出口不带液,增压机功率全部有效利用。
N2+C H4膨胀流程单机膨胀,膨胀机出口不带液,增压机功率全部有效利用。
丙烷预冷混合制冷剂一次分离流程与丙烷预冷混合制冷剂二次分离流程采用同样的丙烷预冷温度,均设有3个丙烷预冷换热器、3个气液分离器及3个丙烷液相节流阀。
混合制冷剂只第30卷 第10期2010年10月煤气与热力GA S&HEATV o.l30N o.10O ct.2010进行一次分离,可采用2组混合制冷剂换热器。
丙烷预冷混合制冷剂二次分离流程丙烷预冷部分与一次分离流程相同。
混合制冷剂采用二次分离,混合制冷剂换热器为3组。
混合制冷剂流程此为无预冷混合制冷剂流程,宜配3组换热器,混合制冷剂配1个气液分离器。
3 冷箱冷负荷天然气液化冷负荷均相同(为1642 104kJ/ h),制冷剂预冷冷负荷随液化流程而变,总供冷量为二者之和。
N2膨胀制冷流程循环物质的量比:5.58;N2预冷负荷:1579 104kJ/h;总供冷量:3221 104kJ/h。
N2+CH4膨胀制冷流程循环物质的量比:4.71;N2+CH4预冷负荷:1123 104kJ/h;总供冷量:2765 104kJ/h。
丙烷预冷一次分离流程丙烷循环物质的量比:1.13;混合制冷剂循环物质的量比:1.6295;混合制冷剂预冷负荷:3322.7 104kJ/h;丙烷供冷量:2011.4 104kJ/h;混合制冷剂供冷量:2953.3 104kJ/h;总供冷量:4964.7 104kJ/h。
丙烷预冷二次分离流程二次分离温度:180K;丙烷循环物质的量比:1.23;混合制冷剂循环物质的量比:1.8923;混合制冷剂预冷负荷:3536 104kJ/h;丙烷供冷量:2175 104kJ/h;混合制冷剂供冷量:3003 104kJ/h;总供冷量:5178 104kJ/h。
混合制冷剂流程循环物质的量比:3.6916;制冷剂预冷量:7509 104kJ/h;制冷剂供冷量:9151 104kJ/h。
4 压缩机轴功率N2膨胀流程 N2压缩机的轴功率:10915k W。
N2+C H4膨胀流程N2+C H4压缩机的轴功率:10421k W。
丙烷预冷一次分离流程丙烷压缩机的轴功率:2051k W;混合制冷剂压缩机的轴功率:2780k W;合计:4831k W。
丙烷预冷二次分离流程丙烷压缩机的轴功率:2233k W;混合制冷剂压缩机的轴功率:2875k W;合计:5108k W。
混合制冷剂流程制冷剂压缩机的轴功率:7482k W。
5 火用损失各液化流程的火用损失见表1。
表1 各液化流程的火用损失k W 项目N2膨胀制冷流程N2+C H4膨胀制冷流程丙烷预冷混合制冷剂一次分离流程丙烷预冷混合制冷剂二次分离流程无预冷混合制冷剂制冷流程压缩机30803148149215782026膨胀机19631942换热器33352128 677 718 712水冷却器13481059 217 2291047节流装置 124 199 240 288 120合计98508476262628133905 6 综合比较此处比较除上述5种流程外,另加上海调峰气源C II液化流程,该流程数据引自文献[1]。
典型天然气液化流程的功耗比较见表2。
二次分离流程功耗理论上应略低于一次分离流程,但因其必须满足3个换热器的热平衡条件,而预冷换热器是气-气换热,液相换热器则是冷凝过程流体与气相制冷剂换热,过冷换热器又是液相流体与气相制冷剂(液体很少,主要是气体)换热。
3个换热器达到热平衡时,对冷量的需求均为非线性关系,且3条曲线的曲率也有较大差异,于是使二次分离流程因增加了1个换热器而使其功耗上升。
经比较,丙烷预冷混合制冷剂一次分离流程的功耗、火用损失二项均为最低。
杜建梅,等:典型天然气液化流程的功耗比较 第30卷 第10期表2 典型天然气液化流程的功耗比较项 目N2膨胀制冷流程N2+C H4膨胀制冷流程丙烷预冷混合制冷剂一次分离流程丙烷预冷混合制冷剂二次分离流程无预冷混合制冷剂制冷流程C II流程备 注天然气各组分物质的量分数CH40.8200.8200.8200.8200.8200.90844C2H60.1120.1120.1120.1120.1120.07025C3H80.0400.0400.0400.0400.0400.00103i-C4H100.0090.0090.0090.0090.0090.02028n-C4H100.0120.0120.0120.0120.012N20.0070.0070.0070.0070.007天然气相对分子质量19.703719.703719.703719.703719.703717.3011 天然气密度/(kg m-3)0.88240.88240.88240.88240.88240.7744 天然气温度/K308308308308308316.15 天然气压力/M Pa4.764.764.764.764.764.8制冷剂各组分物质的量分数CH40.000.560.350.430.300.22448C2H60.000.000.410.310.230.33905C3H80.000.000.180.200.210.07539i-C4H100.000.000.000.000.080.01588n-C4H100.000.000.000.000.070.05402i-C5H120.000.000.000.000.000.14078n-C5H120.000.000.000.000.000.10623N21.000.440.060.060.110.04417制冷剂相对分子质量28.013421.310927.562126.419832.790040.2433制冷剂气相密度/(kg m-3)1.25040.95191.24361.20571.47701.8692天然气流量/(kmo l h-1)10001000100010001000196.163制冷剂流量/(kmo l h-1)55704708276031223691 其制冷剂为多股丙烷流量/(kmo l h-1) 11301230制冷剂循环物质的量比5.5704.7082.7603.1223.691丙烷预冷含丙烷循环比与丙烷预冷功耗之比2.262.161.001.061.551.38以丙烷预冷一次分离为1与丙烷预冷火用损失之比3.763.231.001.071.491.24以丙烷预冷一次分离为1参考文献:[1] 顾安忠,鲁雪生,汪荣顺,等.液化天然气技术[M].北京:机械工业出版社,2003.[2] 王文军,杜建梅,蒋建志,等.煤层气氮膨胀制冷液化工艺参数优化计算[J].煤气与热力,2010,30(3):B09-B12.[3] 范学军,袁树明,杜建梅,等.天然气部分液化工艺计算[J].煤气与热力,2010,30(7):A40-A42.[4] 袁树明,刘兰慧,范学军,等.丙烷预冷混合制冷剂天然气液化流程工艺计算[J].煤气与热力,2010,30(8):B07-B09.作者简介:杜建梅(1969- ),女,山东招远人,高级工程师,学士,从事燃气工程设计与研究工作。
电话:(022)23545514E-ma il:du jianme i69@126.co m收稿日期:2009-12-15; 修回日期:2010-01-30第30卷 第10期 煤气与热力www.w ate 。