Voltage change in the GMAW process due to the influence of a droplet travelling in the arc.
惠普彩色激光打印机 Pro M454 和惠普彩色激光多功能一体机 Pro M479 维修手册说明书
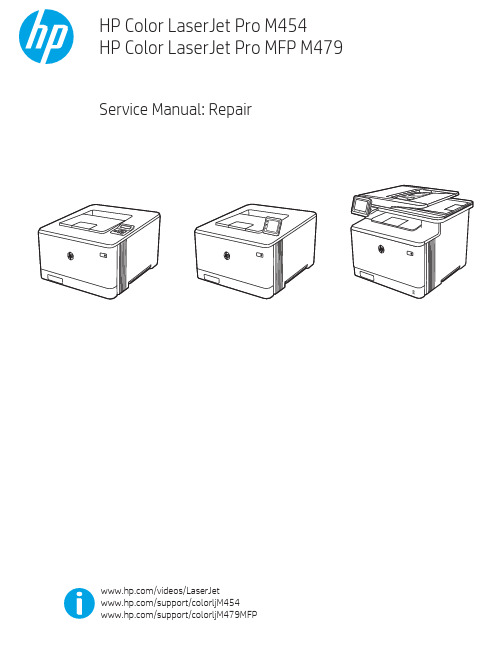
Table -1 Revision history Revision number 1
Revision date 6/2019
Revision notes HP LaserJet Pro M454 HP LaserJet Pro MFP M479 Repair manual initial release
Additional service and support for HP internal personnel HP internal personnel, go to one of the following Web-based Interactive Search Engine (WISE) sites: Americas (AMS) – https:///wise/home/ams-enWISE - English – https:///wise/home/ams-esWISE - Spanish – https:///wise/home/ams-ptWISE - Portuguese – https:///wise/home/ams-frWISE - French Asia Pacific / Japan (APJ) ○ https:///wise/home/apj-enWISE - English ○ https:///wise/home/apj-jaWISE - Japanese ○ https:///wise/home/apj-koWISE - Korean ○ https:///wise/home/apj-zh-HansWISE - Chinese (simplified)
Find information about the following topics ● Service manuals ● Service advisories ● Up-to-date control panel message (CPMD) troubleshooting ● Install and configure ● Printer specifications ● Solutions for printer issues and emerging issues ● Remove and replace part instructions and videos ● Warranty and regulatory information
热影响区宽度的英文
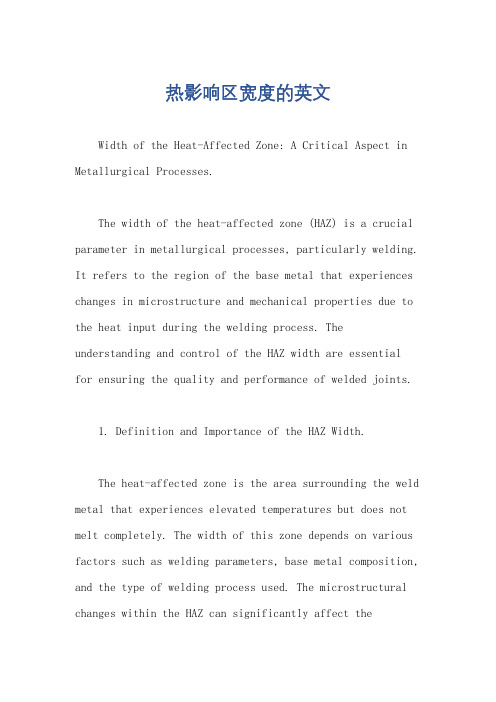
热影响区宽度的英文Width of the Heat-Affected Zone: A Critical Aspect in Metallurgical Processes.The width of the heat-affected zone (HAZ) is a crucial parameter in metallurgical processes, particularly welding. It refers to the region of the base metal that experiences changes in microstructure and mechanical properties due to the heat input during the welding process. The understanding and control of the HAZ width are essentialfor ensuring the quality and performance of welded joints.1. Definition and Importance of the HAZ Width.The heat-affected zone is the area surrounding the weld metal that experiences elevated temperatures but does not melt completely. The width of this zone depends on various factors such as welding parameters, base metal composition, and the type of welding process used. The microstructural changes within the HAZ can significantly affect themechanical properties of the welded joint, including its strength, toughness, and corrosion resistance.2. Factors Influencing the HAZ Width.Welding Parameters: The welding current, voltage, and welding speed significantly affect the heat input and, consequently, the width of the HAZ. Higher heat input results in a wider HAZ.Base Metal Composition: The chemical composition of the base metal determines its thermal conductivity, heat capacity, and phase transformation temperatures. These properties influence how the metal responds to the heat input and, therefore, the width of the HAZ.Welding Process: Different welding processes, such as gas metal arc welding (GMAW), gas tungsten arc welding (GTAW), and submerged arc welding (SAW), have different heat distributions and, thus, affect the HAZ width.3. Impact of the HAZ Width on Welded Joint Properties.Mechanical Properties: The microstructural changes within the HAZ can lead to variations in hardness, ductility, and strength. If the HAZ width is too wide, it can result in a decrease in joint strength and an increase in the risk of cracks.Corrosion Resistance: Changes in the microstructure of the HAZ can affect the corrosion resistance of the welded joint. Wider HAZs may exhibit increased susceptibility to corrosion.Fatigue Resistance: The HAZ width can influence the fatigue life of welded structures. Wider HAZs may introduce stress concentrations and reduce fatigue resistance.4. Controlling the HAZ Width.Selection of Welding Parameters: Careful selection of welding parameters can help limit the heat input and, thus, the width of the HAZ. Adjusting the welding current, voltage, and speed according to the base metal and desiredjoint properties is crucial.Preheat and Postweld Heat Treatment: The application of preheat and postweld heat treatment can control the cooling rate and minimize the risk of harmful microstructural changes within the HAZ.Use of Filler Materials: The selection of appropriate filler materials can influence the microstructural development within the HAZ and, thus, the width.5. Conclusion.The width of the heat-affected zone is a critical aspect in welding and other metallurgical processes. Understanding and controlling this parameter is essential for ensuring the quality and performance of welded joints. By considering factors such as welding parameters, base metal composition, and welding process, it is possible to optimize the HAZ width and achieve optimal welded joint properties.。
博卡电焊机 生成器说明书

Issued February 2018 • Index No. ED/4.4Welder/generator is warranted for three years, parts and labor. Engine is warranted separately by the engine manufacturer.Easier mobility and uses less truck space and payload With its intuitive design, the daily maintenance of our Bobcat welder/generators is faster and easier.Easier Maintenance Safer, more productiveBobcat 250 EFI model shown.The most popular welder/generator • Quieter to operate • Smaller and lighter• More fuel efficient with EFI • Easier to maintainGas or LP Engine-Driven Welder/AC GeneratorBobcat225and 250Miller Electric Mfg. LLCAn ITW Welding Company 1635 West Spencer Street P.O. Box 1079Appleton, WI 54912-1079 USAEquipment Sales US and CanadaPhone: 866-931-9730FAX: 800-637-2315International Phone: 920-735-4554International FAX: 920-735-4125Rugged welder/generators are great for stick and flux-cored welding.Designed for maintenance/repair operations, construction, farm,ranch and generator use.The Bobcat™AdvantageDesigned for reliabilityFrom Appleton, Wis. USA, our welder/generators are the most rugged, durable and long-lasting in the industry. We manufacture them to exceed requirements for extreme working conditions and they are hard-working from the core:•Copper windings and iron generator components for a quality-built machine •Lugged—not soldered—heavy internal leads for better field durability •Superior cooling technologyfor maximum performanceand engine life•Super-tough armor toprotect the welder/generator from accidental impact•Protective armor doors to cover the weldstuds and receptacles as required by OSHAand CSA for jobsite safety•Lift hook integrated into the center frame,which bolts to the machine’s base forgreater durabilityLong runtimesLarge 12-gallon fuel capacity means manyhours of run time before refueling.Versatile AC and DC weld outputProvides quality welds on all types of metals.DC is smooth and easy to run while AC stickis used when arc blow occurs.Quieter and better sound*Significant improvements in soundlevel and quality offer better jobsitecommunication, which provides a safer,more efficient working environmentfor you and your crew. Bobcatwelder/generators have rotated theengine toward the front to create moreefficient airflow, resulting in significantly quieter operation. Now you can start your job earlier in the day and end it later, as well as work around hospitals, businesses, and residential areas.Smaller and lighter design*Bobcat welder/generators take up lessspace on trucks and trailers—leavingmore room on your truck for otherequipment and tools. Plus, they’reeasier to move safely around jobsites—even with weld cables and runninggear attached.*Compared to previous model Easier maintenance*With its intuitive design, the daily maintenance of our Bobcat welder/generators is faster and easier. With front panel maintenance displays, you know when your equipment needs to be serviced. And servicing is simple because of:•Oil checks that can be performed from the top by the front panel •Toolless panels that allow for quick access•Single-side fuel fill and oil drain/filterS fEasier mobilit andAir filterOil fill Oil drain Oil level checkFuel fill Oil filterFuel filter•Front panel fuel and sight gauges provide convenient fuel level indication•Smoother weld output and better generator power while welding •More weld output than 225-amp welder generators—72 percent more power for MIG/flux-cored, 67 percent more for AC welding, and 11 percent more for DC stick Electronic fuel injection (EFI)EFI gas engines optimize the air/fuel ratio forall engine speeds and engine loads, resultingin lower operational costs, fewer emissions, longer runtimes and better performance when compared to carbureted models. TheBobcat™250 Additional FeaturesBobcat 250 recommended option2Exclusive engine and generator packaging design operates cooler and more efficientlyThe engine is rotated towards the front to create more efficient airflow. More efficient airflow and exclusive engine location are significant contributors to reduced sound level and size reduction.Hot air recirculation is eliminated when machine is mounted in tight spots, and internal parts are kept cool for optimal performance.3Reversed Generator AirflowTo select a generator that has enough power output in watts, add the watts for the items you want tosimultaneously run. Tools and appliances with induction motors may require three to seven times the listed wattage when starting. All data listed is approximate —check your tool/appliance for specific wattage requirements.Starting Running Equipment Watts Watts Barn Cleaner (5 hp) 11,600 3,000Silo Unloader (5 hp) 12,200 4,300Portable Conveyor (1/2 hp) 3,400 1,000Milker (5 hp) 10,500 2,800Hand Drill (1/2 inch) 600 600Circular Saw (8-1/4 inch) 1,400 1,400Air Compressor (1-1/2 hp) 8,200 2,200Flood Lights (Vapor) 1,250 1,000Refrigerator/Freezer 2,200 700Sump Pump 1,300 800Millermatic ®212 Auto-Set ™ 6,500 6,500MIG Welder (230 V)Spectrum ®625 X-TREME ™ 6,900 6,900(30 A, 230 V, 1/2-inch cut)The Bobcat ™Generator Power AdvantageAccu-Rated ™—not inflated generator powerOur Accu-Rated ™11,000 watts (12,000 with EFI)of usable peak power isdelivered for a minimum of 30 seconds. Accu-Rated means peak power is usable for maximum generator loads such as plasma cutting, Millermatic ®MIG welders and motor starting. Accu-Rated peak power beats the competition’s very short-duration peak or surge power. Use your peak power, it’s more than a number.Smooth power —not spike powerRevolutionary ten-degree skewed-rotor design optimizes generator performance for smootherpower —not spiked power found with other brands. Better power —better performance.Typical equipment power usageBobcat welder/generators will easily start and run the following equipment:Waveform ComparisonBobcatCompetitorTools and motors are designed to operate within 10 percent of 120/240 V. The powergenerator of the Bobcat provides strong power while keeping the voltage within 10 percent of 120/240 V.This increases tool/motor performance and life.Generator Power Curve10203040506070809010011020406080100120140160180200220AC Power Amps at 120 V025*******108125150050100150200216132264250300A C P o w e r V o l t sAC Power Amps at 240 V4Engine Specifications (Engines warranted separately by the engine manufacturer.)Model Bobcat 225Bobcat 250Welding Mode CC/AC CC/DC CV/DCCC/AC CC/DC CV/DCProcess Stick/TIG Stick/TIG 1MIG/FCAW Stick/TIG Stick/TIG 1MIG/FCAWRated Weld Output at 104°F (40°C)2150 A at 25 V, 100% duty cycle 225 A at 25 V, 100% duty cycle 200 A at 20 V, 100% duty cycle 225 A at 25 V, 100% duty cycle 250 A at 25 V, 60% duty cycle 250 A at 25 V, 100% duty cycle 250 A at 28 V, 100% duty cycle 275 A at 25 V, 60% duty cycleAmp/Volt Ranges 60–160 A 40–225 A 19–28 V 40–250 A 40–250 A 17–28 VSingle-Phase Generator Power Peak: 11,000 wattsContinuous: 9,500 watts 120/240 V, 88/44 A, 60 HzPeak: 11,000 wattsContinuous: 9,500 watts 120/240 V, 88/44 A, 60 Hz EFI ModelPeak: 12,000 wattsContinuous: 10,500 wattsSound Levels at Max. Load/150 A 73.5 dB/72 dB72.5 dB/72 dBNet Weight 3485 lb. (220 kg)501 lb. (227 kg)Dimensions H: 28 in. (711 mm)H: 32.75 in. (832 mm) (to top of exhaust)W: 20 in. (508 mm)D: 40.5 in. (1,029 mm)H: 28 in. (711 mm)H: 32.75 in. (832 mm) (to top of exhaust)W: 20 in. (508 mm)D: 40.5 in. (1,029 mm)Certified by Canadian Standards Association to both the Canadian and U.S. Standards.Note: Derate outputs up to five percent when using LP fuel. 1) DC TIG available above 80 amps. 2) Rated at sea level. 3) Net weight without fuel.*Fuel stabilizer is recommended for gas engines that are used infrequently.**Hose and LP Tank Mounting Assembly and setup are required.Performance DataMounting SpecificationsA.20 in. (508 mm)B.16.5 in. (419 mm)C.1.75 in. (44.5 mm)D.5.12 in. (130 mm)E. 22.3 in. (566 mm)F. 40.32 in. (1,024 mm)G..406 in. (10.3 mm) diameterF r o n t P a n e l0.000.250.500.751.001.251.501.752.0005010015020025030024681012Fuel ConsumptionPower KVA at 100% Duty CycleWeld Amperes at 100% Duty CycleU .S . G a l./h o u rFuel Consumption Data•12-gallon fuel capacity.•On a typical job using 1/8-inch 7018electrodes (125 A, 20% duty cycle) expect about 20 hours (gas) of operation.•Welding at 150 A, 40% duty cycle uses approxi m ately 3/4 gallon per hour —about 16 hours of operation (gas).•Under a continuous load of 4,000 watts of generator power, the Bobcat would run for about 14 hours (gas) of operation.5Note: See or the Full-line Catalog to compare to Trailblazer models.Function and Benefit Guide1.Maintenance display provides fuel level (250 models only), engine hours and oil change interval information.2.Weld process selector switch makes choosing between stick, wire and TIG processes easy. Switch also auto m atically changes polarity with process selection to make sure the machine is easy to set with little effort or knowledge (on 225 model, weld process selector switch is combined with coarse range control).3.Coarse range control225 model —Three DC stick/TIG, one AC TIG, and one wire range are available for output control. Stick ranges are designed forelectrode diameters (3/32, 1/8 and 5/32 inch) making these models very easy to set.250 model —Four stick/TIG and two wire ranges are available for output control. Stick ranges are designed for electrode diameters (3/32, 1/8, 5/32 and 3/16 inch) making these models very easy to set.4.Fine adjust control makes it easy to fine tune amperage within a coarse range. Set control above 7 for best power while welding and to 10 for generator-only use.5.Engine control switch is used to start the engine and then select between auto idle and high speed lock positions.6.Engine choke control is used for easy engine starting.Note: No choke necessary on EFI models.7.120/240 V receptacle with circuit breaker.(For matching plug, order 119172.)8.120 V GFCI receptacles with circuit breakers.Choose the Right Bobcat ™Engine Drive6Order the following from Miller Service Parts.Genuine Miller ®Options *Available as factory option. See ordering information on back page.Genuine Miller ®AccessoriesNever Flat ™TiresAvailable on Bobcat and Trailblazer running gear.•Eliminate costly jobsite downtime•Maintain constant tire pressure and will not develop flats•Protect against punctures•Preserve maneuverability, even when weighed down with heavy welding cable Off-RoadRunning Gear 300909 Gas/LP, with inner tubes 300910 Gas/LP, with Never Flat tires Includes fourheavy-duty 15-inch tires and a rugged handle to provide maximum maneuverability.Off-Road Running Gear withProtective Cage and Never Flat Tires300912 Gas/LP Running gear and rugged cage withcable holders protects your investment and is easy to move around the jobsite.Multi-Terrain Running Gear 300913 Gas/LP,with inner tubes 300914 Gas/LP,with Never Flat tires Includes two heavy-duty 15-inch tires, two 8-inch rubber swivel casters and a heavy-duty handle. Recommended for all surfaces and applications, and is easy to move around the jobsite.Protective Cagewith Cable Holders 300921Gas/LP Rugged cage with cable holders protects yourinvestment. Can beused with running gear, gas cylinder mounting assembly, LP tank mounting assembly, or with trailer.Gas CylinderMounting Assembly 300918GasDesigned for use with multi-terrain running gear, protective cage, or by itself. Includes base tray with bottlebracket, vertical support rack and safety chain.Note: Not for use with LP tank mounting assembly.Not recommended for use with protective cover.Hose and LP Tank Mounting Assembly 300917LPDesigned for use with multi-terrain running gear, protective cage,or by itself. Includes bracket and clamp tomount 33- and 43-pound tanks horizontally, and hose with fittings to converter.Note: Not for use with gas cylinder mounting assembly.Not recommended for use with protective cover.Protective Covers 300919 For gas models without protective cage or running gear (shown)300920 For gas models with protective cage and/or running gearHeavy-duty, water-resistant and mildew-resistant covers protect and maintain the finish of the welder.7MIG/Flux-cored WeldingMillermatic 141 and 211 shown.Millermatic ®141 907612See literature DC/12.42Millermatic ®211 907614See literature DC/12.58Millermatic ®212 Auto-Set ™907405See literature DC/12.46The Millermatic line of MIG welders are complete arc welding power source, wire feeder and gun packages designed for portability and ease of use.Note: The Millermatic machines can be operated utilizing auxiliary power.SuitCase ®X-TREME ™8VS Wire Feeder 951582SuitCase ®X-TREME ™12VS Wire Feeder 951543Lightweight, voltage-sensing wire feeders include secondary contactor, gas valve, drive roll kit and Bernard ™BTB Gun 300 A. See literature M/6.42.Spoolmatic ®30A Spool Gun 130831Air-cooled, 200-amp,one-pound spool gun for aluminum MIG.See literature M/1.73.Requires WC-115A control (137546011).Spoolmate ™3035Spool Gun 195016Use with SGA 100C control and heavy-duty barrel. Spool gun for aluminum andother wires. Four-inch spools; .023–.035 inch (0.6–0.9 mm) aluminum, steel and stainless steel. Rated at 150 amps, 60 percent duty cycle with 20-foot (6 m) cable assembly.SGA 100C Control 043857SGA with contactor required to connectSpoolmate 3035 to CV engine drive. Includes 10-foot (3 m) 115 V power cable and plug, 6-foot (1.8 m) interconnecting cable, and 5-foot (1.5 m) gas hose.Heavy-Duty Barrel for Spoolmate 3035195375Use for demanding applications, rated at 200 A,60 percent duty cycle.Stick (SMAW) WeldingWeld Leads2/0 Stick Cable Set, 50 ft. (15 m) 173851Consists of 50-foot (15 m) 2/0 electrode cable with holder, and 50-foot (15 m) work cable with clamp. 350 A, 100% duty cycle.2/0 Stick Cable Set, 100/50 ft. (30.5/15 m)043952Consists of 100-foot (30.5 m) 2/0 electrode cable with holder, and 50-foot (15 m) work cable with clamp. 300 A, 100% duty cycle.TIG (GTAW) WeldingDynasty ®210 Series For portable AC/DC TIG. See literature AD/4.81.Multiprocess WeldingMultimatic ™200 907518Portable, all-in-one multiprocess package weighs only 29 pounds (13.2 kg), and features excellent arc characteristics. Exclusive multi-voltage plug (MVP ™) provides flexibility to plug into 120- or 240-volt power. Take it anywhere you need to MIG, TIG or stick weld. See literature DC/12.57.Plasma CuttingSpectrum 375 X-TREME and 625 X-TREME shown.Spectrum ®375 X-TREME ™907529See literature PC/9.2.Spectrum ®625 X-TREME ™907579See literature PC/9.6.Spectrum ®875 907583See literature PC/9.8.The Spectrum 375 X-TREME and 625 X-TREME come complete with protective X-CASE ™(not shown).Trailers and HitchesHWY-Mid Frame Trailer 3014381,424-pound (646 kg) capacity highway trailer with welded steel tubing frame, heavy-duty axle with roller bearing hubs and leaf-springsuspension. Includes jack stand, fenders, lights,and dual hitch with 2-inch (50 mm) ball hitch and 3-inch (76 mm) lunette eye.Note: Trailer is shipped unassembled.Cable Tree 043826Provides an area to conveniently wrap weld cables and extension cords.2-In-1 Document/Fire Extinguisher Holder 301236Stores documents and holds a five-pound fire extinguisher.Note: Holder shown mounted on trailer. Fire extinguisher notincluded.Genuine Miller ®Accessories (Continued)Ordering InformationEquipment and Options Stock No. Description Qty. PriceBobcat™225907498001Kohler engine, base model907498 Kohler engine with GFCI receptaclesBobcat™250907500001 Kohler engine, base model907500 Kohler engine with GFCI receptacles907500002 Kohler engine with electric fuel pumpBobcat™250 EFI 907502Kohler engine, base modelBobcat™250 LP 907504Kohler engine with GFCI receptaclesField Options Options listed below can be added to the above packages. Installation is required.GFCI Receptacles 300975Electric Fuel Pump 300976 Recommended for gas engine operations at altitudes above 5,000 feetSpark Arrestor300924Remote Oil Drain and Filter Kit 300923 Front mount for KohlerFull KVA Adapter Cord300517Full KVA Plug 119172Engine Tune-Up Kits See page 6. Order from Miller Service PartsAccessoriesOff-Road Running Gear300909Gas/LP models, with inner tubes300910Gas/LP models, with Never Flat™tiresOff-Road Running Gear with Protective Cage300912 Gas/LP models, with Never Flat™tires.Multi-Terrain Running Gear300913Gas/LP models, with inner tubes300914Gas/LP models, with Never Flat™tiresProtective Cage with Cable Holders300921 Gas/LP modelsGas Cylinder Mounting Assembly 300918 Gas models. Not for use with LP tank mounting assembly.Not recommended for use with protective coverHose and LP Tank Mounting Assembly 300917 LP models. Not for use with gas cylinder mounting assembly.Not recommended for use with protective coverProtective Covers See page 6MIG/Flux-cored WeldingMillermatic®Series MIG Welders See page 7SuitCase®X-TREME Wire Feeders See page 7Spoolmatic®30A Spool Gun 130831 Requires WC-115A Control. See literature M/1.73WC-115A Control 137546011 See literature M/1.73Spoolmate™3035 Spool Gun 195016 See literature M/1.5SGA 100C Control 043857 See literature M/1.5Heavy-Duty Barrel for Spoolmate 3035195375 See literature M/1.5Stick Welding See page 7TIG Welding See page 7Multiprocess Welding See page 7Plasma Cutting See page 7Trailers and HitchesHWY-Mid Frame Trailer301438Trailer with lights, fenders and dual hitch. For highway useCable Tree 043826Trailer-mounted cable holder2-In-1 Document/Fire Extinguisher Holder301236 Stores documents and holds a five-pound fire extinguisherDate: Total Quoted Price:Distributed by:©2018 Miller Electric Mfg. LLC。
关于WPS焊接工艺规程的解释

对弯曲和拉伸不能产生明显影响的因素Can’t produce visible affection on bend ability and tension ability of joint
t 附加重要变素supplemental essential variables
关于WPS焊接工艺规程的解释
•Weld Process Selection 焊接工艺选择
•The “ideal” welding process is that which achieves the minimum specification requirements at the minimum cost...
t A change in groove type (e.g., single-V to doubleV), 坡口形式变化(例如,单V到双V)
PPT文档演模板
关于WPS焊接工艺规程的解释
Essentials in GMAW or FCAW GMAW and FCAW中的重要变素(AWS)
t A change in the type of groove to a square groove and vice versa从任何坡口形式改变为直边或相反
PPT文档演模板
关于WPS焊接工艺规程的解释
Essentials in GMAW or FCAW GMAW and FCAW中的重要变素(AWS)
t A change in diameter, or thickness, or both, not qualified by Table 2工件直径或厚度未在评定范围之 外。
PPT文档演模板
关于WPS焊接工艺规程的解释
焊接检验员试卷
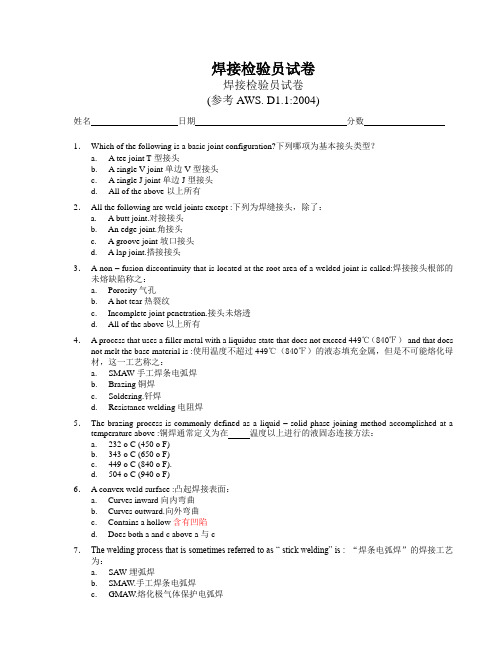
焊接检验员试卷焊接检验员试卷(参考AWS. D1.1:2004)姓名日期分数1.Which of the following is a basic joint configuration?下列哪项为基本接头类型?a. A tee joint T型接头b. A single V joint单边V型接头c. A single J joint单边J型接头d.All of the above以上所有2.All the following are weld joints except :下列为焊缝接头,除了:a. A butt joint.对接接头b.An edge joint.角接头c. A groove joint坡口接头d. A lap joint.搭接接头3.A non – fusion discontinuity that is located at the root area of a welded joint is called:焊接接头根部的未熔缺陷称之:a.Porosity气孔b. A hot tear热裂纹c.Incomplete joint penetration.接头未熔透d.All of the above以上所有4.A process that uses a filler metal with a liquidus state that does not exceed 449℃(840℉)and that does not melt the base material is :使用温度不超过449℃(840℉)的液态填充金属,但是不可能熔化母材,这一工艺称之:a.SMAW手工焊条电弧焊b.Brazing铜焊c.Soldering.钎焊d.Resistance welding电阻焊5.The brazing process is commonly defined as a liquid – solid phase joining method accomplished at a temperature above :铜焊通常定义为在温度以上进行的液固态连接方法:a.232 o C (450 o F)b.343 o C (650 o F)c.449 o C (840 o F).d.504 o C (940 o F)6.A convex weld surface :凸起焊接表面:a.Curves inward向内弯曲b.Curves outward.向外弯曲c.Contains a hollow含有凹陷d.Does both a and c above a与c7.The welding process that is sometimes referred to as “ stick welding” is :“焊条电弧焊”的焊接工艺为:a.SAW埋弧焊b.SMAW.手工焊条电弧焊c.GMAW.熔化极气体保护电弧焊d.GTAW. 气体保护钨极电弧焊8.Tungsten inclusions are found during :夹钨现象通常在中出现:a.GMAW熔化极气体保护电弧焊b.GTAW气体保护钨极电弧焊c.SMAW.手工焊条电弧焊d.None of the above以上都没有9.Embrittlement, caused by a physical or chemical change in the metal, is a reduction in :由物理或者化学变化引起的金属变脆,是的减弱:a.Ductility.延展性b.Hardness硬度c.Hydrogen含氢量d.All of the above以上所有10.T he fillet weld size is based on the :角焊缝的尺寸基于下列:a.Effective fillet weld throat.有效焊喉b.Length of fillet weld.角焊缝长度c.Theoretical weld.理论焊缝d.Length of fillet weld leg角焊角长度11.I n welding, temperature indicating sticks are used to monitor :在焊接中,测温仪用于监测:a.Preheat temperatures.预热温度b.Postheat temperatures.后热温度c.Interpass temperatures.层间温度d.All of the above以上所有12.A discontinuity that appears as a series of the remelted dots beside a weld, resembling a trail left in striking a match is called :焊缝旁边出现的一系列再熔点缺陷,类似闪击留下的痕迹,称之:a.Linear porosity线性孔b.Arc strikes.电弧划伤c.Undercut咬边d.Slag焊渣13.T o be acceptable, a concave fillet weld must have an actual leg dimension that is :能被同意的凹角焊的实际角尺寸务必:a.Longer than the size.长于理论尺寸b.Shorter than the size短于理论尺寸c.Equal to the size等于理论尺寸d.Equal to the throat与焊喉相等14.T he melting and fusing of the filler metal and base metal into a straight continuous weld pass is called a:填充金属焊母材熔融填入直的连续焊道,称之a.Multipass weld多道焊接b.Depressed bead平焊c.Stringer bead. 直焊d.Weave pattern 摆动焊15.A depression on the face of a fillet weld that reduces the cross section of the weld when measured at the depression is called :角焊缝表面量得的减少焊缝横截面的凹陷称之:a.Depressed bead凹槽b.Excessive convexity过分凸起c.Insufficient throat.焊喉不足d.Insufficient leg焊角不足16.A protrusion or rollover of weld metal beyond the toe or root is called :超出焊趾或者焊角的焊接金属突起,称之:a.Overlap焊瘤b.Undercut.咬边c.Reinforcement加强d.Overfill.过多填充17.A round discontinuity that occurs in the weld and is then distributed in line, parallel with the weld is called:焊缝中的圆形不连续,呈线性分布,与焊缝平行,这种不连续称之:a.Melt – through熔透b.Linear porosity.线性气孔c.Cluster porosity簇状气孔d. A crack裂纹18.A welding process in which shielding is provided by the electrode covering is called :用电极遮盖物做保护的焊接工艺称之:a.SMAW.手工焊条电弧焊b.GTAW气体保护钨极电弧焊c.GMAW熔化极气体保护电弧焊d.Brazing铜焊19.A slag – type discontinuity is produced by :渣型不连续由产生:a.SMAW. 手工焊条电弧焊b.GTAW气体保护钨极电弧焊c.GMAW熔化极气体保护电弧焊d.brazing铜焊20.W eld metal that completely fills the groove and is fused to the base metal throughout its total thickness is called:焊接金属完全填充坡口,并完全熔穿母材,称之:a.Partial joint penetration部分接头渗透b.Plate thickness钢板厚度c.Theoretical throat理论焊喉plete joint penetration.全熔透21.A disadvantage of the GMAW process is: 熔化极气体保护电弧焊工艺的缺点为:a.That slag removal is required.需要清除焊渣b.That there is an excessive amount of post – weld cleaning.需要超额的焊后清理c.That shielding gas must be protected from draft 保护气体务必防风d.All of the above.以上所有22.O n a welding symbol, the flag symbol indicates :在焊接符号中,旗状符号表示:a. A shop weld.车间焊缝b. A repair weld.返修焊缝c. A field weld现场焊缝d.Weld – all – around.整周焊缝23.O n a welding symbol, the horizontal line connecting the arrow and the tail is called the :在焊接符号中,连接箭头与尾部的水平线称之:a.Main line主线b.Reference line.参考线c.Symbol line符号线d.AWS line AWS线24.T he theoretical throat dimension for a 10 mm (0.4 inches) leg fillet weld is :10mm(0.4英寸)焊角角焊缝的理论焊喉尺寸为:a. 5 mm (0.2 inches)b.7 mm (0.3 inches).c.10 mm (0.4 inches)d.13 mm (0.5 inches)25.F or a given size weld, the theoretical throat for a concave fillet weld is :关于给定尺寸焊缝,凹角焊理论焊喉为:a.The same for a convex fillet weld与凹角焊一样rger for a convex fillet weld.比凹角焊大c.Smaller for a convex fillet weld.比凹角焊小d.Equal to the effective throat.与有效焊喉一样26.O verlap is a weld profile condition where the angle formed at the junction between the weld and base material is :在焊缝与母材连接处形成的交迭这种焊缝外形条件:a.Less the 90 degrees from the plate surface与钢板表面小于90°b.Equal to 90 degrees from the plate surface. 与钢板表面等于90°c.Greater than 90 degrees from the plate surface. 与钢板表面大于90°d.An internal flaw only detectable with ultrasonic testing.只能用超声波才能发现的缺陷27.T he most critical part of any weld is :任何焊接的要紧部分为:a.The weld reinforcement.焊缝补强b.Correct heat input.正确的热量输入c.Polarity.极性d.The root pass根部焊道28.T he heat – affected zone is the portion of the :热影响区是的一部分:a.Metal that is added to produce the weld joint.用于产生焊接接头的金属b.Base metal that has been melted and solidified.被熔化并凝固的母材c.Base metal that has not been melted but where properties have been altered by the welding heat未熔化,但因焊接而改变性能的母材d.Original metal that is welded.焊接的原母材29.A rc strikes are typically caused by :电弧点击通常由引起:a.Molten particle splashed that are splashed out of the molten puddle熔融坑飞溅出来的熔化颗粒b.Excessive heat during the welding process焊接过程中的过多热量c.The use of improper or wet electrodes使用不适合或者湿焊条d.Welding operator error.焊工错误30.A welding inspector could expect to find a crater crack :焊接检验员希望在发现表面裂纹:a.At the beginning of the weld.焊接开始时b.Somewhere between the beginning and the end of the weld.焊接开始与结束时的某处c.At either the beginning or the end of the weld焊接开始或者结束时d.At the end of the weld.焊接结束时31.T he designer has detailed the joint B-U2-GF for the welding of two structural members. What is the acceptable range of root opening dimensions for that joint configuration ?设计人员全面规定了两个结构部件的焊接接头B-U2-GF。
IEC 60974-1 POWER WAVE 455M STT
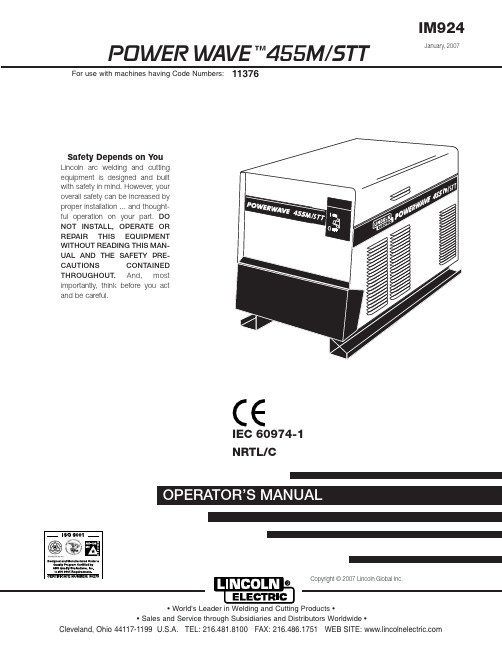
IEC 60974-1™OPERATOR’S MANUALIM924January, 2007Safety Depends on YouLincoln a c welding and cutting equipment is designed and built with safety in mind. However, your overall safety can be increased by proper installation ... and thought-ful ope ation on you pa t.DO NOT INSTALL, OPERATE OR REPAIR THIS EQUIPMENT WITHOUT READING THIS MAN-UAL AND THE SAFETY PRE-CAUTIONS CONTAINED THROUGHOUT.And, most impor tantly, think befor e you act and be careful.Copyright © 2007 Lincoln Global Inc.NRTL/CAUG 06Jan, 07Mar. ‘93viiviiThank Youfor selecting a QUALITY product by Lincoln Electric. We want you to take pride in operating this Lincoln Electric Company product •••as much pride as we have in bringing this product to you!TECHNICAL SPECIFICATIONS - POWER WAVE 455M/STT (CE) (K2203-4)• Lift only with equipment ofFIGURE A.1 - CONNECTION DIAGRAM ON CONNECTION/INPUT ACCESS DOORNOTE: Turn main input power to the machine OFF before performing connection procedure. Failure to do so will result in damage to the machine.POWER WAVE 455M/STT (CE)ROBOTPLC CONTROLLER ANALOG INTERFACEetc.POWER WAVE 455M/STT (CE)POWER WAVE 455M/STT (CE)POWER WAVE 455M/STT (CE)FEED HEADSINGLE HEAD FEEDERDUAL HEAD FEEDERSINGLE HEAD BOOM FEEDERFH 1PF-10RUP TO 4 FEEDERS ALLOWEDUP TO 4 FEED HEADS ALLOWEDWIRE DRIVE MODULETypical Robotic/ Hard Automation(using Wire Drive Module and PF-10R)POWER WAVE 455M/STT (CE)POWER WAVE 455M/STT (CE)POWER WAVE ALTERNATE HARD AUTOMATIC APPLICATION (using a UI, WD Module, and PF-10R)COMBINATION HARD AUTOMATION APPLICATION (w/ Semi-Auto, WD Module, and PF-10R)DUAL HEAD BOOM FEEDER (using two single heads)PF-10RPF-10RWIRE WIRESAFETY PRECAUTIONSRead this entire sec tion of operating instruc tions before operating the machine.ELECTRIC SHOCK can kill.• Do not touch electrically live parts or elec trodes with your skin or wet clothing.• Insulate yourself from the work and ground.• Always wear dry insulating gloves.• Do not use AC welder if your cloth-ing, gloves or work area is damp or if working on, under or inside work-piece.Use the following equipment:-DC manual (stick) welder.-AC welder with reduc ed voltage control.• Do not operate with panels removed.• Disconnect input power before serv-icing.-------------------------------------------------------------ONLY QUALIFIED PERSONS SHOULD INSTALL,USE OR SERVICE THIS EQUIPMENT. READ AND FOLLOW THE MANUFACTURER’S INSTRUC-TIONS, EMPLOYER’S SAFETY PRACTICES AND MATERIAL SAFETY DATA SHEETS (MSDS) FOR CONSUMABLES.-----------------------------------------------------------READ THIS WARNING, PROTECT YOURSELF &OTHERS.the arc,or both,to keep fumes and gases from your breathing zone and general area.WELDING SPARKS can cause fire orheld flammable material.ARC RAYS can burn.• Wear eye, ear, and body protection.INPUT POWERONOFFHIGH TEMPERATUREMACHINE STATUS CIRCUIT BREAKER WIRE FEEDER POSITIVE OUTPUT NEGATIVE OUTPUT 3 PHASE INVERTER INPUT POWER THREE PHASE DIRECT CURRENT GMAWFCAWGTAWOPEN CIRCUIT VOLTAGEINPUT VOLTAGE OUTPUT VOLTAGE INPUT CURRENT OUTPUT CURRENT PROTECTIVE GROUNDWARNING ORCAUTIONGRAPHIC SYMBOLS THAT APPEAR ON THIS MACHINE OR IN THIS MANUALU0U1U2I1I2SMAW11101546141732581213916WELDING ADJUSTMENTSAll adjustments are made on the system component known as the User Interface (Control Box), which con-tains the switches, knobs, and digital displays neces-sary to control both the Power Wave and a Power Feed wire feeder. Typically, the Control Box is supplied as part of the wire feeder. It can be mounted directly on the wire feeder itself, the front of the power source, or mounted separately, as might be done in a welding boom installation.Because the Control Box can be configured with many different options, your system may not have all of the following adjustments. Regardless of availability, all controls are described below. For further information, consult the Power Feed wire feeder instruction manu-al.•WFS / AMPS:In synergic welding modes (synergic CV, pulse GMAW, STT), WFS (wire feed speed) is the dominant control parameter, controlling all other variables. The user adjusts WFS according to factors such as weld size, penetration requirements, heat input, etc. The Power Wave then uses the WFS setting to adjust its output characteristics (output voltage, output current) accord-ing to pre-programmed settings contained in the POWER WAVE 455M/STT(CE). In non-synergic modes, the WFS control behaves more like a conven-tional CV power source where WFS and voltage are independent adjustments. Therefore to maintain the arc characteristics, the operator must adjust the volt-age to compensate for any changes made to the WFS. In constant current modes (stick, TIG) this control adjusts the output current, in amps.•VOLTS / TRIM:In constant voltage modes (synergic CV, standard CV) the control adjusts the welding voltage.In pulse synergic welding modes (pulse GMAW only) the user can change the Trim setting to adjust the arc length. It is adjustable from 0.500 to 1.500. A Trim set-ting of 1.000 is a good starting point for most condi-tions.Power Wave 455M/STT(CE) Only: In STT modes, the user can adjust the Trim setting to change the overall heat input to the weld.• WELDING MODEMay be selected by name (CV/MIG, CC/Stick Crisp,Gouge, etc.) or by a mode number (10, 24, 71, etc.)depending on the Control Box options. Selecting a welding mode determines the output characteristics of the Power Wave power source. For a more complete description of the welding modes available in the Power Wave, see the explanation below.• ARC CONTROLAlso known as Inductance or Wave Control. Allows operator to vary the arc characteristics from "soft" to "harsh" in all weld modes. It is adjustable from -10.0 to +10.0, with a nominal setting of 00.0 (The nominal set-ting of 00.0 may be displayed as OFF on some Power Feed wire feeder control panels). See the Welding Mode descriptions, below, for detailed explanations of how the Arc Control affects each mode.CONSTANT VOLTAGE WELDINGSynergic CV :For each wire feed speed, a corresponding voltage is preprogrammed into the machine through special soft-ware at the factory. The nominal preprogrammed volt-age is the best average voltage for a given wire feed speed, but may be adjusted to preference. When the wire feed speed changes, the Power Wave automati-cally adjusts the voltage level correspondingly to main-tain similar arc characteristics throughout the WFS range.Non Synergic CV:This type of CV mode behaves more like a conven-tional CV power source. Voltage and WFS are inde-pendent adjustments. Therefore to maintain the arc characteristics, the operator must adjust the voltage to compensate for any changes made to the WFS.All CV Modes:Arc Control, often referred to as wave control, adjusts the inductance of the wave shape. The wave control adjustment is similar to the "pinch" function in that it is inversely proportional to inductance. Therefore,increasing wave control greater than 0.0 results in a harsher, colder arc while decreasing the wave control to less than 0.0 provides a softer, hotter arc.(See Figure A.5)SAFETY PRECAUTIONSELECTRIC SHOCK can kill.• Only Qualified personnel sh ouldperform this maintenance.• Turn th e input power OFF at th edisconnect switch or fuse boxbefore working on this equipment.•Do not touch electrically hot parts. ROUTINE MAINTENANCERoutine maintenance consists of periodically blowing out the machine, using a low pressure airstream, to remove accumulated dust and dirt from the intake and outlet louvers, and the cooling channels in the machine.PERIODIC MAINTENANCECalibration of the Power Wave 455M/STT(CE) is criti-cal to its operation. Generally speaking the calibration will not need adjustment. However, neglected or improperly calibrated machines may not yield satisfac-tory weld performance. To ensure optimal performance, the calibration of output Voltage and Current should be checked yearly.CALIBRATION SPECIFICATIONOutput Voltage and Current are calibrated at the facto-ry. Generally speaking the machine calibration will not need adjustment. However, if the weld performance changes, or the yearly calibration check reveals a prob-lem, contact the Lincoln Electric Company for the cali-bration software utility.The calibration procedure itself requires the use of a resistive load bank, and certified actual meters for volt-age and current. The accuracy of the calibration will be directly affected by the accuracy of the measuring equipment you use. Detailed instructions are available with the utility.This Troubleshooting Guide is provided to help you locate and repair possible machine malfunctions. Simply follow the three-step procedure listed below. Step 1.LOCATE PROBLEM(SYMPTOM).Look under the column labeled “PROBLEM (SYMP-TOMS)”. This column describes possible symptoms that the machine may exhibit. Find the listing that best describes the symptom that the machine is exhibiting. Step 2.POSSIBLE CAUSE.The second column labeled “POSSIBLE CAUSE” lists the obvious external possibilities that may contribute to the machine symptom.Step 3.RECOMMENDED COURSE OF ACTION This column provides a course of action for the Possible Cause, generally it states to contact your local Lincoln Authorized Field Service Facility.If you do not understand or are unable to perform the Recommended Course of Action safely, contact your local Lincoln Authorized Field Service Facility.Service and Repair should only be performed by Lincoln Electric Factory Trained Personnel. Unauthorized repairs performed on this equipment may result in danger to the technician and machine operator and will invalidate your factory warranty. For your safety and to avoid Electrical Shock, please observe all safety notes and precautions detailed throughout this manual.__________________________________________________________________________USING THE STATUS LED TO TROUBLESHOOT SYSTEM PROBLEMS The Power Wave / Power Feed are best diagnosed as a system. Each component (power source, user inter-face, and feed head) has a status light, and when a problem occurs it is important to note the condition of each. In addition, errors displayed on the user interface in most cases indicate only that a problem exists in the power source, not what the problem may be. Therefore, prior to cycling power to the system, check the power source status light for error sequences as noted below. This is especially important if the user interface displays "Err 006" or "Err 100" .Included in this section is information about the power source Status LED, and some basic troubleshooting charts for both machine and weld performance.The STATUS LIGHT is a two color light that indicates system errors. Normal operation is a steady green light. Error conditions are indicated in the following chart.NOTE: The POWER WAVE 455M/STT(CE) status light will flash green, and sometimes red and green, for up to one minute when the machine is first turned on. This is a normal situation as the machine goes through a self test at power up.LIGHT CONDITION Status LED is solid green (no blinking). Status LED is blinking green.Status LED is blinking red and green.Status LED is solid red (no blinking). Status LED is blinking red.MEANING1. System OK. Power source communicating normallywith wire feeder and its components.2. Occurs during a reset, and indicates the POWERWAVE 455M/STT(CE) is mapping (identifying) each component in the system. Normal for first 1-10 sec-onds after power is turned on, or if the system con-figuration is changed during operation.3. Non-recoverable system fault. If the PS Status lightis flashing any combination of red and green, errors are present in the POWER WAVE 455M/STT(CE).Read the error code before the machine is turned off.Error Code interpretation through the Status light is detailed in the Service Manual. Individual code digits are flashed in red with a long pause between digits. If more than one code is present, the codes will be sep-arated by a green light.To clear the error, turn power source off, and back on to reset.Non recoverable hardware fault. Generally indicates nothing is connected to the POWER WAVE 455M/STT (CE) wire feeder receptacle. See Trouble Shooting Section.Not applicable.ERROR CODES FOR THE POWERWAVEThe following is a list of possible error codes that the POWER WAVE 455M/STT(CE) can output via the status light (see "Troubleshooting the Power Wave / Power Feed System Using the Status LED." If connected to a PF-10/11 these error codes will generally be accompanied by an "Err 006" or "Err 100" on the user interface display.If for any reason you do not understand the test procedures or are unable to perform the tests/repairs safely, con-If for any reason you do not understand the test procedures or are unable to perform the tests/repairs safely, con-If for any reason you do not understand the test procedures or are unable to perform the tests/repairs safely, con-Connection Diagram Semi-automatic "Simple System" (Electrode Positive, CV/Pulse Configuration shown)Connection Diagram Semi-automatic "Simple System" (Electrode Positive, STT Configuration shown)JapaneseChineseKoreanArabicREAD AND UNDERSTAND THE MANUFACTURER’S INSTRUCTION FOR THIS EQUIPMENT AND THE CONSUMABLES TO BE USED AND FOLLOW YOUR EMPLOYER’S SAFETY PRACTICES.SE RECOMIENDA LEER Y ENTENDER LAS INSTRUCCIONES DEL FABRICANTE PARA EL USO DE ESTE EQUIPO Y LOS CONSUMIBLES QUE VA A UTILIZAR, SIGA LAS MEDIDAS DE SEGURIDAD DE SU SUPERVISOR.LISEZ ET COMPRENEZ LES INSTRUCTIONS DU FABRICANT EN CE QUI REGARDE CET EQUIPMENT ET LES PRODUITS A ETRE EMPLOYES ET SUIVEZ LES PROCEDURES DE SECURITE DE VOTRE EMPLOYEUR.LESEN SIE UND BEFOLGEN SIE DIE BETRIEBSANLEITUNG DER ANLAGE UND DEN ELEKTRODENEINSATZ DES HER-STELLERS. DIE UNFALLVERHÜTUNGSVORSCHRIFTEN DES ARBEITGEBERS SIND EBENFALLS ZU BEACHTEN.JapaneseChineseKoreanArabicLEIA E COMPREENDA AS INSTRUÇÕES DO FABRICANTE PARA ESTE EQUIPAMENTO E AS PARTES DE USO, E SIGA AS PRÁTICAS DE SEGURANÇA DO EMPREGADOR.••• Sales and Service through Subsidiaries and Distributors Worldwide •Cleveland, Ohio 44117-1199 U.S.A. TEL: 216.481.8100 FAX: 216.486.1751 WEB SITE: 。
rebel EMP 215ic 和 Rebel EMP 235ic 多功能工业焊接机说明书

The go-anywhere, weld-anything machine The true multi-process industrial machine THE REBELLION IS GROWING.YOU DON’T KNOW THE MEANING OF A TYPICAL DAY – WHAT IT’S LIKE TO WORK 9 TO 5 AT A DESK. YOU DON’T KNOW WHERE YOU’LL WIND UP ON YOUR NEXT JOB, BUT YOU DO KNOW THAT YOU’LL HAVE TO BE READY FOR ANYTHING. AND WHEN IT COMES TO WELDING, THAT MEANS ANY PROCESS, ANY POWER, ANY MATERIAL, ANYWHERE, AND EVERY TIME. THE ONL Y CHOICE IS REBEL: A PACK OF MACHINES READY TO MOVE WITH EVERYTHING YOU NEED TO GET THE JOB DONE – START TO FINISH. THEY’RE ANYTHING BUT TYPICAL.WHAT MAKES A REBEL?TRUTH // Many machines claim they’re multi-process butare little more than MIG units in disguise. NotRebel. These are true multi-process welders, whichmeans whether you’re welding MIG, Flux-Cored,Stick – even those tricky 6010 rods – or TIG,these welders perform like they were born torun that process. Whether you choose Rebel 215 or the bigger, badder Rebel 235, there are three truths behind every Rebel. They outperform their competitors, they stand up to whatever comes your way in the shop or out in the field, and they make your job easier. You can bet on it. We call it Rebel DNA, and it runs through each and every one of these machines. TRUTH // Y ou’re on-site, out in the field, and in the shop. Y ou need a machine that can go where you go and withstand the harsh environments you face. Rebel can. With a sturdy multi-handle roll cage, steel unibody construction, and IP23S-level protection, Rebel’s rugged exterior gives you the confidence to go where you need to go without fear.TRUTH //Whether you’ve been welding for two years or 20, Rebel’s exclusive sMIG (smartMIG) technology is sure to impress. For rookies, there’s basic mode, which makes setup a breeze. For veterans, the built-in dynamic arc control constantly monitors your weld and adapts to your technique, providing a smooth, stable arc and superior, repeatable welds.w REBEL EMP 215ic: THE GO-ANYWHERE, WELD-ANYTHING MACHINE. TRUE MUL TI-PROCESS.Rebel EMP 215ic has perfected every process,no shortcuts, no compromises, and it will makeyou a multi-process believer. With the 4.3-inchmulti-lingual display, you can easily switch fromprofessional-grade MIG and Flux-Cored to LiftTIG and Stick, including 6010 and 6011 cellulosic and308L electrodes. Plus, it’s even compatible with aspool gun for welding aluminum.ADAPT ABLE DUAL VOL T AGE.Because you never know where your next job may be, you need a machine that’ll run – and run well – no matter your input power. Rebel EMP 215ic runs on 120 V and 230 V single-phase input power, and it will maintain performance down to 90 V without nuisanceerrors. Working in the field? No problem. It runs off a3.7 kVA (120 V) or 7.5 kVA (230 V) generator.sMIG FLUX CORED STICK MIG 53230120 sMIG FLUX CORED MIG 53120 sMIG FLUX CORED STICK TIG 53230120 sMIG FLUX CORED TIG MIG 53230120It’s the machine that started it all byredefining what it means to be multi-process and ready-to-weld – RebelEMP 215ic. Choose this Rebel and you’llget every piece of equipment you needto get going, no matter the process,material, or location. In addition to themulti-process system, there’s alsoRebel EM 215ic (MIG only) and RebelEMS 215ic (MIG/Stick).sMIG FLUX CORED TIG MIG 53230120 sMIG FLUX CORED STICK TIG MIG 53230sMIG FLUX COREDSTICK TIG MIG 53230120CRAZY SMART TECHNOLOGY.This technology we call sMIG (smartMIG)produces less spatter, minimizes weld defects,and adapts to your technique to provide asmooth, stable arc and repeatable welds.Simply set wire diameter and plate thicknessand you’re ready to weld. No matter your skilllevel, setup is quick and easy with basic modefor beginners and advanced mode for the pros.SELECT WIRE DIAMETERSET MATERIAL THICKNESSSTART WELDING AND sMIG DOES THE REST REBEL EMP 215ic TECHNICAL DATACurrent Range5–150 A (120 V); 5–240 A (230 V)MIG (GMAW) Welding Output 130 A/20.5 V (120 V) @ 20% duty cycle 205 A/24.3 V (230 V) @ 25% duty cycleStick (SMAW) Welding Output 90 A/23.6 V (120 V) @ 40% duty cycle 180 A/27.2 V (230 V) @ 25% duty cycleTIG (GTAW) Welding Output 130 A/15.2 V (120 V) @ 40% duty cycle 180 A/17.2 V (230 V) @ 30% duty cycleMax Plate Thickness3/8 in. (9.5 mm)Protection Class IP23SApprovals CSA E60974-1-00; IEC 60974-1Generator Size Recommendation 3.7 kVA (110 V); 7.5 kVA (230 V)Weight40 lb. (18.2 kg)Dimensions (H x W x D)16 in. x 9 in. x 23 in. (406 mm x 229 mm x 584 mm)Warranty 3 years – handle to handle; 1 year – torch; 100% satisfaction guaranteeIndustries Light Fabrication, Repair and Maintenance, Automotive and Restoration, Mechanical Contractors, Civil Construction, Agricultural Equipment, HVAC, Training SchoolsREBEL EMP 235ic: THE TRUE MULTI-PROCESS INDUSTRIAL MACHINE YOU HAVE TO SEE TO BELIEVE. UNPARALLELED PORTABILITY .Weighing in at only 53 pounds, Rebel EMP 235ic is the lightest machine in its class, which means it can go wherever you go. And that’s priceless in today’s demanding industries. With four perfectly placed handles and the ability to detach the power sourcefrom its cart, you’re able to tackle any job, anywhere,with dual voltage capability from 90 V to 270 V .When it comes to getting around andgetting work done, Rebel EMP 235icis second to none. It’s the most mobilewelder in its class and has the powerand performance to crush even themost demanding jobs. In addition tothe multi-process system, a single-process Rebel EM 235ic (MIG only)is also available.THE POWER TO PERFORM. When it comes to portable welders, small means weak, right? Dead wrong. Rebel EMP 235ic is packed with the power to weld up to a half inch on mild steel, measuring in at 235 A at 40% duty cycle with a max output of 250 A/30 V . VERSATILITY THAT CAN’T BE BEAT .Rebel EMP 235ic is three machines in one – MIG,TIG, and Stick. And for welders, that means the daysof having multiple machines are officially over. Y ouroptions are now open with the ability to weld a widerange of metal thicknesses and applications, includingthe full range of .035 in both short arc and spray arc transfer, up to .045 solid wires, and up to .052 coredwires. Plus, Rebel EMP 235ic can also weld Stick rodsup to 5/32 in. and TIG rods up to 3/16 in. sMIG FLUX CORED STICK MIG 53230120sMIG FLUX CORED TIG MIG 53sMIG FLUX CORED STICK TIG 53230120 sMIG FLUX CORED STICK TIG MIG 53230120 sMIG FLUX CORED IG MIG 5390120270 230 FLUX CORED 53120230 sMIG FLUX CORED STICK TIG MIG 53230120 sMIG EXTENDED RANGE UP TO .045 SOLID WIRE.REBEL EMP 235ic TECHNICAL DATACurrent Range5–150 A (120 V); 5–250 A (230 V)MIG (GMAW) Welding Output 120 A/19 V (120 V) @ 40% duty cycle 235 A/26 V (230 V) @ 40% duty cycleStick (SMAW) Welding Output 90 A/23.6 V (120 V) @ 40% duty cycle 210 A/28.4 V (230 V) @ 40% duty cycleTIG (GTAW) Welding Output 130 A/15.2 V (120 V) @ 40% duty cycle 240 A/19.6 V (230 V) @ 40% duty cycleMax Plate Thickness1/2 in. (12.7 mm)Protection Class IP23SApprovals CSA E60974-1-00; UL60974-1; IEC 60974-1Generator Size Recommendation 3.7 kVA (110 V); 7.5 kVA (230 V)Weight53 lb. (24 kg)Dimensions (H x W x D)26.5 in. x 11.5 in. x 19.5 in. (673 mm x 292 mm x 495 mm)Warranty 3 years – handle to handle; 1 year – torch; 100% satisfaction guaranteeIndustries General Fabrication, Repair and Maintenance, Civil Construction, Mechanical Contractors, Automotive and Restoration, Farm and Ranch, HVAC, Training SchoolsEVEN MORE INCREDIBLE STANDARD FEATURES. SOLID CAST ALUMINUM FEEDER.The design of this cast feeder mechanism increasesdurability, decreases wire shavings and bird nesting,provides for easy drive roll changes (no tools required),and delivers consistent feeding performance. All inall it has optimized alignment and long-life drive standcomponents that ensure accurate, smoothwire feeding.LIGHTWEIGHT . The 40-pound Rebel 215 and 53-pound Rebel 235are easy to carry from jobsite to jobsite.MUL TI-MATERIAL. Weld steel, stainless, and aluminum with the optional spool gun.WELD PARAMETER STORAGE.Save up to four welding parameters per process;ideal for switching between jobs.TRIGGER HOLD FUNCTION 2T/4T .Reduces operator fatigue when MIG or TIG welding.INFINITE VOL TAGE CONTROL. Fine-tune the arc characteristic by adjusting thevoltage setting.ADJUSTABLE INDUCTANCE.Perfect for fine-tuning arc stability andcontrolling spatter.ADJUSTABLE BURN-BACK CONTROL. Prevents wire from sticking in the weld pool orburning back, damaging the contact tip.ADJUSTABLE ARC FORCE CONTROL.Optimizes Stick electrode performance and allowsthe operator to increase the arc voltage for a shortperiod of time to avoid arc outs and “sticking” whenthe arc is too short. sMIG FLUX CORED MIG 40120 sMIG FLUX COREDMIG 53120270 230AUTOMATIC HOT START CONTROL. Increases the initial welding current to avoid the electrode sticking to the workpiece; particularly useful for difficult-to-start electrodes.LiftTIG ARC STARTS.Provides TIG arc starts without the use of high frequency. Ideal for the shop or site application where sensitive electronic devices operate.GAS PRE- AND POST-FLOW TIME ADJUSTMENT.Purges gas line and prevents porosity at the start and end of welding; especially useful when MIG welding aluminum.IP23S.The enclosure is built to protect youand your machine. Designed to ahigher standard, Rebel can withstandharsh outdoor environments.WARRANTY.Rebel comes backed with a rock-solid, three-year, handle-to-handle warranty and 100-day, 100% satisfaction guarantee.DUAL SOLENOID VAL VE.When it comes to TIG applications, you have total gas control with Rebel 235’s dual solenoid valve. This additional solenoid valve allows for automatic on/offat ignition and has the ability to set pre- and post-gas flow for proper shielding while also cutting down on gas consumption. For MIG applications, set up a steel/ stainless steel MIG and aluminum spool gun at the same time for maximum productivity without switching back and forth. *Available on Rebel 235 models only.sMIG FLUXCOREDSTICK TIG MIG40230120WHAT’S INCLUDED WITH YOUR REBEL 215.PACKAGE FEATURES EM 215ic EMS 215ic EMP 215ic ProcessMIG X X XFlux-Cored X X XStick (DC)X XTIG (DC)XMaterialsSteel X X XStainless Steel X X XAluminum X X XExclusive FeaturessMIG (.023–.035)X X XsMIG Extended Range (.023–.045)4.3 in. Color LCD/TFT Display X X90–270 V Dual Voltage (extended range)X X XReady-to-Weld (all accessories included – including sampleX X X filler metals)Auto-Detect Spool Gun Capable X X X4 in. Spool Capable X X X8 in. Spool Capable X X X12 in. Spool CapableFour Memory Settings (per process)X XMulti-lingual Display X XBuilt-In Instruction Manual and Spare Parts List X XBuilt-In Weld Parameters X XInductance Control (MIG mode only) X XTrigger Lock (2T, 4T)X XVoltage Trim Adjustment (MIG mode only)X XSCT™ (Short Circuit Termination) X XBurn-Back Adjustment X XPre-flow/Post-flow Adjustment X XSpot Timer Capable X XAutomatic Hot Start X XArc Force Adjustment X XLift Arc XOPTIONAL ACCESSORIES.T weco Spool Gun (Part No. 1027-1397) Spool Gun 160 A, 12 ft. (3.6 m) cable, suits 4 in. (100 mm) spools – required for welding aluminumFoot Control (Part No. W4014450) Foot control contractor on/off and current control with 8-pin male plugand 15 ft. (4.6 m) cableBUNDLED ACCESSORIESEM 215icEMS 215icEMP 215icTweco Fusion 180 A MIG gun with 10 ft. (3 m) cable XX X Tweco 200 A electrode holder with 13 ft. (4 m) cable XX Tweco 17 V TIG torch with 12.5 ft. (3.8 m) cable X Tweco 13 ft. (4 m) ground clamp with leadsX X X Victor argon flowgauge regulator with 12.5 ft. (3.8 m) gas hose X X X 110 V adapter plugX X X Four general purpose 6013 Stick electrodes X X AristoRod 12.50 .030, 8 in., 5 lb. sample spoolXXXBasic Utility Cart (Part No. 0558102325) Utility cart accommodates maximum 7 in. (177.8 mm) diameter cylinderSingle Cylinder Cart (Part No. W4015001) Single cylinder cart accommodates up to 9 in. (228.6 mm) diametercylinder with accessory drawer, plus one parts storage boxnnnnEVERYTHING THAT’S INCLUDED WITH YOUR REBEL 235.PACKAGE FEATURES EM 235ic EMP 235icProcessMIG X XFlux-Cored X XStick (DC)XTIG (DC)XMaterialsSteel X XStainless Steel X XAluminum X XExclusive FeaturessMIG (.023–.035)X XsMIG Extended Range (.023–.045)X X4.3 in. Color LCD/TFT Display X90–270 V Dual Voltage (extended range)X XReady-to-Weld (all accessories included – including sampleX X filler metals)Auto-Detect Spool Gun Capable X X4 in. Spool Capable X X8 in. Spool Capable X X12 in. Spool Capable X XFour Memory Settings (per process)XMulti-lingual Display XBuilt-In Instruction Manual and Spare Parts List XBuilt-In Weld Parameters XInductance Control (MIG mode only) XTrigger Lock (2T, 4T)XVoltage Trim Adjustment (MIG mode only)XSCT™ (Short Circuit Termination) XBurn-Back Adjustment XPre-flow/Post-flow Adjustment XSpot Timer Capable XAutomatic Hot Start XArc Force Adjustment XLift Arc XBUNDLED ACCESSORIES EM 235ic EMP 235icTweco Spray Master 250 MIG gun with 15 ft. (4.6 m) cable X XTweco 200 A electrode holder with 13 ft. (4 m) cable XTweco 13 ft. (4 m) ground clamp with leads X XVictor argon flowgauge regulator with 12.5 ft. (3.8 m) gas hose X X110 V adapter plug X XAtom Arc Acclaim 7018 sample pack Stick electrodes XAristoRod 12.50 .035, 8 in., 11 lb. sample spool X XOPTIONAL ACCESSORIES.ESAB TXH 201 5/8 npt 12.5 ft. TIG T orch Outfit (Part No. 0558102493) T weco 200 A 12 ft. Spool Gun(Part No. 1027-1398)T weco 200 A 25 ft. Spool Gun(Part No. 1027-1399)DARE // /REBEL.Foot Control (Part No. W4014450) Foot control contractor on/off and current control with 8-pin male plug and 15 ft. (4.6 m) cable Single Cylinder Cart (Part No. 0558102491)nnnn nUNRIVALED SERVICE AND SUPPORT.Rebel, like every ESAB machine, is backed by our commitment to superior customer service and support. Our skilled customer service department is prepared to quickly answer any questions, address problems, and help with maintenance and upgrading of machines.For more information on Rebel, visit /rebel.3-YEAR WARRANTY.ESAB’s industry-leading service and support means that if customers do need help, they’llbe protected by the most comprehensive warranty in the business.100% SATISFACTION GUARANTEE.If there’s anything – and we mean anything – you’re not completely happy with inyour first 100 days with your machine, ESAB will make it right, or your money back.ESAB/。
854285-001 1 Memory Module Replacement Instruction

Memory Module Replacement InstructionsBefore you beginObserve the following requirements before removing and replacing memory.WARNING : Never open the cover while the power cord is attached. You might damage your computer or be injured by the spinning fan blades.WARNING : Avoid touching sharp edges inside the computer.CAUTION : Static electricity can damage the electroniccomponents inside the computer. Discharge static electricity by touching the metal cage of the computer before touching any internal parts or electronic components. Tools neededPhillips #2 screwdriver Hex toolSmall screws are easily lost. Remove screws over a surface that enables you to retrieve them if they fall.TroubleshootingIf the computer displays a memory error after you have turned it back on, turn the computer off and unplug the power cord. Open up the memory compartment and make sure the memory module is inserted all the way into the slot, and then press down on it to be sure it is firmly seated.Memory compatibilityThe computer uses SODIMMs (small outline dual in-line memory modules) that must meet the following requirements: ● 204-pin ● DDR4-2133● Unbuffered, non-ECC (64-bit)● 1.2 V● 16 GB maximum installable memoryBecause the memory uses dual channels, you must use the same memory module type for both sockets.NOTE : The actual memory transfer speed might vary, based on the processor used in your computer.NOTE : Memory performance might vary due to different system configurations.Removing the memory module1. Disconnect the power cord and all attached cables from the back of the computer.854285-0012. Using caution, lay the computer down on a flat surface covered with a soft cloth.3. To remove the stand, rotate it upward(1), remove the four hex screws (2), and then lift the stand up and off the computer (3).4. To remove the rear cover, remove the two screw covers (1) and two Phillips screws (2) located in the bottom of the cover. Lift off the cover, and then place it upside down next to the computer(3). The optical drive ismounted on the inside of the rear cover, and a cableconnects it to the system board.5. Locate the memory modules: 1. Hard drive 2.Memory modules6. Remove the five Phillips screws that secure the system board cover (1), and then lift the cover off the computer (2).7. Spread the two retention clips outward (1) until the memory module tilts up at a 45-degree angle. Remove the module (2). Use the same procedure to remove both memory modules.8. Touch the replacement memory module bag to the metal of the computer, and then remove the replacement memory module from the bag.Replacing the memory module1. Align the notched edge of the module with the tab in the slot, and then press the module into the slot at an angle until it is seated (1). Press down on the module until the side retention clips snap into place (2).NOTE : Memorymodules are notched to prevent incorrect insertion.2. Position the system board cover over the system board (1), and then replace the five Phillips screws (2).3. Align the rear cover with the computer and press itdown until it snaps into place (1). Replace the two Phillips screws (2), and then replace the screw covers(3).4. Position the top of the stand on the computer (1), and then replace the four hex screws (2). Rotate the stand downward (3).5. Plug the power cord and any additional cables into the back of the computer.6. Press the power button to turn on the computer.© Copyright 2016 HP Development Company, L.P.The information contained herein is subject to change without notice. The only warranties for HP products and services are set forth in the express warranty statements accompanying suchproducts and services. Nothing herein should be construed as constituting an additional warranty. HP shall not be liable for technical or editorial errors or omissions contained herein.First Edition: May 2016PRINTER: Replace this bo x with Pr inted- In (PI)Statement(s) as per spec.NOTE: This box is simply a placeho lder. PI Statement(s) do n ot have to fit inside the box but sh ould be placed in this area.。
WPS焊接工艺规程(AWS版)

affection on bend ability and tension ability of joint
附加重要变素supplemental essential variables
影响接头冲击性能的因素Affect the toughness of joint
3
Who take charge of compiling WPS? WPS应该由谁制定 应该由谁制定? 应该由谁制定
每个制造者或承包者应按照焊接规范的规定编写合 理的WPS.具体的说WPS是由代表厂家的焊接工程 师编写的。 Each manufacturer and contractor shall prepare written Welding Procedure Specifications which are defined in corresponding welding code.
supervised by AI 授权检验师检查
6
How is a WPS created? 如何创建一个WPS? 如何创建一个
FCAW药芯焊丝保护 FCAW药芯焊丝保护 焊
+
接头形式 joint type
SAW埋弧焊 SAW埋弧焊 GMAW气保焊 GMAW气保焊 SMAW焊条电弧焊 SMAW焊条电弧焊 GTAW钨极氩弧焊 GTAW钨极氩弧焊
General 一般条件
For the PQR groove area, an increase or decrease > 25% in the number of passes 对于与PQR坡口面积相同的,焊道数改变超过 25% A change in position not qualified焊接位置改变为未经评定的位置 。
Part C

规范练习题(PART C)(适用规范:AWS D1.1:2008 StructuralWelding Code—Steel)(本练习题包括:第一部分考试练习题第二部分模拟题和答案)说明:本练习题系AWS 根据AWS D1.1/D1.1M:2008 所编;在考试内容上和AWS D1.1/D1.1M:2006 不会有重要差别,提供给大家作为参考。
本次培训和考试所用规范为AWS D1.1/D1.1M:2006。
第一部分(考试练习题部分)1.For RT of 1-1/2 inch thick plate, which hole-type IQI designation isrequired (Source Side)?对于1-1/2英寸的板厚进行RT时,应选用那种孔型像质指示器(射线源侧)a) 20b) 25c) 30d) 35e) 402.Which of the follow SMAW electrodes is not included in the F2 group?下面那种SMAW焊条不包括在F2组别内?a)E6012b)E6010c)E6013d)E6014e)None of the above 以上都不是3.The maximum weld reinforcement permitted for a welding procedurequalification on pipe or tubing having a wall thickness of 0.208 inch is:壁厚为0.208英寸的管材焊接工艺评定允许的最大焊缝余高是:a)none permitted 不允许b)1/16 inchc)3/16 inchd)3/32 inche)1/8 inch4.For a fillet weld joining 1/2 inch thick statically loaded nontubularmembers, what maximum length of 1/16 inch deep undercut is allowed in any 12 inch length of weld?连接1/2英寸厚的非管材静载荷构件的角焊缝,每12英寸焊缝长度内,允许1/16英寸的咬边长度是多少。
差压变送器故障现场处理流程

差压变送器故障现场处理流程Differential Pressure Transmitter Troubleshooting Procedure.1. Check the Power Supply.Ensure that the transmitter is receiving power.Verify the voltage and amperage at the transmitter terminals.Inspect the wiring for any loose connections or damage.2. Inspect the Mechanical Installation.Make sure that the transmitter is properly mounted and aligned.Check the impulse lines for any leaks or blockages.Inspect the diaphragm or sensing element for any damage or deformation.3. Examine the Electrical Connections.Verify the polarity of the connections.Tighten all electrical terminals.Ensure that the shield wire is properly grounded.4. Calibrate the Transmitter.Apply a known pressure to the transmitter.Adjust the zero and span settings until the output signal corresponds to the applied pressure.5. Check the Output Signal.Monitor the output signal with a voltmeter or ammeter.Verify that the signal is within the expected range.Look for any fluctuations or noise in the signal.6. Diagnose Common Problems.Zero Shift: This can be caused by a damaged diaphragm, a loose connection, or a faulty amplifier.Span Drift: This can be caused by a leak in the impulse lines, a clogged filter, or a problem with the sensor.Output Noise: This can be caused by electrical interference, loose wiring, or a faulty output circuit.7. Repair or Replace the Transmitter.If the problem cannot be resolved through troubleshooting, the transmitter may need to be repaired or replaced.Contact the manufacturer or a qualified technician for assistance.中文回答:压差变送器故障现场处理步骤。
WPS焊接工艺规程(AWS版)详解
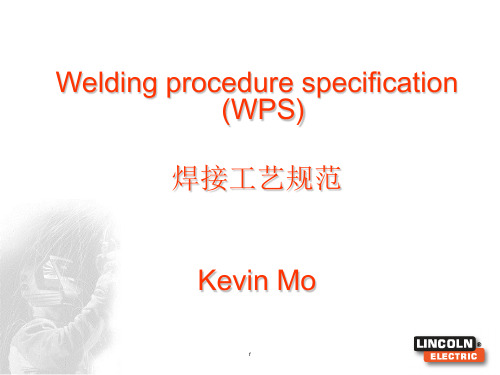
change in the amperage for each diameter每种焊丝 直径的电流变化超过10% A change in type of current (ac or dc) or polarity and mode of transfer (GMAW only)电流极性变化或GMAW过 渡模式变化 A change in the voltage for each diameter,surpass 7% 电压改变超过7% An increase or decrease in the wire feed speed for each electrode diameter surpass 10%送丝速度改变超 过10%
4
Availability of the WPS WPS的可得性
用于产品焊接的WPS,应当在制造现场便于获得
,以供查考,并供授权检验师(AI)检查。 A WPS used for Code production welding shall be available for reference and review by the Authorized Inspector (AI) at the fabrication site.
非重要变素non
essential variables
对弯曲和拉伸不能产生明显影响的因素Can’t produce visible
affection on bend ability and tension ability of joint
附加重要变素supplemental
essential variables
填充材料
Increase in filler metal classification strength增加填料的强度 Change from one electrode classification to any other electrode classification,limited to FCAW从一种焊丝型号改变 到另一种焊丝型号(只限药芯焊丝) Change to an electrode classification not covered in AWS A5.18,A5.20,A5.28,A5.29.焊丝变为在AWS中没有的型号
船舶英语手册

Fore frame Bilge longitudinal bottom longitudinal bottom web longitudinal Deck longitudinal Inner bottom longitudinal Shell side longitudinal Top longitudinal of double bottom Tank after peak tank after water tank AuxilБайду номын сангаасary water tank Auxiliary water ballast tank Bilge tank Bottom tank Bottom side tank Cargo and ballast tank Circulating flow water tank Circulating lubricating oil tank Clean ballast tank Condensate catch tank Dry tank Sealing ring Hinge Handle Balance block welding 焊接
Slopping-bulkhead longitudinal Structure Accessory structure All-welded structure Amidships structure Berthing structure Bottom keel structure Bow structure Braced structure Bridge structure Forecastle structure Framed structure Girder structure manhole Drinking water tank Bilge tank Emergency fresh water tank Fore tank Fore peak tank Hopper side tank Liquid tank Keel tank Starboard tank Topside tank Topside wing tank Small hatch cover Water-tight small hatch cover Weather-tight small hatch cover Single v groove with broad rood face Groove face Groove angle Weld slope Root of joint
气体保护焊工艺流程

气体保护焊工艺流程英文回答:Gas Metal Arc Welding (GMAW)。
Gas metal arc welding (GMAW), also known as metal inert gas (MIG) welding, is a welding process that uses an electric arc between a consumable wire electrode and the workpiece to join metals. The wire electrode is continuously fed into the weld pool, and the arc is shielded by an inert gas, typically argon or helium. This prevents the weld pool from being contaminated by the atmosphere.GMAW is a versatile welding process that can be used to weld a variety of metals, including steel, aluminum, and stainless steel. It is also a relatively fast and efficient welding process, making it ideal for high-production applications.Process Flow.The following is a general overview of the GMAW process flow:1. Preparation: The first step is to prepare the workpiece for welding. This may involve cleaning the surface of the workpiece, removing any rust or dirt, and ensuring that the workpiece is properly clamped in place.2. Setup: Once the workpiece is prepared, the welding equipment must be set up. This includes setting the welding parameters, such as the welding current, voltage, and wire feed rate.3. Welding: The welding process begins by striking an arc between the wire electrode and the workpiece. The arcis then maintained as the wire electrode is fed into the weld pool. The welder must control the speed and direction of the welding torch to ensure that the weld is properly formed.4. Finishing: Once the weld is complete, it must be allowed to cool. The welder may also need to grind or peen the weld to remove any slag or other imperfections.Advantages of GMAW.Versatility: GMAW can be used to weld a variety of metals, including steel, aluminum, and stainless steel.Speed and efficiency: GMAW is a relatively fast and efficient welding process, making it ideal for high-production applications.Portability: GMAW equipment is relatively portable, making it easy to use in a variety of locations.Ease of use: GMAW is a relatively easy-to-learn welding process.Disadvantages of GMAW.Cost: GMAW equipment can be relatively expensive topurchase and maintain.Fumes: GMAW produces fumes that can be harmful to health. Proper ventilation must be used to protect the welder.Spatter: GMAW can produce spatter, which can be a nuisance and can damage the workpiece.中文回答:熔化极气体保护焊工艺流程。
高压主备电源切换流程

高压主备电源切换流程英文回答:High voltage primary and secondary power supply switching process.When it comes to the process of switching between primary and secondary power supplies in high voltage systems, there are several steps that need to be followed to ensure a smooth transition. Let me explain the process in detail.1. Monitoring the primary power supply:Firstly, it is crucial to constantly monitor the primary power supply to ensure its stability and availability. This can be done through various monitoring devices and systems that provide real-time information about the primary power source.2. Detecting a power failure:In the event of a power failure or any other issue with the primary power supply, it is important to have a mechanism in place that can quickly detect the problem.This can be achieved through the use of sensors or monitoring devices that can sense a drop in voltage or an interruption in power supply.3. Activating the secondary power supply:Once a power failure is detected, the switching process begins. The secondary power supply, also known as the backup power supply, needs to be activated to ensure continuous power supply to the system. This can be done manually or automatically, depending on the system's design.4. Transferring the load:After the secondary power supply is activated, the load needs to be transferred from the primary power supply tothe backup power supply. This can be done through the useof switches or circuit breakers that redirect the power flow.5. Verifying the secondary power supply:Once the load is successfully transferred, it is important to verify the stability and reliability of the secondary power supply. This can be done by monitoring the voltage levels, frequency, and other parameters to ensure that the backup power supply is capable of meeting the system's requirements.6. Restoring the primary power supply:Once the primary power supply is restored, the system needs to switch back to the primary source. This can bedone manually or automatically, depending on the system's configuration. The load is transferred back to the primary power supply, and the secondary power supply is deactivated.7. Monitoring and maintenance:After the switching process is complete, it isimportant to continuously monitor the primary and secondary power supplies to ensure their proper functioning. Regular maintenance and testing should be conducted to identify any potential issues and address them promptly.To illustrate the process, let's consider an example of a data center. In a data center, there are multiple servers and networking equipment that require a stable power supply. The primary power supply is provided by the local utility grid, while the secondary power supply is a set of backup generators.In this scenario, the monitoring devices constantly monitor the voltage and frequency of the utility grid. If there is a power failure or a significant drop in voltage, the sensors detect it and trigger the backup generators to start. The load is then transferred from the utility gridto the generators using switches or circuit breakers.Once the utility power is restored, the system automatically switches back to the primary source. The loadis transferred back to the utility grid, and the backup generators are deactivated. Throughout the process, the monitoring devices ensure that the voltage and frequency levels are within the acceptable range.中文回答:高压主备电源切换流程。
MIG (GMAW) 流量管熔合锅炉说明书

Issued January 2019 • Index No. DC/12.49Comes complete with:15 ft. (4.6 m), 250-amp MDX 10 ft. (3 m) work cable with clamp 10 ft. (3 m) industrial power cord (with plug on 200/230 V model)Flow gauge regulator and gas hose for argon or AR/CO 2mixFactory-installed lowered running gear/cylinder rack.030/.035 in. reversible dual-groove drive rolls Extra contact tipsHighest output in its class (250 A at 28 VDC). Weld longer on high-end applications.Infinite voltage control with self-calibrating digital meters that permit presetting of voltage and wire feed speed. Ensures precise parameters and accuracy.Integrated digital timers come complete with presettable preflow/postflow, burnback, spot and delay (stitch) timers. Independent timers for MIG and spool gun.Line voltage compensation keeps power constant even if power input varies by Active Arc Stabilizer™minimizes weld cleanup, and provides excellent starts proven superior to the competition.allows operator to simply pull trigger on MIG gun, spool gun orpush/pull gun. Automatically detects and recalls the voltage, wire feed speed and timer of the active gun. See page 3 for more information.Heavy-duty aluminum two-drive-roll system.energy use and the amount of contaminants pulled though the machine.EZ-Access compartment and parameter chart. Set weld parameters right the first time with convenient flip-down compartment that provides fast access to parameter chart and consumables. See page 3 for more information.Superior aluminum MIG welding with direct connection of optional spool Directly ™200 andSpoolmatic ®spool guns or XR ™push-pull guns. No extra module to buy or install.Welder is warranted for three years, parts and labor.Original main power rectifier parts are warranted for five years.Gun warranted for 90 days, parts and labor.Millermatic ®252MIG Power Source,Wire Feeder and Gun PackageMiller Electric Mfg. LLCAn ITW Welding Company 1635 West Spencer Street P.O. Box 1079Appleton, WI 54912-1079 USAEquipment Sales US and CanadaPhone: 866-931-9730FAX: 800-637-2315International Phone: 920-735-4554International FAX: 920-735-4125IMPROVED!210203040506070809010050100150200250300350400450500W e l d A m p sDuty Cycle Chart51015202530350100200300400Amperes% Duty Cycle Volt/Amp CurvesV o l t sMaxMinPerformance DataControl Panel1.Voltmeter2.Voltage Control3.Wire Speed Meter4.Wire Speed Control*While idling.Note: Operating temperature range: -4° to +104°F (-20° to +40°C). Storage temperature range: -22° to +122°F (-30° to +50°C).Certified by Canadian Standards Association to both the Canadian and U.S. Standards.3Standard Fully Loaded FeaturesOptional Fully Loaded Features4Dual EZ-Change™Low Cylinder Rack with Elevated Gun and Cable Rack 300337Dual cylinder rack allows operators to easily roll cylinders on and off the rack with no lifting. Gun and cable rack keeps cables off the floor and tangle free.Elevated Gun and Cable Rack 300335For use with single cylinder rack. (Included with dual EZ-Change low cylinder rack.) Protective Cover 195142Features side pocket.(Not for use with dual cylinder rack or elevated gun and cable rack.)Argon/Mixed Gas Regulator and Gas Hose 195050Full KVA Adapter Cord 300517Field NEMA 14-50P to NEMA 6-50R. Adapts engine drive 120/240 V plug to common Millermatic®and Spectrum®240 V plug.MIG GunsMDX™-250 MIG Gunwith AccuLock™MDX Consumables1770035 10 ft. (3 m)1770036 12 ft. (3.7 m)1770037 15 ft. (4.6 m), standardIndustrial 250-amp MIG gun with consumablesfor .030/.035 in. (0.8/0.9 mm) wire.MDX™-250 MIG Gunwith Industrial AccuLock™S Consumables1770041 10 ft. (3 m)1770042 12 ft. (3.7 m)1770043 15 ft. (4.6 m)Industrial 250-amp MIG gun with consumablesfor .035/.045 in. (0.9/1.2 mm) wire.Spool GunsSpoolmatic®15A Spool Gun 195156Spoolmatic®30A Spool Gun 130831Ideal for aluminum welding jobs. Air-cooled,one-pound spool gun with 15-foot (4.6 m)or 30-foot (9.1 m) cable assembly. Ratedat 200 amps at100 percent duty cycle.For detailed information, see Spoolmaticliterature M/1.73.Spoolmate™200 Spool Gun 300497Reliable and economical spool gun perfectfor hobbyists and light fabricators whoweld aluminum. Handles .030–.035 inch(0.8–0.9mm) aluminum wires and.023–.035 inch (0.6–0.9mm) steel/stainlesssteel wires. Rated at 160 amps, 60 percent dutycycle with 20-foot cable assembly.For detailedinformation, see Spoolmate literature M/1.47.Optional Spoolmate™200 Head Tubes300591 45-degree head tube300592 9-inch extension head tube243385 5-inch head tubePush-Pull GunsXR-Aluma-Pro™Lite Push-Pull Gun30094825 ft. (7.6 m)Air-cooled gooseneck-style gun for .030–.047 in.(0.8–1.2 mm) aluminum. Rated at 175 amps at60 percent duty cycle.XR-Aluma-Pro™Push-Pull Gun30000015 ft. (4.6 m)30000125 ft. (7.6 m)Air-cooled gooseneck-style gun for .030–.047 in.(0.8–1.2 mm) aluminum. Rated at 300 amps at100 percent duty cycle.U-Grooved Aluminum Drive Rolland Accessory Kits for XR-Aluma-ProPush-Pull Guns195311 .035 in. (0.9 mm)195313 .047 in. (1.2 mm)Kits include Millermatic U-grooved drive rolls,nylon wire guides and contact tips. Genuine Miller®Accessories5 FemaleReceptacleConsumablesFor MDX™-250 MIG GunsStandard Miller®AccuLock™MDX Consumables Smaller consumables and components to access hard-to-reach weldments.Contact Tips (10 per package)T-M023 .023 in. (0.6 mm)T-M030 .030 in. (0.8 mm)T-M035 .035 in. (0.9 mm)T-M045 .045 in. (1.2 mm)NozzlesN-M1200C Copper, 1/2 in. ID, flush, standard N-M1218C Copper, 1/2 in. ID, 1/8 in. recessN-M5800C Copper, 5/8 in. ID, flushN-M5818C Copper, 5/8 in. ID, 1/8 in. recessN-M58XTC Copper, 5/8 in. ID, 1/8 in. stickout Diffuser D-M250Monocoil Replacement Liners10 ft. LinerLM1A-10 .023/.025 in. (0.6 mm)LM2A-10 .030/.035 in. (0.8/0.9 mm)LM3A-10 .035/.045 in. (0.9/1.2 mm)12 ft. LinerLM1A-12 .023/.025 in. (0.6 mm)LM2A-12 .030/.035 in. (0.8/0.9 mm)LM3A-12 .035/.045 in. (0.9/1.2 mm)15 ft. LinerLM1A-15 .023/.025 in. (0.6 mm)LM2A-15 .030/.035 in. (0.8/0.9 mm)LM3A-15 .035/.045 in. (0.9/1.2 mm)Optional Bernard®AccuLock™S Consumables Consumables for increased durability and longer life when guns are used in industrial applications. Contact Tips (10 per package)T-A023CH .023 in. (0.6 mm)T-A030CH .030 in. (0.8 mm)T-A035CH .035 in. (0.9 mm)T-A039CH .039 in. (1.0 mm)T-A045CH .045 in. (1.2 mm)NozzlesN-A5800C Copper, 5/8 in. ID, flush, standard N-A5818C Copper, 5/8 in. ID, 1/8 in. recessN-A5814C Copper, 5/8 in. ID, 1/4 in. recess Diffuser D-MA250For Spoolmatic®Spool Guns andXR™Push-Pull GunsFor Aluminum WireFasTip™Contact Tips (25 per package)206186 Heavy-duty, .030 in. (0.8 mm)206187 Heavy-duty, .035 in. (0.9 mm)206188 Heavy-duty, .040 in. (1.0 mm)206189 Heavy-duty, 3/64 in. (1.2 mm)206191 Heavy-duty, 1/16 in. (1.6 mm)209026 Tapered, .030 in. (0.8 mm)209027 Tapered, .035 in. (0.9 mm)209029 Tapered, 3/64 in. (1.2 mm)206030 Tapered, 1/16 in. (1.6 mm)Screw-On Nozzles199610 Brass, 1/2 in. orifice, tapered199613 Brass, 5/8 in. orifice, tapered199614 Brass, 5/8 in. orifice, tapered HD199611 Brass, 3/4 in. orifice, straight199612 Brass, 3/4 in. orifice, straight HD209035 Copper, 3/8 in. orifice, tapered199615 Copper, 1/2 in. orifice, tapered209036 Copper, 1/2 in. orifice, tapered HD198855 Copper, 5/8 in. orifice, tapered199618 Copper, 5/8 in. orifice, tapered HD207313 Copper, 5/8 in. orifice, tapered 15/16 OD199616 Copper, 3/4 in. orifice, straight199617 Copper, 3/4 in. orifice, straight HDBernard®Centerfire™“T” Series Contact TipsT-035AL .035 in. (0.9 mm)T-047AL .047 in. (1.2 mm)T-062AL 1/16 in. (1.6 mm)Bernard®Centerfire™Small NozzlesNST-3818B Brass, 3/8 in. ID, 1/8 in. tip recessNS-1218B Brass, 1/2 in. ID, 1/8 in. tip recessNS-1200B Brass, 1/2 in. ID, flush tipNS-5818B Brass, 5/8 in. ID, 1/8 in. tip recessNS-1218C Copper, 1/2 in. ID, 1/8 in. tip recessFor Spoolmate™200 Spool GunNote: Spoolmate 200 spool gun ships with (2) .030 in.and (2) .035 in. contact tips and (1) nozzle.For Standard Heavy-Duty Head TubeContact Tips (5 per package)199387.030 in. (0.8 mm)199388 .035 in. (0.9 mm)Nozzle 050622For Optional Head TubesNote: The same consumables are used on 45-degree,5-inch, and 9-inch extension head tubes.Contact Tips (5 per package)199730.024 in. (0.6 mm)(requires V-knurled drive roll 136135)186419.030 in. (0.8 mm)186406.035 in. (0.9 mm)Nozzle 186405For Millermatic®252Note: Machine drive roll kits include two drive rollsand an inlet guide.V-Grooved Drive Roll Kits (solid wire)204579 .030 and .035 in. (0.8 and 0.9 mm)combination (reversible)087131 .024 in. (0.6 mm)079594 .030 in. (0.8 mm)079595 .035 in. (0.9 mm)079596 .045 in. (1.2 mm)V-Knurled Drive Roll Kits(flux-cored or difficult-to-feed wire)079606 .035 in. (0.9 mm)079607 .045 in. (1.2 mm)U-Grooved Drive Roll Kits (aluminum wire)044749 .035 in. (0.9 mm)079599 .047 in. (1.2 mm)Note: Miller®FasTip™, M-Series and Bernard Centerfire™diffusers and consumables are NOT compatible with MDX Series guns.6Ordering InformationSteel Configuration Stock No. Description Qty. PriceMillermatic®252 907321 200(208)/230 V, 60 Hz907322 230/460/575 V, 60 HzMillermatic V-Grooved Drive Roll Kits (solid wire) 087131 .024 in. (0.6 mm)079594 .030 in. (0.8 mm)079595 .035 in.(0.9 mm)079596 .045 in.(1.2 mm)Millermatic V-Knurled Drive Roll Kits (flux-cored) 079606 .035 in. (0.9 mm)079607 .045 in. (1.2 mm)Miller®AccuLock™MDX™Contact Tips T-M023.023 in. (0.6 mm)(10 per package)T-M030.030 in. (0.8 mm)T-M035.035 in. (0.9 mm)T-M045.045 in. (1.2 mm)Miller®AccuLock™MDX™Nozzles N-M1200C Copper, 1/2 in. ID, flush, standardN-M1218C Copper, 1/2 in. ID, 1/8 in. recessN-M5800C Copper, 5/8 in. ID, flushN-M5818C Copper, 5/8 in. ID, 1/8 in. recessN-M58XTC Copper, 5/8 in. ID, 1/8 in. stickoutAluminum Configuration (Spool Gun) For MDX-250 gun consumables and non-aluminum Millermatic 252 drive rolls, see steel configuration chart above.Millermatic®252 Spool Gun Packages 951066 200(208)/230 V, 60 Hz with Spoolmatic®30A, dual cylinder rack,(includes standard MDX™-250 MIG gun) elevated gun and cable rack, regulator and hose951065 230/460/575 V, 60 Hz with Spoolmatic®30A, dual cylinder rack,elevated gun and cable rack, regulator and hoseSpoolmatic®Contact Tips (10 per package)206187 .035 in. (0.9 mm)206188 .040 in. (1.0 mm)206189 .047 in. (1.2 mm)Spoolmatic®Nozzles198855 5/8 in. (16 mm) diameter199618 5/8 in. (16 mm) diameter, HD199616 3/4 in. (19 mm) diameter199617 3/4 in. (19 mm) diameter, HDAluminum Configuration (Push-Pull Gun) For MDX-250 gun consumables and non-aluminum Millermatic 252 drive rolls, see steel configuration chart above.Millermatic®252 907321 200(208)/230 V, 60 Hz(includes standard MDX™-250 MIG gun)907322 230/460/575 V, 60 HzXR-Aluma-Pro™Lite Gun (air-cooled) 300948 25 ft. (7.6 m)XR-Aluma-Pro™Gun (air-cooled) 300000 15 ft. (4.6 m)300001 25 ft. (7.6 m)Millermatic U-Grooved Drive Roll Kits (aluminum) 044749 .035 in. (0.9 mm)079599 .047 in. (1.2 mm)XR-Aluma-Pro U-Grooved Drive Roll Kits 195311 .035 in. (0.9 mm)(required, includes Millermatic U-Grooved Drive Roll Kit) 195313 .047 in. (1.2 mm)XR-Aluma-Pro Lite Contact Tips (10 per package) T-035AL .035 in. (0.9 mm)T-047AL .047 in. (1.2 mm)XR-Aluma-Pro and XR-Pistol Contact Tips (10 per package)206187 .035 in. (0.9 mm)206188 .040 in. (1.0 mm)206189 .047 in. (1.2 mm)Nozzles198855 5/8 in. (16 mm) diameter199618 5/8 in. (16 mm) diameter, HD199616 3/4 in. (19 mm) diameter199617 3/4 in. (19 mm) diameter, HDDate: Total Quoted Price:7Ordering InformationAccessories Stock No. Description Qty. PriceDual EZ-Change™Low Cylinder Rack with 300337Elevated Gun and Cable RackElevated Gun and Cable Rack 300335For use with single cylinder rack(included with dual EZ-Change low cylinder rack)Protective Cover 195142Features side pocketArgon/Mixed Gas Regulator and Gas Hose 195050Full KVA Adapter Cord 300517GunsMDX™-250 MIG Gun 177003510 ft. (3 m), 250 A, .030/.035 in. (0.8/0.9 mm) wirewith AccuLock™MDX Consumables177003612 ft. (3.7 m), 250 A, .030/.035 in. (0.8/0.9 mm) wire177003715 ft. (4.6 m), 250 A, .030/.035 in. (0.8/0.9 mm) wireMDX™-250 MIG Gun 177004110 ft. (3 m), 250 A, .035/.045 in. (0.9/1.2 mm) wirewith Industrial AccuLock™S Consumables 177004212 ft. (3.7 m), 250 A, .035/.045 in. (0.9/1.2 mm) wire177004315 ft. (4.6 m), 250 A, .035/.045 in. (0.9/1.2 mm) wireSpoolmatic®15A 195156 15 ft. (4.6 m), 200 A, .023–1/16 in. (0.6–1.6 mm) for aluminum wireSpoolmatic®30A 130831 30 ft. (9 m), 200 A, .023–1/16 in. (0.6–1.6 mm) for aluminum wireSpoolmate™200300497 20 ft. (6 m), 160 A, .030–.035 in. (0.8–0.9 mm) for aluminum wire,.023–.035 in. (0.6–0.9 mm) for steel/stainless steel wiresOptional Spoolmate™200 Head Tubes 30059145-degree head tube3005929 in. extension head tube243385 5 in. head tubeXR-Aluma-Pro™Lite Gun (air-cooled)300948 25 ft. (7.6 m), 175 A, .030–.047 in. (0.8–1.2 mm) for aluminum wireXR-Aluma-Pro™Gun (air-cooled)300000 15 ft. (4.6 m), 300 A, .030–.047 in. (0.8–1.2 mm) for aluminum wire300001 25 ft. (7.6 m), 300 A, .030–.047 in. (0.8–1.2 mm) for aluminum wireDate:Total Quoted Price:Note: See page 7 for ordering information on the Millermatic 252—available packages, steel and aluminum configurations, and drive roll kits/consumables.Distributed by:©2019 Miller Electric Mfg. LLC。
弧焊机器人摆动跟踪时的焊接电参数特征

山东大学硕士学位论文弧焊机器人摆动跟踪时的焊接电参数特征姓名:***申请学位级别:硕士专业:材料加工工程指导教师:***20050331山东大学硕七学位论文3.3熔深及断面形状的检测16块试件的48种不同焊接工艺条件,对每一种工艺条件获得的焊缝选取两处适当位置进行切割,最终得到48x2=96块试样.对这96块试样进行打磨、腐蚀、抛光处理,拍取金相照片,部分试样金相照片见图3-4。
试样表示方法:如试样5.3.1;表示第五块试件在第三段焊缝上的第一块试样。
(a)试样I-2.2(b)试样2-3·2(c)试样3-3.2(d)试样5·1-2第3章Vee坡口焊接工艺试验(c)试样6.3-2(f)试样7.1.2(g)试样8-3-2(h)试样ll-2.2(i)试样12-2.1(j)试样13·l·l(k)试样15-2.1(1)试样16-l-2图3-4部分试样的焊缝横断面金相照片.2I·第3章Vee坡口焊接工艺试验同时在焊接过程中,利用位移测试仪来检测接头间隙的收缩情况(见图3-11),为以后的工艺试验积累经验。
O1lj36,3'算∞j7.3tj图3一11接头间隙收缩检测示意图其中:士——燃弧距离.起弧点(1.5em),熄弧点(68.5era)×——点固点(1em.36.3era,74.3era)I——位移测试议位置(58era)由位移测试仪测得数据,画出接头间隙收缩量随时间及焊枪位置变化的曲线图,如图3.12和3.13所示.EE删婚娶时问sg捌蓊掣焊枪位置m图3.12接头间隙收缩量与时间关系图图3.13接头间隙收缩量与焊枪位置关系图考虑到试板受热膨胀及点固点位置、大小等因素,可知在这种焊接工艺条件下接头间隙的收缩量较大。
测得的试样部分金相照片见图3.14.(a)试样17.1.I(b)试样17.2。
i山东大学硕士学位论文(c)试样18.1,I(d)试样18-2—1豳3.14试律17、18部分试群金相照片测出试件17眷订18的熔深结果(表3-6),可见试件17(装配时接头间羧l。
马格南能源 MS 系列逆变器 充电器维护与故障排除手册说明书

Page 52© 2012 Magnum Energy, Inc .Maint enance and Troubleshoot ing4.0 Maint enance and Troubleshoot ingThe following information is provided to help you keep your MS Series inverter/charger in optimum operational condition.4.1 Recom m ended I nvert er and Bat t ery CareThe MS Series inverter/charger is designed to provide you with years of trouble-free service. Even though there are no user-serviceable parts, it is recommended that every 6 months you perform thefollowing maintenance steps to ensure optimum performance and extend the life of your batteries.W ARN I N G: Prior to performing any checks, switch OFF both the AC and DC circuits.•Visually inspect the batteries for cracks, leaks, or swelling – replace if necessary •Use baking soda to clean and remove any electrolyte spills or buildups •Check and tighten all battery hold-down clamps (if applicable)• Clean and tighten all battery terminals and connecting cables [10 to 12 ft lbf (13.6 to 16.3N-m)]• Check and fi ll battery water levels (liquid lead acid batteries only)• Check individual battery voltages (load test those that have a voltage difference of more than 0.3 VDC from each other) – replace if necessary• Check all cable runs for signs of cha fi ng – replace if necessary•Check the inverter’s cooling vents – clean as necessary • Check and tighten the inverter’s internal AC terminal block connections [16 in lbf (1.8N-m)]4.2 St orage for Mobile I nst allat ionsWhen placing the RV , boat or truck into storage, it is recommended that you perform the following to ensure the system is properly shut down (or properly con fi gured for storage). This is especially important for maintaining the batteries.•Perform the recommended maintenance steps listed in Section 4.1.• Fully charge the batteries.• Connect AC power (if available) and verify that the breaker to the inverter’s input isswitched ON (to allow battery charging).•Verify the inverter is switched OFF .•Switch OFF all unnecessary AC and DC loads.• Disable the AGS (if installed) when the RV , boat, or truck is in a con fined storage area.W ARN I N G: If an AGS were to start and run the generator for an extended period of time in a con fi ned area, a potentially fatal level of CO (Carbon Monoxide) could accumulate.Maint enance and Troubleshoot ing4.3 Troubleshoot ingThe MS Series inverter/charger is a fairly simple device to troubleshoot. The following chart isPage 53© 2012 Magnum Energy, Inc.Page 54 © 2012 Magnum Energy, Inc .Maint enance and Troubleshoot ing4.4 Perform ing an I nvert er ResetCertain faults require that the inverter be reset. To perform an inverter reset (also known as a soft reset), press and hold the Power ON/OFF button (see Figure 4-1) for approximately fi fteen(15) seconds until the Charging/Inverting Status LED comes on and fl ashes rapidly. Once the rapid fl ashing has begun, release the Power ON/OFF button. The Status LED will go off after the button is released.After the inverter reset is completed, press the Power ON/OFF button to turn the inverter ON.Some older inverter models do not allow an inverter reset. If the inverter reset fails, you will need to perform a power reset using the procedure below. In either case, if an internal fault does not clear, the inverter will require repair at a Magnum Authorized Service Center (ASC).I nfo: The Power ON/OFF pushbutton is a small momentary type switch which operates by lightly pressing and releasing. Be careful not to apply too much force when pushingor the switch might break.Status LED, after approximately15 seconds it should come onand fl ash rapidly to indicate theinverter has reset. The Status LEDwill go off after the pushbutton isreleased.Figure 4-1, Perform ing an I nvert er Reset4.5 Perform ing a Pow er ResetTo perform a power reset (also known as a hard reset):1. Remove all AC power (utility or generator power) to the inverter .2. Open all the inverter DC disconnects (or disconnect the positive battery cable to the inverter).3. Ensure the inverter(s) and the remote are disconnected from all AC and DC power (the remote display will be blank).4. After the inverter(s) has been disconnected from all power for 30 seconds, reconnect the inverter DC disconnects (or reconnect the positive battery cable) and resume operation.I nfo: If DC disconnects are not used, there may be a momentary spark when the positive battery cable is connected to the inverter’s terminal. This is normal and indicates that the inverter’s internal capacitors are being charged.。
变压器异常停电处理流程

变压器异常停电处理流程英文回答:Transformer power outages can occur due to various reasons, such as equipment failures, natural disasters, or human errors. When a transformer experiences an abnormal power outage, it is crucial to follow a proper handling process to ensure safety and minimize downtime.Firstly, upon detecting a power outage, I would immediately notify the relevant authorities, such as the power utility company or the maintenance team. It is essential to report the issue promptly to initiate the necessary actions for resolving the problem. For instance, I might say, "Hey, we've got a power outage on the transformer. I'm calling the utility company now to inform them about the situation."Next, I would assess the situation to determine the cause of the power outage. This may involve conductingvisual inspections, checking for any visible damages or signs of equipment failure. Additionally, I might need to review the power supply records, maintenance logs, orconsult with other experts to gather more information. For example, I could say, "I'm going to inspect the transformer and check if there are any visible damages. I'll alsoreview the maintenance records to see if there were any recent issues reported."Once the cause of the power outage is identified, appropriate measures should be taken to rectify the problem. This may involve repairing or replacing faulty equipment, restoring power supply, or implementing preventive measures to avoid similar incidents in the future. For instance, if the power outage was caused by a blown fuse, I wouldreplace the fuse and conduct tests to ensure proper functioning. I might say, "I've replaced the blown fuse and conducted tests. The power supply is restored, and everything seems to be working fine now."During the process, it is crucial to prioritize safety and take necessary precautions to avoid any accidents orinjuries. This may include wearing appropriate protective gear, following safety protocols, and ensuring proper isolation of the transformer before conducting any repairs. For example, I might say, "I've put on my safety gear and isolated the transformer before starting the repair work. Safety first!"After resolving the power outage issue, it is essential to document the entire incident, including the cause, actions taken, and any recommendations for future improvements. This documentation can be valuable for future reference and help in identifying patterns or recurring problems. For instance, I might say, "I've prepared a detailed report of the power outage incident, including the cause and the steps taken to resolve it. I've also recommended implementing regular maintenance checks to prevent similar issues in the future."中文回答:变压器异常停电可能是由于设备故障、自然灾害或人为错误等原因引起的。
Gilbarco泵错误代码故障排除指南说明书

Troubleshooting Tips#1 – Gilbarco Pump Error CodesIt should be noted to avoid any confusion this bulletin is a summary of all the various codes that we at ERI are aware of. Therefore, this document is our interpretation of these codes, and should only be used as a reference.There are three basic generations of logic development in Gilbarco pumps, which we will deal with in succession.Error codes on Gilbarco pumps show on the PPU (Price per Unit) Display and not on the Console with the exception of the Transac 12G. The PPU Display will show in alternating order the Price and then the Error CodeAll Error Codes will stop the pump from operating and certain Errors will result in loss of communication with older consolesIMPORTANT! - DISCONNECT ALL POWER FROM THE PUMP BEFORE CHANGING OR SERVICING ANY COMPONENTSFor best results, follow this troubleshooting guide in the order it is presented. This will eliminate the simplest possible causes firstPhone: This is a troubleshooting step that you can have the Station Attendant try. This is not possible for all errors in this guideFix: This step MUST be carried out by a service technician, failure to do so could result in damage and loss of warrantyA Master Reset and/or replacement of the Main Controller Board should only be carried out as a last possible option. If a Controller Board must be replaced, a Factory Reset should be performed upon installation to ensure no Data has been retained from previous use or testingError Fixes should be carried out one at a time, this helps to better isolate the actual cause of the problemFirst Generation: 8080 LogicHighline: Start - Fall 1985Multi Product: Start – Fall 1987 (Does not appear in Salesmaker4)This generation only had 2 Error Codes#1Error Code: Blank DisplayDescription: A Pulsing System failure. It can happen on only one hose or on all hoses on a pump. It is important to find out "over the phone" if it is occurring on one hose only, or on all hoses.Causes (Single Hose):- Power Spike- Bad Connection (No Contact or Moisture)- Faulty Pulser- Faulty I.S. Barrier- Broken Pulser WiringCauses (All Hoses): (Multi Product Pumps it may be only all the hoses on one side, all the time)- Faulty Power- Faulty Regulator/Interface Board (These are separate boards on a Multi Product)Phone:1. Have the operator turn off "Control" power to the pump (after isolating it at a self serve).Check with operator to make sure the displays on the pump have gone out, then have them turnpower back on. (put back on console at Self Serve)2. Have them try operating the pump again. (You may have to do this a number of times on a MultiProduct with each hose to determine if any hose on the side ever functions)If the Error occurs again, a service call is necessaryFix (Single Hose):1. Check all exposed wires to pulsers and check all plug connections for security and moisture.2. Swap the Pulser with a known good Pulser (The one on the next hose for example). Try unit again.If it works replace pulser.3. Swap the Barrier with a known good Barrier. Try unit again. If it works change Barrier.4. Check wiring in pump column, conduit and all plug connections in the head of the pump.5. Swap Regulator/Interface with know good boards.#2Error Code: 888.8Description: This problem is referred to as "Logic Lock Up", or in newer books as"Non Existent Memory" which is actually what it is. Technically what happens is that a voltage spikeis induced on the Logic Board causing a Non Existent memory location to be received by the Microprocessor. It then refuses to do anything else until it finds that location. If left alone it willeventually blow its own memory. This means the flashing eights may no longer be happeningwhen you get the service call, the pump may just appear to have lost memory. Memory loss onits own is extremely rare!Causes:- Power Spike or Static- Faulty Flourescent Tubes or Ballast- Bad Neutral or Ground- Faulty Logic Board (Extremely Unlikely)Phone:1. Have the operator turn off "Control" power to the pump (after isolating it at a self serve). Check with the operator to make sure the displays on the pump have gone out, then have them turn power back on. (put back on Console at Self Serves) The pump should now operate until whatever caused the Logic Lock up causes it again. (Remember if the pump lost memory and has no price on it, it will not run until the operator sets the price again.)2. Have the operator check the fluorescent in the pump for flickering, darkened ends or totally out.If any are noted you will have to go the site to change them. Make sure you use proper Tubeswith grounds strips on them. If the problem was a V oltage Spike it may never occur again(however a V oltage Spike usually locks all of the pumps up at the site and you usually recognizeit from this, they also lock up the Consoles easier).Fix:1. If after some time the "Lock Up" occurs again you must take some action. Change the FluorescentTubes in the pump first. Let them run the pumps again, if the "lockup" does not occur again in roughly the same time as from their first call to the second call you have probably fixed the error.2. Check out all wiring to the pump. Pay particular attention to Neutral and Grounding3. If wiring checks O.K., then change the Ballast and check other lighting near the pump. Repair wiring as necessary4. Change Regulator Board if necessary5. If problem still persists, change Logic BoardSecond Generation: Z80 LogicHighline 11B: From Fall 1985Salesmaker4: Start – Fall 1987 (No Multi-Product)#1Error Code: 002.0See First Generation Problem #1#2Error Code: 002.1See First Generation Problem #2#3Error Code: 002.2Description: This is a V olume/Money buffer failure. In other words the Microprocessor checks that the V olume amount times the Price should equal the Money amount but finds it does not, so it shuts the Pump down Causes:- Power Spike/Static- Faulty Logic BoardPhone:1. Have the operator power the pump down and back up as in previous cures. Have them run thepump again. If the problem does not occur again assume the problem was a power spike or staticand there is nothing wrong with the unit.Fix:1. Check all wiring in the pump for proper Neutral and Grounding. Check the doorto the operator panel on the pump to make sure no part of the door or its lock is touching thecommand module plug, allowing static to the Logic Board.2. Change the Logic Board.Description: A Grade assignment has changed after the Pump was powered up last. The operator when calling in will probably complain the Pump has lost memory as their totals will have reset to zero. In fact the totals are still there it is just that the pump is now running on the totalizers for another Grade.Causes: Jumper failure on logic boardFix: Check Jumpers for setting the Grades on the Logic Board and repair as necessary. Make sure Grades are set correctly before powering on the pump.#5Error Code: 002.4Description: The Conversion Factor has changed after Power up. This means thepump is no longer calculating in Litres but may be U.S. or Imperial GallonsCauses: Jumper failure on logic boardFix: Check Jumpers for setting the Conversion Factor on the Logic Board and repair as necessary. Make sure the correct conversion factors have been set correctly before powering on the pump.#6Error Code: 002.5Description: The 2-Wire switch has changed after Power up of the PumpCauses:- The operator panel door of the pump has been opened and the pump has been switched “Off Console” (Self Serve Only)- Faulty 2-Wire SwitchPhone: Have the Operator open the Operator Panel Door on the Pump and check to make sure switch is in the correct position ("On Console at a Self Serve). If the switch was in the correct position, cycle the switch back and forth a couple times to work out any dirt that may have been in it. Then power the pump down and back up again and see if it now functions correctly. If it will not operate in self serve but operates on it own, a service call is necessaryFix: Check the switch on the Display Board or Display Interface Board, replace if not functioning#7Error Code: 002.6Description: The Single/Dual Option setting has changed on the pump after powerup of the Pump. This will usually only occur on a Dual, as you must set Jumper "on" to make a single pump a dual.Causes:- Jumper failure on Logic Board- Faulty Logic BoardFix: Check Single/Dual option jumper for faults, replace the Logic Board if necessary#8Error Code: 002.7Description: The “A” side pump ID # has changedCauses:- Pump # Jumpers have failed- Faulty Logic BoardFix: Check “A” side jumper for faults, replace the Logic Board if necessary#9Error Code: 002.8Description: The “A” side pump ID # has changedCauses: See #8 AboveSolution: See #8 AboveDescription: Invalid Grade assignment or Configuration Change (Salesmaker4 Only)Causes:- Jumper failure on Logic Board- Faulty Logic BoardFix: Check Jumpers for faults, replace Logic Board if Necessary#11Error Code: 003.0Description: Invalid Grade assignment or Configuration Change (Highline 11B Only)Cause: Same as #10 AboveSolution: Same as #10 AboveThird Generation: Modular ElectronicsAll Units: Fall 1987 – On | Spring 1988 – OnCodes “002.0” through “002.8” are identical to previous errors. See Above#1Error Code: 002.9Description: Pump Time-Out ErrorCauses: The unit has been inactive beyond the specified time limit. The transaction is stopped and it will be necessary to turn the pump handle off to clear the error (no power down is needed). Note! This only occurs with software version 50.2 or higher.Phone: Turn the pump handle off and back on (Leave off if the hose isn’t being used)Fix: It may be that the site is not supposed to have a "no flow time-out". In this case the pump configuration has changed and you will have to re configure the pump to "No pump Time-out" as per Function Code 12 of Command Code 10.#2Error Code: 003.0Description: V apor Sense - unit is programmed for Vapor Sense and switch is not hooked up. (This should only occur with version V53.3 software).Cause: Incorrect ProgrammingFix: Re-Program command code 10 function code 7 to “0”#3Error Code: 003.1Description: Totals Data Error. Pump totals memory may be corruptedCauses:- Surge/Static- Faulty Controller Board- Dead/Disconnected Battery- Disconnected/Broken plugs to boardPhone:1. Record Pump Totals2. Perform memory reset (Command code 6 on page 19 of MDE 2022 User Manual)3. The Totals could be put back in by the Operator on a Multi Product or a Salesmaker 4 by performing Command Code 7 on page 21 of MDE 2022, however as this will not work on a Highline 11B unless both sides are Grade 1 or the unit is temporarily re configured to an MPD or Salesmaker 4 under Command Code 10 we donot recommend you even attempt to have the Operator do. Just have them do a shift end and tell them their pump totals for that pump are reset to zero.4. Have the Operator set the prices on the pump in their normal fashion.Fix: Change controller board if code persists#4Error Code: 003.2Description: Pulser Count Failure. The Microprocessor has detected an error between the two pulses coming from the Pulser.Causes:- Surge/Static- Defective Pulser- Defective Interface Board- Defective Controller BoardPhone: Power cycle pumpSoultion (Site):1. Replace pulser with known good unit2. Change Hydraulic Interface Board with known good unit3. Change Controller Board#5Error Code: 003.3Description: Display heaters are on at Power UpCauses:- The displays in the pump were too cold at power up- Defective Heater- Bad Connection between Power Supply and Display- Defective Power Supply- Defective Controller BoardPhone: Wait until displays warm up. If displays aren’t warm within 1 hour after power being applied, a service call is necessaryFix:1. Check for Heater power (24 V AC)on display board. Replace power supply if power not present2. If there is Heater Power (24 V AC) to the Main Display, replace each Main Display with a known good one. Close Bezels to allow to warm up. Be aware that Displays that are cold make take up to an hour to get warm enough to light (at -30 Degrees Celcius this is about a 1/2 hour).3. Replace Controller Board#6Error Code: 003.4Description: Low Battery condition was detected during automatic battery test (See Also TST#8)Causes:- Battery Fuse- Battery- Connection between Battery and Regulator Board- Defective Regulator Board- Controller Board software older than v53.4- Defective Controller BoardPhone: Perform Command Code 9, Function 1 as detailed on page 24 of MDE2022 User Manual. This will override the Error until the next Power Up. If code persists, a service call is necessary1. Check battery fuse and replace if necessary2. Replace battery with known good unit3. Check wiring between Battery and Regulator Board4. Replace Regulator Board with known good unit5. Replace Controller Board with known good unit#7Error Code: 003.5Description: Configuration Data Error. Pump configuration has changedCauses:- Surge/Static- Incorrect Programming- Faulty Controller BoardFix:1. Record Pump Totals2. Perform Command Code 6 as per page 19 of MDE 2022 User Manual3. Re-configure the Pump as per Command Codes 10 through 12 pages 2-1 to 2-17 of MDE2021 Service Manual4. You may now put the pump totals back in a Multi Product or a Salesmaker 4 by performing Command Code 7 on page 21 of MDE2022 User Manual, however on a Highline 111B that is not Grade 1 on both sides you must first temporarily re configure the pump as Salesmaker 4 or Multi Product as per Command Code 10, Function Code 1 on page 2-7 of MDE2021 Service Manual, then enter the totals as per Command Code 7 on page 21 MDE2022 User Manual, then re configure the pump back to be a Highline 111B as per Command Code 10, Function 1 page 2-7 MDE2021 Service Manual (as this can be difficult to accomplish properly we recommend having the operator do a shift cut and start the pump totals at zero for this pump).5. Reset prices as normal#8Error Code: 003.6Description: Unity “Type Code” has changedCause: UnknownFix:1. Re-Configure “Unit Type” as per Function 1 of Command Code 102. If problem persists, replace Controller Board#9Error Code: 003.7Description: PIN code 1 has changedCause: UnknownFix:1. Record Pump Totalizers2. Perform Master Reset (See also TST#6)3. Re-Configure pump and enter totals4. If problem persists, change Controller BoardError Code: 003.8Description: PIN code 2 has changedCause: UnknownFix: See #9 Above#11Error Code: 003.9Description: Cash/Credit option has changedCause: UnknownFix:1. Re-Configure option as per Function Code 2 of Command Code 122. If problem persists, replace Controller Board#12Error Code: 004.0Description: Keylock option has changed (v53.0 or higher only)Cause: UnknownFix: Reprogram Keylock Option Command Code 4, Function Code 2 (0 - No keylock, 1 – Keylock), then power down, turn off battery and power up again.#13Error Code: 004.1Description: Side Exists option has changedCause: UnknownFix:1. Re-Configure “Side Exists” option as per Function Code 3 of Command Code 122. If problem persists, Replace Controller Board#14Error Code: 004.2Description: Manual Mode option has changed (Transac 11 Consoles only)Cause: UnknownFix:1. Re-Configure pump as per Function Code 4 of Command Code 122. If problem persists, replace Controller Board#15Error Code: 004.4Description: The operating handle for the hose flashing is in the ON position upon power-up of the pump Cause: The operating handle is up. Or the handle wiring is shortedPhone: Check to see if the handle is down. Lift and Reset handle. If problem persists, a service call is necessary Fix:1. Check adjustment on handle switch2. Bypass switch. If error disappears, replace switch3. Replace Operating Switch Barrier with known good unit4. Inspect wiring and Fix/Replace as necessary5. Replace Hydraulic Interface with known good unit6. Replace Controller Board。
- 1、下载文档前请自行甄别文档内容的完整性,平台不提供额外的编辑、内容补充、找答案等附加服务。
- 2、"仅部分预览"的文档,不可在线预览部分如存在完整性等问题,可反馈申请退款(可完整预览的文档不适用该条件!)。
- 3、如文档侵犯您的权益,请联系客服反馈,我们会尽快为您处理(人工客服工作时间:9:00-18:30)。
Voltage change in the GMAW process due to the influence of a droplet travelling in the arc Peiyuan Zhu*and S.SimpsonExperimental measurements have been made to investigate the meaning of the fluctuation or noise of electrical signals for the gas metal arc welding process through globular to spray transfer mode,with particular attention being paid to the so-called‘drop spray’transition mode.The results reveal that the welding arc voltage is significantly affected by the molten droplet travelling in the arc.A sharp drop in arc voltage appears just after the detachment of the droplet,reaching its minimum quickly and then recovering,according to the location of the droplet in the arc. Although the full explanation of the feature requires further study,we believe that an important influence is the geometrical effect.The existence of the droplet in the arc path significantly affects the geometrical shape of the arc and arc attachment at the anode,and hence the overall voltage of the arc.Keywords:GMA welding,Droplet transfer,Arc voltageIntroductionGas metal arc welding(GMAW)is a commonly used metal joining industrial technology.Although it is a very well developed industrial process,the complexity of the phenomena that occur in the presence of solid and liquid metal,shielding gas and arc plasma means there are still gaps in our knowledge preventing us from fully under-standing and controlling the process.Over many years of study in thefield,a large number of publications have appeared reporting features and findings of the process,based both on experimental observation and theoretical studies.1–9Among all the features of the GMAW process,metal transfer has attracted most attention around the world.10–14 The formation of the liquid drop and the size of the droplets for various conditions have been both observed experimentally3,5,12,13and simulated in great detail using various theoretical computer models10,11,14,15The interactions between the arc and the formation of a droplet on the wire are understood reasonably well.However,the interaction between the travelling droplet and the surrounding arc has not drawn much research paring the size of a droplet in a typical welding process with the size of the welding arc, it seems that the free travelling droplet will cause serious distortion of the arc,and the degree of the distortion will depend strongly on the size and location of the droplet. Other factors,such as the sheath surrounding the droplet that establishes a potential difference between the arc plasma and the metal droplet,16and both electrical and thermal properties of the liquid metal droplet,will also affect the arc plasma.This paper reports an experimental study to observe the overall impact of a travelling droplet on welding arc characteristics.The possible influence of the arc voltage and currentfluctuations on the formation of the free droplet was observed.This was achieved by correlating precisely the welding arc electrical signals (arc current and voltage)with the shape,size and location of the free droplet images recorded simulta-neously in real time.The authors found that the detachment of the droplet will cause a sharp voltage drop of2–3V.The location of the droplet also seems to have a strong correlation with the arc voltage change during its recovery process.This is particularly clear when GMAW is done in the so-called‘drop spray’17transfer mode,and provides a possible explanation for the regularfluctuation of the arc voltage,which was previously unexplained.It is suggested that a free travelling droplet will affect the arc characteristic significantly because of the geometrical distortion of the arc plasma,and the changes in the arc attachment to the anode,and its influence is responsible for some of the regularfluctuations observed in the arc voltage dynamics.Experimental arrangementThe GMAW process with various welding conditions was performed using a typical industrial welding power source,operating in the constant voltage mode.Copper coated steel electrodes of1.0mm diameter(ER70S-6) andflat steel plates were used as the consumable and workpiece respectively,with contact tip to plate distance of20mm.Argon based shielding gas(y3%O2,y5% CO2,and y92%Ar)was used with aflow rate of 20L min–1throughout this study.School of Electrical&Information Engineering,University of Sydney,NSW2006,Australia*Corresponding author,email Peiyuan@.auß2005IoM Communications LtdPublished by Maney for the Institute of Materials,Minerals and MiningReceived23February2004;accepted24June2004DOI10.1179/174329305X39275Science and Technology of Welding and Joining2005VOL10NO2244Figure1shows a schematic of the experimental arrangement for this study.The arrangement consists of a typical He–Ne laser shadowgraph set-up,a high-speed digital camera,a synchroniser with LCD time display,and a multichannel data acquisition system. The high speed digital camera was capable of recording8000frames s–1,but was operated at a speed of2000frames s–1with camera shutter speed of 561025s.This was fast enough for investigation of the droplet transfer(transfer rates in the order of 102s21)in a typical welding system.The camera was controlled by a personal computer,and the recorded optical image frames were stored in the computer directly.A synchroniser was built and used to synchronise the digital camera with the electrical signal collection system.The synchroniser drives an LCD time display that marks each frame with a time relative to the start of the collection of electrical signals,with a resolution of 1024s.Figure2shows a typical recorded optical image, recorded at a time of0.5245s from the start of electrical signal collection(the digital display has units of1023s). The data acquisition system for measuring welding voltage and current consisted of a multichannel data card,installed in and controlled by a PC computer. The time resolution of the system was set to be1024s,five times higher than the rate of optical image collection.A current probe was used to measure the welding current while the voltage was measured in between the welding plate and the anode nozzle,as shown in Fig.1.With this arrangement,the measured voltage is the sum of three terms,the voltage drop due to the nozzle–anode contact resistance,the voltage drop across the anode wire,and the arc voltage.The arrangement allowed us to observe the dynamics of the consumable wire/droplet(a series of timed optical images)and the welding current and voltage curves at the same time.Results and discussionThe welding current and voltage as a function of time for three different wire feed rates,corresponding to spray(droplet diameter generally smaller than wire diameter),drop spray(droplet diameter slightly larger than wire diameter)and globular(droplet diameter much larger than wire diameter)modes respectively,are compared with each other in Fig.3.The‘drop spray’mode wasfirst observed by Ma18in 1982,and Norris in2003suggested that it shouldbe2A typical sample of a timed laser shadowgraph image, showing a detacheddroplet 1Schematic of the experimental arrangementincluded in a new metal transfer classification list.17Although it appears only at a very narrow band of operation conditions,the clearly regular fluctuations and steady cyclic characteristics make it ideal for understanding the influence of the droplet on the arc plasma.In this research,most of the attention was onthe ‘drop spray’transfer mode.The measurements were made using 1.0mm steelwire,with wire feed rates of 0.1588m s –1(375in min –1)for curve (a),0.1291m s –1(305in min –1)for curve (b)and 0.0931m s –1(220in min –1)for curve (c)in Fig.3.It can be seen from Fig.3that these electrical signals are fluctuating and noisy in general,but in very different manners for different transfer modes.Although it is difficult to interpret the meaning of these signals in full detail,it is clear that these electrical signals reflect the relevant transfer mode’s features and are rich in information.In Fig.3a ,higher frequency in voltage with lower signal level as compared to the other two cases can be seen.This corresponds to a high frequency but smaller sized droplet transfer (spray)mode with a more or less constant arc length.The current curve in Fig.3a shows the lower frequency components,indicating that the inductance of the power supply has limited and smoothed the change in the current,reducing the high frequency component.Figure 3b shows very regular fluctuations in both voltage and current curves,with the frequency being the same as the droplet transfer frequency.This is a key characteristic of the drop spray mode,which has previously been wrongly regarded as being due to power supply modulation.17The fact that these regular fluctuations have the same cyclic period as the droplet transfer rate implies thatthey are related to the droplet transfer processes.The regularity of the fluctuations suggests that the size and the process of each individual droplet transferred in thismode are relatively steady,which was confirmed by therecordings of the droplet images.Figure 3c shows a rather variable high frequency (.50Hz)signal on a low frequency background (3–7Hz).It was found that the droplet size varied a lot and that the transfer mode is actually changing between spray,drop spray and globular modes,with rather significant oscillations in arc length,periodic with the low frequency modules.This is not discussed in detail in this study,since this is a much more complicated situation,as the stick-out instability 7is likely to be causing the low frequency oscillation.The authors believe that the regular voltage fluctua-tions observed in Fig.3b are not due to the change in the stick-out length of the anode wire,for two reasons.First,the stick-out length,and hence the arc length,is relatively steady in this transfer mode,and second,the arc length is at its longest just after droplet detachment and at its shortest just before detachment,whichwould3Typical welding voltage (left)and current (right)as functions of time for a spray,b drop spray and c globular transfermodesinfluence the voltage change in the opposite direction to that observed.Figure 4shows the change in the stick-out length of the anode wire for various stages of a single droplet transfer process in this mode.It can be seen fromFig.4that the stick-out length of the anode wire does not change much in this mode,yielding a relativelysteady arc length.It can also be seen from Fig.4that the stick-out length of the anode increases when droplet detachment is approached and is shortest just after detachment.Characteristic features of drop spray transfer mode As discussed above,the drop spray mode has very regular fluctuations in both voltage and current,with the frequency being the same as the droplet transfer frequency (Fig.3b ).By comparing the electrical signal fluctuations with the laser shadowgraphs for the corresponding times,we find that each cycle of the fluctuation corresponds to one droplet transfer process.The regularity of these fluctua-tions implies that the droplets are all transferred in a very similar manner.The images captured with the high speed camera confirm that the droplet sizes are similar (ranging from 1.26mm to 1.42mm in diameter)at this mode.Therefore,this very stable transfer mode is particularly suitable for investigating the influence of the droplet transfer process on the electrical character-istics of the welding arc.The influence of droplet formation,detachment and travel on the welding arc can be investigated by assessing the droplet images together with the arc voltage signal at the corresponding time.Figure 5shows details of the electrical signals for oneperiod of fluctuation together with nine images,with a point plotted on the voltage curve when an image frame is available at the corresponding time.The nine images were selected after frame by frame investigation of all the images recorded to give a general picture of thedroplet transfer process.The droplet diameter observedfor this case is about 1.3mm.Necking effect and droplet formationIn Fig.5,we can see the liquid necking just before twoindividual droplet detachments,at t 50.5240s andt 50.5370s respectively.Images at t 50.5365s and t 50.5370s show two stagesof the necking process,with the first showing early signof necking,and the latter just before detachment.Fromthese two pictures,we conclude,at lease for this transfermode,that the necking process lasts for about 561023s.The voltage change due to the neckingwould,therefore,naturally occur only in this timeinterval just before detachment.It is hard to measure experimentally the change ofresistance of the liquid on the tip of the wire during thenecking (forming a droplet)process.However,theinfluence of the necking on the voltage change (resis-tance changing during necking)can be estimated bycalculating the change of the resistance of the liquid atnecking using a similar size simulated droplet formationprocess.11We used simulated droplet shapes during the forma-tion 11to estimate the resistance of the droplet at various formation stages by assuming a constant resistivity of 16061026(V cm)for the liquid metal.The resistance of the liquid R can be estimated from R ~ðrS d lwhere r is the resistivity of the liquid metal,l is the liquid length,and S is the cross-sectional area of the liquid.Figure 6shows the simulated droplet shape at various stages of the necking,using the dynamic dropletformation model 11and the estimated resistance of theliquid on the anode tip as a function of the ratio ofliquid volume on the tip to the liquid volume at themoment of detachment.Note that Fig.6provides only an indicative estimation of the resistance for the necking process.It can be seen from Fig.6that the resistance of the liquid does not vary much until the fraction of liquid reaches 0.995.The resistance is of the order of 0.01V ,before it rapidly rises to 0.032V just before detachment.For a 200A current arc,this resistance change implies that a voltage change of the order of half a volt,due to the necking effect,occurs immediately prior to detachment.In Fig.5,we saw a voltage increase of about 0.78V from t 50.5355s,when no obvious neck was observed,to t 50.5372s,when the droplet was detaching.This is in accordance with the neck resistance change estimated from the calculation.However,compared with the random voltage variation level of about 0.5V and a clear voltage drop of 2.5–3V observed after detach-ment,we conclude that the voltage drop after detach-ment cannot be explained as simply a recovery from the necking effect.Characteristic points at droplet detachment time From Fig.5,it is clear that the droplet is detachedbetween 0.5240s (the droplet is still attached)and0.5245s (the droplet has clearly separated with thewire).4Stick-out length for various stage of droplet transfer in drop spray modeSince the detachment of the droplet from the anode wire is a sudden event,it is reasonable to expect a sudden change in the arc at the same time.A turning point of the voltage curve at t 50.5242s was observed,which gives a quite accurate estimation of the detach-ment time.There is no sudden change in welding current (also plotted in Fig.5)at the time of detachment.This can be explained by the fact that the inductance of the power supply not only causes a phase delay but also smooths any sudden changes.The current change is relatively slow,although also periodic,with an averagevalue of about 200A.It is difficult to see a relationshipbetween the droplet transfer process and the currentvariation.The arc voltage has a clear relationship with thedroplet transfer process,through its dependence onparameters such as the arc length and geometry,and thearc–electrode attachment.This characteristic of thevoltage curve provides quite direct information abouthow the droplet transfer affects the welding arc in thedrop spray transfer mode.Through careful study of more laser shadowgraphimages and the voltage curves for each of thesefluctuation periods in this transfer mode,it was foundthat the sudden turning points,which are followed byrather sharp voltage drops,on the voltage curve can betaken as characteristic points corresponding to thedetachment of each droplet.There is often a rise involtage,of the order of about 0.5–1.0V,justbefore5Arc voltage,current and details of droplet transfer for the drop spray modedetachment,which is probably due to the liquid necking effect.The necking voltage change varies,depending on the individual droplet formation and detaching process,and sometimes is not obvious.The sharp decrease in voltage of 2–3V after detach-ment is a characteristic feature of the process.Figure 7shows a section of the voltage curve with the detachment characteristic points marked.Influence of droplet travelling in the arcIt is interesting to see the locations of the droplet at certain points of the voltage curve.In Fig.8,we see that the droplet detaches at point a at t 50.5242s,1.73mm away from the wire tip at point b (t 50.5250s),and about halfway through point c (t 50.5285s),and merges with the pool at t 50.5325s (point d ).At t 50.5365s (point e ),a new neck appears,indicating that detach-ment of the next droplet is about to occur.We observed a 2.6V drop after the detachment of the droplet over about 0.861023to 1.361023s,reaching a minimum at t 50.5250s.After a levelling out,the voltage rises gradually to the nextdetachment.8Droplet at various locations of the arcpathThe droplet in the arc has a significant impact on the arc pressure distribution,due to the geometrical influence,since the droplet diameter we are discussing is about1.3–1.4mm,which is not small compared with the dimension of the arc path,especially near the anode wire.This geometrical influence certainly affects the shape of the arc,and it is understandable that arc voltage would be affected as well.In Fig.9,arc temperature and pressure profiles,for a 200A free burning Ar arc11mm in length,calculated using a two-dimensional free burning model,19are plotted together with a droplet(1.4mm in diameter) on the same scale.The calculation was carried out using similar boundary conditions as those described in Zhu et al.6Thefigure only serves the purpose of geometrical scale comparison of a droplet with a clear path arc(with no droplet in it).The size of the droplet is certainly significant,and the arc will undoubtedly be distorted, and the degree of the distortion will clearly depend on the location of the droplet.From Fig.9,it is concluded that the distortion is most serious when the droplet is near the anode wire tip.Features of spray transfer modesWhile there is a clear correlation between the arc voltage and droplet transfer process in the drop spray transfer mode,the same is not obvious for the spray transfer mode.Figure10shows recorded optical images together with the arc voltage curve(this is a detail of a section of Fig.3a.).For this case,it is not so easy to see the influence of the droplet transfer process at different stages,since the droplet is transferred in lesss time than that needed to travel though the arc path,and there are always several droplets simultaneously at different locations in the arc.Although our image recording rate(2000frames s–1)is only about four times higher than the droplet transfer rate (y500drops s–1),it is clear from our results that the influence of an individual droplet cannot be separated from that of other droplets in the arc path,and the identification of the transfer process stage is more difficult.We conclude that,due to the presence of several droplets at different locations of the arc path simulta-neously,the spray transfer mode has lower amplitude but much less regular voltagefluctuation.In this transfer mode,the arc length and also the arc current do not vary much.Summary and conclusionsExperimental measurements have been made that correlate precisely the electrical dynamics of the GMAW process with the droplet images recorded simultaneously in real time.The results indicate that the electrical signals,in particular thefluctuations in the arc voltage,are rich in information.The droplet formation and transfer process (detachment,travel from the wire tip to welding pool) affect the arc plasma and are responsible,to some degree,for thefluctuations of the voltage curve.One can identify the detachments of the droplets from character-istic maxima of the voltagefluctuations,especially for the transfer modes with droplet size similar or slightly greater than the wire diameter.The results suggest that the welding arc voltage can be significantly affected by a molten droplet travelling in the arc.A rapid drop in arc voltage appears just after the detachment of the droplet.Although a full explanation of the feature requires further study,it is believed that one of the important influences is the geometrical effect of the droplet in the arc.The existence of the droplet in the arc path significantly affects the geometrical shape of the arc,and hence the overall voltage of the arc.This is yet to be confirmed by further study,especially theoretical computer simulations.Reference1.A.Lesnewich:Weld.J.,1958,37,418s–425s.2.J.H.Waszink and L.H.J.Graat:Weld.Res.Suppl.,1983,62,108–116.3.J.C.Needham,C.J.Cooksey and ner:Br.Weld.J.,1960,7,101–114. 10Droplets and voltage curve for stream spray modencaster:‘The physics of welding’,2nd edn;1986,Oxford,Pergamon.5.Y.S.Kim and T.W.Eager:Weld.J.,1993,71,269s–278s.6.P.Zhu,M.Rados and S.W.Simpson:Plasma Sources:Sci.Technol.,1995,4,495–500.7.E.Halmøy:‘Simulation and instabilities in GMAW and SAW’,IIW Document212-895-96;1996,International Institute of Welding.8.P.Zhu,M.Rados and S.W.Simpson:Weld.J.,1997,76,269-S–274-S.9.R.T.Deam,S.W.Simpson and J.Haidar:J.Phys.D.Appl.Phys.,2000,33,1393–1402.10.J.Haidar:J.Appl.Phys.,1998,84,3530–3540.11.S.W.Simpson and P.Zhu:J.Phys.D.Appl.Phys.,1995,28,1594–1600.12.Q.Lin,X.Li and S.W.Simpson:J.Phys.D.Appl.Phys.,2001,34,347–353.13.V.A.Nemchinsky:J.Phys.D.Appl.Phys.,1994,27,1433–1442.14.J.J.Lowke:Austral.Weld.J.Res.Suppl.,1997,42,32–35.15.F.Wang,W.Hou,S.Hu,E.Kannatey-asibu and W.Schultz:J.Phys.D.Appl.Phys.,2003,36,1134–1152.16.M.Mitchner and C.H.Kruger:‘Partially ionized gases’,130;1973,New York,JohnWiley&Sons.17.J.Norrish:‘A review of metal transfer classification in arc welding’,IIW Document XII-1769-03;2003,International Institute of Welding.18.J.Ma:‘Metal transfer in MIG welding’,PhD Thesis,CranfieldInstitute of Technology,1982.19.J.J.Lowke,P.Kovitya and H.P.Schmidt:J.Phys.D.Appl.Phys.,1992,25,1600–1606.。