直拉法生长的硅单晶中的杂质浓度受到许多因素的影响
集成电路技术集成电路工艺原理试卷(练习题库)(2023版)

集成电路技术集成电路工艺原理试卷(练习题库)1、用来做芯片的高纯硅被称为(),英文简称(),有时也被称为()。
2、单晶硅生长常用()和()两种生长方式,生长后的单晶硅被称为()。
3、晶圆的英文是(),其常用的材料是()和()。
4、晶圆制备的九个工艺步骤分别是()、整型、()、磨片倒角、刻蚀、()、清洗、检查和包装。
5、从半导体制造来讲,晶圆中用的最广的晶体平面的密勒符号是()、O 和()。
6、CZ直拉法生长单晶硅是把()变为()并且()的固体硅锭。
7、CZ直拉法的目的是()。
8、影响CZ直拉法的两个主要参数是O和()。
9、晶圆制备中的整型处理包括()、()和()。
10、制备半导体级硅的过程:1、();2、();3、O011、热氧化工艺的基本传输到芯片的不同部分。
77、多层金属化指用来连接硅片上高密度堆积器件的那些金属层。
78、阻挡层金属是淀积金属或金属塞,其作用是增加上下层材料的附着。
79、关键层是指那些线条宽度被刻蚀为器件特征尺寸的金属层。
80、传统互连金属线的材料是铝,即将取代它的金属材料是铜。
81、溅射是个化学过程,而非物理过程。
82、表面起伏的硅片进行平坦化处理,主要采用将低处填平的方法。
83、化学机械平坦化,简称CMP,它是一种表面全局平坦化技术。
84、平滑是一种平坦化类型,它只能使台阶角度圆滑和侧壁倾斜,但高度没有显著变化。
85、反刻是一种传统的平坦化技术,它能够实现全局平坦化。
86、电机电流终点检测不适合用作层间介质的化学机械平坦化。
87、在CMP为零的转换器。
133、CD是指硅片上的最小特征尺寸。
134、集成电路制造就是在硅片上执行一系列复杂的化学或者物理操作。
简而言之,这些操作可以分为四大基本类:薄膜135、人员持续不断地进出净化间,是净化间沾污的最大来源。
136、硅片制造厂可分为六个的区域,各个区域的照明都采用同一种光源以达到标准化。
137、世界上第一块集成电路是用硅半导体材料作为衬底制造的。
硅材料制备新技术及其发展动态考核试卷

B. 杂质类型和浓度
C. 晶体取向
D. 表面态密度
10. 下列哪些技术可以用于制备微米/纳米硅材料?()
A. 溶液相法
B. 气相法
C. 熔融盐法
D. 球磨法
11. 下列哪些是制备多晶硅的常见方法?()
A. 碱性熔融电解法
B. 氯化法
C. 硅烷法
D. 镁热还原法
12. 下列哪些因素会影响硅材料的热导率?()
A. 表面纹理化
B. 金属栅线技术
C. 陷光层技术
D. 所有以上选项
20. 下列哪种方法不属于化学气相沉积法?()
A. 热化学气相沉积
B. 等离子体增强化学气相沉积
C. 激光诱导化学气相沉积
D. 物理气相沉积
二、多选题(本题共20小题,每小题1.5分,共30分,在每小题给出的四个选项中,至少有一项是符合题目要求的)
A. 游离态
B. 化合态
C. 气态
D. 离子态
2. 下列哪种方法不属于硅材料制备的常见方法?()
A. 化学气相沉积
B. 熔融盐电解法
C. 碱性熔融电解法
D. 磁控溅射法
3. 在Czochralski(CZ)法生长单晶硅中,影响单晶硅质量的因素不包括以下哪一项?()
A. 生长速率
B. 温度梯度
C. 溶液浓度
2. 简述多晶硅太阳能电池的工作原理,并列举提高其转换效率的几种常见技术。
3. 详细说明化学气相沉积(CVD)在硅材料制备中的应用,并讨论其优缺点。
4. 分析硅材料在光伏领域的发展趋势,以及可能出现的新技术和挑战。
标准答案
一、单项选择题
1. B
2. D
3. C
直拉法硅单晶中晶转对杂质含量的影响
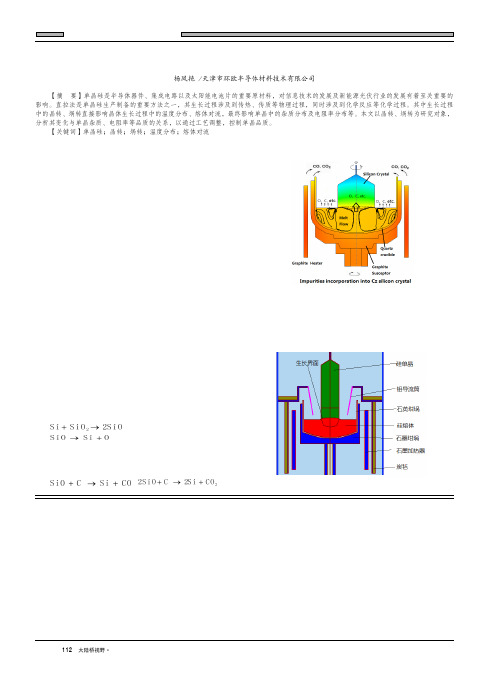
专业研究・Professional Research112 大陆桥视野·2016年第14期1.前言硅材料是信息技术、电子技术和光伏技术最重要的基础材料。
从某种意义上讲, 硅是影响国家未来在高新技术和能源领域实力的战略资源[1]。
自上世纪40 年代起开始使用多晶硅至今, 硅材料的生长技术已趋于完善, 并广泛的应用于红外光谱频率光学元件、红外及射线探测器、集成电路、太阳能电池等[2]。
此外,硅本身的无毒性和高储量现状,决定了它是目前最重要、产量最大、发展最快、用途最广泛的一种半导体材料[3]。
目前,单晶硅完整性好、纯度高、资源丰富、技术成熟、工作效率稳定、光电转换效率高、使用寿命长,也是制备太阳能电池的理想材料。
随着社会的发展,无论半导体级单晶硅还是太阳能级单晶硅,都对单晶硅本身提出了更高的要求,包括杂质含量和缺陷。
在半导体元器件中,杂质含量直接影响电子元器件的电性能参数,严重的可能导致击穿、失效等后果[4]。
在太阳能电池中,杂质含量直接影响少数载流子寿命,最终影响光电转换效率。
本文针对此问题对直拉法以4英寸单晶硅为基础,进行工艺上的探索,以降低单晶硅中杂质含量。
2.直拉硅单晶的工艺特点2.1 工艺流程基本工艺流程直拉硅单晶生长工艺流程包括装料、化料、熔接、引细颈、扩肩、保持、收尾、降温等基本过程。
2.2 杂质来源直拉硅单晶中的品质主要受原料、辅料及拉晶工艺的影响。
其中杂质主要来源于多晶硅原料和辅料(其包括石英埚、碳毡、石墨件等),当原料和辅料确定后,最终晶体内的杂质含量及分布由生长工艺直接决定。
直拉硅单晶中的氧主要来自晶体生长时硅熔体与石英柑锅的反应。
如图1所示,当多晶硅熔化成液相时,液态硅在高温下严重侵蚀石英增锅,其化学反应如下: (2-1) (2-2)绝大部分SiO从熔体表面挥发,部分SiO则在硅熔体中分解形成Si和O离子,氧通过熔体对流形式到生长界面附近,最终进入到晶体中。
硅中的碳原子主要来源于石墨件及碳毡,其化学反应如下:或图1 单晶生长过程中O/C杂质来源与传输过程通过控制单晶的工艺,可以控制熔体对流、气体对流及硅熔体与石英坩埚接触界面的温度,进而影响杂质的引入。
直拉硅单晶的氧和碳

直拉硅单晶的氧和碳直拉硅单晶中的氧和碳是一类很重要的杂质,氧和碳在直拉单晶中,可能形成微沉淀,可能在微沉淀基础上形成微缺陷,严重影响单晶质量,影响大规模集成电路性能和制造。
氧原子在硅单晶中大部以间隙原子状态存在,成Si-O-Si状态或SiO2和SiO4状态,熔点时,氧在固态硅的溶解度为(2.75±0.15)×1018/cm3,在熔硅中的溶解度为(2.20±0.15)×1018/cm3。
直拉硅单晶的氧主要来源于多晶硅,它的含氧量一般为1016/cm3~1017/cm3数量级,而直拉单晶硅中的氧含量一般在6×1017/cm3~2×1018/cm3,可见,单晶生长过程中有大量的氧进入。
石英坩埚对硅单晶的氧沾污非常严重,在1420℃以上高温下,硅熔体和石英坩埚进行化学反应:Si(熔体)+SiO2(固体)=2SiO反应结果,石英坩埚上生成一层固体一氧化硅,并不断溶解于熔硅中,生成一氧化硅气体也会溶解于熔硅,使熔硅氧浓度增高。
氩气氛下拉晶时,氩气中的氧会以不同形成溶入熔硅中,使硅单晶氧浓度增高。
直拉硅单晶一般单晶并没有部氧浓度高,尾部氧浓度低,单晶新面中心氧浓度高,边缘氧浓度低。
硅单晶的这种氧浓度分布既受坩埚污染影响,也受拉晶时氧蒸发和氧分凝效应影响。
坩埚中熔硅虽然离坩埚壁越近氧浓度越高,但在拉晶过程中,被单晶覆盖的熔硅氧不能蒸发,其余部分氧蒸发较快,在熔硅对流作用下,形成单晶中氧含量边缘高中心低的现象。
氧在硅中的平衡分凝系数一般认为是1.25,这很容易解释硅单晶头部含氧高尾部含氧低的事实。
但是,从硅氧二元相图看,氧在硅中的平衡分凝系数应该小于1,这和一般认为氧在硅中平衡分凝系数等于1.25相矛盾。
氧在单晶中分布呈并没有部高尾部低现象可以这样解释:由于多晶硅熔化时温度高,硅和石英坩埚(SiO2)反应激烈,大量的硅氧物进入熔硅,它们比重小,浮于熔硅上部,使得生长的单晶氧含量头部高,单晶在以后生长中,虽然硅和石英坩埚继续反应生成硅氧物进入熔硅,但由于温度较低反应缓慢,而且由于晶体和坩埚转动搅拌熔体中氧蒸发作用增强,使单晶尾部氧含量降低。
集成电路制造技术-原理与工艺 课后习题答案

第一单元:3.比较硅单晶锭CZ,MCZ和FZ三种生长方法的优缺点。
答:CZ直拉法工艺成熟,可拉出大直径硅棒,是目前采用最多的硅棒生产方法。
但直拉法中会使用到坩埚,而坩埚的使用会带来污染。
同时在坩埚中,会有自然对流存在,导致生长条纹和氧的引入。
直拉法生长多是采用液相掺杂,受杂质分凝、杂质蒸发,以及坩埚污染影响大,因此,直拉法生长的单晶硅掺杂浓度的均匀性较差。
MCZ磁控直拉法,在CZ法单晶炉上加一强磁场,高传导熔体硅的流动因切割磁力线而产生洛仑兹力,这相当于增强了熔体的粘性,熔体对流受阻。
能生长无氧、均匀好的大直径单晶硅棒。
设备较直拉法设备复杂得多,造价也高得多,强磁场的存在使得生产成本也大幅提高。
FZ悬浮区熔法,多晶与单晶均由夹具夹着,由高频加热器产生一悬浮的溶区,多晶硅连续通过熔区熔融,在熔区与单晶接触的界面处生长单晶。
与直拉法相比,去掉了坩埚,没有坩埚的污染,因此能生长出无氧的,纯度更高的单晶硅棒。
6.硅气相外延工艺采用的衬底不是准确的晶向,通常偏离[100]或[111]等晶向一个小角度,为什么?答:在外延生长过程中,外延气体进入反应器,气体中的反应剂气相输运到衬底,在高温衬底上发生化学反应,生成的外延物质沿着衬底晶向规则地排列,生长出外延层。
气相外延是由外延气体的气相质量传递和表面外延两个过程完成的。
表面外延过程实质上包含了吸附、分解、迁移、解吸这几个环节,表面过程表明外延生长是横向进行的,是在衬底台阶的结点位置发生的。
因此,在将硅锭切片制备外延衬底时,一般硅片都应偏离主晶面一个小角度。
目的是为了得到原子层台阶和结点位置,以利于表面外延生长。
7. 外延层杂质的分布主要受哪几种因素影响?答:杂质掺杂效率不仅依赖于外延温度、生长速率、气流中掺杂剂的摩尔分数、反应室的几何形状等因素,还依赖于掺杂剂自身的特性。
另外,影响掺杂效率的因素还有衬底的取向和外延层结晶质量。
硅的气相外延工艺中,在外延过程中,衬底和外延层之间存在杂质交换现象,即会出现杂质的再分布现象,主要有自掺杂效应和互扩散效应两种现象引起。
硅工艺 《集成电路制造技术》课程 试题

一、填空题晶圆制备1.用来做芯片的高纯硅被称为(半导体级硅),英文简称(GSG ),有时也被称为(电子级硅)。
2.单晶硅生长常用(CZ法)和(区熔法)两种生长方式,生长后的单晶硅被称为(硅锭)。
3.晶圆的英文是(wafer ),其常用的材料是(硅)和(锗)。
4.晶圆制备的九个工艺步骤分别是整型、定向、标识。
5.从半导体制造来讲,晶圆中用的最广的晶体平面的密勒符号是(100 )、(110 )和(111)。
6.CZ直拉法生长单晶硅是把(融化了的半导体级硅液体)变为(有确定晶向的)并且(被掺杂成p型或n型)的固体硅锭。
7.CZ直拉法的目的是(实现均匀掺杂的同时,并且复制仔晶的结构,得到合适的硅锭直径)。
影响CZ直拉法的两个主要参数是(拉伸速率)和(晶体旋转速率)。
8.晶圆制备中的整型处理包括(去掉两端)、(径向研磨)和(硅片定位边和定位槽)。
9.制备半导体级硅的过程:1(制备工业硅);2(生长硅单晶);3(提纯)。
10.晶片需要经过切片、磨片、抛光后,得到所需晶圆。
氧化10.二氧化硅按结构可分为()和()或()。
11.热氧化工艺的基本设备有三种:(卧式炉)、(立式炉)和(快速热处理炉)。
12.根据氧化剂的不同,热氧化可分为(干氧氧化)、(湿氧氧化)和(水汽氧化)。
13.用于热氧化工艺的立式炉的主要控制系统分为五部分:(工艺腔)、(硅片传输系统)、气体分配系统、尾气系统和(温控系统)。
14.选择性氧化常见的有(局部氧化)和(浅槽隔离),其英语缩略语分别为LOCOS和(STI )。
15.列出热氧化物在硅片制造的4种用途:(掺杂阻挡)、(表面钝化)、场氧化层和(金属层间介质)。
16.可在高温设备中进行的五种工艺分别是(氧化)、(扩散)、(蒸发)、退火和合金。
17.硅片上的氧化物主要通过(热生长)和(淀积)的方法产生,由于硅片表面非常平整,使得产生的氧化物主要为层状结构,所以又称为(薄膜)。
18.卧式炉的工艺腔或炉管是对硅片加热的场所,它由平卧的(石英工艺腔)、(加热器)和(石英舟)组成。
直拉单晶硅中的杂质和位错PPT课件

本征点缺陷对氧沉淀的影响
• 氧沉淀的生成会给硅基体带来很大的应力,只能通过吸收空位以及发射自间隙硅原子,使得应力得到释放。
第18页/共53页
热处理对氧沉淀的影响
• 温度:过饱和度和扩散速率 • 时间:核心在一定的生长速率下的尺寸 • 气氛:硅中引入不同的点缺陷 我们把温度和时间结合在一起考虑为热处理方式,既三个因素简化为 热处理步骤(方式)以及热处理气氛
• 直拉单晶硅中的氧(重点) • 直拉单晶硅中的碳(简要介绍) • 直拉单晶硅中的金属杂质(重点) • 直拉单晶硅中的位错(简要介绍)
目录
第2页/共53页
直拉单晶硅中的氧
• 浓度:1017-1018 cm-1 数量级 • 主要来源:石英坩埚的污染 (1420度),并经过各种温度的热处理 • 存在形式:间隙氧,氧热施主,氧团簇,氧沉淀 • 双刃剑: 内吸杂,破坏器件性能
掺镓的多晶硅
第28页/共53页
第29页/共53页
• 从那里来 • 存在形式 • 基本性质(与氧作用)
直拉单晶硅中的碳
第30页/共53页
从那里来
• 因:原料,直拉单晶炉中存在石墨加热器 • 缘:C + SiO2= SiO + CO CO + Si = SiO + C
第31页/共53页
• 替代位置 • C-O复合体(几个氧有争议) • 间隙位置
第25页/共53页
• 硼浓度 • 氧浓度 • 温度 • 光照强度
硼氧复合体的制约因素(略)
第26页/共53页
如何避免硼氧复合体
• 从氧入手: 区熔单晶硅,磁控直拉单晶硅 • 从硼入手:换成n型单晶硅 • 从硼入手:换成掺镓的单晶硅 • 新的太阳电池工艺,不同升降温工艺和氧化工艺
半导体思考题答案.doc
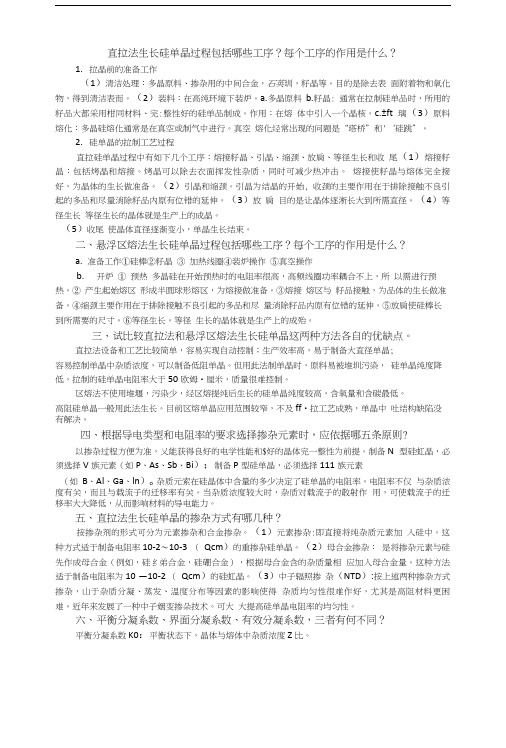
直拉法生长硅单晶过程包括哪些工序?每个工序的作用是什么?1.拉晶前的准备工作(1)清洁处理:多晶原料、掺杂用的中间合金,石英圳,籽晶等。
目的是除去表面附着物和氧化物,得到淸洁表而。
(2)装料:在高纯环境下装炉。
a.多晶原料b.籽晶: 通常在拉制硅单品时,所用的籽品大都采用柑同材料、完:整性好的硅单品制成。
作用:在熔体中引入一个晶核。
c.±ft璃(3)原料熔化:多晶硅熔化通常是在真空或制气中进行。
真空熔化经常出现的问题是“塔桥”和'‘硅跳”。
2.硅单晶的拉制工艺过程直拉硅单晶过程中有如下几个工序:熔接籽晶、引晶、缩颈、放肩、等径生长和收尾(1)熔接籽晶:包括烤晶和熔接。
烤晶可以除去衣面挥发性杂质,同时可减少热冲击。
熔接使籽晶与熔体完全接好,为晶体的生长做准备。
(2)引晶和缩颈。
引晶为结晶的开始, 收颈的主要作用在于排除接触不良引起的多品和尽量消除籽品内原有位错的延伸。
(3)放肩目的是让晶体逐淅长大到所需直径。
(4)等径生长等径生长的晶体就是生产上的成晶。
(5)收尾使晶体直径逐渐变小,单晶生长结束。
二、悬浮区熔法生长硅单晶过程包括哪些工序?每个工序的作用是什么?a.准备工作①硅棒②籽晶③ 加热线圈④装炉操作⑤真空操作b.开炉① 预热多晶硅在开始预热时的电阻率很高,高频线圈功率耦合不上,所以需进行预热。
② 产生起始熔区形成半圆球形熔区,为熔接做准备。
③熔接熔区与籽品接触,为品体的生长做准备。
④缩颈主要作用在于排除接触不良引起的多品和尽量消除籽品内原有位错的延伸。
⑤放肩使硅棒长到所需要的尺寸。
⑥等径生长。
等径生长的晶体就是生产上的成殆。
三、试比较直拉法和悬浮区熔法生长硅单晶这两种方法各自的优缺点。
直拉法设备和工艺比较简单,容易实现自动控制;生产效率高,易于制备大直径单晶;容易控制单晶中杂质浓度,可以制备低阻单晶。
但用此法制单晶时,原料易被堆圳污染,硅单晶纯度降低,拉制的硅单晶电阻率大于50欧姆•厘米,质量很难控制。
大直径直拉硅单晶炉热场的改造及数值模拟(1)

第29卷第4期 人 工 晶 体 学 报 V ol.29 N o.4 2000年11月 JOURNA L OF SY NTHETIC CRY ST A LS N ovember,2000大直径直拉硅单晶炉热场的改造及数值模拟任丙彦,刘彩池,张志成,郝秋艳(河北工业大学半导体材料研究所,天津300130)摘要:为了降低大直径硅单晶生长过程中氧的引入,对常规的406mm(16英寸)热场进行了改造。
设计了以矮加热器为核心的复合式加热器系统,使晶体生长过程中熔体热对流减小。
通过对热场的数值模拟计算,分析了热场的温度分布,发现熔体的纵向温度梯度下降,熔体热对流减小,硅单晶中氧含量降低。
关键词:直拉硅单晶;热场;加热器;热对流;氧含量;数值模拟中图分类号:O78 文献标识码:A 文章编号:10002985X(2000)0420381205 Improvement and Numeric Simulation for H eat Zone inLarge2diameter Si Single Crystals FurnaceREN Bing2yan,LIU Cai2chi,ZH ANG Zhi2cheng,H AO Qiu2yan(Institute of Sem iconductor M aterials,Hebei University of T echnology,T ianjin300130,China)(Received10March2000,accepted15June2000)Abstract:In order to reduce oxygen content in large2diameter C zochralski Si single crystal(CZSi),we have m odified the heat zone in406mm(16in.)system.Thermal convection of melthas been suppressed by our new heat system with com posite heater.Distribution of tem perature filed was calculated by numeric simulation.The result indicated that axial tem perature gradient was decreased due to the decrease of thermal convection in the melt.The concentration of oxygen in CZSi has been reduced.K ey w ords:CZSi;heat zone;heater thermal convection;oxygen concentration;numericsimulation1 引 言传统的直拉(CZ)法生长硅单晶时,氧是主要的非故意掺入的杂质[1]。
半导体工艺-集成电路制造技术-答案-1,2单元

第一单元 习题1. 以直拉法拉制掺硼硅锭,切割后获硅片,在晶锭顶端切下的硅片,硼浓度为3×1015atoms/cm 3。
当熔料的90%已拉出,剩下10%开始生长时,所对应的晶锭上的该位置处切下的硅片,硼浓度是多少?已知:C 0B =3×1015atoms/cm 3;k B =0.35;由ls C C k =得: 硅熔料中硼的初始浓度为:C 0l = C 0B / k B =3×1015 /0.35≈8.57×1015 atoms/cm 3;由10)1(--=k s X kC C 得:剩下10%熔料时,此处晶锭的硼浓度为:C 90%B = k B C 0l ×0.1 kB-1= 0.35×8.57×1015×0.10.35-1=1.34×10162. 硅熔料含0.1%原子百分比的磷,假定溶液总是均匀的,计算当晶体拉出10%,50%,90%时的掺杂浓度。
已知:硅晶体原子密度为:5×1022 atoms/cm 3, 含0.1%原子百分比的磷, 熔料中磷浓度为: C 0p =5×1022 ×0.1%=5×1019atoms/cm 3;k p =0.8由10)1(--=k s X kC C 计算得:C 10%p = k P C 0p ×0.9 kp-1=0.8×5×1019×0.9-0.2=4.09×1019 atoms/cm 3C 50%p =0.8×5×1019×0.5-0.2=4.59×1019 atoms/cm 3C 90%p =0.8×5×1019×0.1-0.2=6.34×1019 atoms/cm 33. 比较硅单晶锭CZ 、MCZ 和FZ 三种生长方法的优缺点?答:CZ 法工艺成熟可拉制大直径硅锭,但受坩锅熔融带来的O 等杂质浓度高,存在一定杂质分布,因此,相对于MCZ 和FZ 法,生长的硅锭质量不高。
集成电路制造技术原理与工艺[王蔚][习题答案(第1单元)
![集成电路制造技术原理与工艺[王蔚][习题答案(第1单元)](https://img.taocdn.com/s3/m/23598a7da417866fb84a8e78.png)
第一单元 习题1. 以直拉法拉制掺硼硅锭,切割后获硅片,在晶锭顶端切下的硅片,硼浓度为3×1015atoms/cm 3。
当熔料的90%已拉出,剩下10%开始生长时,所对应的晶锭上的该位置处切下的硅片,硼浓度是多少?已知:C 0B =3×1015atoms/cm 3;k B =0.35;由ls C C k =得: 硅熔料中硼的初始浓度为:C 0l = C 0B / k B =3×1015 /0.35≈8.57×1015 atoms/cm 3;由10)1(--=k s X kC C 得:剩下10%熔料时,此处晶锭的硼浓度为:C 90%B = k B C 0l ×0.1 kB-1= 0.35×8.57×1015×0.10.35-1=1.34×10162. 硅熔料含0.1%原子百分比的磷,假定溶液总是均匀的,计算当晶体拉出10%,50%,90%时的掺杂浓度。
已知:硅晶体原子密度为:5×1022 atoms/cm 3, 含0.1%原子百分比的磷, 熔料中磷浓度为: C 0p =5×1022 ×0.1%=5×1019atoms/cm 3;k p =0.8由10)1(--=k s X kC C 计算得:C 10%p = k P C 0p ×0.9 kp-1=0.8×5×1019×0.9-0.2=4.09×1019 atoms/cm 3C 50%p =0.8×5×1019×0.5-0.2=4.59×1019 atoms/cm 3C 90%p =0.8×5×1019×0.1-0.2=6.34×1019 atoms/cm 33. 比较硅单晶锭CZ 、MCZ 和FZ 三种生长方法的优缺点?答:CZ 法工艺成熟可拉制大直径硅锭,但受坩锅熔融带来的O 等杂质浓度高,存在一定杂质分布,因此,相对于MCZ 和FZ 法,生长的硅锭质量不高。
直拉法单晶硅中位错影响因素研究进展

第49卷第4期 2021年4月硅 酸 盐 学 报Vol. 49,No. 4 April ,2021JOURNAL OF THE CHINESE CERAMIC SOCIETY DOI :10.14062/j.issn.0454-5648.20200826直拉法单晶硅中位错影响因素研究进展苏文佳,李九龙,杨 伟,李 琛,王军锋(江苏大学能源与动力工程学院,江苏 镇江 212013)摘 要:在介绍了直拉法单晶硅中位错形成及运动机理的基础上,归纳了其生长过程中籽晶热冲击、固液界面、晶体直径和杂质等因素对位错的影响,分析了硼、锗、氮、磷、砷掺杂元素和氧杂质对单晶硅位错行为的影响。
籽晶热冲击会引起位错,而通过缩颈、回熔、籽晶预热以及采用掺杂的籽晶等方式可以使其得到抑制。
凸向熔体的固液界面引起较大的边缘切应力产生边缘位错,当形状为平面时,可抑制位错形成;在重掺n 型单晶硅中,固液界面的演变和{111}边缘面的形成可能促进过冷区域产生并中断顶锥生长,进而引发位错,并且边缘面的长度与熔融等温线的曲率有关;引晶时籽晶的不完全引晶,会产生位错且无法排出晶体,进而延伸至硅棒中;单晶硅直径增大和长晶过程中的直径波动都会增加位错的形成风险。
掺杂是抑制位错形成与运动的有效方法,硼、锗、氮、磷、砷以及氧杂质对位错都起着不同程度的抑制作用,主要原因在于杂质原子对位错的钉扎效应。
最后,针对缩颈工艺、热场设计、掺杂工艺和理论建模等方面,对未来的研究工作做出了展望。
关键词:直拉法;单晶硅;位错;固液界面;籽晶热冲击;晶体直径中图分类号:TB321;O77+2 文献标志码:A 文章编号:0454–5648(2021)04–0723–13 网络出版时间:2021–04–01Research Progress on Influencing Factors of Dislocation in Czochralski SiliconSU Wenjia , LI Jiulong , YANG Wei , LI Chen , WANG Junfeng(School of Energy and Power Engineering, Jiangsu University, Zhenjiang 212013, Jiangsu, China)Abstract: Based on the introduction of the dislocation formation and movement mechanism in Czochralski silicon, the effects of seed crystal thermal shock, solid–liquid interface, crystal diameter, and impurities on the dislocations during the crystal growth process were summarized. The effects of boron, germanium, nitrogen, phosphorus, arsenic doping elements and oxygen impurities on the dislocation behavior of the Czochralski silicon were analyzed. The thermal shock of the seed crystal can lead to the dislocations, which can be suppressed by some methods such as necking, melting back, seed crystal preheating, and the use of doped seed crystal. The solid–liquid interface convex to the melt causes a large edge shear stress to produce the edge dislocations. The formation of dislocations can be suppressed when the shape is flat. In heavily n –type doped single crystal silicon, the evolution of solid–liquid interface and the formation of {111} edge surface may promote the generation of supercooling region and interrupt the growth of top cone, thereby causing the dislocations, and the length of the edge surface is related to the curvature of the melting isotherm. Incomplete seeding of the seed crystal will produce the dislocations that cannot be discharged from the crystal, and then extend to the silicon rod. The increase in the diameter of single crystal silicon and the fluctuation of the diameter during the crystal growth process will increase the risk of dislocation formation. Doping is an effective method to inhibit the formation and movement of dislocations. Boron, germanium, nitrogen, phosphorus, arsenic and oxygen impurities all have different degrees of inhibition on the dislocations mainly due to the pinning effect of impurity atoms on the dislocations. Finally, some future research aspects on necking process, thermal field design, doping process and theoretical modeling were prospected.Keywords: Czochralski method; monocrystalline silicon; dislocation; solid–liquid interface; seed thermal shock; crystal diameter收稿日期:2020–11–02。
直拉法单晶硅生长中的流动及其影响

直拉法单晶硅生长中的流动及其影响
直拉法单晶硅生长是用于制造电子产品的核心技术,它可以用一个原料晶体,并整形晶体,使其具有可用于生产的块状生长单晶硅。
单晶硅生长中的流动包括三个主要方面:熔体流动、物质流动和质量流动。
熔体流动是指以高温的电极的作用下,单晶硅中的熔体产生的流动过程。
物质流动指的是晶体中由于能量源的存在而产生的物质流动,它包括有形(固液,液液,气液)和无形(热和光)流动。
质量流动根据温度和压力的变化,在晶体内部形成的压力有变化,从而影响其形状和结构。
流动在单晶硅生长过程中发挥着重要作用,其对晶体生长的影响也十分显著。
如果熔体流动不足往往会导致晶体的凝固、粗化和折叠,从而影响晶体生长和结构。
而物质流动会改变晶体结构和晶体表面特性,从而影响晶体成型。
同时,质量流动也影响到晶体生长过程,它会影响晶体的形状、尺寸和品质。
因此,在单晶硅生长过程中,熔体流动、物质流动和质量流动的合理控制是提高单晶硅的质量的关键所在,只有在正确控制好上述三种流动的基础上,单晶硅的生长才能有效改善其质量,从而获得高质量的产品。
不同掺杂类型硅片抛光特性的研究

实验结果显示p-Si的掺杂浓度越大,抛光去除速率越小,抛光后 的表面微粗糙度越大,表面微观平整度越差;掺杂浓度相同的pSi的抛光去除速率低于n-Si,而表面微粗糙度高于n-Si。由于化 学机械抛光技术的去除原理主要由硅片表面与碱性抛光液发生 化学反应及抛光垫和抛光磨粒摩擦去除反应生成物两个方面组 成,在抛光压力、转速完全一致的情况下,机械作用对不同硅片 的作用效果基本一致,产生抛光去除速率及抛光后表面微粗糙度 差异的主要原因是不同硅片与抛光液之间的化学作用受到掺杂 剂浓度及种类的影响。
直拉硅单晶的本征缺陷在引入不同的杂质原子时会与杂质原子 进行相互作用,使抛光前的硅片表面形成微缺陷,造成杂质原子 团聚。抛光时,这些微缺陷使硅片表面形成局部微电池,进行局 部电化学反应,其中阳极反应为:Si+6OH-→SiO32--+3H2O+4e-, 阴极反应为:2H++2e-→H2↑。
p-Si中掺有大量B,B参与电化学的阴极反应,使其反应速率下降, 从而令抛光时的化学反应速率下降,不仅导致掺B硅片的抛光去 除速率低,还会使抛光时的机械作用与化学作用的匹配程度降低, 令硅片抛光后的表面粗糙度增大;而n-Si中引入的杂质原子在其 中起到的作用刚好相反,使硅片在抛光时的化学反应加速并与机 械作用更好地匹配从而使硅片抛光结果更好。从上述分析出发, 降低p-Si抛光液的pH,使电化学的阴极反应与阳极反应相对平衡, 抛光时的化学作用与机械作用相匹配,结果p-Si抛光后的表面微 粗糙度降低,表面微观平整度有所改善。
ห้องสมุดไป่ตู้不同掺杂类型硅片抛光特性的研究
如今信息技术飞速发展,大规模集成电路(IC)的制造对衬底硅片 的要求也越来越高,为了提高IC整体性能,硅片加工工艺在硅片 的表面状态、微观平整度等方面的要求都已经达到纳米级。硅 片表面的微观平整度和表面状态主要由抛光过程决定,而抛光的 结果又受到很多因素的影响,其中关于硅片性质对抛光结果的影 响研究较少。
单晶硅生长技术及氧缺陷控制方法

单晶硅生长技术及氧缺陷控制方法摘要:目前电子信息技术以及光伏技术飞速发展,而作为此类技术的基础材料,硅发挥了重要作用。
从某些角度分析,硅(Si)影响了未来科技的发展,是高薪技术进步的基础,因此国家想要发展自身在能源领域以及高新技术领域实力,必须将Si作为战略资源。
作为功能性材料,Si具有各项异性,所以将Si应用于半导体材料需要将其制成硅单晶,并进一步将其加工成为抛光片。
这样才能将Si应用于CI器件的制造中,目前所生产的电子元件中89%以上的均使用硅单晶。
关键词:单晶硅;生长技术;氧缺陷单晶硅的生产需要以半导体单晶硅切割过程中产生的头尾料、单晶硅碎片以及边皮料作为原料。
而生产所用技术目前主要有两种,一种为直拉法,一种则是悬浮区熔法。
制备单晶硅过程中,依照实际的需要还需要添加必要元素,从而增大、减小材料电阻率,掺杂元素主要为第Ⅲ主族元素以及第Ⅴ主族元素。
完成单晶硅材料的制备后,还需要依照半导体材料的需要进行深加工,深加工程序主要包括切片、打磨以及腐蚀和抛光。
而随着单晶硅的生产技术、加工技术的发展,目前的单晶硅逐步向着300mm以上大直径材料发展,且缺陷含量以及杂志含量更低,材料分布更加均匀,且生产成本不断降低、效率更高。
1 单晶硅的概念半导体材料的电学性质和其他物理性质对晶格缺陷以及所含杂质的种类和数量非常敏感。
制作各种半导体器件,尤其是集成电路和大规模集成电路的制作更需要均匀性好的大直径完善单晶。
目前不仅能制造无位错的完善单晶,而且还可以将位错密度控制在一定范围内[1]。
无位错单晶的直径已达到200mm规格化。
2 单晶硅的生长方法2.1 直拉(CZ)法CZ是单晶硅生长中直拉法的简称,其过程相对较为简单,通过从熔硅中利用旋转籽晶对单晶硅进行提拉制备,该种方法生产成本相对较低,且能够大量生产。
因此该项技术在国内太阳能单晶硅片的生产中广泛贵推广开来,直拉法目前使用的技术工艺核心有磁场直拉法、热场构造以及控制氧浓度等。
直拉单晶硅的制备掺杂
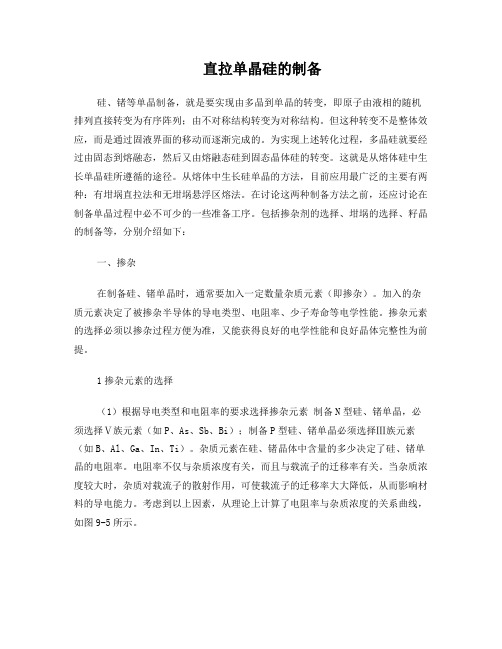
直拉单晶硅的制备硅、锗等单晶制备,就是要实现由多晶到单晶的转变,即原子由液相的随机排列直接转变为有序阵列;由不对称结构转变为对称结构。
但这种转变不是整体效应,而是通过固液界面的移动而逐渐完成的。
为实现上述转化过程,多晶硅就要经过由固态到熔融态,然后又由熔融态硅到固态晶体硅的转变。
这就是从熔体硅中生长单晶硅所遵循的途径。
从熔体中生长硅单晶的方法,目前应用最广泛的主要有两种:有坩埚直拉法和无坩埚悬浮区熔法。
在讨论这两种制备方法之前,还应讨论在制备单晶过程中必不可少的一些准备工序。
包括掺杂剂的选择、坩埚的选择、籽晶的制备等,分别介绍如下:一、掺杂在制备硅、锗单晶时,通常要加入一定数量杂质元素(即掺杂)。
加入的杂质元素决定了被掺杂半导体的导电类型、电阻率、少子寿命等电学性能。
掺杂元素的选择必须以掺杂过程方便为准,又能获得良好的电学性能和良好晶体完整性为前提。
1掺杂元素的选择(1)根据导电类型和电阻率的要求选择掺杂元素制备N型硅、锗单晶,必须选择Ⅴ族元素(如P、As、Sb、Bi);制备P型硅、锗单晶必须选择Ⅲ族元素(如B、Al、Ga、In、Ti)。
杂质元素在硅、锗晶体中含量的多少决定了硅、锗单晶的电阻率。
电阻率不仅与杂质浓度有关,而且与载流子的迁移率有关。
当杂质浓度较大时,杂质对载流子的散射作用,可使载流子的迁移率大大降低,从而影响材料的导电能力。
考虑到以上因素,从理论上计算了电阻率与杂质浓度的关系曲线,如图9-5所示。
在生产工艺上按电阻率的高低分档。
掺杂有三档:轻掺杂(适用于大功率整流级单晶)、中掺杂(适用于晶体管级单晶)、重掺杂(适用于外延衬底级单晶)。
(2)根据杂质元素在硅、锗中溶解度选择掺杂元素各种杂质元素在硅、锗中溶解度相差颇大。
例如,采用大溶解度的杂质,可以达到重掺杂的目的,又不会使杂质元素在晶体中析出影响晶体性能。
下表列出了常用掺杂元素在硅、锗单晶生长时掺入量的极限,超过了极限量,单晶生长不能进行。
第八章硅中的杂质

第八章硅中的杂质半导体硅晶体是高纯材料,对杂质的引入非常敏感,人们有意掺入电活性杂质(如硼、磷等),来控制它的电学性能,以制造不同功能的器件。
但是,在硅晶体生长和器件制造的工艺过程中,常常会由于各种原因无意地引入电活性或非电活性的杂质,这些杂质或者它们所造成的二次缺陷对硅材料和器件的性能有破坏作用,因而引起人们的高度重视。
一般在硅晶体中无意引入的杂质可分为两大类,一类是轻元素杂质,包括氧、碳、氮和氢杂质;另一类是金属杂质,主要是指铁、铜和镍等3d过渡金属。
这些杂质由不同的途径进入硅晶体,对它的机械和电学性能也有不同的影响。
在7.1.1节中已一般地讨论了作为硅中的非本征点缺陷即硅中的杂质的一般性质和行为,本章分别介绍氧、碳、氮、氢杂质和过渡金属杂质在硅中的基本性质,它们在硅中的沉淀,它们之间的相互作用,以及它们对硅材料和器件性能的影响。
8.1 硅中的氧氧是直拉(CZ)硅单晶中最主要的杂质,已被研究四十多年。
硅中的氧浓度一般在1017~1018cm-3数量级,以间隙态存在于硅晶格中。
氧是在晶体生长过程中被引入的,在随后的器件制造工艺过程中,由于硅晶体经历了各种温度的热处理,过饱和的间隙氧会在硅晶体中偏聚和沉淀,形成了氧施主、氧沉淀及二次缺陷。
这些和氧有关的缺陷,对硅材料和器件具有有利和不利的两个方面。
有利的方面是它们能结合器件工艺,形成内吸杂,可以吸除金属杂质;氧杂质还能钉扎位错,提高硅片机械强度。
不利的方面是当氧沉淀过大时,又会导致硅片的翘曲;氧沉淀还能引入大量的二次缺陷。
对硅材料和器件的电学性能有破坏作用。
在半导体硅材料大规模应用的早期,人们认为氧仅仅是有害杂质,努力使之在硅晶体中的浓度降低,在70年代末,人们认识到它能提高硅片的机械强度以及可能具有内吸杂效应,可以加以应用。
在现代硅材料生产中,氧的浓度通常被控制在所需要的范围。
本节介绍硅中氧的引入、硅中氧的基本性质以及它对硅材料和器件性能的影响,还阐述热施主和新施主的性质,重点介绍硅中氧沉淀的形核、长大、形态以及影响氧沉淀生成的因素,最后介绍了内吸杂的概念。
硅材料题库
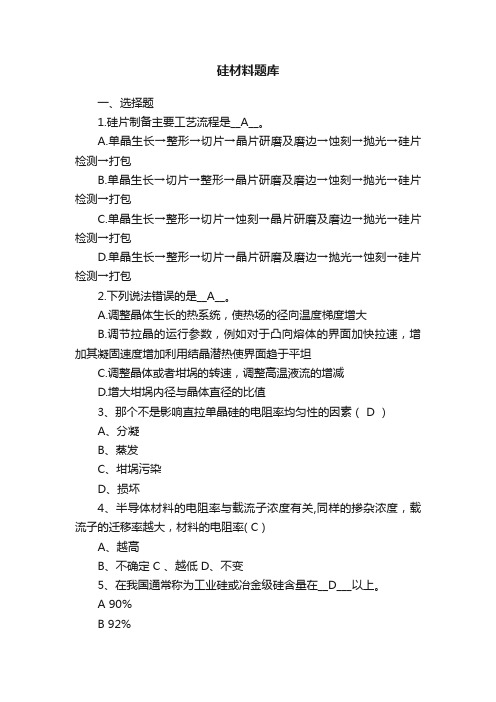
硅材料题库一、选择题1.硅片制备主要工艺流程是__A__。
A.单晶生长→整形→切片→晶片研磨及磨边→蚀刻→抛光→硅片检测→打包B.单晶生长→切片→整形→晶片研磨及磨边→蚀刻→抛光→硅片检测→打包C.单晶生长→整形→切片→蚀刻→晶片研磨及磨边→抛光→硅片检测→打包D.单晶生长→整形→切片→晶片研磨及磨边→抛光→蚀刻→硅片检测→打包2.下列说法错误的是__A__。
A.调整晶体生长的热系统,使热场的径向温度梯度增大B.调节拉晶的运行参数,例如对于凸向熔体的界面加快拉速,增加其凝固速度增加利用结晶潜热使界面趋于平坦C.调整晶体或者坩埚的转速,调整高温液流的增减D.增大坩埚内径与晶体直径的比值3、那个不是影响直拉单晶硅的电阻率均匀性的因素( D )A、分凝B、蒸发C、坩埚污染D、损坏4、半导体材料的电阻率与载流子浓度有关,同样的掺杂浓度,载流子的迁移率越大,材料的电阻率( C )A、越高B、不确定 C 、越低 D、不变5、在我国通常称为工业硅或冶金级硅含量在__D___以上。
A 90%B 92%D 97%6、下列关于硅的说法不正确的是( D )A.硅是非金属元素,它的单质是灰黑色有金属光泽的固体B.硅的导电性能介于金属与绝缘体之间,是良好的半导体材料C.硅的化学性质不活泼,常温下不与任何物质反应D.加热到一定温度时,硅能与氢气、氧气等非金属发生反应7、关于光生伏特效应叙述中错误的是( C )A用能量等于或大于禁带宽度的光子照射p-n结;B p、n区都产生电子—空穴对,产生非平衡载流子;C非平衡载流子不破坏原来的热平衡;D非平衡载流子在内建电场作用下,n区空穴向p区扩散,p区电子向n区扩散;8、对于临界晶核,即与母相达成平衡,可以稳定存在的晶核来说,下列应该满足的条件是( B )(1)、母相压强等于外压强(2)、三个相的化学势相等(3)、新相压强大于外压强(4)、新相压强必须小于外压强A、(1)、(2)、(4)B、(1)、(2)、(3)C、(4)D、(1)、(2)、(3)、(4)9、固相晶化是指非晶硅薄膜在一定的保护气中,在(D )摄氏度以上进行常规热处理。
生物质能课简答题答案

1.简述常规太阳电池片的生产步骤。
答:1.由砂还原成冶金级硅:成分是二氧化硅的砂在电弧炉中用碳还原成硅。
2.冶金级硅提纯为半导体级硅:标准方法有西门子工艺,用盐酸将细碎的冶金级硅颗粒反应成SiHCl3和氢气。
加热混合气体,使半导体级三氯氢硅被氢气还原,此时,硅以细晶粒的多晶硅形式沉积到电加热的硅棒上。
3.半导体级硅转变为单晶硅片:在坩埚中,将半导体级多晶硅熔融,同时,加入器件所需的微量掺杂剂。
利用籽晶从熔融硅中拉出大圆柱形的单晶硅。
再将大单晶硅锭切成薄的硅片。
4.单晶硅片制成太阳能电池:硅片经腐蚀并清洗后,通过高温杂质扩散工艺,掺入杂质。
形成了PN结。
使用真空蒸发工艺来制备附着于n型区和p型区表面的金属电极。
5.太阳能电池封装成防风雨的太阳能电池组件。
2.单晶硅太阳电池与多晶硅太阳电池的性能与制备工艺有哪些不同?答:1)单晶硅是硅原子以金刚石晶格排列而成的连续完整晶体,没有晶界,太阳能电池用单晶硅一般采用CZ直拉单晶法制备而成。
直拉单晶法可生产大尺寸单晶硅,且成本低,质量稳定均一,但其电阻率范围窄,杂质浓度较高,氧含量比较高(~1017 cm-3),氧含量会降低单晶硅太阳能电池的少子寿命,进而降低开路电压、短路电流和光电转换效率。
此外,氧和单晶硅中的掺杂杂质形成的氧络合物在高温下变得很活跃,使得单晶硅电池在高温处理工艺中变得优为敏感。
单晶硅太阳能电池采用碱制绒工艺,可在表面形成金字塔结构,具有很好的陷光效果,因此通常看到的单晶硅太阳能电池表面呈现黑色或暗色。
2)多晶硅是由许多取向不同的硅晶粒组成,不同晶粒之间存在晶界,由于晶界的存在,制备多晶硅对原料质量的要求远远低于单晶硅。
晶界在硅的带隙中引入了额外的缺陷能级,由此产生高的局部区域复合,从而降低了材料整体的少子寿命。
此外,晶界会阻碍少子的扩散,而且为流经p-n结的电流提供了分流路径,从而降低了太阳能电池的性能。
因此为了避免在晶界处发生显著的复合损失,多晶硅晶粒的大小至少在几个mm以上,可减少单位面积上晶界的长度,并且硅晶粒应贯穿太阳能电池,有利于少子的扩散。
- 1、下载文档前请自行甄别文档内容的完整性,平台不提供额外的编辑、内容补充、找答案等附加服务。
- 2、"仅部分预览"的文档,不可在线预览部分如存在完整性等问题,可反馈申请退款(可完整预览的文档不适用该条件!)。
- 3、如文档侵犯您的权益,请联系客服反馈,我们会尽快为您处理(人工客服工作时间:9:00-18:30)。
直拉法生长的硅单晶中的杂质浓度受到许多因素的影响。
掺杂估算所考虑的只是肩部下刚开始等径生长的硅单晶要达到的目标电阻率。
在忽略了一些次要因素后,可以对掺杂量进行大致的估算,作为试拉时的依据,然后可以再根据试拉的结果进行修正。
直拉法生长硅晶体时炉膛中的气氛有正压、减压氩气(也可用氮气)和真空三种。
在不同的气氛下,掺杂剂的蒸发情况不同。
掺杂估算时必须考虑它的影响。
下面我们分别讨论不同气氛下的掺杂估算。
(a)不考虑熔硅中的杂质挥发时的掺杂估算生长用于集成电路和分立器件制造的大直径中、低阻晶体时,普遍采用减压氩(氮)气气氛。
除重掺杂外,在两种气氛下生长硅单晶时都不用纯元素掺杂,而是用掺杂元素与硅的合金与多晶硅共熔掺杂。
这是因为一方面纯元素量太少不易精确计量,另一方面其物理化学性质与硅熔体也相差太远,例如某些元素的熔点比硅低得多,与多晶硅共熔时将于硅熔化前挥发。
CZ法生长是典型的正常凝固过程,在忽略杂质的挥发效应的情形,掺杂剂的轴向分布遵从Pfann关系式(3.149),分布曲线如图3.41所示。
选取晶体肩部位置的电阻率为目标电阻率上限,如果可以忽略杂质的挥发、石英坩埚引入的杂质、多晶硅中的初始杂质浓度和母合金电阻率的不均匀性对于目标电阻率的影响,则可以推出以下的掺杂估算公式。
母合金中的掺杂元素分凝进入晶体,达到与目标电阻率相应的掺杂剂浓度,故有(a+m)CS=keff.Cm .m 式中,a为多晶硅的重量,m 为掺人的母合金的重量;Cm 为母合金中掺杂剂的浓度,keff为有效分凝系数,CS 为晶体肩部位置处目标电阻率对应的杂质浓度。
因而掺入的母合金的重量可由下式计算得到: m=CS/[(keff.Cm -cs)a] 在减压氩气气氛下,生长硅单晶速度为lmm/min时,几种常用掺杂元素在硅中的有效分凝系数的一组数据是:磷为0.406,硼为0.91,锑为0.052。
按式(4.19)估算掺杂量,再根据实际情况加以修正。
一般能够做到比较准确地控制生长成的晶体的电阻率。
(b)考虑熔硅中的杂质挥发时的掺杂估算在真空环境下生长硅单晶或者掺杂剂元素的挥发性很强时,必须考虑掺杂剂的蒸发。
掺杂元素的蒸发系数以Sb、As最大,P、Al较小,硼很小。
掺杂剂的蒸发使其浓度发生的变化可由下式表示:(见插图5个公式为以下6个需要的计算式)NO.1 式中,E为掺杂元素的蒸发系数,AL 为熔体蒸发面积,VL为熔体体积,CL为熔体中掺杂剂的浓度。
对式(4.10)积分,得 NO.2 式中CL0为晶体放肩结束时熔体中的掺杂元素的浓度。
故在考虑熔硅中的杂质挥发的情形,要达到同样的目标电阻率所需要加入的母合金的重量为NO.3 其中t为从母合金熔化到放肩结束这两个时刻之间的时间。
(3)掺杂结果的修正方法在掺杂过程中,由于下列因素得到的结果可能与掺杂估算不一致:(a)多晶硅的杂质浓度的测试不准确。
(b)多晶硅中存在着其他电活性杂质; (c)多晶硅中有明显的杂质补偿; (d)母合金中杂质浓度的数据不准确; (e)石英坩埚材料中主要杂质含量不一致; (f)蒸发系数、坩埚的沾污率等数据的选择不合适; (g)生长硅单晶过程中从开始熔化到收肩的时间控制不严格; (h)生长硅单晶工艺的其他不稳定因素。
如果由于以上因素生长出的晶体的电阻率与掺杂估算有偏离,可在下一次生长硅单晶中应用比例法进行修正。
修正式可用: NO.4 式中,m1为上次生长硅单晶时掺人的合金重量;ρ1为上次生长硅单晶时晶体的电阻率;m2为下次生长硅单晶时应掺入的合金重量;ρ2为下次生长硅单晶时晶体的电阻率。
(4)元素掺杂法的掺杂估算生长外延衬底稳压管、太阳能电池用重掺硅单晶和掺杂用母合金(其电阻率为 0.1-0.000000001欧姆时采用元素掺杂法。
一般采用在多晶熔化后将掺杂剂投入熔硅进行掺杂的方法。
掺杂元素的纯度一般为5~7个“9”。
其掺杂计算如下: (a)当忽略掺杂元素的蒸发时 NO.5 其
中A和A’分别为掺杂元素与硅的原子量。
(b)当考虑掺杂元素的蒸发时 NO.6 式中,A为掺杂元素的原子量;A’为硅的原子量,Cs为重掺杂单晶的杂质浓度,单位是10-9cm-3。
其他符号意义同上。
应当指出,除了上述计算的掺杂量外,还应根据实际情况考虑掺杂时高温冲击引起额外蒸发的杂质,以及炉膛内的掺杂元素在气氛中的分压等因素的影响。
希望对你有帮助。