ML20MnTiB冷镦钢开裂原因分析
低碳冷镦钢冷镦开裂原因分析
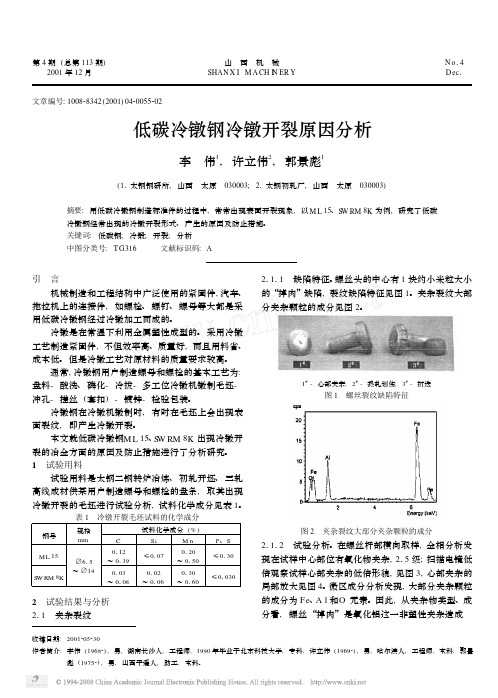
冲孔- 搓丝 (套扣) - 镀锌- 检验包装。
冷镦钢在冷镦机镦制时, 有时在毛坯上会出现表
面裂纹, 即产生冷镦开裂。
本文就低碳冷镦钢M L 15、SW RM 8K 出现冷镦开
裂的冶金方面的原因及防止措施进行了分析研究。
1 试验用料
试验用料是太钢二钢转炉冶炼、 初轧开坯、 三轧
高线成材供某用户制造螺母和螺栓的盘条, 取其出现
折迭裂纹在试样横断面对称的两侧, 各为 2 条平 行的纵向裂纹, 镦制后裂纹张开 (如螺丝头部的外缘 和冷顶锻试样的外侧) , 且裂纹内壁有轻微氧化, 每侧 裂纹的裂纹源均向 2 条裂纹中间延伸。
折迭裂纹产生的原因是, 轧制时孔型或张力等调 整、控制不当, 造成辊缝处“制耳”, 耳子轧后即为折 迭。 3 结论 311 低碳冷镦钢冷顶锻开裂主要有 3 种类型: 夹杂裂 纹、 划伤裂纹和折迭裂纹。 312 夹杂裂纹的特征是在钢材或零件表面有小米粒 大小的 “掉肉”, 留下小坑, 显微镜下为氧化物夹杂。 它是由于炼钢注温高、 注速快、 镇静时间短所致。 313 划伤裂纹的特征是沿纵向较深, 裂纹深处无氧 化、 脱碳, 是由钢材生产和吊运时表面划伤所致。 314 折迭裂纹在钢材或零件两侧对称出现, 且多为纵 向裂纹, 裂纹内壁有轻微氧化。 轧钢时应防止出现 “耳子”, 以避免出现此类裂纹。
图 4 图 3 的局部放大
212 划伤裂纹 21211 划伤裂纹特征: 螺丝头的外缘及杆部有一条纵 向裂纹, 裂纹较深, 裂纹深度的方向约沿着试样直径 方向, 裂纹内未露出内部的 “新金属” (见图 1)。 21212 划伤裂纹的金相分析: 在螺丝杆部横向取样, 观察发现, 在裂纹源处无金属夹杂, 裂纹源延伸处的 钢材组织中也无氧化、 脱碳现象。 21213 综合分析, 缺陷为热轧划伤, 原因是, ①材料 表面缺陷。常见的缺陷特征有材料 45°剪裂、炼钢夹杂
冷镦钢开裂成因分析及质量改进

冷镦钢开裂成因分析及质量改进冷镦钢是一种用途广泛的金属材料,常常用于制作螺栓、螺母等零部件。
在生产过程中,冷镦钢有时会出现开裂的情况,这不仅影响了产品的质量,也增加了生产成本。
对冷镦钢开裂的成因进行分析,并提出质量改进的措施,对于企业的生产和发展具有重要意义。
冷镦钢开裂的成因分析主要包括以下几个方面:原材料质量、冷加工工艺、设备状况、操作技术以及质量控制等方面。
首先是原材料质量。
冷镦钢的开裂与原材料质量有着密切的关系,如果原材料中含有过多的夹杂物、气孔等缺陷,或者材料的组织不均匀,都会导致冷镦钢在冷加工过程中出现开裂的情况。
其次是冷加工工艺。
冷加工工艺的参数设置不当、过程控制不严等因素都可能导致冷镦钢开裂。
冷加工时温度过低或者过高、冷加工过程中受力不均匀等,都会对冷镦钢的质量产生不利影响。
再者是设备状况。
设备的磨损、老化或者不合理的设计都可能导致冷加工过程中对冷镦钢造成损伤,从而引起开裂。
操作技术也是一个重要的因素。
冷加工过程中操作者的技术熟练程度、操作规范程度等都会影响冷镦钢的开裂情况。
如果操作不当、经验不足,都会加剧冷镦钢开裂的风险。
最后是质量控制。
如果生产过程中的质量控制不严格、产品检验不到位,都会让质量不合格的冷镦钢流入市场,增加了产品开裂的风险。
针对以上分析的成因,我们公司提出了以下质量改进措施。
首先是加强原材料的质量控制。
在原材料采购环节,加强对原材料的检验,确保原材料的质量符合要求。
对有质量问题的原材料,及时进行退货处理,避免不良原材料影响产品质量。
其次是优化冷加工工艺。
通过对冷加工工艺参数的优化调整,确保冷加工过程中的温度、压力、速度等参数在合理范围内,减少冷镦钢在冷加工过程中的应力集聚,降低开裂的风险。
再者是加强设备维护和更新。
定期对冷加工设备进行检查、维护和更新,确保设备处于良好的工作状态,避免设备老化和磨损给冷镦钢的质量带来影响。
加强操作技术培训。
对操作者进行系统的技术培训,提高操作者对冷加工过程的理解和技术水平,降低操作不当造成的产品质量问题。
冷镦钢开裂成因分析及质量改进

冷镦钢开裂成因分析及质量改进【摘要】冷镦钢在生产过程中容易出现开裂问题,影响产品质量和生产效率。
本文通过分析冷加工工艺、开裂原因,探讨质量改进策略和监控方法,提出改进生产工艺的建议。
总结认为,冷镦钢开裂问题可通过调整工艺参数和提高生产控制水平来解决,未来可深入研究开裂机理、优化材料配方等方面。
希望通过本文的研究,能够为解决冷镦钢开裂问题提供有效的参考,推动行业质量水平的提升。
【关键词】冷镦钢、开裂成因、质量改进、冷加工工艺、性能影响、质量监控、生产工艺、根本解决方法、研究方向、总结、展望。
1. 引言1.1 冷镦钢开裂成因分析及质量改进冷镦钢是一种常用的金属材料,广泛应用于汽车、机械制造等领域。
冷镦钢在生产过程中经常出现开裂现象,严重影响产品质量和生产效率。
对冷镦钢开裂成因进行分析,并提出质量改进方案至关重要。
本文旨在对冷镦钢开裂成因进行深入分析,探讨影响冷镦钢性能的冷加工工艺因素,并从根本上解决冷镦钢开裂问题。
通过对冷镦钢开裂原因的探讨和质量改进策略的提出,希望能够引起相关行业的重视,提升产品质量和企业生产效率。
在本文中,我们将首先分析冷加工工艺对冷镦钢性能的影响,探讨冷镦钢开裂的根本原因,并提出质量改进策略。
接着,我们将介绍冷镦钢质量监控方法,以及改进冷镦钢生产工艺的具体措施。
我们将总结冷镦钢开裂的根本解决方法,并提出未来研究方向,展望冷镦钢质量改进的发展方向。
希望通过本文的研究,能够为相关行业提供参考,促进冷镦钢质量的提升和行业的发展。
2. 正文2.1 冷加工工艺对冷镦钢性能影响分析冷加工工艺是冷镦钢生产过程中至关重要的环节,其对冷镦钢的性能影响非常显著。
在冷加工工艺中,冷镦钢的变形应力和应变量会大大增加,这会导致冷镦钢的晶粒变形和排列发生变化,从而影响其力学性能。
冷加工过程中会产生大量的加工硬化作用,使得冷镦钢的硬度和强度明显提高,但同时也容易导致其脆性增加,从而增加冷镦钢开裂的风险。
在冷加工工艺中,温度、速度、压力等参数的控制也对冷镦钢的性能有着直接的影响。
冷镦钢开裂成因分析及质量改进

冷镦钢开裂成因分析及质量改进作者:胡志轶来源:《科技风》2019年第16期摘要:在冷镦钢的生产实践过程中,通过分析总结冷镦钢开裂的原因,提出了相应的改进措施,提高了冷镦钢的产品质量,满足下游客户生产需求。
关键词:冷镦钢;开裂;组织;表面缺陷1 绪论冷镦钢是广泛用于制造螺栓、螺母、螺钉、铆钉等各类标准件用钢,它主要是利用金属的塑性,采用冷镦加工成型。
由于冷镦钢在加工过程中形变量大且速度快,所以对钢材的加工性能和机械性能均有严格要求。
通过对生产工艺的不断改进,提高冷镦钢的产品质量,满足客户需求。
2 冷镦钢使用中存在的质量问题通过市场调查发现,冷镦钢在使用过程中出现的主要问题是存在冷镦开裂的现象。
3 造成冷镦钢开裂的主要因素(1)化学成分。
①碳元素。
冷镦钢中碳含量的高低对其韧性有很大影响,碳含量超标会导致冷镦钢在加工过程中出现镦头开裂,造成镦头开裂的另一重要因素是钢中存在球化不完全的碳化物相。
生产过程中要严格将冷镦钢的含碳量按照标准的中下限来加以控制。
②铝元素。
铝在高温下易氧化形成有害杂质,降低钢材的机械性能。
但同时铝元素也具有细化晶粒、改善钢材韧性的作用,可以提高冷镦钢快速镦头以及降低搓丝过程中应变时效等综合性能。
因此,应对其加以适量控制。
③硫、磷元素。
硫和磷为钢中有害元素,其会对钢造成热脆和冷脆现象,所以必须控制在标准范围内,尽可能降低更好。
④硅、锰元素。
硅常被用作脱氧剂加入钢中,少量的硅能够提高钢的强度,但含量较多时则对钢的塑形和韧性产生不利影响。
锰能脱氧并减弱硫的有害作用,从而改善材料的热加工性能。
锰同时会提高钢材的强度、硬度和淬透性,增强加工硬化,从而降低材料的塑性。
⑤氮、氢、氧元素。
氮:随着钢中氮含量的增加,钢材的强度、硬度和脆性升高,但塑形和韧性显著降低,焊接性能变差。
氢:氢是钢中产生白点的根本原因,这些存在于钢中的白点(小裂纹)会使钢材出现氢脆现象。
氧:氧在钢中主要以氧化物的形式存在,随着钢中非铁氧化物的增多,钢材的塑形和韧性明显下降。
冷镦钢开裂成因分析及质量改进
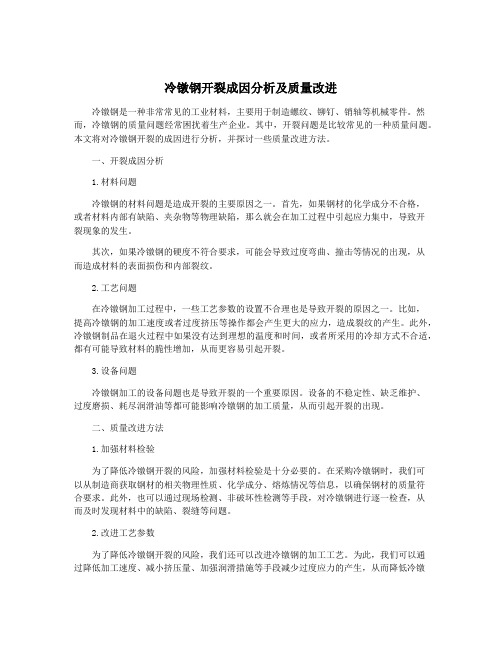
冷镦钢开裂成因分析及质量改进冷镦钢是一种非常常见的工业材料,主要用于制造螺纹、铆钉、销轴等机械零件。
然而,冷镦钢的质量问题经常困扰着生产企业。
其中,开裂问题是比较常见的一种质量问题。
本文将对冷镦钢开裂的成因进行分析,并探讨一些质量改进方法。
一、开裂成因分析1.材料问题冷镦钢的材料问题是造成开裂的主要原因之一。
首先,如果钢材的化学成分不合格,或者材料内部有缺陷、夹杂物等物理缺陷,那么就会在加工过程中引起应力集中,导致开裂现象的发生。
其次,如果冷镦钢的硬度不符合要求,可能会导致过度弯曲、撞击等情况的出现,从而造成材料的表面损伤和内部裂纹。
2.工艺问题在冷镦钢加工过程中,一些工艺参数的设置不合理也是导致开裂的原因之一。
比如,提高冷镦钢的加工速度或者过度挤压等操作都会产生更大的应力,造成裂纹的产生。
此外,冷镦钢制品在退火过程中如果没有达到理想的温度和时间,或者所采用的冷却方式不合适,都有可能导致材料的脆性增加,从而更容易引起开裂。
3.设备问题冷镦钢加工的设备问题也是导致开裂的一个重要原因。
设备的不稳定性、缺乏维护、过度磨损、耗尽润滑油等都可能影响冷镦钢的加工质量,从而引起开裂的出现。
二、质量改进方法1.加强材料检验为了降低冷镦钢开裂的风险,加强材料检验是十分必要的。
在采购冷镦钢时,我们可以从制造商获取钢材的相关物理性质、化学成分、熔炼情况等信息,以确保钢材的质量符合要求。
此外,也可以通过现场检测、非破坏性检测等手段,对冷镦钢进行逐一检查,从而及时发现材料中的缺陷、裂缝等问题。
2.改进工艺参数为了降低冷镦钢开裂的风险,我们还可以改进冷镦钢的加工工艺。
为此,我们可以通过降低加工速度、减小挤压量、加强润滑措施等手段减少过度应力的产生,从而降低冷镦钢开裂的风险。
如果需要进行退火处理,我们也可以控制退火温度和时间,同时改变冷却方式,从而降低材料的脆性。
设备维护是保证生产质量的重要环节,因此,我们应该定期对冷镦机进行保养和检修。
冷镦钢开裂成因分析及质量改进

冷镦钢开裂成因分析及质量改进首先,冷镦钢的开裂与材料本身的内部结构有着密切的关系。
一般来说,冷镦钢的主要组成成分是铁和碳,有些低合金钢还会加入一些其他的合金元素,例如锰、钼、铬等。
这些元素在钢材中形成了各种固相与溶相,并形成了相互之间的复杂的相变关系。
在加工过程中,由于变形强度过大,致使钢材发生了位错等缺陷,造成了材料的内应力增大。
随着内应力的不断积累,最终导致了冷镦钢的开裂。
除此之外,冷镦钢的开裂现象还与外部的工艺条件有着密切的关系。
在冷镦钢的加工过程中,传统的工艺一般采用了多道工序,如毛坯加工、共轭滚后、粗拉削、精拉削等,其中每道工序都有可能引起材料的开裂,特别是在共轭滚后和粗拉削工序中更为常见。
这是因为这两个工序的加工过程都会增加钢材的塑性变形程度,导致材料的内应力增加,从而引起冷镦钢的开裂。
针对这些问题,我们可以采用以下一些措施来改进冷镦钢的质量。
首先,我们可以对冷镦钢的加工条件进行适当的优化。
例如,在毛坯加工、共轭滚后、粗拉削等工序中,应该控制变形度、速度、温度等条件,严格遵守工艺参数。
其次,我们可以采用一些新的成型工艺来降低材料的内应力。
例如,现代的冷镦钢加工工艺已经开始采用单锤冷锻、多锤冷锻等技术,这些技术都能够有效地控制变形程度,降低材料的内应力,从而减少冷镦钢的开裂。
最后,我们可以加强冷镦钢材料的质量控制,从原材料的选择、配料环节开始,大力优化生产工艺,并对检验人员进行严格的培训,确保每个生产环节都能够有效地管理和控制,从而保证冷镦钢材料的质量。
综上所述,冷镦钢的开裂现象是由许多因素引起的,其中材料本身的内部结构和外部工艺条件是主要的原因。
通过优化生产工艺、采用新的冷锻工艺等方式来降低材料的内应力,可以有效地减少冷镦钢的开裂,提高冷镦钢的质量和性能。
冷镦钢开裂成因分析及质量改进

冷镦钢开裂成因分析及质量改进冷镦钢开裂是指在冷镦加工过程中,钢材出现裂纹现象,这种现象严重影响了产品的使用性能和质量,也给生产制造过程带来了一定的损失。
深入分析冷镦钢开裂的成因并进行质量改进非常重要。
一、冷镦钢开裂的成因分析1.原材料质量不合格冷镦钢的原材料主要是钢坯,如果钢坯的质量不合格,如夹杂物含量过高、组织不均匀等,都会导致冷镦钢在加工过程中容易产生开裂现象。
2.冷加工参数设置不合理冷镦是一种冷加工工艺,如果冷加工参数设置不合理,如温度、速度、力度等方面没有精确控制,就会导致钢材变形过大、应力过大,从而引起开裂。
3.模具磨损严重冷镦加工需要使用模具,如果模具磨损严重,就会导致钢材在加工过程中受到不均匀的力度作用,从而导致开裂。
4.加工环境不合理如果冷镦加工的环境温度、湿度等因素不合理,就会导致钢材在加工过程中受到外部环境的影响,从而引起开裂。
二、冷镦钢开裂的质量改进1.严格控制原材料质量从源头上保证原材料的质量,选择质量合格的钢坯,并严格对其进行质量检测,确保原材料质量的稳定性。
3.加强模具维护及时对冷镦加工所使用的模具进行检查和保养,发现磨损严重的模具及时更换,确保模具的使用状态良好,减少对钢材的不良影响。
4.改善加工环境优化冷镦加工的环境,控制好温湿度等因素,营造一个适合冷镦加工的环境条件,减少外部环境对钢材的影响,降低开裂的风险。
5.加强质量控制在冷镦加工过程中,加强对产品质量的检测和控制,对一旦发现开裂等质量问题,及时进行处理和改进,确保产品质量符合要求。
冷镦钢开裂是一个需要认真对待并加以解决的问题,只有深入分析其成因,并从原材料质量、加工参数、模具维护、加工环境和质量控制等方面进行全面改进,才能有效预防和减少冷镦钢的开裂现象,提高产品质量和生产效率。
冷镦钢的表面裂纹成因分析及其控制方法

认为 , 可分成 几 种情 况 , 见表 3 。
表 2 金 相 检 验 的 钢 种 、 格 规
序号
1
批号
9 1 80
钢种
8 A
规格
蚴 中O 2 中O 2 蚴 中o 2
酸洗情 况
未 酸 洗 酸 洗 未 酸 洗 酸 洗 酸 洗 未 酸 洗 未 酸 洗 酸 洗
的形态 , 标记裂纹的相对位置 , 测量裂纹之间的间
距, 并据 此 画 出裂 纹 的相 对位 置 图 。具 体分析 如 下
作者简介 : 吴科成 (93一)男 , 16 , 马钢股份公 司技 术中心 , 工程师 。
维普资讯
总第 3 期 4
吴科成 , 张步海 , 郭湛 : 冷镦钢 的表 面裂纹成 因分析及 其控 制方法
验方法 , 分析冷镦钢 的表面裂纹原因, 采取有效措 施, 提高 了冷镦钢 的合 格率 , 取得 了 良好 的效果。 马钢 冷镦 钢课 题 组 对 凹 O 3中 间 轧 件 和 O 、 、
l 等 规格 的成 品 , O 随机取 样 , 行 酸洗 , 倍 和高 进 低 倍检 验 , 结合 铸 坯 的冶 炼 和 轧 制工 艺 , 表 面裂 并 对 纹 的形成机 理进 行 了分 析 ( 了简 要说 明 , 面 主 为 下
关键词 : 冷镦钢; 成因分析; 裂纹; 控制方法 中图分 类号 :G132 文 献标 识码 : 文 章编 号 :6 2 9 4 2 0 )4— 0 4— T 1. A 17 —9 9 (0 6 0 0 1 0 4
产 品质 量 的稳定 , 仅 决定 企 业 的 经 济效 益 , 不 而且 也决定 企 业 的竞 争 力 和 市场 定 位 。 同样 的产 品, 宝钢 的冷镦 钢产 品 要 比马钢 价 格 每 t 40元 高 0
冷镦钢开裂成因分析及质量改进

冷镦钢开裂成因分析及质量改进冷镦钢指的是冷加工成形的高强度、高硬度钢材。
在冷镦加工过程中,冷镦钢往往会出现开裂的问题,导致产品质量下降。
对冷镦钢开裂成因进行分析并进行质量改进是十分必要的。
冷镦钢开裂的主要成因有以下几点:1. 材料本身质量问题:冷镦钢的质量直接影响其开裂情况。
如果冷镦钢的成分不合理,含有过多的硫、氧等有害元素,或者出现夹杂物、疏松等缺陷,都会导致冷镦钢开裂。
2. 冷镦钢表面氧化:冷镦钢在生产过程中长时间暴露在空气中,容易发生表面氧化。
氧化层的形成使得冷镦钢表面变得较硬,而内部仍保持较软的状态,从而产生内部应力,导致冷镦钢在加工过程中容易出现开裂。
3. 冷镦钢加工工艺问题:冷镦加工是一种高强度、高速度的变形加工,过高的变形应力和变形速率容易导致冷镦钢开裂。
如果冷镦钢的预加工不合理,例如切割时过于猛烈或内部缺陷未得到有效控制,也可能造成冷镦钢的开裂。
为了改进冷镦钢的质量,可以采取以下措施:1. 优化材料成分:合理选择冷镦钢的成分,控制有害元素含量,提升冷镦钢的纯度。
通过合理的炼钢工艺,减少夹杂物和疏松等缺陷的产生,提高冷镦钢的质量。
2. 控制加工工艺参数:合理控制冷镦加工的变形应力和变形速率。
通过调整加工工艺参数,减少冷镦钢的变形应力,降低开裂的风险。
3. 增强表面保护:在冷镦钢加工前,采取有效的措施对冷镦钢进行表面保护,防止氧化层的形成。
可以使用防氧化剂或涂覆防锈剂等方式,保持冷镦钢表面的光洁度和平滑度。
4. 提高预加工质量:在冷镦加工前,对冷镦钢进行必要的预加工,确保冷镦钢的形状完整、表面平整,并且要注意控制内部缺陷的产生。
合理的预加工有助于提高冷镦钢的质量,减少开裂的风险。
冷镦钢开裂是由于材料质量问题、表面氧化、加工工艺问题等多种因素导致的。
通过优化材料成分、控制加工工艺参数、增强表面保护和提高预加工质量等措施,可以有效改进冷镦钢的质量,降低开裂的风险,提升产品的质量水平。
冷镦钢顶锻开裂原因分析及其改进措施

根据现场记录情况,在钢材轧制过程中,曾
出现 短 时 轧 制 不 顺、 断 辊、 待 煤 气 等 不 正 常 现 象,对照钢材生产顺序进行分析发现,绝大部分 脱碳层超标试样,在断辊、待煤气时,恰处于加 热炉高温区位置,且加热温度越高,时间越长, 脱碳越严重。
因此采用快速加热的加热制度,缩短钢坯在 炉内加热段的时间,或采用钢坯的氧化速度大于 脱碳速度的加热制度,可有效控制钢坯的脱碳。
另外,有时会出现单条裂纹。这也是由于折 叠造成的,由于进口导卫、导板安装不正,形成 单侧耳子造成折叠,从而形成单条裂纹。
观察以上两种裂缝的颜色,无金属光泽,即 金属本体没有开裂。
可见,导致冷镦钢开裂的主要原因不是钢材 内部质量问题,而是钢材表面的密集对称发纹和 折叠。解决办法是找出缺陷产生的具体位置,对 轧机进行调整,或对孔型进行适当修改。
3 结语
为保证钢材冷顶锻和脱碳层合格,应注意以 下几点:
(1)在孔型设计时,适当减少压下量,适当 增加轧制道次及翻钢次数,避免轧件在孔型中过 充满现象,以减少皱折及由耳子产生的折叠。
(2)选择硬度高而耐磨的轧辊,提高轧辊的 耐磨性,保证表面光洁,尺寸精确。
(3)采用变形均匀的孔型系统作为精轧孔型 系统,以减少成品裂纹。
(3)钢材表面有密集对称的发纹,是由于孔 型严重磨损,翻钢后压下量过大及轧件在孔型内 的不均匀变形等原因造成。
(4)钢材表面有划痕,是由于导板或导槽等 质量不佳或安装不当,造成轧制时的划伤。 1.1 密集对称发纹的产生和形貌
钢材表面密集对称发纹形貌见图1。
图1 钢材表面密集对称发纹
钢材表面密集对称发纹并不是由于钢的原始 裂纹和皮下气泡演变而来的。因为钢的原始裂纹 和皮下气泡经轧制后,只能是无规律的、分散的 表面裂 纹, 而 且 深 度 较 大 ( 约 2~5mm)。 而 这 种密集对称发纹深度浅,在0.5mm 以下,纵向 整齐密集排列,呈断续状。在钢材表面上有裂纹 与无裂纹区域截然分开,多分布在辊缝处或与辊 缝成90≠处,很有规律。因此认为,这种密集对 称发纹是由于在轧制开坯阶段,在一个方向压下 道次过多、压下量过大或由于在某一孔型中的不 均匀变形,在轧件两侧形成皱折,皱折在轧制中 被拉长,在以后的轧制中不能被消除,有时反而 加剧形成了密集对称发纹。
冷镦钢开裂原因探析及轧制工艺调整

一、前言冷镦钢盘条是萍钢新产品开发中重要的组成部分。
其主要生产工艺流程为:转炉冶炼一吹氩一LF炉精炼一连铸成坯一钢坯加热一粗轧一中轧一预精轧一精轧一吐丝成圈一散卷控冷一集卷一打捆一称重一卸卷一入库。
萍钢生产的冷镦钢在现阶段1/2冷镦开裂率平均在5~8 %,1/3冷镦开裂率达到20%以上,远未达到客户标准。
这种情况不仅影响萍钢的经济效益,而且对萍钢的产品质量形象产生了不利影响。
因此本篇文章将对冷镦钢开裂形貌进行大致分类并提出初步的原因辨别方法,针对一些具有代表性的的特殊问题,结合二轧厂高线的工艺实际状况,就如何尽可能的减少轧制缺陷,对解决措施和调整经验进行总结。
二、冷镦形貌类型及大致原因判断较常见的裂纹形状有三种,图1为平行裂纹,这种平行裂纹如果有规律性,即连续剪切的试样同样产生平行裂纹并有连续性。
基本可以判断为折叠造成。
图2为单条深裂纹,这种裂纹容易观察裂纹源延伸处的钢材组织中有无氧化脱碳。
无氧化脱碳现象,内部金属颜色光亮,裂纹应为夹杂或者严重尖锐划伤造成(注意:成品的轻微或者非尖锐深度划伤在一般1/3冷镦都不会造成裂纹)。
若有氧化铁皮,裂纹应为坯料表面质量缺陷或者严重折叠造成。
图3为单条浅裂纹原因分析较为困难,一般认为是连铸坯表面裂纹所造成产品上产生断续裂纹的情况。
这种铸坯质量不良的断续裂纹情况在1次12mm冷墩钢生产中可以在3#机架轧件表面清楚观察到。
图1平行裂纹萍钢冷镦钢开裂原因探析及二轧钢厂轧制工艺调整二轧钢厂张小军摘要: 对冷镦钢开裂形貌进行大致分类并提出初步的原因辨别方法,针对一些具有代表性的的特殊问题,结合二轧厂高线的工艺实际状况,就如何尽可能的减少轧制缺陷,对解决措施和调整经验进行总结关键词:冷镦钢裂纹夹杂折叠划伤调整轧辊导卫图2单条深裂纹图3单条浅裂纹其他较少出现的裂纹还有外形呈45°剪裂(形状为“<”)原因为塑性不足,可以判断为夹杂;裂纹表面有铁皮包裹,可以认为是折叠或者钢水脱氧不良造成;冷镦形貌为一条裂纹并对称伴随着一条不明显的印痕,认为是在轧制过程中由于单侧耳子造成的平行连续裂纹,一条较深而另一条较浅,浅裂纹经变形延伸消失而深裂纹不能消除,从而表现为一条裂纹,该形貌裂纹一般在其一侧有不明显的与其平行的印痕;另外发生在轧件四周的裂纹位置是否有规律性、连续性、对称性,都可以给我们大致判断裂纹原因带来帮助。
影响冷镦钢质量的因素及控制措施

影响冷镦钢质量的因素及控制措施冷镦钢,又称铆螺钢或冷顶锻钢,是利用金属的塑性,采用冷镦加工成型工艺生产互换性较高的标准件用钢。
冷镦钢产品广泛用于制造螺栓、螺母、螺钉等各类紧固件;另一重要用途是制造冷挤压零部件和各种冷镦成形的零配件,该用途是随着汽车工业发展起来的,逐步扩大到电器、照相机、纺织器材、冷冻机等领域.国内外冷镦钢生产概况1 国内冷镦钢我国冷镦钢的标准化工作起步较晚,尚未形成完整体系,冷镦钢用国家标准仅有3个:GB/T6478—2001《冷镦和冷挤压用钢》,GB/T4232—1993《冷顶锻用不锈钢丝》和GB/T5953—1999《冷镦钢丝》。
冷镦用钢的实物质量尚不能完全满足标准件行业要求,在一定程度上依赖进口。
据海关统计,我国每年进口的紧固件在12~13万t。
随着紧固件工业的迅猛发展,新钢种不断地开发和引进,对外的出口日益增多,汽车、石油、机械各行业的技术进步,对配套的紧固件提出许多新要求,不但是形式尺寸上的,而且是性能与可靠性上的,实际上是对紧固件材料提出更高的要求.我国紧固件行业发生了较大的变化,具体表现:(1)采用国外钢种牌号如10B22M,10B25LHC,MNB123H等,主要是出口订单上规定要使用的牌号;(2)同一牌号的钢种衍生出多个交货状态的品种,如SWRCH35K,有免退火、正火、退火+磷化交货,满足不同用户的需求;(3)大量采用合金、低合金钢种,以适合耐高温、耐高压、耐腐蚀的要求,如SNB5—7,SNB16(JIS4107—94),SNB21-24(JIS4108);(4)采用抗延时断裂用钢生产的钢结构用螺栓抗拉强度超过1200MPa.2 国外冷镦钢国外采用HNDS2制造12.9级螺栓(代替SCM440),延时破断有明显改进,采用45CrNiMoTi在1500MPa级别使用,其性能优于回火马氏体高强度螺栓,贝氏体钢很少见到有(晶界)碳化物析出,避免了穿晶破坏而发生的延时断裂.国外发达国家冷镦钢产业已基本形成规模,重点是根据用户的要求改善冷镦钢材料的质量性能,而产量无太大变化.日本大同为降低标准件材料成本和加工成本,推出了多种不锈钢螺栓和螺钉用钢;高周波钢业开发了一系列不锈冷镦钢新产品,利用设备优势推出SUS系列产品,大大提高了钢的冷镦性能;日本精线为适应建筑行业要求,开发了具有良好耐蚀和冷镦性能、通过淬回火硬化的马氏体冷镦钢。
冷镦钢开裂成因分析及质量改进

冷镦钢开裂成因分析及质量改进冷镦钢开裂是一种非常普遍的质量问题,经常在加工和使用过程中出现,给生产和使用带来了很大的困扰。
对冷镦钢开裂的成因进行深入分析,找出根本原因,通过质量改进措施,提高冷镦钢的质量,对于解决这一问题具有非常重要的意义。
一、冷镦钢开裂的原因1.1 金相组织不均匀冷镦钢在生产加工过程中,如果金相组织不均匀,会导致在冷镦加工过程中,内部应力集中,容易发生裂缝。
特别是在碳化深层不均匀或者套料不均匀等情况下,更容易导致冷镦钢开裂。
1.2 机械加工过程不当冷镦钢在机械加工过程中,如果加工参数设置不合理,如切屑不及时清理、切削速度过快或者刀具磨损严重等情况下,都会导致冷镦钢表面出现裂痕,并最终开裂。
1.3 材料质量不达标冷镦钢的质量问题也可能源自于材料的自身质量不达标。
如果采购到的冷镦钢材料含有太多的夹杂物、气泡或者夹杂物等,都会导致在冷镦加工过程中开裂的风险。
1.4 制程缺陷在冷镦钢的生产制程中,如果存在缺陷,比如温度控制不当、冷却速度过快、退火不均匀等情况下,都会导致冷镦钢表面或内部出现裂纹,最终导致开裂。
1.5 贮存条件不当对于冷镦钢来说,即使其质量本身较好,如果在贮存过程中受到了湿气或者氧化等情况下,都会导致表面产生锈蚀,进而导致冷镦钢在使用过程中开裂。
以上就是冷镦钢开裂的主要原因,通过对这些原因的深入分析,可以发现冷镦钢开裂是一个多方面因素综合作用的结果。
对冷镦钢的质量改进需要综合考虑多个方面的因素。
二、质量改进措施在冷镦钢生产的过程中,应该通过优化工艺流程、控制碳化深度、严格掌握套料的均匀性等手段,来优化冷镦钢的金相组织,确保其均匀性和完整性,降低内部应力集中的风险,从而降低开裂的概率。
2.2 严格控制机械加工参数在采购冷镦钢材料时,应该严格把控材料的质量,采用可靠的供应商,确保材料质量达标,避免过多的夹杂物和气泡等对冷镦钢质量的影响。
2.4 完善生产制程在冷镦钢的生产制程中,应该完善各个环节的工艺流程,确保温度控制的稳定性、冷却速度的均衡性、退火的均匀性等方面,最大限度地降低冷镦钢在生产制程中出现的缺陷和质量问题。
冷镦钢开裂成因分析及质量改进

冷镦钢开裂成因分析及质量改进【摘要】冷镦钢在生产和使用过程中常常出现开裂问题,严重影响产品质量和生产效率。
本文围绕冷镦钢开裂问题展开分析,并提出了相关的成因和改进方案。
通过详细的分析冷镦钢开裂的常见问题和成因,结合提高冷镦钢质量的措施和注意事项,指出了解决冷镦钢开裂问题的方法和提高产品质量的重要性。
通过本文的研究,可以为冷镦钢生产和应用提供参考,帮助生产厂家解决开裂问题,提高产品质量,提升竞争力。
有效地改善生产现状,促进工业发展。
【关键词】冷镦钢、开裂问题、成因分析、质量改进、措施、注意事项、解决方法、产品质量、重要性1. 引言1.1 冷镦钢开裂成因分析及质量改进冷镦钢开裂是钢材生产过程中常见的问题,严重影响产品的质量和使用性能。
为了解决这一问题,需要对冷镦钢开裂的常见问题进行分析,并找出导致开裂的具体原因。
针对开裂问题,制定合适的质量改进方案和措施,以提高冷镦钢产品的质量和性能,减少开裂现象的发生。
冷镦钢开裂的常见问题主要包括内应力过大、组织非均匀、工艺控制不当等。
内应力过大会导致钢材在加工过程中产生裂纹;组织非均匀使得材料在受力时难以均匀变形,易发生开裂;工艺控制不当则会导致加工参数不合理,引起开裂问题。
针对冷镦钢开裂的成因分析,需要从原材料的选择、生产工艺、加工工艺等多个方面进行综合考虑。
在质量改进方面,可以通过优化材料配方、改善生产工艺、加强设备维护等方式来降低开裂风险。
加强质量管理,提高员工素质和技能培训,也是提高产品质量的重要举措。
在冷镦钢的生产过程中,需要特别注意加工温度、冷却速度、加工润滑等因素,以确保产品质量稳定。
通过制定合理的生产工艺流程和严格执行操作规程,可以有效减少开裂问题的发生,提高产品的质量和竞争力。
冷镦钢开裂问题需要系统分析其成因,并针对性地制定改进方案和措施,从而提高产品质量,满足市场需求,增强企业竞争力。
2. 正文2.1 冷镦钢开裂的常见问题,时间等等。
冷镦钢开裂是在生产和加工过程中经常遇到的问题,主要表现为钢材表面或内部出现裂纹,并且会影响产品的质量和使用寿命。
冷镦钢开裂成因分析及质量改进

冷镦钢开裂成因分析及质量改进1. 引言1.1 研究背景冷镦钢是制造各种紧固件、弹簧等产品所必不可少的材料,其质量直接影响着产品的使用性能和安全性。
在生产过程中,冷镦钢常常会出现开裂的现象,给生产带来困扰。
造成冷镦钢开裂的原因多种多样,可能是由于工艺参数控制不当、材料性能不达标、设备维护不到位等原因造成的。
针对冷镦钢开裂问题,相关部门和企业一直在进行改进和探索,但仍然存在许多难题有待解决。
我们有必要深入研究冷镦钢开裂的原因,寻找解决之道,提高冷镦钢的质量,确保产品的稳定性和可靠性。
本文旨在对冷镦钢开裂成因进行分析,并提出相应的质量改进措施,为冷镦钢生产提供参考和借鉴,促进冷镦钢产业的健康发展。
1.2 问题提出在冷镦钢生产过程中,开裂问题一直是一个困扰行业的重要质量难题。
冷镦钢开裂不仅影响产品质量,还会造成生产损失和资源浪费。
目前,虽然针对冷镦钢开裂问题进行了一定的研究和探讨,但相关解决方案仍然有待完善。
如何有效解决冷镦钢开裂问题,提高产品质量,提升生产效率,是当前亟待解决的问题。
对于冷镦钢开裂问题,主要表现为裂纹沿轧制方向扩展,严重影响产品的使用性能和寿命。
这个问题的存在往往直接关系到生产工艺、材料性能和设备状态等多个因素。
需要对冷镦钢开裂问题进行深入分析,找出造成开裂的根本原因,以便制定有效的改进措施。
解决冷镦钢开裂问题不仅仅是一项技术问题,更是关乎企业质量管理和经济效益的重要议题。
加强对冷镦钢开裂问题的研究和探讨,对于提高产品质量,降低生产成本,提升企业竞争力具有重要意义。
【内容已完结】.1.3 研究意义冷镦钢在工业生产中被广泛应用,但在生产过程中经常出现开裂现象,造成生产效率低下、质量不稳定等问题。
对冷镦钢开裂成因进行分析及质量改进具有重要的研究意义。
通过深入研究冷镦钢开裂的原因,可以帮助生产企业更好地了解开裂的机理和规律,有针对性地制定改进措施,提高产品质量和生产效率。
改进冷镦钢制造质量还能有效降低生产成本,提高企业竞争力,提升产品在市场的竞争力。
冷镦钢开裂成因分析及质量改进

冷镦钢开裂成因分析及质量改进冷镦是一种重要的金属加工工艺,广泛应用于汽车、机械、航空航天等领域。
在冷镦过程中,如果出现钢材开裂现象,就会对产品的质量和生产效率造成严重影响。
分析冷镦钢开裂的成因并进行质量改进具有重要的意义。
本文将从冷镦钢的性质、加工工艺和设备方面,对冷镦钢开裂成因进行深入分析,并提出相应的质量改进措施。
一、冷镦钢开裂的成因分析1. 冷镦钢材的性质冷镦钢是一种特殊的金属材料,具有高强度、高韧性和高硬度的特点。
在冷镦过程中,由于受到外力和温度变化的影响,冷镦钢容易出现开裂现象。
冷变形和组织性能是导致开裂的主要原因之一。
冷变形会引起冷镦钢的内应力变化,如果内应力无法得到释放,就会导致钢材发生裂纹。
2. 加工工艺冷镦钢的加工工艺对开裂现象也有着重要影响。
在冷镦过程中,如果加工参数不合理或者操作不当,就会引起钢材的不均匀变形,从而导致开裂。
冷镦设备的质量和性能也会影响到冷镦钢的开裂情况。
3. 设备因素二、质量改进措施为了减少冷镦钢的开裂现象,可以优化冷镦钢的组织性能,以提高其耐冲击性和韧性。
具体操作方式包括采用适当的退火工艺和合理的工艺参数,以减少冷镦钢的内应力,从而降低开裂风险。
2. 合理调整冷镦工艺参数在冷镦钢的加工过程中,需要合理调整加工参数,避免过大的冷变形和不均匀的应力分布。
要注意加工过程中的润滑和冷却,以保证冷镦钢的表面质量和加工稳定性。
3. 加强冷镦设备的维护和管理冷镦设备的正常运转对冷镦钢的质量具有十分重要的作用。
为了降低冷镦钢的开裂风险,需要加强冷镦设备的维护和管理工作,确保设备的性能和稳定性。
4. 加强人员培训和操作规范在冷镦钢的加工过程中,操作人员的素质和操作规范也对产品的质量有着直接影响。
需要加强人员的培训,提高其操作技能和工艺素养,以减少操作不当对产品质量的影响。
冷镦产品开裂原因分析报告范文

冷镦产品开裂原因分析报告范文## Analysis Report on the Causes of Cracking in Cold Headed Products ##。
### English Answer: ###。
Introduction:Cold heading is a metal forming process that involves the deformation of metal wire or rod into a desired shape using a series of cold forging operations. This process is widely used in the production of various components such as bolts, screws, rivets, and other fasteners. However, cracking is a common issue that can occur during cold heading operations, leading to the rejection of finished products and potential safety hazards.Causes of Cracking:Cracking in cold headed products can be attributed toseveral factors, including:Material Properties: The composition and mechanical properties of the metal being used can influence its susceptibility to cracking. Factors such as hardness, strength, and ductility play a crucial role in determining the material's ability to withstand the stresses andstrains encountered during cold heading.Process Parameters: The parameters of the cold heading process, such as the amount of force applied, the speed of deformation, and the temperature of the workpiece, can affect the likelihood of cracking. Excessive force or rapid deformation rates can lead to excessive strain and potentially cause cracks.Tooling Design and Condition: The design and condition of the tooling used in the cold heading process can contribute to cracking. Improperly designed or worn-out tooling can create stress concentrations or introduce defects that can initiate cracks during deformation.Lubrication: Insufficient or improper lubrication during the cold heading process can increase friction between the workpiece and the tooling, generating heat and leading to the formation of cracks.Surface Condition: The surface condition of the workpiece can also influence its propensity to crack. Defects such as scratches, nicks, or inclusions can act as stress risers and provide nucleation sites for cracks.Prevention and Mitigation Strategies:To prevent and mitigate cracking in cold headed products, several strategies can be employed:Material Selection: Careful selection of the material based on its composition and mechanical properties is essential. Alloys with higher ductility and lower hardness are generally more resistant to cracking.Process Optimization: Optimizing the process parameters, such as force, speed, and temperature, can helpreduce the likelihood of cracking. Balancing the amount of force applied with the material's properties and process speed is crucial.Tooling Maintenance: Regular maintenance andinspection of tooling is necessary to ensure its proper functioning. Worn-out or damaged tooling should be replaced to prevent stress concentrations and surface defects.Proper Lubrication: Adequate lubrication throughoutthe cold heading process is essential to minimize friction and heat generation. Selecting the appropriate lubricantfor the specific material and process conditions is crucial.Surface Preparation: Proper surface preparation of the workpiece, including removal of any defects or imperfections, can help reduce the likelihood of crack initiation during deformation.### 中文回答, ###。
冷镦开裂

冷镦钢开裂原因分析及预防摘要介绍国内冷镦钢的生产概况,从钢坯加热、表面质量、脱碳、冷镦性能、工艺调整等方面指出冷镦钢生产的技术要求,探讨冷镦钢成品中所存在的质量问题,同时提出提高冷镦钢质量的措施。
关键词冷镦钢;表面质量;开裂;黑线前言冷镦钢盘条主要用于制作标准件螺钉,用户加工过程为:除鳞→拉拔→退火→冷镦→搓丝→热处理→电镀→入库。
预计每年全国需冷镦钢盘条约达500万吨,如此大的市场空间还吸引着国内外其他厂家的目光,因此,冷镦钢盘条具有很大的潜力市场。
由于冷镦下游产品是由线材经过多道次拉拔,热处理等工艺生产出来的,因此对冷镦钢线材的质量控制提出了很高的要求,无论是成分组织、表面质量、尺寸精度还是通条性能等方面均要求严格。
1 冷镦开裂原因在2006年9、10月份,由于高线设备改造后工艺调整不当及存在的相关问题,用户反馈在加工过程中冷镦开裂,由此产生的质量异议占异议总量的95%占以上。
我厂通过近几年的不懈努力,使冷礅钢线材实现了稳定的批量生产。
在生产实践中我们发现表面质量缺陷是导致冷镦开裂最直接的原因。
主要分三种:(1)线材表面折叠,主要是由于压下量过大、孔型过充满或导卫开口度过大,轧件尺寸过小而倒坯形成耳子,在随后的轧制过程中产生折叠。
(2)导槽、导辊、活套轮以及轧线上所有与轧件有直接接触的物体被磨损或存在棱角与毛刺,都有可能使轧件划伤而最终导致裂纹。
(3)孔型、导卫磨损严重、轧线不对中、错辊、导卫安装不当或对中不好,以及进钢时导卫晃动等,使轧件在孔型内变形不均匀,形成耳子、棱子、轧痕也是造成其后镦裂的隐患。
1.1 对称双裂纹产生原因根据以上成因,可以把镦裂分为平行双面连续裂纹、单条单面连续裂纹、断续裂纹等3种。
如图(1)和图(2)中所示为平行双面连续裂纹。
是在生产过程中轧件产生双边耳子,在后续道次图(1)图(2)轧制中形成折叠而产生。
双边耳子的产生多是由于压下调整不当、孔型过充满、各机架断面尺寸控制不合理、张力控制不稳定等引起。
线材高碳钢冷墩易出现裂纹的原因及对策

线材高碳钢冷墩易出现裂纹的原因及对策
有关冶金专家对线材高碳钢冷墩易出现裂纹的原因及对策的观点是:
高碳钢冷墩出现裂纹原因有二:
1.炼钢以及连铸过程中出现钢坯夹杂造成冷墩裂纹。
2.轧钢在轧制过程中产生一些表面缺陷比如重叠,加热过烧等原因造成冷墩裂纹。
解决办法加强各个工序的工艺操作,严格执行工艺制度。
其次轧后控制冷却也很重要此外:应该从1、生产各工序质量控制情况一一进行分析,查找出异常因素;2、对出现裂纹的线材进行高倍检测,看看裂纹周围的组织及夹杂物情况,在返回在工序中进行分析,具体是那个工序的问题。
没有手段和检验数据,盲目得去认为和判定原因都是不科学和徒劳的。
还有认为:原因不复杂,钢质不纯N高,氧化物夹杂等超标,可以和拉拔性能要求对比一下。
- 1、下载文档前请自行甄别文档内容的完整性,平台不提供额外的编辑、内容补充、找答案等附加服务。
- 2、"仅部分预览"的文档,不可在线预览部分如存在完整性等问题,可反馈申请退款(可完整预览的文档不适用该条件!)。
- 3、如文档侵犯您的权益,请联系客服反馈,我们会尽快为您处理(人工客服工作时间:9:00-18:30)。
第35卷 第1期2010年1月HEAT T RE AT ME NT OF MET ALSVol 135No 11January 2010ML20M nT iB 冷镦钢开裂原因分析华 蔚(宝钢股份研究院,上海 201900)摘要:ML20MnTi B 冷镦钢丝在镦制内六角螺栓时发生了开裂现象。
用光学显微镜、扫描电子显微镜和洛氏硬度计对ML20MnTi B 高强度螺栓开裂的显微组织、硬度和合金元素分布状态进行分析。
结果表明,导致ML20M nTi B 盘条镦制螺栓开裂的原因是盘条组织异常和表面缺陷。
关键词:冷镦钢;盘条;螺栓;裂纹中图分类号:TG163183 文献标志码:B 文章编号:025426051(2010)0120117204Crack ana lysis of ML 20M nT iB cold head i n g steelHUA W ei(Baosteel Research I nsitute,Baoshan Ir on and Steel Co .,L td .,Shanghai 201900,China )Abstract:Cracks occurred in hexagon s ocket head bolts of ML20M nTi B cold heading steel wire 1The m icr ostructure,hardness and all oying element distributi on of high strength bolt made of ML20M nTi B were analyzed by op tical m icr oscopy,scanning electr on m icr oscopy and Rock well hardness res pectively 1The results show that the cracking cause are structural heter ogenity and surface defects on the wire r od 1Key words:cold heading steel;wire r od;bolt;crack收稿日期:2008208219作者简介:华 蔚(1963—),女,江苏无锡人,高级工程师,主要从事金属材料研发工作,发表论文7篇。
联系电话:021*********,E 2mail:hua wei@baosteel 1com 冷镦钢广泛用于制造螺栓、螺母、螺钉、自攻螺钉等各类紧固件和各种冷镦成形的零配件[122],在冷镦钢加工过程中,变形量很大(60%~70%),所承受的变形速度很高,因此要求冷镦钢具有良好的加工性能和力学性能。
最近研究[3]表明,冷镦钢尤其是优质冷镦钢与进口冷镦钢相比主要差别体现在材料性能和冷镦技术上。
主要问题是钢中杂质元素的控制和盘条的表面缺陷。
宝钢开发、专用于加工1019级强度的内六角螺栓的ML20MnTi B 冷镦钢。
在产品试制过程中,出现了一些质量问题,影响镦制螺栓的成材率。
本文针对ML20MnTi B 钢<18mm 盘条经拉拔成<15mm 钢棒后,再冷镦成螺栓时出现的表面开裂进行了分析。
1 试验材料及方法对镦制螺栓开裂的材料,在<18mm 热轧盘条和<15mm 冷拔钢丝随机抽样。
采用ARL4460型化学直读光谱仪对试样进行了化学成分分析,见表1。
其生产工艺流程为:150t 电弧炉冶炼→LF 精炼表1 ML20M nT i B 冷镦钢化学成分(质量分数,%)Table 1 Che m i ca l co m positi on of ML20M nT i B cold head i n g steel(wt%)试样号C Si Mn P S Ti B H O Fe盘条0122012311410101601006010690100101000101003余量钢丝012201231146010160100601066010*********010025余量Q /BQB 517—20030117~0124≤01301130~1160≤01030≤010300104~0110010005~010035——余量→VD 真空脱气处理→连铸小方坯→钢坯探伤、修磨→加热炉→高线机组轧制→斯泰尔摩冷却→冷镦钢盘条成品→检验合格→出厂。
由表1可知,钢中硫、磷、氧、氢含量较低,钢质纯净度较高。
其它合金元素的化学成分都符合宝山钢铁股份有限公司企业标准Q /BQB 517—2003《冷镦钢盘条》的要求。
2 试验结果211 宏观观察从热轧盘条和拉拔钢丝样品上可以看出,盘条表面光滑,无任何缺陷存在。
而拉拔后的钢丝表面局部区域有较多的麻坑状缺陷及表面直道划痕存在,如图1所示。
118 第35卷图1 ML20MnTi B 钢拉拔后钢丝表面缺陷(a )麻坑状缺陷;(b )直道划痕缺陷Fig 11 Surface defects ofML20M nTi B steel wire after dra wing(a )p it defects;(b )nick defects212 微观分析为了进一步分析拉拔钢丝表面缺陷的产生原因,对盘条和钢丝的显微组织、表面缺陷的形貌进行了观察。
将盘条沿横截面剖开并制成金相试样,在LE I CA MEF4A 型金相显微镜下观察。
发现盘条试样的边缘组织异常,为晶粒粗大的魏氏体组织,而且盘条边部氧化层较厚见图2(a )。
经过显微镜内标尺测定,氧化层厚度为0105mm 。
远离盘条边缘的组织无异常,为珠光体+铁素体组织,并且组织细小,如图2(b )所示。
在盘条的纵截面上,观察了试样抛光态的夹杂物图2 ML20MnTi B 钢横截面显微组织(a )盘条边部魏氏体组织;(b )铁素体+珠光体组织Fig 12 M icr ostructure of ML20MnTi B steel cr oss secti on(a )widmanstatten structure;(b )ferrite +pearlite structure情况,钢中氧化物、硫化物夹杂级别都控制在015~110级。
在试样的整个截面上,分布着小块状、形貌和颜色类似于氮化物夹杂,这类夹杂物析出数量较多,并且颗粒大小不均匀,在LE I CA Q600S 定量金相显微镜上进行各参数的测定,单位面积颗粒分布见表2。
在观察钢丝缺陷部位时,发现试样横截面边缘存在深浅不一的孔洞和局部区域的结疤及裂纹缺陷,裂纹内也有该类夹杂物存在,经过S 24200扫描电子显微镜及能谱仪分析确定为Ti N 夹杂,如图3所示。
表2 ML20M nT i B 钢丝氮化物颗粒分布Table 2 D istr i buti on of n itr i de parti cle of ML20M nT i B w i re steel试样单位面积氮化物数/(个・mm -2)单位面积不同宽度氮化物数/(个・mm -2)0~2μm2~4μm 4~6μm 6~8μm>8μm 最大宽度/μm钢丝56423234214盘条52132586815213 硬度测定显微组织观察表明,盘条边缘组织和盘条心部组织完全不同,盘条边缘组织异常,为晶粒粗大的魏氏体组织,而盘条心部为正常的铁素体+珠光体组织。
盘条经过冷拉成钢丝,再经过球化退火后的组织为球状珠光体。
为了对比盘条缺陷部位与盘条正常部位的硬度差异,以及冷拔钢丝退火后的硬度变化,采用FR 23E L 型数字式洛氏硬度计测定盘条和钢丝不同部位的硬度值,如表3所示。
根据标准件厂提供的资料,正常盘条硬度值应为98~110HRB 之间,钢丝经中间退火后,其心部的硬度值为85~90HRB ,并且表面硬度值比心部硬度值略高第1期华 蔚:ML20M nTi B 冷镦钢开裂原因分析119 表3 ML20M nT i B 钢盘条不同部位的硬度值Table 3 Hardness a t d i fferen t positi on s ofML20M nT i B steel rod测定部位硬度/HRB平均硬度/HRB盘条边缘75796673盘条心部85817982拉拔钢丝边缘50505853拉拔钢丝心部81818181图3 ML20M nTi B 钢拉拔钢丝裂纹内夹杂物能谱图Fig 13 Eenergy s pectru m of the cracking inclusi on ofML20M nTi B wire steel after cold dra wing1~2HRB 。
然而从盘条、钢丝硬度值上分析,盘条边缘和心部的硬度值偏低,盘条边缘硬度在66~79HRB ,盘条心部硬度在79~85HRB ,盘条边缘硬度低于盘条心部硬度,这与标准件厂所要求的正常盘条硬度值变化规律相违背。
进一步分析拉拔钢丝边缘和心部硬度的变化情况,可以看出,钢丝边缘硬度只有50~58HRB ,而钢丝心部硬度则为81HRB 。
钢丝硬度数据表明,盘条边缘组织异常不仅对盘条冷拔性能有影响,而且对最终成品钢丝硬度也有影响。
3 分析讨论分析钢丝表面麻坑缺陷处的形貌和组织可以看出,麻坑处表面氧化皮经酸洗后已全部剥落,沿缺陷部位剖开后观察,靠近试样表面有较多的结疤状缺陷,而且存在较多的氧化皮,这说明钢丝麻坑处的缺陷在钢丝拉拔前就已存在,即盘条在轧制过程中,由于辊环、导卫表面粘钢或表面粗糙致使盘条表面产生结疤现象。
结疤处的氧化物在钢丝酸洗过程中剥落,从而导致钢丝表面出现大量的麻坑缺陷并使钢丝在冷拔时发生开裂。
分析盘条直道划痕缺陷处的显微形貌可以看出,横截面直道周围有大量深浅不一的氧化孔洞,孔洞周围无裂纹存在。
由于生产高强度螺栓的工艺流程较复杂,即高线盘条→酸洗→拉拔(油拉)→中间退火→二次拉拔(石灰干拉)→冷镦成形→热处理→发黑→包装等工序。
通过对直道划痕冷拔并经过中间退火钢丝试样的组织分析,钢丝的基体组织为球状珠光体,为正常的球化退火组织。
根据标准件厂提供的资料,中间退火工艺为:加热温度在700℃以上,保温时间≥3h,然后随炉冷却到500℃,出炉空冷。
由于钢丝在拉拔过程中经过球化退火,从组织上无法判定直道缺陷处的脱碳情况,但是盘条组织和硬度的异常会加剧钢丝在后道拉拔过程中表面缺陷的产生,并影响钢丝的冷拔性能。
盘条组织异常和心部硬度偏低,与钢坯的加热温度过高和加热时间过长有关,致使钢坯表层氧化脱碳严重和奥氏体晶粒吞并长大,盘条热加工后,如果冷却速度控制不好,过冷奥氏体转变成晶粒较粗大的魏氏组织,形成这类组织对盘条的综合性能不利,造成盘条总体硬度值偏低和严重不均匀,并产生了盘条表面硬度低于心部硬度的反常现象。