热轧钢板成型开裂原因
造成热轧卷板边裂的几种原因分析

造成热轧卷板边裂的几种原因分析
造成热轧卷板边裂的几种原因
1、脱氧不良、浇注异常。
2、铸坯待轧时过热过烧是翘边边裂的主要原因。
3、钢水残余元素铜含量超标。
4、板坯在均热炉的进出温度与时间。
5、铸坯表面横裂纹(包括深振痕)和边部细小纵裂纹,在加热和
轧制过程中不断扩展,钢液在凝固以及铸坯在冷却、均热、轧制、层流冷却和卷取等过程中的热应力、机械应力以及相变应力等作用力超过钢的塑性变形抗力。
6、钢坯内在缺陷、加热温度偏高及加热不均匀。
7、连铸坯皮下边部存在针孔状气泡,在加热过程中因表面金属氧
化,气泡暴露以及连铸边部存在角横裂等缺陷,角横裂和气孔在轧制过程中不能焊和而产生边裂。
2008年12月27日。
热轧不锈钢边裂原因
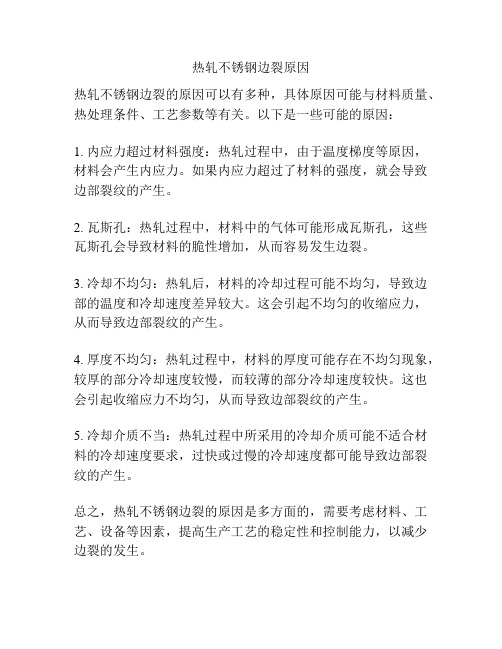
热轧不锈钢边裂原因
热轧不锈钢边裂的原因可以有多种,具体原因可能与材料质量、热处理条件、工艺参数等有关。
以下是一些可能的原因:
1. 内应力超过材料强度:热轧过程中,由于温度梯度等原因,材料会产生内应力。
如果内应力超过了材料的强度,就会导致边部裂纹的产生。
2. 瓦斯孔:热轧过程中,材料中的气体可能形成瓦斯孔,这些瓦斯孔会导致材料的脆性增加,从而容易发生边裂。
3. 冷却不均匀:热轧后,材料的冷却过程可能不均匀,导致边部的温度和冷却速度差异较大。
这会引起不均匀的收缩应力,从而导致边部裂纹的产生。
4. 厚度不均匀:热轧过程中,材料的厚度可能存在不均匀现象,较厚的部分冷却速度较慢,而较薄的部分冷却速度较快。
这也会引起收缩应力不均匀,从而导致边部裂纹的产生。
5. 冷却介质不当:热轧过程中所采用的冷却介质可能不适合材料的冷却速度要求,过快或过慢的冷却速度都可能导致边部裂纹的产生。
总之,热轧不锈钢边裂的原因是多方面的,需要考虑材料、工艺、设备等因素,提高生产工艺的稳定性和控制能力,以减少边裂的发生。
钢材出现断裂的原因分析

钢材出现断裂的原因分析用于各行业的钢材品种达数千种之多。
每种钢材都因不同的性能、化学成分或合金种类和含量而具有不同的商品名称。
虽然断裂韧性值大大方便了每种钢的选择,然而这些参数很难适用于所有钢材。
主要原因有:第一,因为在钢的冶炼时需加入一定数量的某种或多种合金元素,成材后再经简单热处理便可获得不同的显微组织,从而改变了钢的原有性能;第二,因为炼钢和浇注过程中产生的缺陷,特别是集中缺陷(如气孔、夹杂等)在轧制时极其敏感,并且在同一化学成分钢的不同炉次之间,甚至在同一钢坯的不同部位发生不同的改变,从而影响钢材的质量。
由于钢材韧性主要取决于显微结构和缺陷的分散(严防集中缺陷)度,而不是化学成分。
所以,经热处理后韧性会发生很大变化。
要深入探究钢材性能及其断裂原因,还需掌握物理冶金学和显微组织与钢材韧性的关系。
1. 铁素体-珠光体钢断裂铁素体-珠光体钢占钢总产量的绝大多数。
它们通常是含碳量在0.05%~0.20%之间的铁-碳和为提高屈服强度及韧性而加入的其它少量合金元素的合金。
铁素体-珠光体的显微组织由BBC铁(铁素体)、0.01%C、可溶合金和Fe3C组成。
在碳含量很低的碳钢中,渗碳体颗粒(碳化物)停留在铁素体晶粒边界和晶粒之中。
但当碳含量高于0.02%时,绝大多数的Fe3C形成具有某些铁素体的片状结构,而称为珠光体,同时趋向于作为“晶粒”和球结(晶界析出物)分散在铁素体基体中。
含碳量在0.10%~0.20%的低碳钢显微组织中,珠光体含量占10%~25%。
尽管珠光体颗粒很坚硬,但却能非常广泛地分散在铁素体基体上,并且围绕铁素体轻松地变形。
通常,铁素体的晶粒尺寸会随着珠光体含量的增加而减小。
因为珠光体球结的形成和转化会妨碍铁素体晶粒长大。
因此,珠光体会通过升高d-1/2(d为晶粒平均直径)而间接升高拉伸屈服应力δy。
从断裂分析的观点看,在低碳钢中有两种含碳量范围的钢,其性能令人关注。
一是,含碳量在0.03%以下,碳以珠光体球结的形式存在,对钢的韧性影响较小;二是,含碳量较高时,以球光体形式直接影响韧性和夏比曲线。
热轧棒料产生裂纹原因

热轧棒料产生裂纹原因
热轧棒料在生产过程中可能出现裂纹,其原因复杂,可能受到多种因素的影响。
以下是一些可能导致热轧棒料产生裂纹的原因:
1.冶炼和铸造问题:原材料的质量和冶炼工艺可能会对
热轧棒料的质量产生影响。
不合格的原材料、合金成分不均匀、铸造时的温度不当等都可能导致裂纹。
2.轧制工艺问题:轧制过程中的工艺参数,如轧制温度、
压下率、冷却速率等,如果没有正确控制,可能导致热轧棒料表面和内部出现应力集中,从而引发裂纹。
3.结晶器温度不均匀:如果结晶器温度分布不均匀,部
分区域的温度过高或过低,可能导致热轧棒料产生不均匀的组织结构,从而引发裂纹。
4.冷却不足:在热轧后,如果冷却速率不足,棒料内部
的温度不能迅速降低,可能导致应力积累,从而导致裂纹的发生。
5.内在缺陷:原材料或在制造过程中可能存在内在的缺
陷,如夹杂物、气泡等,这些缺陷可能成为裂纹的起始点。
6.质量控制问题:生产过程中的质量控制不严格,检测
手段不到位,可能导致未能及时发现并处理潜在的问题,从而造成裂纹。
为了预防和减少热轧棒料的裂纹问题,生产过程中需要加强对原材料、工艺和质量的监控,确保各个环节的合理性和稳定性。
热轧带钢边裂原因分析

DW H# 低倍检验 为了对钢坯进 行 质 量 判 定 ! 对同批的连铸坯进 行了低倍热 酸 蚀 宏 观 检 验 ! 其 低 倍 组 织 见 图 !" 从 柱 状 晶 粗 大! 皮 下 裂 纹 #W 角 图 ! 中可以看出 ! , 级! 部裂纹 )W 中心裂纹 ! 级和非金属夹杂 #W ,级! ,级" 可见 ! 连铸坯存在着一定的低倍组织缺陷 "
锯齿状 " 有的已经氧化呈现锈斑 " 且裂纹向内延伸 ’ DW D# 化学成分分析 钢的化学成分不仅影响钢的性能 " 也使其显微组 织有所差异 " 笔者将大包取样测得的化学成分与其轧 制后的带钢的化学成分进行对比 " 结果列于表 # ’ 从表 # 中可以 看 出 " 中间包的含碳量与轧制后 钢卷的含量不同 " 轧制后钢卷的含碳量明显要低 " 且 低于该种钢的国标最低值 "W " [\ ’
!!!"
"
!!!!"
质量控制
化学成分分析及金相检验等方法 " 对出现边裂的带钢卷进行了解剖 摘 # 要 !采用低倍组织试验 ! 分析 # 结果表明 " 钢坯的内在缺陷 ! 加热温度偏高及加热不均匀是产生边裂的主要原因 #
关键词 !边裂 $低倍组织 $显微组织 $夹杂 $粗晶 $脱碳 $过热 中图分类号 ! ! # ’ ( # ) !### 文献标识码 !*### 文章编号 ! # " " # + ) " # ! ! " " ) # ! + " [ ! $ + " )
热轧带钢边裂缺陷成因分析
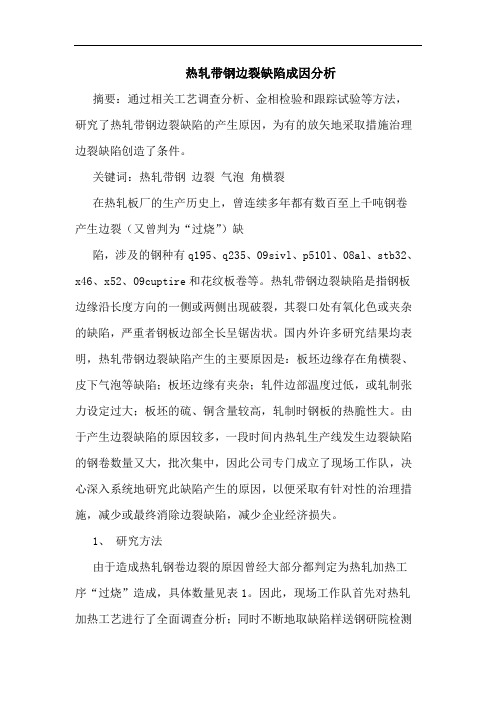
热轧带钢边裂缺陷成因分析摘要:通过相关工艺调查分析、金相检验和跟踪试验等方法,研究了热轧带钢边裂缺陷的产生原因,为有的放矢地采取措施治理边裂缺陷创造了条件。
关键词:热轧带钢边裂气泡角横裂在热轧板厂的生产历史上,曾连续多年都有数百至上千吨钢卷产生边裂(又曾判为“过烧”)缺陷,涉及的钢种有q195、q235、09sivl、p510l、08al、stb32、x46、x52、09cuptire和花纹板卷等。
热轧带钢边裂缺陷是指钢板边缘沿长度方向的一侧或两侧出现破裂,其裂口处有氧化色或夹杂的缺陷,严重者钢板边部全长呈锯齿状。
国内外许多研究结果均表明,热轧带钢边裂缺陷产生的主要原因是:板坯边缘存在角横裂、皮下气泡等缺陷;板坯边缘有夹杂;轧件边部温度过低,或轧制张力设定过大;板坯的硫、铜含量较高,轧制时钢板的热脆性大。
由于产生边裂缺陷的原因较多,一段时间内热轧生产线发生边裂缺陷的钢卷数量又大,批次集中,因此公司专门成立了现场工作队,决心深入系统地研究此缺陷产生的原因,以便采取有针对性的治理措施,减少或最终消除边裂缺陷,减少企业经济损失。
1、研究方法由于造成热轧钢卷边裂的原因曾经大部分都判定为热轧加热工序“过烧”造成,具体数量见表1。
因此,现场工作队首先对热轧加热工艺进行了全面调查分析;同时不断地取缺陷样送钢研院检测中心进行金相和电镜检验分析;为进一步验证缺陷原因的调查分析结果,还专门进行了跟踪试验进行验证。
2、研究结果2.1 热轧加热工艺调查研究针对一段时间内热轧带钢边裂缺陷频繁发生的情况,现场工作队对发生边裂缺陷的63个炉次的热轧加热工艺进行了调查,调查结果见表2。
其中q235g—31炉次, p510l—16炉次,hp295—7炉次, stb32—5炉次, x46和x52—3炉次以及q195lc—1炉次。
从表2可以看出,尽管x46和x52的加热温度靠规程下限,以及q195lc的加热温度靠规程上限,但是发生边裂缺陷的各钢种的热轧加热工艺都符合规程要求。
Q235B热轧钢带冷弯开裂原因分析及措施

21 0 0年 1 O月
金 属 材 料 与 冶 金 工 程
M ETAL M ATE ALS AND E RI M TAL URGY ENGI L NEE NG RI
V 0 - NO. l38 5 0 c 2 0 t 01
Q2 5 3 B热 轧钢 带冷 弯开 裂 制 拉 长 使 钢 材 表 面 产 生 裂 纹 源 。 当 然 ,次要 原 因 的根 源 还 在 于 钢 水 气体 含 量 高 导致 铸 坯存 在 皮 下
气 泡 。而 在 这 些 非 金 属夹 杂 物 中 ,又 以 C 类 ( 酸 盐 )和 D 类 ( 状 氧 化物 )夹 杂 为 最 多 和等 级 最 高 。 基 硅 环
氧 在 固 态 钢 中 的溶 解 度 非 常小 ,几 乎 全 部
以 氧化 物 夹 杂 的形 式存 在 于 钢 中 ,因 氧 化 物 夹
1 开 裂 试 样 金 相 组 织 和 夹 杂 物 等 级
检 验
为 找 出冷 弯 开 裂 原 因 ,制定 出改 善 冷 弯性
能 的 工艺 措 施 ,并 对 Q2 5 热轧 卷 板 冷 弯 开裂 3B
c a k n i t t du t t e te b le p d r s ox d z d e o l r c g s ha e o h se l ilt e i e mi i ie s r usy, s b u a e u bb e i i u c t n o s bu l
ABS TRACT : T e c n i e a l h s a n h mi a x mi a i n a d sr c u e a a y i h o s r b e p y i l a d c e c l e a n t n t t r n l ss d c o u
汽车大梁钢成型开裂的原因分析

209管理及其他M anagement and other汽车大梁钢成型开裂的原因分析杨成鑫(厦门海洋职业技术学院,福建 厦门 361102)摘 要:结合生产实际,针对汽车大梁用热轧钢板冲压开裂问题展开分析研究。
结果表明:夹杂物是造成钢板冲压开裂的主要原因。
通过从铁水预处理、转炉初炼、LF 炉精炼到连铸全过程控制夹杂物形成,强化夹杂物去除工序,最终解决了汽车大梁用热轧钢板冲压开裂难题。
关键词:汽车大梁;冲压开裂;夹杂物中图分类号:U466 文献标识码:A 文章编号:11-5004(2020)07-0209-2收稿日期:2020-04作者简介:杨成鑫,男,生于1984年,汉族,福建泉州人,本科,实验师,研究方向:冶金工程。
我国制造业在快速的发展,冲压钣金件的复杂性和可变性越来越大。
汽车大梁钢主要应用于重卡汽车底盘上的纵梁、衬梁、横梁以及前后车桥等结构件,这些部件在汽车行驶过程中几乎承载了货物的全部重量,其综合性能对整车的行驶安全和使用寿命至关重要[1]。
冲压后的纵梁形状简单,一般采用槽钢或U 形梁,除了一般的机械性能外,还对宽冷弯工艺性能要求很高。
因为横梁和加强筋比桁条更复杂,因此在冲压过程中它们更容易破裂。
不合理的材料选择和原材料质量的波动往往都会导致了冲压的时候出现了裂缝,这样会给加工的企业以及材料的供应商带来一定的经济损失。
所以,我们从原材料的铸造工艺进行有效分析,并实施有效的工艺改进措施,使得原材料从冶金质量上更上一层,最终达到所需的使用要求。
1 化学成分及显微组织的分析1.1 化学成分的分析我们以低碳、高锰和适宜的钛微合金化复合设计方案用于汽车大梁钢的冶炼。
其中,适当地增加锰含量以补偿由低碳含量引起的抗拉强度的降低。
通过一定分析,发现化学成分满足国标GB/T3273-2005的要求。
1.2 组织和夹杂物的分析利用光学显微镜对大梁钢的组织、带状组织和夹杂物进行分析,结果表明,显微组织为铁素体(F)+珠光体(P),珠光体体积分数为10%,晶粒度为10.5级,心部带状组织为1.0级,非金属夹杂物属于脆性夹杂,且略高于正常的水平,这样会引起在变形过程中因为变形不协调而增加开裂的几率[2]。
钢材轧制缺陷及原因
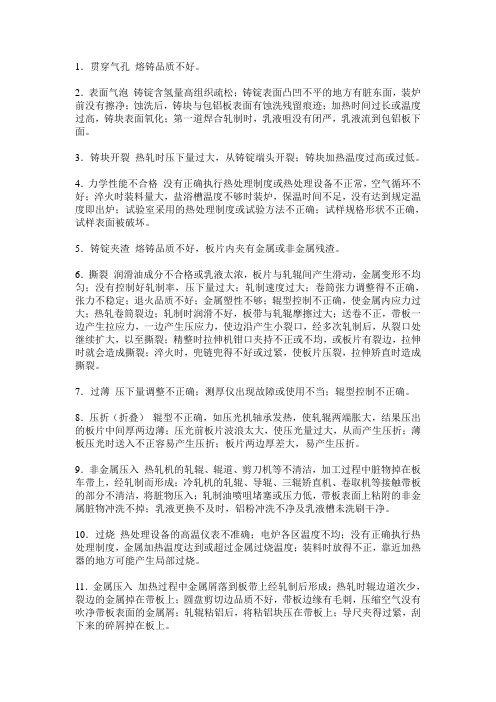
1.贯穿气孔熔铸品质不好。
2.表面气泡铸锭含氢量高组织疏松;铸锭表面凸凹不平的地方有脏东面,装炉前没有擦净;蚀洗后,铸块与包铝板表面有蚀洗残留痕迹;加热时间过长或温度过高,铸块表面氧化;第一道焊合轧制时,乳液咀没有闭严,乳液流到包铝板下面。
3.铸块开裂热轧时压下量过大,从铸锭端头开裂;铸块加热温度过高或过低。
4.力学性能不合格没有正确执行热处理制度或热处理设备不正常,空气循环不好;淬火时装料量大,盐浴槽温度不够时装炉,保温时间不足,没有达到规定温度即出炉;试验室采用的热处理制度或试验方法不正确;试样规格形状不正确,试样表面被破坏。
5.铸锭夹渣熔铸品质不好,板片内夹有金属或非金属残渣。
6.撕裂润滑油成分不合格或乳液太浓,板片与轧辊间产生滑动,金属变形不均匀;没有控制好轧制率,压下量过大;轧制速度过大;卷筒张力调整得不正确,张力不稳定;退火品质不好;金属塑性不够;辊型控制不正确,使金属内应力过大;热轧卷筒裂边;轧制时润滑不好,板带与轧辊摩擦过大;送卷不正,带板一边产生拉应力,一边产生压应力,使边沿产生小裂口,经多次轧制后,从裂口处继续扩大,以至撕裂;精整时拉伸机钳口夹持不正或不均,或板片有裂边,拉伸时就会造成撕裂;淬火时,兜链兜得不好或过紧,使板片压裂,拉伸矫直时造成撕裂。
7.过薄压下量调整不正确;测厚仪出现故障或使用不当;辊型控制不正确。
8.压折(折叠)辊型不正确,如压光机轴承发热,使轧辊两端胀大,结果压出的板片中间厚两边薄;压光前板片波浪太大,使压光量过大,从而产生压折;薄板压光时送入不正容易产生压折;板片两边厚差大,易产生压折。
9.非金属压入热轧机的轧辊、辊道、剪刀机等不清洁,加工过程中脏物掉在板车带上,经轧制而形成;冷轧机的轧辊、导辊、三辊矫直机、卷取机等接触带板的部分不清洁,将脏物压入;轧制油喷咀堵塞或压力低,带板表面上粘附的非金属脏物冲洗不掉;乳液更换不及时,铝粉冲洗不净及乳液槽未洗刷干净。
浅析棒材表面裂纹特点及产生原因

浅析棒材表面裂纹特点及产生原因引言:表面裂纹是热轧棒材表面缺陷中最常见的一种,为清除这些缺陷,往往不得不花费大量的人力物力,有时还会严重影响企业的正常生产和经济效益。
二轧车间自09年元月投产以来,生产的产品经常有表面裂纹的缺陷产生,8月中旬以后,表面裂纹尤其严重,不同钢种,不同规格,热送和冷装均出现裂纹,没有明显的规律,因表面裂纹压钢1400余吨,给轧钢精整工段的修磨工作带来巨大的压力。
为此,轧钢部专门成立攻关小组,会同炼钢及质量部,对裂纹的产生原因进行了分析,取得了一些成效,但由于种种原因,没有达到预期的效果。
结合对现场裂纹钢材一些数据的统计,参考国内相关专家的一些研究结果,提出了一些看法,希望能对解决二轧热轧棒材表面裂纹问题有所帮助。
1、裂纹的常见种类及特点:1.1 裂纹分类由于查不到棒材表面裂纹的准确分类,参照其他厂家的习惯,我们将表面裂纹分为以下几类:直型裂纹:指裂纹总长60%以上基本呈直线且偏角小于30度的裂纹。
曲型裂纹(不规则裂纹):除直型裂纹以外的裂纹。
长型裂纹:指裂纹长度大于等于300mm的表面裂纹。
短型裂纹:指裂纹长度小于300mm的表面裂纹。
宽型裂纹:指裂纹最大宽度大于等于1mm的表面裂纹。
窄型裂纹:指裂纹最大宽度小于1mm的表面裂纹。
深型裂纹:指裂纹深度大于0.4表面裂纹。
浅型裂纹:指裂纹深度小于0.4表面裂纹。
密型裂纹:指在圆周角小于等于30度所对应的圆周面上裂纹条数大于等于3条的裂纹。
疏型裂纹:指在圆周角小于等于30度所对应的圆周面上裂纹条数小于3条的裂纹。
由于二轧出现的裂纹对钢种没有特殊的针对性,为简化分析,主要针对45#钢进行统计分析,统计分析的批次其化学成分符合45#钢的标准要求。
1.2 二轧车间裂纹的特点:我们对这些裂纹进行了仔细观察,总结了这些裂纹的表观特征:中间宽,两头细,呈凸透镜状,绝大多数裂纹长约10~30mm,中间宽约1~2mm,这些裂纹有单独出现的,大部分成簇状出现的,另外一部分是直长型,有通根长的,也有中间间断的出现,还有一部分就是密集不规则型。
J4不锈钢热轧板冷轧横裂原因分析

试样正常部位的非金属夹杂物主要以 B 类 为主 , 2. 0级 ,级别不是很高 ,对材料的影响不大 。 金 相组织为奥氏体 +少量铁素体 +少量显微气
3 分析讨论
现场调查及询问用户相关技术人员 ,结合试 验结果分析认为 ,酸退及轧制工艺问题不大 ,并且
a)
b)
远离裂纹正常部位
c)
d)
次裂纹部位
图 4 试样裂纹 、显微气泡与组织间关系 500 × Figure 4 The relationship among the cracks, m icro bubbles and structures in the samp le (500 ×)
参考文献
[ 1 ] 徐飙 ,王龙妹 ,朱京希 ,王福 ,徐军 ,戚国平. 节镍型奥氏体 不锈钢冷 轧 断 带 的 影 响 因 素. 金 属 热 处 理 , 2007 年 , 32 (6).
[ 2 ] 肖纪美. 不锈钢的金属学问题 . 北京 :冶金工业出版社 , 1983, 41 - 62.
[ 3 ] 王肇愉. 铬锰氮钢中气体问题的探讨 [ J ]. 铸工 , 1981 ( 3) : 32 - 35. 编辑 杜青泉
Key words: J4 hot rolling p late; transverse crack; m icro bubbles; analysis
某公司生产的规格为 3. 0 mm ×1 250 mm 的 J4奥氏体不锈钢热轧板 ,经 1 020℃酸洗退火 ,纵 向分切成 3. 0 mm ×740 mm 以及 3. 0 mm ×510 mm 后 ,客户进行冷轧 。当轧到 1. 23 mm ×740 mm 时表面出现大量横裂纹 ,沿板宽横向无规则 分布 。个别横裂纹呈穿透状 ,未穿透的横裂纹部 位背面有明显的痕迹 ,横裂形态如图 1所示 。
热轧钢带边裂形成原因分析及控制

热轧钢带边裂形成原因分析及控制摘要:文章主要是采用到宏观检验、金相检验等的方式分析了热轧钢带边裂的原因,通过分析可知铸坯存在着原始表面裂纹等的缺陷,是导致热轧钢带边裂的主因素。
关键词:热轧钢带;边裂;显微组织;夹杂;粗晶前言热轧钢带边裂是热轧生产过程中最常见的一种质量缺陷,同时也是有关人员应当关注和解决的质量问题。
热轧钢带边裂问题的存在会影响到企业的发展,造成企业的经济损失,为此有关人员应当对其边裂的形成进行分析,采取到针对性的解决措施,才能够为企业的发展奠定良好的基础。
1试样的制备及试验方法对产生边裂缺陷的钢卷进行宏观检验f11,观察边裂部位的裂纹形态、分布、尺寸等。
边裂钢带上有缺陷的部位截取金相试样,研磨、抛光后在金相显微镜观察裂纹的形态及分布,腐蚀后观察组织状态、晶粒度、脱碳层。
利用扫描电镜观测钢板表面裂纹内部情况,通过能谱分析填充物及内夹杂物的具体成分。
2检验结果2.1宏观分析从宏观上看囝,存在边裂的钢卷边部参差不齐,一侧或两侧的边部呈连续或间断的树皮状或严重的锯齿状,侧边附近的表面伴有不规则的裂纹。
现为山东泰山钢铁集团新材料研究所助理工程师,从事金属材料检测分析工作。
近的两轧制表面有沿轧制方向分布的细长裂纹,这种细长的裂纹宽度在0.1-0.5mm,两轧制表面整个宽度方向都有沿轧制方向分布,长度一般在3-100mm范围内,两平行裂纹的间距在4~8mm。
2.2金相检验边裂检验在有严重破边缺陷的钢板上,分别在缺陷处取样,磨制成金相样观察,发现缺陷处有大量的裂纹,裂纹及其分支向里延伸,裂纹内充满氧化铁。
裂纹基本上都是由钢板边缘向板内延伸。
试样经硝酸酒精腐蚀后,发现裂纹附近的组织与其它正常部位的组织明显不一样,晶粒粗大,并有较明显的变形特征,还有明显的流线,裂纹附近有晶粒不均现象。
边裂的尾端存在晶界氧化和内氧化。
表面裂纹带钢轧制表面上密集分布的裂纹裂纹可见深度一般在0.1~0.4mm,有些裂纹内部有分支细小裂纹向里延伸,裂纹内充满氧化铁。
热轧圆钢皮下“裂纹”形成原因分析及改进措施
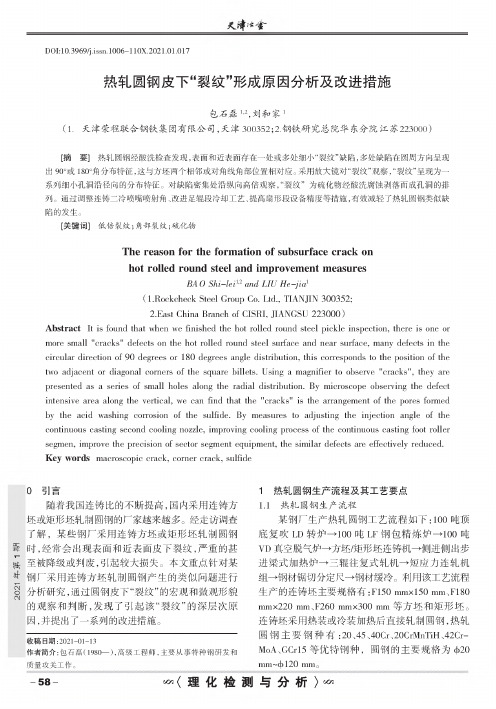
DOI:10.3969/j.issn.l006-110X.2021.01.017热轧圆钢皮下“裂纹”形成原因分析及改进措施包石磊1,2,刘和家1(! 天津荣程联合钢铁集团有限公司,天津300352;2.钢铁研究总院华东分院江苏223000)[摘 要]热轧圆钢经酸洗检查发现,表面和近表面存在一处或多处细小“裂纹”缺陷,多处缺陷在圆周方向呈现岀90$或1,0$角分布特征,这与方坯两个相邻或对角线角部位置相对应。
采用放大镜对“裂纹”观察,“裂纹”呈现为一系列细小孔洞沿径向的分布特征。
对缺陷密集处沿纵向高倍观察,“裂纹”为硫化物经酸洗腐蚀剥落而成孔洞的排 列。
通过调整连铸二冷喷嘴喷射角、改进足辊段冷却工艺、提高扇形段设备精度等措施,有效减轻了热轧圆钢类似缺陷的发生。
[关键词]低倍裂纹;角部裂纹;硫化物The reason for the formation of subsur^ce crack on hot rolled round steel and improvement measuresBA 0 Shi-lei 1,2 and LIU He-jic*(l.QocCcCecC Sted Gronp Co. L u U, TIANJIN 300352;2.Ent Chin BrancO of CISRI, JIANGSU 223000)Abstract It is found that when we finished the hot rolled round steel pickle inspection, there is one ormore small "cracks" defects on the hot rolled round steel surface and near surface, many defects in the circular direction of 90 degrees or 180 degrees angle distribution, this corresponds to the position of thetwo adjacent or diagonal corners of the square billets. Using a magnifier to observe "cracks", they are presented as a series of small holes along the radial distribution. By microscope observing the defect intensive area along the vertical, we can find that the "cracks" is the arrangement of the pores formedby the acid washing corrosion of the sulfide. By measures to adjusting the injection angle of the continuous casting second cooling nozzle, improving cooling process of the continuous casting foot roller segmen, improve the precision of sector segment equipment, the similar defects are effectively reduced.Key words macroscopic crack, corner crack, sulfide0引言随着我国连铸比的不断提高,国内采用连铸方 坯或矩形坯轧制圆钢的厂家越来越多。
热轧板Q235B裂纹成因分析

热轧板Q235B裂纹成因分析【摘要】利用金相和扫描电镜等分析手段,对热轧板Q235B裂纹进行分析。
结果表明,铸坯存在原始表面裂纹、表层气孔等缺陷是产生裂纹的主要原因,铸坯近表层的夹杂物富集,促进了轧制过程中裂纹的扩展,铸坯的局部过烧,使边部晶粒异常长大,加剧了裂纹发展。
【关键词】热轧板Q235B;裂纹;金相;扫描电镜;夹杂0.前言热连轧厂生产的普碳系列钢种Q235B出现严重裂纹,主要表现为边裂和布满钢带整个表面的小纵裂。
本研究对Q235B裂纹进行了试验、分析,对缺陷的形成机理及原因进行探讨,提出工艺改进措施。
1.缺陷描述Q235B的裂纹分两种形态,主要指边裂和布满钢带整个表面的小纵裂。
边裂表现为深度较深,有明显的裂口,严重的成烂边;小纵裂表现为距钢卷边部较远,分布在整个钢卷表面,经冷弯后出现起皮现象。
2.成因分析对缺陷部位截取金相试样,研磨、抛光后在金相显微镜观察裂纹的形态和分布,腐蚀后观测组织、形态;利用扫描电镜观测钢板表面裂纹内部情况,通过能普分析夹杂物的成分;通过以上手段,查找缺陷成因。
2.1硫含量分析对同一时期生产的Q235B裂纹炉次与无裂纹炉次的S含量进行了对比,发现裂纹出现的炉次S含量较无裂纹的高,S含量对成品钢板裂纹有一定影响。
2.2金相分析缺陷部分金相显示,裂纹附近有明显的脱碳现象,裂纹深度大于200um,有明显的裂口,说明这类裂纹在铸坯上已经形成,而钢带的局部位置晶粒粗大,存在过烧现象[1]。
2.3扫描电镜分析经扫描电镜、能普分析,裂纹内部填充物是氧化铁及氧化物夹杂。
裂纹内部两侧基体氧化严重,有大量的内氧化原点,裂纹处存在轧制变形流线、晶粒不均,这说明该缺陷在轧制前就已经存在[2]。
2.4夹杂物分析裂纹周围存在密集分布的点状夹杂,从夹杂成分看以硫化锰(铁)、锰硅酸盐为主,同时有磷元素的存在。
从夹杂物的分布和尺寸来看,主要是硫化物和硅酸盐夹杂,是以共晶形式或者高温加热后冷却过程中析出的夹杂,夹杂物含量较高,从评级情况看A类夹杂物达到3级。
热轧板Q235B裂纹成因分析

热轧板Q235B裂纹成因分析【摘要】利用金相和扫描电镜等分析手段,对热轧板Q235B裂纹进行分析。
结果表明,铸坯存在原始表面裂纹、表层气孔等缺陷是产生裂纹的主要原因,铸坯近表层的夹杂物富集,促进了轧制过程中裂纹的扩展,铸坯的局部过烧,使边部晶粒异常长大,加剧了裂纹发展。
【关键词】热轧板Q235B;裂纹;金相;扫描电镜;夹杂0.前言热连轧厂生产的普碳系列钢种Q235B出现严重裂纹,主要表现为边裂和布满钢带整个表面的小纵裂。
本研究对Q235B裂纹进行了试验、分析,对缺陷的形成机理及原因进行探讨,提出工艺改进措施。
1.缺陷描述Q235B的裂纹分两种形态,主要指边裂和布满钢带整个表面的小纵裂。
边裂表现为深度较深,有明显的裂口,严重的成烂边;小纵裂表现为距钢卷边部较远,分布在整个钢卷表面,经冷弯后出现起皮现象。
2.成因分析对缺陷部位截取金相试样,研磨、抛光后在金相显微镜观察裂纹的形态和分布,腐蚀后观测组织、形态;利用扫描电镜观测钢板表面裂纹内部情况,通过能普分析夹杂物的成分;通过以上手段,查找缺陷成因。
2.1硫含量分析对同一时期生产的Q235B裂纹炉次与无裂纹炉次的S含量进行了对比,发现裂纹出现的炉次S含量较无裂纹的高,S含量对成品钢板裂纹有一定影响。
2.2金相分析缺陷部分金相显示,裂纹附近有明显的脱碳现象,裂纹深度大于200um,有明显的裂口,说明这类裂纹在铸坯上已经形成,而钢带的局部位置晶粒粗大,存在过烧现象[1]。
2.3扫描电镜分析经扫描电镜、能普分析,裂纹内部填充物是氧化铁及氧化物夹杂。
裂纹内部两侧基体氧化严重,有大量的内氧化原点,裂纹处存在轧制变形流线、晶粒不均,这说明该缺陷在轧制前就已经存在[2]。
2.4夹杂物分析裂纹周围存在密集分布的点状夹杂,从夹杂成分看以硫化锰(铁)、锰硅酸盐为主,同时有磷元素的存在。
从夹杂物的分布和尺寸来看,主要是硫化物和硅酸盐夹杂,是以共晶形式或者高温加热后冷却过程中析出的夹杂,夹杂物含量较高,从评级情况看A类夹杂物达到3级。
J4不锈钢热轧板冷轧横裂原因分析
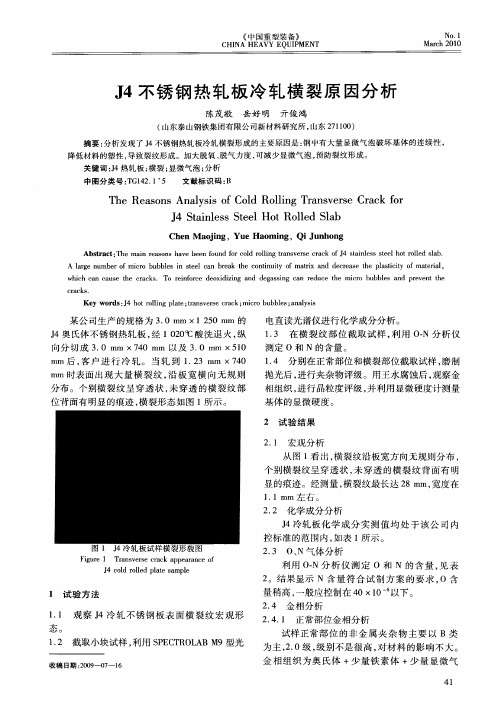
J od r l d p ae s mp e 4 c l ol l t a l e
1 试 验方法
量 稍高 , 一般 应控 制在 4 0×1 以下 。 0
2 4 金 相分 析 . 2 4 1 正常 部位金 相 分析 .. 试样 正 常部 位 的 非 金 属 夹 杂 物 主 要 以 B类 为 主 ,. , 2 0级 级别 不 是很 高 , 材 料 的影 响不 大 。 对
A lr e n mb ro c o b b l s i te a r a h o t ut f marx a d d c e s h lsii fma ei l a g u e fmir u b e n s lc n b e k t e c n i i o t n e r a e t e pa t t o t r , e n y i cy a
Ke r s J o o l g p ae ta s e s r c mir u b e ; n lss y wo d : 4 h t l n lt ;r n v r e c a k; c o b b l s a ay i r i
某 公 司生产 的规 格 为 3 0ml X1 5 . T 2 0mm 的 l
whih c n c us h r c s To en o c d o i zn n d g s i c n r d e t e c a a e te ca k . r if r e e xdiig a d e a sng a e uc h mir ub e a e e t t c o b bls nd prv n he c a ks rc .
2 1 宏观 分析 .
从 图 1看 出 , 裂纹 沿板 宽方 向无规 则 分布 , 横 个 别横 裂纹 呈穿 透状 , 穿 透 的横 裂 纹 背 面有 明 未 显 的痕 迹 。经测 量 , 横裂 纹最 长达 2 m, 度在 8m 宽
- 1、下载文档前请自行甄别文档内容的完整性,平台不提供额外的编辑、内容补充、找答案等附加服务。
- 2、"仅部分预览"的文档,不可在线预览部分如存在完整性等问题,可反馈申请退款(可完整预览的文档不适用该条件!)。
- 3、如文档侵犯您的权益,请联系客服反馈,我们会尽快为您处理(人工客服工作时间:9:00-18:30)。
热轧钢板成型开裂原因
热轧钢板成型开裂的原因可以有多种。
以下列举了一些常见的原因:
1. 压力不均匀:在热轧过程中,如果板坯的变形过程中施加的压力不均匀,可能会导致应力集中,在局部区域产生开裂。
2. 温度不均匀:热轧过程中,如果板坯的温度分布不均匀,可能会导致板坯内部的应力不均匀,进而产生开裂。
3. 缺陷存在:热轧钢板在生产过程中可能存在各种缺陷,如夹杂物、气泡等。
这些缺陷会削弱钢板的强度和韧性,容易导致开裂。
4. 冷却速度过快:热轧后,钢板需要冷却。
如果冷却速度过快,可能会导致钢板内部产生应力,从而引发开裂。
5. 压辊问题:热轧过程中,如果压辊的表面磨损或凹陷,可能会在板坯上留下凸起或凹陷的痕迹,进而导致开裂。
这些是热轧钢板成型开裂的一些常见原因,通过加强生产工艺控制、提高材料质量和完善设备维护,可以有效降低开裂的风险。